Introduction to Manufacturing Chapter 14 Forging Engr 241
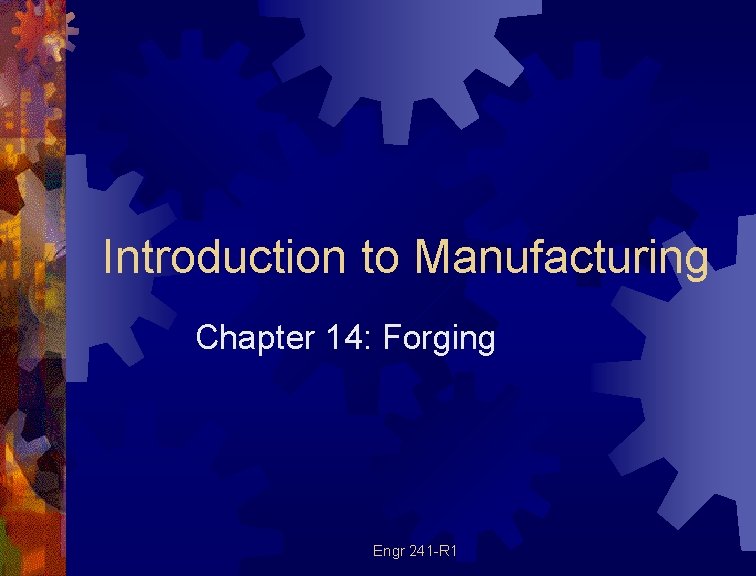
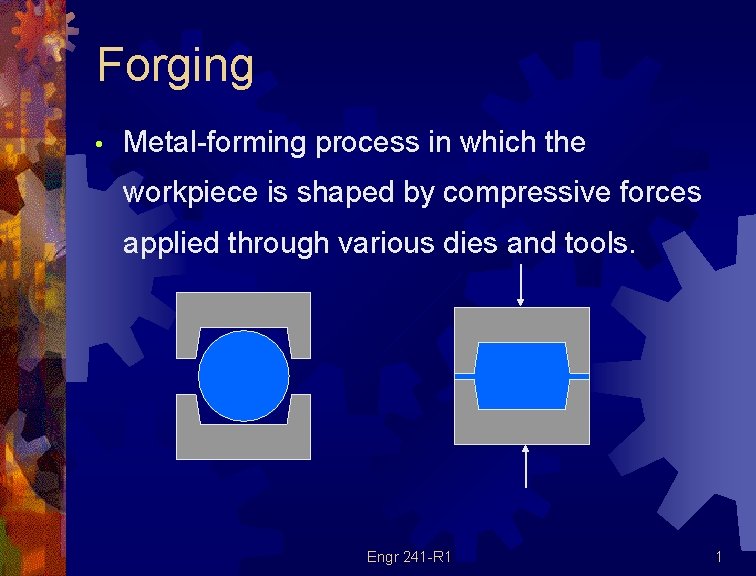
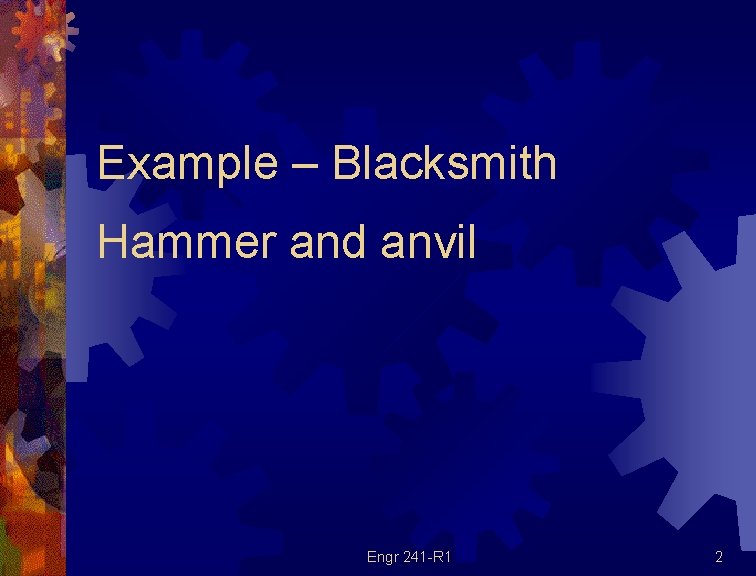
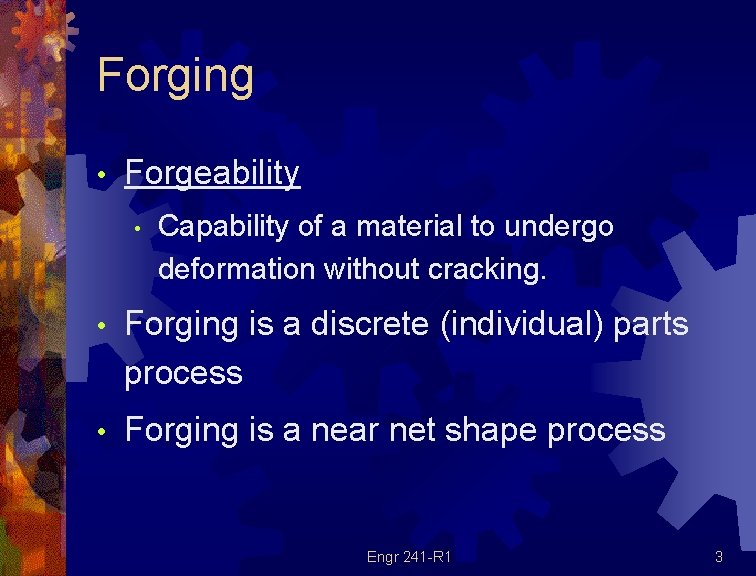
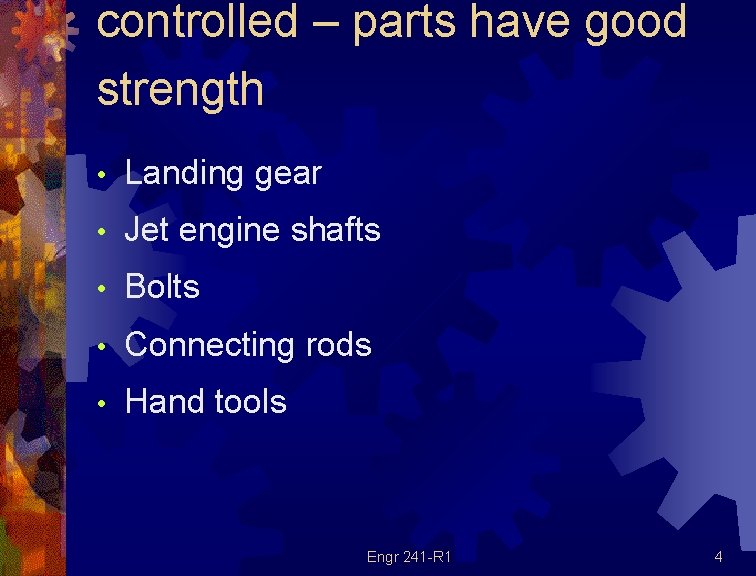
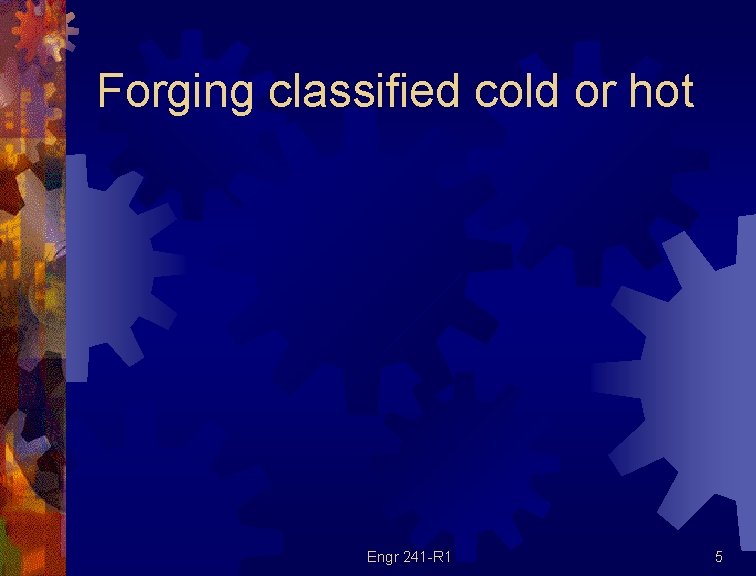
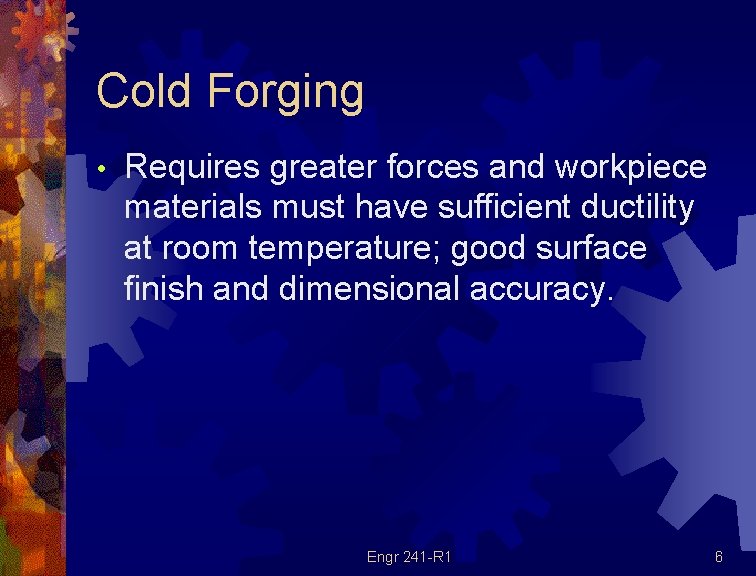
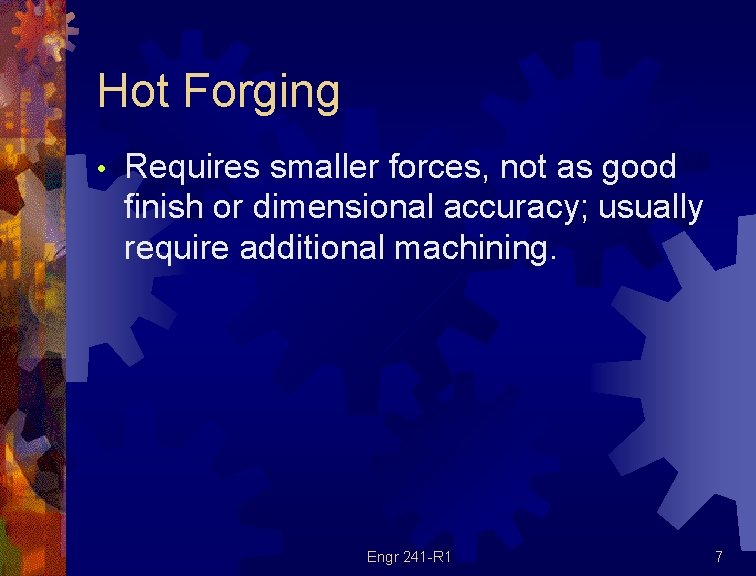
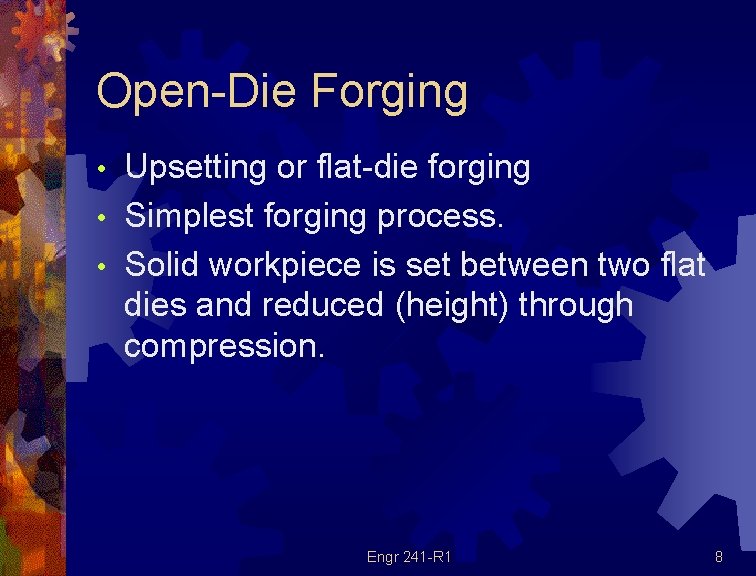
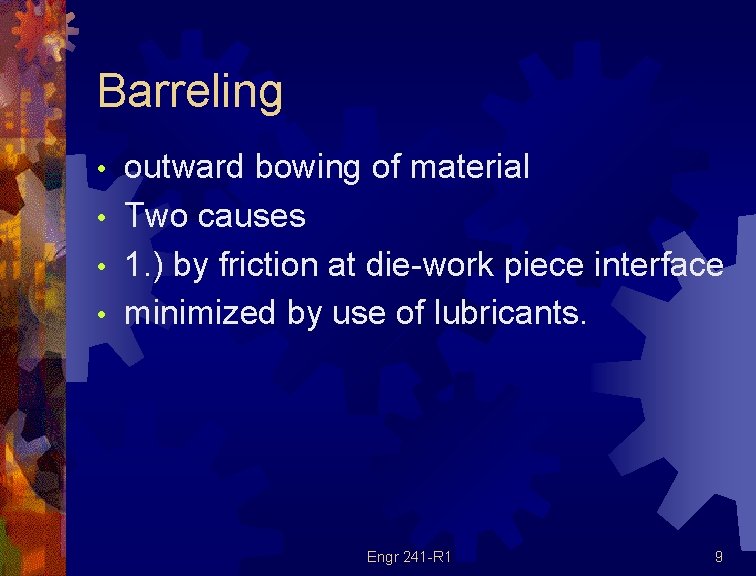
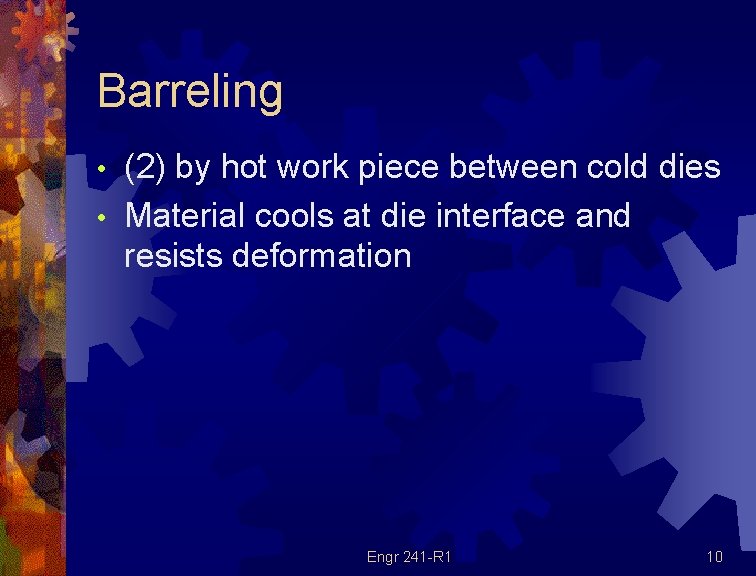
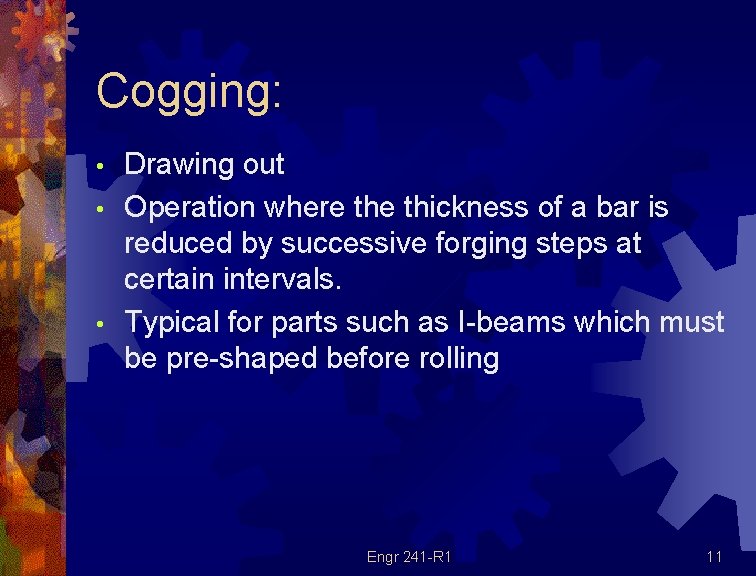
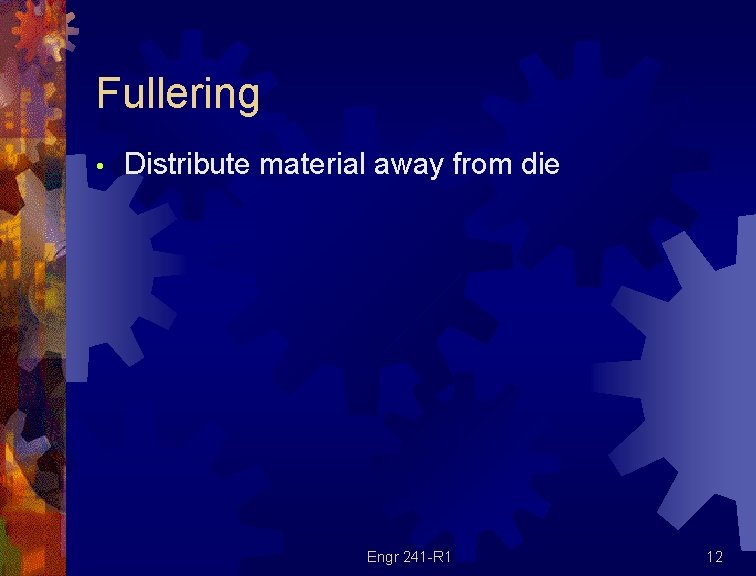
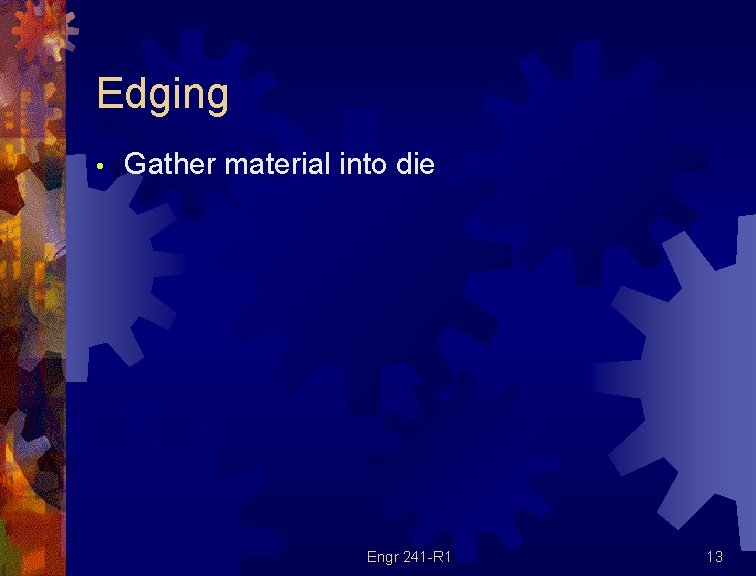
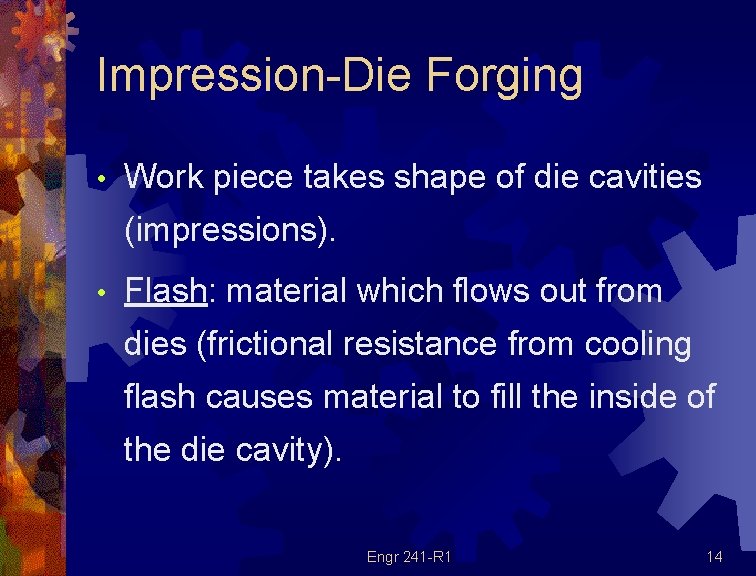
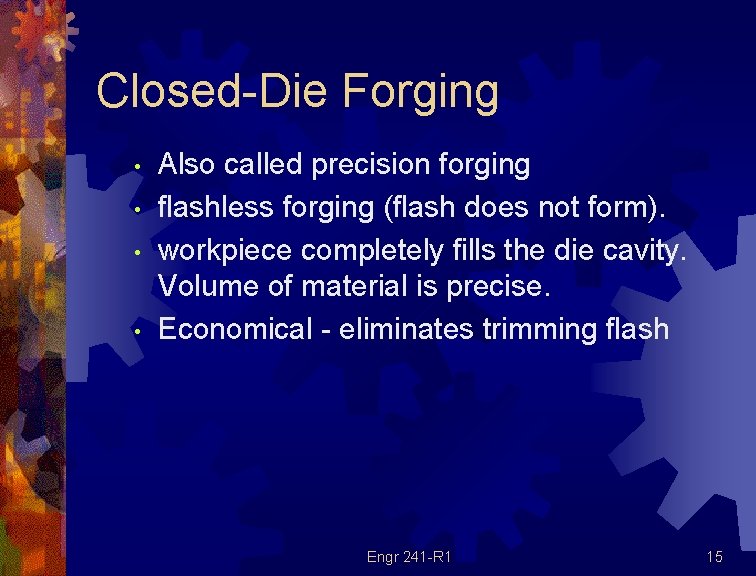
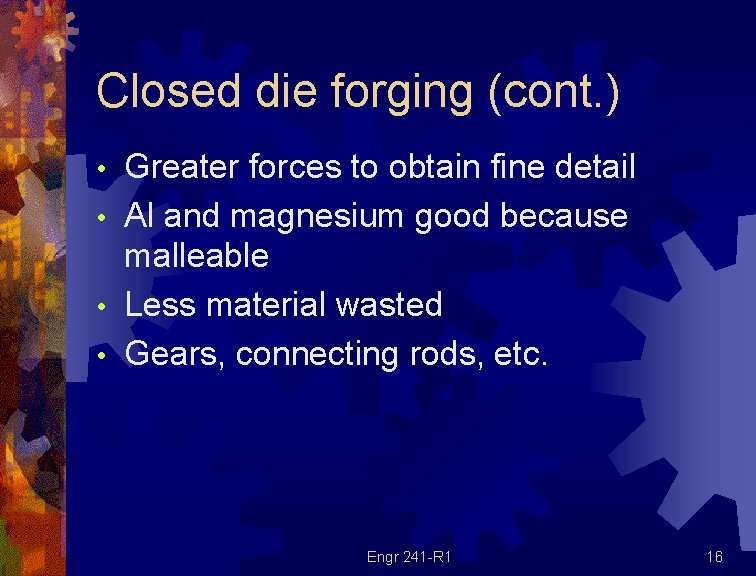
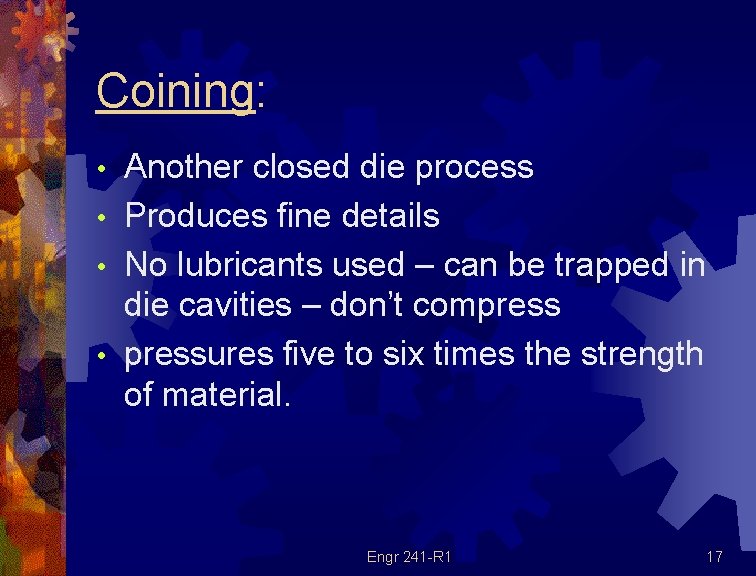
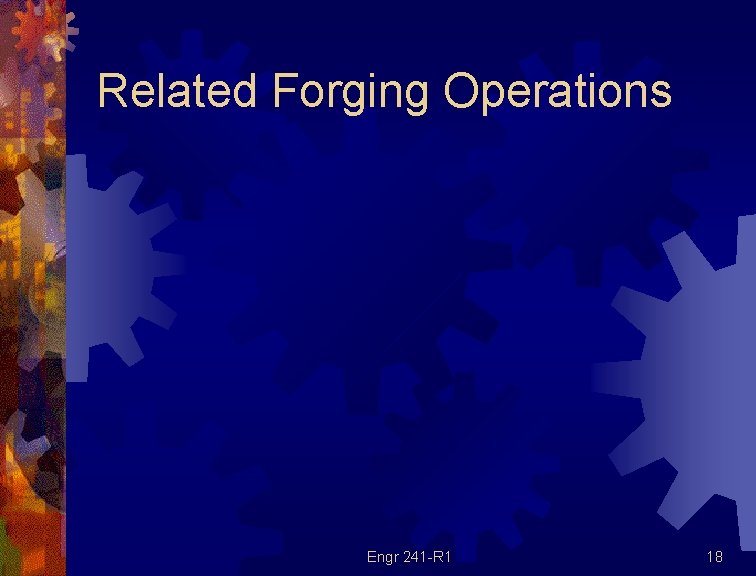
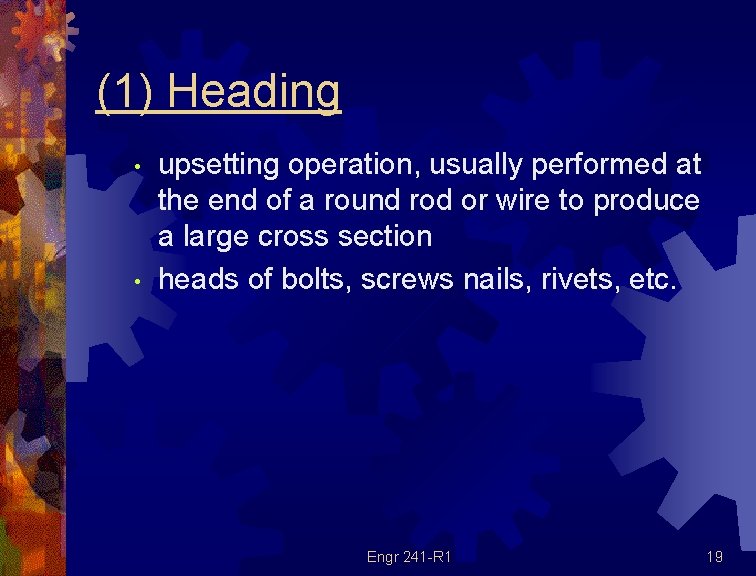
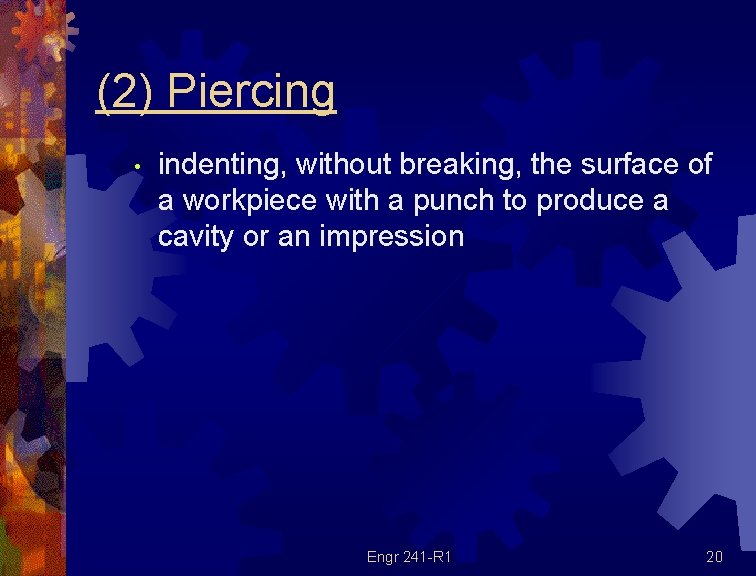
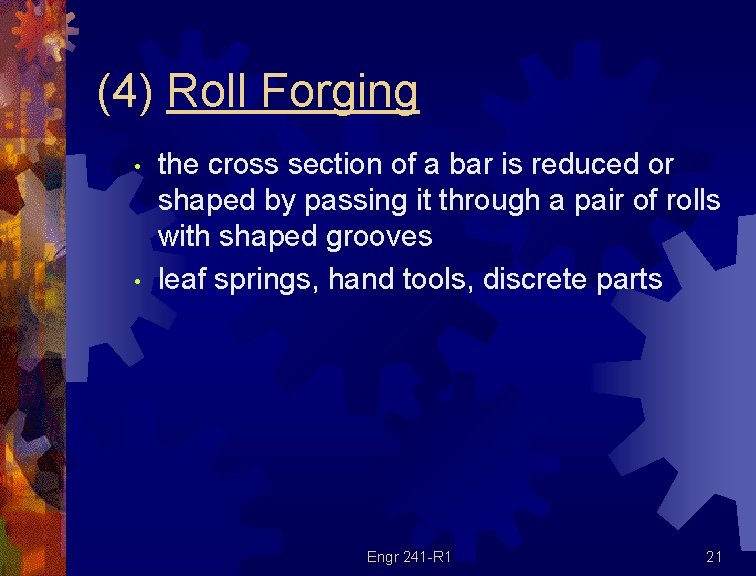
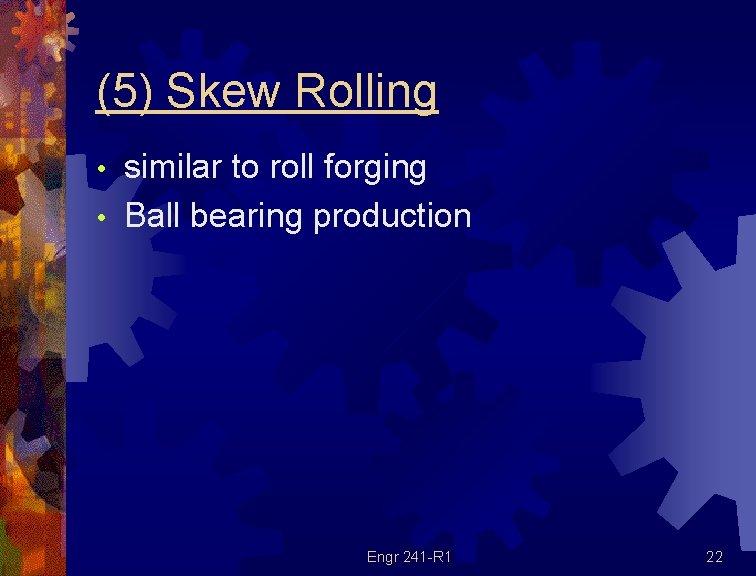
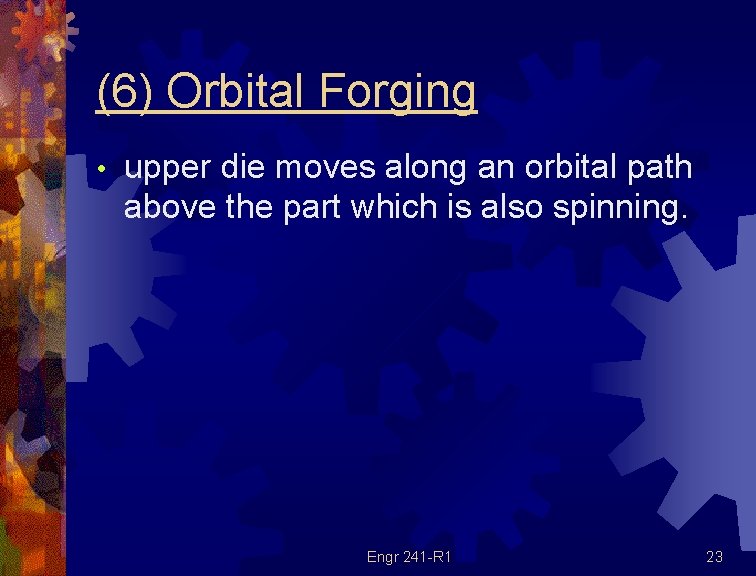
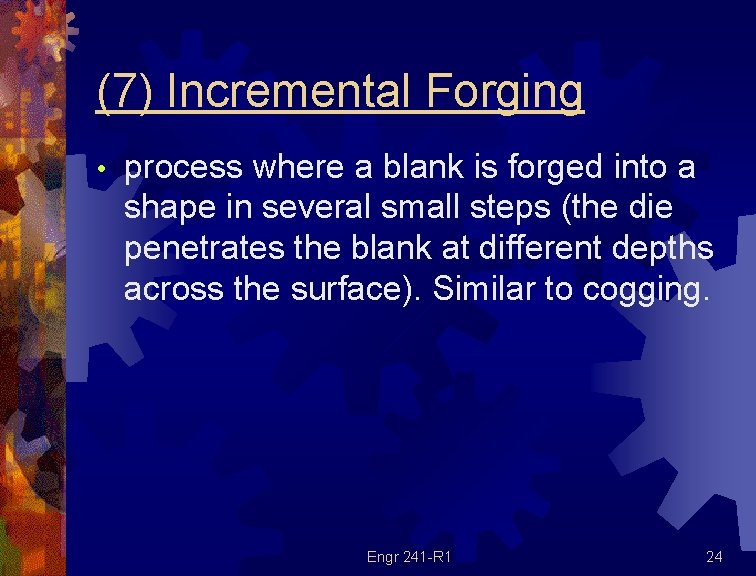
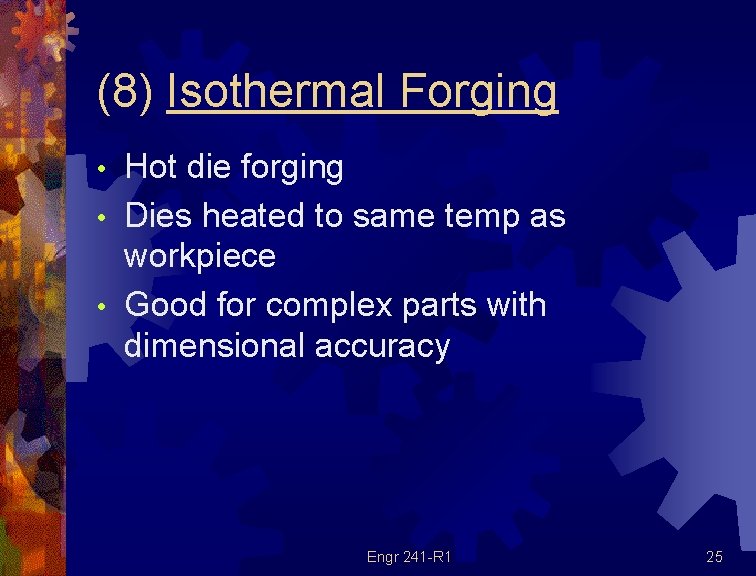
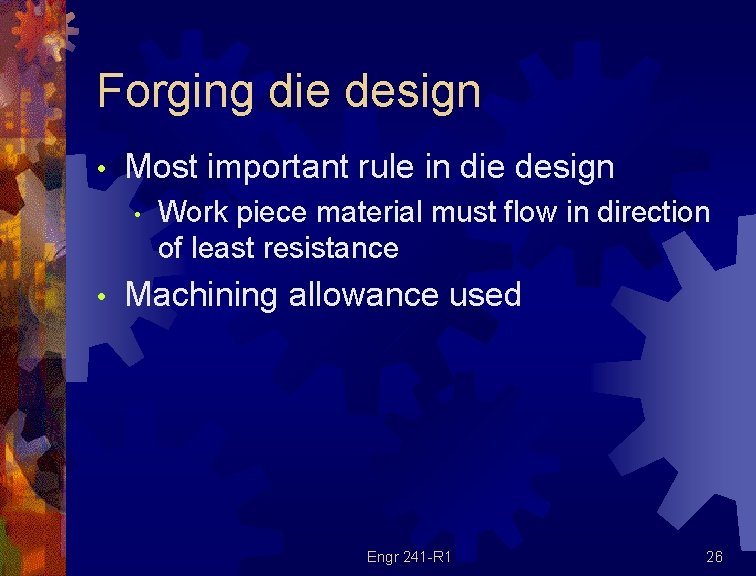
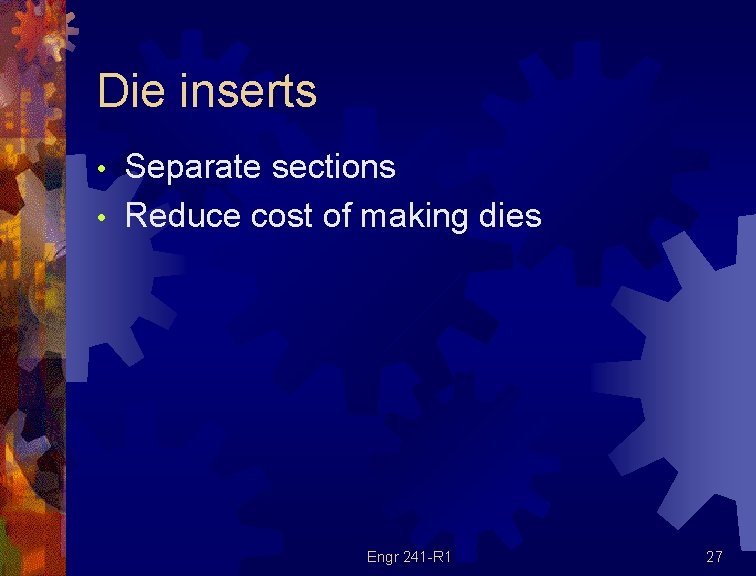
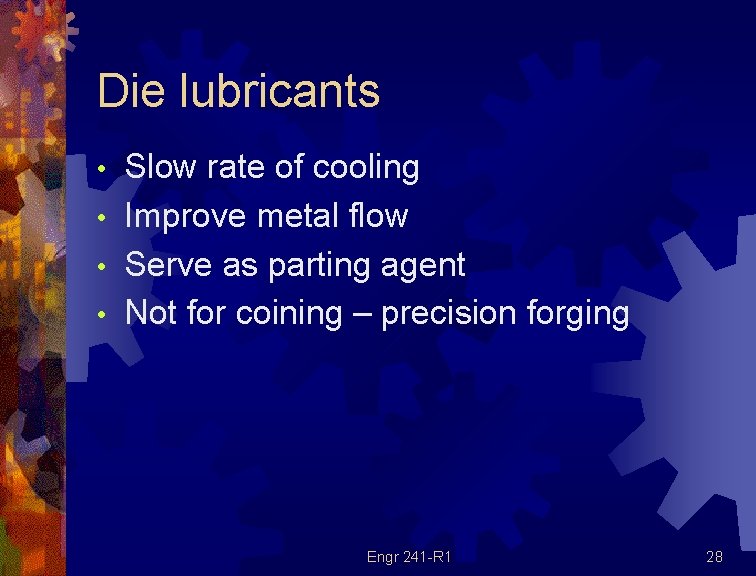
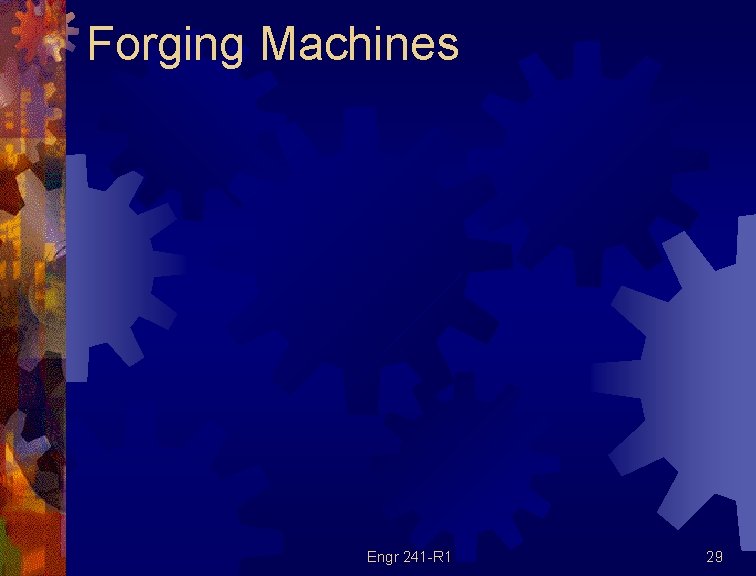
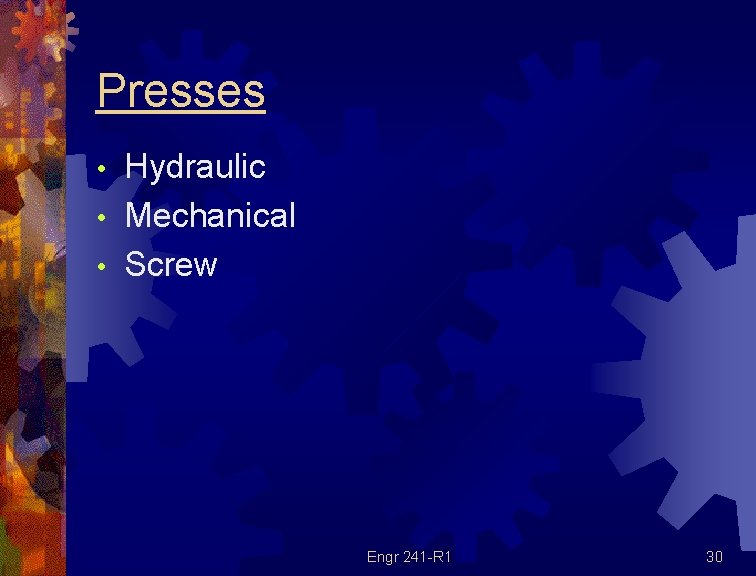
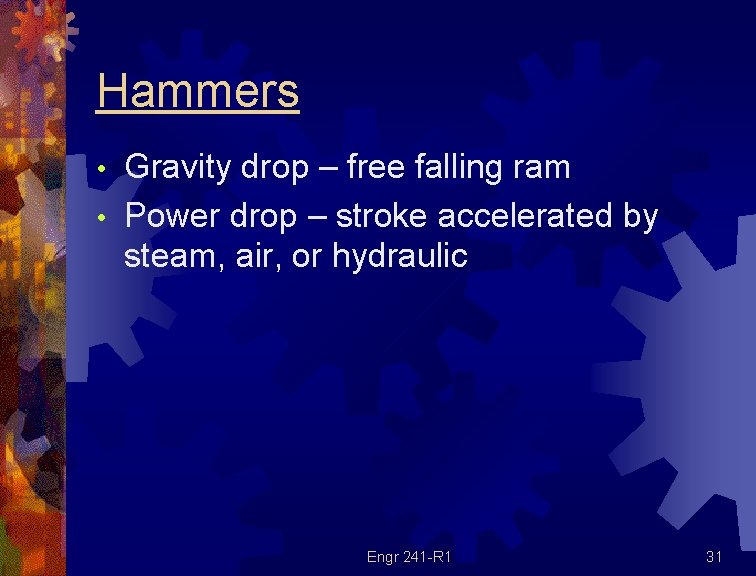
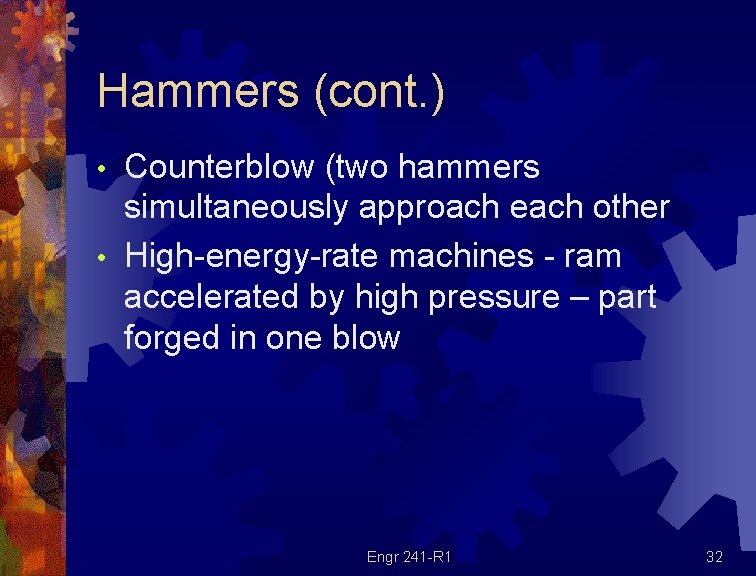
- Slides: 33
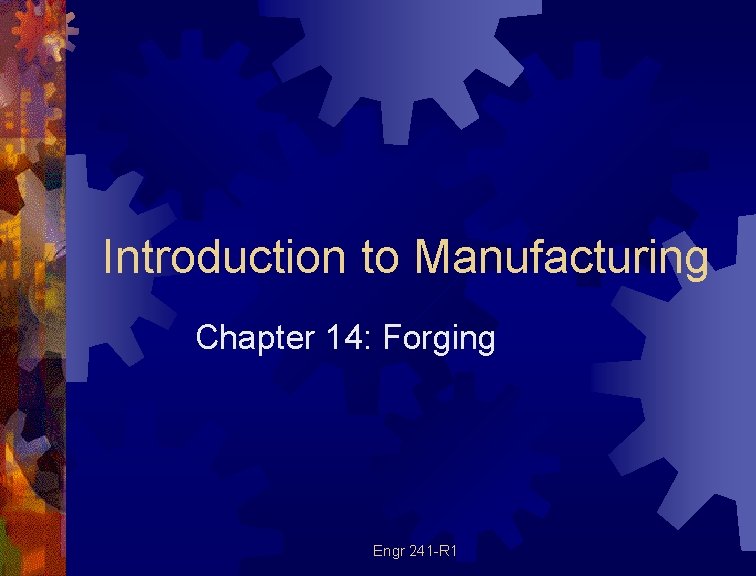
Introduction to Manufacturing Chapter 14: Forging Engr 241 -R 1
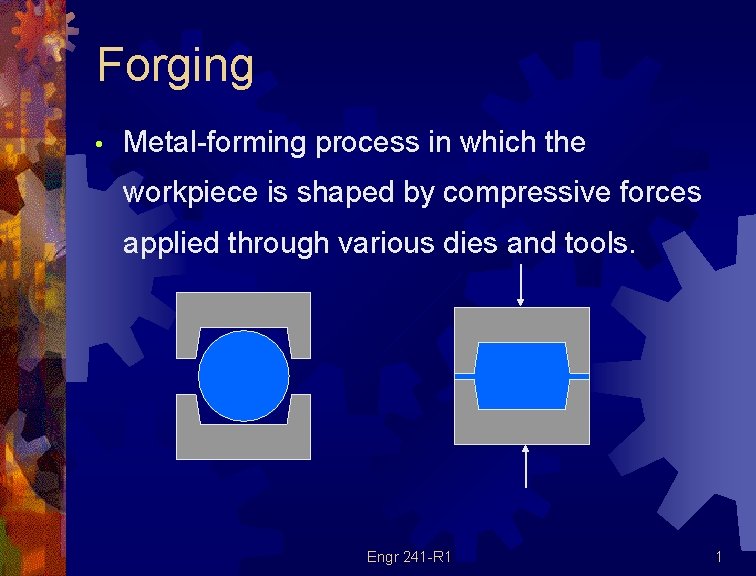
Forging • Metal-forming process in which the workpiece is shaped by compressive forces applied through various dies and tools. Engr 241 -R 1 1
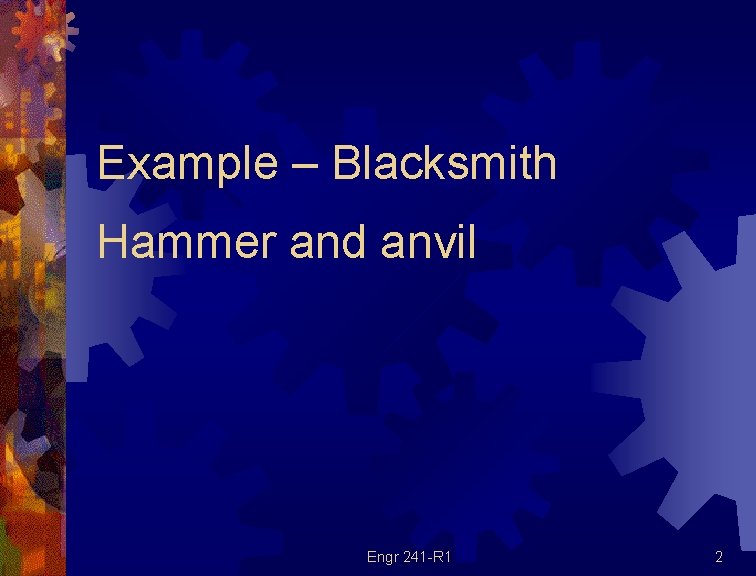
Example – Blacksmith Hammer and anvil Engr 241 -R 1 2
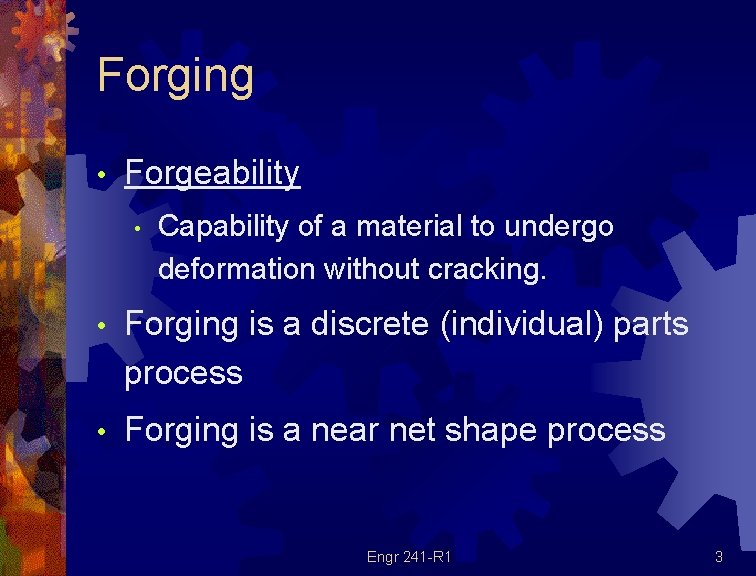
Forging • Forgeability • Capability of a material to undergo deformation without cracking. • Forging is a discrete (individual) parts process • Forging is a near net shape process Engr 241 -R 1 3
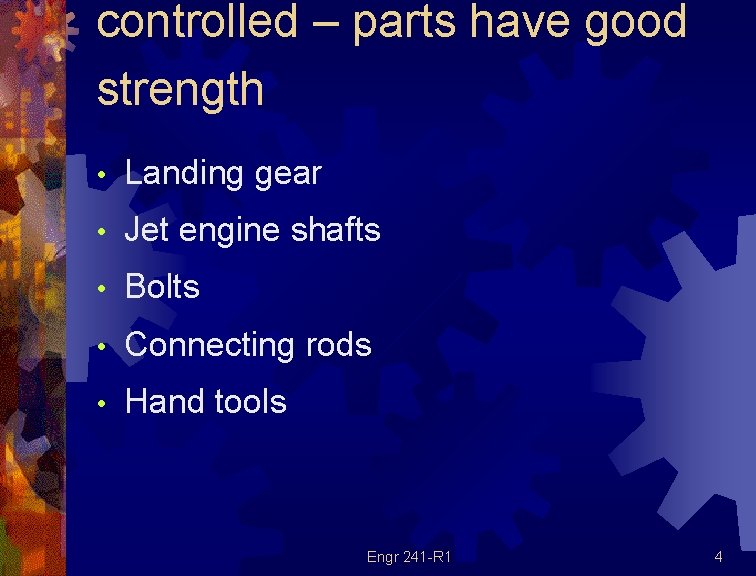
controlled – parts have good strength • Landing gear • Jet engine shafts • Bolts • Connecting rods • Hand tools Engr 241 -R 1 4
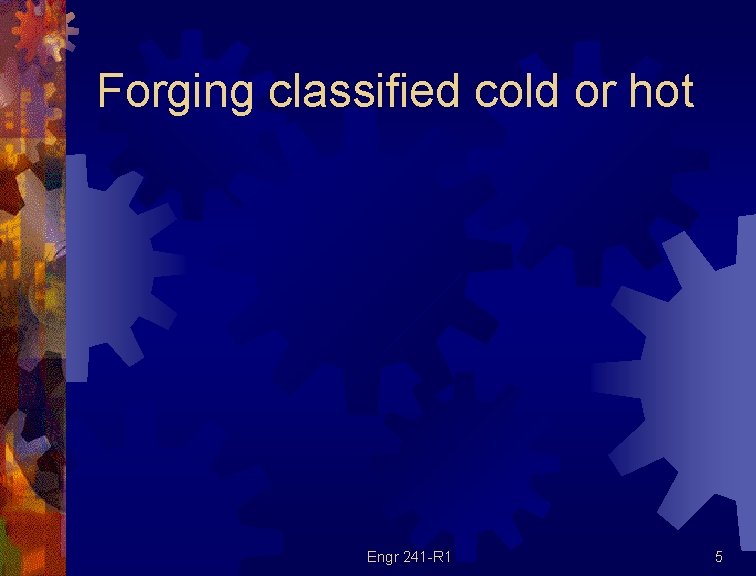
Forging classified cold or hot Engr 241 -R 1 5
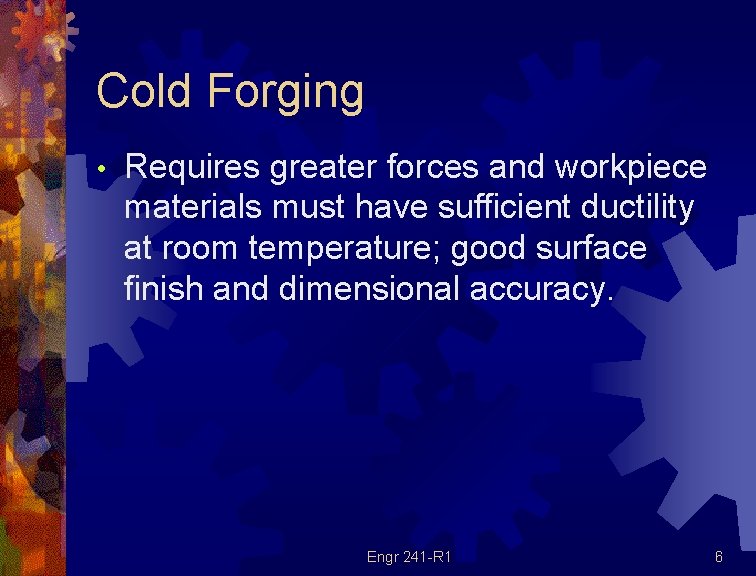
Cold Forging • Requires greater forces and workpiece materials must have sufficient ductility at room temperature; good surface finish and dimensional accuracy. Engr 241 -R 1 6
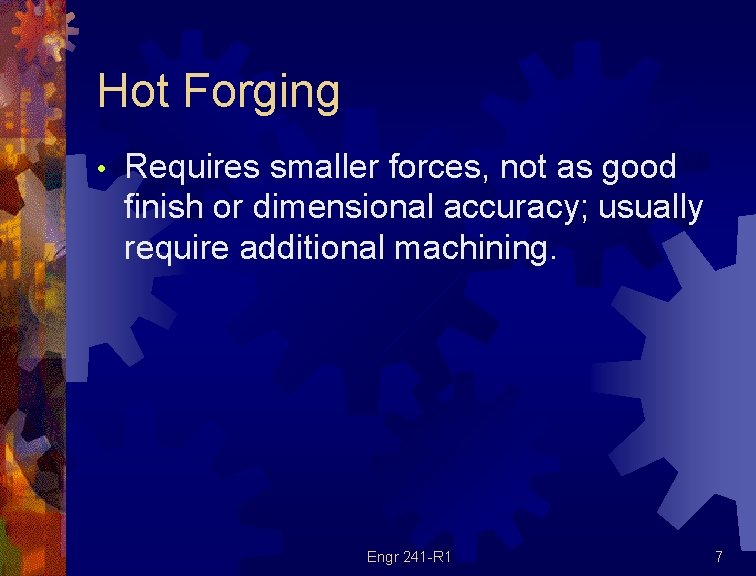
Hot Forging • Requires smaller forces, not as good finish or dimensional accuracy; usually require additional machining. Engr 241 -R 1 7
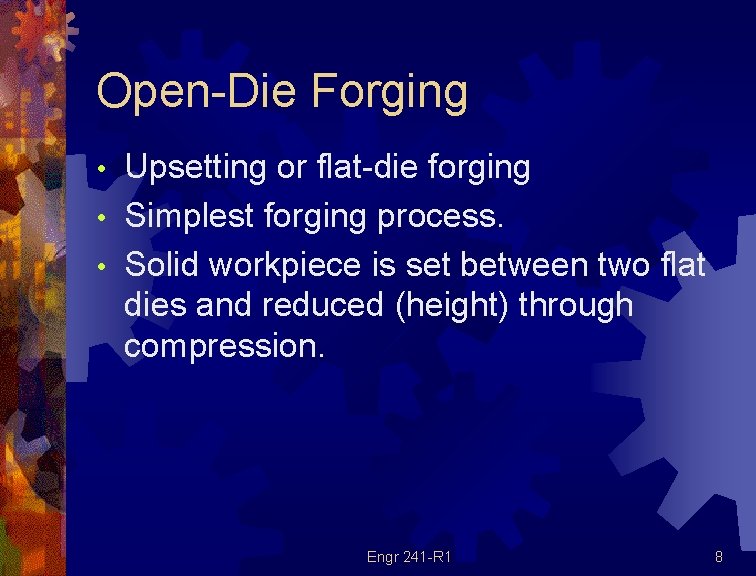
Open-Die Forging Upsetting or flat-die forging • Simplest forging process. • Solid workpiece is set between two flat dies and reduced (height) through compression. • Engr 241 -R 1 8
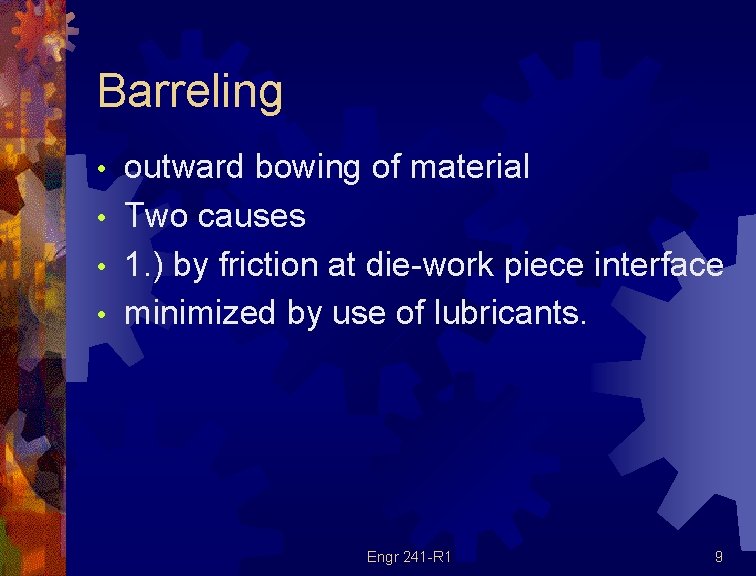
Barreling outward bowing of material • Two causes • 1. ) by friction at die-work piece interface • minimized by use of lubricants. • Engr 241 -R 1 9
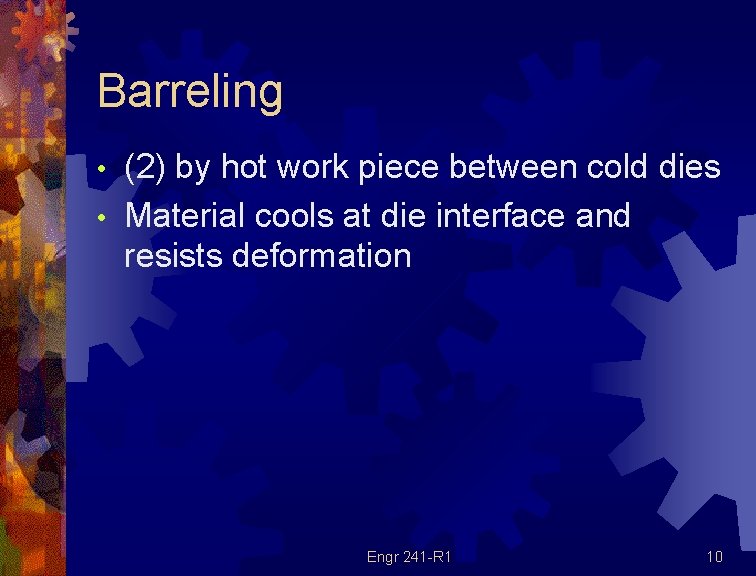
Barreling (2) by hot work piece between cold dies • Material cools at die interface and resists deformation • Engr 241 -R 1 10
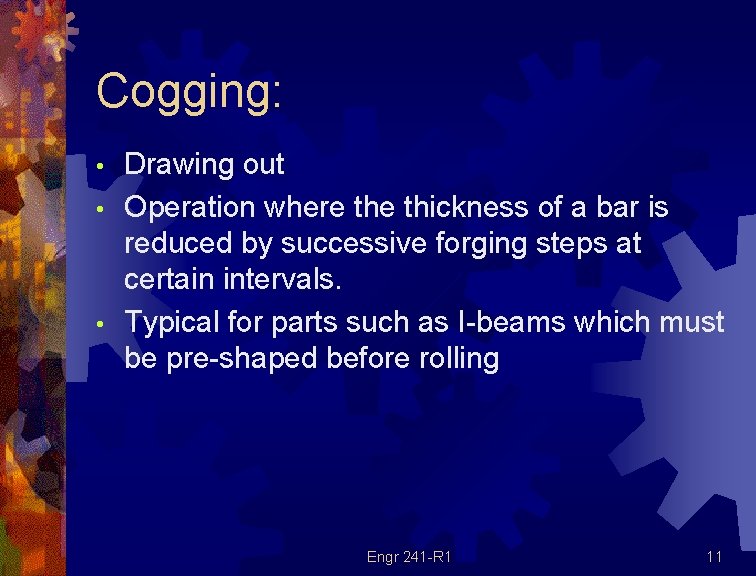
Cogging: Drawing out • Operation where thickness of a bar is reduced by successive forging steps at certain intervals. • Typical for parts such as I-beams which must be pre-shaped before rolling • Engr 241 -R 1 11
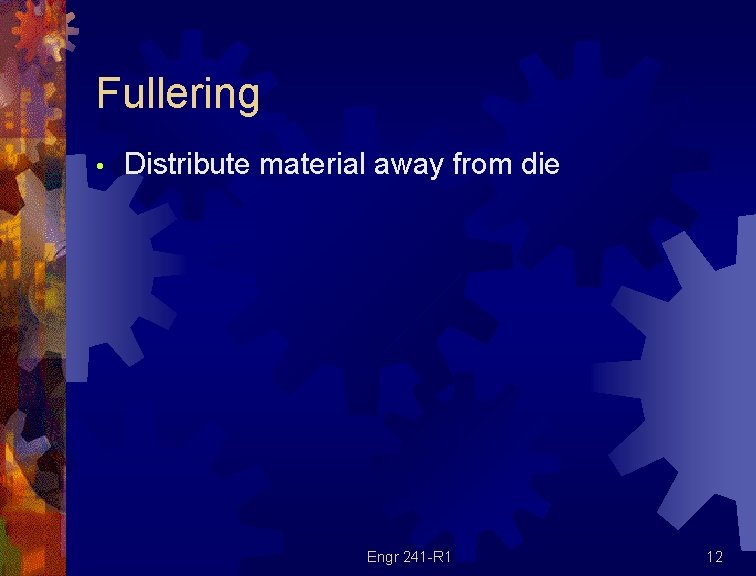
Fullering • Distribute material away from die Engr 241 -R 1 12
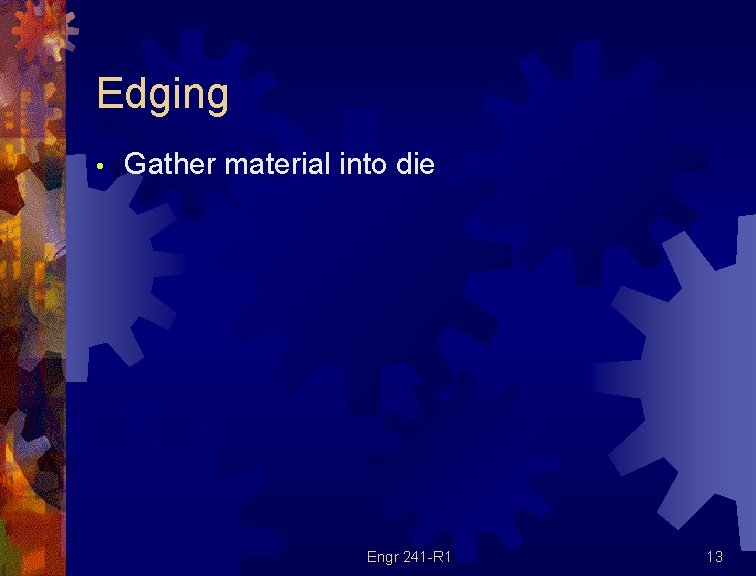
Edging • Gather material into die Engr 241 -R 1 13
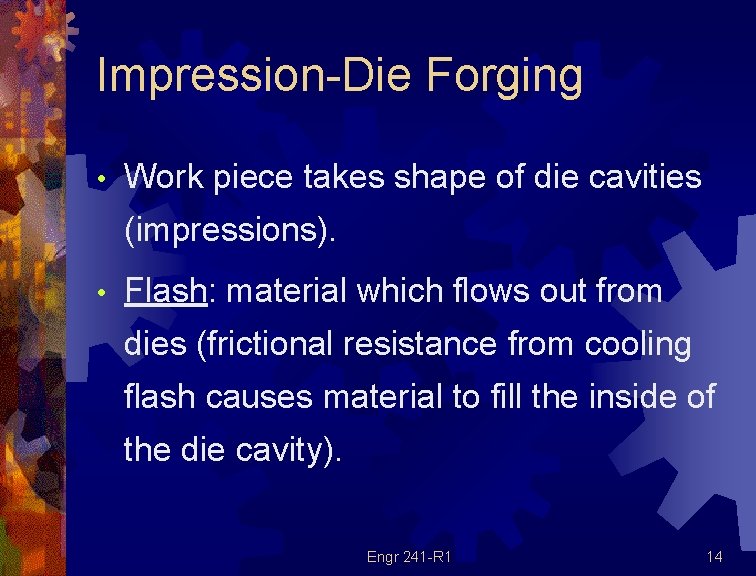
Impression-Die Forging • Work piece takes shape of die cavities (impressions). • Flash: material which flows out from dies (frictional resistance from cooling flash causes material to fill the inside of the die cavity). Engr 241 -R 1 14
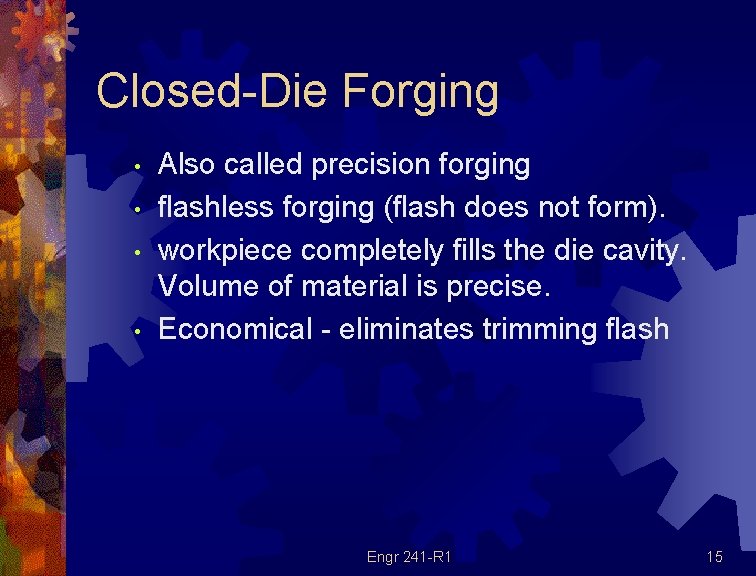
Closed-Die Forging • • Also called precision forging flashless forging (flash does not form). workpiece completely fills the die cavity. Volume of material is precise. Economical - eliminates trimming flash Engr 241 -R 1 15
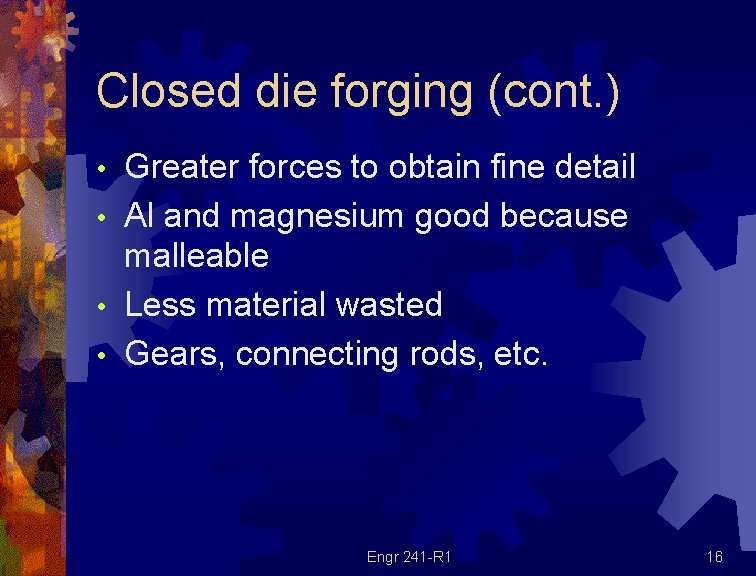
Closed die forging (cont. ) Greater forces to obtain fine detail • Al and magnesium good because malleable • Less material wasted • Gears, connecting rods, etc. • Engr 241 -R 1 16
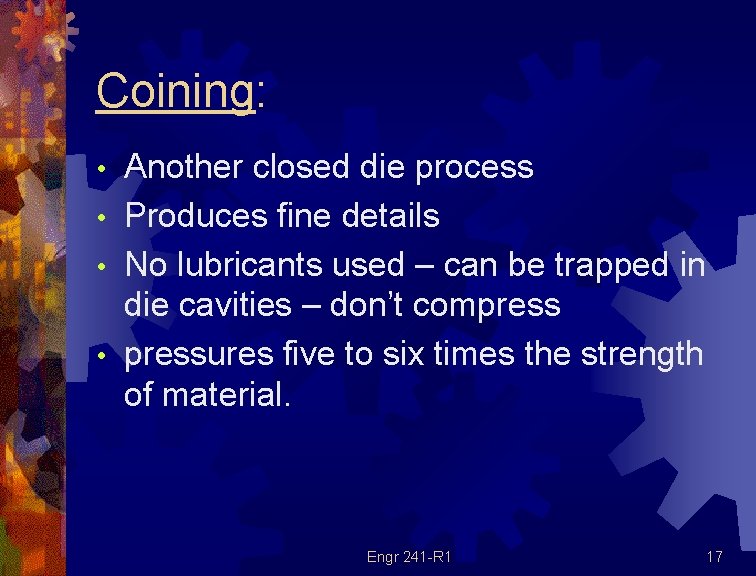
Coining: Another closed die process • Produces fine details • No lubricants used – can be trapped in die cavities – don’t compress • pressures five to six times the strength of material. • Engr 241 -R 1 17
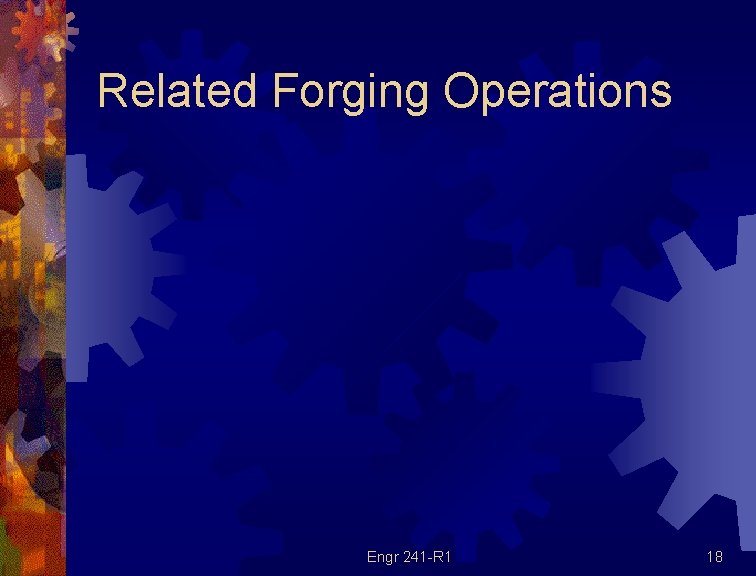
Related Forging Operations Engr 241 -R 1 18
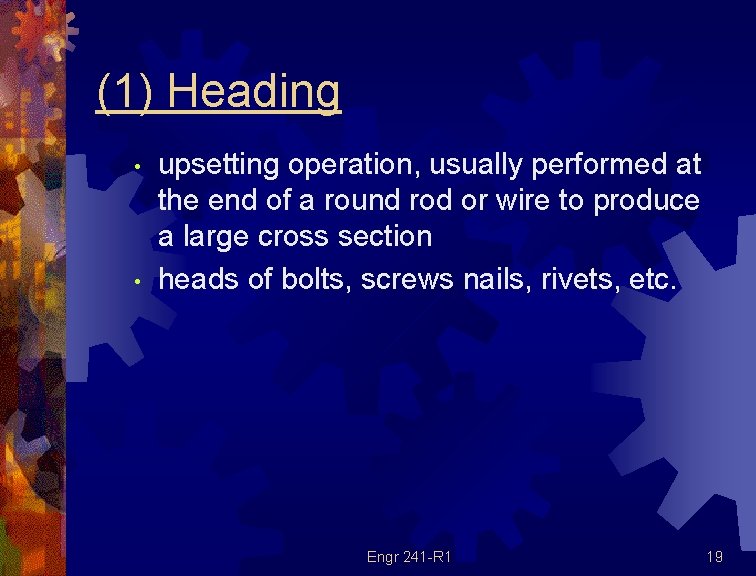
(1) Heading • • upsetting operation, usually performed at the end of a round rod or wire to produce a large cross section heads of bolts, screws nails, rivets, etc. Engr 241 -R 1 19
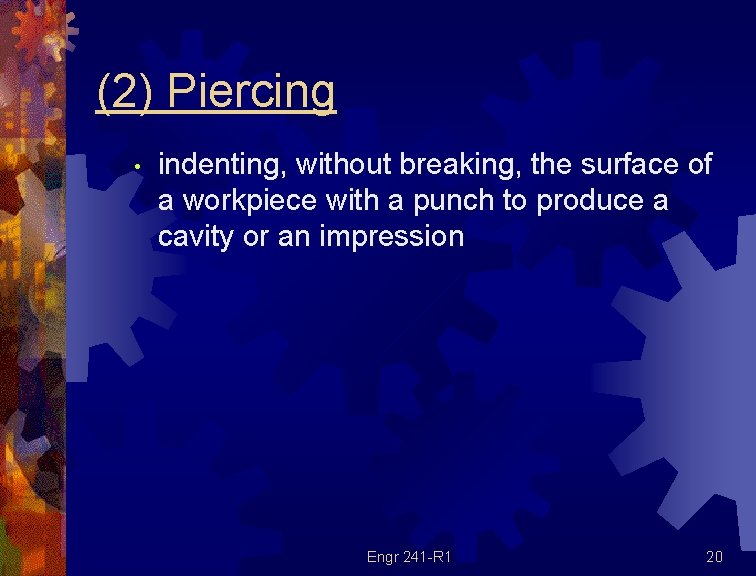
(2) Piercing • indenting, without breaking, the surface of a workpiece with a punch to produce a cavity or an impression Engr 241 -R 1 20
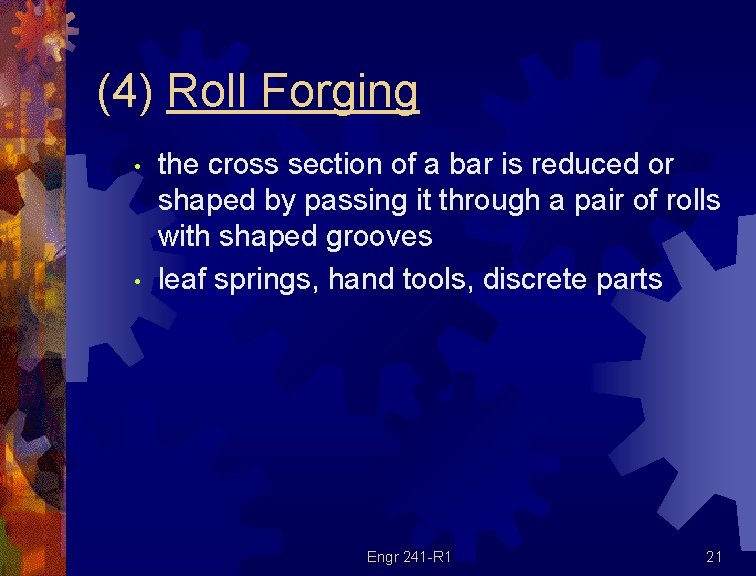
(4) Roll Forging • • the cross section of a bar is reduced or shaped by passing it through a pair of rolls with shaped grooves leaf springs, hand tools, discrete parts Engr 241 -R 1 21
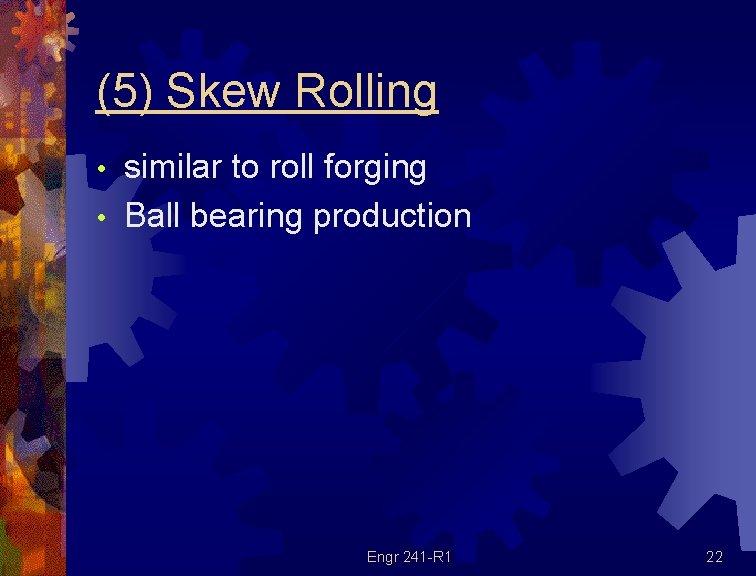
(5) Skew Rolling similar to roll forging • Ball bearing production • Engr 241 -R 1 22
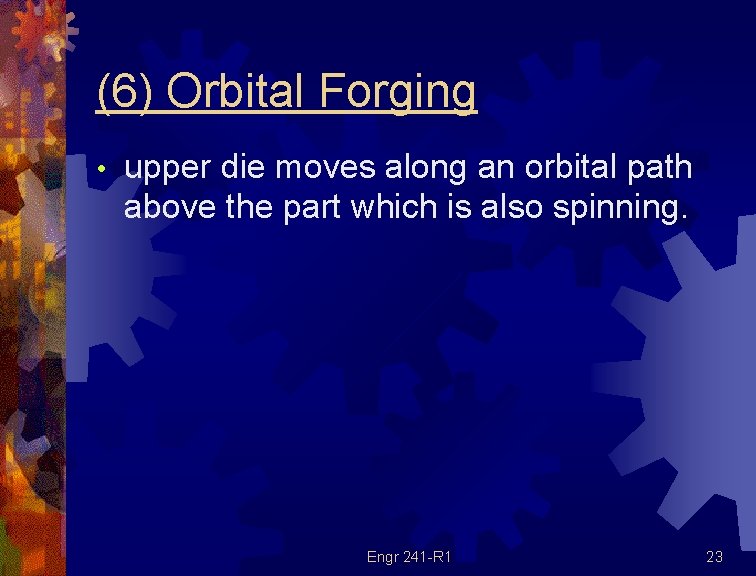
(6) Orbital Forging • upper die moves along an orbital path above the part which is also spinning. Engr 241 -R 1 23
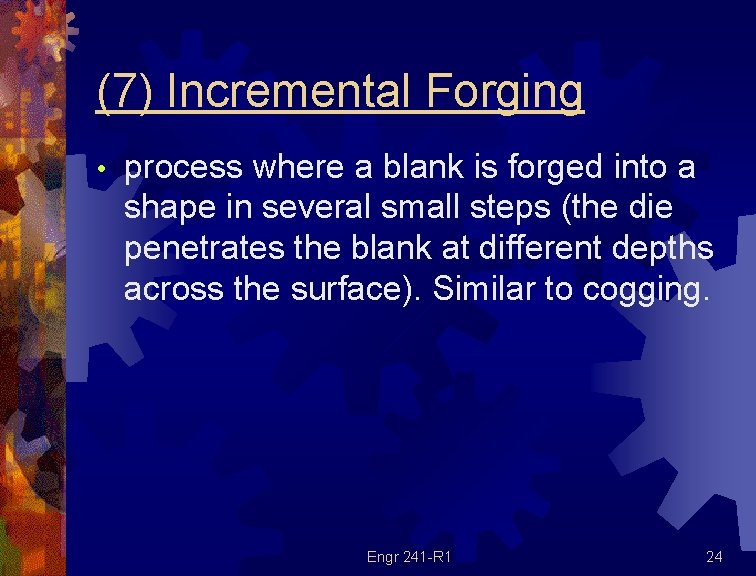
(7) Incremental Forging • process where a blank is forged into a shape in several small steps (the die penetrates the blank at different depths across the surface). Similar to cogging. Engr 241 -R 1 24
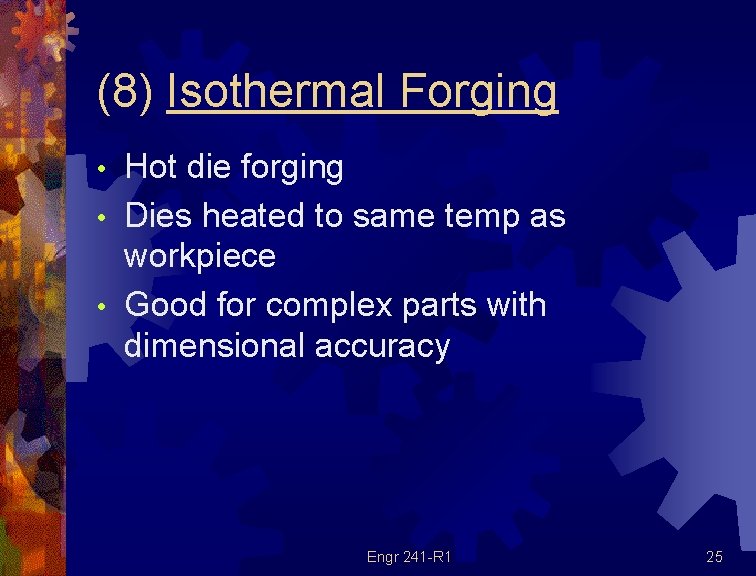
(8) Isothermal Forging Hot die forging • Dies heated to same temp as workpiece • Good for complex parts with dimensional accuracy • Engr 241 -R 1 25
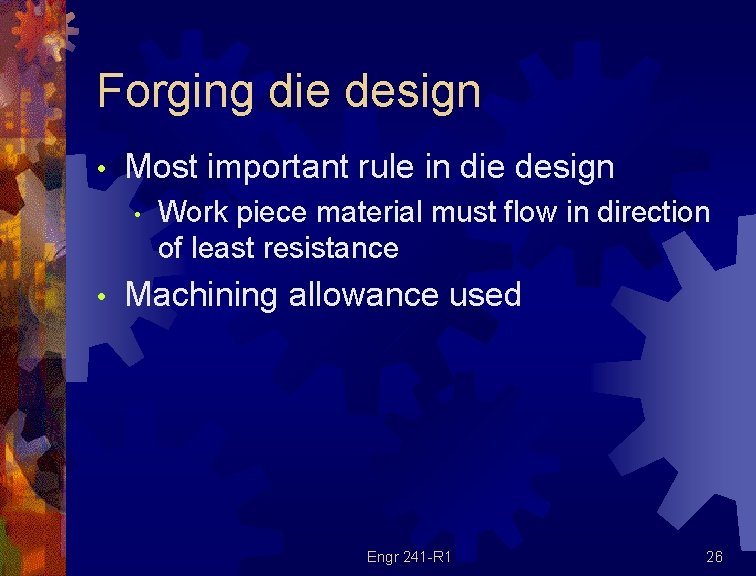
Forging die design • Most important rule in die design • • Work piece material must flow in direction of least resistance Machining allowance used Engr 241 -R 1 26
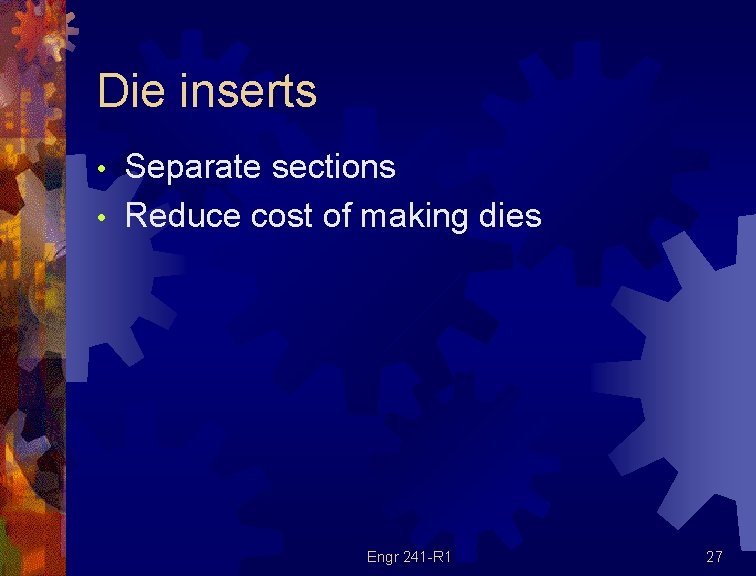
Die inserts Separate sections • Reduce cost of making dies • Engr 241 -R 1 27
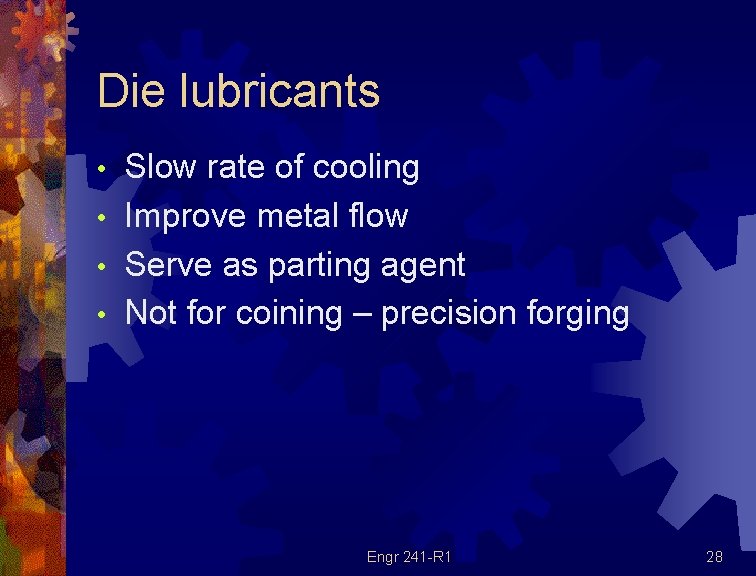
Die lubricants Slow rate of cooling • Improve metal flow • Serve as parting agent • Not for coining – precision forging • Engr 241 -R 1 28
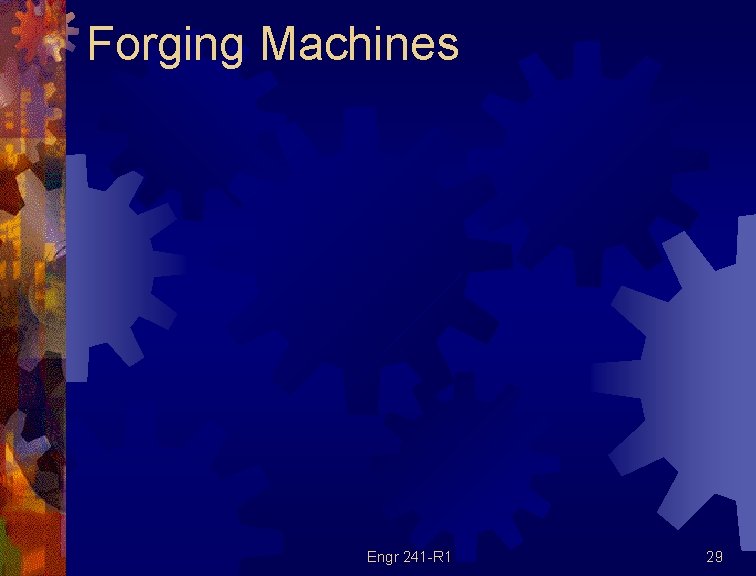
Forging Machines Engr 241 -R 1 29
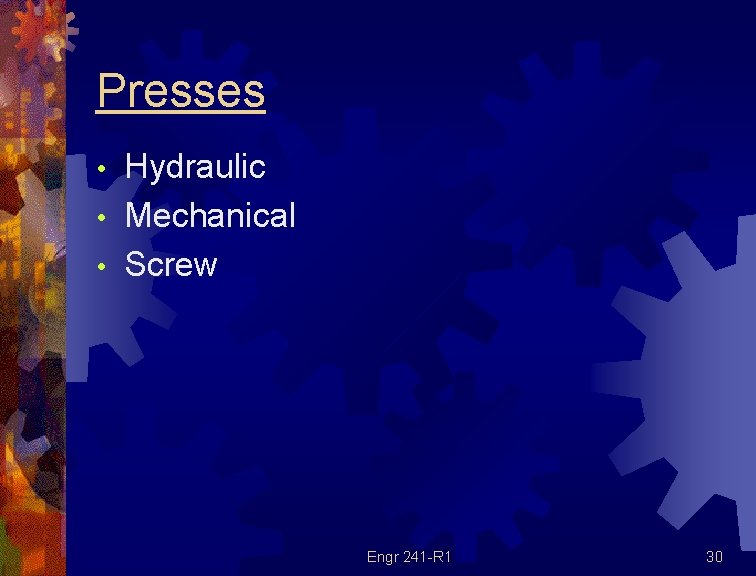
Presses Hydraulic • Mechanical • Screw • Engr 241 -R 1 30
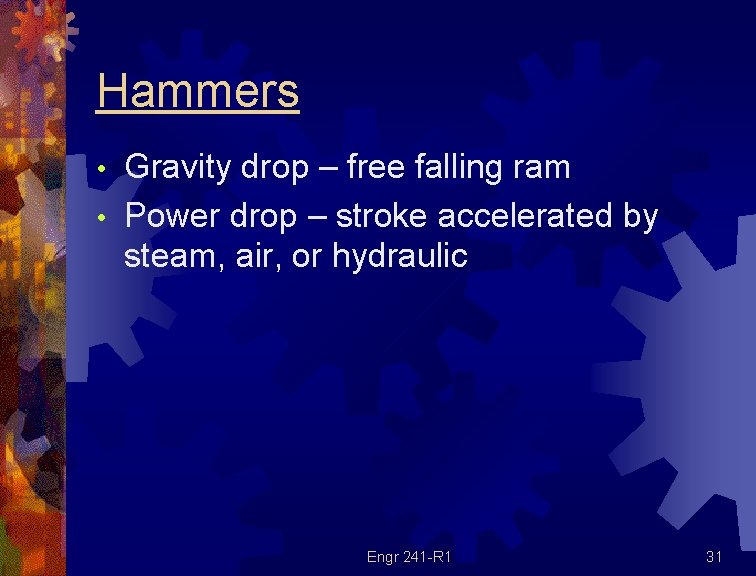
Hammers Gravity drop – free falling ram • Power drop – stroke accelerated by steam, air, or hydraulic • Engr 241 -R 1 31
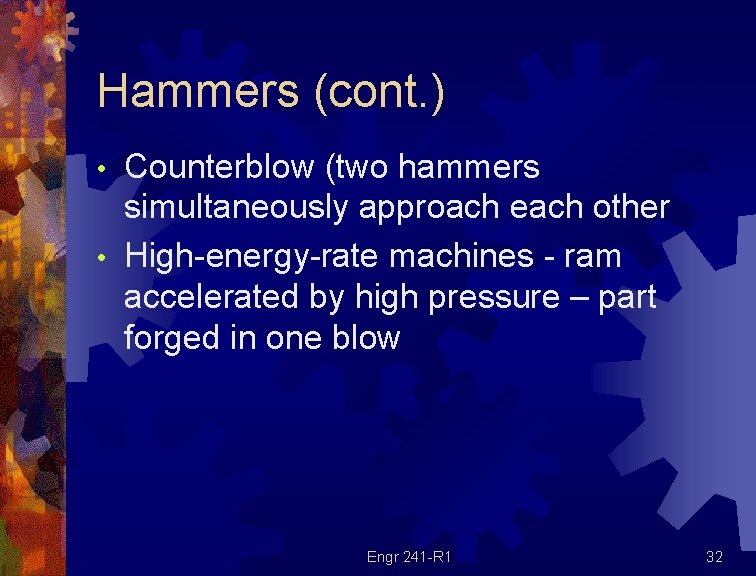
Hammers (cont. ) Counterblow (two hammers simultaneously approach each other • High-energy-rate machines - ram accelerated by high pressure – part forged in one blow • Engr 241 -R 1 32
Manufacturing cost vs non manufacturing cost
Job costing definition
Controllable expenses examples
Manufacturing cost vs non manufacturing cost
Additive manufacturing vs subtractive manufacturing
Chapter 7 lesson 2 forging a new constitution
Chapter 14 forging the national economy
Engr 1181
Sjsu engineering 10
Engr 201
Engr 1182
Engr 350
Engr 1182
Engr 482
Engr 1330
Engr 1330
Engr 112
Engr 240
Engr 10 sjsu
Engr 1181
Mala tiskana slova
Cpe 301 unr
Engr 1181
Engr 1181
Engr 248
Nfpa 241 pdf
Purdue phys 241
241 bce
Tenth thousandth
Fon 241
Cob 241
Ceng 241
Psyco 241
Cs 241 vector mp