CENTRAL PLANT OPTIMIZATION 1 Johnson Controls Inc Central
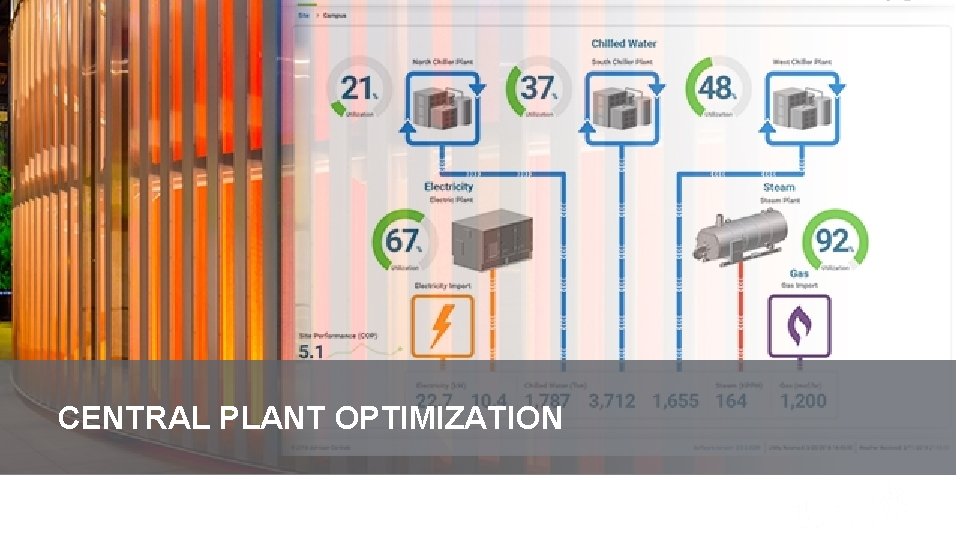
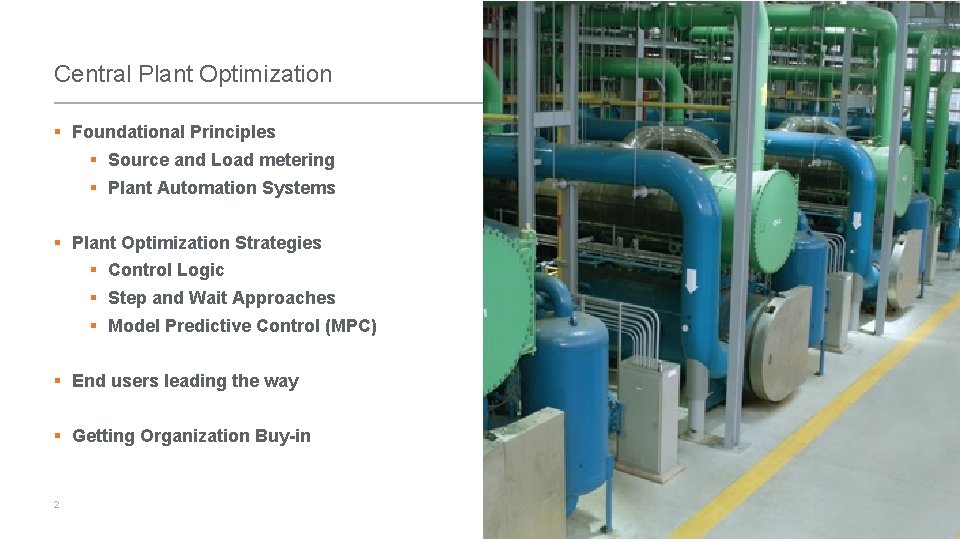
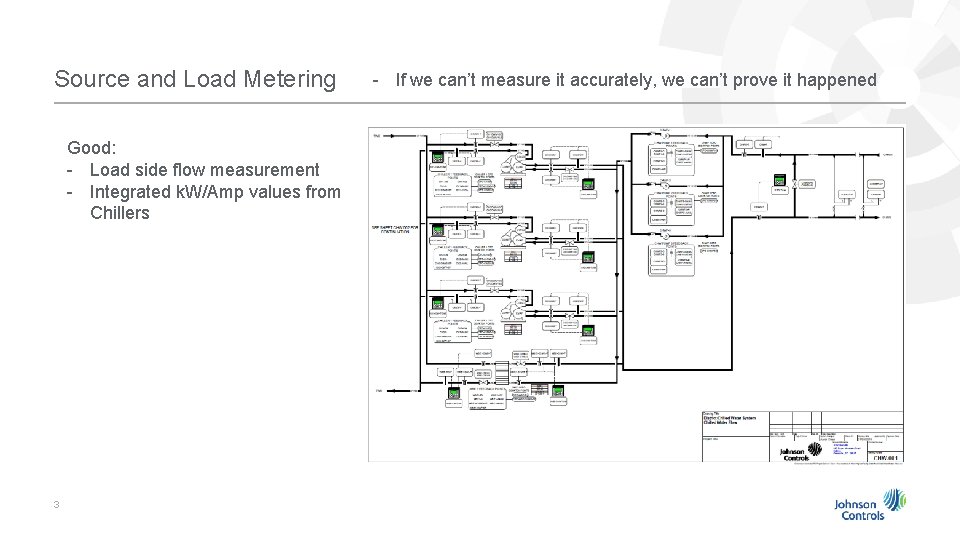
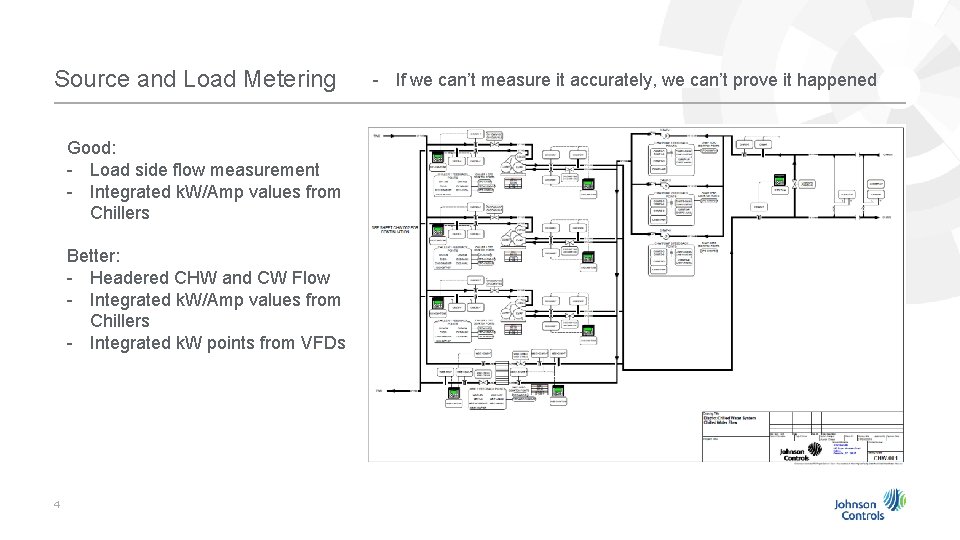
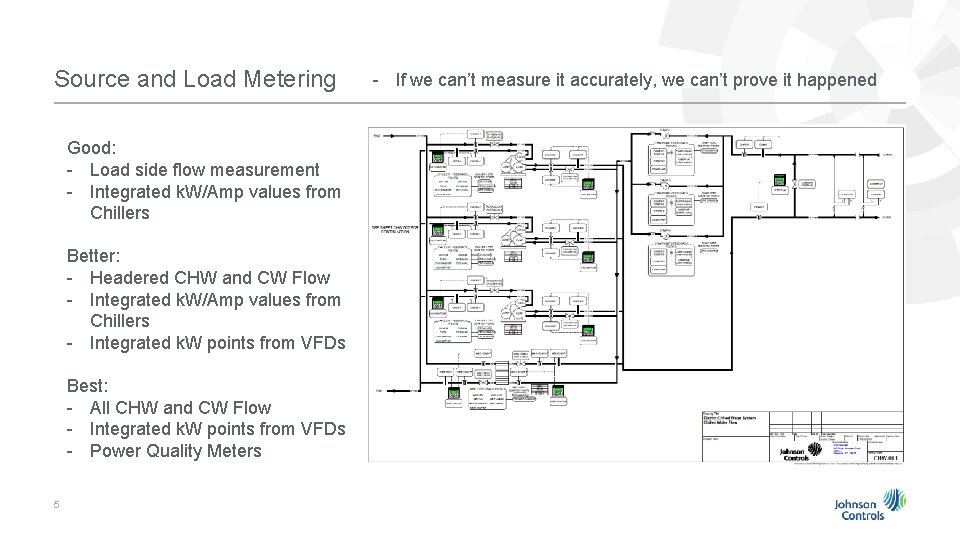
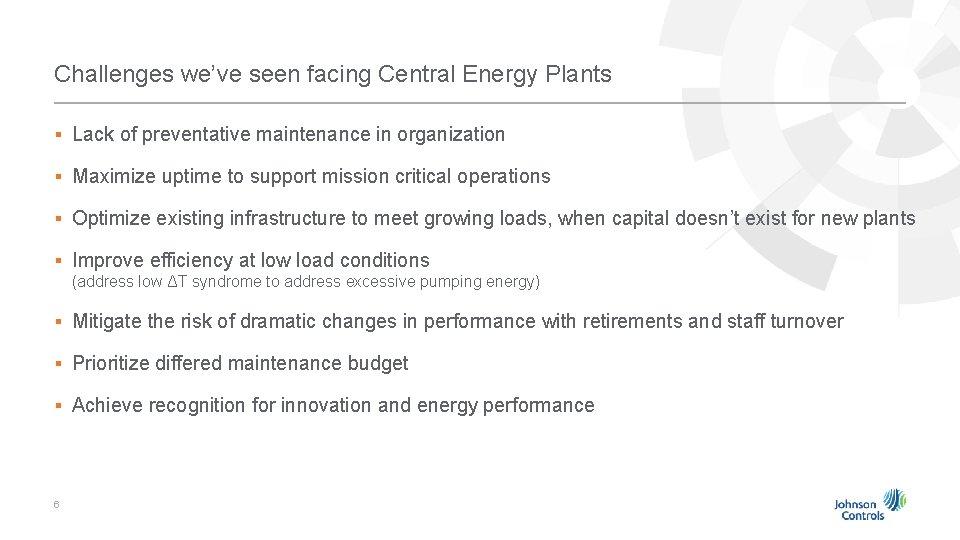
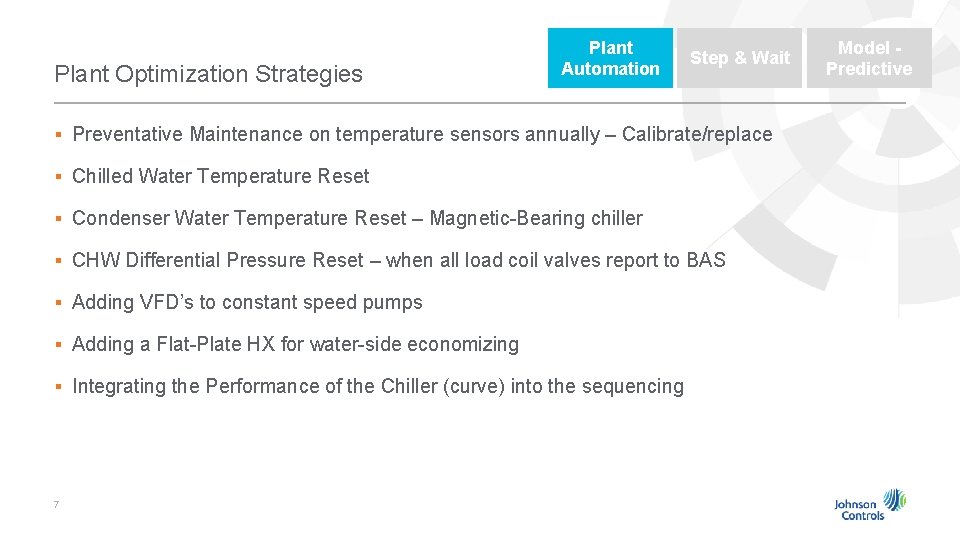
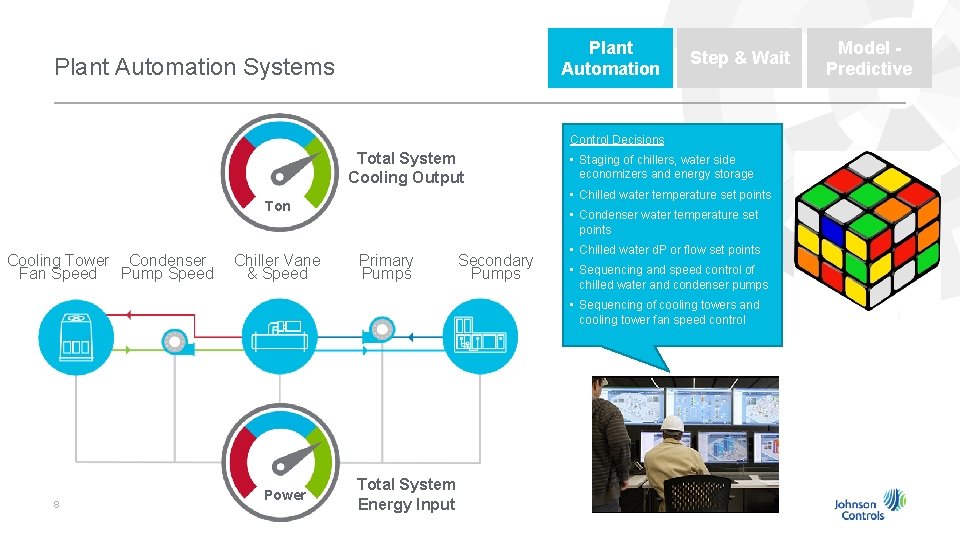
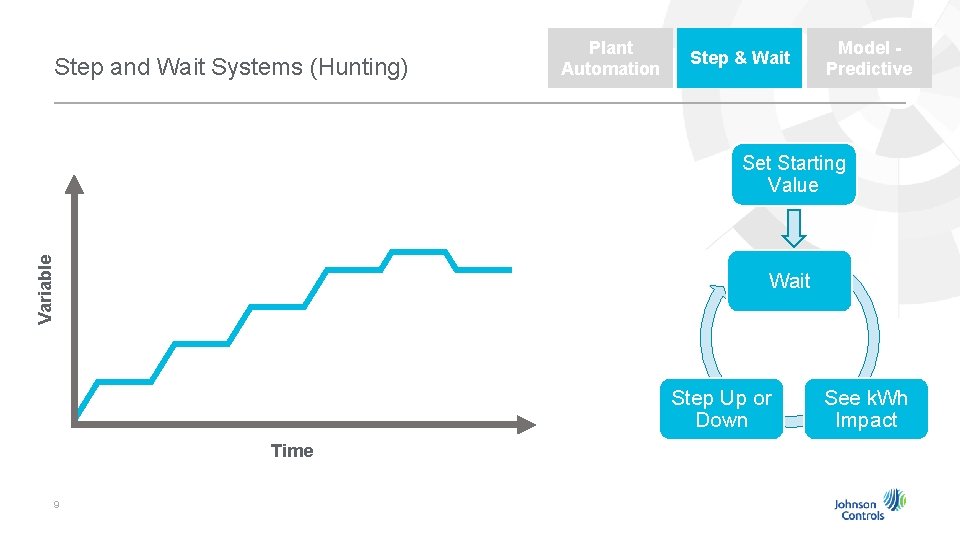
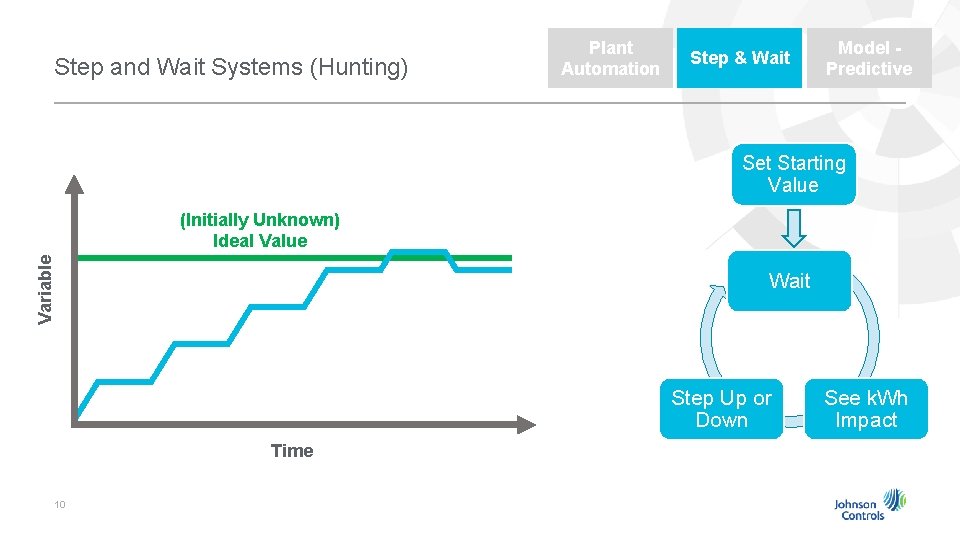
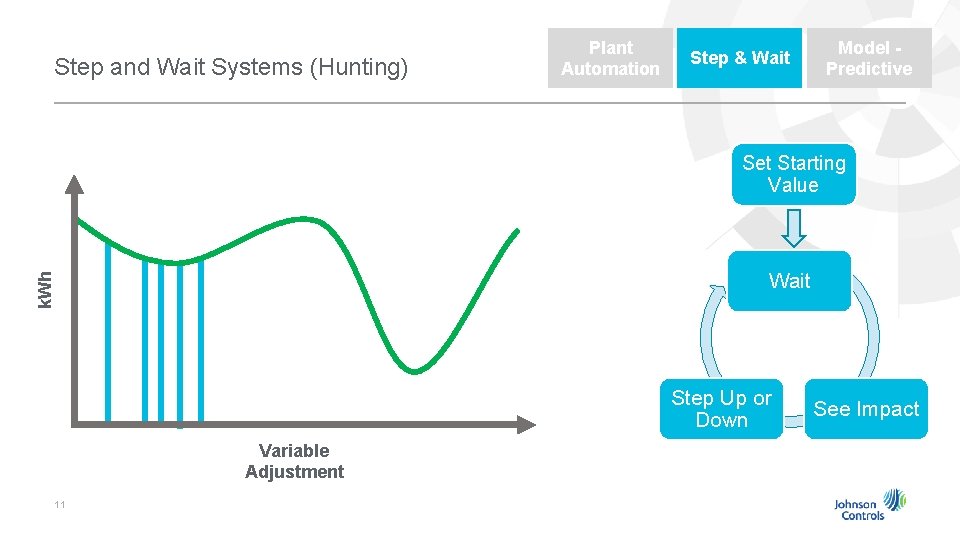
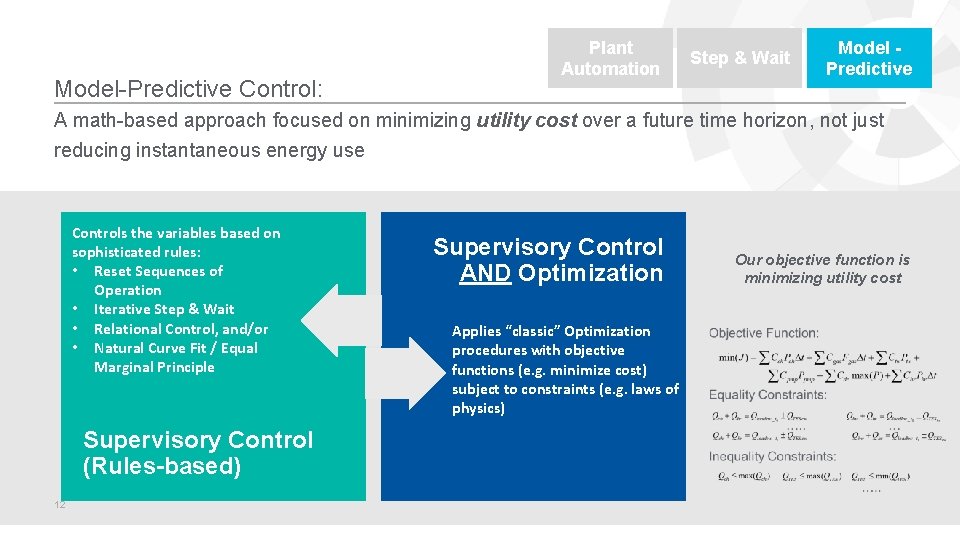
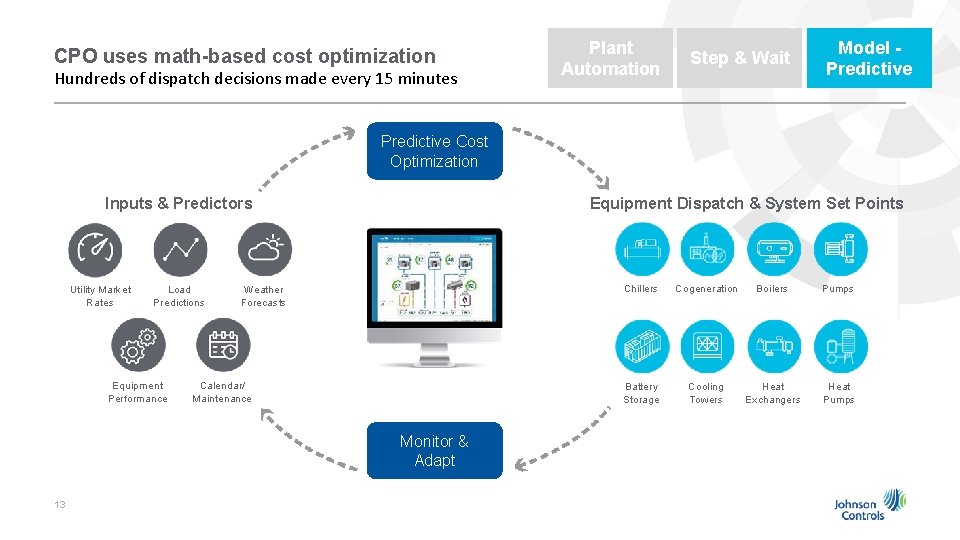
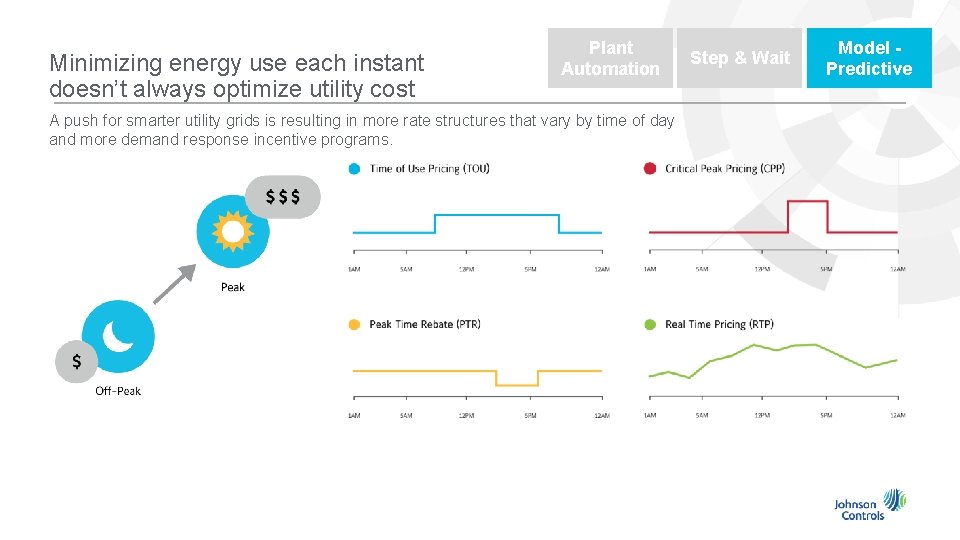
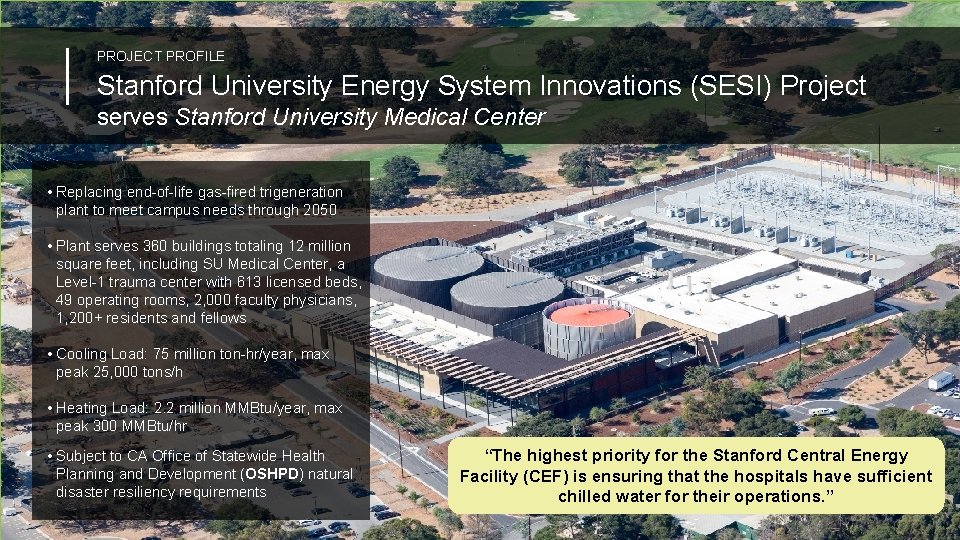
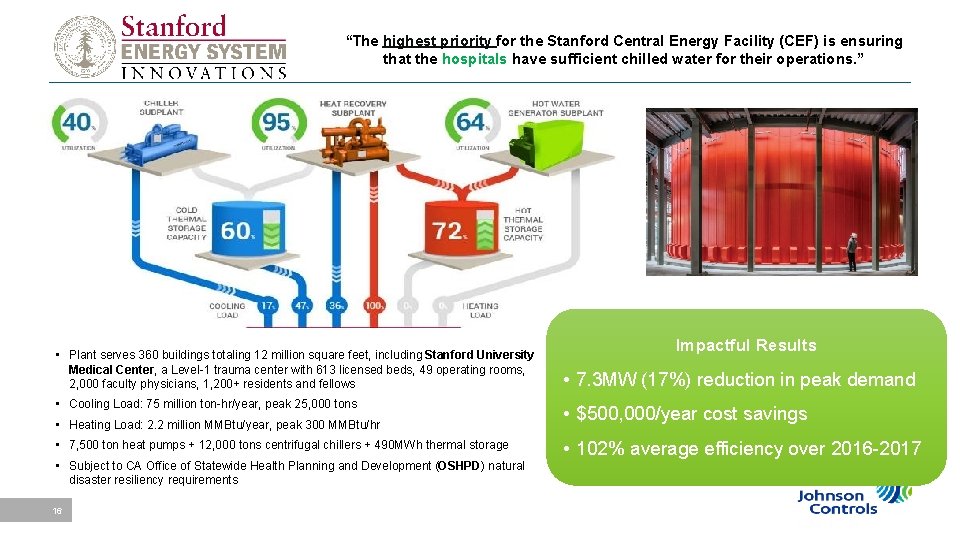
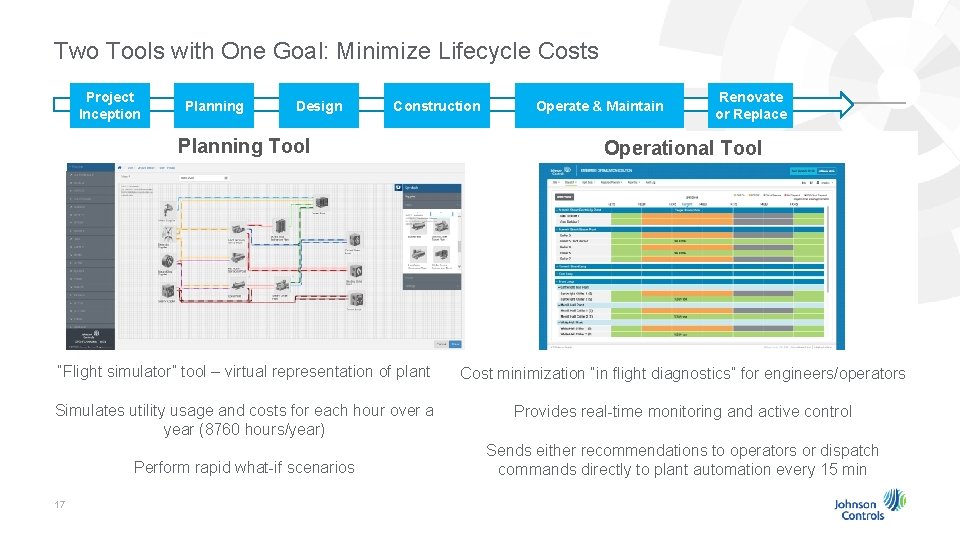
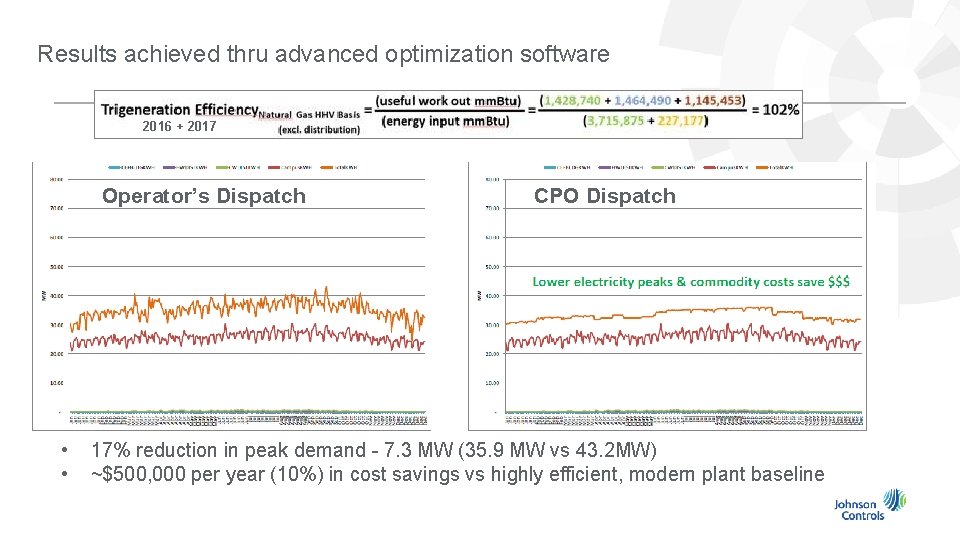
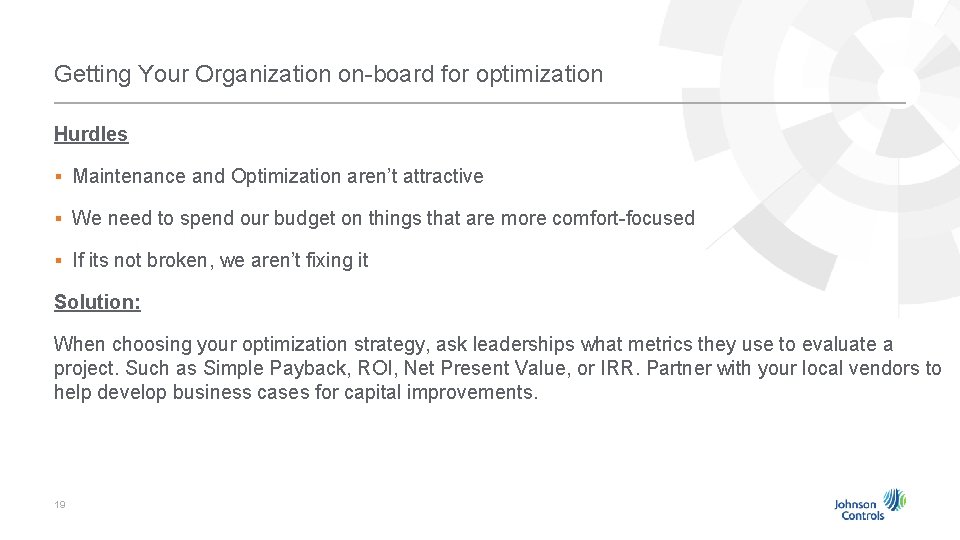
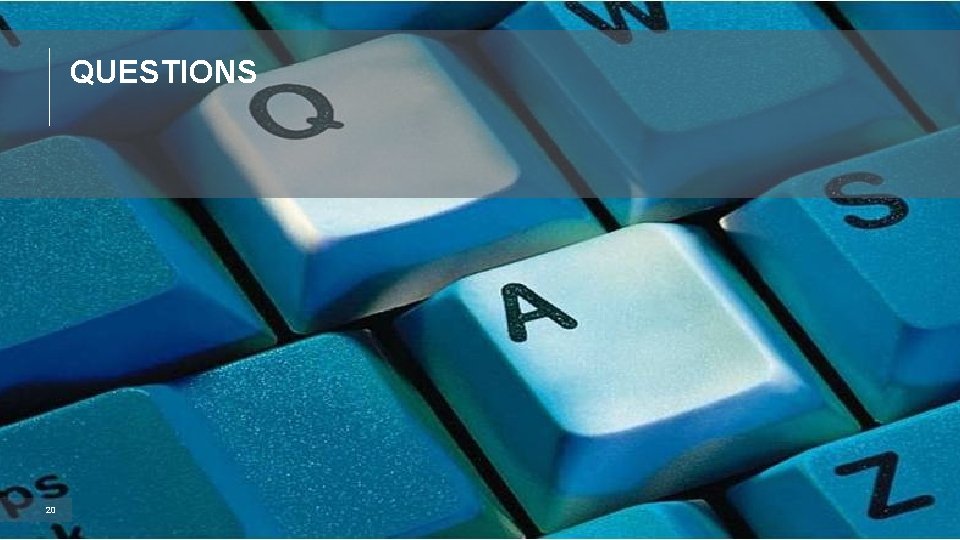
- Slides: 20
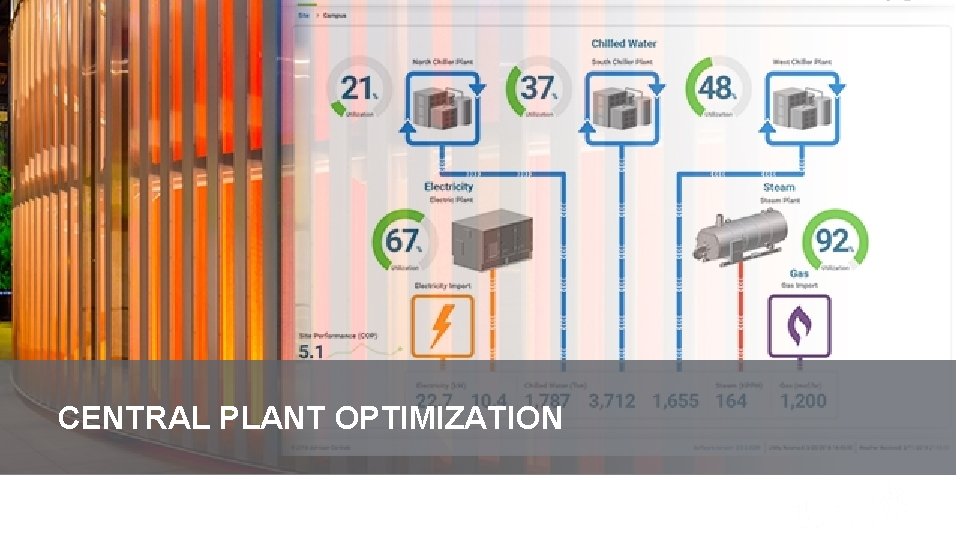
CENTRAL PLANT OPTIMIZATION 1 Johnson Controls, Inc.
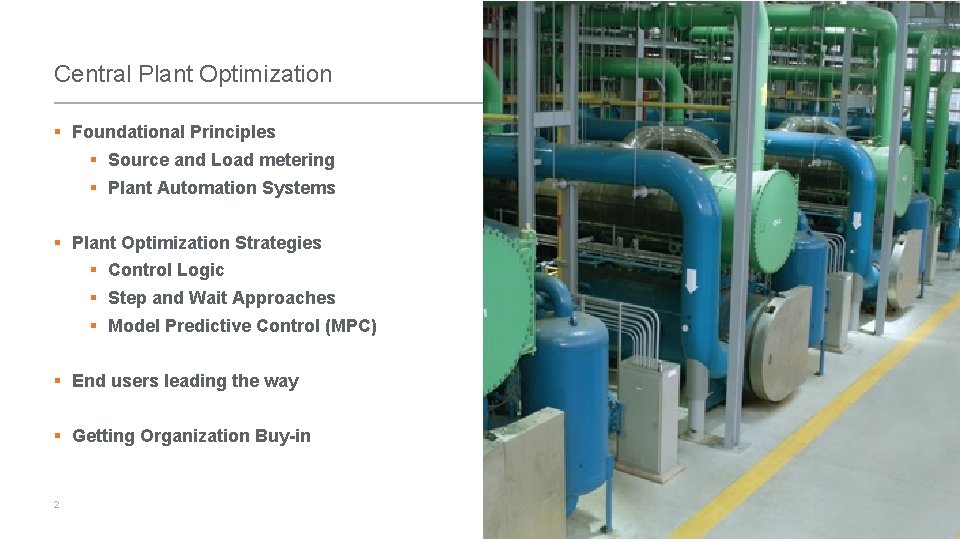
Central Plant Optimization § Foundational Principles § Source and Load metering § Plant Automation Systems § Plant Optimization Strategies § Control Logic § Step and Wait Approaches § Model Predictive Control (MPC) § End users leading the way § Getting Organization Buy-in 2
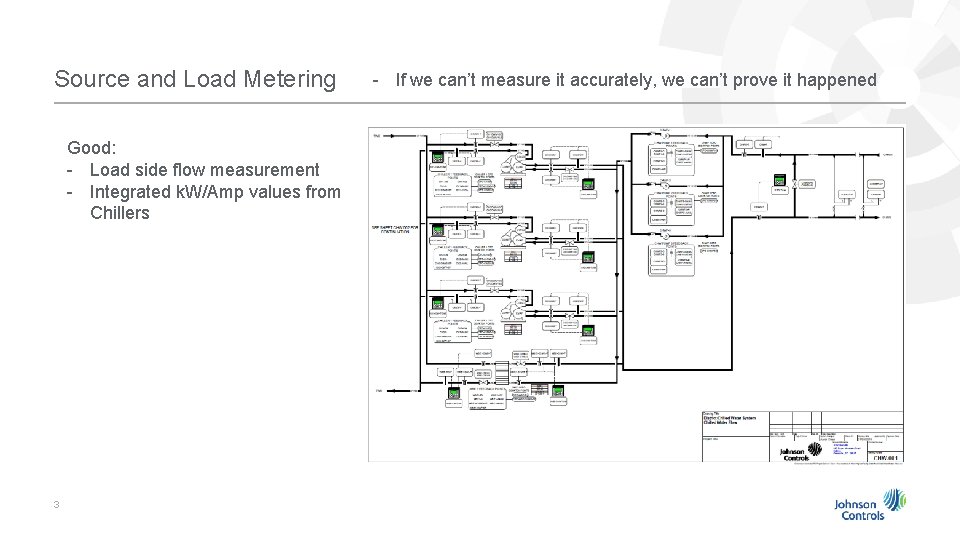
Source and Load Metering Good: - Load side flow measurement - Integrated k. W/Amp values from Chillers 3 - If we can’t measure it accurately, we can’t prove it happened
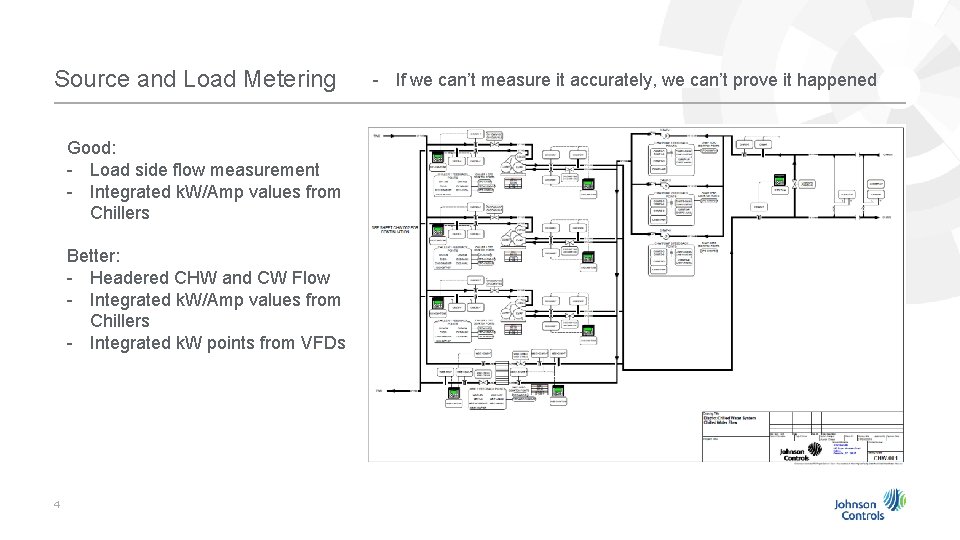
Source and Load Metering Good: - Load side flow measurement - Integrated k. W/Amp values from Chillers Better: - Headered CHW and CW Flow - Integrated k. W/Amp values from Chillers - Integrated k. W points from VFDs 4 - If we can’t measure it accurately, we can’t prove it happened
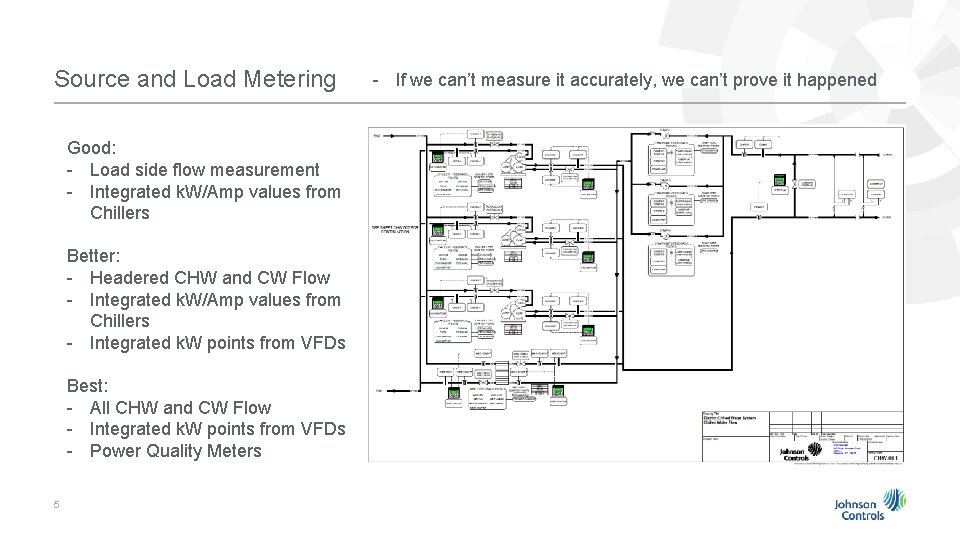
Source and Load Metering Good: - Load side flow measurement - Integrated k. W/Amp values from Chillers Better: - Headered CHW and CW Flow - Integrated k. W/Amp values from Chillers - Integrated k. W points from VFDs Best: - All CHW and CW Flow - Integrated k. W points from VFDs - Power Quality Meters 5 - If we can’t measure it accurately, we can’t prove it happened
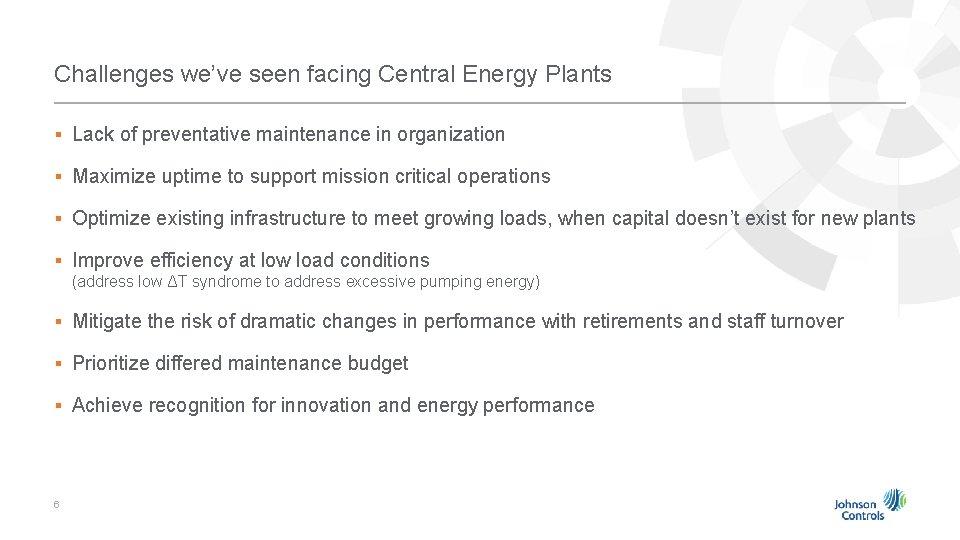
Challenges we’ve seen facing Central Energy Plants § Lack of preventative maintenance in organization § Maximize uptime to support mission critical operations § Optimize existing infrastructure to meet growing loads, when capital doesn’t exist for new plants § Improve efficiency at low load conditions (address low ΔT syndrome to address excessive pumping energy) § Mitigate the risk of dramatic changes in performance with retirements and staff turnover § Prioritize differed maintenance budget § Achieve recognition for innovation and energy performance 6
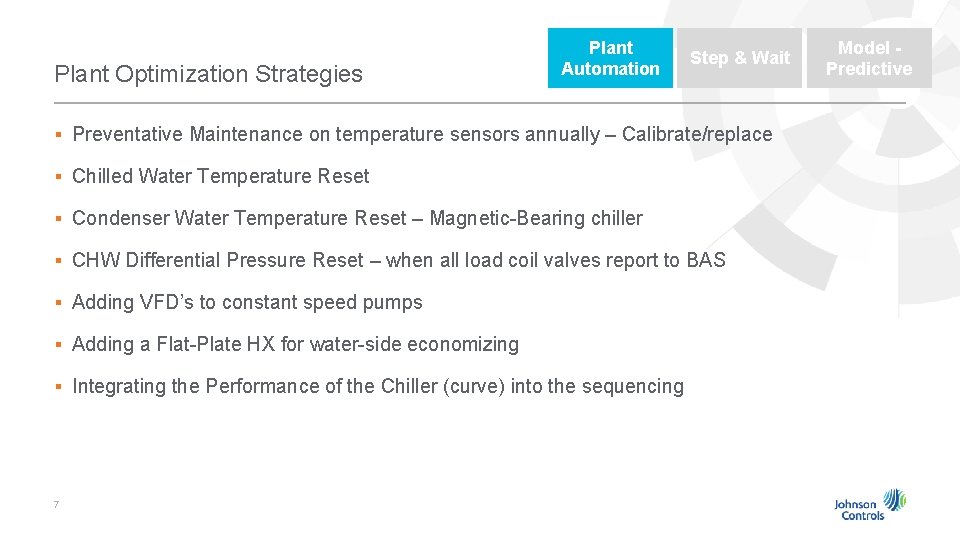
Plant Optimization Strategies Plant Automation Step & Wait § Preventative Maintenance on temperature sensors annually – Calibrate/replace § Chilled Water Temperature Reset § Condenser Water Temperature Reset – Magnetic-Bearing chiller § CHW Differential Pressure Reset – when all load coil valves report to BAS § Adding VFD’s to constant speed pumps § Adding a Flat-Plate HX for water-side economizing § Integrating the Performance of the Chiller (curve) into the sequencing 7 Model Predictive
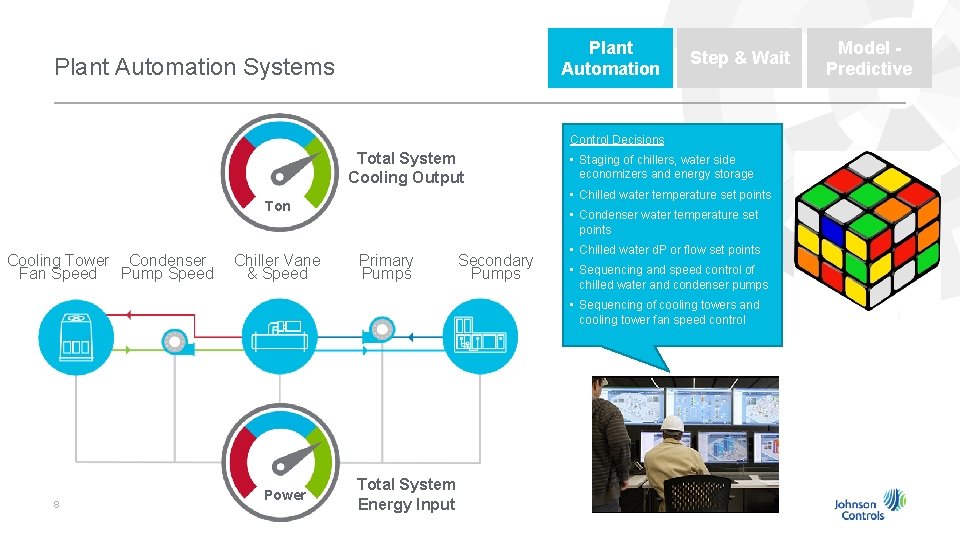
Plant Automation Systems Step & Wait Control Decisions Total System Cooling Output • Chilled water temperature set points Ton Cooling Tower Condenser Pump Speed Fan Speed Chiller Vane & Speed • Staging of chillers, water side economizers and energy storage • Condenser water temperature set points Primary Pumps Secondary Pumps • Chilled water d. P or flow set points • Sequencing and speed control of chilled water and condenser pumps • Sequencing of cooling towers and cooling tower fan speed control 8 Power Total System Energy Input Model Predictive
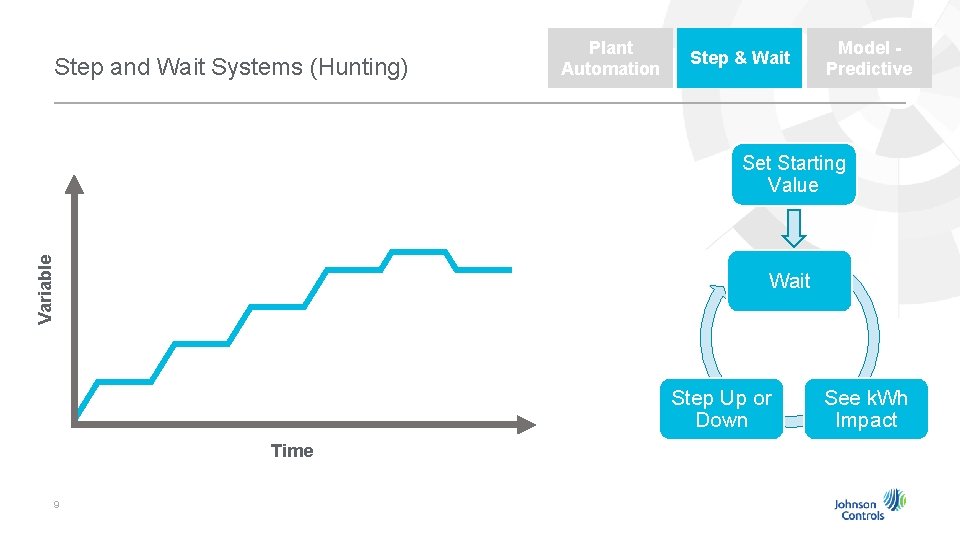
Step and Wait Systems (Hunting) Plant Automation Step & Wait Model Predictive Variable Set Starting Value Wait Step Up or Down Time 9 See k. Wh Impact
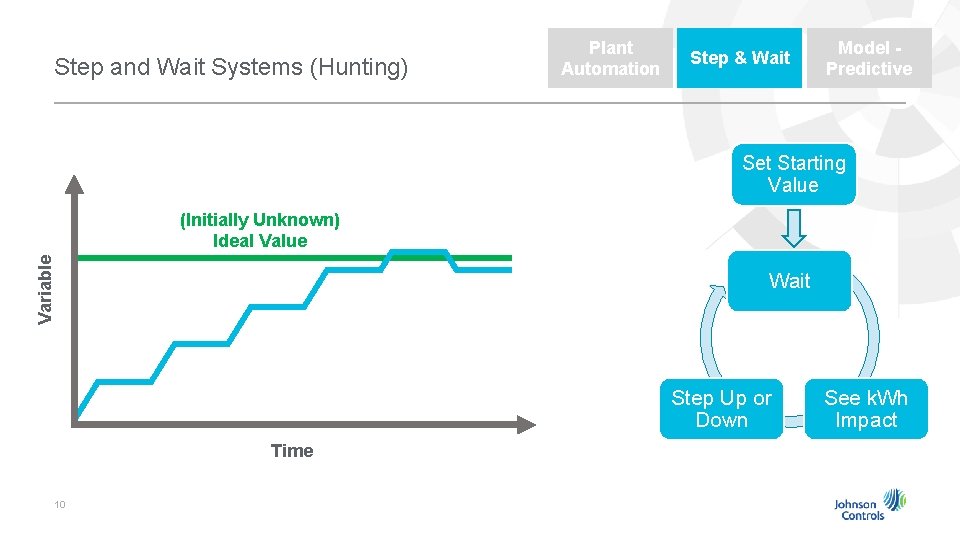
Step and Wait Systems (Hunting) Plant Automation Step & Wait Model Predictive Set Starting Value Variable (Initially Unknown) Ideal Value Wait Step Up or Down Time 10 See k. Wh Impact
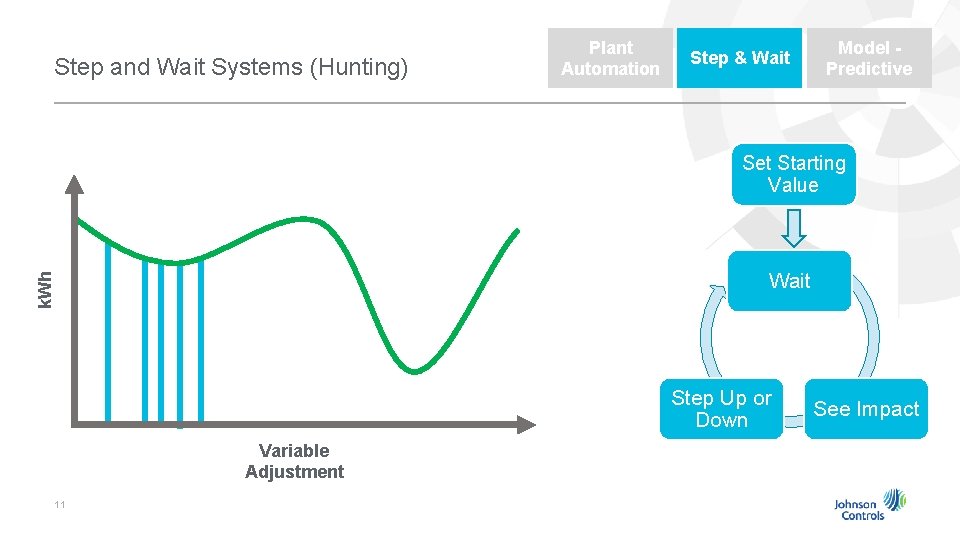
Step and Wait Systems (Hunting) Plant Automation Step & Wait Model Predictive Set Starting Value k. Wh Wait Step Up or Down Variable Adjustment 11 See Impact
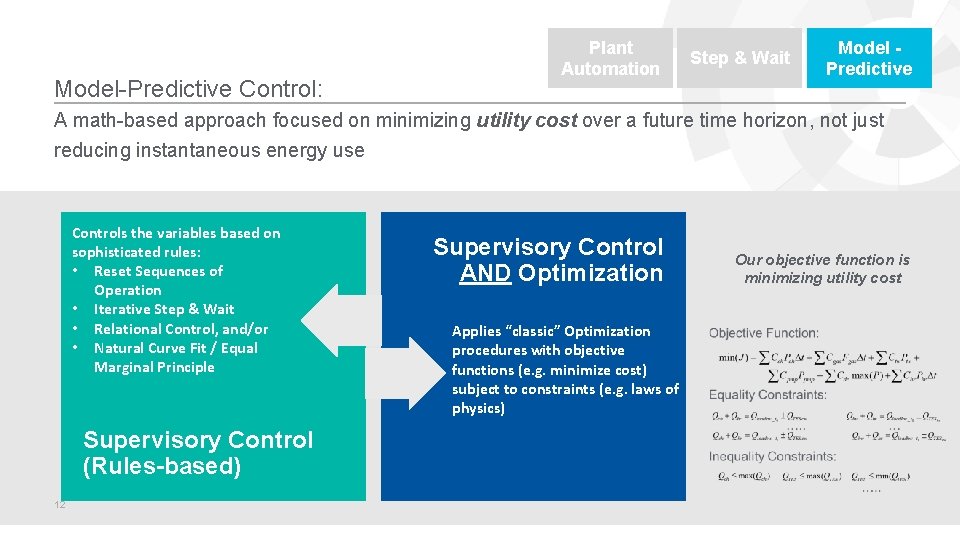
Model-Predictive Control: Plant Automation Step & Wait Model Predictive A math-based approach focused on minimizing utility cost over a future time horizon, not just reducing instantaneous energy use Controls the variables based on sophisticated rules: • Reset Sequences of Operation • Iterative Step & Wait • Relational Control, and/or • Natural Curve Fit / Equal Marginal Principle Supervisory Control (Rules-based) 12 Supervisory Control AND Optimization Applies “classic” Optimization procedures with objective functions (e. g. minimize cost) subject to constraints (e. g. laws of physics) Our objective function is minimizing utility cost
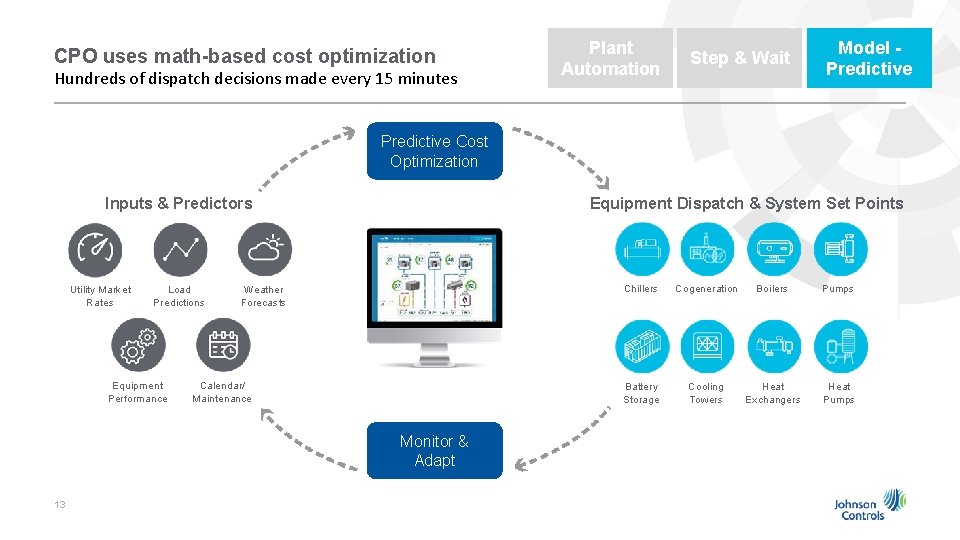
CPO uses math-based cost optimization Hundreds of dispatch decisions made every 15 minutes Plant Automation Step & Wait Model Predictive Cost Optimization Inputs & Predictors Utility Market Rates Load Predictions Equipment Performance Equipment Dispatch & System Set Points Weather Forecasts Calendar/ Maintenance Monitor & Adapt 13 Chillers Cogeneration Boilers Pumps Battery Storage Cooling Towers Heat Exchangers Heat Pumps
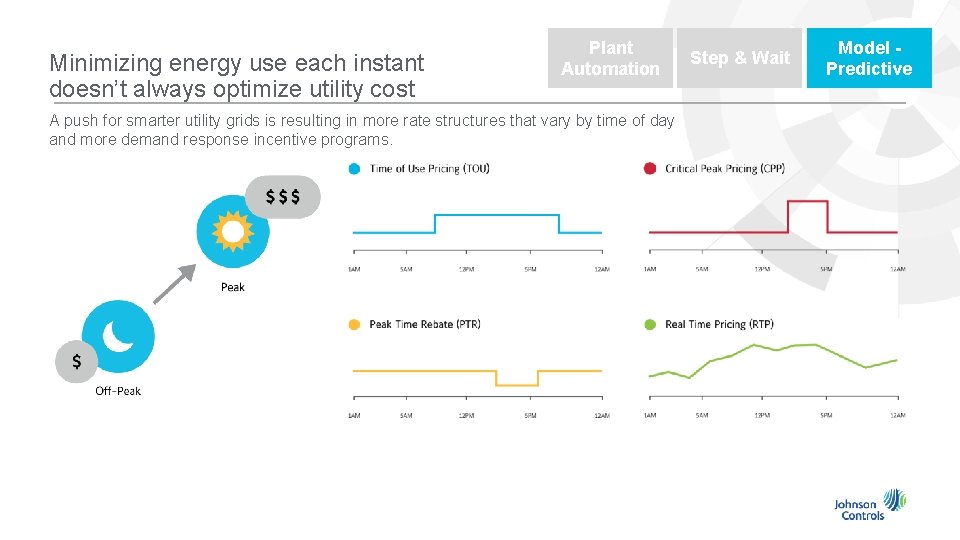
Minimizing energy use each instant doesn’t always optimize utility cost Plant Automation A push for smarter utility grids is resulting in more rate structures that vary by time of day and more demand response incentive programs. Step & Wait Model Predictive
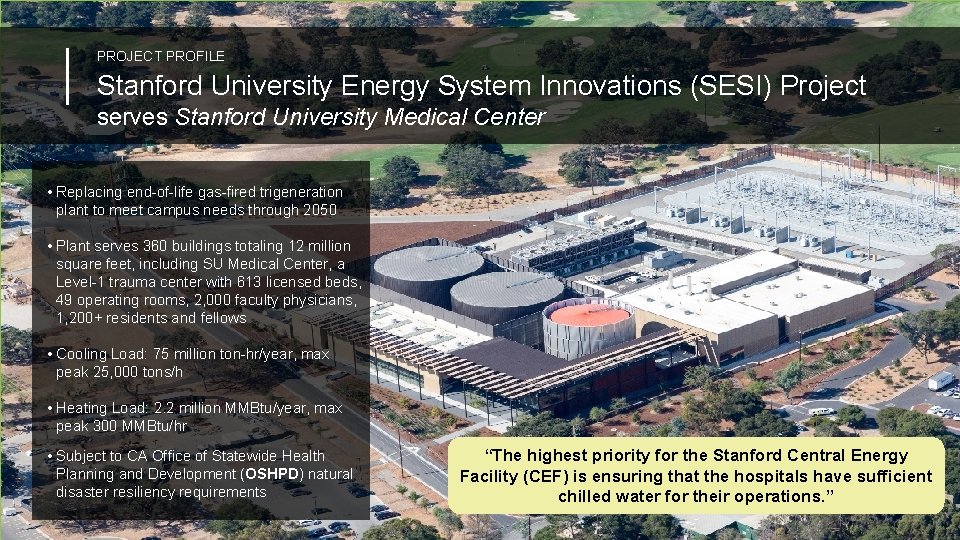
PROJECT PROFILE Stanford University Energy System Innovations (SESI) Project serves Stanford University Medical Center • Replacing end-of-life gas-fired trigeneration plant to meet campus needs through 2050 • Plant serves 360 buildings totaling 12 million square feet, including SU Medical Center, a Level-1 trauma center with 613 licensed beds, 49 operating rooms, 2, 000 faculty physicians, 1, 200+ residents and fellows • Cooling Load: 75 million ton-hr/year, max peak 25, 000 tons/h • Heating Load: 2. 2 million MMBtu/year, max peak 300 MMBtu/hr • Subject to CA Office of Statewide Health Planning and Development (OSHPD) natural disaster resiliency requirements “The highest priority for the Stanford Central Energy Facility (CEF) is ensuring that the hospitals have sufficient chilled water for their operations. ”
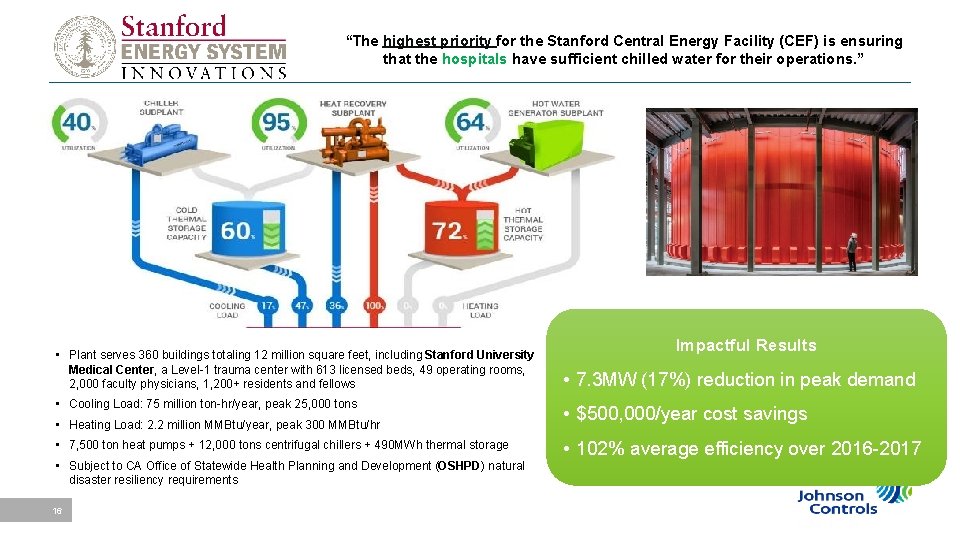
“The highest priority for the Stanford Central Energy Facility (CEF) is ensuring that the hospitals have sufficient chilled water for their operations. ” • Plant serves 360 buildings totaling 12 million square feet, including Stanford University Medical Center, a Level-1 trauma center with 613 licensed beds, 49 operating rooms, 2, 000 faculty physicians, 1, 200+ residents and fellows • Cooling Load: 75 million ton-hr/year, peak 25, 000 tons • Heating Load: 2. 2 million MMBtu/year, peak 300 MMBtu/hr • 7, 500 ton heat pumps + 12, 000 tons centrifugal chillers + 490 MWh thermal storage • Subject to CA Office of Statewide Health Planning and Development (OSHPD) natural disaster resiliency requirements 16 Johnson Controls, Inc. Impactful Results • 7. 3 MW (17%) reduction in peak demand • $500, 000/year cost savings • 102% average efficiency over 2016 -2017
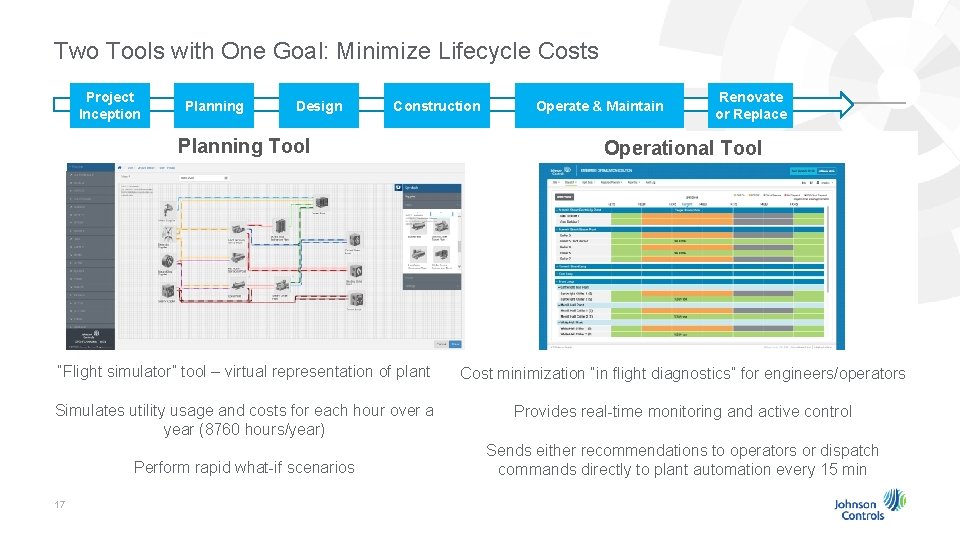
Two Tools with One Goal: Minimize Lifecycle Costs Project Inception Planning Design Construction Operate & Maintain Renovate or Replace Planning Tool Operational Tool “Flight simulator” tool – virtual representation of plant Cost minimization “in flight diagnostics” for engineers/operators Simulates utility usage and costs for each hour over a year (8760 hours/year) Provides real-time monitoring and active control Perform rapid what-if scenarios 17 Sends either recommendations to operators or dispatch commands directly to plant automation every 15 min
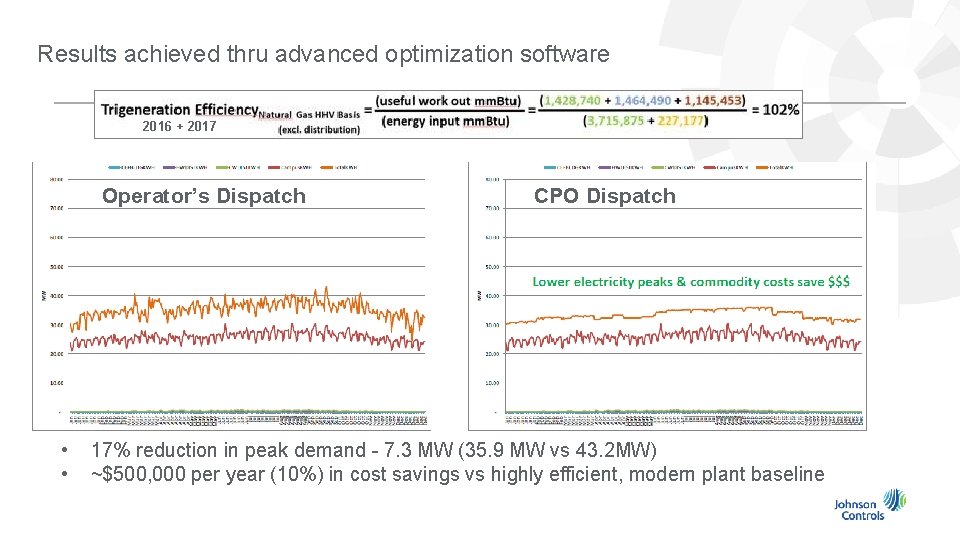
Results achieved thru advanced optimization software 2016 + 2017 Operator’s Dispatch • • CPO Dispatch 17% reduction in peak demand - 7. 3 MW (35. 9 MW vs 43. 2 MW) ~$500, 000 per year (10%) in cost savings vs highly efficient, modern plant baseline
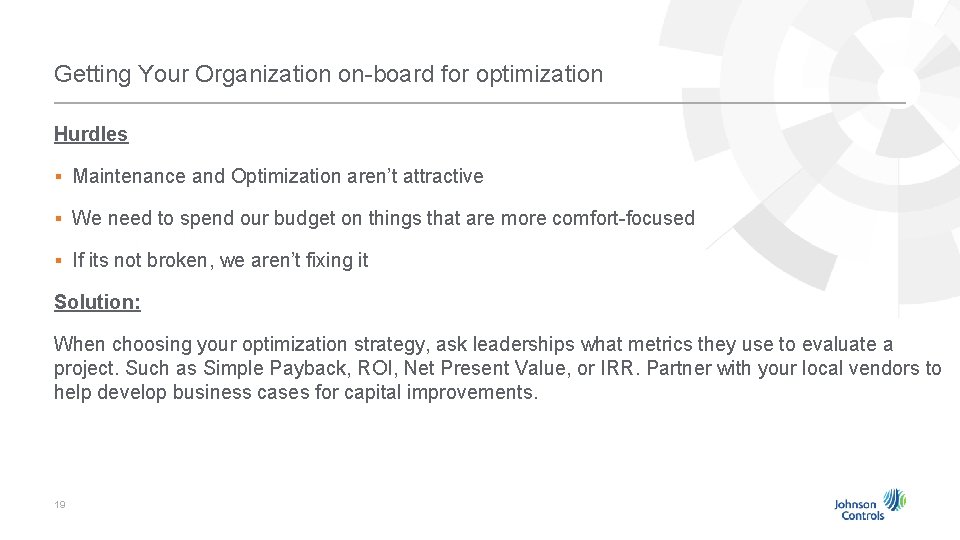
Getting Your Organization on-board for optimization Hurdles § Maintenance and Optimization aren’t attractive § We need to spend our budget on things that are more comfort-focused § If its not broken, we aren’t fixing it Solution: When choosing your optimization strategy, ask leaderships what metrics they use to evaluate a project. Such as Simple Payback, ROI, Net Present Value, or IRR. Partner with your local vendors to help develop business cases for capital improvements. 19
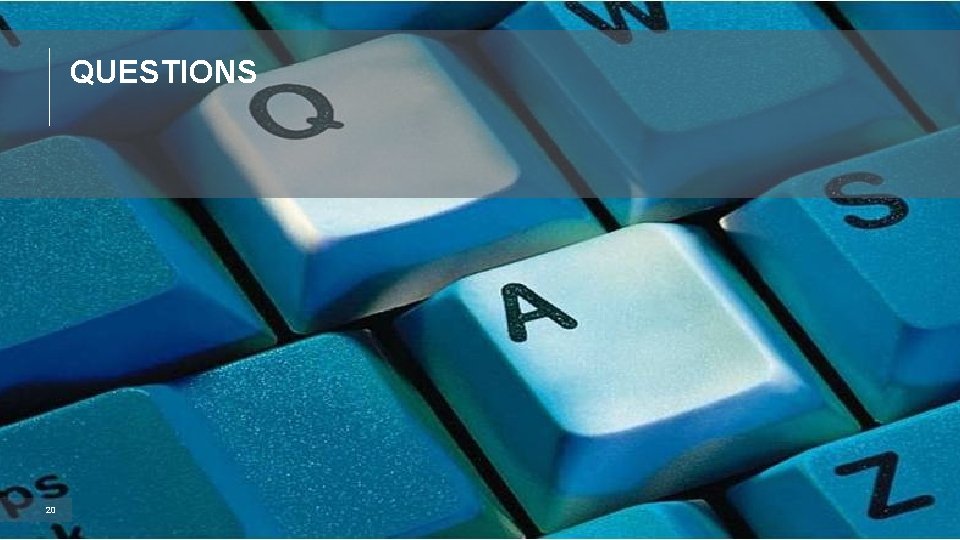
QUESTIONS 20
Johnson controls chiller plant optimization
General controls vs application controls
He who controls the past controls the future
Sw suwitupc
Johnson controls peru
Johnson controls international kft
Johnson controls
Easyparts jci
Swot analysis johnson and johnson
Johnson and johnson bcg matrix
Laurie johnson brad johnson
Credo values
Johnson and johnson organizational structure
Understanding the mirai botnet
Johnson and johnson swot analysis
Jjeds johnson
Dreikurs classroom management theory
Johnson and johnson md&d
Voyager plant optimization
Plant introduction in plant breeding
Plant breeding for disease resistance