Cumulative Design Review Team 22 Driver Assist Electrical
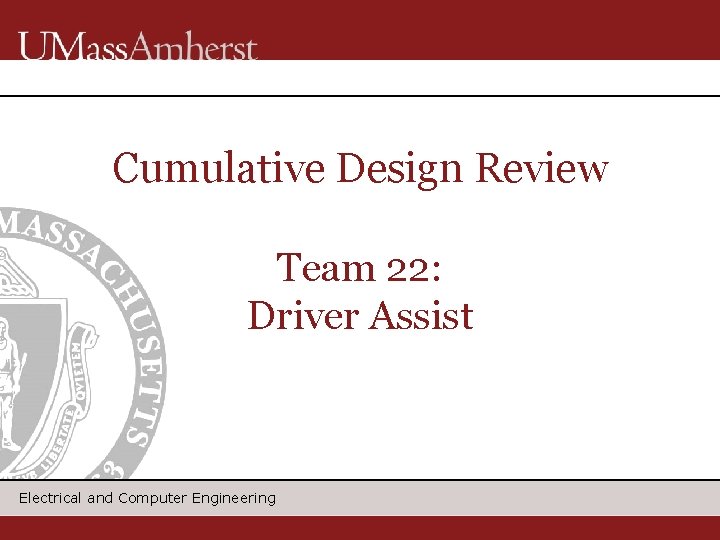
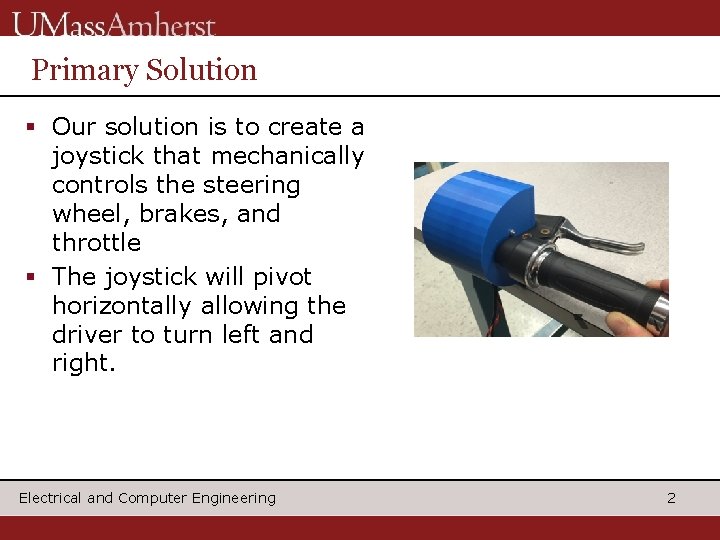
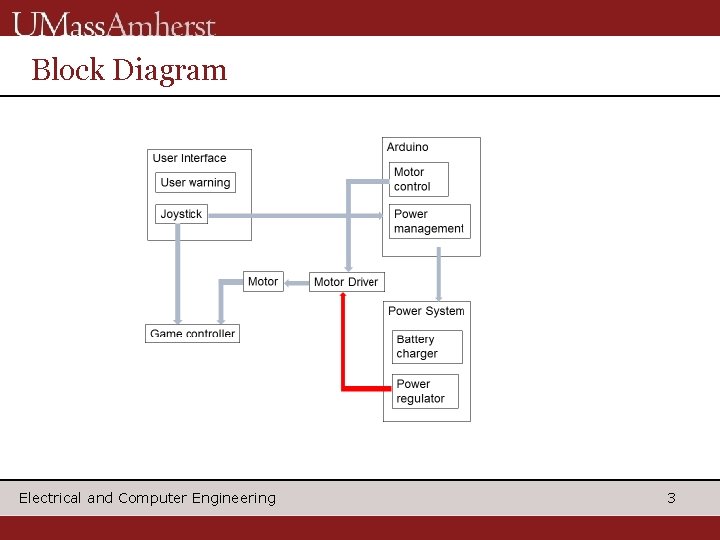
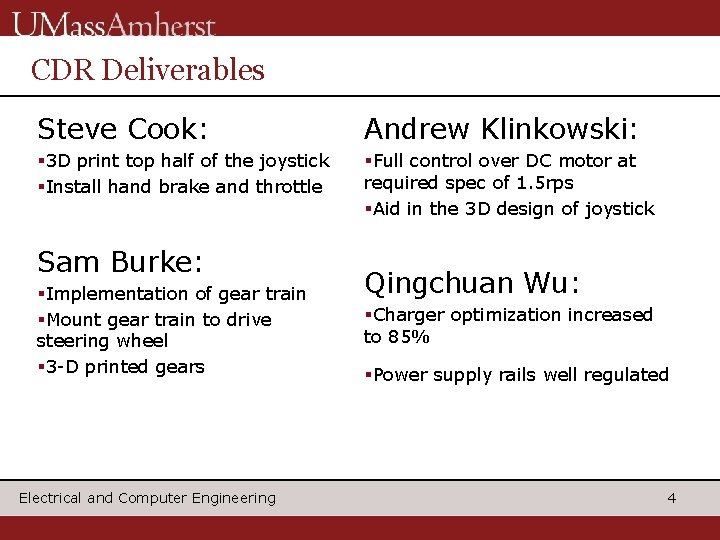
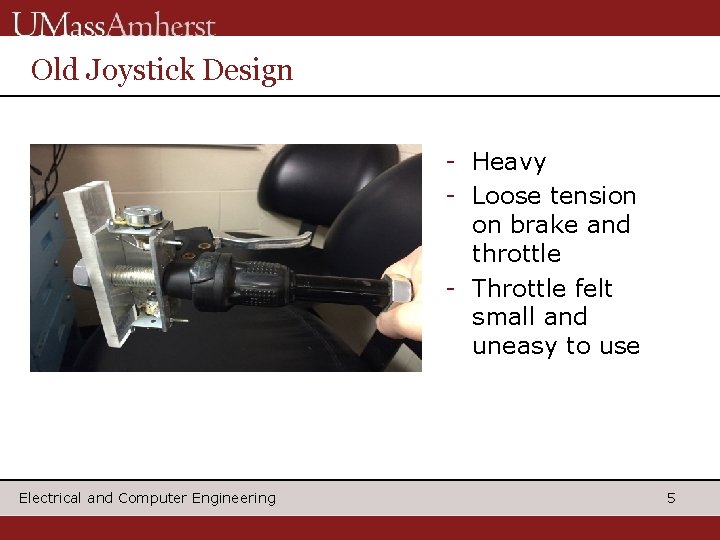
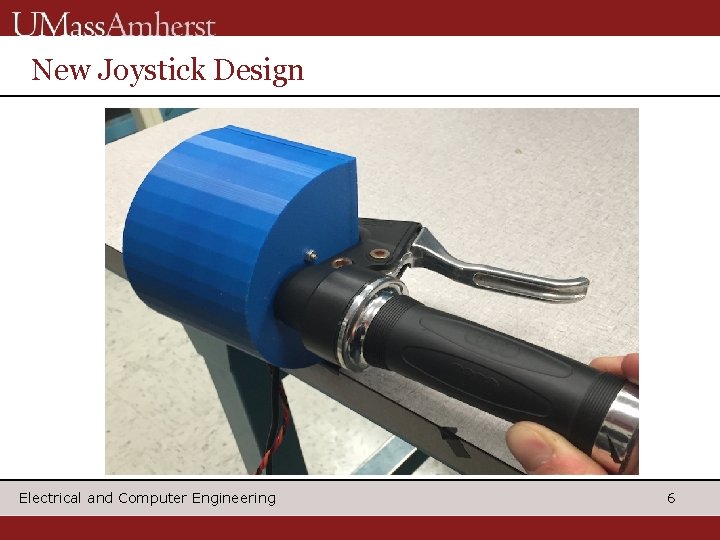
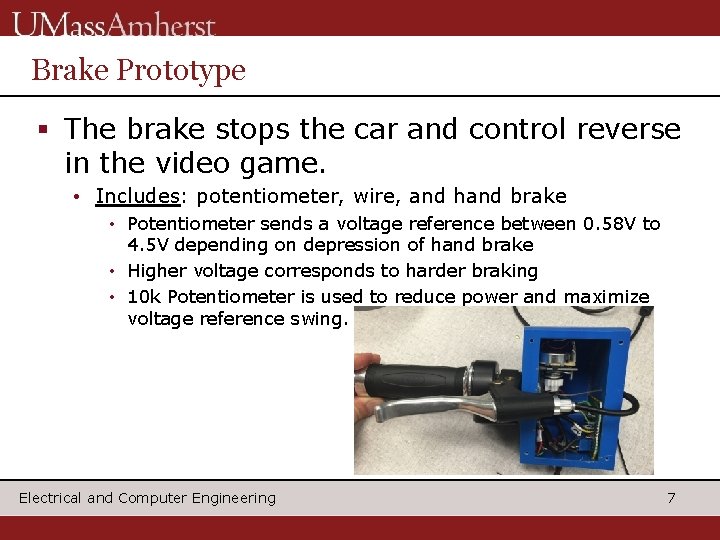
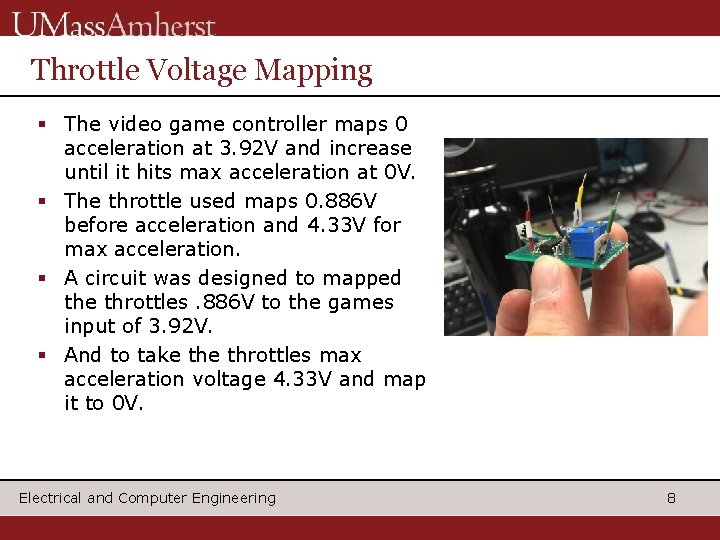
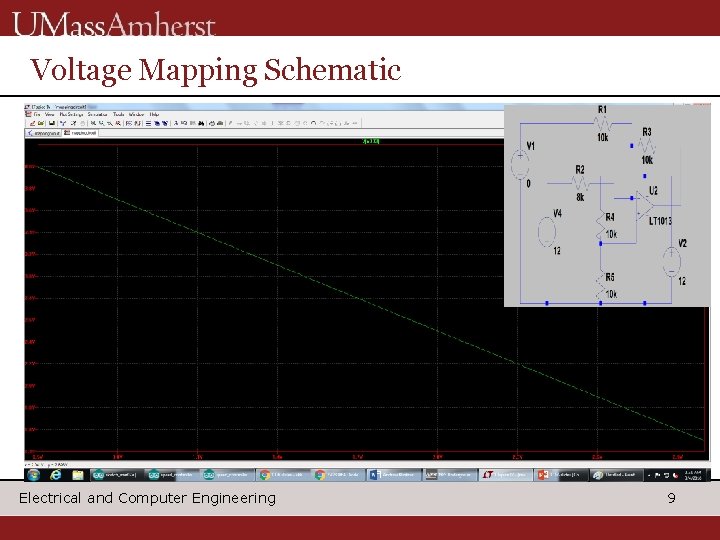
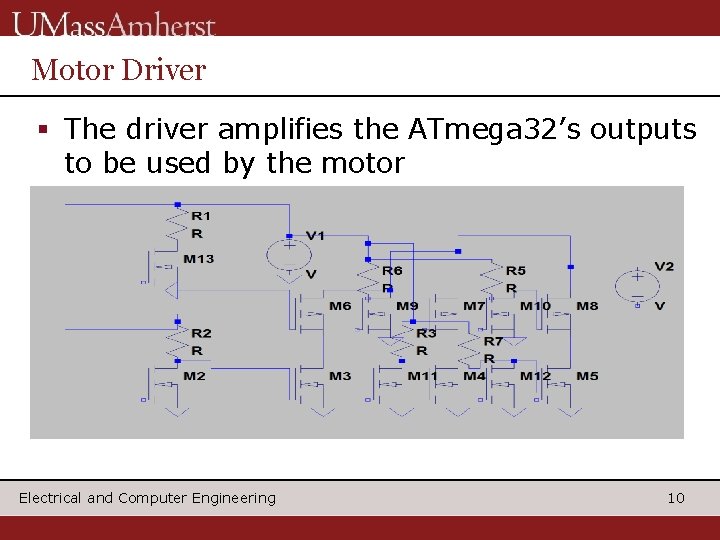
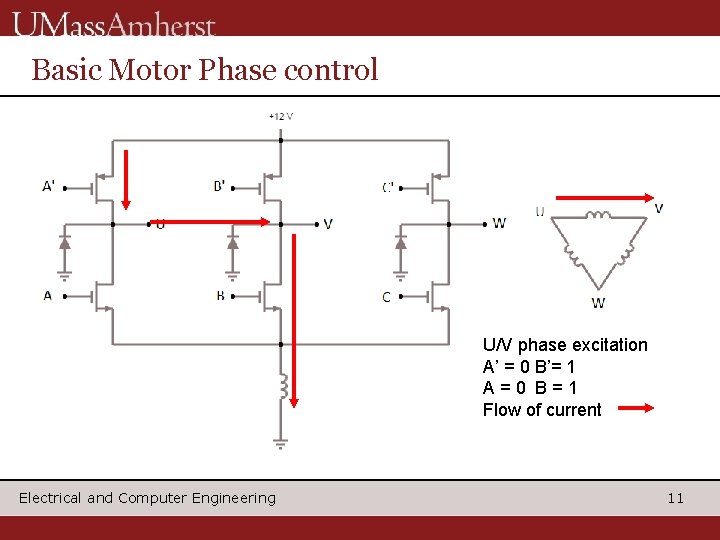
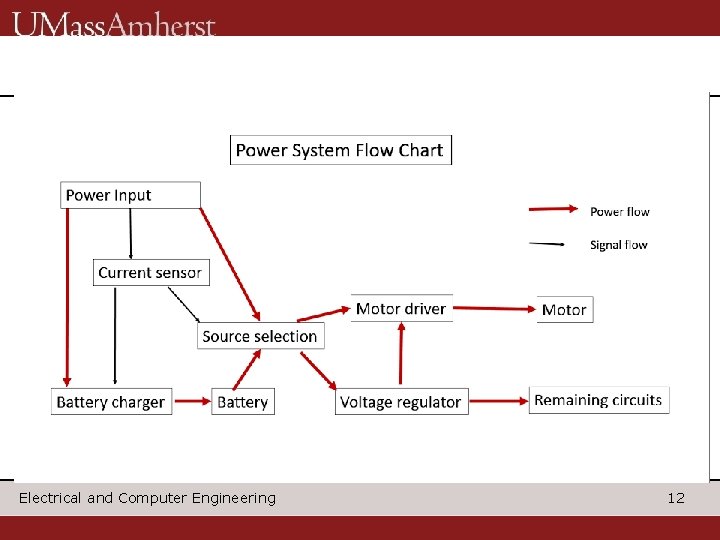
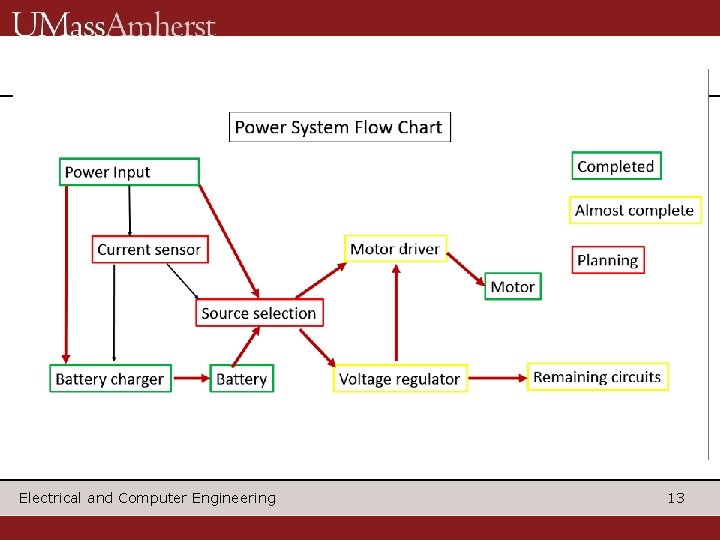
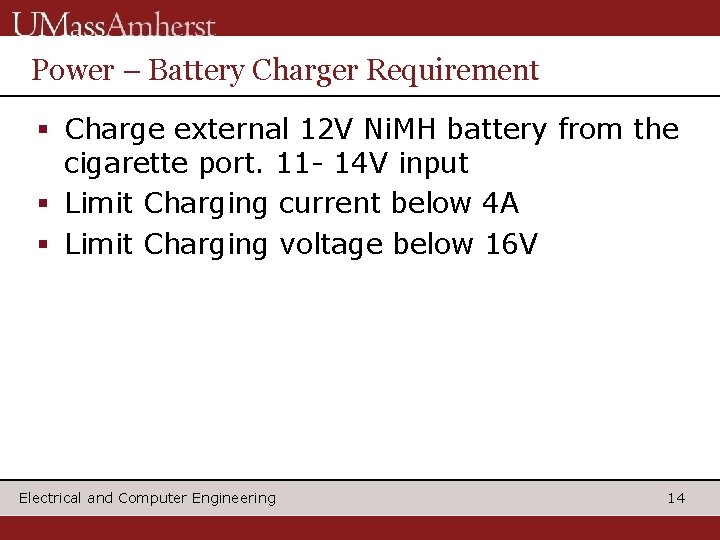
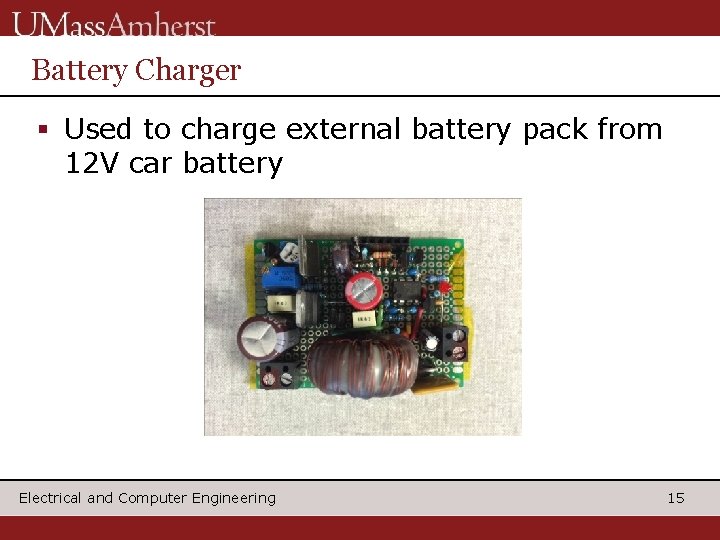
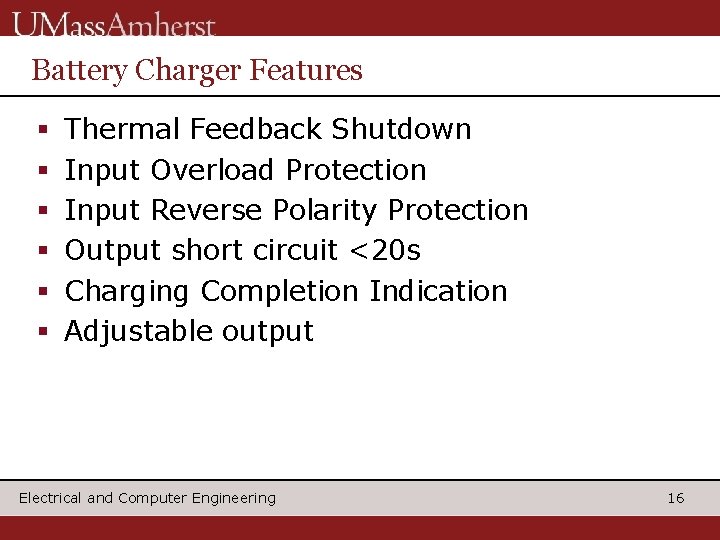
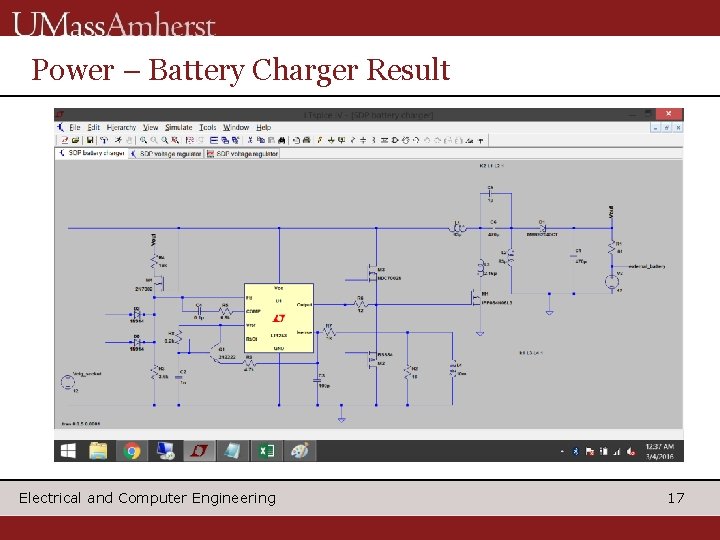
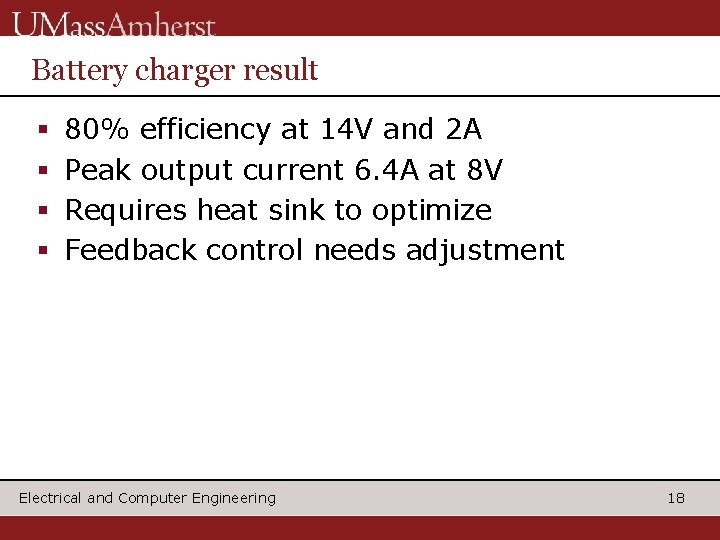
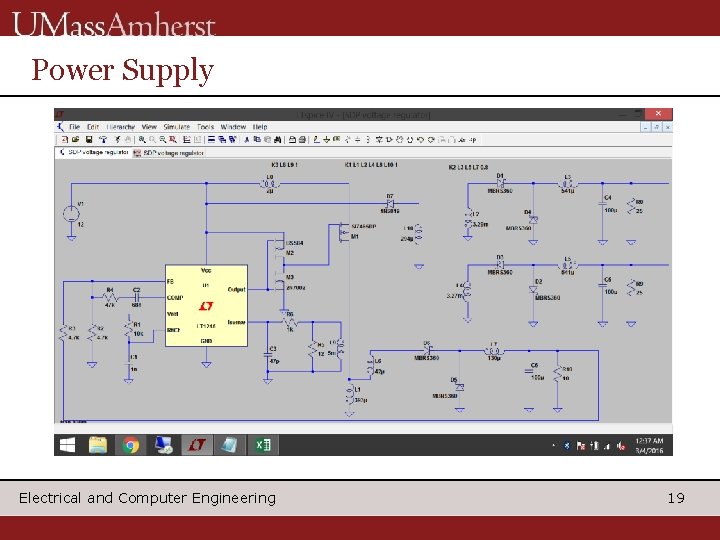
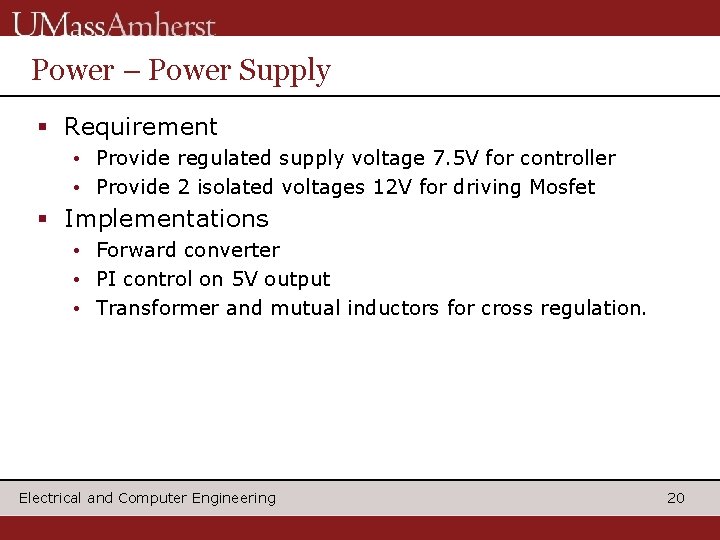
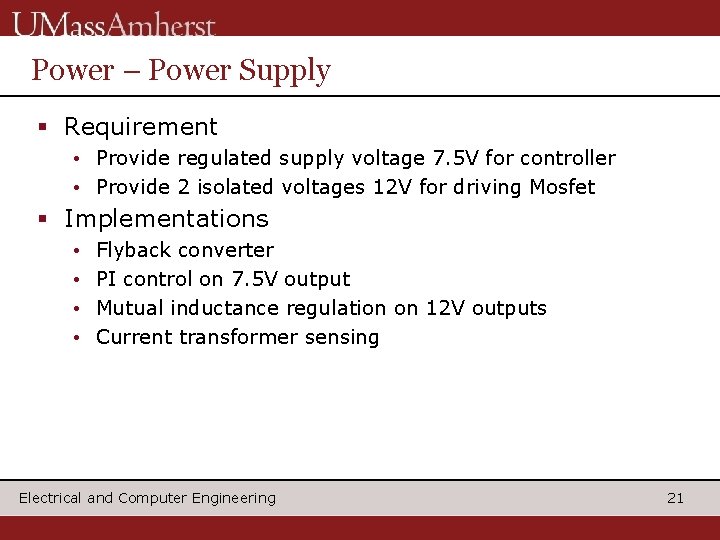
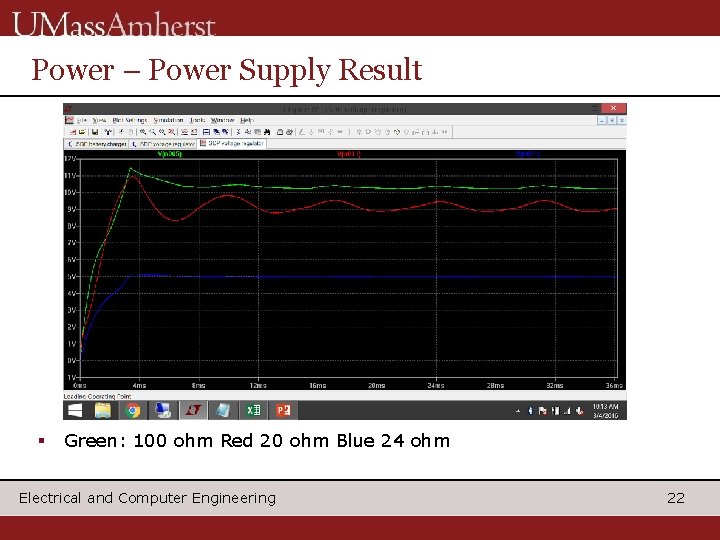
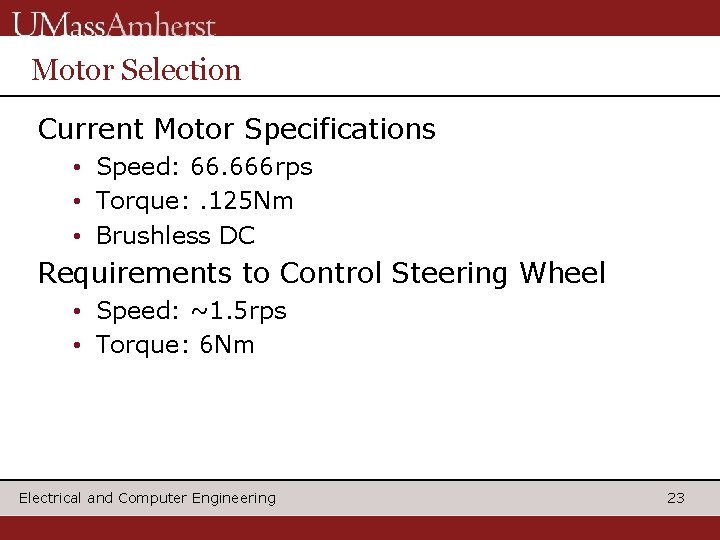
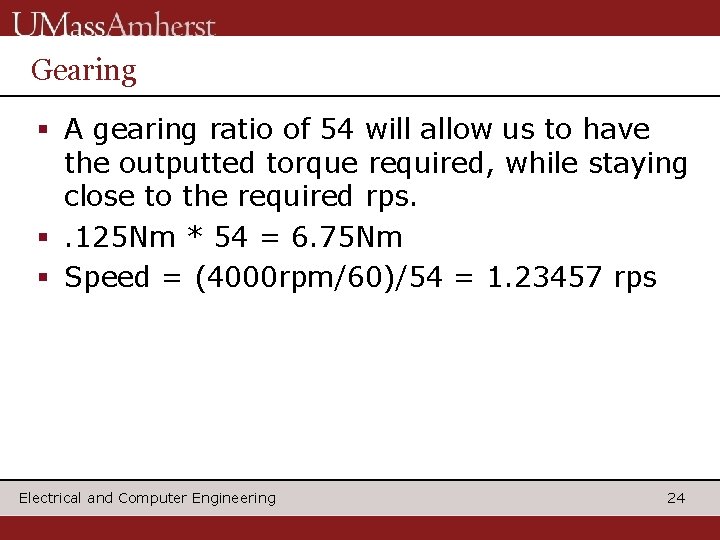
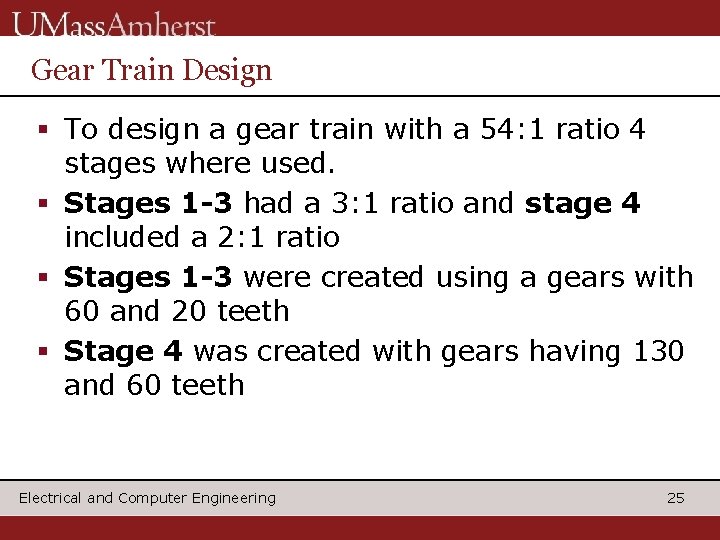
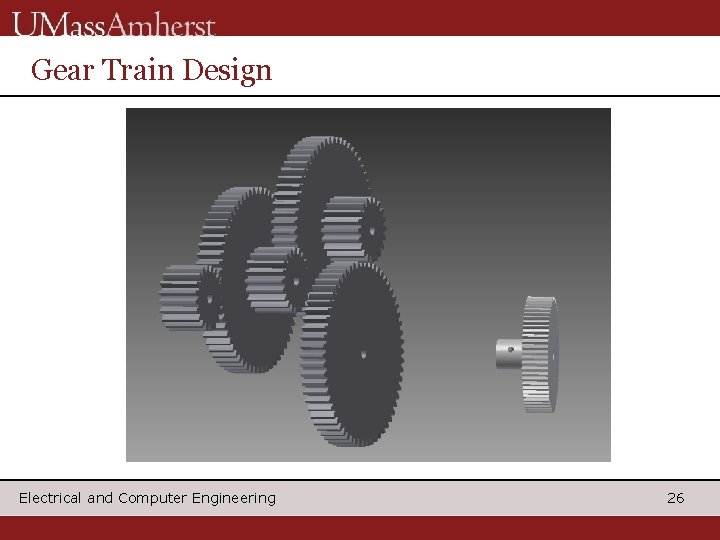
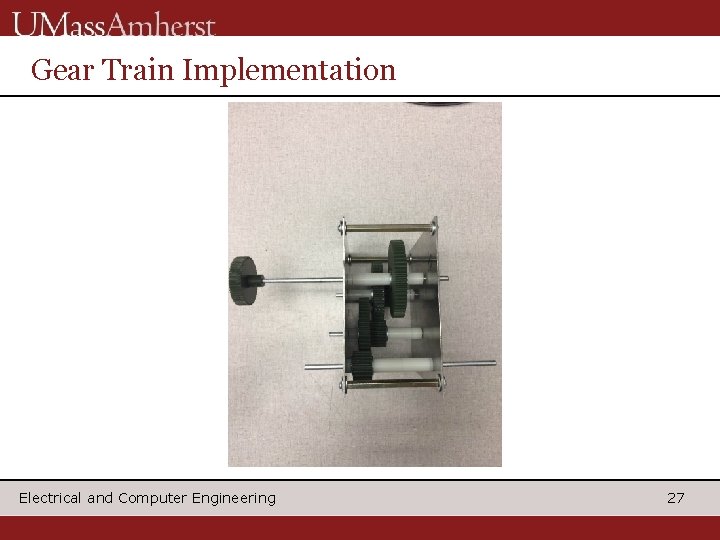
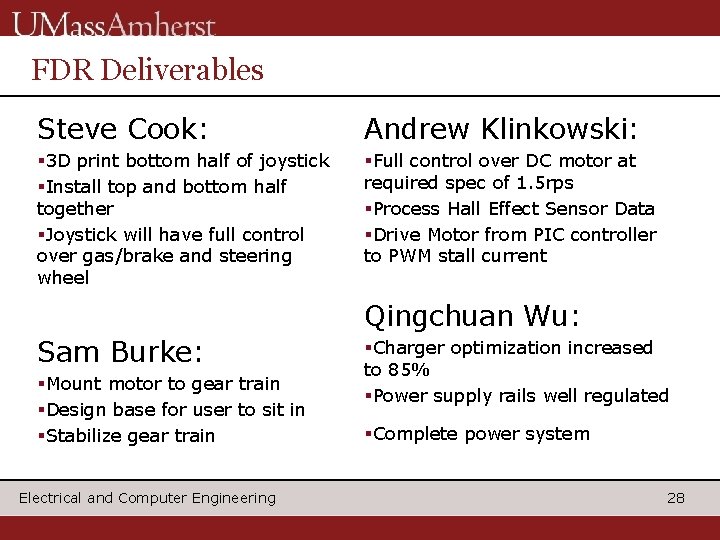
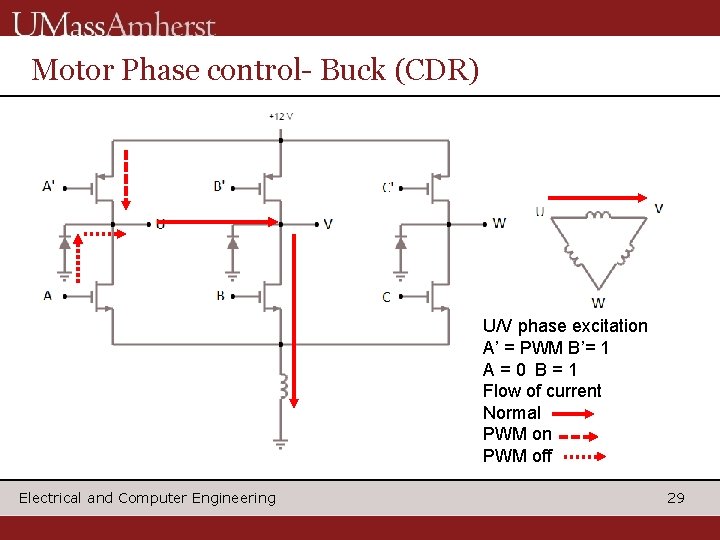
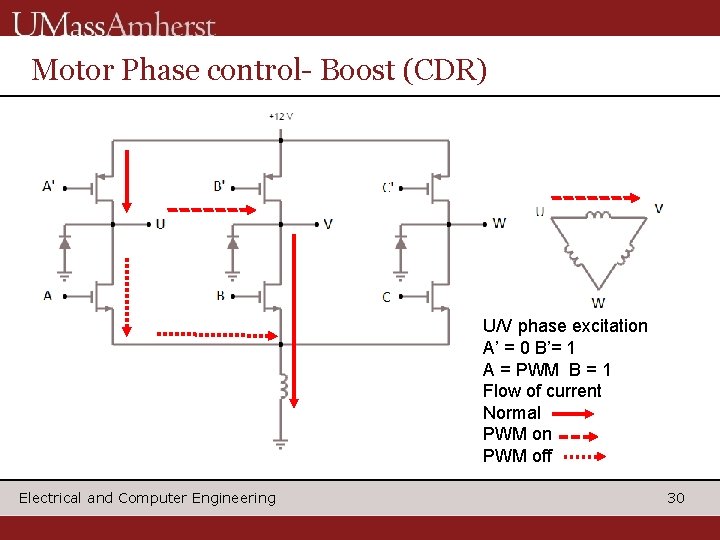
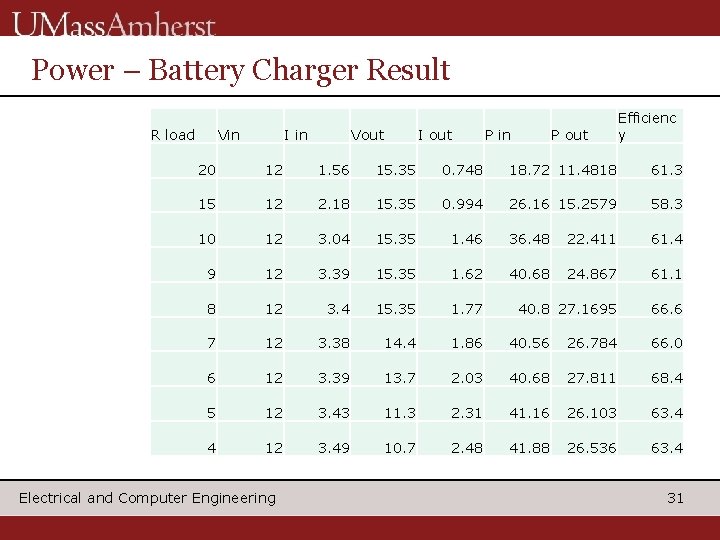
- Slides: 31
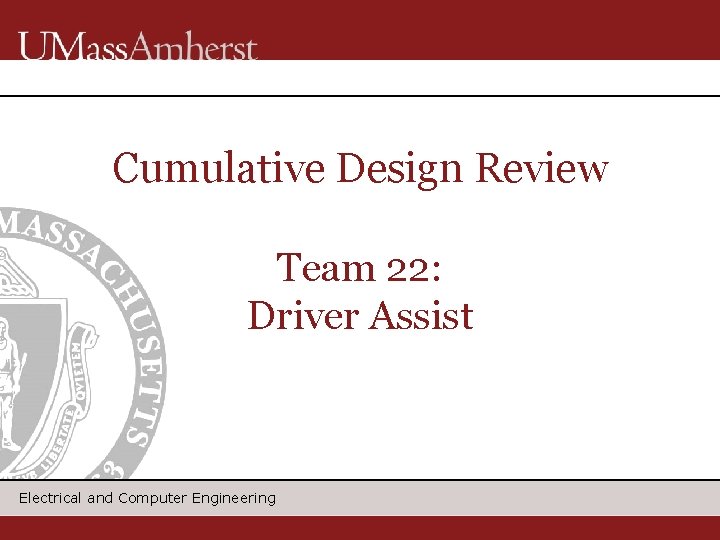
Cumulative Design Review Team 22: Driver Assist Electrical and Computer Engineering
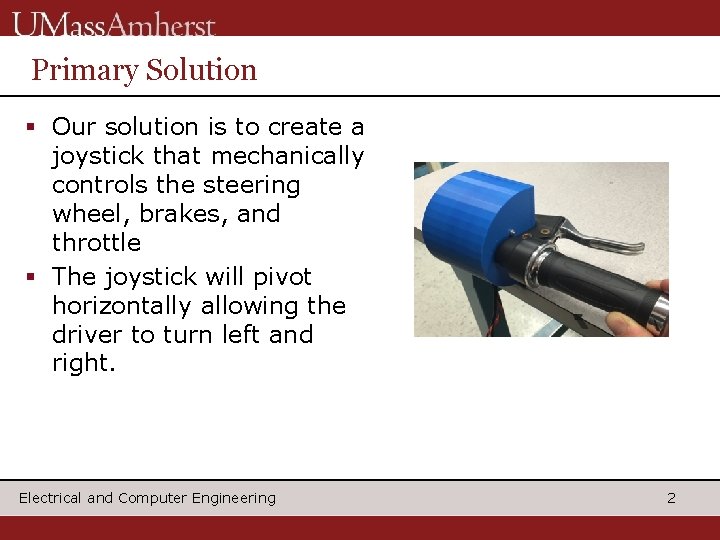
Primary Solution § Our solution is to create a joystick that mechanically controls the steering wheel, brakes, and throttle § The joystick will pivot horizontally allowing the driver to turn left and right. Electrical and Computer Engineering 2
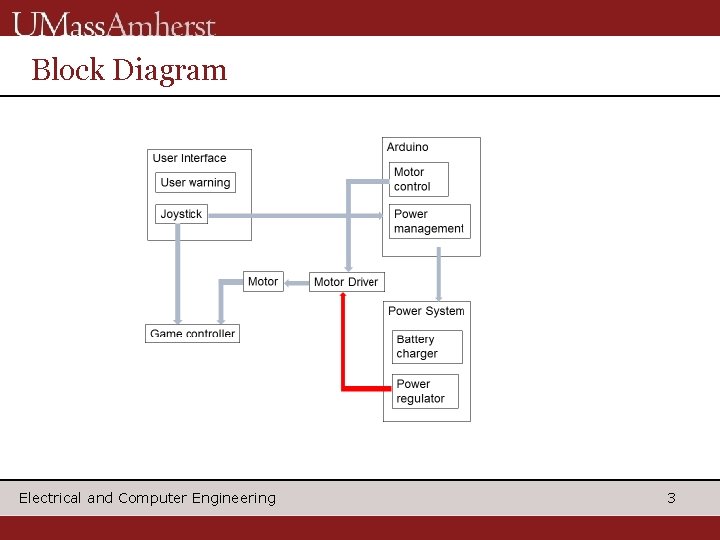
Block Diagram Electrical and Computer Engineering 3
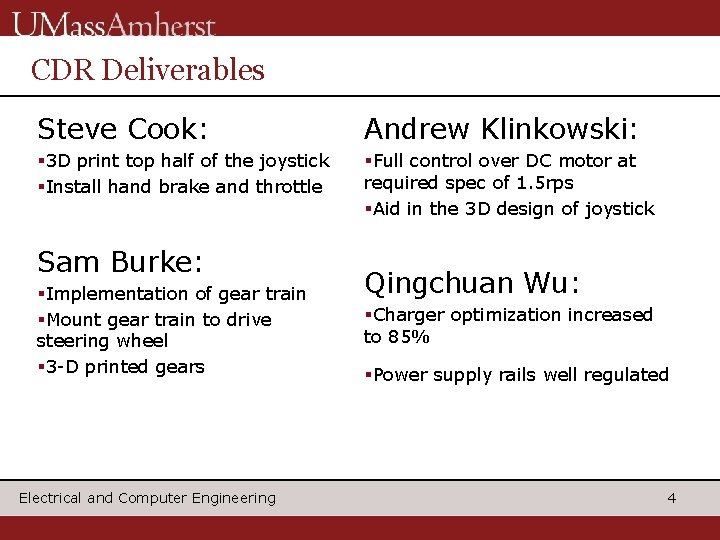
CDR Deliverables Steve Cook: Andrew Klinkowski: § 3 D print top half of the joystick §Install hand brake and throttle §Full control over DC motor at required spec of 1. 5 rps §Aid in the 3 D design of joystick Sam Burke: §Implementation of gear train §Mount gear train to drive steering wheel § 3 -D printed gears Electrical and Computer Engineering Qingchuan Wu: §Charger optimization increased to 85% §Power supply rails well regulated 4
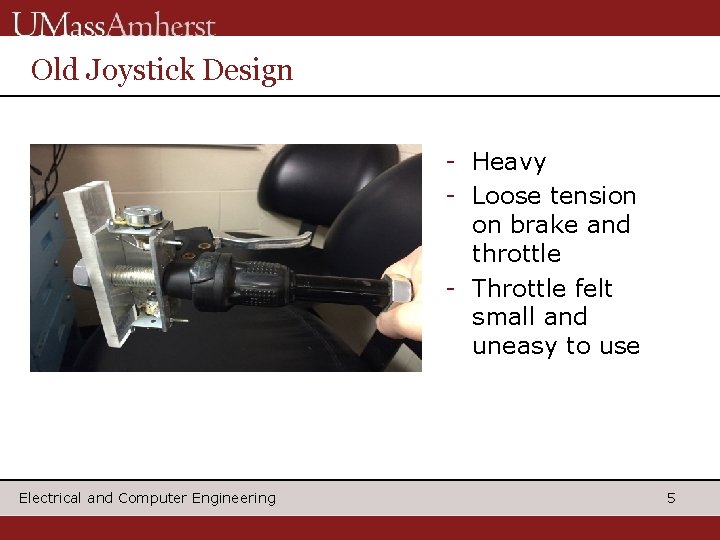
Old Joystick Design - Heavy - Loose tension on brake and throttle - Throttle felt small and uneasy to use Electrical and Computer Engineering 5
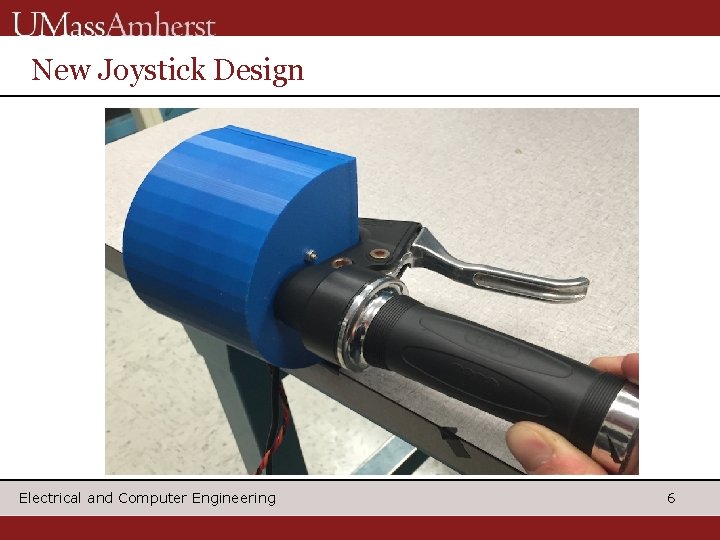
New Joystick Design Electrical and Computer Engineering 6
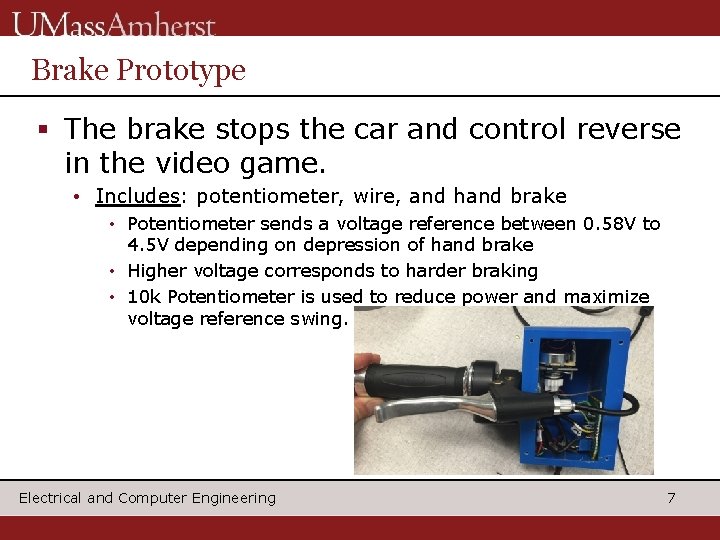
Brake Prototype § The brake stops the car and control reverse in the video game. • Includes: potentiometer, wire, and hand brake • Potentiometer sends a voltage reference between 0. 58 V to 4. 5 V depending on depression of hand brake • Higher voltage corresponds to harder braking • 10 k Potentiometer is used to reduce power and maximize voltage reference swing. Electrical and Computer Engineering 7
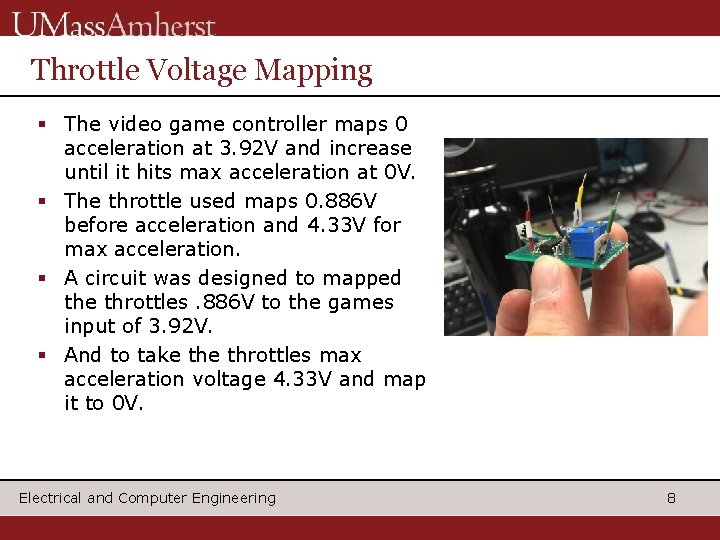
Throttle Voltage Mapping § The video game controller maps 0 acceleration at 3. 92 V and increase until it hits max acceleration at 0 V. § The throttle used maps 0. 886 V before acceleration and 4. 33 V for max acceleration. § A circuit was designed to mapped the throttles. 886 V to the games input of 3. 92 V. § And to take throttles max acceleration voltage 4. 33 V and map it to 0 V. Electrical and Computer Engineering 8
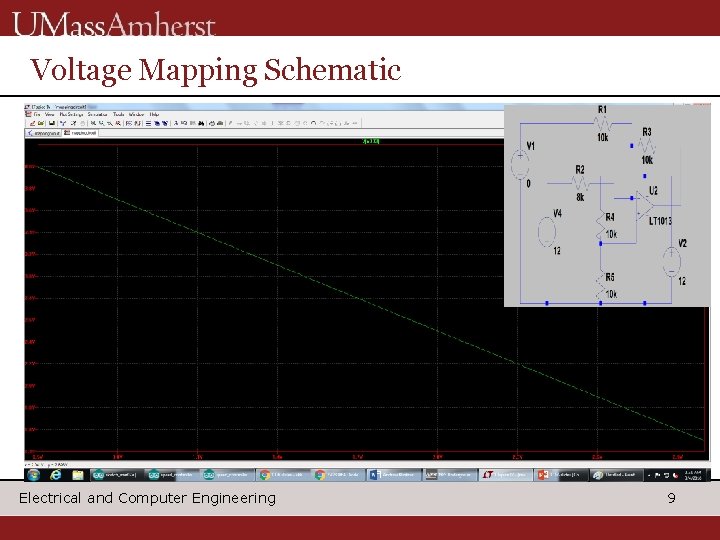
Voltage Mapping Schematic Electrical and Computer Engineering 9
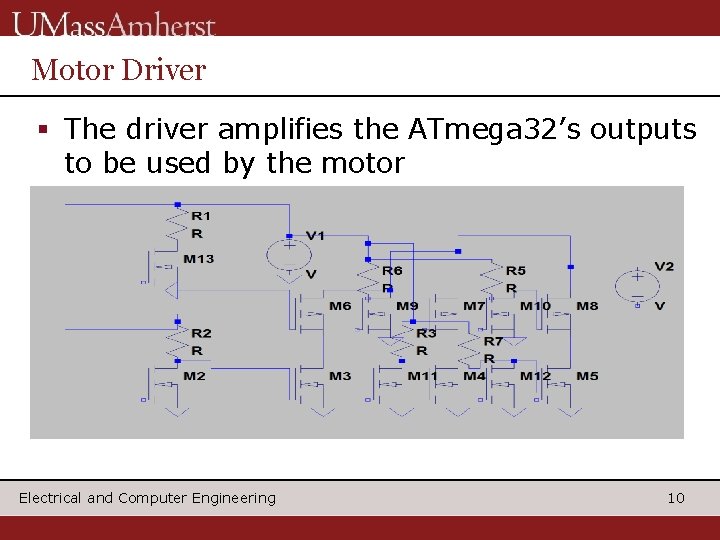
Motor Driver § The driver amplifies the ATmega 32’s outputs to be used by the motor Electrical and Computer Engineering 10
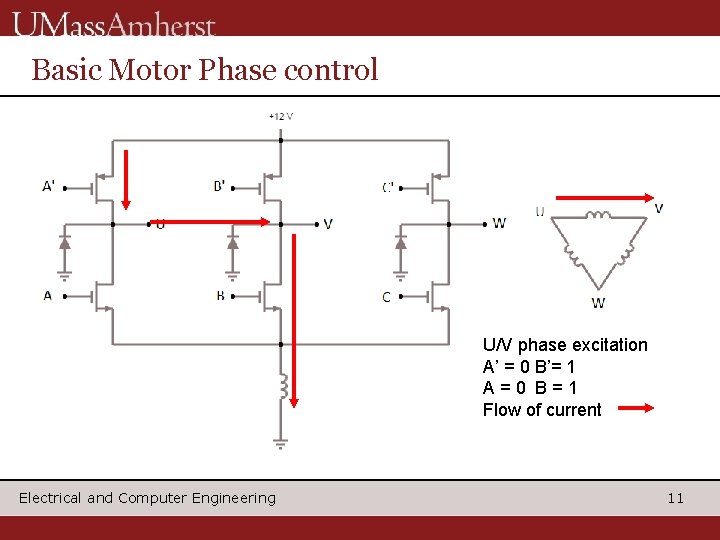
Basic Motor Phase control U/V phase excitation A’ = 0 B’= 1 A=0 B=1 Flow of current Electrical and Computer Engineering 11
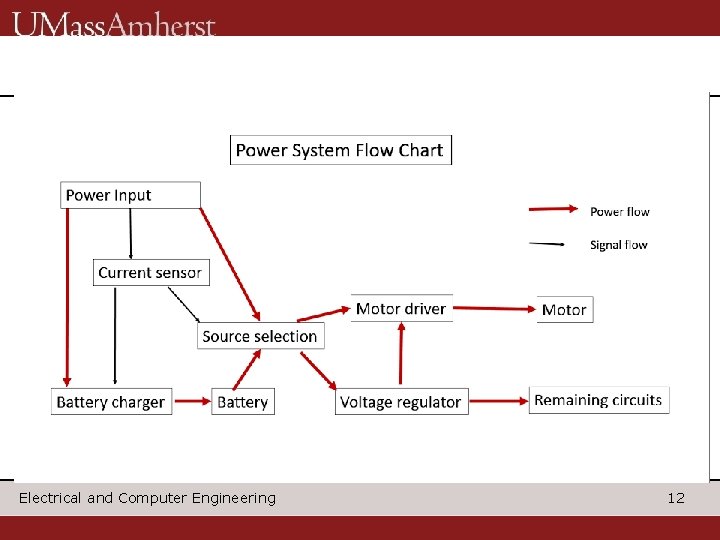
Electrical and Computer Engineering 12
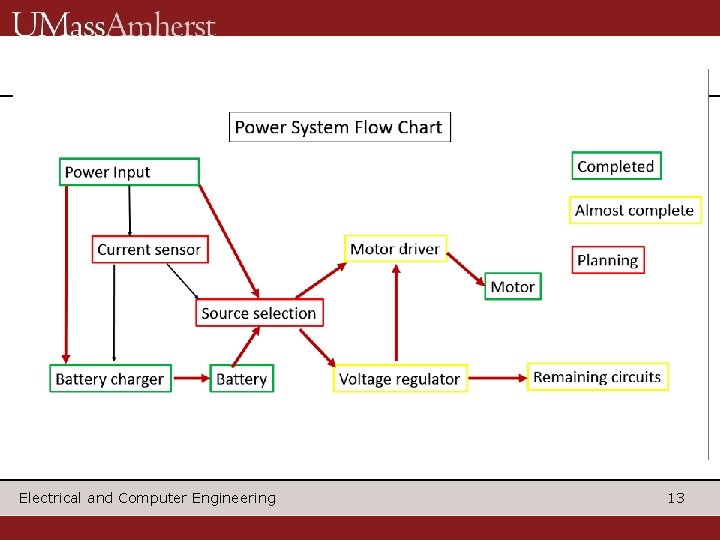
Electrical and Computer Engineering 13
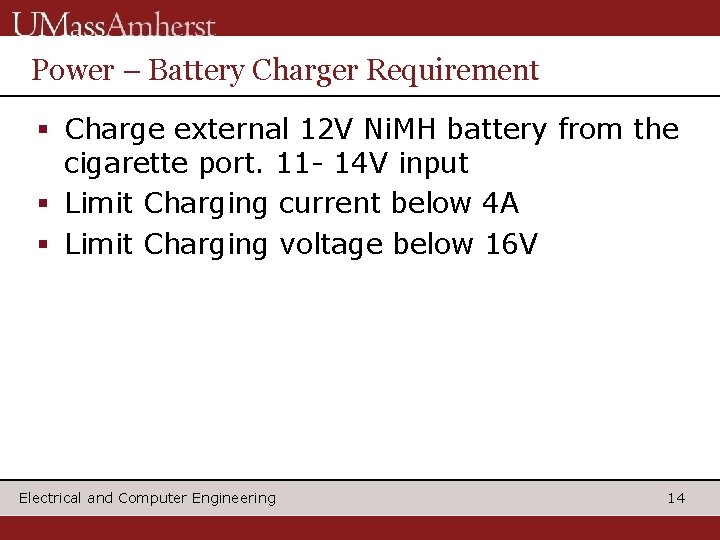
Power – Battery Charger Requirement § Charge external 12 V Ni. MH battery from the cigarette port. 11 - 14 V input § Limit Charging current below 4 A § Limit Charging voltage below 16 V Electrical and Computer Engineering 14
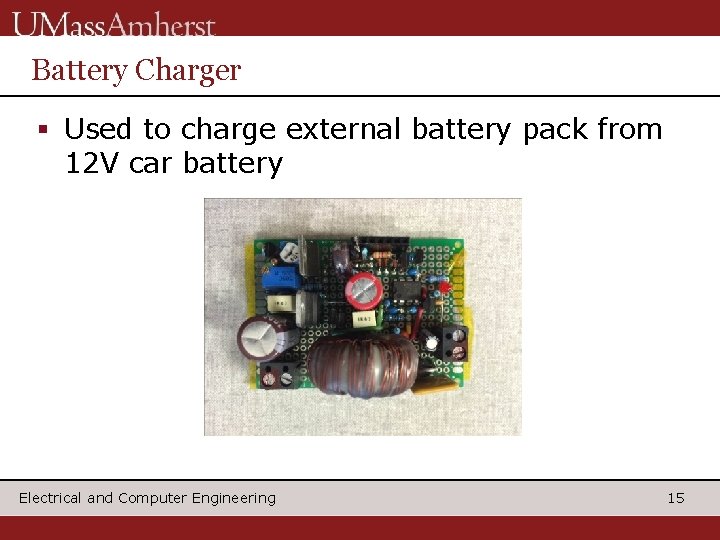
Battery Charger § Used to charge external battery pack from 12 V car battery Electrical and Computer Engineering 15
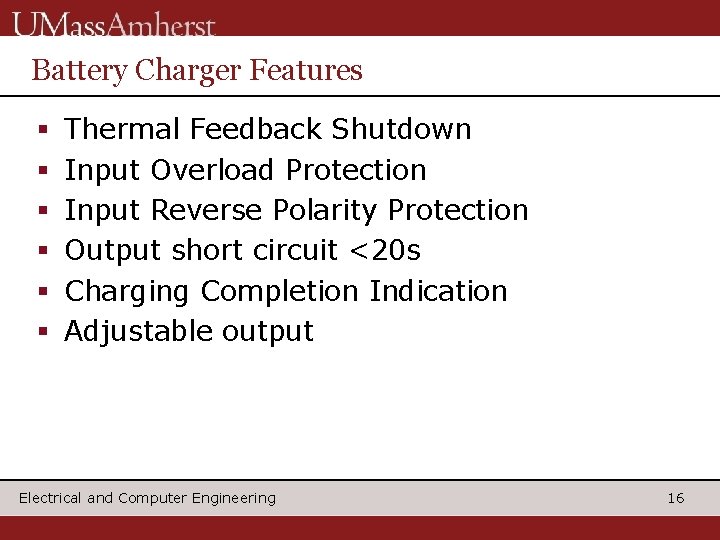
Battery Charger Features § § § Thermal Feedback Shutdown Input Overload Protection Input Reverse Polarity Protection Output short circuit <20 s Charging Completion Indication Adjustable output Electrical and Computer Engineering 16
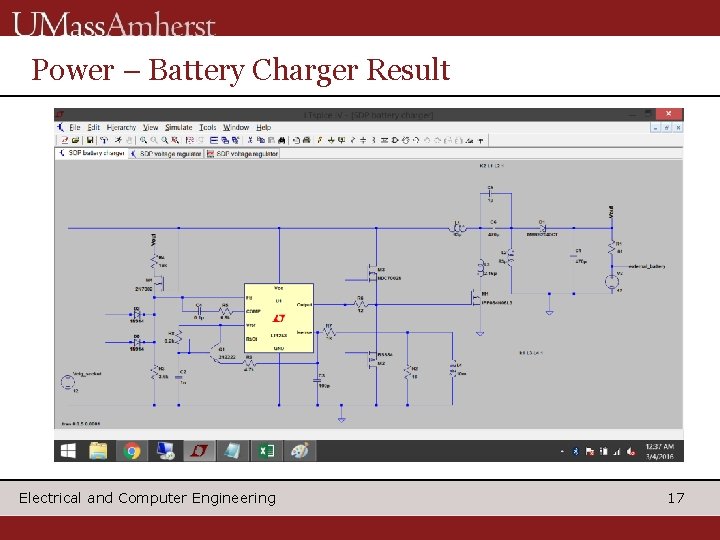
Power – Battery Charger Result Electrical and Computer Engineering 17
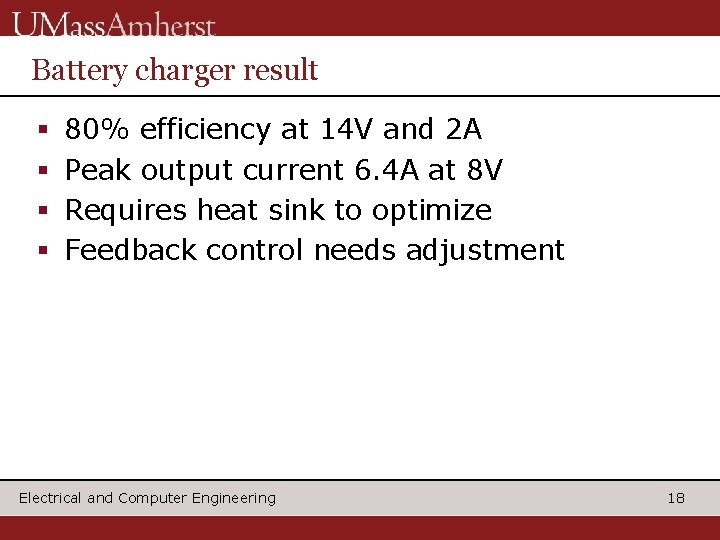
Battery charger result § § 80% efficiency at 14 V and 2 A Peak output current 6. 4 A at 8 V Requires heat sink to optimize Feedback control needs adjustment Electrical and Computer Engineering 18
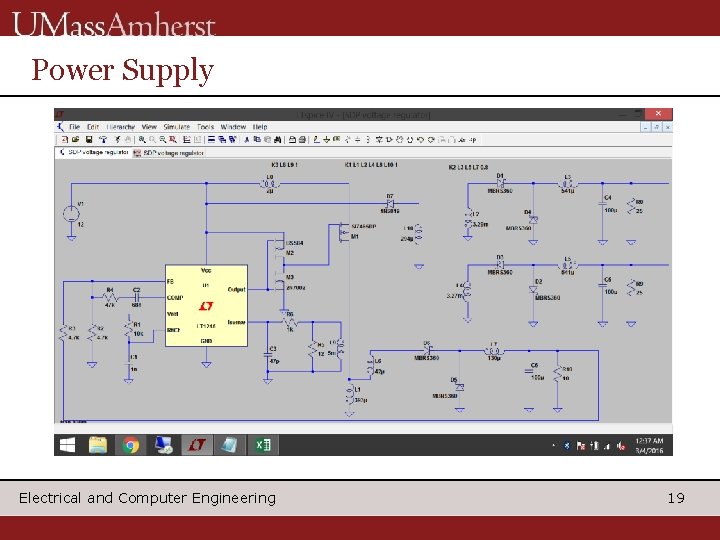
Power Supply Electrical and Computer Engineering 19
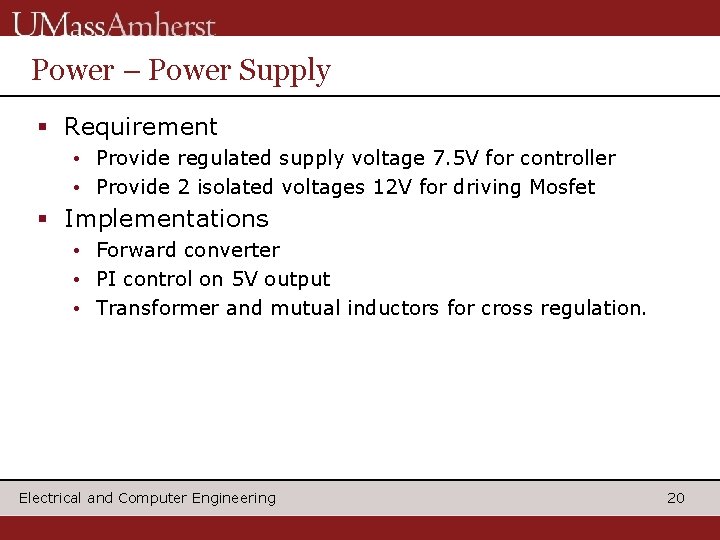
Power – Power Supply § Requirement • Provide regulated supply voltage 7. 5 V for controller • Provide 2 isolated voltages 12 V for driving Mosfet § Implementations • Forward converter • PI control on 5 V output • Transformer and mutual inductors for cross regulation. Electrical and Computer Engineering 20
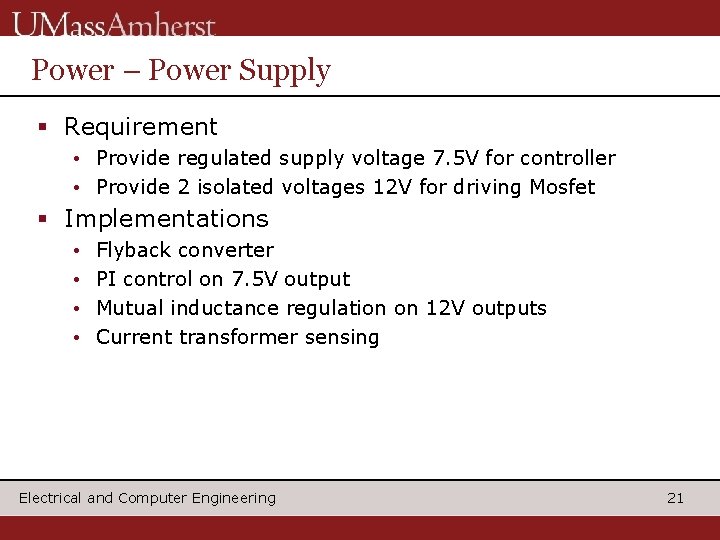
Power – Power Supply § Requirement • Provide regulated supply voltage 7. 5 V for controller • Provide 2 isolated voltages 12 V for driving Mosfet § Implementations • • Flyback converter PI control on 7. 5 V output Mutual inductance regulation on 12 V outputs Current transformer sensing Electrical and Computer Engineering 21
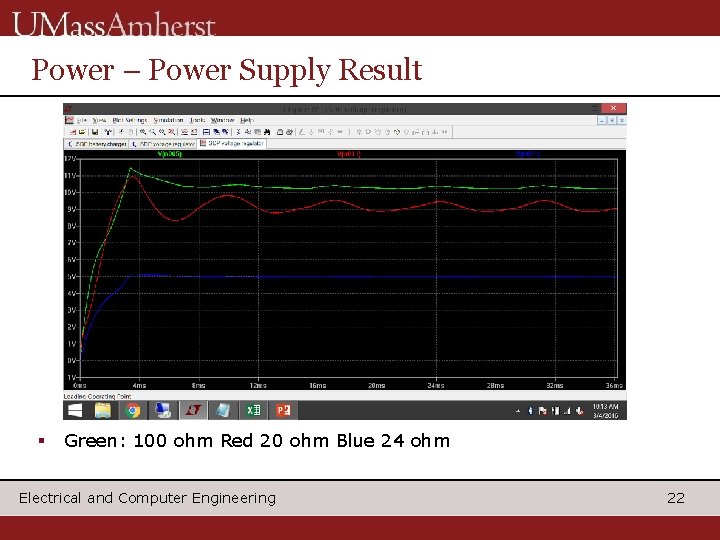
Power – Power Supply Result § Green: 100 ohm Red 20 ohm Blue 24 ohm Electrical and Computer Engineering 22
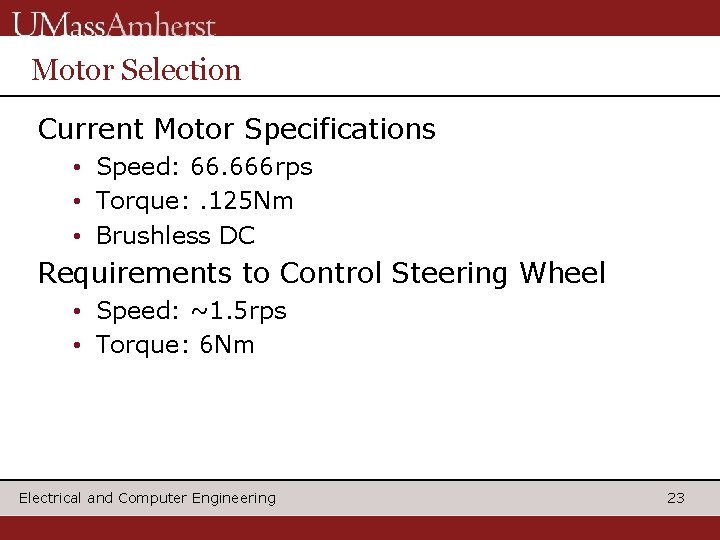
Motor Selection Current Motor Specifications • Speed: 66. 666 rps • Torque: . 125 Nm • Brushless DC Requirements to Control Steering Wheel • Speed: ~1. 5 rps • Torque: 6 Nm Electrical and Computer Engineering 23
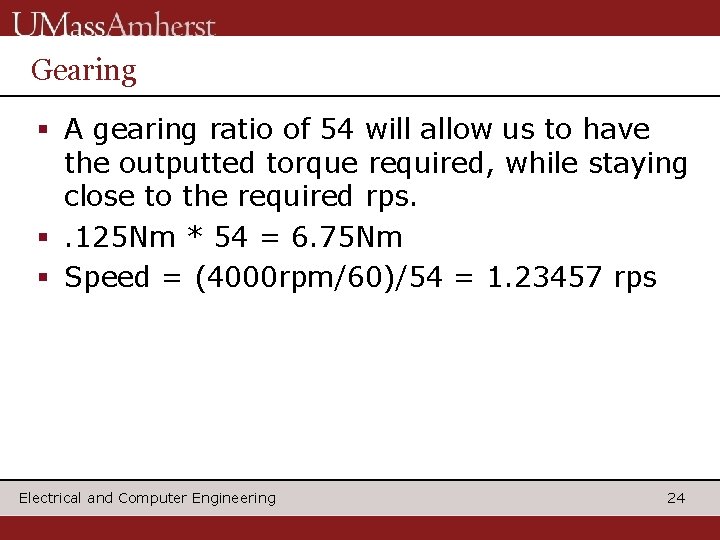
Gearing § A gearing ratio of 54 will allow us to have the outputted torque required, while staying close to the required rps. §. 125 Nm * 54 = 6. 75 Nm § Speed = (4000 rpm/60)/54 = 1. 23457 rps Electrical and Computer Engineering 24
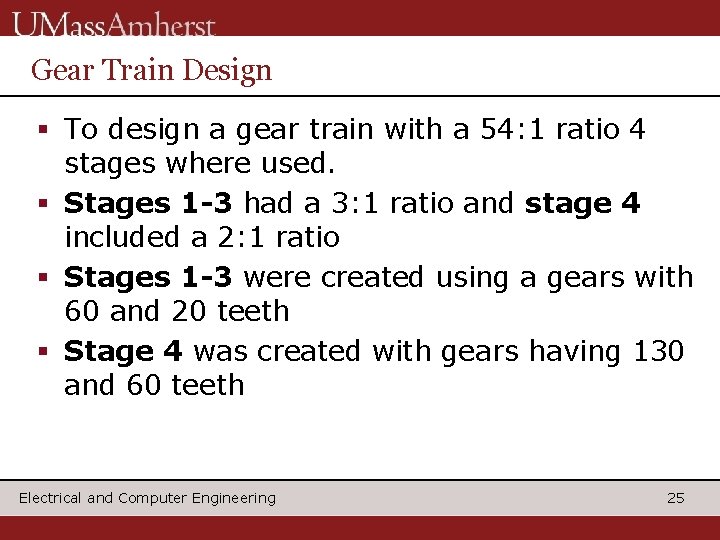
Gear Train Design § To design a gear train with a 54: 1 ratio 4 stages where used. § Stages 1 -3 had a 3: 1 ratio and stage 4 included a 2: 1 ratio § Stages 1 -3 were created using a gears with 60 and 20 teeth § Stage 4 was created with gears having 130 and 60 teeth Electrical and Computer Engineering 25
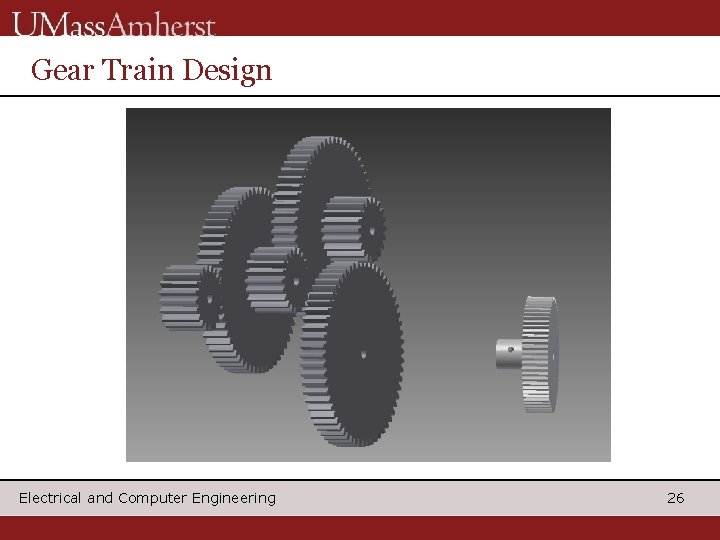
Gear Train Design Electrical and Computer Engineering 26
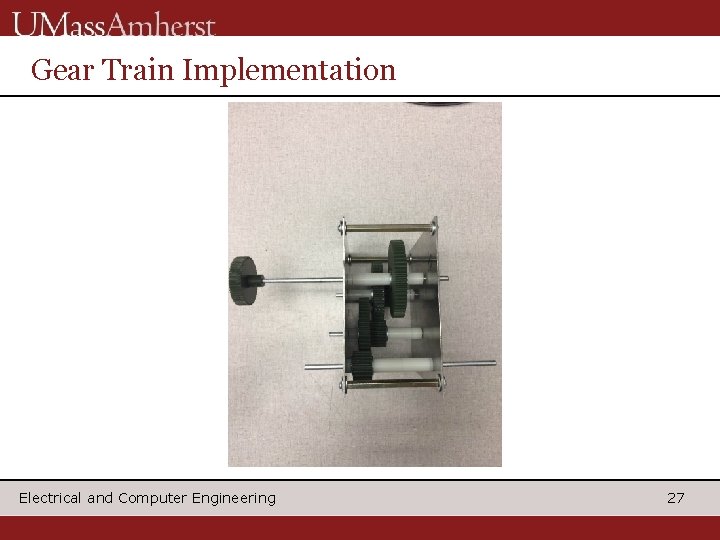
Gear Train Implementation Electrical and Computer Engineering 27
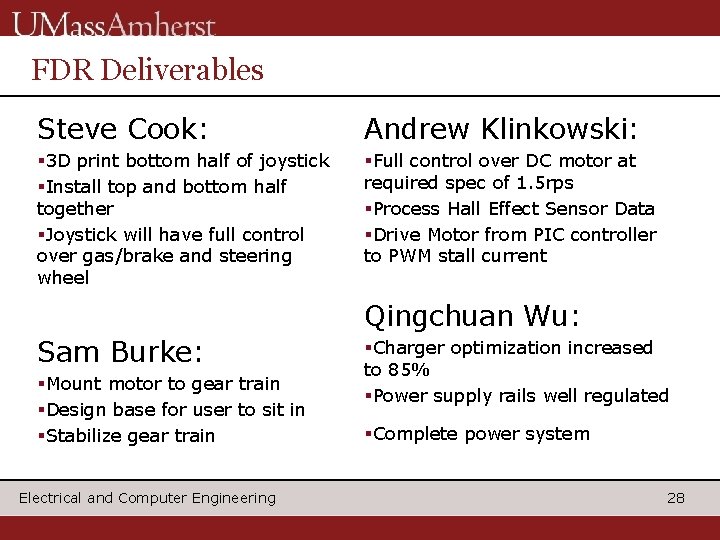
FDR Deliverables Steve Cook: Andrew Klinkowski: § 3 D print bottom half of joystick §Install top and bottom half together §Joystick will have full control over gas/brake and steering wheel §Full control over DC motor at required spec of 1. 5 rps §Process Hall Effect Sensor Data §Drive Motor from PIC controller to PWM stall current Qingchuan Wu: Sam Burke: §Mount motor to gear train §Design base for user to sit in §Stabilize gear train Electrical and Computer Engineering §Charger optimization increased to 85% §Power supply rails well regulated §Complete power system 28
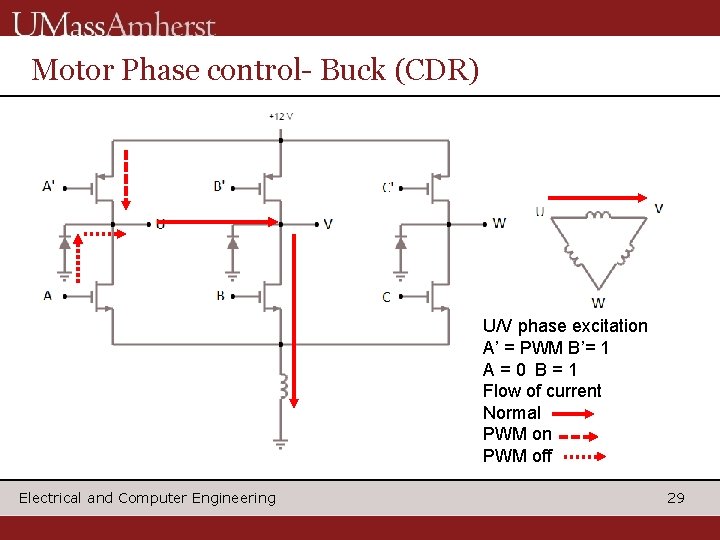
Motor Phase control- Buck (CDR) U/V phase excitation A’ = PWM B’= 1 A=0 B=1 Flow of current Normal PWM on PWM off Electrical and Computer Engineering 29
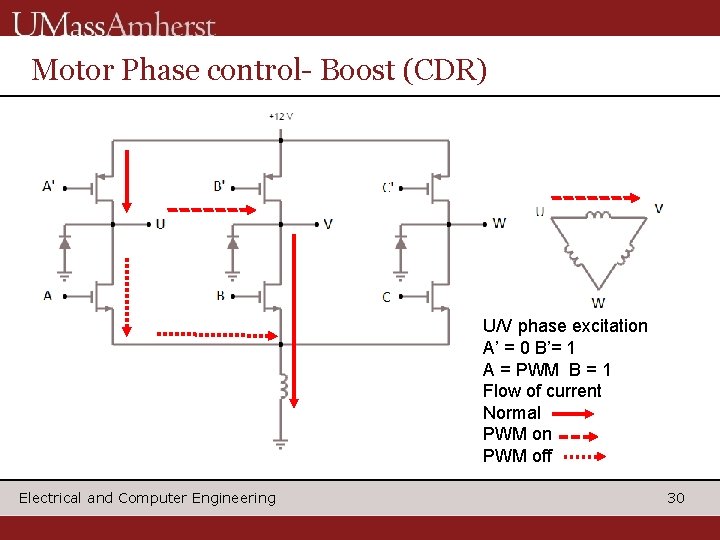
Motor Phase control- Boost (CDR) U/V phase excitation A’ = 0 B’= 1 A = PWM B = 1 Flow of current Normal PWM on PWM off Electrical and Computer Engineering 30
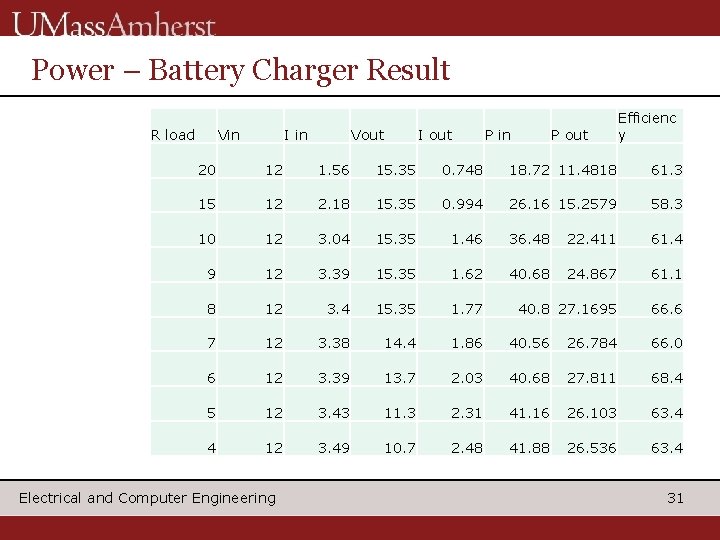
Power – Battery Charger Result R load Vin I in Vout I out P in P out Efficienc y 20 12 1. 56 15. 35 0. 748 18. 72 11. 4818 61. 3 15 12 2. 18 15. 35 0. 994 26. 16 15. 2579 58. 3 10 12 3. 04 15. 35 1. 46 36. 48 22. 411 61. 4 9 12 3. 39 15. 35 1. 62 40. 68 24. 867 61. 1 8 12 3. 4 15. 35 1. 77 40. 8 27. 1695 66. 6 7 12 3. 38 14. 4 1. 86 40. 56 26. 784 66. 0 6 12 3. 39 13. 7 2. 03 40. 68 27. 811 68. 4 5 12 3. 43 11. 3 2. 31 41. 16 26. 103 63. 4 4 12 3. 49 10. 7 2. 48 41. 88 26. 536 63. 4 Electrical and Computer Engineering 31
Assist electrical
Column formation
Umdf reflector
Redcap choa
Usmc counseling sheet
Quality assist
Leslie miller md
Cisco smart assist
Peer assist adalah
Als assist
The whips assist the party leaders by
Travel guard ez tips
Pam assist counselling
Brake assist system
Intelligent assist device
One teach, one assist pros and cons
The first step in diagnosing a hydro-boost problem is
Assist user guide
Plan rubi colmedica
Pbx call assist 2
School mental health assist
Medi assist escalation matrix
Cisco smart assist
Kristiina jokinen
Gx assist side effects
Park assist 2
Mission assist
Thymosin and thymopoietin assist in the maturation of:
Info assist
What cognitive strategies assist our problem solving
Team spirit becomes team infatuation
Team spirit becomes team infatuation