Update on UT related cooling parameters and procedures
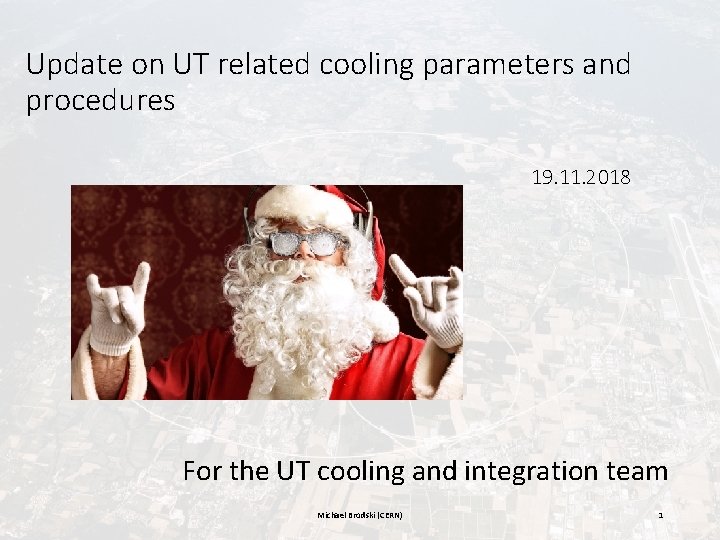
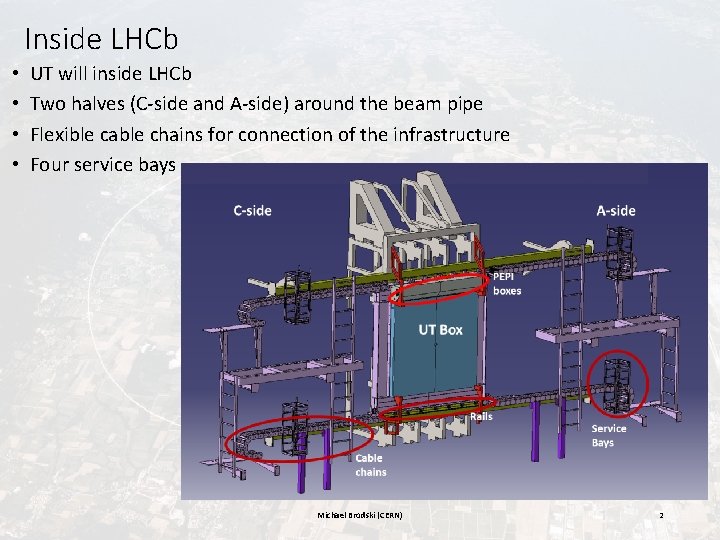
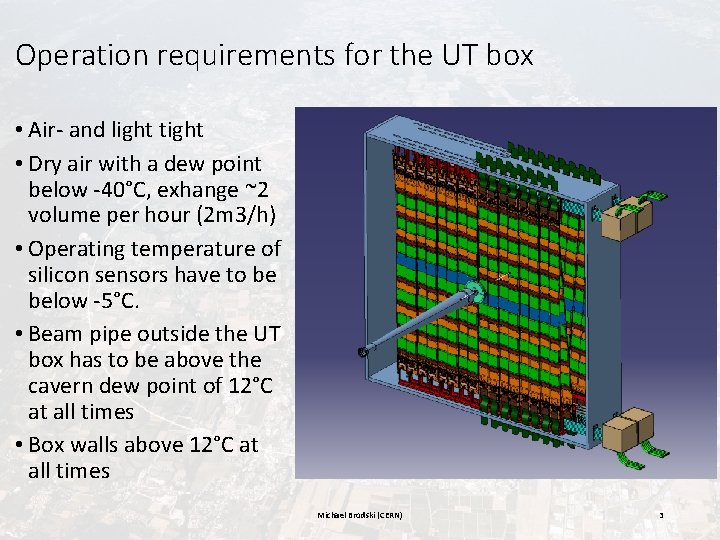
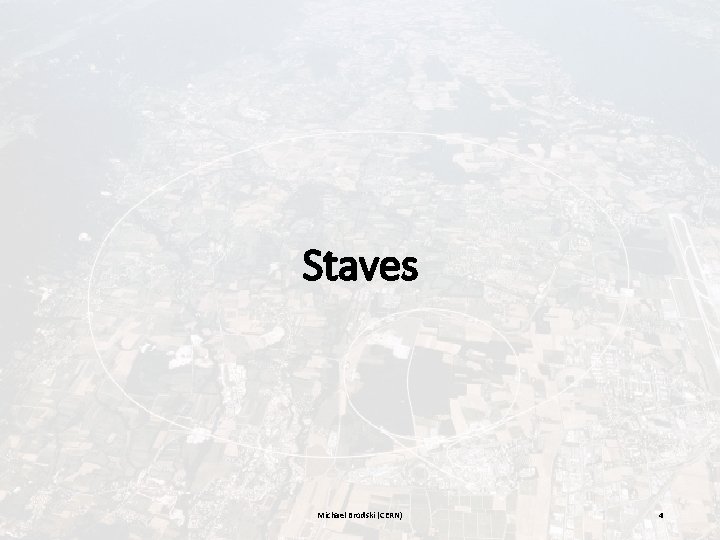
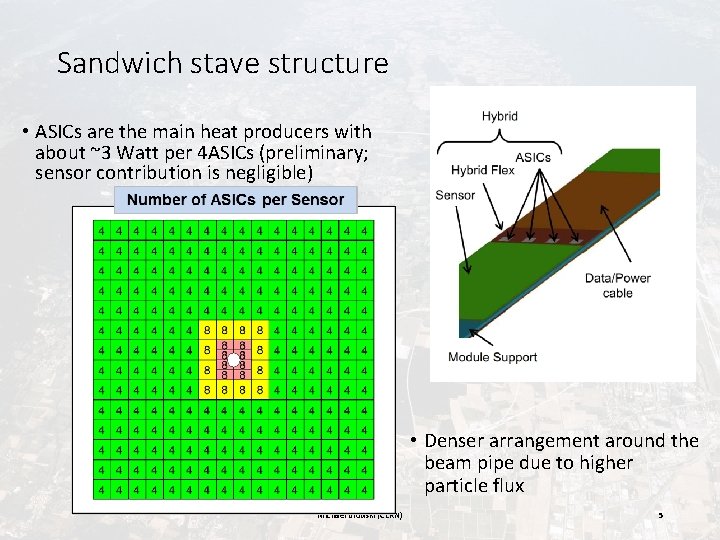
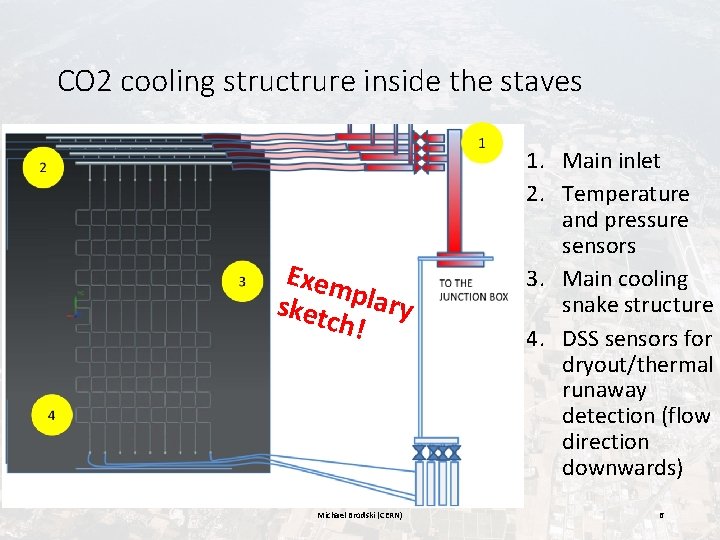
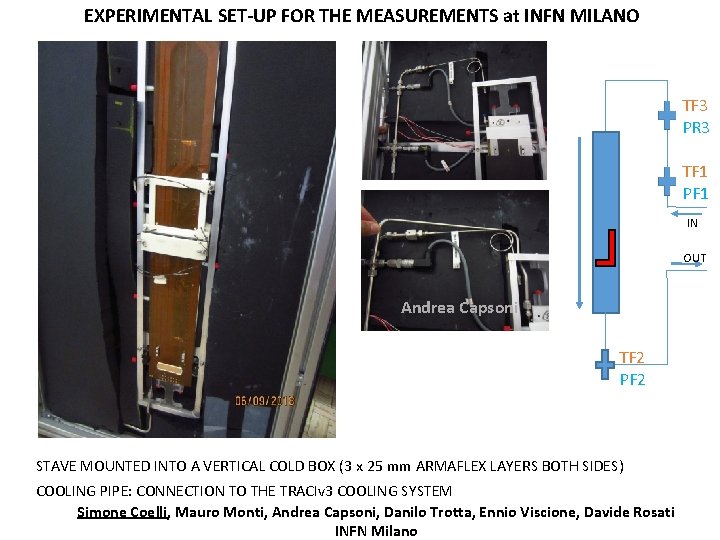
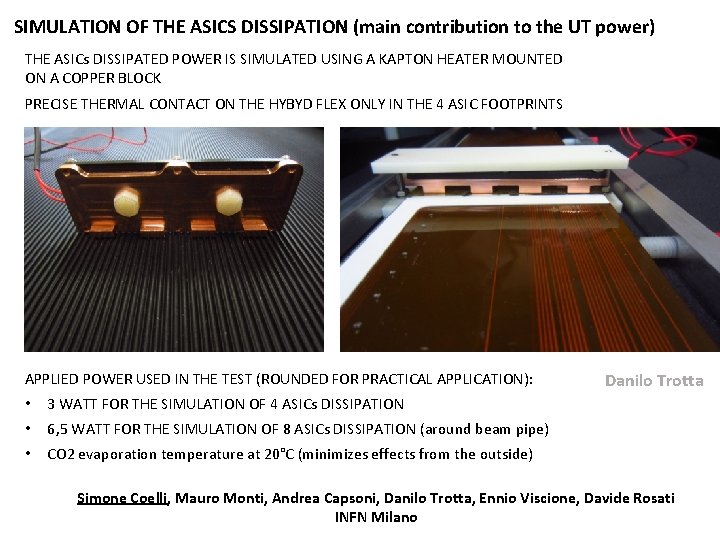
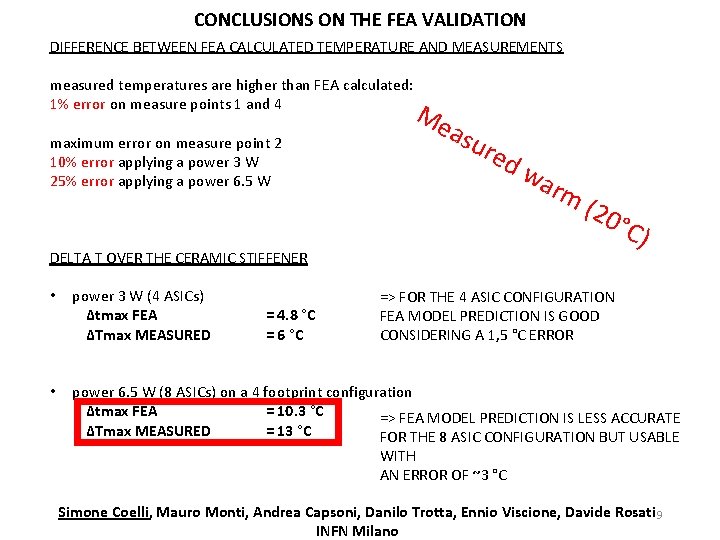
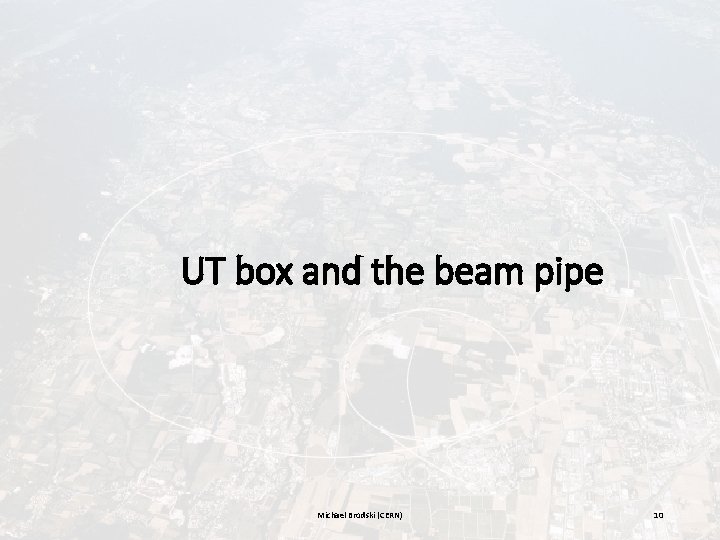
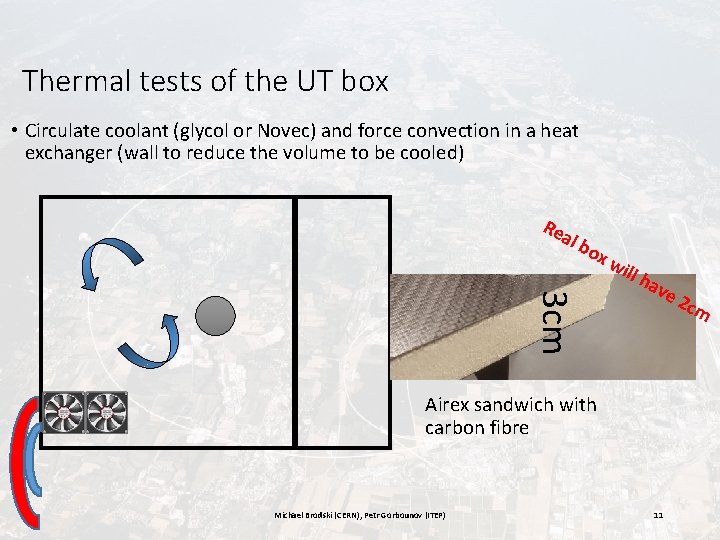
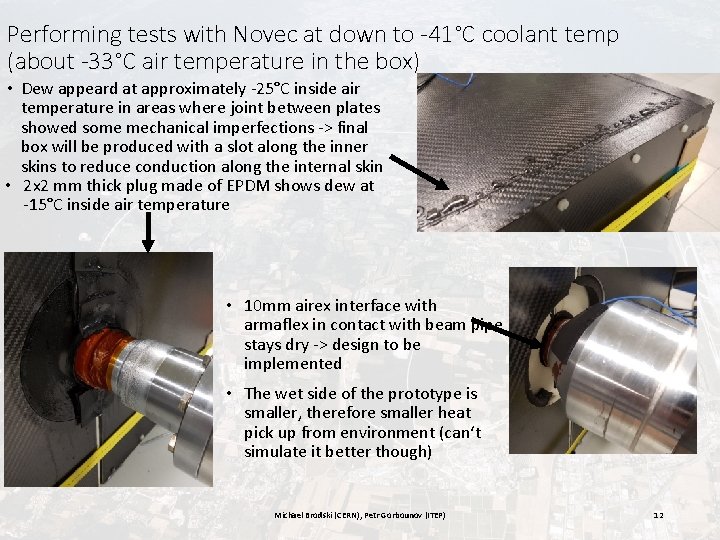
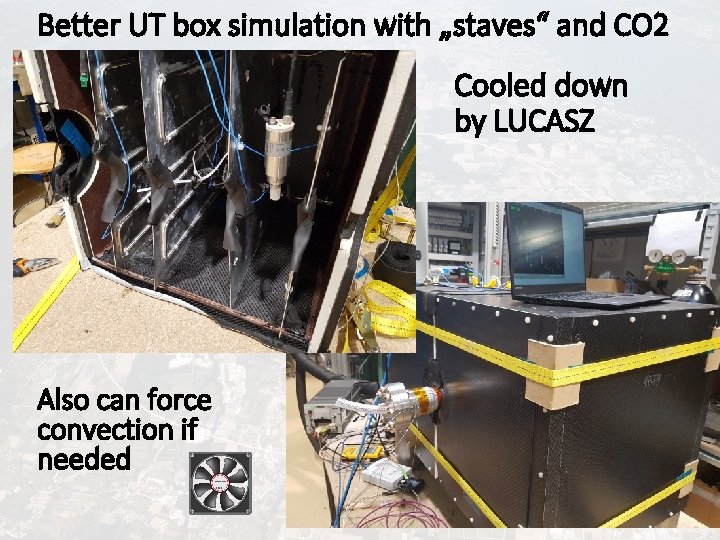
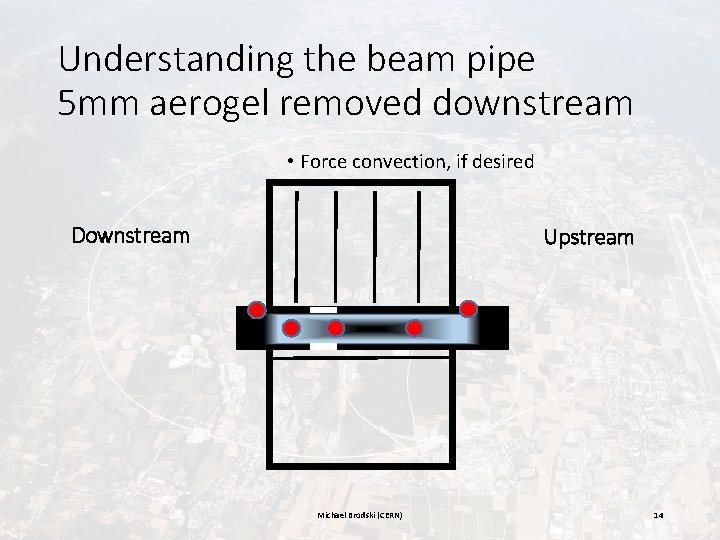
![Lowest possible temperature with forced convection Object/Position Temperature [°C] CO 2 evaporation -37 Air Lowest possible temperature with forced convection Object/Position Temperature [°C] CO 2 evaporation -37 Air](https://slidetodoc.com/presentation_image/4dae367aba640911218eea6a98d1c0f2/image-15.jpg)
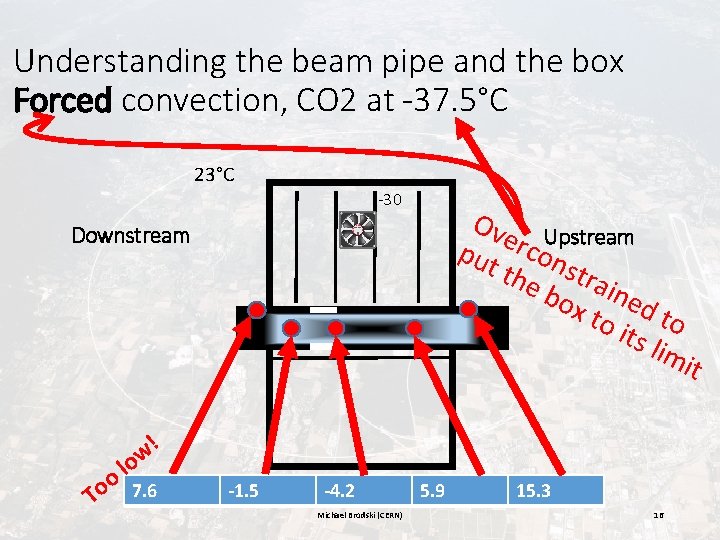
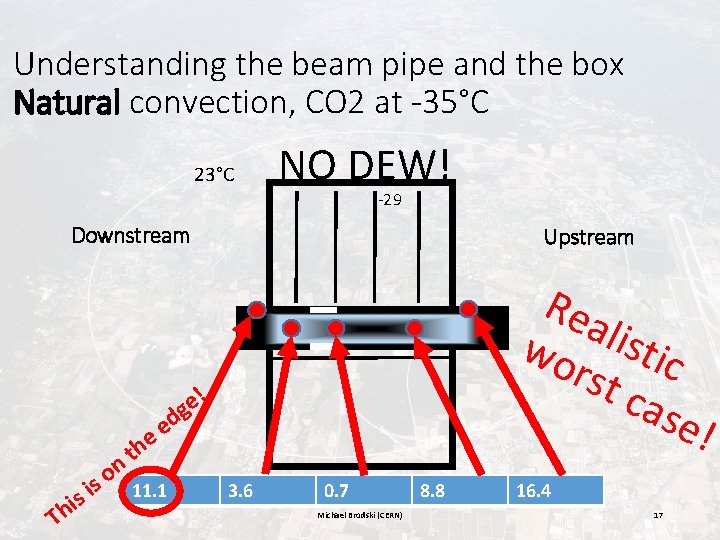
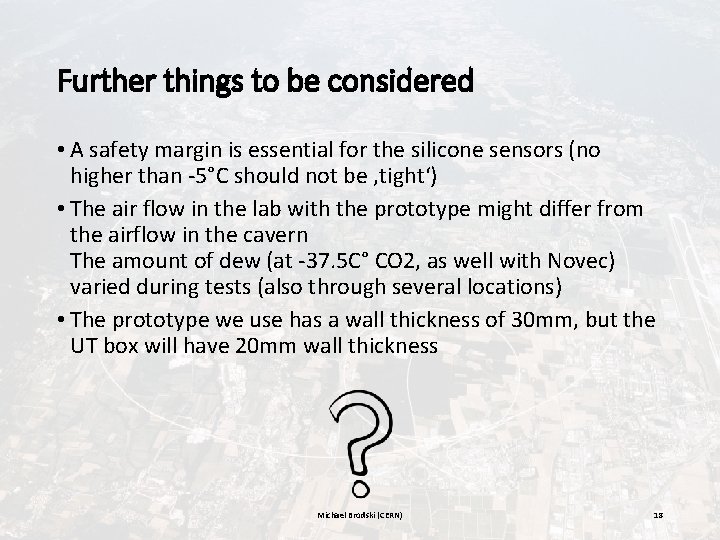
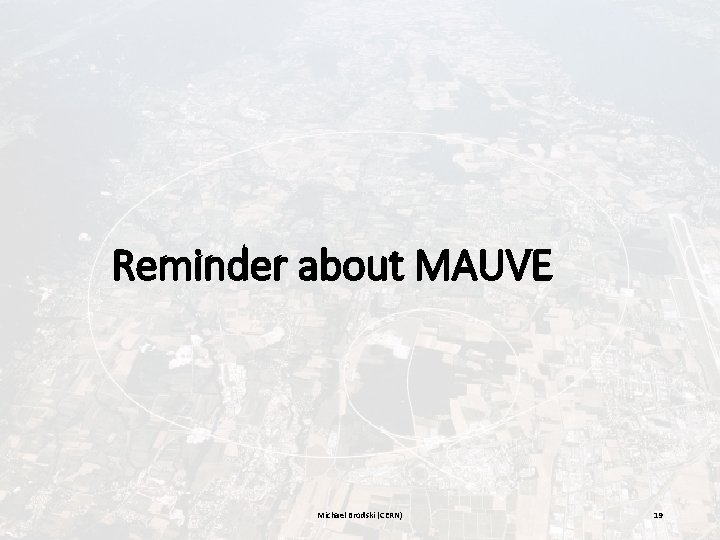
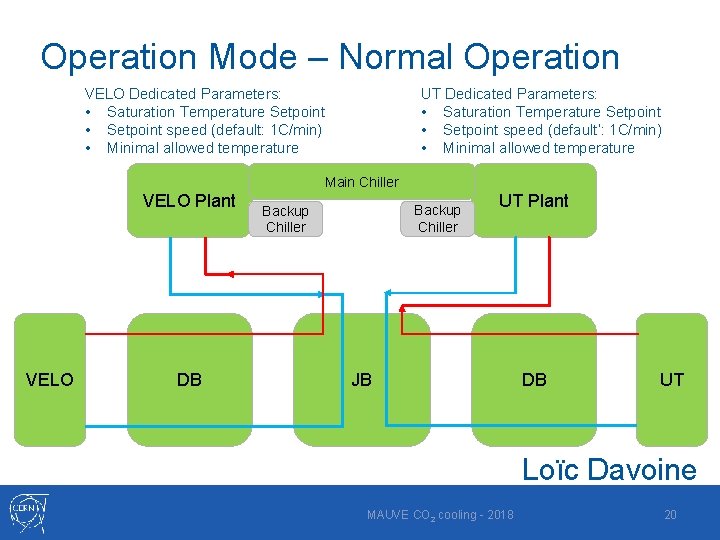
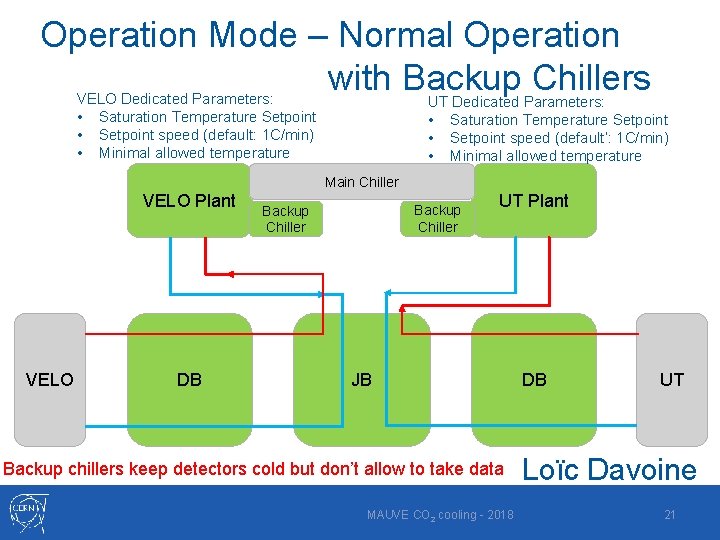
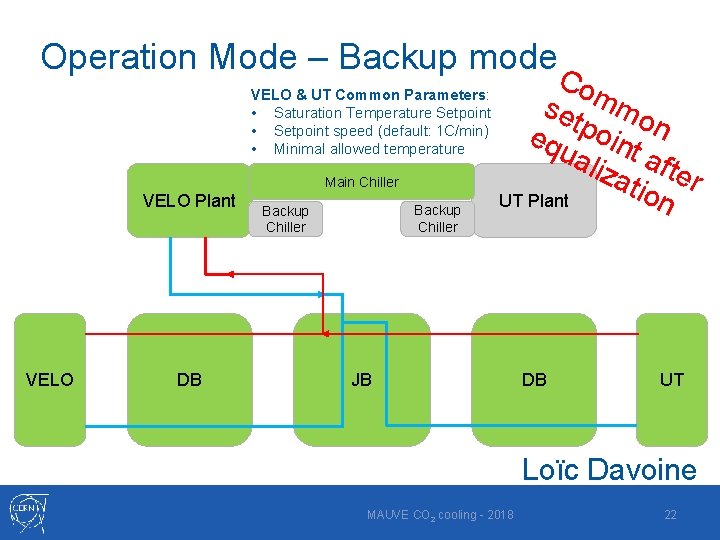
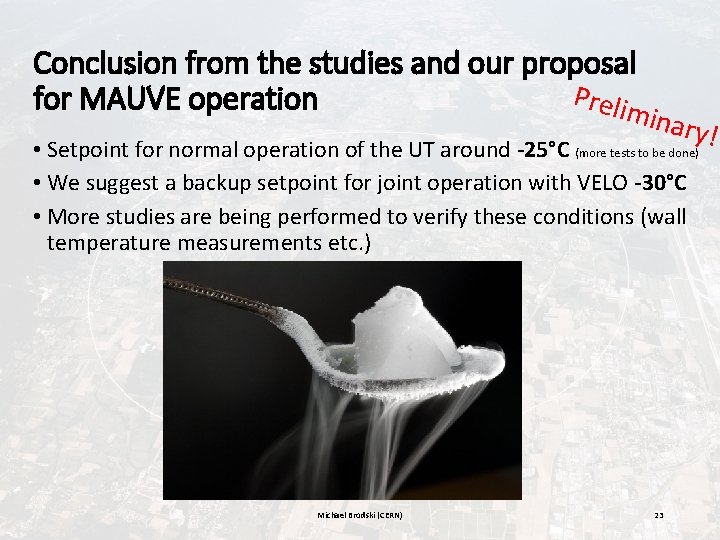
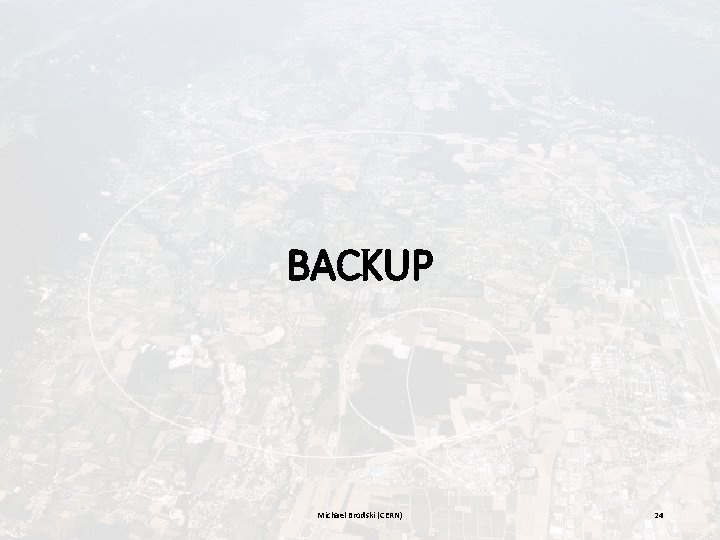
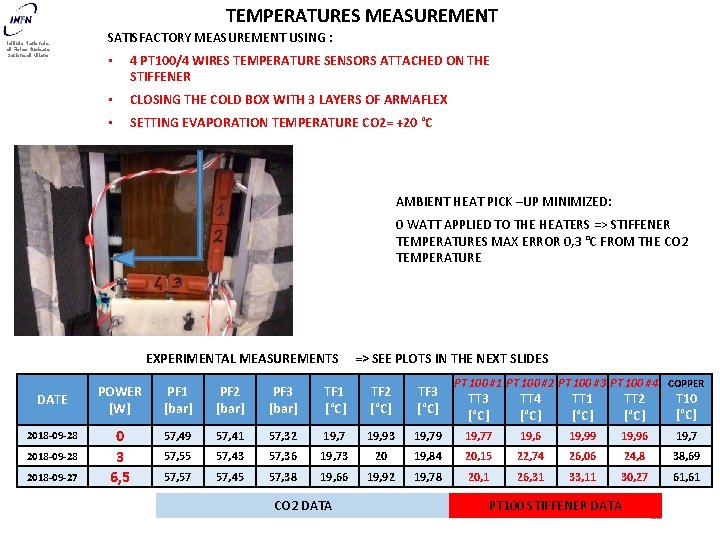
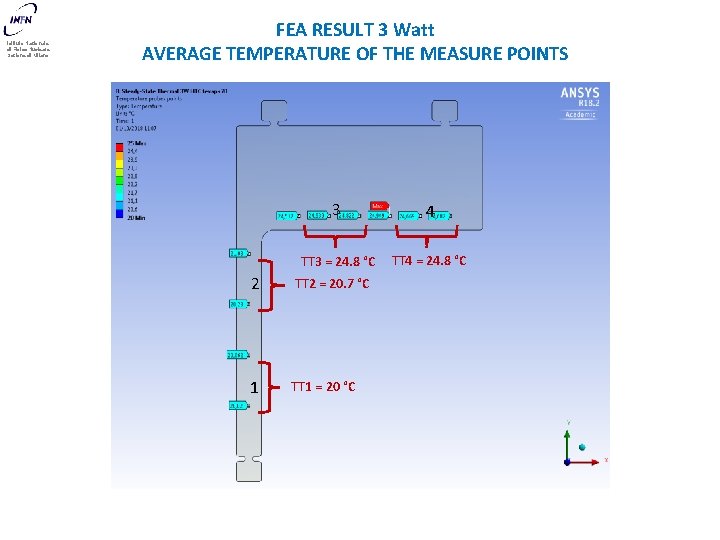
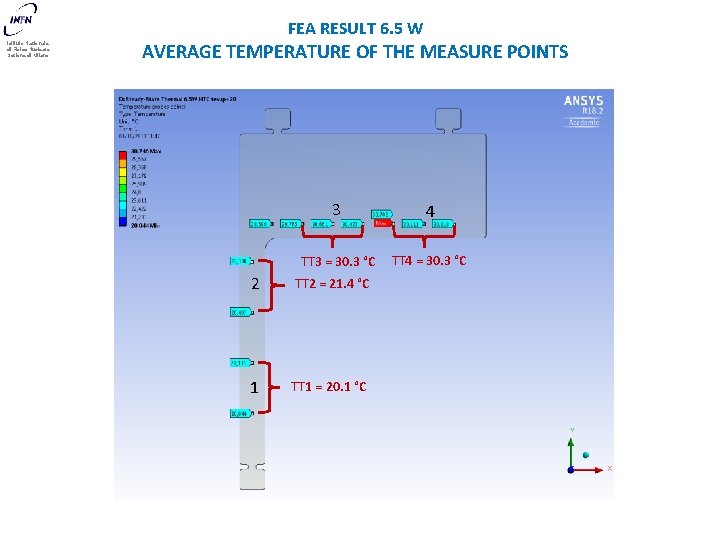
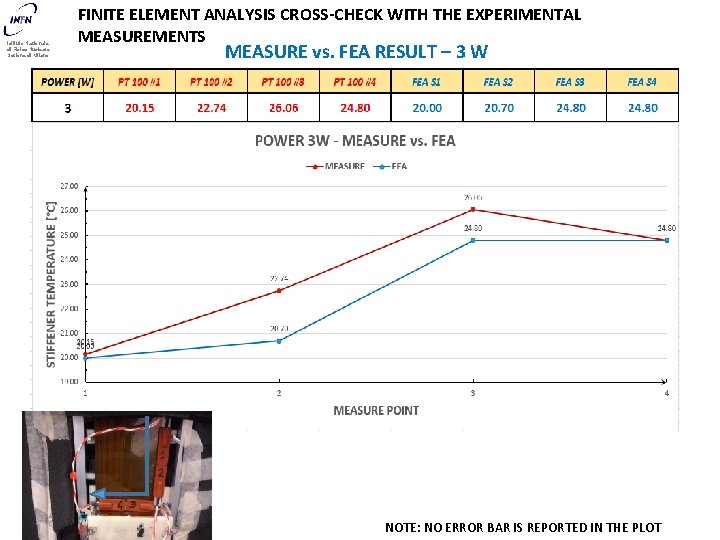
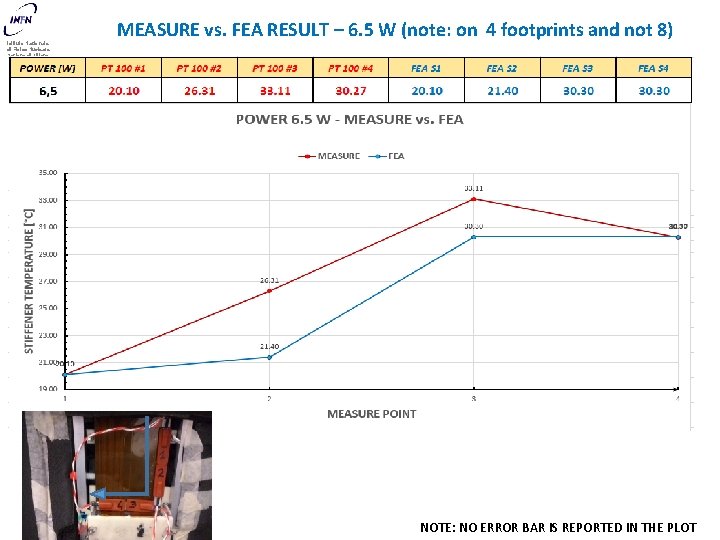
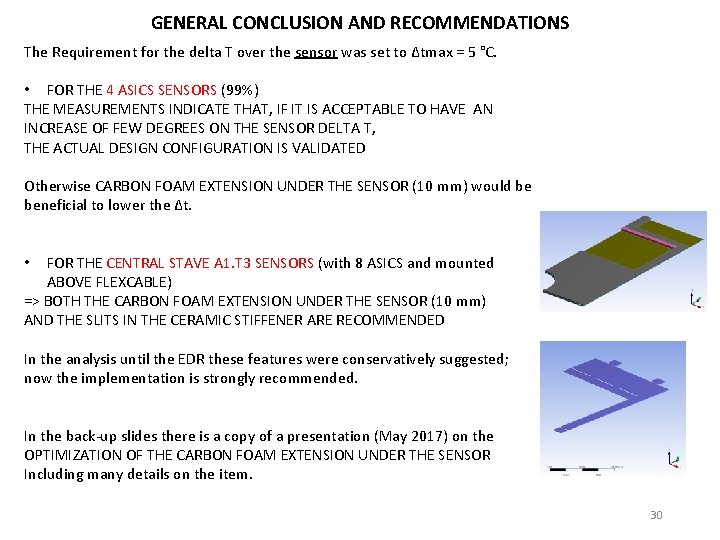
- Slides: 30
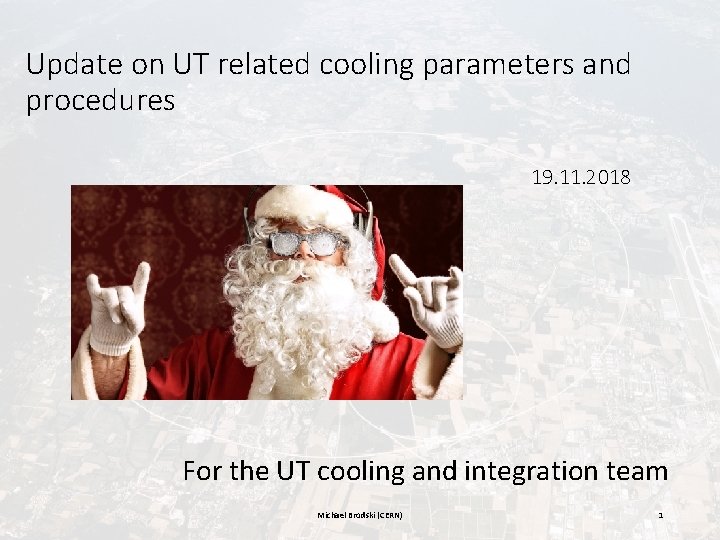
Update on UT related cooling parameters and procedures 19. 11. 2018 For the UT cooling and integration team Michael Brodski (CERN) 1
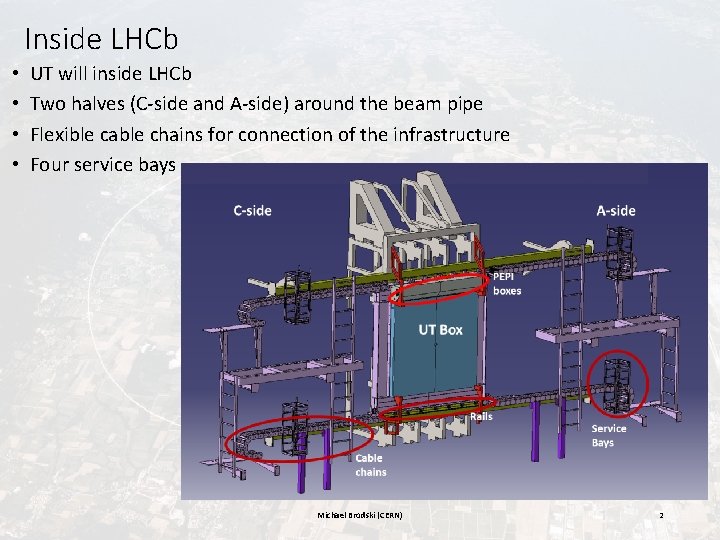
Inside LHCb • • UT will inside LHCb Two halves (C-side and A-side) around the beam pipe Flexible cable chains for connection of the infrastructure Four service bays Michael Brodski (CERN) 2
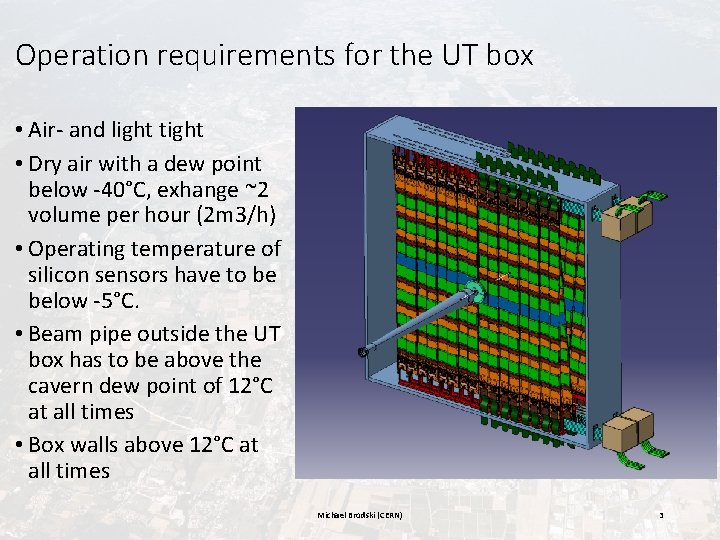
Operation requirements for the UT box • Air- and light tight • Dry air with a dew point below -40°C, exhange ~2 volume per hour (2 m 3/h) • Operating temperature of silicon sensors have to be below -5°C. • Beam pipe outside the UT box has to be above the cavern dew point of 12°C at all times • Box walls above 12°C at all times Michael Brodski (CERN) 3
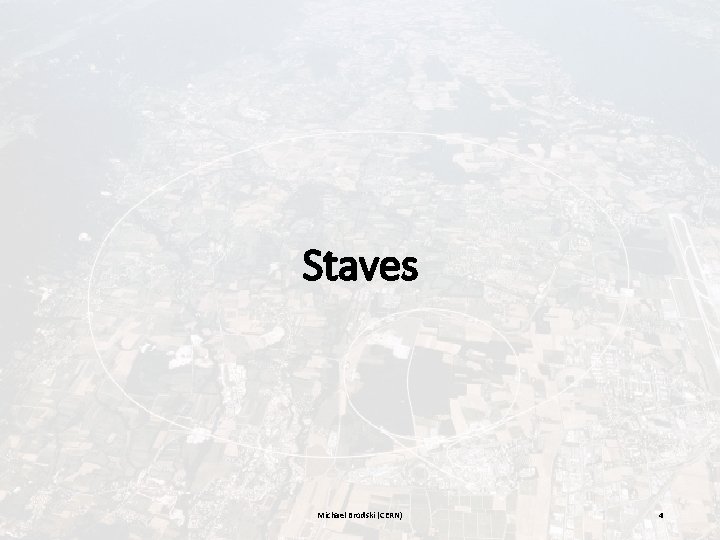
Staves Michael Brodski (CERN) 4
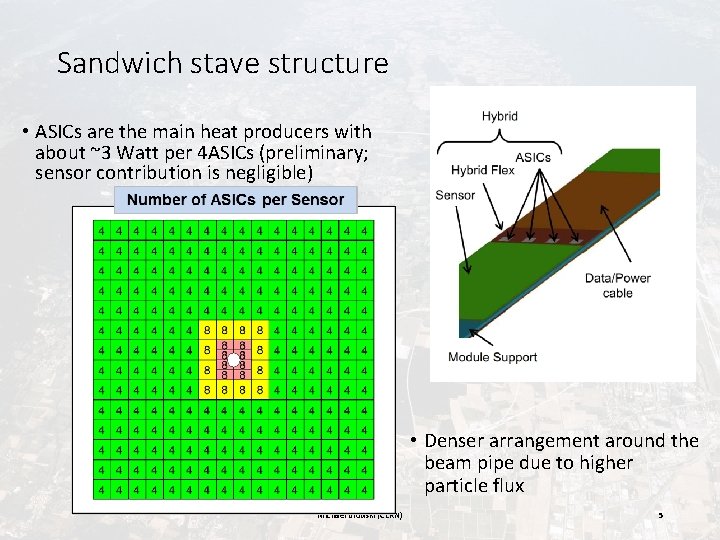
Sandwich stave structure • ASICs are the main heat producers with about ~3 Watt per 4 ASICs (preliminary; sensor contribution is negligible) • Denser arrangement around the beam pipe due to higher particle flux Michael Brodski (CERN) 5
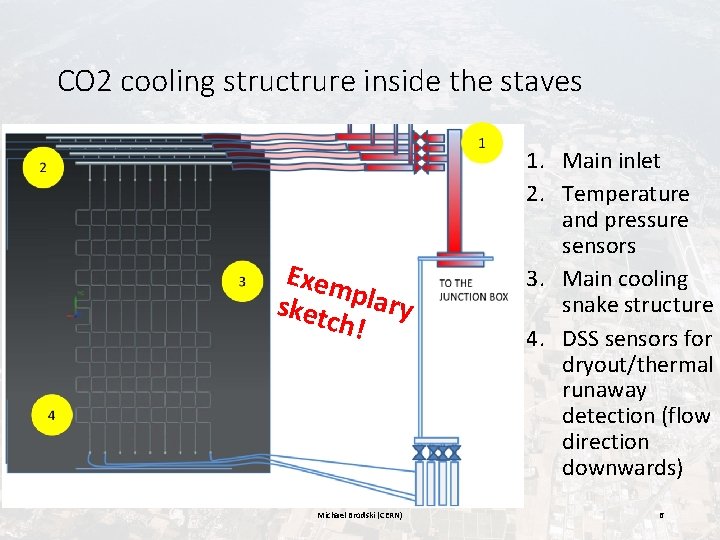
CO 2 cooling structrure inside the staves Exem sketc plary h! Michael Brodski (CERN) 1. Main inlet 2. Temperature and pressure sensors 3. Main cooling snake structure 4. DSS sensors for dryout/thermal runaway detection (flow direction downwards) 6
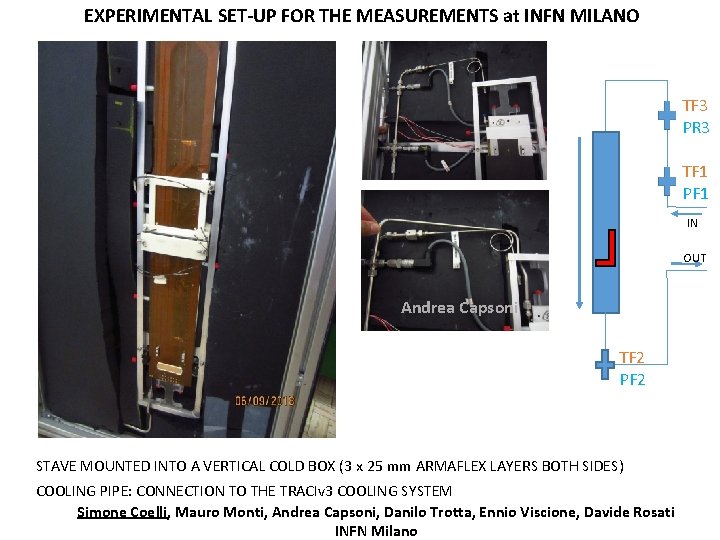
EXPERIMENTAL SET-UP FOR THE MEASUREMENTS at INFN MILANO TF 3 PR 3 TF 1 PF 1 IN OUT Andrea Capsoni TF 2 PF 2 STAVE MOUNTED INTO A VERTICAL COLD BOX (3 x 25 mm ARMAFLEX LAYERS BOTH SIDES) COOLING PIPE: CONNECTION TO THE TRACIv 3 COOLING SYSTEM Simone Coelli, Mauro Monti, Andrea Capsoni, Danilo Trotta, Ennio Viscione, Davide Rosati INFN Milano
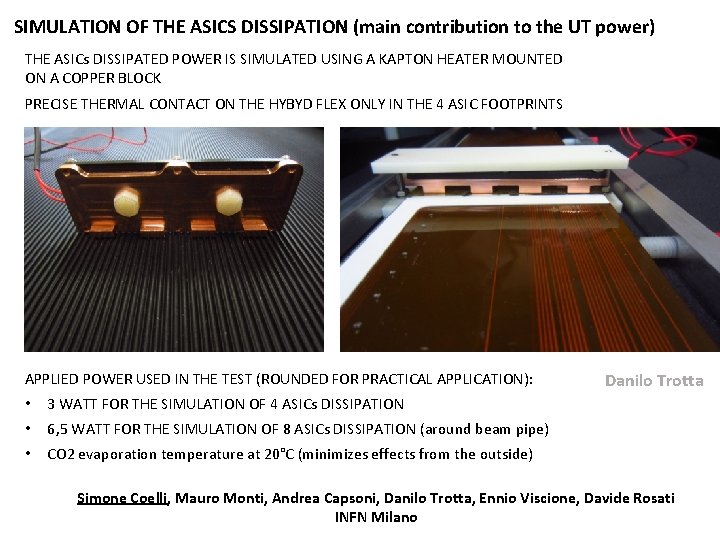
SIMULATION OF THE ASICS DISSIPATION (main contribution to the UT power) THE ASICs DISSIPATED POWER IS SIMULATED USING A KAPTON HEATER MOUNTED ON A COPPER BLOCK PRECISE THERMAL CONTACT ON THE HYBYD FLEX ONLY IN THE 4 ASIC FOOTPRINTS APPLIED POWER USED IN THE TEST (ROUNDED FOR PRACTICAL APPLICATION): • 3 WATT FOR THE SIMULATION OF 4 ASICs DISSIPATION • 6, 5 WATT FOR THE SIMULATION OF 8 ASICs DISSIPATION (around beam pipe) • CO 2 evaporation temperature at 20°C (minimizes effects from the outside) Danilo Trotta Simone Coelli, Mauro Monti, Andrea Capsoni, Danilo Trotta, Ennio Viscione, Davide Rosati INFN Milano
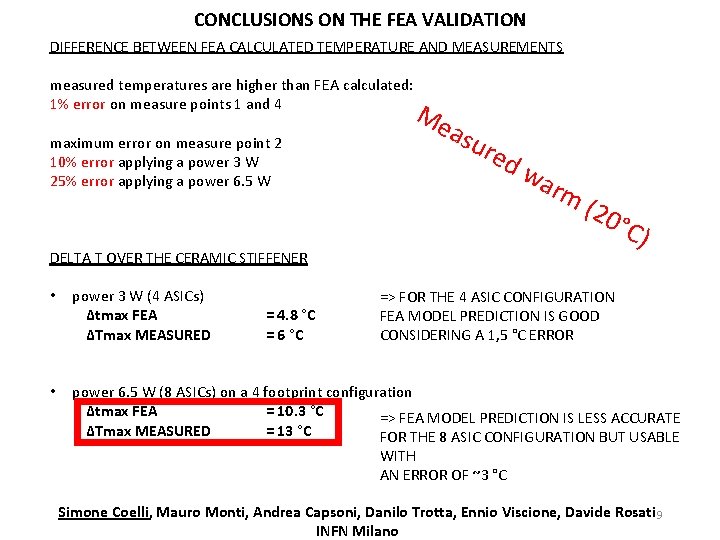
CONCLUSIONS ON THE FEA VALIDATION DIFFERENCE BETWEEN FEA CALCULATED TEMPERATURE AND MEASUREMENTS measured temperatures are higher than FEA calculated: 1% error on measure points 1 and 4 maximum error on measure point 2 10% error applying a power 3 W 25% error applying a power 6. 5 W Me asu red wa rm (20 ° DELTA T OVER THE CERAMIC STIFFENER • • power 3 W (4 ASICs) Δtmax FEA ΔTmax MEASURED = 4. 8 °C = 6 °C C) => FOR THE 4 ASIC CONFIGURATION FEA MODEL PREDICTION IS GOOD CONSIDERING A 1, 5 °C ERROR power 6. 5 W (8 ASICs) on a 4 footprint configuration Δtmax FEA = 10. 3 °C => FEA MODEL PREDICTION IS LESS ACCURATE ΔTmax MEASURED = 13 °C FOR THE 8 ASIC CONFIGURATION BUT USABLE WITH AN ERROR OF ~3 °C Simone Coelli, Mauro Monti, Andrea Capsoni, Danilo Trotta, Ennio Viscione, Davide Rosati 9 INFN Milano
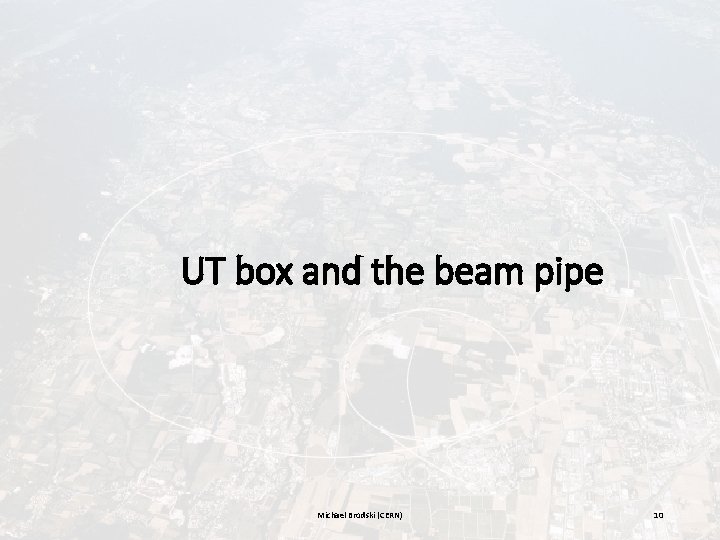
UT box and the beam pipe Michael Brodski (CERN) 10
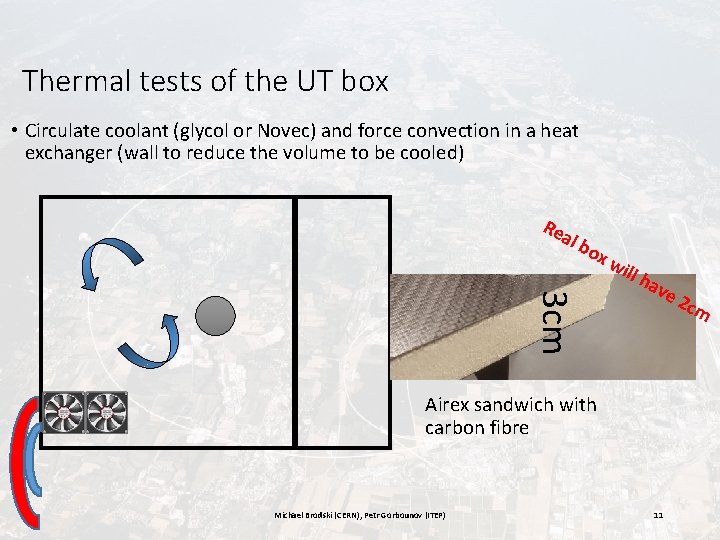
Thermal tests of the UT box • Circulate coolant (glycol or Novec) and force convection in a heat exchanger (wall to reduce the volume to be cooled) Re al b ox w ill h 3 cm ave Airex sandwich with carbon fibre Michael Brodski (CERN), Petr Gorbounov (ITEP) 11 2 cm
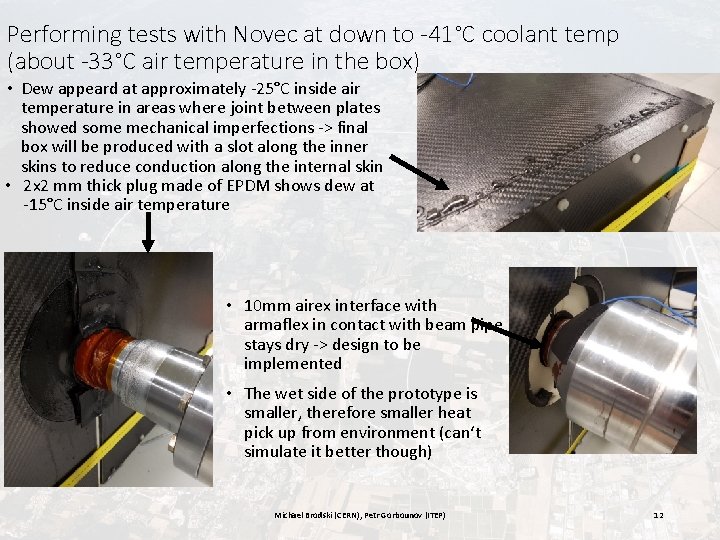
Performing tests with Novec at down to -41°C coolant temp (about -33°C air temperature in the box) • Dew appeard at approximately -25°C inside air temperature in areas where joint between plates showed some mechanical imperfections -> final box will be produced with a slot along the inner skins to reduce conduction along the internal skin • 2 x 2 mm thick plug made of EPDM shows dew at -15°C inside air temperature • 10 mm airex interface with armaflex in contact with beam pipe stays dry -> design to be implemented • The wet side of the prototype is smaller, therefore smaller heat pick up from environment (can‘t simulate it better though) Michael Brodski (CERN), Petr Gorbounov (ITEP) 12
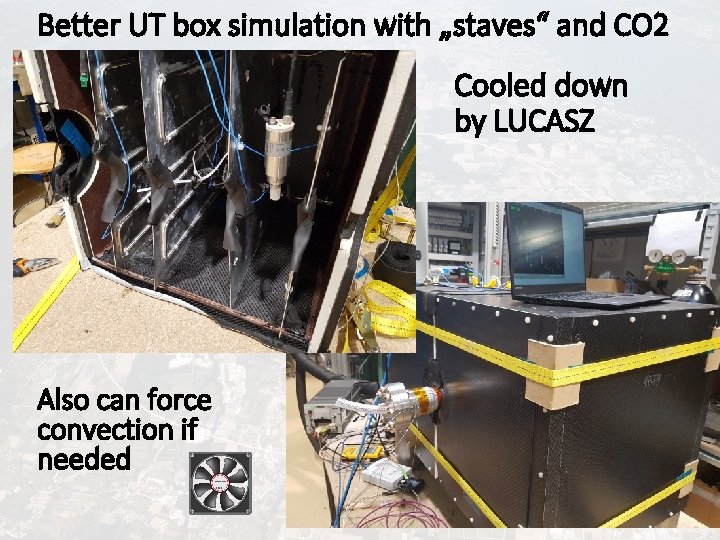
Better UT box simulation with „staves“ and CO 2 Cooled down by LUCASZ Also can force convection if needed Michael Brodski (CERN) 13
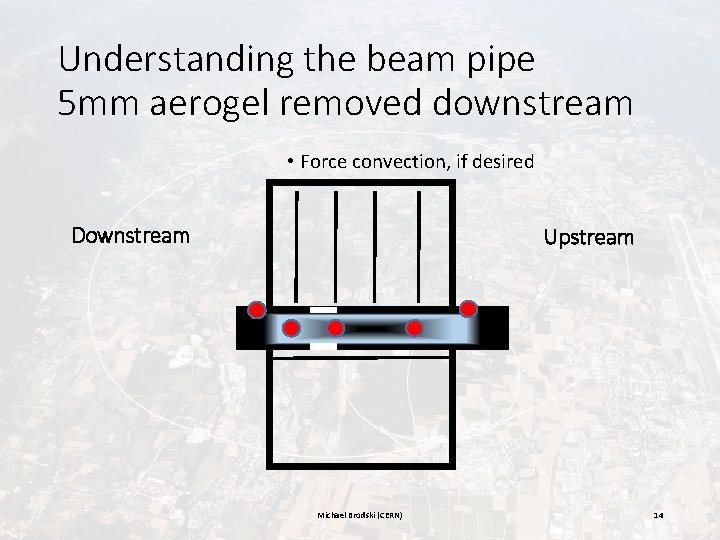
Understanding the beam pipe 5 mm aerogel removed downstream • Force convection, if desired Downstream Upstream Michael Brodski (CERN) 14
![Lowest possible temperature with forced convection ObjectPosition Temperature C CO 2 evaporation 37 Air Lowest possible temperature with forced convection Object/Position Temperature [°C] CO 2 evaporation -37 Air](https://slidetodoc.com/presentation_image/4dae367aba640911218eea6a98d1c0f2/image-15.jpg)
Lowest possible temperature with forced convection Object/Position Temperature [°C] CO 2 evaporation -37 Air inside ~-30 Alu Plates -31 Top outside wall 13. 9 Top inside wall -20. 8 Bottom inside wall -22. 3 Bottom outside wall 14. 6 BP (2310 mm from IP) 3. 9 BP (2445 mm from IP) -6. 1 BP (2705 mm from IP) -3. 1 Air outside 22 on W E D ! x O o N b he Michael Brodski (CERN) 15
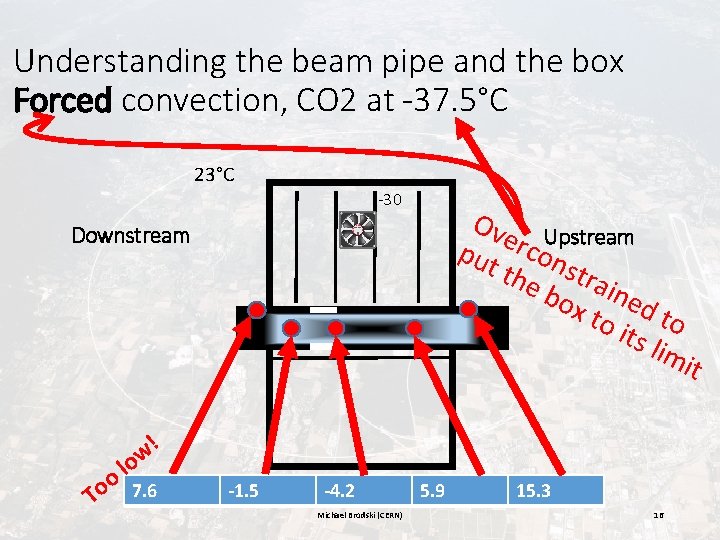
Understanding the beam pipe and the box Forced convection, CO 2 at -37. 5°C 23°C -30 Ov Upstream put ercon the stra box ined to i to ts l imi Downstream t o o T ! w lo 7. 6 -1. 5 -4. 2 Michael Brodski (CERN) 5. 9 15. 3 16
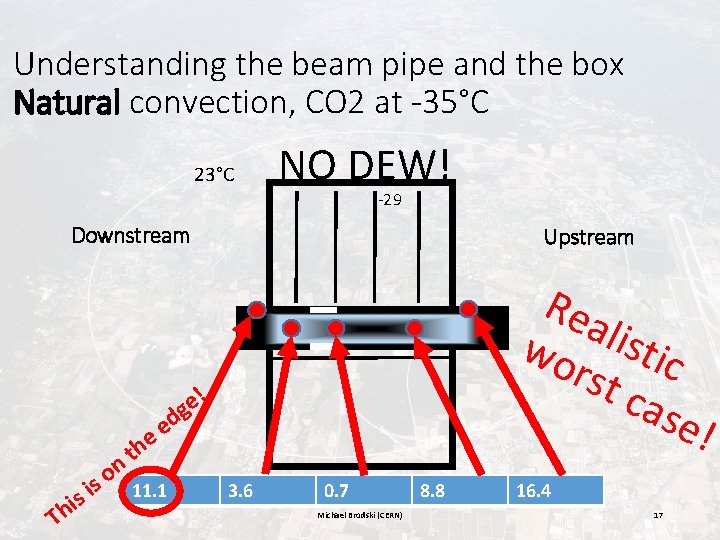
Understanding the beam pipe and the box Natural convection, CO 2 at -35°C 23°C NO DEW! -29 Downstream Upstream Rea wo listic rst cas e! ! e dg e e h Th i is s t n o 11. 1 3. 6 0. 7 Michael Brodski (CERN) 8. 8 16. 4 17
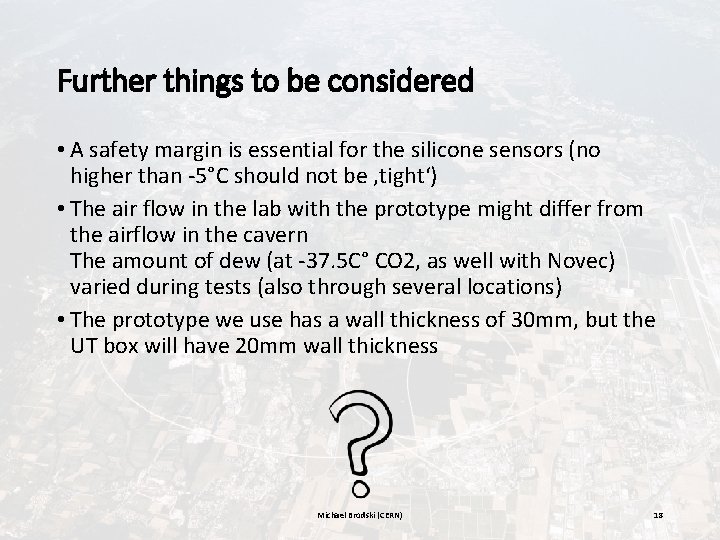
Further things to be considered • A safety margin is essential for the silicone sensors (no higher than -5°C should not be ‚tight‘) • The air flow in the lab with the prototype might differ from the airflow in the cavern The amount of dew (at -37. 5 C° CO 2, as well with Novec) varied during tests (also through several locations) • The prototype we use has a wall thickness of 30 mm, but the UT box will have 20 mm wall thickness Michael Brodski (CERN) 18
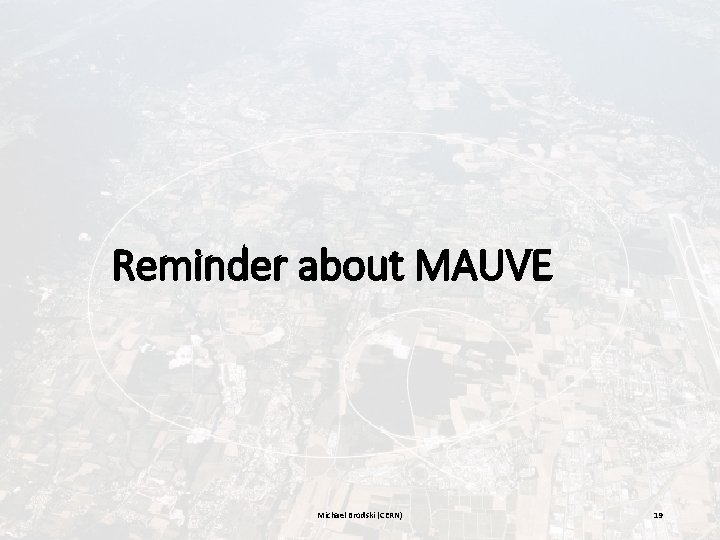
Reminder about MAUVE Michael Brodski (CERN) 19
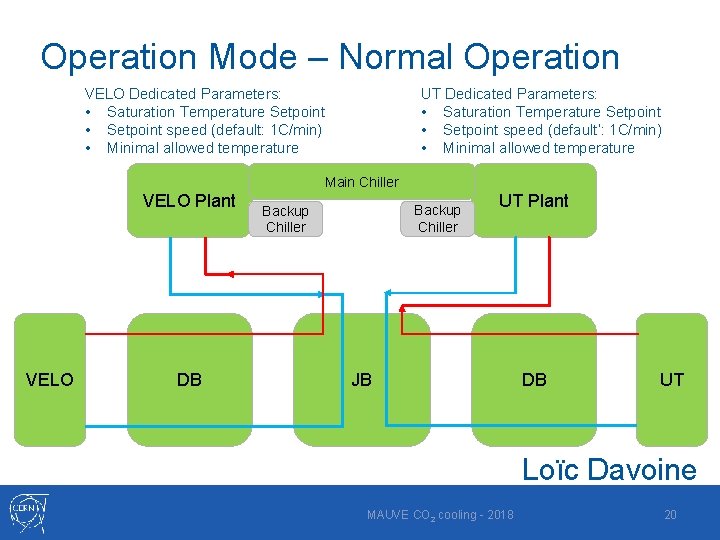
Operation Mode – Normal Operation UT Dedicated Parameters: • Saturation Temperature Setpoint • Setpoint speed (default’: 1 C/min) • Minimal allowed temperature VELO Dedicated Parameters: • Saturation Temperature Setpoint • Setpoint speed (default: 1 C/min) • Minimal allowed temperature Main Chiller VELO Plant VELO DB Backup Chiller UT Plant JB DB UT Loïc Davoine MAUVE CO 2 cooling - 2018 20
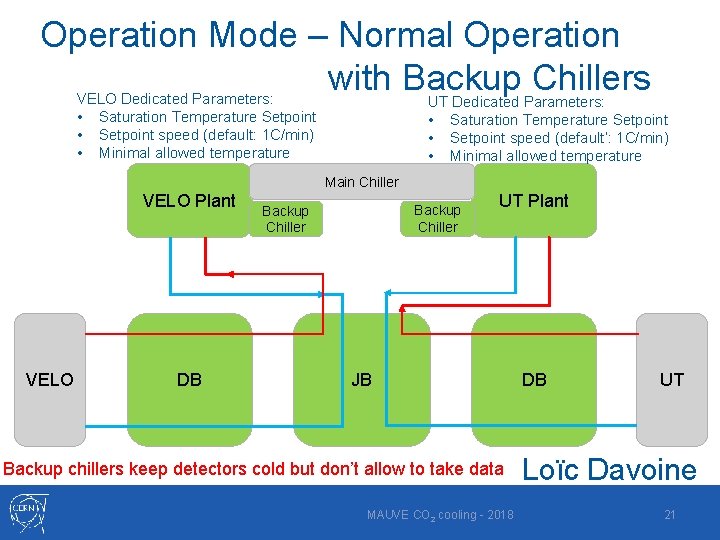
Operation Mode – Normal Operation with Backup Chillers VELO Dedicated Parameters: UT Dedicated Parameters: • • • Saturation Temperature Setpoint speed (default: 1 C/min) Minimal allowed temperature • • • Saturation Temperature Setpoint speed (default’: 1 C/min) Minimal allowed temperature Main Chiller VELO Plant VELO DB Backup Chiller UT Plant JB Backup chillers keep detectors cold but don’t allow to take data MAUVE CO 2 cooling - 2018 DB UT Loïc Davoine 21
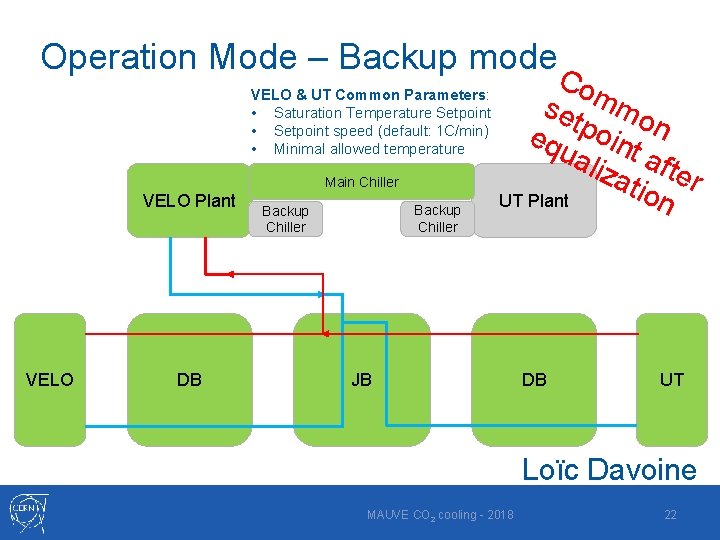
Operation Mode – Backup mode. C VELO & UT Common Parameters: • Saturation Temperature Setpoint • Setpoint speed (default: 1 C/min) • Minimal allowed temperature Main Chiller VELO Plant VELO DB Backup Chiller om set mo eq point n ua liza after tion UT Plant JB DB UT Loïc Davoine MAUVE CO 2 cooling - 2018 22
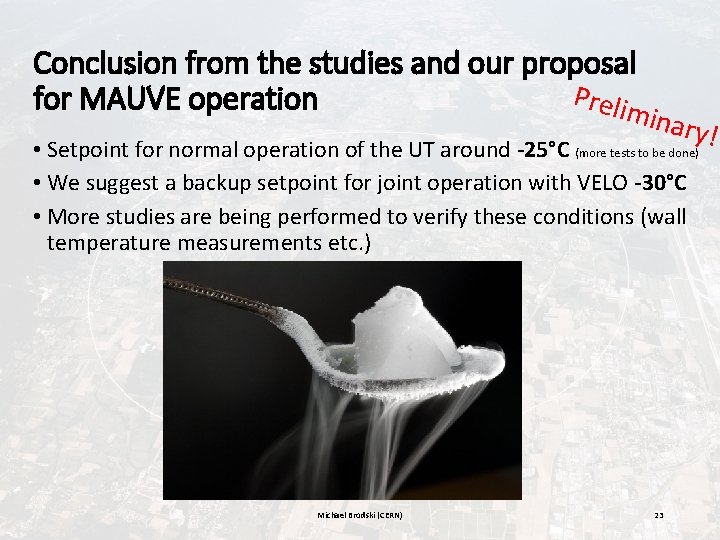
Conclusion from the studies and our proposal Preli for MAUVE operation m inary ! • Setpoint for normal operation of the UT around -25°C (more tests to be done) • We suggest a backup setpoint for joint operation with VELO -30°C • More studies are being performed to verify these conditions (wall temperature measurements etc. ) Michael Brodski (CERN) 23
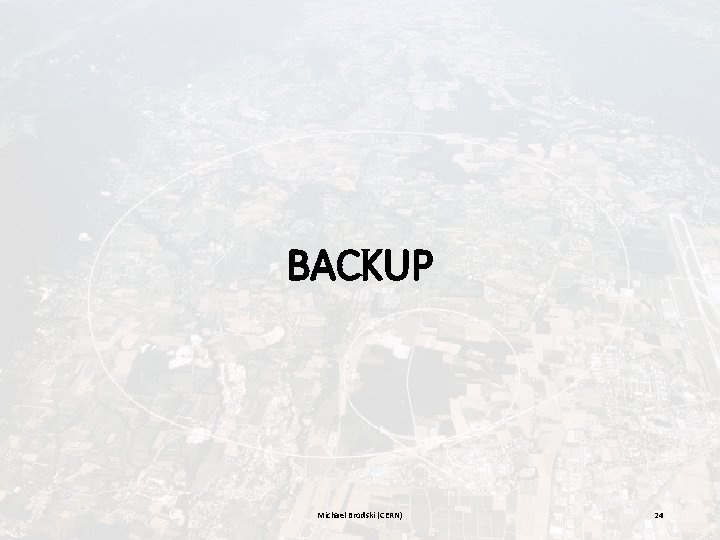
BACKUP Michael Brodski (CERN) 24
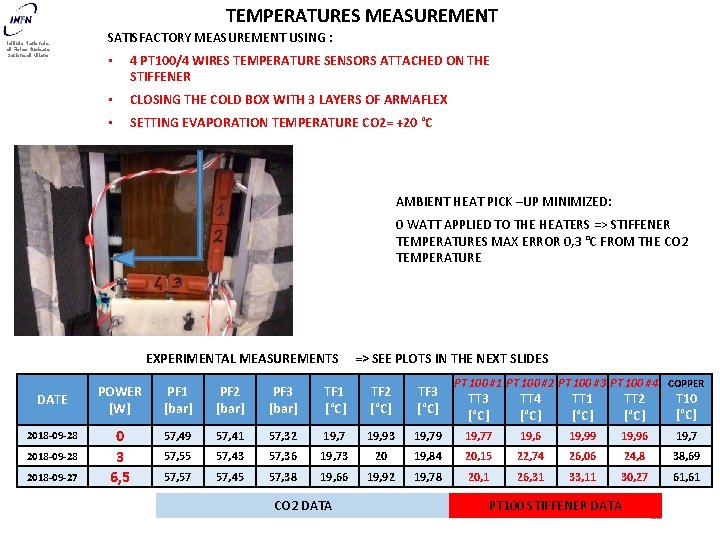
TEMPERATURES MEASUREMENT Istituto Nazionale di Fisica Nucleare Sezione di Milano SATISFACTORY MEASUREMENT USING : • 4 PT 100/4 WIRES TEMPERATURE SENSORS ATTACHED ON THE STIFFENER • CLOSING THE COLD BOX WITH 3 LAYERS OF ARMAFLEX • SETTING EVAPORATION TEMPERATURE CO 2= +20 °C AMBIENT HEAT PICK –UP MINIMIZED: 0 WATT APPLIED TO THE HEATERS => STIFFENER TEMPERATURES MAX ERROR 0, 3 °C FROM THE CO 2 TEMPERATURE EXPERIMENTAL MEASUREMENTS DATE 2018 -09 -28 2018 -09 -27 => SEE PLOTS IN THE NEXT SLIDES POWER [W] PF 1 [bar] PF 2 [bar] PF 3 [bar] TF 1 [°C] TF 2 [°C] TF 3 [°C] 0 3 6, 5 57, 49 57, 41 57, 32 19, 7 19, 93 57, 55 57, 43 57, 36 19, 73 57, 57 57, 45 57, 38 19, 66 CO 2 DATA PT 100 #1 PT 100 #2 PT 100 #3 PT 100 #4 COPPER TT 3 [°C] TT 4 [°C] TT 1 [°C] TT 2 [°C] T 10 [°C] 19, 79 19, 77 19, 6 19, 99 19, 96 19, 7 20 19, 84 20, 15 22, 74 26, 06 24, 8 38, 69 19, 92 19, 78 20, 1 26, 31 33, 11 30, 27 61, 61 PT 100 STIFFENER DATA 25
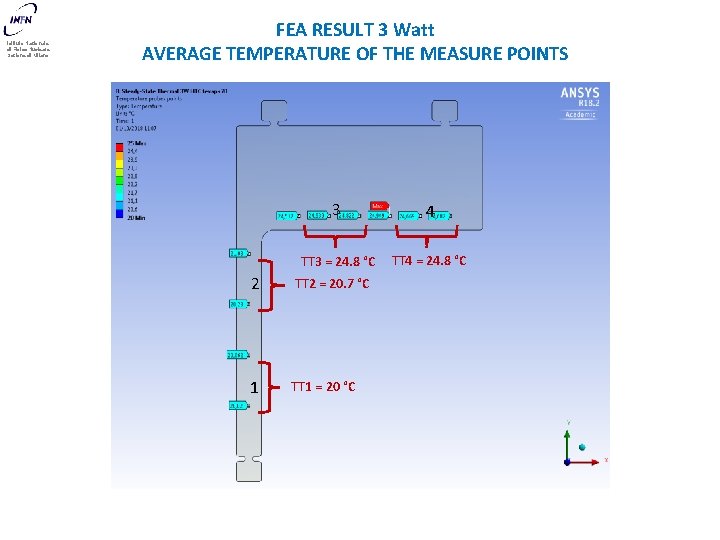
Istituto Nazionale di Fisica Nucleare Sezione di Milano FEA RESULT 3 Watt AVERAGE TEMPERATURE OF THE MEASURE POINTS 3 4 TT 3 = 24. 8 °C TT 4 = 24. 8 °C 2 TT 2 = 20. 7 °C 1 TT 1 = 20 °C
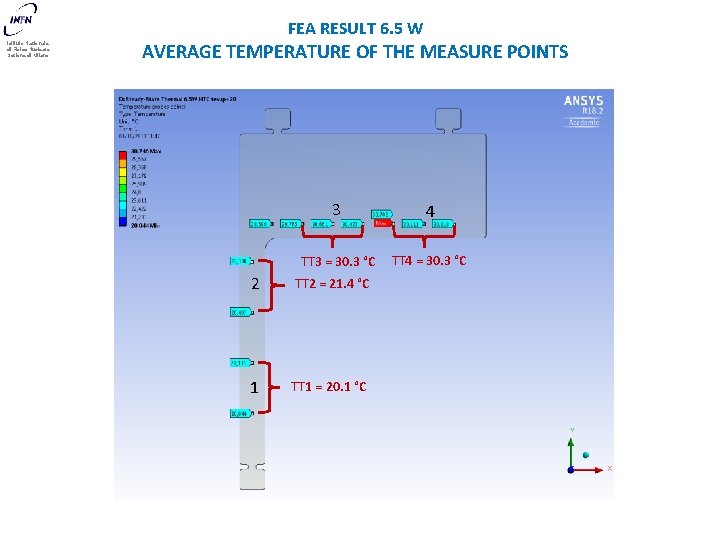
FEA RESULT 6. 5 W Istituto Nazionale di Fisica Nucleare Sezione di Milano AVERAGE TEMPERATURE OF THE MEASURE POINTS 3 4 TT 3 = 30. 3 °C TT 4 = 30. 3 °C 2 TT 2 = 21. 4 °C 1 TT 1 = 20. 1 °C
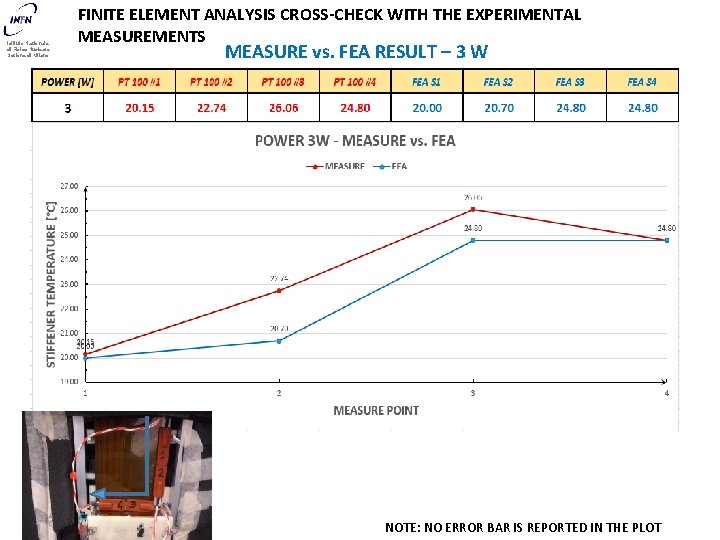
Istituto Nazionale di Fisica Nucleare Sezione di Milano FINITE ELEMENT ANALYSIS CROSS-CHECK WITH THE EXPERIMENTAL MEASUREMENTS MEASURE vs. FEA RESULT – 3 W NOTE: NO ERROR BAR IS REPORTED IN THE PLOT
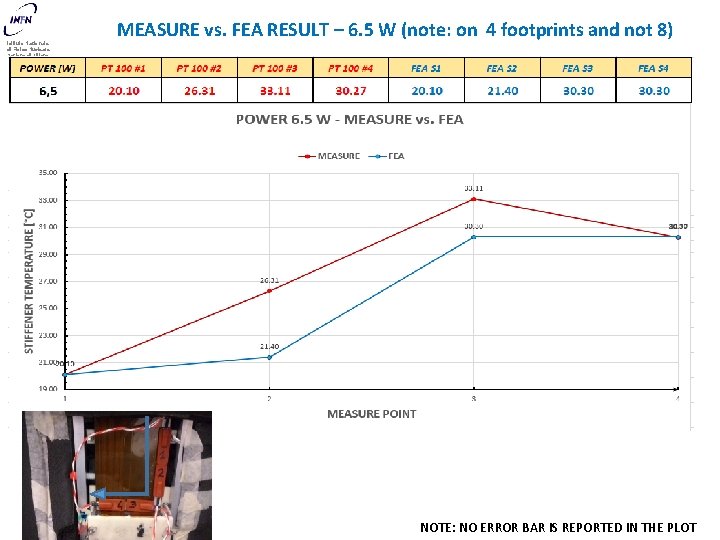
Istituto Nazionale di Fisica Nucleare Sezione di Milano MEASURE vs. FEA RESULT – 6. 5 W (note: on 4 footprints and not 8) NOTE: NO ERROR BAR IS REPORTED IN THE PLOT
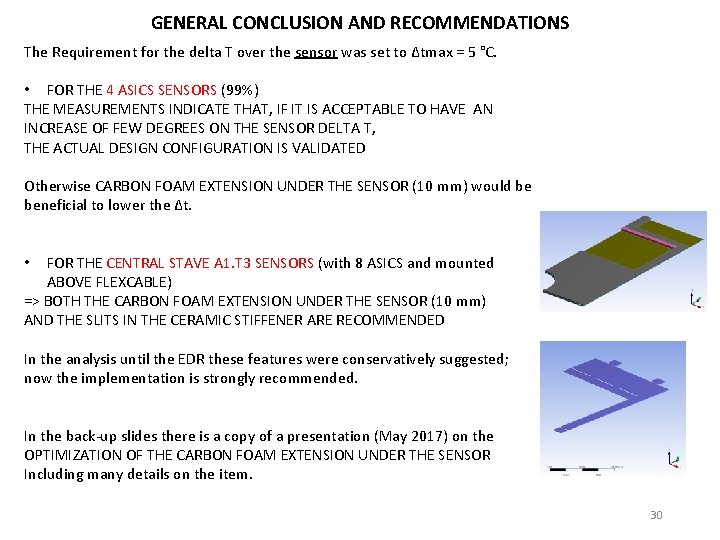
GENERAL CONCLUSION AND RECOMMENDATIONS The Requirement for the delta T over the sensor was set to Δtmax = 5 °C. • FOR THE 4 ASICS SENSORS (99%) THE MEASUREMENTS INDICATE THAT, IF IT IS ACCEPTABLE TO HAVE AN INCREASE OF FEW DEGREES ON THE SENSOR DELTA T, THE ACTUAL DESIGN CONFIGURATION IS VALIDATED Otherwise CARBON FOAM EXTENSION UNDER THE SENSOR (10 mm) would be beneficial to lower the Δt. FOR THE CENTRAL STAVE A 1. T 3 SENSORS (with 8 ASICS and mounted ABOVE FLEXCABLE) => BOTH THE CARBON FOAM EXTENSION UNDER THE SENSOR (10 mm) AND THE SLITS IN THE CERAMIC STIFFENER ARE RECOMMENDED • In the analysis until the EDR these features were conservatively suggested; now the implementation is strongly recommended. In the back-up slides there is a copy of a presentation (May 2017) on the OPTIMIZATION OF THE CARBON FOAM EXTENSION UNDER THE SENSOR Including many details on the item. 30
Is an alternative of log based recovery.
Physical fitness two types
What is skill-related fitness? *
Food and beverage product knowledge
Bsbhrm506
Purchasing, receiving, storing and issuing
Liz owns stock in nar heating/cooling
Air conditioning heat load calculation software
Engine lubrication and cooling system
Mounds of cooling brown and white
Heating and cooling curve
Sea breeze
Lubrication of couling systems
Frazier heating and cooling
Physical behavior of matter
Cooling load calculation example
Thermo bello
H&c heating and cooling
Physical behavior of matter heating and cooling curves
Jon snow golden ratio
Heating curve
Thermo bello
Kale heating and cooling
Is vaporization endothermic or exothermic
Sieb heating and cooling
Specific heat
Lesson 4: parameters and return make
Lesson 3: parameters and return practice
Common critical values
Lesson 3 parameters and return practice 7
Intrinsic parameters of food