AUTONOMOUS HAULAGE MINING TRUCKS AUTOMATED CONTROL SYSTEM OVERVIEW
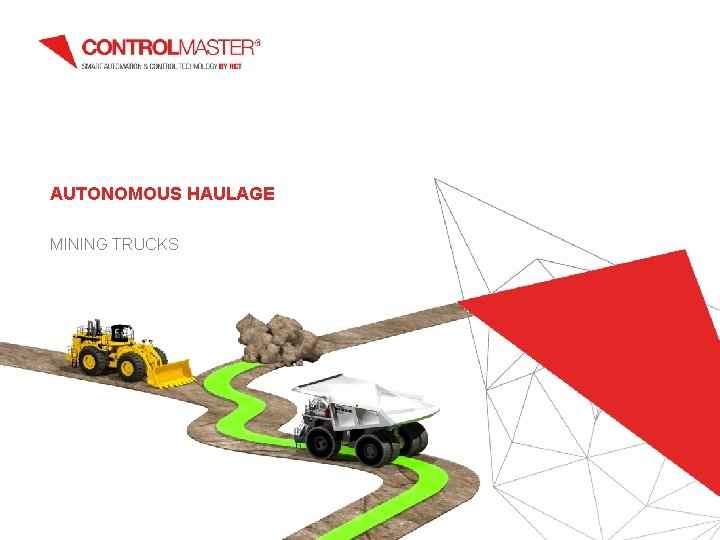
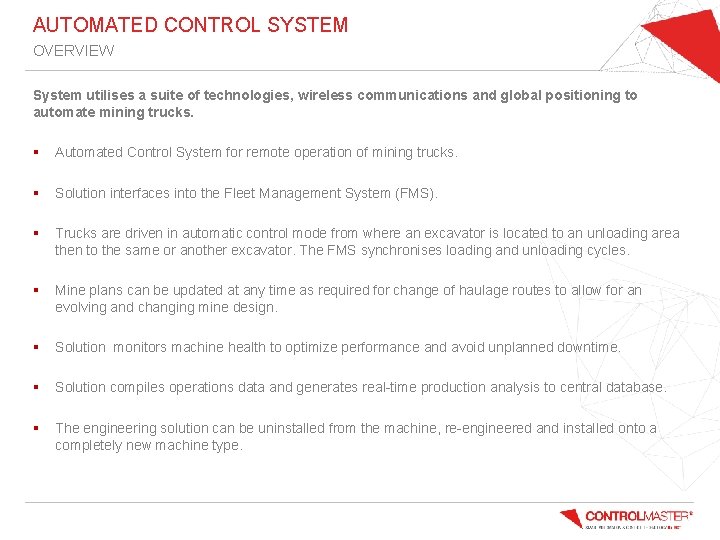
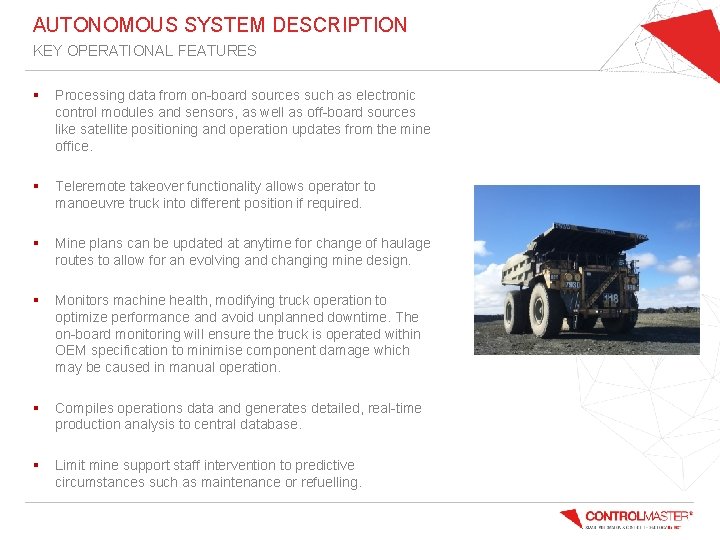
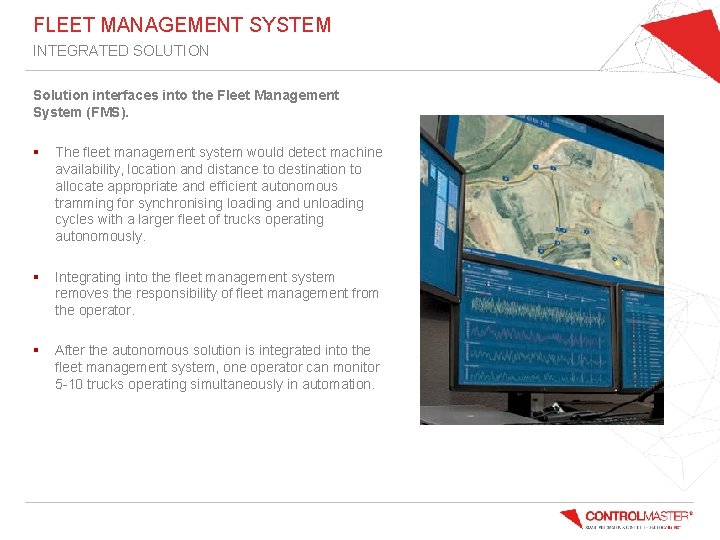
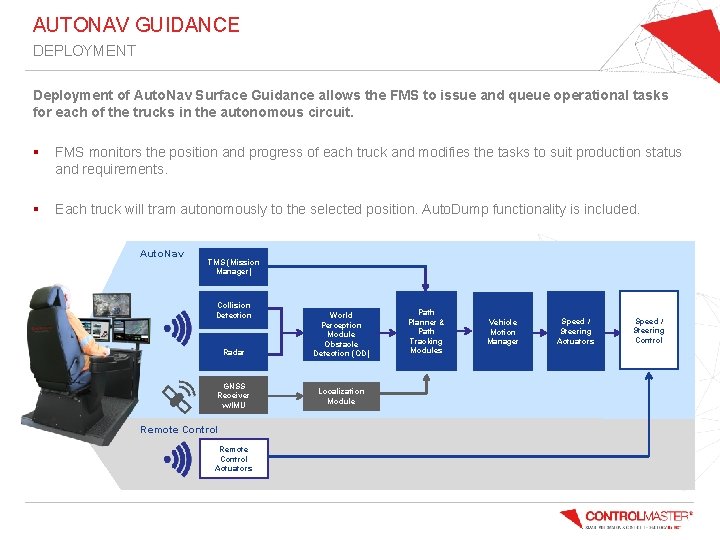
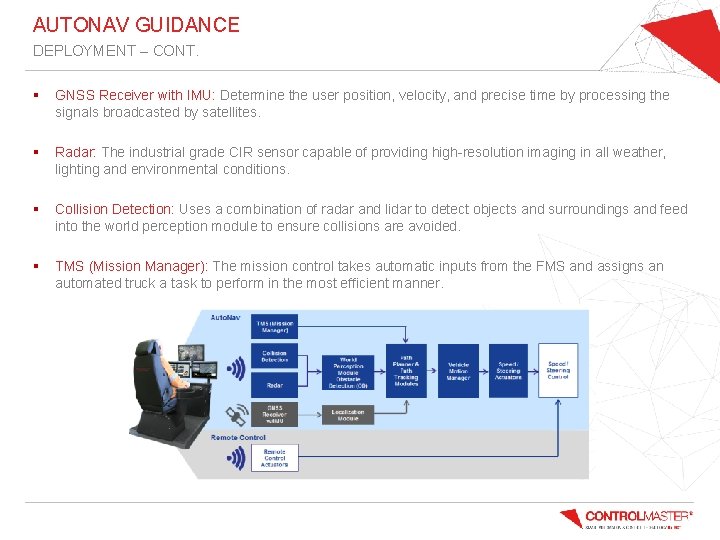
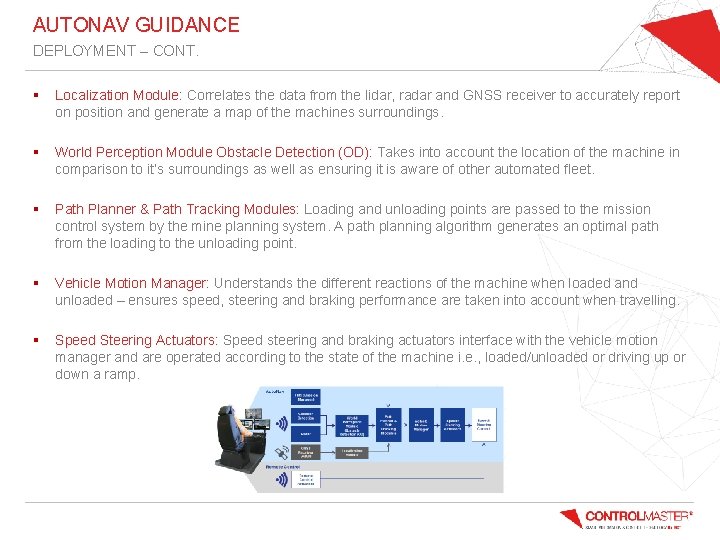
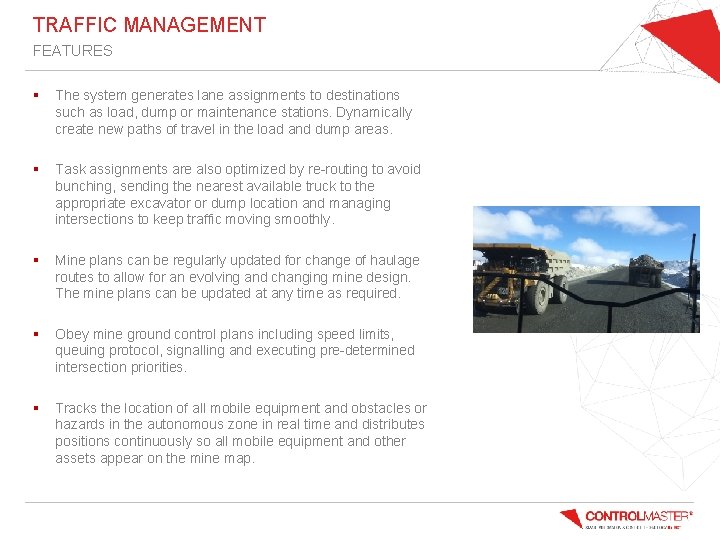
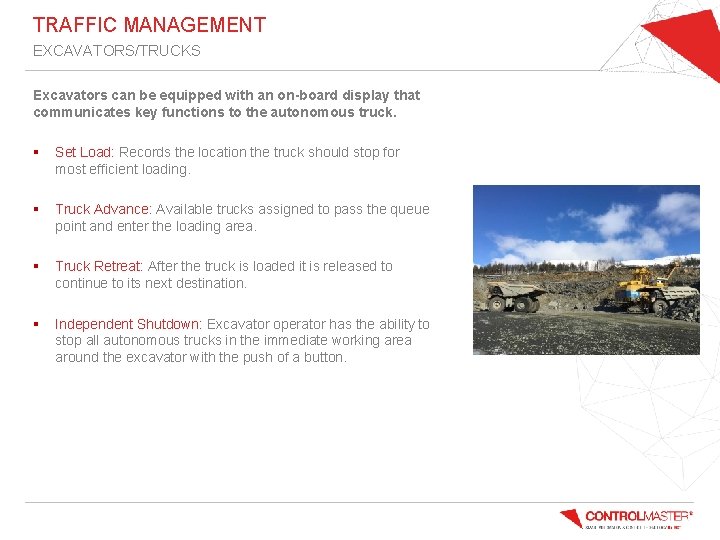
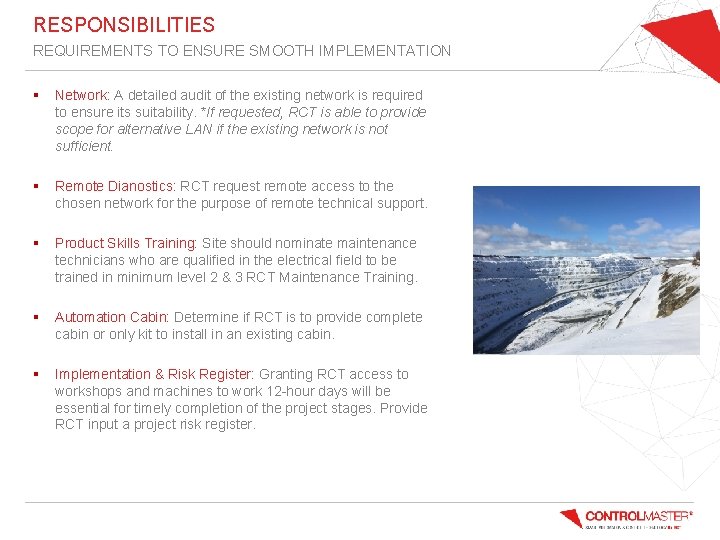
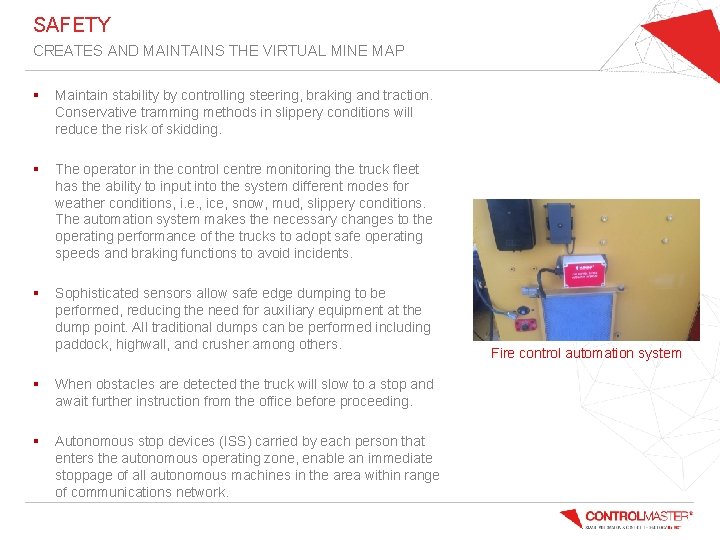
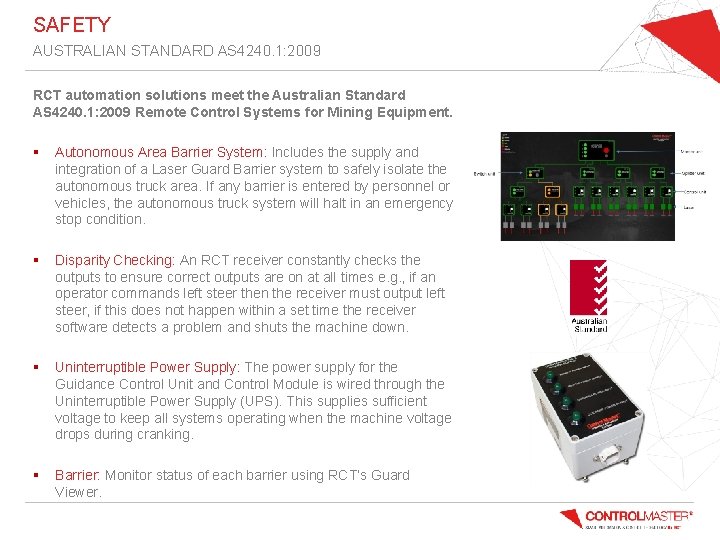
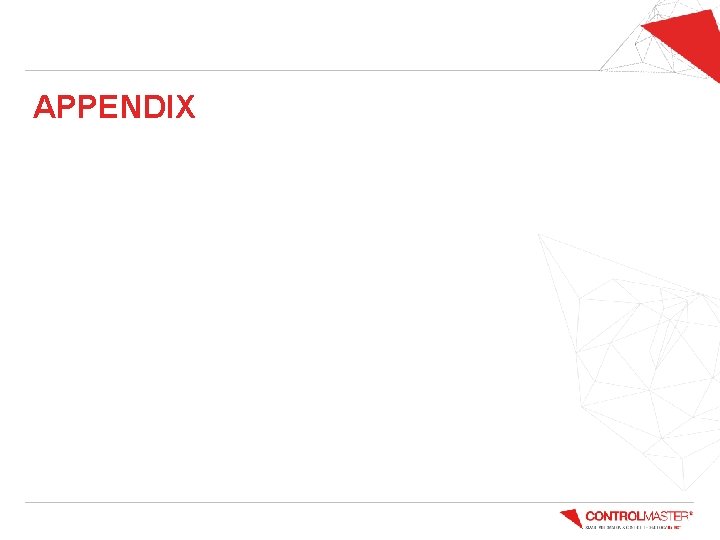
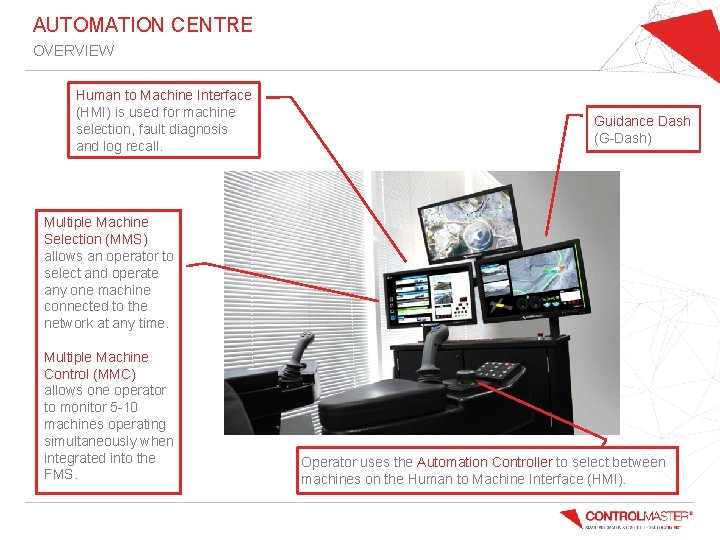
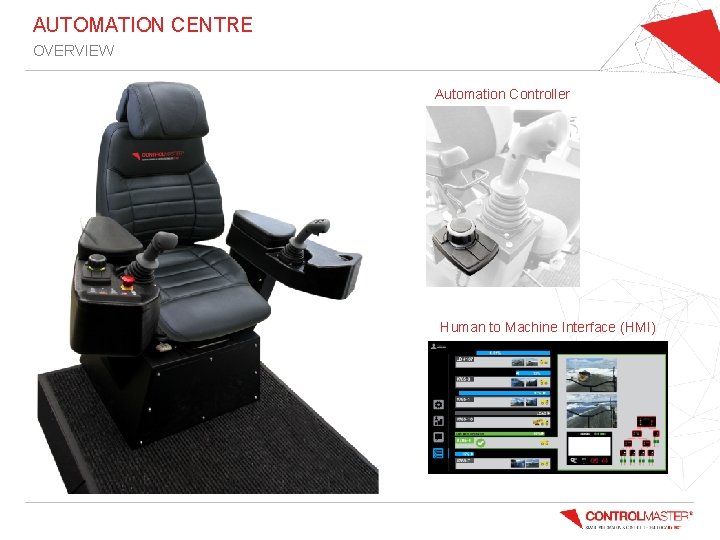
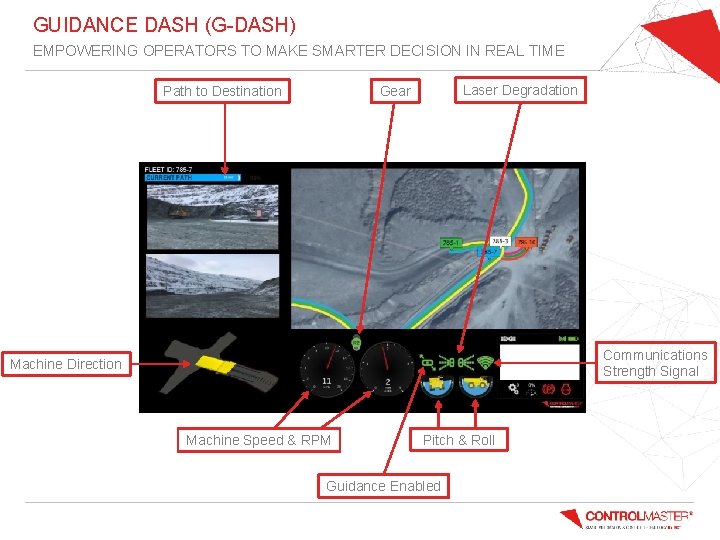
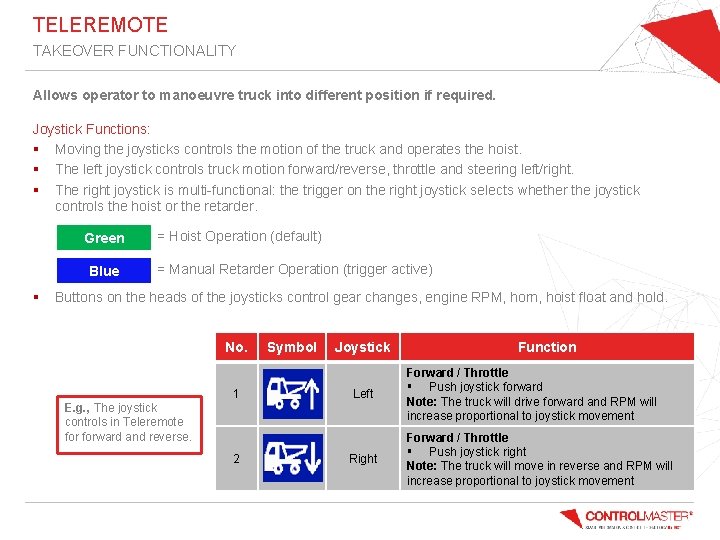
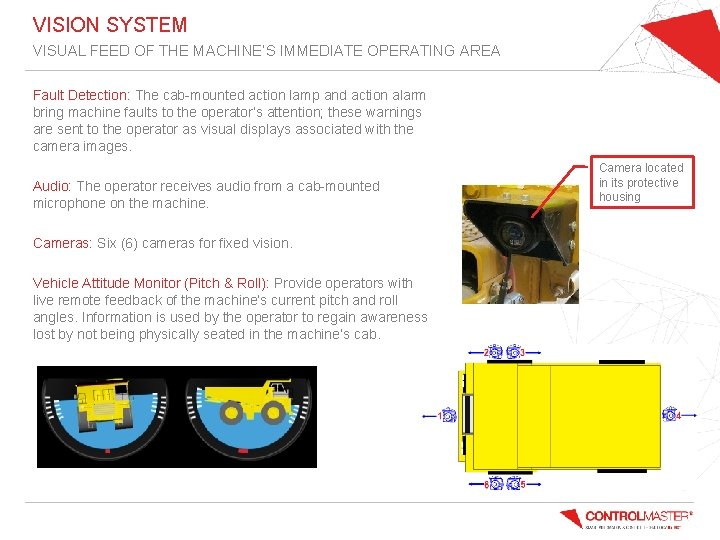
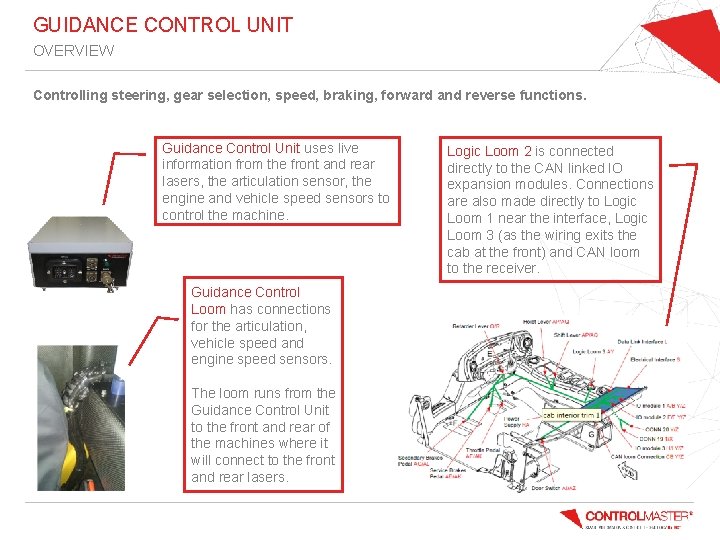
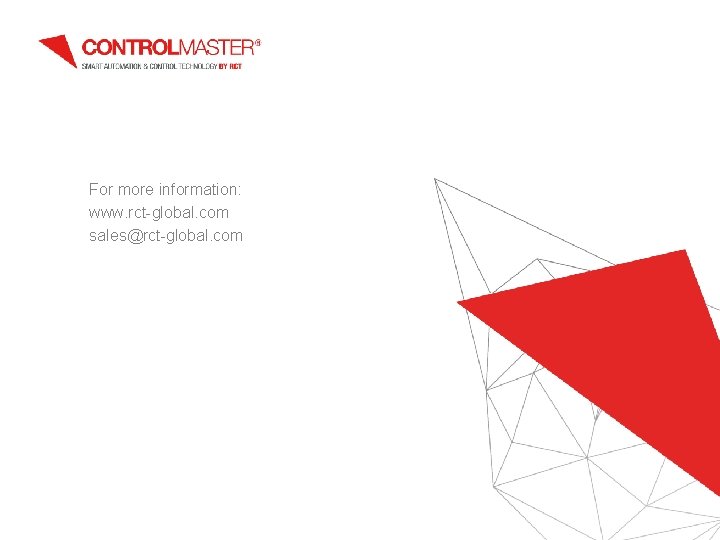
- Slides: 20
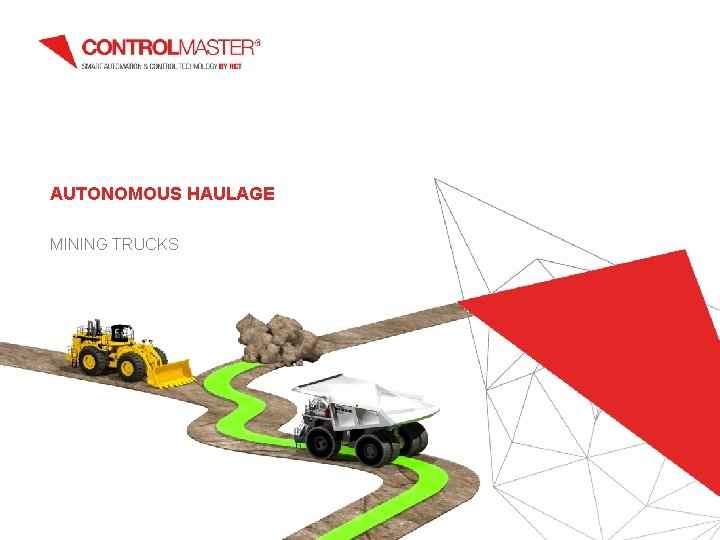
AUTONOMOUS HAULAGE MINING TRUCKS
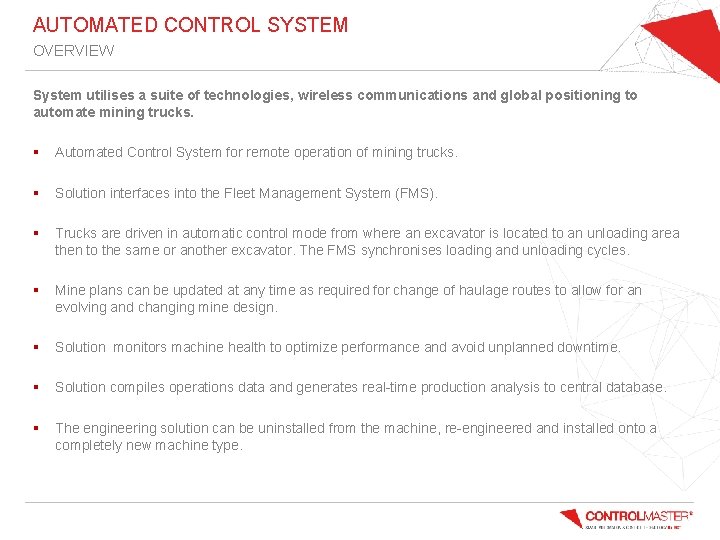
AUTOMATED CONTROL SYSTEM OVERVIEW System utilises a suite of technologies, wireless communications and global positioning to automate mining trucks. § Automated Control System for remote operation of mining trucks. § Solution interfaces into the Fleet Management System (FMS). § Trucks are driven in automatic control mode from where an excavator is located to an unloading area then to the same or another excavator. The FMS synchronises loading and unloading cycles. § Mine plans can be updated at any time as required for change of haulage routes to allow for an evolving and changing mine design. § Solution monitors machine health to optimize performance and avoid unplanned downtime. § Solution compiles operations data and generates real-time production analysis to central database. § The engineering solution can be uninstalled from the machine, re-engineered and installed onto a completely new machine type.
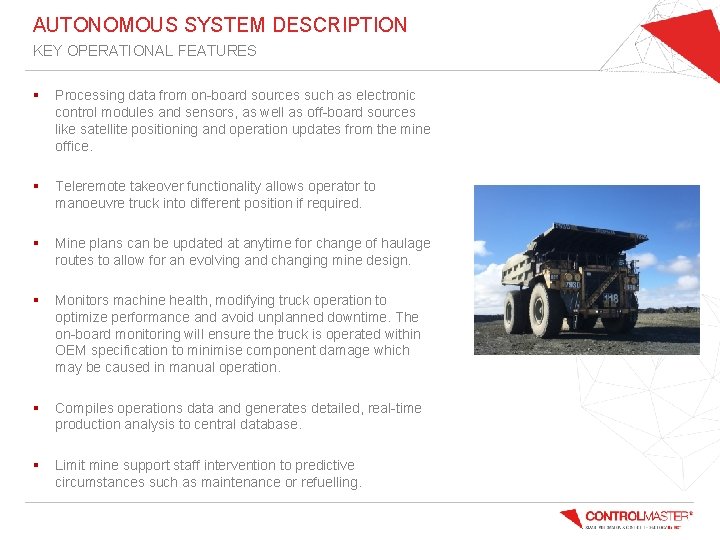
AUTONOMOUS SYSTEM DESCRIPTION KEY OPERATIONAL FEATURES § Processing data from on-board sources such as electronic control modules and sensors, as well as off-board sources like satellite positioning and operation updates from the mine office. § Teleremote takeover functionality allows operator to manoeuvre truck into different position if required. § Mine plans can be updated at anytime for change of haulage routes to allow for an evolving and changing mine design. § Monitors machine health, modifying truck operation to optimize performance and avoid unplanned downtime. The on-board monitoring will ensure the truck is operated within OEM specification to minimise component damage which may be caused in manual operation. § Compiles operations data and generates detailed, real-time production analysis to central database. § Limit mine support staff intervention to predictive circumstances such as maintenance or refuelling.
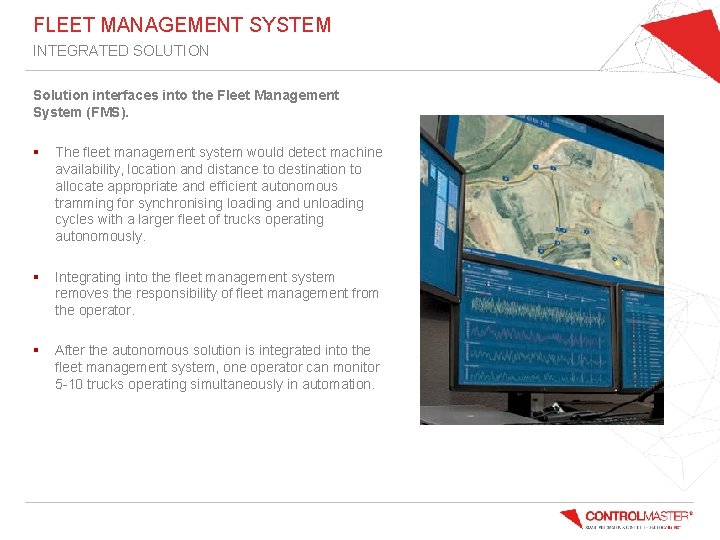
FLEET MANAGEMENT SYSTEM INTEGRATED SOLUTION Solution interfaces into the Fleet Management System (FMS). § The fleet management system would detect machine availability, location and distance to destination to allocate appropriate and efficient autonomous tramming for synchronising loading and unloading cycles with a larger fleet of trucks operating autonomously. § Integrating into the fleet management system removes the responsibility of fleet management from the operator. § After the autonomous solution is integrated into the fleet management system, one operator can monitor 5 -10 trucks operating simultaneously in automation.
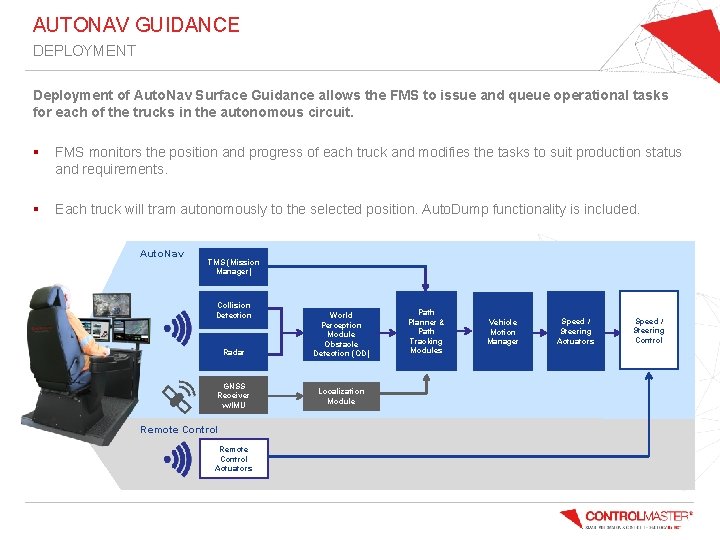
AUTONAV GUIDANCE DEPLOYMENT Deployment of Auto. Nav Surface Guidance allows the FMS to issue and queue operational tasks for each of the trucks in the autonomous circuit. § FMS monitors the position and progress of each truck and modifies the tasks to suit production status and requirements. § Each truck will tram autonomously to the selected position. Auto. Dump functionality is included. Auto. Nav TMS (Mission Manager) Collision Detection Radar World Perception Module Obstacle Detection (OD) GNSS Receiver w/IMU Localization Module Remote Control Actuators Path Planner & Path Tracking Modules Vehicle Motion Manager Speed / Steering Actuators Speed / Steering Control
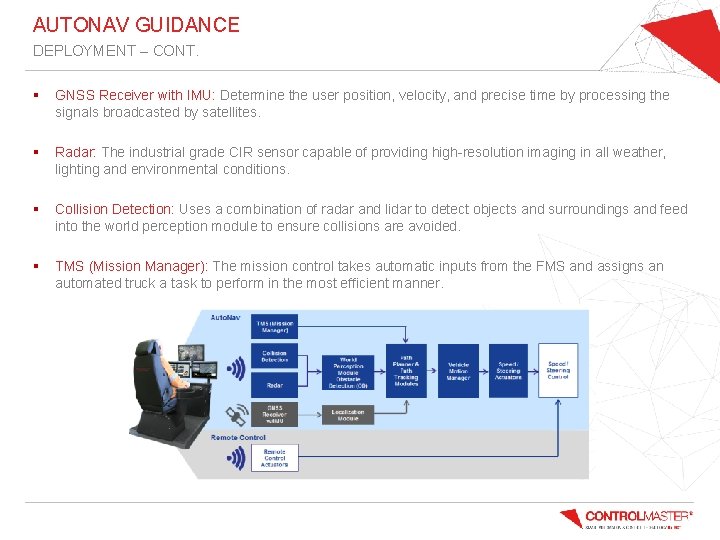
AUTONAV GUIDANCE DEPLOYMENT – CONT. § GNSS Receiver with IMU: Determine the user position, velocity, and precise time by processing the signals broadcasted by satellites. § Radar: The industrial grade CIR sensor capable of providing high-resolution imaging in all weather, lighting and environmental conditions. § Collision Detection: Uses a combination of radar and lidar to detect objects and surroundings and feed into the world perception module to ensure collisions are avoided. § TMS (Mission Manager): The mission control takes automatic inputs from the FMS and assigns an automated truck a task to perform in the most efficient manner.
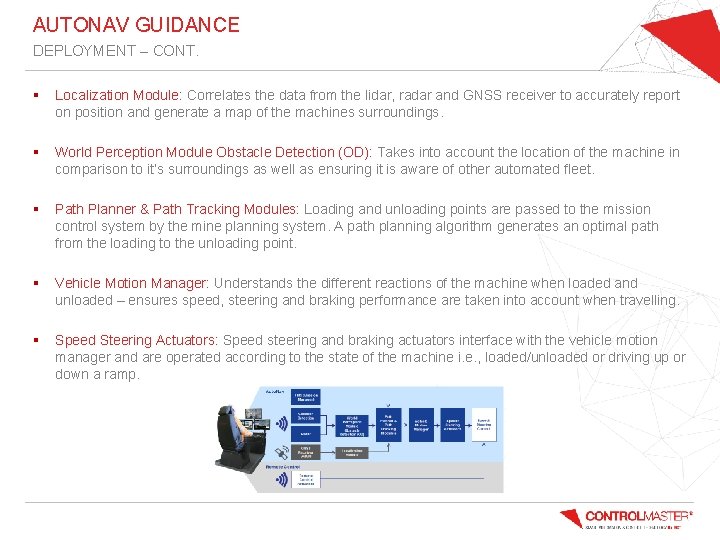
AUTONAV GUIDANCE DEPLOYMENT – CONT. § Localization Module: Correlates the data from the lidar, radar and GNSS receiver to accurately report on position and generate a map of the machines surroundings. § World Perception Module Obstacle Detection (OD): Takes into account the location of the machine in comparison to it’s surroundings as well as ensuring it is aware of other automated fleet. § Path Planner & Path Tracking Modules: Loading and unloading points are passed to the mission control system by the mine planning system. A path planning algorithm generates an optimal path from the loading to the unloading point. § Vehicle Motion Manager: Understands the different reactions of the machine when loaded and unloaded – ensures speed, steering and braking performance are taken into account when travelling. § Speed Steering Actuators: Speed steering and braking actuators interface with the vehicle motion manager and are operated according to the state of the machine i. e. , loaded/unloaded or driving up or down a ramp.
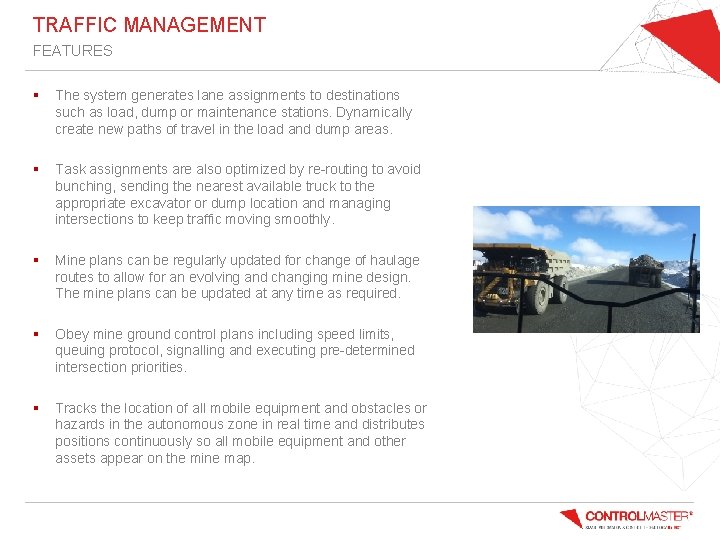
TRAFFIC MANAGEMENT FEATURES § The system generates lane assignments to destinations such as load, dump or maintenance stations. Dynamically create new paths of travel in the load and dump areas. § Task assignments are also optimized by re-routing to avoid bunching, sending the nearest available truck to the appropriate excavator or dump location and managing intersections to keep traffic moving smoothly. § Mine plans can be regularly updated for change of haulage routes to allow for an evolving and changing mine design. The mine plans can be updated at any time as required. § Obey mine ground control plans including speed limits, queuing protocol, signalling and executing pre-determined intersection priorities. § Tracks the location of all mobile equipment and obstacles or hazards in the autonomous zone in real time and distributes positions continuously so all mobile equipment and other assets appear on the mine map.
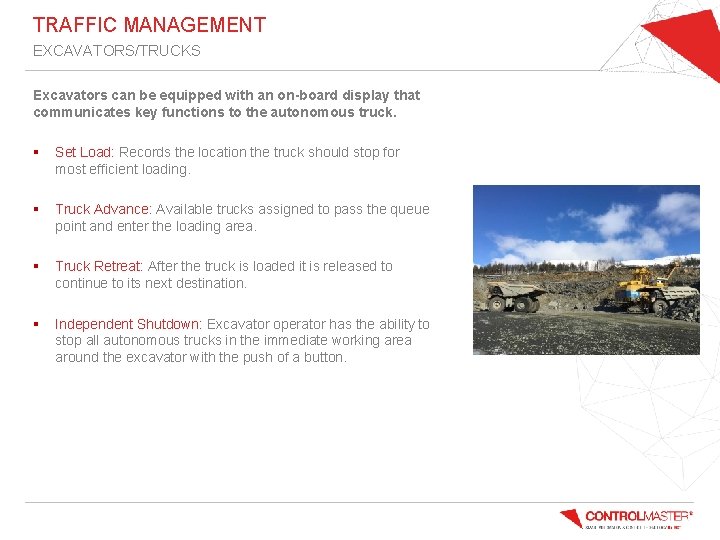
TRAFFIC MANAGEMENT EXCAVATORS/TRUCKS Excavators can be equipped with an on-board display that communicates key functions to the autonomous truck. § Set Load: Records the location the truck should stop for most efficient loading. § Truck Advance: Available trucks assigned to pass the queue point and enter the loading area. § Truck Retreat: After the truck is loaded it is released to continue to its next destination. § Independent Shutdown: Excavator operator has the ability to stop all autonomous trucks in the immediate working area around the excavator with the push of a button.
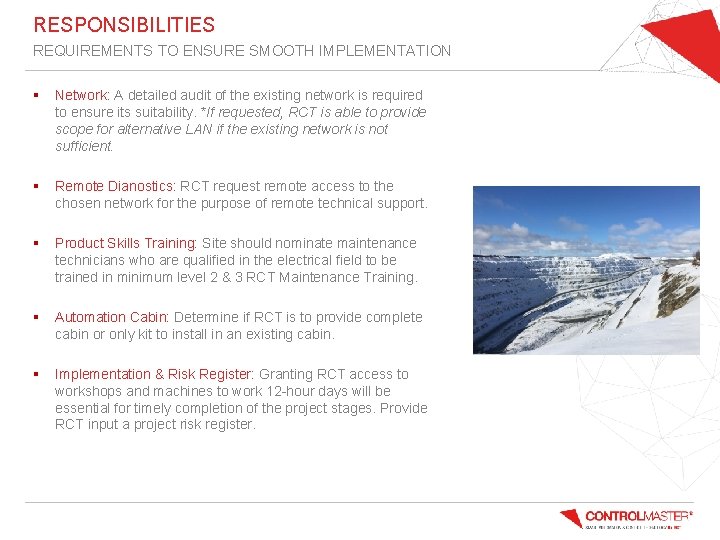
RESPONSIBILITIES REQUIREMENTS TO ENSURE SMOOTH IMPLEMENTATION § Network: A detailed audit of the existing network is required to ensure its suitability. *If requested, RCT is able to provide scope for alternative LAN if the existing network is not sufficient. § Remote Dianostics: RCT request remote access to the chosen network for the purpose of remote technical support. § Product Skills Training: Site should nominate maintenance technicians who are qualified in the electrical field to be trained in minimum level 2 & 3 RCT Maintenance Training. § Automation Cabin: Determine if RCT is to provide complete cabin or only kit to install in an existing cabin. § Implementation & Risk Register: Granting RCT access to workshops and machines to work 12 -hour days will be essential for timely completion of the project stages. Provide RCT input a project risk register.
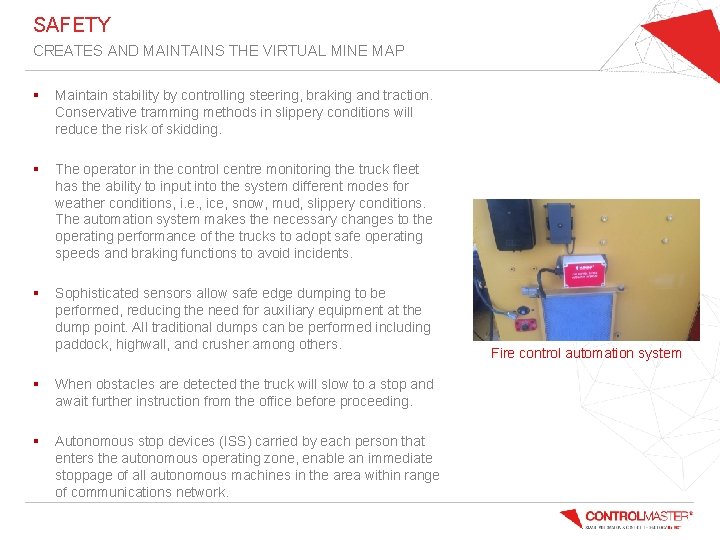
SAFETY CREATES AND MAINTAINS THE VIRTUAL MINE MAP § Maintain stability by controlling steering, braking and traction. Conservative tramming methods in slippery conditions will reduce the risk of skidding. § The operator in the control centre monitoring the truck fleet has the ability to input into the system different modes for weather conditions, i. e. , ice, snow, mud, slippery conditions. The automation system makes the necessary changes to the operating performance of the trucks to adopt safe operating speeds and braking functions to avoid incidents. § Sophisticated sensors allow safe edge dumping to be performed, reducing the need for auxiliary equipment at the dump point. All traditional dumps can be performed including paddock, highwall, and crusher among others. § When obstacles are detected the truck will slow to a stop and await further instruction from the office before proceeding. § Autonomous stop devices (ISS) carried by each person that enters the autonomous operating zone, enable an immediate stoppage of all autonomous machines in the area within range of communications network. Fire control automation system
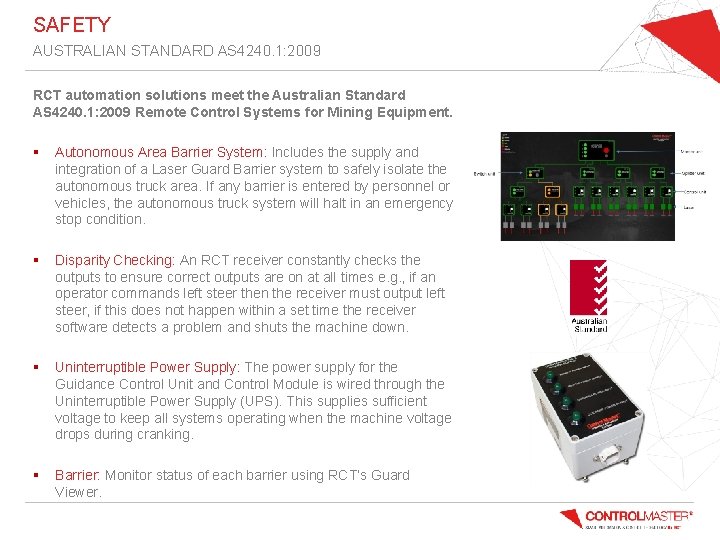
SAFETY AUSTRALIAN STANDARD AS 4240. 1: 2009 RCT automation solutions meet the Australian Standard AS 4240. 1: 2009 Remote Control Systems for Mining Equipment. § Autonomous Area Barrier System: Includes the supply and integration of a Laser Guard Barrier system to safely isolate the autonomous truck area. If any barrier is entered by personnel or vehicles, the autonomous truck system will halt in an emergency stop condition. § Disparity Checking: An RCT receiver constantly checks the outputs to ensure correct outputs are on at all times e. g. , if an operator commands left steer then the receiver must output left steer, if this does not happen within a set time the receiver software detects a problem and shuts the machine down. § Uninterruptible Power Supply: The power supply for the Guidance Control Unit and Control Module is wired through the Uninterruptible Power Supply (UPS). This supplies sufficient voltage to keep all systems operating when the machine voltage drops during cranking. § Barrier: Monitor status of each barrier using RCT’s Guard Viewer.
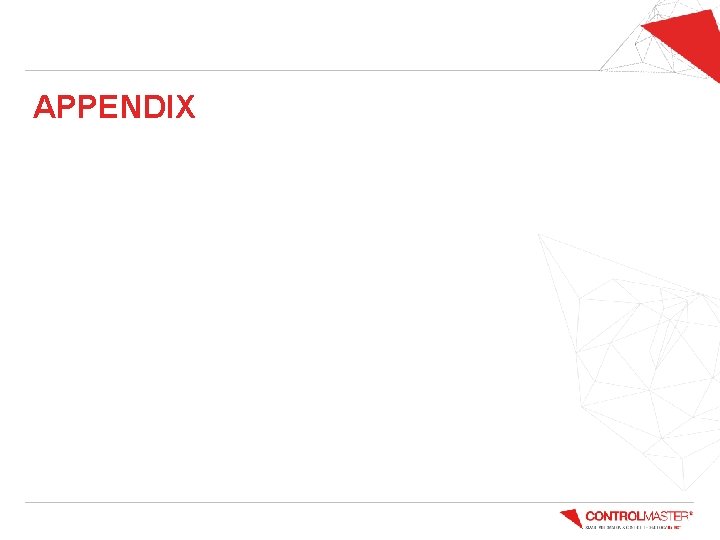
APPENDIX
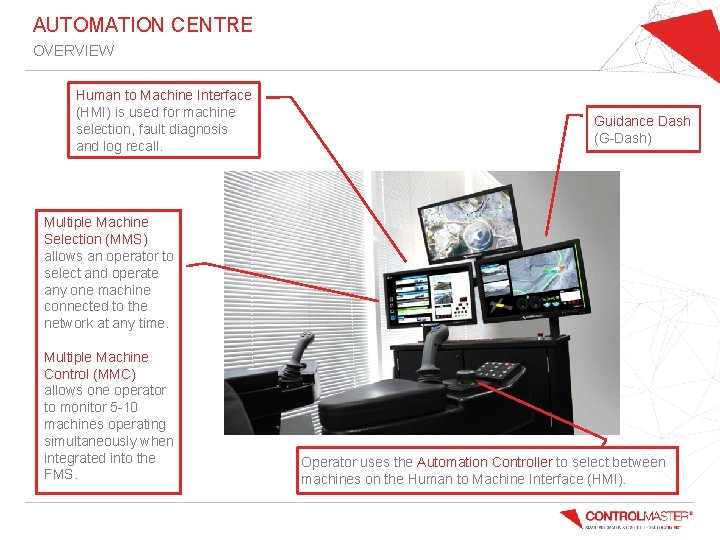
AUTOMATION CENTRE OVERVIEW Human to Machine Interface (HMI) is used for machine selection, fault diagnosis and log recall. Guidance Dash (G-Dash) Multiple Machine Selection (MMS) allows an operator to select and operate any one machine connected to the network at any time. Multiple Machine Control (MMC) allows one operator to monitor 5 -10 machines operating simultaneously when integrated into the FMS. Operator uses the Automation Controller to select between machines on the Human to Machine Interface (HMI).
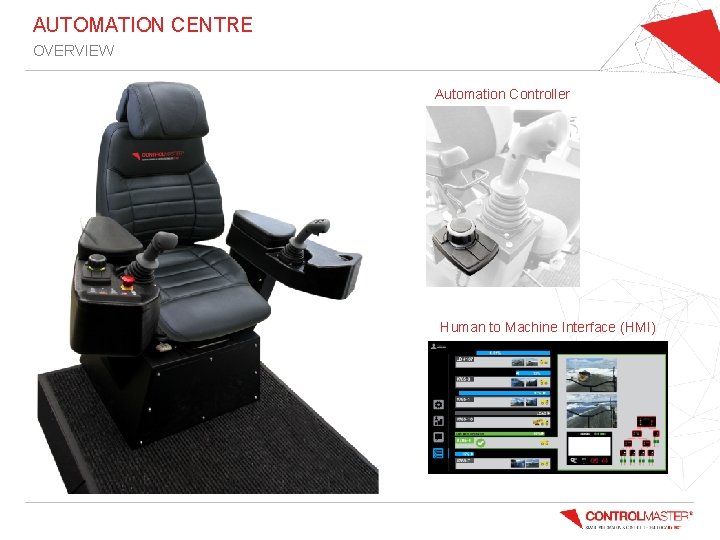
AUTOMATION CENTRE OVERVIEW Automation Controller Human to Machine Interface (HMI)
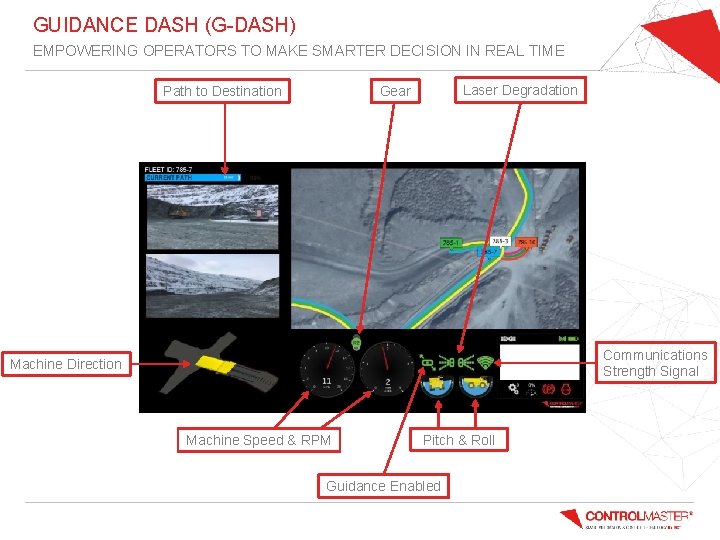
GUIDANCE DASH (G-DASH) EMPOWERING OPERATORS TO MAKE SMARTER DECISION IN REAL TIME Path to Destination Laser Degradation Gear Communications Strength Signal Machine Direction Machine Speed & RPM Pitch & Roll Guidance Enabled
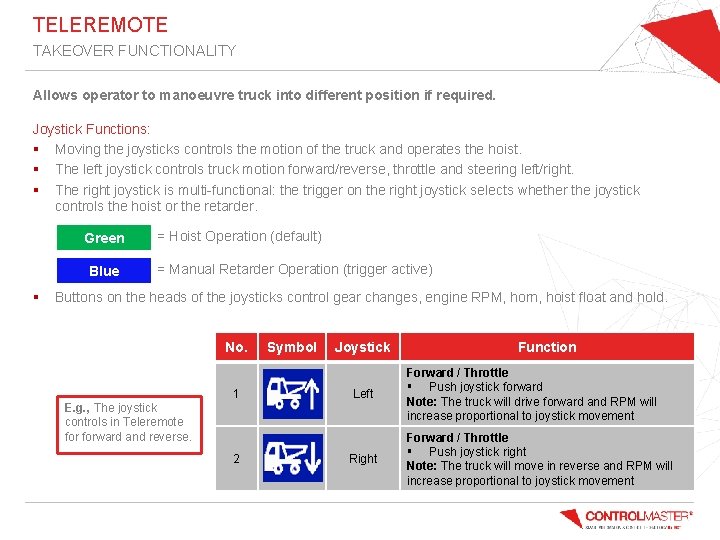
TELEREMOTE TAKEOVER FUNCTIONALITY Allows operator to manoeuvre truck into different position if required. Joystick Functions: § Moving the joysticks controls the motion of the truck and operates the hoist. § The left joystick controls truck motion forward/reverse, throttle and steering left/right. § The right joystick is multi-functional: the trigger on the right joystick selects whether the joystick controls the hoist or the retarder. Green Blue § = Hoist Operation (default) = Manual Retarder Operation (trigger active) Buttons on the heads of the joysticks control gear changes, engine RPM, horn, hoist float and hold. No. 1 Symbol Joystick Left E. g. , The joystick controls in Teleremote forward and reverse. 2 Right Function Forward / Throttle § Push joystick forward Note: The truck will drive forward and RPM will increase proportional to joystick movement Forward / Throttle § Push joystick right Note: The truck will move in reverse and RPM will increase proportional to joystick movement
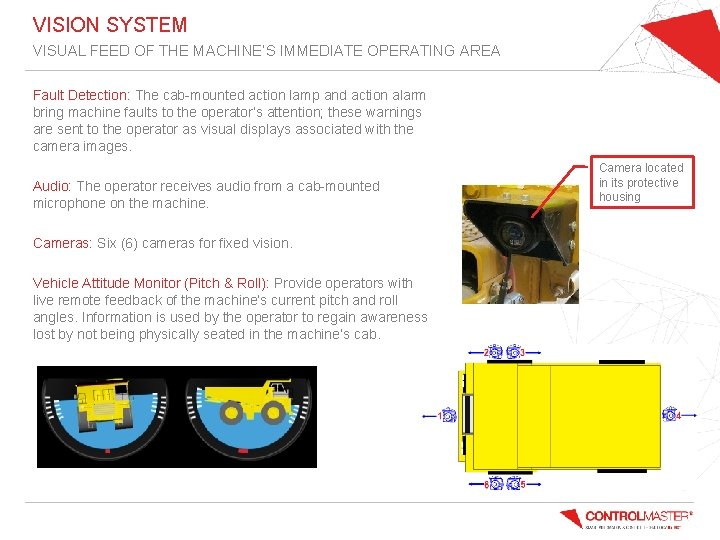
VISION SYSTEM VISUAL FEED OF THE MACHINE’S IMMEDIATE OPERATING AREA Fault Detection: The cab-mounted action lamp and action alarm bring machine faults to the operator’s attention; these warnings are sent to the operator as visual displays associated with the camera images. Audio: The operator receives audio from a cab-mounted microphone on the machine. Cameras: Six (6) cameras for fixed vision. Vehicle Attitude Monitor (Pitch & Roll): Provide operators with live remote feedback of the machine’s current pitch and roll angles. Information is used by the operator to regain awareness lost by not being physically seated in the machine’s cab. Camera located in its protective housing
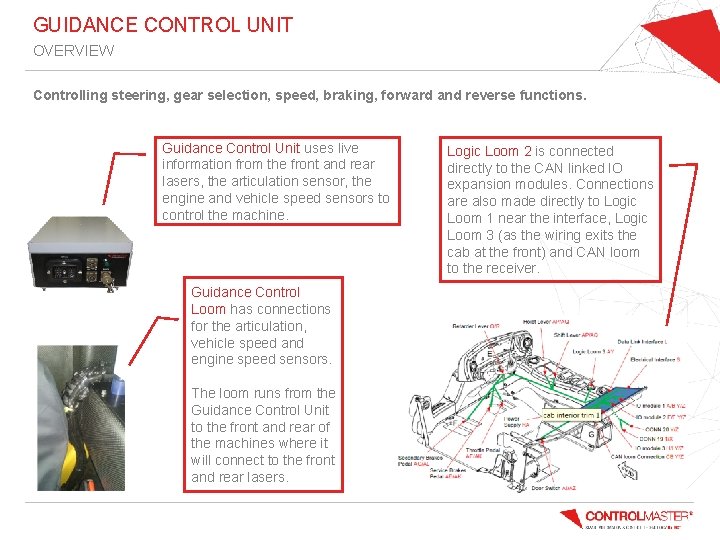
GUIDANCE CONTROL UNIT OVERVIEW Controlling steering, gear selection, speed, braking, forward and reverse functions. Guidance Control Unit uses live information from the front and rear lasers, the articulation sensor, the engine and vehicle speed sensors to control the machine. Guidance Control Loom has connections for the articulation, vehicle speed and engine speed sensors. The loom runs from the Guidance Control Unit to the front and rear of the machines where it will connect to the front and rear lasers. Logic Loom 2 is connected directly to the CAN linked IO expansion modules. Connections are also made directly to Logic Loom 1 near the interface, Logic Loom 3 (as the wiring exits the cab at the front) and CAN loom to the receiver.
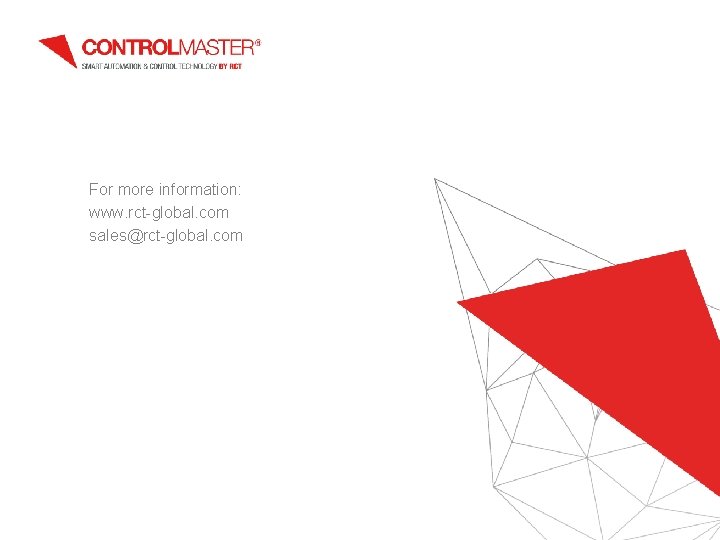
For more information: www. rct-global. com sales@rct-global. com
"scania" "trucks buy" or "best trucks" or commercial
Automation haulage
Diesen v samson
Sub mm2
Limitade
Gps fuel monitoring system
Trajectory data mining an overview
Strip mining vs open pit mining
Strip mining vs open pit mining
Difference between strip mining and open pit mining
Difference between text mining and web mining
Mining multimedia databases
Mining complex types of data in data mining
Autonomous system adalah
The centers of gravity of the three trucks
Maz vrachtwagen
Corner mount cranes
Lift trucks ports and terminal
29 cfr 1910 osha 178
Mobile spray rigs
Osha 1910 forklift