Optical Alignment with Computer Generated Holograms James H
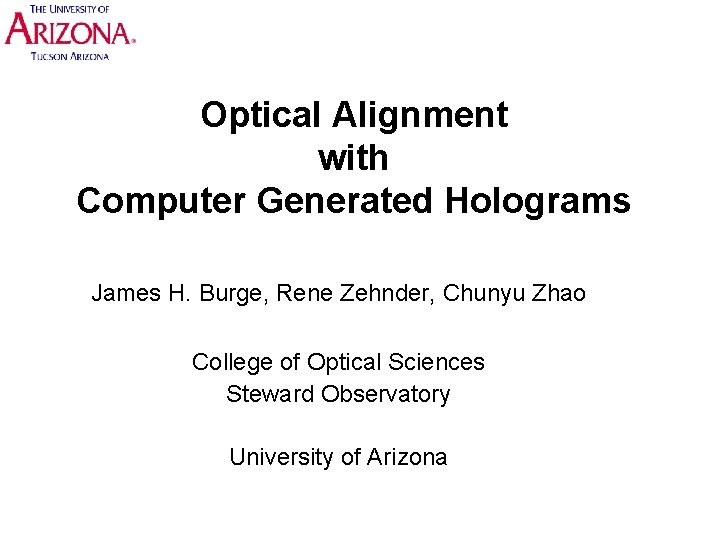
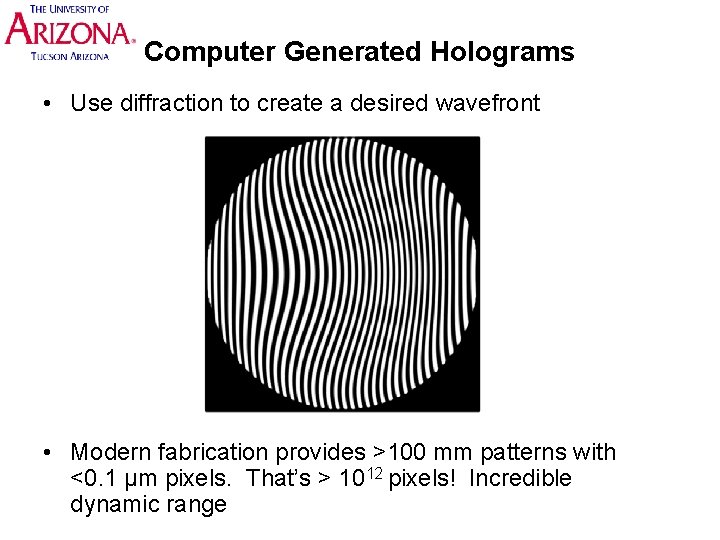
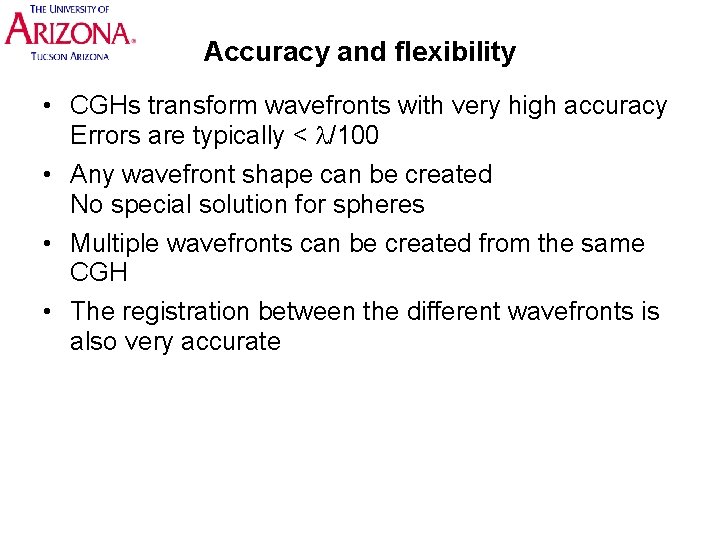
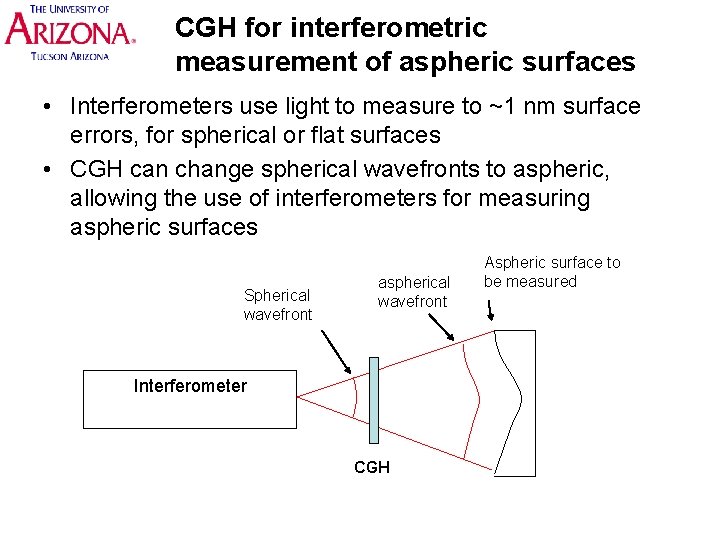
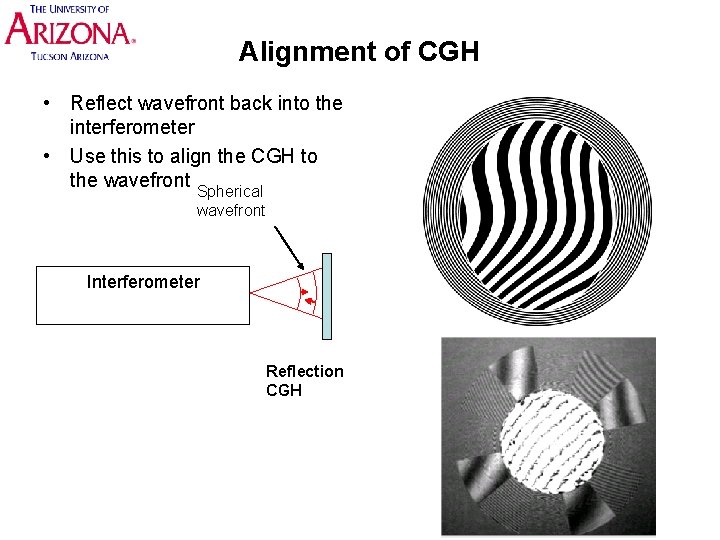
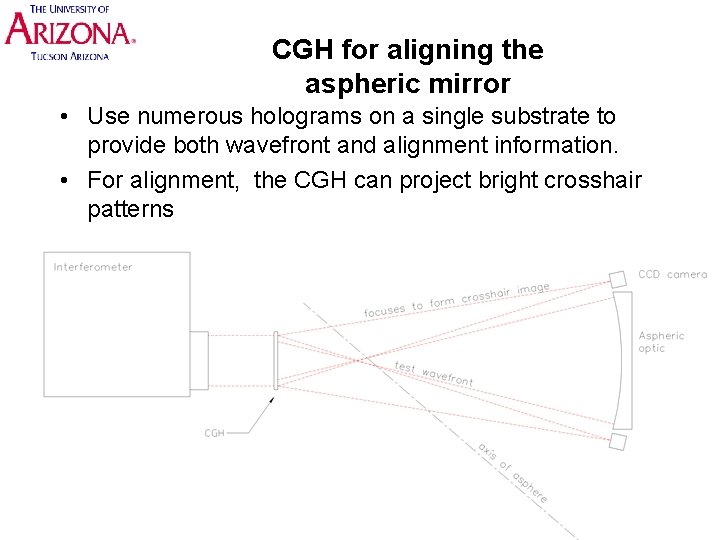
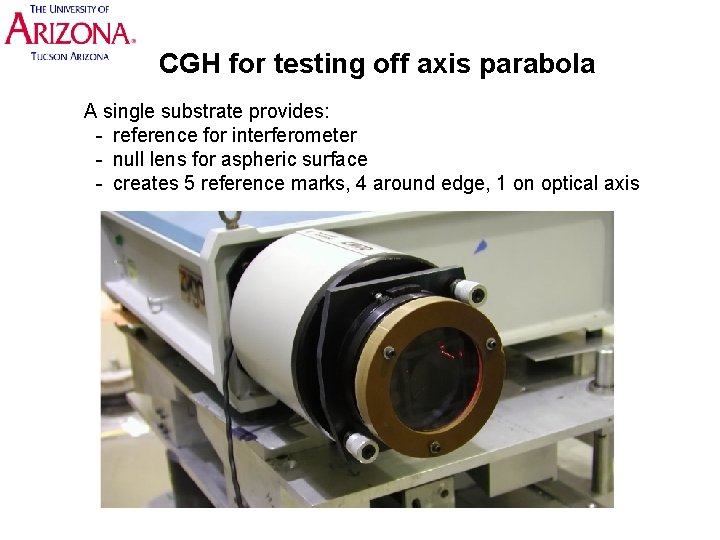
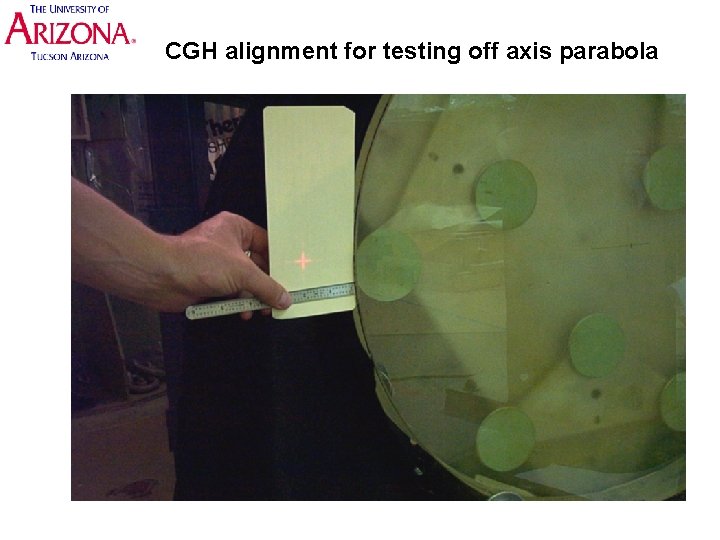
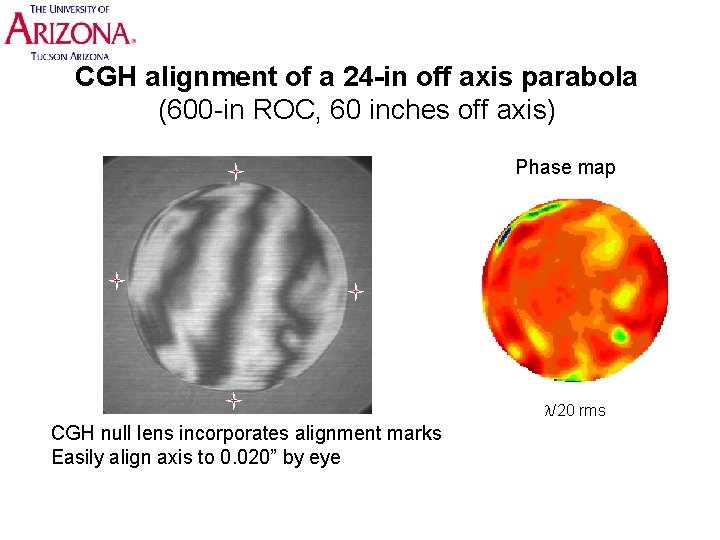
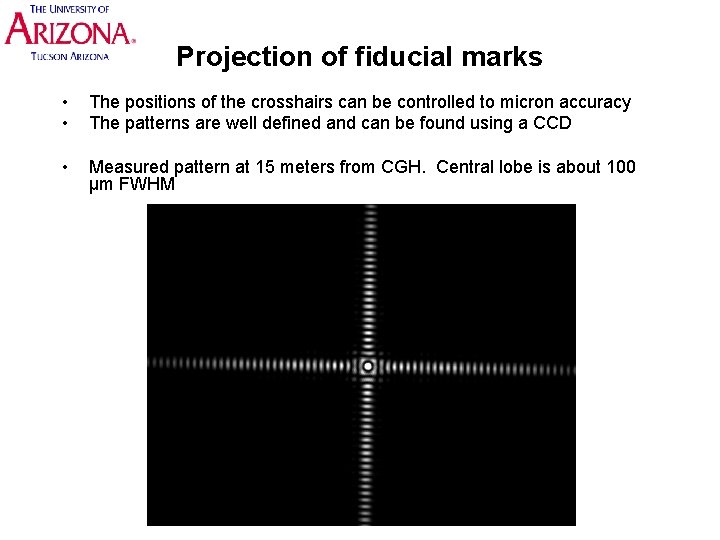
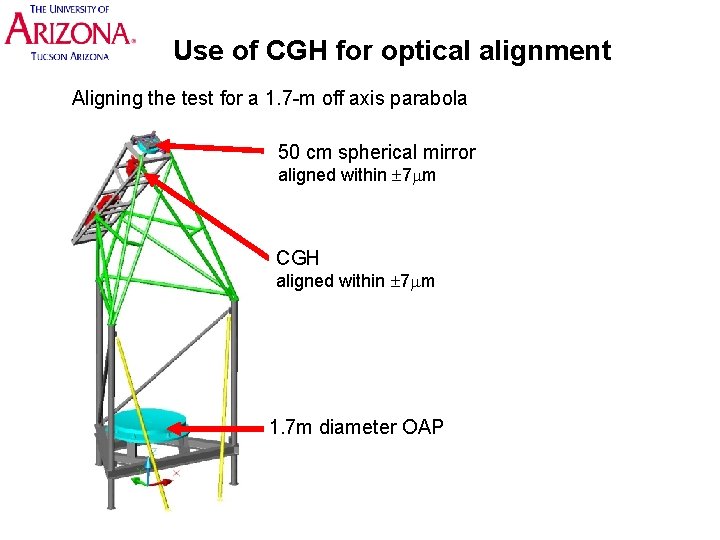
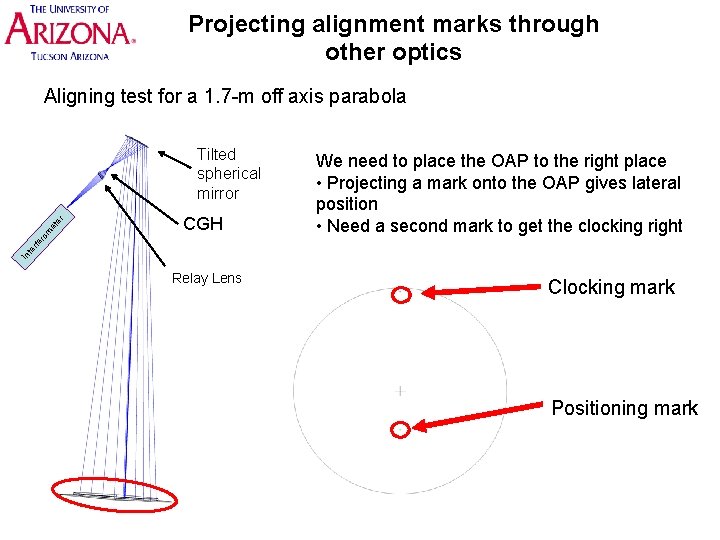
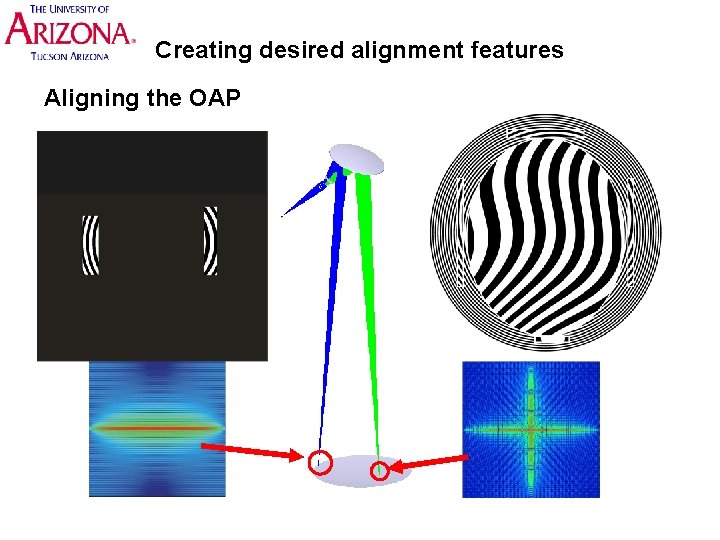
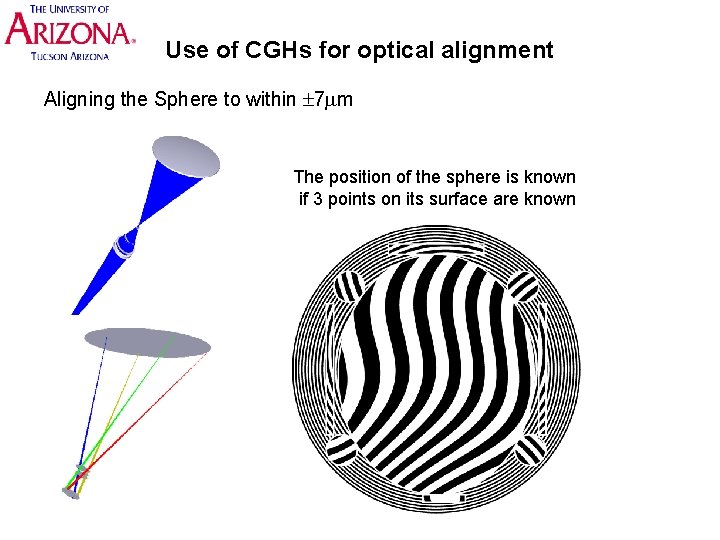
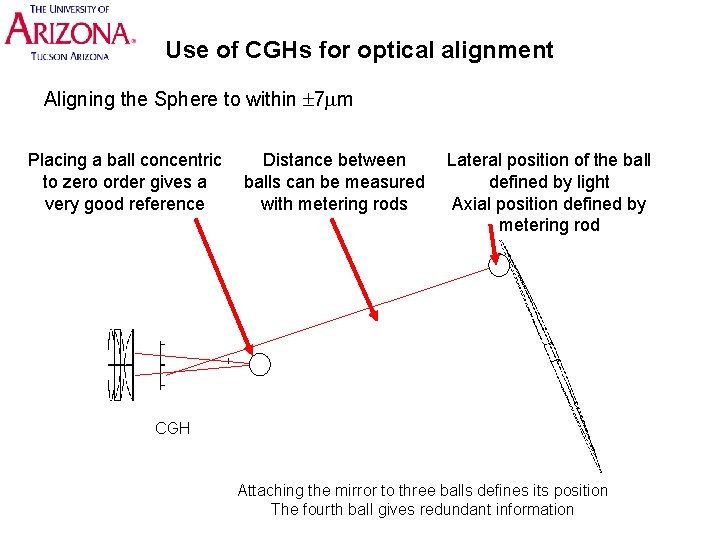
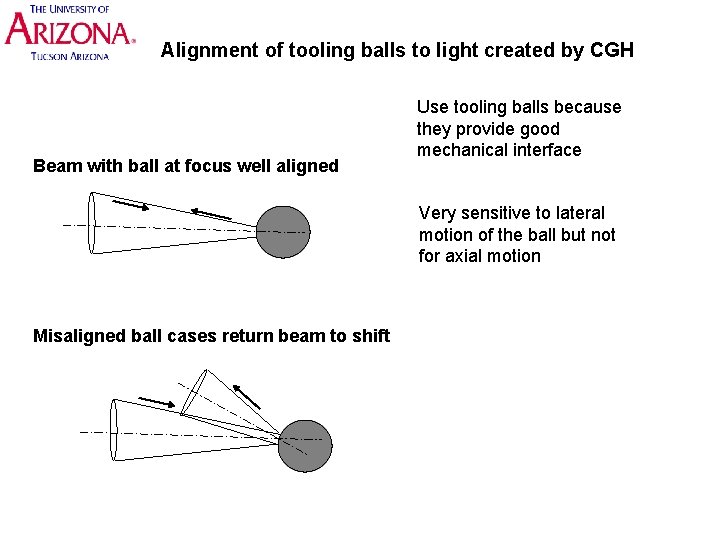
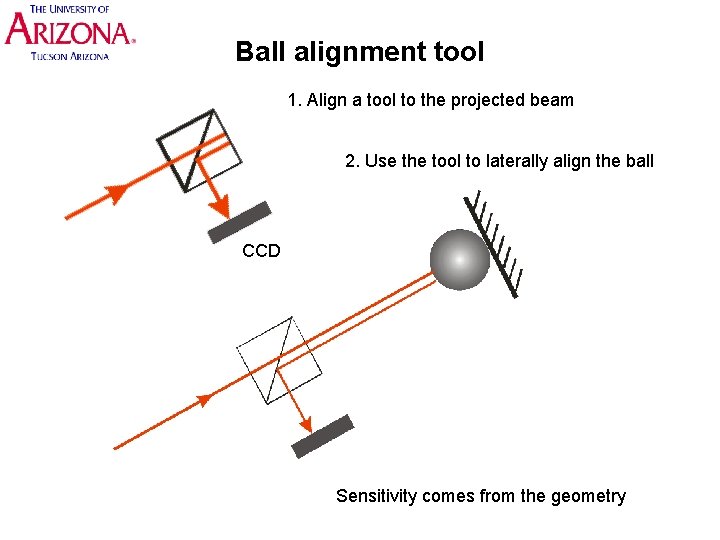
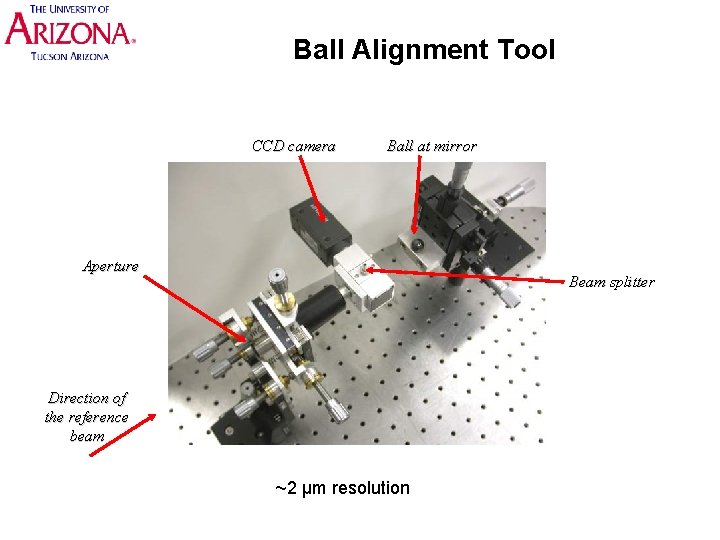
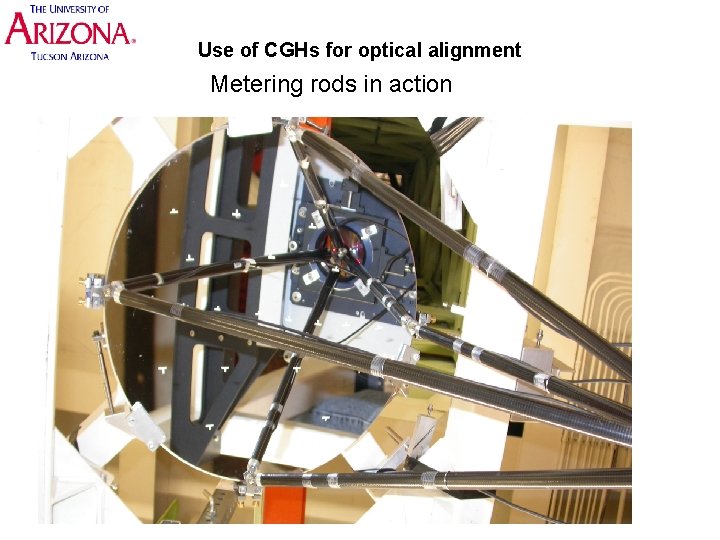
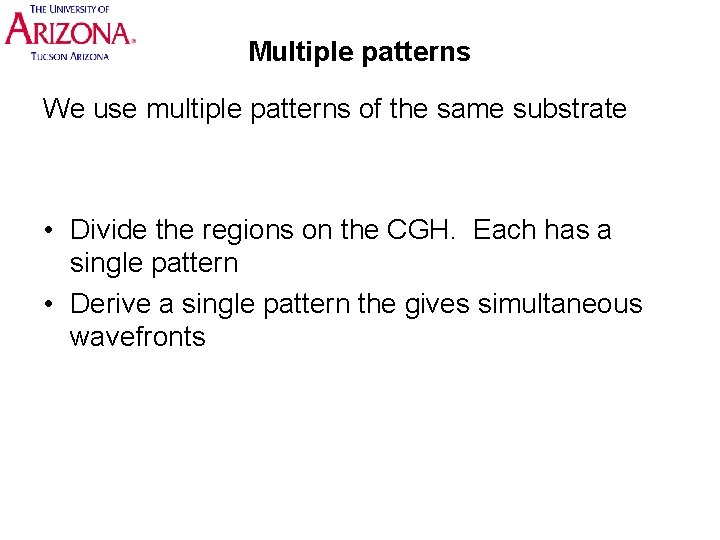
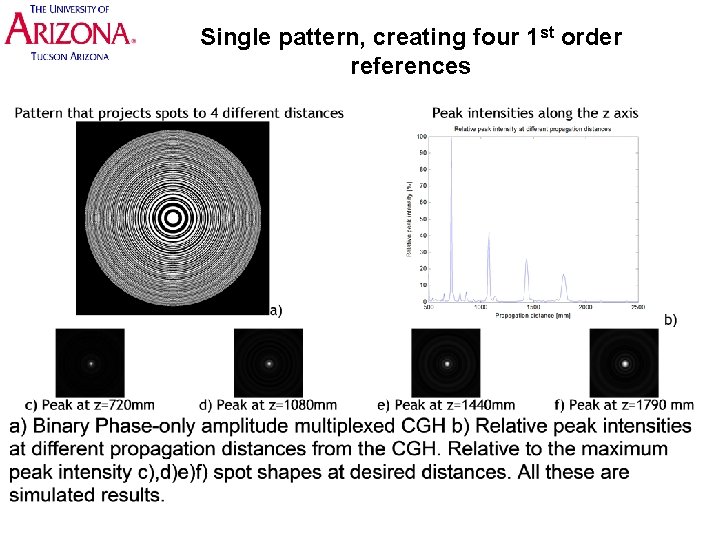

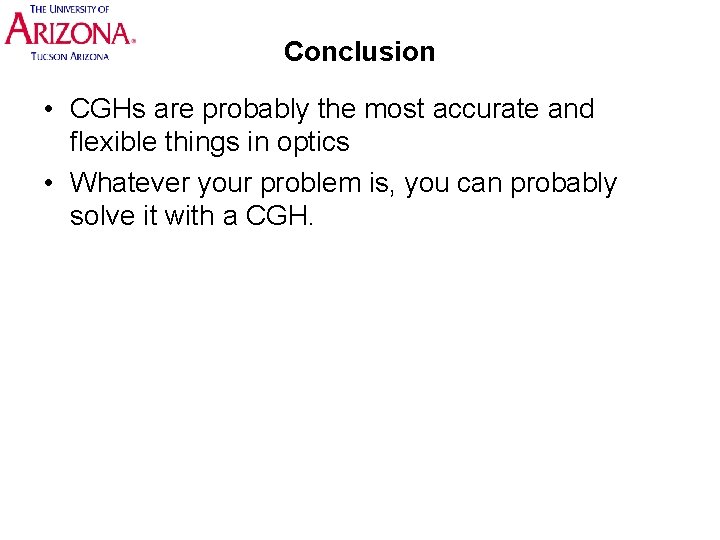
- Slides: 23
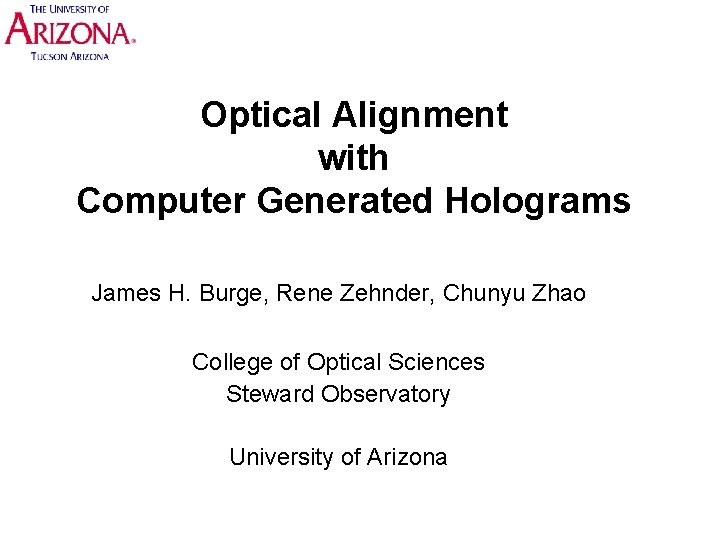
Optical Alignment with Computer Generated Holograms James H. Burge, Rene Zehnder, Chunyu Zhao College of Optical Sciences Steward Observatory University of Arizona
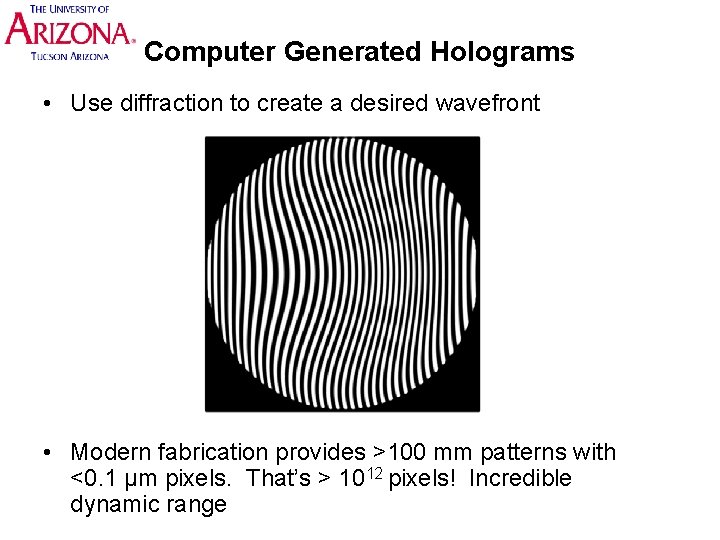
Computer Generated Holograms • Use diffraction to create a desired wavefront • Modern fabrication provides >100 mm patterns with <0. 1 µm pixels. That’s > 1012 pixels! Incredible dynamic range
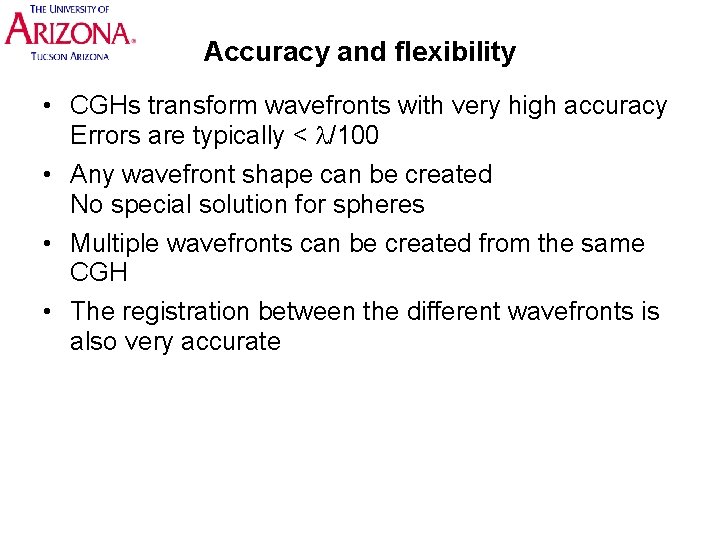
Accuracy and flexibility • CGHs transform wavefronts with very high accuracy Errors are typically < l/100 • Any wavefront shape can be created No special solution for spheres • Multiple wavefronts can be created from the same CGH • The registration between the different wavefronts is also very accurate
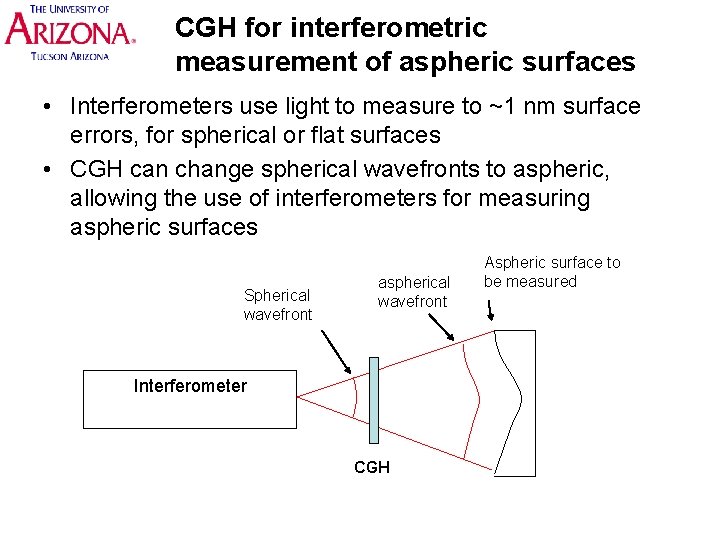
CGH for interferometric measurement of aspheric surfaces • Interferometers use light to measure to ~1 nm surface errors, for spherical or flat surfaces • CGH can change spherical wavefronts to aspheric, allowing the use of interferometers for measuring aspheric surfaces Spherical wavefront aspherical wavefront Interferometer CGH Aspheric surface to be measured
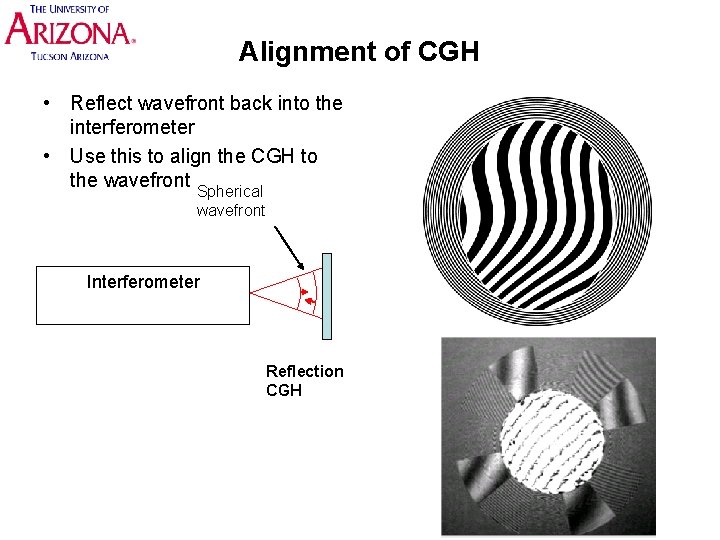
Alignment of CGH • Reflect wavefront back into the interferometer • Use this to align the CGH to the wavefront Spherical wavefront Interferometer Reflection CGH
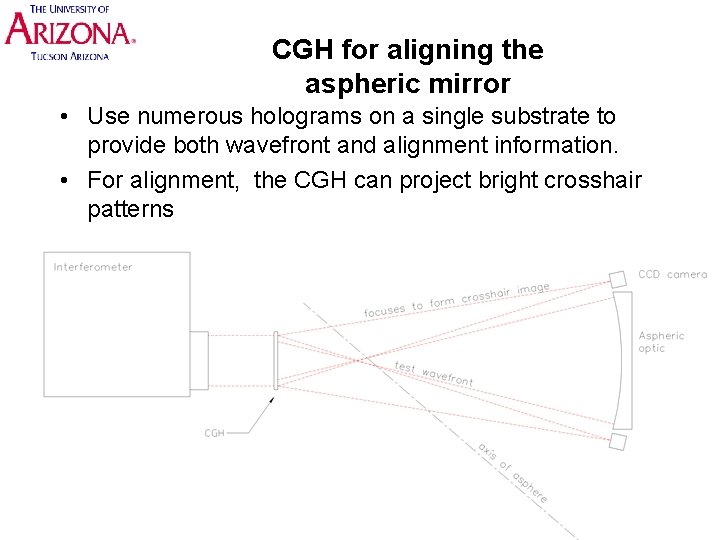
CGH for aligning the aspheric mirror • Use numerous holograms on a single substrate to provide both wavefront and alignment information. • For alignment, the CGH can project bright crosshair patterns
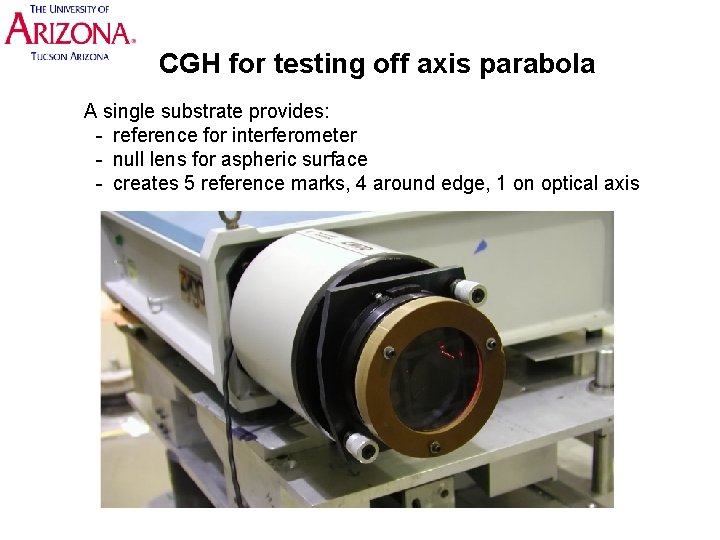
CGH for testing off axis parabola A single substrate provides: - reference for interferometer - null lens for aspheric surface - creates 5 reference marks, 4 around edge, 1 on optical axis
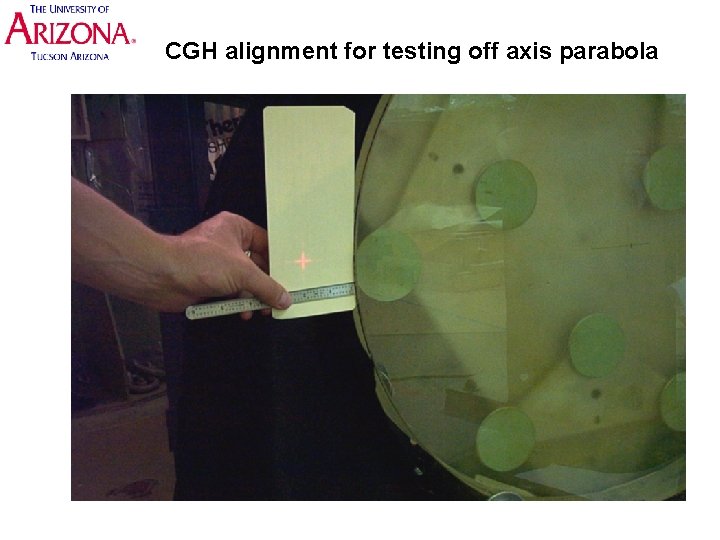
CGH alignment for testing off axis parabola
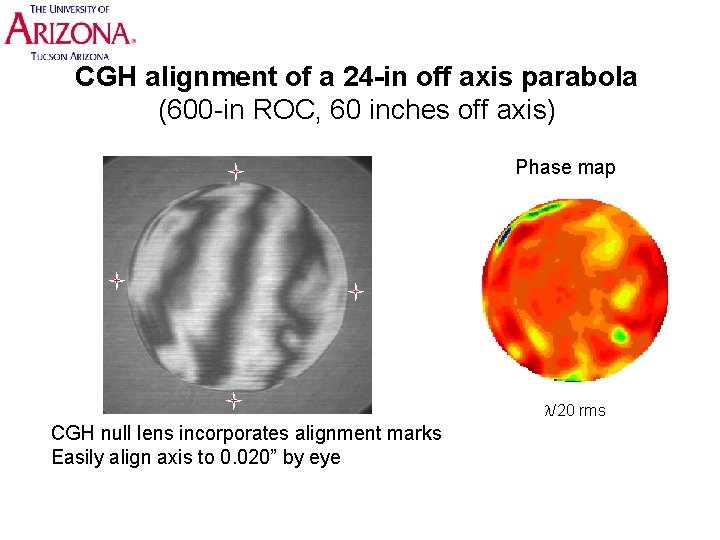
CGH alignment of a 24 -in off axis parabola (600 -in ROC, 60 inches off axis) Phase map l/20 rms CGH null lens incorporates alignment marks Easily align axis to 0. 020” by eye
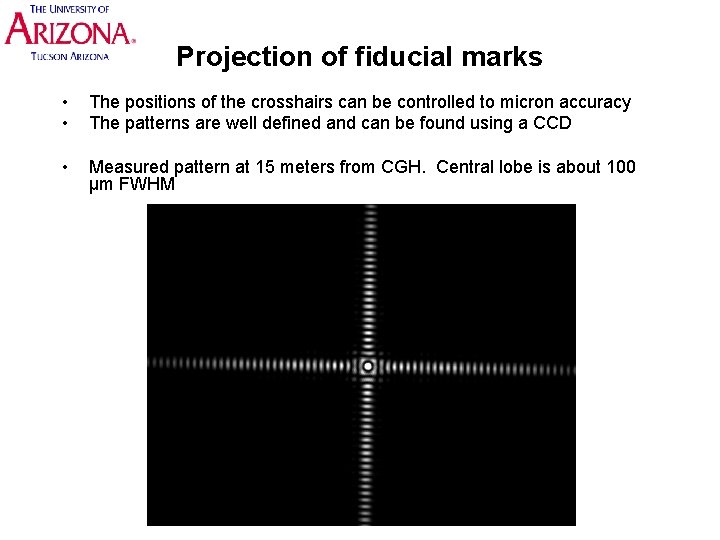
Projection of fiducial marks • • The positions of the crosshairs can be controlled to micron accuracy The patterns are well defined and can be found using a CCD • Measured pattern at 15 meters from CGH. Central lobe is about 100 µm FWHM
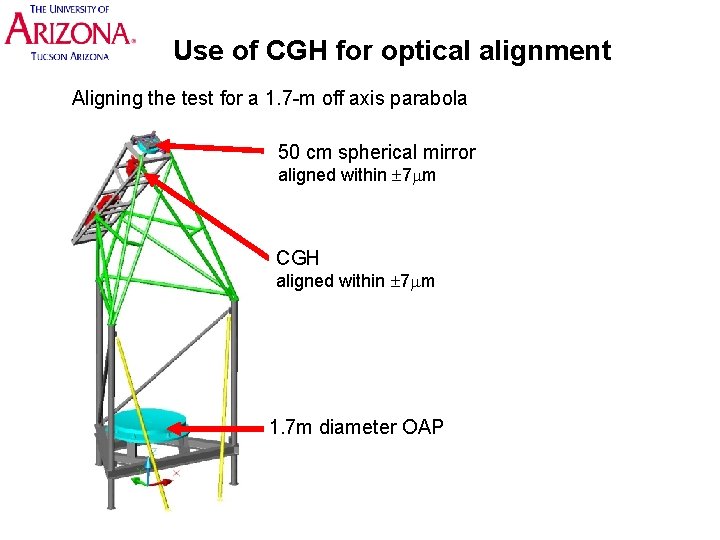
Use of CGH for optical alignment Aligning the test for a 1. 7 -m off axis parabola 50 cm spherical mirror aligned within 7 m CGH aligned within 7 m 1. 7 m diameter OAP
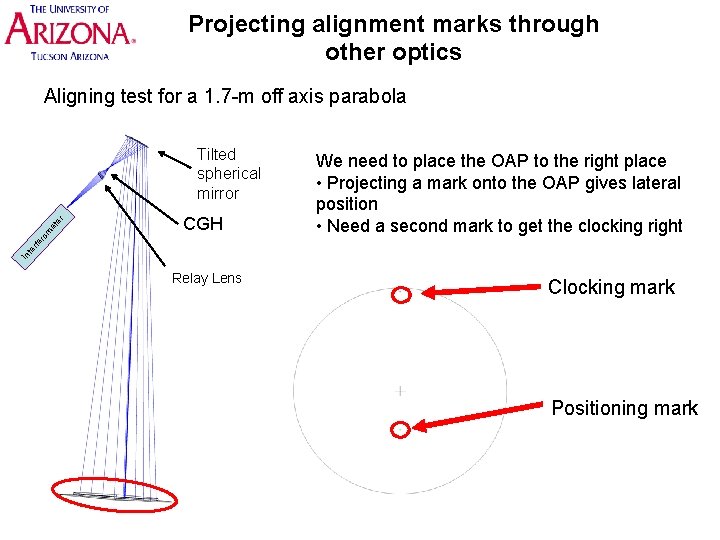
Projecting alignment marks through other optics Aligning test for a 1. 7 -m off axis parabola CGH We need to place the OAP to the right place • Projecting a mark onto the OAP gives lateral position • Need a second mark to get the clocking right In te rfe ro m et er Tilted spherical mirror Relay Lens Clocking mark Positioning mark
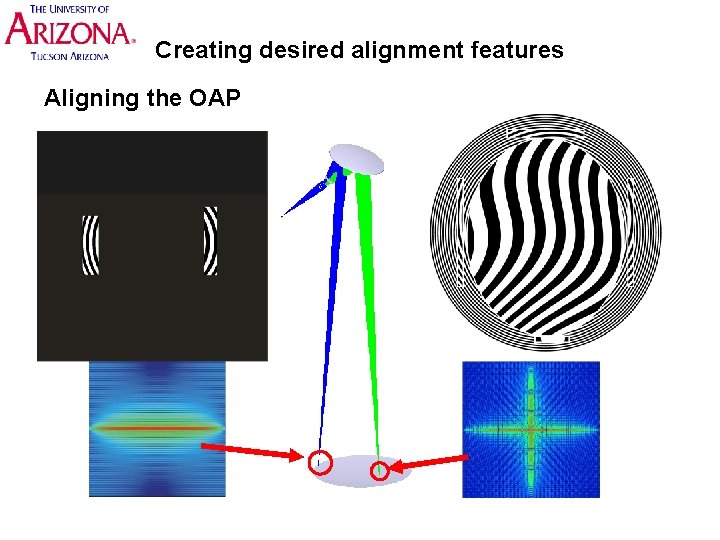
Creating desired alignment features Aligning the OAP
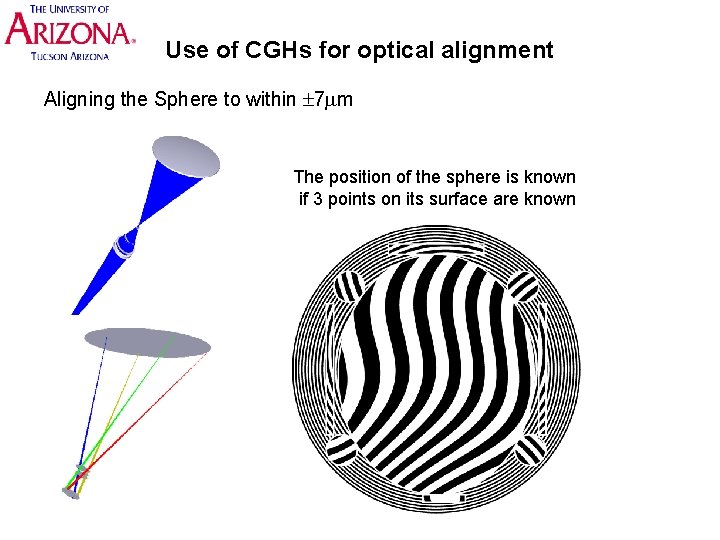
Use of CGHs for optical alignment Aligning the Sphere to within 7 m The position of the sphere is known if 3 points on its surface are known
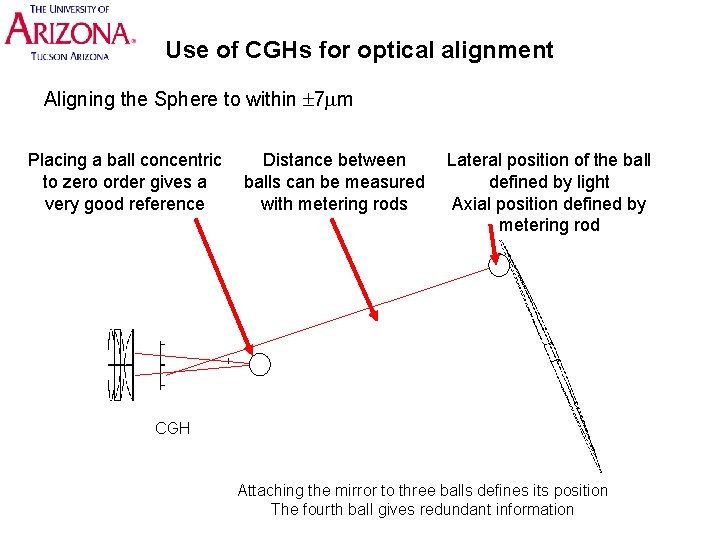
Use of CGHs for optical alignment Aligning the Sphere to within 7 m Placing a ball concentric to zero order gives a very good reference Distance between balls can be measured with metering rods Lateral position of the ball defined by light Axial position defined by metering rod CGH Attaching the mirror to three balls defines its position The fourth ball gives redundant information
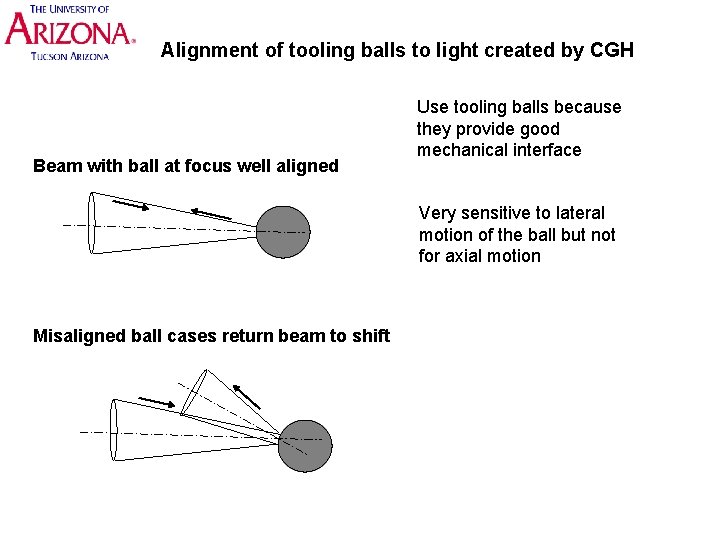
Alignment of tooling balls to light created by CGH Beam with ball at focus well aligned Use tooling balls because they provide good mechanical interface Very sensitive to lateral motion of the ball but not for axial motion Misaligned ball cases return beam to shift
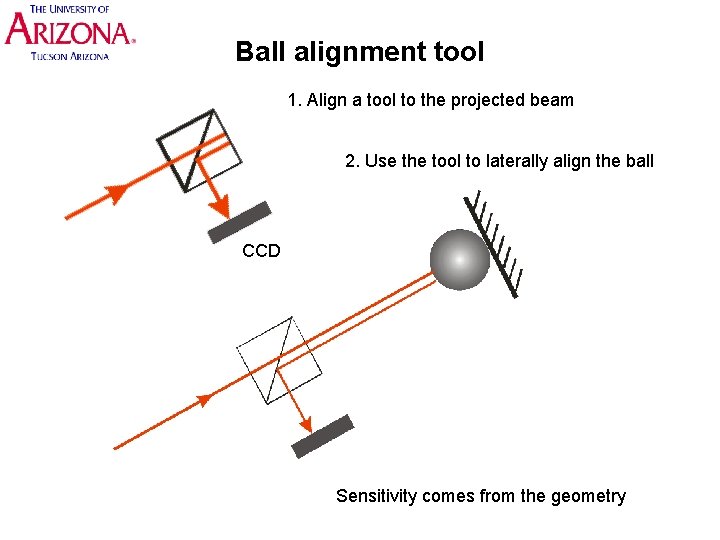
Ball alignment tool 1. Align a tool to the projected beam 2. Use the tool to laterally align the ball CCD Sensitivity comes from the geometry
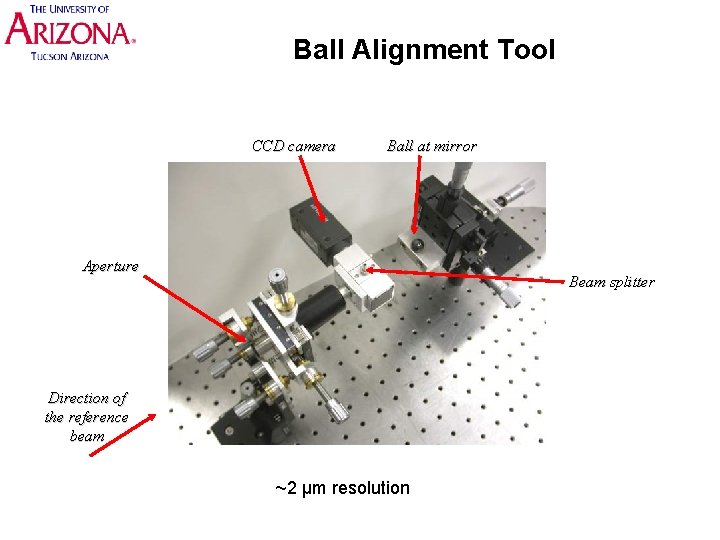
Ball Alignment Tool CCD camera Ball at mirror Aperture Beam splitter Direction of the reference beam ~2 µm resolution
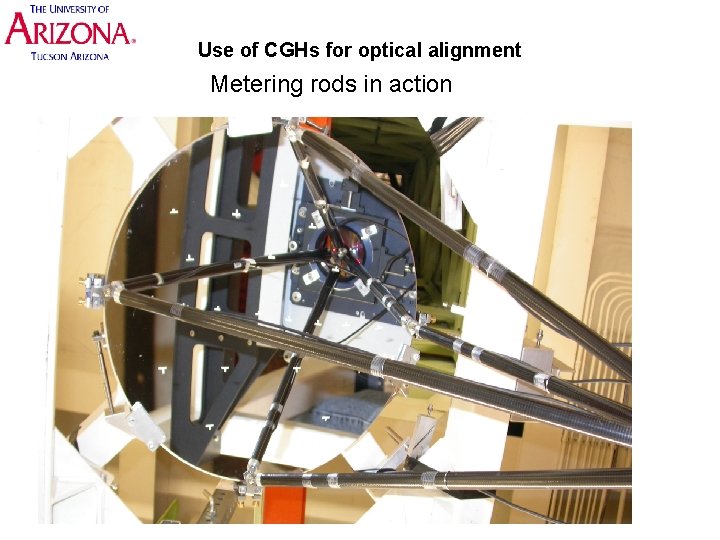
Use of CGHs for optical alignment Metering rods in action
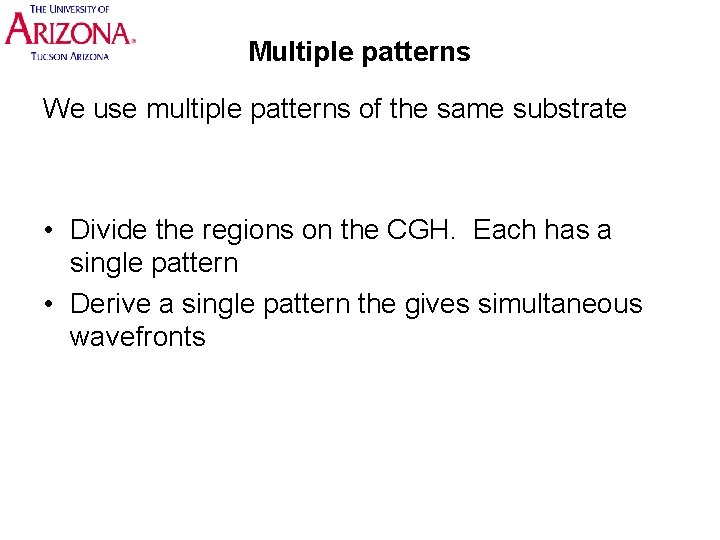
Multiple patterns We use multiple patterns of the same substrate • Divide the regions on the CGH. Each has a single pattern • Derive a single pattern the gives simultaneous wavefronts
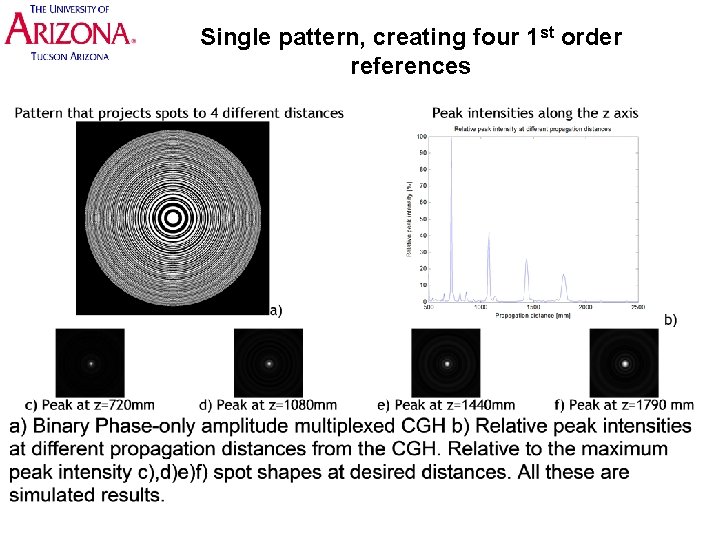
Single pattern, creating four 1 st order references

Single CGH with multiple references CGH creating multiple wavefronts Position sensing detector
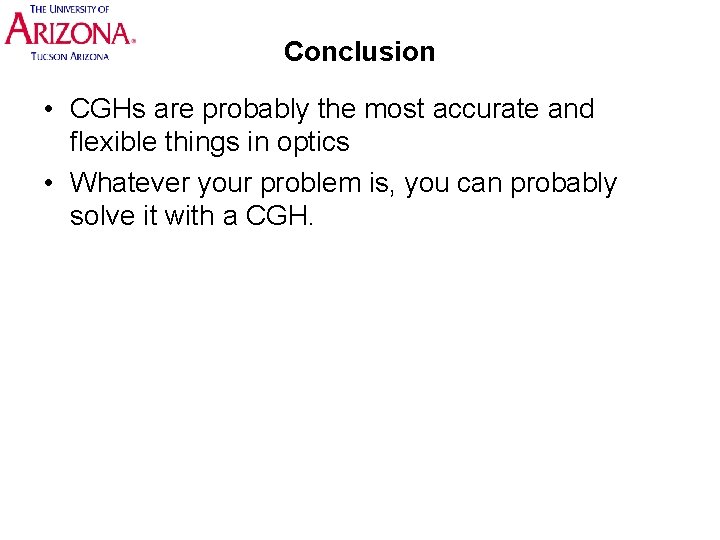
Conclusion • CGHs are probably the most accurate and flexible things in optics • Whatever your problem is, you can probably solve it with a CGH.
Compare two sequences
Dna substitution
Sequence alignment
Global alignment vs local alignment
Global vs local alignment
Precision optical alignment service
Computer generated reports
The trailside killer
Russell odom and clay lawson
Mobile user-generated content
How lift is generated
Procedurally generated music
What are presentation graphics programs?
What is the angle generated by a clockwise rotation?
Bnet pnm
An 8 pole dc shunt generator with 778 wave
User generated content journalism
Find all abelian groups (up to isomorphism) of order 360.
How is thermal energy generated
Image by generated photos
Rld cards contain
Electric current is generated due to
Kesler science
How do batteries work