Cost Management ACCOUNTING AND CONTROL HANSEN MOWEN 1
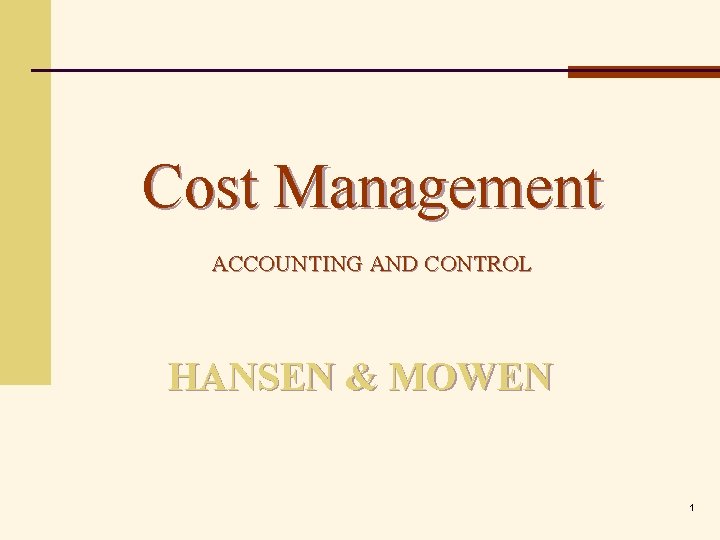
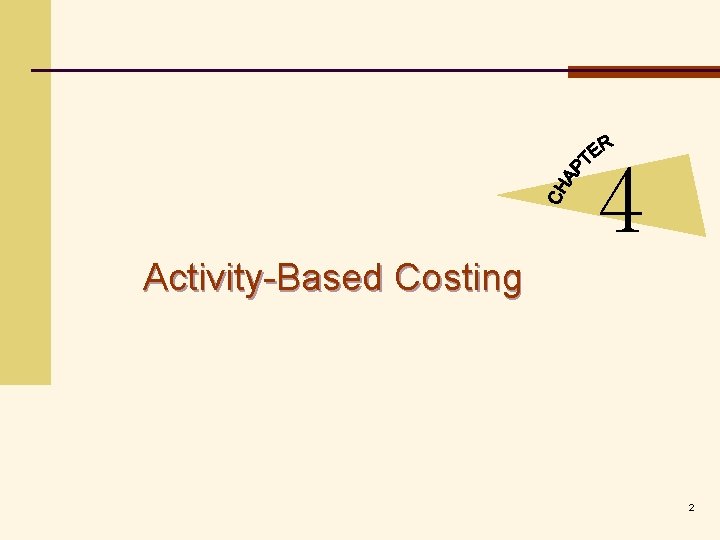
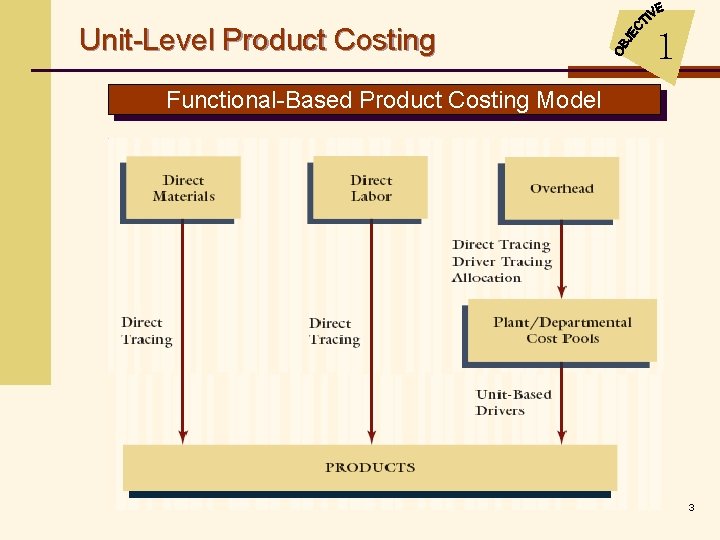
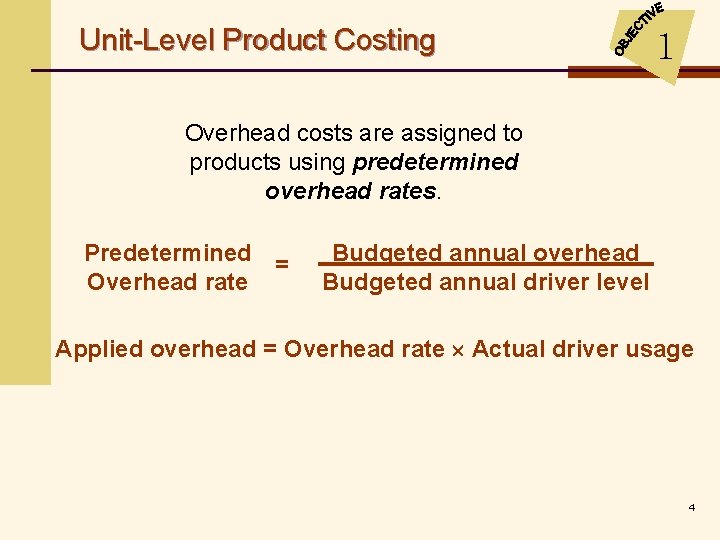
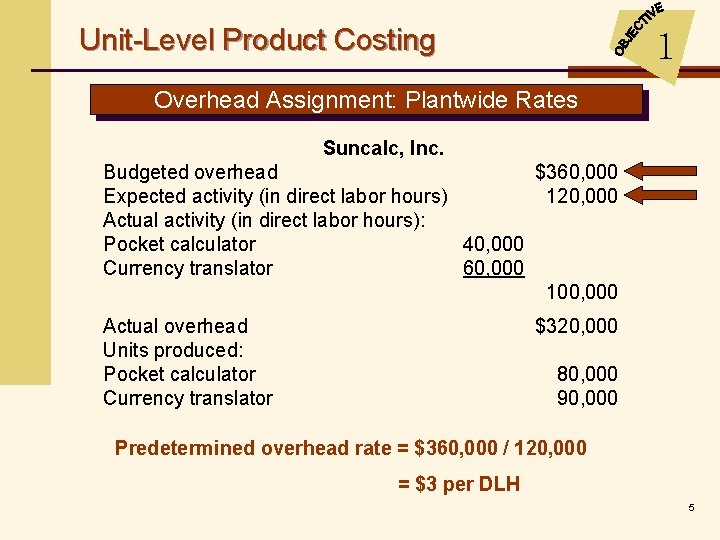
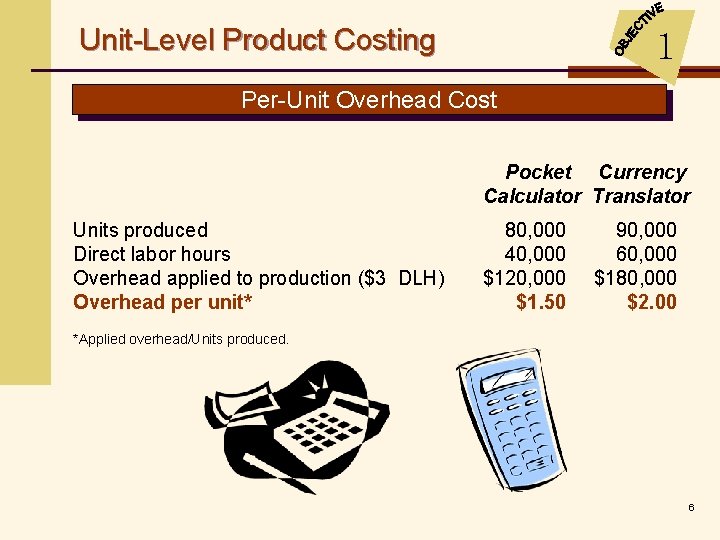
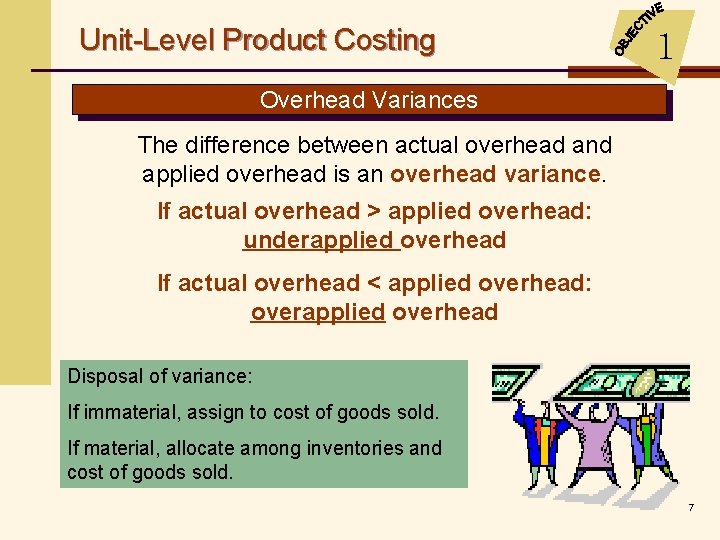
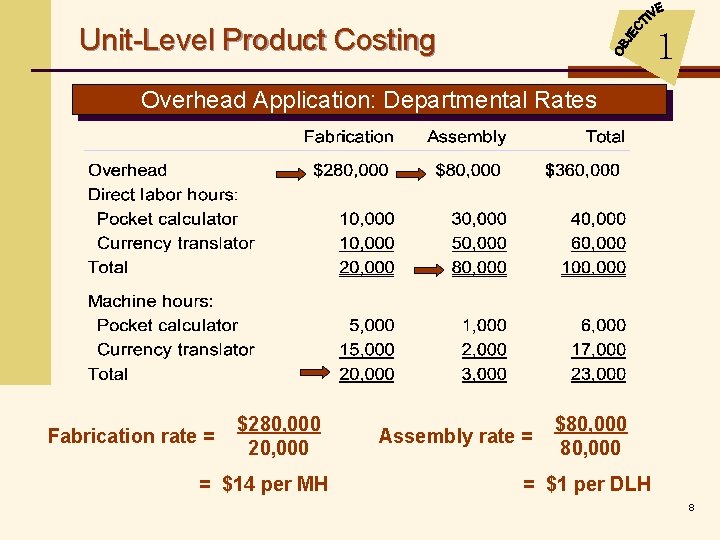
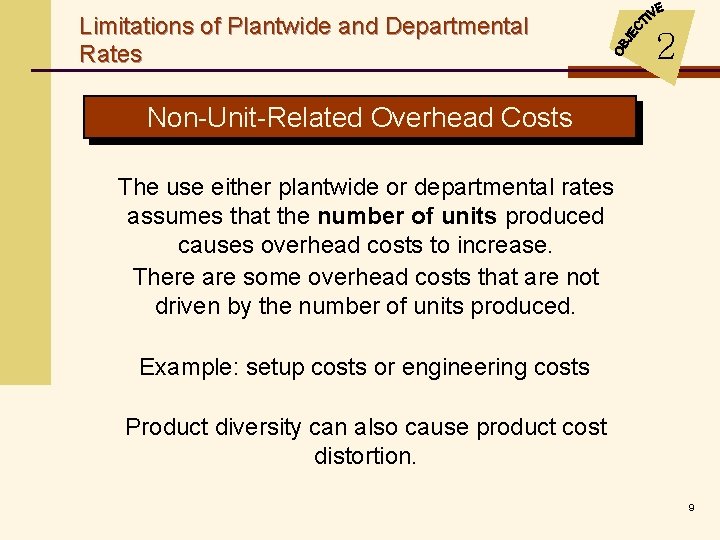
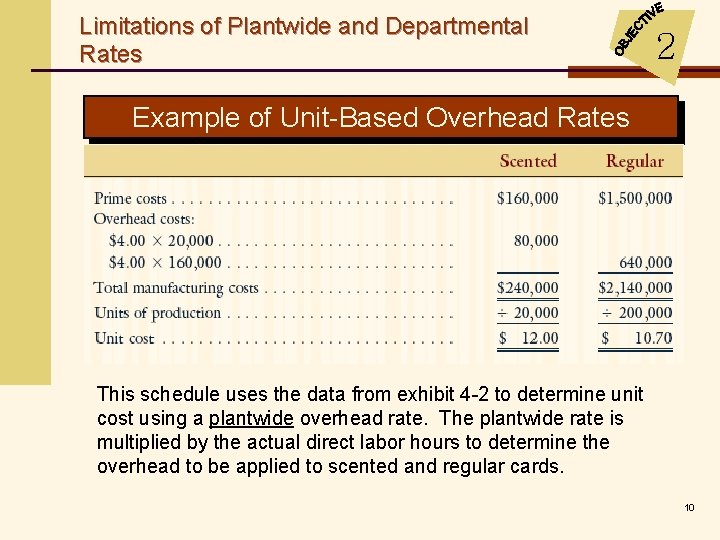
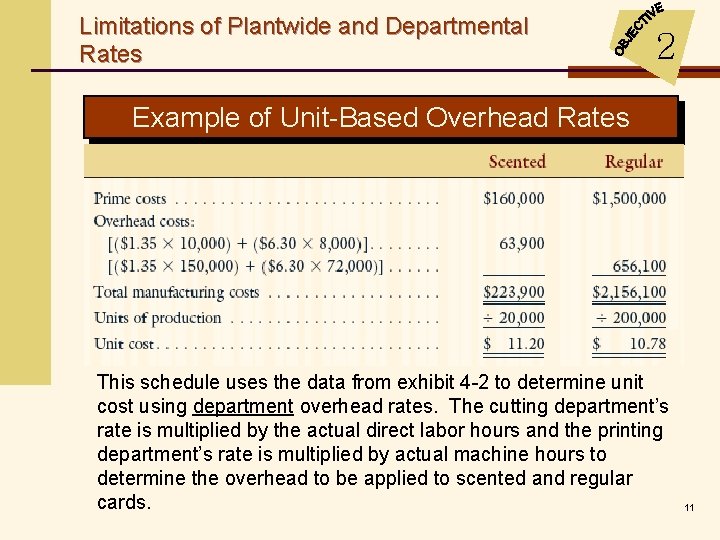
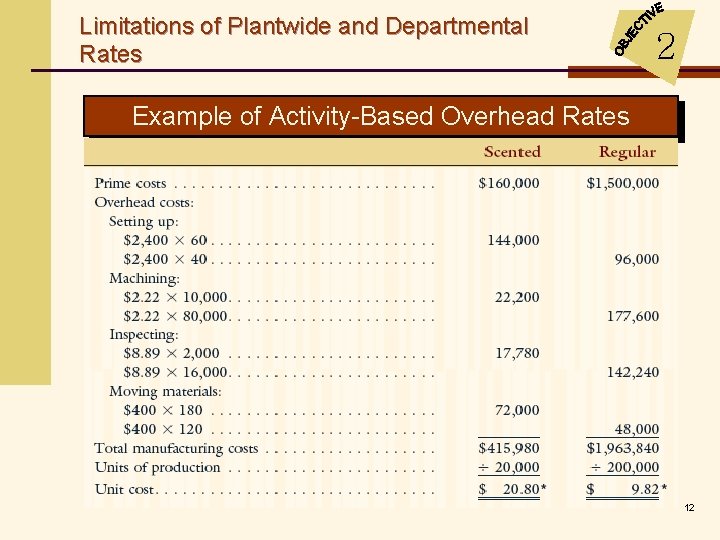
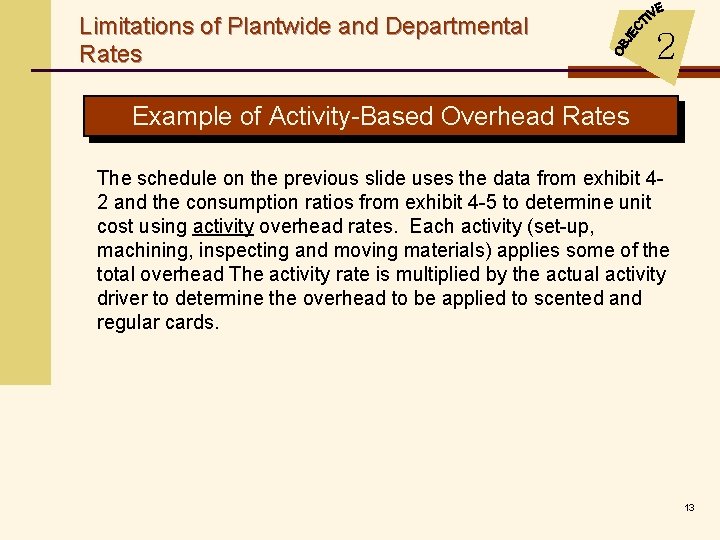
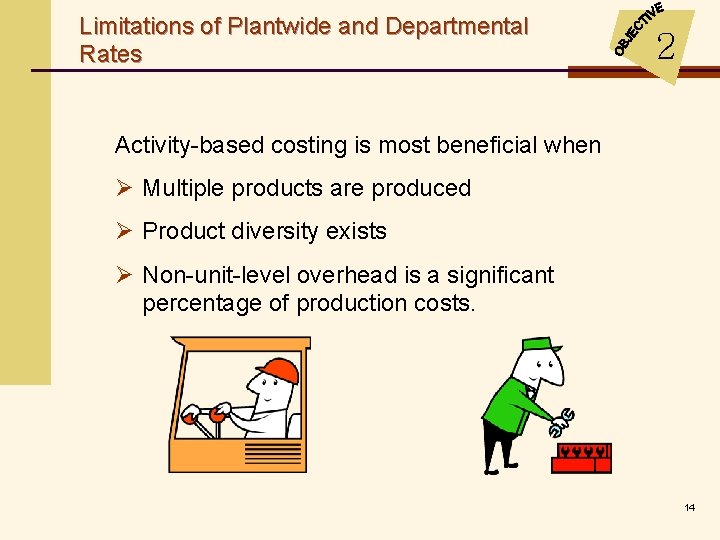
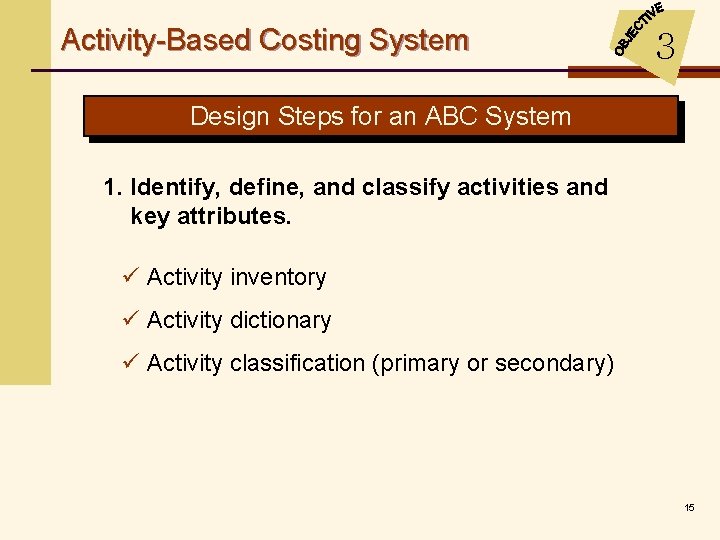
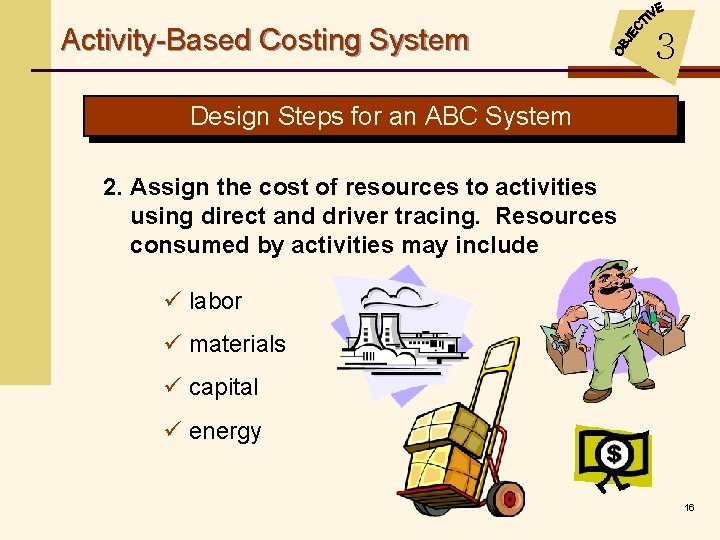
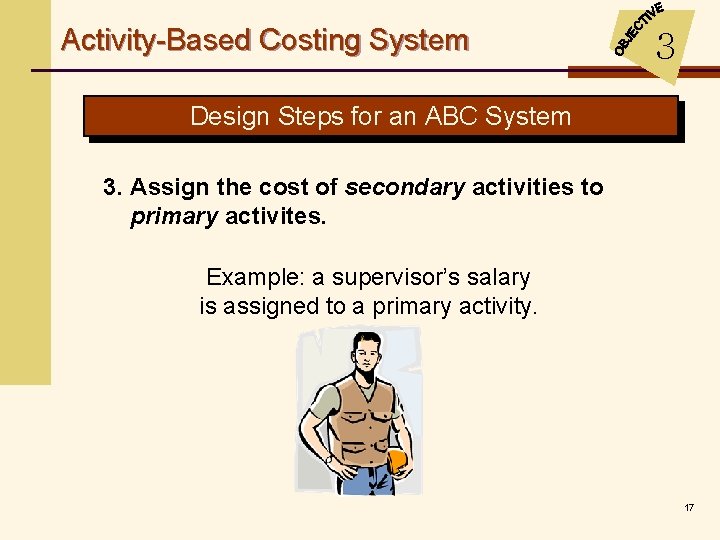
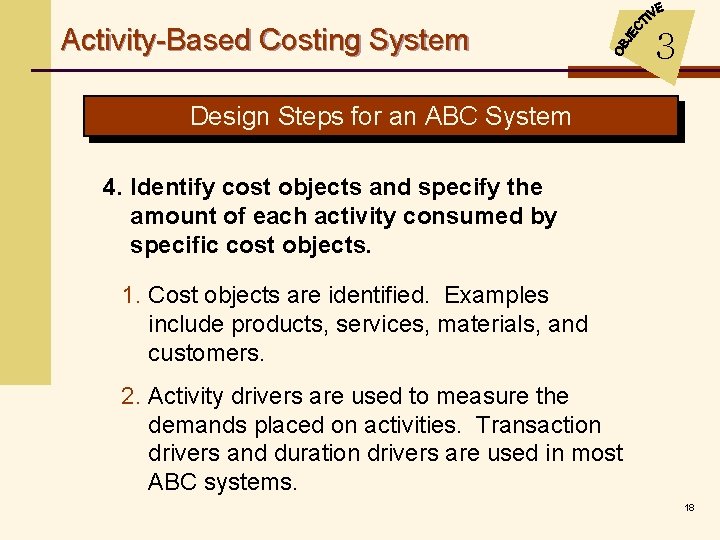
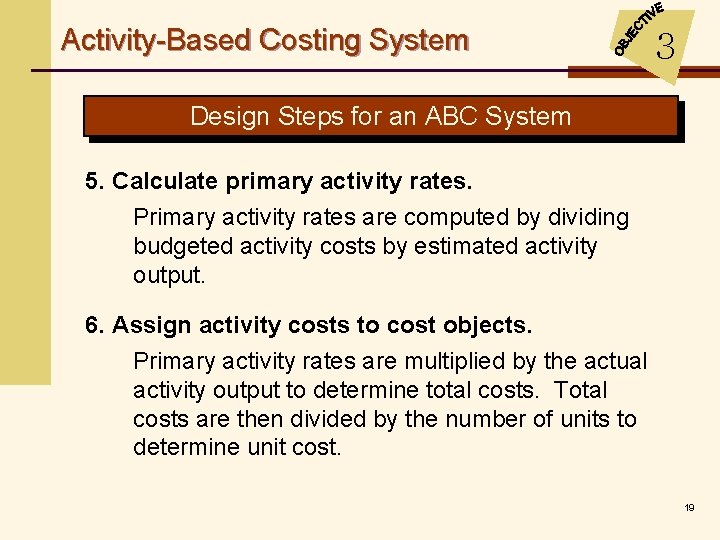
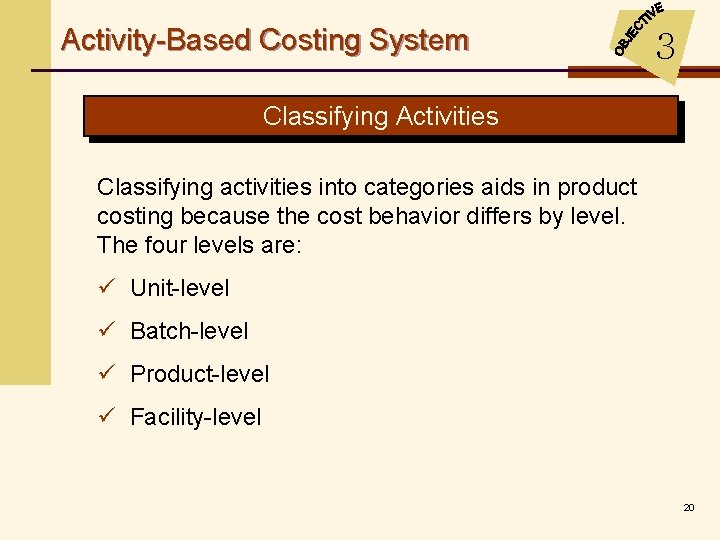
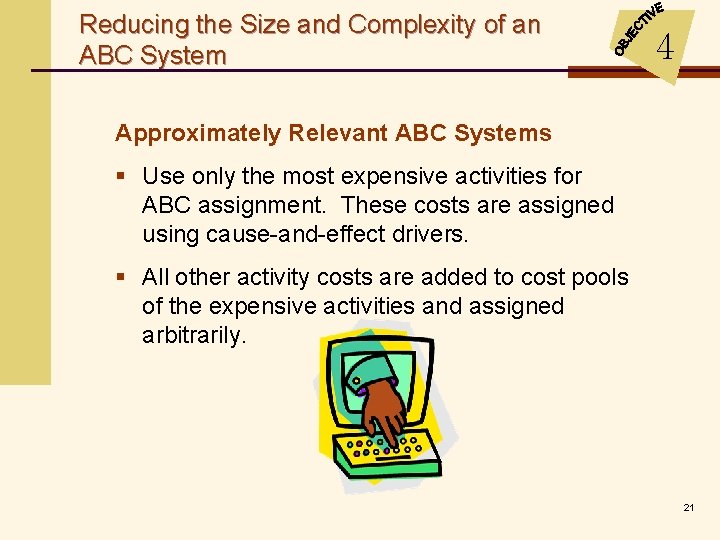
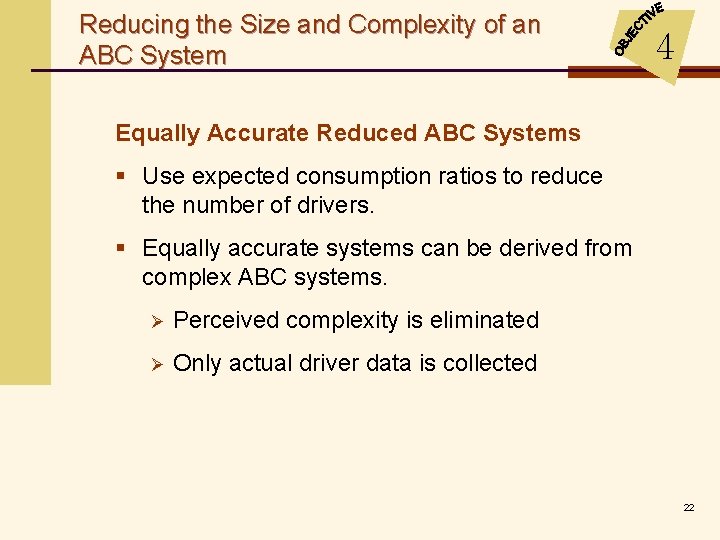
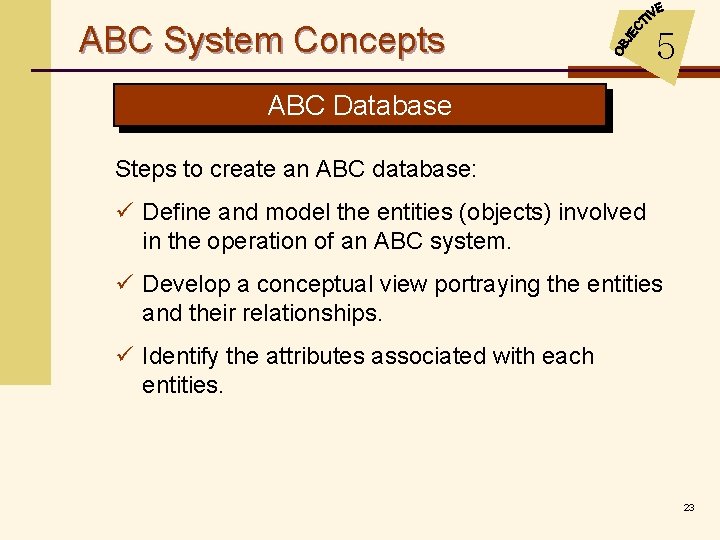
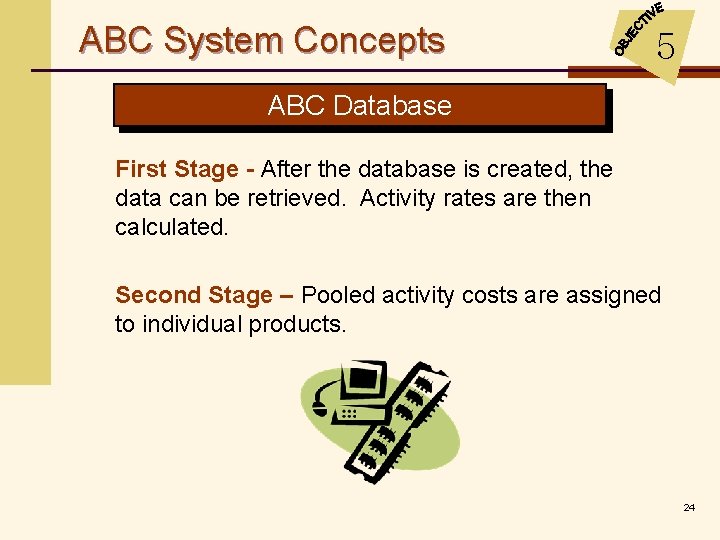
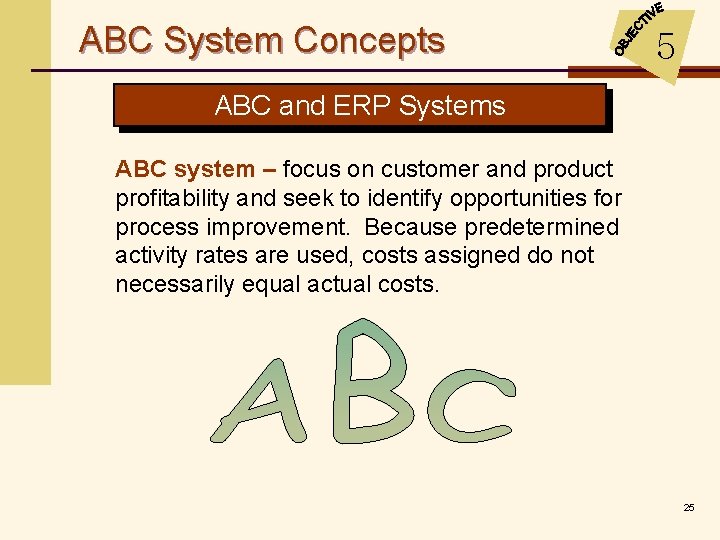
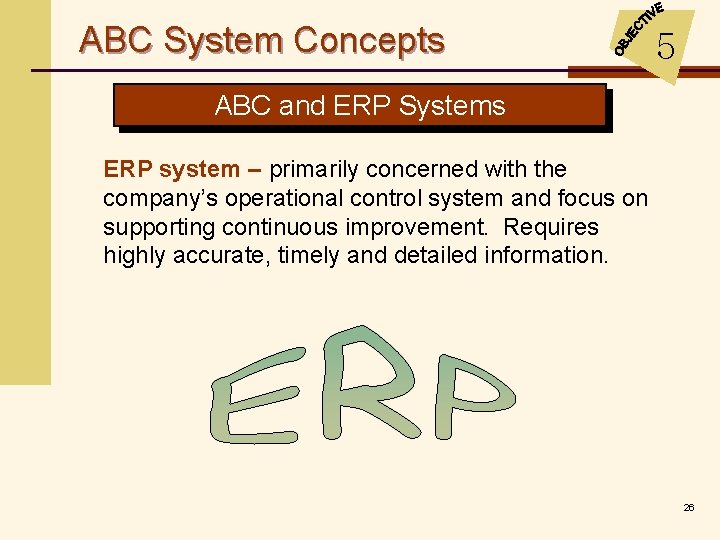
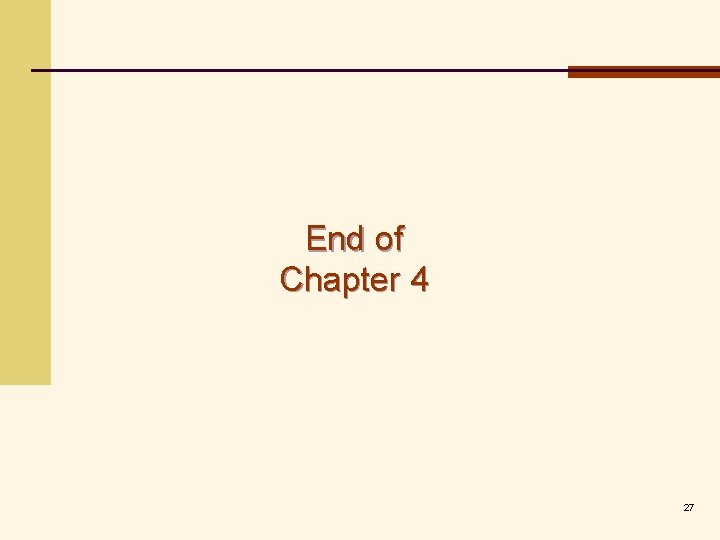
- Slides: 27
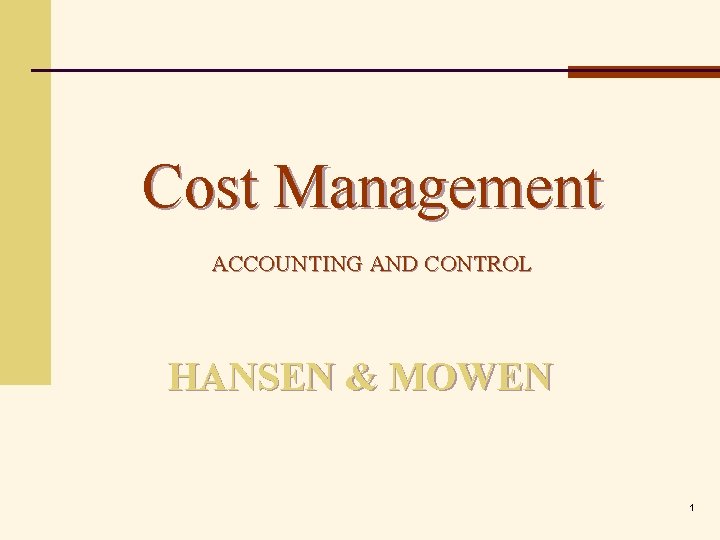
Cost Management ACCOUNTING AND CONTROL HANSEN & MOWEN 1
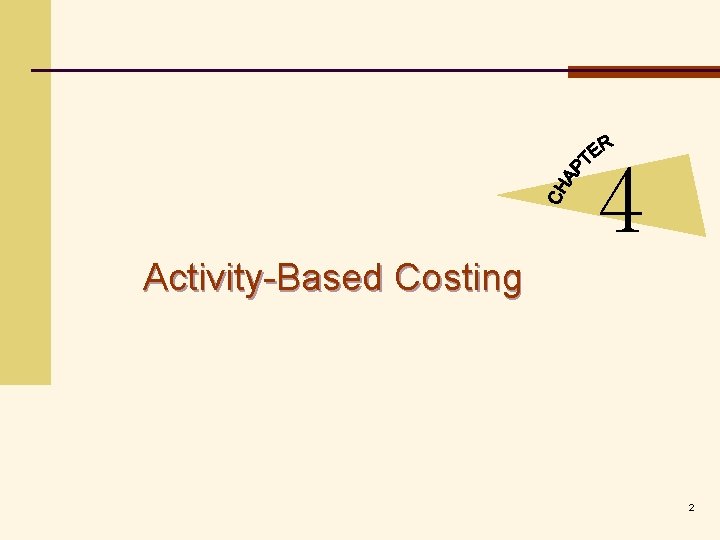
4 Activity-Based Costing 2
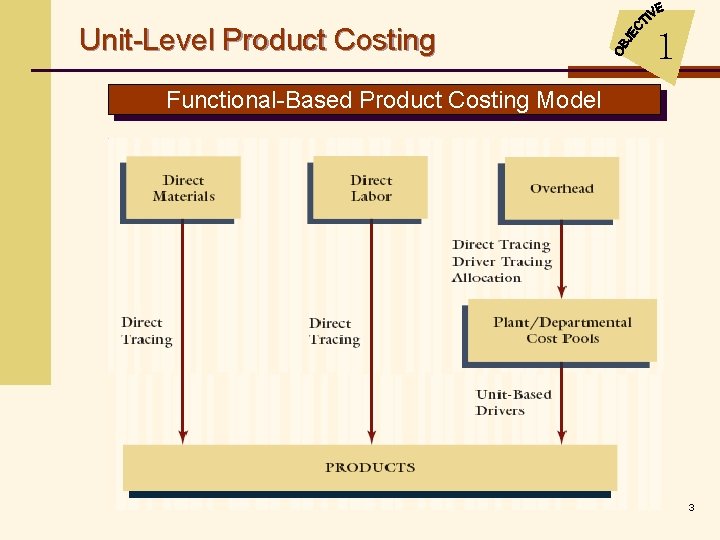
Unit-Level Product Costing 1 Functional-Based Product Costing Model 3
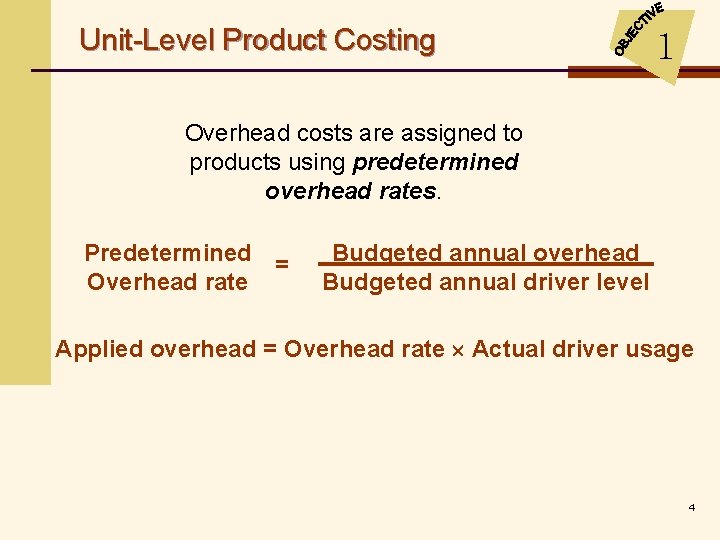
Unit-Level Product Costing 1 Overhead costs are assigned to products using predetermined overhead rates. Predetermined = Overhead rate Budgeted annual overhead Budgeted annual driver level Applied overhead = Overhead rate Actual driver usage 4
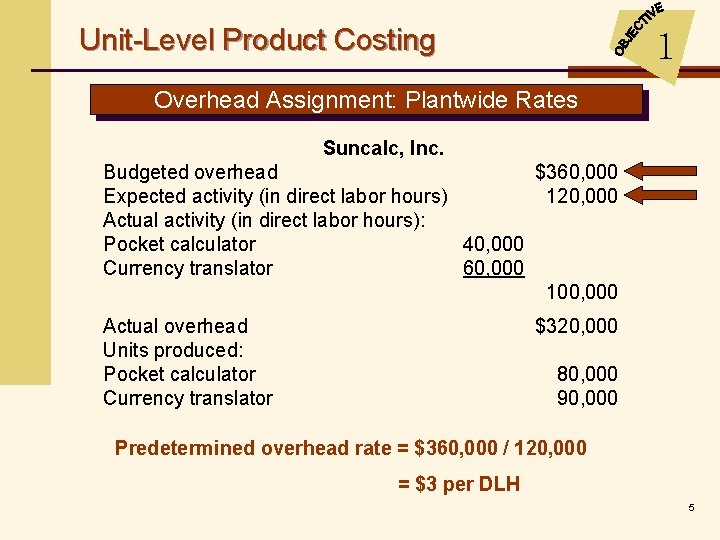
Unit-Level Product Costing 1 Overhead Assignment: Plantwide Rates Suncalc, Inc. Budgeted overhead $360, 000 Expected activity (in direct labor hours) 120, 000 Actual activity (in direct labor hours): Pocket calculator 40, 000 Currency translator 60, 000 100, 000 Actual overhead Units produced: Pocket calculator Currency translator $320, 000 80, 000 90, 000 Predetermined overhead rate = $360, 000 / 120, 000 = $3 per DLH 5
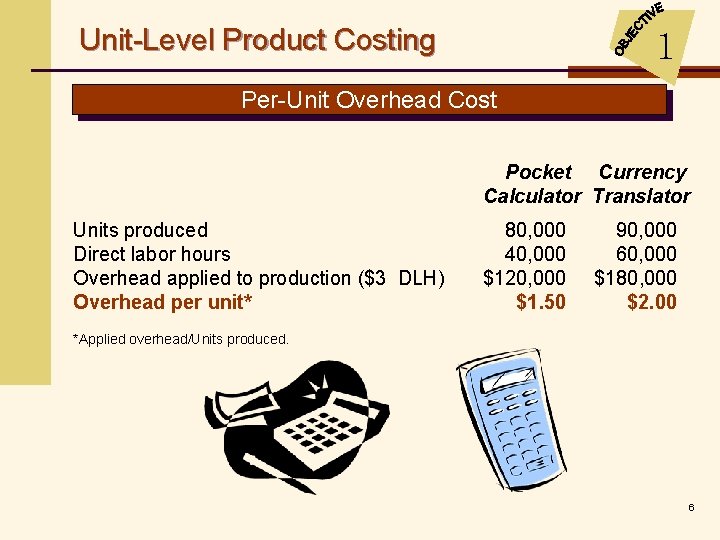
Unit-Level Product Costing 1 Per-Unit Overhead Cost Pocket Currency Calculator Translator Units produced Direct labor hours Overhead applied to production ($3 DLH) Overhead per unit* 80, 000 40, 000 $120, 000 $1. 50 90, 000 60, 000 $180, 000 $2. 00 *Applied overhead/Units produced. 6
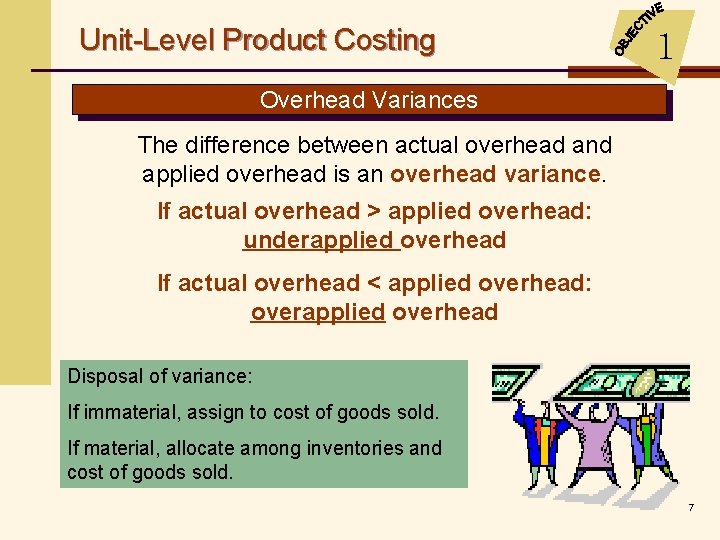
Unit-Level Product Costing 1 Overhead Variances The difference between actual overhead and applied overhead is an overhead variance. If actual overhead > applied overhead: underapplied overhead If actual overhead < applied overhead: overapplied overhead Disposal of variance: If immaterial, assign to cost of goods sold. If material, allocate among inventories and cost of goods sold. 7
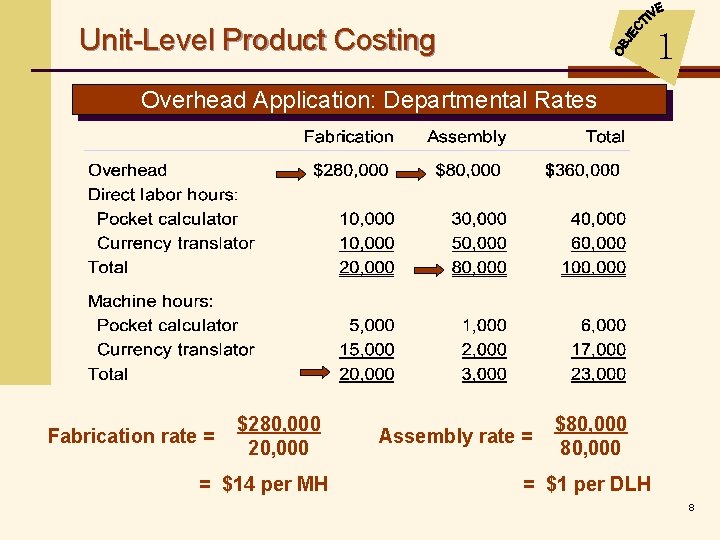
Unit-Level Product Costing 1 Overhead Application: Departmental Rates Fabrication rate = $280, 000 20, 000 = $14 per MH Assembly rate = $80, 000 = $1 per DLH 8
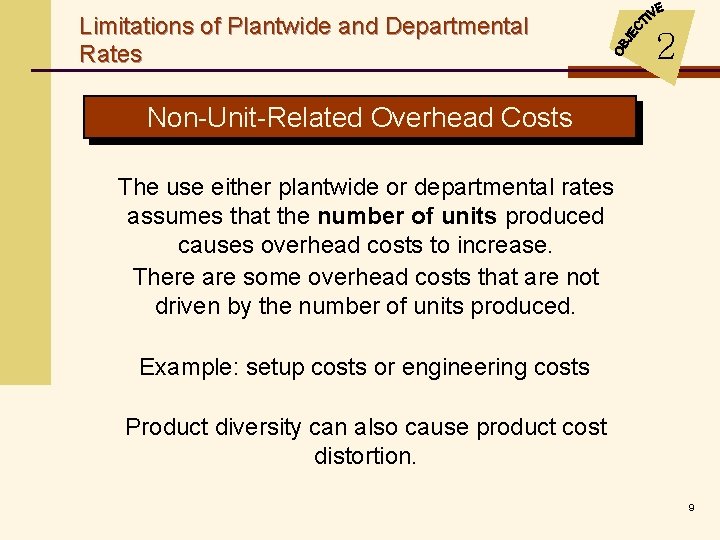
Limitations of Plantwide and Departmental Rates 2 Non-Unit-Related Overhead Costs The use either plantwide or departmental rates assumes that the number of units produced causes overhead costs to increase. There are some overhead costs that are not driven by the number of units produced. Example: setup costs or engineering costs Product diversity can also cause product cost distortion. 9
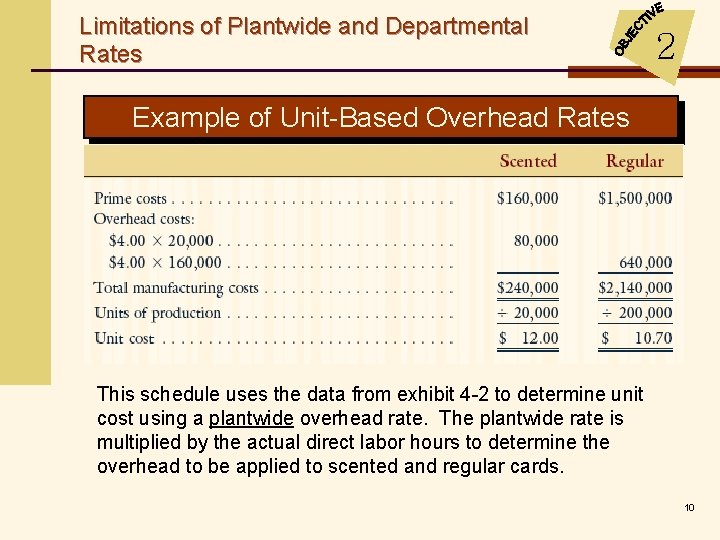
Limitations of Plantwide and Departmental Rates 2 Example of Unit-Based Overhead Rates This schedule uses the data from exhibit 4 -2 to determine unit cost using a plantwide overhead rate. The plantwide rate is multiplied by the actual direct labor hours to determine the overhead to be applied to scented and regular cards. 10
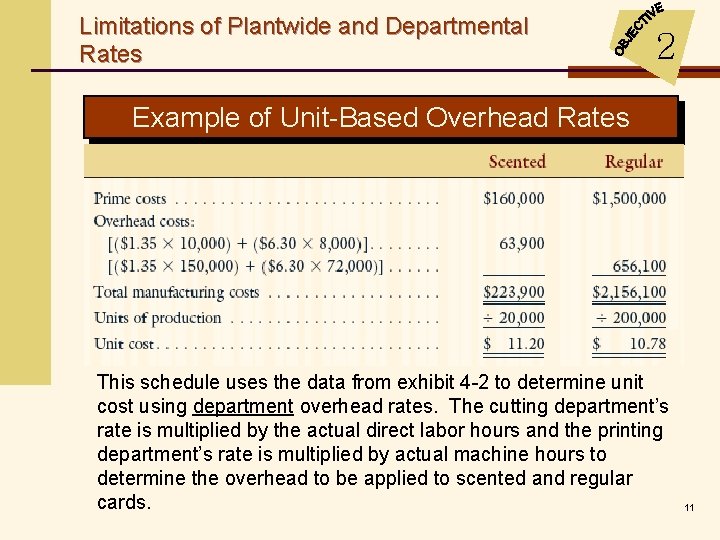
Limitations of Plantwide and Departmental Rates 2 Example of Unit-Based Overhead Rates This schedule uses the data from exhibit 4 -2 to determine unit cost using department overhead rates. The cutting department’s rate is multiplied by the actual direct labor hours and the printing department’s rate is multiplied by actual machine hours to determine the overhead to be applied to scented and regular cards. 11
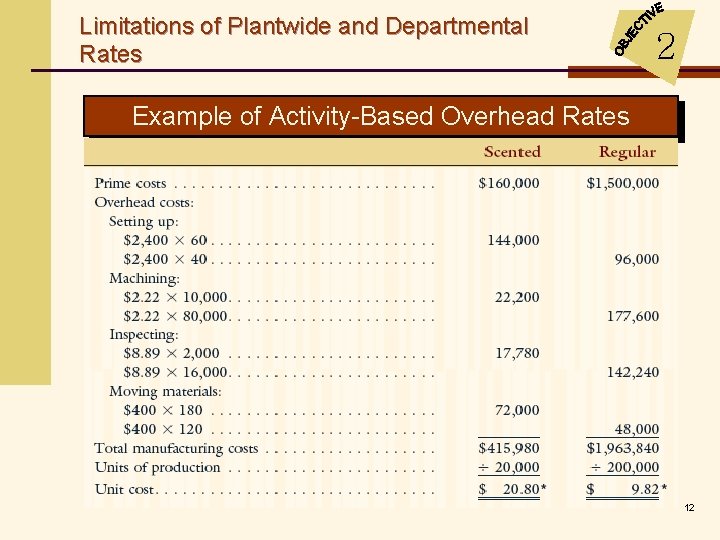
Limitations of Plantwide and Departmental Rates 2 Example of Activity-Based Overhead Rates 12
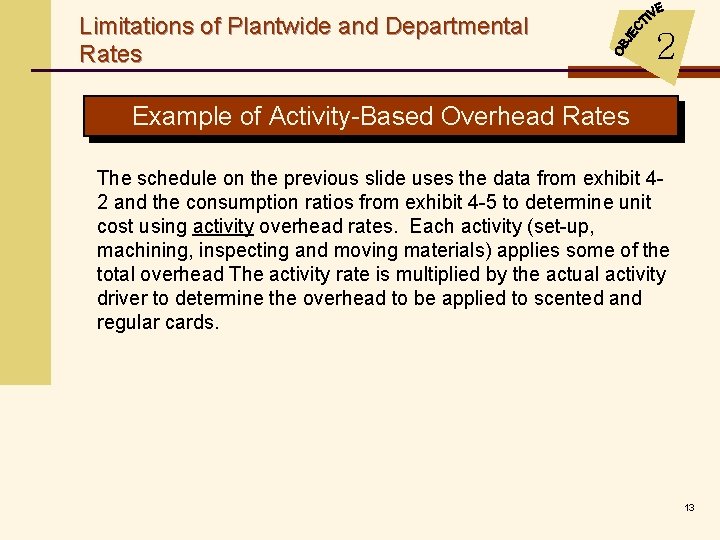
Limitations of Plantwide and Departmental Rates 2 Example of Activity-Based Overhead Rates The schedule on the previous slide uses the data from exhibit 42 and the consumption ratios from exhibit 4 -5 to determine unit cost using activity overhead rates. Each activity (set-up, machining, inspecting and moving materials) applies some of the total overhead The activity rate is multiplied by the actual activity driver to determine the overhead to be applied to scented and regular cards. 13
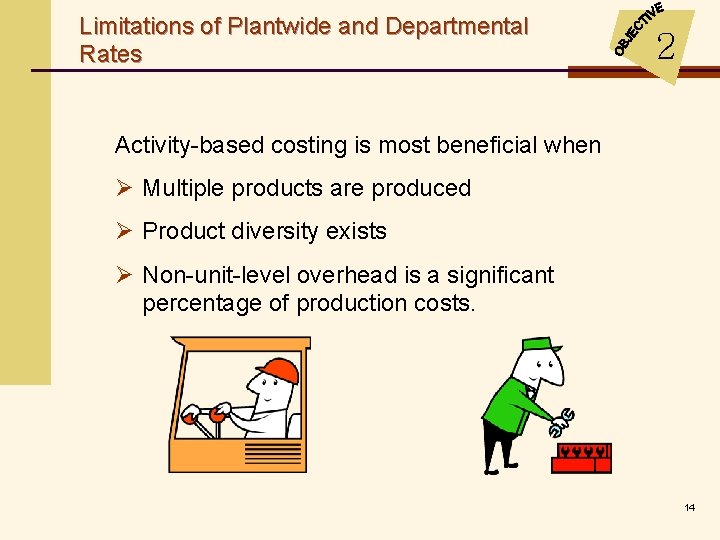
Limitations of Plantwide and Departmental Rates 2 Activity-based costing is most beneficial when Ø Multiple products are produced Ø Product diversity exists Ø Non-unit-level overhead is a significant percentage of production costs. 14
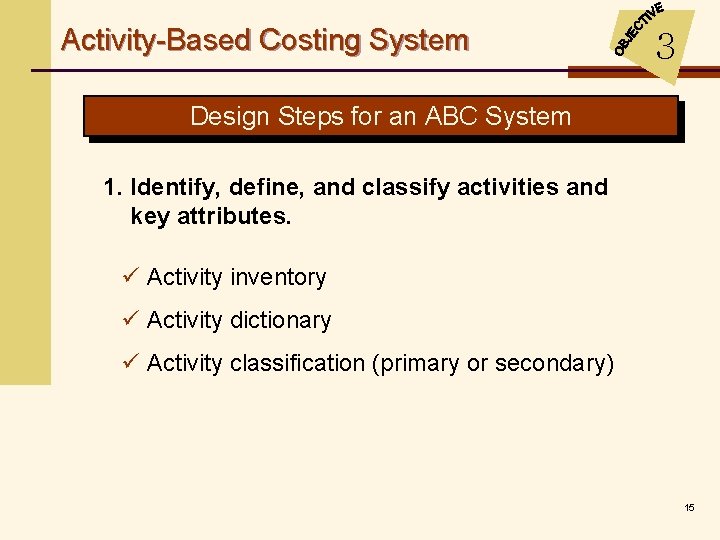
Activity-Based Costing System 3 Design Steps for an ABC System 1. Identify, define, and classify activities and key attributes. ü Activity inventory ü Activity dictionary ü Activity classification (primary or secondary) 15
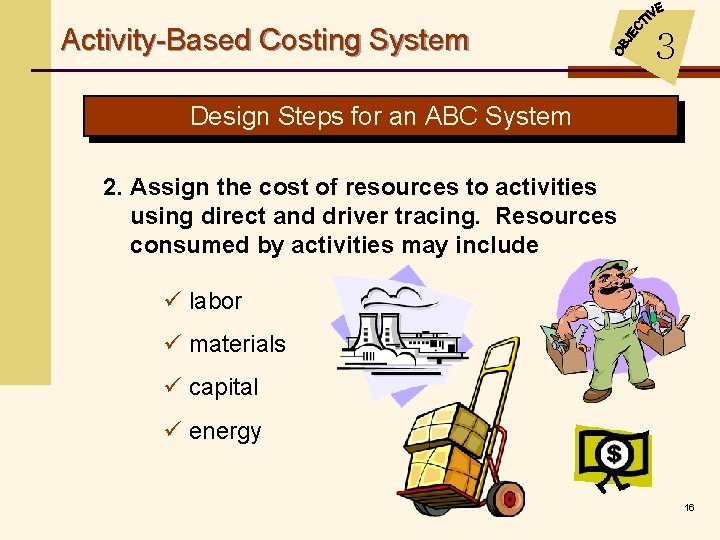
Activity-Based Costing System 3 Design Steps for an ABC System 2. Assign the cost of resources to activities using direct and driver tracing. Resources consumed by activities may include ü labor ü materials ü capital ü energy 16
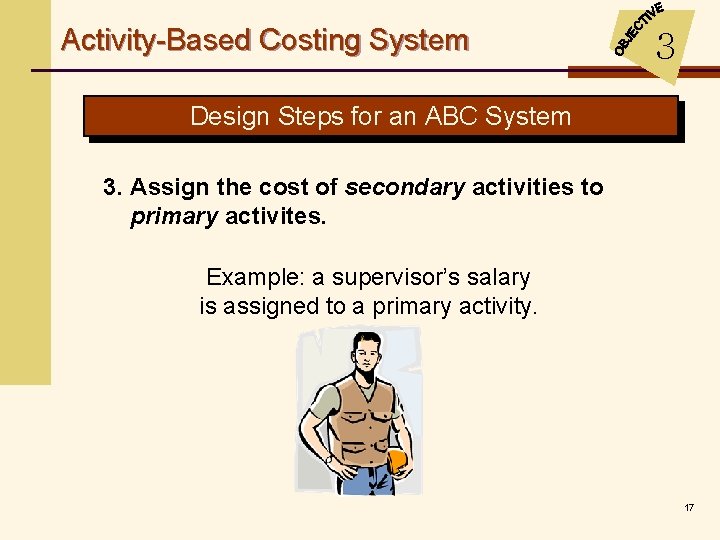
Activity-Based Costing System 3 Design Steps for an ABC System 3. Assign the cost of secondary activities to primary activites. Example: a supervisor’s salary is assigned to a primary activity. 17
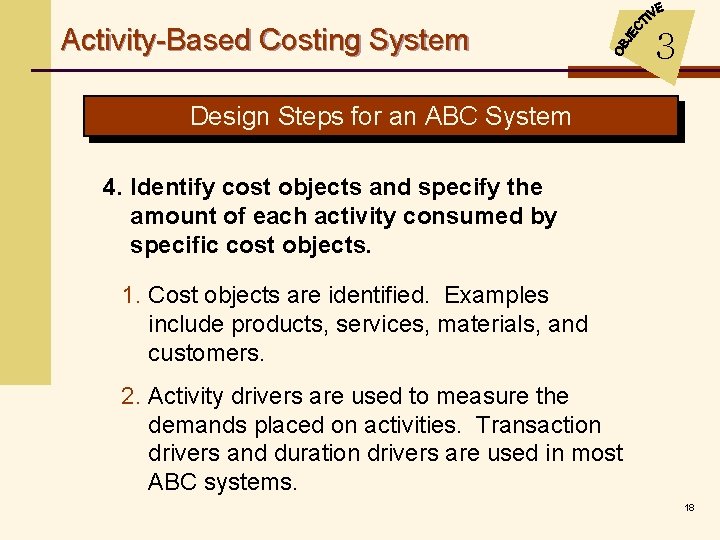
Activity-Based Costing System 3 Design Steps for an ABC System 4. Identify cost objects and specify the amount of each activity consumed by specific cost objects. 1. Cost objects are identified. Examples include products, services, materials, and customers. 2. Activity drivers are used to measure the demands placed on activities. Transaction drivers and duration drivers are used in most ABC systems. 18
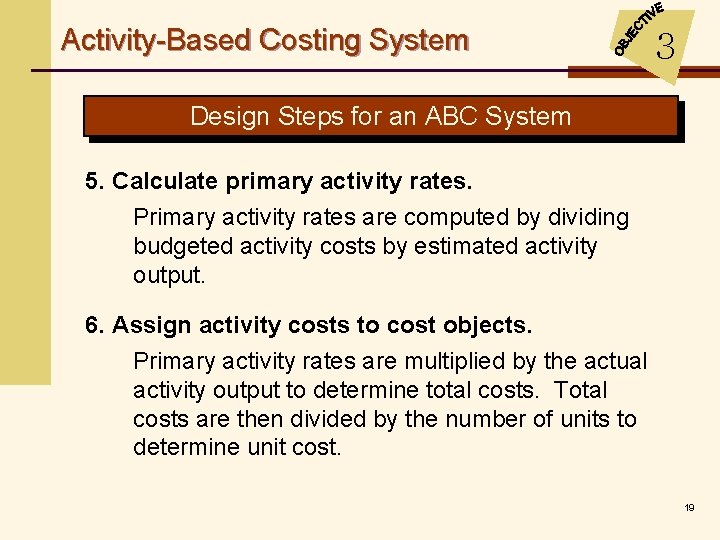
Activity-Based Costing System 3 Design Steps for an ABC System 5. Calculate primary activity rates. Primary activity rates are computed by dividing budgeted activity costs by estimated activity output. 6. Assign activity costs to cost objects. Primary activity rates are multiplied by the actual activity output to determine total costs. Total costs are then divided by the number of units to determine unit cost. 19
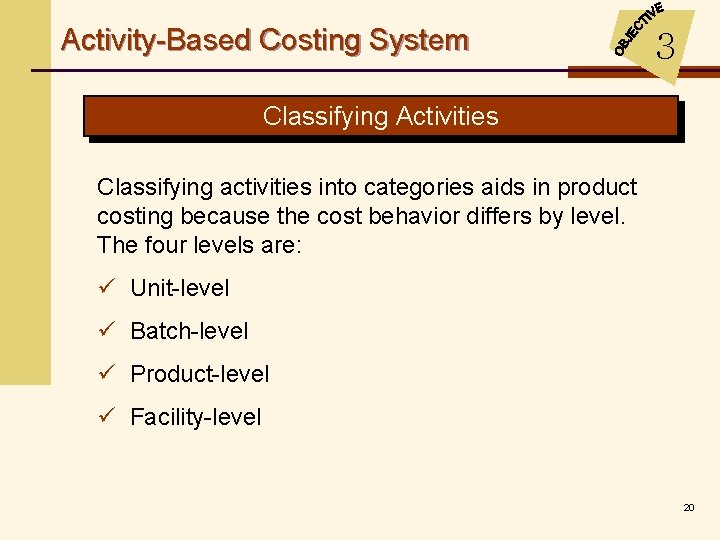
Activity-Based Costing System 3 Classifying Activities Classifying activities into categories aids in product costing because the cost behavior differs by level. The four levels are: ü Unit-level ü Batch-level ü Product-level ü Facility-level 20
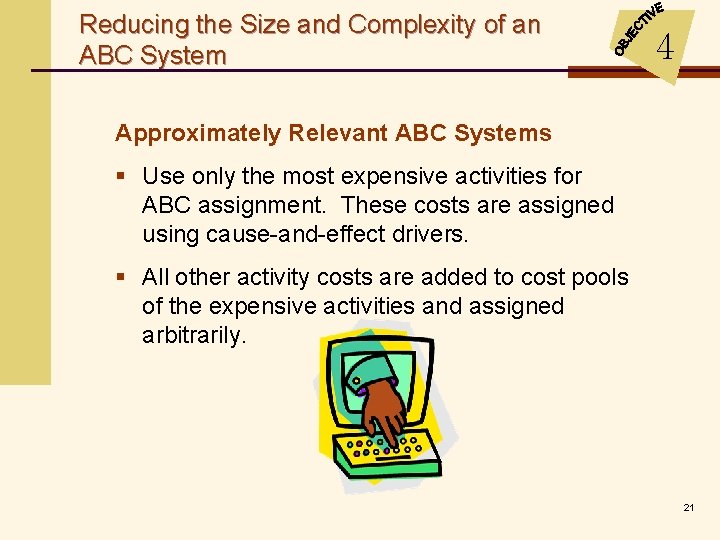
Reducing the Size and Complexity of an ABC System 4 Approximately Relevant ABC Systems § Use only the most expensive activities for ABC assignment. These costs are assigned using cause-and-effect drivers. § All other activity costs are added to cost pools of the expensive activities and assigned arbitrarily. 21
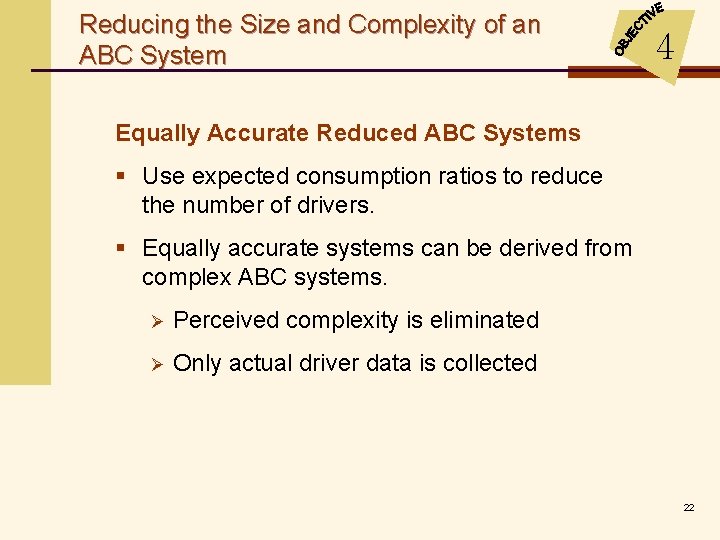
Reducing the Size and Complexity of an ABC System 4 Equally Accurate Reduced ABC Systems § Use expected consumption ratios to reduce the number of drivers. § Equally accurate systems can be derived from complex ABC systems. Ø Perceived complexity is eliminated Ø Only actual driver data is collected 22
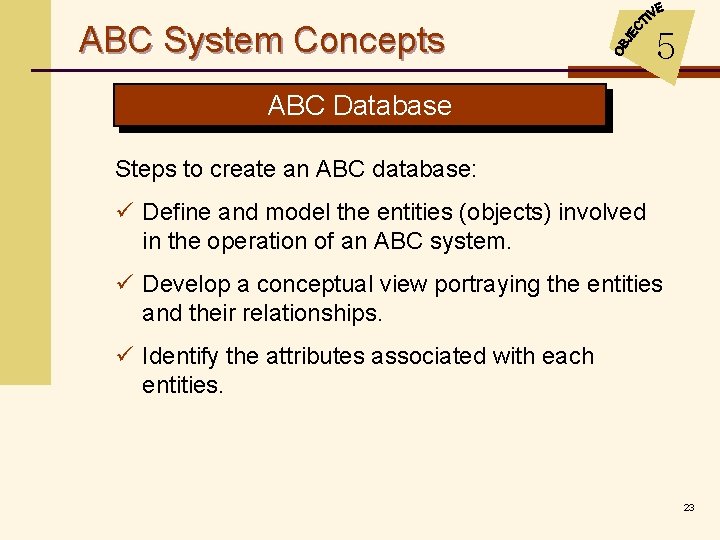
ABC System Concepts 5 ABC Database Steps to create an ABC database: ü Define and model the entities (objects) involved in the operation of an ABC system. ü Develop a conceptual view portraying the entities and their relationships. ü Identify the attributes associated with each entities. 23
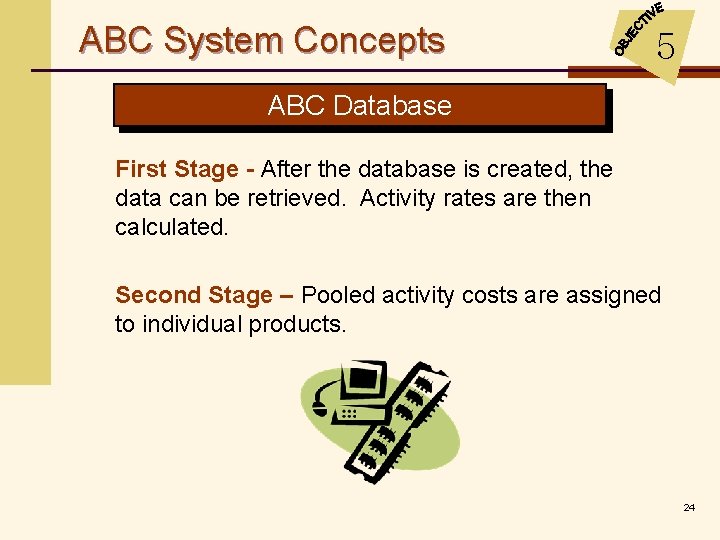
ABC System Concepts 5 ABC Database First Stage - After the database is created, the data can be retrieved. Activity rates are then calculated. Second Stage – Pooled activity costs are assigned to individual products. 24
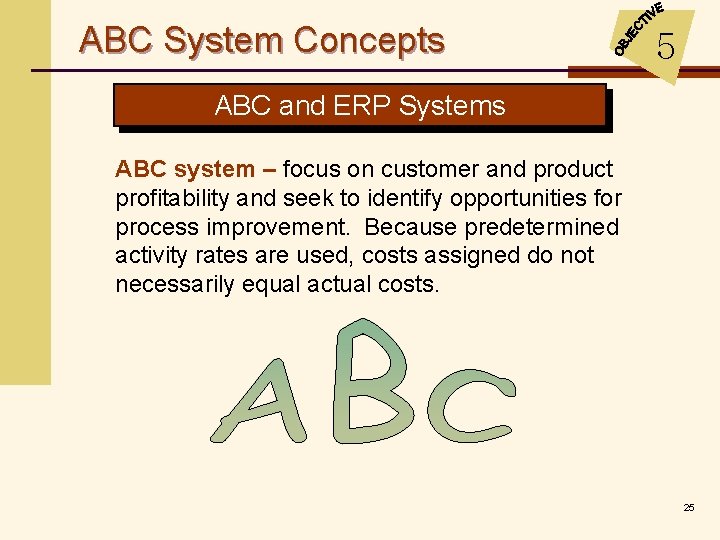
ABC System Concepts 5 ABC and ERP Systems ABC system – focus on customer and product profitability and seek to identify opportunities for process improvement. Because predetermined activity rates are used, costs assigned do not necessarily equal actual costs. 25
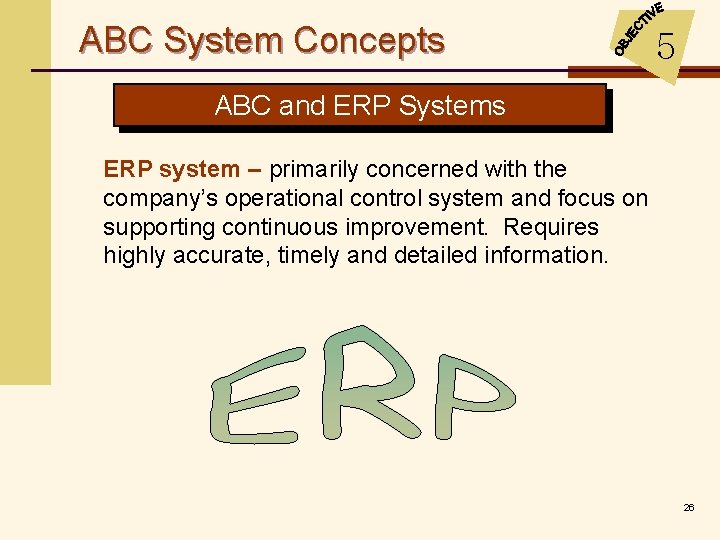
ABC System Concepts 5 ABC and ERP Systems ERP system – primarily concerned with the company’s operational control system and focus on supporting continuous improvement. Requires highly accurate, timely and detailed information. 26
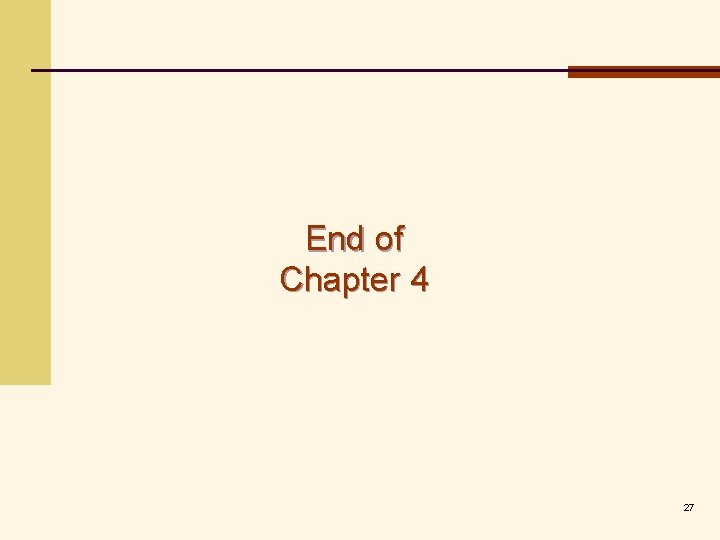
End of Chapter 4 27
Cost management hansen
Slidetodoc.com
Cost management accounting and control
Cost management accounting and control
Cost control and cost reduction difference
Cost control and cost reduction difference
Cost control and cost reduction project report
Cost control and cost reduction project report
Kaizen costing ppt
Advanced cost and management accounting ppt
Social responsibility of management ppt
Drury management and cost accounting
Drury c management and cost accounting
Relevant cost in management accounting
The tail by joyce hansen
Cost accumulation and cost assignment
Cost accumulation and cost assignment
Cost pools
Cost accumulation and cost assignment
Standerd costing
Distinguish between average cost and marginal cost
Job order costing vs process costing
Ordering cost and carrying cost
Opportunity cost vs trade off
Cost structure refers to the relative proportion of
Job costing definition
Nature of cost accounting
Managerial accounting cost concepts