PDCA Plan Do Check Act Larry Osentoski Mike
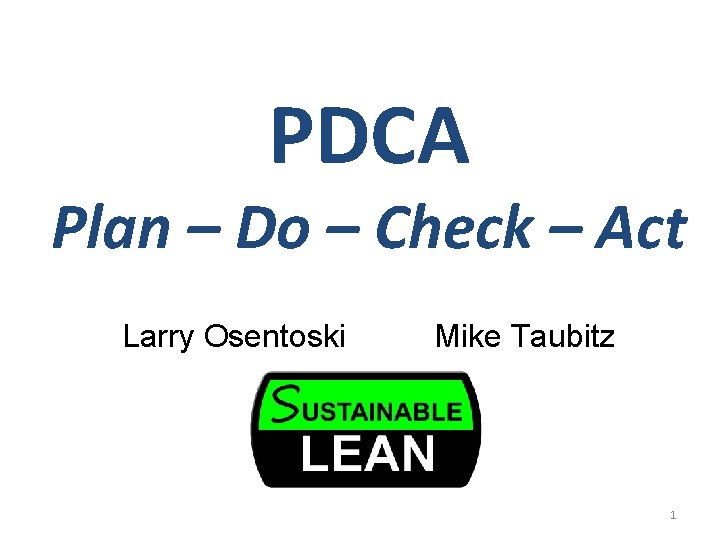
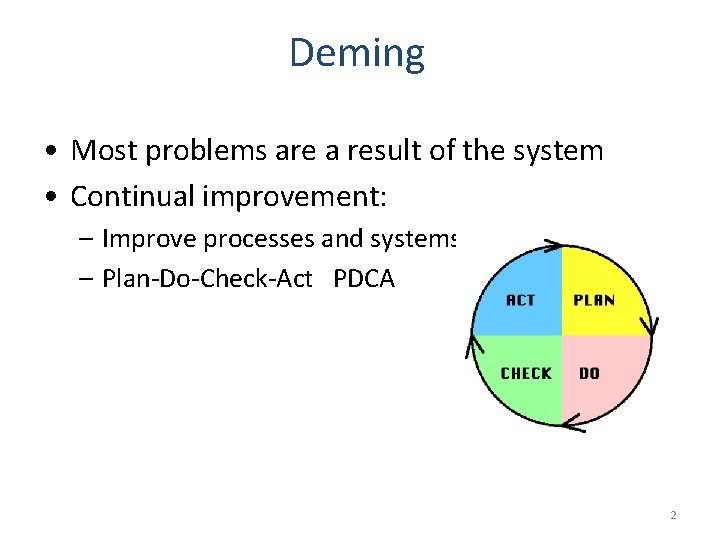
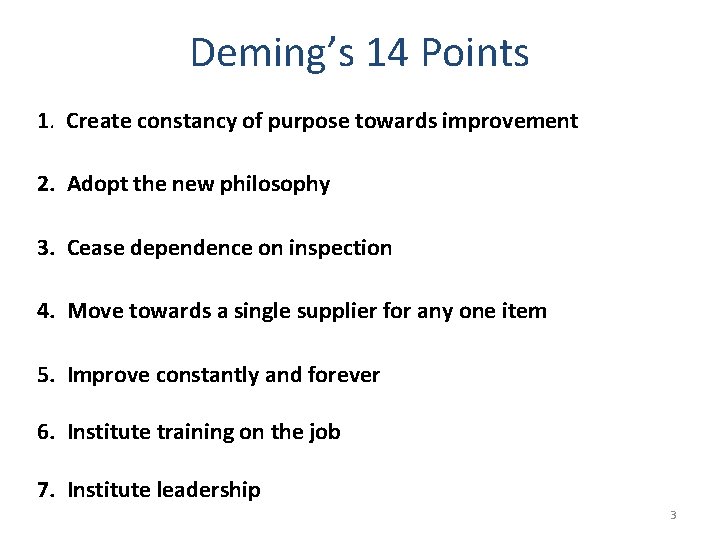
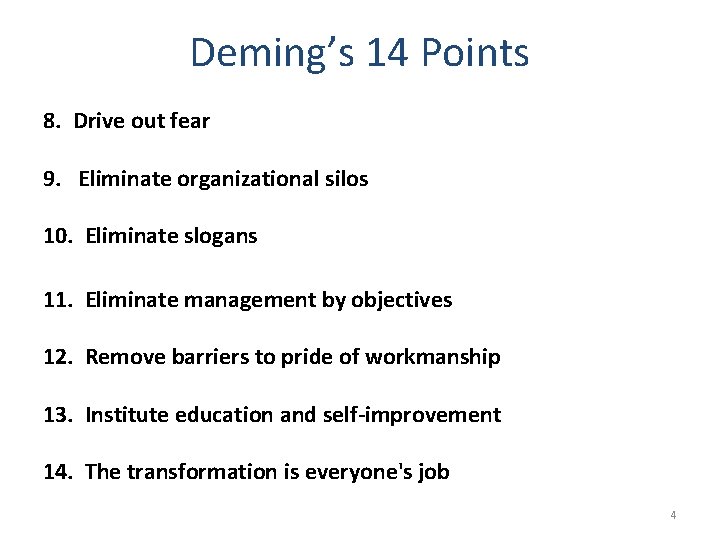
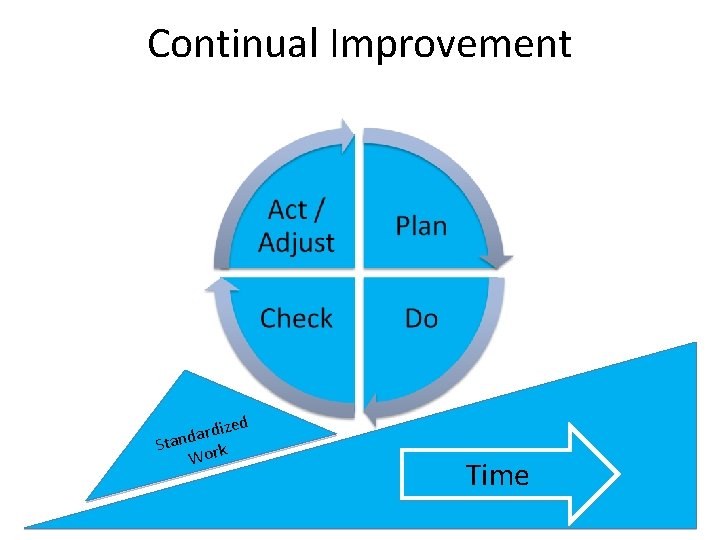
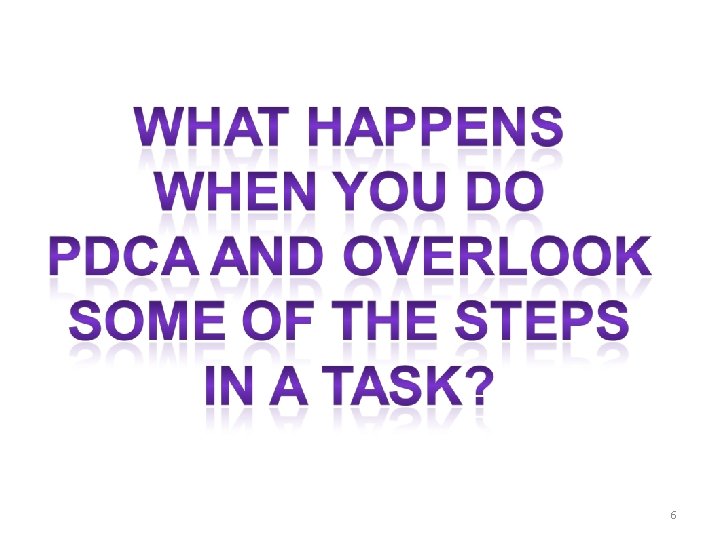
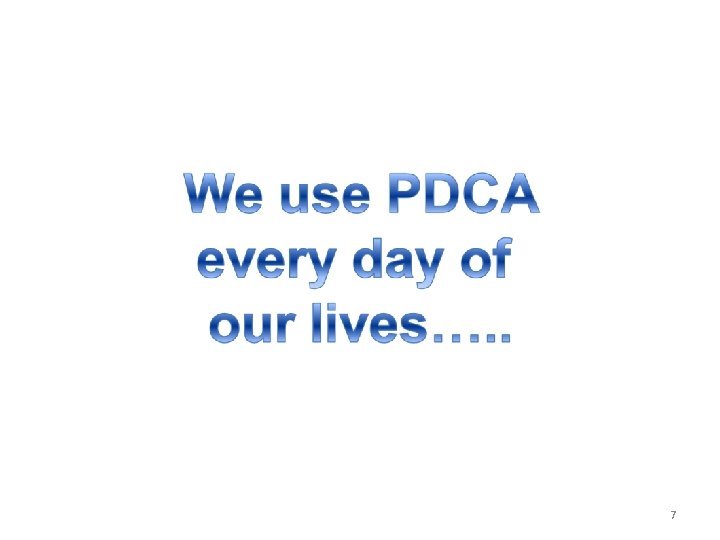
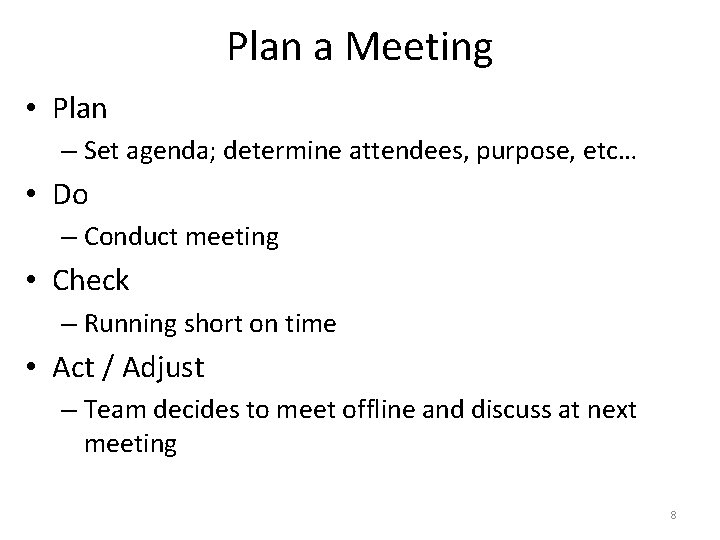
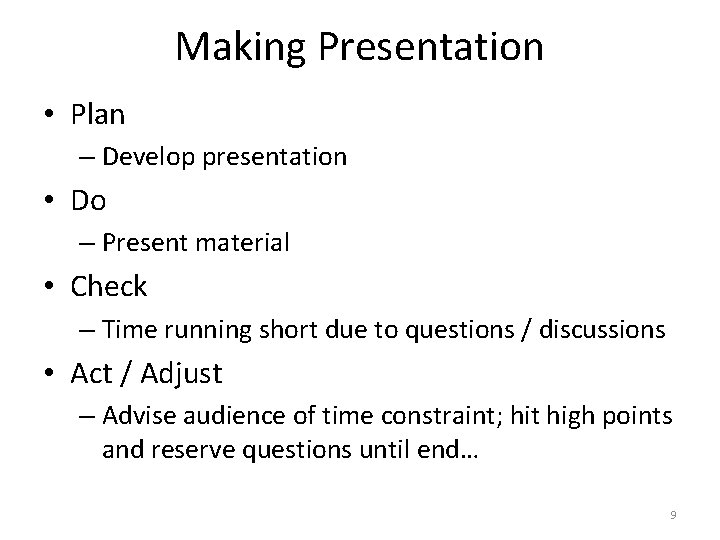
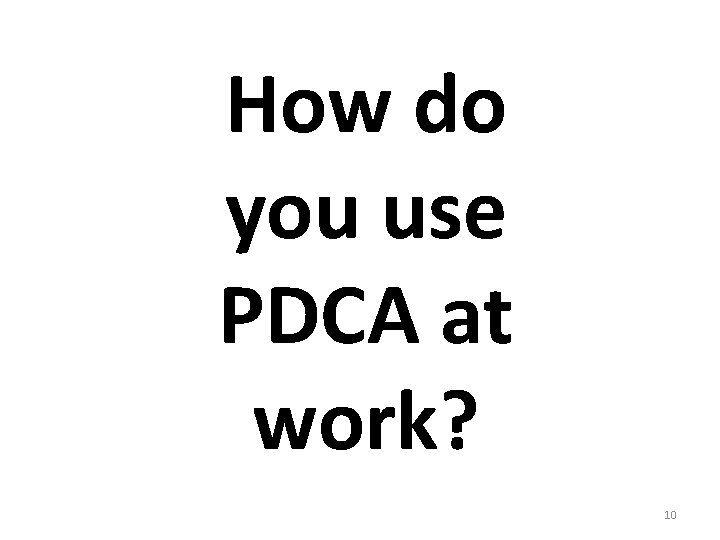
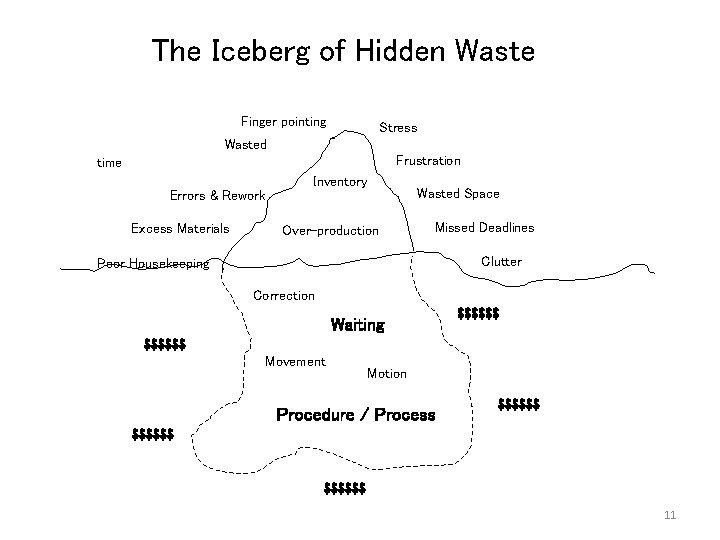
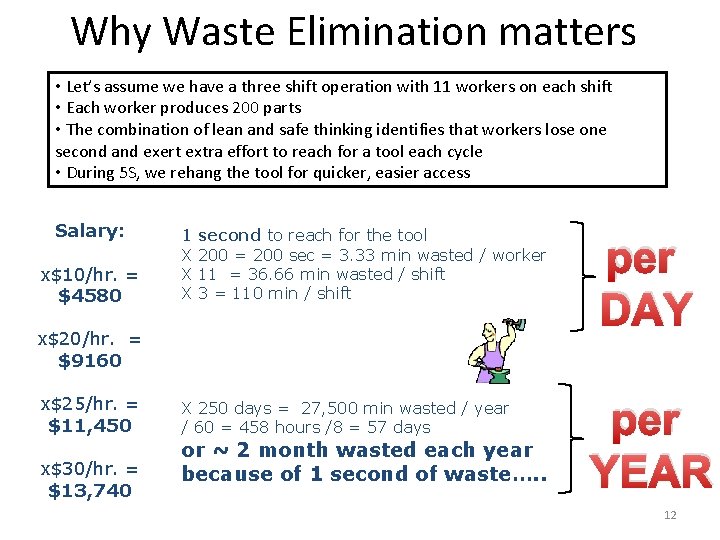

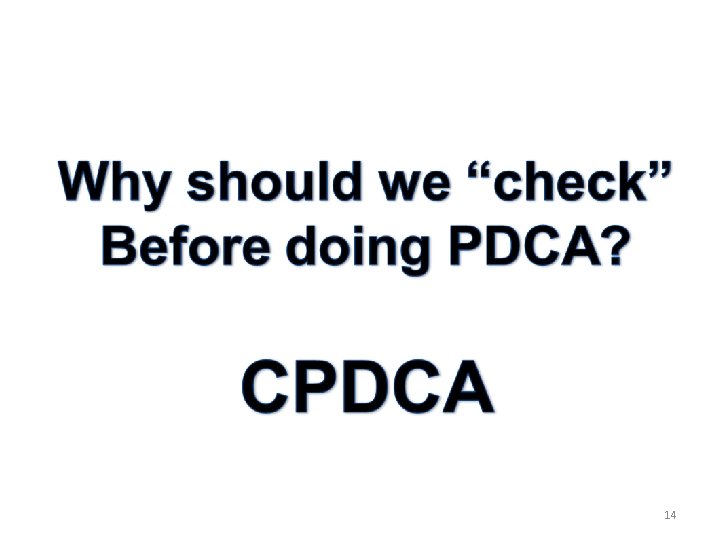
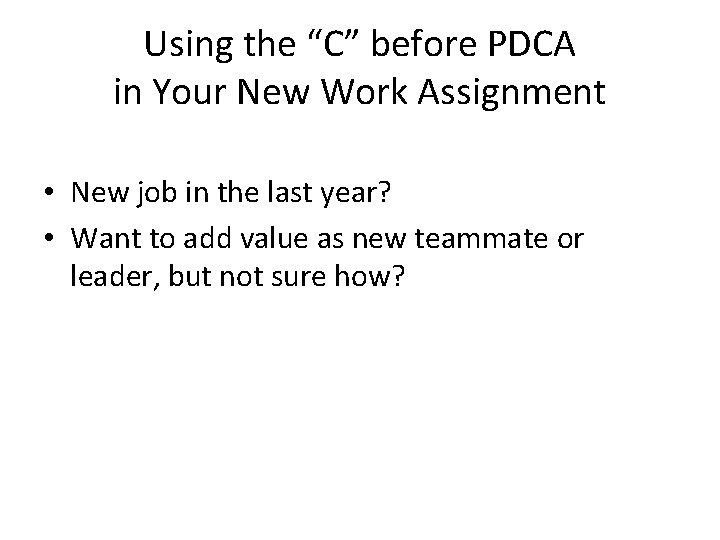
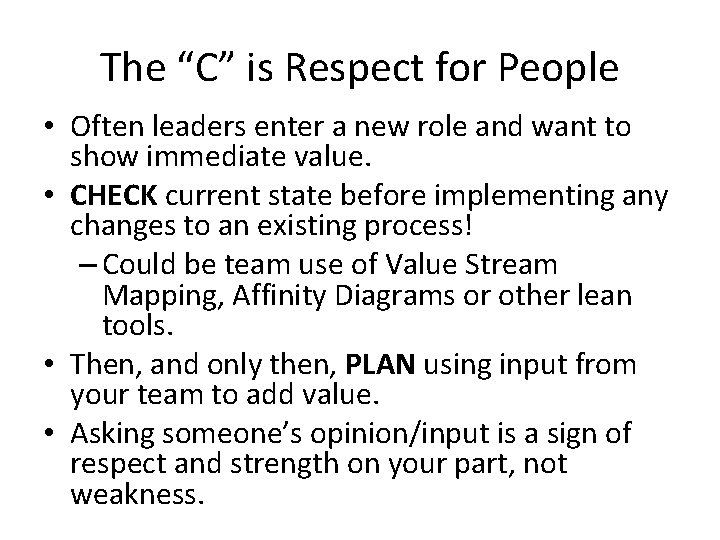
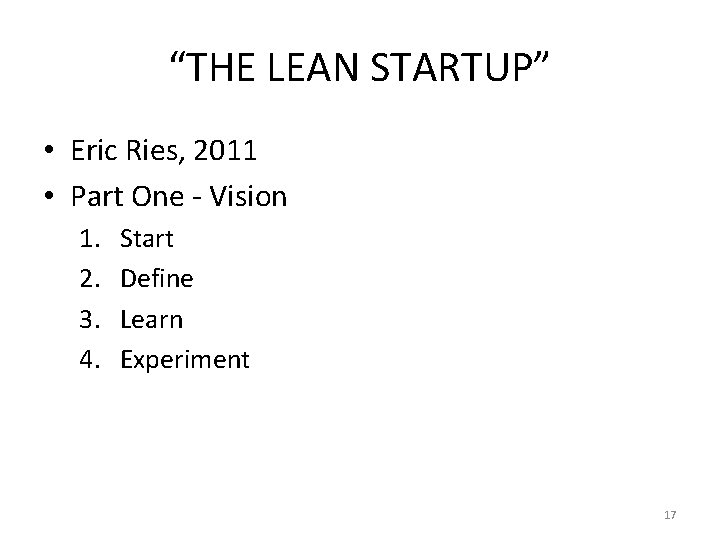
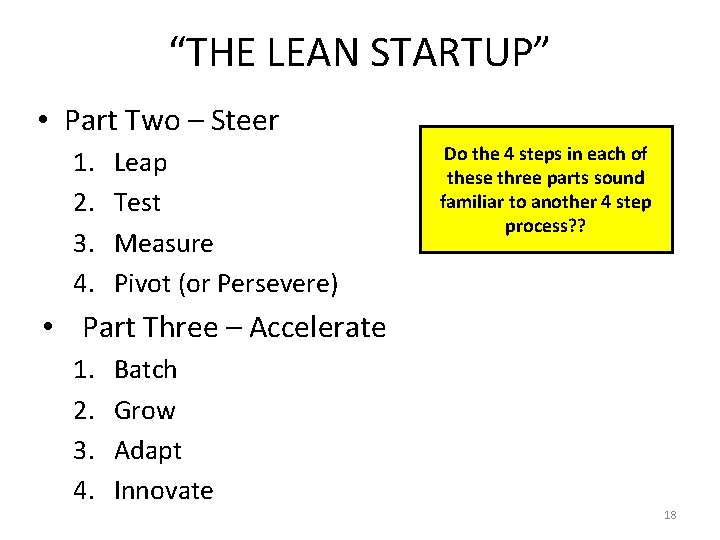
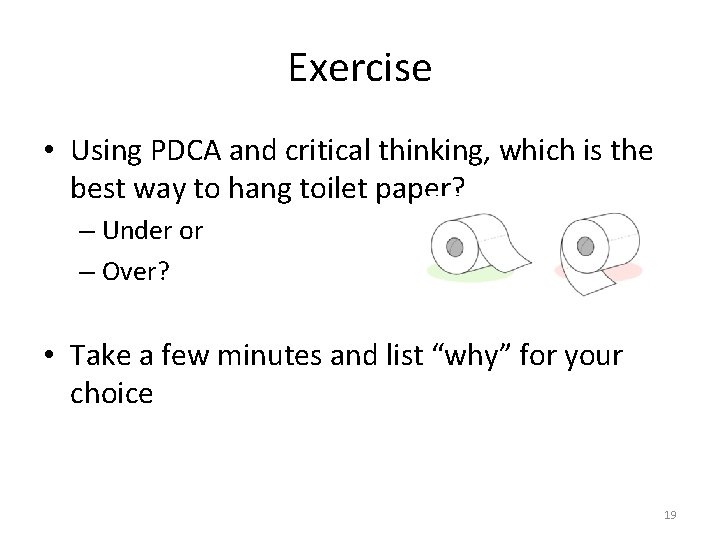
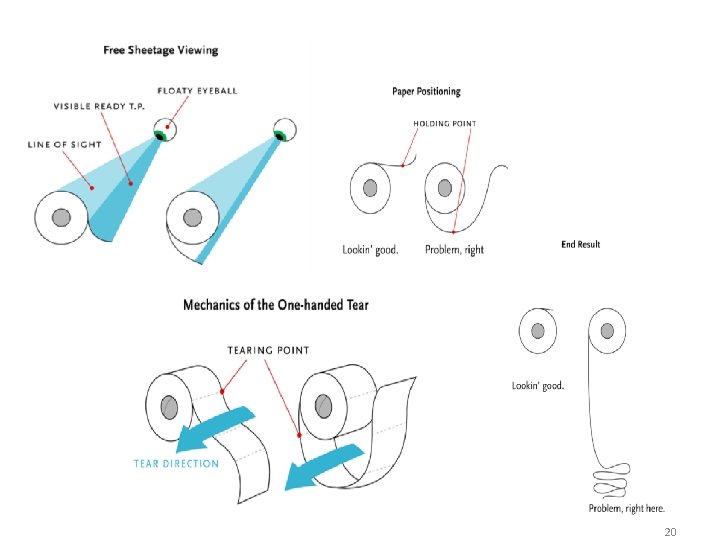
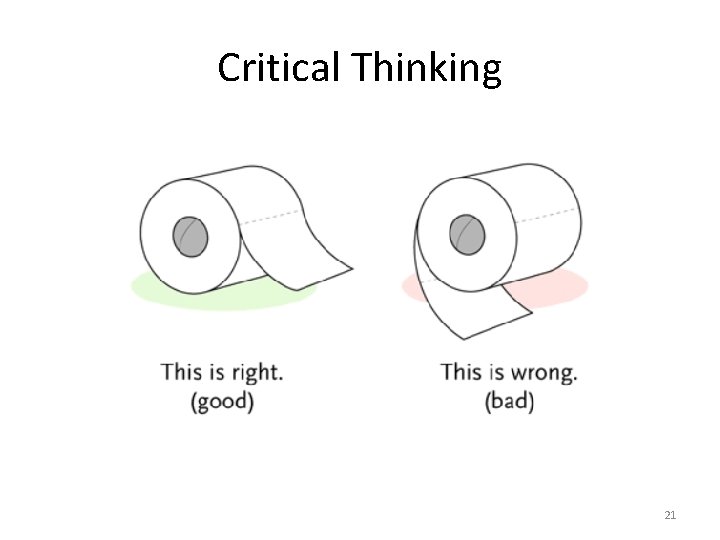
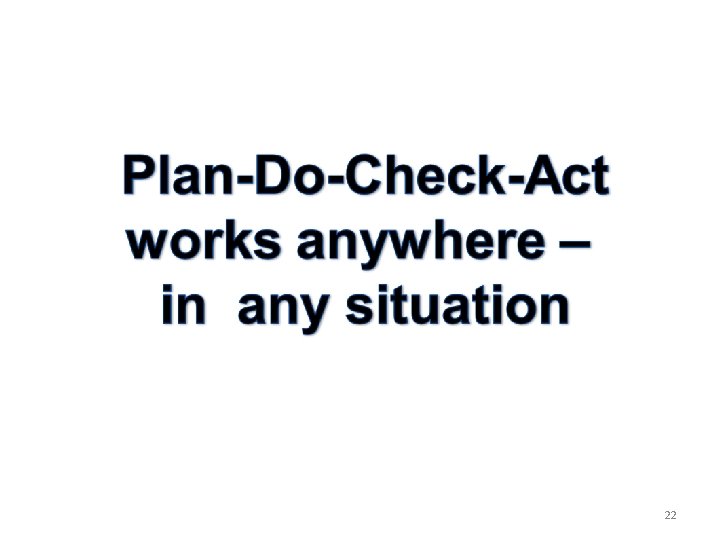
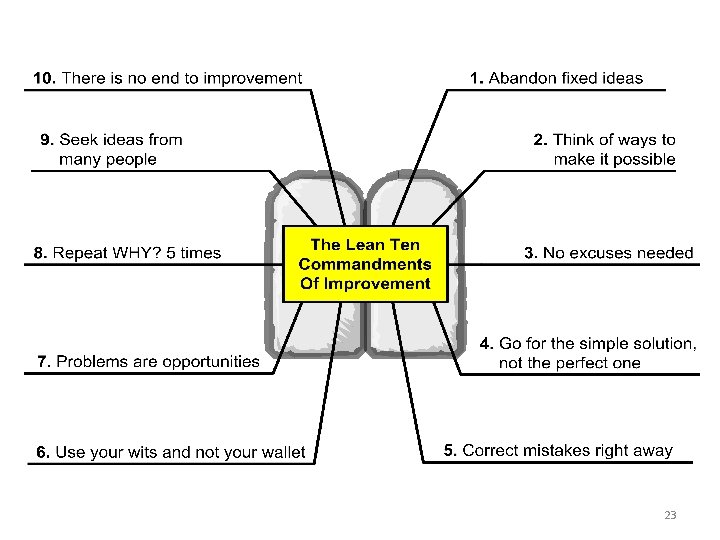
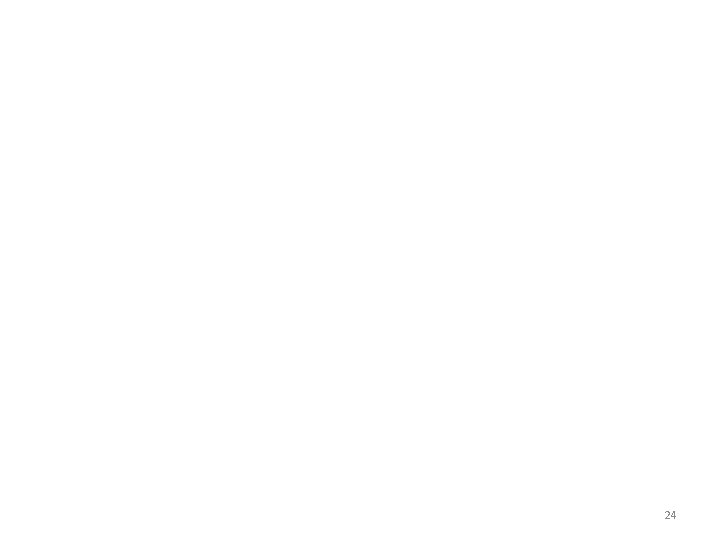
- Slides: 24
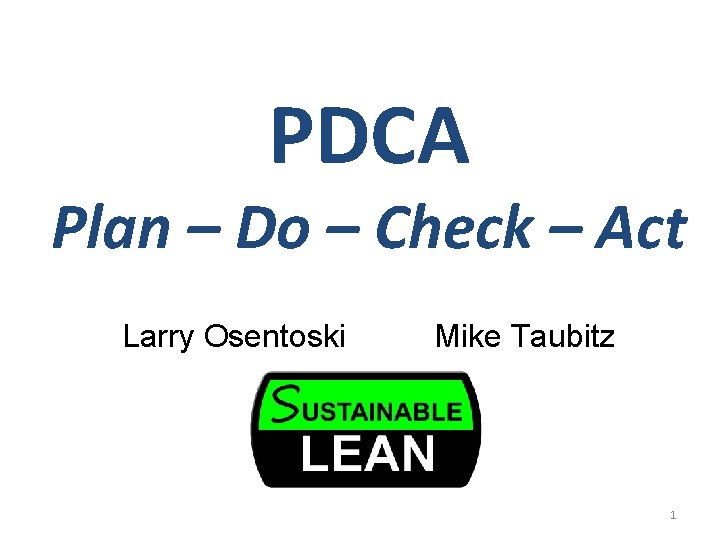
PDCA Plan – Do – Check – Act Larry Osentoski Mike Taubitz 1
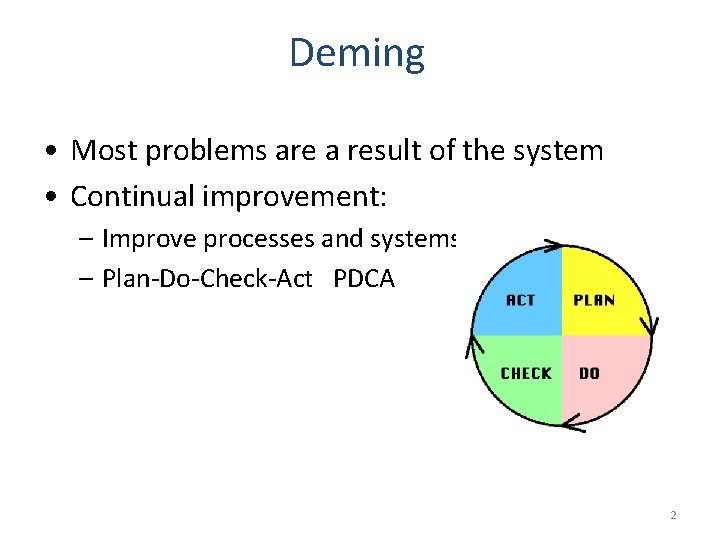
Deming • Most problems are a result of the system • Continual improvement: – Improve processes and systems – Plan-Do-Check-Act PDCA 2
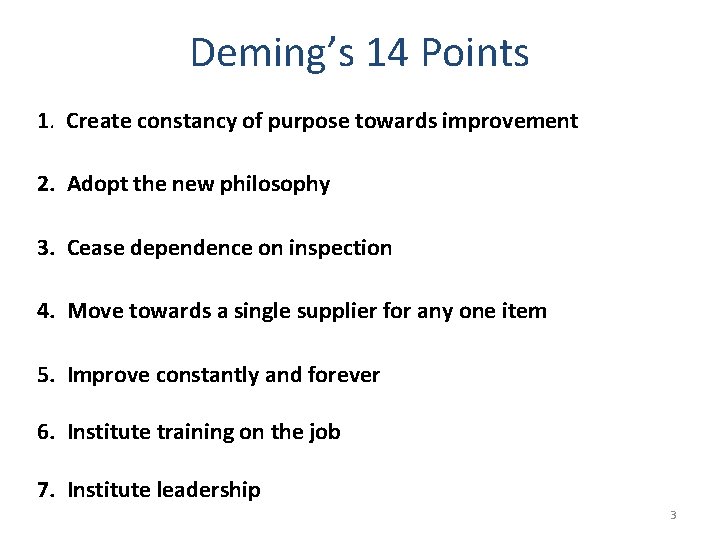
Deming’s 14 Points 1. Create constancy of purpose towards improvement 2. Adopt the new philosophy 3. Cease dependence on inspection 4. Move towards a single supplier for any one item 5. Improve constantly and forever 6. Institute training on the job 7. Institute leadership 3
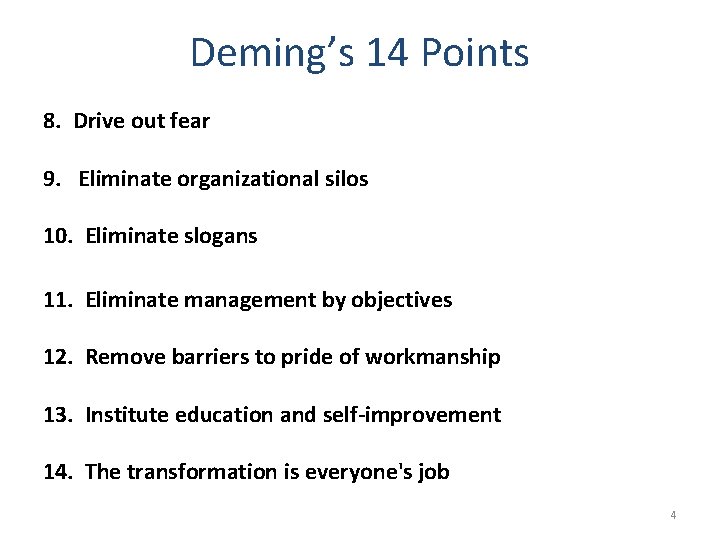
Deming’s 14 Points 8. Drive out fear 9. Eliminate organizational silos 10. Eliminate slogans 11. Eliminate management by objectives 12. Remove barriers to pride of workmanship 13. Institute education and self-improvement 14. The transformation is everyone's job 4
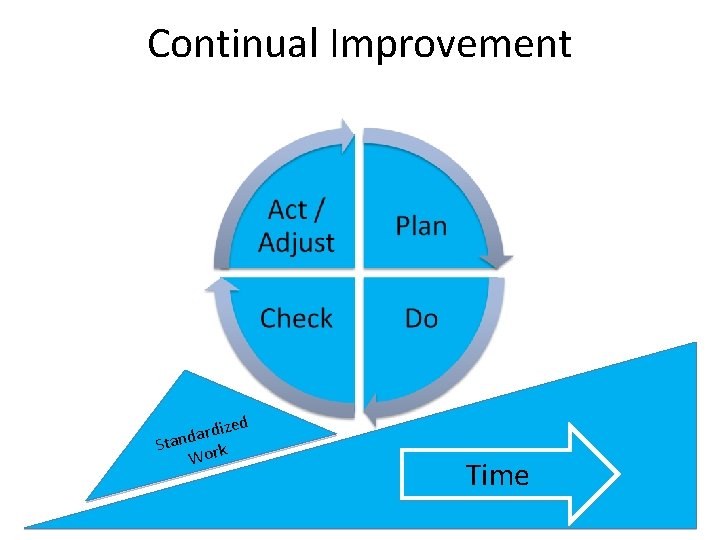
Continual Improvement ized d r a d Stan rk Wo Time 5 5
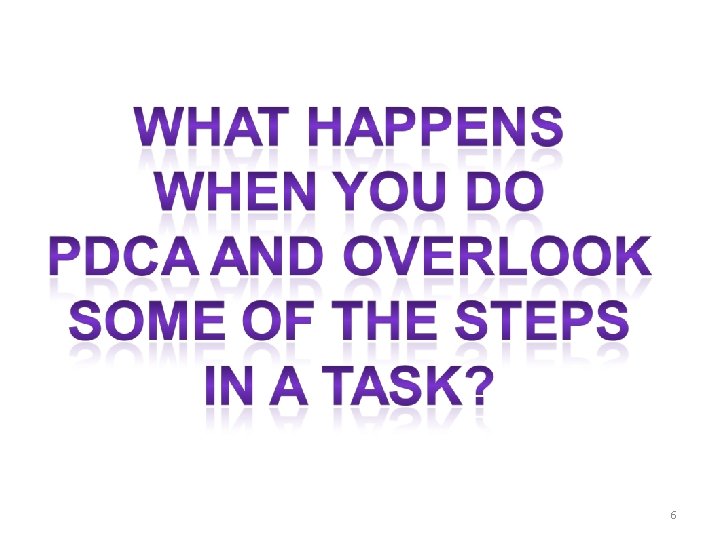
6
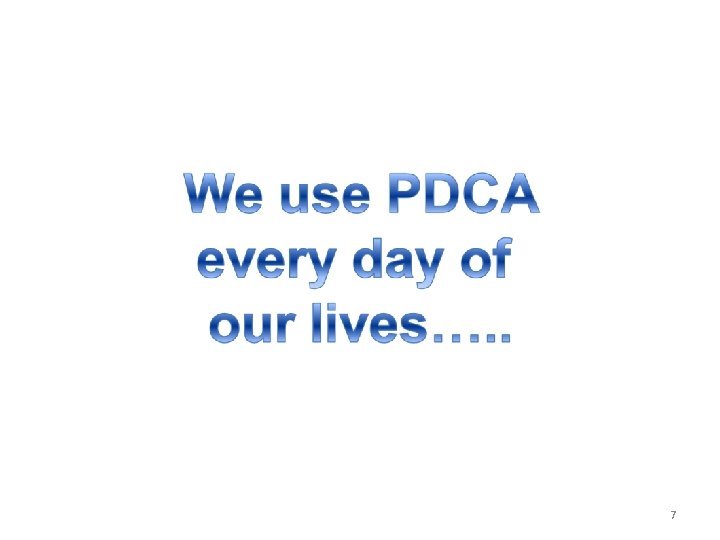
7
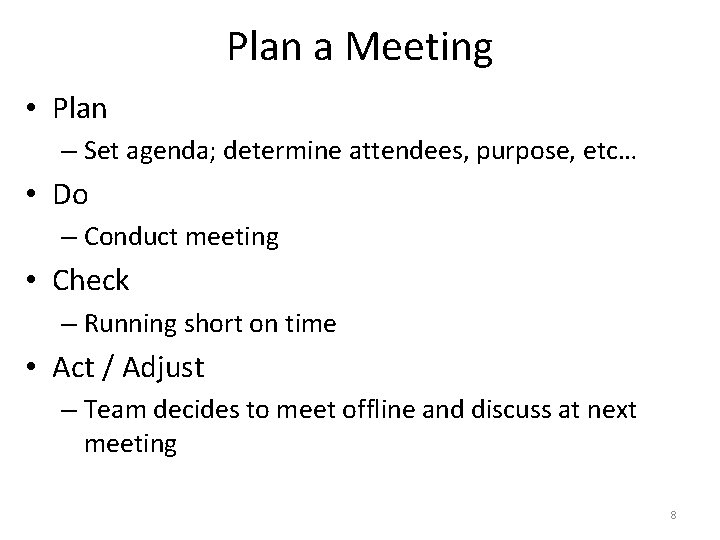
Plan a Meeting • Plan – Set agenda; determine attendees, purpose, etc… • Do – Conduct meeting • Check – Running short on time • Act / Adjust – Team decides to meet offline and discuss at next meeting 8
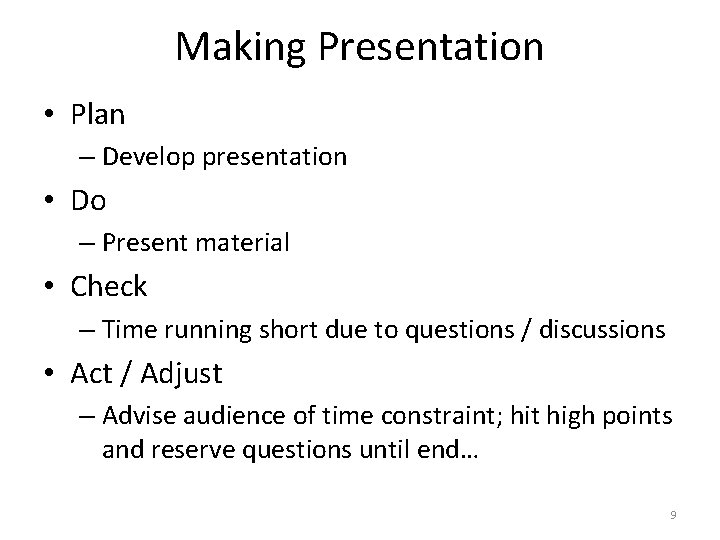
Making Presentation • Plan – Develop presentation • Do – Present material • Check – Time running short due to questions / discussions • Act / Adjust – Advise audience of time constraint; hit high points and reserve questions until end… 9
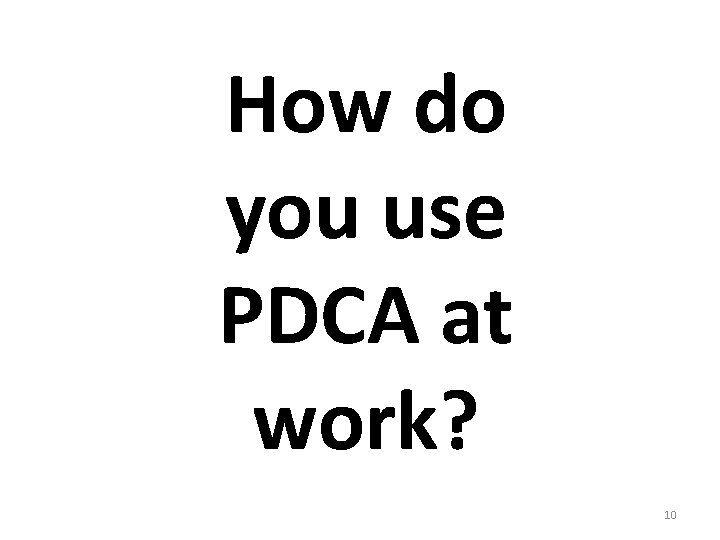
How do you use PDCA at work? 10
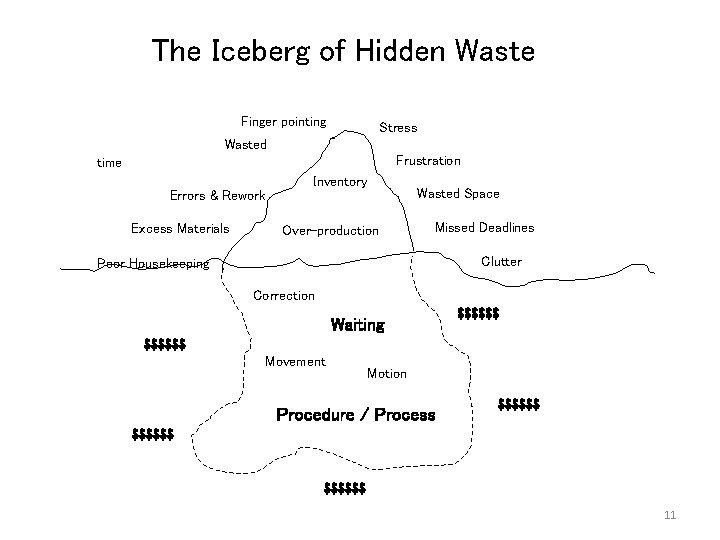
The Iceberg of Hidden Waste Finger pointing Stress Wasted Frustration time Errors & Rework Excess Materials Inventory Over-production Wasted Space Missed Deadlines Clutter Poor Housekeeping Correction Waiting $$$$$$ Movement Motion Procedure / Process $$$$$$ 11
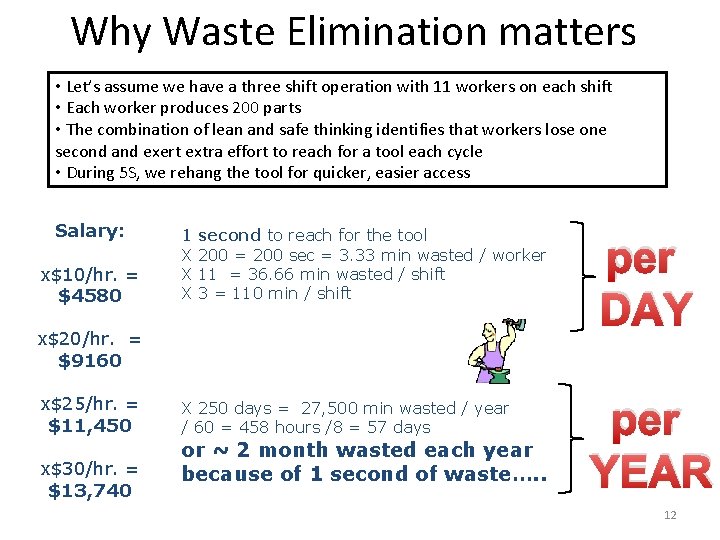
Why Waste Elimination matters • Let’s assume we have a three shift operation with 11 workers on each shift • Each worker produces 200 parts • The combination of lean and safe thinking identifies that workers lose one second and exert extra effort to reach for a tool each cycle • During 5 S, we rehang the tool for quicker, easier access Salary: x$10/hr. = $4580 1 X X X second to reach for the tool 200 = 200 sec = 3. 33 min wasted / worker 11 = 36. 66 min wasted / shift 3 = 110 min / shift x$20/hr. = $9160 x$25/hr. = $11, 450 x$30/hr. = $13, 740 X 250 days = 27, 500 min wasted / year / 60 = 458 hours /8 = 57 days or ~ 2 month wasted each year because of 1 second of waste…. . per DAY per YEAR 12

Individual & Partner Exercise • Think about how you use PDCA in your professional life – Can it help reduce waste in your job? • Partner up with someone near you – Use PDCA reference • Share thoughts 1. 2. 3. 4. Correction Over production Motion Material movement 5. Waiting 6. Inventory 7. Process 13
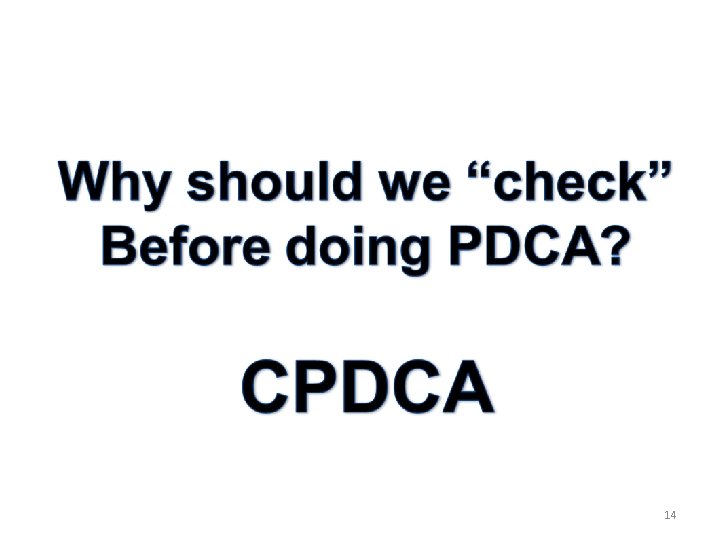
14
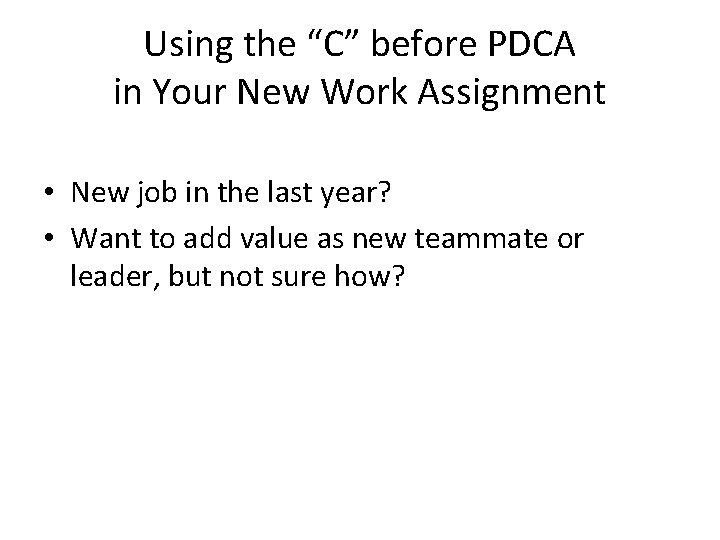
Using the “C” before PDCA in Your New Work Assignment • New job in the last year? • Want to add value as new teammate or leader, but not sure how?
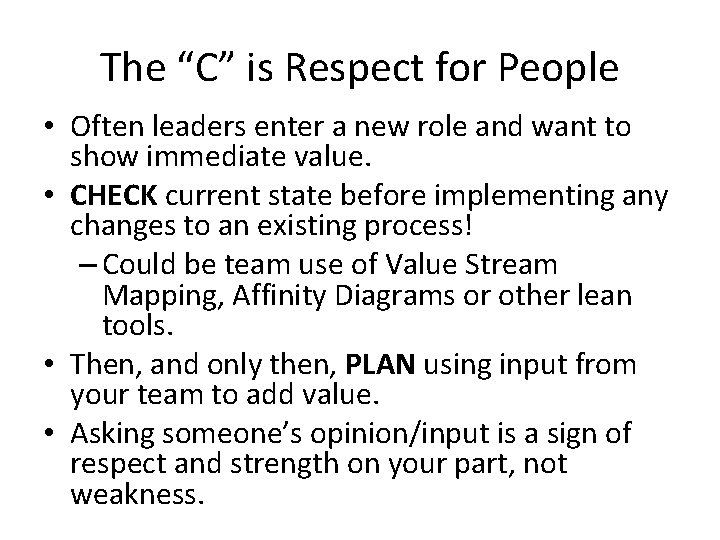
The “C” is Respect for People • Often leaders enter a new role and want to show immediate value. • CHECK current state before implementing any changes to an existing process! – Could be team use of Value Stream Mapping, Affinity Diagrams or other lean tools. • Then, and only then, PLAN using input from your team to add value. • Asking someone’s opinion/input is a sign of respect and strength on your part, not weakness.
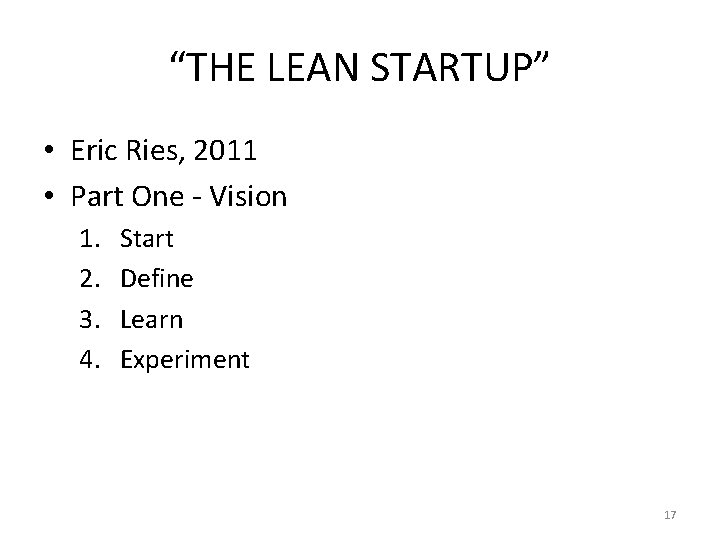
“THE LEAN STARTUP” • Eric Ries, 2011 • Part One - Vision 1. 2. 3. 4. Start Define Learn Experiment 17
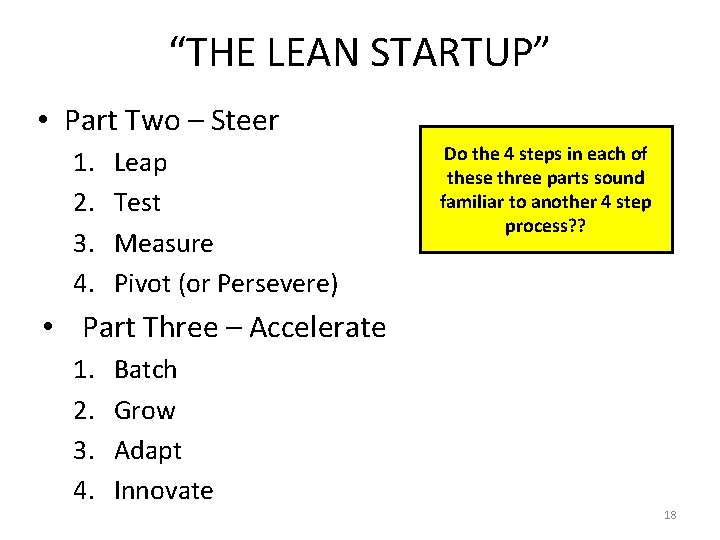
“THE LEAN STARTUP” • Part Two – Steer 1. 2. 3. 4. Leap Test Measure Pivot (or Persevere) Do the 4 steps in each of these three parts sound familiar to another 4 step process? ? • Part Three – Accelerate 1. 2. 3. 4. Batch Grow Adapt Innovate 18
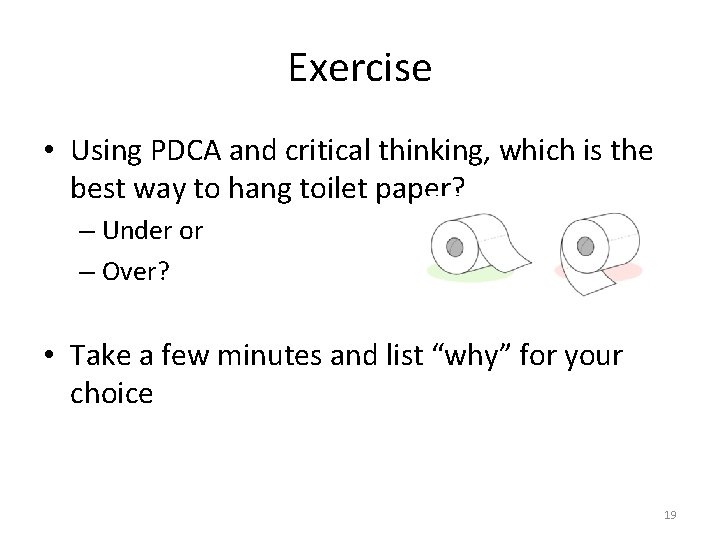
Exercise • Using PDCA and critical thinking, which is the best way to hang toilet paper? – Under or – Over? • Take a few minutes and list “why” for your choice 19
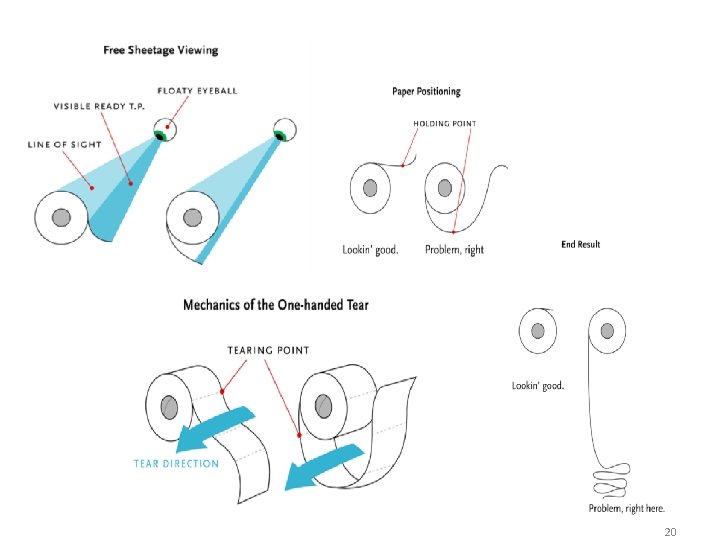
20
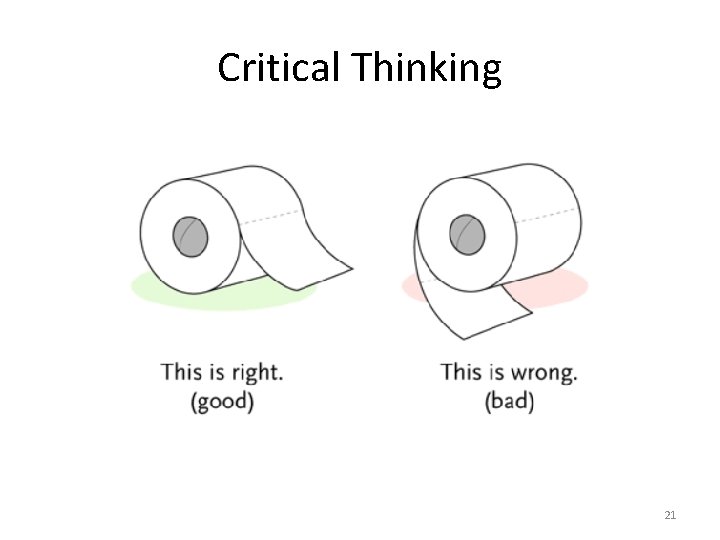
Critical Thinking 21
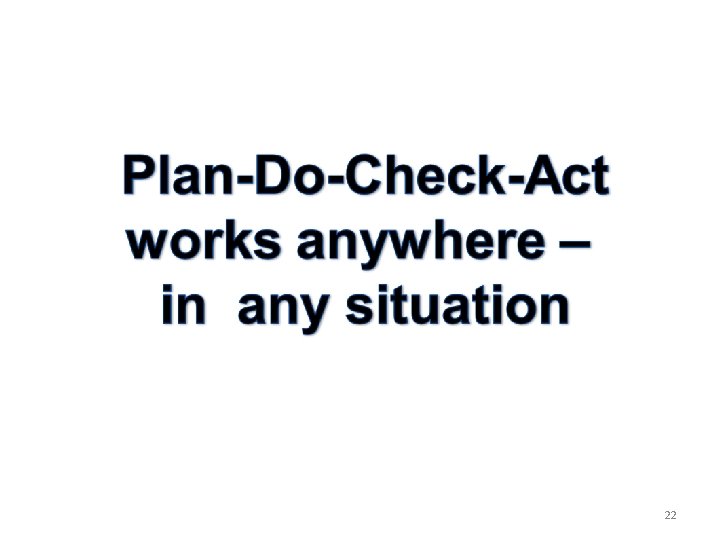
22
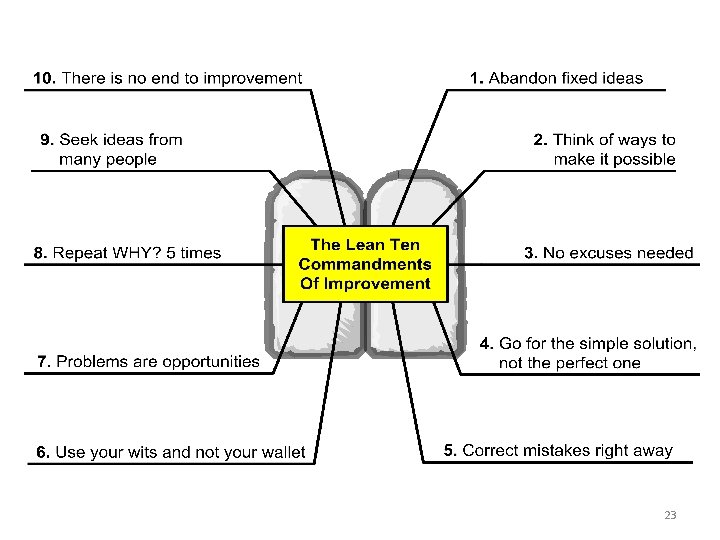
23
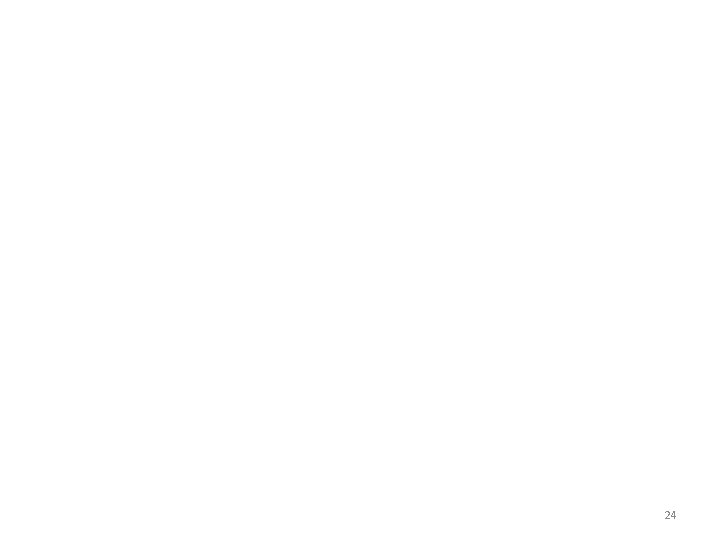
24
Logistieke doelstellingen voorbeelden
Plan do check act
Pdca sa
Manfaat pdsa
Pdsa-cykeln
Reddingsborden
Dmaic x pdca
8 step problem solving training
Capdca
Premier bet mali
Iso 27001 pdca
8 step problem solving
Pdca itil
Focus pdca
O ciclo pdca
Pdca model
Pdca model
Ciclo pdca fluxograma
Pdca příklad
Ciclo pdca
Dto diagnostico do trabalho operacional
Pdca doc
Cia+
Act 1 act 2 act 3
Behavior check in check out sheet