Office of the Secretary of Defense Microelectronics Activity
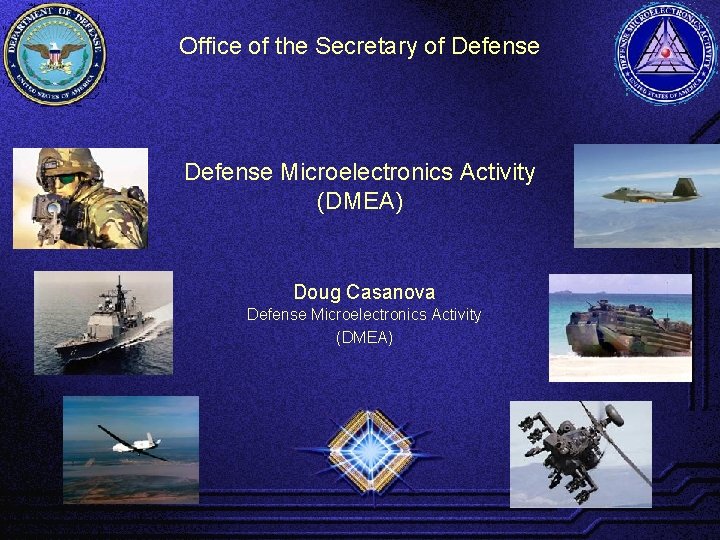
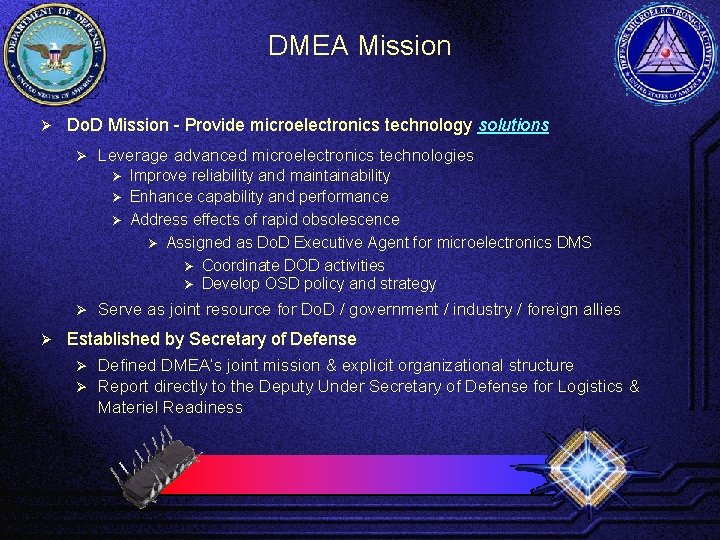
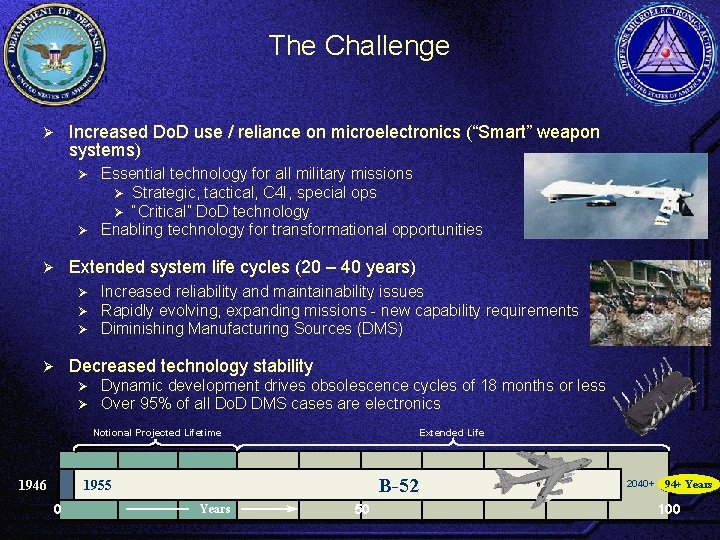
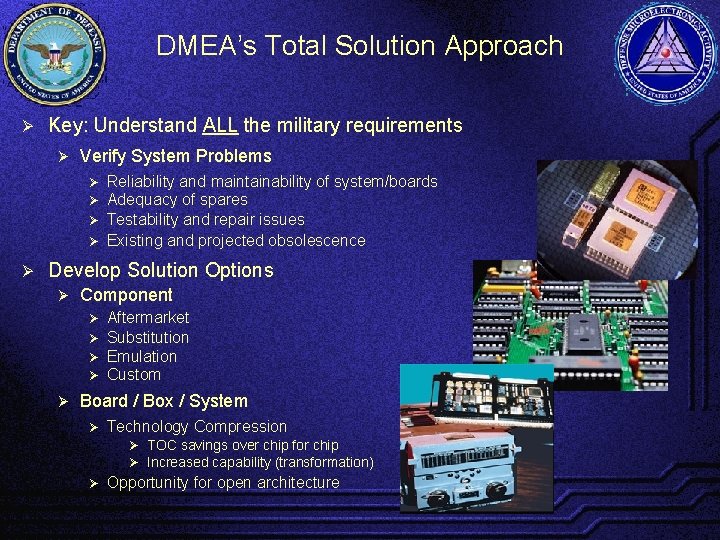
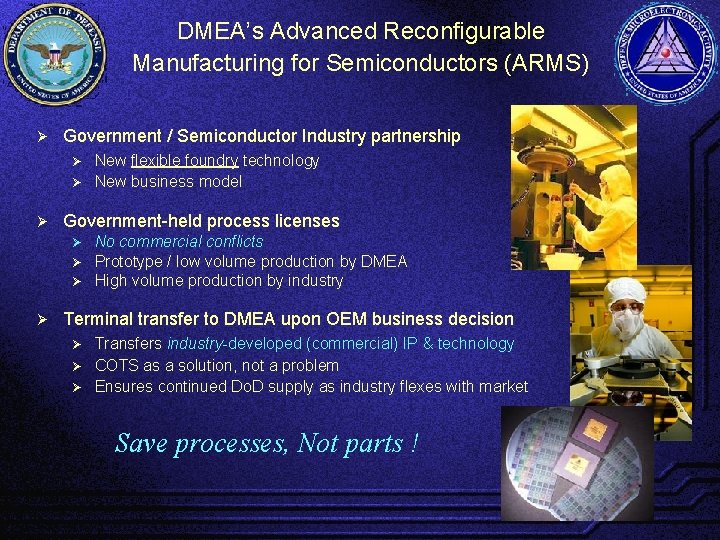
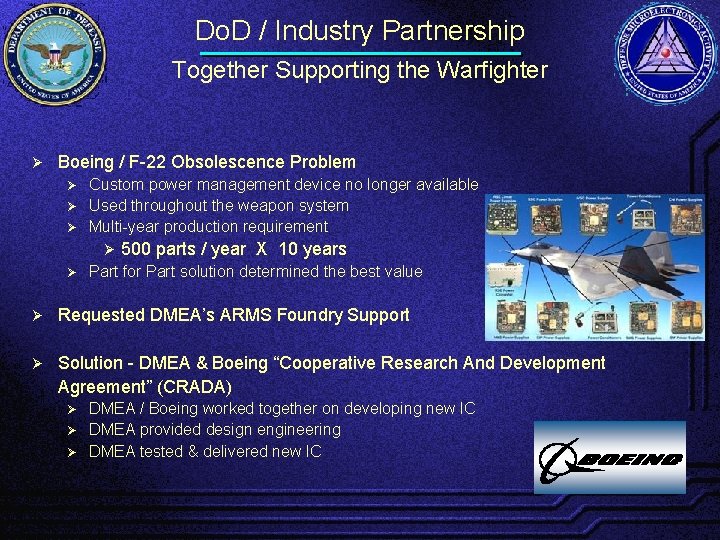
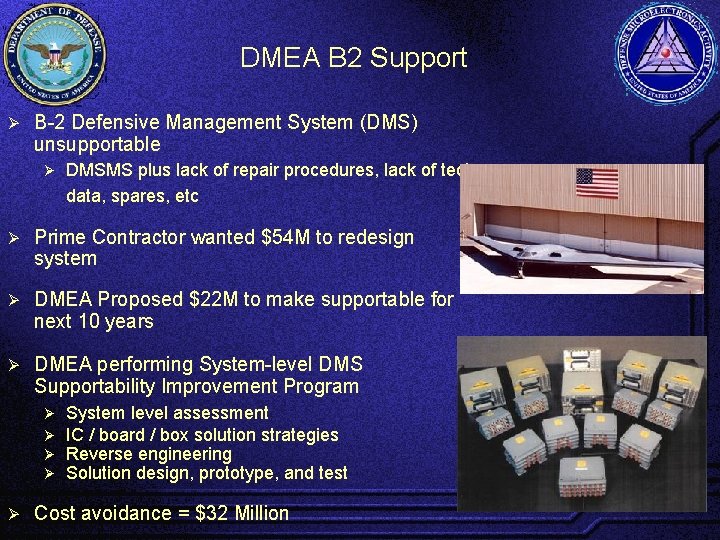
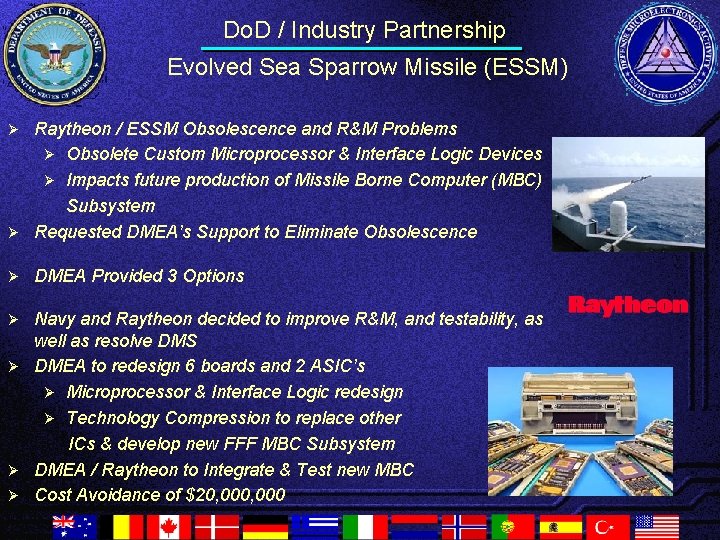
- Slides: 8
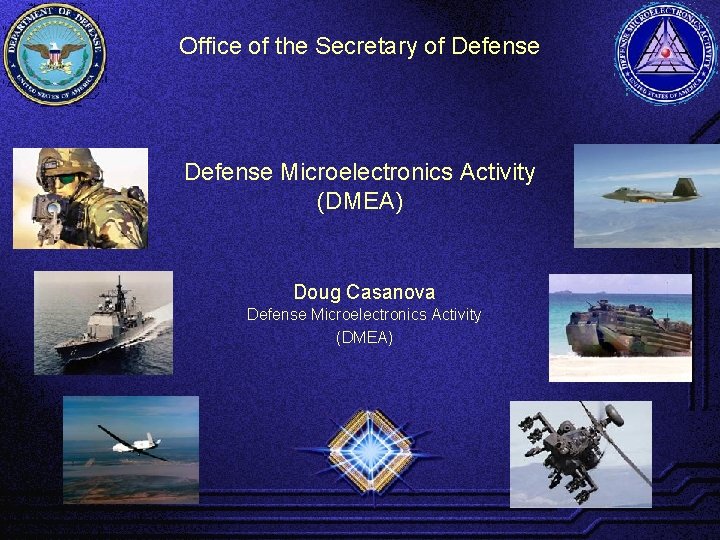
Office of the Secretary of Defense Microelectronics Activity (DMEA) Doug Casanova Defense Microelectronics Activity (DMEA)
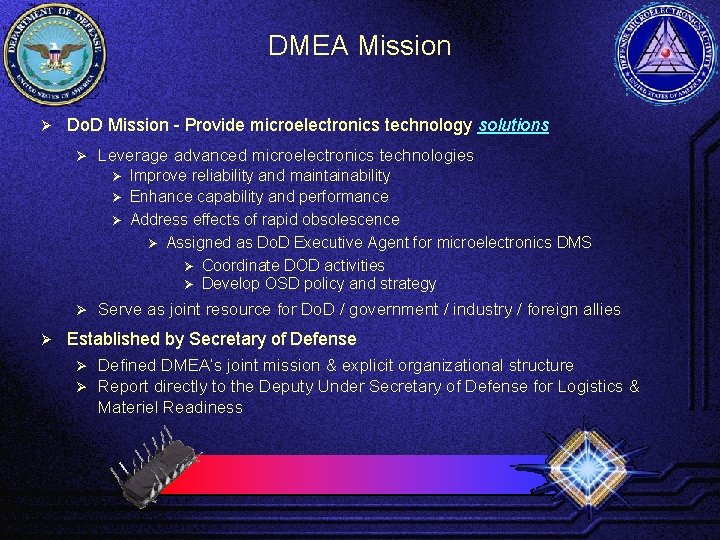
DMEA Mission Ø Do. D Mission - Provide microelectronics technology solutions Ø Leverage advanced microelectronics technologies Improve reliability and maintainability Ø Enhance capability and performance Ø Address effects of rapid obsolescence Ø Assigned as Do. D Executive Agent for microelectronics DMS Ø Coordinate DOD activities Ø Develop OSD policy and strategy Ø Ø Ø Serve as joint resource for Do. D / government / industry / foreign allies Established by Secretary of Defense Defined DMEA’s joint mission & explicit organizational structure Ø Report directly to the Deputy Under Secretary of Defense for Logistics & Materiel Readiness Ø
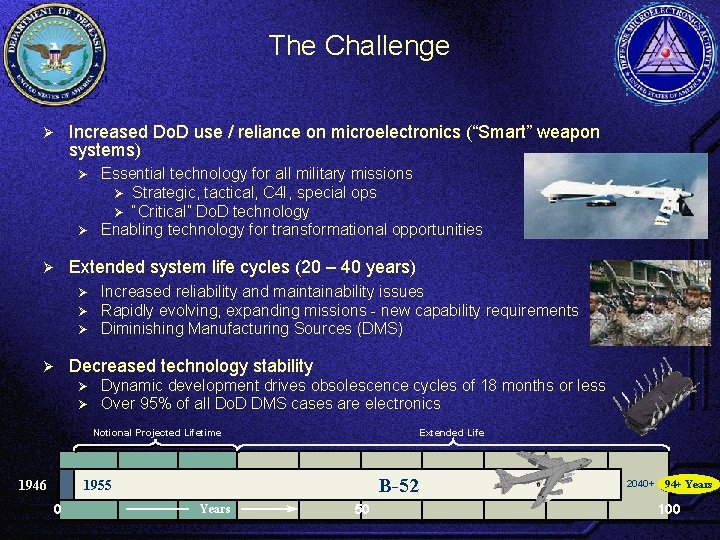
The Challenge Ø Increased Do. D use / reliance on microelectronics (“Smart” weapon systems) Essential technology for all military missions Ø Strategic, tactical, C 4 I, special ops Ø “Critical” Do. D technology Ø Enabling technology for transformational opportunities Ø Ø Extended system life cycles (20 – 40 years) Ø Ø Increased reliability and maintainability issues Rapidly evolving, expanding missions - new capability requirements Diminishing Manufacturing Sources (DMS) Decreased technology stability Ø Ø Dynamic development drives obsolescence cycles of 18 months or less Over 95% of all Do. D DMS cases are electronics Notional Projected Lifetime 1946 Extended Life B-52 1955 0 Years 50 2040+ 94+ Years 100
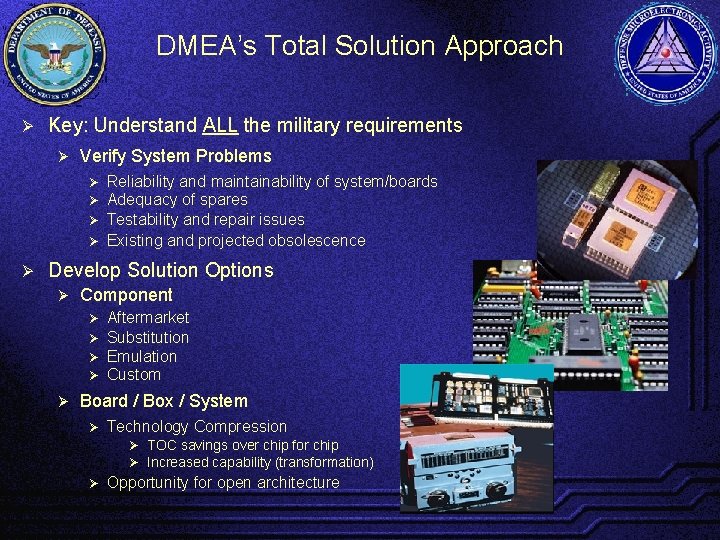
DMEA’s Total Solution Approach Ø Key: Understand ALL the military requirements Ø Verify System Problems Reliability and maintainability of system/boards Adequacy of spares Ø Testability and repair issues Ø Existing and projected obsolescence Ø Ø Ø Develop Solution Options Ø Component Ø Ø Ø Aftermarket Substitution Emulation Custom Board / Box / System Ø Technology Compression Ø TOC savings over chip for chip Ø Increased capability (transformation) Ø Opportunity for open architecture
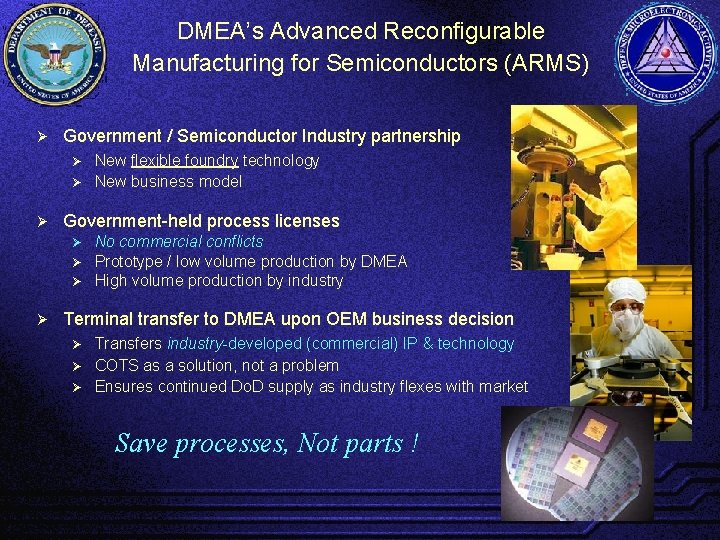
DMEA’s Advanced Reconfigurable Manufacturing for Semiconductors (ARMS) Ø Government / Semiconductor Industry partnership New flexible foundry technology Ø New business model Ø Ø Government-held process licenses Ø Ø No commercial conflicts Prototype / low volume production by DMEA High volume production by industry Terminal transfer to DMEA upon OEM business decision Transfers industry-developed (commercial) IP & technology Ø COTS as a solution, not a problem Ø Ensures continued Do. D supply as industry flexes with market Ø Save processes, Not parts !
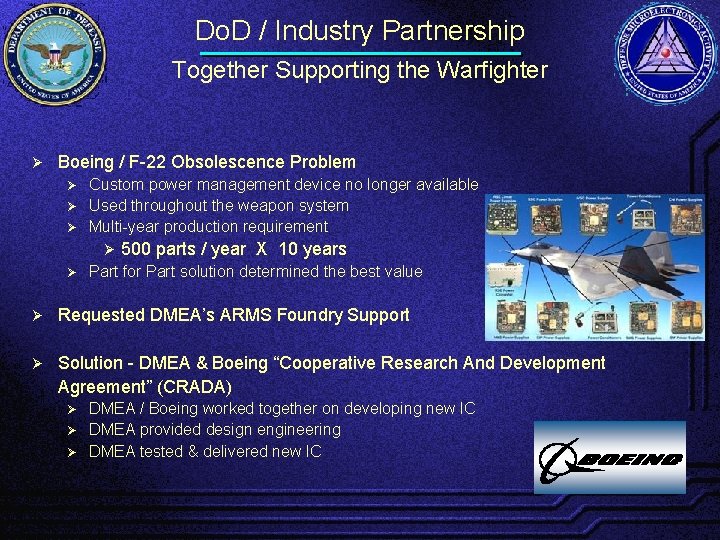
Do. D / Industry Partnership Together Supporting the Warfighter Ø Boeing / F-22 Obsolescence Problem Custom power management device no longer available Ø Used throughout the weapon system Ø Multi-year production requirement Ø Ø Ø 500 parts / year X 10 years Part for Part solution determined the best value Ø Requested DMEA’s ARMS Foundry Support Ø Solution - DMEA & Boeing “Cooperative Research And Development Agreement” (CRADA) DMEA / Boeing worked together on developing new IC Ø DMEA provided design engineering Ø DMEA tested & delivered new IC Ø
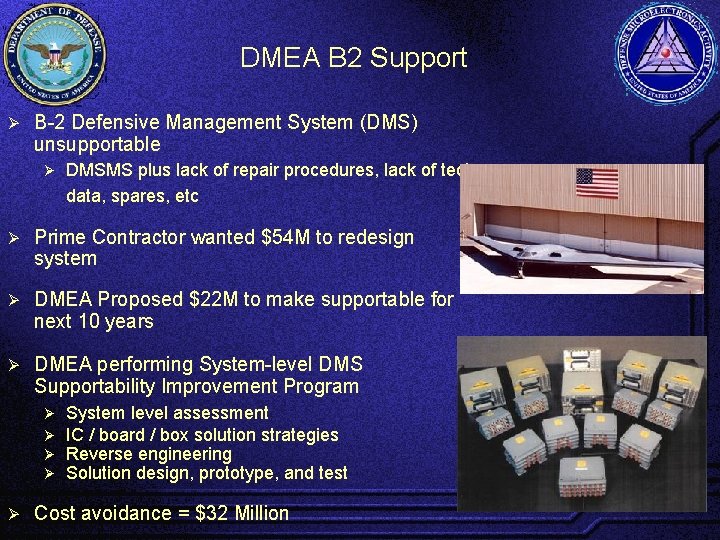
DMEA B 2 Support Ø B-2 Defensive Management System (DMS) unsupportable Ø DMSMS plus lack of repair procedures, lack of tech data, spares, etc Ø Prime Contractor wanted $54 M to redesign system Ø DMEA Proposed $22 M to make supportable for next 10 years Ø DMEA performing System-level DMS Supportability Improvement Program Ø Ø Ø System level assessment IC / board / box solution strategies Reverse engineering Solution design, prototype, and test Cost avoidance = $32 Million
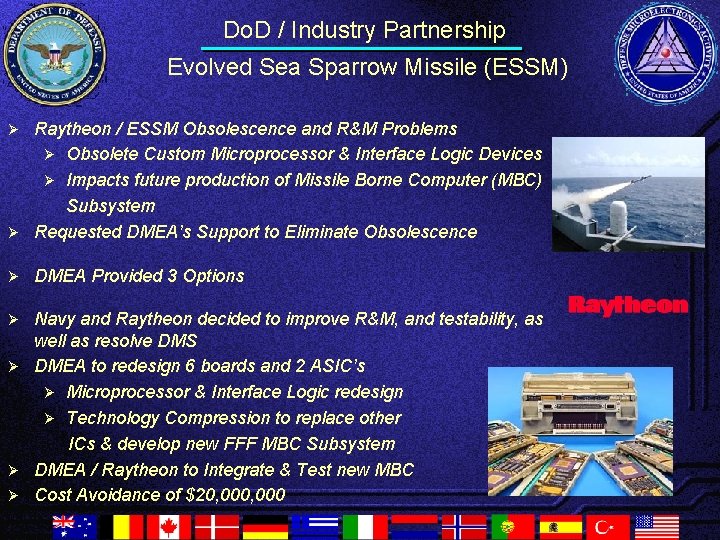
Do. D / Industry Partnership Evolved Sea Sparrow Missile (ESSM) Raytheon / ESSM Obsolescence and R&M Problems Ø Obsolete Custom Microprocessor & Interface Logic Devices Ø Impacts future production of Missile Borne Computer (MBC) Subsystem Ø Requested DMEA’s Support to Eliminate Obsolescence Ø Ø DMEA Provided 3 Options Navy and Raytheon decided to improve R&M, and testability, as well as resolve DMS Ø DMEA to redesign 6 boards and 2 ASIC’s Ø Microprocessor & Interface Logic redesign Ø Technology Compression to replace other ICs & develop new FFF MBC Subsystem Ø DMEA / Raytheon to Integrate & Test new MBC Ø Cost Avoidance of $20, 000 Ø