Review of the HQ and LHQ coil Winding
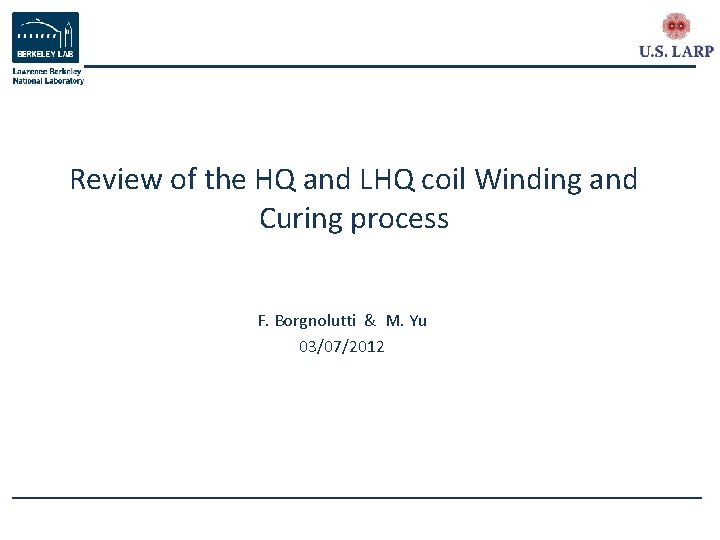
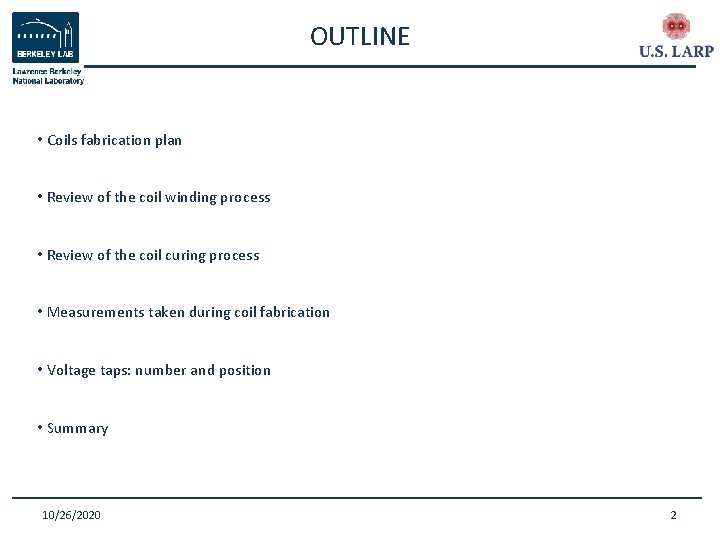
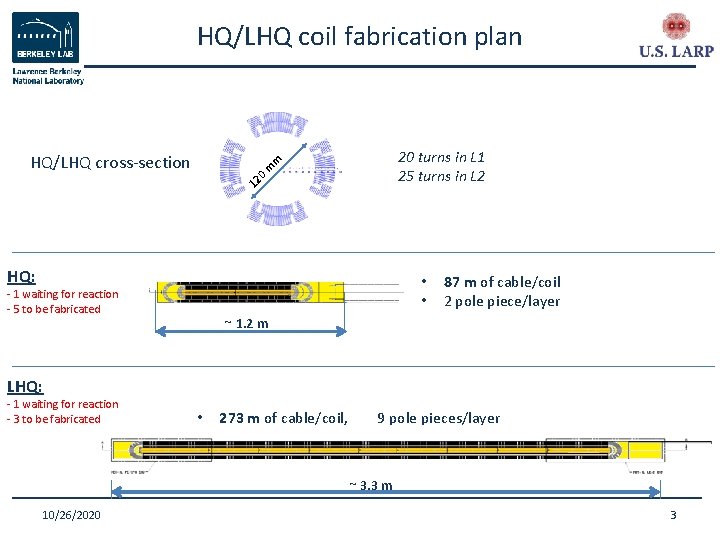
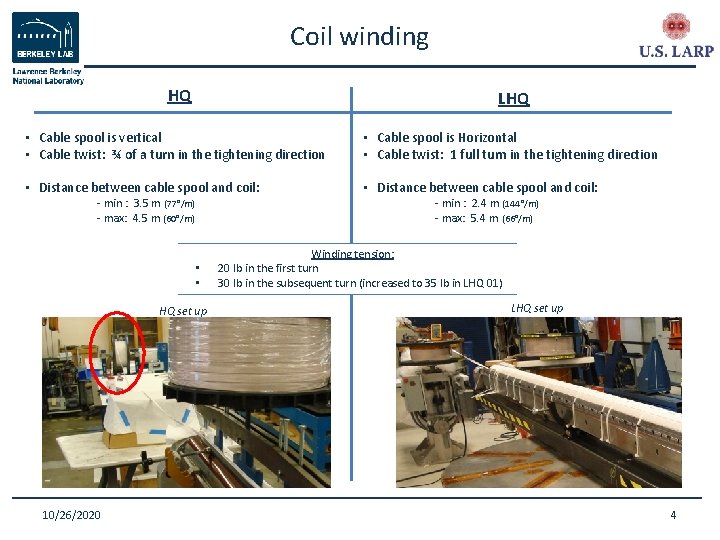
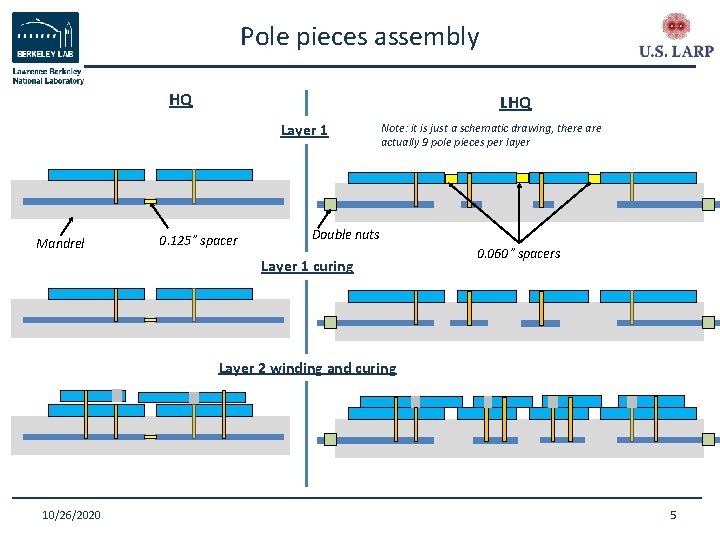
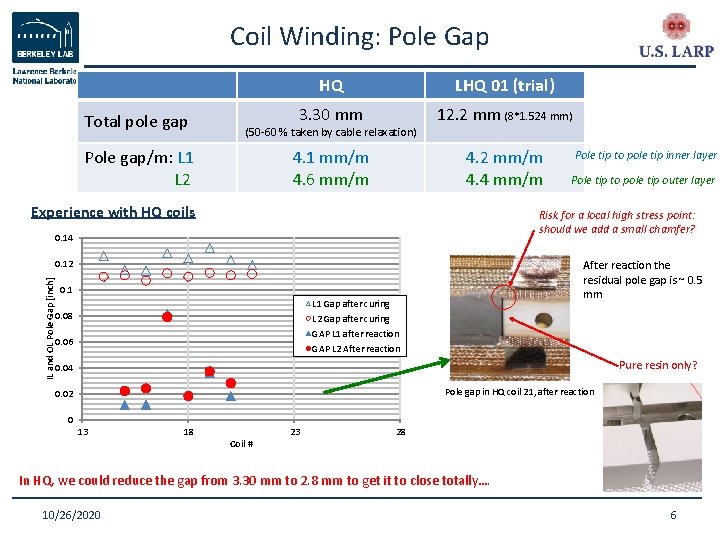
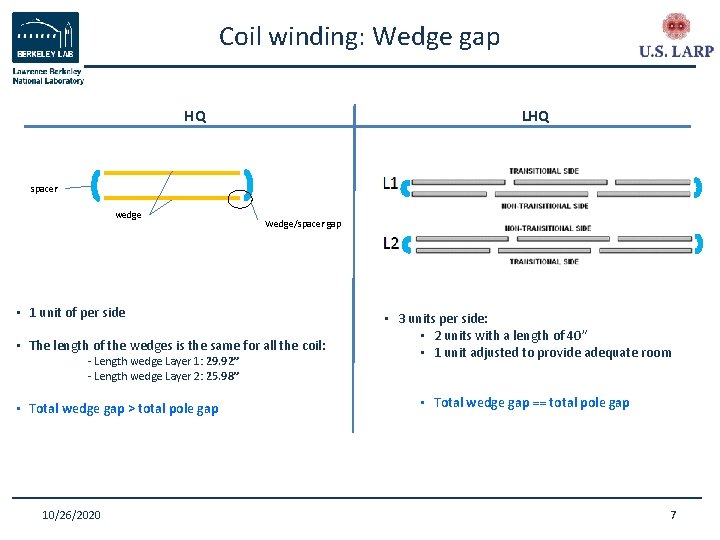
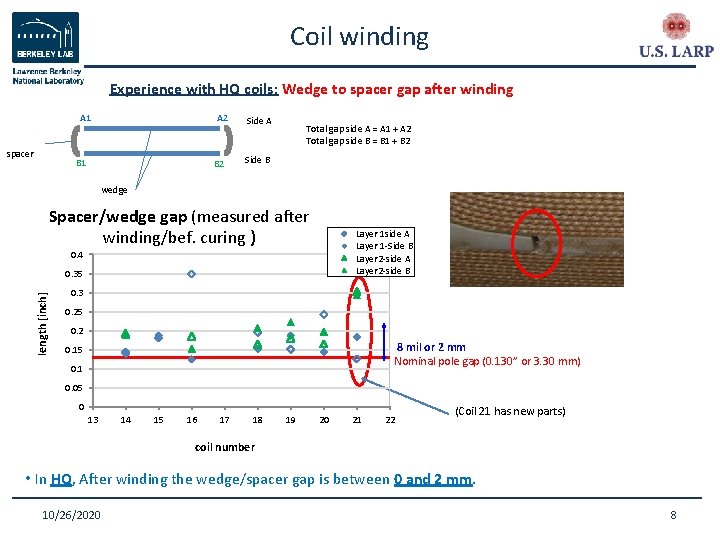
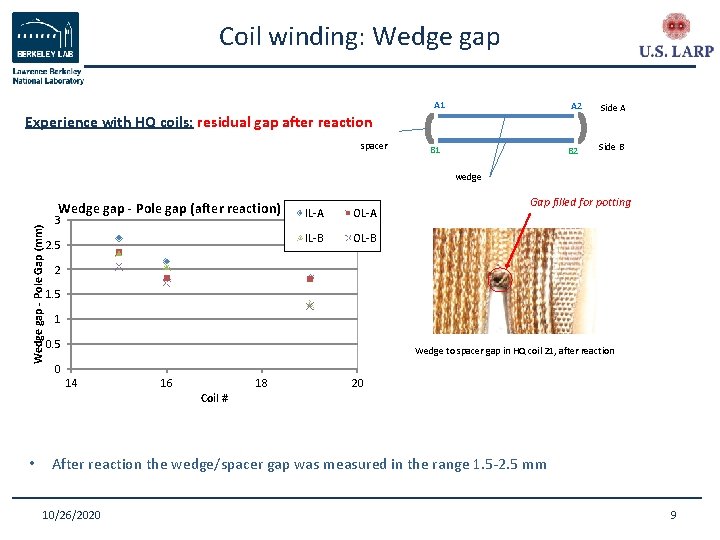
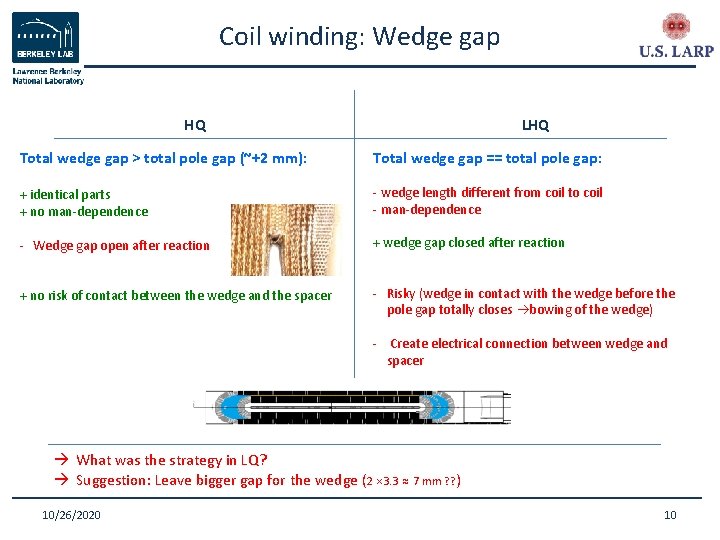
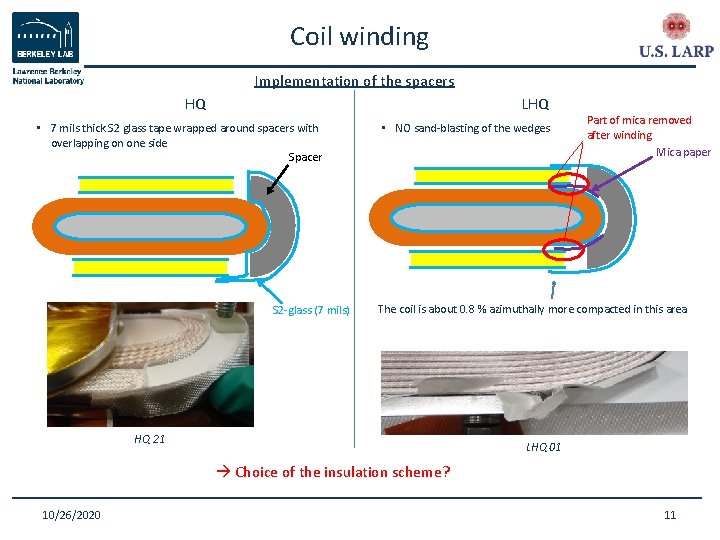
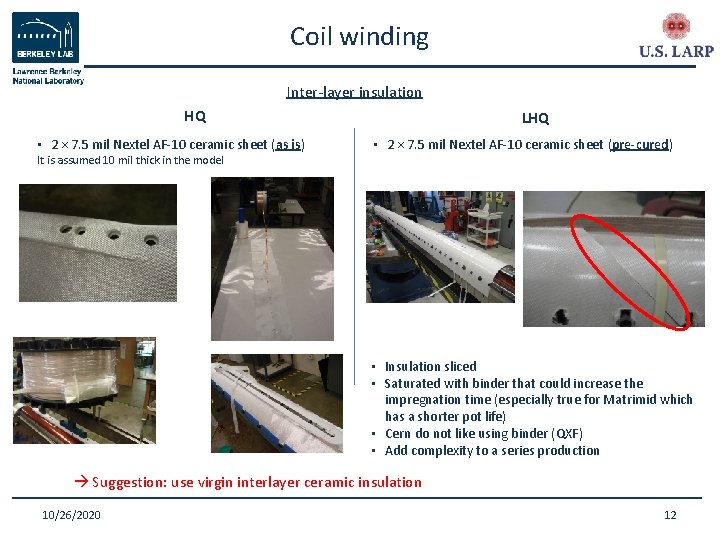
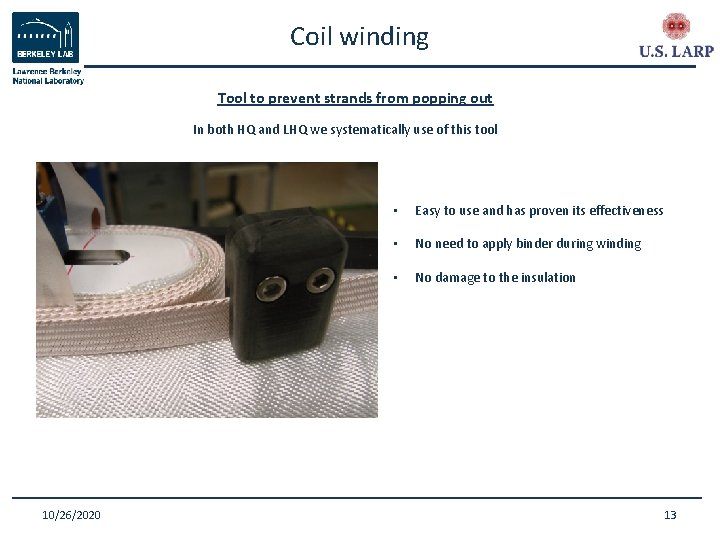
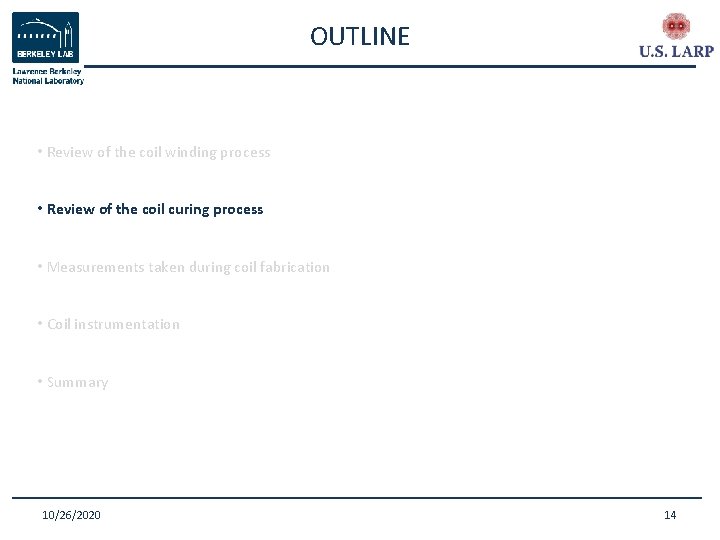
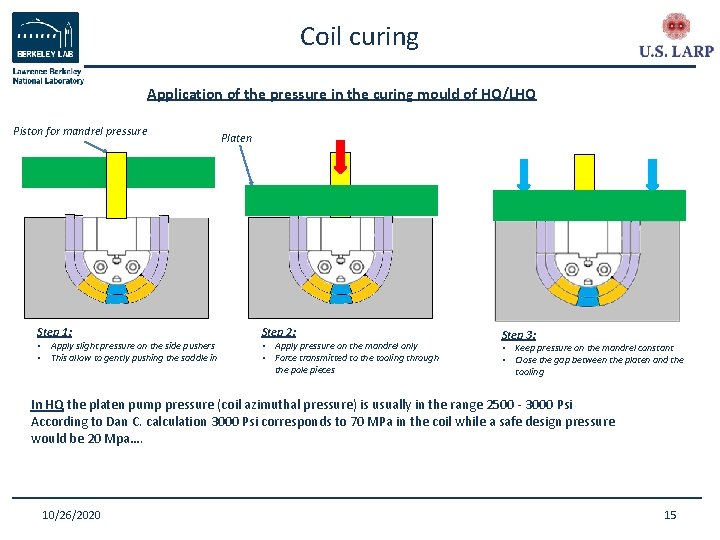
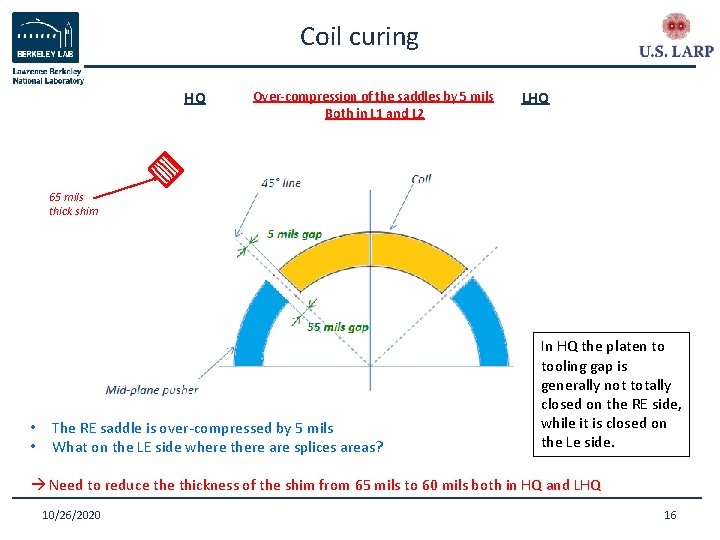
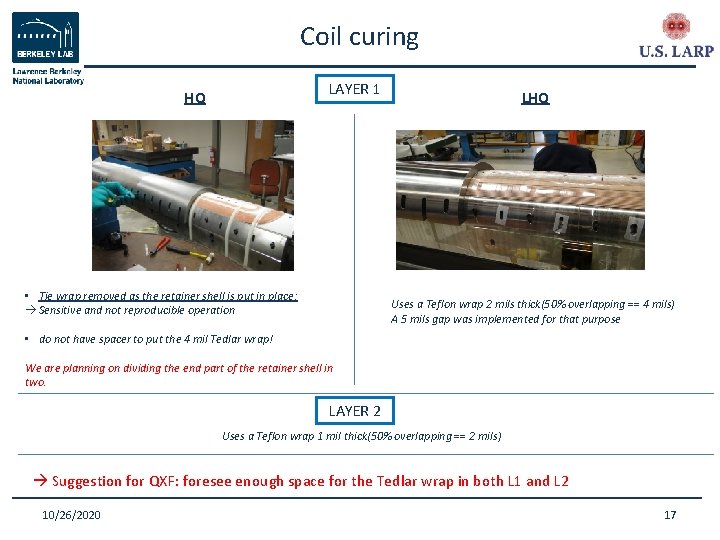
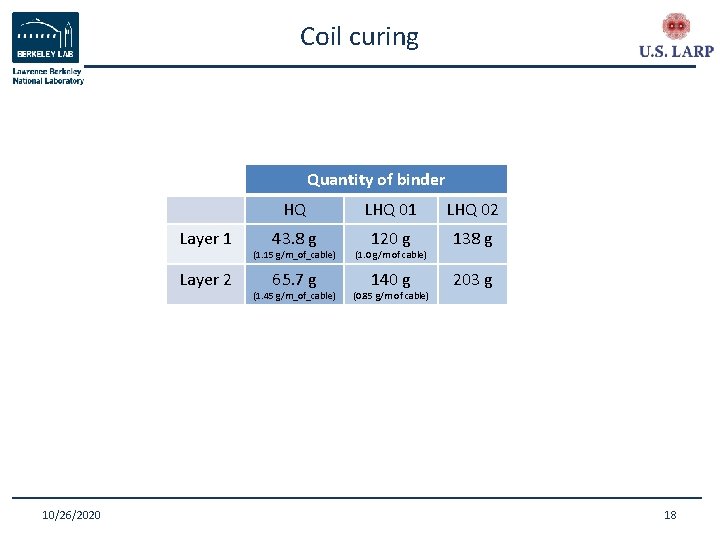
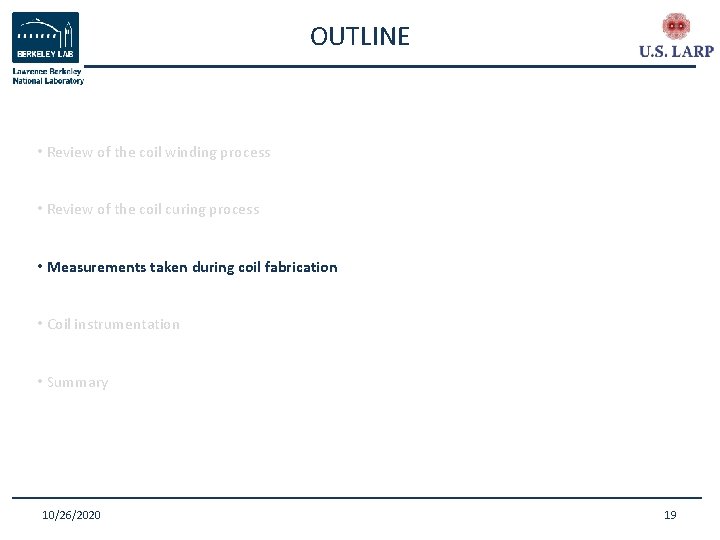
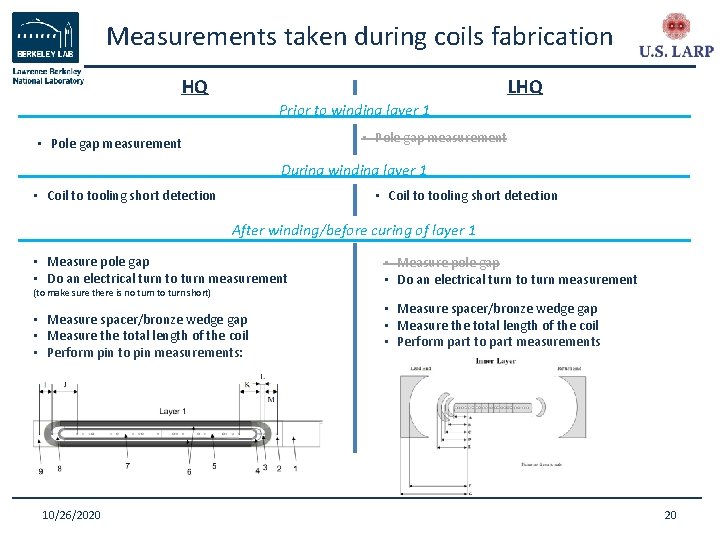
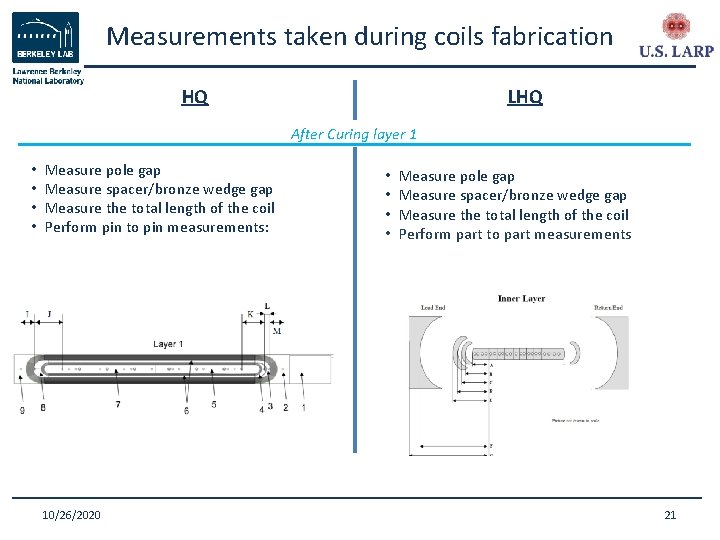
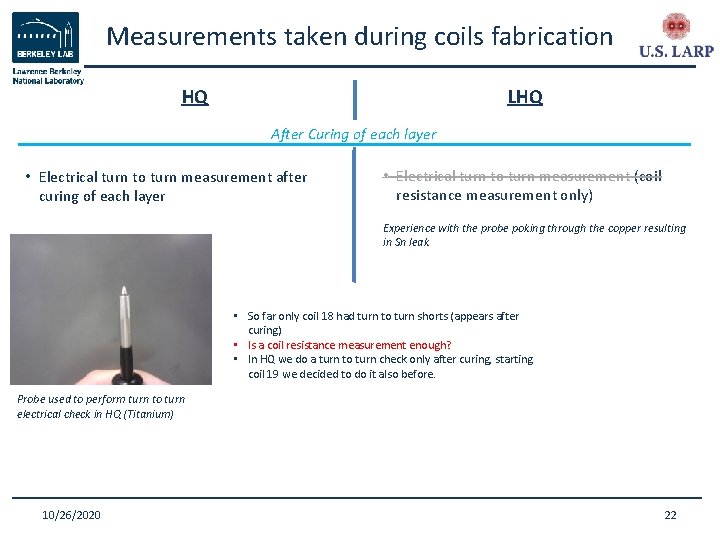
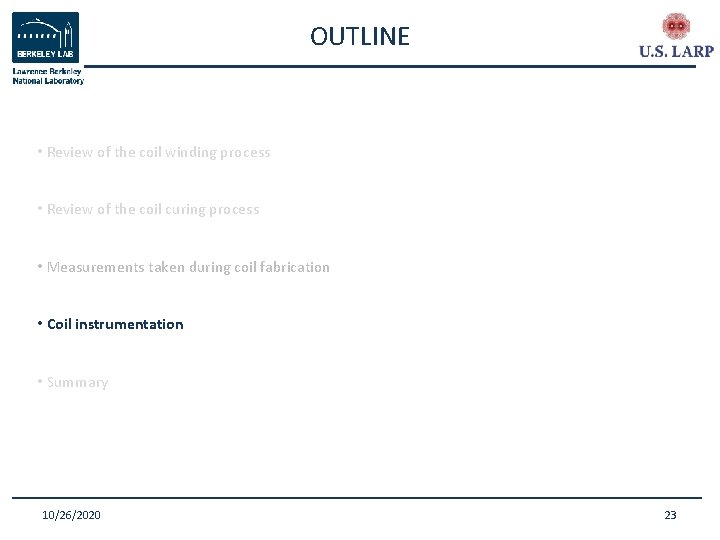
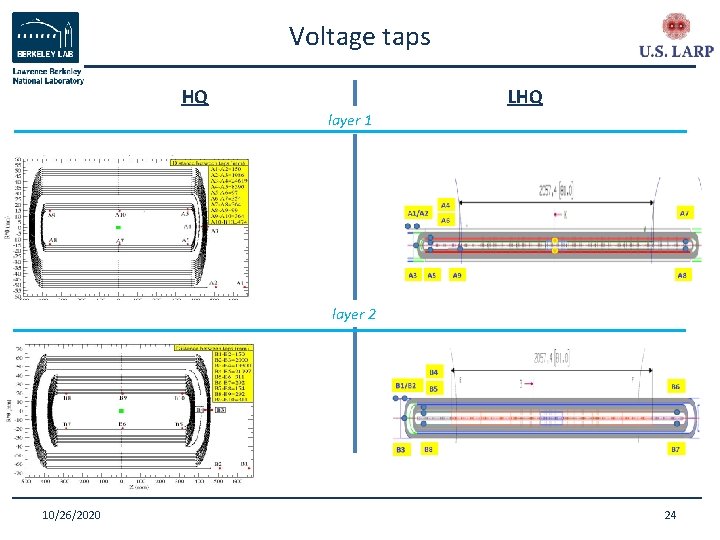
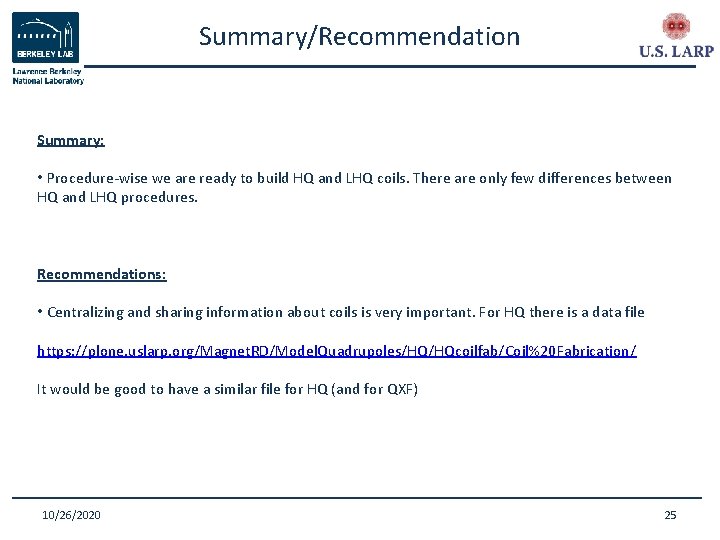
- Slides: 25
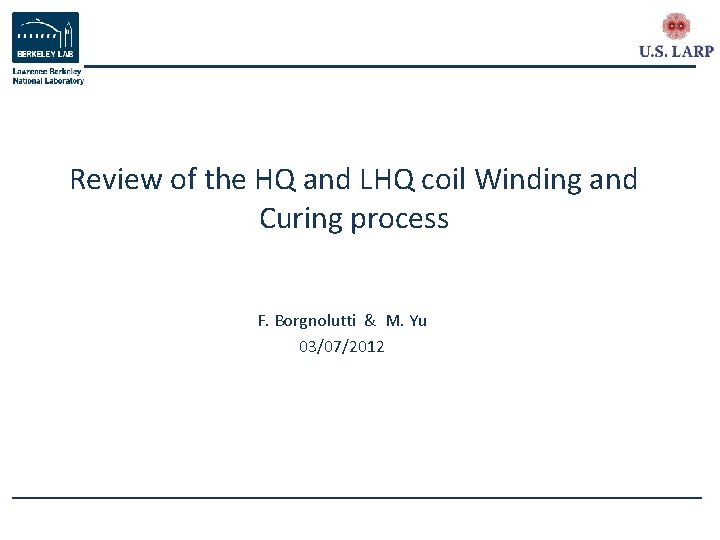
Review of the HQ and LHQ coil Winding and Curing process F. Borgnolutti & M. Yu 03/07/2012
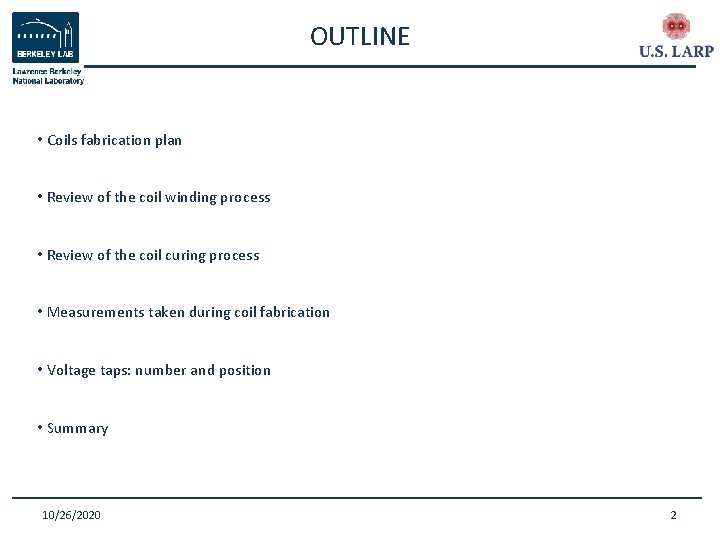
OUTLINE • Coils fabrication plan • Review of the coil winding process • Review of the coil curing process • Measurements taken during coil fabrication • Voltage taps: number and position • Summary 10/26/2020 2
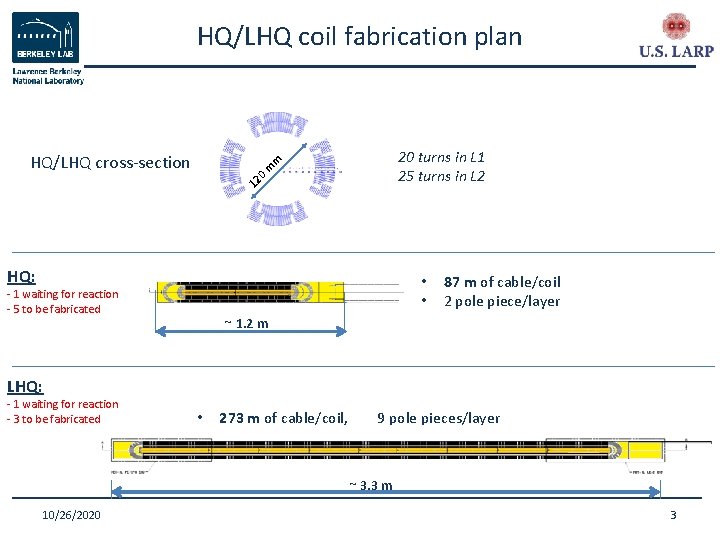
HQ/LHQ coil fabrication plan 20 turns in L 1 25 turns in L 2 12 0 m m HQ/LHQ cross-section HQ: • • - 1 waiting for reaction - 5 to be fabricated 87 m of cable/coil 2 pole piece/layer ~ 1. 2 m LHQ: - 1 waiting for reaction - 3 to be fabricated • 273 m of cable/coil, 9 pole pieces/layer ~ 3. 3 m 10/26/2020 3
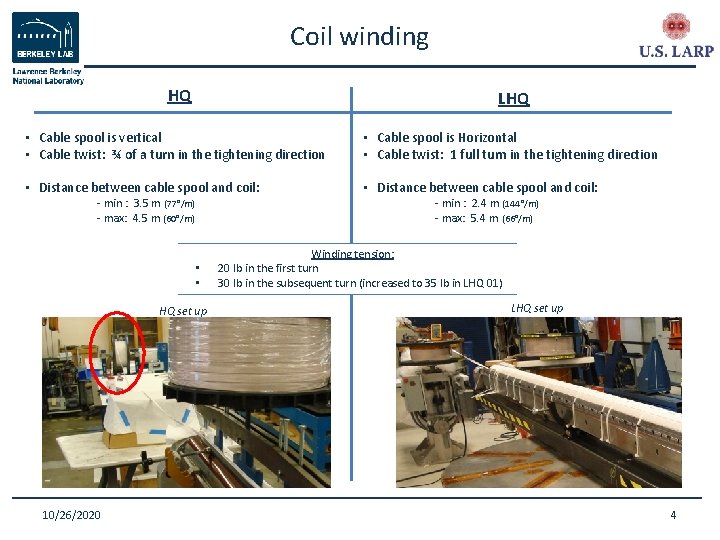
Coil winding HQ LHQ • Cable spool is vertical • Cable twist: ¾ of a turn in the tightening direction • Cable spool is Horizontal • Cable twist: 1 full turn in the tightening direction • Distance between cable spool and coil: - min : 3. 5 m (77°/m) - max: 4. 5 m (60°/m) • • HQ set up 10/26/2020 - min : 2. 4 m (144°/m) - max: 5. 4 m (66°/m) Winding tension: 20 lb in the first turn 30 lb in the subsequent turn (increased to 35 lb in LHQ 01) LHQ set up 4
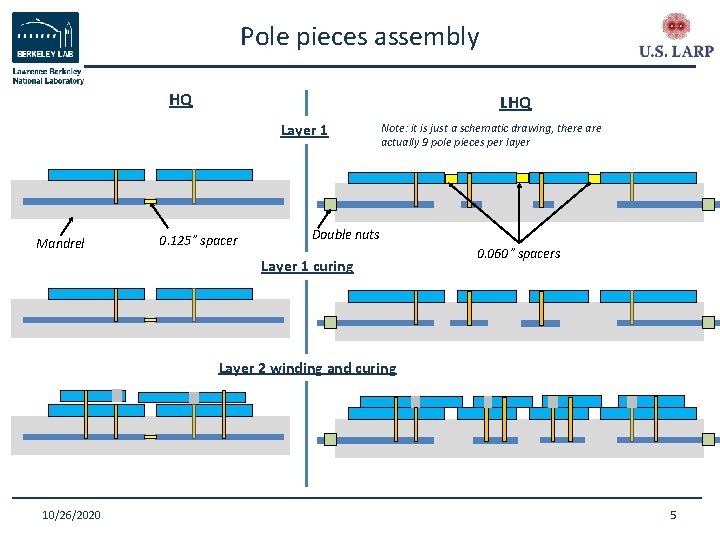
Pole pieces assembly HQ Layer 1 Mandrel 0. 125” spacer Note: it is just a schematic drawing, there actually 9 pole pieces per layer Double nuts Layer 1 curing 0. 060” spacers Layer 2 winding and curing 10/26/2020 5
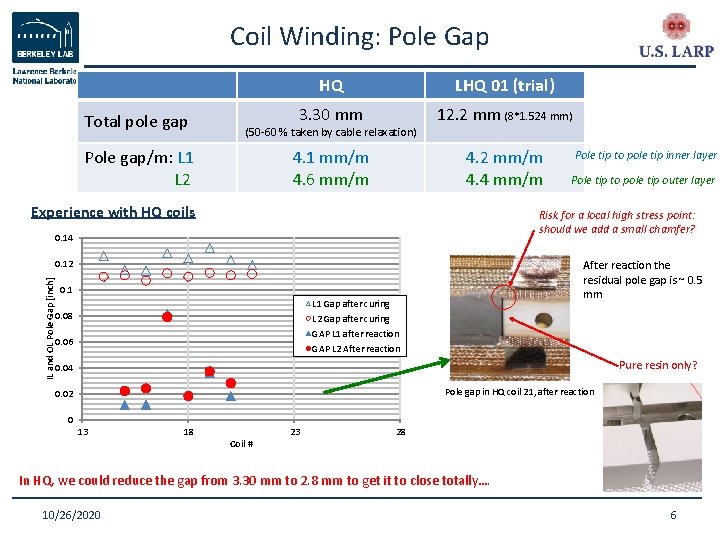
Coil Winding: Pole Gap Total pole gap HQ LHQ 01 (trial) 3. 30 mm 12. 2 mm (8*1. 524 mm) 4. 1 mm/m 4. 6 mm/m 4. 2 mm/m 4. 4 mm/m (50 -60 % taken by cable relaxation) Pole gap/m: L 1 L 2 Experience with HQ coils Pole tip to pole tip outer layer Risk for a local high stress point: should we add a small chamfer? 0. 14 0. 12 IL and OL Pole Gap [inch] Pole tip to pole tip inner layer After reaction the residual pole gap is ~ 0. 5 mm 0. 1 L 1 Gap after curing 0. 08 L 2 Gap after curing GAP L 1 after reaction 0. 06 GAP L 2 After reaction Pure resin only? 0. 04 Pole gap in HQ coil 21, after reaction 0. 02 0 13 18 Coil # 23 28 In HQ, we could reduce the gap from 3. 30 mm to 2. 8 mm to get it to close totally…. 10/26/2020 6
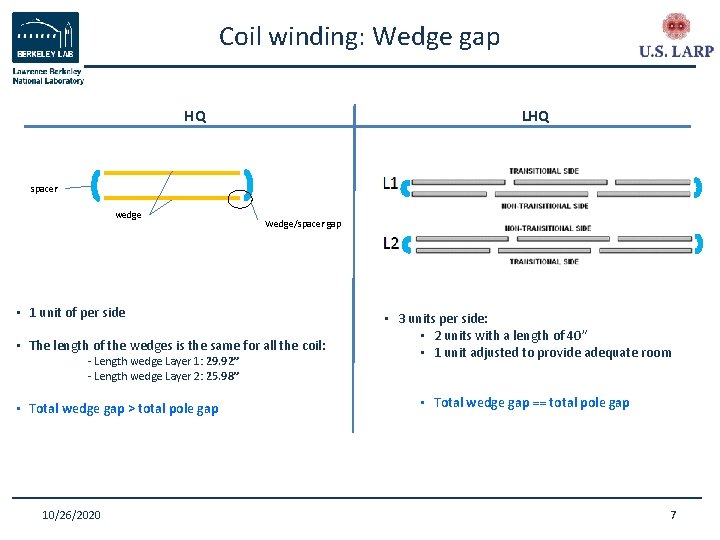
Coil winding: Wedge gap HQ LHQ spacer wedge Wedge/spacer gap • 1 unit of per side • The length of the wedges is the same for all the coil: - Length wedge Layer 1: 29. 92” - Length wedge Layer 2: 25. 98” • Total wedge gap > total pole gap 10/26/2020 • 3 units per side: • 2 units with a length of 40” • 1 unit adjusted to provide adequate room • Total wedge gap == total pole gap 7
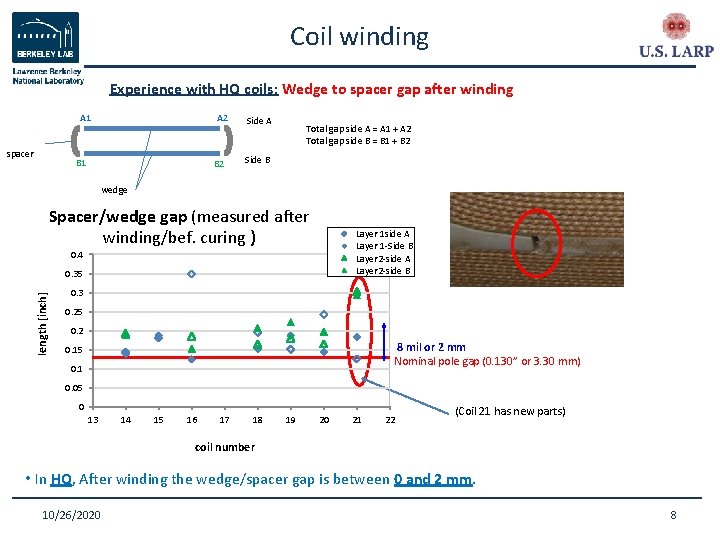
Coil winding Experience with HQ coils: Wedge to spacer gap after winding A 1 spacer B 1 A 2 Side A B 2 Side B Total gap side A = A 1 + A 2 Total gap side B = B 1 + B 2 wedge Spacer/wedge gap (measured after winding/bef. curing ) Layer 1 side A Layer 1 -Side B Layer 2 -side A Layer 2 -side B 0. 4 length [inch] 0. 35 0. 3 0. 25 0. 2 8 mil or 2 mm Nominal pole gap (0. 130” or 3. 30 mm) 0. 15 0. 1 0. 05 0 13 14 15 16 17 18 19 20 21 22 (Coil 21 has new parts) coil number • In HQ, After winding the wedge/spacer gap is between 0 and 2 mm. 10/26/2020 8
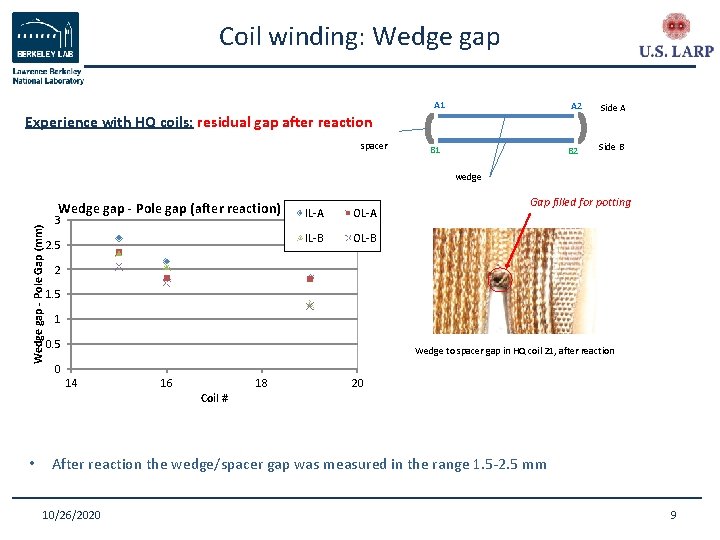
Coil winding: Wedge gap A 1 Experience with HQ coils: residual gap after reaction spacer B 1 A 2 Side A B 2 Side B wedge Wedge gap - Pole Gap (mm) Wedge gap - Pole gap (after reaction) 3 2. 5 OL-A IL-B OL-B Gap filled for potting 2 1. 5 1 0. 5 Wedge to spacer gap in HQ coil 21, after reaction 0 14 • IL-A 16 Coil # 18 20 After reaction the wedge/spacer gap was measured in the range 1. 5 -2. 5 mm 10/26/2020 9
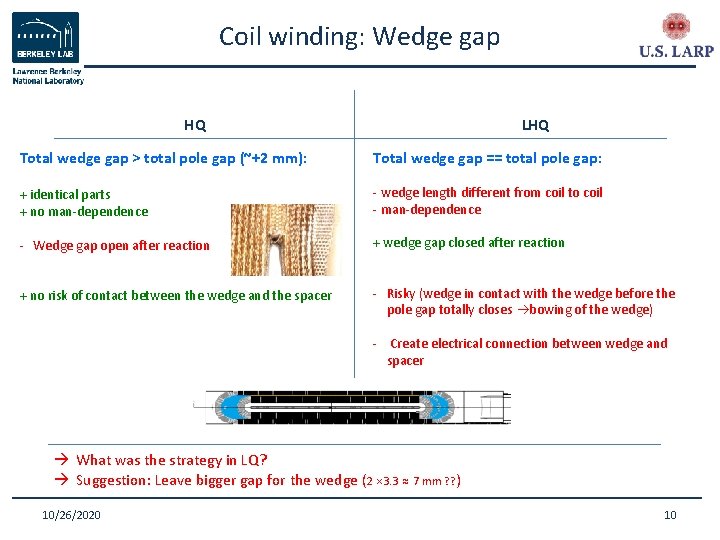
Coil winding: Wedge gap HQ LHQ Total wedge gap > total pole gap (~+2 mm): Total wedge gap == total pole gap: + identical parts + no man-dependence - wedge length different from coil to coil - man-dependence - Wedge gap open after reaction + wedge gap closed after reaction + no risk of contact between the wedge and the spacer - Risky (wedge in contact with the wedge before the pole gap totally closes bowing of the wedge) - Create electrical connection between wedge and spacer What was the strategy in LQ? Suggestion: Leave bigger gap for the wedge (2 × 3. 3 ≈ 10/26/2020 7 mm ? ? ) 10
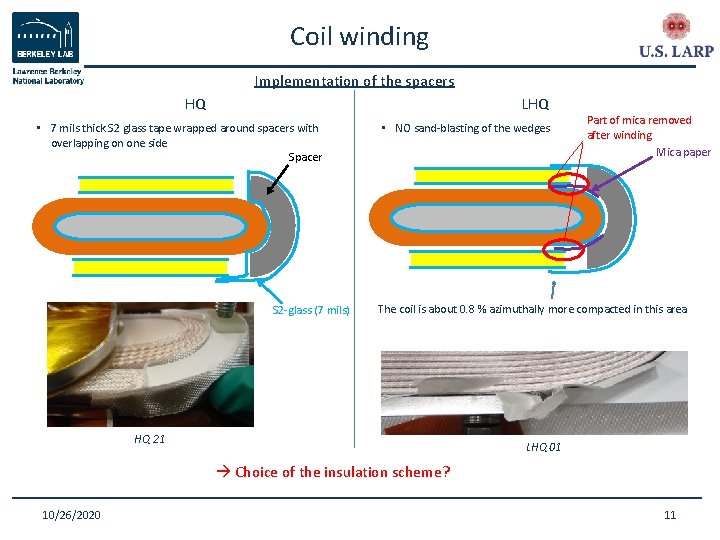
Coil winding Implementation of the spacers HQ LHQ • 7 mils thick S 2 glass tape wrapped around spacers with overlapping on one side Spacer S 2 -glass (7 mils) • NO sand-blasting of the wedges Part of mica removed after winding Mica paper The coil is about 0. 8 % azimuthally more compacted in this area HQ 21 LHQ 01 Choice of the insulation scheme? 10/26/2020 11
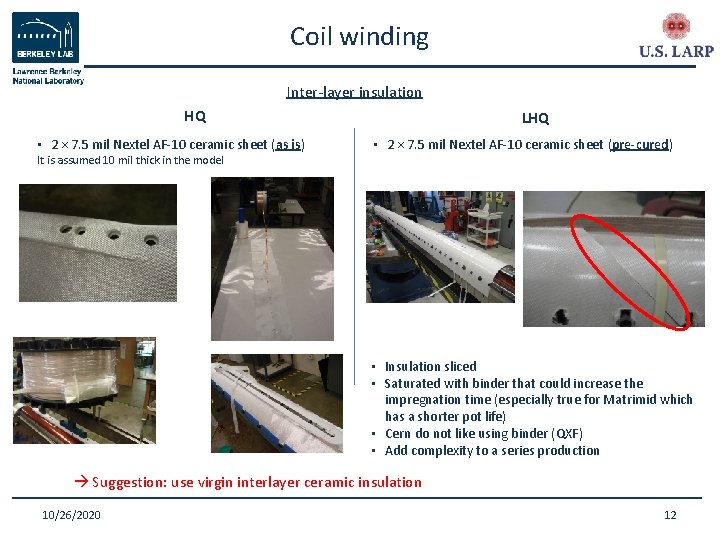
Coil winding Inter-layer insulation HQ • 2 × 7. 5 mil Nextel AF-10 ceramic sheet (as is) It is assumed 10 mil thick in the model LHQ • 2 × 7. 5 mil Nextel AF-10 ceramic sheet (pre-cured) • Insulation sliced • Saturated with binder that could increase the impregnation time (especially true for Matrimid which has a shorter pot life) • Cern do not like using binder (QXF) • Add complexity to a series production Suggestion: use virgin interlayer ceramic insulation 10/26/2020 12
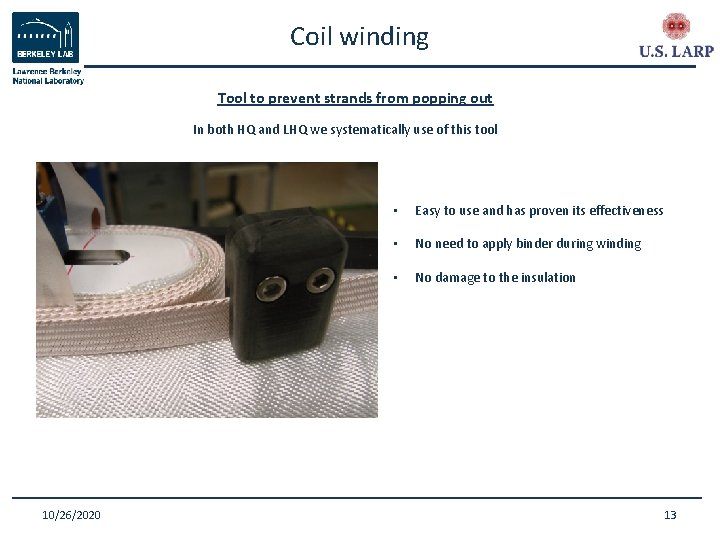
Coil winding Tool to prevent strands from popping out In both HQ and LHQ we systematically use of this tool 10/26/2020 • Easy to use and has proven its effectiveness • No need to apply binder during winding • No damage to the insulation 13
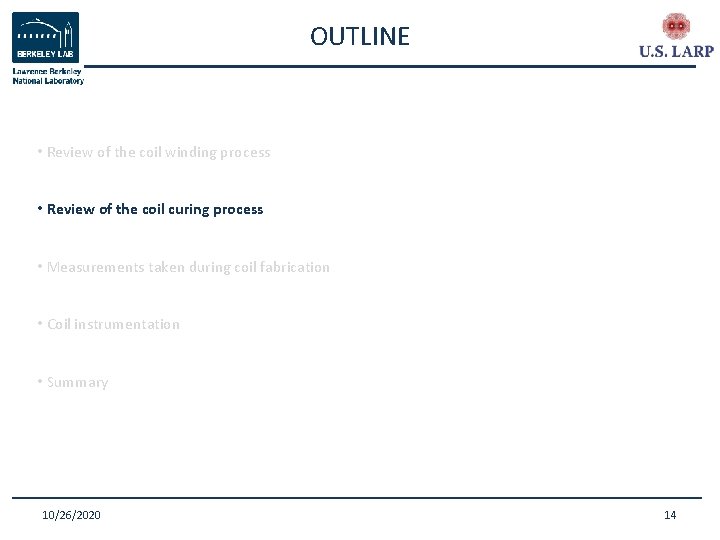
OUTLINE • Review of the coil winding process • Review of the coil curing process • Measurements taken during coil fabrication • Coil instrumentation • Summary 10/26/2020 14
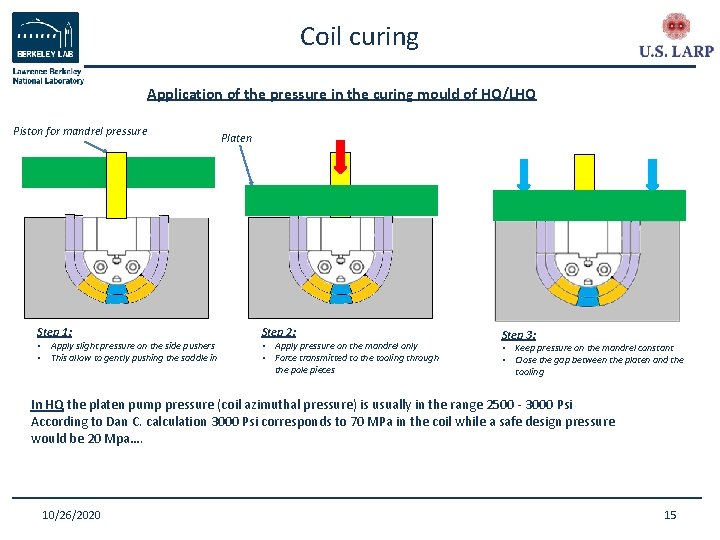
Coil curing Application of the pressure in the curing mould of HQ/LHQ Piston for mandrel pressure Step 1: • Apply slight pressure on the side pushers • This allow to gently pushing the saddle in Platen Step 2: • Apply pressure on the mandrel only • Force transmitted to the tooling through the pole pieces Step 3: • Keep pressure on the mandrel constant • Close the gap between the platen and the tooling In HQ the platen pump pressure (coil azimuthal pressure) is usually in the range 2500 - 3000 Psi According to Dan C. calculation 3000 Psi corresponds to 70 MPa in the coil while a safe design pressure would be 20 Mpa…. 10/26/2020 15
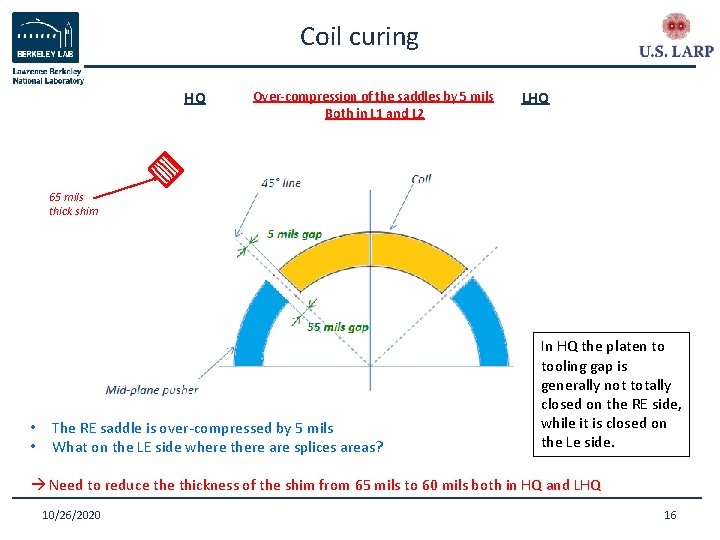
Coil curing HQ Over-compression of the saddles by 5 mils Both in L 1 and L 2 LHQ 65 mils thick shim • • The RE saddle is over-compressed by 5 mils What on the LE side where there are splices areas? In HQ the platen to tooling gap is generally not totally closed on the RE side, while it is closed on the Le side. Need to reduce thickness of the shim from 65 mils to 60 mils both in HQ and LHQ 10/26/2020 16
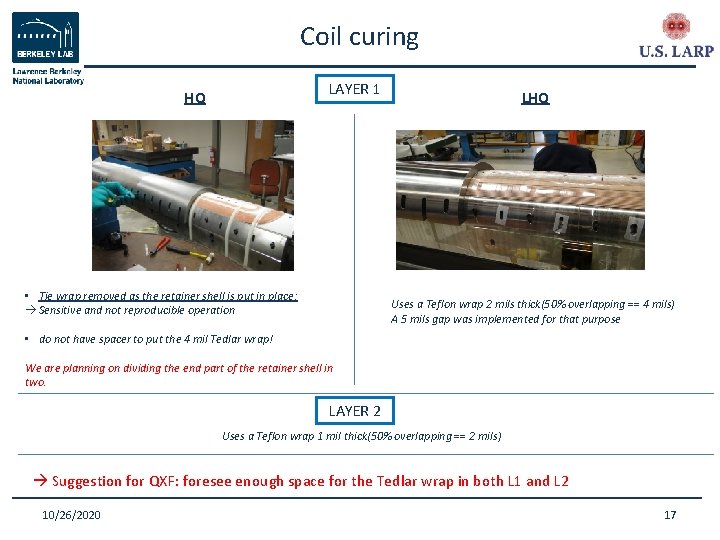
Coil curing LAYER 1 HQ • Tie wrap removed as the retainer shell is put in place: Sensitive and not reproducible operation LHQ Uses a Teflon wrap 2 mils thick(50% overlapping == 4 mils) A 5 mils gap was implemented for that purpose • do not have spacer to put the 4 mil Tedlar wrap! We are planning on dividing the end part of the retainer shell in two. LAYER 2 Uses a Teflon wrap 1 mil thick(50% overlapping == 2 mils) Suggestion for QXF: foresee enough space for the Tedlar wrap in both L 1 and L 2 10/26/2020 17
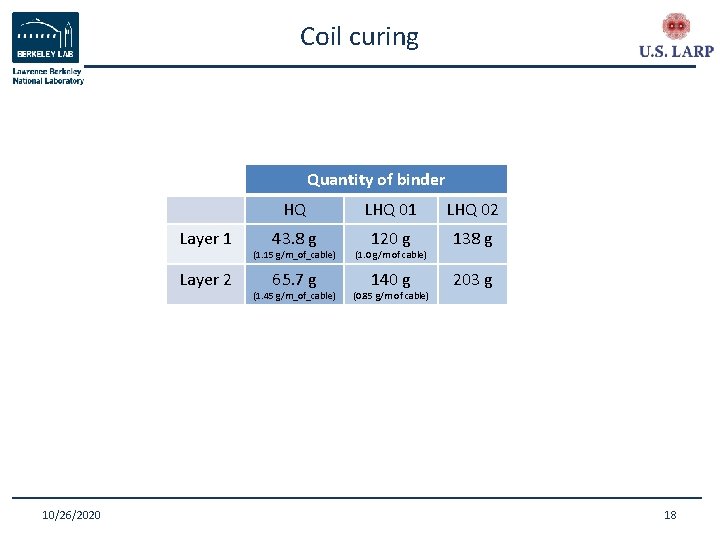
Coil curing Quantity of binder Layer 1 Layer 2 10/26/2020 HQ LHQ 01 LHQ 02 43. 8 g 120 g 138 g 140 g 203 g (1. 15 g/m_of_cable) 65. 7 g (1. 45 g/m_of_cable) (1. 0 g/m of cable) (0. 85 g/m of cable) 18
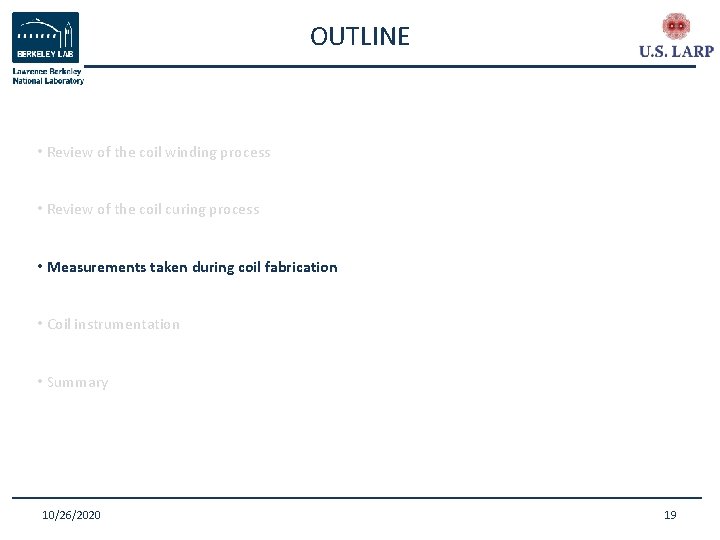
OUTLINE • Review of the coil winding process • Review of the coil curing process • Measurements taken during coil fabrication • Coil instrumentation • Summary 10/26/2020 19
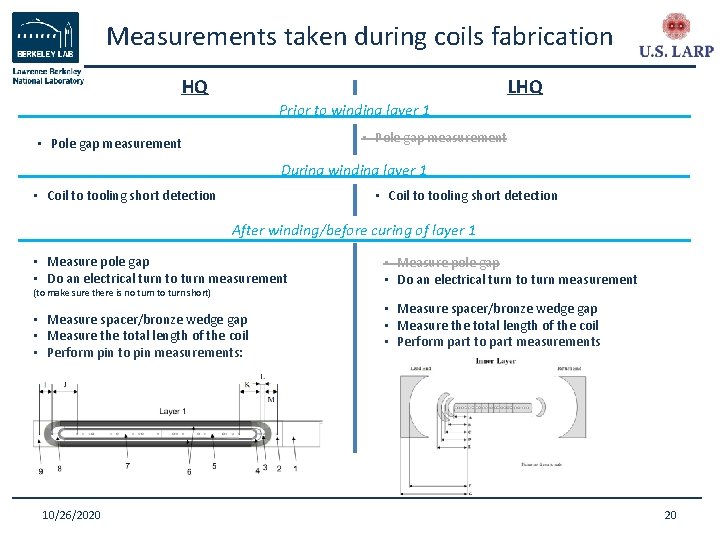
Measurements taken during coils fabrication HQ LHQ Prior to winding layer 1 • Pole gap measurement During winding layer 1 • Coil to tooling short detection After winding/before curing of layer 1 • Measure pole gap • Do an electrical turn to turn measurement (to make sure there is no turn to turn short) • Measure spacer/bronze wedge gap • Measure the total length of the coil • Perform pin to pin measurements: 10/26/2020 • Measure pole gap • Do an electrical turn to turn measurement • Measure spacer/bronze wedge gap • Measure the total length of the coil • Perform part to part measurements 20
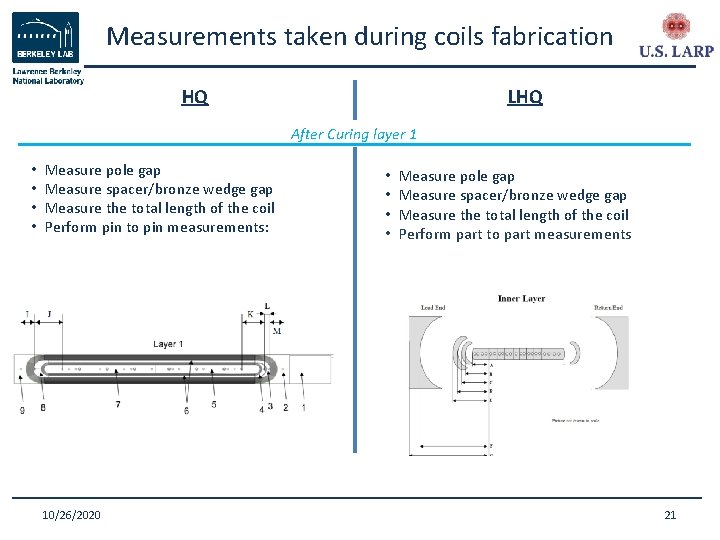
Measurements taken during coils fabrication HQ LHQ After Curing layer 1 • • Measure pole gap Measure spacer/bronze wedge gap Measure the total length of the coil Perform pin to pin measurements: 10/26/2020 • • Measure pole gap Measure spacer/bronze wedge gap Measure the total length of the coil Perform part to part measurements 21
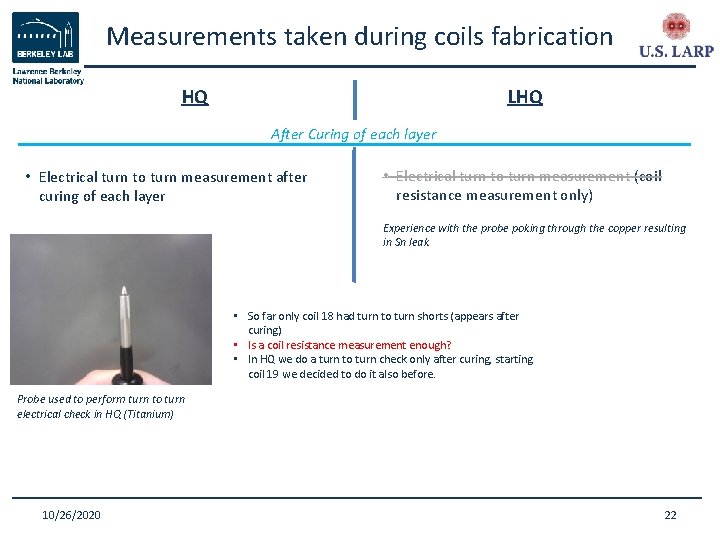
Measurements taken during coils fabrication HQ LHQ After Curing of each layer • Electrical turn to turn measurement after curing of each layer • Electrical turn to turn measurement (coil resistance measurement only) Experience with the probe poking through the copper resulting in Sn leak • So far only coil 18 had turn to turn shorts (appears after curing) • Is a coil resistance measurement enough? • In HQ we do a turn to turn check only after curing, starting coil 19 we decided to do it also before. Probe used to perform turn to turn electrical check in HQ (Titanium) 10/26/2020 22
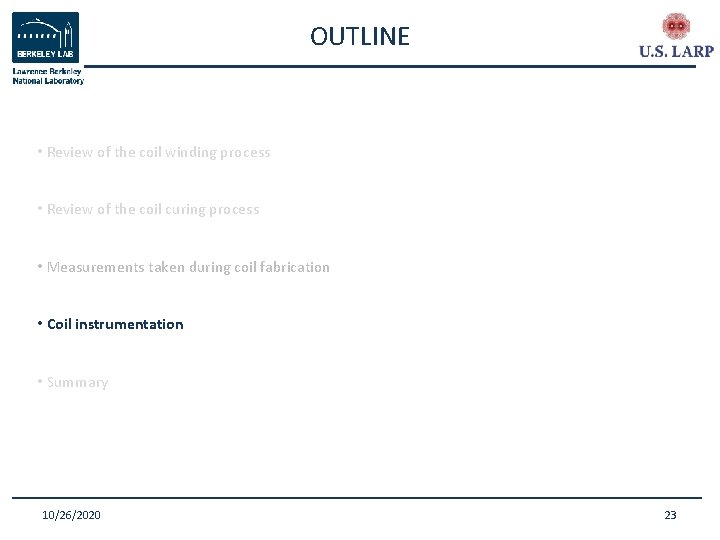
OUTLINE • Review of the coil winding process • Review of the coil curing process • Measurements taken during coil fabrication • Coil instrumentation • Summary 10/26/2020 23
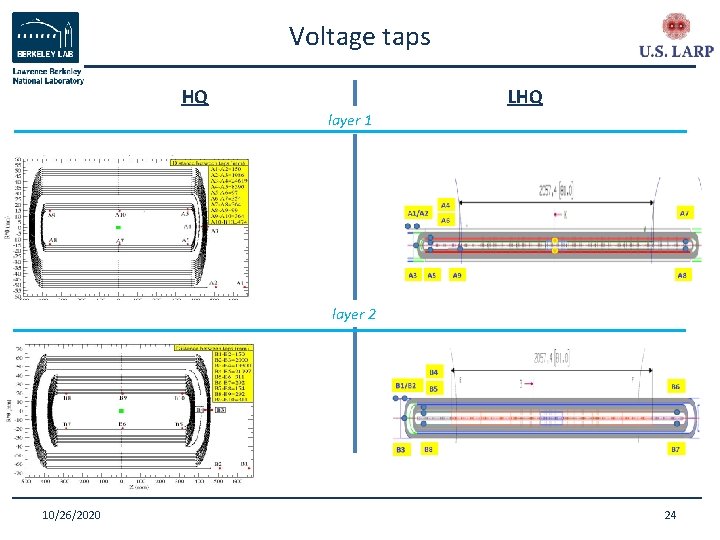
Voltage taps HQ LHQ layer 1 layer 2 10/26/2020 24
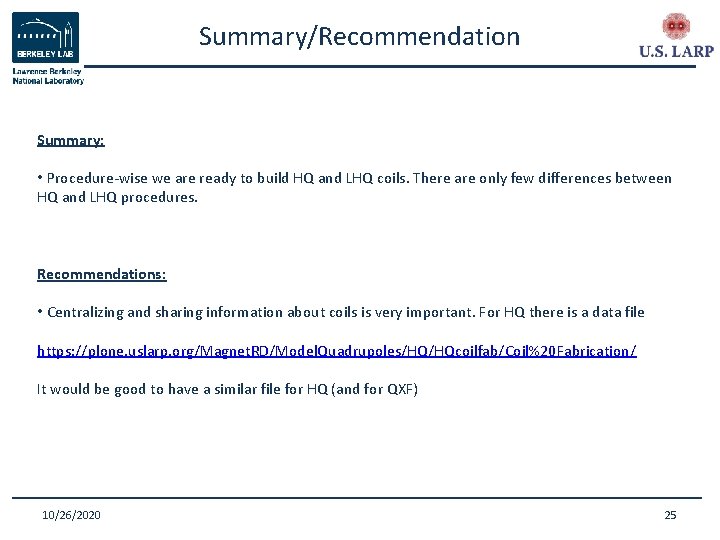
Summary/Recommendation Summary: • Procedure-wise we are ready to build HQ and LHQ coils. There are only few differences between HQ and LHQ procedures. Recommendations: • Centralizing and sharing information about coils is very important. For HQ there is a data file https: //plone. uslarp. org/Magnet. RD/Model. Quadrupoles/HQ/HQcoilfab/Coil%20 Fabrication/ It would be good to have a similar file for HQ (and for QXF) 10/26/2020 25
Armature of dc machine
Final control
Series coil and multi-turn coil
Maximum efficiency of transformer
Drum winding prepreg machine
Primary and secondary coil
Coil pitch and pole pitch
Ac motor armature winding diagram
Object of winding
24 slot 4 pole winding diagram
Winding up vs liquidation
Generator rotor testing
9 section perm wind
Sipro winding
Wet filament winding
Véronique haslund
Filament winding machine design
Dlrk winding
Wave winding parallel paths
Helical winding in transformer
Occipital lobe main function
Lobes of cerebrum
Dc motor armature winding diagram
Winding one point perspective
Sarcomere sliding filament model
Field pole