Textile Printing Textile Printing Defined as Localised form
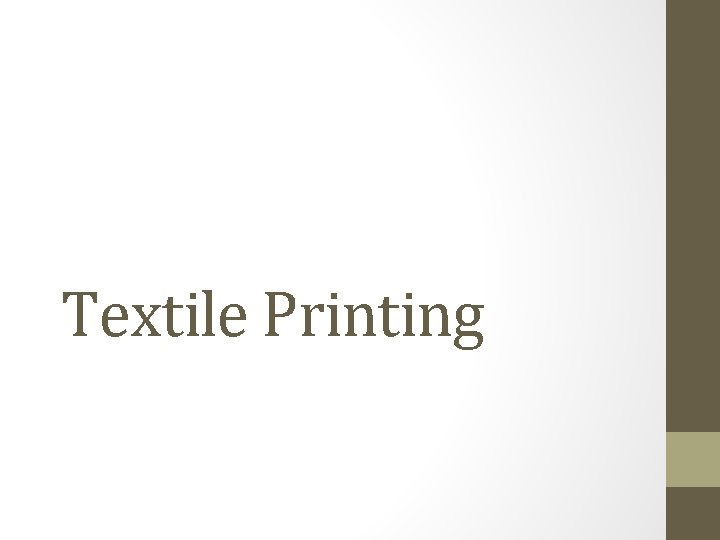
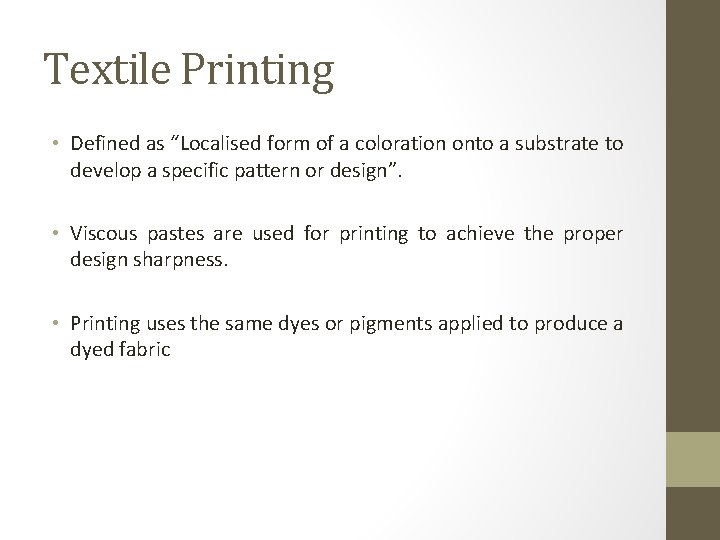
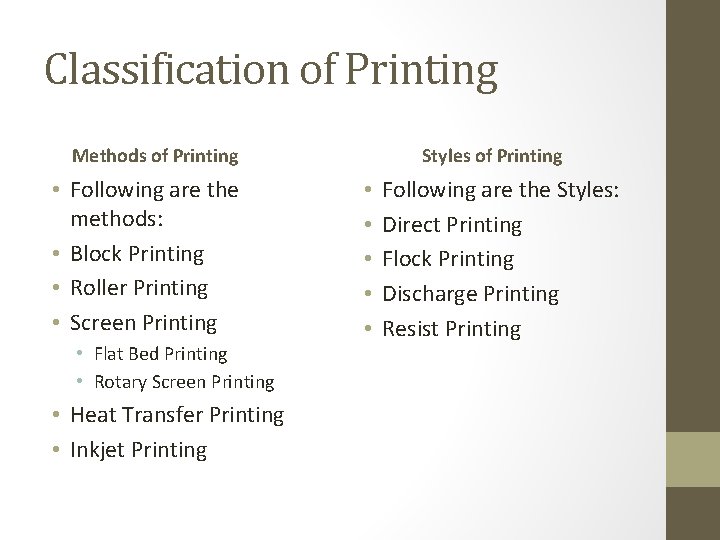
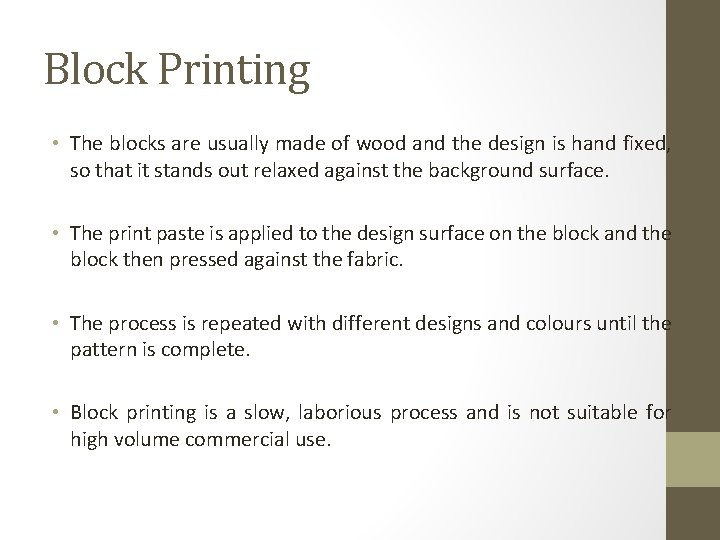
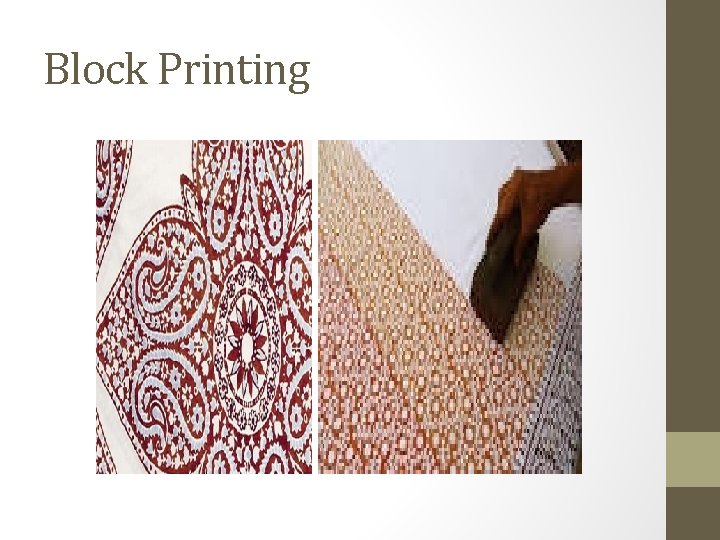
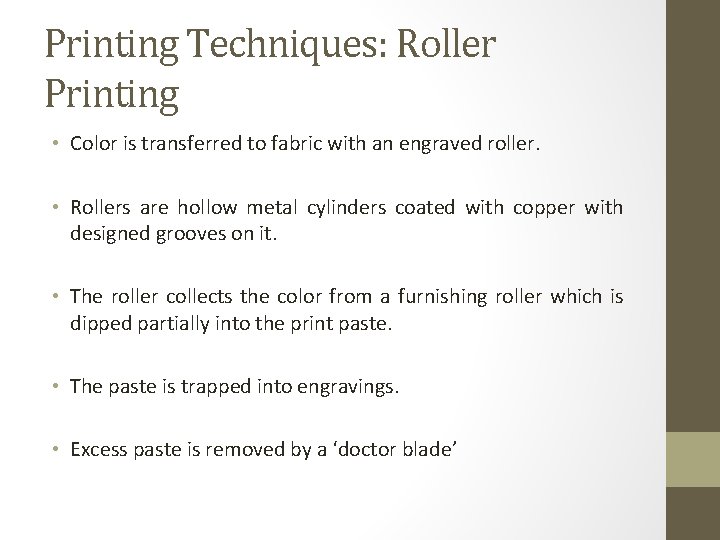
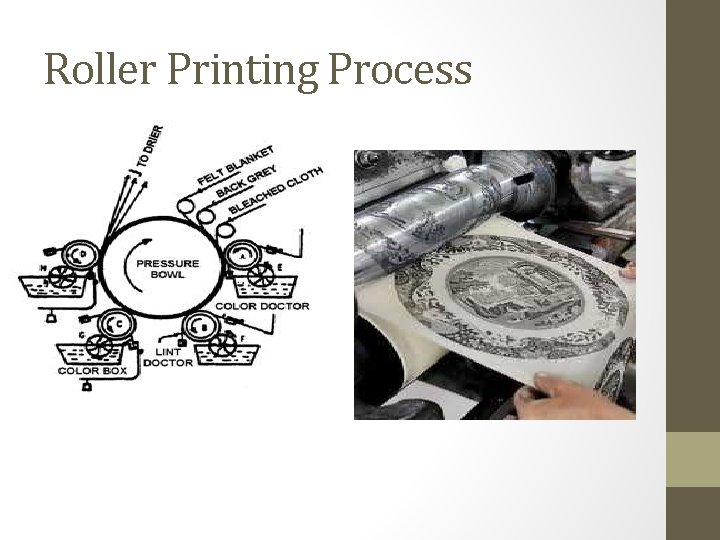
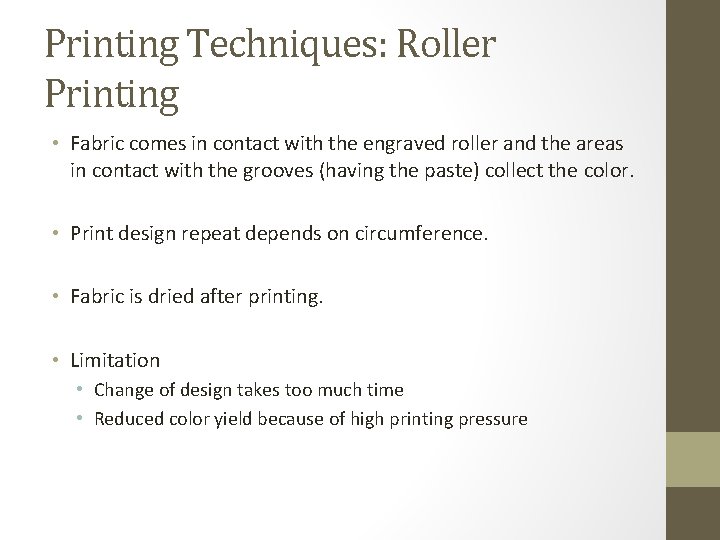
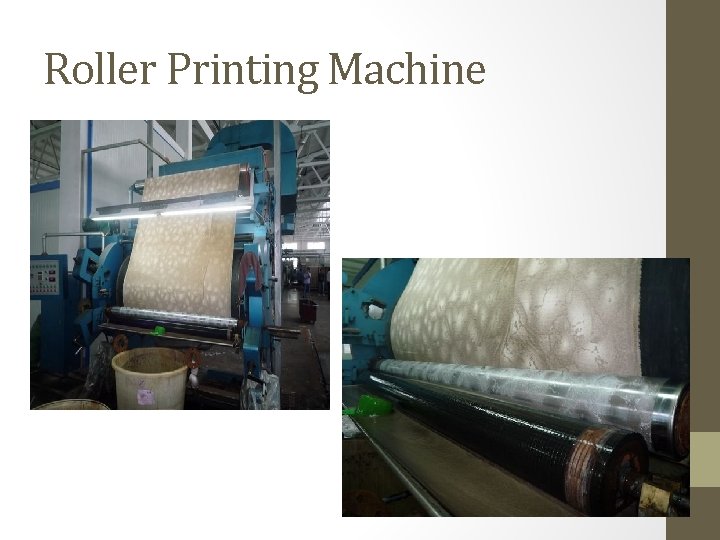
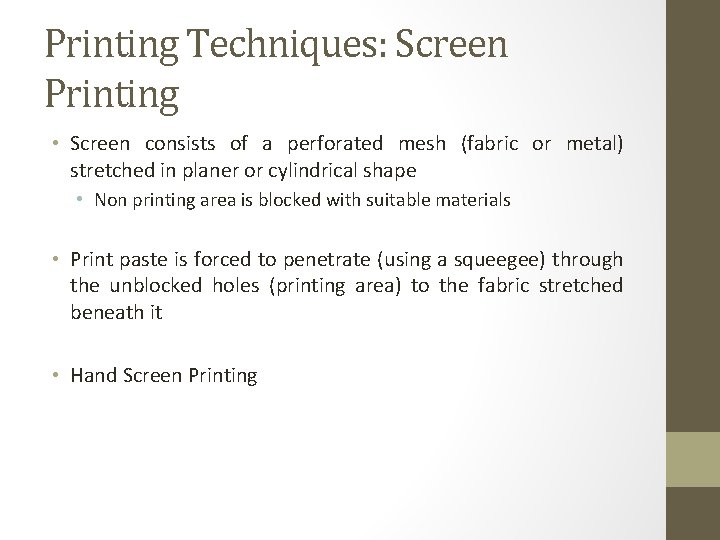
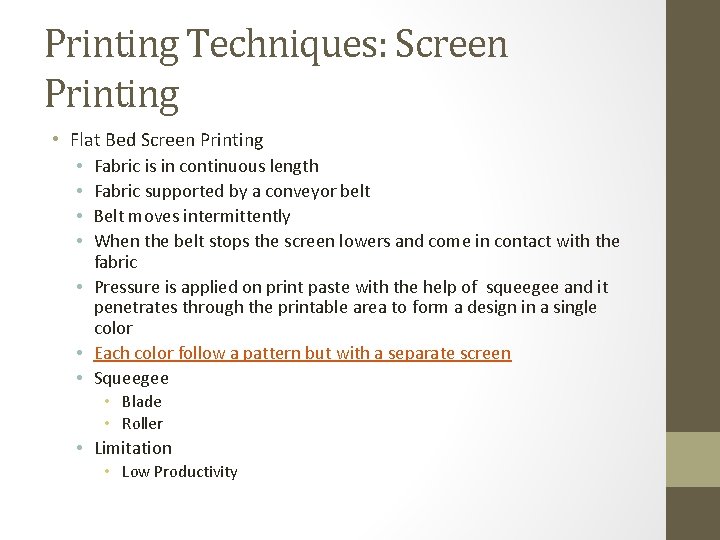
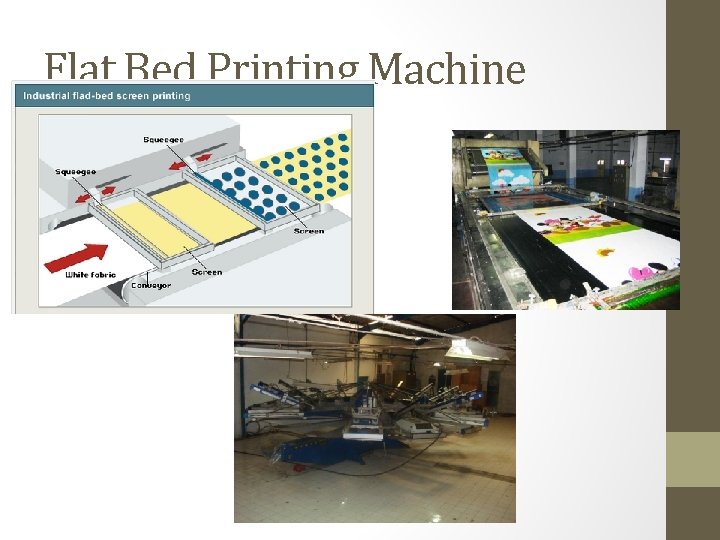
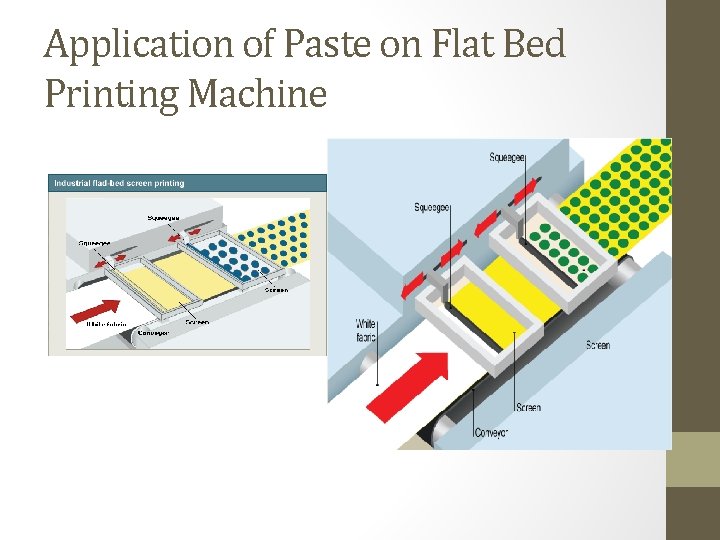
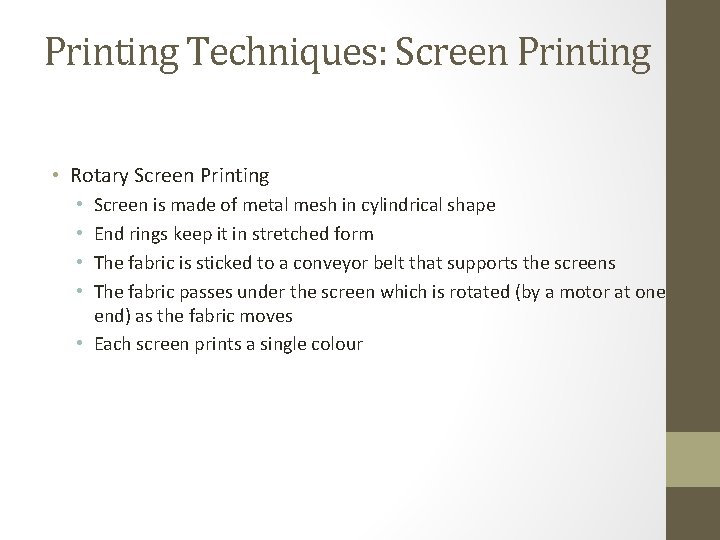
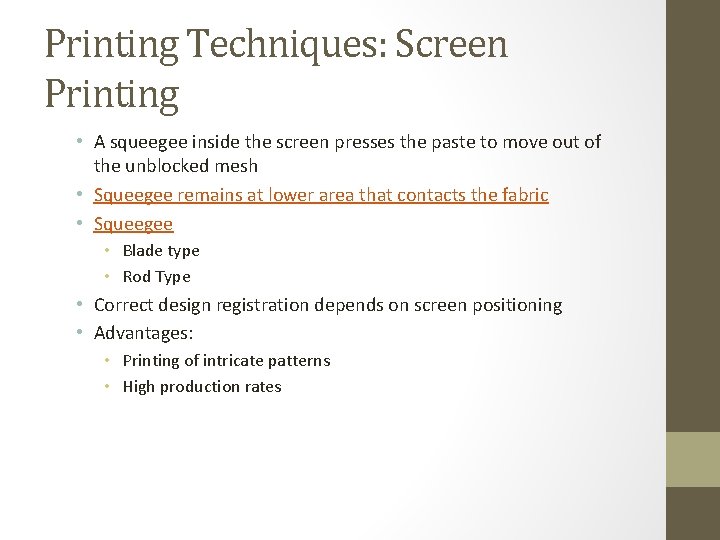
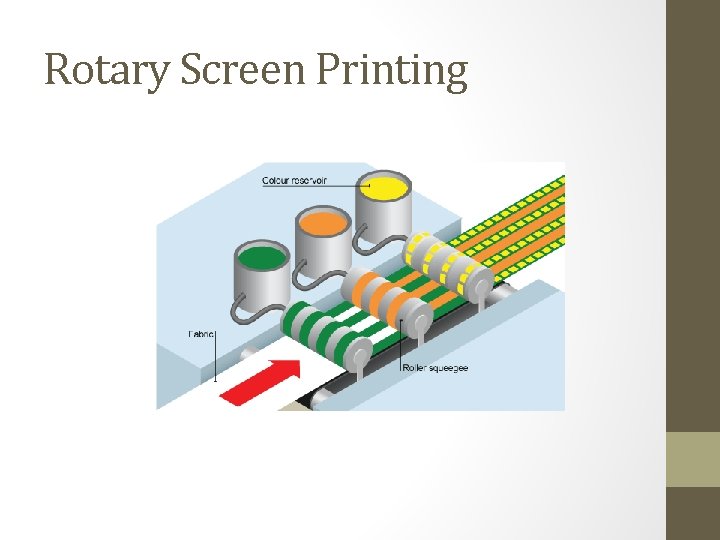
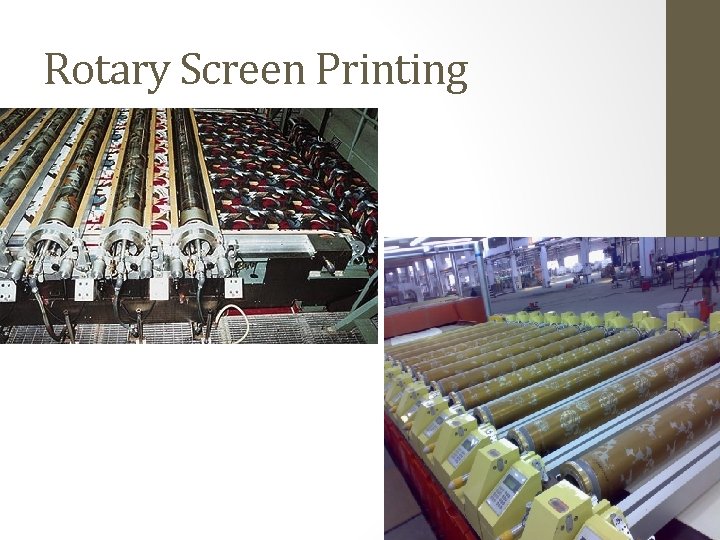

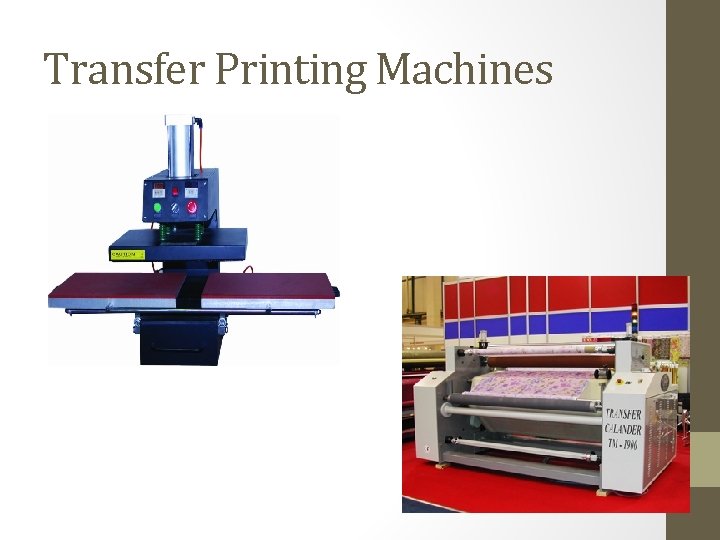
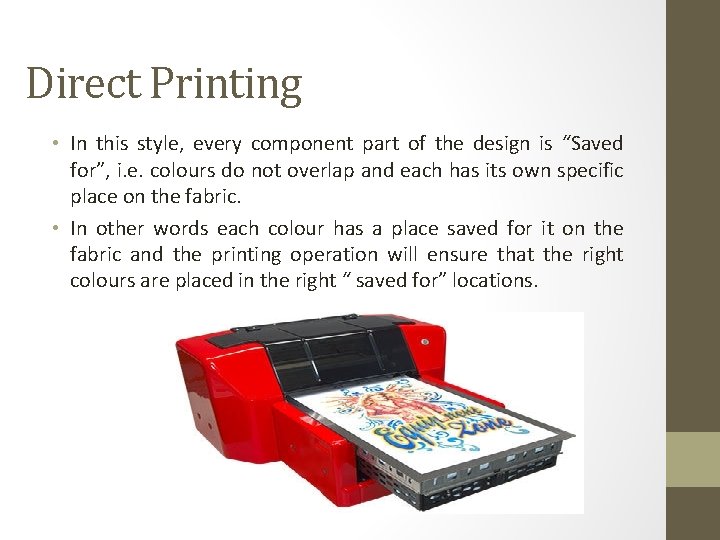
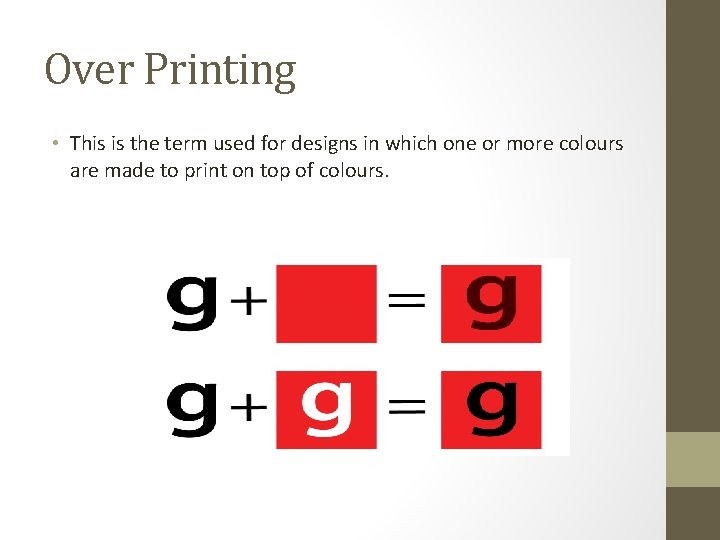
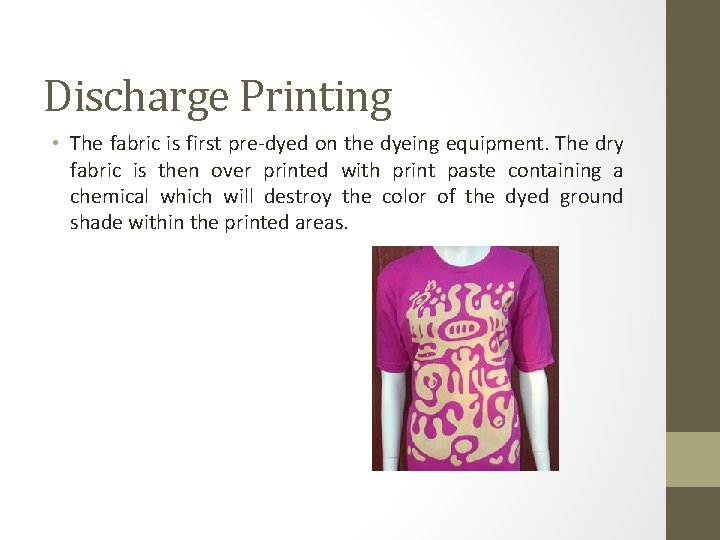
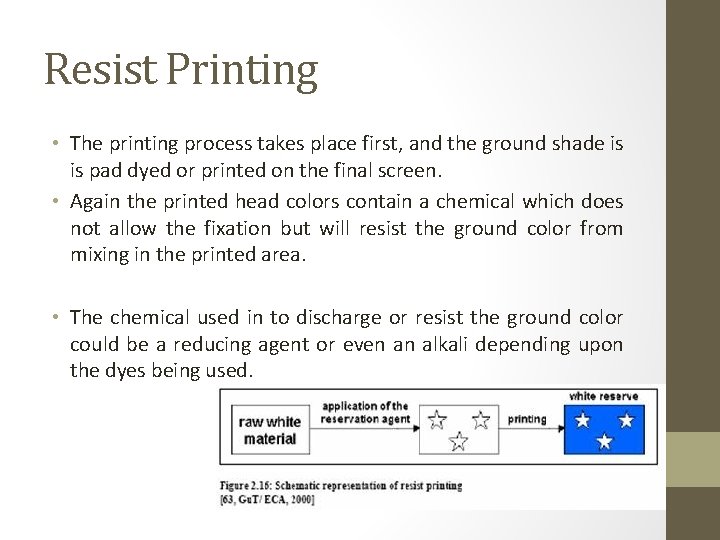
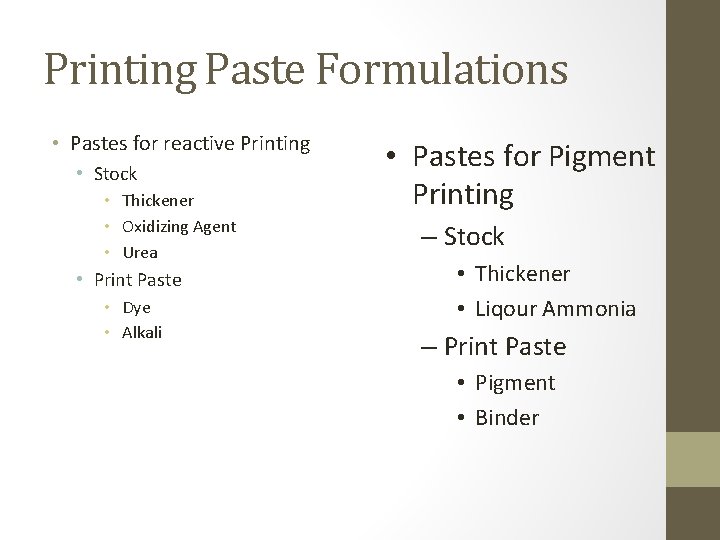
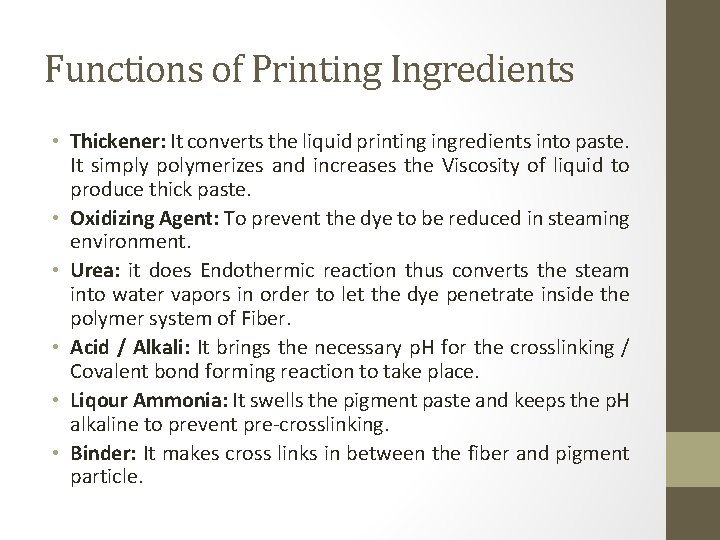
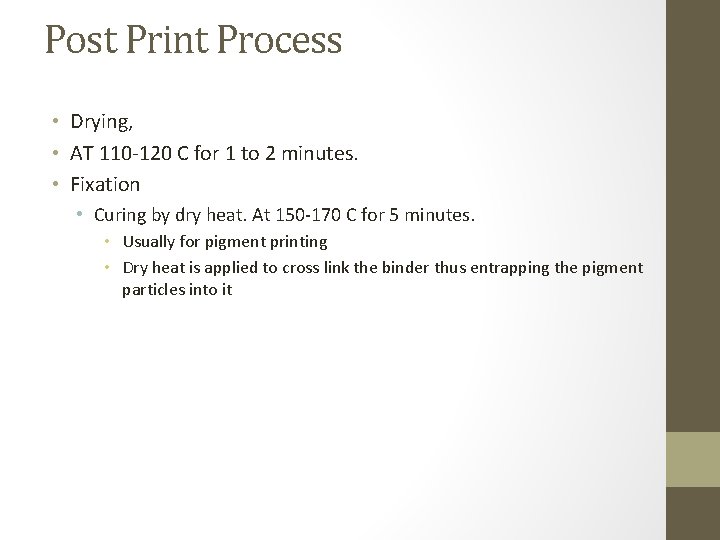
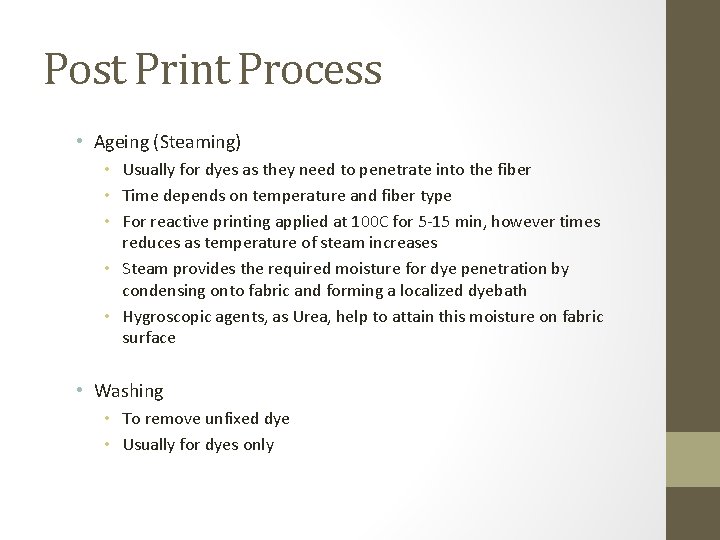
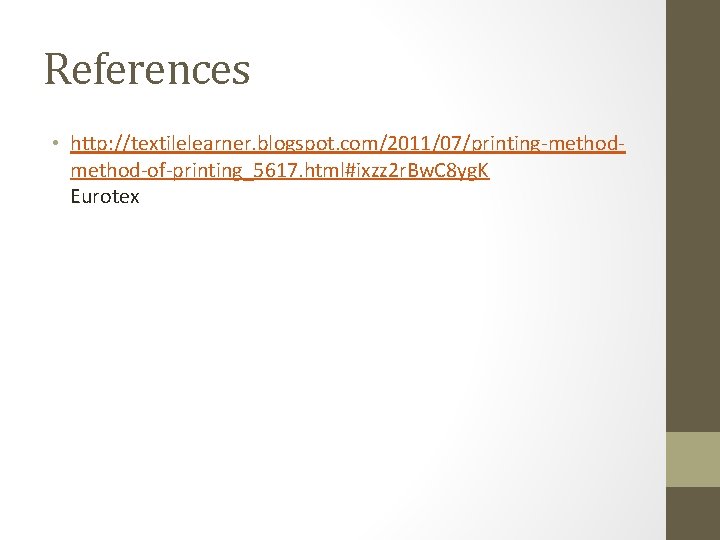
- Slides: 28
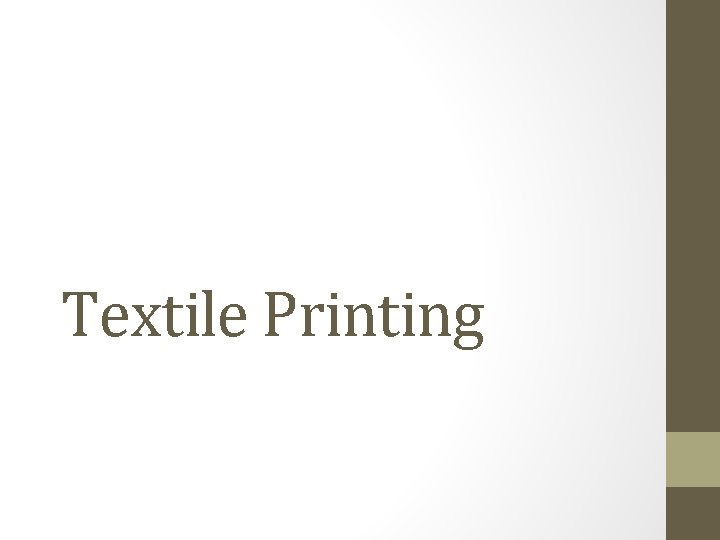
Textile Printing
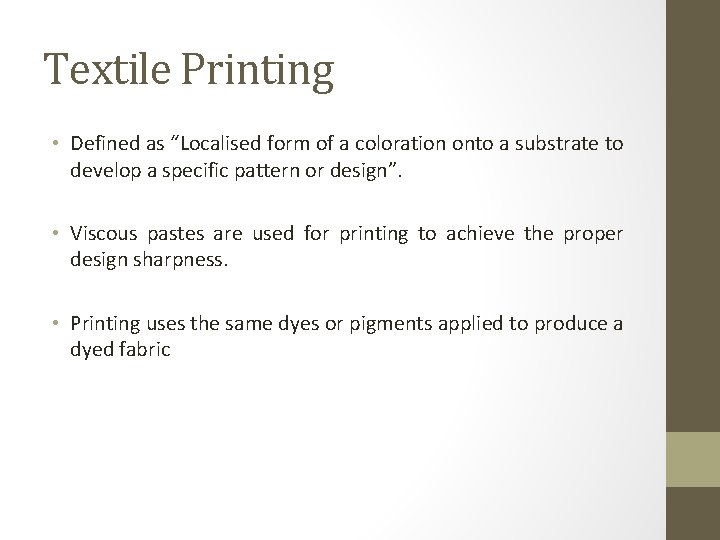
Textile Printing • Defined as “Localised form of a coloration onto a substrate to develop a specific pattern or design”. • Viscous pastes are used for printing to achieve the proper design sharpness. • Printing uses the same dyes or pigments applied to produce a dyed fabric
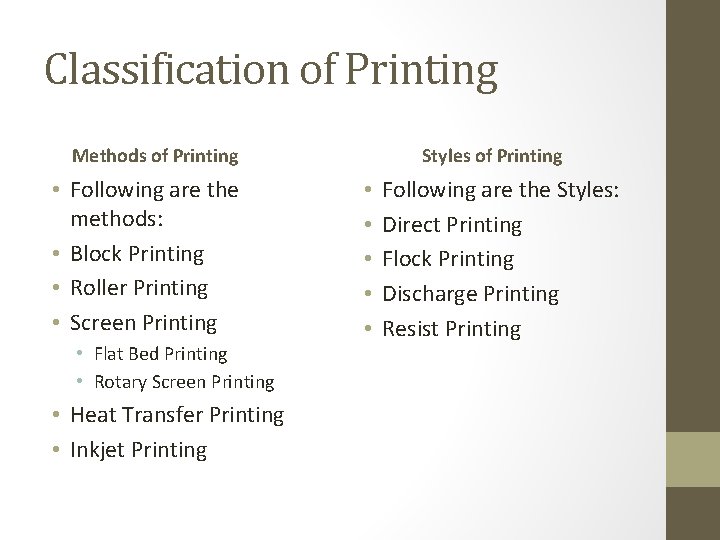
Classification of Printing Methods of Printing • Following are the methods: • Block Printing • Roller Printing • Screen Printing • Flat Bed Printing • Rotary Screen Printing • Heat Transfer Printing • Inkjet Printing Styles of Printing • • • Following are the Styles: Direct Printing Flock Printing Discharge Printing Resist Printing
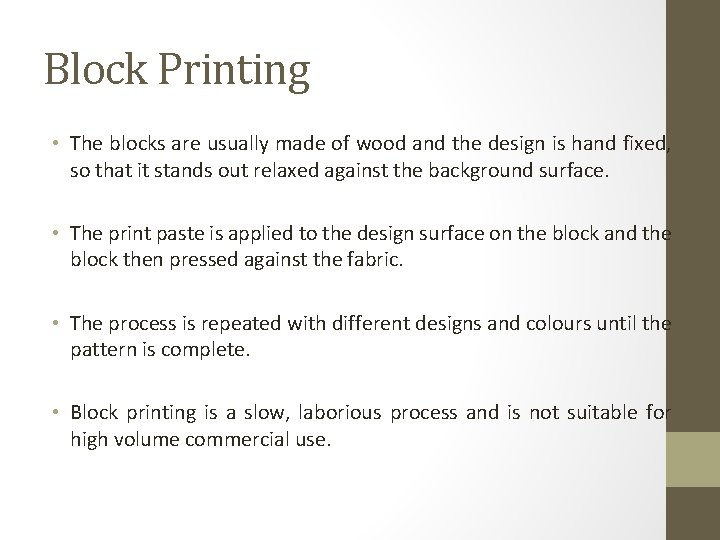
Block Printing • The blocks are usually made of wood and the design is hand fixed, so that it stands out relaxed against the background surface. • The print paste is applied to the design surface on the block and the block then pressed against the fabric. • The process is repeated with different designs and colours until the pattern is complete. • Block printing is a slow, laborious process and is not suitable for high volume commercial use.
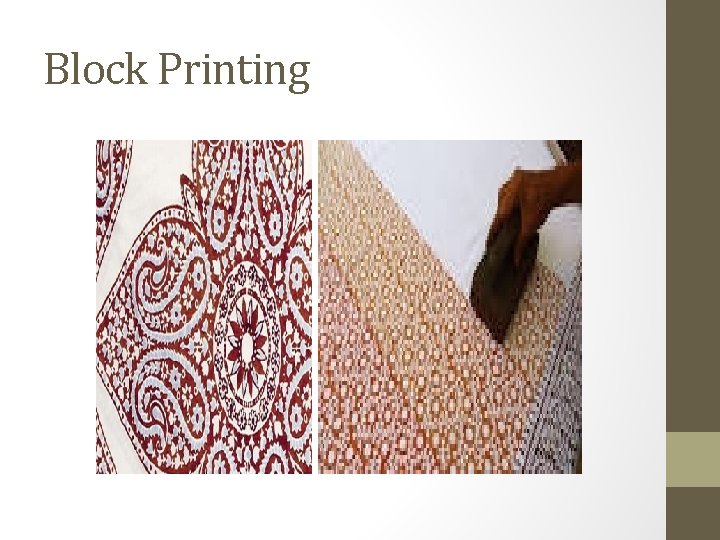
Block Printing
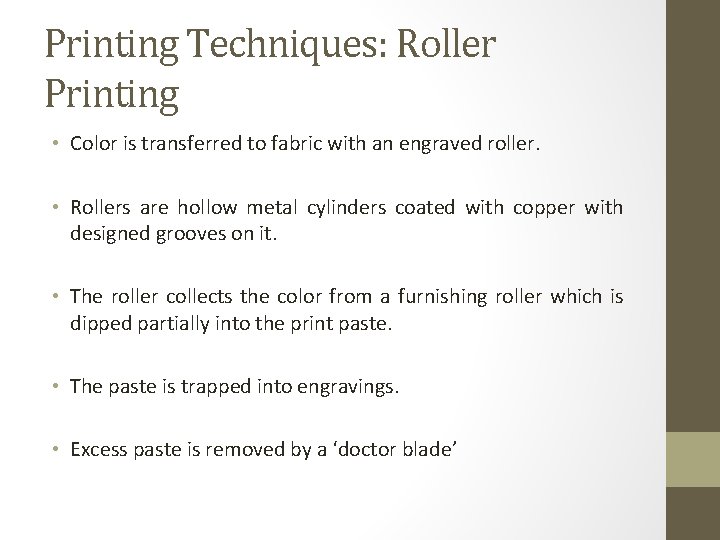
Printing Techniques: Roller Printing • Color is transferred to fabric with an engraved roller. • Rollers are hollow metal cylinders coated with copper with designed grooves on it. • The roller collects the color from a furnishing roller which is dipped partially into the print paste. • The paste is trapped into engravings. • Excess paste is removed by a ‘doctor blade’
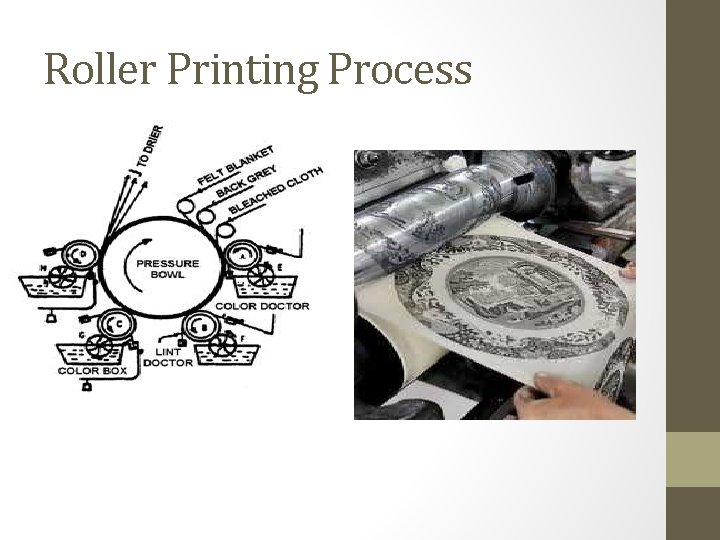
Roller Printing Process
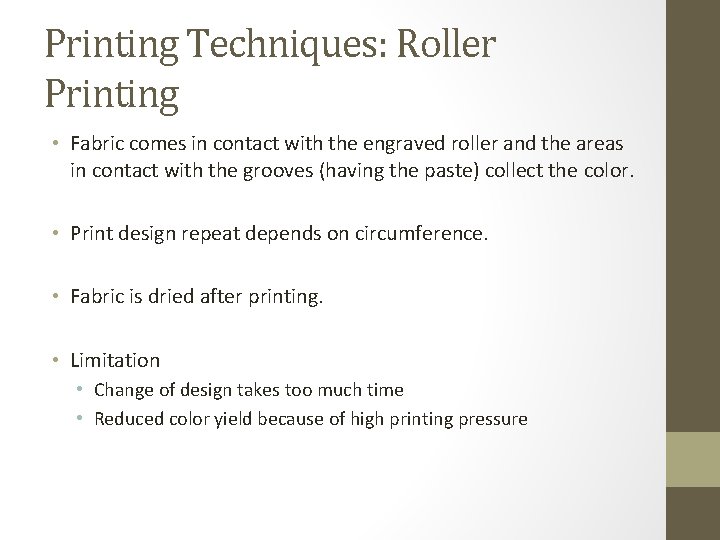
Printing Techniques: Roller Printing • Fabric comes in contact with the engraved roller and the areas in contact with the grooves (having the paste) collect the color. • Print design repeat depends on circumference. • Fabric is dried after printing. • Limitation • Change of design takes too much time • Reduced color yield because of high printing pressure
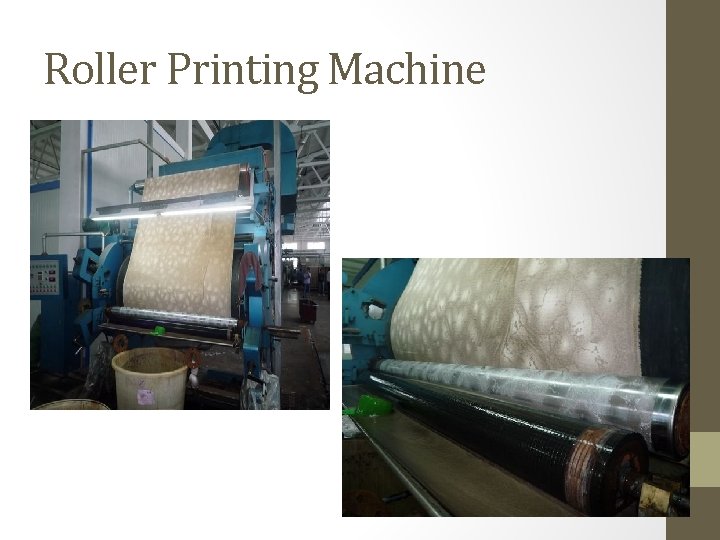
Roller Printing Machine
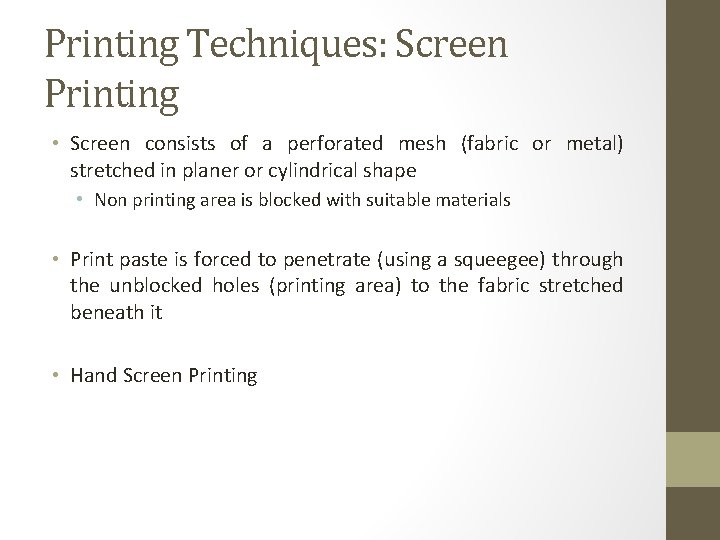
Printing Techniques: Screen Printing • Screen consists of a perforated mesh (fabric or metal) stretched in planer or cylindrical shape • Non printing area is blocked with suitable materials • Print paste is forced to penetrate (using a squeegee) through the unblocked holes (printing area) to the fabric stretched beneath it • Hand Screen Printing
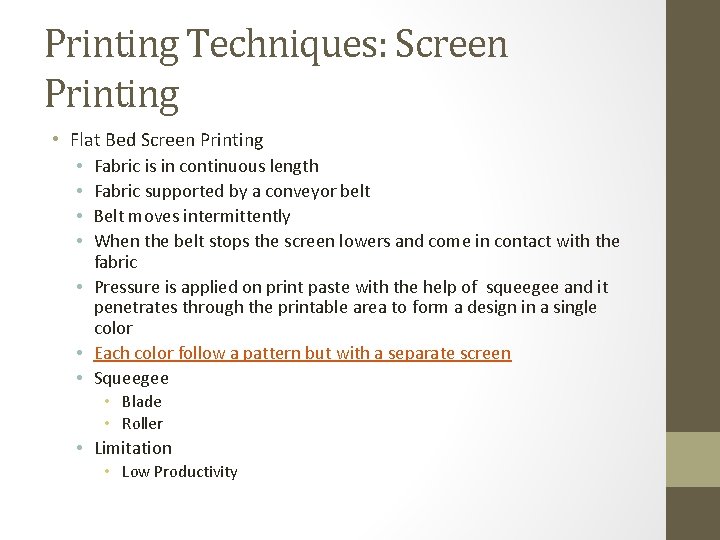
Printing Techniques: Screen Printing • Flat Bed Screen Printing • Fabric is in continuous length • Fabric supported by a conveyor belt • Belt moves intermittently • When the belt stops the screen lowers and come in contact with the fabric • Pressure is applied on print paste with the help of squeegee and it penetrates through the printable area to form a design in a single color • Each color follow a pattern but with a separate screen • Squeegee • Blade • Roller • Limitation • Low Productivity
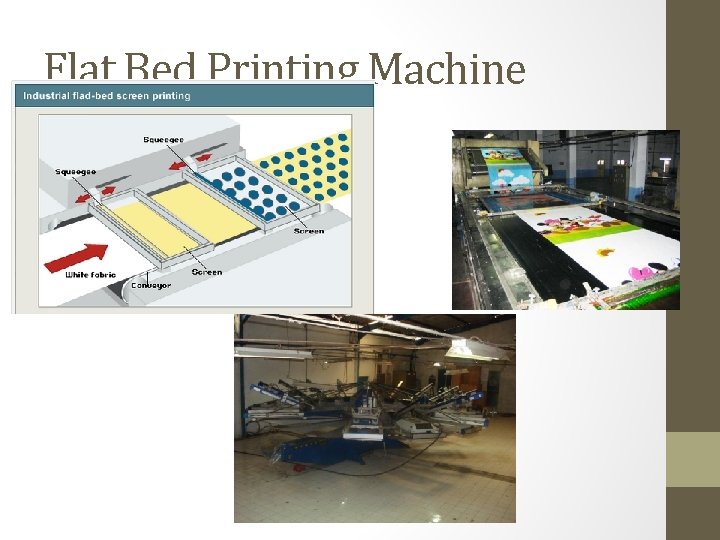
Flat Bed Printing Machine
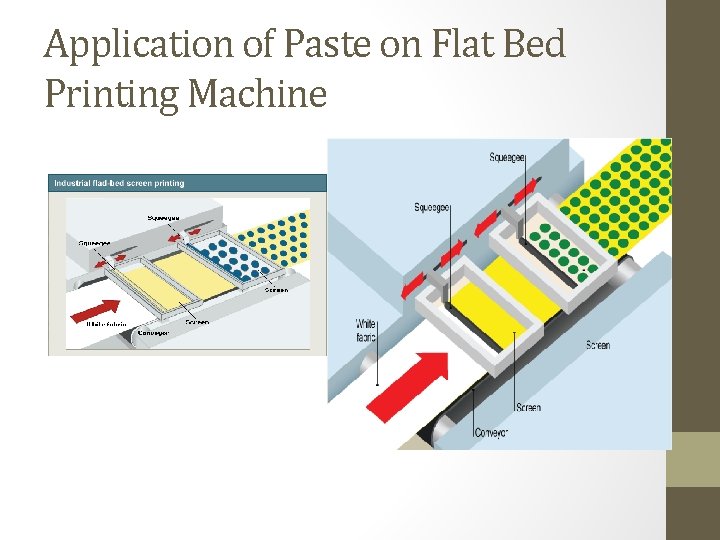
Application of Paste on Flat Bed Printing Machine
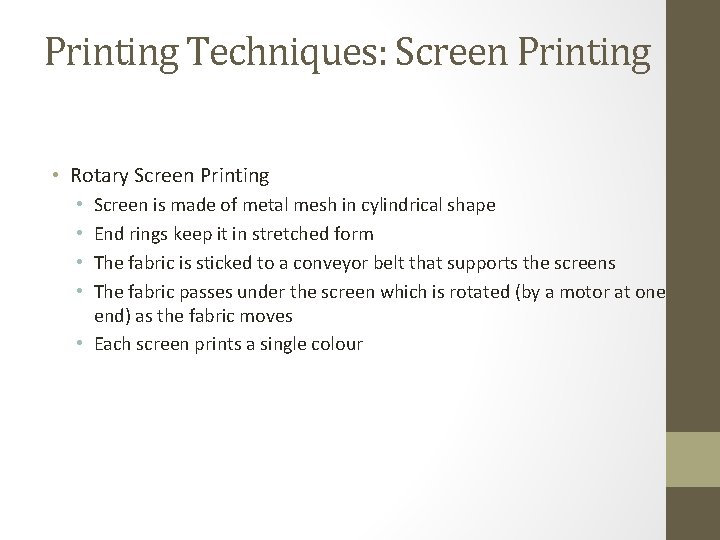
Printing Techniques: Screen Printing • Rotary Screen Printing Screen is made of metal mesh in cylindrical shape End rings keep it in stretched form The fabric is sticked to a conveyor belt that supports the screens The fabric passes under the screen which is rotated (by a motor at one end) as the fabric moves • Each screen prints a single colour • •
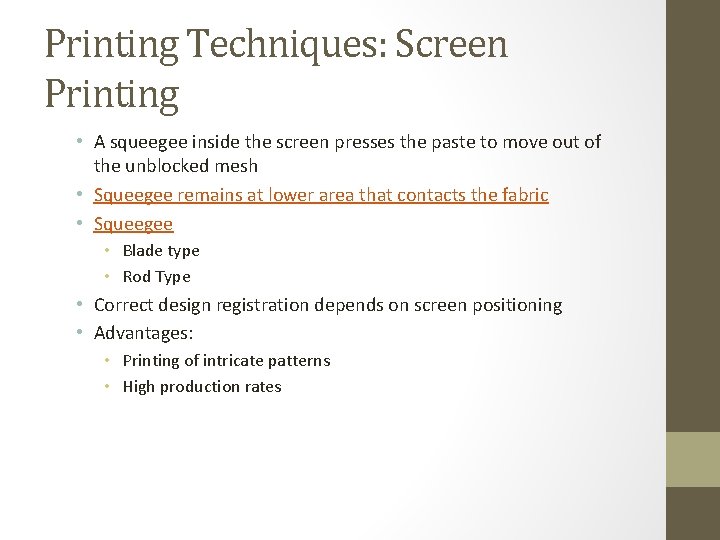
Printing Techniques: Screen Printing • A squeegee inside the screen presses the paste to move out of the unblocked mesh • Squeegee remains at lower area that contacts the fabric • Squeegee • Blade type • Rod Type • Correct design registration depends on screen positioning • Advantages: • Printing of intricate patterns • High production rates
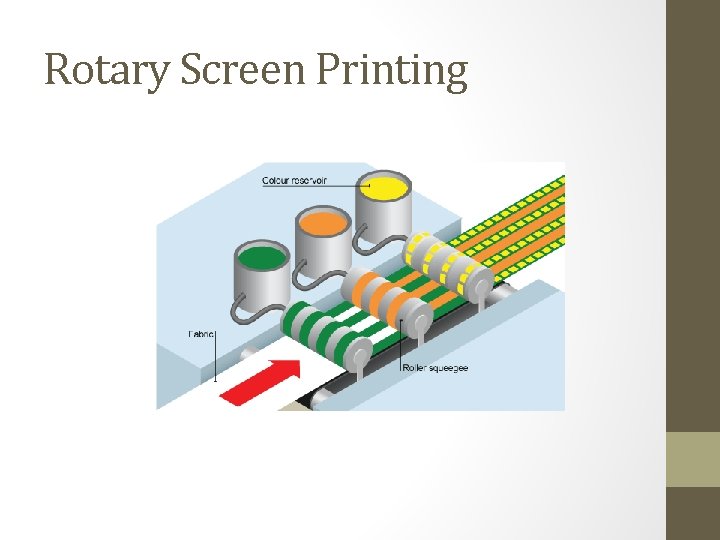
Rotary Screen Printing
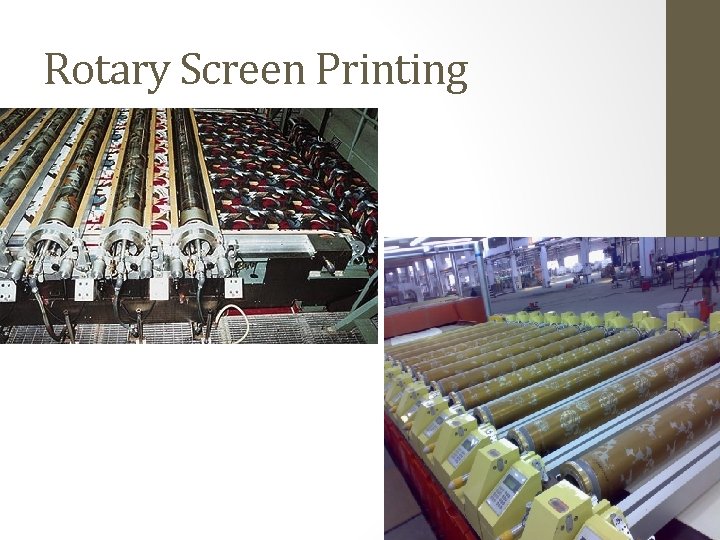
Rotary Screen Printing

Printing Techniques: Transfer Printing • Uses special “Transferable dyes” that sublimate on heating • When heat is applied to the material having the printed dyes it transfers on to the fabric which is in contact with it • The dyes are first printed on a cellulosic paper • The paper in along with fabric passes under the heating arrangement • Temperature of heating calendar or belt may be up to 180 C • No after treatment is usually required • Disadvantages • Vapor phase printing is limited to synthetics only so not used extensively on bulk scale
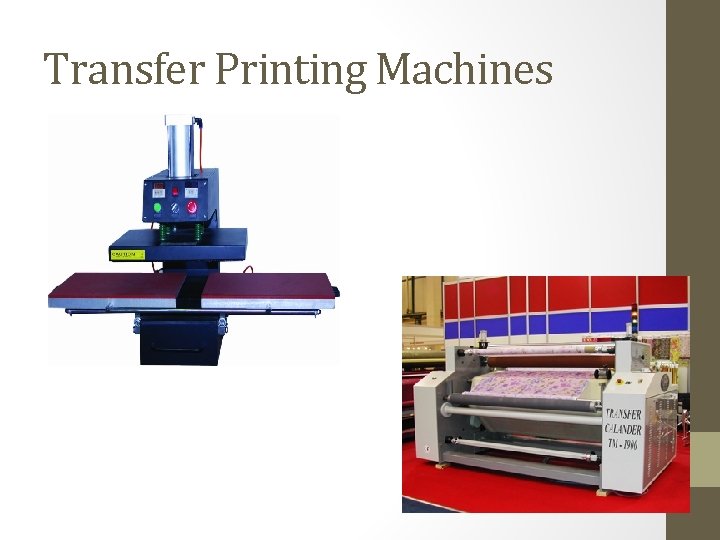
Transfer Printing Machines
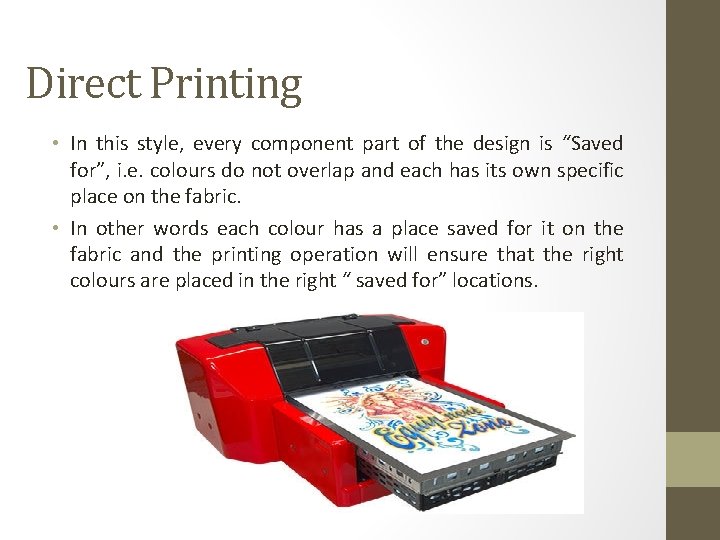
Direct Printing • In this style, every component part of the design is “Saved for”, i. e. colours do not overlap and each has its own specific place on the fabric. • In other words each colour has a place saved for it on the fabric and the printing operation will ensure that the right colours are placed in the right “ saved for” locations.
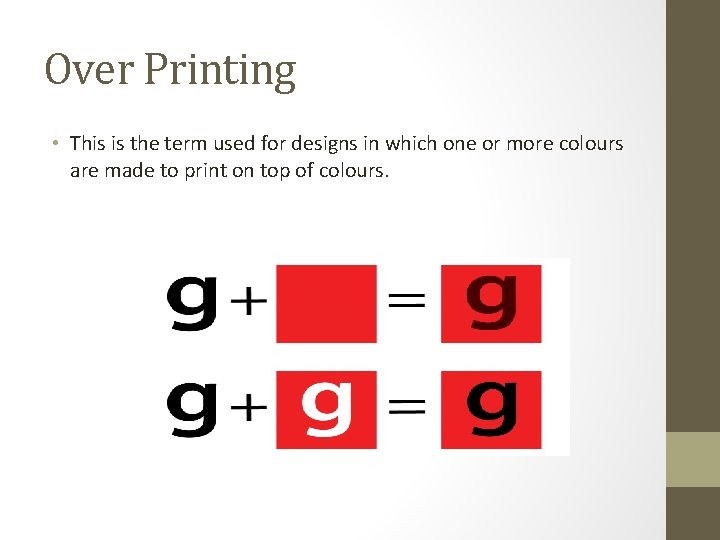
Over Printing • This is the term used for designs in which one or more colours are made to print on top of colours.
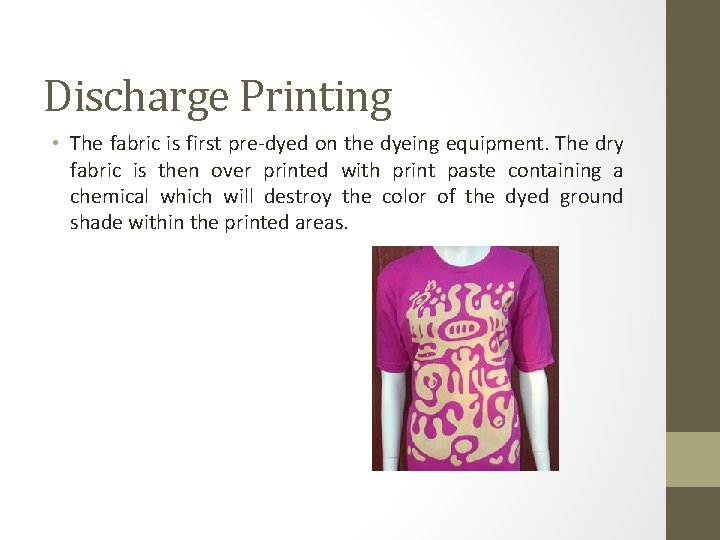
Discharge Printing • The fabric is first pre-dyed on the dyeing equipment. The dry fabric is then over printed with print paste containing a chemical which will destroy the color of the dyed ground shade within the printed areas.
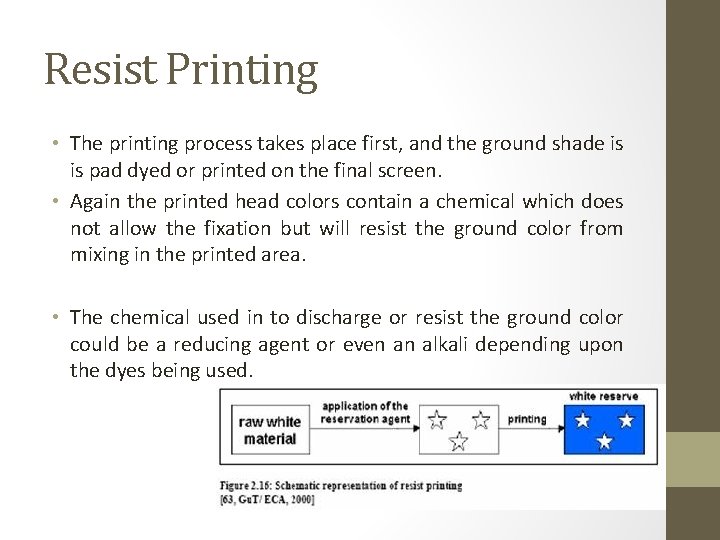
Resist Printing • The printing process takes place first, and the ground shade is is pad dyed or printed on the final screen. • Again the printed head colors contain a chemical which does not allow the fixation but will resist the ground color from mixing in the printed area. • The chemical used in to discharge or resist the ground color could be a reducing agent or even an alkali depending upon the dyes being used.
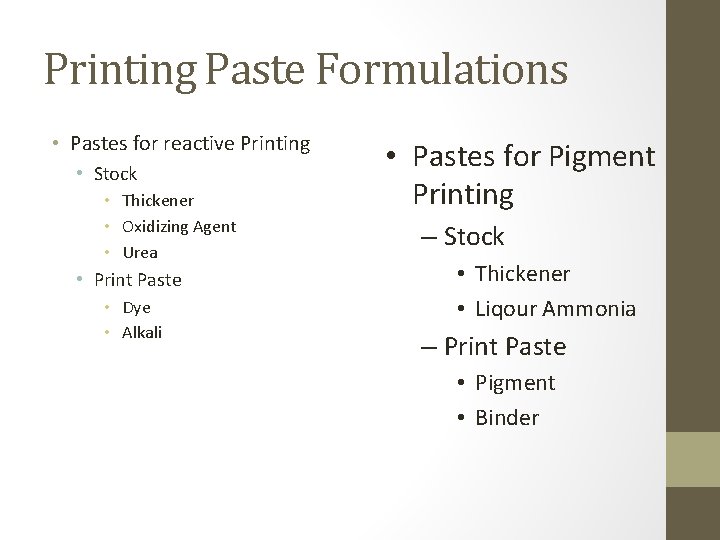
Printing Paste Formulations • Pastes for reactive Printing • Stock • Thickener • Oxidizing Agent • Urea • Print Paste • Dye • Alkali • Pastes for Pigment Printing – Stock • Thickener • Liqour Ammonia – Print Paste • Pigment • Binder
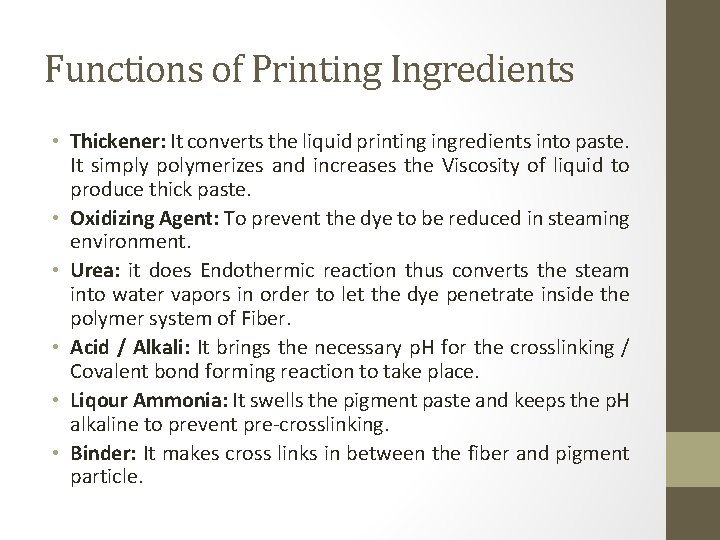
Functions of Printing Ingredients • Thickener: It converts the liquid printing ingredients into paste. It simply polymerizes and increases the Viscosity of liquid to produce thick paste. • Oxidizing Agent: To prevent the dye to be reduced in steaming environment. • Urea: it does Endothermic reaction thus converts the steam into water vapors in order to let the dye penetrate inside the polymer system of Fiber. • Acid / Alkali: It brings the necessary p. H for the crosslinking / Covalent bond forming reaction to take place. • Liqour Ammonia: It swells the pigment paste and keeps the p. H alkaline to prevent pre-crosslinking. • Binder: It makes cross links in between the fiber and pigment particle.
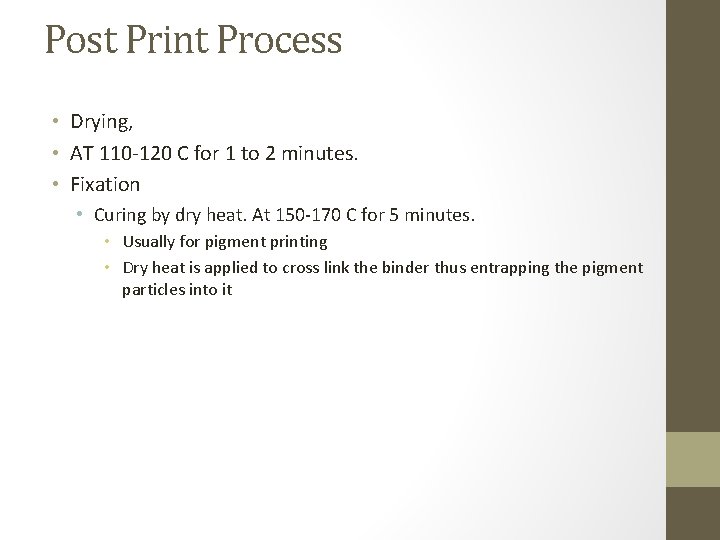
Post Print Process • Drying, • AT 110 -120 C for 1 to 2 minutes. • Fixation • Curing by dry heat. At 150 -170 C for 5 minutes. • Usually for pigment printing • Dry heat is applied to cross link the binder thus entrapping the pigment particles into it
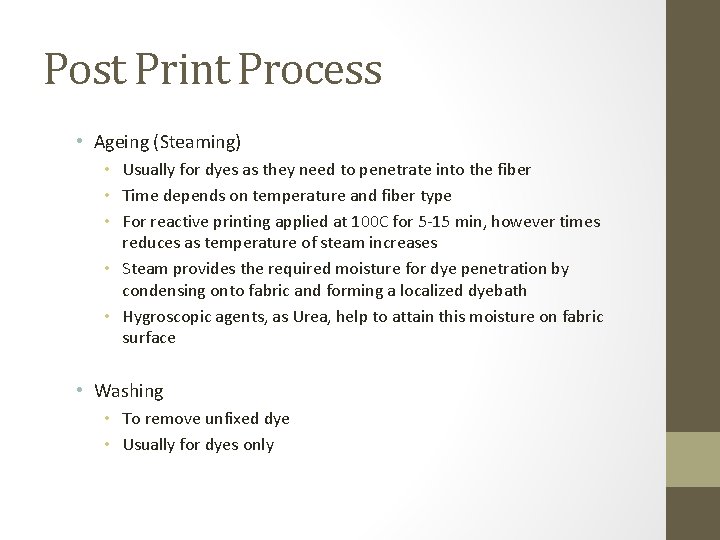
Post Print Process • Ageing (Steaming) • Usually for dyes as they need to penetrate into the fiber • Time depends on temperature and fiber type • For reactive printing applied at 100 C for 5 -15 min, however times reduces as temperature of steam increases • Steam provides the required moisture for dye penetration by condensing onto fabric and forming a localized dyebath • Hygroscopic agents, as Urea, help to attain this moisture on fabric surface • Washing • To remove unfixed dye • Usually for dyes only
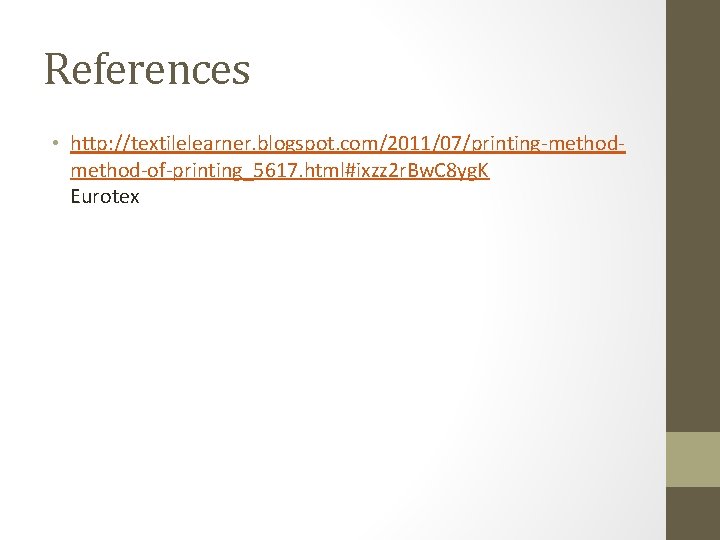
References • http: //textilelearner. blogspot. com/2011/07/printing-method-of-printing_5617. html#ixzz 2 r. Bw. C 8 yg. K Eurotex
Casting
What is the collection of well defined objects
Present continuous negative interrogative
Smart printing solutions ltd
Types of industrial printing
Brief history of printing
Broadnax printing
Contact printing
Bidmas examples
Cheque book printer
Uwl library hours
Cern printer
Sdn oph
Hangzhou definition ap world history
Proximity printing
Ionography printing process
Smart printing
Enterprise mobile printing
Uu solis id
Follow me printing kyocera
Pad printing basics
Dinastiyang tsina
Proximity printing
Maintop windows 10
How has the printing press impacted society
Reverse offset printing
Dgs printing
Chapter 30 money growth and inflation
Gravure cylinder cell types