Solar Powered Charging Station Final Presentation Design Team
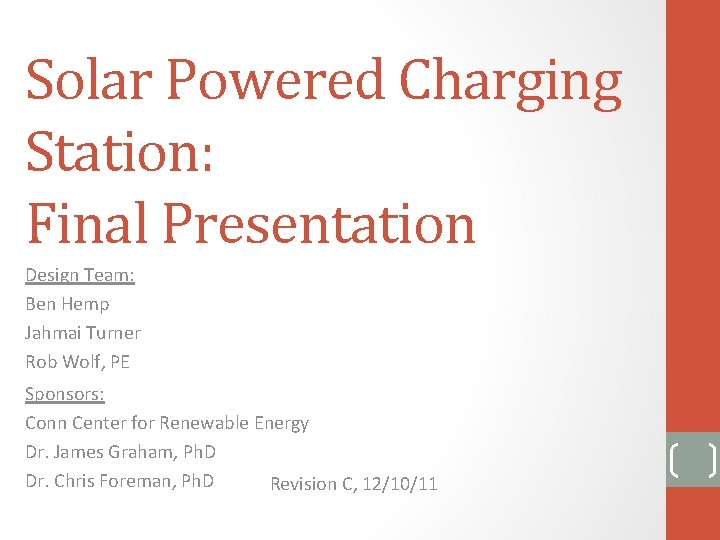
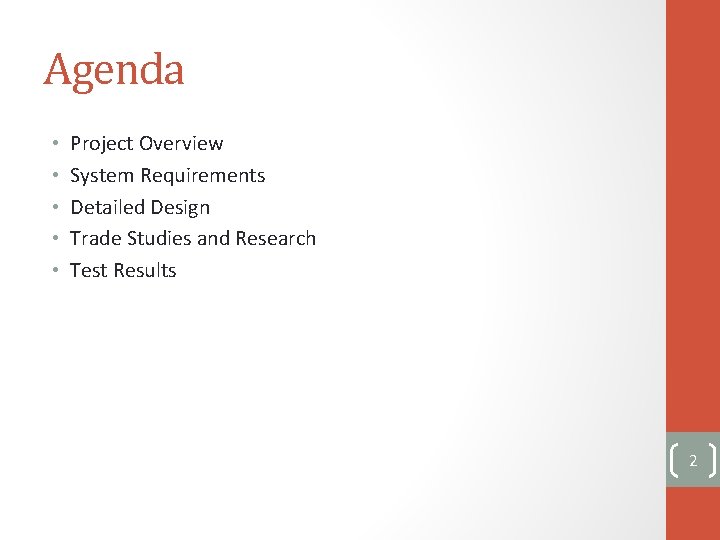
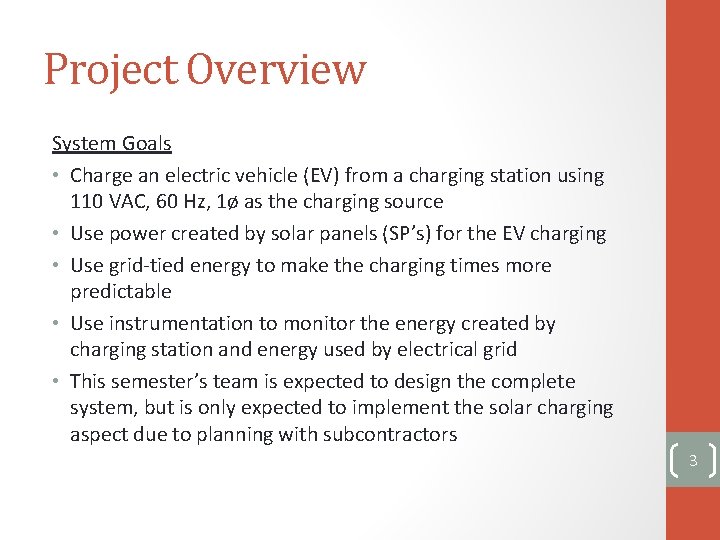
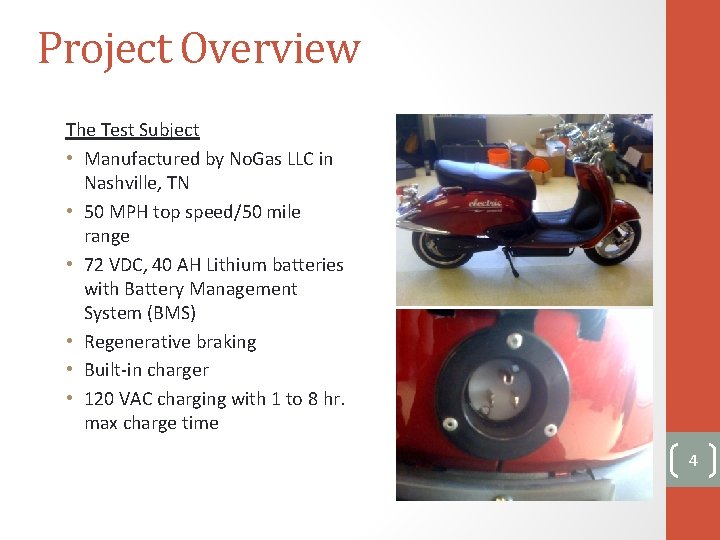
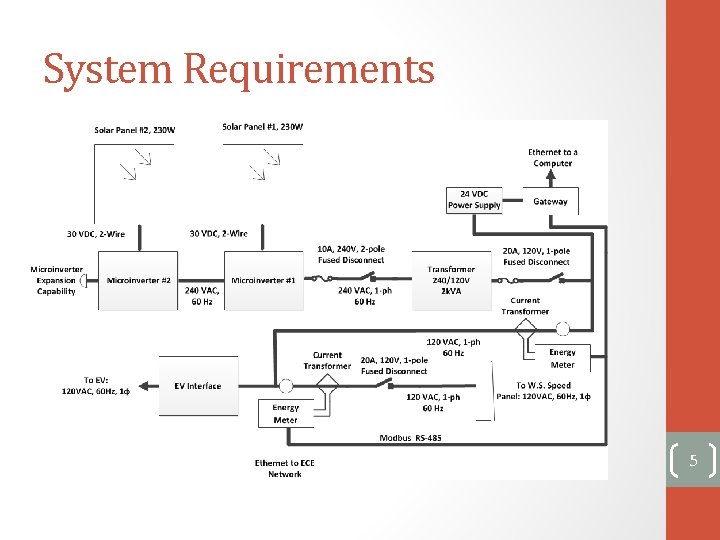
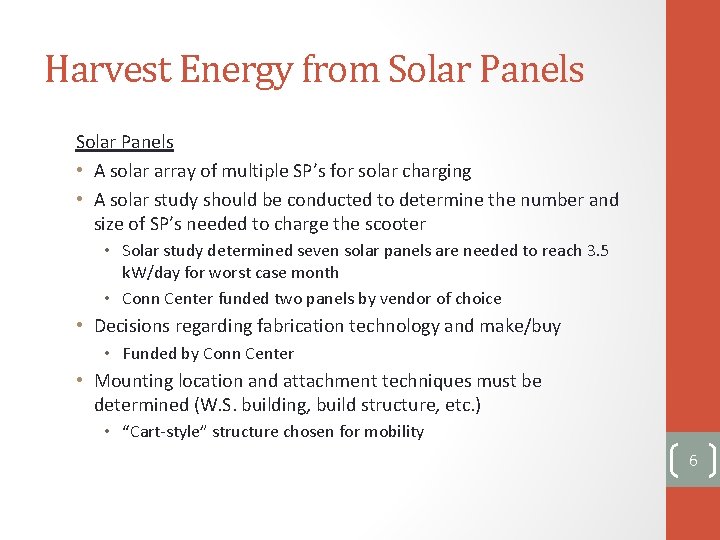
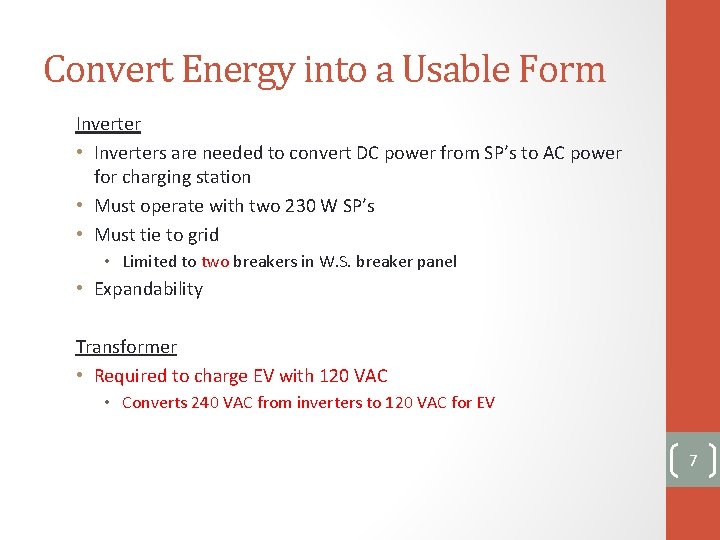
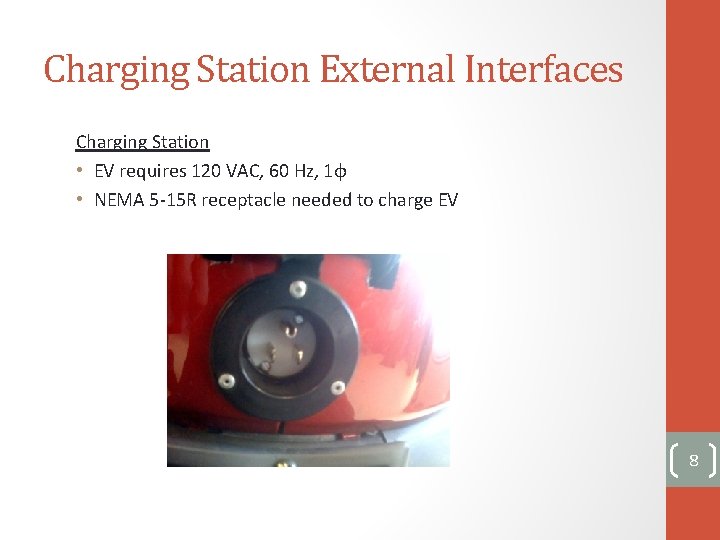
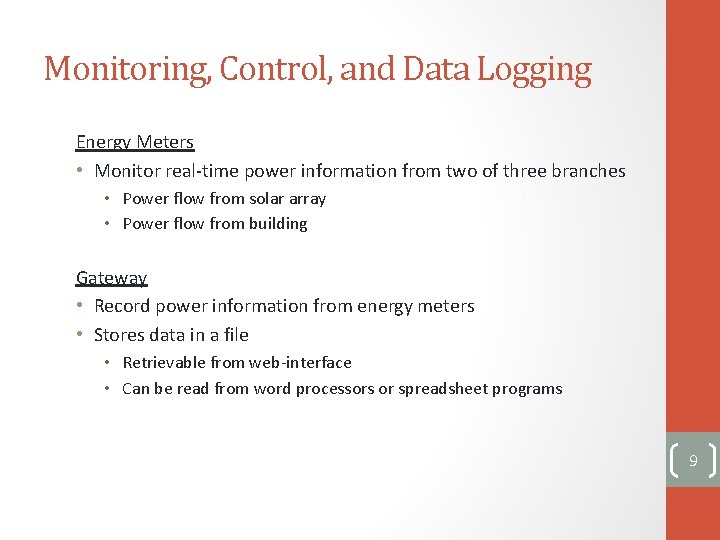
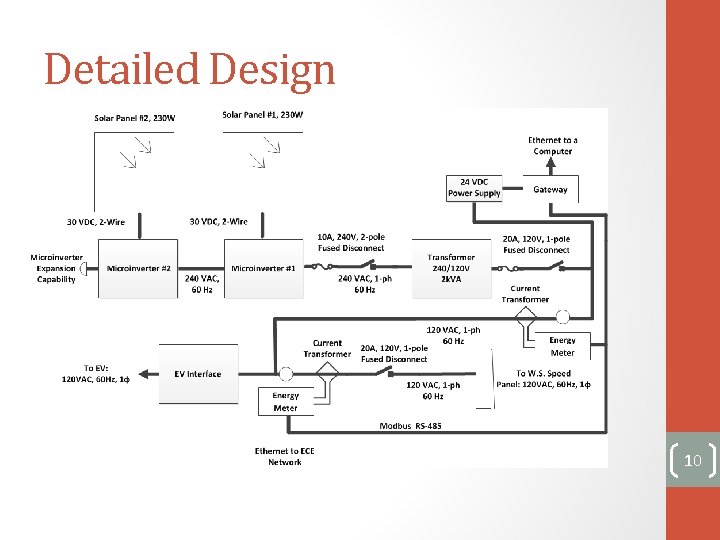
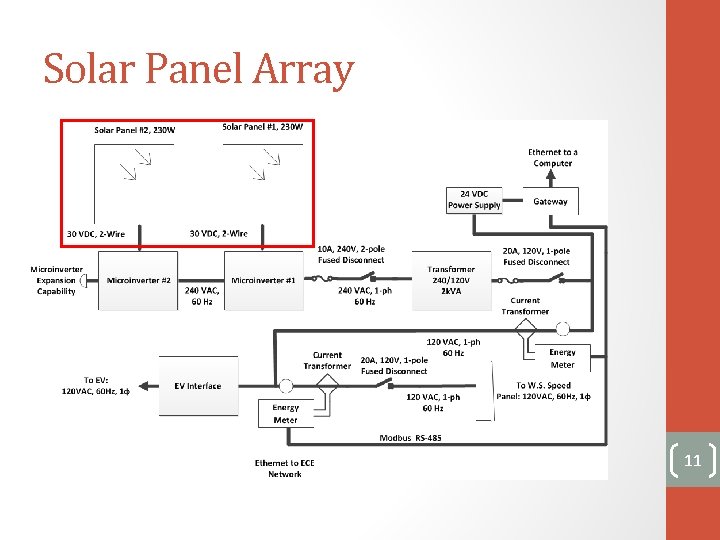
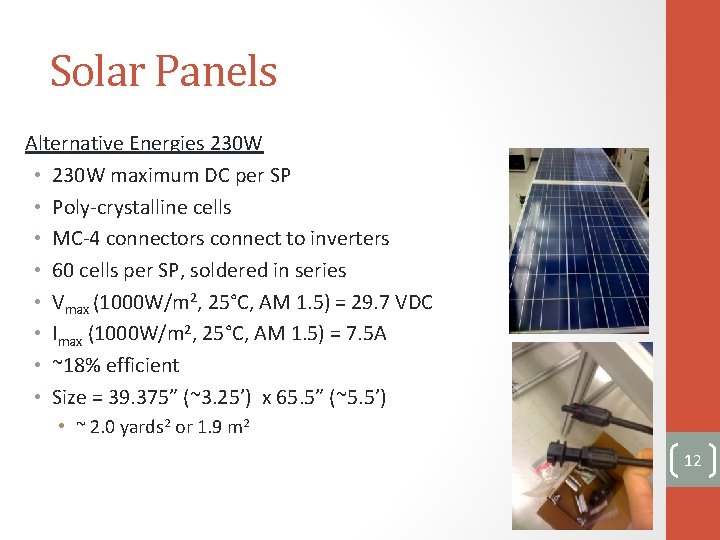
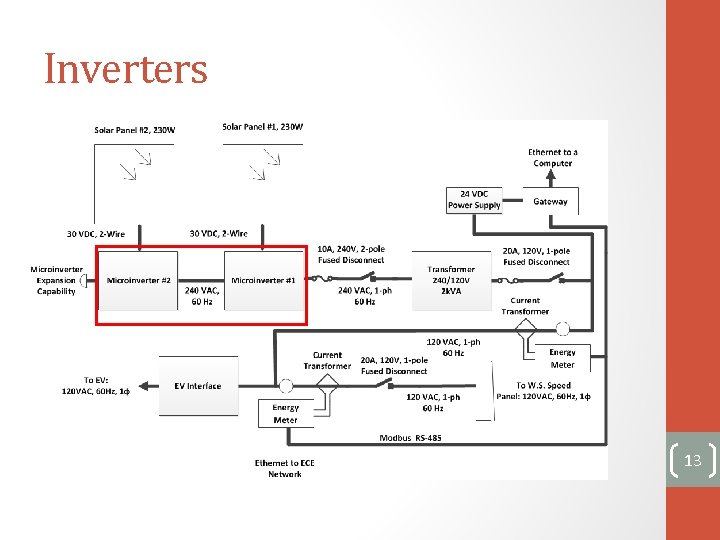
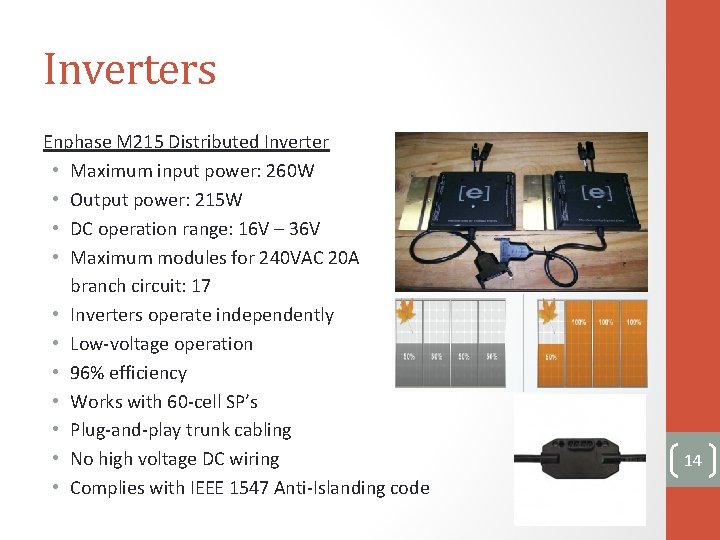
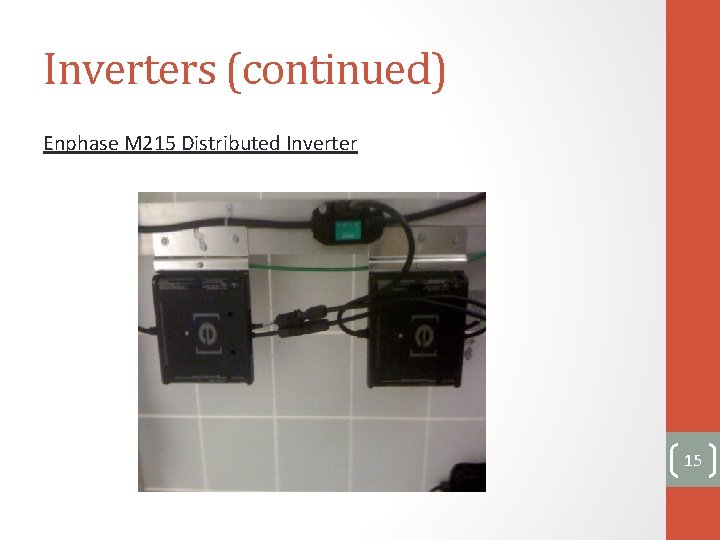
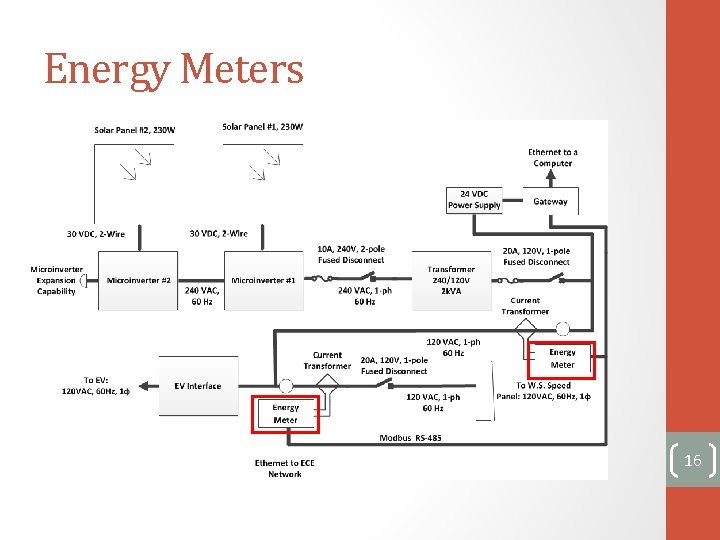
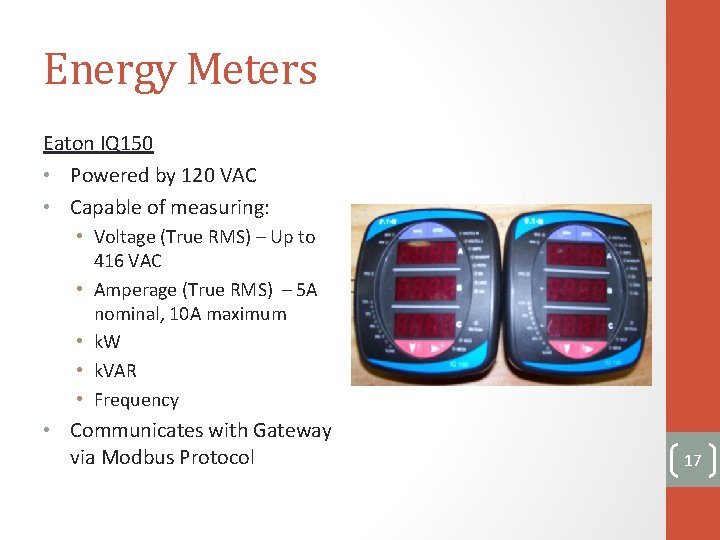
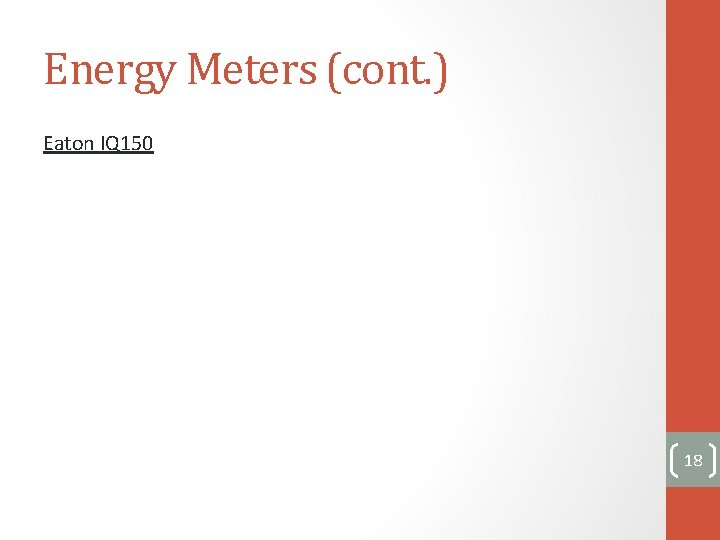
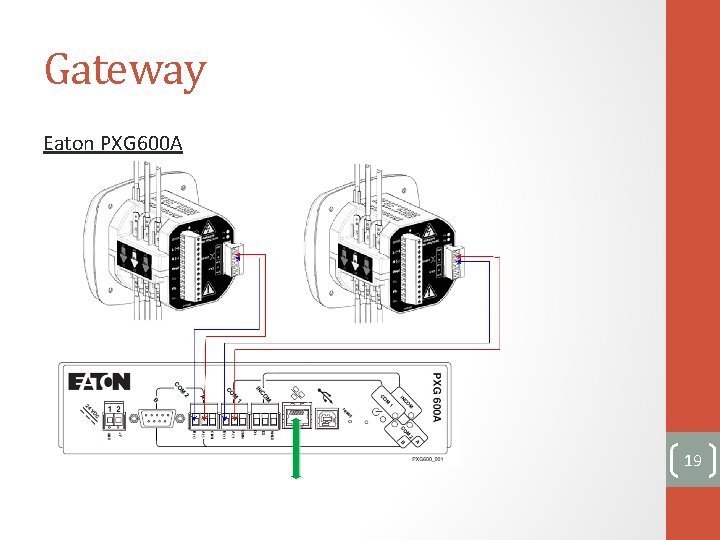
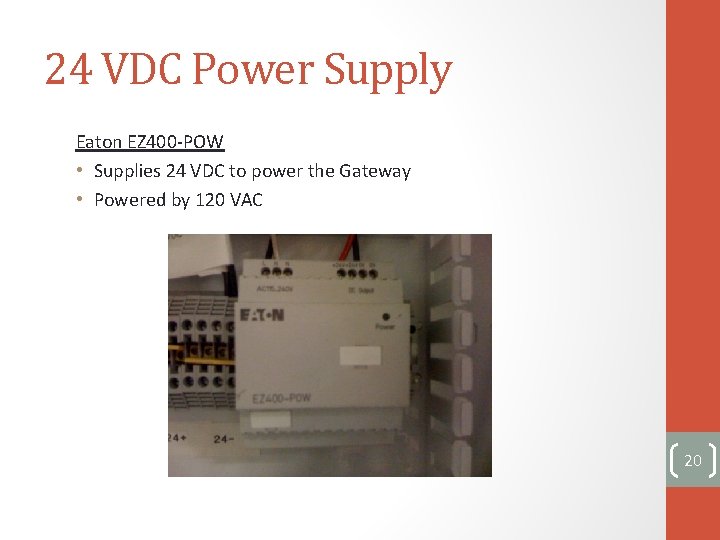
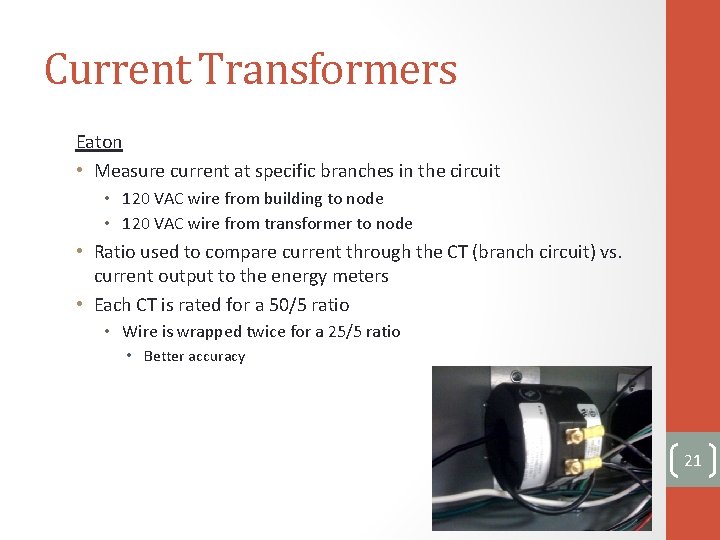
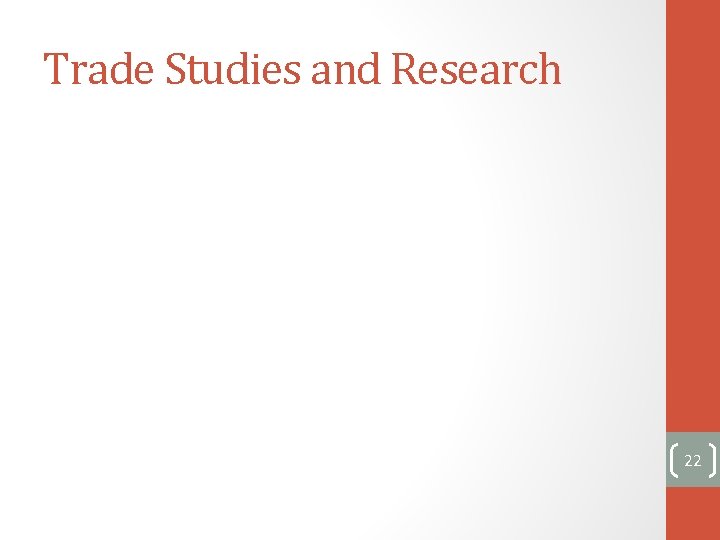

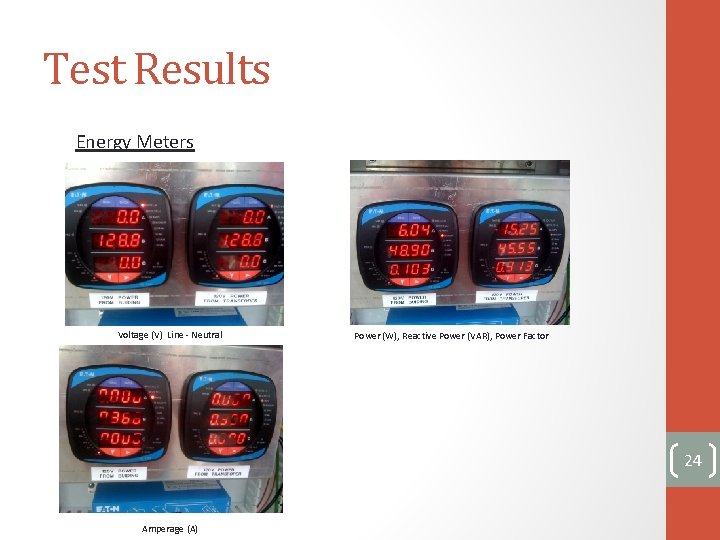
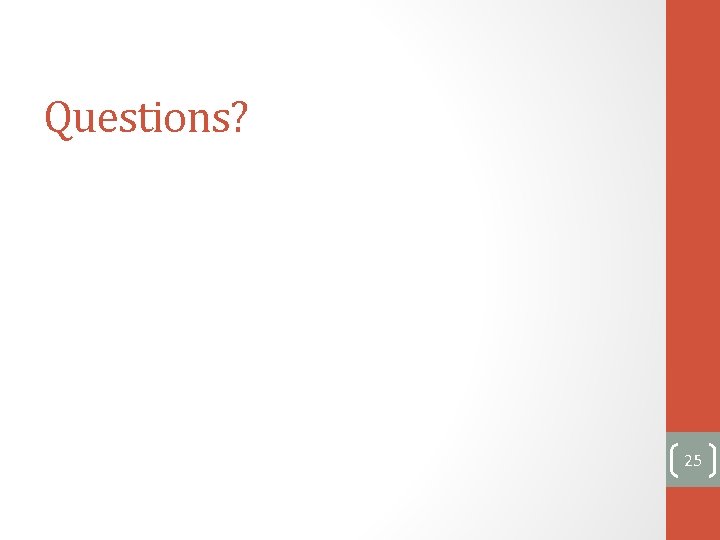
- Slides: 25
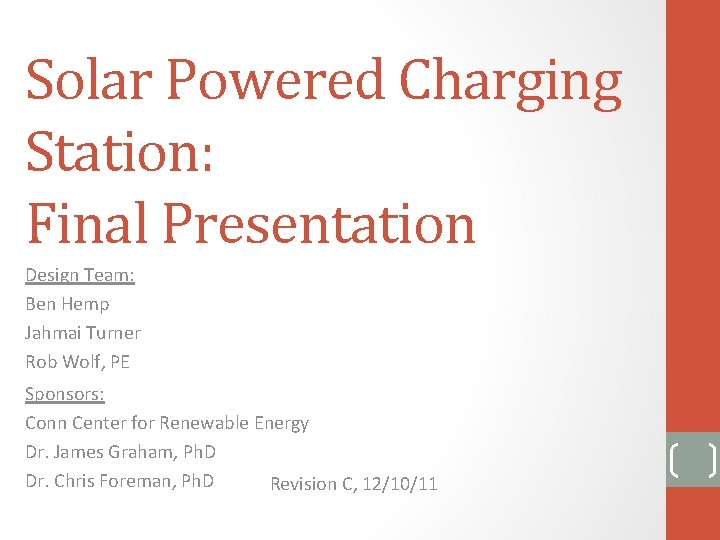
Solar Powered Charging Station: Final Presentation Design Team: Ben Hemp Jahmai Turner Rob Wolf, PE Sponsors: Conn Center for Renewable Energy Dr. James Graham, Ph. D Dr. Chris Foreman, Ph. D Revision C, 12/10/11
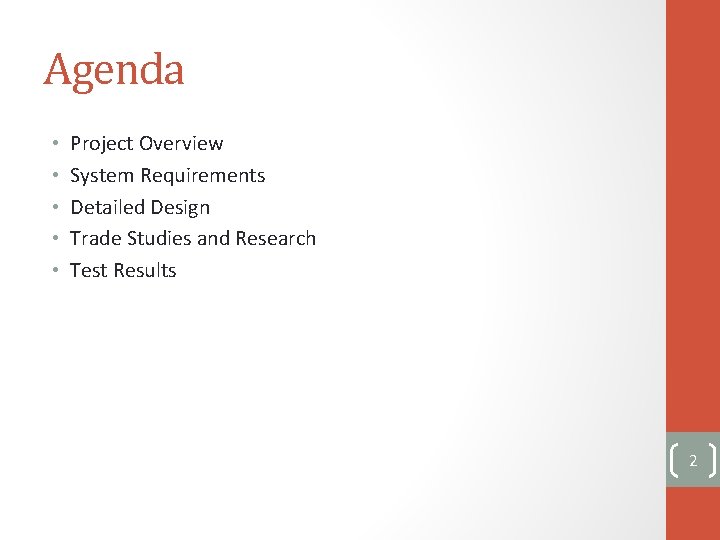
Agenda • • • Project Overview System Requirements Detailed Design Trade Studies and Research Test Results 2
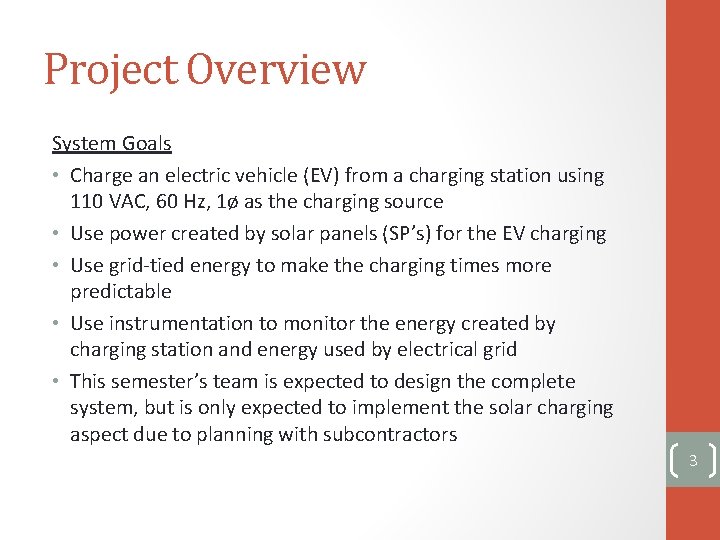
Project Overview System Goals • Charge an electric vehicle (EV) from a charging station using 110 VAC, 60 Hz, 1ø as the charging source • Use power created by solar panels (SP’s) for the EV charging • Use grid-tied energy to make the charging times more predictable • Use instrumentation to monitor the energy created by charging station and energy used by electrical grid • This semester’s team is expected to design the complete system, but is only expected to implement the solar charging aspect due to planning with subcontractors 3
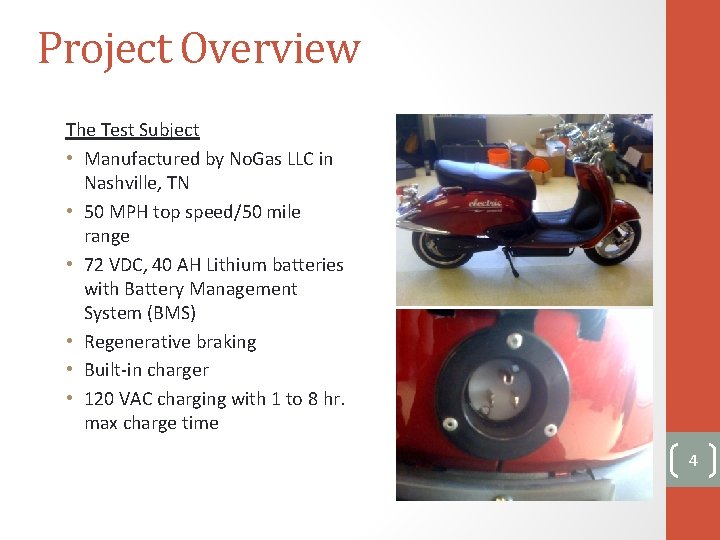
Project Overview The Test Subject • Manufactured by No. Gas LLC in Nashville, TN • 50 MPH top speed/50 mile range • 72 VDC, 40 AH Lithium batteries with Battery Management System (BMS) • Regenerative braking • Built-in charger • 120 VAC charging with 1 to 8 hr. max charge time 4
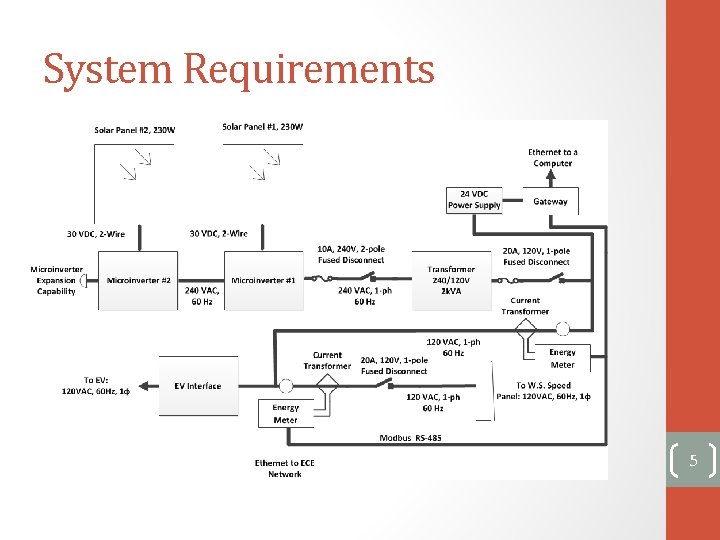
System Requirements 5
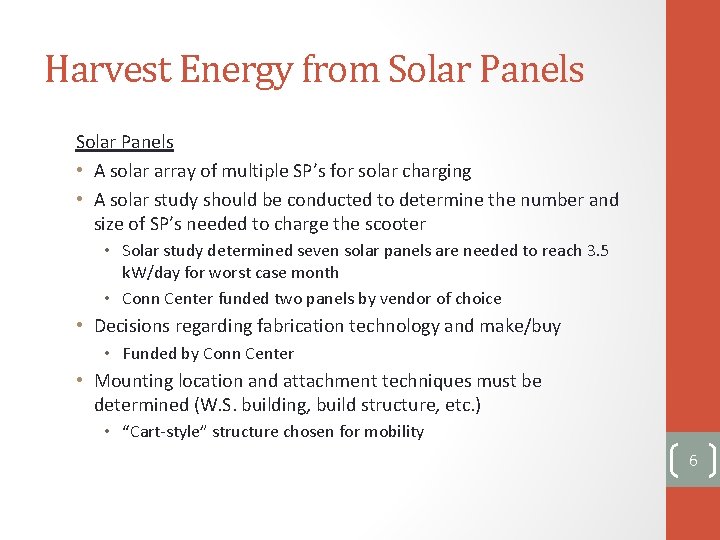
Harvest Energy from Solar Panels • A solar array of multiple SP’s for solar charging • A solar study should be conducted to determine the number and size of SP’s needed to charge the scooter • Solar study determined seven solar panels are needed to reach 3. 5 k. W/day for worst case month • Conn Center funded two panels by vendor of choice • Decisions regarding fabrication technology and make/buy • Funded by Conn Center • Mounting location and attachment techniques must be determined (W. S. building, build structure, etc. ) • “Cart-style” structure chosen for mobility 6
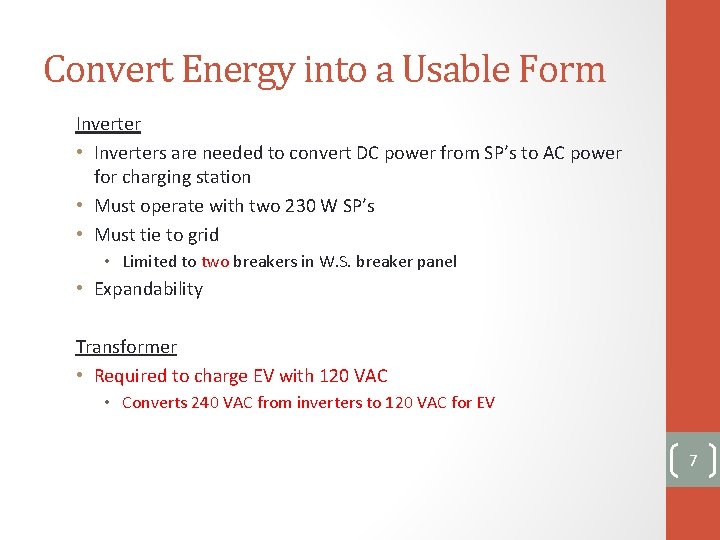
Convert Energy into a Usable Form Inverter • Inverters are needed to convert DC power from SP’s to AC power for charging station • Must operate with two 230 W SP’s • Must tie to grid • Limited to two breakers in W. S. breaker panel • Expandability Transformer • Required to charge EV with 120 VAC • Converts 240 VAC from inverters to 120 VAC for EV 7
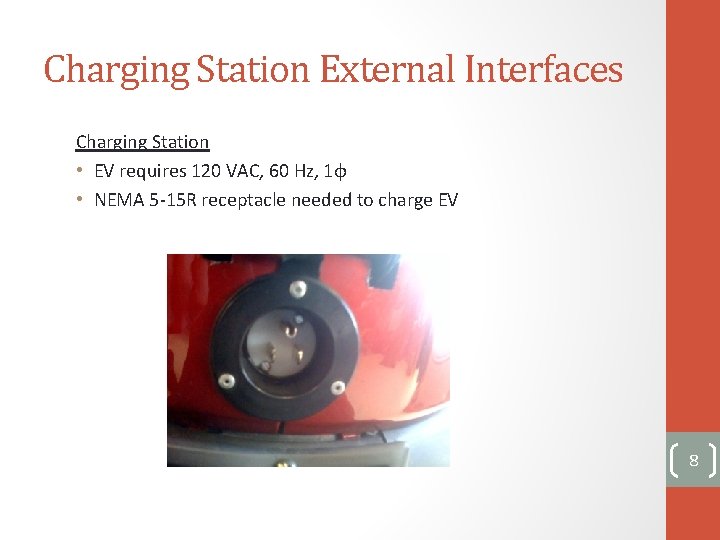
Charging Station External Interfaces Charging Station • EV requires 120 VAC, 60 Hz, 1ɸ • NEMA 5 -15 R receptacle needed to charge EV 8
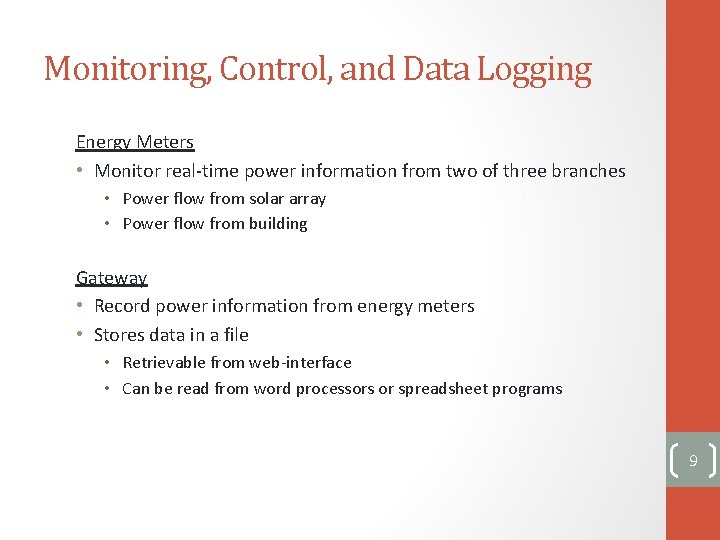
Monitoring, Control, and Data Logging Energy Meters • Monitor real-time power information from two of three branches • Power flow from solar array • Power flow from building Gateway • Record power information from energy meters • Stores data in a file • Retrievable from web-interface • Can be read from word processors or spreadsheet programs 9
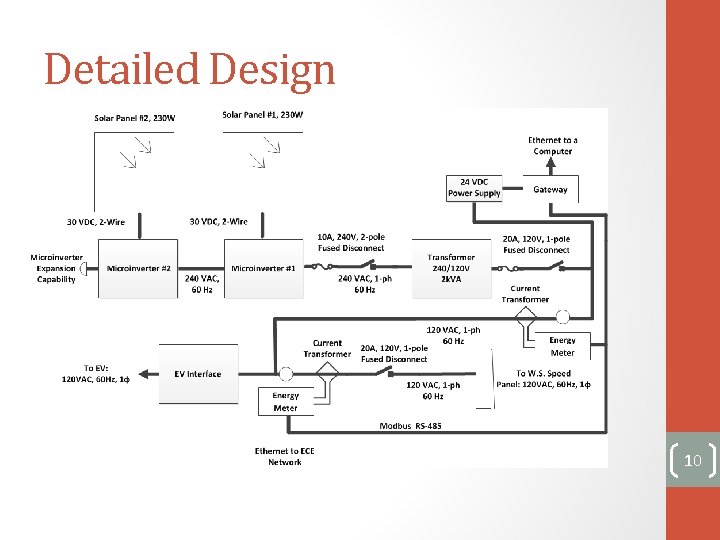
Detailed Design 10
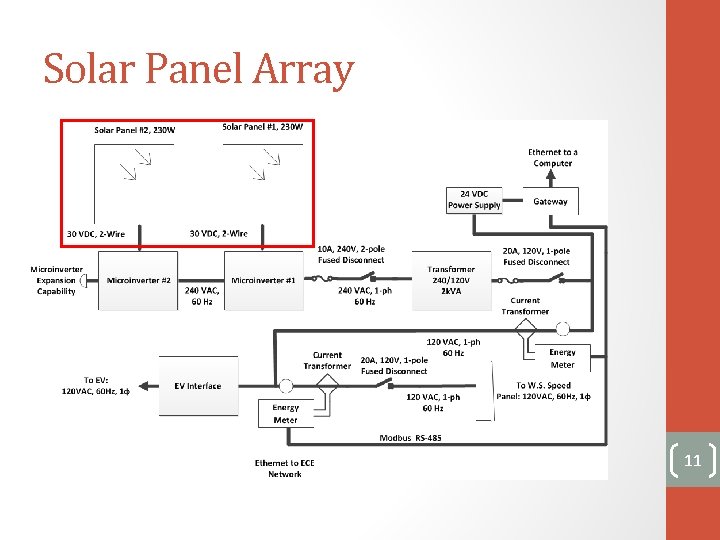
Solar Panel Array 11
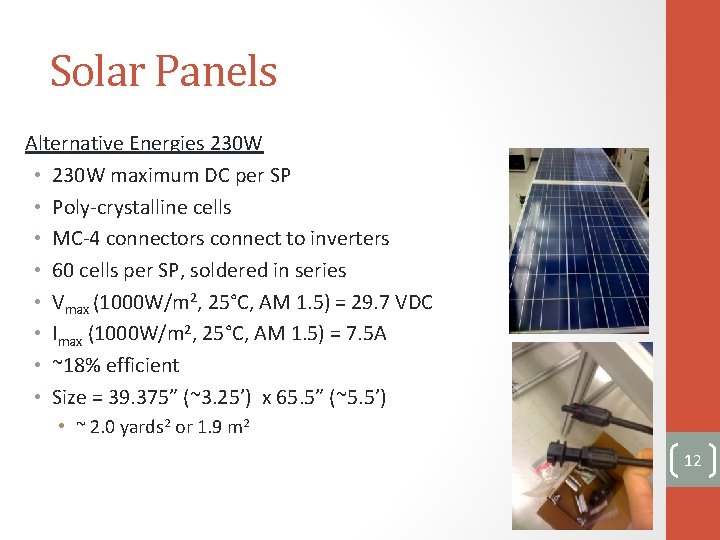
Solar Panels Alternative Energies 230 W • 230 W maximum DC per SP • Poly-crystalline cells • MC-4 connectors connect to inverters • 60 cells per SP, soldered in series • Vmax (1000 W/m 2, 25°C, AM 1. 5) = 29. 7 VDC • Imax (1000 W/m 2, 25°C, AM 1. 5) = 7. 5 A • ~18% efficient • Size = 39. 375” (~3. 25’) x 65. 5” (~5. 5’) • ~ 2. 0 yards 2 or 1. 9 m 2 12
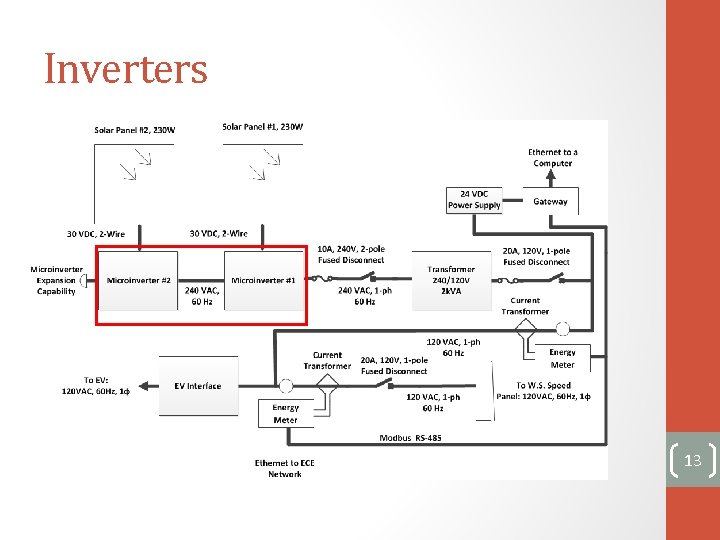
Inverters 13
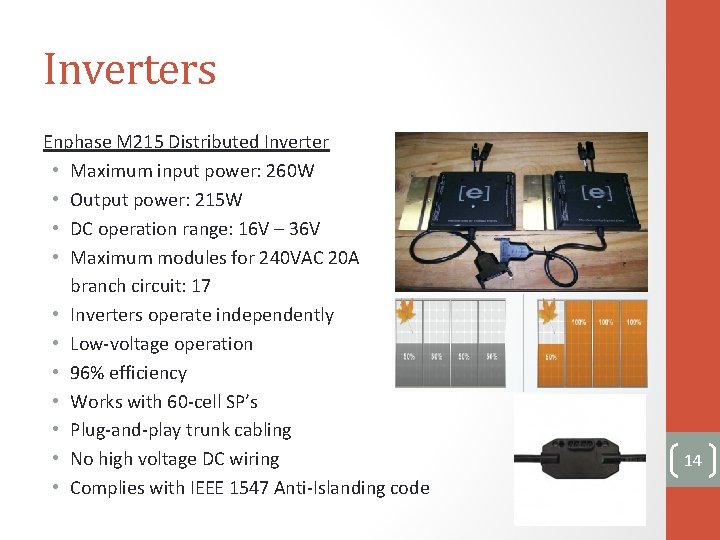
Inverters Enphase M 215 Distributed Inverter • Maximum input power: 260 W • Output power: 215 W • DC operation range: 16 V – 36 V • Maximum modules for 240 VAC 20 A branch circuit: 17 • Inverters operate independently • Low-voltage operation • 96% efficiency • Works with 60 -cell SP’s • Plug-and-play trunk cabling • No high voltage DC wiring • Complies with IEEE 1547 Anti-Islanding code 14
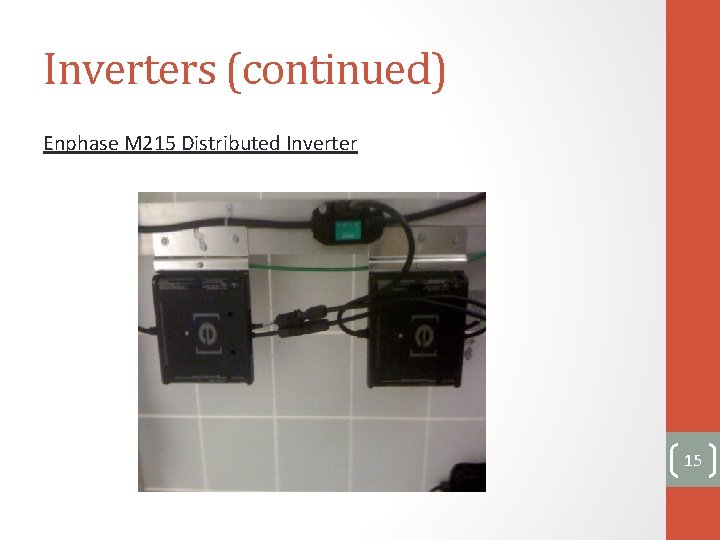
Inverters (continued) Enphase M 215 Distributed Inverter 15
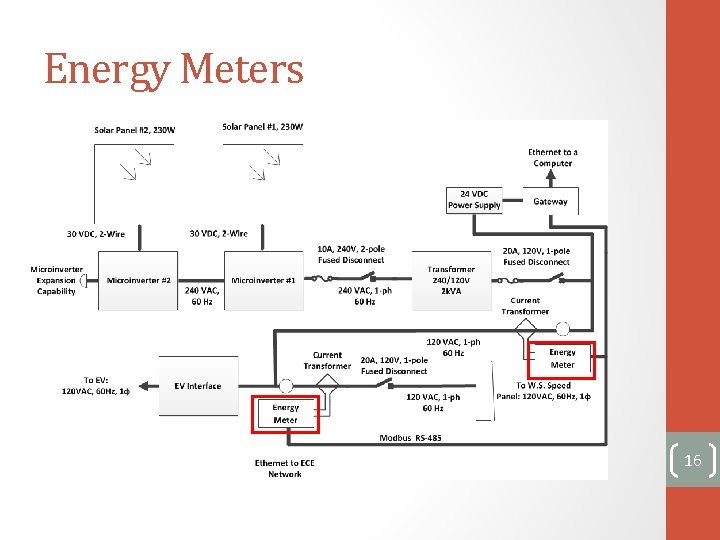
Energy Meters 16
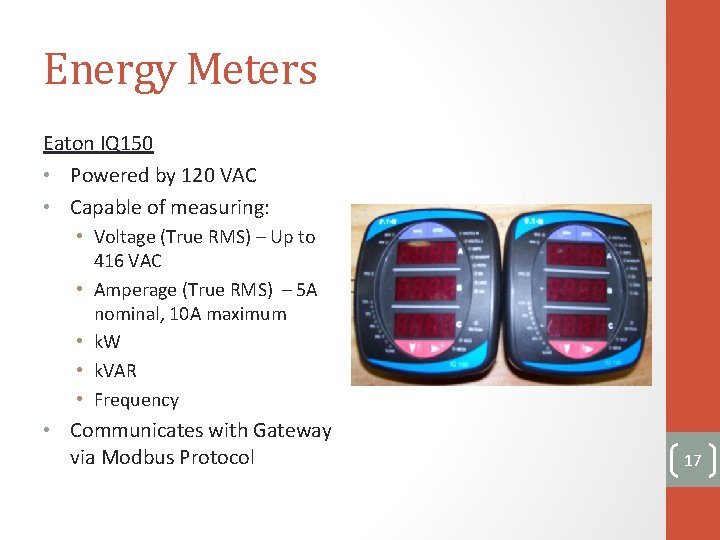
Energy Meters Eaton IQ 150 • Powered by 120 VAC • Capable of measuring: • Voltage (True RMS) – Up to 416 VAC • Amperage (True RMS) – 5 A nominal, 10 A maximum • k. W • k. VAR • Frequency • Communicates with Gateway via Modbus Protocol 17
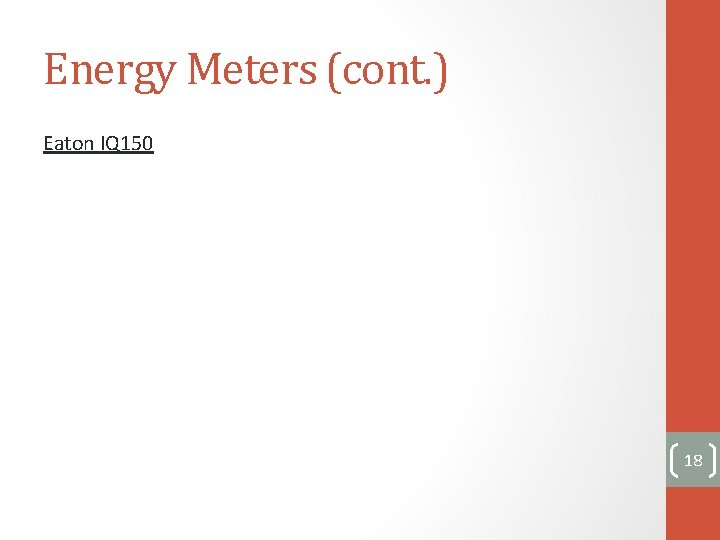
Energy Meters (cont. ) Eaton IQ 150 18
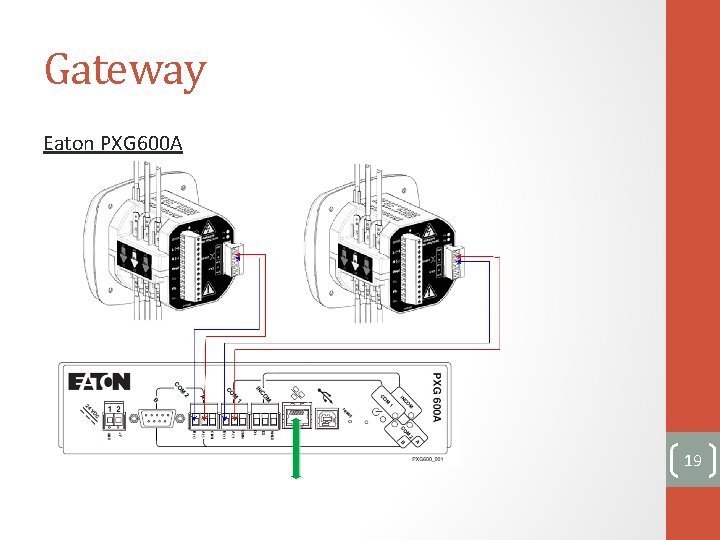
Gateway Eaton PXG 600 A 19
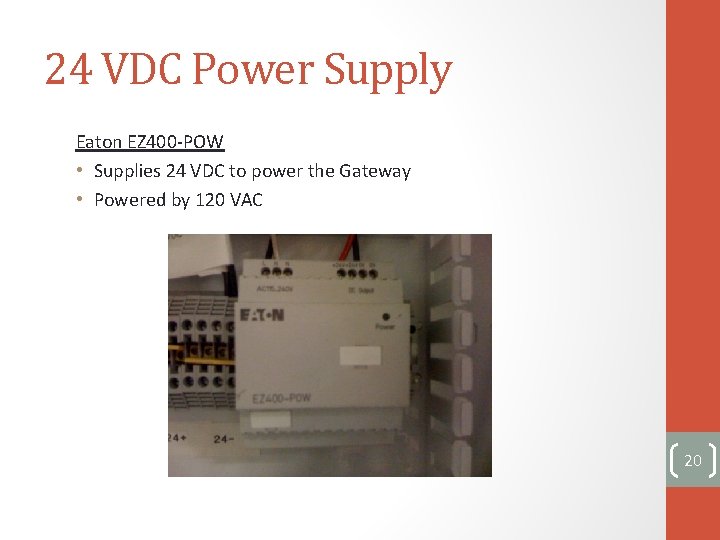
24 VDC Power Supply Eaton EZ 400 -POW • Supplies 24 VDC to power the Gateway • Powered by 120 VAC 20
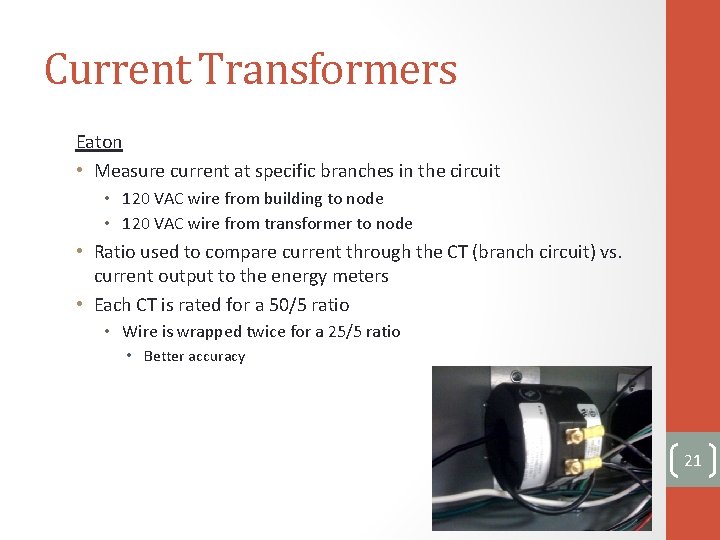
Current Transformers Eaton • Measure current at specific branches in the circuit • 120 VAC wire from building to node • 120 VAC wire from transformer to node • Ratio used to compare current through the CT (branch circuit) vs. current output to the energy meters • Each CT is rated for a 50/5 ratio • Wire is wrapped twice for a 25/5 ratio • Better accuracy 21
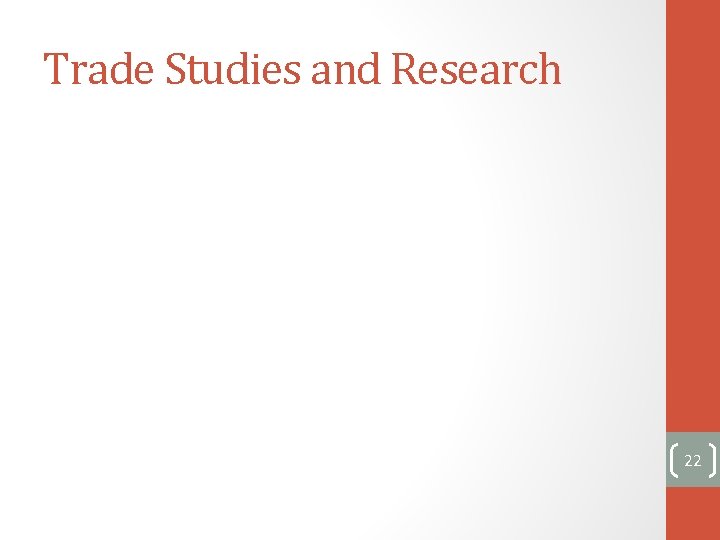
Trade Studies and Research 22

Test Results 23
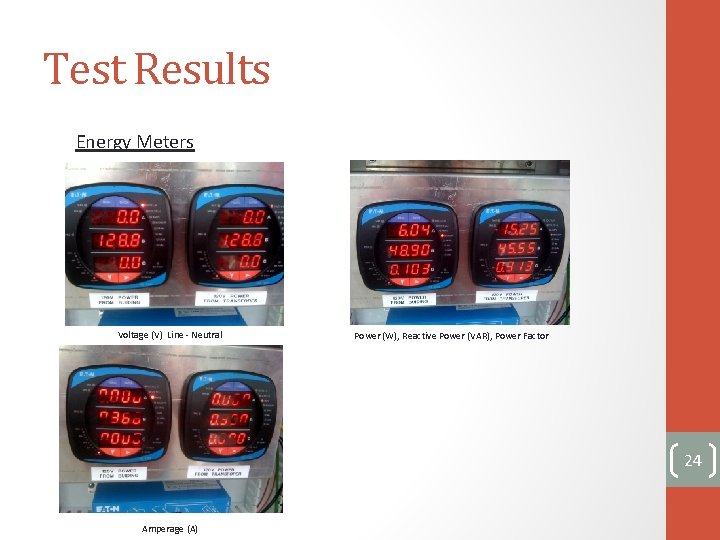
Test Results Energy Meters Voltage (V) Line - Neutral Power (W), Reactive Power (VAR), Power Factor 24 Amperage (A)
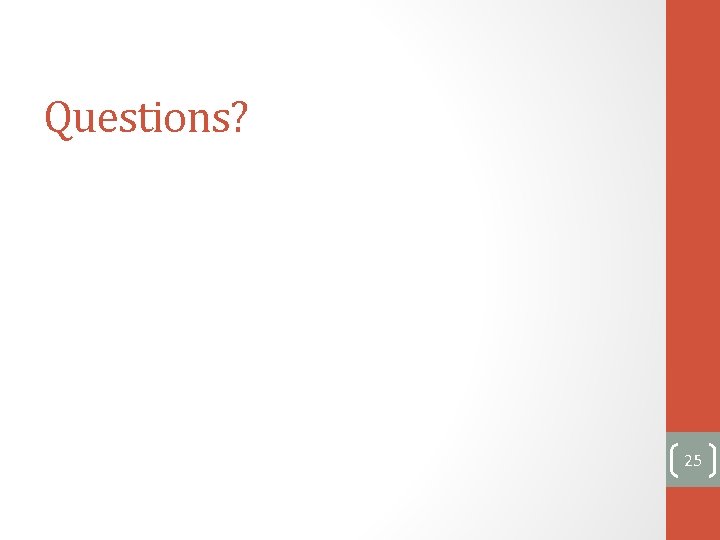
Questions? 25
Wilson solar powered grill
Solar powered router
Solar powered ham radio
Rac charging stations
Ev charging station installation montana
Virta global charging station
Solar panel table
Wholesale solar.com
Inexhaustible source of energy
Sap business one analytics powered by sap hana
Night the soup tasted of corpses
Horse powered reading
Health powered kids
Zappos powered by service
Balloon-powered car conclusion
Powered by simple machines
Wind powered car project
Water powered factories
When is a powered industrial truck considered unattended
29 cfr 1910 osha 178
A pneumatic drill is commonly used
Potato light bulb
29 cfr 1910 powered industrial trucks
Powered flyers
Clinical pharmacology powered by clinicalkey
Bicycle powered water pump