PTRT 1317 Natural Gas Processing I Chapter 9
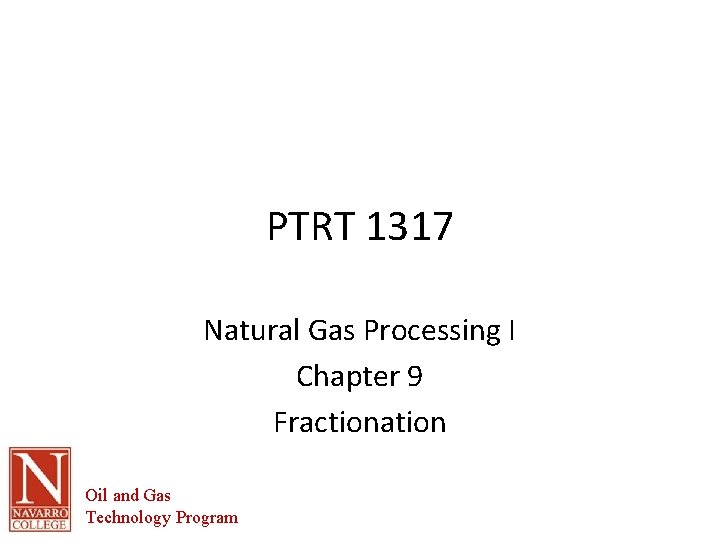
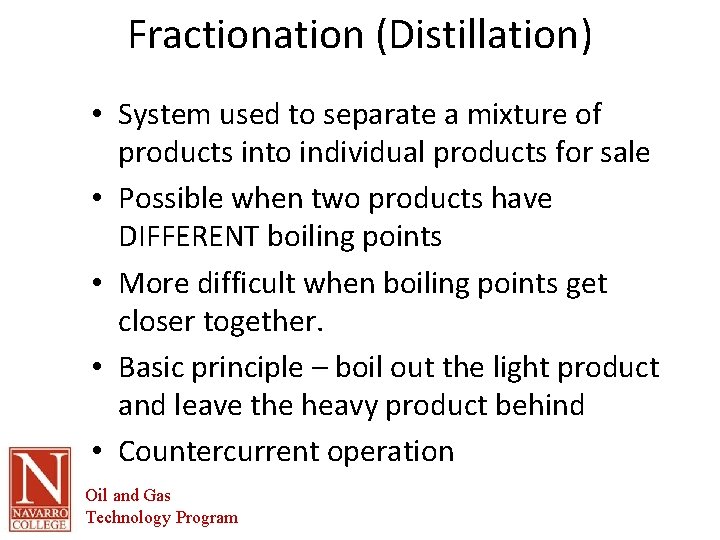
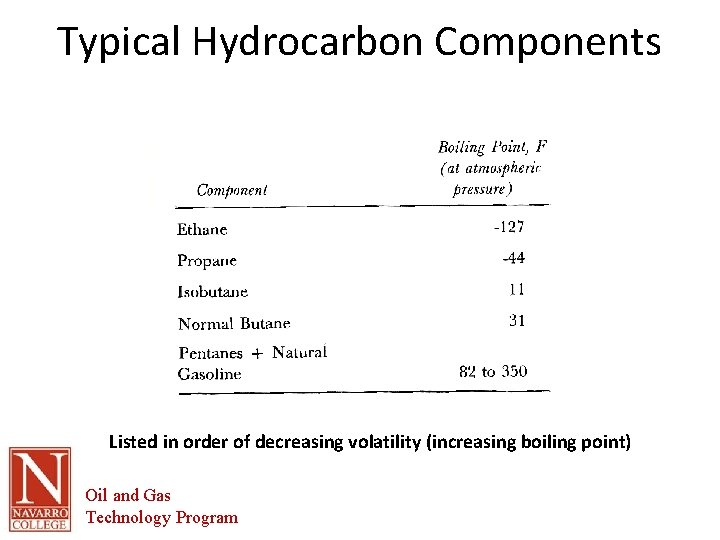
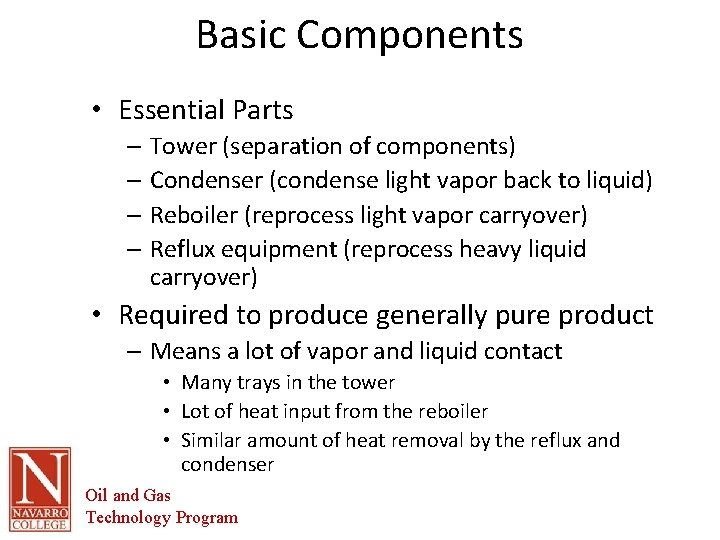
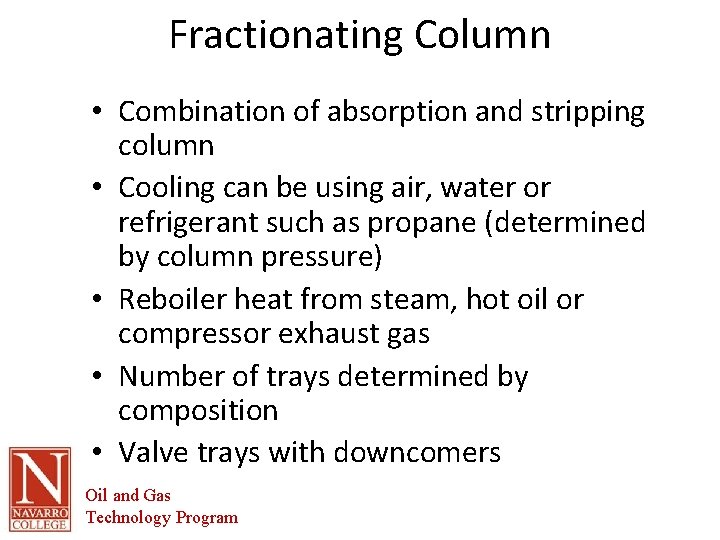
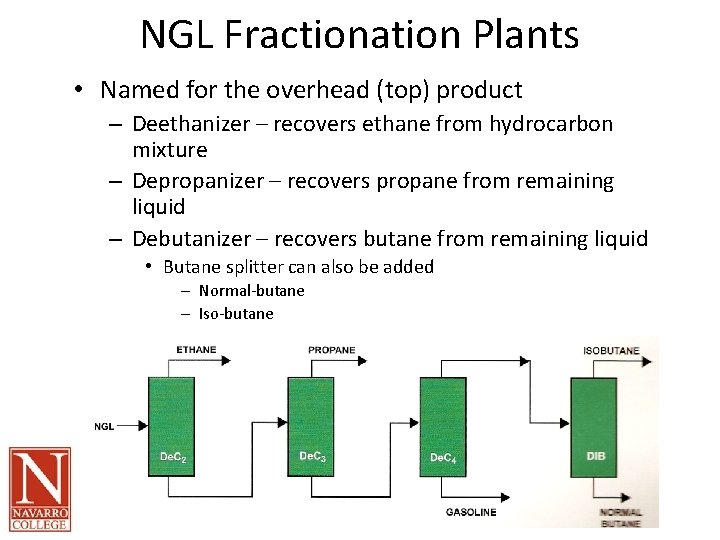
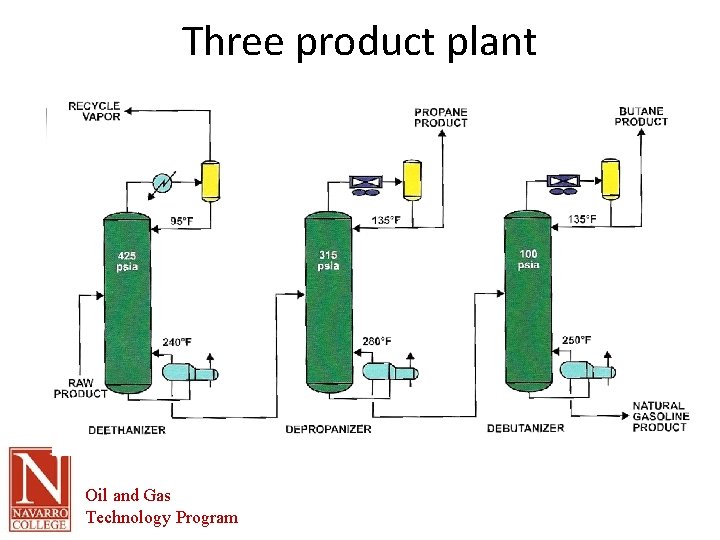
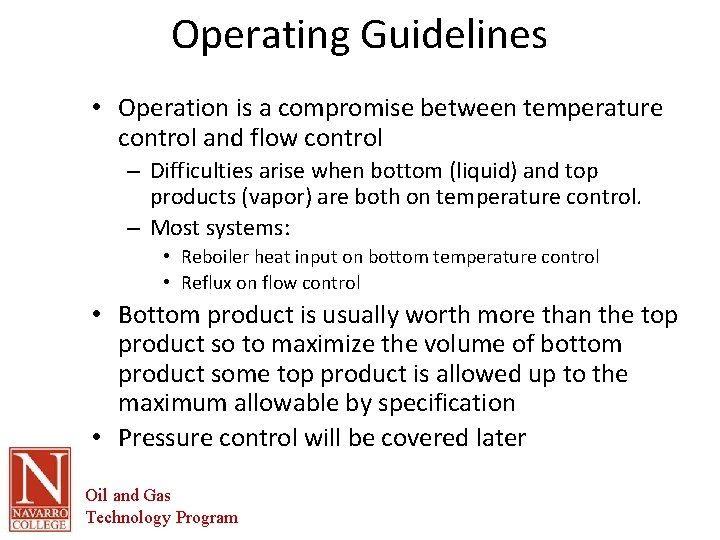
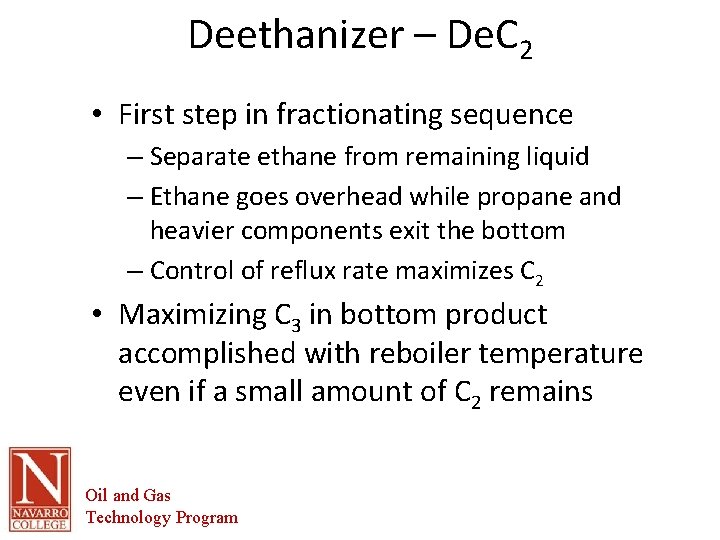
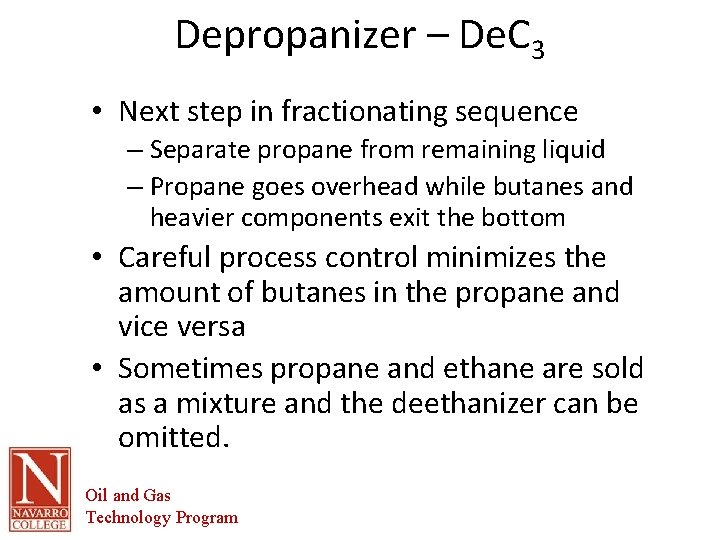
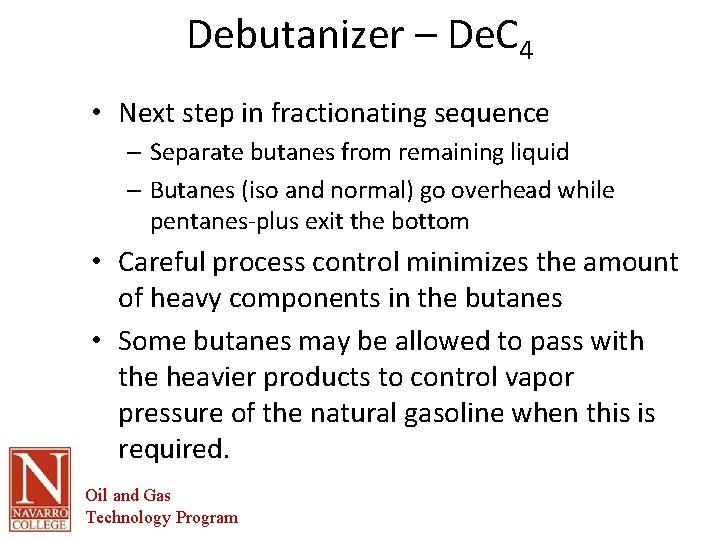
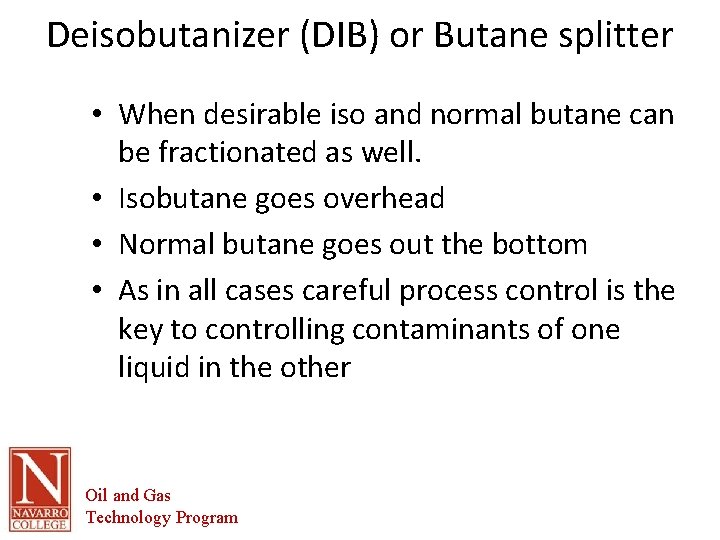
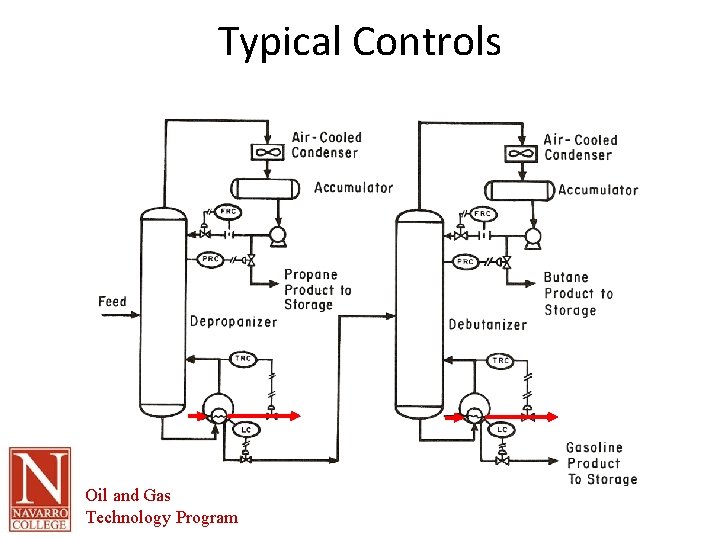
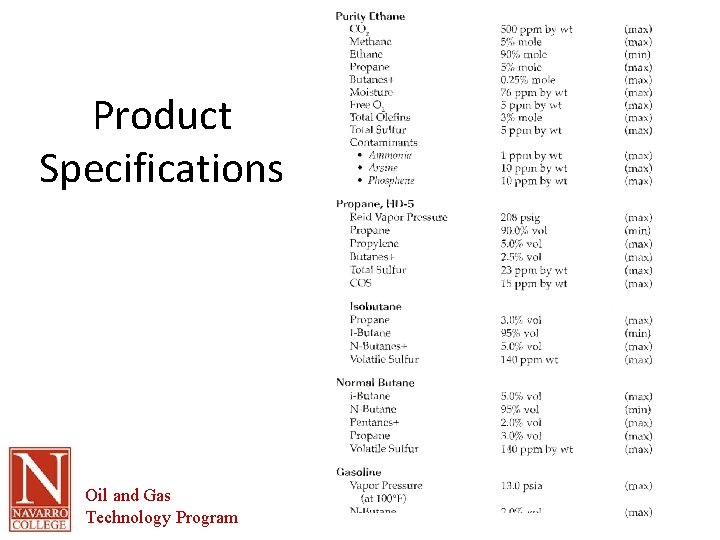
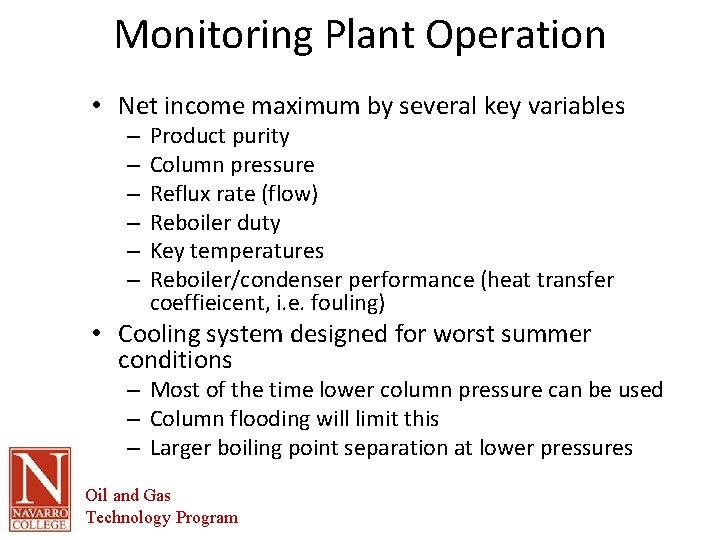
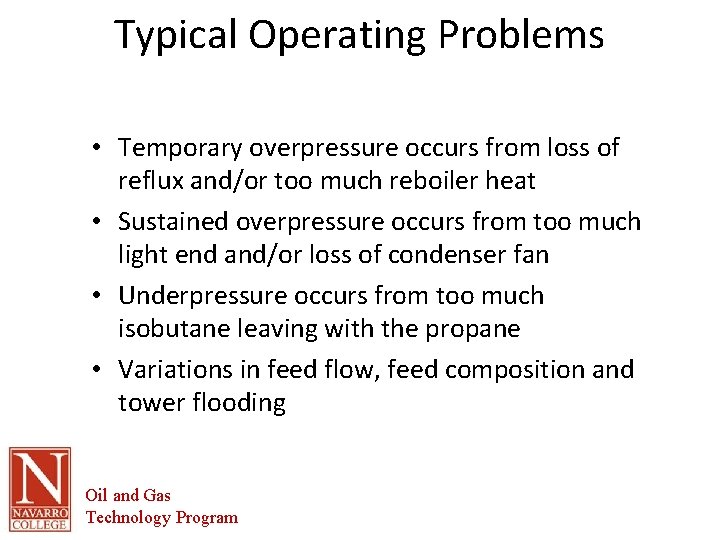
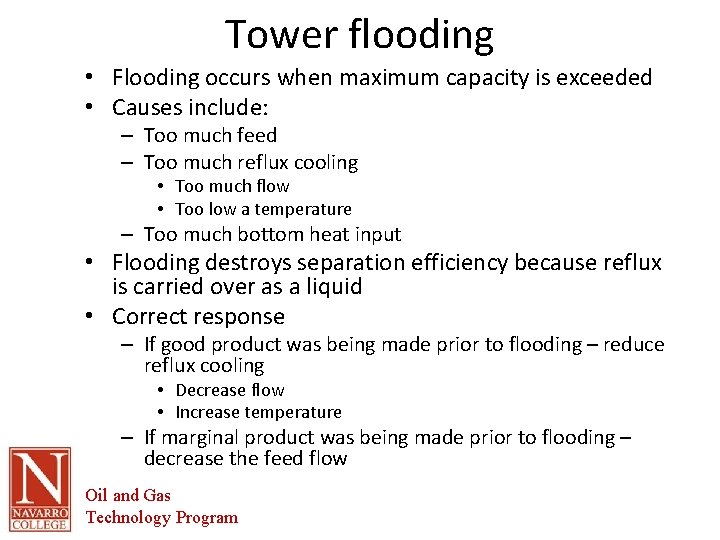
- Slides: 17
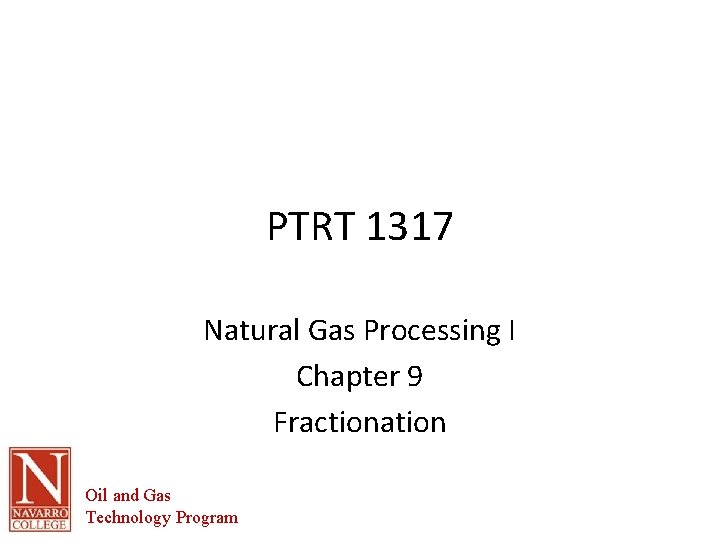
PTRT 1317 Natural Gas Processing I Chapter 9 Fractionation Oil and Gas Technology Program
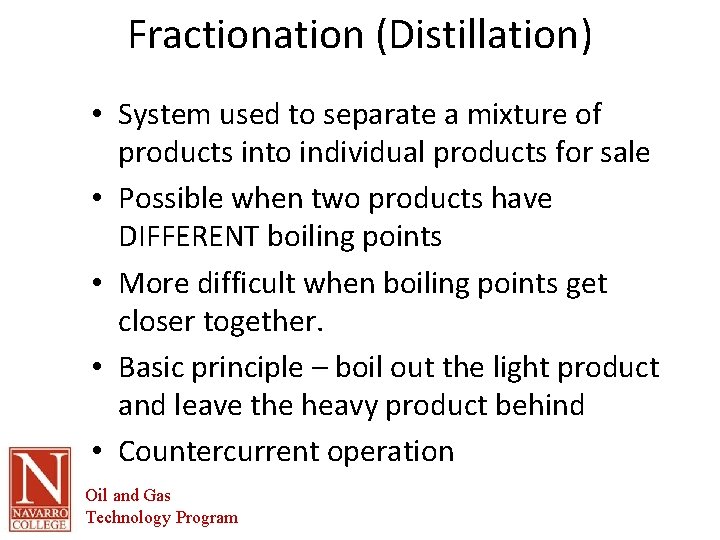
Fractionation (Distillation) • System used to separate a mixture of products into individual products for sale • Possible when two products have DIFFERENT boiling points • More difficult when boiling points get closer together. • Basic principle – boil out the light product and leave the heavy product behind • Countercurrent operation Oil and Gas Technology Program
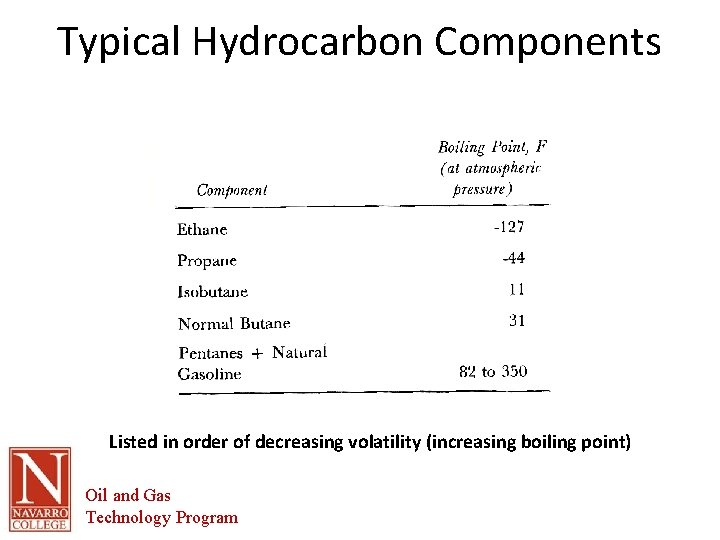
Typical Hydrocarbon Components Listed in order of decreasing volatility (increasing boiling point) Oil and Gas Technology Program
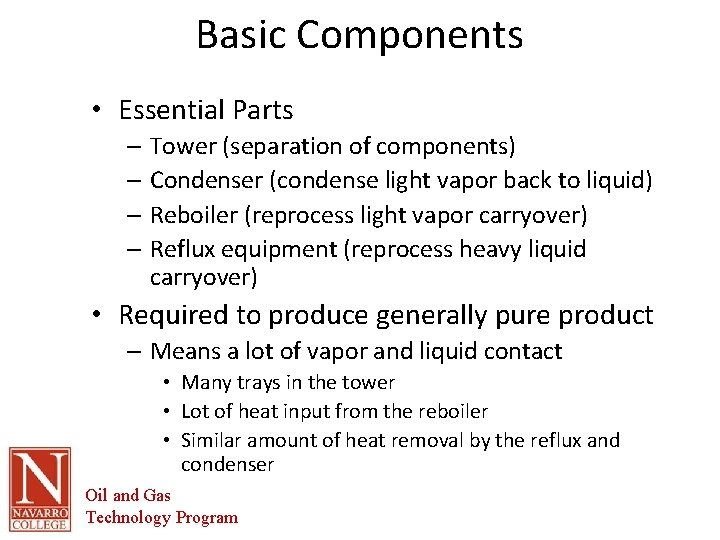
Basic Components • Essential Parts – Tower (separation of components) – Condenser (condense light vapor back to liquid) – Reboiler (reprocess light vapor carryover) – Reflux equipment (reprocess heavy liquid carryover) • Required to produce generally pure product – Means a lot of vapor and liquid contact • Many trays in the tower • Lot of heat input from the reboiler • Similar amount of heat removal by the reflux and condenser Oil and Gas Technology Program
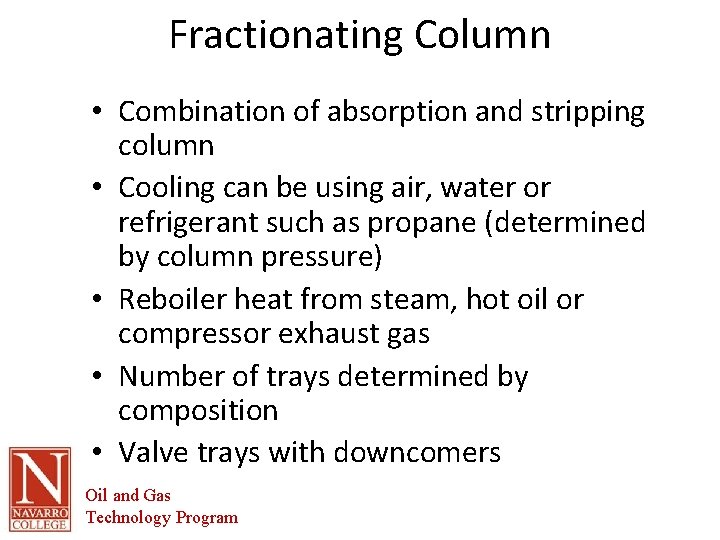
Fractionating Column • Combination of absorption and stripping column • Cooling can be using air, water or refrigerant such as propane (determined by column pressure) • Reboiler heat from steam, hot oil or compressor exhaust gas • Number of trays determined by composition • Valve trays with downcomers Oil and Gas Technology Program
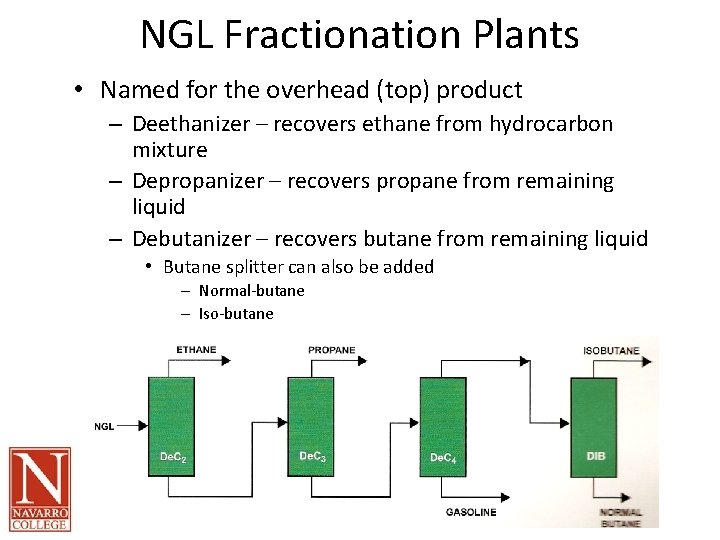
NGL Fractionation Plants • Named for the overhead (top) product – Deethanizer – recovers ethane from hydrocarbon mixture – Depropanizer – recovers propane from remaining liquid – Debutanizer – recovers butane from remaining liquid • Butane splitter can also be added – Normal-butane – Iso-butane Oil and Gas Technology Program
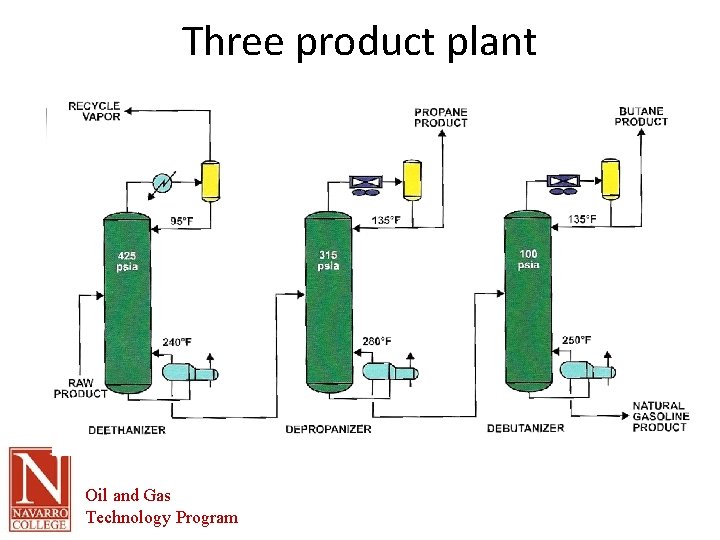
Three product plant Oil and Gas Technology Program
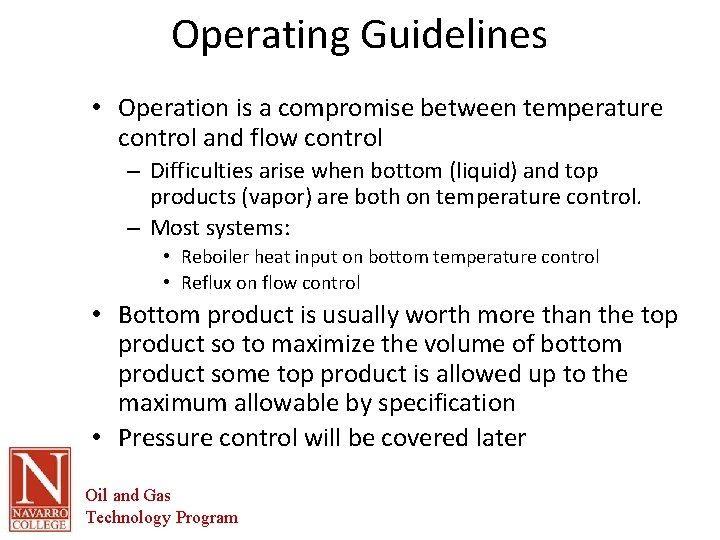
Operating Guidelines • Operation is a compromise between temperature control and flow control – Difficulties arise when bottom (liquid) and top products (vapor) are both on temperature control. – Most systems: • Reboiler heat input on bottom temperature control • Reflux on flow control • Bottom product is usually worth more than the top product so to maximize the volume of bottom product some top product is allowed up to the maximum allowable by specification • Pressure control will be covered later Oil and Gas Technology Program
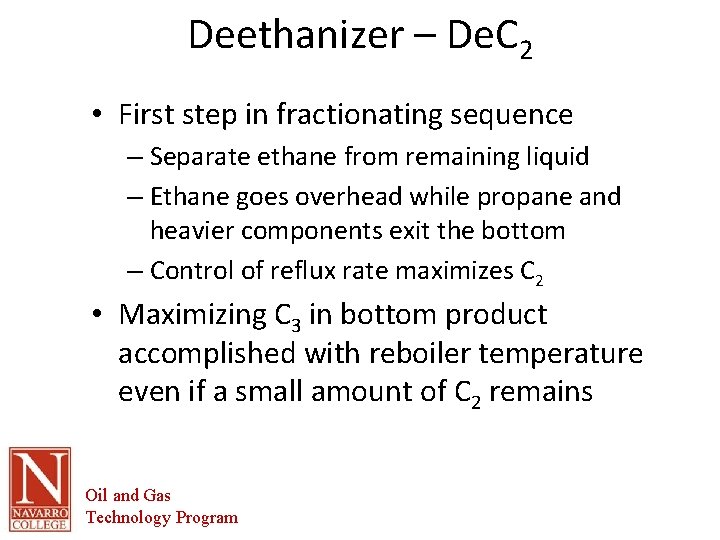
Deethanizer – De. C 2 • First step in fractionating sequence – Separate ethane from remaining liquid – Ethane goes overhead while propane and heavier components exit the bottom – Control of reflux rate maximizes C 2 • Maximizing C 3 in bottom product accomplished with reboiler temperature even if a small amount of C 2 remains Oil and Gas Technology Program
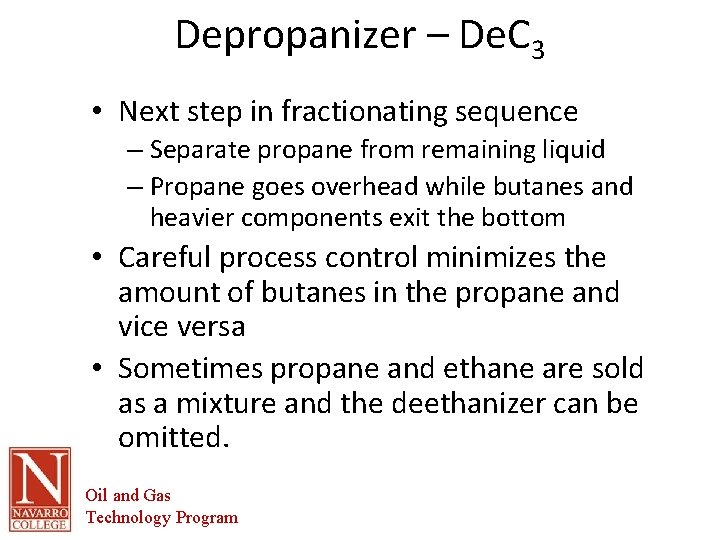
Depropanizer – De. C 3 • Next step in fractionating sequence – Separate propane from remaining liquid – Propane goes overhead while butanes and heavier components exit the bottom • Careful process control minimizes the amount of butanes in the propane and vice versa • Sometimes propane and ethane are sold as a mixture and the deethanizer can be omitted. Oil and Gas Technology Program
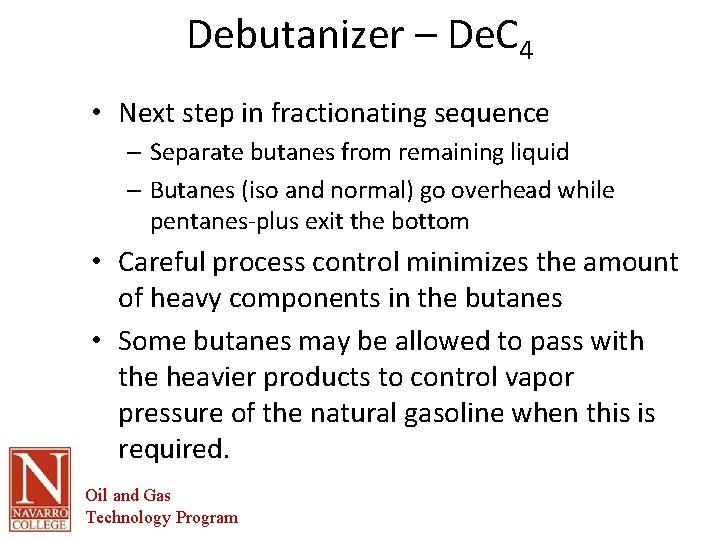
Debutanizer – De. C 4 • Next step in fractionating sequence – Separate butanes from remaining liquid – Butanes (iso and normal) go overhead while pentanes-plus exit the bottom • Careful process control minimizes the amount of heavy components in the butanes • Some butanes may be allowed to pass with the heavier products to control vapor pressure of the natural gasoline when this is required. Oil and Gas Technology Program
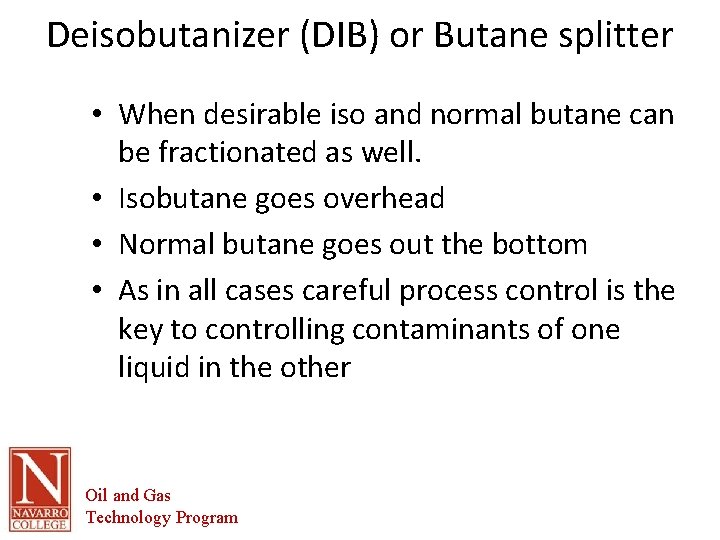
Deisobutanizer (DIB) or Butane splitter • When desirable iso and normal butane can be fractionated as well. • Isobutane goes overhead • Normal butane goes out the bottom • As in all cases careful process control is the key to controlling contaminants of one liquid in the other Oil and Gas Technology Program
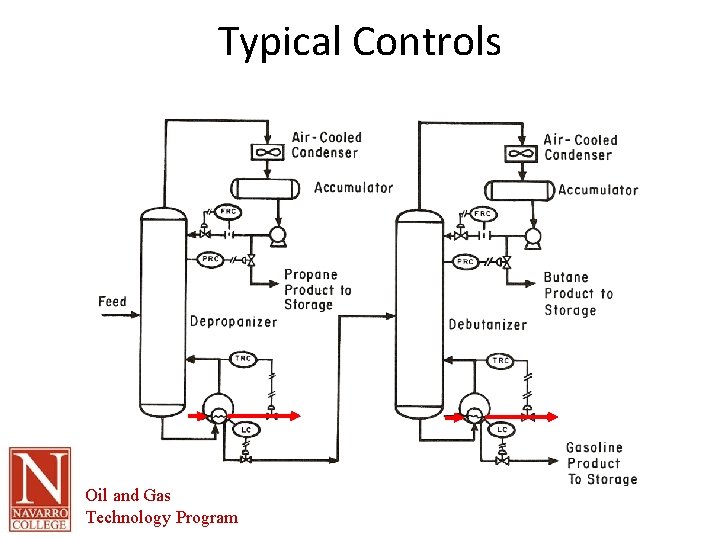
Typical Controls Oil and Gas Technology Program
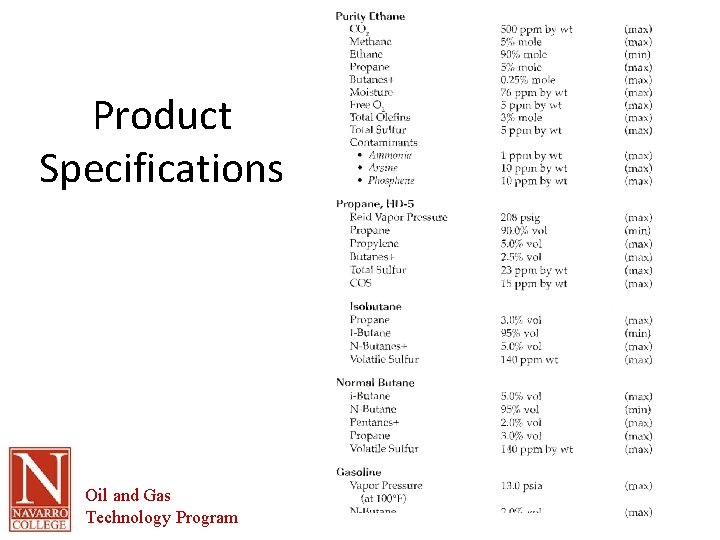
Product Specifications Oil and Gas Technology Program
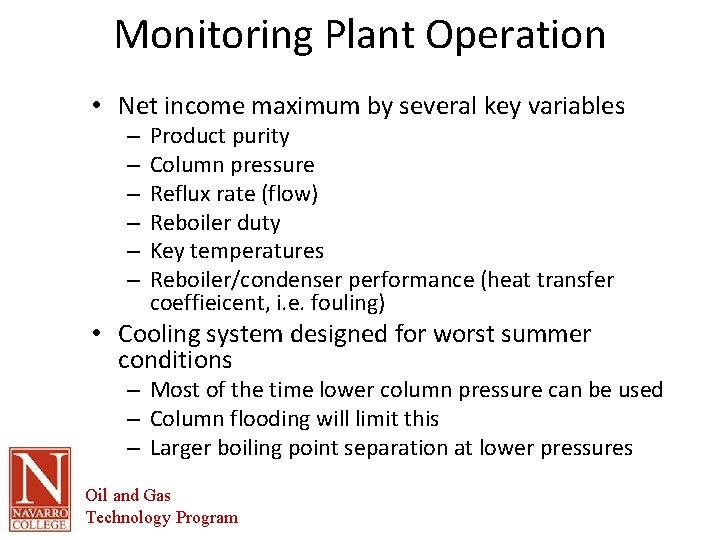
Monitoring Plant Operation • Net income maximum by several key variables – – – Product purity Column pressure Reflux rate (flow) Reboiler duty Key temperatures Reboiler/condenser performance (heat transfer coeffieicent, i. e. fouling) • Cooling system designed for worst summer conditions – Most of the time lower column pressure can be used – Column flooding will limit this – Larger boiling point separation at lower pressures Oil and Gas Technology Program
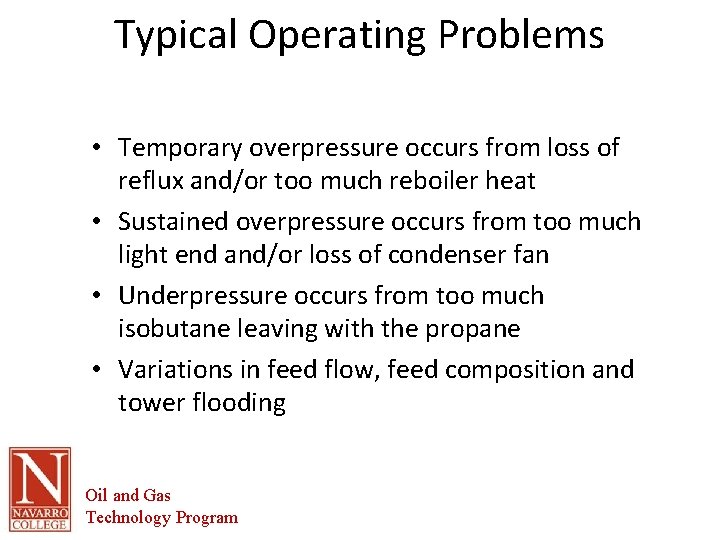
Typical Operating Problems • Temporary overpressure occurs from loss of reflux and/or too much reboiler heat • Sustained overpressure occurs from too much light end and/or loss of condenser fan • Underpressure occurs from too much isobutane leaving with the propane • Variations in feed flow, feed composition and tower flooding Oil and Gas Technology Program
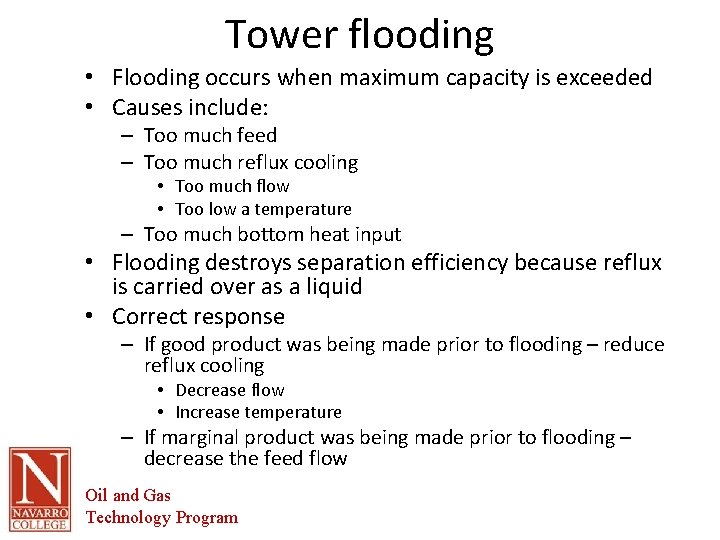
Tower flooding • Flooding occurs when maximum capacity is exceeded • Causes include: – Too much feed – Too much reflux cooling • Too much flow • Too low a temperature – Too much bottom heat input • Flooding destroys separation efficiency because reflux is carried over as a liquid • Correct response – If good product was being made prior to flooding – reduce reflux cooling • Decrease flow • Increase temperature – If marginal product was being made prior to flooding – decrease the feed flow Oil and Gas Technology Program
Bottom up and top down processing
Gloria suarez
Bottom up processing example
Neighborhood processing in image processing
Differentiate primary and secondary processing
Point processing in image processing
Histogram processing in digital image processing
Parallel processing vs concurrent processing
Laplacian filter
Point processing
Morphological processing in digital image processing
Bottom up vs top down processing
Batch processing vs interactive processing
Pseudo reduced specific volume
Imaginary gas
Differences between ideal gas and real gas
Ideal gas vs perfect gas
Reason for bhopal gas tragedy