RollsRoyce University Technology Center in High Mach Propulsion
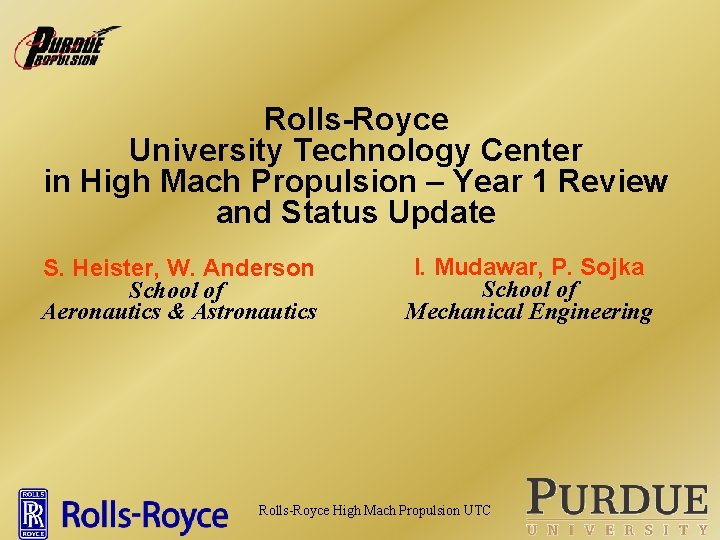
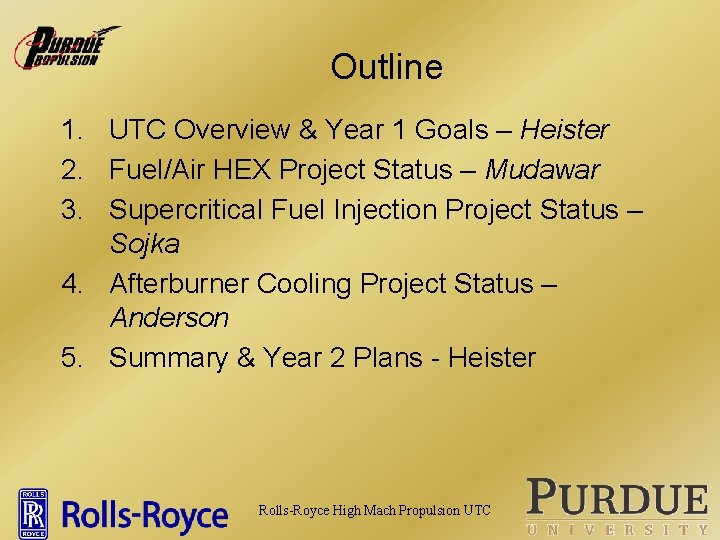
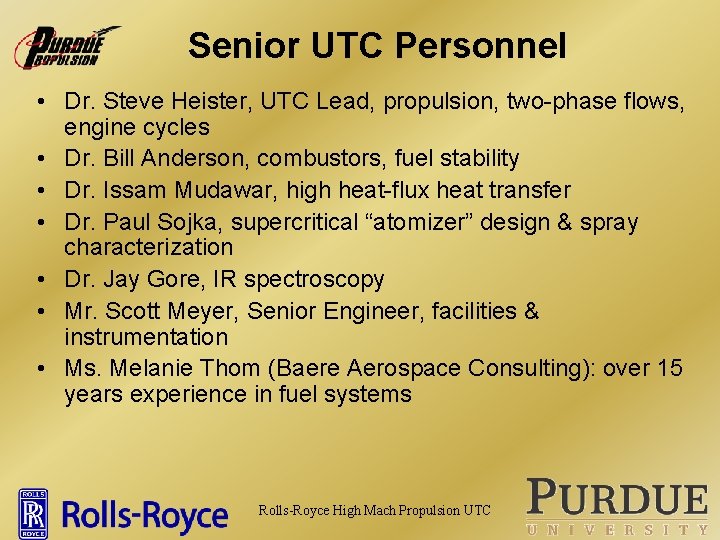
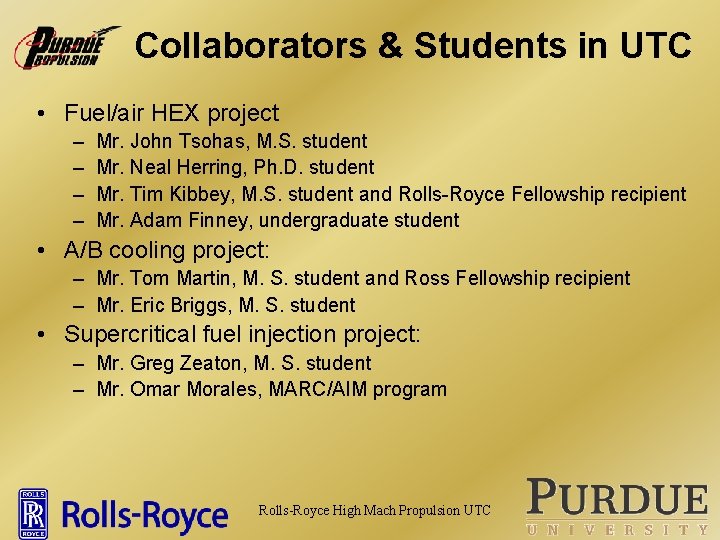
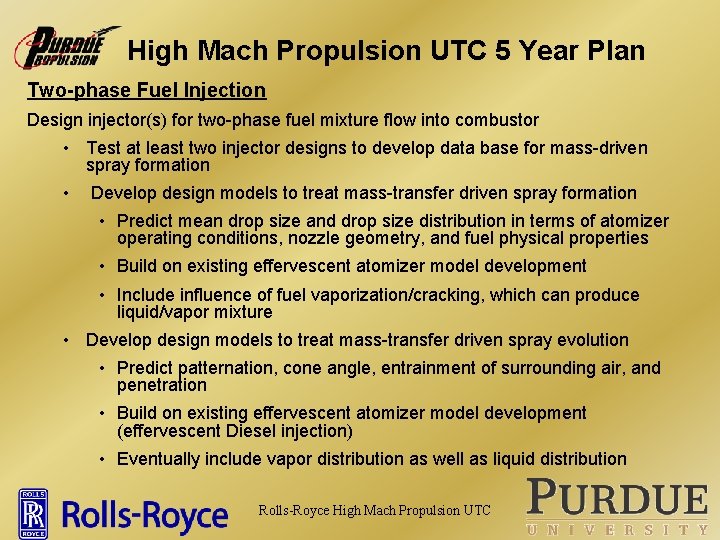
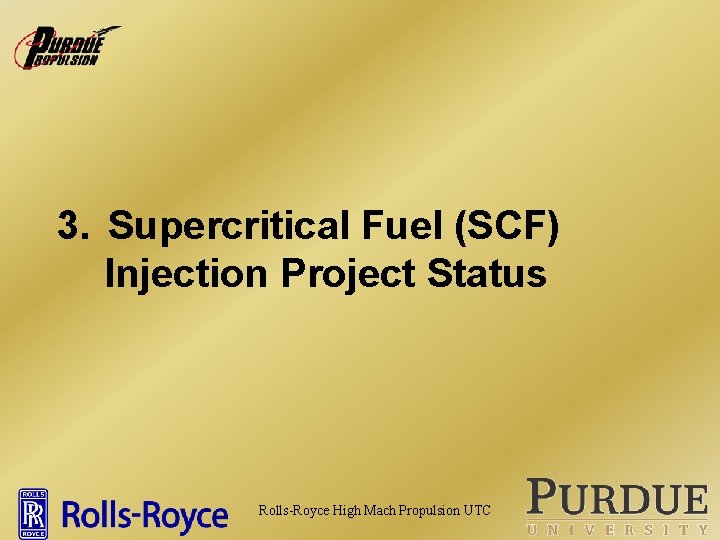
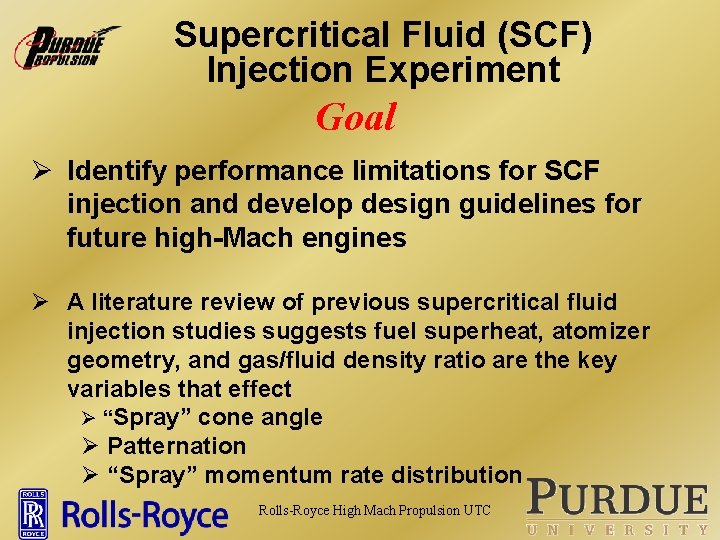
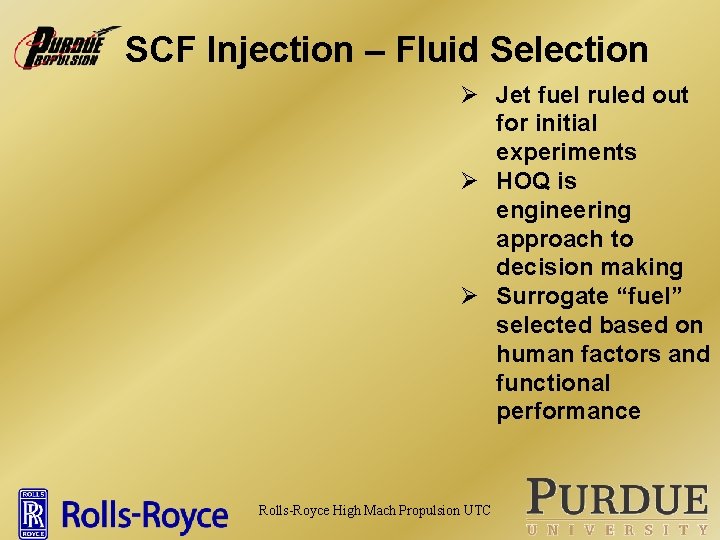
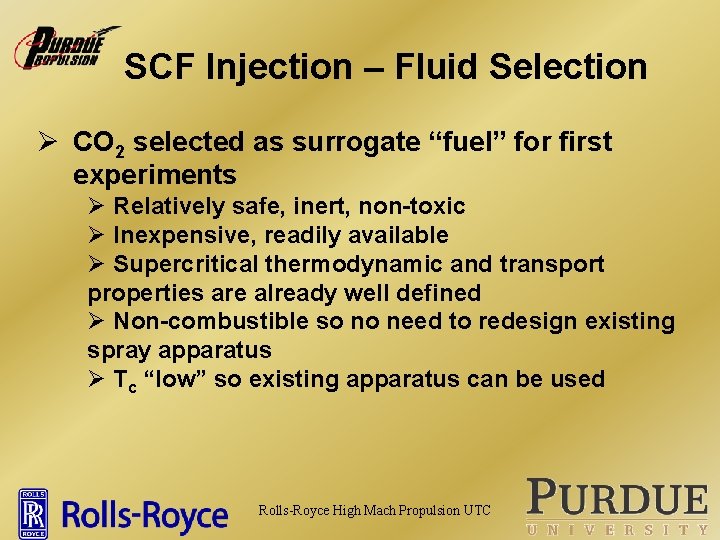
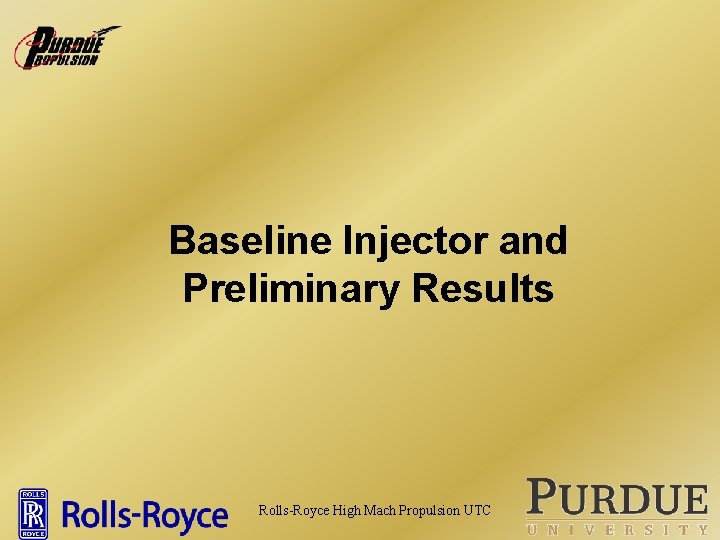
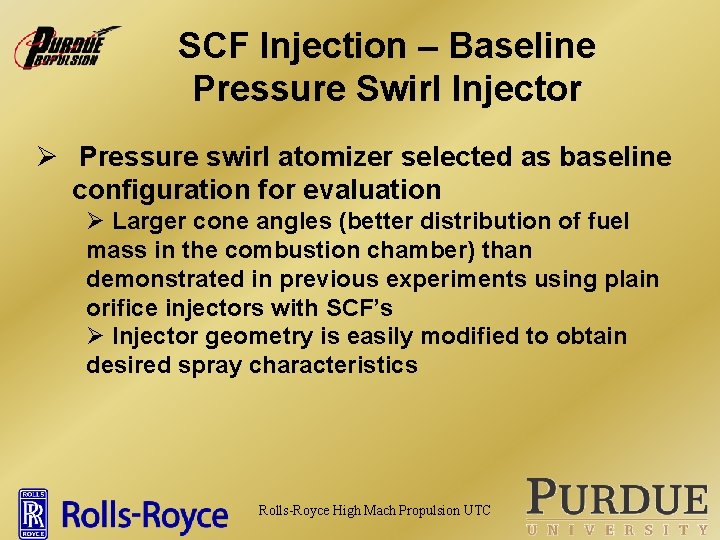
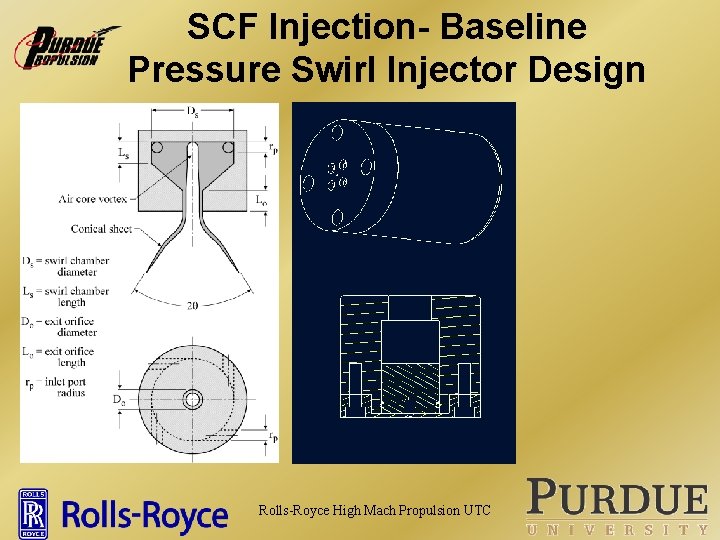
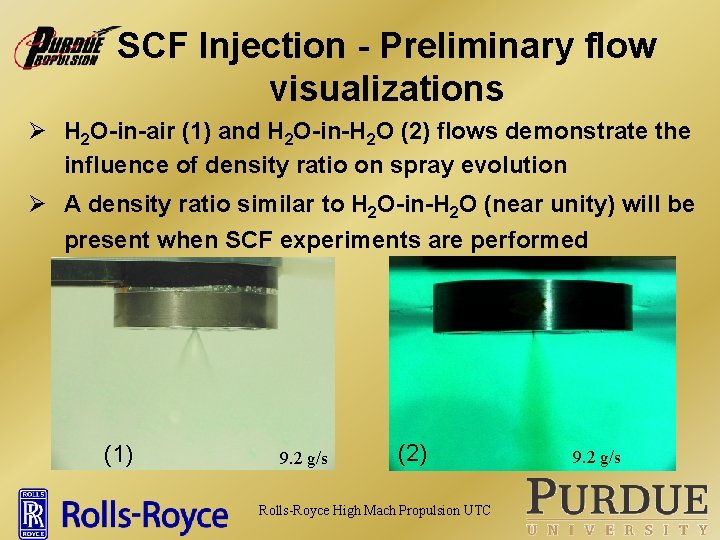
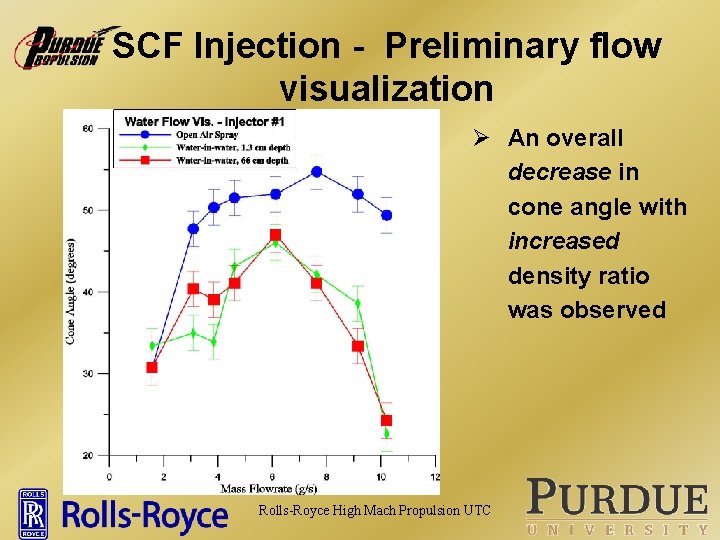
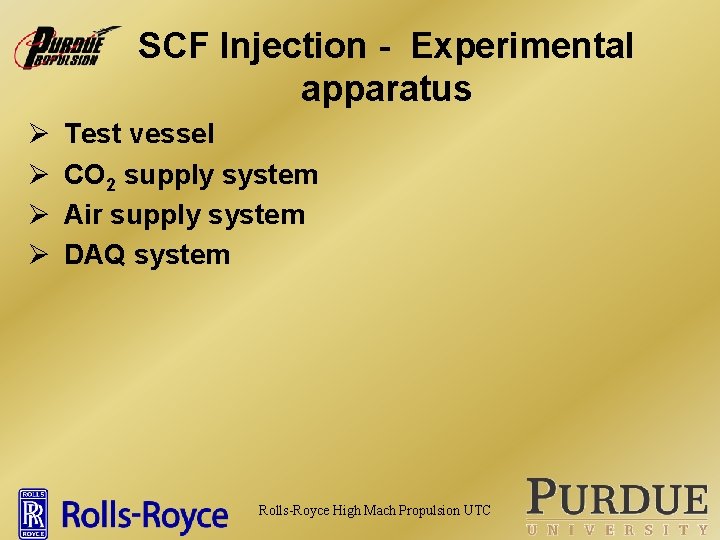
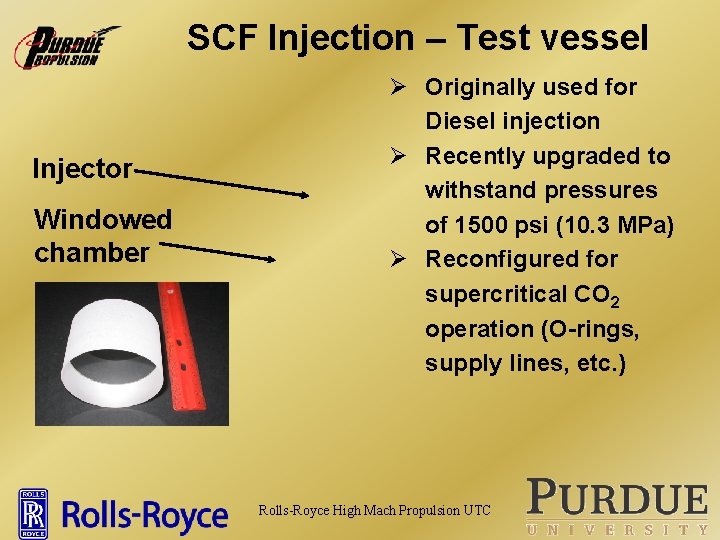
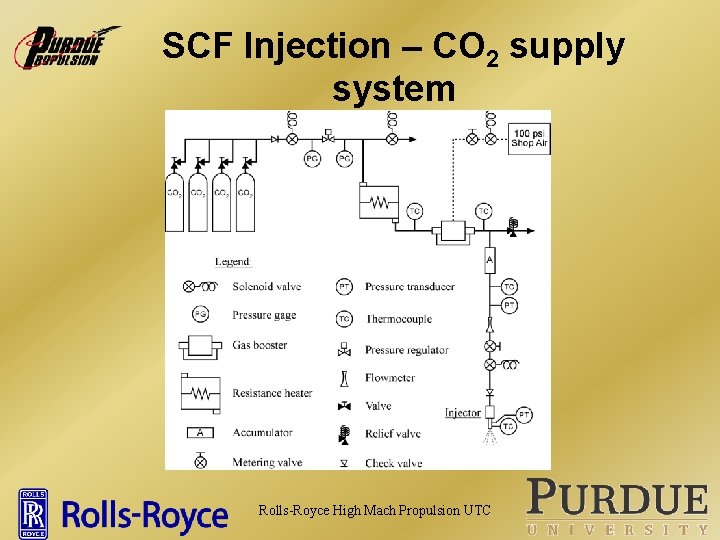
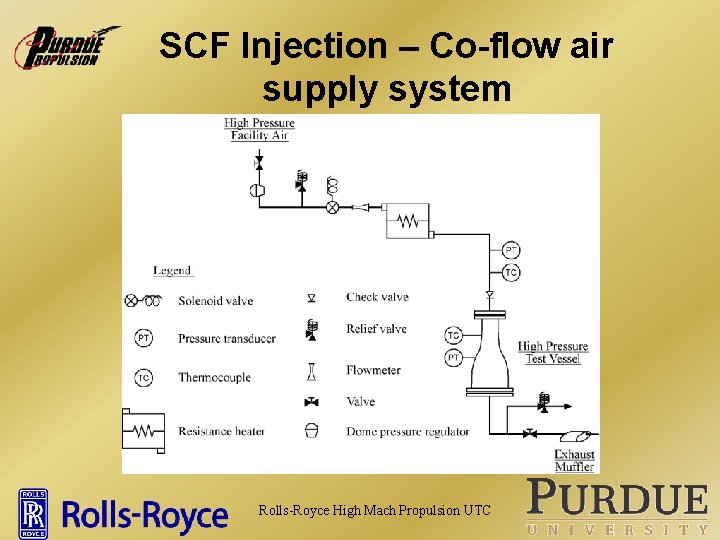
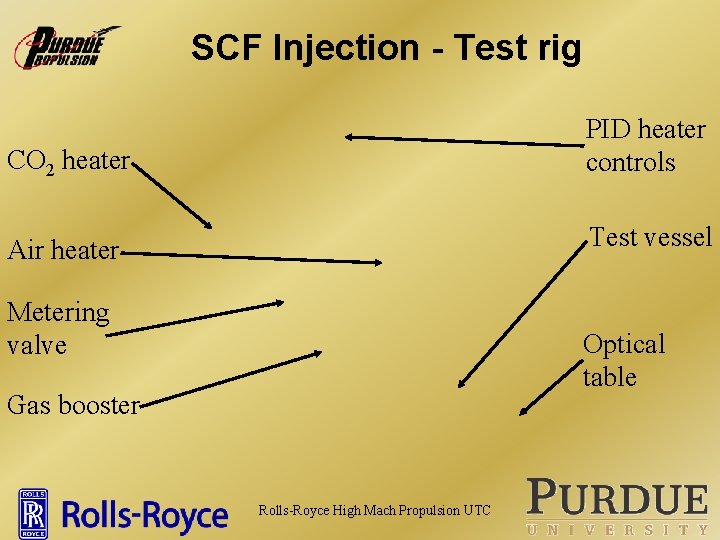
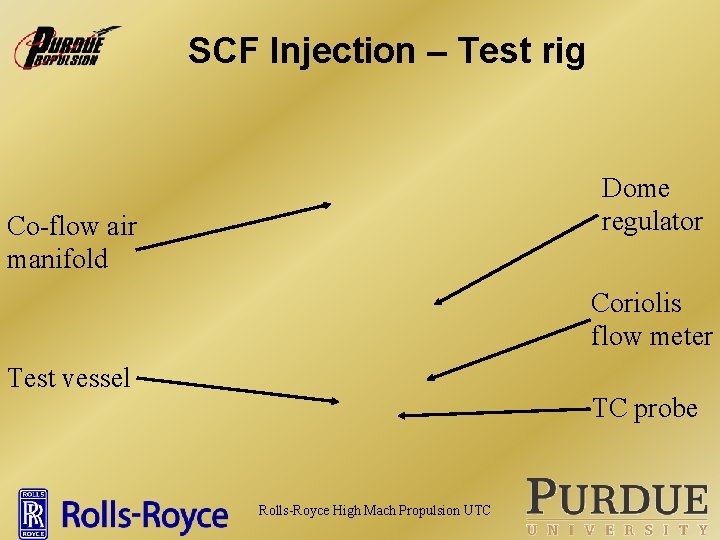
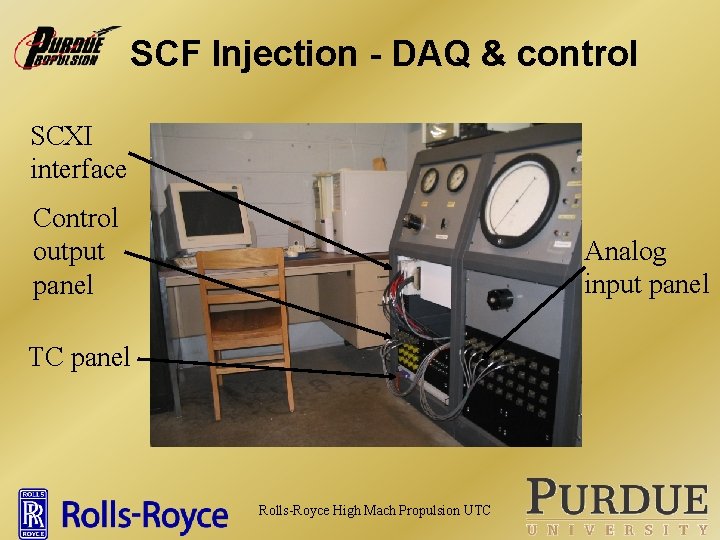
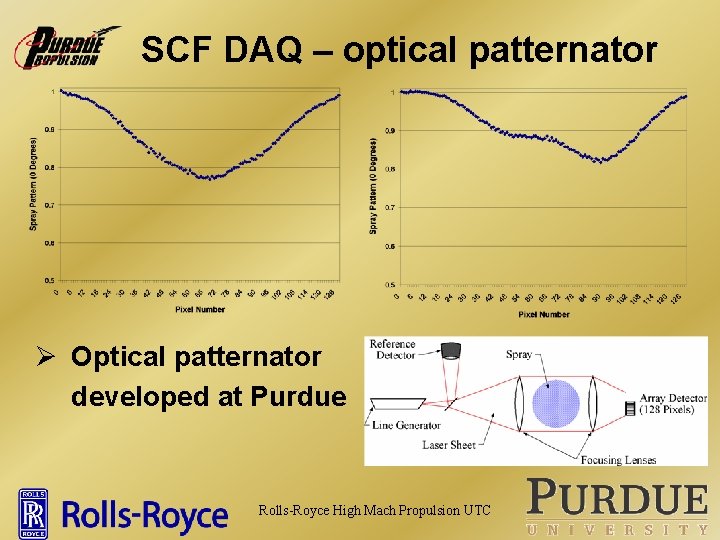
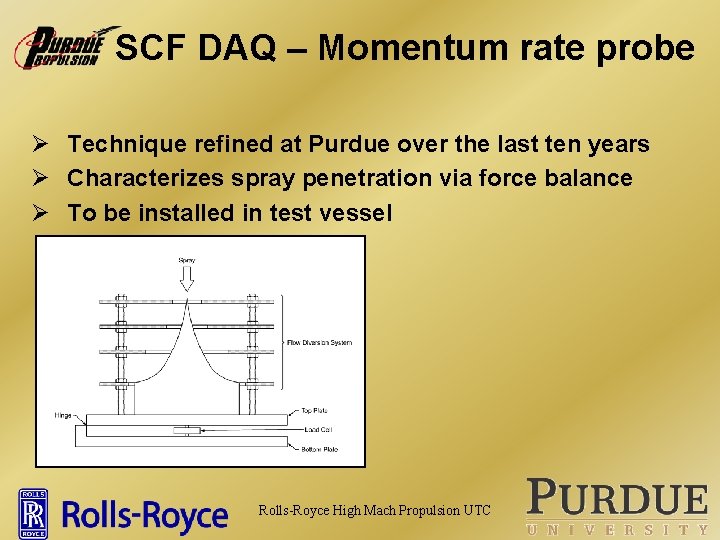
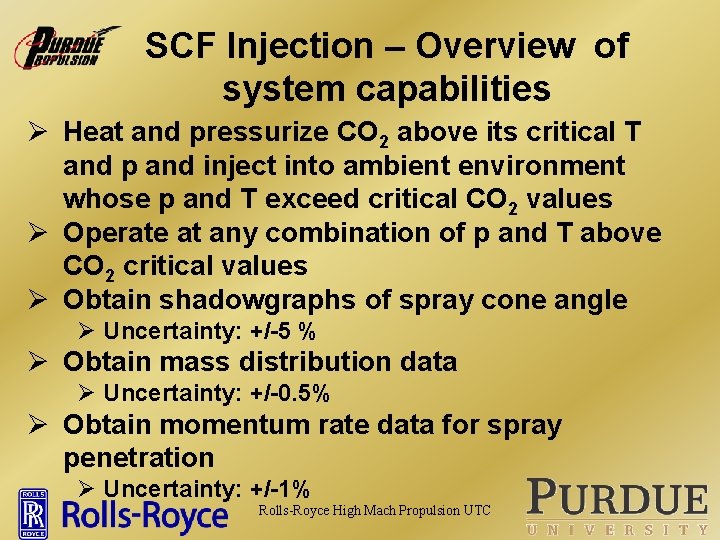
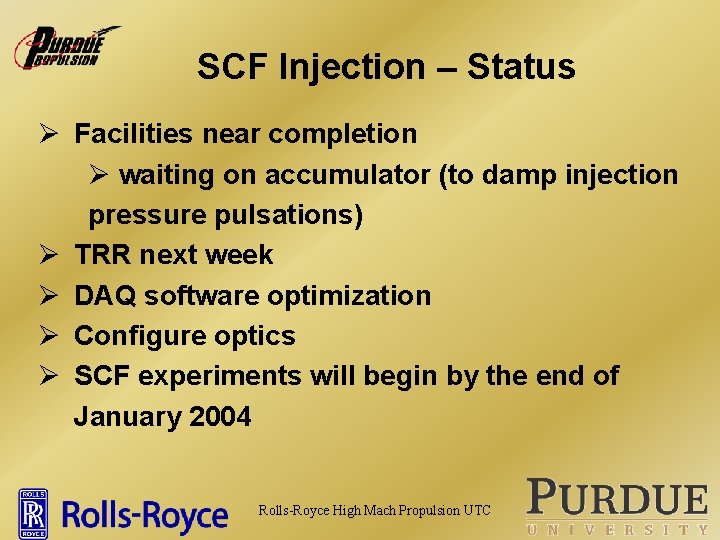
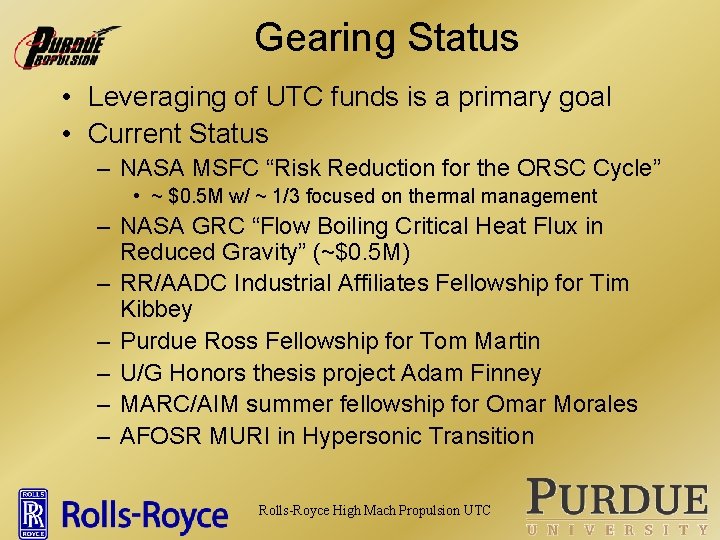
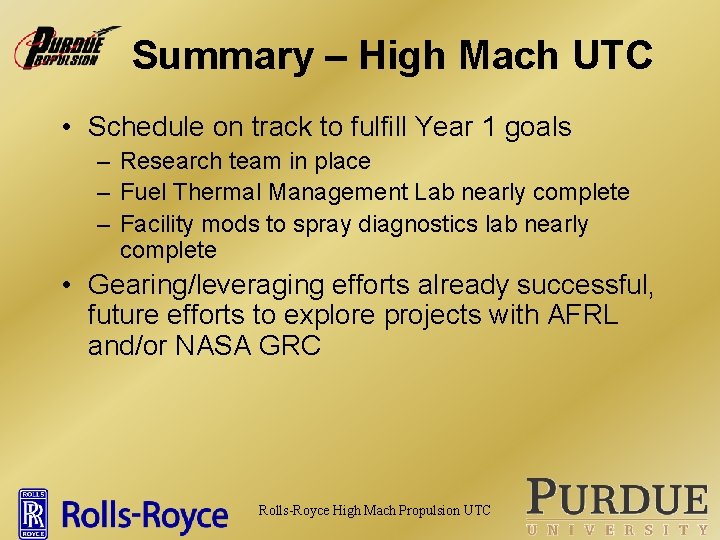
- Slides: 27
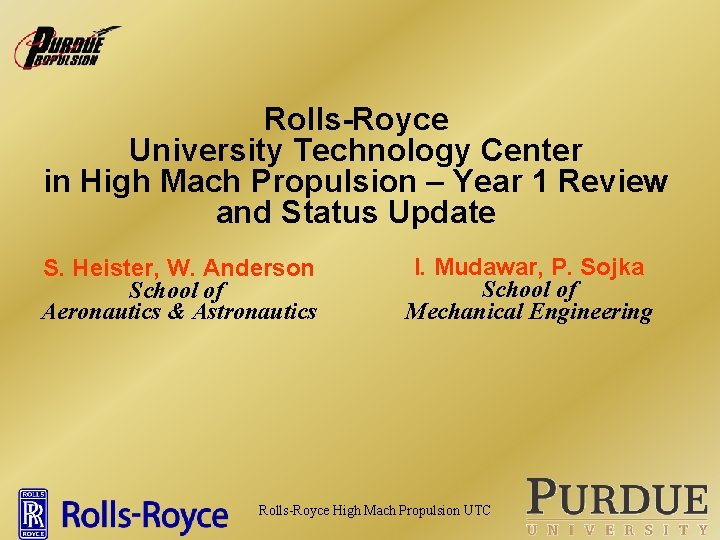
Rolls-Royce University Technology Center in High Mach Propulsion – Year 1 Review and Status Update S. Heister, W. Anderson School of Aeronautics & Astronautics I. Mudawar, P. Sojka School of Mechanical Engineering Rolls-Royce High Mach Propulsion UTC
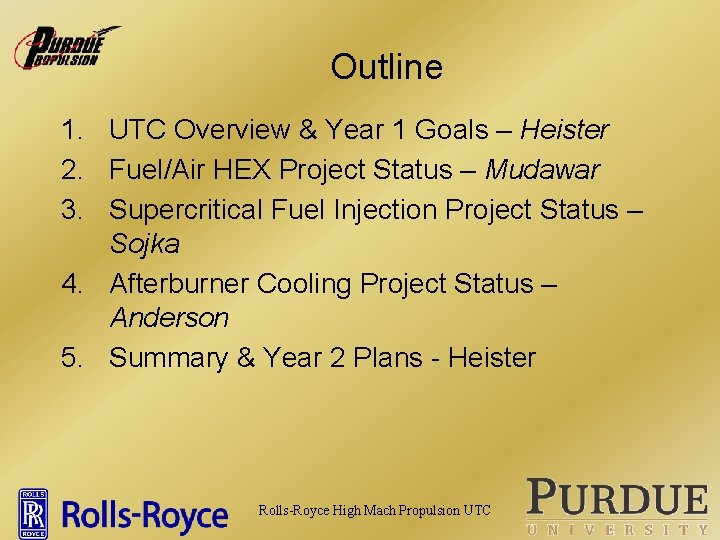
Outline 1. UTC Overview & Year 1 Goals – Heister 2. Fuel/Air HEX Project Status – Mudawar 3. Supercritical Fuel Injection Project Status – Sojka 4. Afterburner Cooling Project Status – Anderson 5. Summary & Year 2 Plans - Heister Rolls-Royce High Mach Propulsion UTC
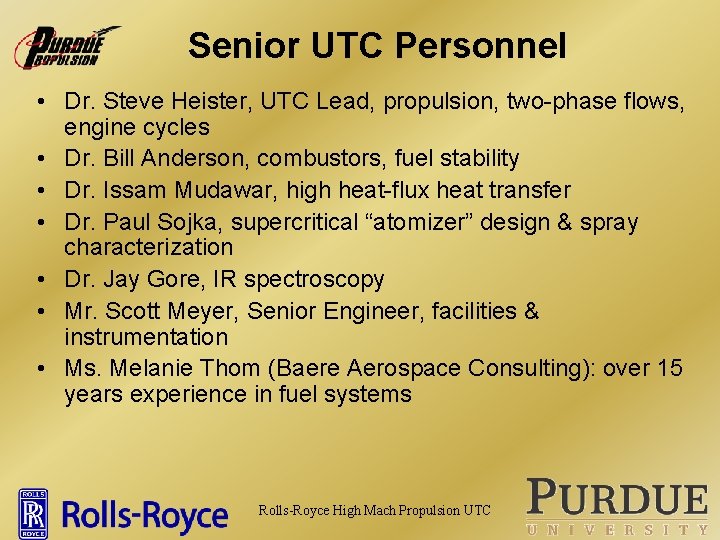
Senior UTC Personnel • Dr. Steve Heister, UTC Lead, propulsion, two-phase flows, engine cycles • Dr. Bill Anderson, combustors, fuel stability • Dr. Issam Mudawar, high heat-flux heat transfer • Dr. Paul Sojka, supercritical “atomizer” design & spray characterization • Dr. Jay Gore, IR spectroscopy • Mr. Scott Meyer, Senior Engineer, facilities & instrumentation • Ms. Melanie Thom (Baere Aerospace Consulting): over 15 years experience in fuel systems Rolls-Royce High Mach Propulsion UTC
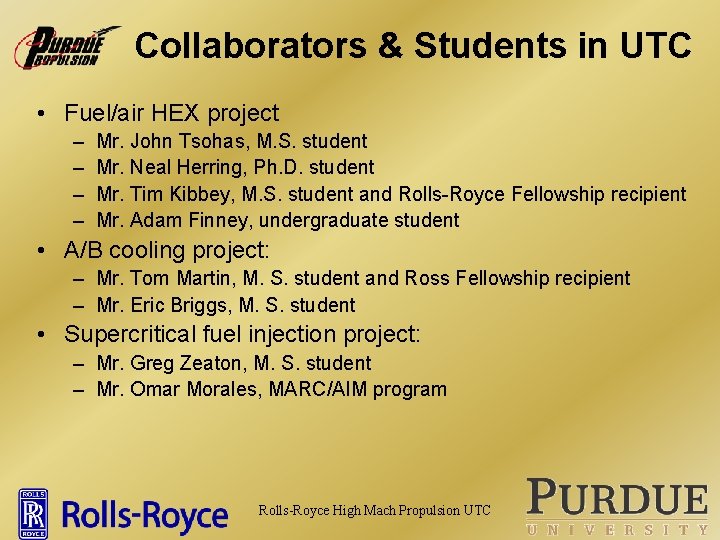
Collaborators & Students in UTC • Fuel/air HEX project – – Mr. John Tsohas, M. S. student Mr. Neal Herring, Ph. D. student Mr. Tim Kibbey, M. S. student and Rolls-Royce Fellowship recipient Mr. Adam Finney, undergraduate student • A/B cooling project: – Mr. Tom Martin, M. S. student and Ross Fellowship recipient – Mr. Eric Briggs, M. S. student • Supercritical fuel injection project: – Mr. Greg Zeaton, M. S. student – Mr. Omar Morales, MARC/AIM program Rolls-Royce High Mach Propulsion UTC
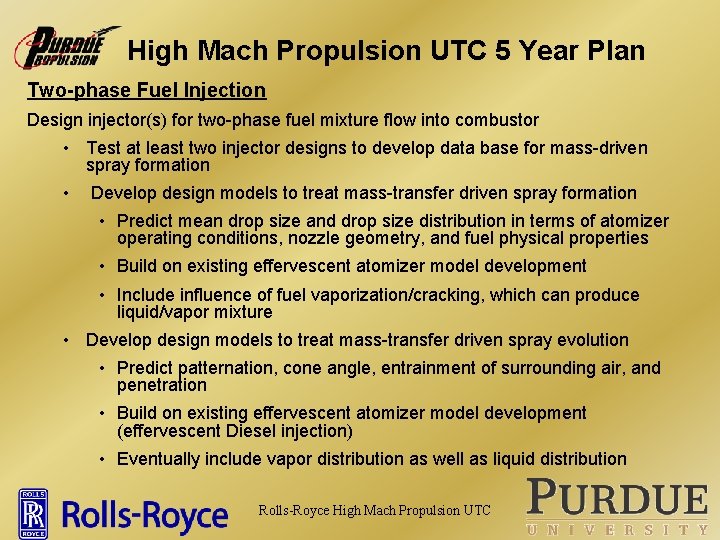
High Mach Propulsion UTC 5 Year Plan Two-phase Fuel Injection Design injector(s) for two-phase fuel mixture flow into combustor • Test at least two injector designs to develop data base for mass-driven spray formation • Develop design models to treat mass-transfer driven spray formation • Predict mean drop size and drop size distribution in terms of atomizer operating conditions, nozzle geometry, and fuel physical properties • Build on existing effervescent atomizer model development • Include influence of fuel vaporization/cracking, which can produce liquid/vapor mixture • Develop design models to treat mass-transfer driven spray evolution • Predict patternation, cone angle, entrainment of surrounding air, and penetration • Build on existing effervescent atomizer model development (effervescent Diesel injection) • Eventually include vapor distribution as well as liquid distribution Rolls-Royce High Mach Propulsion UTC
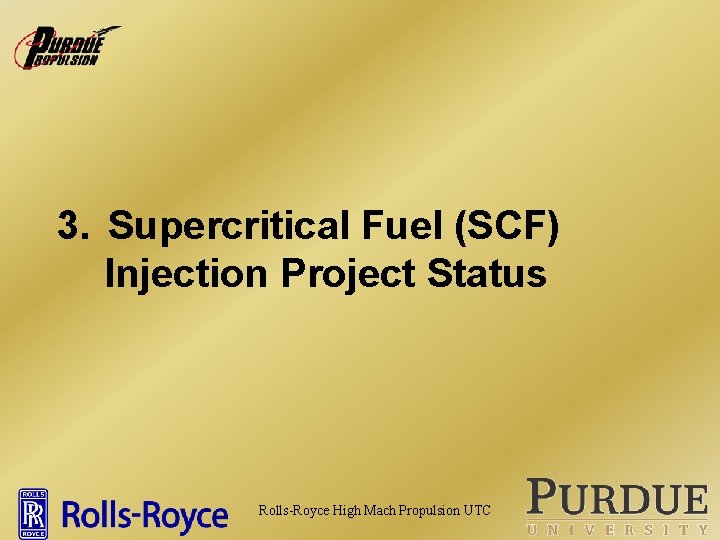
3. Supercritical Fuel (SCF) Injection Project Status Rolls-Royce High Mach Propulsion UTC
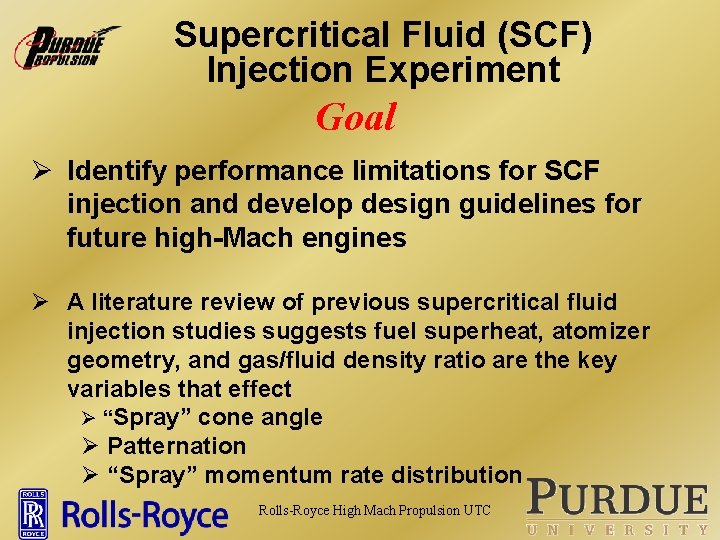
Supercritical Fluid (SCF) Injection Experiment Goal Ø Identify performance limitations for SCF injection and develop design guidelines for future high-Mach engines Ø A literature review of previous supercritical fluid injection studies suggests fuel superheat, atomizer geometry, and gas/fluid density ratio are the key variables that effect Ø “Spray” cone angle Ø Patternation Ø “Spray” momentum rate distribution Rolls-Royce High Mach Propulsion UTC
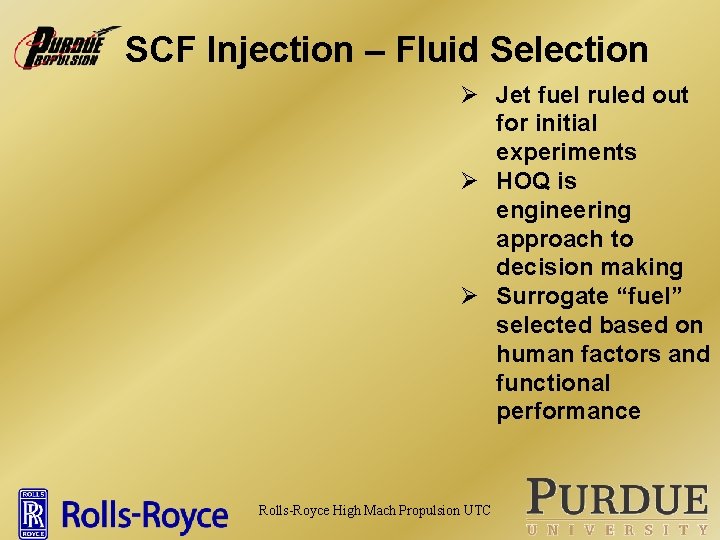
SCF Injection – Fluid Selection Ø Jet fuel ruled out for initial experiments Ø HOQ is engineering approach to decision making Ø Surrogate “fuel” selected based on human factors and functional performance Rolls-Royce High Mach Propulsion UTC
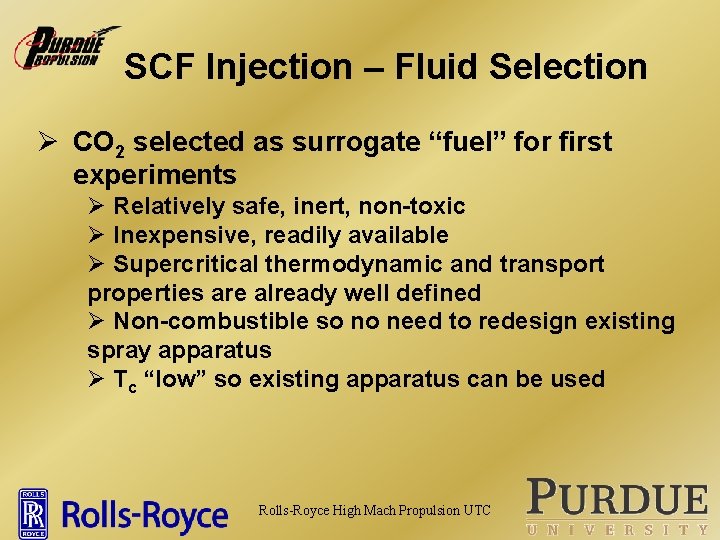
SCF Injection – Fluid Selection Ø CO 2 selected as surrogate “fuel” for first experiments Ø Relatively safe, inert, non-toxic Ø Inexpensive, readily available Ø Supercritical thermodynamic and transport properties are already well defined Ø Non-combustible so no need to redesign existing spray apparatus Ø Tc “low” so existing apparatus can be used Rolls-Royce High Mach Propulsion UTC
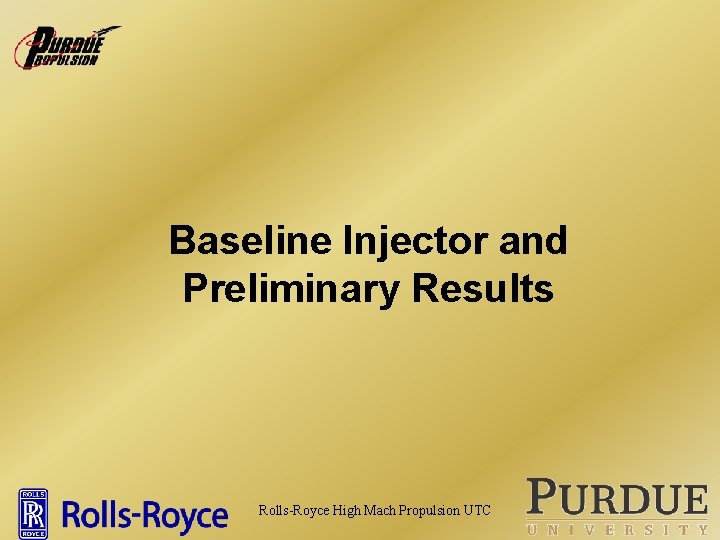
Baseline Injector and Preliminary Results Rolls-Royce High Mach Propulsion UTC
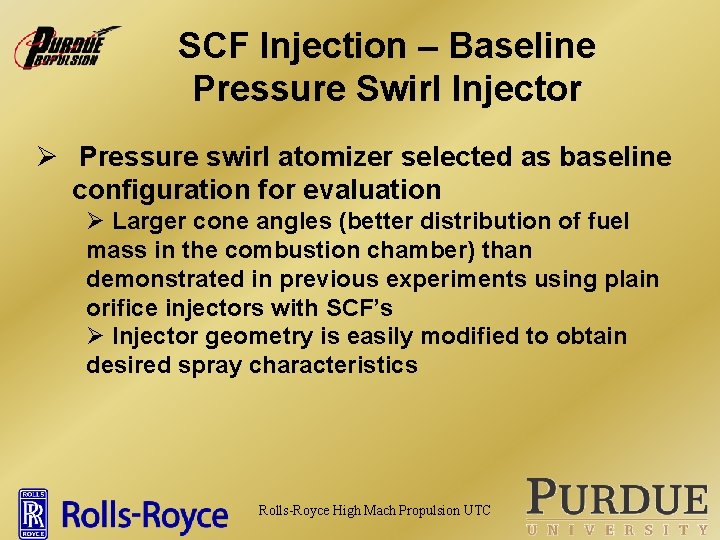
SCF Injection – Baseline Pressure Swirl Injector Ø Pressure swirl atomizer selected as baseline configuration for evaluation Ø Larger cone angles (better distribution of fuel mass in the combustion chamber) than demonstrated in previous experiments using plain orifice injectors with SCF’s Ø Injector geometry is easily modified to obtain desired spray characteristics Rolls-Royce High Mach Propulsion UTC
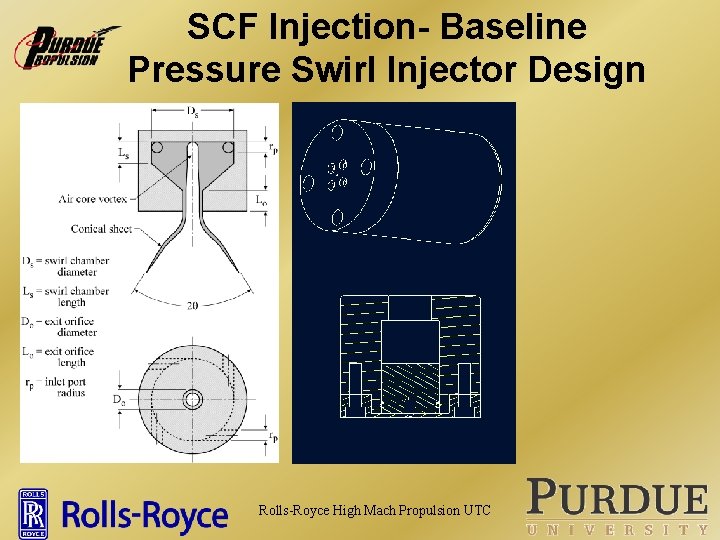
SCF Injection- Baseline Pressure Swirl Injector Design Rolls-Royce High Mach Propulsion UTC
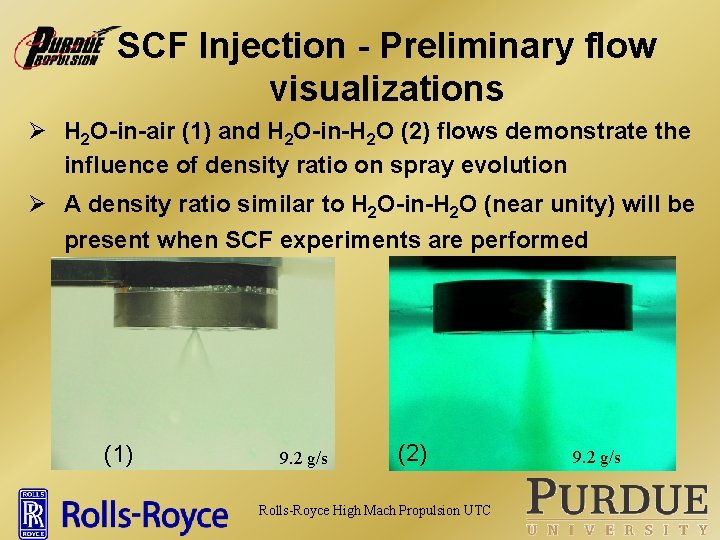
SCF Injection - Preliminary flow visualizations Ø H 2 O-in-air (1) and H 2 O-in-H 2 O (2) flows demonstrate the influence of density ratio on spray evolution Ø A density ratio similar to H 2 O-in-H 2 O (near unity) will be present when SCF experiments are performed (1) 9. 2 g/s (2) Rolls-Royce High Mach Propulsion UTC 9. 2 g/s
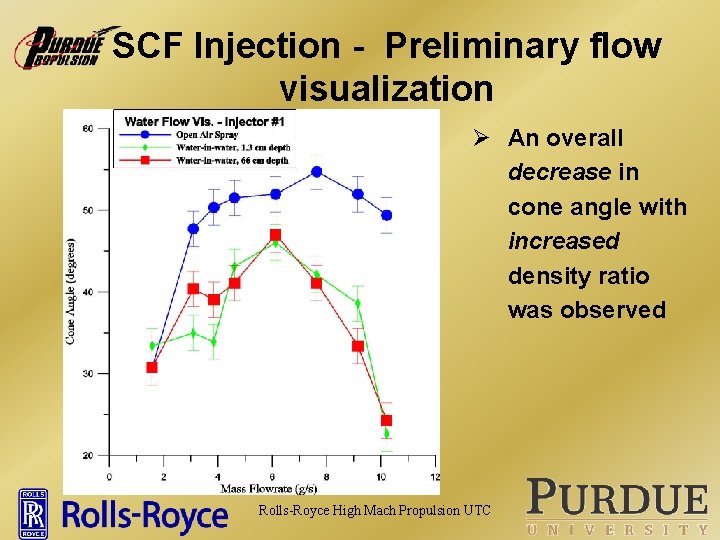
SCF Injection - Preliminary flow visualization Ø An overall decrease in cone angle with increased density ratio was observed Rolls-Royce High Mach Propulsion UTC
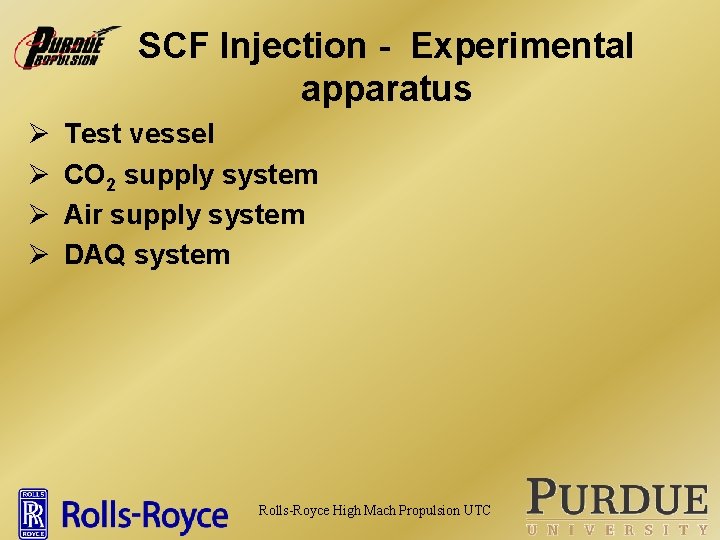
SCF Injection - Experimental apparatus Ø Ø Test vessel CO 2 supply system Air supply system DAQ system Rolls-Royce High Mach Propulsion UTC
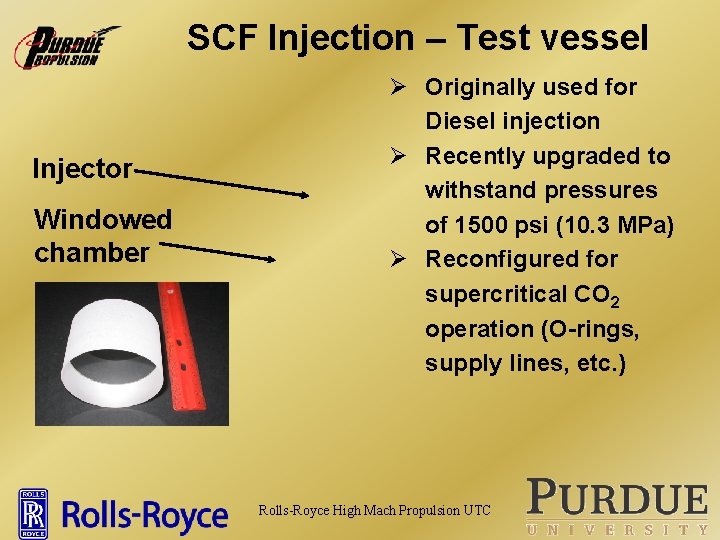
SCF Injection – Test vessel Injector Windowed chamber Ø Originally used for Diesel injection Ø Recently upgraded to withstand pressures of 1500 psi (10. 3 MPa) Ø Reconfigured for supercritical CO 2 operation (O-rings, supply lines, etc. ) Rolls-Royce High Mach Propulsion UTC
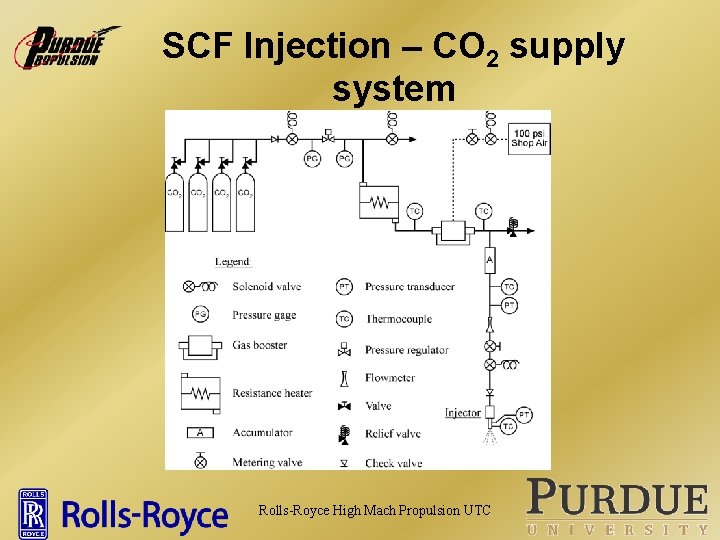
SCF Injection – CO 2 supply system Rolls-Royce High Mach Propulsion UTC
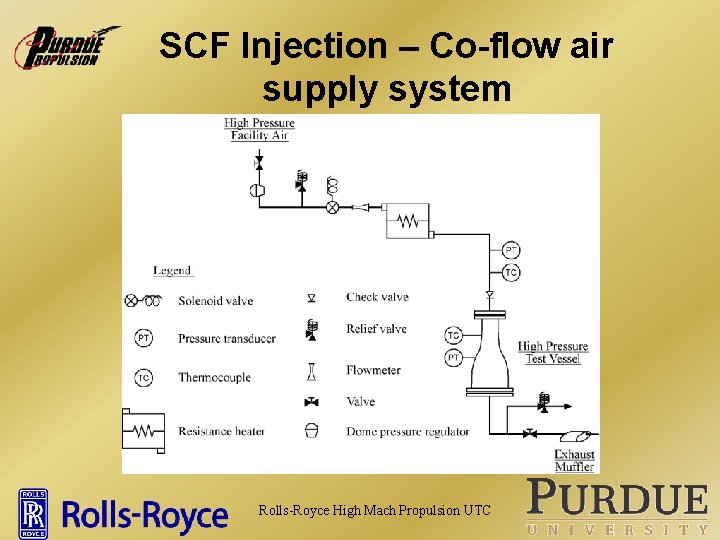
SCF Injection – Co-flow air supply system Rolls-Royce High Mach Propulsion UTC
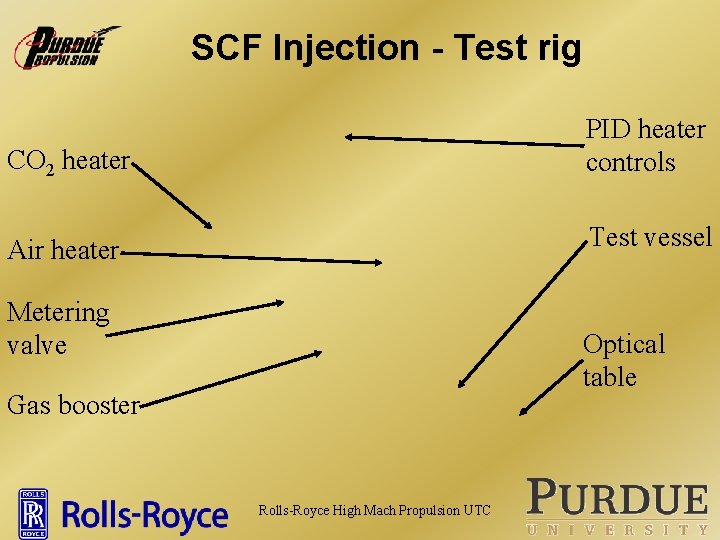
SCF Injection - Test rig CO 2 heater PID heater controls Air heater Test vessel Metering valve Optical table Gas booster Rolls-Royce High Mach Propulsion UTC
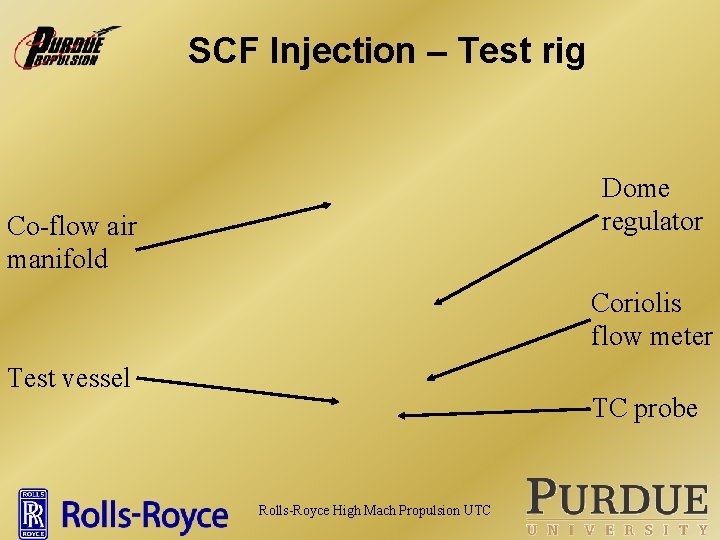
SCF Injection – Test rig Dome regulator Co-flow air manifold Coriolis flow meter Test vessel TC probe Rolls-Royce High Mach Propulsion UTC
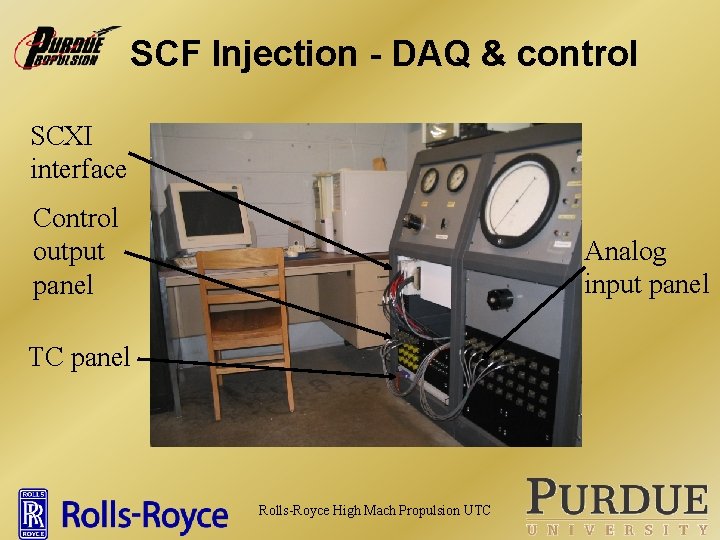
SCF Injection - DAQ & control SCXI interface Control output panel Analog input panel TC panel Rolls-Royce High Mach Propulsion UTC
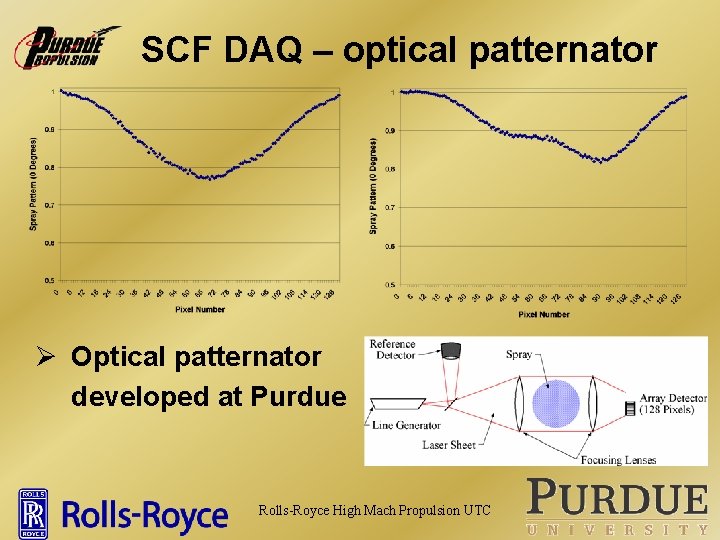
SCF DAQ – optical patternator Ø Optical patternator developed at Purdue Rolls-Royce High Mach Propulsion UTC
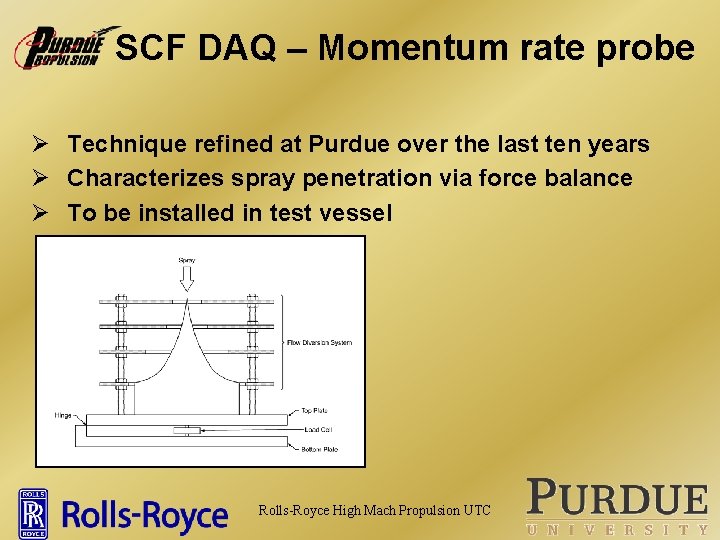
SCF DAQ – Momentum rate probe Ø Technique refined at Purdue over the last ten years Ø Characterizes spray penetration via force balance Ø To be installed in test vessel Rolls-Royce High Mach Propulsion UTC
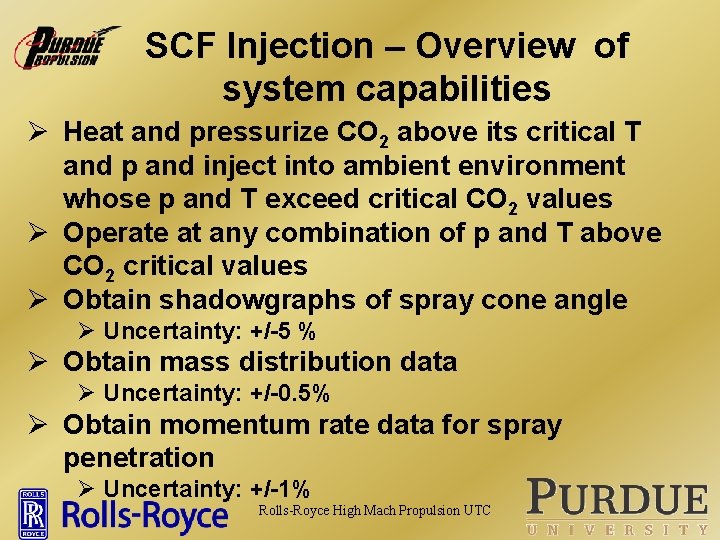
SCF Injection – Overview of system capabilities Ø Heat and pressurize CO 2 above its critical T and p and inject into ambient environment whose p and T exceed critical CO 2 values Ø Operate at any combination of p and T above CO 2 critical values Ø Obtain shadowgraphs of spray cone angle Ø Uncertainty: +/-5 % Ø Obtain mass distribution data Ø Uncertainty: +/-0. 5% Ø Obtain momentum rate data for spray penetration Ø Uncertainty: +/-1% Rolls-Royce High Mach Propulsion UTC
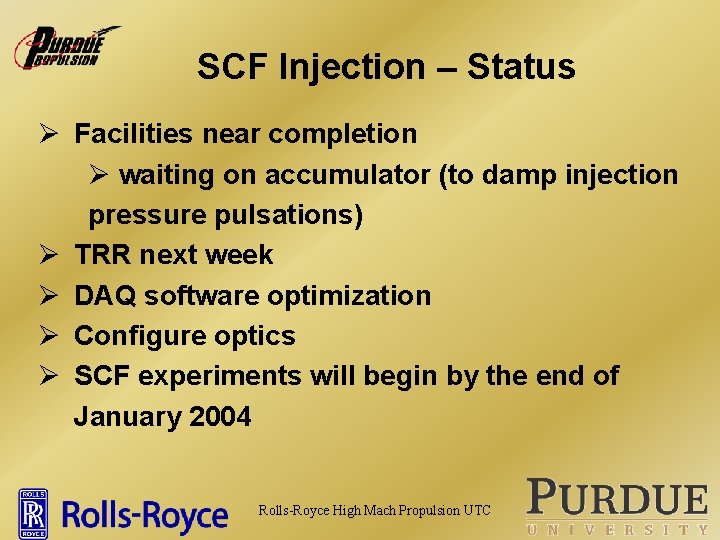
SCF Injection – Status Ø Facilities near completion Ø waiting on accumulator (to damp injection pressure pulsations) Ø TRR next week Ø DAQ software optimization Ø Configure optics Ø SCF experiments will begin by the end of January 2004 Rolls-Royce High Mach Propulsion UTC
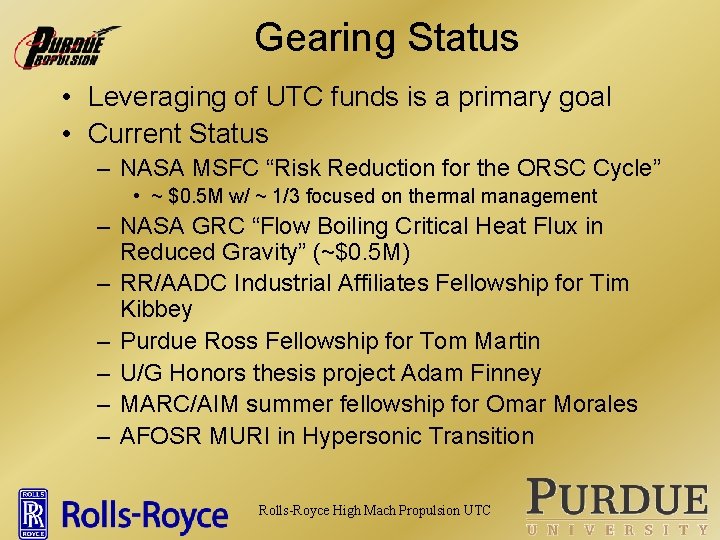
Gearing Status • Leveraging of UTC funds is a primary goal • Current Status – NASA MSFC “Risk Reduction for the ORSC Cycle” • ~ $0. 5 M w/ ~ 1/3 focused on thermal management – NASA GRC “Flow Boiling Critical Heat Flux in Reduced Gravity” (~$0. 5 M) – RR/AADC Industrial Affiliates Fellowship for Tim Kibbey – Purdue Ross Fellowship for Tom Martin – U/G Honors thesis project Adam Finney – MARC/AIM summer fellowship for Omar Morales – AFOSR MURI in Hypersonic Transition Rolls-Royce High Mach Propulsion UTC
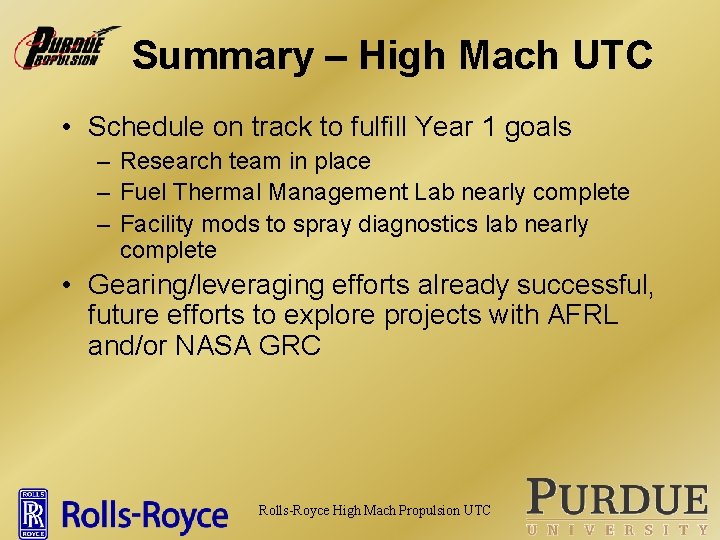
Summary – High Mach UTC • Schedule on track to fulfill Year 1 goals – Research team in place – Fuel Thermal Management Lab nearly complete – Facility mods to spray diagnostics lab nearly complete • Gearing/leveraging efforts already successful, future efforts to explore projects with AFRL and/or NASA GRC Rolls-Royce High Mach Propulsion UTC
Inertial propulsion
Propulsión en el sistema digestivo
Mouvement de bennet
Propulsion efficiency
Cps supplier portal
Propulsion efficiency
Stern landing vessel propulsion
Vasimr
Nuclear propulsion officer
Spacex chemical engineer salary
Siva de scalzo
Nuclear propulsion
Propellantless propulsion
Nuclear thermal propulsion
10 year old sarah stands on a skateboard
Mach's principle
Dreidimensionaler potentialtopf
Prandtl glauert rule
Mach zehnder modulator optisystem
Mach number formula
Mach number formula
Aerodynamic shape vs aerofoil shape
Sơ đồ mạch điện chiều dòng điện
Process management in mach
Mach disk
Mach band effect in computer graphics
Irene mach
Mach number in fluid mechanics