Waste management hierarchy waste reduction prevention recycling WASTE
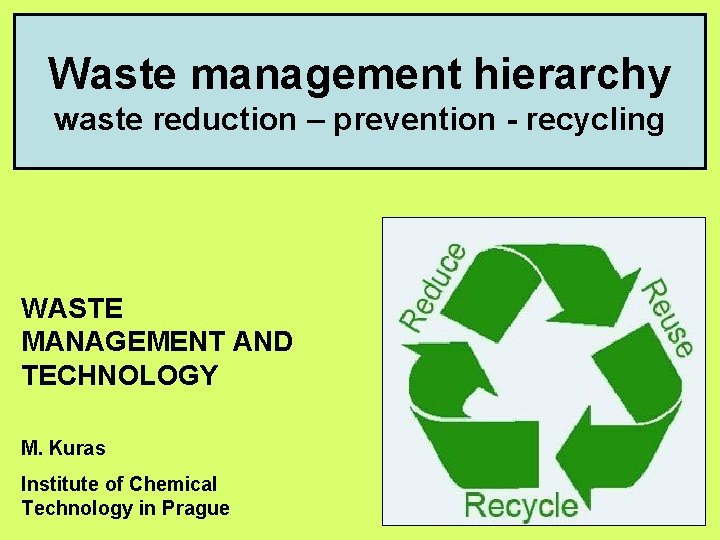
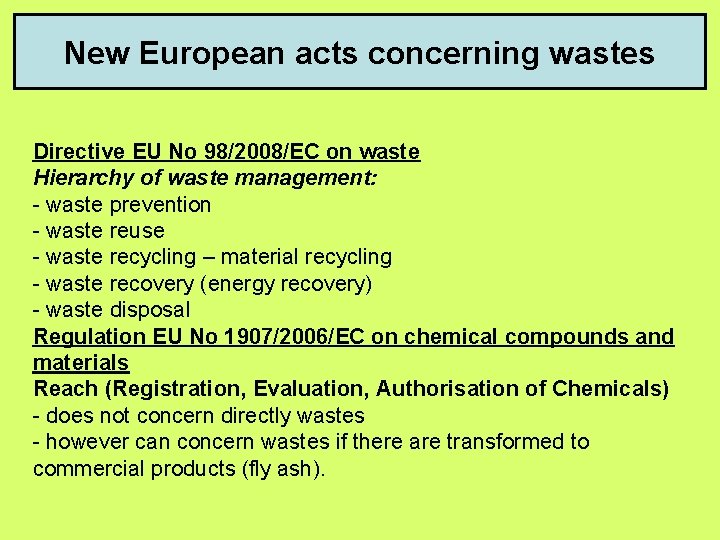
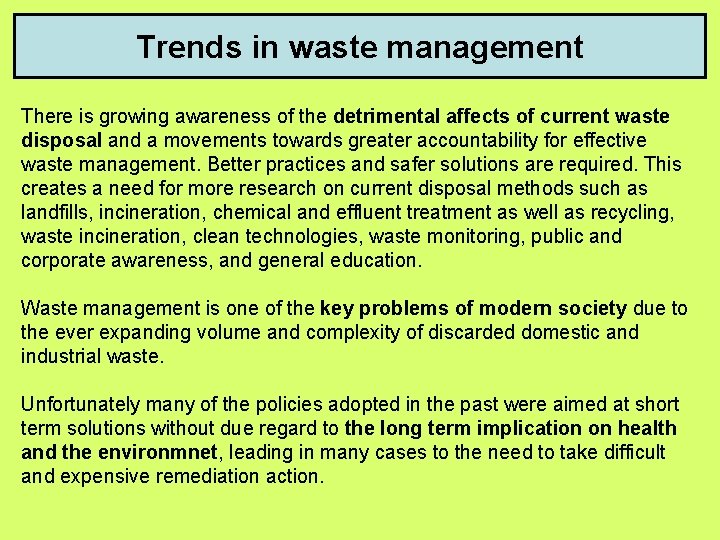
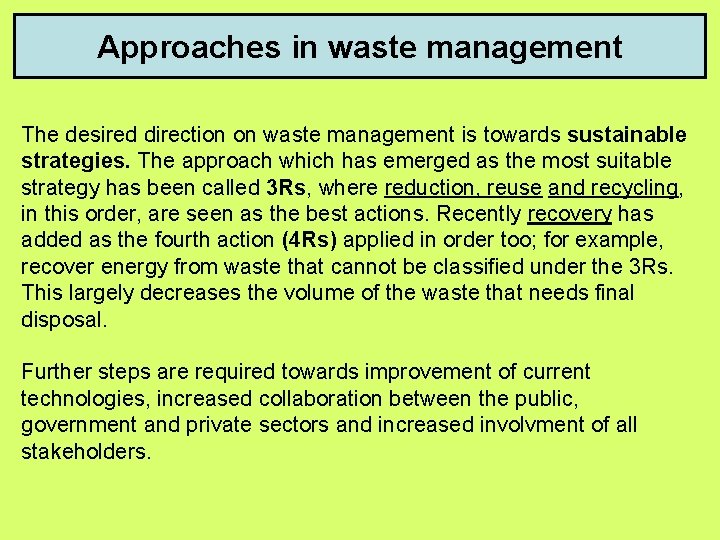
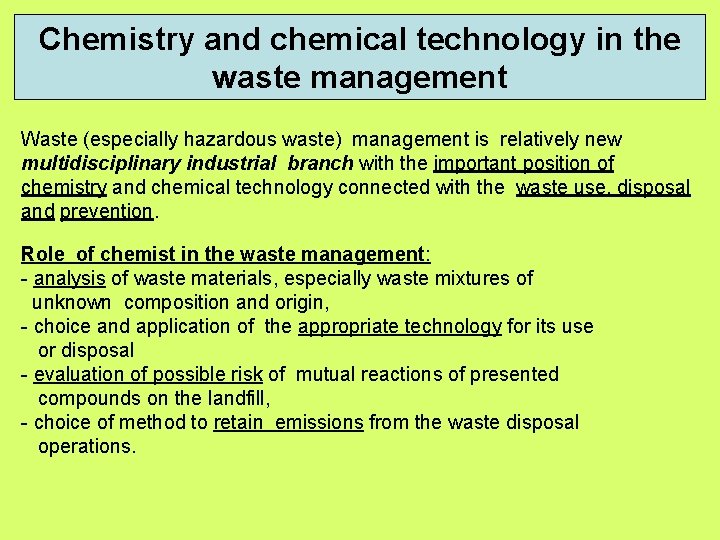
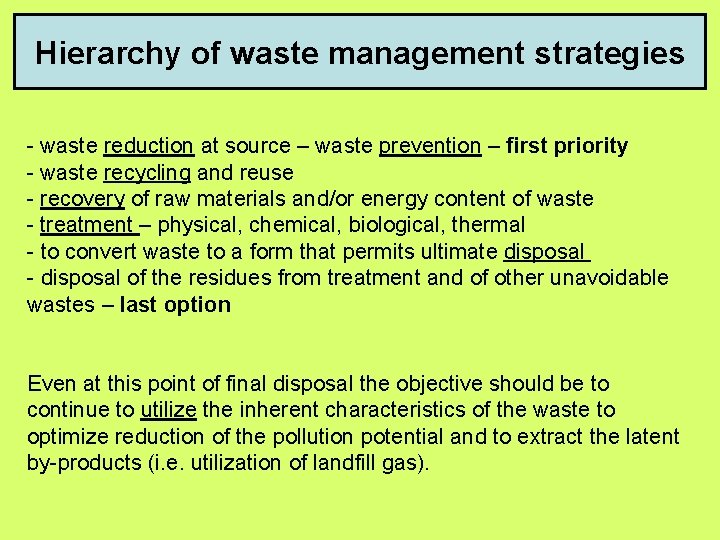
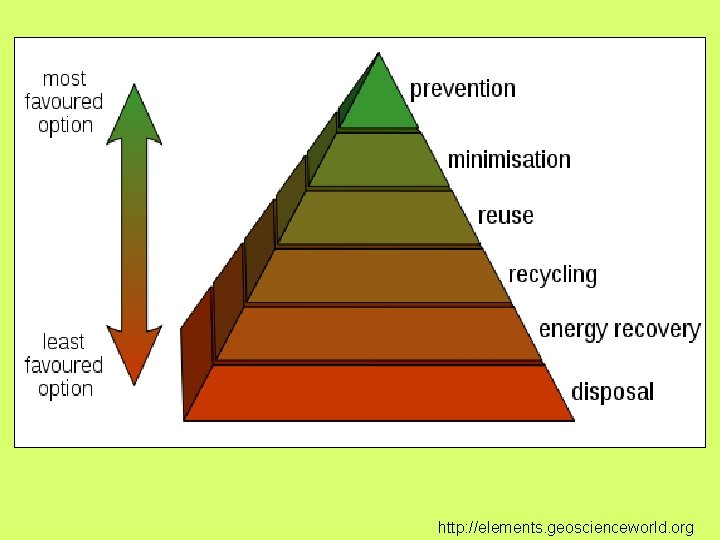
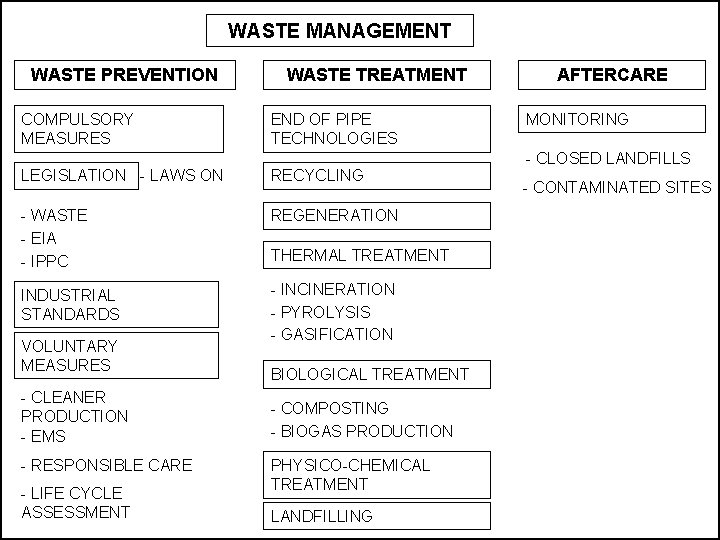
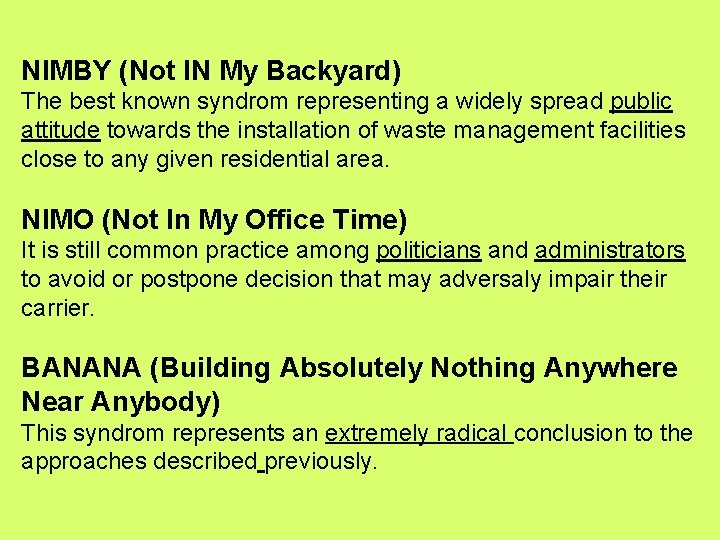
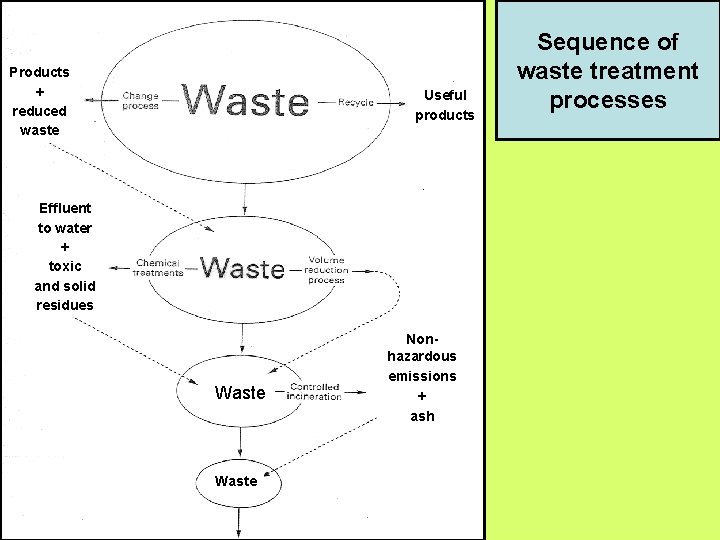
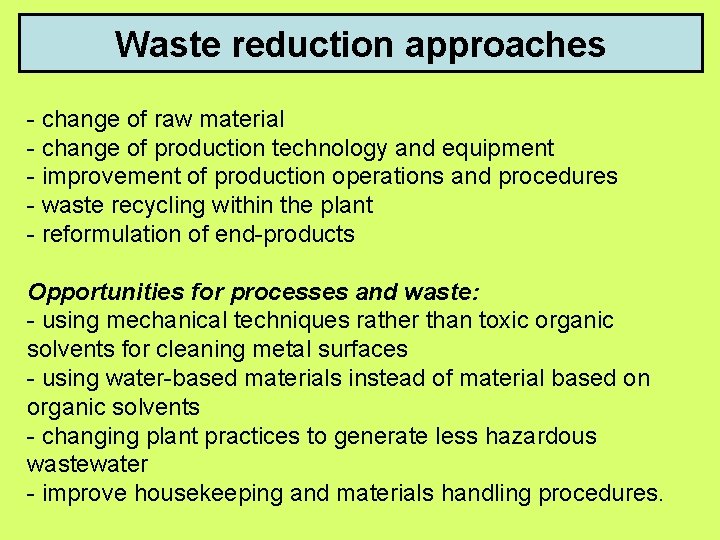
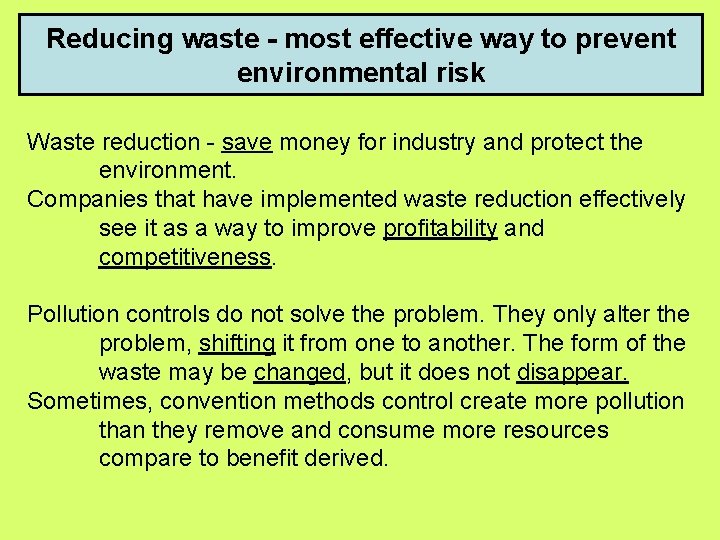
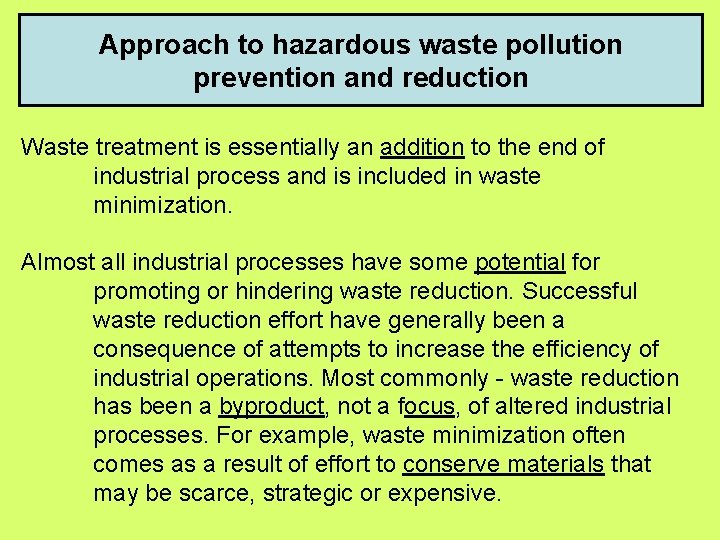
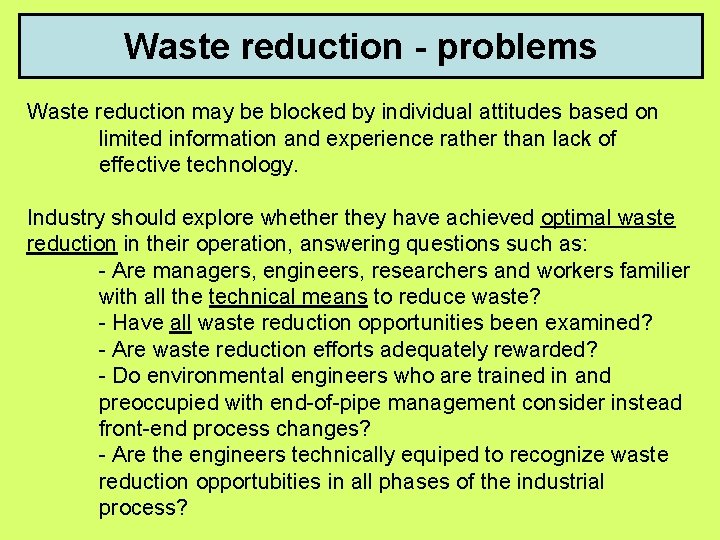
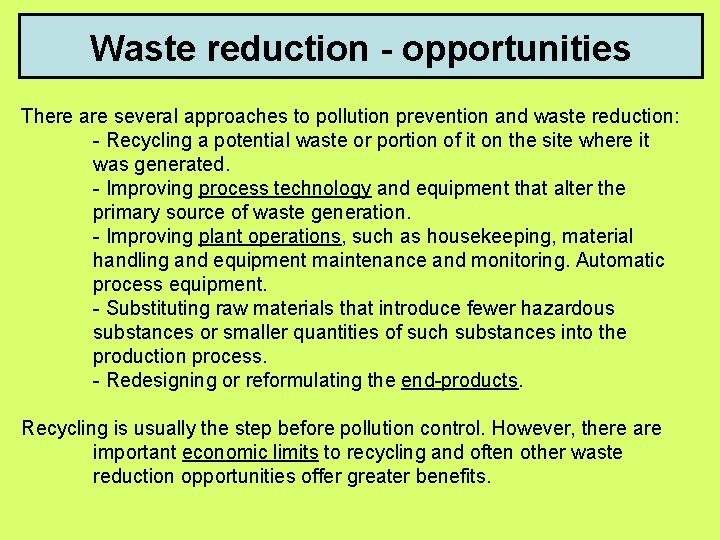
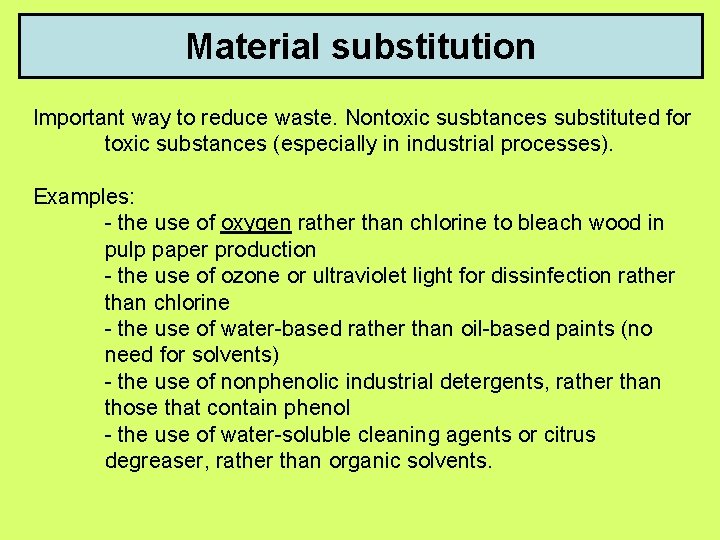
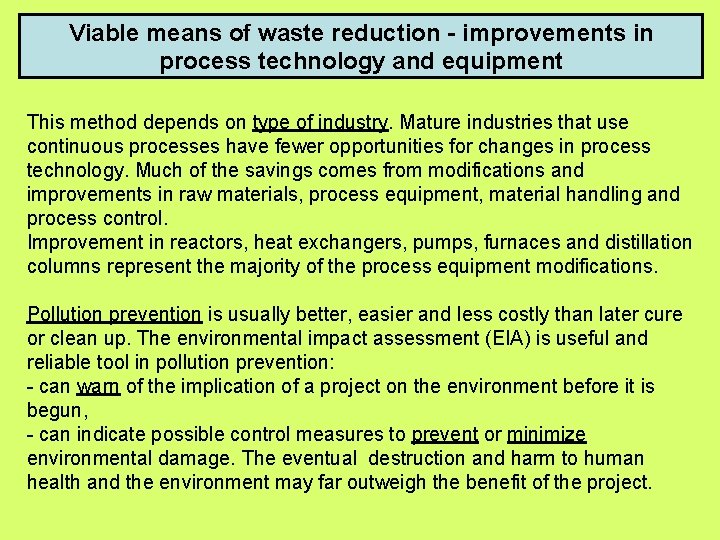
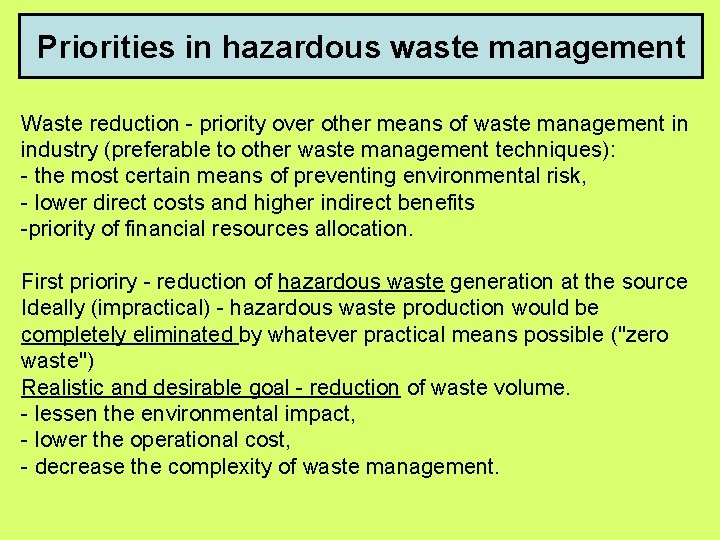
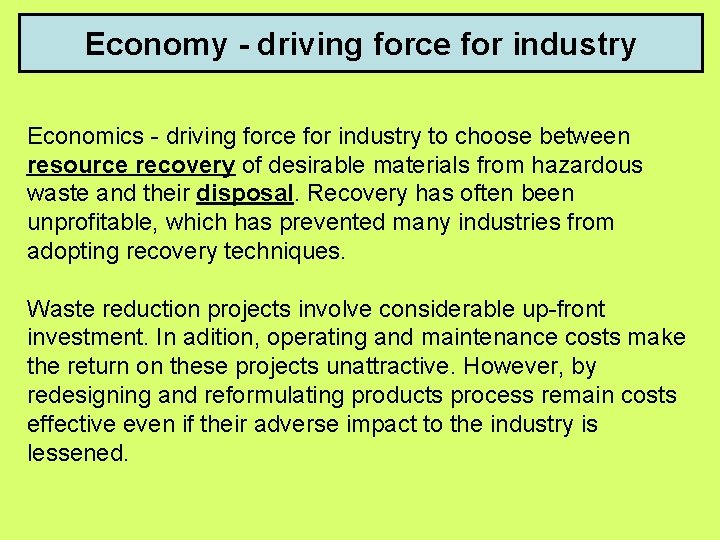
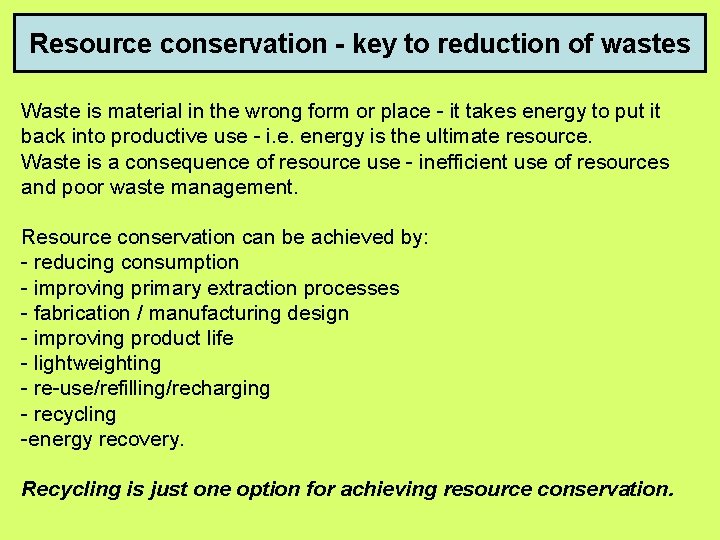
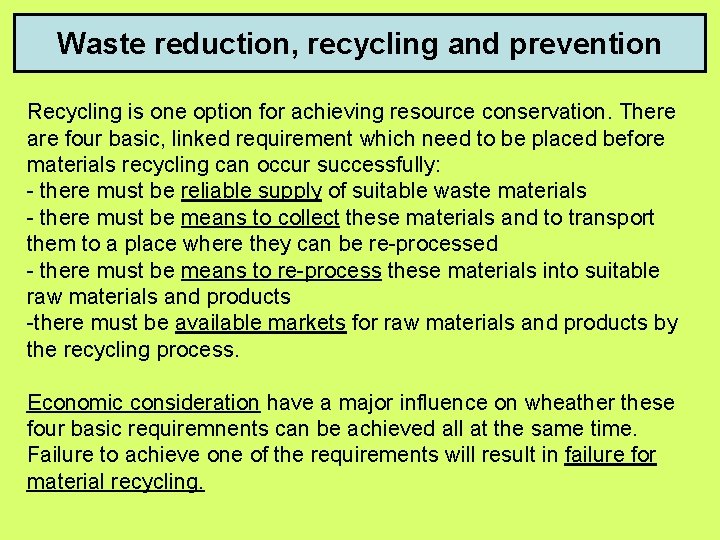
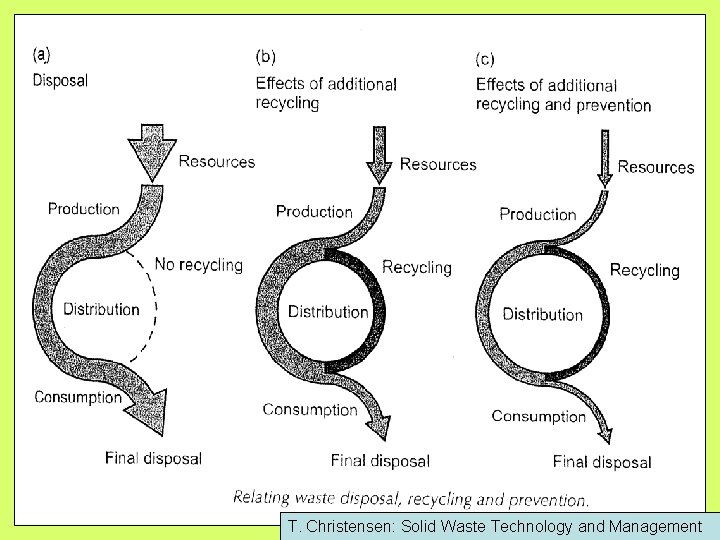
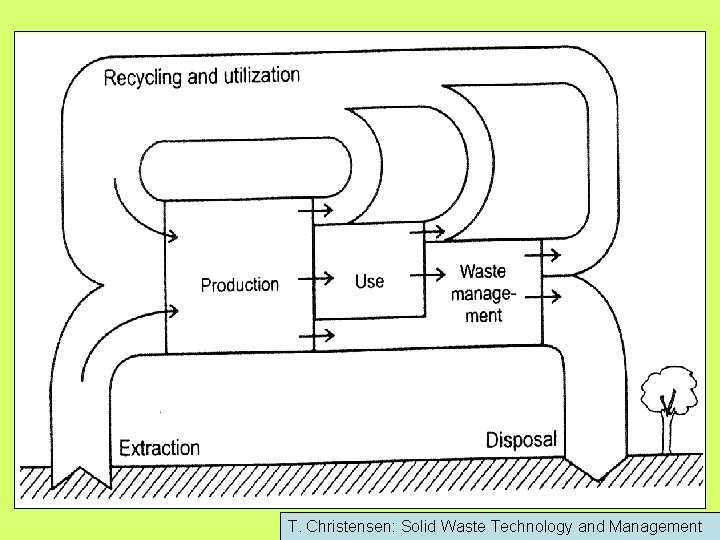
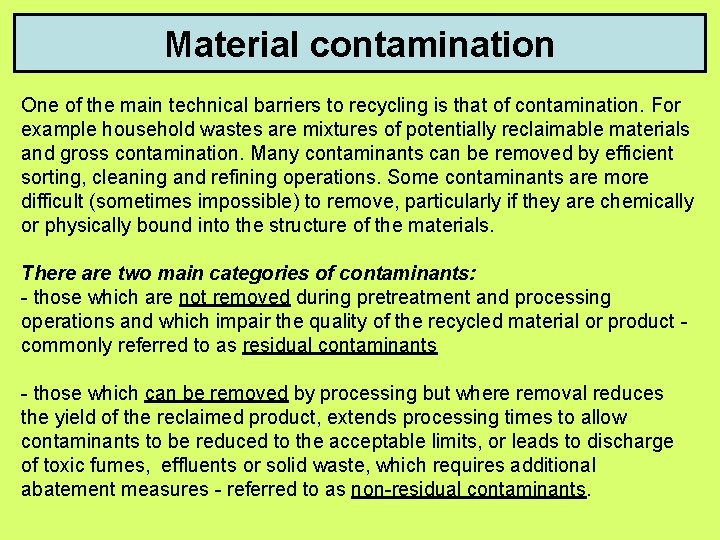
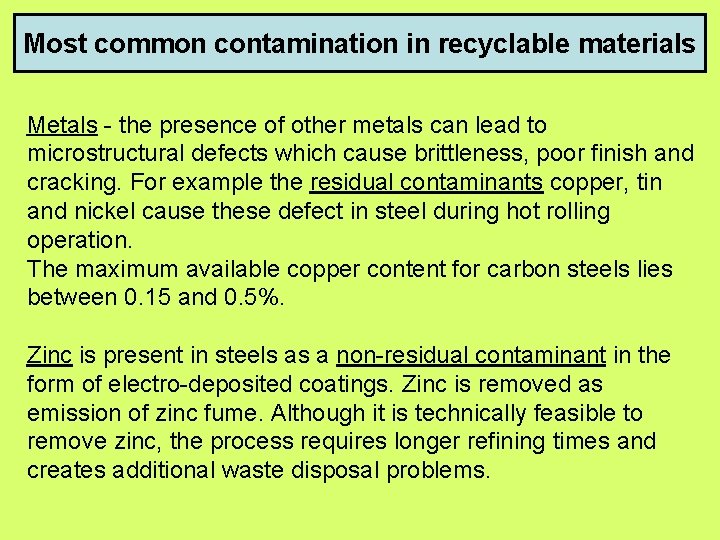
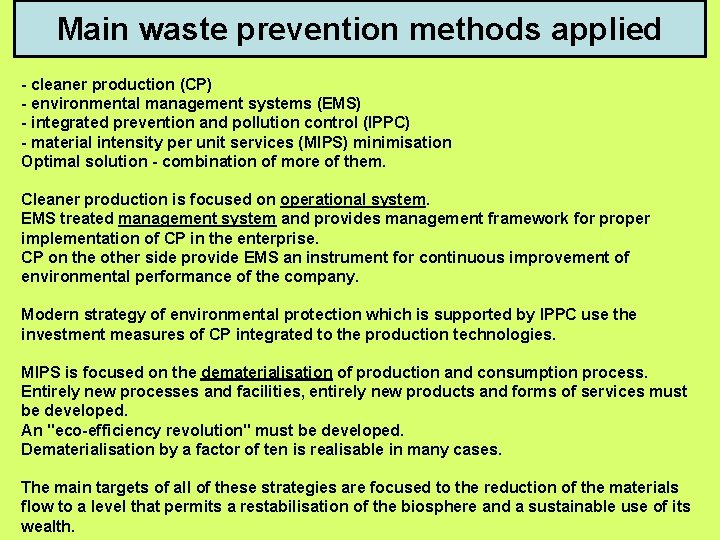
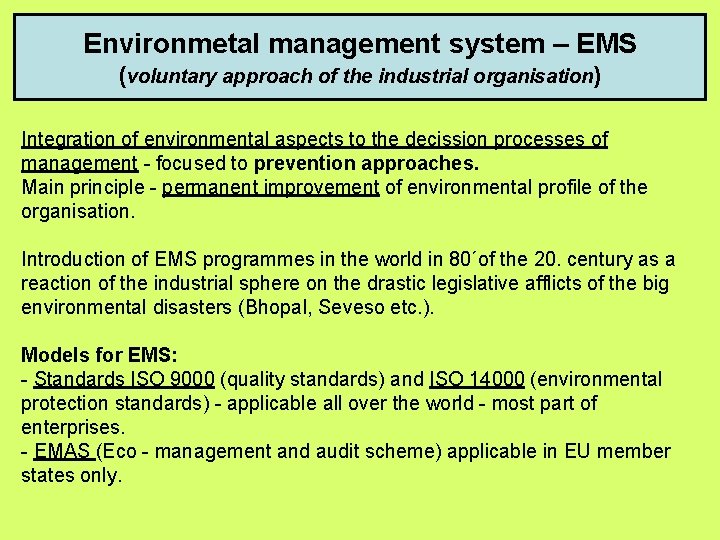
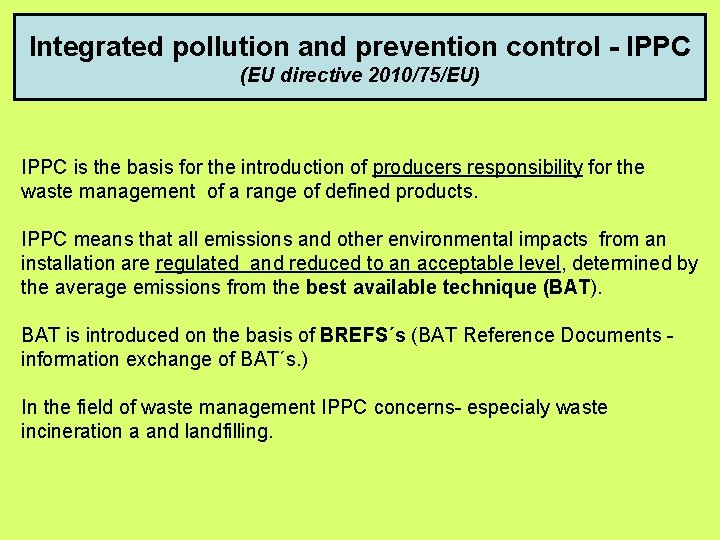
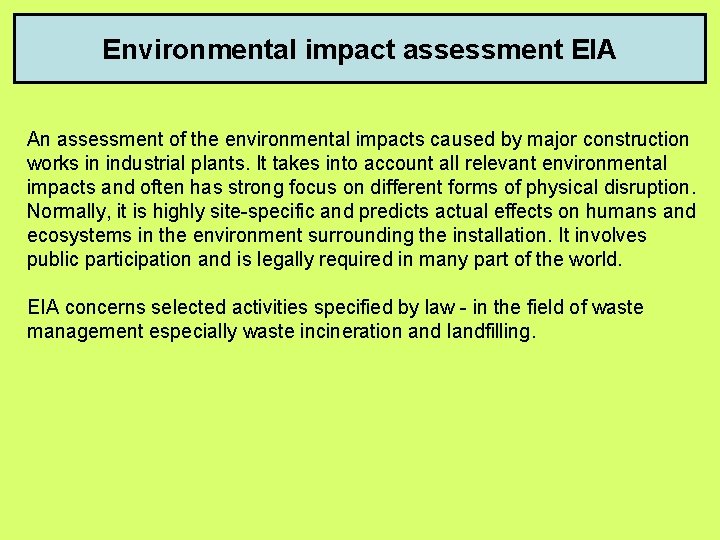
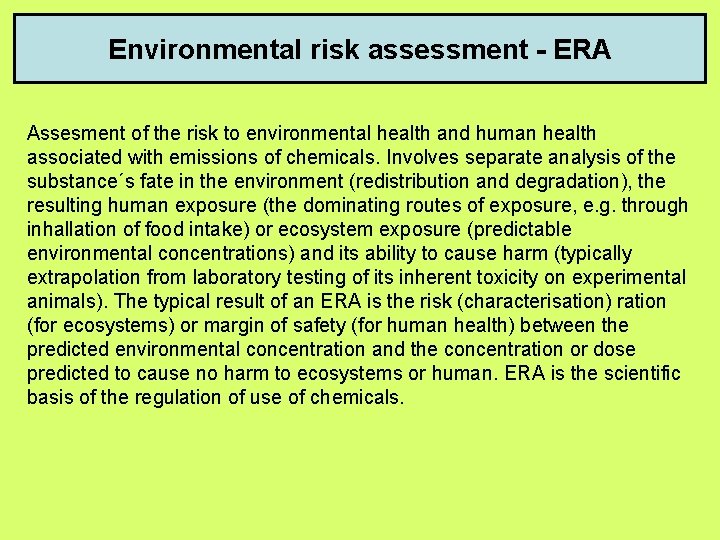
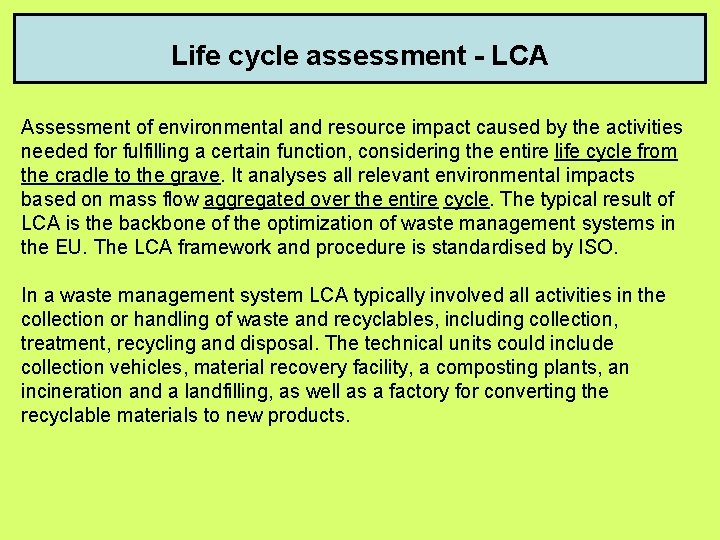
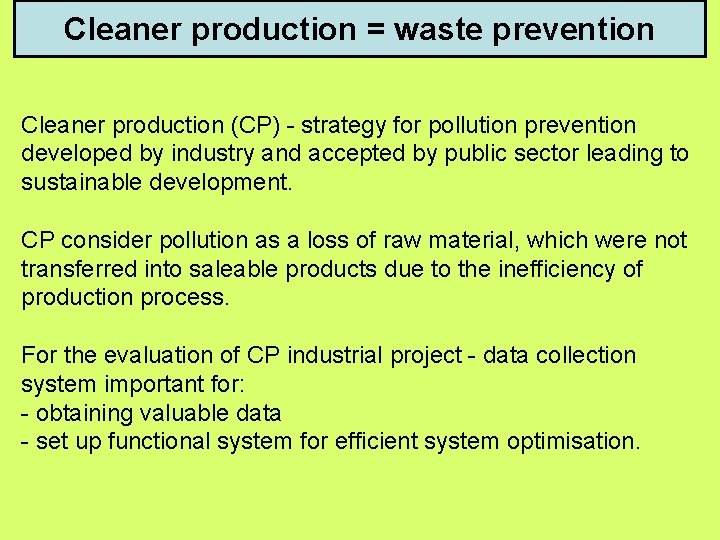
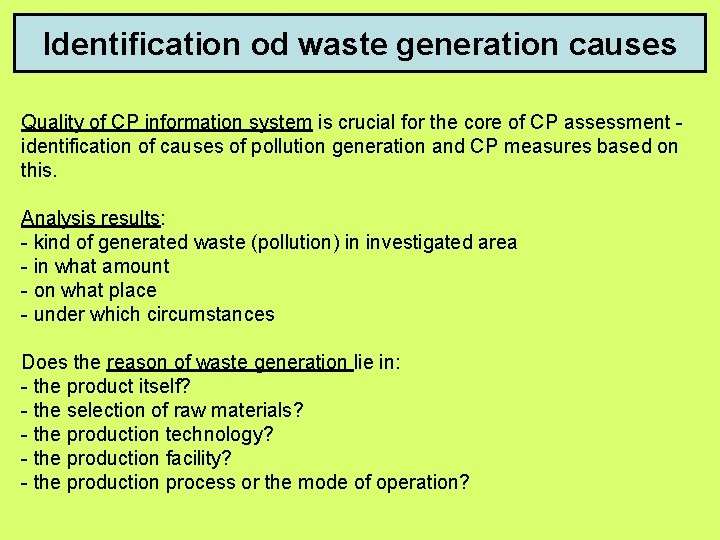
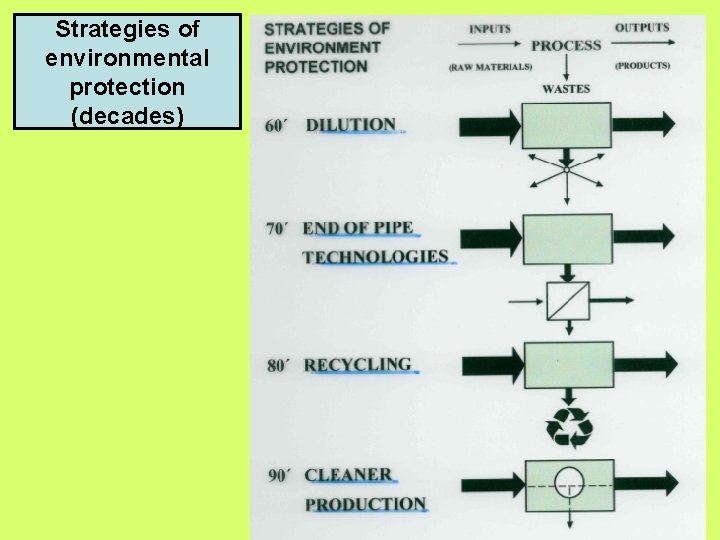
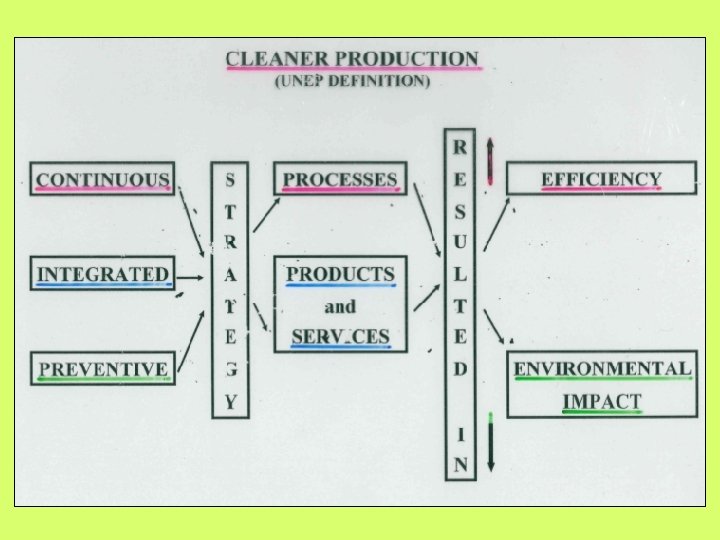
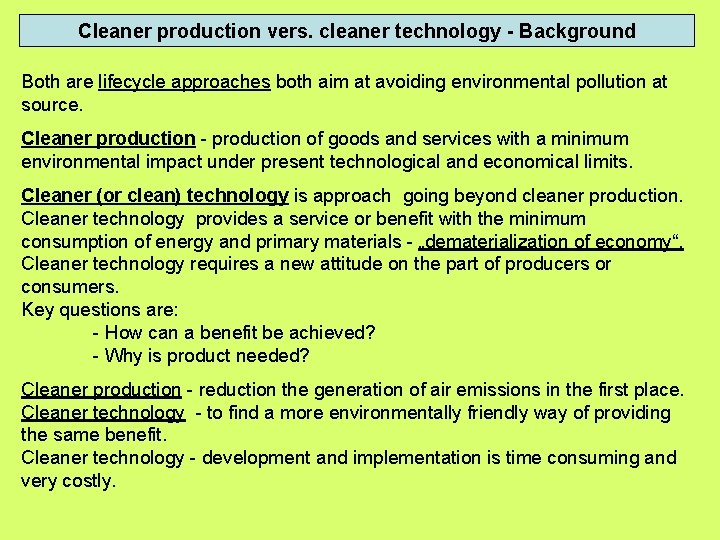
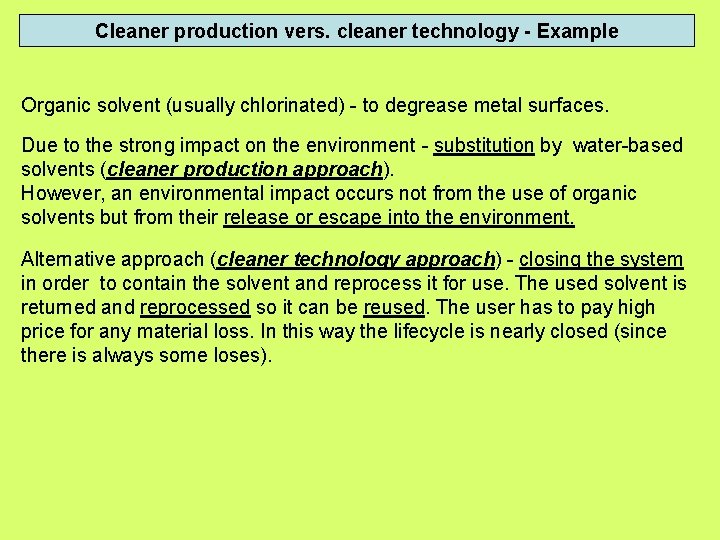
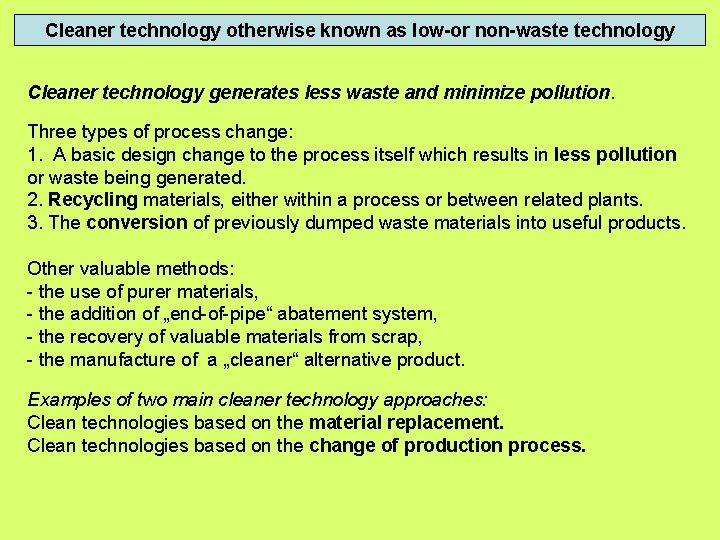
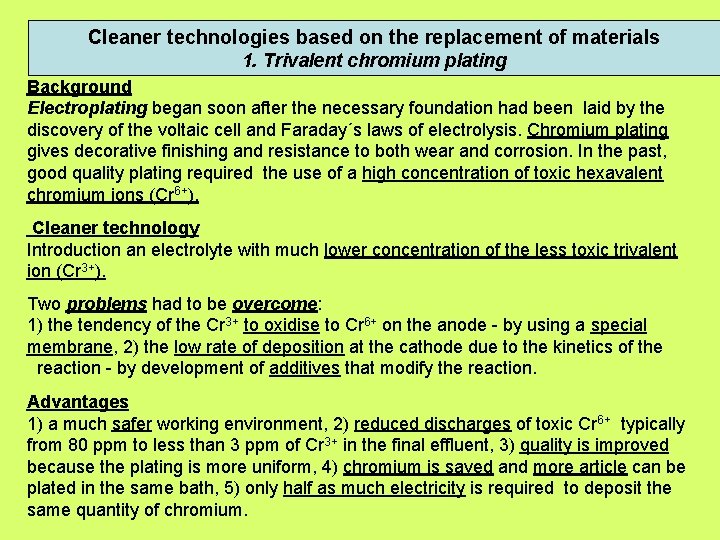
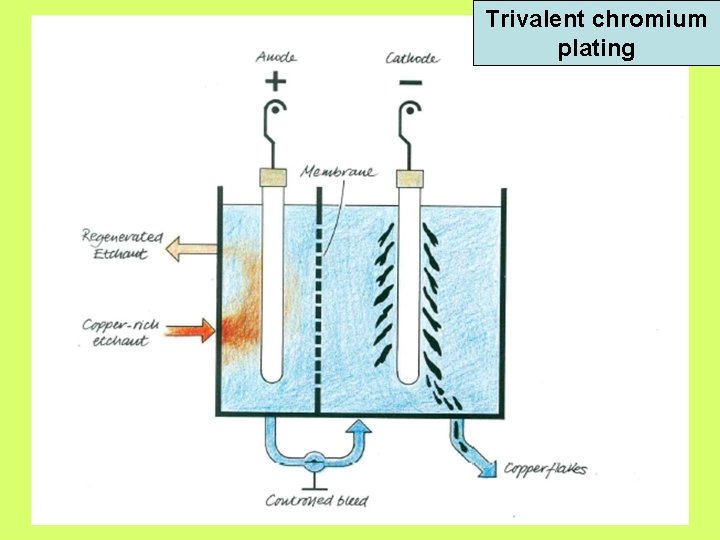
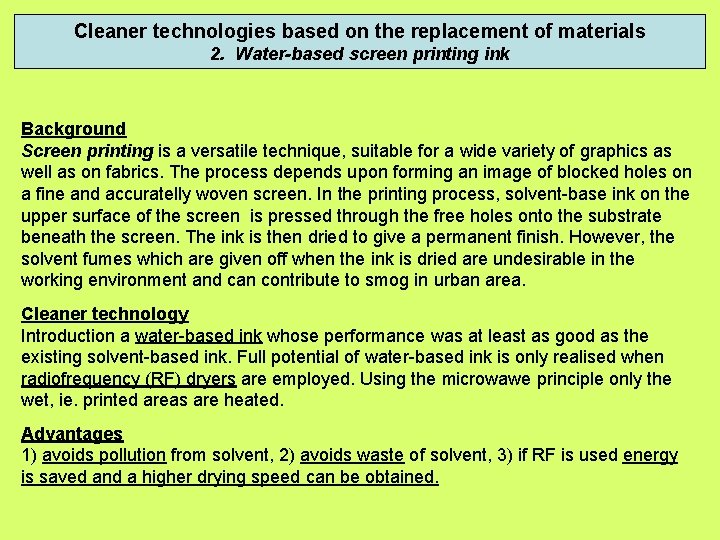

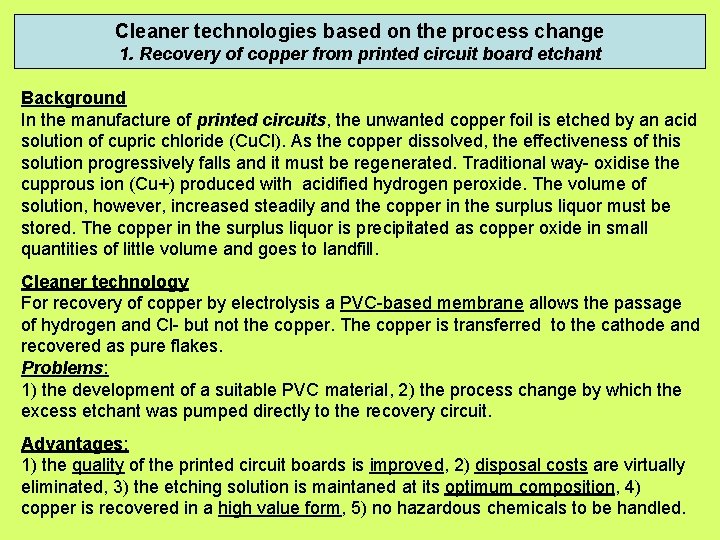
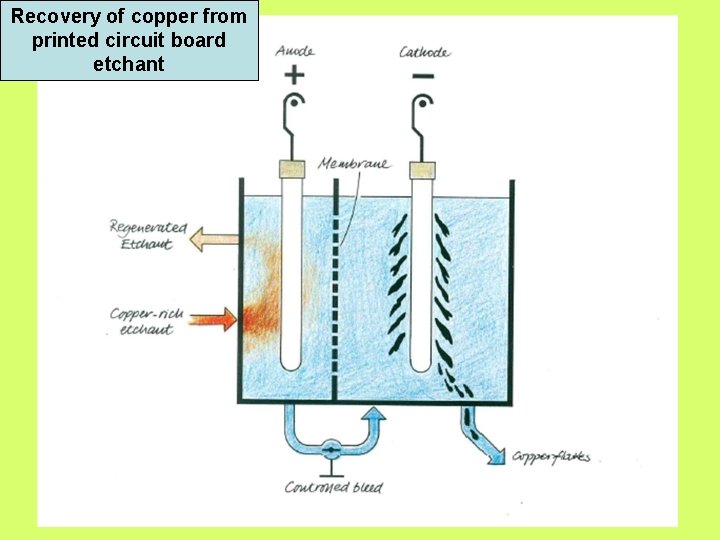

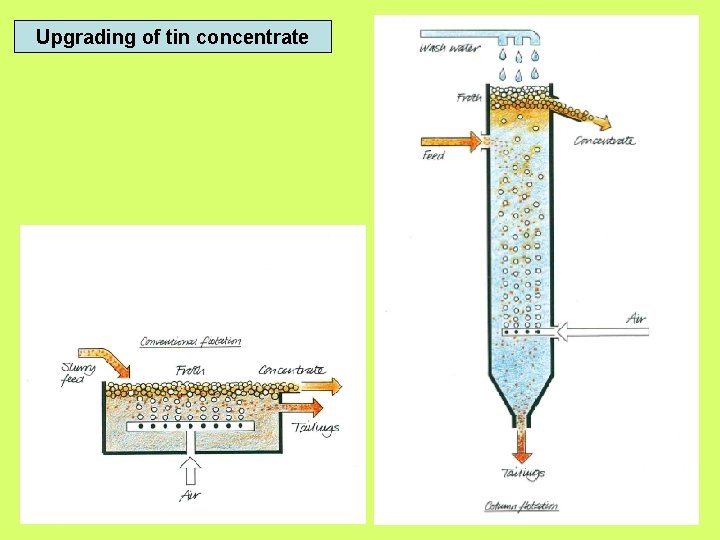
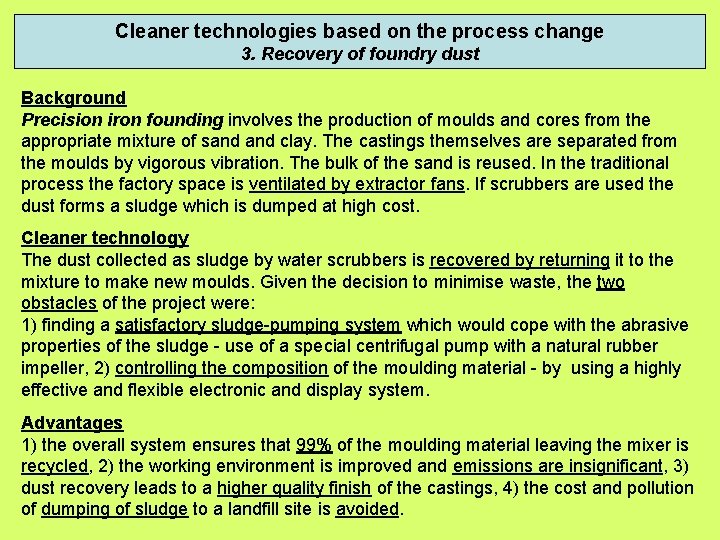
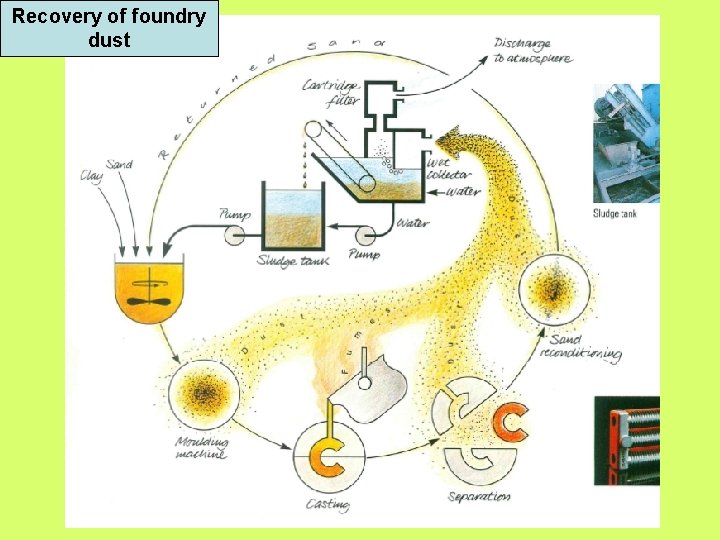
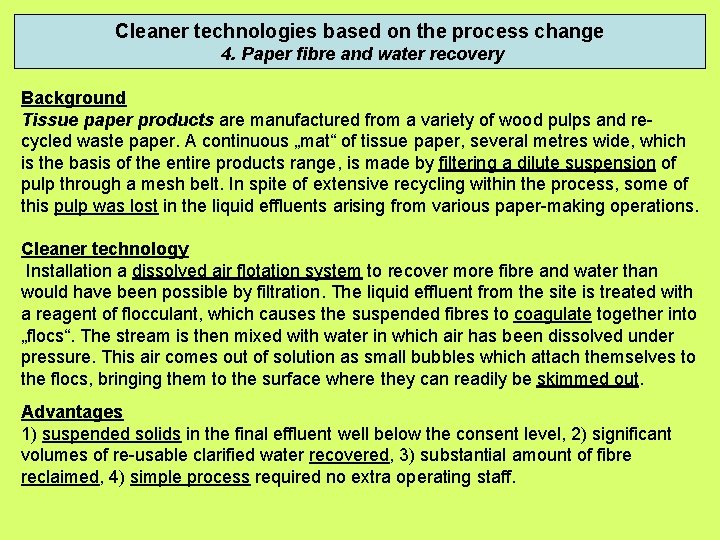
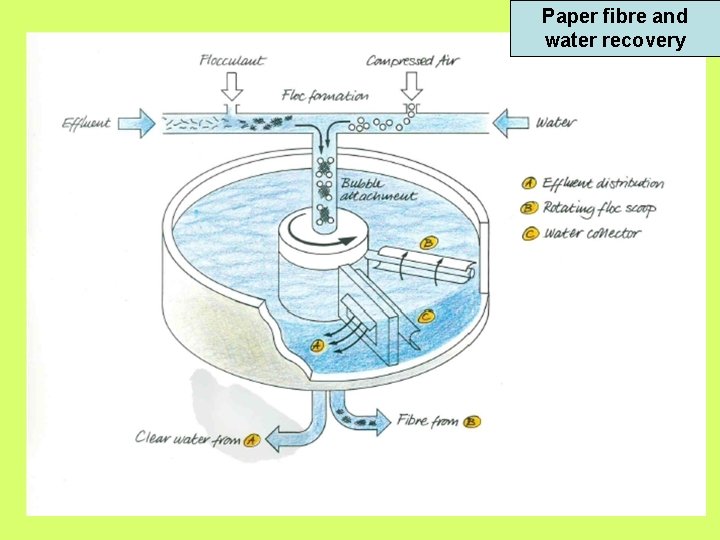
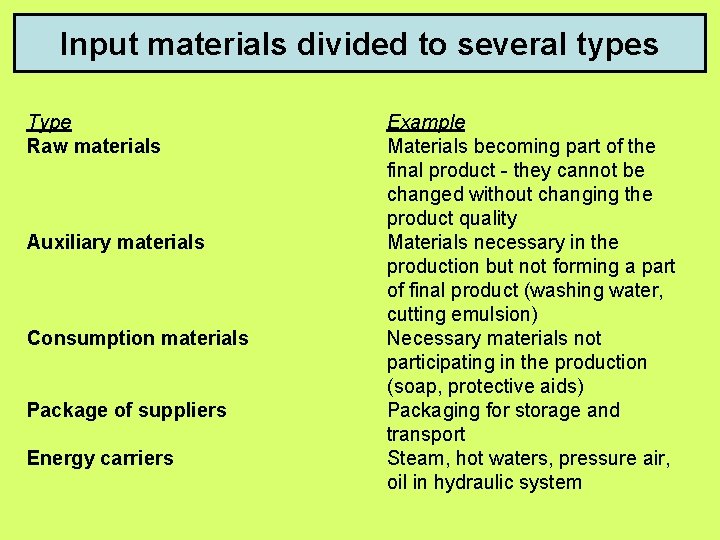
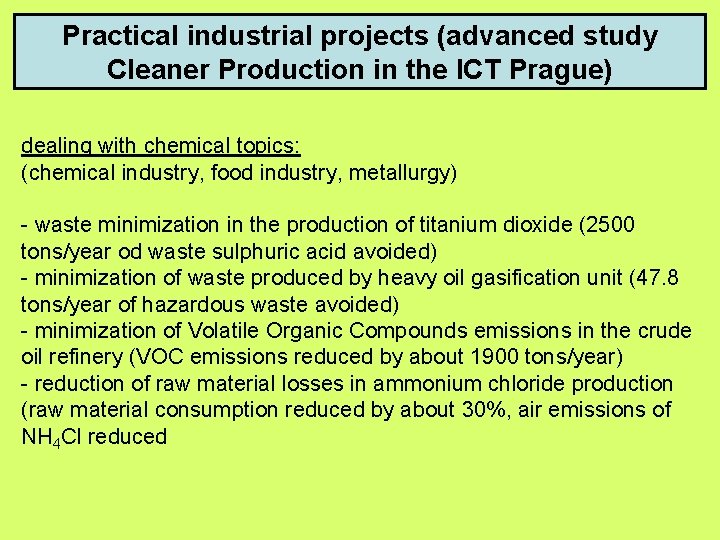
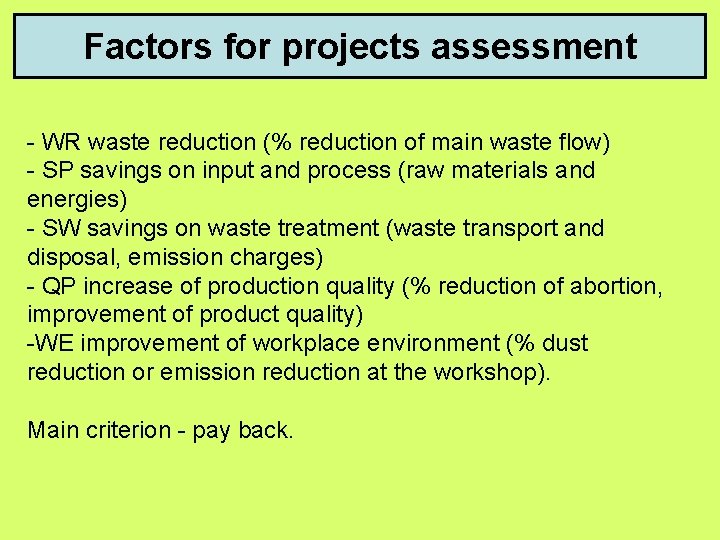
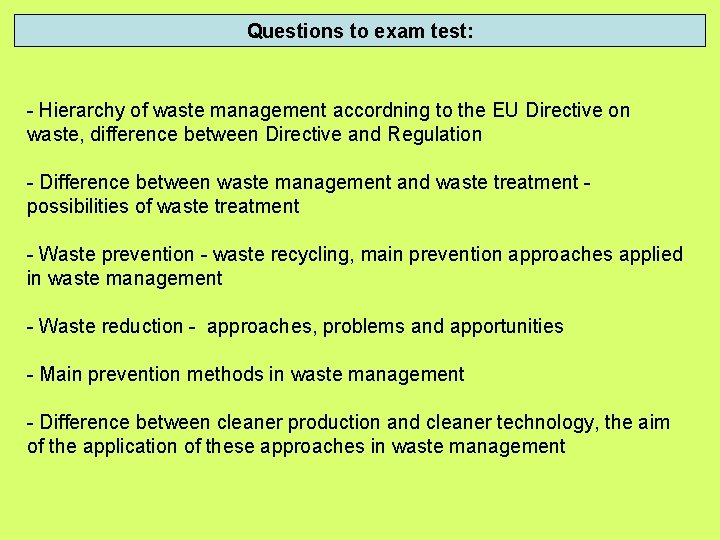
- Slides: 54
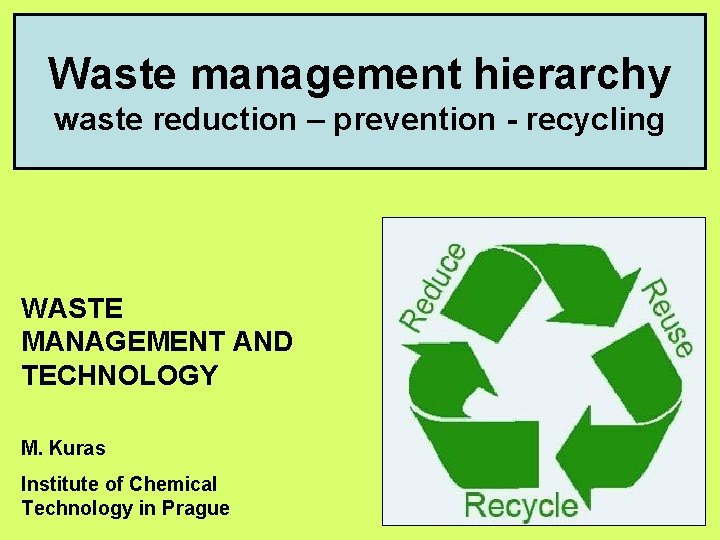
Waste management hierarchy waste reduction – prevention - recycling WASTE MANAGEMENT AND TECHNOLOGY M. Kuras Institute of Chemical Technology in Prague
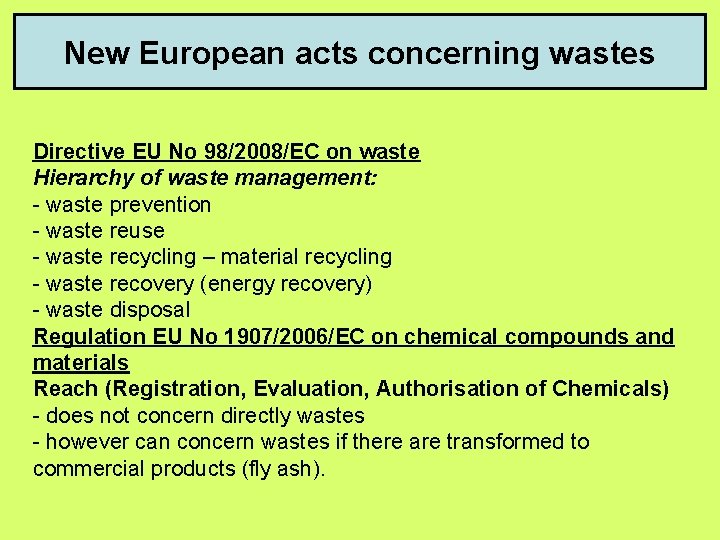
New European acts concerning wastes Directive EU No 98/2008/EC on waste Hierarchy of waste management: - waste prevention - waste reuse - waste recycling – material recycling - waste recovery (energy recovery) - waste disposal Regulation EU No 1907/2006/EC on chemical compounds and materials Reach (Registration, Evaluation, Authorisation of Chemicals) - does not concern directly wastes - however can concern wastes if there are transformed to commercial products (fly ash).
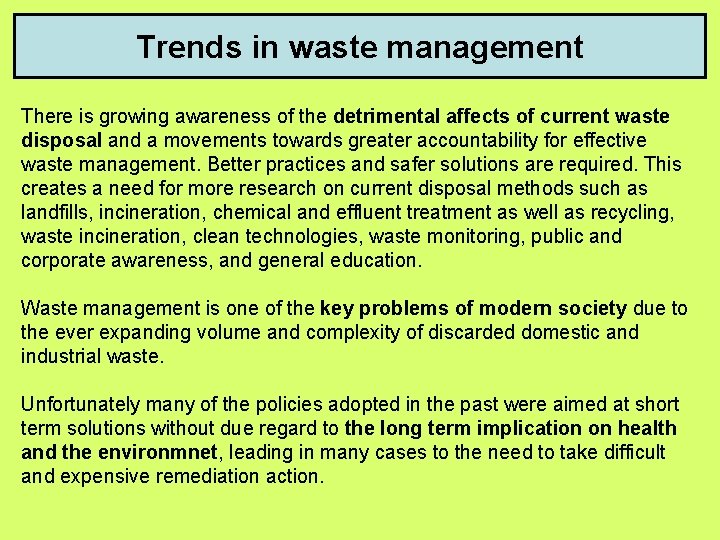
Trends in waste management There is growing awareness of the detrimental affects of current waste disposal and a movements towards greater accountability for effective waste management. Better practices and safer solutions are required. This creates a need for more research on current disposal methods such as landfills, incineration, chemical and effluent treatment as well as recycling, waste incineration, clean technologies, waste monitoring, public and corporate awareness, and general education. Waste management is one of the key problems of modern society due to the ever expanding volume and complexity of discarded domestic and industrial waste. Unfortunately many of the policies adopted in the past were aimed at short term solutions without due regard to the long term implication on health and the environmnet, leading in many cases to the need to take difficult and expensive remediation action.
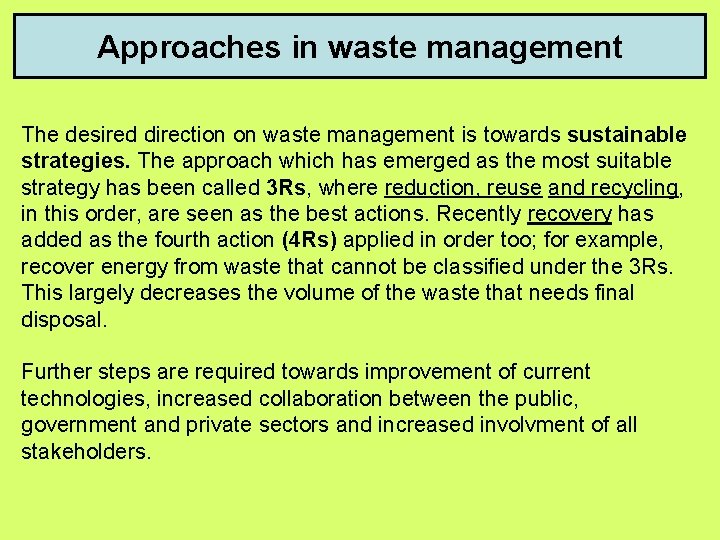
Approaches in waste management The desired direction on waste management is towards sustainable strategies. The approach which has emerged as the most suitable strategy has been called 3 Rs, where reduction, reuse and recycling, in this order, are seen as the best actions. Recently recovery has added as the fourth action (4 Rs) applied in order too; for example, recover energy from waste that cannot be classified under the 3 Rs. This largely decreases the volume of the waste that needs final disposal. Further steps are required towards improvement of current technologies, increased collaboration between the public, government and private sectors and increased involvment of all stakeholders.
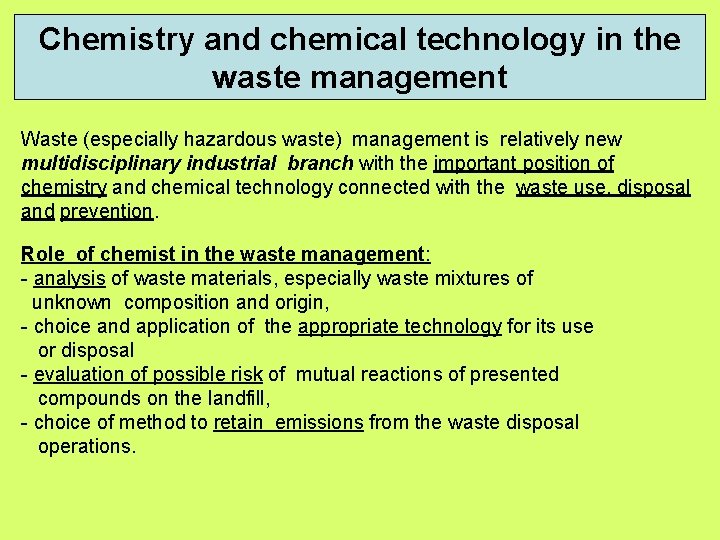
Chemistry and chemical technology in the waste management Waste (especially hazardous waste) management is relatively new multidisciplinary industrial branch with the important position of chemistry and chemical technology connected with the waste use, disposal and prevention. Role of chemist in the waste management: - analysis of waste materials, especially waste mixtures of unknown composition and origin, - choice and application of the appropriate technology for its use or disposal - evaluation of possible risk of mutual reactions of presented compounds on the landfill, - choice of method to retain emissions from the waste disposal operations.
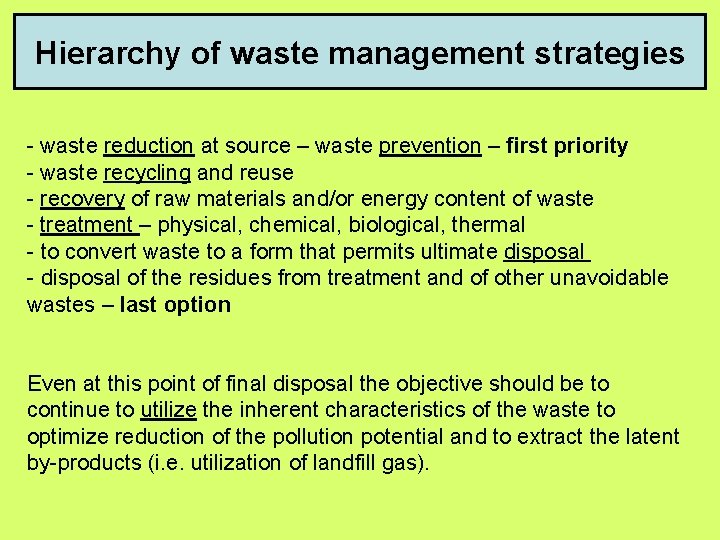
Hierarchy of waste management strategies - waste reduction at source – waste prevention – first priority - waste recycling and reuse - recovery of raw materials and/or energy content of waste - treatment – physical, chemical, biological, thermal - to convert waste to a form that permits ultimate disposal - disposal of the residues from treatment and of other unavoidable wastes – last option Even at this point of final disposal the objective should be to continue to utilize the inherent characteristics of the waste to optimize reduction of the pollution potential and to extract the latent by-products (i. e. utilization of landfill gas).
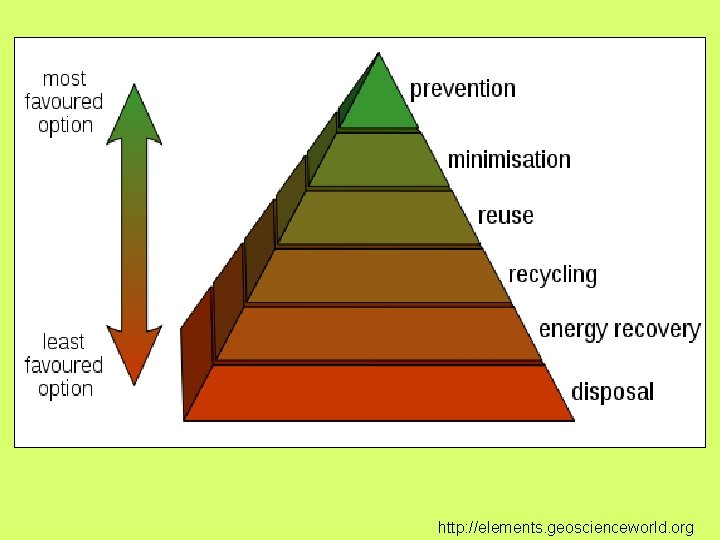
http: //elements. geoscienceworld. org
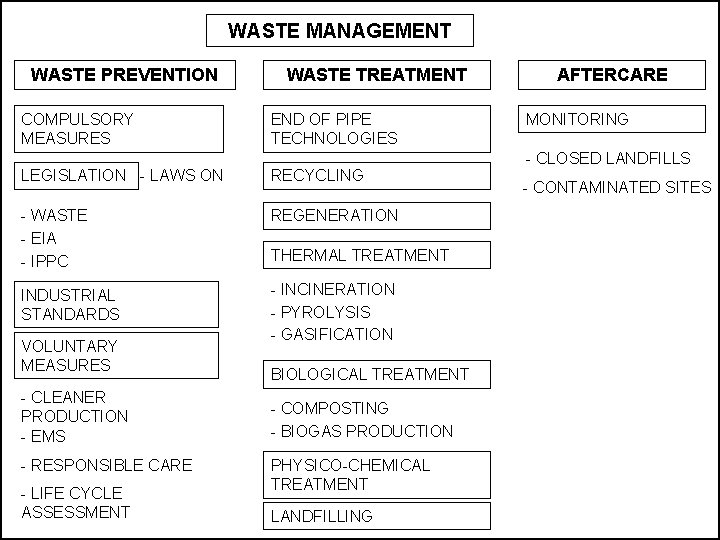
WASTE MANAGEMENT WASTE PREVENTION COMPULSORY MEASURES WASTE TREATMENT END OF PIPE TECHNOLOGIES LEGISLATION - LAWS ON RECYCLING - WASTE - EIA - IPPC REGENERATION INDUSTRIAL STANDARDS - INCINERATION - PYROLYSIS - GASIFICATION VOLUNTARY MEASURES - CLEANER PRODUCTION - EMS - RESPONSIBLE CARE - LIFE CYCLE ASSESSMENT THERMAL TREATMENT BIOLOGICAL TREATMENT - COMPOSTING - BIOGAS PRODUCTION PHYSICO-CHEMICAL TREATMENT LANDFILLING AFTERCARE MONITORING - CLOSED LANDFILLS - CONTAMINATED SITES
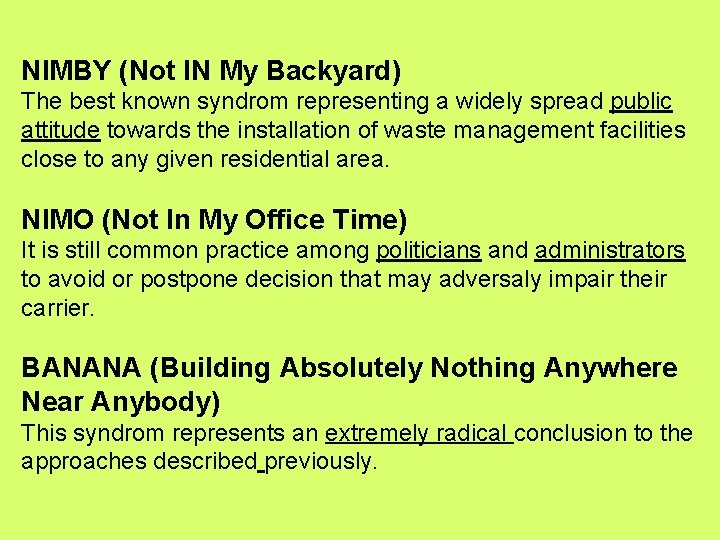
NIMBY (Not IN My Backyard) The best known syndrom representing a widely spread public attitude towards the installation of waste management facilities close to any given residential area. NIMO (Not In My Office Time) It is still common practice among politicians and administrators to avoid or postpone decision that may adversaly impair their carrier. BANANA (Building Absolutely Nothing Anywhere Near Anybody) This syndrom represents an extremely radical conclusion to the approaches described previously.
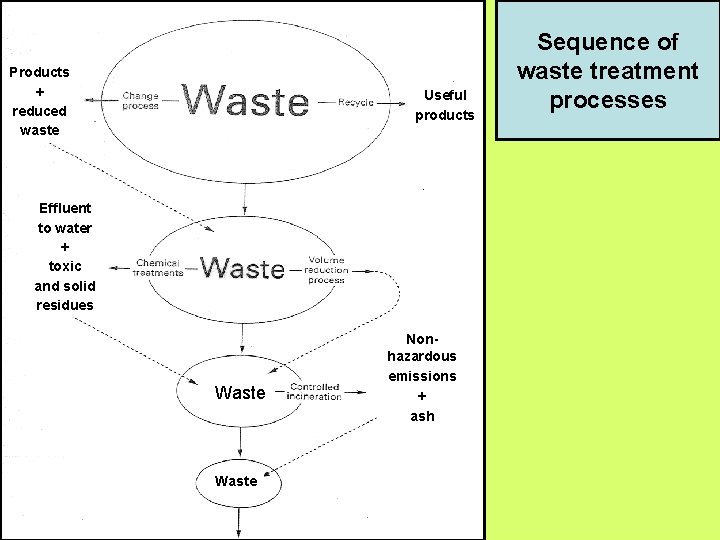
Products + reduced waste Useful products Effluent to water + toxic and solid residues Waste Nonhazardous emissions + ash Sequence of waste treatment processes
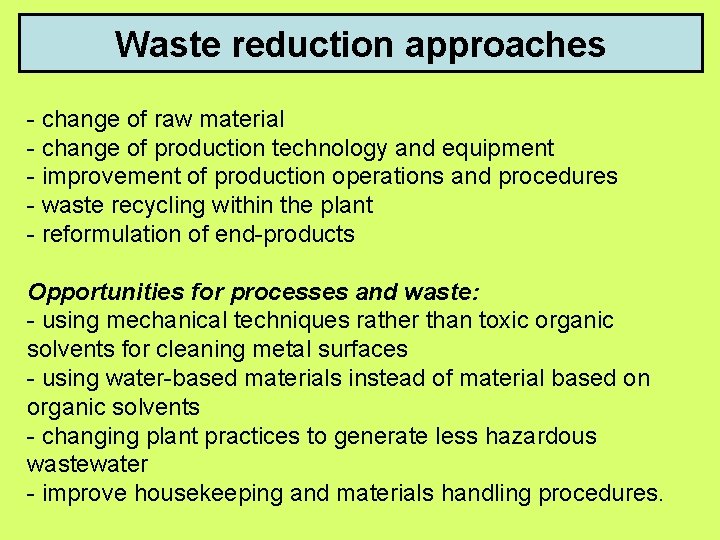
Waste reduction approaches - change of raw material - change of production technology and equipment - improvement of production operations and procedures - waste recycling within the plant - reformulation of end-products Opportunities for processes and waste: - using mechanical techniques rather than toxic organic solvents for cleaning metal surfaces - using water-based materials instead of material based on organic solvents - changing plant practices to generate less hazardous wastewater - improve housekeeping and materials handling procedures.
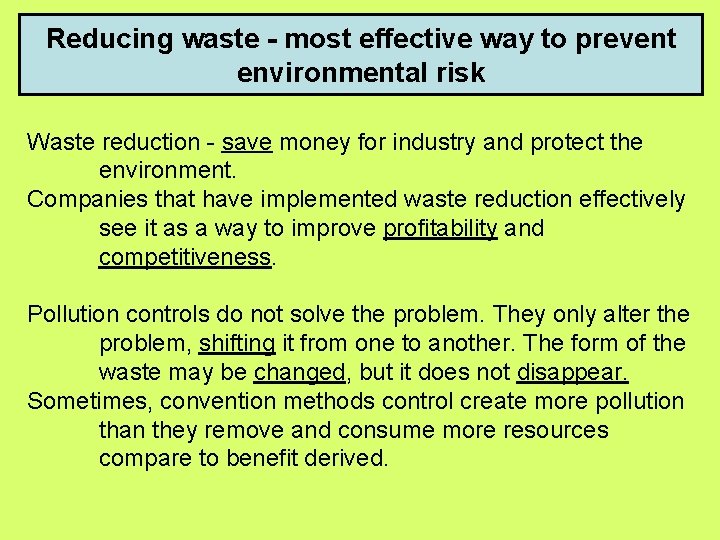
Reducing waste - most effective way to prevent environmental risk Waste reduction - save money for industry and protect the environment. Companies that have implemented waste reduction effectively see it as a way to improve profitability and competitiveness. Pollution controls do not solve the problem. They only alter the problem, shifting it from one to another. The form of the waste may be changed, but it does not disappear. Sometimes, convention methods control create more pollution than they remove and consume more resources compare to benefit derived.
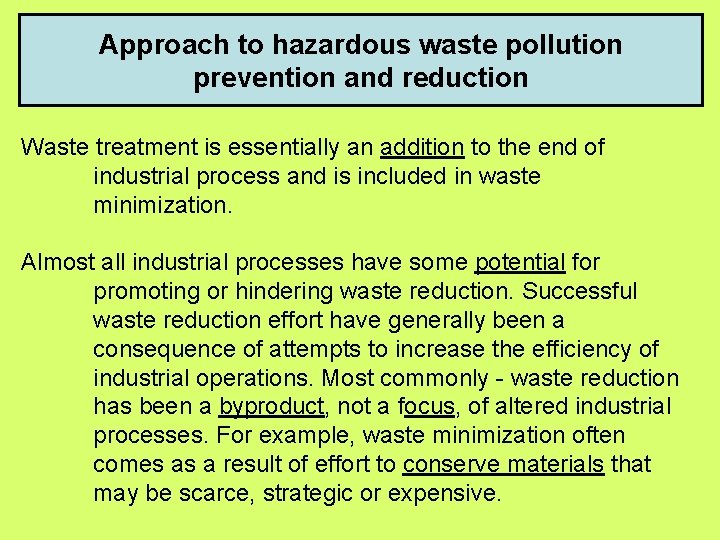
Approach to hazardous waste pollution prevention and reduction Waste treatment is essentially an addition to the end of industrial process and is included in waste minimization. Almost all industrial processes have some potential for promoting or hindering waste reduction. Successful waste reduction effort have generally been a consequence of attempts to increase the efficiency of industrial operations. Most commonly - waste reduction has been a byproduct, not a focus, of altered industrial processes. For example, waste minimization often comes as a result of effort to conserve materials that may be scarce, strategic or expensive.
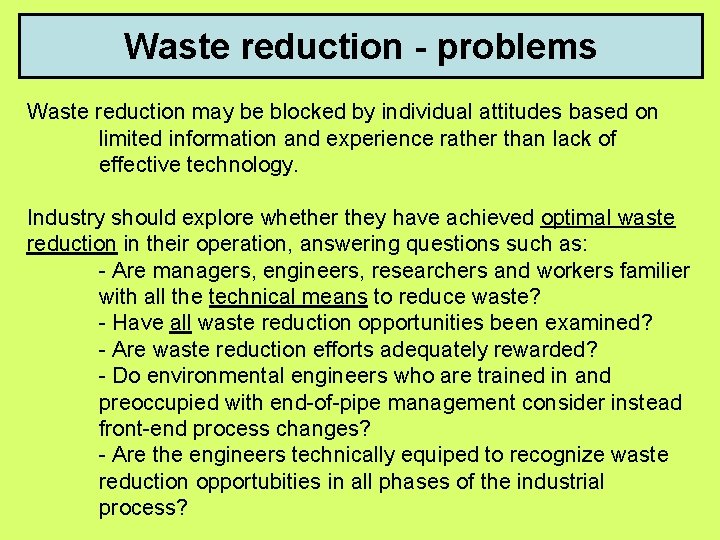
Waste reduction - problems Waste reduction may be blocked by individual attitudes based on limited information and experience rather than lack of effective technology. Industry should explore whether they have achieved optimal waste reduction in their operation, answering questions such as: - Are managers, engineers, researchers and workers familier with all the technical means to reduce waste? - Have all waste reduction opportunities been examined? - Are waste reduction efforts adequately rewarded? - Do environmental engineers who are trained in and preoccupied with end-of-pipe management consider instead front-end process changes? - Are the engineers technically equiped to recognize waste reduction opportubities in all phases of the industrial process?
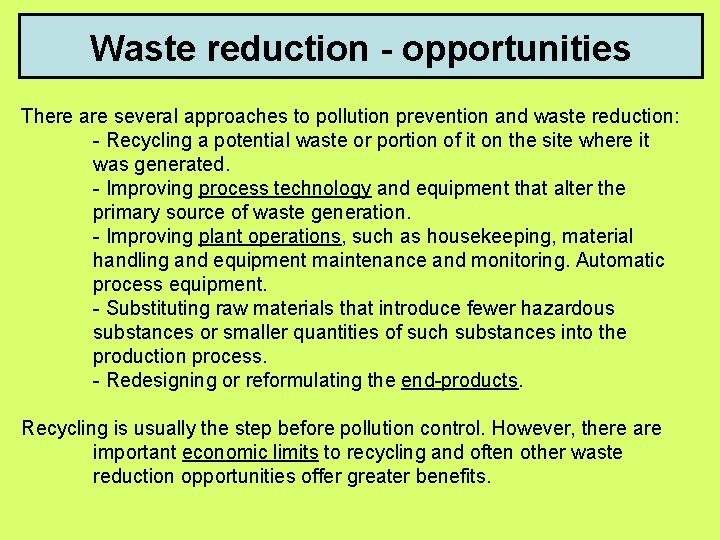
Waste reduction - opportunities There are several approaches to pollution prevention and waste reduction: - Recycling a potential waste or portion of it on the site where it was generated. - Improving process technology and equipment that alter the primary source of waste generation. - Improving plant operations, such as housekeeping, material handling and equipment maintenance and monitoring. Automatic process equipment. - Substituting raw materials that introduce fewer hazardous substances or smaller quantities of such substances into the production process. - Redesigning or reformulating the end-products. Recycling is usually the step before pollution control. However, there are important economic limits to recycling and often other waste reduction opportunities offer greater benefits.
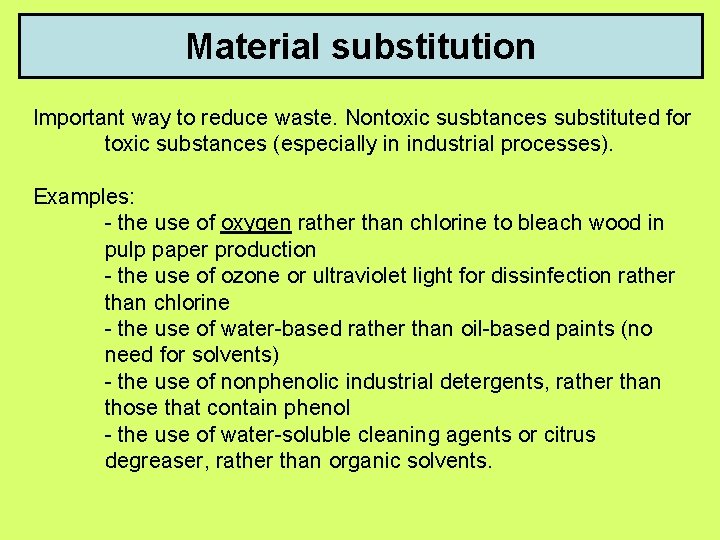
Material substitution Important way to reduce waste. Nontoxic susbtances substituted for toxic substances (especially in industrial processes). Examples: - the use of oxygen rather than chlorine to bleach wood in pulp paper production - the use of ozone or ultraviolet light for dissinfection rather than chlorine - the use of water-based rather than oil-based paints (no need for solvents) - the use of nonphenolic industrial detergents, rather than those that contain phenol - the use of water-soluble cleaning agents or citrus degreaser, rather than organic solvents.
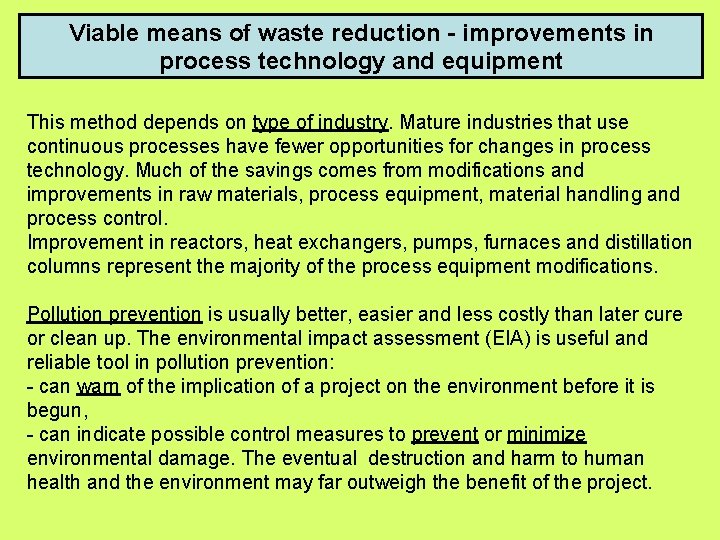
Viable means of waste reduction - improvements in process technology and equipment This method depends on type of industry. Mature industries that use continuous processes have fewer opportunities for changes in process technology. Much of the savings comes from modifications and improvements in raw materials, process equipment, material handling and process control. Improvement in reactors, heat exchangers, pumps, furnaces and distillation columns represent the majority of the process equipment modifications. Pollution prevention is usually better, easier and less costly than later cure or clean up. The environmental impact assessment (EIA) is useful and reliable tool in pollution prevention: - can warn of the implication of a project on the environment before it is begun, - can indicate possible control measures to prevent or minimize environmental damage. The eventual destruction and harm to human health and the environment may far outweigh the benefit of the project.
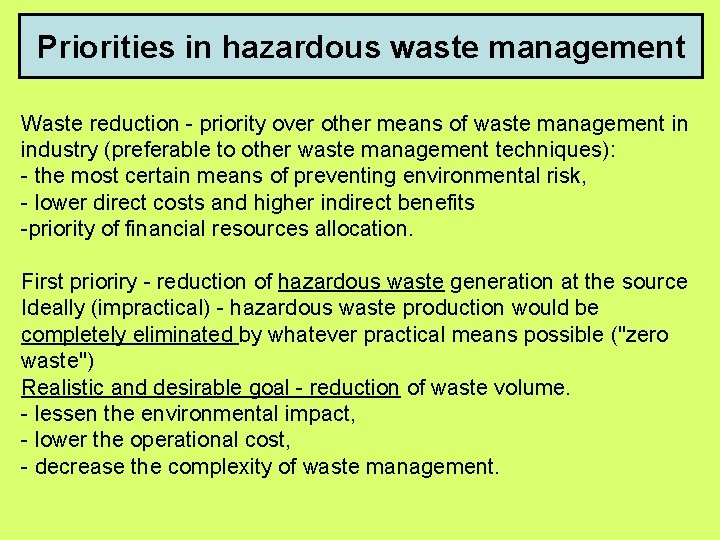
Priorities in hazardous waste management Waste reduction - priority over other means of waste management in industry (preferable to other waste management techniques): - the most certain means of preventing environmental risk, - lower direct costs and higher indirect benefits -priority of financial resources allocation. First prioriry - reduction of hazardous waste generation at the source Ideally (impractical) - hazardous waste production would be completely eliminated by whatever practical means possible ("zero waste") Realistic and desirable goal - reduction of waste volume. - lessen the environmental impact, - lower the operational cost, - decrease the complexity of waste management.
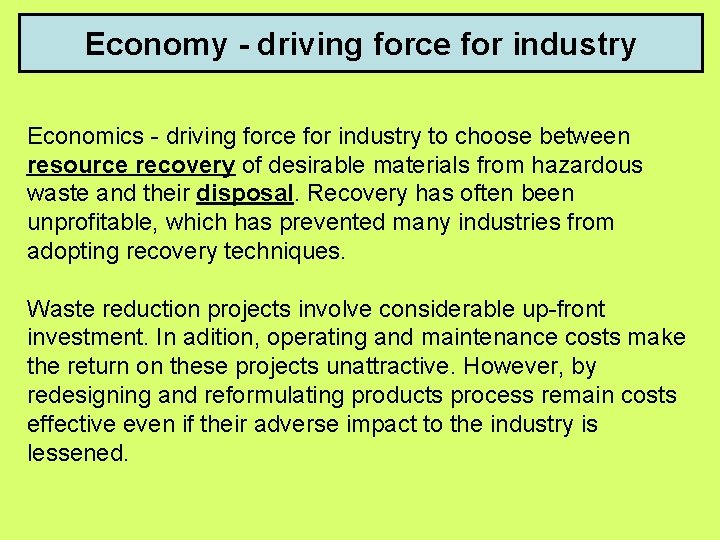
Economy - driving force for industry Economics - driving force for industry to choose between resource recovery of desirable materials from hazardous waste and their disposal. Recovery has often been unprofitable, which has prevented many industries from adopting recovery techniques. Waste reduction projects involve considerable up-front investment. In adition, operating and maintenance costs make the return on these projects unattractive. However, by redesigning and reformulating products process remain costs effective even if their adverse impact to the industry is lessened.
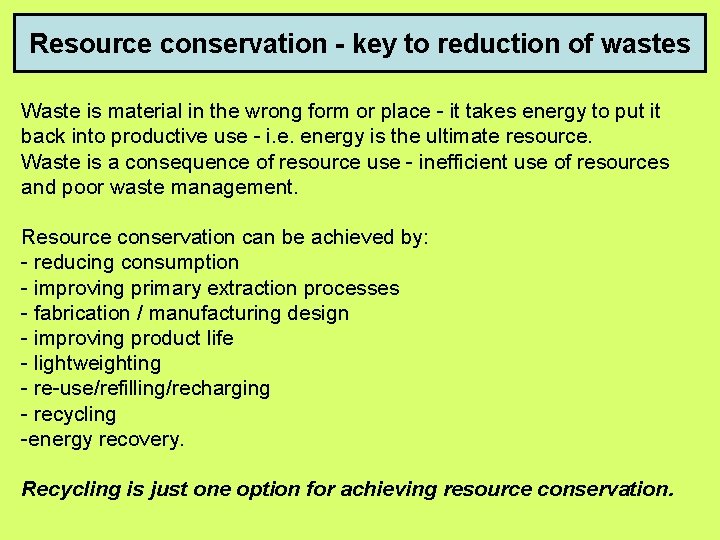
Resource conservation - key to reduction of wastes Waste is material in the wrong form or place - it takes energy to put it back into productive use - i. e. energy is the ultimate resource. Waste is a consequence of resource use - inefficient use of resources and poor waste management. Resource conservation can be achieved by: - reducing consumption - improving primary extraction processes - fabrication / manufacturing design - improving product life - lightweighting - re-use/refilling/recharging - recycling -energy recovery. Recycling is just one option for achieving resource conservation.
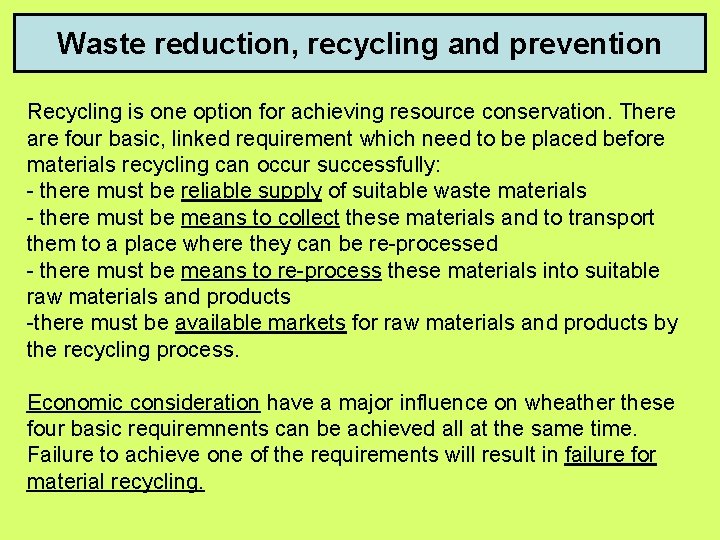
Waste reduction, recycling and prevention Recycling is one option for achieving resource conservation. There are four basic, linked requirement which need to be placed before materials recycling can occur successfully: - there must be reliable supply of suitable waste materials - there must be means to collect these materials and to transport them to a place where they can be re-processed - there must be means to re-process these materials into suitable raw materials and products -there must be available markets for raw materials and products by the recycling process. Economic consideration have a major influence on wheather these four basic requiremnents can be achieved all at the same time. Failure to achieve one of the requirements will result in failure for material recycling.
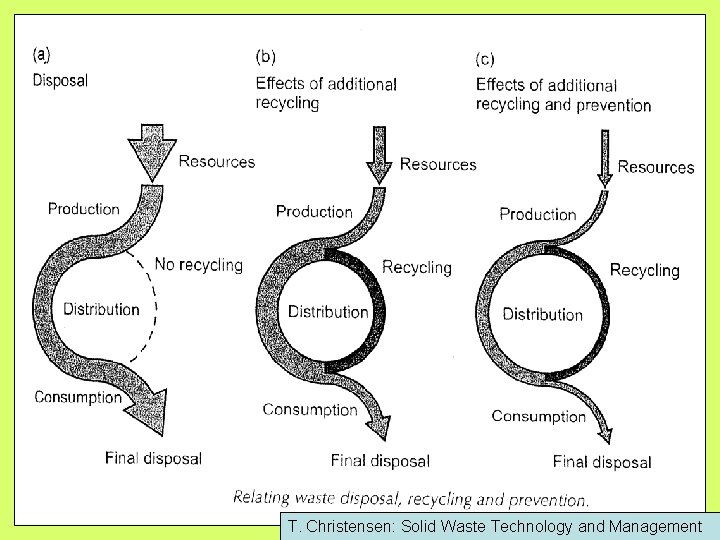
T. Christensen: Solid Waste Technology and Management
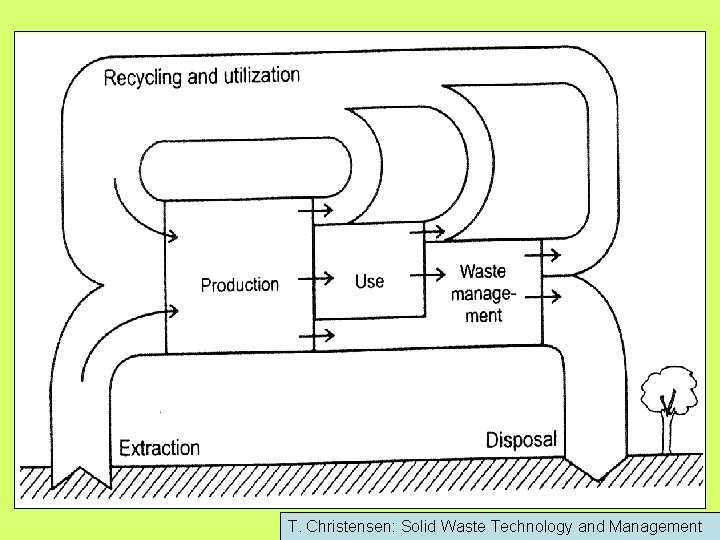
T. Christensen: Solid Waste Technology and Management
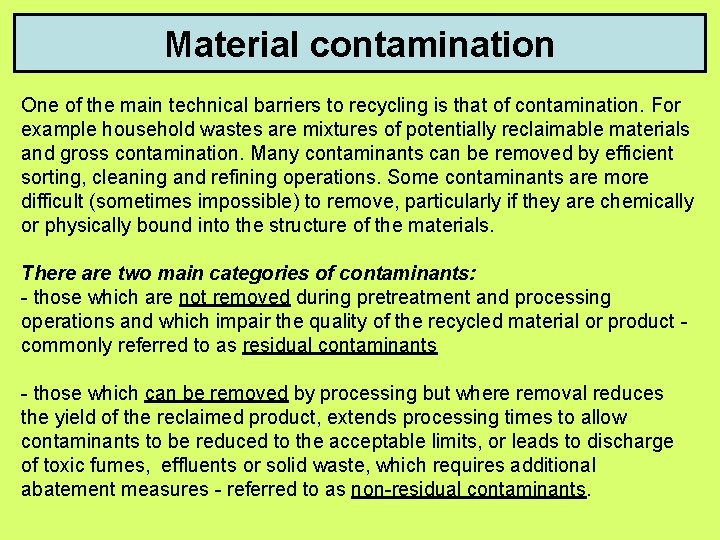
Material contamination One of the main technical barriers to recycling is that of contamination. For example household wastes are mixtures of potentially reclaimable materials and gross contamination. Many contaminants can be removed by efficient sorting, cleaning and refining operations. Some contaminants are more difficult (sometimes impossible) to remove, particularly if they are chemically or physically bound into the structure of the materials. There are two main categories of contaminants: - those which are not removed during pretreatment and processing operations and which impair the quality of the recycled material or product commonly referred to as residual contaminants - those which can be removed by processing but where removal reduces the yield of the reclaimed product, extends processing times to allow contaminants to be reduced to the acceptable limits, or leads to discharge of toxic fumes, effluents or solid waste, which requires additional abatement measures - referred to as non-residual contaminants.
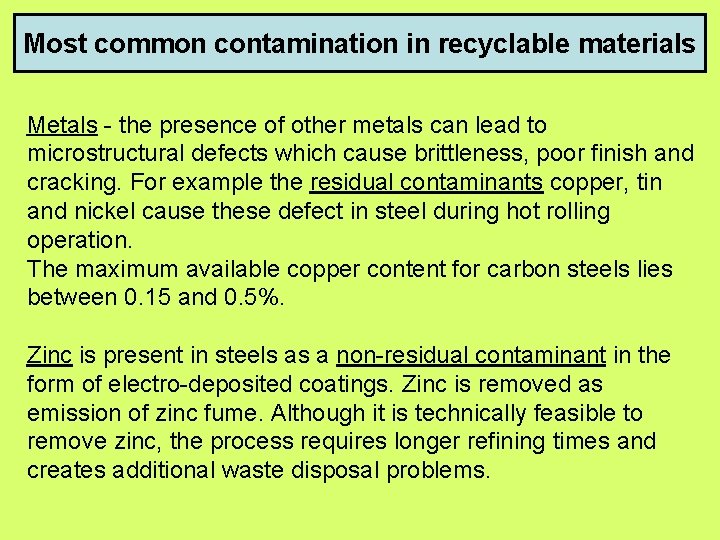
Most common contamination in recyclable materials Metals - the presence of other metals can lead to microstructural defects which cause brittleness, poor finish and cracking. For example the residual contaminants copper, tin and nickel cause these defect in steel during hot rolling operation. The maximum available copper content for carbon steels lies between 0. 15 and 0. 5%. Zinc is present in steels as a non-residual contaminant in the form of electro-deposited coatings. Zinc is removed as emission of zinc fume. Although it is technically feasible to remove zinc, the process requires longer refining times and creates additional waste disposal problems.
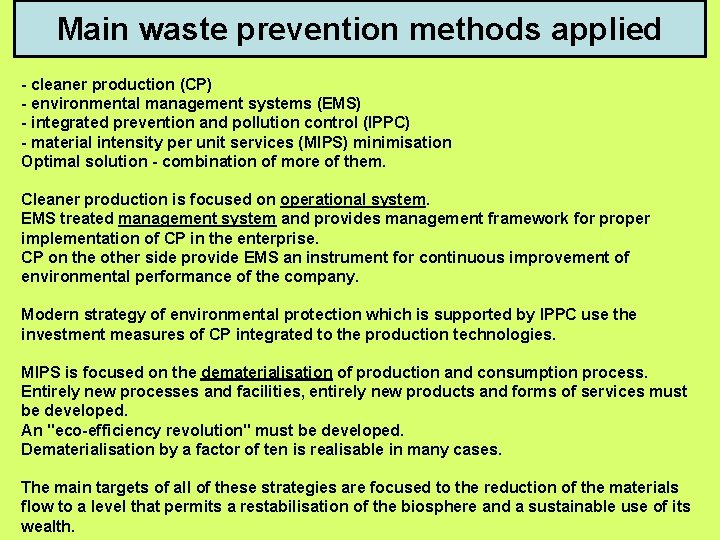
Main waste prevention methods applied - cleaner production (CP) - environmental management systems (EMS) - integrated prevention and pollution control (IPPC) - material intensity per unit services (MIPS) minimisation Optimal solution - combination of more of them. Cleaner production is focused on operational system. EMS treated management system and provides management framework for proper implementation of CP in the enterprise. CP on the other side provide EMS an instrument for continuous improvement of environmental performance of the company. Modern strategy of environmental protection which is supported by IPPC use the investment measures of CP integrated to the production technologies. MIPS is focused on the dematerialisation of production and consumption process. Entirely new processes and facilities, entirely new products and forms of services must be developed. An "eco-efficiency revolution" must be developed. Dematerialisation by a factor of ten is realisable in many cases. The main targets of all of these strategies are focused to the reduction of the materials flow to a level that permits a restabilisation of the biosphere and a sustainable use of its wealth.
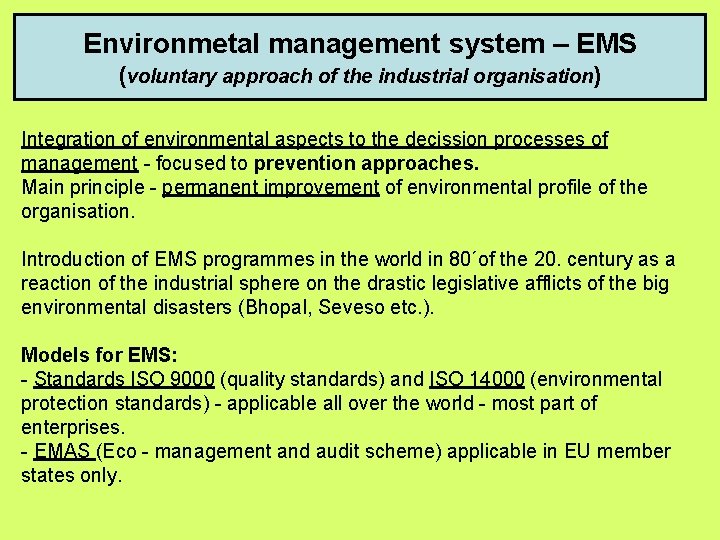
Environmetal management system – EMS (voluntary approach of the industrial organisation) Integration of environmental aspects to the decission processes of management - focused to prevention approaches. Main principle - permanent improvement of environmental profile of the organisation. Introduction of EMS programmes in the world in 80´of the 20. century as a reaction of the industrial sphere on the drastic legislative afflicts of the big environmental disasters (Bhopal, Seveso etc. ). Models for EMS: - Standards ISO 9000 (quality standards) and ISO 14000 (environmental protection standards) - applicable all over the world - most part of enterprises. - EMAS (Eco - management and audit scheme) applicable in EU member states only.
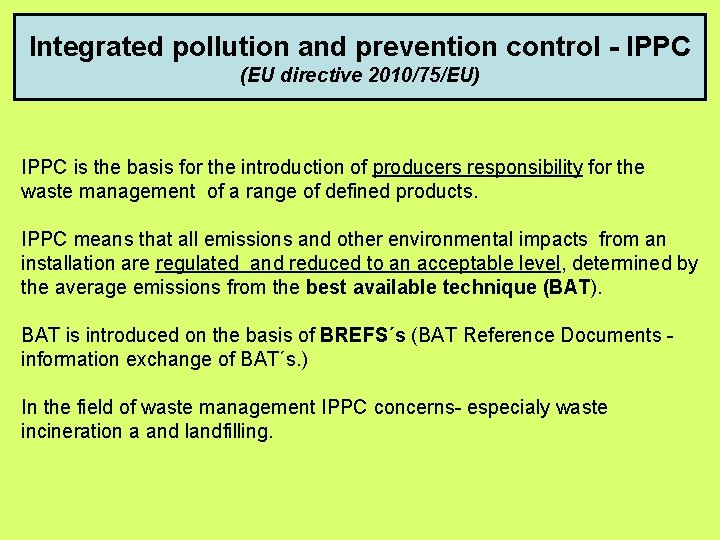
Integrated pollution and prevention control - IPPC (EU directive 2010/75/EU) IPPC is the basis for the introduction of producers responsibility for the waste management of a range of defined products. IPPC means that all emissions and other environmental impacts from an installation are regulated and reduced to an acceptable level, determined by the average emissions from the best available technique (BAT). BAT is introduced on the basis of BREFS´s (BAT Reference Documents information exchange of BAT´s. ) In the field of waste management IPPC concerns- especialy waste incineration a and landfilling.
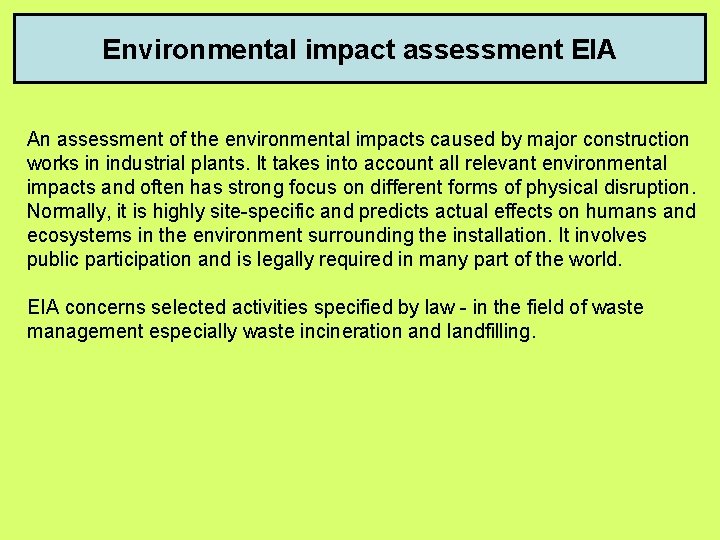
Environmental impact assessment EIA An assessment of the environmental impacts caused by major construction works in industrial plants. It takes into account all relevant environmental impacts and often has strong focus on different forms of physical disruption. Normally, it is highly site-specific and predicts actual effects on humans and ecosystems in the environment surrounding the installation. It involves public participation and is legally required in many part of the world. EIA concerns selected activities specified by law - in the field of waste management especially waste incineration and landfilling.
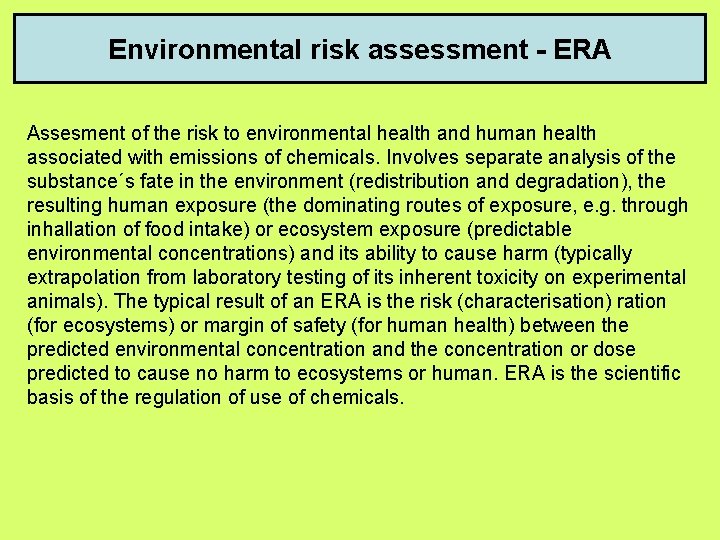
Environmental risk assessment - ERA Assesment of the risk to environmental health and human health associated with emissions of chemicals. Involves separate analysis of the substance´s fate in the environment (redistribution and degradation), the resulting human exposure (the dominating routes of exposure, e. g. through inhallation of food intake) or ecosystem exposure (predictable environmental concentrations) and its ability to cause harm (typically extrapolation from laboratory testing of its inherent toxicity on experimental animals). The typical result of an ERA is the risk (characterisation) ration (for ecosystems) or margin of safety (for human health) between the predicted environmental concentration and the concentration or dose predicted to cause no harm to ecosystems or human. ERA is the scientific basis of the regulation of use of chemicals.
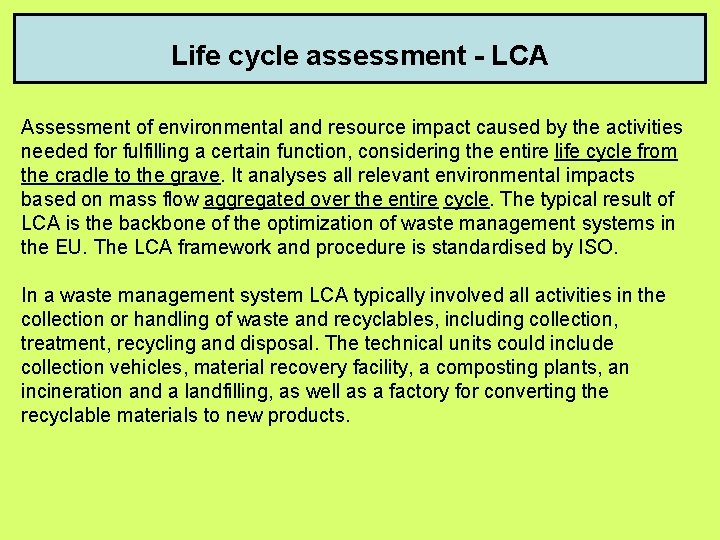
Life cycle assessment - LCA Assessment of environmental and resource impact caused by the activities needed for fulfilling a certain function, considering the entire life cycle from the cradle to the grave. It analyses all relevant environmental impacts based on mass flow aggregated over the entire cycle. The typical result of LCA is the backbone of the optimization of waste management systems in the EU. The LCA framework and procedure is standardised by ISO. In a waste management system LCA typically involved all activities in the collection or handling of waste and recyclables, including collection, treatment, recycling and disposal. The technical units could include collection vehicles, material recovery facility, a composting plants, an incineration and a landfilling, as well as a factory for converting the recyclable materials to new products.
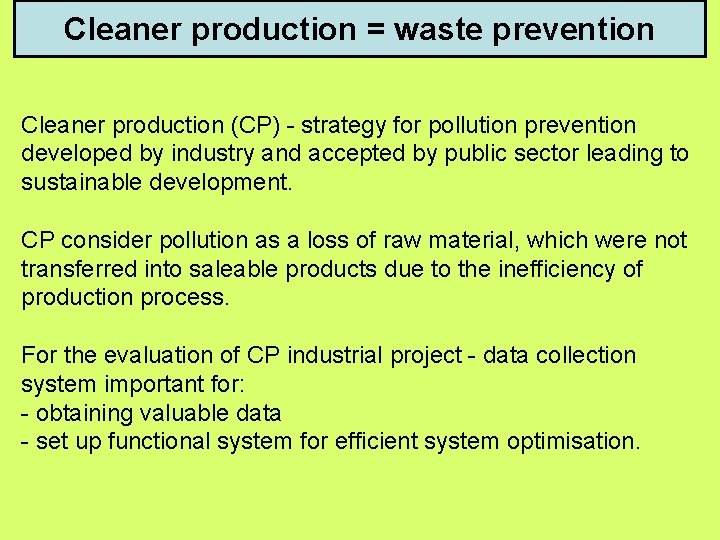
Cleaner production = waste prevention Cleaner production (CP) - strategy for pollution prevention developed by industry and accepted by public sector leading to sustainable development. CP consider pollution as a loss of raw material, which were not transferred into saleable products due to the inefficiency of production process. For the evaluation of CP industrial project - data collection system important for: - obtaining valuable data - set up functional system for efficient system optimisation.
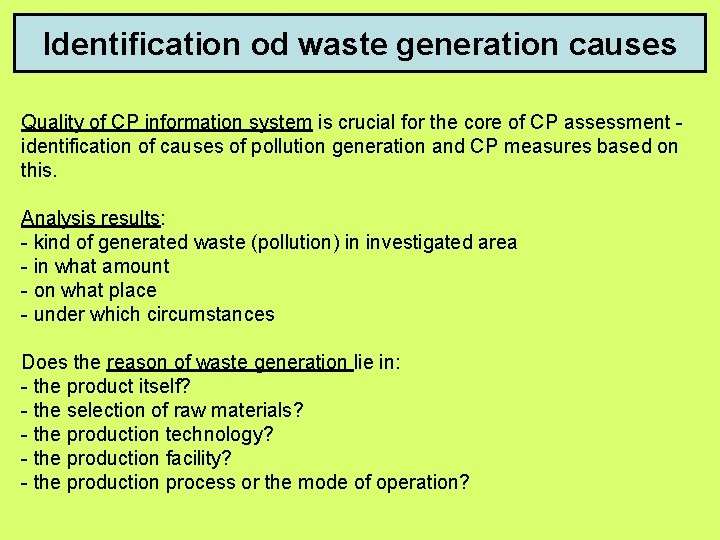
Identification od waste generation causes Quality of CP information system is crucial for the core of CP assessment identification of causes of pollution generation and CP measures based on this. Analysis results: - kind of generated waste (pollution) in investigated area - in what amount - on what place - under which circumstances Does the reason of waste generation lie in: - the product itself? - the selection of raw materials? - the production technology? - the production facility? - the production process or the mode of operation?
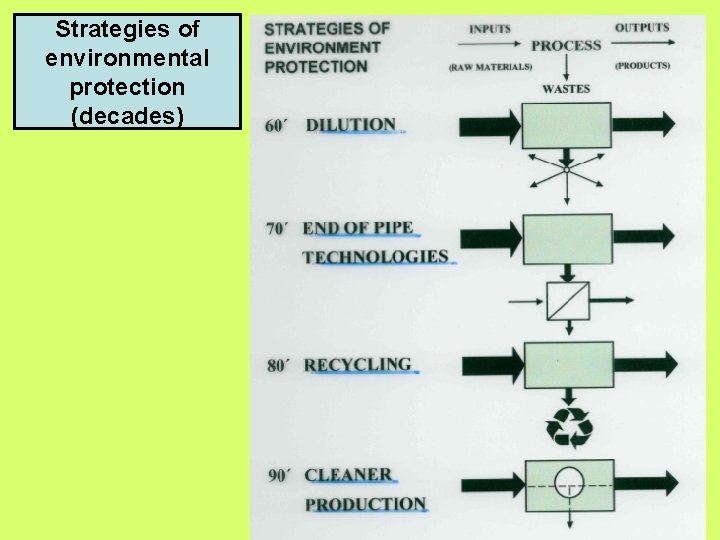
Strategies of environmental protection (decades)
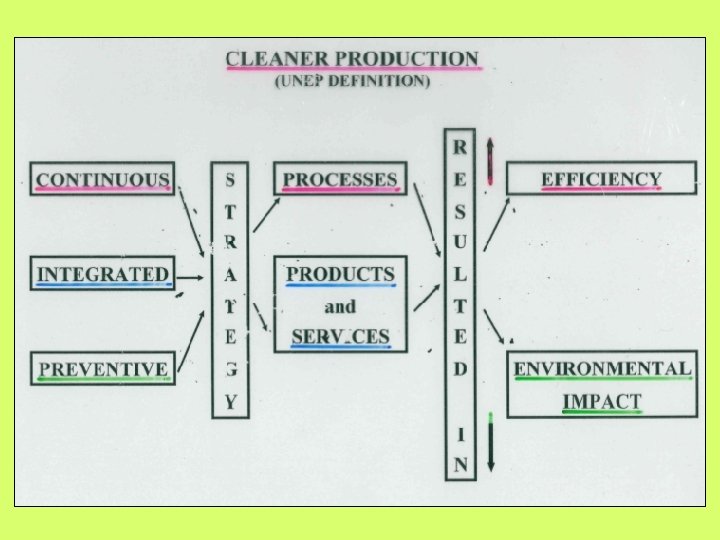
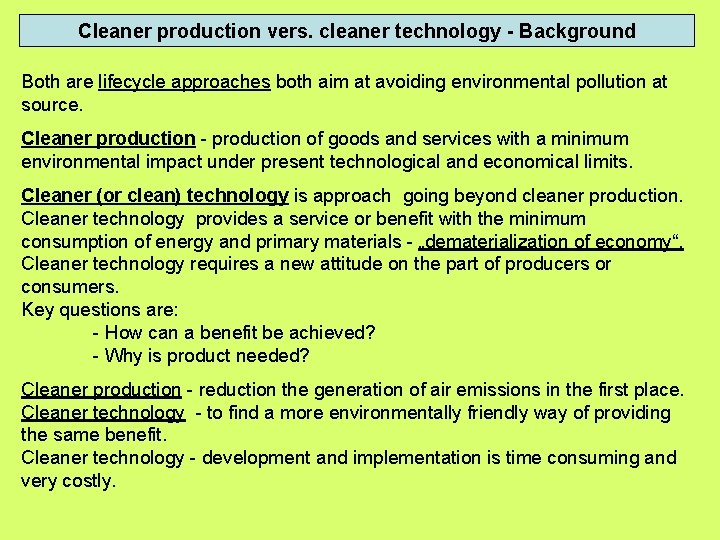
Cleaner production vers. cleaner technology - Background Both are lifecycle approaches both aim at avoiding environmental pollution at source. Cleaner production - production of goods and services with a minimum environmental impact under present technological and economical limits. Cleaner (or clean) technology is approach going beyond cleaner production. Cleaner technology provides a service or benefit with the minimum consumption of energy and primary materials - „dematerialization of economy“. Cleaner technology requires a new attitude on the part of producers or consumers. Key questions are: - How can a benefit be achieved? - Why is product needed? Cleaner production - reduction the generation of air emissions in the first place. Cleaner technology - to find a more environmentally friendly way of providing the same benefit. Cleaner technology - development and implementation is time consuming and very costly.
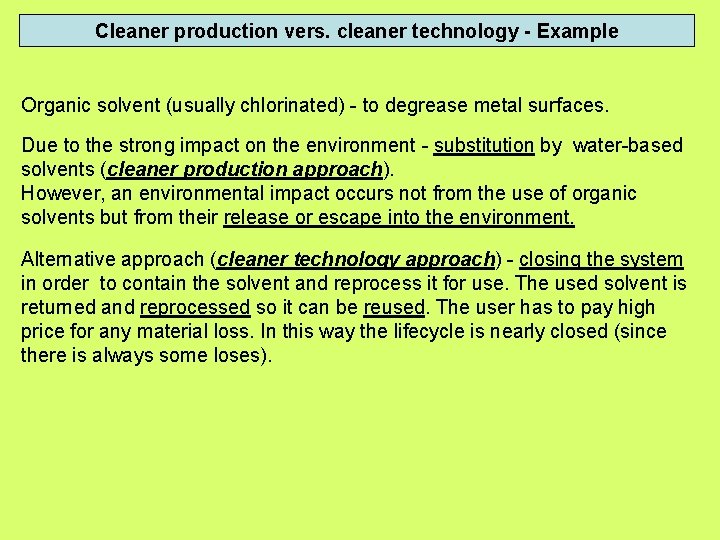
Cleaner production vers. cleaner technology - Example Organic solvent (usually chlorinated) - to degrease metal surfaces. Due to the strong impact on the environment - substitution by water-based solvents (cleaner production approach). However, an environmental impact occurs not from the use of organic solvents but from their release or escape into the environment. Alternative approach (cleaner technology approach) - closing the system in order to contain the solvent and reprocess it for use. The used solvent is returned and reprocessed so it can be reused. The user has to pay high price for any material loss. In this way the lifecycle is nearly closed (since there is always some loses).
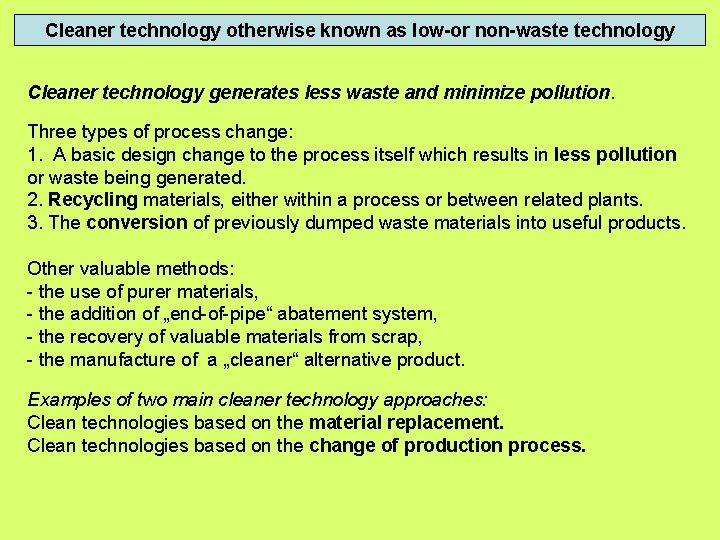
Cleaner technology otherwise known as low-or non-waste technology Cleaner technology generates less waste and minimize pollution. Three types of process change: 1. A basic design change to the process itself which results in less pollution or waste being generated. 2. Recycling materials, either within a process or between related plants. 3. The conversion of previously dumped waste materials into useful products. Other valuable methods: - the use of purer materials, - the addition of „end-of-pipe“ abatement system, - the recovery of valuable materials from scrap, - the manufacture of a „cleaner“ alternative product. Examples of two main cleaner technology approaches: Clean technologies based on the material replacement. Clean technologies based on the change of production process.
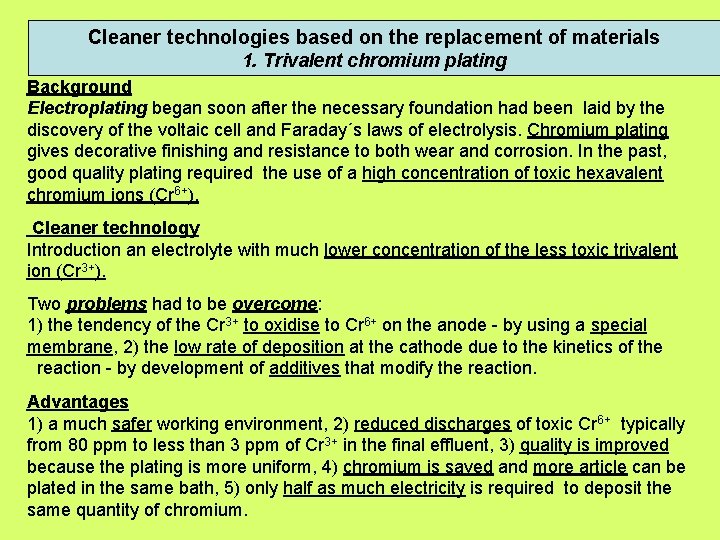
Cleaner technologies based on the replacement of materials 1. Trivalent chromium plating Background Electroplating began soon after the necessary foundation had been laid by the discovery of the voltaic cell and Faraday´s laws of electrolysis. Chromium plating gives decorative finishing and resistance to both wear and corrosion. In the past, good quality plating required the use of a high concentration of toxic hexavalent chromium ions (Cr 6+). Cleaner technology Introduction an electrolyte with much lower concentration of the less toxic trivalent ion (Cr 3+). Two problems had to be overcome: 1) the tendency of the Cr 3+ to oxidise to Cr 6+ on the anode - by using a special membrane, 2) the low rate of deposition at the cathode due to the kinetics of the reaction - by development of additives that modify the reaction. Advantages 1) a much safer working environment, 2) reduced discharges of toxic Cr 6+ typically from 80 ppm to less than 3 ppm of Cr 3+ in the final effluent, 3) quality is improved because the plating is more uniform, 4) chromium is saved and more article can be plated in the same bath, 5) only half as much electricity is required to deposit the same quantity of chromium.
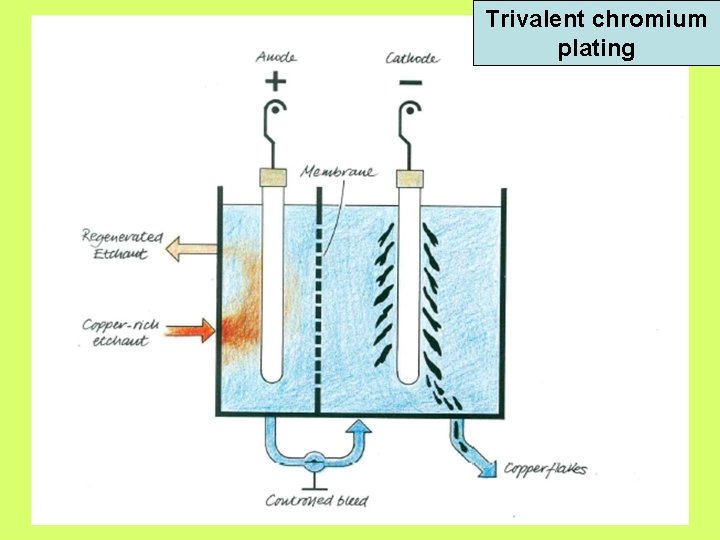
Trivalent chromium plating
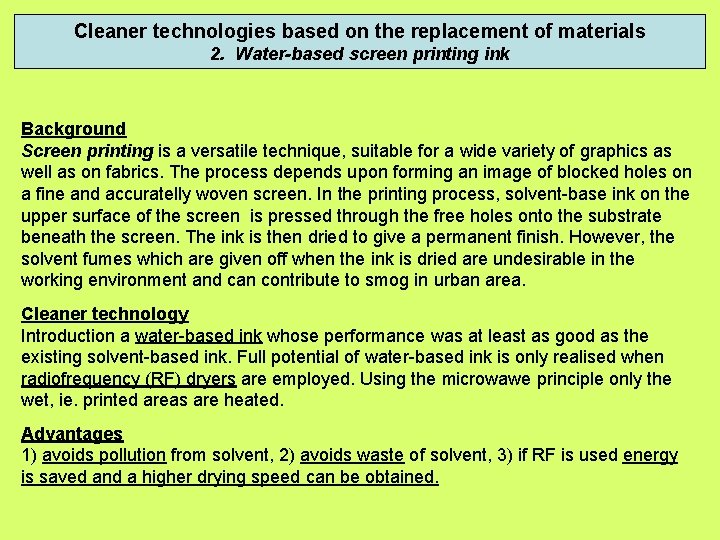
Cleaner technologies based on the replacement of materials 2. Water-based screen printing ink Background Screen printing is a versatile technique, suitable for a wide variety of graphics as well as on fabrics. The process depends upon forming an image of blocked holes on a fine and accuratelly woven screen. In the printing process, solvent-base ink on the upper surface of the screen is pressed through the free holes onto the substrate beneath the screen. The ink is then dried to give a permanent finish. However, the solvent fumes which are given off when the ink is dried are undesirable in the working environment and can contribute to smog in urban area. Cleaner technology Introduction a water-based ink whose performance was at least as good as the existing solvent-based ink. Full potential of water-based ink is only realised when radiofrequency (RF) dryers are employed. Using the microwawe principle only the wet, ie. printed areas are heated. Advantages 1) avoids pollution from solvent, 2) avoids waste of solvent, 3) if RF is used energy is saved and a higher drying speed can be obtained.

Water-based screen printing ink
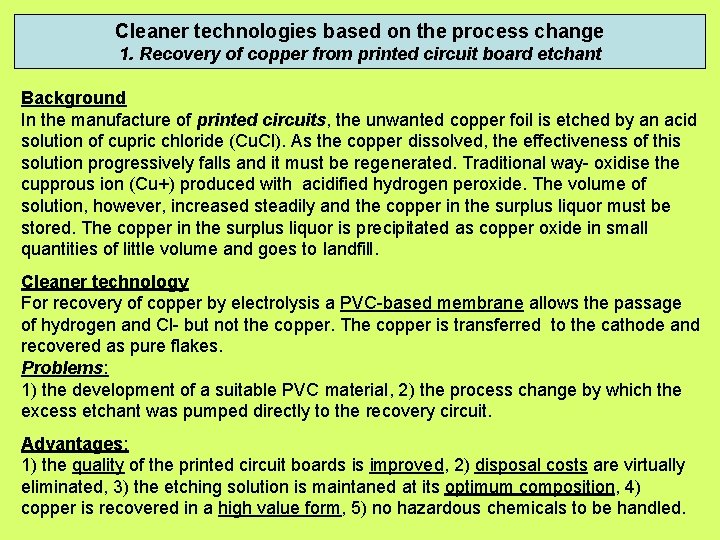
Cleaner technologies based on the process change 1. Recovery of copper from printed circuit board etchant Background In the manufacture of printed circuits, the unwanted copper foil is etched by an acid solution of cupric chloride (Cu. Cl). As the copper dissolved, the effectiveness of this solution progressively falls and it must be regenerated. Traditional way- oxidise the cupprous ion (Cu+) produced with acidified hydrogen peroxide. The volume of solution, however, increased steadily and the copper in the surplus liquor must be stored. The copper in the surplus liquor is precipitated as copper oxide in small quantities of little volume and goes to landfill. Cleaner technology For recovery of copper by electrolysis a PVC-based membrane allows the passage of hydrogen and Cl- but not the copper. The copper is transferred to the cathode and recovered as pure flakes. Problems: 1) the development of a suitable PVC material, 2) the process change by which the excess etchant was pumped directly to the recovery circuit. Advantages: 1) the quality of the printed circuit boards is improved, 2) disposal costs are virtually eliminated, 3) the etching solution is maintaned at its optimum composition, 4) copper is recovered in a high value form, 5) no hazardous chemicals to be handled.
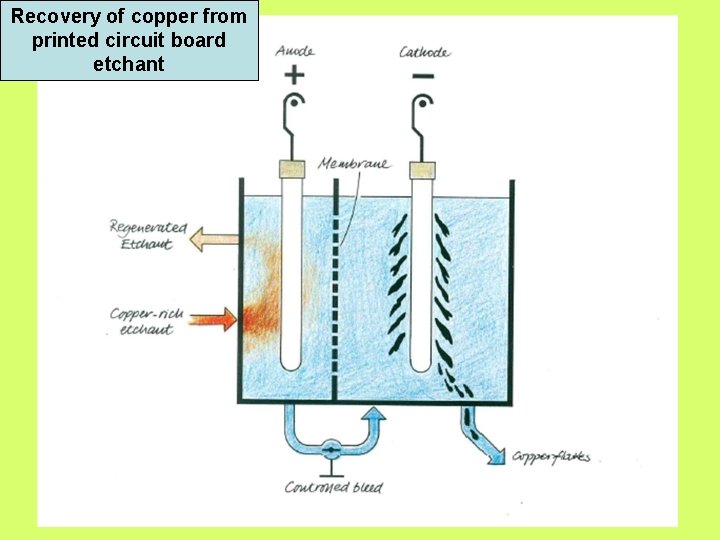
Recovery of copper from printed circuit board etchant

Cleaner technologies based on the process change 2. Upgrading of tin concentrate Background Tin ore has been mined from the earlier times. There has been a steady improvement in the percentage of tin in the concentrate which is sent to the smelter. The traditional concentration process involves a number of steps culminating in the flotation. The slurry containing the tin ore flows cross- current to the rising bubbles which float as a foam carrrying the tin-rich particles. Cleaner technology The separation and upgrading of the ore has been improved by introducing column flotation. The rising bubbles and falling ore flow counter-current, giving the effect of multiple stages of normal flotation. A water wash gives improved separation at the top of the column. Advantages 1) less waste from the smelting process, 2) less energy used for smelting.
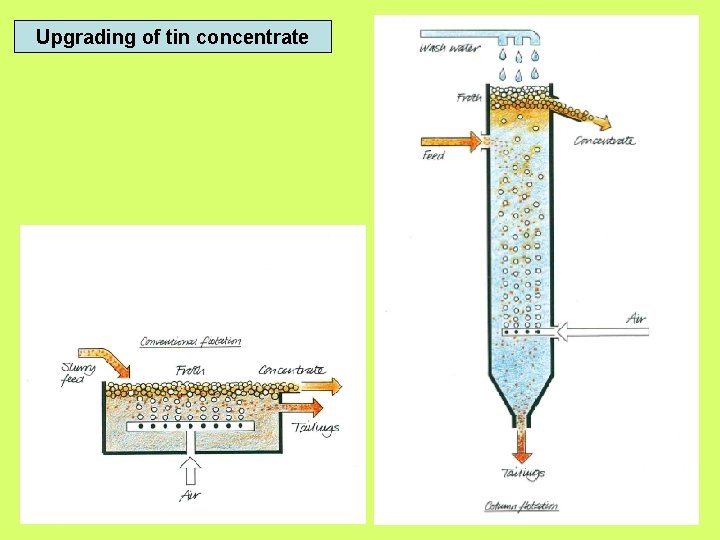
Upgrading of tin concentrate
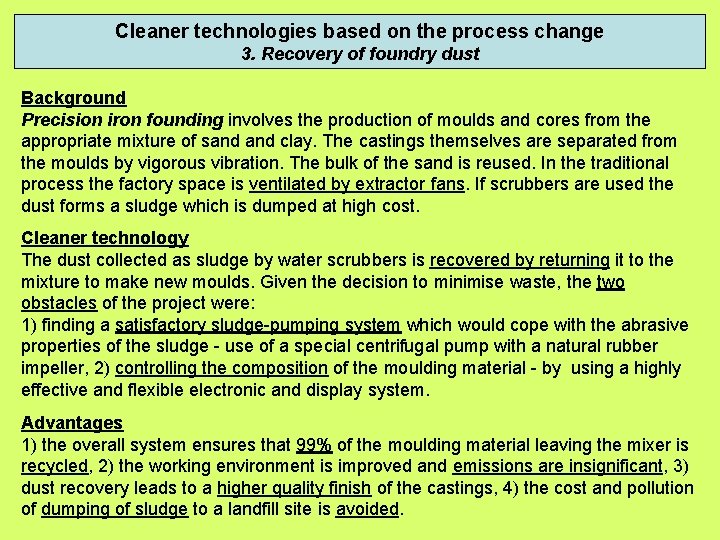
Cleaner technologies based on the process change 3. Recovery of foundry dust Background Precision iron founding involves the production of moulds and cores from the appropriate mixture of sand clay. The castings themselves are separated from the moulds by vigorous vibration. The bulk of the sand is reused. In the traditional process the factory space is ventilated by extractor fans. If scrubbers are used the dust forms a sludge which is dumped at high cost. Cleaner technology The dust collected as sludge by water scrubbers is recovered by returning it to the mixture to make new moulds. Given the decision to minimise waste, the two obstacles of the project were: 1) finding a satisfactory sludge-pumping system which would cope with the abrasive properties of the sludge - use of a special centrifugal pump with a natural rubber impeller, 2) controlling the composition of the moulding material - by using a highly effective and flexible electronic and display system. Advantages 1) the overall system ensures that 99% of the moulding material leaving the mixer is recycled, 2) the working environment is improved and emissions are insignificant, 3) dust recovery leads to a higher quality finish of the castings, 4) the cost and pollution of dumping of sludge to a landfill site is avoided.
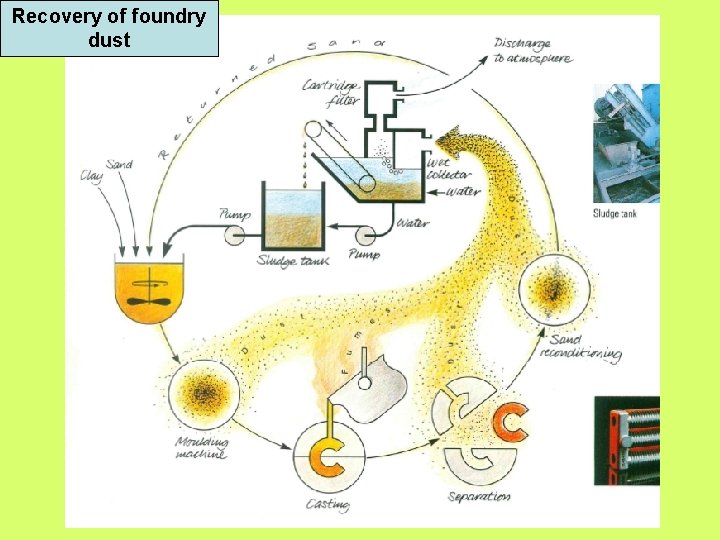
Recovery of foundry dust
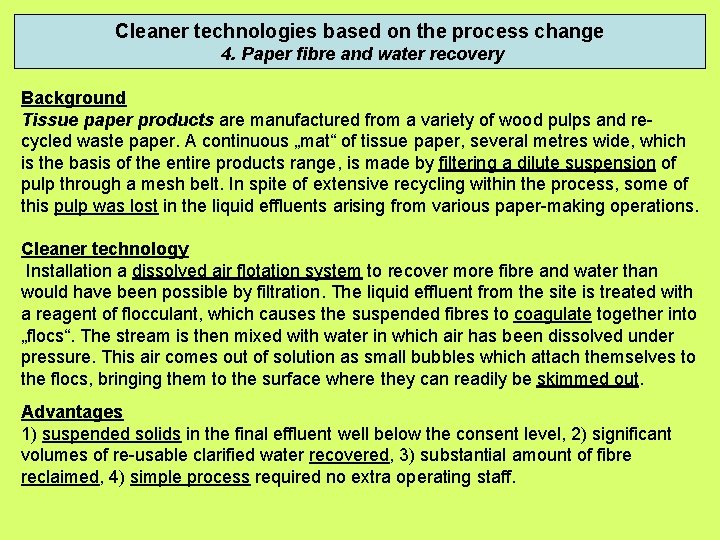
Cleaner technologies based on the process change 4. Paper fibre and water recovery Background Tissue paper products are manufactured from a variety of wood pulps and recycled waste paper. A continuous „mat“ of tissue paper, several metres wide, which is the basis of the entire products range, is made by filtering a dilute suspension of pulp through a mesh belt. In spite of extensive recycling within the process, some of this pulp was lost in the liquid effluents arising from various paper-making operations. Cleaner technology Installation a dissolved air flotation system to recover more fibre and water than would have been possible by filtration. The liquid effluent from the site is treated with a reagent of flocculant, which causes the suspended fibres to coagulate together into „flocs“. The stream is then mixed with water in which air has been dissolved under pressure. This air comes out of solution as small bubbles which attach themselves to the flocs, bringing them to the surface where they can readily be skimmed out. Advantages 1) suspended solids in the final effluent well below the consent level, 2) significant volumes of re-usable clarified water recovered, 3) substantial amount of fibre reclaimed, 4) simple process required no extra operating staff.
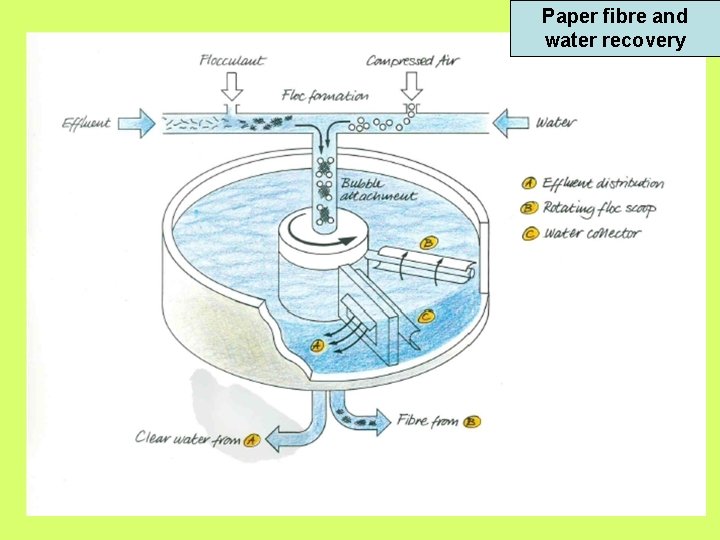
Paper fibre and water recovery
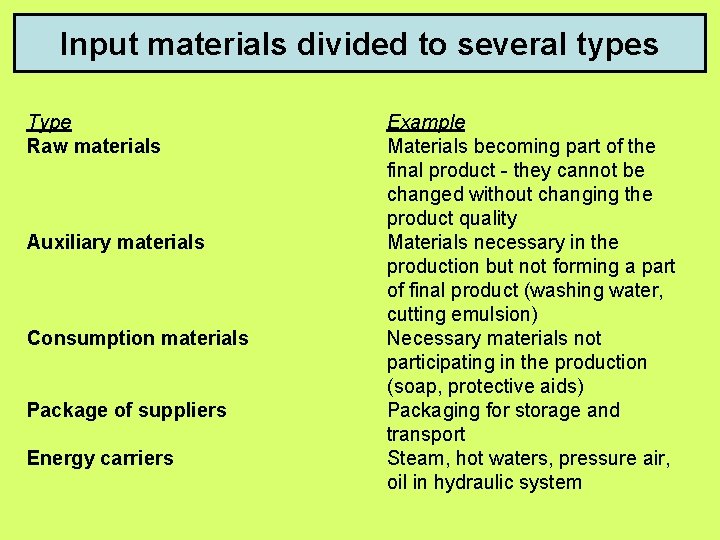
Input materials divided to several types Type Raw materials Auxiliary materials Consumption materials Package of suppliers Energy carriers Example Materials becoming part of the final product - they cannot be changed without changing the product quality Materials necessary in the production but not forming a part of final product (washing water, cutting emulsion) Necessary materials not participating in the production (soap, protective aids) Packaging for storage and transport Steam, hot waters, pressure air, oil in hydraulic system
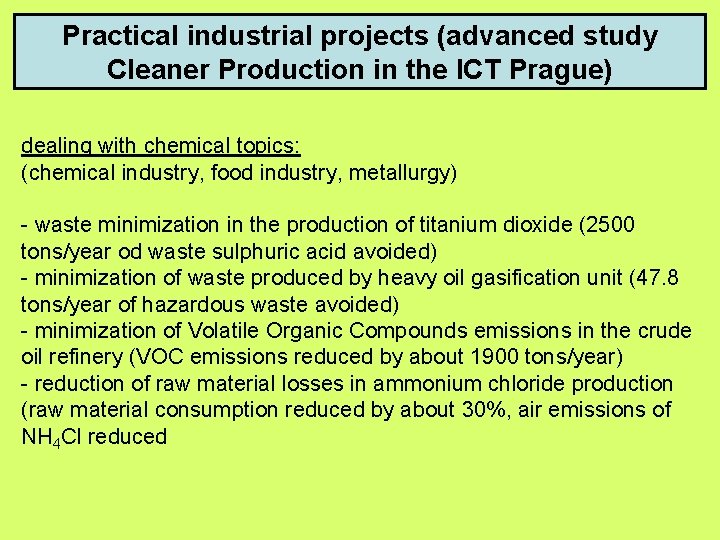
Practical industrial projects (advanced study Cleaner Production in the ICT Prague) dealing with chemical topics: (chemical industry, food industry, metallurgy) - waste minimization in the production of titanium dioxide (2500 tons/year od waste sulphuric acid avoided) - minimization of waste produced by heavy oil gasification unit (47. 8 tons/year of hazardous waste avoided) - minimization of Volatile Organic Compounds emissions in the crude oil refinery (VOC emissions reduced by about 1900 tons/year) - reduction of raw material losses in ammonium chloride production (raw material consumption reduced by about 30%, air emissions of NH 4 Cl reduced
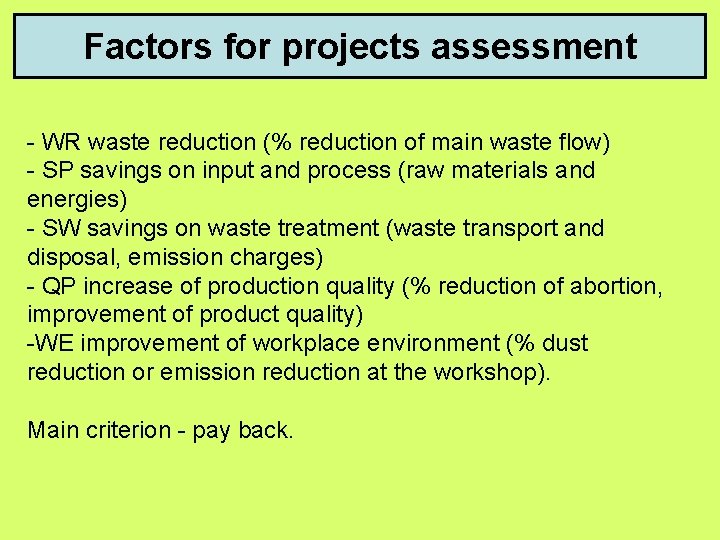
Factors for projects assessment - WR waste reduction (% reduction of main waste flow) - SP savings on input and process (raw materials and energies) - SW savings on waste treatment (waste transport and disposal, emission charges) - QP increase of production quality (% reduction of abortion, improvement of product quality) -WE improvement of workplace environment (% dust reduction or emission reduction at the workshop). Main criterion - pay back.
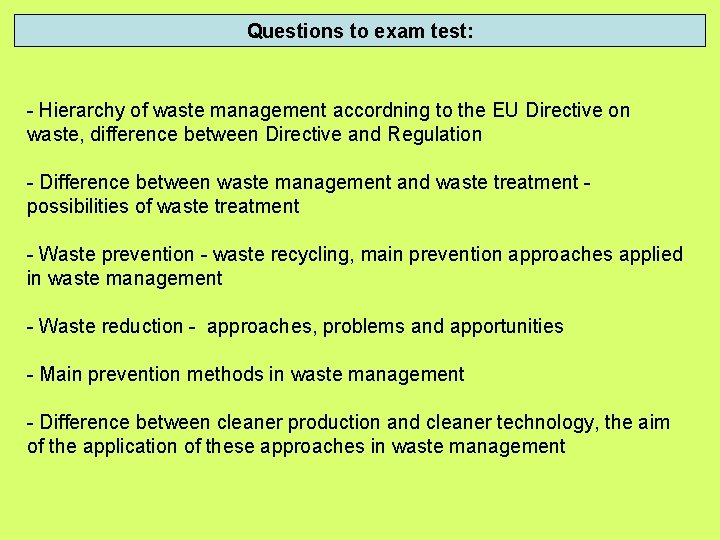
Questions to exam test: - Hierarchy of waste management accordning to the EU Directive on waste, difference between Directive and Regulation - Difference between waste management and waste treatment possibilities of waste treatment - Waste prevention - waste recycling, main prevention approaches applied in waste management - Waste reduction - approaches, problems and apportunities - Main prevention methods in waste management - Difference between cleaner production and cleaner technology, the aim of the application of these approaches in waste management
Primary prevention secondary prevention tertiary prevention
Hierarchy of waste management
Neal road recycling and waste facility
Recycling of solid waste
Leather waste recycling
Teton county integrated solid waste and recycling
Cd waste recycling
Composting and recycling municipal solid waste "torrent"
Food loss and waste
Barangay disaster risk reduction management plan
Drrm law
National disaster risk reduction and management framework
Management-research question hierarchy example
Business process levels
Schools organizational structure
Management research question hierarchy
Sustainable barbados recycling centre
Stafford county recycling
Recycling advantages and disadvantages
Thermoset recycling
3 benefits of recycling
Designer polymers
Textile chemical recycling
Plastic things that can be recycled
Mixed recycling chesterfield
Salt switch recycling
Recycling services procurement
Plastic recycling flow chart
St helier recycling
Midwest organics recycling
In situ cleaning
Paragraph on recycling
Eco2go recycling
Recycling in the biosphere
Malden trash
Chapter 9 vehicle maintenance
Recycling in the biosphere
Owasso recycling center
Summary of the nitrogen cycle
Swot analysis of plastic recycling company
Philadelphia recycling mine
United electronics recycling
Tonbridge and malling bins
V
Salt switch recycling
Recycling puerto rico
Processing used materials into new products
Cherokee county ga electronics recycling
Motive force
Bee green recycling
Kane county recycle
Unicor recycling
Nyc recycling sorting
Chestermere garbage
Shingle recycling san antonio texas