HEALTH AND SAFETY MANAGEMENT SYSTEM OHSAS 18001 Nicola
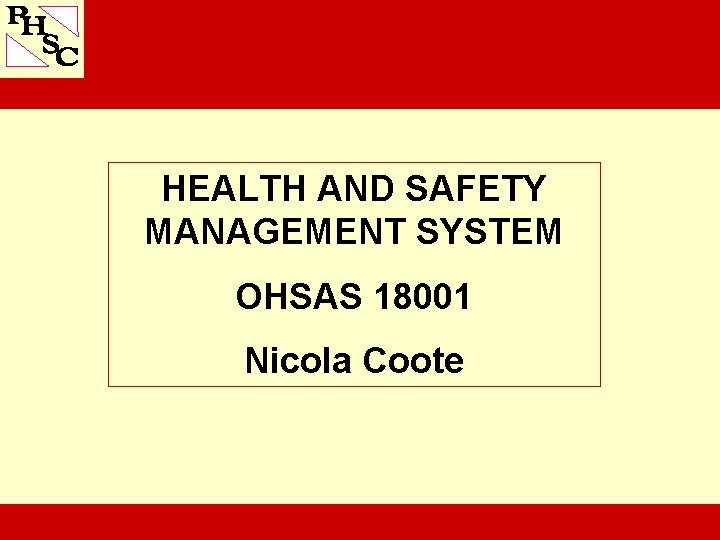
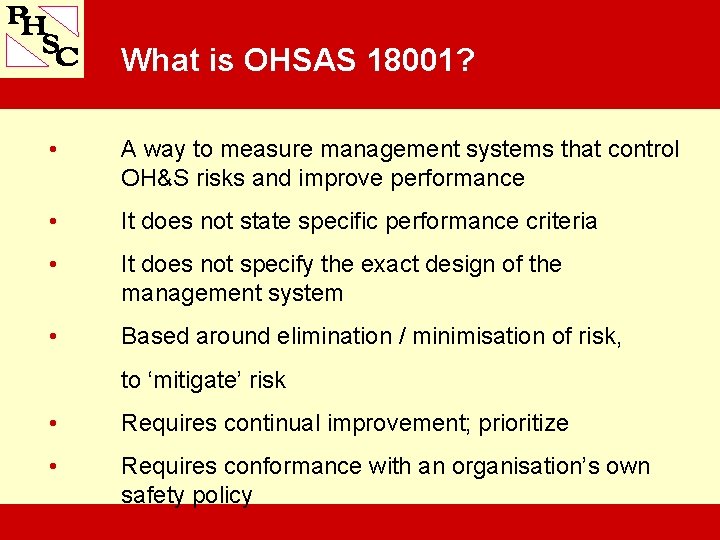
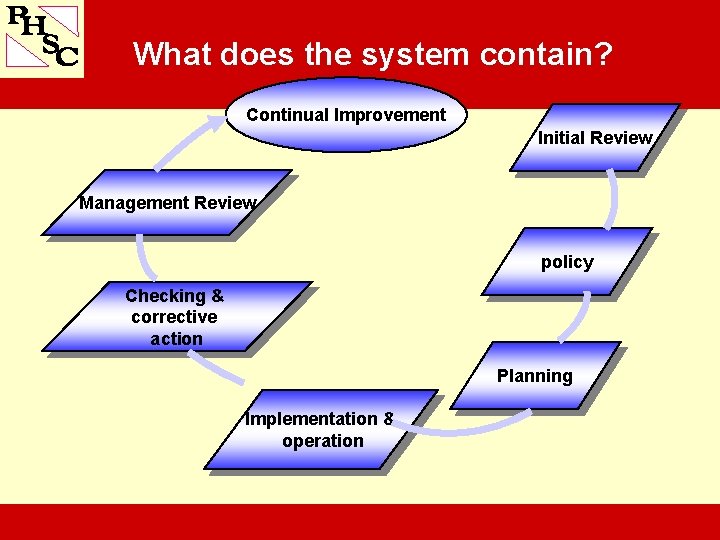
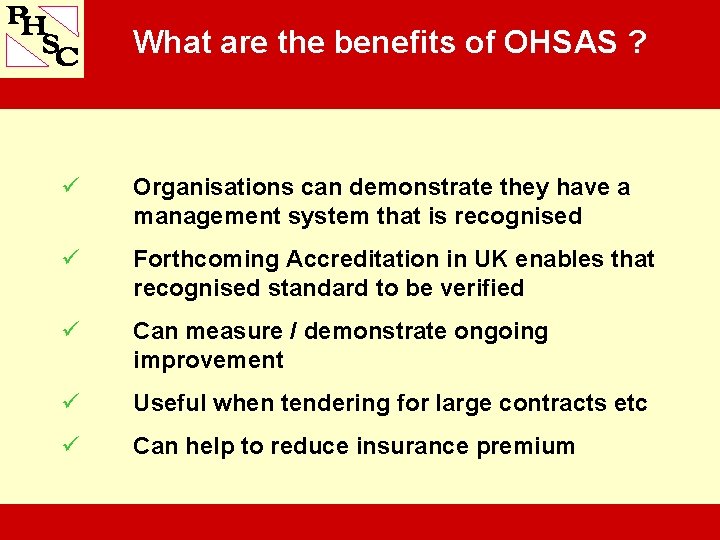
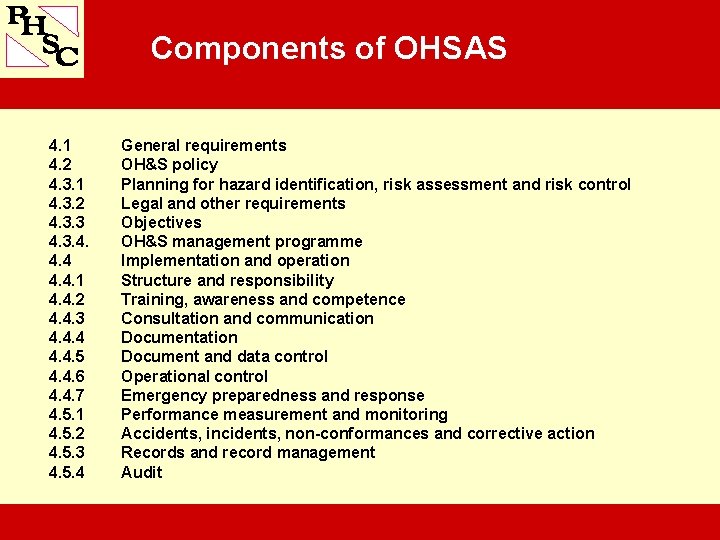
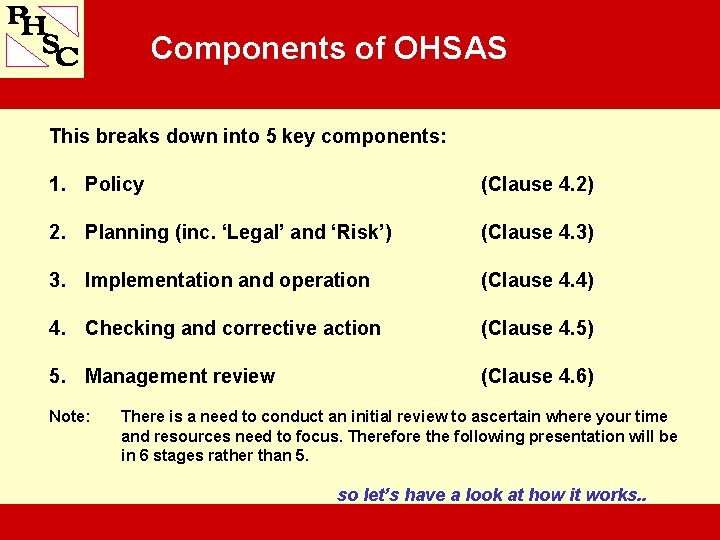
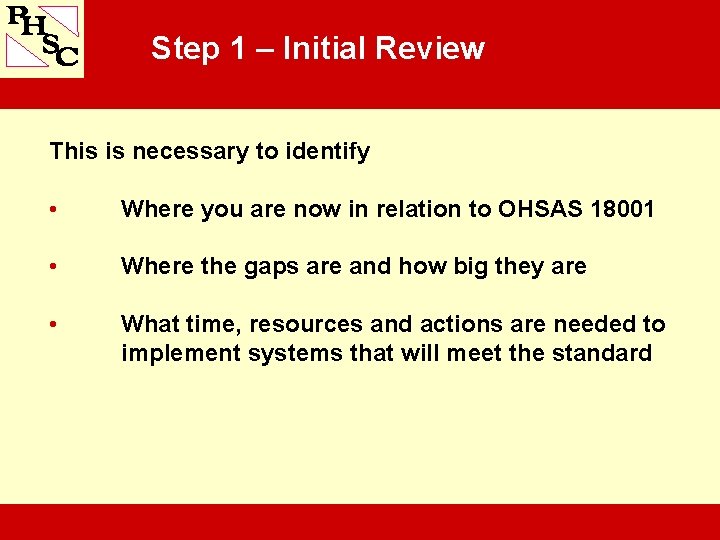
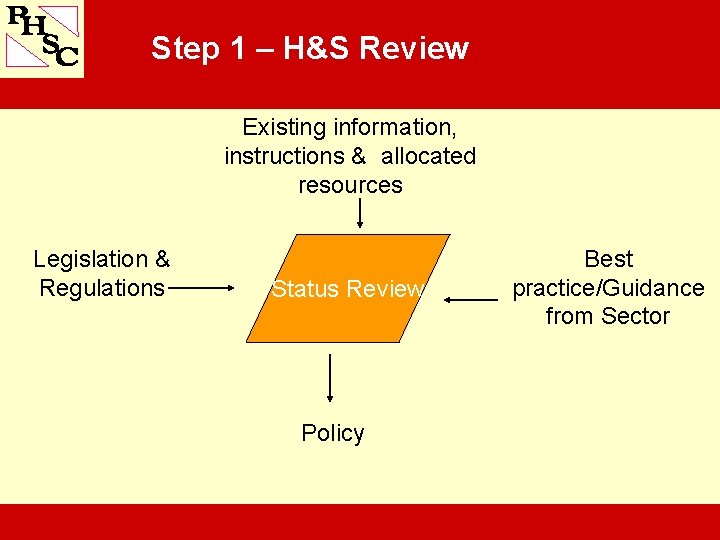
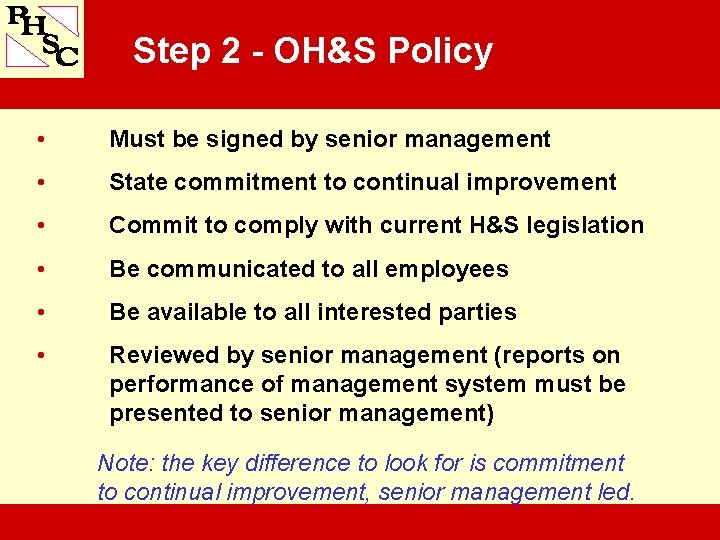
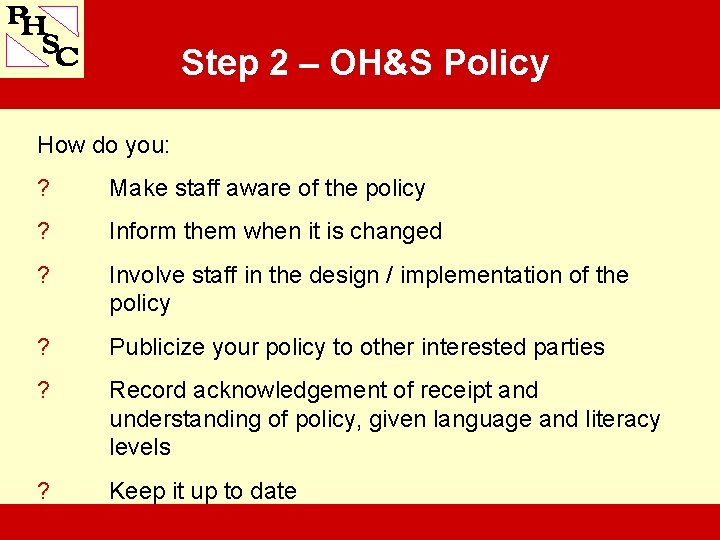
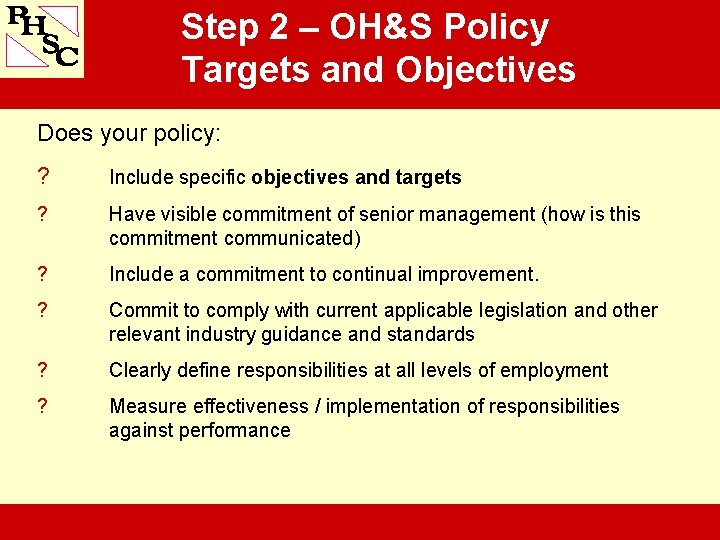
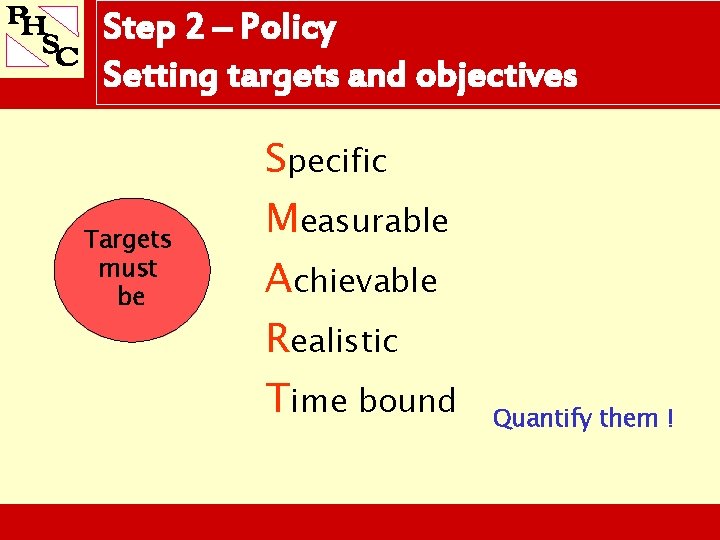
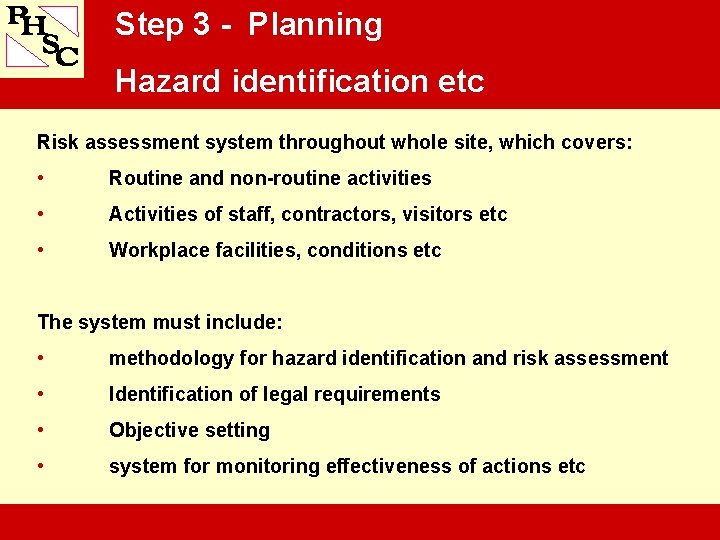
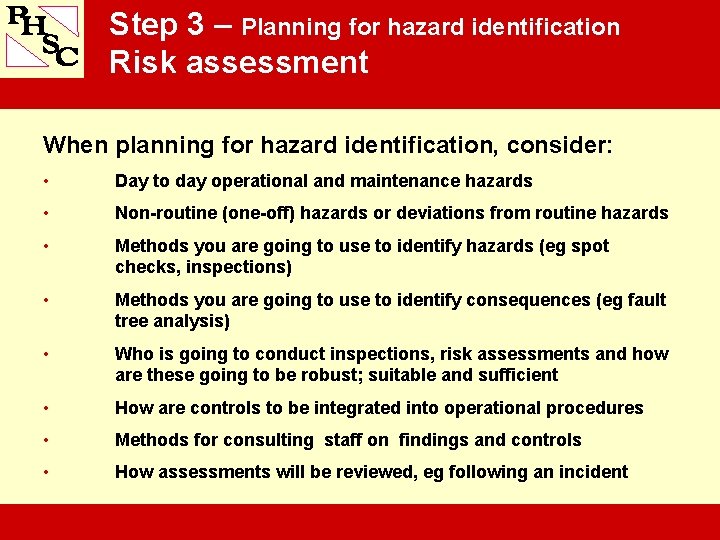
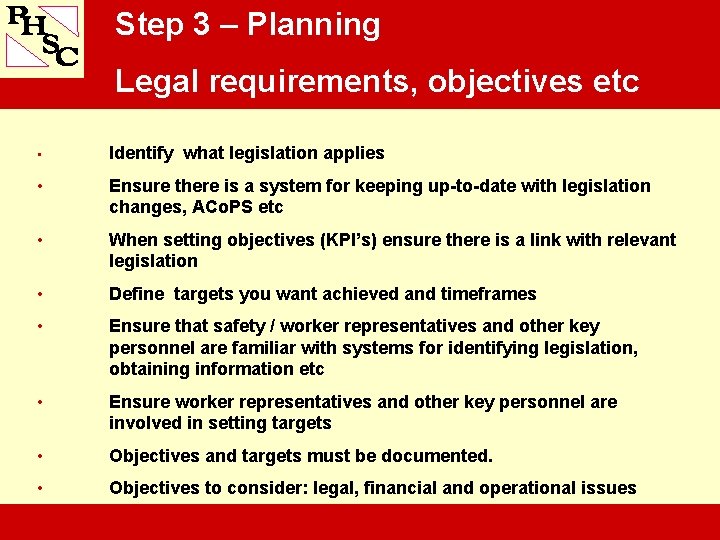
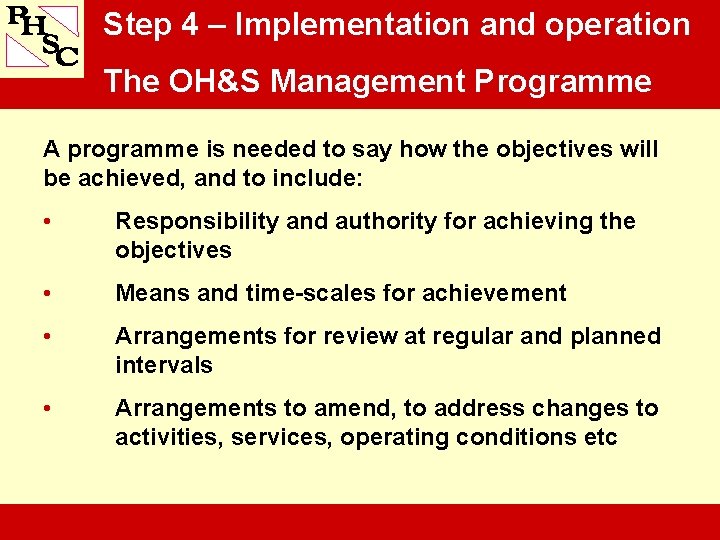
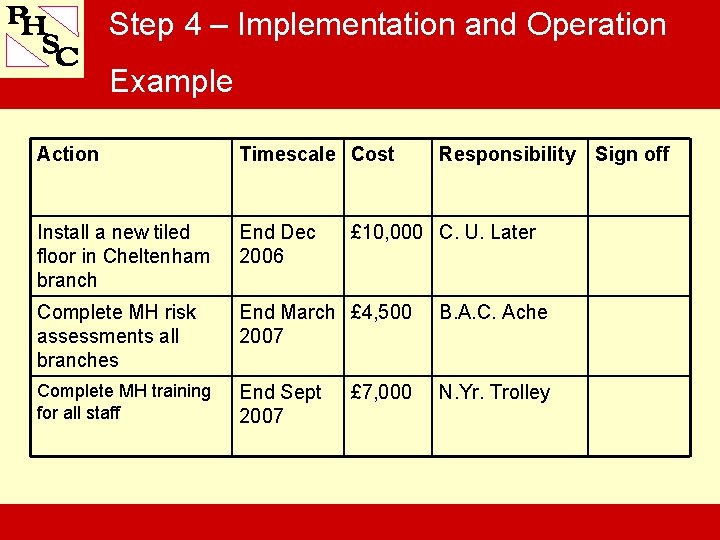
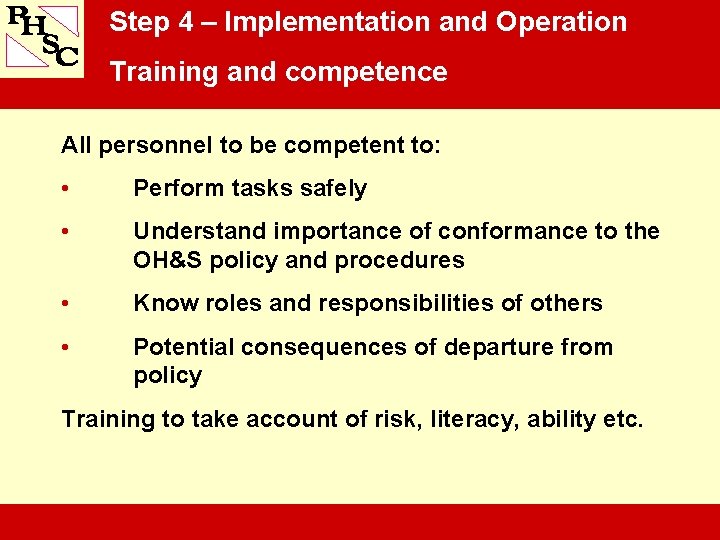
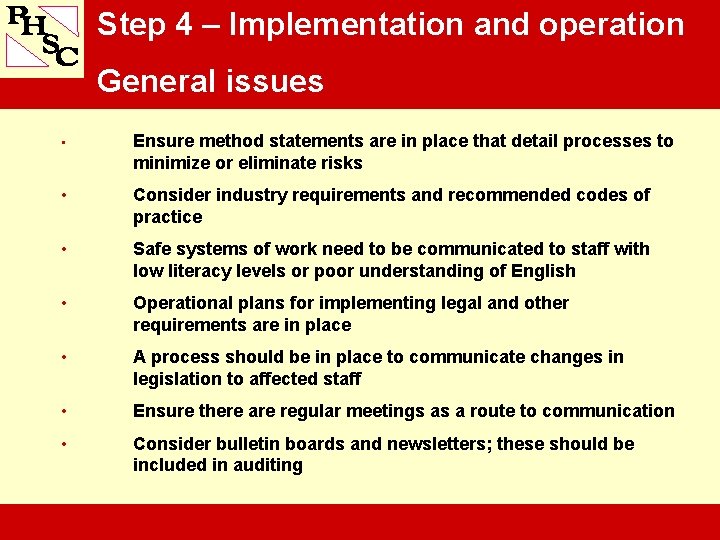
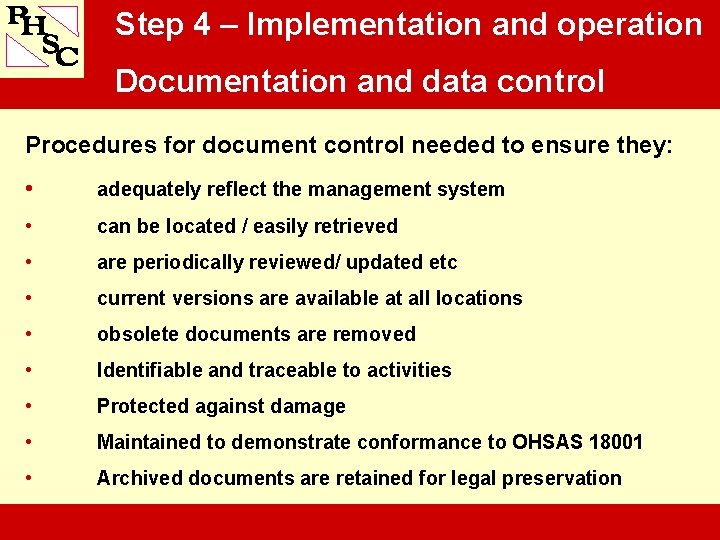
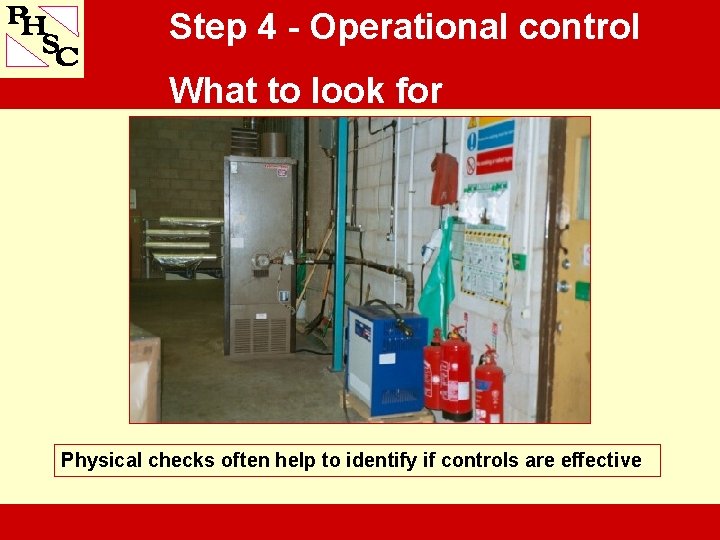
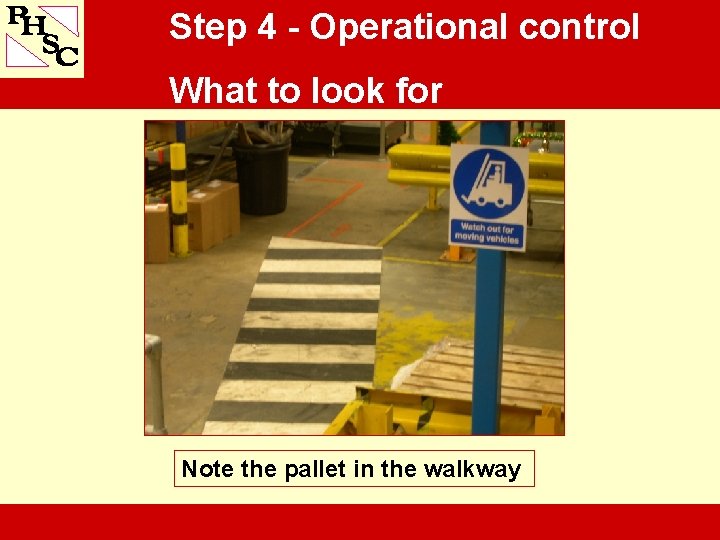
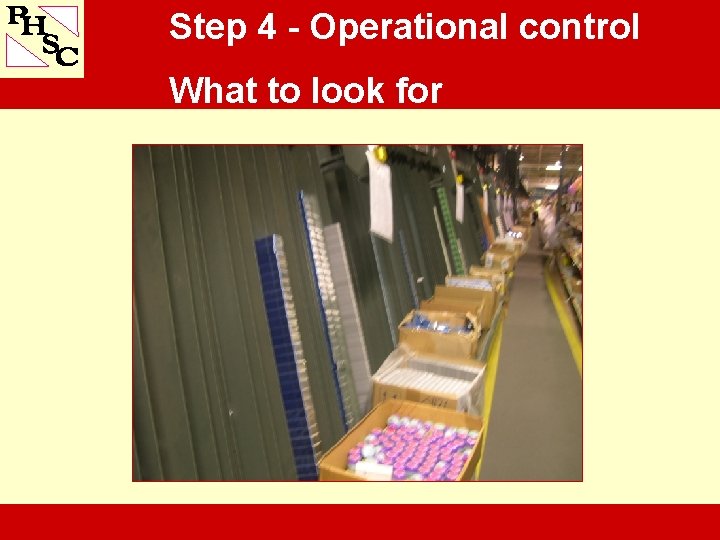
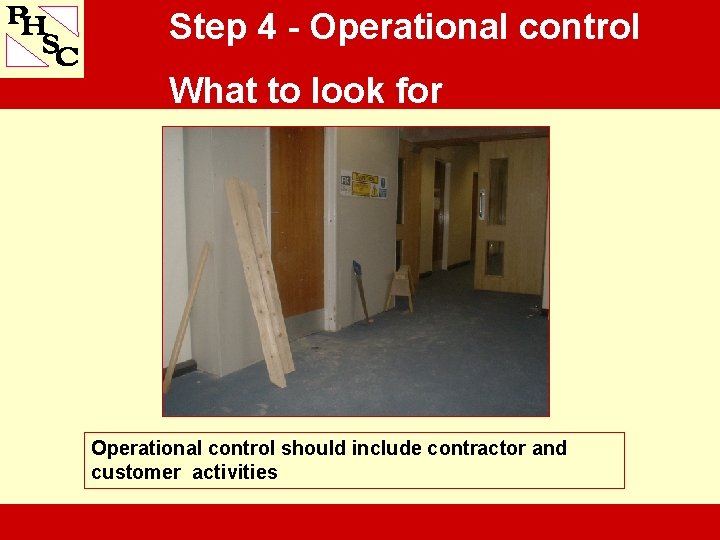
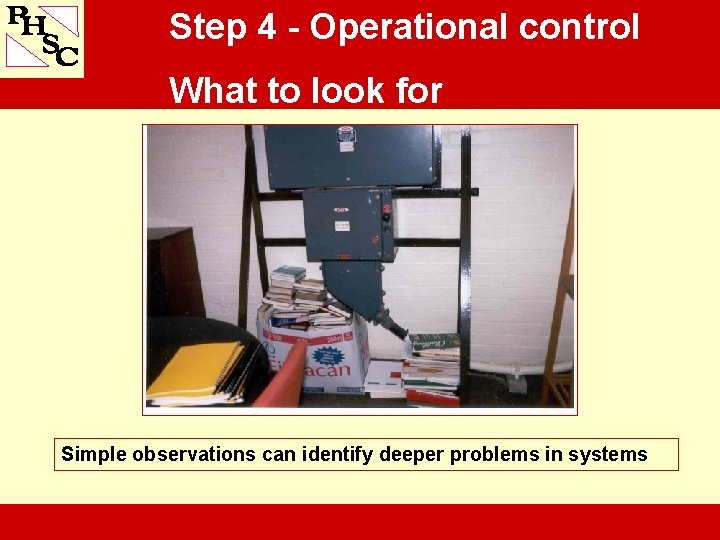
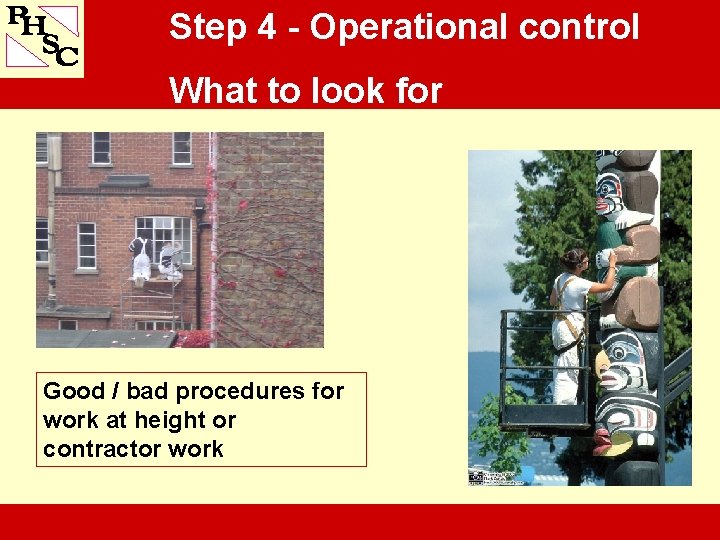
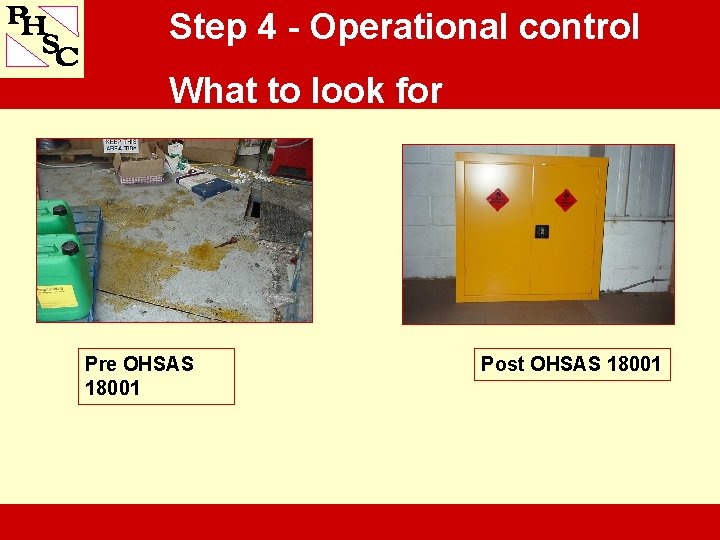
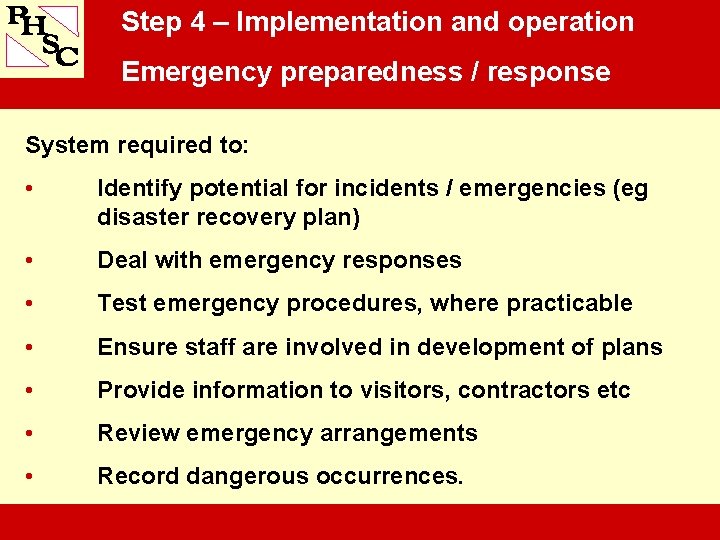
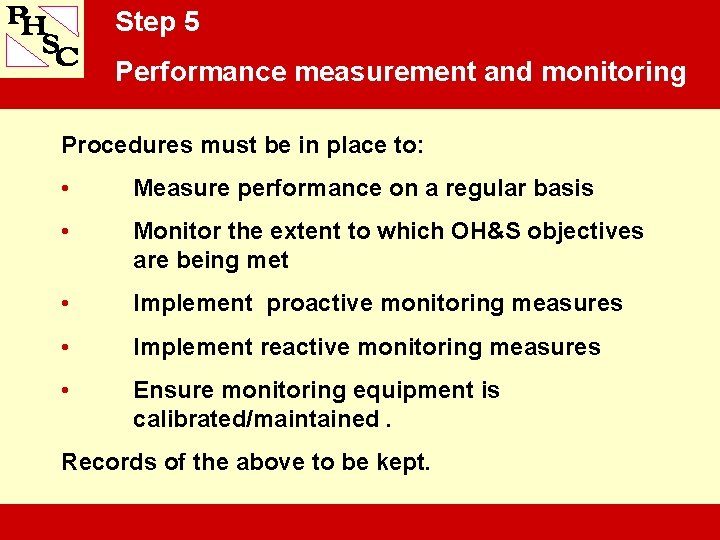
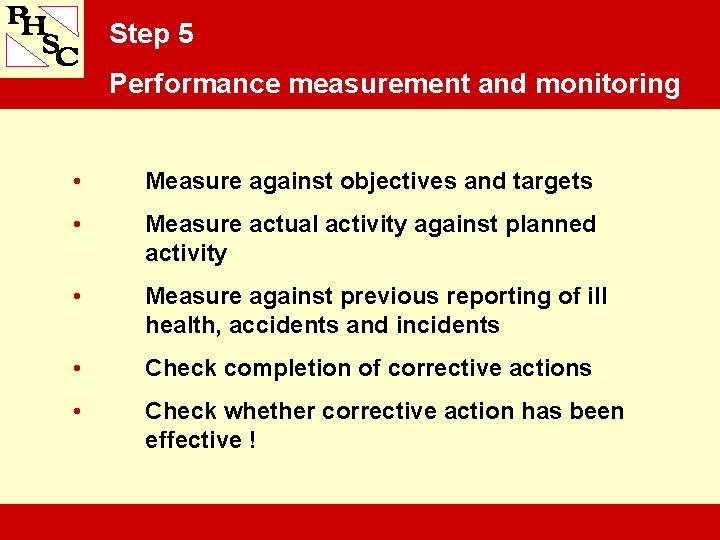
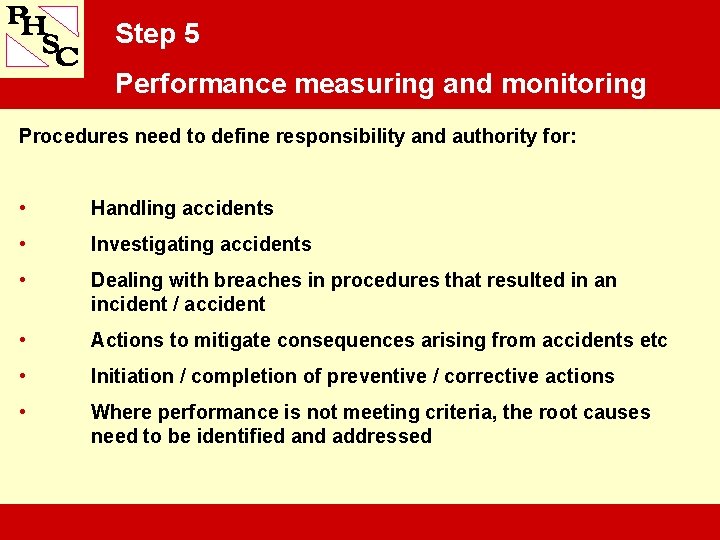
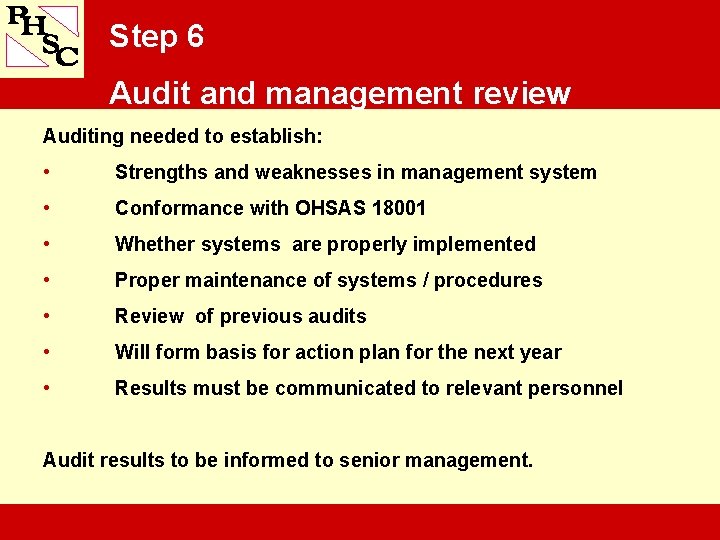
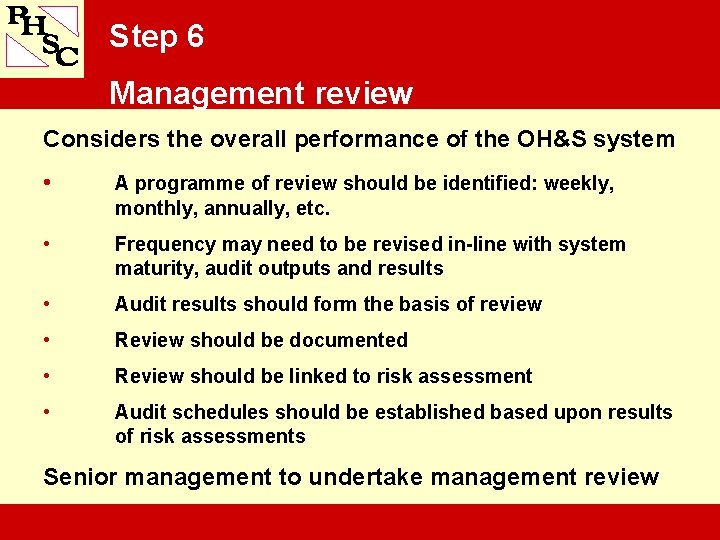
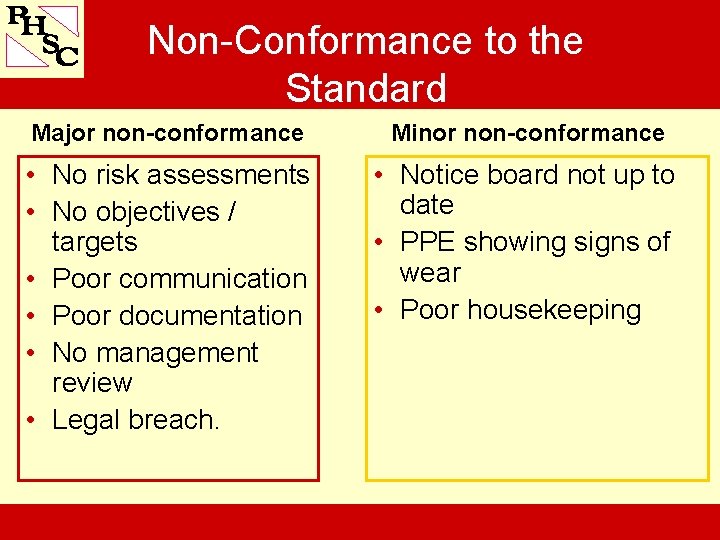
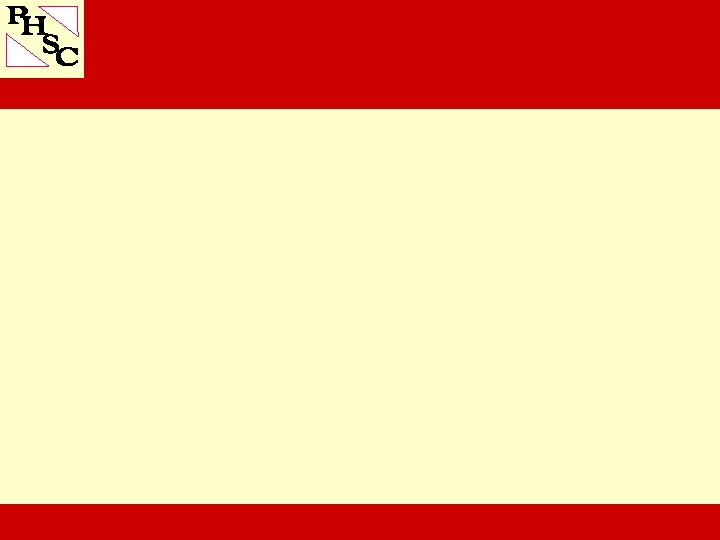
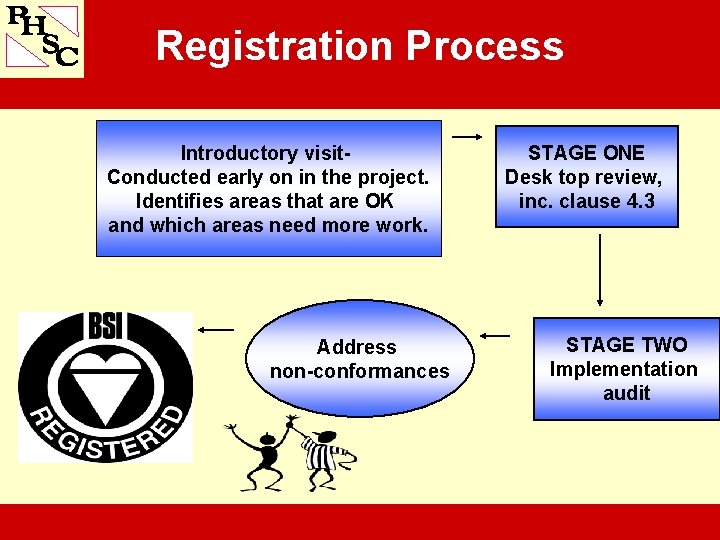
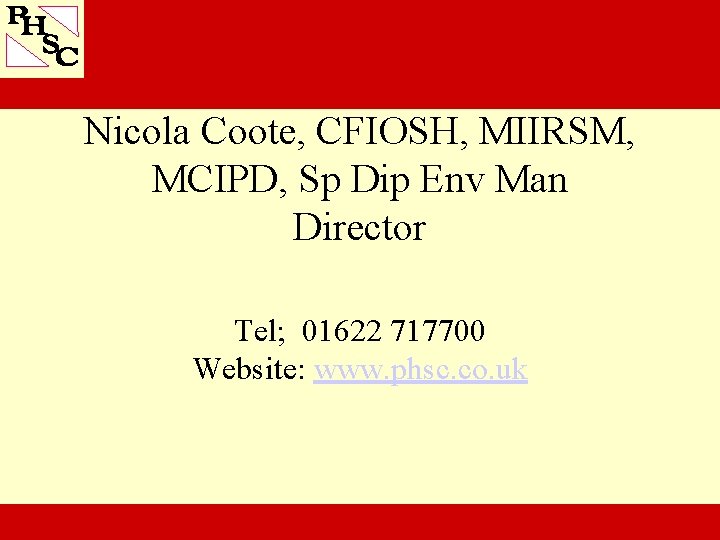
- Slides: 37
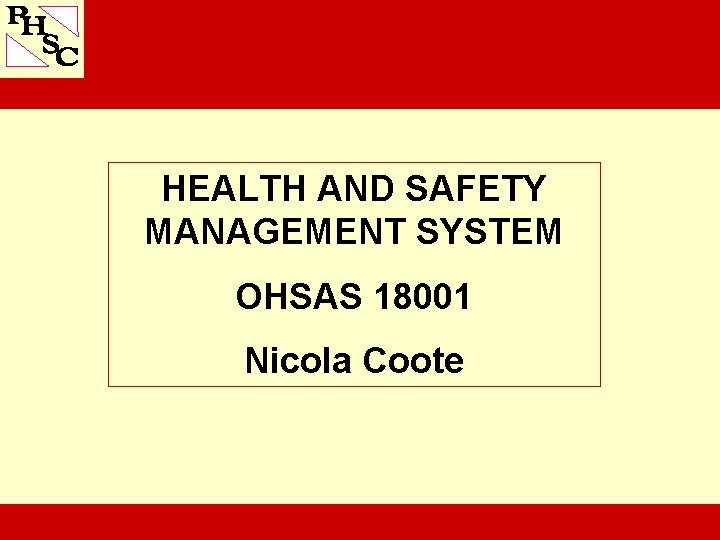
HEALTH AND SAFETY MANAGEMENT SYSTEM OHSAS 18001 Nicola Coote
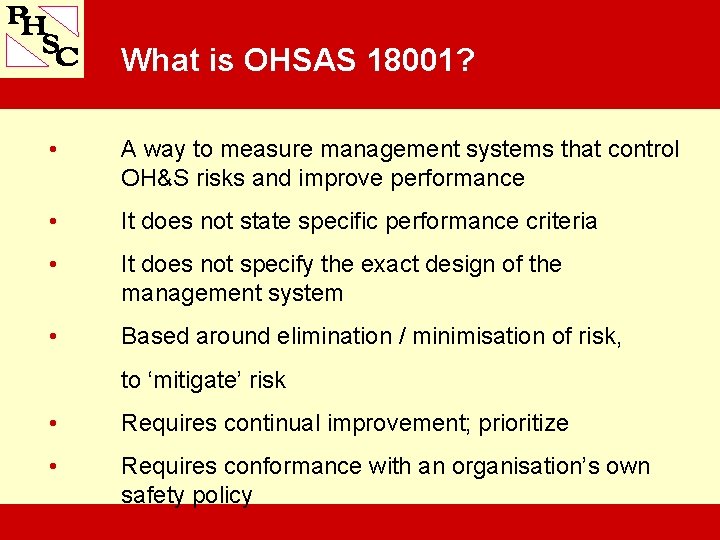
What is OHSAS 18001? • A way to measure management systems that control OH&S risks and improve performance • It does not state specific performance criteria • It does not specify the exact design of the management system • Based around elimination / minimisation of risk, to ‘mitigate’ risk • Requires continual improvement; prioritize • Requires conformance with an organisation’s own safety policy
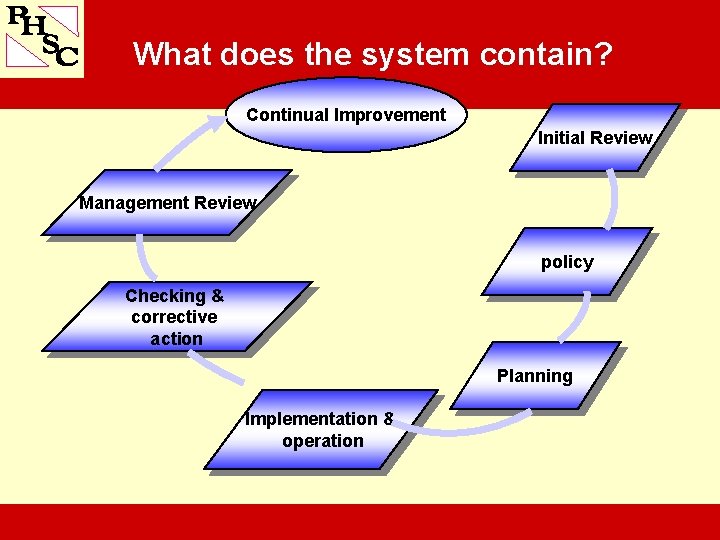
What does the system contain? Continual Improvement Initial Review Management Review policy Checking & corrective action Planning Implementation & operation
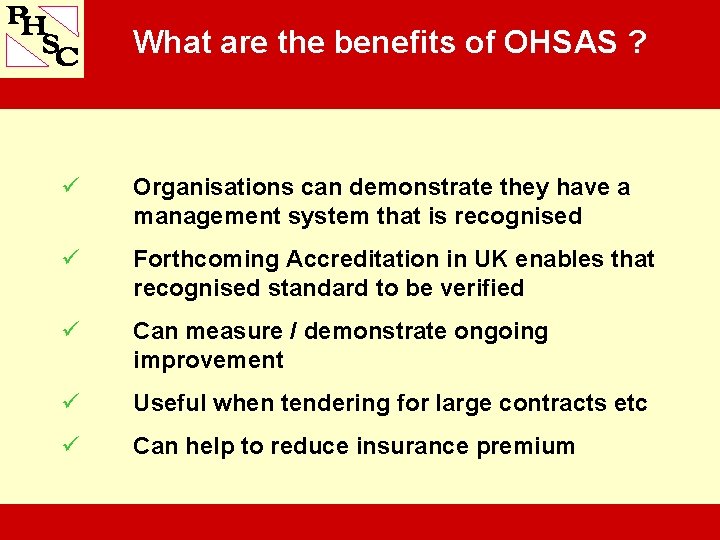
What are the benefits of OHSAS ? ü Organisations can demonstrate they have a management system that is recognised ü Forthcoming Accreditation in UK enables that recognised standard to be verified ü Can measure / demonstrate ongoing improvement ü Useful when tendering for large contracts etc ü Can help to reduce insurance premium
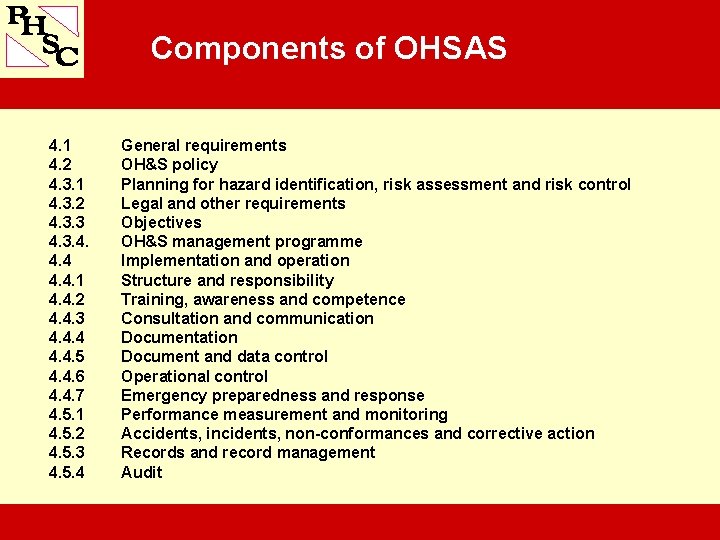
Components of OHSAS 4. 1 4. 2 4. 3. 1 4. 3. 2 4. 3. 3 4. 3. 4. 4. 4. 1 4. 4. 2 4. 4. 3 4. 4. 4. 5 4. 4. 6 4. 4. 7 4. 5. 1 4. 5. 2 4. 5. 3 4. 5. 4 General requirements OH&S policy Planning for hazard identification, risk assessment and risk control Legal and other requirements Objectives OH&S management programme Implementation and operation Structure and responsibility Training, awareness and competence Consultation and communication Document and data control Operational control Emergency preparedness and response Performance measurement and monitoring Accidents, incidents, non-conformances and corrective action Records and record management Audit
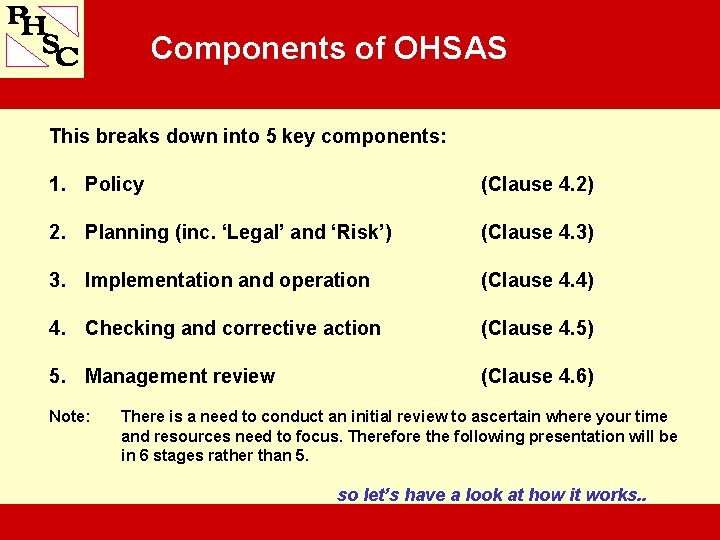
Components of OHSAS This breaks down into 5 key components: 1. Policy (Clause 4. 2) 2. Planning (inc. ‘Legal’ and ‘Risk’) (Clause 4. 3) 3. Implementation and operation (Clause 4. 4) 4. Checking and corrective action (Clause 4. 5) 5. Management review (Clause 4. 6) Note: There is a need to conduct an initial review to ascertain where your time and resources need to focus. Therefore the following presentation will be in 6 stages rather than 5. so let’s have a look at how it works. .
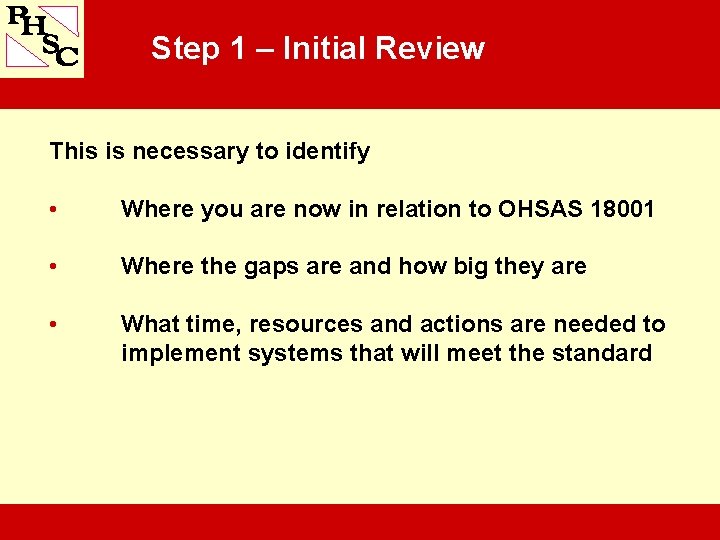
Step 1 – Initial Review This is necessary to identify • Where you are now in relation to OHSAS 18001 • Where the gaps are and how big they are • What time, resources and actions are needed to implement systems that will meet the standard
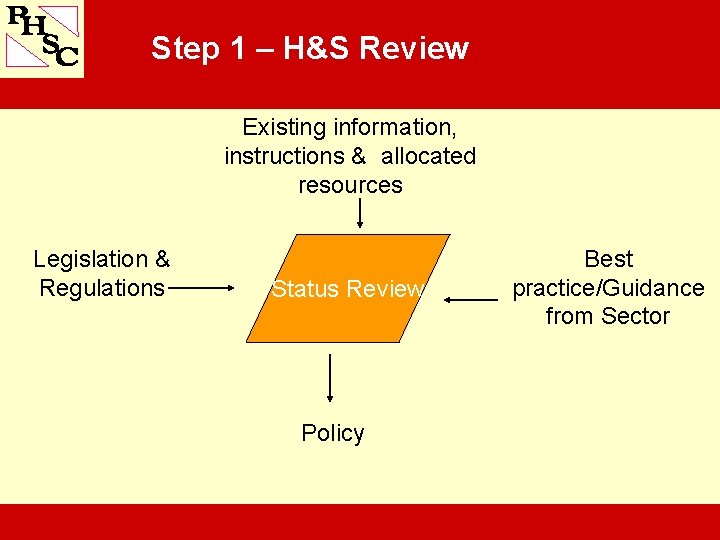
Step 1 – H&S Review Existing information, instructions & allocated resources Legislation & Regulations Status Review Policy Best practice/Guidance from Sector
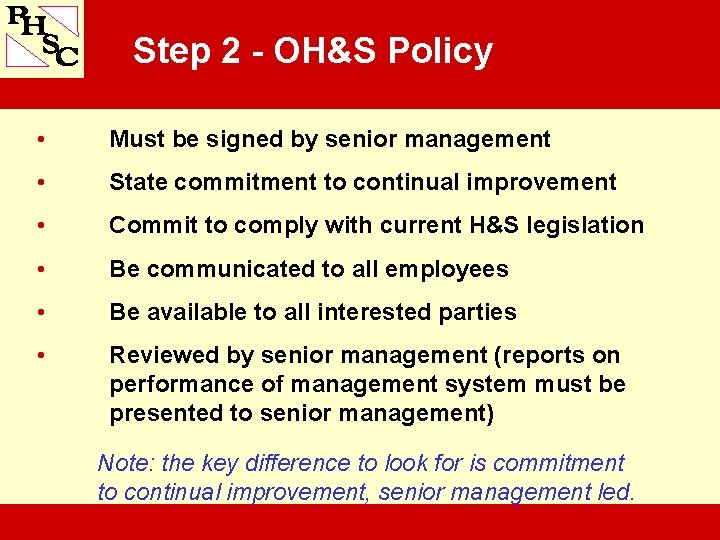
Step 2 - OH&S Policy • Must be signed by senior management • State commitment to continual improvement • Commit to comply with current H&S legislation • Be communicated to all employees • Be available to all interested parties • Reviewed by senior management (reports on performance of management system must be presented to senior management) Note: the key difference to look for is commitment to continual improvement, senior management led.
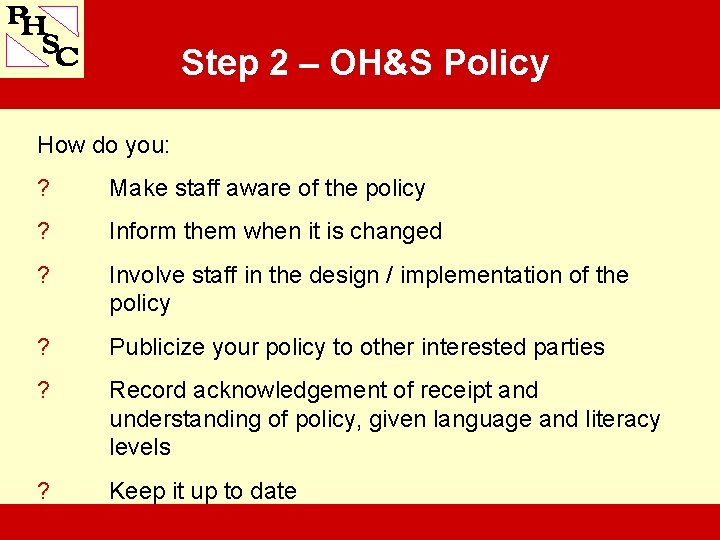
Step 2 – OH&S Policy How do you: ? Make staff aware of the policy ? Inform them when it is changed ? Involve staff in the design / implementation of the policy ? Publicize your policy to other interested parties ? Record acknowledgement of receipt and understanding of policy, given language and literacy levels ? Keep it up to date
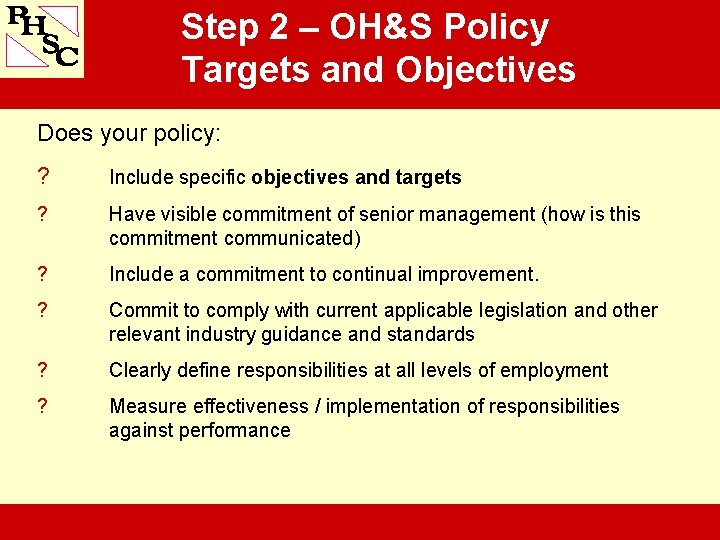
Step 2 – OH&S Policy Targets and Objectives Does your policy: ? Include specific objectives and targets ? Have visible commitment of senior management (how is this commitment communicated) ? Include a commitment to continual improvement. ? Commit to comply with current applicable legislation and other relevant industry guidance and standards ? Clearly define responsibilities at all levels of employment ? Measure effectiveness / implementation of responsibilities against performance
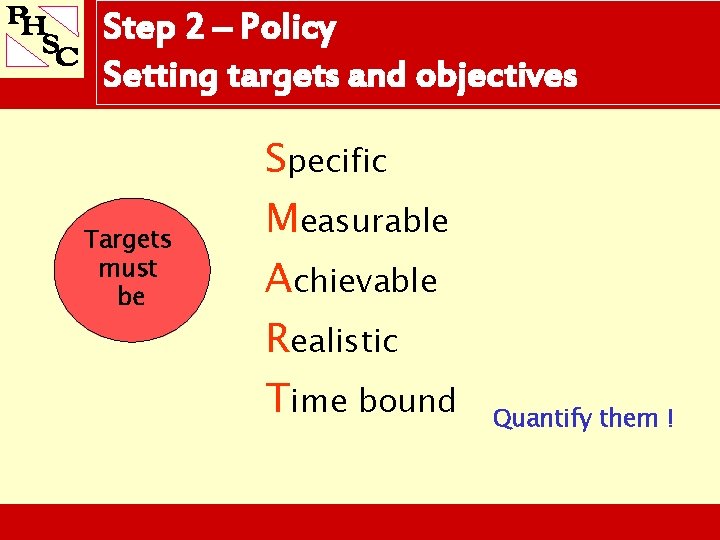
Step 2 – Policy Setting targets and objectives Targets must be Specific Measurable Achievable Realistic Time bound Quantify them !
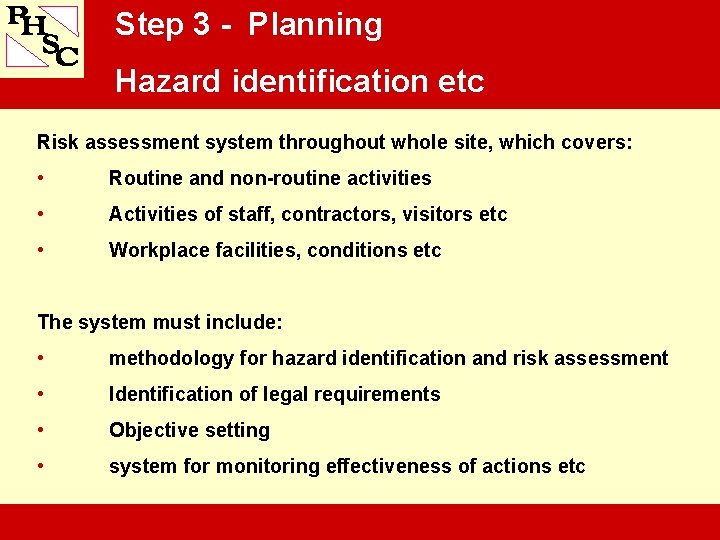
Step 3 - Planning Hazard identification etc Risk assessment system throughout whole site, which covers: • Routine and non-routine activities • Activities of staff, contractors, visitors etc • Workplace facilities, conditions etc The system must include: • methodology for hazard identification and risk assessment • Identification of legal requirements • Objective setting • system for monitoring effectiveness of actions etc
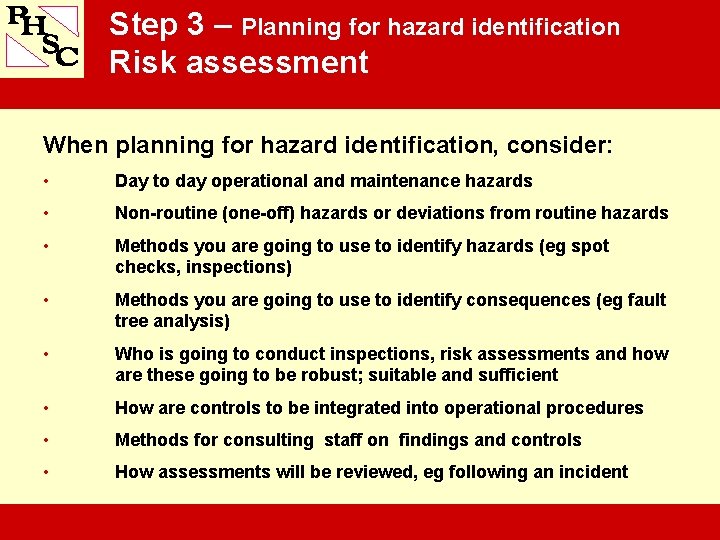
Step 3 – Planning for hazard identification Risk assessment When planning for hazard identification, consider: • Day to day operational and maintenance hazards • Non-routine (one-off) hazards or deviations from routine hazards • Methods you are going to use to identify hazards (eg spot checks, inspections) • Methods you are going to use to identify consequences (eg fault tree analysis) • Who is going to conduct inspections, risk assessments and how are these going to be robust; suitable and sufficient • How are controls to be integrated into operational procedures • Methods for consulting staff on findings and controls • How assessments will be reviewed, eg following an incident
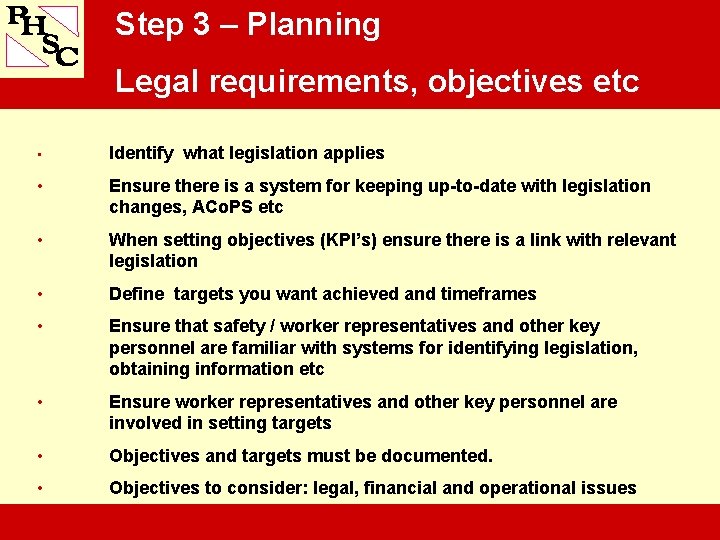
Step 3 – Planning Legal requirements, objectives etc • Identify what legislation applies • Ensure there is a system for keeping up-to-date with legislation changes, ACo. PS etc • When setting objectives (KPI’s) ensure there is a link with relevant legislation • Define targets you want achieved and timeframes • Ensure that safety / worker representatives and other key personnel are familiar with systems for identifying legislation, obtaining information etc • Ensure worker representatives and other key personnel are involved in setting targets • Objectives and targets must be documented. • Objectives to consider: legal, financial and operational issues
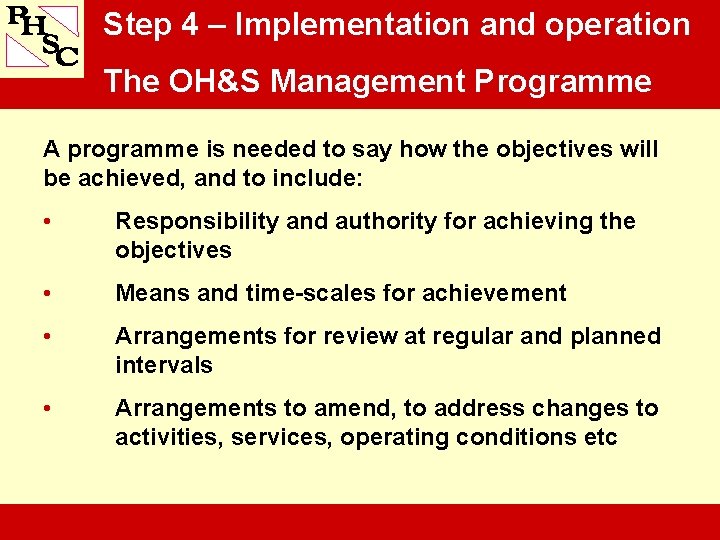
Step 4 – Implementation and operation The OH&S Management Programme A programme is needed to say how the objectives will be achieved, and to include: • Responsibility and authority for achieving the objectives • Means and time-scales for achievement • Arrangements for review at regular and planned intervals • Arrangements to amend, to address changes to activities, services, operating conditions etc
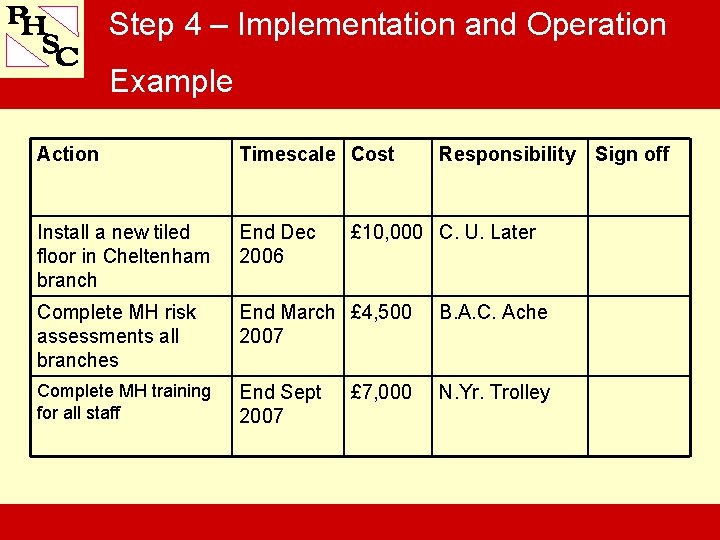
Step 4 – Implementation and Operation Example Action Timescale Cost Responsibility Sign off Install a new tiled floor in Cheltenham branch End Dec 2006 Complete MH risk assessments all branches End March £ 4, 500 2007 B. A. C. Ache Complete MH training for all staff End Sept 2007 N. Yr. Trolley £ 10, 000 C. U. Later £ 7, 000
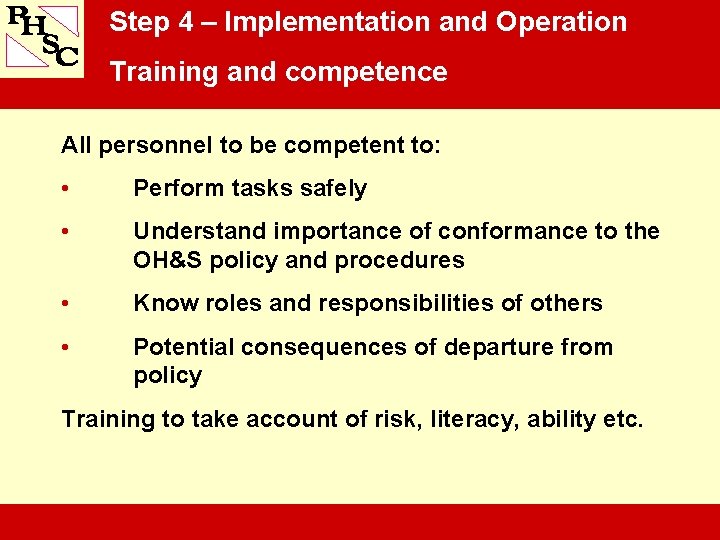
Step 4 – Implementation and Operation Training and competence All personnel to be competent to: • Perform tasks safely • Understand importance of conformance to the OH&S policy and procedures • Know roles and responsibilities of others • Potential consequences of departure from policy Training to take account of risk, literacy, ability etc.
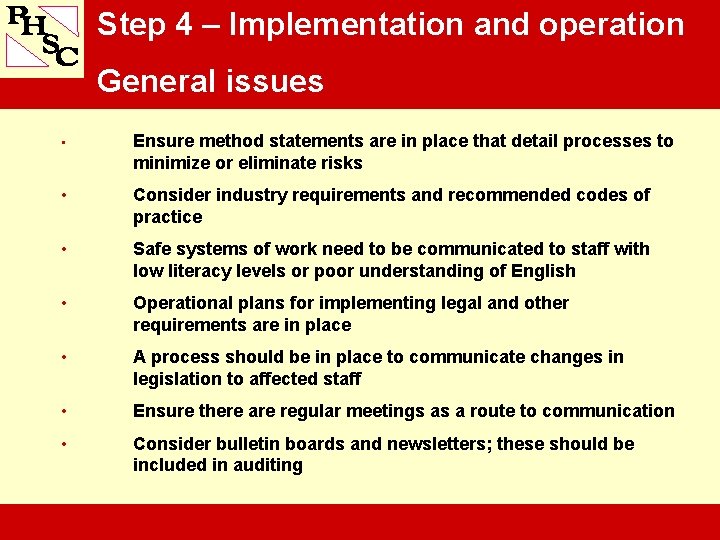
Step 4 – Implementation and operation General issues • Ensure method statements are in place that detail processes to minimize or eliminate risks • Consider industry requirements and recommended codes of practice • Safe systems of work need to be communicated to staff with low literacy levels or poor understanding of English • Operational plans for implementing legal and other requirements are in place • A process should be in place to communicate changes in legislation to affected staff • Ensure there are regular meetings as a route to communication • Consider bulletin boards and newsletters; these should be included in auditing
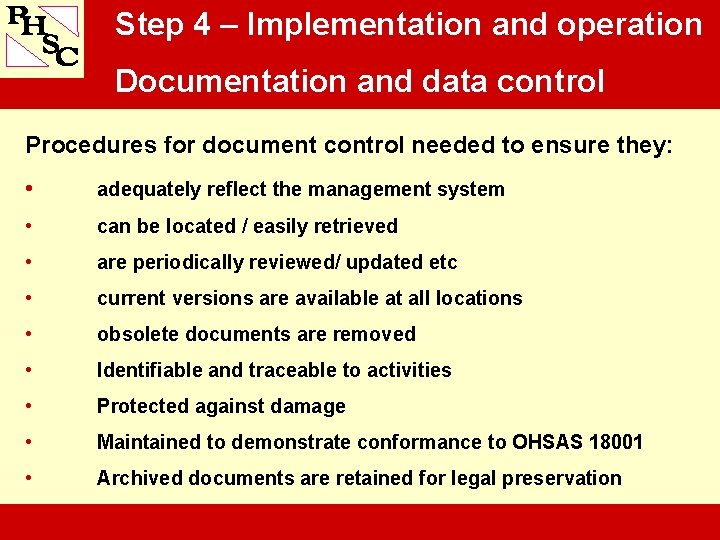
Step 4 – Implementation and operation Documentation and data control Procedures for document control needed to ensure they: • adequately reflect the management system • can be located / easily retrieved • are periodically reviewed/ updated etc • current versions are available at all locations • obsolete documents are removed • Identifiable and traceable to activities • Protected against damage • Maintained to demonstrate conformance to OHSAS 18001 • Archived documents are retained for legal preservation
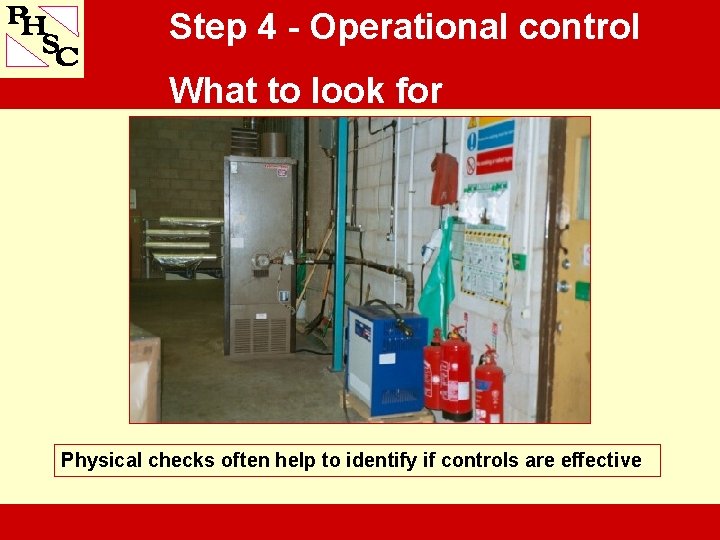
Step 4 - Operational control What to look for Physical checks often help to identify if controls are effective
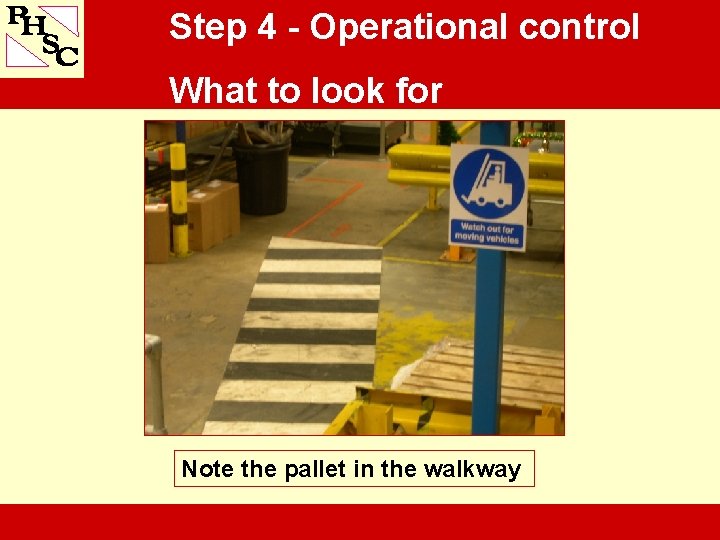
Step 4 - Operational control What to look for Note the pallet in the walkway
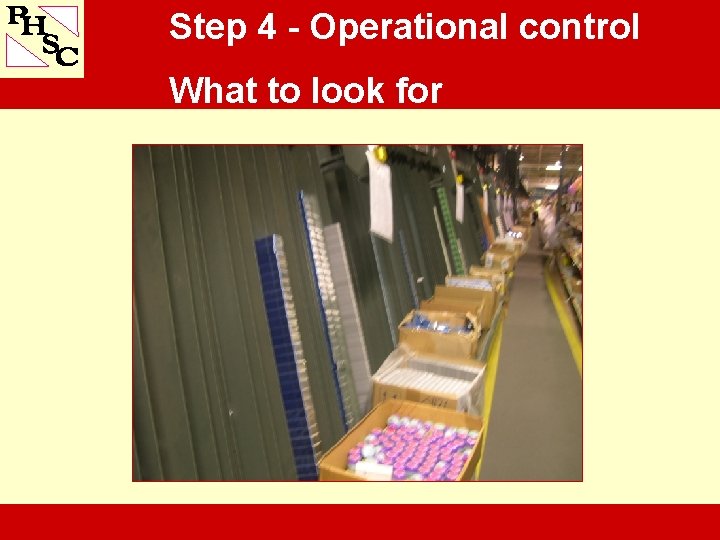
Step 4 - Operational control What to look for
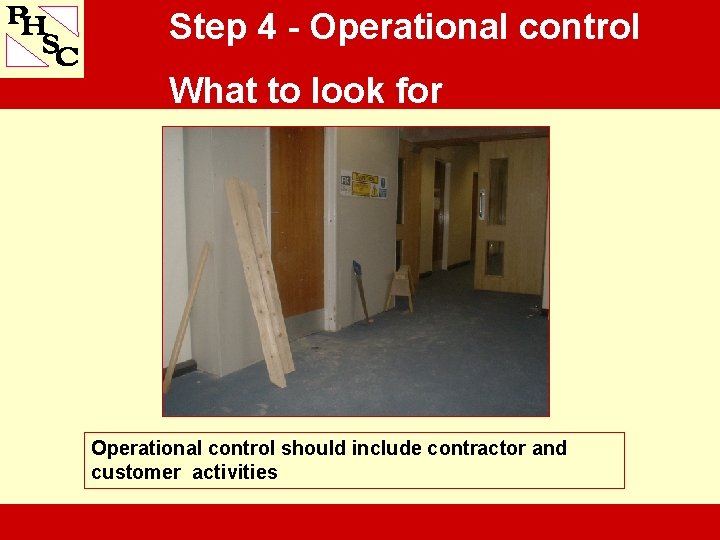
Step 4 - Operational control What to look for Operational control should include contractor and customer activities
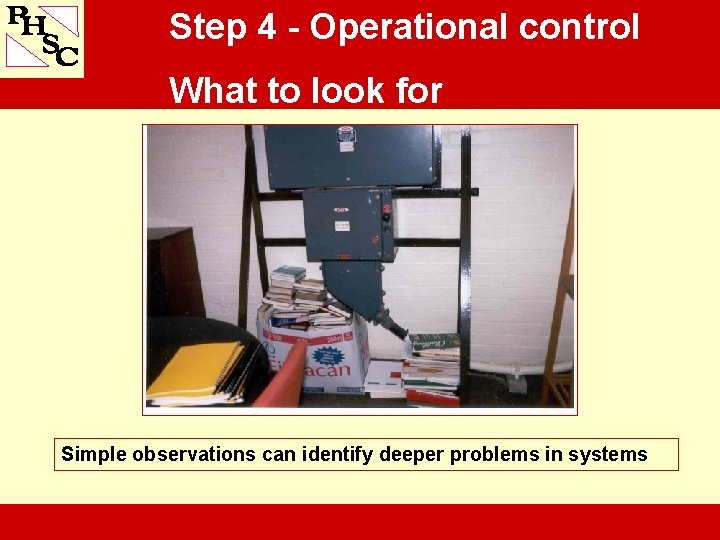
Step 4 - Operational control What to look for Simple observations can identify deeper problems in systems
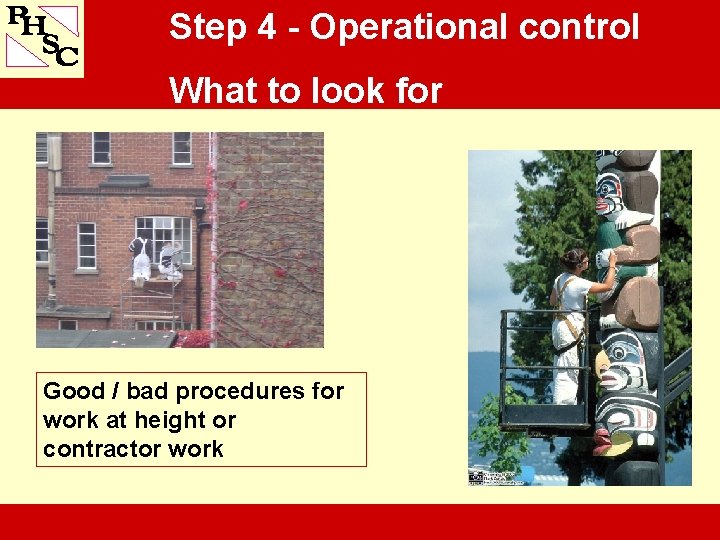
Step 4 - Operational control What to look for Good / bad procedures for work at height or contractor work
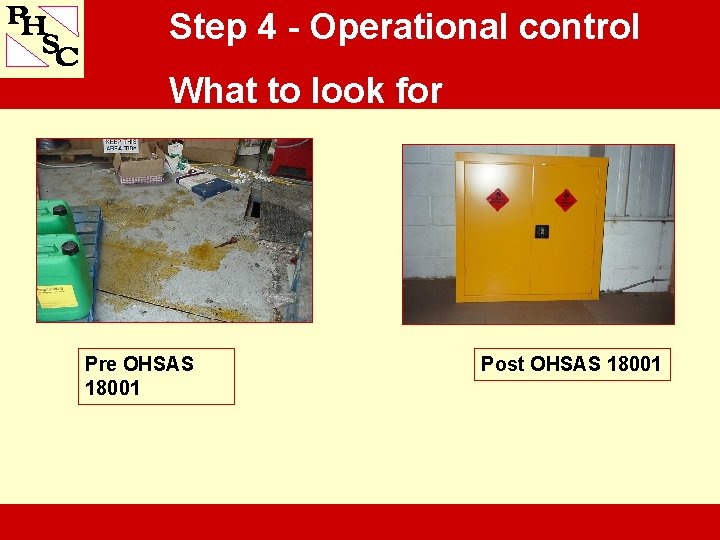
Step 4 - Operational control What to look for Pre OHSAS 18001 Post OHSAS 18001
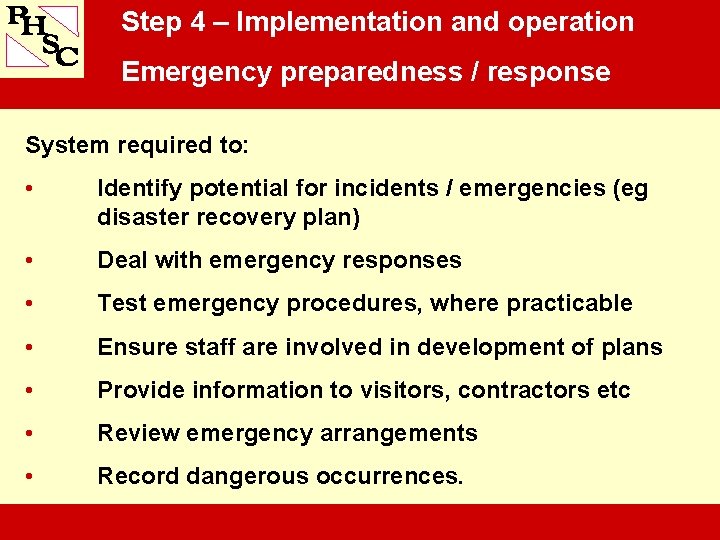
Step 4 – Implementation and operation Emergency preparedness / response System required to: • Identify potential for incidents / emergencies (eg disaster recovery plan) • Deal with emergency responses • Test emergency procedures, where practicable • Ensure staff are involved in development of plans • Provide information to visitors, contractors etc • Review emergency arrangements • Record dangerous occurrences.
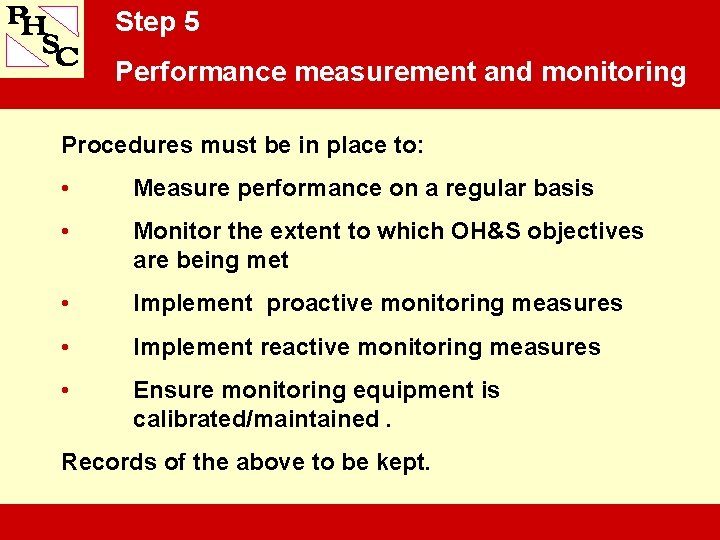
Step 5 Performance measurement and monitoring Procedures must be in place to: • Measure performance on a regular basis • Monitor the extent to which OH&S objectives are being met • Implement proactive monitoring measures • Implement reactive monitoring measures • Ensure monitoring equipment is calibrated/maintained. Records of the above to be kept.
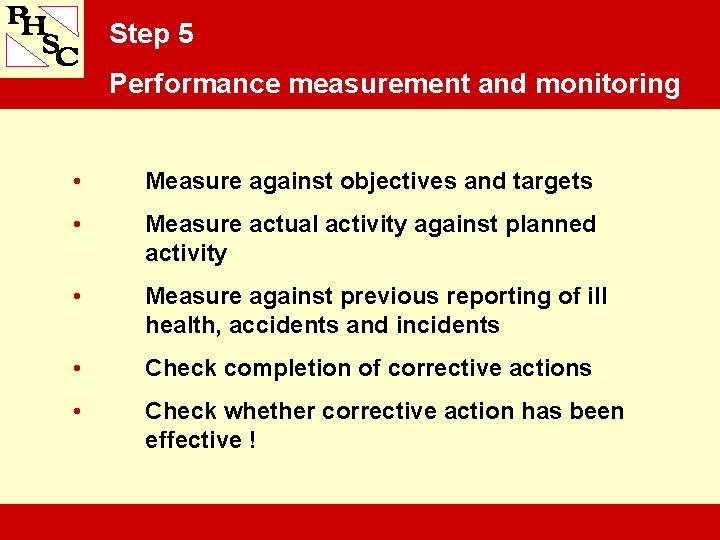
Step 5 Performance measurement and monitoring • Measure against objectives and targets • Measure actual activity against planned activity • Measure against previous reporting of ill health, accidents and incidents • Check completion of corrective actions • Check whether corrective action has been effective !
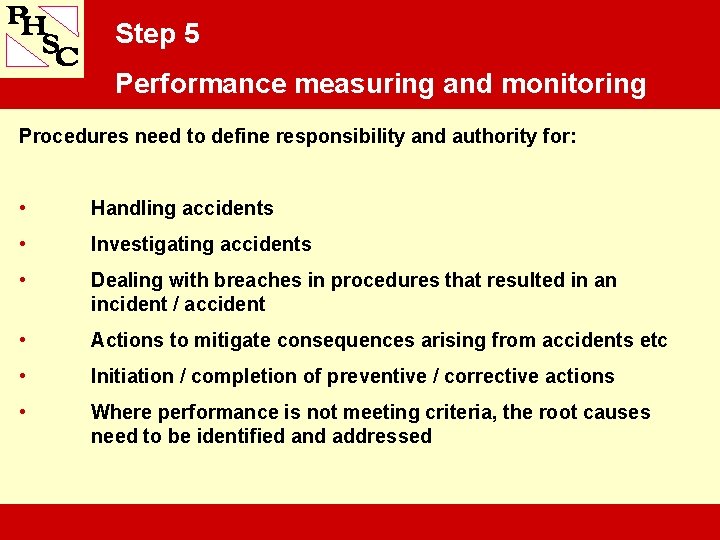
Step 5 Performance measuring and monitoring Procedures need to define responsibility and authority for: • Handling accidents • Investigating accidents • Dealing with breaches in procedures that resulted in an incident / accident • Actions to mitigate consequences arising from accidents etc • Initiation / completion of preventive / corrective actions • Where performance is not meeting criteria, the root causes need to be identified and addressed
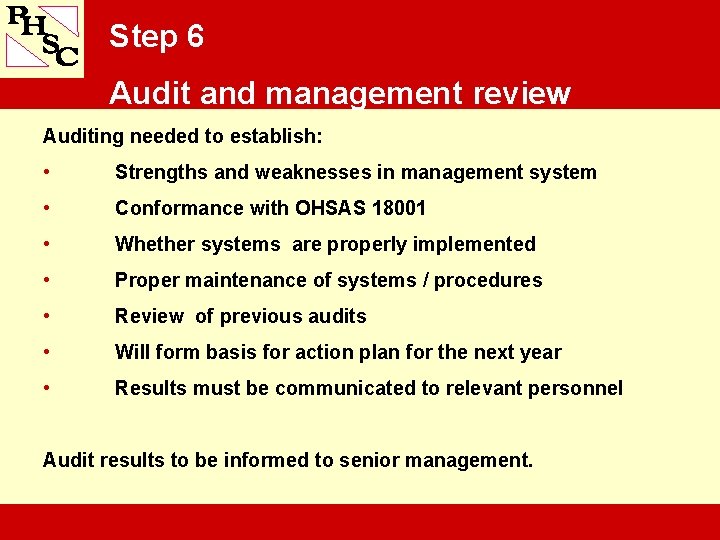
Step 6 Audit and management review Auditing needed to establish: • Strengths and weaknesses in management system • Conformance with OHSAS 18001 • Whether systems are properly implemented • Proper maintenance of systems / procedures • Review of previous audits • Will form basis for action plan for the next year • Results must be communicated to relevant personnel Audit results to be informed to senior management.
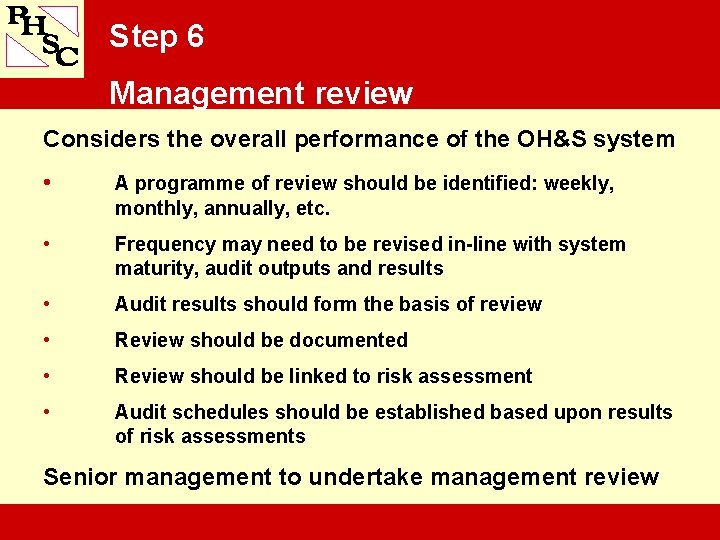
Step 6 Management review Considers the overall performance of the OH&S system • A programme of review should be identified: weekly, monthly, annually, etc. • Frequency may need to be revised in-line with system maturity, audit outputs and results • Audit results should form the basis of review • Review should be documented • Review should be linked to risk assessment • Audit schedules should be established based upon results of risk assessments Senior management to undertake management review
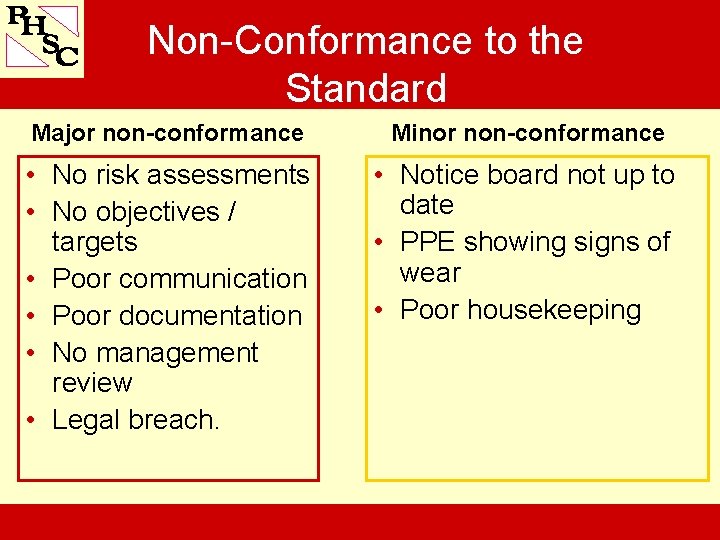
Non-Conformance to the Standard Major non-conformance Minor non-conformance • No risk assessments • No objectives / targets • Poor communication • Poor documentation • No management review • Legal breach. • Notice board not up to date • PPE showing signs of wear • Poor housekeeping
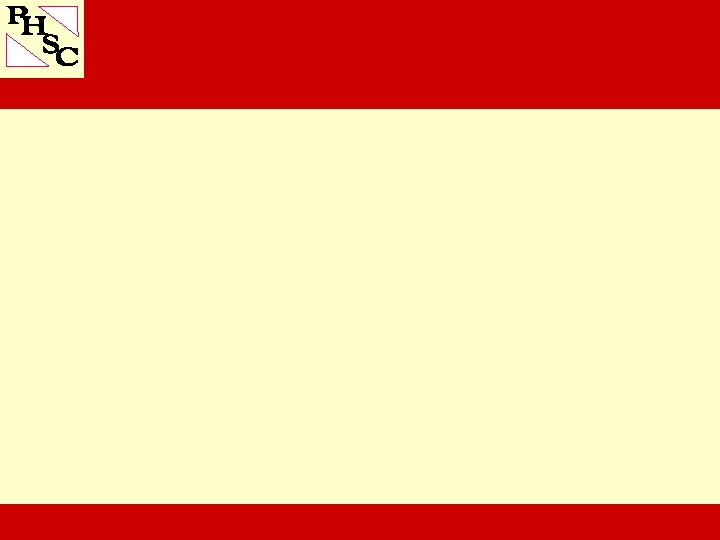
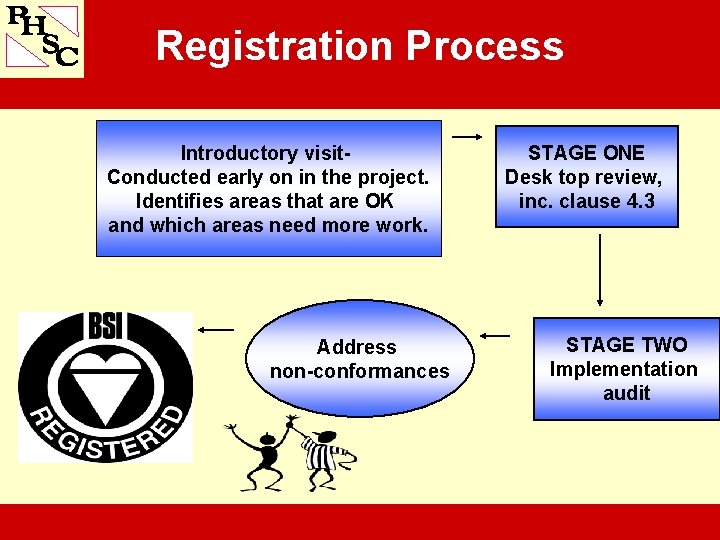
Registration Process Introductory visit- Conducted early on in the project. Identifies areas that are OK and which areas need more work. Address non-conformances STAGE ONE Desk top review, inc. clause 4. 3 STAGE TWO Implementation audit
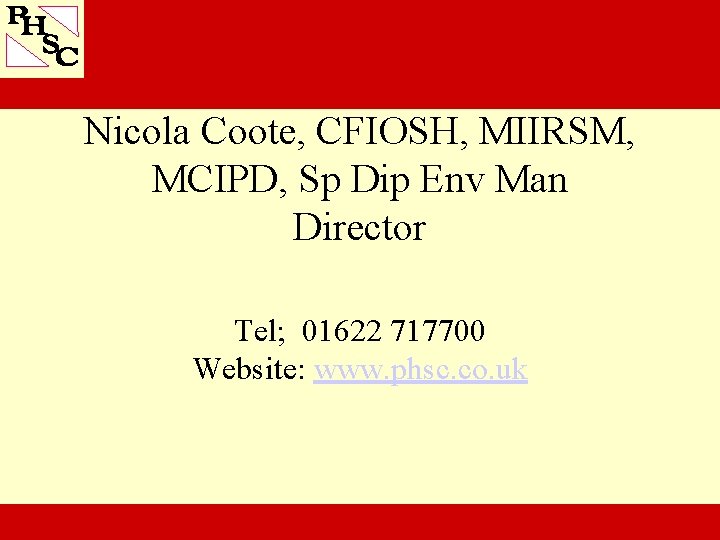
Nicola Coote, CFIOSH, MIIRSM, MCIPD, Sp Dip Env Man Director Tel; 01622 717700 Website: www. phsc. co. uk
Ohsas 18001 management representative appointment
Ohsas 18001:1999
Ohsas 18001 temel felsefesi
Ohsas 18001 e kılavuzluk bilgisi veren standarttır
Iso 9001 iso 14001 ohsas 18001 comparison
Ohsas 18001:2008
Food safety management system template
Ohsas 9000
Ohsas 18000
Normas ohsas 18000
Ohsas 18801
Nbr 18801
Hse management standards analysis tool
Hsg218
Steamboat willie apush
Contractor safety management system tata steel
Safety management system faa
Intelex document control
Icao safety management system
Doe integrated safety management
Bs 8800 safety management system
Key elements of food safety management system
Safety incident management system
Api rp 1173
Seguridad operacional (sms)
Driver safety management system
Ccps process safety elements
Transport canada safety management system
Nicola carozza
Nicola licata
Nicola cezzi
Nicola allen knutsford
Dawn marie wesley
Książka ponad wszystko
Nicola bacchetta
Reiseberufe
Nicola sheldon
Nicola cezzi