LARP Hi Lumi AUP Coil Winding Curing Review
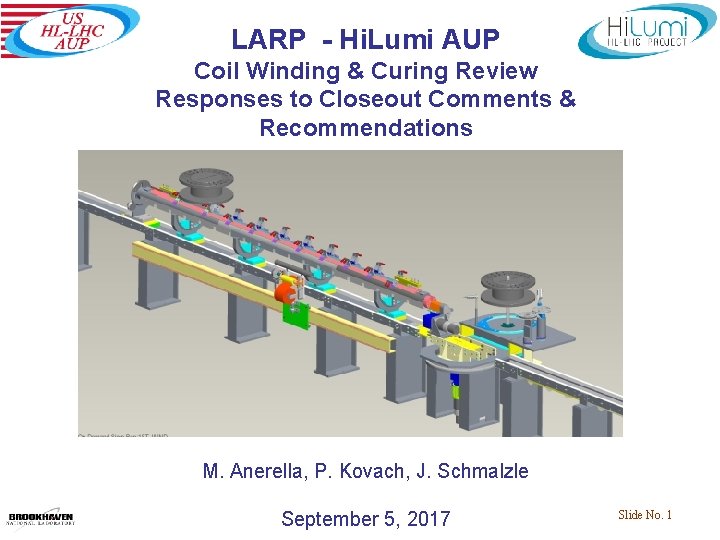
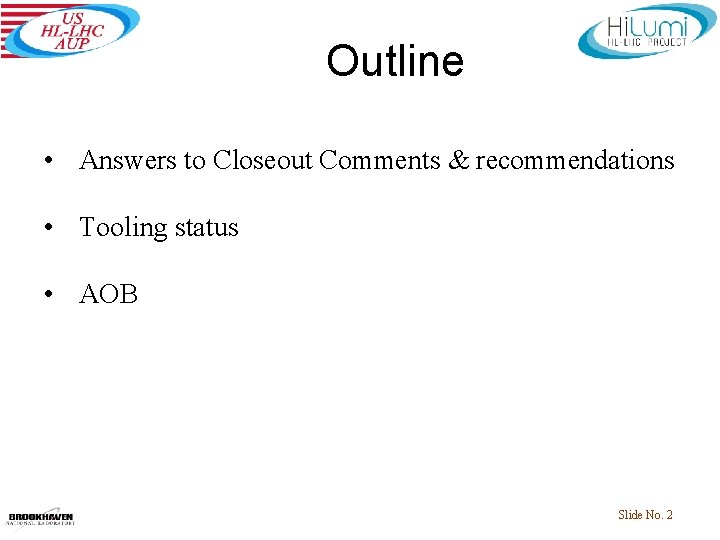
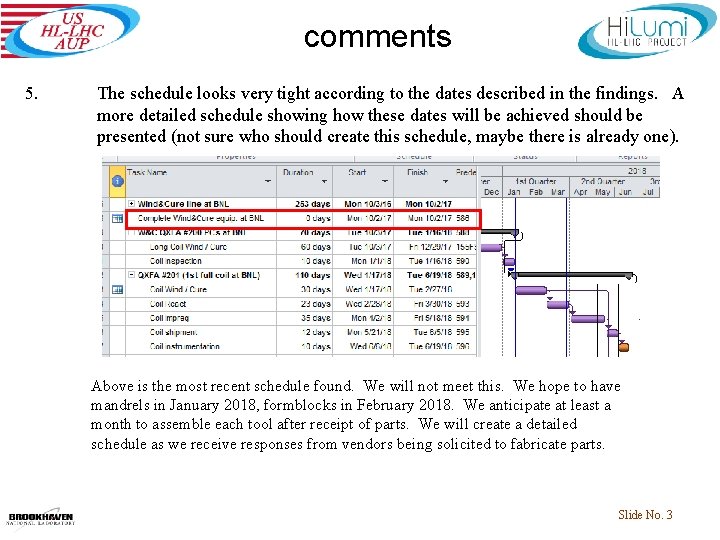
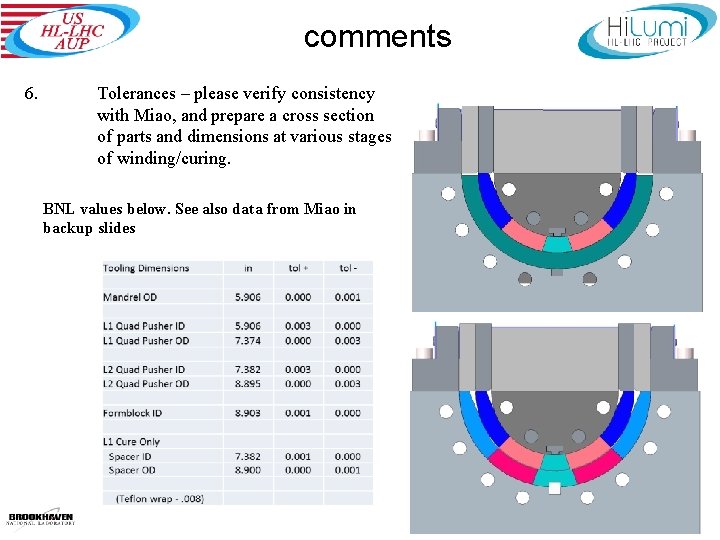
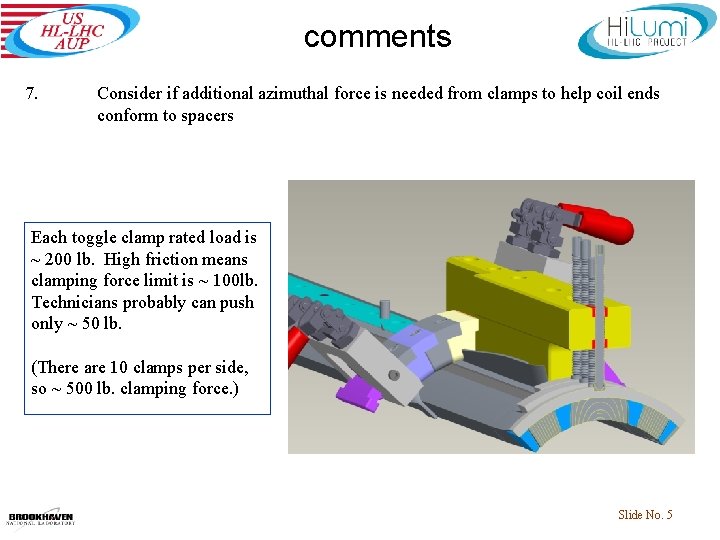
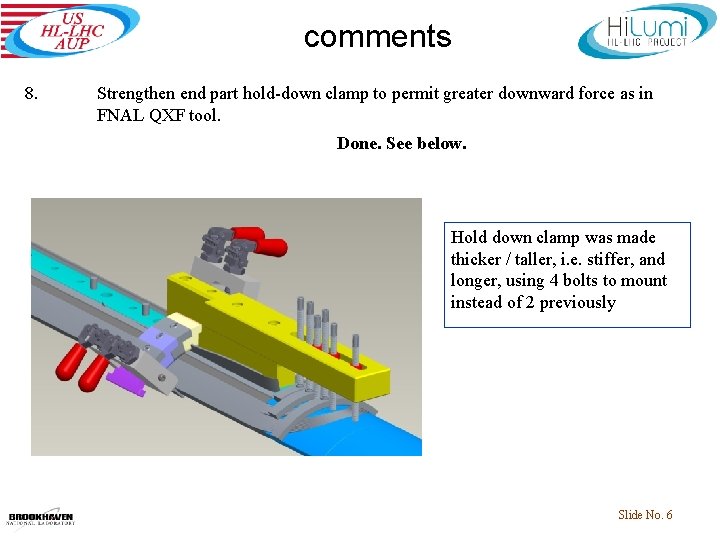
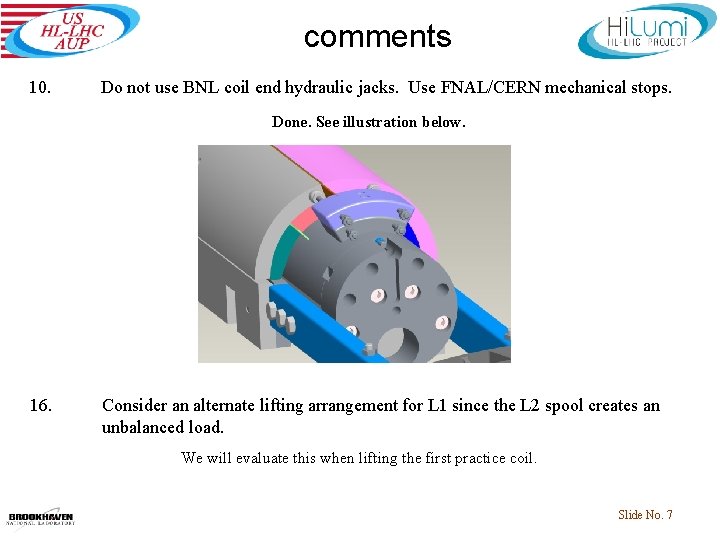
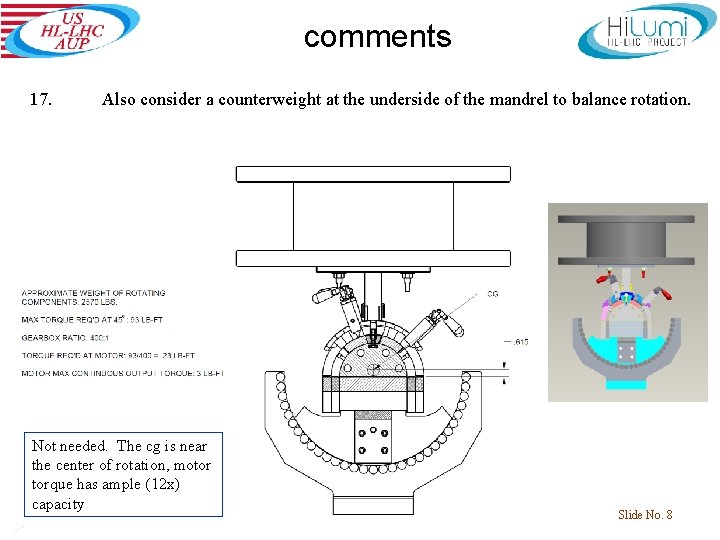
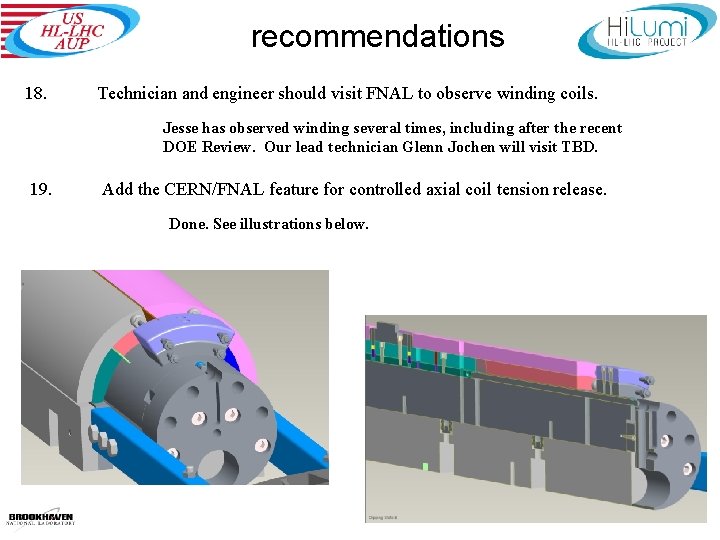
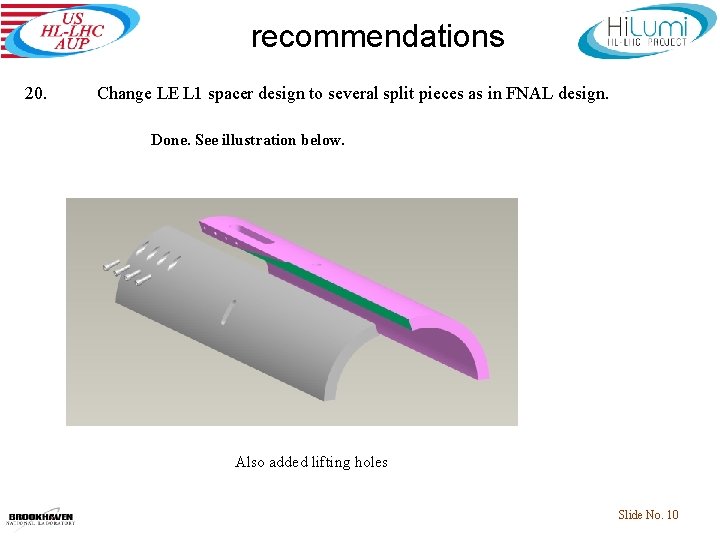
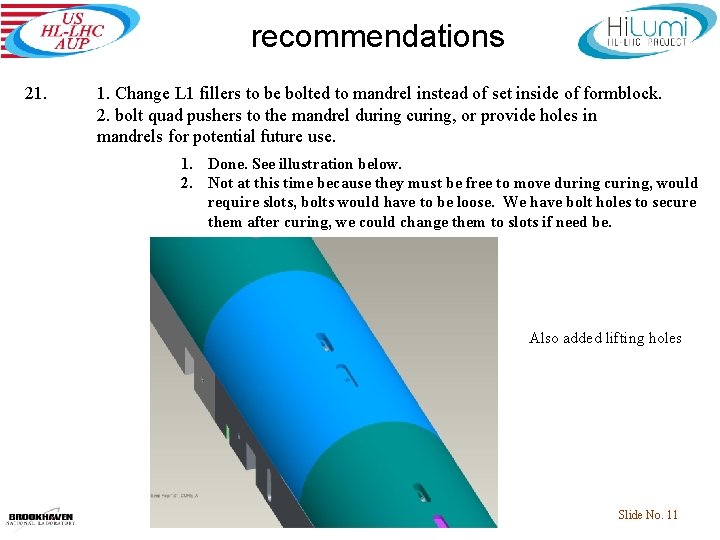
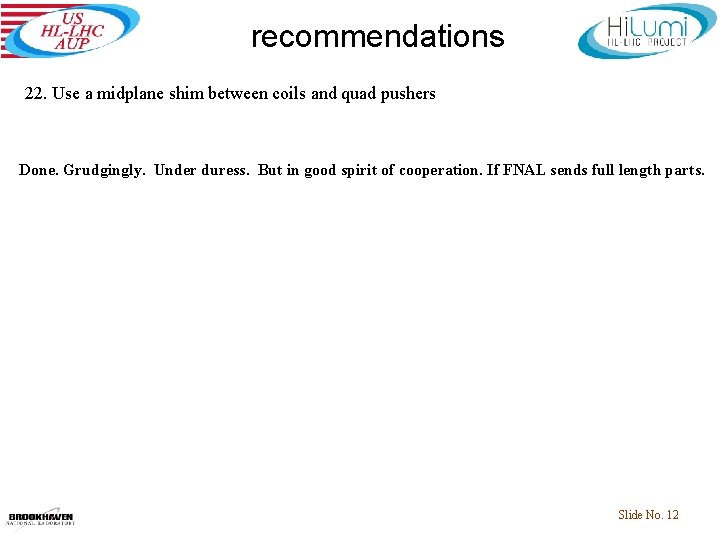
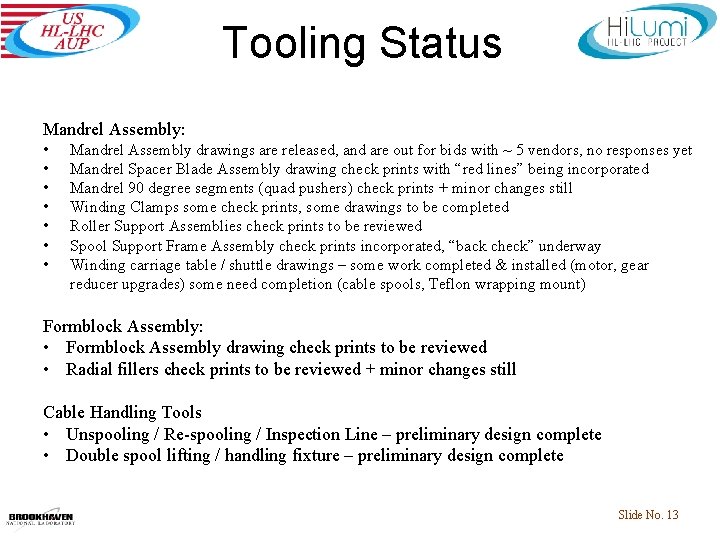
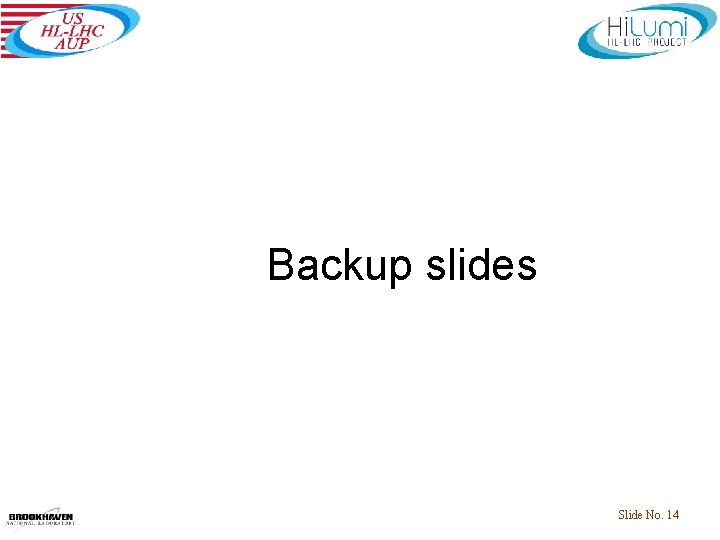
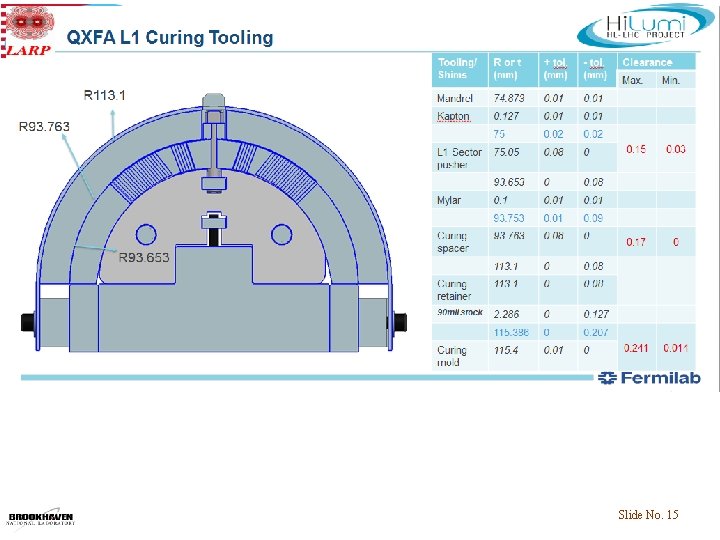
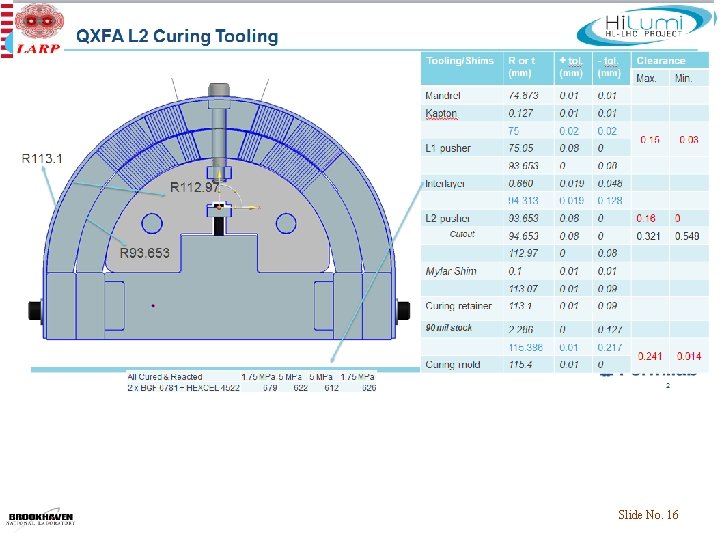
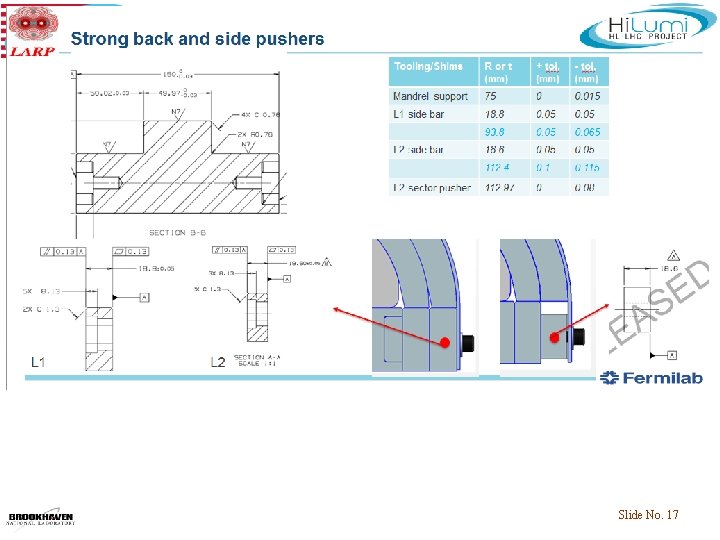
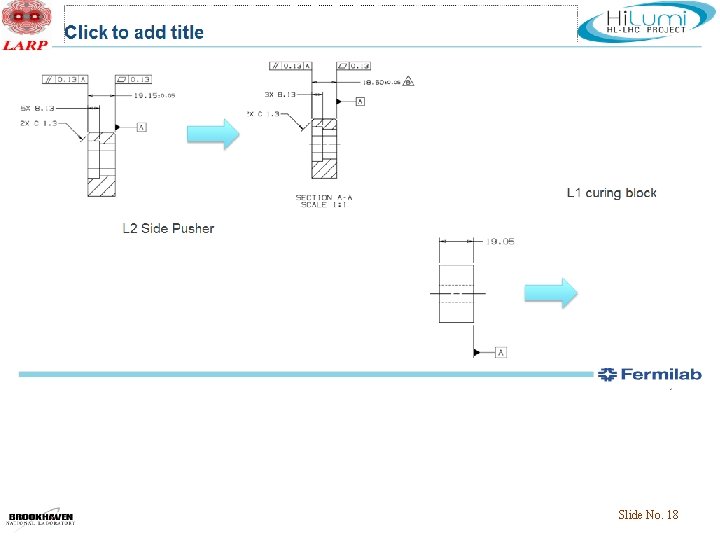
- Slides: 18
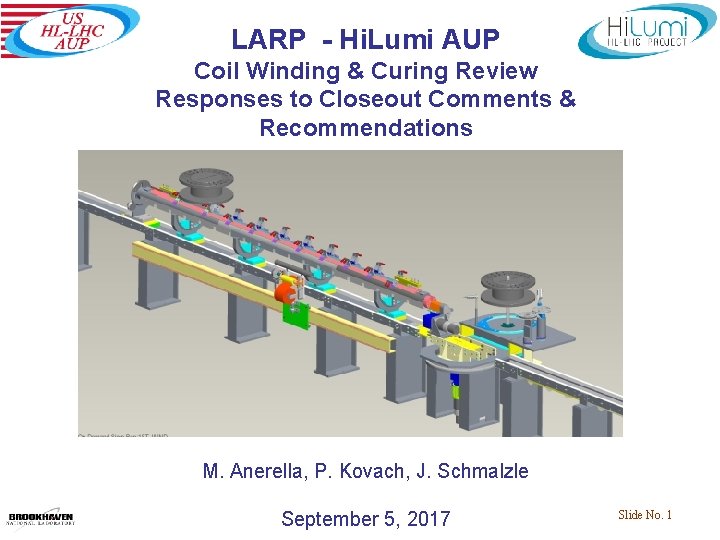
LARP - Hi. Lumi AUP Coil Winding & Curing Review Responses to Closeout Comments & Recommendations M. Anerella, P. Kovach, J. Schmalzle September 5, 2017 Slide No. 1
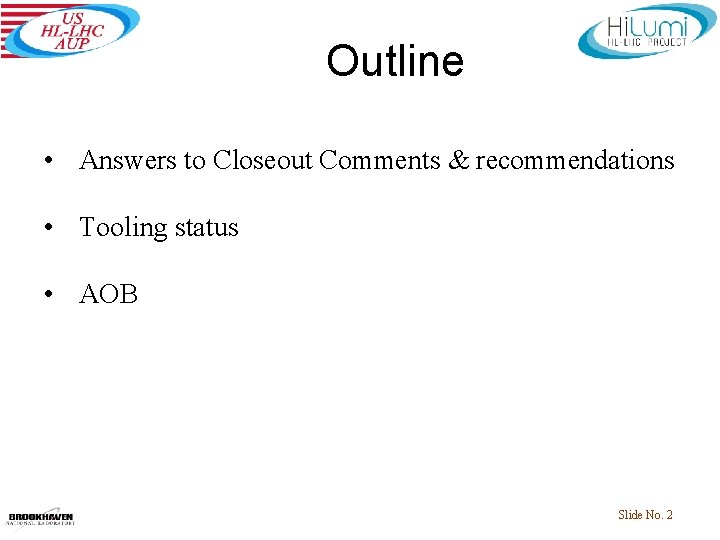
Outline • Answers to Closeout Comments & recommendations • Tooling status • AOB Slide No. 2
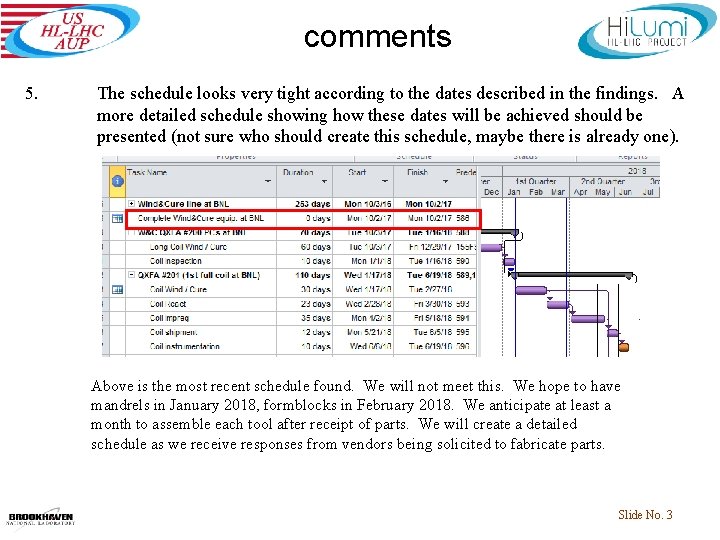
comments 5. The schedule looks very tight according to the dates described in the findings. A more detailed schedule showing how these dates will be achieved should be presented (not sure who should create this schedule, maybe there is already one). Above is the most recent schedule found. We will not meet this. We hope to have mandrels in January 2018, formblocks in February 2018. We anticipate at least a month to assemble each tool after receipt of parts. We will create a detailed schedule as we receive responses from vendors being solicited to fabricate parts. Slide No. 3
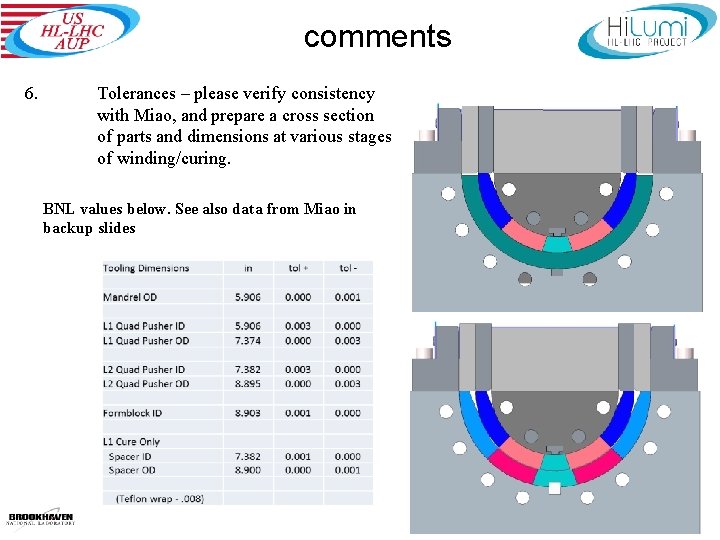
comments 6. Tolerances – please verify consistency with Miao, and prepare a cross section of parts and dimensions at various stages of winding/curing. BNL values below. See also data from Miao in backup slides Slide No. 4
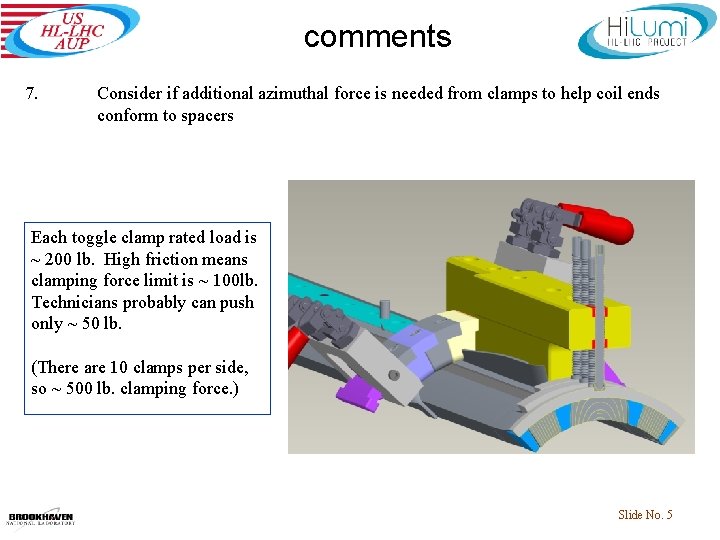
comments 7. Consider if additional azimuthal force is needed from clamps to help coil ends conform to spacers Each toggle clamp rated load is ~ 200 lb. High friction means clamping force limit is ~ 100 lb. Technicians probably can push only ~ 50 lb. (There are 10 clamps per side, so ~ 500 lb. clamping force. ) Slide No. 5
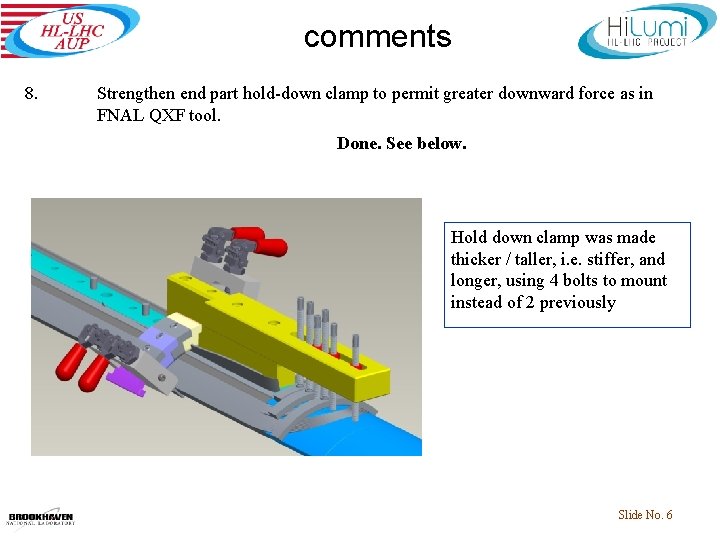
comments 8. Strengthen end part hold-down clamp to permit greater downward force as in FNAL QXF tool. Done. See below. Hold down clamp was made thicker / taller, i. e. stiffer, and longer, using 4 bolts to mount instead of 2 previously Slide No. 6
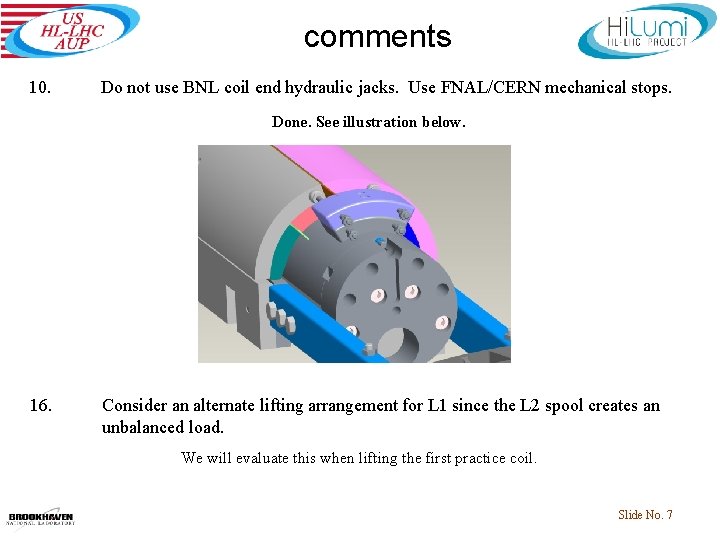
comments 10. Do not use BNL coil end hydraulic jacks. Use FNAL/CERN mechanical stops. Done. See illustration below. 16. Consider an alternate lifting arrangement for L 1 since the L 2 spool creates an unbalanced load. We will evaluate this when lifting the first practice coil. Slide No. 7
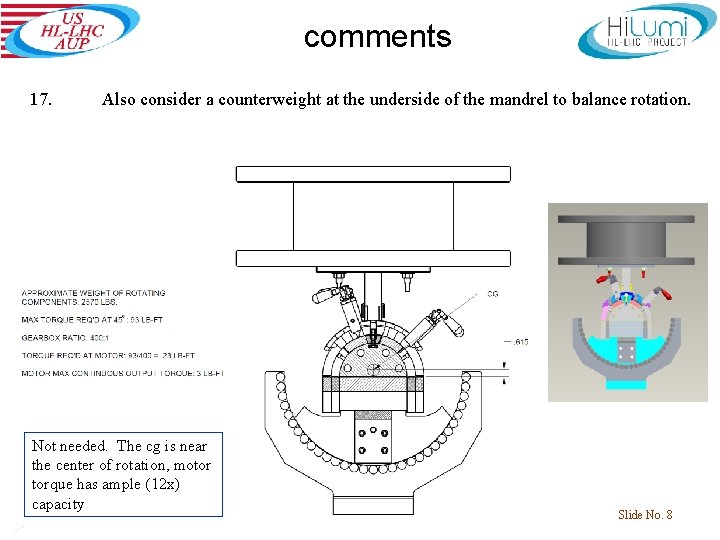
comments 17. Also consider a counterweight at the underside of the mandrel to balance rotation. Not needed. The cg is near the center of rotation, motor torque has ample (12 x) capacity Slide No. 8
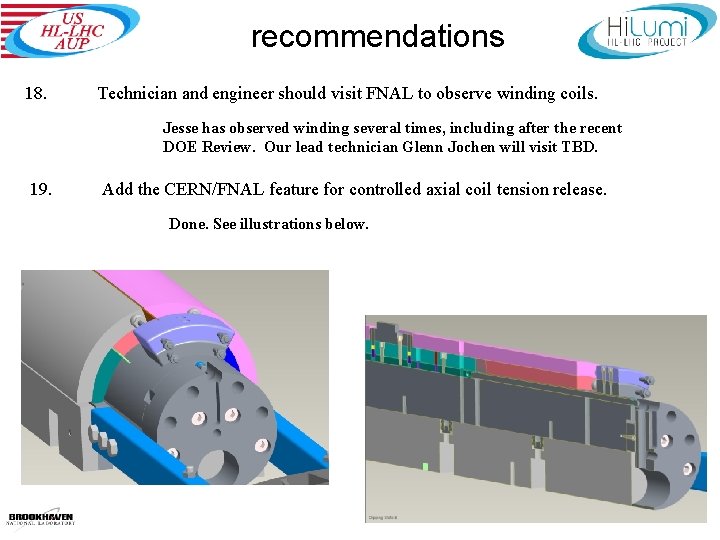
recommendations 18. Technician and engineer should visit FNAL to observe winding coils. Jesse has observed winding several times, including after the recent DOE Review. Our lead technician Glenn Jochen will visit TBD. 19. Add the CERN/FNAL feature for controlled axial coil tension release. Done. See illustrations below. Slide No. 9
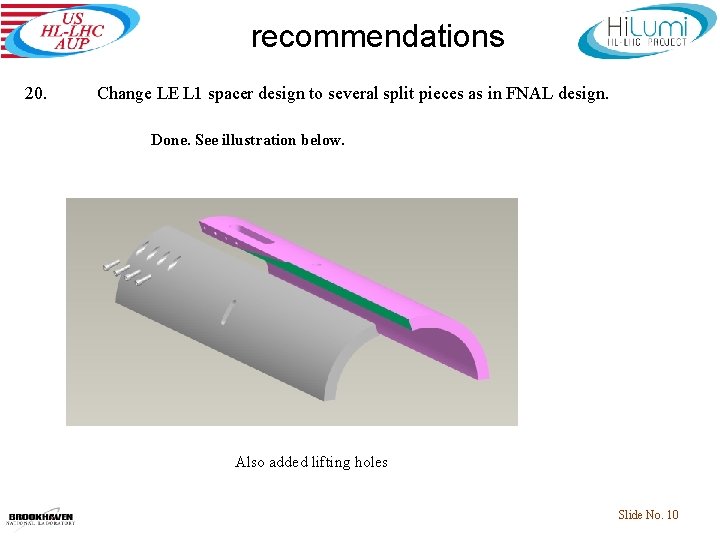
recommendations 20. Change LE L 1 spacer design to several split pieces as in FNAL design. Done. See illustration below. Also added lifting holes Slide No. 10
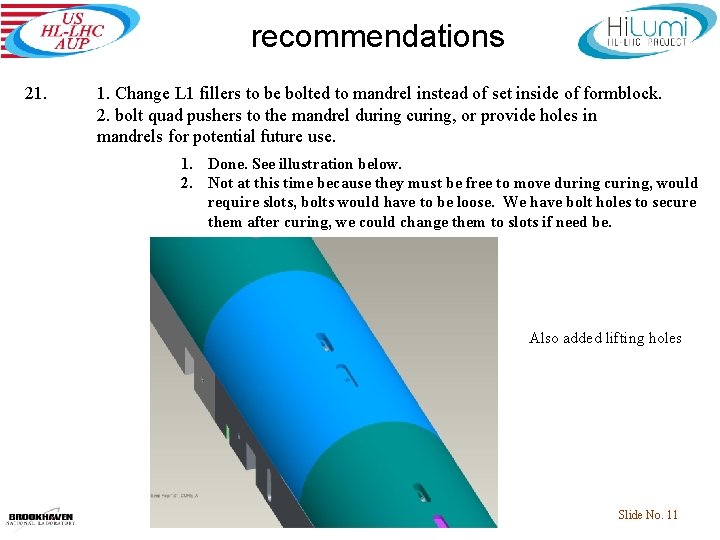
recommendations 21. 1. Change L 1 fillers to be bolted to mandrel instead of set inside of formblock. 2. bolt quad pushers to the mandrel during curing, or provide holes in mandrels for potential future use. 1. Done. See illustration below. 2. Not at this time because they must be free to move during curing, would require slots, bolts would have to be loose. We have bolt holes to secure them after curing, we could change them to slots if need be. Also added lifting holes Slide No. 11
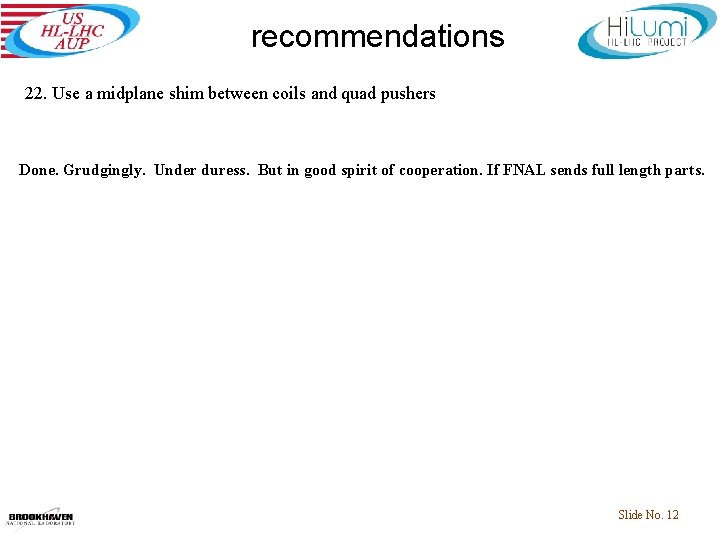
recommendations 22. Use a midplane shim between coils and quad pushers Done. Grudgingly. Under duress. But in good spirit of cooperation. If FNAL sends full length parts. Slide No. 12
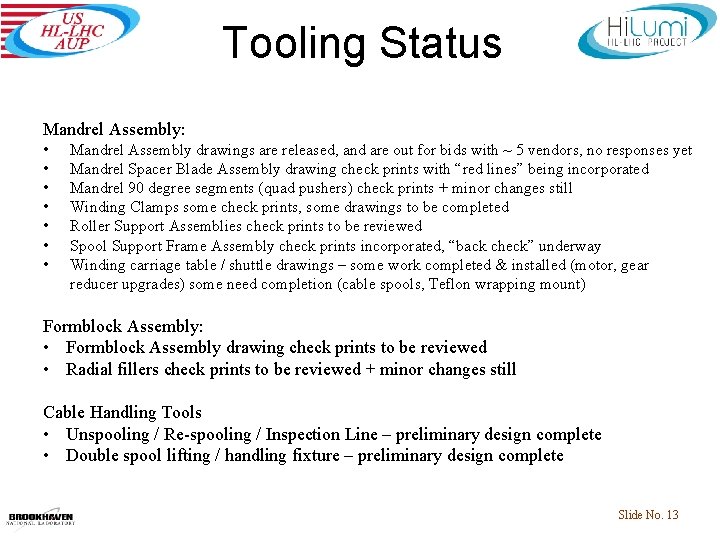
Tooling Status Mandrel Assembly: • • Mandrel Assembly drawings are released, and are out for bids with ~ 5 vendors, no responses yet Mandrel Spacer Blade Assembly drawing check prints with “red lines” being incorporated Mandrel 90 degree segments (quad pushers) check prints + minor changes still Winding Clamps some check prints, some drawings to be completed Roller Support Assemblies check prints to be reviewed Spool Support Frame Assembly check prints incorporated, “back check” underway Winding carriage table / shuttle drawings – some work completed & installed (motor, gear reducer upgrades) some need completion (cable spools, Teflon wrapping mount) Formblock Assembly: • Formblock Assembly drawing check prints to be reviewed • Radial fillers check prints to be reviewed + minor changes still Cable Handling Tools • Unspooling / Re-spooling / Inspection Line – preliminary design complete • Double spool lifting / handling fixture – preliminary design complete Slide No. 13
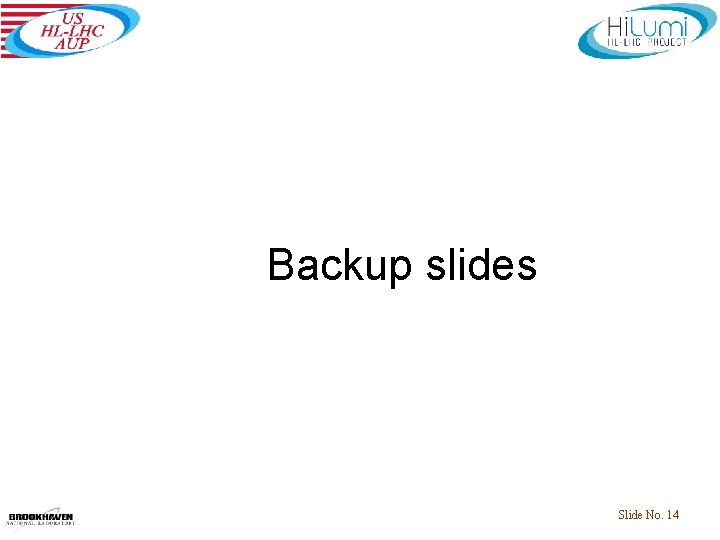
Backup slides Slide No. 14
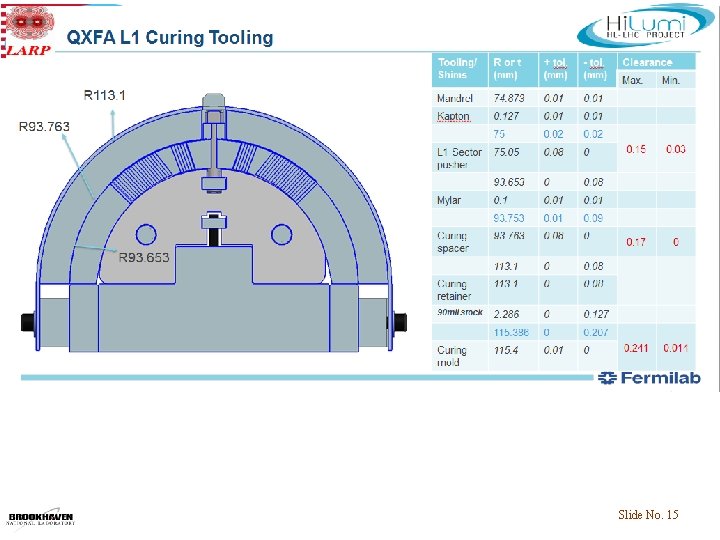
Slide No. 15
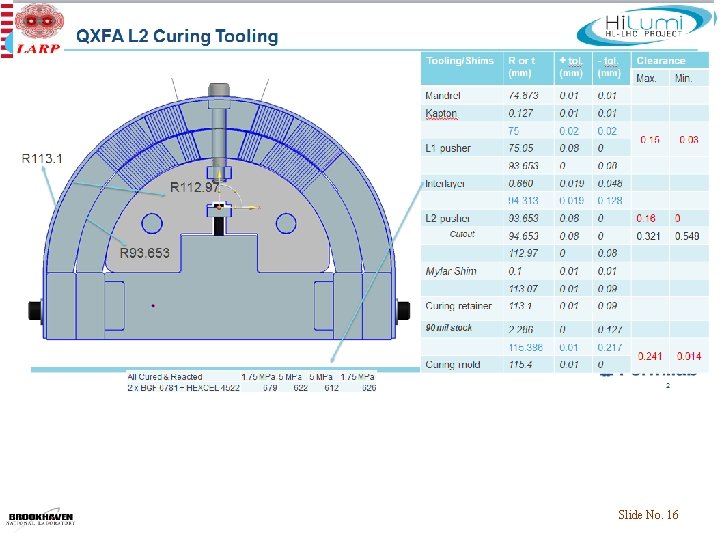
Slide No. 16
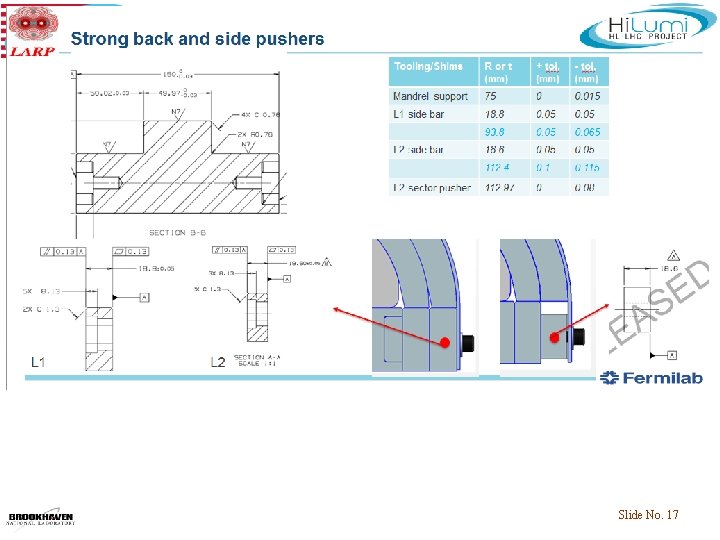
Slide No. 17
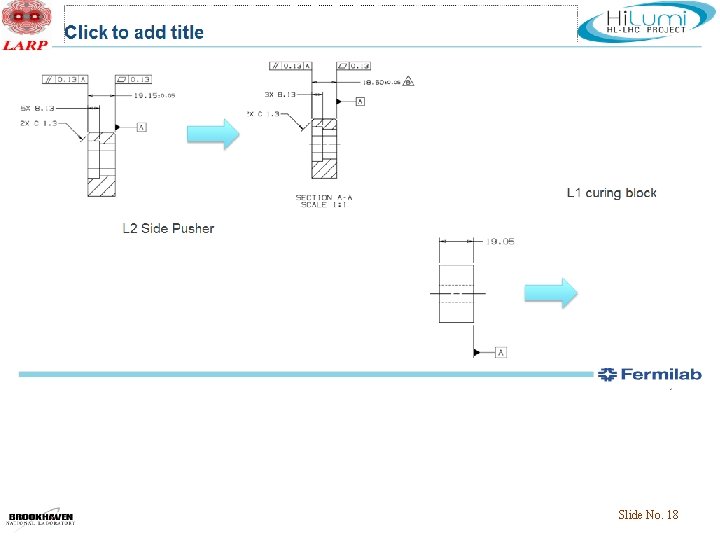
Slide No. 18
Pole core and pole shoe
Field winding vs armature winding
Series coil and multi-turn coil
Biggest larp event in america
Larp logiciel
What does aup mean
Isrs 4400 revised
Aup
Aup dorms
Aup ranking
Tlv: lumi
Lumi della ragione
Wire handling
Phillips lumi
7 minuni ale lumii antice
Lumi rossi
Cele 25 de minuni ale lumii moderne
Lumi sps
Tire retreading air tools