P Paul XIGWCRTMIS 8221 5429 PIJ Pixel Placement
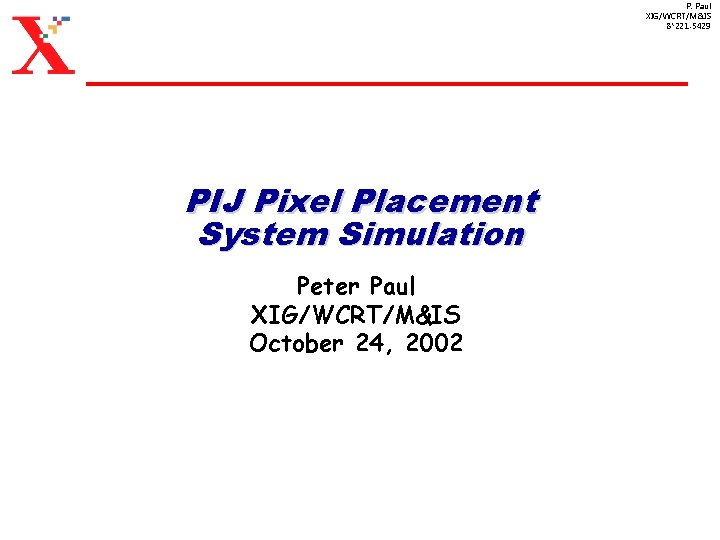
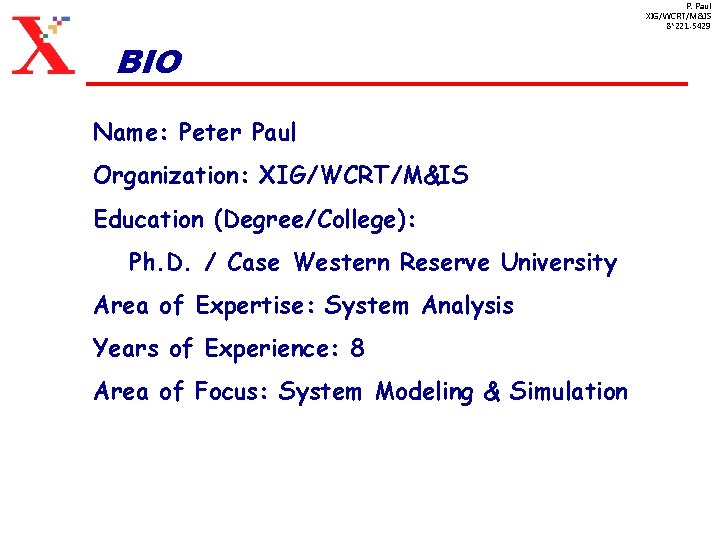
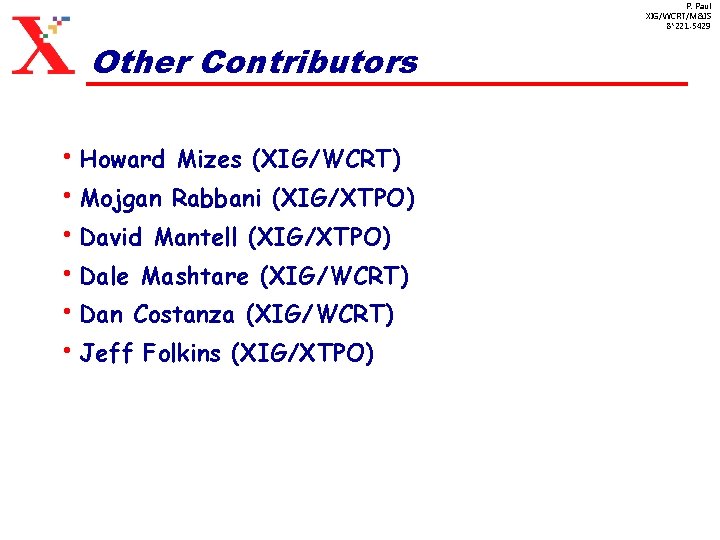
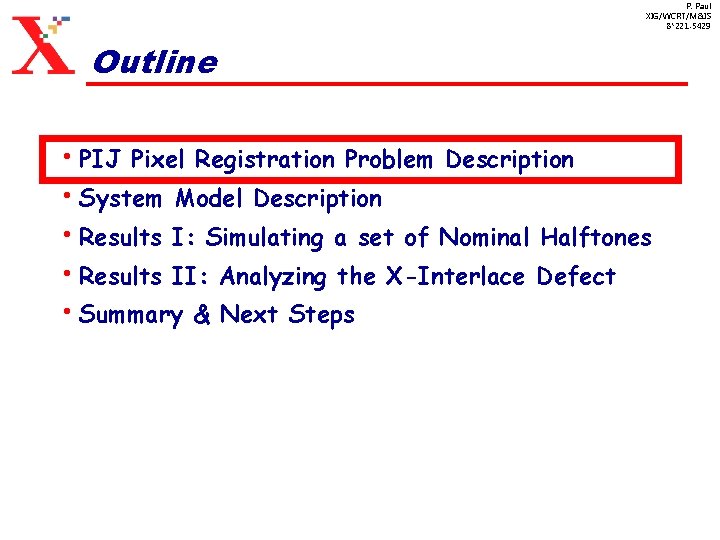
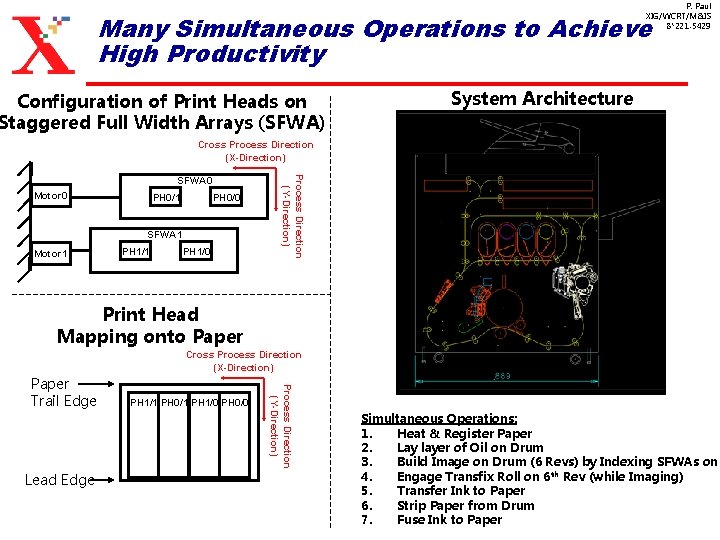
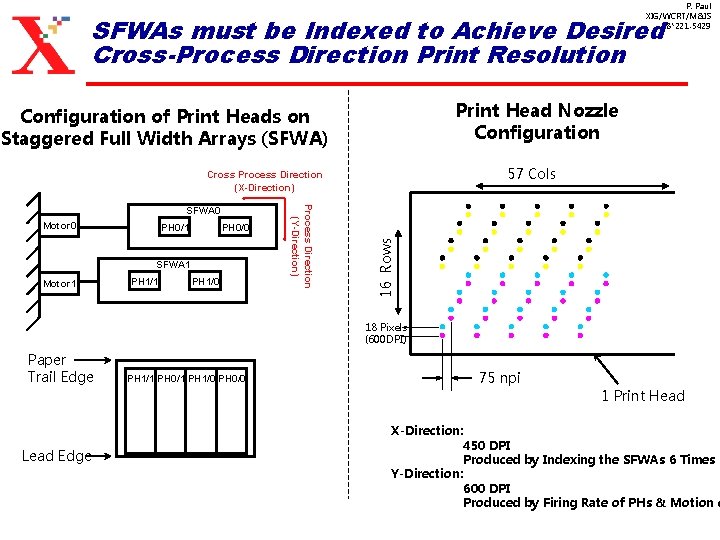
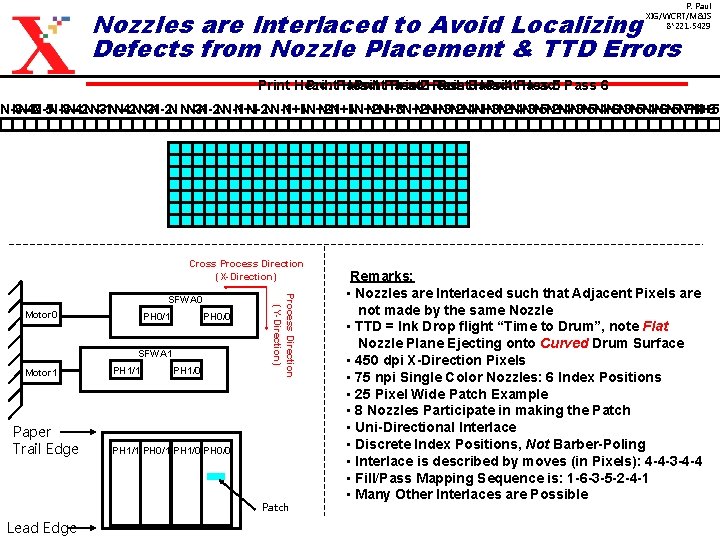
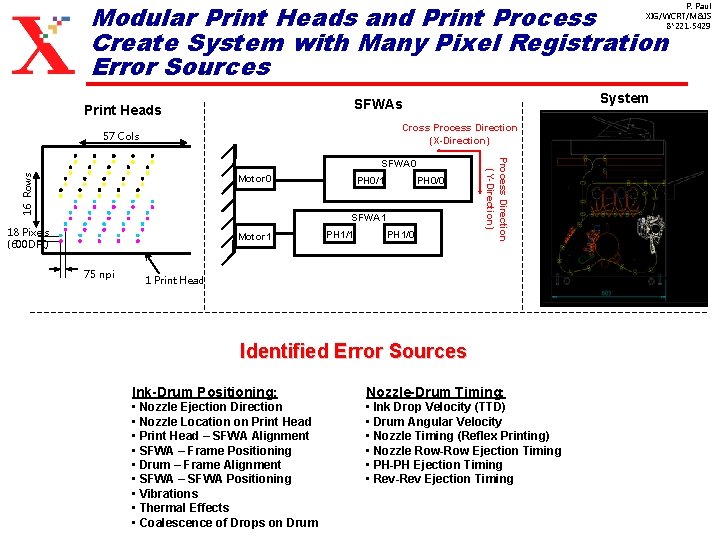
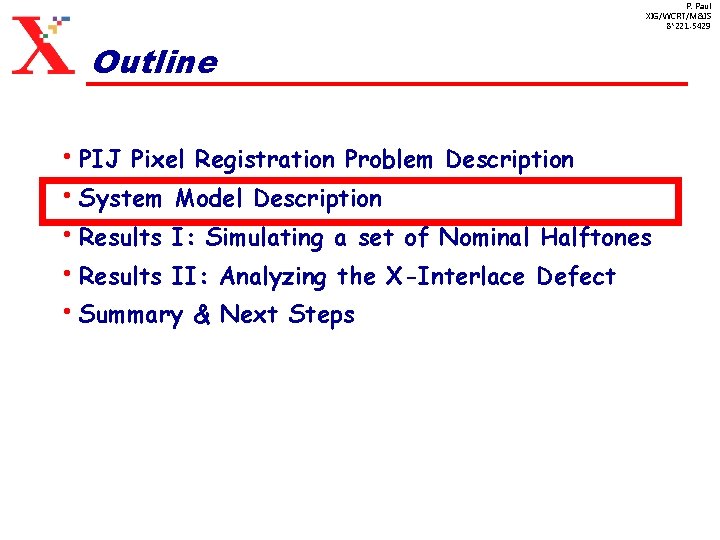
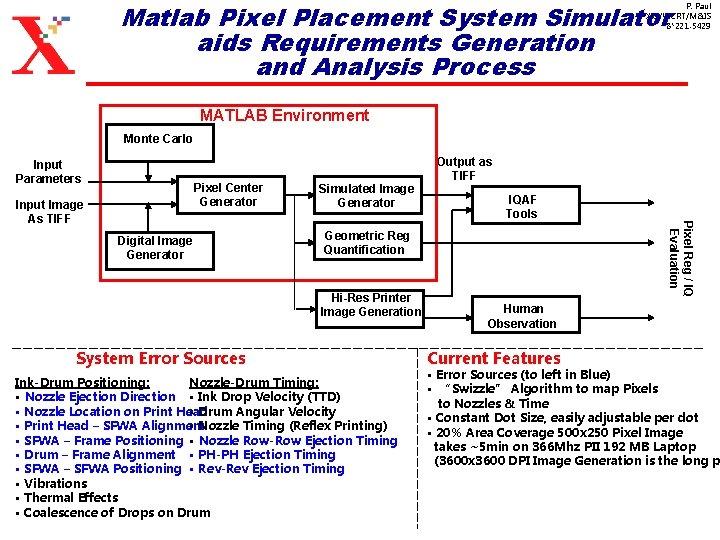
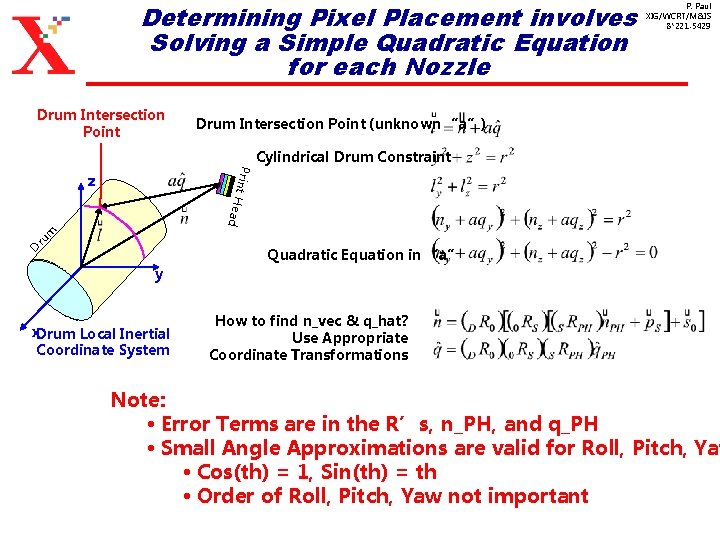
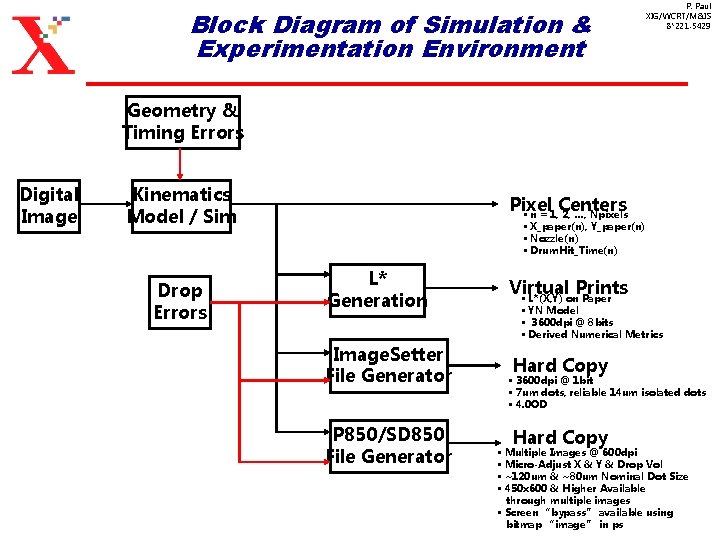
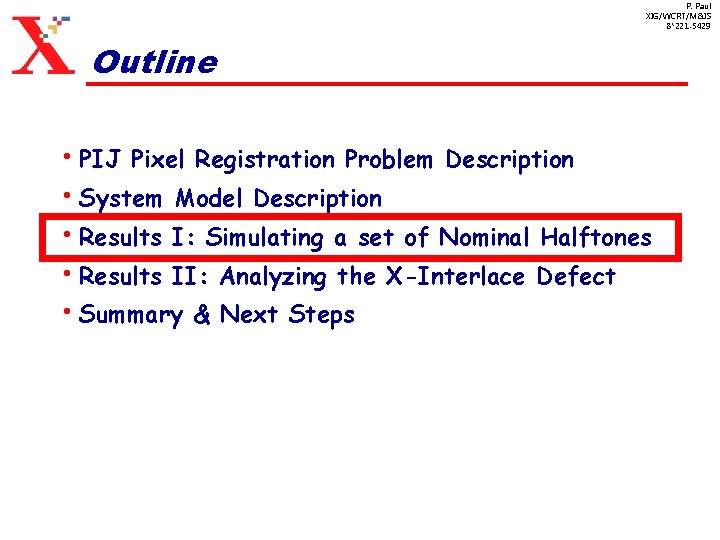
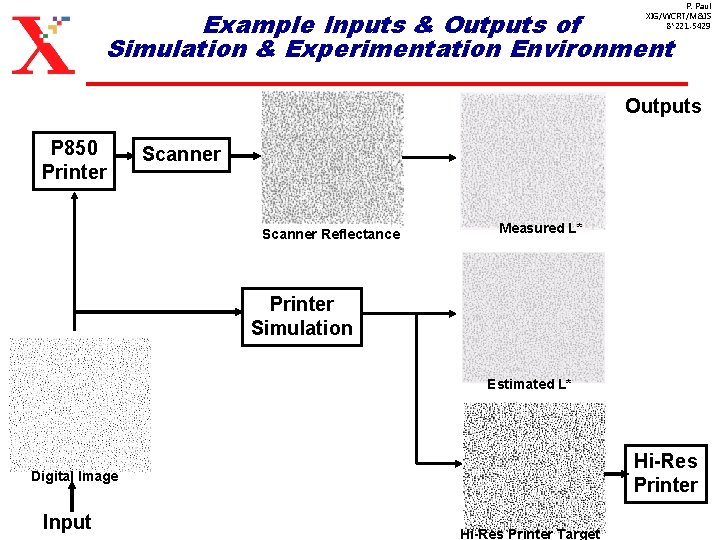
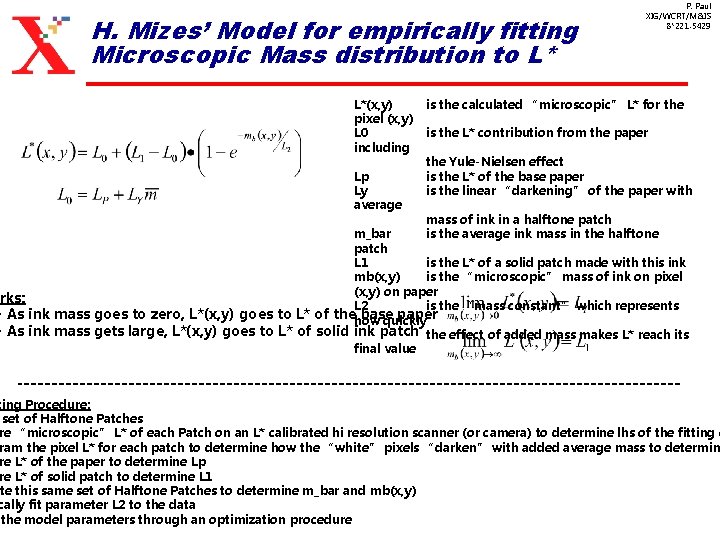
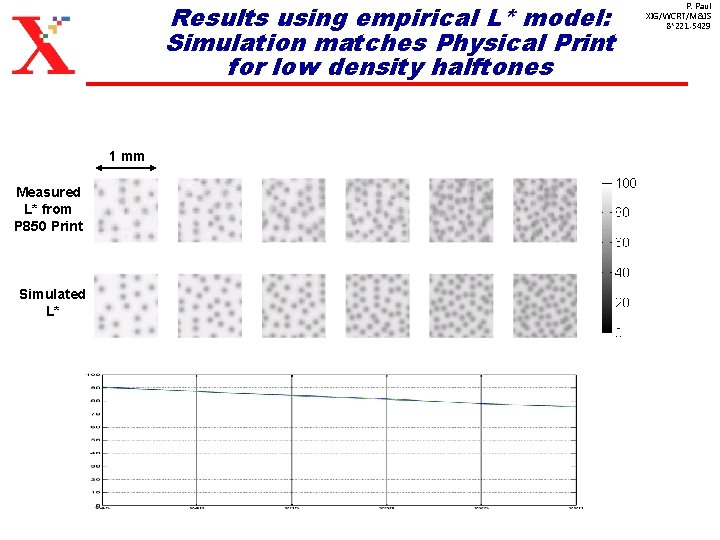
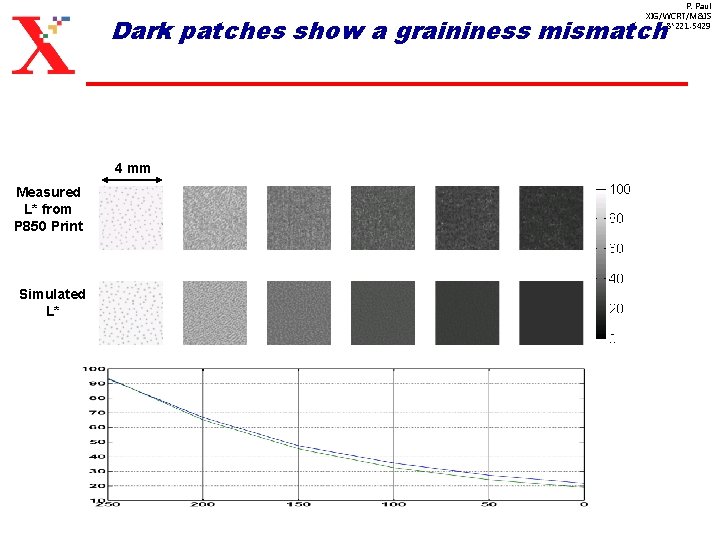
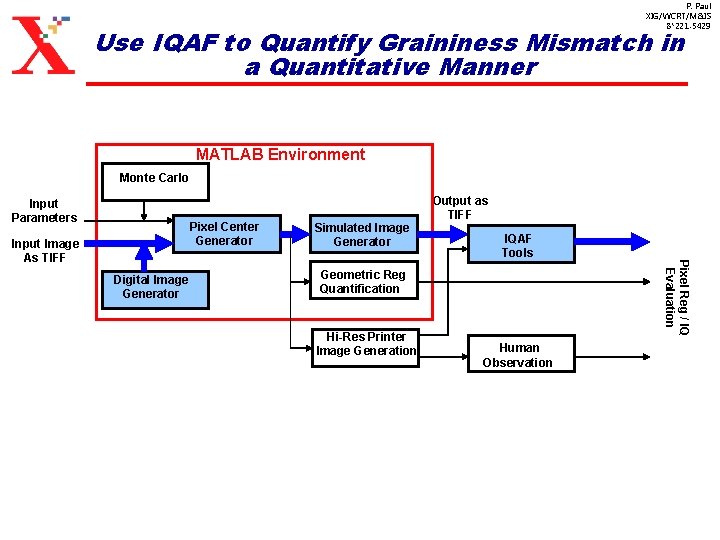
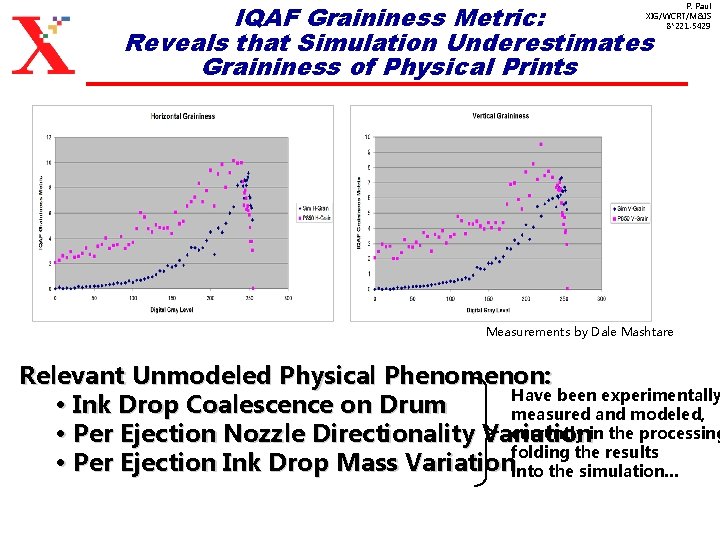
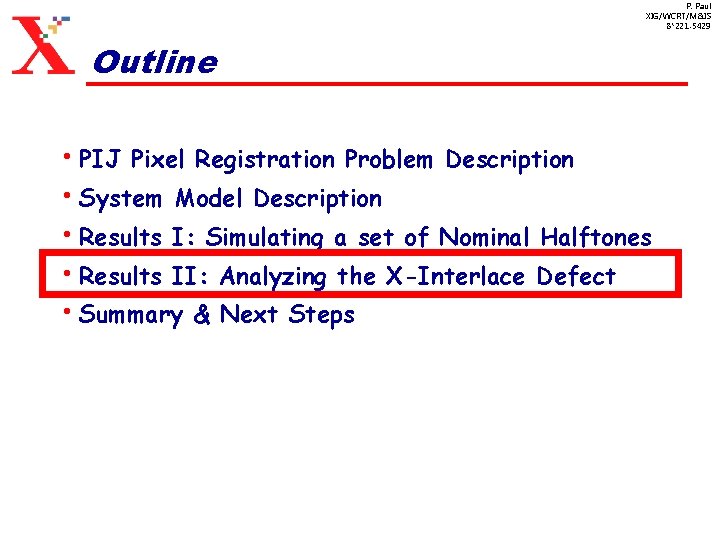
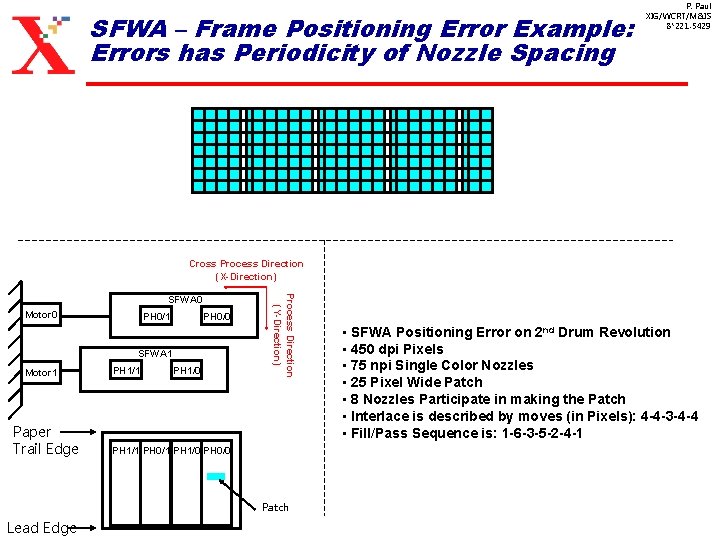
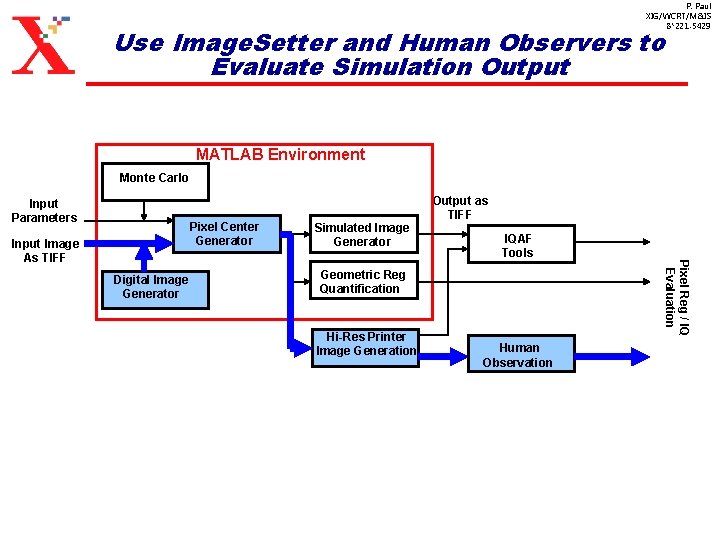
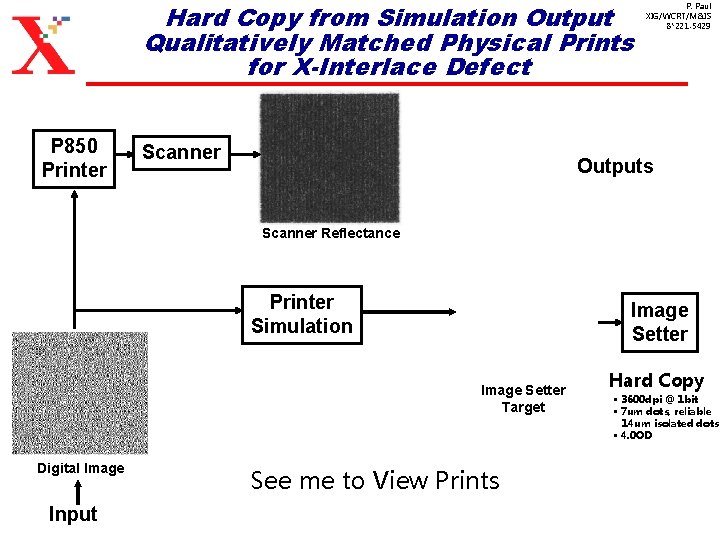
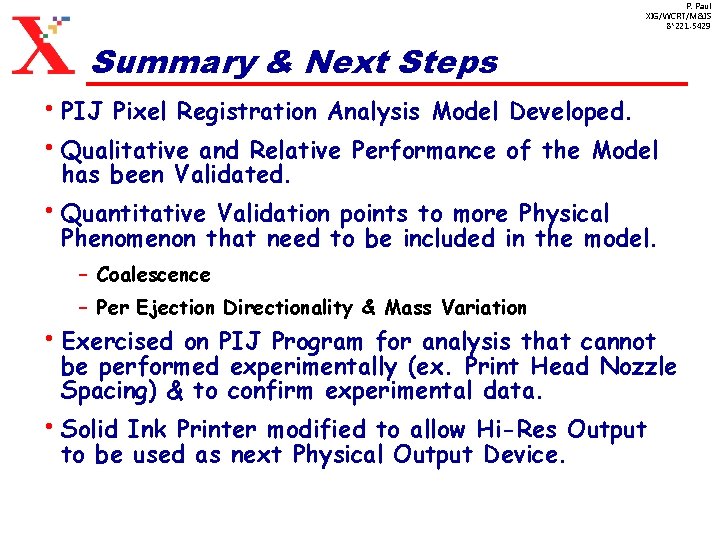
- Slides: 24
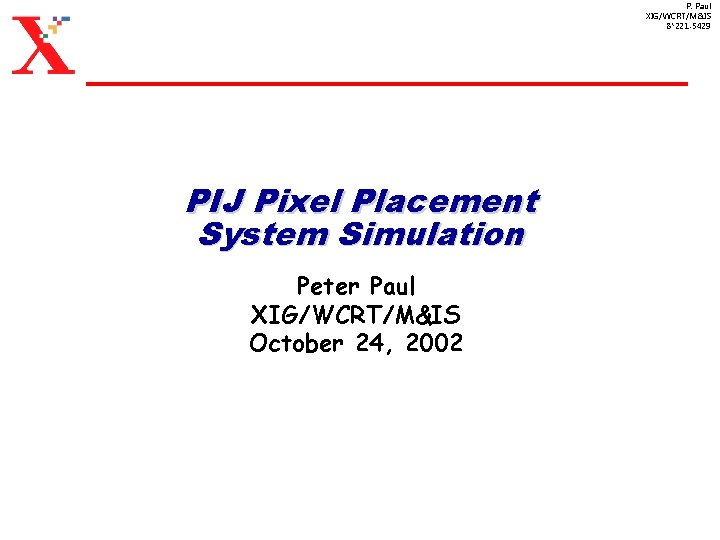
P. Paul XIG/WCRT/M&IS 8*221 -5429 PIJ Pixel Placement System Simulation Peter Paul XIG/WCRT/M&IS October 24, 2002
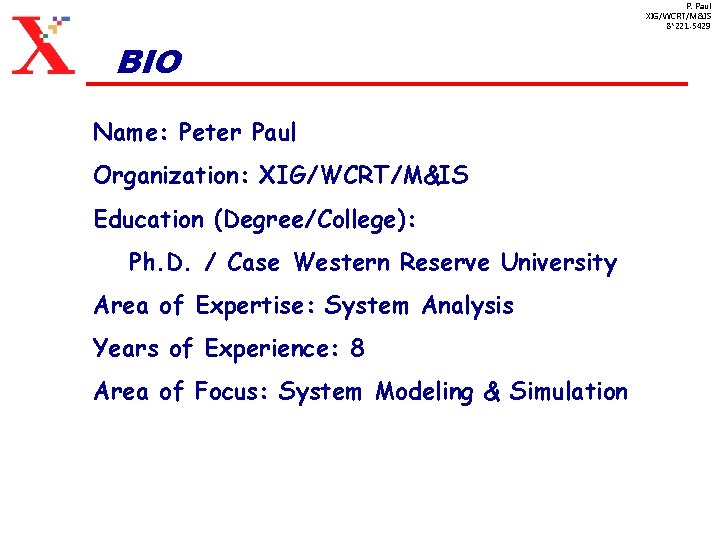
P. Paul XIG/WCRT/M&IS 8*221 -5429 BIO Name: Peter Paul Organization: XIG/WCRT/M&IS Education (Degree/College): Ph. D. / Case Western Reserve University Area of Expertise: System Analysis Years of Experience: 8 Area of Focus: System Modeling & Simulation
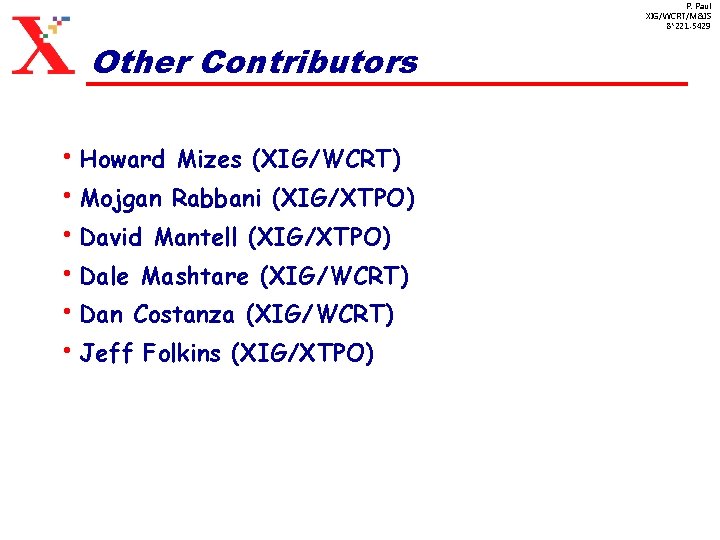
P. Paul XIG/WCRT/M&IS 8*221 -5429 Other Contributors • Howard Mizes (XIG/WCRT) • Mojgan Rabbani (XIG/XTPO) • David Mantell (XIG/XTPO) • Dale Mashtare (XIG/WCRT) • Dan Costanza (XIG/WCRT) • Jeff Folkins (XIG/XTPO)
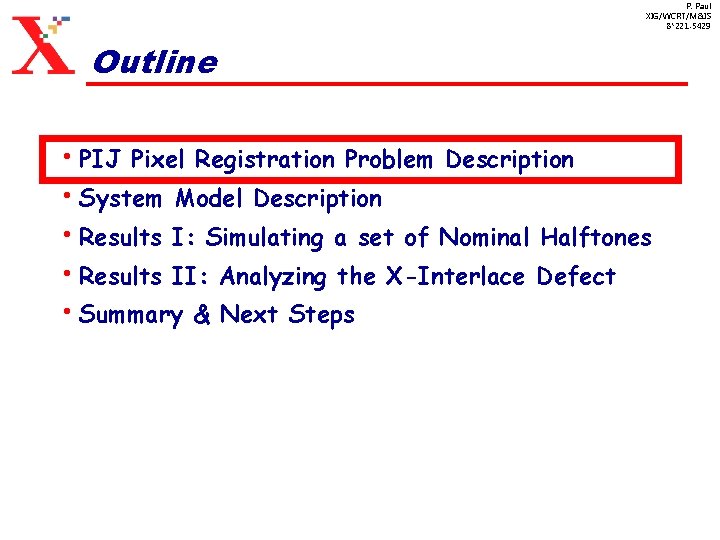
P. Paul XIG/WCRT/M&IS 8*221 -5429 Outline • PIJ Pixel Registration Problem Description • System Model Description • Results I: Simulating a set of Nominal Halftones • Results II: Analyzing the X-Interlace Defect • Summary & Next Steps
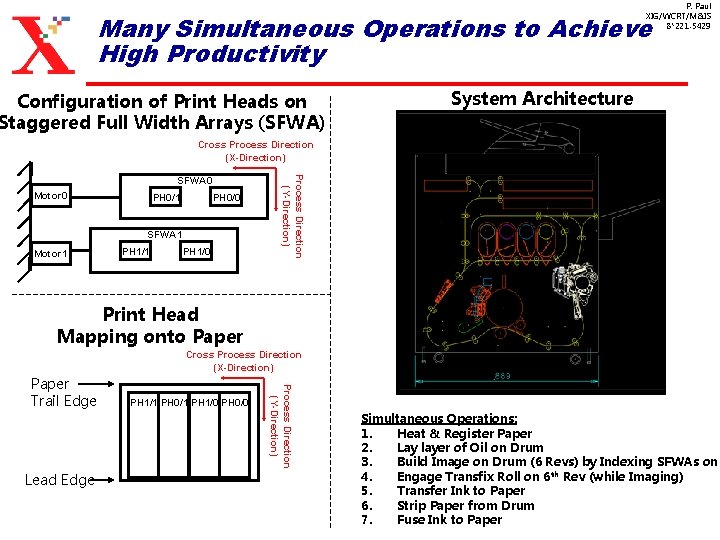
P. Paul XIG/WCRT/M&IS 8*221 -5429 Many Simultaneous Operations to Achieve High Productivity Configuration of Print Heads on Staggered Full Width Arrays (SFWA) System Architecture Cross Process Direction (X-Direction) PH 0/1 PH 0/0 SFWA 1 Motor 1 PH 1/0 Process Direction (Y-Direction) SFWA 0 Motor 0 Print Head Mapping onto Paper Cross Process Direction (X-Direction) Lead Edge PH 1/1 PH 0/1 PH 1/0 PH 0/0 Process Direction (Y-Direction) Paper Trail Edge Simultaneous Operations: 1. Heat & Register Paper 2. Lay layer of Oil on Drum 3. Build Image on Drum (6 Revs) by Indexing SFWAs on 4. Engage Transfix Roll on 6 th Rev (while Imaging) 5. Transfer Ink to Paper 6. Strip Paper from Drum 7. Fuse Ink to Paper
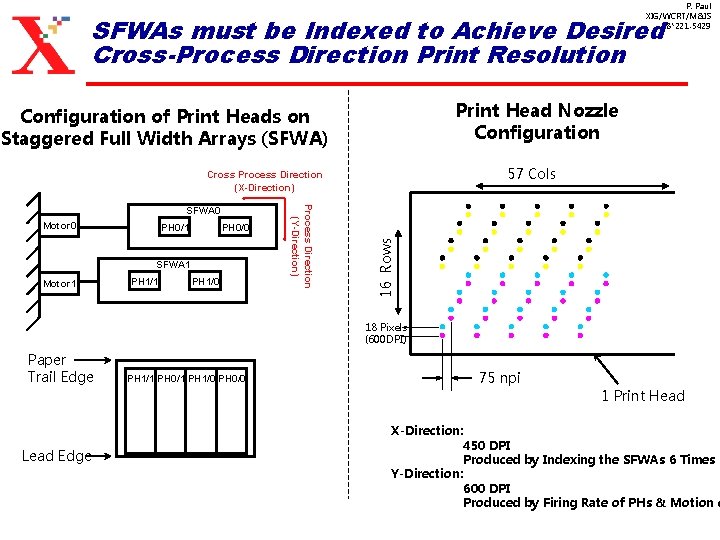
P. Paul XIG/WCRT/M&IS 8*221 -5429 SFWAs must be Indexed to Achieve Desired Cross-Process Direction Print Resolution Print Head Nozzle Configuration of Print Heads on Staggered Full Width Arrays (SFWA) 57 Cols Motor 0 PH 0/1 PH 0/0 SFWA 1 Motor 1 PH 1/0 Process Direction (Y-Direction) SFWA 0 16 Rows Cross Process Direction (X-Direction) 18 Pixels (600 DPI) Paper Trail Edge Lead Edge PH 1/1 PH 0/1 PH 1/0 PH 0/0 75 npi 1 Print Head X-Direction: 450 DPI Produced by Indexing the SFWAs 6 Times Y-Direction: 600 DPI Produced by Firing Rate of PHs & Motion o
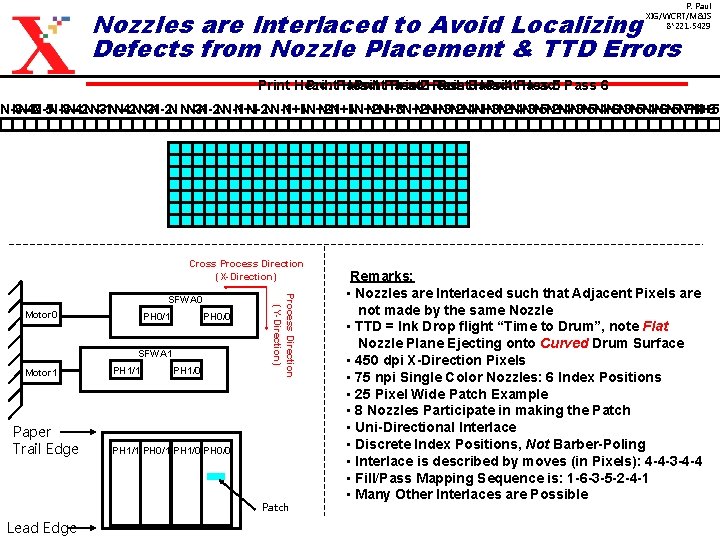
P. Paul XIG/WCRT/M&IS 8*221 -5429 Nozzles are Interlaced to Avoid Localizing Defects from Nozzle Placement & TTD Errors Print Head: Print 1 Pass Head: Print 2 Head: Pass 3 Head: 4 Pass Print Head: 5 Pass 6 Print. Pass Head: N-5 N-3 N-2 NN-1 NN+2 N+1 N+2 N+3 N+4 N-2 N-4 N-1 N-4 N-2 NN-1 N+1 NN+2 N+3 N+1 N+4 N+2 N+5 N+3 N+6 N+4 N+7 N+5 N-3 N-4 N-2 N-3 N-1 N-2 N N-3 N-1 N+1 NN+2 N+1 N+3 N+2 N+3 N+4 N+5 N+6 Cross Process Direction (X-Direction) Motor 0 PH 0/1 PH 0/0 SFWA 1 Motor 1 Paper Trail Edge PH 1/1 PH 1/0 Process Direction (Y-Direction) SFWA 0 PH 1/1 PH 0/1 PH 1/0 PH 0/0 Patch Lead Edge Remarks: • Nozzles are Interlaced such that Adjacent Pixels are not made by the same Nozzle • TTD = Ink Drop flight “Time to Drum”, note Flat Nozzle Plane Ejecting onto Curved Drum Surface • 450 dpi X-Direction Pixels • 75 npi Single Color Nozzles: 6 Index Positions • 25 Pixel Wide Patch Example • 8 Nozzles Participate in making the Patch • Uni-Directional Interlace • Discrete Index Positions, Not Barber-Poling • Interlace is described by moves (in Pixels): 4 -4 -3 -4 -4 • Fill/Pass Mapping Sequence is: 1 -6 -3 -5 -2 -4 -1 • Many Other Interlaces are Possible
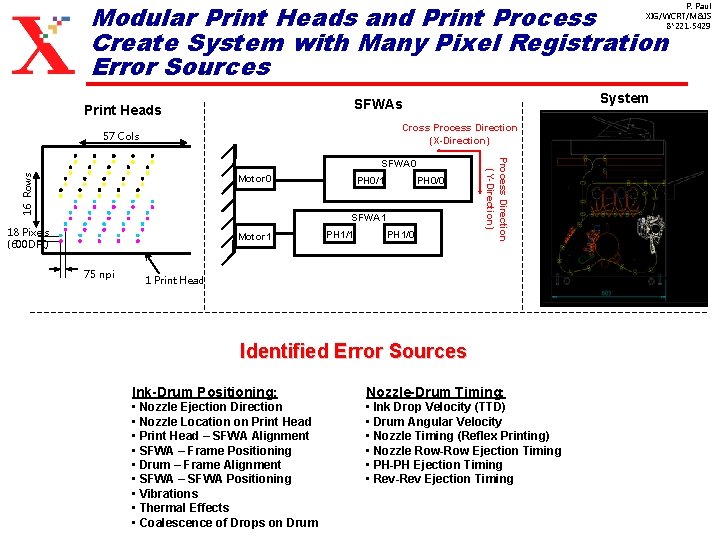
Modular Print Heads and Print Process Create System with Many Pixel Registration Error Sources P. Paul XIG/WCRT/M&IS 8*221 -5429 System SFWAs Print Heads Cross Process Direction (X-Direction) 57 Cols 16 Rows Motor 0 PH 0/1 PH 0/0 SFWA 1 18 Pixels (600 DPI) Motor 1 75 npi PH 1/1 PH 1/0 Process Direction (Y-Direction) SFWA 0 1 Print Head Identified Error Sources Ink-Drum Positioning: Nozzle-Drum Timing: • Nozzle Ejection Direction • Nozzle Location on Print Head • Print Head – SFWA Alignment • SFWA – Frame Positioning • Drum – Frame Alignment • SFWA – SFWA Positioning • Vibrations • Thermal Effects • Coalescence of Drops on Drum • Ink Drop Velocity (TTD) • Drum Angular Velocity • Nozzle Timing (Reflex Printing) • Nozzle Row-Row Ejection Timing • PH-PH Ejection Timing • Rev-Rev Ejection Timing
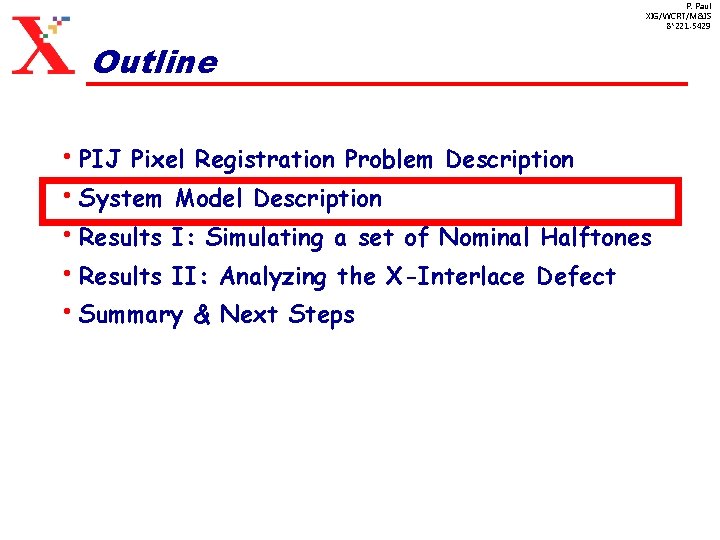
P. Paul XIG/WCRT/M&IS 8*221 -5429 Outline • PIJ Pixel Registration Problem Description • System Model Description • Results I: Simulating a set of Nominal Halftones • Results II: Analyzing the X-Interlace Defect • Summary & Next Steps
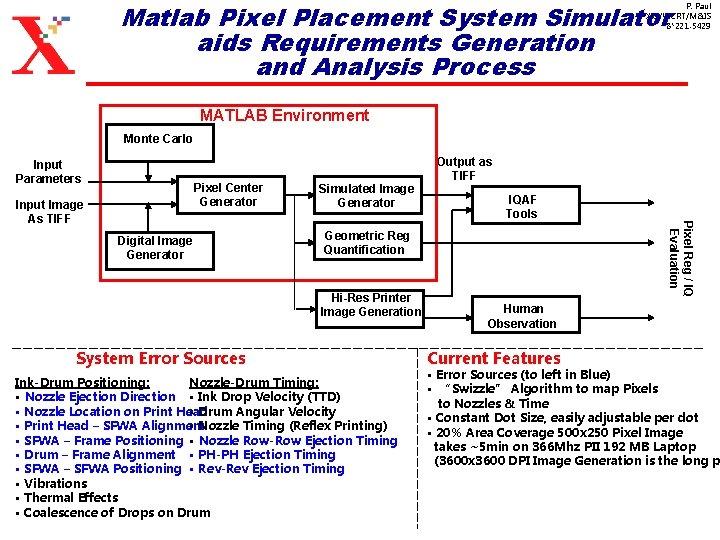
Matlab Pixel Placement System Simulator aids Requirements Generation and Analysis Process P. Paul XIG/WCRT/M&IS 8*221 -5429 MATLAB Environment Monte Carlo Input Parameters Pixel Center Generator Digital Image Generator IQAF Tools Geometric Reg Quantification Hi-Res Printer Image Generation System Error Sources Ink-Drum Positioning: Nozzle-Drum Timing: • Nozzle Ejection Direction • Ink Drop Velocity (TTD) • Nozzle Location on Print Head • Drum Angular Velocity • Print Head – SFWA Alignment • Nozzle Timing (Reflex Printing) • SFWA – Frame Positioning • Nozzle Row-Row Ejection Timing • Drum – Frame Alignment • PH-PH Ejection Timing • SFWA – SFWA Positioning • Rev-Rev Ejection Timing • Vibrations • Thermal Effects • Coalescence of Drops on Drum Pixel Reg / IQ Evaluation Input Image As TIFF Simulated Image Generator Output as TIFF Human Observation Current Features • Error Sources (to left in Blue) • “Swizzle” Algorithm to map Pixels to Nozzles & Time • Constant Dot Size, easily adjustable per dot • 20% Area Coverage 500 x 250 Pixel Image takes ~5 min on 366 Mhz PII 192 MB Laptop (3600 x 3600 DPI Image Generation is the long p
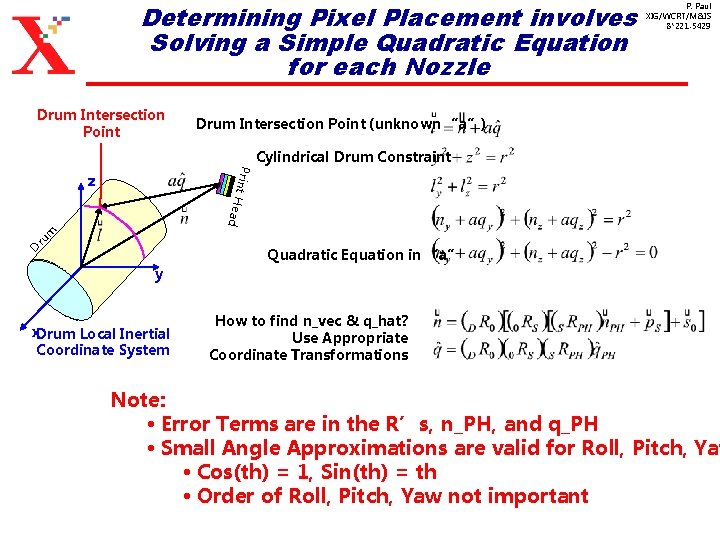
Determining Pixel Placement involves Solving a Simple Quadratic Equation for each Nozzle Drum Intersection Point P. Paul XIG/WCRT/M&IS 8*221 -5429 Drum Intersection Point (unknown “a”) Cylindrical Drum Constraint Print H z D ru m ead y x. Drum Local Inertial Coordinate System Quadratic Equation in “a” How to find n_vec & q_hat? Use Appropriate Coordinate Transformations Note: • Error Terms are in the R’s, n_PH, and q_PH • Small Angle Approximations are valid for Roll, Pitch, Yaw • Cos(th) = 1, Sin(th) = th • Order of Roll, Pitch, Yaw not important
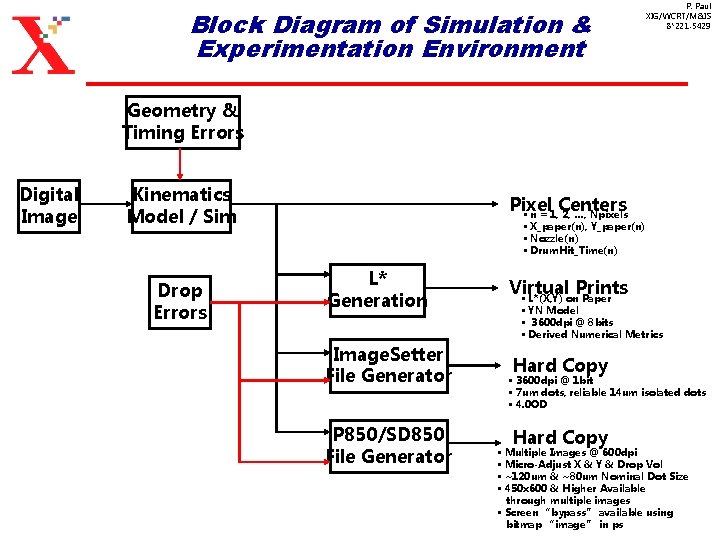
Block Diagram of Simulation & Experimentation Environment P. Paul XIG/WCRT/M&IS 8*221 -5429 Geometry & Timing Errors Digital Image Kinematics Model / Sim Drop Errors Pixel Centers • n = 1, 2, …, Npixels • X_paper(n), Y_paper(n) • Nozzle(n) • Drum. Hit_Time(n) L* Generation Image. Setter File Generator P 850/SD 850 File Generator Virtual Prints • L*(X, Y) on Paper • YN Model • 3600 dpi @ 8 bits • Derived Numerical Metrics Hard Copy • 3600 dpi @ 1 bit • 7 um dots, reliable 14 um isolated dots • 4. 0 OD Hard Copy • Multiple Images @ 600 dpi • Micro-Adjust X & Y & Drop Vol • ~120 um & ~80 um Nominal Dot Size • 450 x 600 & Higher Available through multiple images • Screen “bypass” available using bitmap “image” in ps
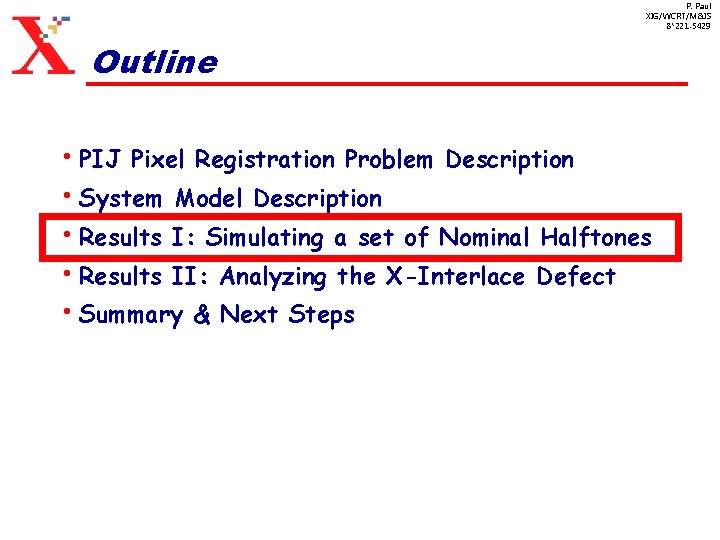
P. Paul XIG/WCRT/M&IS 8*221 -5429 Outline • PIJ Pixel Registration Problem Description • System Model Description • Results I: Simulating a set of Nominal Halftones • Results II: Analyzing the X-Interlace Defect • Summary & Next Steps
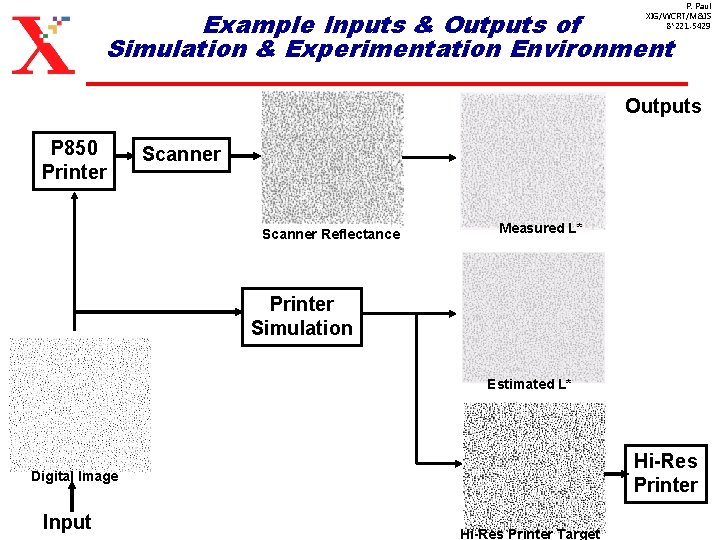
P. Paul XIG/WCRT/M&IS 8*221 -5429 Example Inputs & Outputs of Simulation & Experimentation Environment Outputs P 850 Printer Scanner Reflectance Measured L* Printer Simulation Estimated L* Hi-Res Printer Digital Image Input Hi-Res Printer Target
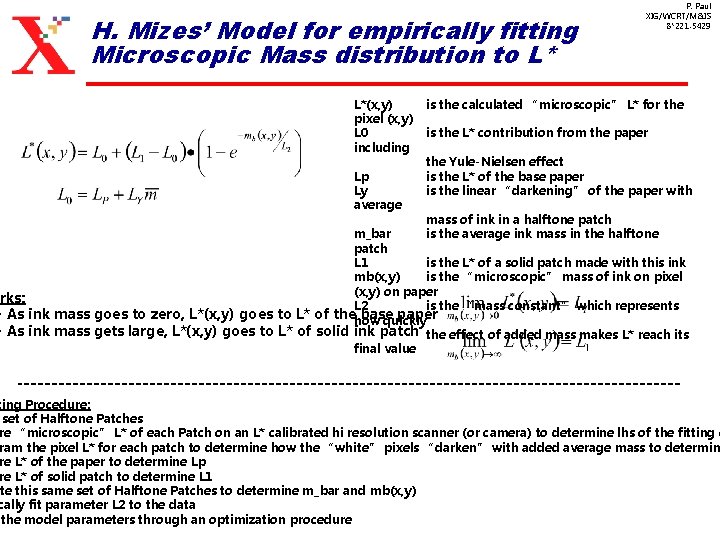
H. Mizes’ Model for empirically fitting Microscopic Mass distribution to L* L*(x, y) pixel (x, y) L 0 including Lp Ly average P. Paul XIG/WCRT/M&IS 8*221 -5429 is the calculated “microscopic” L* for the is the L* contribution from the paper the Yule-Nielsen effect is the L* of the base paper is the linear “darkening” of the paper with mass of ink in a halftone patch is the average ink mass in the halftone m_bar patch L 1 is the L* of a solid patch made with this ink mb(x, y) is the “microscopic” mass of ink on pixel (x, y) on paper arks: L 2 is the “mass constant” which represents • As ink mass goes to zero, L*(x, y) goes to L* of thehow base paper quickly • As ink mass gets large, L*(x, y) goes to L* of solid ink patch the effect of added mass makes L* reach its final value ting Procedure: set of Halftone Patches re “microscopic” L* of each Patch on an L* calibrated hi resolution scanner (or camera) to determine lhs of the fitting e ram the pixel L* for each patch to determine how the “white” pixels “darken” with added average mass to determin re L* of the paper to determine Lp re L* of solid patch to determine L 1 te this same set of Halftone Patches to determine m_bar and mb(x, y) cally fit parameter L 2 to the data the model parameters through an optimization procedure
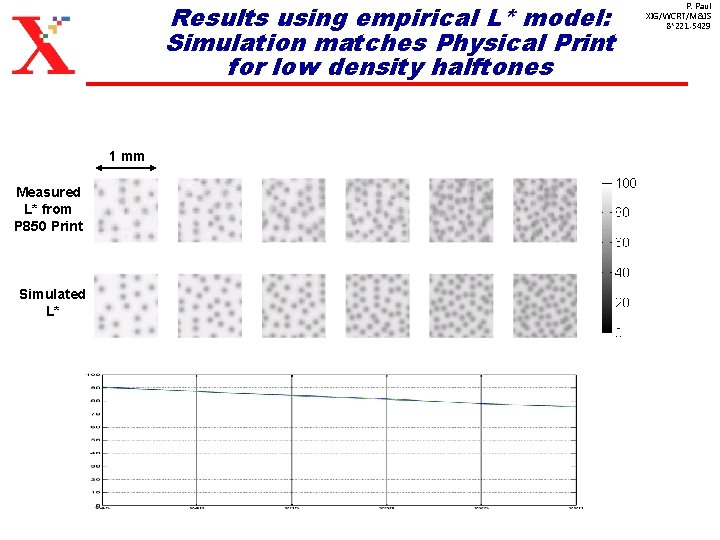
Results using empirical L* model: Simulation matches Physical Print for low density halftones 1 mm Measured L* from P 850 Print Simulated L* P. Paul XIG/WCRT/M&IS 8*221 -5429
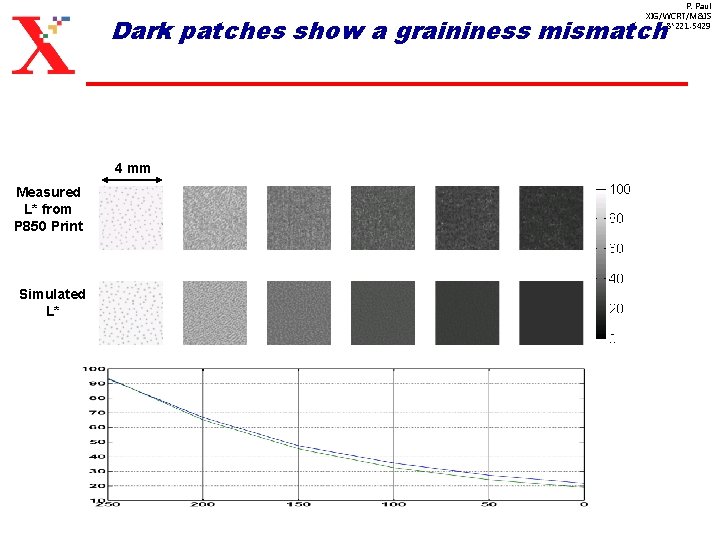
P. Paul XIG/WCRT/M&IS 8*221 -5429 Dark patches show a graininess mismatch 4 mm Measured L* from P 850 Print Simulated L*
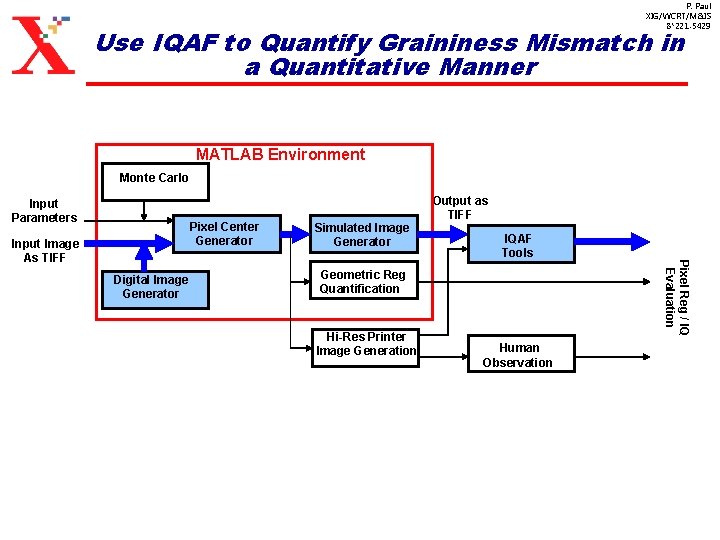
P. Paul XIG/WCRT/M&IS 8*221 -5429 Use IQAF to Quantify Graininess Mismatch in a Quantitative Manner MATLAB Environment Monte Carlo Input Parameters Pixel Center Generator Digital Image Generator IQAF Tools Geometric Reg Quantification Hi-Res Printer Image Generation Human Observation Pixel Reg / IQ Evaluation Input Image As TIFF Simulated Image Generator Output as TIFF
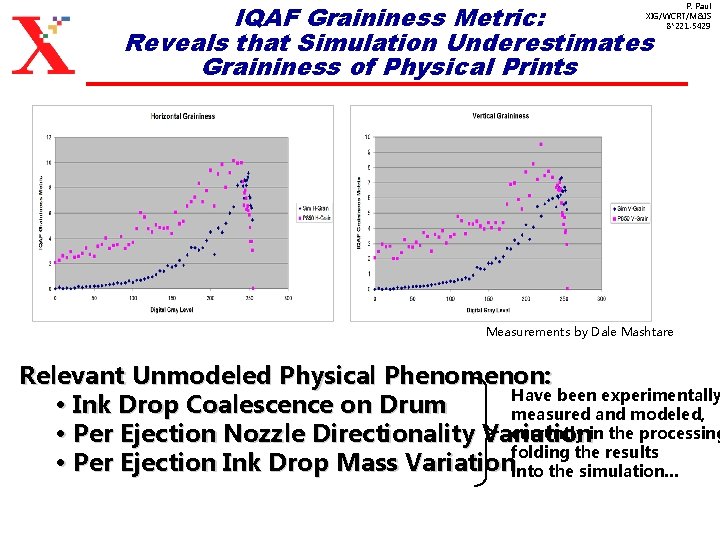
IQAF Graininess Metric: Reveals that Simulation Underestimates Graininess of Physical Prints P. Paul XIG/WCRT/M&IS 8*221 -5429 Measurements by Dale Mashtare Relevant Unmodeled Physical Phenomenon: Have been experimentally • Ink Drop Coalescence on Drum measured and modeled, currently in the processing • Per Ejection Nozzle Directionality Variation folding the results • Per Ejection Ink Drop Mass Variationinto the simulation…
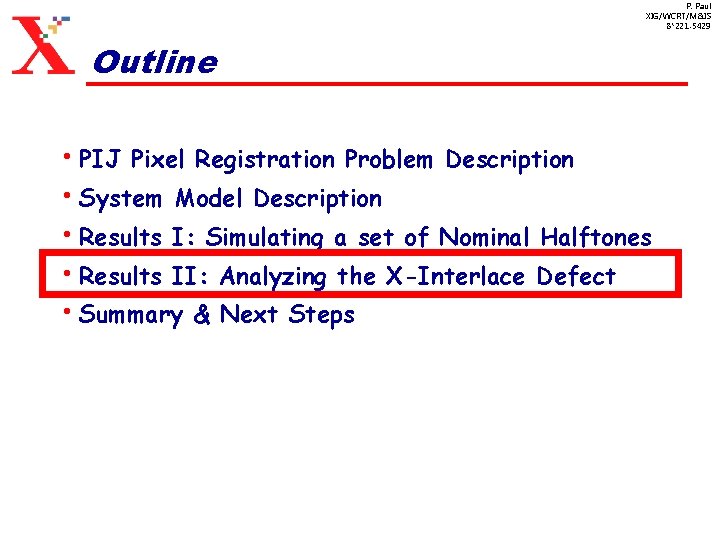
P. Paul XIG/WCRT/M&IS 8*221 -5429 Outline • PIJ Pixel Registration Problem Description • System Model Description • Results I: Simulating a set of Nominal Halftones • Results II: Analyzing the X-Interlace Defect • Summary & Next Steps
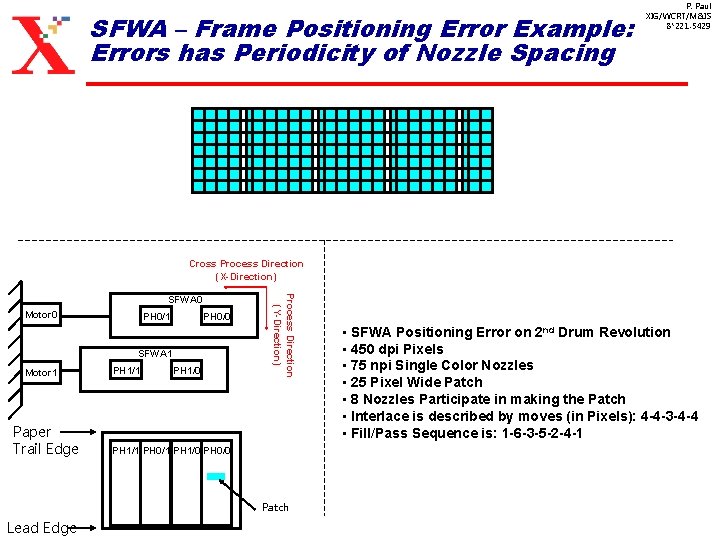
SFWA – Frame Positioning Error Example: Errors has Periodicity of Nozzle Spacing P. Paul XIG/WCRT/M&IS 8*221 -5429 Cross Process Direction (X-Direction) Motor 0 PH 0/1 PH 0/0 SFWA 1 Motor 1 Paper Trail Edge PH 1/1 PH 1/0 Process Direction (Y-Direction) SFWA 0 PH 1/1 PH 0/1 PH 1/0 PH 0/0 Patch Lead Edge • SFWA Positioning Error on 2 nd Drum Revolution • 450 dpi Pixels • 75 npi Single Color Nozzles • 25 Pixel Wide Patch • 8 Nozzles Participate in making the Patch • Interlace is described by moves (in Pixels): 4 -4 -3 -4 -4 • Fill/Pass Sequence is: 1 -6 -3 -5 -2 -4 -1
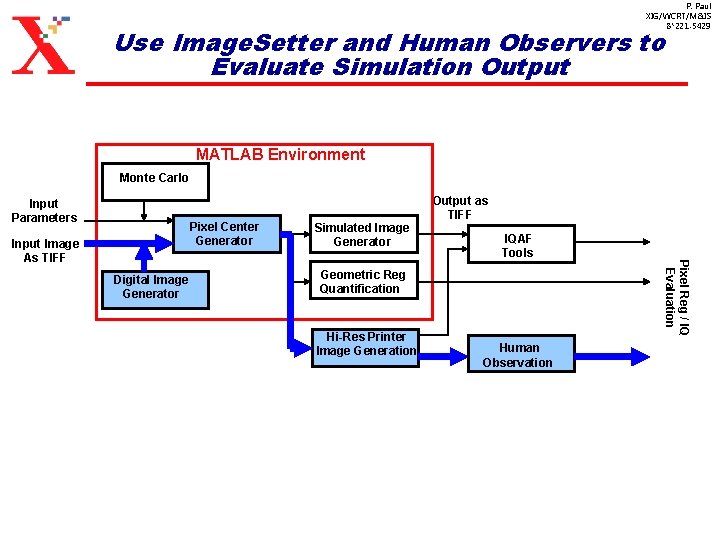
P. Paul XIG/WCRT/M&IS 8*221 -5429 Use Image. Setter and Human Observers to Evaluate Simulation Output MATLAB Environment Monte Carlo Input Parameters Pixel Center Generator Digital Image Generator IQAF Tools Geometric Reg Quantification Hi-Res Printer Image Generation Human Observation Pixel Reg / IQ Evaluation Input Image As TIFF Simulated Image Generator Output as TIFF
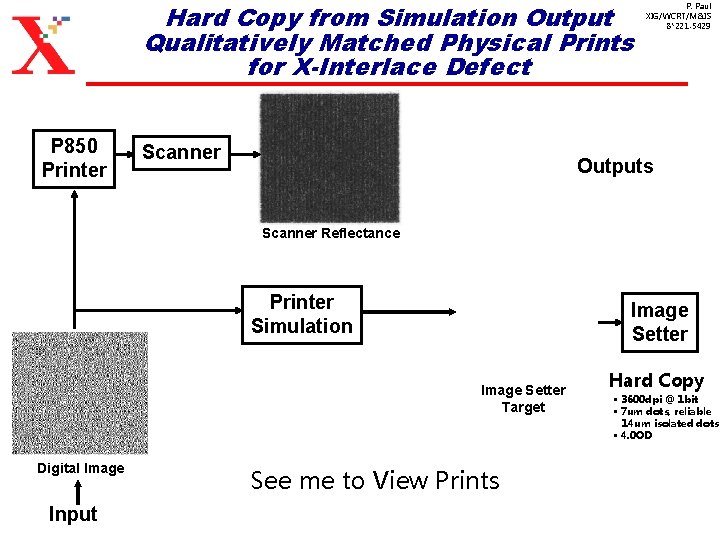
Hard Copy from Simulation Output Qualitatively Matched Physical Prints for X-Interlace Defect P 850 Printer Scanner P. Paul XIG/WCRT/M&IS 8*221 -5429 Outputs Scanner Reflectance Printer Simulation Image Setter Target Digital Image Input See me to View Prints Hard Copy • 3600 dpi @ 1 bit • 7 um dots, reliable 14 um isolated dots • 4. 0 OD
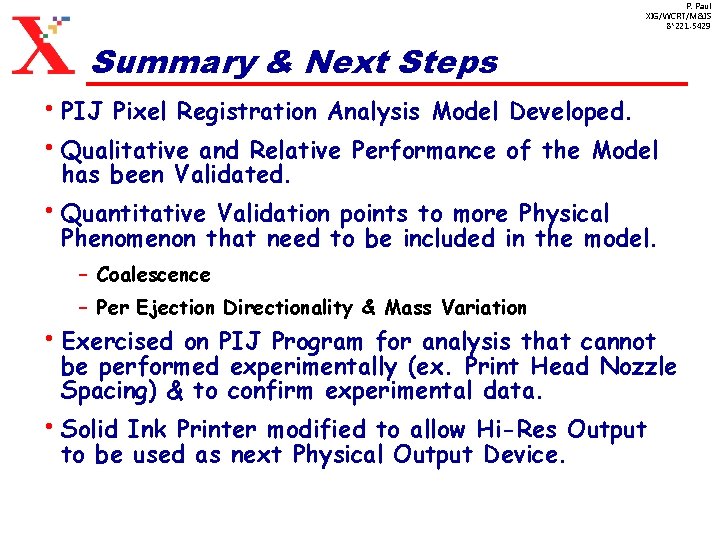
P. Paul XIG/WCRT/M&IS 8*221 -5429 Summary & Next Steps • PIJ Pixel Registration Analysis Model Developed. • Qualitative and Relative Performance of the Model has been Validated. • Quantitative Validation points to more Physical Phenomenon that need to be included in the model. – Coalescence – Per Ejection Directionality & Mass Variation • Exercised on PIJ Program for analysis that cannot be performed experimentally (ex. Print Head Nozzle Spacing) & to confirm experimental data. • Solid Ink Printer modified to allow Hi-Res Output to be used as next Physical Output Device.
Nie jedz i nie pij przy komputerze
Pravda nebo pij
Nie pij wody po zjedzeniu ryby
Nie jedz i nie pij przy komputerze
Petra riedler
Micro pixel
Pixel aspect ratio
What is bitmap and pixmap in computer graphics
Chart text
The distance between pixels p and q
9thz
Colour 23042008
Pixel shift
Qual tipo de filtro é o de canny?
Tera pixel
Pixel purity index is to determine
For coordinates p(2,3) the 4 neighbors of pixel p are
Relationship between pixels
Pixel electronics
Pixel ladder
Geometric transformations
Windows architecture
Assembly language draw pixel
Basic relationships between pixels
Identify a method for testing a pixel inside polygon or not