PLT 303 Electrical Drives Chapter 1 Introduction To
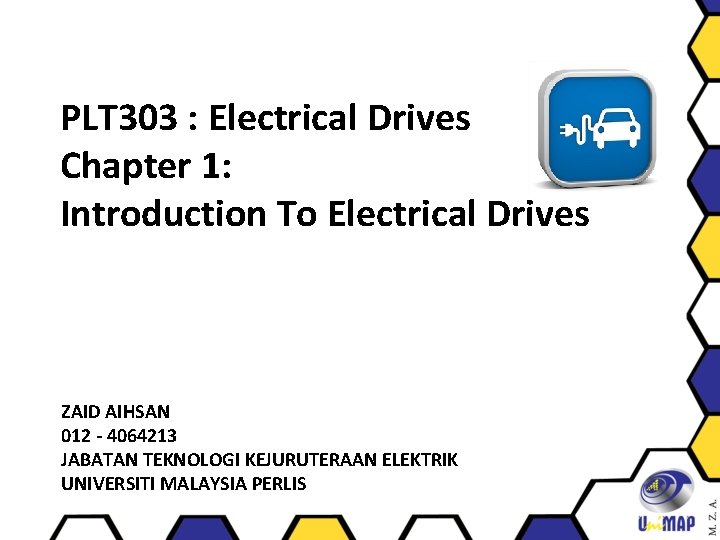
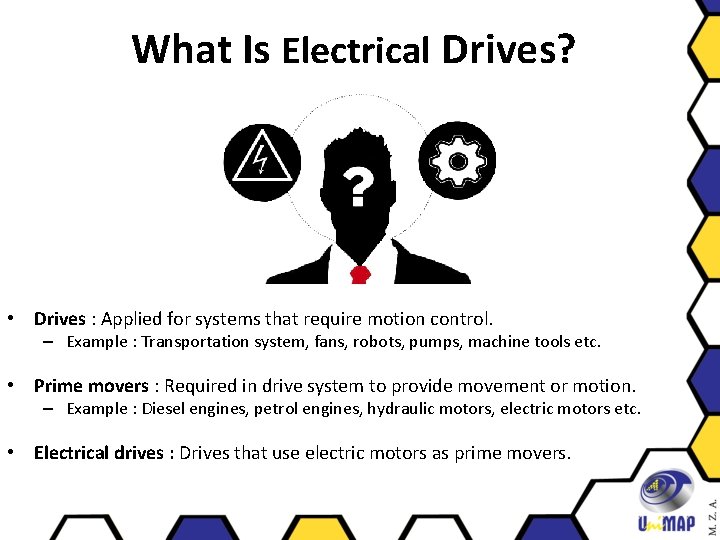
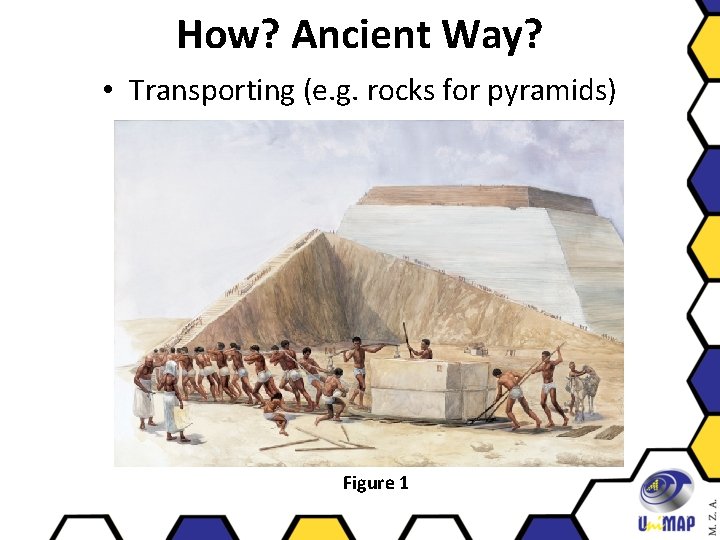
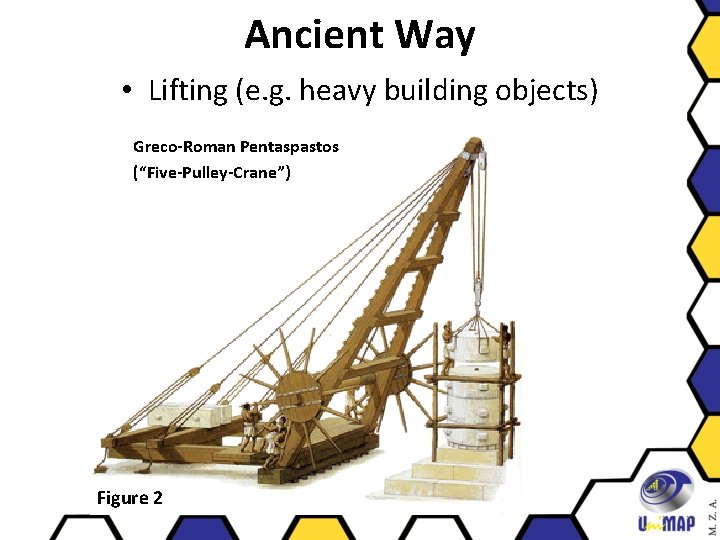
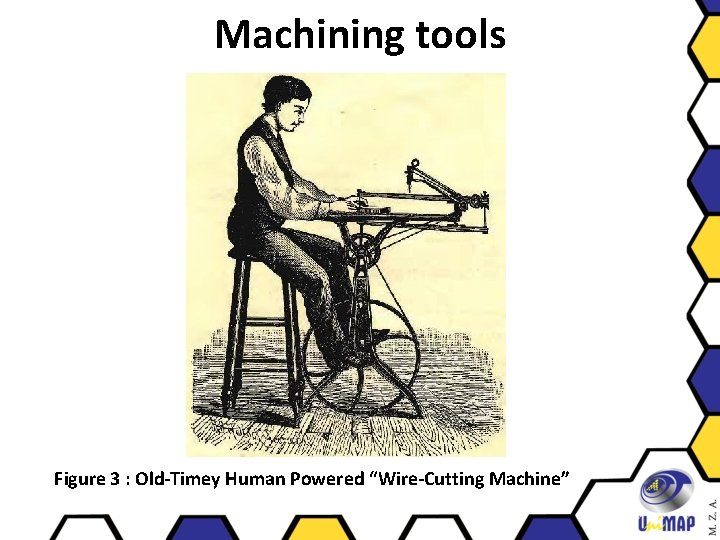
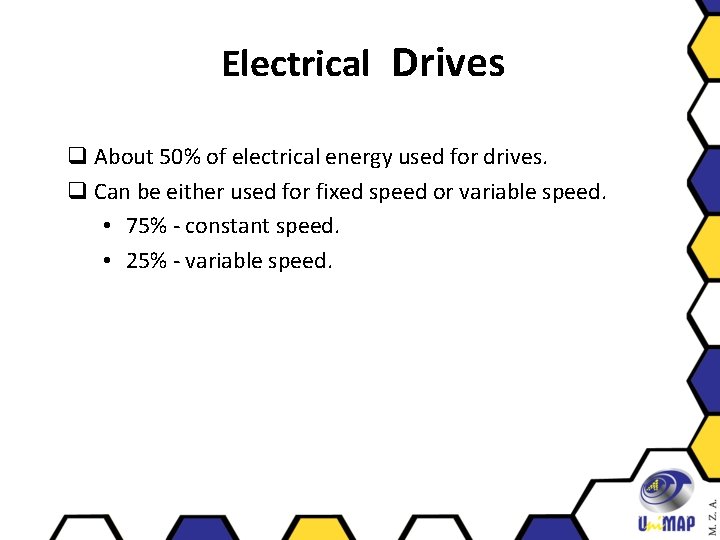
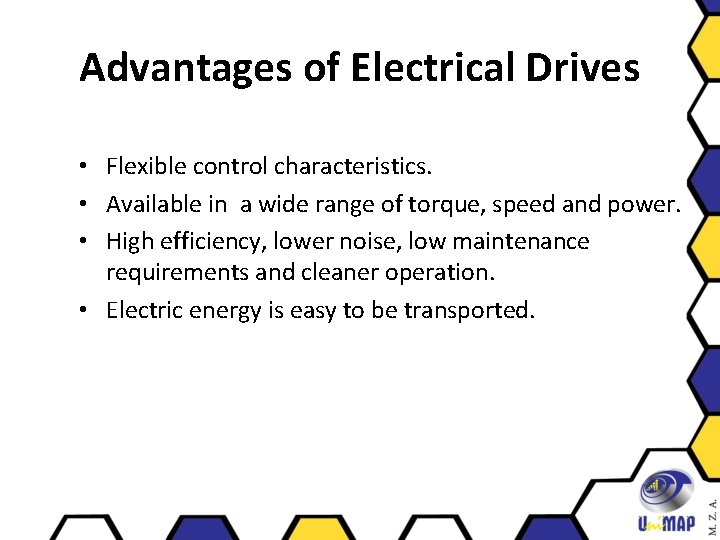
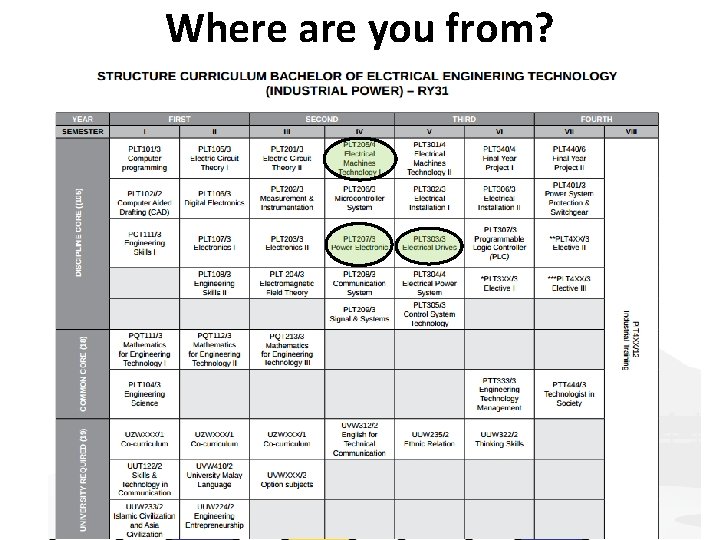
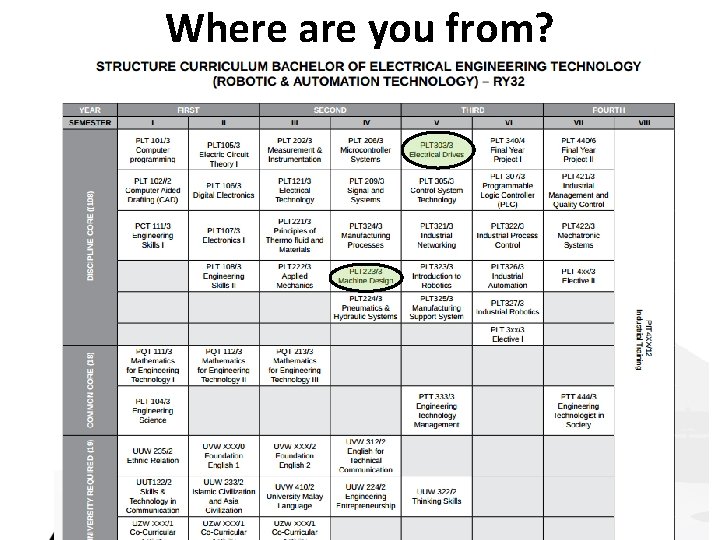
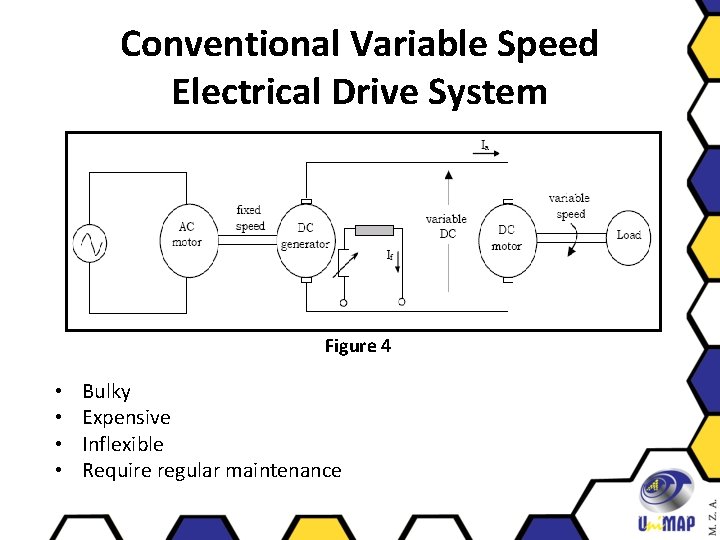
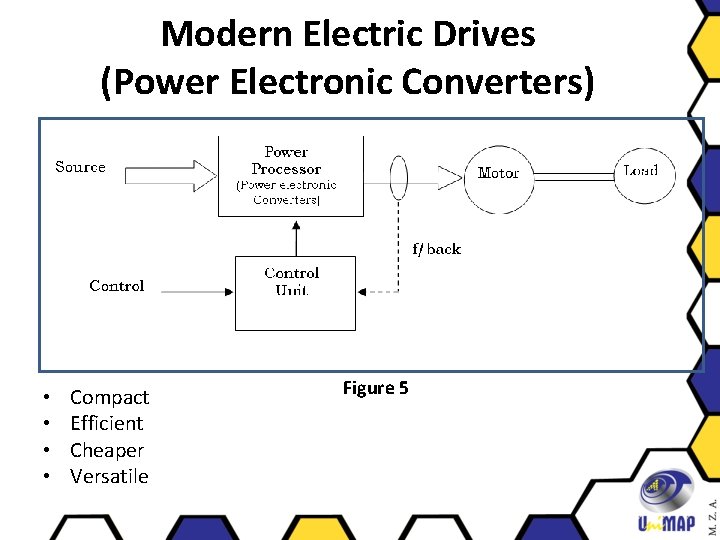
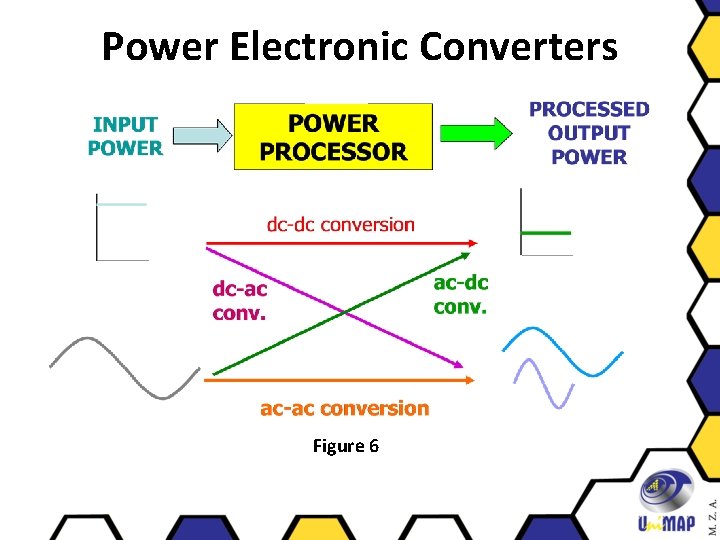
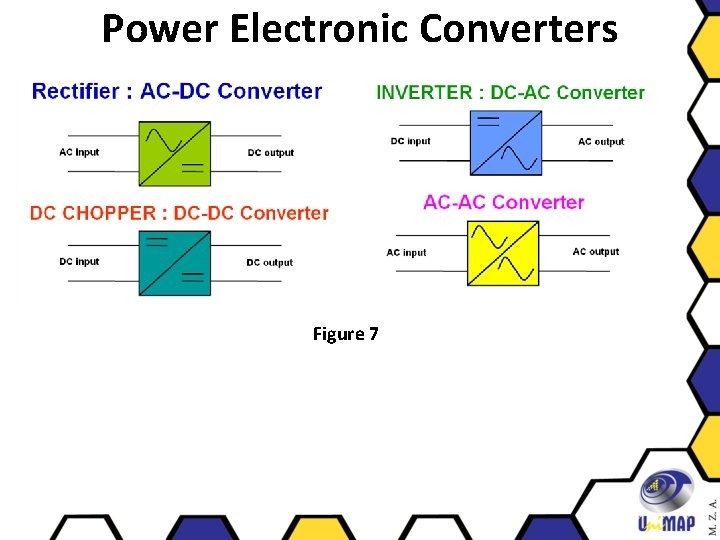
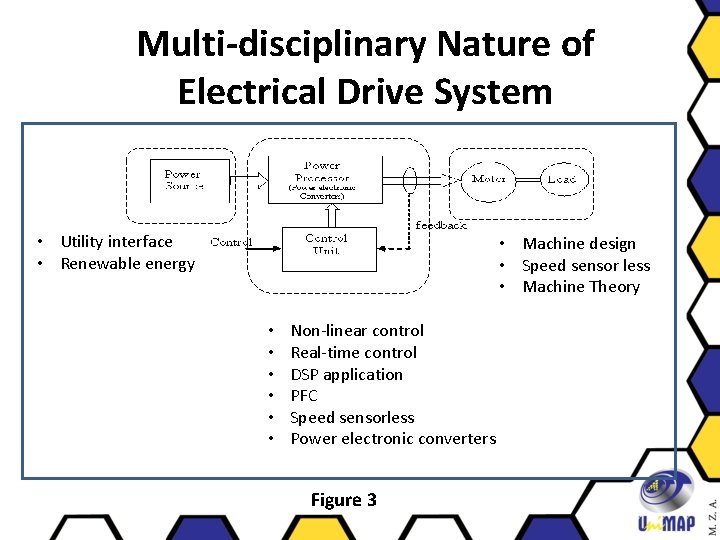
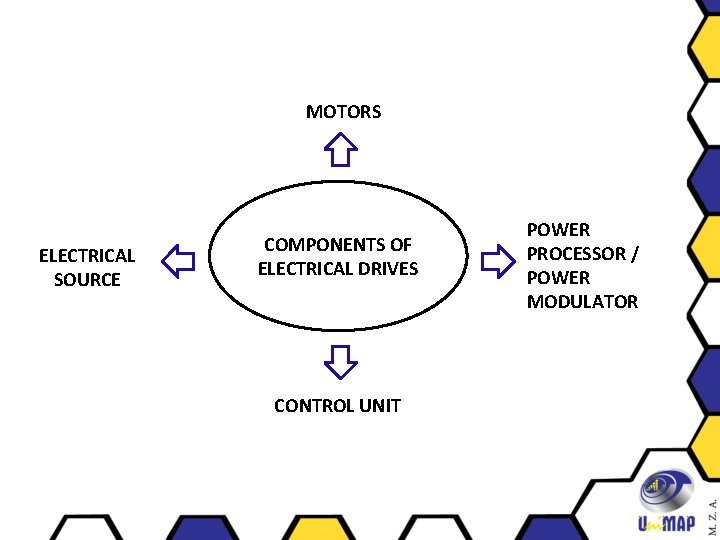
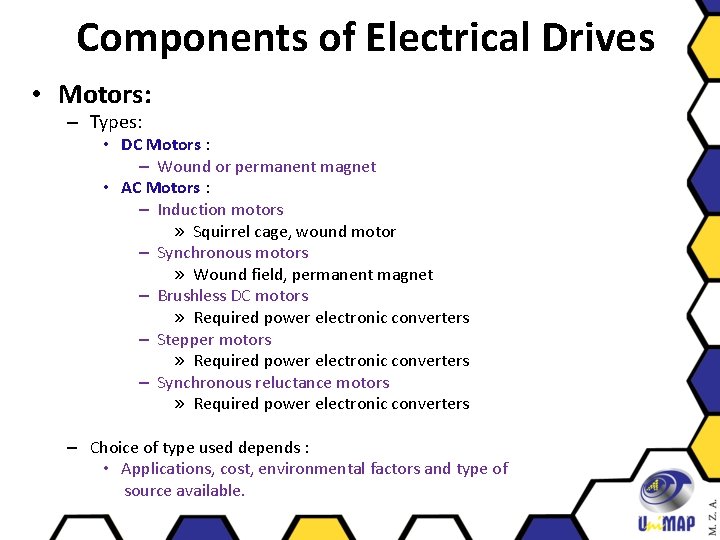
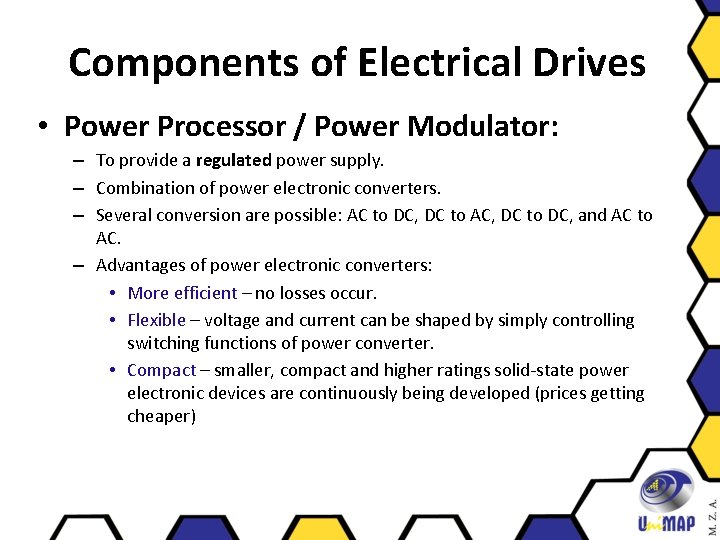
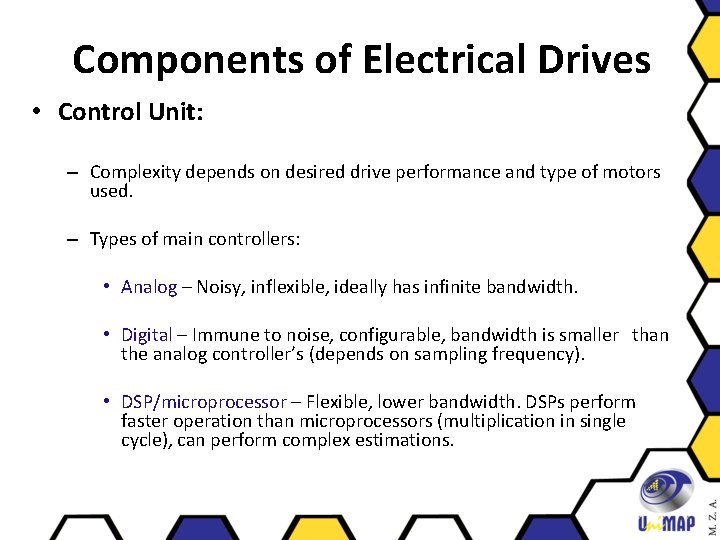
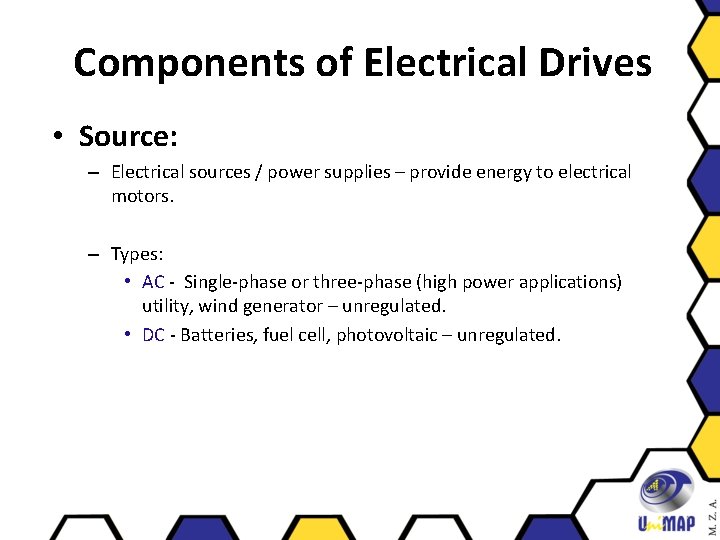
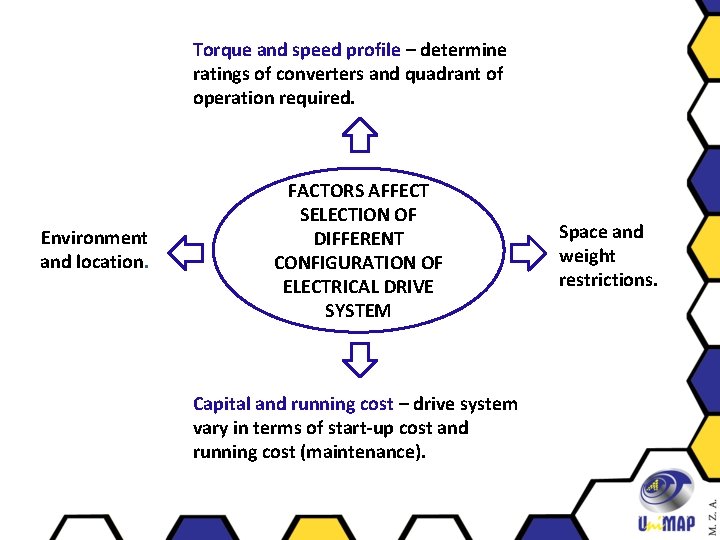
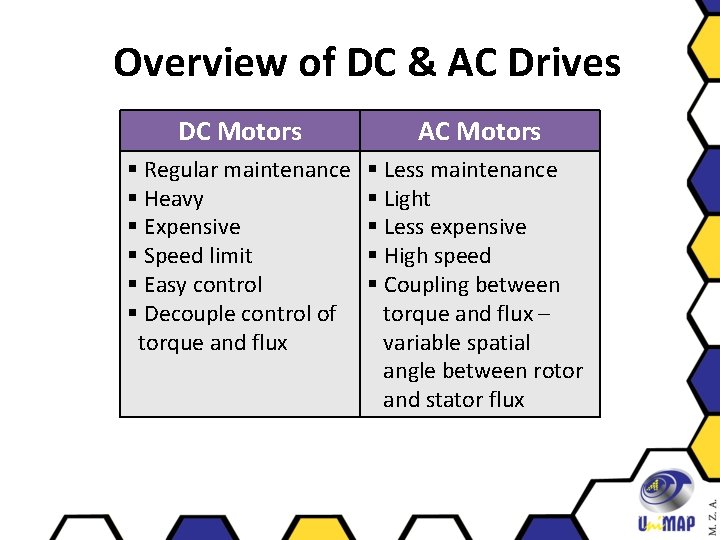
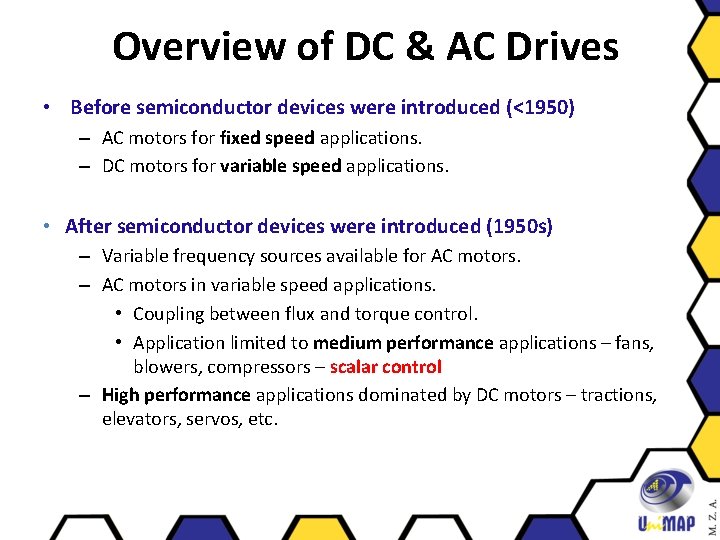
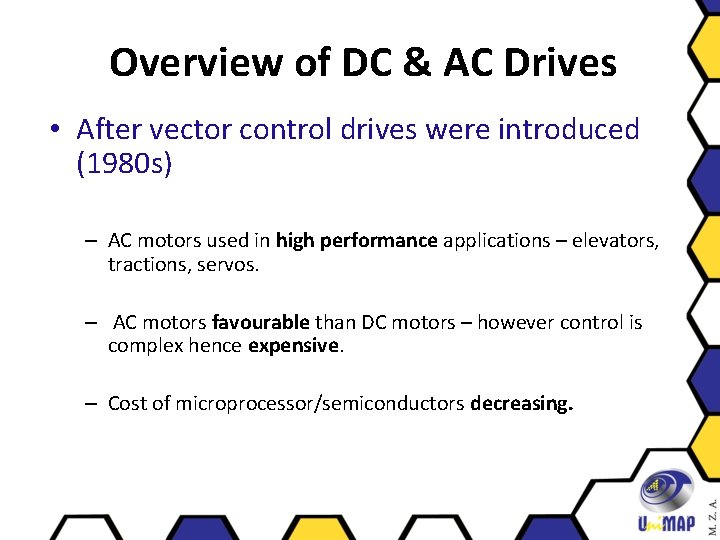
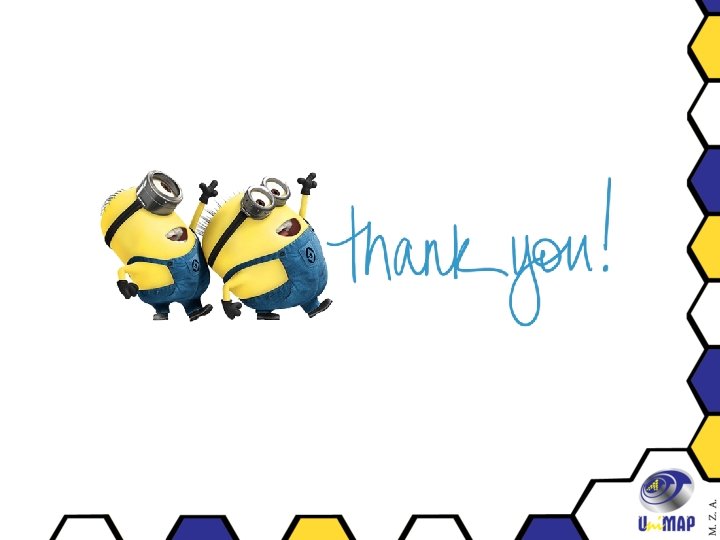
- Slides: 24
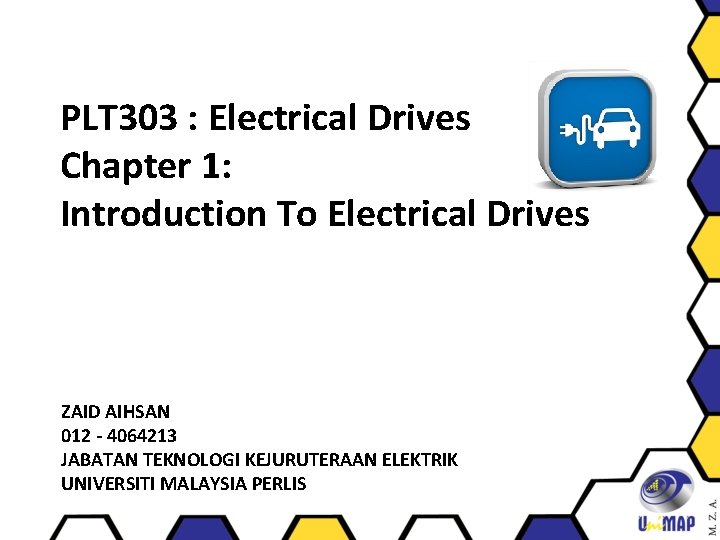
PLT 303 : Electrical Drives Chapter 1: Introduction To Electrical Drives ZAID AIHSAN 012 - 4064213 JABATAN TEKNOLOGI KEJURUTERAAN ELEKTRIK UNIVERSITI MALAYSIA PERLIS
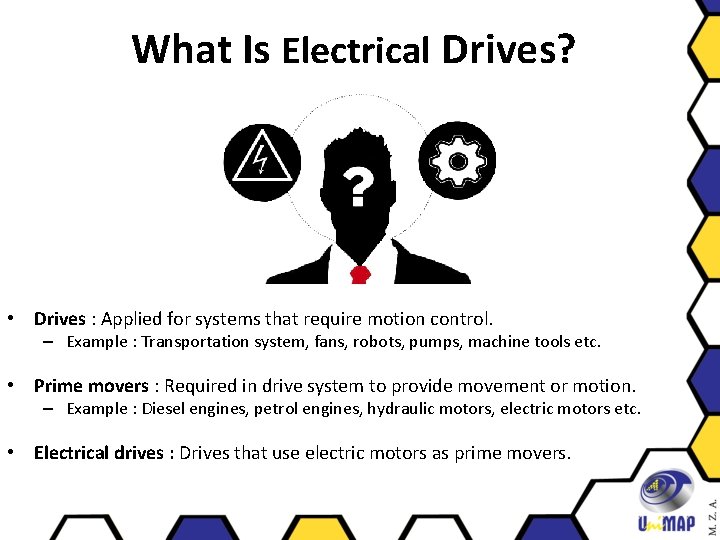
What Is Electrical Drives? • Drives : Applied for systems that require motion control. – Example : Transportation system, fans, robots, pumps, machine tools etc. • Prime movers : Required in drive system to provide movement or motion. – Example : Diesel engines, petrol engines, hydraulic motors, electric motors etc. • Electrical drives : Drives that use electric motors as prime movers.
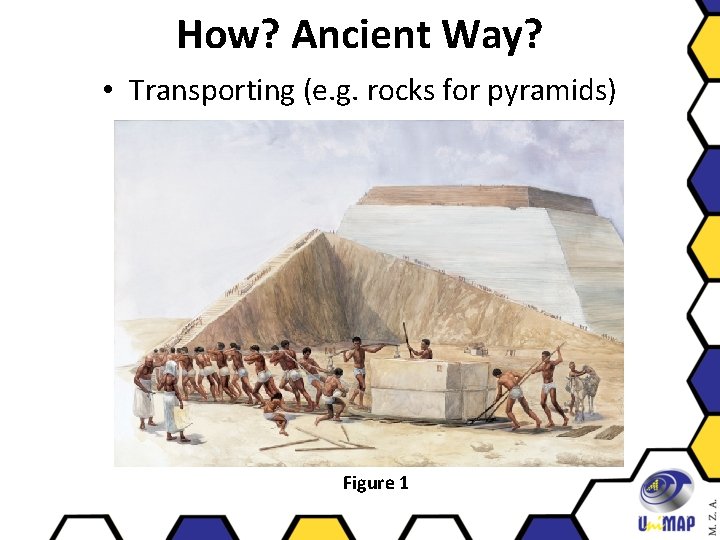
How? Ancient Way? • Transporting (e. g. rocks for pyramids) Figure 1
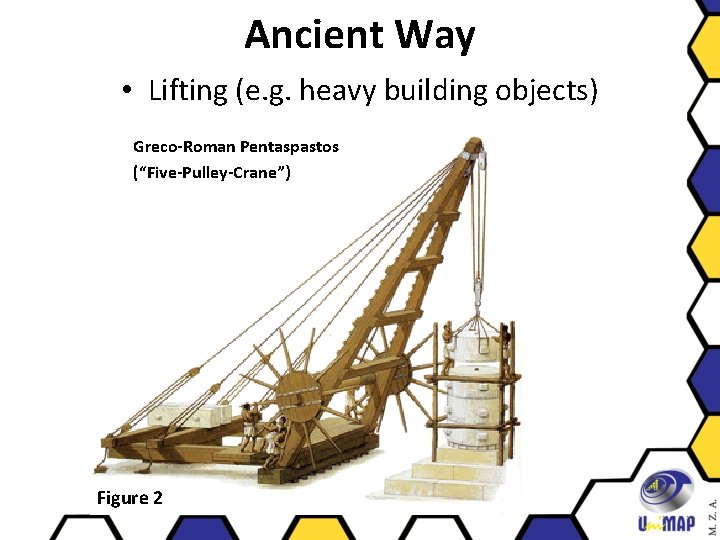
Ancient Way • Lifting (e. g. heavy building objects) Greco-Roman Pentaspastos (“Five-Pulley-Crane”) Figure 2
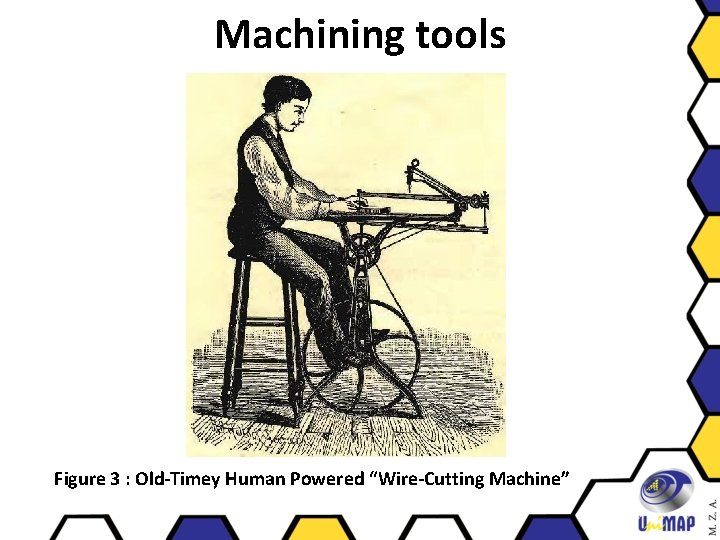
Machining tools Figure 3 : Old-Timey Human Powered “Wire-Cutting Machine”
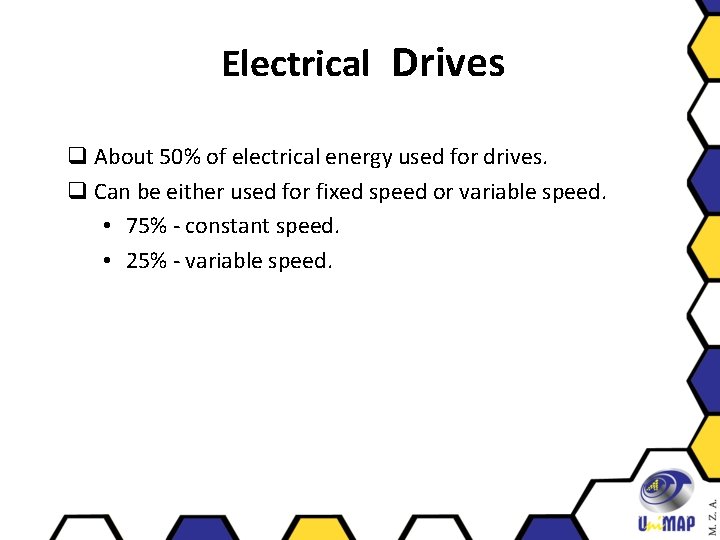
Electrical Drives q About 50% of electrical energy used for drives. q Can be either used for fixed speed or variable speed. • 75% - constant speed. • 25% - variable speed.
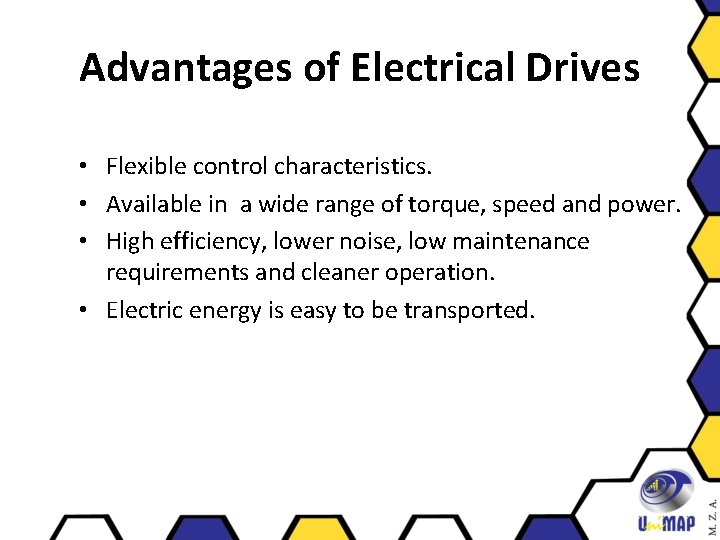
Advantages of Electrical Drives • Flexible control characteristics. • Available in a wide range of torque, speed and power. • High efficiency, lower noise, low maintenance requirements and cleaner operation. • Electric energy is easy to be transported.
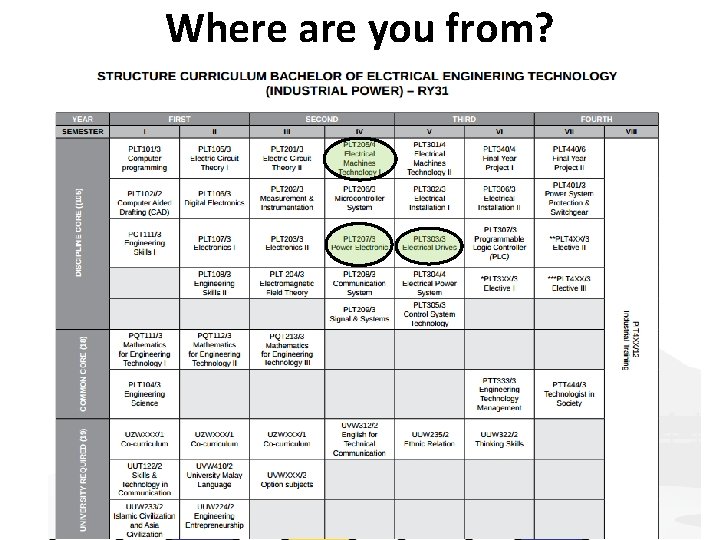
Where are you from?
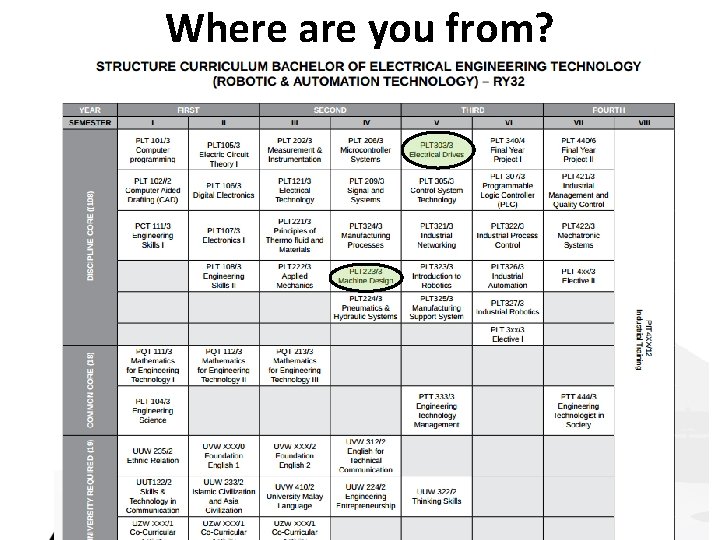
Where are you from?
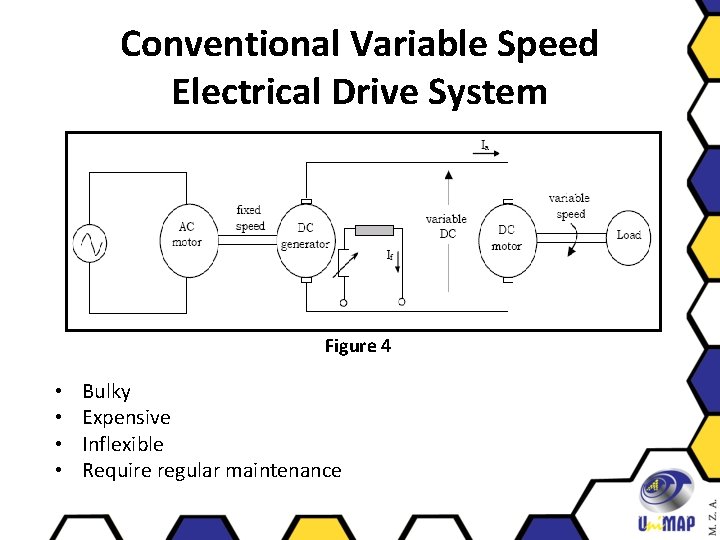
Conventional Variable Speed Electrical Drive System Figure 4 • • Bulky Expensive Inflexible Require regular maintenance
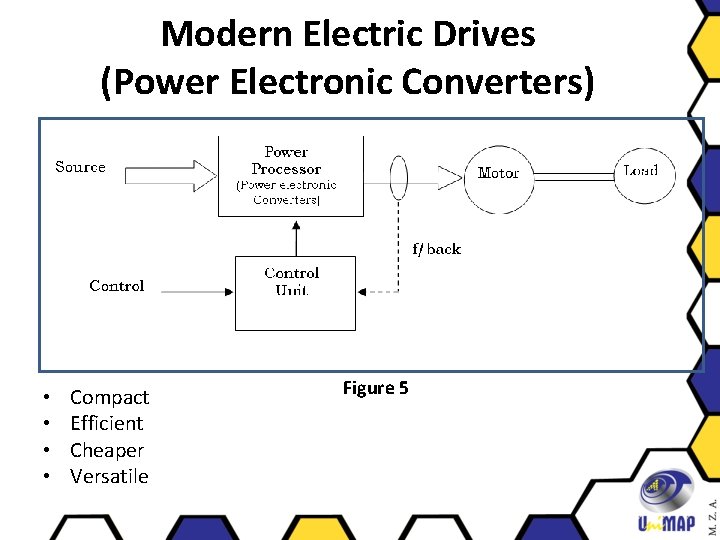
Modern Electric Drives (Power Electronic Converters) • • Compact Efficient Cheaper Versatile Figure 5
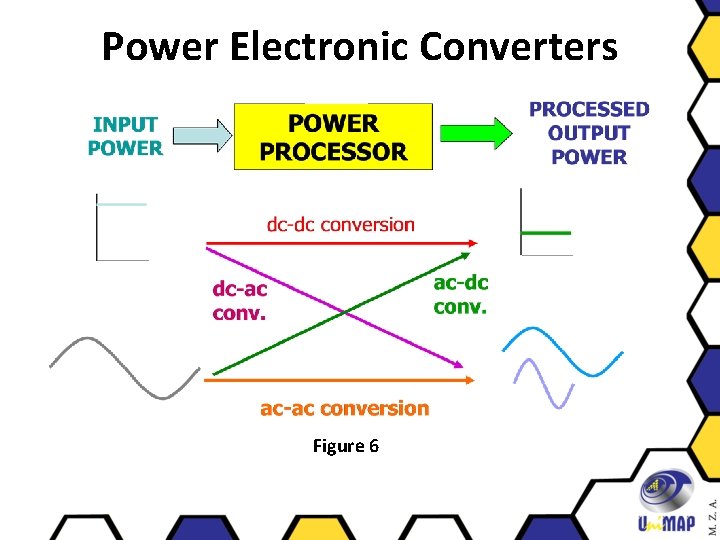
Power Electronic Converters Figure 6
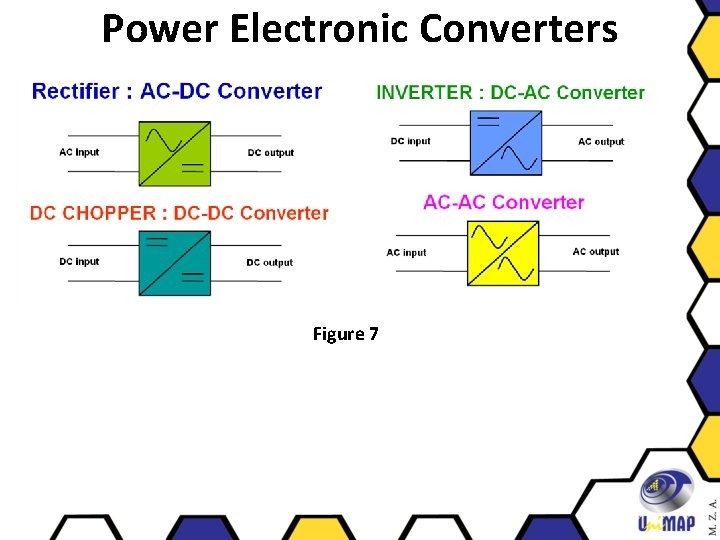
Power Electronic Converters Figure 7
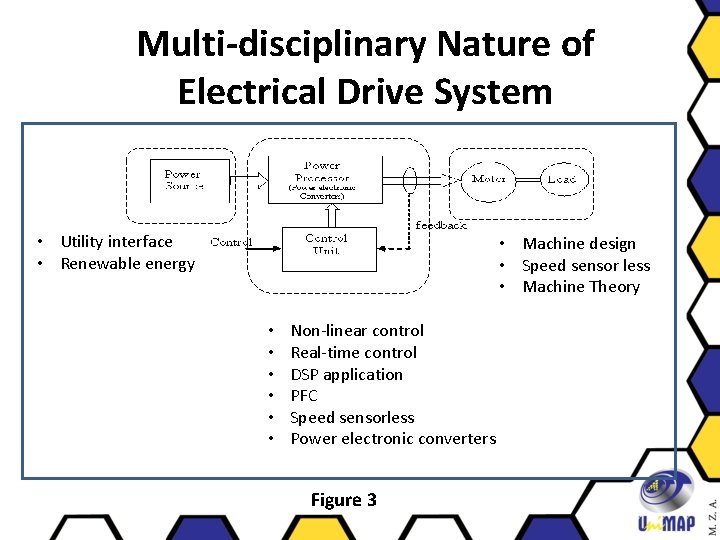
Multi-disciplinary Nature of Electrical Drive System • Utility interface • Renewable energy • Machine design • Speed sensor less • Machine Theory • • • Non-linear control Real-time control DSP application PFC Speed sensorless Power electronic converters Figure 3
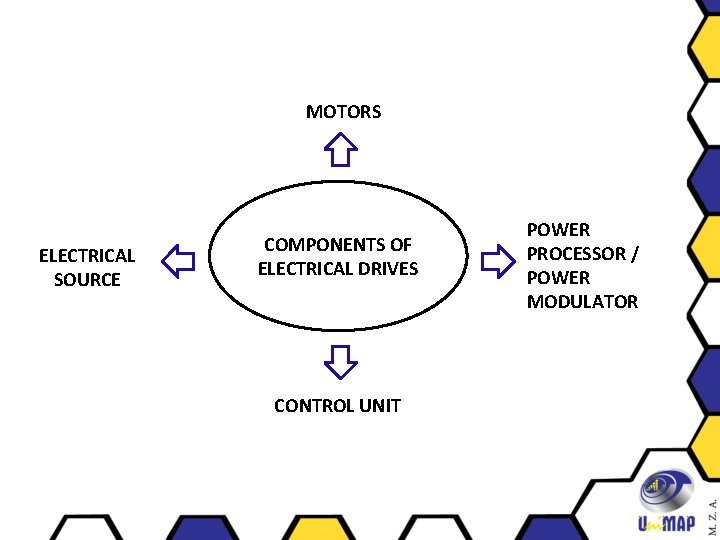
MOTORS ELECTRICAL SOURCE COMPONENTS OF ELECTRICAL DRIVES CONTROL UNIT POWER PROCESSOR / POWER MODULATOR
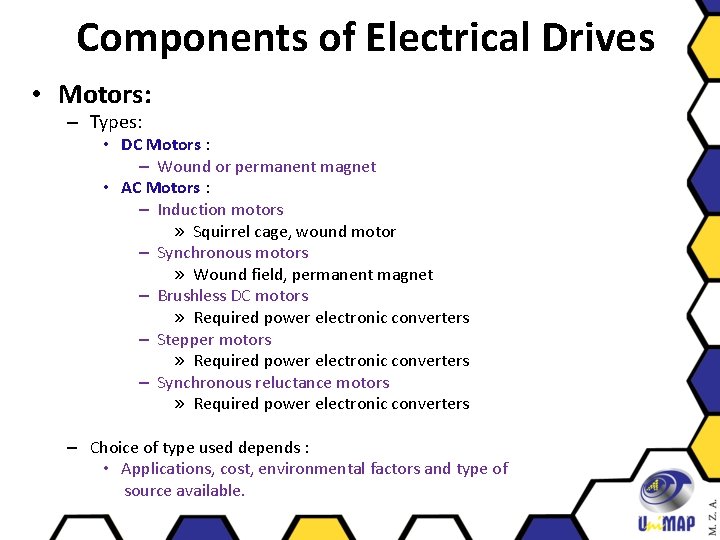
Components of Electrical Drives • Motors: – Types: • DC Motors : – Wound or permanent magnet • AC Motors : – Induction motors » Squirrel cage, wound motor – Synchronous motors » Wound field, permanent magnet – Brushless DC motors » Required power electronic converters – Stepper motors » Required power electronic converters – Synchronous reluctance motors » Required power electronic converters – Choice of type used depends : • Applications, cost, environmental factors and type of source available.
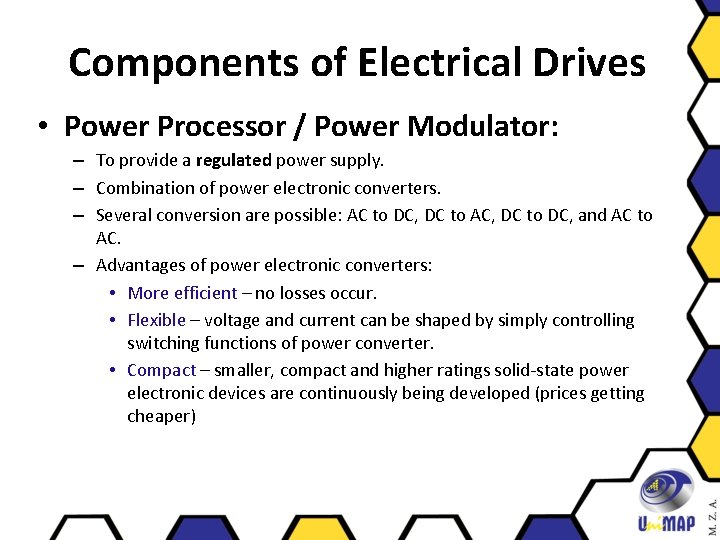
Components of Electrical Drives • Power Processor / Power Modulator: – To provide a regulated power supply. – Combination of power electronic converters. – Several conversion are possible: AC to DC, DC to AC, DC to DC, and AC to AC. – Advantages of power electronic converters: • More efficient – no losses occur. • Flexible – voltage and current can be shaped by simply controlling switching functions of power converter. • Compact – smaller, compact and higher ratings solid-state power electronic devices are continuously being developed (prices getting cheaper)
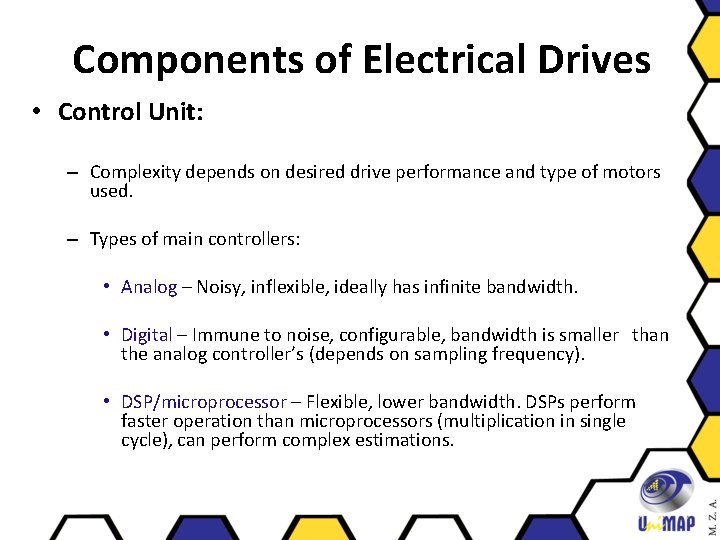
Components of Electrical Drives • Control Unit: – Complexity depends on desired drive performance and type of motors used. – Types of main controllers: • Analog – Noisy, inflexible, ideally has infinite bandwidth. • Digital – Immune to noise, configurable, bandwidth is smaller than the analog controller’s (depends on sampling frequency). • DSP/microprocessor – Flexible, lower bandwidth. DSPs perform faster operation than microprocessors (multiplication in single cycle), can perform complex estimations.
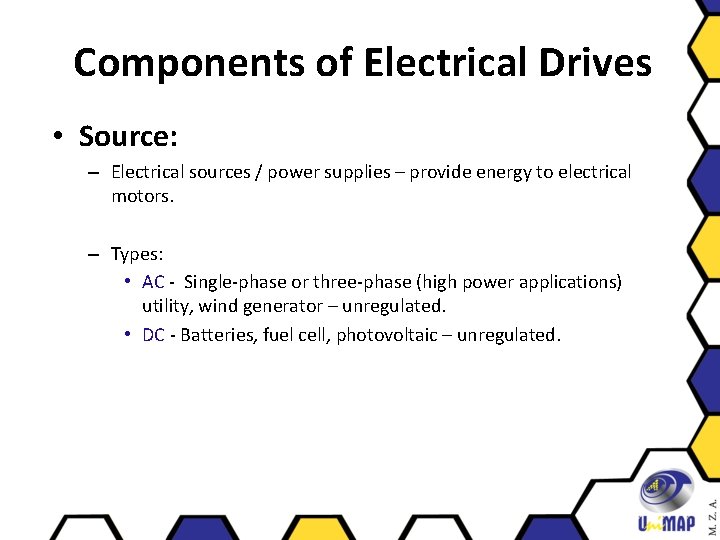
Components of Electrical Drives • Source: – Electrical sources / power supplies – provide energy to electrical motors. – Types: • AC - Single-phase or three-phase (high power applications) utility, wind generator – unregulated. • DC - Batteries, fuel cell, photovoltaic – unregulated.
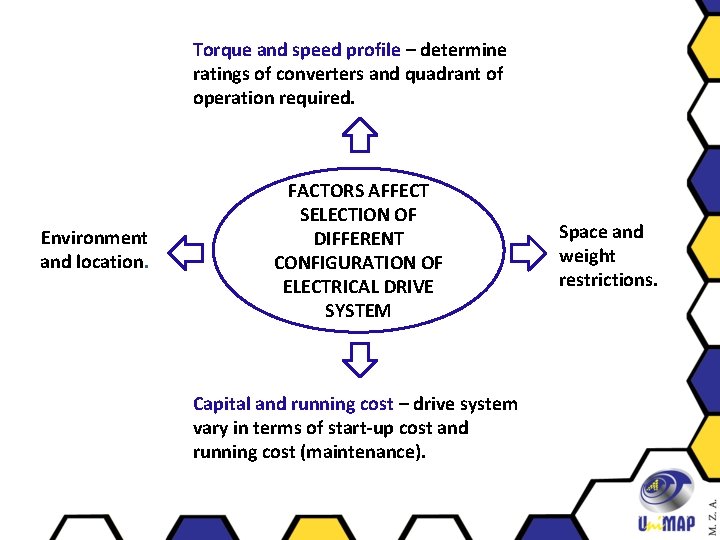
Torque and speed profile – determine ratings of converters and quadrant of operation required. Environment and location. FACTORS AFFECT SELECTION OF DIFFERENT CONFIGURATION OF ELECTRICAL DRIVE SYSTEM Capital and running cost – drive system vary in terms of start-up cost and running cost (maintenance). Space and weight restrictions.
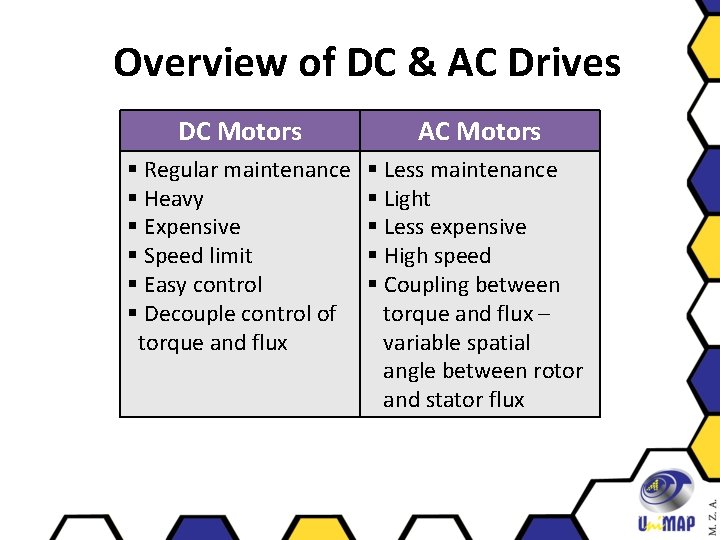
Overview of DC & AC Drives DC Motors AC Motors § Regular maintenance § Heavy § Expensive § Speed limit § Easy control § Decouple control of torque and flux § Less maintenance § Light § Less expensive § High speed § Coupling between torque and flux – variable spatial angle between rotor and stator flux
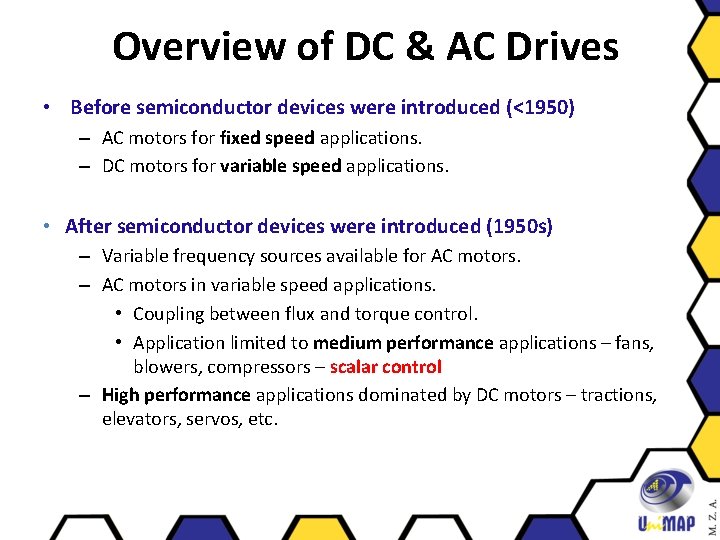
Overview of DC & AC Drives • Before semiconductor devices were introduced (<1950) – AC motors for fixed speed applications. – DC motors for variable speed applications. • After semiconductor devices were introduced (1950 s) – Variable frequency sources available for AC motors. – AC motors in variable speed applications. • Coupling between flux and torque control. • Application limited to medium performance applications – fans, blowers, compressors – scalar control – High performance applications dominated by DC motors – tractions, elevators, servos, etc.
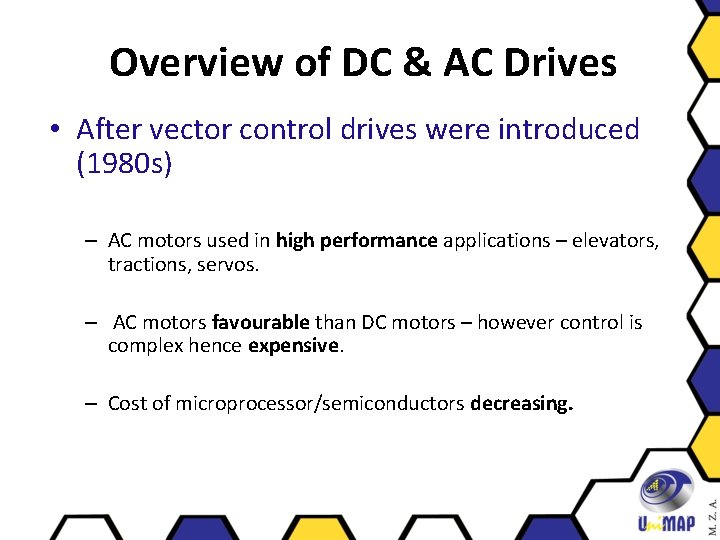
Overview of DC & AC Drives • After vector control drives were introduced (1980 s) – AC motors used in high performance applications – elevators, tractions, servos. – AC motors favourable than DC motors – however control is complex hence expensive. – Cost of microprocessor/semiconductors decreasing.
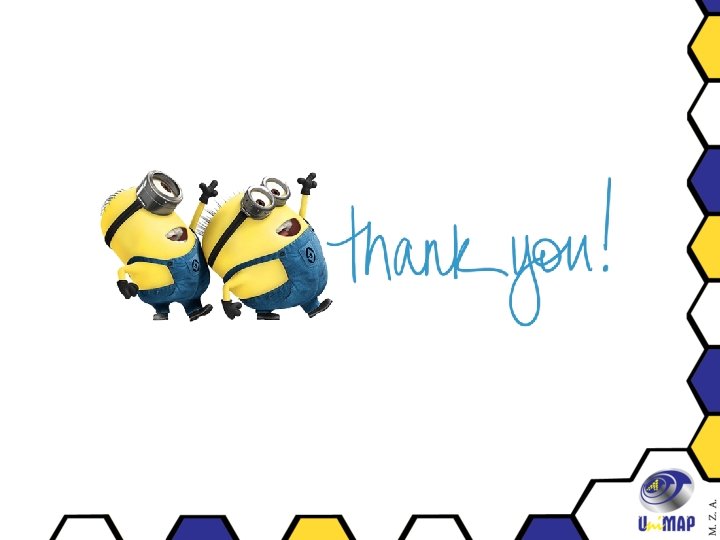
Electrical drives and control
38cfr3.303
Vir 303
Emin gun sirer
Ruger no 1 accuracy improvement
Zoo 303
Sis-303
Vicentiu covrig
Explain kravis and linder theory.
Economic 303
Dywizjon 303 klp
6974-6459-0121-7236-303
Life orientation grade 7 term 2 exam papers
Uib290
Www.coloradoui.gov.myuiemployer
Mktg 303
Bilgiyi işleme modelinin eğitim ortamında uygulamaları
Cse 303
Wbc ip message blasts/abn lympho
Plt abn distribution
Plt 404
Striscio di sangue
Plt scheme
Plt fuzzy set
Plt electronics