41 st GasLift Workshop Houston Texas USA June
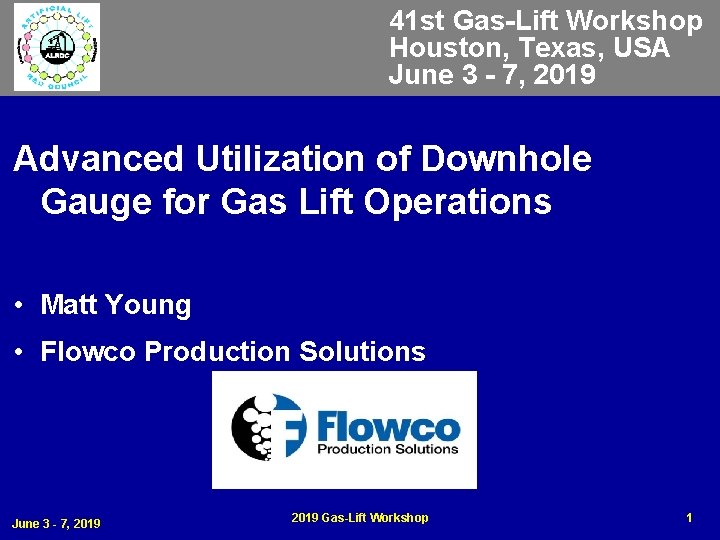
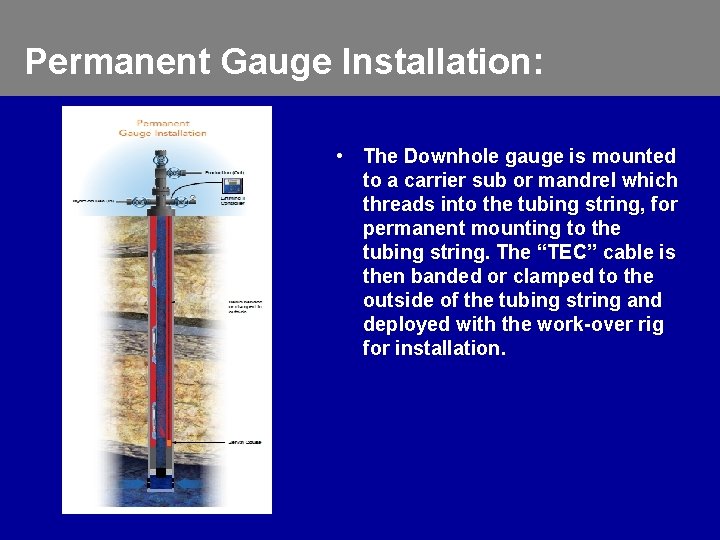
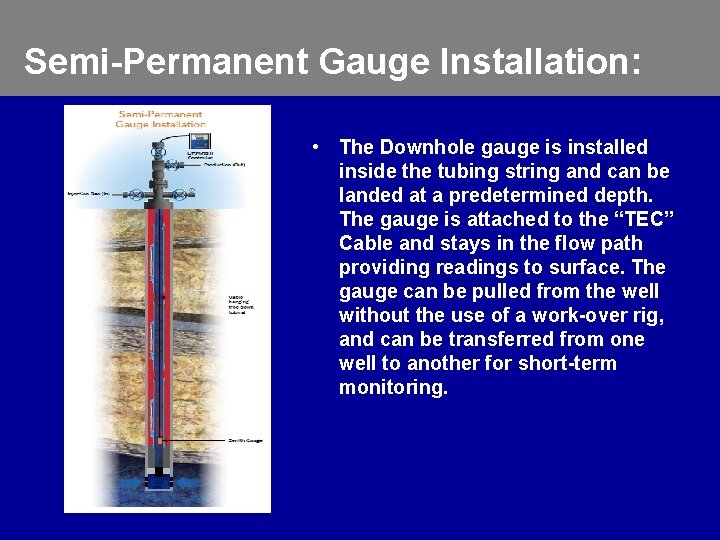
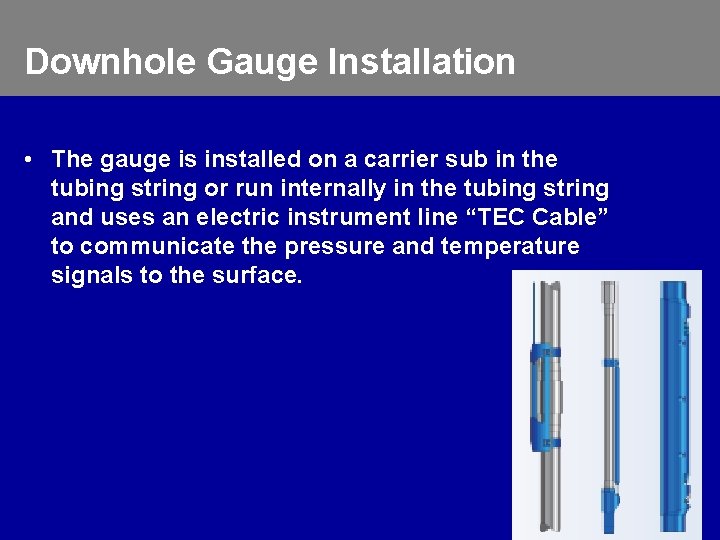
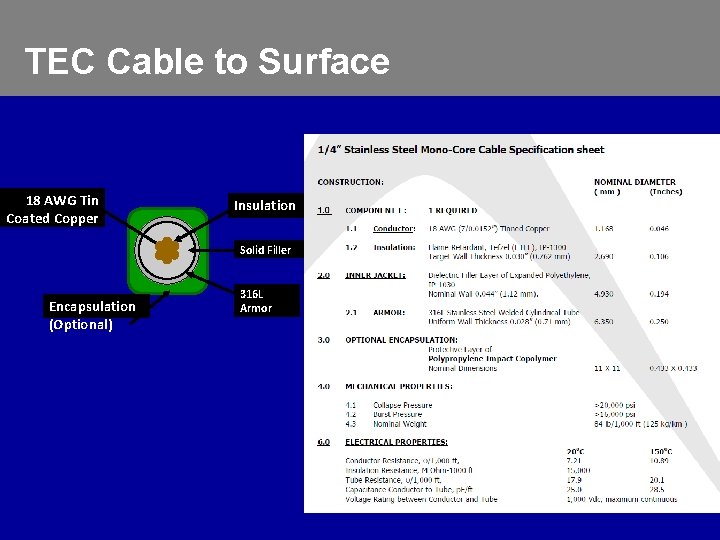
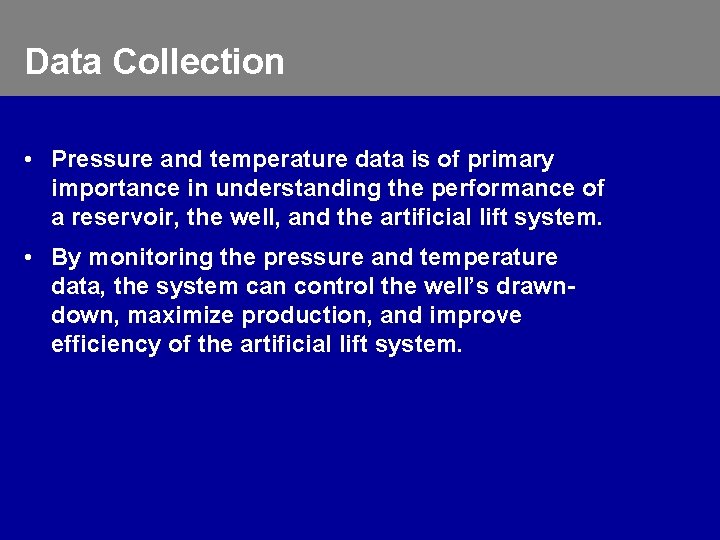
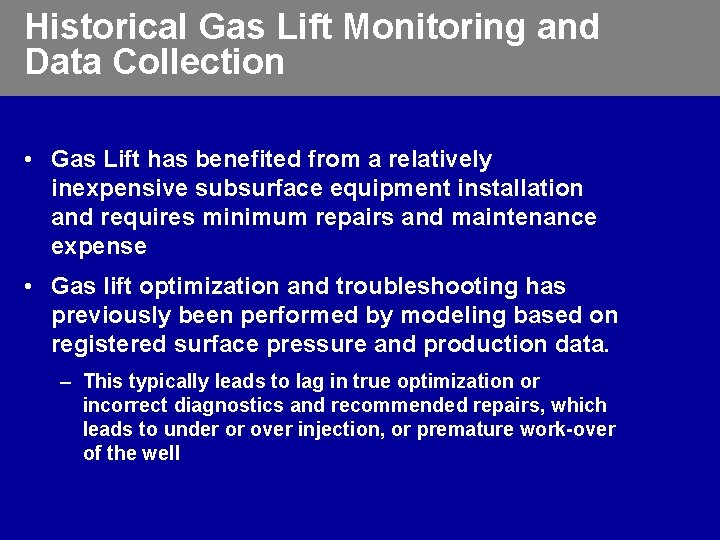
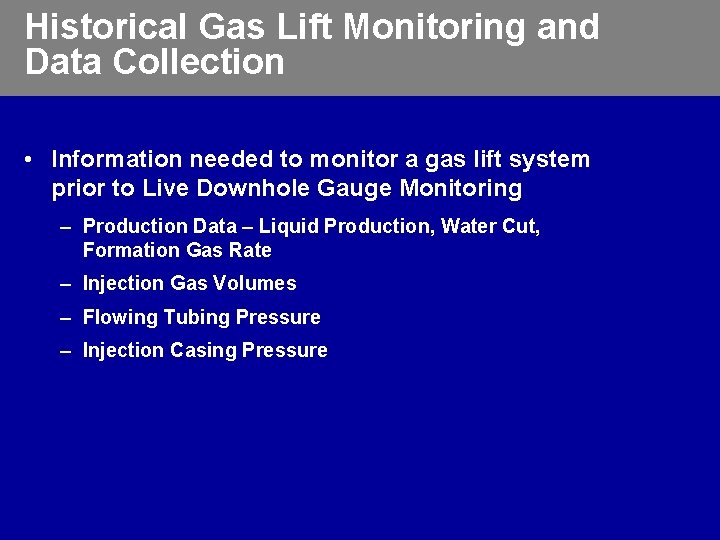
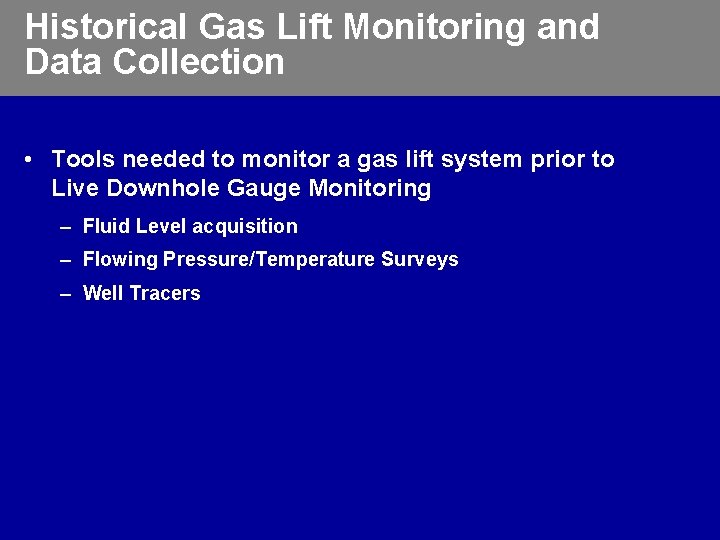
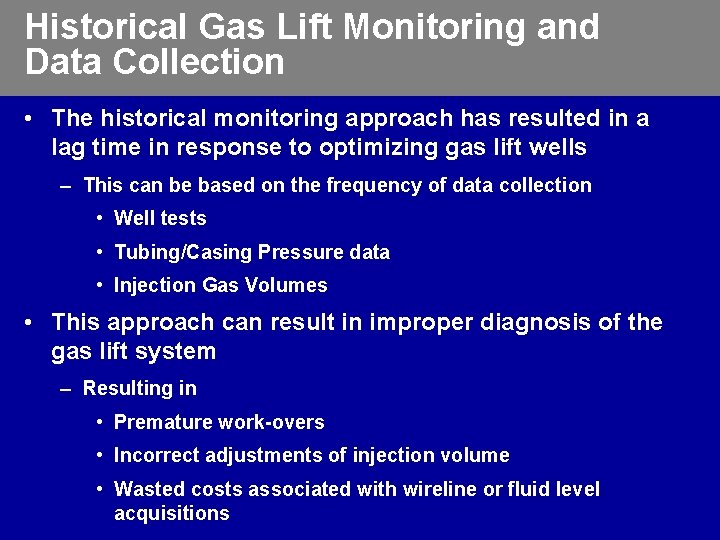
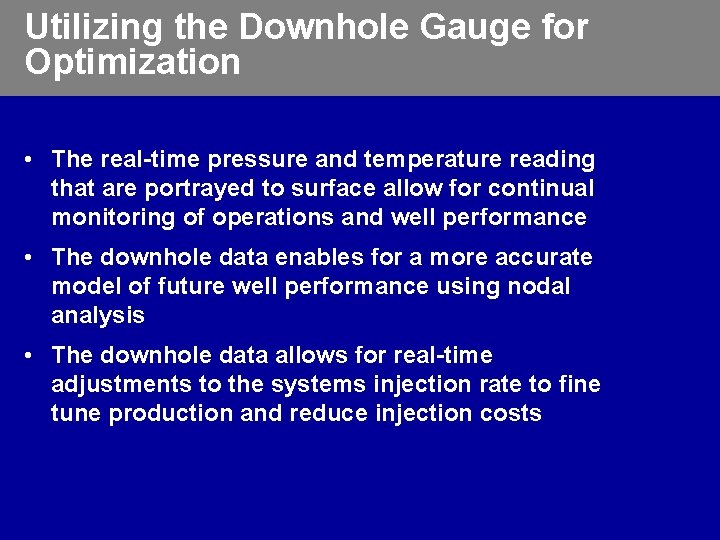
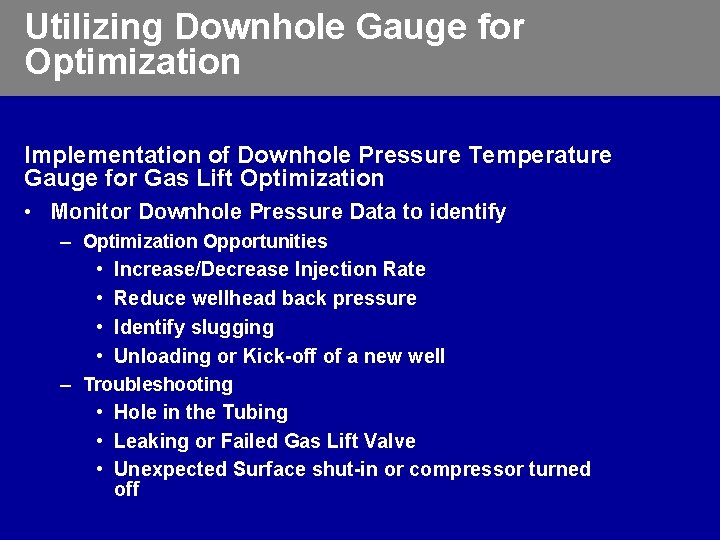
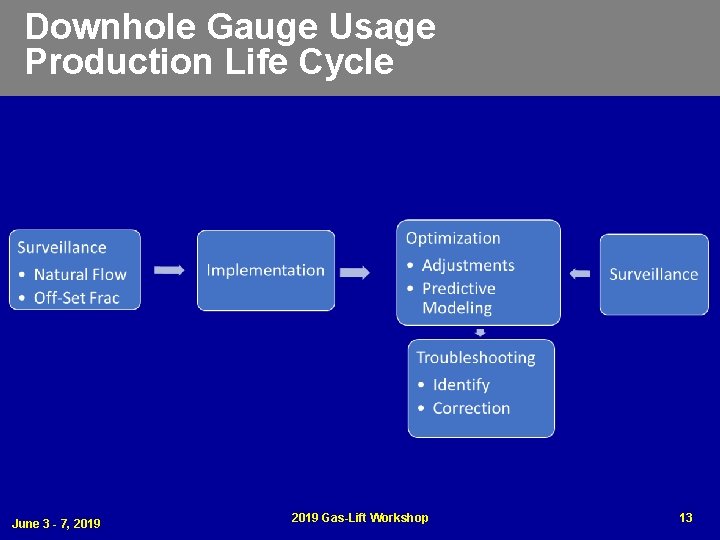
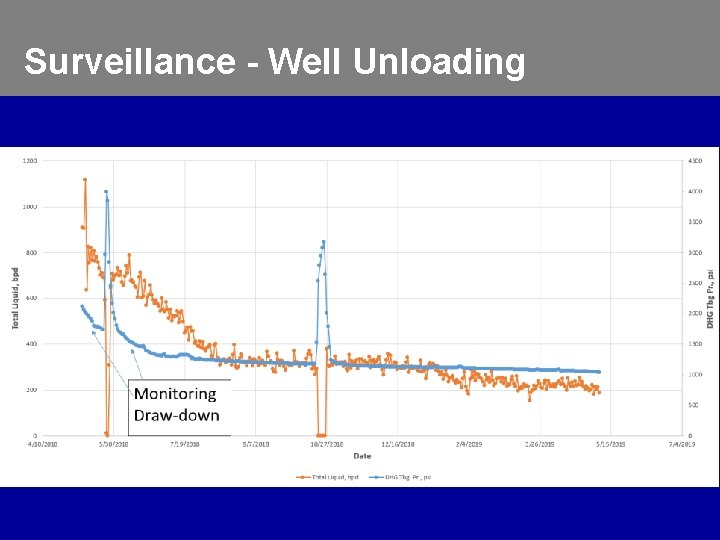
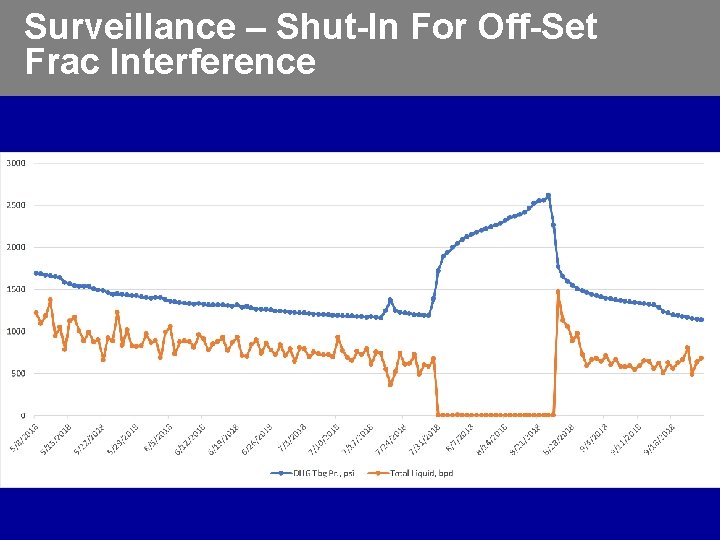
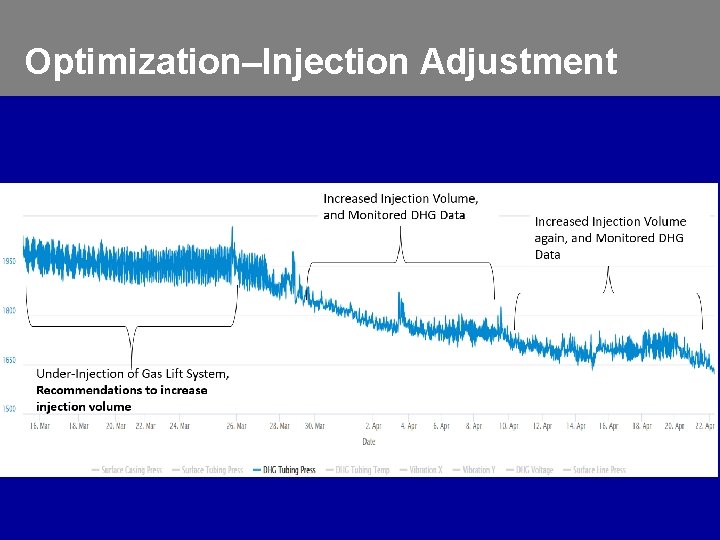
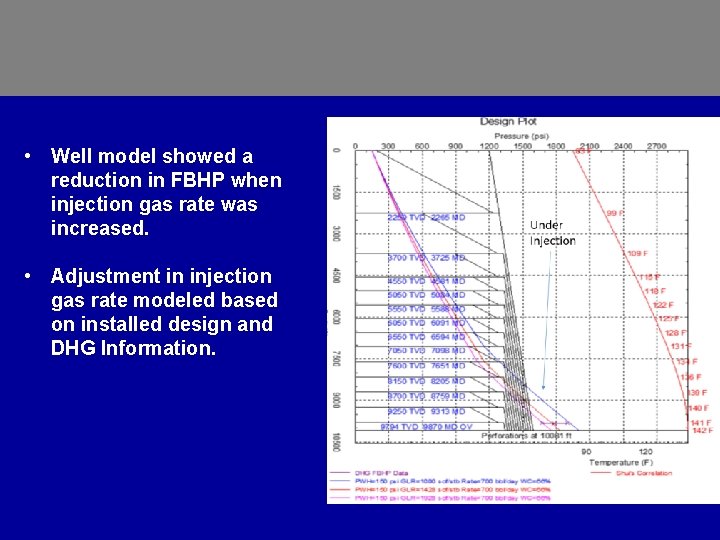
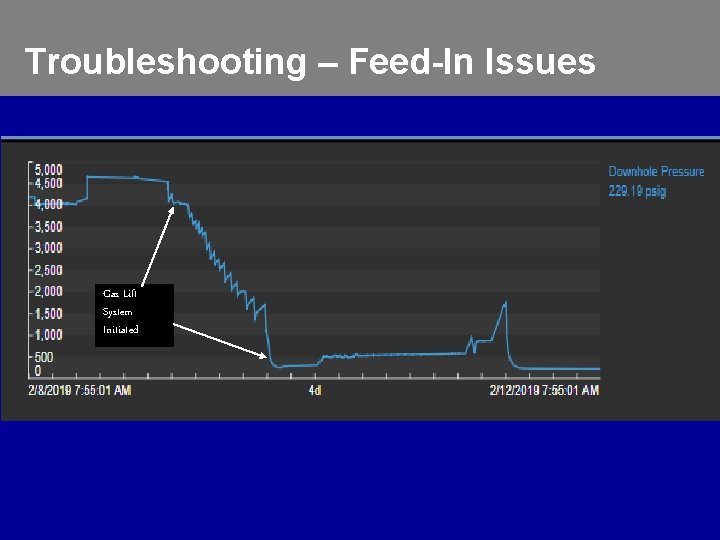
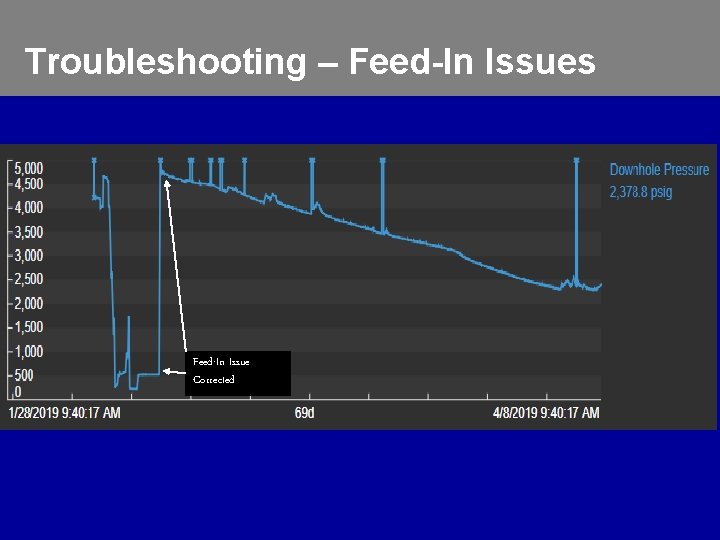
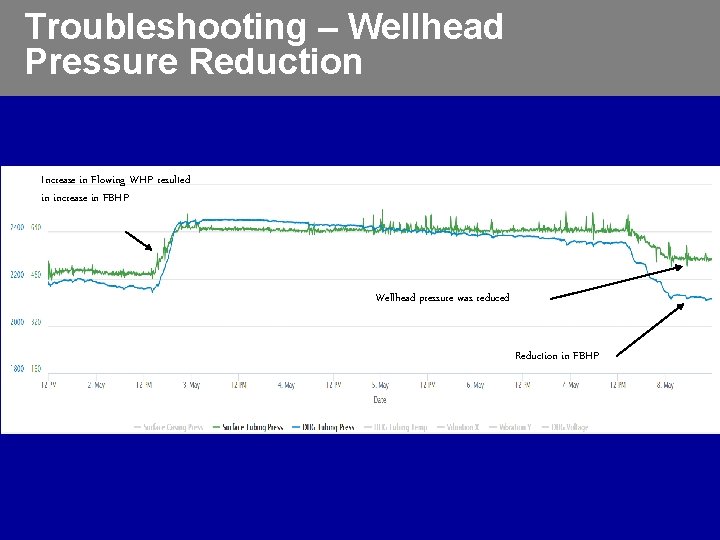
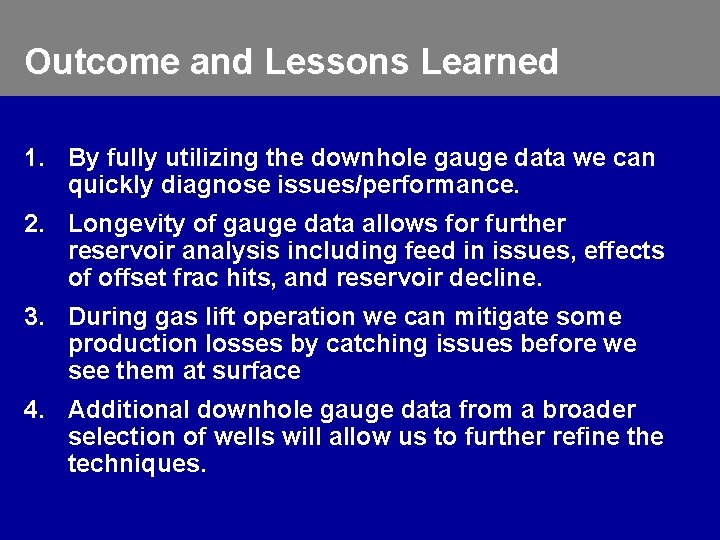
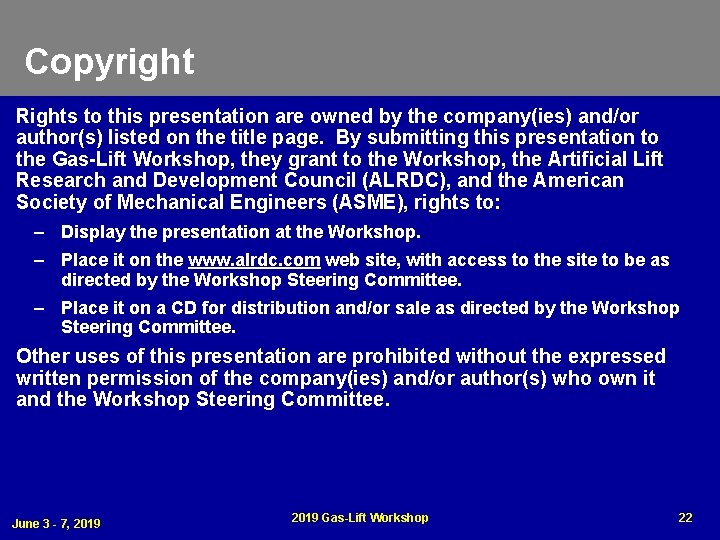
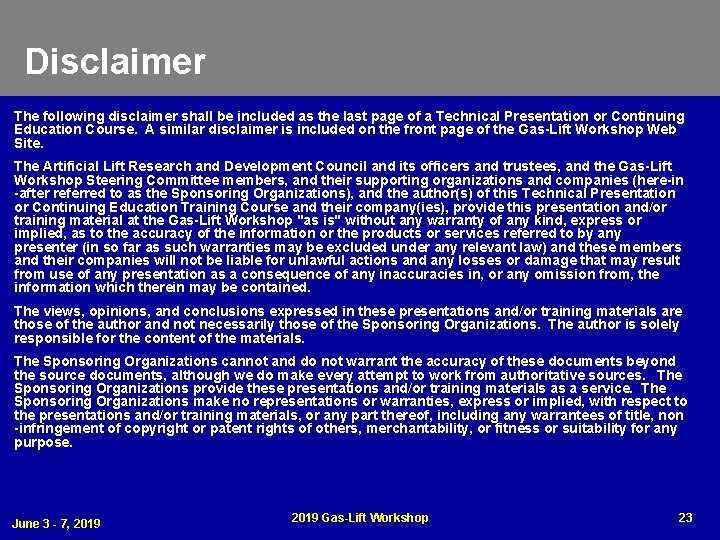
- Slides: 23
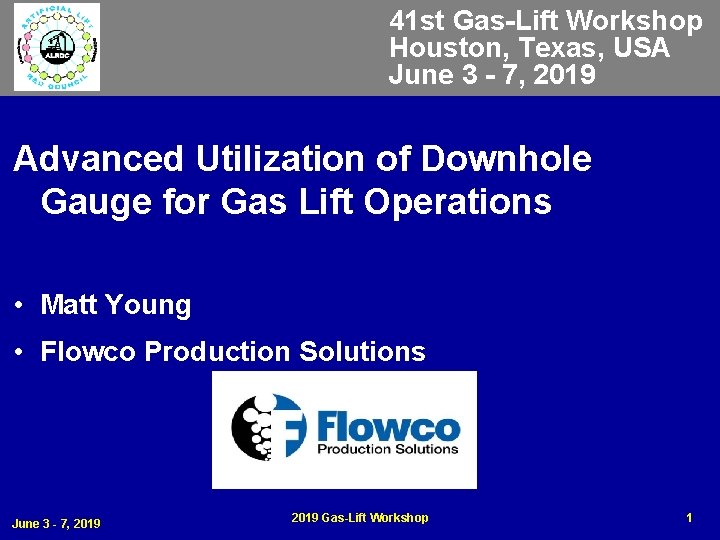
41 st Gas-Lift Workshop Houston, Texas, USA June 3 - 7, 2019 Advanced Utilization of Downhole Gauge for Gas Lift Operations • Matt Young • Flowco Production Solutions June 3 - 7, 2019 Gas-Lift Workshop 1
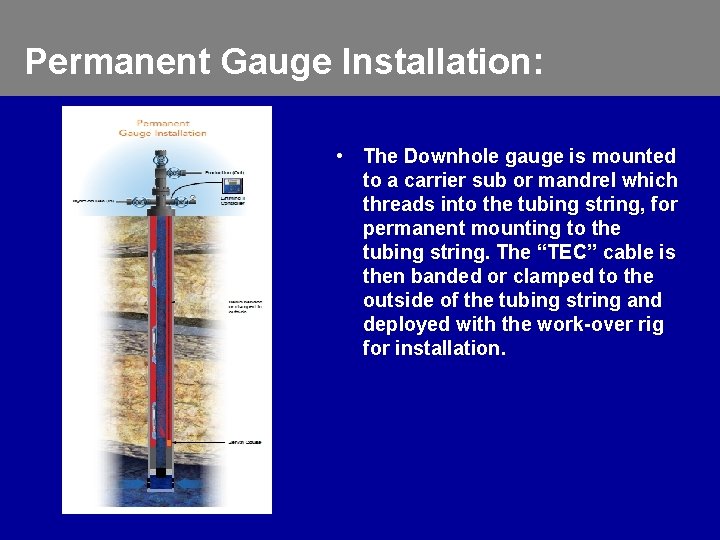
Permanent Gauge Installation: • The Downhole gauge is mounted to a carrier sub or mandrel which threads into the tubing string, for permanent mounting to the tubing string. The “TEC” cable is then banded or clamped to the outside of the tubing string and deployed with the work-over rig for installation.
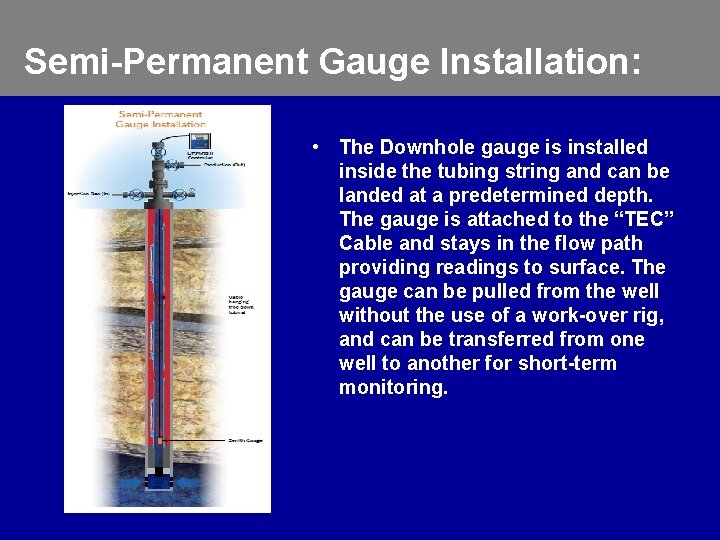
Semi-Permanent Gauge Installation: • The Downhole gauge is installed inside the tubing string and can be landed at a predetermined depth. The gauge is attached to the “TEC” Cable and stays in the flow path providing readings to surface. The gauge can be pulled from the well without the use of a work-over rig, and can be transferred from one well to another for short-term monitoring.
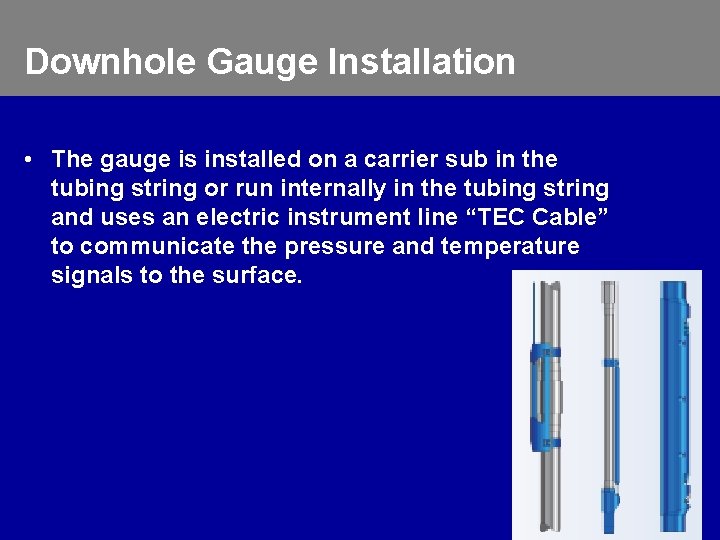
Downhole Gauge Installation • The gauge is installed on a carrier sub in the tubing string or run internally in the tubing string and uses an electric instrument line “TEC Cable” to communicate the pressure and temperature signals to the surface.
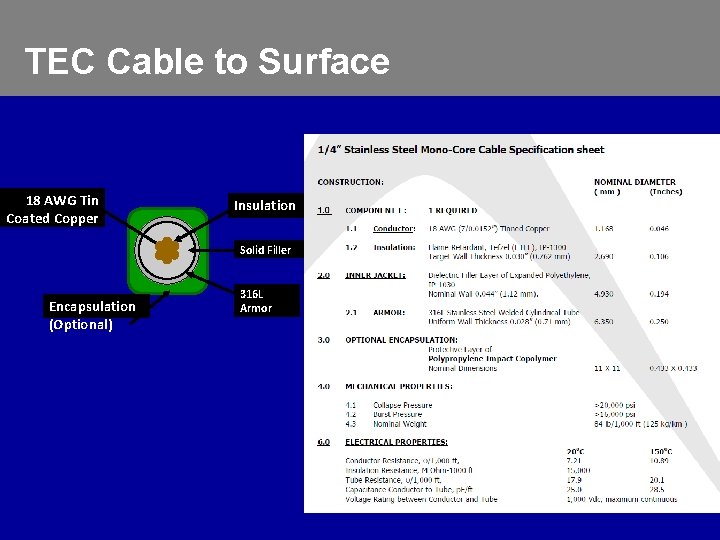
TEC Cable to Surface 18 AWG Tin Coated Copper Insulation Solid Filler Encapsulation (Optional) 316 L Armor
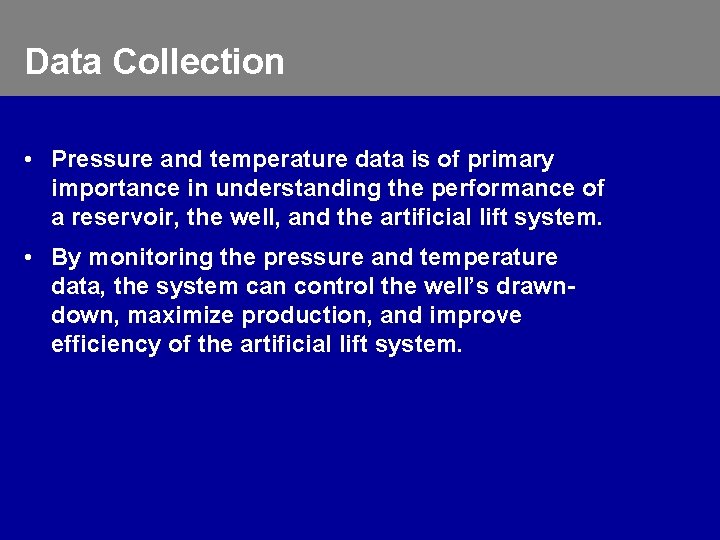
Data Collection • Pressure and temperature data is of primary importance in understanding the performance of a reservoir, the well, and the artificial lift system. • By monitoring the pressure and temperature data, the system can control the well’s drawndown, maximize production, and improve efficiency of the artificial lift system.
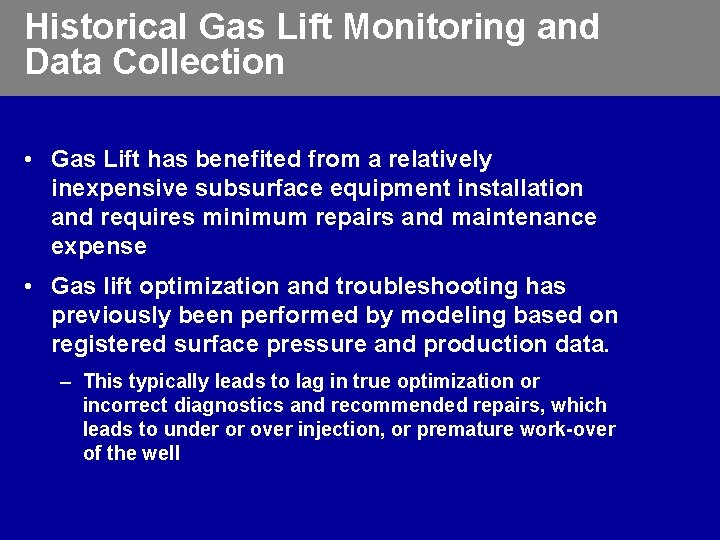
Historical Gas Lift Monitoring and Data Collection • Gas Lift has benefited from a relatively inexpensive subsurface equipment installation and requires minimum repairs and maintenance expense • Gas lift optimization and troubleshooting has previously been performed by modeling based on registered surface pressure and production data. – This typically leads to lag in true optimization or incorrect diagnostics and recommended repairs, which leads to under or over injection, or premature work-over of the well
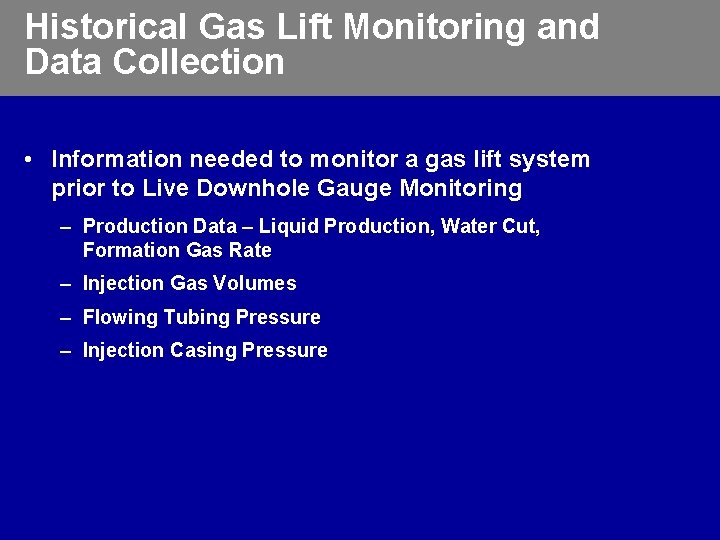
Historical Gas Lift Monitoring and Data Collection • Information needed to monitor a gas lift system prior to Live Downhole Gauge Monitoring – Production Data – Liquid Production, Water Cut, Formation Gas Rate – Injection Gas Volumes – Flowing Tubing Pressure – Injection Casing Pressure
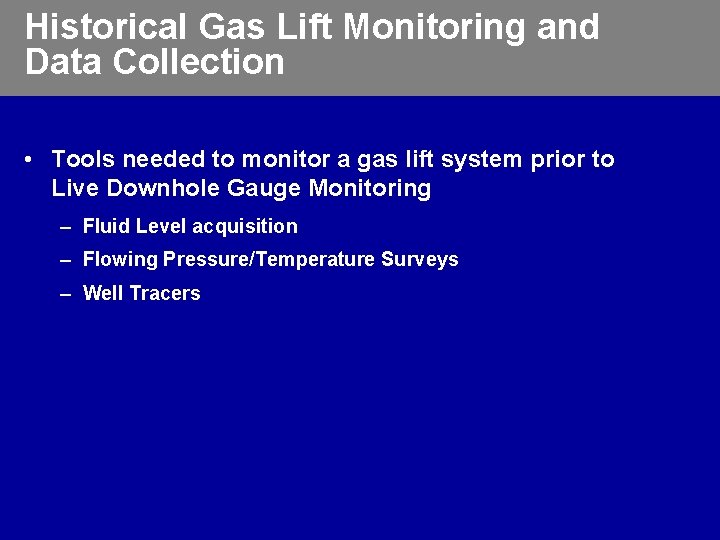
Historical Gas Lift Monitoring and Data Collection • Tools needed to monitor a gas lift system prior to Live Downhole Gauge Monitoring – Fluid Level acquisition – Flowing Pressure/Temperature Surveys – Well Tracers
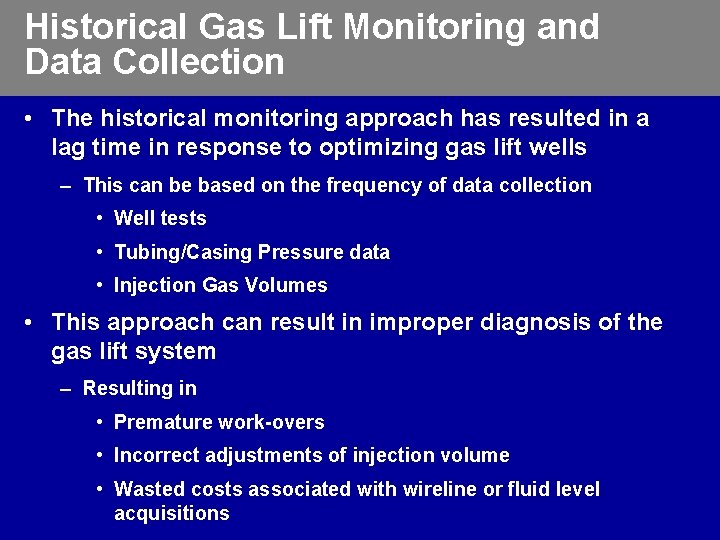
Historical Gas Lift Monitoring and Data Collection • The historical monitoring approach has resulted in a lag time in response to optimizing gas lift wells – This can be based on the frequency of data collection • Well tests • Tubing/Casing Pressure data • Injection Gas Volumes • This approach can result in improper diagnosis of the gas lift system – Resulting in • Premature work-overs • Incorrect adjustments of injection volume • Wasted costs associated with wireline or fluid level acquisitions
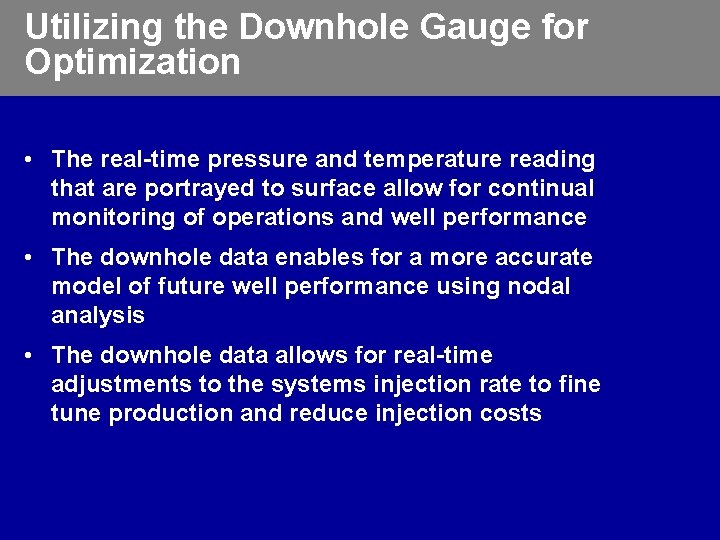
Utilizing the Downhole Gauge for Optimization • The real-time pressure and temperature reading that are portrayed to surface allow for continual monitoring of operations and well performance • The downhole data enables for a more accurate model of future well performance using nodal analysis • The downhole data allows for real-time adjustments to the systems injection rate to fine tune production and reduce injection costs
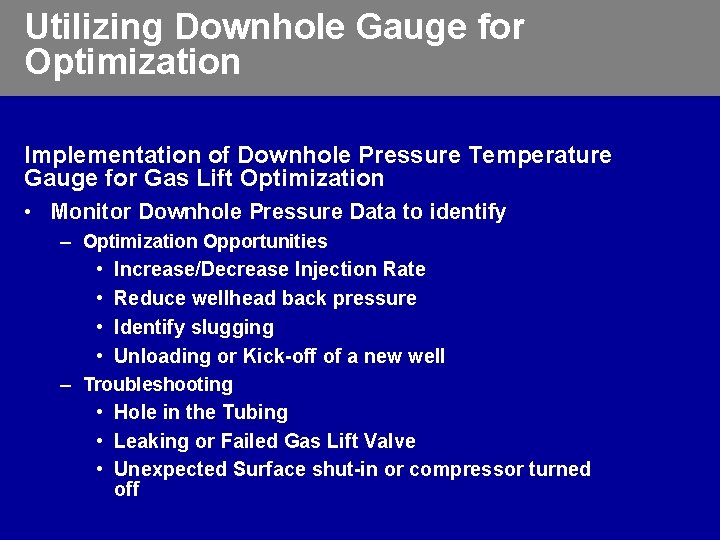
Utilizing Downhole Gauge for Optimization Implementation of Downhole Pressure Temperature Gauge for Gas Lift Optimization • Monitor Downhole Pressure Data to identify – Optimization Opportunities • Increase/Decrease Injection Rate • Reduce wellhead back pressure • Identify slugging • Unloading or Kick-off of a new well – Troubleshooting • Hole in the Tubing • Leaking or Failed Gas Lift Valve • Unexpected Surface shut-in or compressor turned off
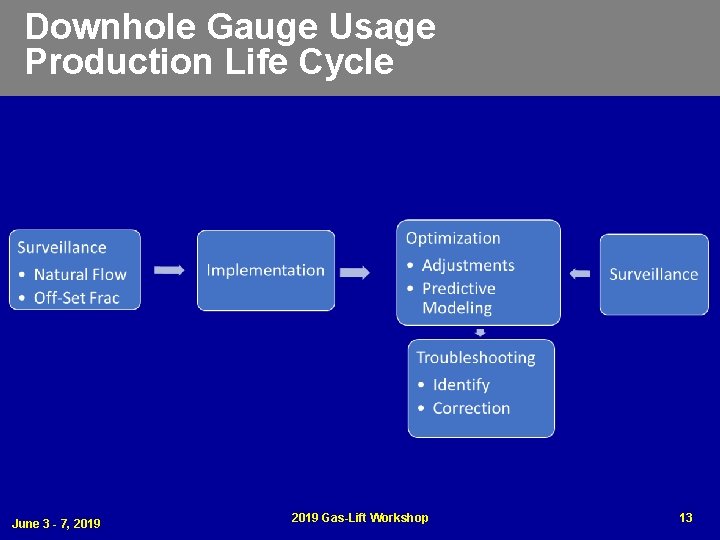
Downhole Gauge Usage Production Life Cycle June 3 - 7, 2019 Gas-Lift Workshop 13
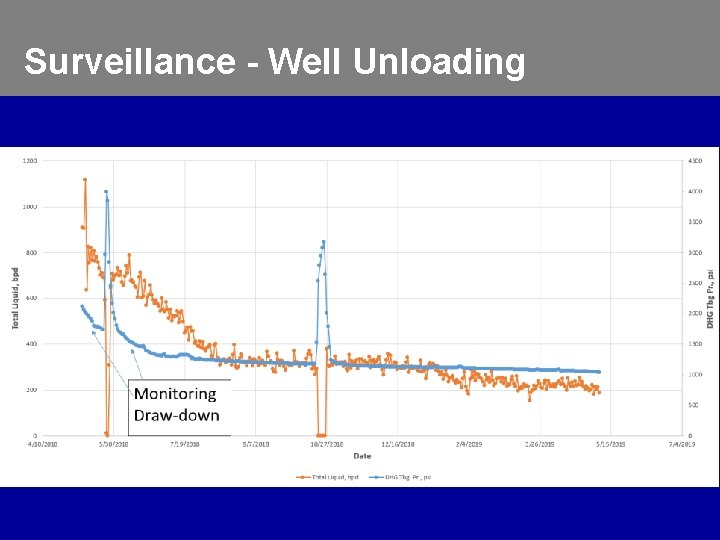
Surveillance - Well Unloading
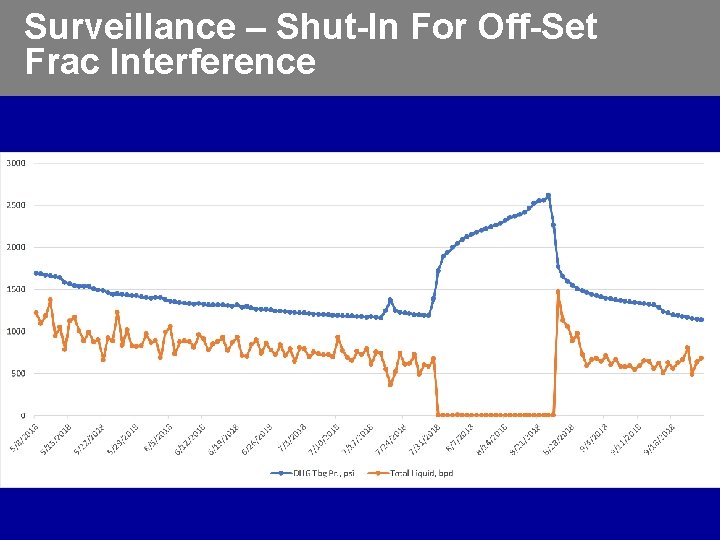
Surveillance – Shut-In For Off-Set Frac Interference
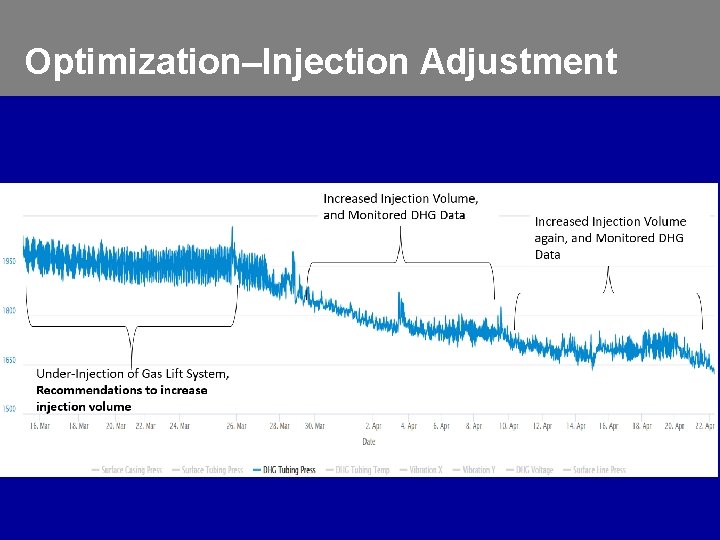
Optimization–Injection Adjustment Under-Injection of Gas Lift System, Recommendations to increase injection volume
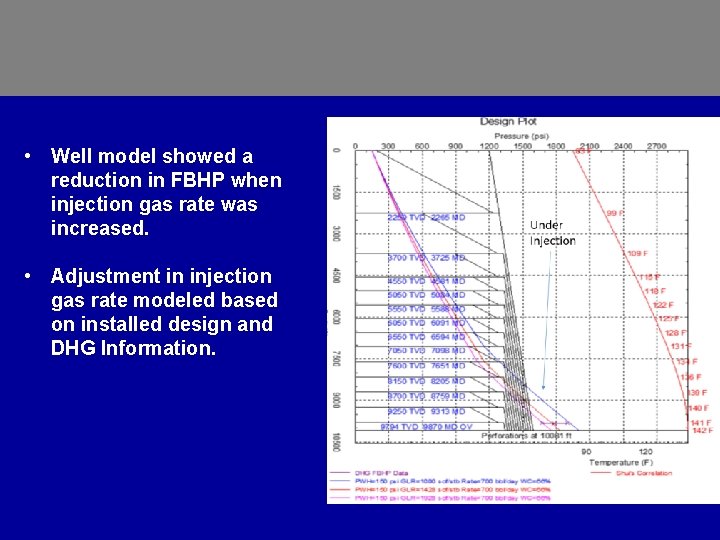
• Well model showed a reduction in FBHP when injection gas rate was increased. • Adjustment in injection gas rate modeled based on installed design and DHG Information.
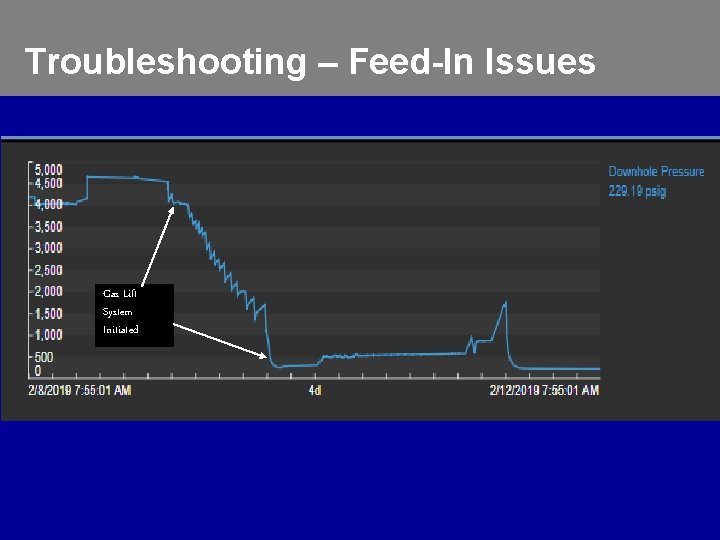
Troubleshooting – Feed-In Issues Well Shut-In Gas Lift System Initiated
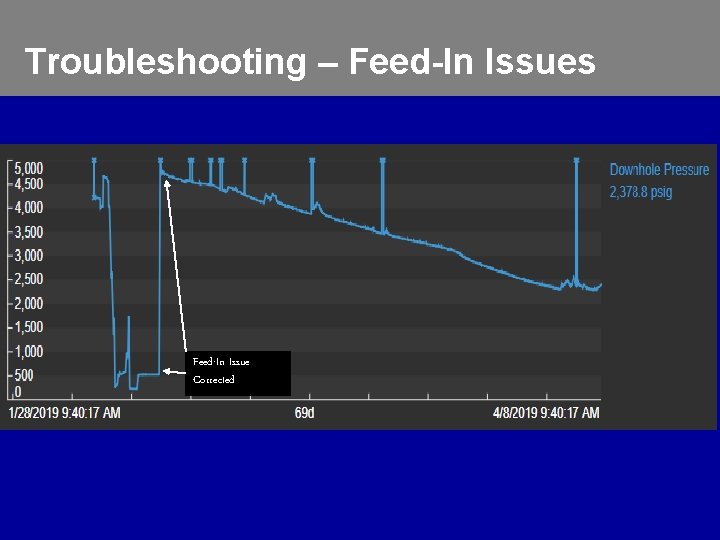
Troubleshooting – Feed-In Issues Feed-In Issue Corrected
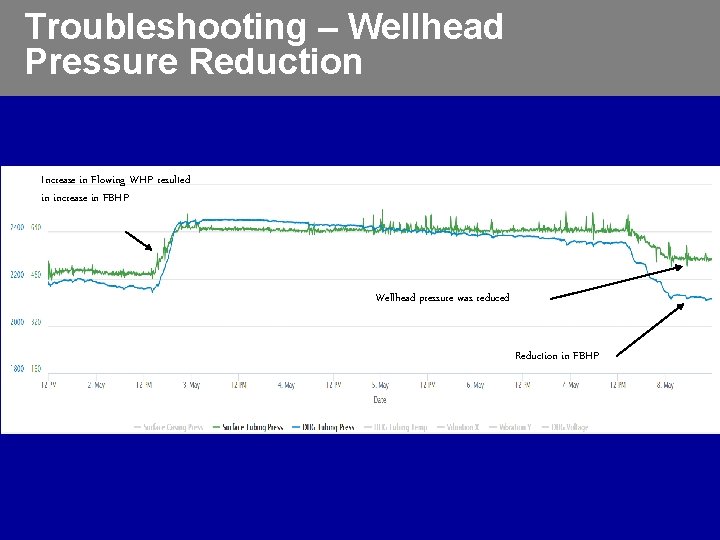
Troubleshooting – Wellhead Pressure Reduction Increase in Flowing WHP resulted in increase in FBHP Wellhead pressure was reduced Reduction in FBHP
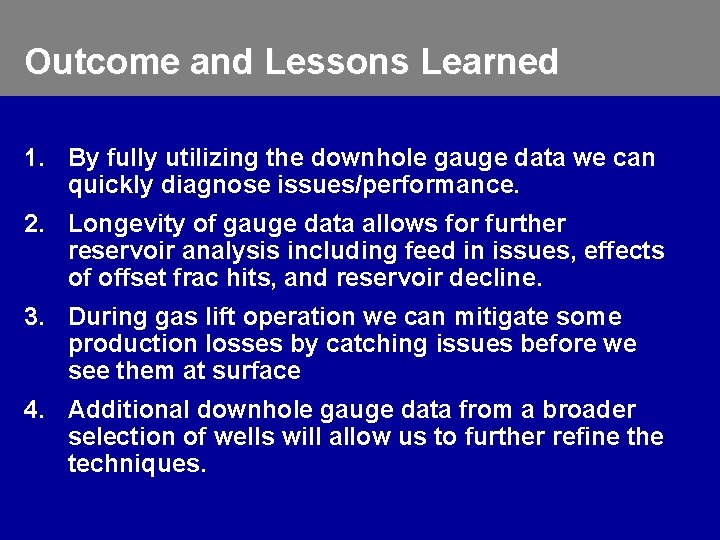
Outcome and Lessons Learned 1. By fully utilizing the downhole gauge data we can quickly diagnose issues/performance. 2. Longevity of gauge data allows for further reservoir analysis including feed in issues, effects of offset frac hits, and reservoir decline. 3. During gas lift operation we can mitigate some production losses by catching issues before we see them at surface 4. Additional downhole gauge data from a broader selection of wells will allow us to further refine the techniques.
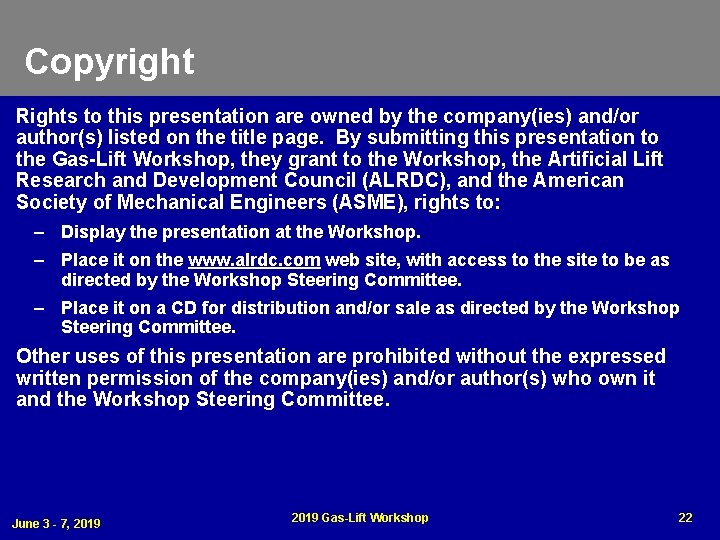
Copyright Rights to this presentation are owned by the company(ies) and/or author(s) listed on the title page. By submitting this presentation to the Gas-Lift Workshop, they grant to the Workshop, the Artificial Lift Research and Development Council (ALRDC), and the American Society of Mechanical Engineers (ASME), rights to: – Display the presentation at the Workshop. – Place it on the www. alrdc. com web site, with access to the site to be as directed by the Workshop Steering Committee. – Place it on a CD for distribution and/or sale as directed by the Workshop Steering Committee. Other uses of this presentation are prohibited without the expressed written permission of the company(ies) and/or author(s) who own it and the Workshop Steering Committee. June 3 - 7, 2019 Gas-Lift Workshop 22
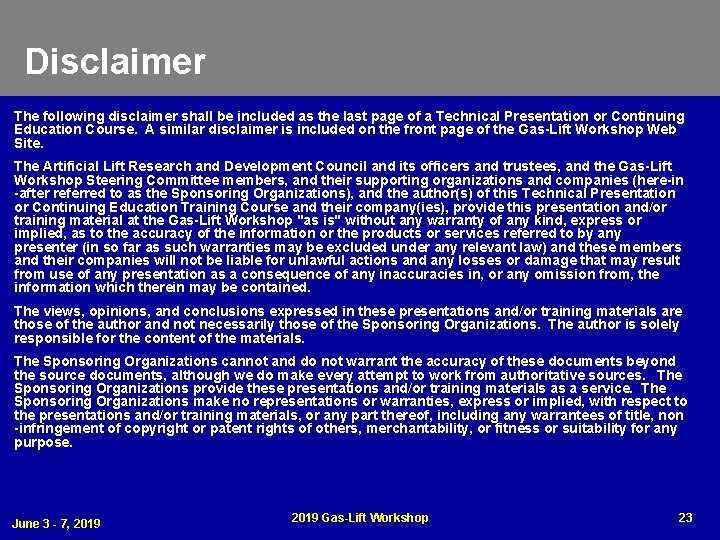
Disclaimer The following disclaimer shall be included as the last page of a Technical Presentation or Continuing Education Course. A similar disclaimer is included on the front page of the Gas-Lift Workshop Web Site. The Artificial Lift Research and Development Council and its officers and trustees, and the Gas-Lift Workshop Steering Committee members, and their supporting organizations and companies (here-in -after referred to as the Sponsoring Organizations), and the author(s) of this Technical Presentation or Continuing Education Training Course and their company(ies), provide this presentation and/or training material at the Gas-Lift Workshop "as is" without any warranty of any kind, express or implied, as to the accuracy of the information or the products or services referred to by any presenter (in so far as such warranties may be excluded under any relevant law) and these members and their companies will not be liable for unlawful actions and any losses or damage that may result from use of any presentation as a consequence of any inaccuracies in, or any omission from, the information which therein may be contained. The views, opinions, and conclusions expressed in these presentations and/or training materials are those of the author and not necessarily those of the Sponsoring Organizations. The author is solely responsible for the content of the materials. The Sponsoring Organizations cannot and do not warrant the accuracy of these documents beyond the source documents, although we do make every attempt to work from authoritative sources. The Sponsoring Organizations provide these presentations and/or training materials as a service. The Sponsoring Organizations make no representations or warranties, express or implied, with respect to the presentations and/or training materials, or any part thereof, including any warrantees of title, non -infringement of copyright or patent rights of others, merchantability, or fitness or suitability for any purpose. June 3 - 7, 2019 Gas-Lift Workshop 23
Houston isd foundation houston, tx
Houston texas to hawaii
Joint processing center houston
June 15 1215
Lake june head start
Grade 7 life orientation term 1 notes
Elephant riding in phuket texto completo respuestas
June 23
June 2005 calendar
June 2018 chemistry regents
Tobias spears
Ward 34 ninewells
Holy june
June 22 to july 22
Confined placental mosaicism
June's journey
Danswer
Summary period: june 2021 poem
June canavan foundation
30 days has september
June 21 2019 geometry regents
June preschool newsletter
Dr june james
Good morning welcome june