GLAST LAT Project March 24 2003 GLAST Large
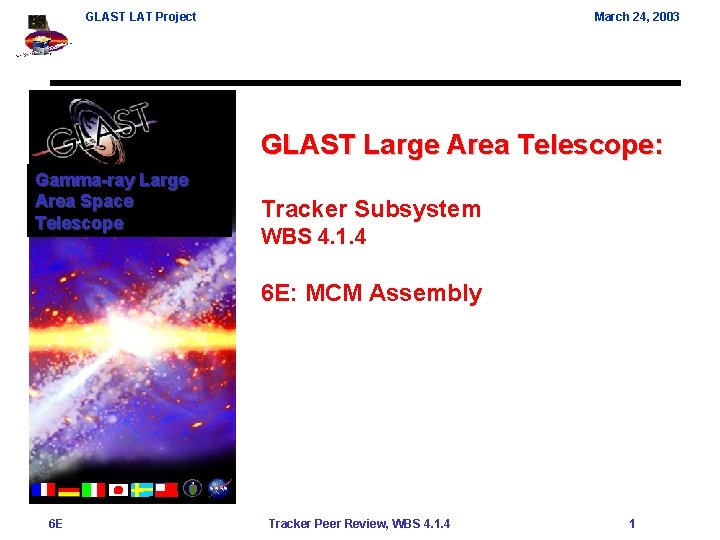
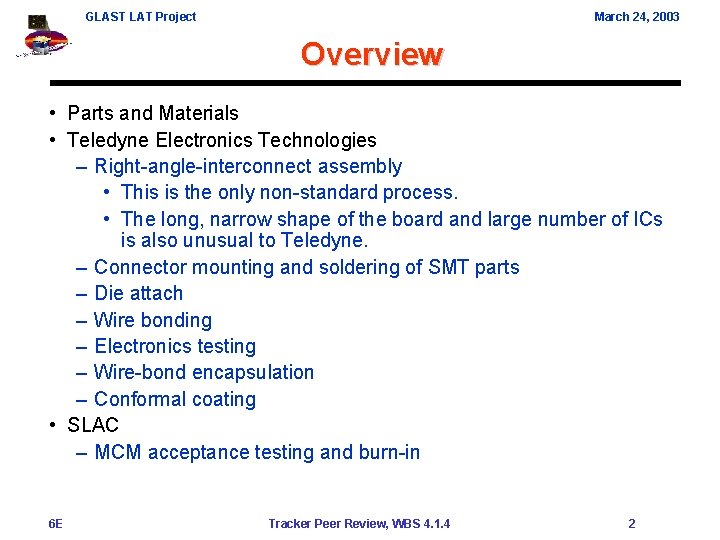
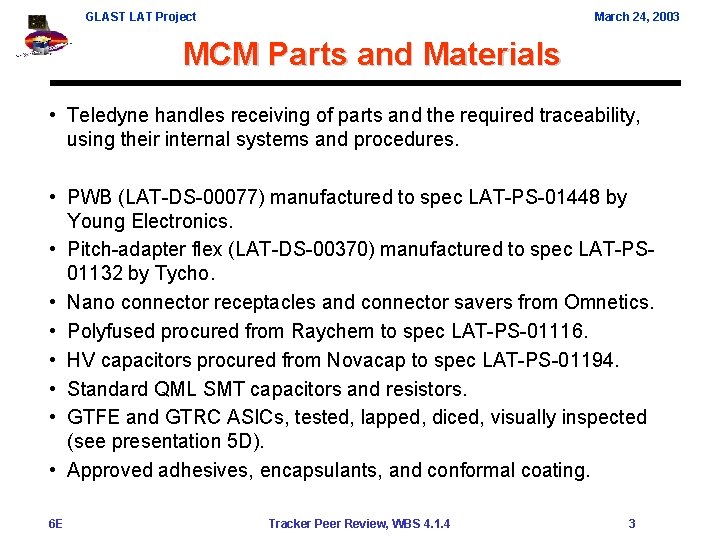
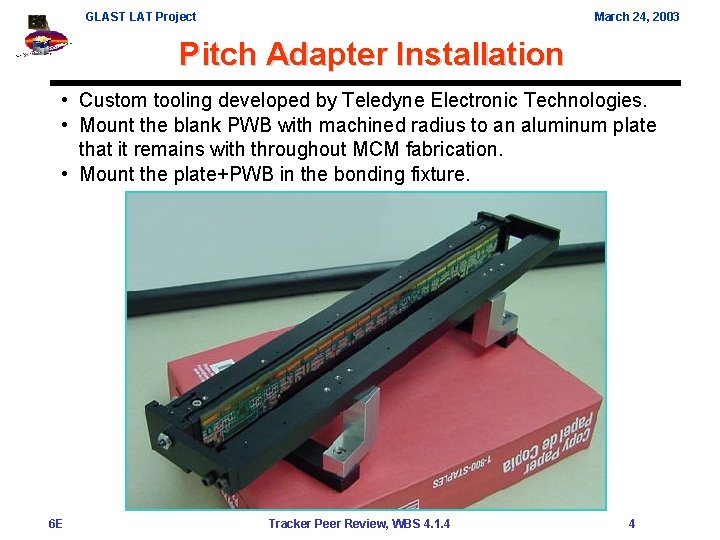
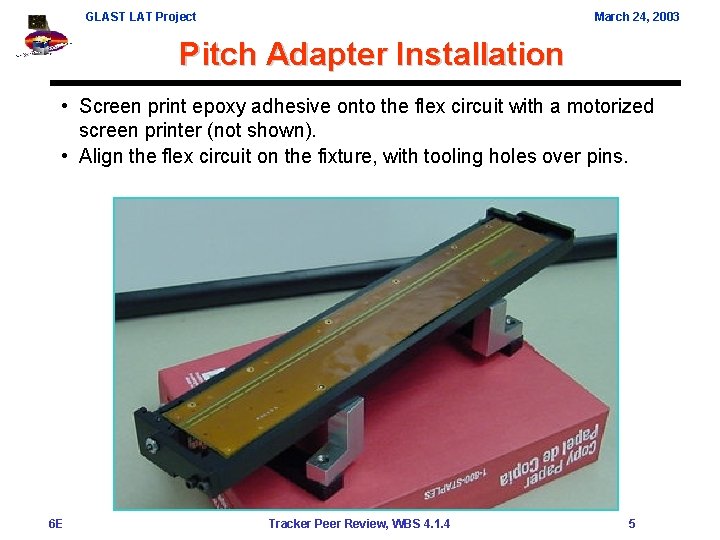
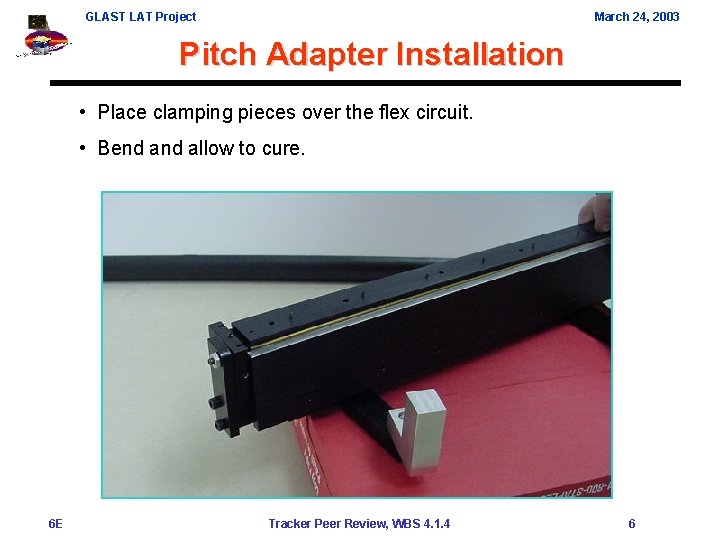
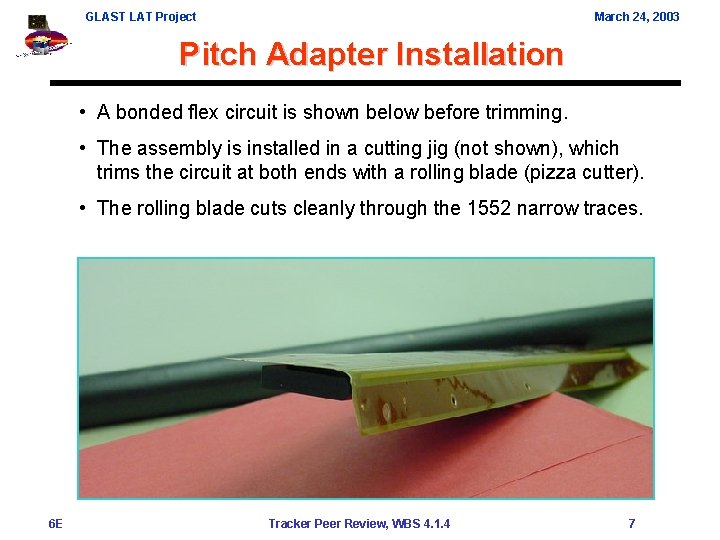
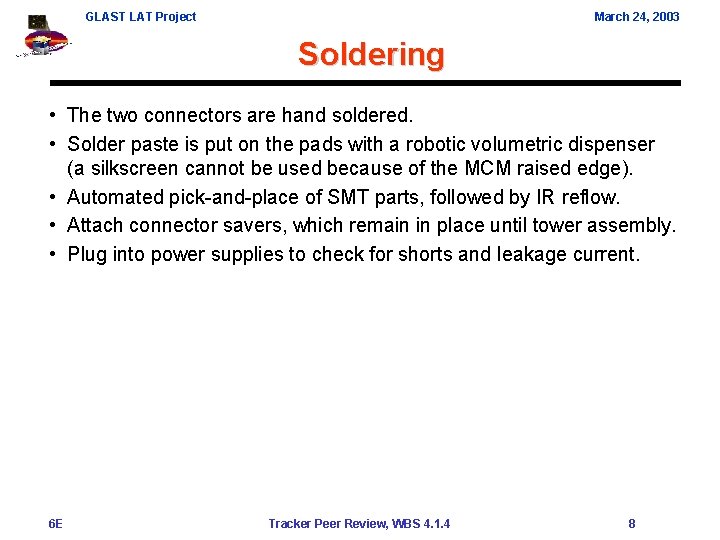
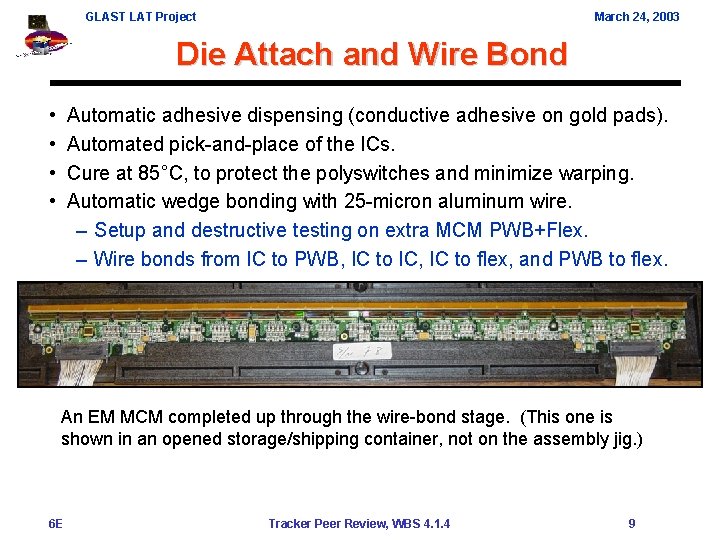
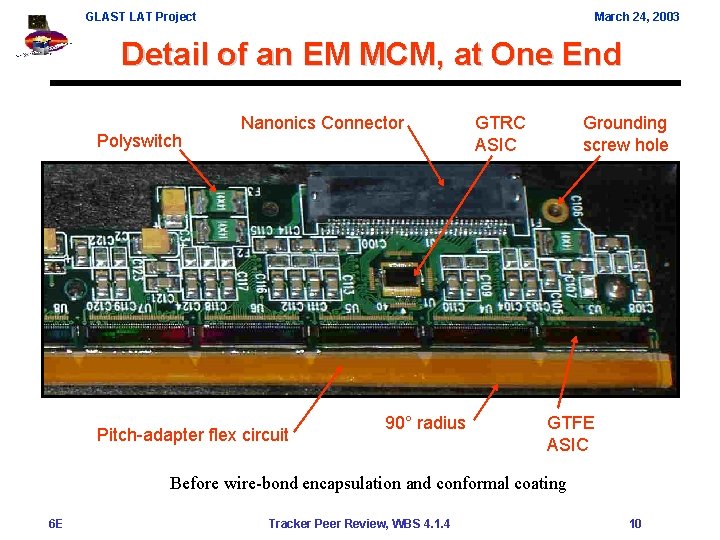
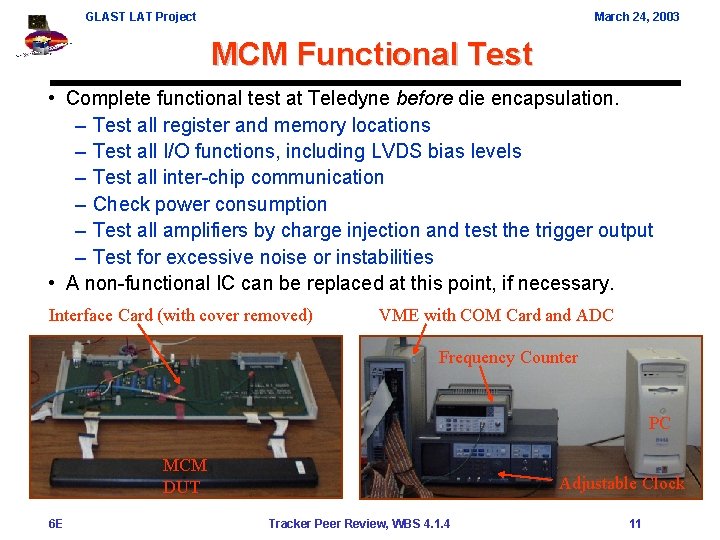
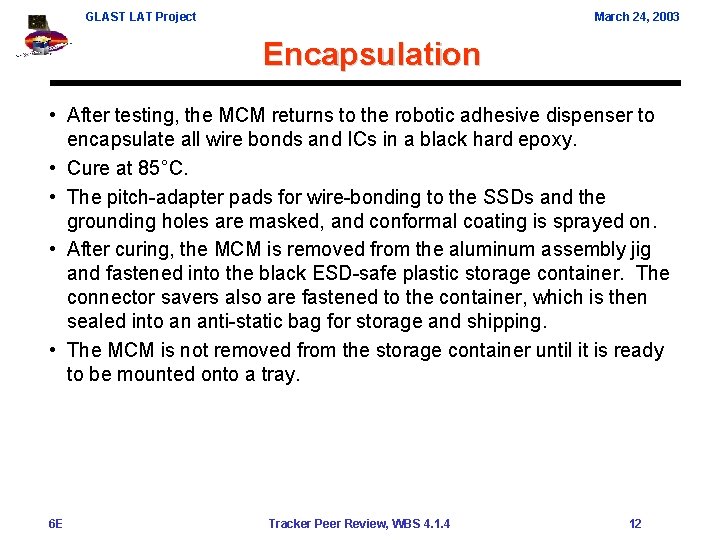
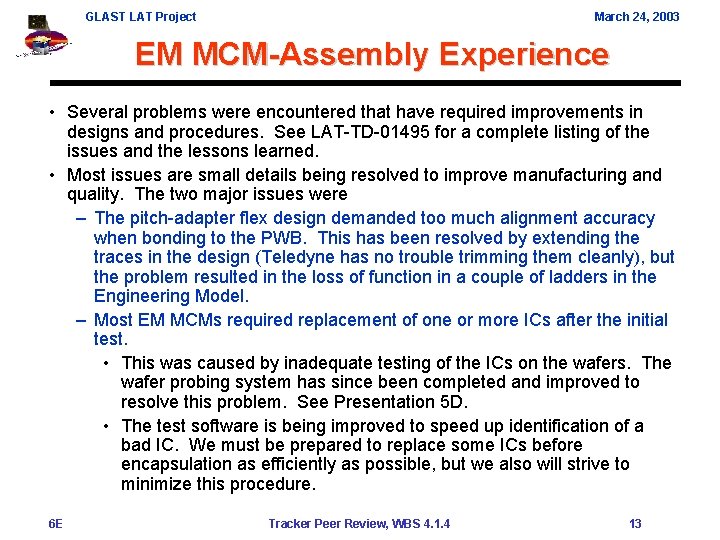
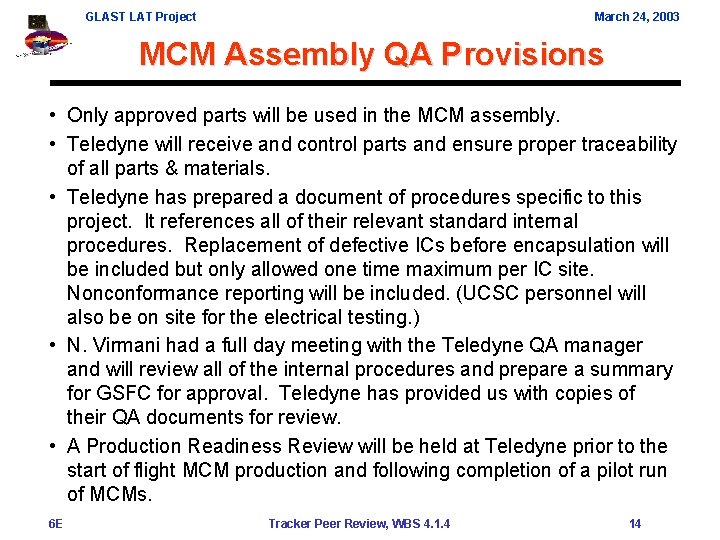
- Slides: 14
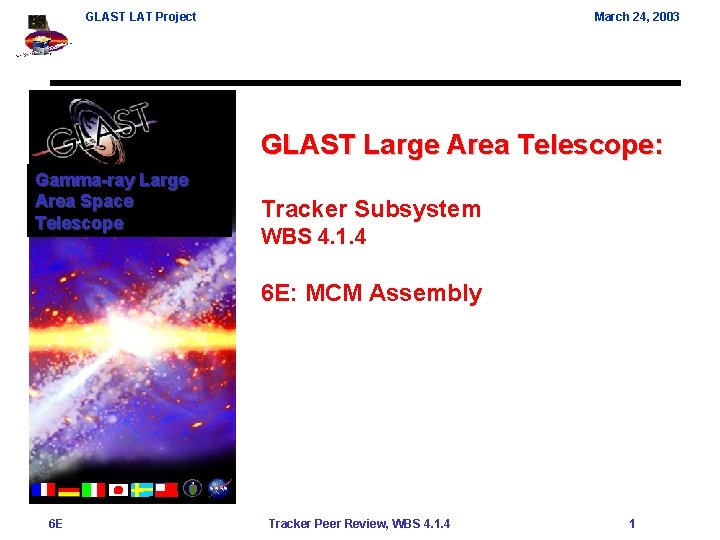
GLAST LAT Project March 24, 2003 GLAST Large Area Telescope: Gamma-ray Large Area Space Telescope Tracker Subsystem WBS 4. 1. 4 6 E: MCM Assembly 6 E Tracker Peer Review, WBS 4. 1. 4 1
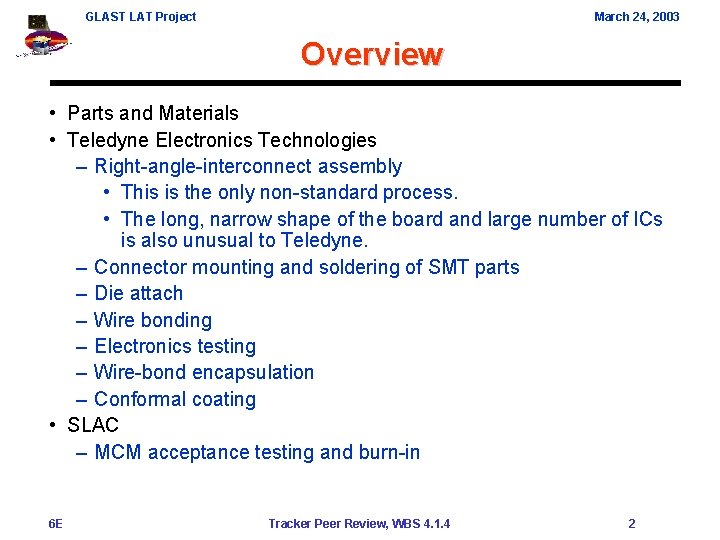
GLAST LAT Project March 24, 2003 Overview • Parts and Materials • Teledyne Electronics Technologies – Right-angle-interconnect assembly • This is the only non-standard process. • The long, narrow shape of the board and large number of ICs is also unusual to Teledyne. – Connector mounting and soldering of SMT parts – Die attach – Wire bonding – Electronics testing – Wire-bond encapsulation – Conformal coating • SLAC – MCM acceptance testing and burn-in 6 E Tracker Peer Review, WBS 4. 1. 4 2
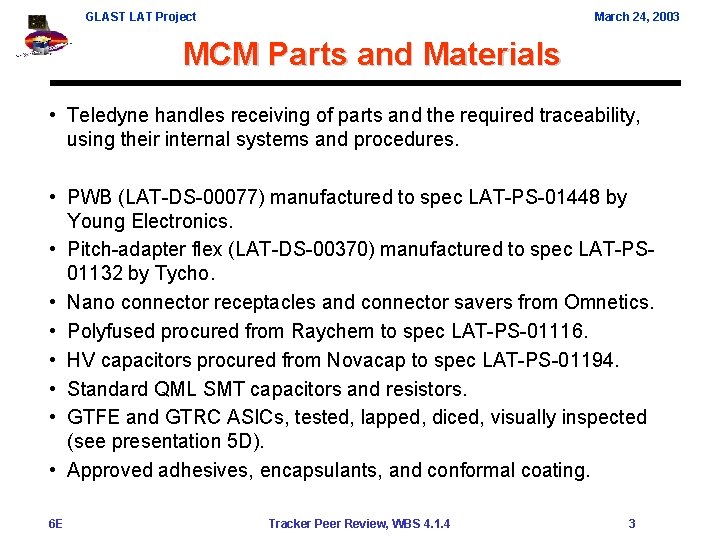
GLAST LAT Project March 24, 2003 MCM Parts and Materials • Teledyne handles receiving of parts and the required traceability, using their internal systems and procedures. • PWB (LAT-DS-00077) manufactured to spec LAT-PS-01448 by Young Electronics. • Pitch-adapter flex (LAT-DS-00370) manufactured to spec LAT-PS 01132 by Tycho. • Nano connector receptacles and connector savers from Omnetics. • Polyfused procured from Raychem to spec LAT-PS-01116. • HV capacitors procured from Novacap to spec LAT-PS-01194. • Standard QML SMT capacitors and resistors. • GTFE and GTRC ASICs, tested, lapped, diced, visually inspected (see presentation 5 D). • Approved adhesives, encapsulants, and conformal coating. 6 E Tracker Peer Review, WBS 4. 1. 4 3
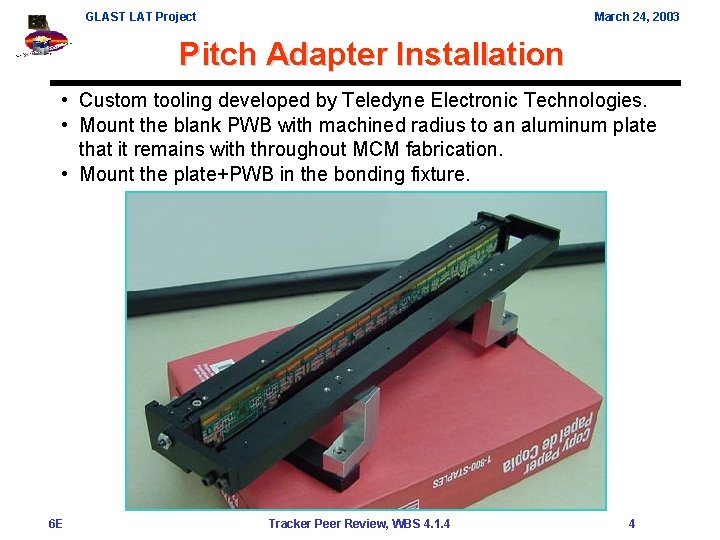
GLAST LAT Project March 24, 2003 Pitch Adapter Installation • Custom tooling developed by Teledyne Electronic Technologies. • Mount the blank PWB with machined radius to an aluminum plate that it remains with throughout MCM fabrication. • Mount the plate+PWB in the bonding fixture. 6 E Tracker Peer Review, WBS 4. 1. 4 4
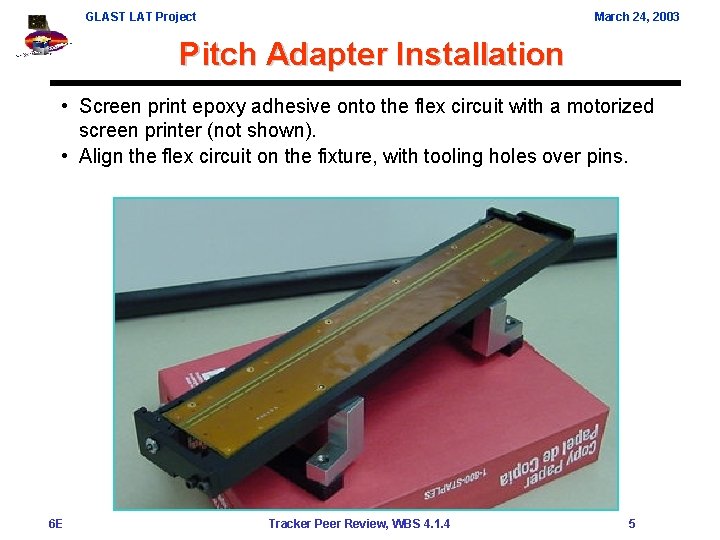
GLAST LAT Project March 24, 2003 Pitch Adapter Installation • Screen print epoxy adhesive onto the flex circuit with a motorized screen printer (not shown). • Align the flex circuit on the fixture, with tooling holes over pins. 6 E Tracker Peer Review, WBS 4. 1. 4 5
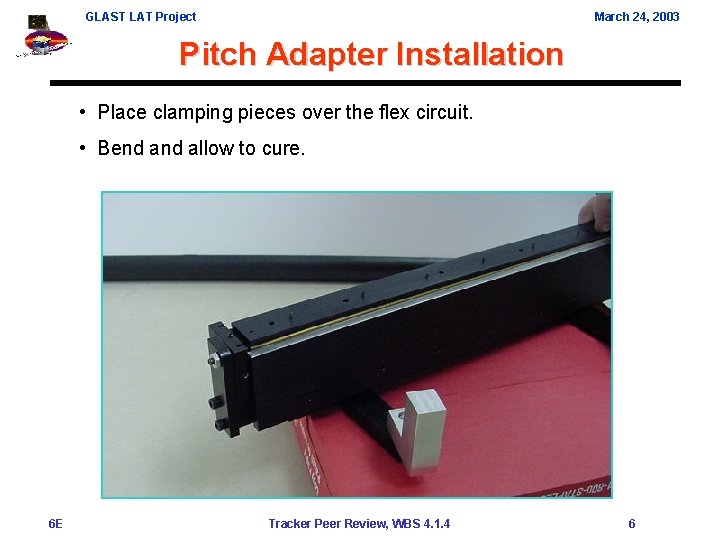
GLAST LAT Project March 24, 2003 Pitch Adapter Installation • Place clamping pieces over the flex circuit. • Bend allow to cure. 6 E Tracker Peer Review, WBS 4. 1. 4 6
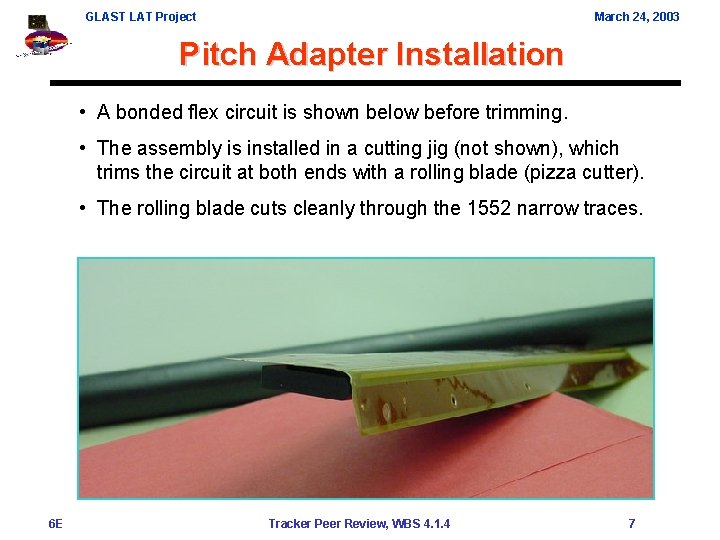
GLAST LAT Project March 24, 2003 Pitch Adapter Installation • A bonded flex circuit is shown below before trimming. • The assembly is installed in a cutting jig (not shown), which trims the circuit at both ends with a rolling blade (pizza cutter). • The rolling blade cuts cleanly through the 1552 narrow traces. 6 E Tracker Peer Review, WBS 4. 1. 4 7
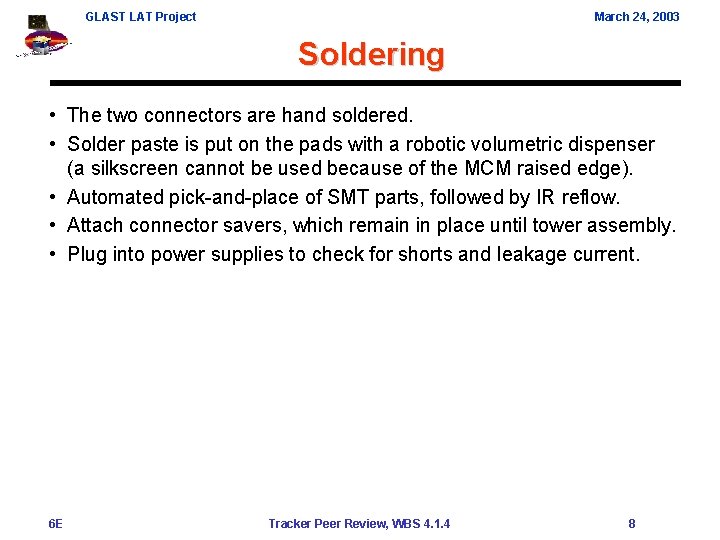
GLAST LAT Project March 24, 2003 Soldering • The two connectors are hand soldered. • Solder paste is put on the pads with a robotic volumetric dispenser (a silkscreen cannot be used because of the MCM raised edge). • Automated pick-and-place of SMT parts, followed by IR reflow. • Attach connector savers, which remain in place until tower assembly. • Plug into power supplies to check for shorts and leakage current. 6 E Tracker Peer Review, WBS 4. 1. 4 8
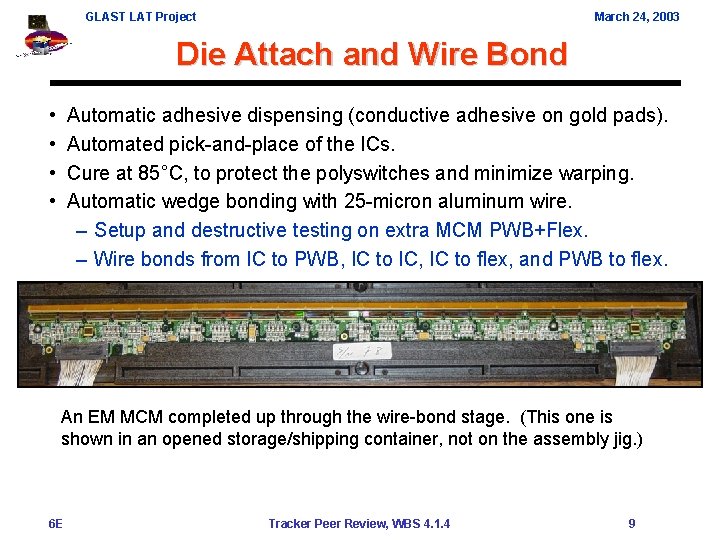
GLAST LAT Project March 24, 2003 Die Attach and Wire Bond • • Automatic adhesive dispensing (conductive adhesive on gold pads). Automated pick-and-place of the ICs. Cure at 85°C, to protect the polyswitches and minimize warping. Automatic wedge bonding with 25 -micron aluminum wire. – Setup and destructive testing on extra MCM PWB+Flex. – Wire bonds from IC to PWB, IC to IC, IC to flex, and PWB to flex. An EM MCM completed up through the wire-bond stage. (This one is shown in an opened storage/shipping container, not on the assembly jig. ) 6 E Tracker Peer Review, WBS 4. 1. 4 9
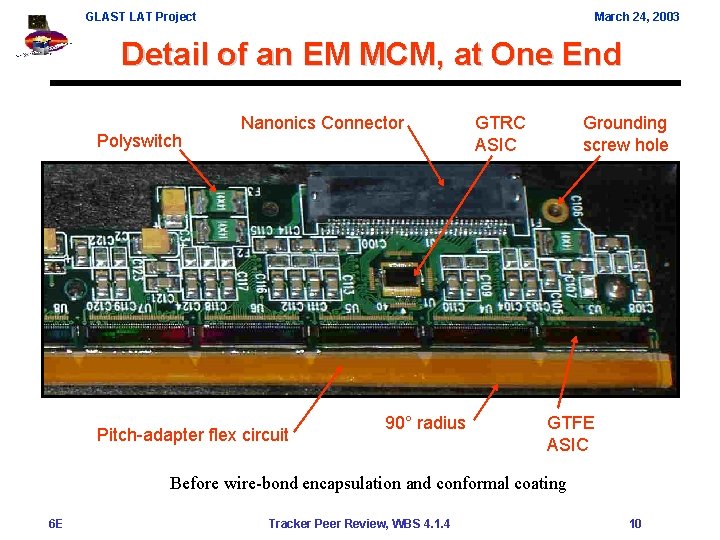
GLAST LAT Project March 24, 2003 Detail of an EM MCM, at One End Polyswitch Nanonics Connector Pitch-adapter flex circuit 90° radius GTRC ASIC Grounding screw hole GTFE ASIC Before wire-bond encapsulation and conformal coating 6 E Tracker Peer Review, WBS 4. 1. 4 10
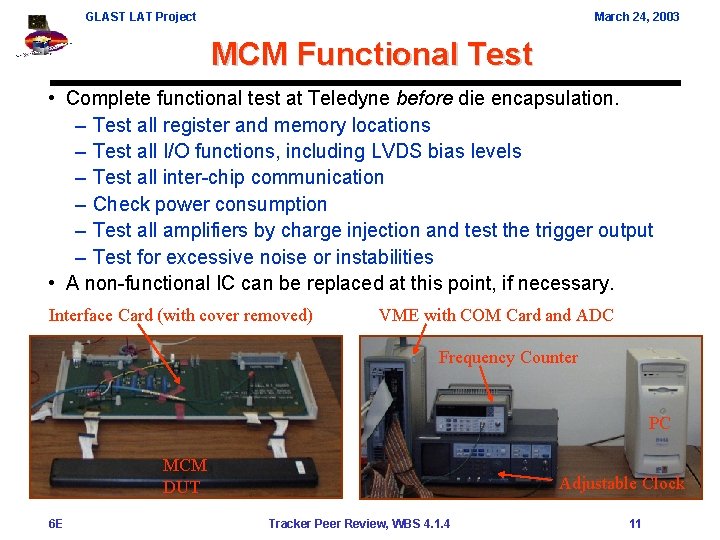
GLAST LAT Project March 24, 2003 MCM Functional Test • Complete functional test at Teledyne before die encapsulation. – Test all register and memory locations – Test all I/O functions, including LVDS bias levels – Test all inter-chip communication – Check power consumption – Test all amplifiers by charge injection and test the trigger output – Test for excessive noise or instabilities • A non-functional IC can be replaced at this point, if necessary. Interface Card (with cover removed) VME with COM Card and ADC Frequency Counter PC MCM DUT 6 E Adjustable Clock Tracker Peer Review, WBS 4. 1. 4 11
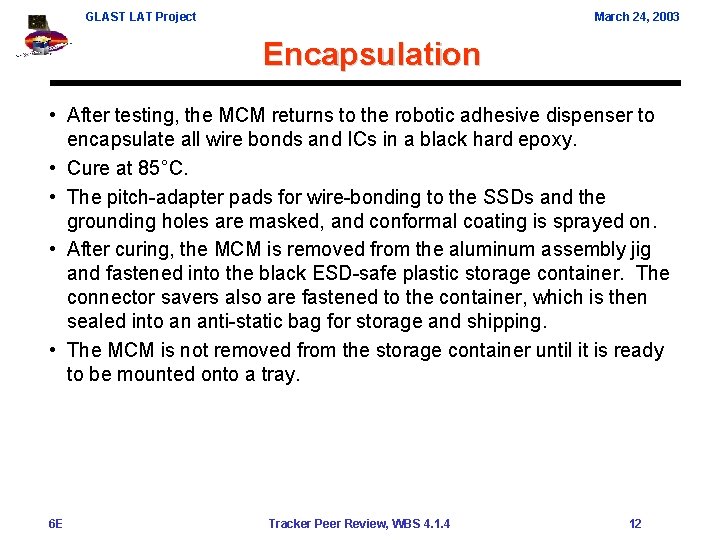
GLAST LAT Project March 24, 2003 Encapsulation • After testing, the MCM returns to the robotic adhesive dispenser to encapsulate all wire bonds and ICs in a black hard epoxy. • Cure at 85°C. • The pitch-adapter pads for wire-bonding to the SSDs and the grounding holes are masked, and conformal coating is sprayed on. • After curing, the MCM is removed from the aluminum assembly jig and fastened into the black ESD-safe plastic storage container. The connector savers also are fastened to the container, which is then sealed into an anti-static bag for storage and shipping. • The MCM is not removed from the storage container until it is ready to be mounted onto a tray. 6 E Tracker Peer Review, WBS 4. 1. 4 12
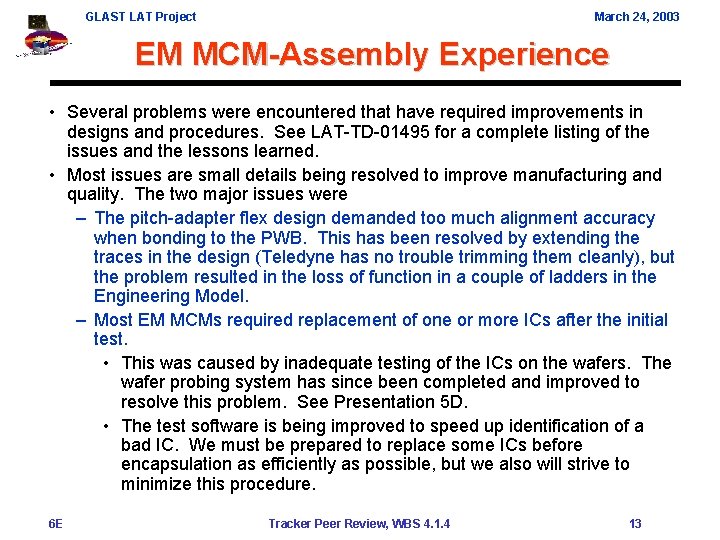
GLAST LAT Project March 24, 2003 EM MCM-Assembly Experience • Several problems were encountered that have required improvements in designs and procedures. See LAT-TD-01495 for a complete listing of the issues and the lessons learned. • Most issues are small details being resolved to improve manufacturing and quality. The two major issues were – The pitch-adapter flex design demanded too much alignment accuracy when bonding to the PWB. This has been resolved by extending the traces in the design (Teledyne has no trouble trimming them cleanly), but the problem resulted in the loss of function in a couple of ladders in the Engineering Model. – Most EM MCMs required replacement of one or more ICs after the initial test. • This was caused by inadequate testing of the ICs on the wafers. The wafer probing system has since been completed and improved to resolve this problem. See Presentation 5 D. • The test software is being improved to speed up identification of a bad IC. We must be prepared to replace some ICs before encapsulation as efficiently as possible, but we also will strive to minimize this procedure. 6 E Tracker Peer Review, WBS 4. 1. 4 13
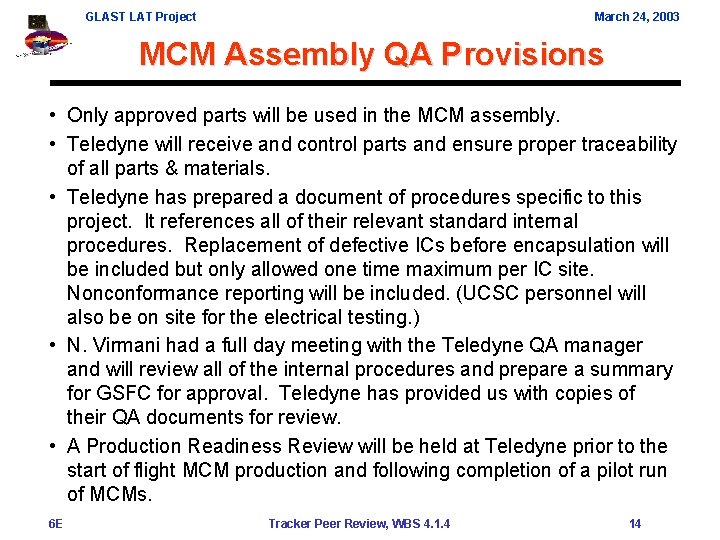
GLAST LAT Project March 24, 2003 MCM Assembly QA Provisions • Only approved parts will be used in the MCM assembly. • Teledyne will receive and control parts and ensure proper traceability of all parts & materials. • Teledyne has prepared a document of procedures specific to this project. It references all of their relevant standard internal procedures. Replacement of defective ICs before encapsulation will be included but only allowed one time maximum per IC site. Nonconformance reporting will be included. (UCSC personnel will also be on site for the electrical testing. ) • N. Virmani had a full day meeting with the Teledyne QA manager and will review all of the internal procedures and prepare a summary for GSFC for approval. Teledyne has provided us with copies of their QA documents for review. • A Production Readiness Review will be held at Teledyne prior to the start of flight MCM production and following completion of a pilot run of MCMs. 6 E Tracker Peer Review, WBS 4. 1. 4 14
Glast tm
Poikilodermia civatte
Poland national anthem lyrics
Decs order no.11, s.1987
Ms project 2003 tutorial
Ms project 2007
Project server 2003
Project server 2003 database
Długość pewnej linii kolejowej to około 318 km
Acromioclavicular ligament
Pani asia kupiła 7 bułek
Po'lat haqida malumot
Absolute location of oslo
Lat dorsi innervation
Anterior capsule stretch