Ductile Phase Toughening of Tungsten Composites G R
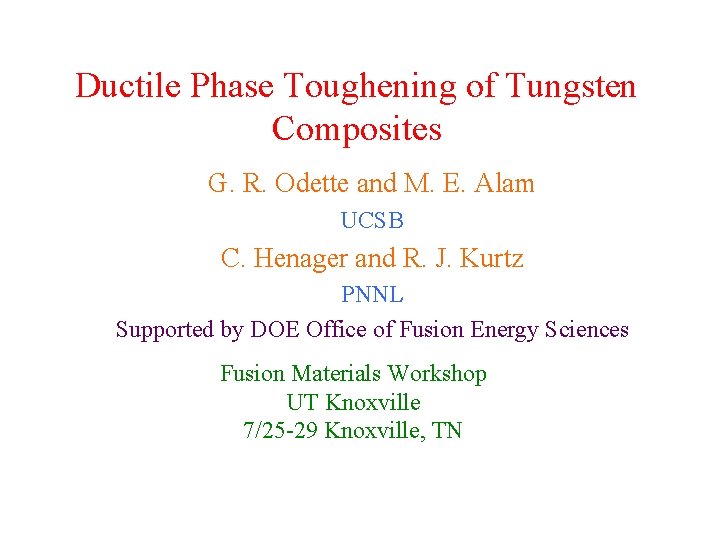
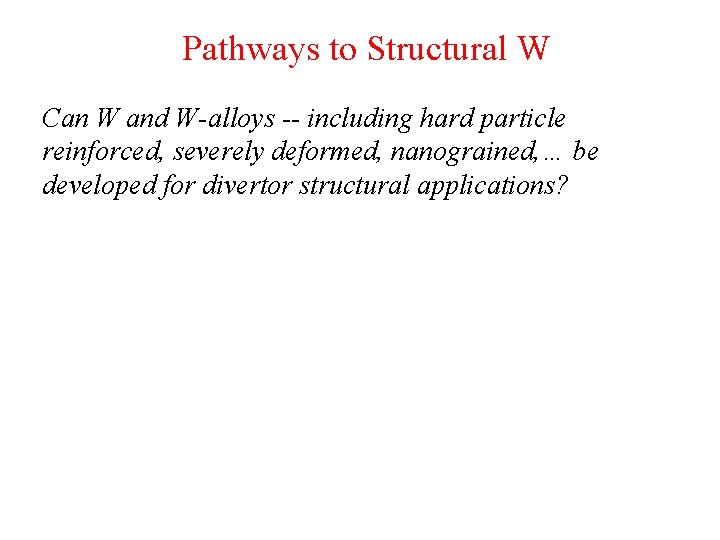
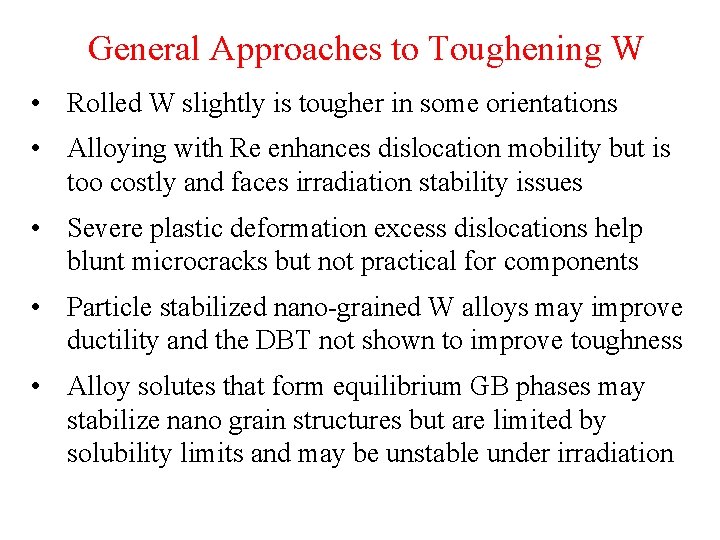
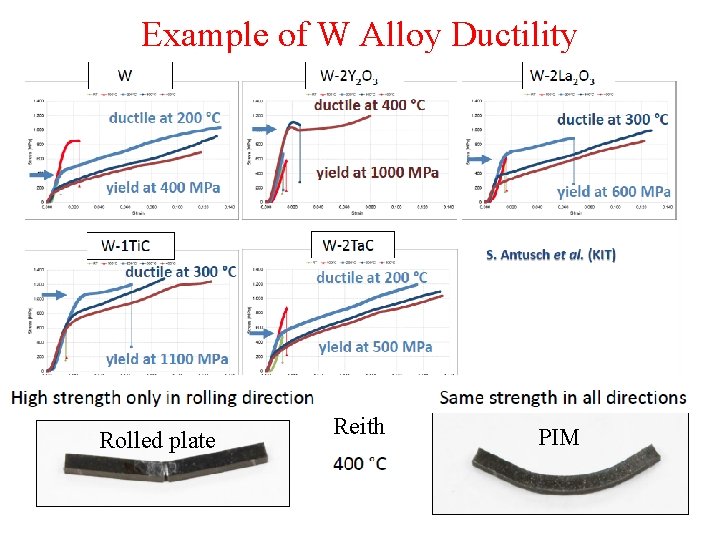
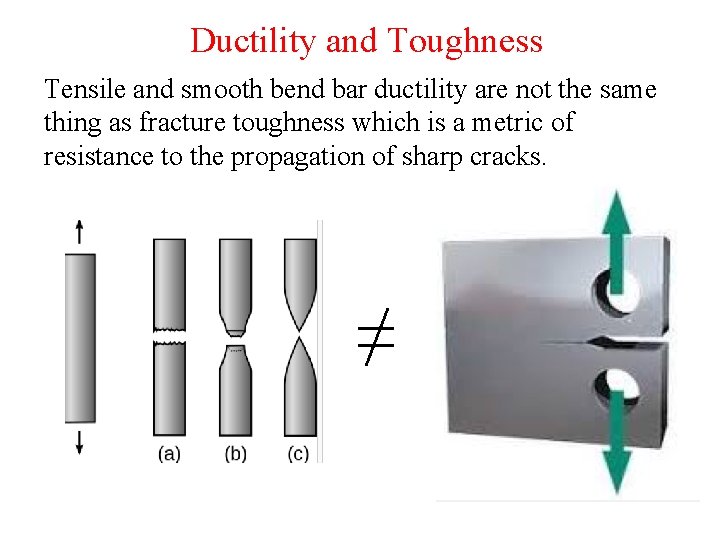
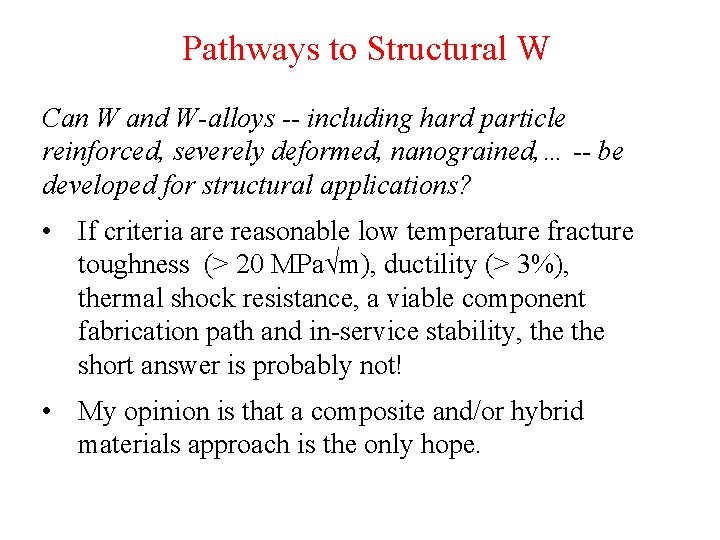
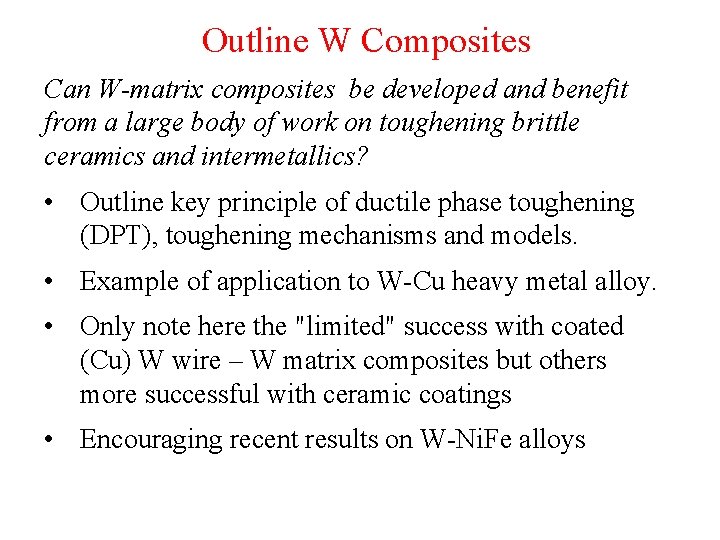
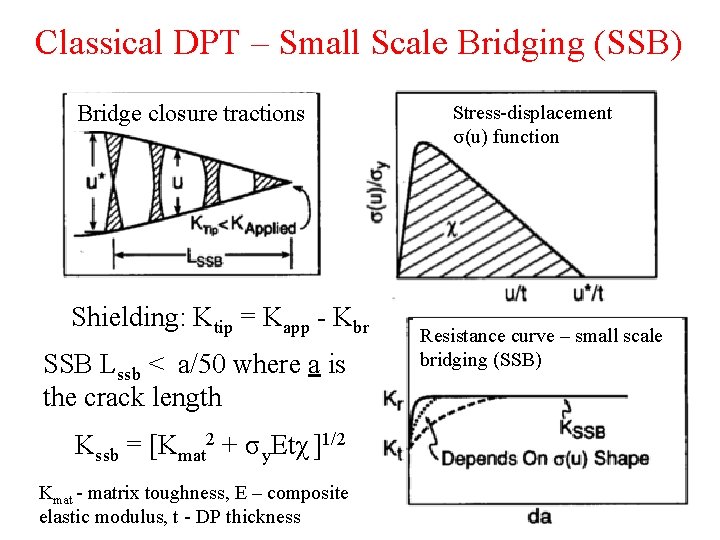
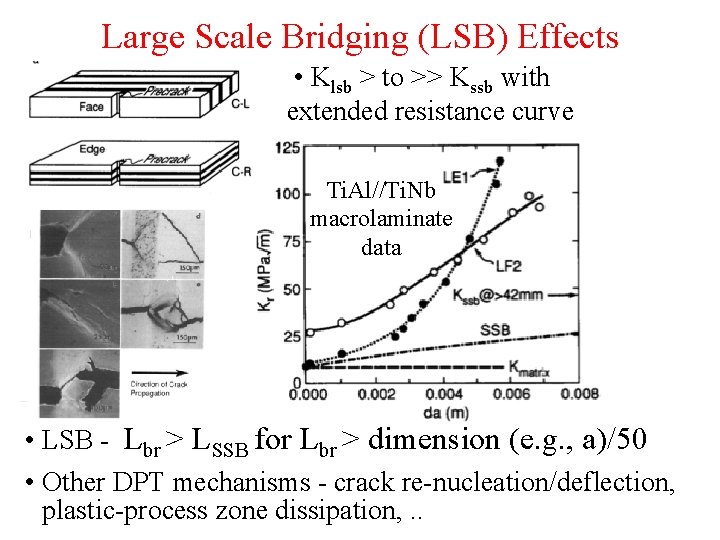
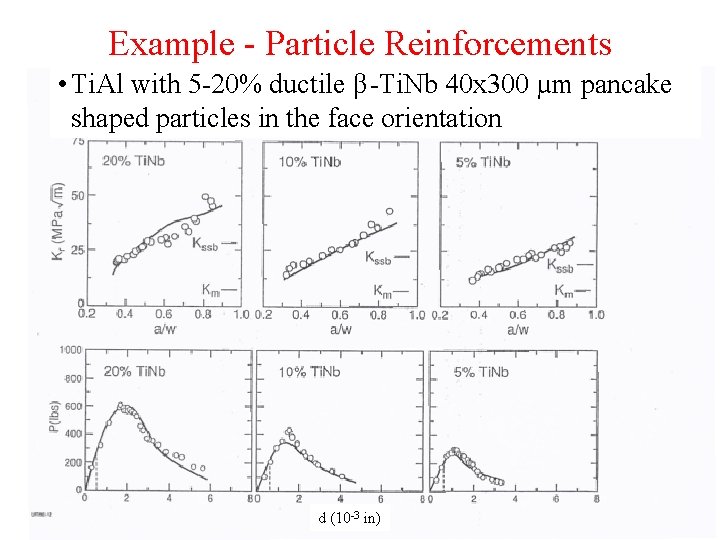
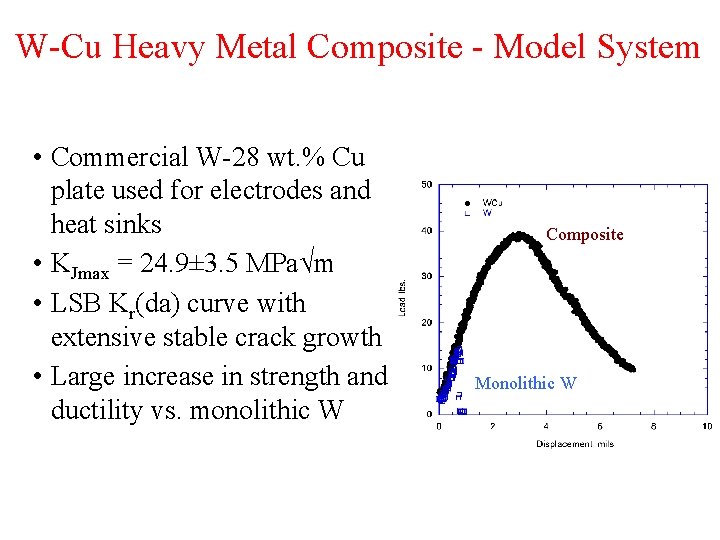
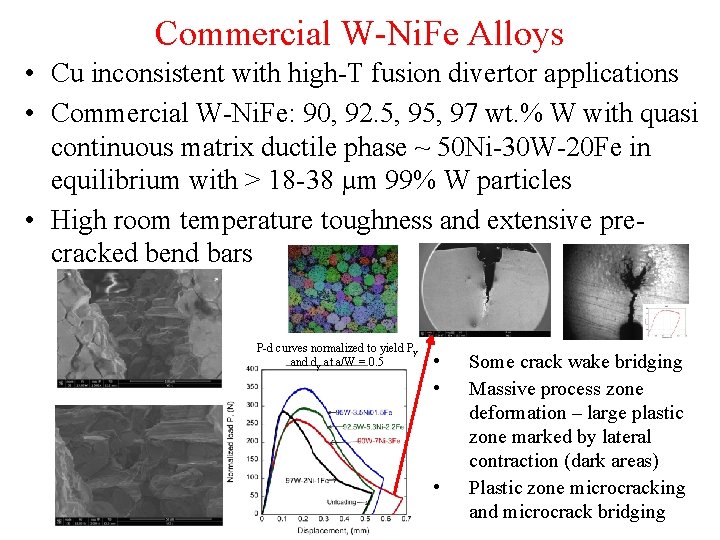
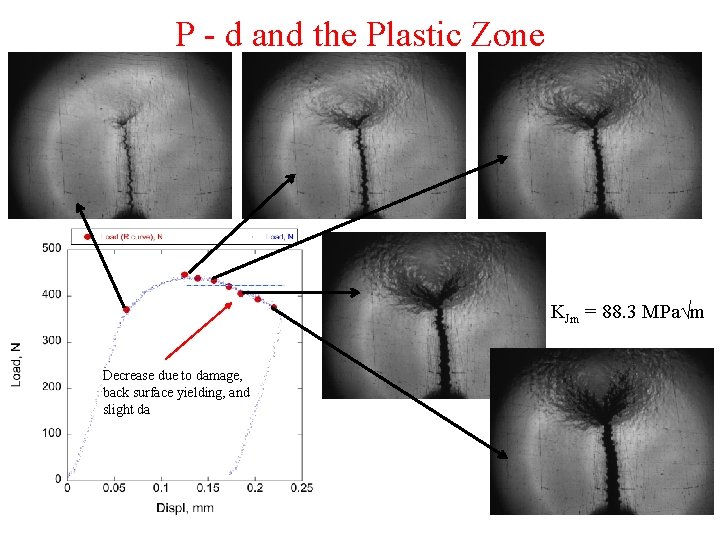
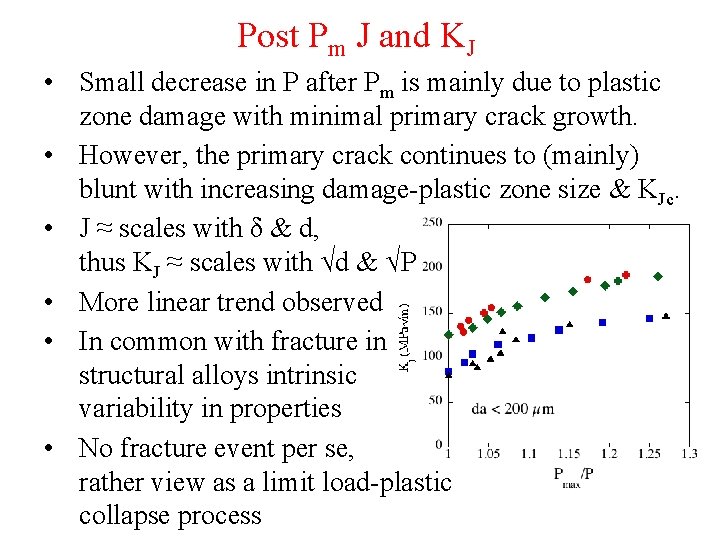
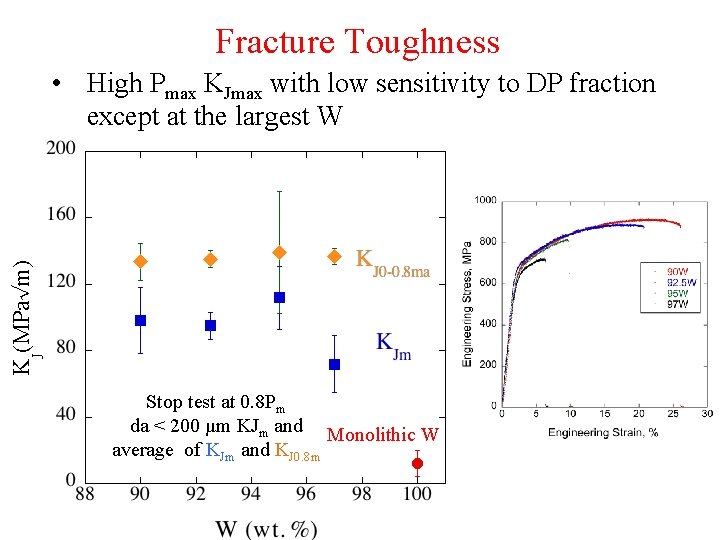
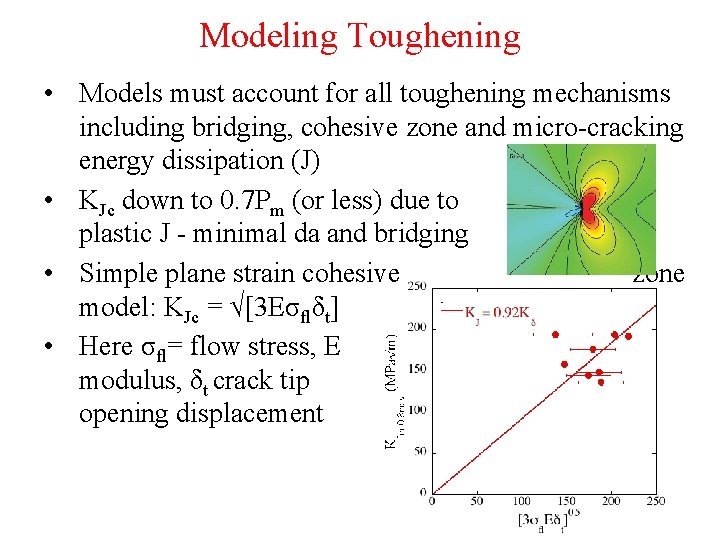
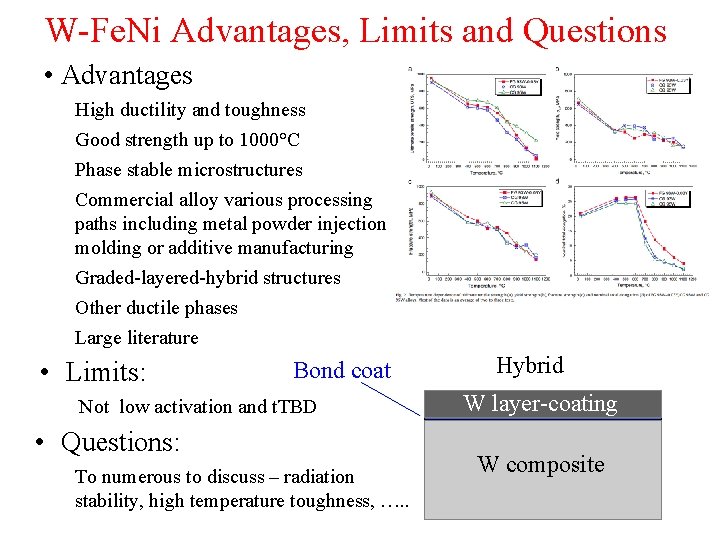
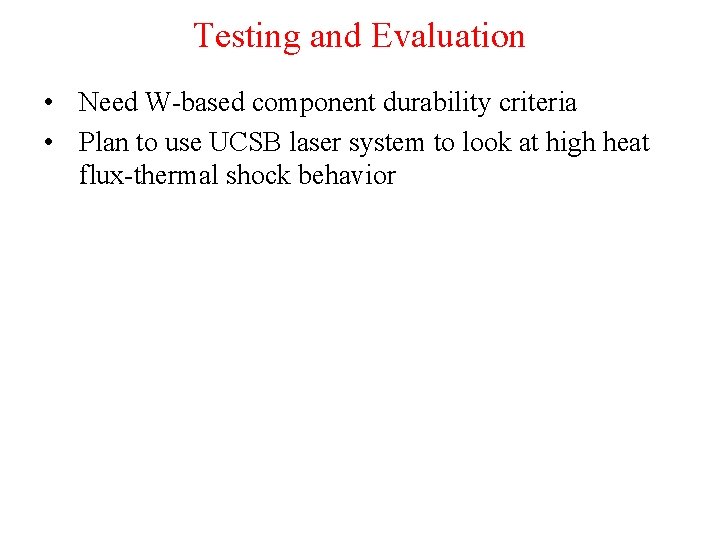
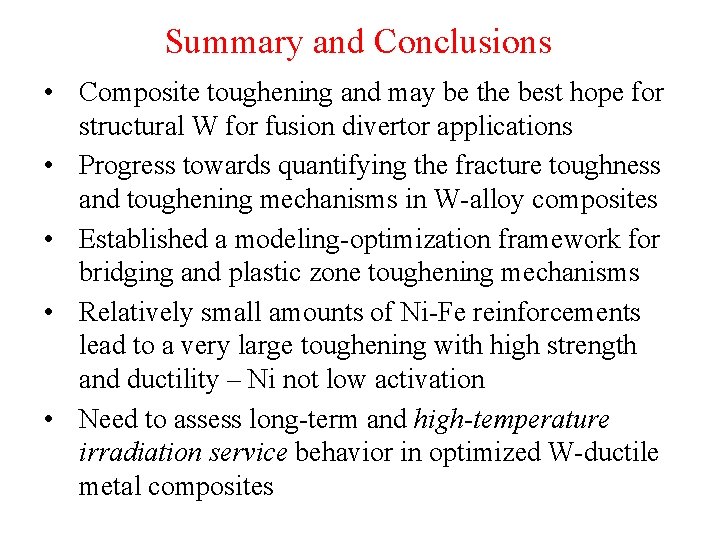
- Slides: 19
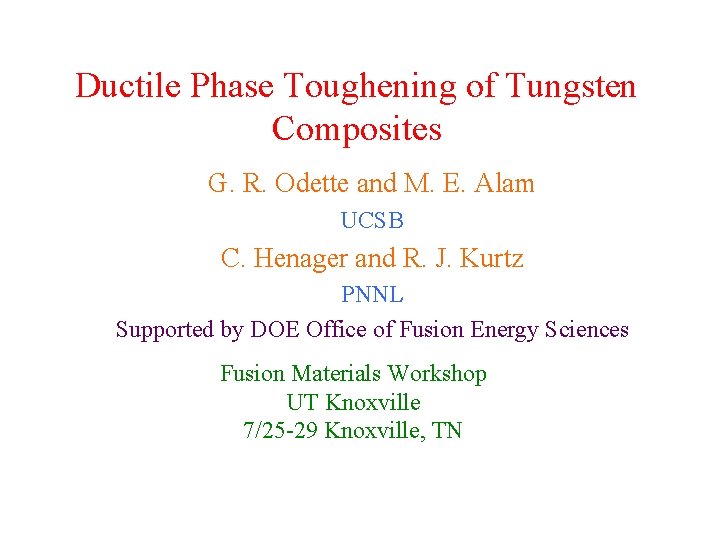
Ductile Phase Toughening of Tungsten Composites G. R. Odette and M. E. Alam UCSB C. Henager and R. J. Kurtz PNNL Supported by DOE Office of Fusion Energy Sciences Fusion Materials Workshop UT Knoxville 7/25 -29 Knoxville, TN
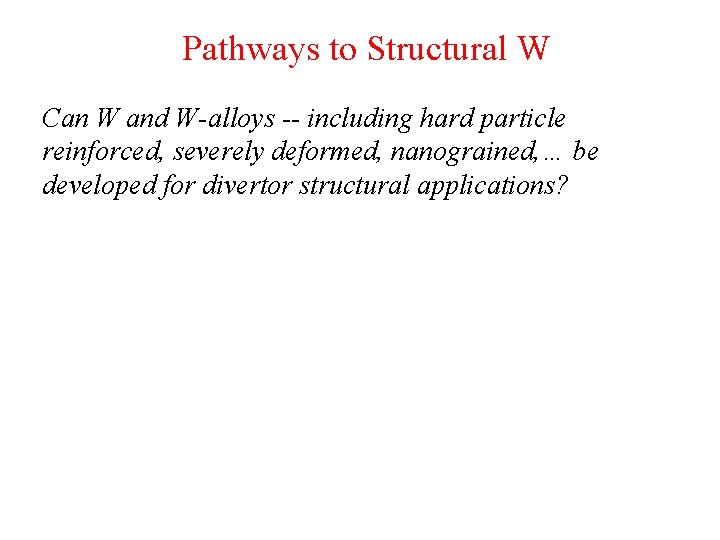
Pathways to Structural W Can W and W-alloys -- including hard particle reinforced, severely deformed, nanograined, … be developed for divertor structural applications?
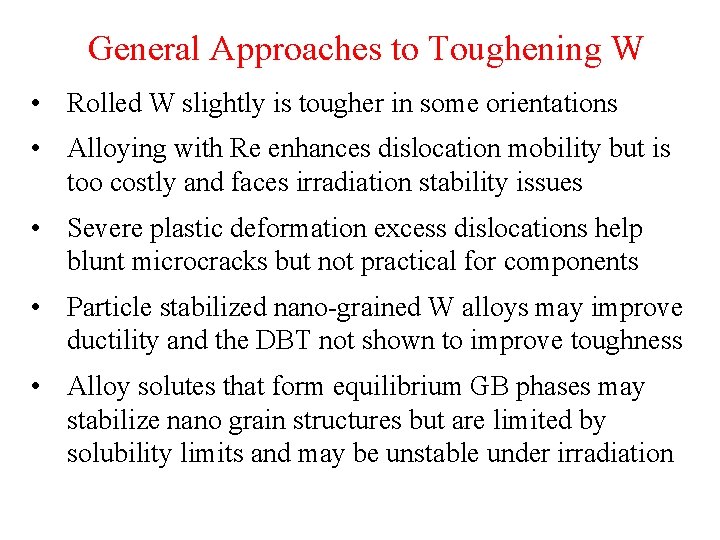
General Approaches to Toughening W • Rolled W slightly is tougher in some orientations • Alloying with Re enhances dislocation mobility but is too costly and faces irradiation stability issues • Severe plastic deformation excess dislocations help blunt microcracks but not practical for components • Particle stabilized nano-grained W alloys may improve ductility and the DBT not shown to improve toughness • Alloy solutes that form equilibrium GB phases may stabilize nano grain structures but are limited by solubility limits and may be unstable under irradiation
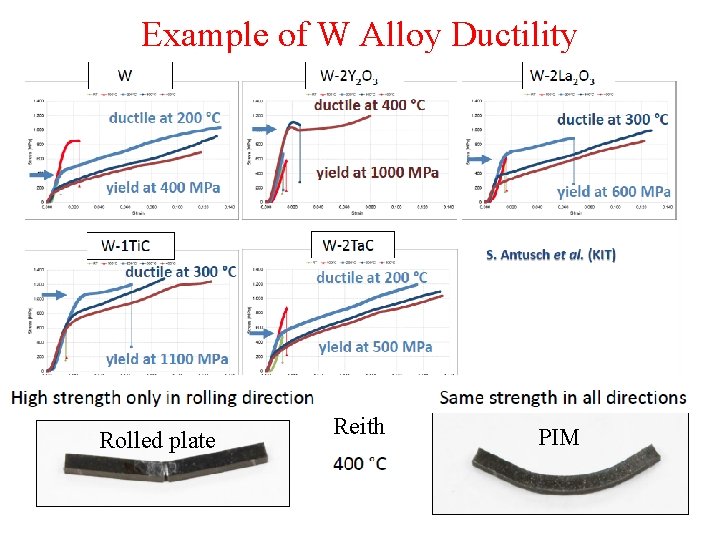
Example of W Alloy Ductility Rolled plate Reith PIM
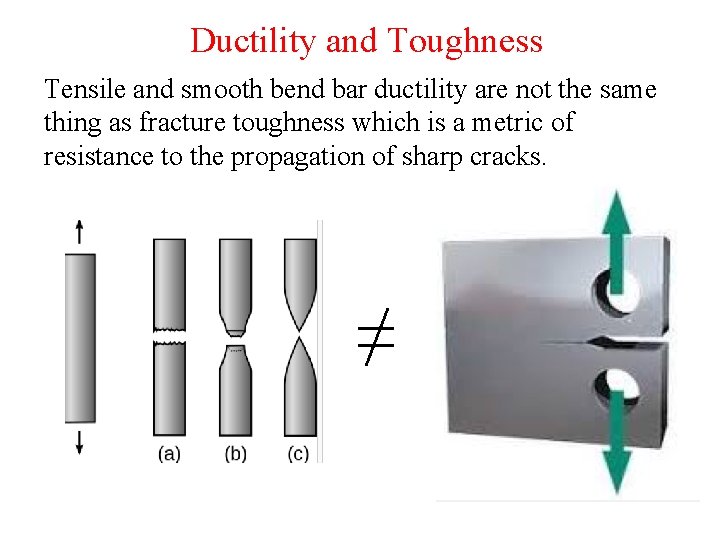
Ductility and Toughness Tensile and smooth bend bar ductility are not the same thing as fracture toughness which is a metric of resistance to the propagation of sharp cracks. ≠
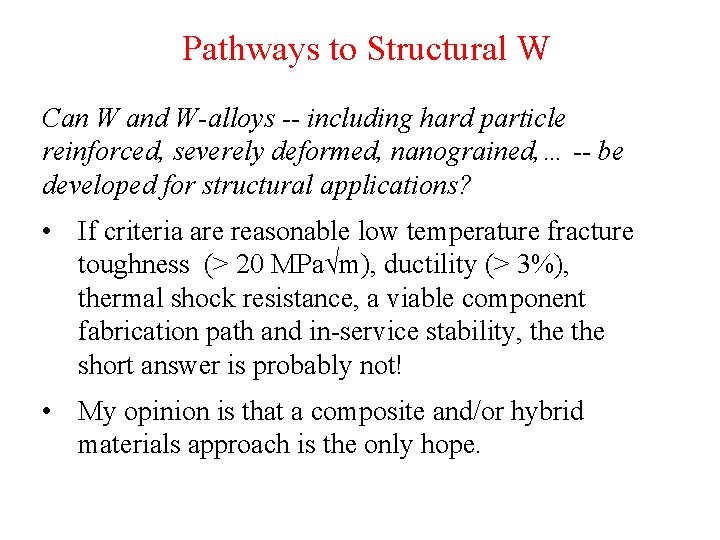
Pathways to Structural W Can W and W-alloys -- including hard particle reinforced, severely deformed, nanograined, … -- be developed for structural applications? • If criteria are reasonable low temperature fracture toughness (> 20 MPa√m), ductility (> 3%), thermal shock resistance, a viable component fabrication path and in-service stability, the short answer is probably not! • My opinion is that a composite and/or hybrid materials approach is the only hope.
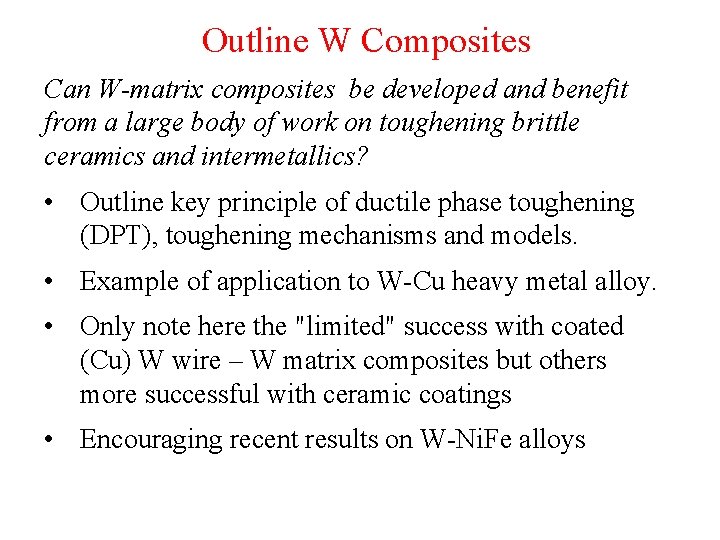
Outline W Composites Can W-matrix composites be developed and benefit from a large body of work on toughening brittle ceramics and intermetallics? • Outline key principle of ductile phase toughening (DPT), toughening mechanisms and models. • Example of application to W-Cu heavy metal alloy. • Only note here the "limited" success with coated (Cu) W wire – W matrix composites but others more successful with ceramic coatings • Encouraging recent results on W-Ni. Fe alloys
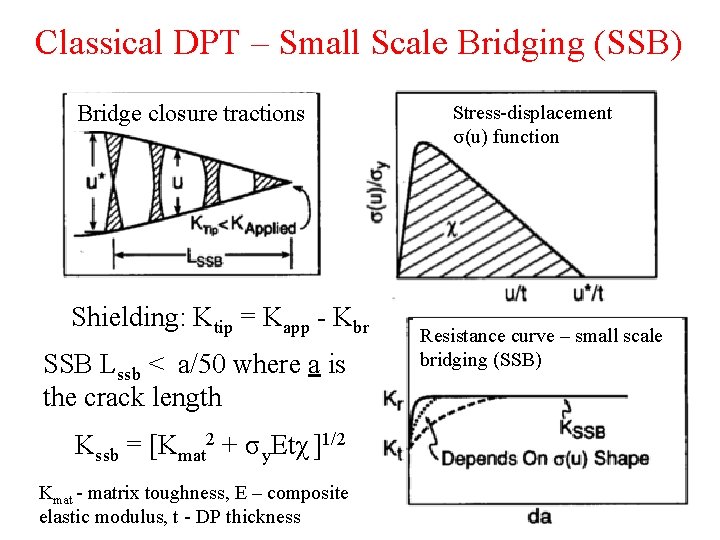
Classical DPT – Small Scale Bridging (SSB) Bridge closure tractions Shielding: Ktip = Kapp - Kbr SSB Lssb < a/50 where a is the crack length Kssb = [Kmat 2 + σ y. Etχ ]1/2 Kmat - matrix toughness, E – composite elastic modulus, t - DP thickness Stress-displacement σ(u) function Resistance curve – small scale bridging (SSB)
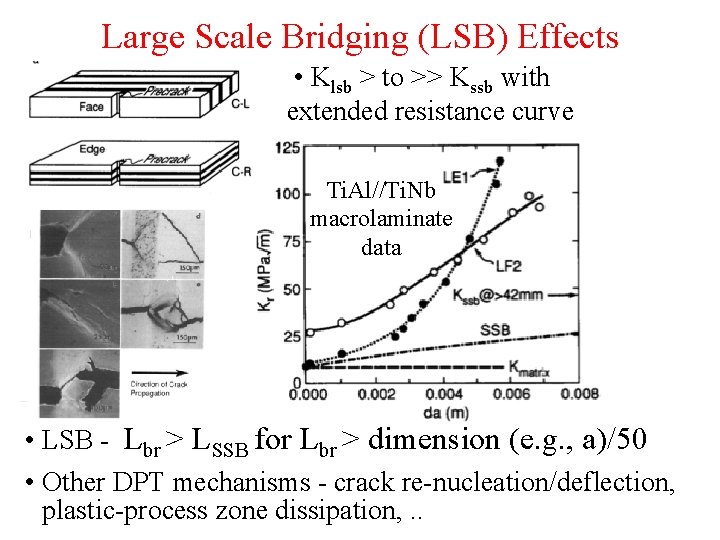
Large Scale Bridging (LSB) Effects • Klsb > to >> Kssb with extended resistance curve xxx Measure s(u) Ti. Al//Ti. Nb macrolaminate data • LSB - Lbr > LSSB for Lbr > dimension (e. g. , a)/50 • Other DPT mechanisms - crack re-nucleation/deflection, plastic-process zone dissipation, . .
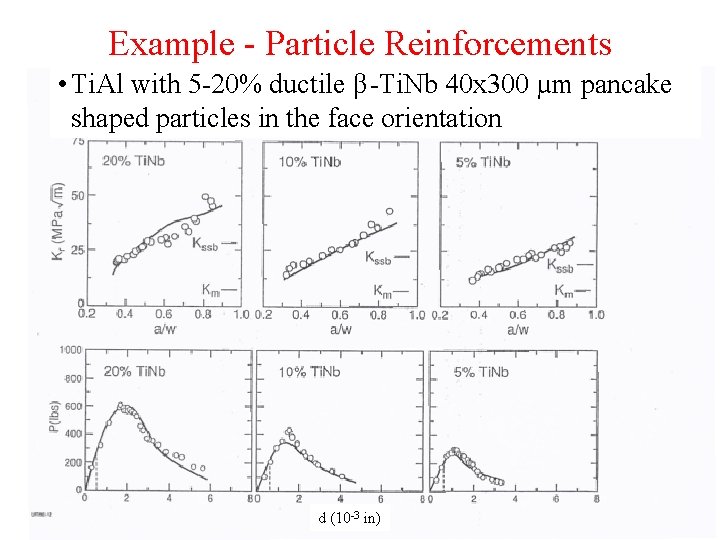
Example - Particle Reinforcements • Ti. Al with 5 -20% ductile β-Ti. Nb 40 x 300 µm pancake shaped particles in the face orientation d (10 -3 in)
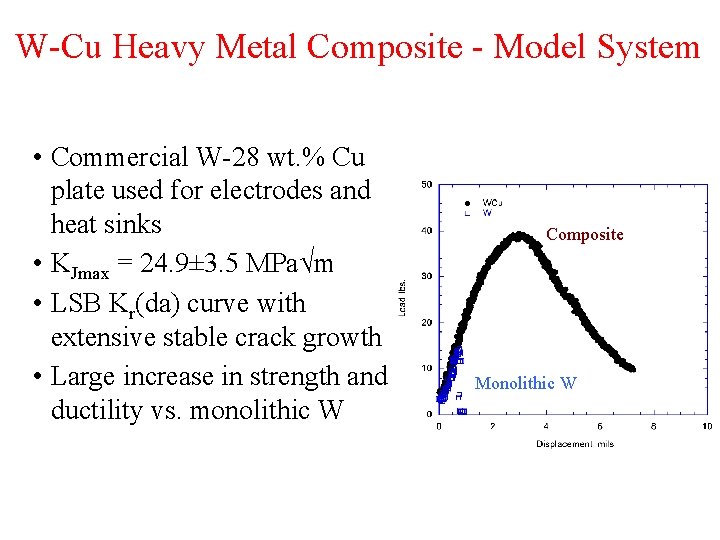
W-Cu Heavy Metal Composite - Model System • Commercial W-28 wt. % Cu plate used for electrodes and heat sinks • KJmax = 24. 9± 3. 5 MPa√m • LSB Kr(da) curve with extensive stable crack growth • Large increase in strength and ductility vs. monolithic W Composite Monolithic W
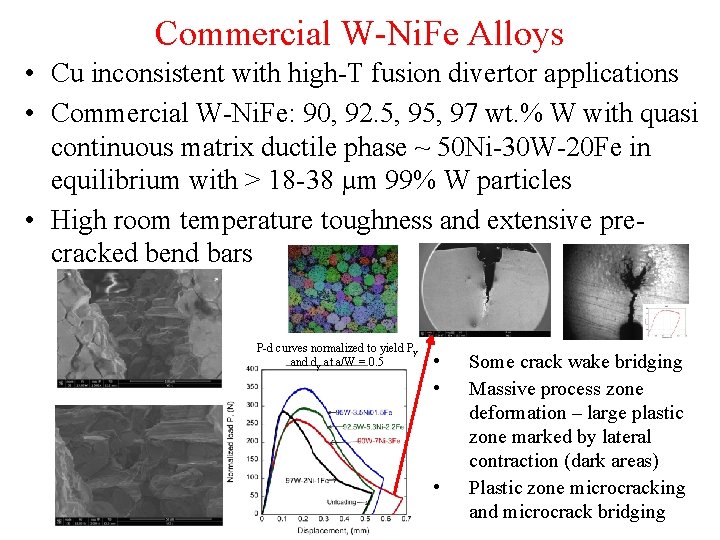
Commercial W-Ni. Fe Alloys • Cu inconsistent with high-T fusion divertor applications • Commercial W-Ni. Fe: 90, 92. 5, 97 wt. % W with quasi continuous matrix ductile phase ~ 50 Ni-30 W-20 Fe in equilibrium with > 18 -38 µm 99% W particles • High room temperature toughness and extensive precracked bend bars P-d curves normalized to yield P y and dy at a/W = 0. 5 • • • Some crack wake bridging Massive process zone deformation – large plastic zone marked by lateral contraction (dark areas) Plastic zone microcracking and microcrack bridging
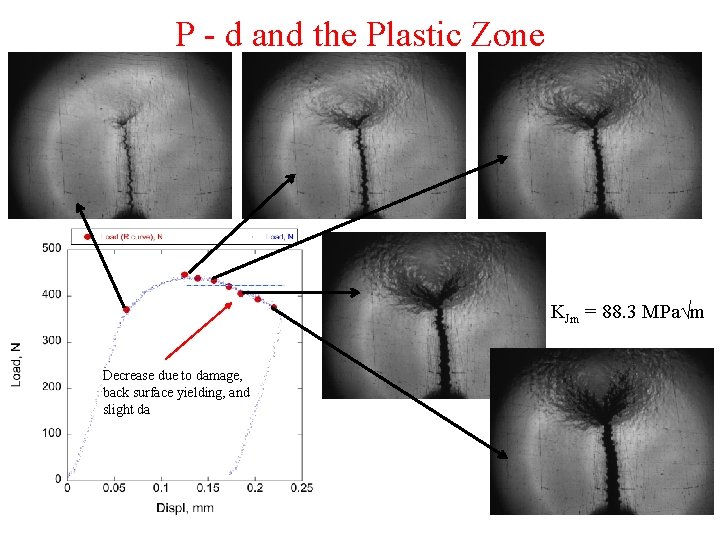
P - d and the Plastic Zone KJm = 88. 3 MPa√m Decrease due to damage, back surface yielding, and slight da 13
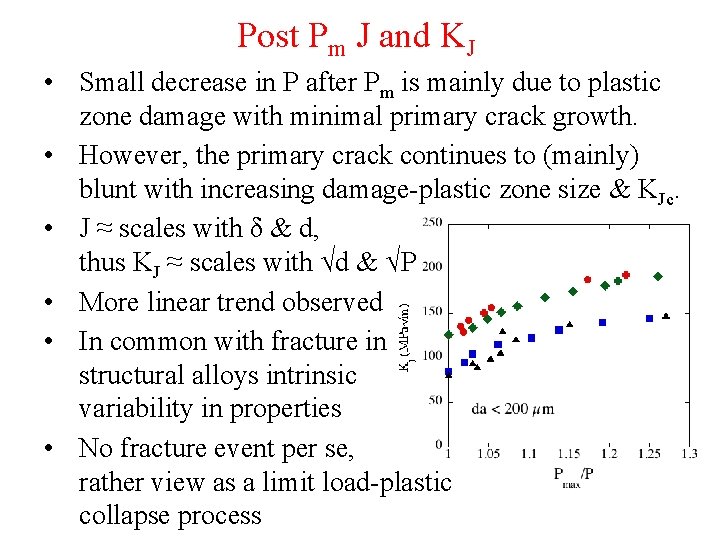
Post Pm J and KJ • Small decrease in P after Pm is mainly due to plastic zone damage with minimal primary crack growth. • However, the primary crack continues to (mainly) blunt with increasing damage-plastic zone size & KJc. • J ≈ scales with δ & d, thus KJ ≈ scales with √d & √P • More linear trend observed • In common with fracture in structural alloys intrinsic variability in properties • No fracture event per se, rather view as a limit load-plastic collapse process
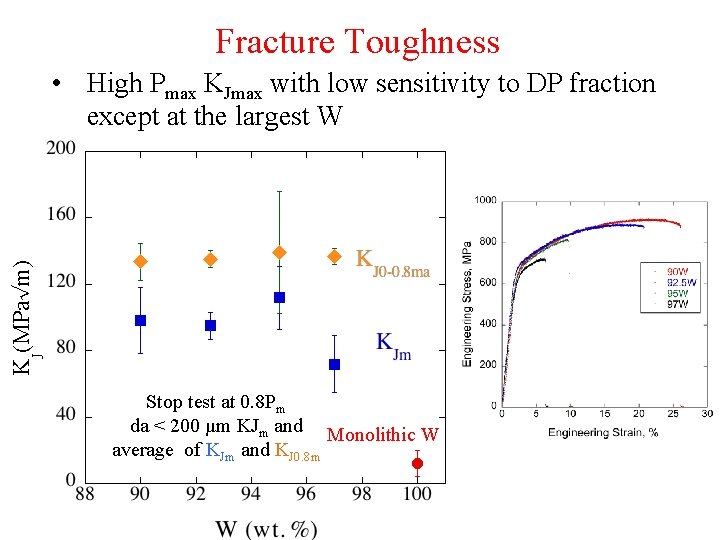
Fracture Toughness • High Pmax KJmax with low sensitivity to DP fraction except at the largest W Stop test at 0. 8 Pm da < 200 µm KJm and Monolithic W average of KJm and KJ 0. 8 m
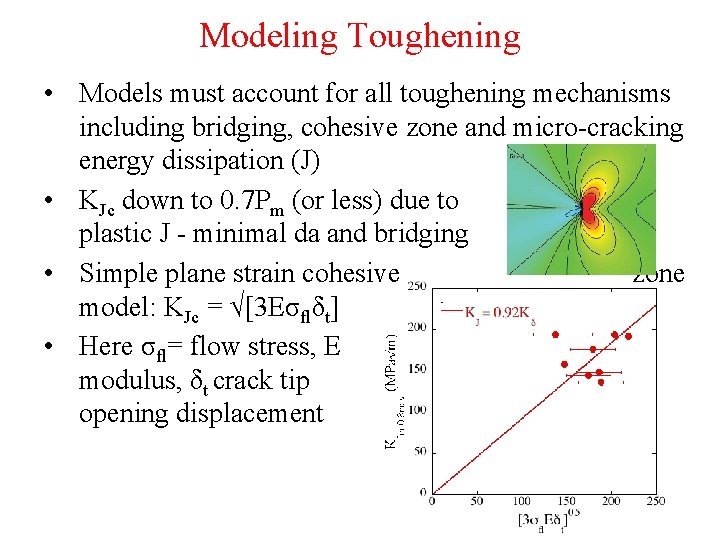
Modeling Toughening • Models must account for all toughening mechanisms including bridging, cohesive zone and micro-cracking energy dissipation (J) • KJc down to 0. 7 Pm (or less) due to plastic J - minimal da and bridging • Simple plane strain cohesive zone model: KJc = √[3 Eσflδt] • Here σfl= flow stress, E modulus, δt crack tip opening displacement
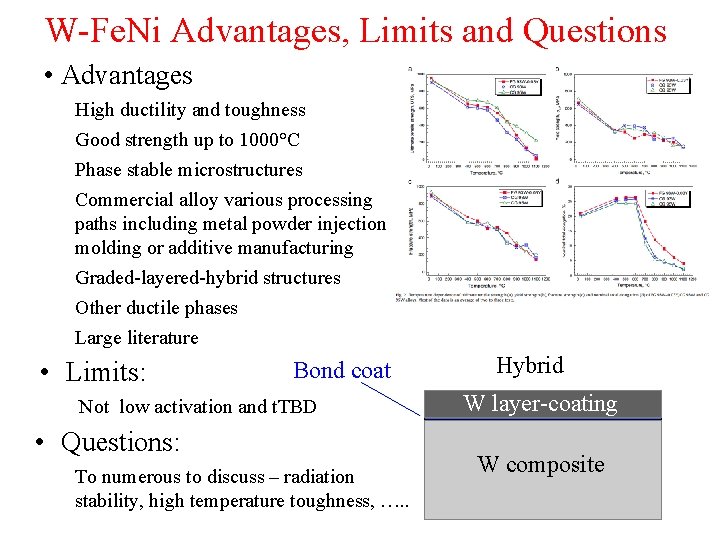
W-Fe. Ni Advantages, Limits and Questions • Advantages High ductility and toughness Good strength up to 1000°C Phase stable microstructures Commercial alloy various processing paths including metal powder injection molding or additive manufacturing Graded-layered-hybrid structures Other ductile phases Large literature • Limits: Bond coat Not low activation and t. TBD • Questions: To numerous to discuss – radiation stability, high temperature toughness, …. . Hybrid W layer-coating W composite
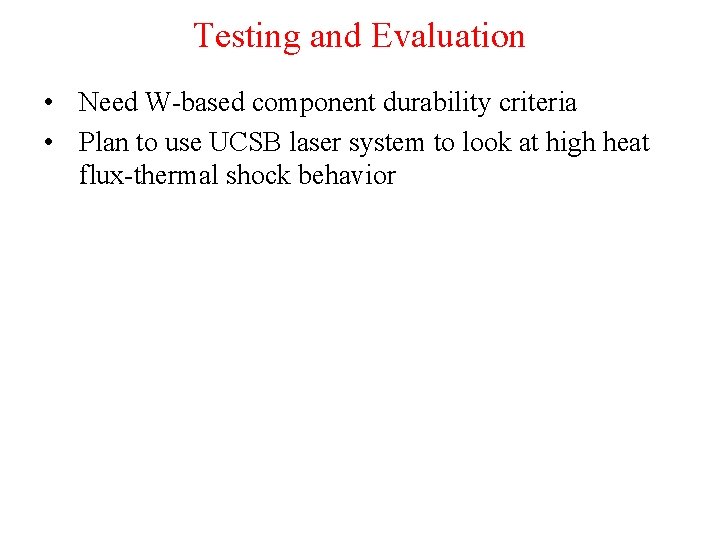
Testing and Evaluation • Need W-based component durability criteria • Plan to use UCSB laser system to look at high heat flux-thermal shock behavior
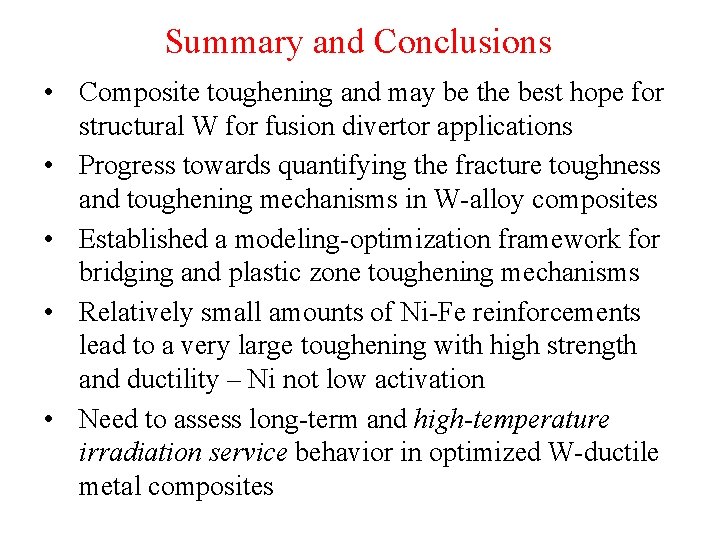
Summary and Conclusions • Composite toughening and may be the best hope for structural W for fusion divertor applications • Progress towards quantifying the fracture toughness and toughening mechanisms in W-alloy composites • Established a modeling-optimization framework for bridging and plastic zone toughening mechanisms • Relatively small amounts of Ni-Fe reinforcements lead to a very large toughening with high strength and ductility – Ni not low activation • Need to assess long-term and high-temperature irradiation service behavior in optimized W-ductile metal composites
Interior wall finishes material
Testimonial evidence.
Replsi
Ceramic matrix composites definition
Matrix materials zrt
Definition of matrix in composite materials
Astm d7332
Isotropic material stiffness matrix
Composites in sports
Structural composites industries llc
Ceramic matrix composites definition
Maine marine composites
Composites and components ofsted
Warp clock composites
Bts europlastics et composites option conception outillage
Garage composites
Advantages and disadvantages of thermoplastics
Define composite in dentistry
Brittle vs ductile deformation
Machinability of metals