Solar Powered Charging Station Final Presentation Design Team
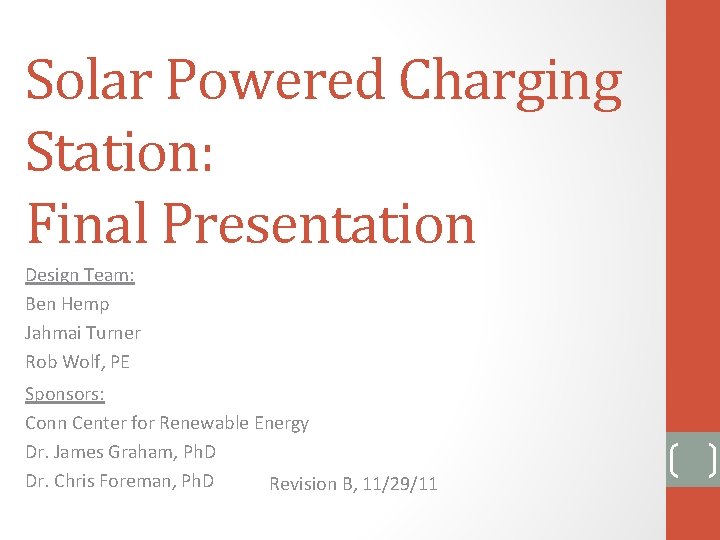
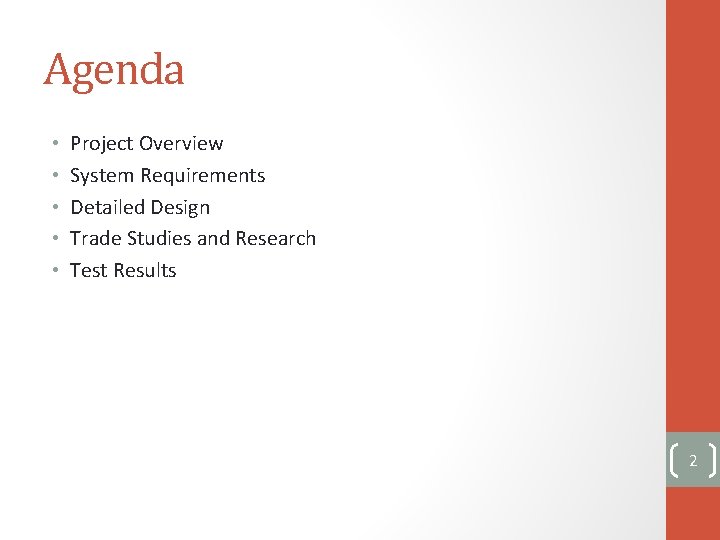
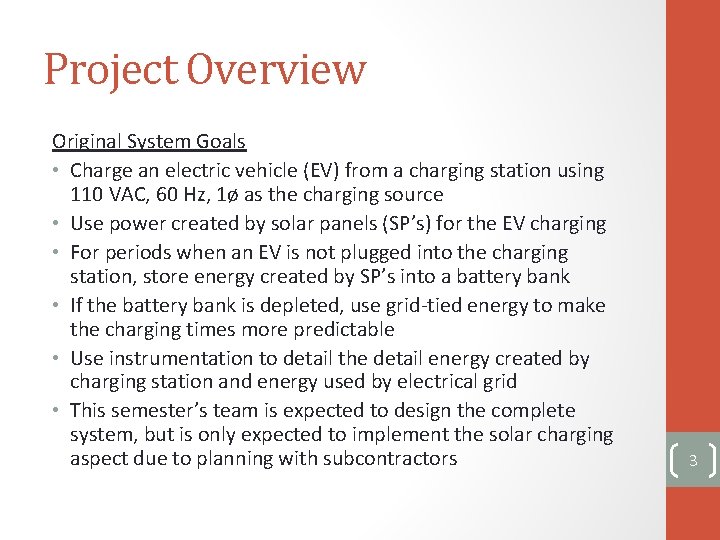
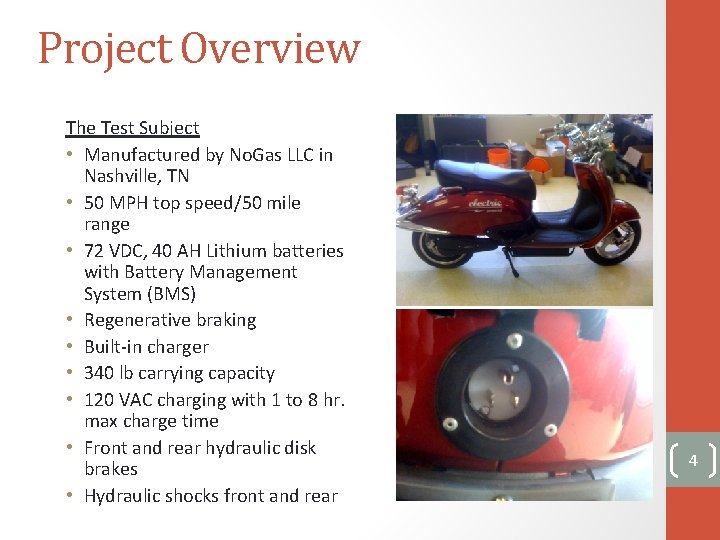
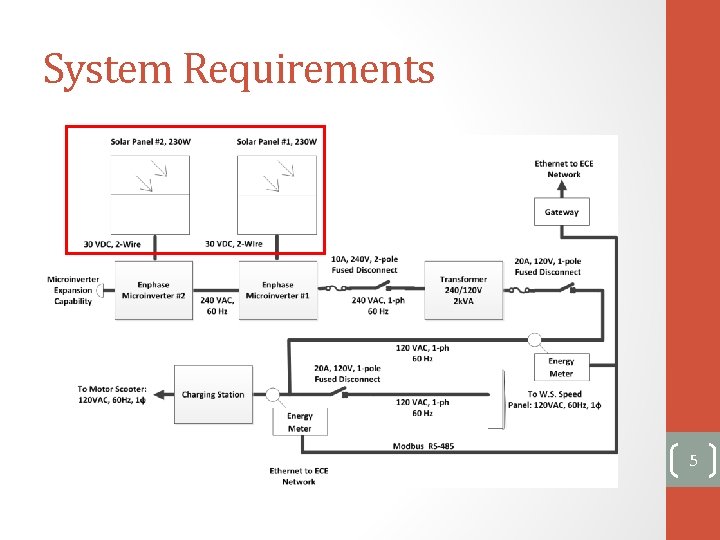
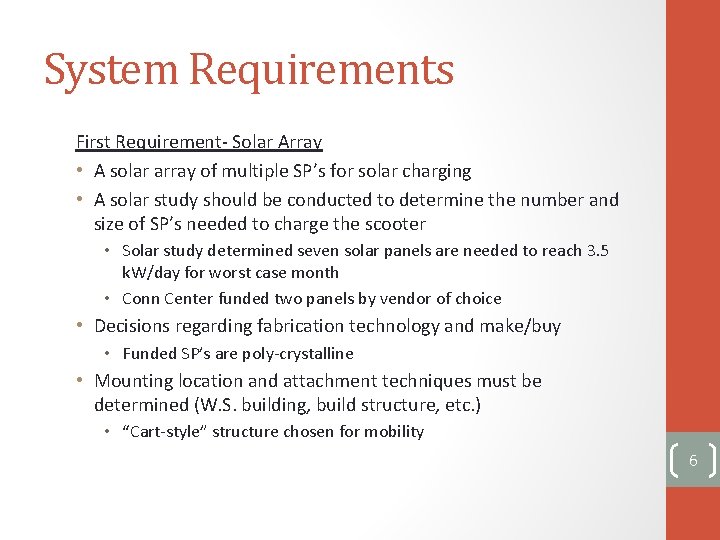
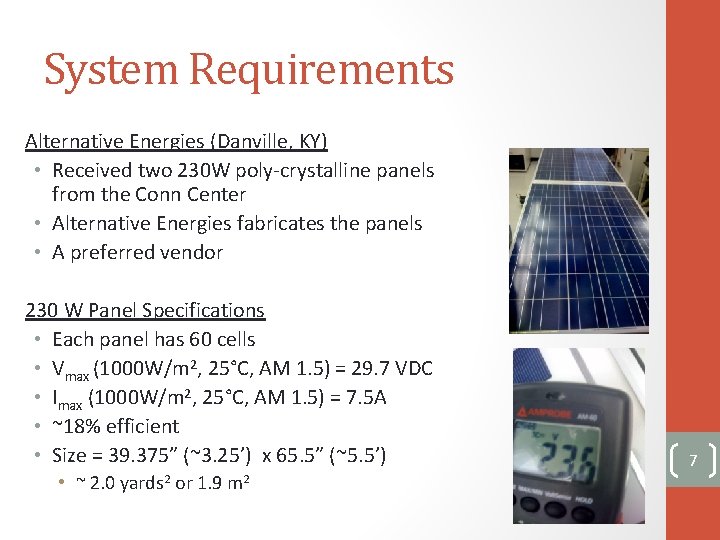
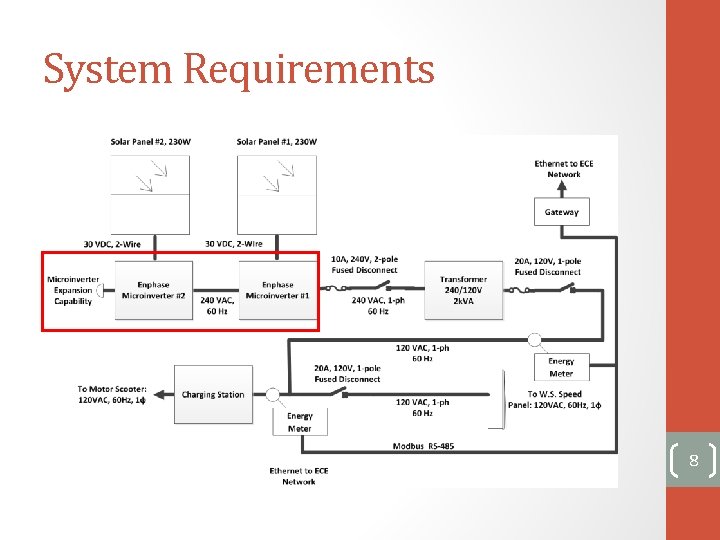
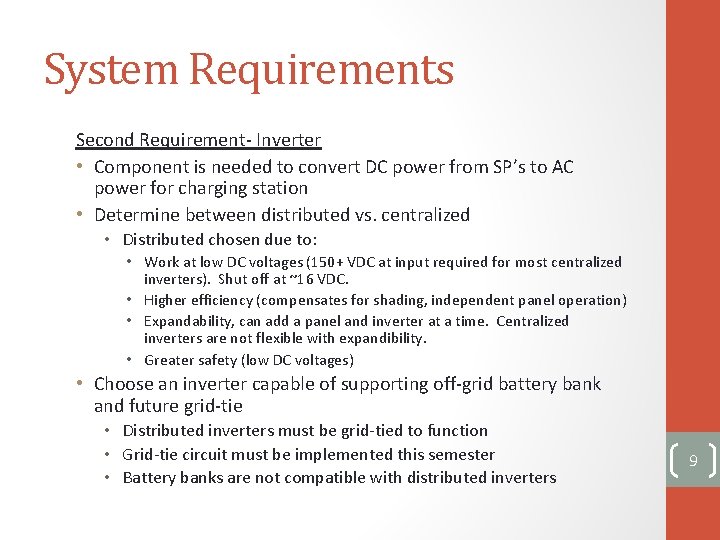
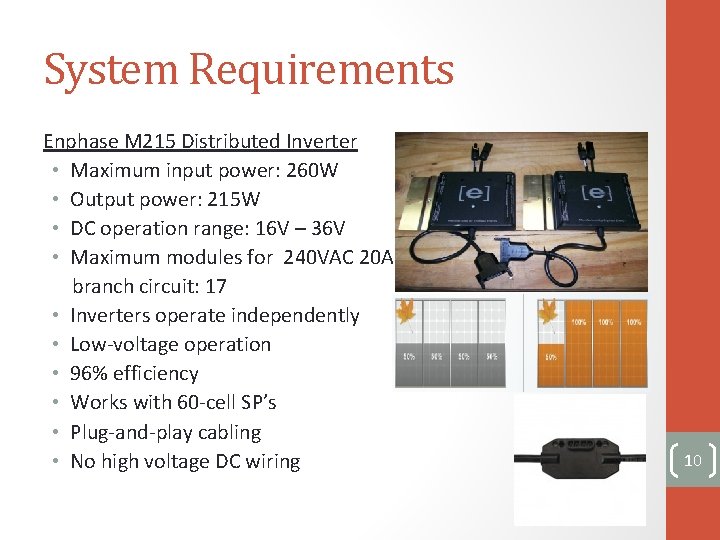
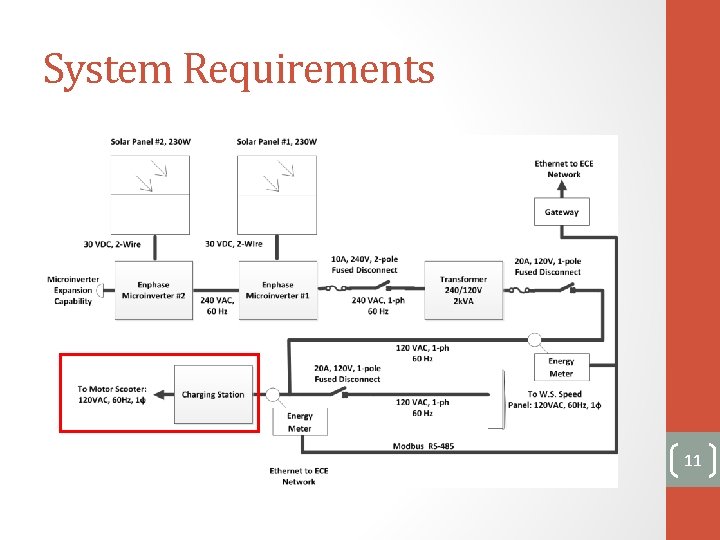
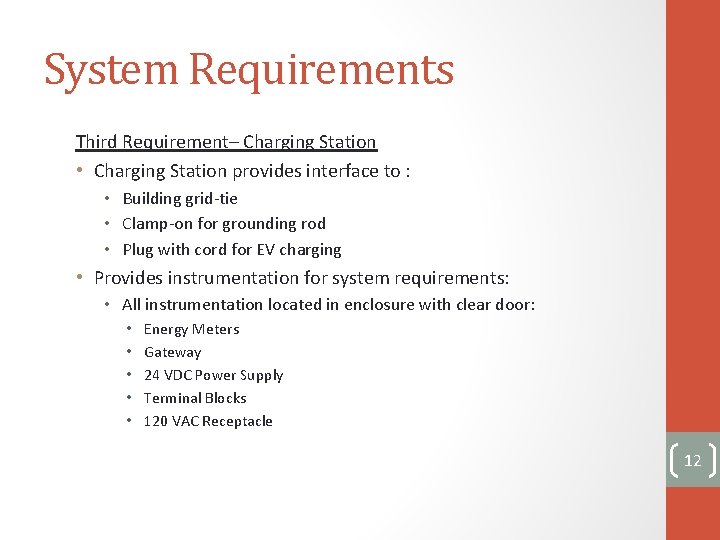
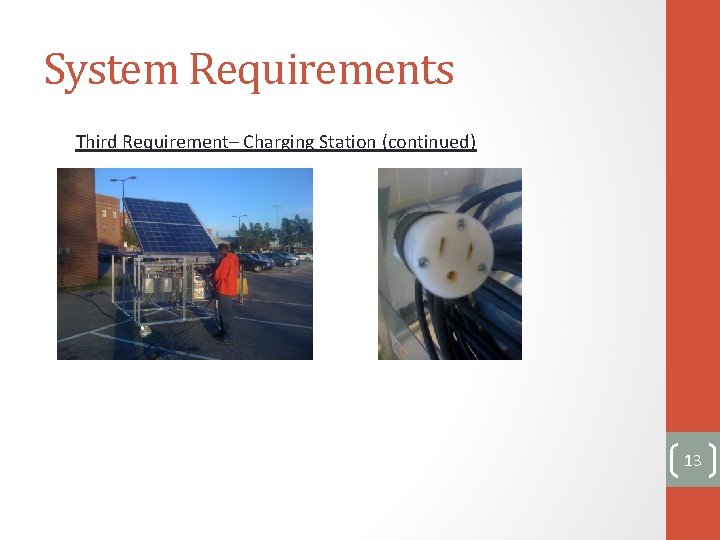
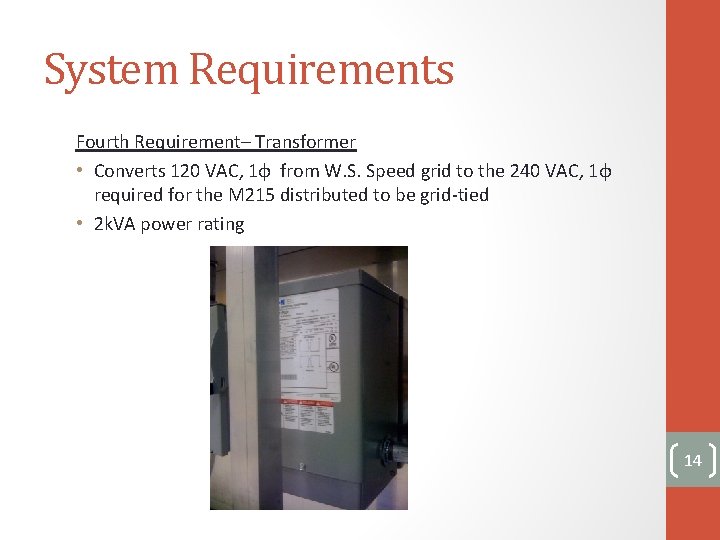
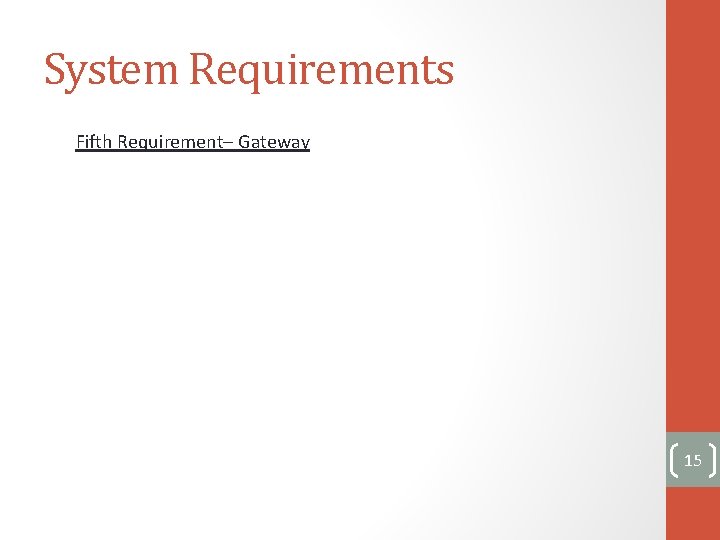
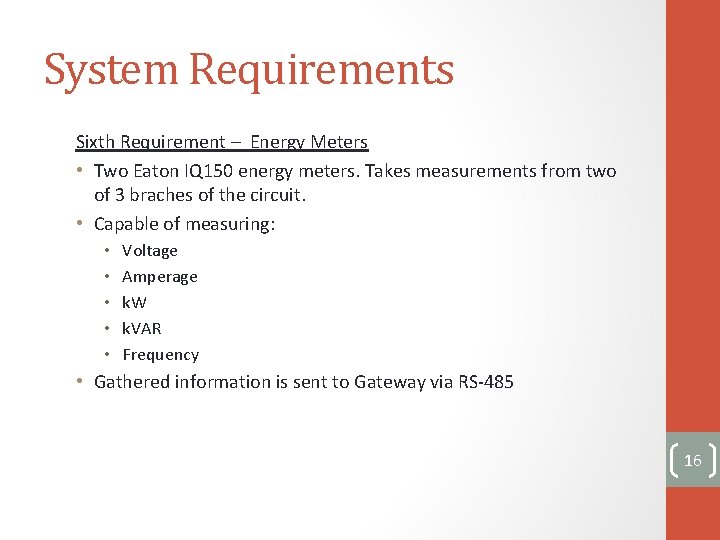
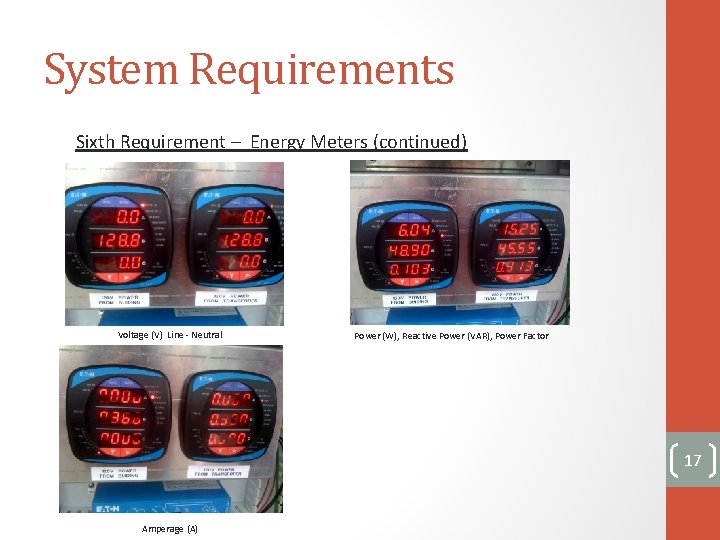
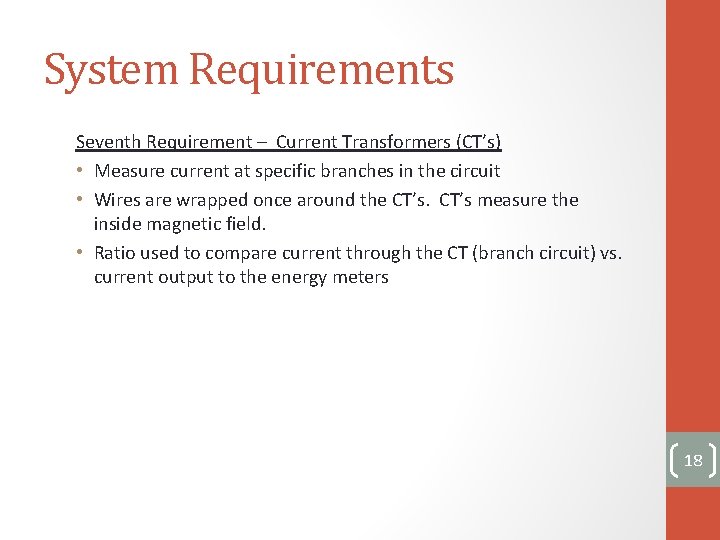
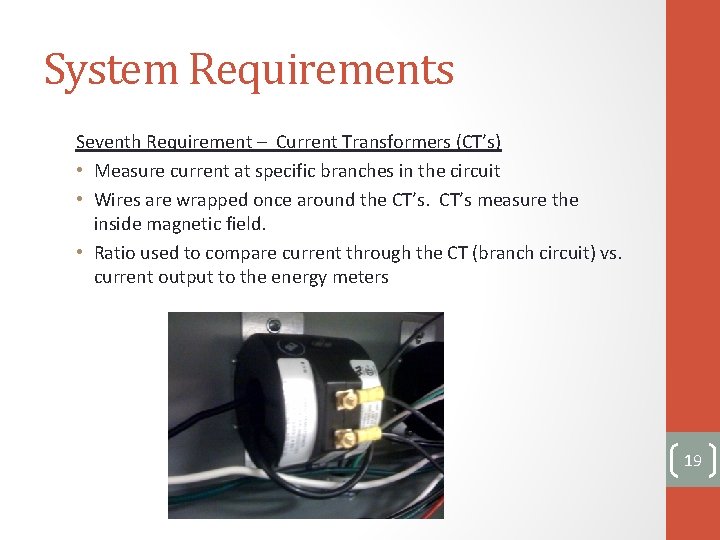
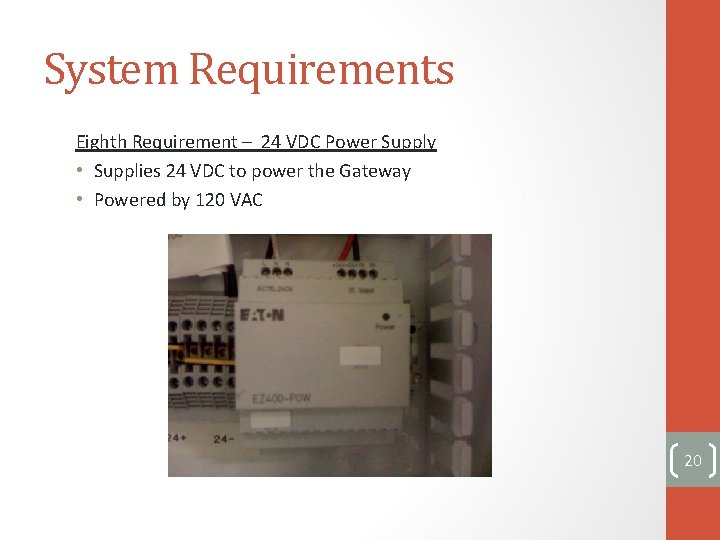
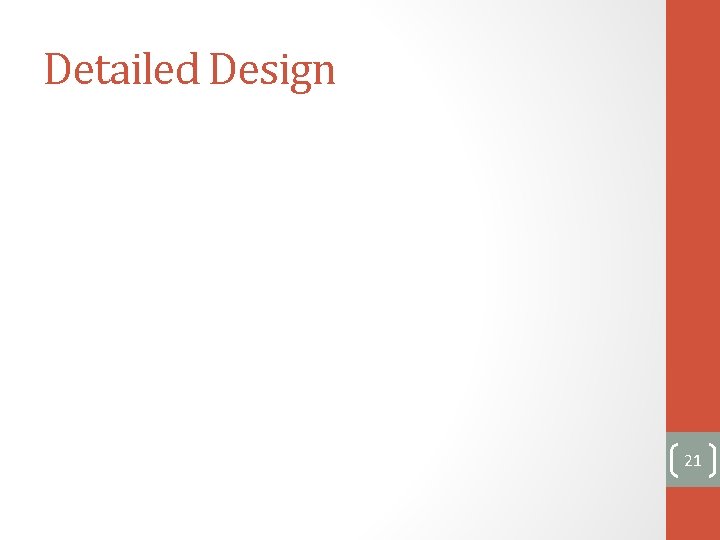

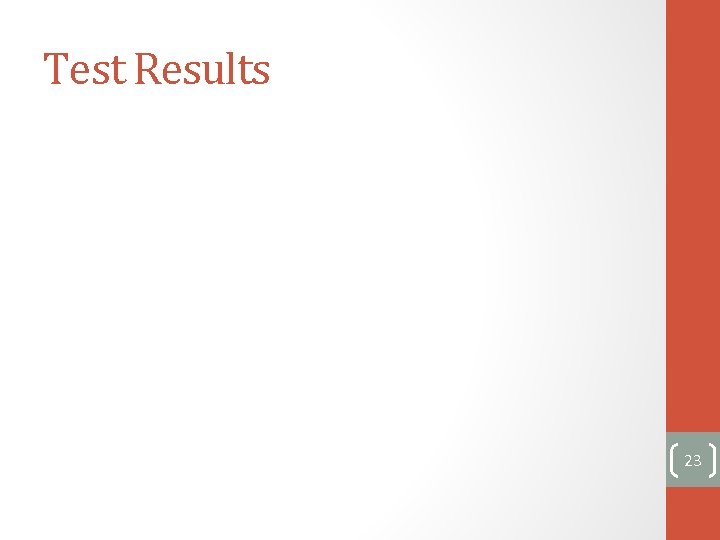
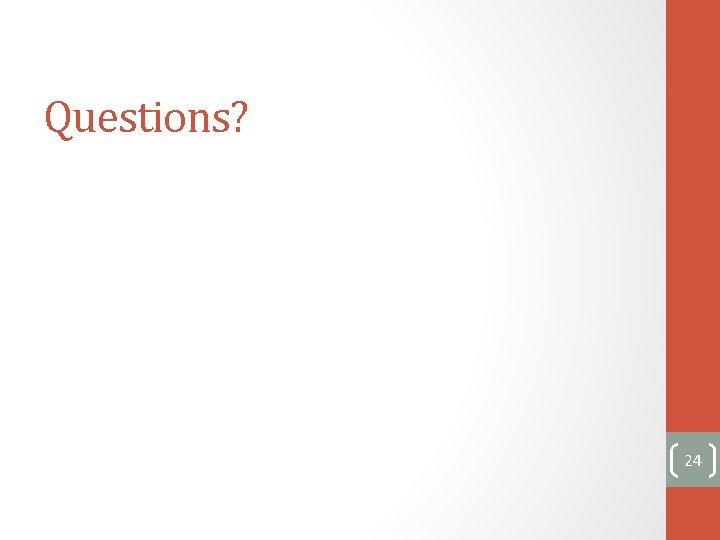
- Slides: 24
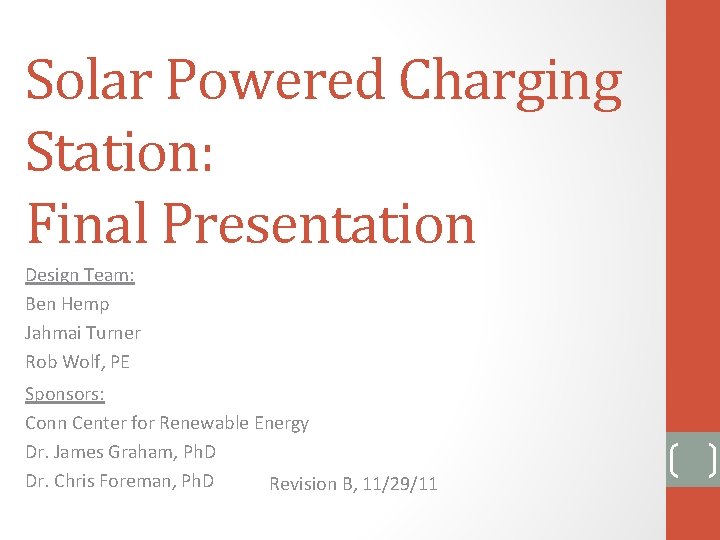
Solar Powered Charging Station: Final Presentation Design Team: Ben Hemp Jahmai Turner Rob Wolf, PE Sponsors: Conn Center for Renewable Energy Dr. James Graham, Ph. D Dr. Chris Foreman, Ph. D Revision B, 11/29/11
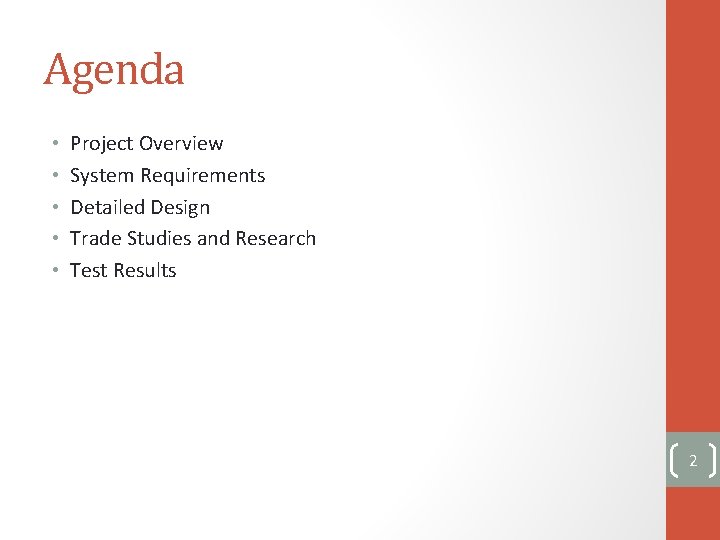
Agenda • • • Project Overview System Requirements Detailed Design Trade Studies and Research Test Results 2
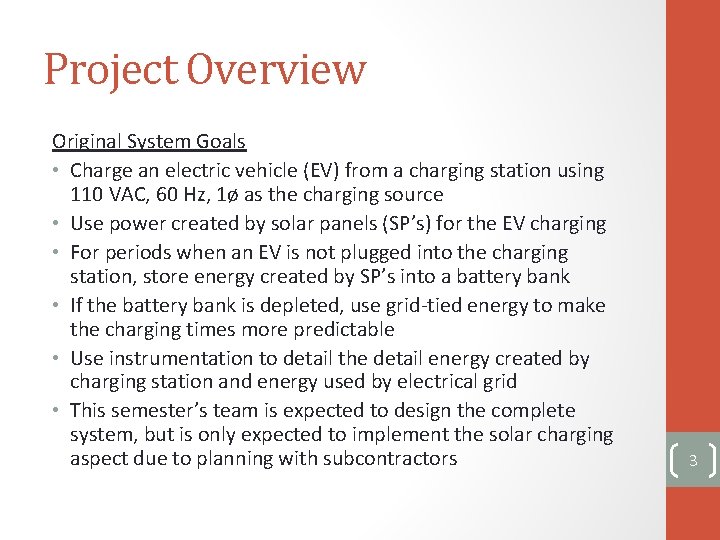
Project Overview Original System Goals • Charge an electric vehicle (EV) from a charging station using 110 VAC, 60 Hz, 1ø as the charging source • Use power created by solar panels (SP’s) for the EV charging • For periods when an EV is not plugged into the charging station, store energy created by SP’s into a battery bank • If the battery bank is depleted, use grid-tied energy to make the charging times more predictable • Use instrumentation to detail the detail energy created by charging station and energy used by electrical grid • This semester’s team is expected to design the complete system, but is only expected to implement the solar charging aspect due to planning with subcontractors 3
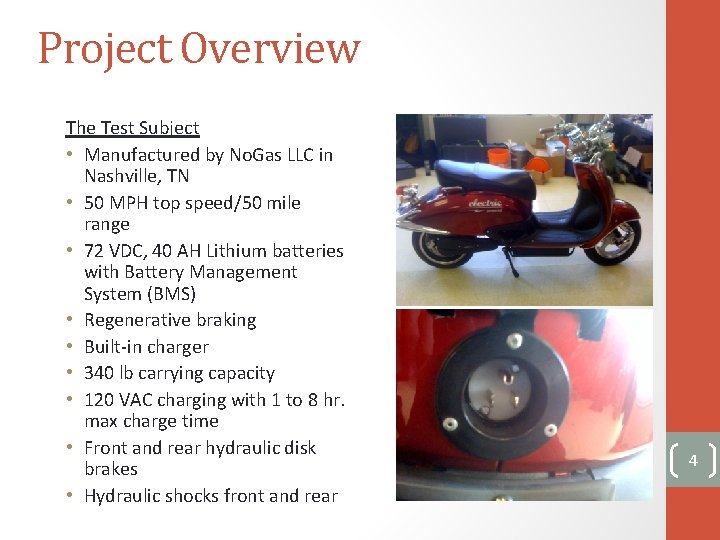
Project Overview The Test Subject • Manufactured by No. Gas LLC in Nashville, TN • 50 MPH top speed/50 mile range • 72 VDC, 40 AH Lithium batteries with Battery Management System (BMS) • Regenerative braking • Built-in charger • 340 lb carrying capacity • 120 VAC charging with 1 to 8 hr. max charge time • Front and rear hydraulic disk brakes • Hydraulic shocks front and rear 4
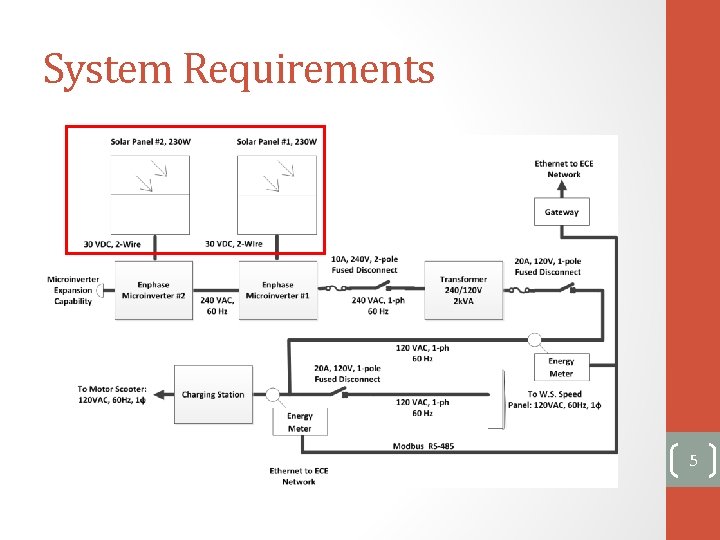
System Requirements 5
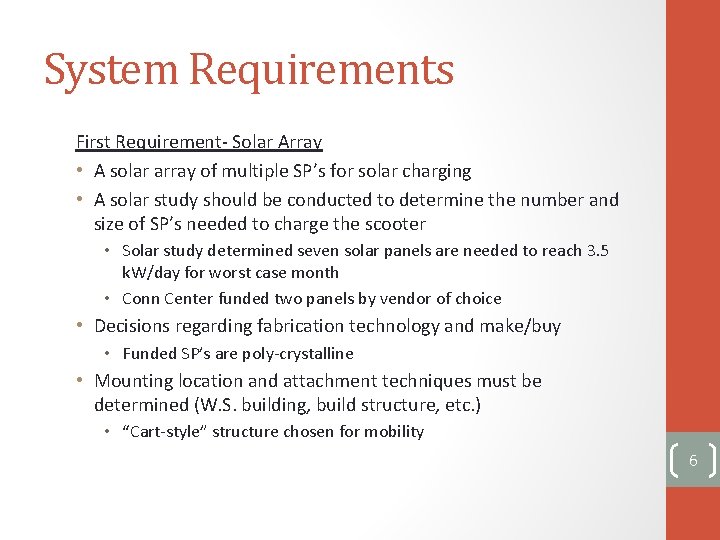
System Requirements First Requirement- Solar Array • A solar array of multiple SP’s for solar charging • A solar study should be conducted to determine the number and size of SP’s needed to charge the scooter • Solar study determined seven solar panels are needed to reach 3. 5 k. W/day for worst case month • Conn Center funded two panels by vendor of choice • Decisions regarding fabrication technology and make/buy • Funded SP’s are poly-crystalline • Mounting location and attachment techniques must be determined (W. S. building, build structure, etc. ) • “Cart-style” structure chosen for mobility 6
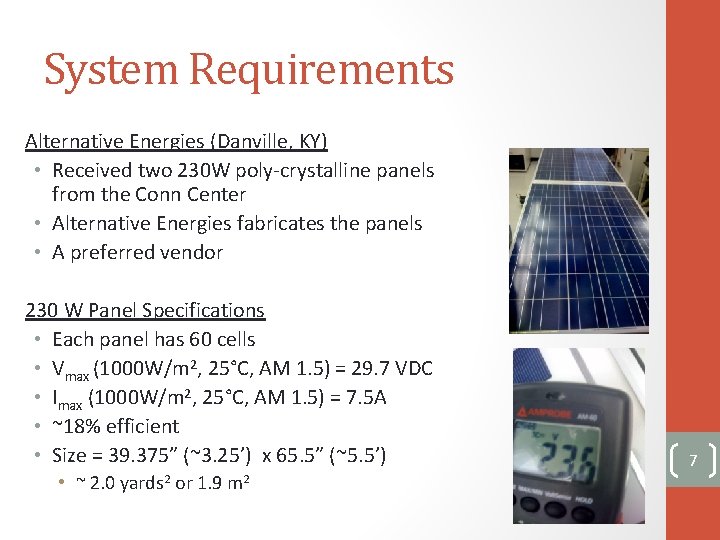
System Requirements Alternative Energies (Danville, KY) • Received two 230 W poly-crystalline panels from the Conn Center • Alternative Energies fabricates the panels • A preferred vendor 230 W Panel Specifications • Each panel has 60 cells • Vmax (1000 W/m 2, 25°C, AM 1. 5) = 29. 7 VDC • Imax (1000 W/m 2, 25°C, AM 1. 5) = 7. 5 A • ~18% efficient • Size = 39. 375” (~3. 25’) x 65. 5” (~5. 5’) • ~ 2. 0 yards 2 or 1. 9 m 2 7
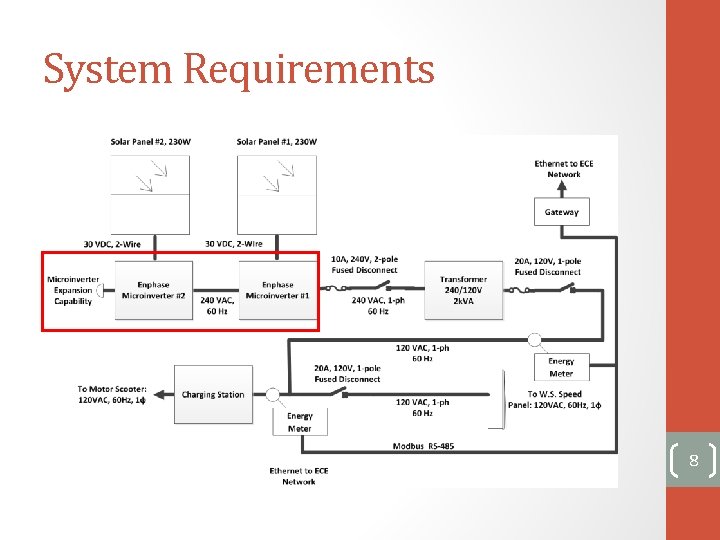
System Requirements 8
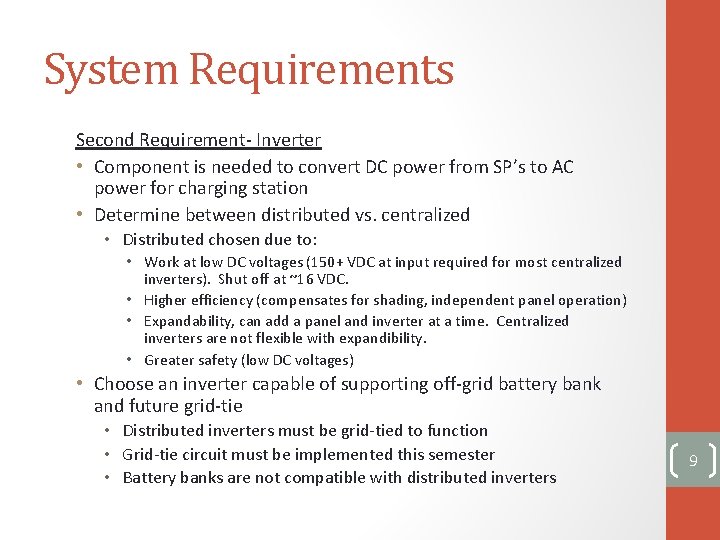
System Requirements Second Requirement- Inverter • Component is needed to convert DC power from SP’s to AC power for charging station • Determine between distributed vs. centralized • Distributed chosen due to: • Work at low DC voltages (150+ VDC at input required for most centralized inverters). Shut off at ~16 VDC. • Higher efficiency (compensates for shading, independent panel operation) • Expandability, can add a panel and inverter at a time. Centralized inverters are not flexible with expandibility. • Greater safety (low DC voltages) • Choose an inverter capable of supporting off-grid battery bank and future grid-tie • Distributed inverters must be grid-tied to function • Grid-tie circuit must be implemented this semester • Battery banks are not compatible with distributed inverters 9
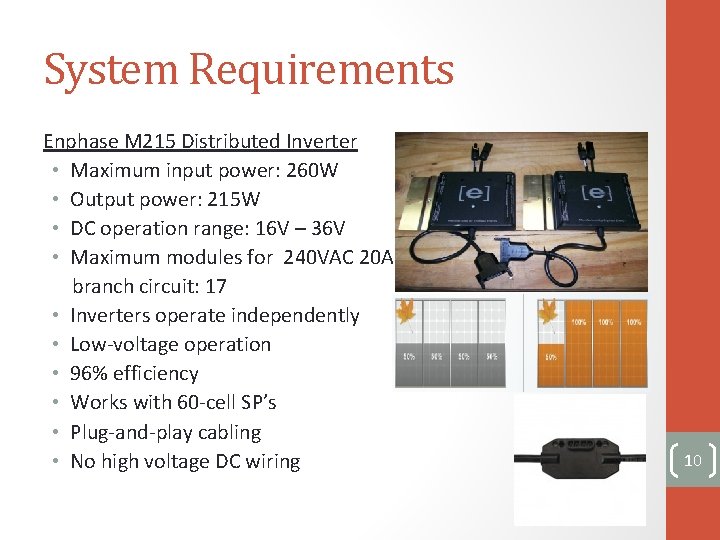
System Requirements Enphase M 215 Distributed Inverter • Maximum input power: 260 W • Output power: 215 W • DC operation range: 16 V – 36 V • Maximum modules for 240 VAC 20 A branch circuit: 17 • Inverters operate independently • Low-voltage operation • 96% efficiency • Works with 60 -cell SP’s • Plug-and-play cabling • No high voltage DC wiring 10
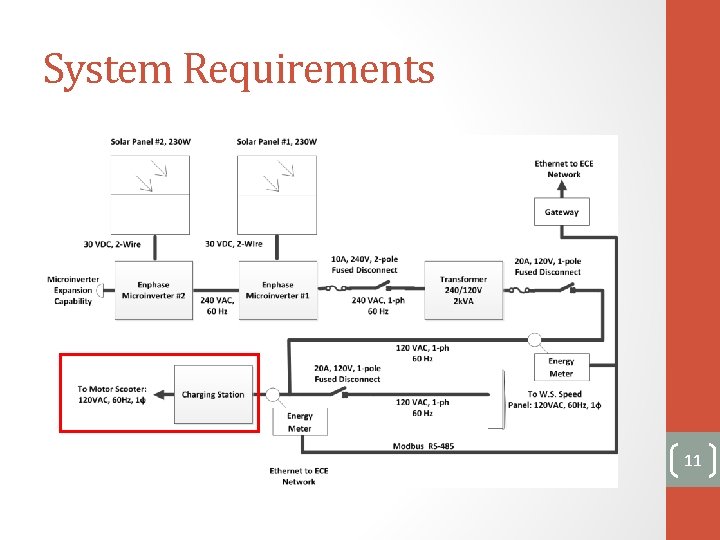
System Requirements 11
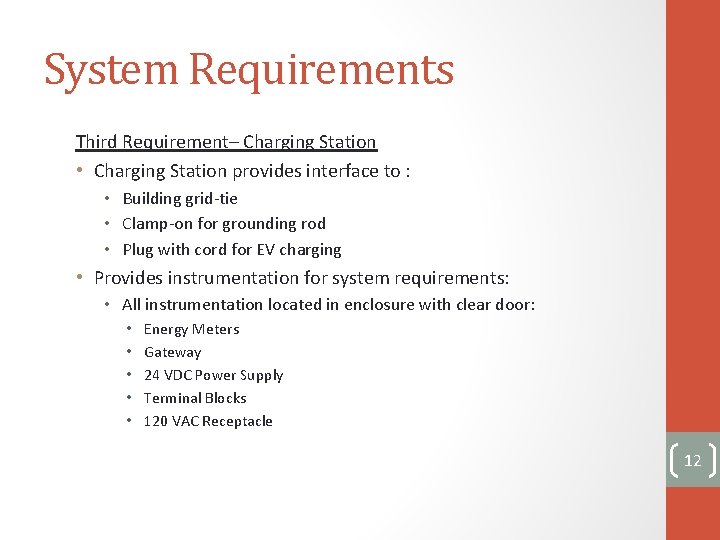
System Requirements Third Requirement– Charging Station • Charging Station provides interface to : • Building grid-tie • Clamp-on for grounding rod • Plug with cord for EV charging • Provides instrumentation for system requirements: • All instrumentation located in enclosure with clear door: • • • Energy Meters Gateway 24 VDC Power Supply Terminal Blocks 120 VAC Receptacle 12
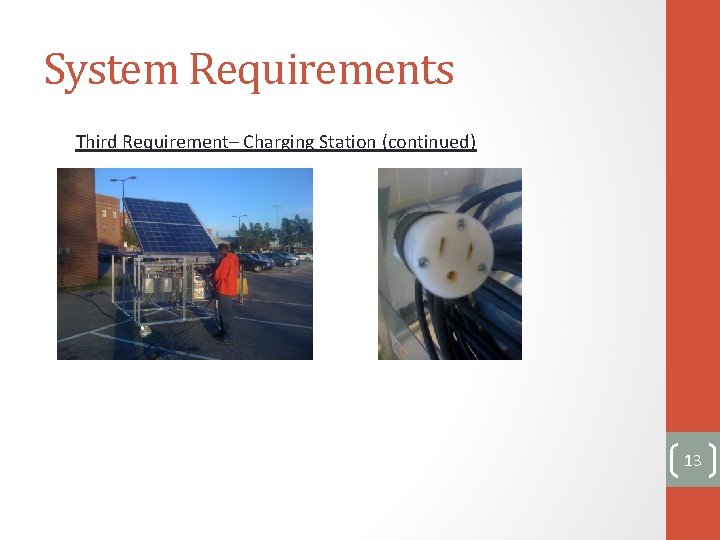
System Requirements Third Requirement– Charging Station (continued) 13
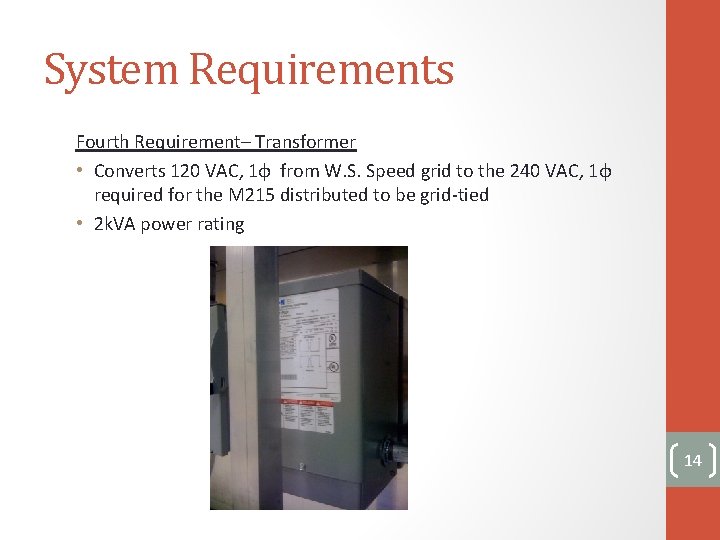
System Requirements Fourth Requirement– Transformer • Converts 120 VAC, 1ɸ from W. S. Speed grid to the 240 VAC, 1ɸ required for the M 215 distributed to be grid-tied • 2 k. VA power rating 14
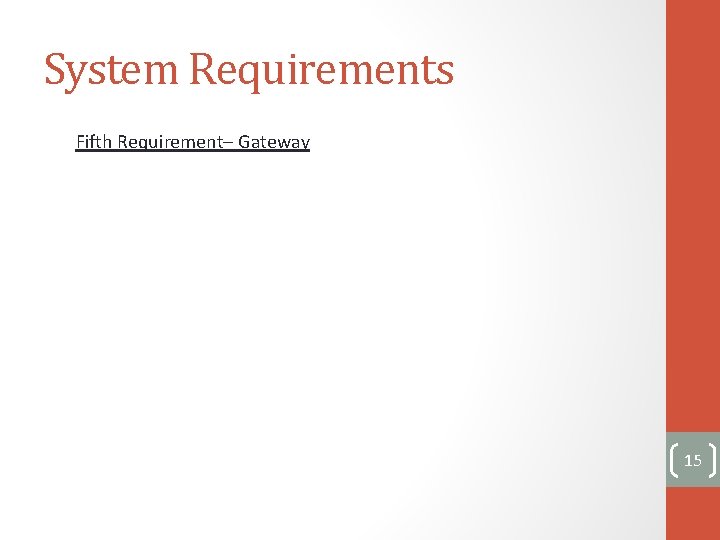
System Requirements Fifth Requirement– Gateway 15
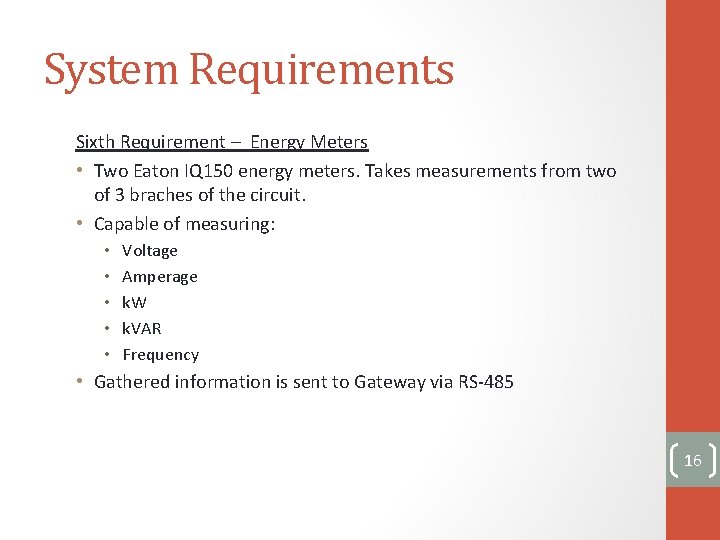
System Requirements Sixth Requirement – Energy Meters • Two Eaton IQ 150 energy meters. Takes measurements from two of 3 braches of the circuit. • Capable of measuring: • • • Voltage Amperage k. W k. VAR Frequency • Gathered information is sent to Gateway via RS-485 16
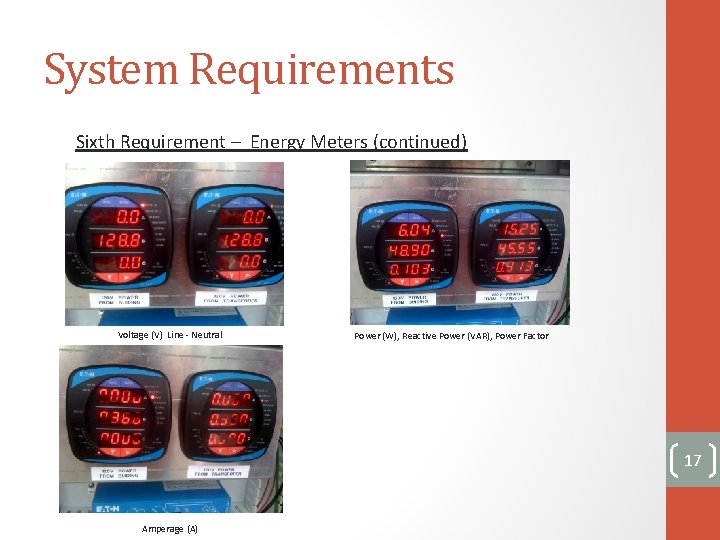
System Requirements Sixth Requirement – Energy Meters (continued) Voltage (V) Line - Neutral Power (W), Reactive Power (VAR), Power Factor 17 Amperage (A)
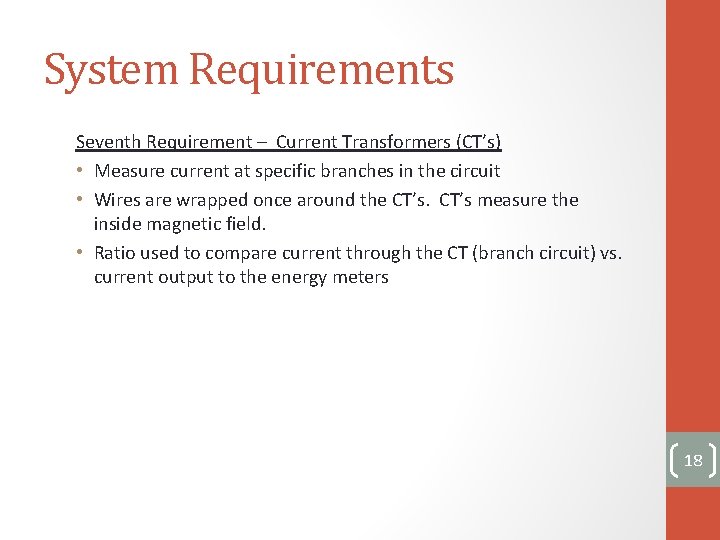
System Requirements Seventh Requirement – Current Transformers (CT’s) • Measure current at specific branches in the circuit • Wires are wrapped once around the CT’s measure the inside magnetic field. • Ratio used to compare current through the CT (branch circuit) vs. current output to the energy meters 18
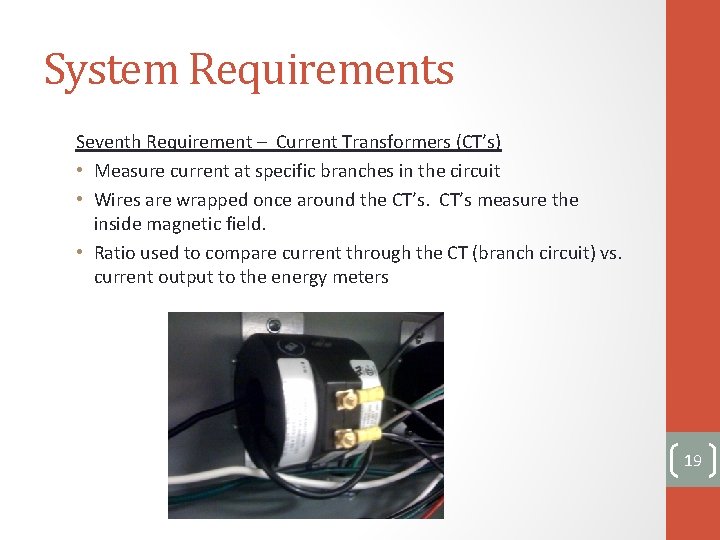
System Requirements Seventh Requirement – Current Transformers (CT’s) • Measure current at specific branches in the circuit • Wires are wrapped once around the CT’s measure the inside magnetic field. • Ratio used to compare current through the CT (branch circuit) vs. current output to the energy meters 19
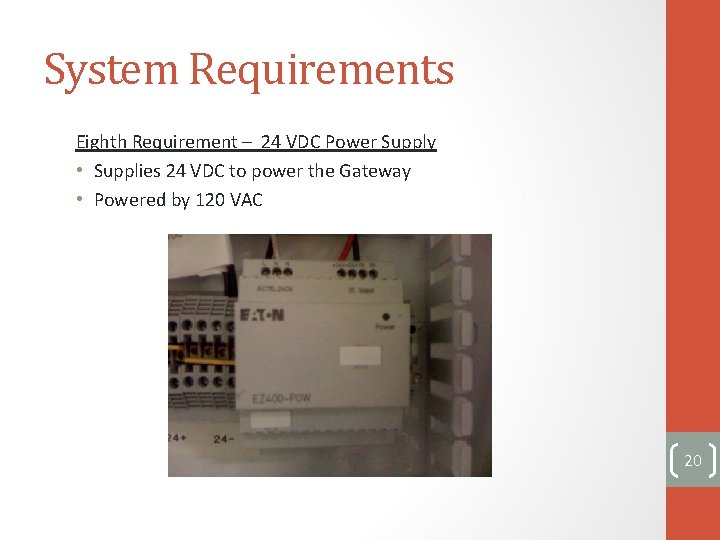
System Requirements Eighth Requirement – 24 VDC Power Supply • Supplies 24 VDC to power the Gateway • Powered by 120 VAC 20
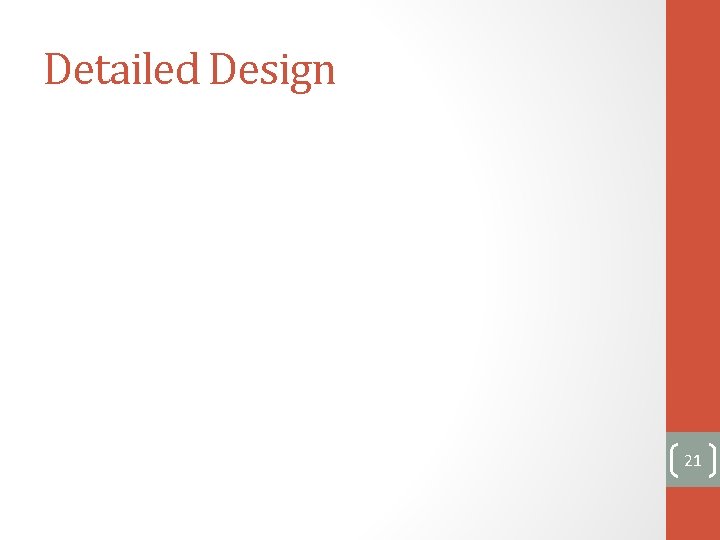
Detailed Design 21

Trade Studies and Research 22
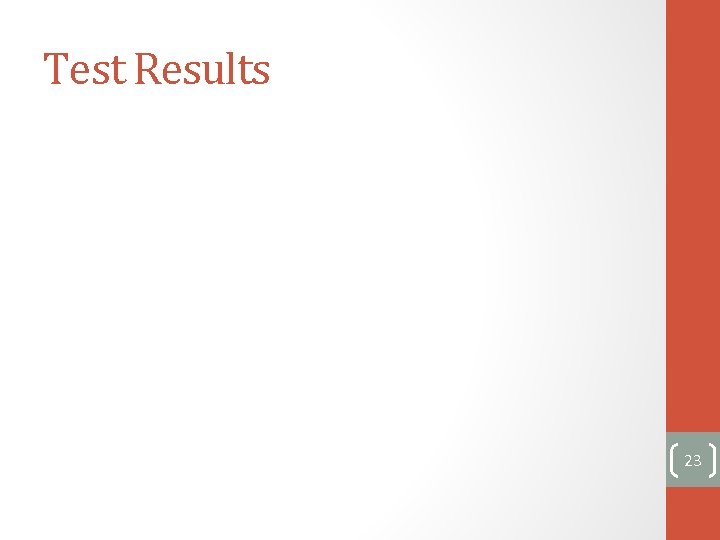
Test Results 23
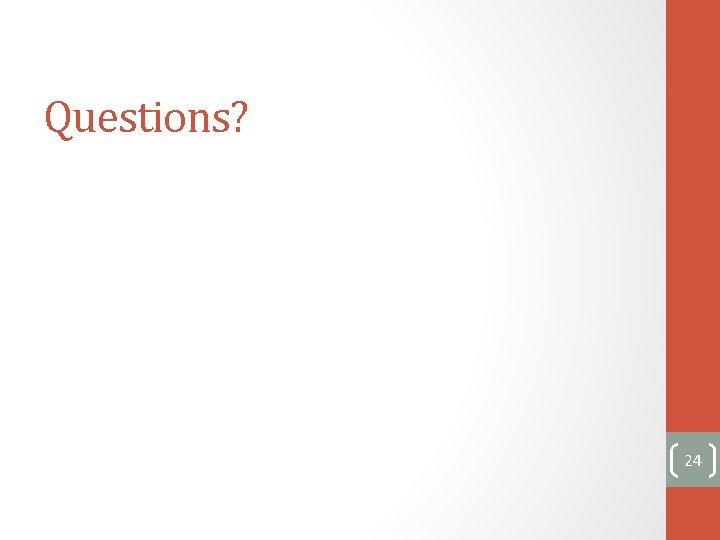
Questions? 24
Wilson solar grill
Solar powered router
Energy ham
Rac electric highway
Ev charger installation montana
Virta global charging station
Thermolite solar charging system
Wholesale sun solar panels
Inexhaustible source of energy
Sap business one analytic
Night the soup tasted of corpses
Horse powered reading
Health powered kids
Zappos 800 number
Baking soda and vinegar car
Powered by simple machines
Wind powered car project
Water powered factories
When is a powered industrial truck considered unattended
29 cfr 1910 powered industrial trucks
A pneumatic drill is commonly used
Potato light bulb
Osha 1910 forklift
Grade 6 flight
Clinical pharmacology powered by clinicalkey