Lasfouten l l l 1 We kunnen aannemen
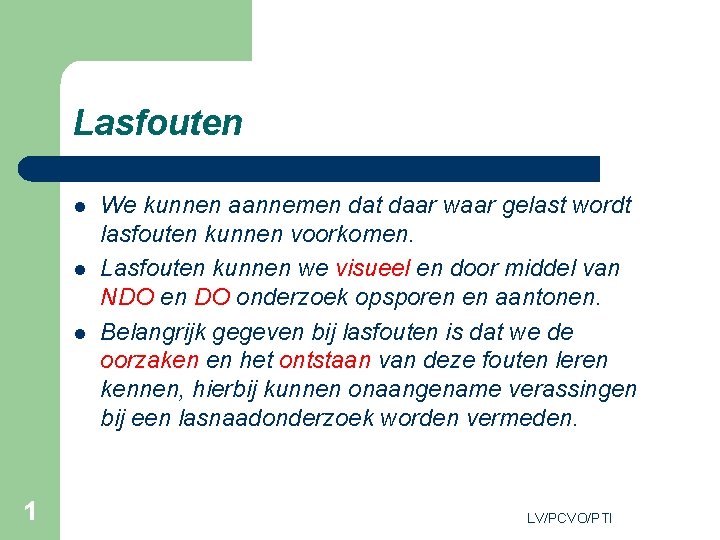
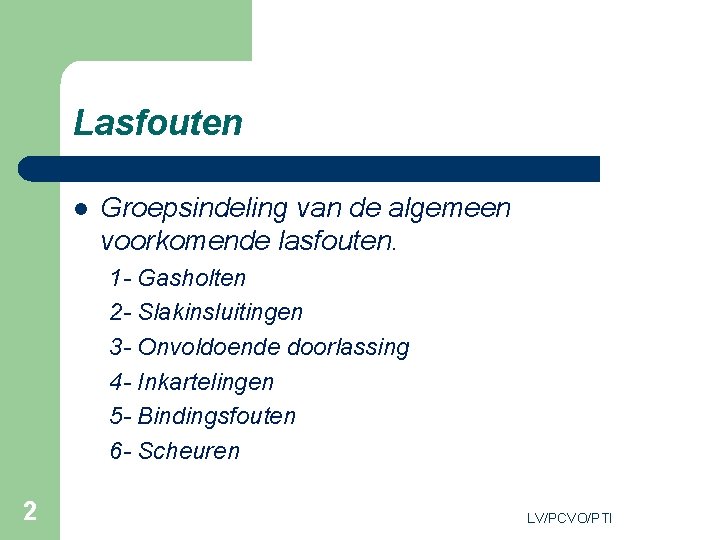
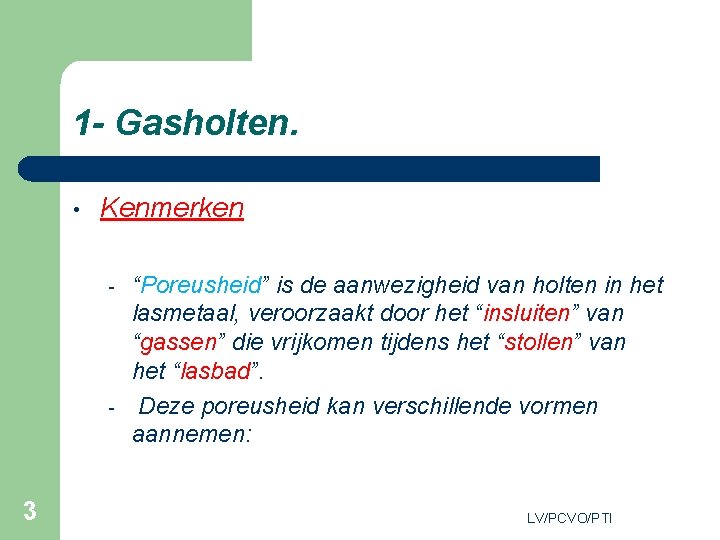
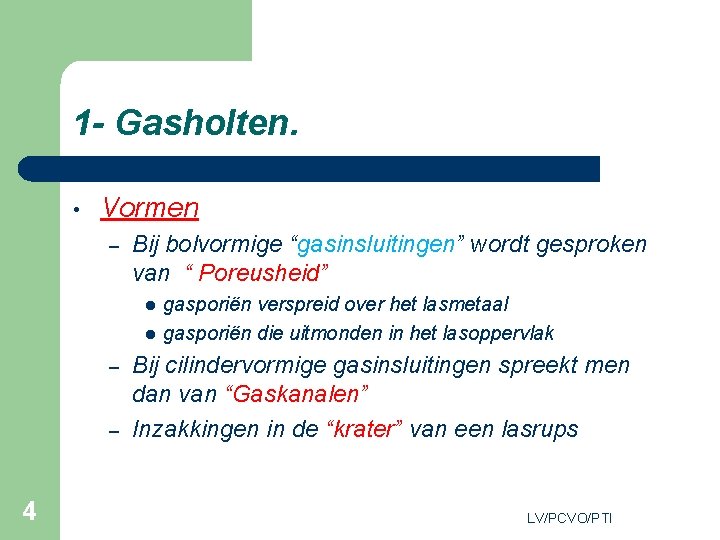
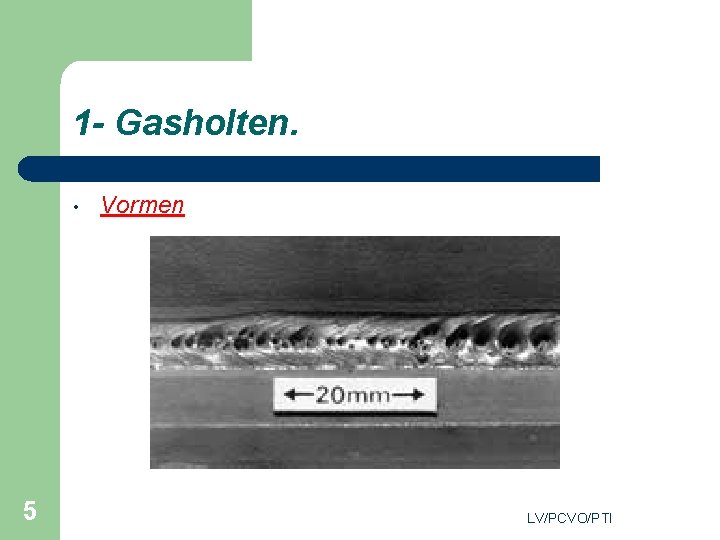
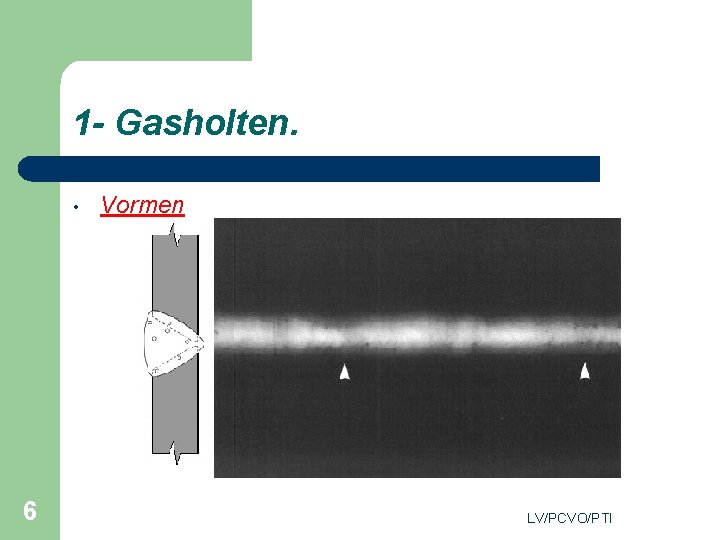
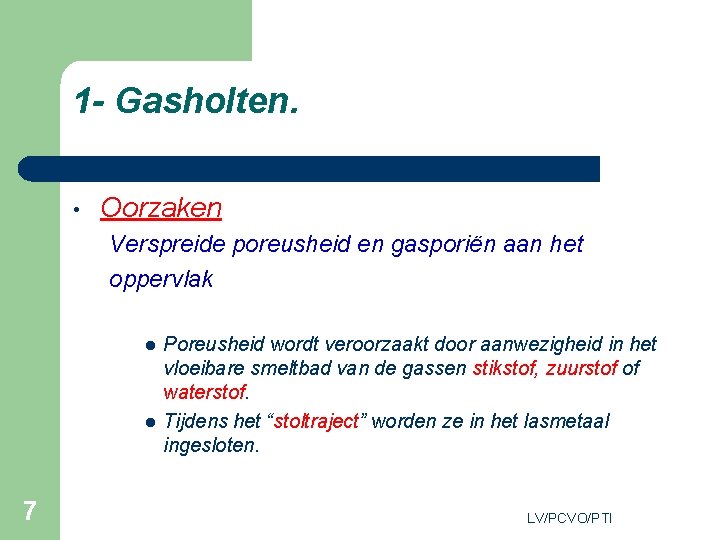
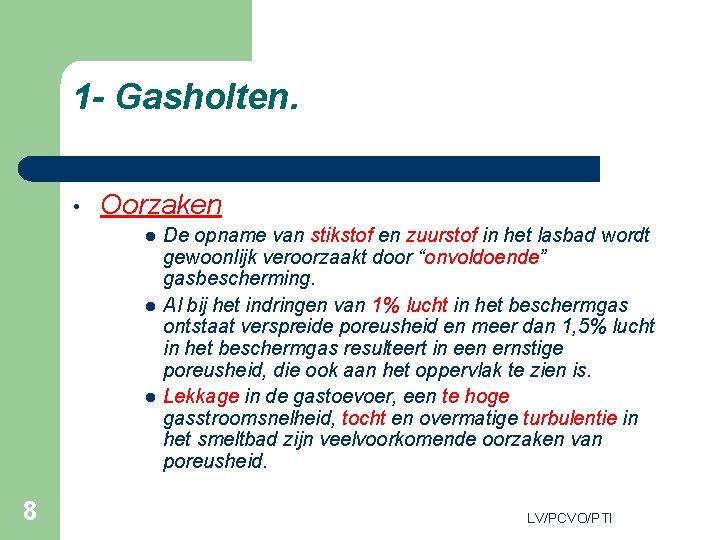
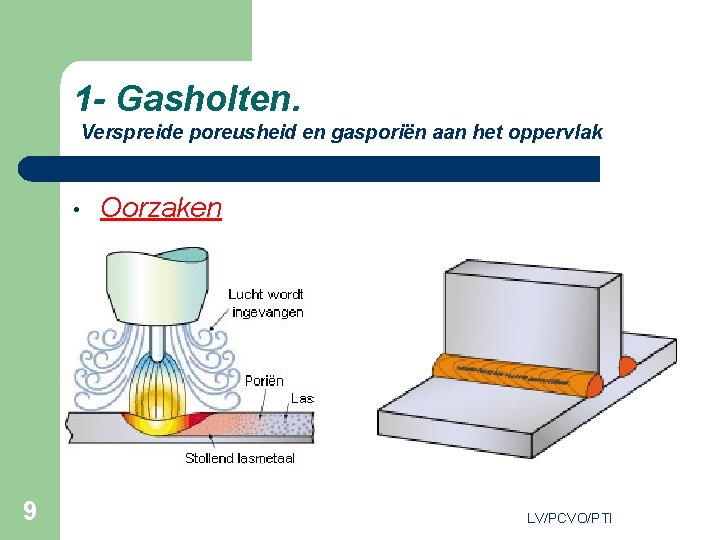
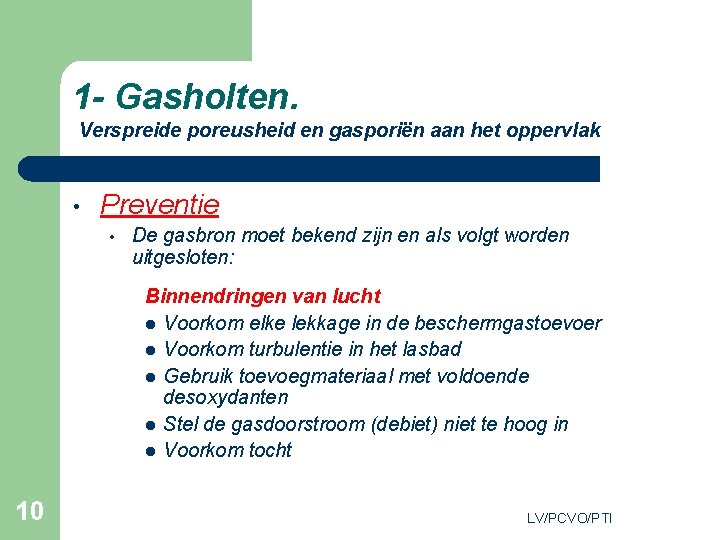
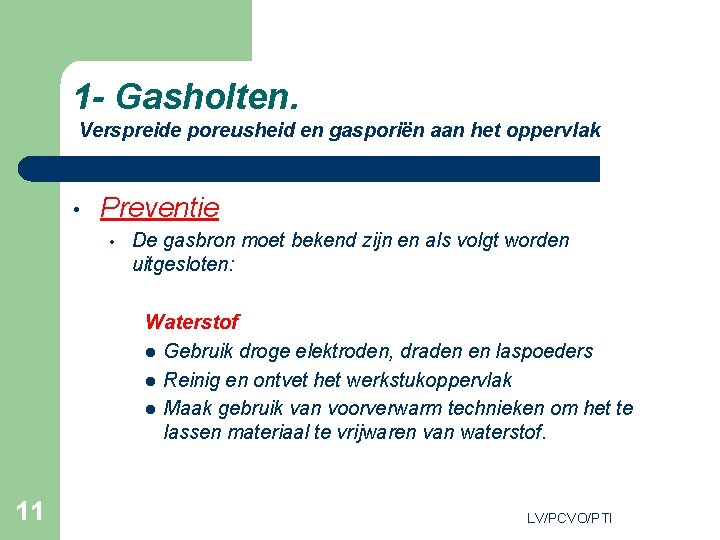
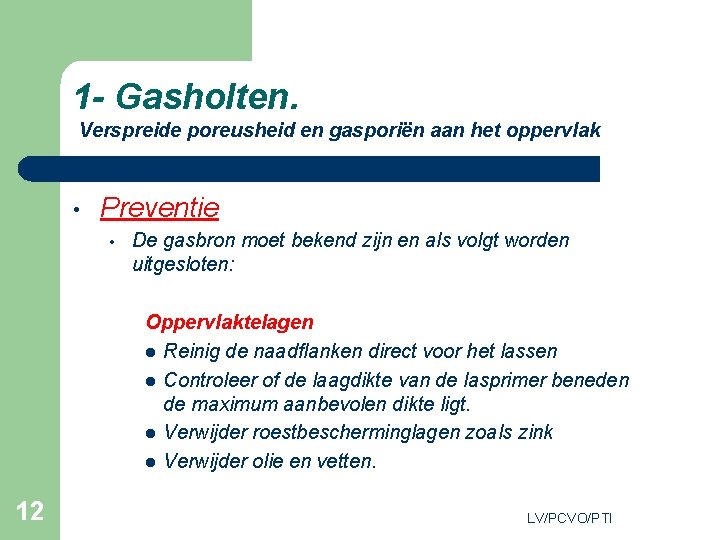
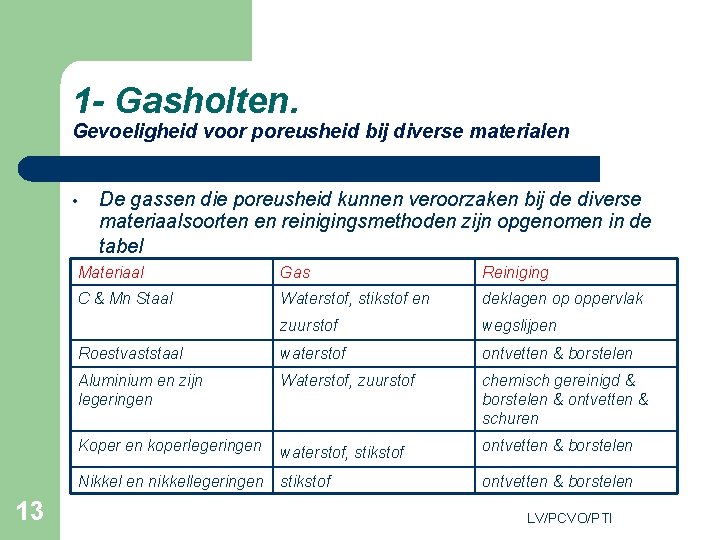
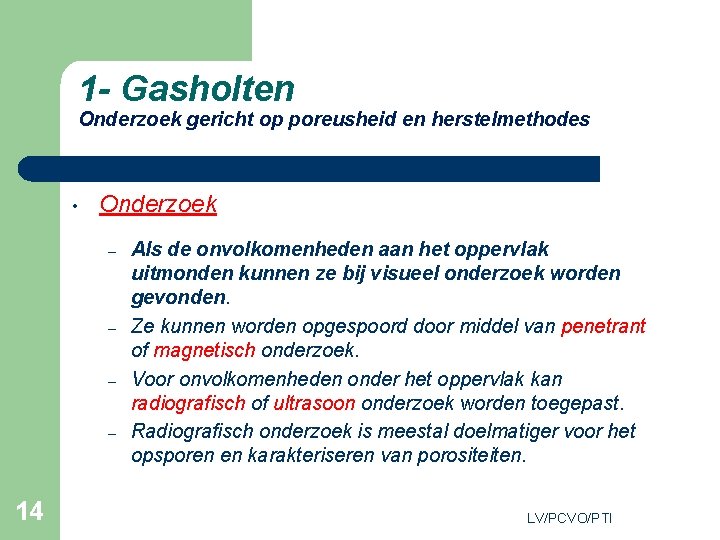
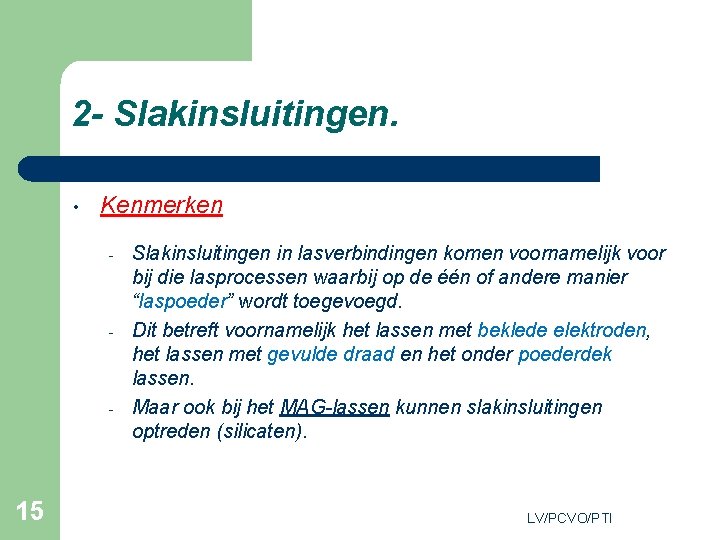
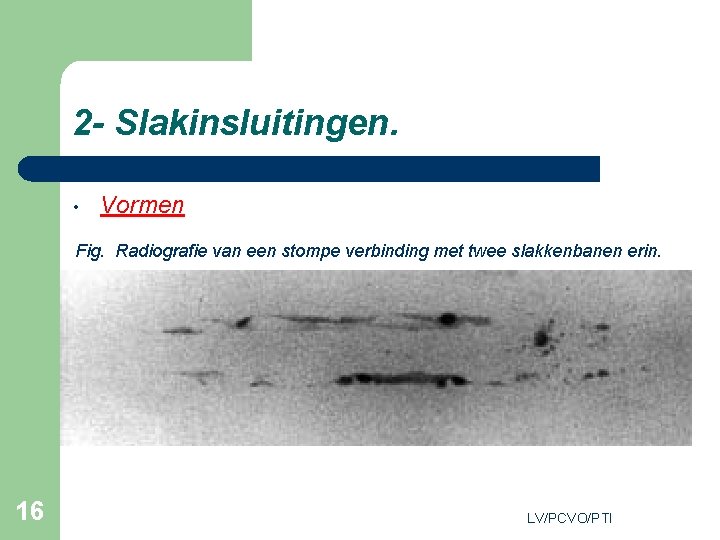
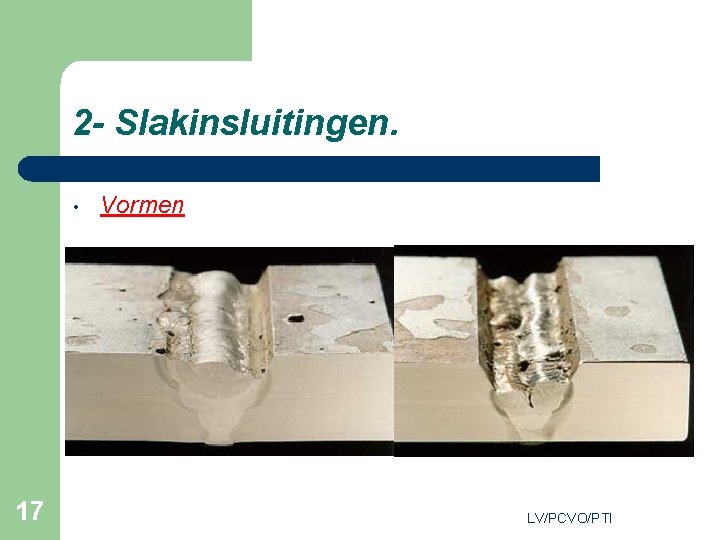
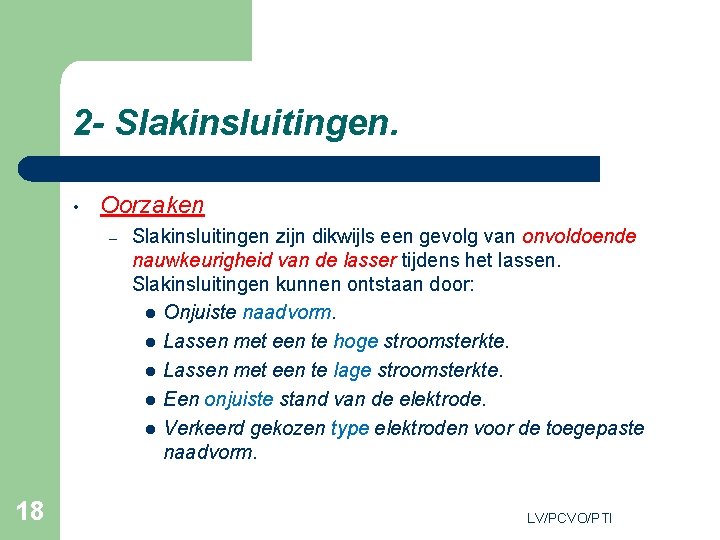
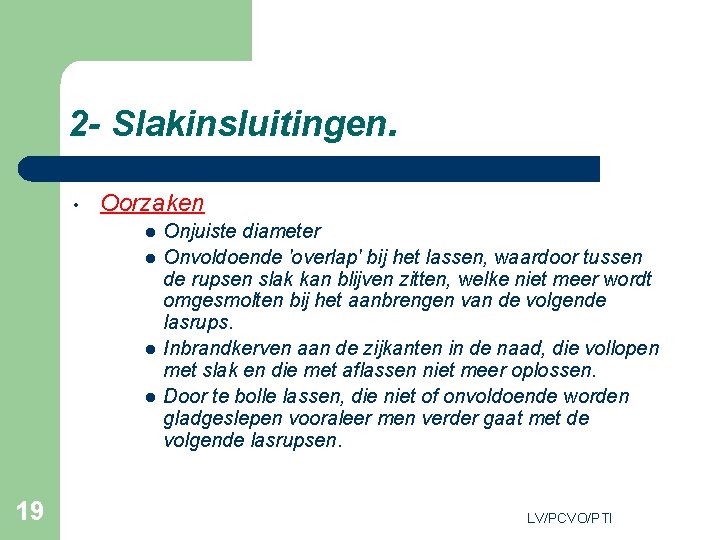
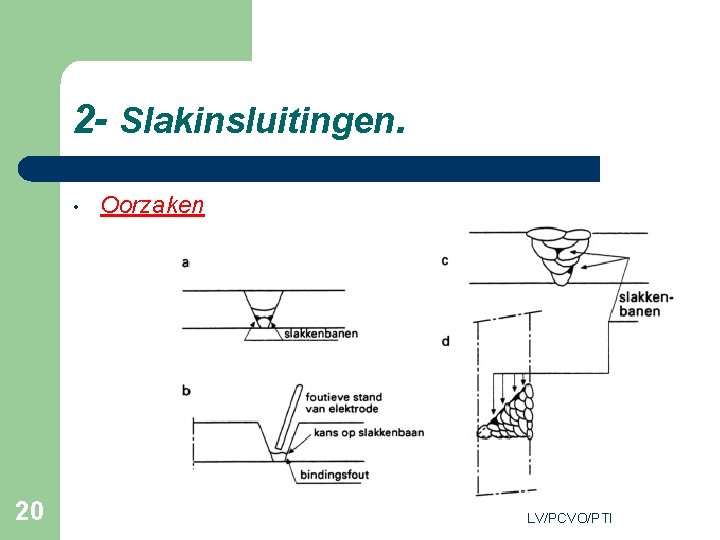
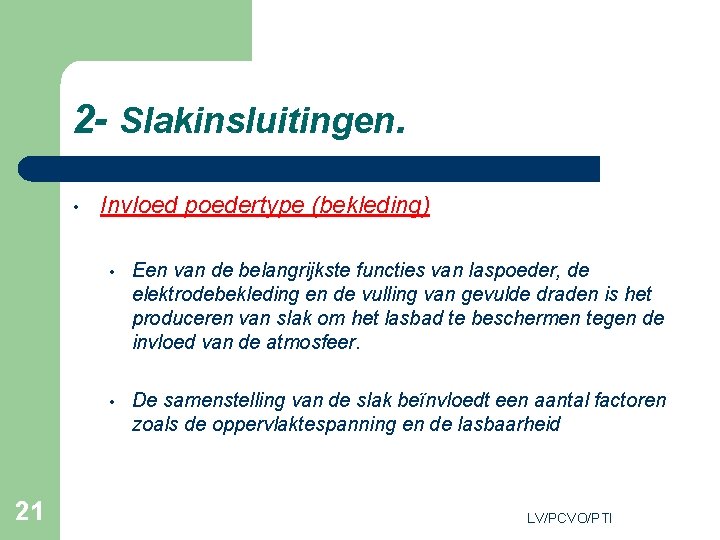
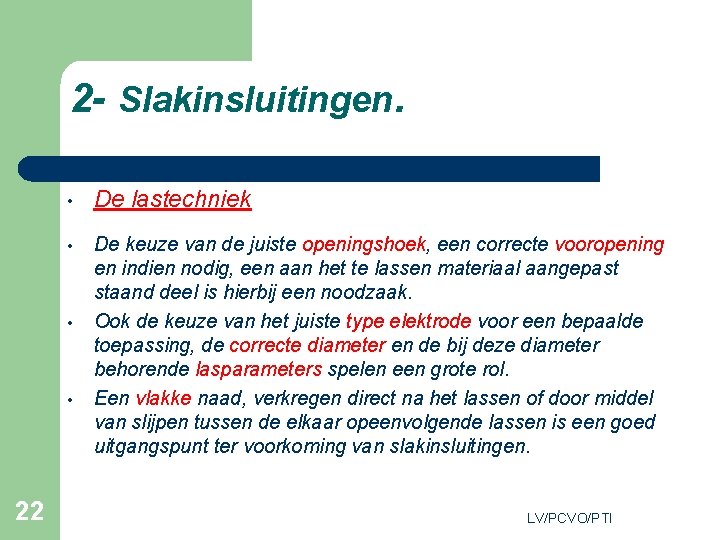
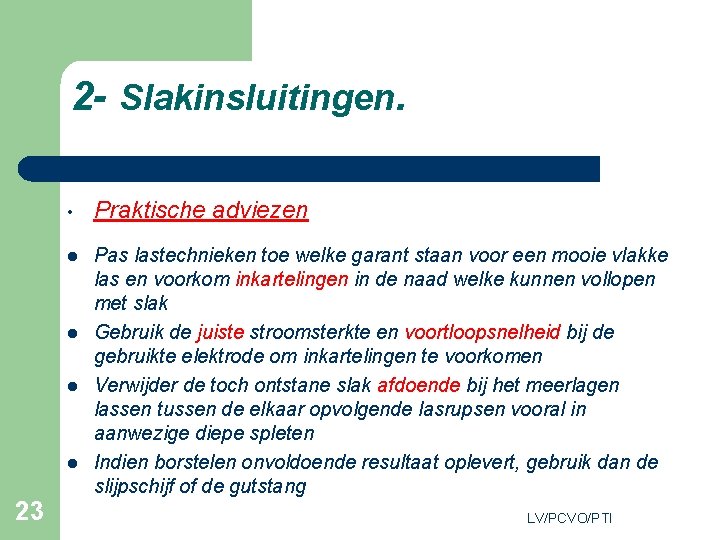
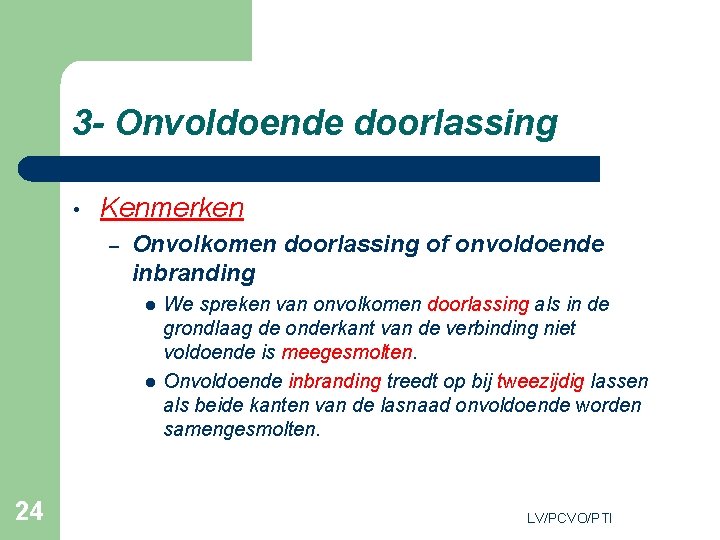
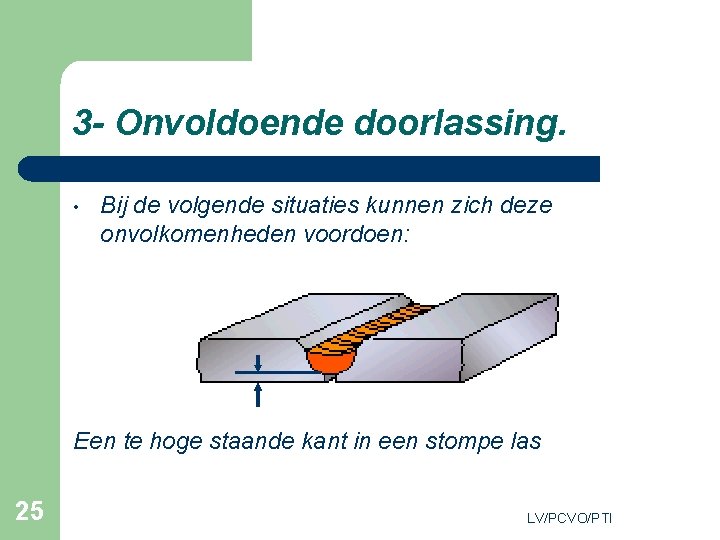
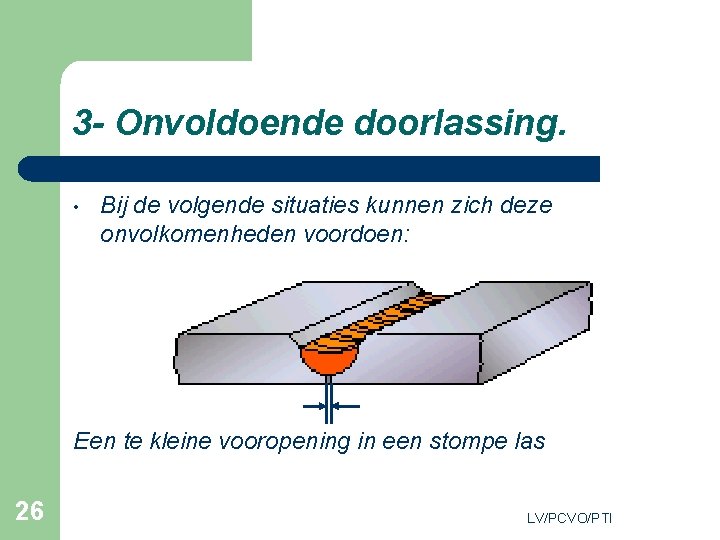
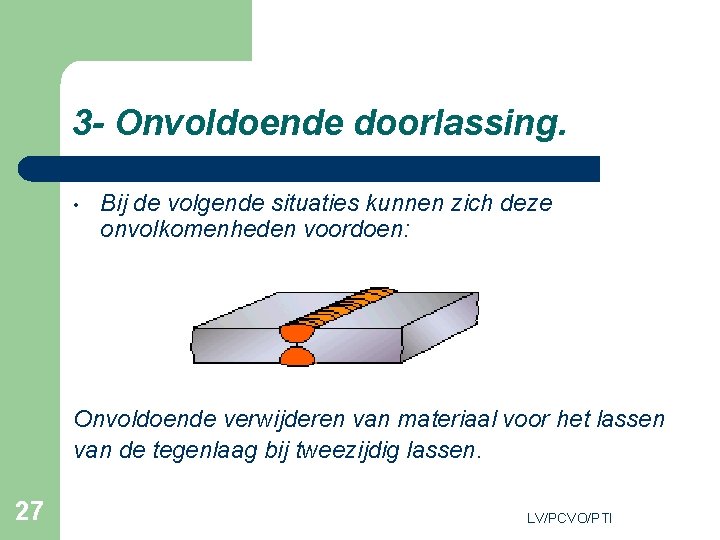
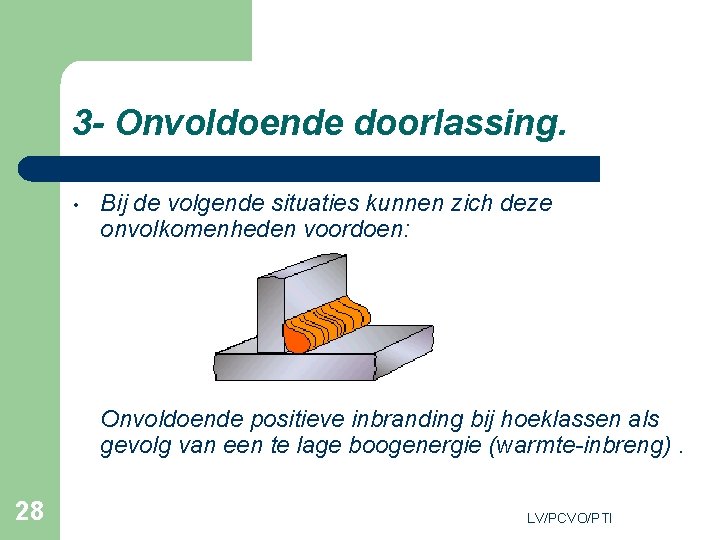
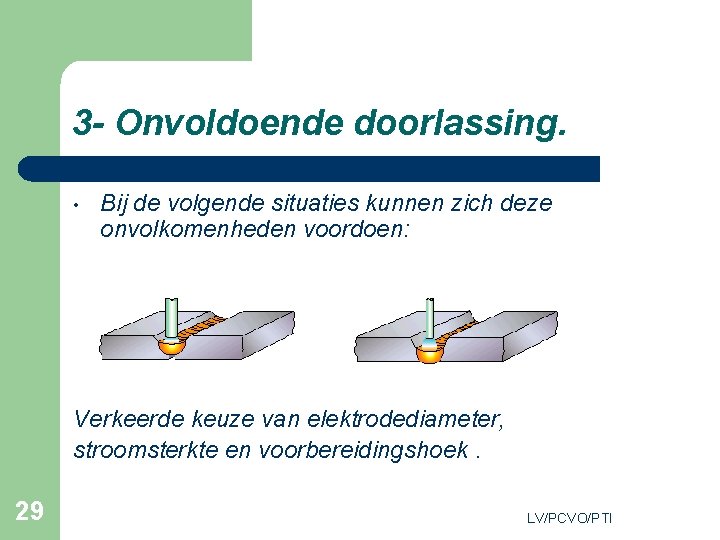
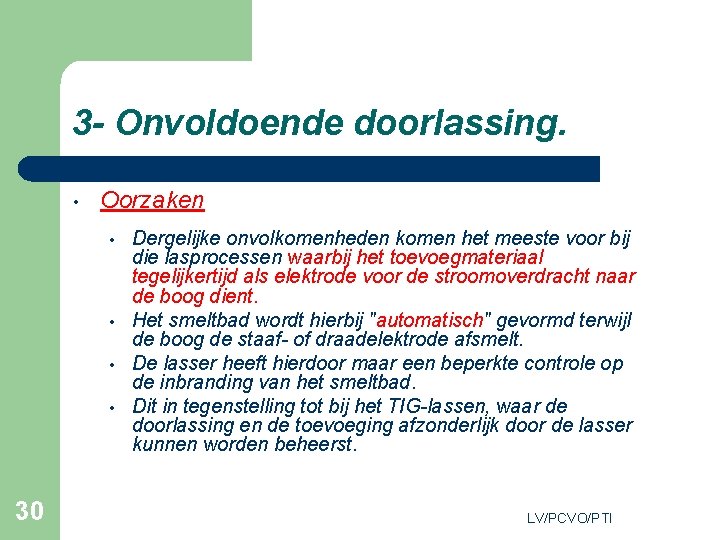
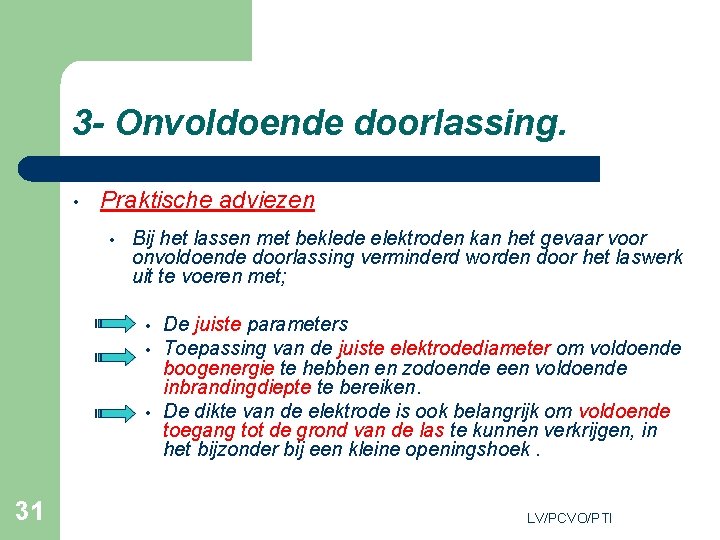
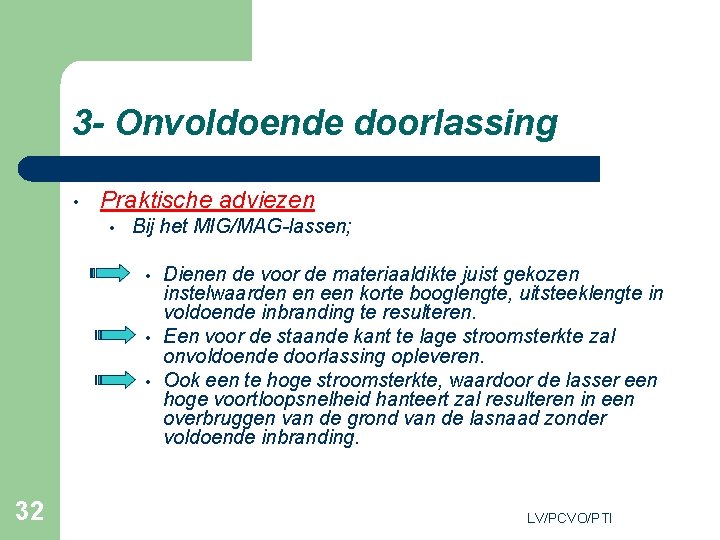
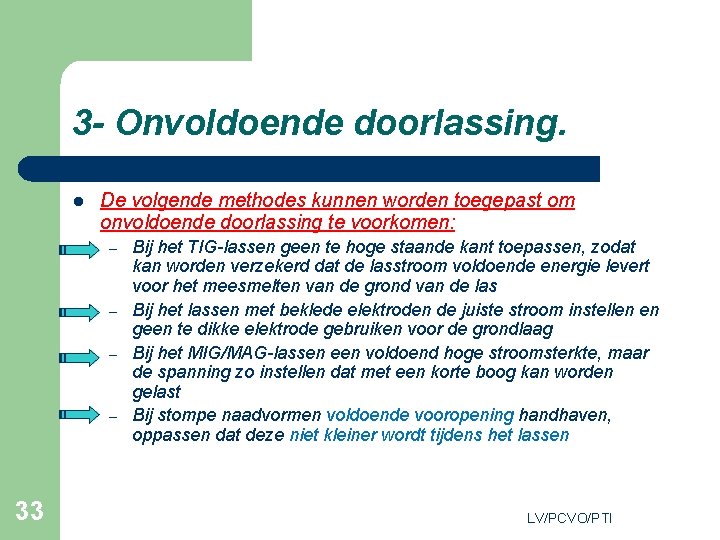
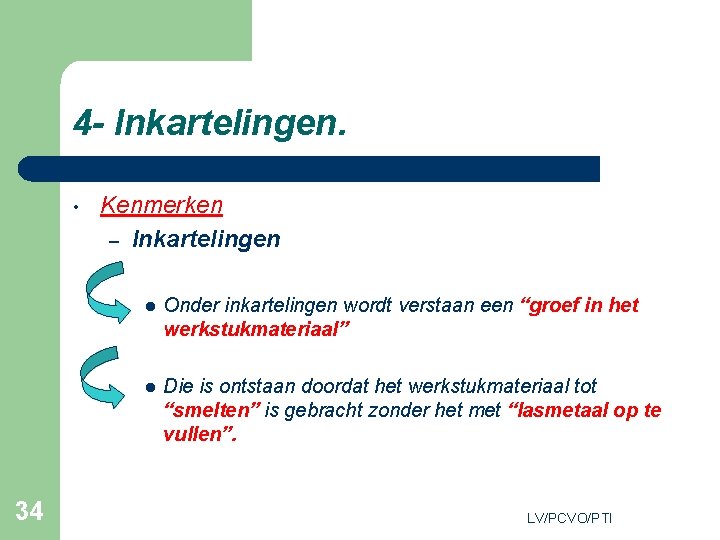
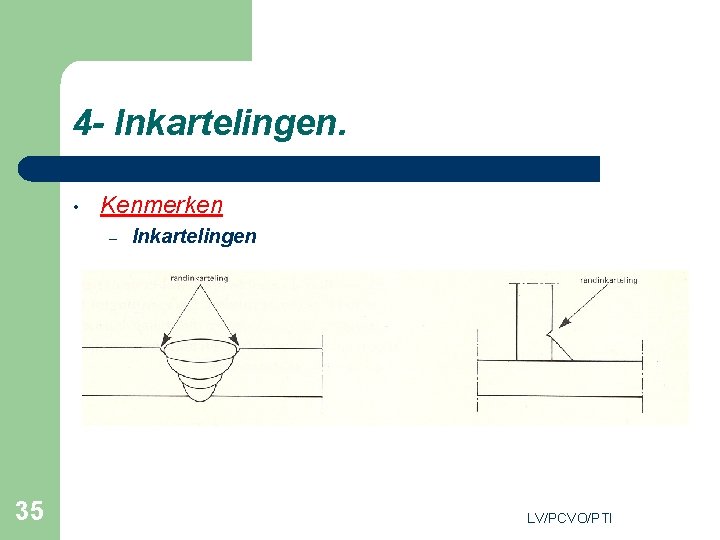
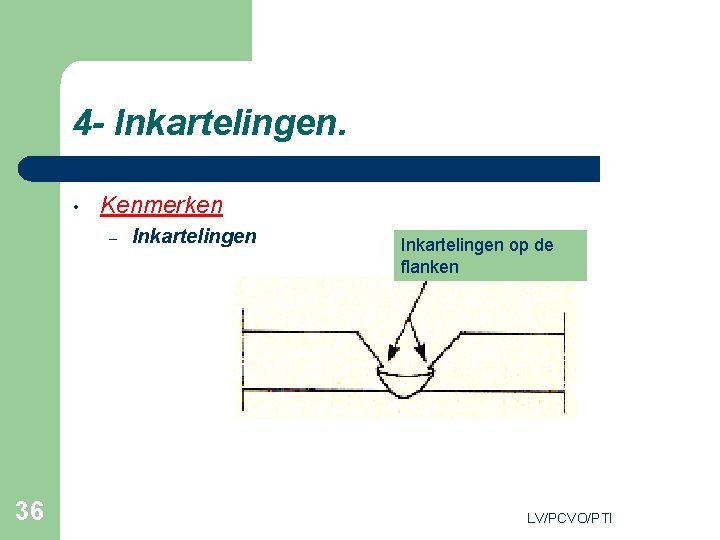
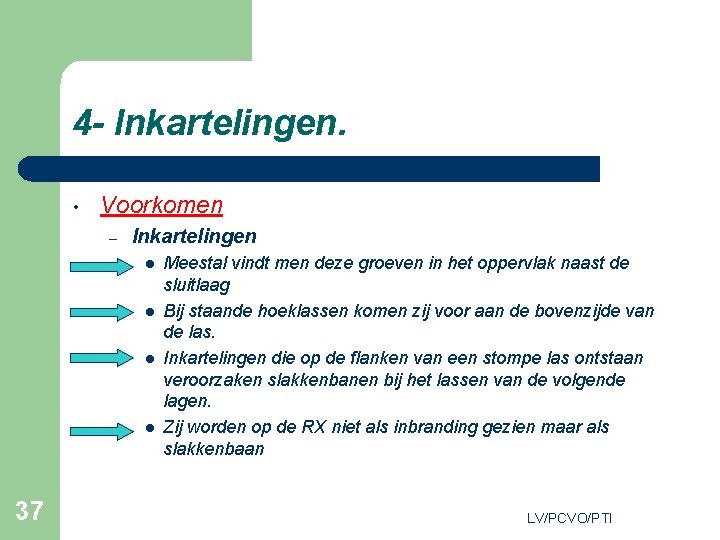
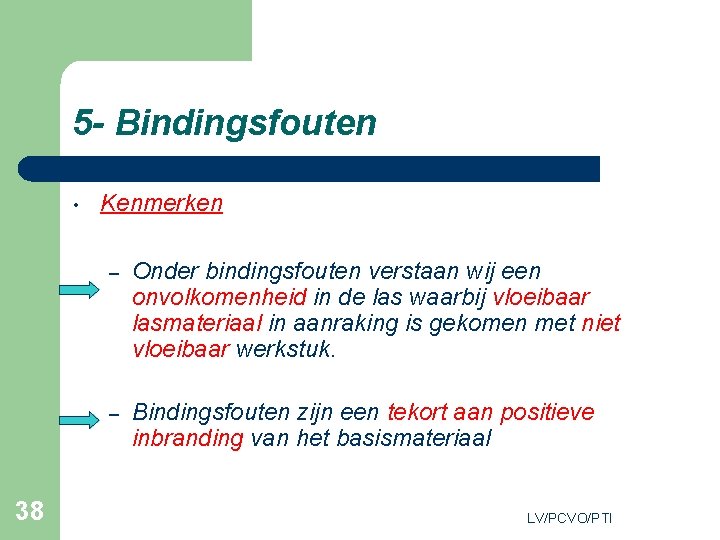
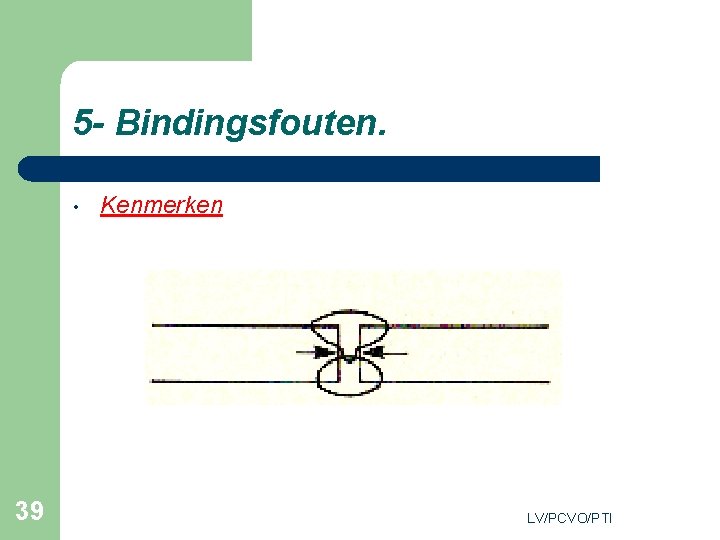
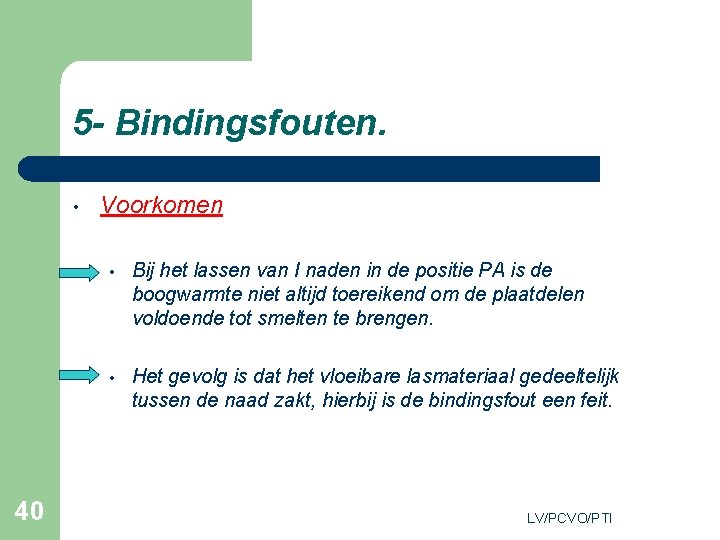
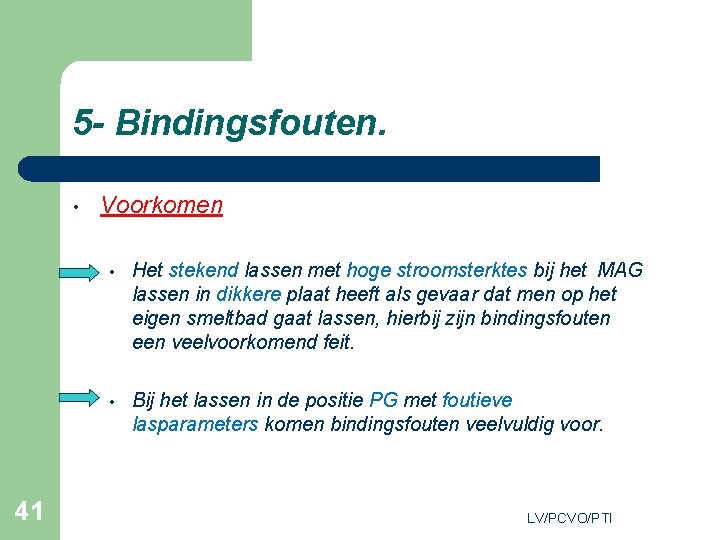
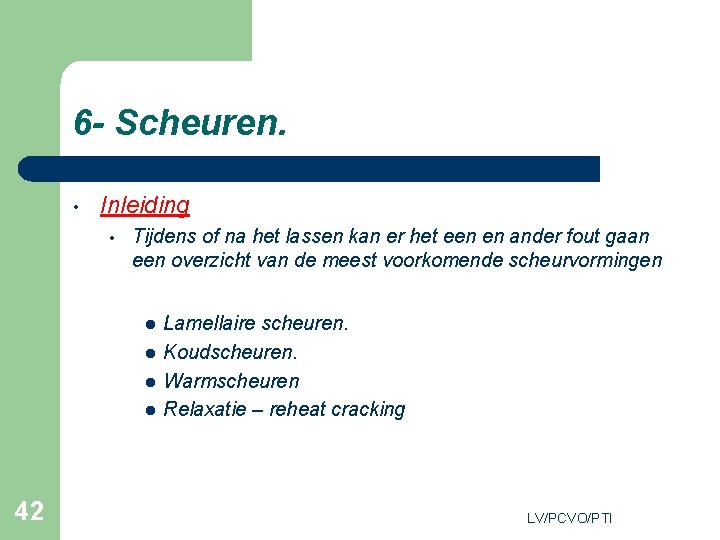
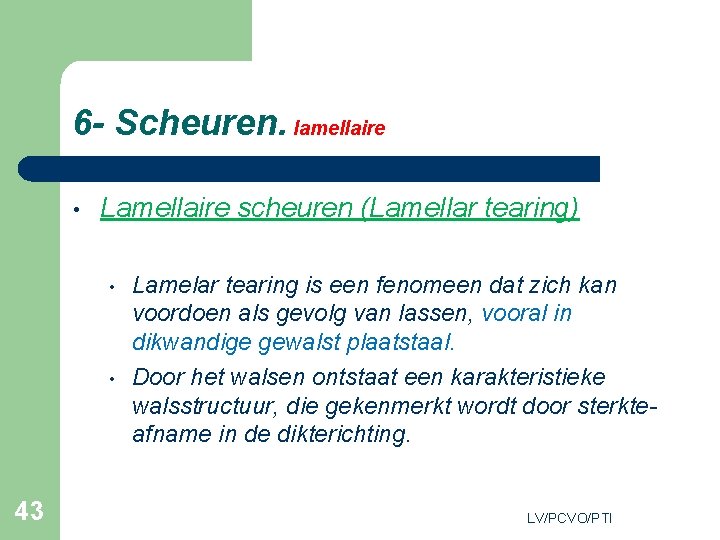
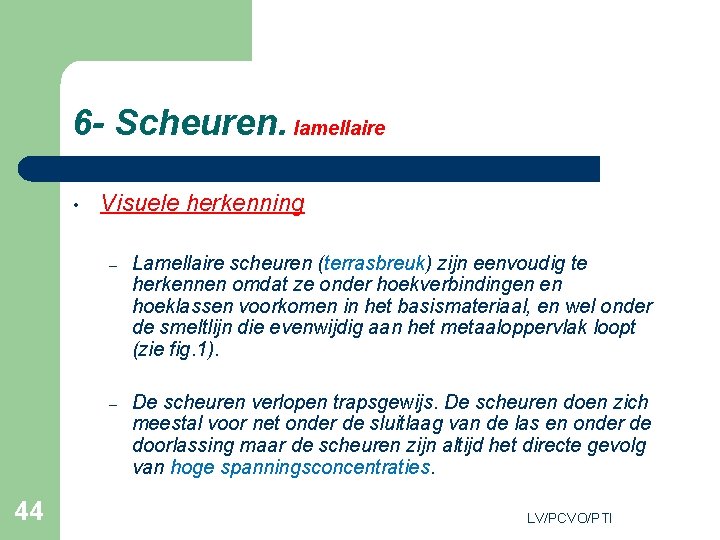
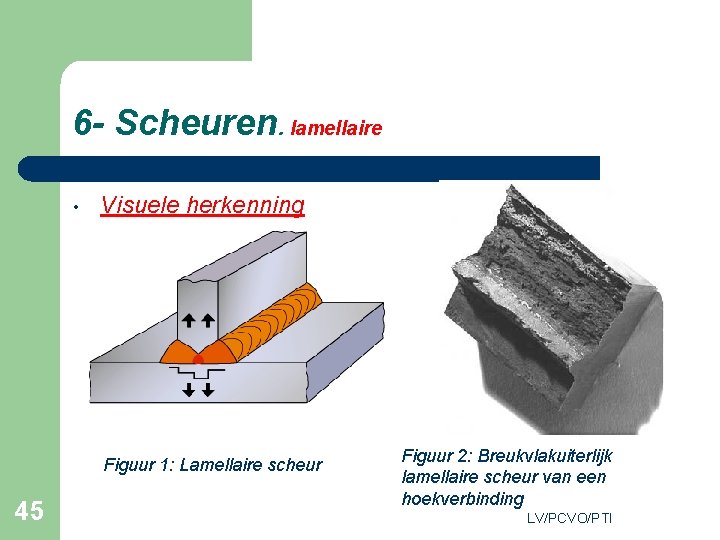
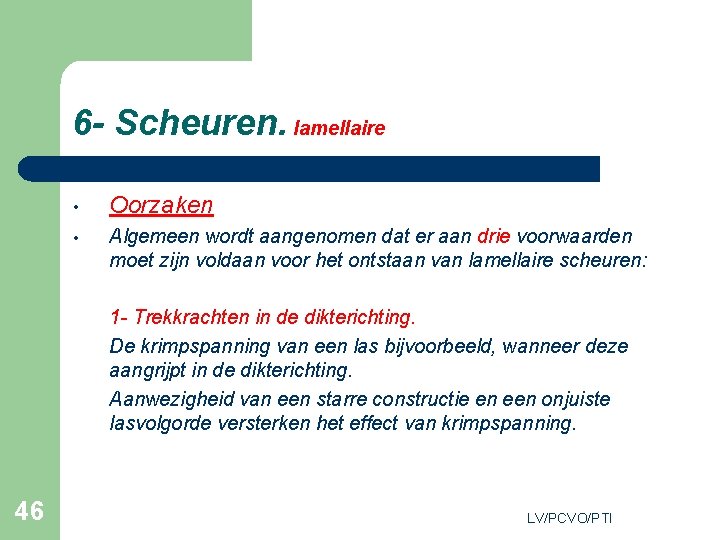
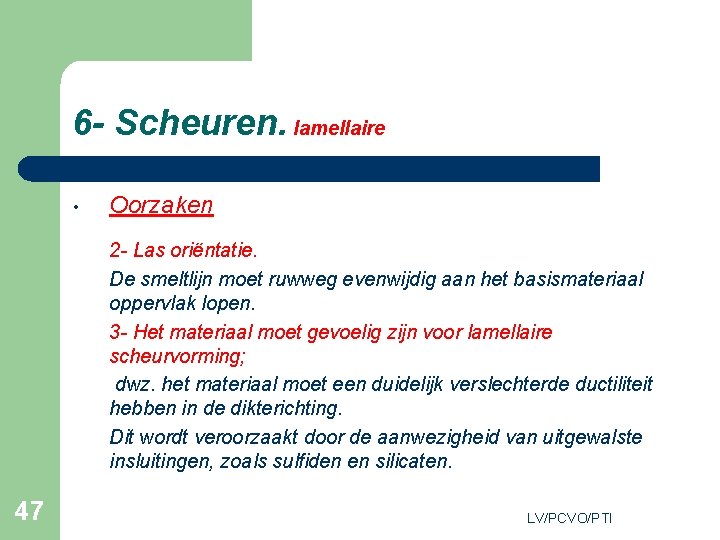
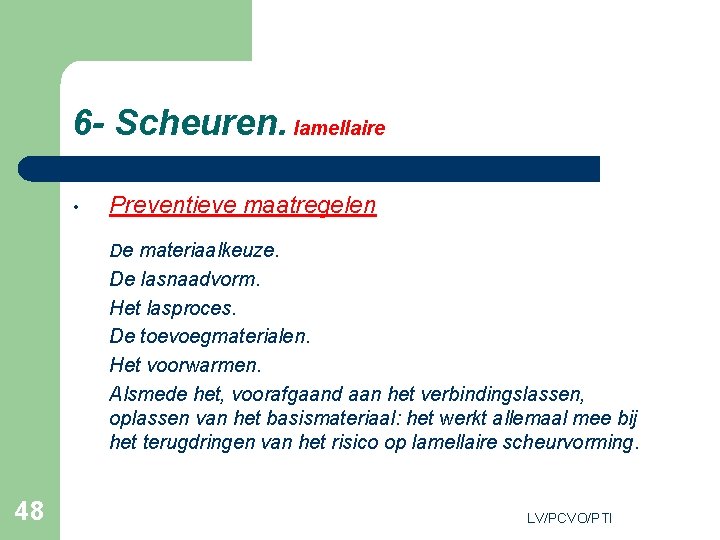
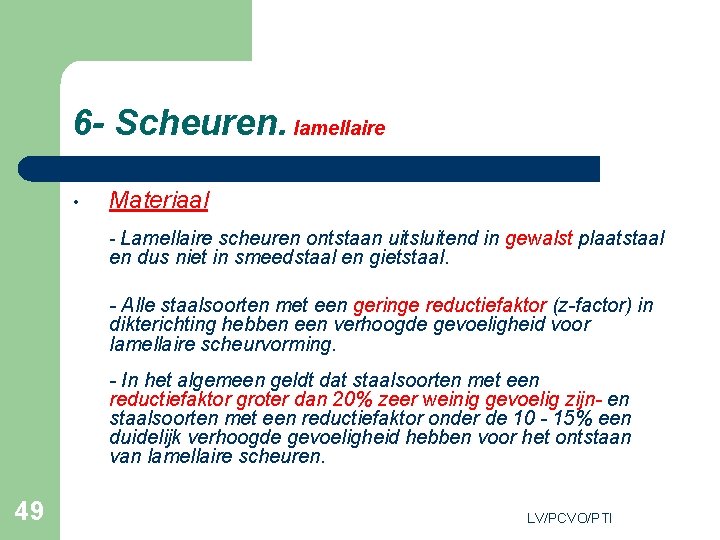
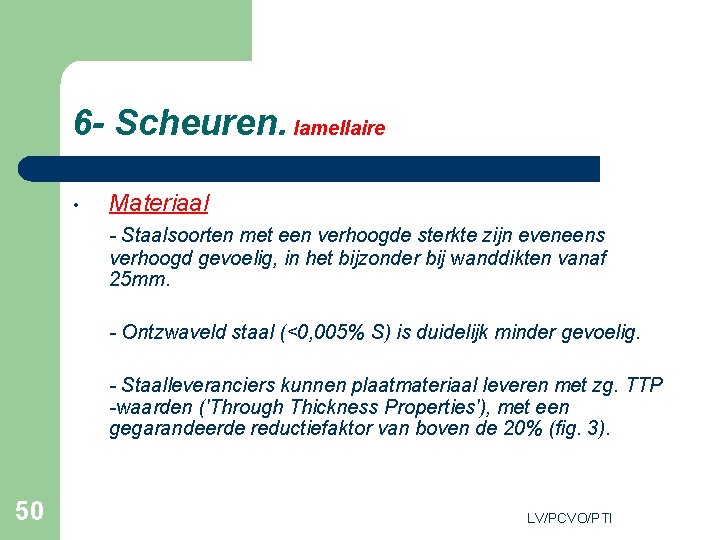
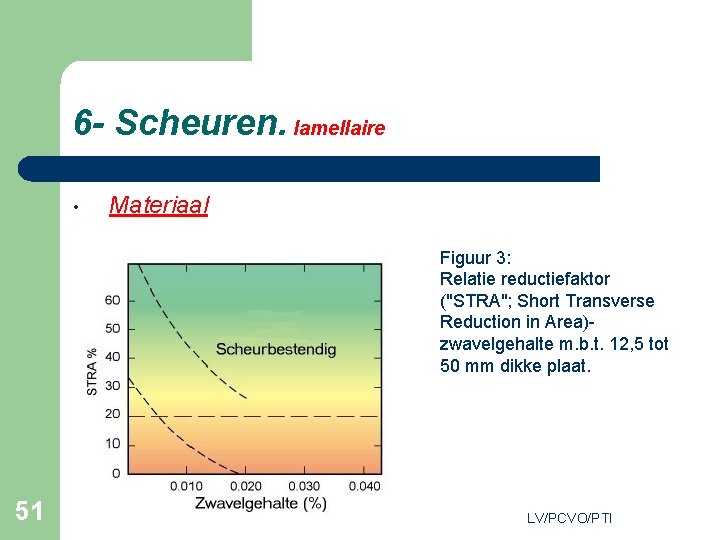
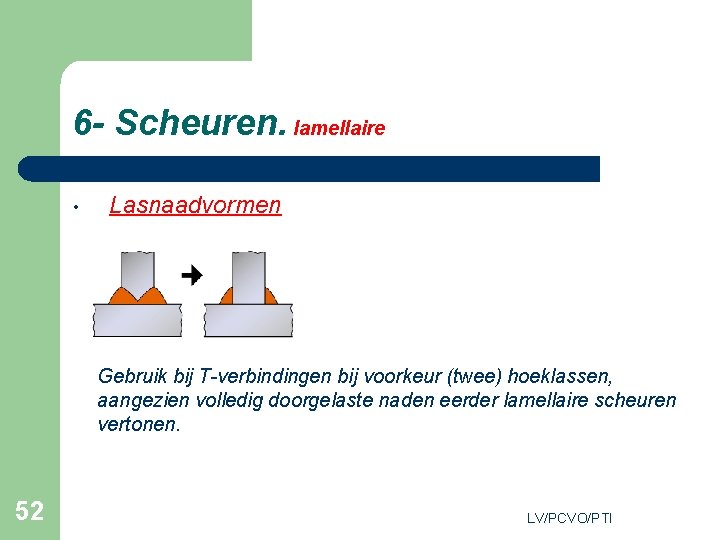
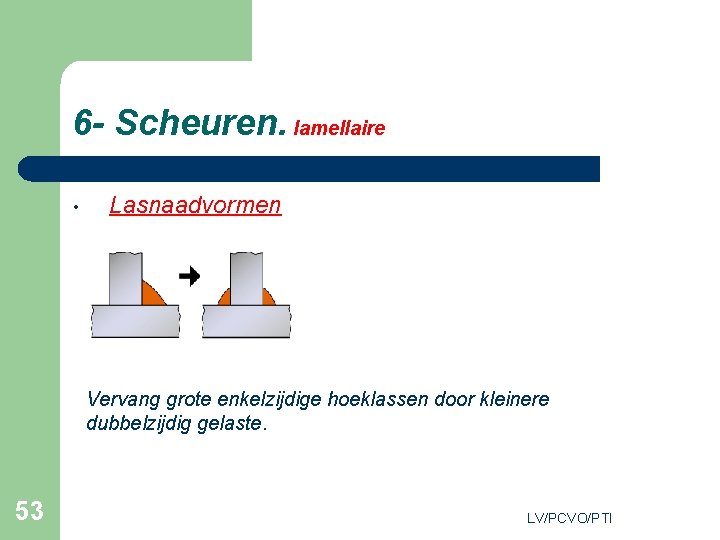
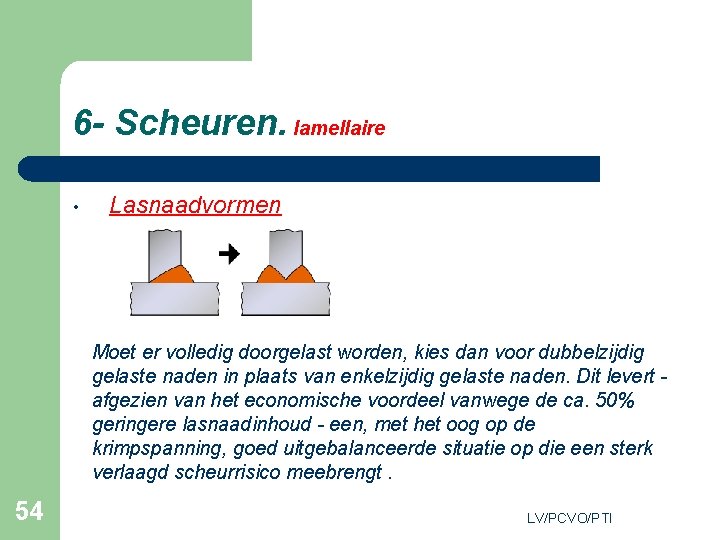
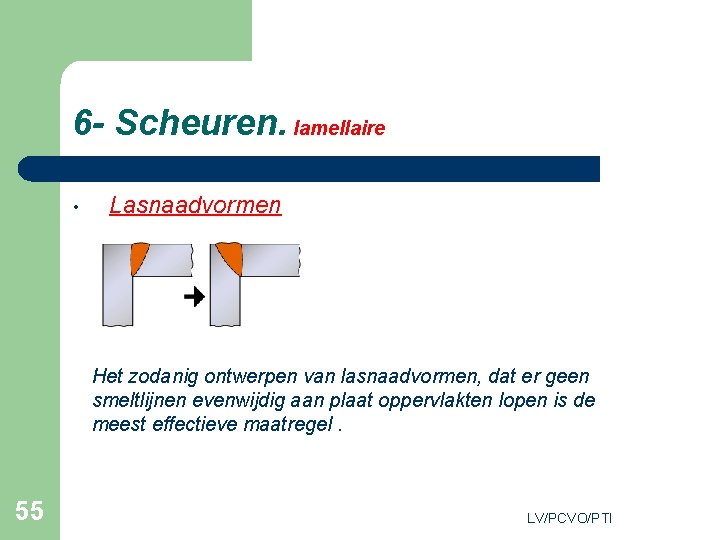

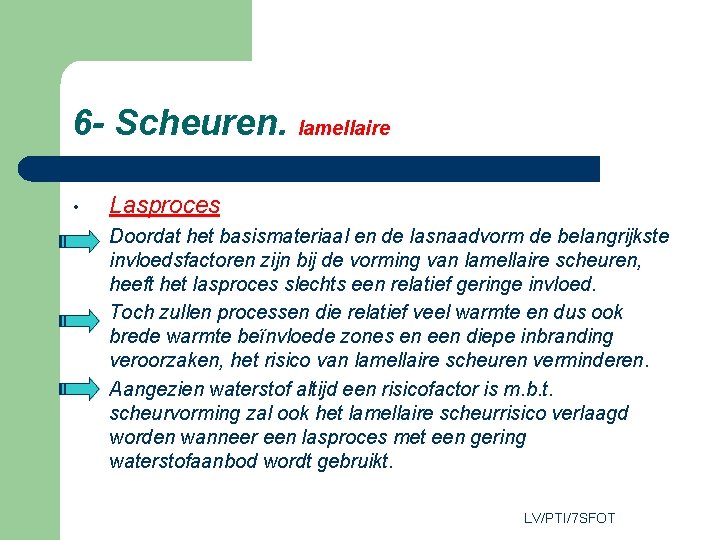
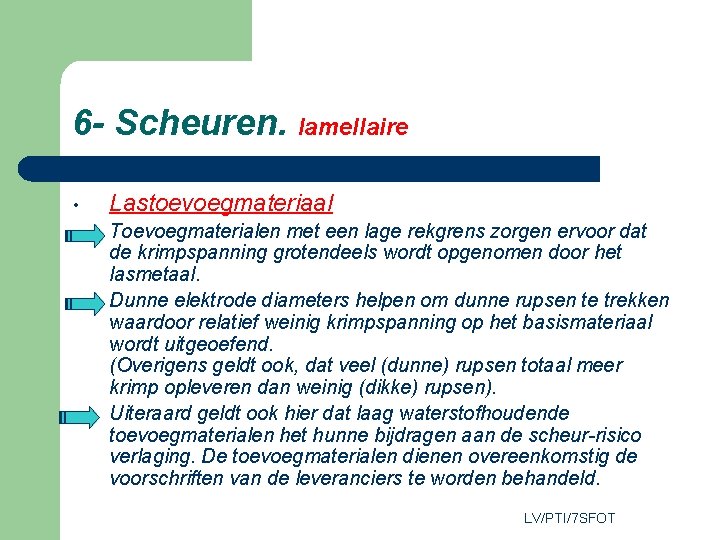
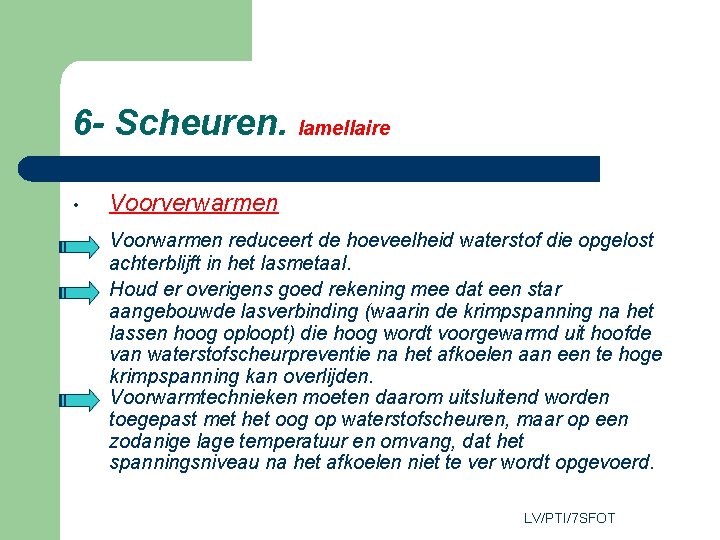
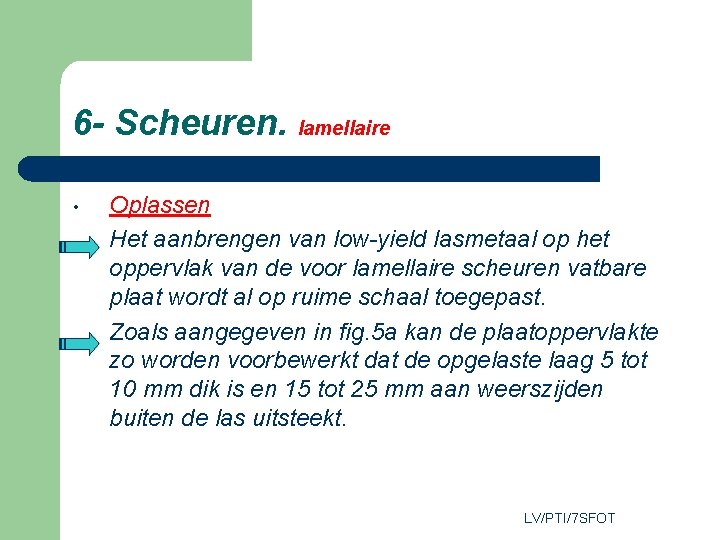
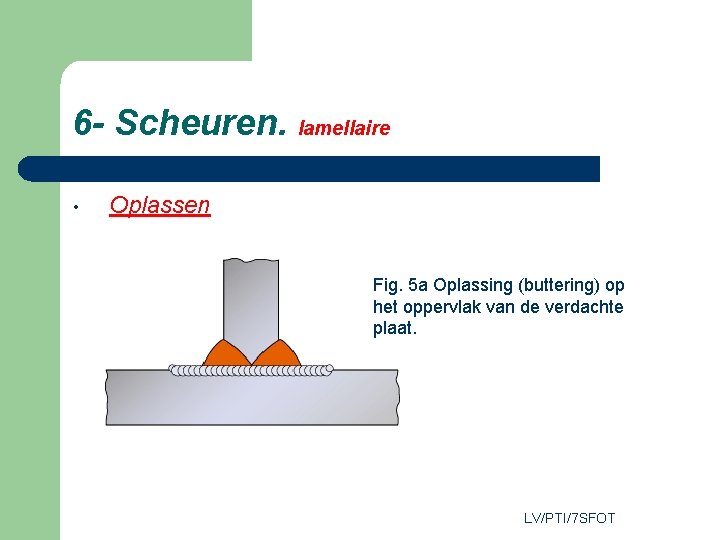
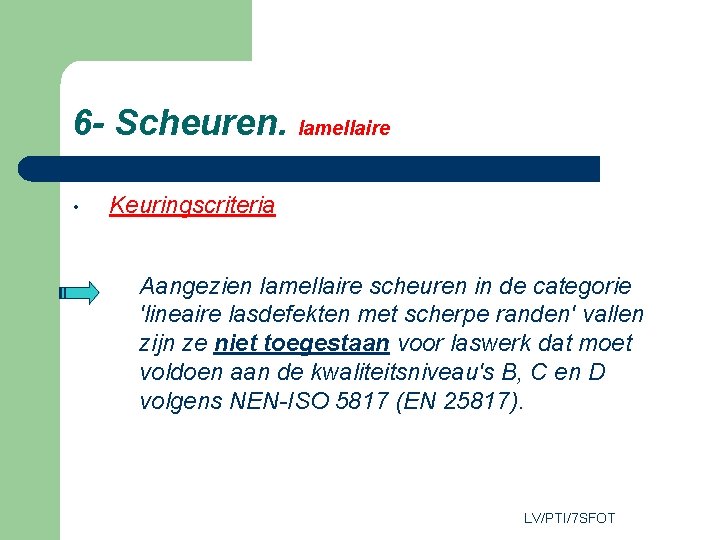
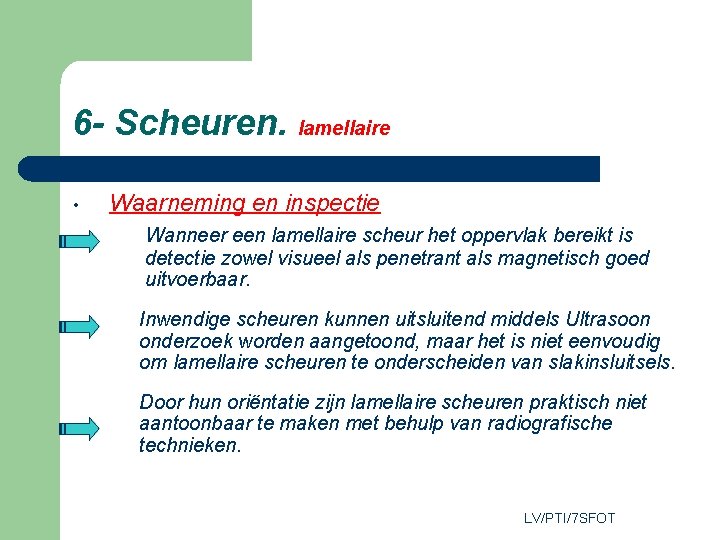
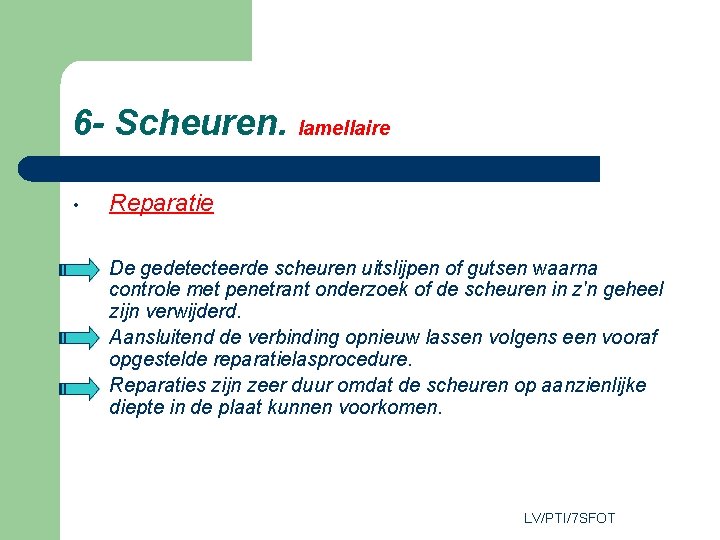
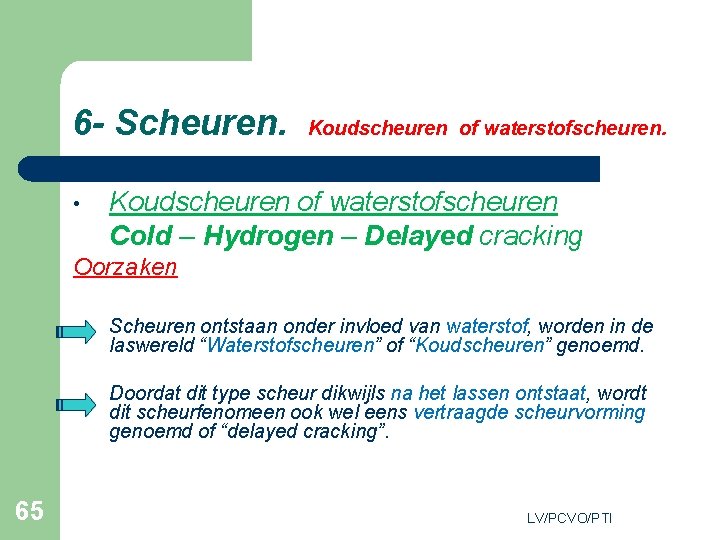
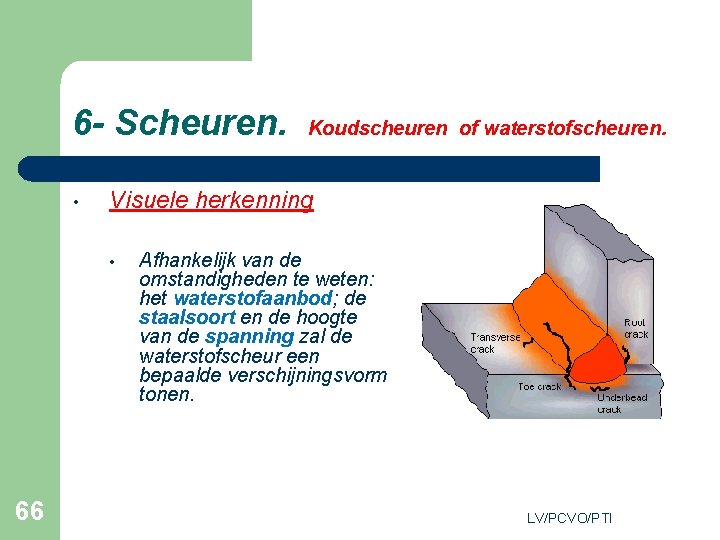
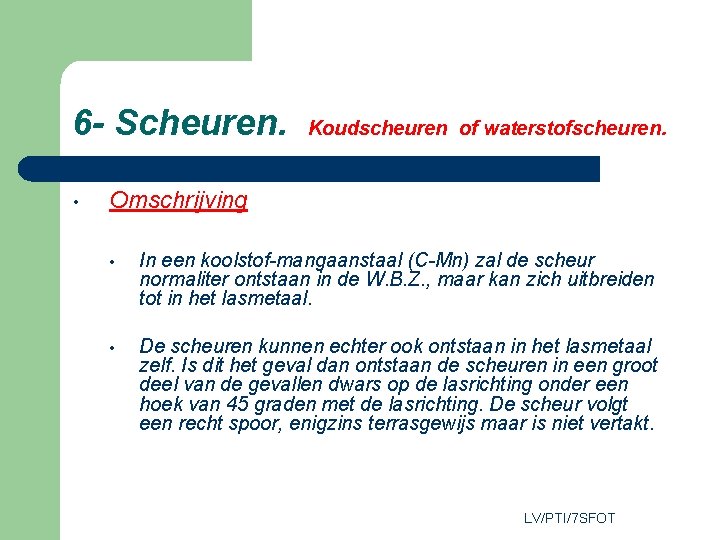
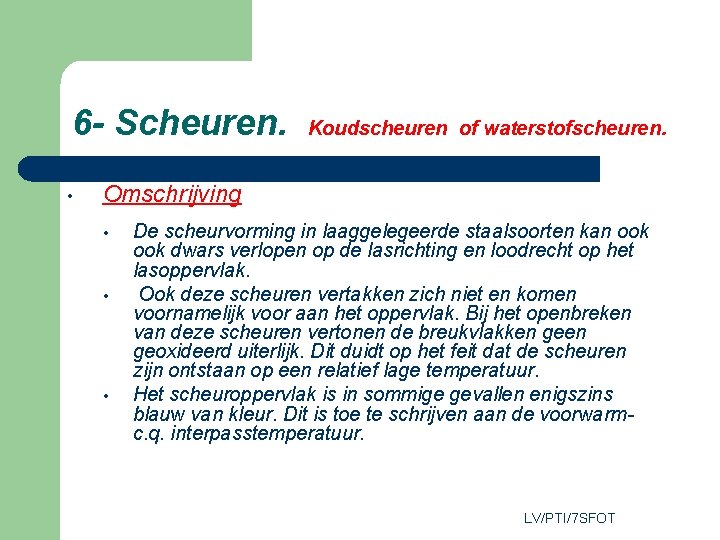
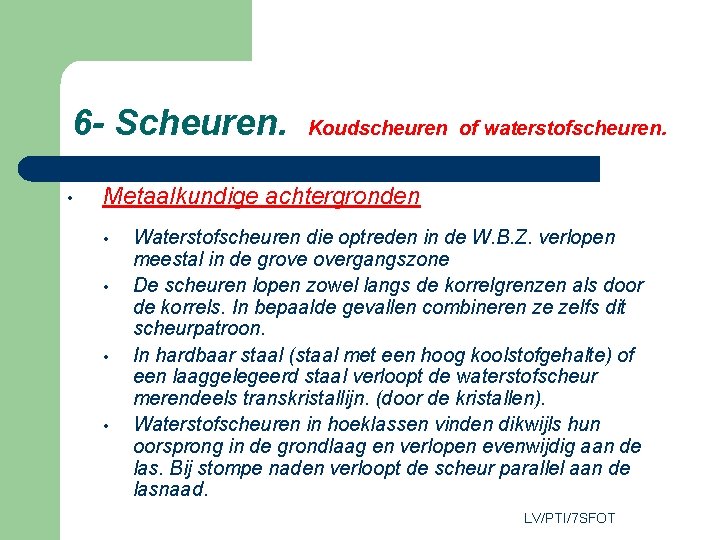
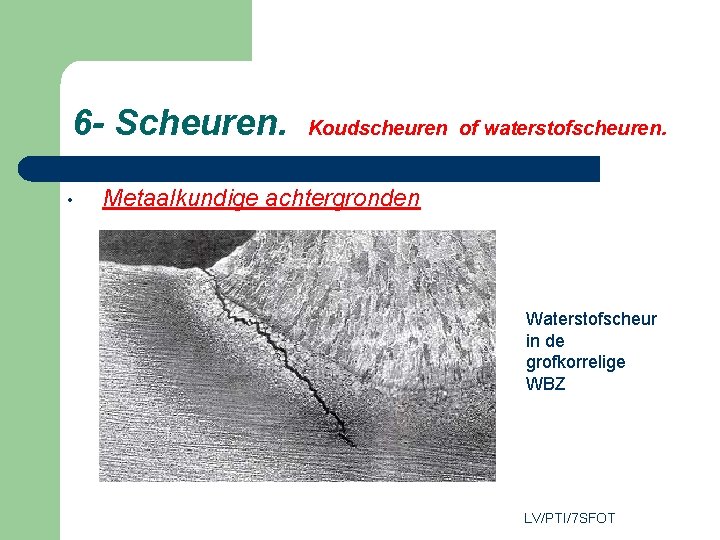
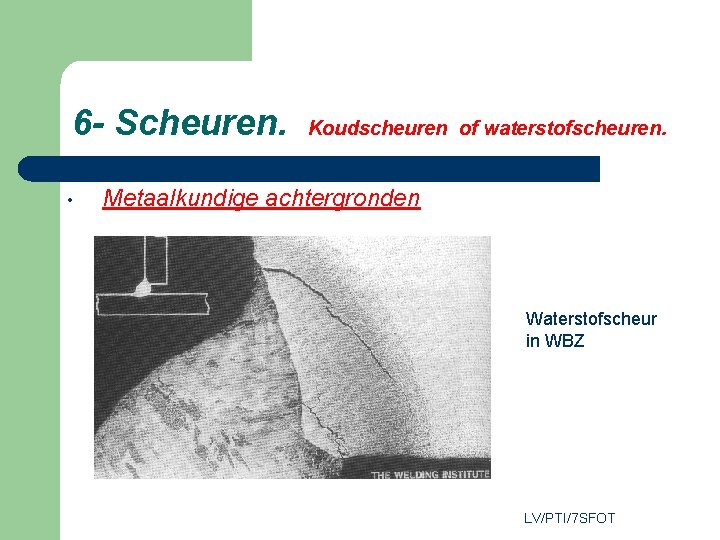
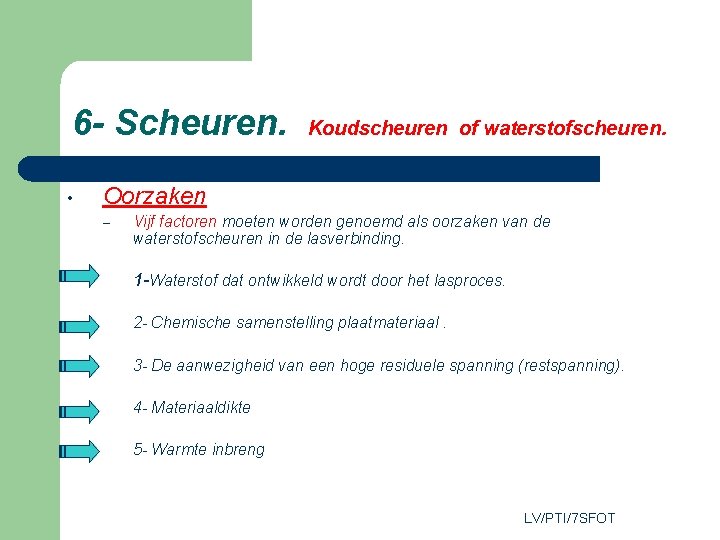
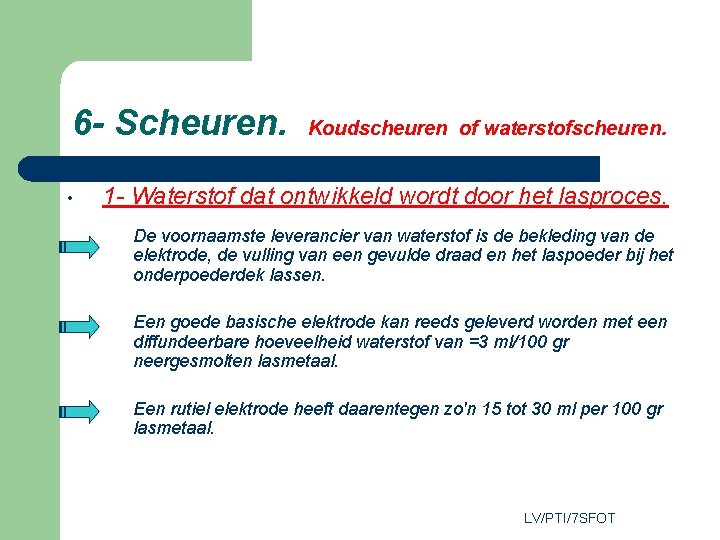
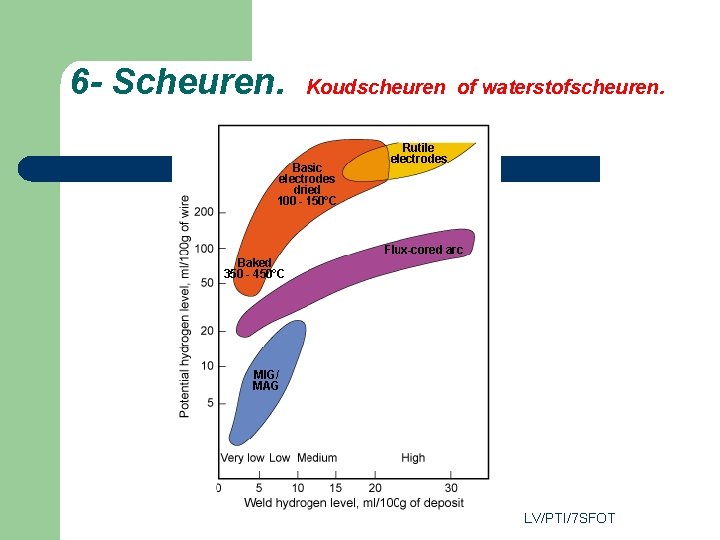
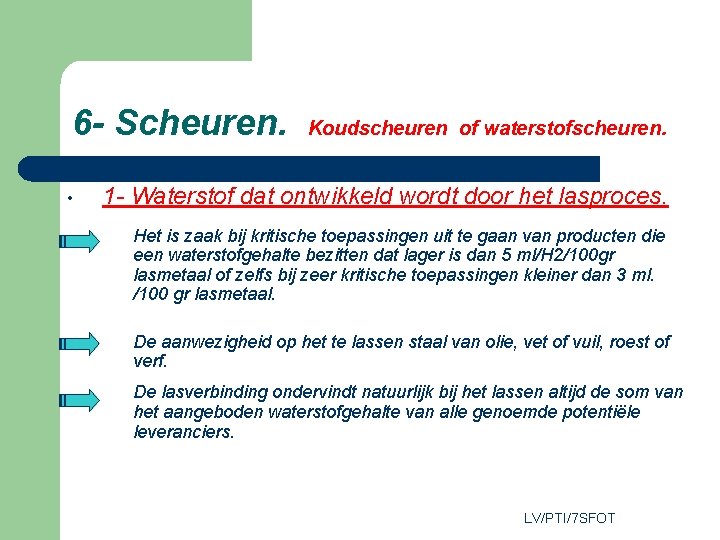
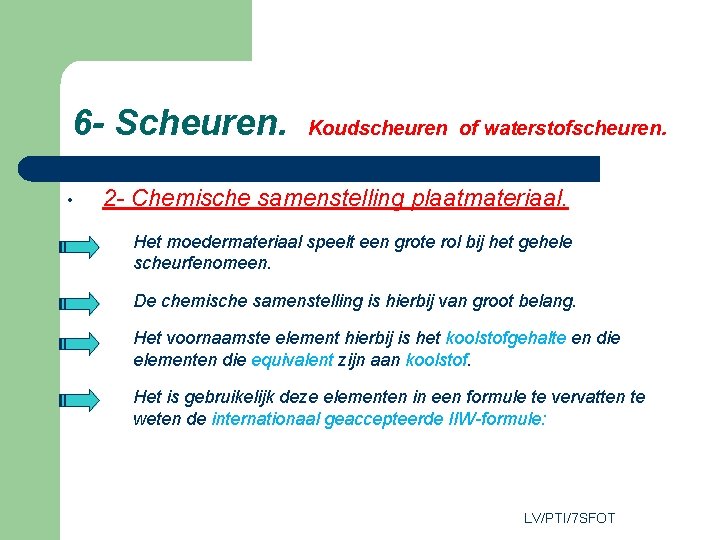
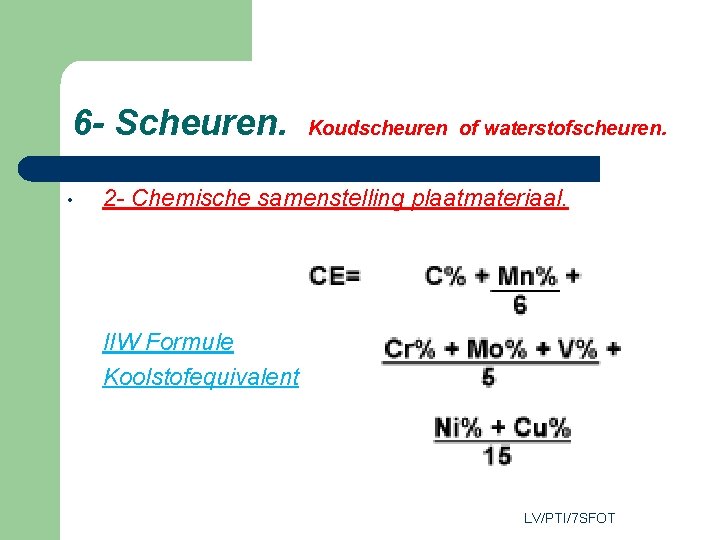
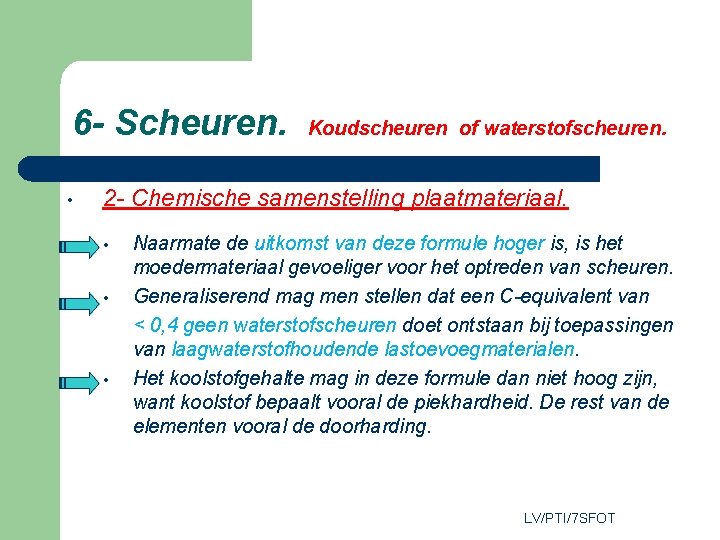
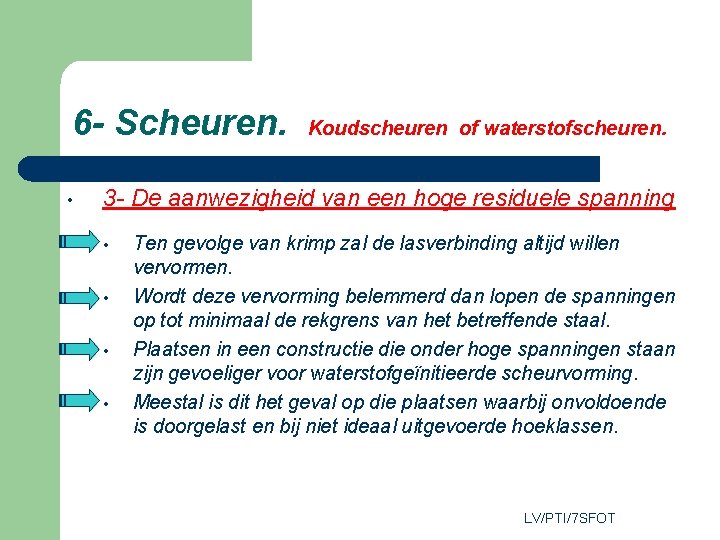
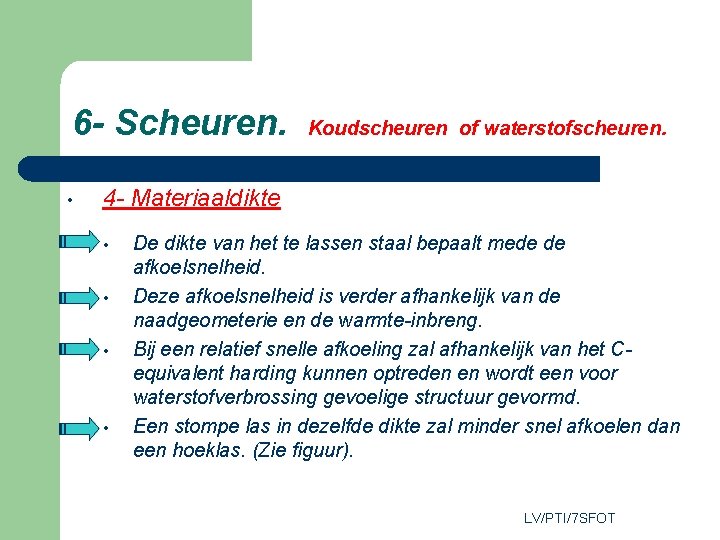
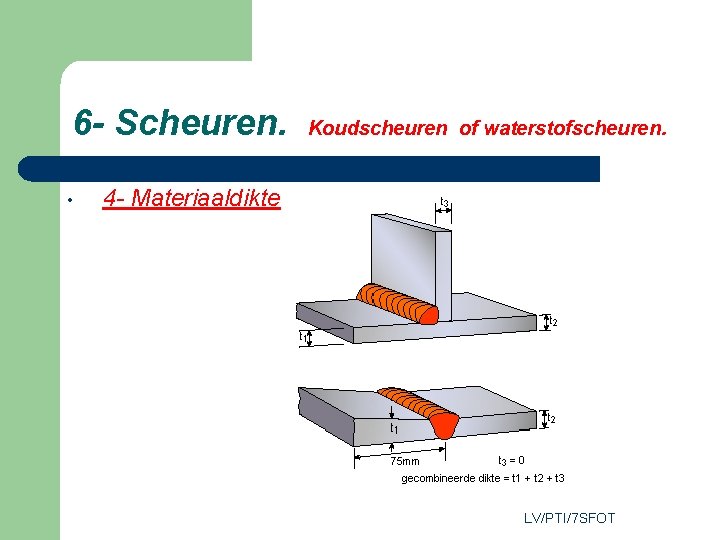
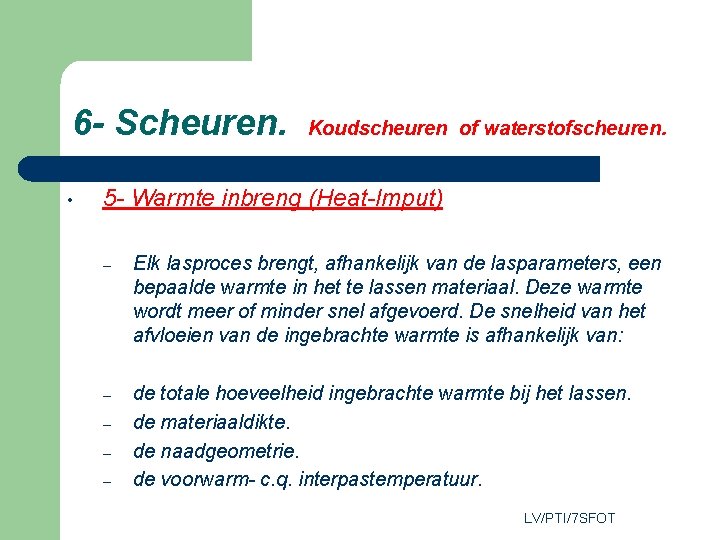
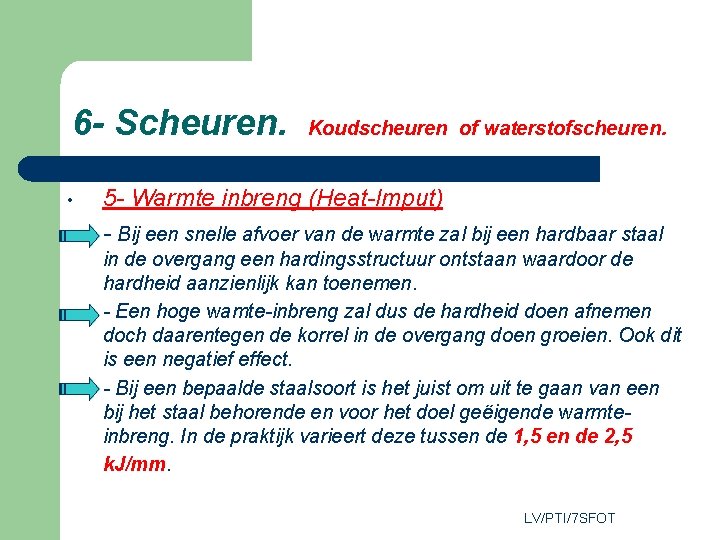
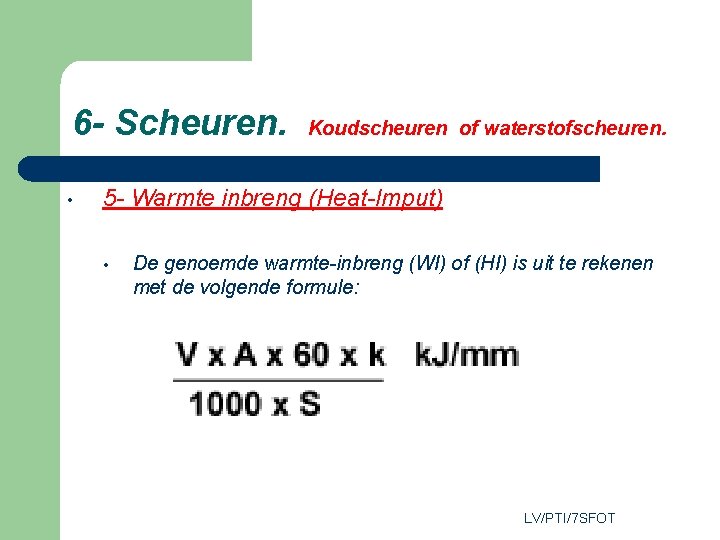
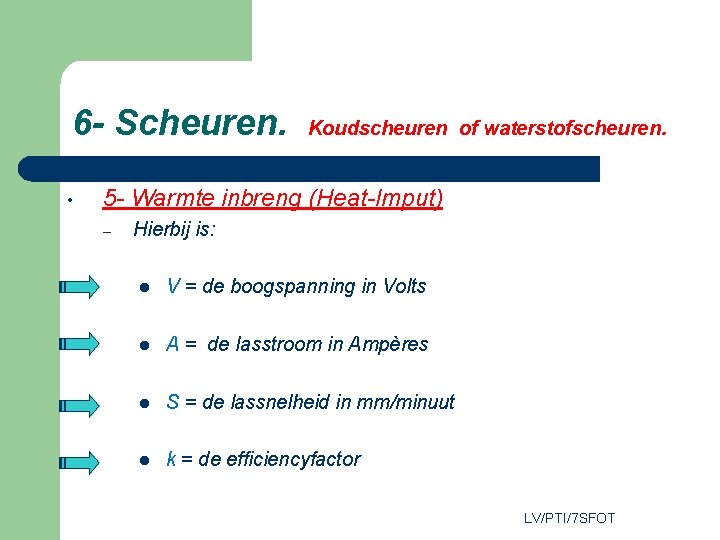
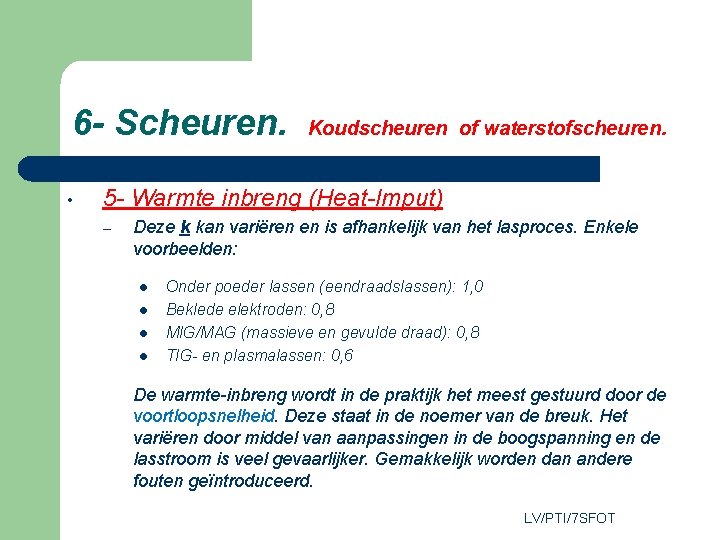
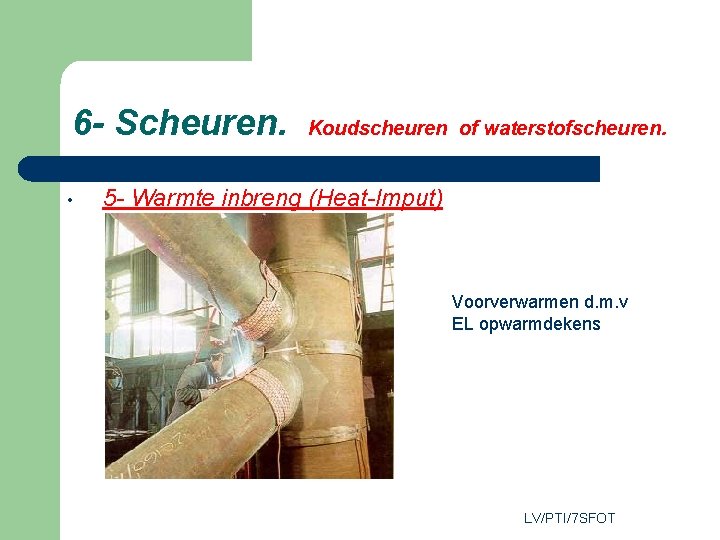

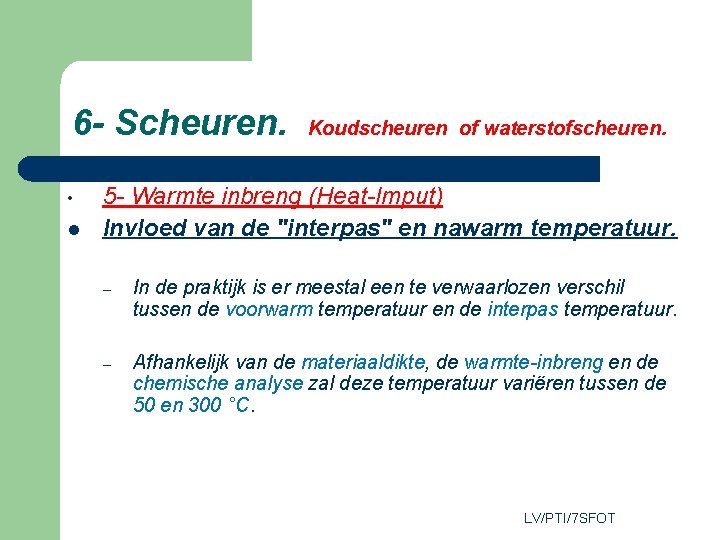
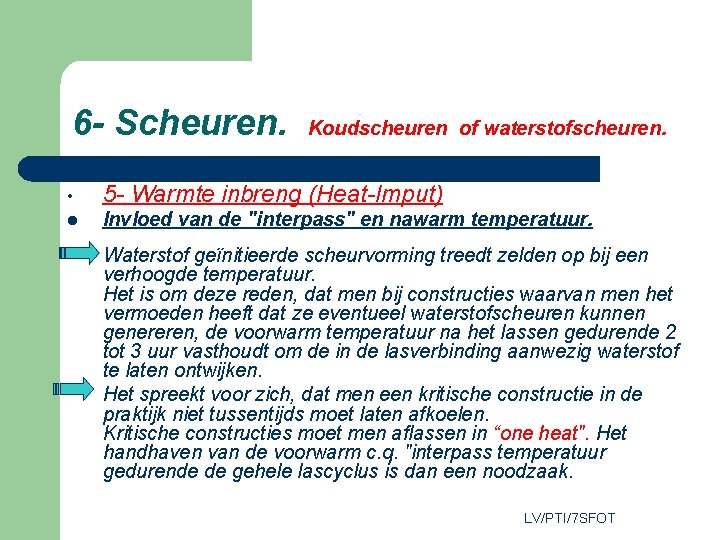
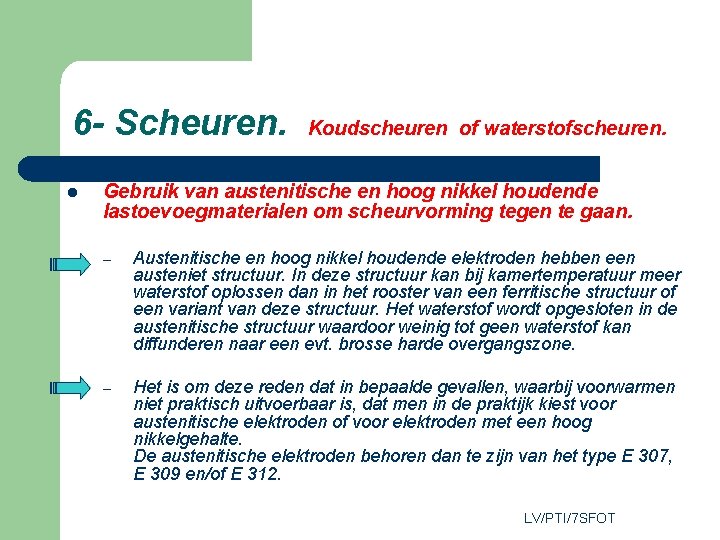
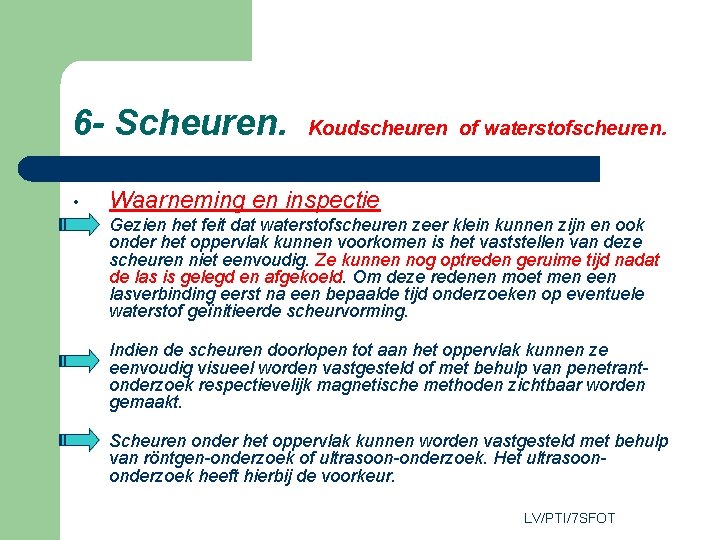
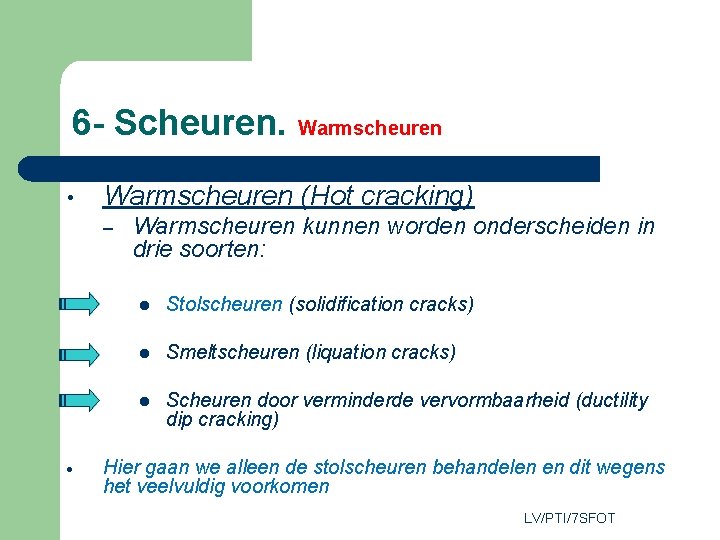
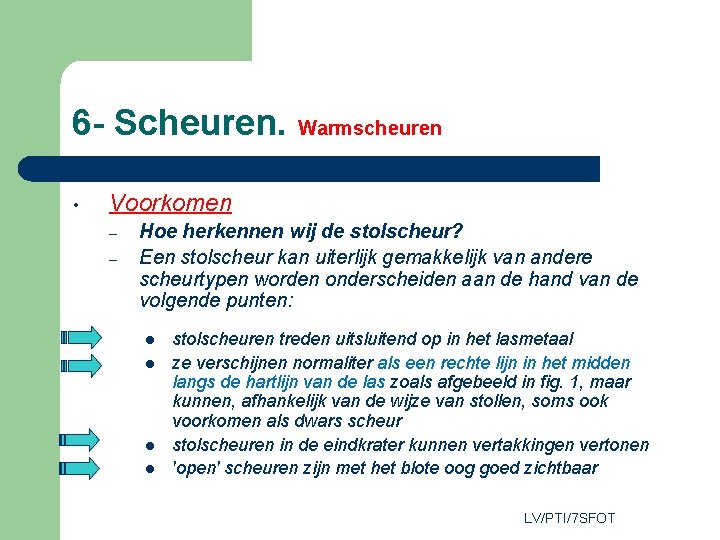
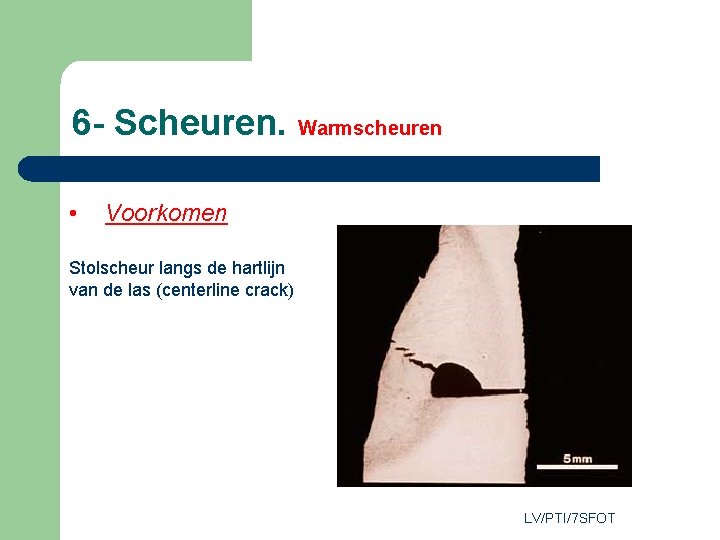
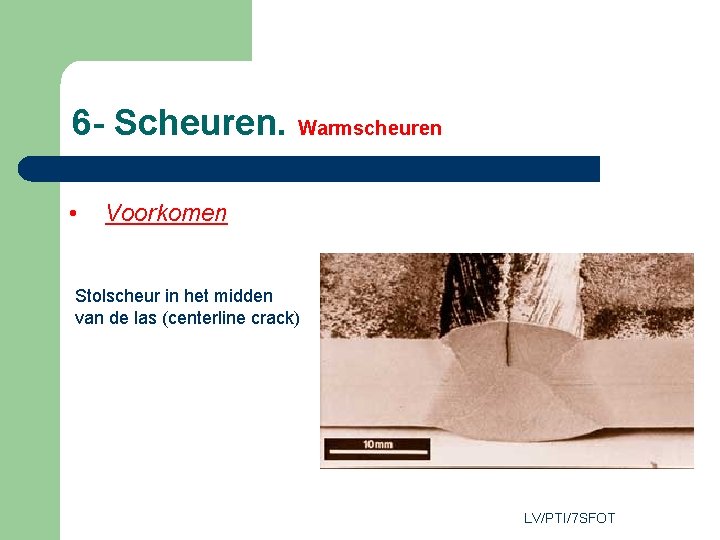
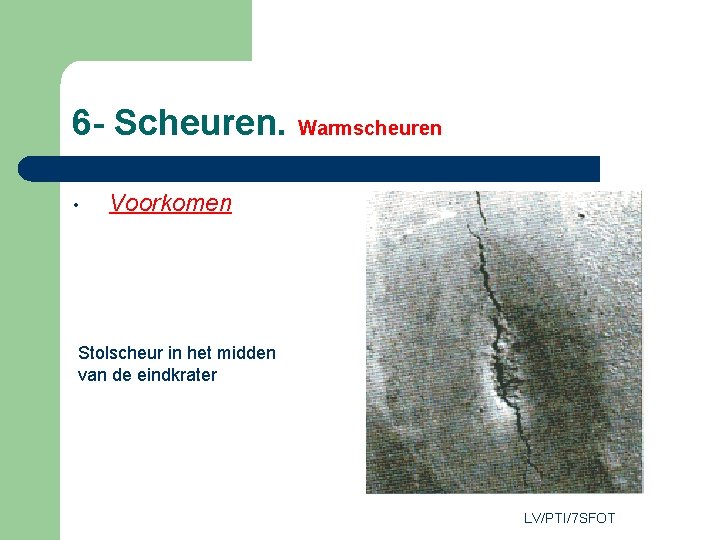

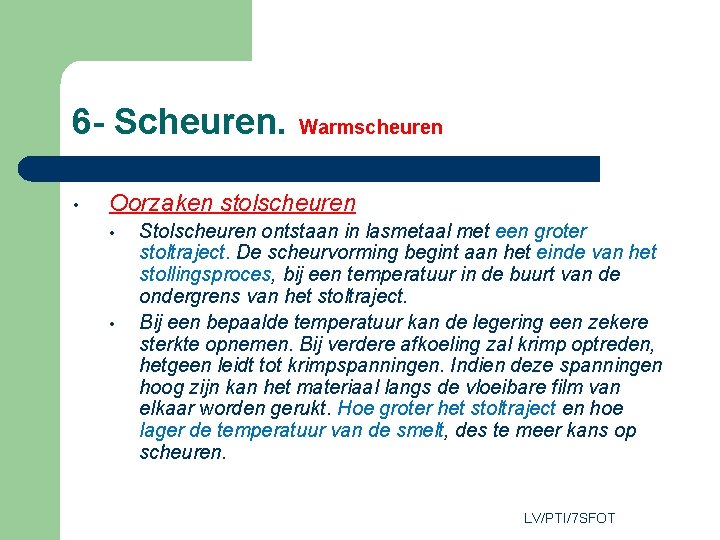
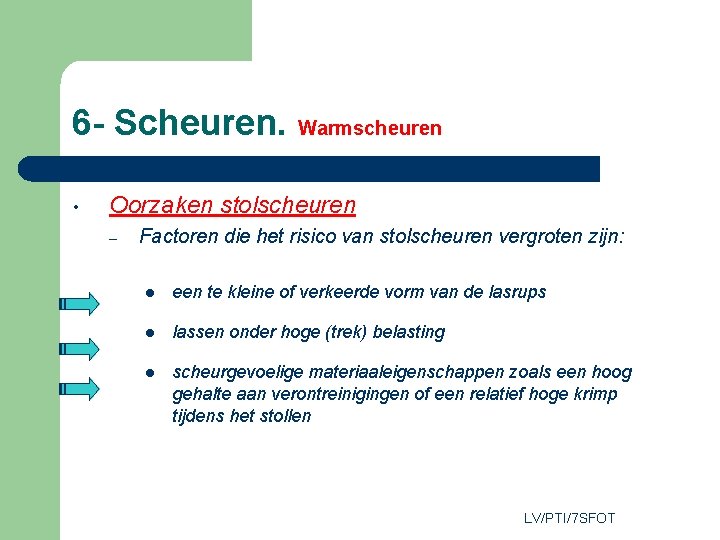
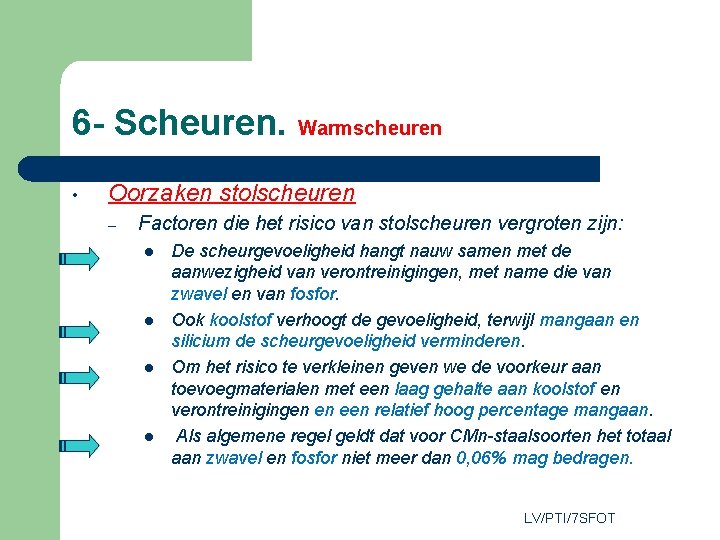
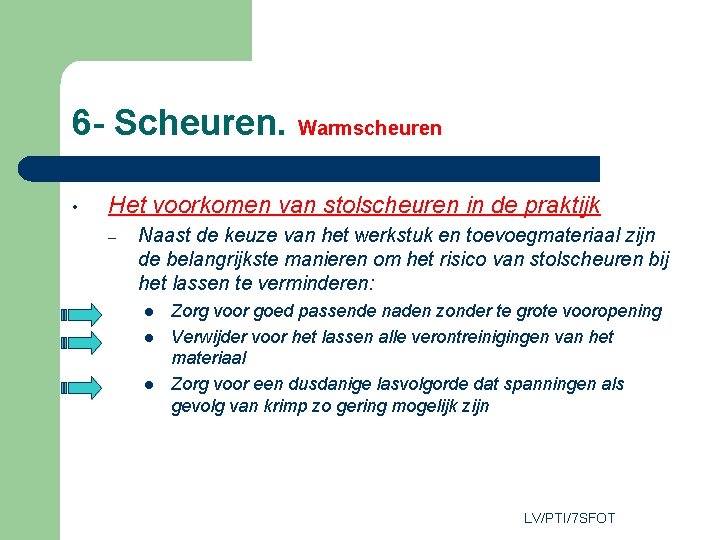
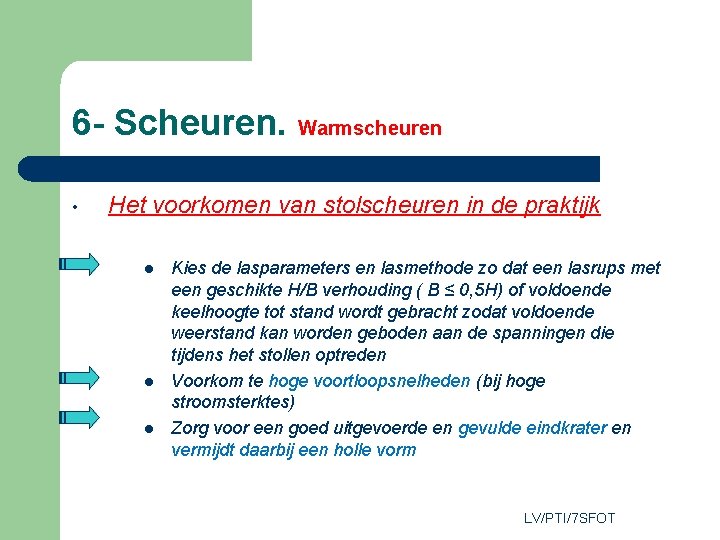
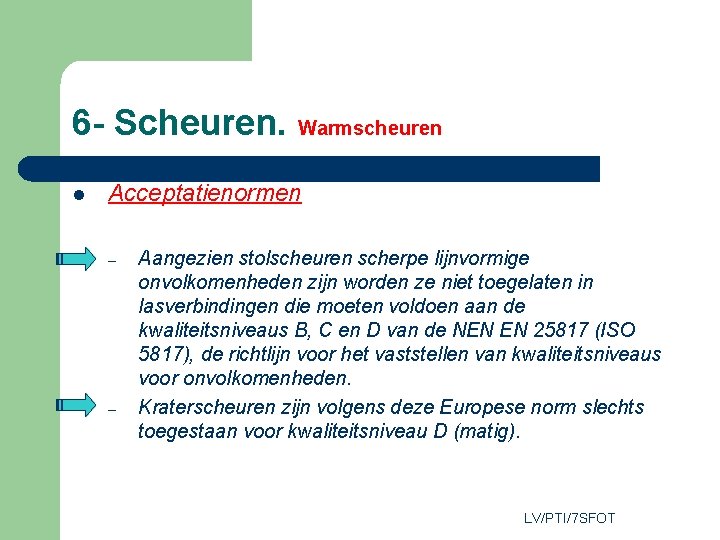
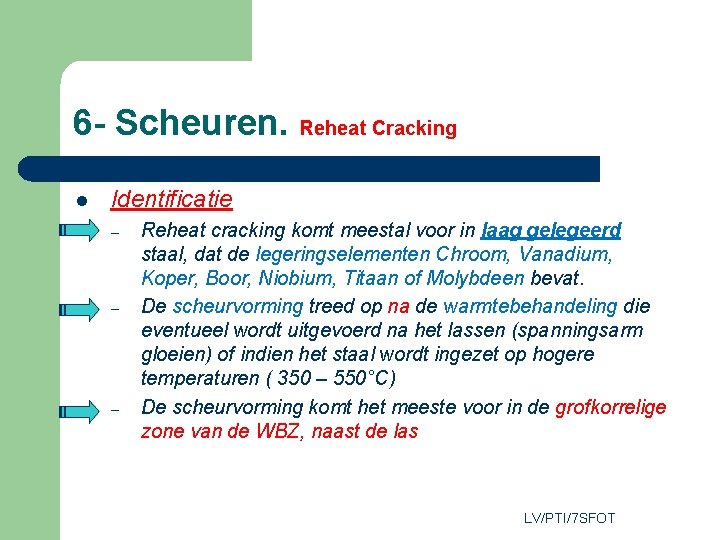
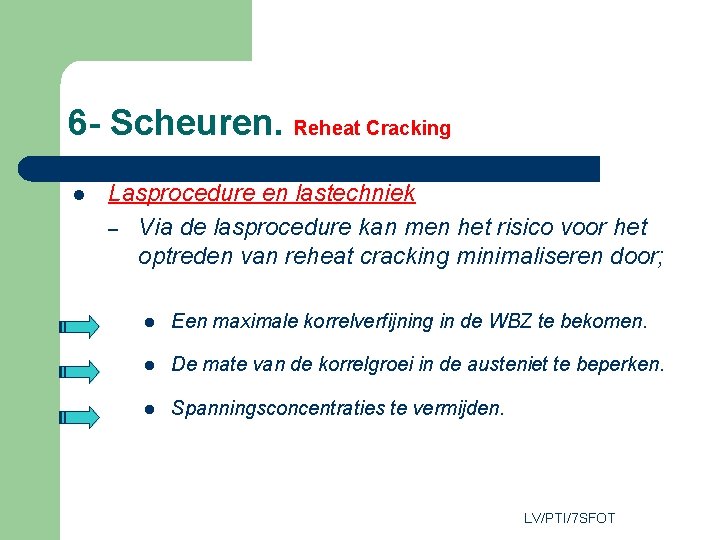
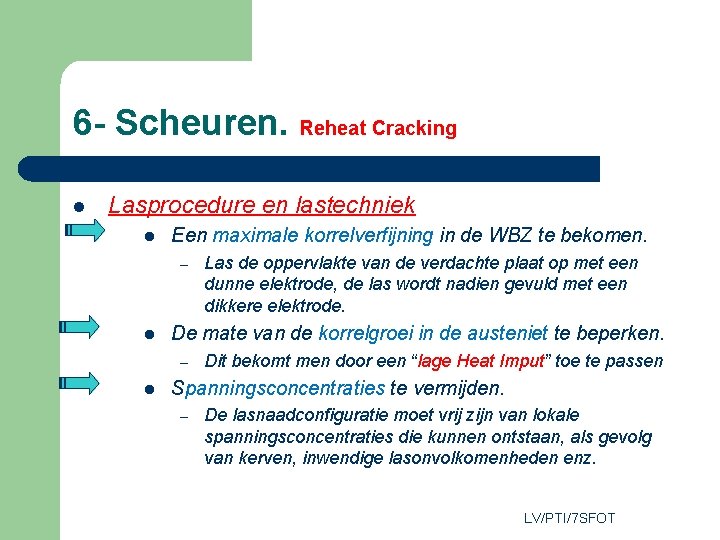
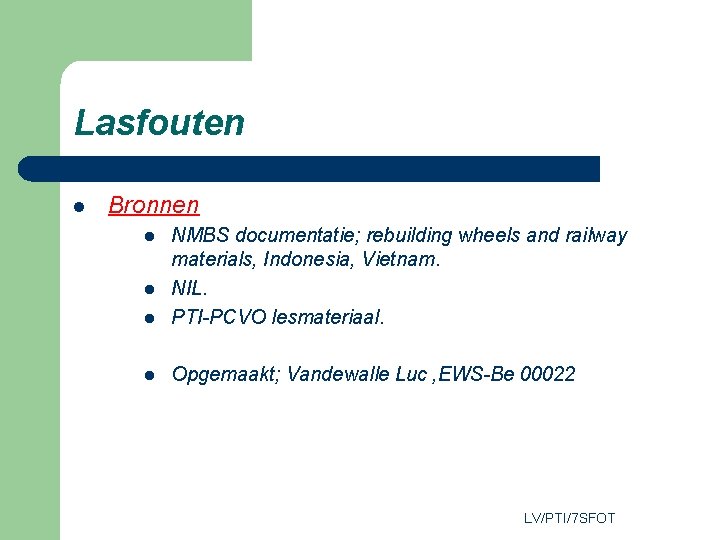
- Slides: 108
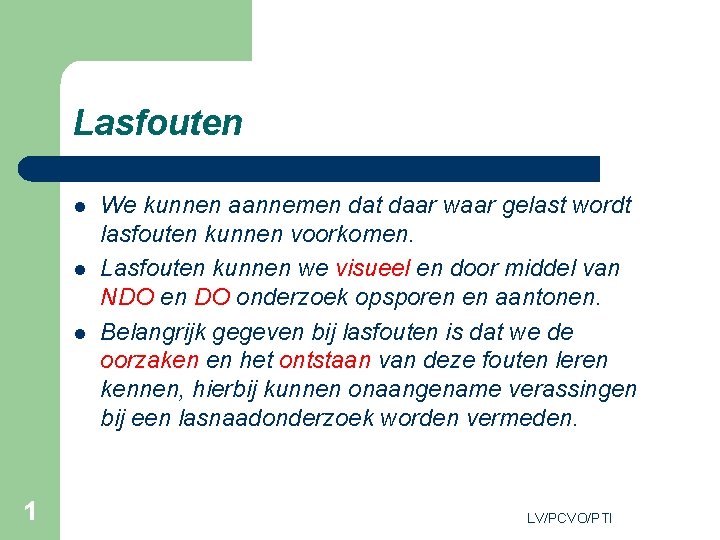
Lasfouten l l l 1 We kunnen aannemen dat daar waar gelast wordt lasfouten kunnen voorkomen. Lasfouten kunnen we visueel en door middel van NDO en DO onderzoek opsporen en aantonen. Belangrijk gegeven bij lasfouten is dat we de oorzaken en het ontstaan van deze fouten leren kennen, hierbij kunnen onaangename verassingen bij een lasnaadonderzoek worden vermeden. LV/PCVO/PTI
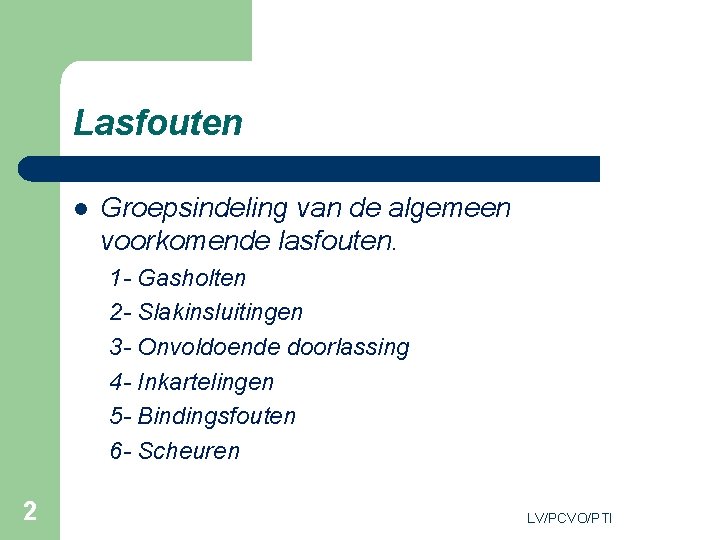
Lasfouten l Groepsindeling van de algemeen voorkomende lasfouten. 1 - Gasholten 2 - Slakinsluitingen 3 - Onvoldoende doorlassing 4 - Inkartelingen 5 - Bindingsfouten 6 - Scheuren 2 LV/PCVO/PTI
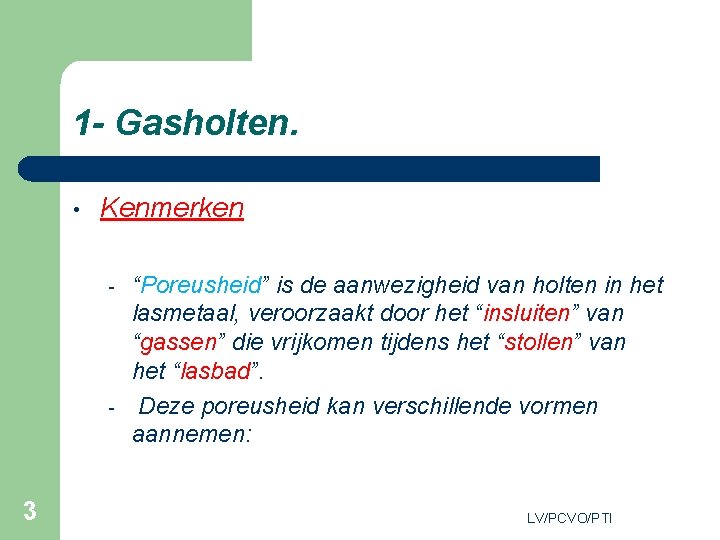
1 - Gasholten. • Kenmerken - - 3 “Poreusheid” is de aanwezigheid van holten in het lasmetaal, veroorzaakt door het “insluiten” van “gassen” die vrijkomen tijdens het “stollen” van het “lasbad”. Deze poreusheid kan verschillende vormen aannemen: LV/PCVO/PTI
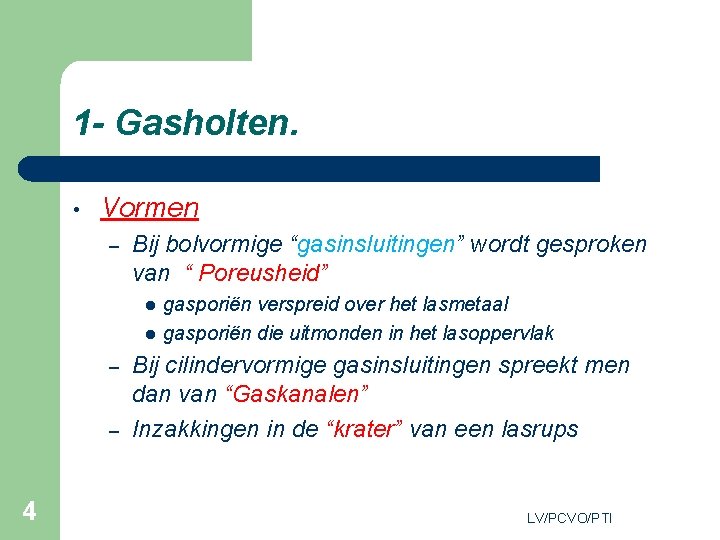
1 - Gasholten. • Vormen – Bij bolvormige “gasinsluitingen” wordt gesproken van “ Poreusheid” l l – – 4 gasporiën verspreid over het lasmetaal gasporiën die uitmonden in het lasoppervlak Bij cilindervormige gasinsluitingen spreekt men dan van “Gaskanalen” Inzakkingen in de “krater” van een lasrups LV/PCVO/PTI
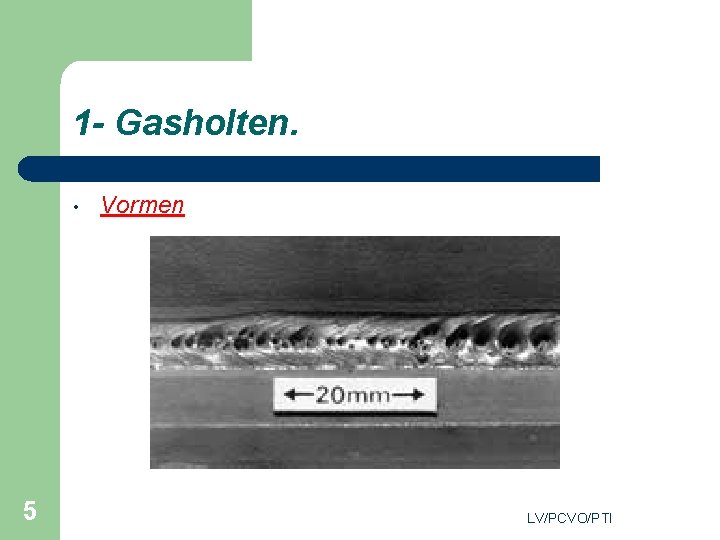
1 - Gasholten. • 5 Vormen LV/PCVO/PTI
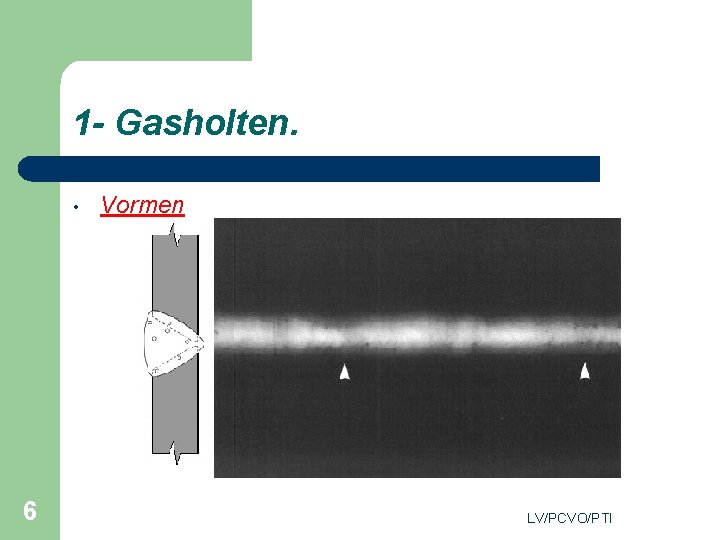
1 - Gasholten. • 6 Vormen LV/PCVO/PTI
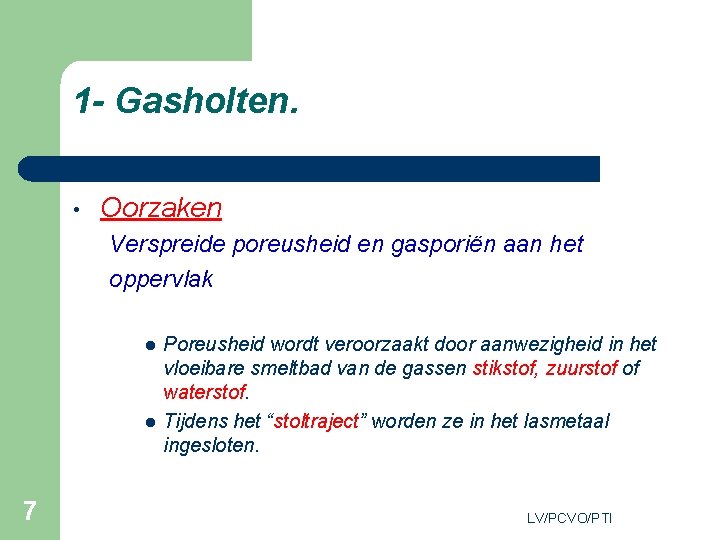
1 - Gasholten. • Oorzaken Verspreide poreusheid en gasporiën aan het oppervlak l l 7 Poreusheid wordt veroorzaakt door aanwezigheid in het vloeibare smeltbad van de gassen stikstof, zuurstof of waterstof. Tijdens het “stoltraject” worden ze in het lasmetaal ingesloten. LV/PCVO/PTI
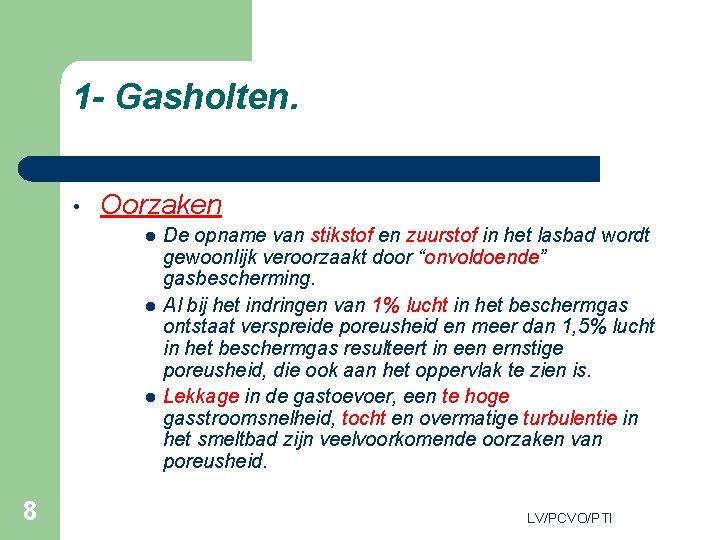
1 - Gasholten. • Oorzaken l l l 8 De opname van stikstof en zuurstof in het lasbad wordt gewoonlijk veroorzaakt door “onvoldoende” gasbescherming. Al bij het indringen van 1% lucht in het beschermgas ontstaat verspreide poreusheid en meer dan 1, 5% lucht in het beschermgas resulteert in een ernstige poreusheid, die ook aan het oppervlak te zien is. Lekkage in de gastoevoer, een te hoge gasstroomsnelheid, tocht en overmatige turbulentie in het smeltbad zijn veelvoorkomende oorzaken van poreusheid. LV/PCVO/PTI
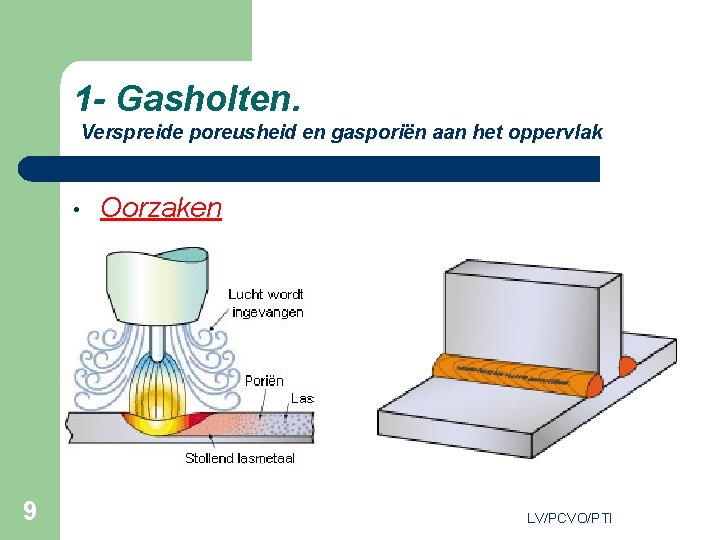
1 - Gasholten. Verspreide poreusheid en gasporiën aan het oppervlak • 9 Oorzaken LV/PCVO/PTI
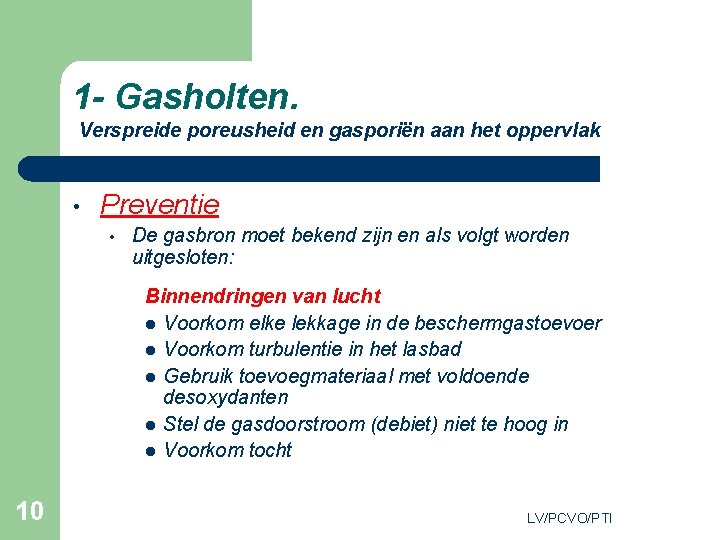
1 - Gasholten. Verspreide poreusheid en gasporiën aan het oppervlak • Preventie • De gasbron moet bekend zijn en als volgt worden uitgesloten: Binnendringen van lucht l Voorkom elke lekkage in de beschermgastoevoer l Voorkom turbulentie in het lasbad l Gebruik toevoegmateriaal met voldoende desoxydanten l Stel de gasdoorstroom (debiet) niet te hoog in l Voorkom tocht 10 LV/PCVO/PTI
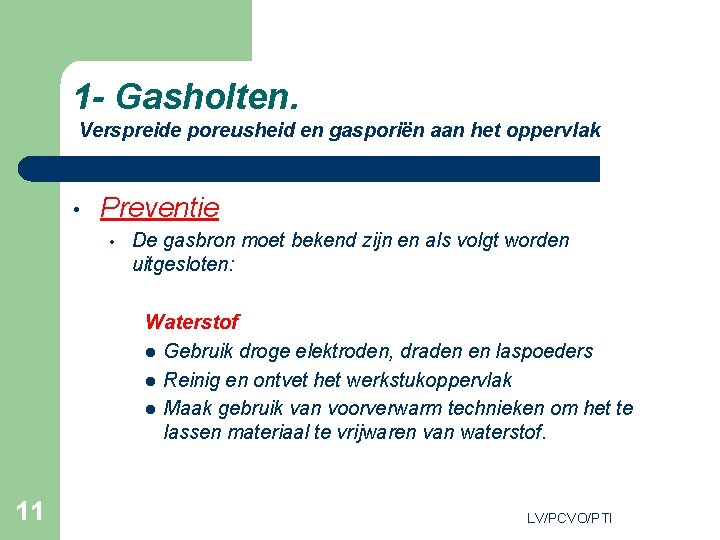
1 - Gasholten. Verspreide poreusheid en gasporiën aan het oppervlak • Preventie • De gasbron moet bekend zijn en als volgt worden uitgesloten: Waterstof l Gebruik droge elektroden, draden en laspoeders l Reinig en ontvet het werkstukoppervlak l Maak gebruik van voorverwarm technieken om het te lassen materiaal te vrijwaren van waterstof. 11 LV/PCVO/PTI
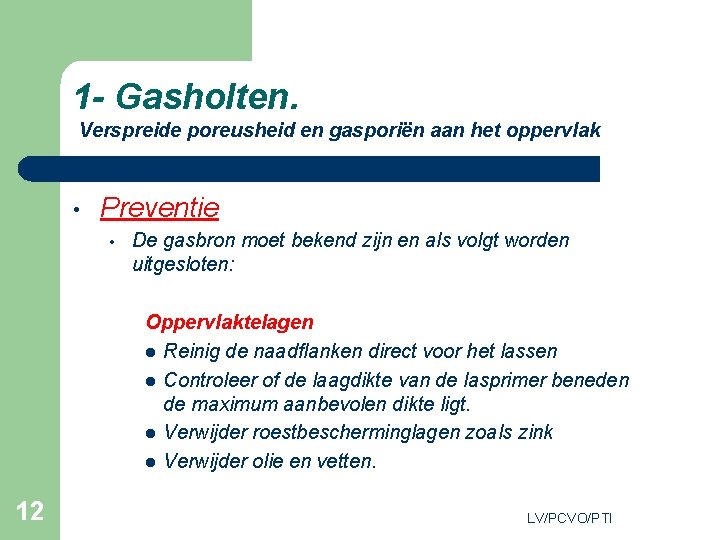
1 - Gasholten. Verspreide poreusheid en gasporiën aan het oppervlak • Preventie • De gasbron moet bekend zijn en als volgt worden uitgesloten: Oppervlaktelagen l Reinig de naadflanken direct voor het lassen l Controleer of de laagdikte van de lasprimer beneden de maximum aanbevolen dikte ligt. l Verwijder roestbescherminglagen zoals zink l Verwijder olie en vetten. 12 LV/PCVO/PTI
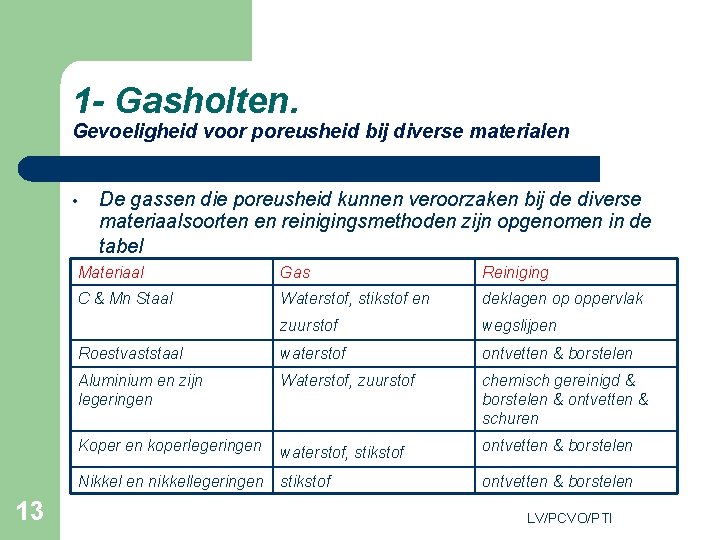
1 - Gasholten. Gevoeligheid voor poreusheid bij diverse materialen • 13 De gassen die poreusheid kunnen veroorzaken bij de diverse materiaalsoorten en reinigingsmethoden zijn opgenomen in de tabel Materiaal Gas Reiniging C & Mn Staal Waterstof, stikstof en deklagen op oppervlak zuurstof wegslijpen Roestvaststaal waterstof ontvetten & borstelen Aluminium en zijn legeringen Waterstof, zuurstof chemisch gereinigd & borstelen & ontvetten & schuren Koper en koperlegeringen waterstof, stikstof ontvetten & borstelen Nikkel en nikkellegeringen stikstof ontvetten & borstelen LV/PCVO/PTI
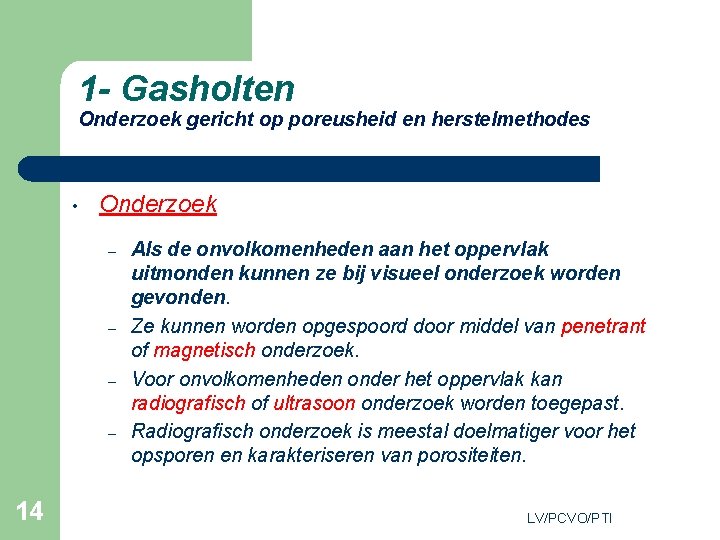
1 - Gasholten Onderzoek gericht op poreusheid en herstelmethodes • Onderzoek – – 14 Als de onvolkomenheden aan het oppervlak uitmonden kunnen ze bij visueel onderzoek worden gevonden. Ze kunnen worden opgespoord door middel van penetrant of magnetisch onderzoek. Voor onvolkomenheden onder het oppervlak kan radiografisch of ultrasoon onderzoek worden toegepast. Radiografisch onderzoek is meestal doelmatiger voor het opsporen en karakteriseren van porositeiten. LV/PCVO/PTI
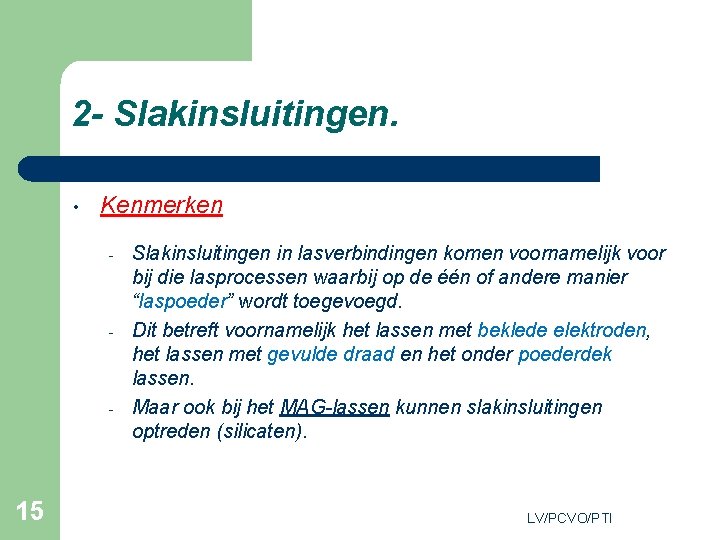
2 - Slakinsluitingen. • Kenmerken - - - 15 Slakinsluitingen in lasverbindingen komen voornamelijk voor bij die lasprocessen waarbij op de één of andere manier “laspoeder” wordt toegevoegd. Dit betreft voornamelijk het lassen met beklede elektroden, het lassen met gevulde draad en het onder poederdek lassen. Maar ook bij het MAG-lassen kunnen slakinsluitingen optreden (silicaten). LV/PCVO/PTI
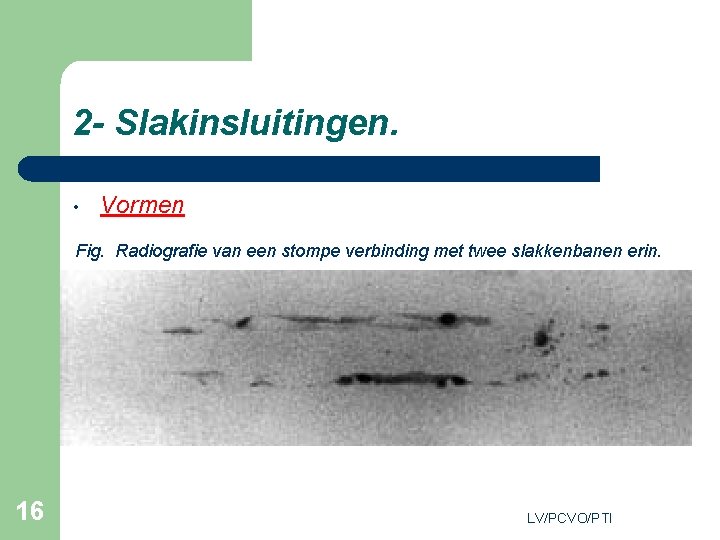
2 - Slakinsluitingen. • Vormen Fig. Radiografie van een stompe verbinding met twee slakkenbanen erin. 16 LV/PCVO/PTI
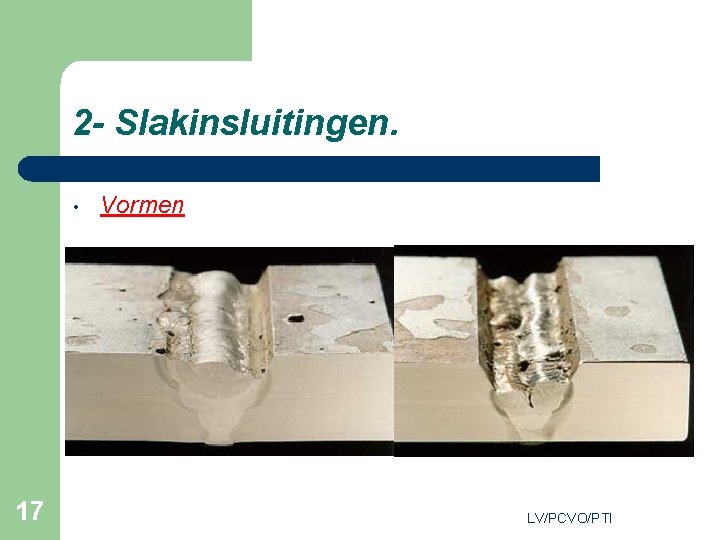
2 - Slakinsluitingen. • 17 Vormen LV/PCVO/PTI
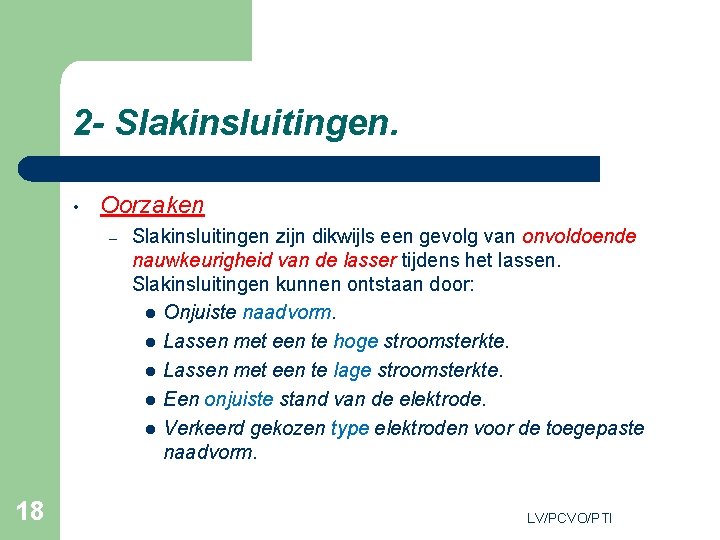
2 - Slakinsluitingen. • Oorzaken – 18 Slakinsluitingen zijn dikwijls een gevolg van onvoldoende nauwkeurigheid van de lasser tijdens het lassen. Slakinsluitingen kunnen ontstaan door: l Onjuiste naadvorm. l Lassen met een te hoge stroomsterkte. l Lassen met een te lage stroomsterkte. l Een onjuiste stand van de elektrode. l Verkeerd gekozen type elektroden voor de toegepaste naadvorm. LV/PCVO/PTI
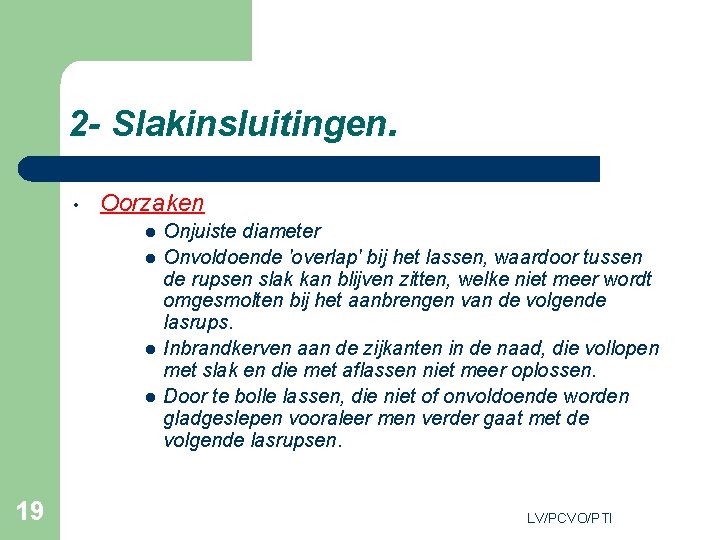
2 - Slakinsluitingen. • Oorzaken l l 19 Onjuiste diameter Onvoldoende 'overlap' bij het lassen, waardoor tussen de rupsen slak kan blijven zitten, welke niet meer wordt omgesmolten bij het aanbrengen van de volgende lasrups. Inbrandkerven aan de zijkanten in de naad, die vollopen met slak en die met aflassen niet meer oplossen. Door te bolle lassen, die niet of onvoldoende worden gladgeslepen vooraleer men verder gaat met de volgende lasrupsen. LV/PCVO/PTI
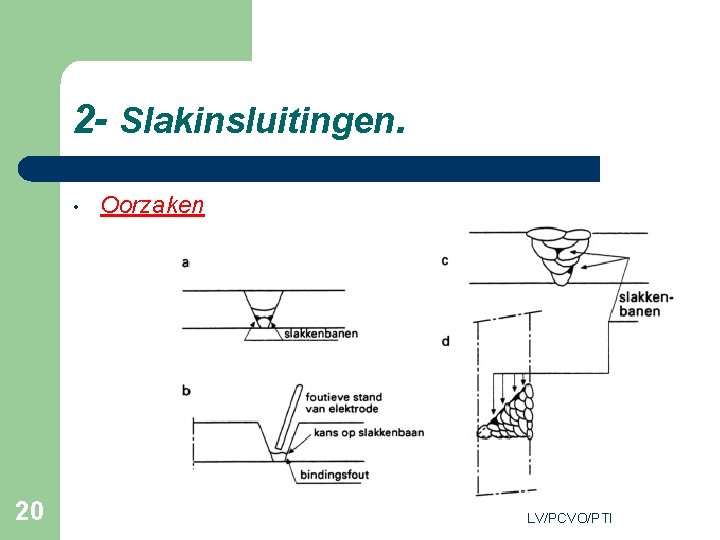
2 - Slakinsluitingen. • 20 Oorzaken LV/PCVO/PTI
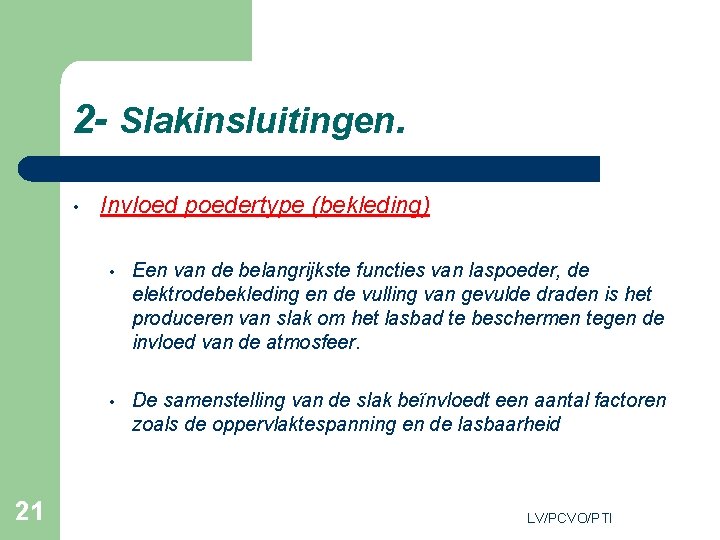
2 - Slakinsluitingen. • 21 Invloed poedertype (bekleding) • Een van de belangrijkste functies van laspoeder, de elektrodebekleding en de vulling van gevulde draden is het produceren van slak om het lasbad te beschermen tegen de invloed van de atmosfeer. • De samenstelling van de slak beïnvloedt een aantal factoren zoals de oppervlaktespanning en de lasbaarheid LV/PCVO/PTI
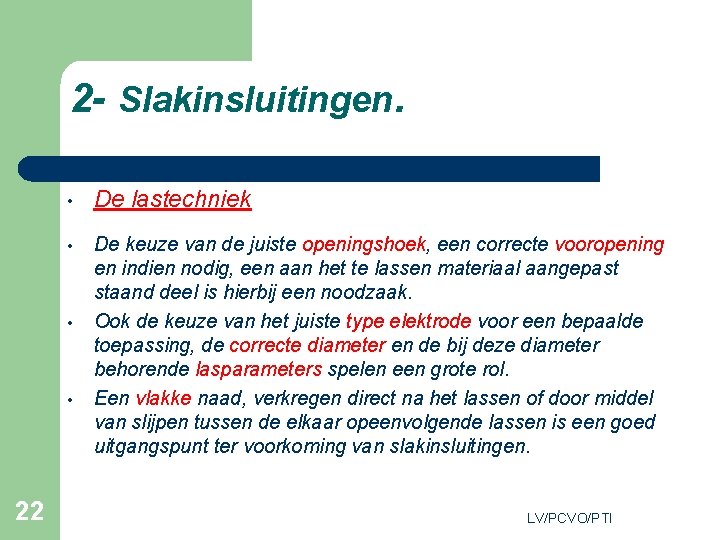
2 - Slakinsluitingen. • De lastechniek • De keuze van de juiste openingshoek, een correcte vooropening en indien nodig, een aan het te lassen materiaal aangepast staand deel is hierbij een noodzaak. Ook de keuze van het juiste type elektrode voor een bepaalde toepassing, de correcte diameter en de bij deze diameter behorende lasparameters spelen een grote rol. Een vlakke naad, verkregen direct na het lassen of door middel van slijpen tussen de elkaar opeenvolgende lassen is een goed uitgangspunt ter voorkoming van slakinsluitingen. • • 22 LV/PCVO/PTI
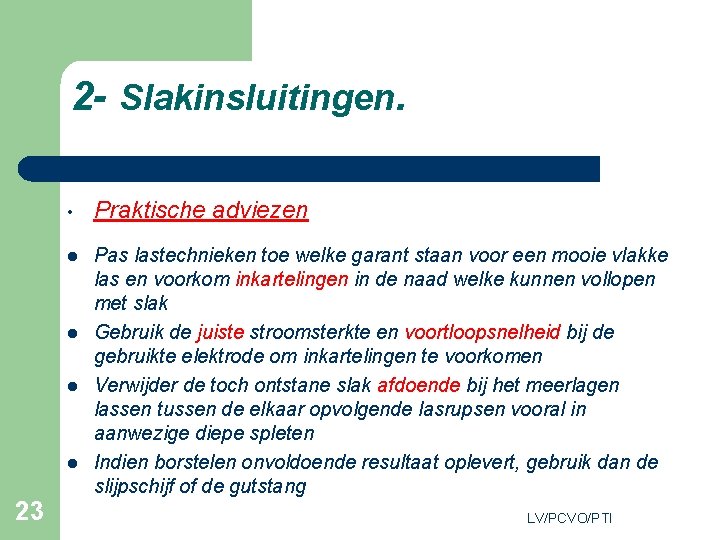
2 - Slakinsluitingen. • Praktische adviezen l Pas lastechnieken toe welke garant staan voor een mooie vlakke las en voorkom inkartelingen in de naad welke kunnen vollopen met slak Gebruik de juiste stroomsterkte en voortloopsnelheid bij de gebruikte elektrode om inkartelingen te voorkomen Verwijder de toch ontstane slak afdoende bij het meerlagen lassen tussen de elkaar opvolgende lasrupsen vooral in aanwezige diepe spleten Indien borstelen onvoldoende resultaat oplevert, gebruik dan de slijpschijf of de gutstang l l l 23 LV/PCVO/PTI
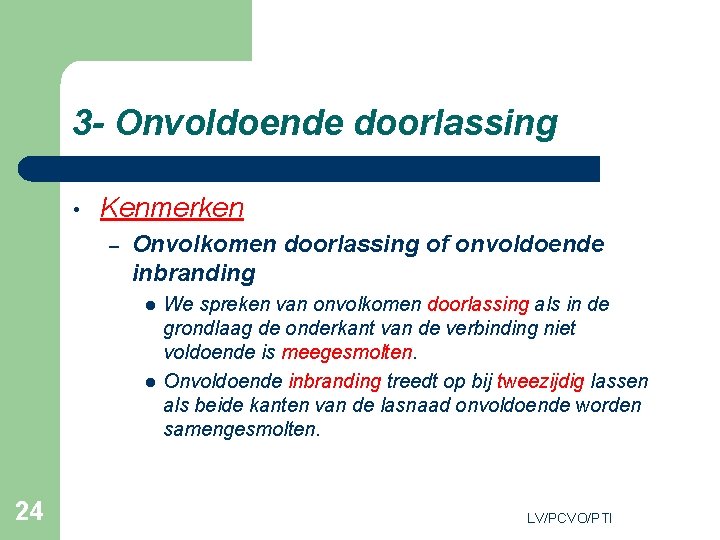
3 - Onvoldoende doorlassing • Kenmerken – Onvolkomen doorlassing of onvoldoende inbranding l l 24 We spreken van onvolkomen doorlassing als in de grondlaag de onderkant van de verbinding niet voldoende is meegesmolten. Onvoldoende inbranding treedt op bij tweezijdig lassen als beide kanten van de lasnaad onvoldoende worden samengesmolten. LV/PCVO/PTI
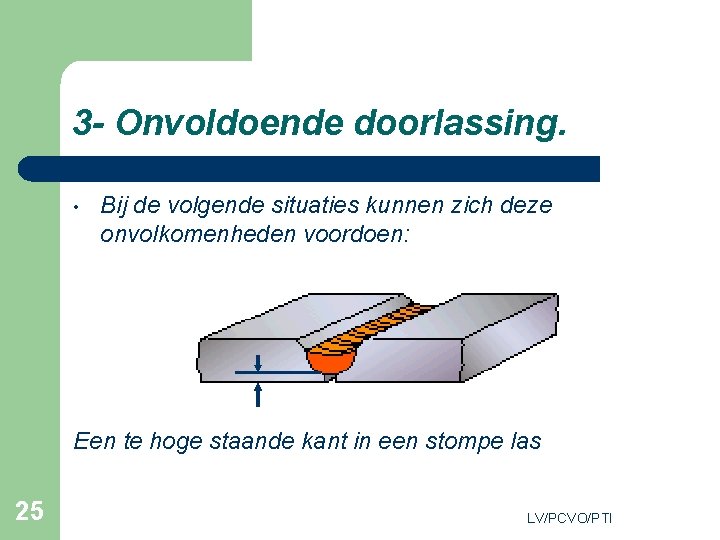
3 - Onvoldoende doorlassing. • Bij de volgende situaties kunnen zich deze onvolkomenheden voordoen: Een te hoge staande kant in een stompe las 25 LV/PCVO/PTI
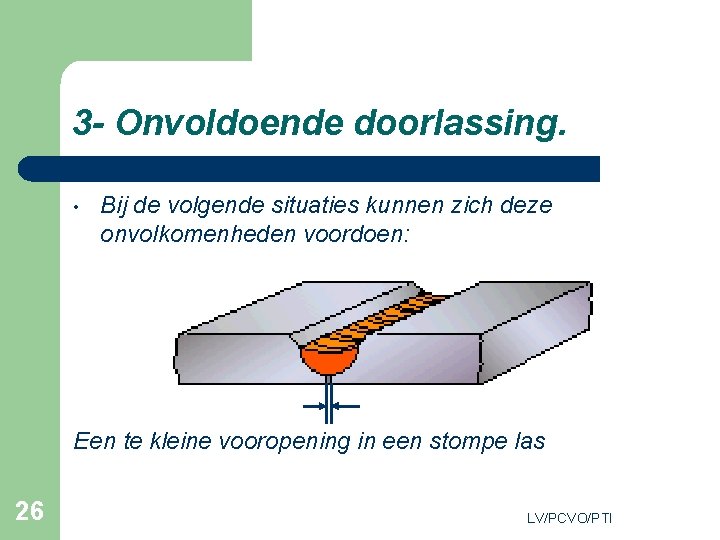
3 - Onvoldoende doorlassing. • Bij de volgende situaties kunnen zich deze onvolkomenheden voordoen: Een te kleine vooropening in een stompe las 26 LV/PCVO/PTI
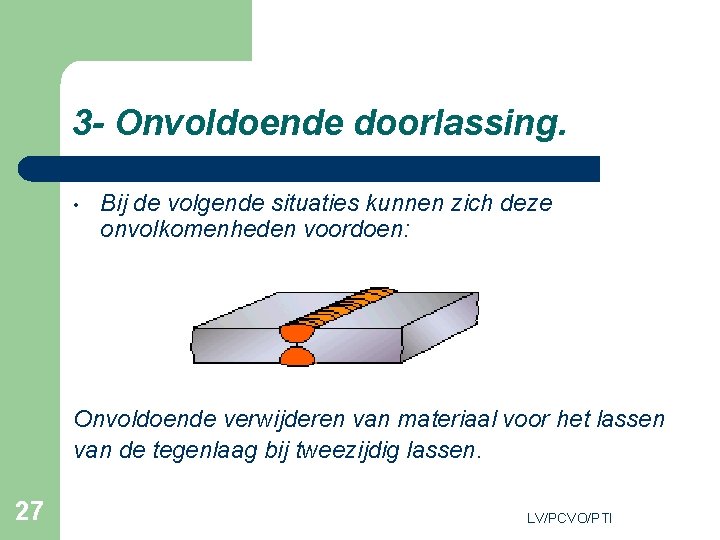
3 - Onvoldoende doorlassing. • Bij de volgende situaties kunnen zich deze onvolkomenheden voordoen: Onvoldoende verwijderen van materiaal voor het lassen van de tegenlaag bij tweezijdig lassen. 27 LV/PCVO/PTI
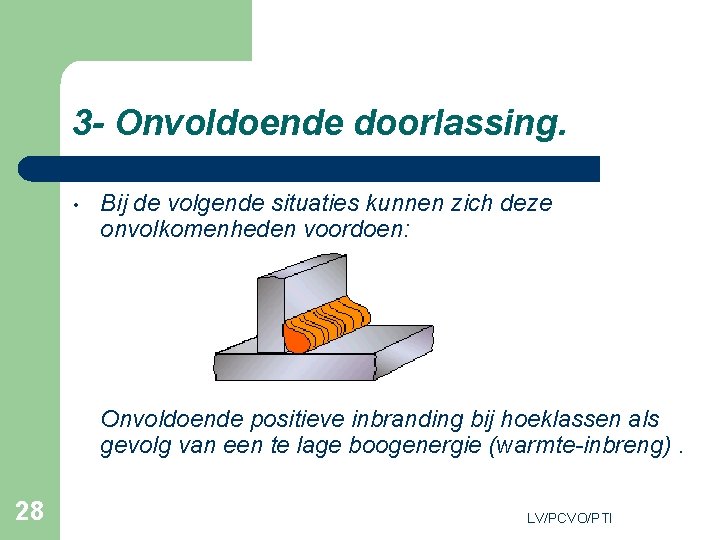
3 - Onvoldoende doorlassing. • Bij de volgende situaties kunnen zich deze onvolkomenheden voordoen: Onvoldoende positieve inbranding bij hoeklassen als gevolg van een te lage boogenergie (warmte-inbreng). 28 LV/PCVO/PTI
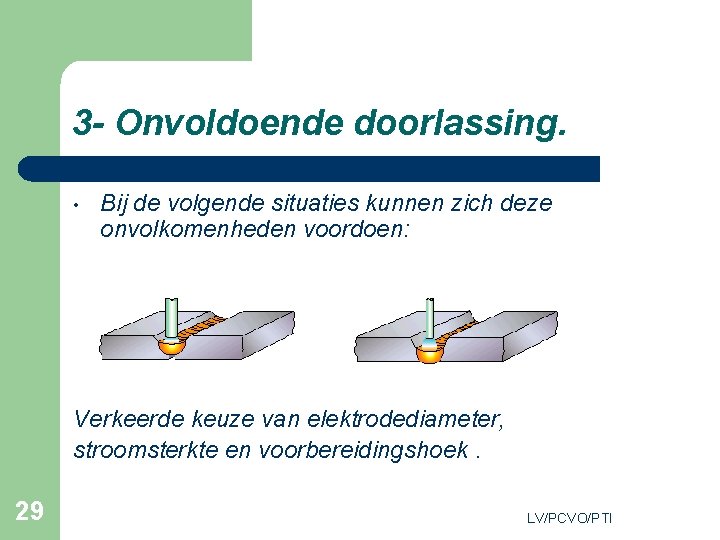
3 - Onvoldoende doorlassing. • Bij de volgende situaties kunnen zich deze onvolkomenheden voordoen: Verkeerde keuze van elektrodediameter, stroomsterkte en voorbereidingshoek. 29 LV/PCVO/PTI
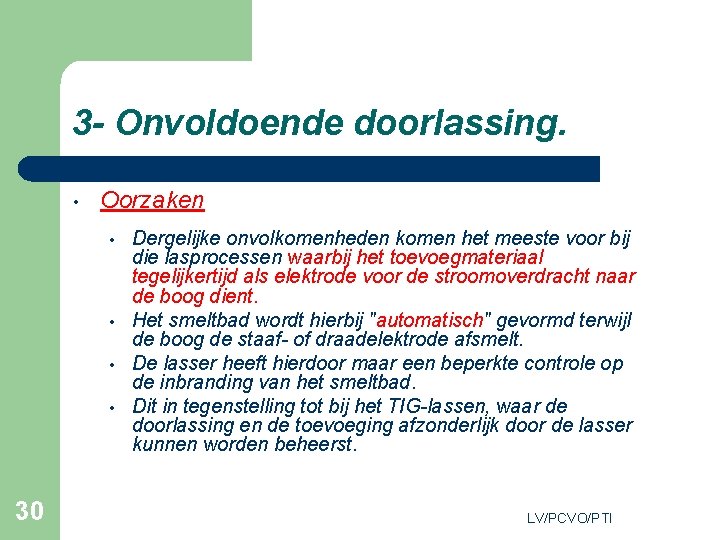
3 - Onvoldoende doorlassing. • Oorzaken • • 30 Dergelijke onvolkomenheden komen het meeste voor bij die lasprocessen waarbij het toevoegmateriaal tegelijkertijd als elektrode voor de stroomoverdracht naar de boog dient. Het smeltbad wordt hierbij "automatisch" gevormd terwijl de boog de staaf- of draadelektrode afsmelt. De lasser heeft hierdoor maar een beperkte controle op de inbranding van het smeltbad. Dit in tegenstelling tot bij het TIG-lassen, waar de doorlassing en de toevoeging afzonderlijk door de lasser kunnen worden beheerst. LV/PCVO/PTI
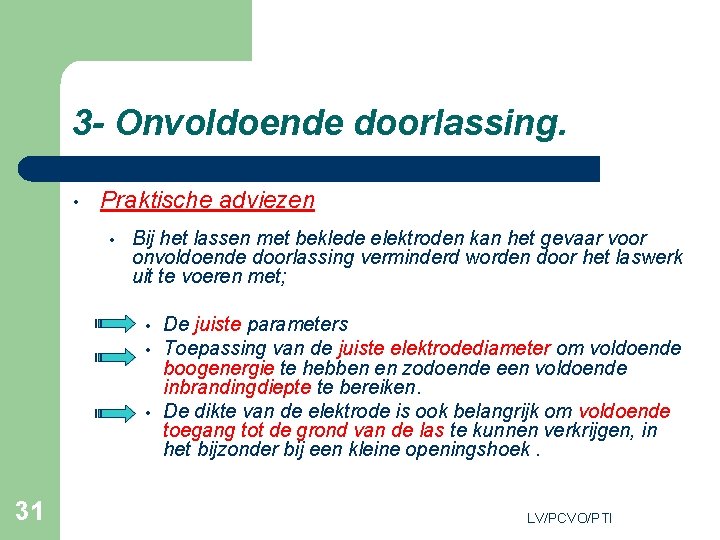
3 - Onvoldoende doorlassing. • Praktische adviezen • Bij het lassen met beklede elektroden kan het gevaar voor onvoldoende doorlassing verminderd worden door het laswerk uit te voeren met; • • • 31 De juiste parameters Toepassing van de juiste elektrodediameter om voldoende boogenergie te hebben en zodoende een voldoende inbrandingdiepte te bereiken. De dikte van de elektrode is ook belangrijk om voldoende toegang tot de grond van de las te kunnen verkrijgen, in het bijzonder bij een kleine openingshoek. LV/PCVO/PTI
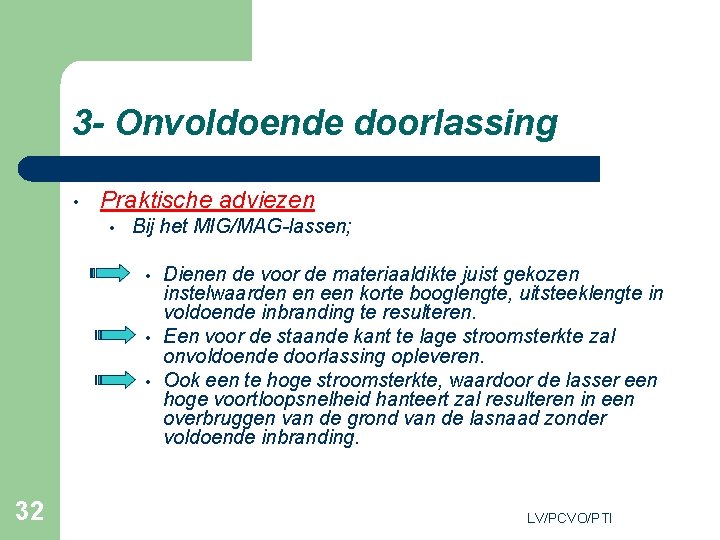
3 - Onvoldoende doorlassing • Praktische adviezen • Bij het MIG/MAG-lassen; • • • 32 Dienen de voor de materiaaldikte juist gekozen instelwaarden en een korte booglengte, uitsteeklengte in voldoende inbranding te resulteren. Een voor de staande kant te lage stroomsterkte zal onvoldoende doorlassing opleveren. Ook een te hoge stroomsterkte, waardoor de lasser een hoge voortloopsnelheid hanteert zal resulteren in een overbruggen van de grond van de lasnaad zonder voldoende inbranding. LV/PCVO/PTI
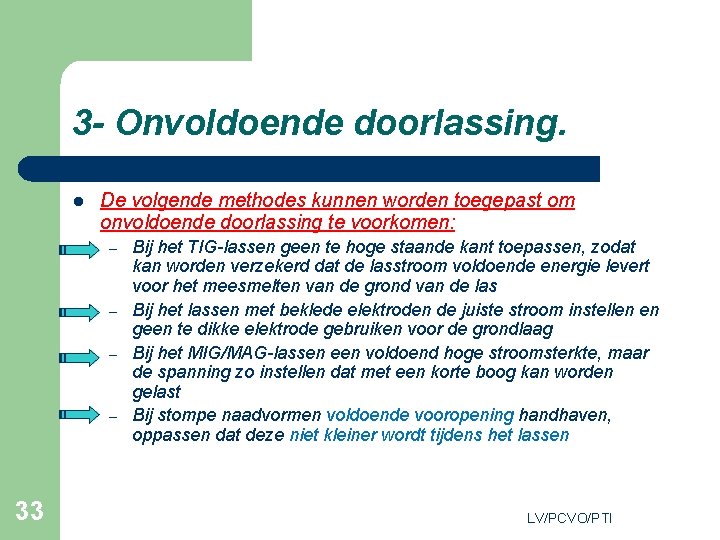
3 - Onvoldoende doorlassing. l De volgende methodes kunnen worden toegepast om onvoldoende doorlassing te voorkomen: – – 33 Bij het TIG-lassen geen te hoge staande kant toepassen, zodat kan worden verzekerd dat de lasstroom voldoende energie levert voor het meesmelten van de grond van de las Bij het lassen met beklede elektroden de juiste stroom instellen en geen te dikke elektrode gebruiken voor de grondlaag Bij het MIG/MAG-lassen een voldoend hoge stroomsterkte, maar de spanning zo instellen dat met een korte boog kan worden gelast Bij stompe naadvormen voldoende vooropening handhaven, oppassen dat deze niet kleiner wordt tijdens het lassen LV/PCVO/PTI
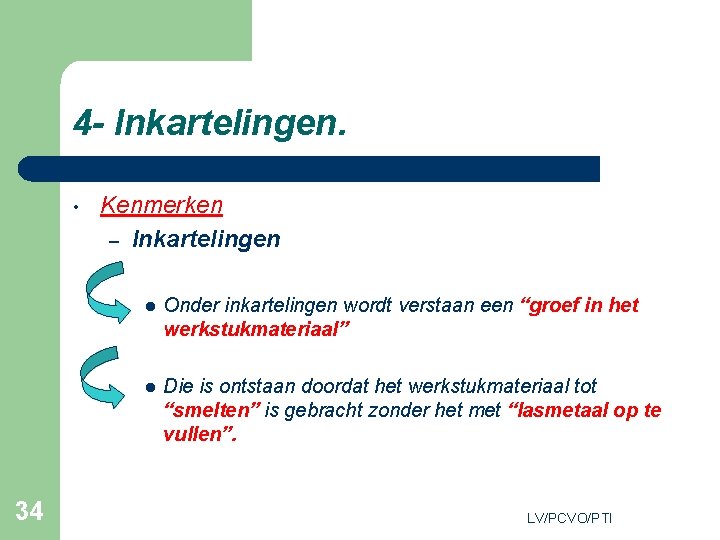
4 - Inkartelingen. • 34 Kenmerken – Inkartelingen l Onder inkartelingen wordt verstaan een “groef in het werkstukmateriaal” l Die is ontstaan doordat het werkstukmateriaal tot “smelten” is gebracht zonder het met “lasmetaal op te vullen”. LV/PCVO/PTI
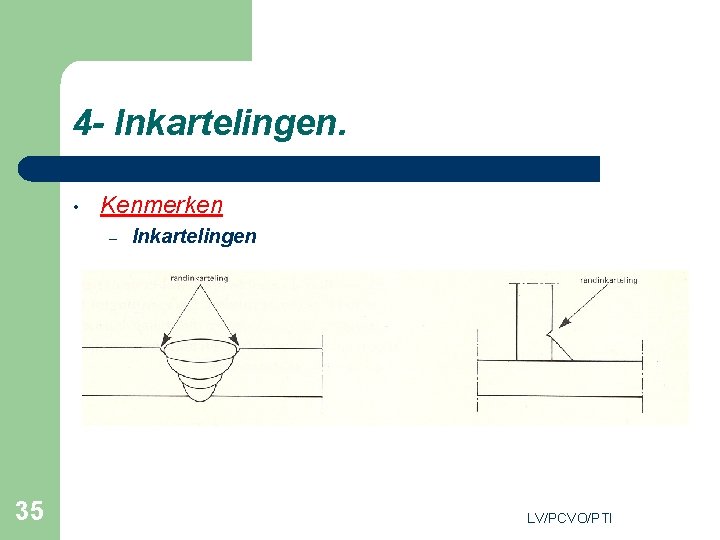
4 - Inkartelingen. • Kenmerken – 35 Inkartelingen LV/PCVO/PTI
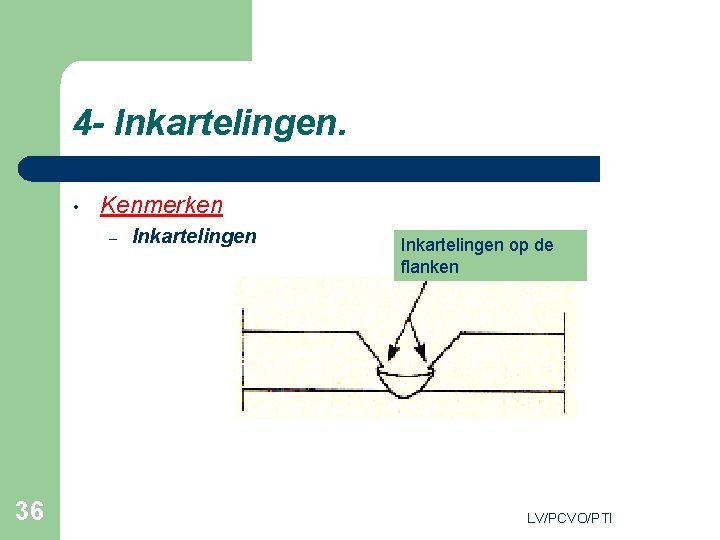
4 - Inkartelingen. • Kenmerken – 36 Inkartelingen op de flanken LV/PCVO/PTI
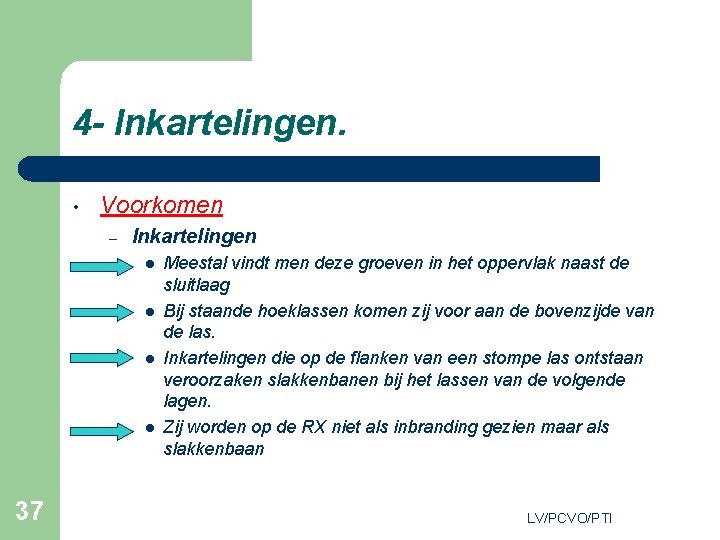
4 - Inkartelingen. • Voorkomen – Inkartelingen l l 37 Meestal vindt men deze groeven in het oppervlak naast de sluitlaag Bij staande hoeklassen komen zij voor aan de bovenzijde van de las. Inkartelingen die op de flanken van een stompe las ontstaan veroorzaken slakkenbanen bij het lassen van de volgende lagen. Zij worden op de RX niet als inbranding gezien maar als slakkenbaan LV/PCVO/PTI
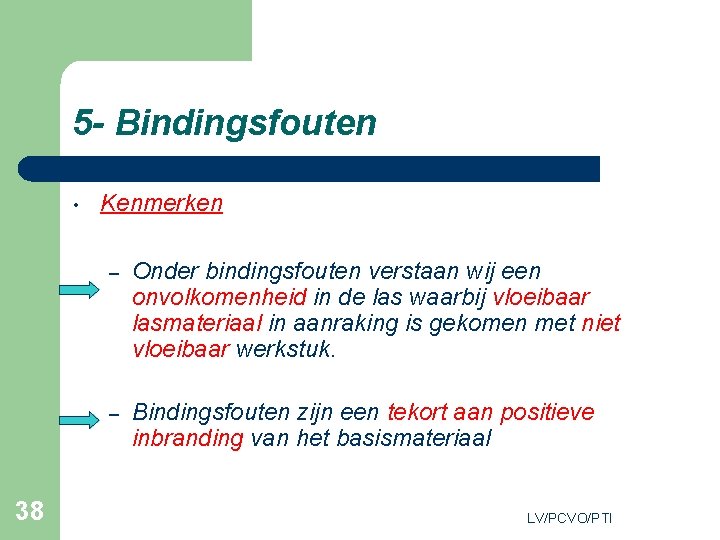
5 - Bindingsfouten • 38 Kenmerken – Onder bindingsfouten verstaan wij een onvolkomenheid in de las waarbij vloeibaar lasmateriaal in aanraking is gekomen met niet vloeibaar werkstuk. – Bindingsfouten zijn een tekort aan positieve inbranding van het basismateriaal LV/PCVO/PTI
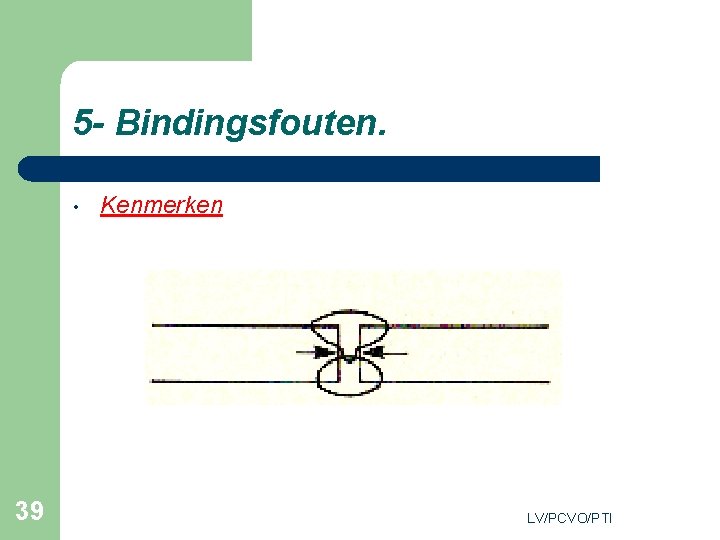
5 - Bindingsfouten. • 39 Kenmerken LV/PCVO/PTI
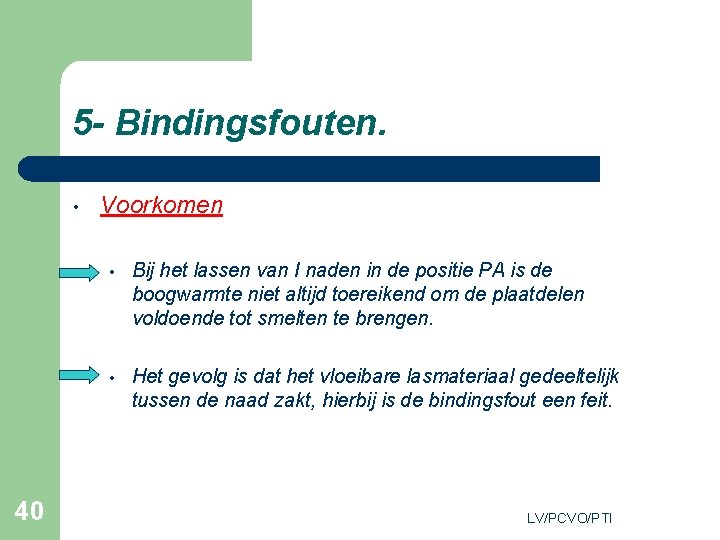
5 - Bindingsfouten. • 40 Voorkomen • Bij het lassen van I naden in de positie PA is de boogwarmte niet altijd toereikend om de plaatdelen voldoende tot smelten te brengen. • Het gevolg is dat het vloeibare lasmateriaal gedeeltelijk tussen de naad zakt, hierbij is de bindingsfout een feit. LV/PCVO/PTI
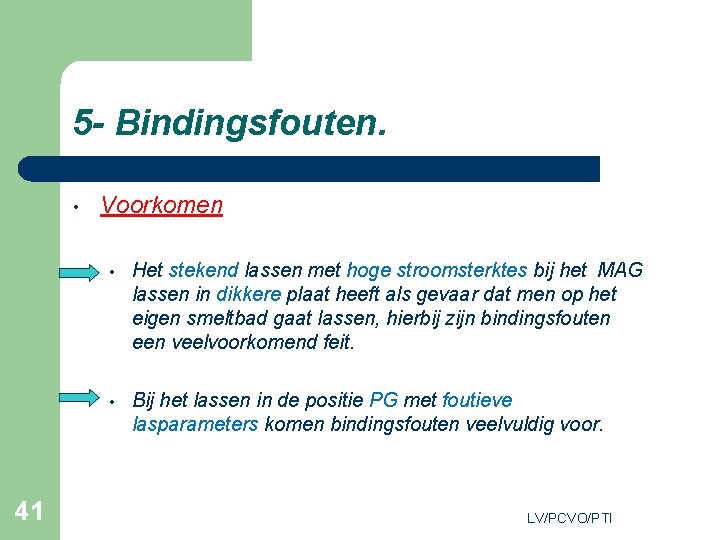
5 - Bindingsfouten. • 41 Voorkomen • Het stekend lassen met hoge stroomsterktes bij het MAG lassen in dikkere plaat heeft als gevaar dat men op het eigen smeltbad gaat lassen, hierbij zijn bindingsfouten een veelvoorkomend feit. • Bij het lassen in de positie PG met foutieve lasparameters komen bindingsfouten veelvuldig voor. LV/PCVO/PTI
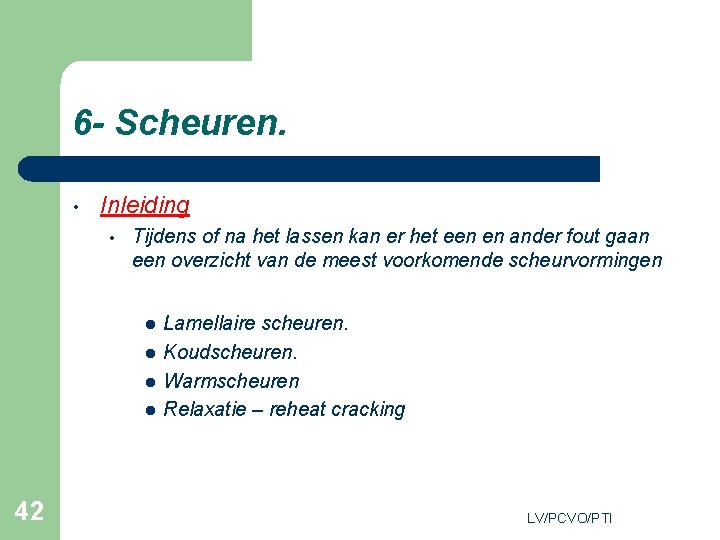
6 - Scheuren. • Inleiding • Tijdens of na het lassen kan er het een en ander fout gaan een overzicht van de meest voorkomende scheurvormingen l l 42 Lamellaire scheuren. Koudscheuren. Warmscheuren Relaxatie – reheat cracking LV/PCVO/PTI
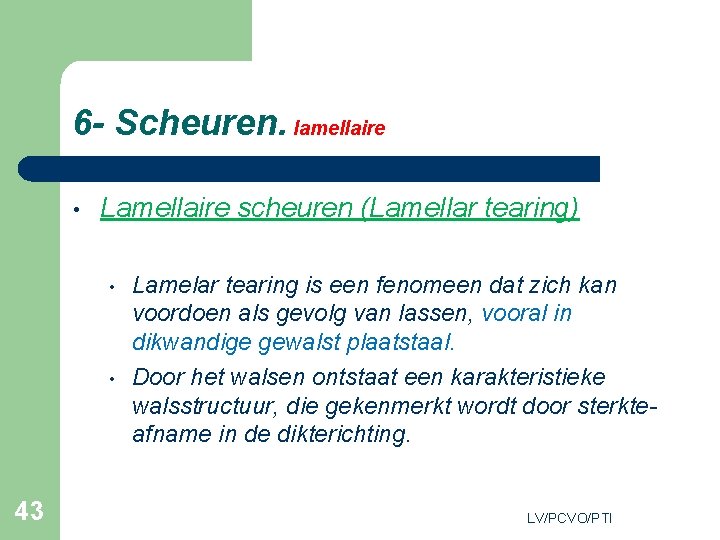
6 - Scheuren. lamellaire • Lamellaire scheuren (Lamellar tearing) • • 43 Lamelar tearing is een fenomeen dat zich kan voordoen als gevolg van lassen, vooral in dikwandige gewalst plaatstaal. Door het walsen ontstaat een karakteristieke walsstructuur, die gekenmerkt wordt door sterkteafname in de dikterichting. LV/PCVO/PTI
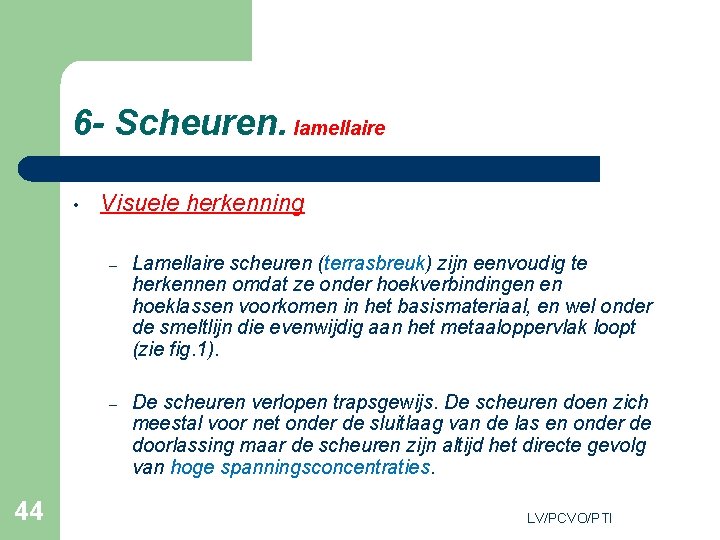
6 - Scheuren. lamellaire • 44 Visuele herkenning – Lamellaire scheuren (terrasbreuk) zijn eenvoudig te herkennen omdat ze onder hoekverbindingen en hoeklassen voorkomen in het basismateriaal, en wel onder de smeltlijn die evenwijdig aan het metaaloppervlak loopt (zie fig. 1). – De scheuren verlopen trapsgewijs. De scheuren doen zich meestal voor net onder de sluitlaag van de las en onder de doorlassing maar de scheuren zijn altijd het directe gevolg van hoge spanningsconcentraties. LV/PCVO/PTI
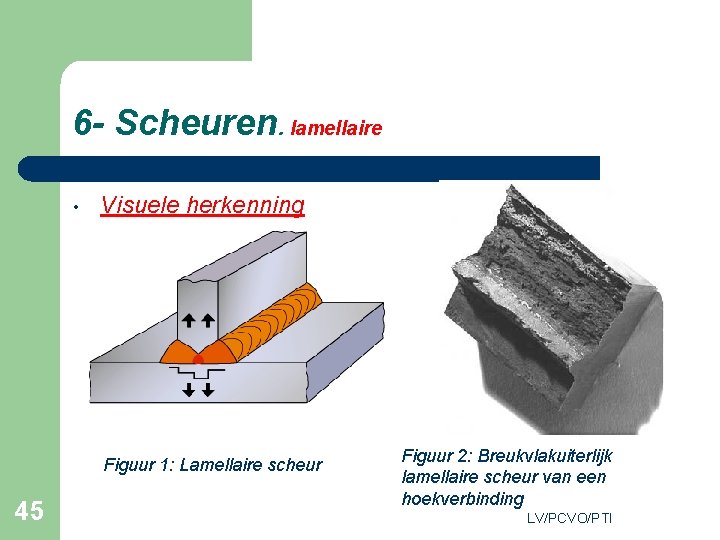
6 - Scheuren. lamellaire • Visuele herkenning Figuur 1: Lamellaire scheur 45 Figuur 2: Breukvlakuiterlijk lamellaire scheur van een hoekverbinding LV/PCVO/PTI
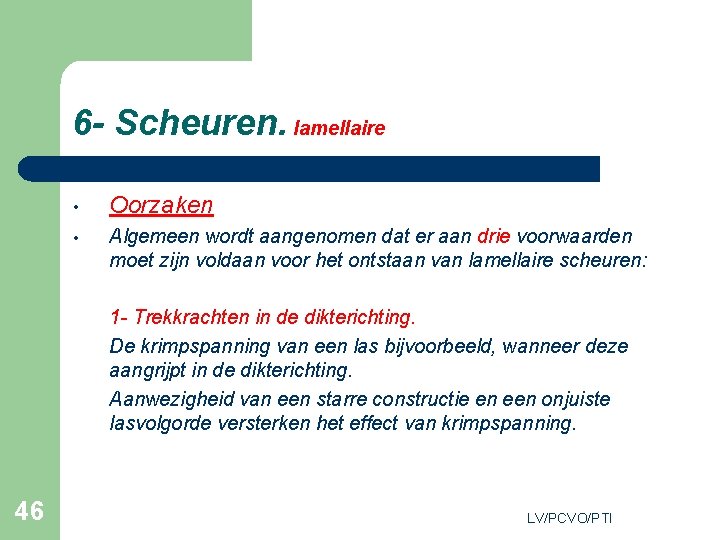
6 - Scheuren. lamellaire • Oorzaken • Algemeen wordt aangenomen dat er aan drie voorwaarden moet zijn voldaan voor het ontstaan van lamellaire scheuren: 1 - Trekkrachten in de dikterichting. De krimpspanning van een las bijvoorbeeld, wanneer deze aangrijpt in de dikterichting. Aanwezigheid van een starre constructie en een onjuiste lasvolgorde versterken het effect van krimpspanning. 46 LV/PCVO/PTI
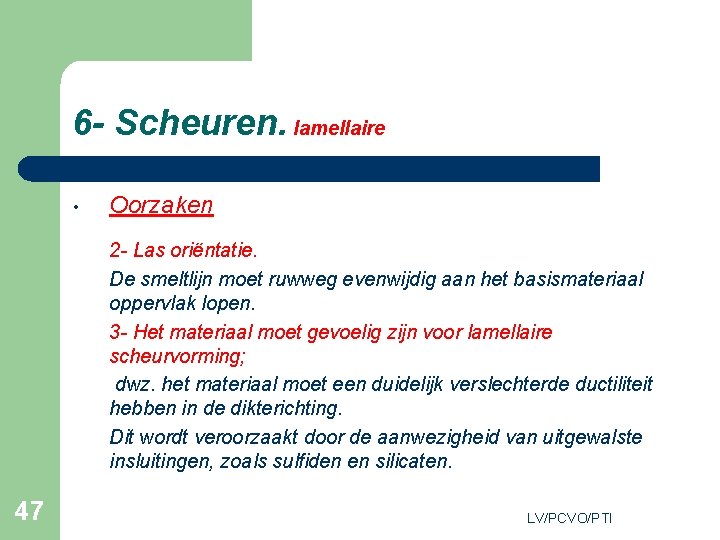
6 - Scheuren. lamellaire • Oorzaken 2 - Las oriëntatie. De smeltlijn moet ruwweg evenwijdig aan het basismateriaal oppervlak lopen. 3 - Het materiaal moet gevoelig zijn voor lamellaire scheurvorming; dwz. het materiaal moet een duidelijk verslechterde ductiliteit hebben in de dikterichting. Dit wordt veroorzaakt door de aanwezigheid van uitgewalste insluitingen, zoals sulfiden en silicaten. 47 LV/PCVO/PTI
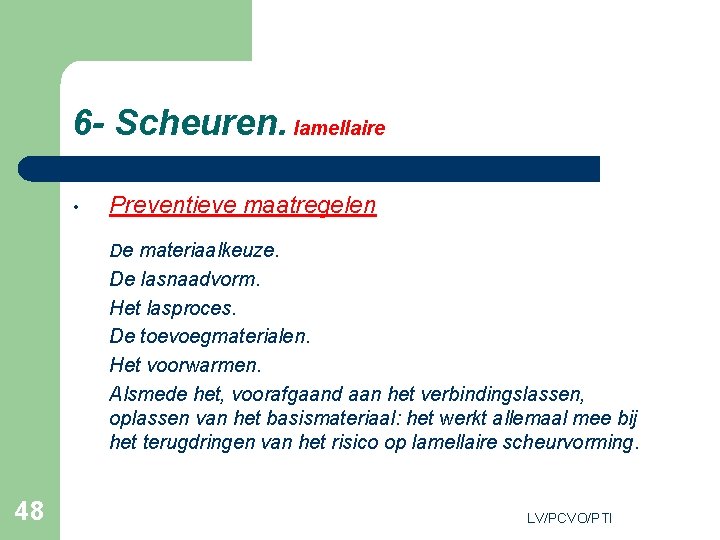
6 - Scheuren. lamellaire • Preventieve maatregelen De materiaalkeuze. De lasnaadvorm. Het lasproces. De toevoegmaterialen. Het voorwarmen. Alsmede het, voorafgaand aan het verbindingslassen, oplassen van het basismateriaal: het werkt allemaal mee bij het terugdringen van het risico op lamellaire scheurvorming. 48 LV/PCVO/PTI
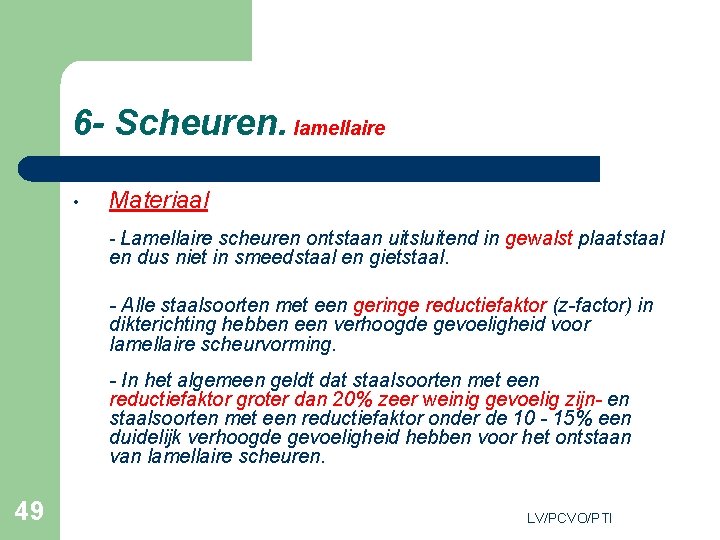
6 - Scheuren. lamellaire • Materiaal - Lamellaire scheuren ontstaan uitsluitend in gewalst plaatstaal en dus niet in smeedstaal en gietstaal. - Alle staalsoorten met een geringe reductiefaktor (z-factor) in dikterichting hebben een verhoogde gevoeligheid voor lamellaire scheurvorming. - In het algemeen geldt dat staalsoorten met een reductiefaktor groter dan 20% zeer weinig gevoelig zijn- en staalsoorten met een reductiefaktor onder de 10 - 15% een duidelijk verhoogde gevoeligheid hebben voor het ontstaan van lamellaire scheuren. 49 LV/PCVO/PTI
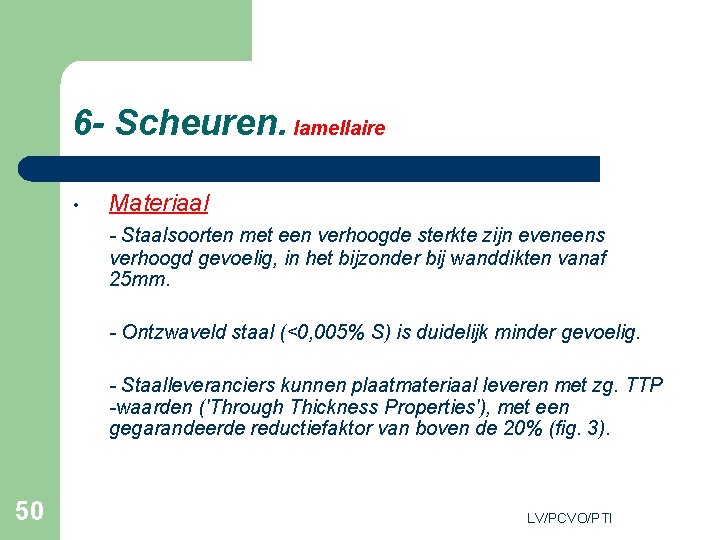
6 - Scheuren. lamellaire • Materiaal - Staalsoorten met een verhoogde sterkte zijn eveneens verhoogd gevoelig, in het bijzonder bij wanddikten vanaf 25 mm. - Ontzwaveld staal (<0, 005% S) is duidelijk minder gevoelig. - Staalleveranciers kunnen plaatmateriaal leveren met zg. TTP -waarden ('Through Thickness Properties'), met een gegarandeerde reductiefaktor van boven de 20% (fig. 3). 50 LV/PCVO/PTI
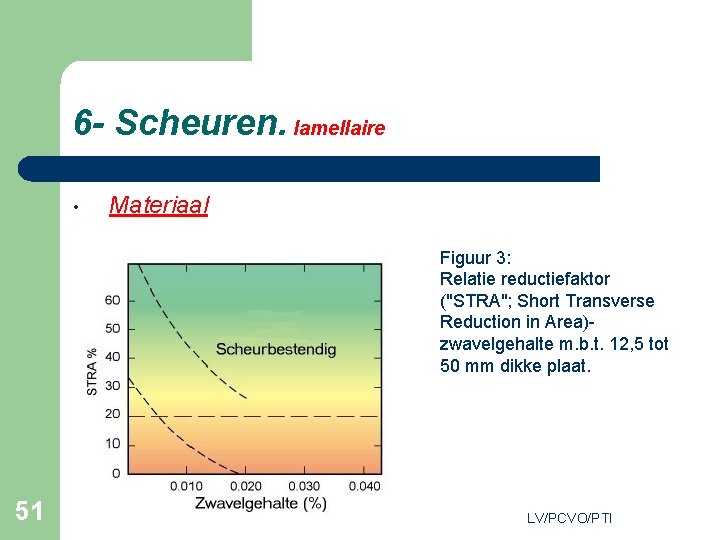
6 - Scheuren. lamellaire • Materiaal Figuur 3: Relatie reductiefaktor ("STRA"; Short Transverse Reduction in Area)zwavelgehalte m. b. t. 12, 5 tot 50 mm dikke plaat. 51 LV/PCVO/PTI
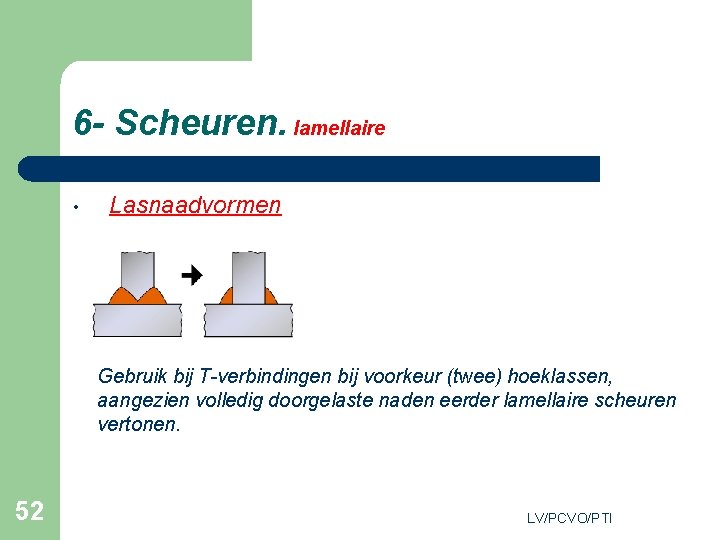
6 - Scheuren. lamellaire • Lasnaadvormen Gebruik bij T-verbindingen bij voorkeur (twee) hoeklassen, aangezien volledig doorgelaste naden eerder lamellaire scheuren vertonen. 52 LV/PCVO/PTI
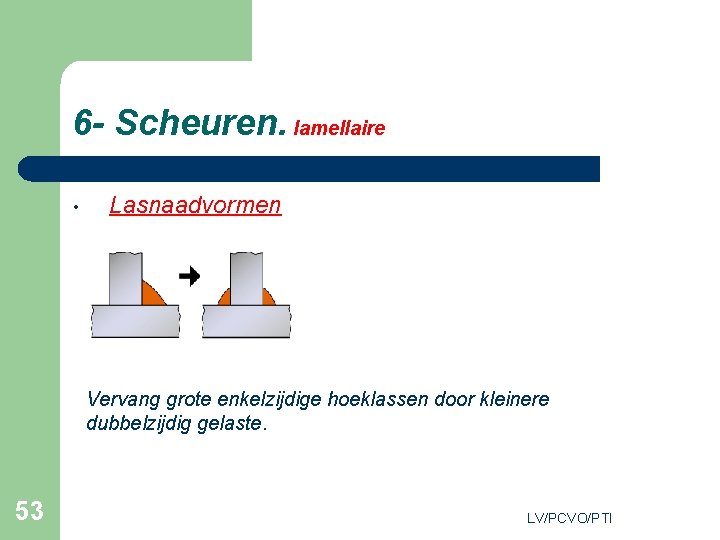
6 - Scheuren. lamellaire • Lasnaadvormen Vervang grote enkelzijdige hoeklassen door kleinere dubbelzijdig gelaste. 53 LV/PCVO/PTI
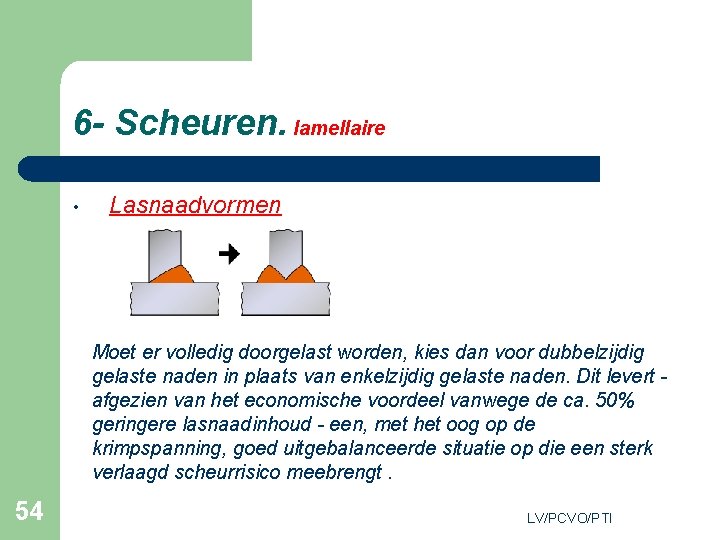
6 - Scheuren. lamellaire • Lasnaadvormen Moet er volledig doorgelast worden, kies dan voor dubbelzijdig gelaste naden in plaats van enkelzijdig gelaste naden. Dit levert afgezien van het economische voordeel vanwege de ca. 50% geringere lasnaadinhoud - een, met het oog op de krimpspanning, goed uitgebalanceerde situatie op die een sterk verlaagd scheurrisico meebrengt. 54 LV/PCVO/PTI
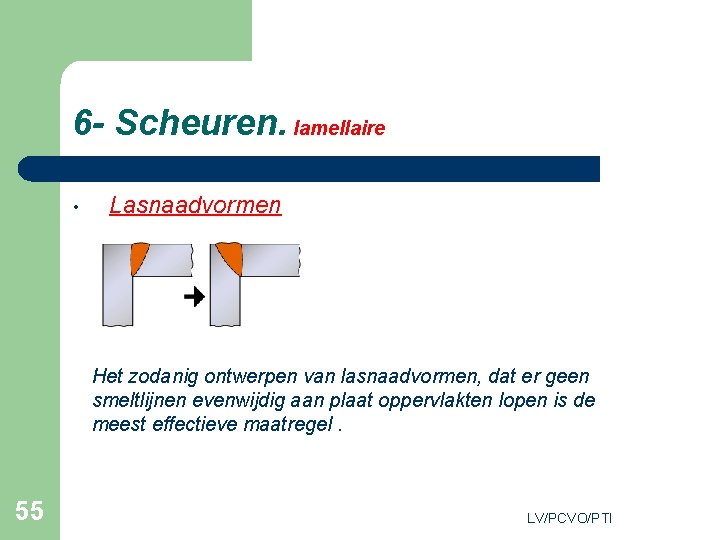
6 - Scheuren. lamellaire • Lasnaadvormen Het zodanig ontwerpen van lasnaadvormen, dat er geen smeltlijnen evenwijdig aan plaat oppervlakten lopen is de meest effectieve maatregel. 55 LV/PCVO/PTI

6 - Scheuren. lamellaire • Lasnaad afmeting Lamellaire scheuren zullen eerder ontstaan onder grote lasnaden, en met name wanneer de beenlengte van de hoeklas- cq. de diepte van de stompe lasnaad groter wordt dan 20 mm. LV/PTI/7 SFOT
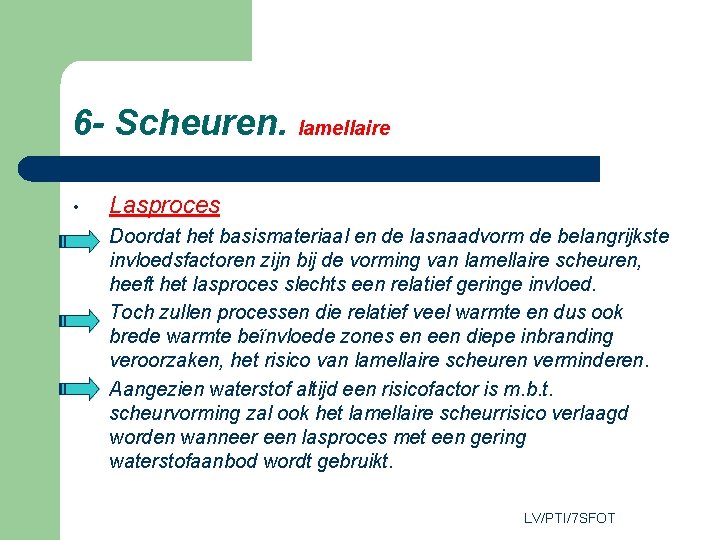
6 - Scheuren. lamellaire • Lasproces Doordat het basismateriaal en de lasnaadvorm de belangrijkste invloedsfactoren zijn bij de vorming van lamellaire scheuren, heeft het lasproces slechts een relatief geringe invloed. Toch zullen processen die relatief veel warmte en dus ook brede warmte beïnvloede zones en een diepe inbranding veroorzaken, het risico van lamellaire scheuren verminderen. Aangezien waterstof altijd een risicofactor is m. b. t. scheurvorming zal ook het lamellaire scheurrisico verlaagd worden wanneer een lasproces met een gering waterstofaanbod wordt gebruikt. LV/PTI/7 SFOT
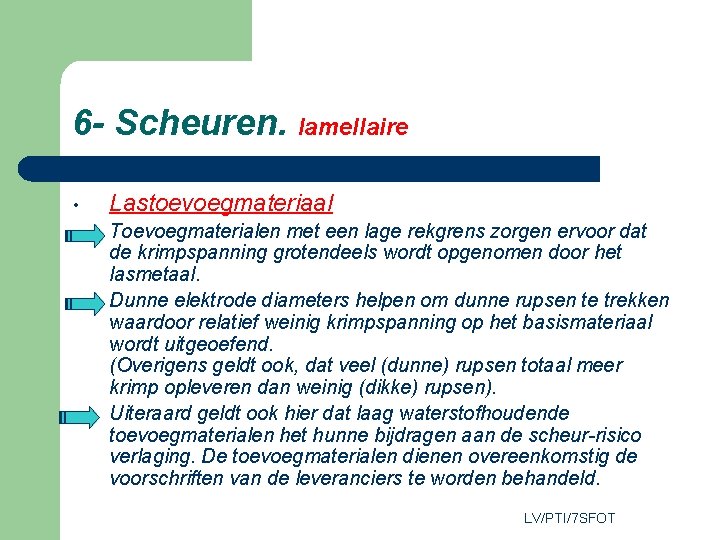
6 - Scheuren. lamellaire • Lastoevoegmateriaal Toevoegmaterialen met een lage rekgrens zorgen ervoor dat de krimpspanning grotendeels wordt opgenomen door het lasmetaal. Dunne elektrode diameters helpen om dunne rupsen te trekken waardoor relatief weinig krimpspanning op het basismateriaal wordt uitgeoefend. (Overigens geldt ook, dat veel (dunne) rupsen totaal meer krimp opleveren dan weinig (dikke) rupsen). Uiteraard geldt ook hier dat laag waterstofhoudende toevoegmaterialen het hunne bijdragen aan de scheur-risico verlaging. De toevoegmaterialen dienen overeenkomstig de voorschriften van de leveranciers te worden behandeld. LV/PTI/7 SFOT
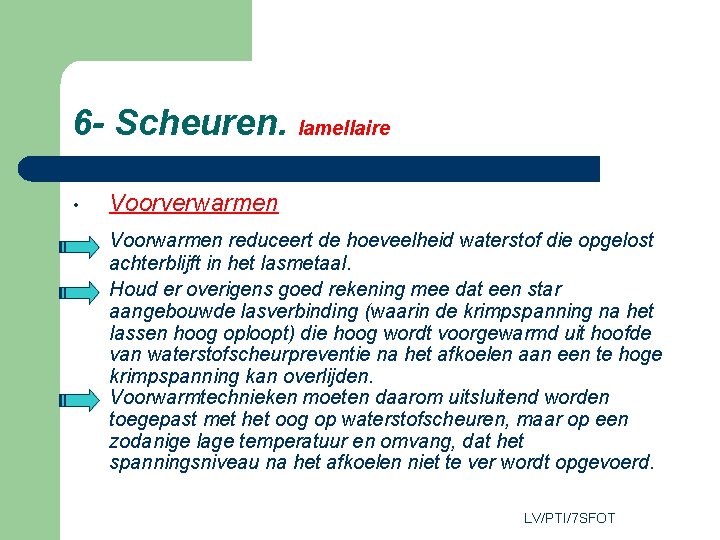
6 - Scheuren. lamellaire • Voorverwarmen Voorwarmen reduceert de hoeveelheid waterstof die opgelost achterblijft in het lasmetaal. Houd er overigens goed rekening mee dat een star aangebouwde lasverbinding (waarin de krimpspanning na het lassen hoog oploopt) die hoog wordt voorgewarmd uit hoofde van waterstofscheurpreventie na het afkoelen aan een te hoge krimpspanning kan overlijden. Voorwarmtechnieken moeten daarom uitsluitend worden toegepast met het oog op waterstofscheuren, maar op een zodanige lage temperatuur en omvang, dat het spanningsniveau na het afkoelen niet te ver wordt opgevoerd. LV/PTI/7 SFOT
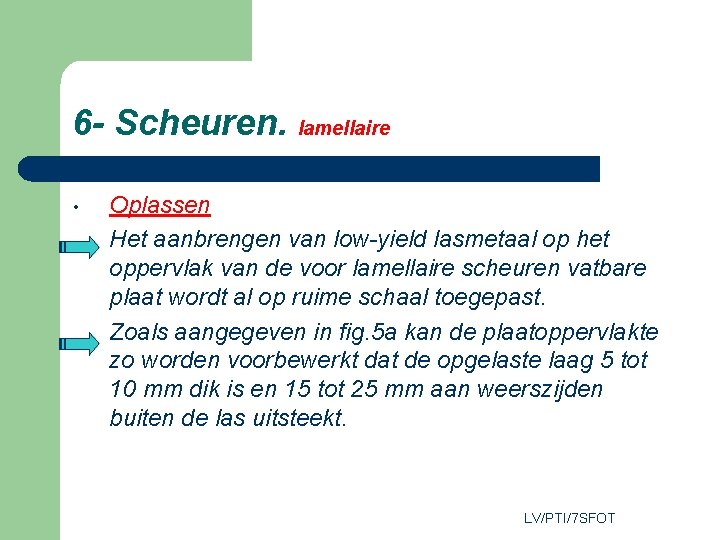
6 - Scheuren. lamellaire • Oplassen Het aanbrengen van low-yield lasmetaal op het oppervlak van de voor lamellaire scheuren vatbare plaat wordt al op ruime schaal toegepast. Zoals aangegeven in fig. 5 a kan de plaatoppervlakte zo worden voorbewerkt dat de opgelaste laag 5 tot 10 mm dik is en 15 tot 25 mm aan weerszijden buiten de las uitsteekt. LV/PTI/7 SFOT
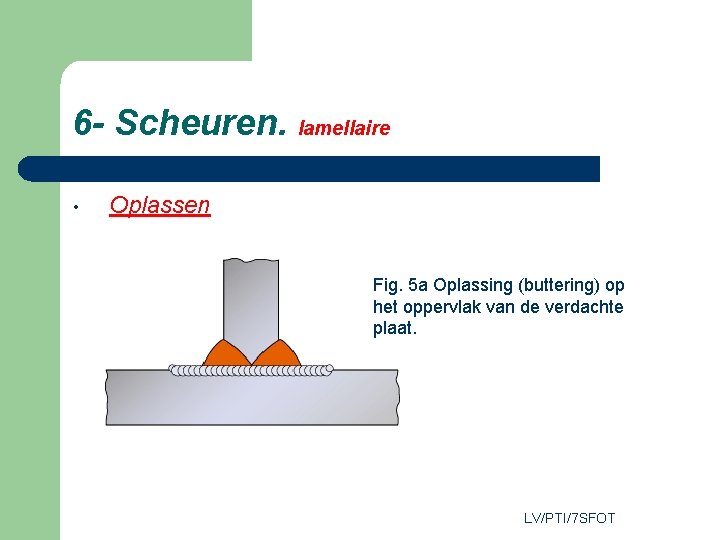
6 - Scheuren. lamellaire • Oplassen Fig. 5 a Oplassing (buttering) op het oppervlak van de verdachte plaat. LV/PTI/7 SFOT
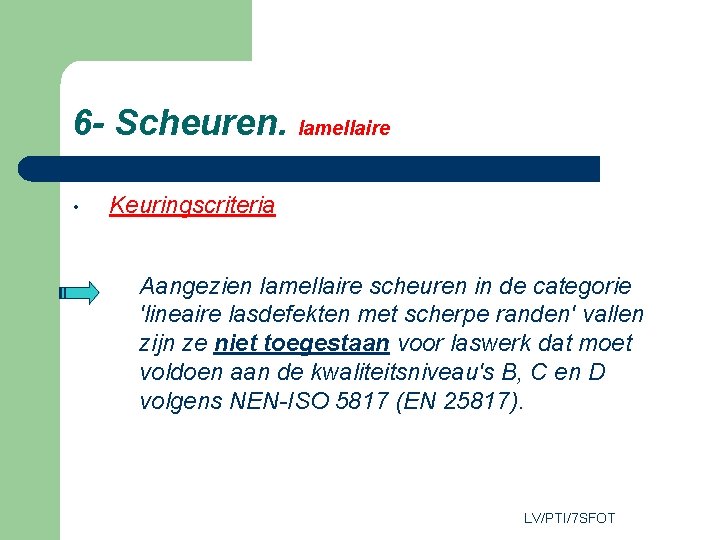
6 - Scheuren. lamellaire • Keuringscriteria Aangezien lamellaire scheuren in de categorie 'lineaire lasdefekten met scherpe randen' vallen zijn ze niet toegestaan voor laswerk dat moet voldoen aan de kwaliteitsniveau's B, C en D volgens NEN-ISO 5817 (EN 25817). LV/PTI/7 SFOT
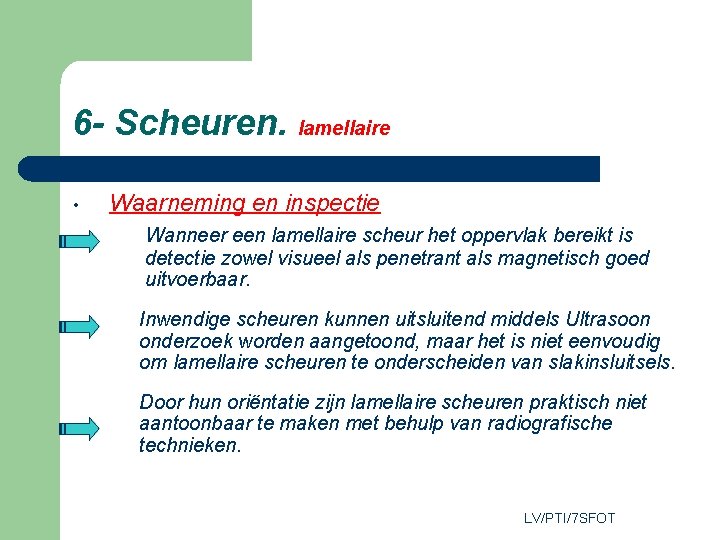
6 - Scheuren. lamellaire • Waarneming en inspectie Wanneer een lamellaire scheur het oppervlak bereikt is detectie zowel visueel als penetrant als magnetisch goed uitvoerbaar. Inwendige scheuren kunnen uitsluitend middels Ultrasoon onderzoek worden aangetoond, maar het is niet eenvoudig om lamellaire scheuren te onderscheiden van slakinsluitsels. Door hun oriëntatie zijn lamellaire scheuren praktisch niet aantoonbaar te maken met behulp van radiografische technieken. LV/PTI/7 SFOT
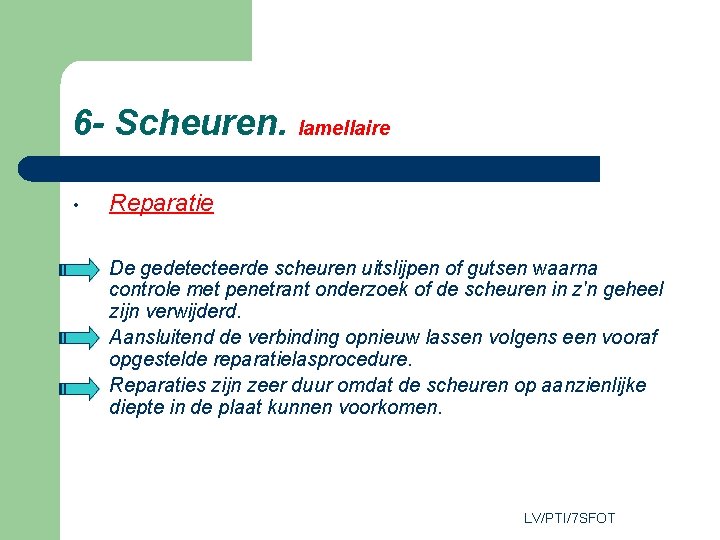
6 - Scheuren. lamellaire • Reparatie De gedetecteerde scheuren uitslijpen of gutsen waarna controle met penetrant onderzoek of de scheuren in z'n geheel zijn verwijderd. Aansluitend de verbinding opnieuw lassen volgens een vooraf opgestelde reparatielasprocedure. Reparaties zijn zeer duur omdat de scheuren op aanzienlijke diepte in de plaat kunnen voorkomen. LV/PTI/7 SFOT
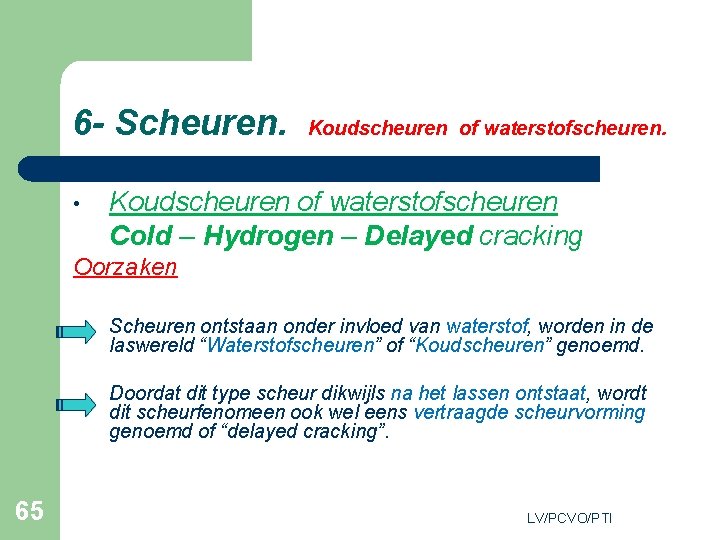
6 - Scheuren. • Koudscheuren of waterstofscheuren Cold – Hydrogen – Delayed cracking Oorzaken Scheuren ontstaan onder invloed van waterstof, worden in de laswereld “Waterstofscheuren” of “Koudscheuren” genoemd. Doordat dit type scheur dikwijls na het lassen ontstaat, wordt dit scheurfenomeen ook wel eens vertraagde scheurvorming genoemd of “delayed cracking”. 65 LV/PCVO/PTI
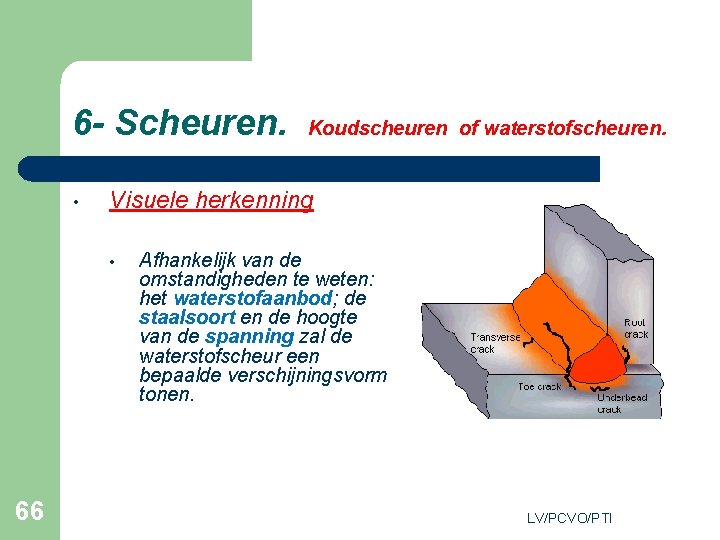
6 - Scheuren. • Visuele herkenning • 66 Koudscheuren of waterstofscheuren. Afhankelijk van de omstandigheden te weten: het waterstofaanbod; de staalsoort en de hoogte van de spanning zal de waterstofscheur een bepaalde verschijningsvorm tonen. LV/PCVO/PTI
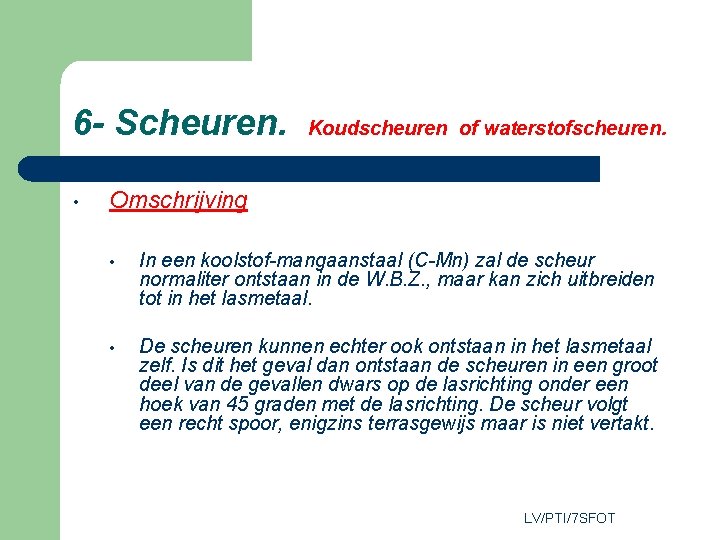
6 - Scheuren. • Koudscheuren of waterstofscheuren. Omschrijving • In een koolstof-mangaanstaal (C-Mn) zal de scheur normaliter ontstaan in de W. B. Z. , maar kan zich uitbreiden tot in het lasmetaal. • De scheuren kunnen echter ook ontstaan in het lasmetaal zelf. Is dit het geval dan ontstaan de scheuren in een groot deel van de gevallen dwars op de lasrichting onder een hoek van 45 graden met de lasrichting. De scheur volgt een recht spoor, enigzins terrasgewijs maar is niet vertakt. LV/PTI/7 SFOT
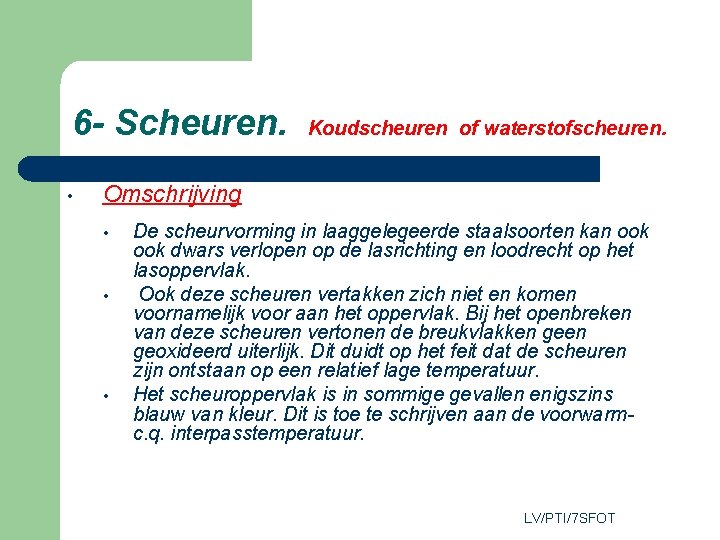
6 - Scheuren. • Koudscheuren of waterstofscheuren. Omschrijving • • • De scheurvorming in laaggelegeerde staalsoorten kan ook dwars verlopen op de lasrichting en loodrecht op het lasoppervlak. Ook deze scheuren vertakken zich niet en komen voornamelijk voor aan het oppervlak. Bij het openbreken van deze scheuren vertonen de breukvlakken geoxideerd uiterlijk. Dit duidt op het feit dat de scheuren zijn ontstaan op een relatief lage temperatuur. Het scheuroppervlak is in sommige gevallen enigszins blauw van kleur. Dit is toe te schrijven aan de voorwarmc. q. interpasstemperatuur. LV/PTI/7 SFOT
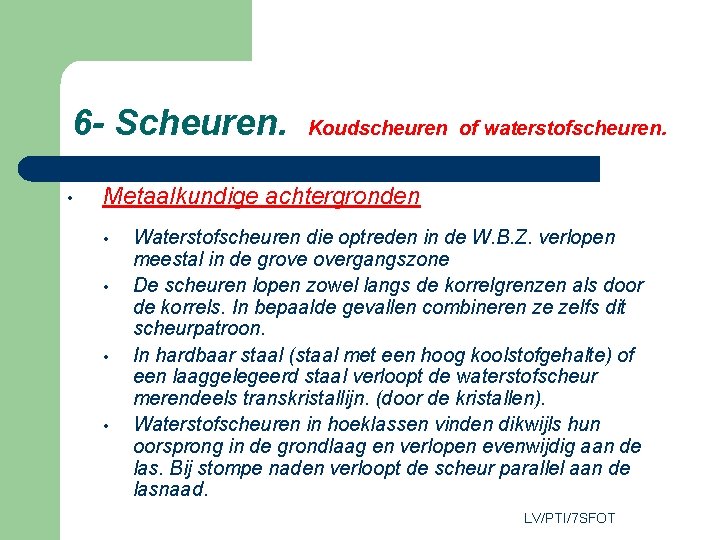
6 - Scheuren. • Koudscheuren of waterstofscheuren. Metaalkundige achtergronden • • Waterstofscheuren die optreden in de W. B. Z. verlopen meestal in de grove overgangszone De scheuren lopen zowel langs de korrelgrenzen als door de korrels. In bepaalde gevallen combineren ze zelfs dit scheurpatroon. In hardbaar staal (staal met een hoog koolstofgehalte) of een laaggelegeerd staal verloopt de waterstofscheur merendeels transkristallijn. (door de kristallen). Waterstofscheuren in hoeklassen vinden dikwijls hun oorsprong in de grondlaag en verlopen evenwijdig aan de las. Bij stompe naden verloopt de scheur parallel aan de lasnaad. LV/PTI/7 SFOT
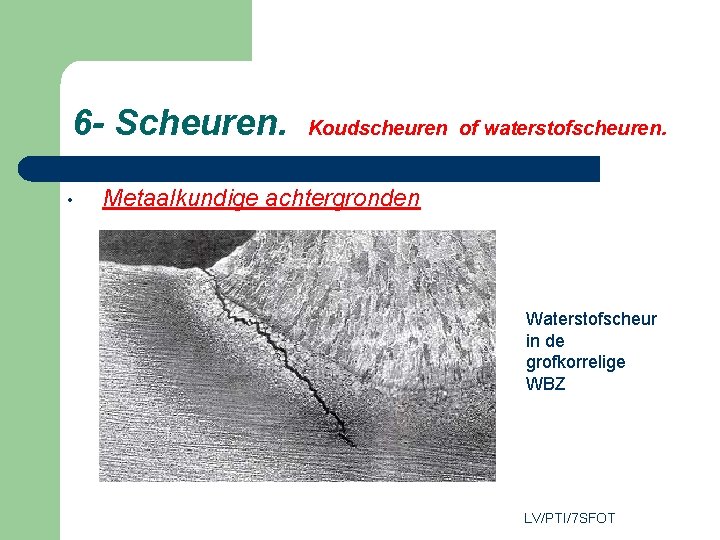
6 - Scheuren. • Koudscheuren of waterstofscheuren. Metaalkundige achtergronden Waterstofscheur in de grofkorrelige WBZ LV/PTI/7 SFOT
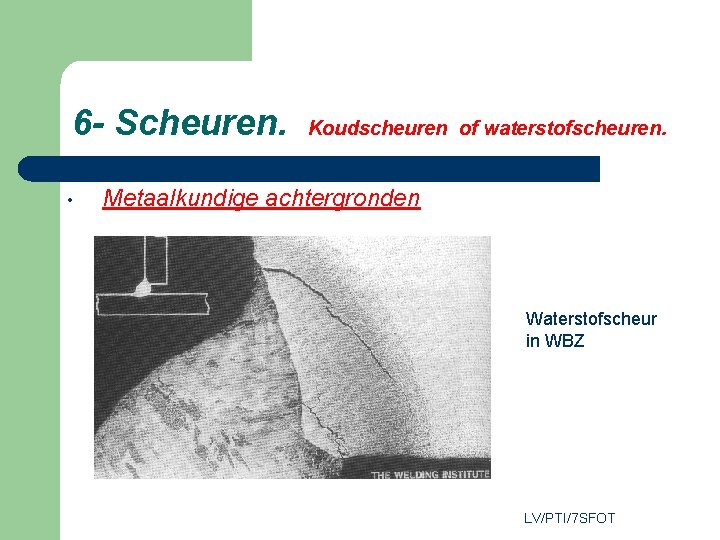
6 - Scheuren. • Koudscheuren of waterstofscheuren. Metaalkundige achtergronden Waterstofscheur in WBZ LV/PTI/7 SFOT
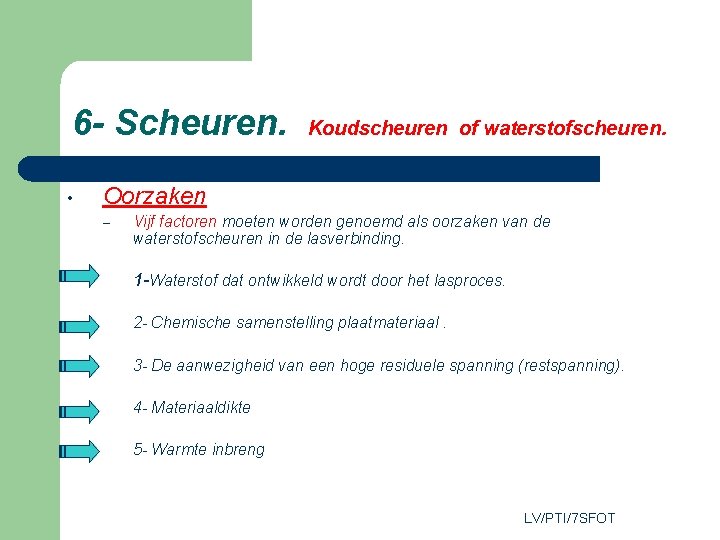
6 - Scheuren. • Koudscheuren of waterstofscheuren. Oorzaken – Vijf factoren moeten worden genoemd als oorzaken van de waterstofscheuren in de lasverbinding. 1 -Waterstof dat ontwikkeld wordt door het lasproces. 2 - Chemische samenstelling plaatmateriaal. 3 - De aanwezigheid van een hoge residuele spanning (restspanning). 4 - Materiaaldikte 5 - Warmte inbreng LV/PTI/7 SFOT
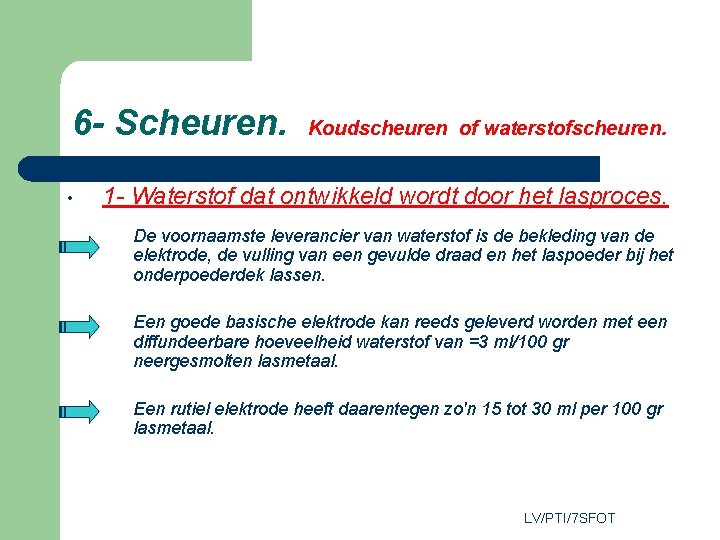
6 - Scheuren. • Koudscheuren of waterstofscheuren. 1 - Waterstof dat ontwikkeld wordt door het lasproces. De voornaamste leverancier van waterstof is de bekleding van de elektrode, de vulling van een gevulde draad en het laspoeder bij het onderpoederdek lassen. Een goede basische elektrode kan reeds geleverd worden met een diffundeerbare hoeveelheid waterstof van =3 ml/100 gr neergesmolten lasmetaal. Een rutiel elektrode heeft daarentegen zo'n 15 tot 30 ml per 100 gr lasmetaal. LV/PTI/7 SFOT
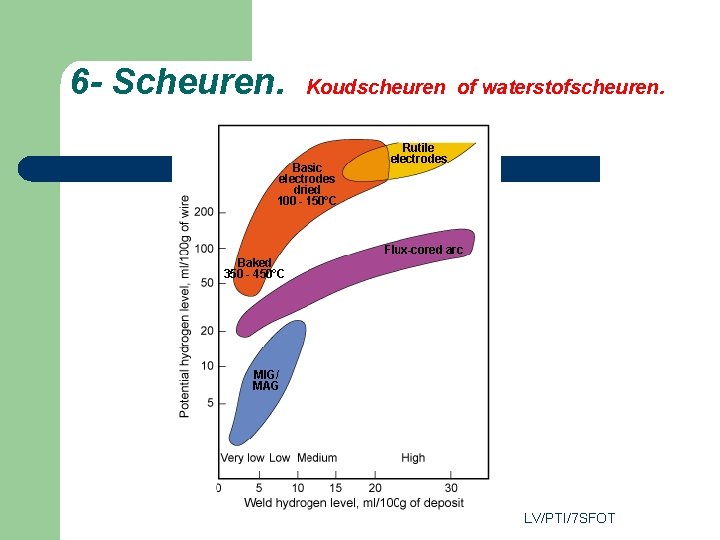
6 - Scheuren. Koudscheuren of waterstofscheuren. LV/PTI/7 SFOT
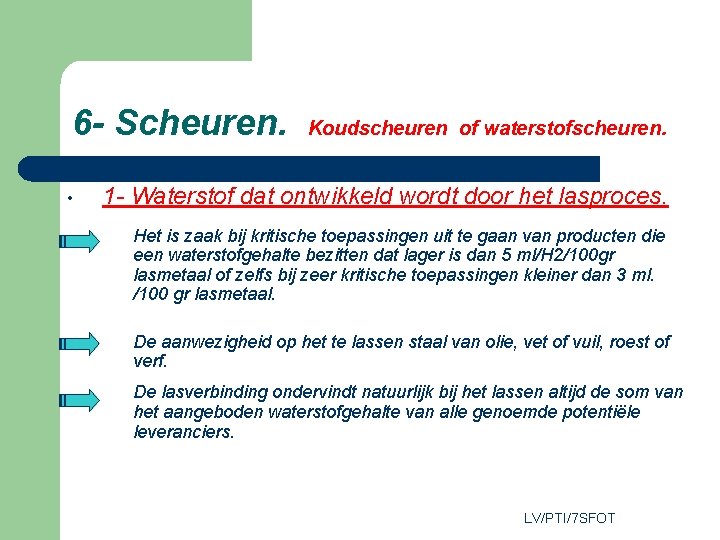
6 - Scheuren. • Koudscheuren of waterstofscheuren. 1 - Waterstof dat ontwikkeld wordt door het lasproces. Het is zaak bij kritische toepassingen uit te gaan van producten die een waterstofgehalte bezitten dat lager is dan 5 ml/H 2/100 gr lasmetaal of zelfs bij zeer kritische toepassingen kleiner dan 3 ml. /100 gr lasmetaal. De aanwezigheid op het te lassen staal van olie, vet of vuil, roest of verf. De lasverbinding ondervindt natuurlijk bij het lassen altijd de som van het aangeboden waterstofgehalte van alle genoemde potentiële leveranciers. LV/PTI/7 SFOT
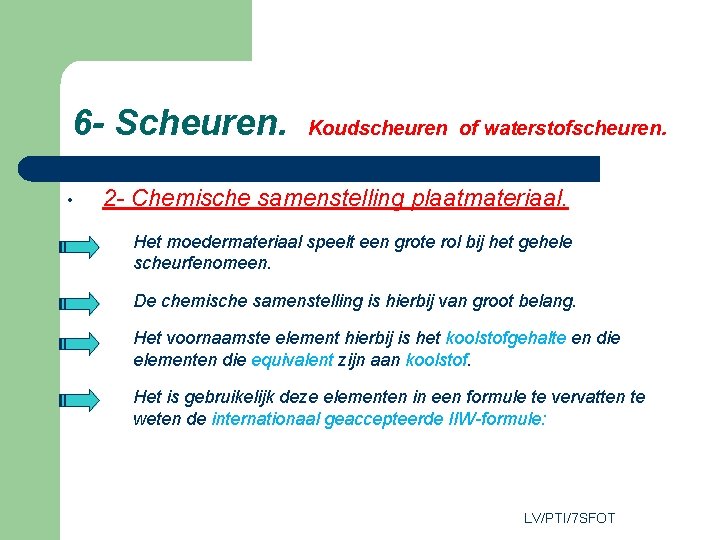
6 - Scheuren. • Koudscheuren of waterstofscheuren. 2 - Chemische samenstelling plaatmateriaal. Het moedermateriaal speelt een grote rol bij het gehele scheurfenomeen. De chemische samenstelling is hierbij van groot belang. Het voornaamste element hierbij is het koolstofgehalte en die elementen die equivalent zijn aan koolstof. Het is gebruikelijk deze elementen in een formule te vervatten te weten de internationaal geaccepteerde IIW-formule: LV/PTI/7 SFOT
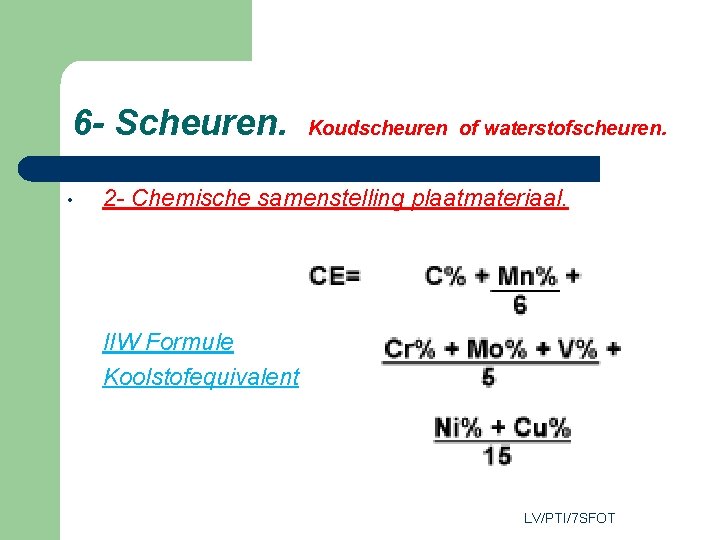
6 - Scheuren. • Koudscheuren of waterstofscheuren. 2 - Chemische samenstelling plaatmateriaal. IIW Formule Koolstofequivalent LV/PTI/7 SFOT
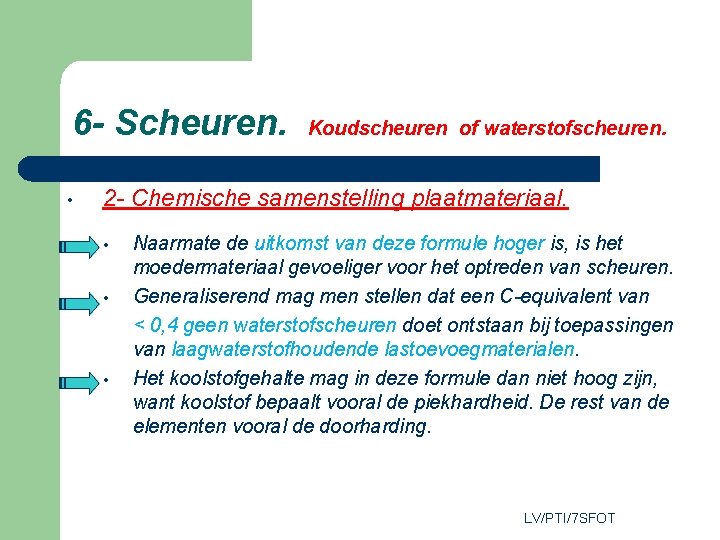
6 - Scheuren. • Koudscheuren of waterstofscheuren. 2 - Chemische samenstelling plaatmateriaal. • • • Naarmate de uitkomst van deze formule hoger is, is het moedermateriaal gevoeliger voor het optreden van scheuren. Generaliserend mag men stellen dat een C-equivalent van < 0, 4 geen waterstofscheuren doet ontstaan bij toepassingen van laagwaterstofhoudende lastoevoegmaterialen. Het koolstofgehalte mag in deze formule dan niet hoog zijn, want koolstof bepaalt vooral de piekhardheid. De rest van de elementen vooral de doorharding. LV/PTI/7 SFOT
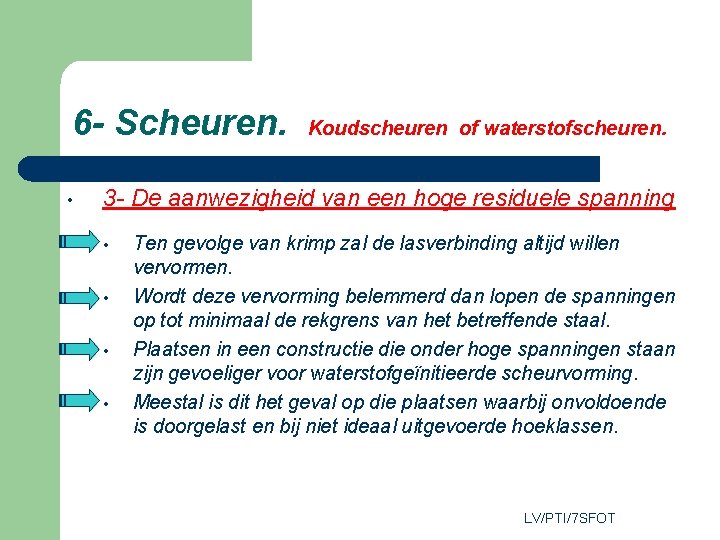
6 - Scheuren. • Koudscheuren of waterstofscheuren. 3 - De aanwezigheid van een hoge residuele spanning • • Ten gevolge van krimp zal de lasverbinding altijd willen vervormen. Wordt deze vervorming belemmerd dan lopen de spanningen op tot minimaal de rekgrens van het betreffende staal. Plaatsen in een constructie die onder hoge spanningen staan zijn gevoeliger voor waterstofgeïnitieerde scheurvorming. Meestal is dit het geval op die plaatsen waarbij onvoldoende is doorgelast en bij niet ideaal uitgevoerde hoeklassen. LV/PTI/7 SFOT
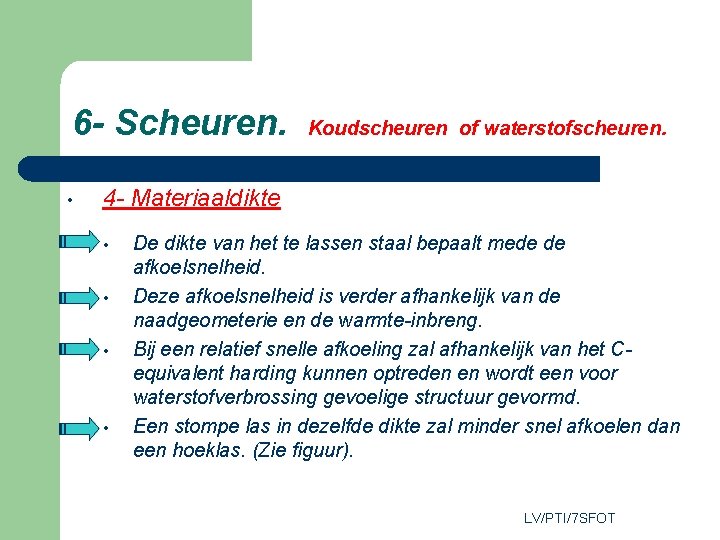
6 - Scheuren. • Koudscheuren of waterstofscheuren. 4 - Materiaaldikte • • De dikte van het te lassen staal bepaalt mede de afkoelsnelheid. Deze afkoelsnelheid is verder afhankelijk van de naadgeometerie en de warmte-inbreng. Bij een relatief snelle afkoeling zal afhankelijk van het Cequivalent harding kunnen optreden en wordt een voor waterstofverbrossing gevoelige structuur gevormd. Een stompe las in dezelfde dikte zal minder snel afkoelen dan een hoeklas. (Zie figuur). LV/PTI/7 SFOT
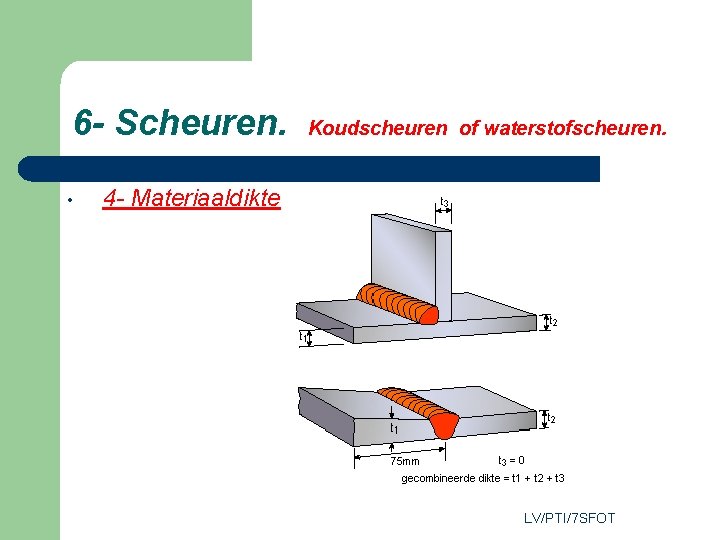
6 - Scheuren. • Koudscheuren of waterstofscheuren. 4 - Materiaaldikte LV/PTI/7 SFOT
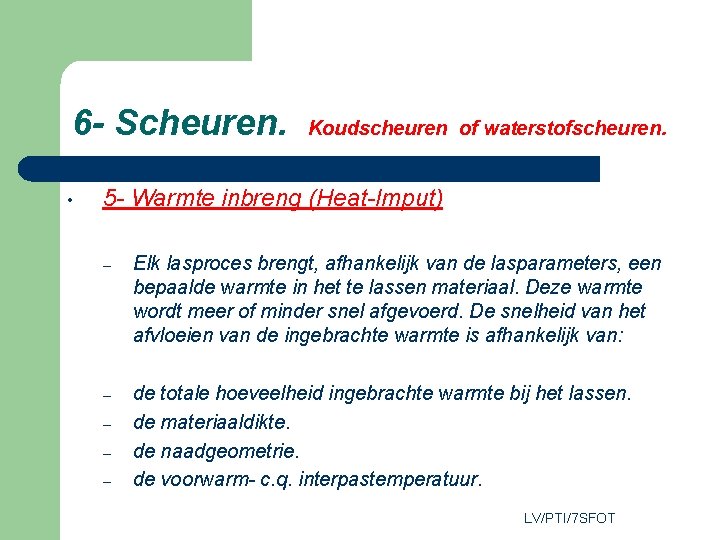
6 - Scheuren. • Koudscheuren of waterstofscheuren. 5 - Warmte inbreng (Heat-Imput) – Elk lasproces brengt, afhankelijk van de lasparameters, een bepaalde warmte in het te lassen materiaal. Deze warmte wordt meer of minder snel afgevoerd. De snelheid van het afvloeien van de ingebrachte warmte is afhankelijk van: – de totale hoeveelheid ingebrachte warmte bij het lassen. de materiaaldikte. de naadgeometrie. de voorwarm- c. q. interpastemperatuur. – – – LV/PTI/7 SFOT
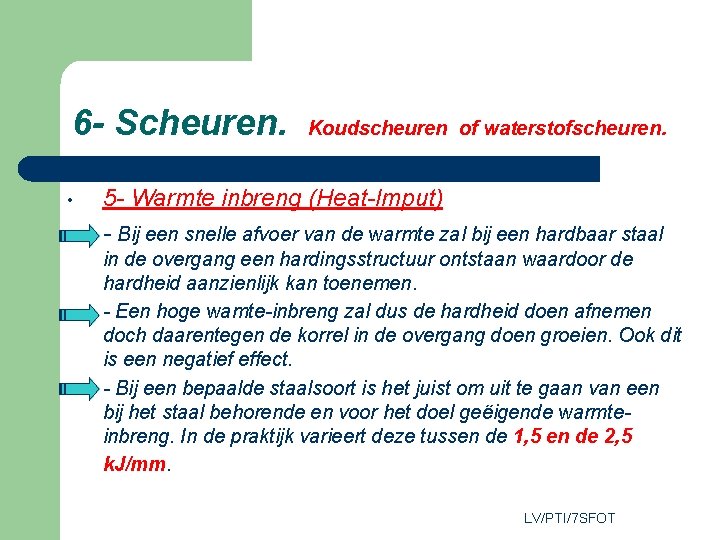
6 - Scheuren. • Koudscheuren of waterstofscheuren. 5 - Warmte inbreng (Heat-Imput) - Bij een snelle afvoer van de warmte zal bij een hardbaar staal in de overgang een hardingsstructuur ontstaan waardoor de hardheid aanzienlijk kan toenemen. - Een hoge wamte-inbreng zal dus de hardheid doen afnemen doch daarentegen de korrel in de overgang doen groeien. Ook dit is een negatief effect. - Bij een bepaalde staalsoort is het juist om uit te gaan van een bij het staal behorende en voor het doel geëigende warmteinbreng. In de praktijk varieert deze tussen de 1, 5 en de 2, 5 k. J/mm. LV/PTI/7 SFOT
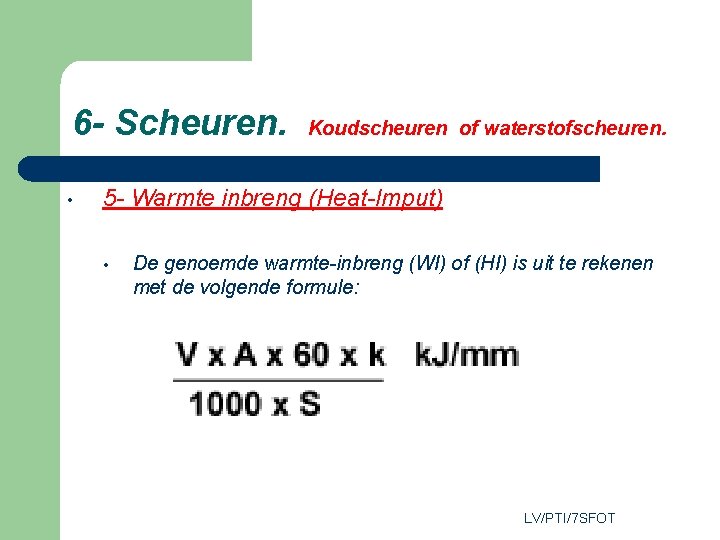
6 - Scheuren. • Koudscheuren of waterstofscheuren. 5 - Warmte inbreng (Heat-Imput) • De genoemde warmte-inbreng (WI) of (HI) is uit te rekenen met de volgende formule: LV/PTI/7 SFOT
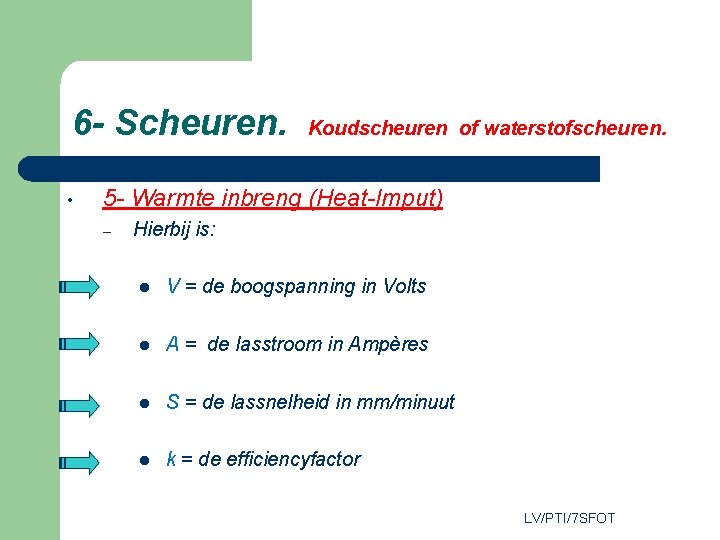
6 - Scheuren. • Koudscheuren of waterstofscheuren. 5 - Warmte inbreng (Heat-Imput) – Hierbij is: l V = de boogspanning in Volts l A = de lasstroom in Ampères l S = de lassnelheid in mm/minuut l k = de efficiencyfactor LV/PTI/7 SFOT
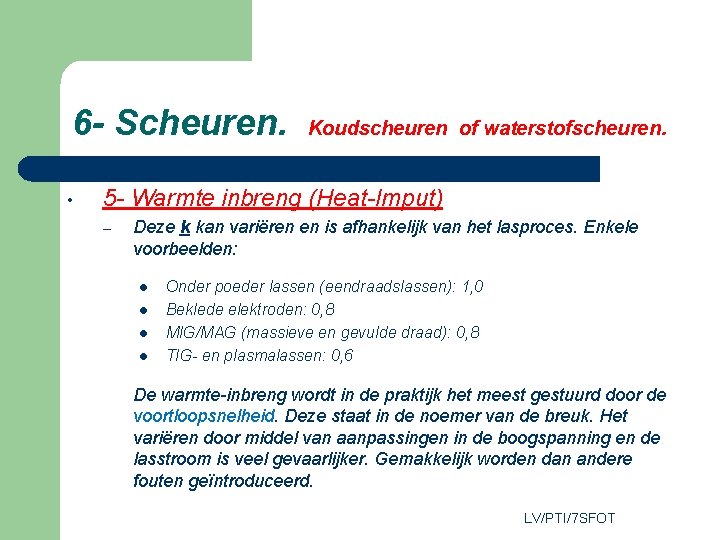
6 - Scheuren. • Koudscheuren of waterstofscheuren. 5 - Warmte inbreng (Heat-Imput) – Deze k kan variëren en is afhankelijk van het lasproces. Enkele voorbeelden: l l Onder poeder lassen (eendraadslassen): 1, 0 Beklede elektroden: 0, 8 MIG/MAG (massieve en gevulde draad): 0, 8 TIG- en plasmalassen: 0, 6 De warmte-inbreng wordt in de praktijk het meest gestuurd door de voortloopsnelheid. Deze staat in de noemer van de breuk. Het variëren door middel van aanpassingen in de boogspanning en de lasstroom is veel gevaarlijker. Gemakkelijk worden dan andere fouten geïntroduceerd. LV/PTI/7 SFOT
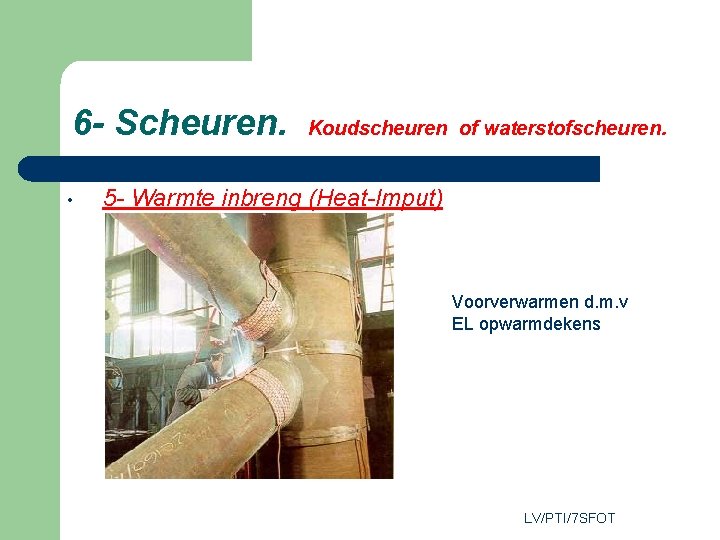
6 - Scheuren. • Koudscheuren of waterstofscheuren. 5 - Warmte inbreng (Heat-Imput) Voorverwarmen d. m. v EL opwarmdekens LV/PTI/7 SFOT

6 - Scheuren. • • Koudscheuren of waterstofscheuren. 5 - Warmte inbreng (Heat-Imput) Invloed voorwarmen. • • Het effect van voorwarmen bij het lassen is groot. Immers een verhoogde temperatuur geeft de eventueel aanwezige waterstof de tijd uit de lasverbinding te diffunderen. Bovendien wordt de afkoelsnelheid van de lasverbinding vertraagd, waardoor de kans op het ontstaan van een harde, brosse structuur wordt verkleind zoniet wordt uitgesloten. LV/PTI/7 SFOT
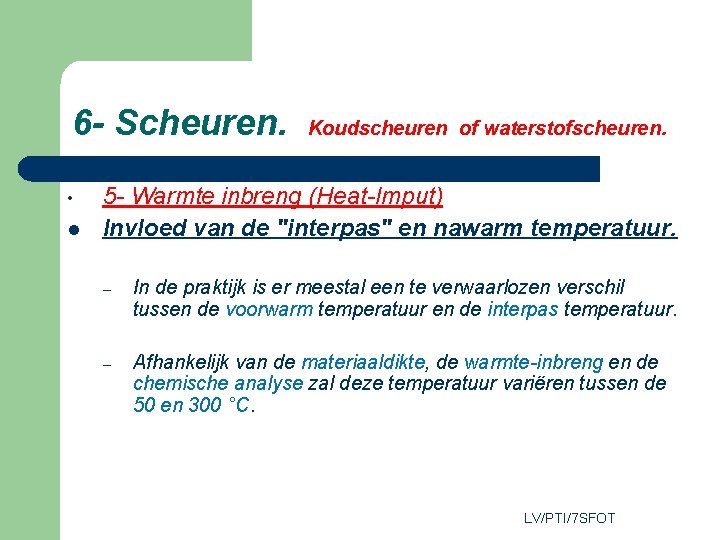
6 - Scheuren. • l Koudscheuren of waterstofscheuren. 5 - Warmte inbreng (Heat-Imput) Invloed van de "interpas" en nawarm temperatuur. – In de praktijk is er meestal een te verwaarlozen verschil tussen de voorwarm temperatuur en de interpas temperatuur. – Afhankelijk van de materiaaldikte, de warmte-inbreng en de chemische analyse zal deze temperatuur variëren tussen de 50 en 300 °C. LV/PTI/7 SFOT
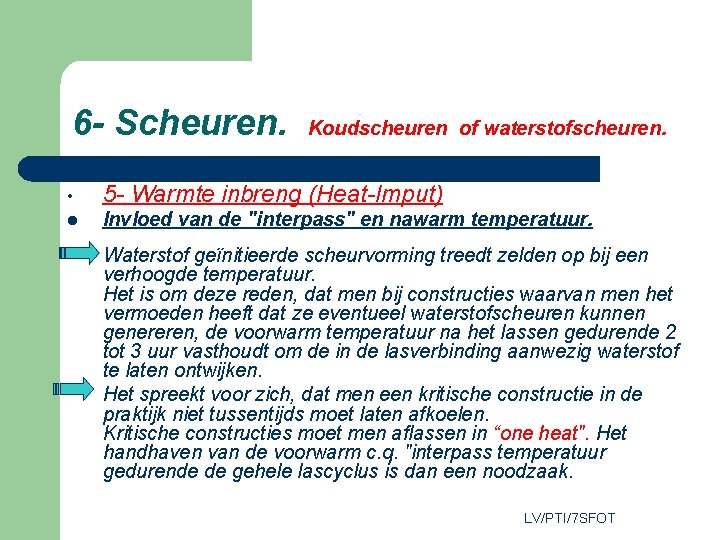
6 - Scheuren. Koudscheuren of waterstofscheuren. • 5 - Warmte inbreng (Heat-Imput) l Invloed van de "interpass" en nawarm temperatuur. Waterstof geïnitieerde scheurvorming treedt zelden op bij een verhoogde temperatuur. Het is om deze reden, dat men bij constructies waarvan men het vermoeden heeft dat ze eventueel waterstofscheuren kunnen genereren, de voorwarm temperatuur na het lassen gedurende 2 tot 3 uur vasthoudt om de in de lasverbinding aanwezig waterstof te laten ontwijken. Het spreekt voor zich, dat men een kritische constructie in de praktijk niet tussentijds moet laten afkoelen. Kritische constructies moet men aflassen in “one heat". Het handhaven van de voorwarm c. q. "interpass temperatuur gedurende de gehele lascyclus is dan een noodzaak. LV/PTI/7 SFOT
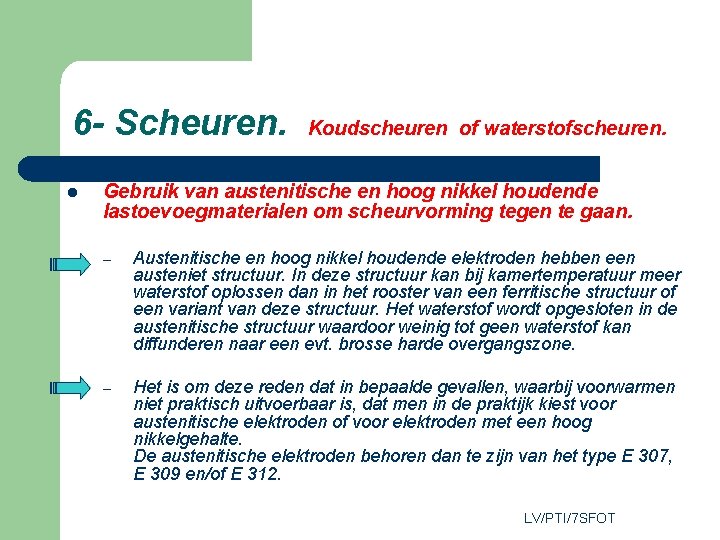
6 - Scheuren. l Koudscheuren of waterstofscheuren. Gebruik van austenitische en hoog nikkel houdende lastoevoegmaterialen om scheurvorming tegen te gaan. – Austenitische en hoog nikkel houdende elektroden hebben een austeniet structuur. In deze structuur kan bij kamertemperatuur meer waterstof oplossen dan in het rooster van een ferritische structuur of een variant van deze structuur. Het waterstof wordt opgesloten in de austenitische structuur waardoor weinig tot geen waterstof kan diffunderen naar een evt. brosse harde overgangszone. – Het is om deze reden dat in bepaalde gevallen, waarbij voorwarmen niet praktisch uitvoerbaar is, dat men in de praktijk kiest voor austenitische elektroden of voor elektroden met een hoog nikkelgehalte. De austenitische elektroden behoren dan te zijn van het type E 307, E 309 en/of E 312. LV/PTI/7 SFOT
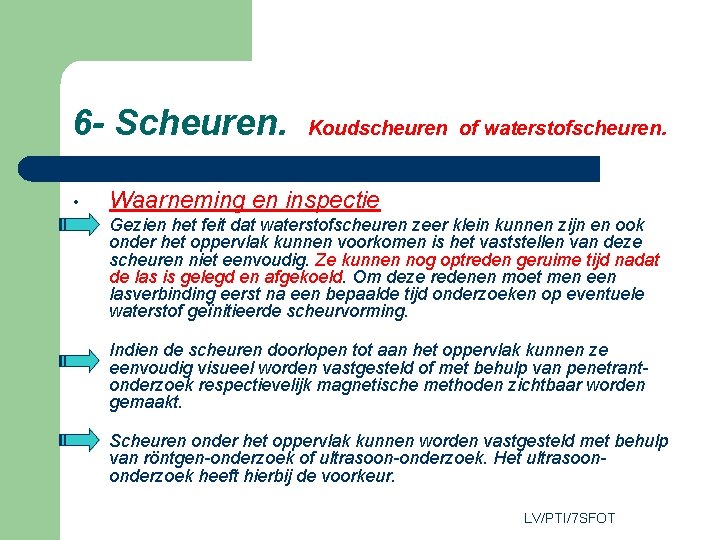
6 - Scheuren. • Koudscheuren of waterstofscheuren. Waarneming en inspectie Gezien het feit dat waterstofscheuren zeer klein kunnen zijn en ook onder het oppervlak kunnen voorkomen is het vaststellen van deze scheuren niet eenvoudig. Ze kunnen nog optreden geruime tijd nadat de las is gelegd en afgekoeld. Om deze redenen moet men een lasverbinding eerst na een bepaalde tijd onderzoeken op eventuele waterstof geïnitieerde scheurvorming. Indien de scheuren doorlopen tot aan het oppervlak kunnen ze eenvoudig visueel worden vastgesteld of met behulp van penetrantonderzoek respectievelijk magnetische methoden zichtbaar worden gemaakt. Scheuren onder het oppervlak kunnen worden vastgesteld met behulp van röntgen-onderzoek of ultrasoon-onderzoek. Het ultrasoononderzoek heeft hierbij de voorkeur. LV/PTI/7 SFOT
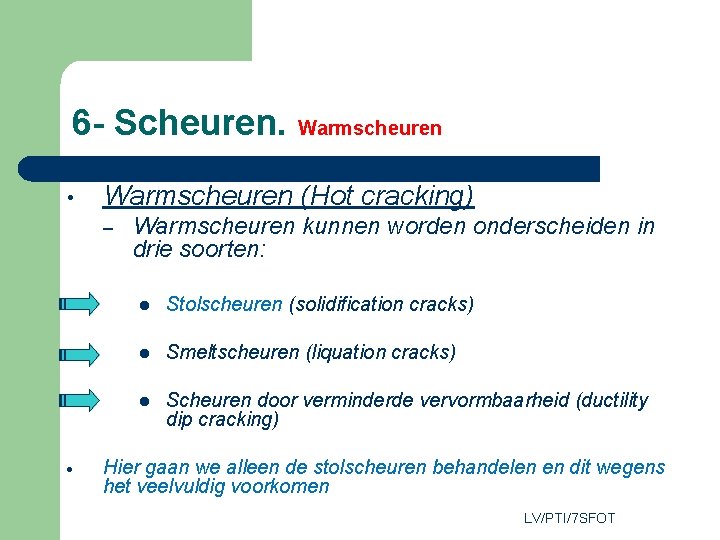
6 - Scheuren. Warmscheuren • Warmscheuren (Hot cracking) – Warmscheuren kunnen worden onderscheiden in drie soorten: l Stolscheuren (solidification cracks) l Smeltscheuren (liquation cracks) l Scheuren door verminderde vervormbaarheid (ductility dip cracking) Hier gaan we alleen de stolscheuren behandelen en dit wegens het veelvuldig voorkomen LV/PTI/7 SFOT
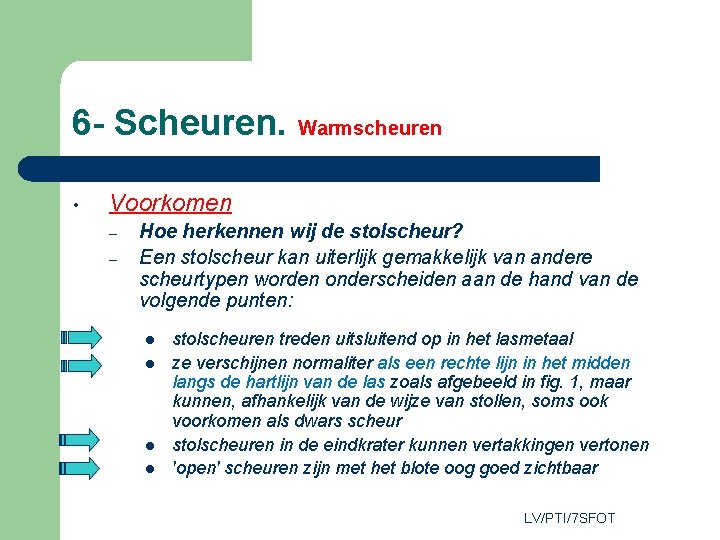
6 - Scheuren. Warmscheuren • Voorkomen – – Hoe herkennen wij de stolscheur? Een stolscheur kan uiterlijk gemakkelijk van andere scheurtypen worden onderscheiden aan de hand van de volgende punten: l l stolscheuren treden uitsluitend op in het lasmetaal ze verschijnen normaliter als een rechte lijn in het midden langs de hartlijn van de las zoals afgebeeld in fig. 1, maar kunnen, afhankelijk van de wijze van stollen, soms ook voorkomen als dwars scheur stolscheuren in de eindkrater kunnen vertakkingen vertonen 'open' scheuren zijn met het blote oog goed zichtbaar LV/PTI/7 SFOT
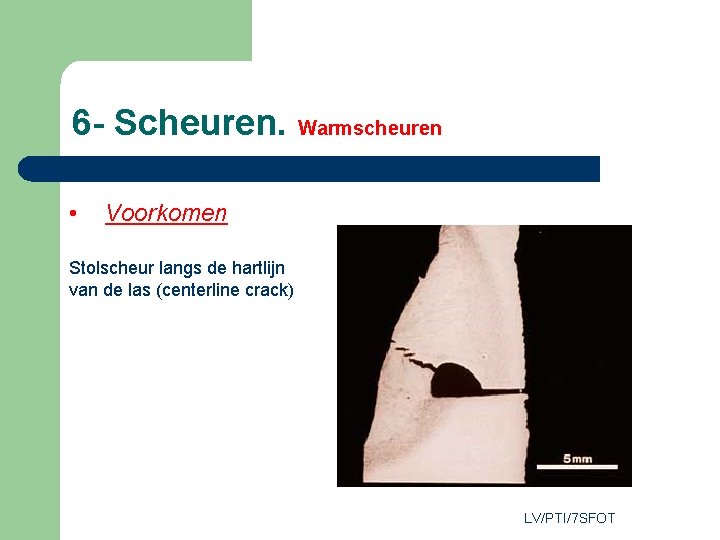
6 - Scheuren. Warmscheuren • Voorkomen Stolscheur langs de hartlijn van de las (centerline crack) LV/PTI/7 SFOT
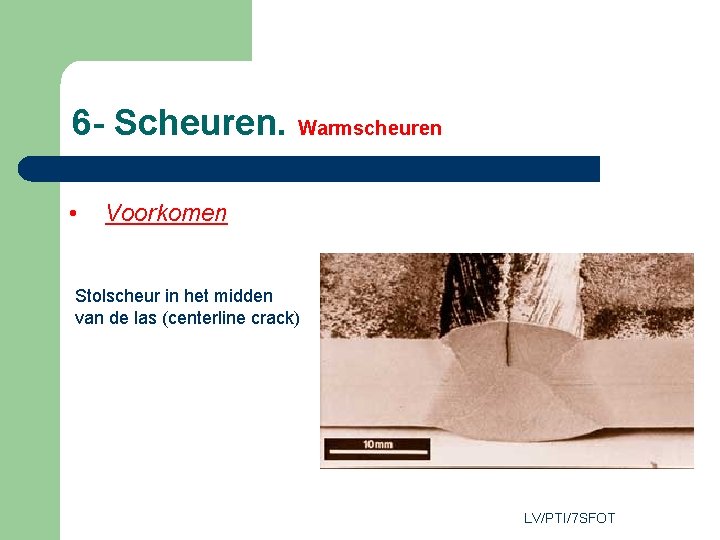
6 - Scheuren. Warmscheuren • Voorkomen Stolscheur in het midden van de las (centerline crack) LV/PTI/7 SFOT
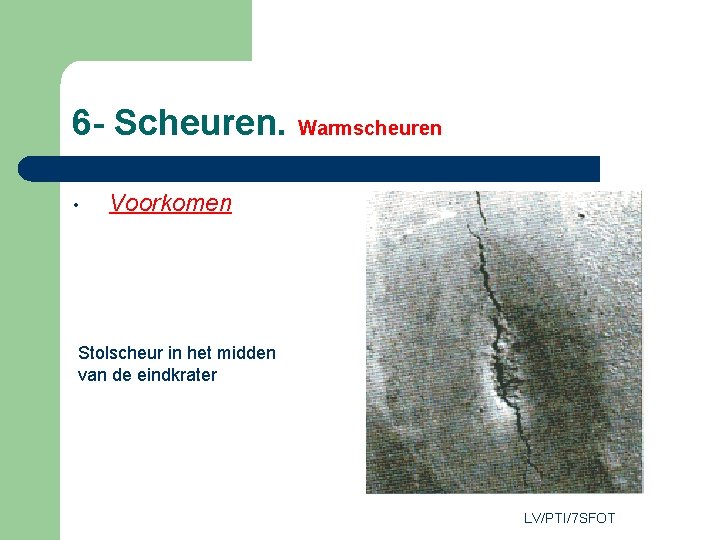
6 - Scheuren. Warmscheuren • Voorkomen Stolscheur in het midden van de eindkrater LV/PTI/7 SFOT

6 - Scheuren. Warmscheuren • Metaalkundige aspecten • • De scheuren worden gevormd aan het einde van het stollingsproces en zijn interkristallijn. Hun vorm is een weergave van de wijze waarop de stolling is verlopen. De kristallen groeien gedurende het stollen gebruikelijk in de richting vanuit de relatief koude kanten van het moedermateriaal naar het midden van het smeltbad. De laatst overgebleven smelt bevat de meeste verontreinigingen. LV/PTI/7 SFOT
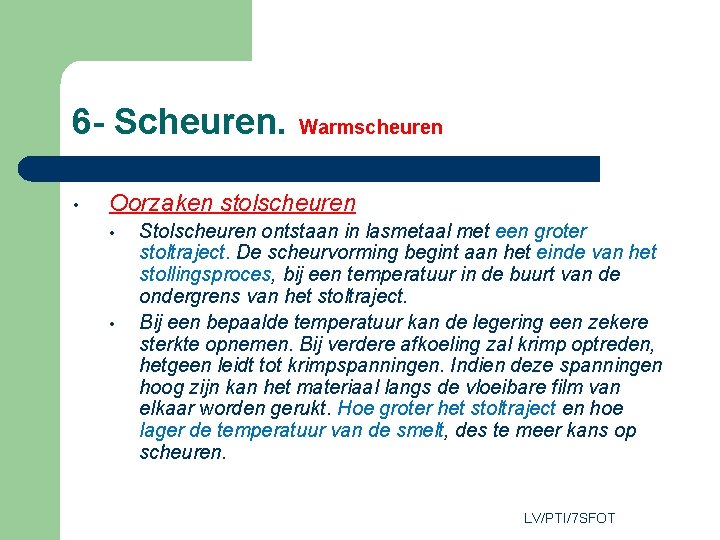
6 - Scheuren. • Warmscheuren Oorzaken stolscheuren • • Stolscheuren ontstaan in lasmetaal met een groter stoltraject. De scheurvorming begint aan het einde van het stollingsproces, bij een temperatuur in de buurt van de ondergrens van het stoltraject. Bij een bepaalde temperatuur kan de legering een zekere sterkte opnemen. Bij verdere afkoeling zal krimp optreden, hetgeen leidt tot krimpspanningen. Indien deze spanningen hoog zijn kan het materiaal langs de vloeibare film van elkaar worden gerukt. Hoe groter het stoltraject en hoe lager de temperatuur van de smelt, des te meer kans op scheuren. LV/PTI/7 SFOT
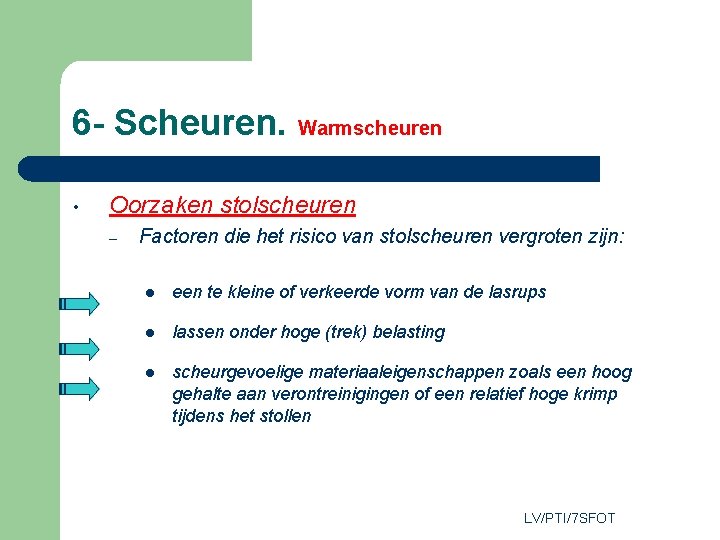
6 - Scheuren. Warmscheuren • Oorzaken stolscheuren – Factoren die het risico van stolscheuren vergroten zijn: l een te kleine of verkeerde vorm van de lasrups l lassen onder hoge (trek) belasting l scheurgevoelige materiaaleigenschappen zoals een hoog gehalte aan verontreinigingen of een relatief hoge krimp tijdens het stollen LV/PTI/7 SFOT
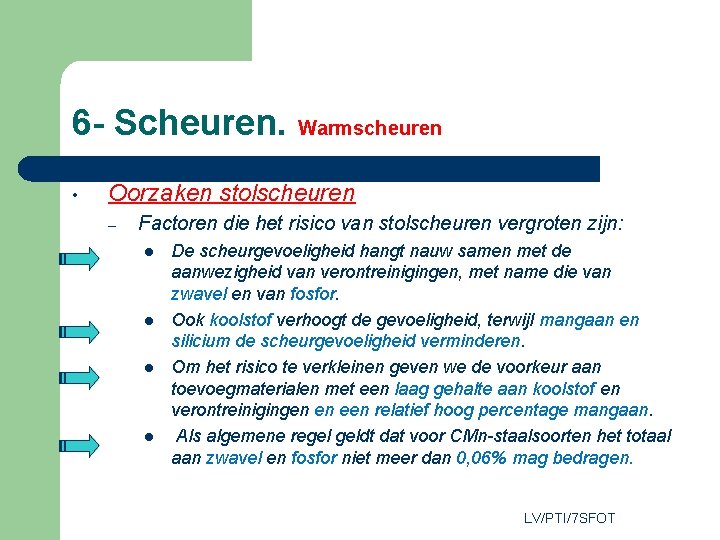
6 - Scheuren. Warmscheuren • Oorzaken stolscheuren – Factoren die het risico van stolscheuren vergroten zijn: l l De scheurgevoeligheid hangt nauw samen met de aanwezigheid van verontreinigingen, met name die van zwavel en van fosfor. Ook koolstof verhoogt de gevoeligheid, terwijl mangaan en silicium de scheurgevoeligheid verminderen. Om het risico te verkleinen geven we de voorkeur aan toevoegmaterialen met een laag gehalte aan koolstof en verontreinigingen en een relatief hoog percentage mangaan. Als algemene regel geldt dat voor CMn-staalsoorten het totaal aan zwavel en fosfor niet meer dan 0, 06% mag bedragen. LV/PTI/7 SFOT
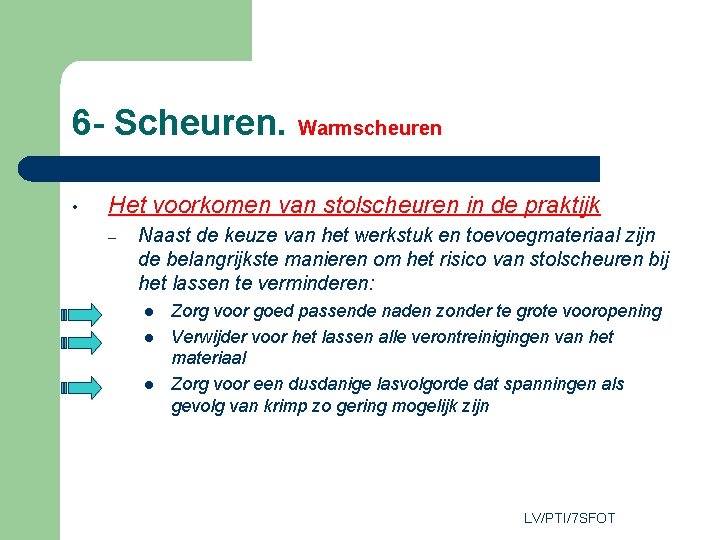
6 - Scheuren. Warmscheuren • Het voorkomen van stolscheuren in de praktijk – Naast de keuze van het werkstuk en toevoegmateriaal zijn de belangrijkste manieren om het risico van stolscheuren bij het lassen te verminderen: l l l Zorg voor goed passende naden zonder te grote vooropening Verwijder voor het lassen alle verontreinigingen van het materiaal Zorg voor een dusdanige lasvolgorde dat spanningen als gevolg van krimp zo gering mogelijk zijn LV/PTI/7 SFOT
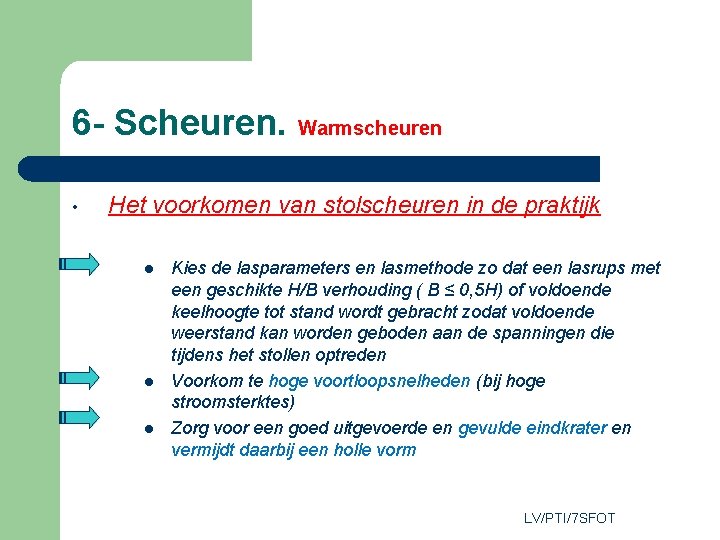
6 - Scheuren. Warmscheuren • Het voorkomen van stolscheuren in de praktijk l l l Kies de lasparameters en lasmethode zo dat een lasrups met een geschikte H/B verhouding ( B ≤ 0, 5 H) of voldoende keelhoogte tot stand wordt gebracht zodat voldoende weerstand kan worden geboden aan de spanningen die tijdens het stollen optreden Voorkom te hoge voortloopsnelheden (bij hoge stroomsterktes) Zorg voor een goed uitgevoerde en gevulde eindkrater en vermijdt daarbij een holle vorm LV/PTI/7 SFOT
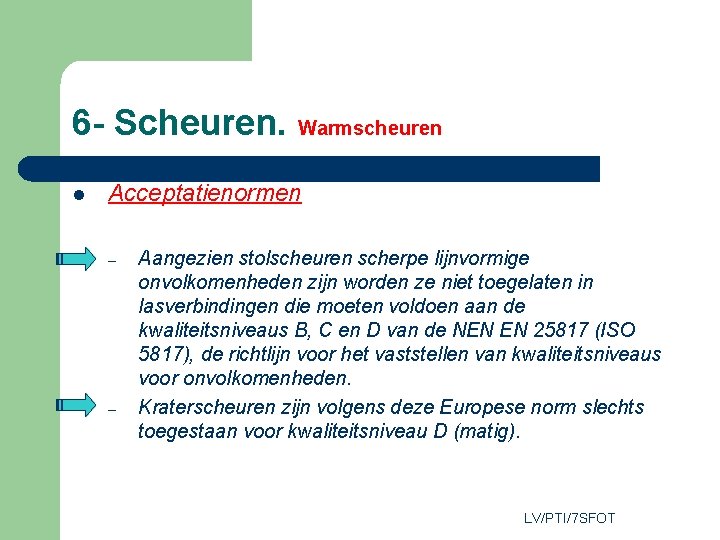
6 - Scheuren. Warmscheuren l Acceptatienormen – – Aangezien stolscheuren scherpe lijnvormige onvolkomenheden zijn worden ze niet toegelaten in lasverbindingen die moeten voldoen aan de kwaliteitsniveaus B, C en D van de NEN EN 25817 (ISO 5817), de richtlijn voor het vaststellen van kwaliteitsniveaus voor onvolkomenheden. Kraterscheuren zijn volgens deze Europese norm slechts toegestaan voor kwaliteitsniveau D (matig). LV/PTI/7 SFOT
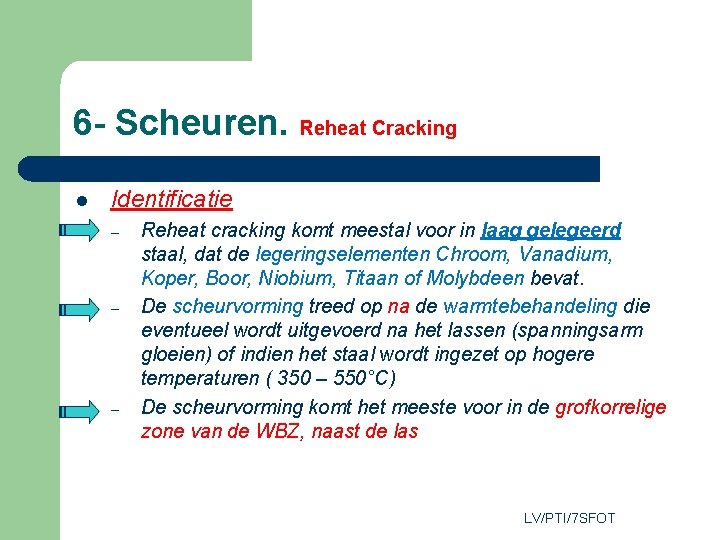
6 - Scheuren. Reheat Cracking l Identificatie – – – Reheat cracking komt meestal voor in laag gelegeerd staal, dat de legeringselementen Chroom, Vanadium, Koper, Boor, Niobium, Titaan of Molybdeen bevat. De scheurvorming treed op na de warmtebehandeling die eventueel wordt uitgevoerd na het lassen (spanningsarm gloeien) of indien het staal wordt ingezet op hogere temperaturen ( 350 – 550°C) De scheurvorming komt het meeste voor in de grofkorrelige zone van de WBZ, naast de las LV/PTI/7 SFOT
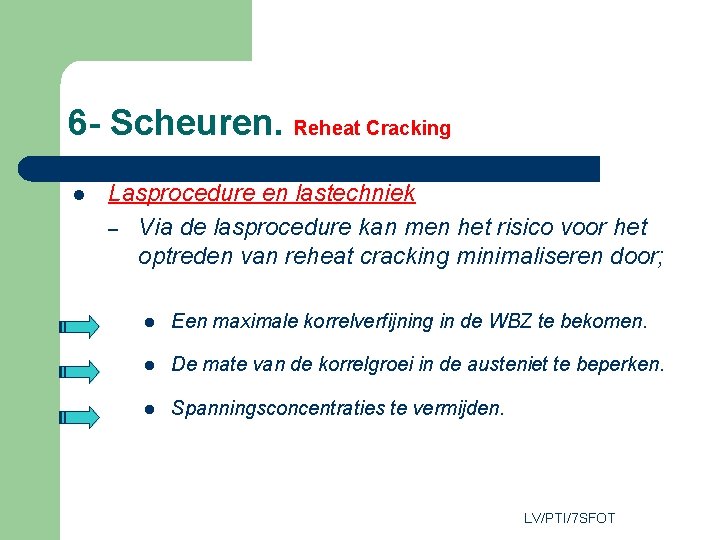
6 - Scheuren. Reheat Cracking l Lasprocedure en lastechniek – Via de lasprocedure kan men het risico voor het optreden van reheat cracking minimaliseren door; l Een maximale korrelverfijning in de WBZ te bekomen. l De mate van de korrelgroei in de austeniet te beperken. l Spanningsconcentraties te vermijden. LV/PTI/7 SFOT
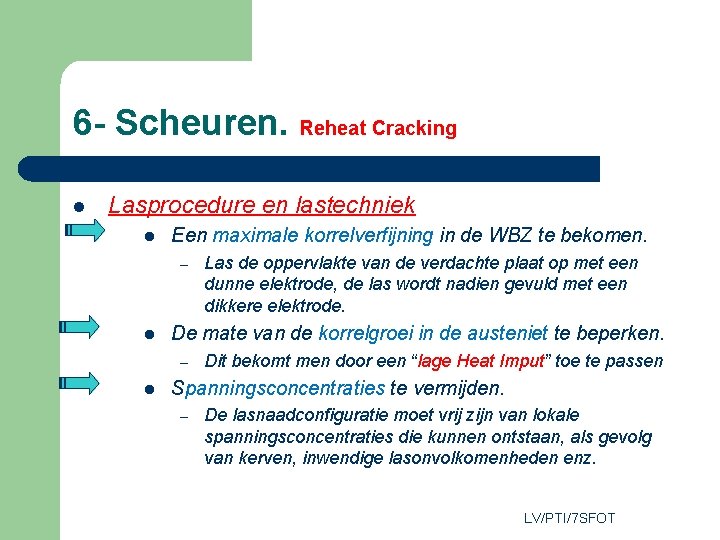
6 - Scheuren. Reheat Cracking l Lasprocedure en lastechniek l Een maximale korrelverfijning in de WBZ te bekomen. – l De mate van de korrelgroei in de austeniet te beperken. – l Las de oppervlakte van de verdachte plaat op met een dunne elektrode, de las wordt nadien gevuld met een dikkere elektrode. Dit bekomt men door een “lage Heat Imput” toe te passen Spanningsconcentraties te vermijden. – De lasnaadconfiguratie moet vrij zijn van lokale spanningsconcentraties die kunnen ontstaan, als gevolg van kerven, inwendige lasonvolkomenheden enz. LV/PTI/7 SFOT
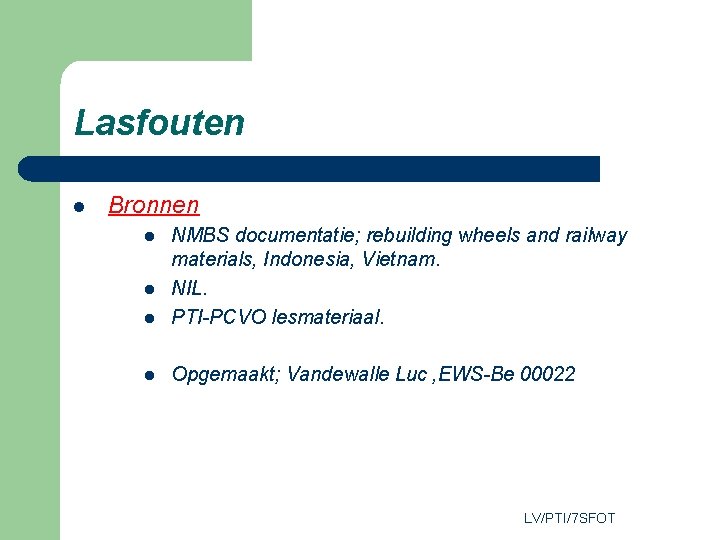
Lasfouten l Bronnen l NMBS documentatie; rebuilding wheels and railway materials, Indonesia, Vietnam. NIL. PTI-PCVO lesmateriaal. l Opgemaakt; Vandewalle Luc , EWS-Be 00022 l l LV/PTI/7 SFOT