Single Stage Press Diaphragms Diaphragm Material A Diaphragm
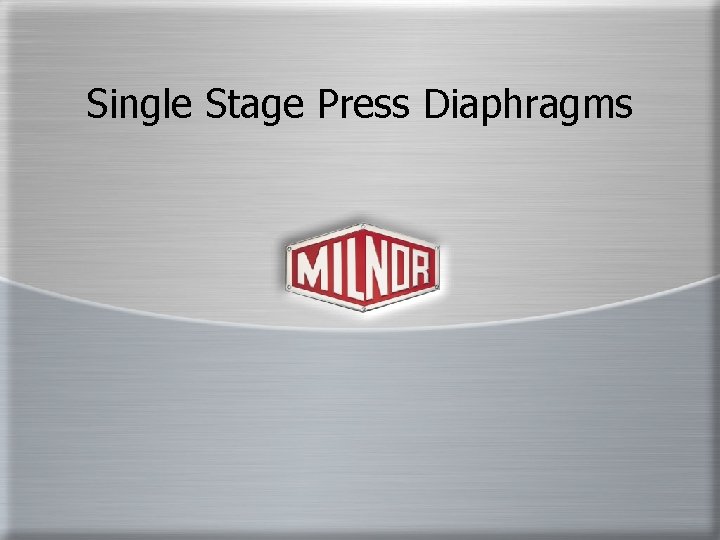
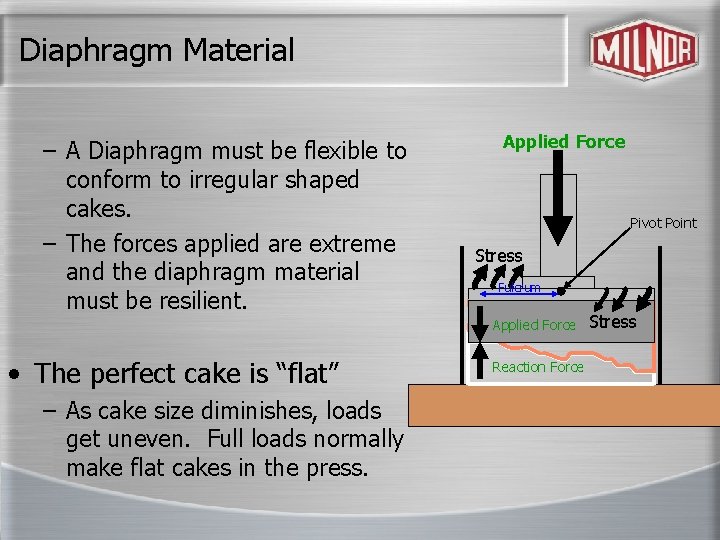
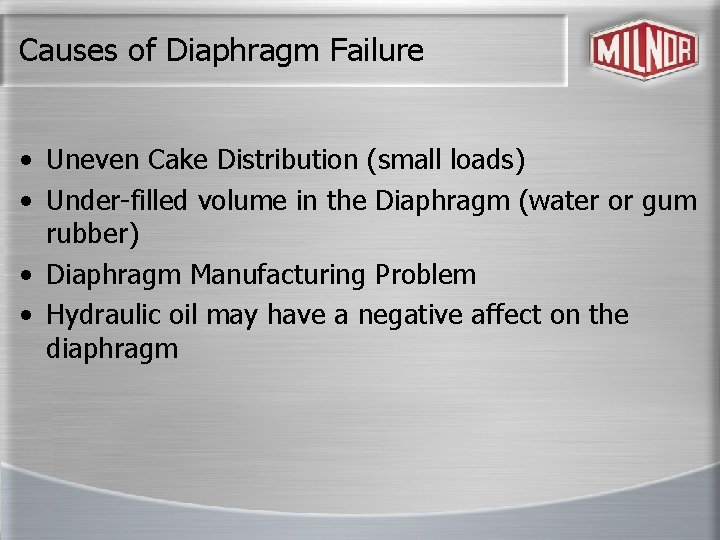
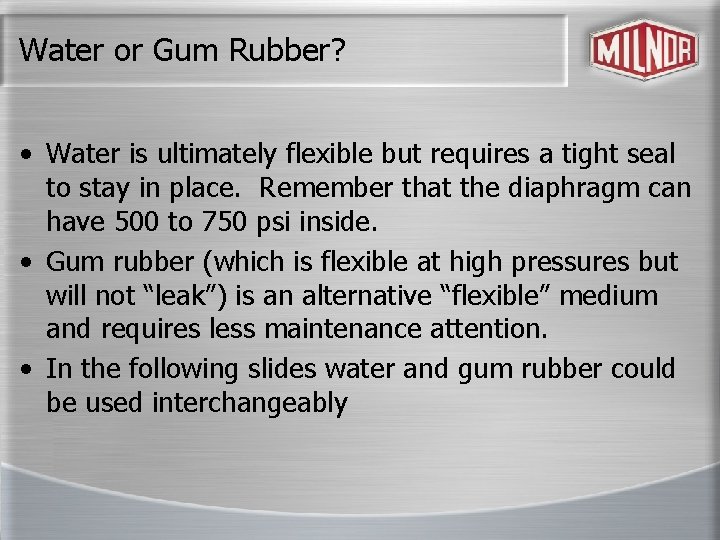

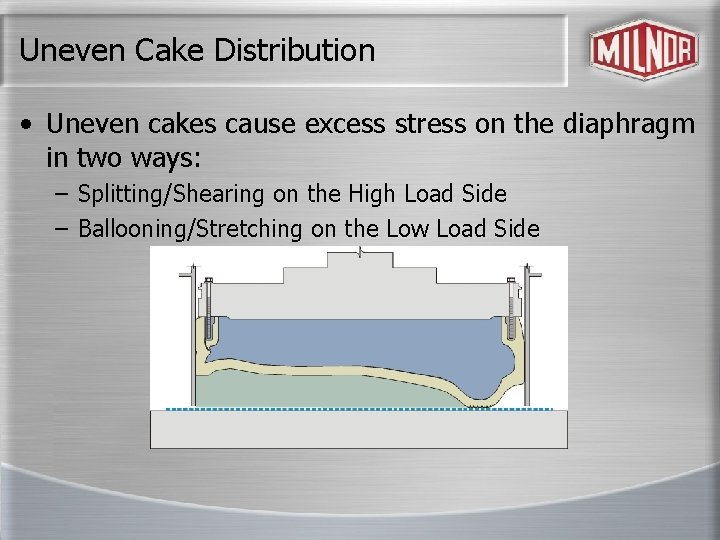
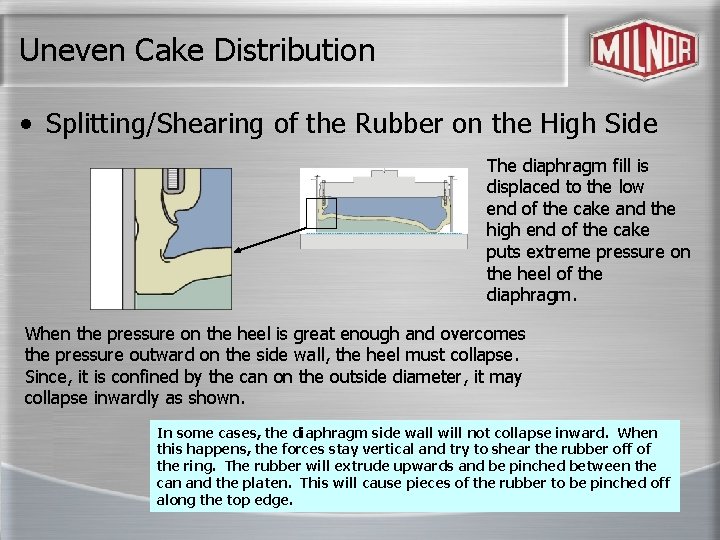
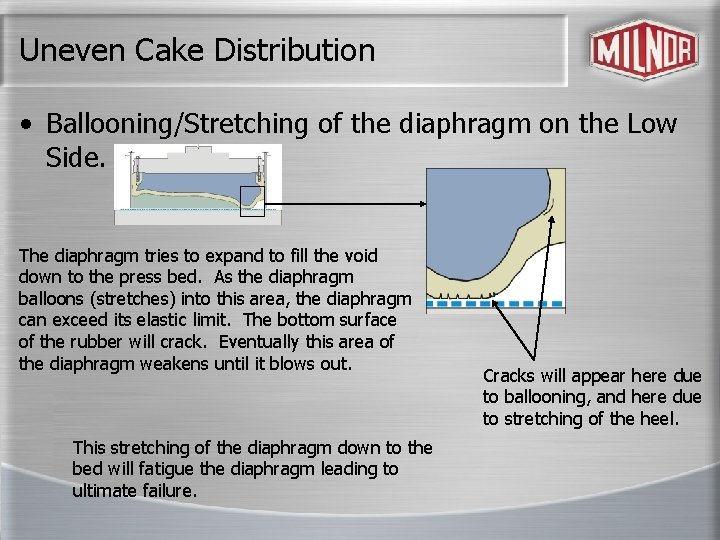
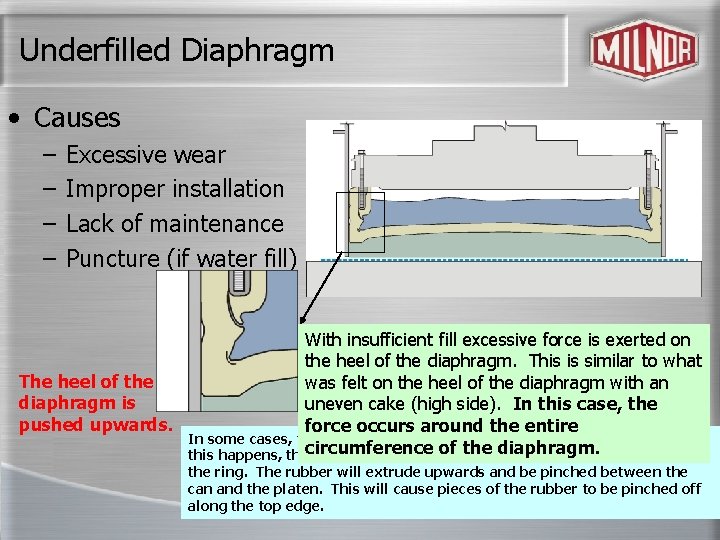
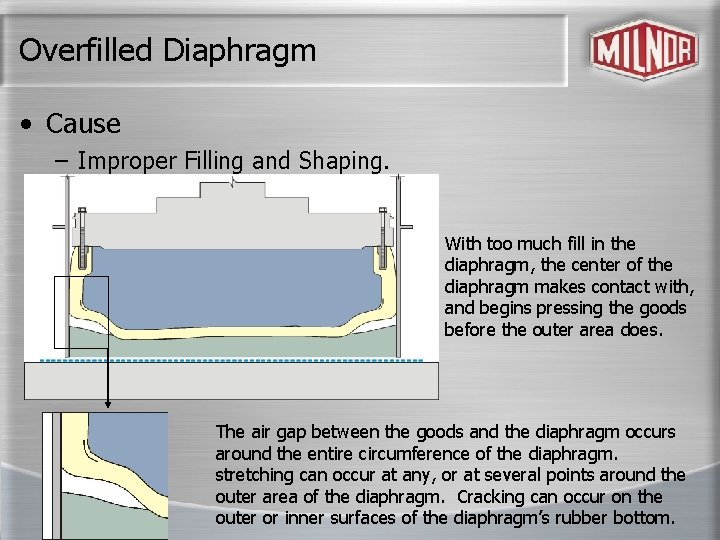
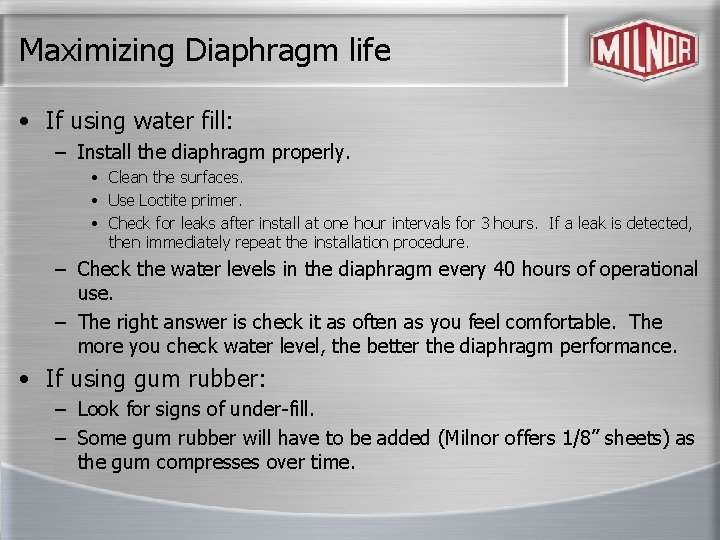
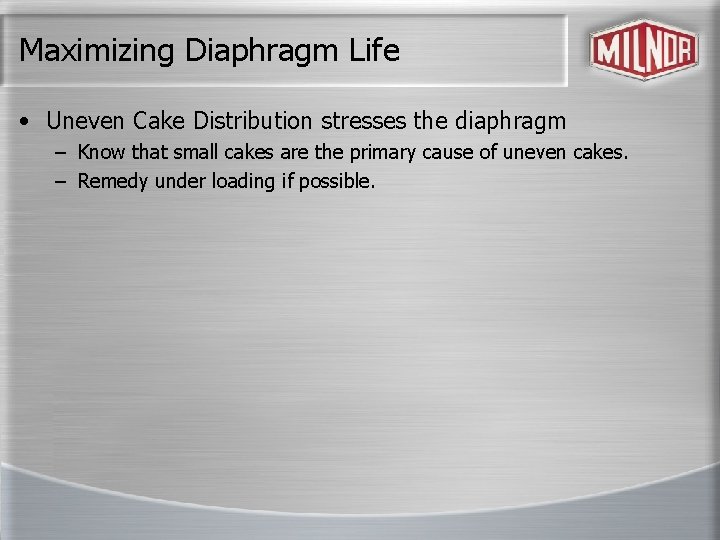
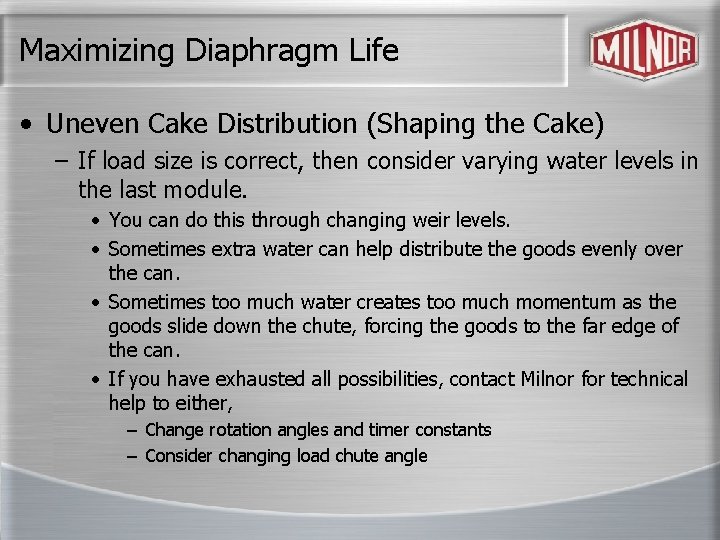
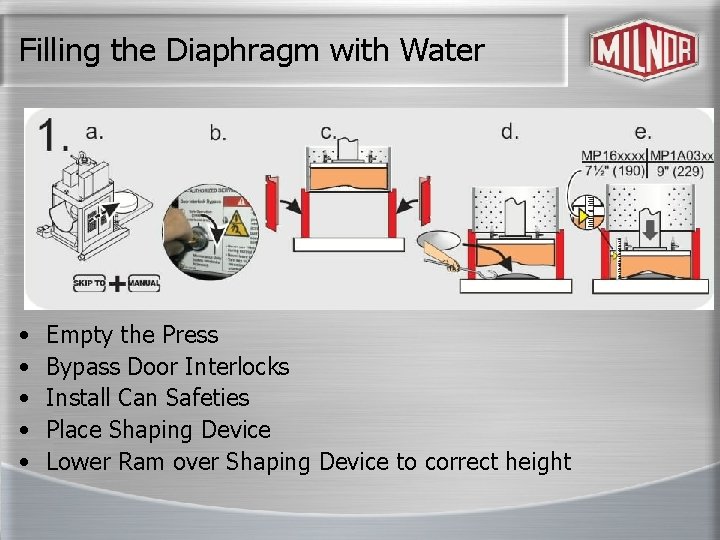
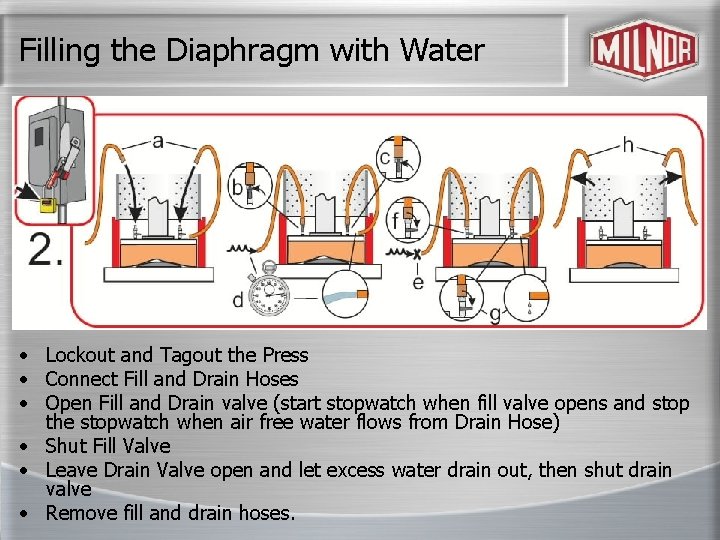
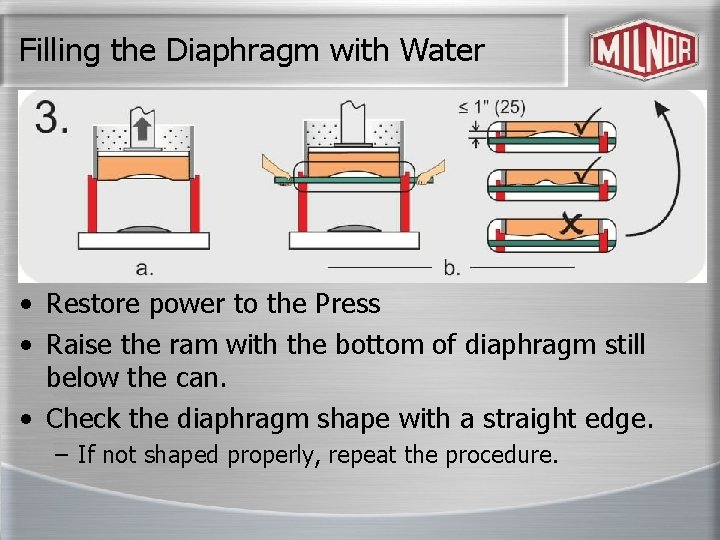
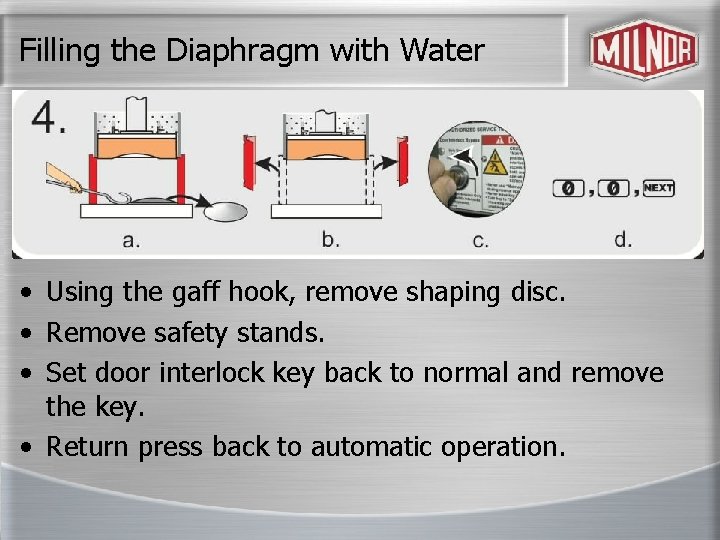
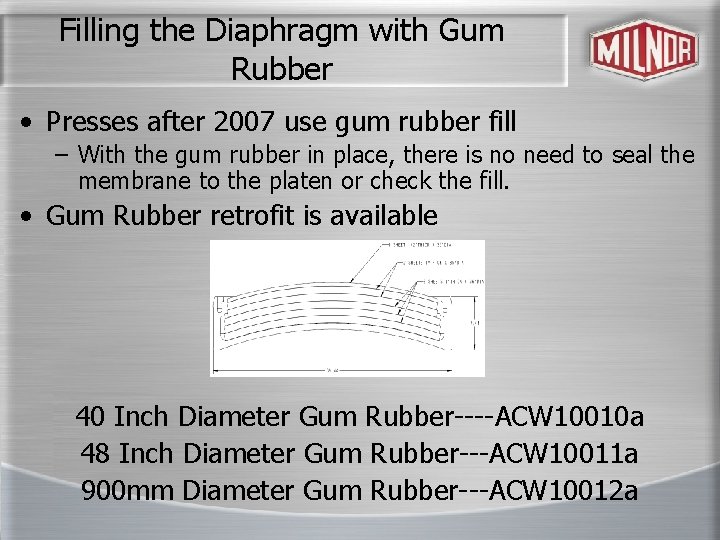
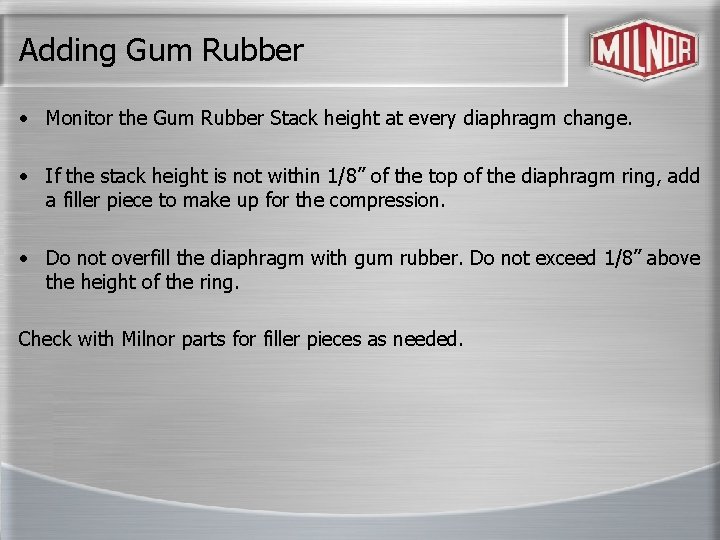
- Slides: 19
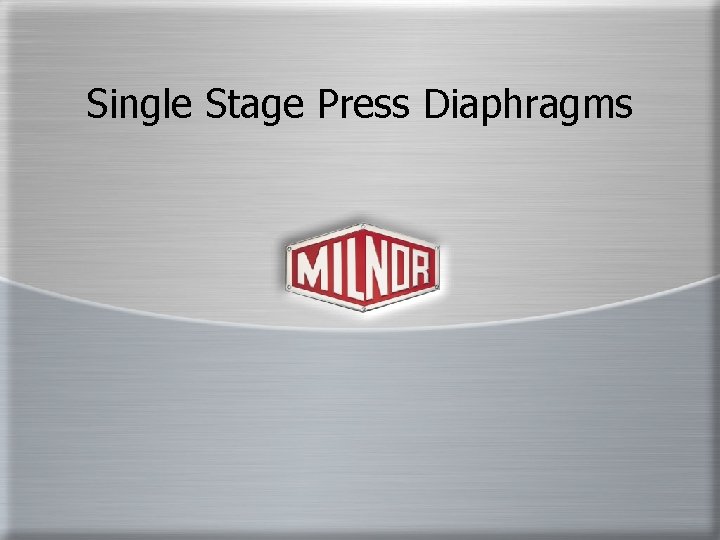
Single Stage Press Diaphragms
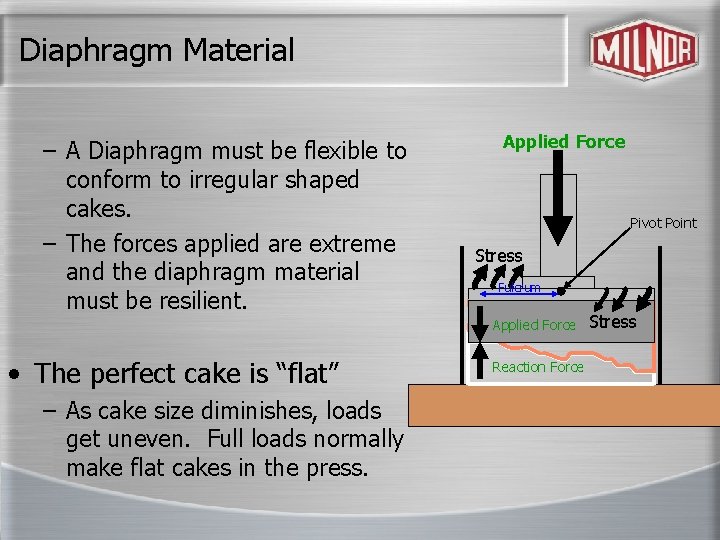
Diaphragm Material – A Diaphragm must be flexible to conform to irregular shaped cakes. – The forces applied are extreme and the diaphragm material must be resilient. Applied Force Pivot Point Stress Fulcrum Applied Force • The perfect cake is “flat” – As cake size diminishes, loads get uneven. Full loads normally make flat cakes in the press. Reaction Force Stress
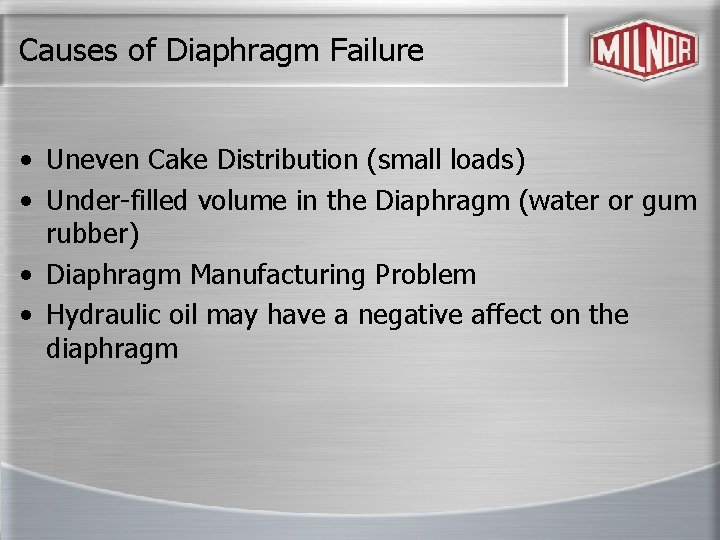
Causes of Diaphragm Failure • Uneven Cake Distribution (small loads) • Under-filled volume in the Diaphragm (water or gum rubber) • Diaphragm Manufacturing Problem • Hydraulic oil may have a negative affect on the diaphragm
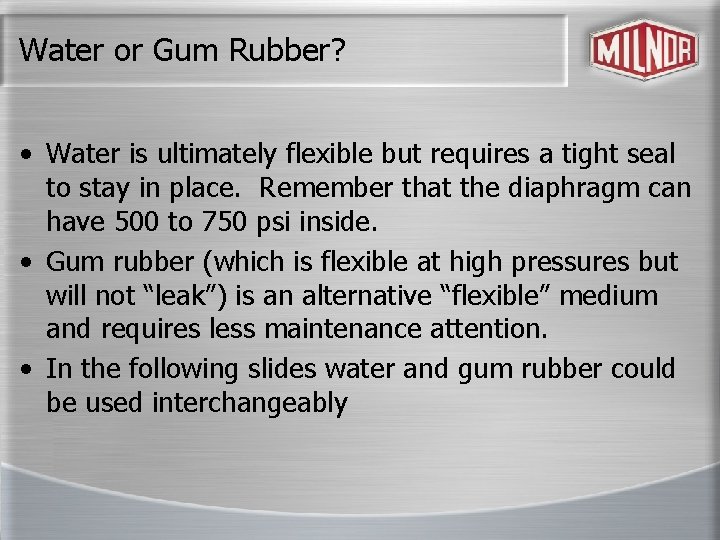
Water or Gum Rubber? • Water is ultimately flexible but requires a tight seal to stay in place. Remember that the diaphragm can have 500 to 750 psi inside. • Gum rubber (which is flexible at high pressures but will not “leak”) is an alternative “flexible” medium and requires less maintenance attention. • In the following slides water and gum rubber could be used interchangeably

Uneven Cake Distribution 1. Platen, Hub, and Cylinder 2. Water or Gum Rubber 3. Diaphragm 4. Goods 5. Press Bed 6. Diaphragm Ring On small cakes, typically the high point will be on the side of the can opposite the load. chute. The low point will be directly under the load chute.
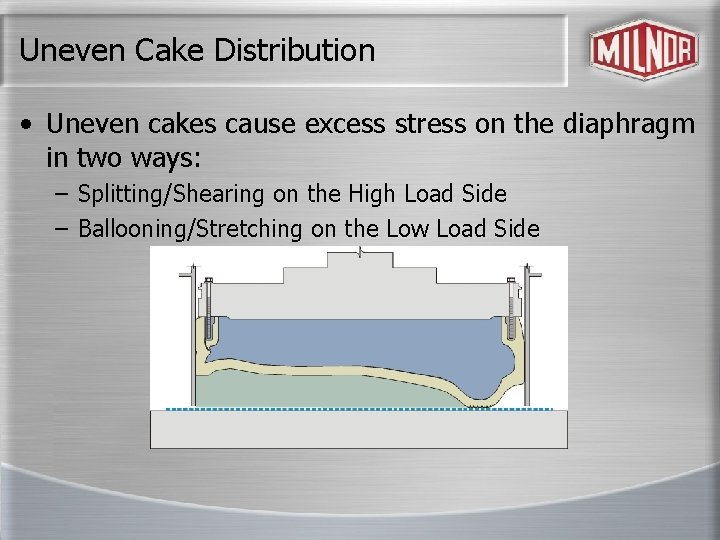
Uneven Cake Distribution • Uneven cakes cause excess stress on the diaphragm in two ways: – Splitting/Shearing on the High Load Side – Ballooning/Stretching on the Low Load Side
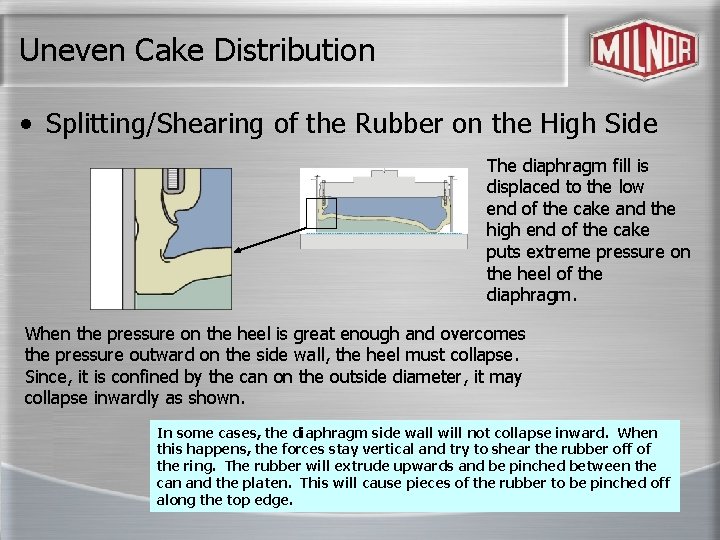
Uneven Cake Distribution • Splitting/Shearing of the Rubber on the High Side The diaphragm fill is displaced to the low end of the cake and the high end of the cake puts extreme pressure on the heel of the diaphragm. When the pressure on the heel is great enough and overcomes the pressure outward on the side wall, the heel must collapse. Since, it is confined by the can on the outside diameter, it may collapse inwardly as shown. In some cases, the diaphragm side wall will not collapse inward. When this happens, the forces stay vertical and try to shear the rubber off of the ring. The rubber will extrude upwards and be pinched between the can and the platen. This will cause pieces of the rubber to be pinched off along the top edge.
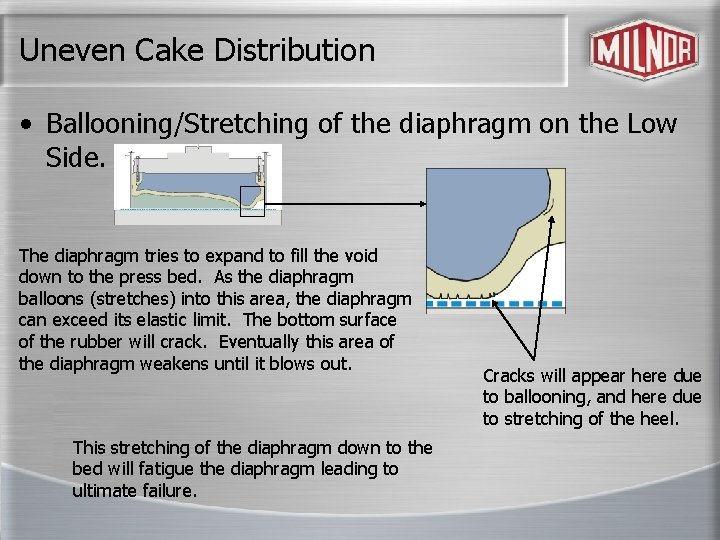
Uneven Cake Distribution • Ballooning/Stretching of the diaphragm on the Low Side. The diaphragm tries to expand to fill the void down to the press bed. As the diaphragm balloons (stretches) into this area, the diaphragm can exceed its elastic limit. The bottom surface of the rubber will crack. Eventually this area of the diaphragm weakens until it blows out. This stretching of the diaphragm down to the bed will fatigue the diaphragm leading to ultimate failure. Cracks will appear here due to ballooning, and here due to stretching of the heel.
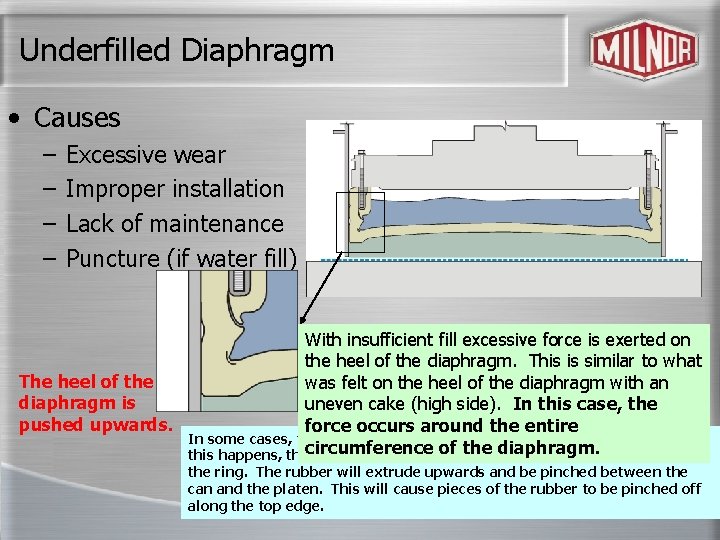
Underfilled Diaphragm • Causes – – Excessive wear Improper installation Lack of maintenance Puncture (if water fill) With insufficient fill excessive force is exerted on the heel of the diaphragm. This is similar to what The heel of the was felt on the heel of the diaphragm with an diaphragm is uneven cake (high side). In this case, the pushed upwards. force occurs around the entire In some cases, the diaphragm side wall will not collapse inward. When ofand the this happens, thecircumference forces stay vertical trydiaphragm. to shear the rubber off of the ring. The rubber will extrude upwards and be pinched between the can and the platen. This will cause pieces of the rubber to be pinched off along the top edge.
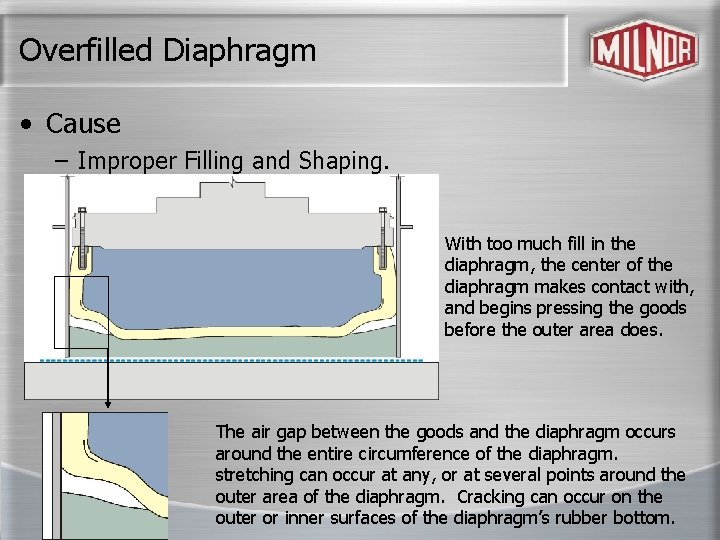
Overfilled Diaphragm • Cause – Improper Filling and Shaping. With too much fill in the diaphragm, the center of the diaphragm makes contact with, and begins pressing the goods before the outer area does. The air gap between the goods and the diaphragm occurs around the entire circumference of the diaphragm. stretching can occur at any, or at several points around the outer area of the diaphragm. Cracking can occur on the outer or inner surfaces of the diaphragm’s rubber bottom.
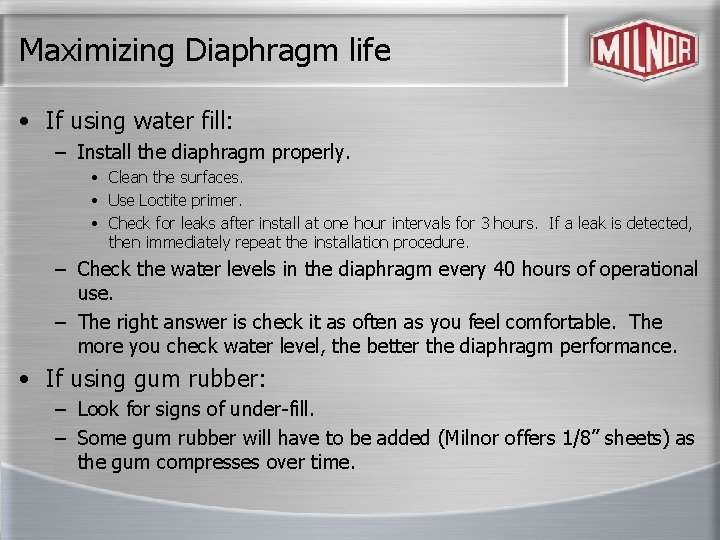
Maximizing Diaphragm life • If using water fill: – Install the diaphragm properly. • Clean the surfaces. • Use Loctite primer. • Check for leaks after install at one hour intervals for 3 hours. If a leak is detected, then immediately repeat the installation procedure. – Check the water levels in the diaphragm every 40 hours of operational use. – The right answer is check it as often as you feel comfortable. The more you check water level, the better the diaphragm performance. • If using gum rubber: – Look for signs of under-fill. – Some gum rubber will have to be added (Milnor offers 1/8” sheets) as the gum compresses over time.
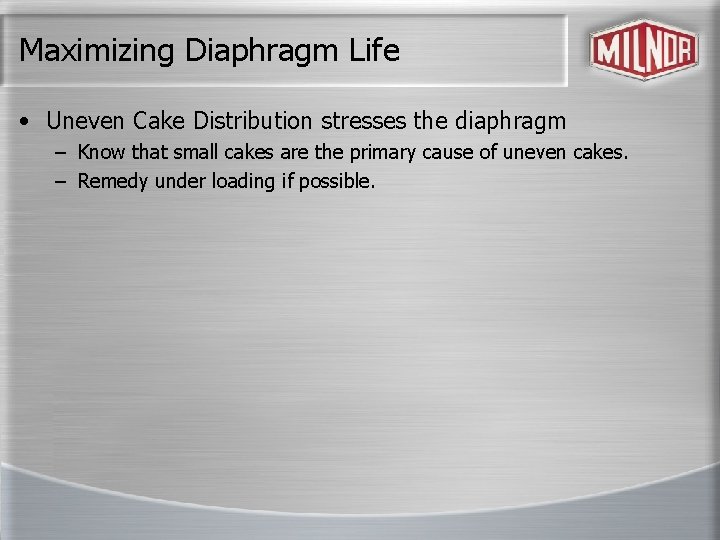
Maximizing Diaphragm Life • Uneven Cake Distribution stresses the diaphragm – Know that small cakes are the primary cause of uneven cakes. – Remedy under loading if possible.
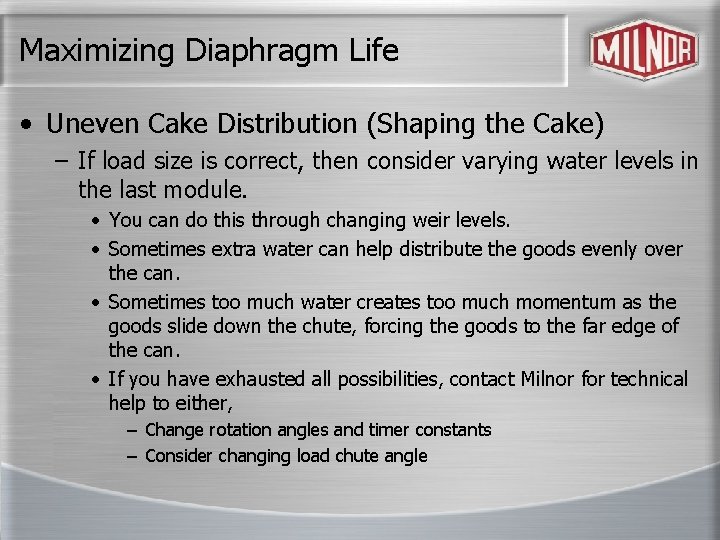
Maximizing Diaphragm Life • Uneven Cake Distribution (Shaping the Cake) – If load size is correct, then consider varying water levels in the last module. • You can do this through changing weir levels. • Sometimes extra water can help distribute the goods evenly over the can. • Sometimes too much water creates too much momentum as the goods slide down the chute, forcing the goods to the far edge of the can. • If you have exhausted all possibilities, contact Milnor for technical help to either, – Change rotation angles and timer constants – Consider changing load chute angle
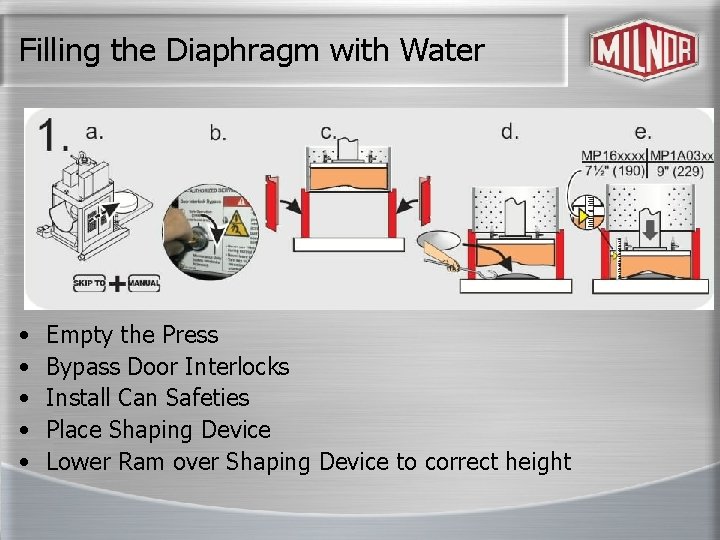
Filling the Diaphragm with Water • • • Empty the Press Bypass Door Interlocks Install Can Safeties Place Shaping Device Lower Ram over Shaping Device to correct height
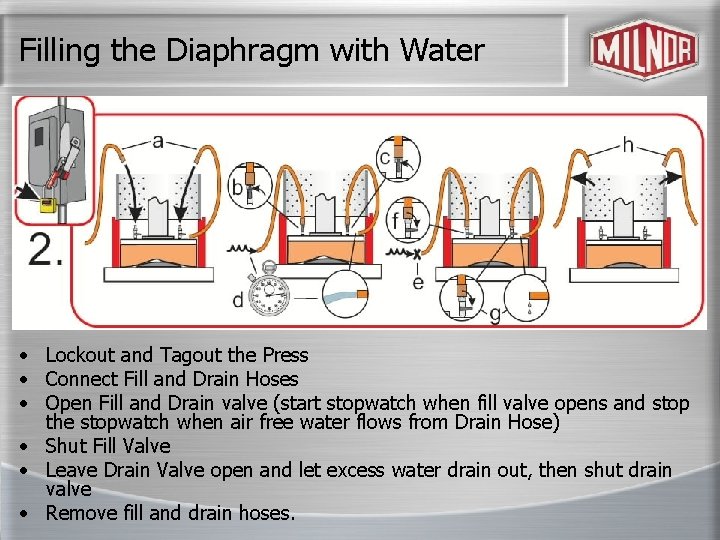
Filling the Diaphragm with Water • Lockout and Tagout the Press • Connect Fill and Drain Hoses • Open Fill and Drain valve (start stopwatch when fill valve opens and stop the stopwatch when air free water flows from Drain Hose) • Shut Fill Valve • Leave Drain Valve open and let excess water drain out, then shut drain valve • Remove fill and drain hoses.
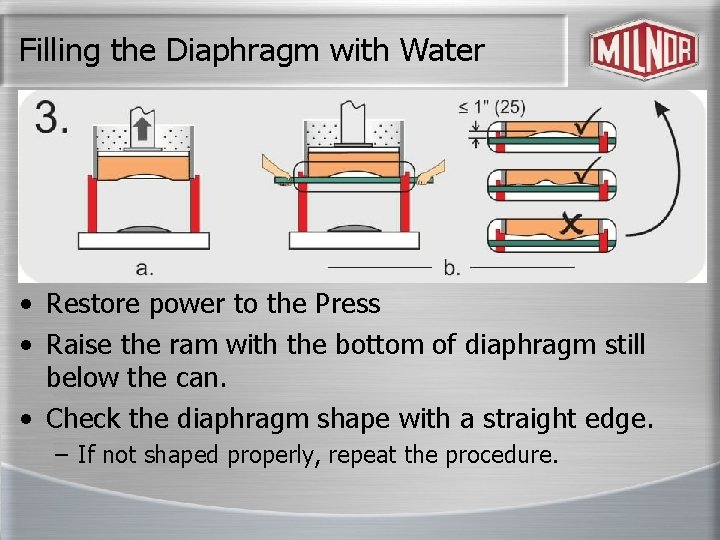
Filling the Diaphragm with Water • Restore power to the Press • Raise the ram with the bottom of diaphragm still below the can. • Check the diaphragm shape with a straight edge. – If not shaped properly, repeat the procedure.
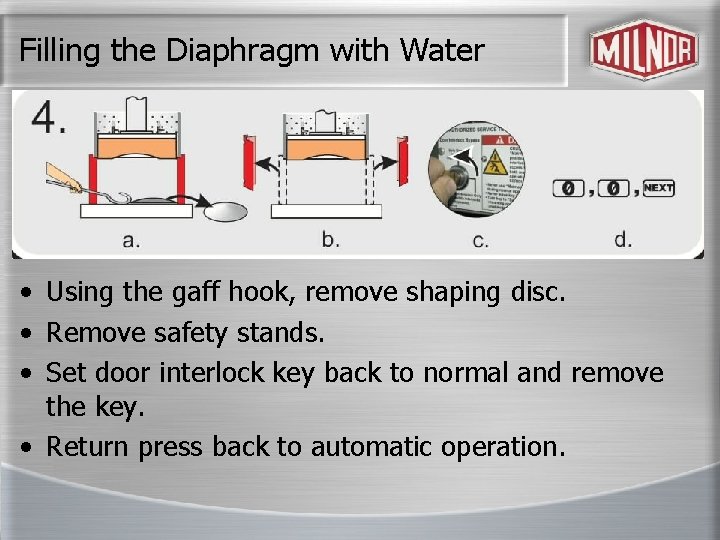
Filling the Diaphragm with Water • Using the gaff hook, remove shaping disc. • Remove safety stands. • Set door interlock key back to normal and remove the key. • Return press back to automatic operation.
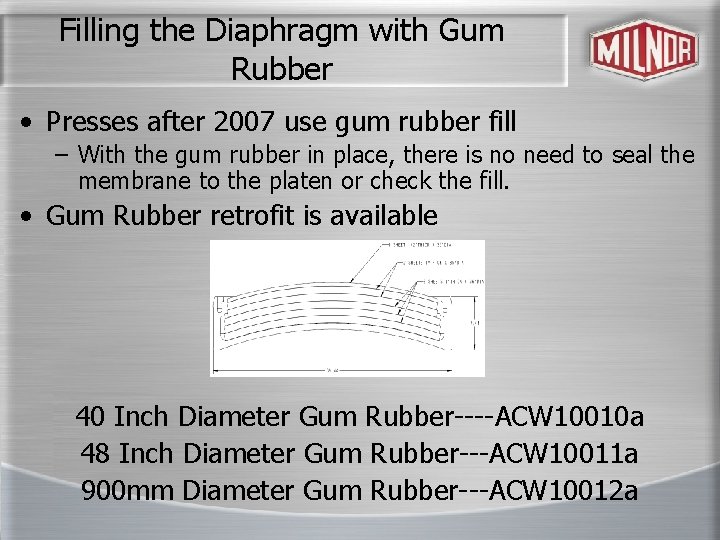
Filling the Diaphragm with Gum Rubber • Presses after 2007 use gum rubber fill – With the gum rubber in place, there is no need to seal the membrane to the platen or check the fill. • Gum Rubber retrofit is available 40 Inch Diameter Gum Rubber----ACW 10010 a 48 Inch Diameter Gum Rubber---ACW 10011 a 900 mm Diameter Gum Rubber---ACW 10012 a
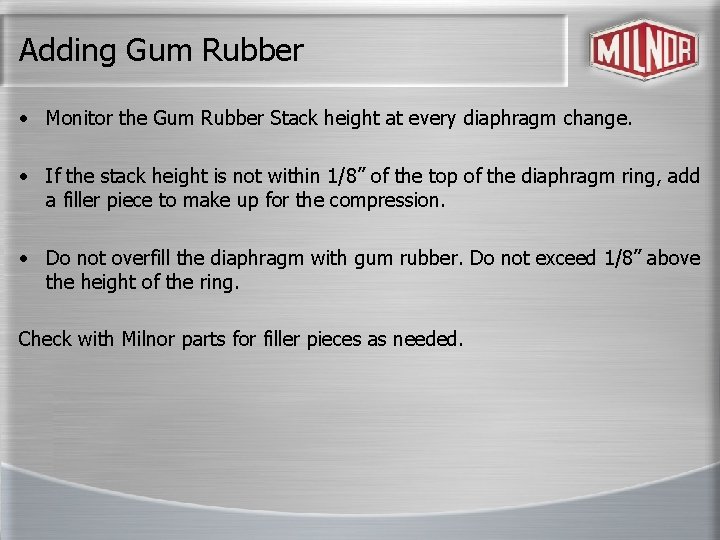
Adding Gum Rubber • Monitor the Gum Rubber Stack height at every diaphragm change. • If the stack height is not within 1/8” of the top of the diaphragm ring, add a filler piece to make up for the compression. • Do not overfill the diaphragm with gum rubber. Do not exceed 1/8” above the height of the ring. Check with Milnor parts for filler pieces as needed.
Relaxation vocabulary
What is a two stage tender
Geometric symbols and their meanings
Standard costing formula
Cultural relativism
Refers to the knowledge language values customs
Example of material culture
Useful and harmful materials pictures
Sisd example
Dataxin
Single channel single phase example
What is residual income
Single stage transistor amplifier
Single stage business case
Single equilibrium stage
Stage 1 denial stage 2
Position control definition
Stage left vs right
Downstage and upstage
Stage right and left