Letting the Tail Wag the Dog How the
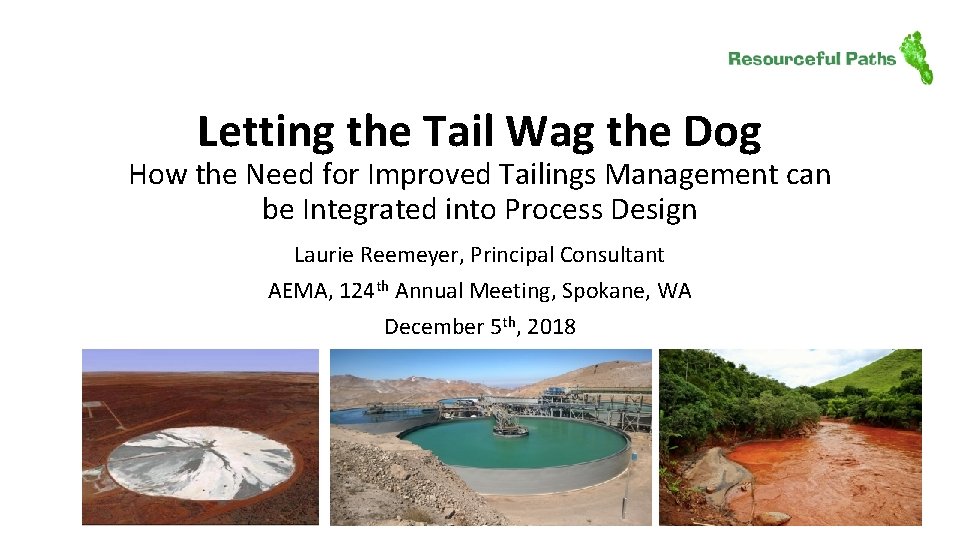
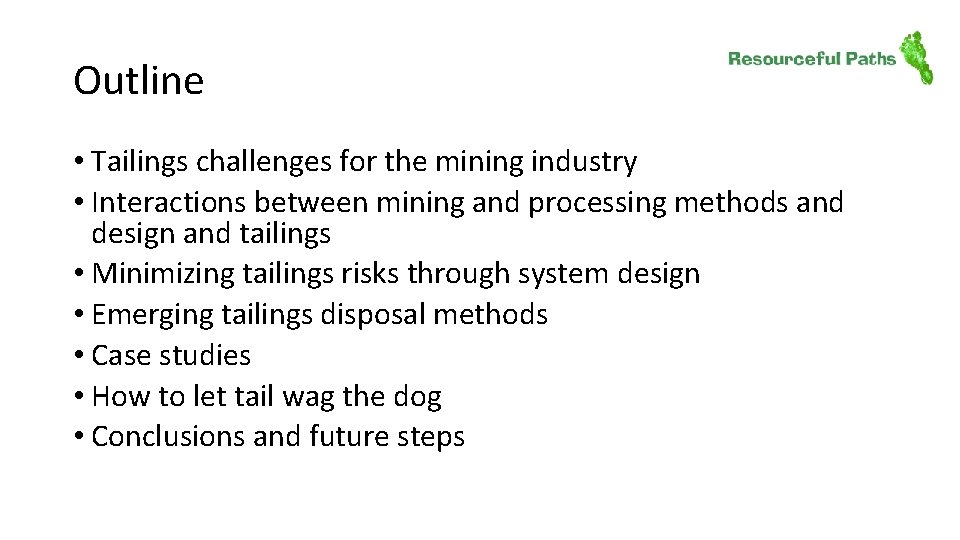
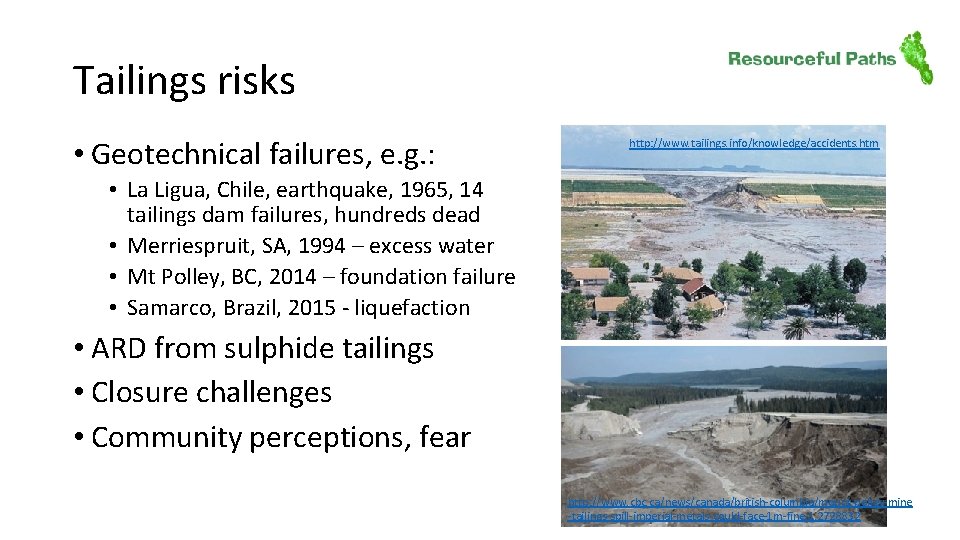
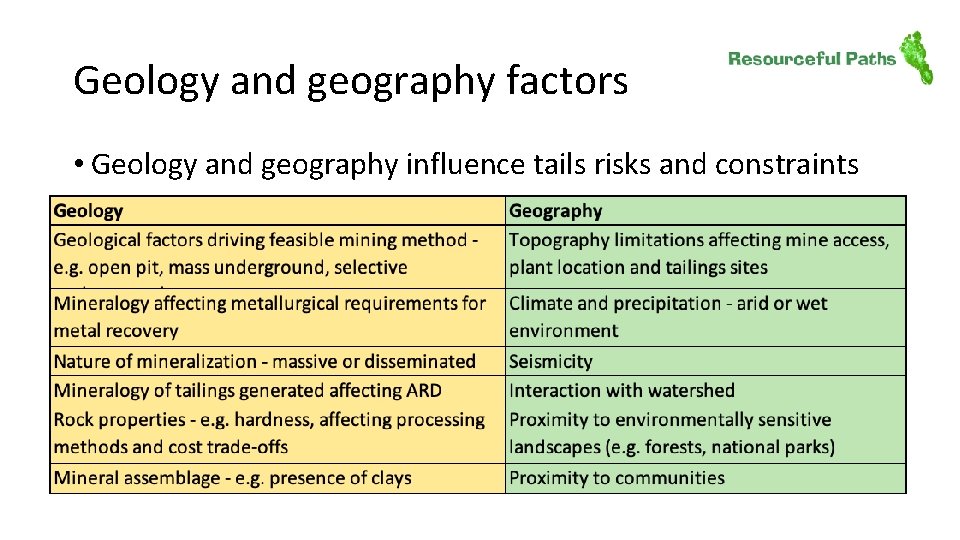
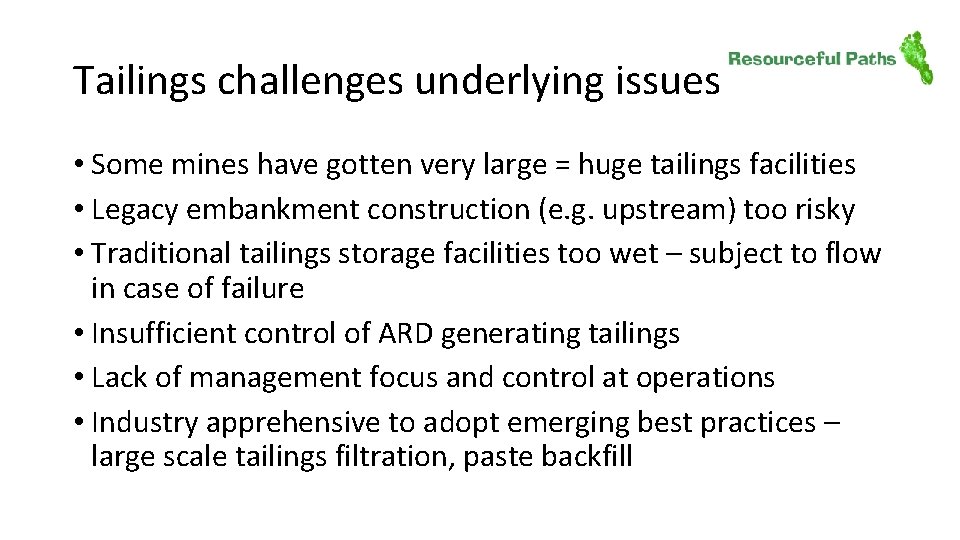
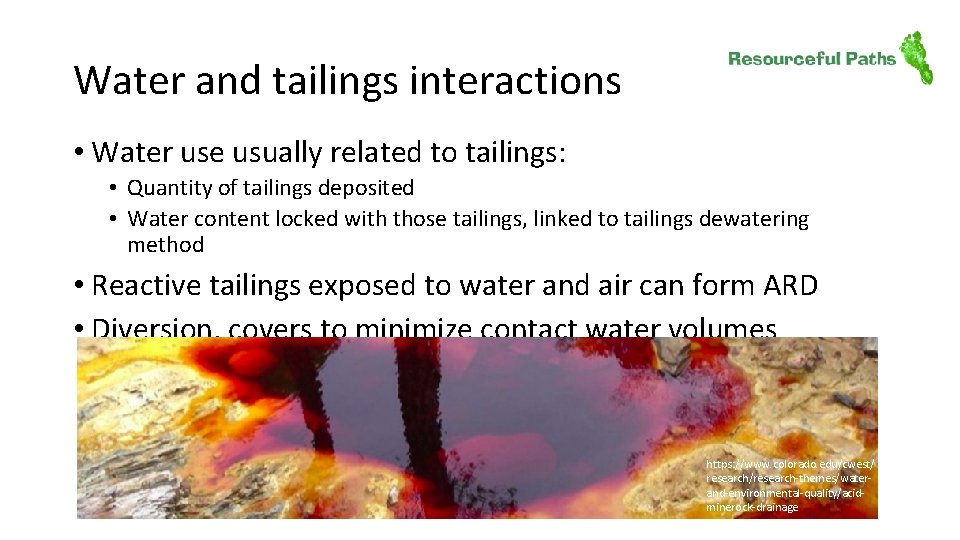
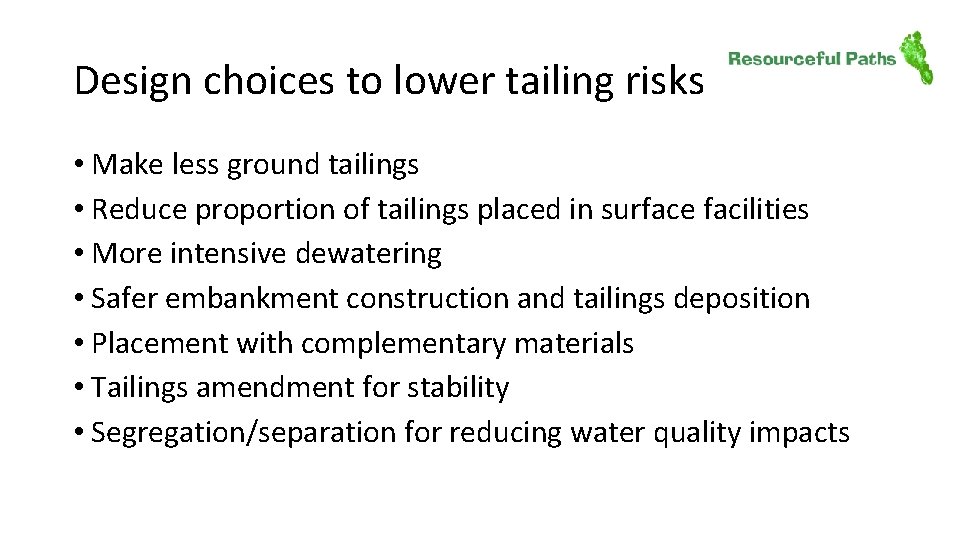
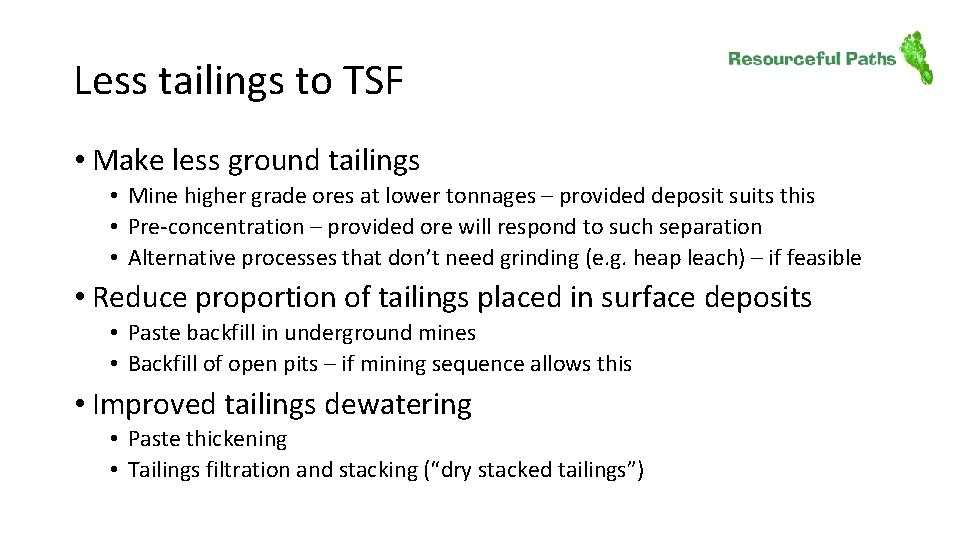
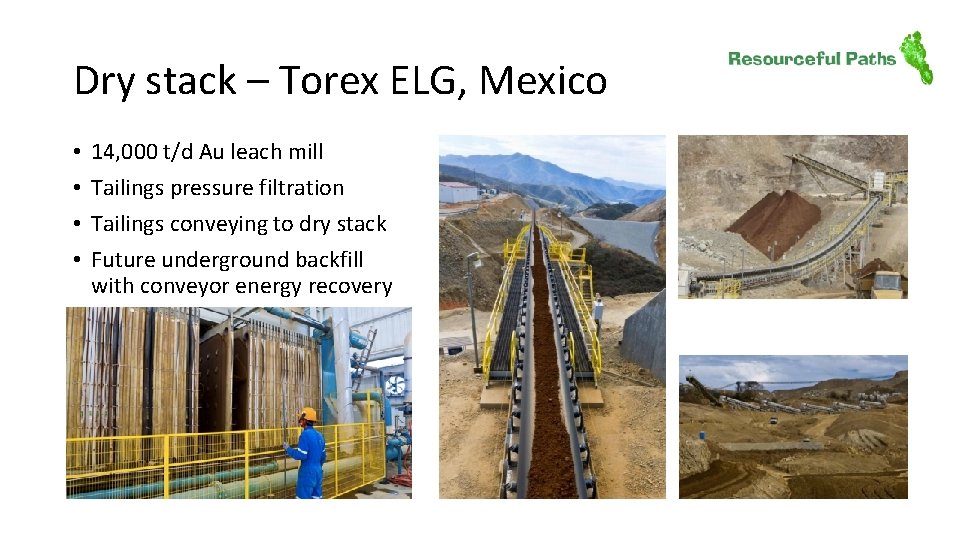
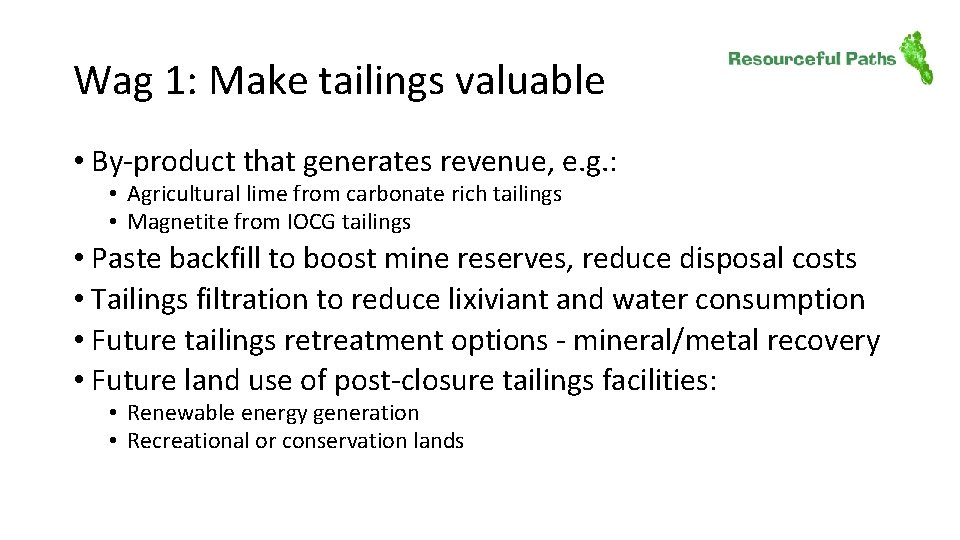
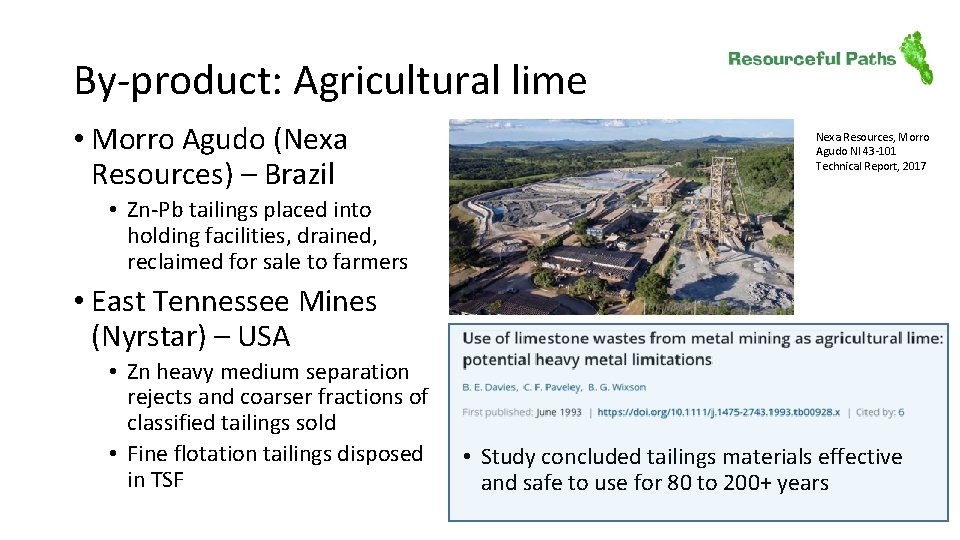
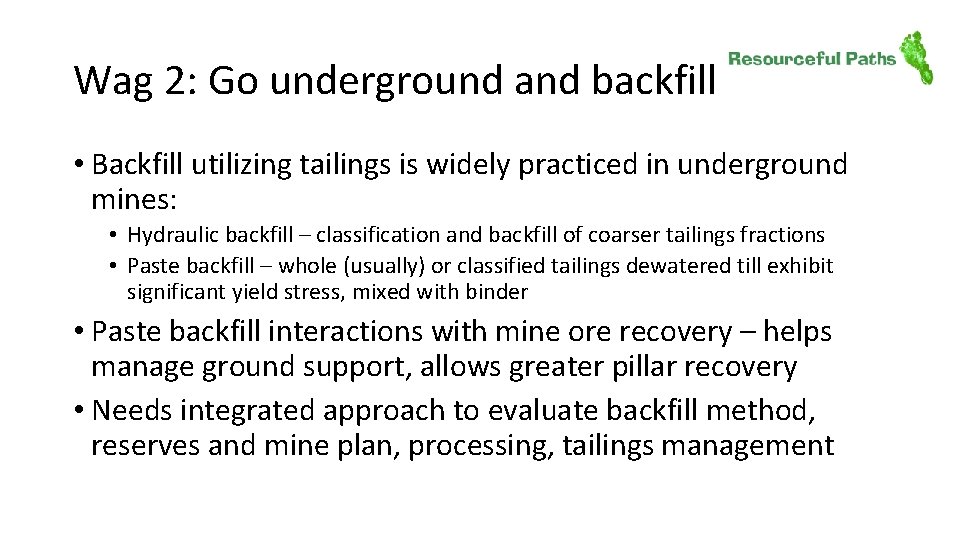
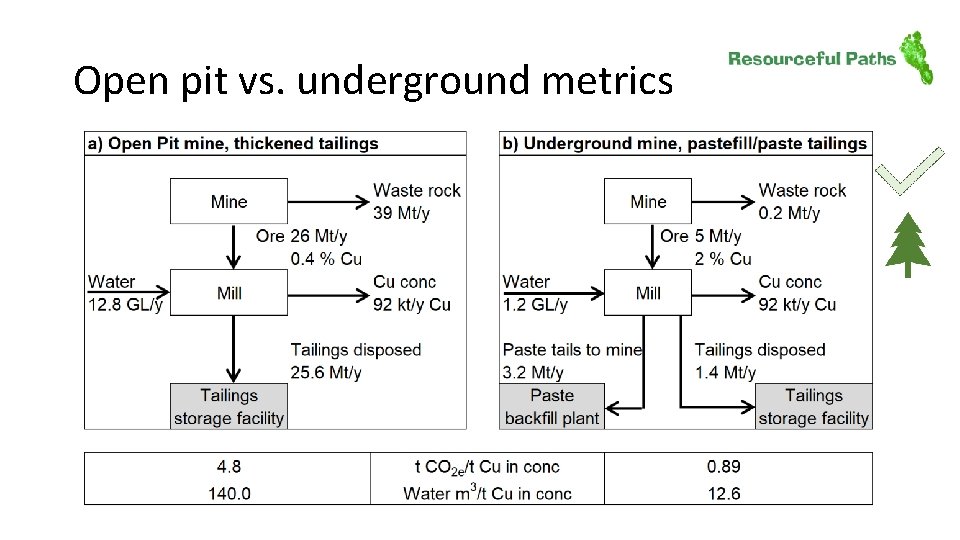
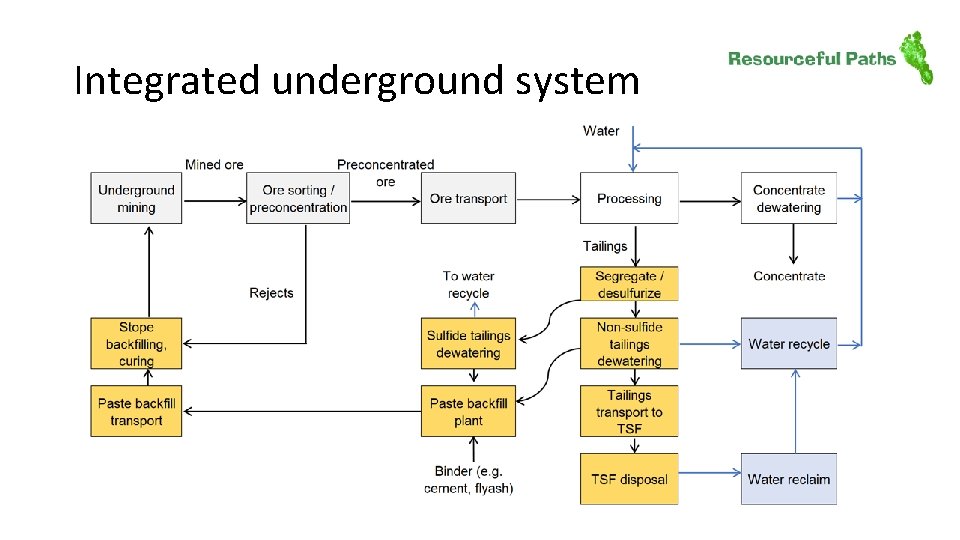
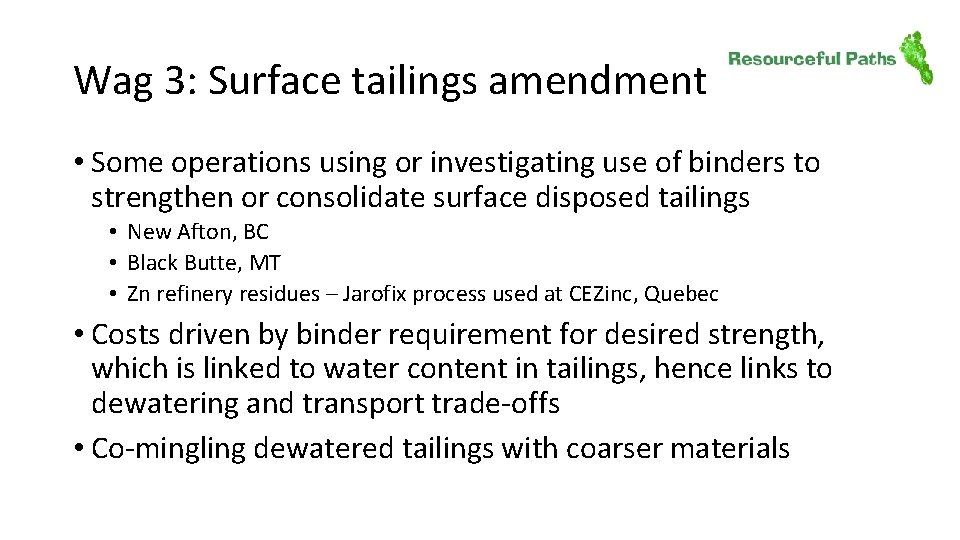
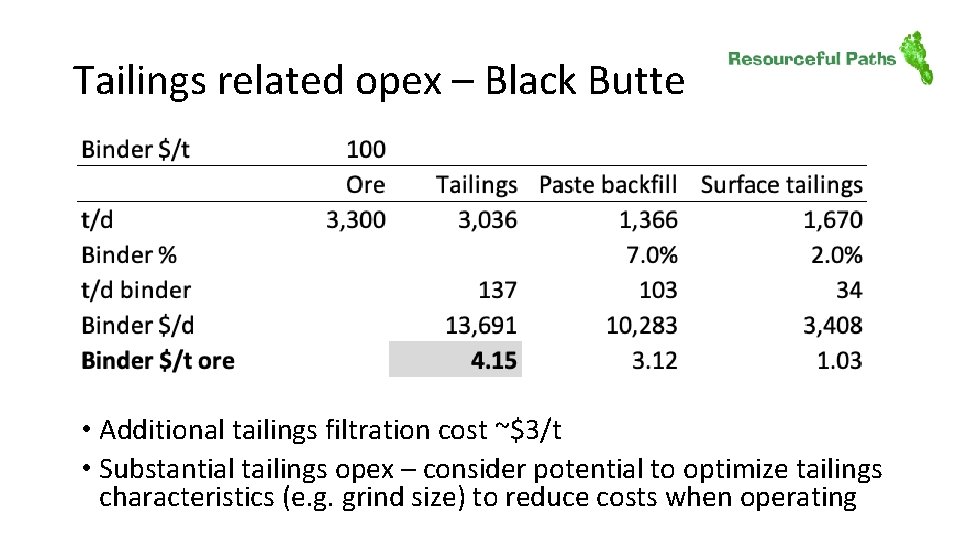
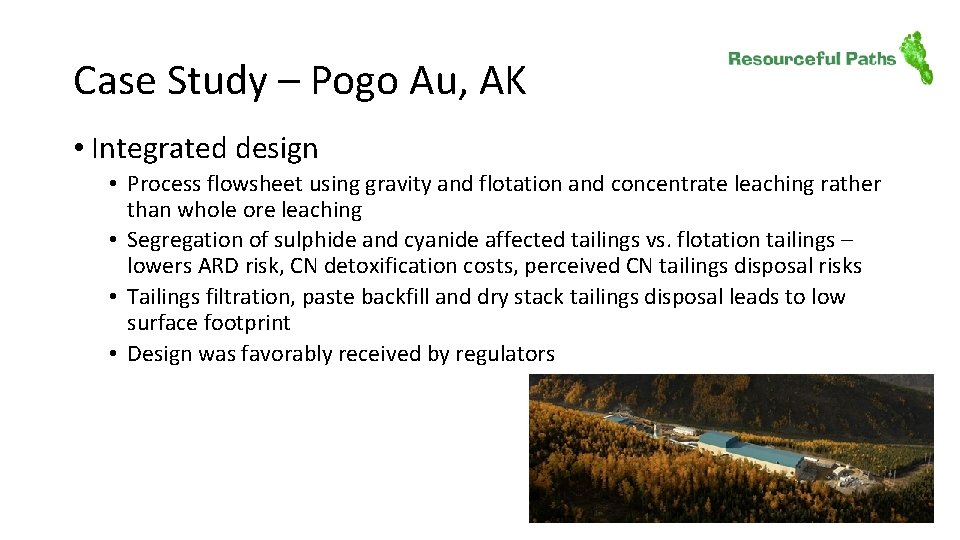
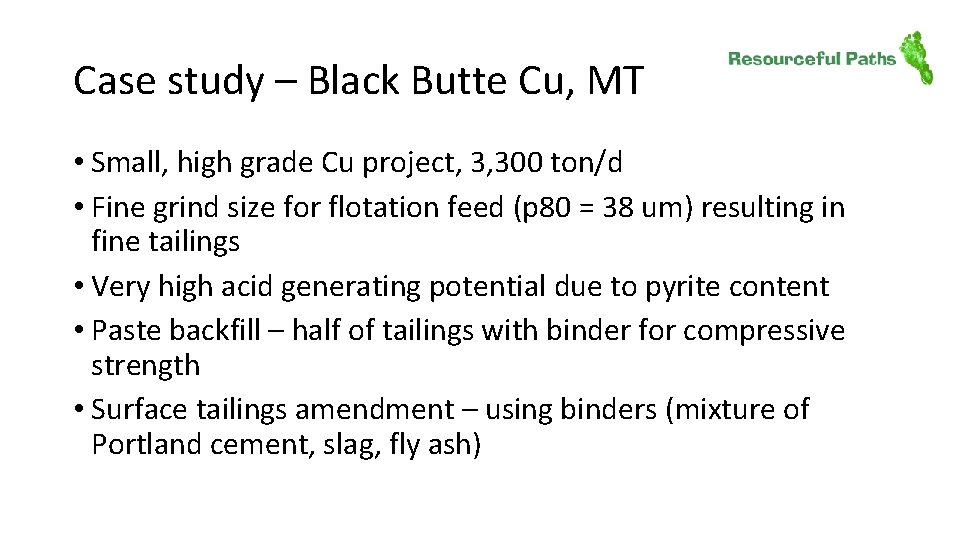
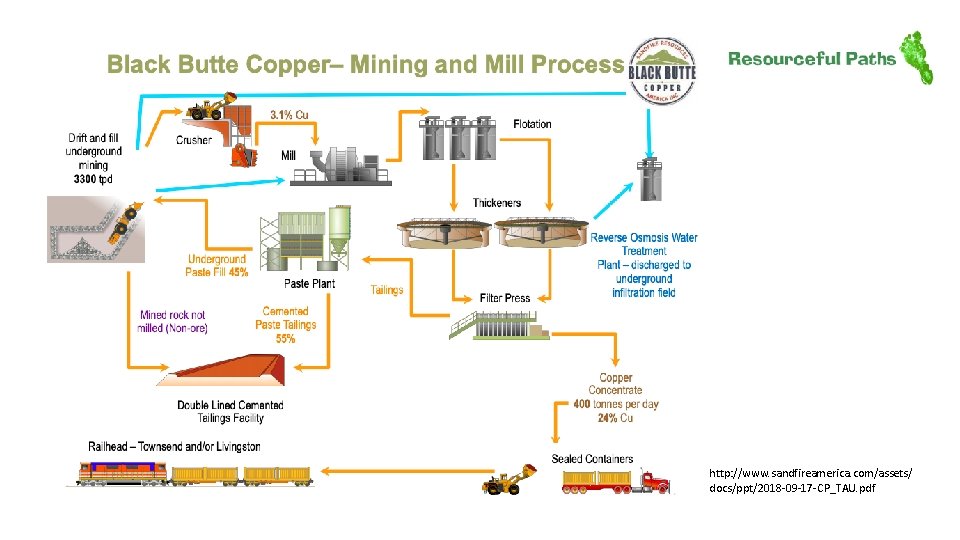
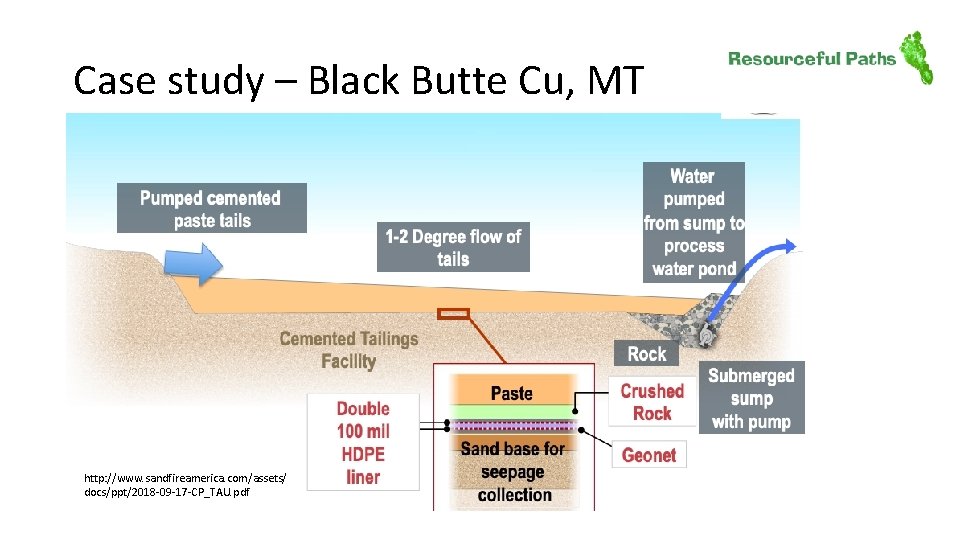
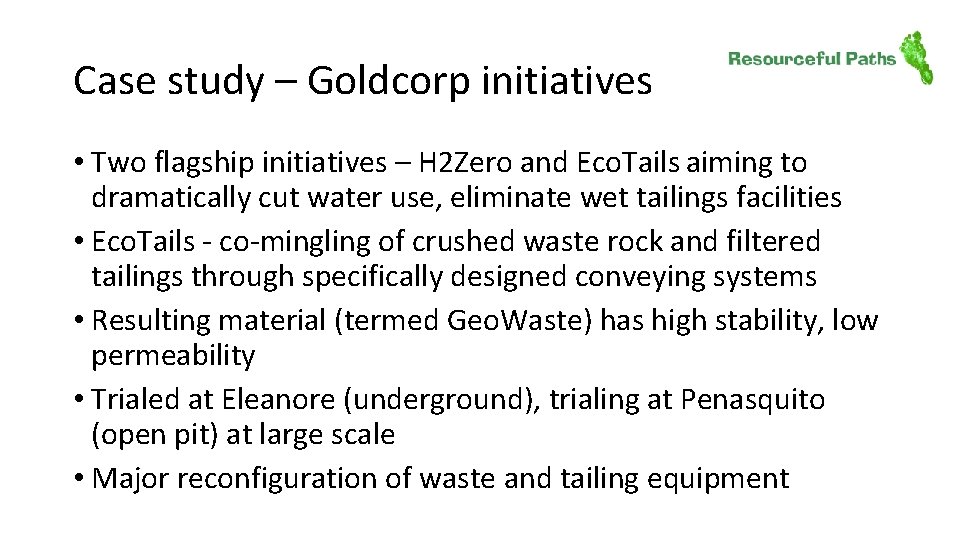
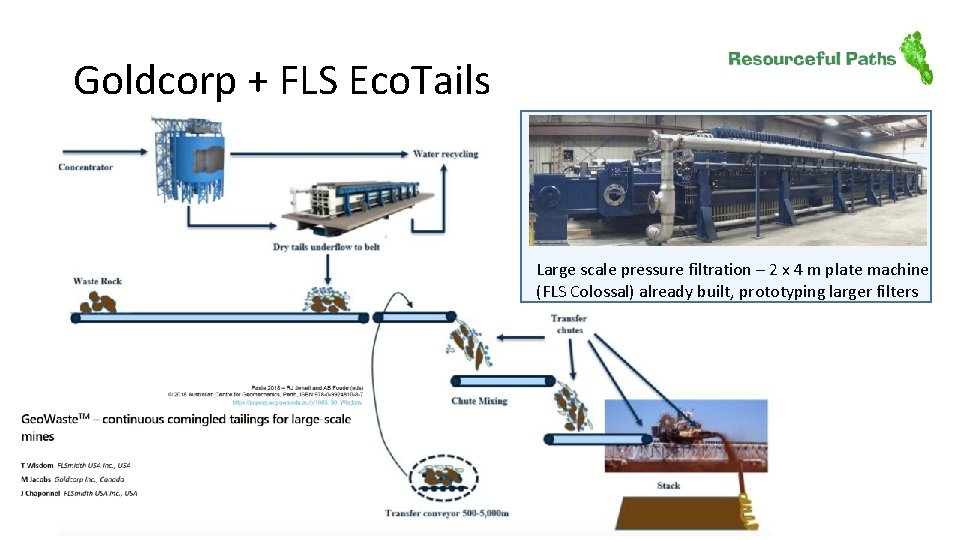
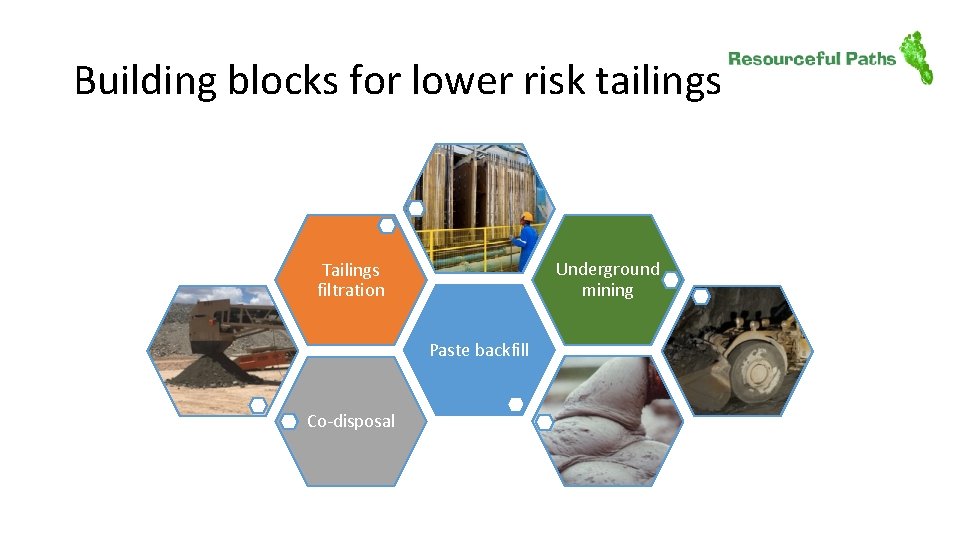

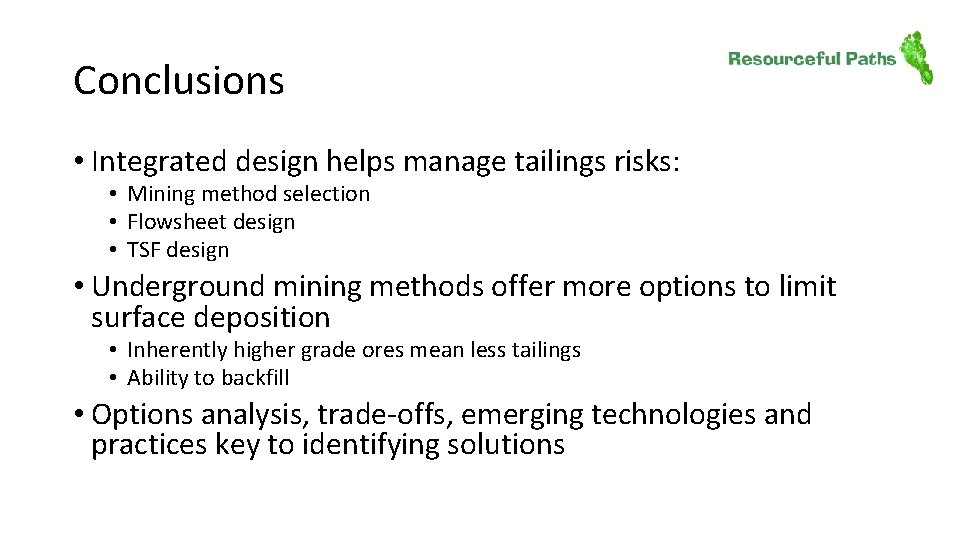
- Slides: 25
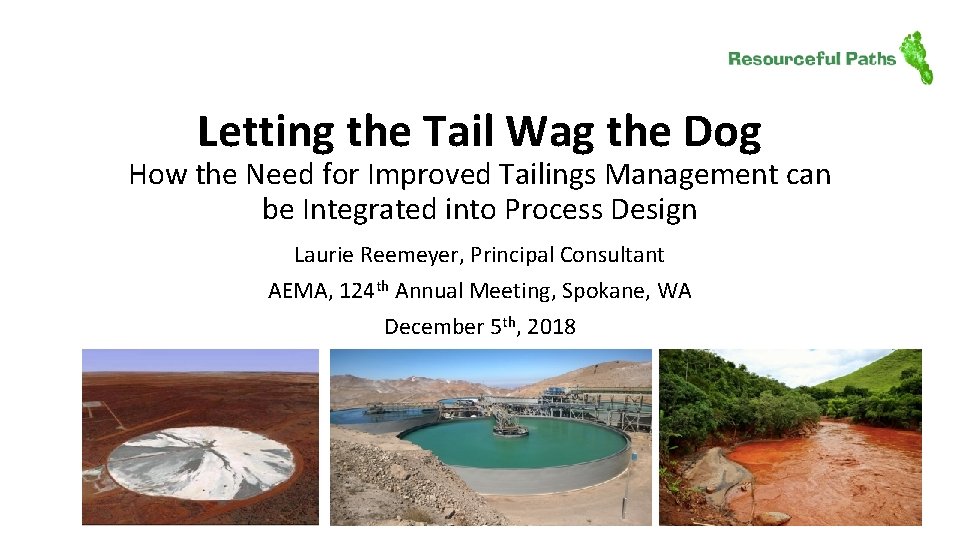
Letting the Tail Wag the Dog How the Need for Improved Tailings Management can be Integrated into Process Design Laurie Reemeyer, Principal Consultant AEMA, 124 th Annual Meeting, Spokane, WA December 5 th, 2018
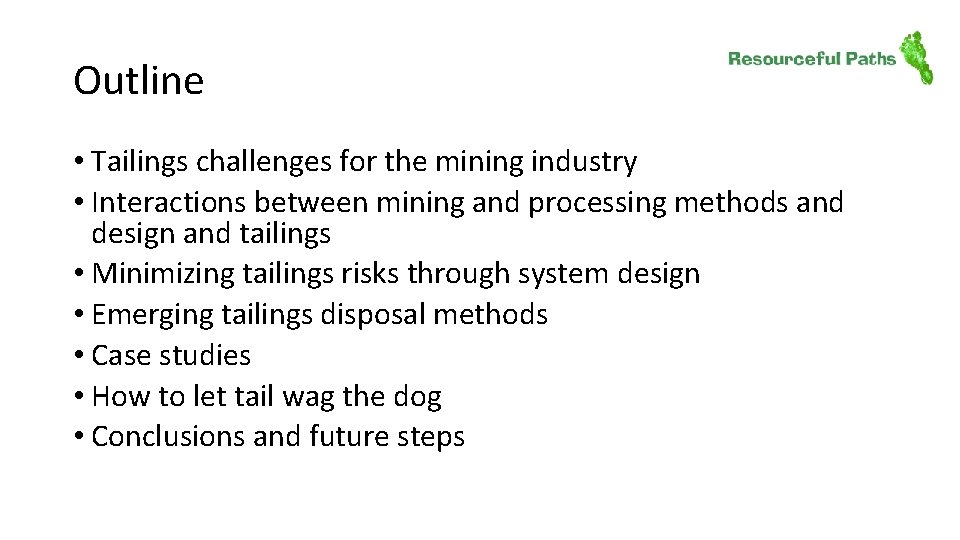
Outline • Tailings challenges for the mining industry • Interactions between mining and processing methods and design and tailings • Minimizing tailings risks through system design • Emerging tailings disposal methods • Case studies • How to let tail wag the dog • Conclusions and future steps
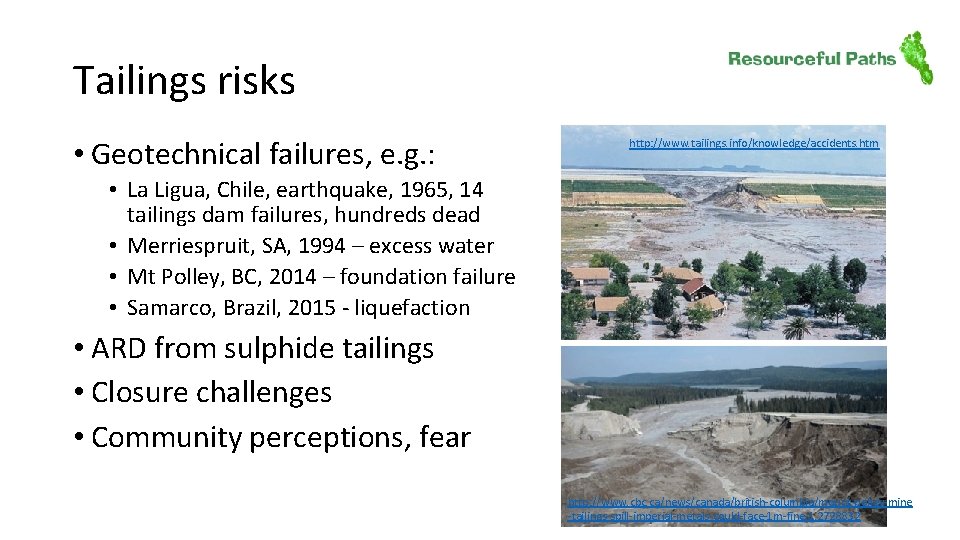
Tailings risks • Geotechnical failures, e. g. : http: //www. tailings. info/knowledge/accidents. htm • La Ligua, Chile, earthquake, 1965, 14 tailings dam failures, hundreds dead • Merriespruit, SA, 1994 – excess water • Mt Polley, BC, 2014 – foundation failure • Samarco, Brazil, 2015 - liquefaction • ARD from sulphide tailings • Closure challenges • Community perceptions, fear http: //www. cbc. ca/news/canada/british-columbia/mount-polley-mine -tailings-spill-imperial-metals-could-face-1 m-fine-1. 2728832
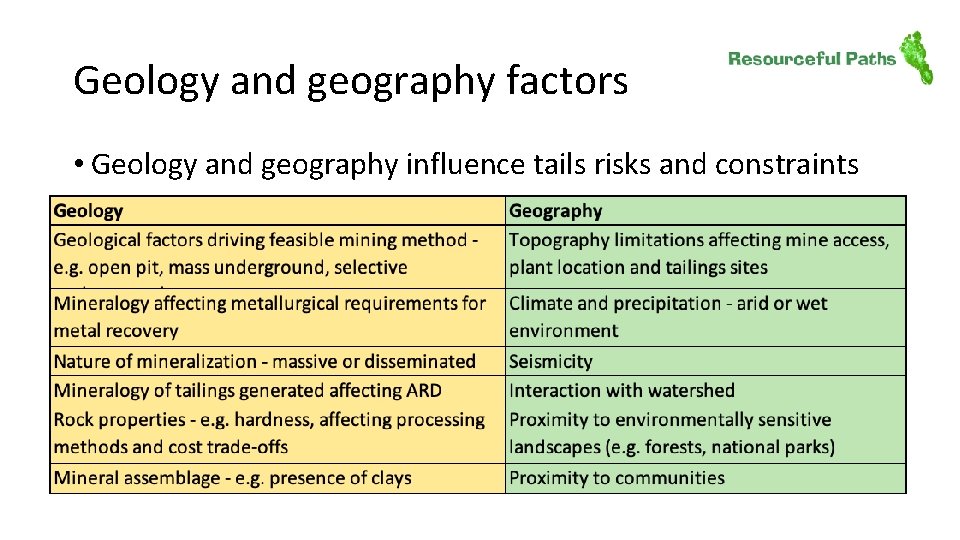
Geology and geography factors • Geology and geography influence tails risks and constraints
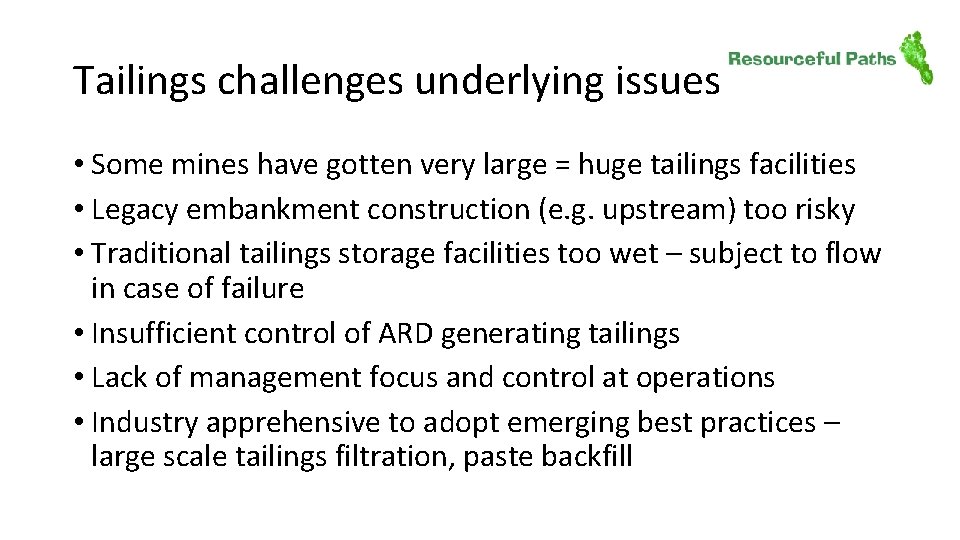
Tailings challenges underlying issues • Some mines have gotten very large = huge tailings facilities • Legacy embankment construction (e. g. upstream) too risky • Traditional tailings storage facilities too wet – subject to flow in case of failure • Insufficient control of ARD generating tailings • Lack of management focus and control at operations • Industry apprehensive to adopt emerging best practices – large scale tailings filtration, paste backfill
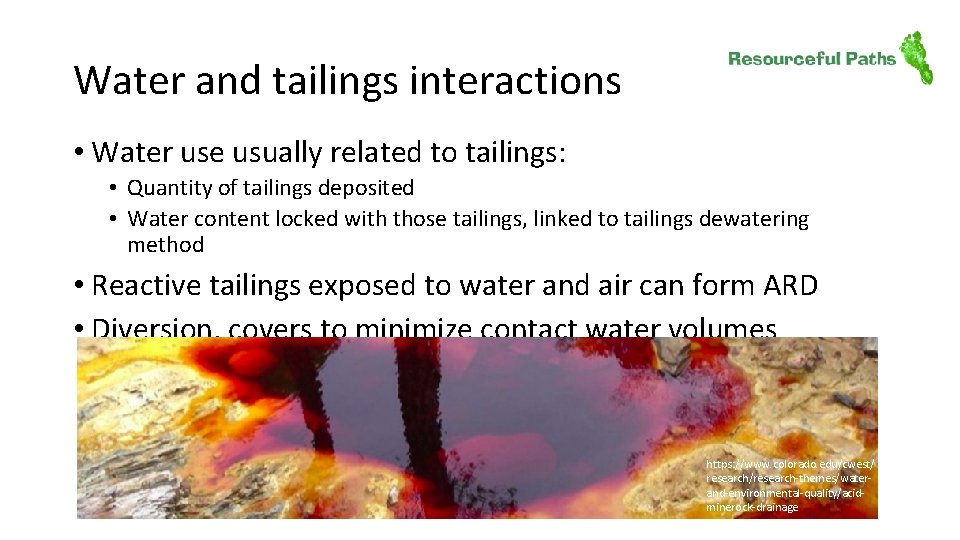
Water and tailings interactions • Water use usually related to tailings: • Quantity of tailings deposited • Water content locked with those tailings, linked to tailings dewatering method • Reactive tailings exposed to water and air can form ARD • Diversion, covers to minimize contact water volumes https: //www. colorado. edu/cwest/ research/research-themes/waterand-environmental-quality/acidminerock-drainage
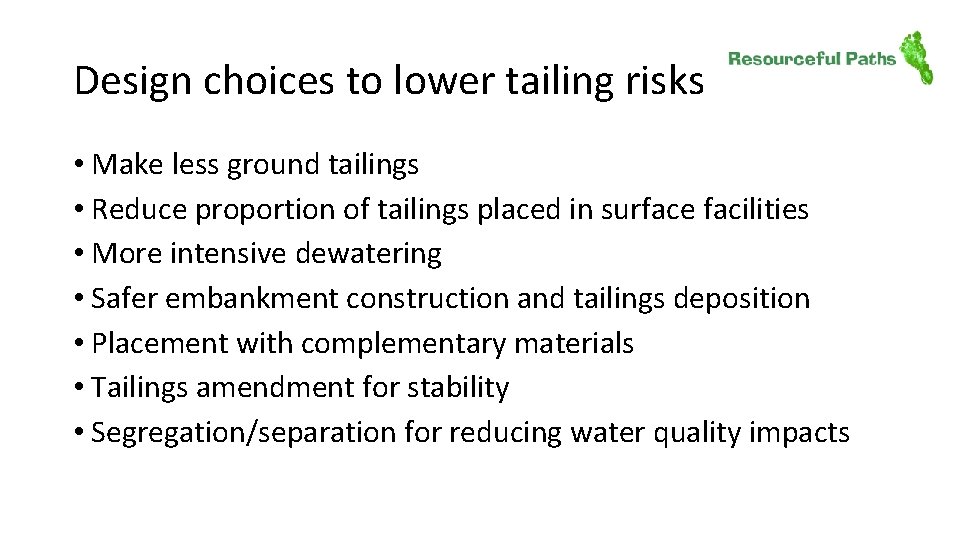
Design choices to lower tailing risks • Make less ground tailings • Reduce proportion of tailings placed in surface facilities • More intensive dewatering • Safer embankment construction and tailings deposition • Placement with complementary materials • Tailings amendment for stability • Segregation/separation for reducing water quality impacts
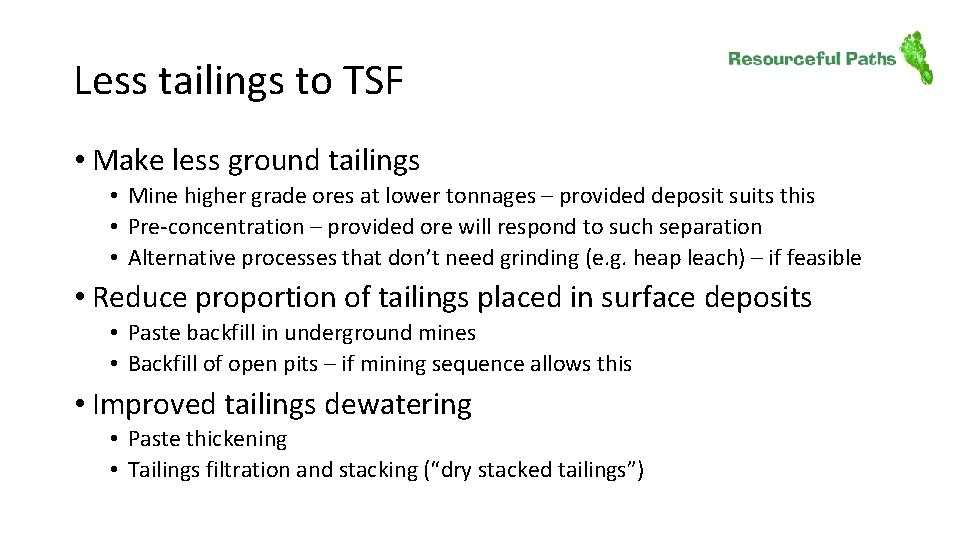
Less tailings to TSF • Make less ground tailings • Mine higher grade ores at lower tonnages – provided deposit suits this • Pre-concentration – provided ore will respond to such separation • Alternative processes that don’t need grinding (e. g. heap leach) – if feasible • Reduce proportion of tailings placed in surface deposits • Paste backfill in underground mines • Backfill of open pits – if mining sequence allows this • Improved tailings dewatering • Paste thickening • Tailings filtration and stacking (“dry stacked tailings”)
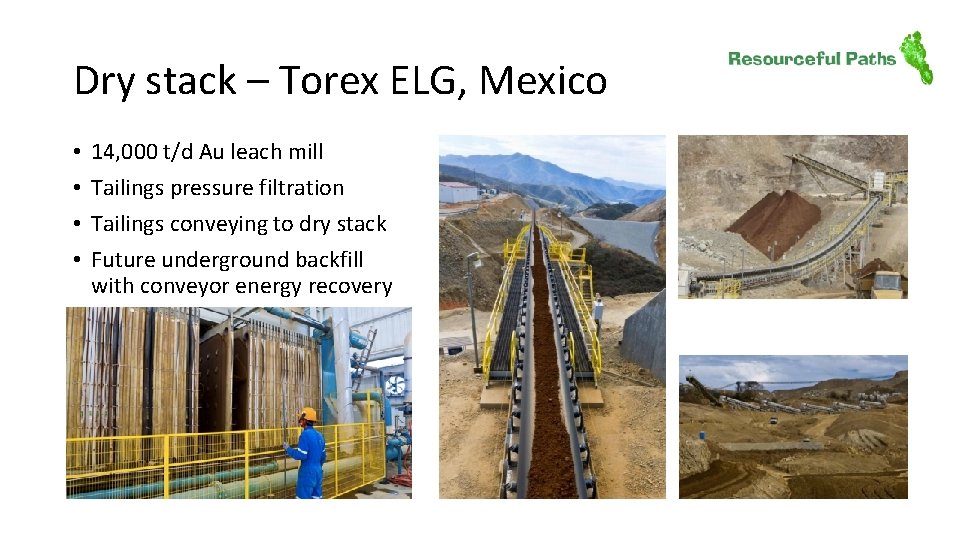
Dry stack – Torex ELG, Mexico • • 14, 000 t/d Au leach mill Tailings pressure filtration Tailings conveying to dry stack Future underground backfill with conveyor energy recovery
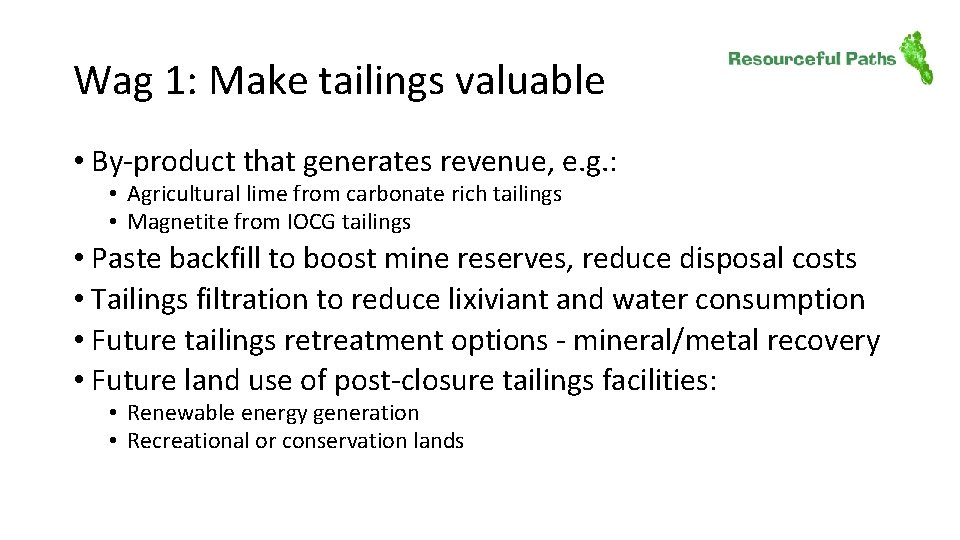
Wag 1: Make tailings valuable • By-product that generates revenue, e. g. : • Agricultural lime from carbonate rich tailings • Magnetite from IOCG tailings • Paste backfill to boost mine reserves, reduce disposal costs • Tailings filtration to reduce lixiviant and water consumption • Future tailings retreatment options - mineral/metal recovery • Future land use of post-closure tailings facilities: • Renewable energy generation • Recreational or conservation lands
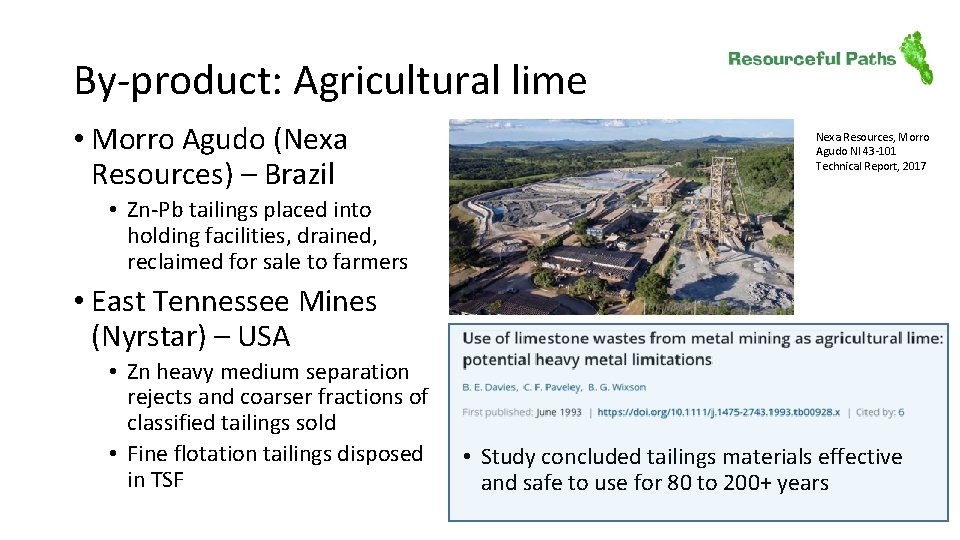
By-product: Agricultural lime • Morro Agudo (Nexa Resources) – Brazil Nexa Resources, Morro Agudo NI 43 -101 Technical Report, 2017 • Zn-Pb tailings placed into holding facilities, drained, reclaimed for sale to farmers • East Tennessee Mines (Nyrstar) – USA • Zn heavy medium separation rejects and coarser fractions of classified tailings sold • Fine flotation tailings disposed in TSF • Study concluded tailings materials effective and safe to use for 80 to 200+ years
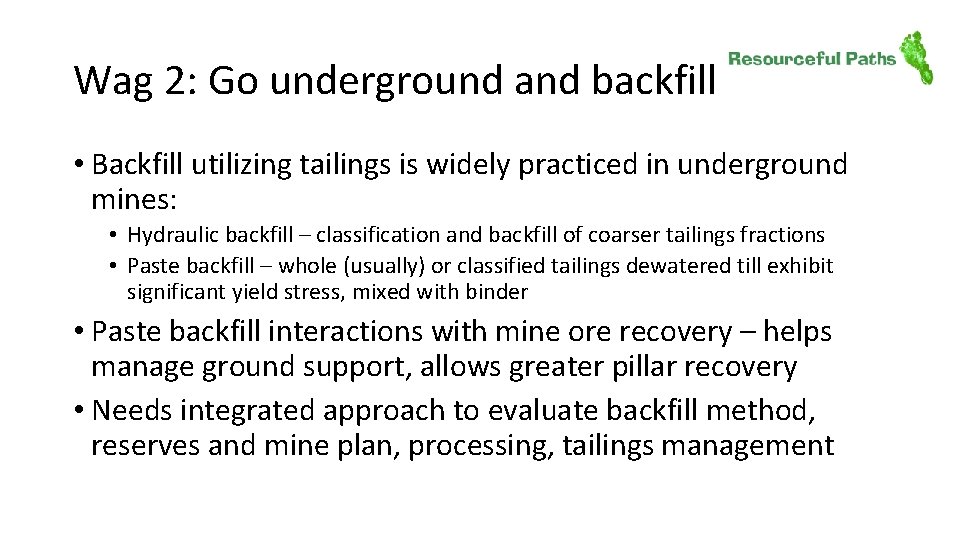
Wag 2: Go underground and backfill • Backfill utilizing tailings is widely practiced in underground mines: • Hydraulic backfill – classification and backfill of coarser tailings fractions • Paste backfill – whole (usually) or classified tailings dewatered till exhibit significant yield stress, mixed with binder • Paste backfill interactions with mine ore recovery – helps manage ground support, allows greater pillar recovery • Needs integrated approach to evaluate backfill method, reserves and mine plan, processing, tailings management
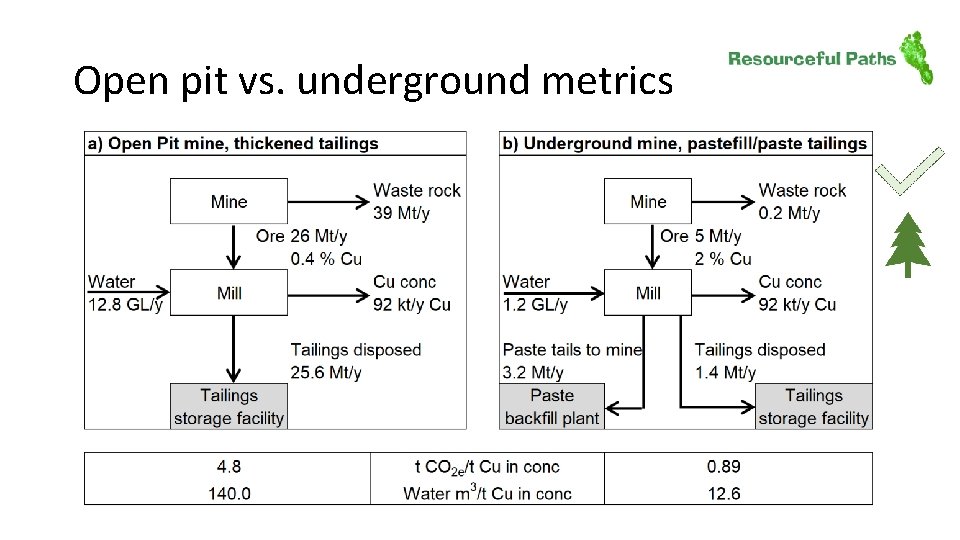
Open pit vs. underground metrics
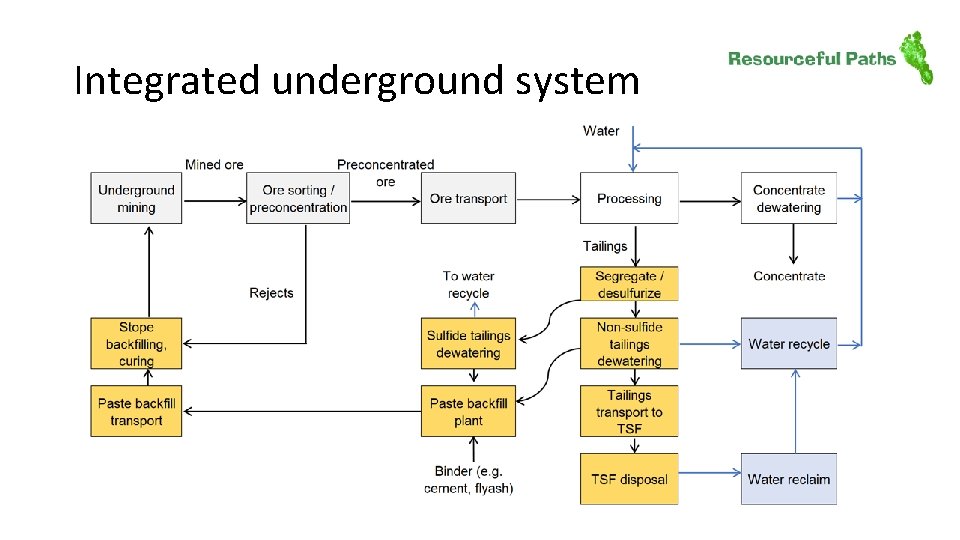
Integrated underground system
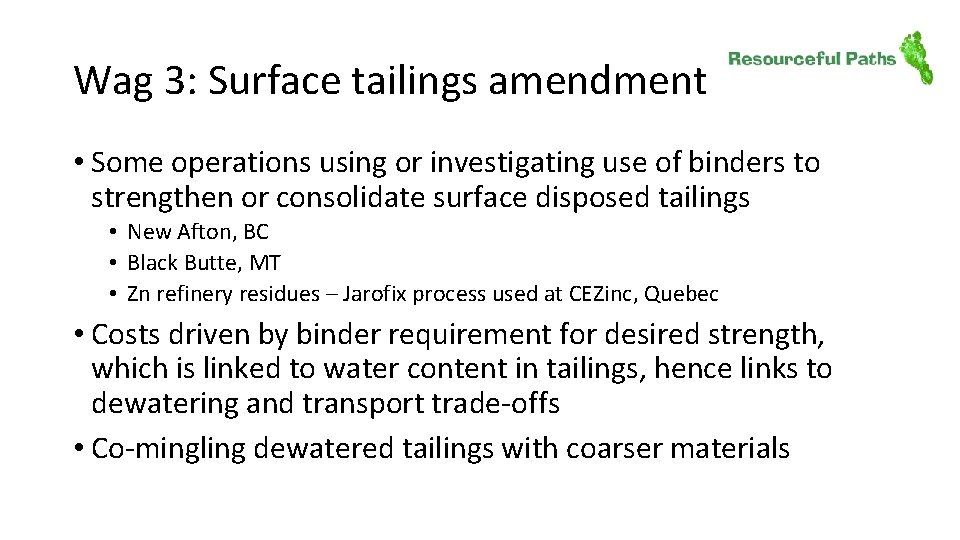
Wag 3: Surface tailings amendment • Some operations using or investigating use of binders to strengthen or consolidate surface disposed tailings • New Afton, BC • Black Butte, MT • Zn refinery residues – Jarofix process used at CEZinc, Quebec • Costs driven by binder requirement for desired strength, which is linked to water content in tailings, hence links to dewatering and transport trade-offs • Co-mingling dewatered tailings with coarser materials
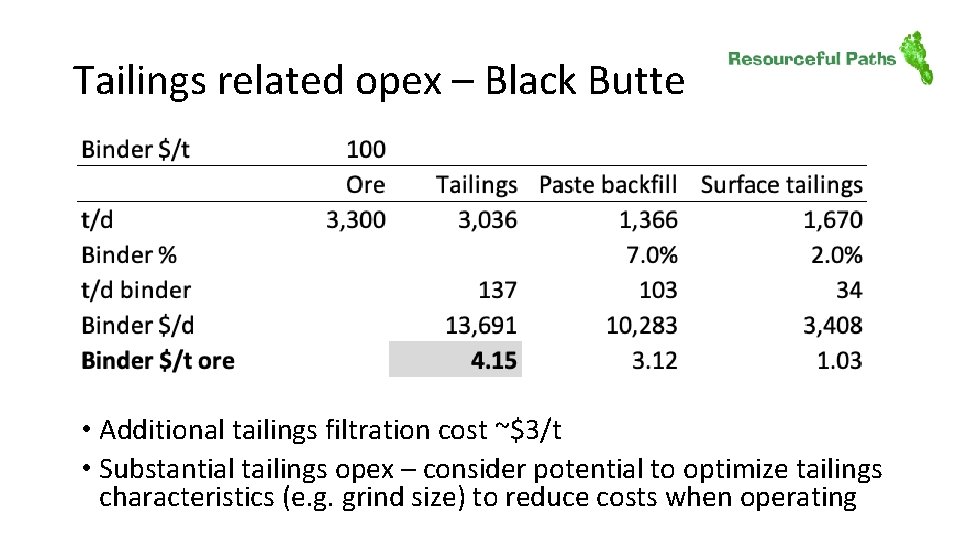
Tailings related opex – Black Butte • Additional tailings filtration cost ~$3/t • Substantial tailings opex – consider potential to optimize tailings characteristics (e. g. grind size) to reduce costs when operating
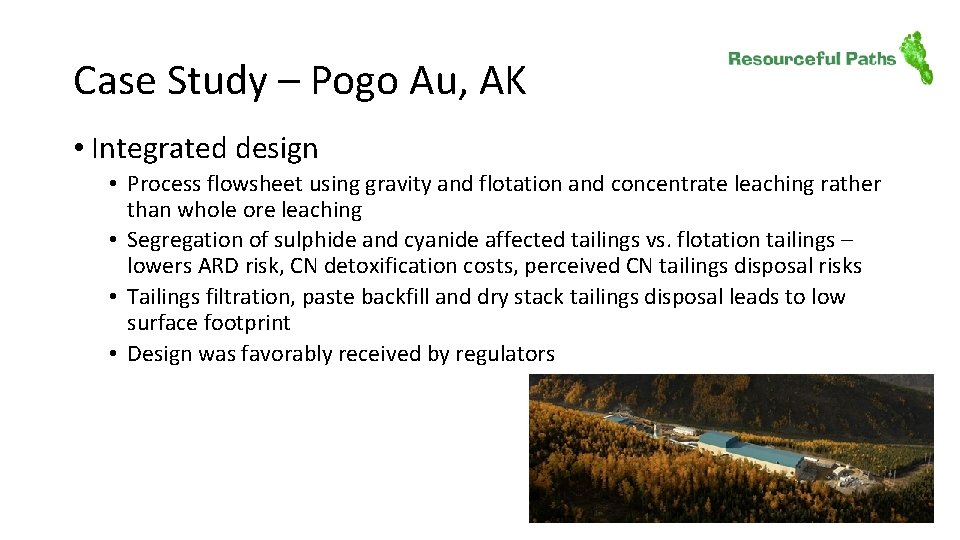
Case Study – Pogo Au, AK • Integrated design • Process flowsheet using gravity and flotation and concentrate leaching rather than whole ore leaching • Segregation of sulphide and cyanide affected tailings vs. flotation tailings – lowers ARD risk, CN detoxification costs, perceived CN tailings disposal risks • Tailings filtration, paste backfill and dry stack tailings disposal leads to low surface footprint • Design was favorably received by regulators
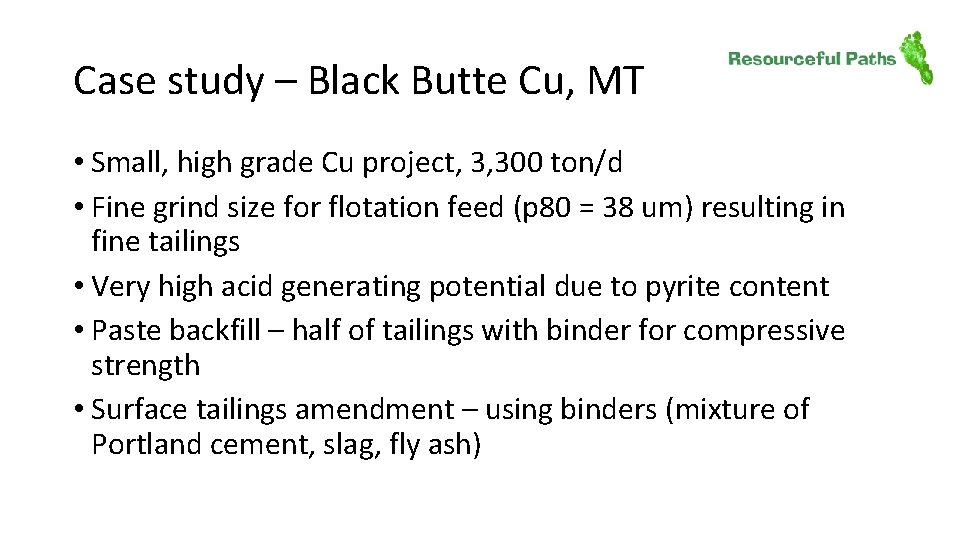
Case study – Black Butte Cu, MT • Small, high grade Cu project, 3, 300 ton/d • Fine grind size for flotation feed (p 80 = 38 um) resulting in fine tailings • Very high acid generating potential due to pyrite content • Paste backfill – half of tailings with binder for compressive strength • Surface tailings amendment – using binders (mixture of Portland cement, slag, fly ash)
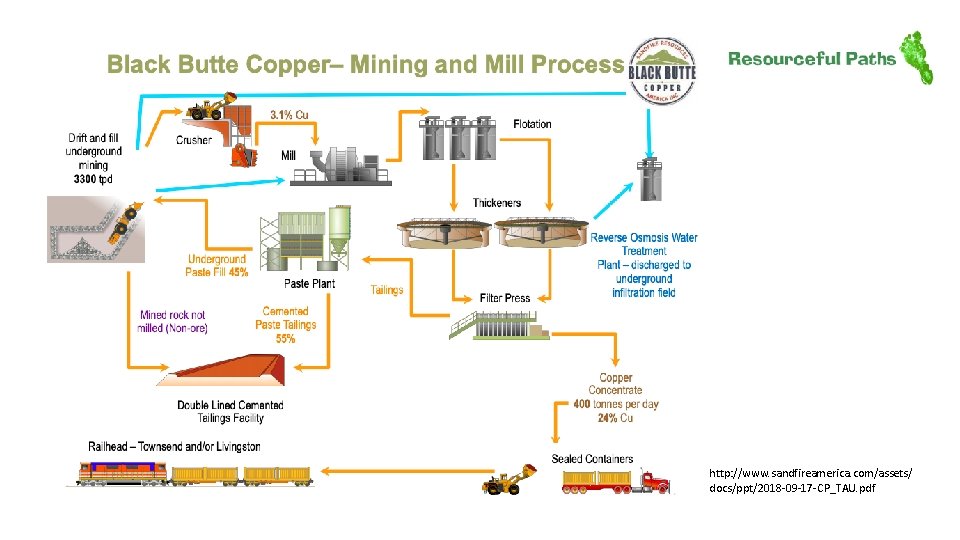
Case study – Black Butte Cu, MT http: //www. sandfireamerica. com/assets/ docs/ppt/2018 -09 -17 -CP_TAU. pdf
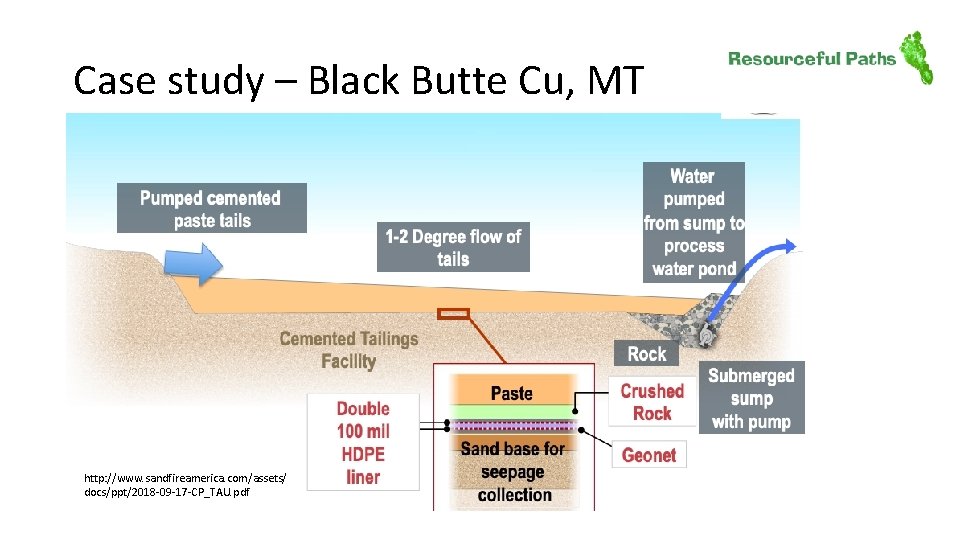
Case study – Black Butte Cu, MT http: //www. sandfireamerica. com/assets/ docs/ppt/2018 -09 -17 -CP_TAU. pdf
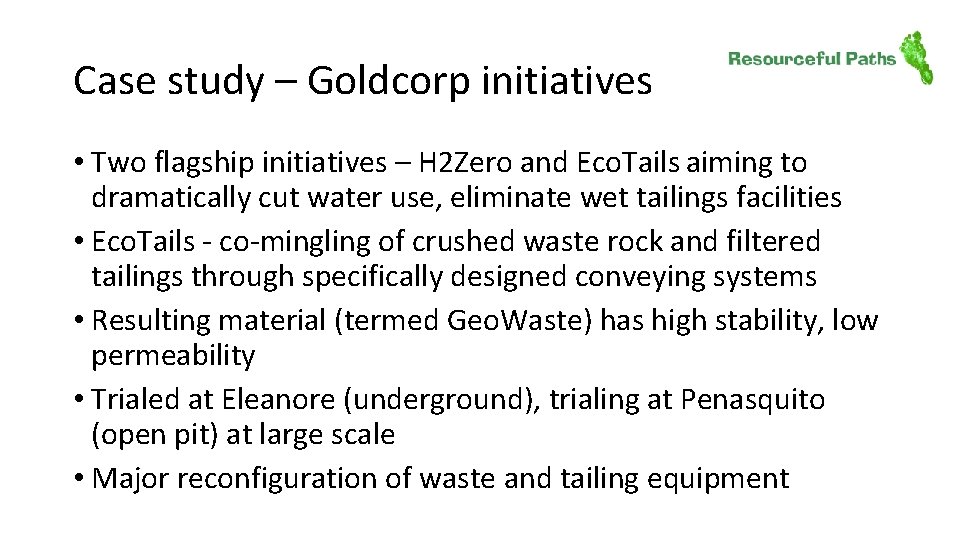
Case study – Goldcorp initiatives • Two flagship initiatives – H 2 Zero and Eco. Tails aiming to dramatically cut water use, eliminate wet tailings facilities • Eco. Tails - co-mingling of crushed waste rock and filtered tailings through specifically designed conveying systems • Resulting material (termed Geo. Waste) has high stability, low permeability • Trialed at Eleanore (underground), trialing at Penasquito (open pit) at large scale • Major reconfiguration of waste and tailing equipment
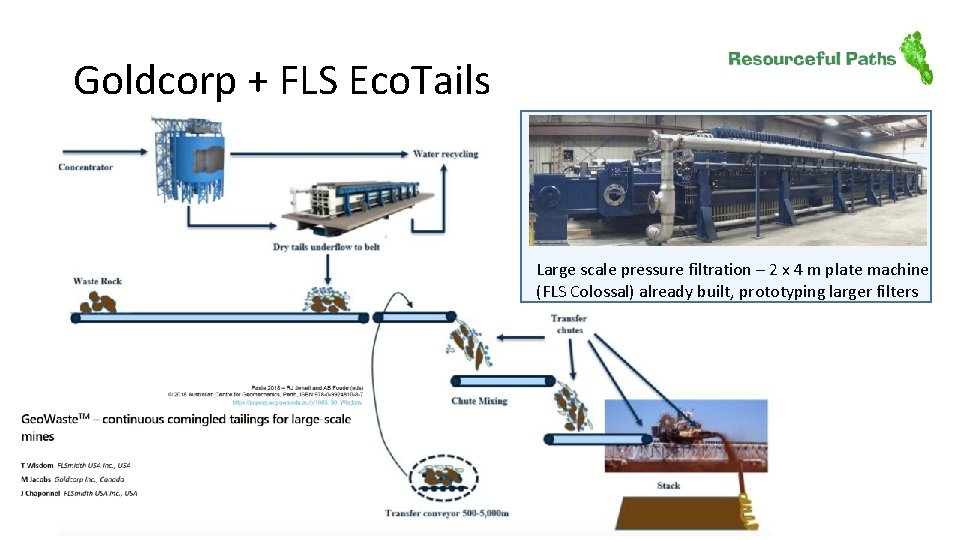
Goldcorp + FLS Eco. Tails Large scale pressure filtration – 2 x 4 m plate machine (FLS Colossal) already built, prototyping larger filters
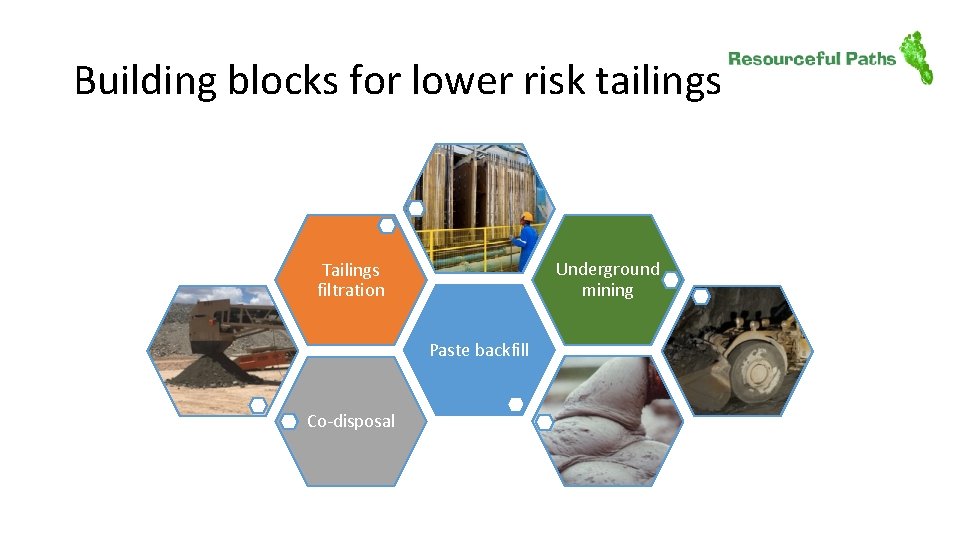
Building blocks for lower risk tailings Underground mining Tailings filtration Paste backfill Co-disposal

When tails should wag the dog… • Mining in environmentally sensitive areas – minimizing footprint is key – consider underground mining, paste backfill • Arid areas – tailings filtration to conserve water, plus design changes to lower total operating costs including tailings • When there are strong synergies with process alternatives that also reduce energy, water, reagent and grinding media consumption and costs
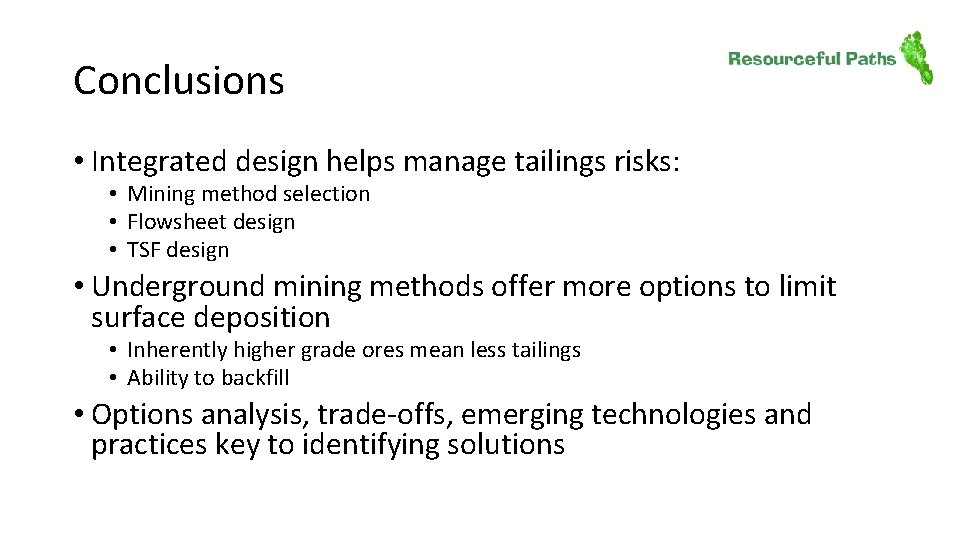
Conclusions • Integrated design helps manage tailings risks: • Mining method selection • Flowsheet design • TSF design • Underground mining methods offer more options to limit surface deposition • Inherently higher grade ores mean less tailings • Ability to backfill • Options analysis, trade-offs, emerging technologies and practices key to identifying solutions
Ltenant
Bee sickle dance
Billiard ball effect shotgun
Mikrometr na nanometr
Indot letting prep schedule
Tyrone ware
The drink and the drugs won't flush him out
Conclusion for blood donation project
Native american letting go ceremony
Personal pronouns complement
Animal farm chapter 9 and 10
Laura welcher
Direct and indirect recursion
Balloon framing vs platform framing
Contoh soal uji pihak kanan
Tail fibers
Conveyor return roller guards
How do helicopters move forward
Alkyl tail
Lists in prolog
Queues definition
Impulse and reaction turbine
The zoo dangerous curves
Blood spatter patterns
Long tail demand
The newspaper report contained important information