When is Lean too Lean Discrete Event Simulation
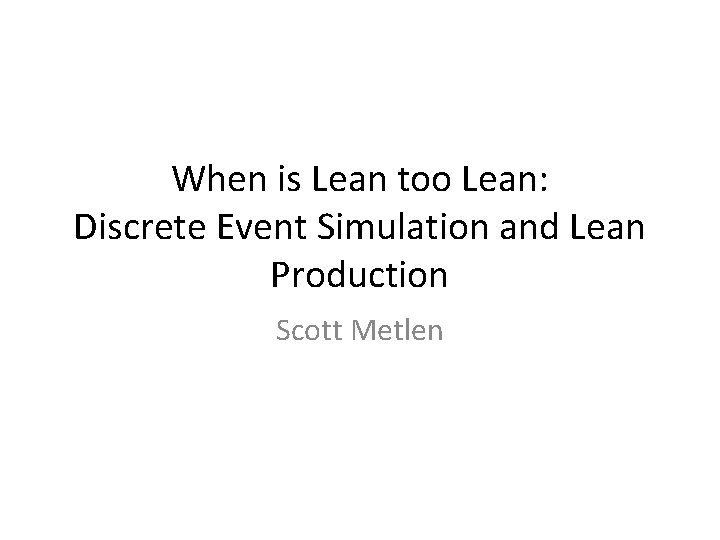
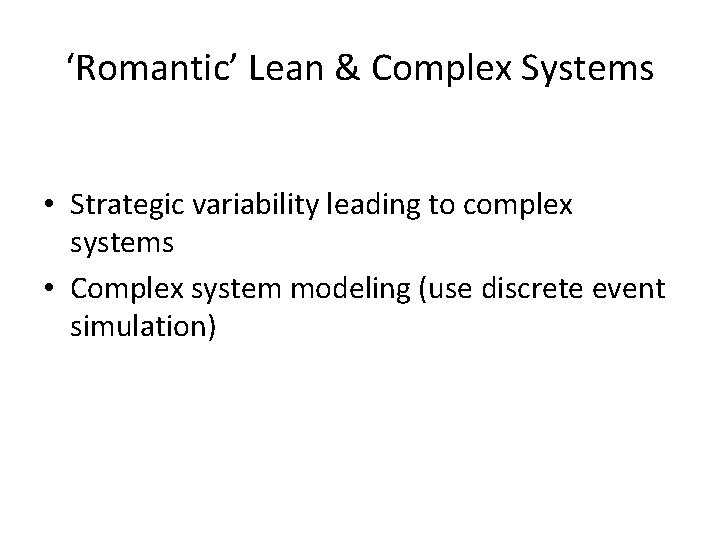
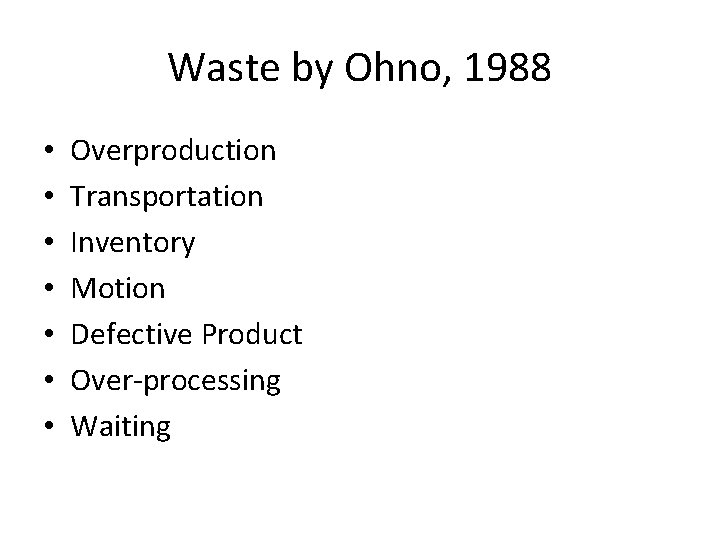
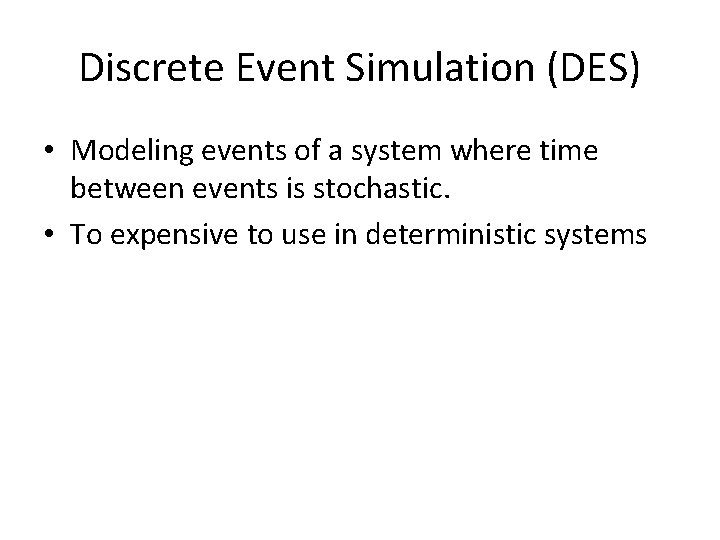
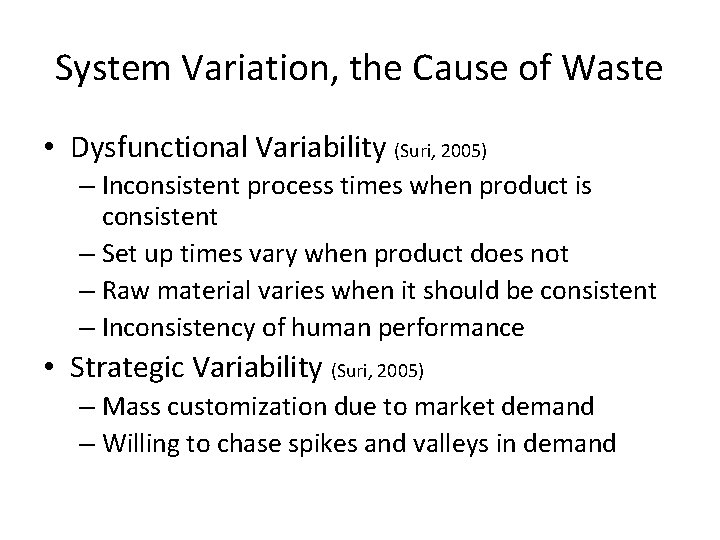
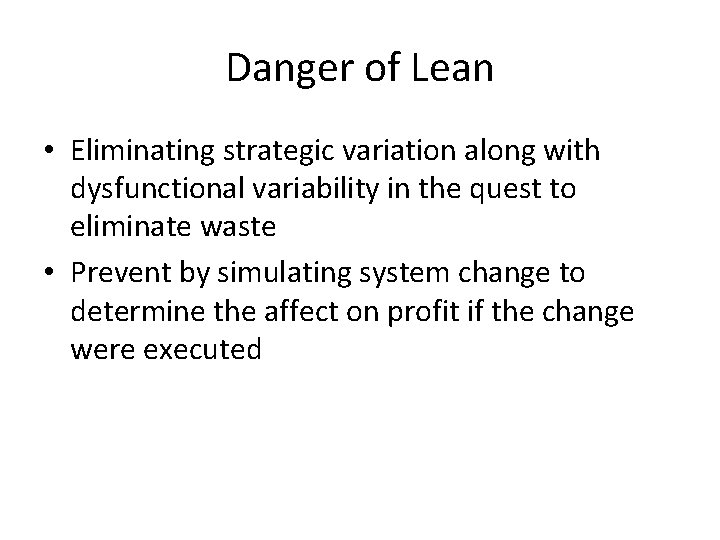
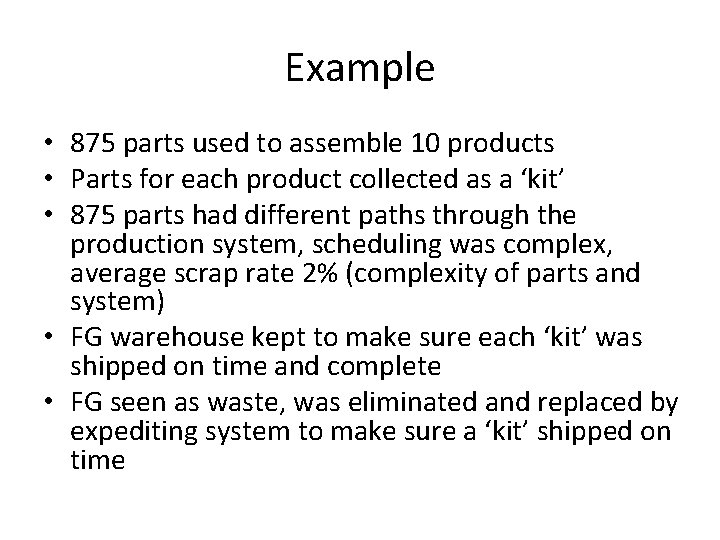
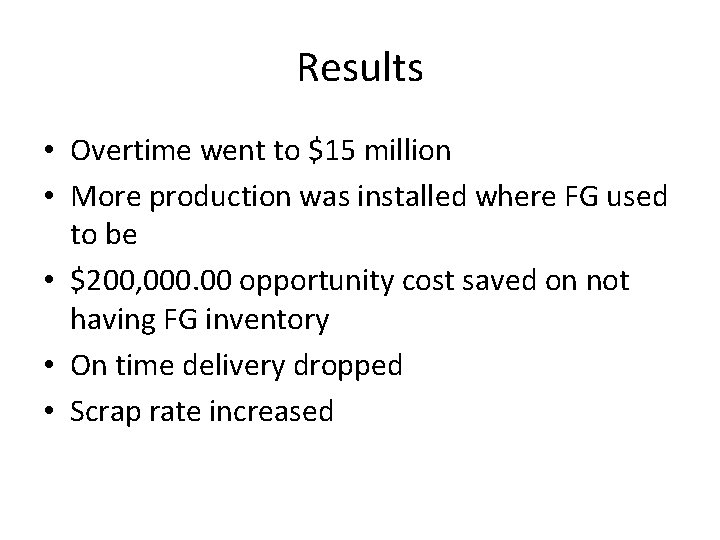
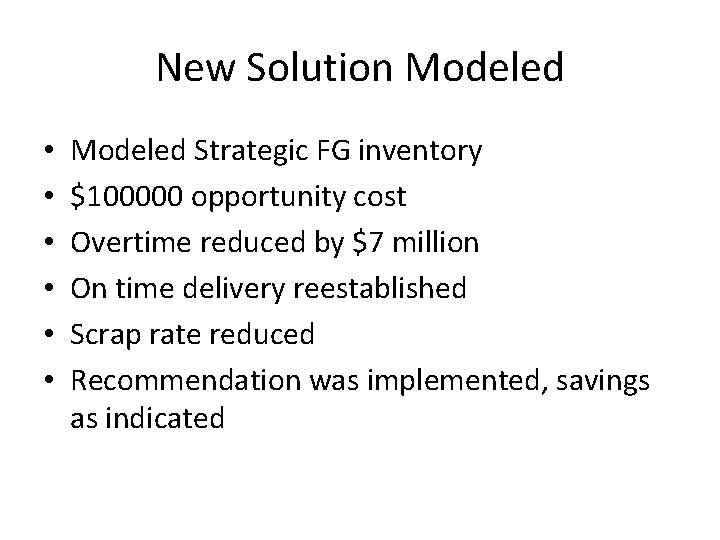
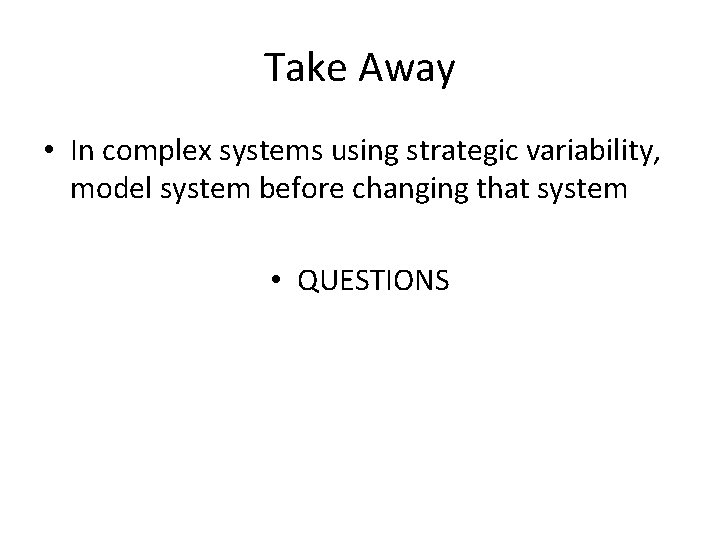
- Slides: 10
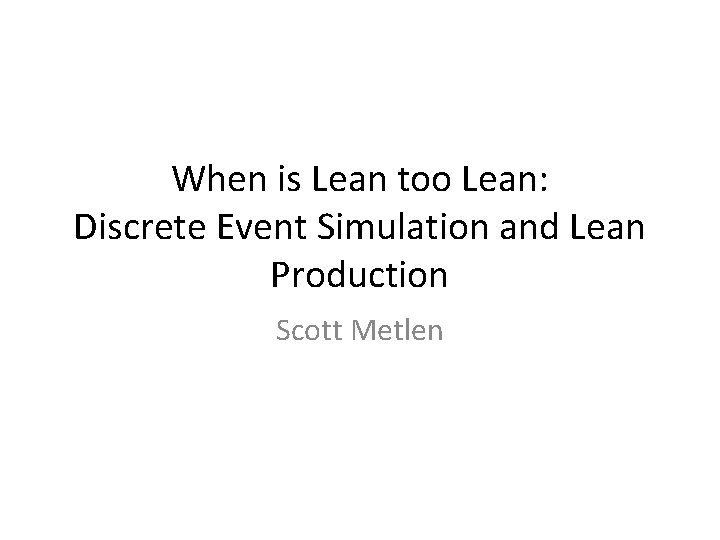
When is Lean too Lean: Discrete Event Simulation and Lean Production Scott Metlen
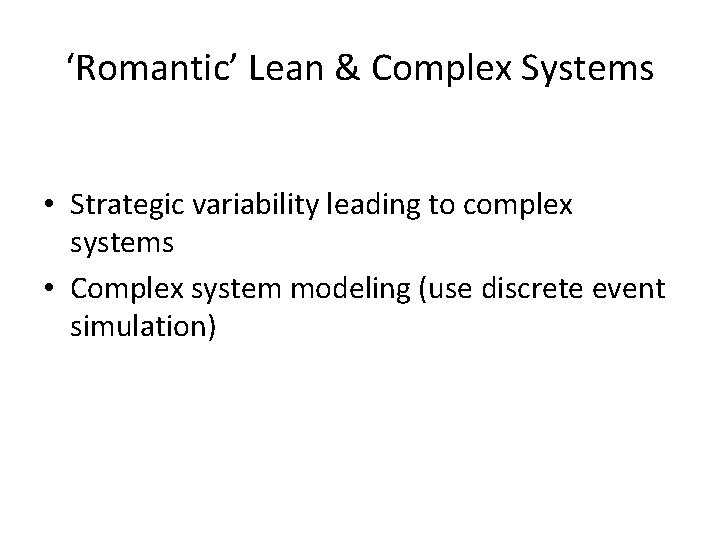
‘Romantic’ Lean & Complex Systems • Strategic variability leading to complex systems • Complex system modeling (use discrete event simulation)
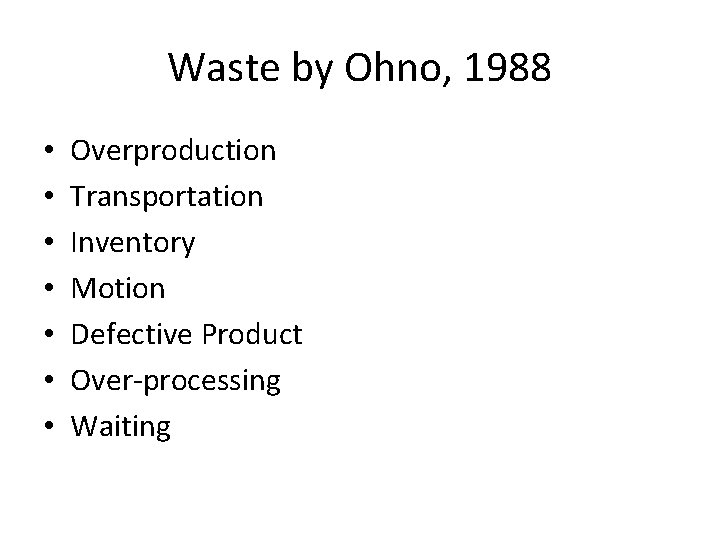
Waste by Ohno, 1988 • • Overproduction Transportation Inventory Motion Defective Product Over-processing Waiting
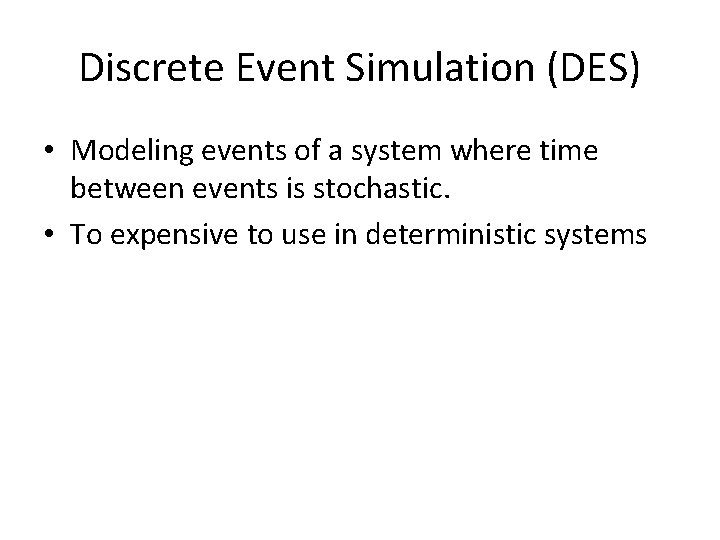
Discrete Event Simulation (DES) • Modeling events of a system where time between events is stochastic. • To expensive to use in deterministic systems
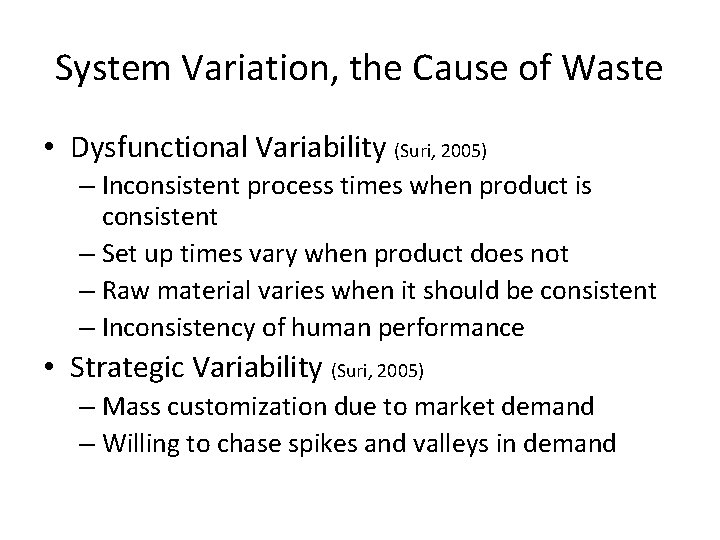
System Variation, the Cause of Waste • Dysfunctional Variability (Suri, 2005) – Inconsistent process times when product is consistent – Set up times vary when product does not – Raw material varies when it should be consistent – Inconsistency of human performance • Strategic Variability (Suri, 2005) – Mass customization due to market demand – Willing to chase spikes and valleys in demand
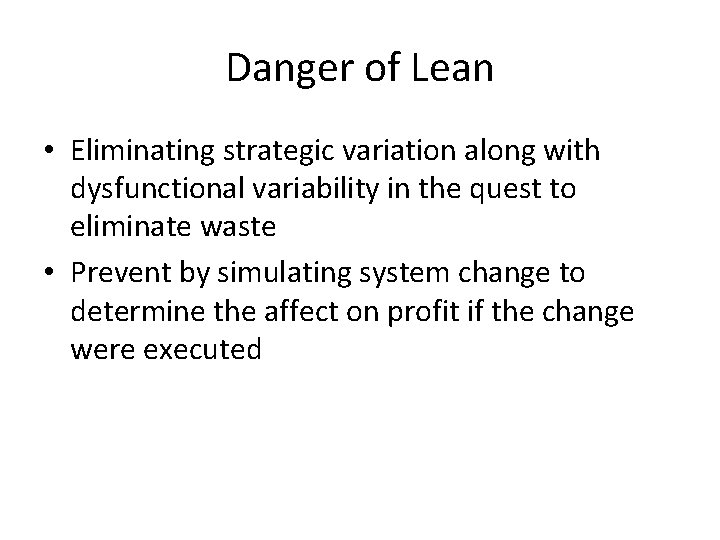
Danger of Lean • Eliminating strategic variation along with dysfunctional variability in the quest to eliminate waste • Prevent by simulating system change to determine the affect on profit if the change were executed
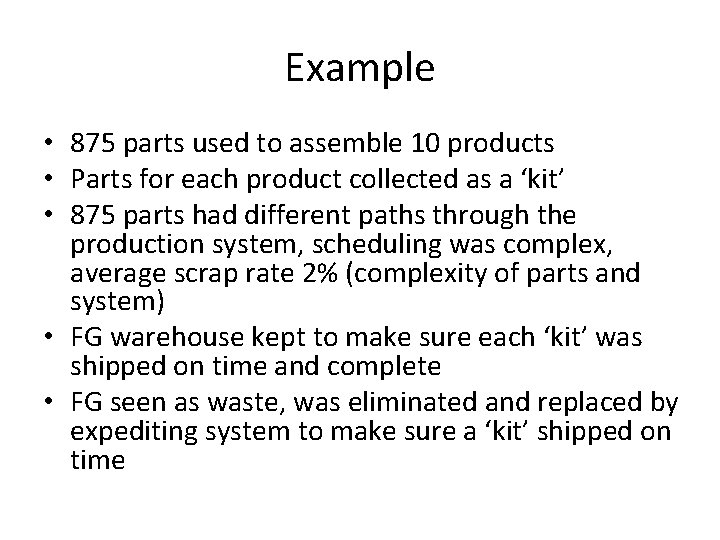
Example • 875 parts used to assemble 10 products • Parts for each product collected as a ‘kit’ • 875 parts had different paths through the production system, scheduling was complex, average scrap rate 2% (complexity of parts and system) • FG warehouse kept to make sure each ‘kit’ was shipped on time and complete • FG seen as waste, was eliminated and replaced by expediting system to make sure a ‘kit’ shipped on time
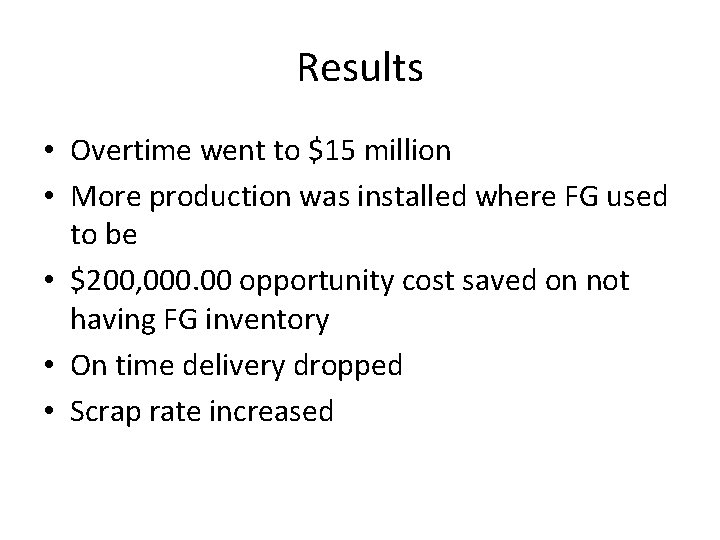
Results • Overtime went to $15 million • More production was installed where FG used to be • $200, 000. 00 opportunity cost saved on not having FG inventory • On time delivery dropped • Scrap rate increased
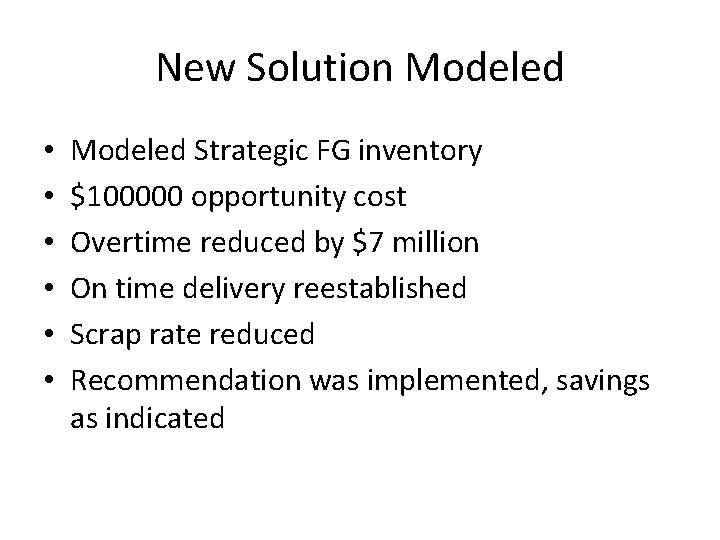
New Solution Modeled • • • Modeled Strategic FG inventory $100000 opportunity cost Overtime reduced by $7 million On time delivery reestablished Scrap rate reduced Recommendation was implemented, savings as indicated
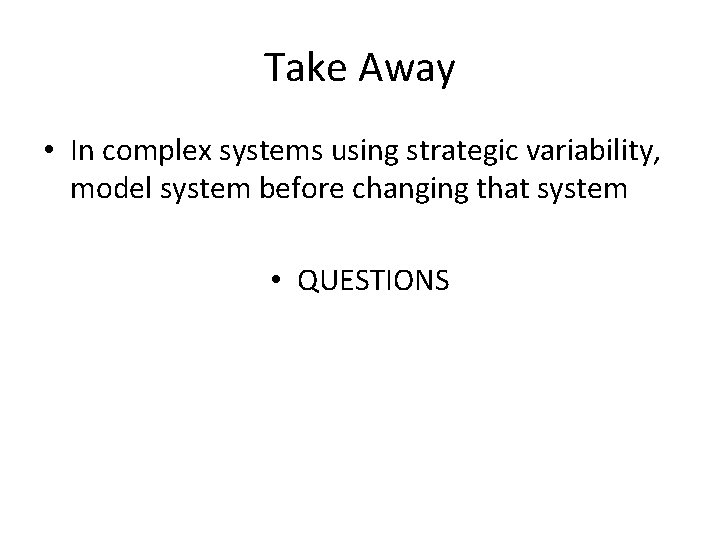
Take Away • In complex systems using strategic variability, model system before changing that system • QUESTIONS
Quantifiers too much too many enough
Parallel discrete event simulation
Not too big not too small just right
Research questions
Too foreign for home too foreign for here
Too much money is chasing too few goods
Too anointed to be disappointed
Too broad and too narrow examples
Too broad and too narrow examples
Not too narrow not too deep
Iso 18404 training