WP 10 RFQ 3 design Alexej Grudiev 5
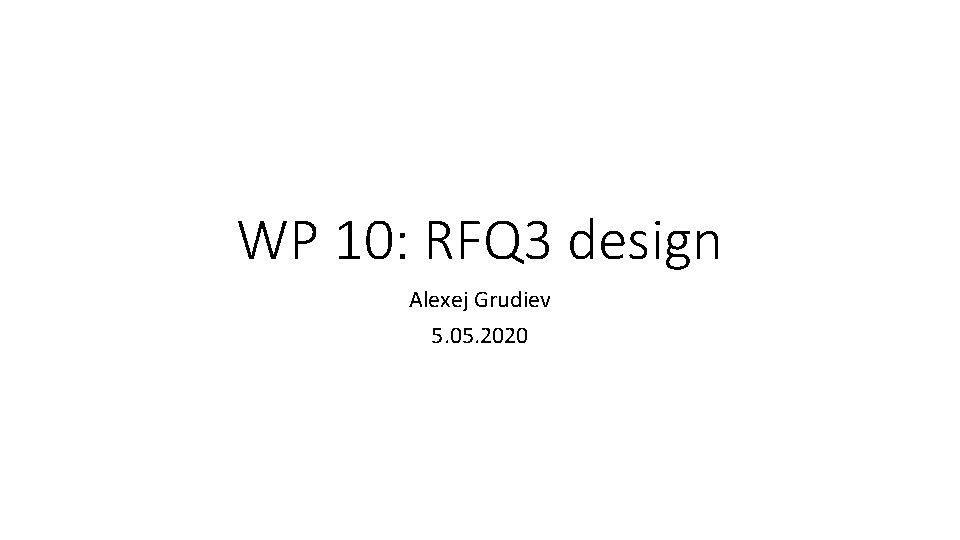
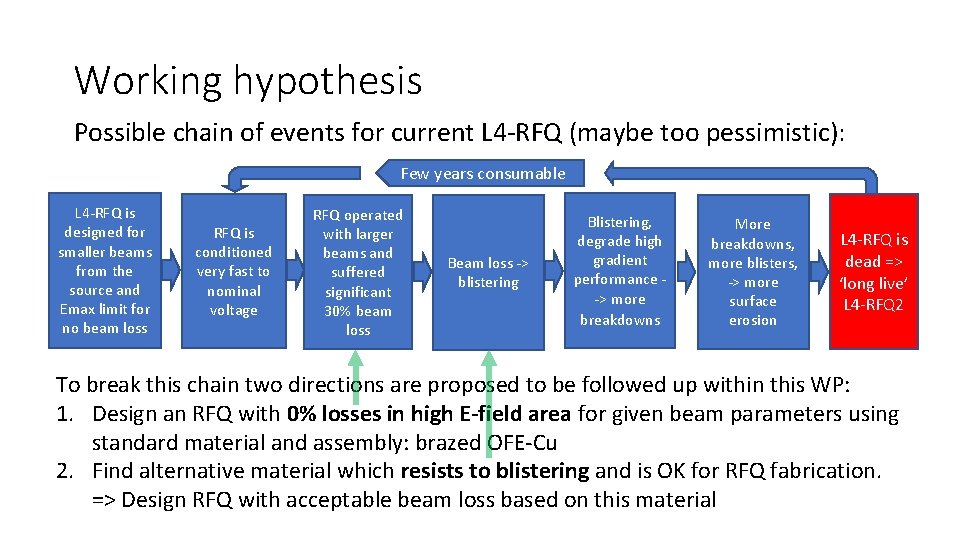
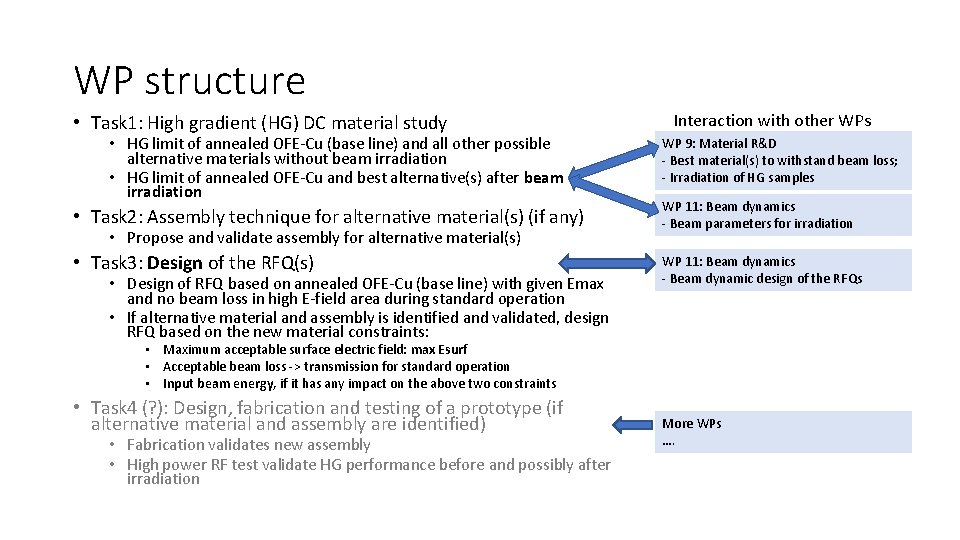
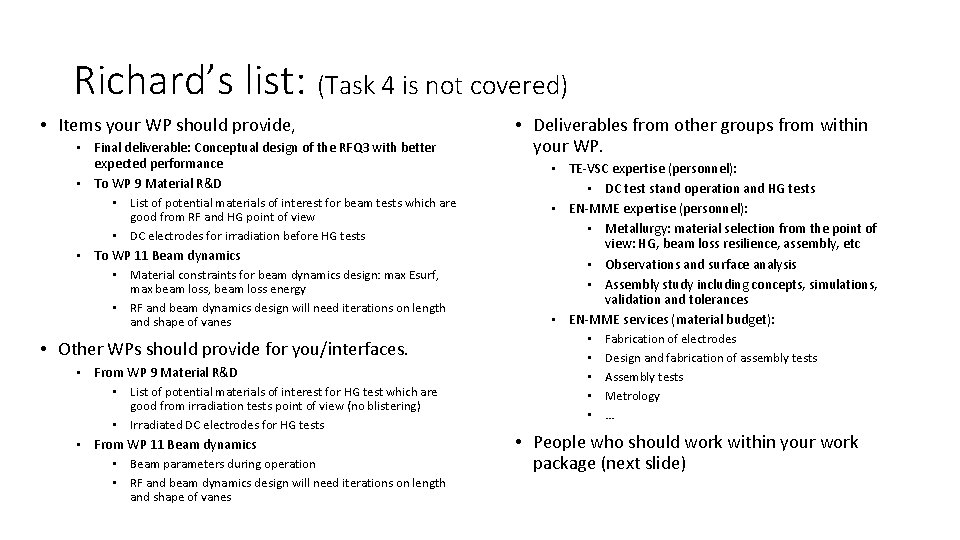
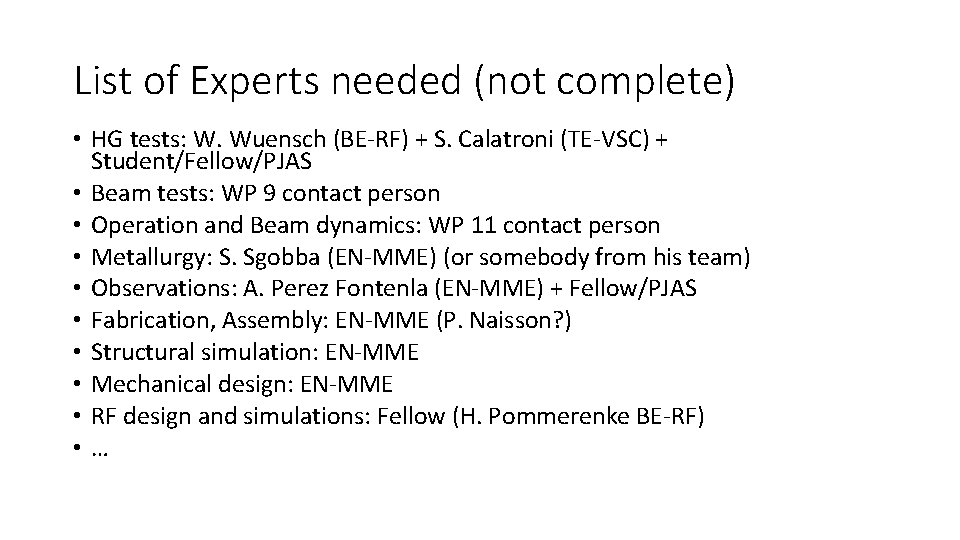
- Slides: 5
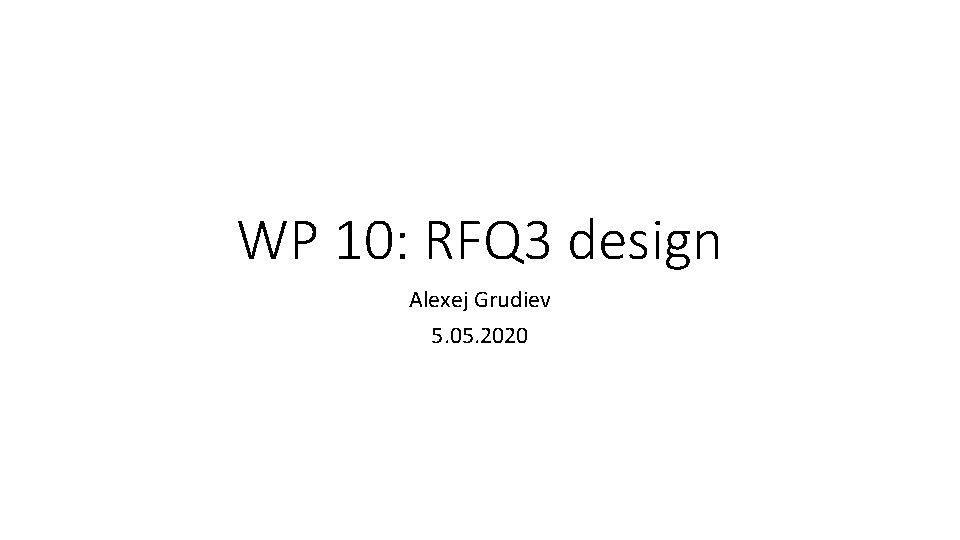
WP 10: RFQ 3 design Alexej Grudiev 5. 05. 2020
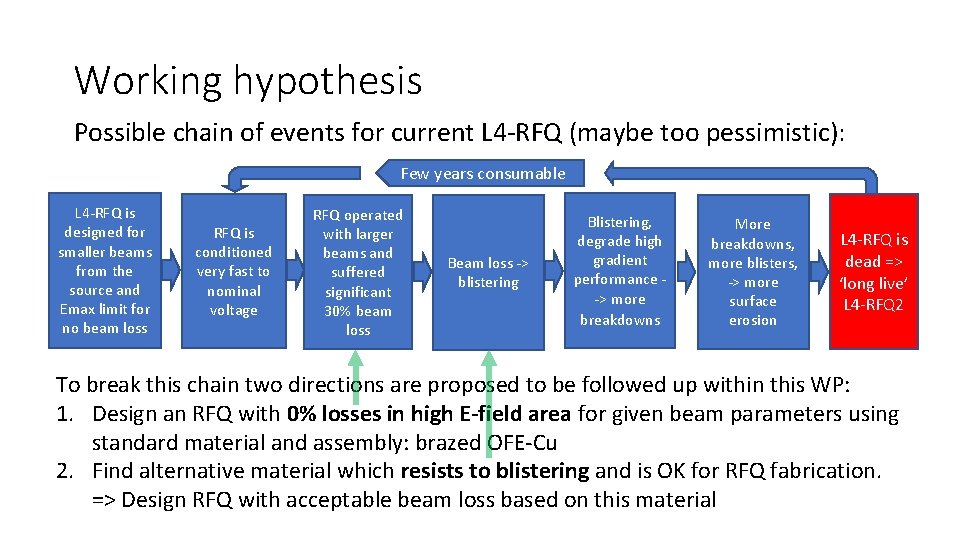
Working hypothesis Possible chain of events for current L 4 -RFQ (maybe too pessimistic): Few years consumable L 4 -RFQ is designed for smaller beams from the source and Emax limit for no beam loss RFQ is conditioned very fast to nominal voltage RFQ operated with larger beams and suffered significant 30% beam loss Beam loss -> blistering Blistering, degrade high gradient performance -> more breakdowns More breakdowns, more blisters, -> more surface erosion L 4 -RFQ is dead => ‘long live’ L 4 -RFQ 2 To break this chain two directions are proposed to be followed up within this WP: 1. Design an RFQ with 0% losses in high E-field area for given beam parameters using standard material and assembly: brazed OFE-Cu 2. Find alternative material which resists to blistering and is OK for RFQ fabrication. => Design RFQ with acceptable beam loss based on this material
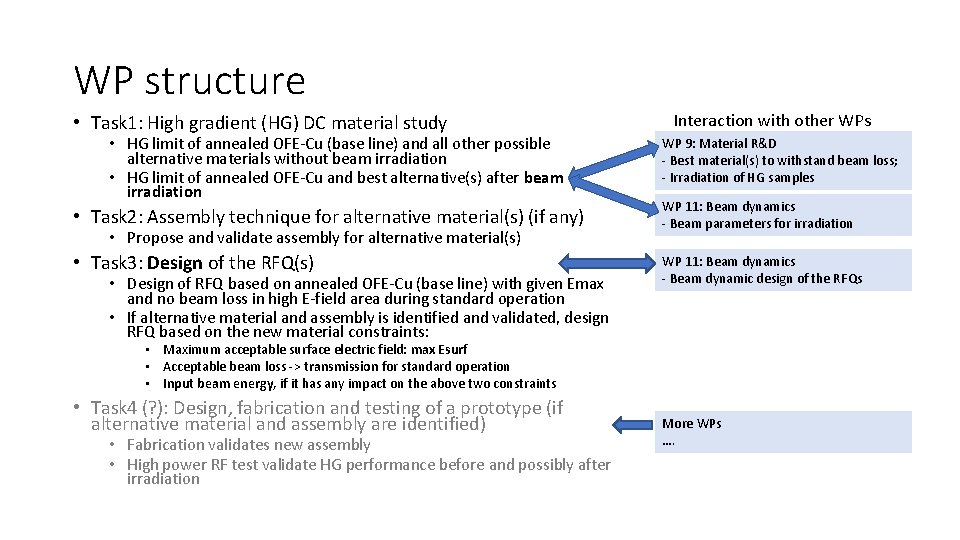
WP structure • Task 1: High gradient (HG) DC material study • HG limit of annealed OFE-Cu (base line) and all other possible alternative materials without beam irradiation • HG limit of annealed OFE-Cu and best alternative(s) after beam irradiation Interaction with other WPs WP 9: Material R&D - Best material(s) to withstand beam loss; - Irradiation of HG samples • Task 2: Assembly technique for alternative material(s) (if any) WP 11: Beam dynamics - Beam parameters for irradiation • Task 3: Design of the RFQ(s) WP 11: Beam dynamics - Beam dynamic design of the RFQs • Propose and validate assembly for alternative material(s) • Design of RFQ based on annealed OFE-Cu (base line) with given Emax and no beam loss in high E-field area during standard operation • If alternative material and assembly is identified and validated, design RFQ based on the new material constraints: • Maximum acceptable surface electric field: max Esurf • Acceptable beam loss -> transmission for standard operation • Input beam energy, if it has any impact on the above two constraints • Task 4 (? ): Design, fabrication and testing of a prototype (if alternative material and assembly are identified) • Fabrication validates new assembly • High power RF test validate HG performance before and possibly after irradiation More WPs ….
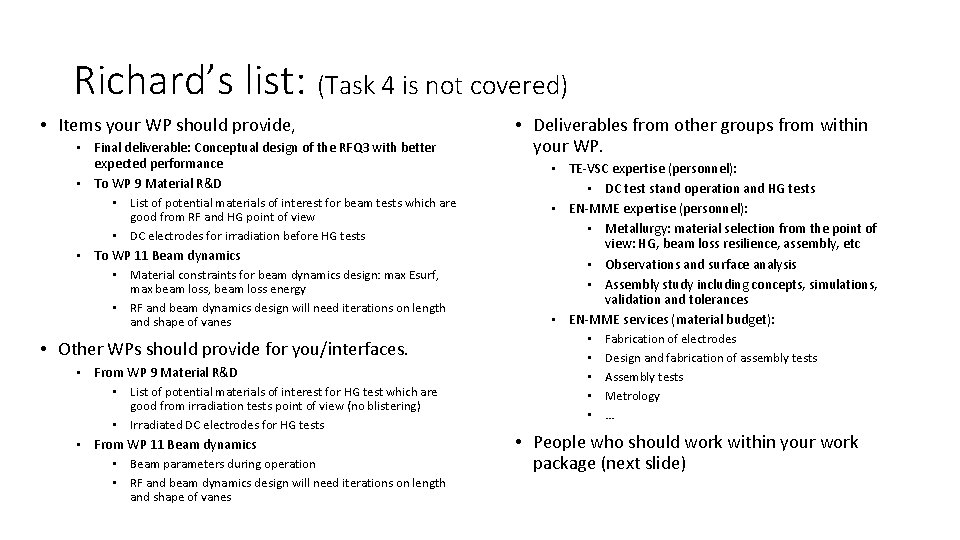
Richard’s list: (Task 4 is not covered) • Items your WP should provide, • Final deliverable: Conceptual design of the RFQ 3 with better expected performance • To WP 9 Material R&D • List of potential materials of interest for beam tests which are good from RF and HG point of view • DC electrodes for irradiation before HG tests • To WP 11 Beam dynamics • Material constraints for beam dynamics design: max Esurf, max beam loss, beam loss energy • RF and beam dynamics design will need iterations on length and shape of vanes • Other WPs should provide for you/interfaces. • From WP 9 Material R&D • List of potential materials of interest for HG test which are good from irradiation tests point of view (no blistering) • Irradiated DC electrodes for HG tests • From WP 11 Beam dynamics • Beam parameters during operation • RF and beam dynamics design will need iterations on length and shape of vanes • Deliverables from other groups from within your WP. • TE-VSC expertise (personnel): • DC test stand operation and HG tests • EN-MME expertise (personnel): • Metallurgy: material selection from the point of view: HG, beam loss resilience, assembly, etc • Observations and surface analysis • Assembly study including concepts, simulations, validation and tolerances • EN-MME services (material budget): • • • Fabrication of electrodes Design and fabrication of assembly tests Assembly tests Metrology … • People who should work within your work package (next slide)
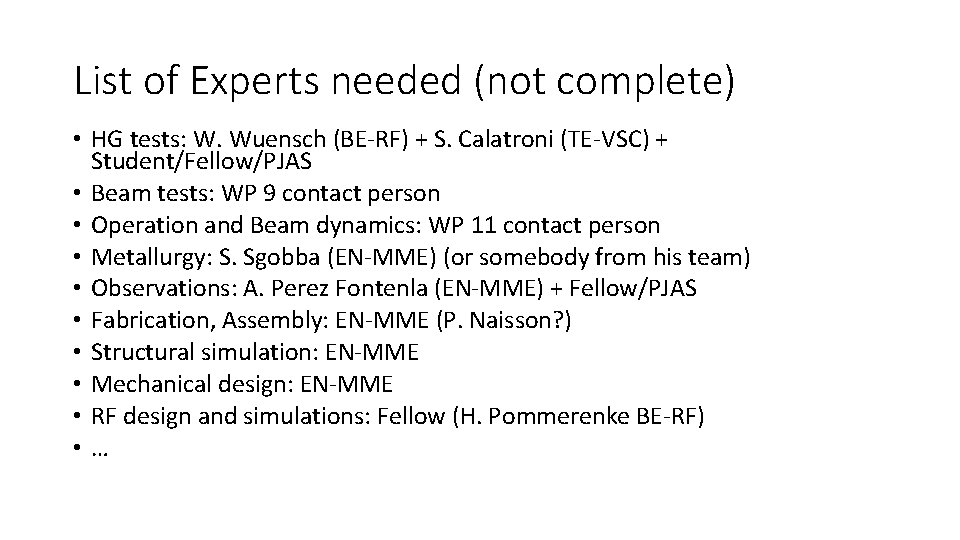
List of Experts needed (not complete) • HG tests: W. Wuensch (BE-RF) + S. Calatroni (TE-VSC) + Student/Fellow/PJAS • Beam tests: WP 9 contact person • Operation and Beam dynamics: WP 11 contact person • Metallurgy: S. Sgobba (EN-MME) (or somebody from his team) • Observations: A. Perez Fontenla (EN-MME) + Fellow/PJAS • Fabrication, Assembly: EN-MME (P. Naisson? ) • Structural simulation: EN-MME • Mechanical design: EN-MME • RF design and simulations: Fellow (H. Pommerenke BE-RF) • …