ENGR 480 Manufacturing Systems Spring 2015 ENGR 480
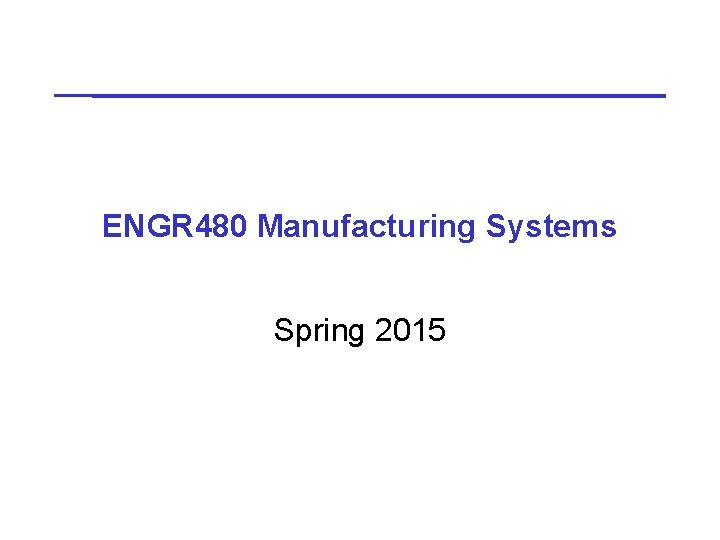
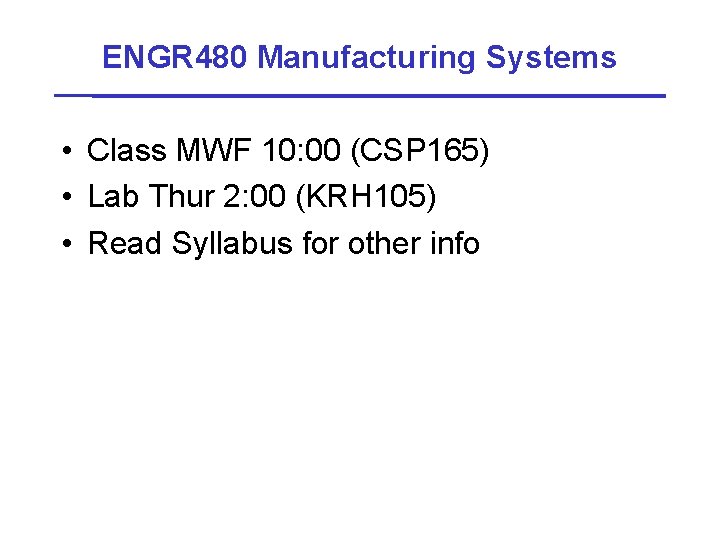
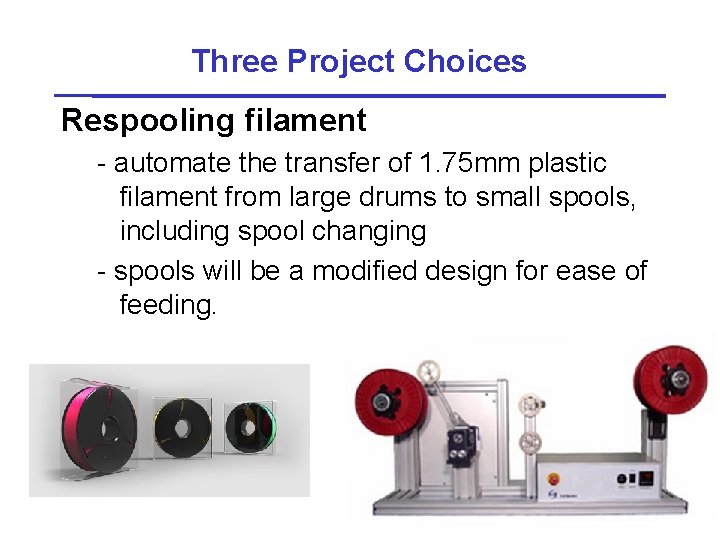
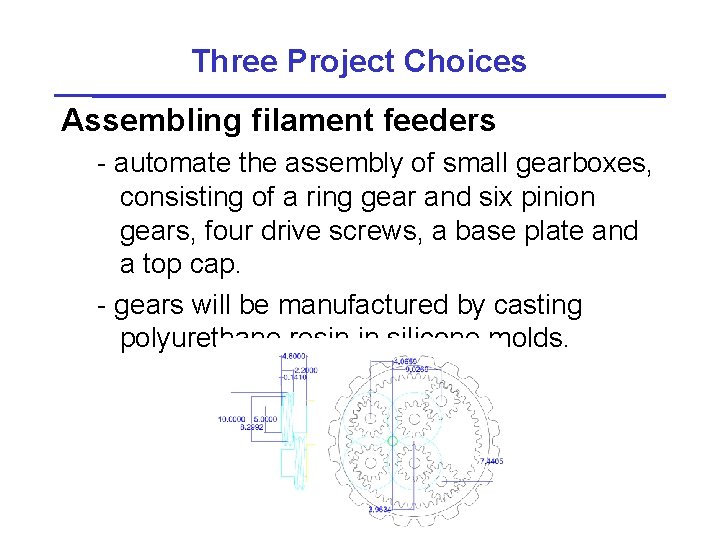
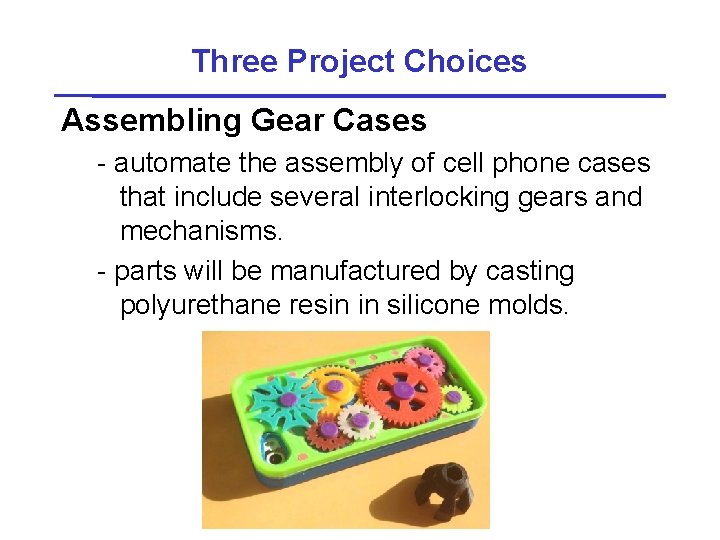
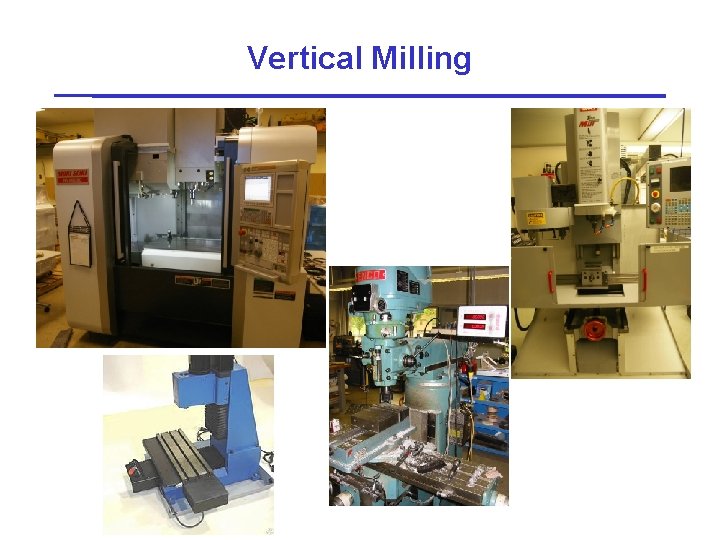
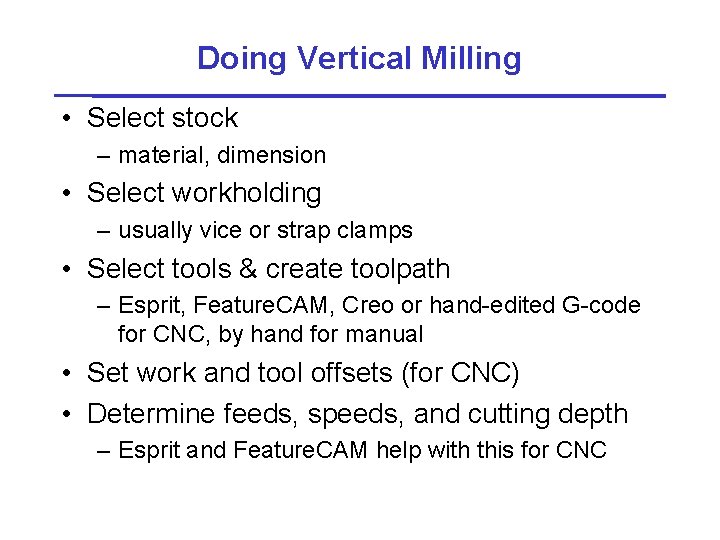
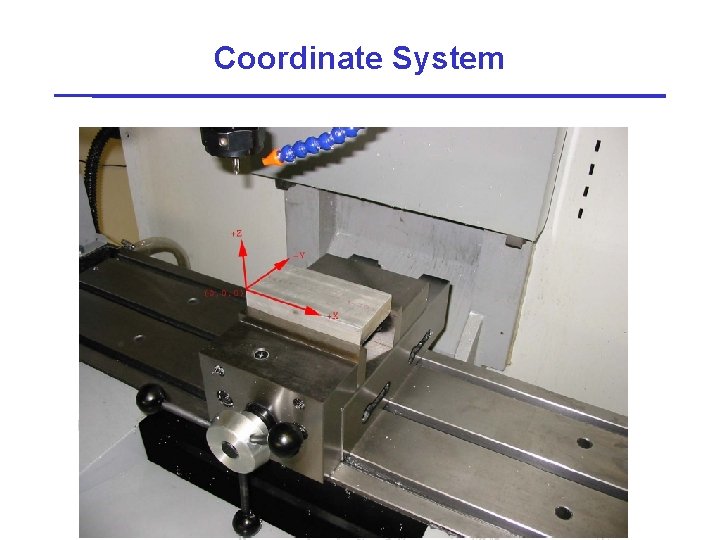
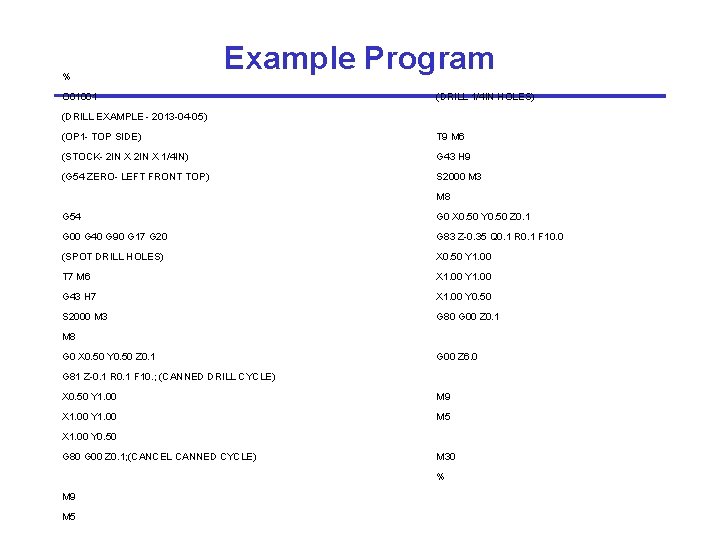
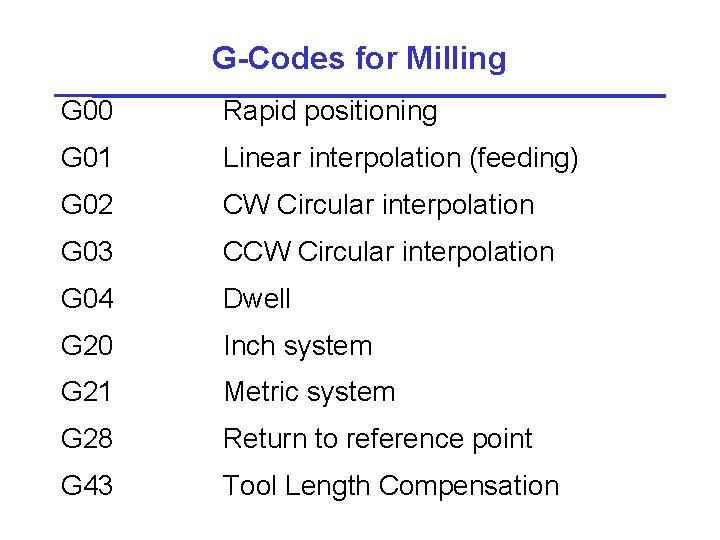
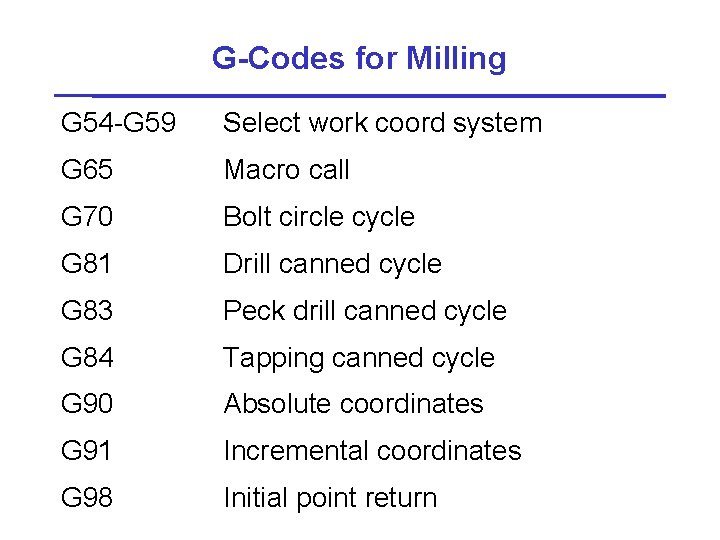

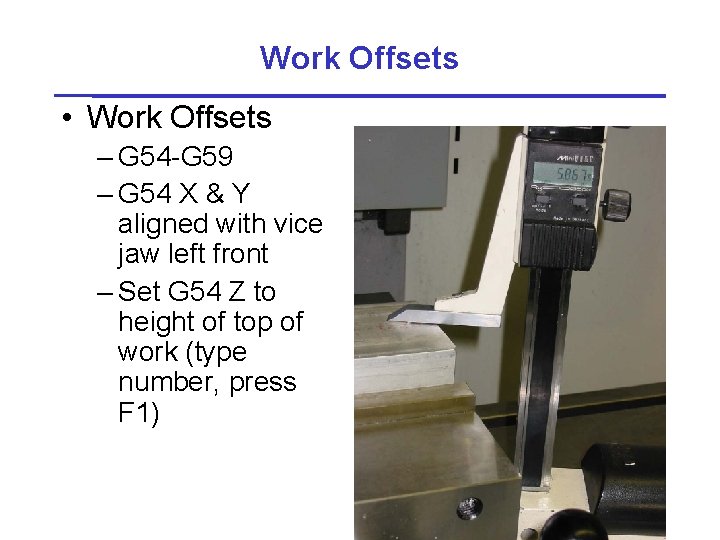
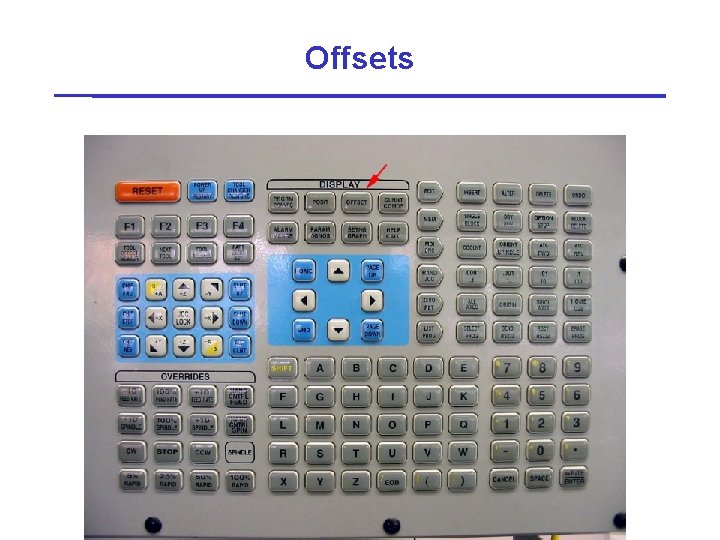
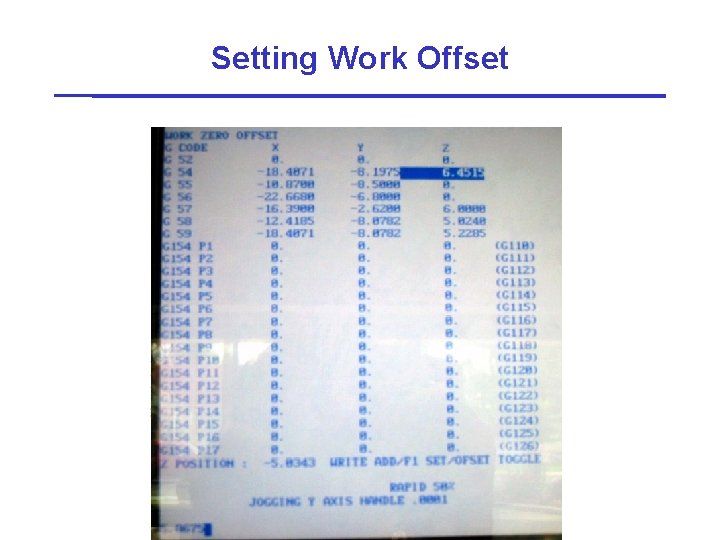
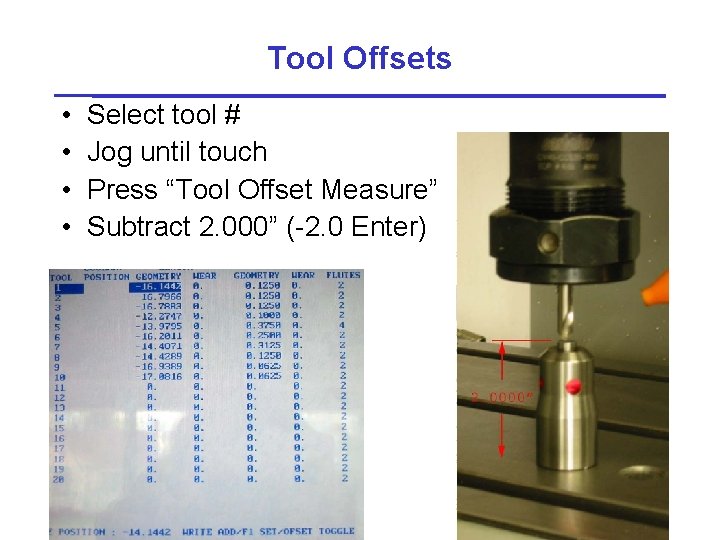
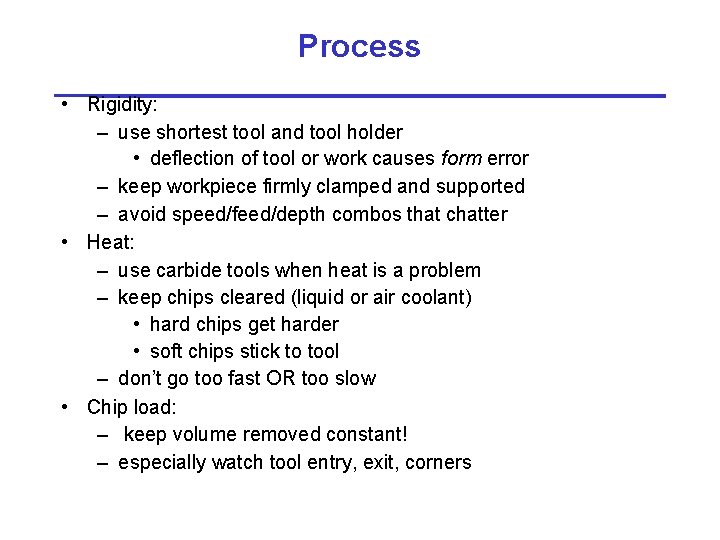
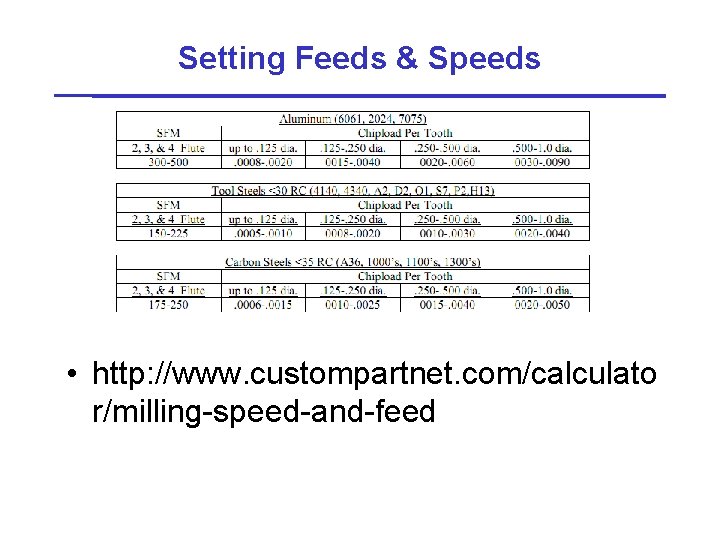
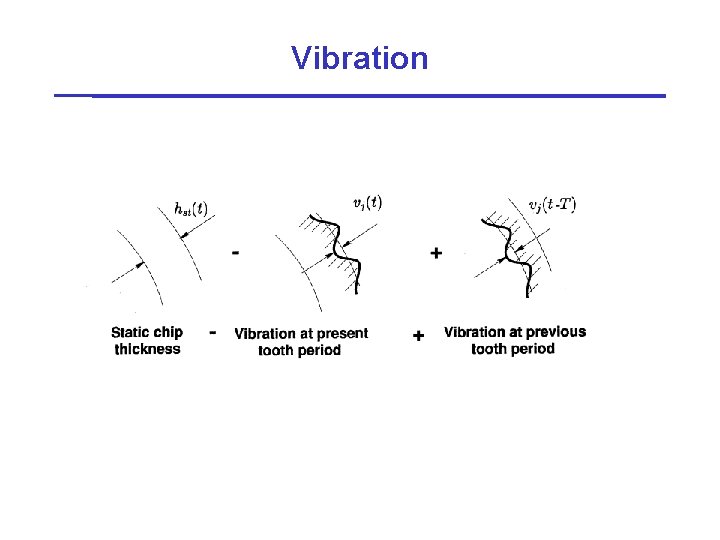
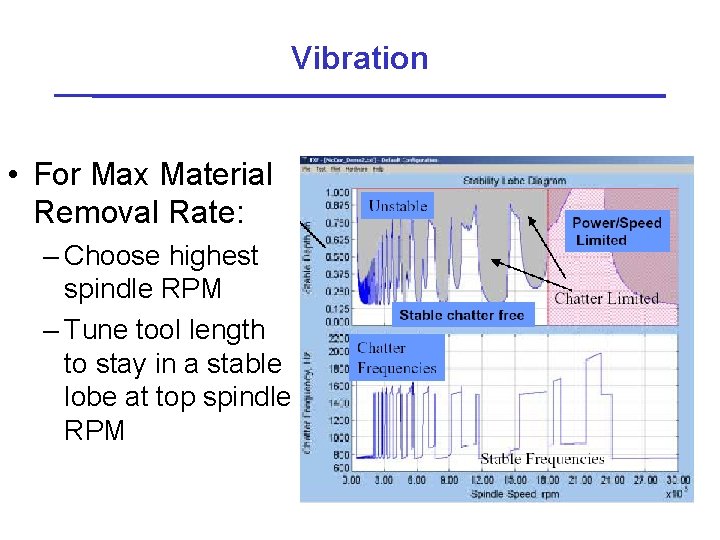
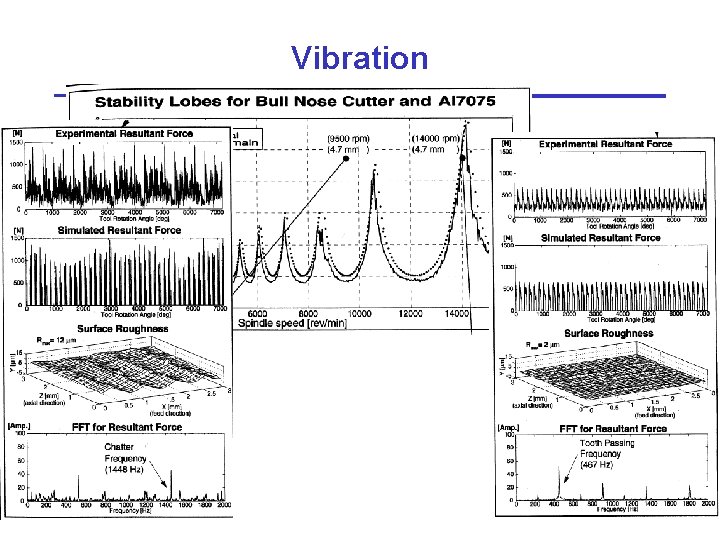
- Slides: 21
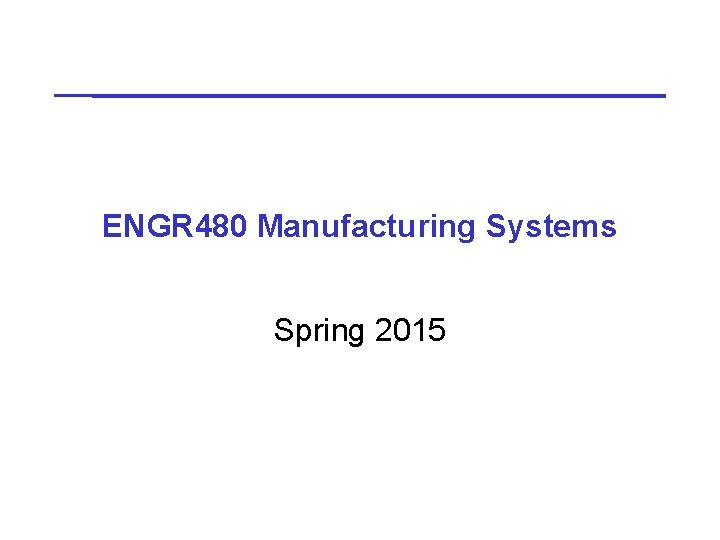
ENGR 480 Manufacturing Systems Spring 2015
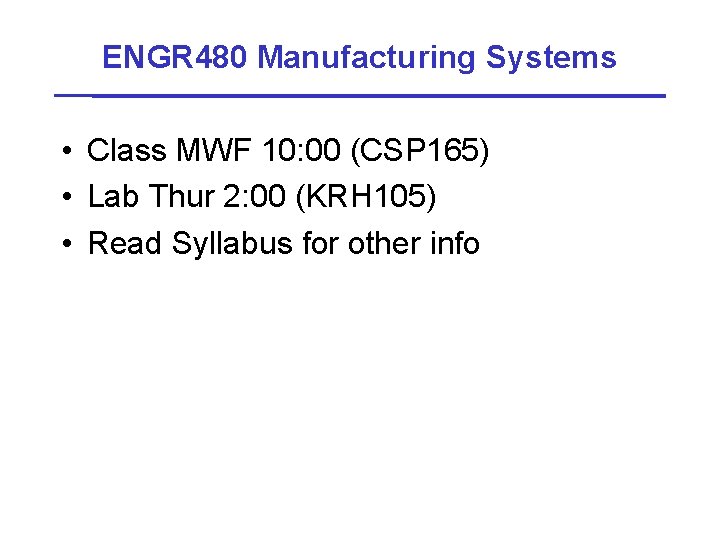
ENGR 480 Manufacturing Systems • Class MWF 10: 00 (CSP 165) • Lab Thur 2: 00 (KRH 105) • Read Syllabus for other info
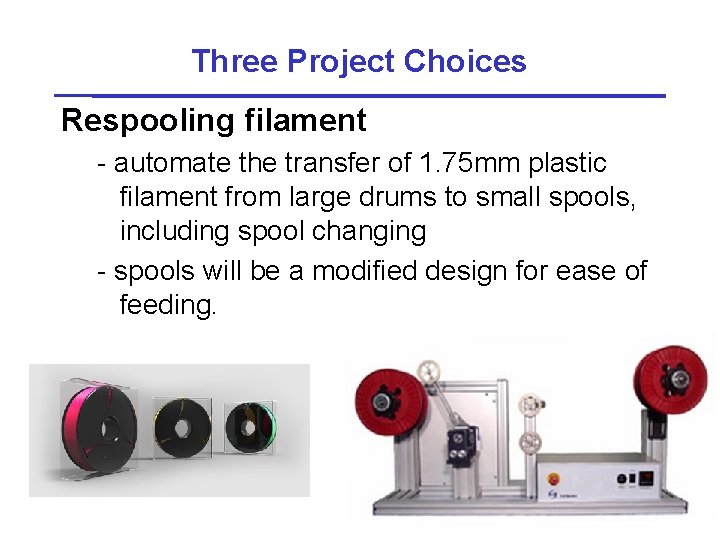
Three Project Choices Respooling filament - automate the transfer of 1. 75 mm plastic filament from large drums to small spools, including spool changing - spools will be a modified design for ease of feeding.
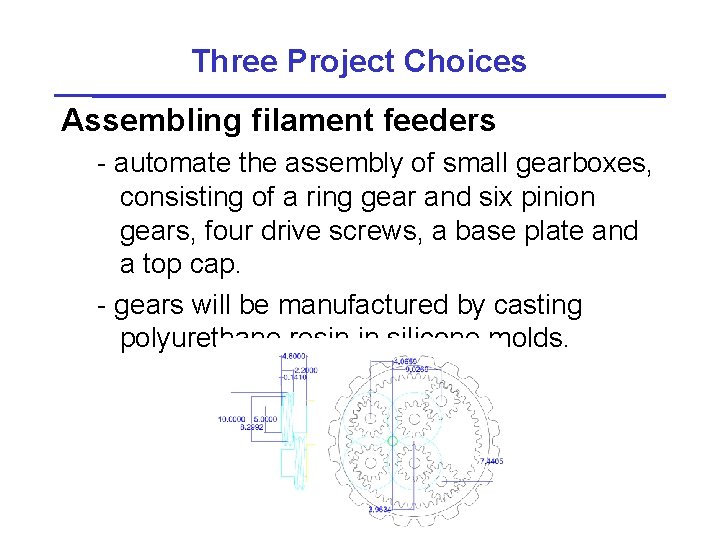
Three Project Choices Assembling filament feeders - automate the assembly of small gearboxes, consisting of a ring gear and six pinion gears, four drive screws, a base plate and a top cap. - gears will be manufactured by casting polyurethane resin in silicone molds.
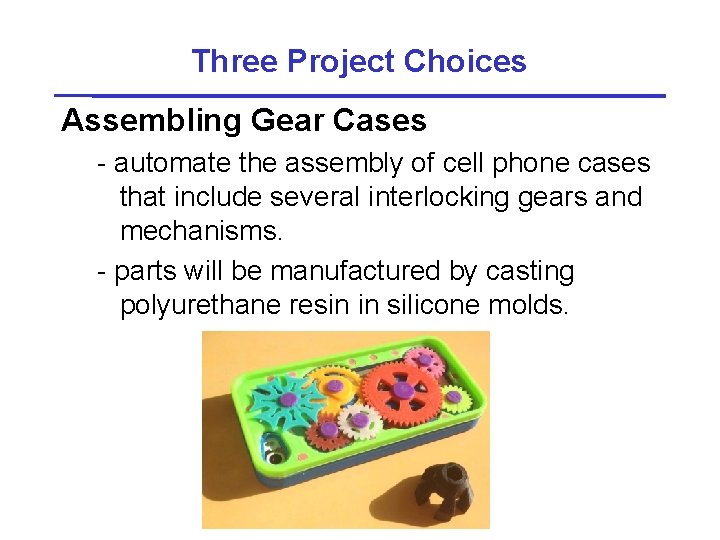
Three Project Choices Assembling Gear Cases - automate the assembly of cell phone cases that include several interlocking gears and mechanisms. - parts will be manufactured by casting polyurethane resin in silicone molds.
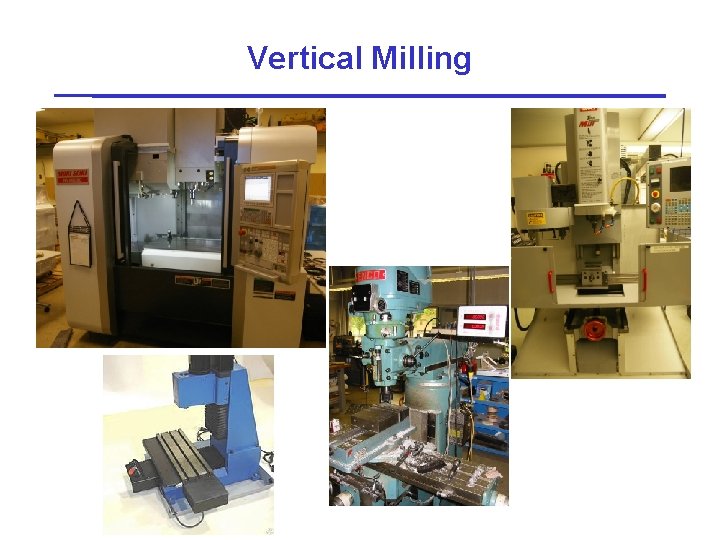
Vertical Milling
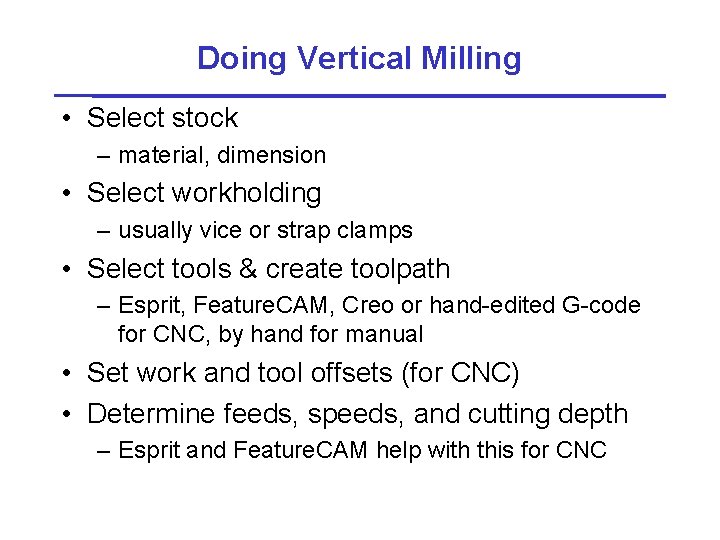
Doing Vertical Milling • Select stock – material, dimension • Select workholding – usually vice or strap clamps • Select tools & create toolpath – Esprit, Feature. CAM, Creo or hand-edited G-code for CNC, by hand for manual • Set work and tool offsets (for CNC) • Determine feeds, speeds, and cutting depth – Esprit and Feature. CAM help with this for CNC
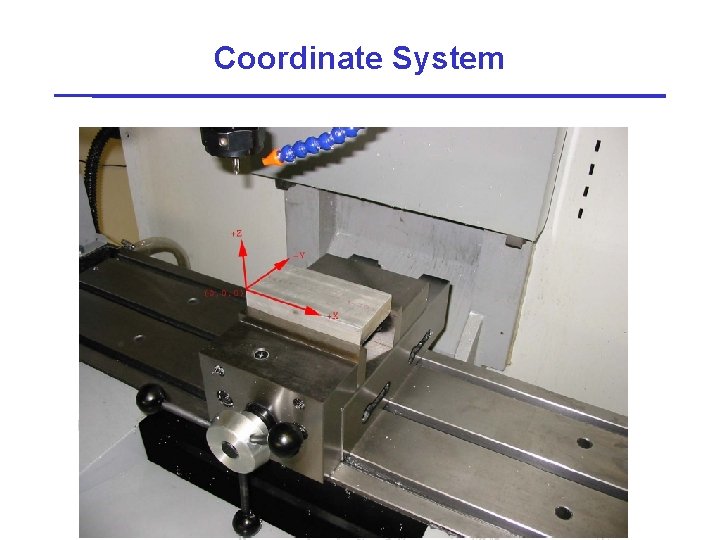
Coordinate System
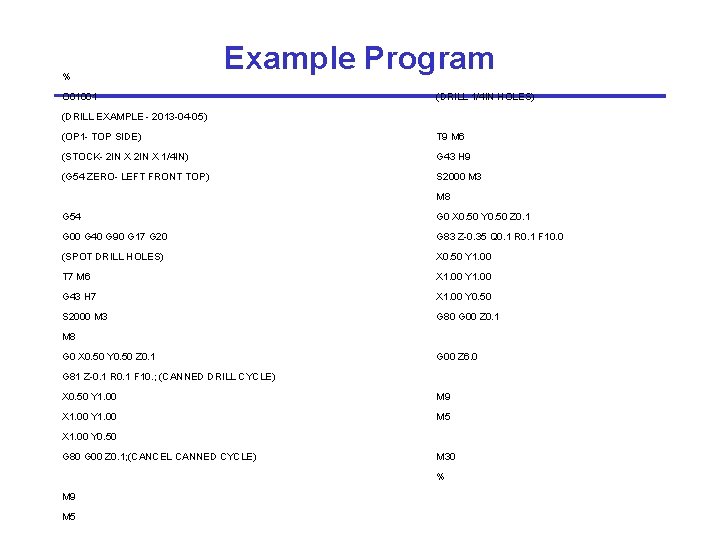
% Example Program O 01001 (DRILL 1/4 IN HOLES) (DRILL EXAMPLE - 2013 -04 -05) (OP 1 - TOP SIDE) T 9 M 6 (STOCK- 2 IN X 1/4 IN) G 43 H 9 (G 54 ZERO- LEFT FRONT TOP) S 2000 M 3 M 8 G 54 G 0 X 0. 50 Y 0. 50 Z 0. 1 G 00 G 40 G 90 G 17 G 20 G 83 Z-0. 35 Q 0. 1 R 0. 1 F 10. 0 (SPOT DRILL HOLES) X 0. 50 Y 1. 00 T 7 M 6 X 1. 00 Y 1. 00 G 43 H 7 X 1. 00 Y 0. 50 S 2000 M 3 G 80 G 00 Z 0. 1 M 8 G 0 X 0. 50 Y 0. 50 Z 0. 1 G 00 Z 6. 0 G 81 Z-0. 1 R 0. 1 F 10. ; (CANNED DRILL CYCLE) X 0. 50 Y 1. 00 M 9 X 1. 00 Y 1. 00 M 5 X 1. 00 Y 0. 50 G 80 G 00 Z 0. 1; (CANCEL CANNED CYCLE) M 30 % M 9 M 5
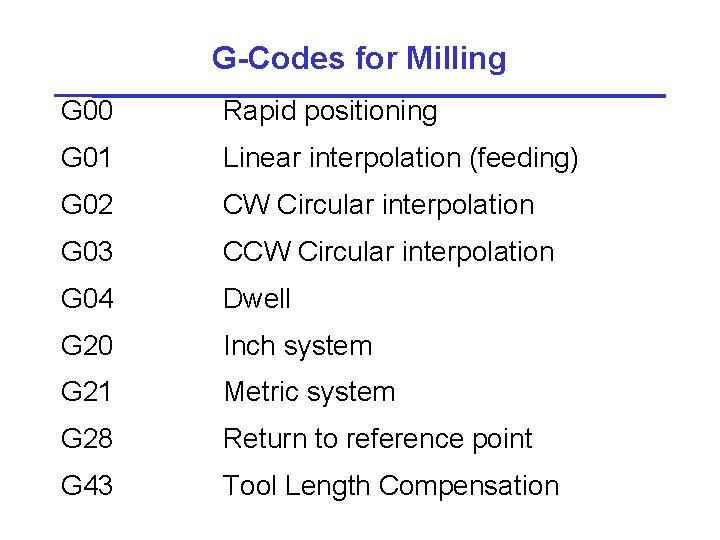
G-Codes for Milling G 00 Rapid positioning G 01 Linear interpolation (feeding) G 02 CW Circular interpolation G 03 CCW Circular interpolation G 04 Dwell G 20 Inch system G 21 Metric system G 28 Return to reference point G 43 Tool Length Compensation
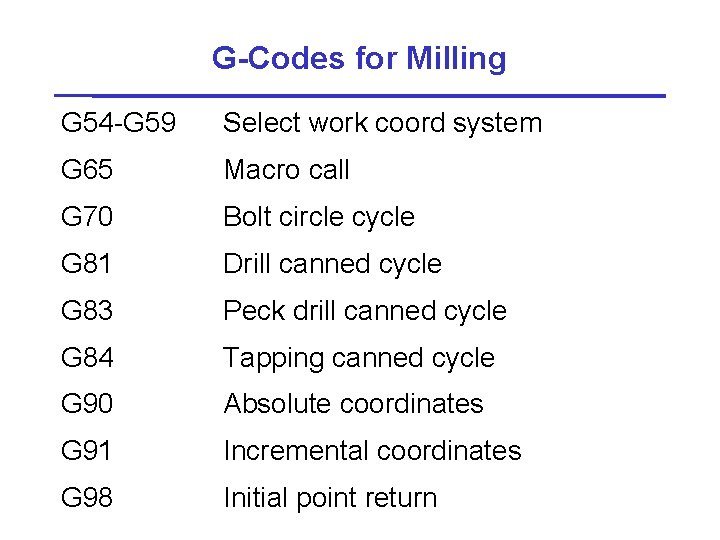
G-Codes for Milling G 54 -G 59 Select work coord system G 65 Macro call G 70 Bolt circle cycle G 81 Drill canned cycle G 83 Peck drill canned cycle G 84 Tapping canned cycle G 90 Absolute coordinates G 91 Incremental coordinates G 98 Initial point return

M-Codes for Milling M 00 Program Stop M 01 Opt. Program Stop (panel controlled) M 03 Start spindle (normal rotation) M 04 Start spindle (reverse rotation) M 05 Stop spindle M 06 Tool change M 08 Start coolant M 09 Stop coolant M 30 Program end
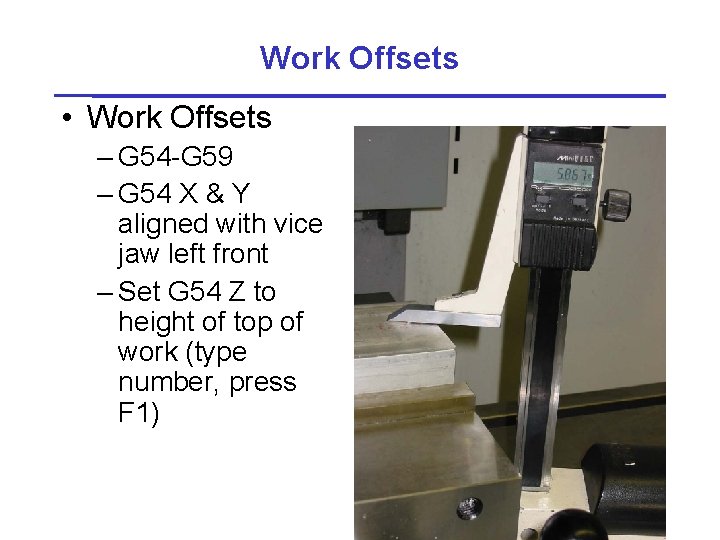
Work Offsets • Work Offsets – G 54 -G 59 – G 54 X & Y aligned with vice jaw left front – Set G 54 Z to height of top of work (type number, press F 1)
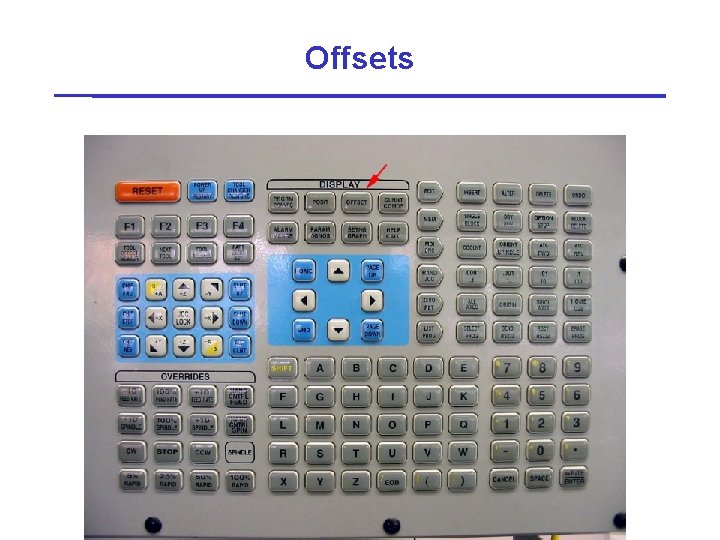
Offsets
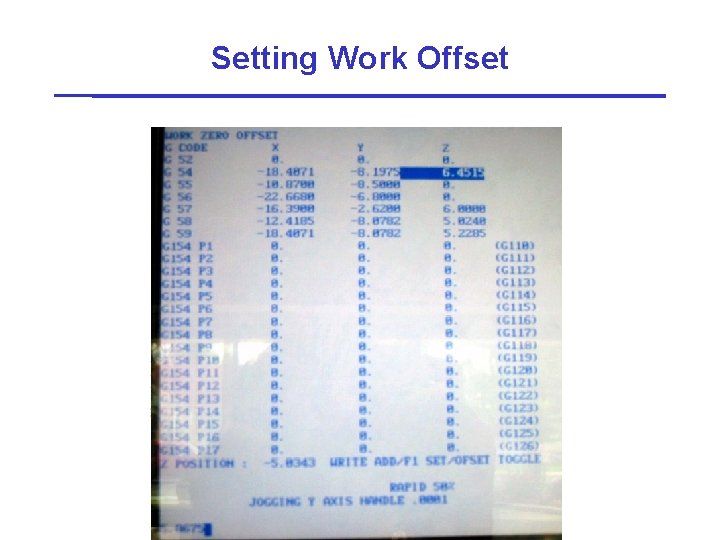
Setting Work Offset
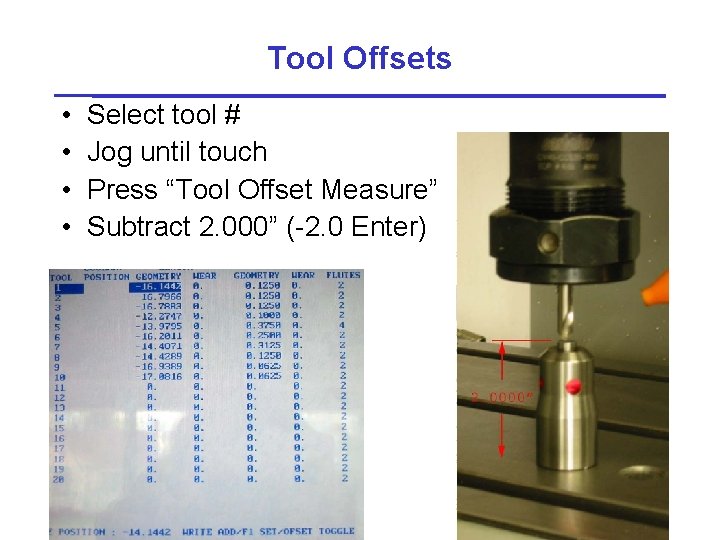
Tool Offsets • • Select tool # Jog until touch Press “Tool Offset Measure” Subtract 2. 000” (-2. 0 Enter)
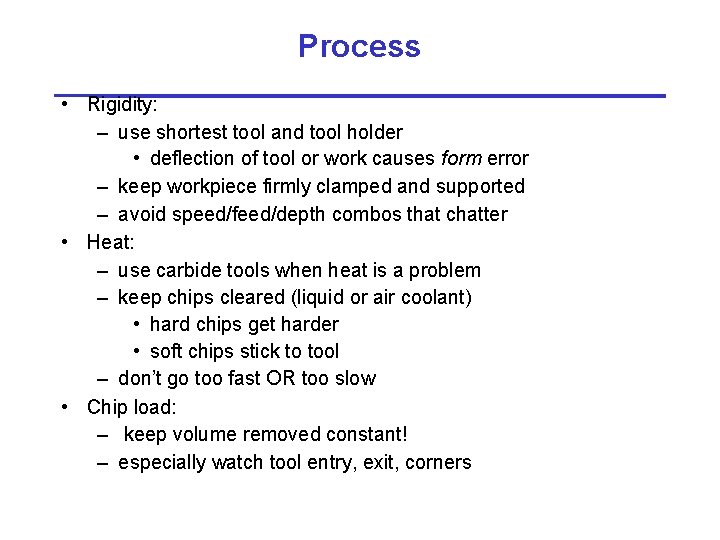
Process • Rigidity: – use shortest tool and tool holder • deflection of tool or work causes form error – keep workpiece firmly clamped and supported – avoid speed/feed/depth combos that chatter • Heat: – use carbide tools when heat is a problem – keep chips cleared (liquid or air coolant) • hard chips get harder • soft chips stick to tool – don’t go too fast OR too slow • Chip load: – keep volume removed constant! – especially watch tool entry, exit, corners
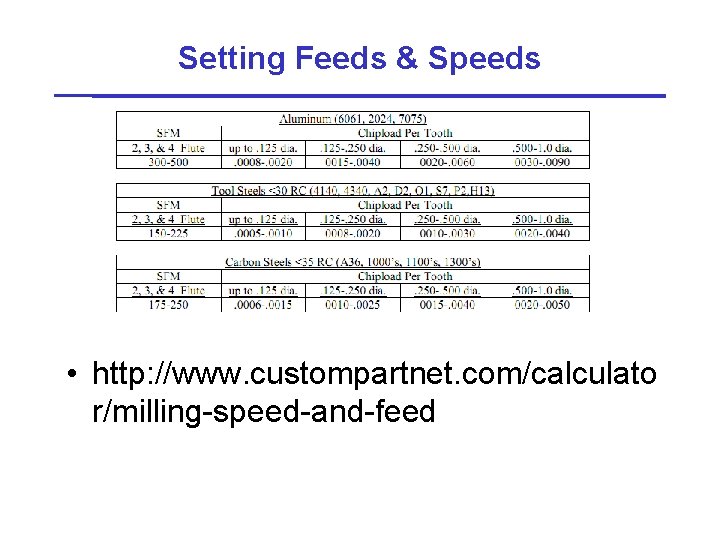
Setting Feeds & Speeds • http: //www. custompartnet. com/calculato r/milling-speed-and-feed
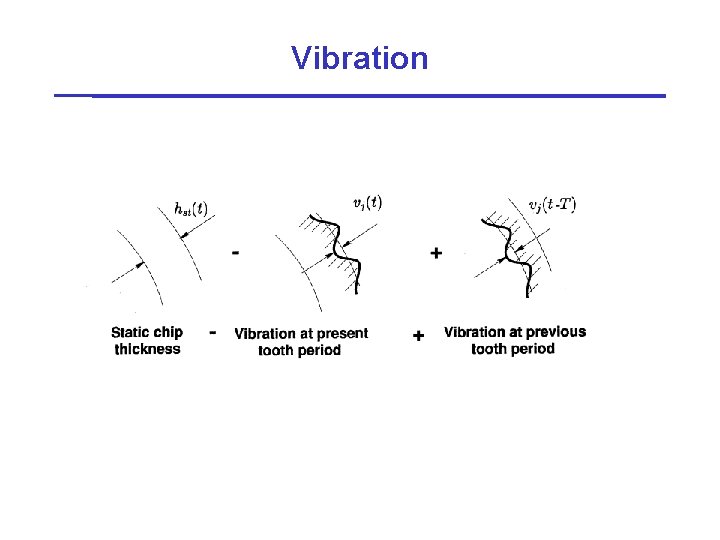
Vibration
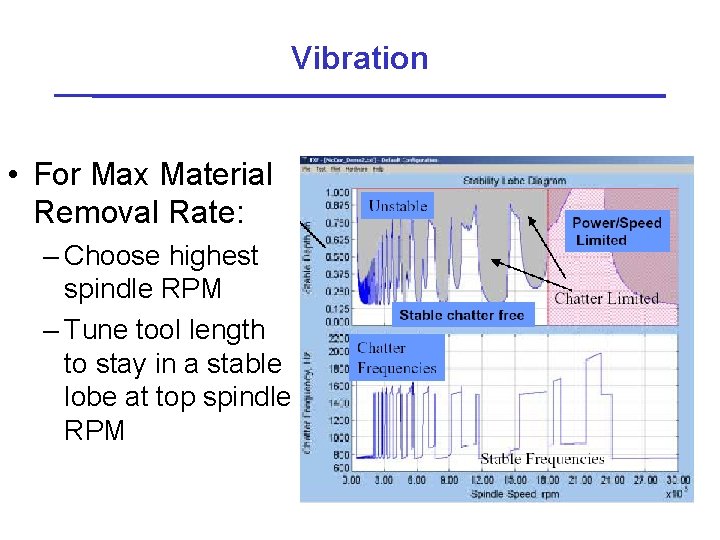
Vibration • For Max Material Removal Rate: – Choose highest spindle RPM – Tune tool length to stay in a stable lobe at top spindle RPM
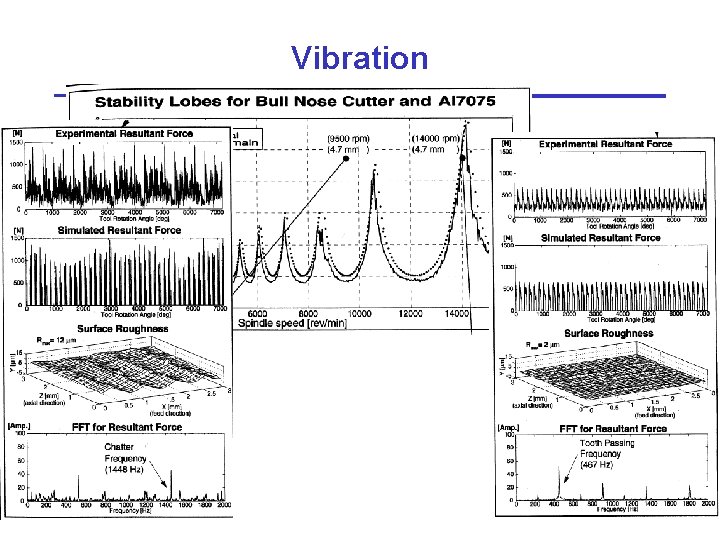
Vibration
480+480
Manufacturing cost vs non manufacturing cost
Job order costing vs process costing
Uncontrollable cost example
Manufacturing cost vs non manufacturing cost
Additive manufacturing steps
Spring break 2015
Bae yong-kyun
Months spring
Computer control of manufacturing systems
Cms manufacturing systems
Introduction to manufacturing systems
Manufacturing systems modeling and analysis
Engr 1181 osu
Sjsu engineering 10
Engr 201
Engr 1182
Engr 350
Performance task: roller coaster design
Engr 482
Engr 1330
Engr 1330 ttu