Lean Hospitals Improving Quality Patient Safety and Employee
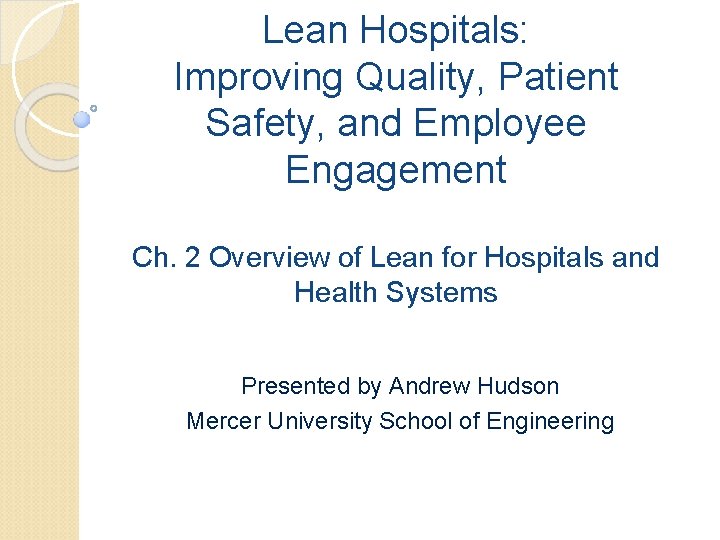
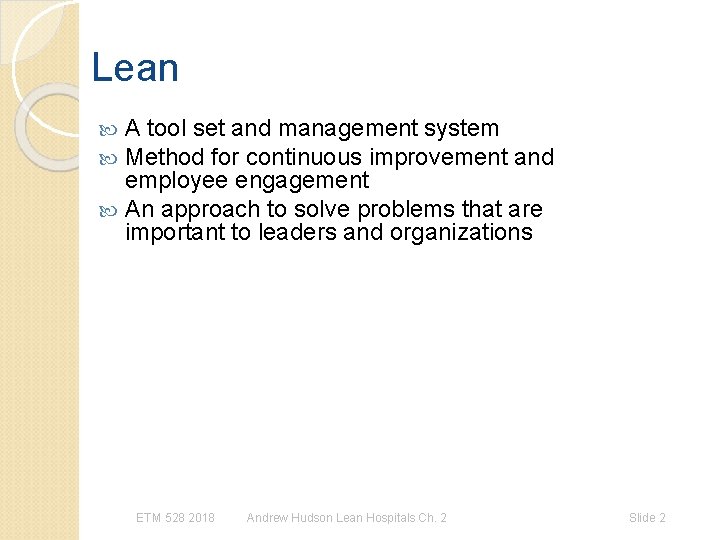
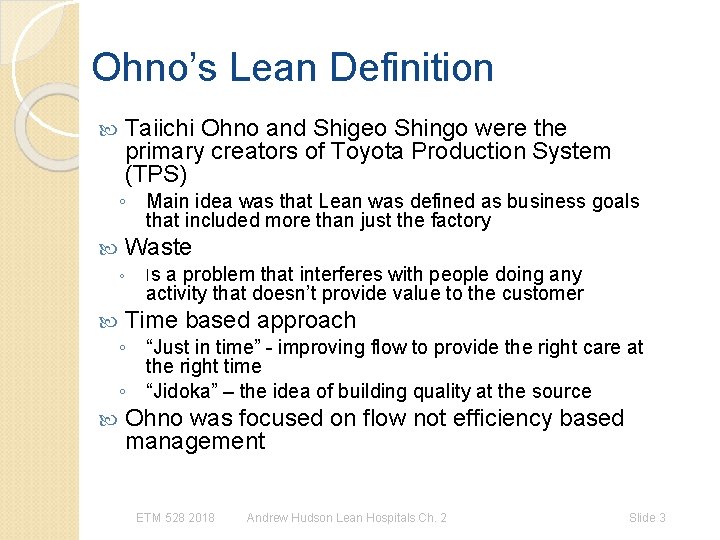
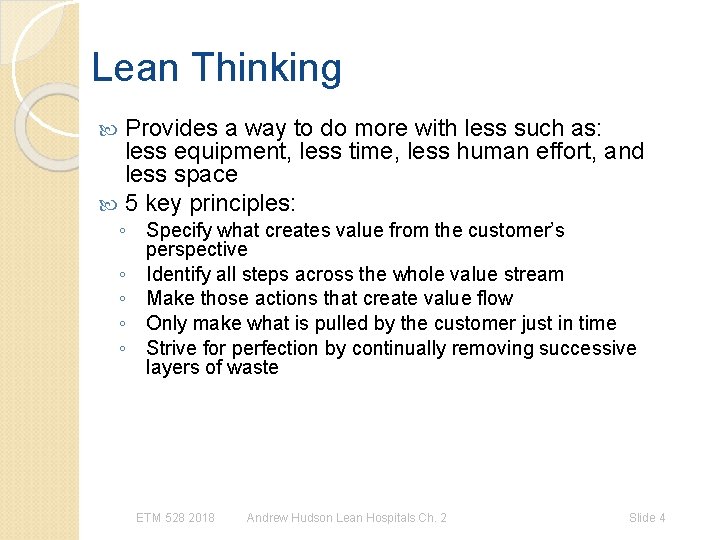
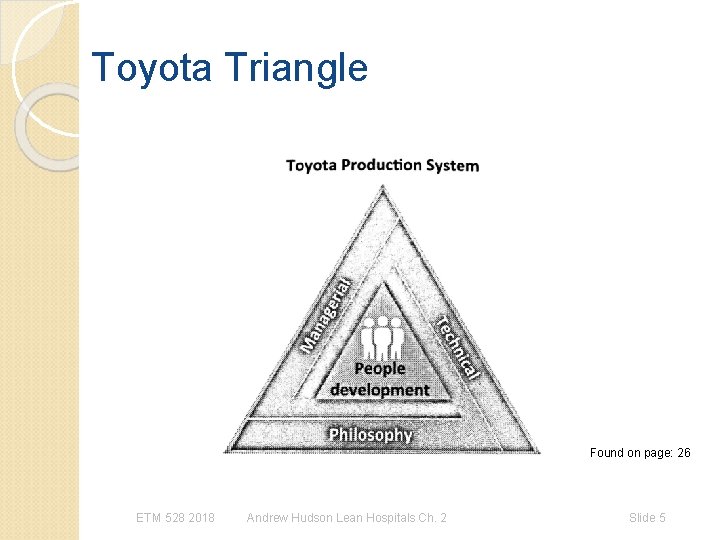
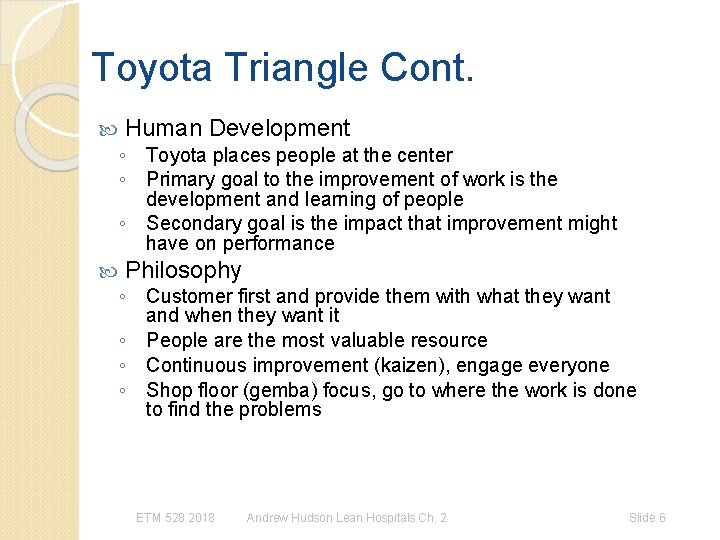
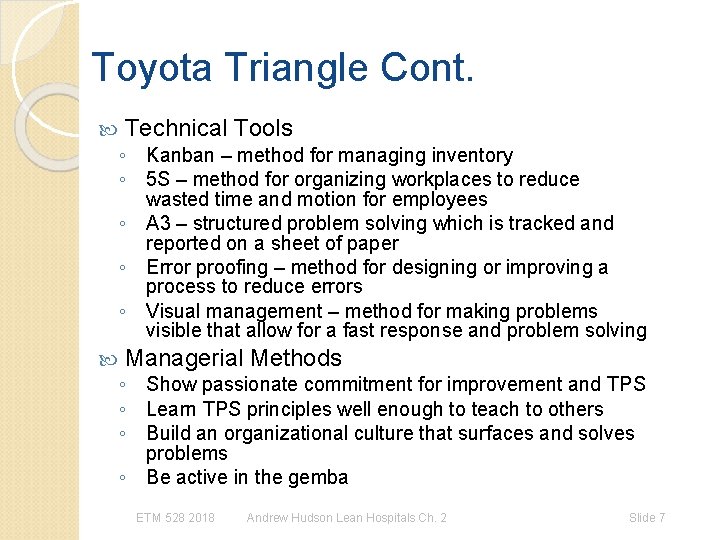
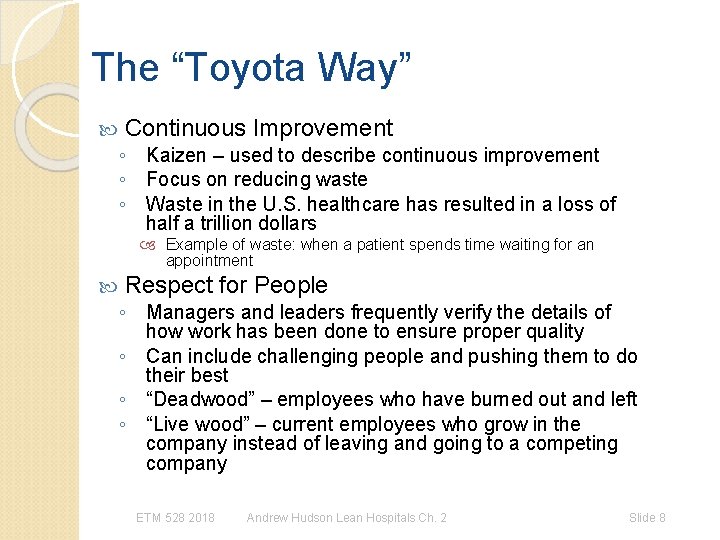
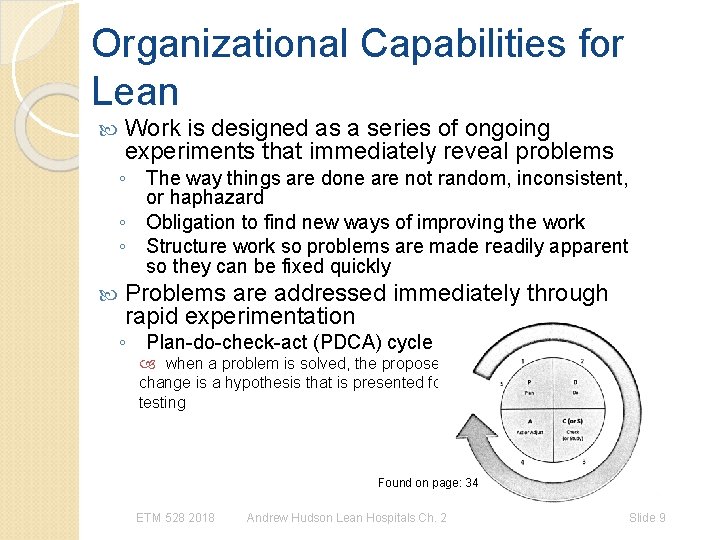
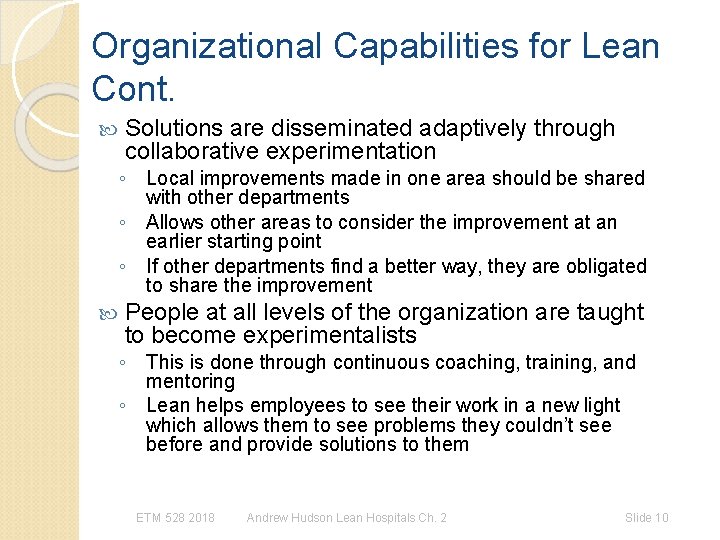
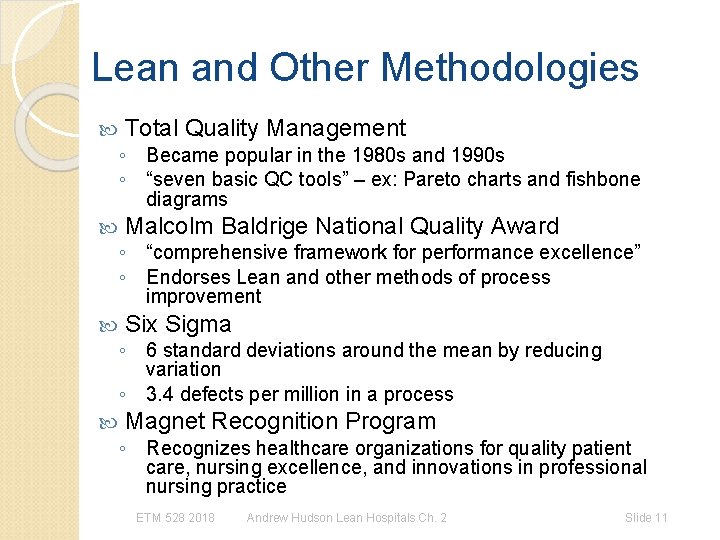
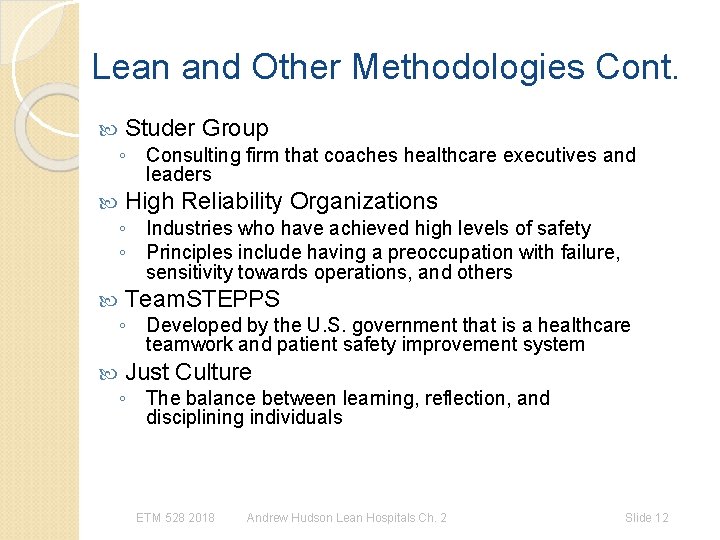
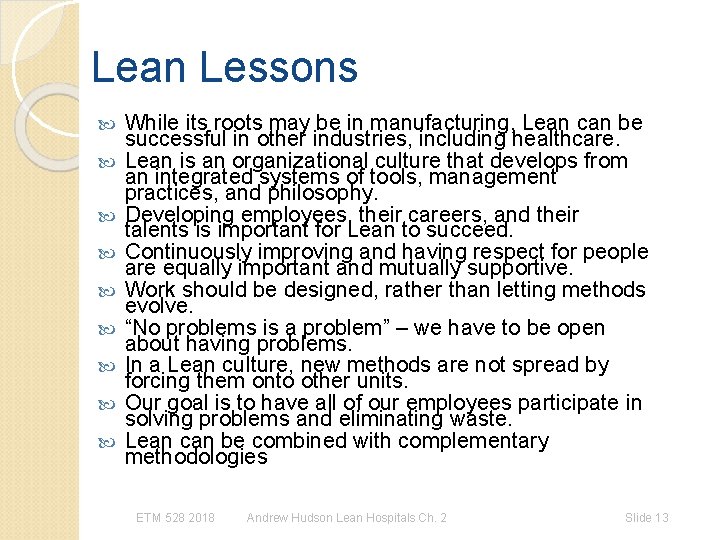

- Slides: 14
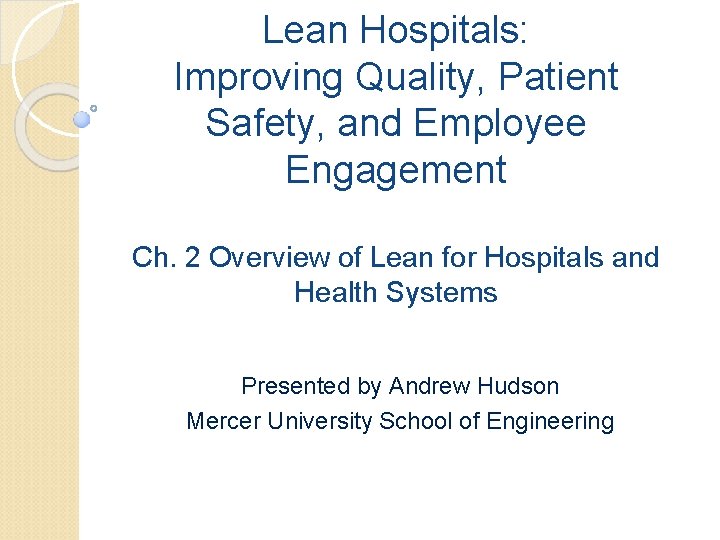
Lean Hospitals: Improving Quality, Patient Safety, and Employee Engagement Ch. 2 Overview of Lean for Hospitals and Health Systems Presented by Andrew Hudson Mercer University School of Engineering
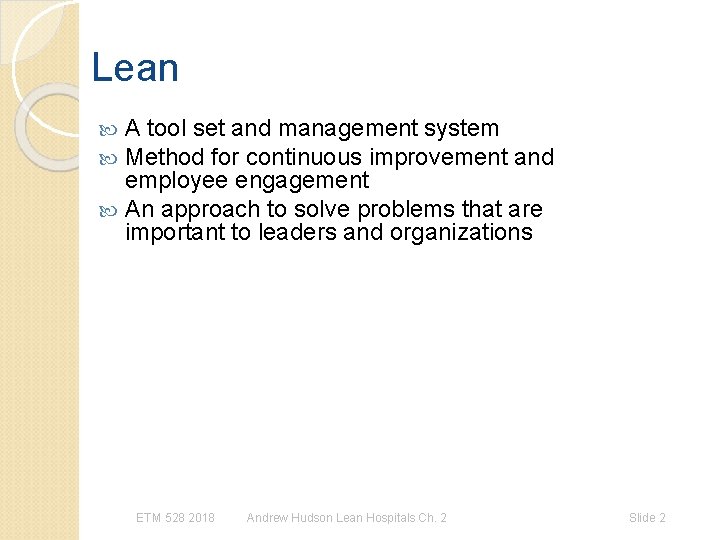
Lean A tool set and management system Method for continuous improvement and employee engagement An approach to solve problems that are important to leaders and organizations ETM 528 2018 Andrew Hudson Lean Hospitals Ch. 2 Slide 2
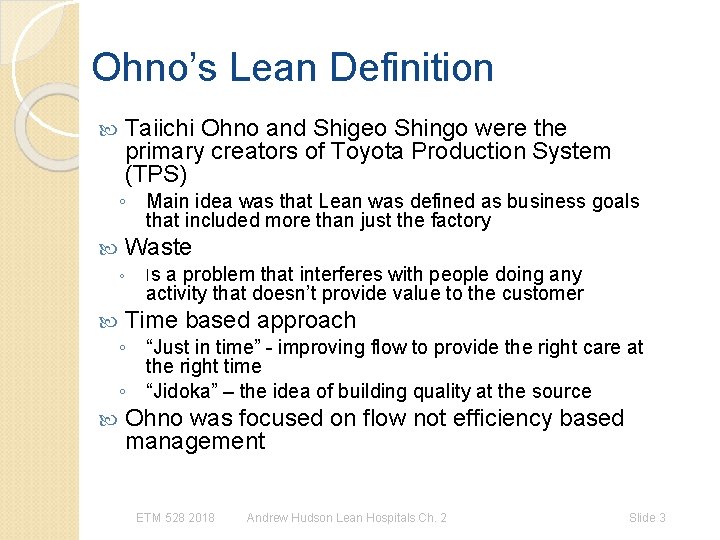
Ohno’s Lean Definition Taiichi Ohno and Shigeo Shingo were the primary creators of Toyota Production System (TPS) ◦ Main idea was that Lean was defined as business goals that included more than just the factory Waste ◦ Is a problem that interferes with people doing any activity that doesn’t provide value to the customer Time based approach ◦ “Just in time” - improving flow to provide the right care at the right time ◦ “Jidoka” – the idea of building quality at the source Ohno was focused on flow not efficiency based management ETM 528 2018 Andrew Hudson Lean Hospitals Ch. 2 Slide 3
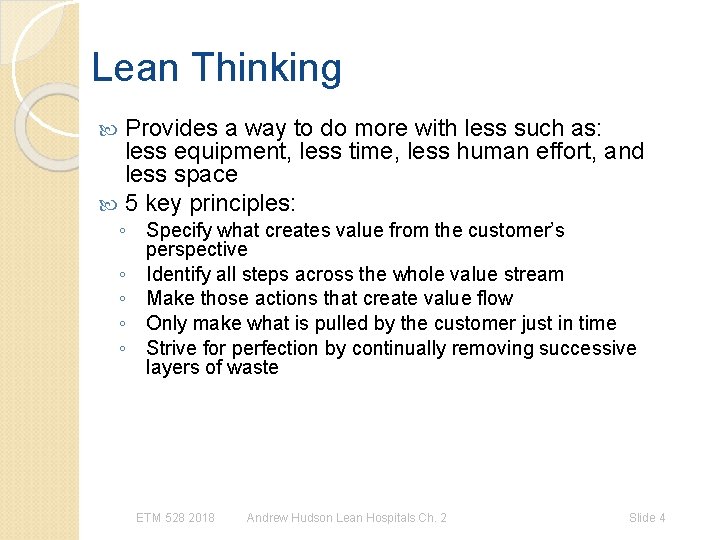
Lean Thinking Provides a way to do more with less such as: less equipment, less time, less human effort, and less space 5 key principles: ◦ Specify what creates value from the customer’s perspective ◦ Identify all steps across the whole value stream ◦ Make those actions that create value flow ◦ Only make what is pulled by the customer just in time ◦ Strive for perfection by continually removing successive layers of waste ETM 528 2018 Andrew Hudson Lean Hospitals Ch. 2 Slide 4
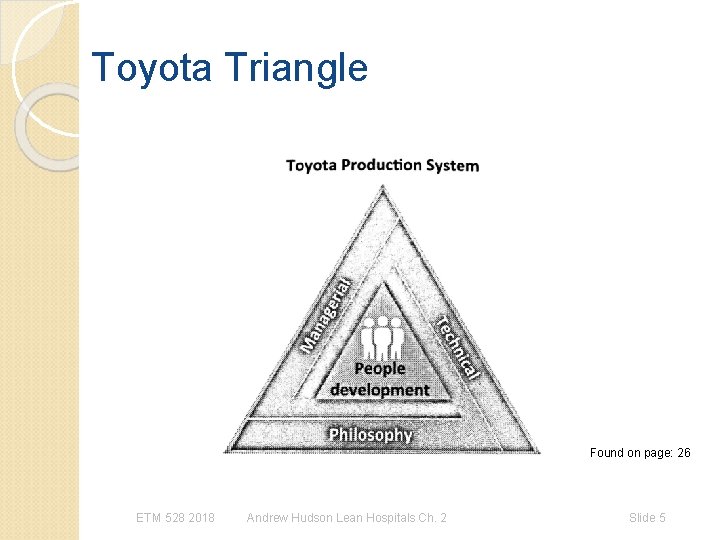
Toyota Triangle Found on page: 26 ETM 528 2018 Andrew Hudson Lean Hospitals Ch. 2 Slide 5
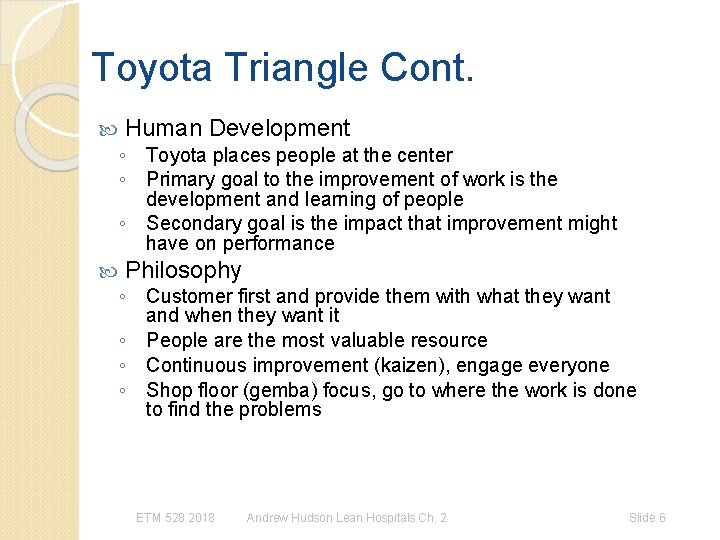
Toyota Triangle Cont. Human Development ◦ Toyota places people at the center ◦ Primary goal to the improvement of work is the development and learning of people ◦ Secondary goal is the impact that improvement might have on performance Philosophy ◦ Customer first and provide them with what they want and when they want it ◦ People are the most valuable resource ◦ Continuous improvement (kaizen), engage everyone ◦ Shop floor (gemba) focus, go to where the work is done to find the problems ETM 528 2018 Andrew Hudson Lean Hospitals Ch. 2 Slide 6
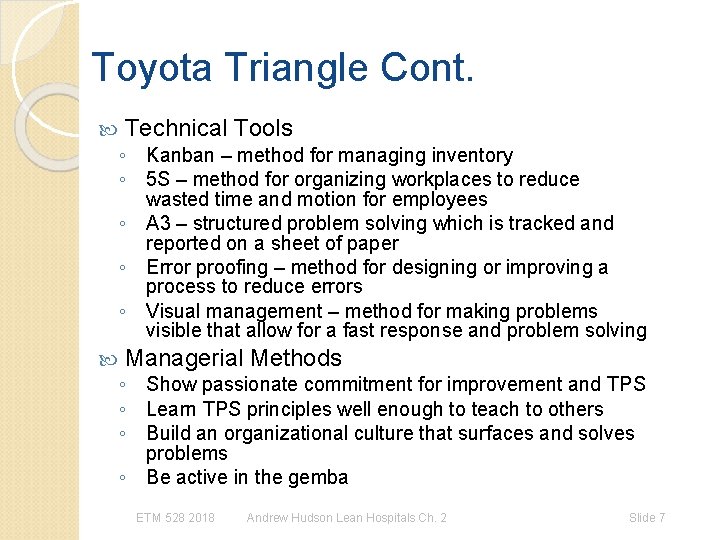
Toyota Triangle Cont. Technical Tools ◦ Kanban – method for managing inventory ◦ 5 S – method for organizing workplaces to reduce wasted time and motion for employees ◦ A 3 – structured problem solving which is tracked and reported on a sheet of paper ◦ Error proofing – method for designing or improving a process to reduce errors ◦ Visual management – method for making problems visible that allow for a fast response and problem solving Managerial Methods ◦ Show passionate commitment for improvement and TPS ◦ Learn TPS principles well enough to teach to others ◦ Build an organizational culture that surfaces and solves problems ◦ Be active in the gemba ETM 528 2018 Andrew Hudson Lean Hospitals Ch. 2 Slide 7
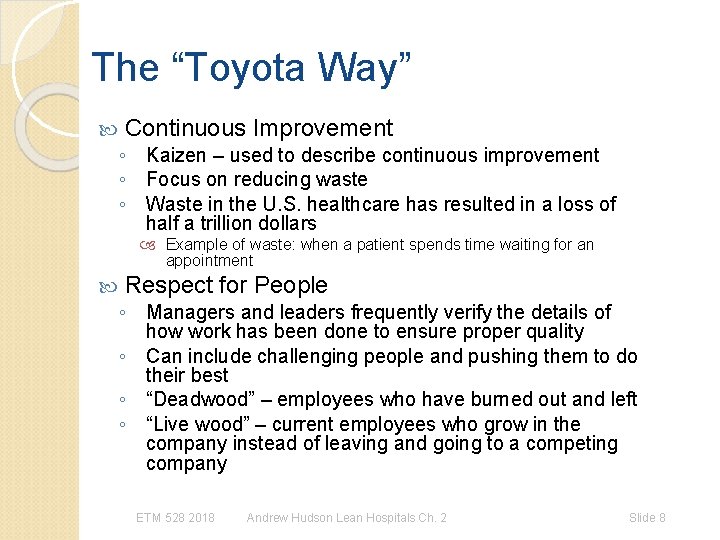
The “Toyota Way” Continuous Improvement ◦ Kaizen – used to describe continuous improvement ◦ Focus on reducing waste ◦ Waste in the U. S. healthcare has resulted in a loss of half a trillion dollars Example of waste: when a patient spends time waiting for an appointment Respect for People ◦ Managers and leaders frequently verify the details of how work has been done to ensure proper quality ◦ Can include challenging people and pushing them to do their best ◦ “Deadwood” – employees who have burned out and left ◦ “Live wood” – current employees who grow in the company instead of leaving and going to a competing company ETM 528 2018 Andrew Hudson Lean Hospitals Ch. 2 Slide 8
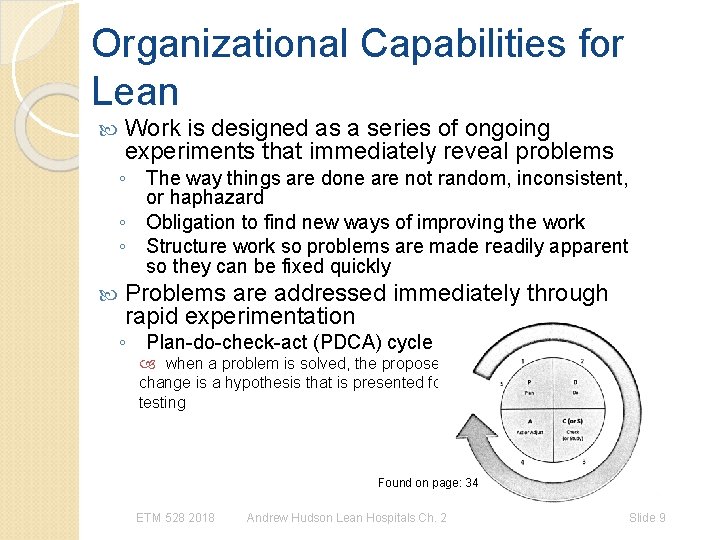
Organizational Capabilities for Lean Work is designed as a series of ongoing experiments that immediately reveal problems ◦ The way things are done are not random, inconsistent, or haphazard ◦ Obligation to find new ways of improving the work ◦ Structure work so problems are made readily apparent so they can be fixed quickly Problems are addressed immediately through rapid experimentation ◦ Plan-do-check-act (PDCA) cycle when a problem is solved, the proposed change is a hypothesis that is presented for testing Found on page: 34 ETM 528 2018 Andrew Hudson Lean Hospitals Ch. 2 Slide 9
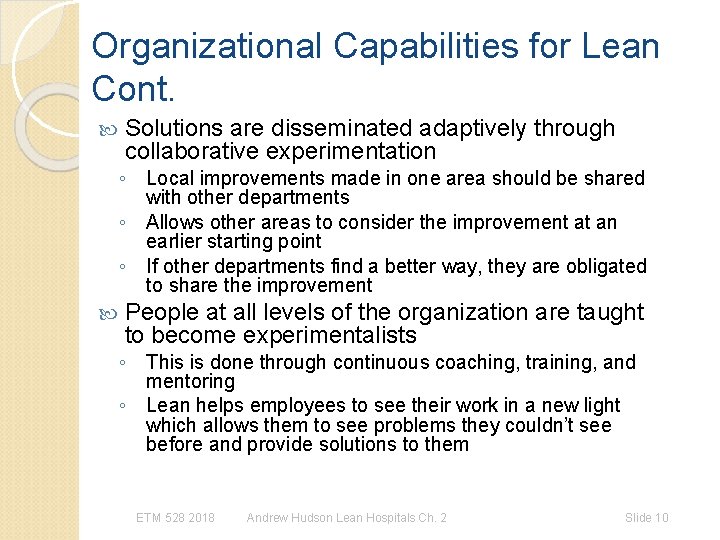
Organizational Capabilities for Lean Cont. Solutions are disseminated adaptively through collaborative experimentation ◦ Local improvements made in one area should be shared with other departments ◦ Allows other areas to consider the improvement at an earlier starting point ◦ If other departments find a better way, they are obligated to share the improvement People at all levels of the organization are taught to become experimentalists ◦ This is done through continuous coaching, training, and mentoring ◦ Lean helps employees to see their work in a new light which allows them to see problems they couldn’t see before and provide solutions to them ETM 528 2018 Andrew Hudson Lean Hospitals Ch. 2 Slide 10
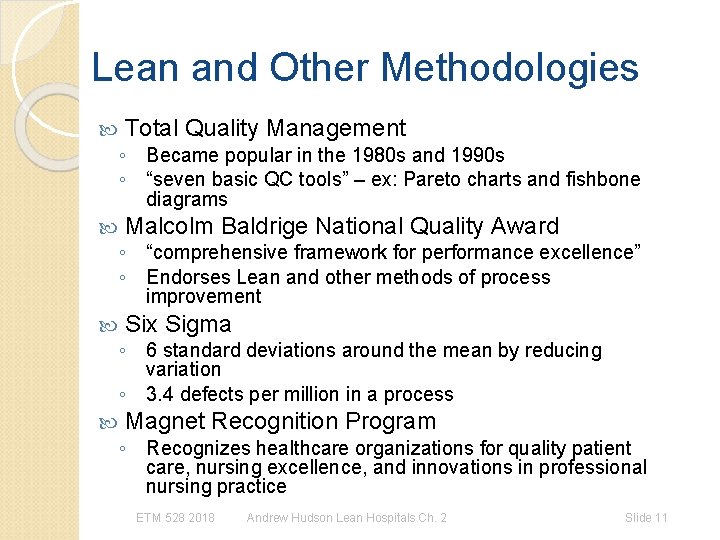
Lean and Other Methodologies Total Quality Management ◦ Became popular in the 1980 s and 1990 s ◦ “seven basic QC tools” – ex: Pareto charts and fishbone diagrams Malcolm Baldrige National Quality Award ◦ “comprehensive framework for performance excellence” ◦ Endorses Lean and other methods of process improvement Six Sigma ◦ 6 standard deviations around the mean by reducing variation ◦ 3. 4 defects per million in a process Magnet Recognition Program ◦ Recognizes healthcare organizations for quality patient care, nursing excellence, and innovations in professional nursing practice ETM 528 2018 Andrew Hudson Lean Hospitals Ch. 2 Slide 11
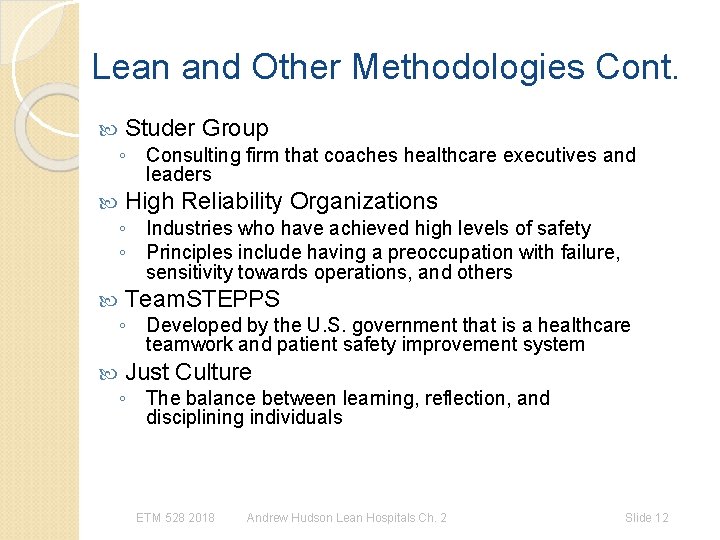
Lean and Other Methodologies Cont. Studer Group ◦ Consulting firm that coaches healthcare executives and leaders High Reliability Organizations ◦ Industries who have achieved high levels of safety ◦ Principles include having a preoccupation with failure, sensitivity towards operations, and others Team. STEPPS ◦ Developed by the U. S. government that is a healthcare teamwork and patient safety improvement system Just Culture ◦ The balance between learning, reflection, and disciplining individuals ETM 528 2018 Andrew Hudson Lean Hospitals Ch. 2 Slide 12
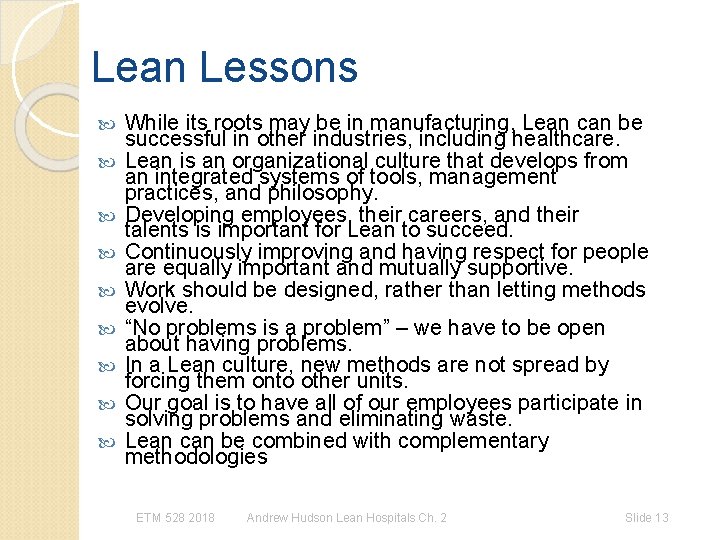
Lean Lessons While its roots may be in manufacturing, Lean can be successful in other industries, including healthcare. Lean is an organizational culture that develops from an integrated systems of tools, management practices, and philosophy. Developing employees, their careers, and their talents is important for Lean to succeed. Continuously improving and having respect for people are equally important and mutually supportive. Work should be designed, rather than letting methods evolve. “No problems is a problem” – we have to be open about having problems. In a Lean culture, new methods are not spread by forcing them onto other units. Our goal is to have all of our employees participate in solving problems and eliminating waste. Lean can be combined with complementary methodologies ETM 528 2018 Andrew Hudson Lean Hospitals Ch. 2 Slide 13

Source Graban, M. (2017). Lean hospitals: Improving quality, patient safety, and employee engagement. Boca Raton: Taylor & Francis. ETM 528 2018 Andrew Hudson Lean Hospitals Ch. 2 Slide 14
Lean hospitals
Graban lean hospitals download
A nurse floats to a busy surgical unit
Patient safety and quality care movement
User registration process flow diagram
Improving the patient journey
Service quality and productivity
Quality business a level
Employee attitudes and employee performance
Listening gap communication
Gaps model for improving service quality
Ahrq antibiotic stewardship
Lean production and quality management
Patient 2 patient
Exposure control plan bloodborne pathogens