Variation and Control Charts A Leadership Perspective Please
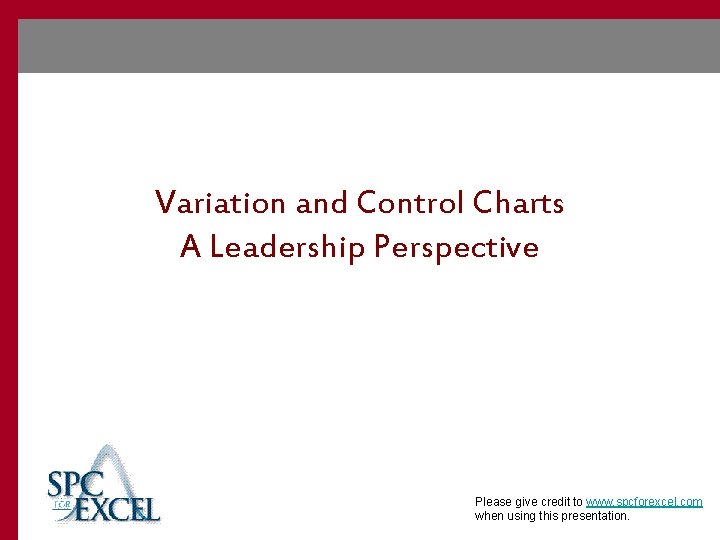
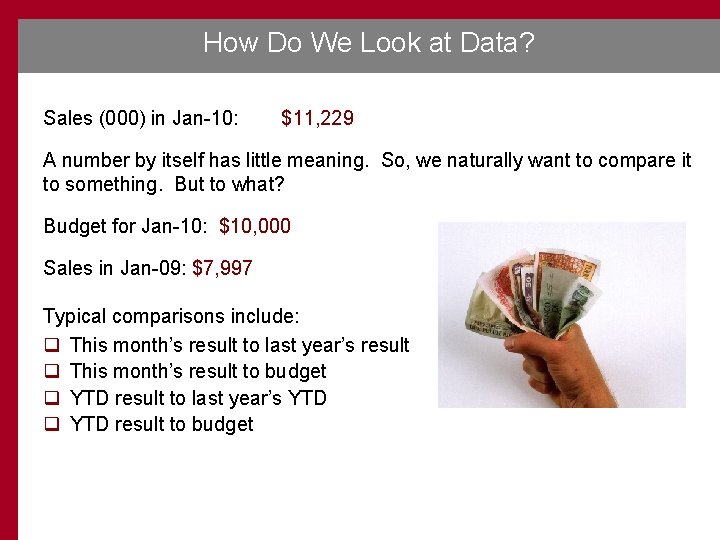
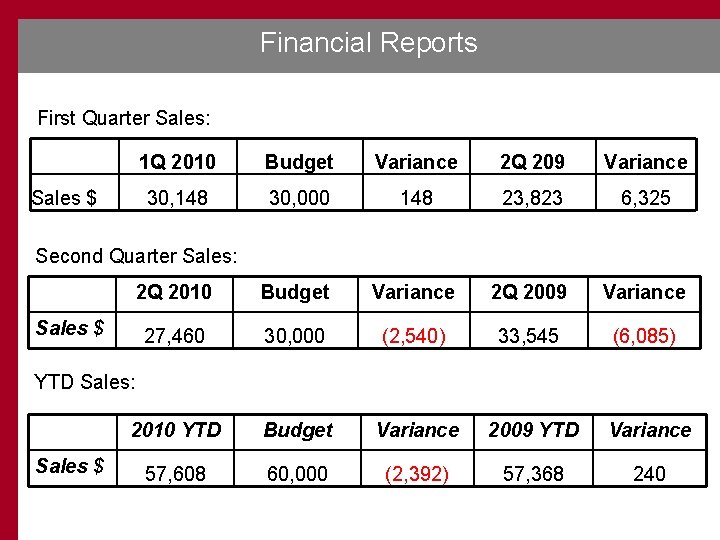
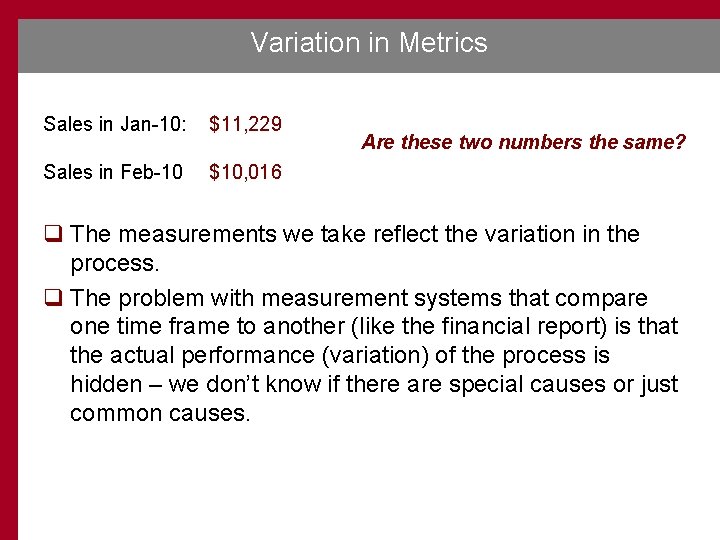
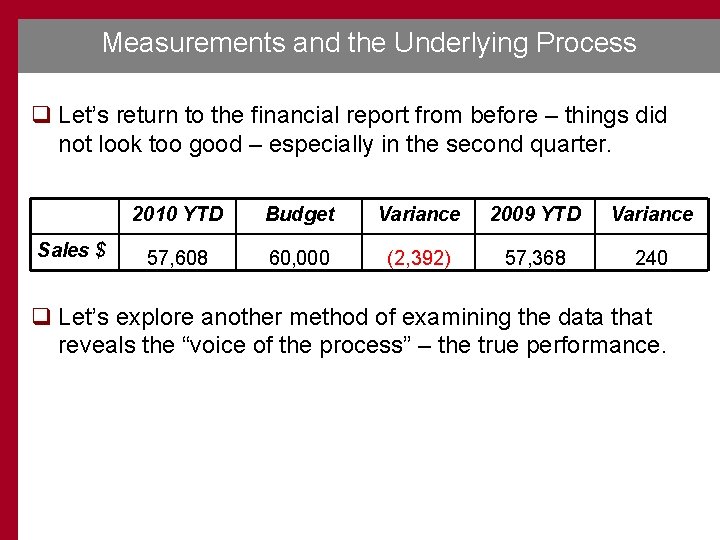
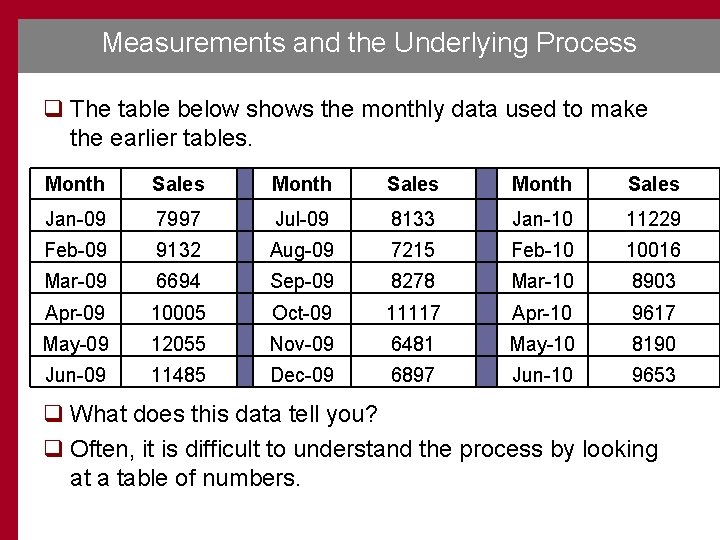
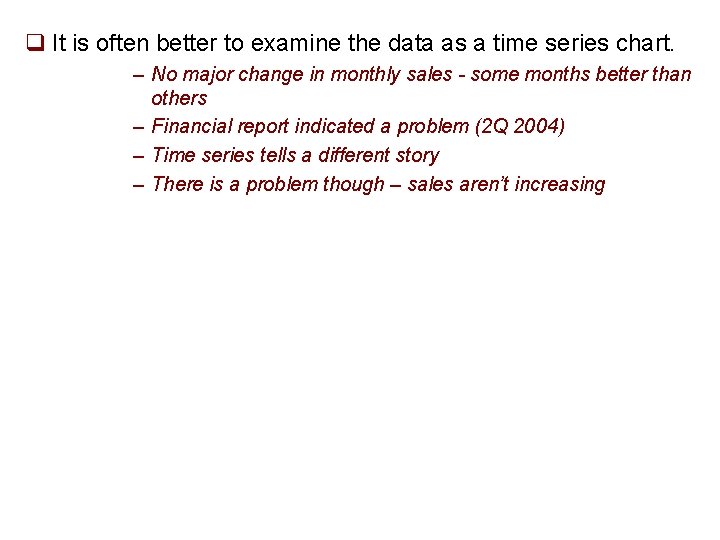
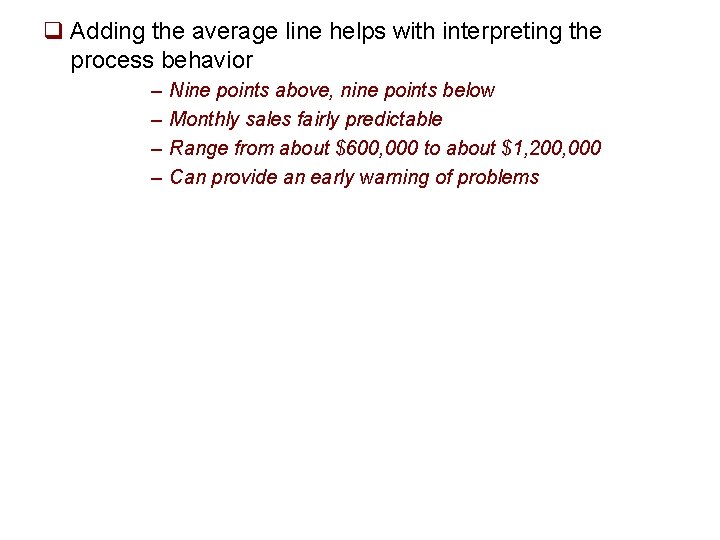
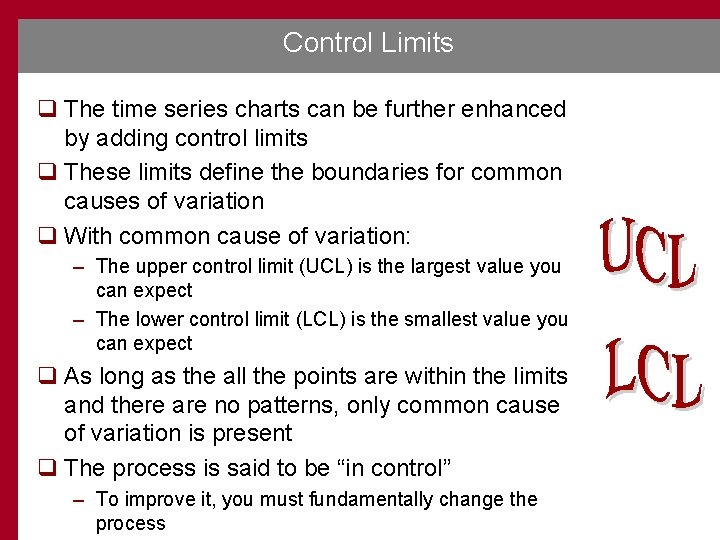
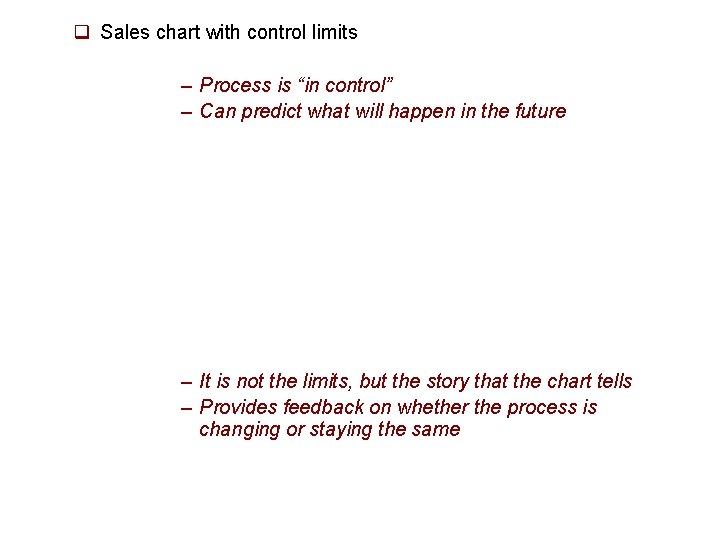
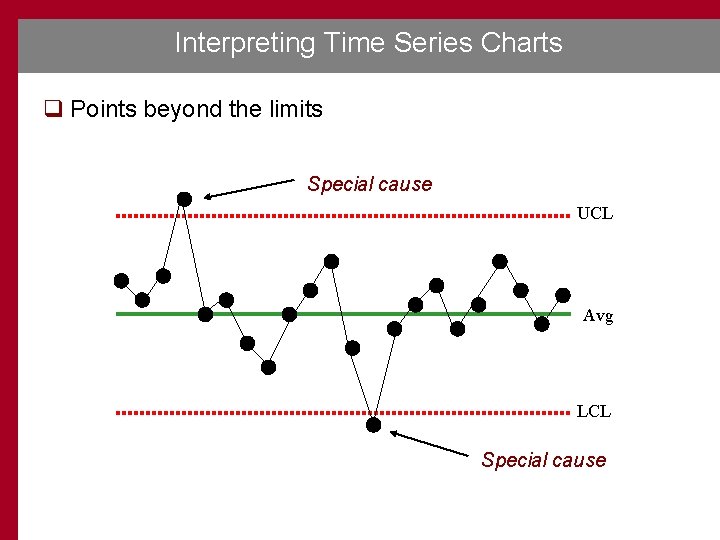
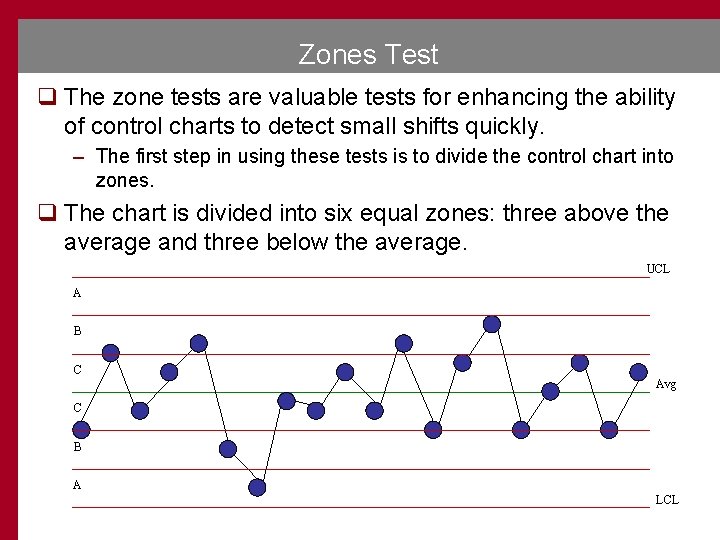
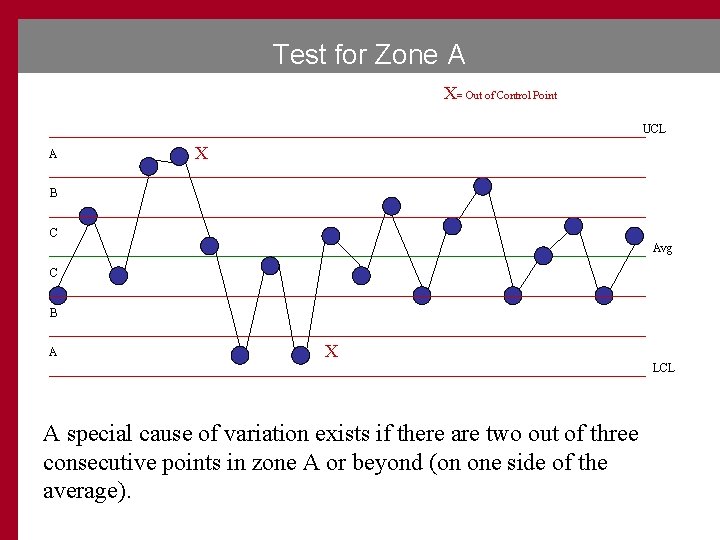
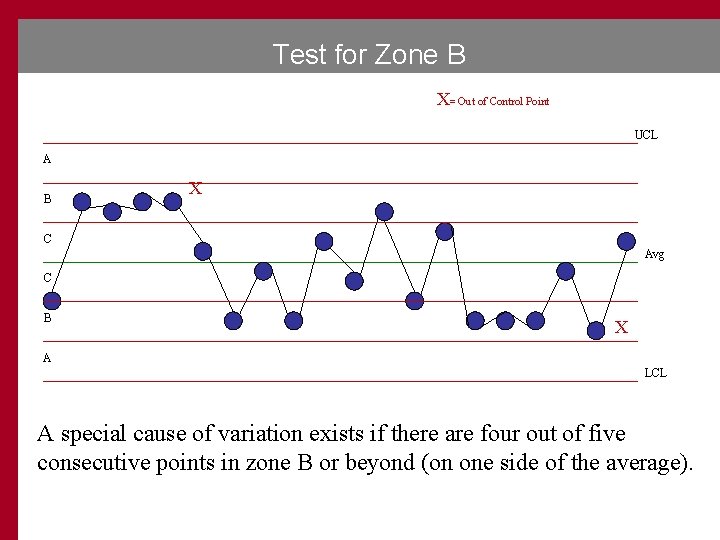
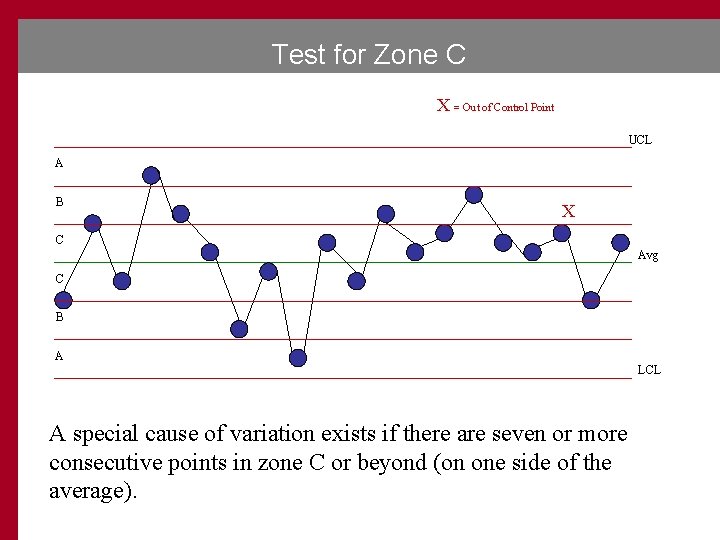
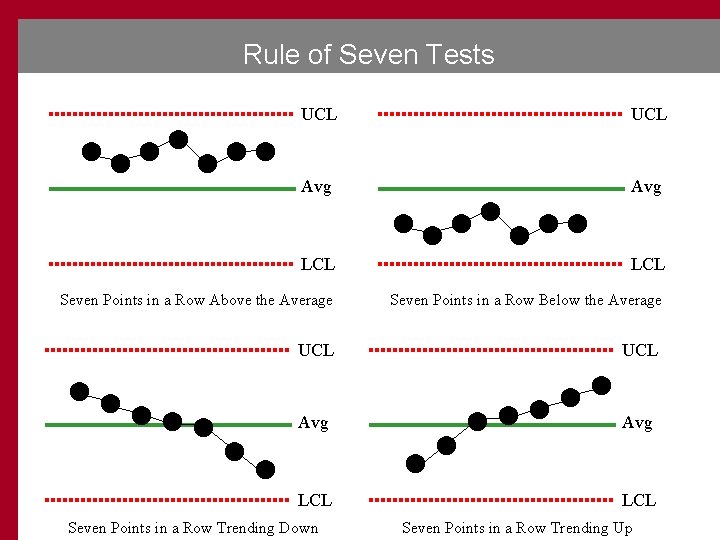
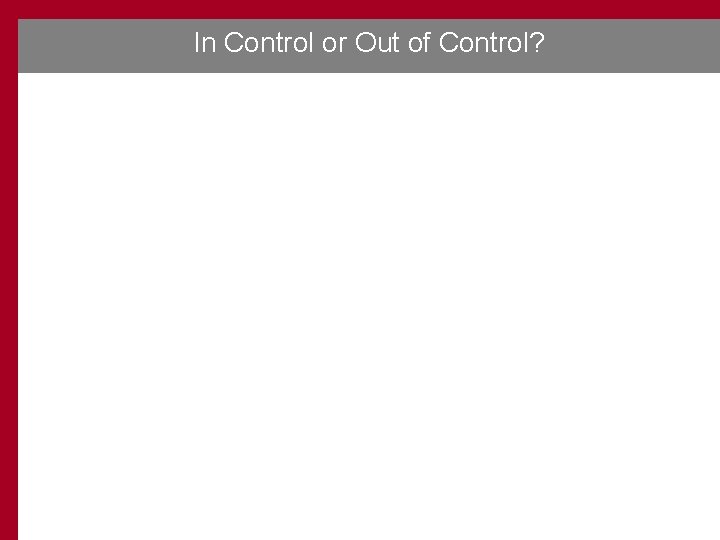
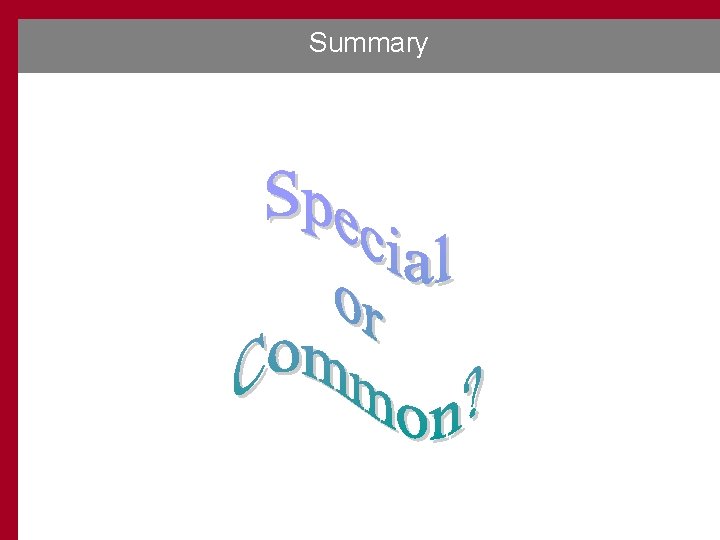
- Slides: 18
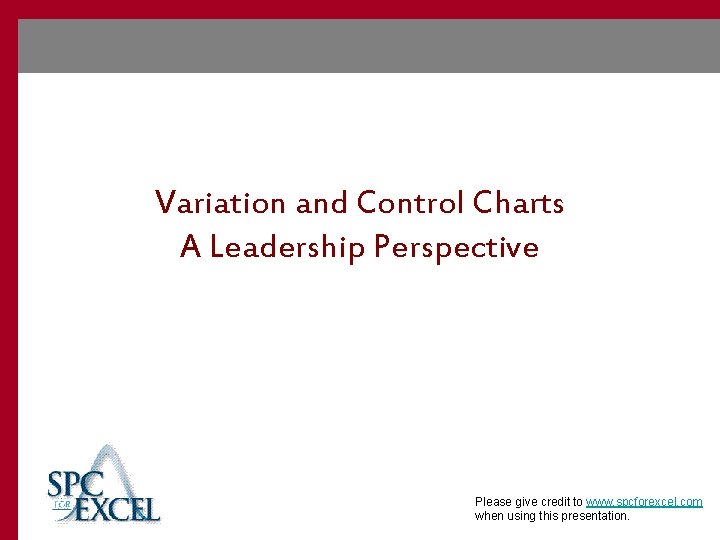
Variation and Control Charts A Leadership Perspective Please give credit to www. spcforexcel. com when using this presentation.
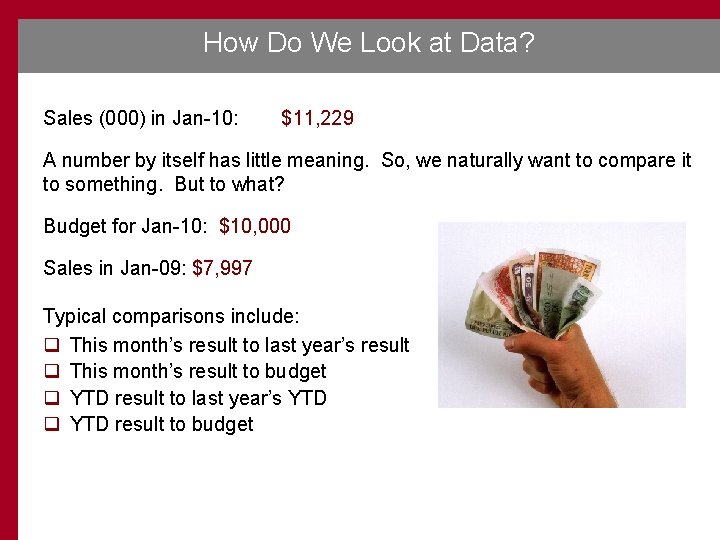
How Do We Look at Data? Sales (000) in Jan-10: $11, 229 A number by itself has little meaning. So, we naturally want to compare it to something. But to what? Budget for Jan-10: $10, 000 Sales in Jan-09: $7, 997 Typical comparisons include: q This month’s result to last year’s result q This month’s result to budget q YTD result to last year’s YTD q YTD result to budget
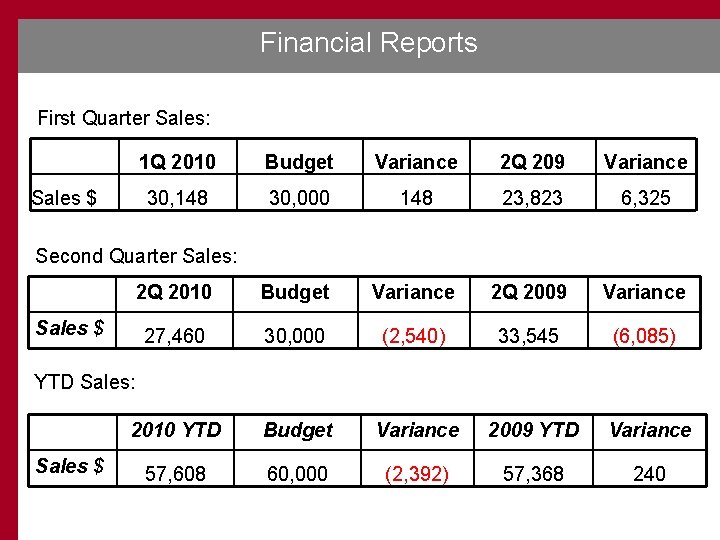
Financial Reports First Quarter Sales: 1 Q 2010 Budget Variance 2 Q 209 Variance 30, 148 30, 000 148 23, 823 6, 325 2 Q 2010 Budget Variance 2 Q 2009 Variance 27, 460 30, 000 (2, 540) 33, 545 (6, 085) 2010 YTD Budget Variance 2009 YTD Variance 57, 608 60, 000 (2, 392) 57, 368 240 Sales $ Second Quarter Sales: Sales $ YTD Sales: Sales $
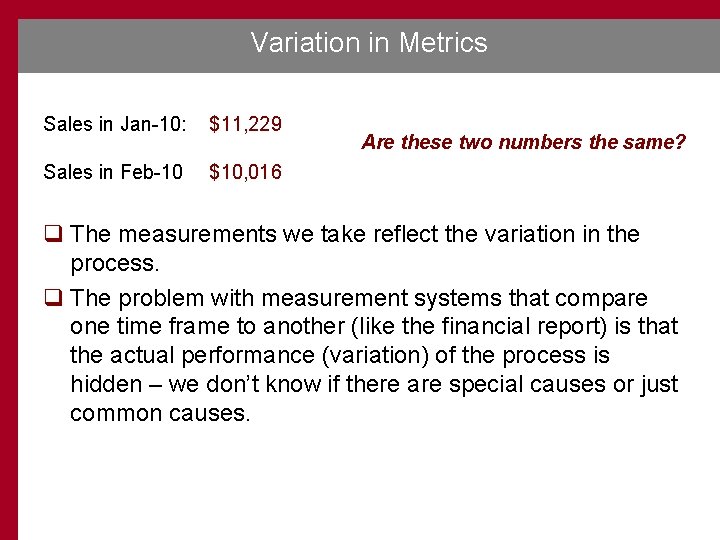
Variation in Metrics Sales in Jan-10: $11, 229 Sales in Feb-10 $10, 016 Are these two numbers the same? q The measurements we take reflect the variation in the process. q The problem with measurement systems that compare one time frame to another (like the financial report) is that the actual performance (variation) of the process is hidden – we don’t know if there are special causes or just common causes.
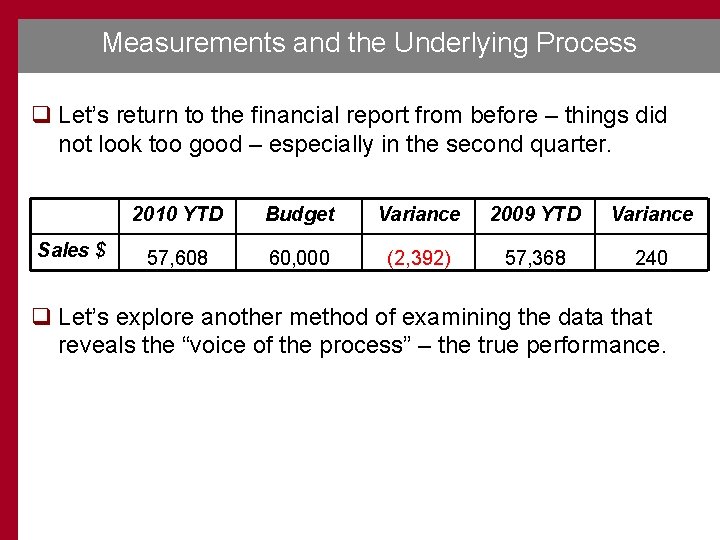
Measurements and the Underlying Process q Let’s return to the financial report from before – things did not look too good – especially in the second quarter. Sales $ 2010 YTD Budget Variance 2009 YTD Variance 57, 608 60, 000 (2, 392) 57, 368 240 q Let’s explore another method of examining the data that reveals the “voice of the process” – the true performance.
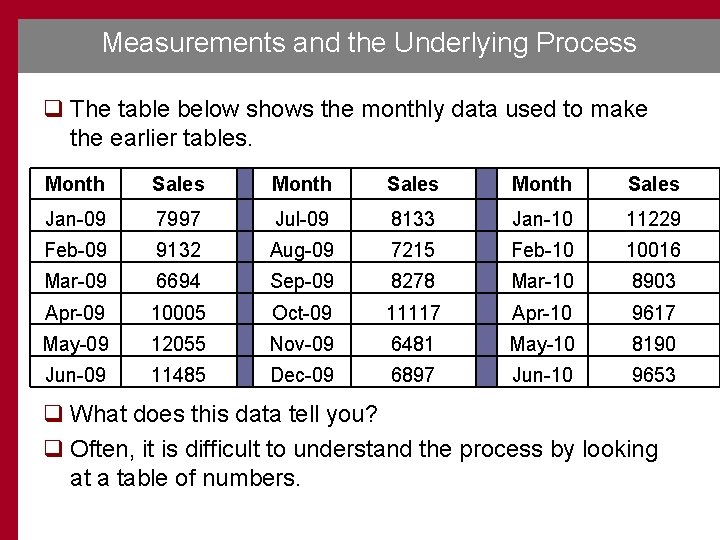
Measurements and the Underlying Process q The table below shows the monthly data used to make the earlier tables. Month Sales Jan-09 7997 Jul-09 8133 Jan-10 11229 Feb-09 9132 Aug-09 7215 Feb-10 10016 Mar-09 6694 Sep-09 8278 Mar-10 8903 Apr-09 10005 Oct-09 11117 Apr-10 9617 May-09 12055 Nov-09 6481 May-10 8190 Jun-09 11485 Dec-09 6897 Jun-10 9653 q What does this data tell you? q Often, it is difficult to understand the process by looking at a table of numbers.
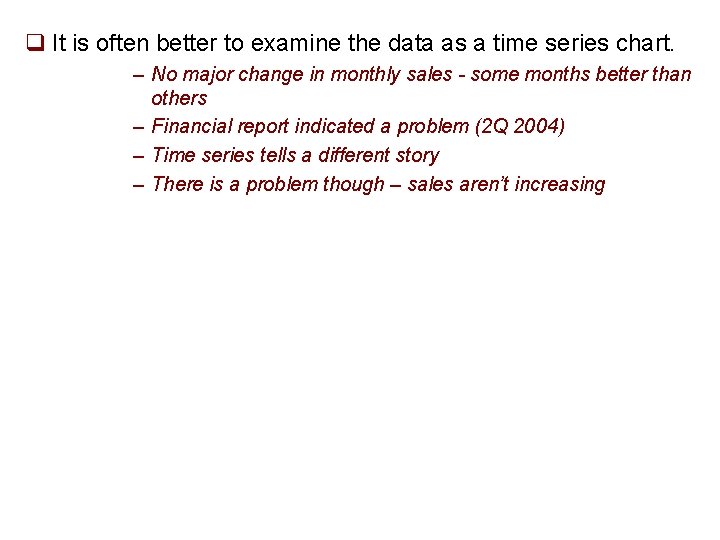
q It is often better to examine the data as a time series chart. – No major change in monthly sales - some months better than others – Financial report indicated a problem (2 Q 2004) – Time series tells a different story – There is a problem though – sales aren’t increasing
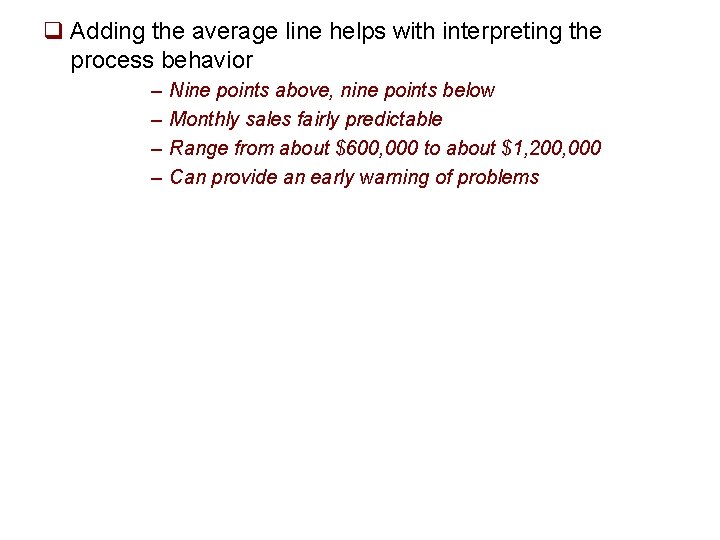
q Adding the average line helps with interpreting the process behavior – – Nine points above, nine points below Monthly sales fairly predictable Range from about $600, 000 to about $1, 200, 000 Can provide an early warning of problems
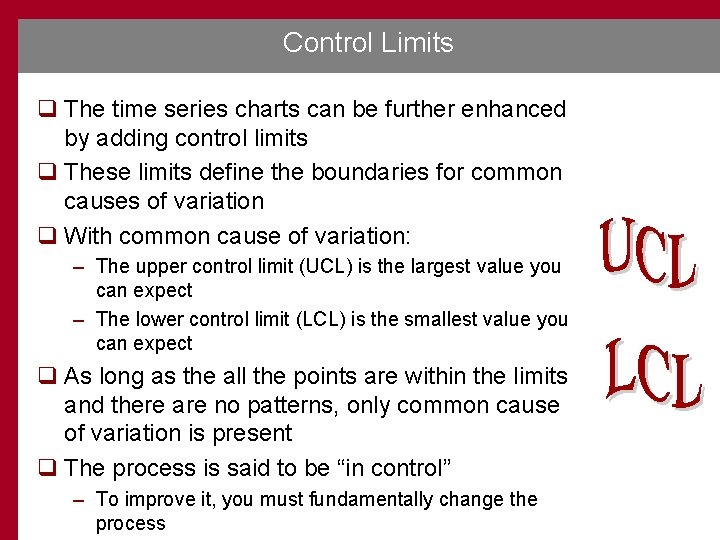
Control Limits q The time series charts can be further enhanced by adding control limits q These limits define the boundaries for common causes of variation q With common cause of variation: – The upper control limit (UCL) is the largest value you can expect – The lower control limit (LCL) is the smallest value you can expect q As long as the all the points are within the limits and there are no patterns, only common cause of variation is present q The process is said to be “in control” – To improve it, you must fundamentally change the process
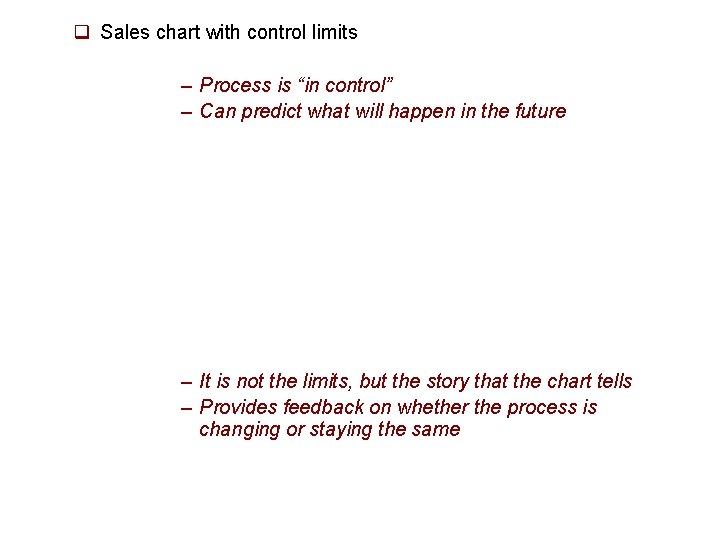
q Sales chart with control limits – Process is “in control” – Can predict what will happen in the future – It is not the limits, but the story that the chart tells – Provides feedback on whether the process is changing or staying the same
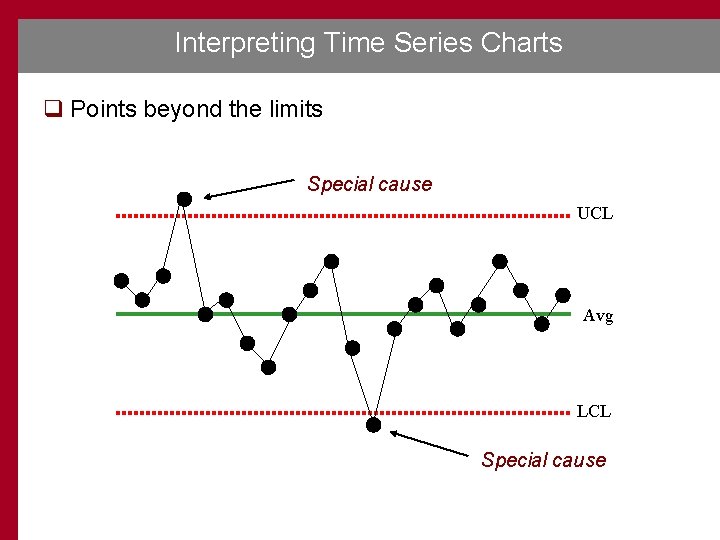
Interpreting Time Series Charts q Points beyond the limits Special cause UCL Avg LCL Special cause
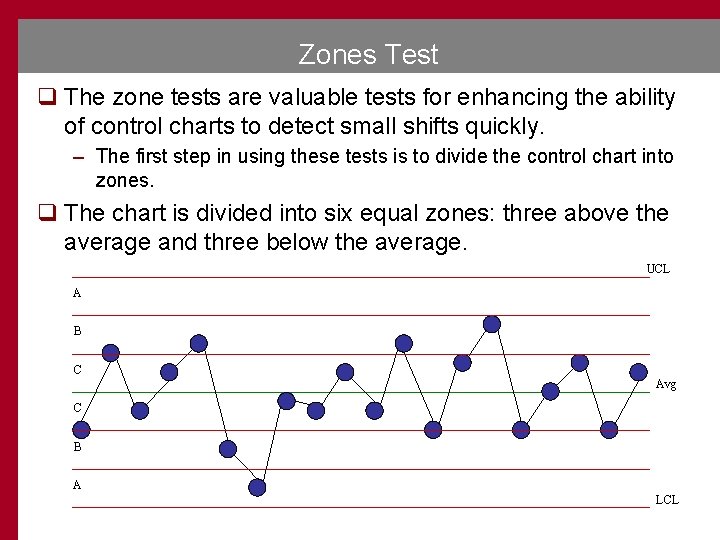
Zones Test q The zone tests are valuable tests for enhancing the ability of control charts to detect small shifts quickly. – The first step in using these tests is to divide the control chart into zones. q The chart is divided into six equal zones: three above the average and three below the average. UCL A B C Avg C B A LCL
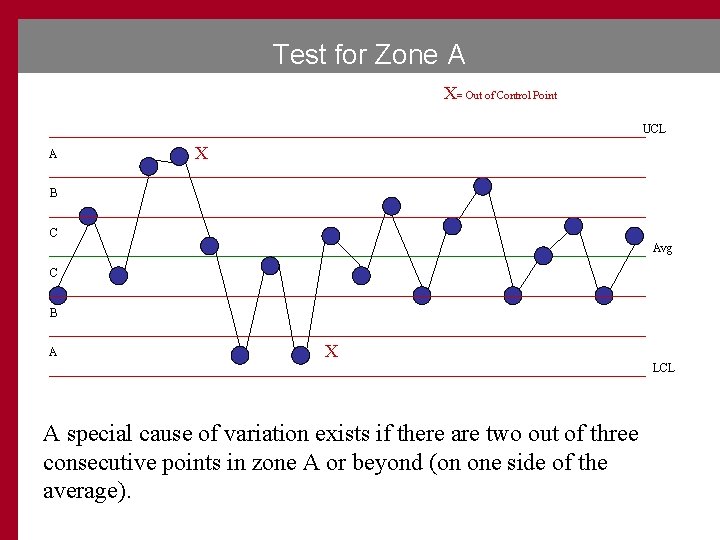
Test for Zone A X= Out of Control Point UCL A X B C Avg C B A X A special cause of variation exists if there are two out of three consecutive points in zone A or beyond (on one side of the average). LCL
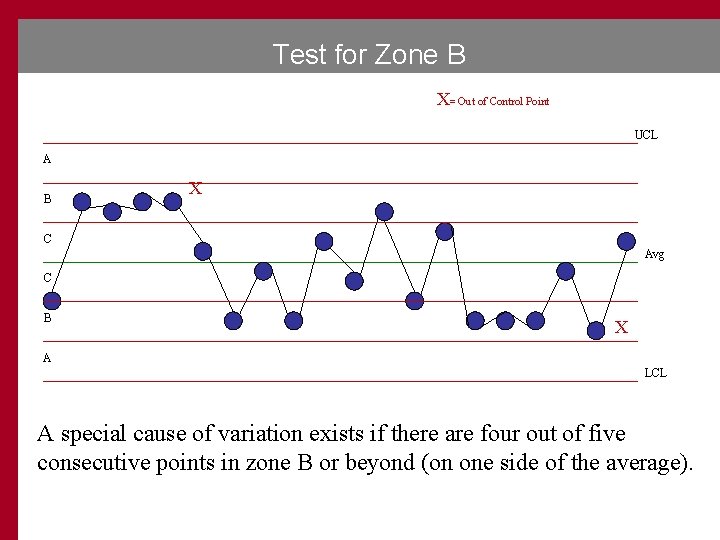
Test for Zone B X= Out of Control Point UCL A B X C Avg C B X A LCL A special cause of variation exists if there are four out of five consecutive points in zone B or beyond (on one side of the average).
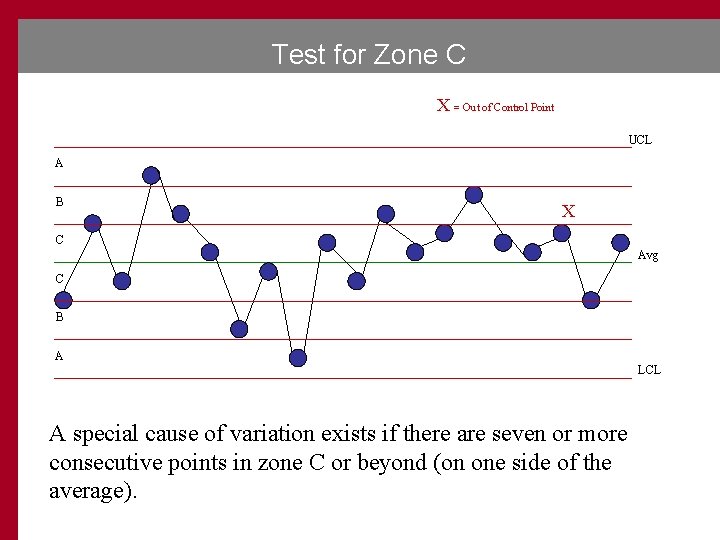
Test for Zone C X = Out of Control Point UCL A B X C Avg C B A LCL A special cause of variation exists if there are seven or more consecutive points in zone C or beyond (on one side of the average).
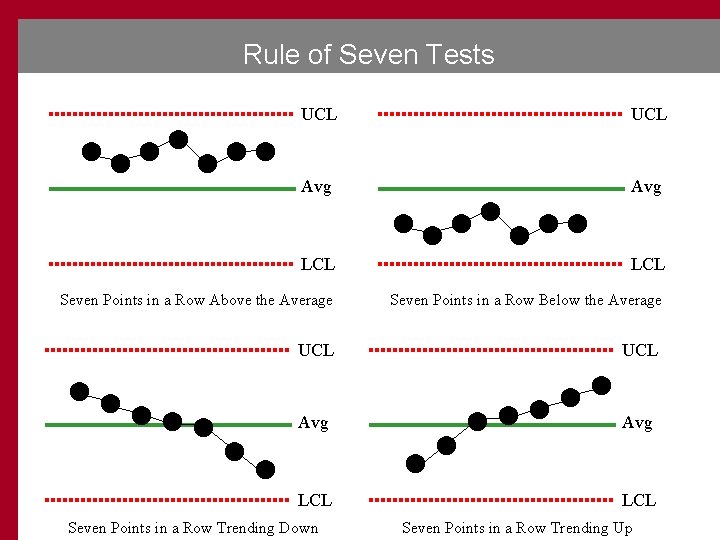
Rule of Seven Tests UCL Avg LCL Seven Points in a Row Above the Average Seven Points in a Row Below the Average UCL Avg LCL Seven Points in a Row Trending Down Seven Points in a Row Trending Up
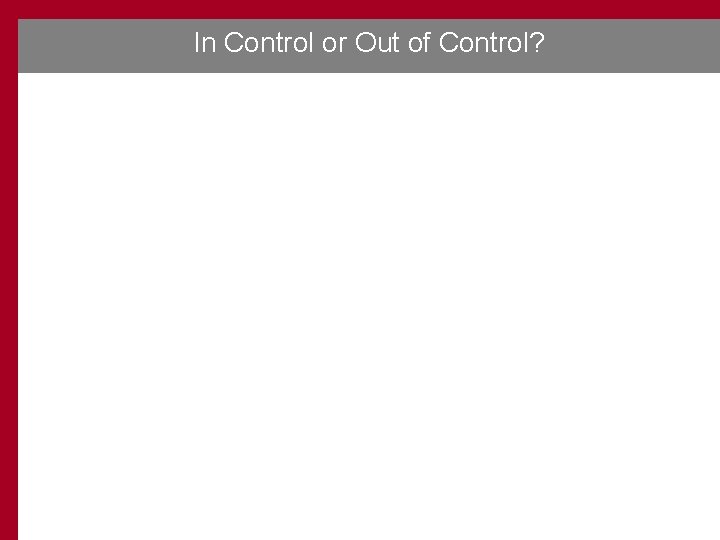
In Control or Out of Control?
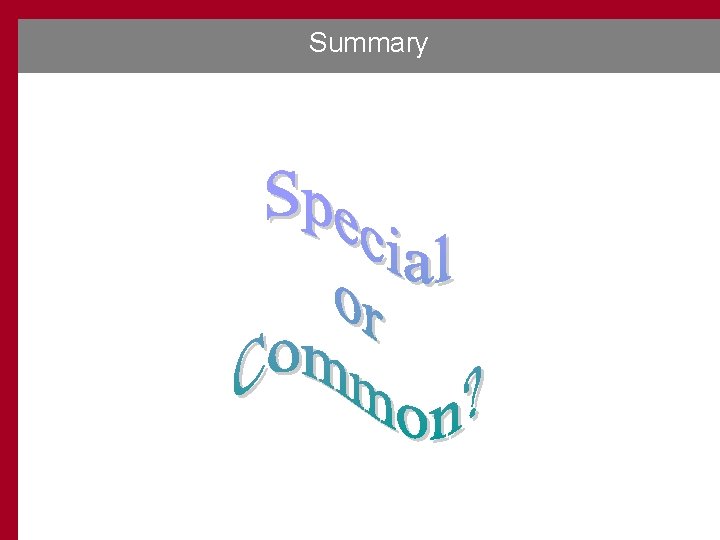
Summary
Which graph represents a function with direct variation
Examples of direct variation graphs
Coefficient of determination formula in regression
Will you please be quiet please raymond carver
Quality control charts
Attribute control charts
Who developed control chart
Weco rules for control charts
Defect chart
Attribute control chart
20%ของ300
Spc in operations management
Transactional vs transformational leadership
1 point perspective vs 2 point perspective
Silo perspective vs business process perspective
Statistical process
Toxic triangle of destructive leadership
Adaptive leadership style
Situational leadership vs adaptive leadership