Chalmers University of Technology Dynamic Mode Decomposition applied
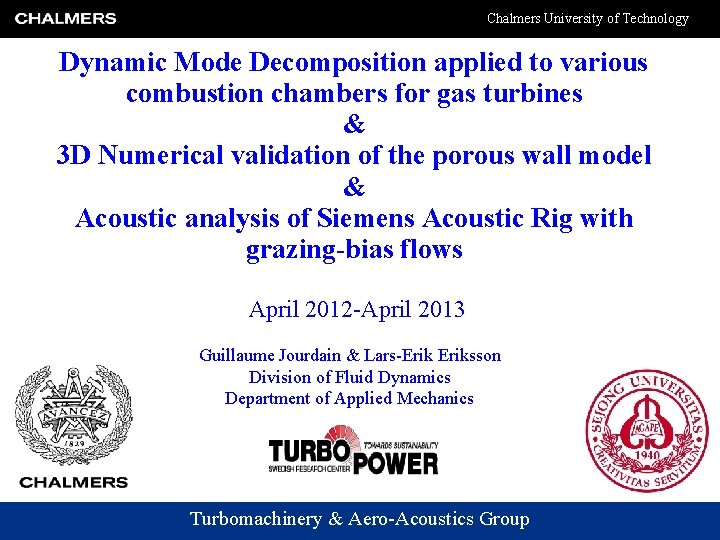
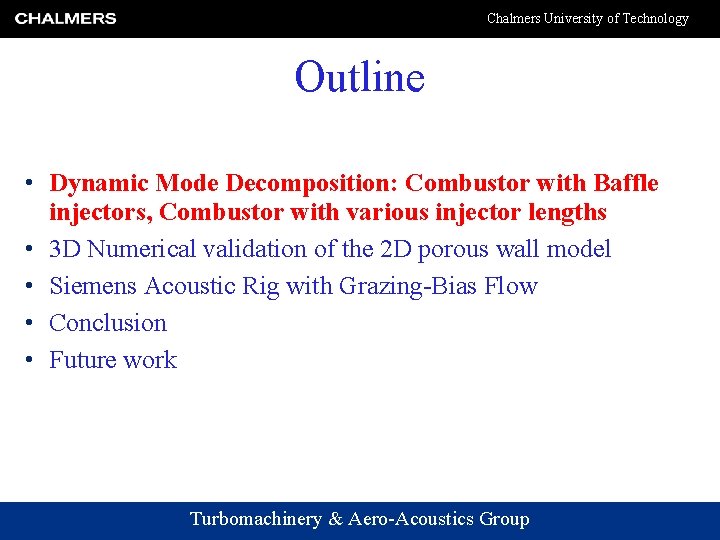
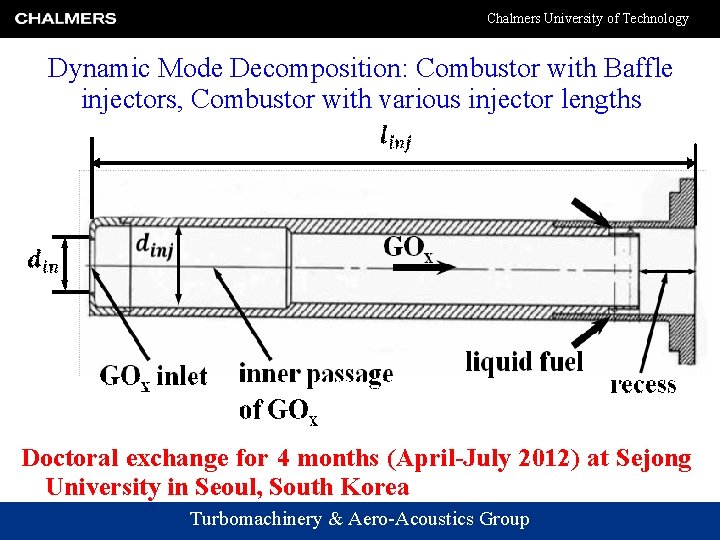
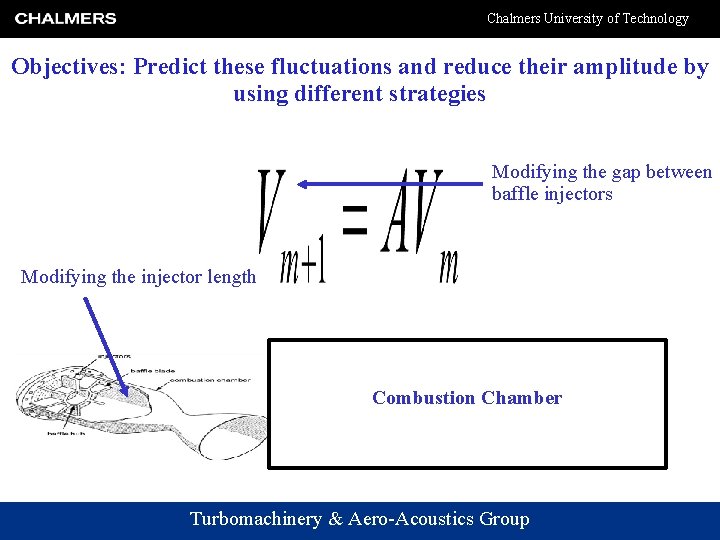
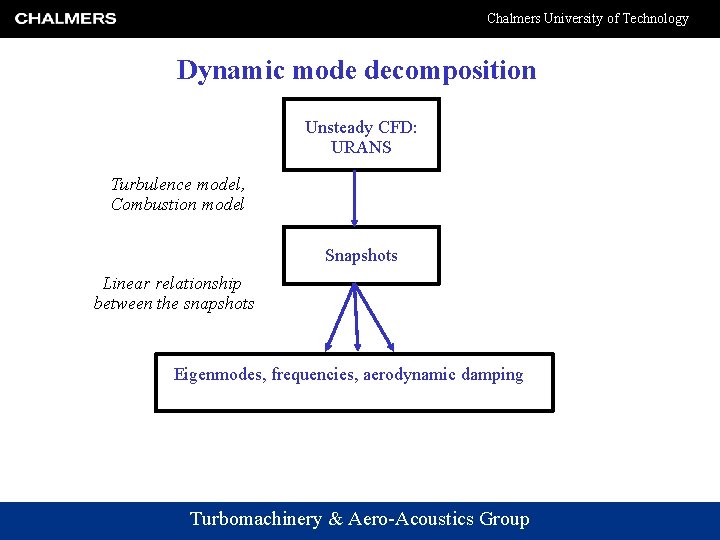
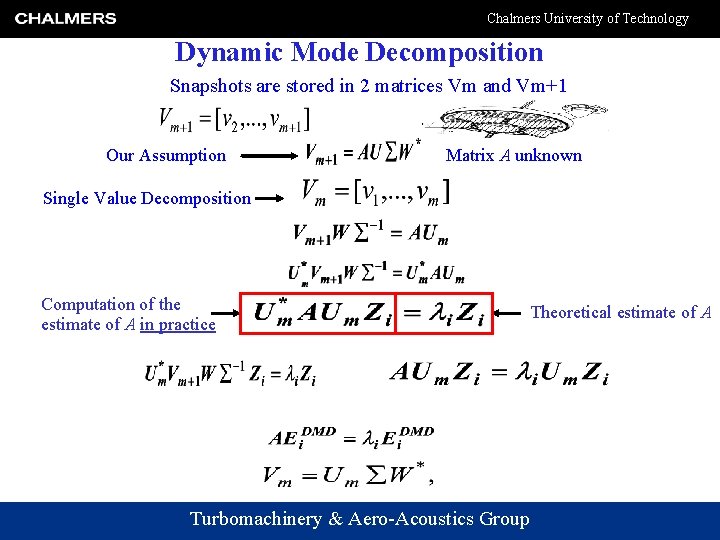
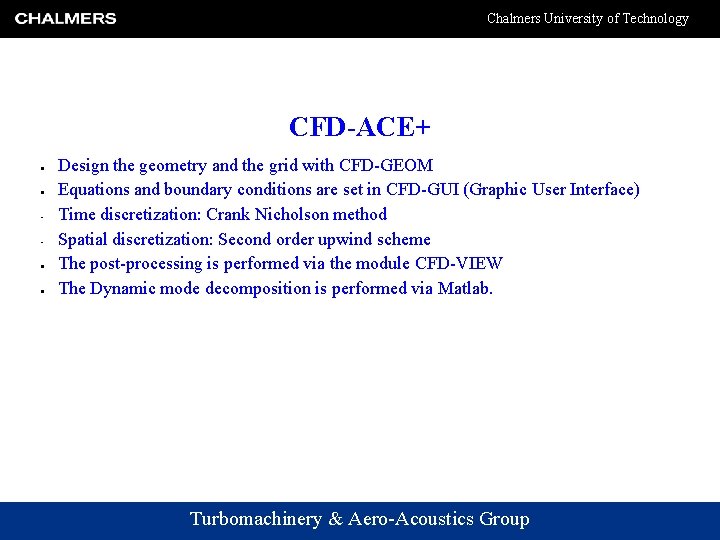
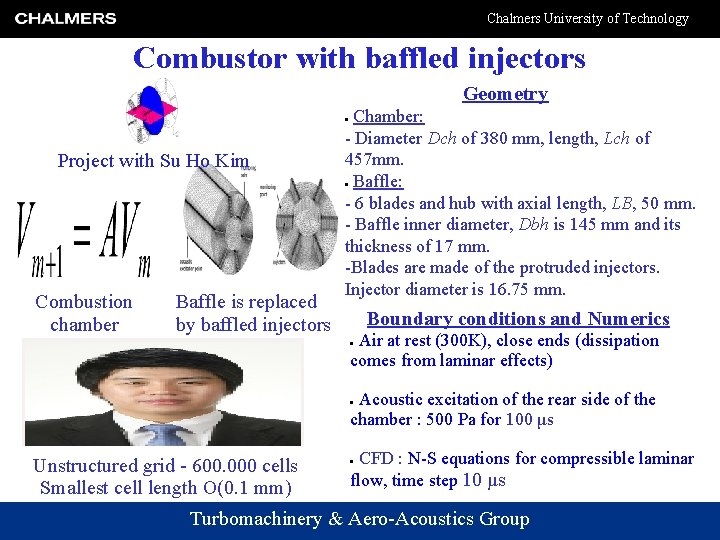
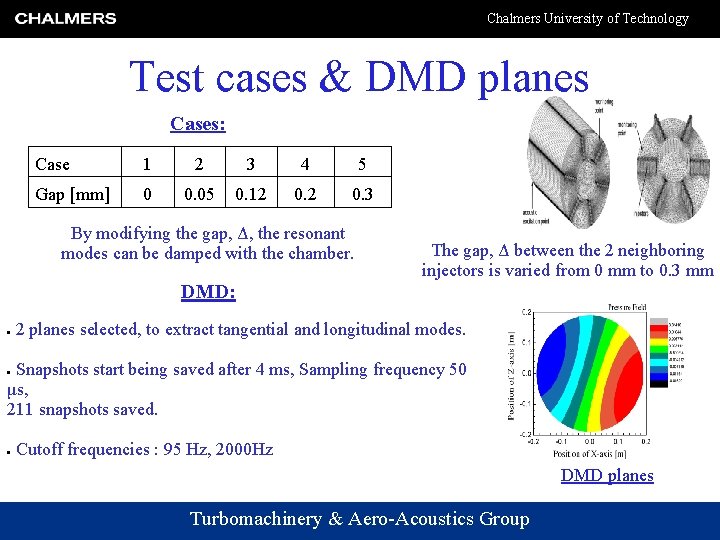
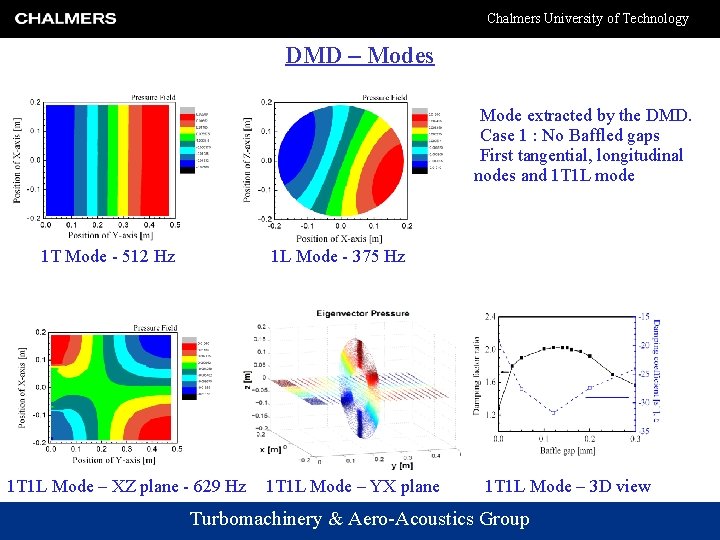
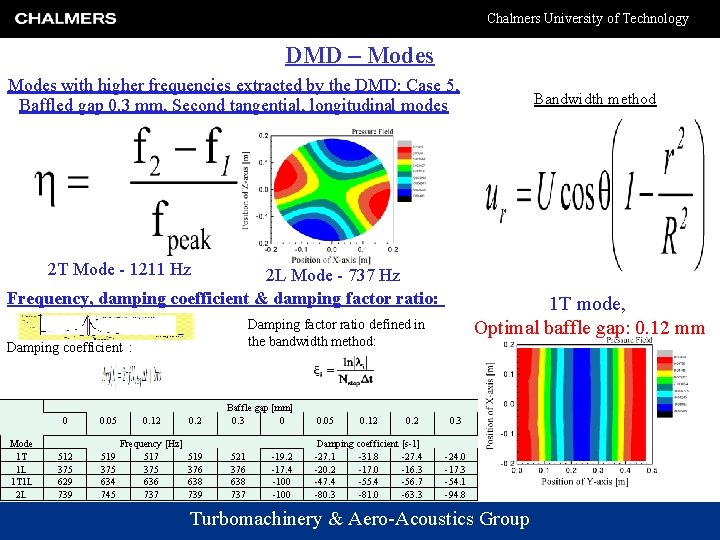
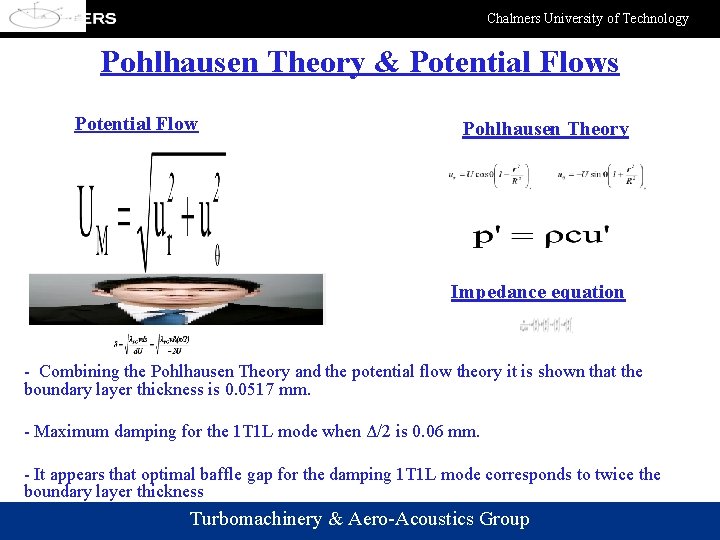
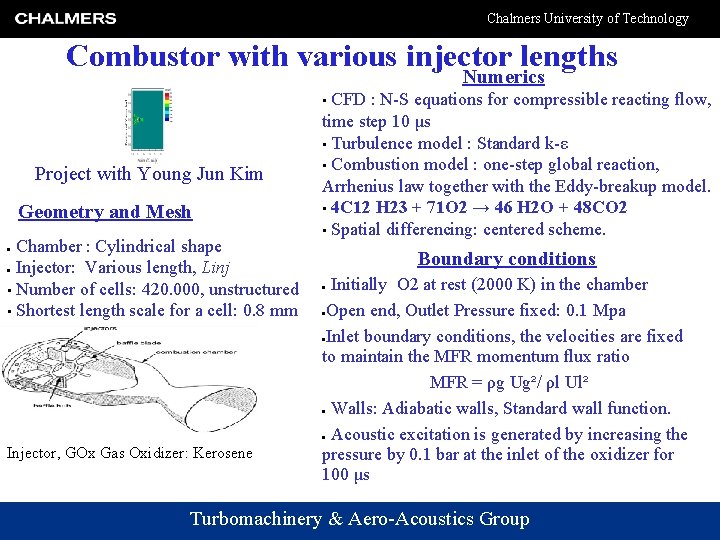
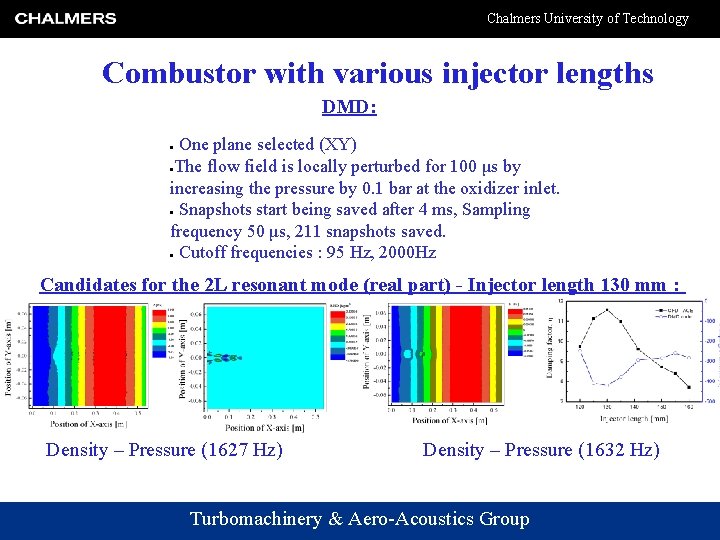
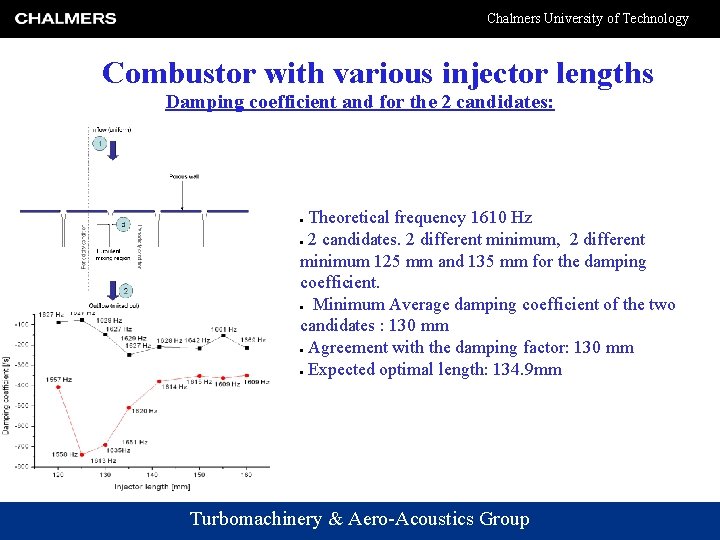
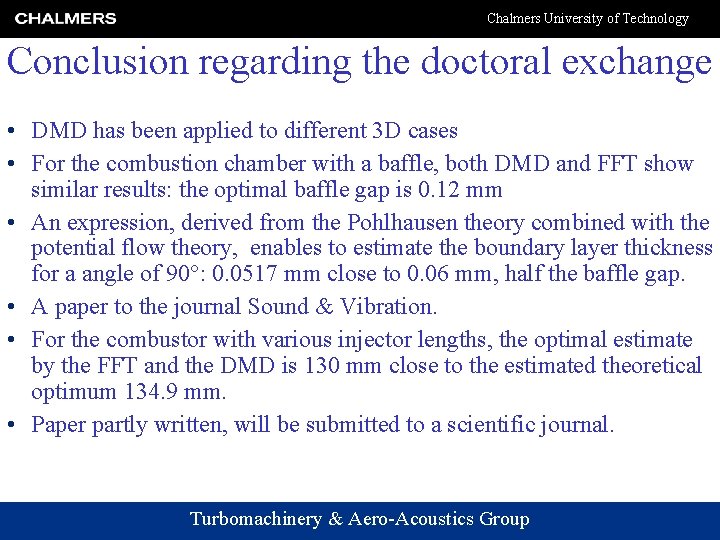

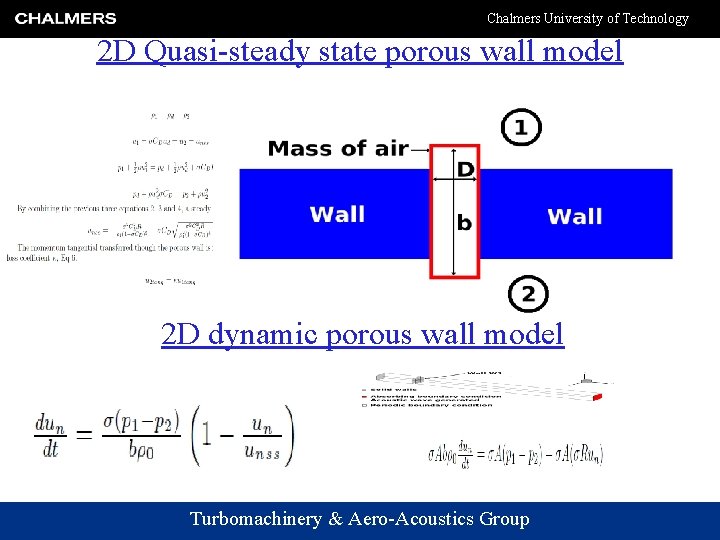
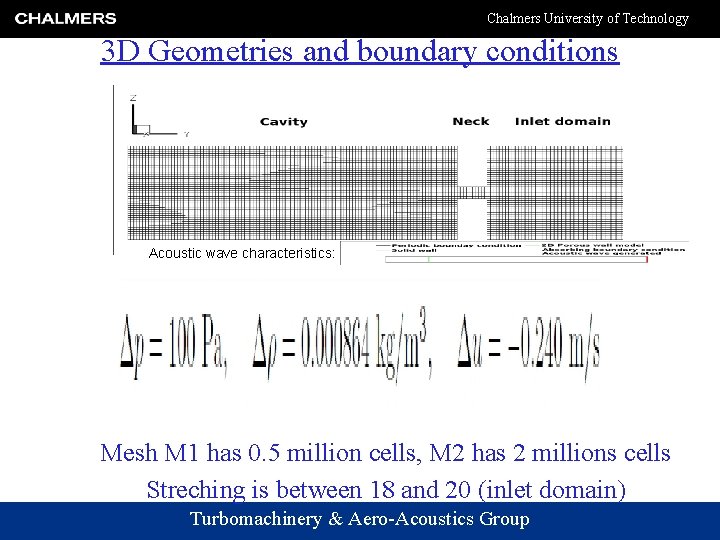
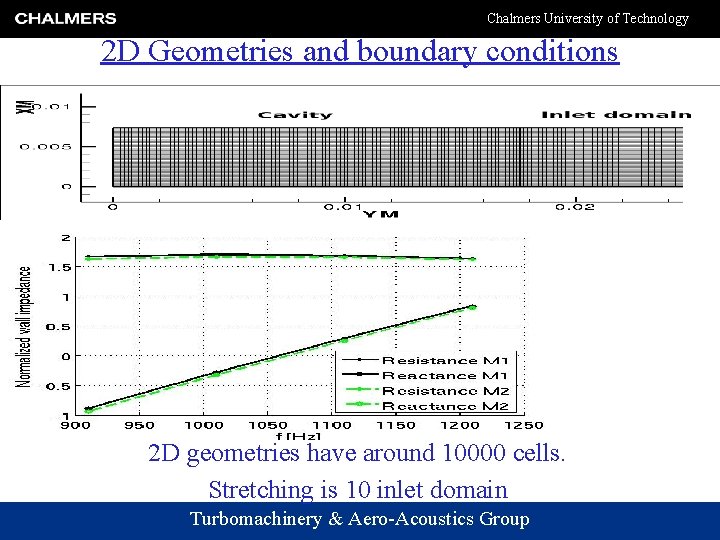
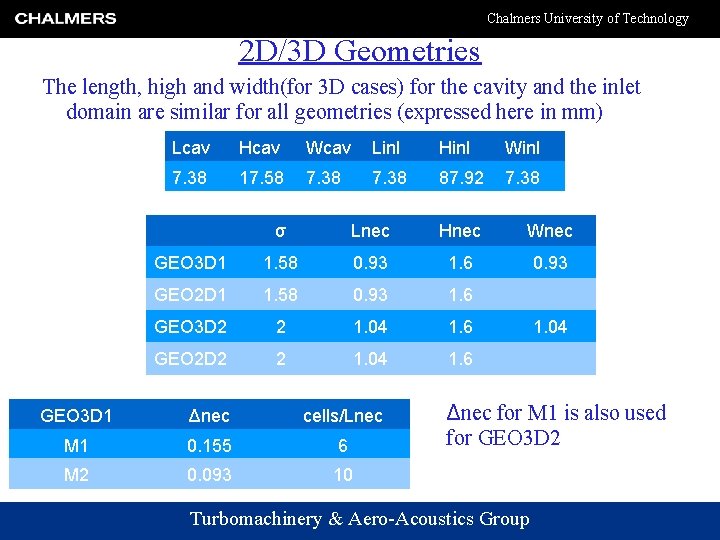
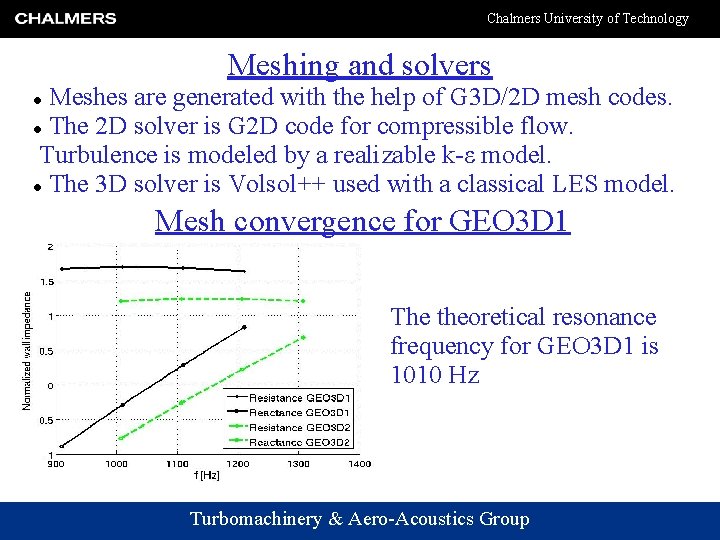
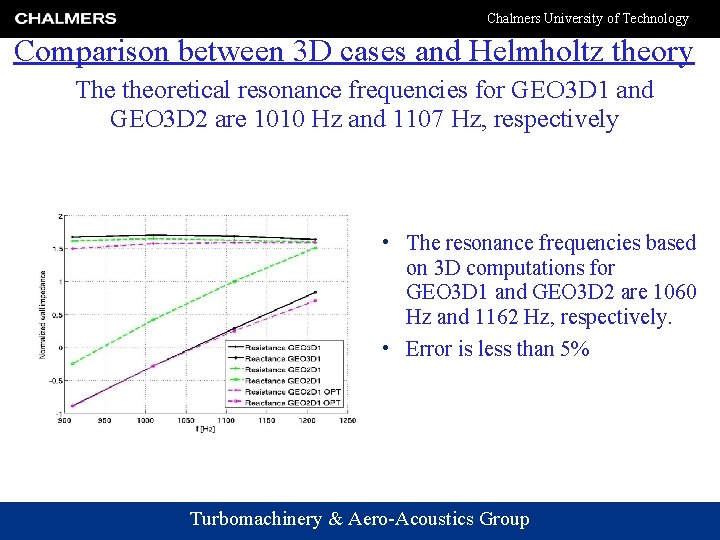
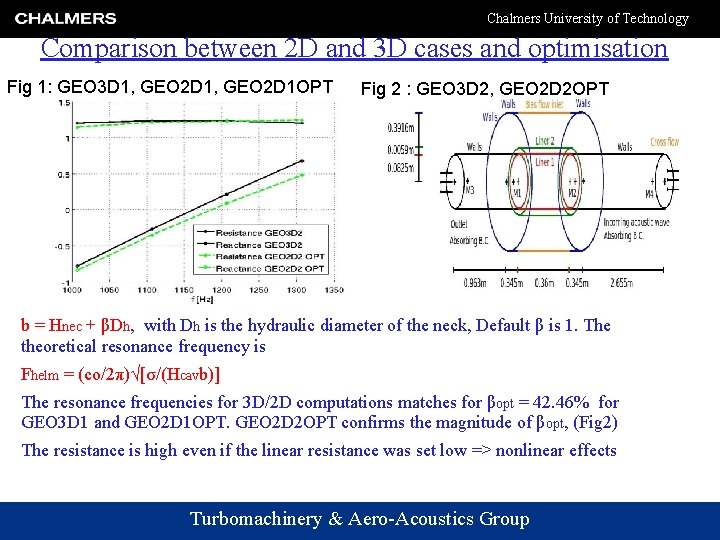
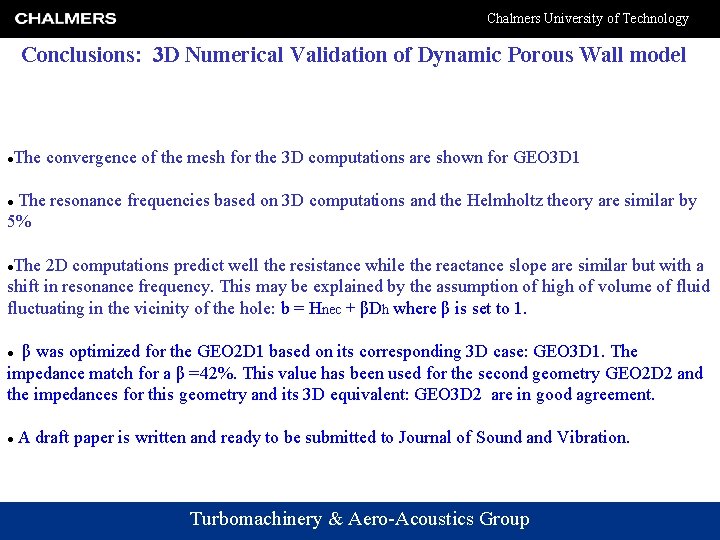
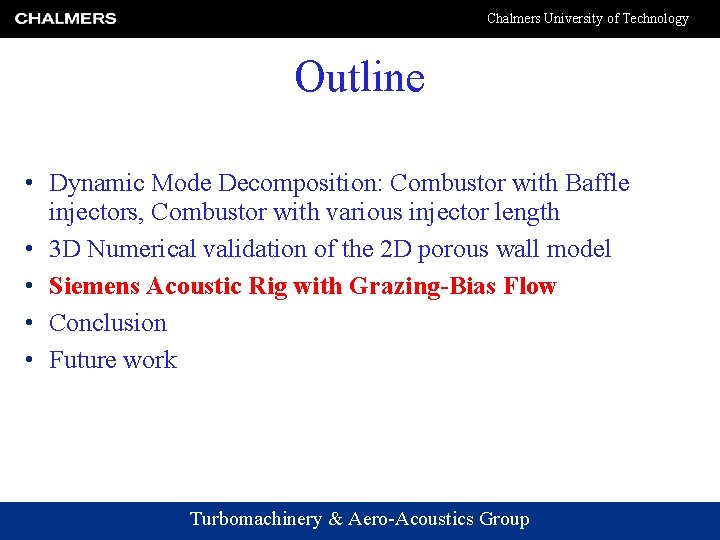
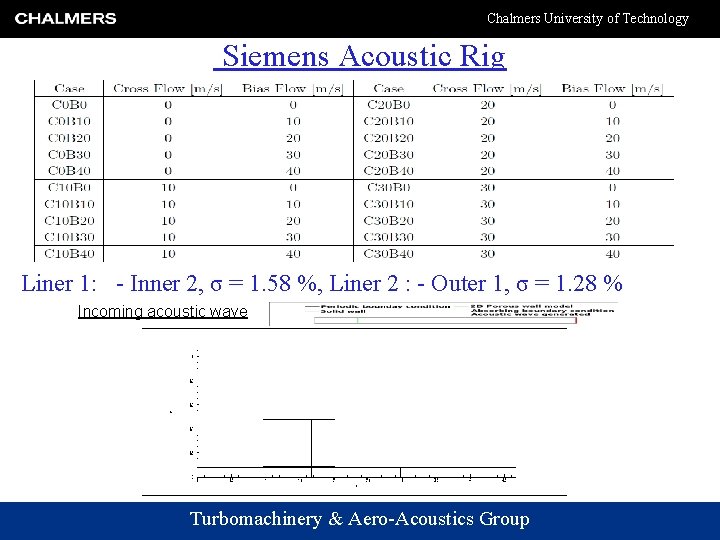
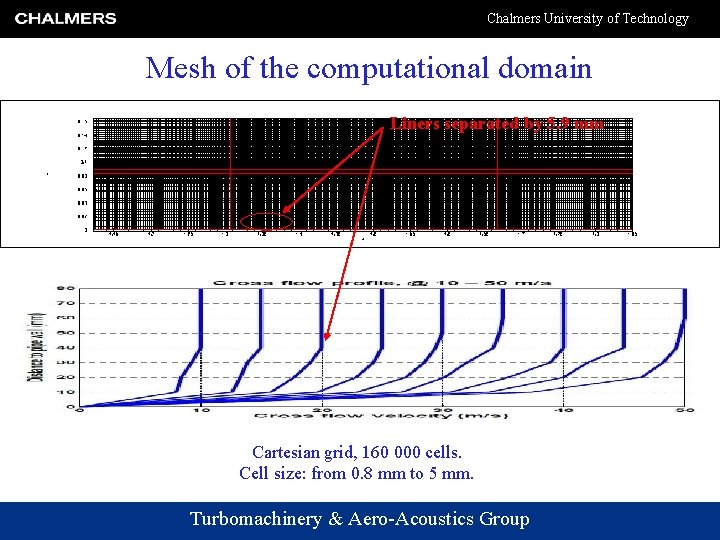
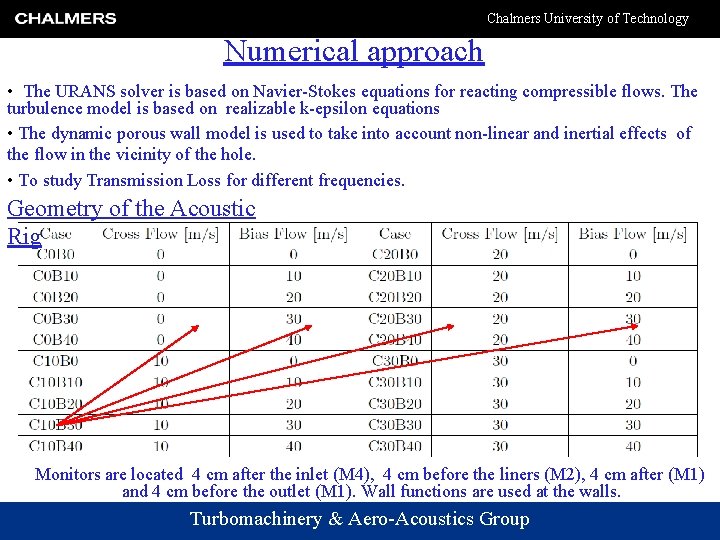
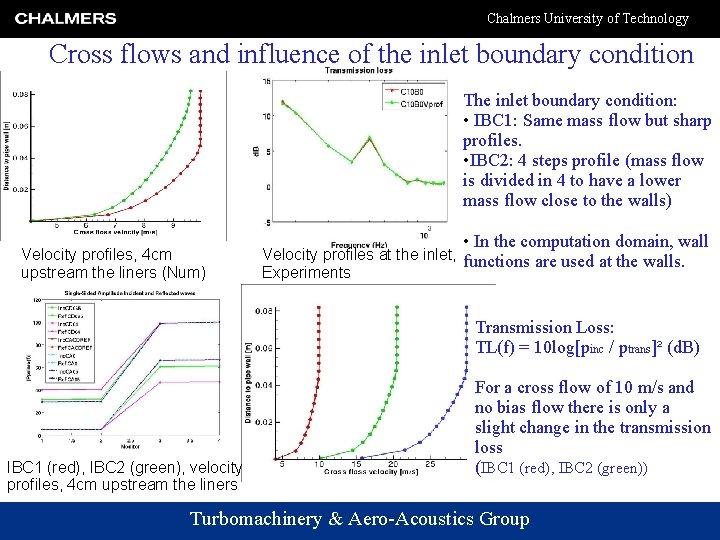
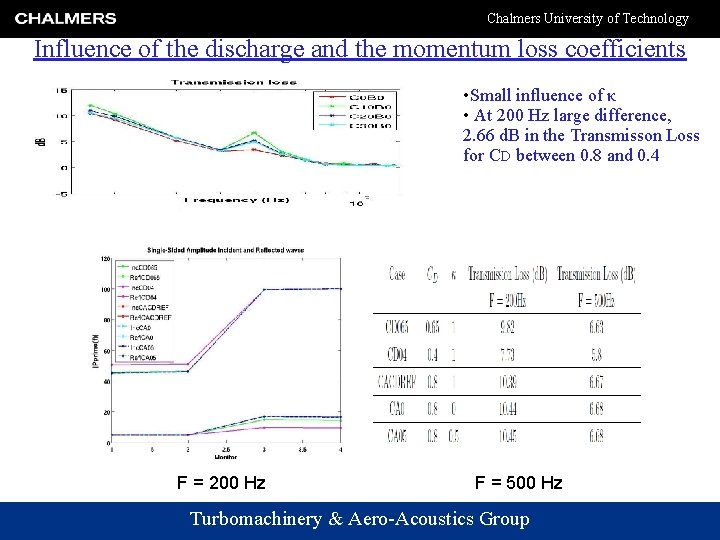
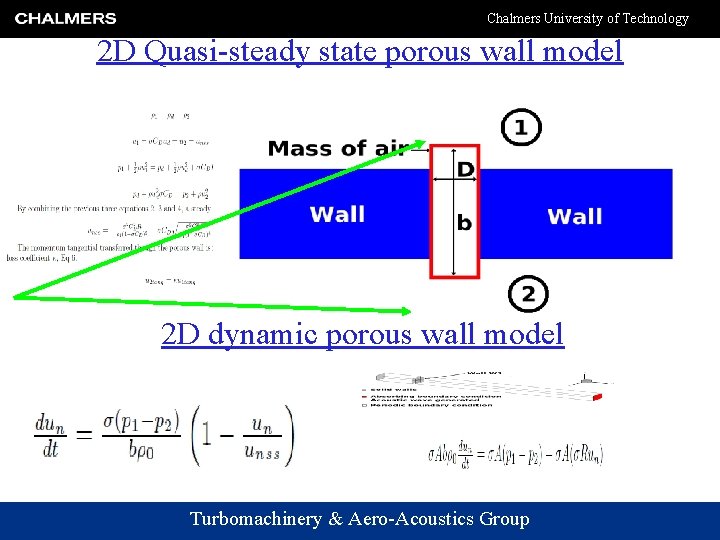
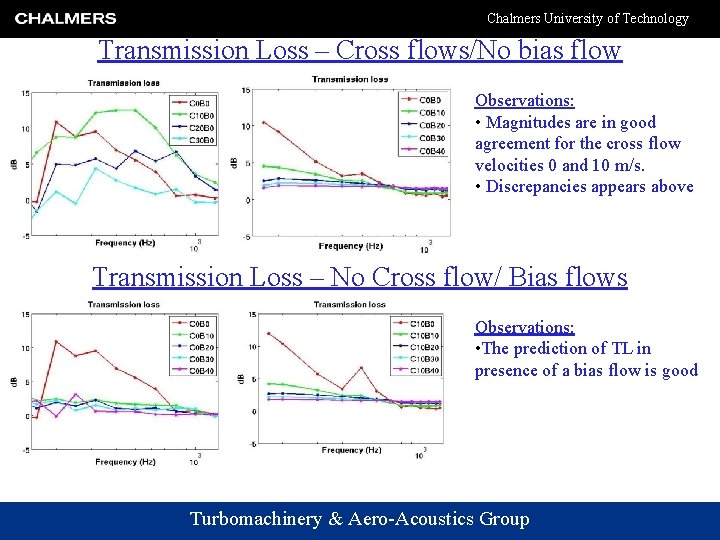
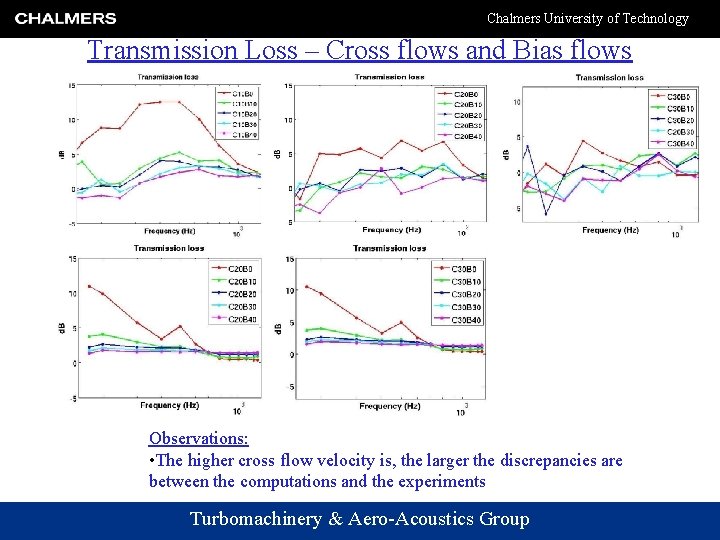
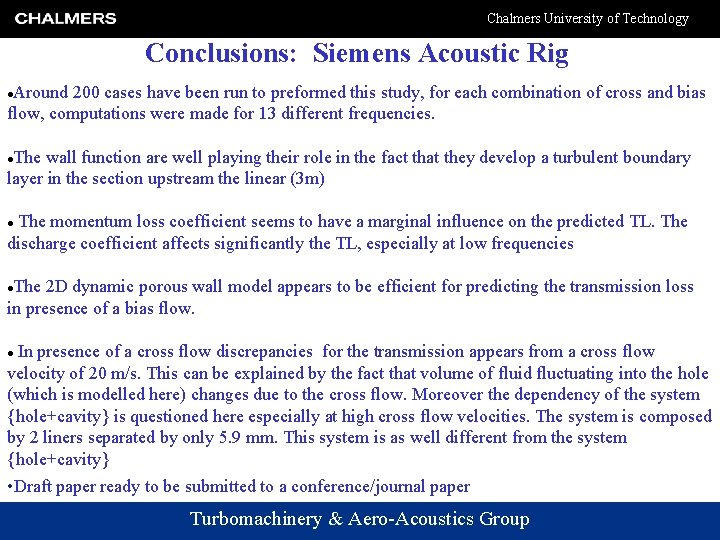
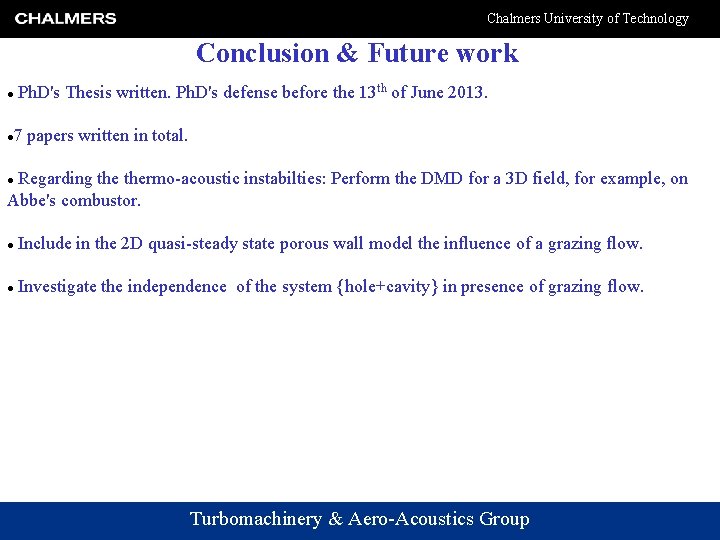
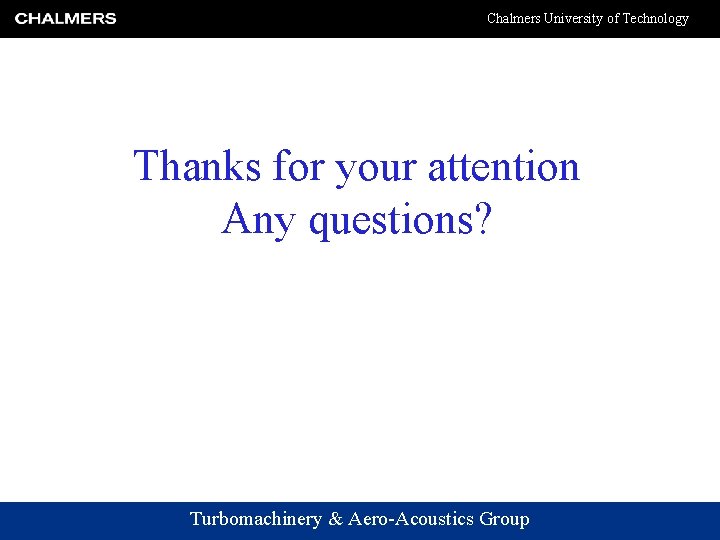
- Slides: 37
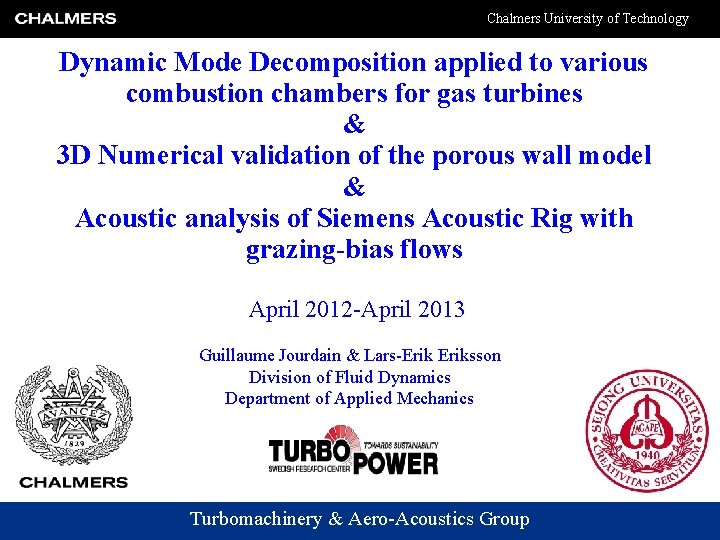
Chalmers University of Technology Dynamic Mode Decomposition applied to various combustion chambers for gas turbines & 3 D Numerical validation of the porous wall model & Acoustic analysis of Siemens Acoustic Rig with grazing-bias flows April 2012 -April 2013 Guillaume Jourdain & Lars-Eriksson Division of Fluid Dynamics Department of Applied Mechanics Turbomachinery & Aero-Acoustics Group
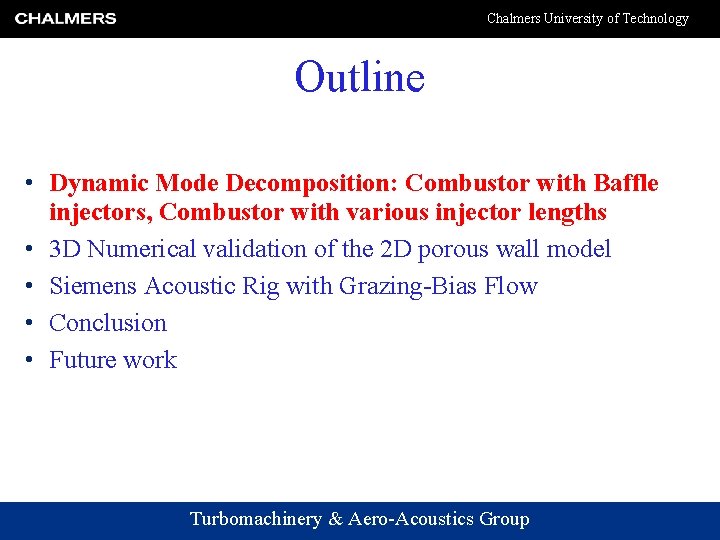
Chalmers University of Technology Outline • Dynamic Mode Decomposition: Combustor with Baffle injectors, Combustor with various injector lengths • 3 D Numerical validation of the 2 D porous wall model • Siemens Acoustic Rig with Grazing-Bias Flow • Conclusion • Future work Turbomachinery & Aero-Acoustics Group
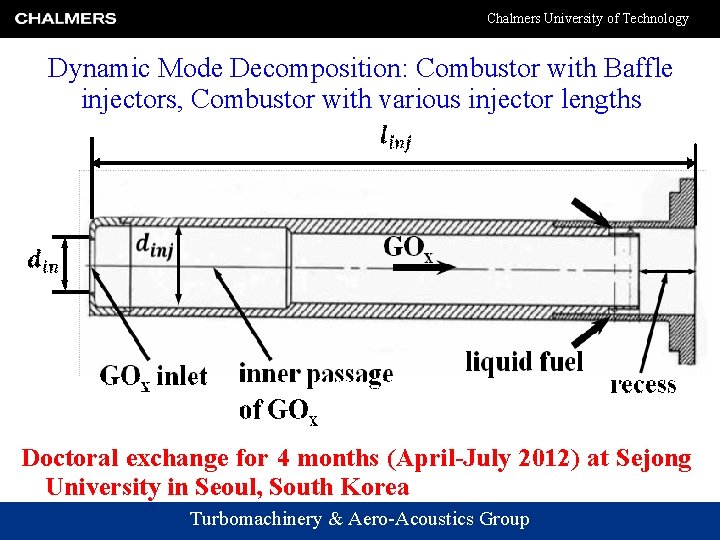
Chalmers University of Technology Dynamic Mode Decomposition: Combustor with Baffle injectors, Combustor with various injector lengths Doctoral exchange for 4 months (April-July 2012) at Sejong University in Seoul, South Korea Turbomachinery & Aero-Acoustics Group
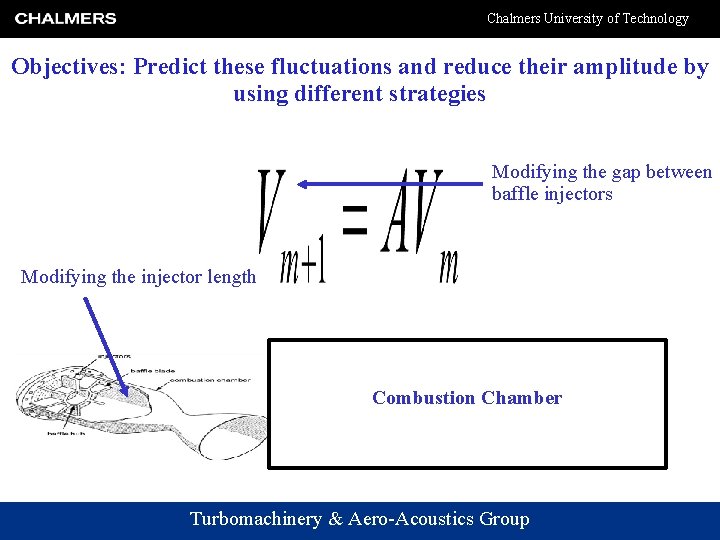
Chalmers University of Technology Objectives: Predict these fluctuations and reduce their amplitude by using different strategies Modifying the gap between baffle injectors Modifying the injector length Combustion Chamber Turbomachinery & Aero-Acoustics Group
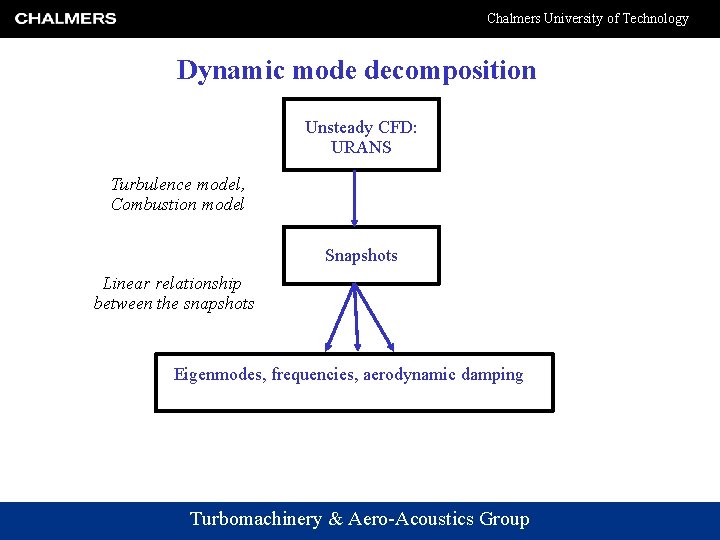
Chalmers University of Technology Dynamic mode decomposition Unsteady CFD: URANS Turbulence model, Combustion model Snapshots Linear relationship between the snapshots Eigenmodes, frequencies, aerodynamic damping Turbomachinery & Aero-Acoustics Group
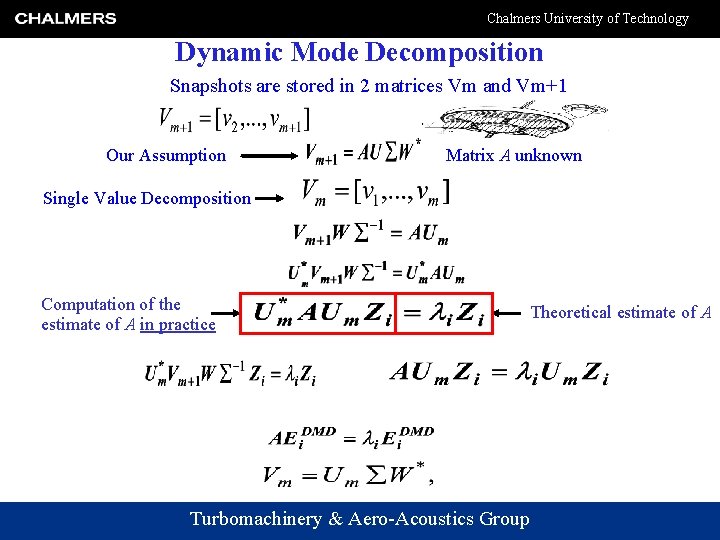
Chalmers University of Technology Dynamic Mode Decomposition Snapshots are stored in 2 matrices Vm and Vm+1 Our Assumption Matrix A unknown Single Value Decomposition Computation of the estimate of A in practice Turbomachinery & Aero-Acoustics Group Theoretical estimate of A
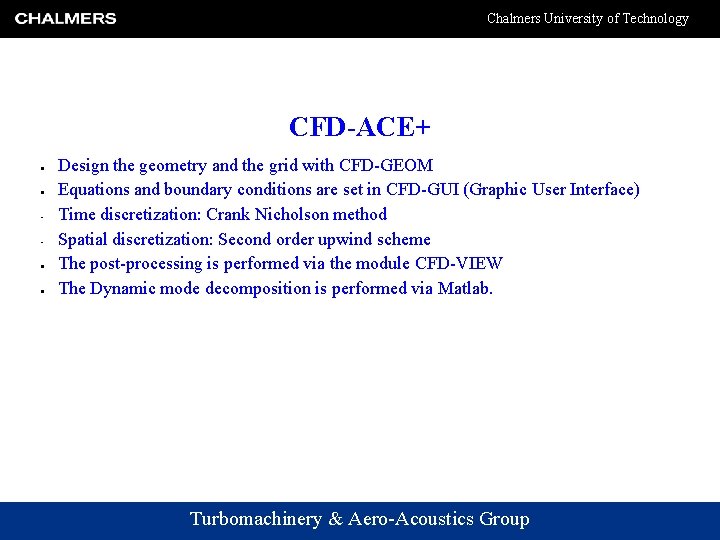
Chalmers University of Technology CFD-ACE+ Design the geometry and the grid with CFD-GEOM Equations and boundary conditions are set in CFD-GUI (Graphic User Interface) Time discretization: Crank Nicholson method Spatial discretization: Second order upwind scheme The post-processing is performed via the module CFD-VIEW The Dynamic mode decomposition is performed via Matlab. Turbomachinery & Aero-Acoustics Group
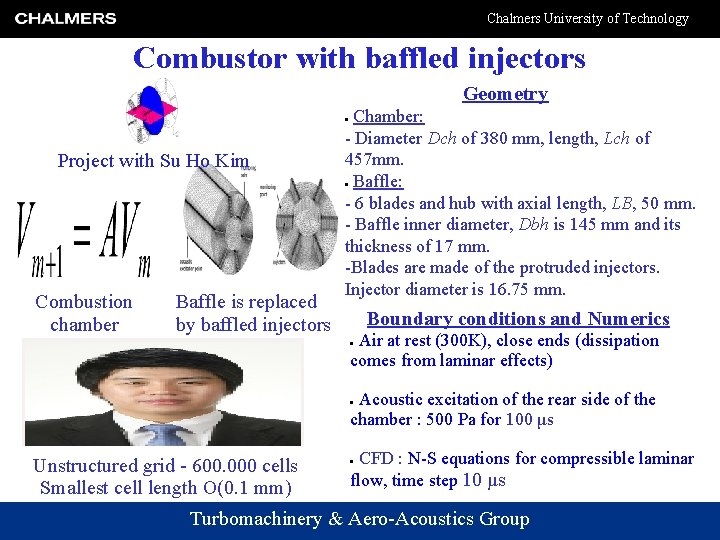
Chalmers University of Technology Combustor with baffled injectors Geometry Chamber: - Diameter Dch of 380 mm, length, Lch of 457 mm. Baffle: - 6 blades and hub with axial length, LB, 50 mm. - Baffle inner diameter, Dbh is 145 mm and its thickness of 17 mm. -Blades are made of the protruded injectors. Injector diameter is 16. 75 mm. Project with Su Ho Kim Combustion chamber Baffle is replaced by baffled injectors Boundary conditions and Numerics Air at rest (300 K), close ends (dissipation comes from laminar effects) Acoustic excitation of the rear side of the chamber : 500 Pa for 100 μs Unstructured grid - 600. 000 cells Smallest cell length O(0. 1 mm) CFD : N-S equations for compressible laminar flow, time step 10 μs Turbomachinery & Aero-Acoustics Group
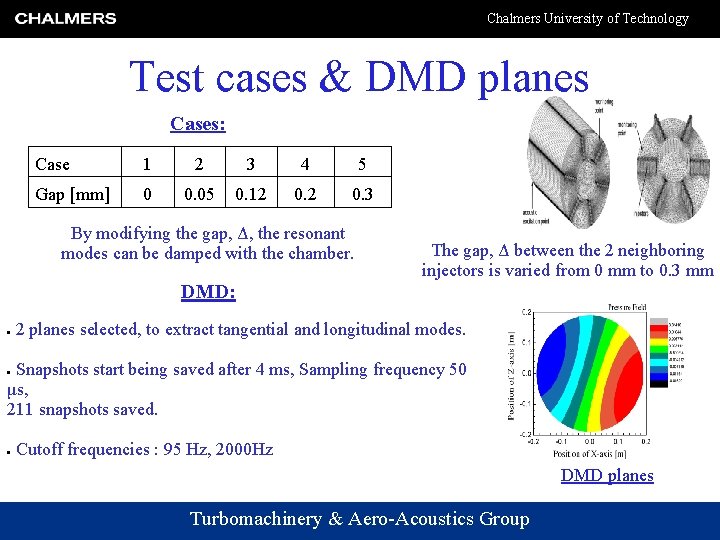
Chalmers University of Technology Test cases & DMD planes Cases: Case 1 2 3 4 5 Gap [mm] 0 0. 05 0. 12 0. 3 By modifying the gap, Δ, the resonant modes can be damped with the chamber. The gap, Δ between the 2 neighboring injectors is varied from 0 mm to 0. 3 mm DMD: 2 planes selected, to extract tangential and longitudinal modes. Snapshots start being saved after 4 ms, Sampling frequency 50 μs, 211 snapshots saved. Cutoff frequencies : 95 Hz, 2000 Hz DMD planes Turbomachinery & Aero-Acoustics Group
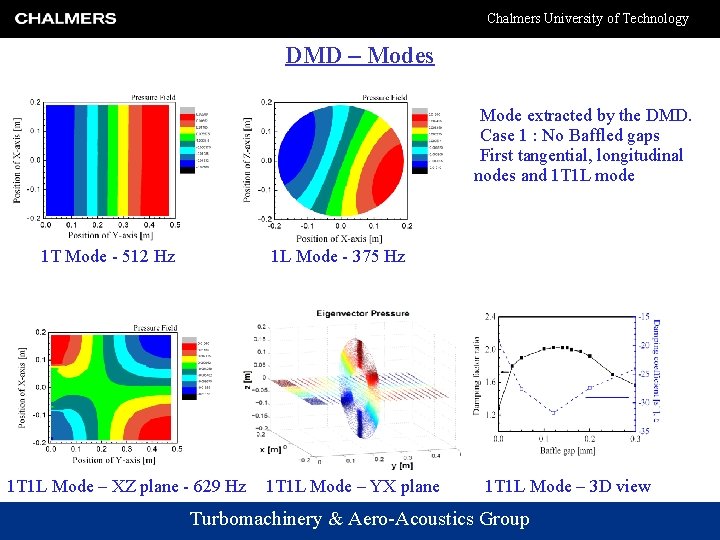
Chalmers University of Technology DMD – Modes • Mode extracted by the DMD. • Case 1 : No Baffled gaps • First tangential, longitudinal modes and 1 T 1 L mode 1 T Mode - 512 Hz 1 L Mode - 375 Hz 1 T 1 L Mode – XZ plane - 629 Hz 1 T 1 L Mode – YX plane 1 T 1 L Mode – 3 D view Turbomachinery & Aero-Acoustics Group
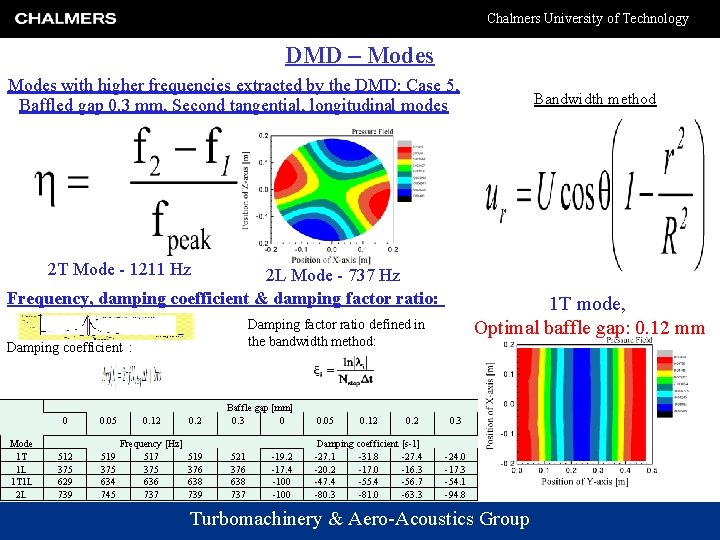
Chalmers University of Technology DMD – Modes with higher frequencies extracted by the DMD: Case 5, Baffled gap 0. 3 mm, Second tangential, longitudinal modes Bandwidth method 2 T Mode - 1211 Hz 2 L Mode - 737 Hz Frequency, damping coefficient & damping factor ratio: Damping factor ratio defined in the bandwidth method: Damping coefficient : Mode 1 T 1 L 2 L 1 T mode, Optimal baffle gap: 0. 12 mm 0 0. 05 0. 12 0. 2 512 375 629 739 519 375 634 745 Frequency [Hz] 517 375 636 737 519 376 638 739 Baffle gap [mm] 0. 3 0 521 376 638 737 -19. 2 -17. 4 -100 0. 05 0. 12 0. 2 Damping coefficient [s-1] -27. 1 -31. 8 -27. 4 -20. 2 -17. 0 -16. 3 -47. 4 -55. 4 -56. 7 -80. 3 -81. 0 -63. 3 0. 3 -24. 0 -17. 3 -54. 1 -94. 8 Turbomachinery & Aero-Acoustics Group
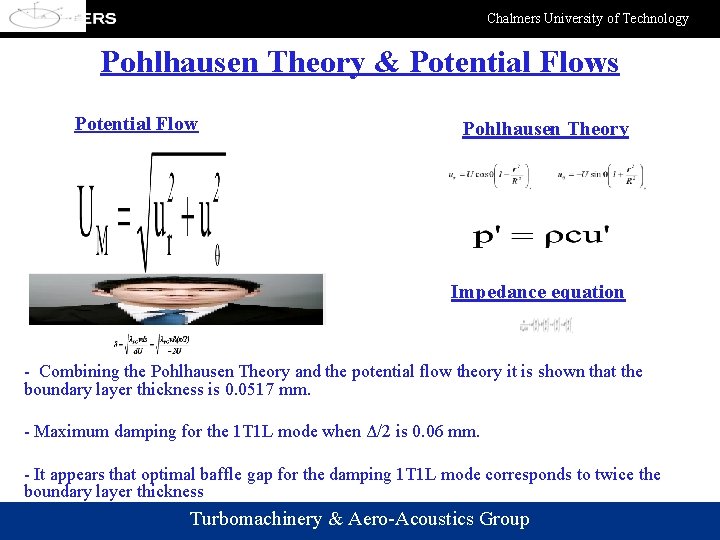
Chalmers University of Technology Pohlhausen Theory & Potential Flows Potential Flow Pohlhausen Theory Impedance equation - Combining the Pohlhausen Theory and the potential flow theory it is shown that the boundary layer thickness is 0. 0517 mm. - Maximum damping for the 1 T 1 L mode when Δ/2 is 0. 06 mm. - It appears that optimal baffle gap for the damping 1 T 1 L mode corresponds to twice the boundary layer thickness Turbomachinery & Aero-Acoustics Group
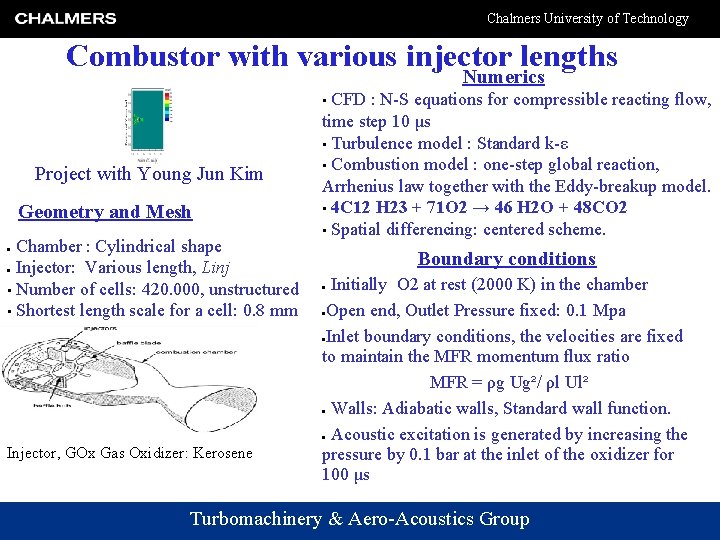
Chalmers University of Technology Combustor with various injector lengths Numerics CFD : N-S equations for compressible reacting flow, time step 10 μs • Turbulence model : Standard k-ε • Combustion model : one-step global reaction, Arrhenius law together with the Eddy-breakup model. • 4 C 12 H 23 + 71 O 2 → 46 H 2 O + 48 CO 2 • Spatial differencing: centered scheme. • Project with Young Jun Kim Geometry and Mesh Chamber : Cylindrical shape Injector: Various length, Linj • Number of cells: 420. 000, unstructured • Shortest length scale for a cell: 0. 8 mm Injector, GOx Gas Oxidizer: Kerosene Boundary conditions Initially O 2 at rest (2000 K) in the chamber Open end, Outlet Pressure fixed: 0. 1 Mpa Inlet boundary conditions, the velocities are fixed to maintain the MFR momentum flux ratio MFR = ρg Ug²/ ρl Ul² Walls: Adiabatic walls, Standard wall function. Acoustic excitation is generated by increasing the pressure by 0. 1 bar at the inlet of the oxidizer for 100 μs Turbomachinery & Aero-Acoustics Group
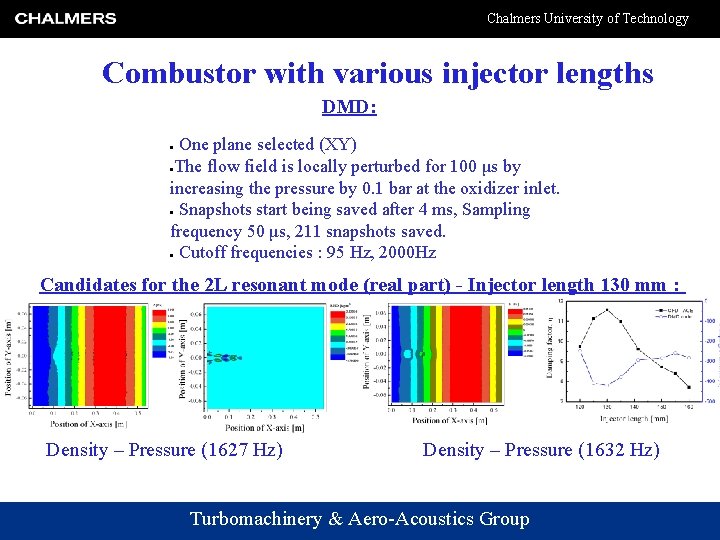
Chalmers University of Technology Combustor with various injector lengths DMD: One plane selected (XY) The flow field is locally perturbed for 100 μs by increasing the pressure by 0. 1 bar at the oxidizer inlet. Snapshots start being saved after 4 ms, Sampling frequency 50 μs, 211 snapshots saved. Cutoff frequencies : 95 Hz, 2000 Hz Candidates for the 2 L resonant mode (real part) - Injector length 130 mm : Density – Pressure (1627 Hz) Density – Pressure (1632 Hz) Turbomachinery & Aero-Acoustics Group
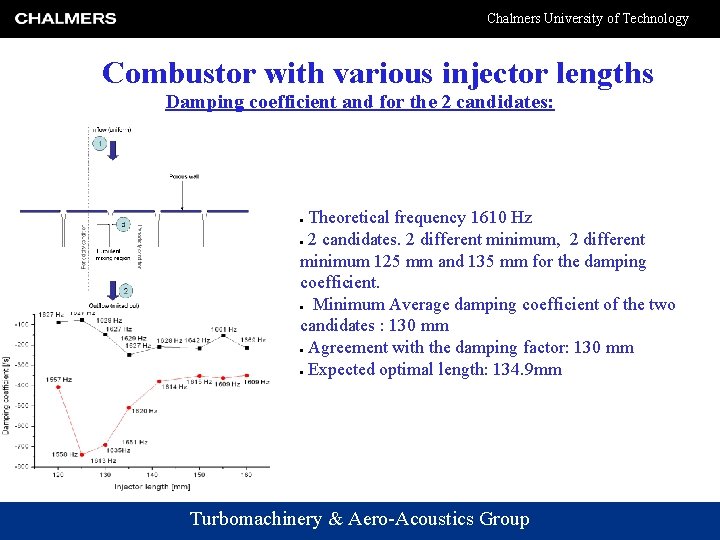
Chalmers University of Technology Combustor with various injector lengths Damping coefficient and for the 2 candidates: Theoretical frequency 1610 Hz 2 candidates. 2 different minimum, 2 different minimum 125 mm and 135 mm for the damping coefficient. Minimum Average damping coefficient of the two candidates : 130 mm Agreement with the damping factor: 130 mm Expected optimal length: 134. 9 mm Turbomachinery & Aero-Acoustics Group
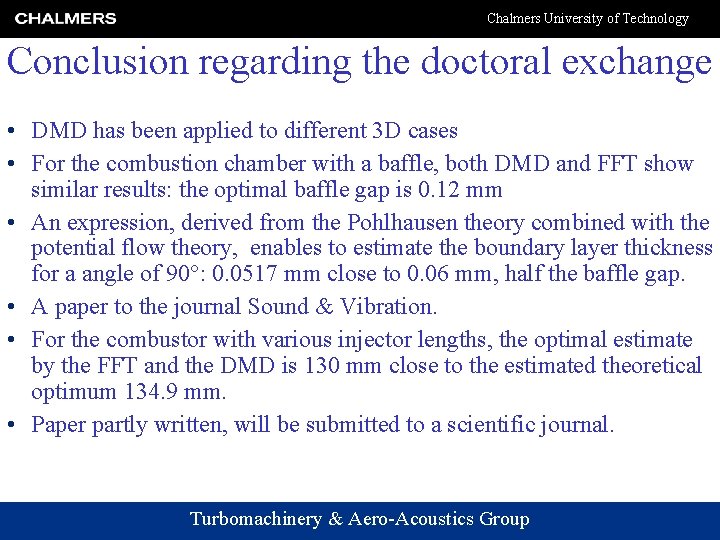
Chalmers University of Technology Conclusion regarding the doctoral exchange • DMD has been applied to different 3 D cases • For the combustion chamber with a baffle, both DMD and FFT show similar results: the optimal baffle gap is 0. 12 mm • An expression, derived from the Pohlhausen theory combined with the potential flow theory, enables to estimate the boundary layer thickness for a angle of 90°: 0. 0517 mm close to 0. 06 mm, half the baffle gap. • A paper to the journal Sound & Vibration. • For the combustor with various injector lengths, the optimal estimate by the FFT and the DMD is 130 mm close to the estimated theoretical optimum 134. 9 mm. • Paper partly written, will be submitted to a scientific journal. Turbomachinery & Aero-Acoustics Group

Chalmers University of Technology Outline • Dynamic Mode Decomposition: Combustor with Baffle injectors, Combustor with various injector length • 3 D Numerical validation of the 2 D porous wall model • Siemens Acoustic Rig with Grazing-Bias Flow • Conclusion • Future work Turbomachinery & Aero-Acoustics Group
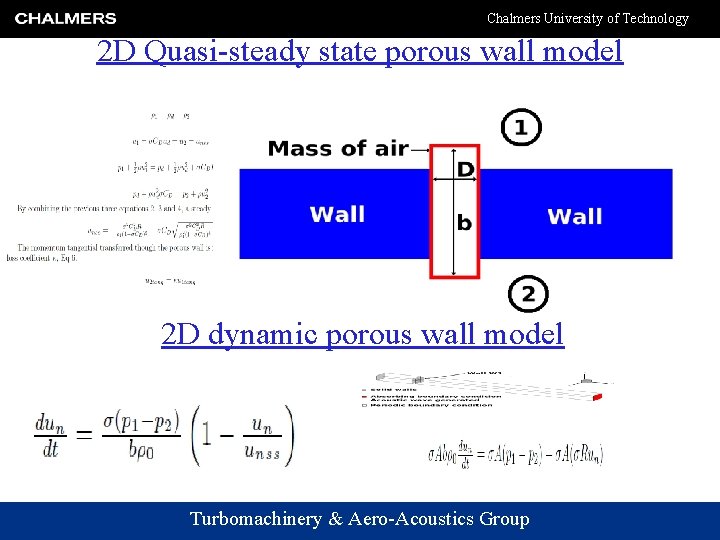
Chalmers University of Technology 2 D Quasi-steady state porous wall model 2 D dynamic porous wall model Turbomachinery & Aero-Acoustics Group
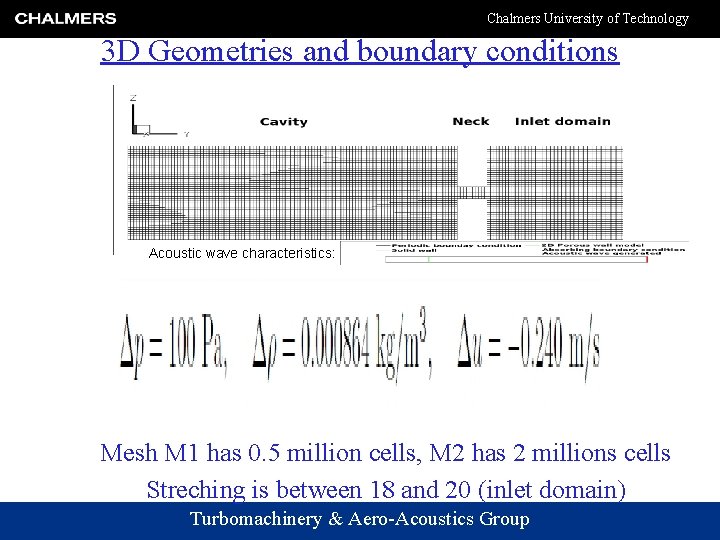
Chalmers University of Technology 3 D Geometries and boundary conditions Acoustic wave characteristics: Mesh M 1 has 0. 5 million cells, M 2 has 2 millions cells Streching is between 18 and 20 (inlet domain) Turbomachinery & Aero-Acoustics Group
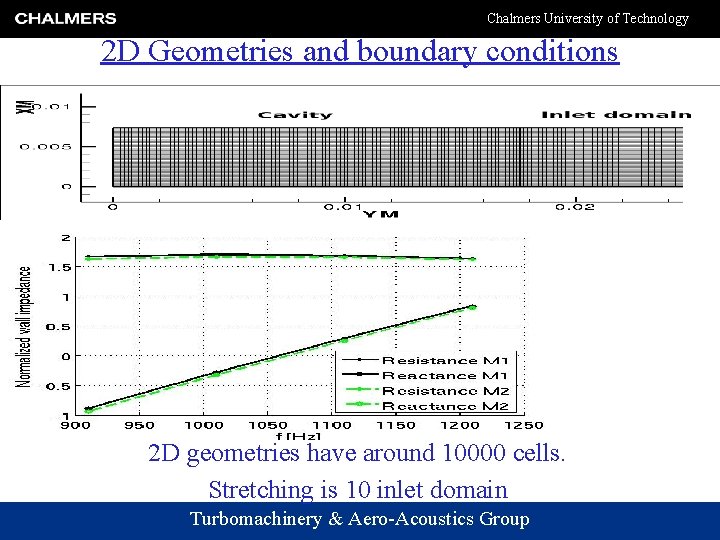
Chalmers University of Technology 2 D Geometries and boundary conditions 2 D geometries have around 10000 cells. Stretching is 10 inlet domain Turbomachinery & Aero-Acoustics Group
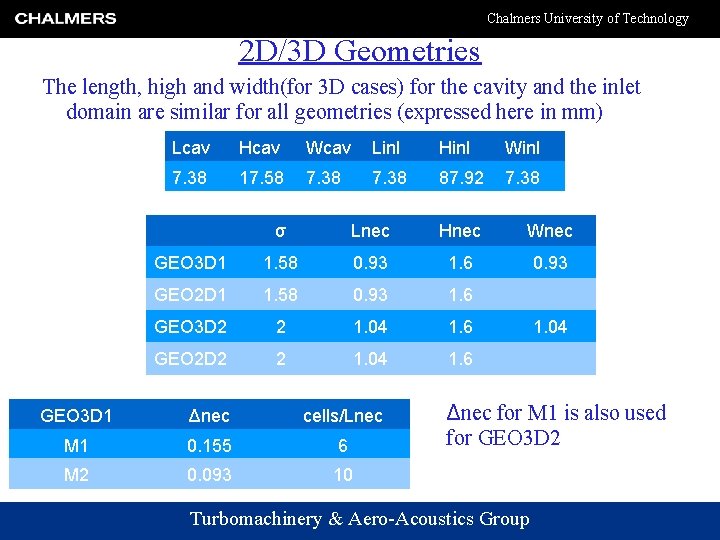
Chalmers University of Technology 2 D/3 D Geometries The length, high and width(for 3 D cases) for the cavity and the inlet domain are similar for all geometries (expressed here in mm) Lcav Hcav Wcav Linl Hinl Winl 7. 38 17. 58 7. 38 87. 92 7. 38 σ Lnec Hnec Wnec GEO 3 D 1 1. 58 0. 93 1. 6 0. 93 GEO 2 D 1 1. 58 0. 93 1. 6 GEO 3 D 2 2 1. 04 1. 6 GEO 2 D 2 2 1. 04 1. 6 GEO 3 D 1 Δnec cells/Lnec M 1 0. 155 6 M 2 0. 093 10 1. 04 Δnec for M 1 is also used for GEO 3 D 2 Turbomachinery & Aero-Acoustics Group
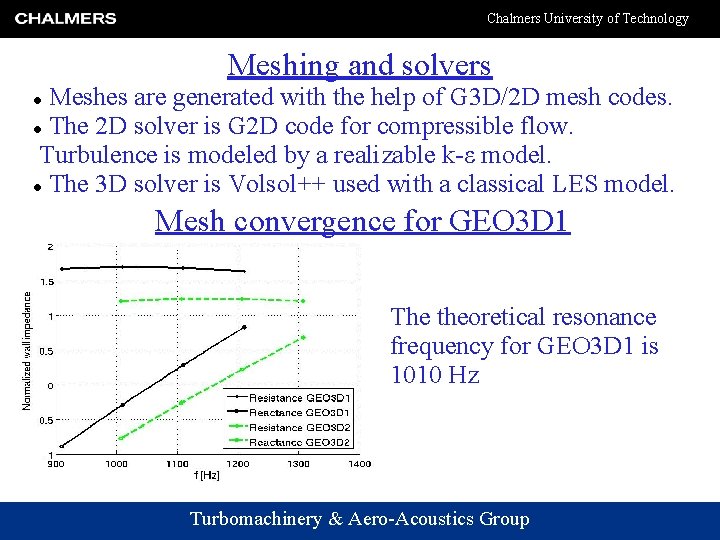
Chalmers University of Technology Meshing and solvers Meshes are generated with the help of G 3 D/2 D mesh codes. The 2 D solver is G 2 D code for compressible flow. Turbulence is modeled by a realizable k-ε model. The 3 D solver is Volsol++ used with a classical LES model. Mesh convergence for GEO 3 D 1 The theoretical resonance frequency for GEO 3 D 1 is 1010 Hz Turbomachinery & Aero-Acoustics Group
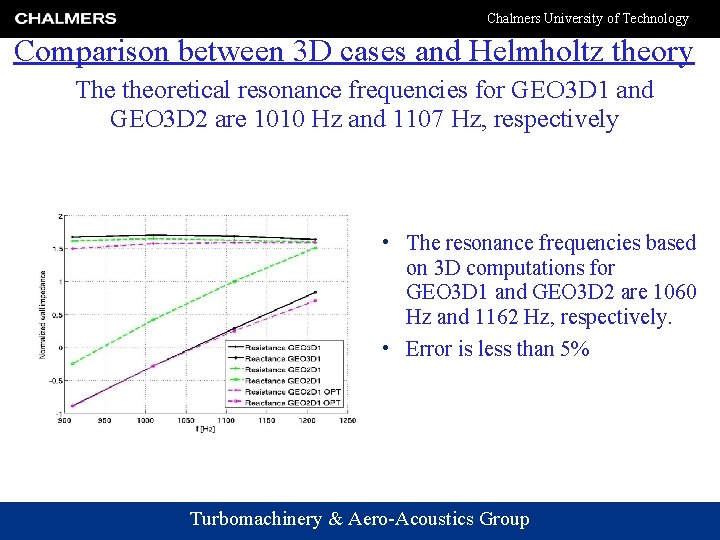
Chalmers University of Technology Comparison between 3 D cases and Helmholtz theory The theoretical resonance frequencies for GEO 3 D 1 and GEO 3 D 2 are 1010 Hz and 1107 Hz, respectively • The resonance frequencies based on 3 D computations for GEO 3 D 1 and GEO 3 D 2 are 1060 Hz and 1162 Hz, respectively. • Error is less than 5% Turbomachinery & Aero-Acoustics Group
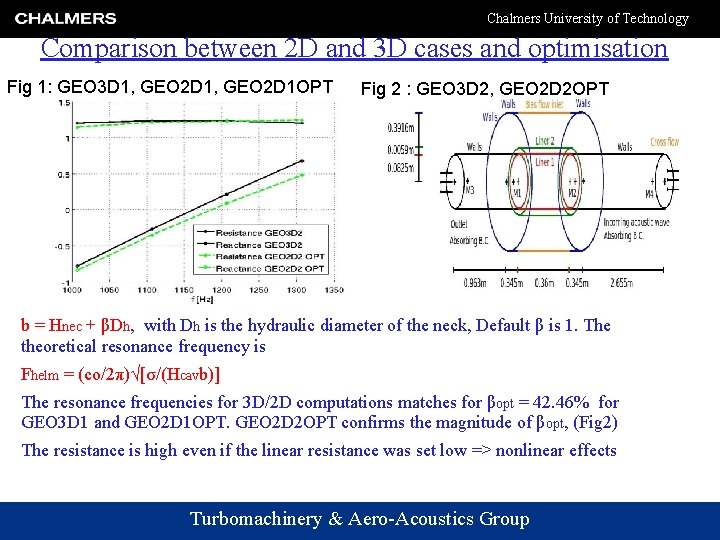
Chalmers University of Technology Comparison between 2 D and 3 D cases and optimisation Fig 1: GEO 3 D 1, GEO 2 D 1 OPT Fig 2 : GEO 3 D 2, GEO 2 D 2 OPT b = Hnec + βDh, with Dh is the hydraulic diameter of the neck, Default β is 1. The theoretical resonance frequency is Fhelm = (co/2π)√[σ/(Hcavb)] The resonance frequencies for 3 D/2 D computations matches for βopt = 42. 46% for GEO 3 D 1 and GEO 2 D 1 OPT. GEO 2 D 2 OPT confirms the magnitude of βopt, (Fig 2) The resistance is high even if the linear resistance was set low => nonlinear effects Turbomachinery & Aero-Acoustics Group
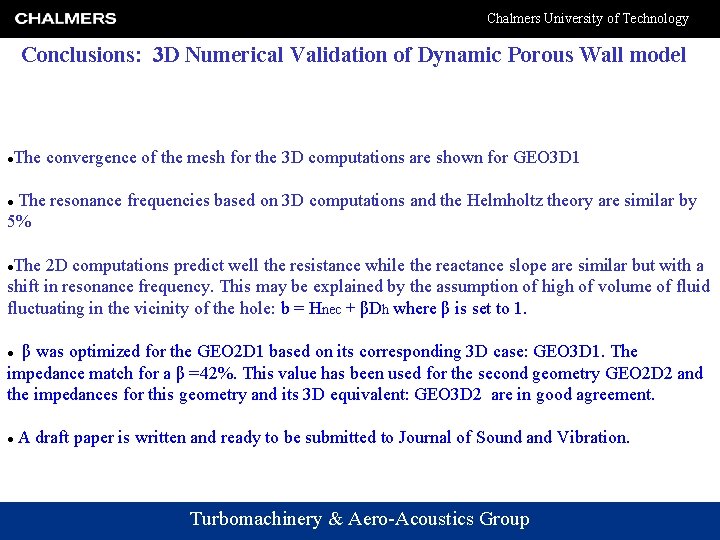
Chalmers University of Technology Conclusions: 3 D Numerical Validation of Dynamic Porous Wall model The convergence of the mesh for the 3 D computations are shown for GEO 3 D 1 The resonance frequencies based on 3 D computations and the Helmholtz theory are similar by 5% The 2 D computations predict well the resistance while the reactance slope are similar but with a shift in resonance frequency. This may be explained by the assumption of high of volume of fluid fluctuating in the vicinity of the hole: b = Hnec + βDh where β is set to 1. β was optimized for the GEO 2 D 1 based on its corresponding 3 D case: GEO 3 D 1. The impedance match for a β =42%. This value has been used for the second geometry GEO 2 D 2 and the impedances for this geometry and its 3 D equivalent: GEO 3 D 2 are in good agreement. A draft paper is written and ready to be submitted to Journal of Sound and Vibration. Turbomachinery & Aero-Acoustics Group
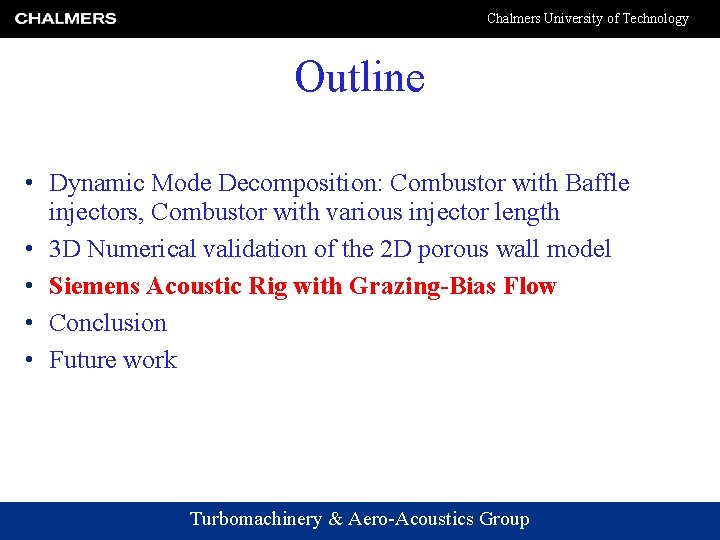
Chalmers University of Technology Outline • Dynamic Mode Decomposition: Combustor with Baffle injectors, Combustor with various injector length • 3 D Numerical validation of the 2 D porous wall model • Siemens Acoustic Rig with Grazing-Bias Flow • Conclusion • Future work Turbomachinery & Aero-Acoustics Group
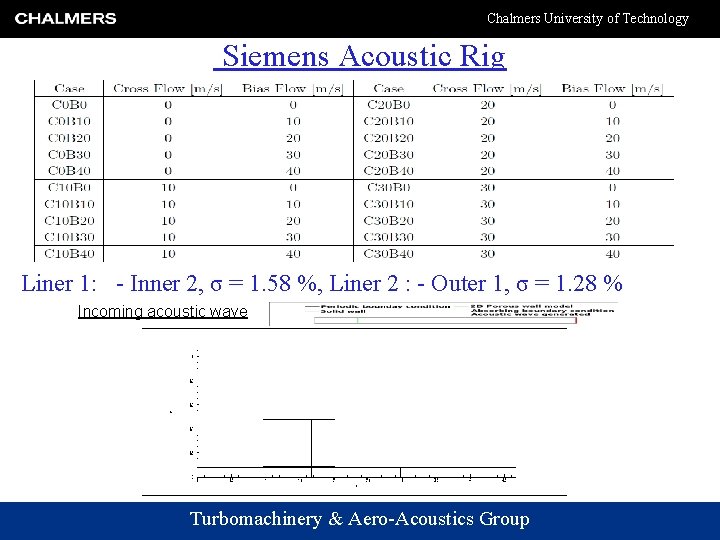
Chalmers University of Technology Siemens Acoustic Rig Liner 1: - Inner 2, σ = 1. 58 %, Liner 2 : - Outer 1, σ = 1. 28 % Incoming acoustic wave Turbomachinery & Aero-Acoustics Group
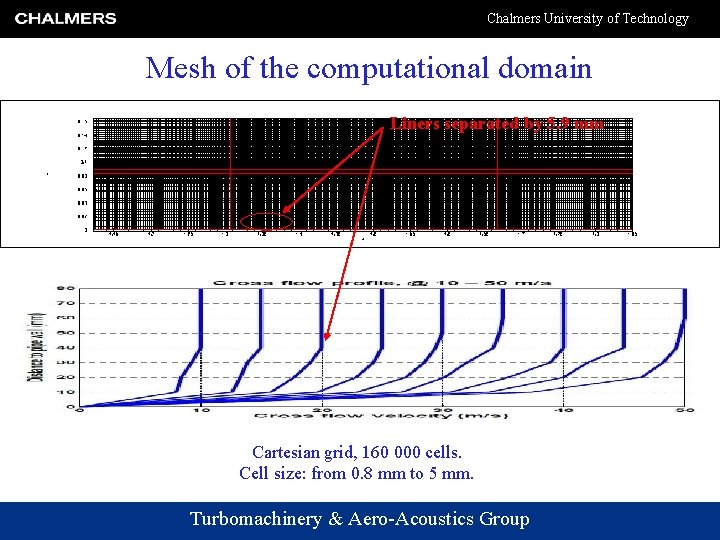
Chalmers University of Technology Mesh of the computational domain Liners separated by 5. 9 mm Cartesian grid, 160 000 cells. Cell size: from 0. 8 mm to 5 mm. Turbomachinery & Aero-Acoustics Group
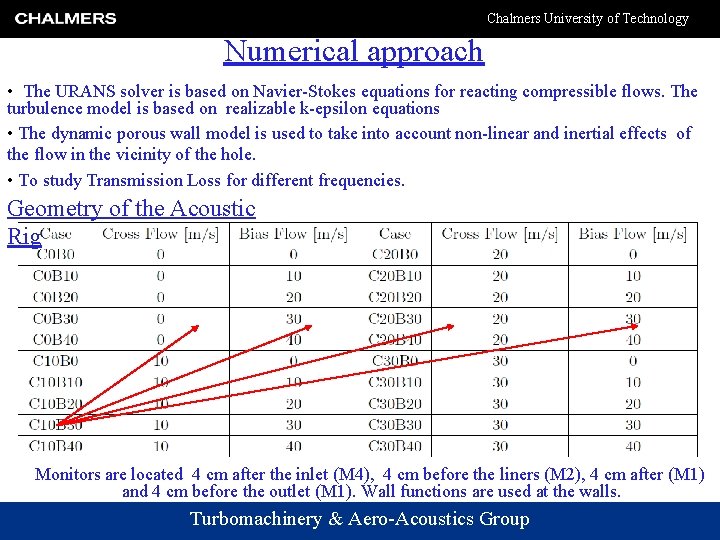
Chalmers University of Technology Numerical approach • The URANS solver is based on Navier-Stokes equations for reacting compressible flows. The turbulence model is based on realizable k-epsilon equations • The dynamic porous wall model is used to take into account non-linear and inertial effects of the flow in the vicinity of the hole. • To study Transmission Loss for different frequencies. Geometry of the Acoustic Rig Monitors are located 4 cm after the inlet (M 4), 4 cm before the liners (M 2), 4 cm after (M 1) and 4 cm before the outlet (M 1). Wall functions are used at the walls. Turbomachinery & Aero-Acoustics Group
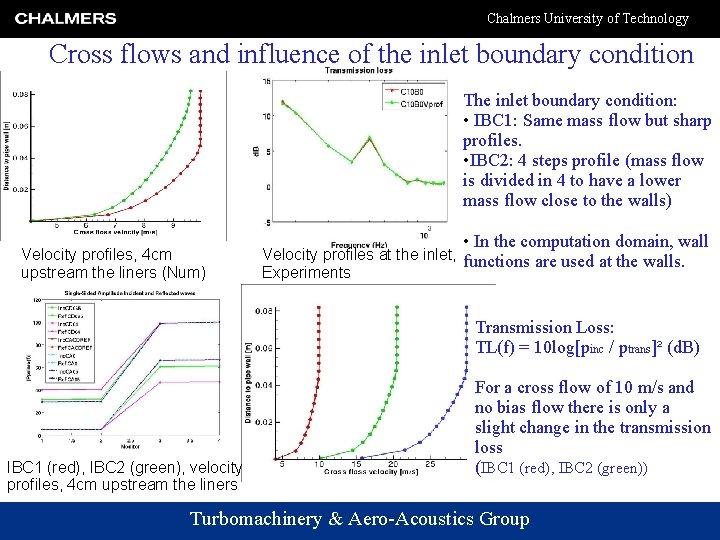
Chalmers University of Technology Cross flows and influence of the inlet boundary condition The inlet boundary condition: • IBC 1: Same mass flow but sharp profiles. • IBC 2: 4 steps profile (mass flow is divided in 4 to have a lower mass flow close to the walls) Velocity profiles, 4 cm upstream the liners (Num) • In the computation domain, wall Velocity profiles at the inlet, functions are used at the walls. Experiments Transmission Loss: TL(f) = 10 log[pinc / ptrans]² (d. B) IBC 1 (red), IBC 2 (green), velocity profiles, 4 cm upstream the liners For a cross flow of 10 m/s and no bias flow there is only a slight change in the transmission loss (IBC 1 (red), IBC 2 (green)) Turbomachinery & Aero-Acoustics Group
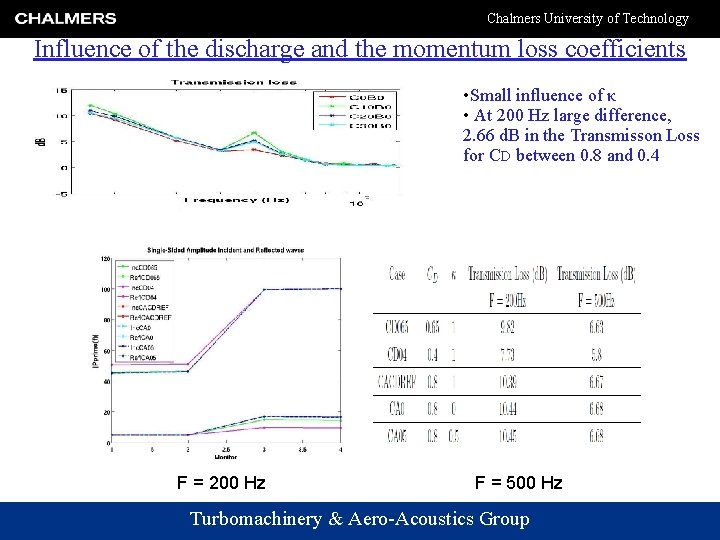
Chalmers University of Technology Influence of the discharge and the momentum loss coefficients • Small influence of κ • At 200 Hz large difference, 2. 66 d. B in the Transmisson Loss for CD between 0. 8 and 0. 4 F = 200 Hz F = 500 Hz Turbomachinery & Aero-Acoustics Group
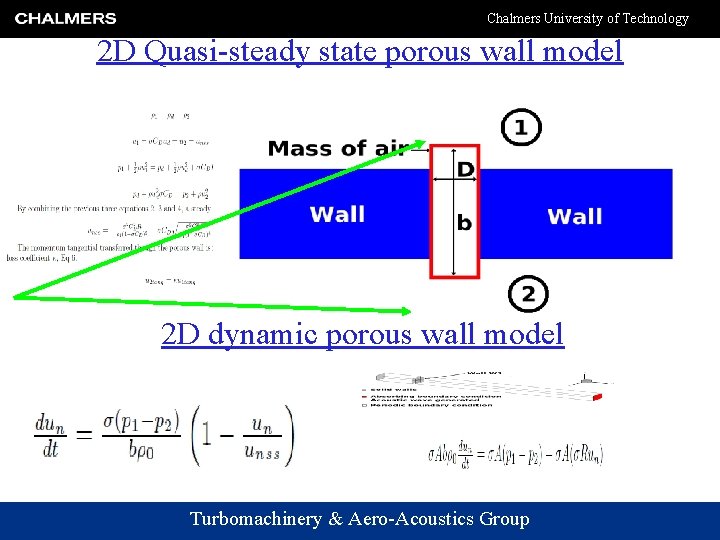
Chalmers University of Technology 2 D Quasi-steady state porous wall model 2 D dynamic porous wall model Turbomachinery & Aero-Acoustics Group
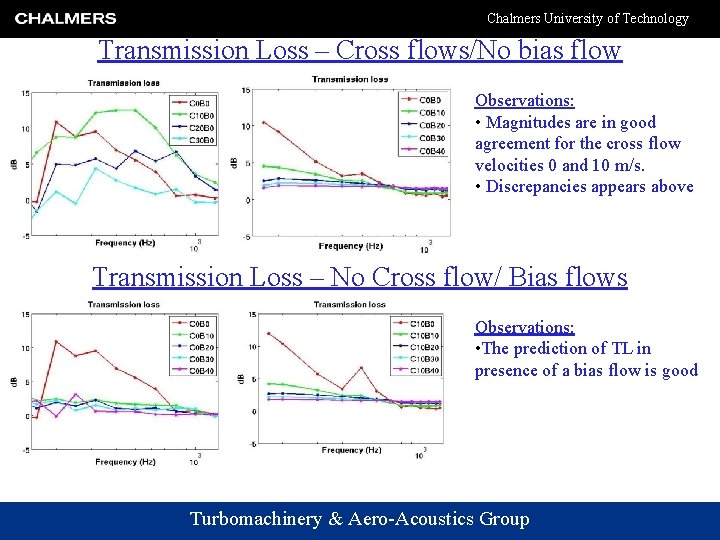
Chalmers University of Technology Transmission Loss – Cross flows/No bias flow Observations: • Magnitudes are in good agreement for the cross flow velocities 0 and 10 m/s. • Discrepancies appears above Transmission Loss – No Cross flow/ Bias flows Observations: • The prediction of TL in presence of a bias flow is good Turbomachinery & Aero-Acoustics Group
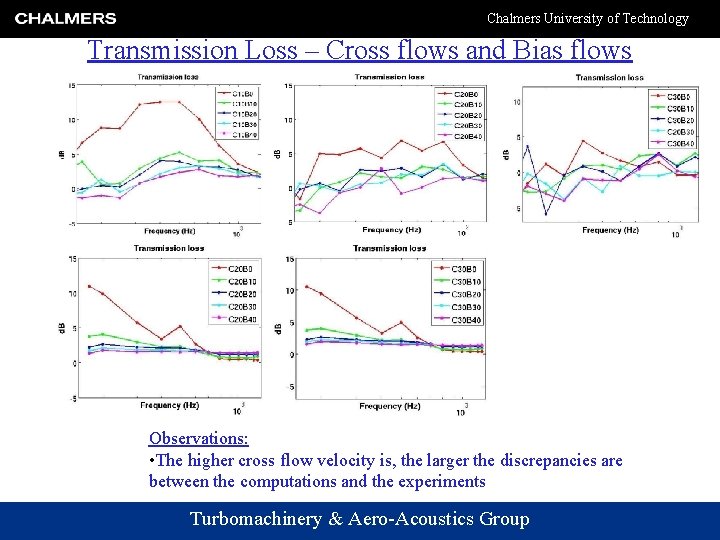
Chalmers University of Technology Transmission Loss – Cross flows and Bias flows Observations: • The higher cross flow velocity is, the larger the discrepancies are between the computations and the experiments Turbomachinery & Aero-Acoustics Group
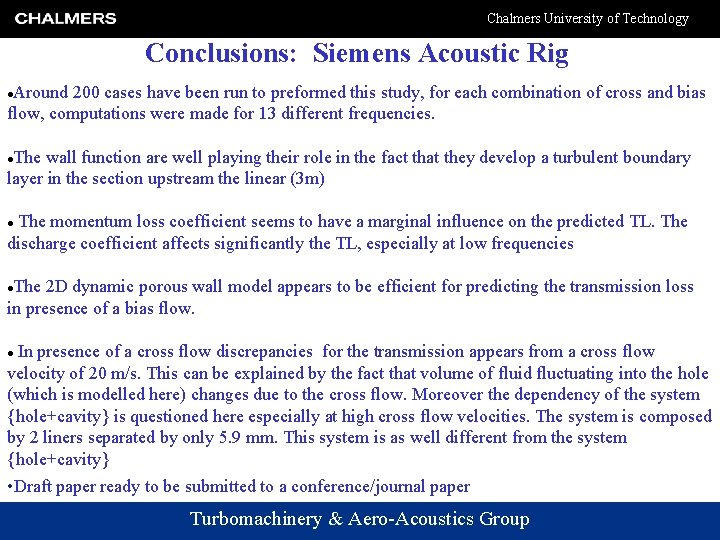
Chalmers University of Technology Conclusions: Siemens Acoustic Rig Around 200 cases have been run to preformed this study, for each combination of cross and bias flow, computations were made for 13 different frequencies. The wall function are well playing their role in the fact that they develop a turbulent boundary layer in the section upstream the linear (3 m) The momentum loss coefficient seems to have a marginal influence on the predicted TL. The discharge coefficient affects significantly the TL, especially at low frequencies The 2 D dynamic porous wall model appears to be efficient for predicting the transmission loss in presence of a bias flow. In presence of a cross flow discrepancies for the transmission appears from a cross flow velocity of 20 m/s. This can be explained by the fact that volume of fluid fluctuating into the hole (which is modelled here) changes due to the cross flow. Moreover the dependency of the system {hole+cavity} is questioned here especially at high cross flow velocities. The system is composed by 2 liners separated by only 5. 9 mm. This system is as well different from the system {hole+cavity} • Draft paper ready to be submitted to a conference/journal paper Turbomachinery & Aero-Acoustics Group
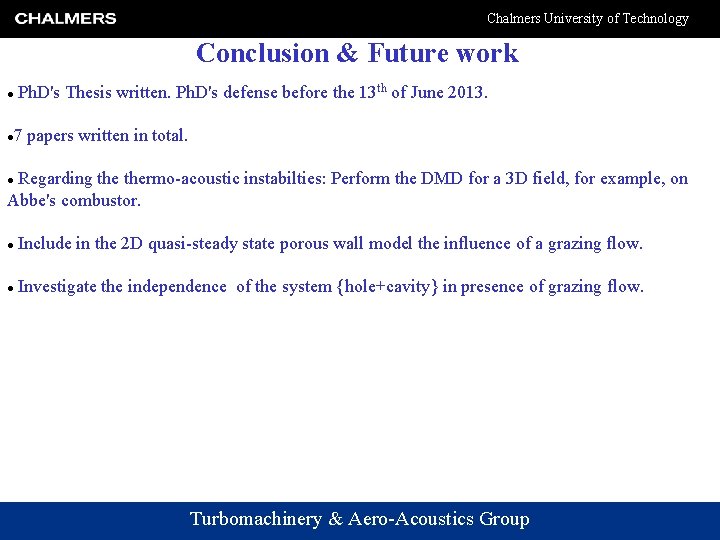
Chalmers University of Technology Conclusion & Future work Ph. D's Thesis written. Ph. D's defense before the 13 th of June 2013. 7 papers written in total. Regarding thermo-acoustic instabilties: Perform the DMD for a 3 D field, for example, on Abbe's combustor. Include in the 2 D quasi-steady state porous wall model the influence of a grazing flow. Investigate the independence of the system {hole+cavity} in presence of grazing flow. Turbomachinery & Aero-Acoustics Group
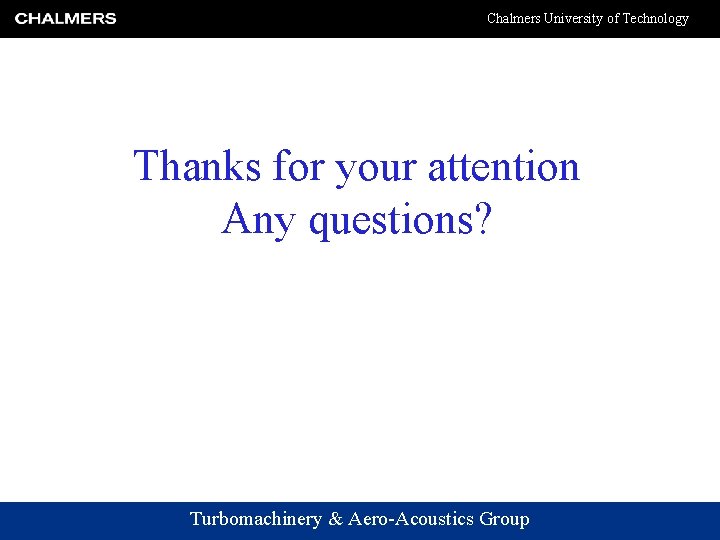
Chalmers University of Technology Thanks for your attention Any questions? Turbomachinery & Aero-Acoustics Group
Chalmers university of technology
Chalmers university of technology
Chalmers university of technology
Amplitude mode
Mode of motions in size separation methods
Focus mode and diffuse mode
Mode địa chỉ tức thì là mode
Difference between real mode and virtual mode of 80386
8051 timer interrupt
Gartner mode 1 mode 2
Perbedaan (planning mode) dan (evolutionary mode)
Reset pin in 8086
Al reef institute of logistics and applied technology
Is bilkent university good
Applied technology building ball state
Van hall larenstein, university of applied sciences
Vaasa university of applied sciences
Oulu university of applied sciences
Weihenstephan-triesdorf university of applied sciences
Kodolányi jános university of applied sciences
Western norway university of applied sciences
Esslingen university of applied science
Piraeus university of applied sciences
Jade university of applied sciences
Isparta university of applied sciences
Eberswalde university of applied sciences
Business management courses winnipeg
Mischhybrid
International university of applied sciences bad honnef
Brock university applied linguistics
Mkm subu
Pirzmak
Transferered
Chalmers singularity
Ivica crnkovic chalmers
Thomas chalmers y el trabajo social
Staffan björk chalmers
Pingpong chalmers