QUALITY MANAGEMENT QUALITY What Is Quality There are
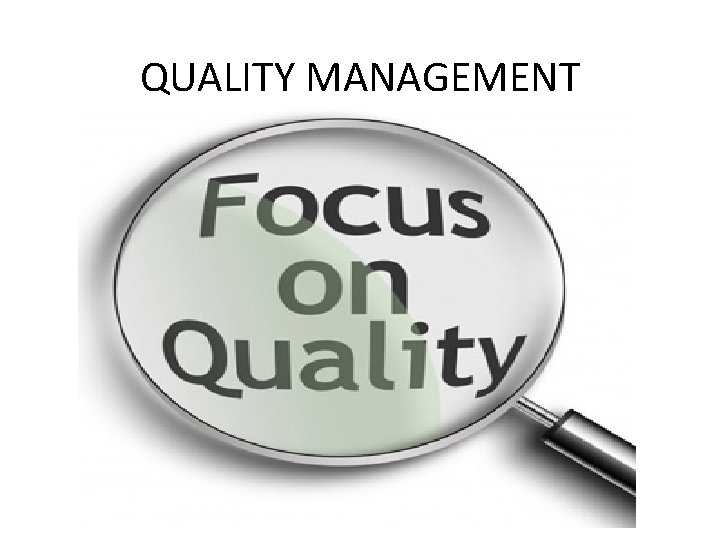
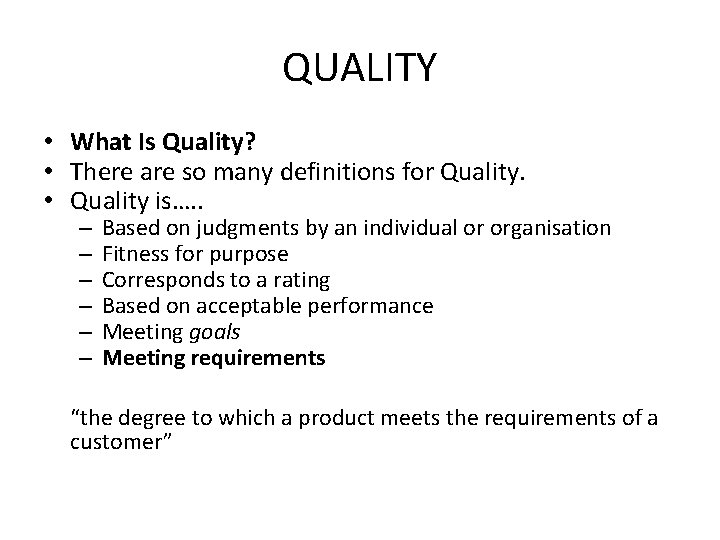
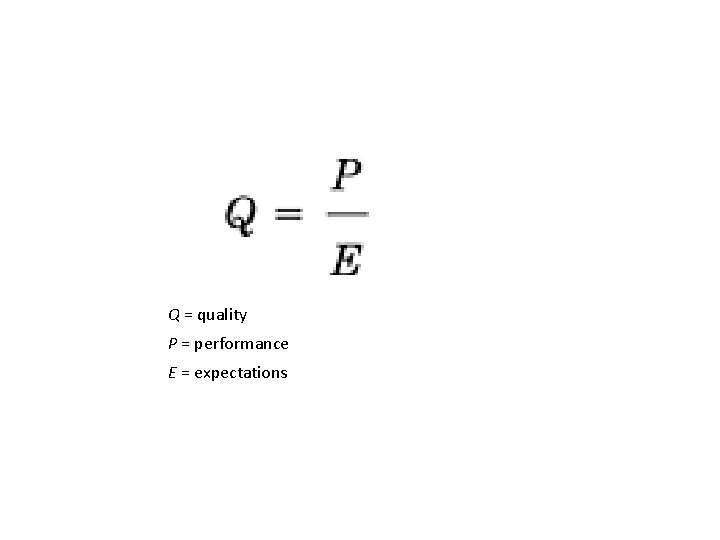
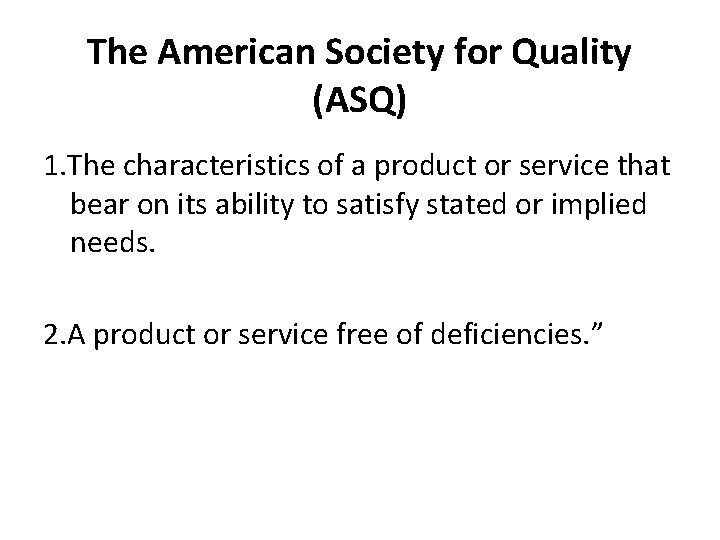
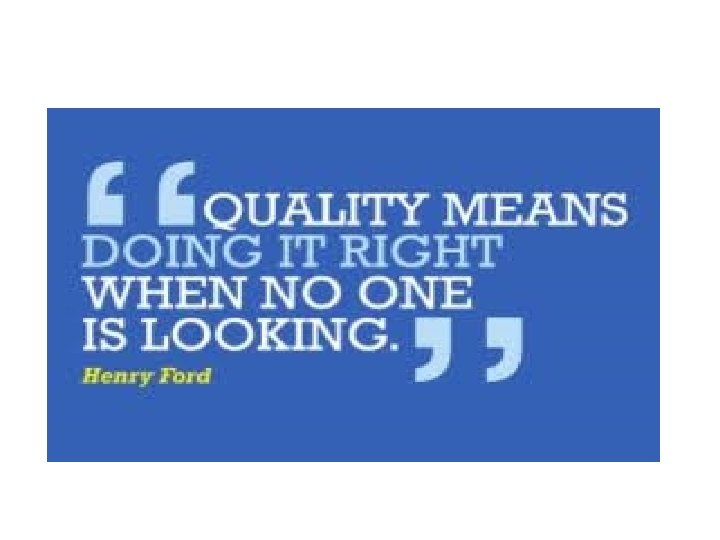
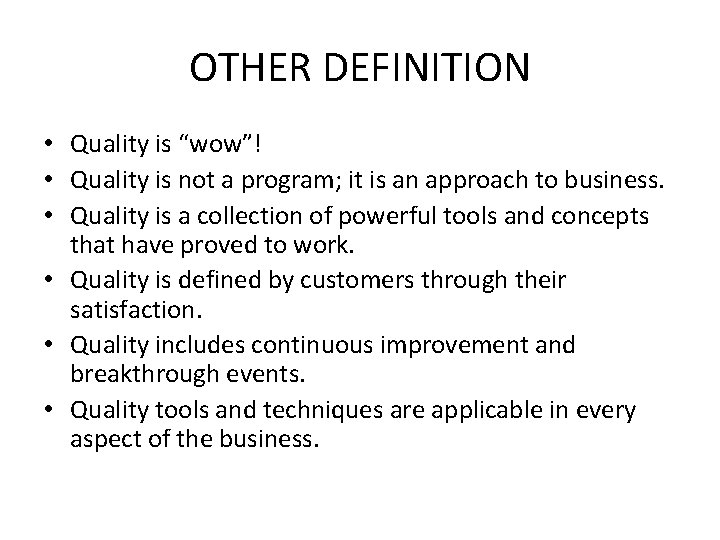
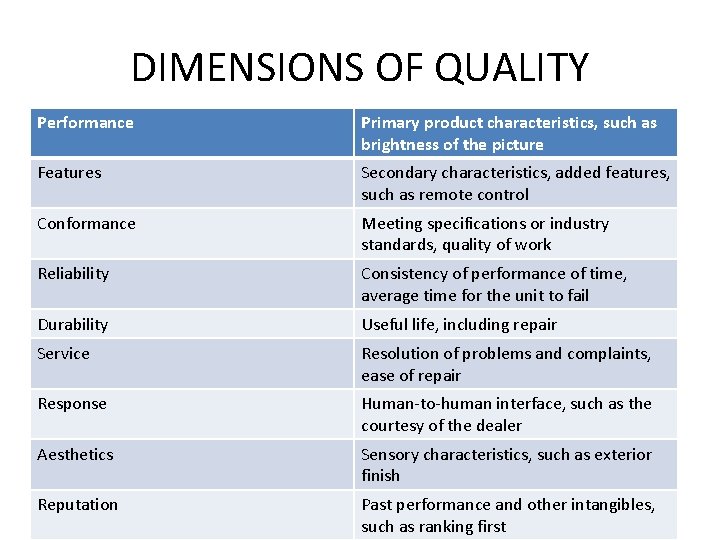
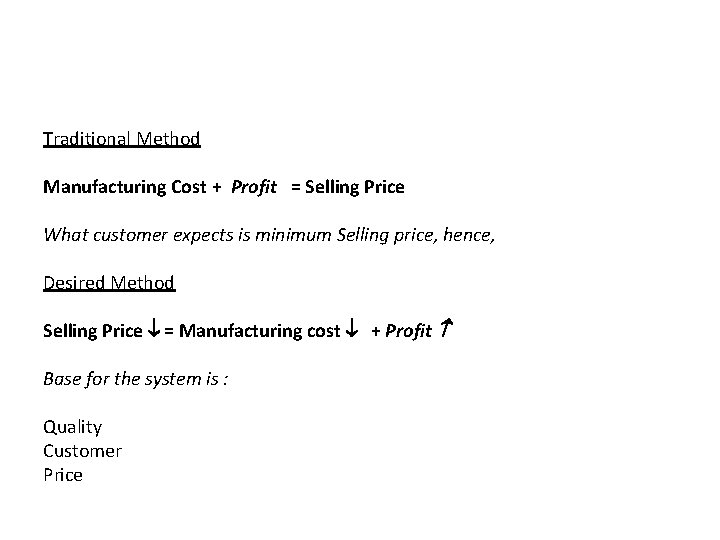
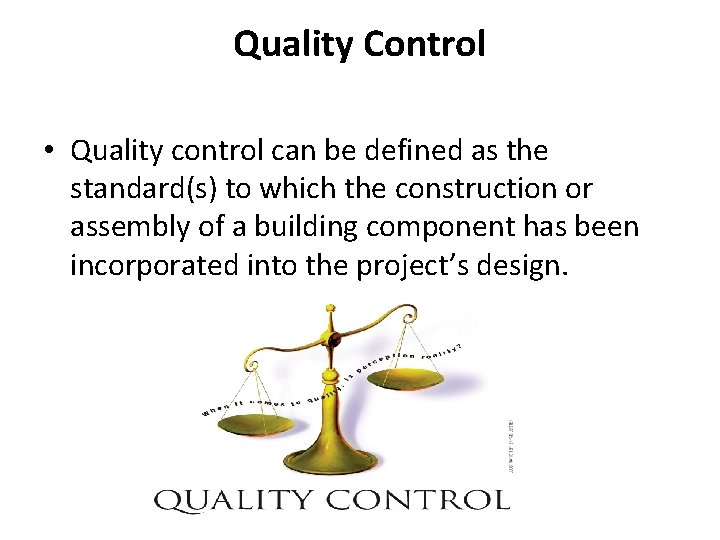
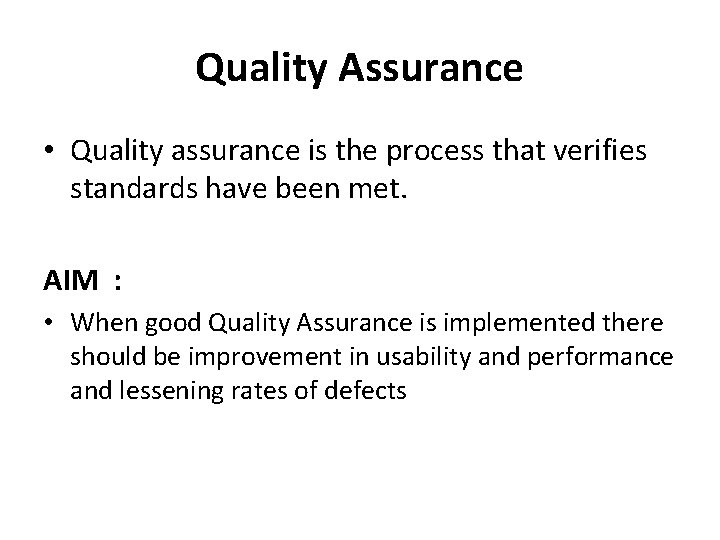
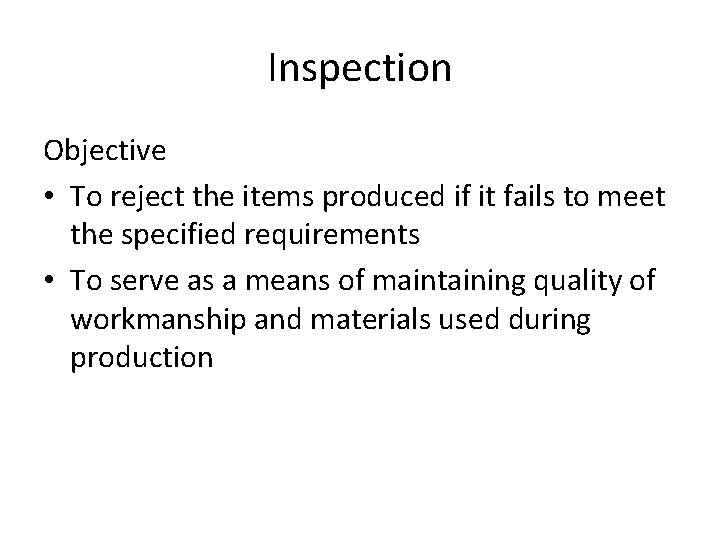
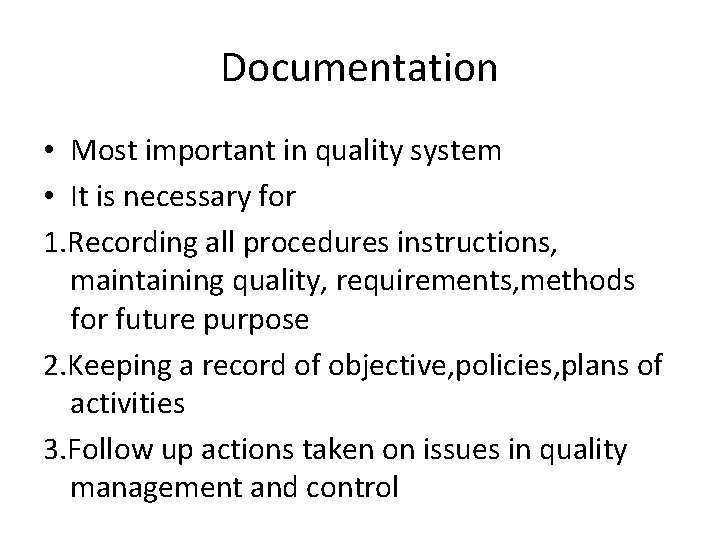
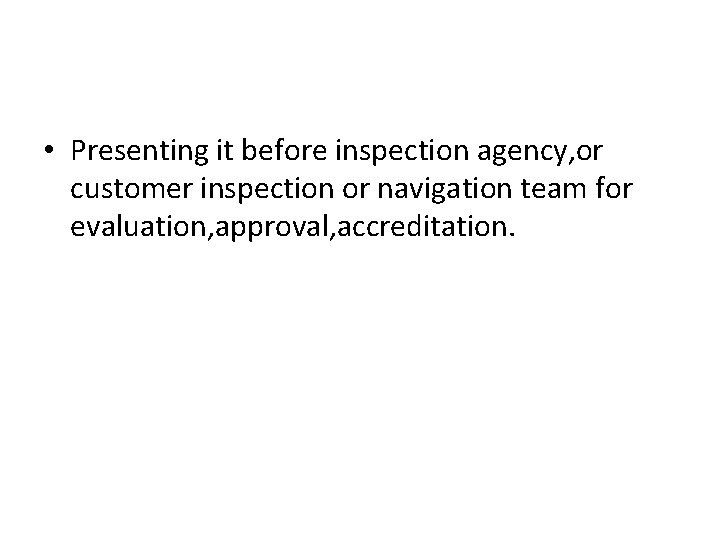
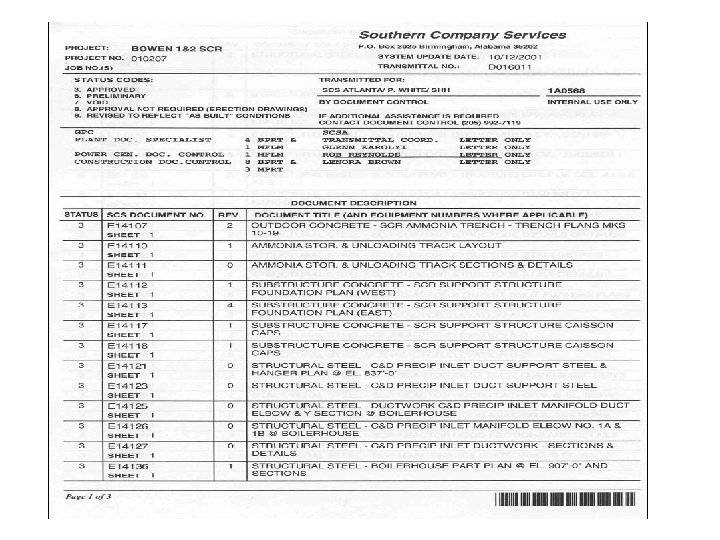
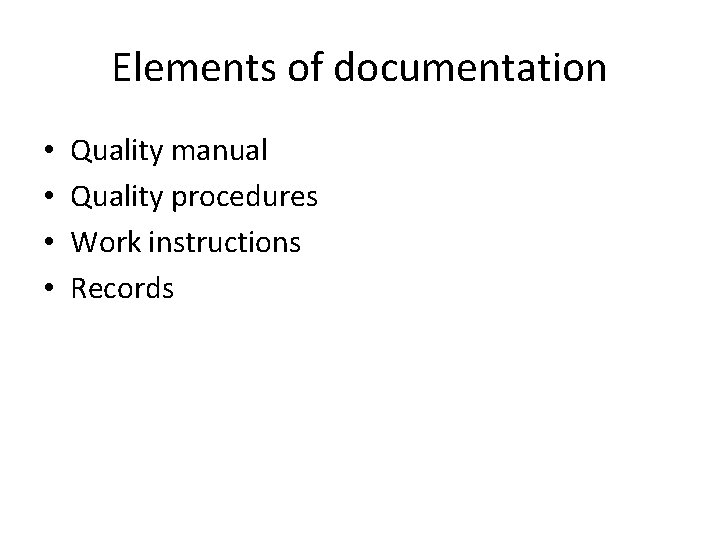
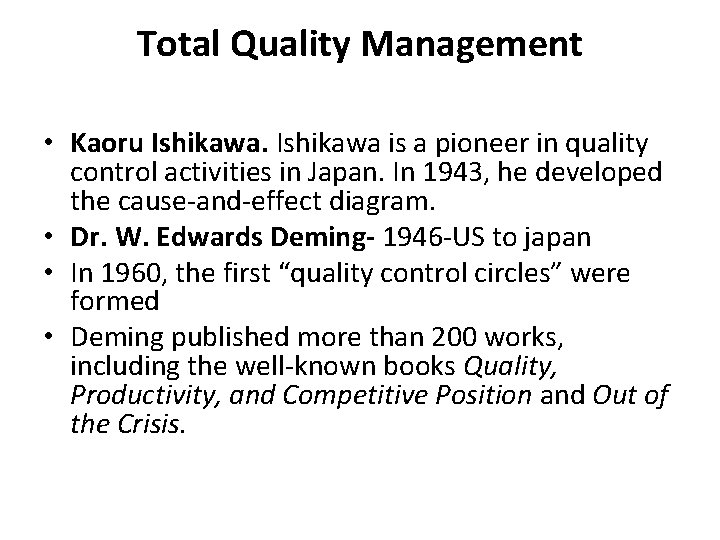
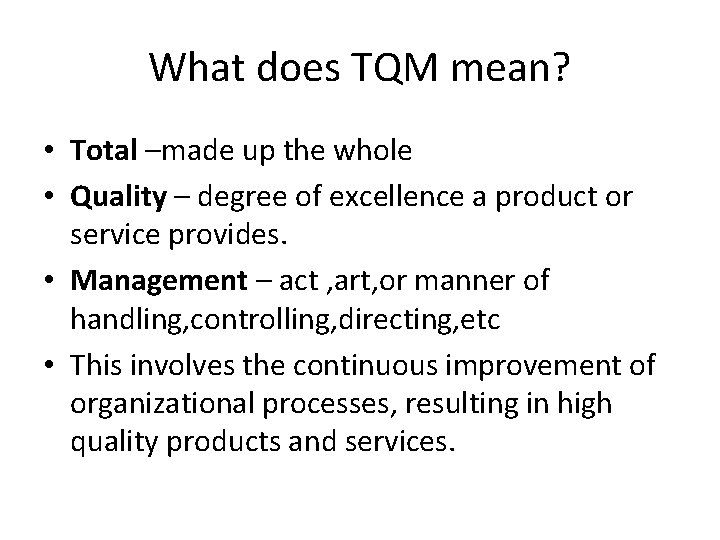
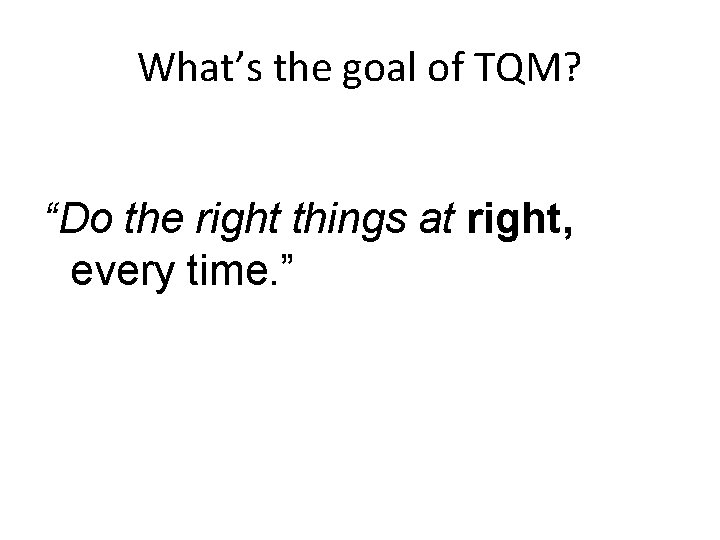
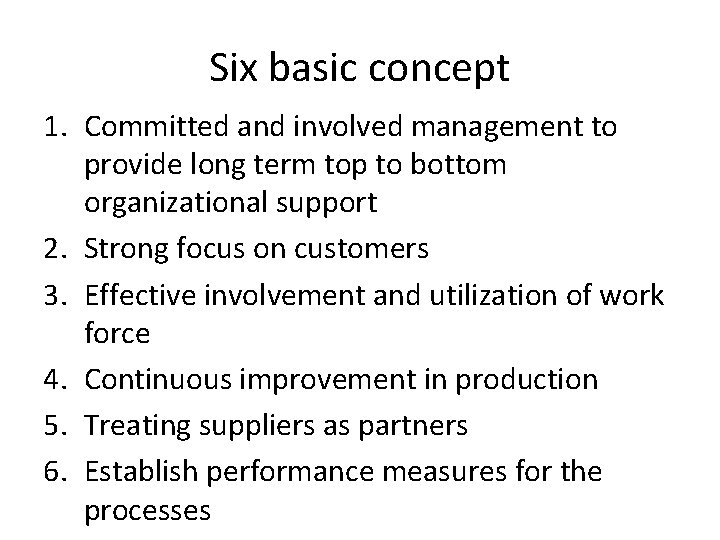
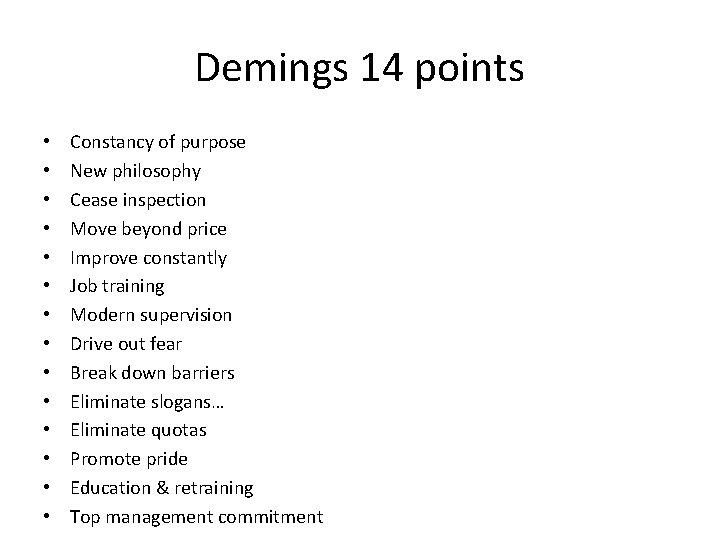
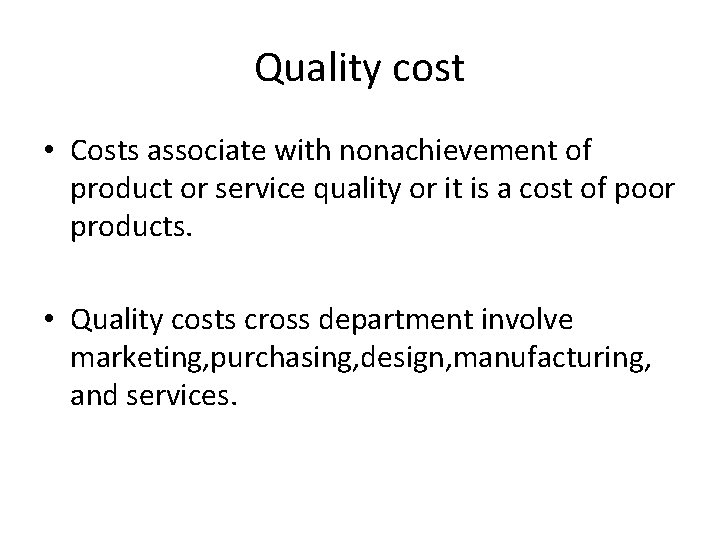
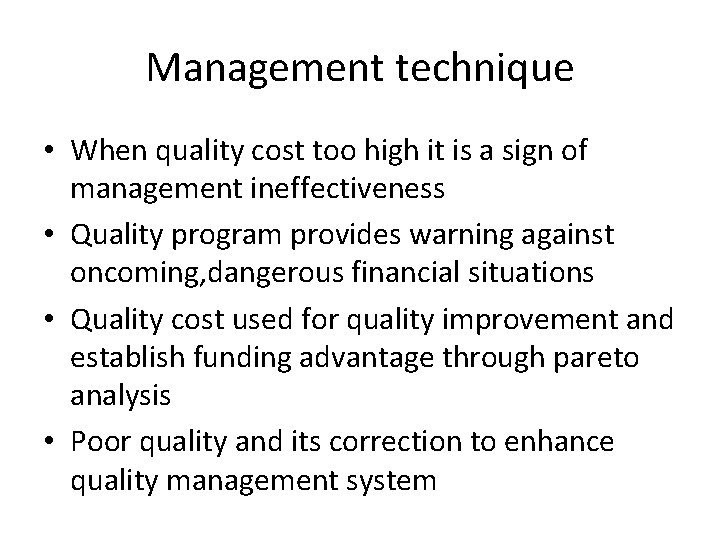
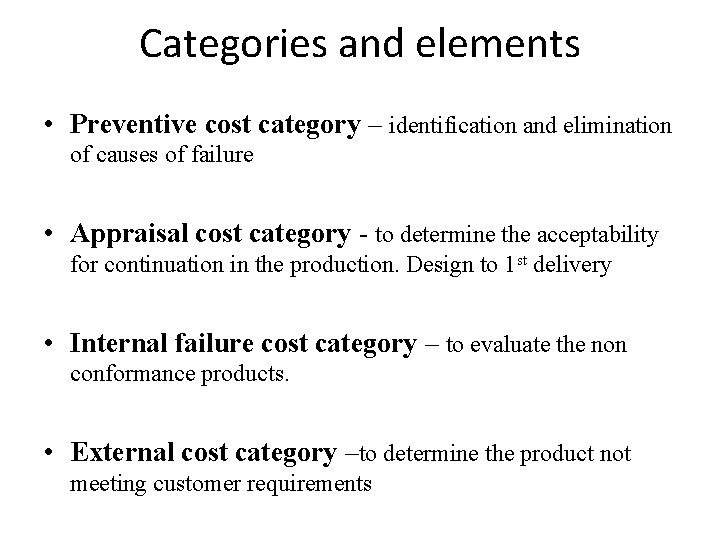
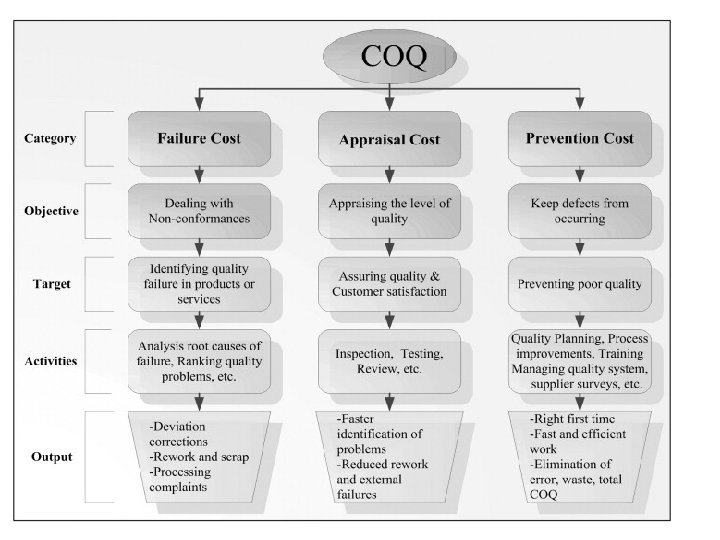
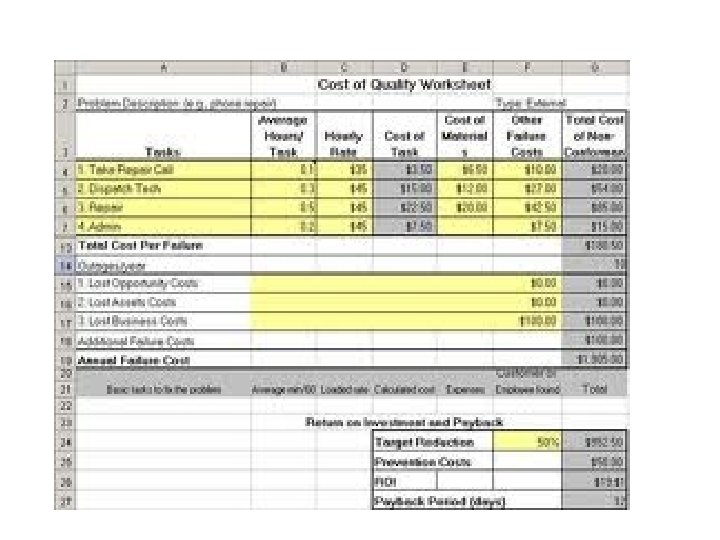
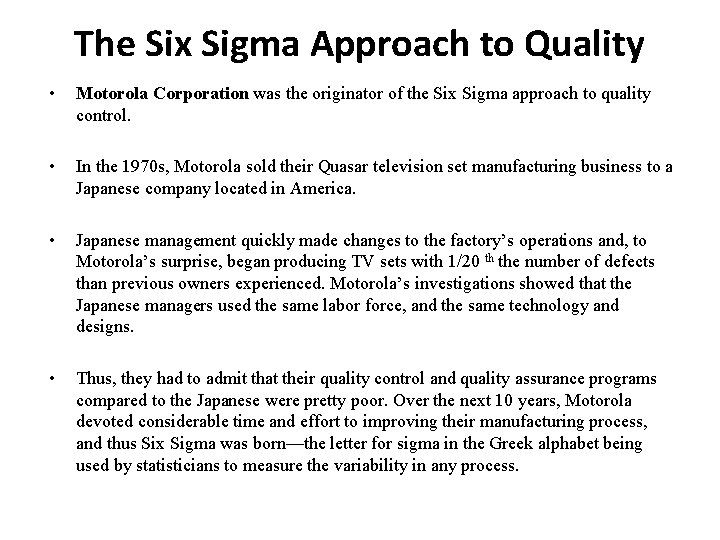
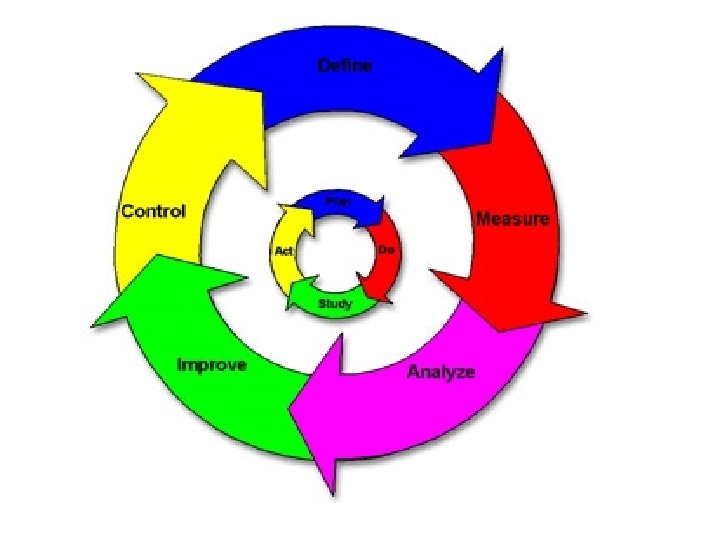
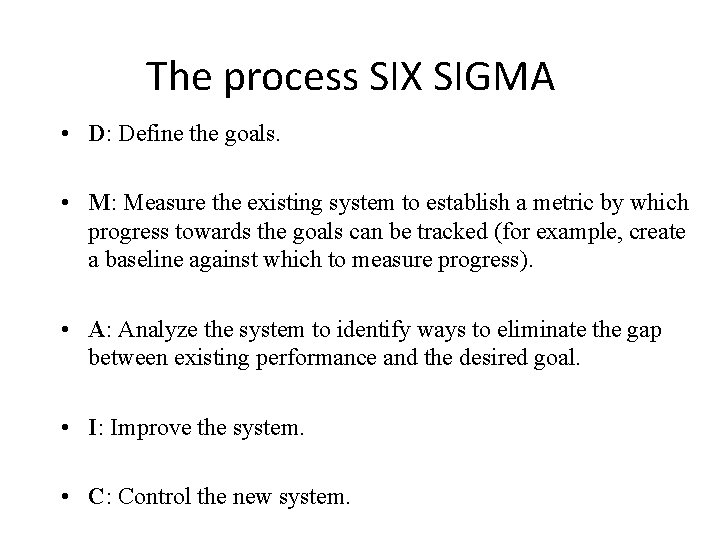
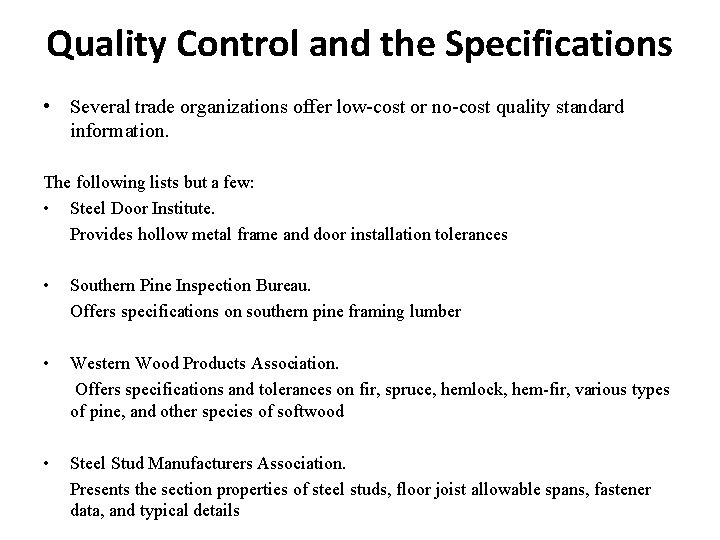
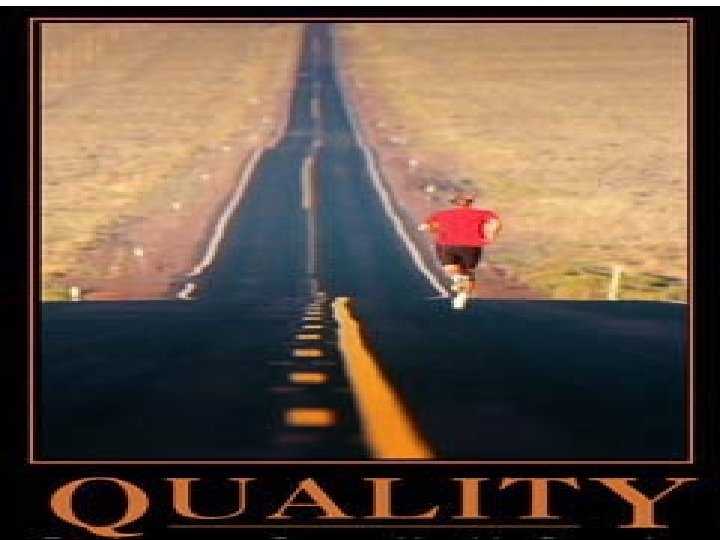
- Slides: 30
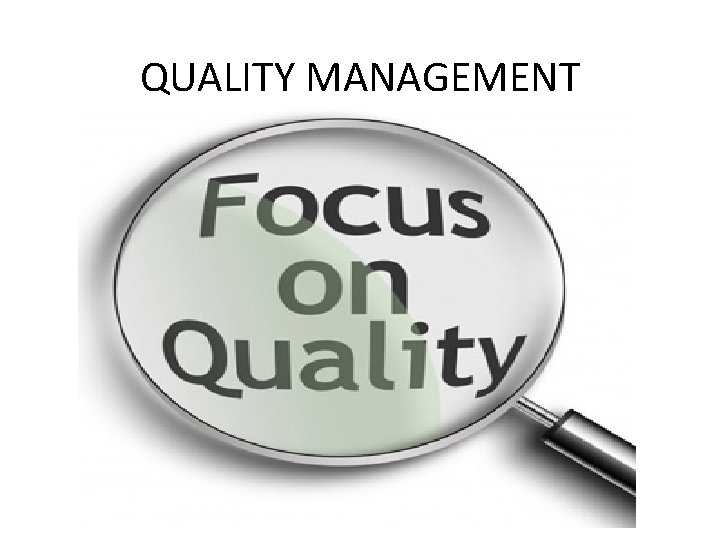
QUALITY MANAGEMENT
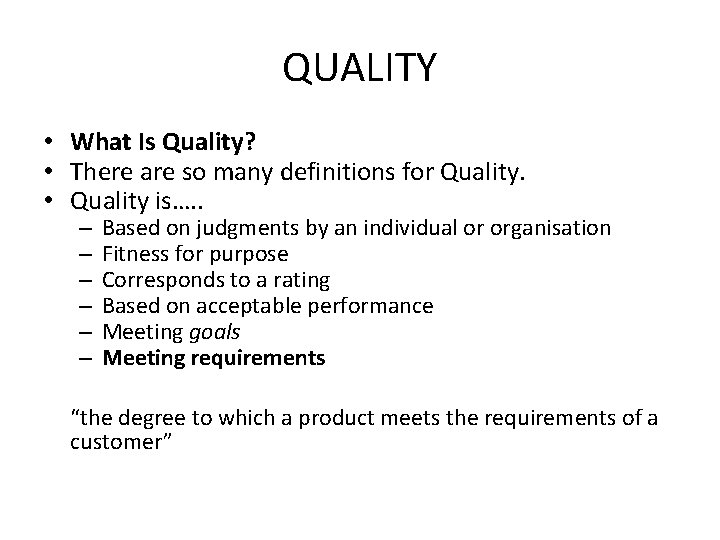
QUALITY • What Is Quality? • There are so many definitions for Quality. • Quality is…. . – – – Based on judgments by an individual or organisation Fitness for purpose Corresponds to a rating Based on acceptable performance Meeting goals Meeting requirements “the degree to which a product meets the requirements of a customer”
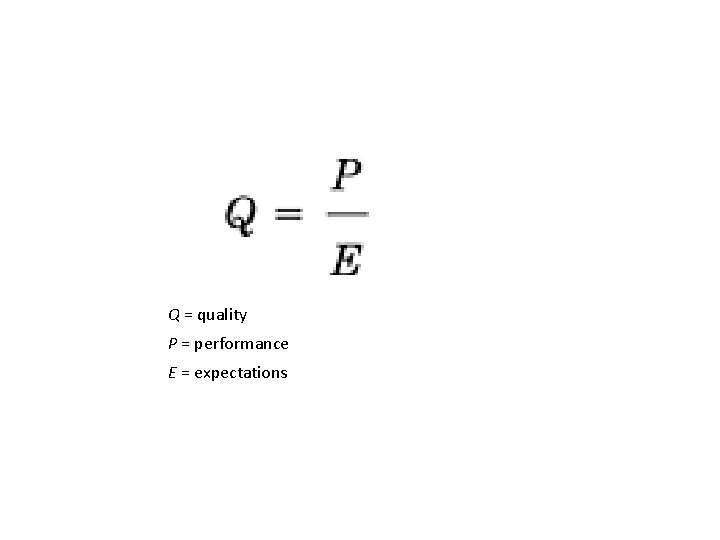
Q = quality P = performance E = expectations
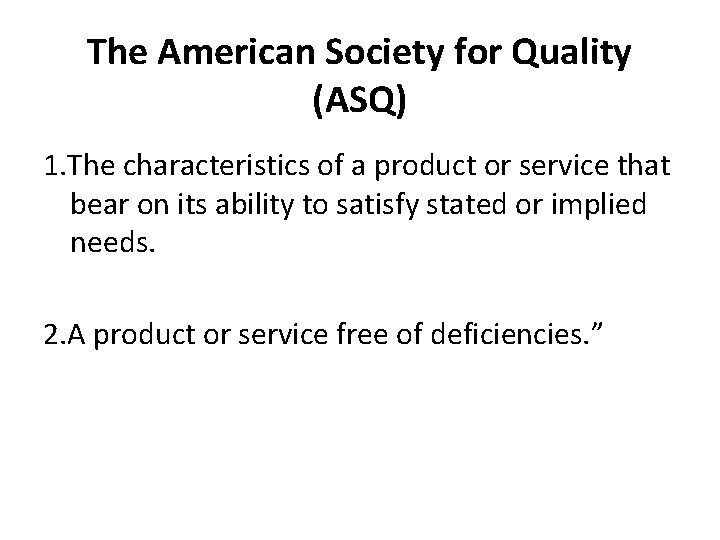
The American Society for Quality (ASQ) 1. The characteristics of a product or service that bear on its ability to satisfy stated or implied needs. 2. A product or service free of deficiencies. ”
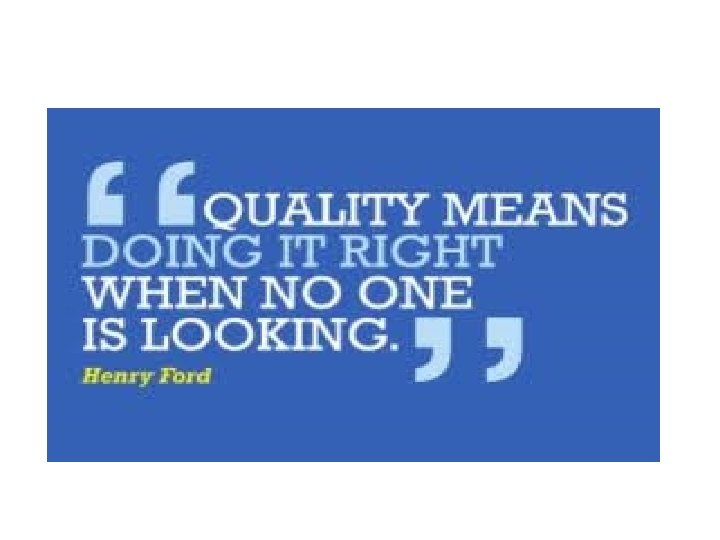
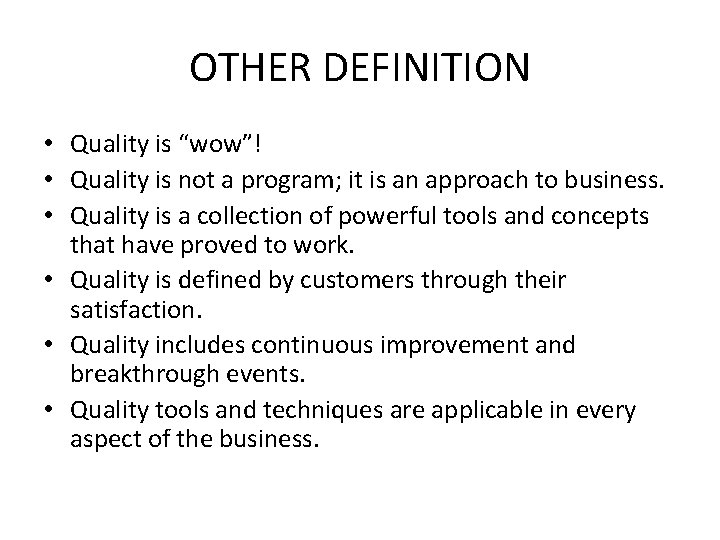
OTHER DEFINITION • Quality is “wow”! • Quality is not a program; it is an approach to business. • Quality is a collection of powerful tools and concepts that have proved to work. • Quality is defined by customers through their satisfaction. • Quality includes continuous improvement and breakthrough events. • Quality tools and techniques are applicable in every aspect of the business.
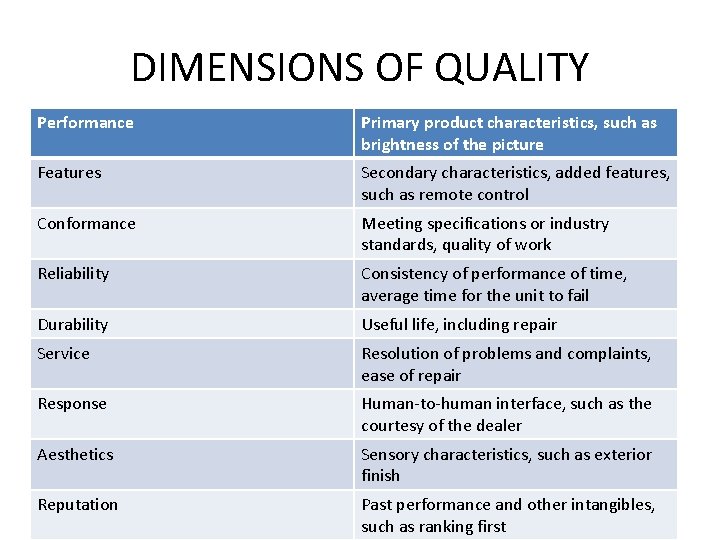
DIMENSIONS OF QUALITY Performance Primary product characteristics, such as brightness of the picture Features Secondary characteristics, added features, such as remote control Conformance Meeting specifications or industry standards, quality of work Reliability Consistency of performance of time, average time for the unit to fail Durability Useful life, including repair Service Resolution of problems and complaints, ease of repair Response Human-to-human interface, such as the courtesy of the dealer Aesthetics Sensory characteristics, such as exterior finish Reputation Past performance and other intangibles, such as ranking first
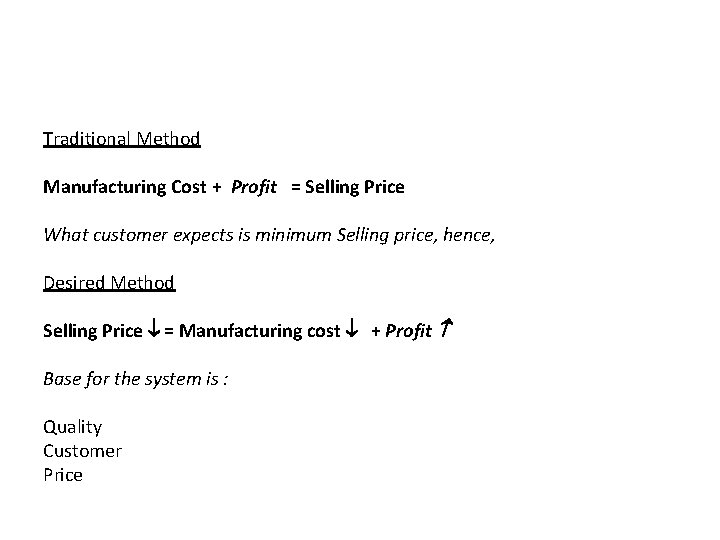
Traditional Method Manufacturing Cost + Profit = Selling Price What customer expects is minimum Selling price, hence, Desired Method Selling Price = Manufacturing cost + Profit Base for the system is : Quality Customer Price
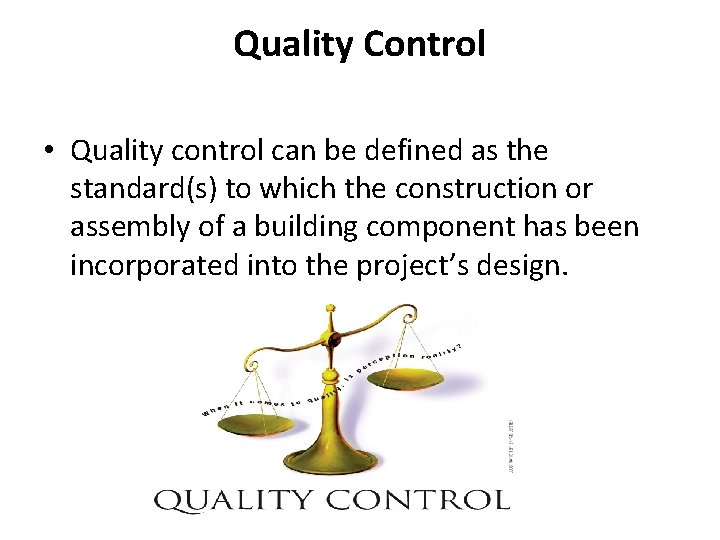
Quality Control • Quality control can be defined as the standard(s) to which the construction or assembly of a building component has been incorporated into the project’s design.
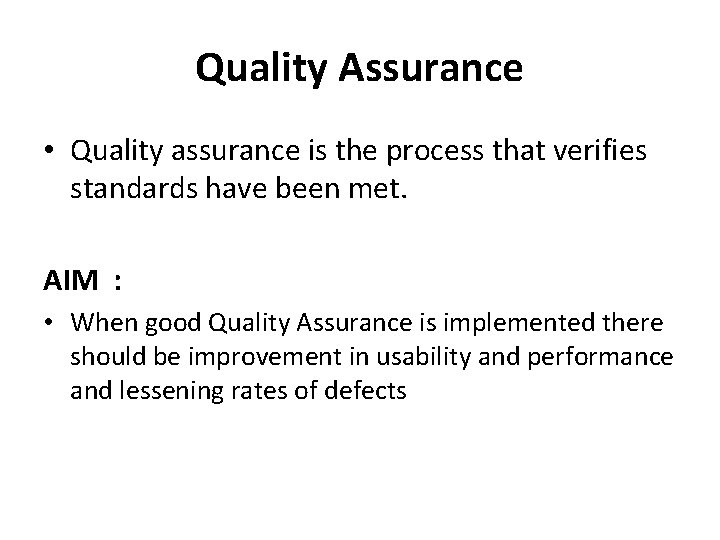
Quality Assurance • Quality assurance is the process that verifies standards have been met. AIM : • When good Quality Assurance is implemented there should be improvement in usability and performance and lessening rates of defects
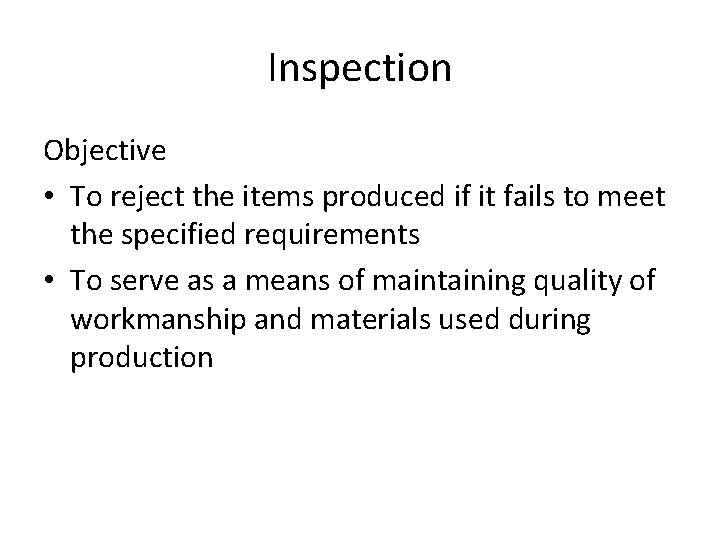
Inspection Objective • To reject the items produced if it fails to meet the specified requirements • To serve as a means of maintaining quality of workmanship and materials used during production
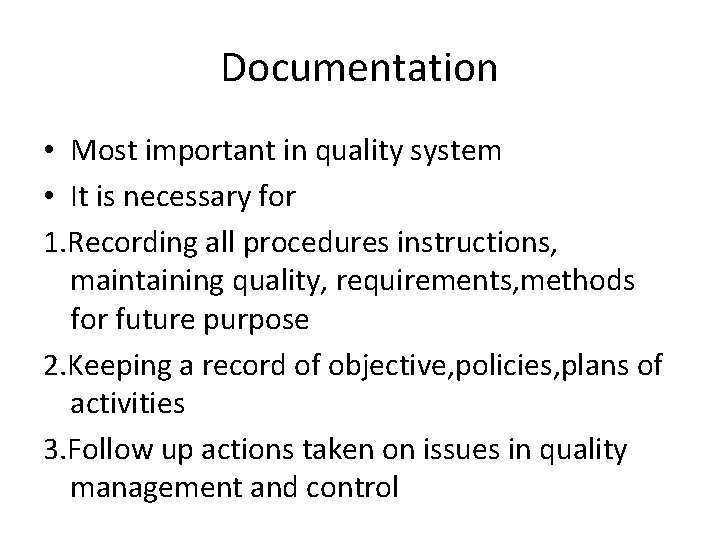
Documentation • Most important in quality system • It is necessary for 1. Recording all procedures instructions, maintaining quality, requirements, methods for future purpose 2. Keeping a record of objective, policies, plans of activities 3. Follow up actions taken on issues in quality management and control
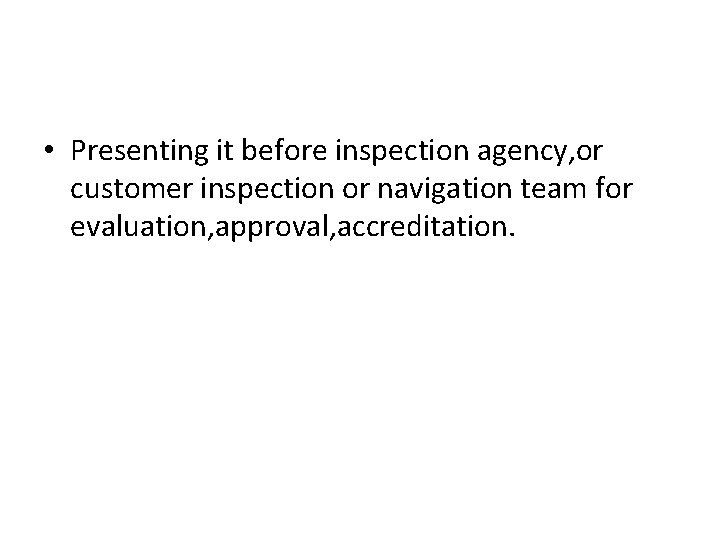
• Presenting it before inspection agency, or customer inspection or navigation team for evaluation, approval, accreditation.
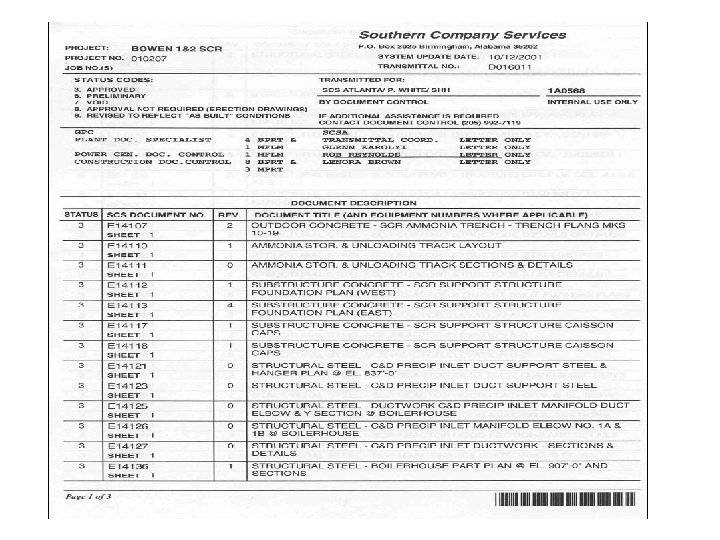
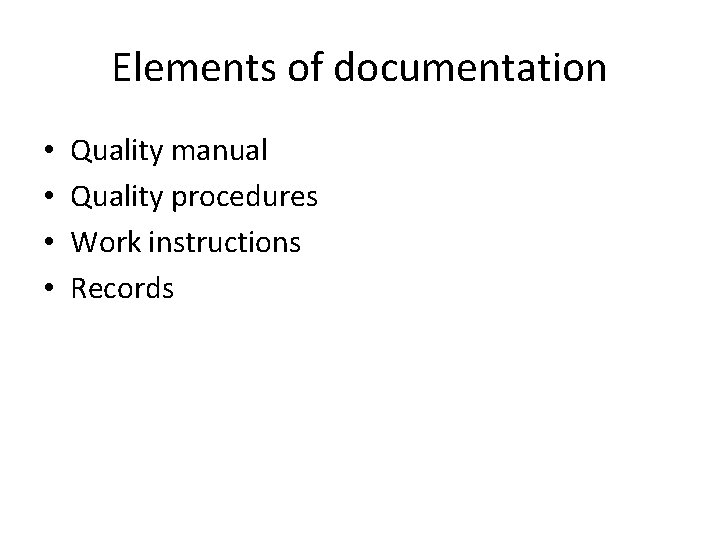
Elements of documentation • • Quality manual Quality procedures Work instructions Records
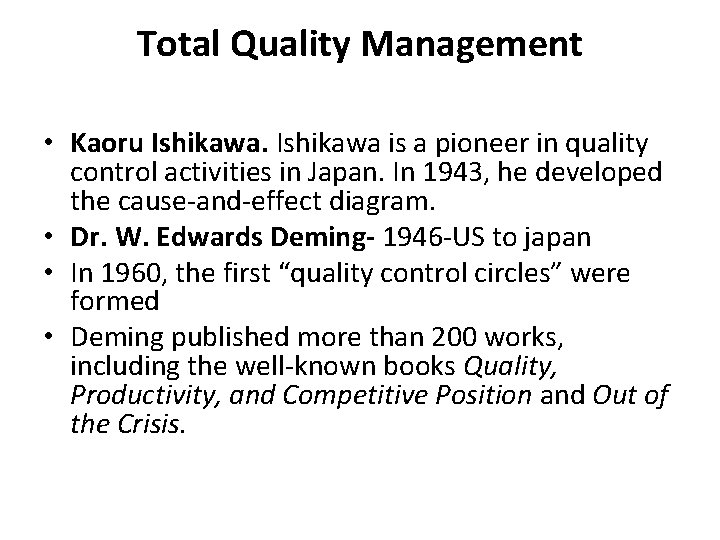
Total Quality Management • Kaoru Ishikawa is a pioneer in quality control activities in Japan. In 1943, he developed the cause-and-effect diagram. • Dr. W. Edwards Deming- 1946 -US to japan • In 1960, the first “quality control circles” were formed • Deming published more than 200 works, including the well-known books Quality, Productivity, and Competitive Position and Out of the Crisis.
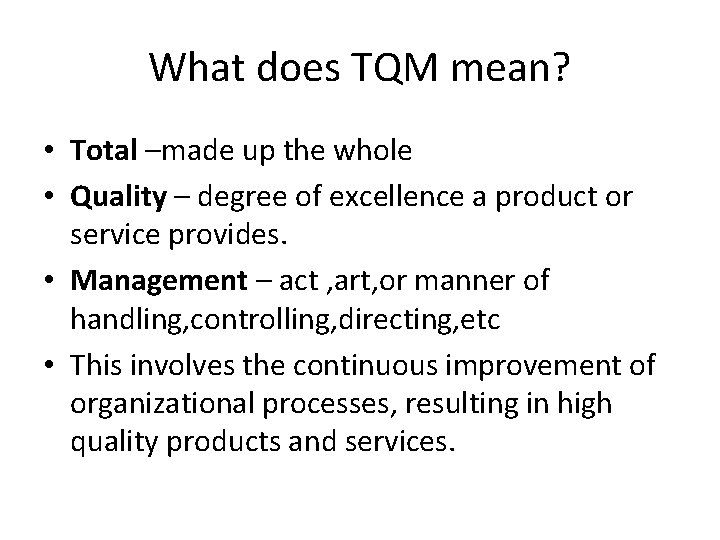
What does TQM mean? • Total –made up the whole • Quality – degree of excellence a product or service provides. • Management – act , art, or manner of handling, controlling, directing, etc • This involves the continuous improvement of organizational processes, resulting in high quality products and services.
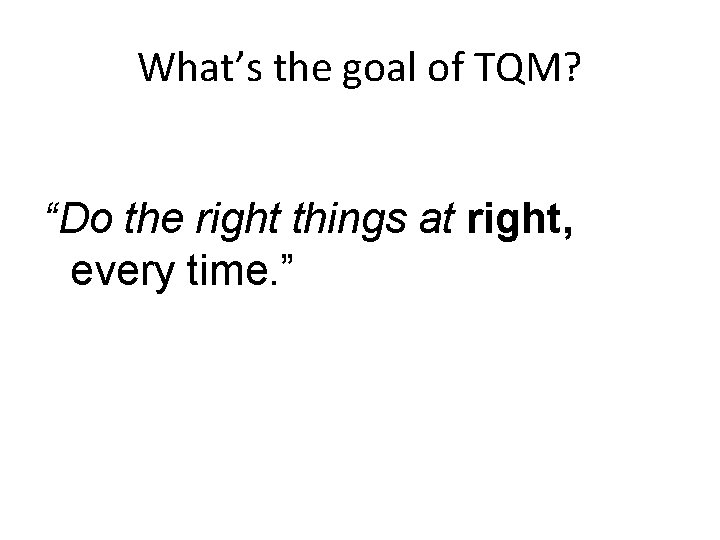
What’s the goal of TQM? “Do the right things at right, every time. ”
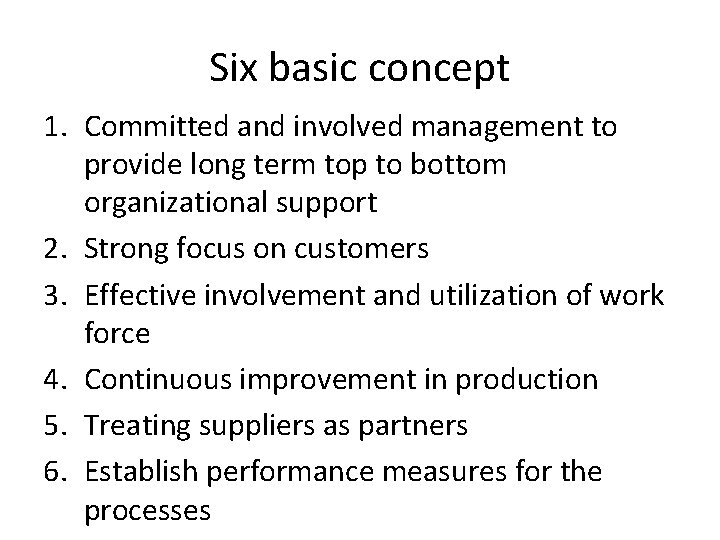
Six basic concept 1. Committed and involved management to provide long term top to bottom organizational support 2. Strong focus on customers 3. Effective involvement and utilization of work force 4. Continuous improvement in production 5. Treating suppliers as partners 6. Establish performance measures for the processes
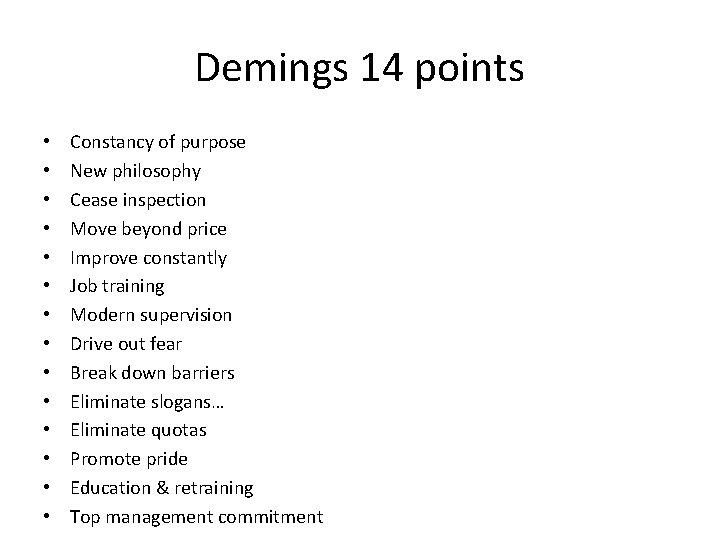
Demings 14 points • • • • Constancy of purpose New philosophy Cease inspection Move beyond price Improve constantly Job training Modern supervision Drive out fear Break down barriers Eliminate slogans… Eliminate quotas Promote pride Education & retraining Top management commitment
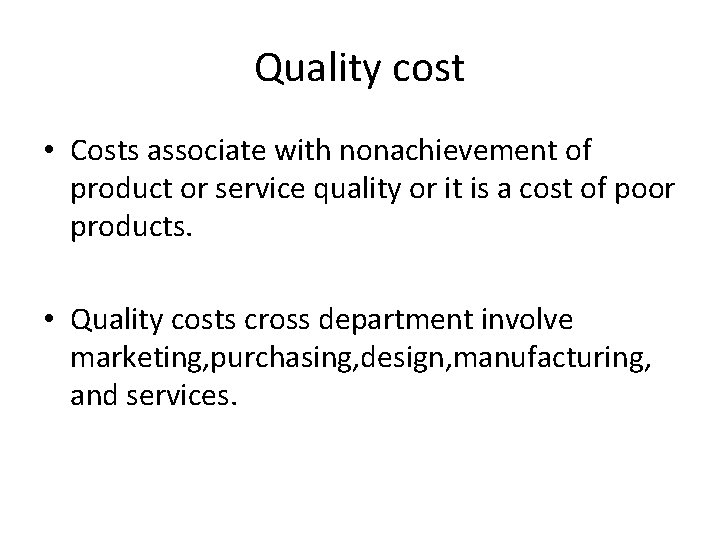
Quality cost • Costs associate with nonachievement of product or service quality or it is a cost of poor products. • Quality costs cross department involve marketing, purchasing, design, manufacturing, and services.
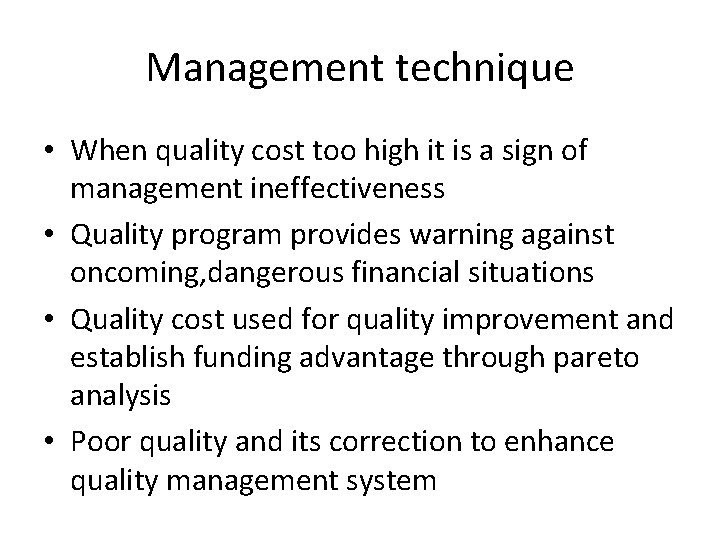
Management technique • When quality cost too high it is a sign of management ineffectiveness • Quality program provides warning against oncoming, dangerous financial situations • Quality cost used for quality improvement and establish funding advantage through pareto analysis • Poor quality and its correction to enhance quality management system
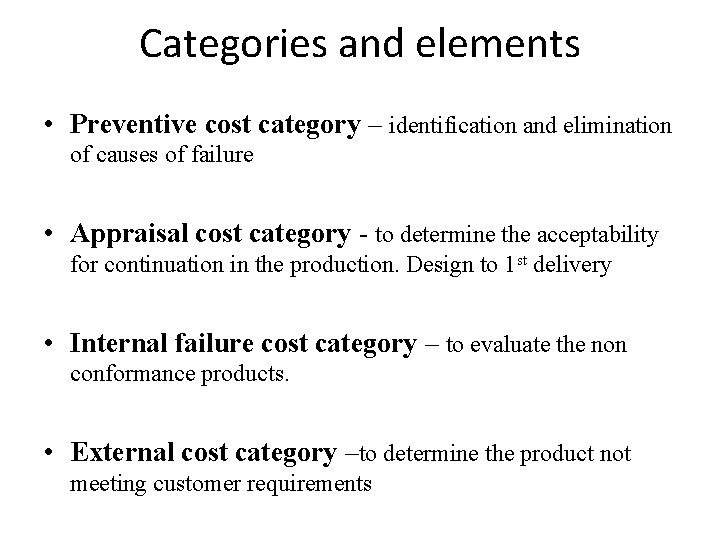
Categories and elements • Preventive cost category – identification and elimination of causes of failure • Appraisal cost category - to determine the acceptability for continuation in the production. Design to 1 st delivery • Internal failure cost category – to evaluate the non conformance products. • External cost category –to determine the product not meeting customer requirements
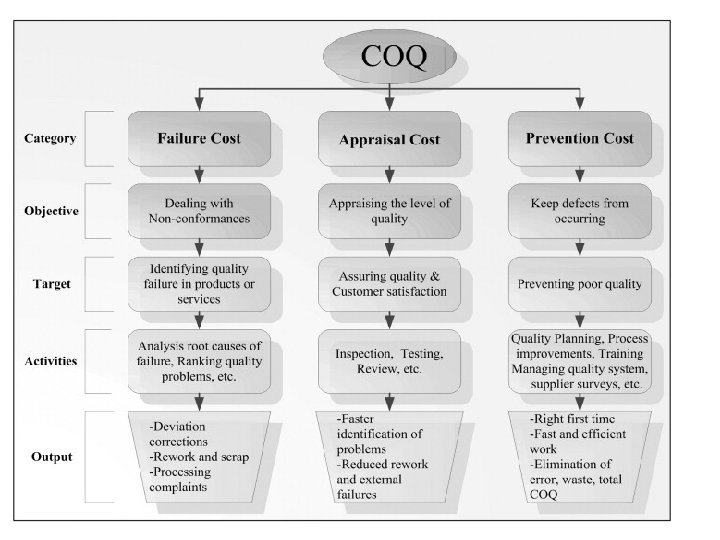
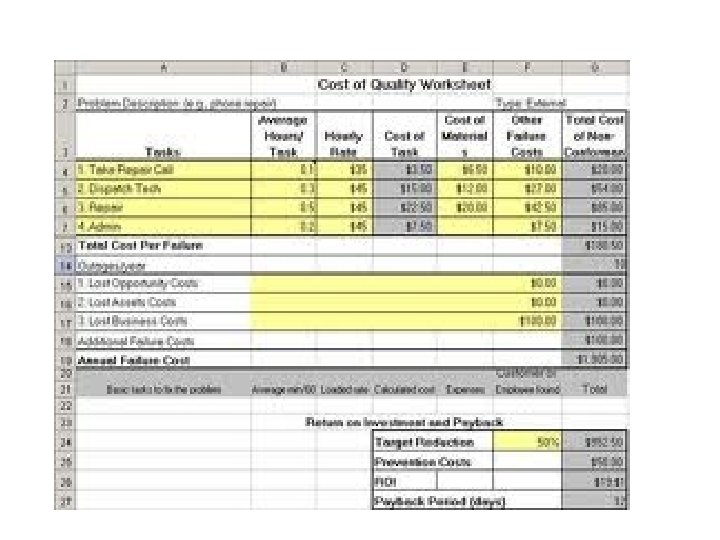
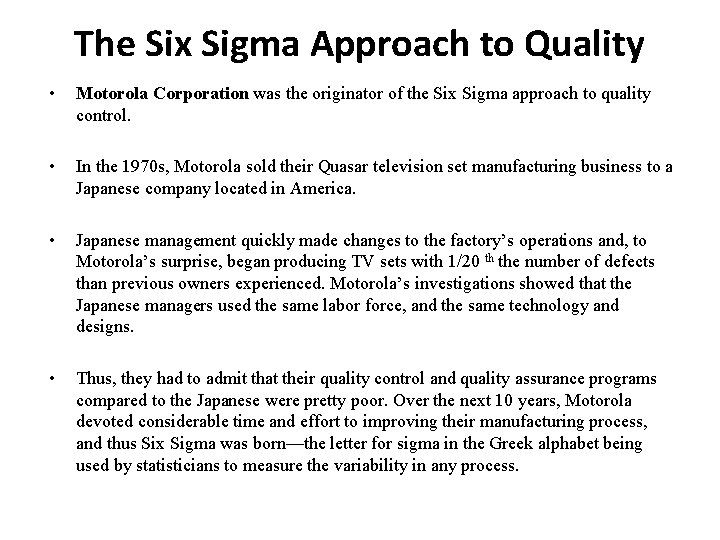
The Six Sigma Approach to Quality • Motorola Corporation was the originator of the Six Sigma approach to quality control. • In the 1970 s, Motorola sold their Quasar television set manufacturing business to a Japanese company located in America. • Japanese management quickly made changes to the factory’s operations and, to Motorola’s surprise, began producing TV sets with 1/20 th the number of defects than previous owners experienced. Motorola’s investigations showed that the Japanese managers used the same labor force, and the same technology and designs. • Thus, they had to admit that their quality control and quality assurance programs compared to the Japanese were pretty poor. Over the next 10 years, Motorola devoted considerable time and effort to improving their manufacturing process, and thus Six Sigma was born—the letter for sigma in the Greek alphabet being used by statisticians to measure the variability in any process.
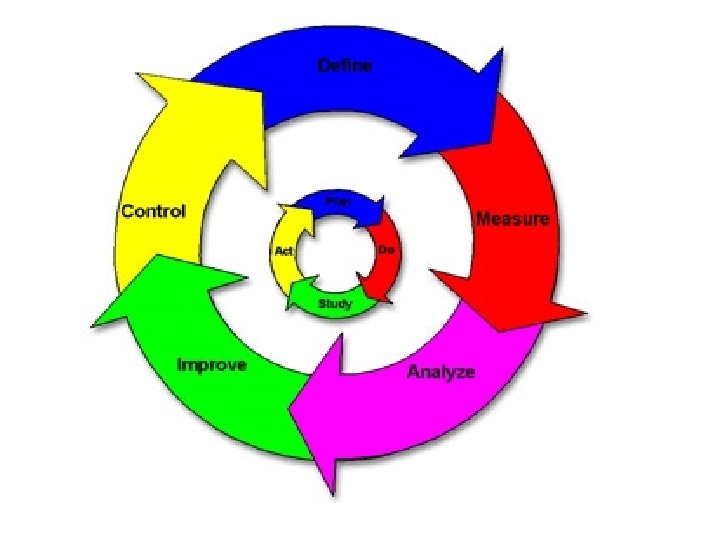
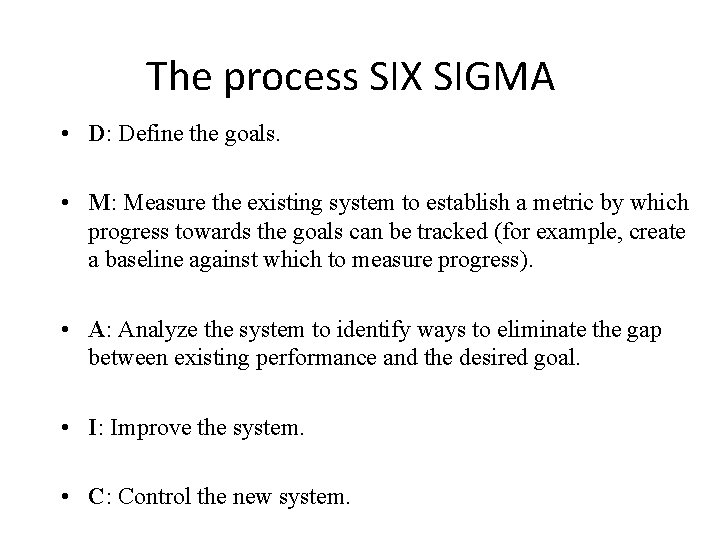
The process SIX SIGMA • D: Define the goals. • M: Measure the existing system to establish a metric by which progress towards the goals can be tracked (for example, create a baseline against which to measure progress). • A: Analyze the system to identify ways to eliminate the gap between existing performance and the desired goal. • I: Improve the system. • C: Control the new system.
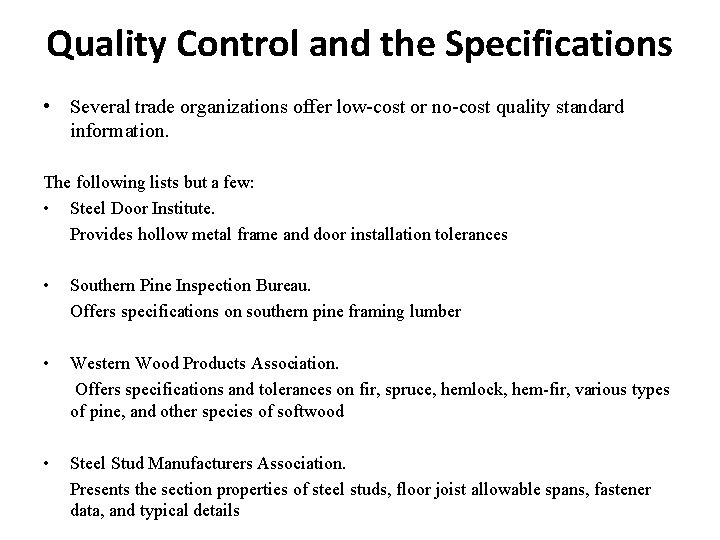
Quality Control and the Specifications • Several trade organizations offer low-cost or no-cost quality standard information. The following lists but a few: • Steel Door Institute. Provides hollow metal frame and door installation tolerances • Southern Pine Inspection Bureau. Offers specifications on southern pine framing lumber • Western Wood Products Association. Offers specifications and tolerances on fir, spruce, hemlock, hem-fir, various types of pine, and other species of softwood • Steel Stud Manufacturers Association. Presents the section properties of steel studs, floor joist allowable spans, fastener data, and typical details
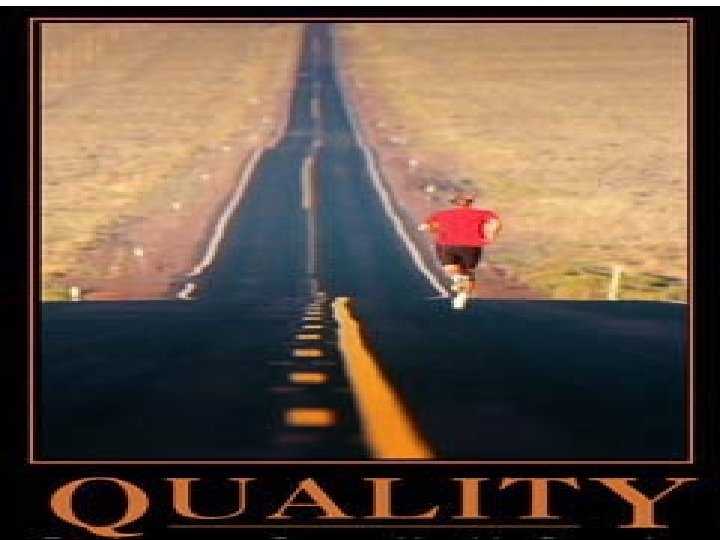
Insidan region jh
Tema there is there are
What part of speech is open
There is there are negative form
Countable and uncountable there is there are
There isn't any chicken
There is there are
Mathematics is john's favorite subject
Here there over there
Some any an a
El ketchup es contable o incontable
Pep unit
Ingilizce gramer zamanlar tablosu
Exercising game
There is there are
Arehay
There's and there are
If there is no struggle there is no progress explanation
Quality management in operations management
Enterprise resource planning ppt
Operations management with total quality management book
Pyramid levels of management
Management pyramid
Top management and middle management
Quality assurance vs quality control
Plan quality management pmp
Pmbok quality assurance vs quality control
Process of nursing audit
Compliance vs quality
Quality assurance vs quality control
Quality guru