EML 2023 Rapid Prototyping Lecture 1 Additive Rapid
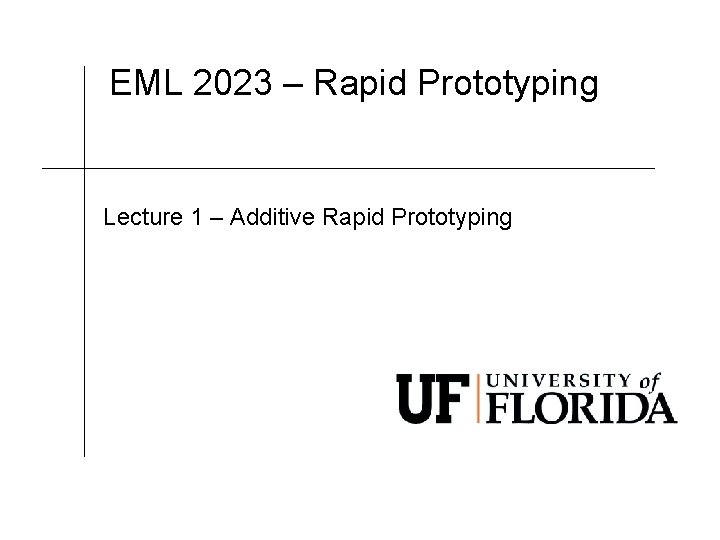
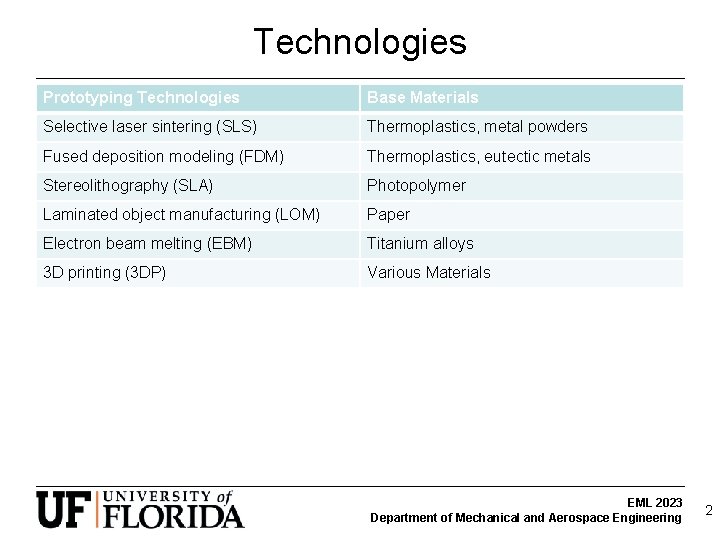
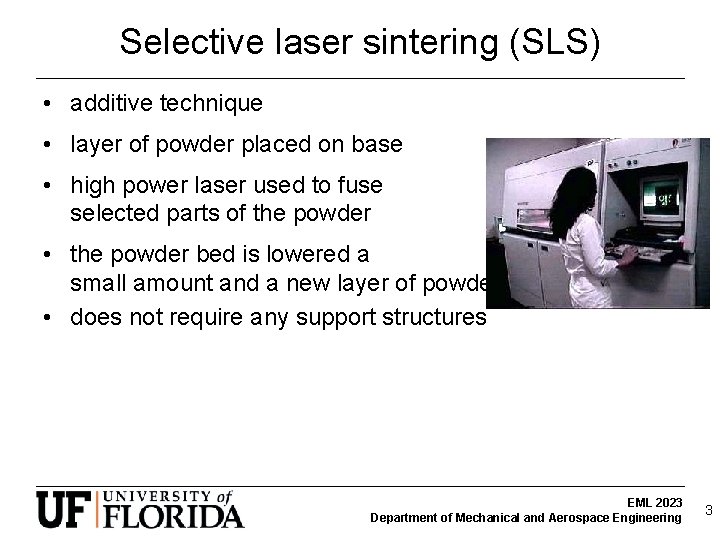
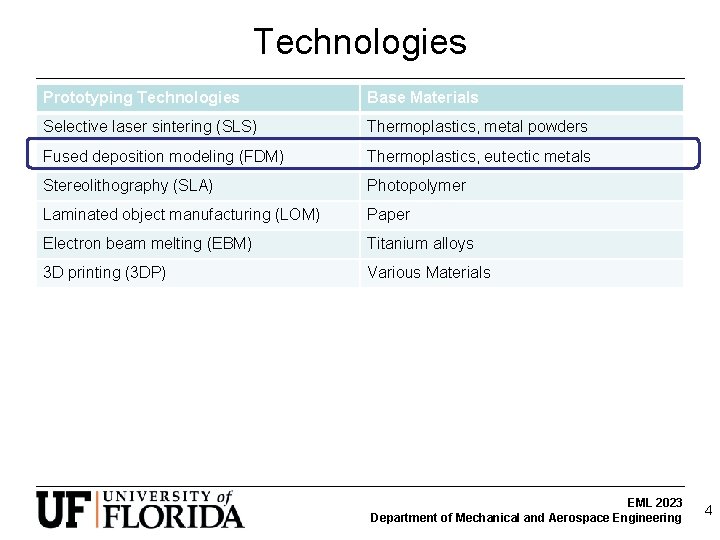
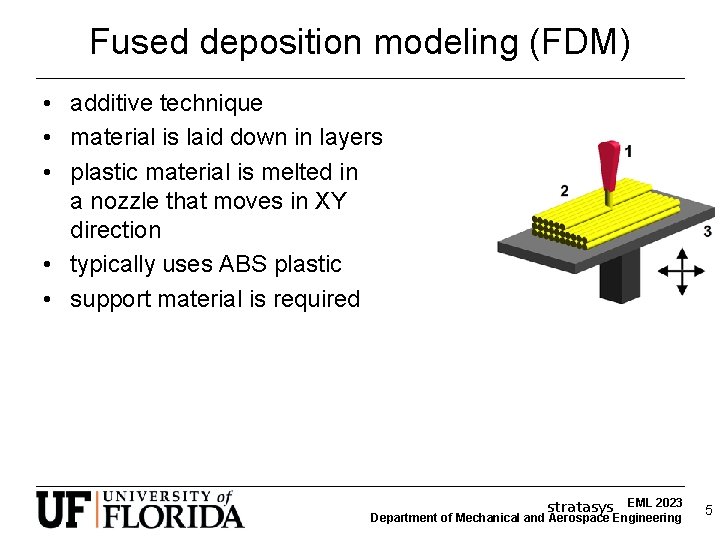
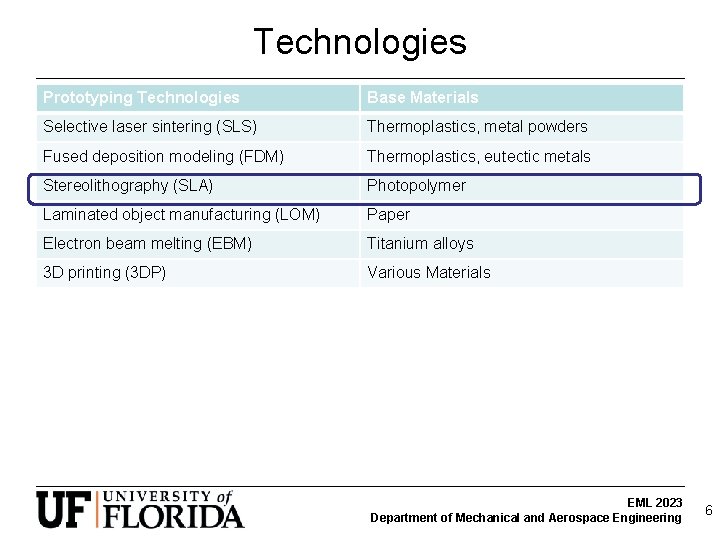
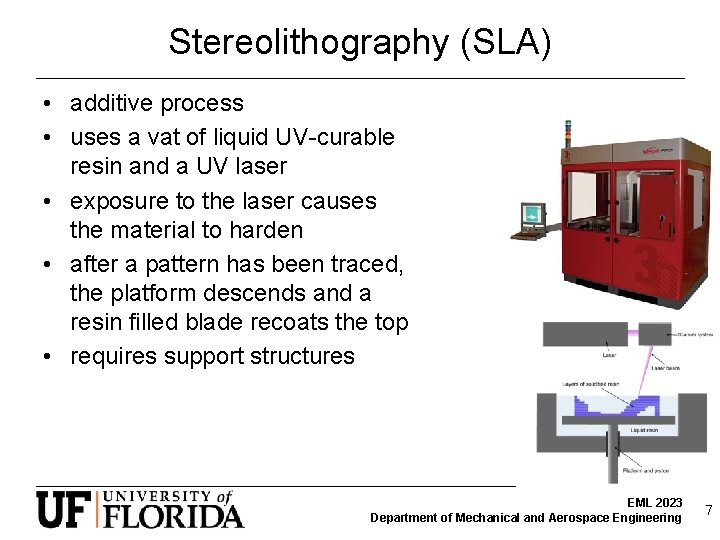
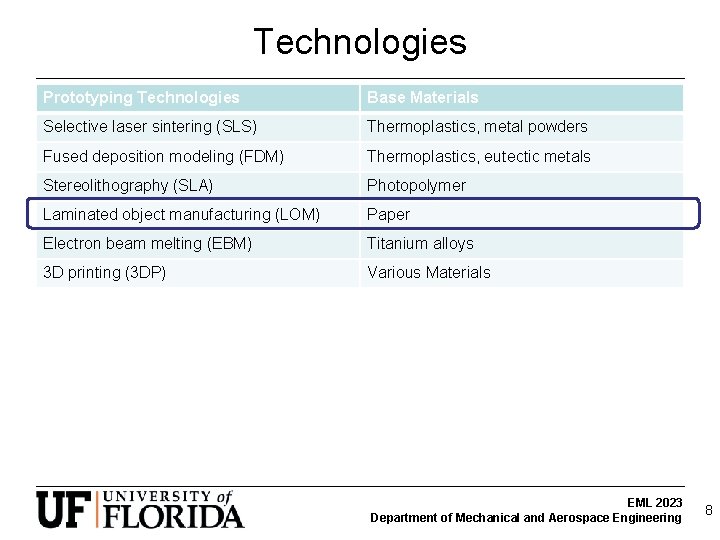
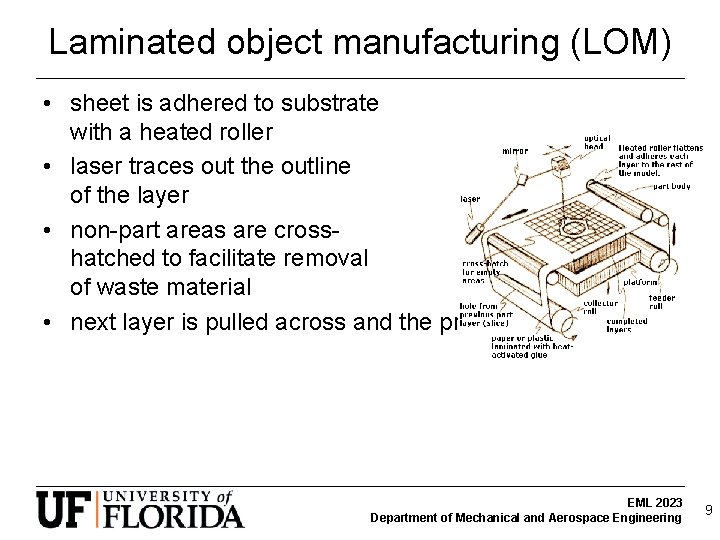
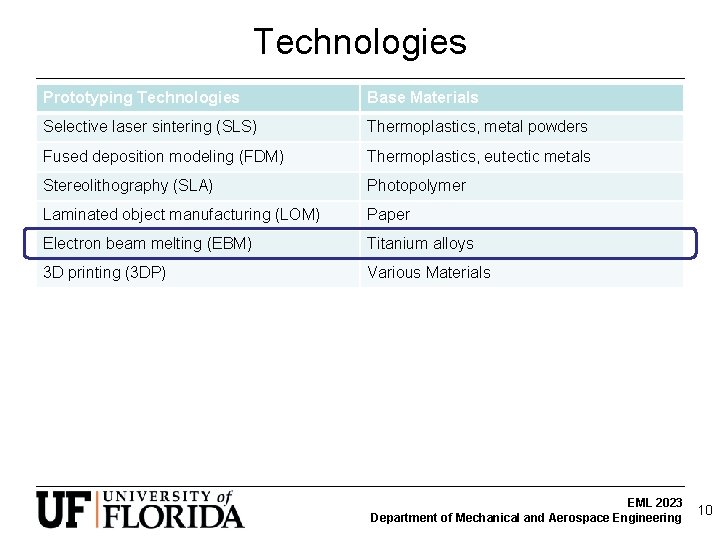
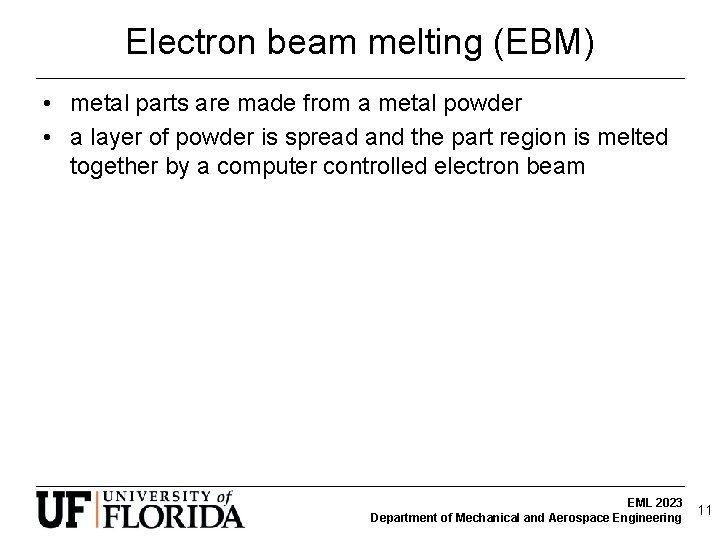
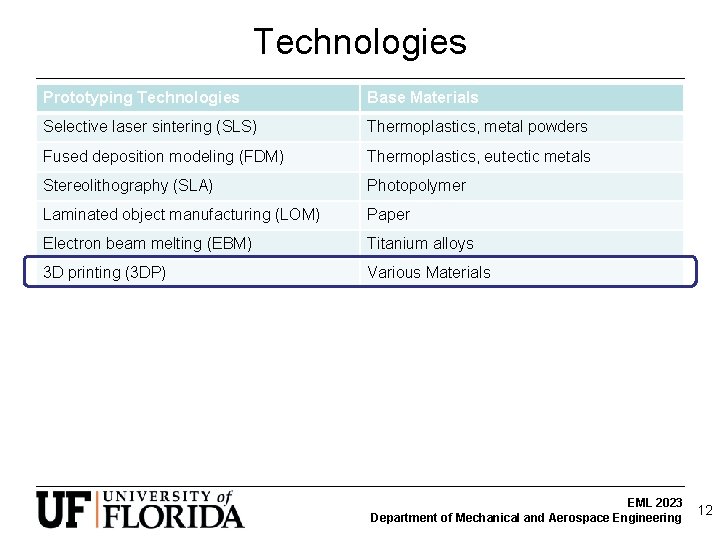
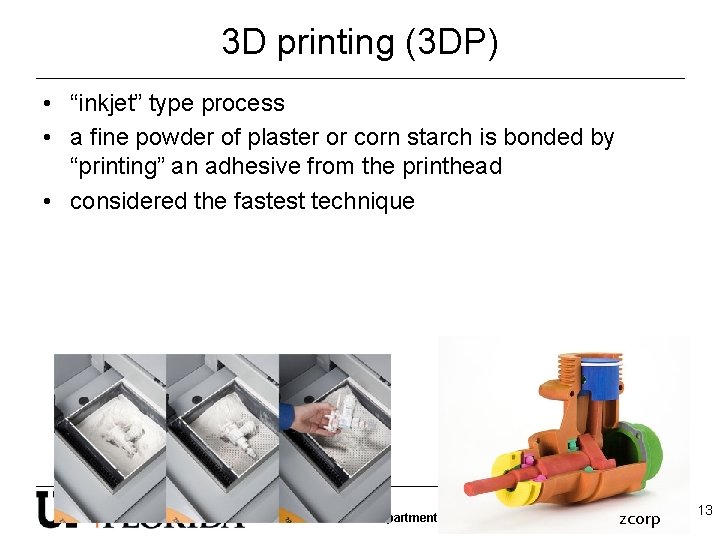
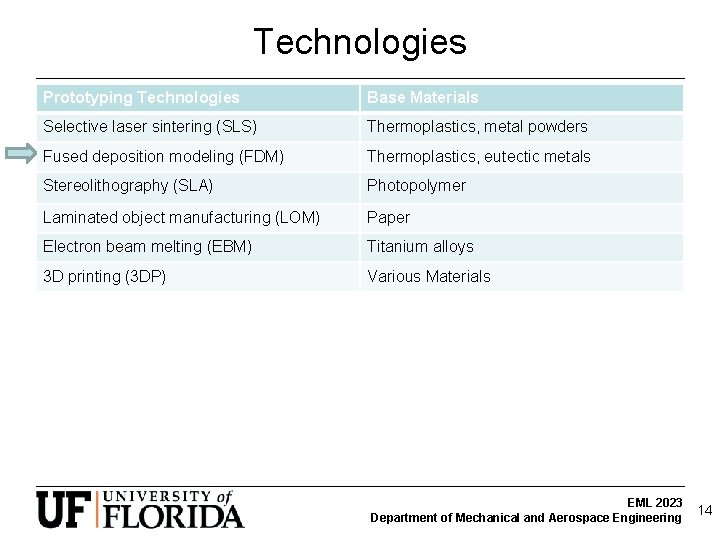
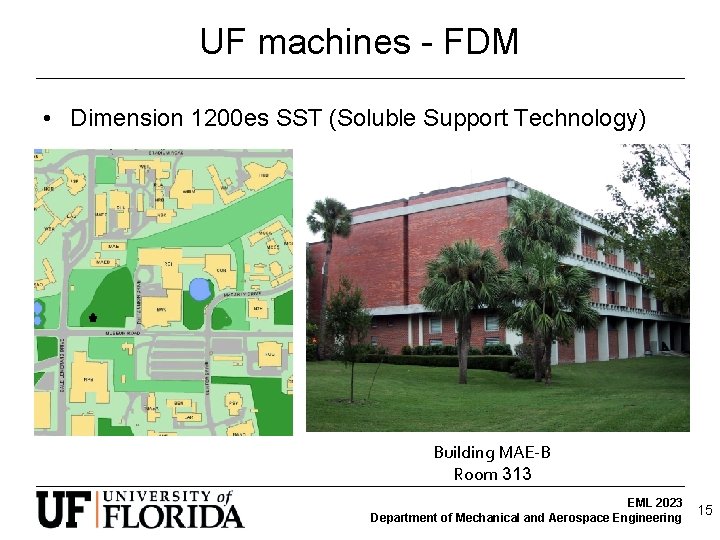
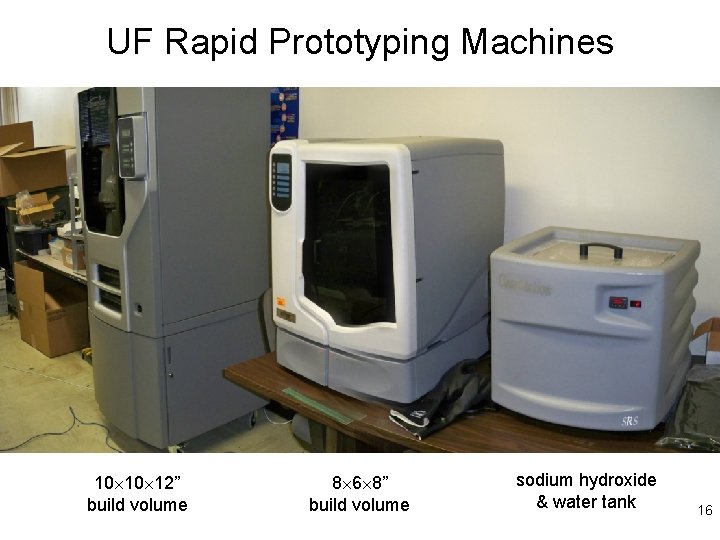
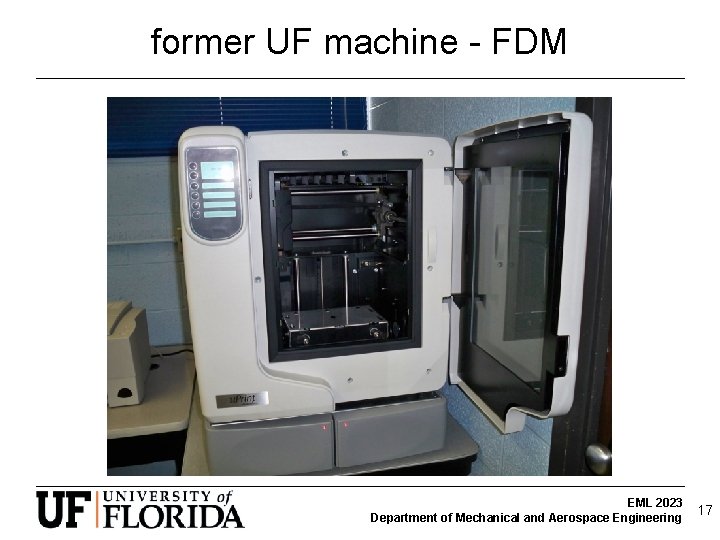
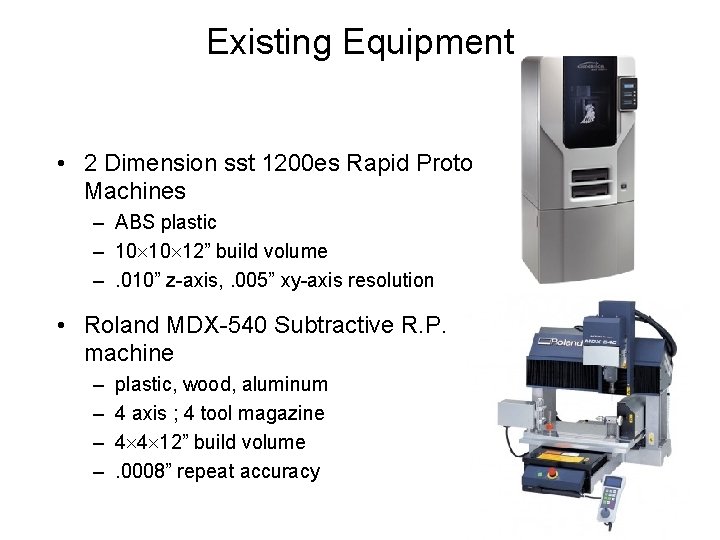
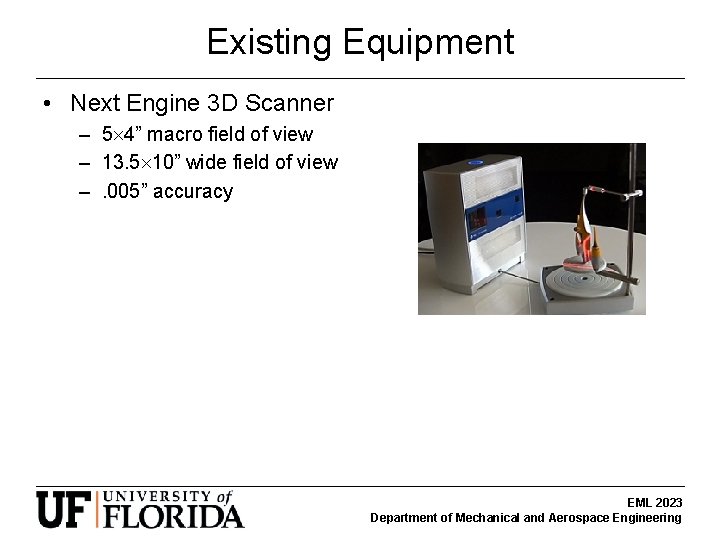
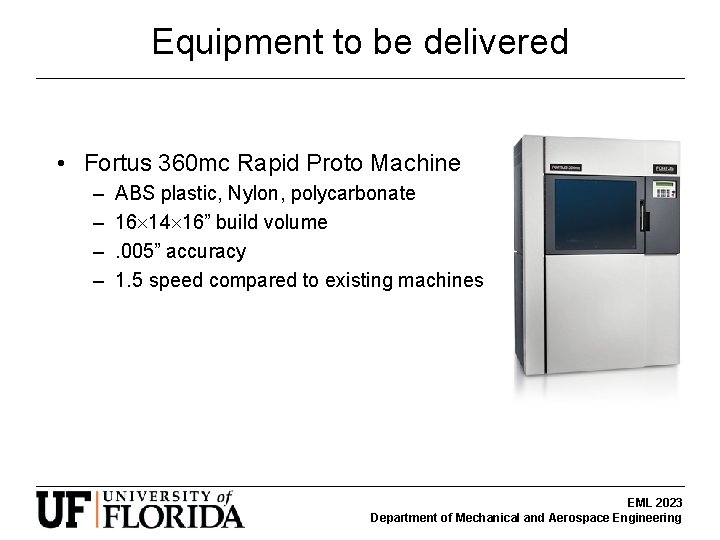
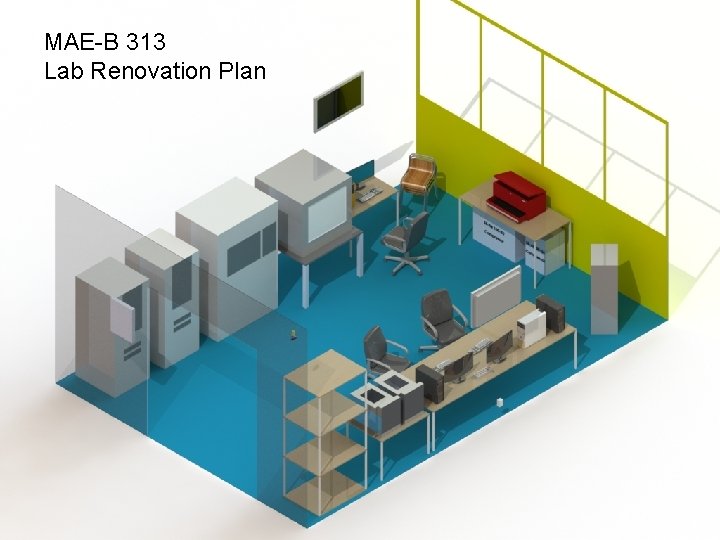
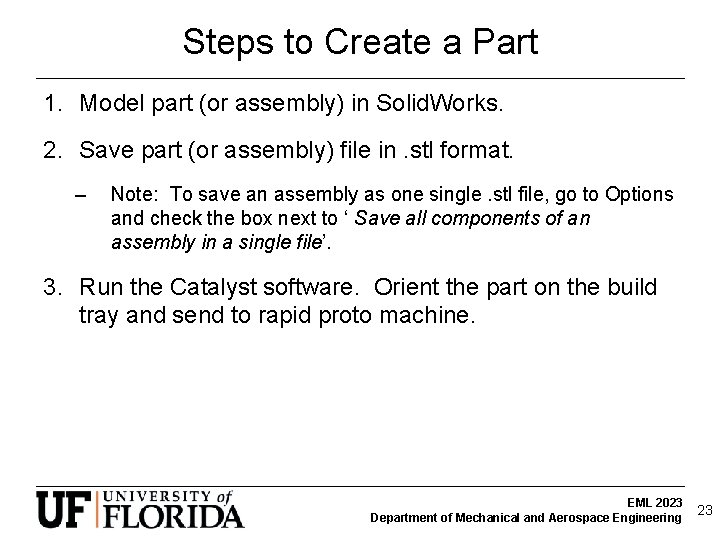
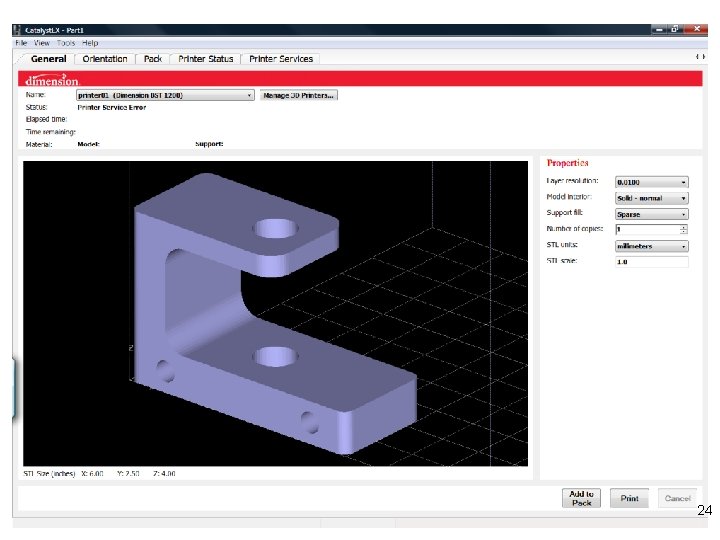
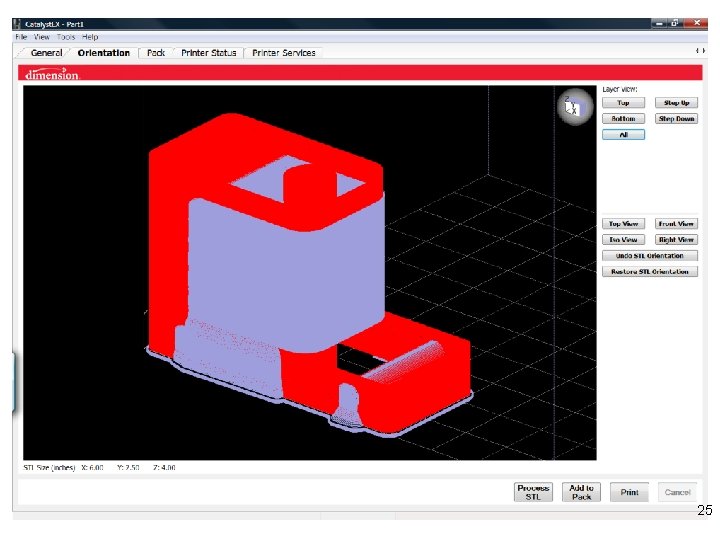

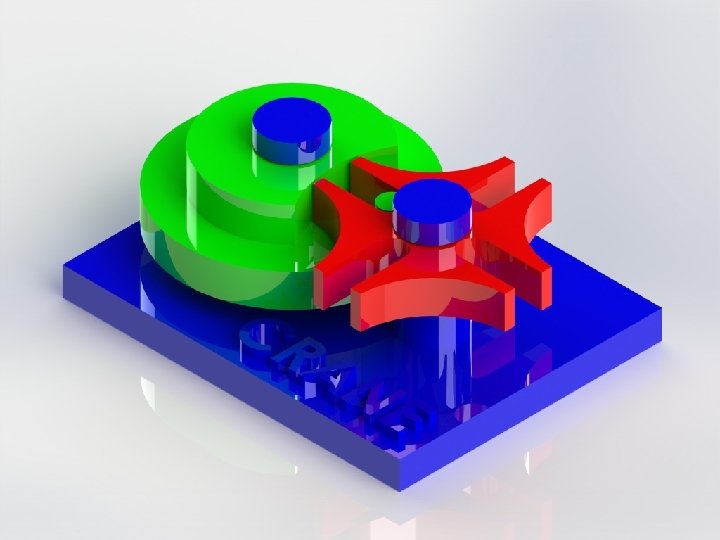
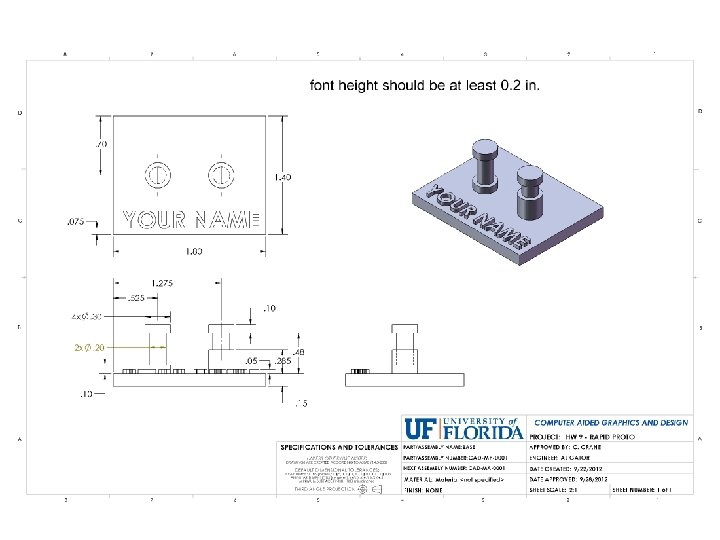
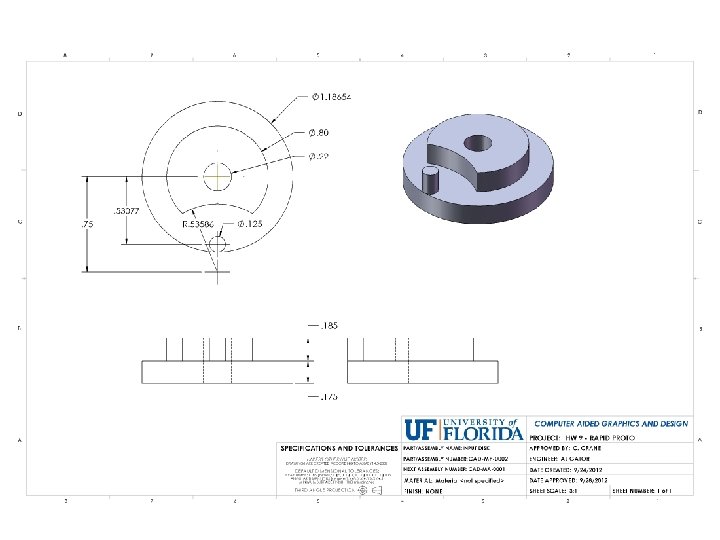
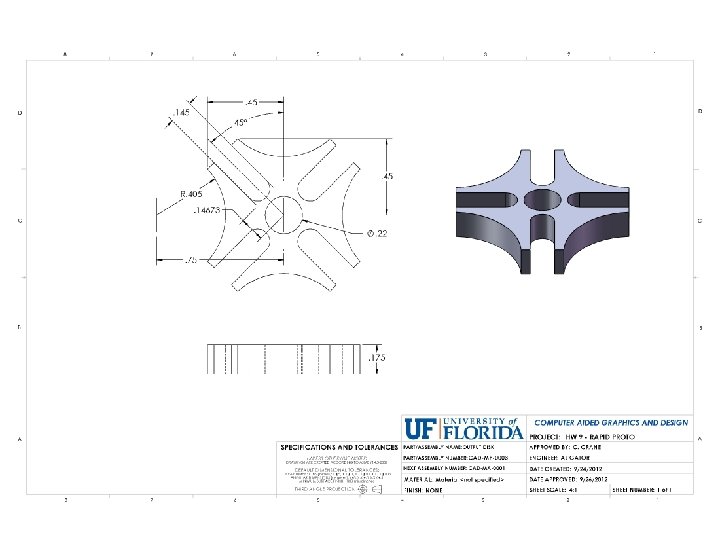
- Slides: 29
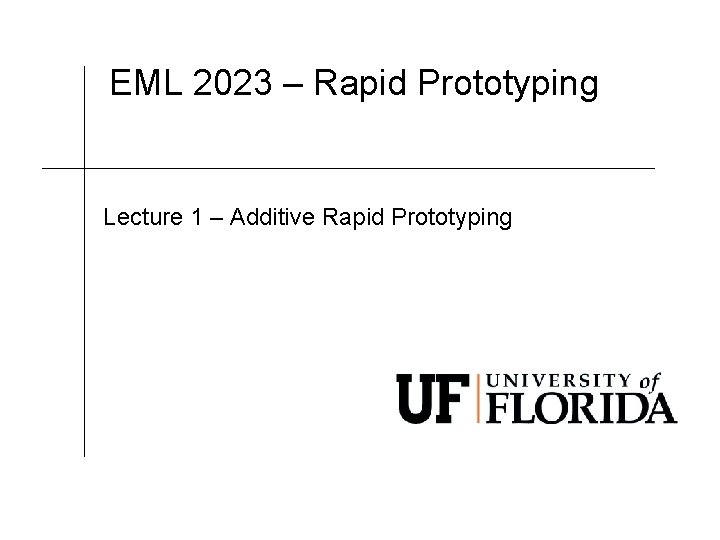
EML 2023 – Rapid Prototyping Lecture 1 – Additive Rapid Prototyping
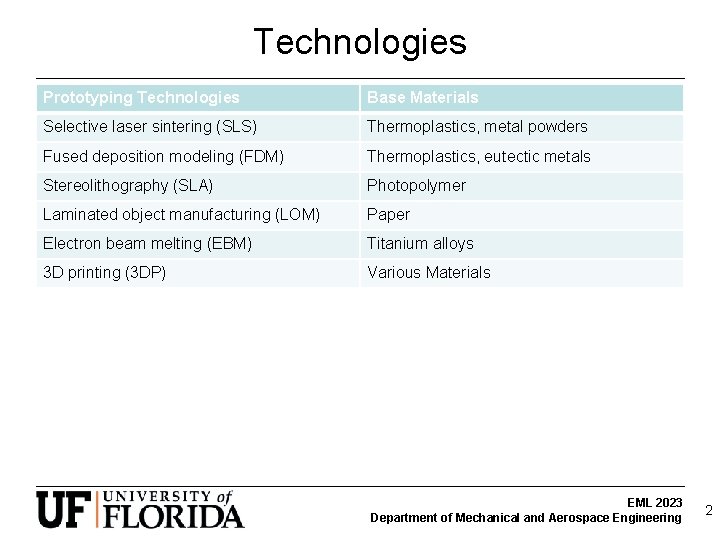
Technologies Prototyping Technologies Base Materials Selective laser sintering (SLS) Thermoplastics, metal powders Fused deposition modeling (FDM) Thermoplastics, eutectic metals Stereolithography (SLA) Photopolymer Laminated object manufacturing (LOM) Paper Electron beam melting (EBM) Titanium alloys 3 D printing (3 DP) Various Materials EML 2023 Department of Mechanical and Aerospace Engineering 2
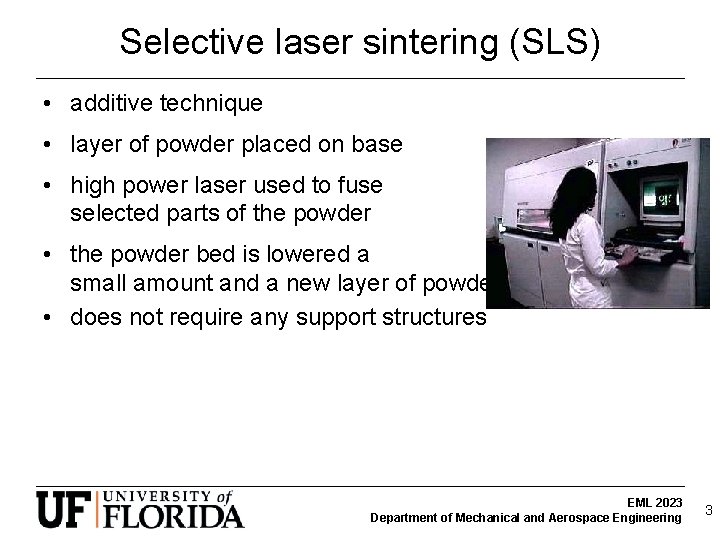
Selective laser sintering (SLS) • additive technique • layer of powder placed on base • high power laser used to fuse selected parts of the powder • the powder bed is lowered a small amount and a new layer of powder is spread • does not require any support structures EML 2023 Department of Mechanical and Aerospace Engineering 3
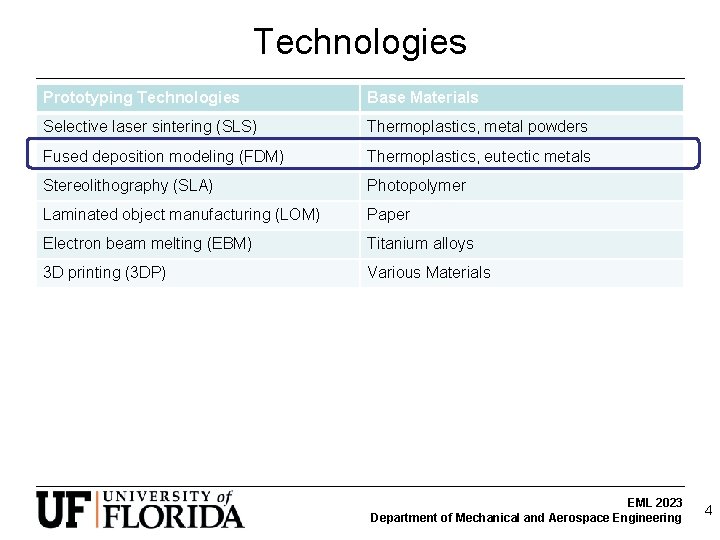
Technologies Prototyping Technologies Base Materials Selective laser sintering (SLS) Thermoplastics, metal powders Fused deposition modeling (FDM) Thermoplastics, eutectic metals Stereolithography (SLA) Photopolymer Laminated object manufacturing (LOM) Paper Electron beam melting (EBM) Titanium alloys 3 D printing (3 DP) Various Materials EML 2023 Department of Mechanical and Aerospace Engineering 4
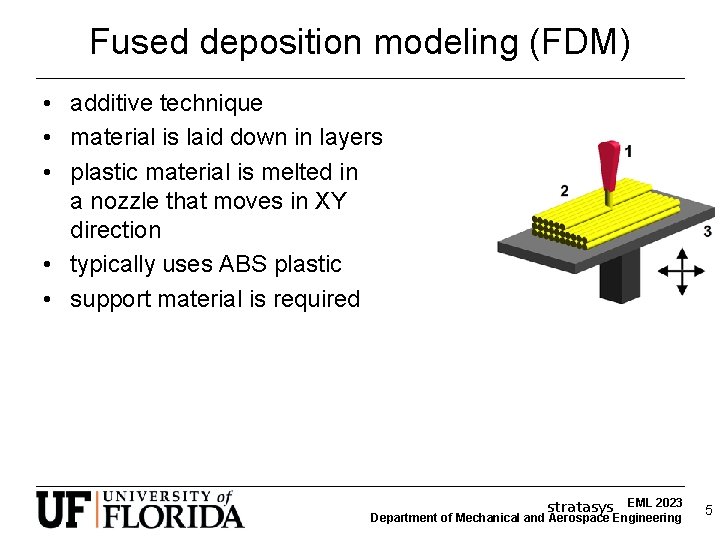
Fused deposition modeling (FDM) • additive technique • material is laid down in layers • plastic material is melted in a nozzle that moves in XY direction • typically uses ABS plastic • support material is required stratasys EML 2023 Department of Mechanical and Aerospace Engineering 5
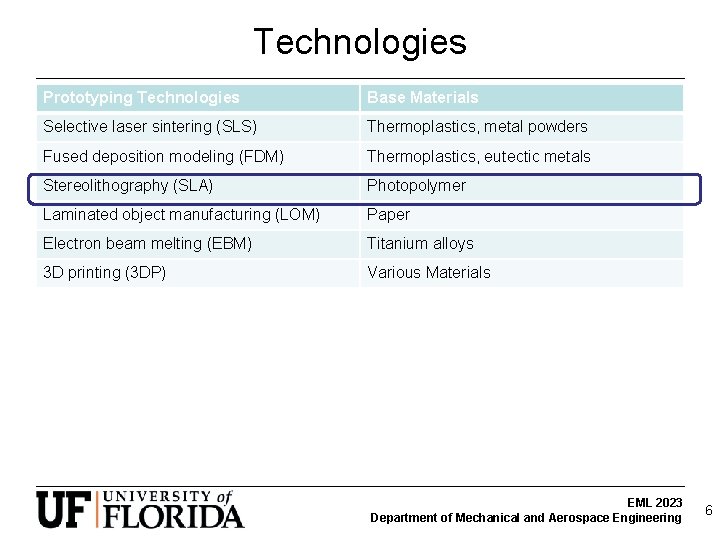
Technologies Prototyping Technologies Base Materials Selective laser sintering (SLS) Thermoplastics, metal powders Fused deposition modeling (FDM) Thermoplastics, eutectic metals Stereolithography (SLA) Photopolymer Laminated object manufacturing (LOM) Paper Electron beam melting (EBM) Titanium alloys 3 D printing (3 DP) Various Materials EML 2023 Department of Mechanical and Aerospace Engineering 6
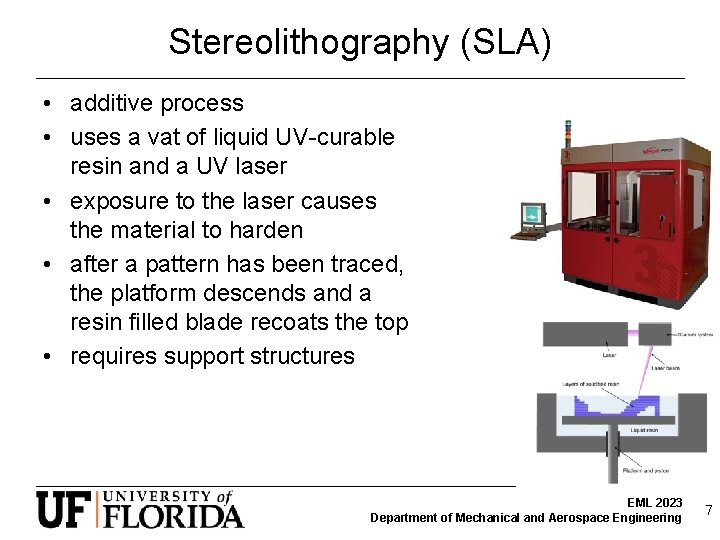
Stereolithography (SLA) • additive process • uses a vat of liquid UV-curable resin and a UV laser • exposure to the laser causes the material to harden • after a pattern has been traced, the platform descends and a resin filled blade recoats the top • requires support structures EML 2023 Department of Mechanical and Aerospace Engineering 7
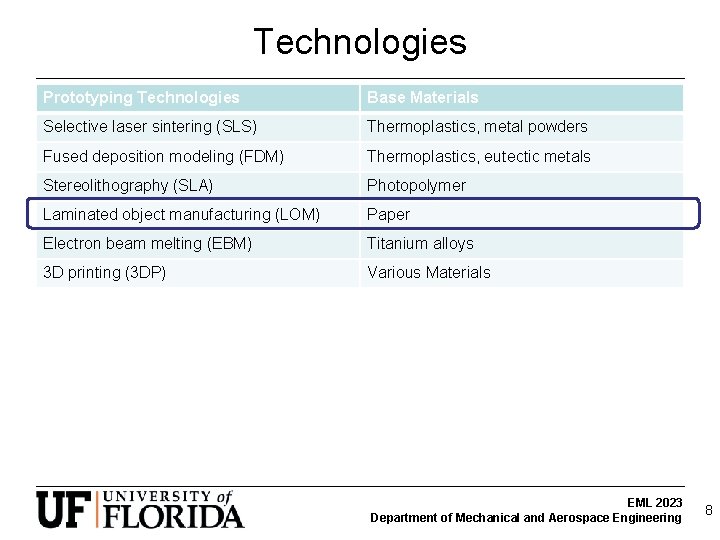
Technologies Prototyping Technologies Base Materials Selective laser sintering (SLS) Thermoplastics, metal powders Fused deposition modeling (FDM) Thermoplastics, eutectic metals Stereolithography (SLA) Photopolymer Laminated object manufacturing (LOM) Paper Electron beam melting (EBM) Titanium alloys 3 D printing (3 DP) Various Materials EML 2023 Department of Mechanical and Aerospace Engineering 8
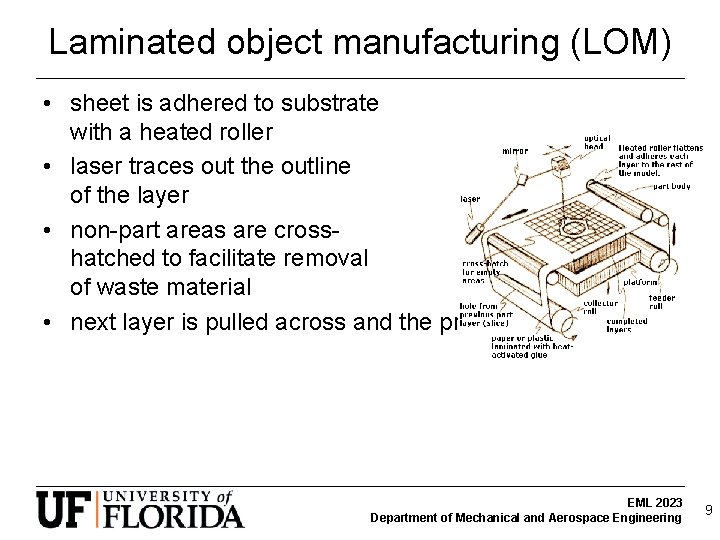
Laminated object manufacturing (LOM) • sheet is adhered to substrate with a heated roller • laser traces out the outline of the layer • non-part areas are crosshatched to facilitate removal of waste material • next layer is pulled across and the process is repeated EML 2023 Department of Mechanical and Aerospace Engineering 9
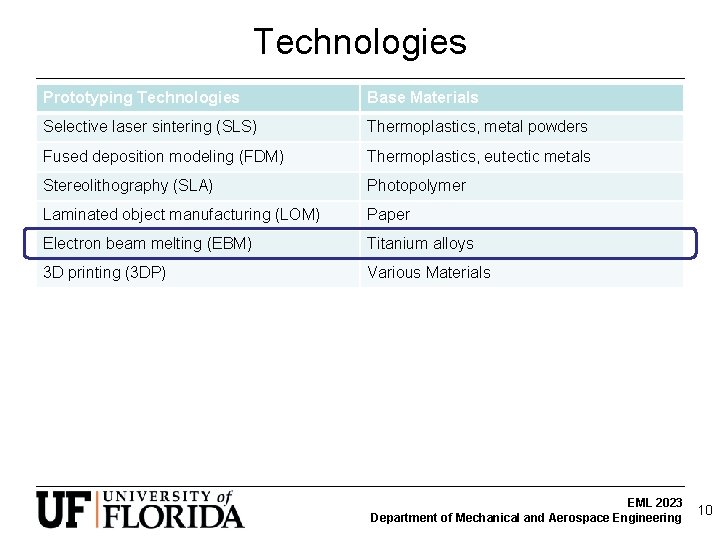
Technologies Prototyping Technologies Base Materials Selective laser sintering (SLS) Thermoplastics, metal powders Fused deposition modeling (FDM) Thermoplastics, eutectic metals Stereolithography (SLA) Photopolymer Laminated object manufacturing (LOM) Paper Electron beam melting (EBM) Titanium alloys 3 D printing (3 DP) Various Materials EML 2023 Department of Mechanical and Aerospace Engineering 10
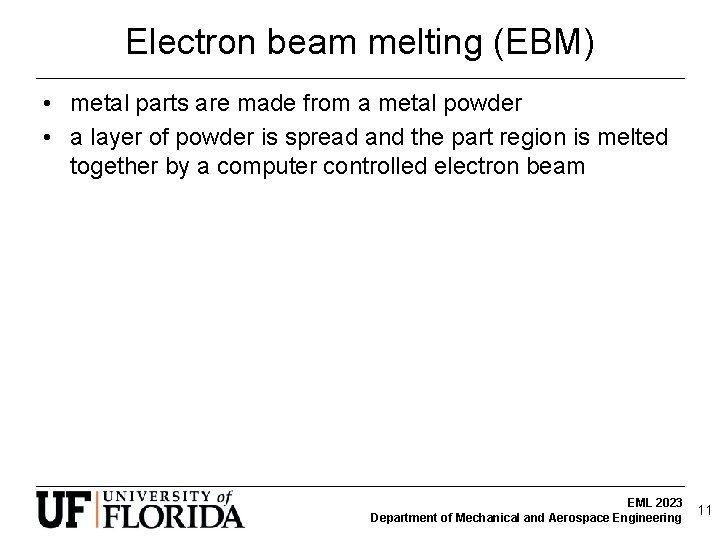
Electron beam melting (EBM) • metal parts are made from a metal powder • a layer of powder is spread and the part region is melted together by a computer controlled electron beam EML 2023 Department of Mechanical and Aerospace Engineering 11
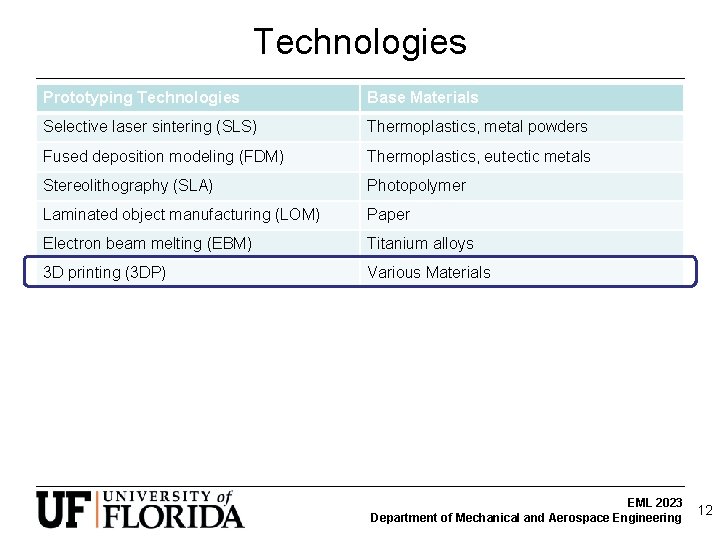
Technologies Prototyping Technologies Base Materials Selective laser sintering (SLS) Thermoplastics, metal powders Fused deposition modeling (FDM) Thermoplastics, eutectic metals Stereolithography (SLA) Photopolymer Laminated object manufacturing (LOM) Paper Electron beam melting (EBM) Titanium alloys 3 D printing (3 DP) Various Materials EML 2023 Department of Mechanical and Aerospace Engineering 12
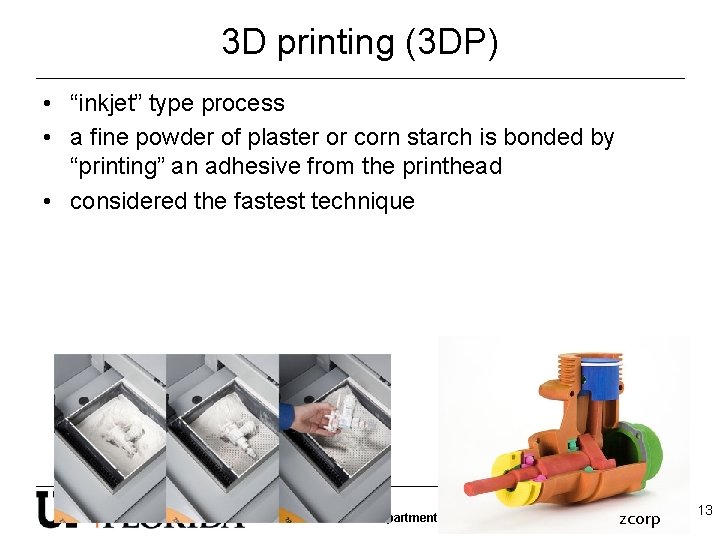
3 D printing (3 DP) • “inkjet” type process • a fine powder of plaster or corn starch is bonded by “printing” an adhesive from the printhead • considered the fastest technique EML 2023 Department of Mechanical and Aerospace Engineering zcorp 13
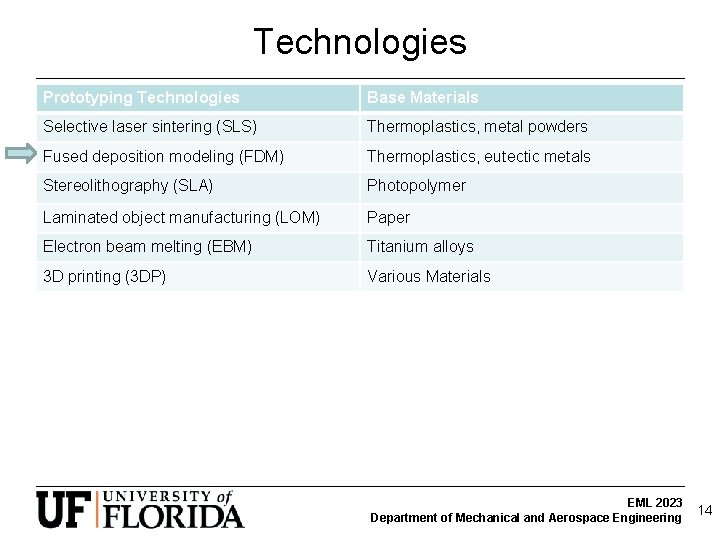
Technologies Prototyping Technologies Base Materials Selective laser sintering (SLS) Thermoplastics, metal powders Fused deposition modeling (FDM) Thermoplastics, eutectic metals Stereolithography (SLA) Photopolymer Laminated object manufacturing (LOM) Paper Electron beam melting (EBM) Titanium alloys 3 D printing (3 DP) Various Materials EML 2023 Department of Mechanical and Aerospace Engineering 14
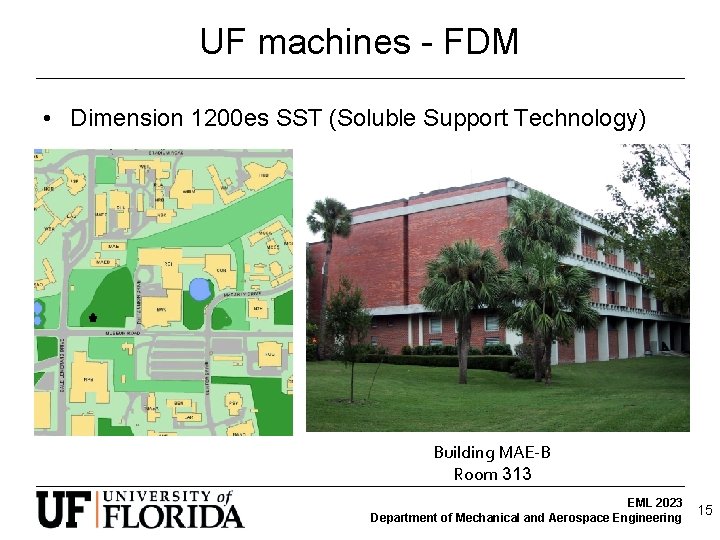
UF machines - FDM • Dimension 1200 es SST (Soluble Support Technology) Building MAE-B Room 313 EML 2023 Department of Mechanical and Aerospace Engineering 15
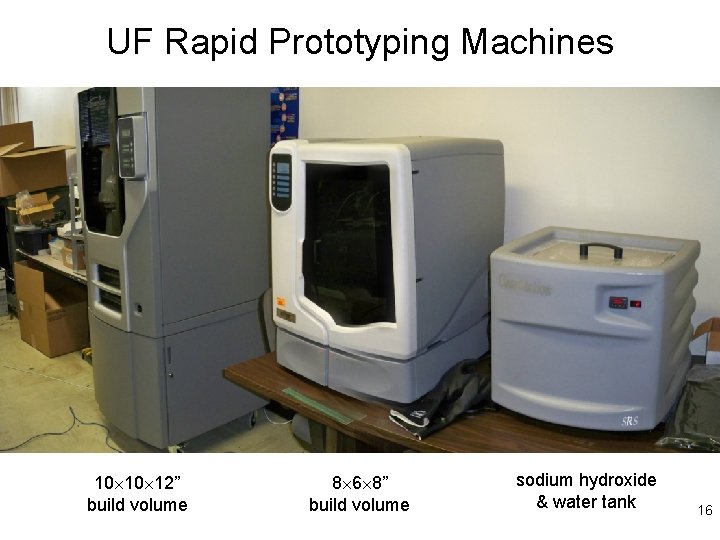
UF Rapid Prototyping Machines 10 10 12” build volume 8 6 8” build volume sodium hydroxide & water tank 16
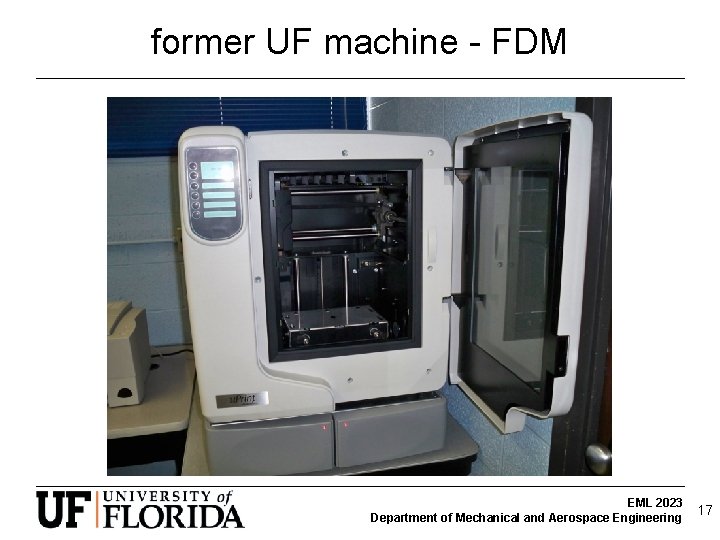
former UF machine - FDM EML 2023 Department of Mechanical and Aerospace Engineering 17
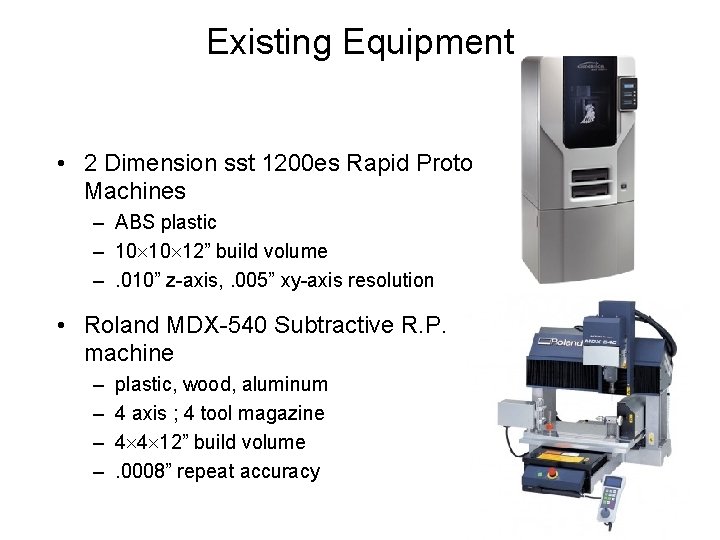
Existing Equipment • 2 Dimension sst 1200 es Rapid Proto Machines – ABS plastic – 10 10 12” build volume –. 010” z-axis, . 005” xy-axis resolution • Roland MDX-540 Subtractive R. P. machine – – plastic, wood, aluminum 4 axis ; 4 tool magazine 4 4 12” build volume. 0008” repeat accuracy
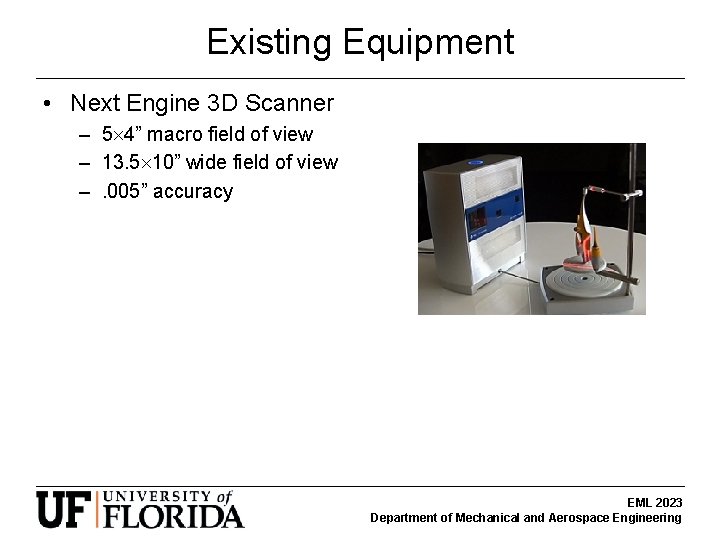
Existing Equipment • Next Engine 3 D Scanner – 5 4” macro field of view – 13. 5 10” wide field of view –. 005” accuracy EML 2023 Department of Mechanical and Aerospace Engineering
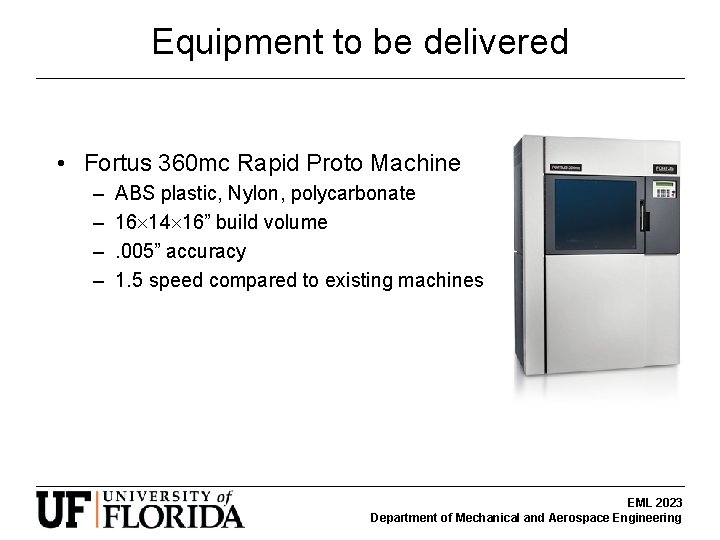
Equipment to be delivered • Fortus 360 mc Rapid Proto Machine – – ABS plastic, Nylon, polycarbonate 16 14 16” build volume. 005” accuracy 1. 5 speed compared to existing machines EML 2023 Department of Mechanical and Aerospace Engineering
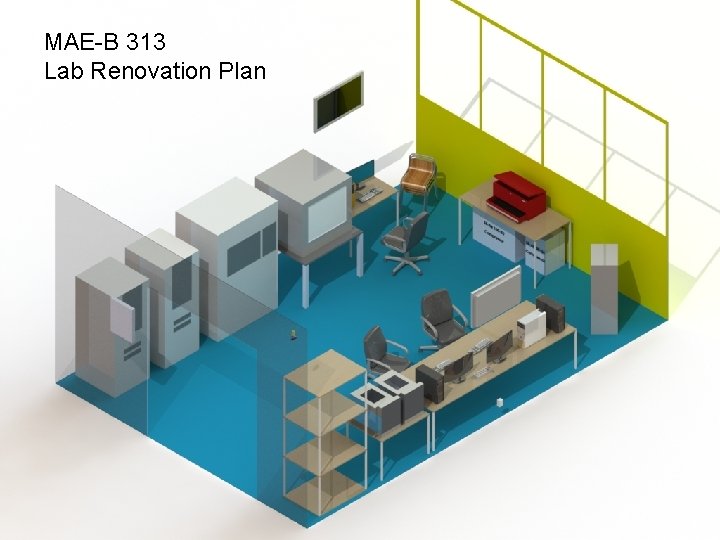
MAE-B 313 Lab Renovation Plan EML 2023 Department of Mechanical and Aerospace Engineering
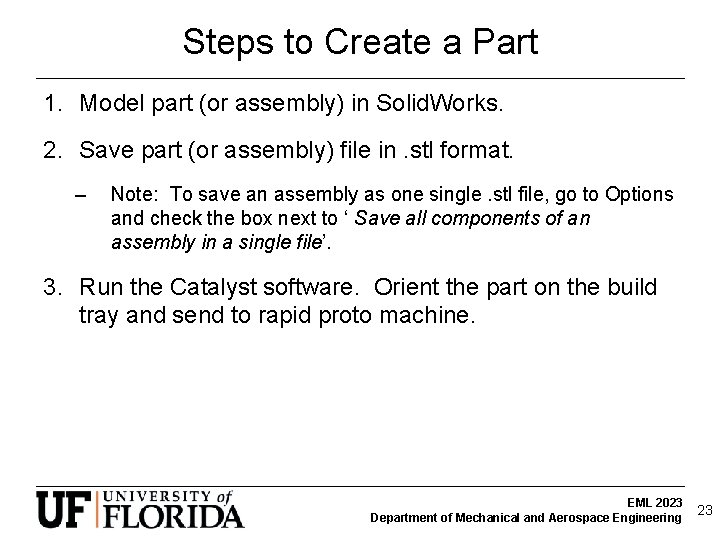
Steps to Create a Part 1. Model part (or assembly) in Solid. Works. 2. Save part (or assembly) file in. stl format. – Note: To save an assembly as one single. stl file, go to Options and check the box next to ‘ Save all components of an assembly in a single file’. 3. Run the Catalyst software. Orient the part on the build tray and send to rapid proto machine. EML 2023 Department of Mechanical and Aerospace Engineering 23
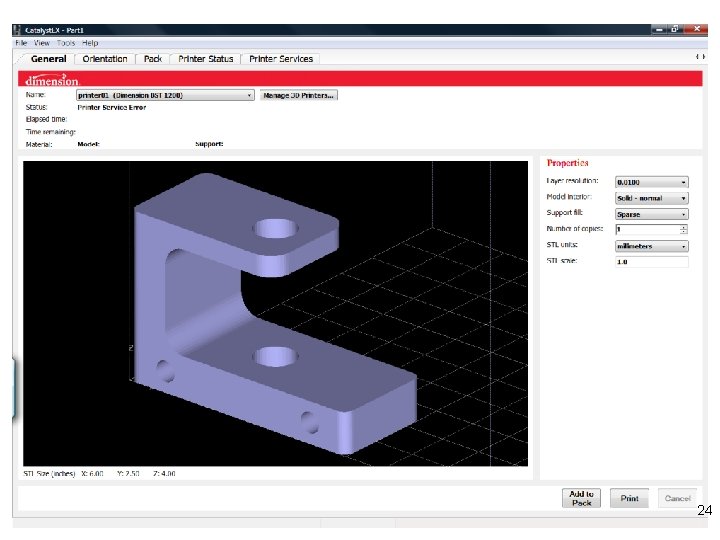
24
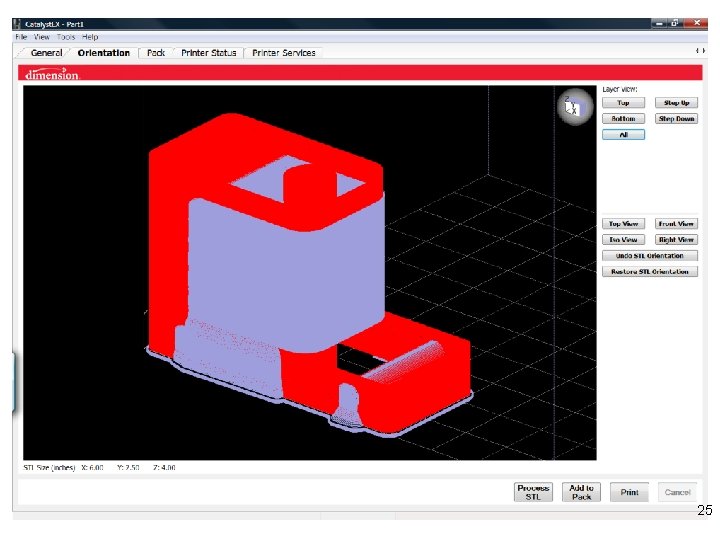
25

26
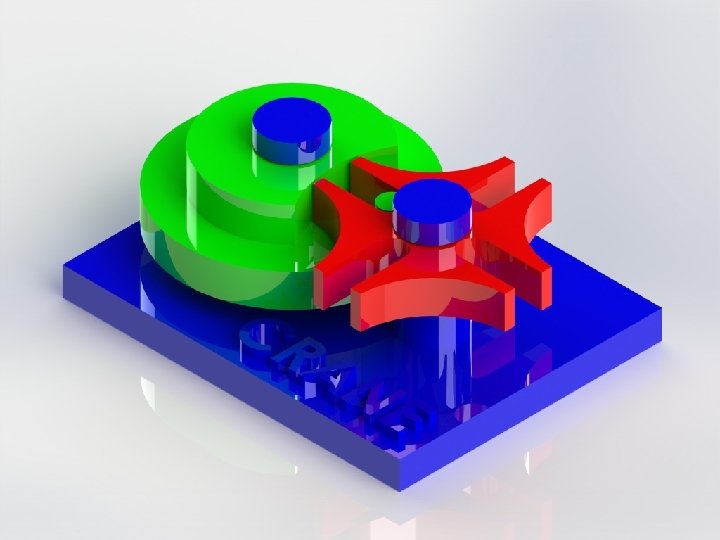
27
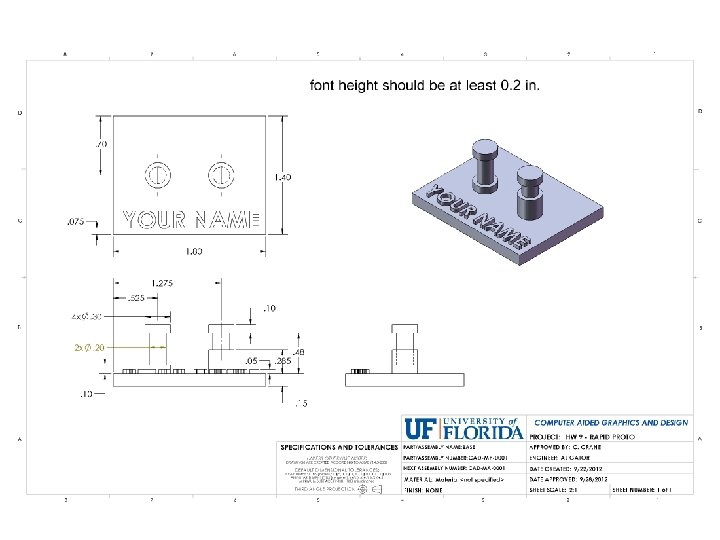
28
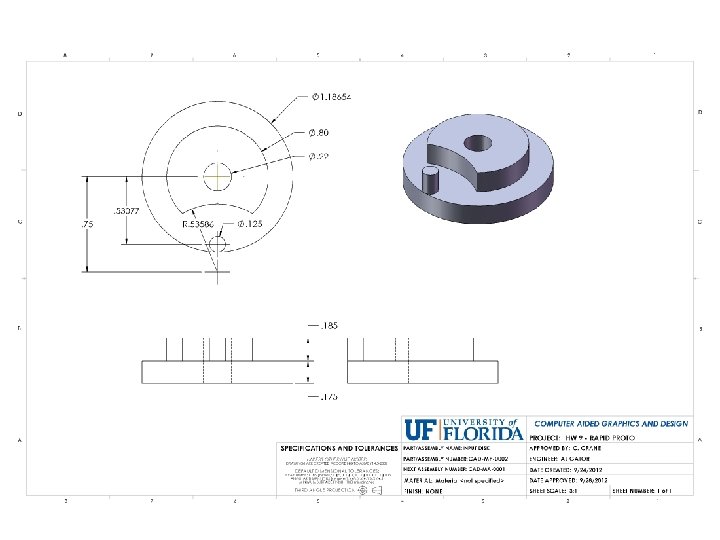
29
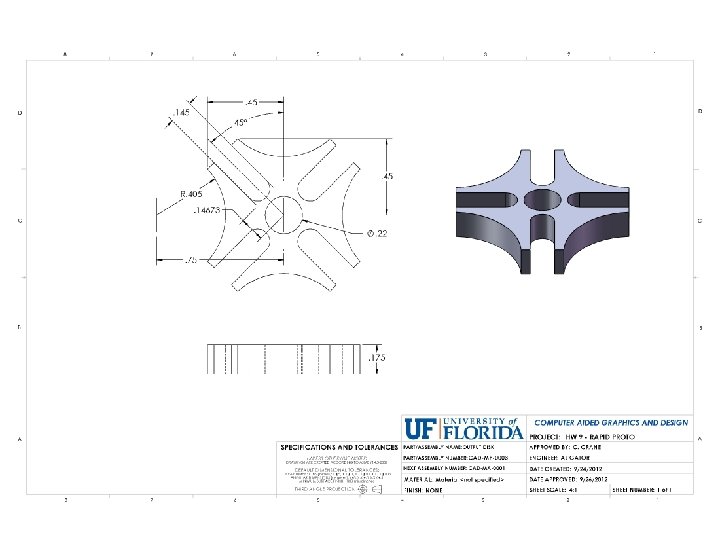
30
What is a clearance fit
Solidworks download
Eml 2023
Uf eml 2023
Eml2023
Predictive maintenance wikipedia
Rapid prototyping
Lom rapid prototyping
Rapid prototyping
Synchronize and stabilize model
Rapid prototyping video
Rad design workshop
Cmu rapid prototyping
Powder based rapid prototyping
Prototyping definition
Solid ground curing diagram
Rapid prototyping rp
Bentuk awal contoh atau standar ukuran dari sebuah
Compare stl and slc file format
Prototyping methodology
Liquid based rapid prototyping
Fineline rapid prototyping
Rapid prototyping could be an advantageous methodology
Mexico rapid prototyping
Rapid prototyping model in software engineering
Rapid prototyping pro metal system
01:640:244 lecture notes - lecture 15: plat, idah, farad
Metal lath uses
Ciclo del proyecto bajo el eml
Health systems building blocks