Update of CLIC accelerating structure design Hao Zha
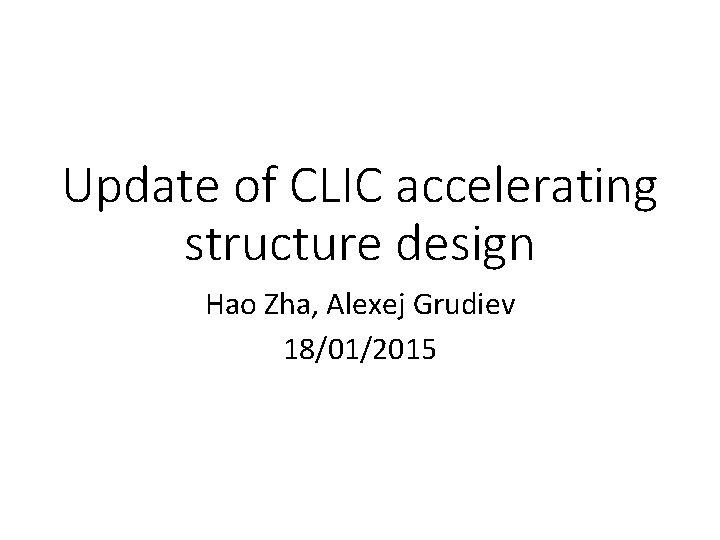
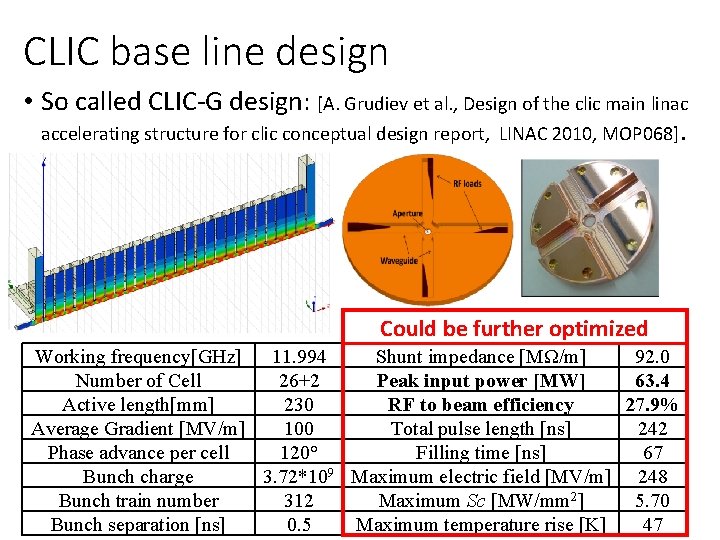
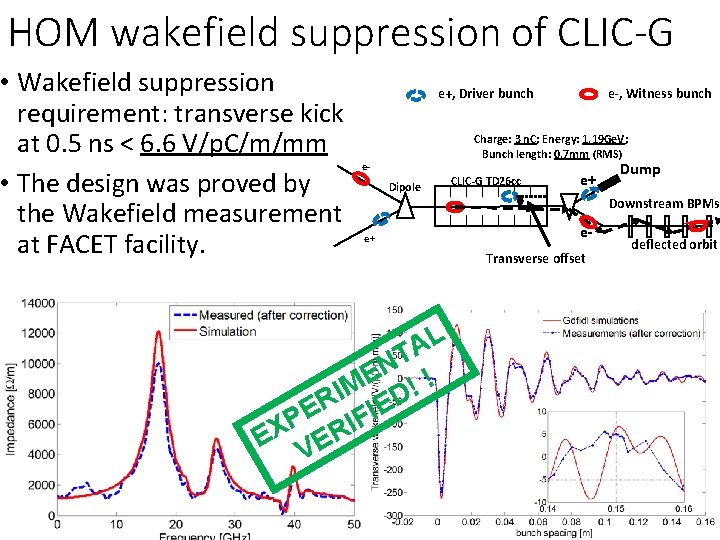
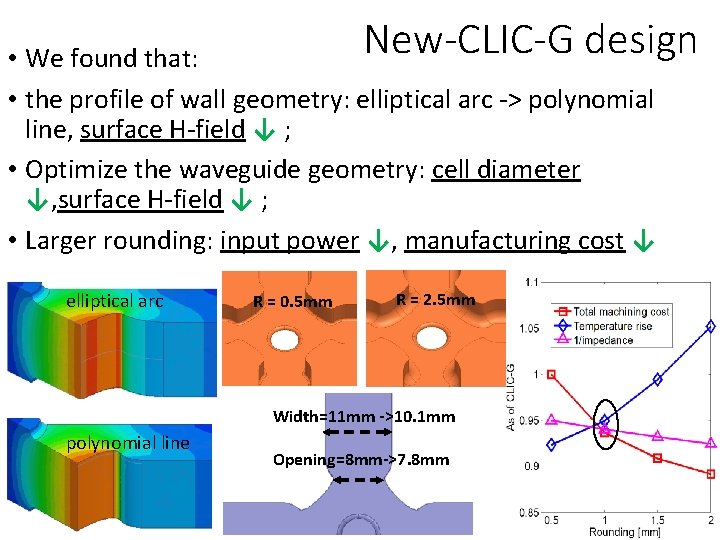

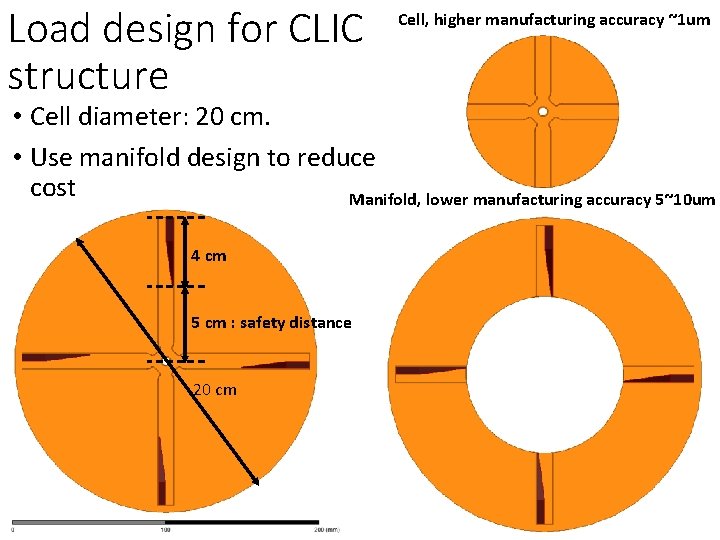
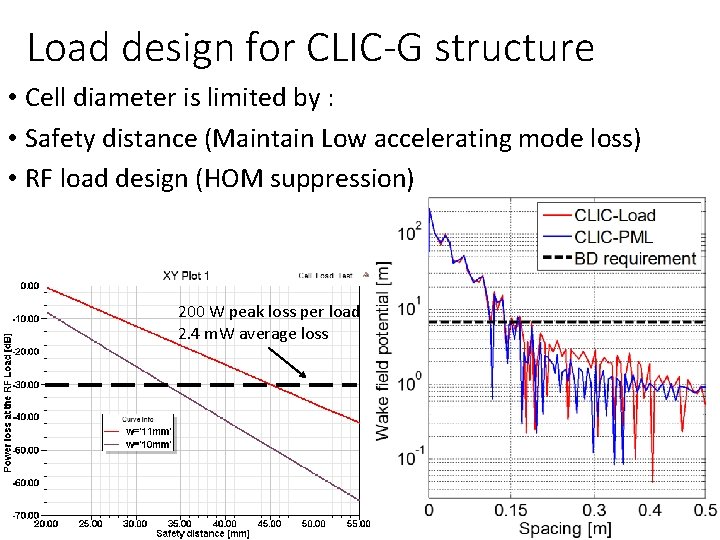
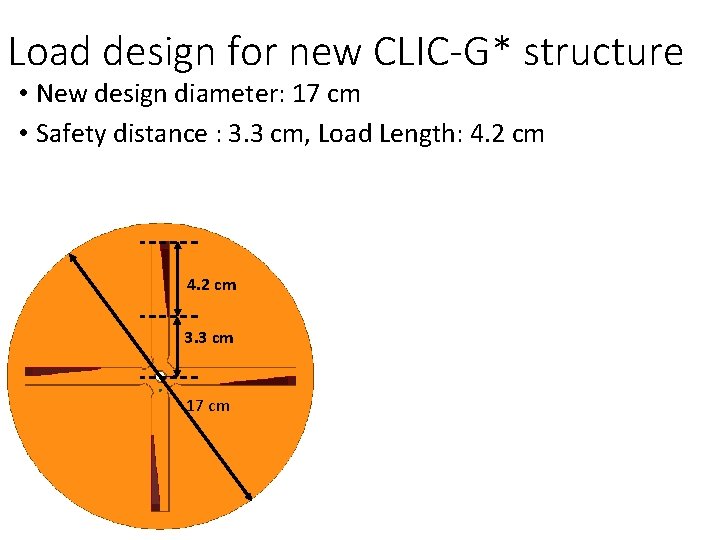
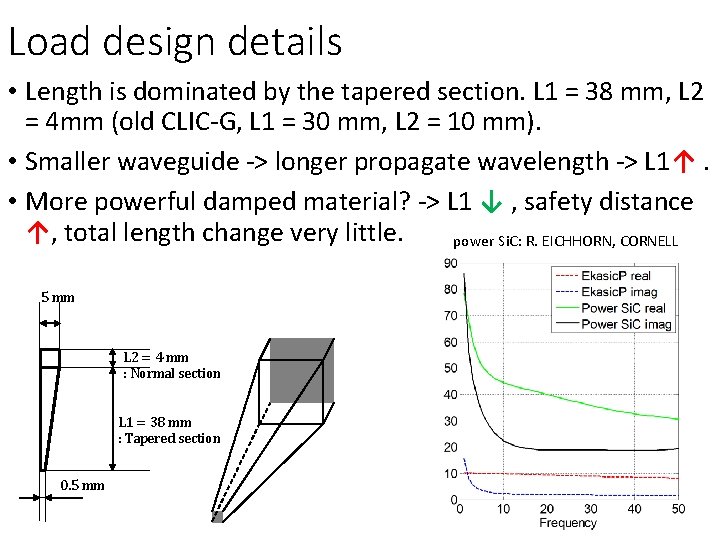
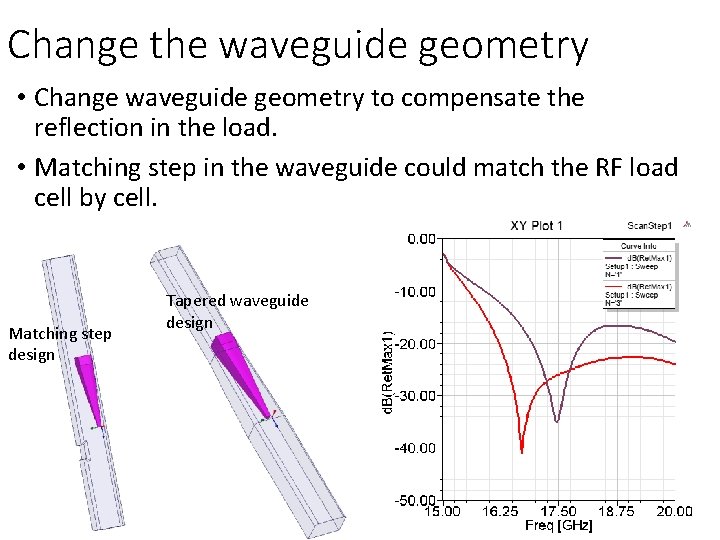
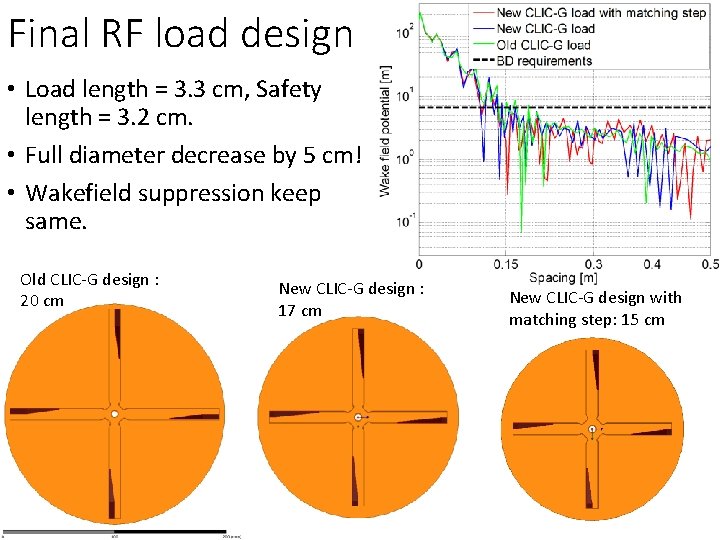
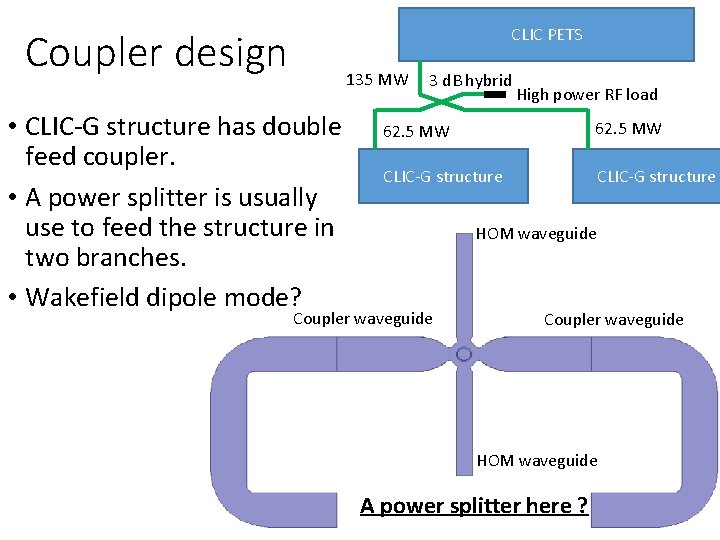
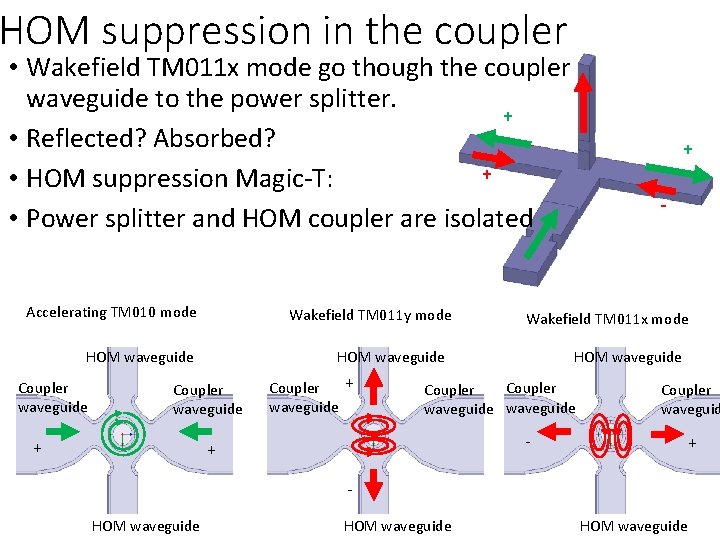
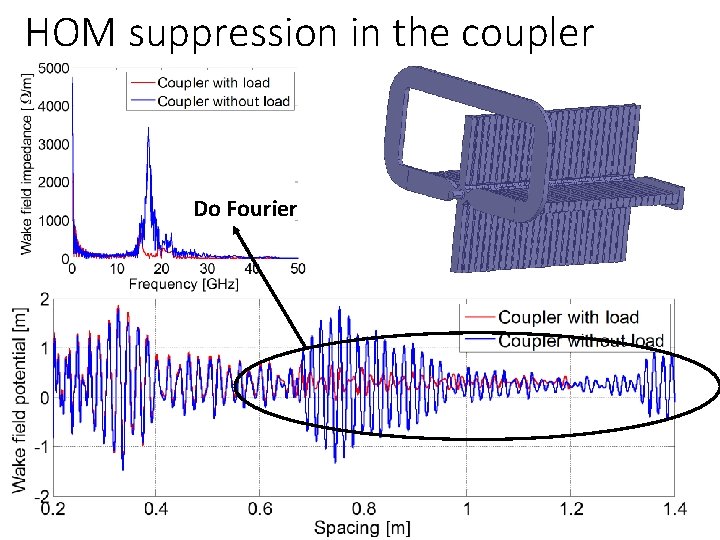
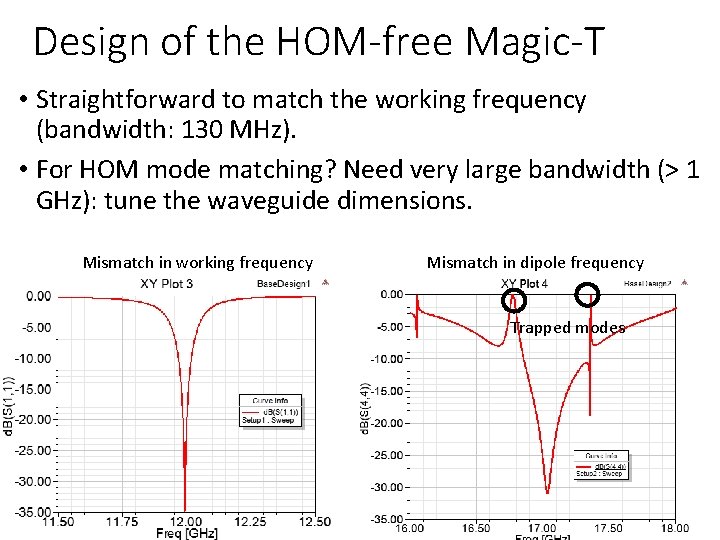
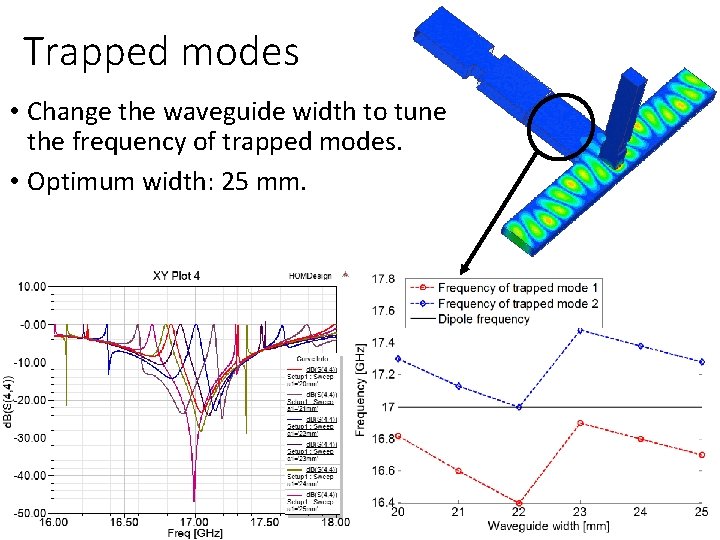
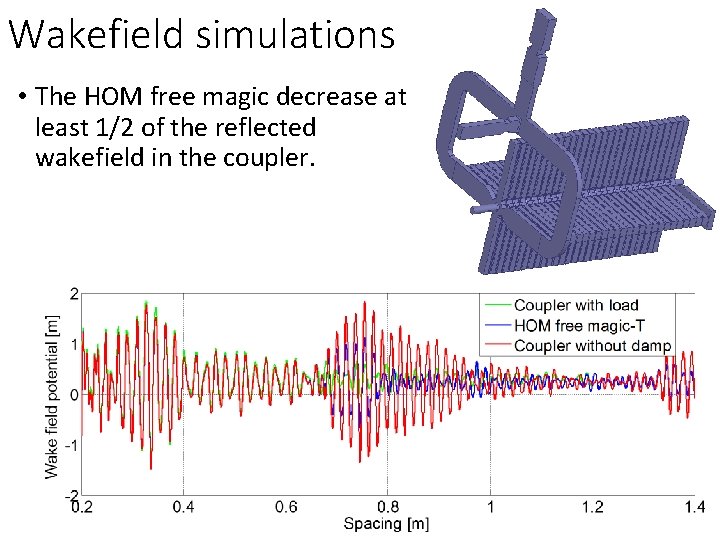
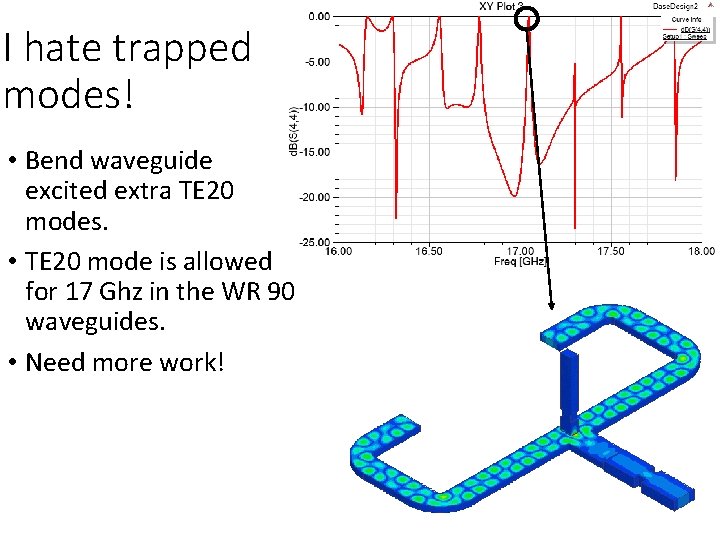
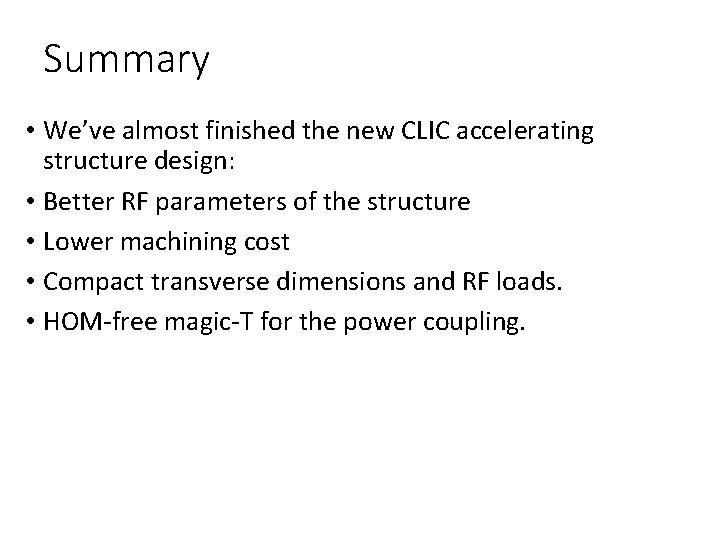
- Slides: 19
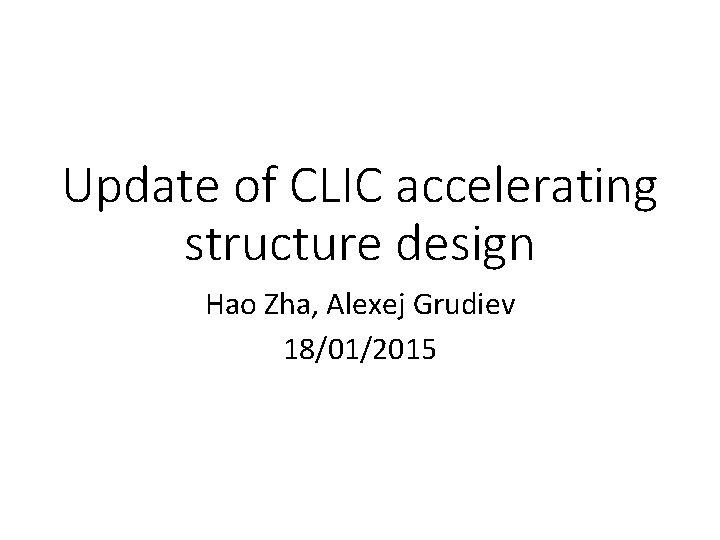
Update of CLIC accelerating structure design Hao Zha, Alexej Grudiev 18/01/2015
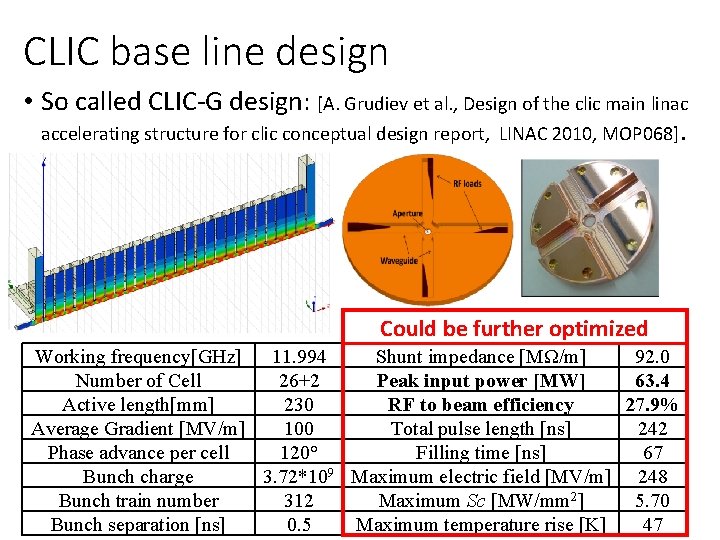
CLIC base line design • So called CLIC-G design: [A. Grudiev et al. , Design of the clic main linac accelerating structure for clic conceptual design report, LINAC 2010, MOP 068]. Could be further optimized Working frequency[GHz] 11. 994 Shunt impedance [MΩ/m] 92. 0 Number of Cell 26+2 Peak input power [MW] 63. 4 Active length[mm] 230 RF to beam efficiency 27. 9% Average Gradient [MV/m] 100 Total pulse length [ns] 242 Phase advance per cell 120° Filling time [ns] 67 Bunch charge 3. 72*109 Maximum electric field [MV/m] 248 Bunch train number 312 Maximum Sc [MW/mm 2] 5. 70 Bunch separation [ns] 0. 5 Maximum temperature rise [K] 47
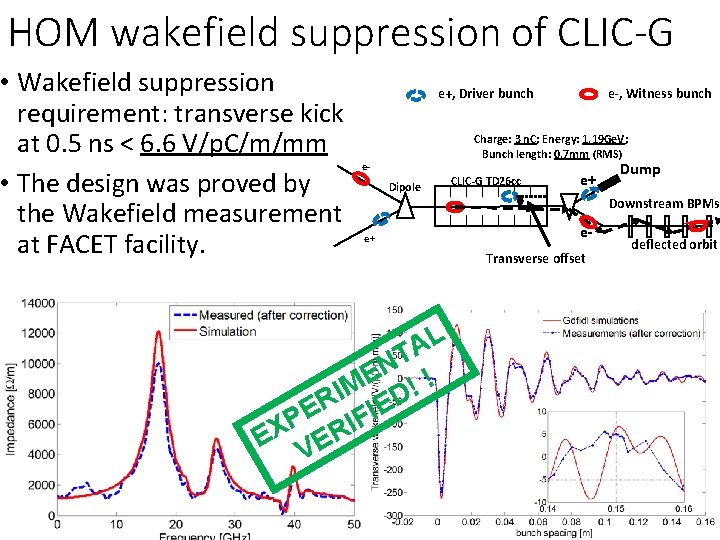
HOM wakefield suppression of CLIC-G • Wakefield suppression requirement: transverse kick at 0. 5 ns < 6. 6 V/p. C/m/mm • The design was proved by the Wakefield measurement at FACET facility. e-, Witness bunch e+, Driver bunch Charge: 3 n. C; Energy: 1. 19 Ge. V; Bunch length: 0. 7 mm (RMS) e- Dipole CLIC-G TD 26 cc e+ Dump Downstream BPMs e+ L A T N E !! M I D R E E IFI P EX VER e. Transverse offset deflected orbit
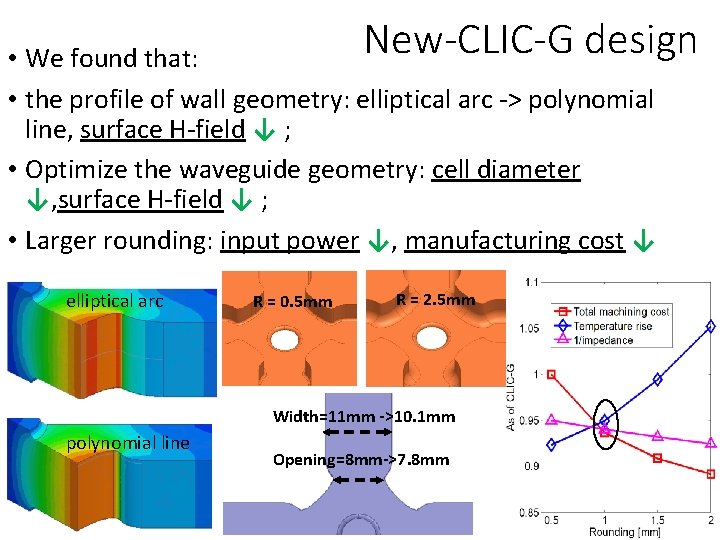
New-CLIC-G design • We found that: • the profile of wall geometry: elliptical arc -> polynomial line, surface H-field ↓ ; • Optimize the waveguide geometry: cell diameter ↓, surface H-field ↓ ; • Larger rounding: input power ↓, manufacturing cost ↓ elliptical arc R = 0. 5 mm R = 2. 5 mm Width=11 mm ->10. 1 mm polynomial line Opening=8 mm->7. 8 mm

New-CLIC-G design • Now we have a lower surface field , lower input power , lower cost design: CLIC-G*. • Manufacturing is now undergoing (anticipate high power CLIC-G* test in 2016). Rounding[mm] 0. 5 Manufacturing cost -reduction Shunt impedance 92. 0 [MΩ/m] Peak input power [MW] 63. 4 RF to beam efficiency 27. 9% Filling time [ns] Maximum electric field [MV/m] Maximum Sc [MW/mm 2] Maximum temperature rise [K] 1. 0 7%↓ 95. 4↑ 67 248 62. 3↓ 28. 4% ↑ 66↓ 250↑ 5. 70 52 5. 65↓ 41↓
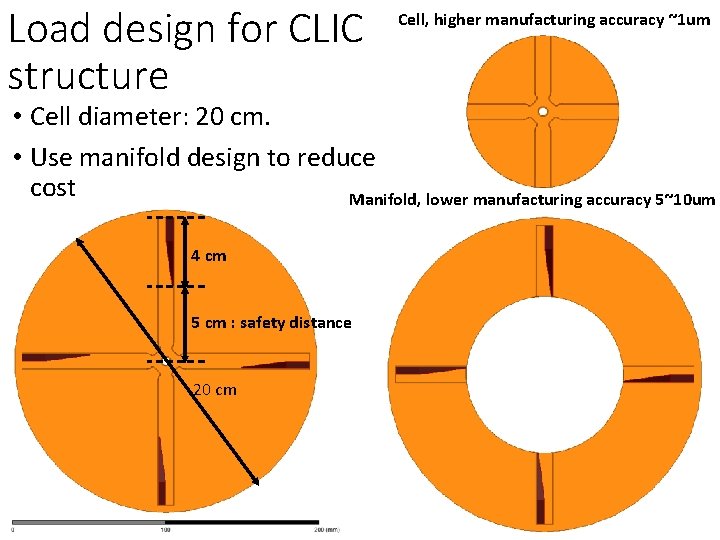
Load design for CLIC structure Cell, higher manufacturing accuracy ~1 um • Cell diameter: 20 cm. • Use manifold design to reduce cost Manifold, lower manufacturing accuracy 5~10 um 4 cm 5 cm : safety distance 20 cm
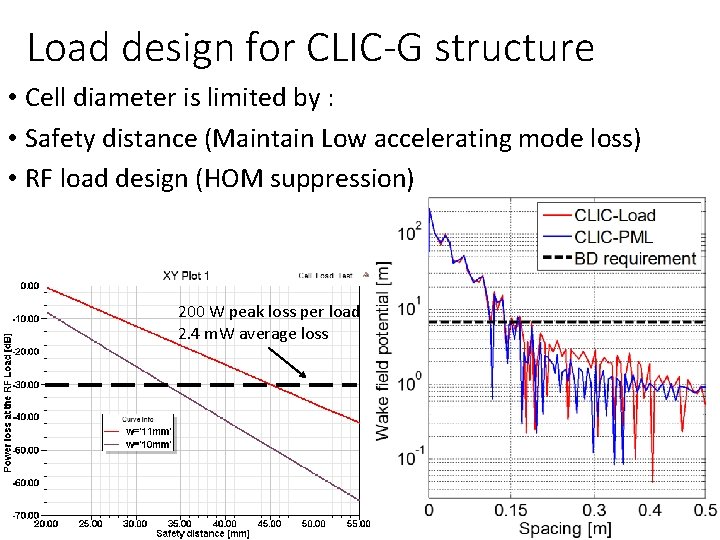
Load design for CLIC-G structure • Cell diameter is limited by : • Safety distance (Maintain Low accelerating mode loss) • RF load design (HOM suppression) 200 W peak loss per load 2. 4 m. W average loss
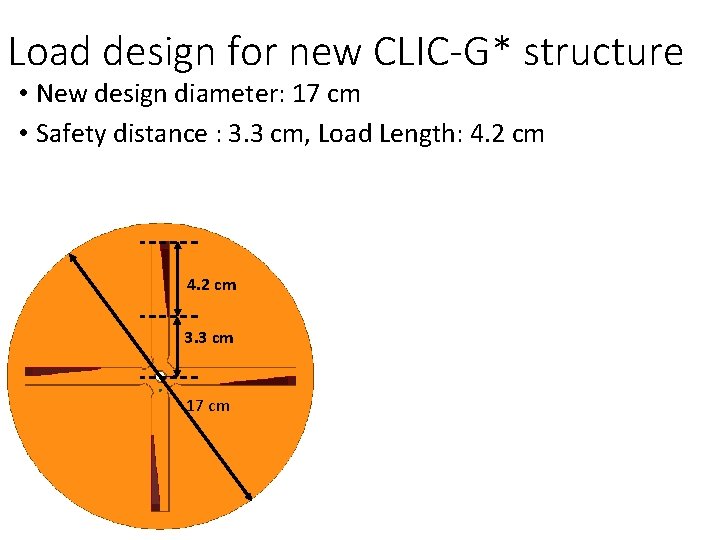
Load design for new CLIC-G* structure • New design diameter: 17 cm • Safety distance : 3. 3 cm, Load Length: 4. 2 cm 3. 3 cm 17 cm
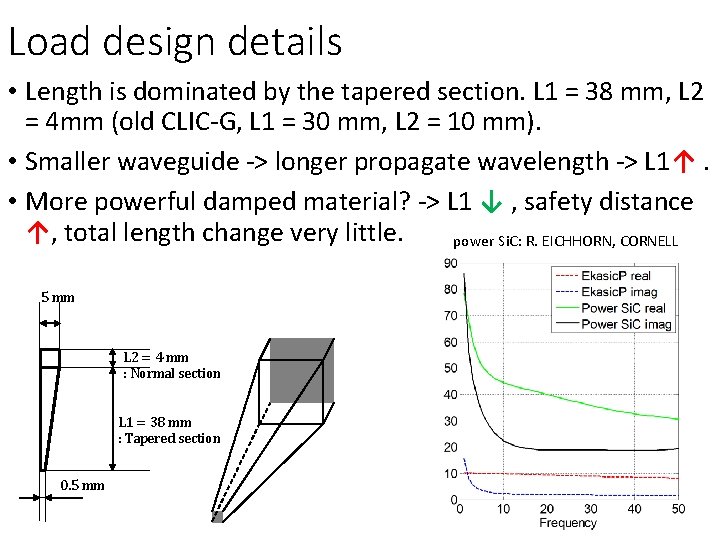
Load design details • Length is dominated by the tapered section. L 1 = 38 mm, L 2 = 4 mm (old CLIC-G, L 1 = 30 mm, L 2 = 10 mm). • Smaller waveguide -> longer propagate wavelength -> L 1↑. • More powerful damped material? -> L 1 ↓ , safety distance ↑, total length change very little. power Si. C: R. EICHHORN, CORNELL 5 mm L 2 = 4 mm : Normal section L 1 = 38 mm : Tapered section 0. 5 mm
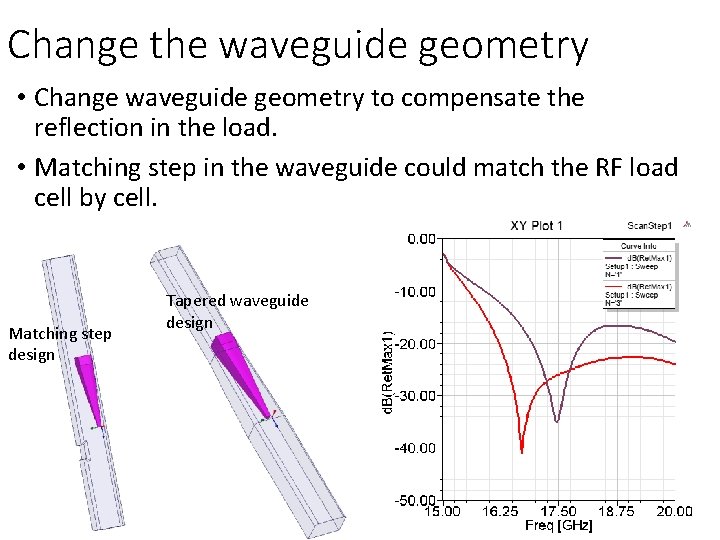
Change the waveguide geometry • Change waveguide geometry to compensate the reflection in the load. • Matching step in the waveguide could match the RF load cell by cell. Matching step design Tapered waveguide design
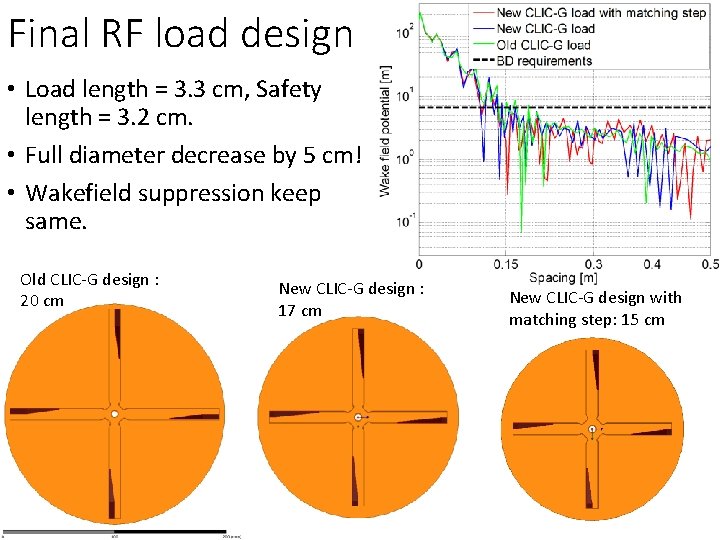
Final RF load design • Load length = 3. 3 cm, Safety length = 3. 2 cm. • Full diameter decrease by 5 cm! • Wakefield suppression keep same. Old CLIC-G design : 20 cm New CLIC-G design : 17 cm New CLIC-G design with matching step: 15 cm
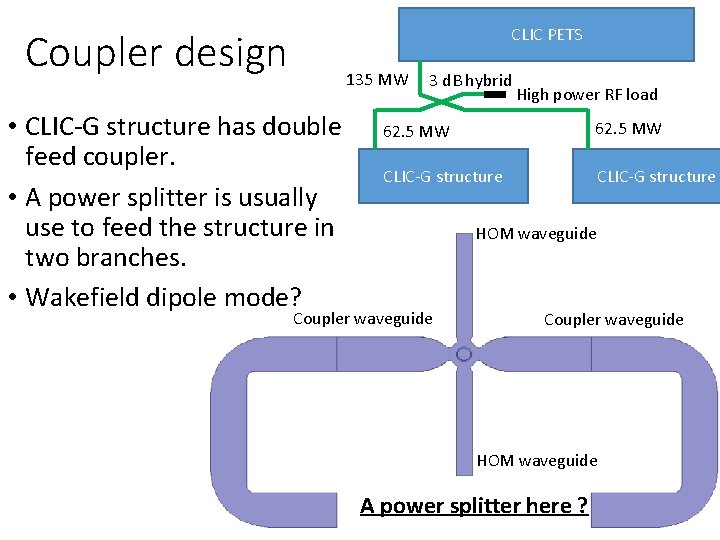
CLIC PETS Coupler design 135 MW • CLIC-G structure has double feed coupler. • A power splitter is usually use to feed the structure in two branches. • Wakefield dipole mode? 3 d. B hybrid High power RF load 62. 5 MW CLIC-G structure HOM waveguide Coupler waveguide HOM waveguide A power splitter here ?
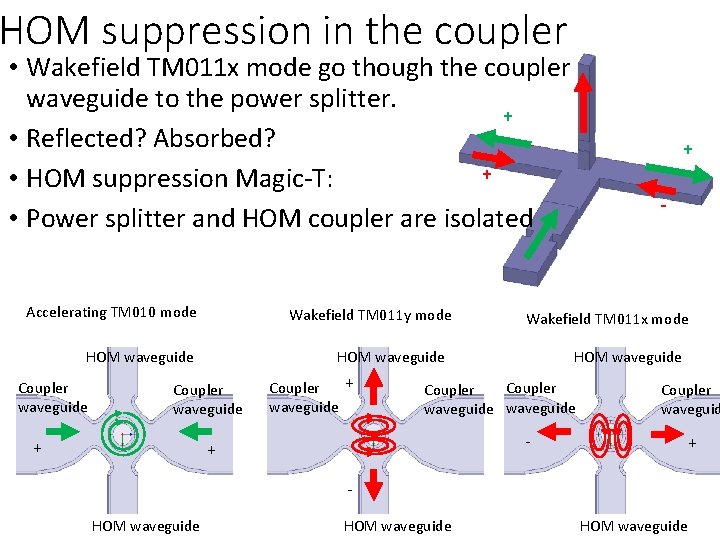
HOM suppression in the coupler • Wakefield TM 011 x mode go though the coupler waveguide to the power splitter. + • Reflected? Absorbed? + • HOM suppression Magic-T: • Power splitter and HOM coupler are isolated Accelerating TM 010 mode Wakefield TM 011 y mode HOM waveguide Coupler waveguide + + Coupler waveguide - Wakefield TM 011 x mode HOM waveguide Coupler waveguide + HOM waveguide Coupler waveguide - + Coupler waveguid + HOM waveguide
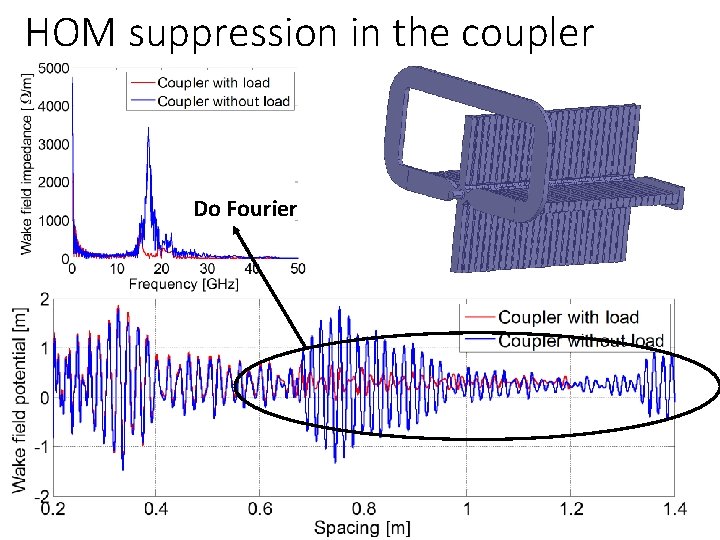
HOM suppression in the coupler Do Fourier
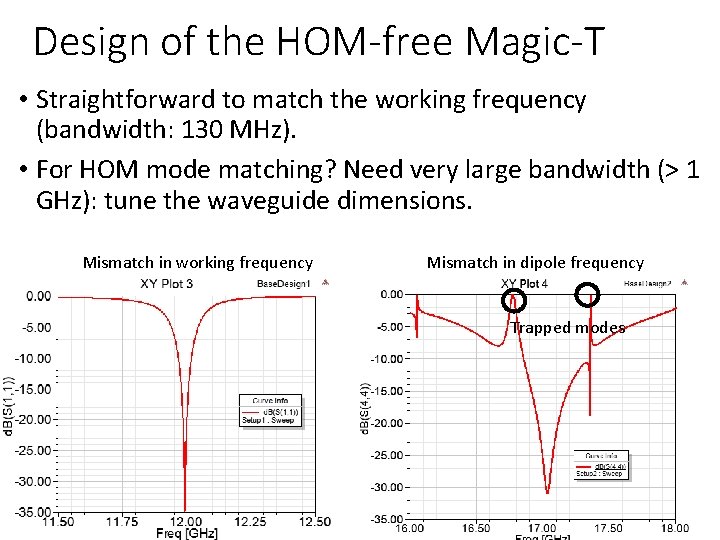
Design of the HOM-free Magic-T • Straightforward to match the working frequency (bandwidth: 130 MHz). • For HOM mode matching? Need very large bandwidth (> 1 GHz): tune the waveguide dimensions. Mismatch in working frequency Mismatch in dipole frequency Trapped modes
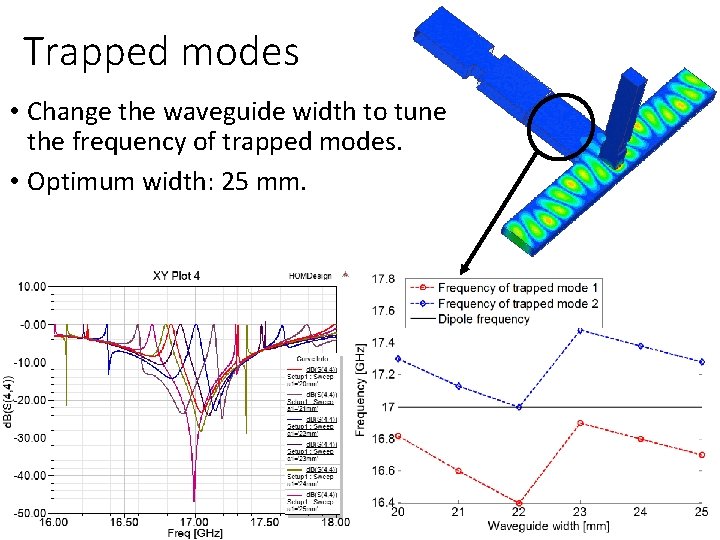
Trapped modes • Change the waveguide width to tune the frequency of trapped modes. • Optimum width: 25 mm.
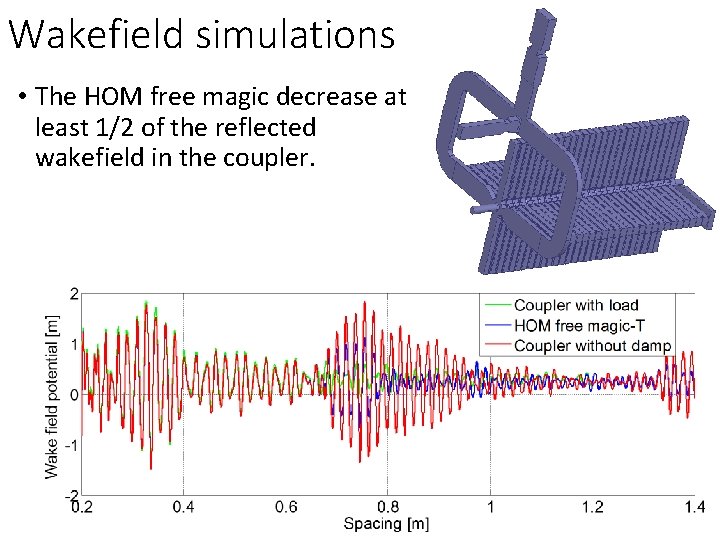
Wakefield simulations • The HOM free magic decrease at least 1/2 of the reflected wakefield in the coupler.
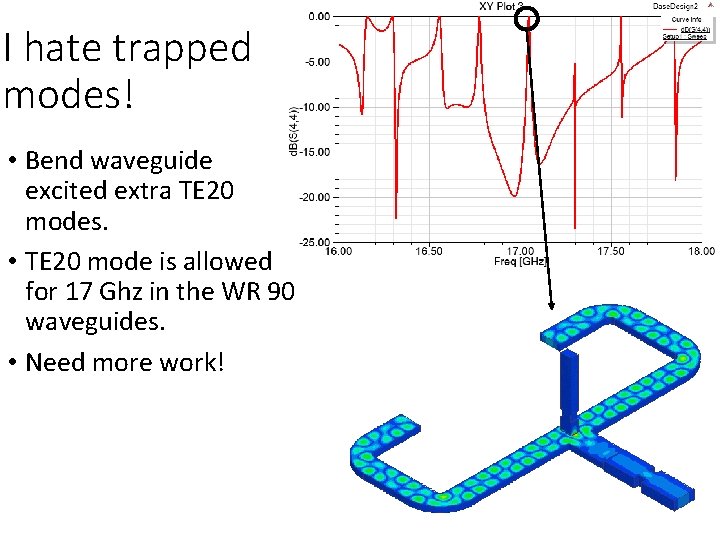
I hate trapped modes! • Bend waveguide excited extra TE 20 modes. • TE 20 mode is allowed for 17 Ghz in the WR 90 waveguides. • Need more work!
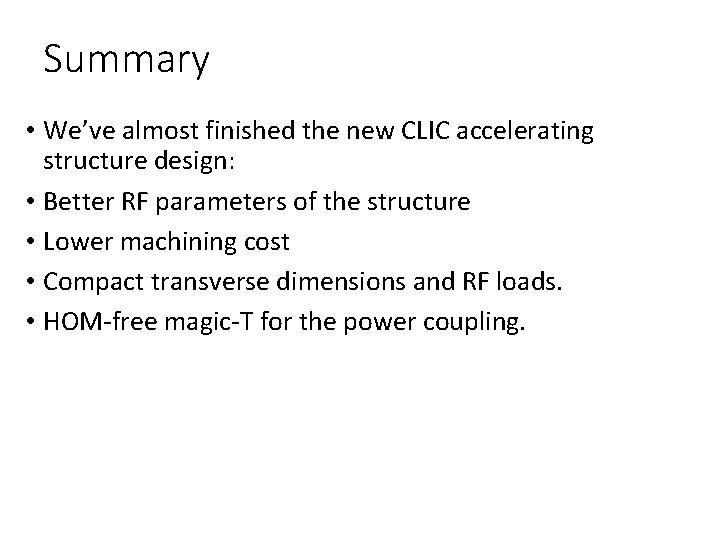
Summary • We’ve almost finished the new CLIC accelerating structure design: • Better RF parameters of the structure • Lower machining cost • Compact transverse dimensions and RF loads. • HOM-free magic-T for the power coupling.
Da zha hao
Wo de mingzi shi pronunciation
Nanxi zha
Is an alternative of log based recovery.
Accelerating rate calorimeter
Law of accelerating returns
50000x200
Accelerated implementation methodology
Accelerating high performance
Advanced materials
Son clochette saint nicolas
Dead clic
Palabras con la letra v
How to compute net of vat
Rception
Secretaria de energia 1102
Clic paris emeraude
Clic mesosistolico
Clic
Imagenes de clic