Screening tests of an oneshot forming process of
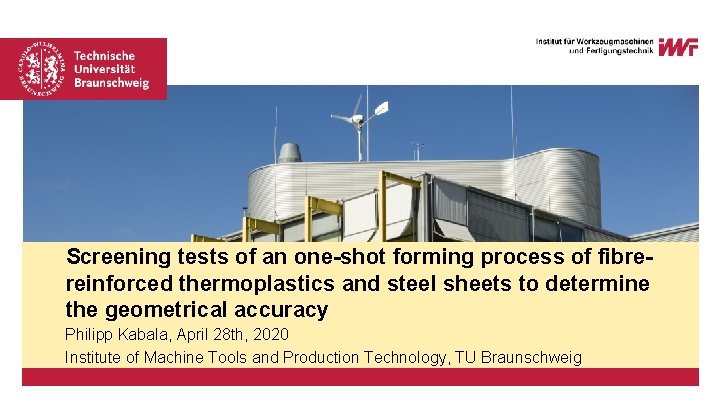
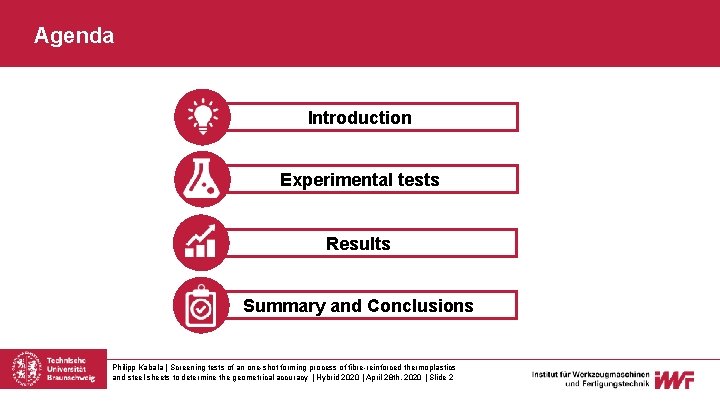
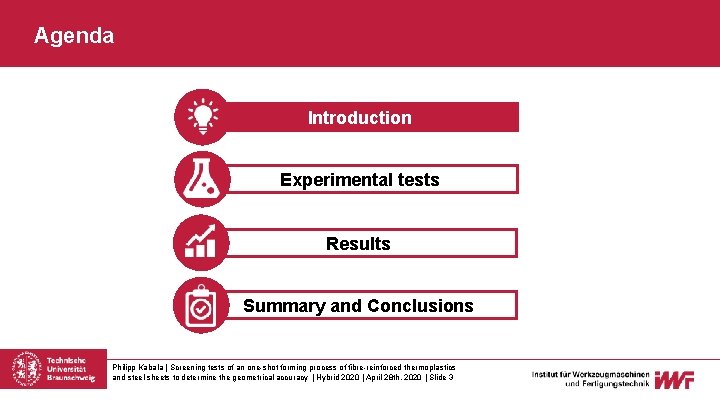
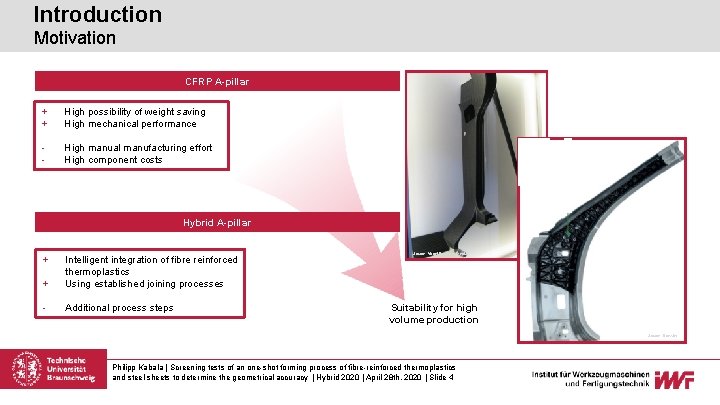
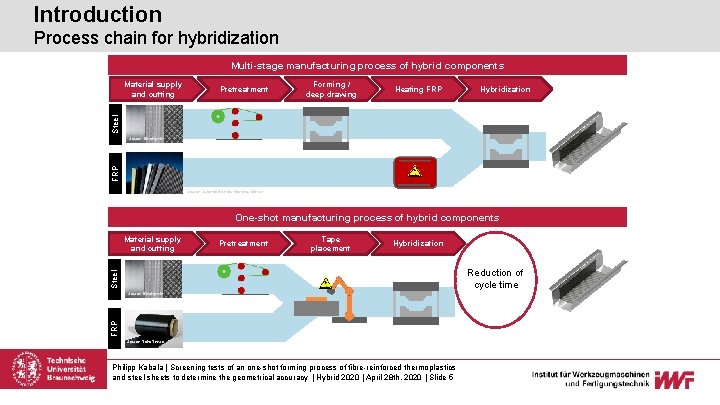
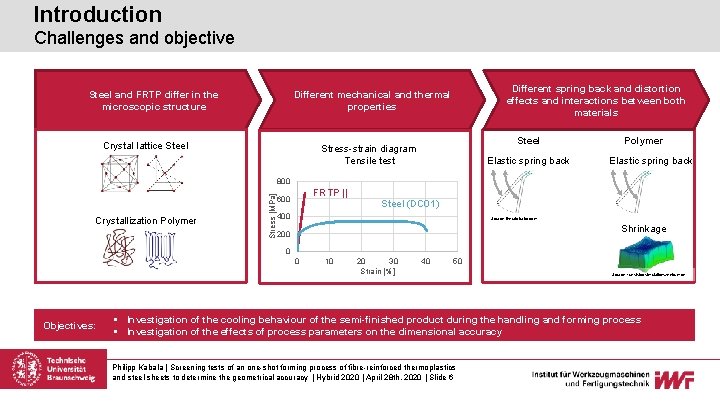
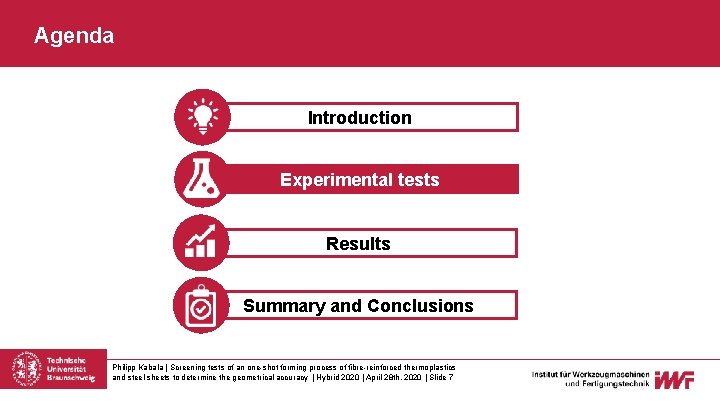
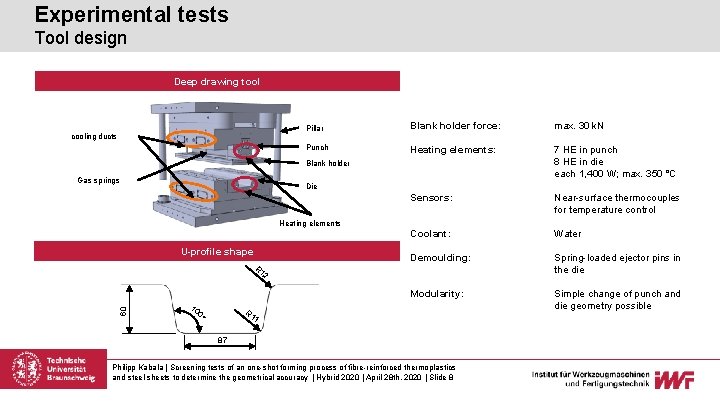
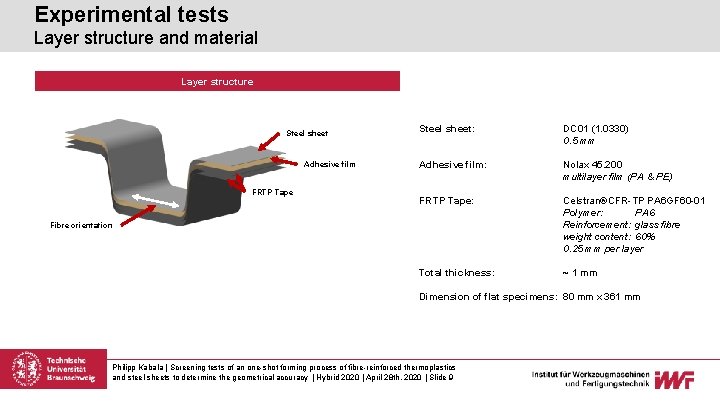
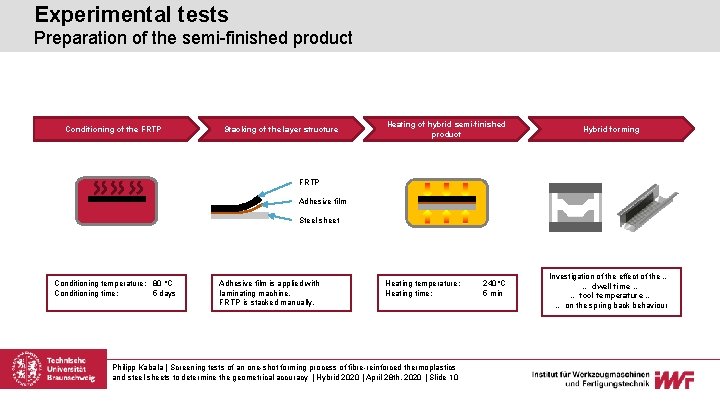

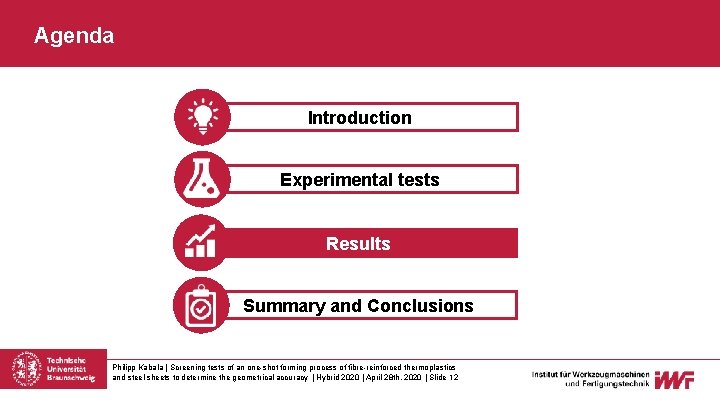
![Results Specimen temperature during forming Temperature curves of the specimen during forming Temperature [°C] Results Specimen temperature during forming Temperature curves of the specimen during forming Temperature [°C]](https://slidetodoc.com/presentation_image_h/108eaa47b39a4066c73ce0f0f9c191e4/image-13.jpg)
![Results Influence of the dwell time Spring back [°C] Investigation of a dwell time Results Influence of the dwell time Spring back [°C] Investigation of a dwell time](https://slidetodoc.com/presentation_image_h/108eaa47b39a4066c73ce0f0f9c191e4/image-14.jpg)
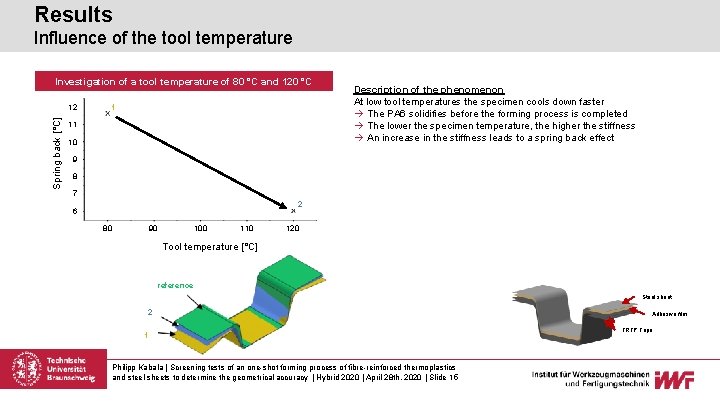
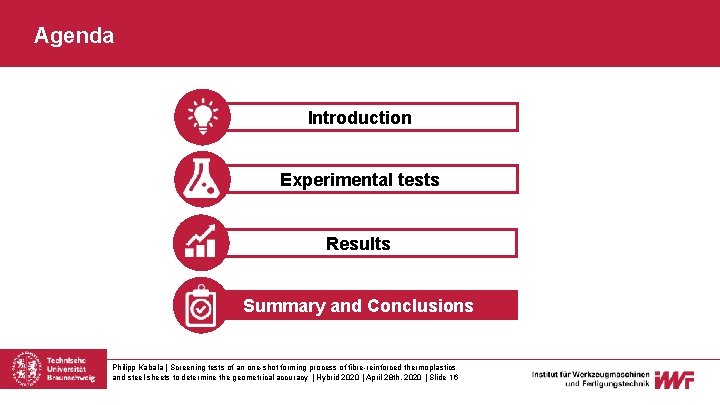
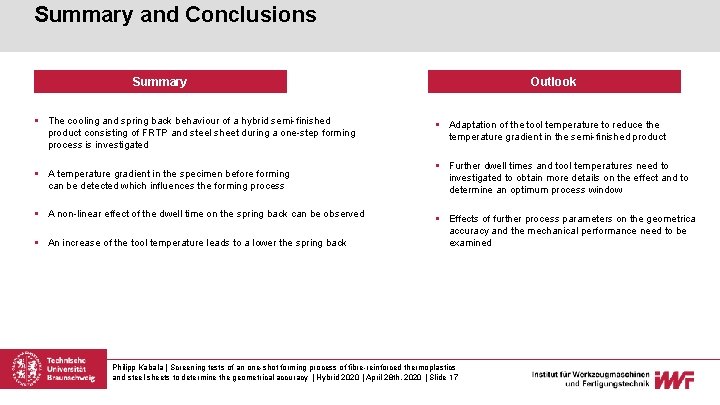
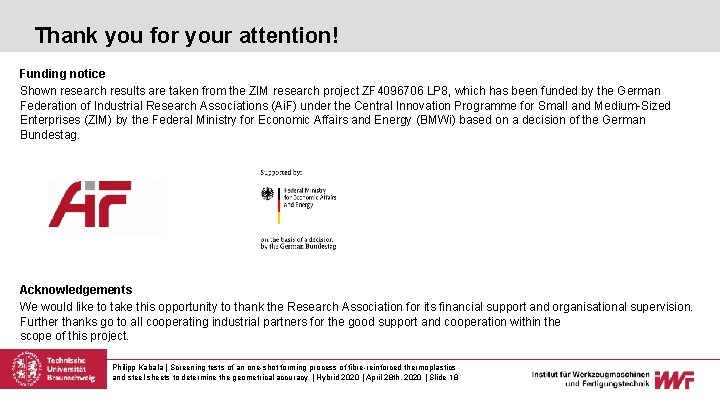
- Slides: 18
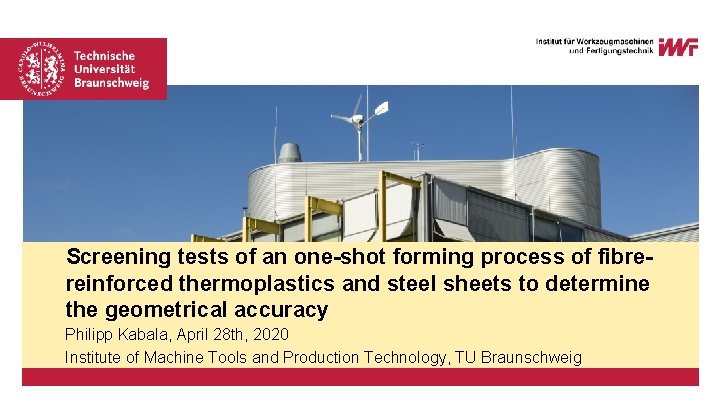
Screening tests of an one-shot forming process of fibrereinforced thermoplastics and steel sheets to determine the geometrical accuracy Philipp Kabala, April 28 th, 2020 Institute of Machine Tools and Production Technology, TU Braunschweig
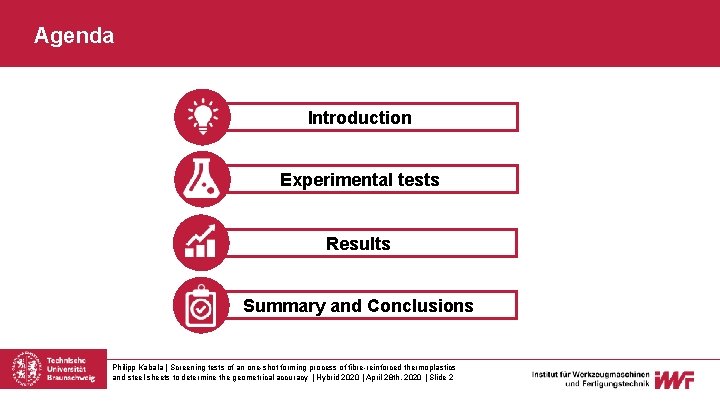
Agenda Introduction Experimental tests Results Summary and Conclusions Philipp Kabala | Screening tests of an one-shot forming process of fibre-reinforced thermoplastics and steel sheets to determine the geometrical accuracy | Hybrid 2020 | April 28 th, 2020 | Slide 2
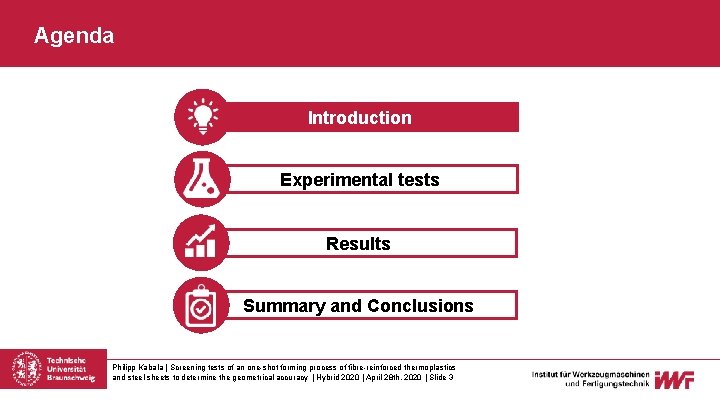
Agenda Introduction Experimental tests Results Summary and Conclusions Philipp Kabala | Screening tests of an one-shot forming process of fibre-reinforced thermoplastics and steel sheets to determine the geometrical accuracy | Hybrid 2020 | April 28 th, 2020 | Slide 3
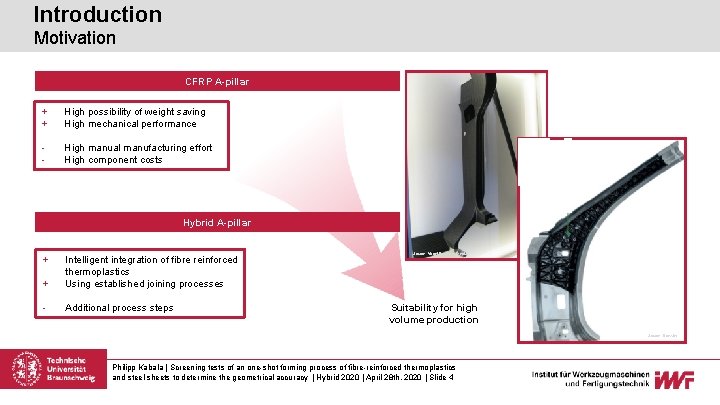
Introduction Motivation CFRP A-pillar + + High possibility of weight saving High mechanical performance - High manual manufacturing effort High component costs Hybrid A-pillar + + Intelligent integration of fibre reinforced thermoplastics Using established joining processes - Additional process steps Source: Vogel Business Media Suitability for high volume production Source: Drössler Philipp Kabala | Screening tests of an one-shot forming process of fibre-reinforced thermoplastics and steel sheets to determine the geometrical accuracy | Hybrid 2020 | April 28 th, 2020 | Slide 4
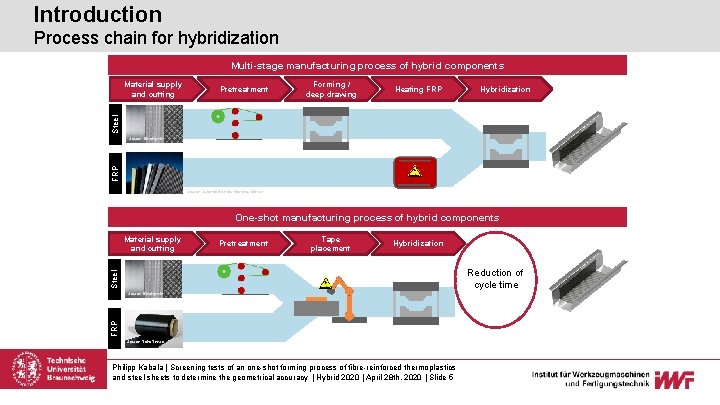
Introduction Process chain for hybridization Multi-stage manufacturing process of hybrid components Pretreatment Forming / deep drawing Heating FRP Hybridization Steel Material supply and cutting FRP Source: Blechgenie Source: automobilkonstruktion. industrie. de One-shot manufacturing process of hybrid components Material supply and cutting Pretreatment Tape placement Hybridization Steel Reduction of cycle time FRP Source: Blechgenie Source: Toho Tenax Philipp Kabala | Screening tests of an one-shot forming process of fibre-reinforced thermoplastics and steel sheets to determine the geometrical accuracy | Hybrid 2020 | April 28 th, 2020 | Slide 5
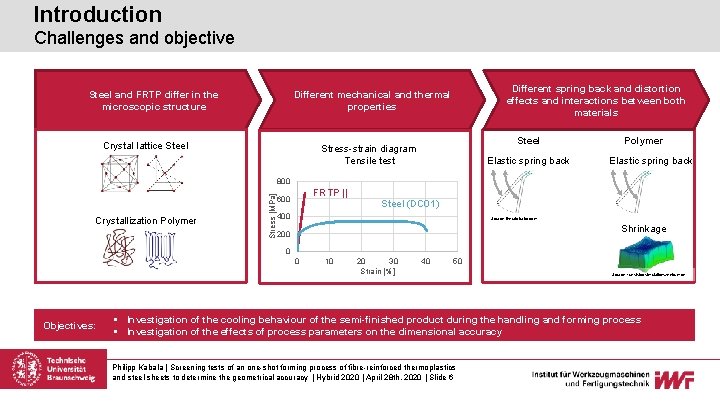
Introduction Challenges and objective Different spring back and distortion effects and interactions between both materials Different mechanical and thermal properties Steel and FRTP differ in the microscopic structure Crystal lattice Steel Stress-strain diagram Tensile test Elastic spring back Polymer Elastic spring back Crystallization Polymer Stress [MPa] 800 FRTP || 600 Steel (DC 01) 400 Source: thefabricator. com Shrinkage 200 0 0 Objectives: 10 20 30 Strain [%] 40 50 Source: kunststoff-simulationszentrum. de § Investigation of the cooling behaviour of the semi-finished product during the handling and forming process § Investigation of the effects of process parameters on the dimensional accuracy Philipp Kabala | Screening tests of an one-shot forming process of fibre-reinforced thermoplastics and steel sheets to determine the geometrical accuracy | Hybrid 2020 | April 28 th, 2020 | Slide 6
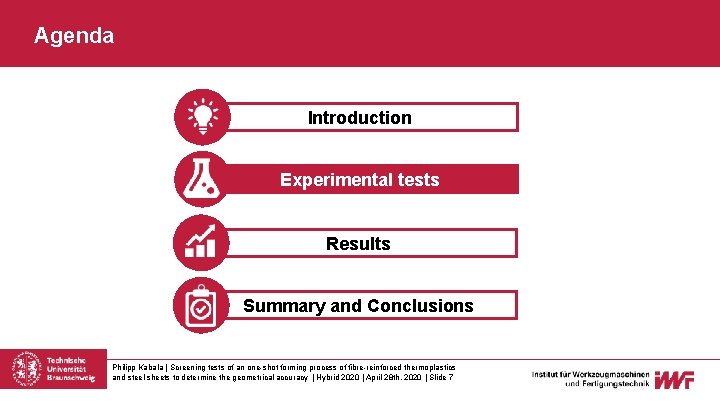
Agenda Introduction Experimental tests Results Summary and Conclusions Philipp Kabala | Screening tests of an one-shot forming process of fibre-reinforced thermoplastics and steel sheets to determine the geometrical accuracy | Hybrid 2020 | April 28 th, 2020 | Slide 7
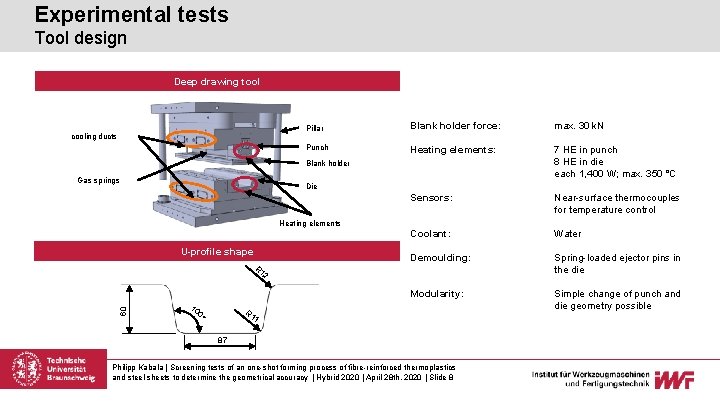
Experimental tests Tool design Deep drawing tool cooling ducts Pillar Blank holder force: max. 30 k. N Punch Heating elements: 7 HE in punch 8 HE in die each 1, 400 W; max. 350 °C Sensors: Near-surface thermocouples for temperature control Coolant: Water Demoulding: Spring-loaded ejector pins in the die Modularity: Simple change of punch and die geometry possible Blank holder Gas springs Die Heating elements U-profile shape 60 R 1 2 10 0° R 1 1 87 Philipp Kabala | Screening tests of an one-shot forming process of fibre-reinforced thermoplastics and steel sheets to determine the geometrical accuracy | Hybrid 2020 | April 28 th, 2020 | Slide 8
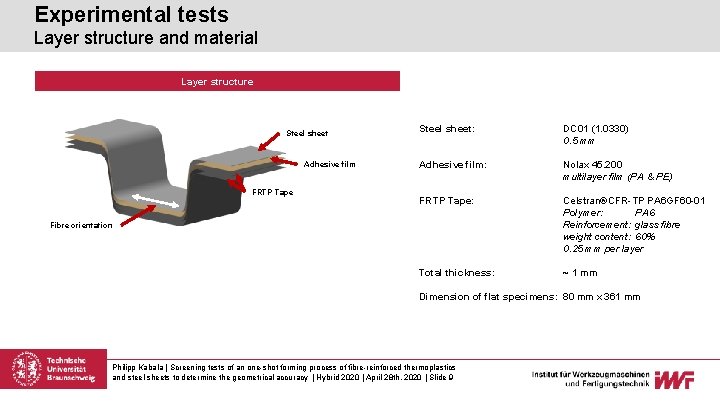
Experimental tests Layer structure and material Layer structure Steel sheet Adhesive film FRTP Tape Steel sheet: DC 01 (1. 0330) 0. 5 mm Adhesive film: Nolax 45. 200 multilayer film (PA & PE) FRTP Tape: Celstran®CFR-TP PA 6 GF 60 -01 Polymer: PA 6 Reinforcement: glass fibre weight content: 60% 0. 25 mm per layer Total thickness: ~ 1 mm Fibre orientation Dimension of flat specimens: 80 mm x 361 mm Philipp Kabala | Screening tests of an one-shot forming process of fibre-reinforced thermoplastics and steel sheets to determine the geometrical accuracy | Hybrid 2020 | April 28 th, 2020 | Slide 9
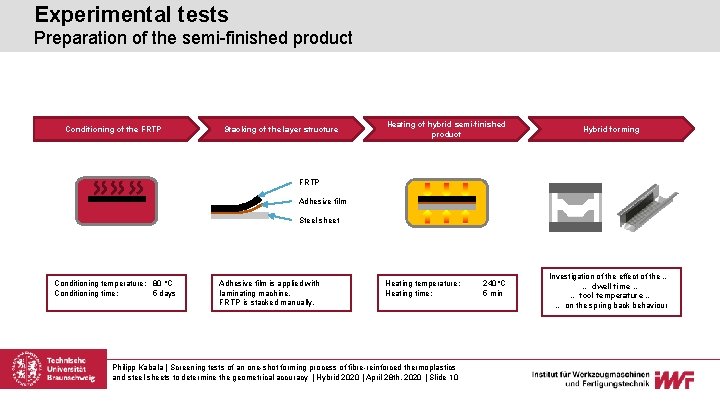
Experimental tests Preparation of the semi-finished product Conditioning of the FRTP Stacking of the layer structure Heating of hybrid semi-finished product Hybrid forming FRTP Adhesive film Steel sheet Conditioning temperature: 80 °C Conditioning time: 5 days Adhesive film is applied with laminating machine. FRTP is stacked manually. Heating temperature: Heating time: Philipp Kabala | Screening tests of an one-shot forming process of fibre-reinforced thermoplastics and steel sheets to determine the geometrical accuracy | Hybrid 2020 | April 28 th, 2020 | Slide 10 240°C 5 min Investigation of the effect of the … … dwell time … … tool temperature … … on the spring back behaviour

Experimental tests Measurement of the dimensional accuracy of the specimens Matching digitalized specimens and reference model to measure the springback/springin effect Scanning (digitalization) of the specimens with optical measuring system Extracting a reference model from CAD design specimen reference model angular deviation on the flank Philipp Kabala | Screening tests of an one-shot forming process of fibre-reinforced thermoplastics and steel sheets to determine the geometrical accuracy | Hybrid 2020 | April 28 th, 2020 | Slide 11
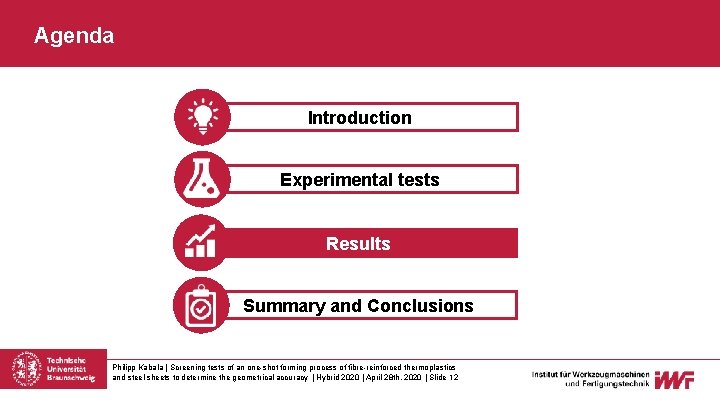
Agenda Introduction Experimental tests Results Summary and Conclusions Philipp Kabala | Screening tests of an one-shot forming process of fibre-reinforced thermoplastics and steel sheets to determine the geometrical accuracy | Hybrid 2020 | April 28 th, 2020 | Slide 12
![Results Specimen temperature during forming Temperature curves of the specimen during forming Temperature C Results Specimen temperature during forming Temperature curves of the specimen during forming Temperature [°C]](https://slidetodoc.com/presentation_image_h/108eaa47b39a4066c73ce0f0f9c191e4/image-13.jpg)
Results Specimen temperature during forming Temperature curves of the specimen during forming Temperature [°C] 250 T 1 (120°C) 200 T 2 (120°C) 150 T 1 (80°C) 100 50 0 T 2 (80°C) Start forming -30 -20 0 -10 10 Time [s] 20 30 40 50 Results: § Temperature gradient occurs in the semi-finished product § Outer areas cool down faster due to direct contact with the tool before forming § Central area is not in contact with the tool before forming § No significant change in temperature can be detected after 20 to 30 s § Longer dwell times are not necessary and uneconomic § With shorter dwell times, the specimen is not completely cooled to the tool temperature § Adhesive could be still in a viscous state T 1 T 2 18 0 80 To ensure the solidification of the adhesive and to reduce the cycle time, the optimum dwell time is 20 to 30 s Philipp Kabala | Screening tests of an one-shot forming process of fibre-reinforced thermoplastics and steel sheets to determine the geometrical accuracy | Hybrid 2020 | April 28 th, 2020 | Slide 13
![Results Influence of the dwell time Spring back C Investigation of a dwell time Results Influence of the dwell time Spring back [°C] Investigation of a dwell time](https://slidetodoc.com/presentation_image_h/108eaa47b39a4066c73ce0f0f9c191e4/image-14.jpg)
Results Influence of the dwell time Spring back [°C] Investigation of a dwell time of 5, 20 and 60 s 3 18 16 14 1 Description of the phenomenon between point 1 and 2: At short dwell times the specimen is not cooled to the tool temperature à This results in a greater temperature difference between the specimen and the environment à The higher the temperature difference, the greater thermal distortion à Coefficient of thermal expansion of PA 6 is higher than that of steel Description of the phenomenon between point 2 and 3: Both dwell times are sufficiently long to cool the specimen to the tool temperature 12 2 0 20 10 30 40 Dwell time [s] 50 60 At long dwell times thermal energy introduced into the specimen by the tool increases à The longer the heat input, the higher the proportion of densely packed crystalline structures in PA 6 à Densely packed crystalline structures lead to strong shrinkage effects reference 2 1 3 Philipp Kabala | Screening tests of an one-shot forming process of fibre-reinforced thermoplastics and steel sheets to determine the geometrical accuracy | Hybrid 2020 | April 28 th, 2020 | Slide 14 Steel sheet Adhesive film FRTP Tape
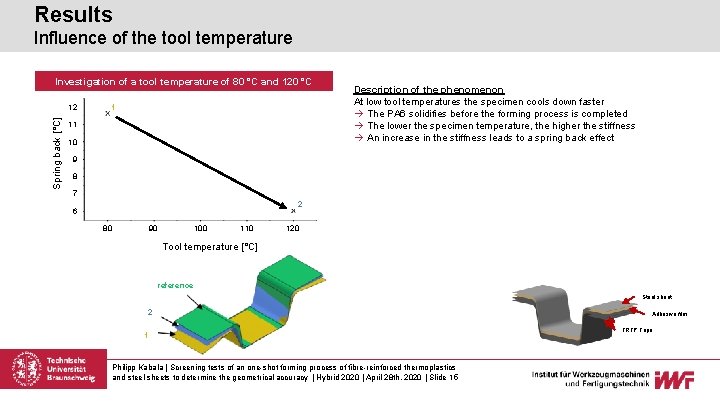
Results Influence of the tool temperature Investigation of a tool temperature of 80 °C and 120 °C 12 Spring back [°C] s 1 11 10 Description of the phenomenon At low tool temperatures the specimen cools down faster à The PA 6 solidifies before the forming process is completed à The lower the specimen temperature, the higher the stiffness à An increase in the stiffness leads to a spring back effect 9 8 7 2 6 90 80 100 110 120 Tool temperature [°C] reference Steel sheet 2 1 Philipp Kabala | Screening tests of an one-shot forming process of fibre-reinforced thermoplastics and steel sheets to determine the geometrical accuracy | Hybrid 2020 | April 28 th, 2020 | Slide 15 Adhesive film FRTP Tape
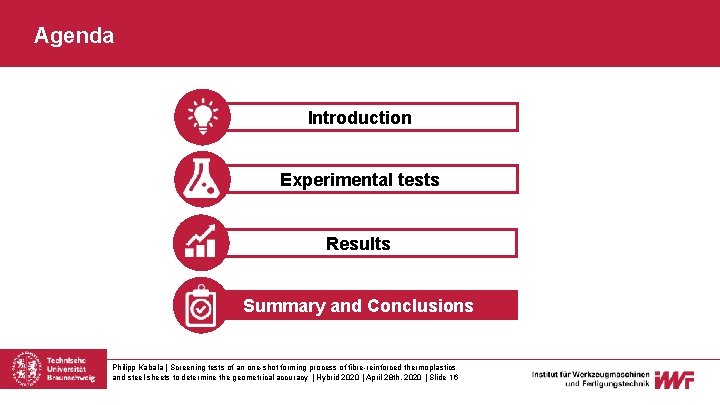
Agenda Introduction Experimental tests Results Summary and Conclusions Philipp Kabala | Screening tests of an one-shot forming process of fibre-reinforced thermoplastics and steel sheets to determine the geometrical accuracy | Hybrid 2020 | April 28 th, 2020 | Slide 16
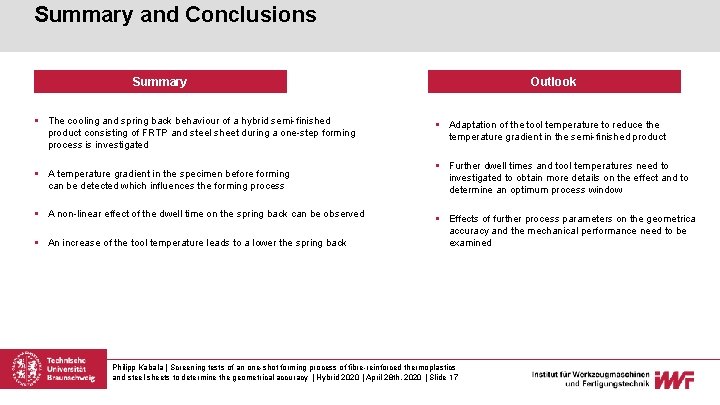
Summary and Conclusions Outlook Summary § The cooling and spring back behaviour of a hybrid semi-finished product consisting of FRTP and steel sheet during a one-step forming process is investigated § Adaptation of the tool temperature to reduce the temperature gradient in the semi-finished product § A temperature gradient in the specimen before forming can be detected which influences the forming process § Further dwell times and tool temperatures need to investigated to obtain more details on the effect and to determine an optimum process window § A non-linear effect of the dwell time on the spring back can be observed § An increase of the tool temperature leads to a lower the spring back § Effects of further process parameters on the geometrica accuracy and the mechanical performance need to be examined Philipp Kabala | Screening tests of an one-shot forming process of fibre-reinforced thermoplastics and steel sheets to determine the geometrical accuracy | Hybrid 2020 | April 28 th, 2020 | Slide 17
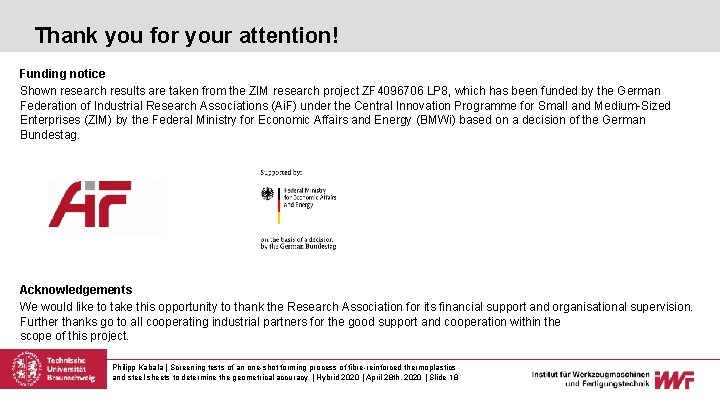
Thank you for your attention! Funding notice Shown research results are taken from the ZIM research project ZF 4096706 LP 8, which has been funded by the German Federation of Industrial Research Associations (Ai. F) under the Central Innovation Programme for Small and Medium-Sized Enterprises (ZIM) by the Federal Ministry for Economic Affairs and Energy (BMWi) based on a decision of the German Bundestag. Acknowledgements We would like to take this opportunity to thank the Research Association for its financial support and organisational supervision. Further thanks go to all cooperating industrial partners for the good support and cooperation within the scope of this project. Philipp Kabala | Screening tests of an one-shot forming process of fibre-reinforced thermoplastics and steel sheets to determine the geometrical accuracy | Hybrid 2020 | April 28 th, 2020 | Slide 18
Ace different tests iq tests still
Proses metal forming
Forming process in sheet metal
Particulate forming process in ceramics
Stages of vacuum forming
Different stages of team development
Storming norming conforming performing
Corynebacterium diphtheriae spore forming
Disadvantages of cold working
Draw bead
Casting forming and welding mcq
Forming and solving equations worksheet
Forming and solving linear equations worksheet
Ionic bonding problems
Readers increase their knowledge by forming synthesis.
Organs forming the respiratory passageway
Forming research design
Bulk deformation and sheet metal forming
4 soil forming processes