2 SHORT WELDED RAILS SWR 2 1 Track
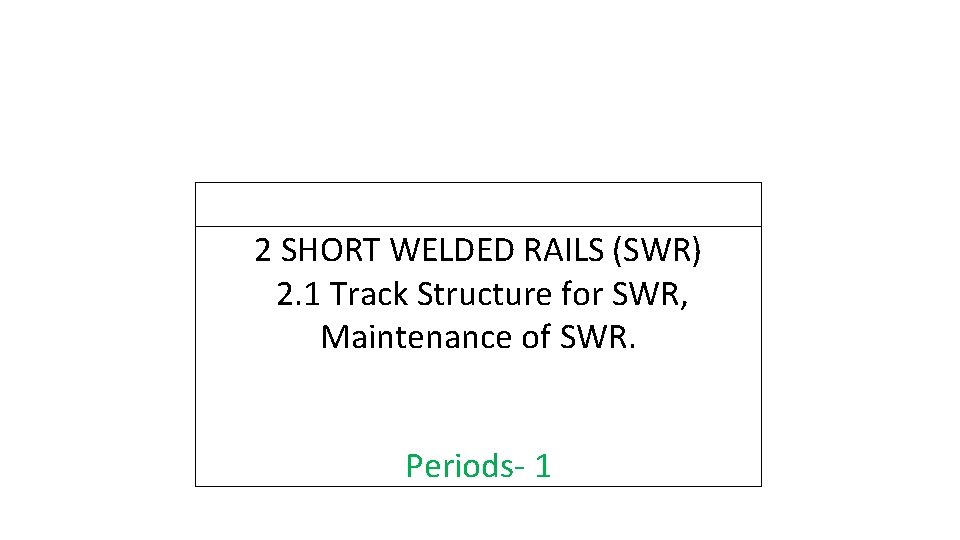
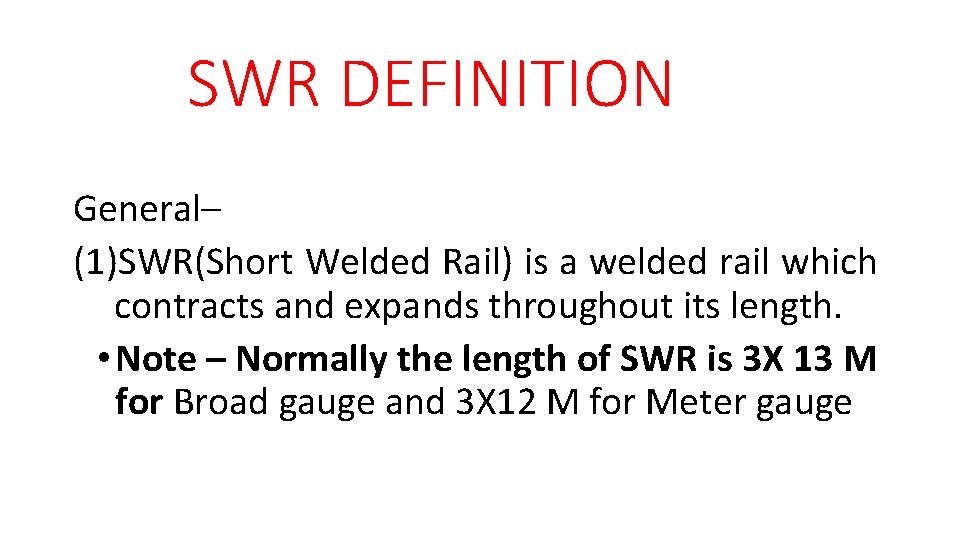
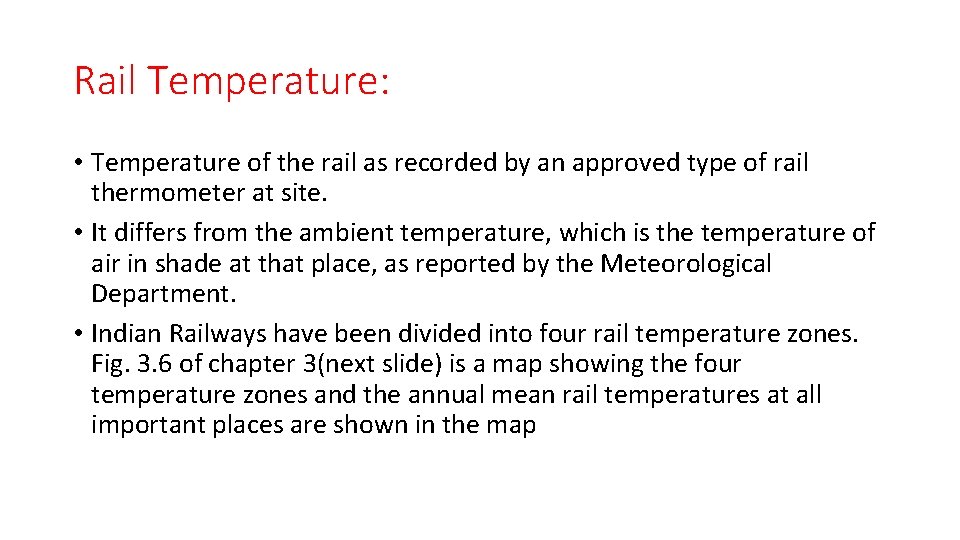
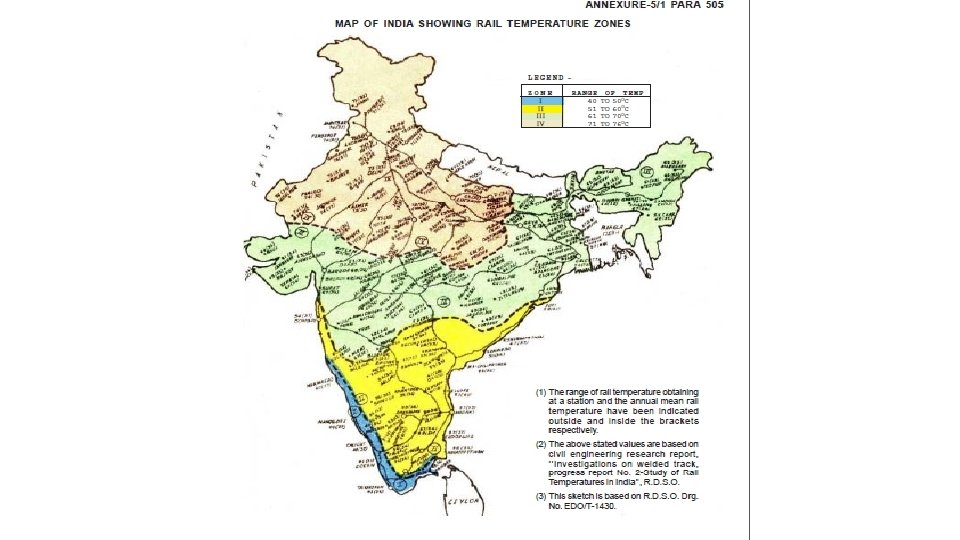
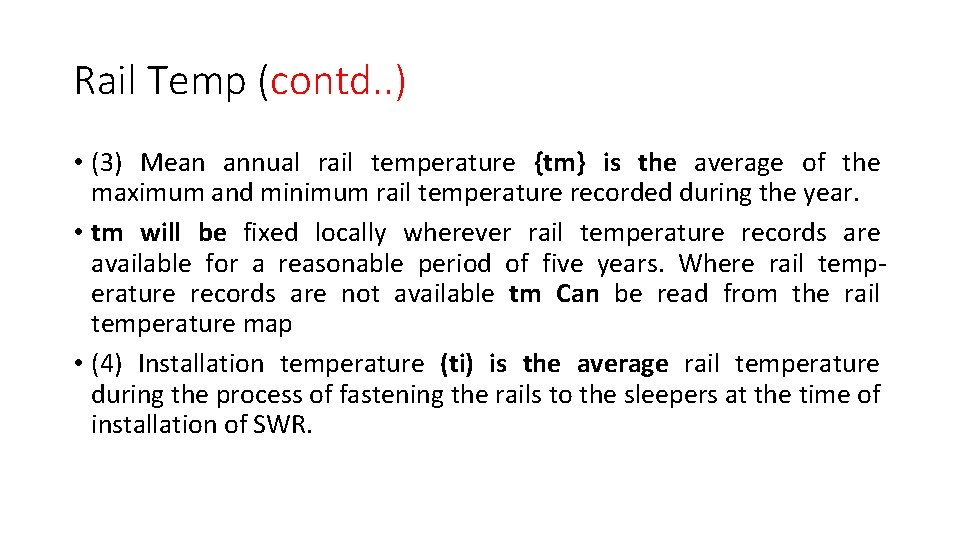
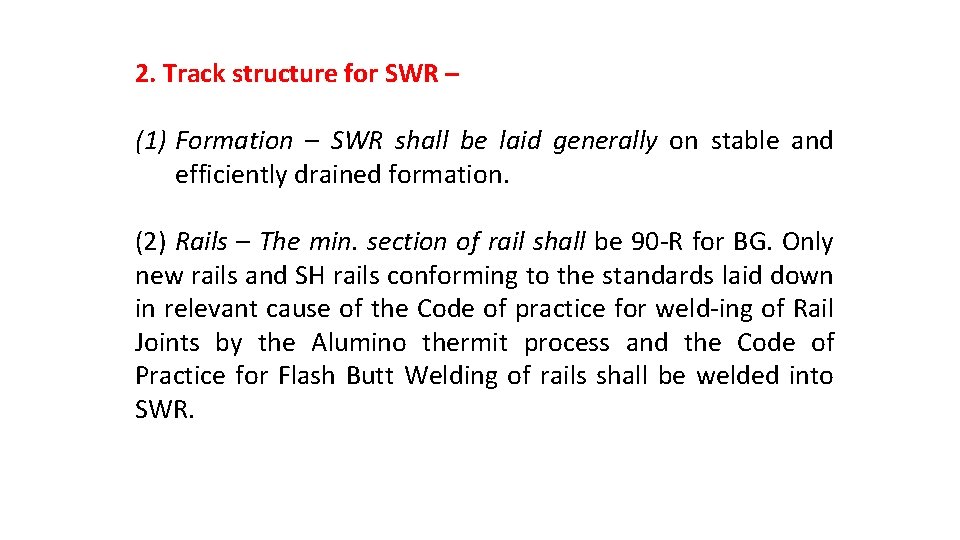
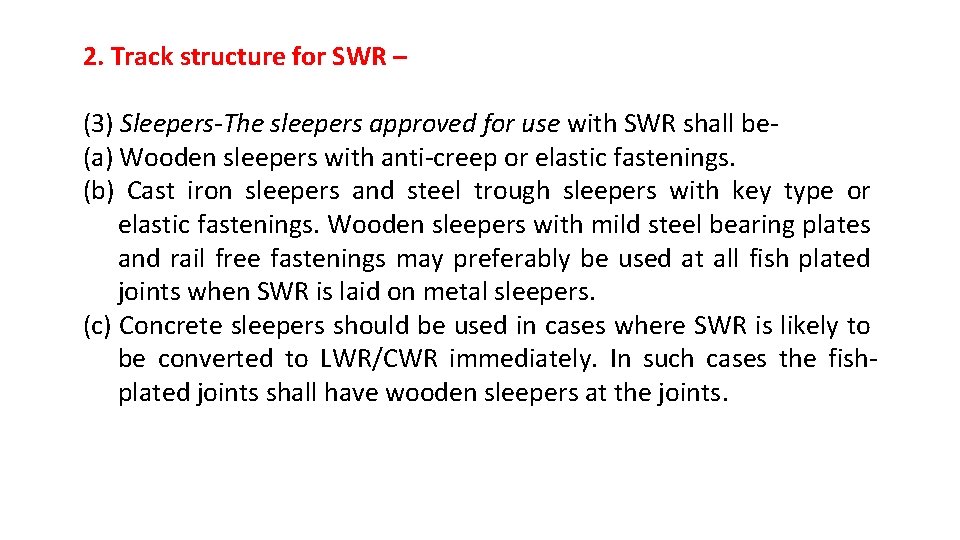
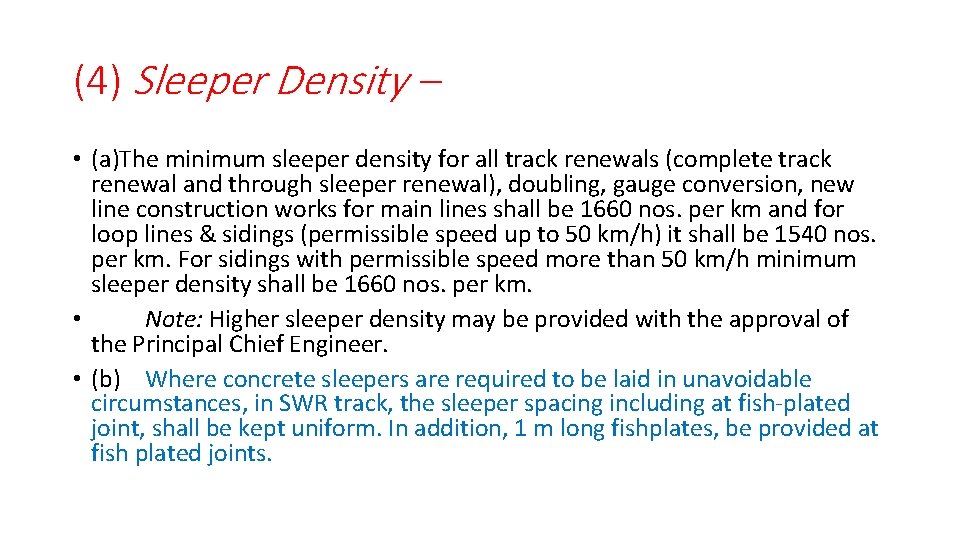
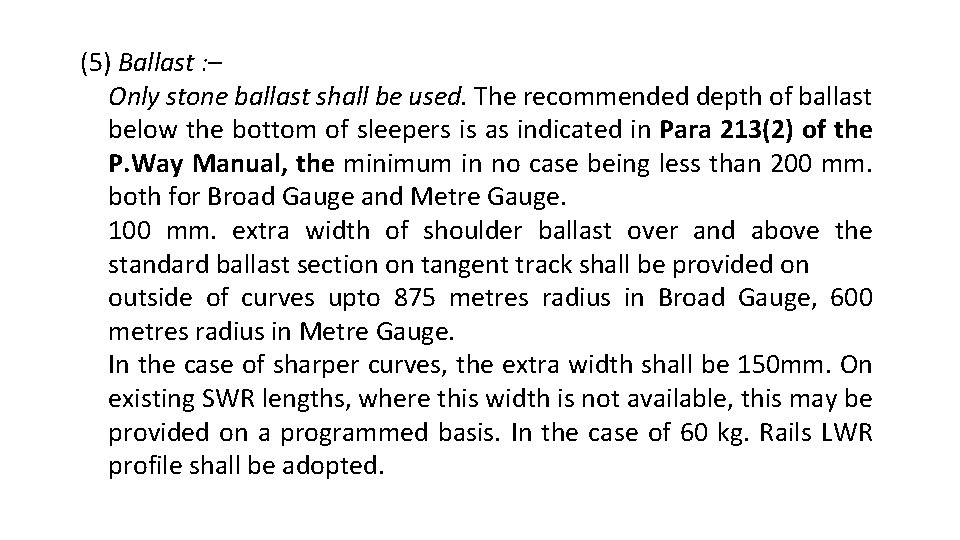
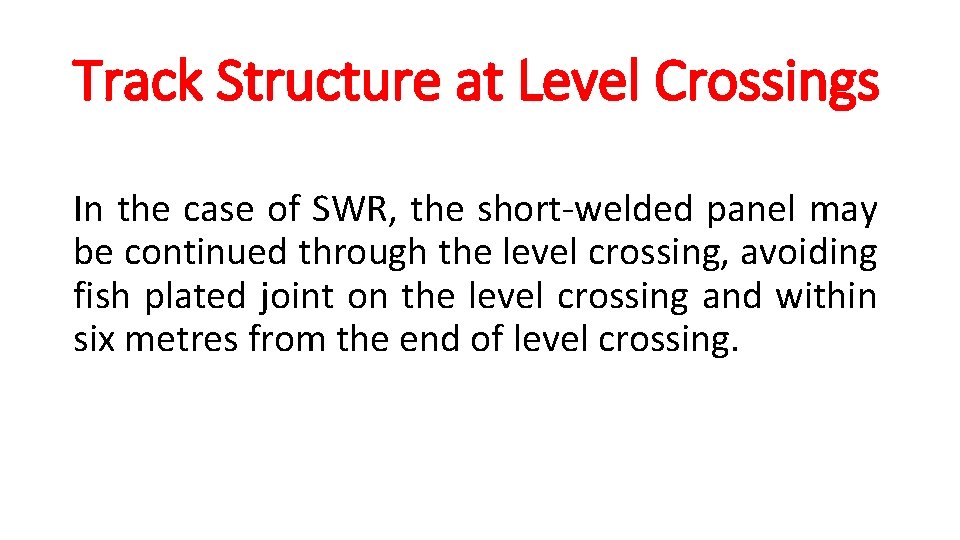
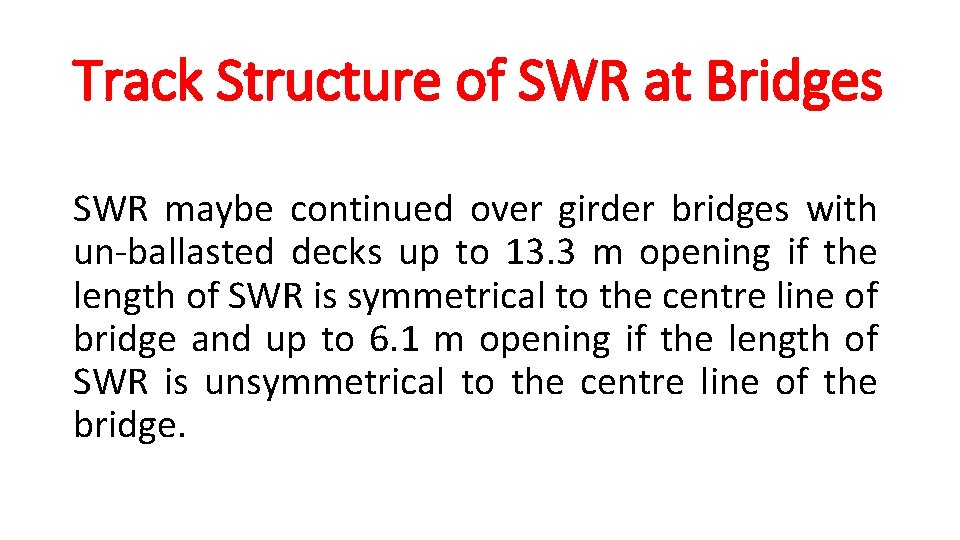
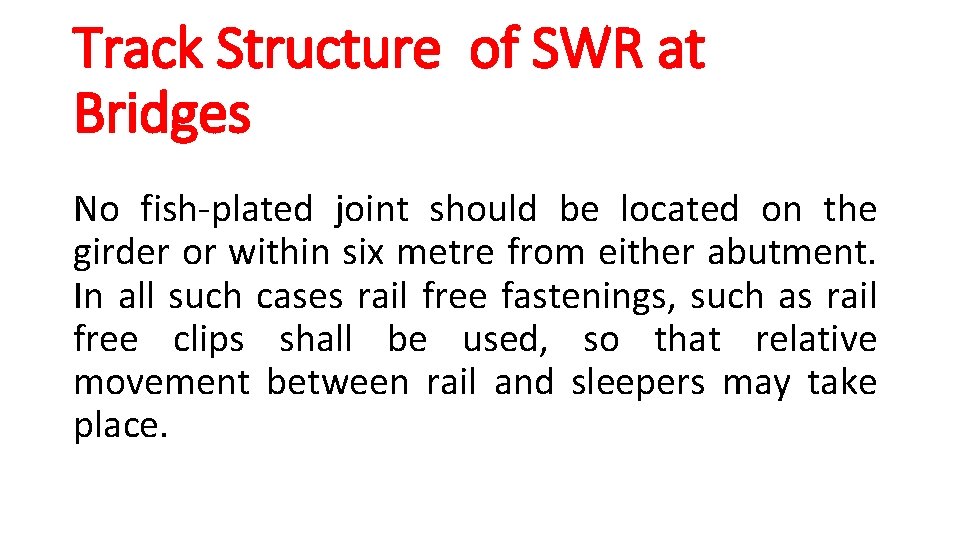
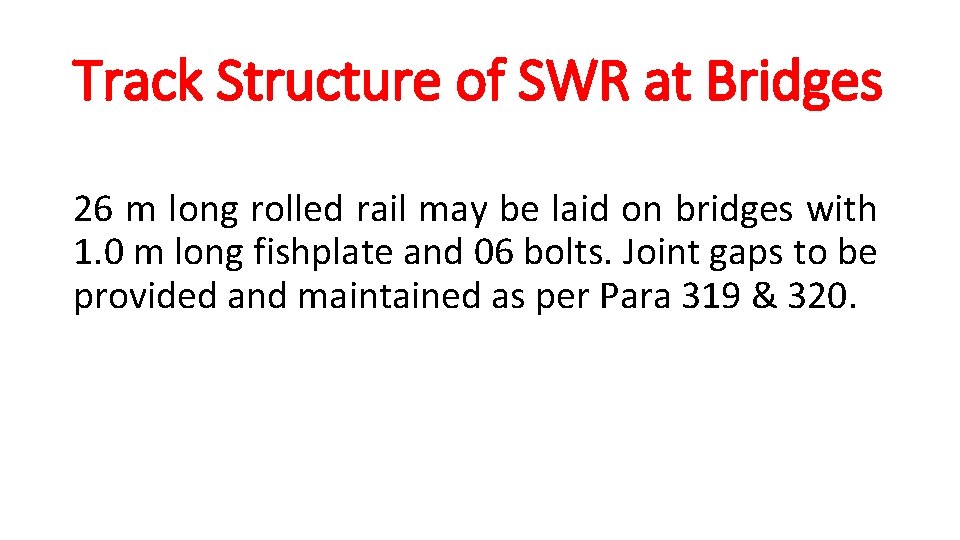
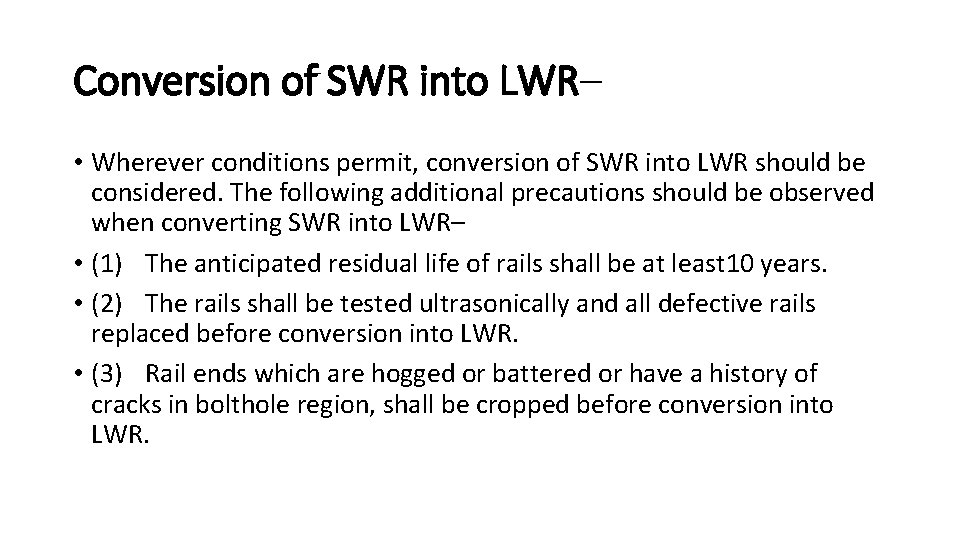
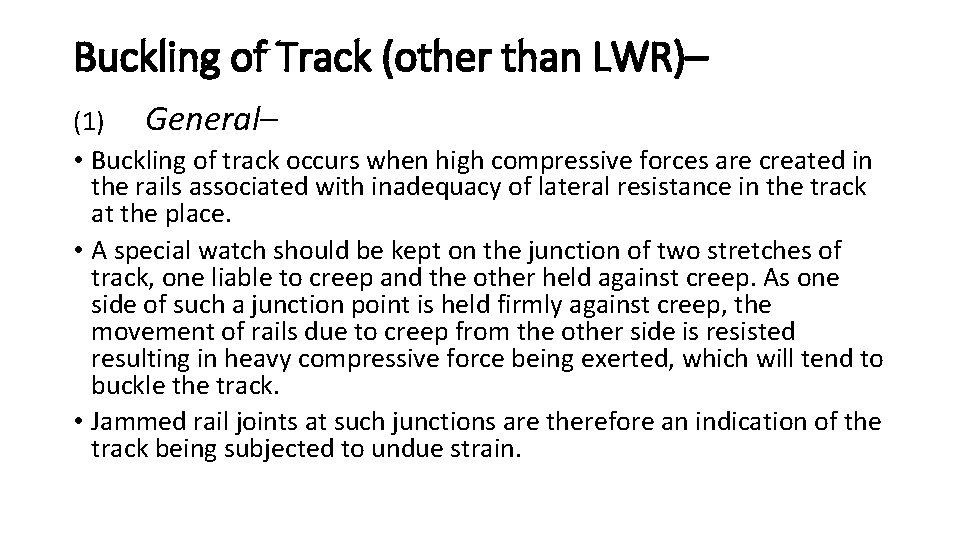
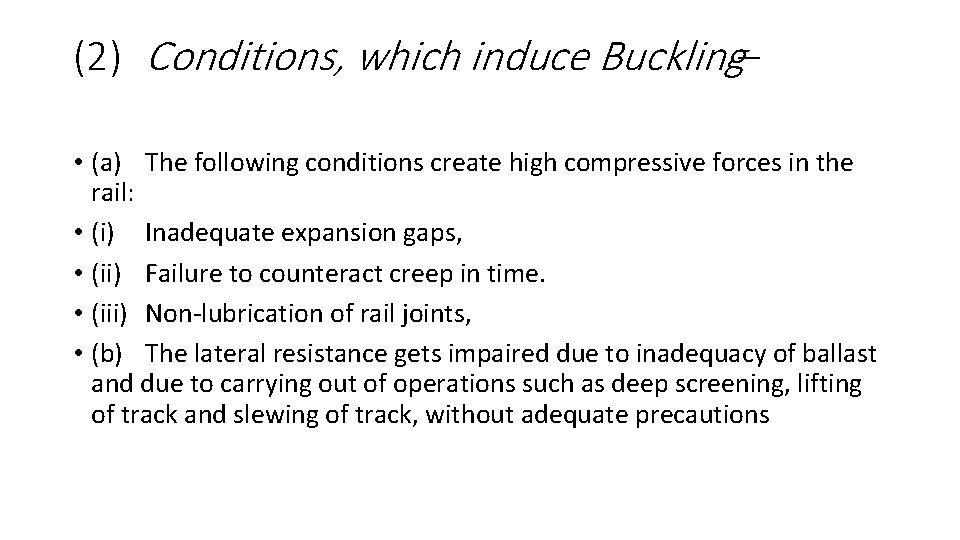
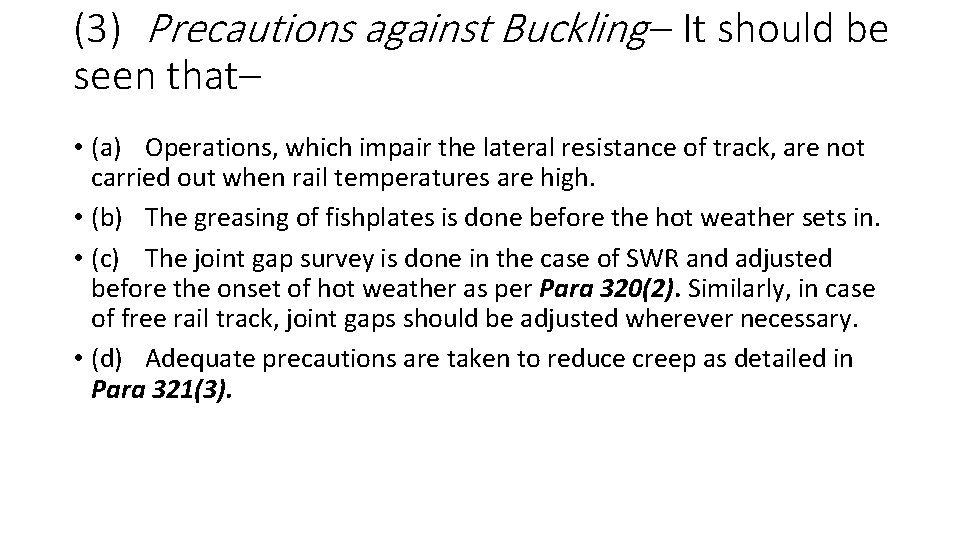
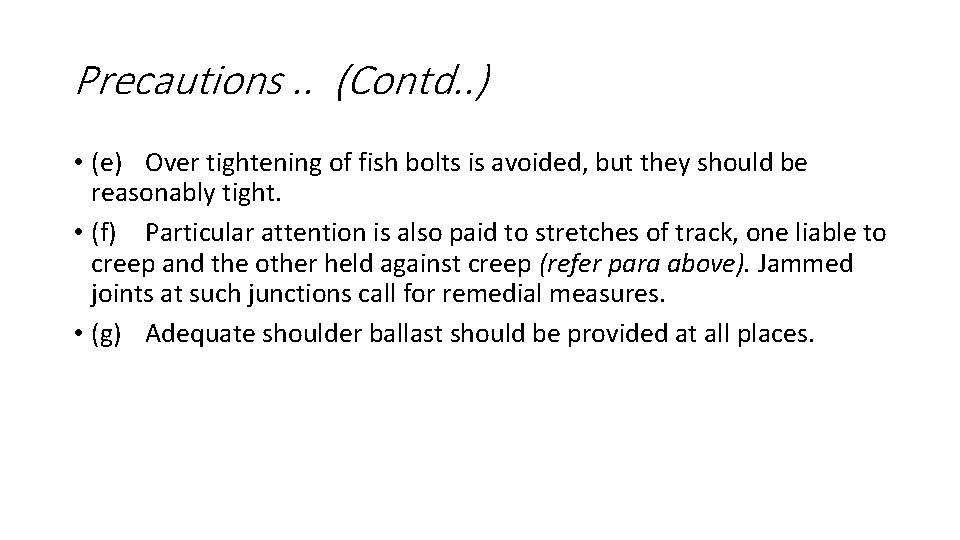
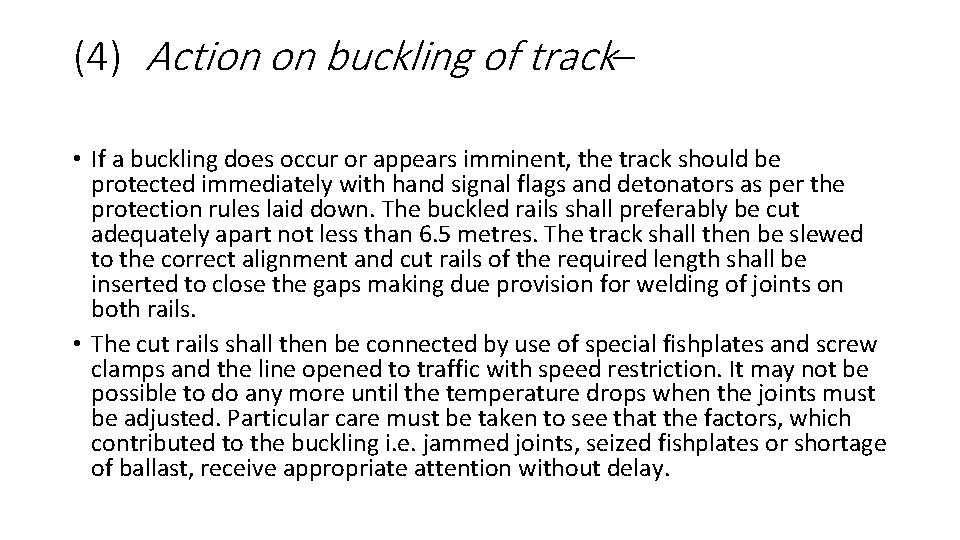
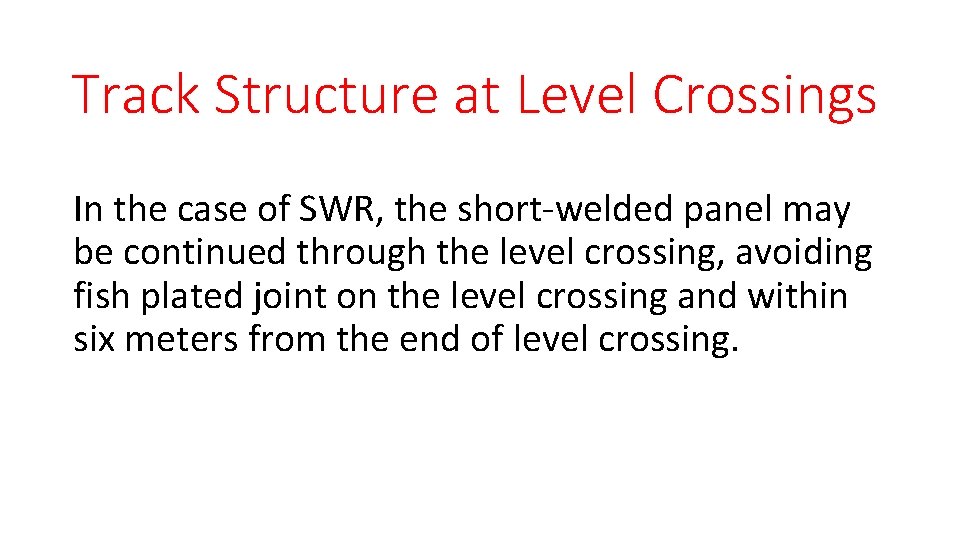
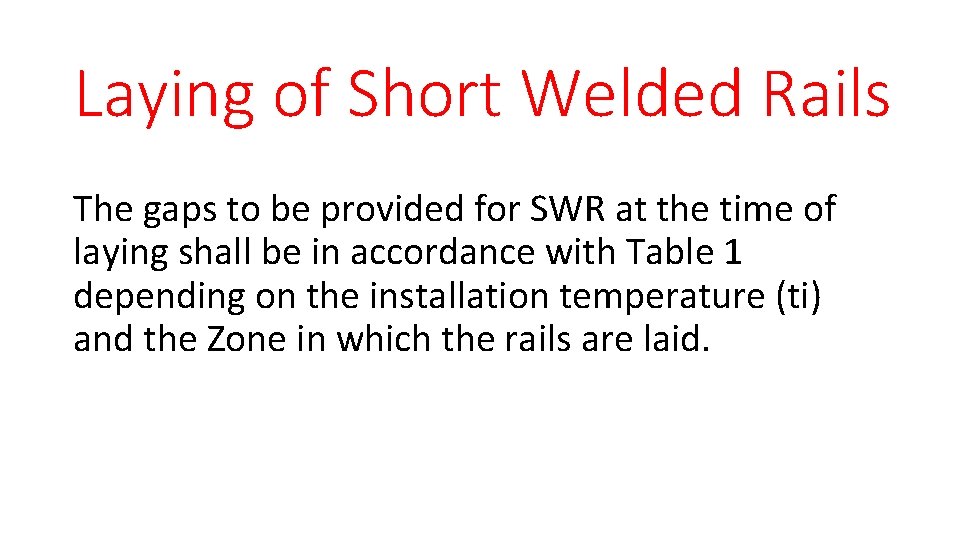
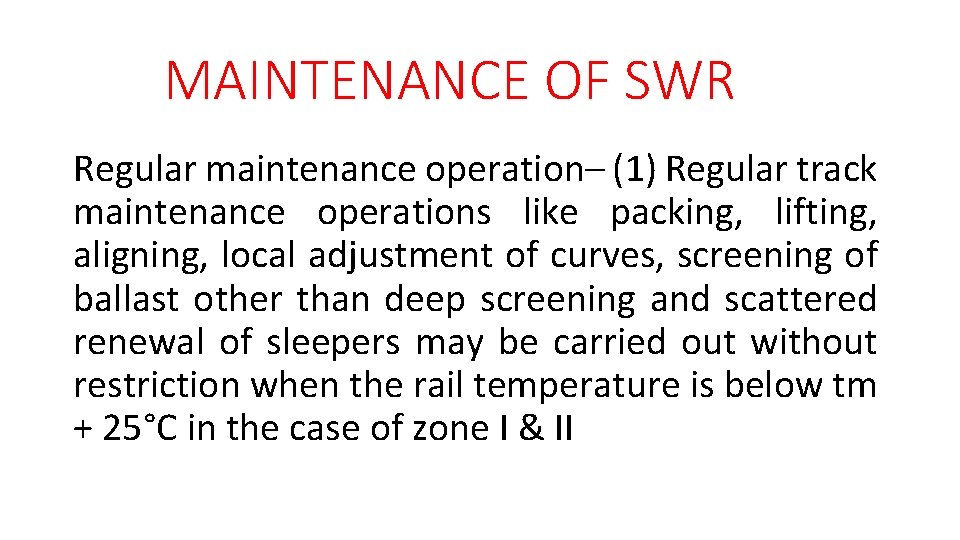
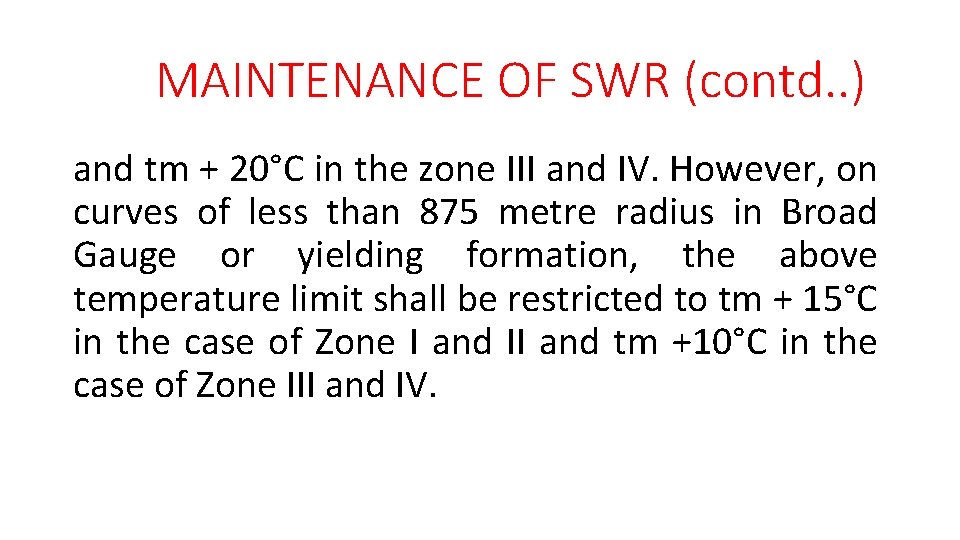
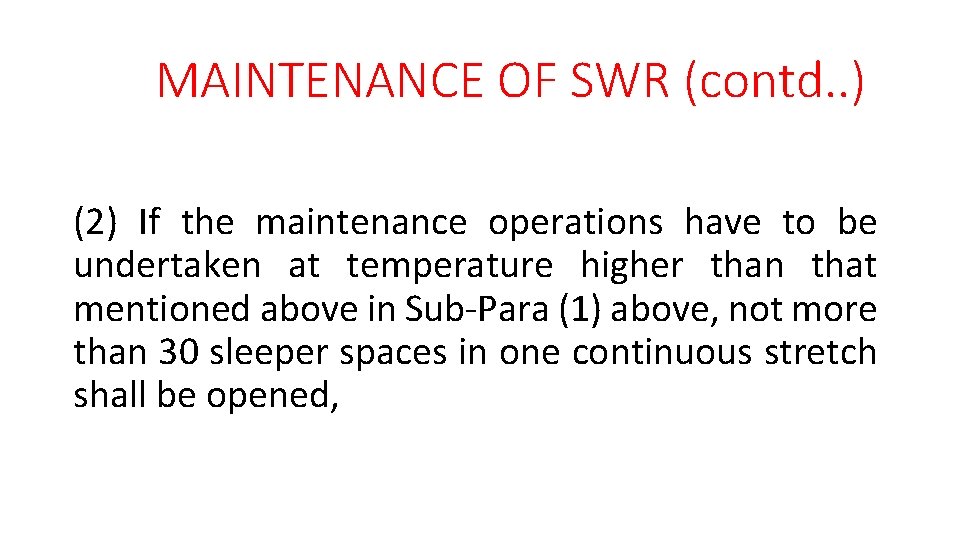
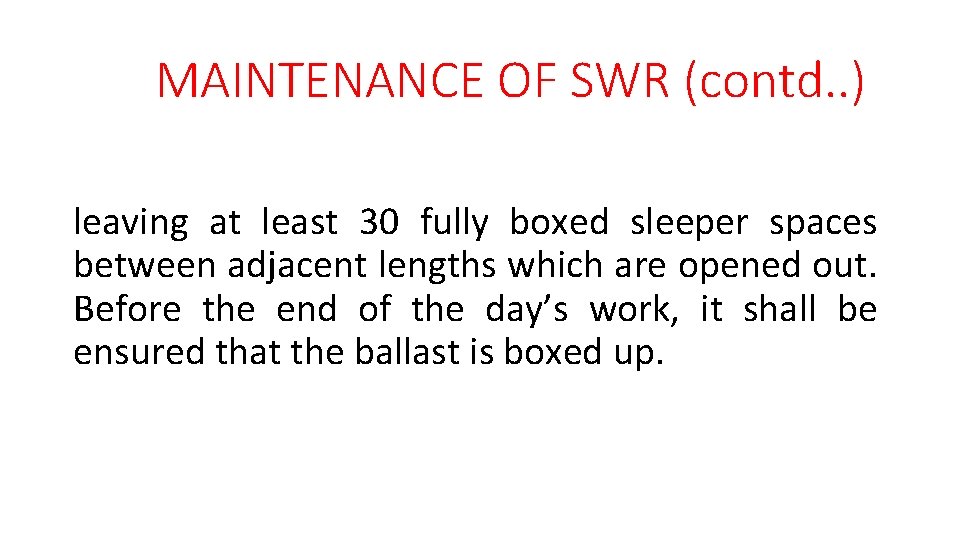
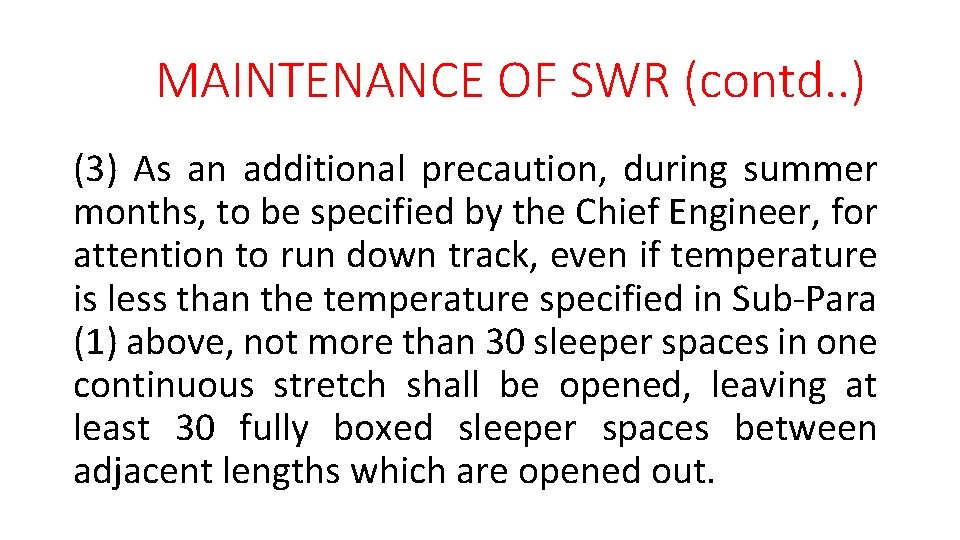
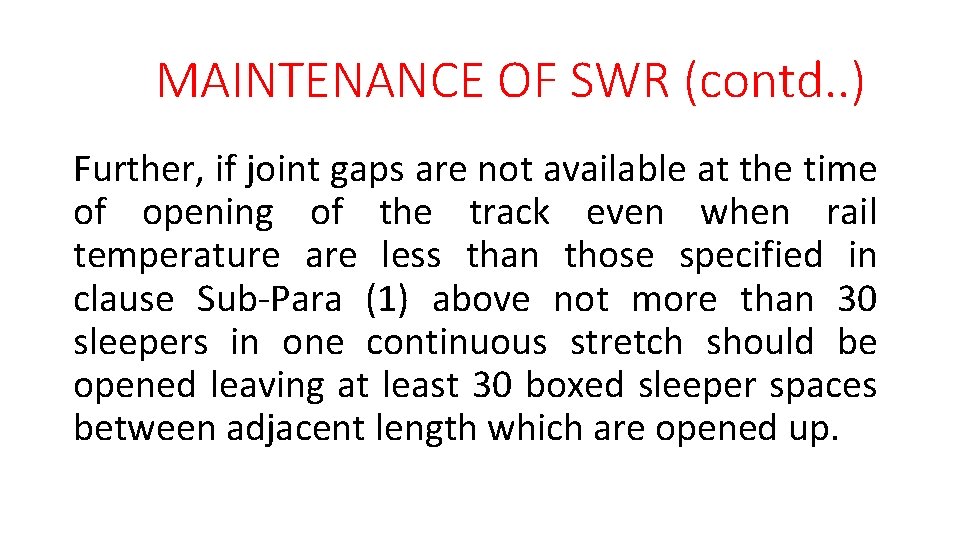
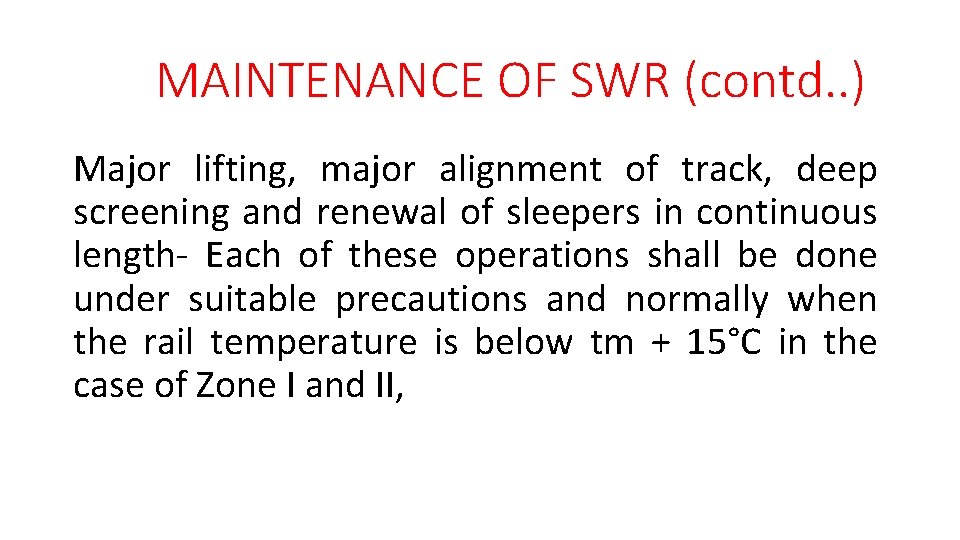
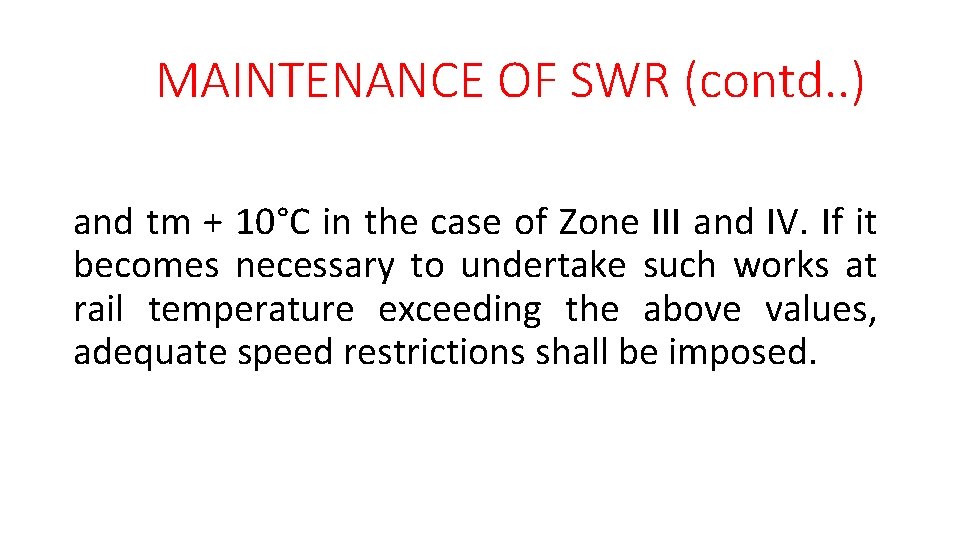
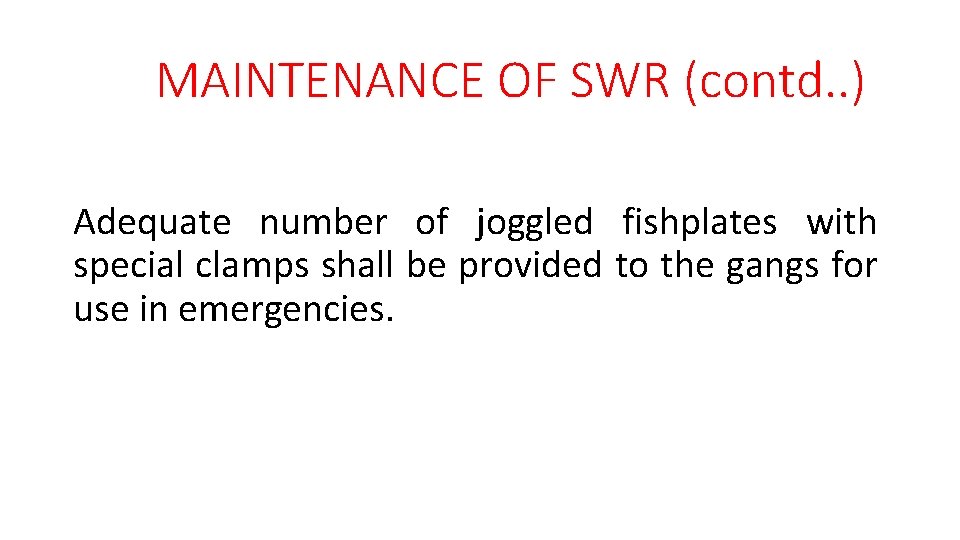
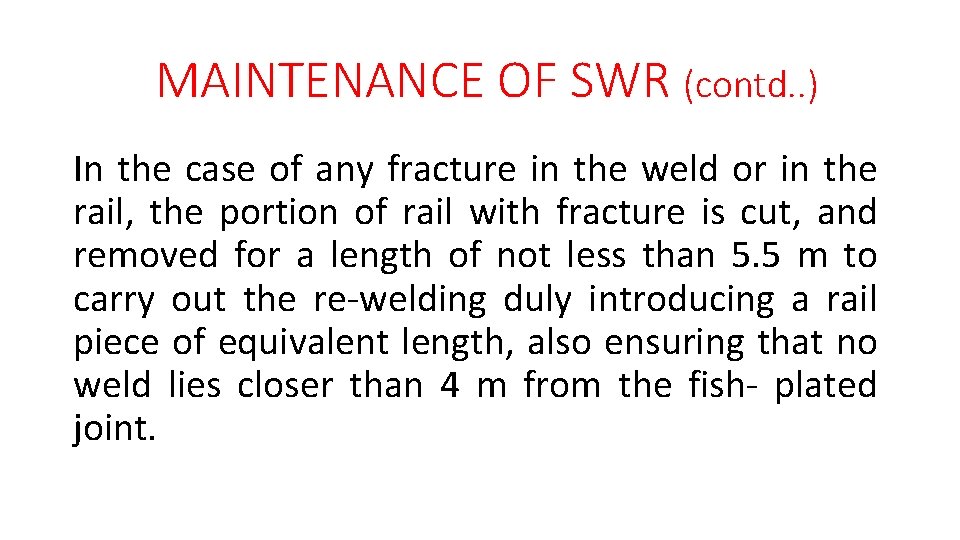
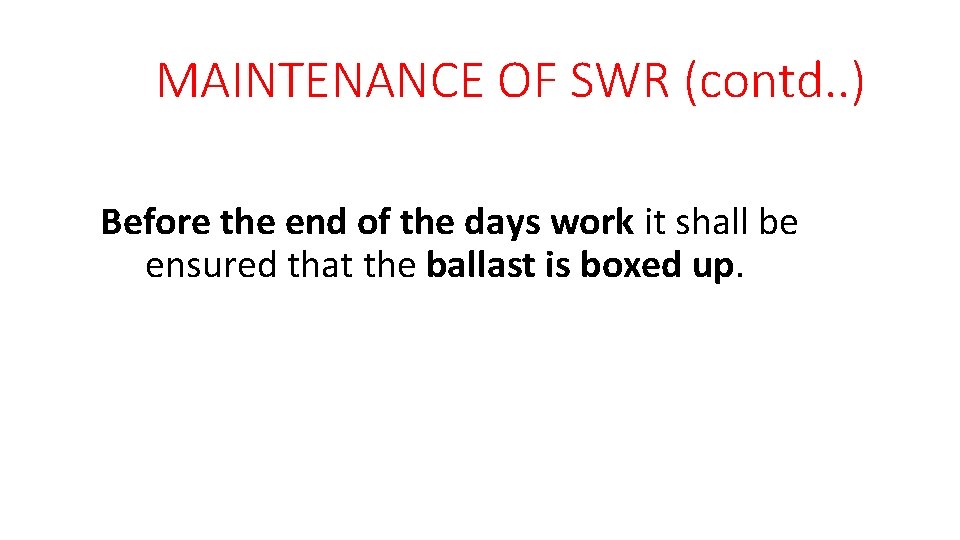
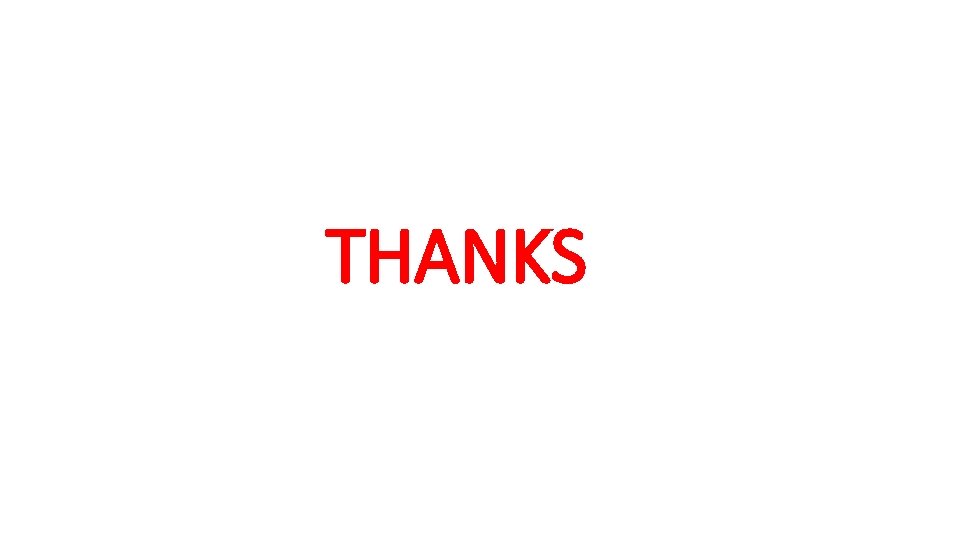
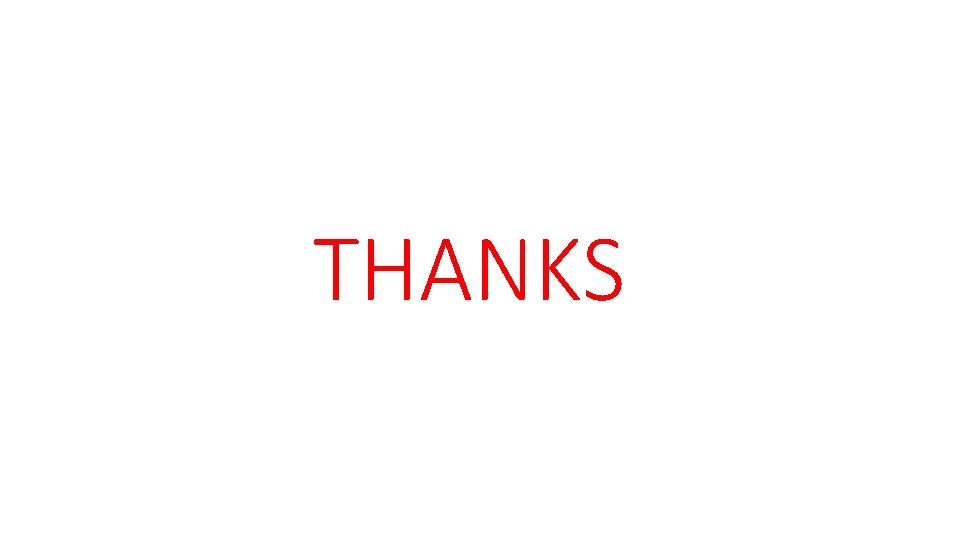
- Slides: 34
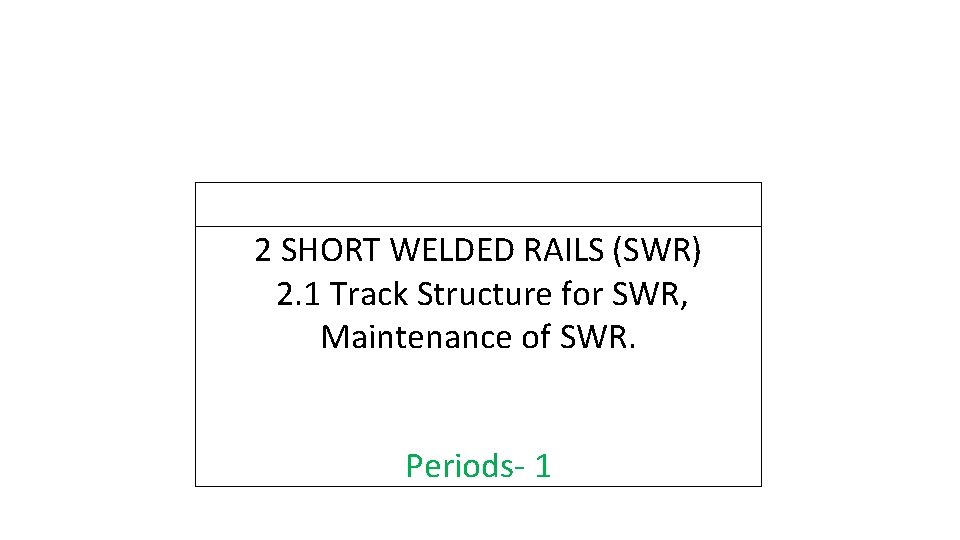
2 SHORT WELDED RAILS (SWR) 2. 1 Track Structure for SWR, Maintenance of SWR. Periods- 1
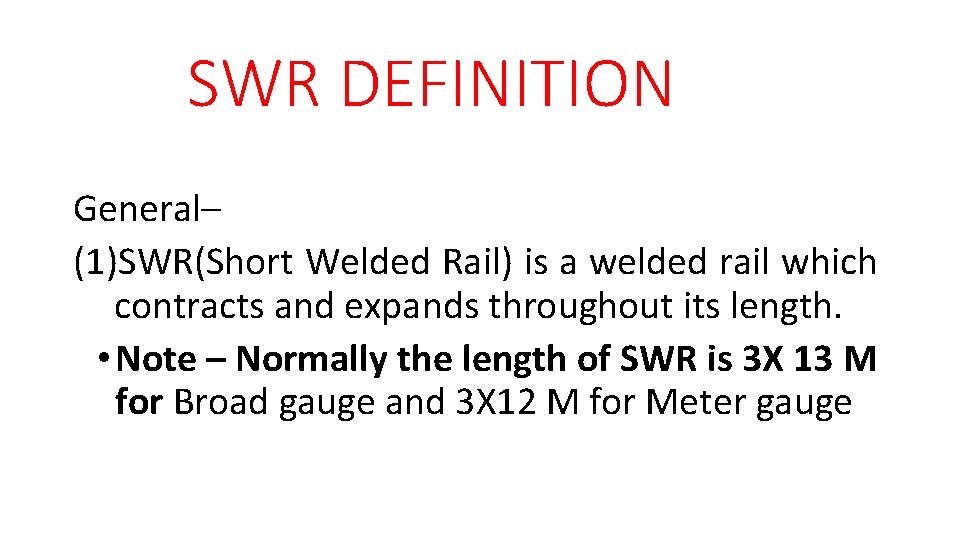
SWR DEFINITION General– (1)SWR(Short Welded Rail) is a welded rail which contracts and expands throughout its length. • Note – Normally the length of SWR is 3 X 13 M for Broad gauge and 3 X 12 M for Meter gauge
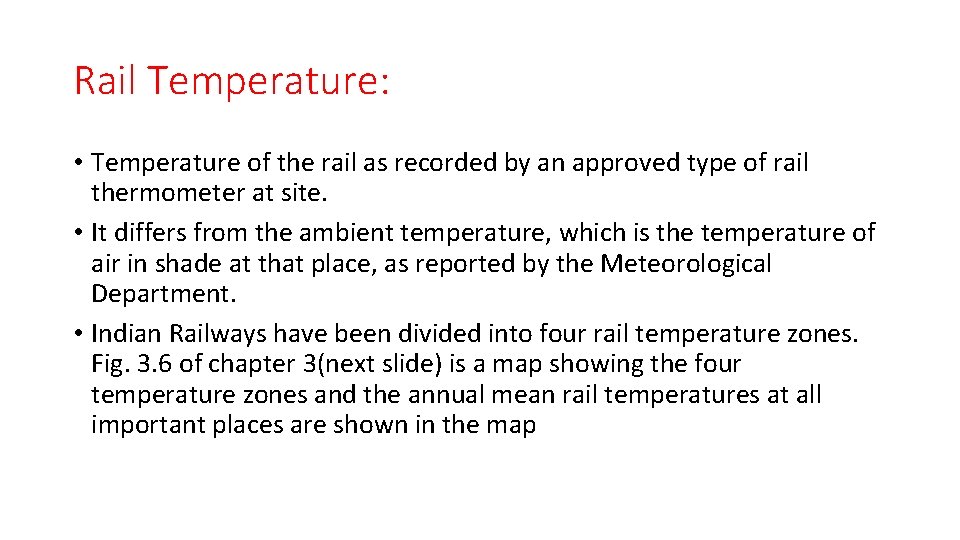
Rail Temperature: • Temperature of the rail as recorded by an approved type of rail thermometer at site. • It differs from the ambient temperature, which is the temperature of air in shade at that place, as reported by the Meteorological Department. • Indian Railways have been divided into four rail temperature zones. Fig. 3. 6 of chapter 3(next slide) is a map showing the four temperature zones and the annual mean rail temperatures at all important places are shown in the map
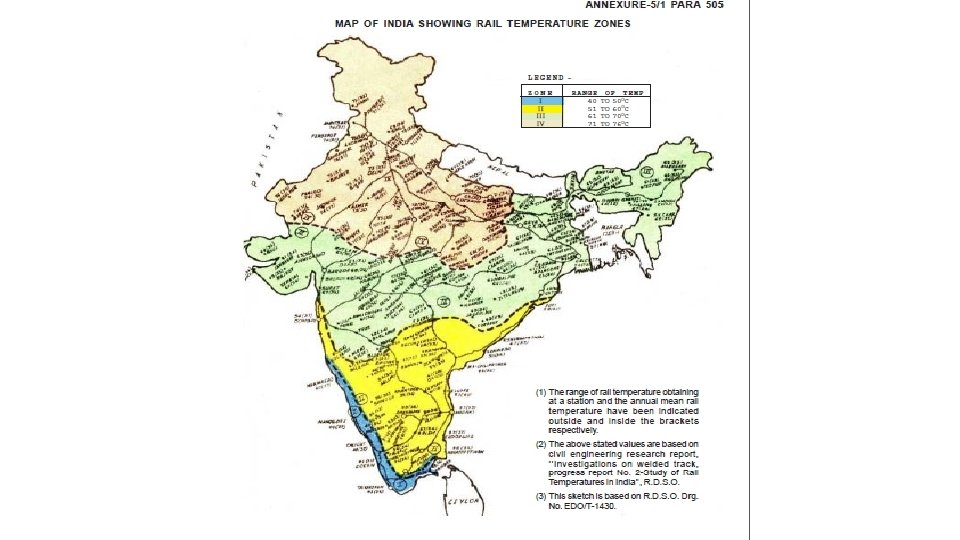
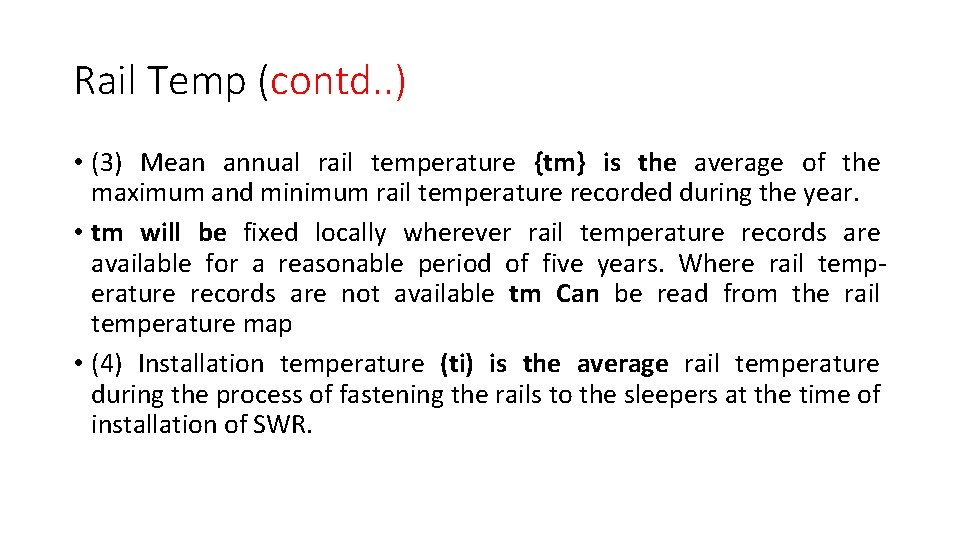
Rail Temp (contd. . ) • (3) Mean annual rail temperature {tm} is the average of the maximum and minimum rail temperature recorded during the year. • tm will be fixed locally wherever rail temperature records are available for a reasonable period of five years. Where rail temperature records are not available tm Can be read from the rail temperature map • (4) Installation temperature (ti) is the average rail temperature during the process of fastening the rails to the sleepers at the time of installation of SWR.
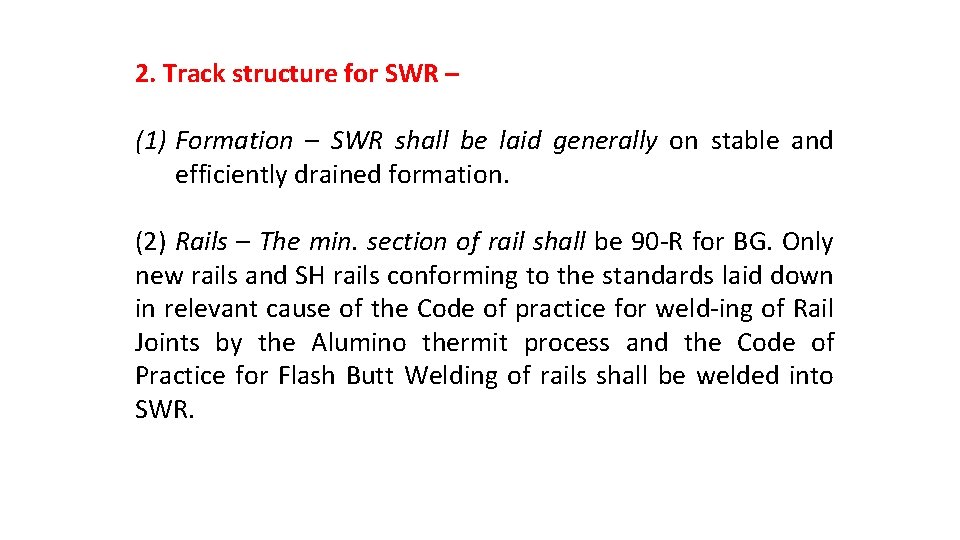
2. Track structure for SWR – (1) Formation – SWR shall be laid generally on stable and efficiently drained formation. (2) Rails – The min. section of rail shall be 90 -R for BG. Only new rails and SH rails conforming to the standards laid down in relevant cause of the Code of practice for weld-ing of Rail Joints by the Alumino thermit process and the Code of Practice for Flash Butt Welding of rails shall be welded into SWR.
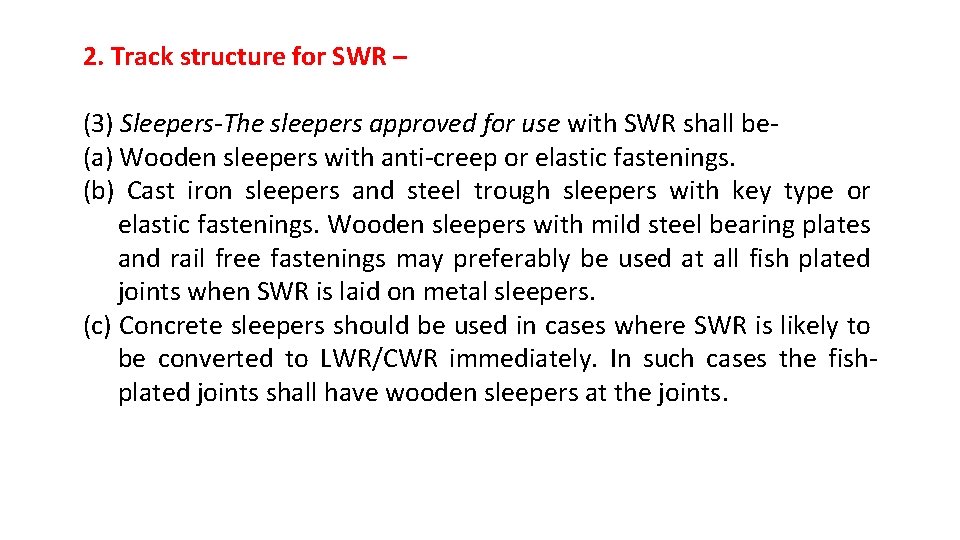
2. Track structure for SWR – (3) Sleepers-The sleepers approved for use with SWR shall be(a) Wooden sleepers with anti-creep or elastic fastenings. (b) Cast iron sleepers and steel trough sleepers with key type or elastic fastenings. Wooden sleepers with mild steel bearing plates and rail free fastenings may preferably be used at all fish plated joints when SWR is laid on metal sleepers. (c) Concrete sleepers should be used in cases where SWR is likely to be converted to LWR/CWR immediately. In such cases the fishplated joints shall have wooden sleepers at the joints.
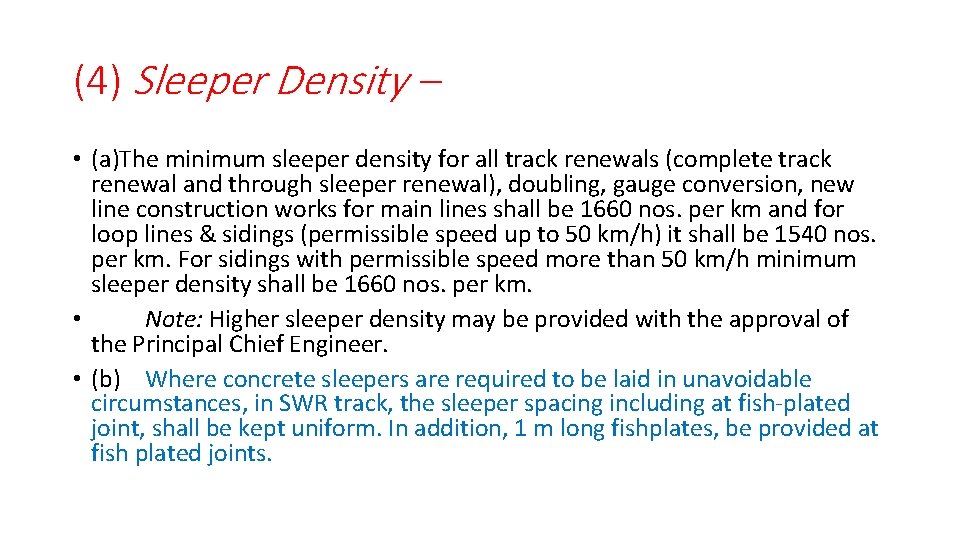
(4) Sleeper Density – • (a)The minimum sleeper density for all track renewals (complete track renewal and through sleeper renewal), doubling, gauge conversion, new line construction works for main lines shall be 1660 nos. per km and for loop lines & sidings (permissible speed up to 50 km/h) it shall be 1540 nos. per km. For sidings with permissible speed more than 50 km/h minimum sleeper density shall be 1660 nos. per km. • Note: Higher sleeper density may be provided with the approval of the Principal Chief Engineer. • (b) Where concrete sleepers are required to be laid in unavoidable circumstances, in SWR track, the sleeper spacing including at fish-plated joint, shall be kept uniform. In addition, 1 m long fishplates, be provided at fish plated joints.
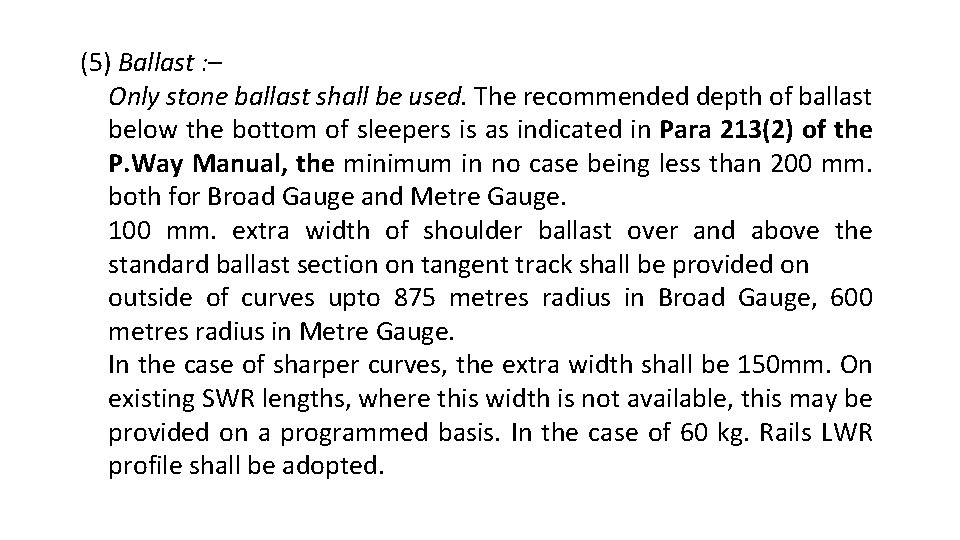
(5) Ballast : – Only stone ballast shall be used. The recommended depth of ballast below the bottom of sleepers is as indicated in Para 213(2) of the P. Way Manual, the minimum in no case being less than 200 mm. both for Broad Gauge and Metre Gauge. 100 mm. extra width of shoulder ballast over and above the standard ballast section on tangent track shall be provided on outside of curves upto 875 metres radius in Broad Gauge, 600 metres radius in Metre Gauge. In the case of sharper curves, the extra width shall be 150 mm. On existing SWR lengths, where this width is not available, this may be provided on a programmed basis. In the case of 60 kg. Rails LWR profile shall be adopted.
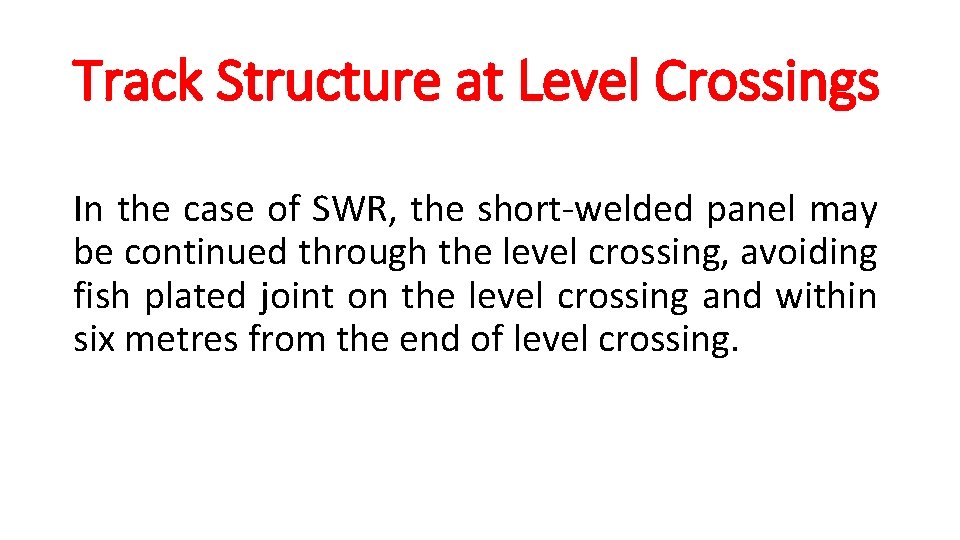
Track Structure at Level Crossings In the case of SWR, the short-welded panel may be continued through the level crossing, avoiding fish plated joint on the level crossing and within six metres from the end of level crossing.
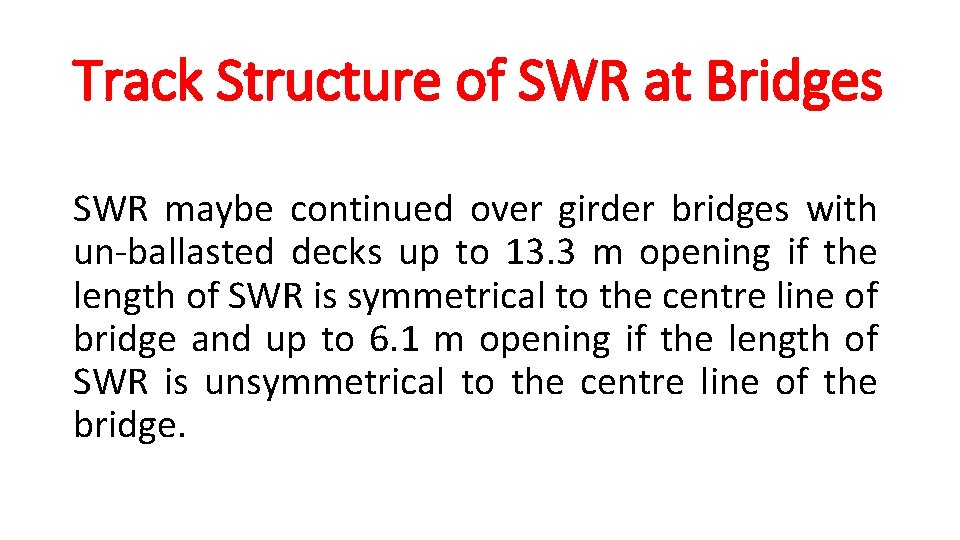
Track Structure of SWR at Bridges SWR maybe continued over girder bridges with un-ballasted decks up to 13. 3 m opening if the length of SWR is symmetrical to the centre line of bridge and up to 6. 1 m opening if the length of SWR is unsymmetrical to the centre line of the bridge.
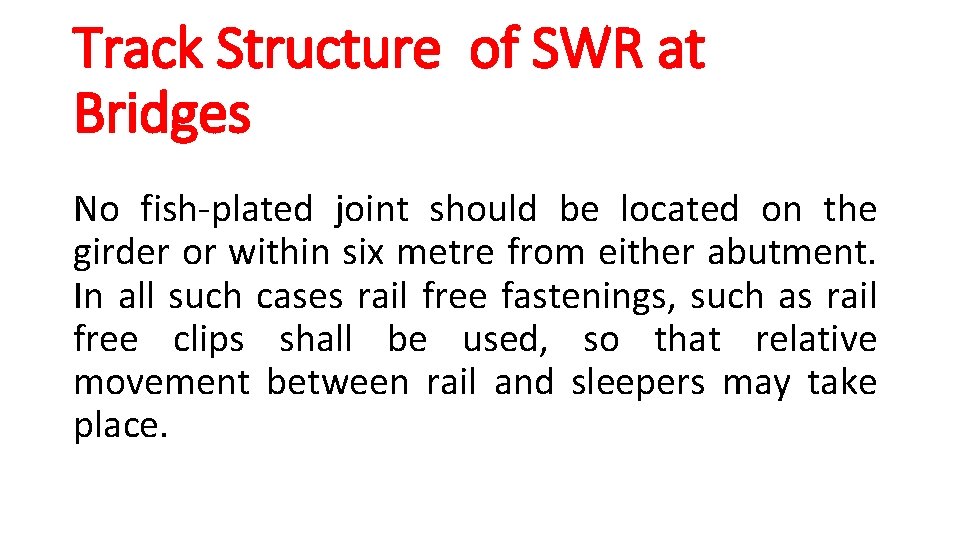
Track Structure of SWR at Bridges No fish-plated joint should be located on the girder or within six metre from either abutment. In all such cases rail free fastenings, such as rail free clips shall be used, so that relative movement between rail and sleepers may take place.
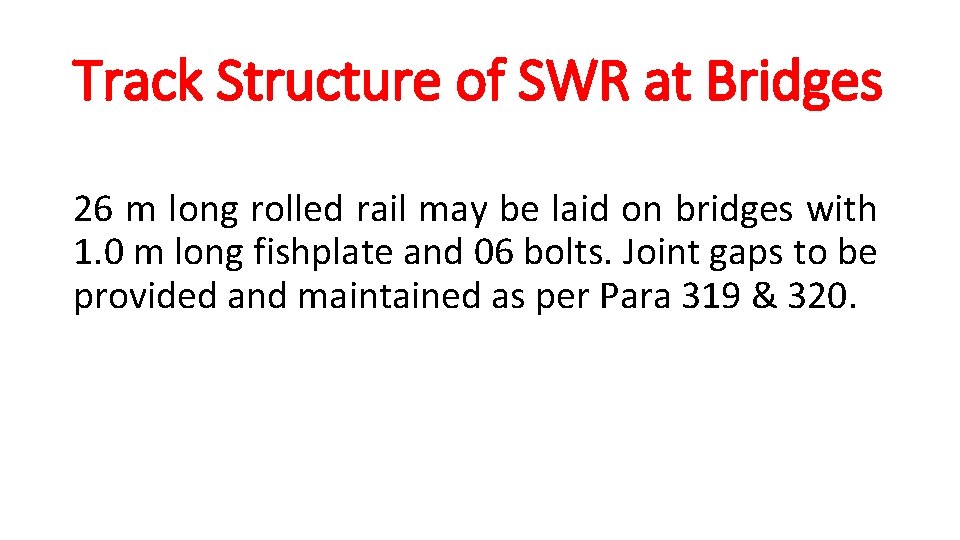
Track Structure of SWR at Bridges 26 m long rolled rail may be laid on bridges with 1. 0 m long fishplate and 06 bolts. Joint gaps to be provided and maintained as per Para 319 & 320.
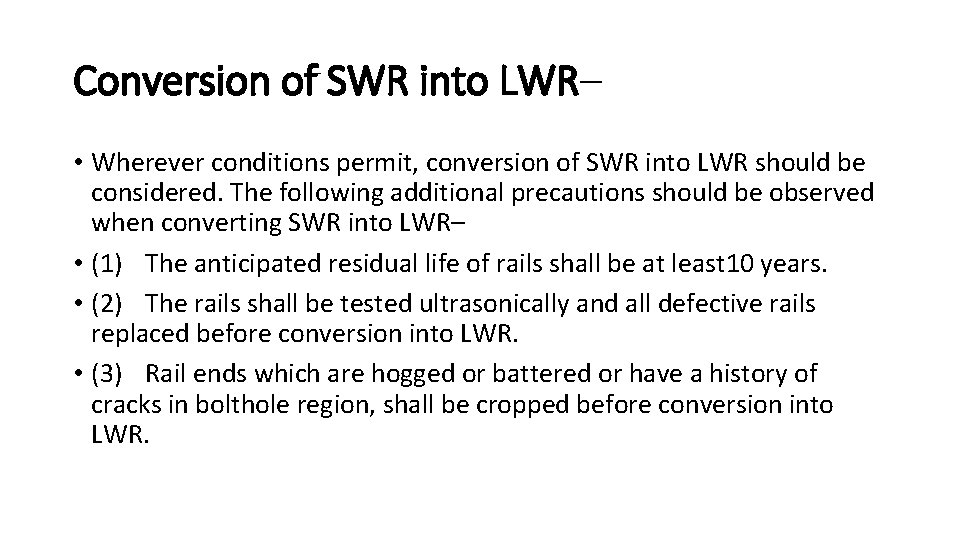
Conversion of SWR into LWR– • Wherever conditions permit, conversion of SWR into LWR should be considered. The following additional precautions should be observed when converting SWR into LWR– • (1) The anticipated residual life of rails shall be at least 10 years. • (2) The rails shall be tested ultrasonically and all defective rails replaced before conversion into LWR. • (3) Rail ends which are hogged or battered or have a history of cracks in bolthole region, shall be cropped before conversion into LWR.
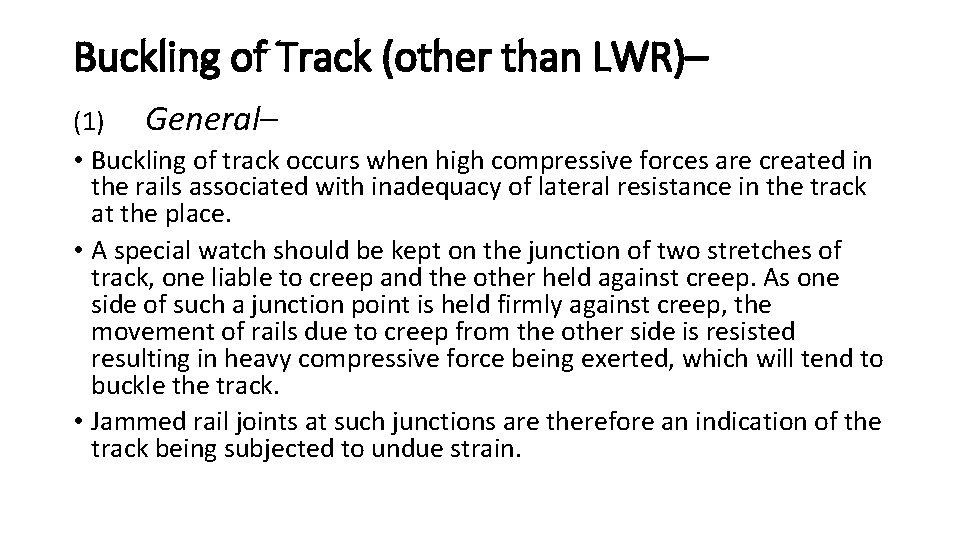
Buckling of Track (other than LWR)– (1) General– • Buckling of track occurs when high compressive forces are created in the rails associated with inadequacy of lateral resistance in the track at the place. • A special watch should be kept on the junction of two stretches of track, one liable to creep and the other held against creep. As one side of such a junction point is held firmly against creep, the movement of rails due to creep from the other side is resisted resulting in heavy compressive force being exerted, which will tend to buckle the track. • Jammed rail joints at such junctions are therefore an indication of the track being subjected to undue strain.
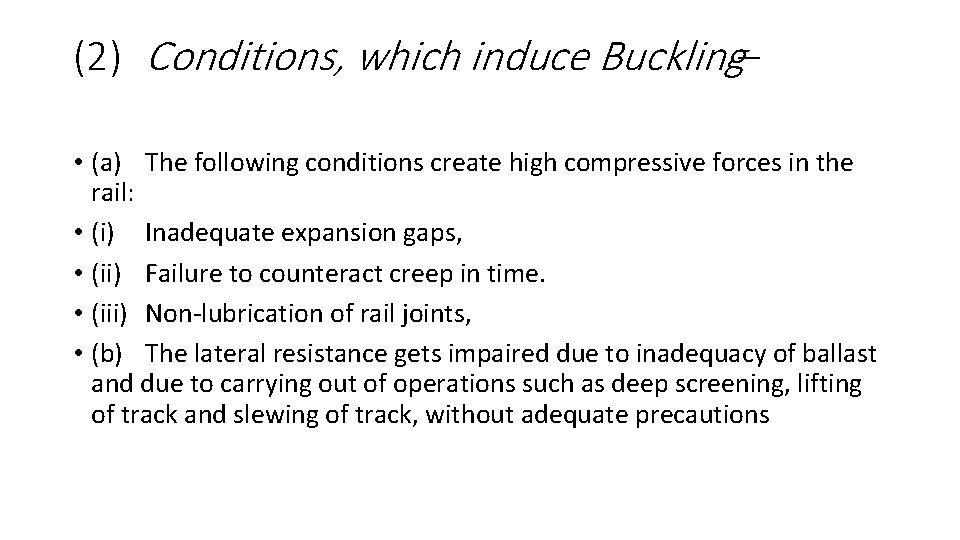
(2) Conditions, which induce Buckling– • (a) The following conditions create high compressive forces in the rail: • (i) Inadequate expansion gaps, • (ii) Failure to counteract creep in time. • (iii) Non-lubrication of rail joints, • (b) The lateral resistance gets impaired due to inadequacy of ballast and due to carrying out of operations such as deep screening, lifting of track and slewing of track, without adequate precautions
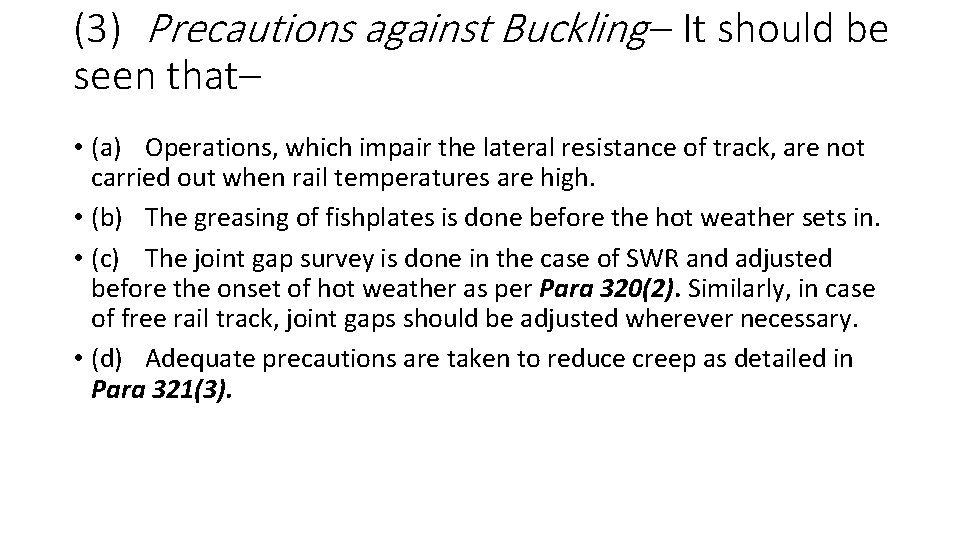
(3) Precautions against Buckling – It should be seen that– • (a) Operations, which impair the lateral resistance of track, are not carried out when rail temperatures are high. • (b) The greasing of fishplates is done before the hot weather sets in. • (c) The joint gap survey is done in the case of SWR and adjusted before the onset of hot weather as per Para 320(2). Similarly, in case of free rail track, joint gaps should be adjusted wherever necessary. • (d) Adequate precautions are taken to reduce creep as detailed in Para 321(3).
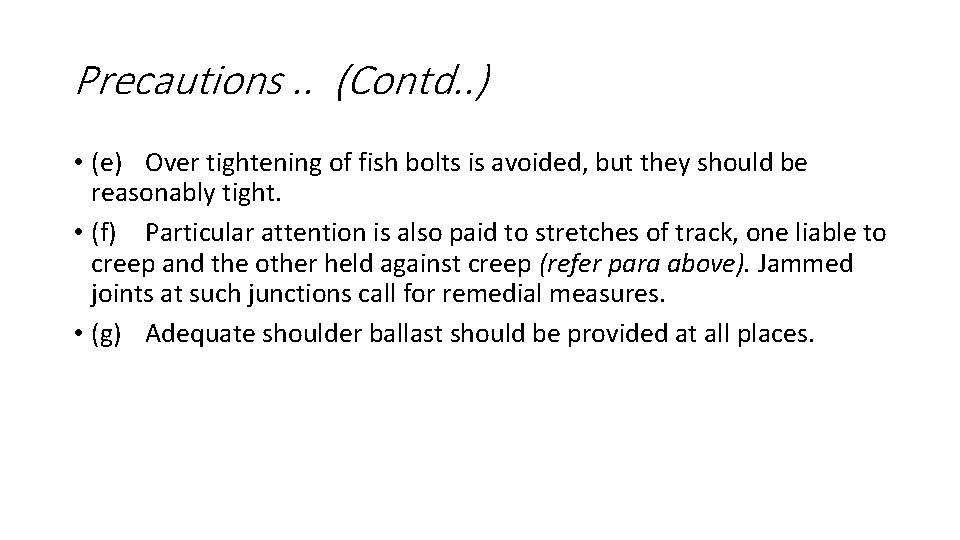
Precautions. . (Contd. . ) • (e) Over tightening of fish bolts is avoided, but they should be reasonably tight. • (f) Particular attention is also paid to stretches of track, one liable to creep and the other held against creep (refer para above). Jammed joints at such junctions call for remedial measures. • (g) Adequate shoulder ballast should be provided at all places.
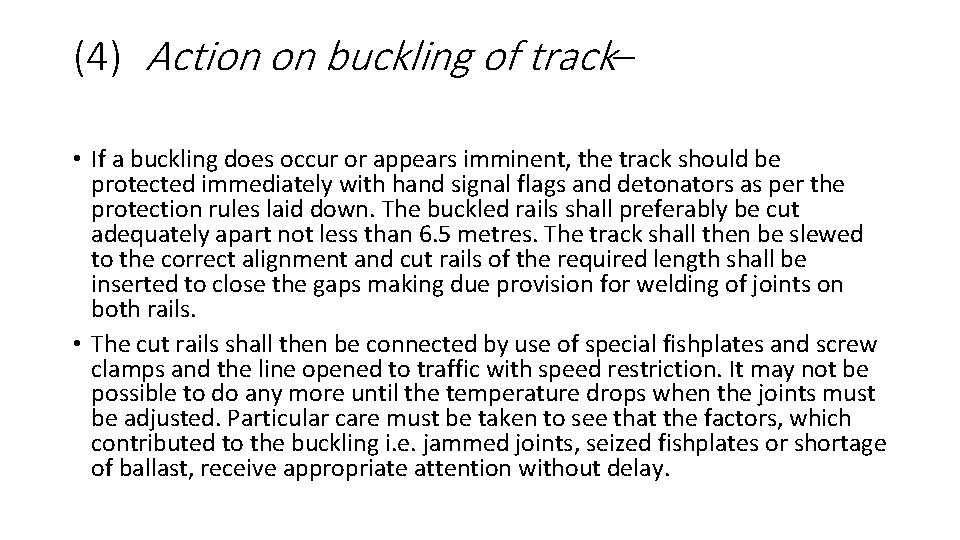
(4) Action on buckling of track– • If a buckling does occur or appears imminent, the track should be protected immediately with hand signal flags and detonators as per the protection rules laid down. The buckled rails shall preferably be cut adequately apart not less than 6. 5 metres. The track shall then be slewed to the correct alignment and cut rails of the required length shall be inserted to close the gaps making due provision for welding of joints on both rails. • The cut rails shall then be connected by use of special fishplates and screw clamps and the line opened to traffic with speed restriction. It may not be possible to do any more until the temperature drops when the joints must be adjusted. Particular care must be taken to see that the factors, which contributed to the buckling i. e. jammed joints, seized fishplates or shortage of ballast, receive appropriate attention without delay.
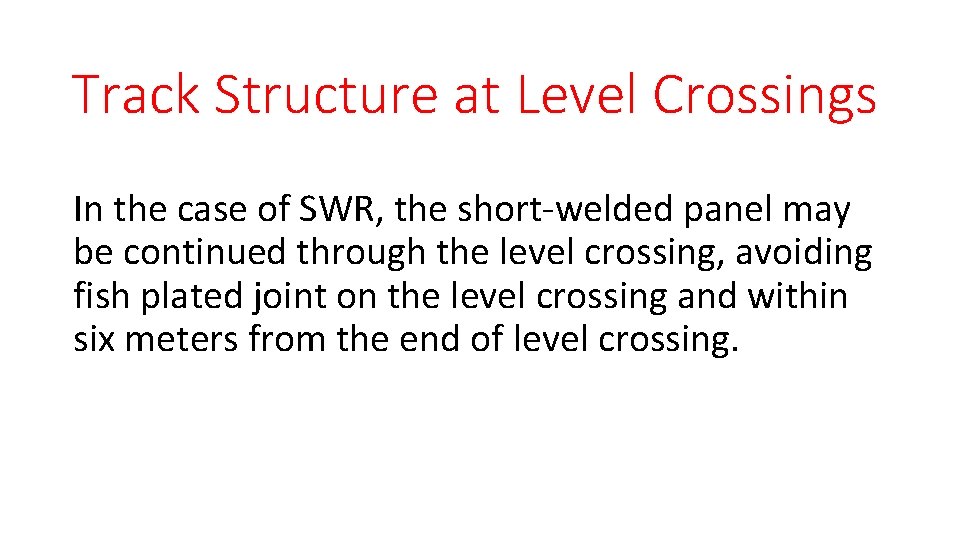
Track Structure at Level Crossings In the case of SWR, the short-welded panel may be continued through the level crossing, avoiding fish plated joint on the level crossing and within six meters from the end of level crossing.
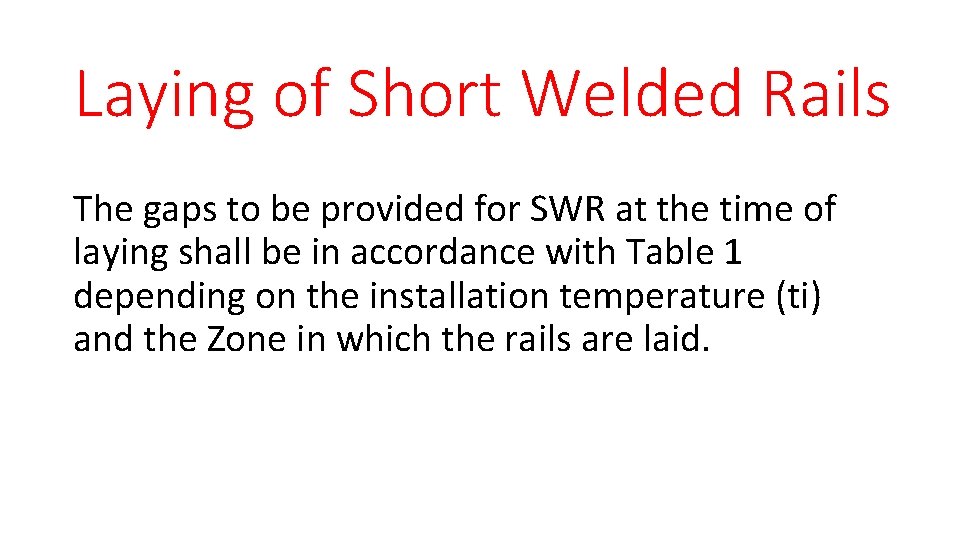
Laying of Short Welded Rails The gaps to be provided for SWR at the time of laying shall be in accordance with Table 1 depending on the installation temperature (ti) and the Zone in which the rails are laid.
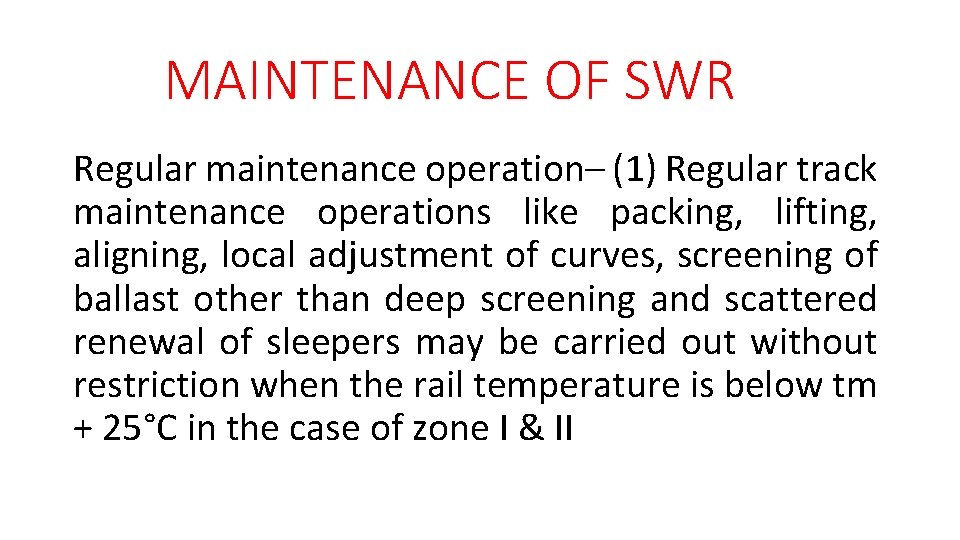
MAINTENANCE OF SWR Regular maintenance operation– (1) Regular track maintenance operations like packing, lifting, aligning, local adjustment of curves, screening of ballast other than deep screening and scattered renewal of sleepers may be carried out without restriction when the rail temperature is below tm + 25°C in the case of zone I & II
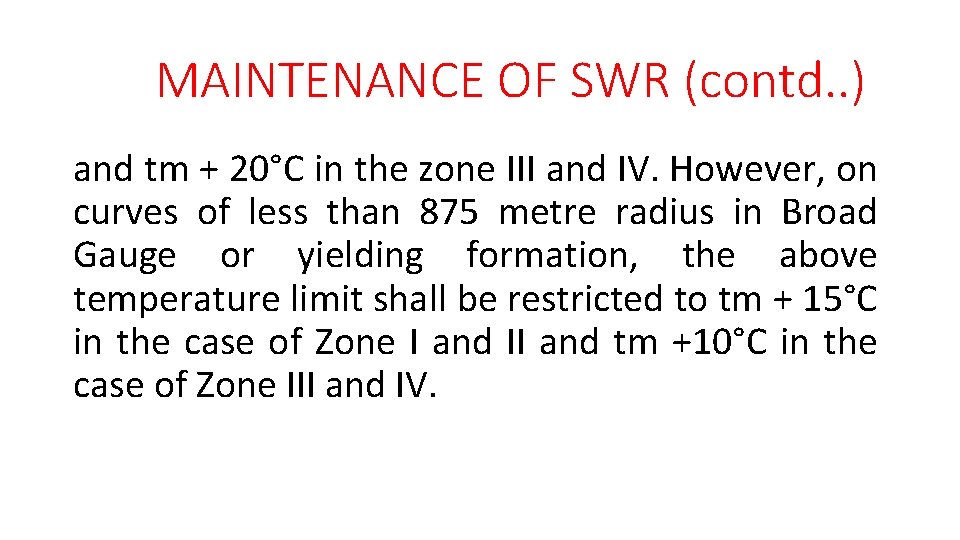
MAINTENANCE OF SWR (contd. . ) and tm + 20°C in the zone III and IV. However, on curves of less than 875 metre radius in Broad Gauge or yielding formation, the above temperature limit shall be restricted to tm + 15°C in the case of Zone I and II and tm +10°C in the case of Zone III and IV.
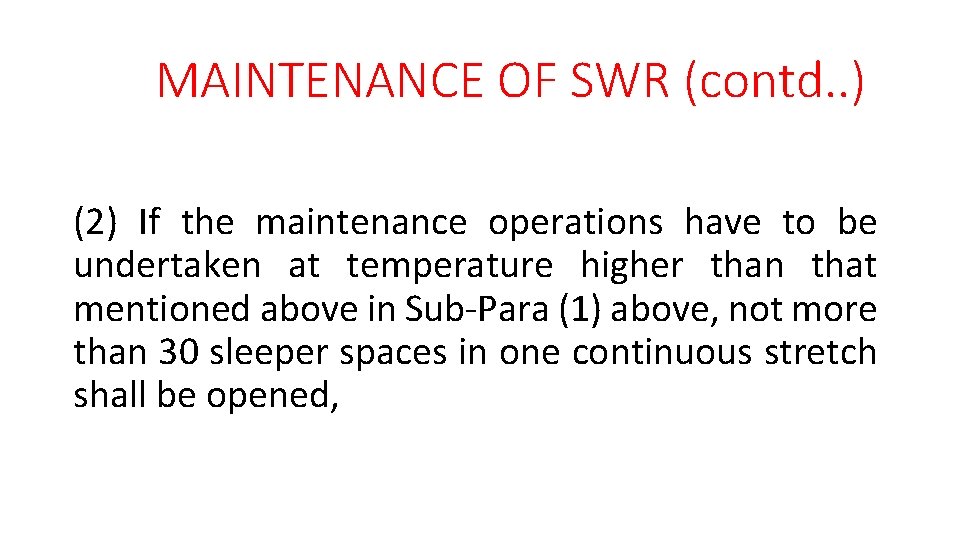
MAINTENANCE OF SWR (contd. . ) (2) If the maintenance operations have to be undertaken at temperature higher than that mentioned above in Sub-Para (1) above, not more than 30 sleeper spaces in one continuous stretch shall be opened,
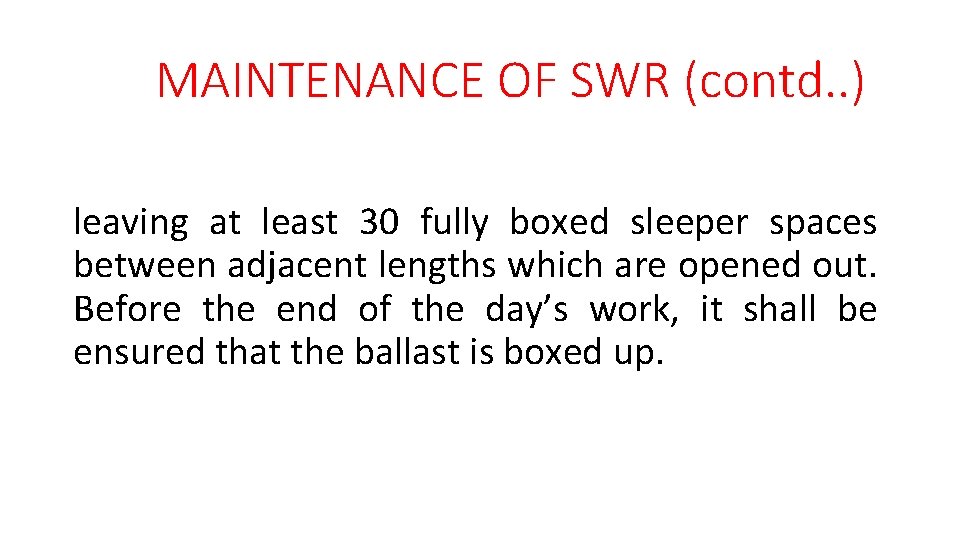
MAINTENANCE OF SWR (contd. . ) leaving at least 30 fully boxed sleeper spaces between adjacent lengths which are opened out. Before the end of the day’s work, it shall be ensured that the ballast is boxed up.
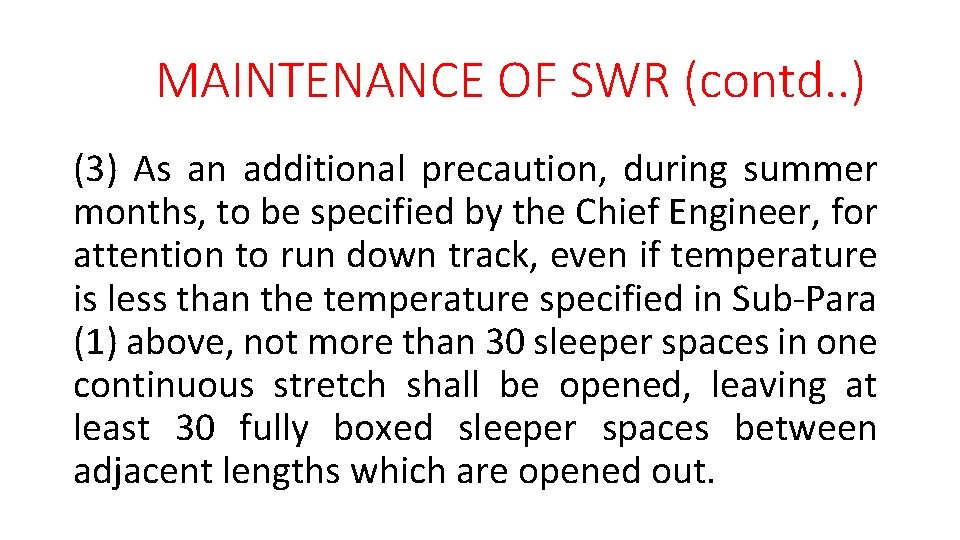
MAINTENANCE OF SWR (contd. . ) (3) As an additional precaution, during summer months, to be specified by the Chief Engineer, for attention to run down track, even if temperature is less than the temperature specified in Sub-Para (1) above, not more than 30 sleeper spaces in one continuous stretch shall be opened, leaving at least 30 fully boxed sleeper spaces between adjacent lengths which are opened out.
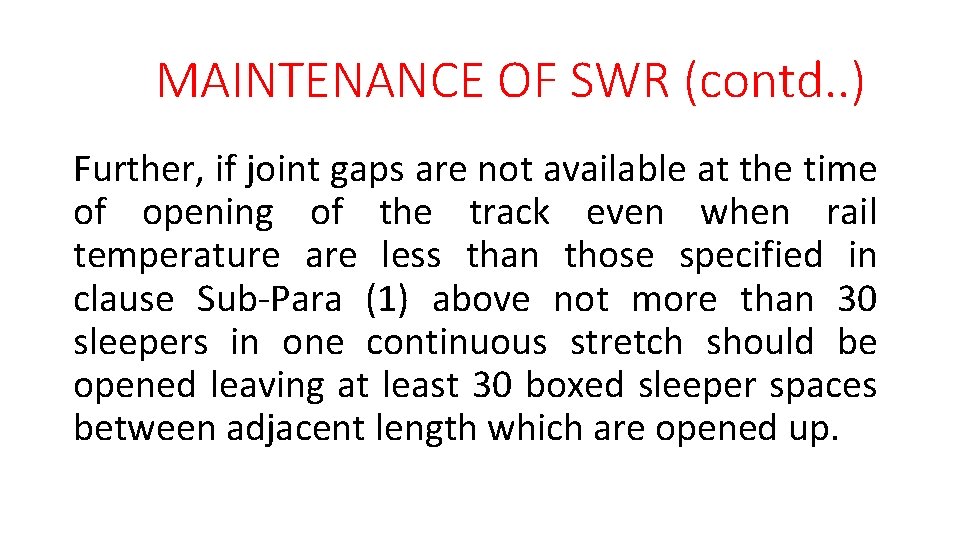
MAINTENANCE OF SWR (contd. . ) Further, if joint gaps are not available at the time of opening of the track even when rail temperature are less than those specified in clause Sub-Para (1) above not more than 30 sleepers in one continuous stretch should be opened leaving at least 30 boxed sleeper spaces between adjacent length which are opened up.
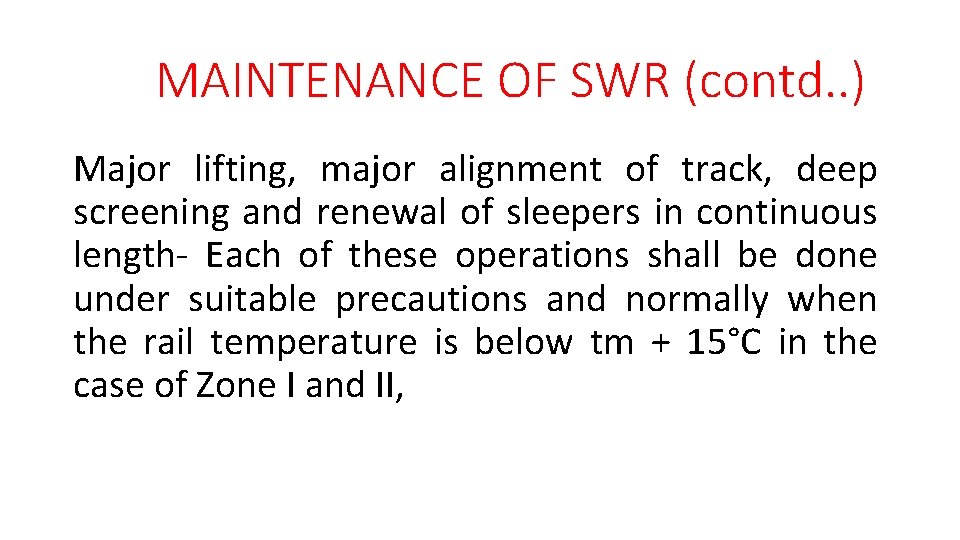
MAINTENANCE OF SWR (contd. . ) Major lifting, major alignment of track, deep screening and renewal of sleepers in continuous length- Each of these operations shall be done under suitable precautions and normally when the rail temperature is below tm + 15°C in the case of Zone I and II,
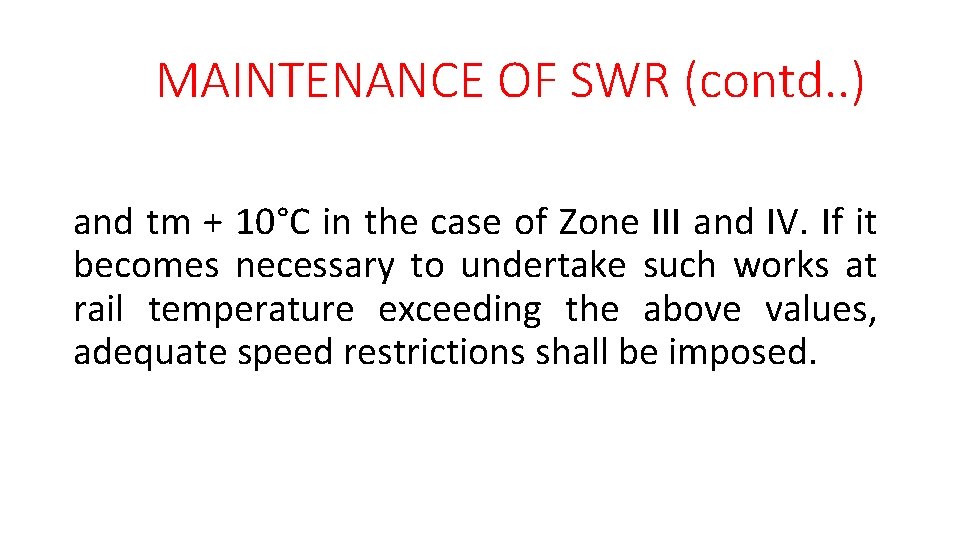
MAINTENANCE OF SWR (contd. . ) and tm + 10°C in the case of Zone III and IV. If it becomes necessary to undertake such works at rail temperature exceeding the above values, adequate speed restrictions shall be imposed.
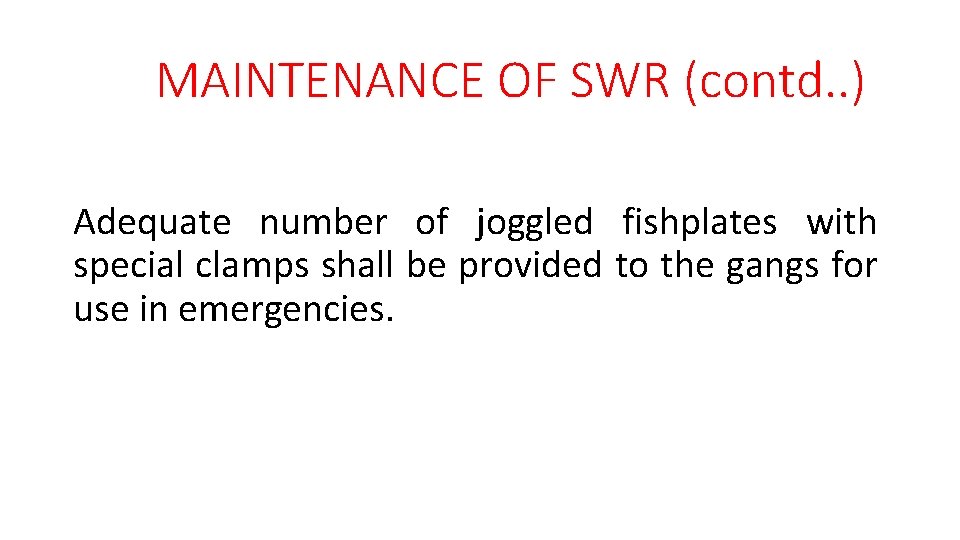
MAINTENANCE OF SWR (contd. . ) Adequate number of joggled fishplates with special clamps shall be provided to the gangs for use in emergencies.
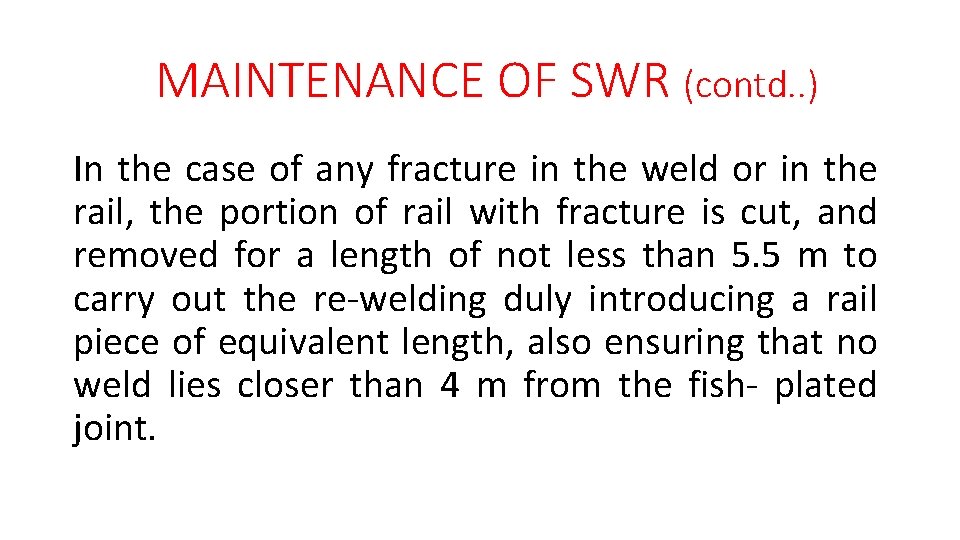
MAINTENANCE OF SWR (contd. . ) In the case of any fracture in the weld or in the rail, the portion of rail with fracture is cut, and removed for a length of not less than 5. 5 m to carry out the re-welding duly introducing a rail piece of equivalent length, also ensuring that no weld lies closer than 4 m from the fish- plated joint.
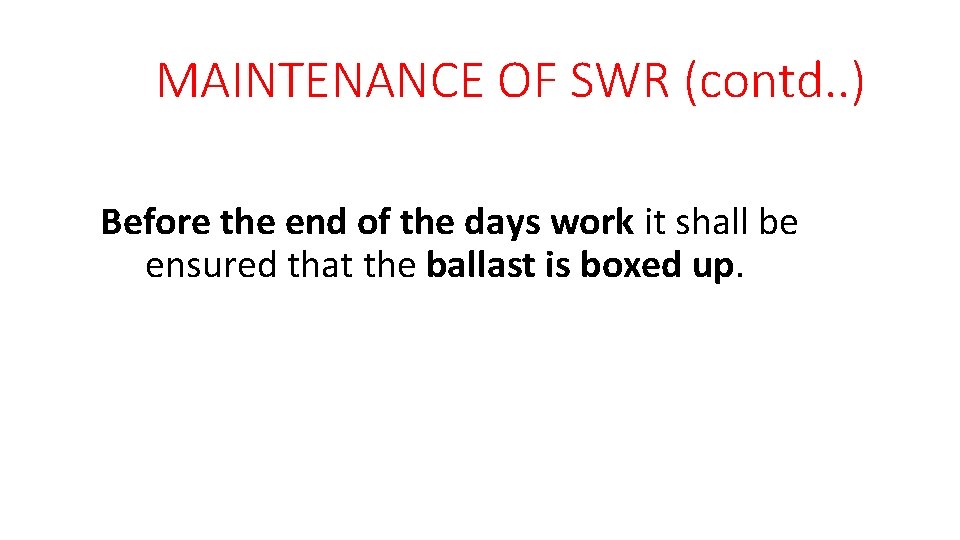
MAINTENANCE OF SWR (contd. . ) Before the end of the days work it shall be ensured that the ballast is boxed up.
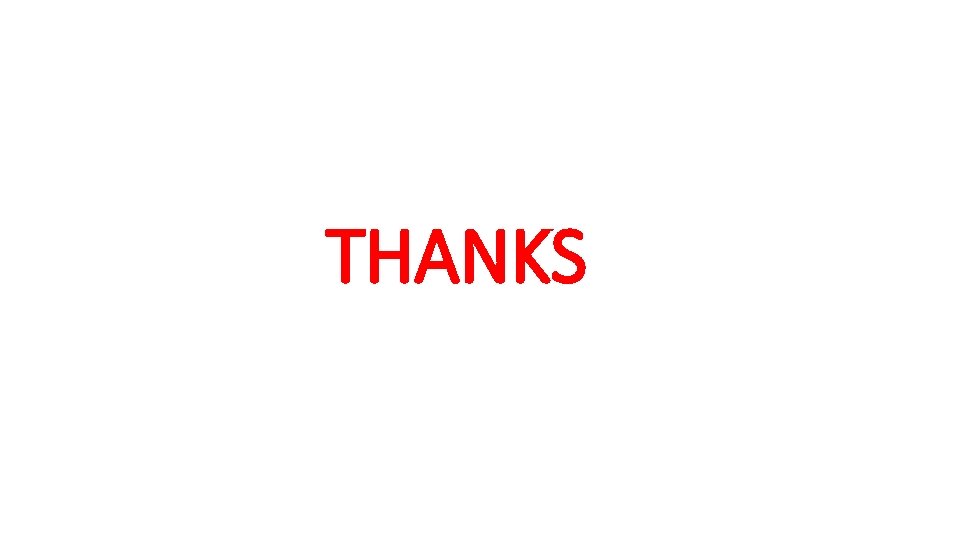
THANKS
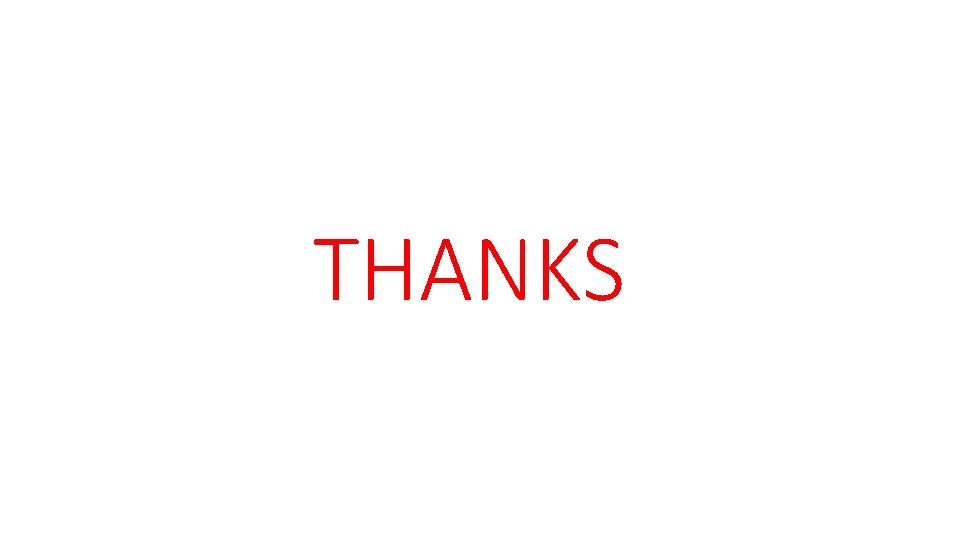
THANKS
Tall + short h
Electrical length
Nano vna saver
Swr meter harbor freight
Short welded rail
Electronic returnless fuel systems use the
Rails sti vs polymorphic
Rails chat
Rocket sled on rails
Transportation engineering
Jonathan slide rails
The two outside rails of the double helix are called
Comfort device assignment
Rails send sms
Seizure precautions bed rails
Ruby on rails gui
Generator slide rails
Influxdb collectd
Flat footed rail
Continuous tubular rails
Wear of rails
Seizure precautions bed rails
Ruby hadoop
Ruby validates_presence_of
Rails webrick
Dhh rails
Versine
Rails session model
Rails unit testing
Ruby on rails demo
Double headed rails definition
Stairway safety presentation
Ruby gem おすすめ
Jonathan slide rails
Manual ultrasonic testing