Root Cause Analysis Thomas S Arneson 1192020 Focus
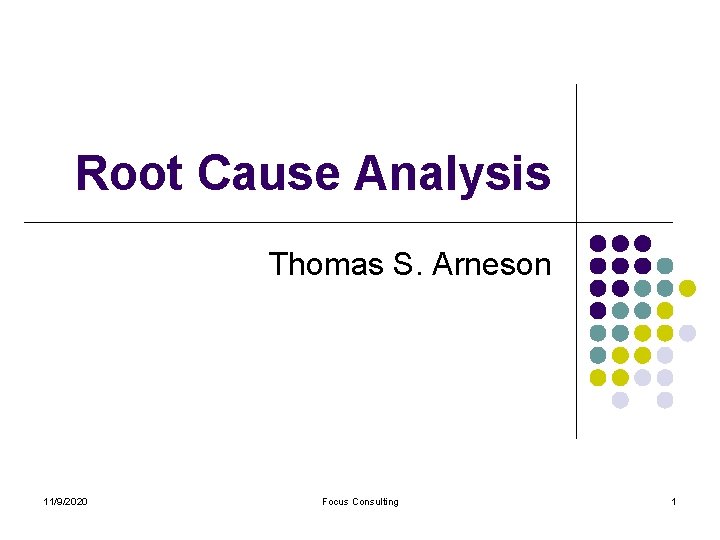

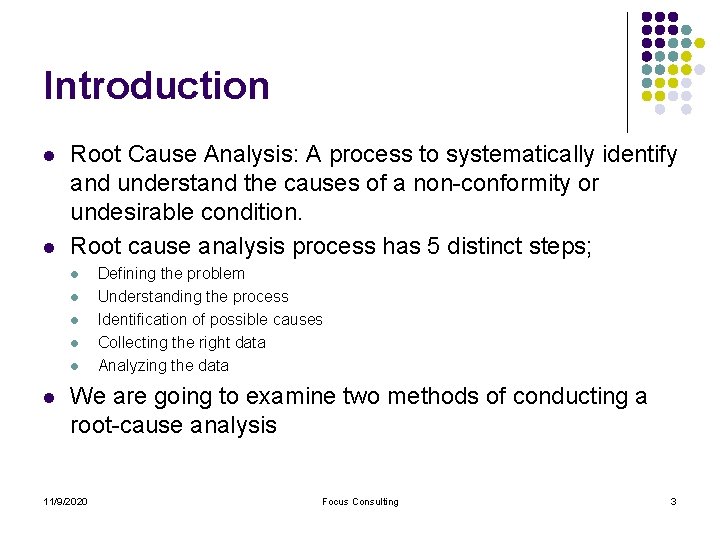
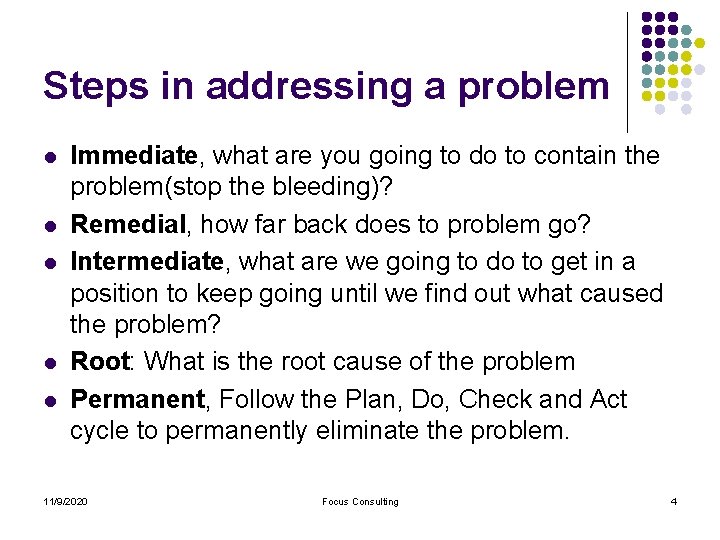
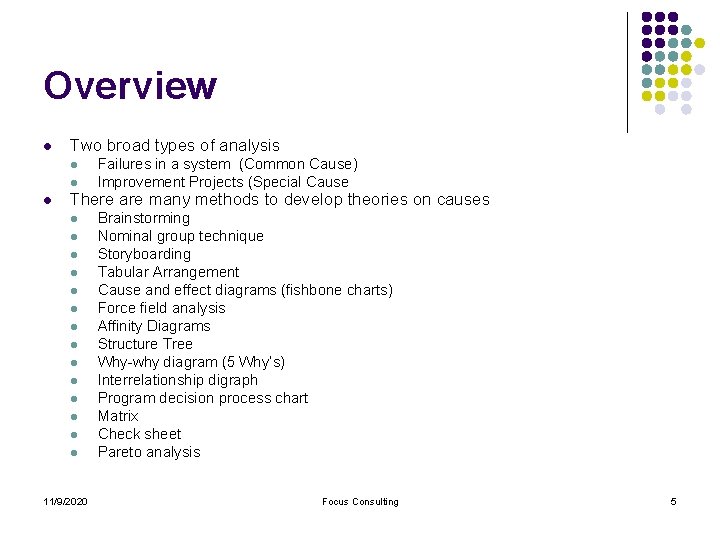
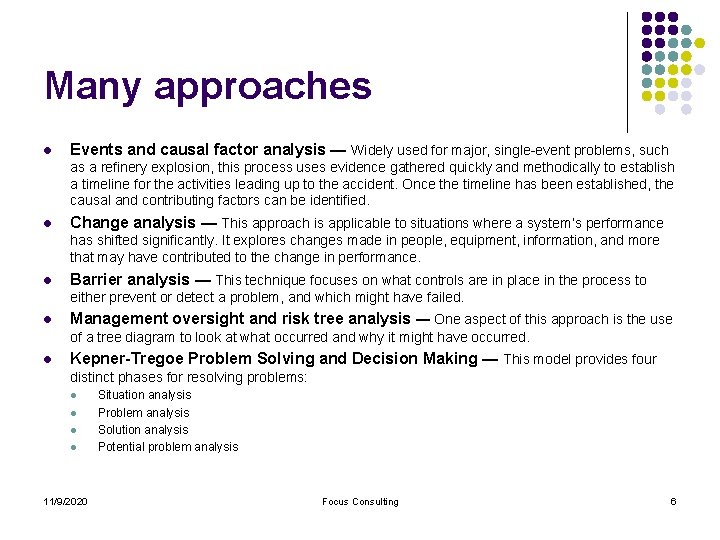
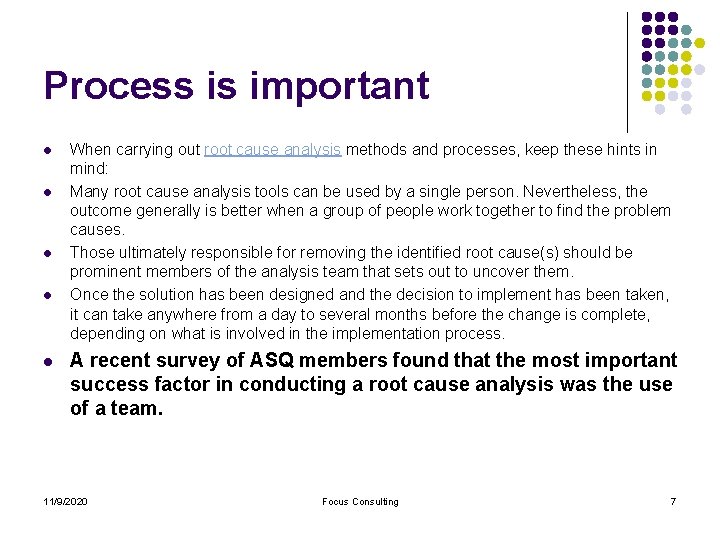
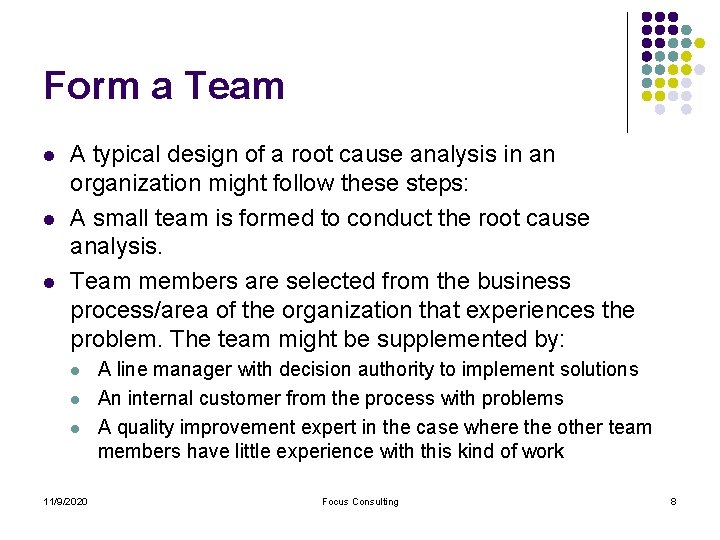
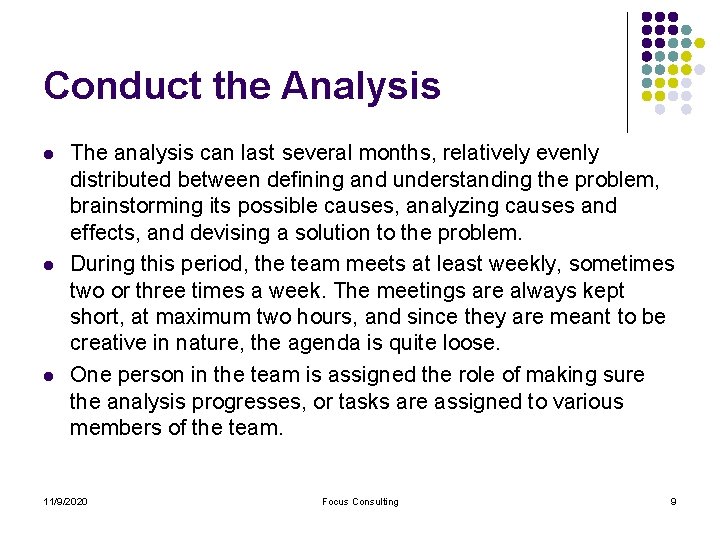
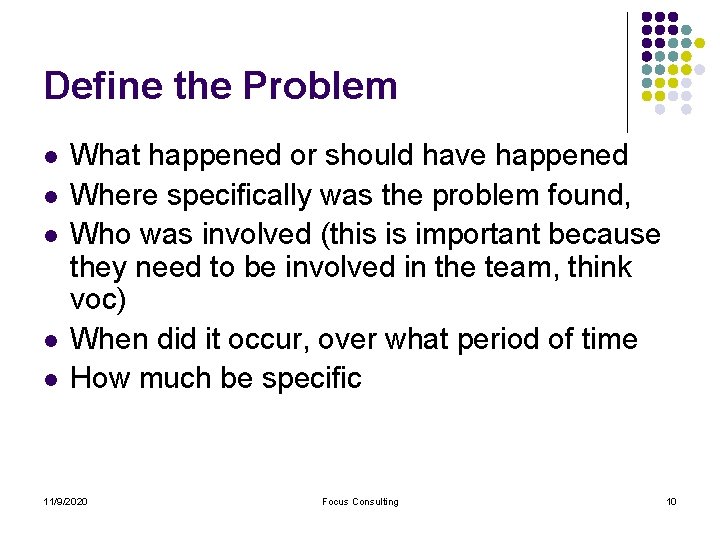
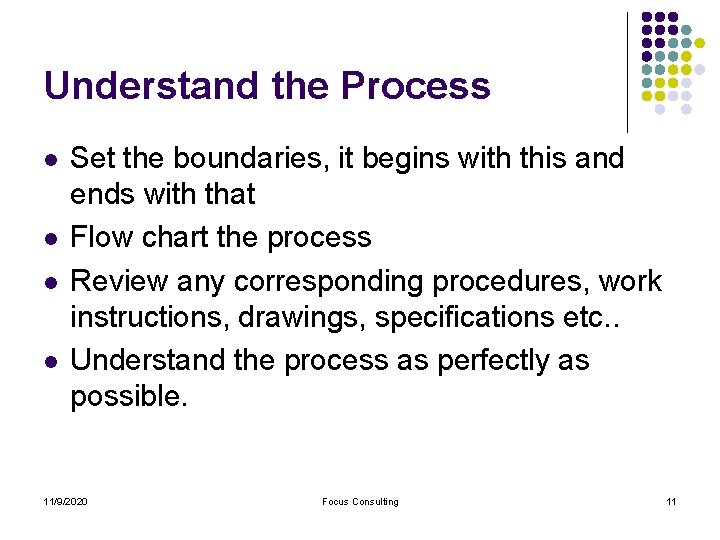
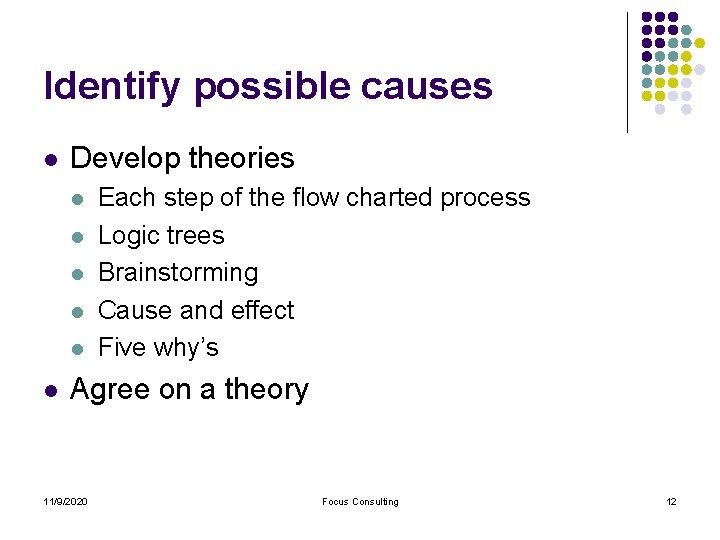
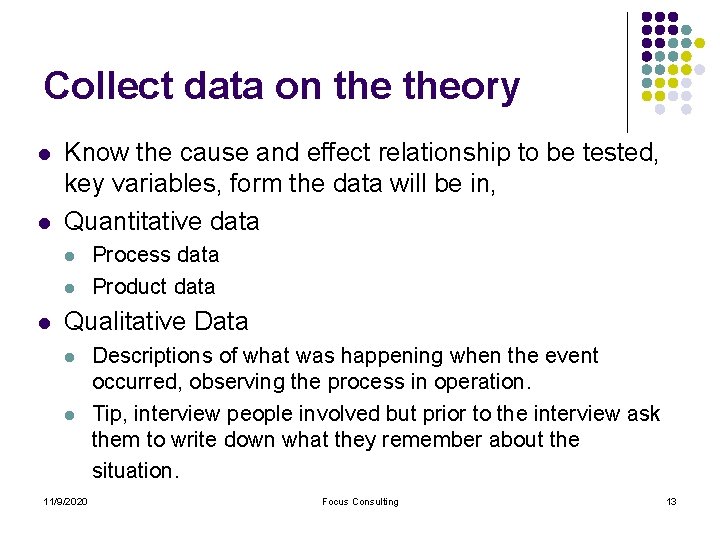
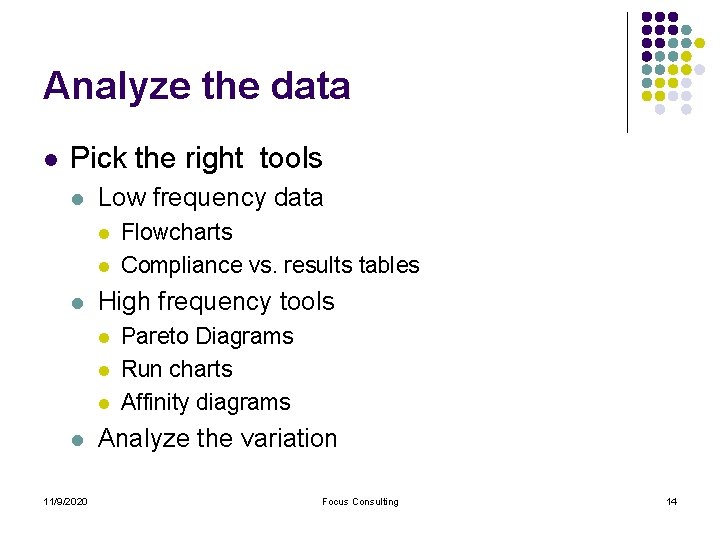
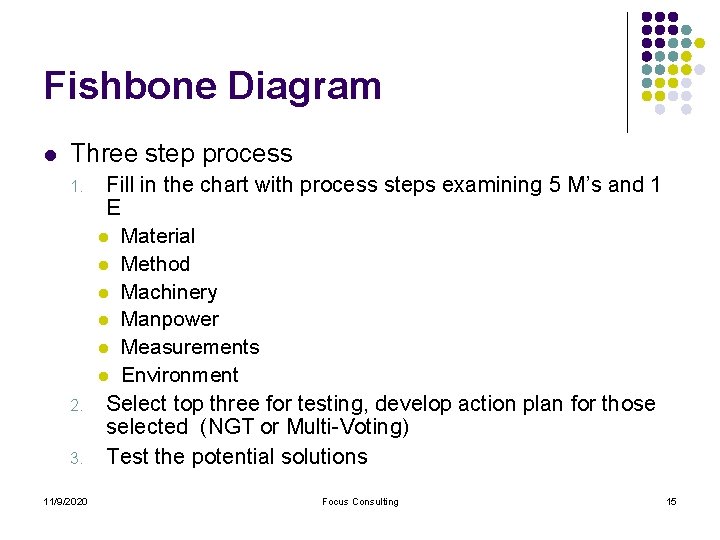
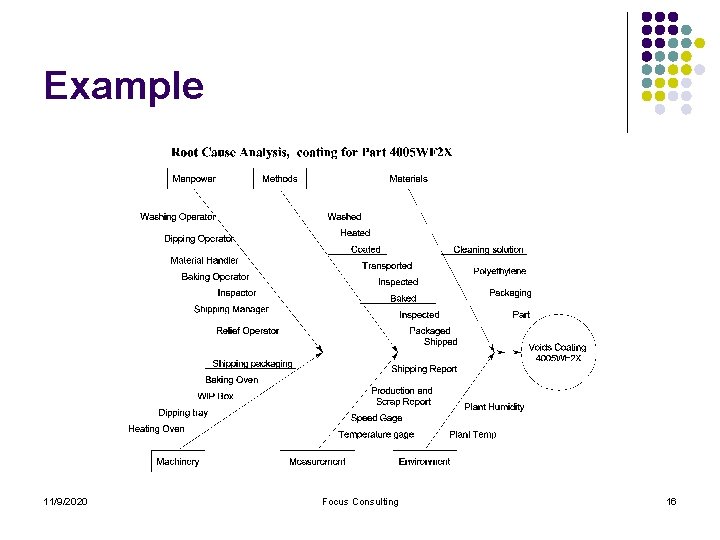
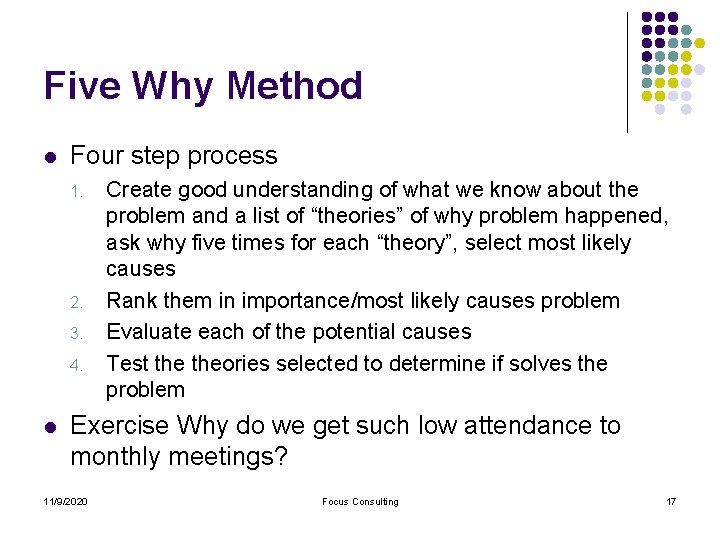
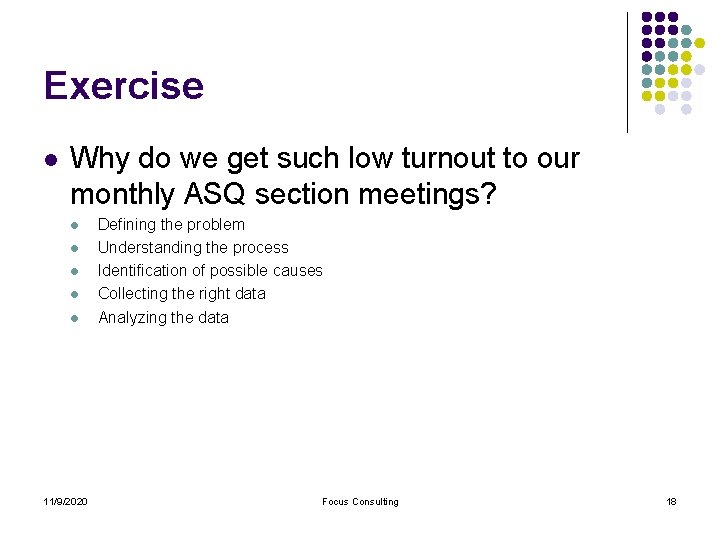
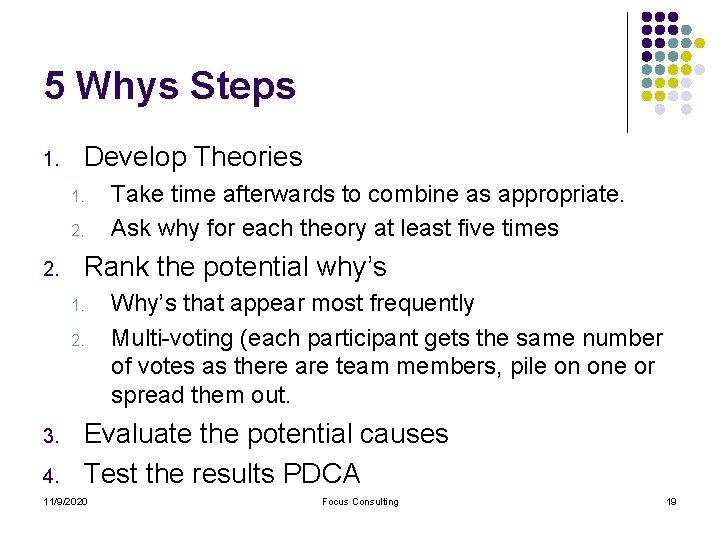
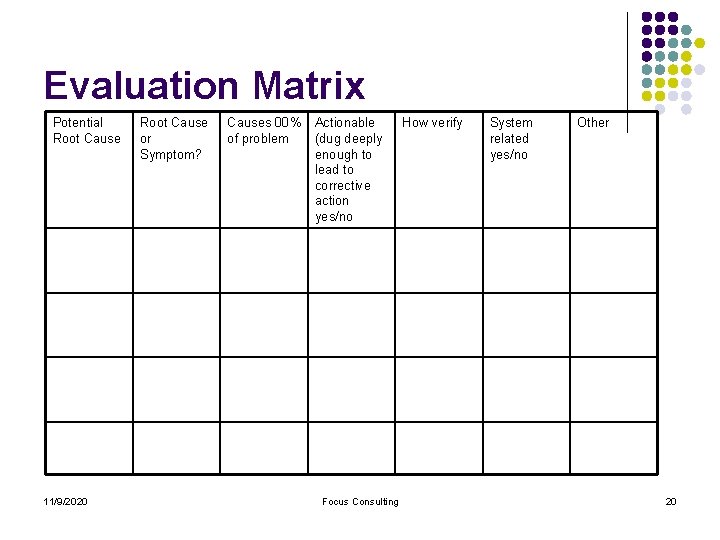
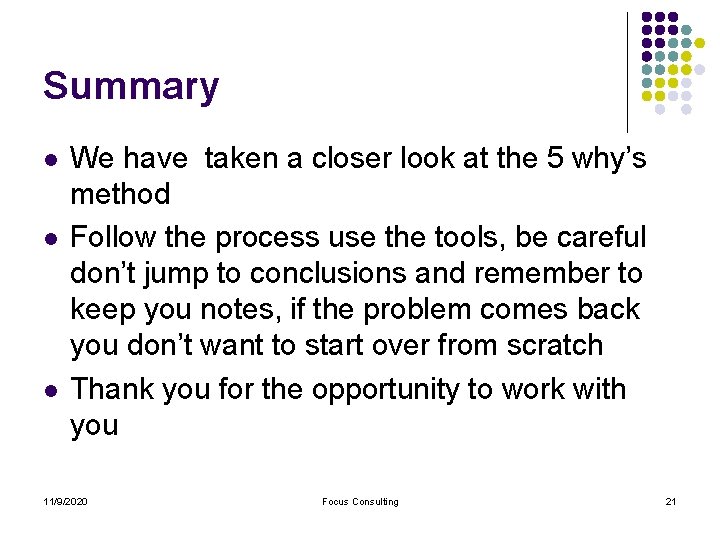
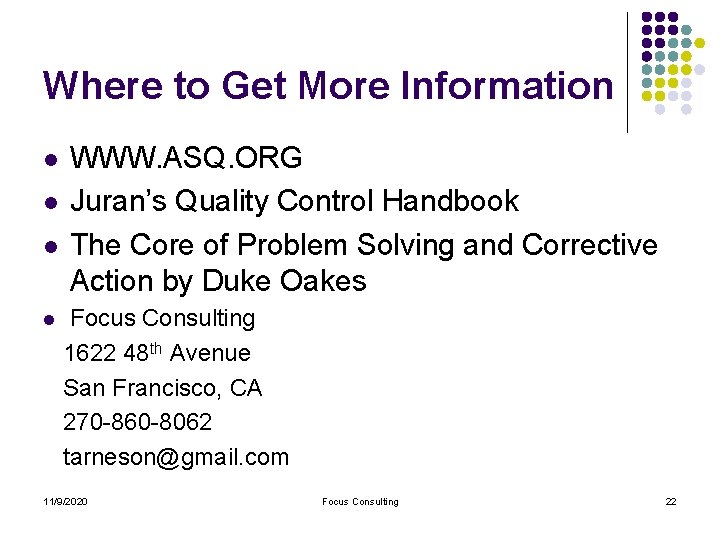
- Slides: 22
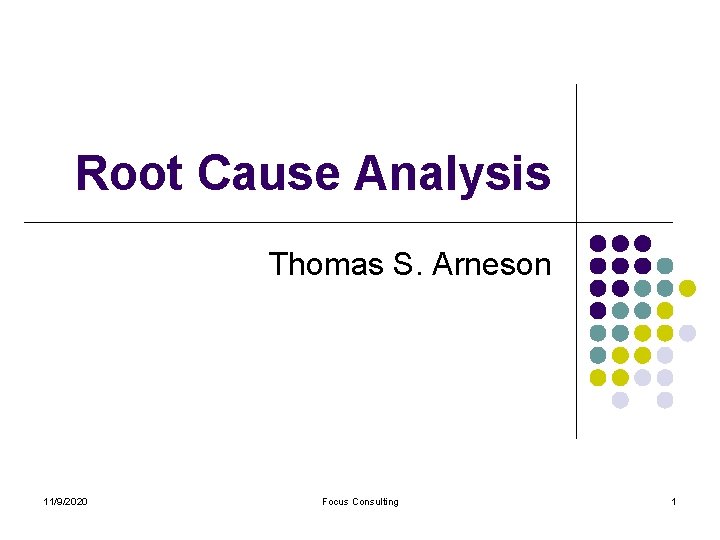
Root Cause Analysis Thomas S. Arneson 11/9/2020 Focus Consulting 1

Agenda l l l Introductions and the index card. It’s the process more than the tools that matter. A couple of tools l l l Fishbone Diagram Five Why’s Table Conducting Root-Cause Analysis on a real problem using the Five Why’s Table 11/9/2020 Focus Consulting 2
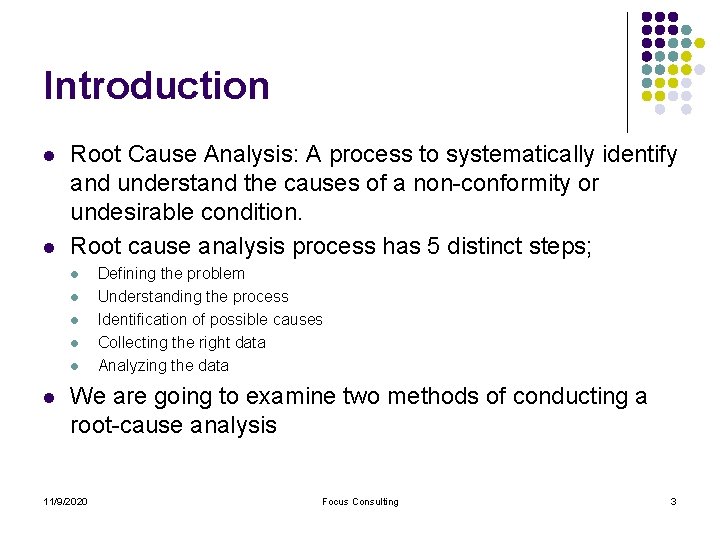
Introduction l l Root Cause Analysis: A process to systematically identify and understand the causes of a non-conformity or undesirable condition. Root cause analysis process has 5 distinct steps; l l l Defining the problem Understanding the process Identification of possible causes Collecting the right data Analyzing the data We are going to examine two methods of conducting a root-cause analysis 11/9/2020 Focus Consulting 3
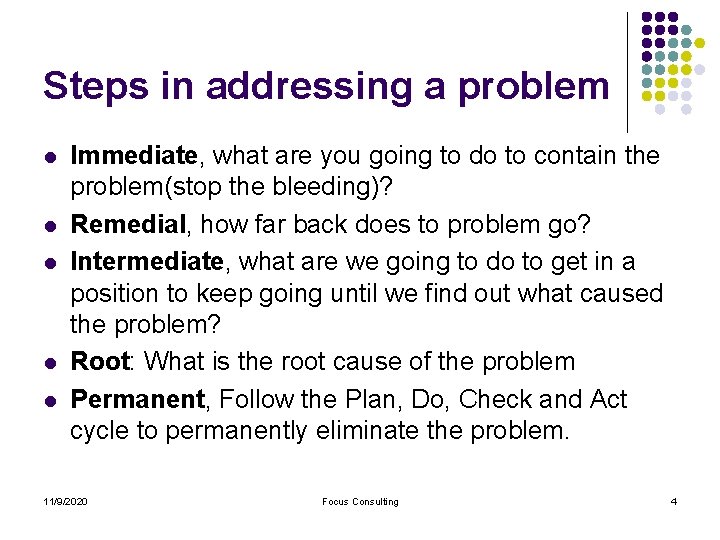
Steps in addressing a problem l l l Immediate, what are you going to do to contain the problem(stop the bleeding)? Remedial, how far back does to problem go? Intermediate, what are we going to do to get in a position to keep going until we find out what caused the problem? Root: What is the root cause of the problem Permanent, Follow the Plan, Do, Check and Act cycle to permanently eliminate the problem. 11/9/2020 Focus Consulting 4
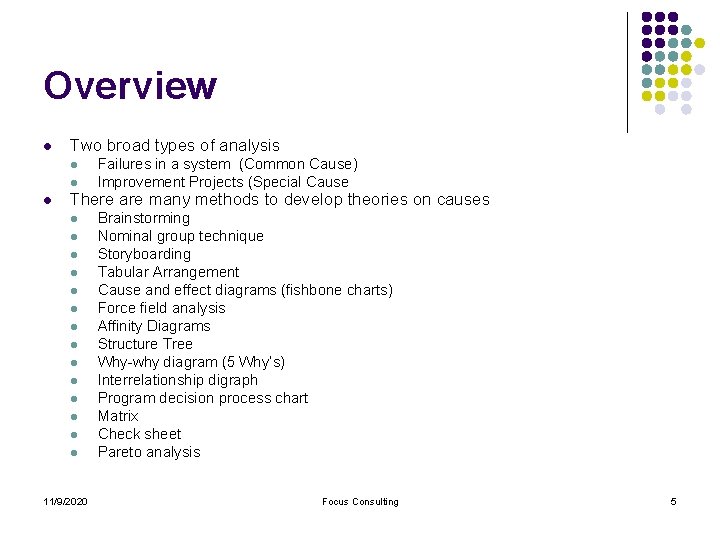
Overview l Two broad types of analysis l l l Failures in a system (Common Cause) Improvement Projects (Special Cause There are many methods to develop theories on causes l l l l 11/9/2020 Brainstorming Nominal group technique Storyboarding Tabular Arrangement Cause and effect diagrams (fishbone charts) Force field analysis Affinity Diagrams Structure Tree Why-why diagram (5 Why’s) Interrelationship digraph Program decision process chart Matrix Check sheet Pareto analysis Focus Consulting 5
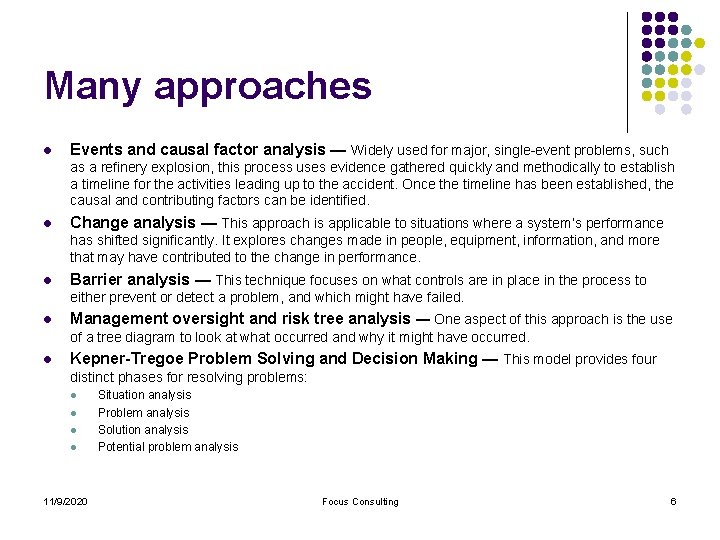
Many approaches l Events and causal factor analysis — Widely used for major, single-event problems, such as a refinery explosion, this process uses evidence gathered quickly and methodically to establish a timeline for the activities leading up to the accident. Once the timeline has been established, the causal and contributing factors can be identified. l Change analysis — This approach is applicable to situations where a system’s performance has shifted significantly. It explores changes made in people, equipment, information, and more that may have contributed to the change in performance. l Barrier analysis — This technique focuses on what controls are in place in the process to either prevent or detect a problem, and which might have failed. l Management oversight and risk tree analysis — One aspect of this approach is the use of a tree diagram to look at what occurred and why it might have occurred. l Kepner-Tregoe Problem Solving and Decision Making — This model provides four distinct phases for resolving problems: l l 11/9/2020 Situation analysis Problem analysis Solution analysis Potential problem analysis Focus Consulting 6
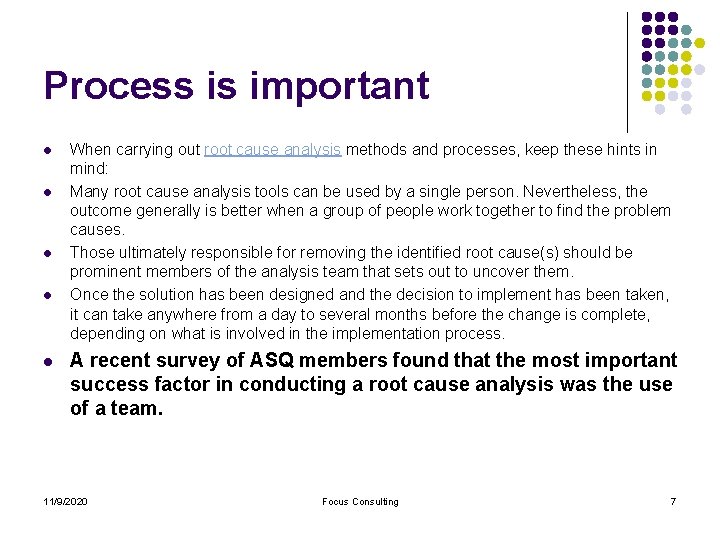
Process is important l l l When carrying out root cause analysis methods and processes, keep these hints in mind: Many root cause analysis tools can be used by a single person. Nevertheless, the outcome generally is better when a group of people work together to find the problem causes. Those ultimately responsible for removing the identified root cause(s) should be prominent members of the analysis team that sets out to uncover them. Once the solution has been designed and the decision to implement has been taken, it can take anywhere from a day to several months before the change is complete, depending on what is involved in the implementation process. A recent survey of ASQ members found that the most important success factor in conducting a root cause analysis was the use of a team. 11/9/2020 Focus Consulting 7
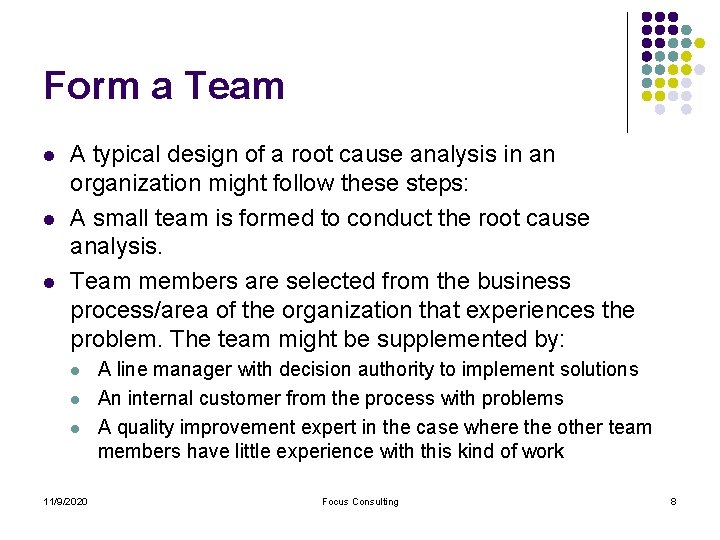
Form a Team l l l A typical design of a root cause analysis in an organization might follow these steps: A small team is formed to conduct the root cause analysis. Team members are selected from the business process/area of the organization that experiences the problem. The team might be supplemented by: l l l 11/9/2020 A line manager with decision authority to implement solutions An internal customer from the process with problems A quality improvement expert in the case where the other team members have little experience with this kind of work Focus Consulting 8
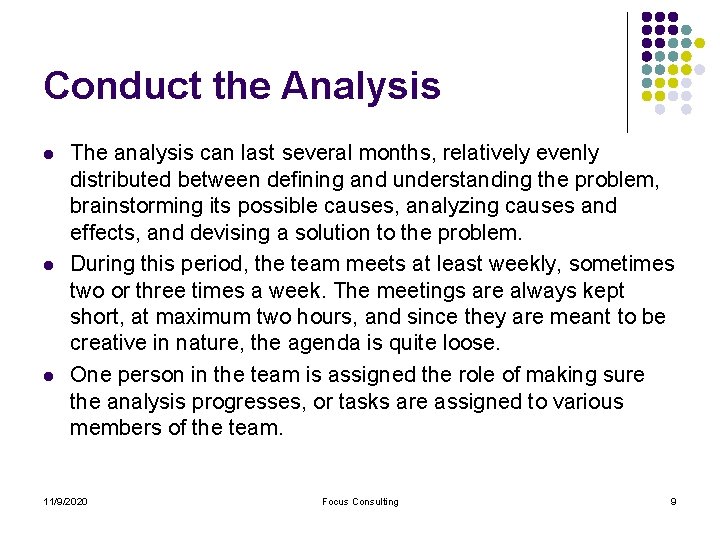
Conduct the Analysis l l l The analysis can last several months, relatively evenly distributed between defining and understanding the problem, brainstorming its possible causes, analyzing causes and effects, and devising a solution to the problem. During this period, the team meets at least weekly, sometimes two or three times a week. The meetings are always kept short, at maximum two hours, and since they are meant to be creative in nature, the agenda is quite loose. One person in the team is assigned the role of making sure the analysis progresses, or tasks are assigned to various members of the team. 11/9/2020 Focus Consulting 9
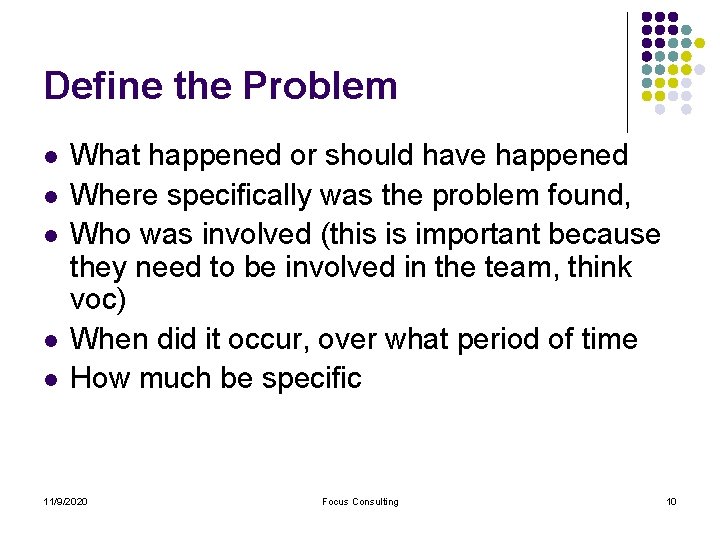
Define the Problem l l l What happened or should have happened Where specifically was the problem found, Who was involved (this is important because they need to be involved in the team, think voc) When did it occur, over what period of time How much be specific 11/9/2020 Focus Consulting 10
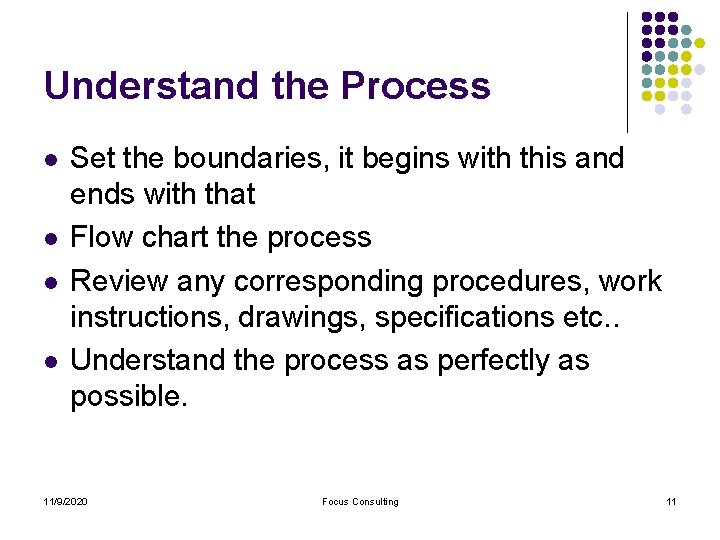
Understand the Process l l Set the boundaries, it begins with this and ends with that Flow chart the process Review any corresponding procedures, work instructions, drawings, specifications etc. . Understand the process as perfectly as possible. 11/9/2020 Focus Consulting 11
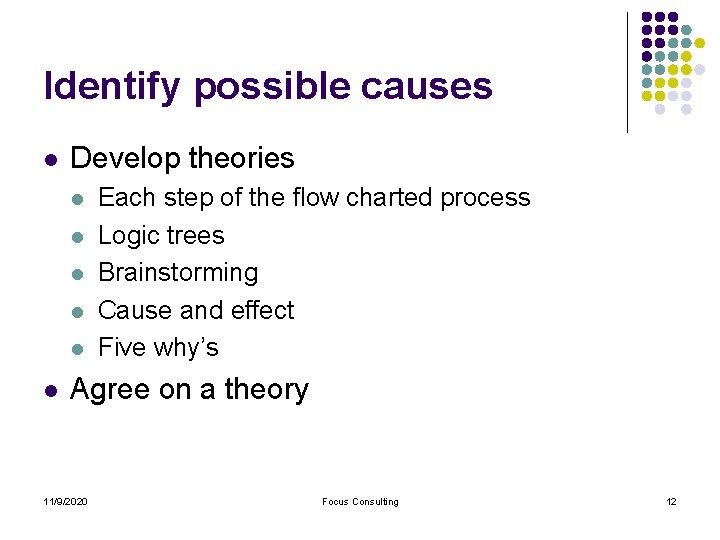
Identify possible causes l Develop theories l l l Each step of the flow charted process Logic trees Brainstorming Cause and effect Five why’s Agree on a theory 11/9/2020 Focus Consulting 12
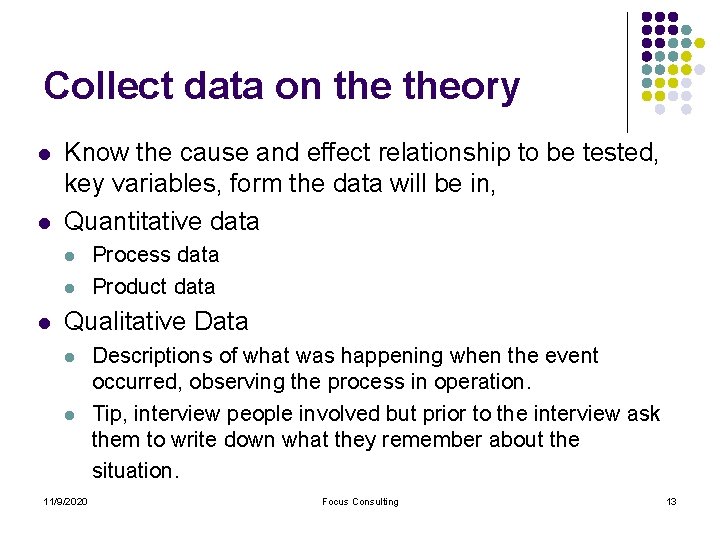
Collect data on theory l l Know the cause and effect relationship to be tested, key variables, form the data will be in, Quantitative data l l l Process data Product data Qualitative Data l l 11/9/2020 Descriptions of what was happening when the event occurred, observing the process in operation. Tip, interview people involved but prior to the interview ask them to write down what they remember about the situation. Focus Consulting 13
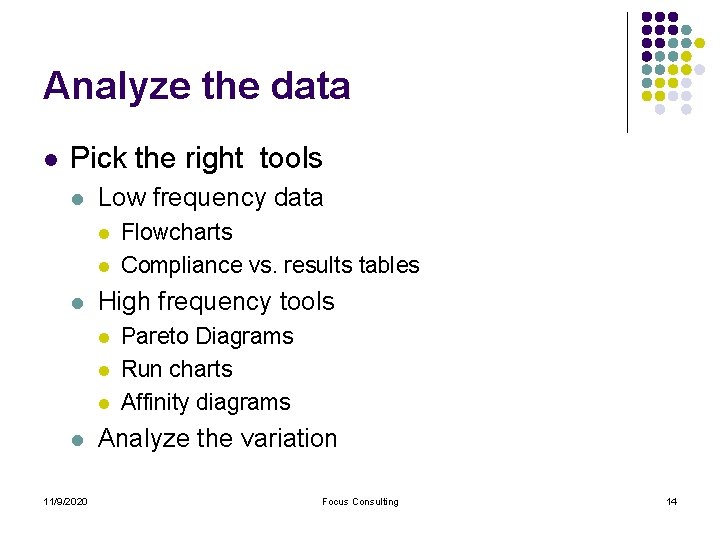
Analyze the data l Pick the right tools l Low frequency data l l l High frequency tools l l 11/9/2020 Flowcharts Compliance vs. results tables Pareto Diagrams Run charts Affinity diagrams Analyze the variation Focus Consulting 14
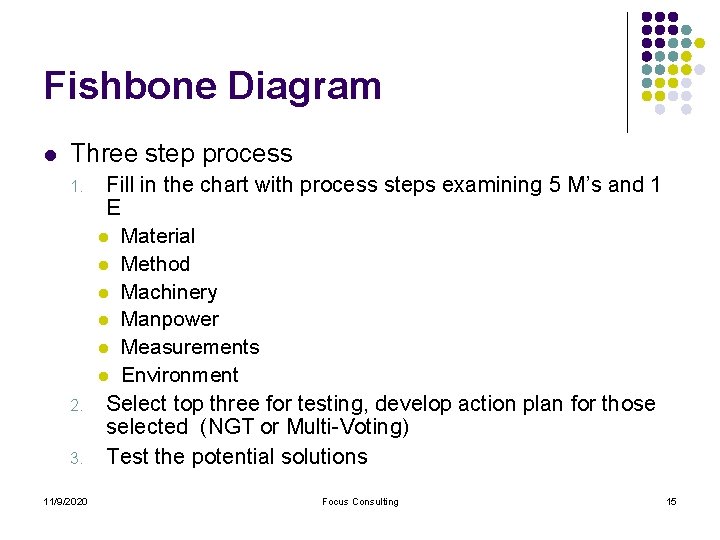
Fishbone Diagram l Three step process 1. 2. 3. 11/9/2020 Fill in the chart with process steps examining 5 M’s and 1 E l Material l Method l Machinery l Manpower l Measurements l Environment Select top three for testing, develop action plan for those selected (NGT or Multi-Voting) Test the potential solutions Focus Consulting 15
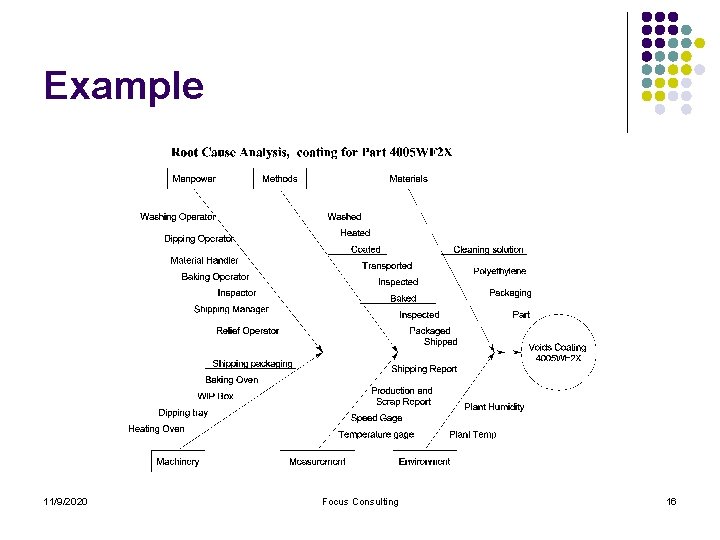
Example 11/9/2020 Focus Consulting 16
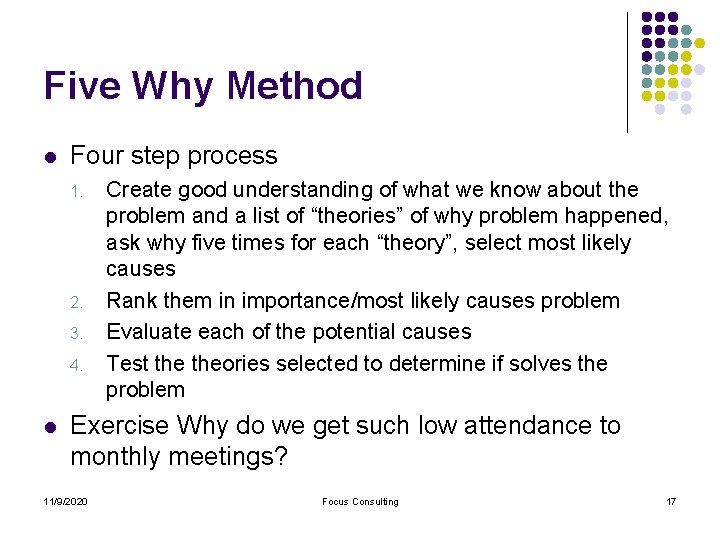
Five Why Method l Four step process 1. 2. 3. 4. l Create good understanding of what we know about the problem and a list of “theories” of why problem happened, ask why five times for each “theory”, select most likely causes Rank them in importance/most likely causes problem Evaluate each of the potential causes Test theories selected to determine if solves the problem Exercise Why do we get such low attendance to monthly meetings? 11/9/2020 Focus Consulting 17
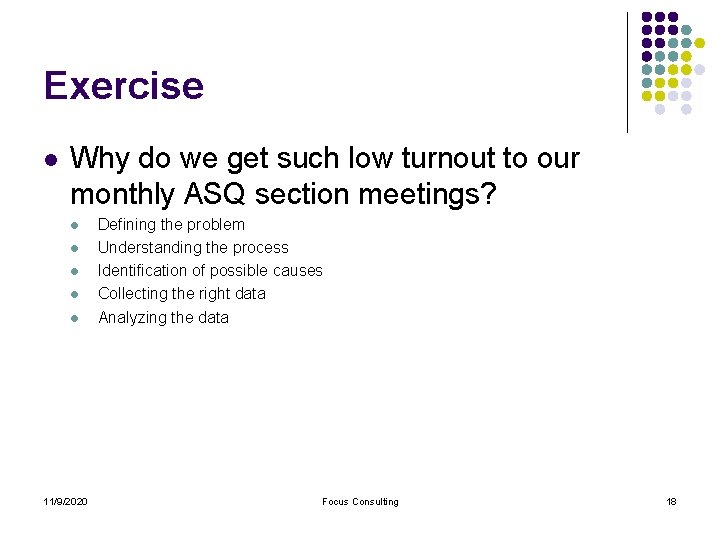
Exercise l Why do we get such low turnout to our monthly ASQ section meetings? l l l 11/9/2020 Defining the problem Understanding the process Identification of possible causes Collecting the right data Analyzing the data Focus Consulting 18
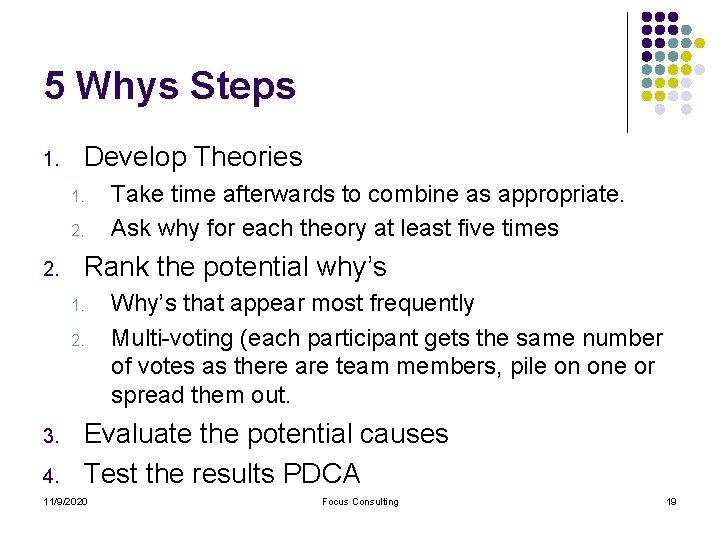
5 Whys Steps 1. Develop Theories 1. 2. Rank the potential why’s 1. 2. 3. 4. Take time afterwards to combine as appropriate. Ask why for each theory at least five times Why’s that appear most frequently Multi-voting (each participant gets the same number of votes as there are team members, pile on one or spread them out. Evaluate the potential causes Test the results PDCA 11/9/2020 Focus Consulting 19
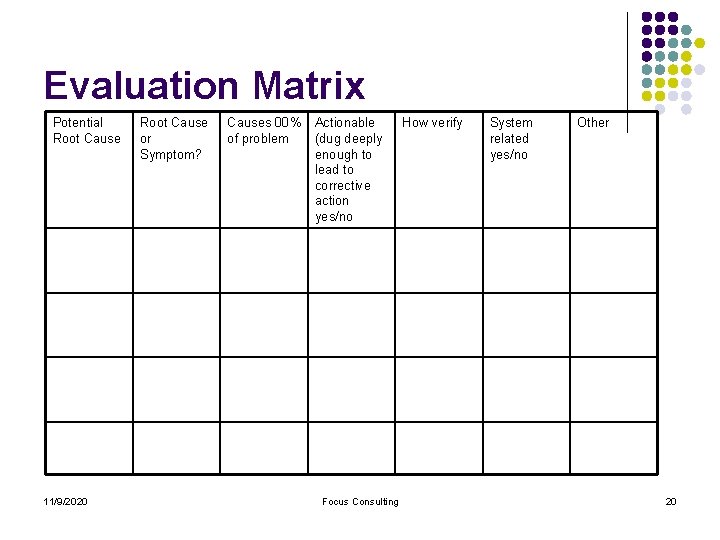
Evaluation Matrix Potential Root Cause 11/9/2020 Root Cause or Symptom? Causes 00% of problem Actionable (dug deeply enough to lead to corrective action yes/no Focus Consulting How verify System related yes/no Other 20
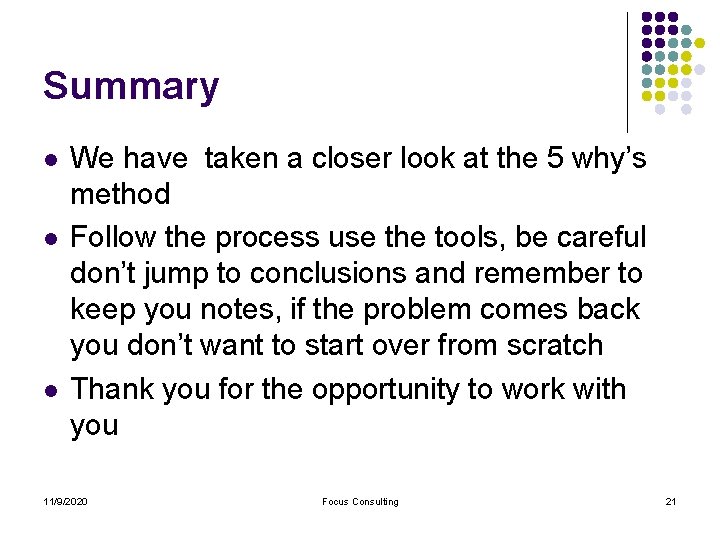
Summary l l l We have taken a closer look at the 5 why’s method Follow the process use the tools, be careful don’t jump to conclusions and remember to keep you notes, if the problem comes back you don’t want to start over from scratch Thank you for the opportunity to work with you 11/9/2020 Focus Consulting 21
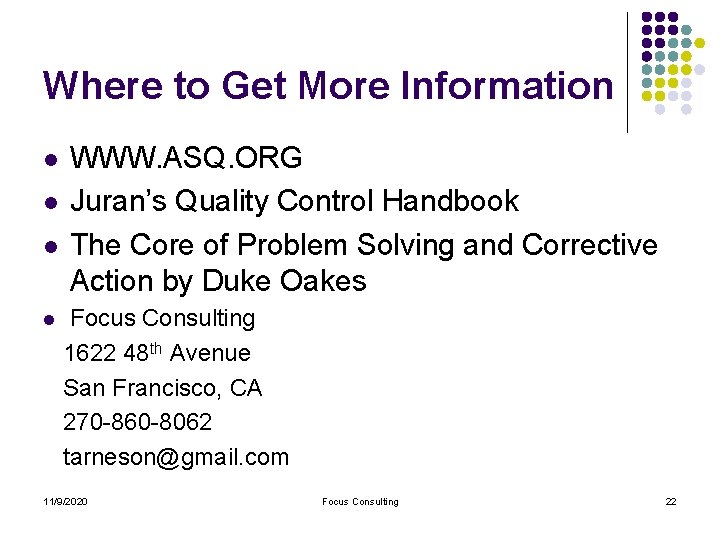
Where to Get More Information l l WWW. ASQ. ORG Juran’s Quality Control Handbook The Core of Problem Solving and Corrective Action by Duke Oakes Focus Consulting 1622 48 th Avenue San Francisco, CA 270 -860 -8062 tarneson@gmail. com 11/9/2020 Focus Consulting 22
9:09 pm
Pop art signs
Lisa arneson
Needle tool clay definition
Focus on form vs focus on forms
Porter's generic business strategies
Cost focus and differentiation focus
Actor focus vs object focus
Root cause analysis sop
Root cause analysis slide
Dmiac
M&m fishbone diagram
Fishbone diagram kaizen
Contoh root cause analysis 5 why
London protocol template
Fishbone's menu
Name of diagram
Root cause analysis tutorial
Sentinal event
Jefferson memorial root cause analysis
Root cause analysis slide
Jefferson memorial root cause analysis
Analysis