Typical Textures part 2 Thermomechanical Processing TMP of
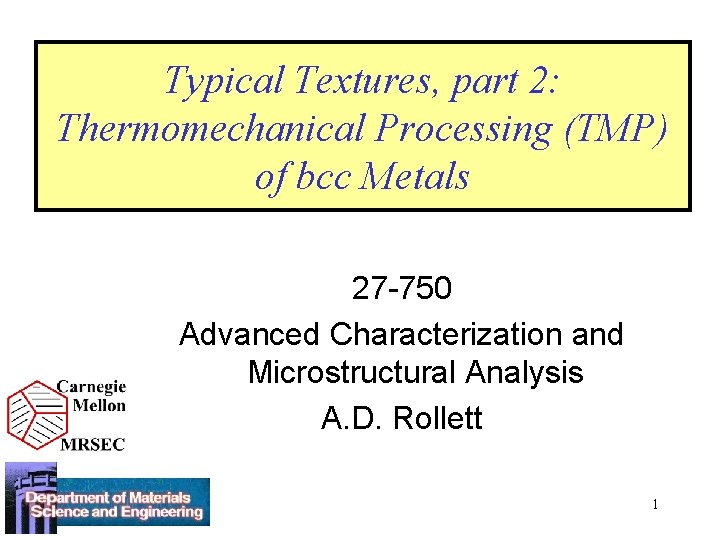
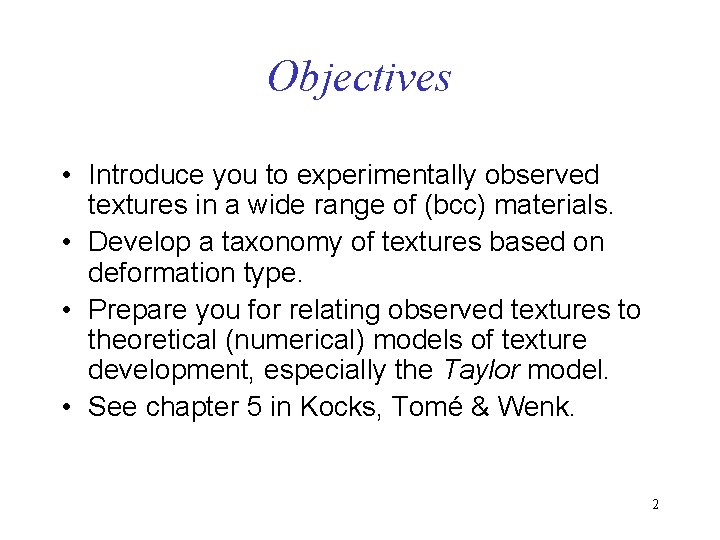
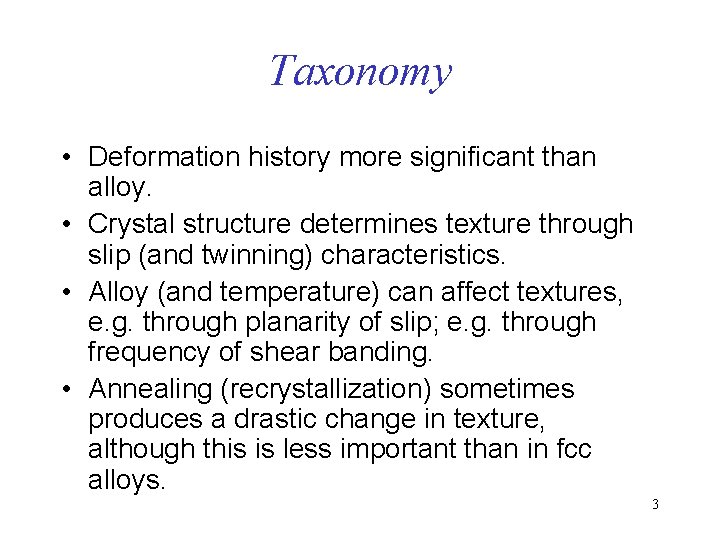
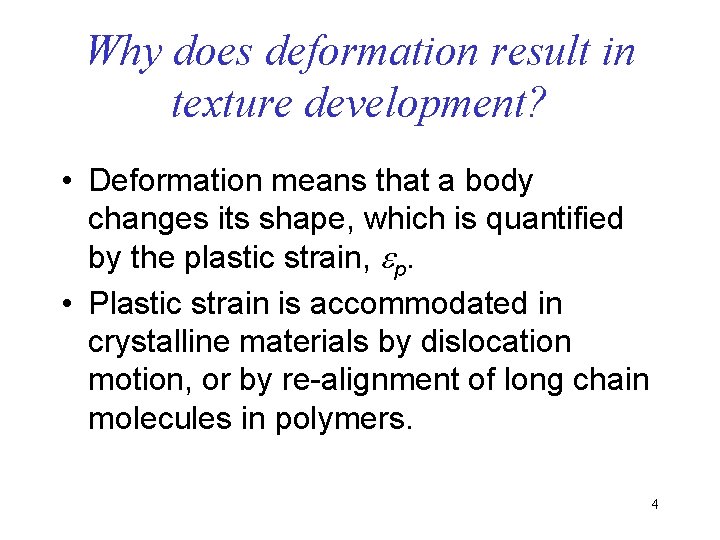
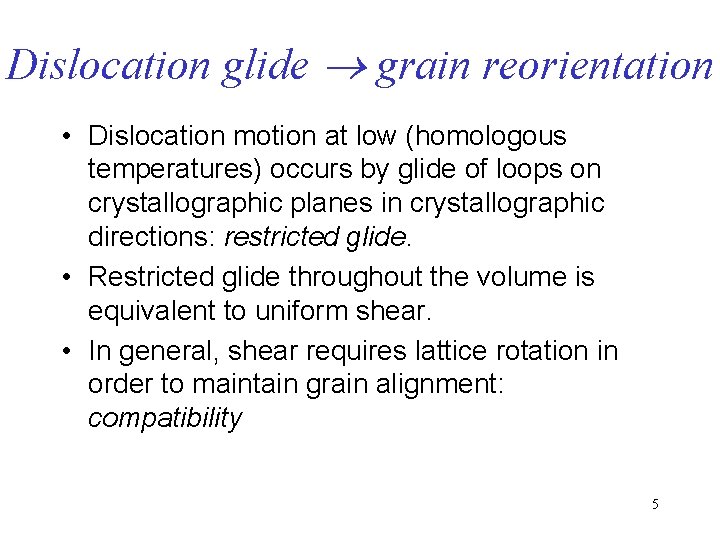
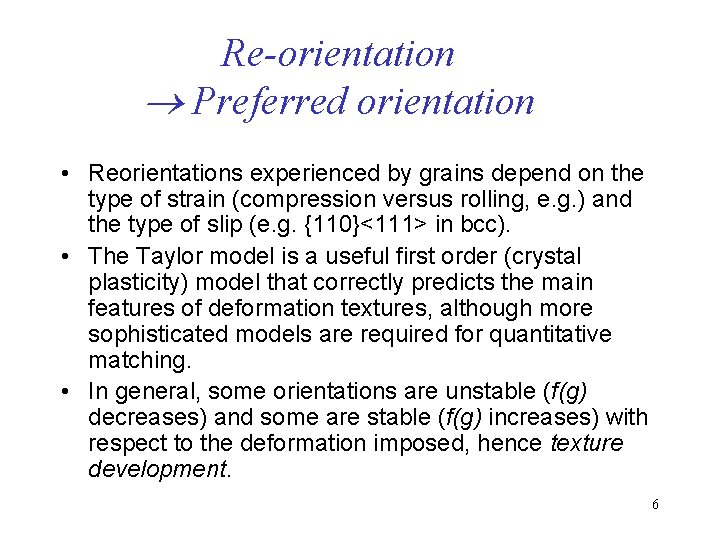
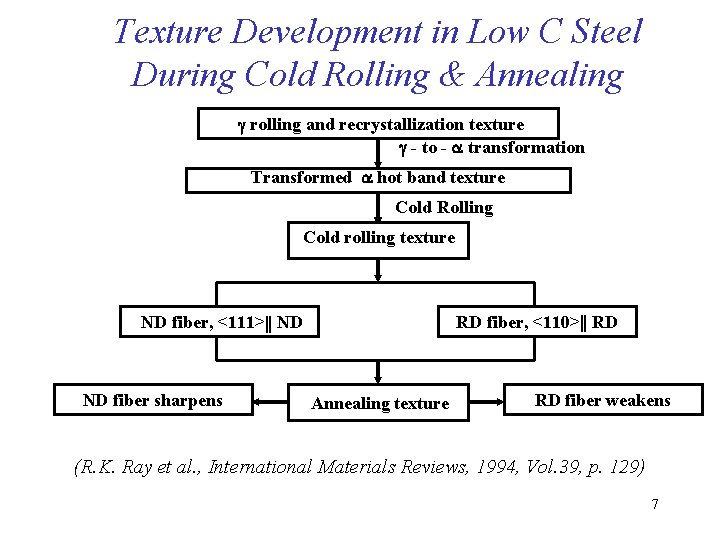
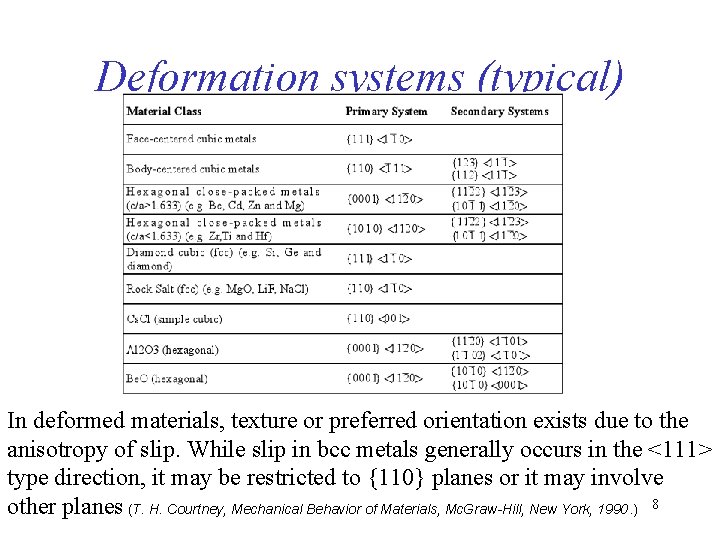
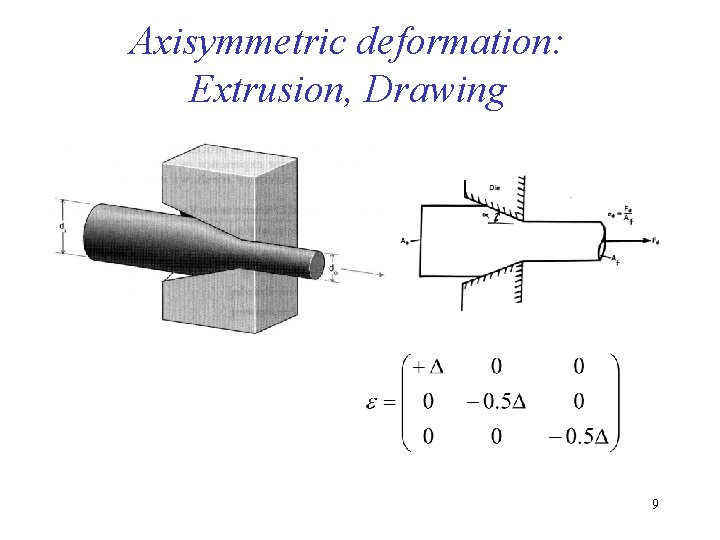
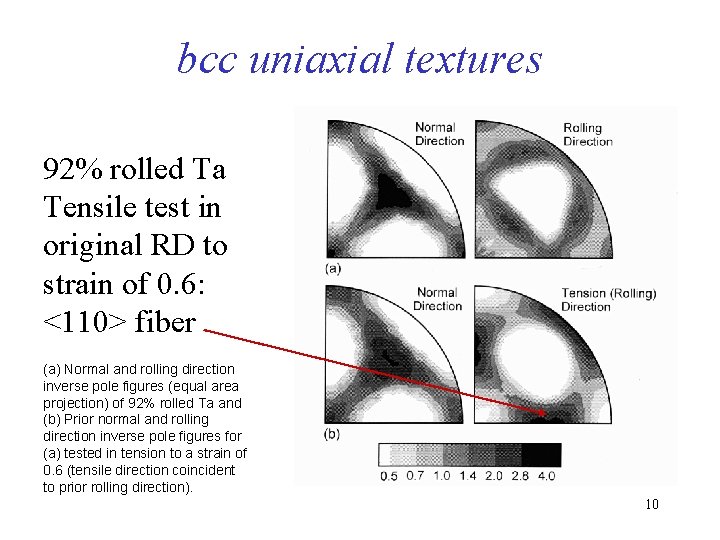
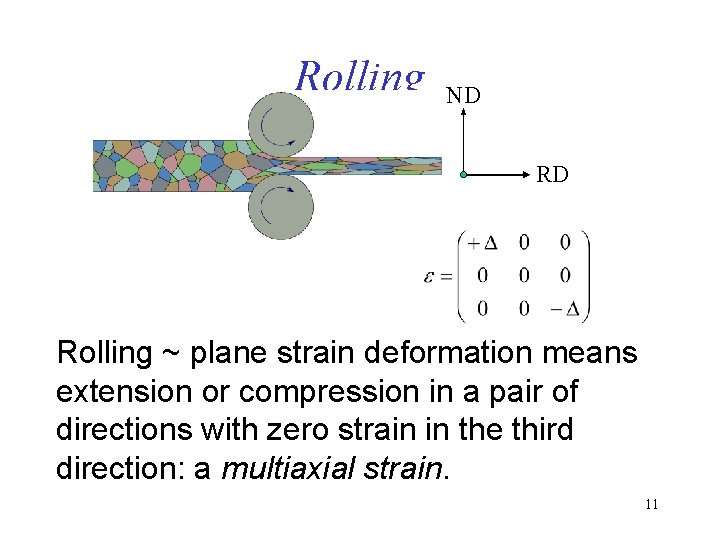
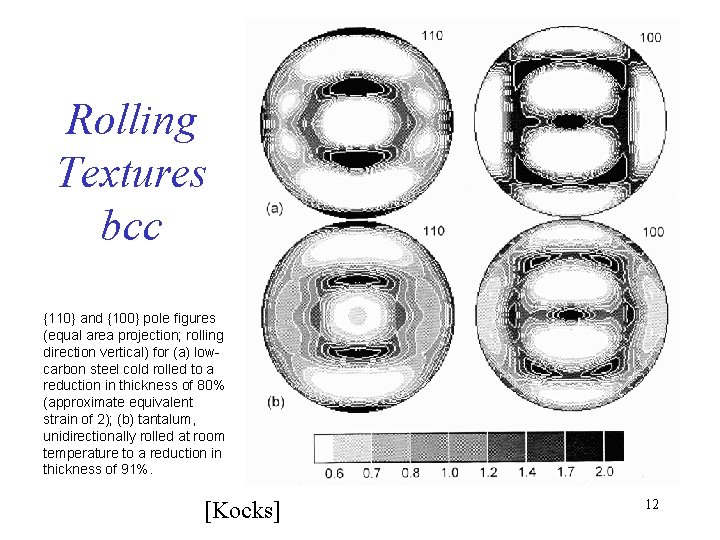
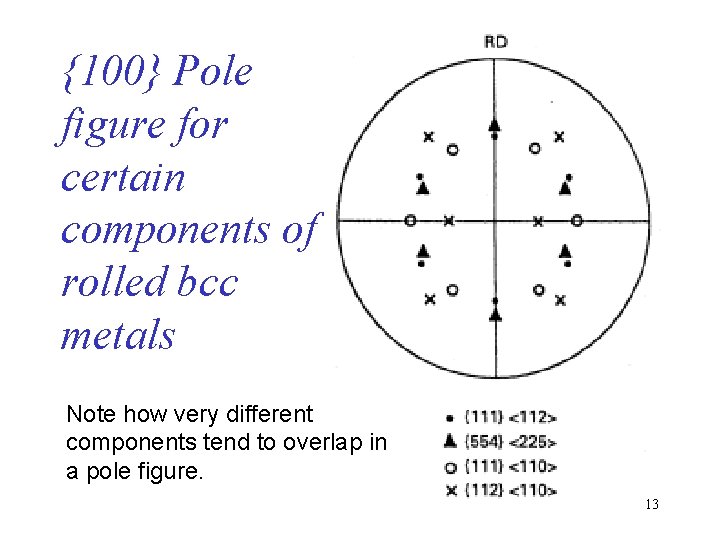
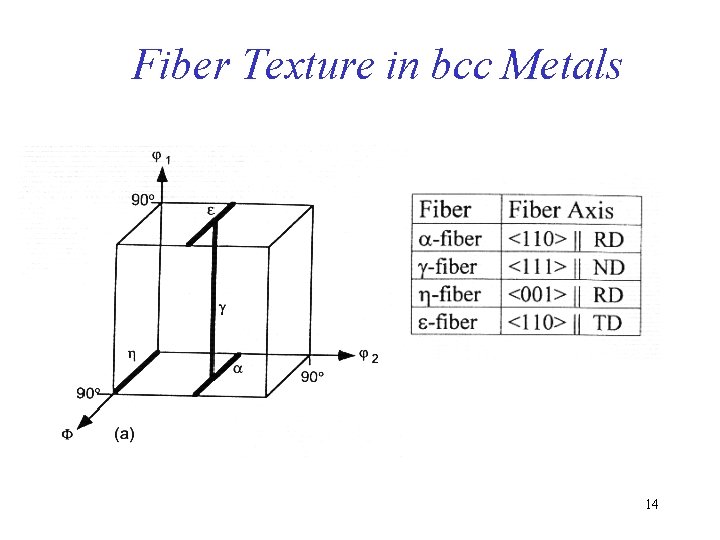
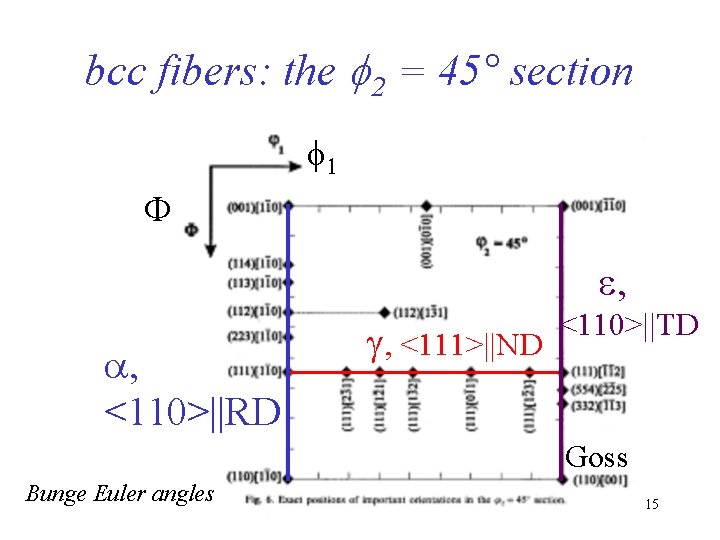
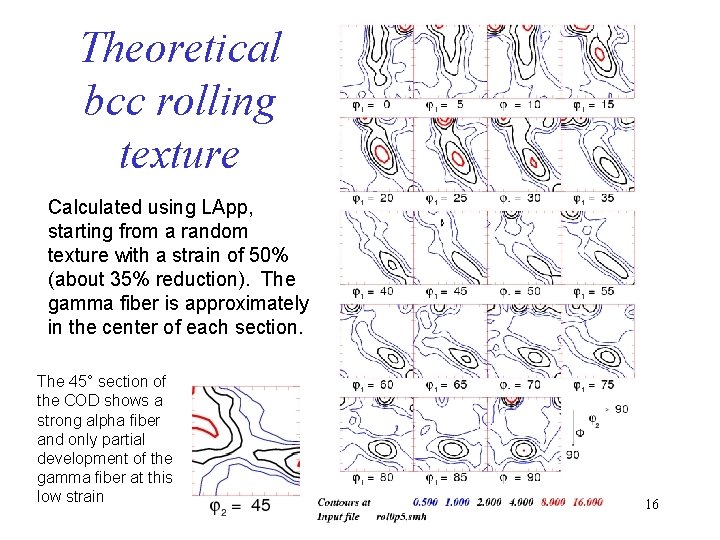
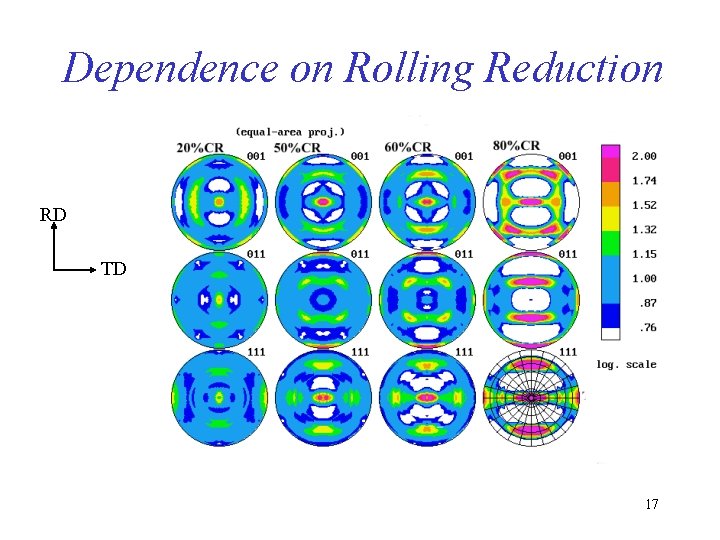
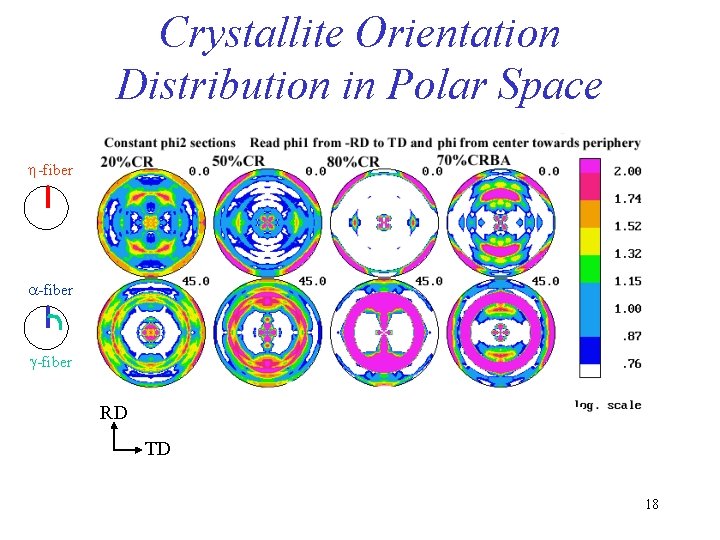
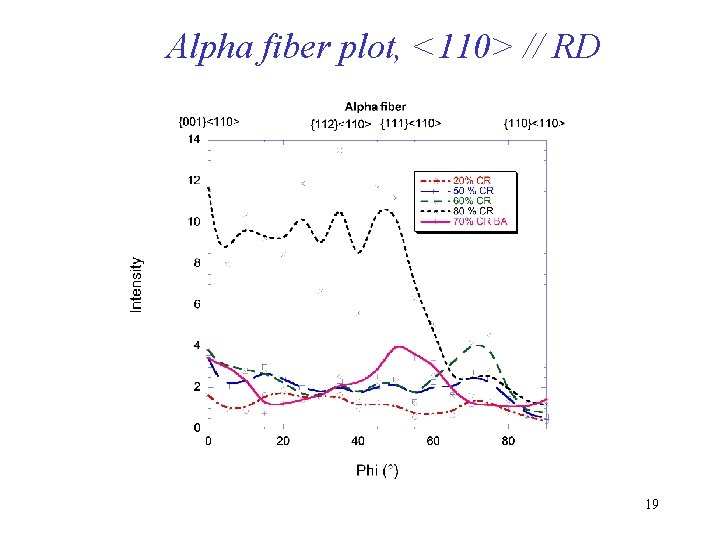
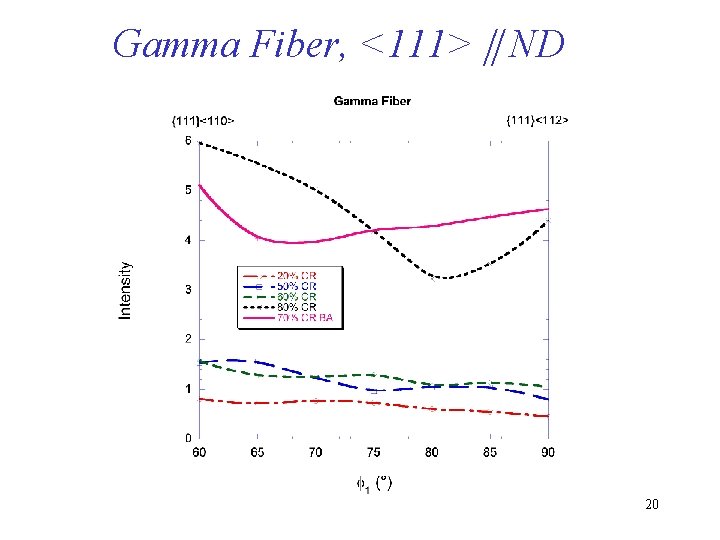
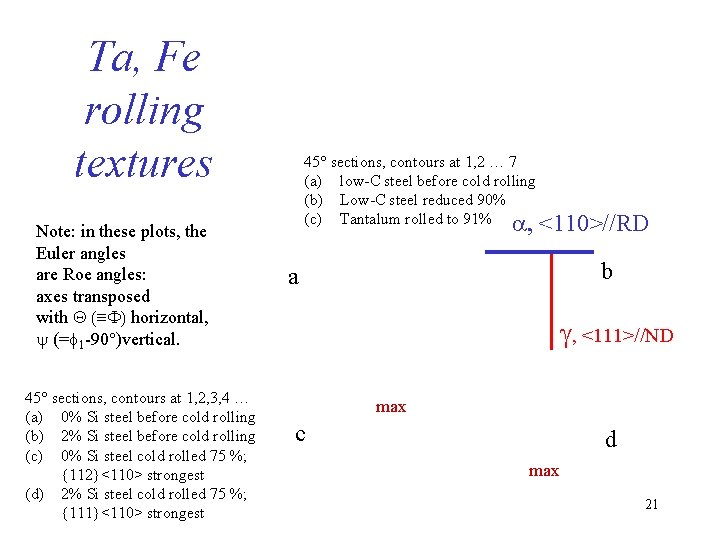
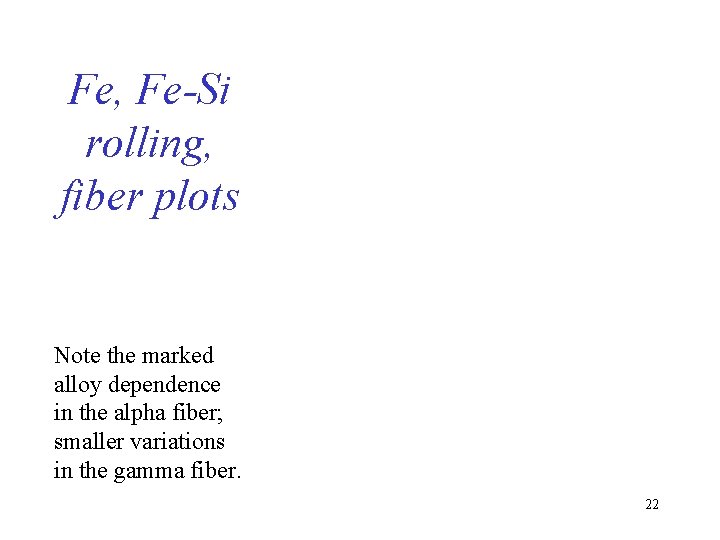
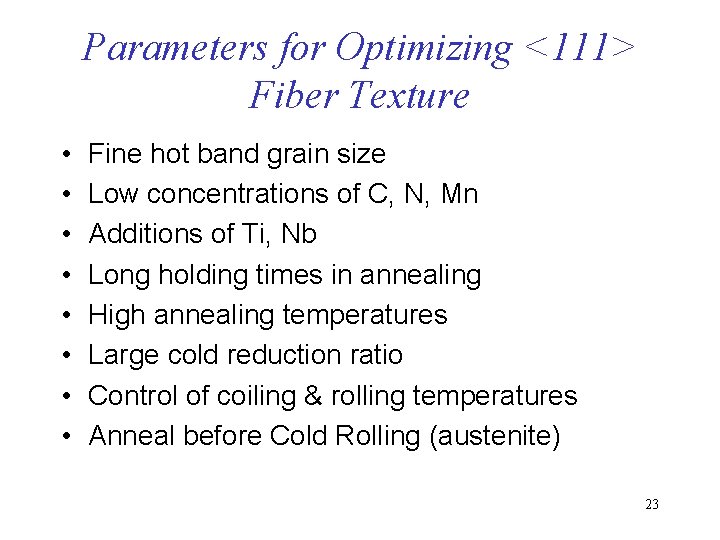
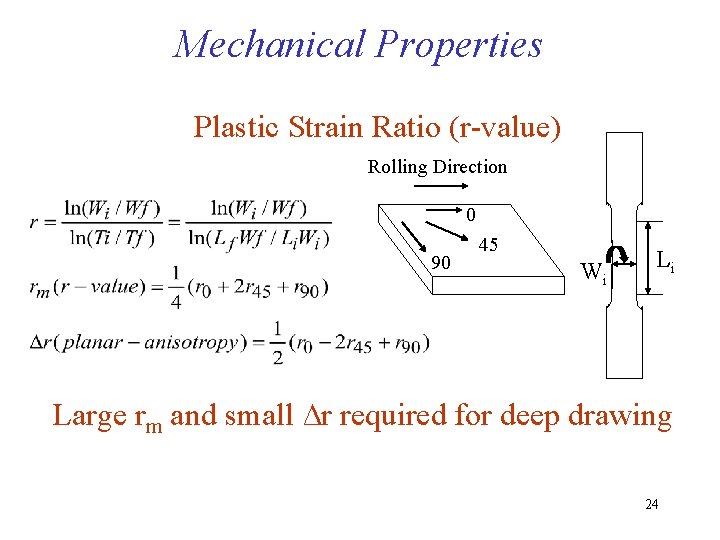
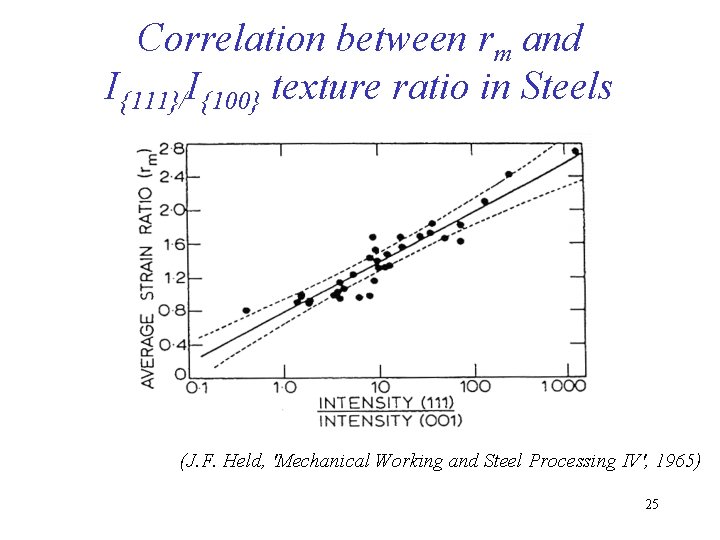
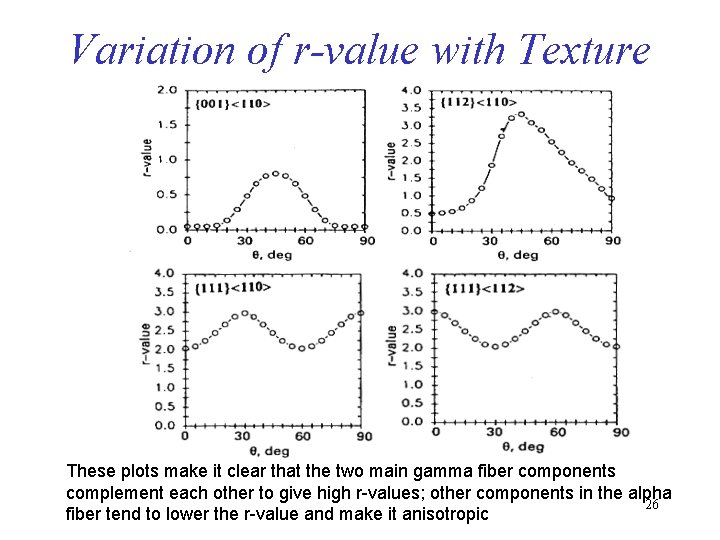
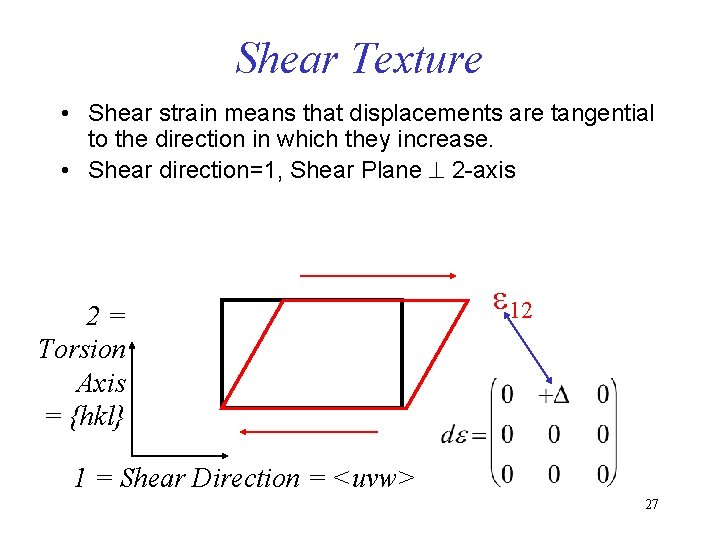
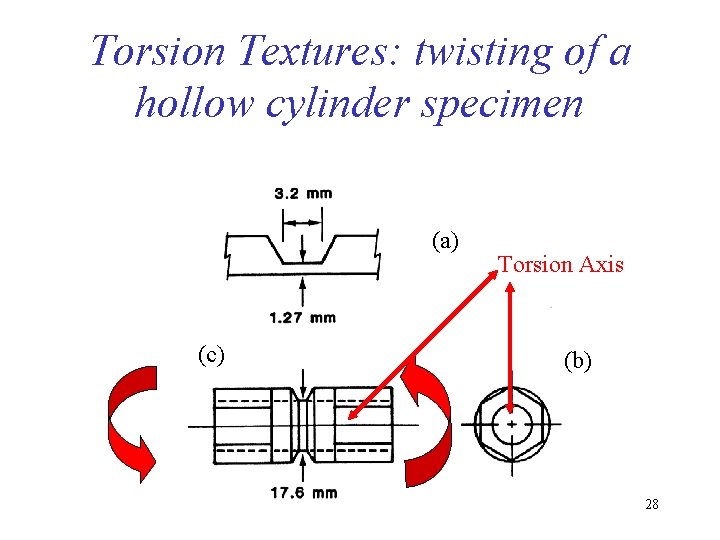
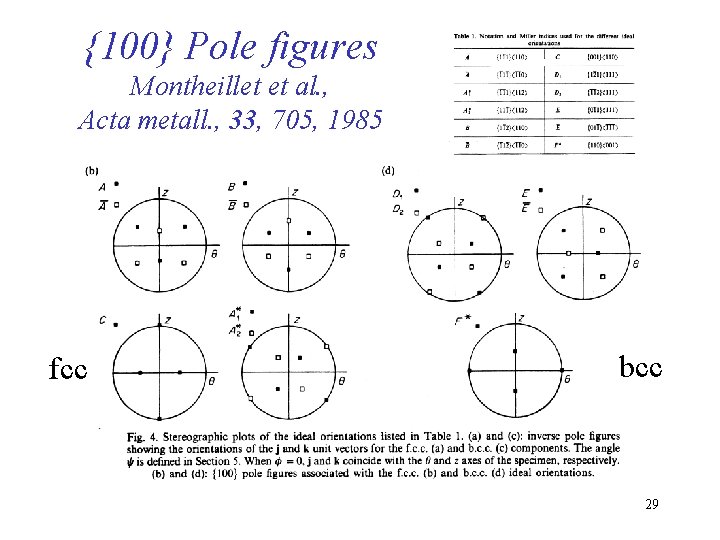
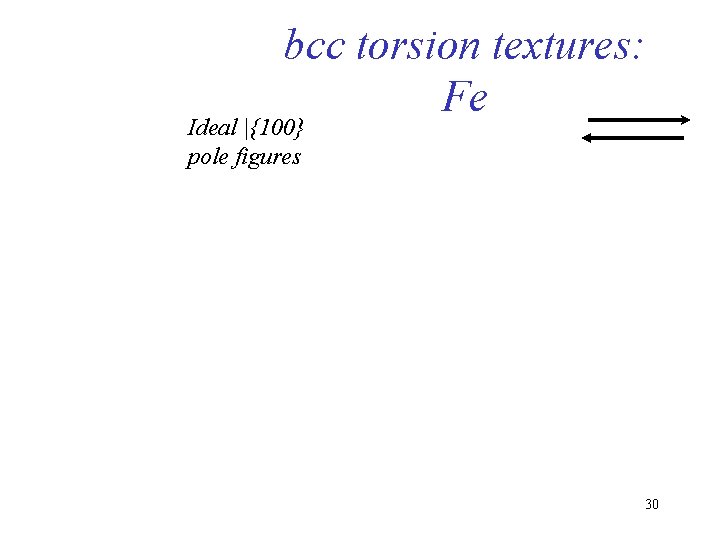
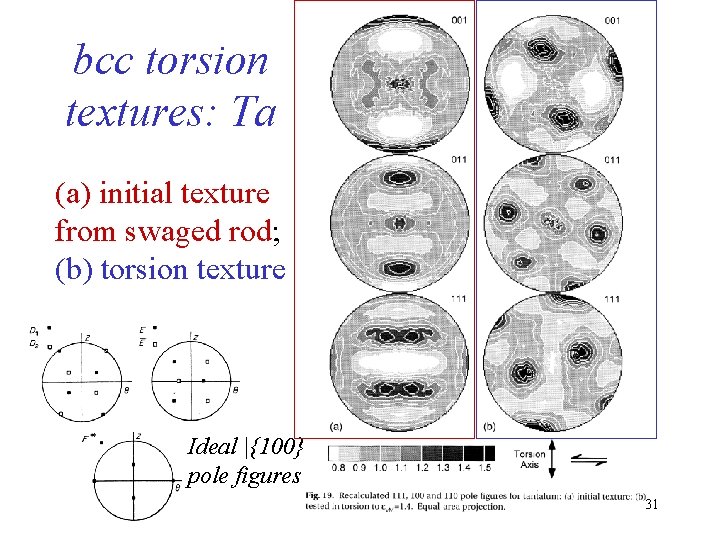
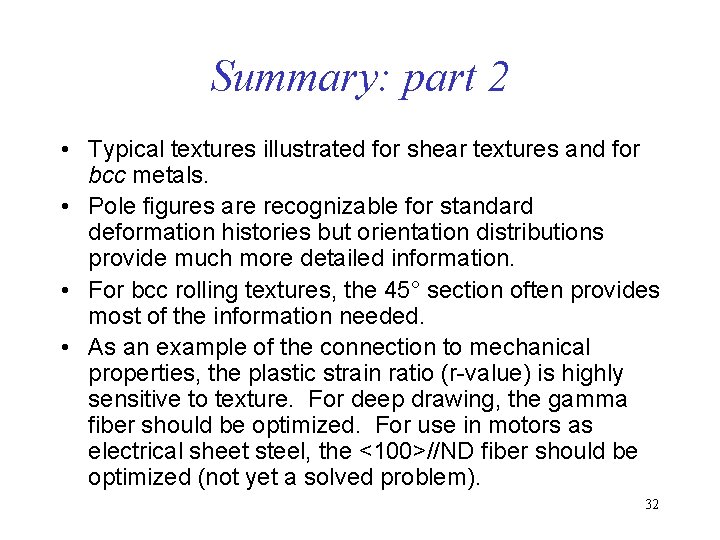
- Slides: 32
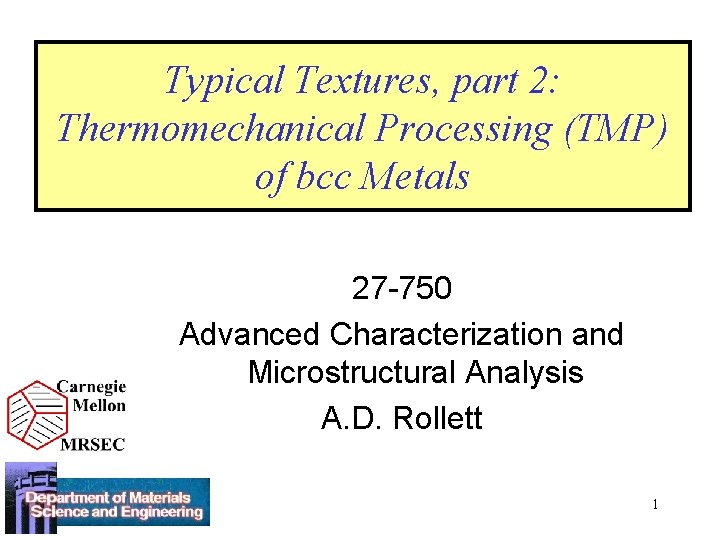
Typical Textures, part 2: Thermomechanical Processing (TMP) of bcc Metals 27 -750 Advanced Characterization and Microstructural Analysis A. D. Rollett 1
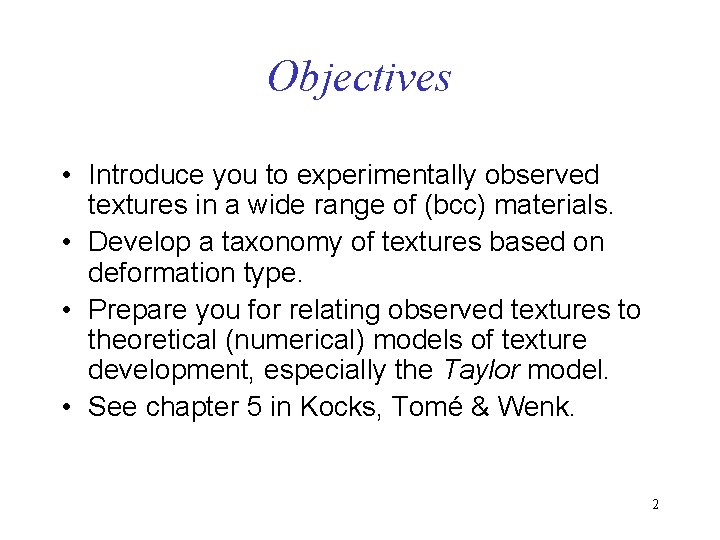
Objectives • Introduce you to experimentally observed textures in a wide range of (bcc) materials. • Develop a taxonomy of textures based on deformation type. • Prepare you for relating observed textures to theoretical (numerical) models of texture development, especially the Taylor model. • See chapter 5 in Kocks, Tomé & Wenk. 2
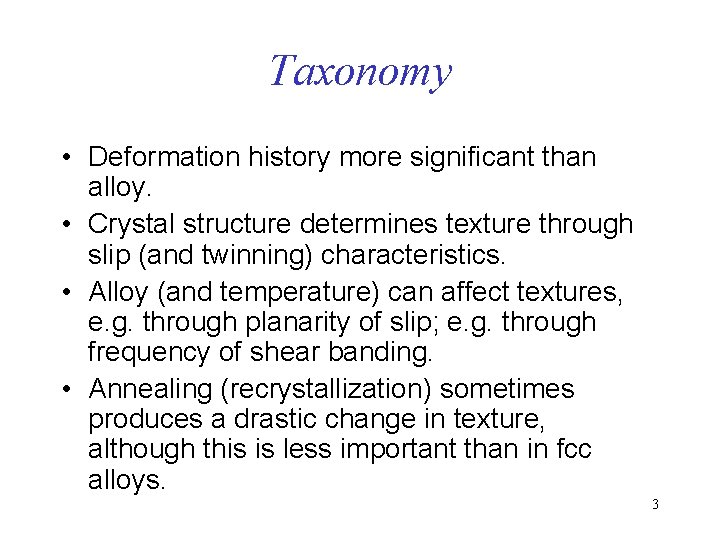
Taxonomy • Deformation history more significant than alloy. • Crystal structure determines texture through slip (and twinning) characteristics. • Alloy (and temperature) can affect textures, e. g. through planarity of slip; e. g. through frequency of shear banding. • Annealing (recrystallization) sometimes produces a drastic change in texture, although this is less important than in fcc alloys. 3
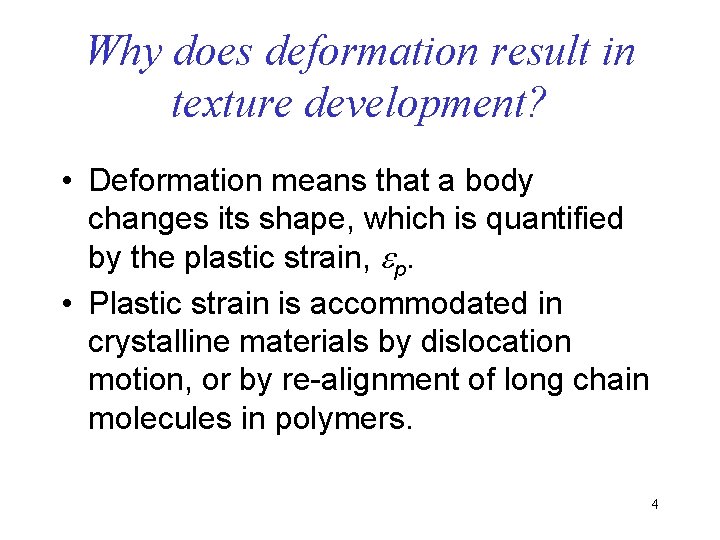
Why does deformation result in texture development? • Deformation means that a body changes its shape, which is quantified by the plastic strain, ep. • Plastic strain is accommodated in crystalline materials by dislocation motion, or by re-alignment of long chain molecules in polymers. 4
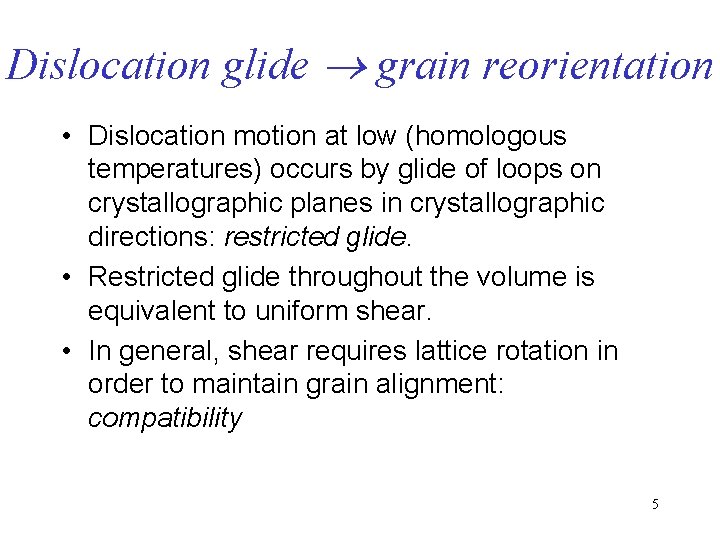
Dislocation glide grain reorientation • Dislocation motion at low (homologous temperatures) occurs by glide of loops on crystallographic planes in crystallographic directions: restricted glide. • Restricted glide throughout the volume is equivalent to uniform shear. • In general, shear requires lattice rotation in order to maintain grain alignment: compatibility 5
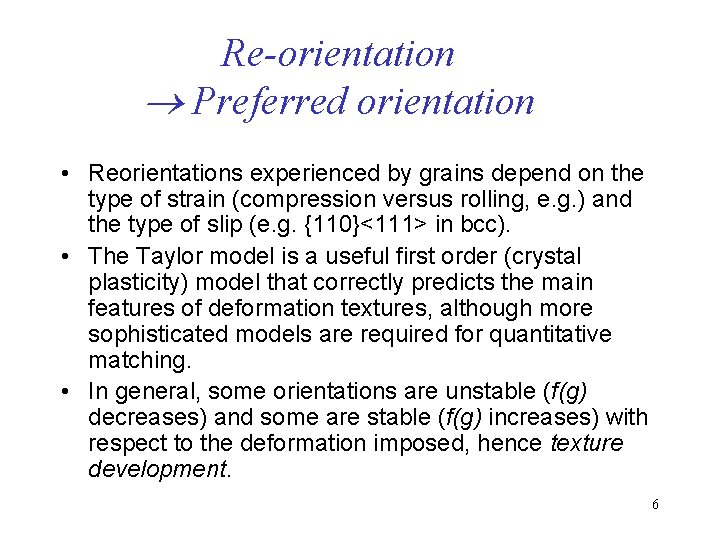
Re-orientation Preferred orientation • Reorientations experienced by grains depend on the type of strain (compression versus rolling, e. g. ) and the type of slip (e. g. {110}<111> in bcc). • The Taylor model is a useful first order (crystal plasticity) model that correctly predicts the main features of deformation textures, although more sophisticated models are required for quantitative matching. • In general, some orientations are unstable (f(g) decreases) and some are stable (f(g) increases) with respect to the deformation imposed, hence texture development. 6
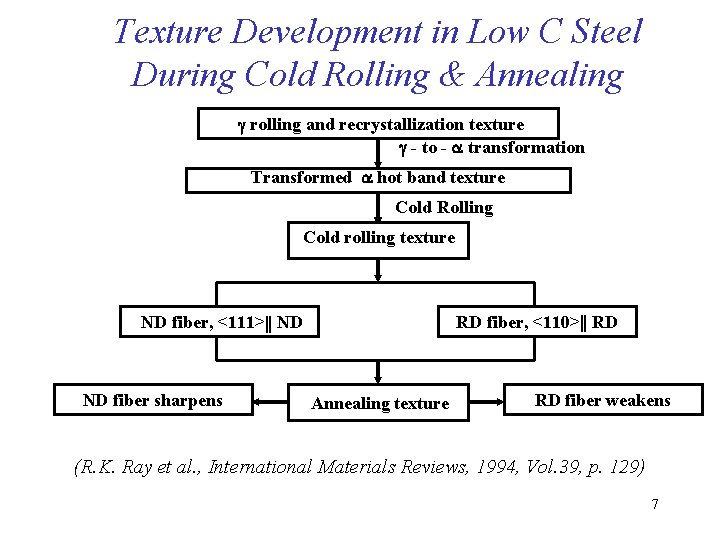
Texture Development in Low C Steel During Cold Rolling & Annealing rolling and recrystallization texture - to - transformation Transformed hot band texture Cold Rolling Cold rolling texture RD fiber, <110> RD ND fiber, <111> ND ND fiber sharpens Annealing texture RD fiber weakens (R. K. Ray et al. , International Materials Reviews, 1994, Vol. 39, p. 129) 7
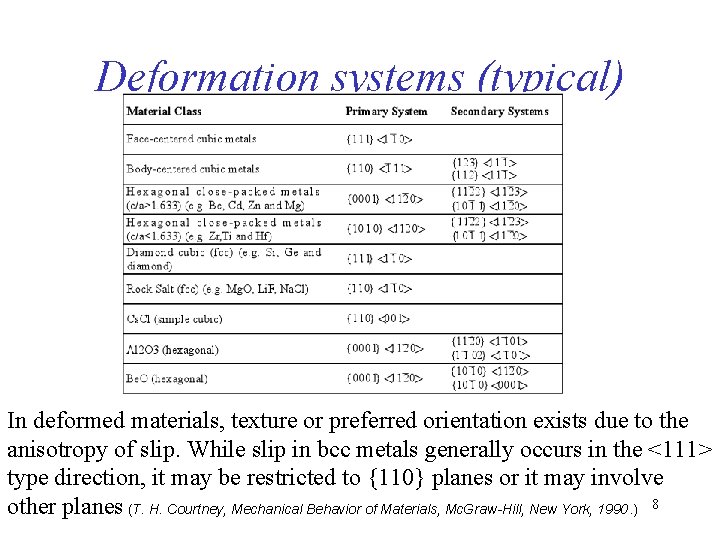
Deformation systems (typical) In deformed materials, texture or preferred orientation exists due to the anisotropy of slip. While slip in bcc metals generally occurs in the <111> type direction, it may be restricted to {110} planes or it may involve other planes (T. H. Courtney, Mechanical Behavior of Materials, Mc. Graw-Hill, New York, 1990. ) 8
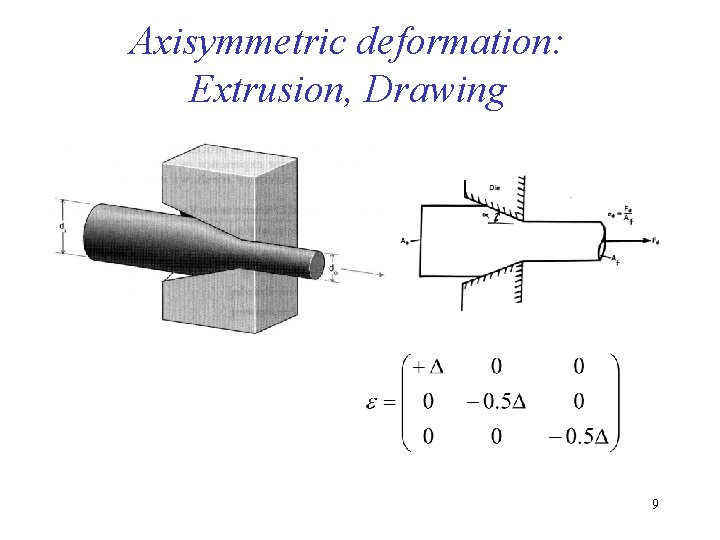
Axisymmetric deformation: Extrusion, Drawing 9
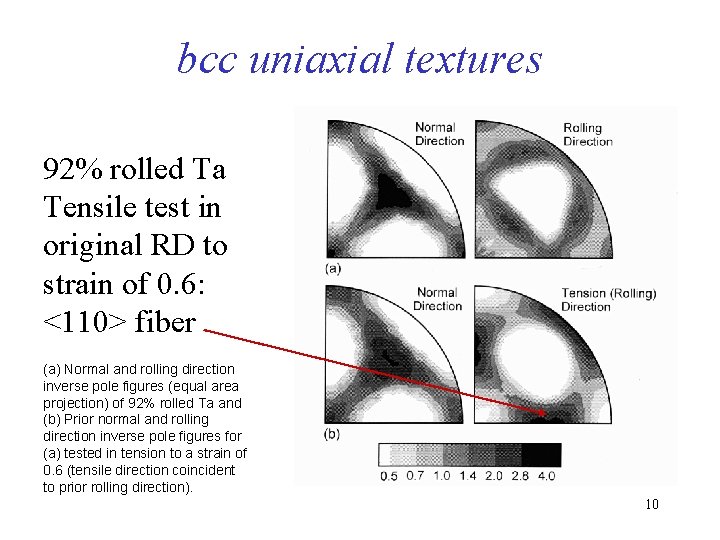
bcc uniaxial textures 92% rolled Ta Tensile test in original RD to strain of 0. 6: <110> fiber (a) Normal and rolling direction inverse pole figures (equal area projection) of 92% rolled Ta and (b) Prior normal and rolling direction inverse pole figures for (a) tested in tension to a strain of 0. 6 (tensile direction coincident to prior rolling direction). 10
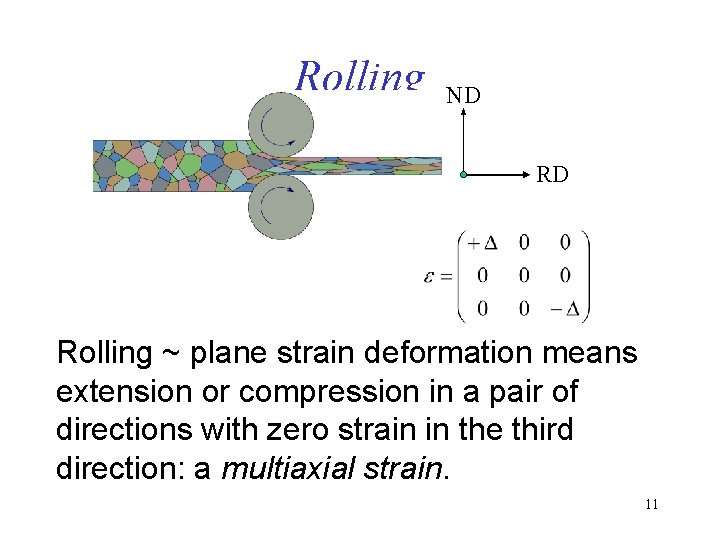
Rolling ND RD Rolling ~ plane strain deformation means extension or compression in a pair of directions with zero strain in the third direction: a multiaxial strain. 11
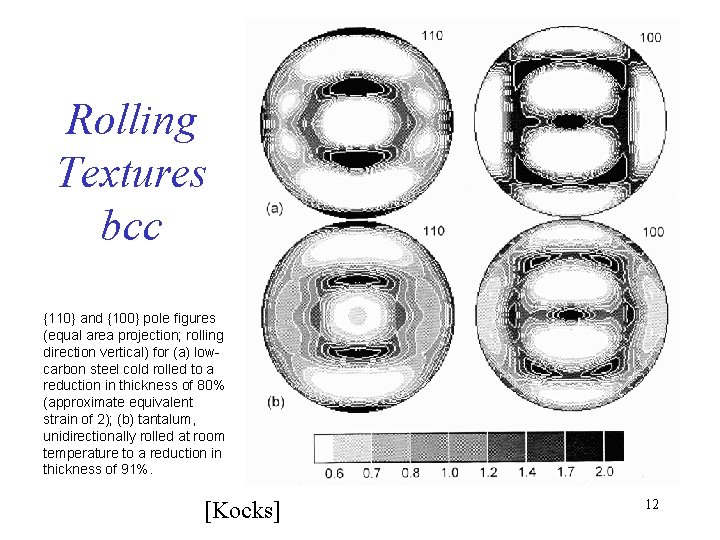
Rolling Textures bcc {110} and {100} pole figures (equal area projection; rolling direction vertical) for (a) lowcarbon steel cold rolled to a reduction in thickness of 80% (approximate equivalent strain of 2); (b) tantalum, unidirectionally rolled at room temperature to a reduction in thickness of 91%. [Kocks] 12
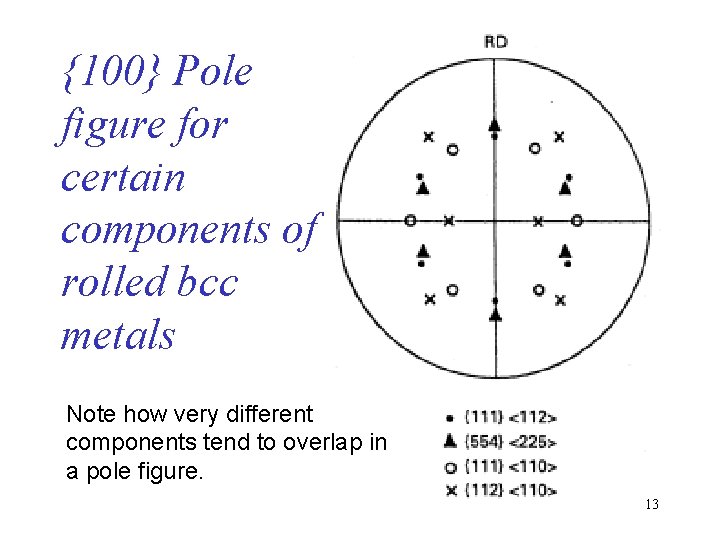
{100} Pole figure for certain components of rolled bcc metals Note how very different components tend to overlap in a pole figure. 13
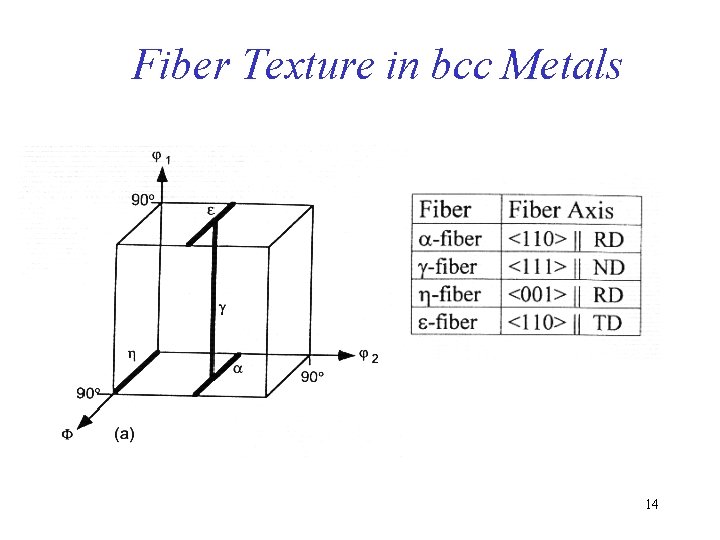
Fiber Texture in bcc Metals 14
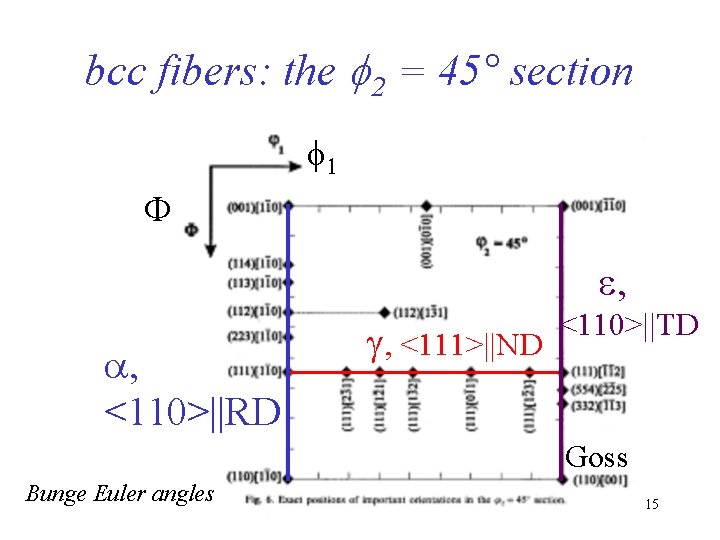
bcc fibers: the f 2 = 45° section 1 e, a, <110>||RD g, <111>||ND <110>||TD Goss Bunge Euler angles 15
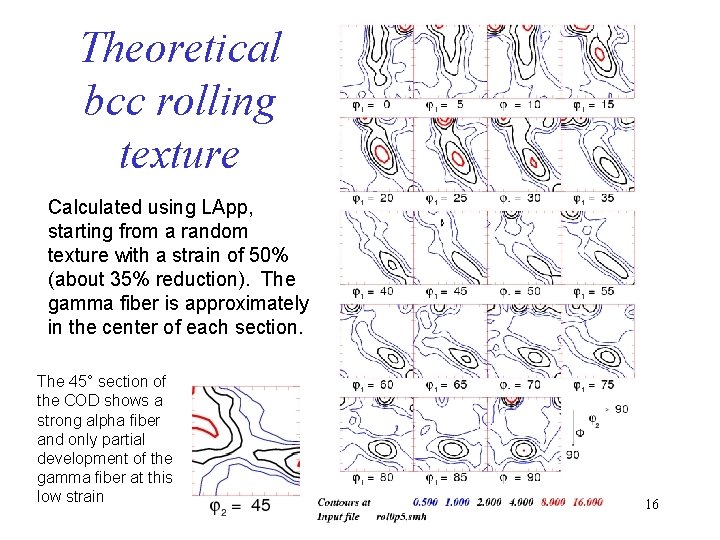
Theoretical bcc rolling texture Calculated using LApp, starting from a random texture with a strain of 50% (about 35% reduction). The gamma fiber is approximately in the center of each section. The 45° section of the COD shows a strong alpha fiber and only partial development of the gamma fiber at this low strain 16
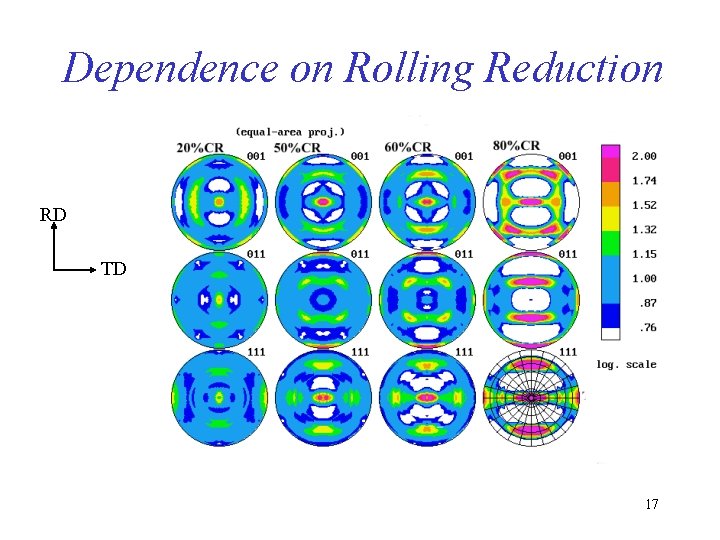
Dependence on Rolling Reduction RD TD 17
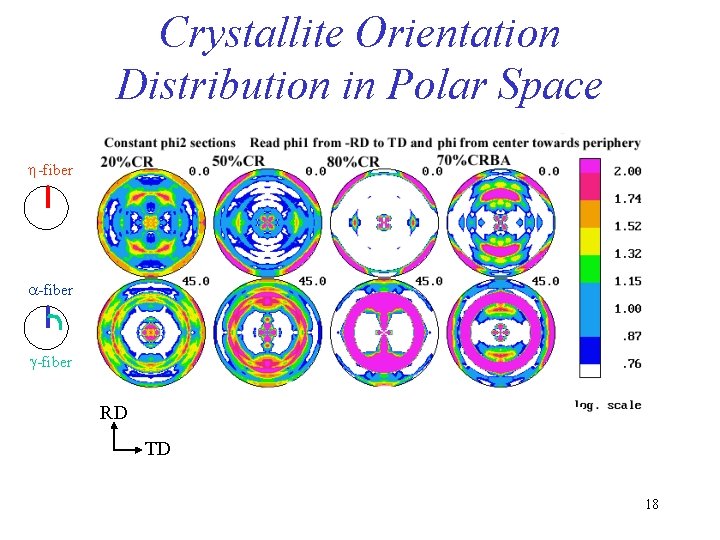
Crystallite Orientation Distribution in Polar Space h-fiber a-fiber g-fiber RD TD 18
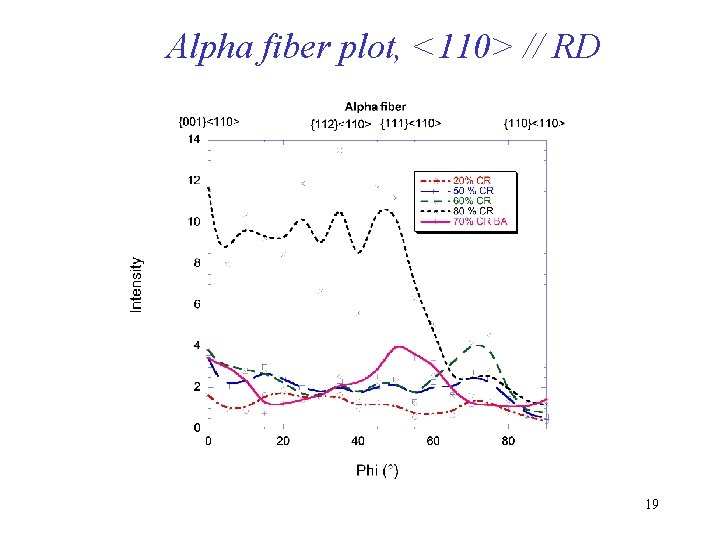
Alpha fiber plot, <110> // RD 19
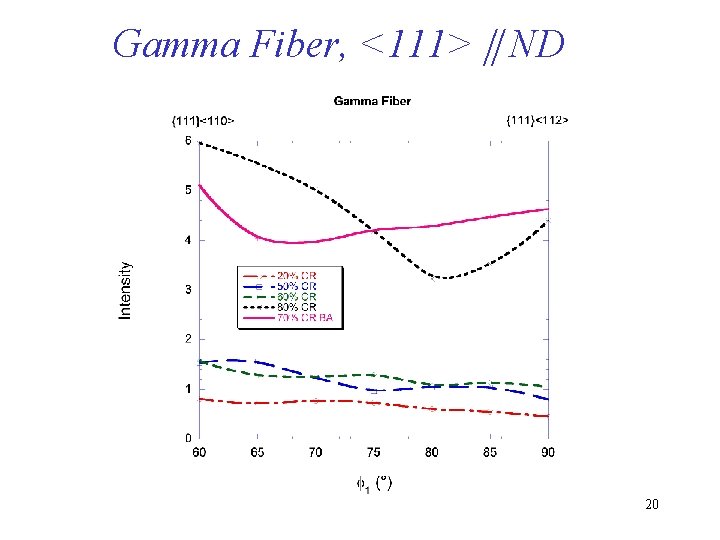
Gamma Fiber, <111> ND 20
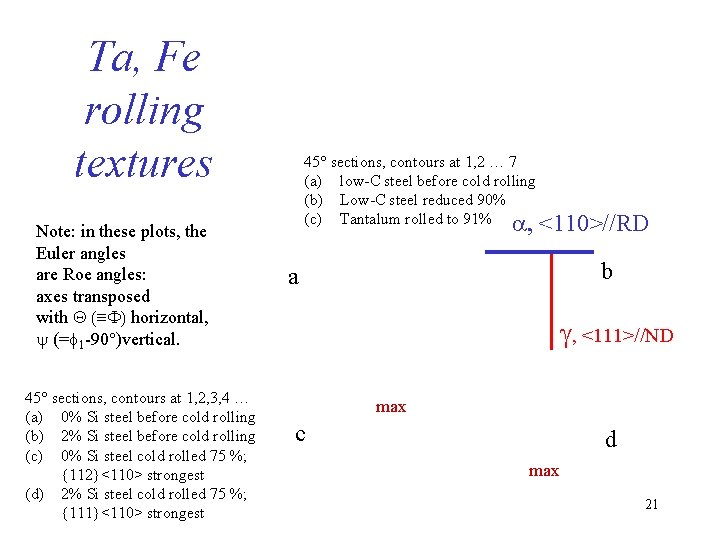
Ta, Fe rolling textures Note: in these plots, the Euler angles are Roe angles: axes transposed with Q horizontal, y (= 1 -90°)vertical. 45° sections, contours at 1, 2, 3, 4 … (a) 0% Si steel before cold rolling (b) 2% Si steel before cold rolling (c) 0% Si steel cold rolled 75 %; {112}<110> strongest (d) 2% Si steel cold rolled 75 %; {111}<110> strongest 45° sections, contours at 1, 2 … 7 (a) low-C steel before cold rolling (b) Low-C steel reduced 90% (c) Tantalum rolled to 91% a, <110>//RD b a g, <111>//ND max c d max 21
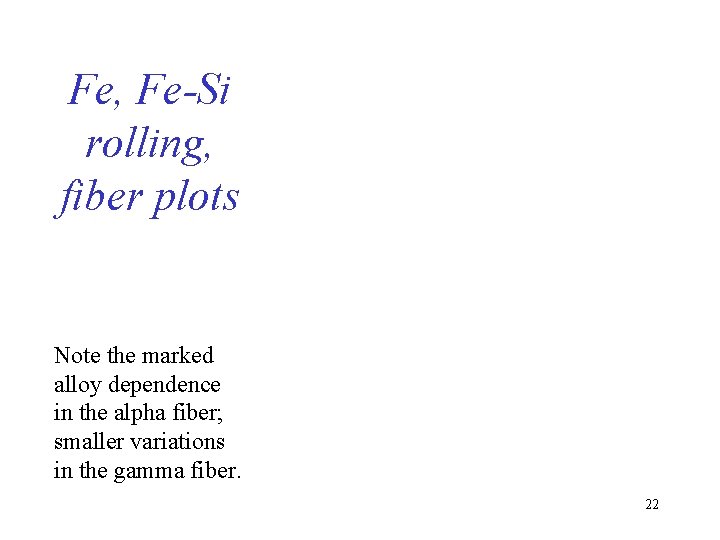
Fe, Fe-Si rolling, fiber plots Note the marked alloy dependence in the alpha fiber; smaller variations in the gamma fiber. 22
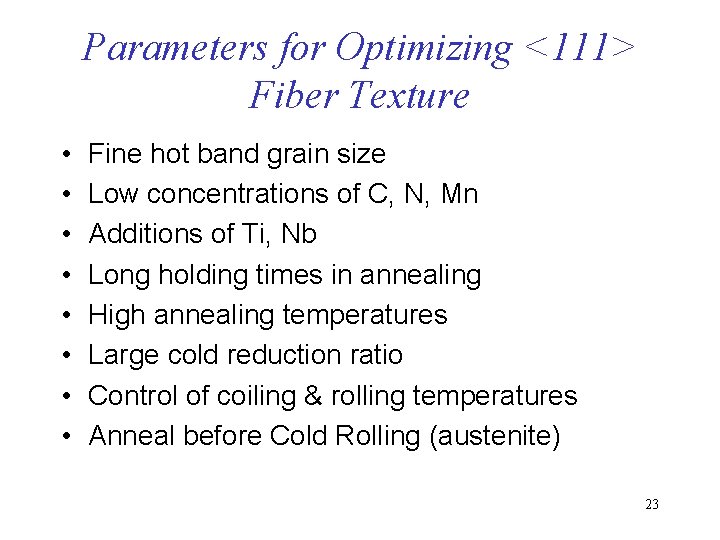
Parameters for Optimizing <111> Fiber Texture • • Fine hot band grain size Low concentrations of C, N, Mn Additions of Ti, Nb Long holding times in annealing High annealing temperatures Large cold reduction ratio Control of coiling & rolling temperatures Anneal before Cold Rolling (austenite) 23
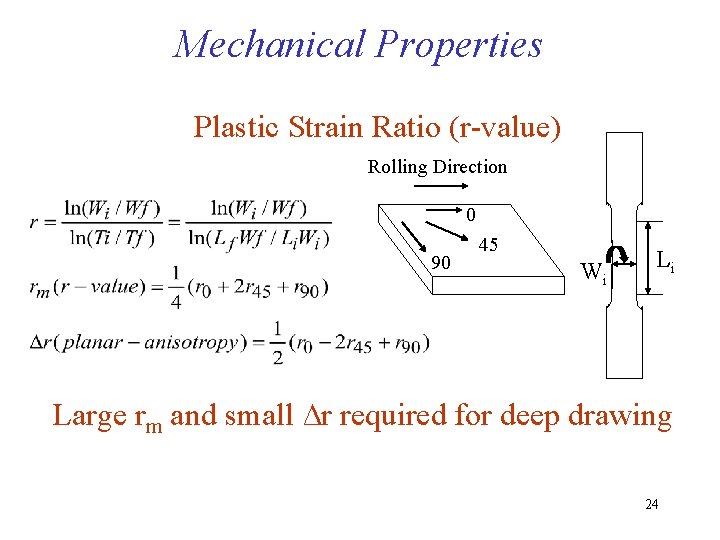
Mechanical Properties Plastic Strain Ratio (r-value) Rolling Direction 0 90 45 Wi Li Large rm and small ∆r required for deep drawing 24
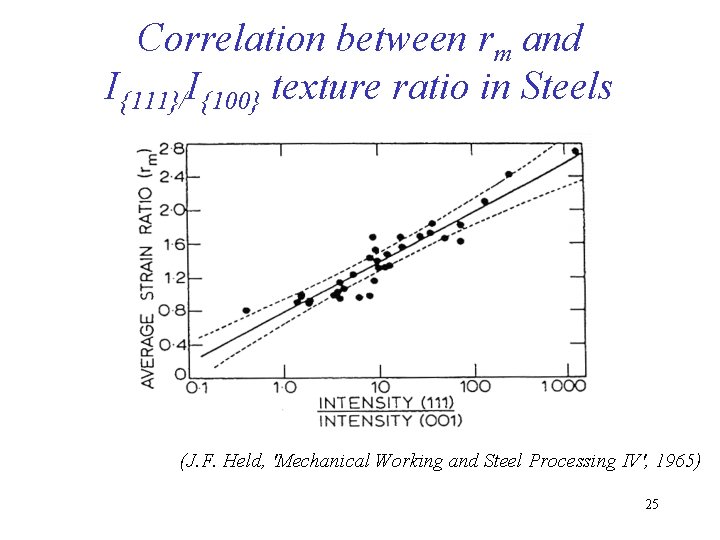
Correlation between rm and I{111}/I{100} texture ratio in Steels (J. F. Held, 'Mechanical Working and Steel Processing IV', 1965) 25
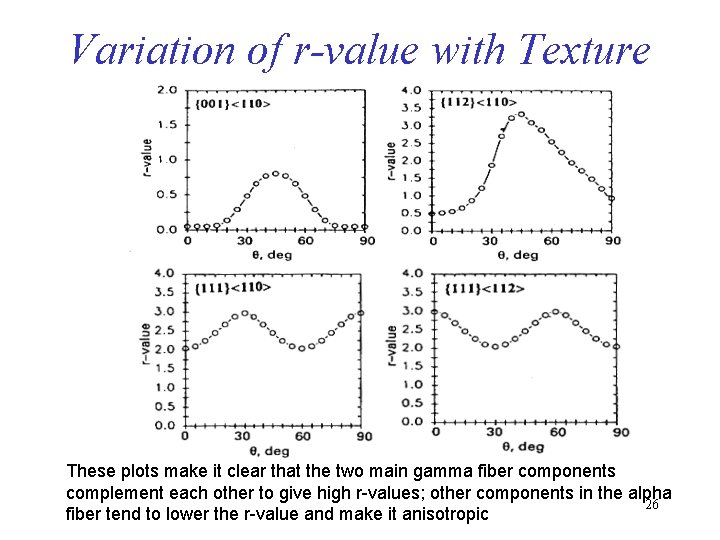
Variation of r-value with Texture These plots make it clear that the two main gamma fiber components complement each other to give high r-values; other components in the alpha 26 fiber tend to lower the r-value and make it anisotropic
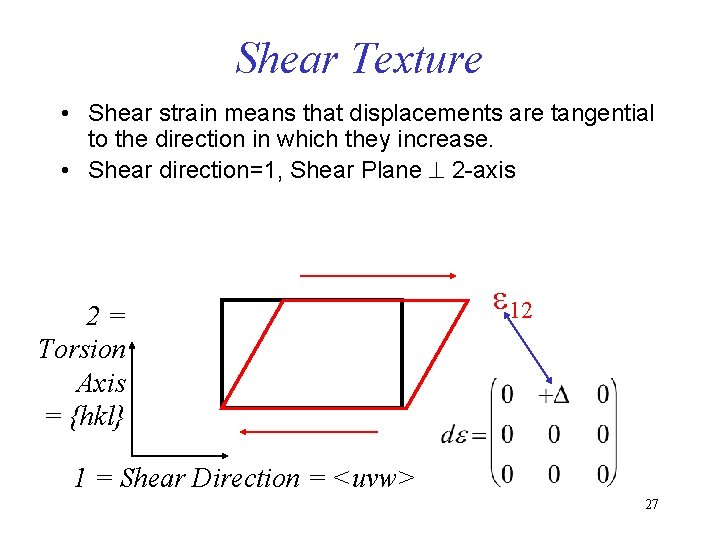
Shear Texture • Shear strain means that displacements are tangential to the direction in which they increase. • Shear direction=1, Shear Plane 2 -axis 2= Torsion Axis = {hkl} e 12 1 = Shear Direction = <uvw> 27
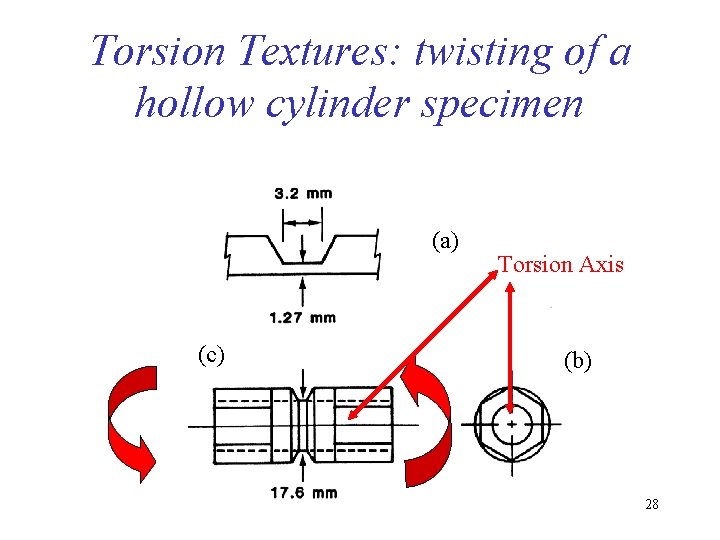
Torsion Textures: twisting of a hollow cylinder specimen (a) (c) Torsion Axis (b) 28
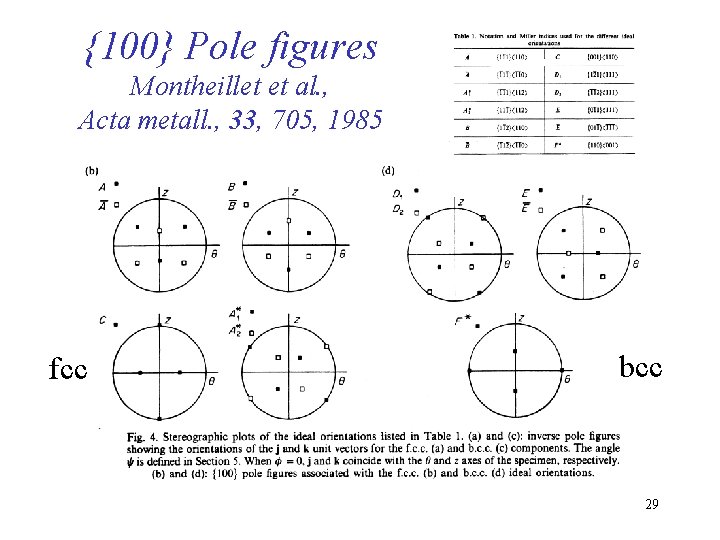
{100} Pole figures Montheillet et al. , Acta metall. , 33, 705, 1985 fcc bcc 29
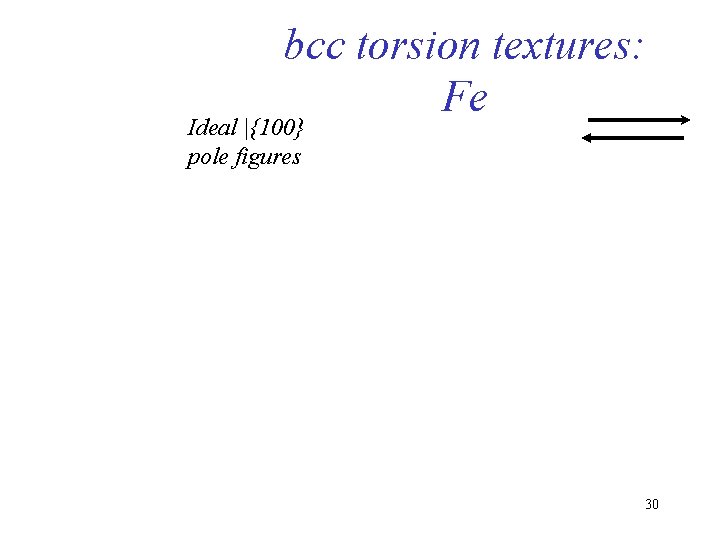
bcc torsion textures: Fe Ideal |{100} pole figures 30
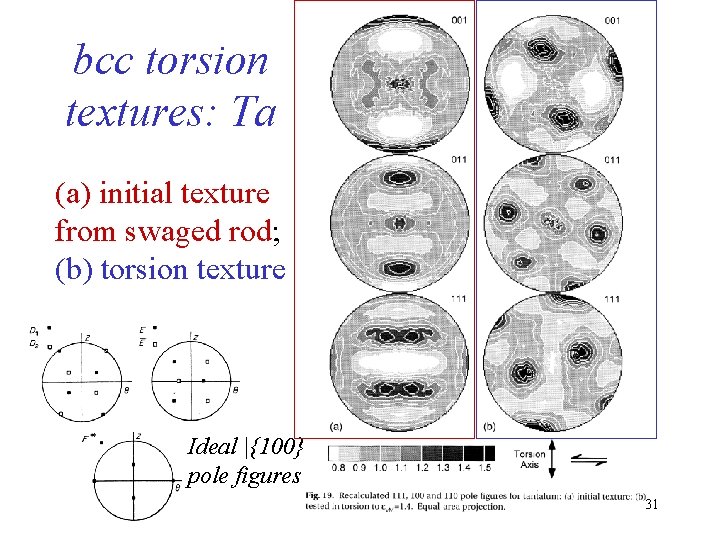
bcc torsion textures: Ta (a) initial texture from swaged rod; (b) torsion texture Ideal |{100} pole figures 31
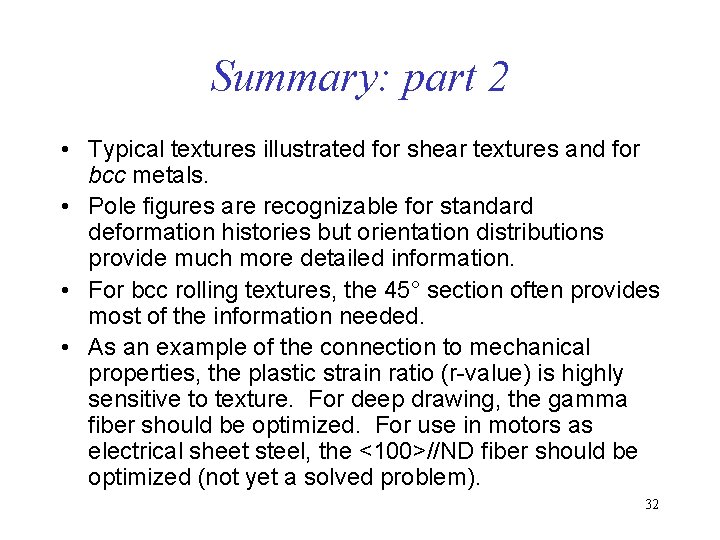
Summary: part 2 • Typical textures illustrated for shear textures and for bcc metals. • Pole figures are recognizable for standard deformation histories but orientation distributions provide much more detailed information. • For bcc rolling textures, the 45° section often provides most of the information needed. • As an example of the connection to mechanical properties, the plastic strain ratio (r-value) is highly sensitive to texture. For deep drawing, the gamma fiber should be optimized. For use in motors as electrical sheet steel, the <100>//ND fiber should be optimized (not yet a solved problem). 32
Structural lines in clothing
Tmp presentation
Pov
Varicela zoster
Hilton tmp
Prisma flex
Tmp tempoe
Partially resident textures
Rendering fur with three dimensional textures
Illusion textures
Rock textures chart
Metamorphic textures
Metamorphic textures
What is simulated texture in art
Invented texture
Cuda texture object example
Textures drape fabric
Atiyeh ghoreyshi
A surface that reflects a soft dull light
What is point processing in digital image processing
Batch processing and interactive processing
Bottom-up processing examples
Histogram processing in digital image processing
Digital image processing
High boost filtering matlab
Parallel processing vs concurrent processing
Top-down processing vs bottom-up processing
What is primary and secondary processing
Nonlinear image processing
Top bottom processing
Bottom up processing vs top down processing
Fractal
Four part processing model for word recognition