Hazard Management Implement and Monitor Workplace Health Safety
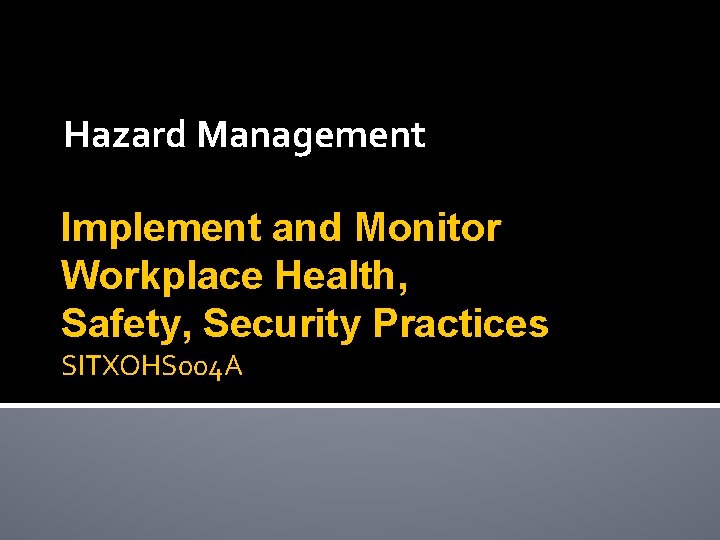
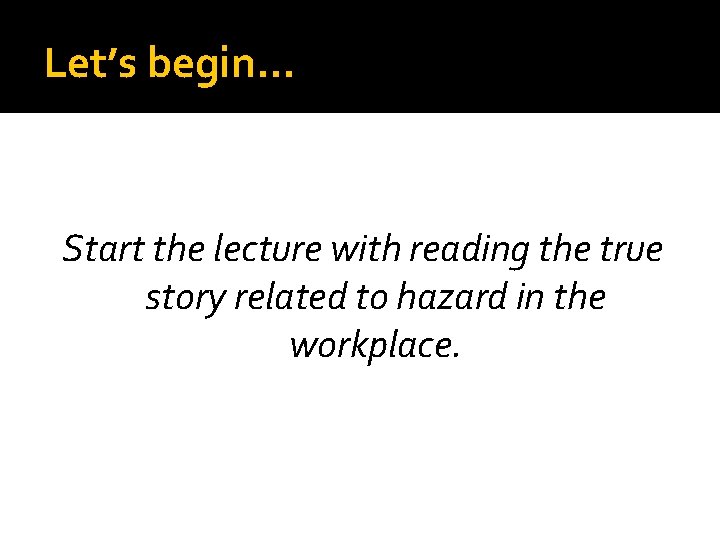
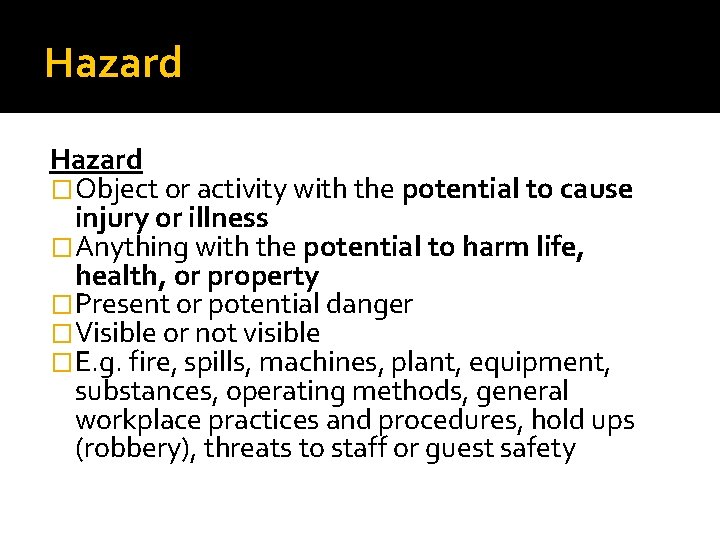

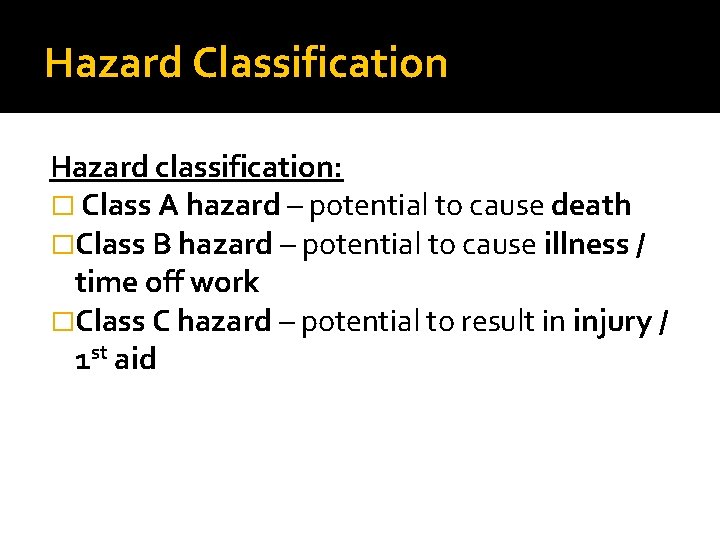
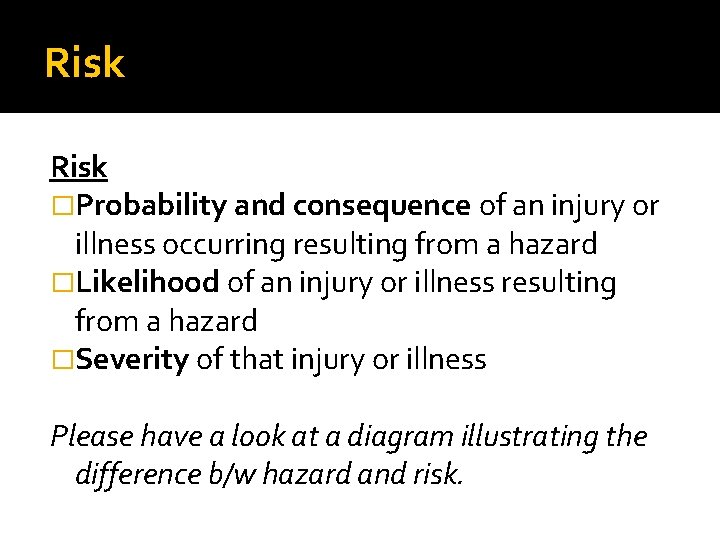
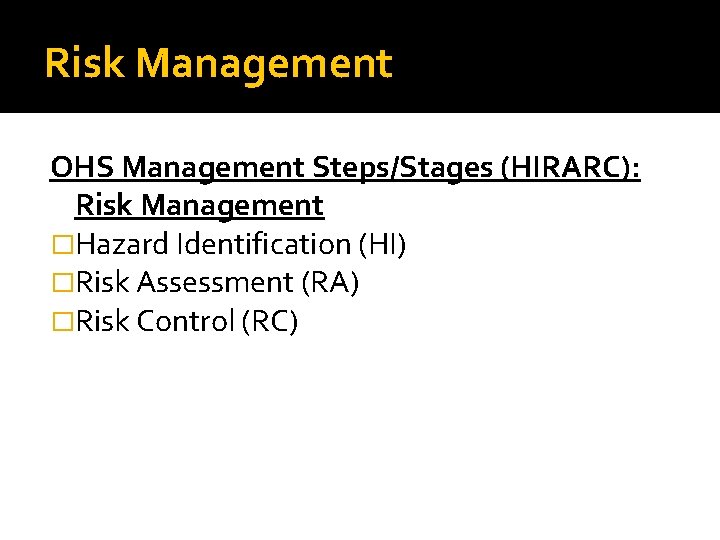
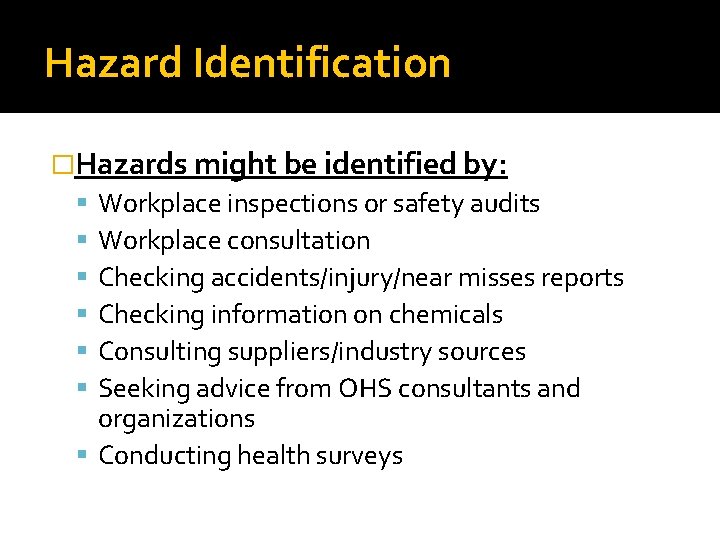
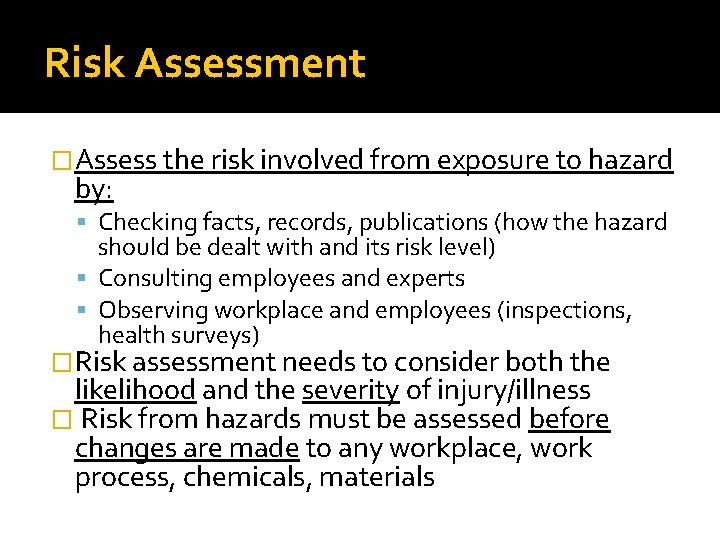
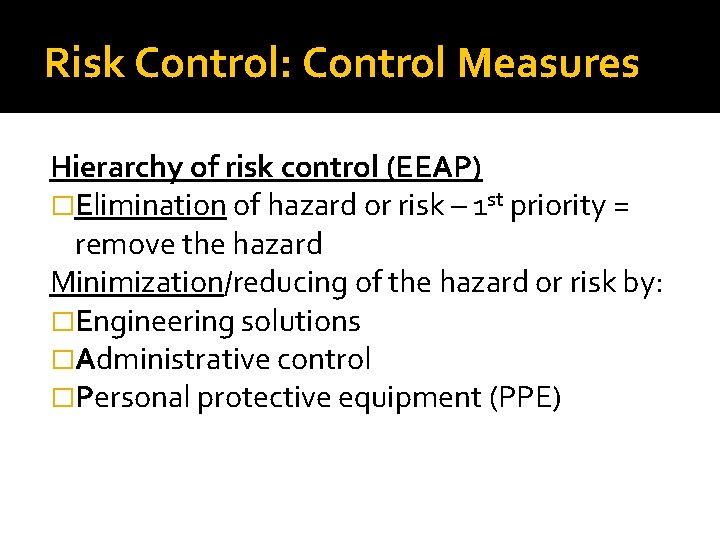
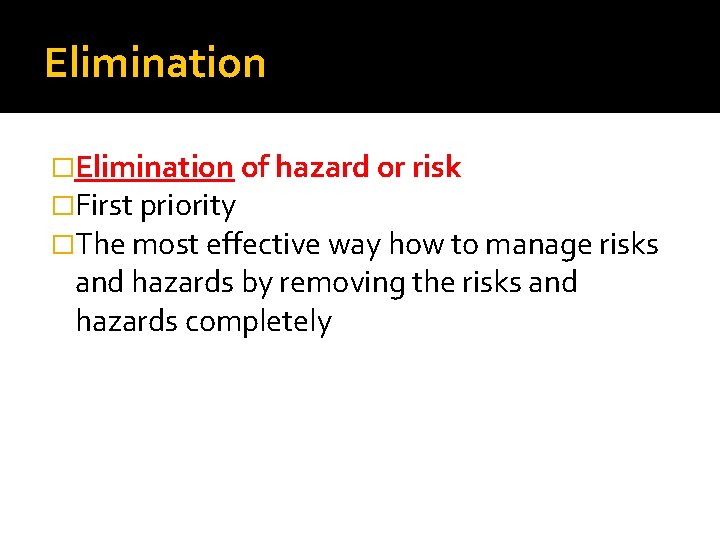
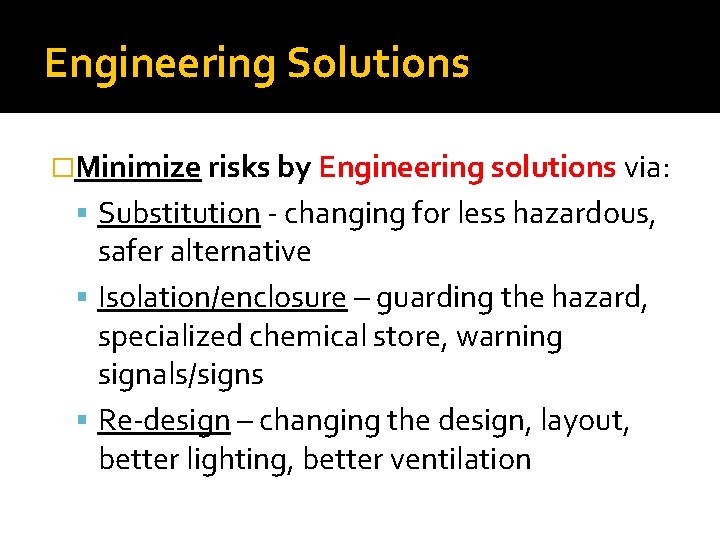
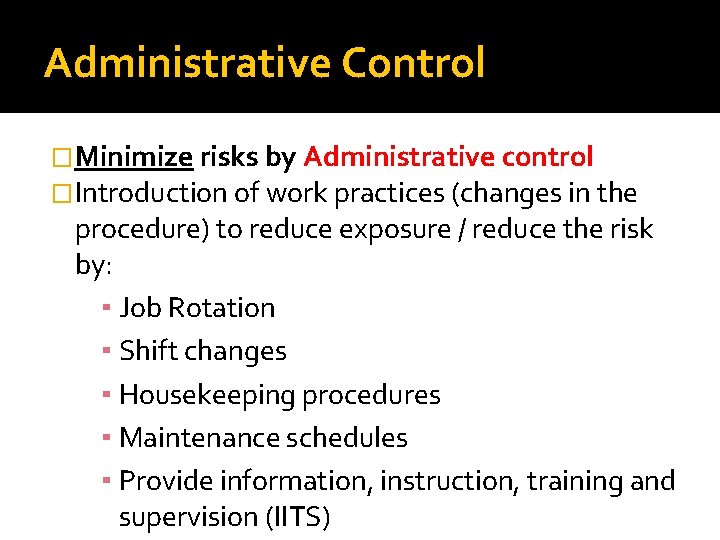
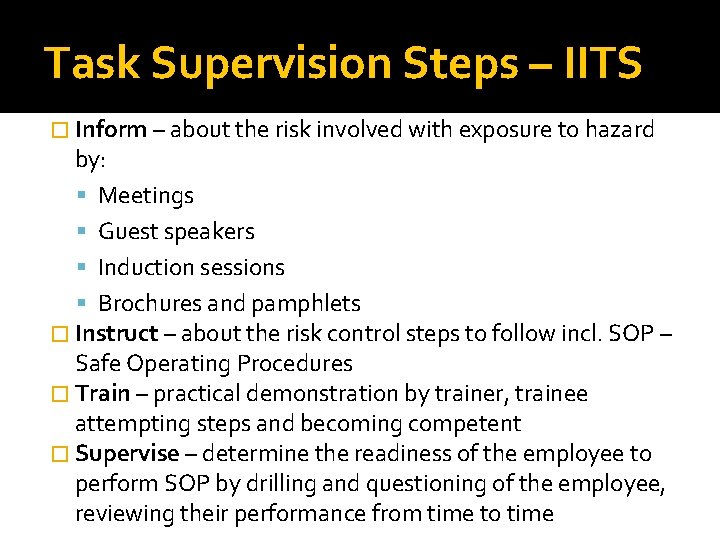
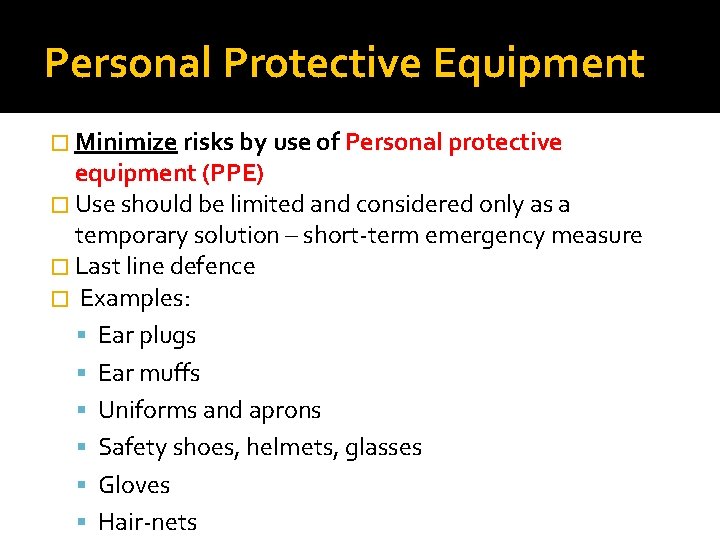
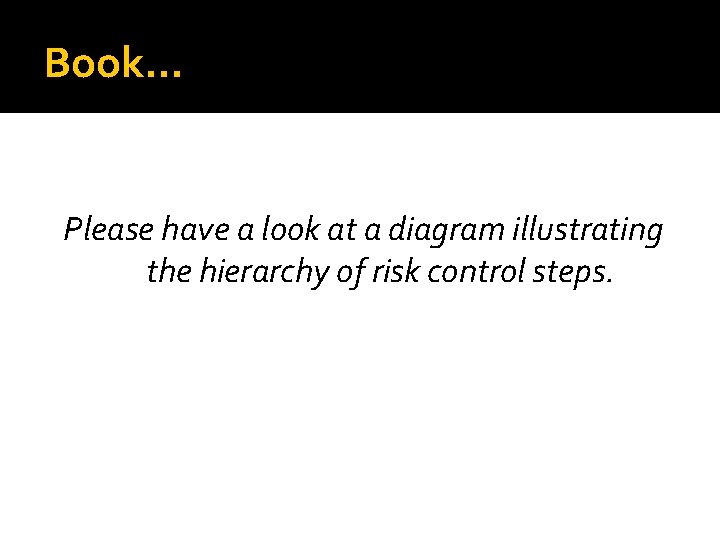
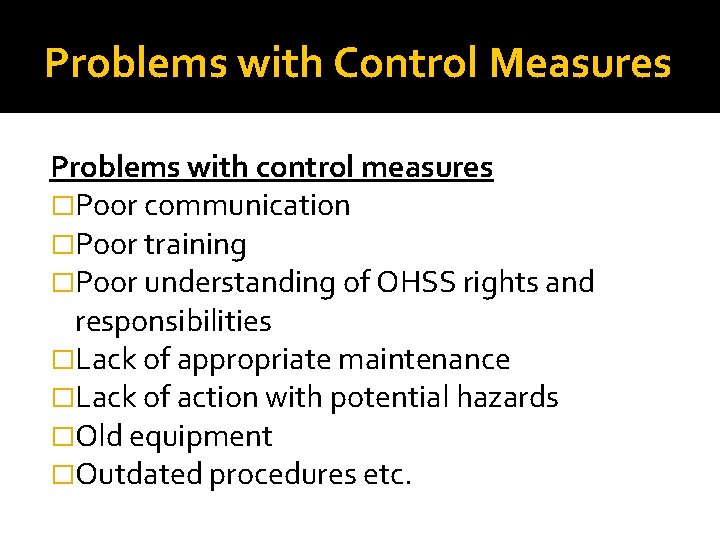
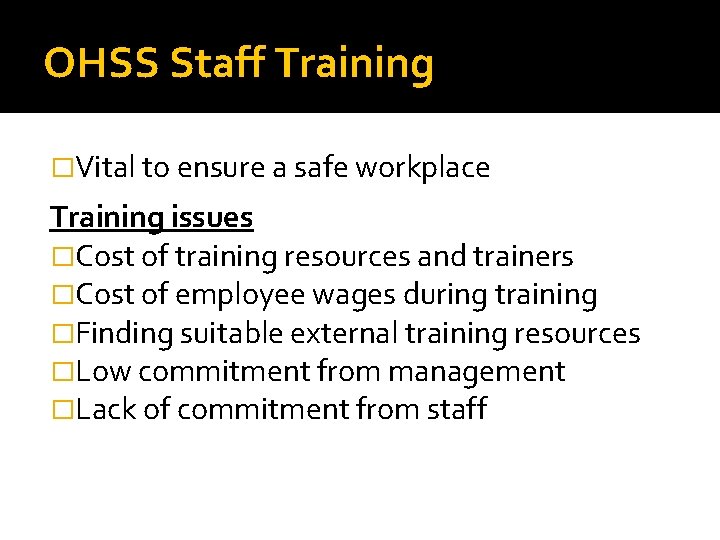
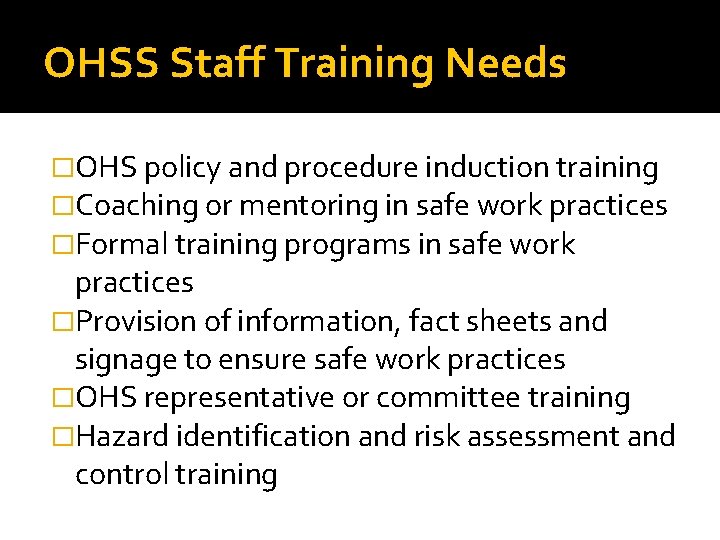
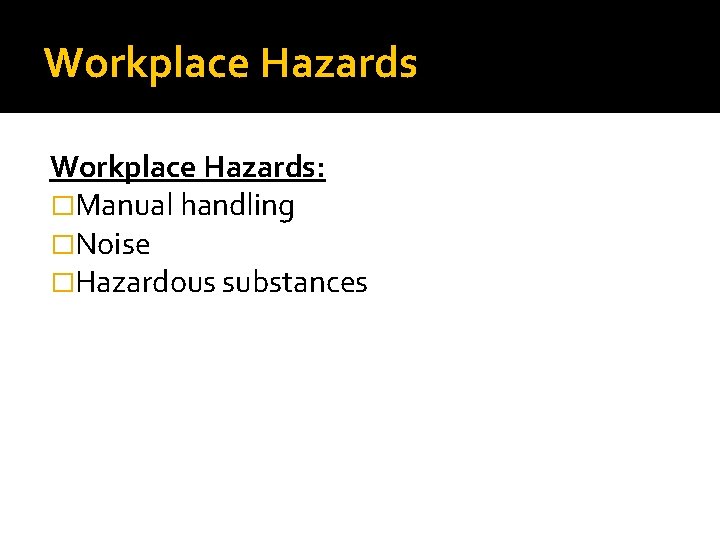
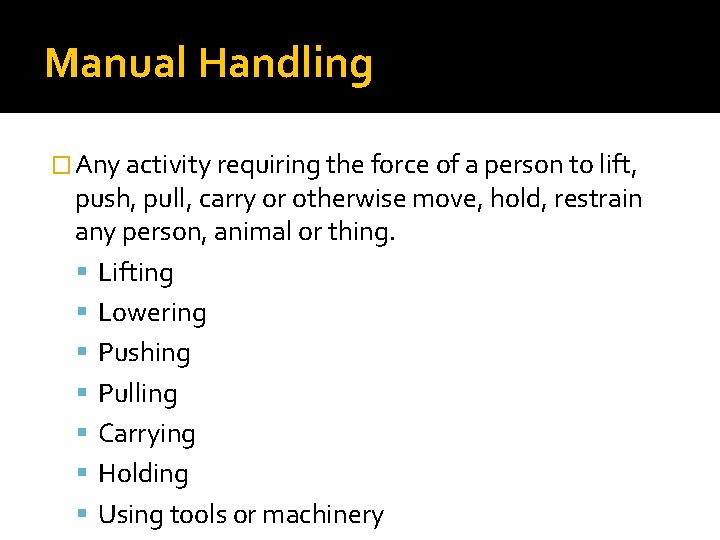
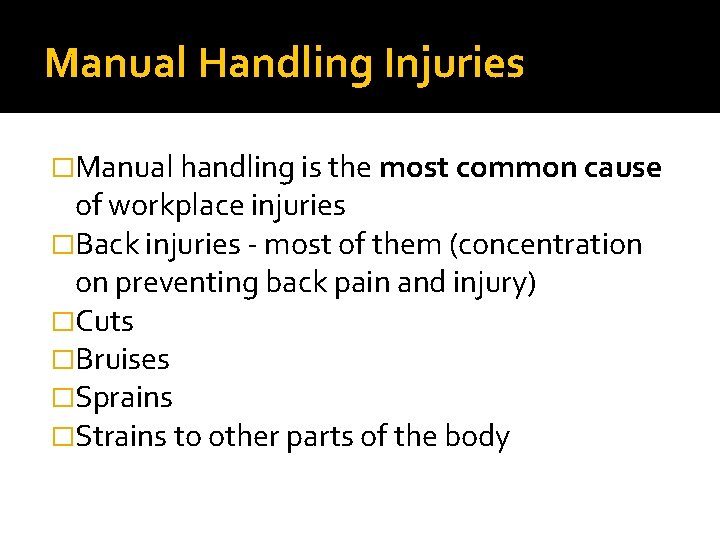
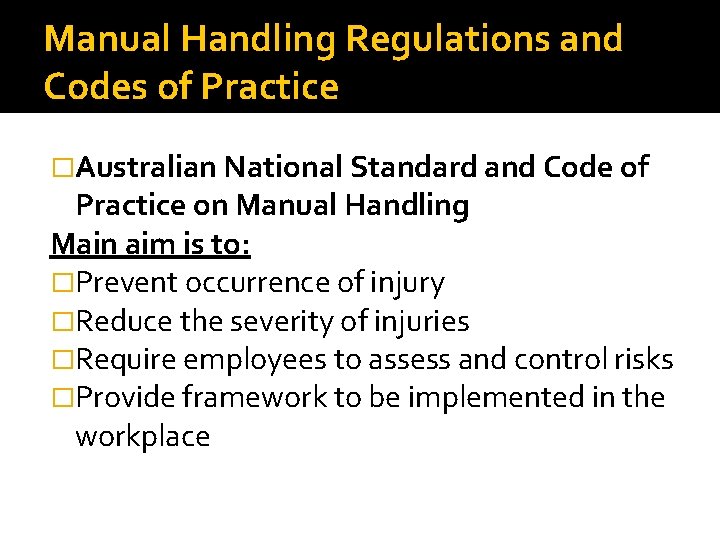
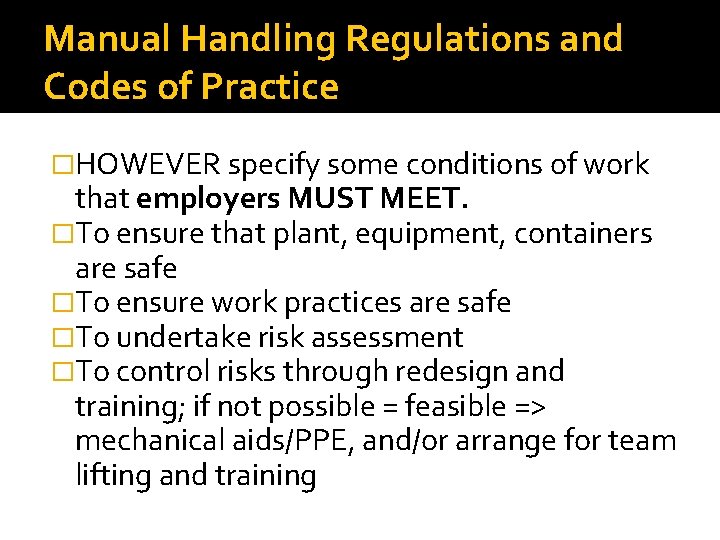
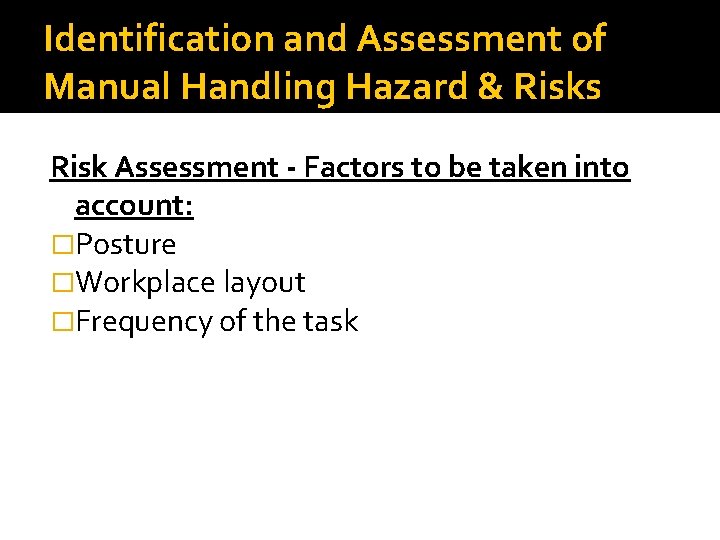
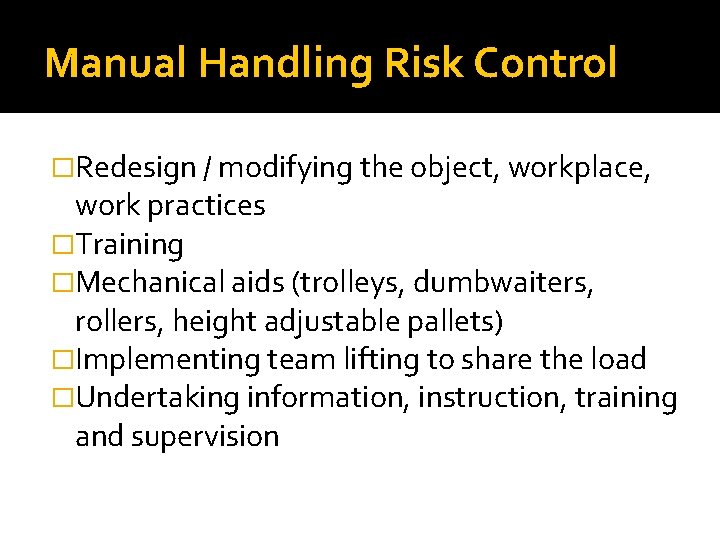
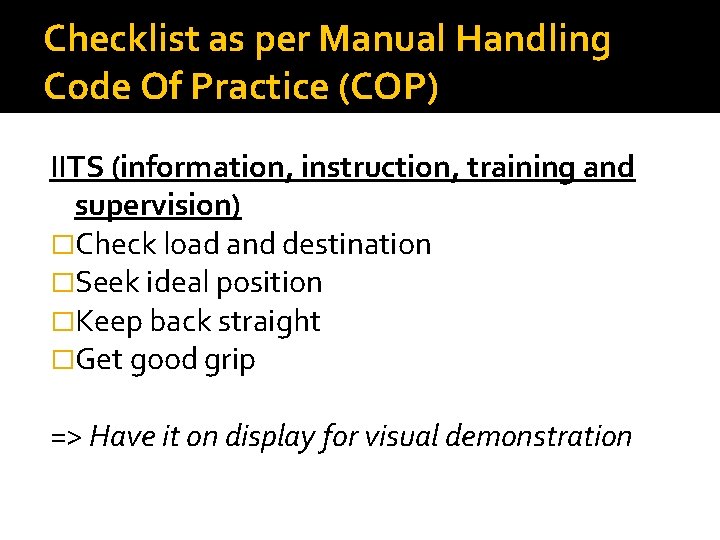
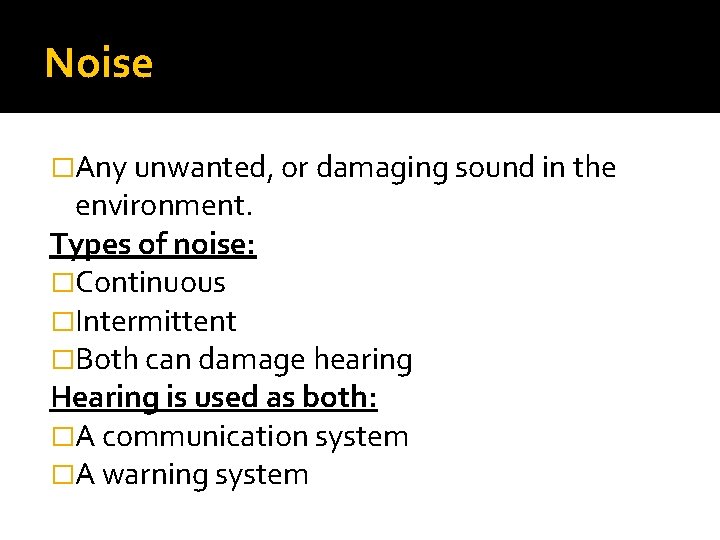
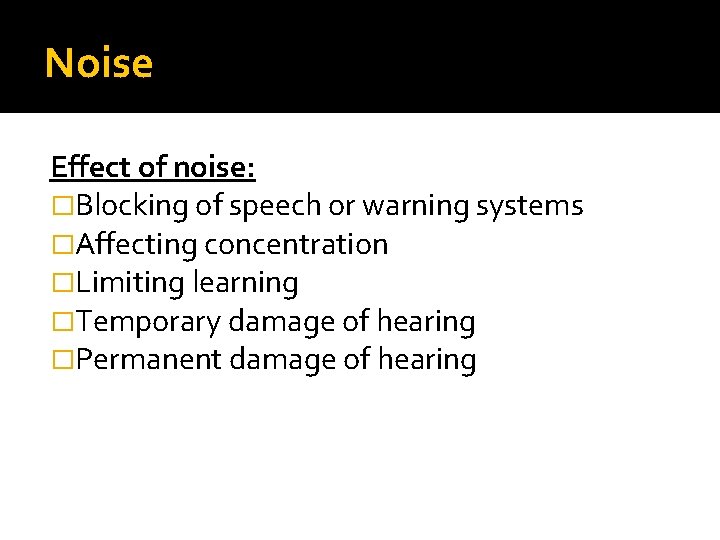
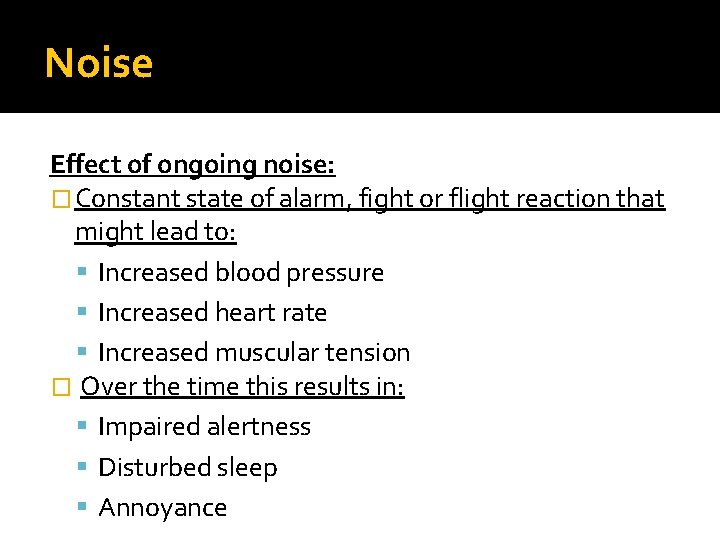
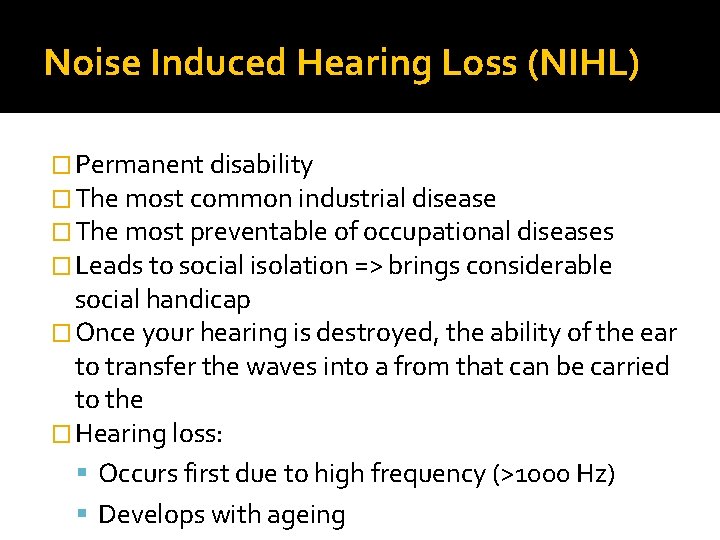
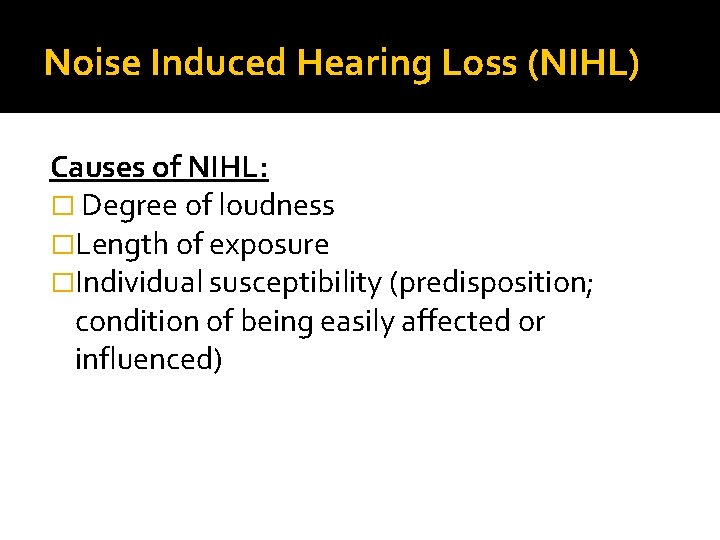
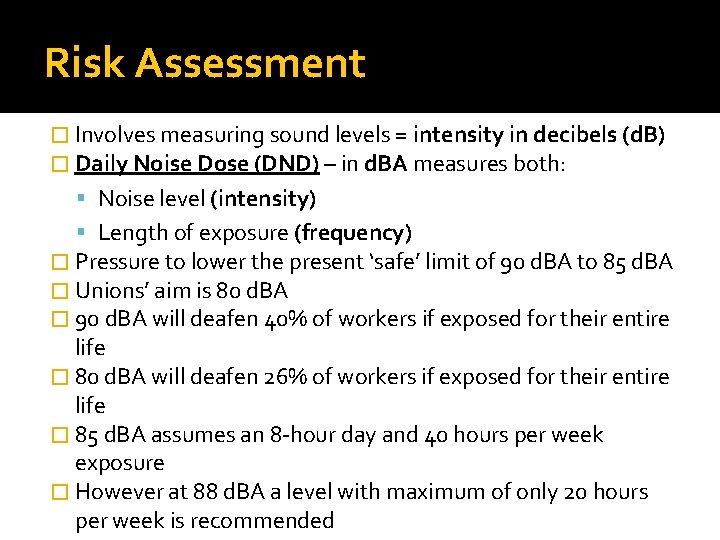
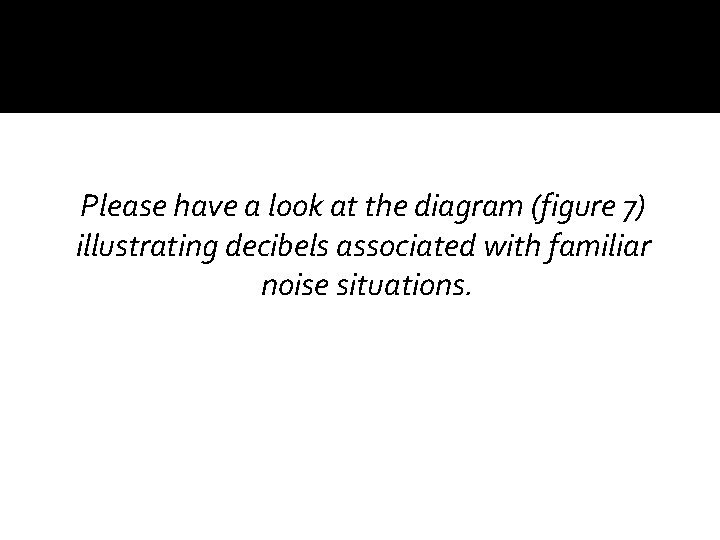
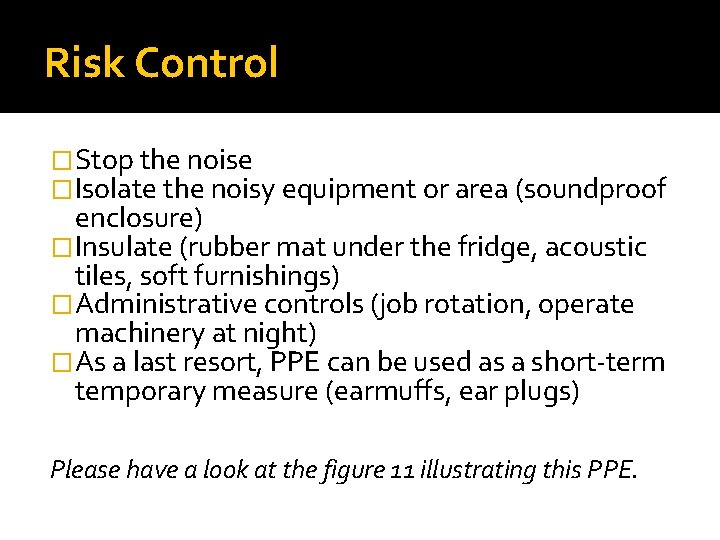
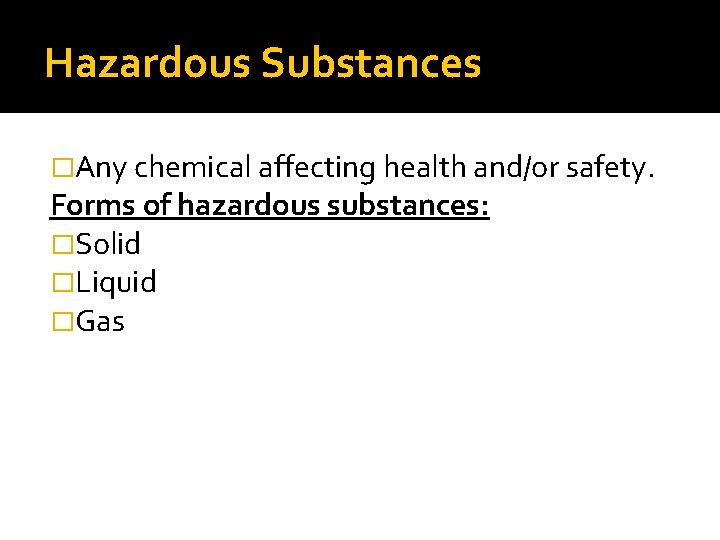
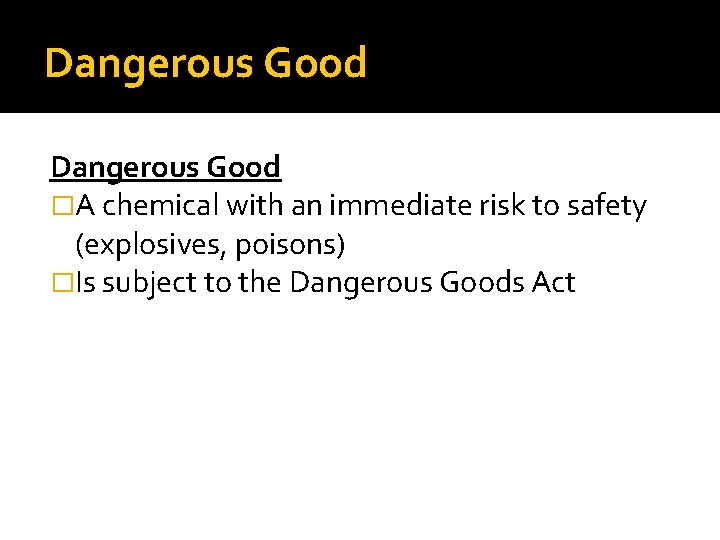
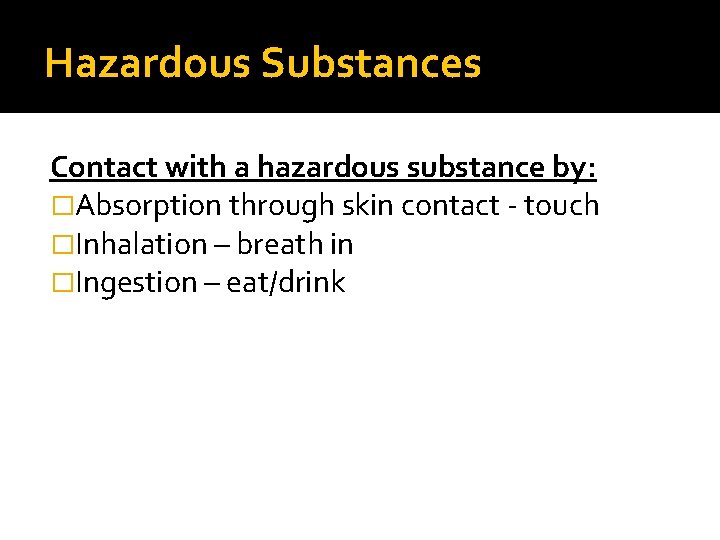
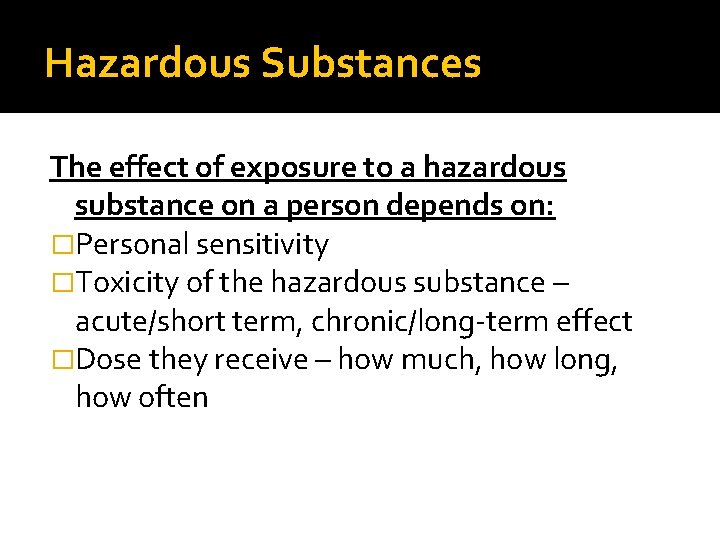
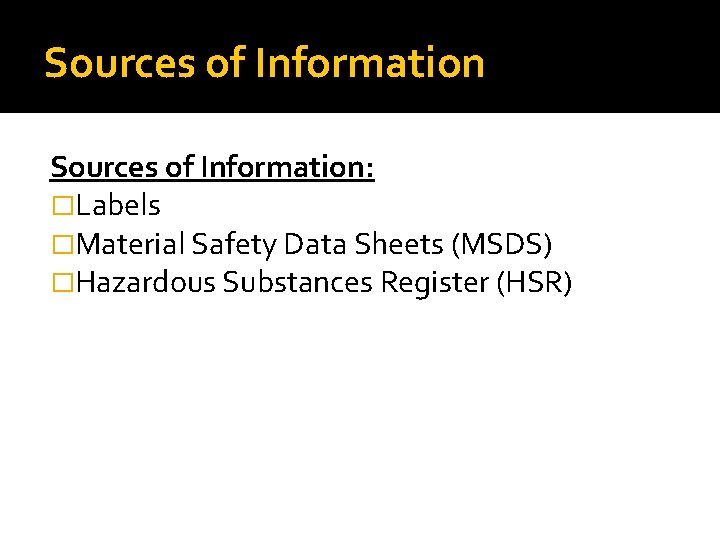
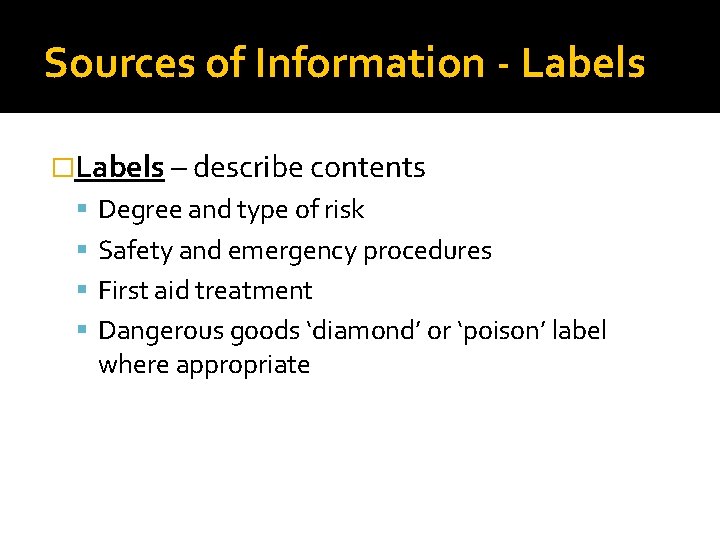
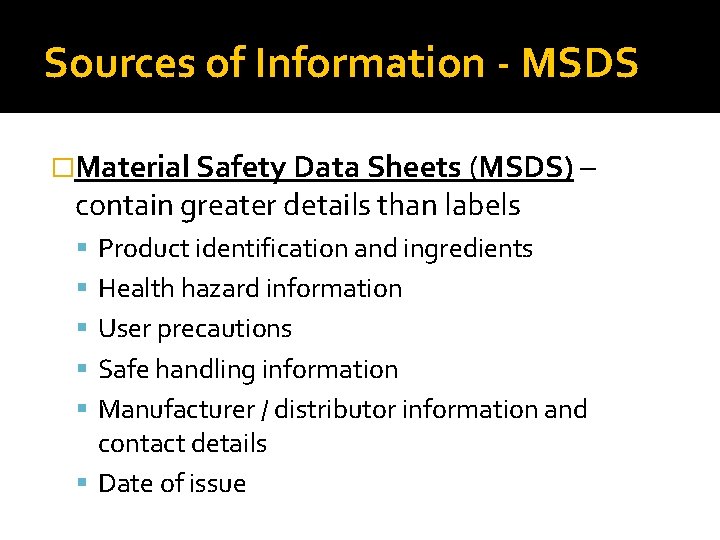
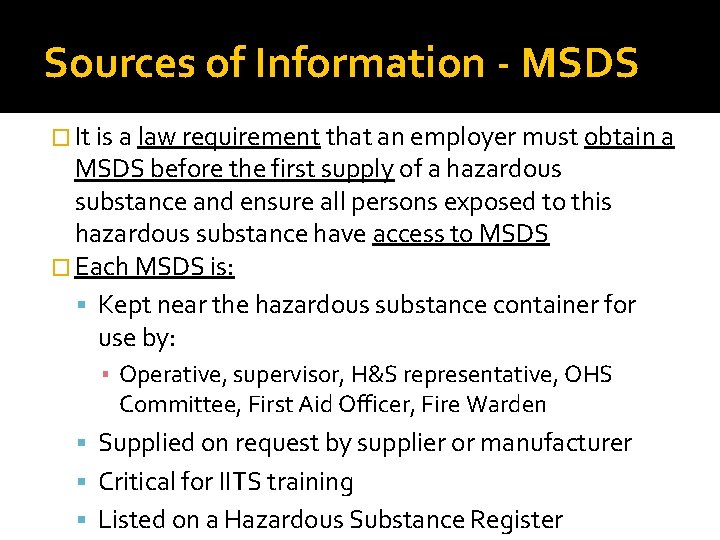
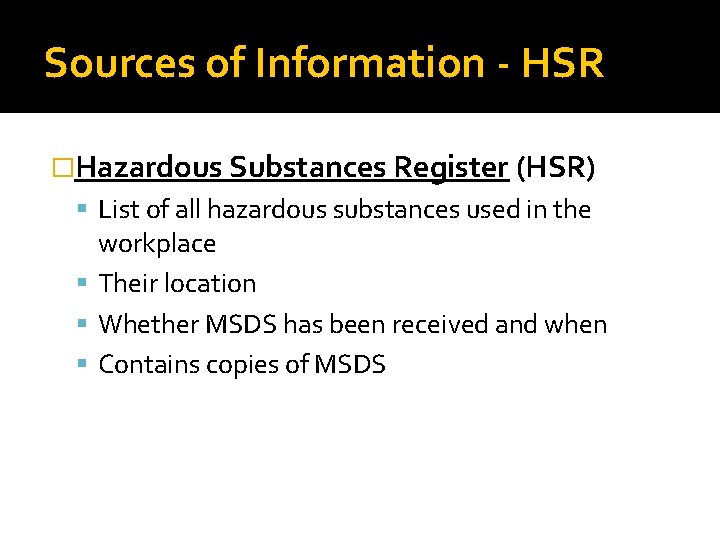

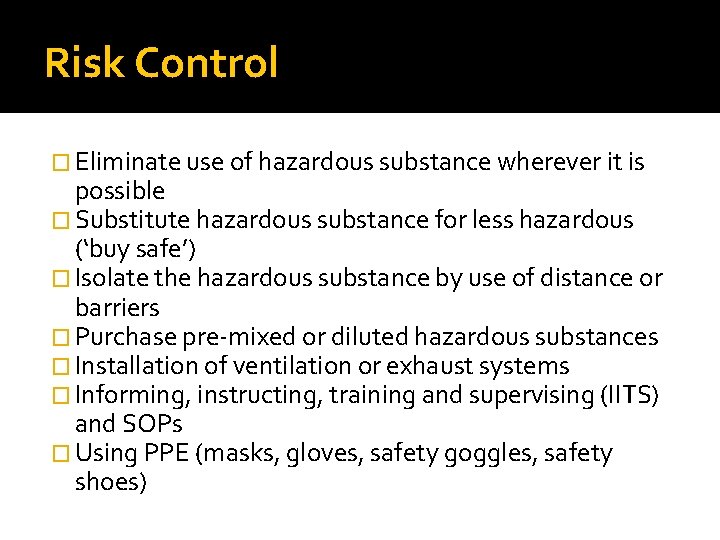
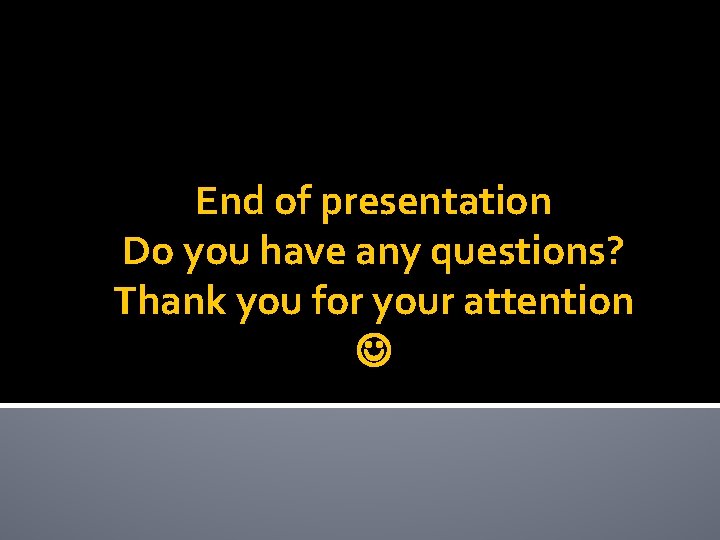
- Slides: 47
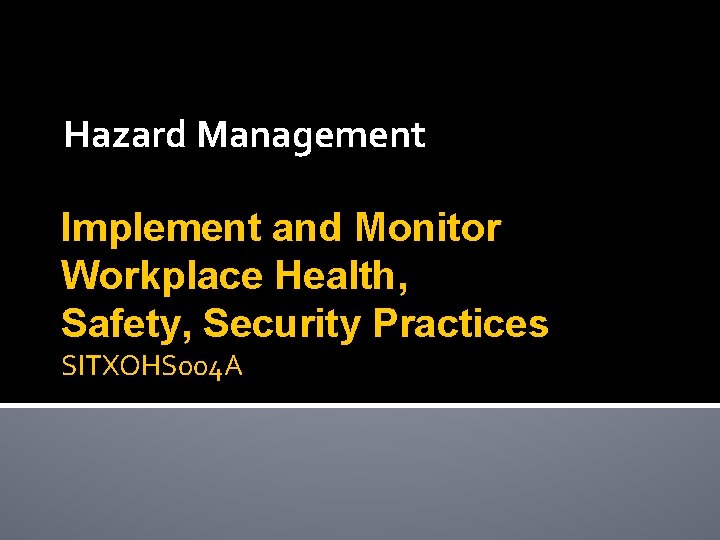
Hazard Management Implement and Monitor Workplace Health, Safety, Security Practices SITXOHS 004 A
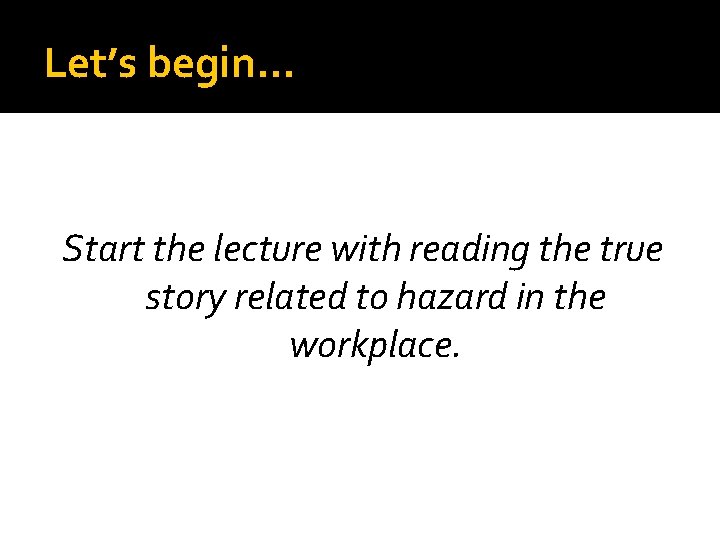
Let’s begin… Start the lecture with reading the true story related to hazard in the workplace.
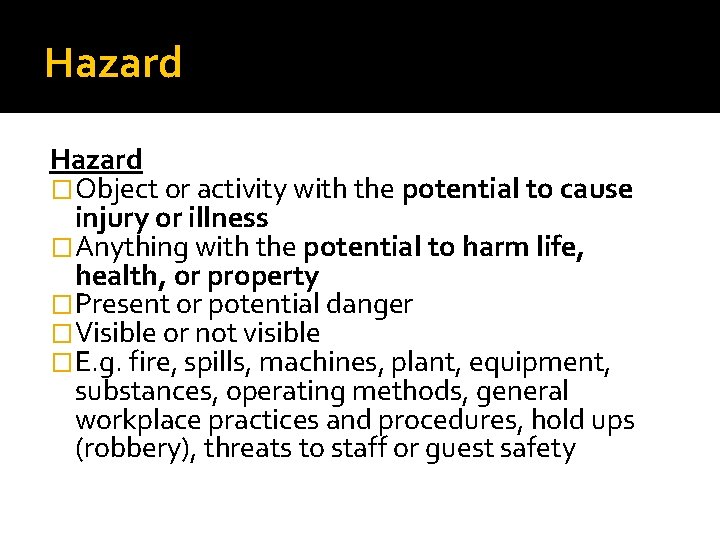
Hazard �Object or activity with the potential to cause injury or illness �Anything with the potential to harm life, health, or property �Present or potential danger �Visible or not visible �E. g. fire, spills, machines, plant, equipment, substances, operating methods, general workplace practices and procedures, hold ups (robbery), threats to staff or guest safety

Types of Hazard Types of hazard: �Safety hazards – can lead to injury �Health hazards – can lead to illness/disease
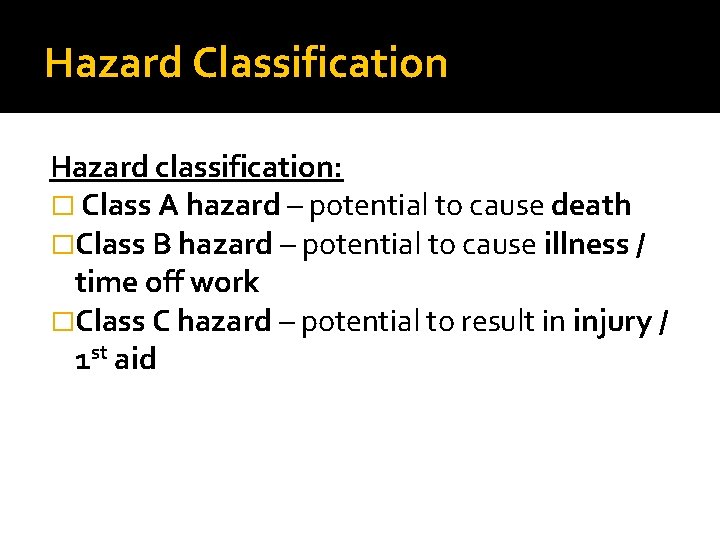
Hazard Classification Hazard classification: � Class A hazard – potential to cause death �Class B hazard – potential to cause illness / time off work �Class C hazard – potential to result in injury / 1 st aid
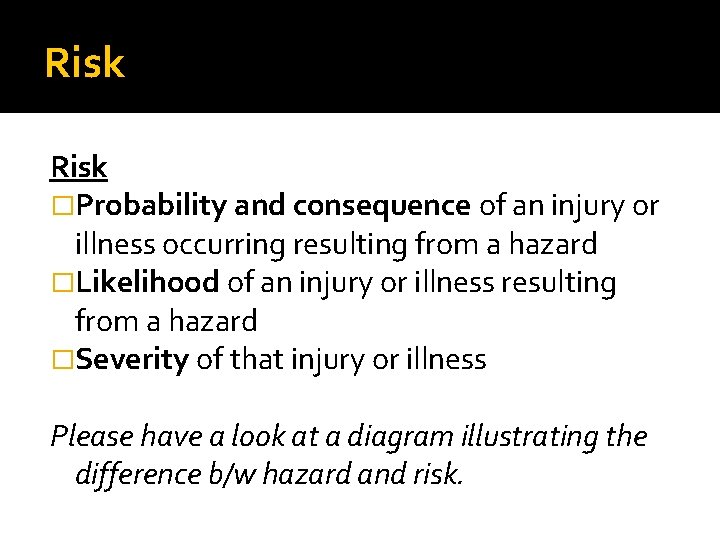
Risk �Probability and consequence of an injury or illness occurring resulting from a hazard �Likelihood of an injury or illness resulting from a hazard �Severity of that injury or illness Please have a look at a diagram illustrating the difference b/w hazard and risk.
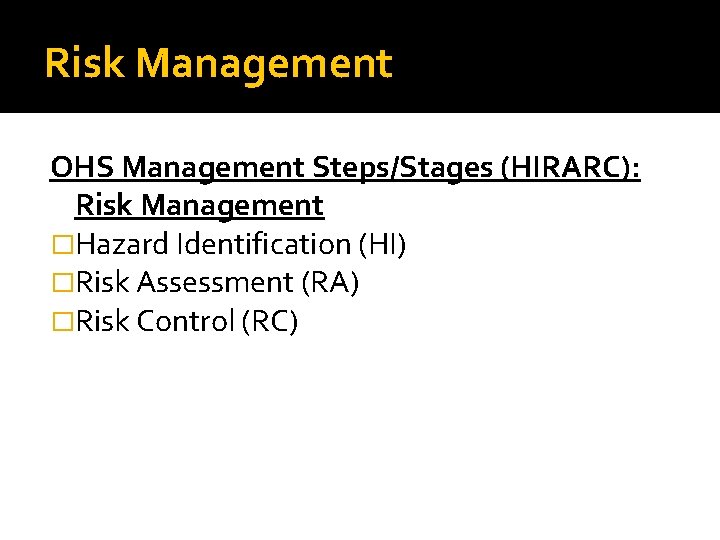
Risk Management OHS Management Steps/Stages (HIRARC): Risk Management �Hazard Identification (HI) �Risk Assessment (RA) �Risk Control (RC)
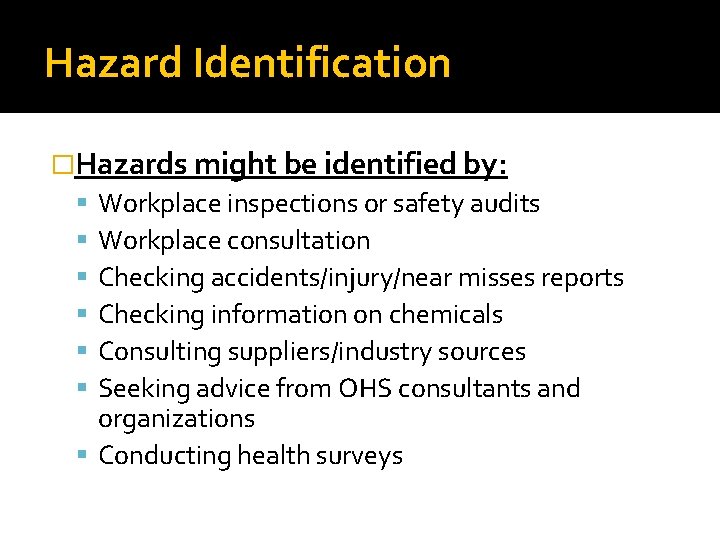
Hazard Identification �Hazards might be identified by: Workplace inspections or safety audits Workplace consultation Checking accidents/injury/near misses reports Checking information on chemicals Consulting suppliers/industry sources Seeking advice from OHS consultants and organizations Conducting health surveys
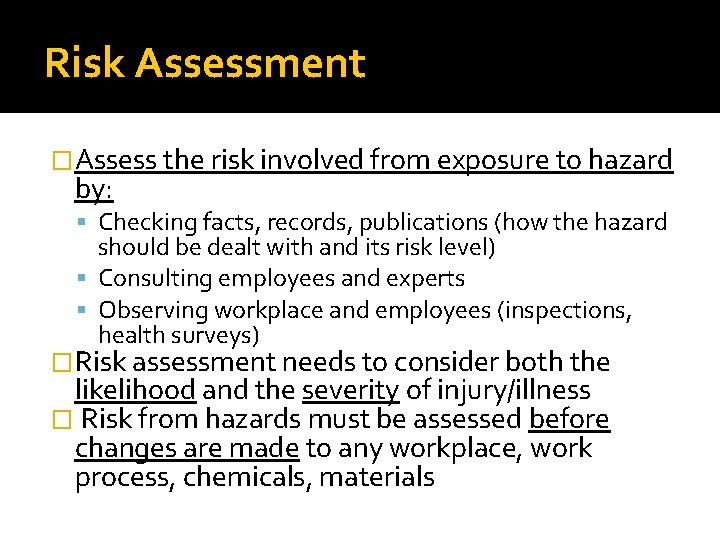
Risk Assessment �Assess the risk involved from exposure to hazard by: Checking facts, records, publications (how the hazard should be dealt with and its risk level) Consulting employees and experts Observing workplace and employees (inspections, health surveys) �Risk assessment needs to consider both the likelihood and the severity of injury/illness � Risk from hazards must be assessed before changes are made to any workplace, work process, chemicals, materials
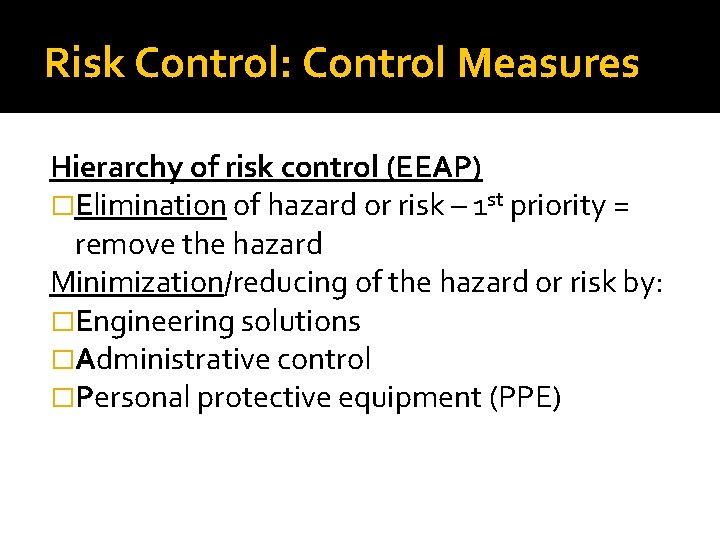
Risk Control: Control Measures Hierarchy of risk control (EEAP) �Elimination of hazard or risk – 1 st priority = remove the hazard Minimization/reducing of the hazard or risk by: �Engineering solutions �Administrative control �Personal protective equipment (PPE)
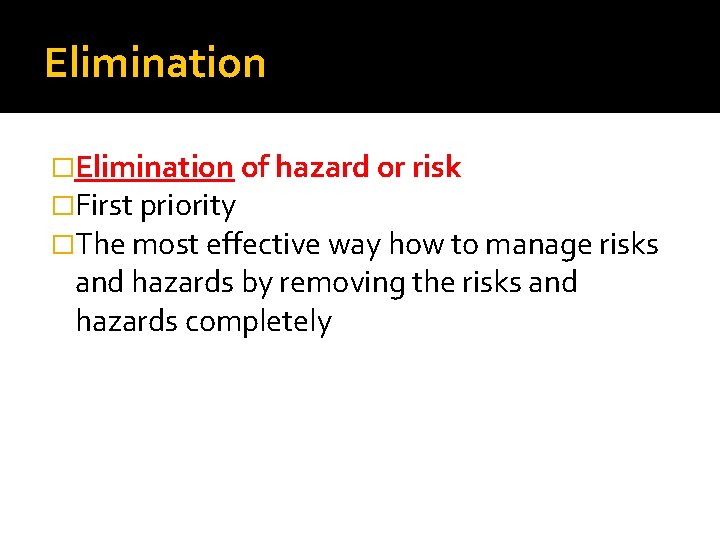
Elimination �Elimination of hazard or risk �First priority �The most effective way how to manage risks and hazards by removing the risks and hazards completely
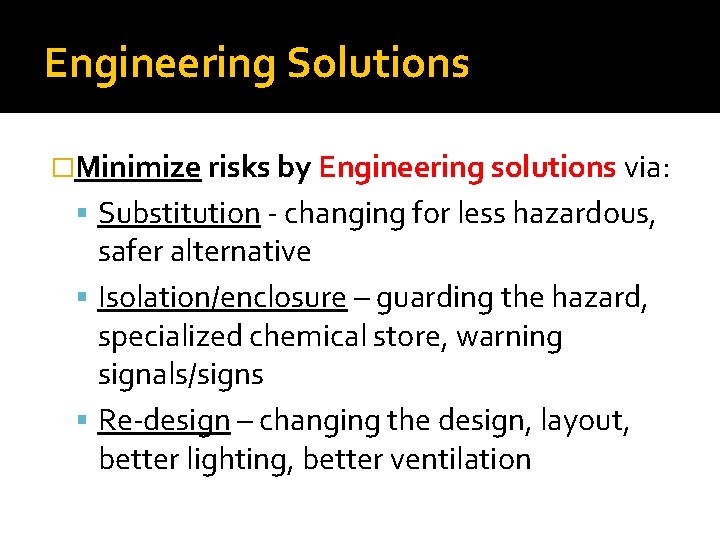
Engineering Solutions �Minimize risks by Engineering solutions via: Substitution - changing for less hazardous, safer alternative Isolation/enclosure – guarding the hazard, specialized chemical store, warning signals/signs Re-design – changing the design, layout, better lighting, better ventilation
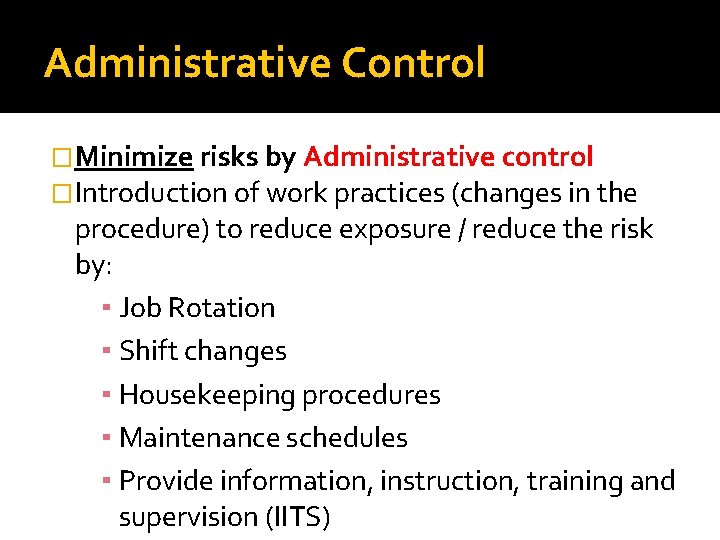
Administrative Control �Minimize risks by Administrative control �Introduction of work practices (changes in the procedure) to reduce exposure / reduce the risk by: ▪ Job Rotation ▪ Shift changes ▪ Housekeeping procedures ▪ Maintenance schedules ▪ Provide information, instruction, training and supervision (IITS)
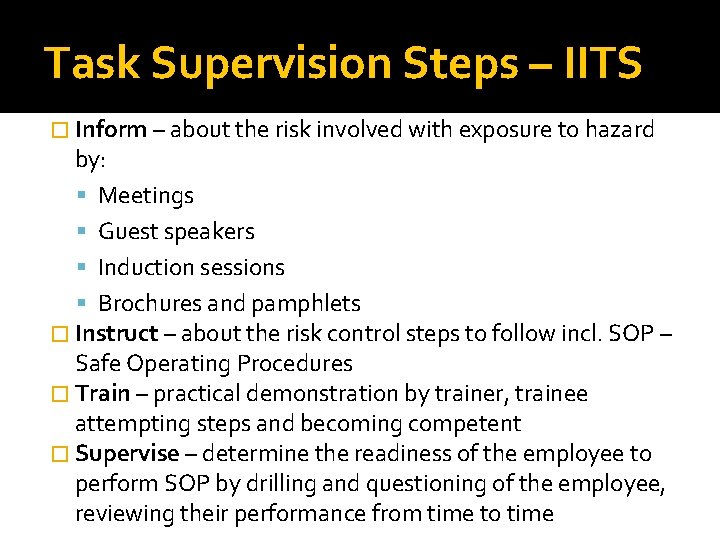
Task Supervision Steps – IITS � Inform – about the risk involved with exposure to hazard by: Meetings Guest speakers Induction sessions Brochures and pamphlets � Instruct – about the risk control steps to follow incl. SOP – Safe Operating Procedures � Train – practical demonstration by trainer, trainee attempting steps and becoming competent � Supervise – determine the readiness of the employee to perform SOP by drilling and questioning of the employee, reviewing their performance from time to time
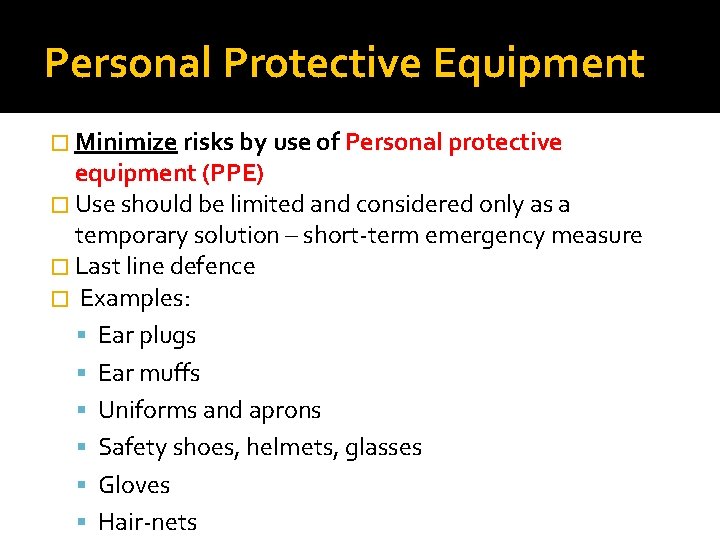
Personal Protective Equipment � Minimize risks by use of Personal protective equipment (PPE) � Use should be limited and considered only as a temporary solution – short-term emergency measure � Last line defence � Examples: Ear plugs Ear muffs Uniforms and aprons Safety shoes, helmets, glasses Gloves Hair-nets
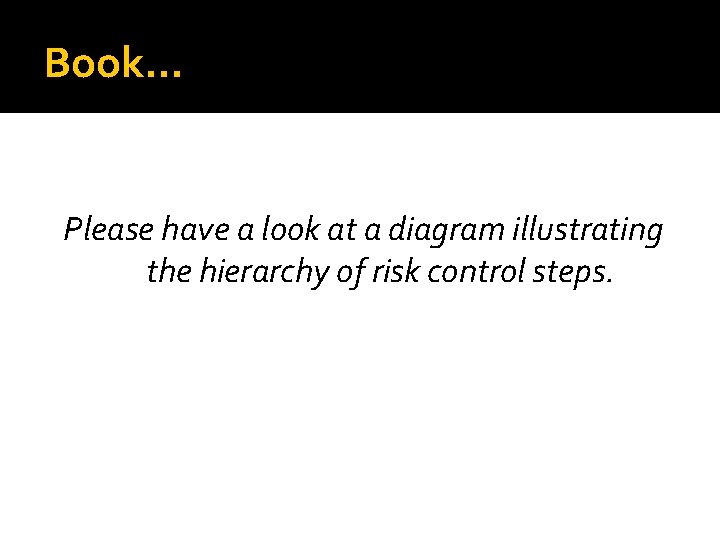
Book… Please have a look at a diagram illustrating the hierarchy of risk control steps.
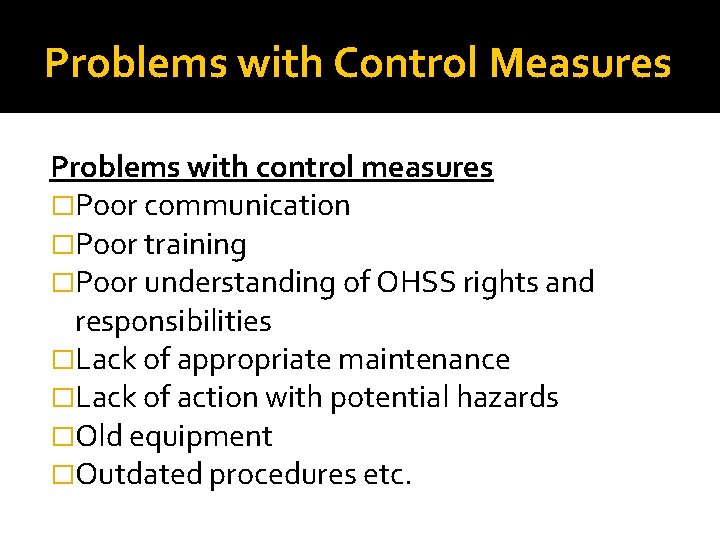
Problems with Control Measures Problems with control measures �Poor communication �Poor training �Poor understanding of OHSS rights and responsibilities �Lack of appropriate maintenance �Lack of action with potential hazards �Old equipment �Outdated procedures etc.
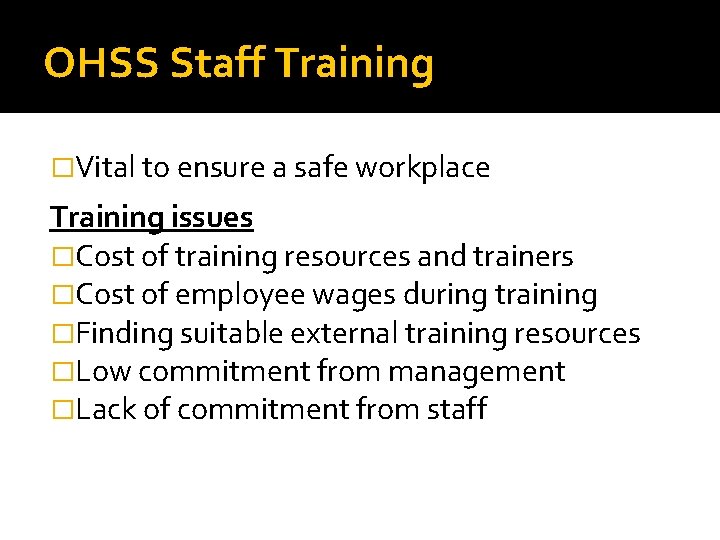
OHSS Staff Training �Vital to ensure a safe workplace Training issues �Cost of training resources and trainers �Cost of employee wages during training �Finding suitable external training resources �Low commitment from management �Lack of commitment from staff
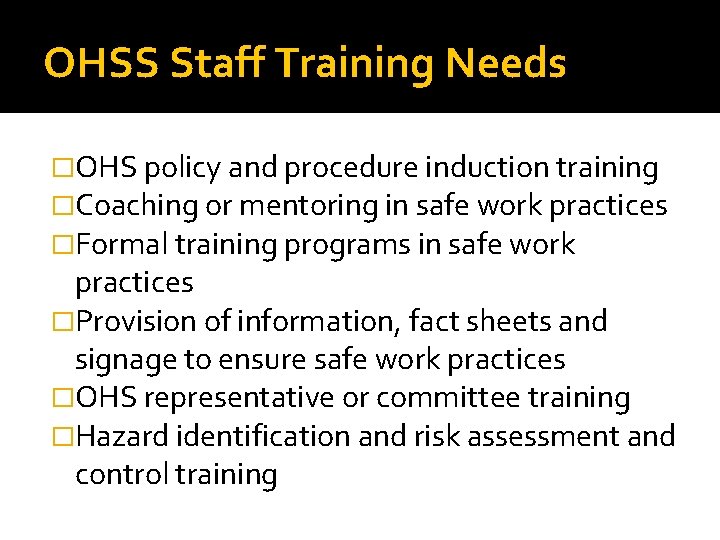
OHSS Staff Training Needs �OHS policy and procedure induction training �Coaching or mentoring in safe work practices �Formal training programs in safe work practices �Provision of information, fact sheets and signage to ensure safe work practices �OHS representative or committee training �Hazard identification and risk assessment and control training
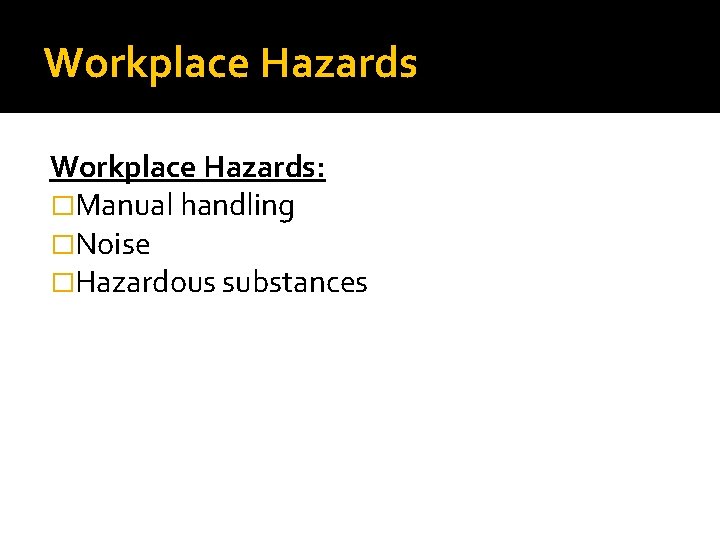
Workplace Hazards: �Manual handling �Noise �Hazardous substances
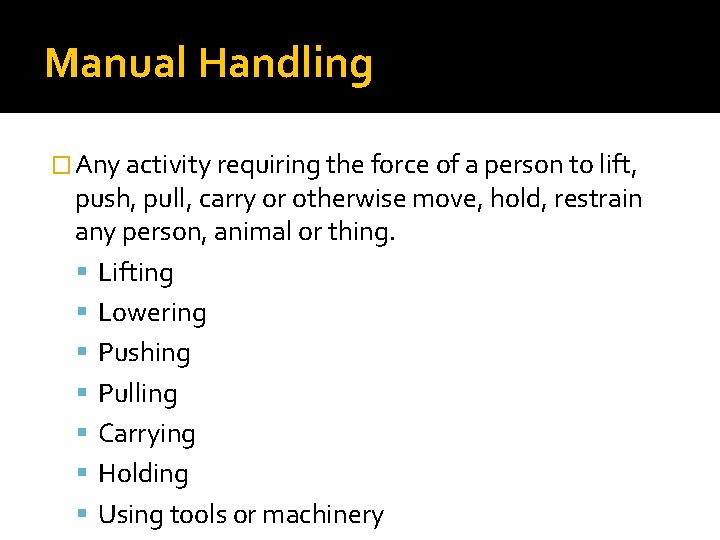
Manual Handling � Any activity requiring the force of a person to lift, push, pull, carry or otherwise move, hold, restrain any person, animal or thing. Lifting Lowering Pushing Pulling Carrying Holding Using tools or machinery
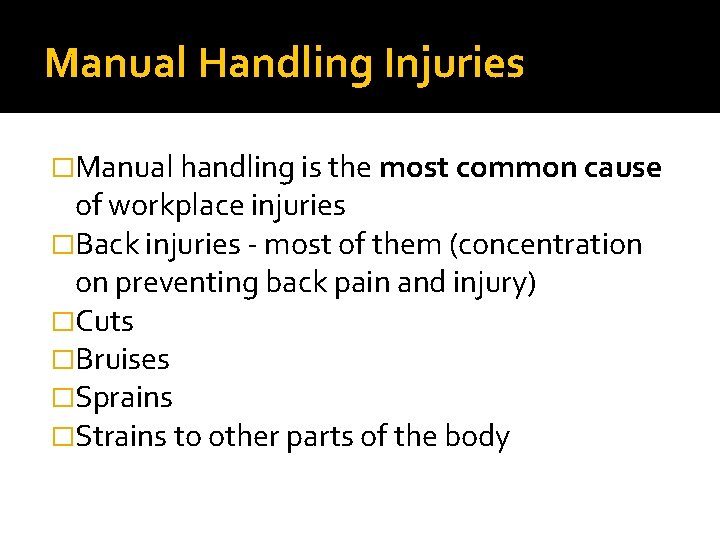
Manual Handling Injuries �Manual handling is the most common cause of workplace injuries �Back injuries - most of them (concentration on preventing back pain and injury) �Cuts �Bruises �Sprains �Strains to other parts of the body
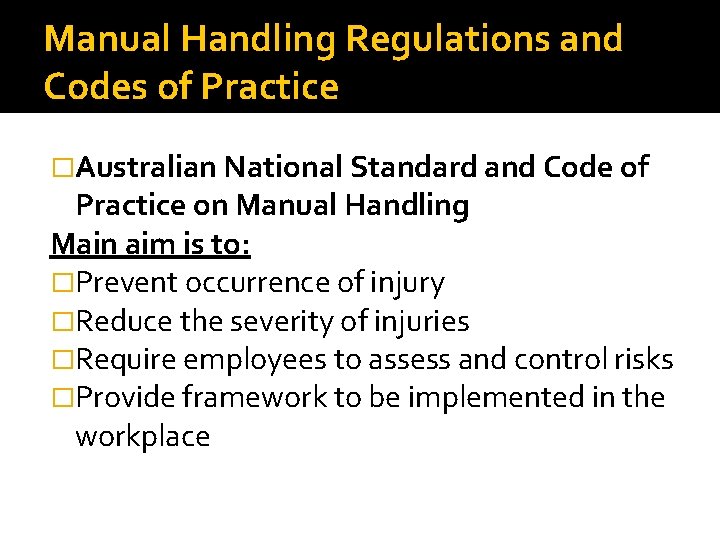
Manual Handling Regulations and Codes of Practice �Australian National Standard and Code of Practice on Manual Handling Main aim is to: �Prevent occurrence of injury �Reduce the severity of injuries �Require employees to assess and control risks �Provide framework to be implemented in the workplace
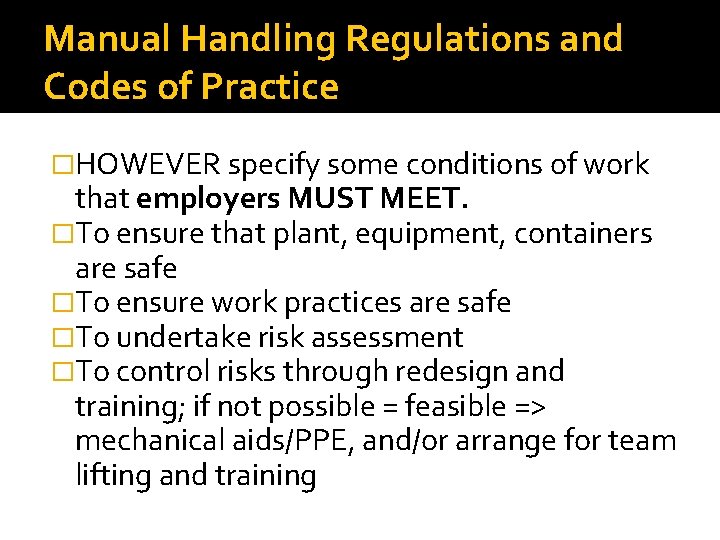
Manual Handling Regulations and Codes of Practice �HOWEVER specify some conditions of work that employers MUST MEET. �To ensure that plant, equipment, containers are safe �To ensure work practices are safe �To undertake risk assessment �To control risks through redesign and training; if not possible = feasible => mechanical aids/PPE, and/or arrange for team lifting and training
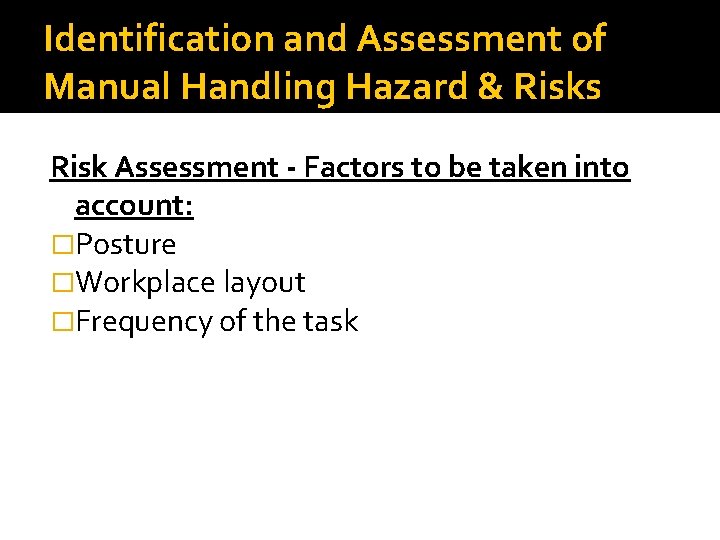
Identification and Assessment of Manual Handling Hazard & Risks Risk Assessment - Factors to be taken into account: �Posture �Workplace layout �Frequency of the task
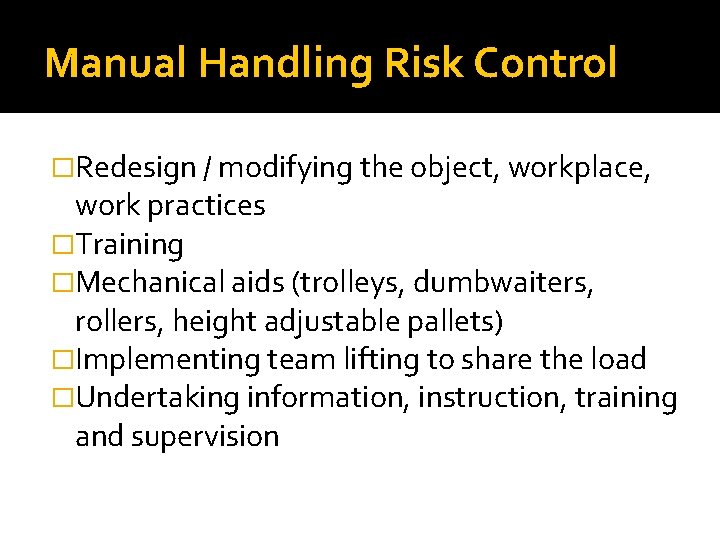
Manual Handling Risk Control �Redesign / modifying the object, workplace, work practices �Training �Mechanical aids (trolleys, dumbwaiters, rollers, height adjustable pallets) �Implementing team lifting to share the load �Undertaking information, instruction, training and supervision
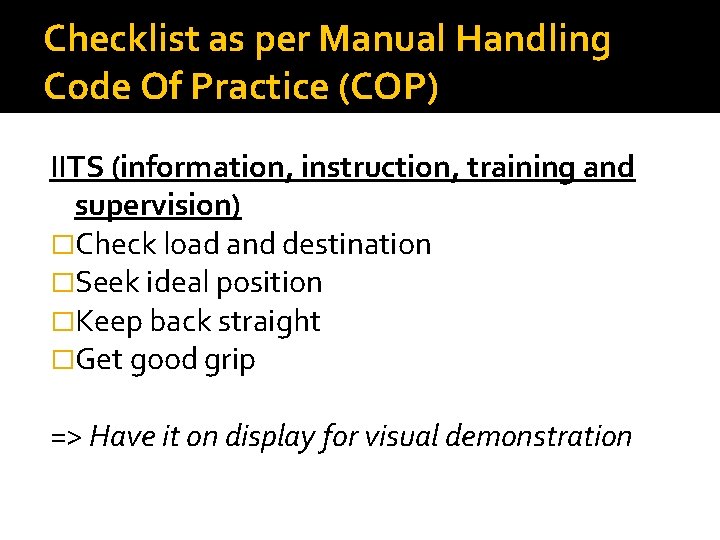
Checklist as per Manual Handling Code Of Practice (COP) IITS (information, instruction, training and supervision) �Check load and destination �Seek ideal position �Keep back straight �Get good grip => Have it on display for visual demonstration
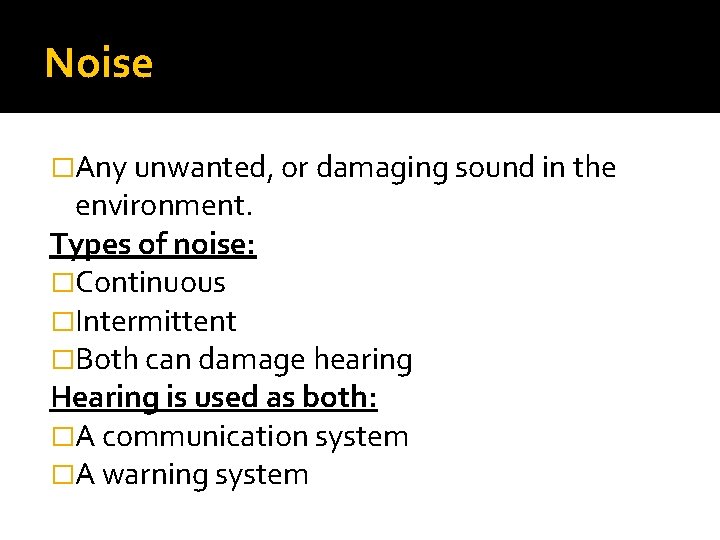
Noise �Any unwanted, or damaging sound in the environment. Types of noise: �Continuous �Intermittent �Both can damage hearing Hearing is used as both: �A communication system �A warning system
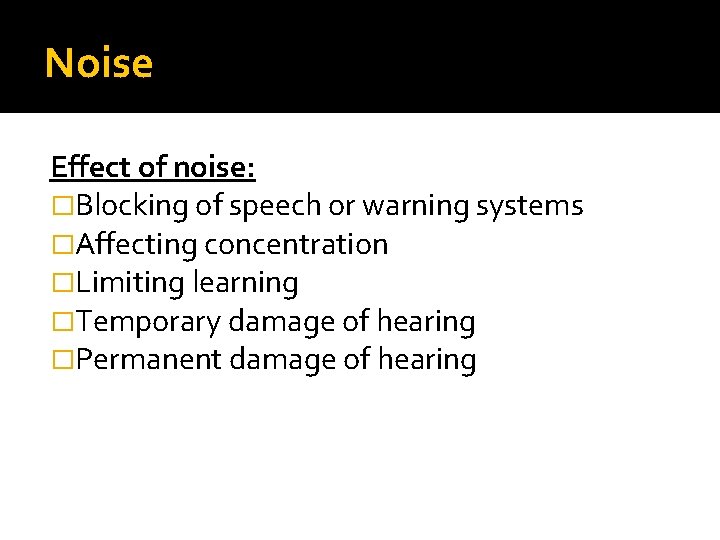
Noise Effect of noise: �Blocking of speech or warning systems �Affecting concentration �Limiting learning �Temporary damage of hearing �Permanent damage of hearing
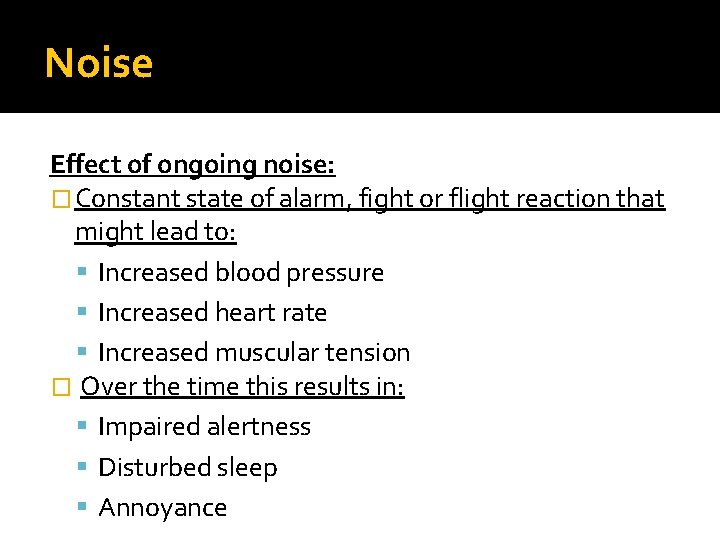
Noise Effect of ongoing noise: � Constant state of alarm, fight or flight reaction that might lead to: Increased blood pressure Increased heart rate Increased muscular tension � Over the time this results in: Impaired alertness Disturbed sleep Annoyance
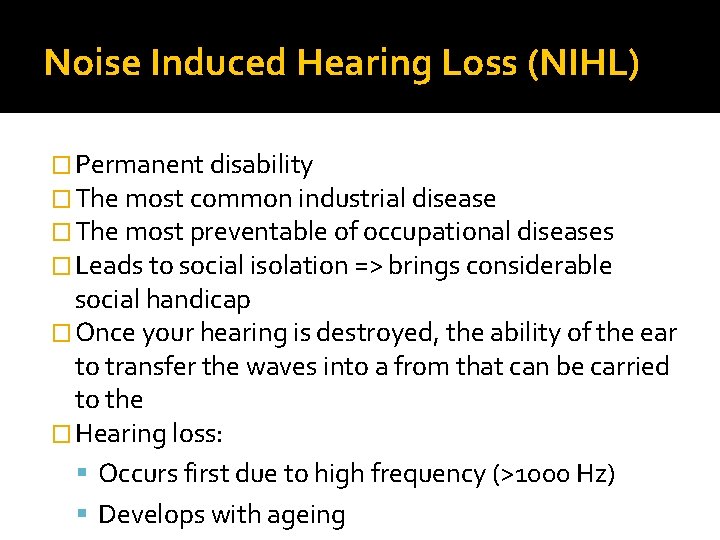
Noise Induced Hearing Loss (NIHL) � Permanent disability � The most common industrial disease � The most preventable of occupational diseases � Leads to social isolation => brings considerable social handicap � Once your hearing is destroyed, the ability of the ear to transfer the waves into a from that can be carried to the � Hearing loss: Occurs first due to high frequency (>1000 Hz) Develops with ageing
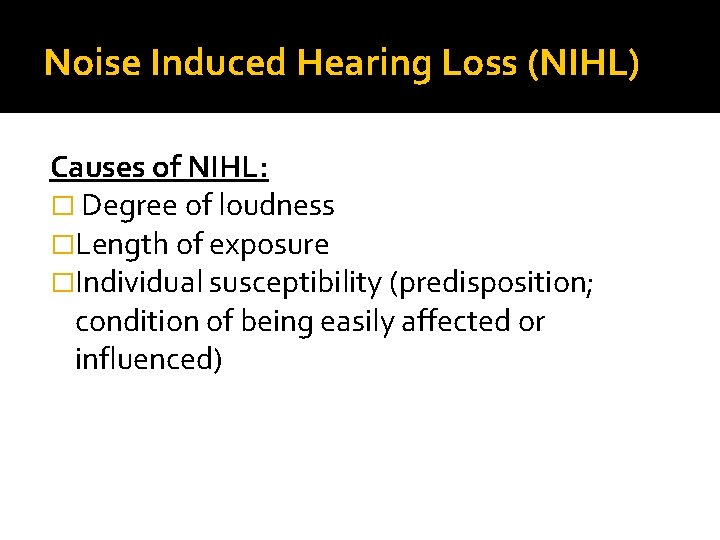
Noise Induced Hearing Loss (NIHL) Causes of NIHL: � Degree of loudness �Length of exposure �Individual susceptibility (predisposition; condition of being easily affected or influenced)
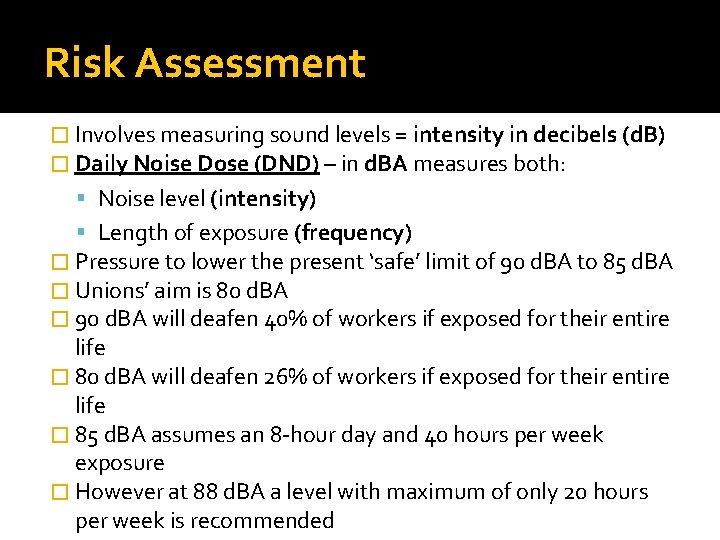
Risk Assessment � Involves measuring sound levels = intensity in decibels (d. B) � Daily Noise Dose (DND) – in d. BA measures both: Noise level (intensity) Length of exposure (frequency) � Pressure to lower the present ‘safe’ limit of 90 d. BA to 85 d. BA � Unions’ aim is 80 d. BA � 90 d. BA will deafen 40% of workers if exposed for their entire life � 80 d. BA will deafen 26% of workers if exposed for their entire life � 85 d. BA assumes an 8 -hour day and 40 hours per week exposure � However at 88 d. BA a level with maximum of only 20 hours per week is recommended
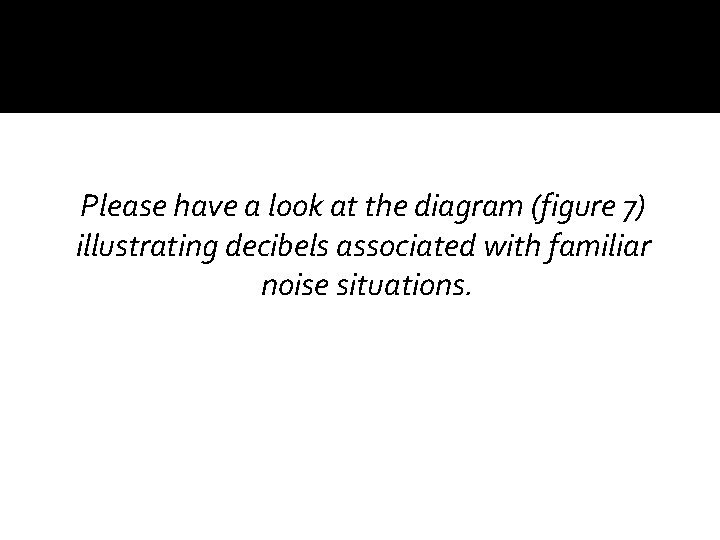
Please have a look at the diagram (figure 7) illustrating decibels associated with familiar noise situations.
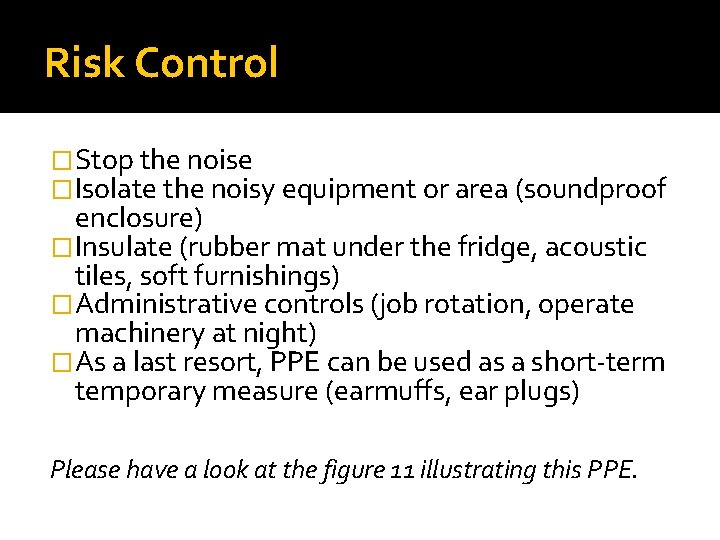
Risk Control �Stop the noise �Isolate the noisy equipment or area (soundproof enclosure) �Insulate (rubber mat under the fridge, acoustic tiles, soft furnishings) �Administrative controls (job rotation, operate machinery at night) �As a last resort, PPE can be used as a short-term temporary measure (earmuffs, ear plugs) Please have a look at the figure 11 illustrating this PPE.
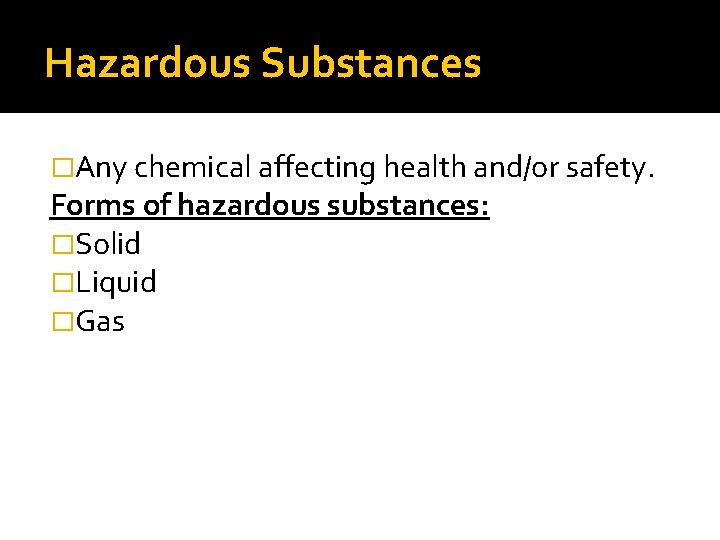
Hazardous Substances �Any chemical affecting health and/or safety. Forms of hazardous substances: �Solid �Liquid �Gas
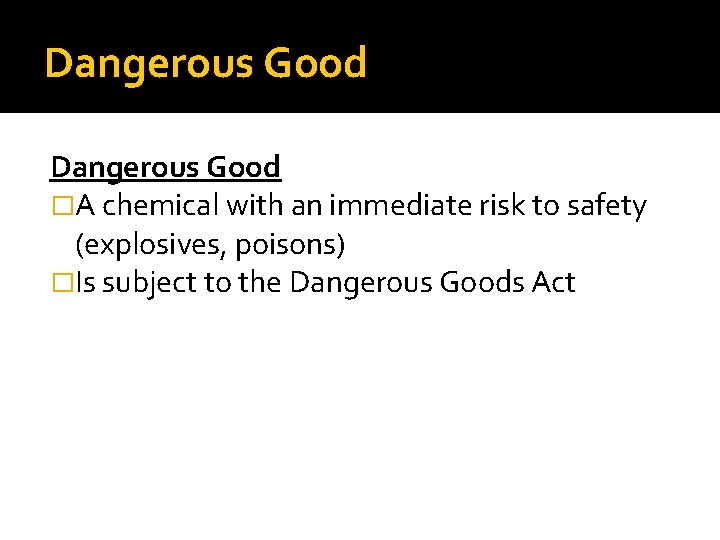
Dangerous Good �A chemical with an immediate risk to safety (explosives, poisons) �Is subject to the Dangerous Goods Act
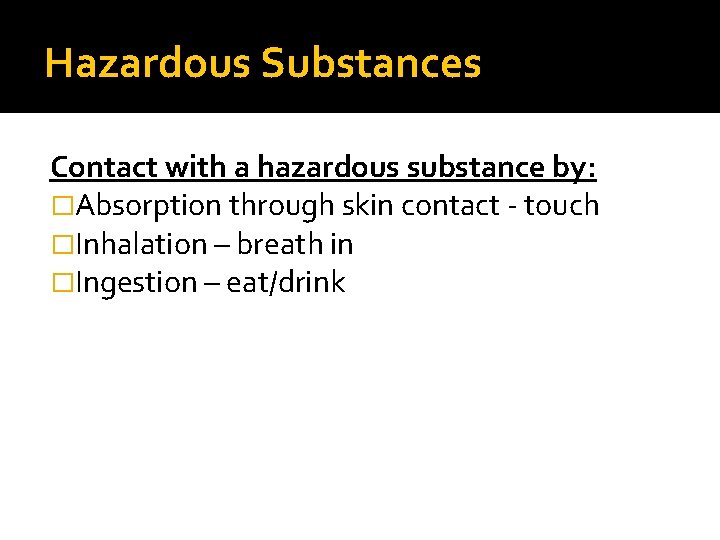
Hazardous Substances Contact with a hazardous substance by: �Absorption through skin contact - touch �Inhalation – breath in �Ingestion – eat/drink
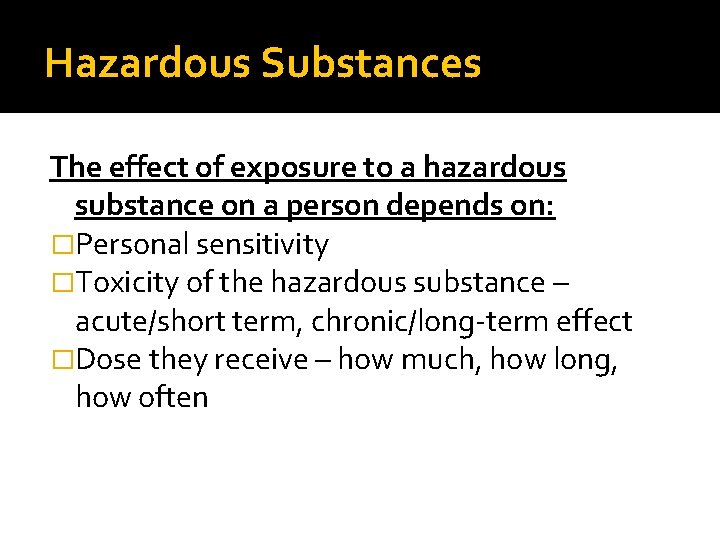
Hazardous Substances The effect of exposure to a hazardous substance on a person depends on: �Personal sensitivity �Toxicity of the hazardous substance – acute/short term, chronic/long-term effect �Dose they receive – how much, how long, how often
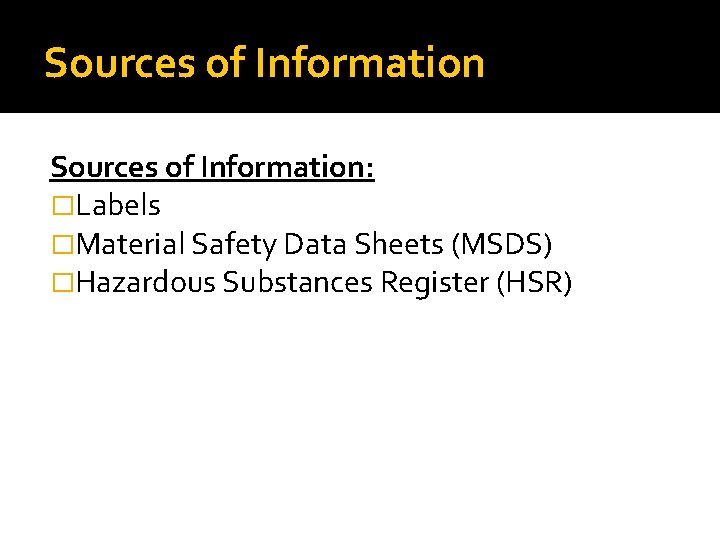
Sources of Information: �Labels �Material Safety Data Sheets (MSDS) �Hazardous Substances Register (HSR)
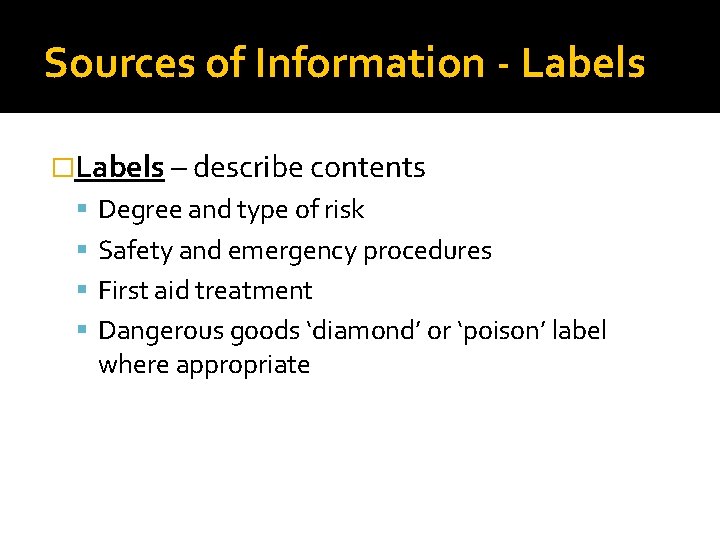
Sources of Information - Labels �Labels – describe contents Degree and type of risk Safety and emergency procedures First aid treatment Dangerous goods ‘diamond’ or ‘poison’ label where appropriate
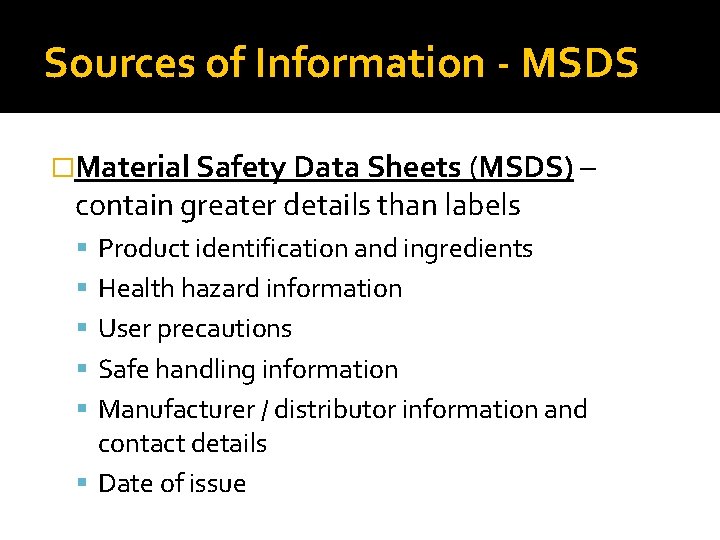
Sources of Information - MSDS �Material Safety Data Sheets (MSDS) – contain greater details than labels Product identification and ingredients Health hazard information User precautions Safe handling information Manufacturer / distributor information and contact details Date of issue
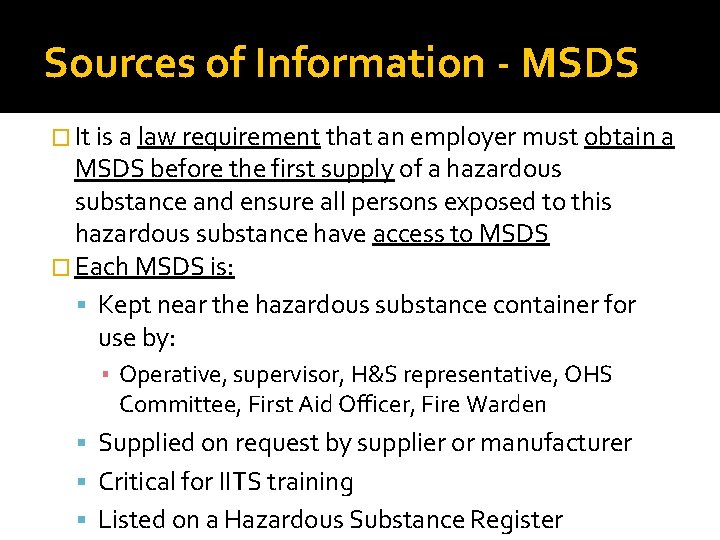
Sources of Information - MSDS � It is a law requirement that an employer must obtain a MSDS before the first supply of a hazardous substance and ensure all persons exposed to this hazardous substance have access to MSDS � Each MSDS is: Kept near the hazardous substance container for use by: ▪ Operative, supervisor, H&S representative, OHS Committee, First Aid Officer, Fire Warden Supplied on request by supplier or manufacturer Critical for IITS training Listed on a Hazardous Substance Register
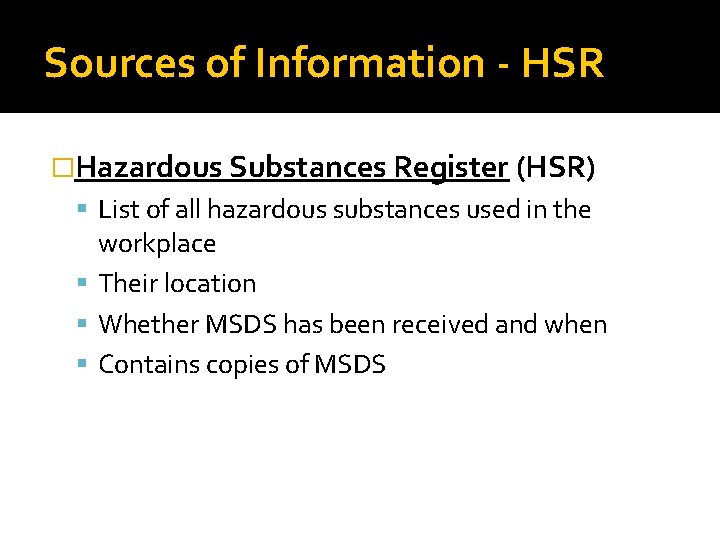
Sources of Information - HSR �Hazardous Substances Register (HSR) List of all hazardous substances used in the workplace Their location Whether MSDS has been received and when Contains copies of MSDS

Sources of Information - HSR �It is a law requirement that an employer must ensure a register is kept and maintained for all hazardous substances used at the workplace �Access to HSR should be given to: Employees Emergency services Government authorities �It is a law requirement that the use of hazardous substances in the workplace must be reviewed at least every 5 years
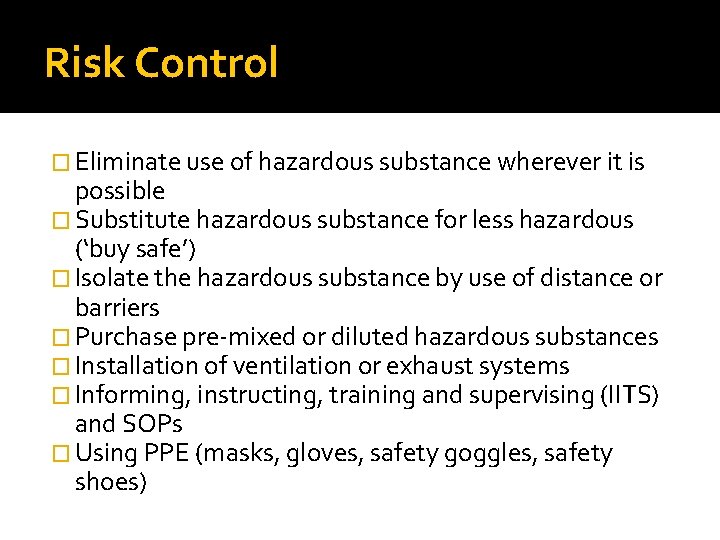
Risk Control � Eliminate use of hazardous substance wherever it is possible � Substitute hazardous substance for less hazardous (‘buy safe’) � Isolate the hazardous substance by use of distance or barriers � Purchase pre-mixed or diluted hazardous substances � Installation of ventilation or exhaust systems � Informing, instructing, training and supervising (IITS) and SOPs � Using PPE (masks, gloves, safety goggles, safety shoes)
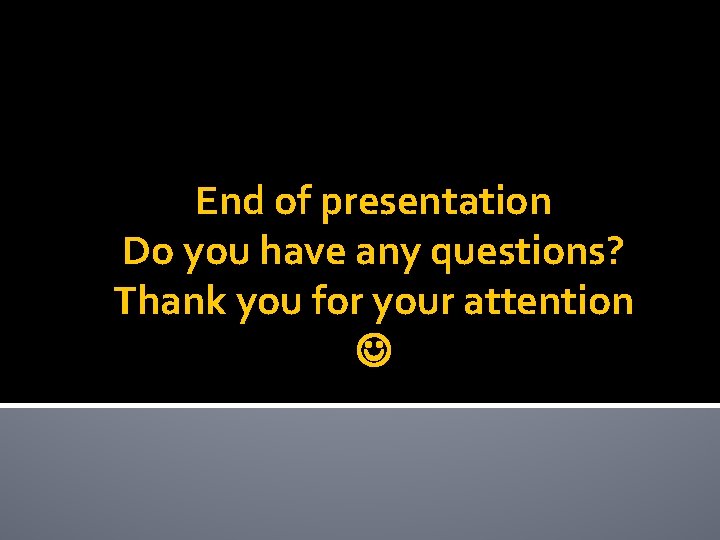
End of presentation Do you have any questions? Thank you for your attention
Ict workplace health and safety
Develop and implement a food safety program
How to monitor and improve workplace operations
Sitxfsa001a
Implement food safety procedures
Workplace hazard
Eeeme
Mis issues in strategy implementation
Implement change management with these six steps
Osha safety signs and symbols
Safety at work vocabulary
Chapter 10 workplace safety procedures
Back safety in the workplace
Osha safety videos
Sun safety in the workplace
Office hazards
What are two goals of storing knives correctly
Health and safety management system template
Hsg218
Hsg218
Hazard communication safety training quiz answers
Gregory carter
Touch current vs leakage current
Eschew the implement of correction and vitiate the scion
Implement tasks that promote reasoning and problem solving
Classes salsa and swing implement an interface dance
Medicinal preparation definition
Workplace health without borders
Federal public service workplace mental health strategy
Federal public service workplace mental health strategy
Toxic hazard symbol
Health hazard
Health hazard examples
Hazard management cycle vs park model
Pc health monitor
Monitor health status
Non invasive health monitor
Reiser implement
Permanent product recording aba
Implement steering
Acquiring capital to implement strategies
Bandenmaten
Develop vs implement
Your startup wants to implement an order fulfillment
Storage area network diagram
Polynomial addition in data structure using linked list
Why are user interfaces hard to implement
3 stage pipeline arm organization