Athermalization Techniques in Infrared Systems OPTI 521 Fall
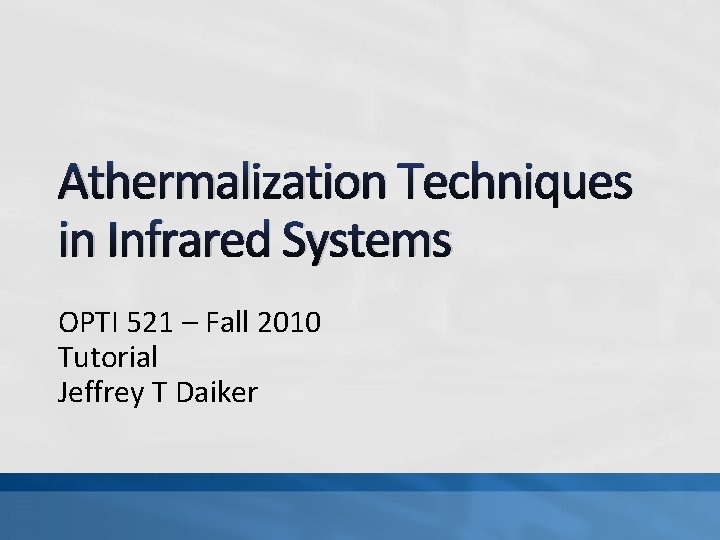
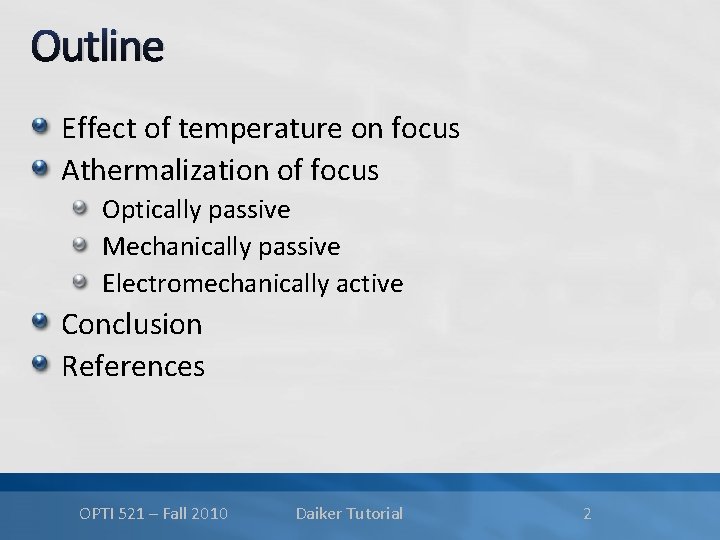
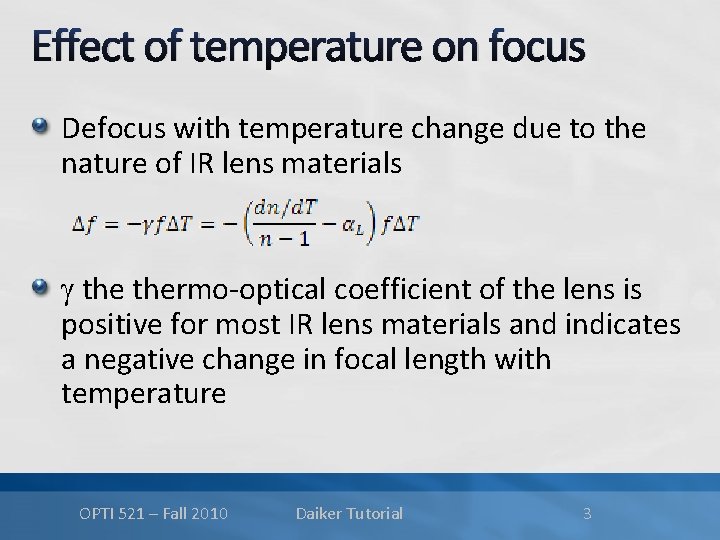
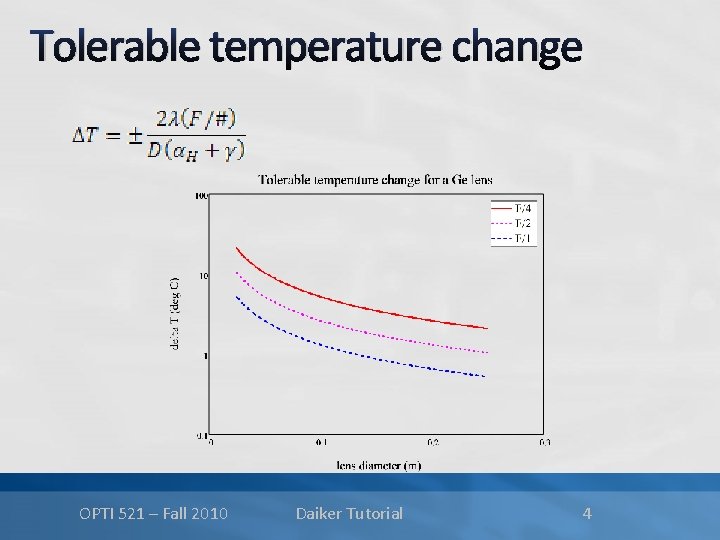
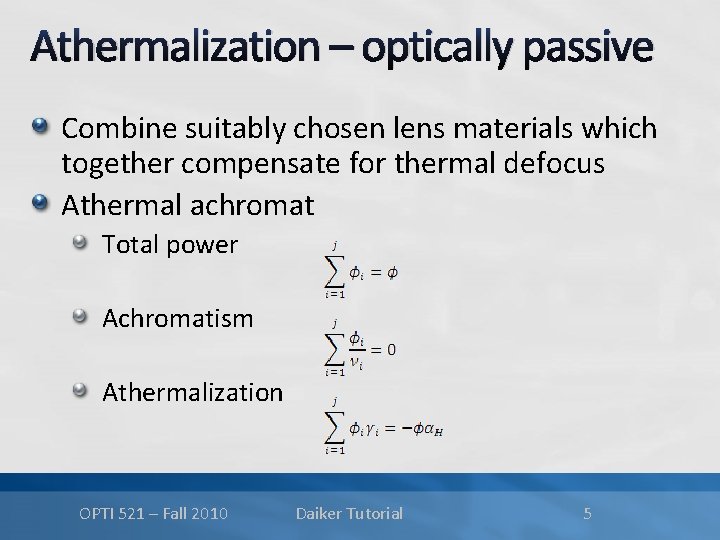
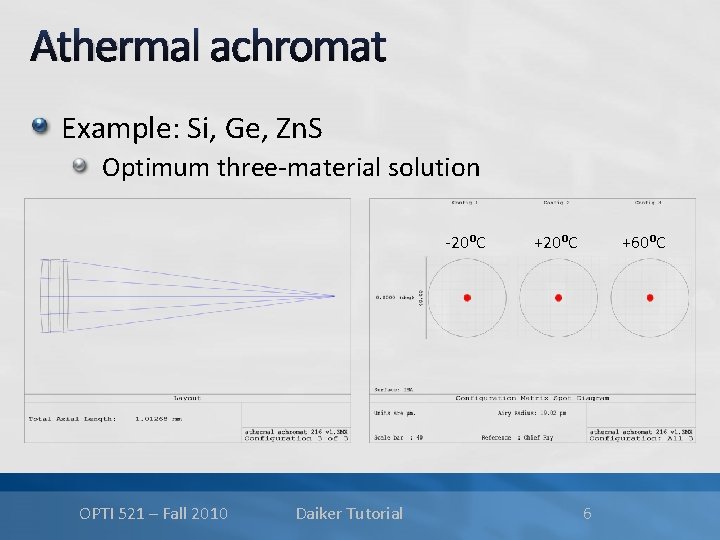
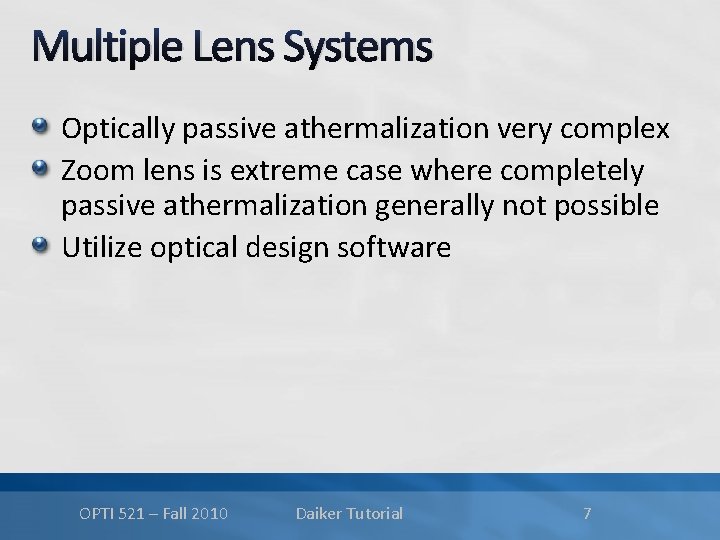
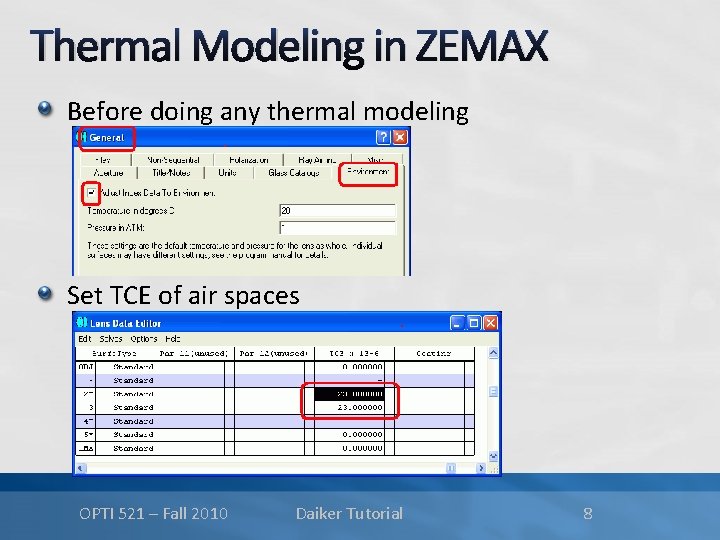
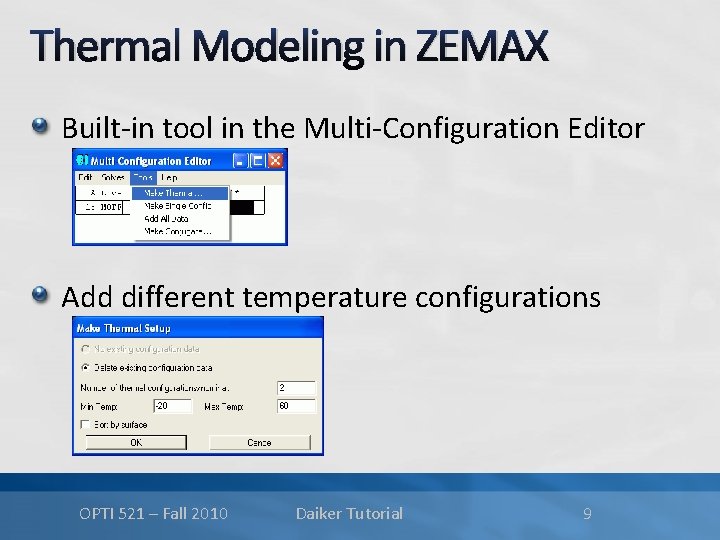
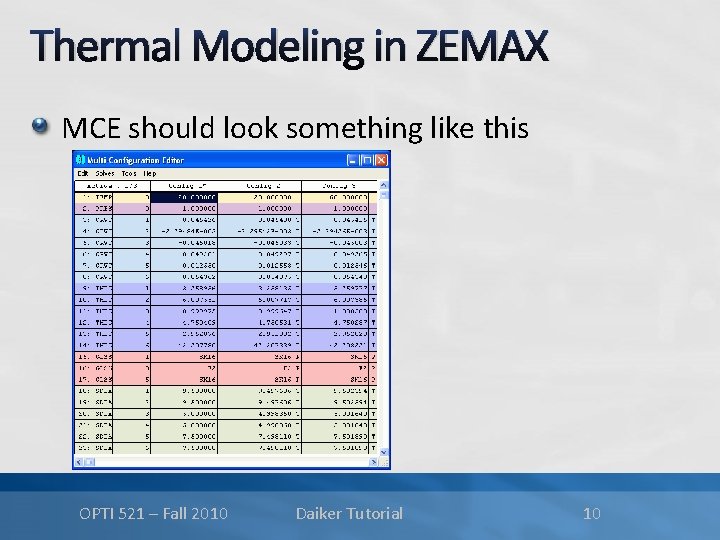
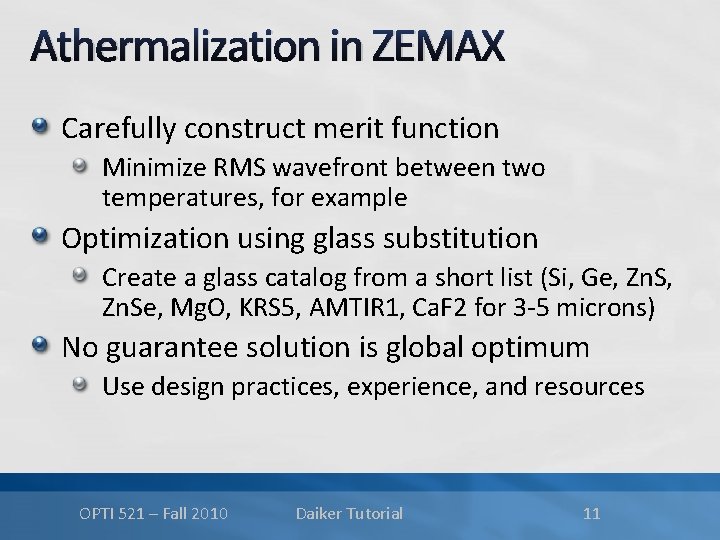
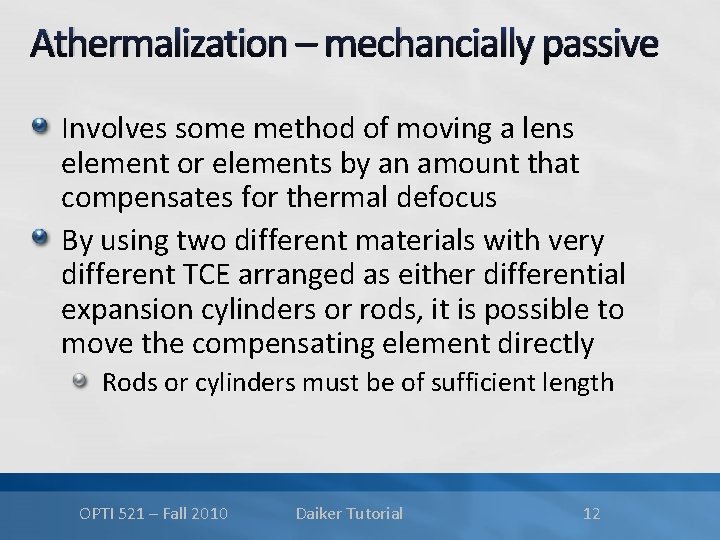
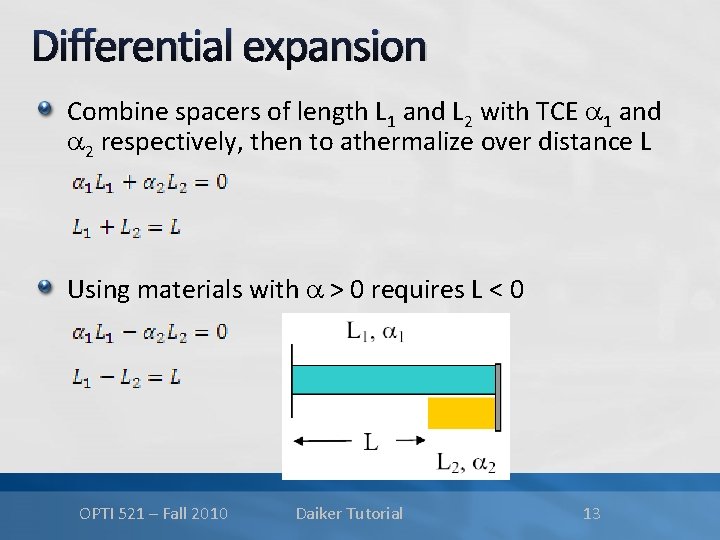
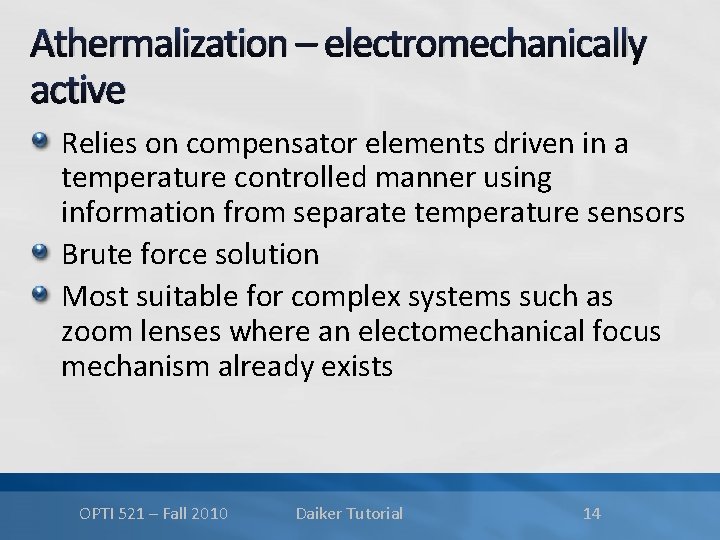
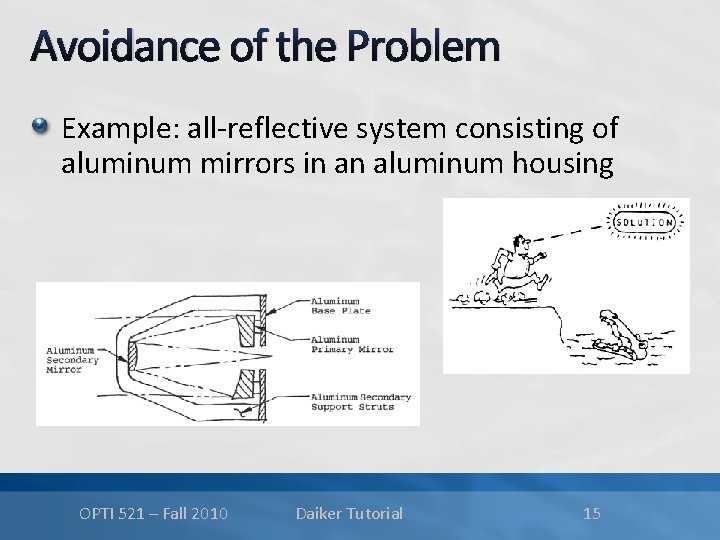
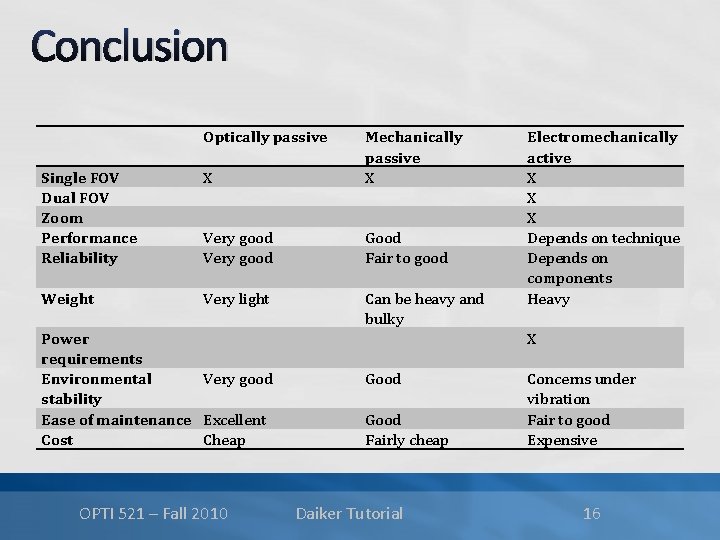
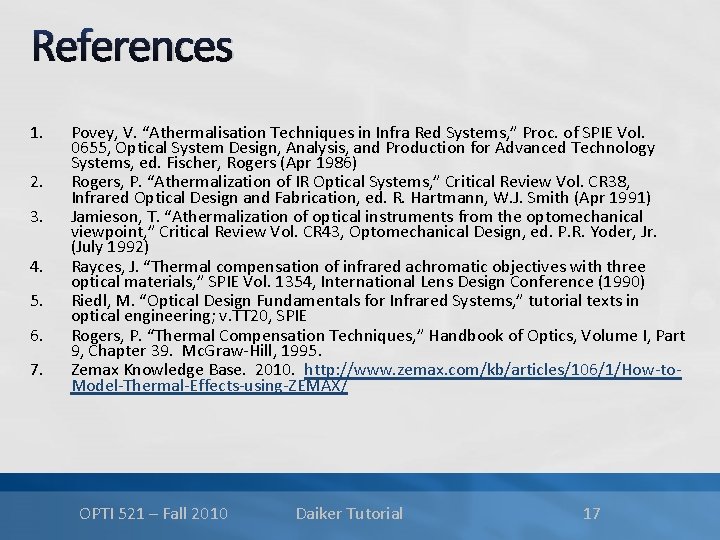
- Slides: 17
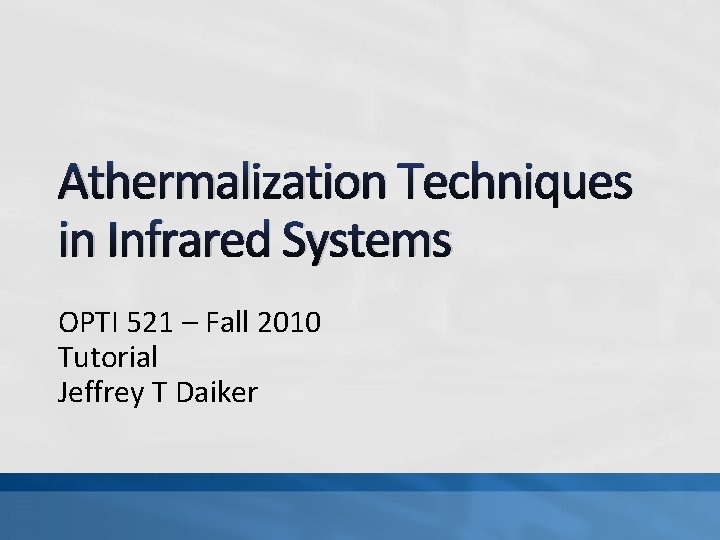
Athermalization Techniques in Infrared Systems OPTI 521 – Fall 2010 Tutorial Jeffrey T Daiker
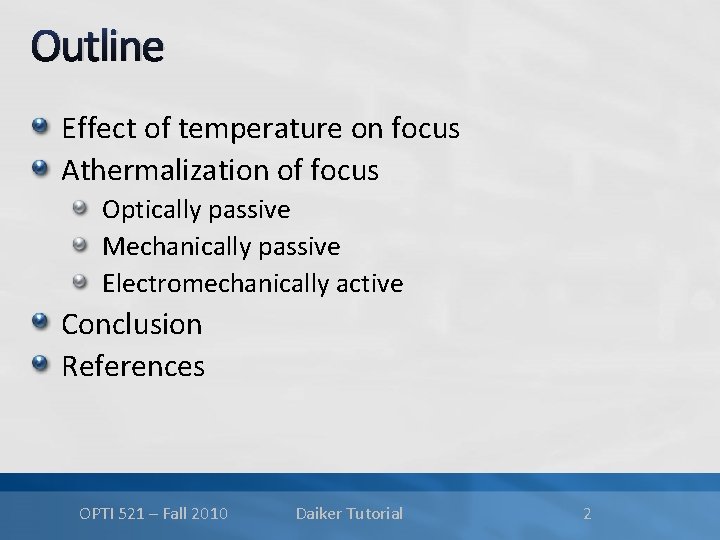
Outline Effect of temperature on focus Athermalization of focus Optically passive Mechanically passive Electromechanically active Conclusion References OPTI 521 – Fall 2010 Daiker Tutorial 2
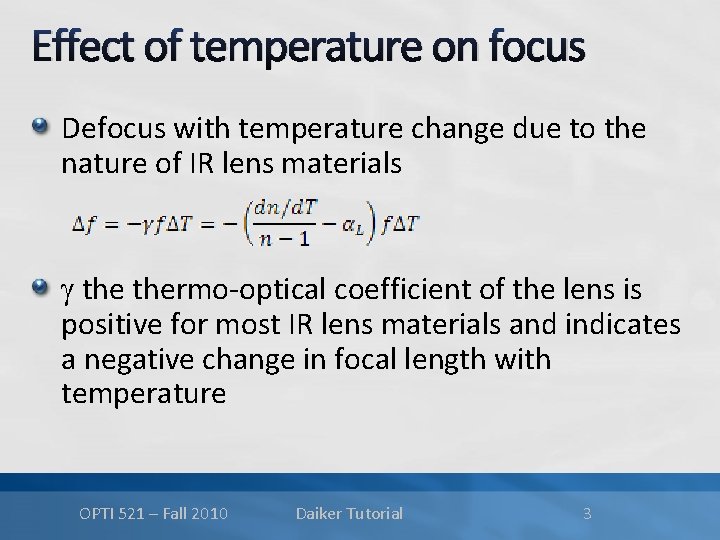
Effect of temperature on focus Defocus with temperature change due to the nature of IR lens materials g thermo-optical coefficient of the lens is positive for most IR lens materials and indicates a negative change in focal length with temperature OPTI 521 – Fall 2010 Daiker Tutorial 3
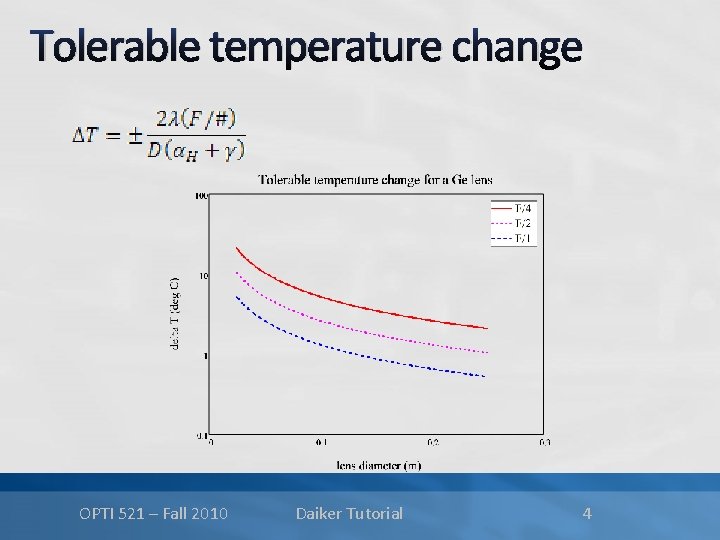
Tolerable temperature change OPTI 521 – Fall 2010 Daiker Tutorial 4
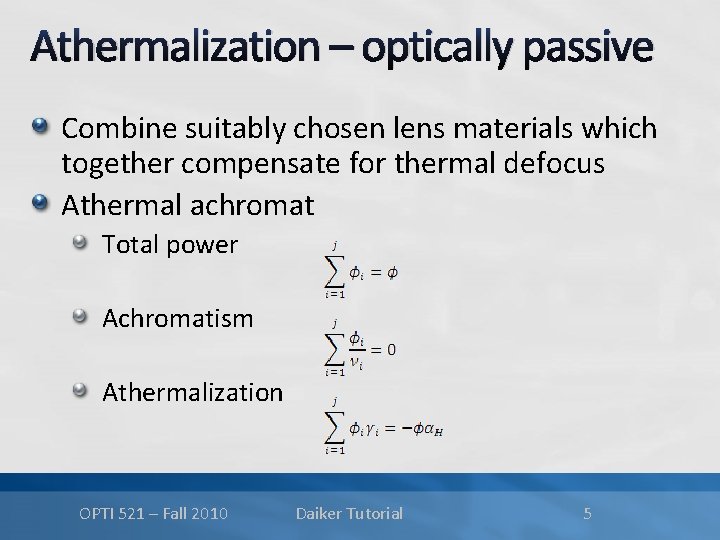
Athermalization – optically passive Combine suitably chosen lens materials which together compensate for thermal defocus Athermal achromat Total power Achromatism Athermalization OPTI 521 – Fall 2010 Daiker Tutorial 5
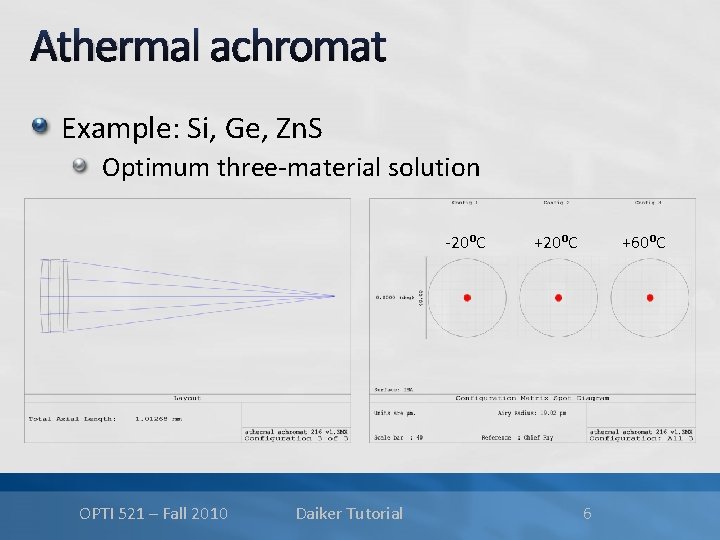
Athermal achromat Example: Si, Ge, Zn. S Optimum three-material solution -20⁰C OPTI 521 – Fall 2010 Daiker Tutorial +20⁰C +60⁰C 6
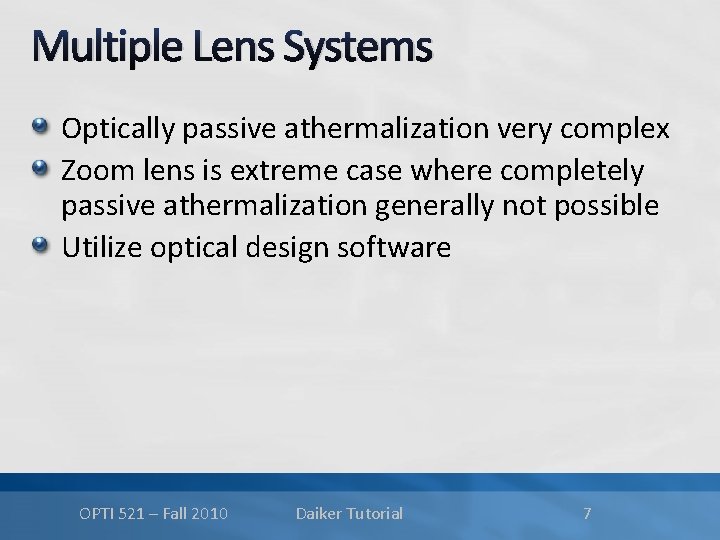
Multiple Lens Systems Optically passive athermalization very complex Zoom lens is extreme case where completely passive athermalization generally not possible Utilize optical design software OPTI 521 – Fall 2010 Daiker Tutorial 7
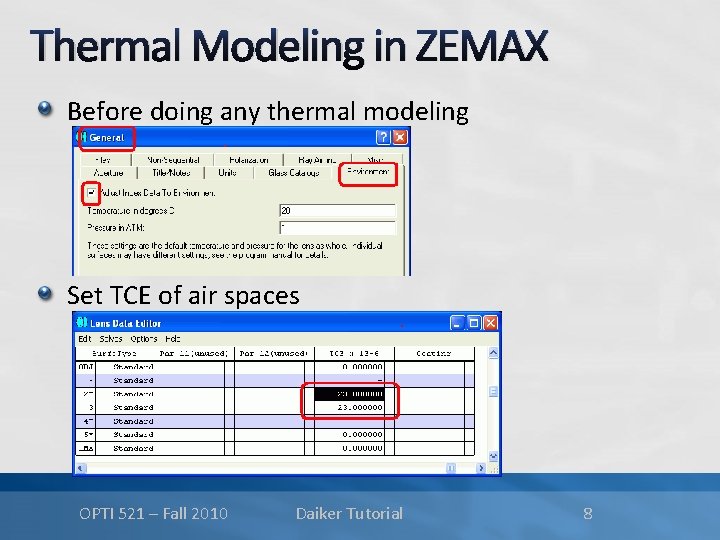
Thermal Modeling in ZEMAX Before doing any thermal modeling Set TCE of air spaces OPTI 521 – Fall 2010 Daiker Tutorial 8
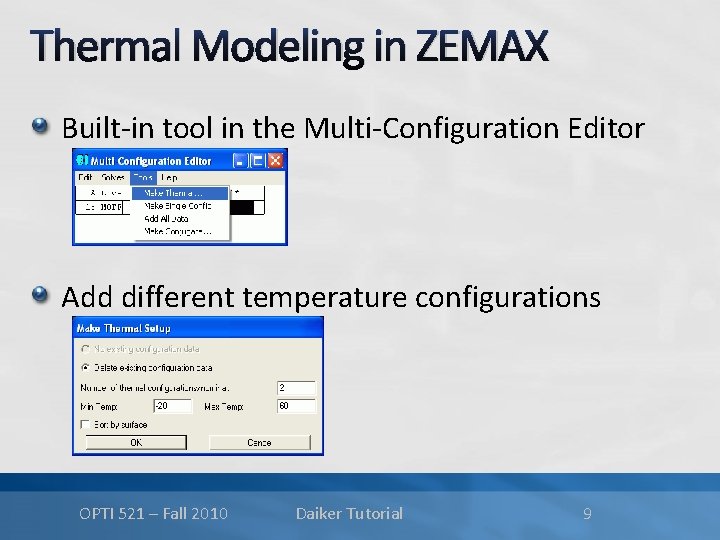
Thermal Modeling in ZEMAX Built-in tool in the Multi-Configuration Editor Add different temperature configurations OPTI 521 – Fall 2010 Daiker Tutorial 9
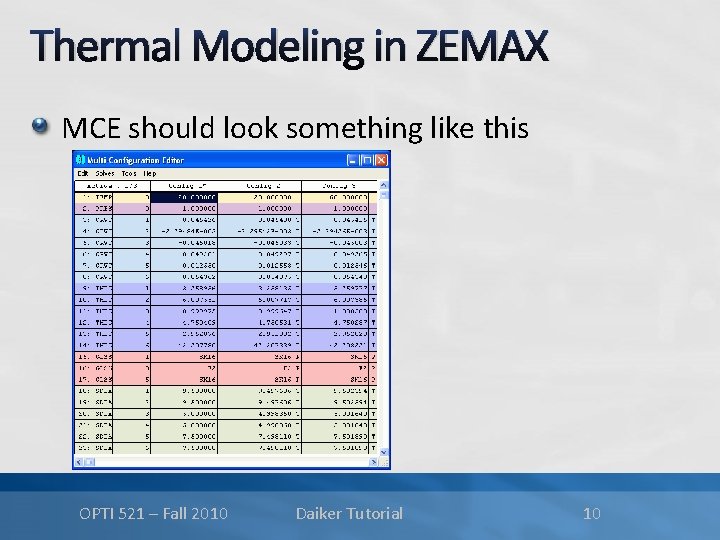
Thermal Modeling in ZEMAX MCE should look something like this OPTI 521 – Fall 2010 Daiker Tutorial 10
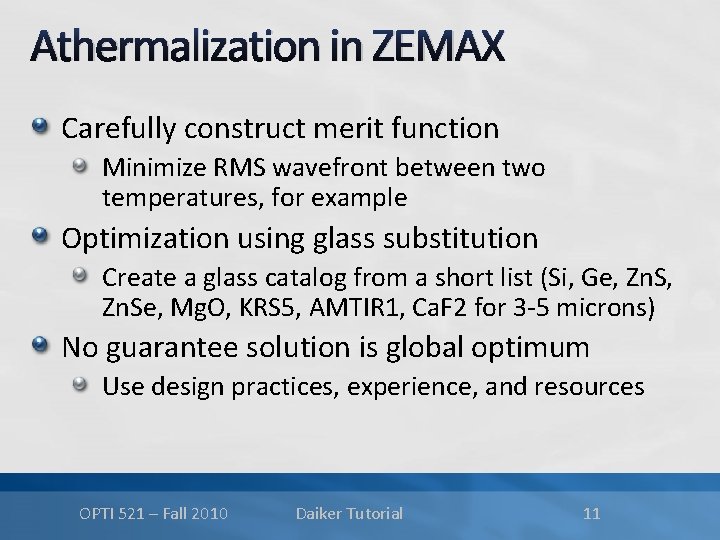
Athermalization in ZEMAX Carefully construct merit function Minimize RMS wavefront between two temperatures, for example Optimization using glass substitution Create a glass catalog from a short list (Si, Ge, Zn. Se, Mg. O, KRS 5, AMTIR 1, Ca. F 2 for 3 -5 microns) No guarantee solution is global optimum Use design practices, experience, and resources OPTI 521 – Fall 2010 Daiker Tutorial 11
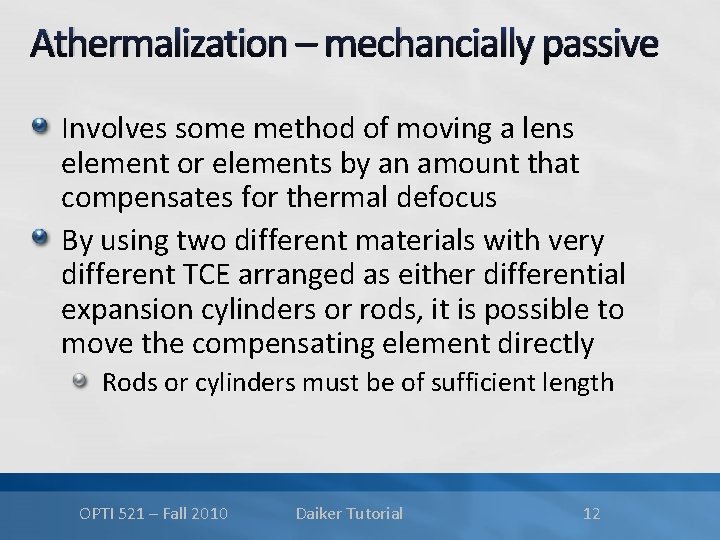
Athermalization – mechancially passive Involves some method of moving a lens element or elements by an amount that compensates for thermal defocus By using two different materials with very different TCE arranged as either differential expansion cylinders or rods, it is possible to move the compensating element directly Rods or cylinders must be of sufficient length OPTI 521 – Fall 2010 Daiker Tutorial 12
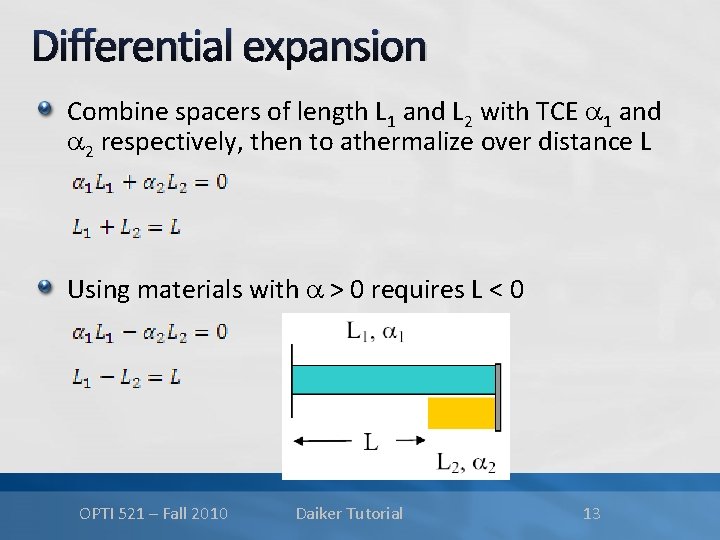
Differential expansion Combine spacers of length L 1 and L 2 with TCE a 1 and a 2 respectively, then to athermalize over distance L Using materials with a > 0 requires L < 0 OPTI 521 – Fall 2010 Daiker Tutorial 13
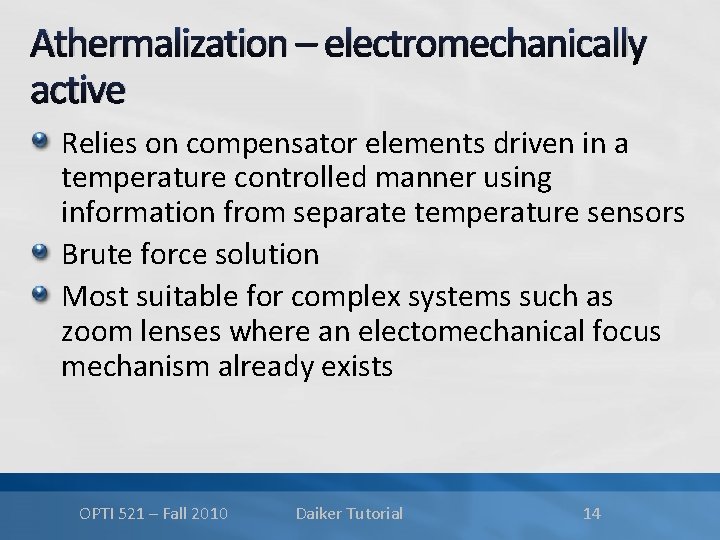
Athermalization – electromechanically active Relies on compensator elements driven in a temperature controlled manner using information from separate temperature sensors Brute force solution Most suitable for complex systems such as zoom lenses where an electomechanical focus mechanism already exists OPTI 521 – Fall 2010 Daiker Tutorial 14
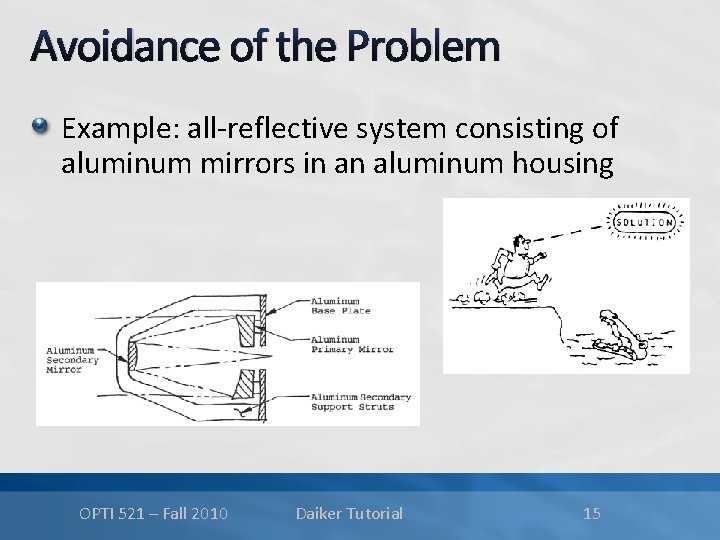
Avoidance of the Problem Example: all-reflective system consisting of aluminum mirrors in an aluminum housing OPTI 521 – Fall 2010 Daiker Tutorial 15
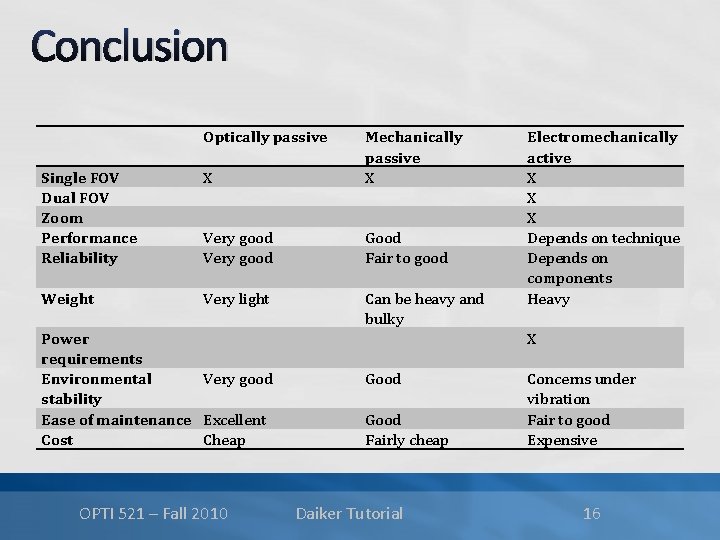
Conclusion Optically passive Single FOV Dual FOV Zoom Performance Reliability X Mechanically passive X Very good Good Fair to good Weight Very light Can be heavy and bulky Power requirements Environmental Very good stability Ease of maintenance Excellent Cost Cheap OPTI 521 – Fall 2010 Electromechanically active X X X Depends on technique Depends on components Heavy X Good Fairly cheap Daiker Tutorial Concerns under vibration Fair to good Expensive 16
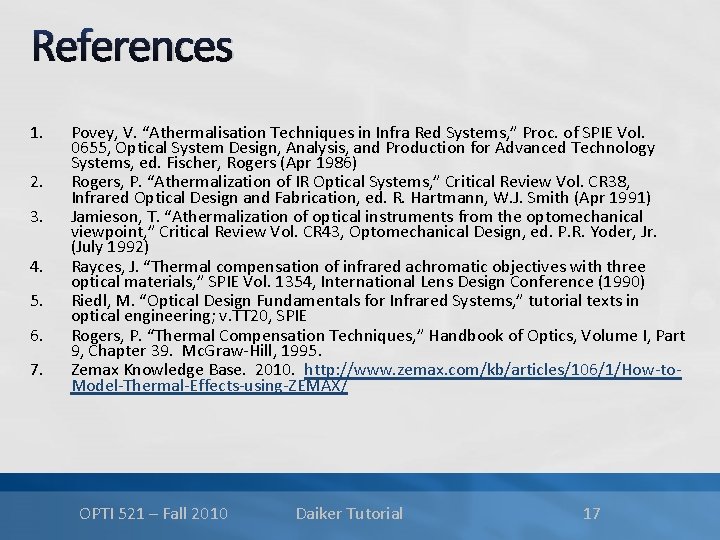
References 1. 2. 3. 4. 5. 6. 7. Povey, V. “Athermalisation Techniques in Infra Red Systems, ” Proc. of SPIE Vol. 0655, Optical System Design, Analysis, and Production for Advanced Technology Systems, ed. Fischer, Rogers (Apr 1986) Rogers, P. “Athermalization of IR Optical Systems, ” Critical Review Vol. CR 38, Infrared Optical Design and Fabrication, ed. R. Hartmann, W. J. Smith (Apr 1991) Jamieson, T. “Athermalization of optical instruments from the optomechanical viewpoint, ” Critical Review Vol. CR 43, Optomechanical Design, ed. P. R. Yoder, Jr. (July 1992) Rayces, J. “Thermal compensation of infrared achromatic objectives with three optical materials, ” SPIE Vol. 1354, International Lens Design Conference (1990) Riedl, M. “Optical Design Fundamentals for Infrared Systems, ” tutorial texts in optical engineering; v. TT 20, SPIE Rogers, P. “Thermal Compensation Techniques, ” Handbook of Optics, Volume I, Part 9, Chapter 39. Mc. Graw-Hill, 1995. Zemax Knowledge Base. 2010. http: //www. zemax. com/kb/articles/106/1/How-to. Model-Thermal-Effects-using-ZEMAX/ OPTI 521 – Fall 2010 Daiker Tutorial 17