Figure 8 1 Engineering drawing of the steer
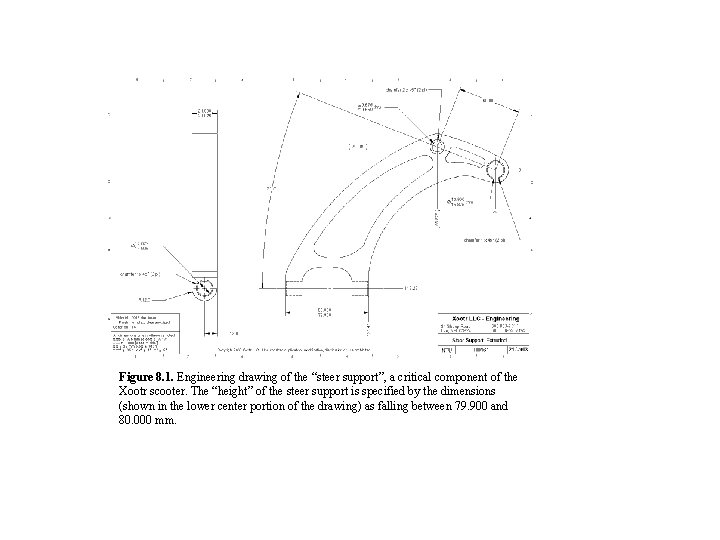
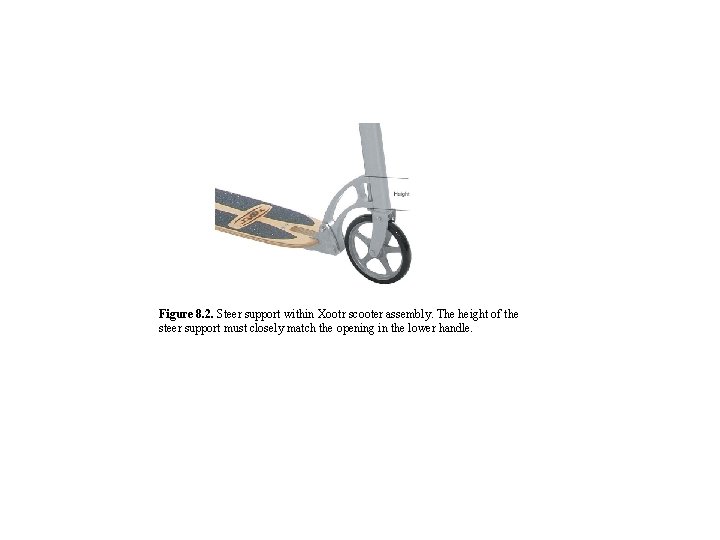
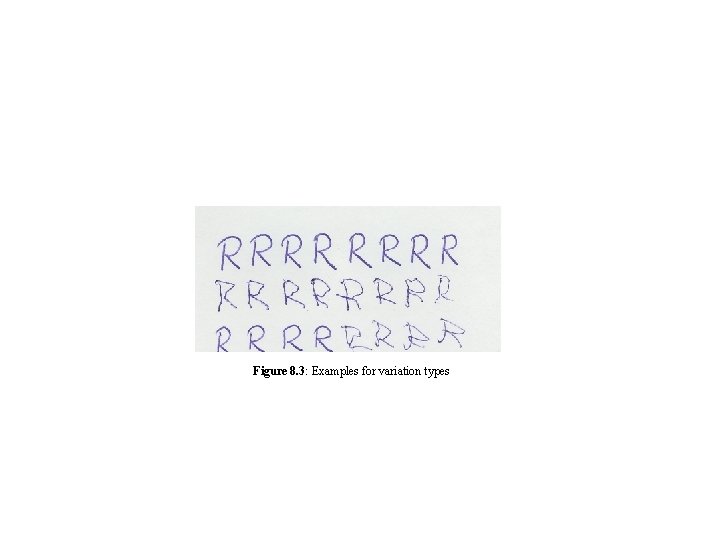
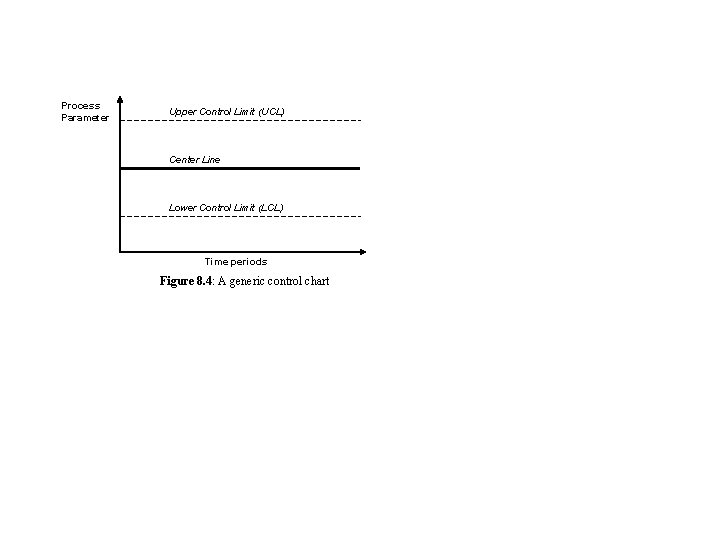
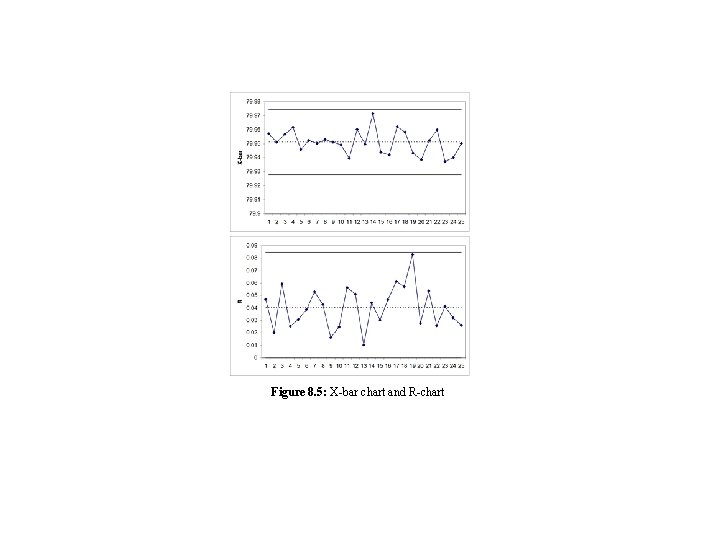
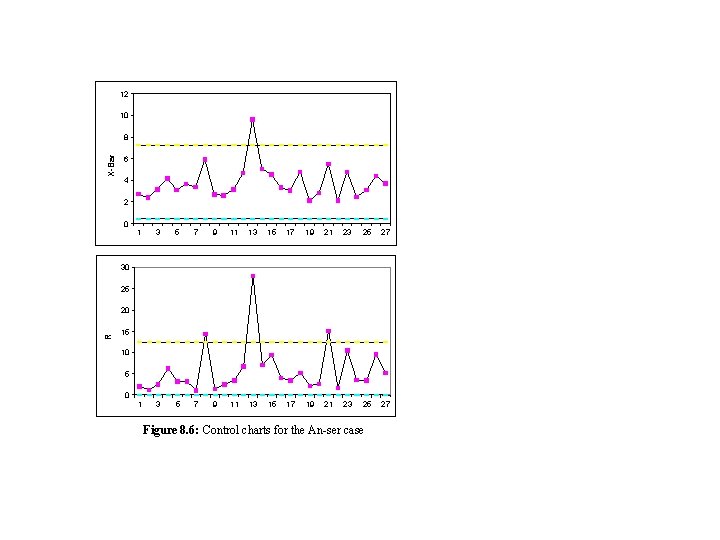
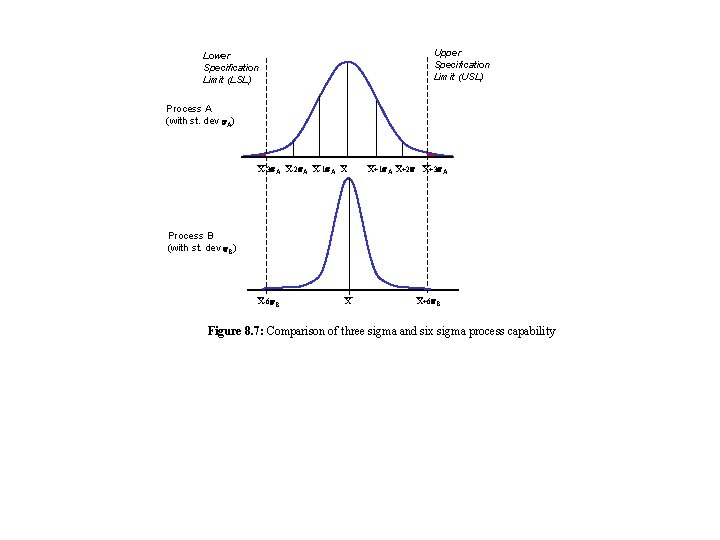
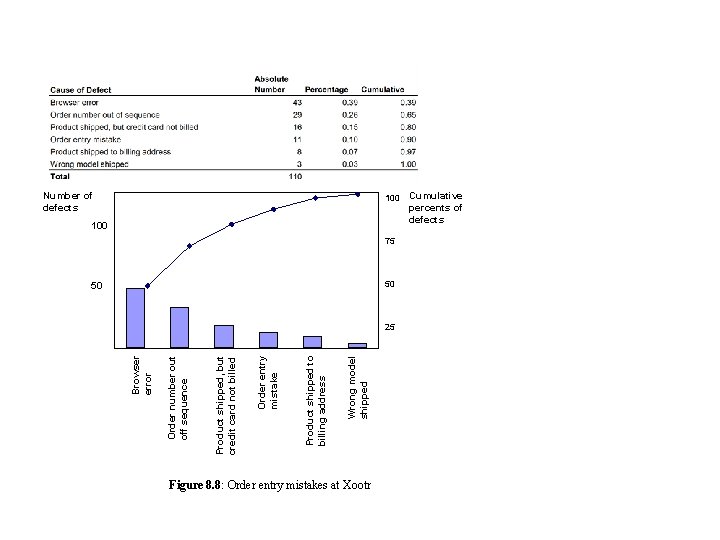
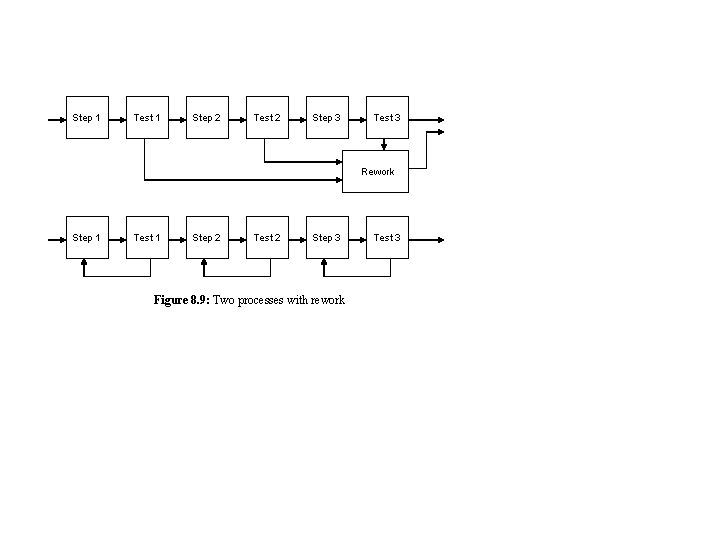
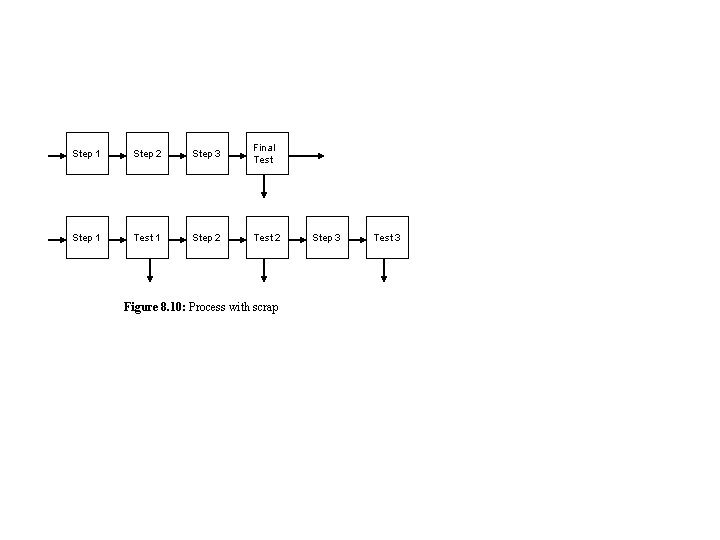
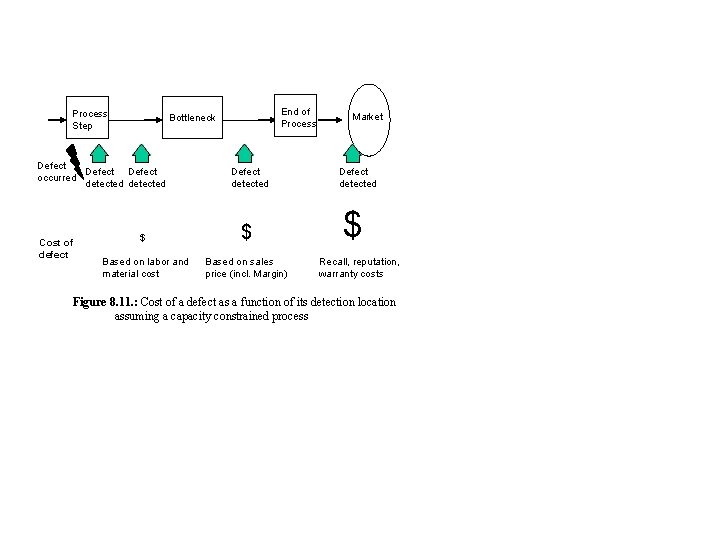
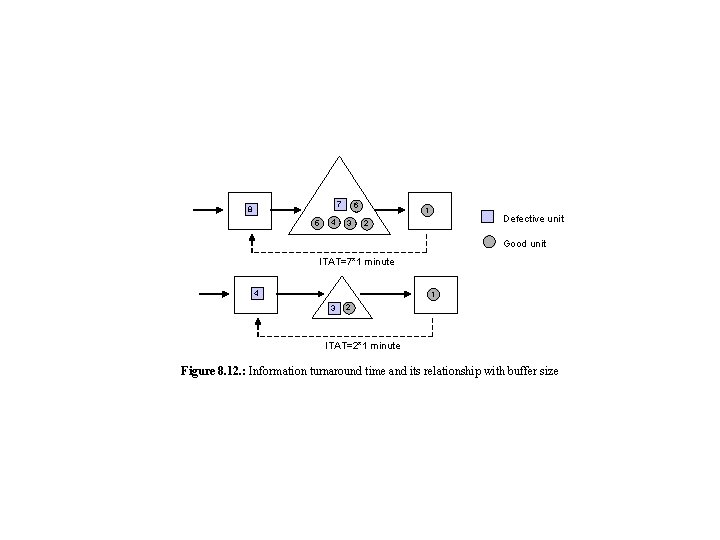

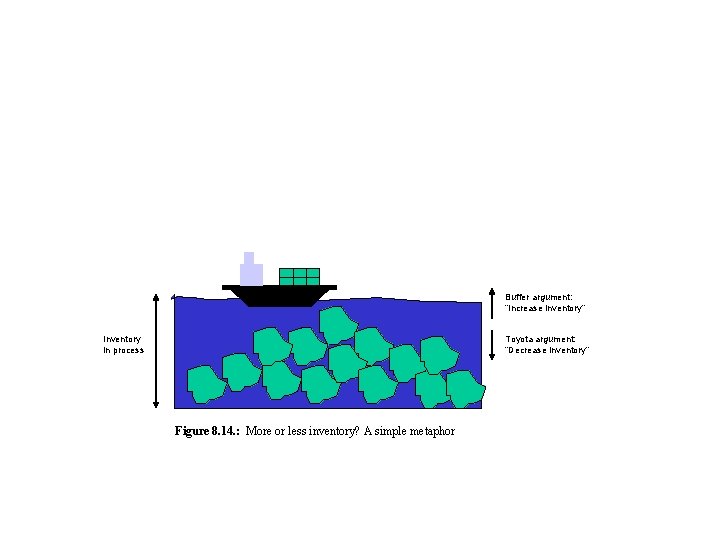
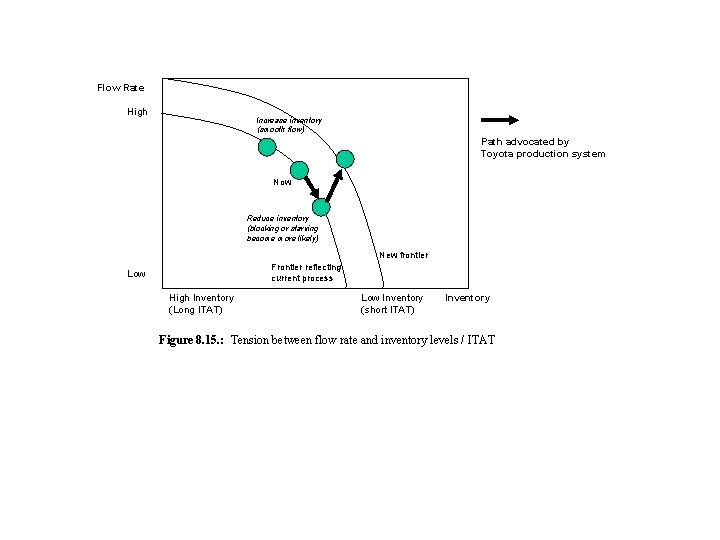
- Slides: 15
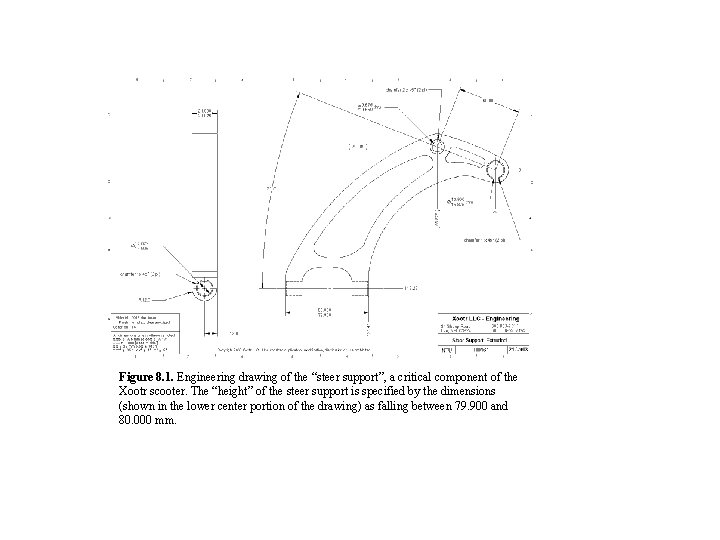
Figure 8. 1. Engineering drawing of the “steer support”, a critical component of the Xootr scooter. The “height” of the steer support is specified by the dimensions (shown in the lower center portion of the drawing) as falling between 79. 900 and 80. 000 mm.
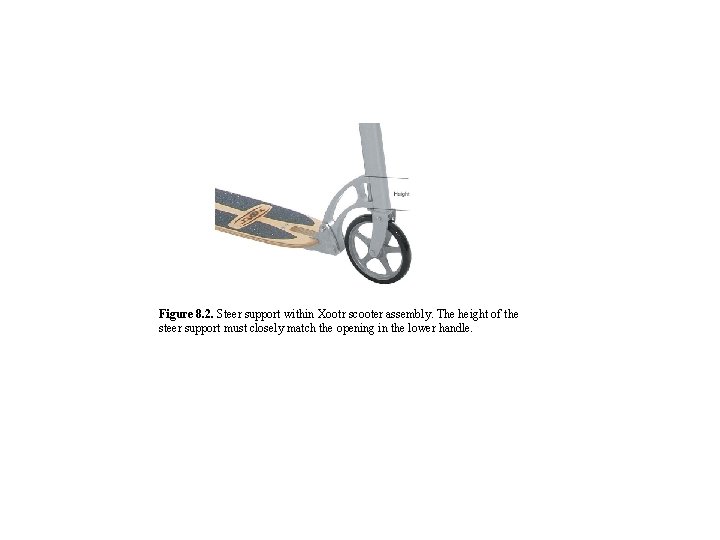
Figure 8. 2. Steer support within Xootr scooter assembly. The height of the steer support must closely match the opening in the lower handle.
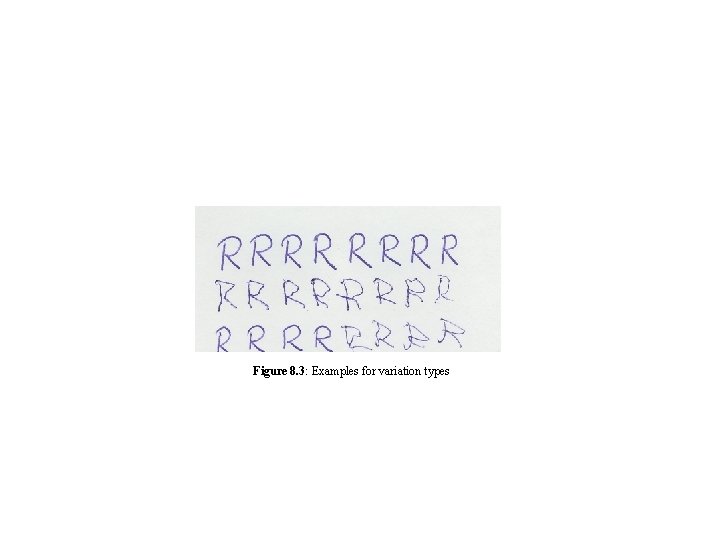
Figure 8. 3: Examples for variation types
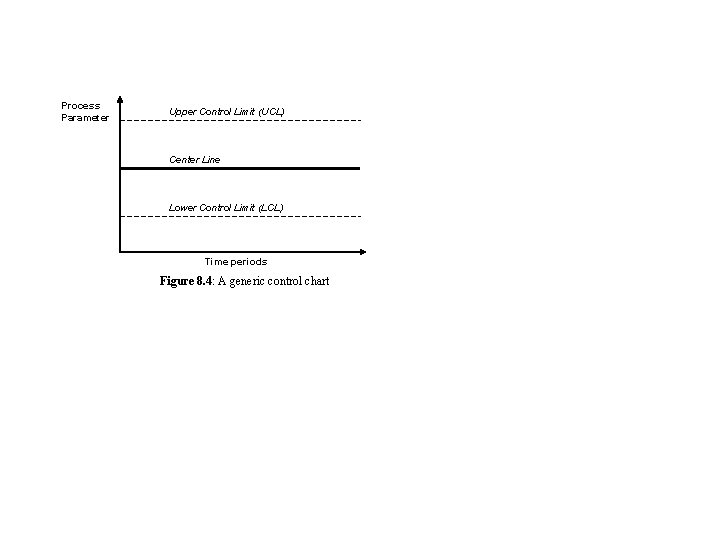
Process Parameter Upper Control Limit (UCL) Center Line Lower Control Limit (LCL) Time periods Figure 8. 4: A generic control chart
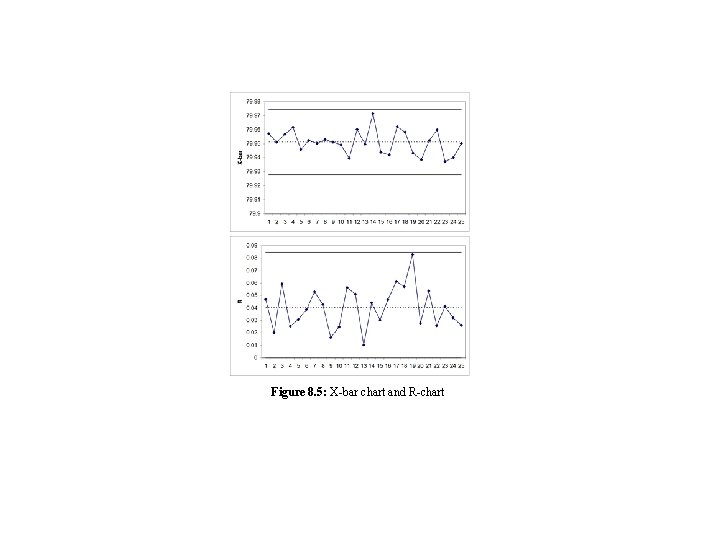
Figure 8. 5: X-bar chart and R-chart
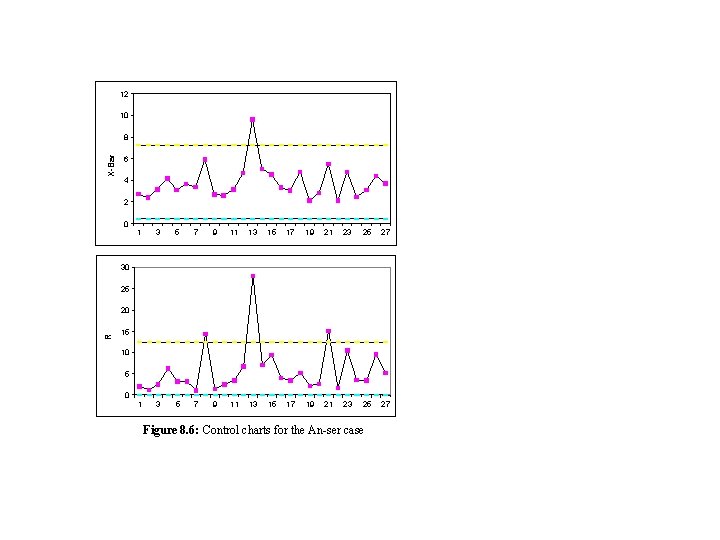
12 10 X-Bar 8 6 4 2 0 1 3 5 7 9 11 13 15 17 19 21 23 25 27 30 25 R 20 15 10 5 0 Figure 8. 6: Control charts for the An-ser case
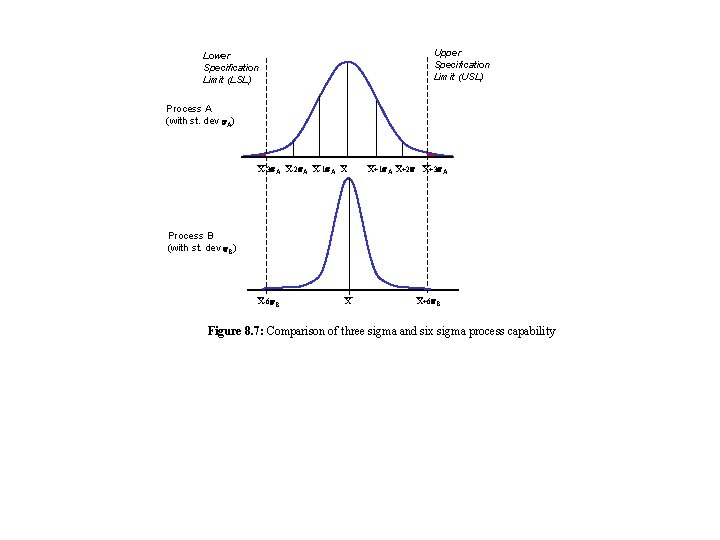
Upper Specification Limit (USL) Lower Specification Limit (LSL) Process A (with st. dev A) X-3 A X-2 A X-1 A X X+1 A X+2 X+3 A 3 Process B (with st. dev B) X-6 B X X+6 B Figure 8. 7: Comparison of three sigma and six sigma process capability
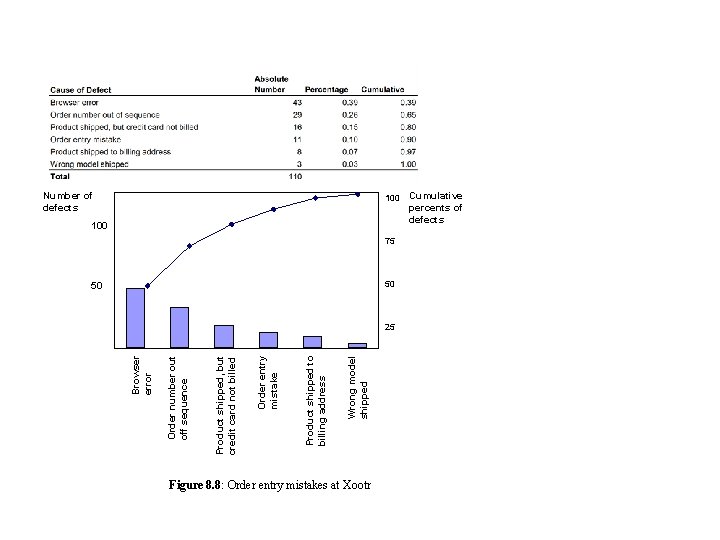
Wrong model shipped Product shipped to billing address Order entry mistake Product shipped, but credit card not billed Order number out off sequence Browser error Number of defects 100 Cumulative 100 percents of defects 75 50 50 25 Figure 8. 8: Order entry mistakes at Xootr
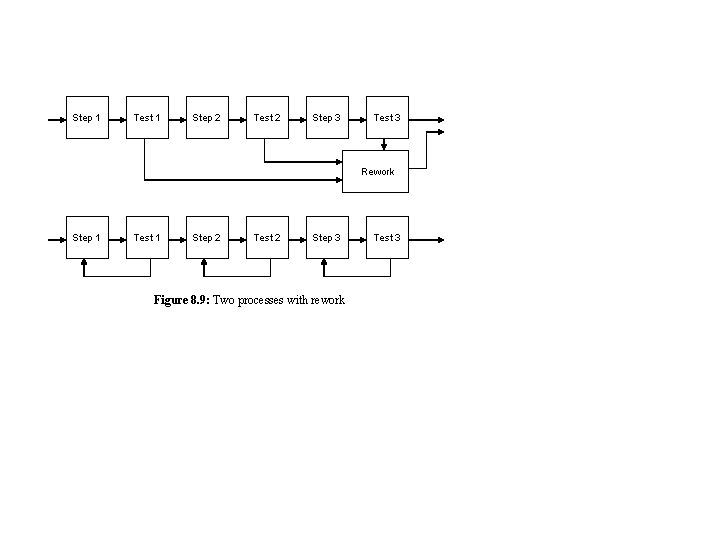
Step 1 Test 1 Step 2 Test 2 Step 3 Test 3 Rework Step 1 Test 1 Step 2 Test 2 Step 3 Figure 8. 9: Two processes with rework Test 3
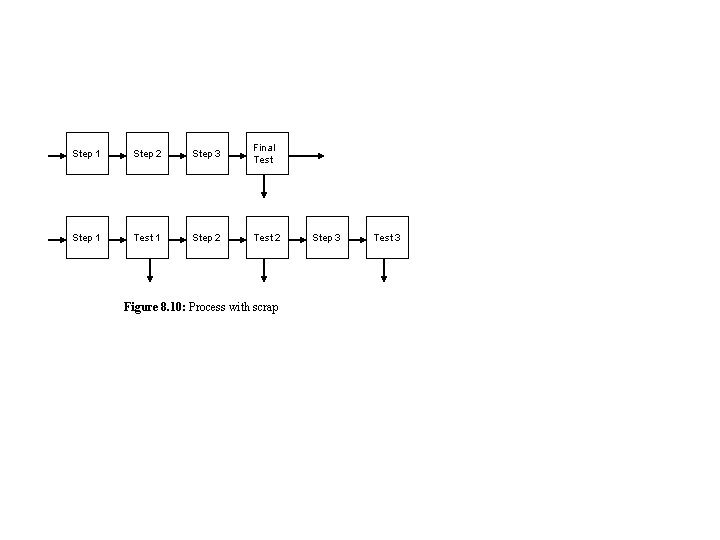
Step 1 Step 2 Step 3 Final Test Step 1 Test 1 Step 2 Test 2 Figure 8. 10: Process with scrap Step 3 Test 3
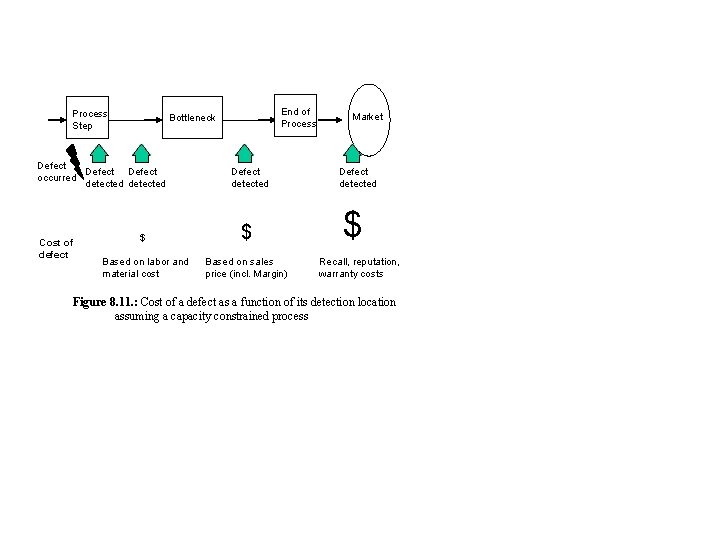
Process Step Defect occurred detected Cost of defect End of Process Bottleneck Defect detected $ $ Based on labor and material cost Based on sales price (incl. Margin) Market Defect detected $ Recall, reputation, warranty costs Figure 8. 11. : Cost of a defect as a function of its detection location assuming a capacity constrained process
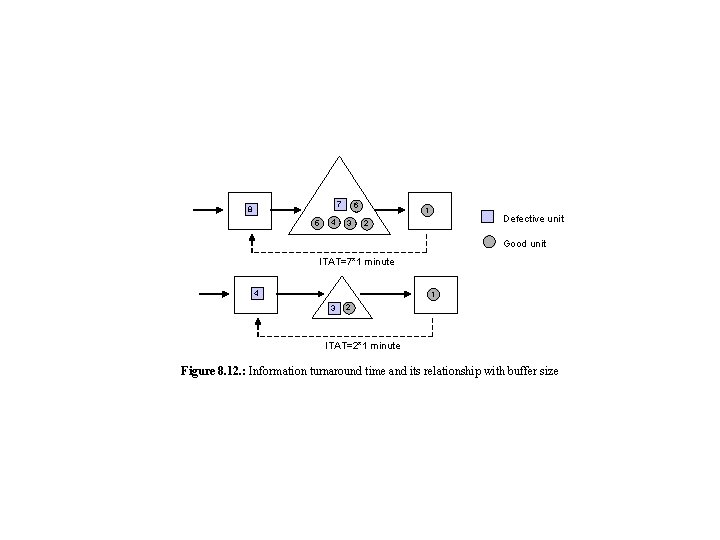
7 8 5 4 6 3 1 Defective unit 2 Good unit ITAT=7*1 minute 4 1 3 2 ITAT=2*1 minute Figure 8. 12. : Information turnaround time and its relationship with buffer size

Direction of production flow upstream downstream an anb K Authorize production of next unit ban an b Kan ban Kan Figure 8. 13. : Simplified mechanics of a Kanban system
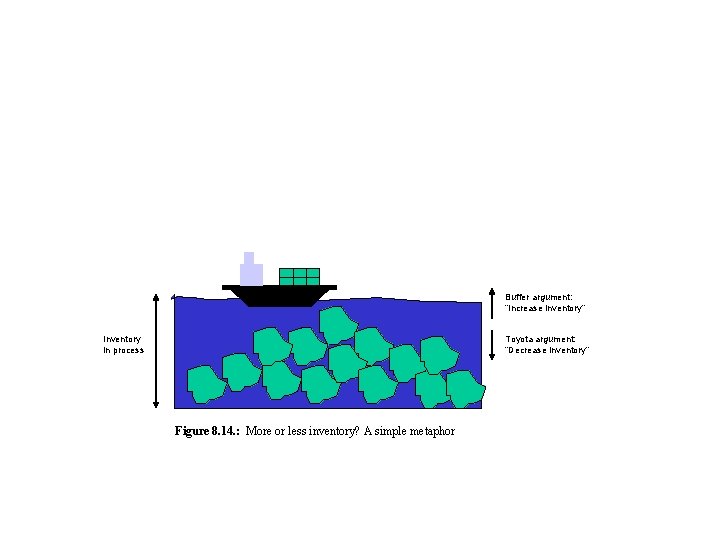
Buffer argument: “Increase inventory” Inventory in process Toyota argument: “Decrease inventory” Figure 8. 14. : More or less inventory? A simple metaphor
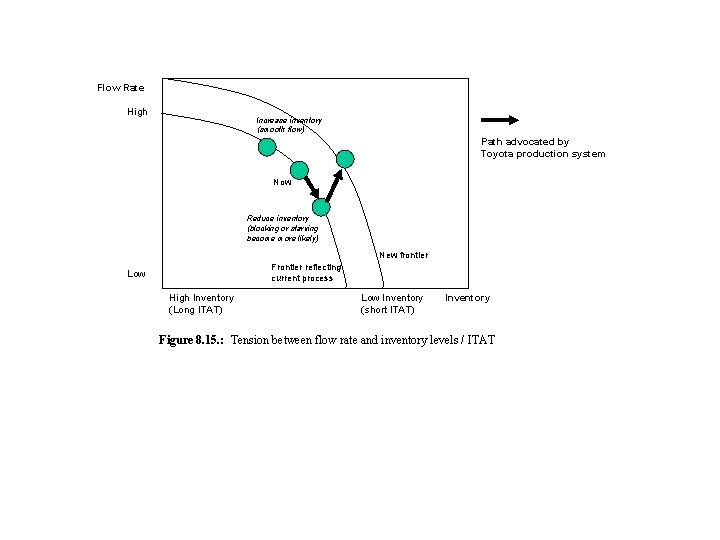
Flow Rate High Increase inventory (smooth flow) Path advocated by Toyota production system Now Reduce inventory (blocking or starving become more likely) New frontier Frontier reflecting current process Low High Inventory (Long ITAT) Low Inventory (short ITAT) Inventory Figure 8. 15. : Tension between flow rate and inventory levels / ITAT
Pictorial drawing in technical drawing
Trimble implement guidance
Understeer
Fwd torque steer
Steering straight backward
Course to steer
Steer by wire system
Judging market steers
Ag leader steer command
Drivetrain design
Stomp stay steer
Anterior vagal trunk
Bum steer cow
Engine on half power ahead - steer 182 degrees port side.
David steer
Chapter 6 performing basic vehicle maneuvers