2016 Kappa Electronics Motor Control Training Series 2016
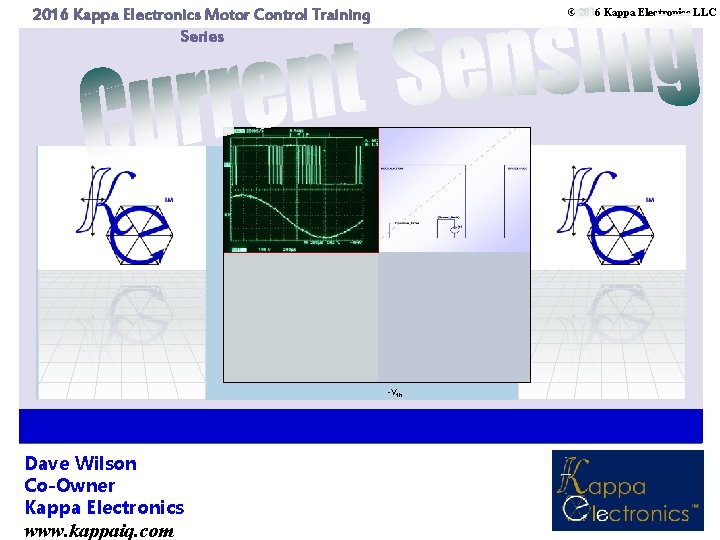
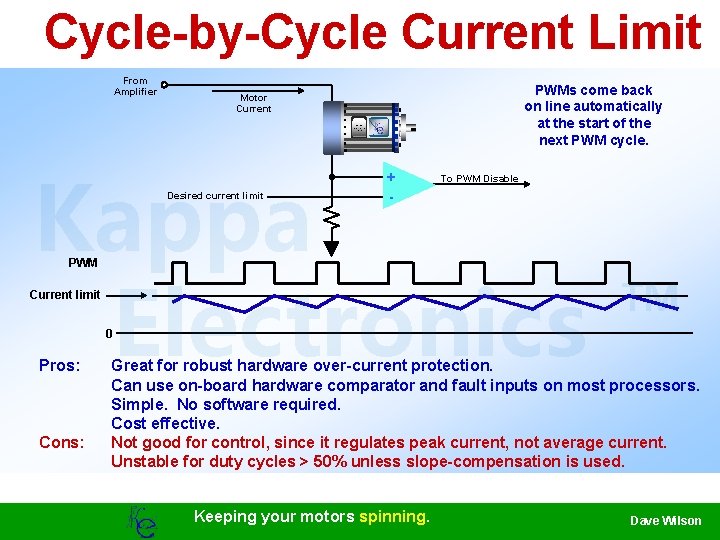
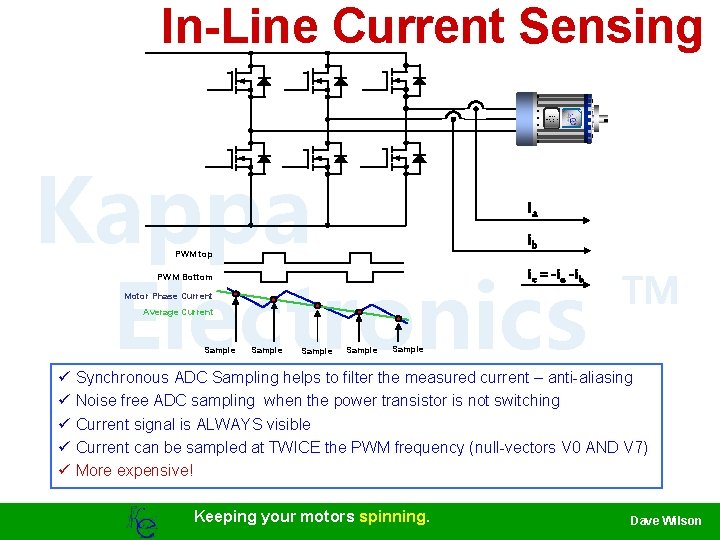
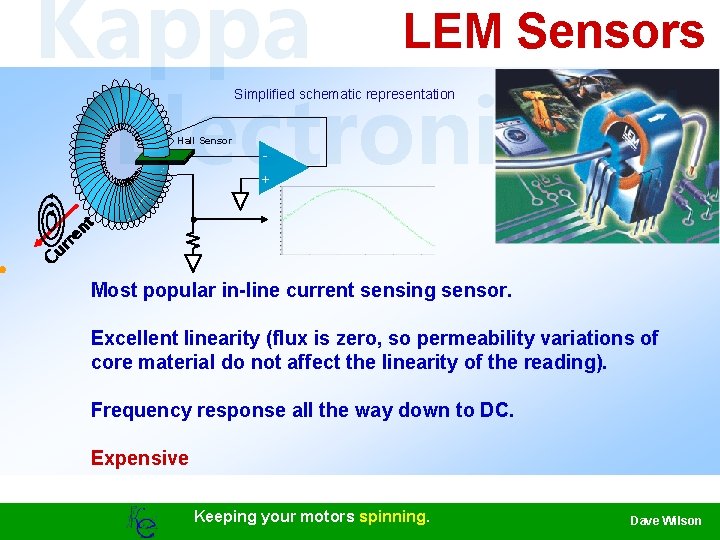

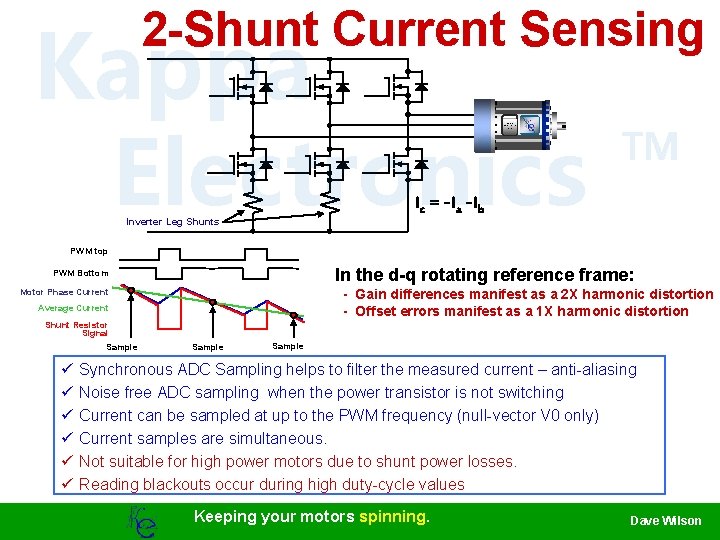
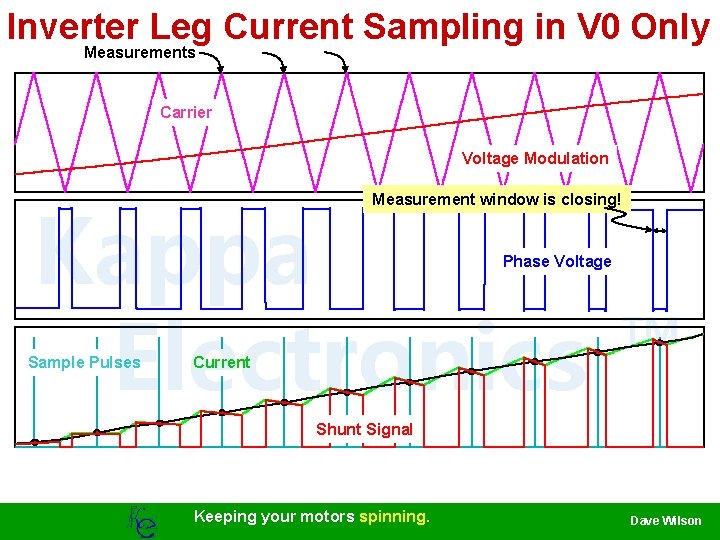
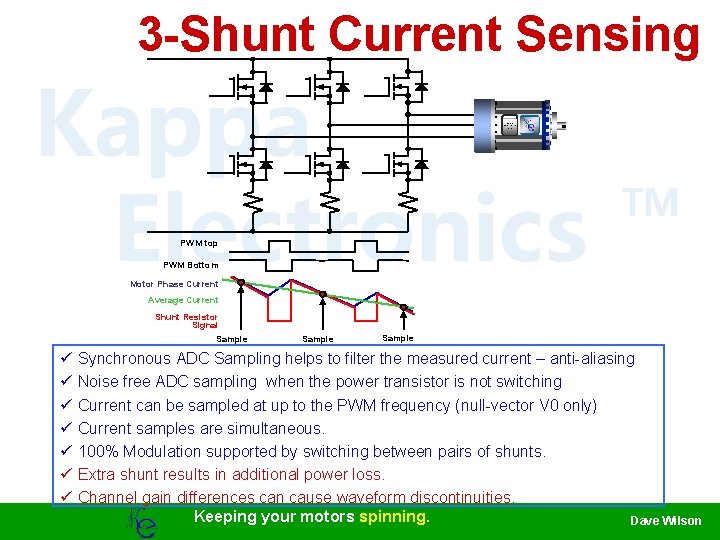
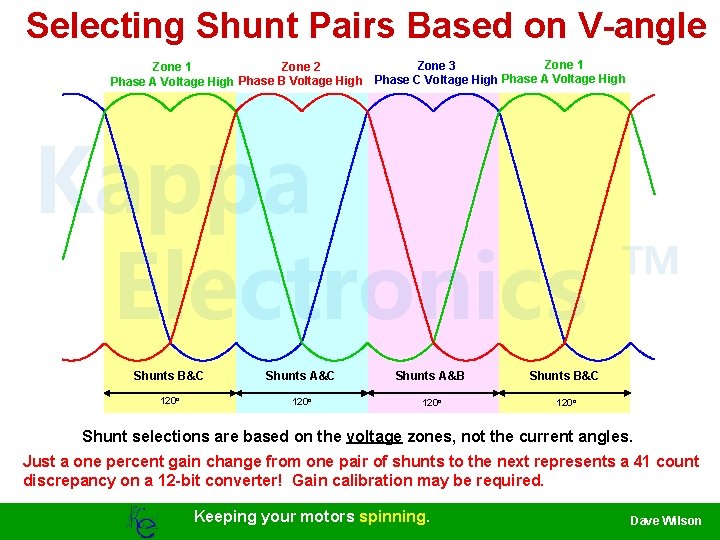
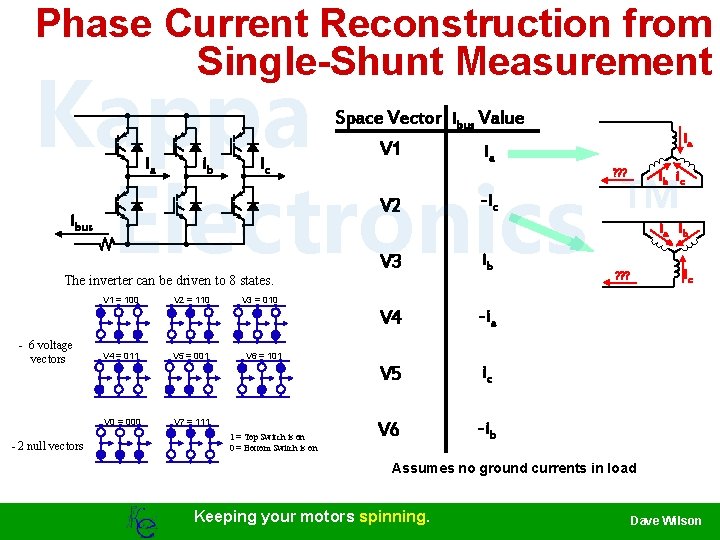
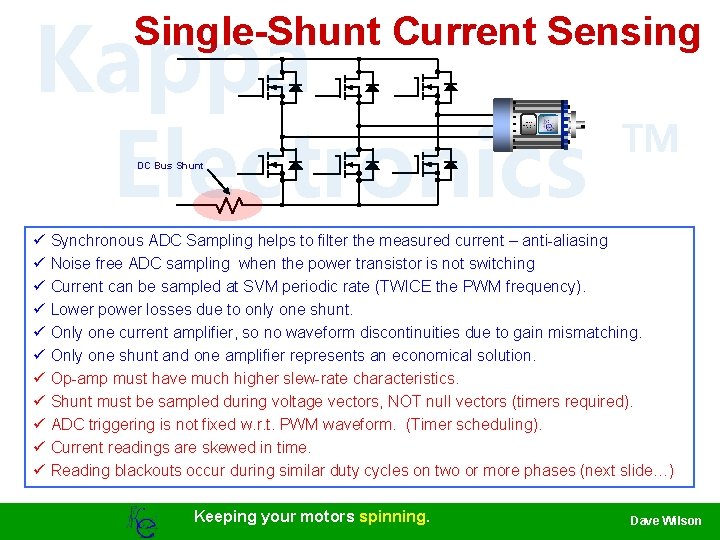
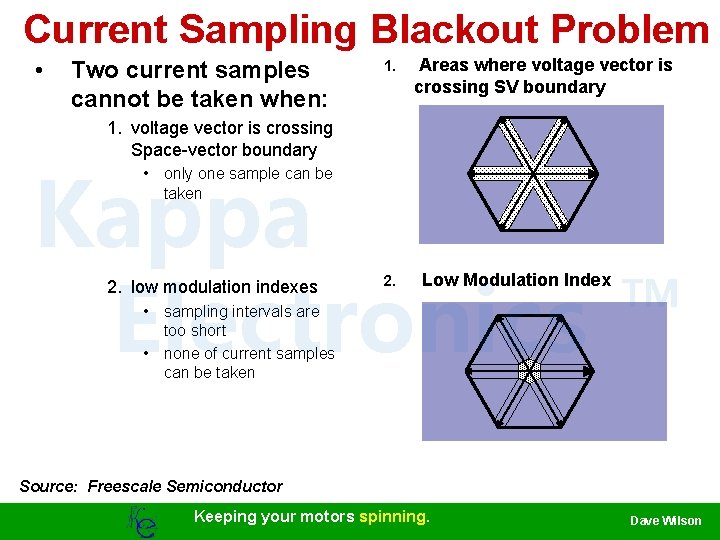
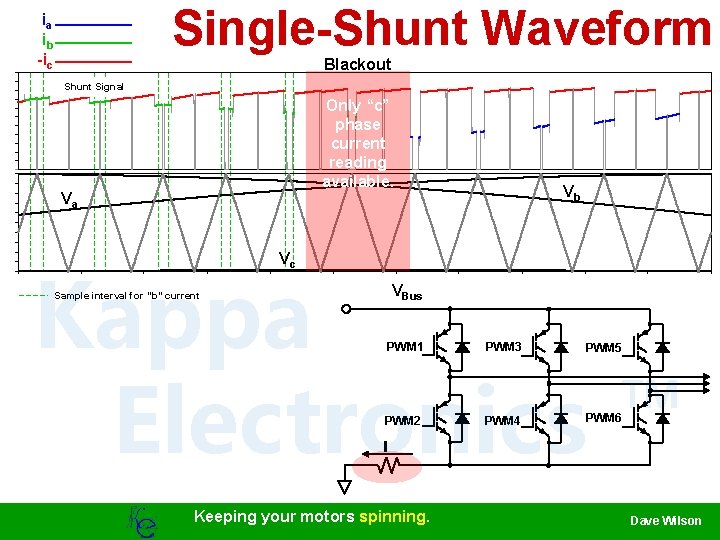
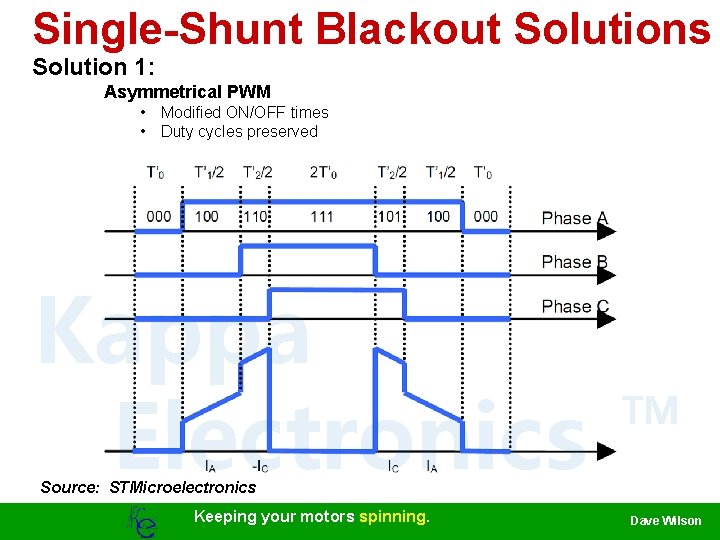
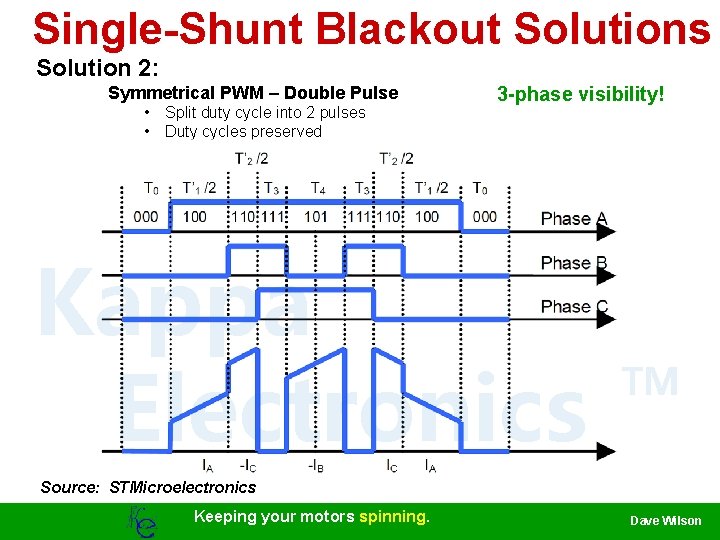
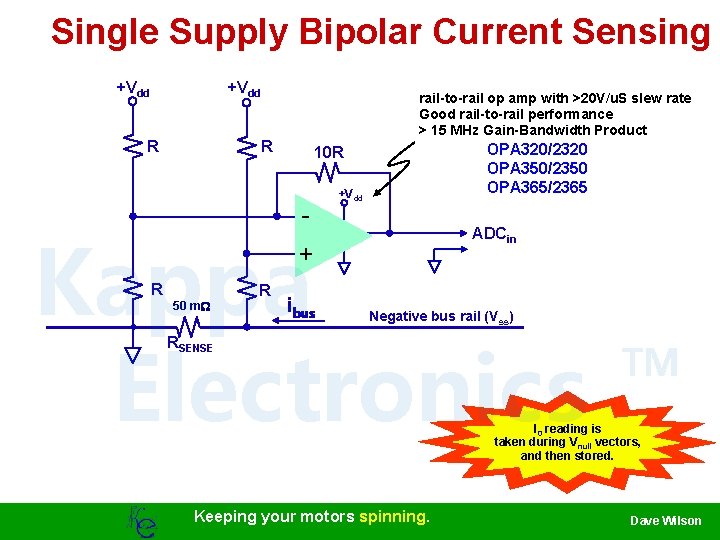
- Slides: 16
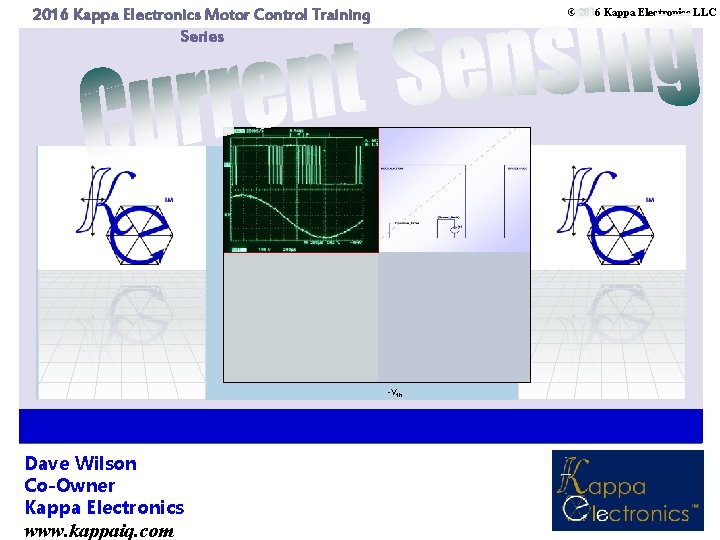
2016 Kappa Electronics Motor Control Training Series © 2016 Kappa Electronics LLC -Vth Dave Wilson Co-Owner Kappa Electronics www. kappaiq. com
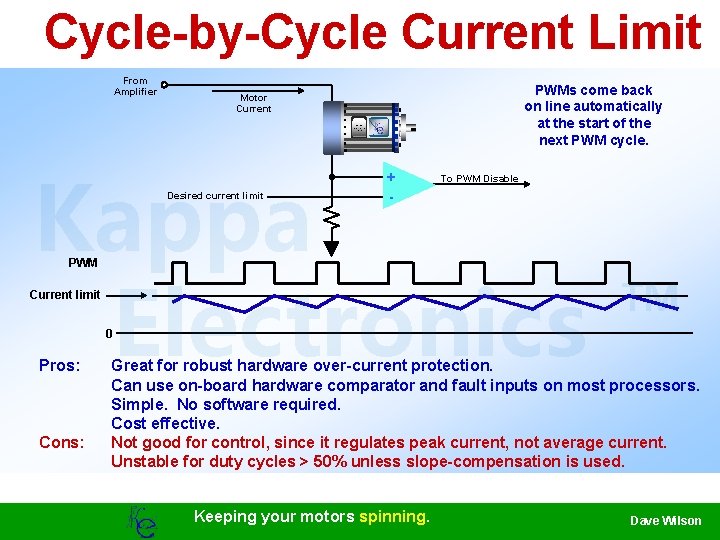
Cycle-by-Cycle Current Limit From Amplifier PWMs come back on line automatically at the start of the next PWM cycle. Motor Current Dave’s Motor Control Center Kappa Electronics Desired current limit + - To PWM Disable PWM Current limit TM 0 Pros: Cons: Great for robust hardware over-current protection. Can use on-board hardware comparator and fault inputs on most processors. Simple. No software required. Cost effective. Not good for control, since it regulates peak current, not average current. Unstable for duty cycles > 50% unless slope-compensation is used. Keeping your motors spinning. Dave Wilson
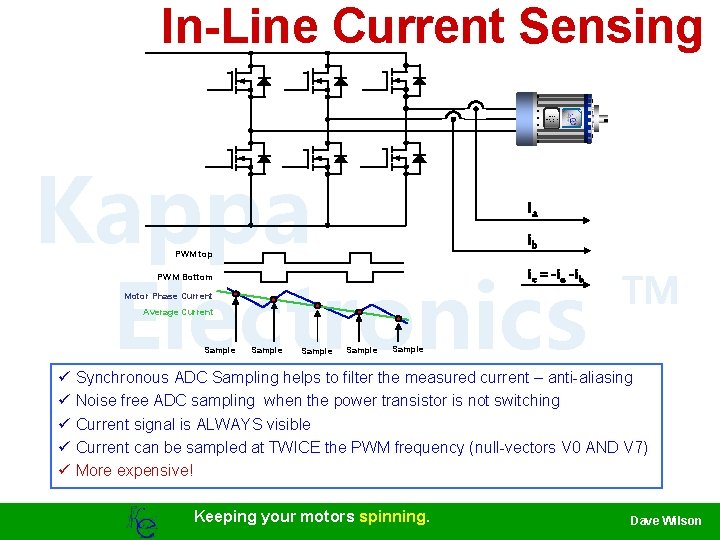
In-Line Current Sensing Dave’s Motor Control Center Kappa Electronics ia ib PWM top ic = -ia -ib PWM Bottom Motor Phase Current Average Current Sample ü ü ü Sample TM Sample Synchronous ADC Sampling helps to filter the measured current – anti-aliasing Noise free ADC sampling when the power transistor is not switching Current signal is ALWAYS visible Current can be sampled at TWICE the PWM frequency (null-vectors V 0 AND V 7) More expensive! Keeping your motors spinning. Dave Wilson
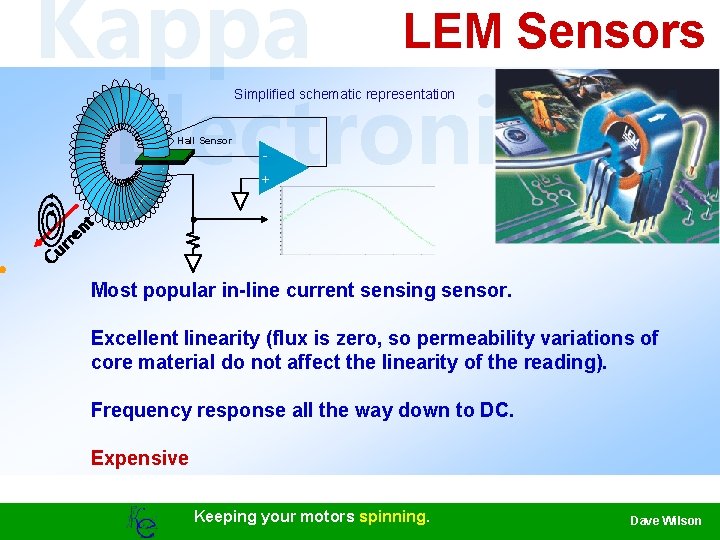
Kappa LEM Sensors TM Electronics Simplified schematic representation Hall Sensor - + t n re r Cu Most popular in-line current sensing sensor. Excellent linearity (flux is zero, so permeability variations of core material do not affect the linearity of the reading). Frequency response all the way down to DC. Expensive Keeping your motors spinning. Dave Wilson

In-Line Current Sampling in Both V 0 and V 7 Measurements Kappa Electronics Carrier Voltage Modulation TM Phase Voltage Sample Pulses Keeping your motors spinning. Phase Current Dave Wilson
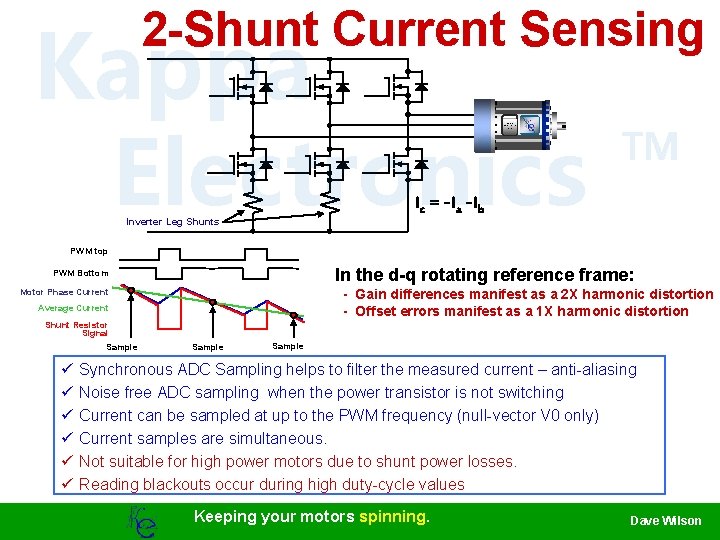
2 -Shunt Current Sensing Kappa Electronics Dave’s Motor Control Center TM ic = -ia -ib Inverter Leg Shunts PWM top In the d-q rotating reference frame: PWM Bottom - Gain differences manifest as a 2 X harmonic distortion - Offset errors manifest as a 1 X harmonic distortion Motor Phase Current Average Current Shunt Resistor Signal Sample ü ü ü Sample Synchronous ADC Sampling helps to filter the measured current – anti-aliasing Noise free ADC sampling when the power transistor is not switching Current can be sampled at up to the PWM frequency (null-vector V 0 only) Current samples are simultaneous. Not suitable for high power motors due to shunt power losses. Reading blackouts occur during high duty-cycle values Keeping your motors spinning. Dave Wilson
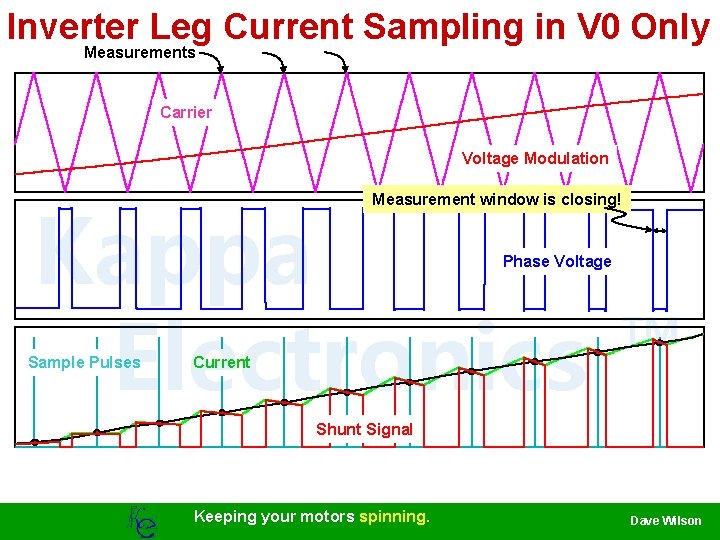
Inverter Leg Current Sampling in V 0 Only Measurements Carrier Voltage Modulation Measurement window is closing! Kappa Electronics Phase Voltage Sample Pulses Current TM Shunt Signal Keeping your motors spinning. Dave Wilson
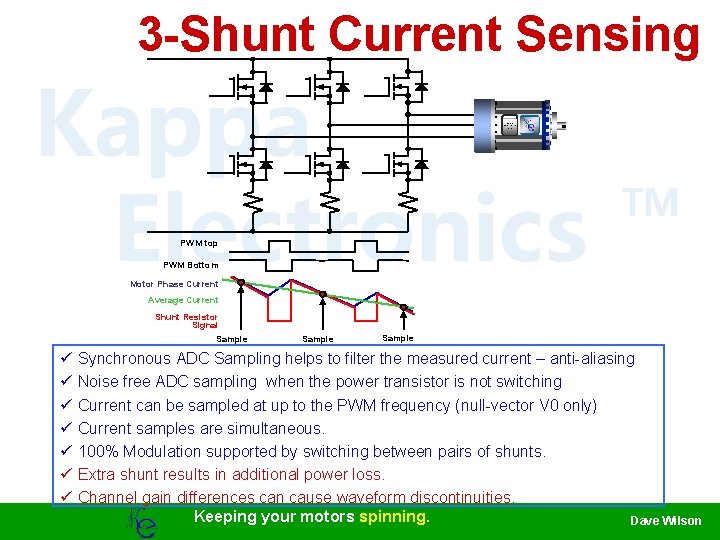
3 -Shunt Current Sensing Kappa Electronics Dave’s Motor Control Center TM PWM top PWM Bottom Motor Phase Current Average Current Shunt Resistor Signal Sample ü ü ü ü Sample Synchronous ADC Sampling helps to filter the measured current – anti-aliasing Noise free ADC sampling when the power transistor is not switching Current can be sampled at up to the PWM frequency (null-vector V 0 only) Current samples are simultaneous. 100% Modulation supported by switching between pairs of shunts. Extra shunt results in additional power loss. Channel gain differences can cause waveform discontinuities. Keeping your motors spinning. Dave Wilson
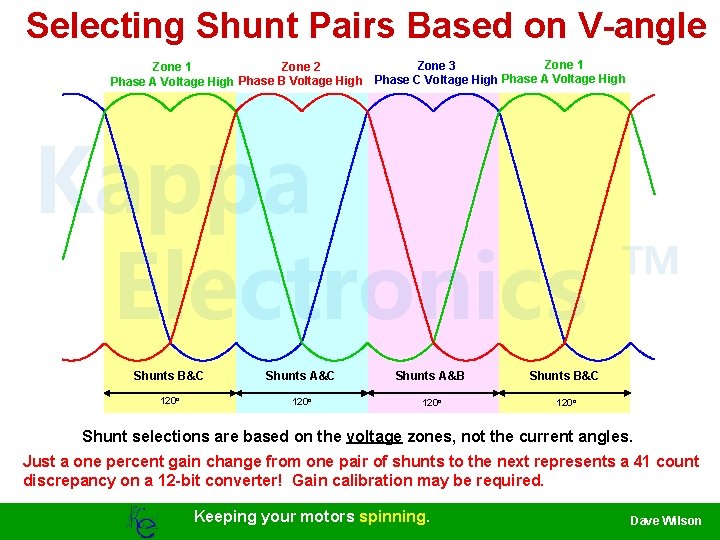
Selecting Shunt Pairs Based on V-angle Zone 1 Zone 3 Zone 2 Zone 1 Phase A Voltage High Phase B Voltage High Phase C Voltage High Kappa Electronics Shunts B&C Shunts A&B Shunts B&C 120 o TM Shunt selections are based on the voltage zones, not the current angles. Just a one percent gain change from one pair of shunts to the next represents a 41 count discrepancy on a 12 -bit converter! Gain calibration may be required. Keeping your motors spinning. Dave Wilson
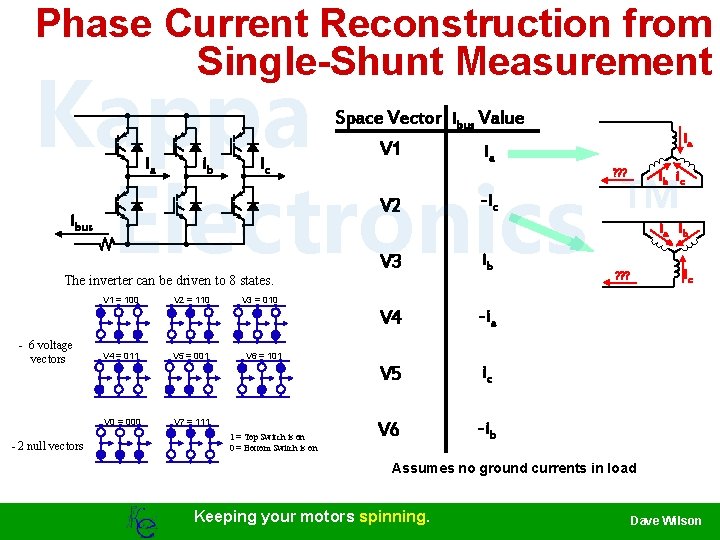
Phase Current Reconstruction from Single-Shunt Measurement Kappa Electronics Space Vector ibus Value ia ib ic V 2 ibus The inverter can be driven to 8 states. V 1 = 100 - 6 voltage vectors V 4 = 011 V 0 = 000 - 2 null vectors V 1 V 2 = 110 V 5 = 001 ia -ic V 3 ib V 4 -ia V 5 ic V 6 -ib V 3 = 010 ia ? ? ? ib ic TM ia ib ic ? ? ? V 6 = 101 V 7 = 111 1 = Top Switch is on 0 = Bottom Switch is on Assumes no ground currents in load Keeping your motors spinning. Dave Wilson
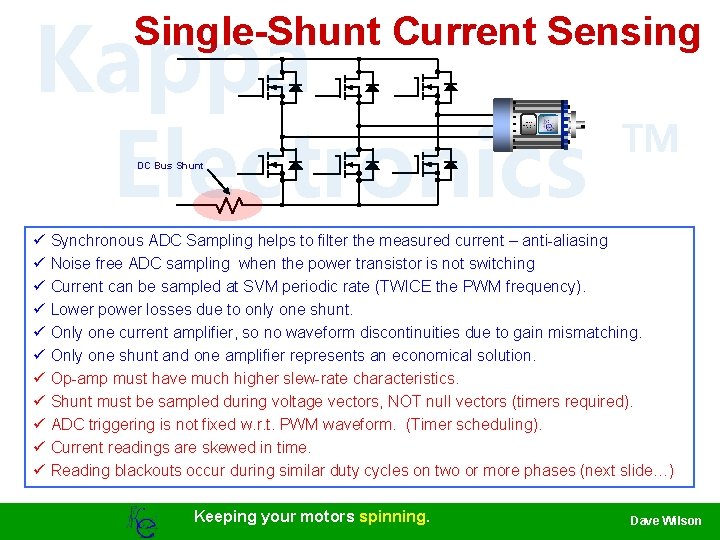
Kappa Electronics Single-Shunt Current Sensing Dave’s Motor Control Center DC Bus Shunt ü ü ü TM Synchronous ADC Sampling helps to filter the measured current – anti-aliasing Noise free ADC sampling when the power transistor is not switching Current can be sampled at SVM periodic rate (TWICE the PWM frequency). Lower power losses due to only one shunt. Only one current amplifier, so no waveform discontinuities due to gain mismatching. Only one shunt and one amplifier represents an economical solution. Op-amp must have much higher slew-rate characteristics. Shunt must be sampled during voltage vectors, NOT null vectors (timers required). ADC triggering is not fixed w. r. t. PWM waveform. (Timer scheduling). Current readings are skewed in time. Reading blackouts occur during similar duty cycles on two or more phases (next slide…) Keeping your motors spinning. Dave Wilson
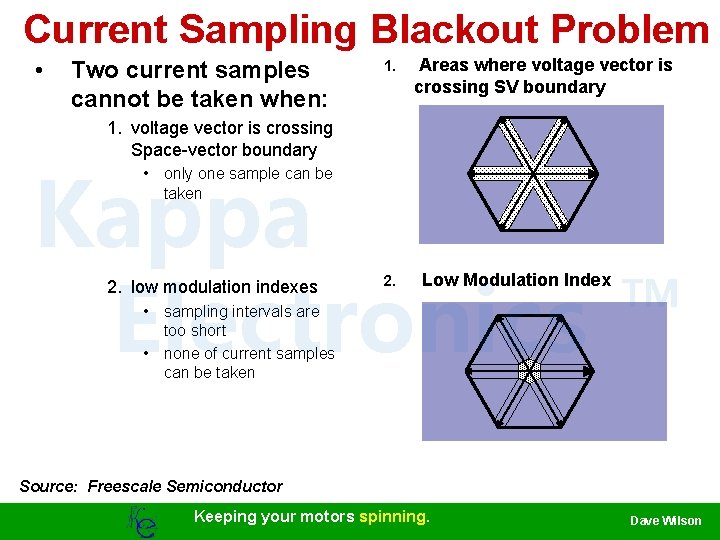
Current Sampling Blackout Problem • Two current samples cannot be taken when: 1. Areas where voltage vector is crossing SV boundary 1. voltage vector is crossing Space-vector boundary Kappa Electronics • only one sample can be taken 2. low modulation indexes 2. Low Modulation Index • sampling intervals are too short • none of current samples can be taken TM Source: Freescale Semiconductor Keeping your motors spinning. Dave Wilson
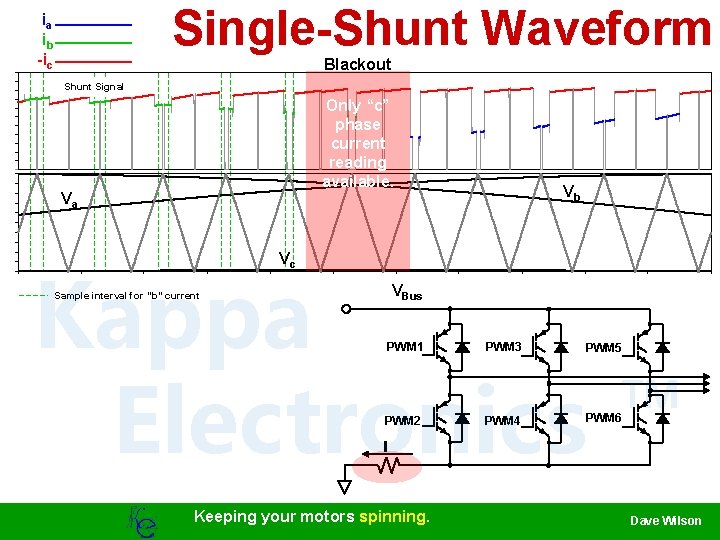
Single-Shunt Waveform ia ib -ic Blackout Shunt Signal Only “c” phase current reading available. Va Vb Vc Kappa Electronics VBus Sample interval for “b” current PWM 1 PWM 2 PWM 3 PWM 5 PWM 4 PWM 6 TM i Keeping your motors spinning. Dave Wilson
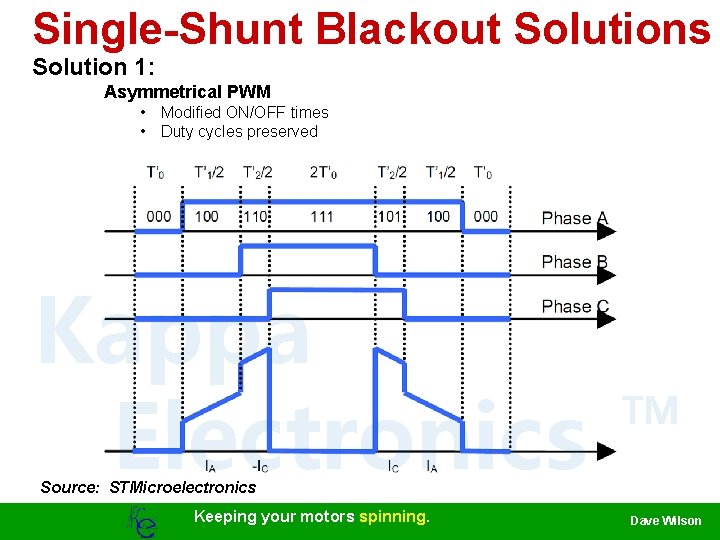
Single-Shunt Blackout Solutions Solution 1: Asymmetrical PWM • Modified ON/OFF times • Duty cycles preserved Kappa Electronics TM Source: STMicroelectronics Keeping your motors spinning. Dave Wilson
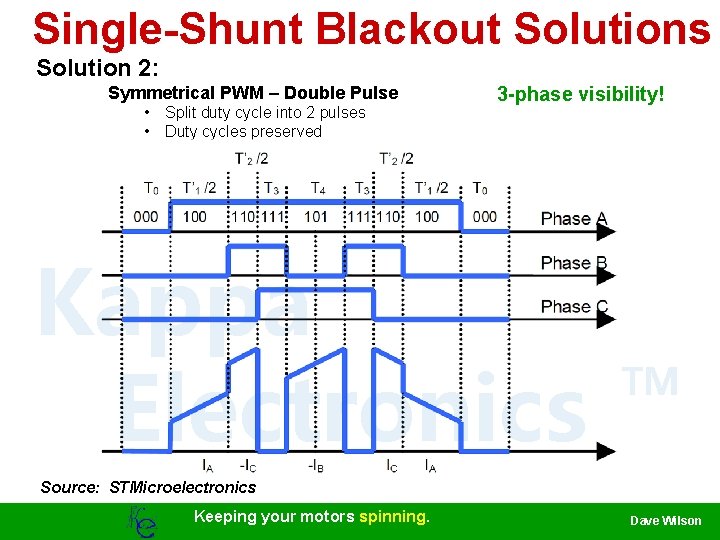
Single-Shunt Blackout Solutions Solution 2: Symmetrical PWM – Double Pulse • Split duty cycle into 2 pulses • Duty cycles preserved 3 -phase visibility! Kappa Electronics TM Source: STMicroelectronics Keeping your motors spinning. Dave Wilson
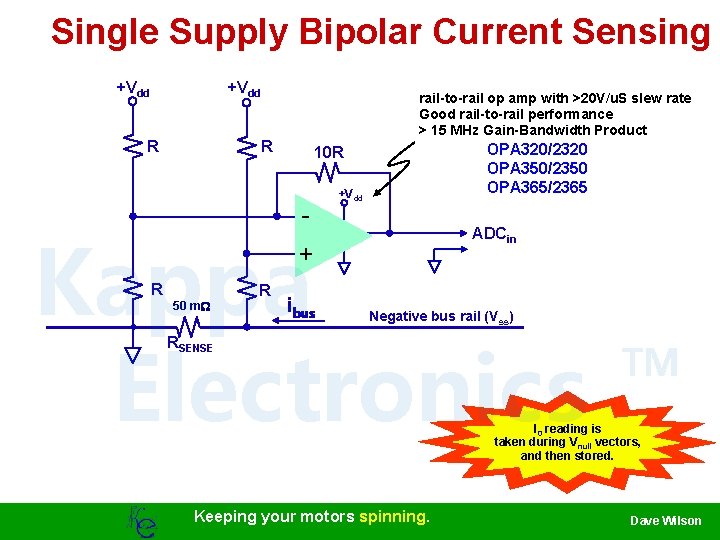
Single Supply Bipolar Current Sensing +Vdd R rail-to-rail op amp with >20 V/u. S slew rate Good rail-to-rail performance > 15 MHz Gain-Bandwidth Product R OPA 320/2320 OPA 350/2350 OPA 365/2365 10 R - +Vdd Kappa Electronics ADCin + R R 50 m. W ibus Negative bus rail (Vss) RSENSE TM I 0 reading is taken during Vnull vectors, and then stored. Keeping your motors spinning. Dave Wilson
Kappa electronics
Kappa electronics
Kappa electronics
An ideal traction system should have
Digital motor electronics bmw
Enem ppl 2016 para reciclar um motor
Three phase synchronous generator
A motor unit consists of a motor neuron and
Principle of synchronous motor
Ac motor vs dc motor
Ee 216
Torque speed characteristics of dc series motor
Maclaurin series vs taylor series
Balmer series lyman series
Taylor series of composite function
Deret maclaurin
Ibm p series