MONOFILAMENT EXTRUSION PROCESS Monofilaments are wirelike polymeric strands
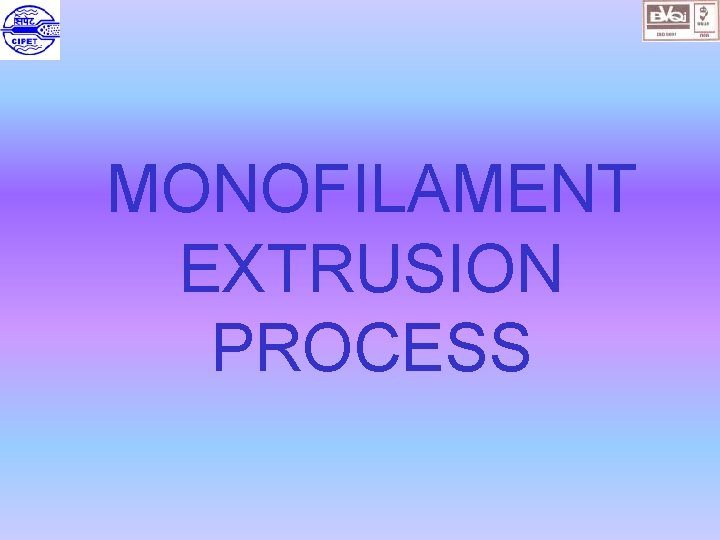
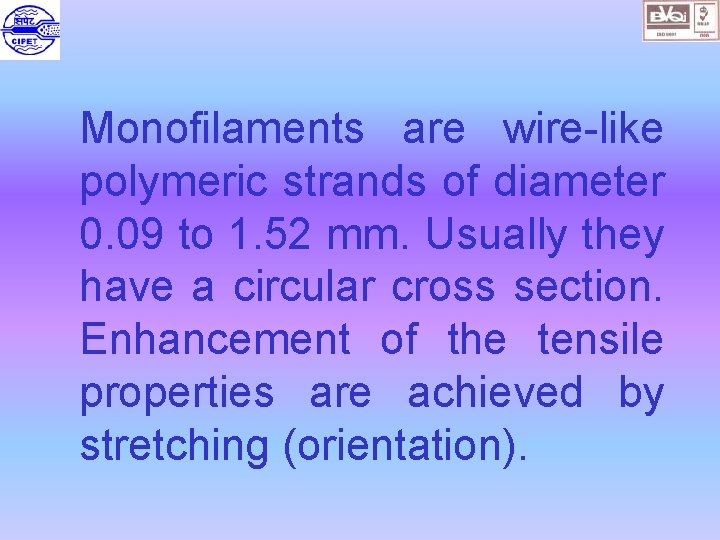
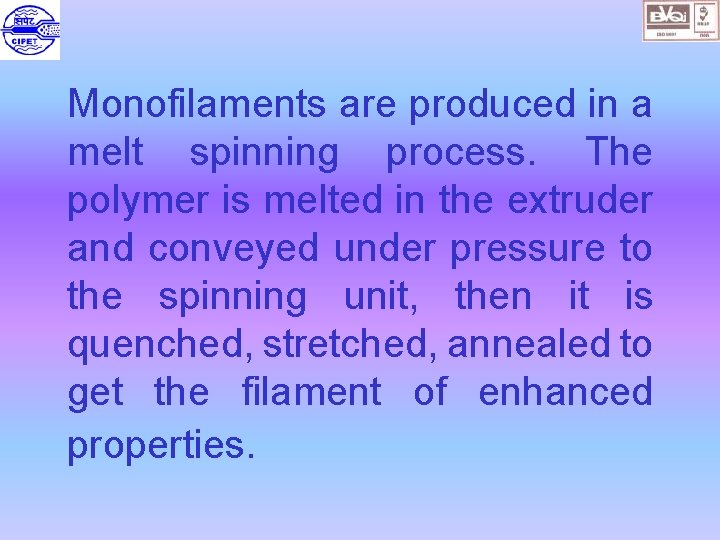
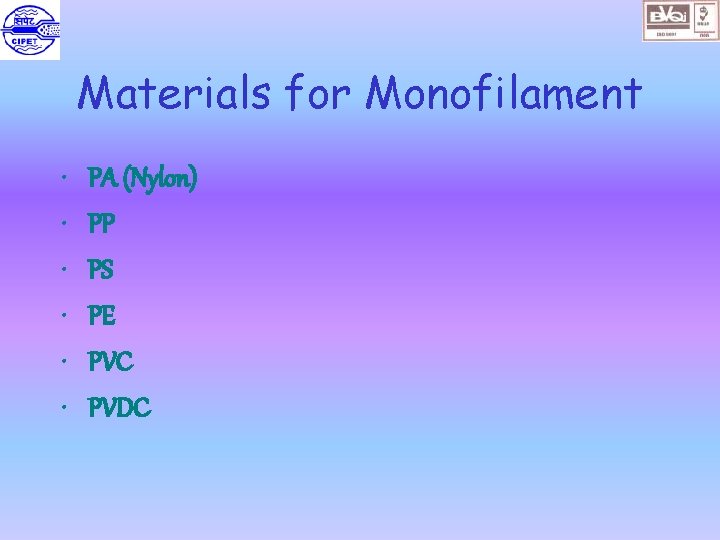
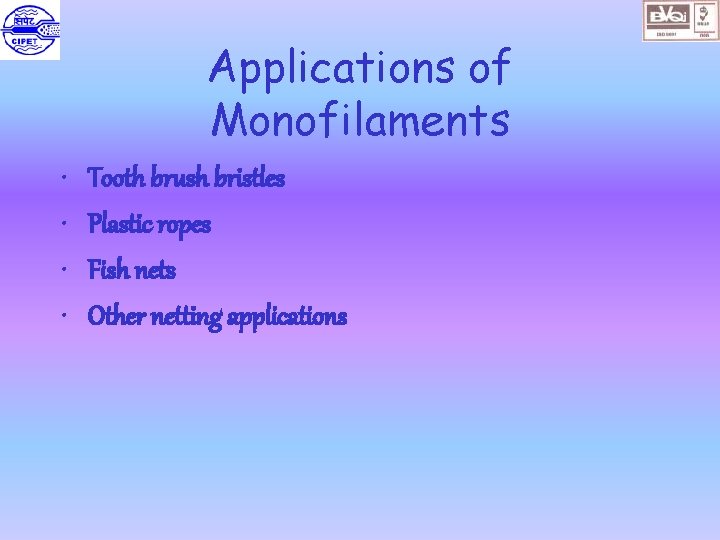
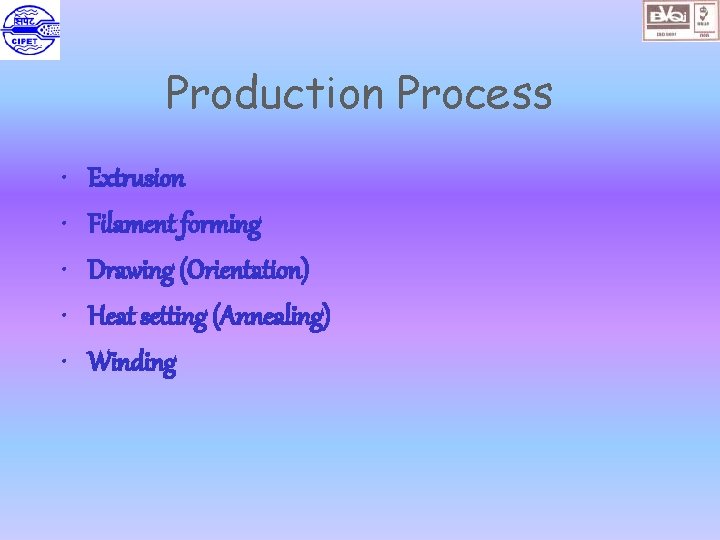
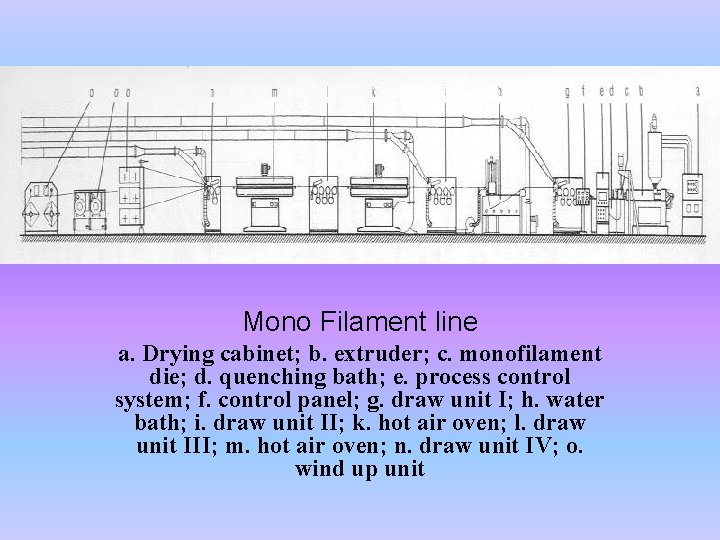
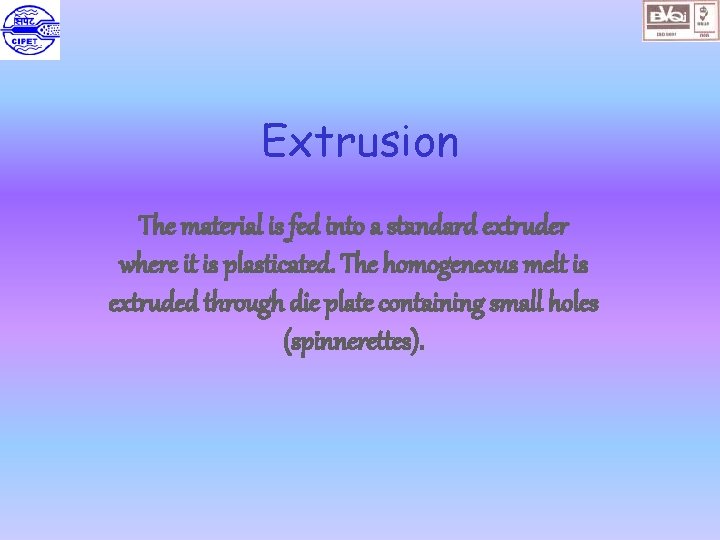
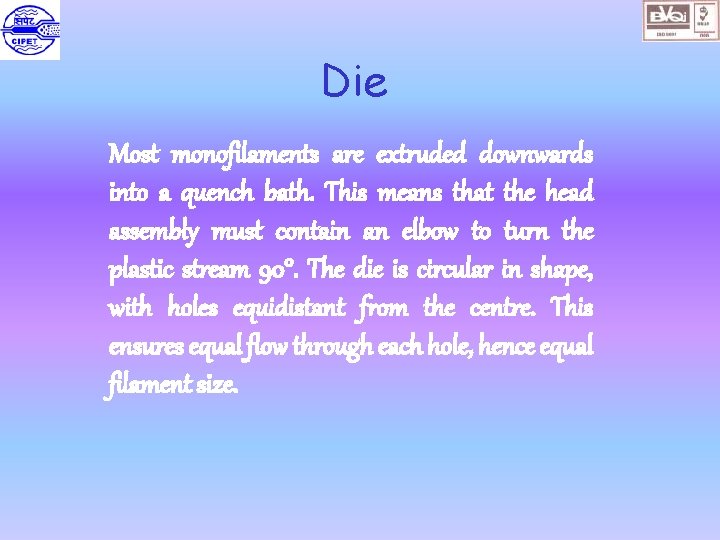
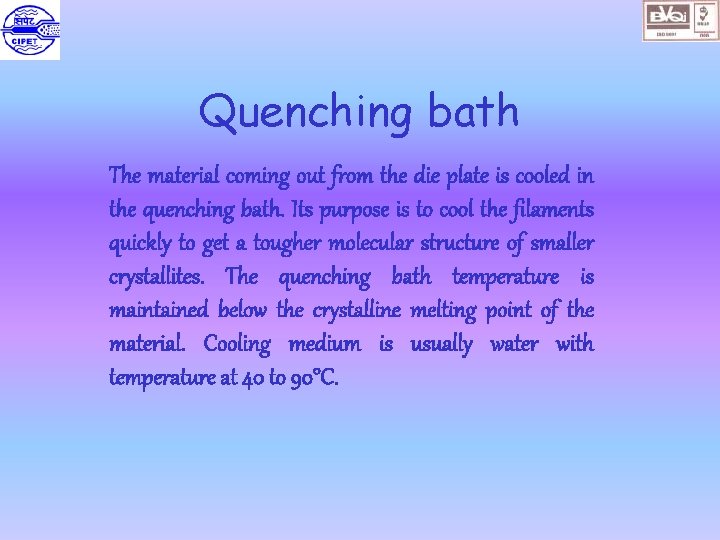
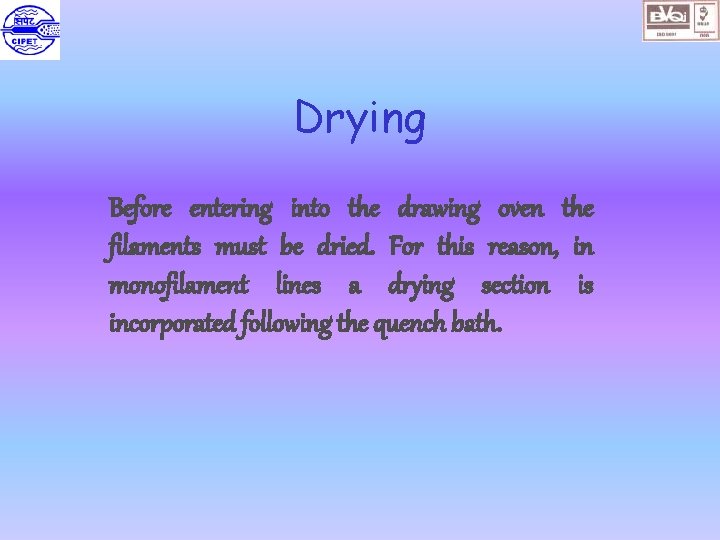
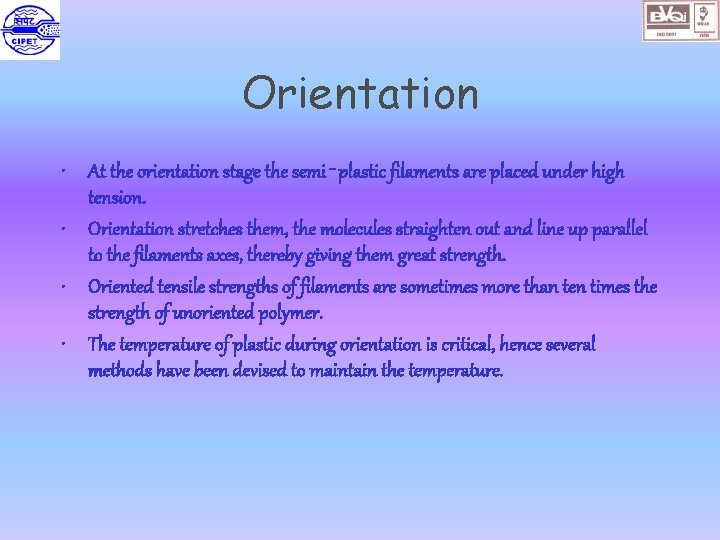
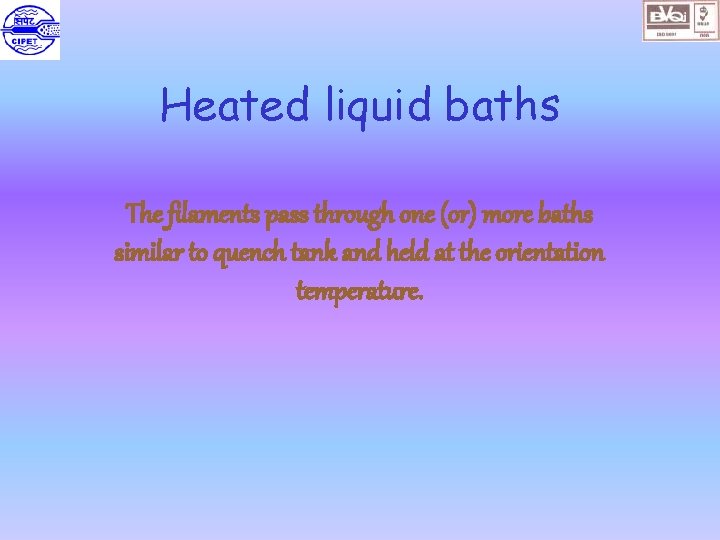
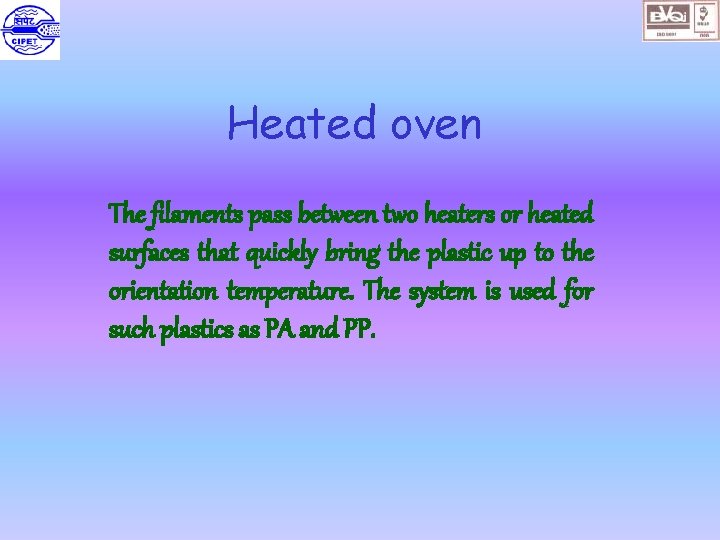
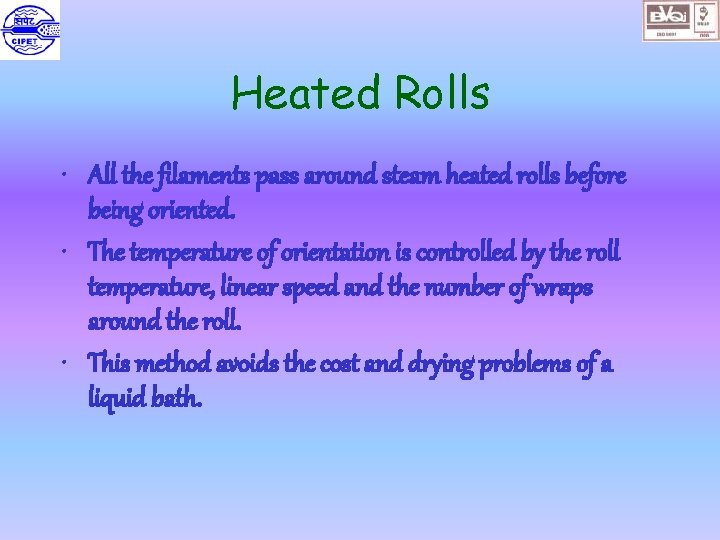
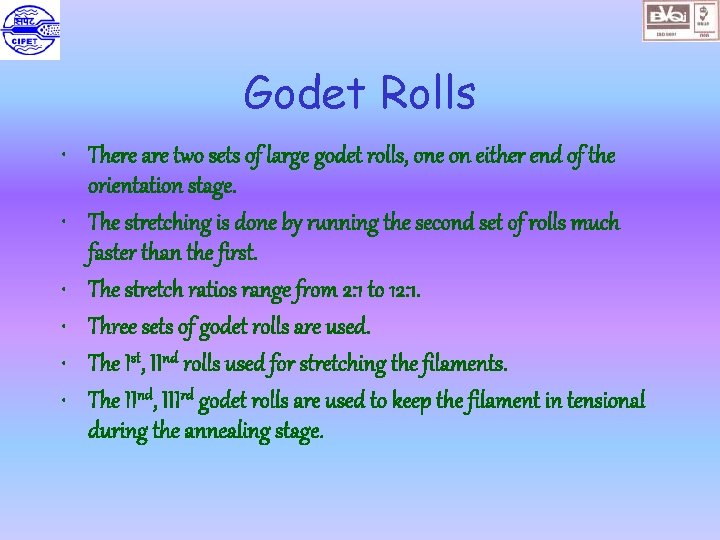
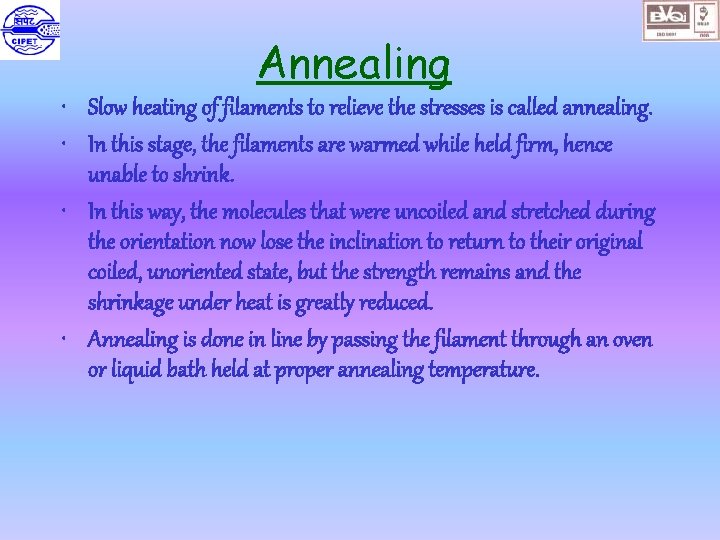
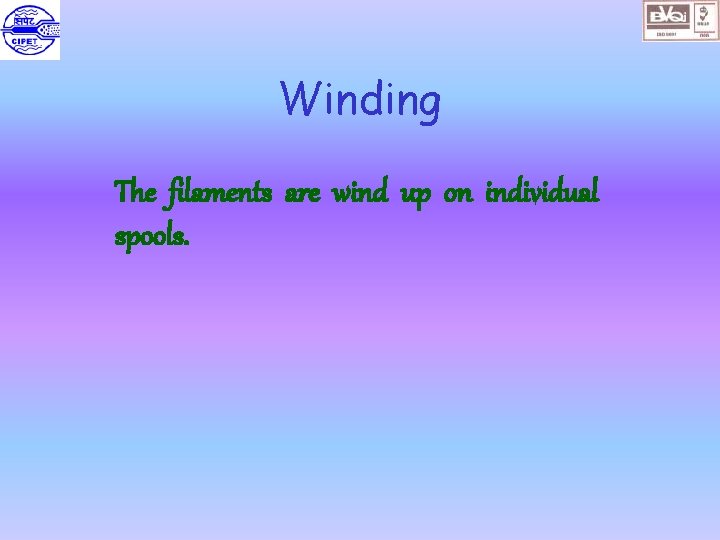
- Slides: 18
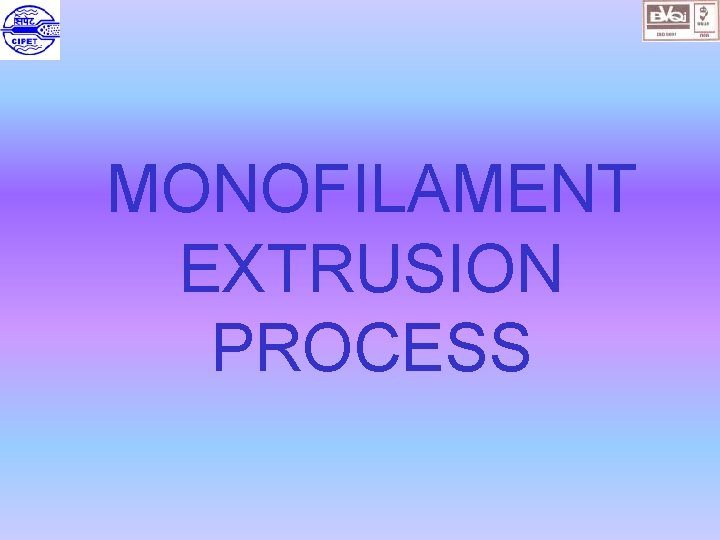
MONOFILAMENT EXTRUSION PROCESS
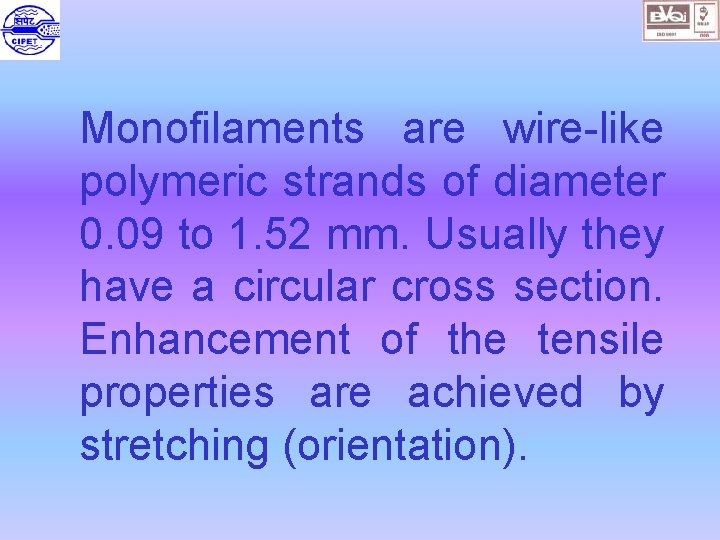
Monofilaments are wire-like polymeric strands of diameter 0. 09 to 1. 52 mm. Usually they have a circular cross section. Enhancement of the tensile properties are achieved by stretching (orientation).
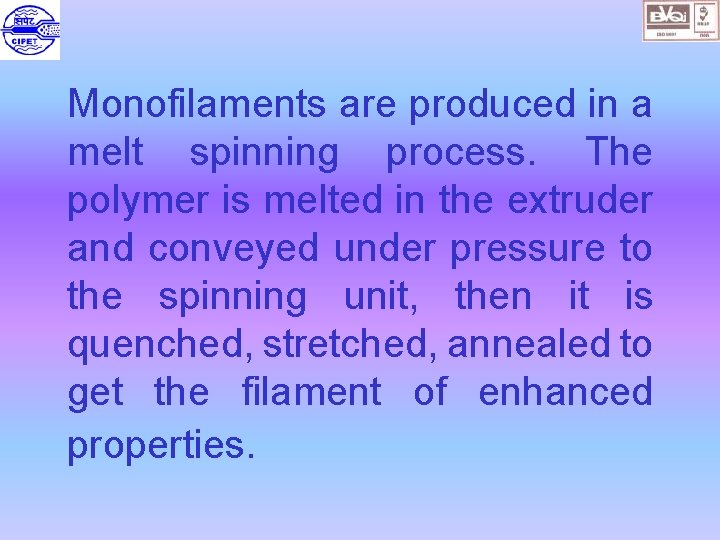
Monofilaments are produced in a melt spinning process. The polymer is melted in the extruder and conveyed under pressure to the spinning unit, then it is quenched, stretched, annealed to get the filament of enhanced properties.
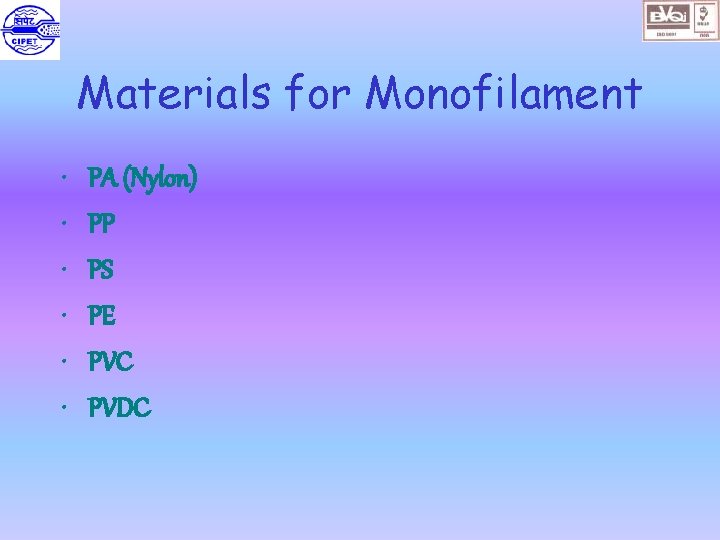
Materials for Monofilament • • • PA (Nylon) PP PS PE PVC PVDC
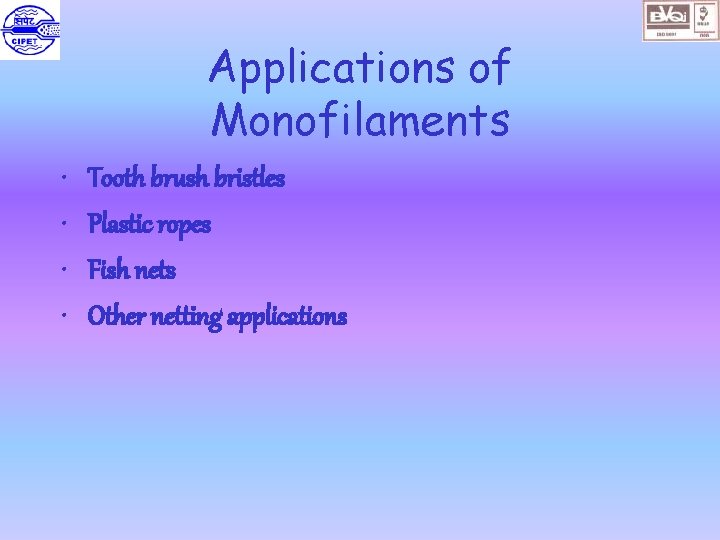
Applications of Monofilaments • • Tooth brush bristles Plastic ropes Fish nets Other netting applications
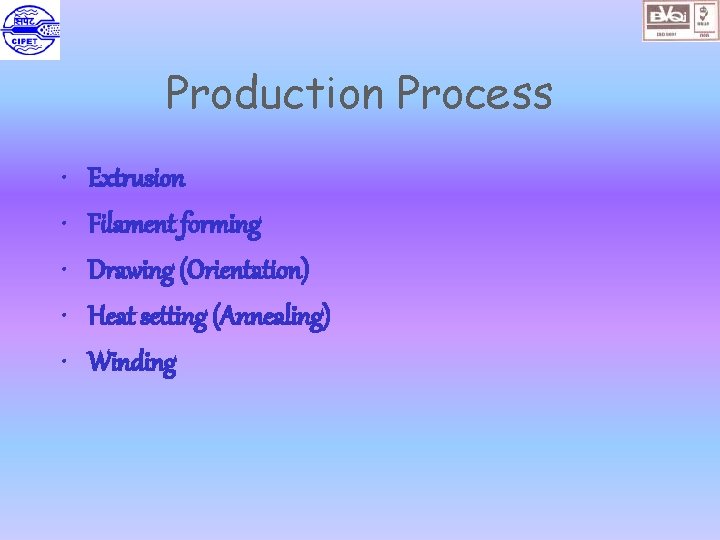
Production Process • • • Extrusion Filament forming Drawing (Orientation) Heat setting (Annealing) Winding
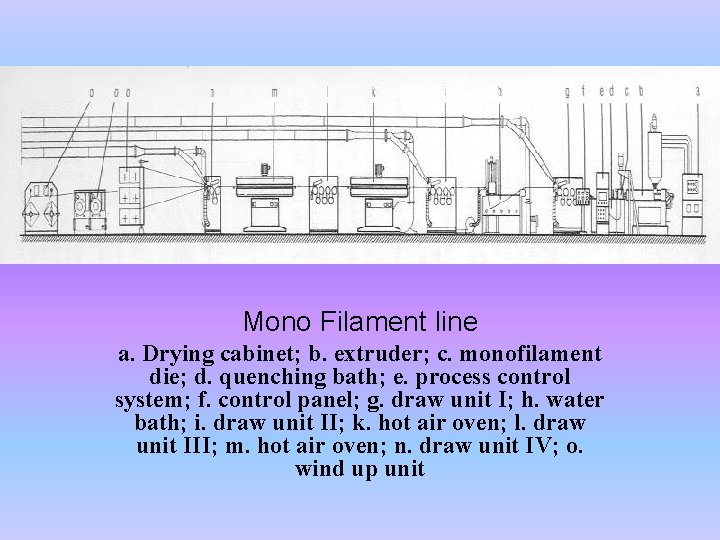
Mono Filament line a. Drying cabinet; b. extruder; c. monofilament die; d. quenching bath; e. process control system; f. control panel; g. draw unit I; h. water bath; i. draw unit II; k. hot air oven; l. draw unit III; m. hot air oven; n. draw unit IV; o. wind up unit
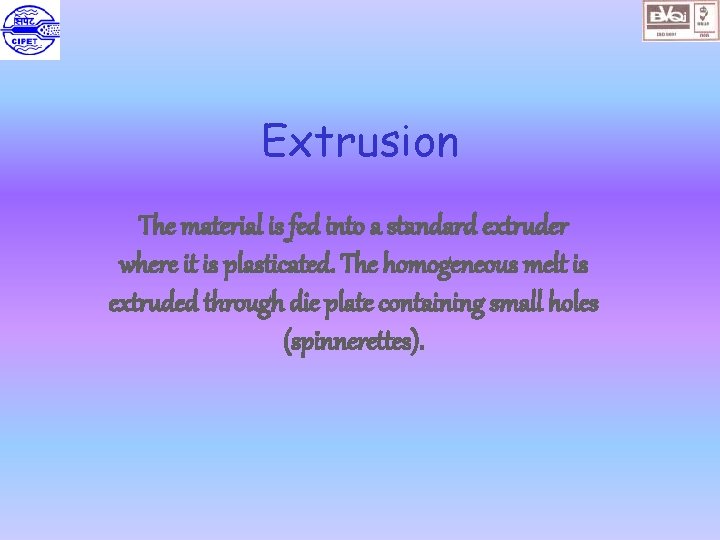
Extrusion The material is fed into a standard extruder where it is plasticated. The homogeneous melt is extruded through die plate containing small holes (spinnerettes).
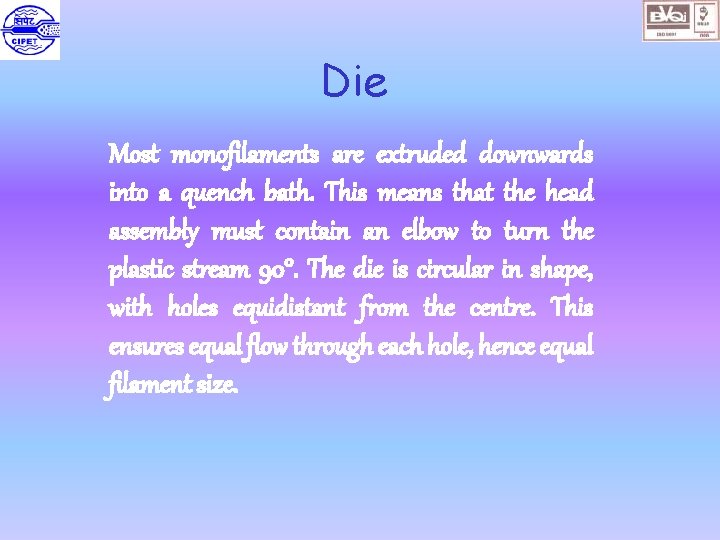
Die Most monofilaments are extruded downwards into a quench bath. This means that the head assembly must contain an elbow to turn the plastic stream 90°. The die is circular in shape, with holes equidistant from the centre. This ensures equal flow through each hole, hence equal filament size.
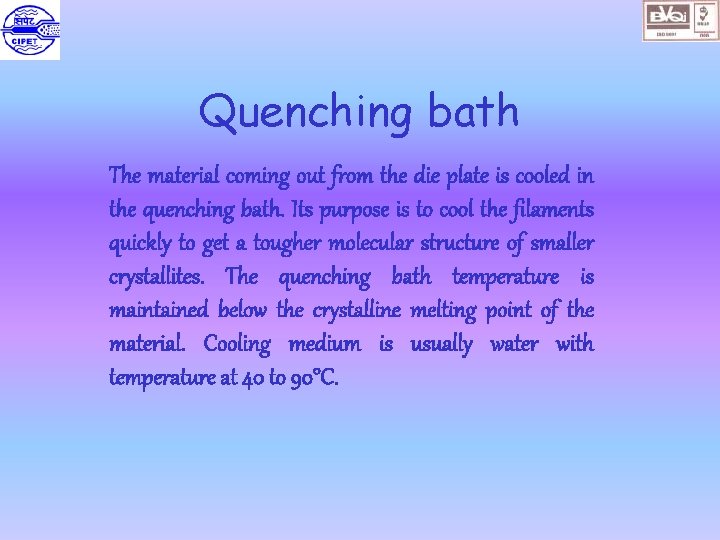
Quenching bath The material coming out from the die plate is cooled in the quenching bath. Its purpose is to cool the filaments quickly to get a tougher molecular structure of smaller crystallites. The quenching bath temperature is maintained below the crystalline melting point of the material. Cooling medium is usually water with temperature at 40 to 90°C.
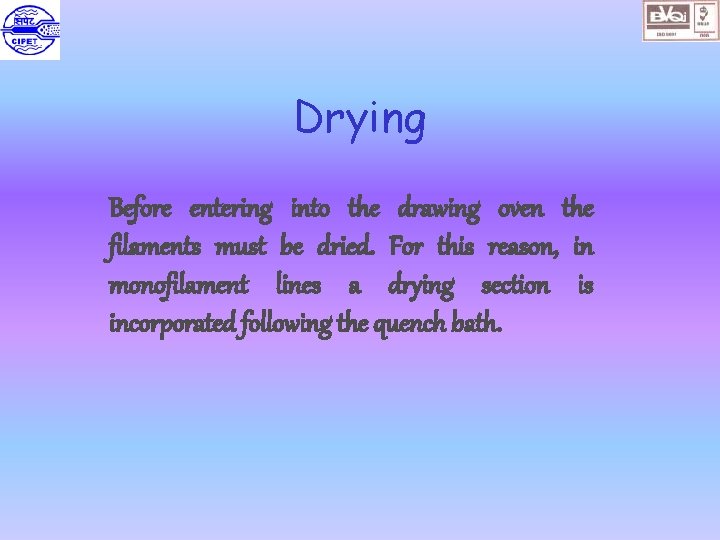
Drying Before entering into the drawing oven the filaments must be dried. For this reason, in monofilament lines a drying section is incorporated following the quench bath.
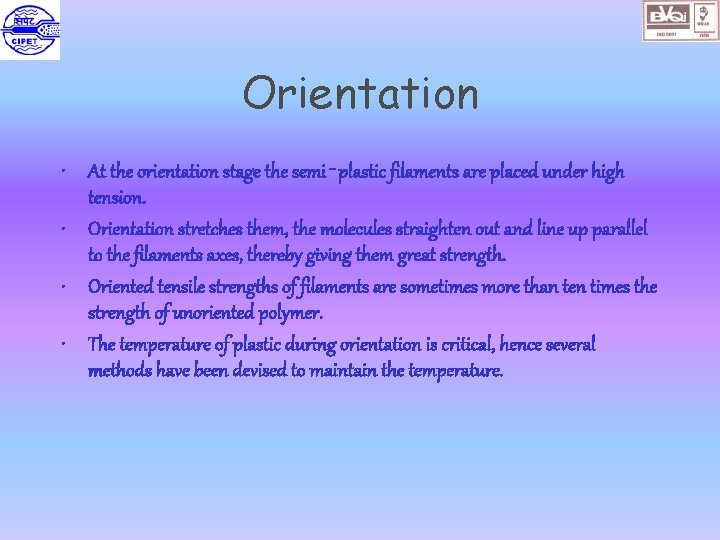
Orientation • At the orientation stage the semi‑plastic filaments are placed under high tension. • Orientation stretches them, the molecules straighten out and line up parallel to the filaments axes, thereby giving them great strength. • Oriented tensile strengths of filaments are sometimes more than ten times the strength of unoriented polymer. • The temperature of plastic during orientation is critical, hence several methods have been devised to maintain the temperature.
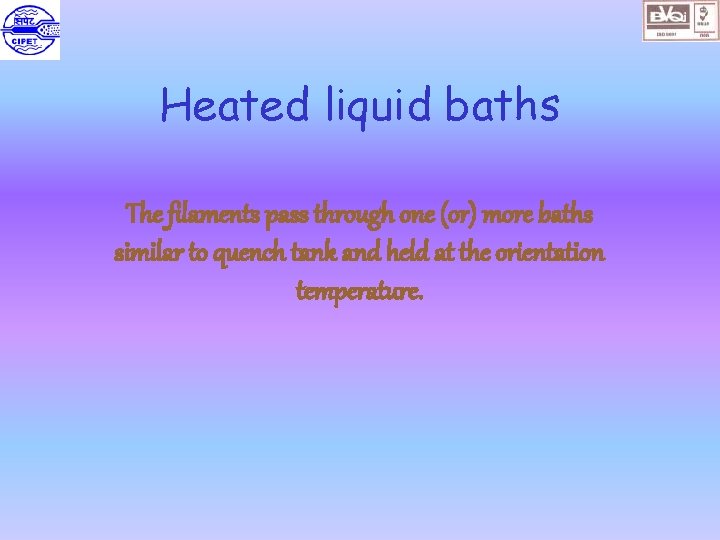
Heated liquid baths The filaments pass through one (or) more baths similar to quench tank and held at the orientation temperature.
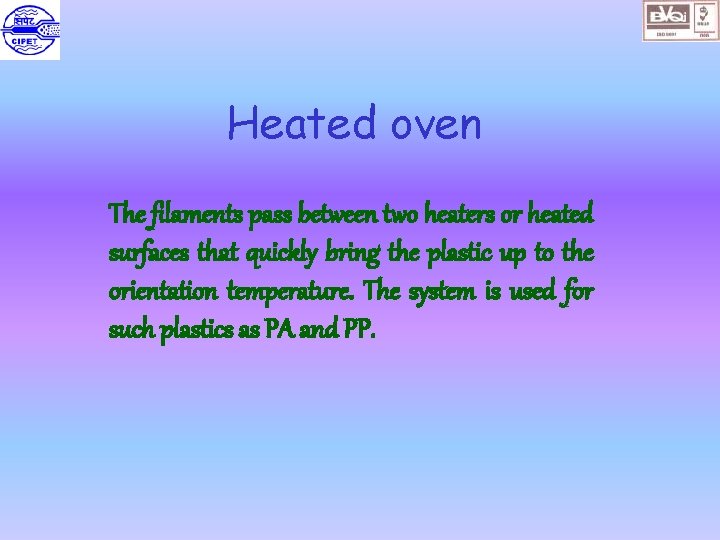
Heated oven The filaments pass between two heaters or heated surfaces that quickly bring the plastic up to the orientation temperature. The system is used for such plastics as PA and PP.
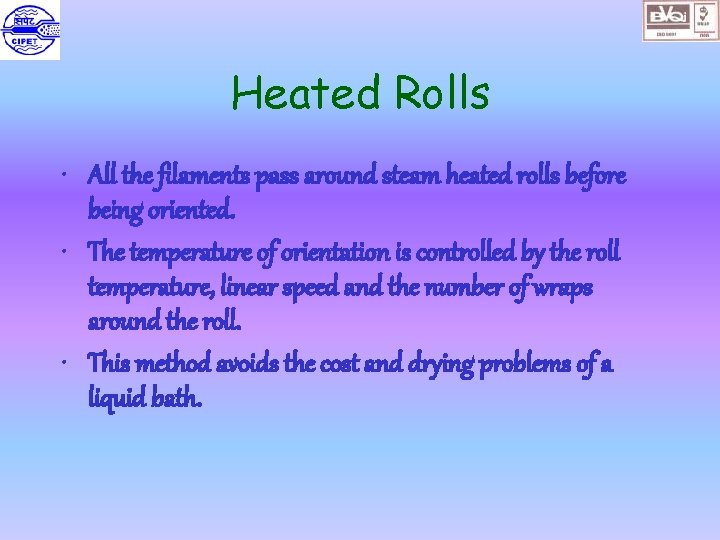
Heated Rolls • All the filaments pass around steam heated rolls before being oriented. • The temperature of orientation is controlled by the roll temperature, linear speed and the number of wraps around the roll. • This method avoids the cost and drying problems of a liquid bath.
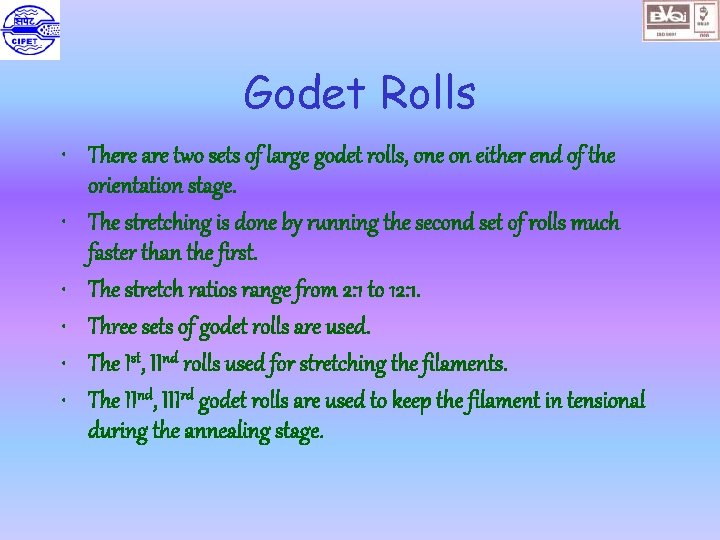
Godet Rolls • There are two sets of large godet rolls, one on either end of the orientation stage. • The stretching is done by running the second set of rolls much faster than the first. • The stretch ratios range from 2: 1 to 12: 1. • Three sets of godet rolls are used. • The Ist, IInd rolls used for stretching the filaments. • The IInd, IIIrd godet rolls are used to keep the filament in tensional during the annealing stage.
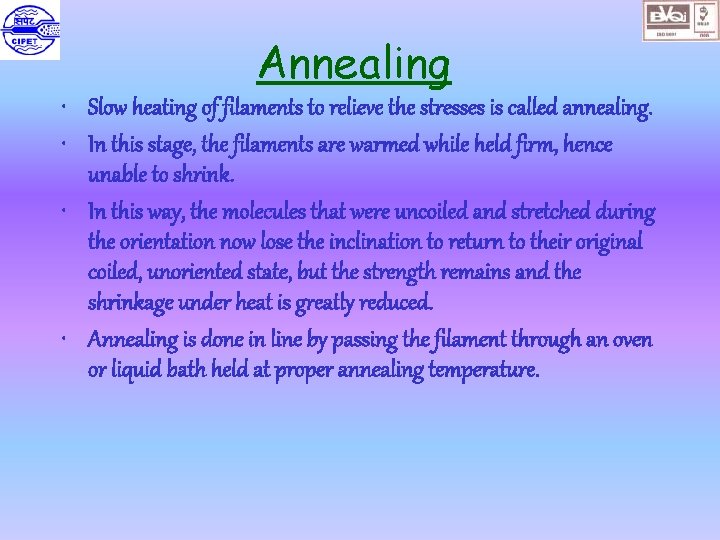
Annealing • Slow heating of filaments to relieve the stresses is called annealing. • In this stage, the filaments are warmed while held firm, hence unable to shrink. • In this way, the molecules that were uncoiled and stretched during the orientation now lose the inclination to return to their original coiled, unoriented state, but the strength remains and the shrinkage under heat is greatly reduced. • Annealing is done in line by passing the filament through an oven or liquid bath held at proper annealing temperature.
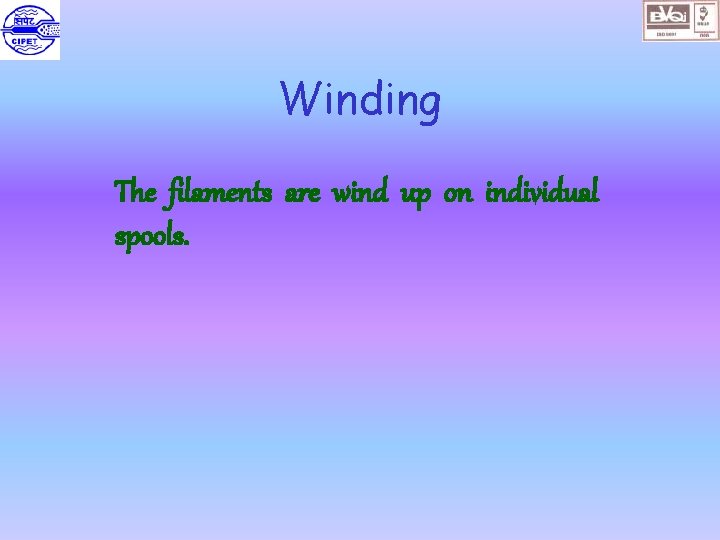
Winding The filaments are wind up on individual spools.
Mono extruder
Pc hollow sheet extrusion machine
Antigentest åre
Polymer in dentistry
Draw the polymeric backbones of silicones and phosphagenes
Gene interaction example
Extrusion molding process
Plastic extrusion defects
Drawing and extrusion
The extrusion process
Impact extrusion process
Side extrusion process
Pressure extrusion
Advantages and disadvantages of blow moulding
Classification of extrusion process
Chargaff rule definition
What are the 4 strands of sexuality
Sokratiske spørgsmål
Domain and strands of ppst