SNMS Supplier Network Management System SNMS Guideline for
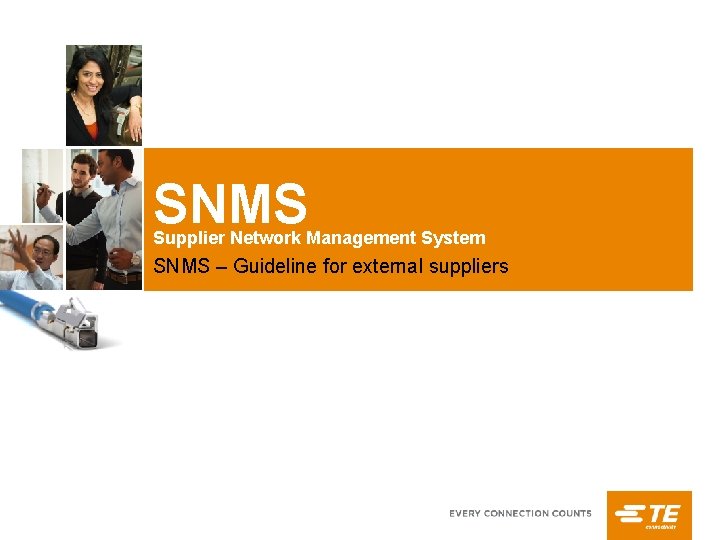
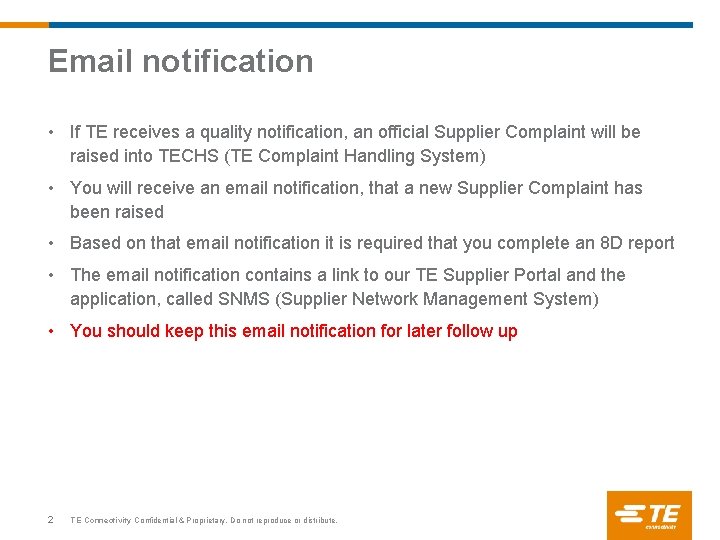
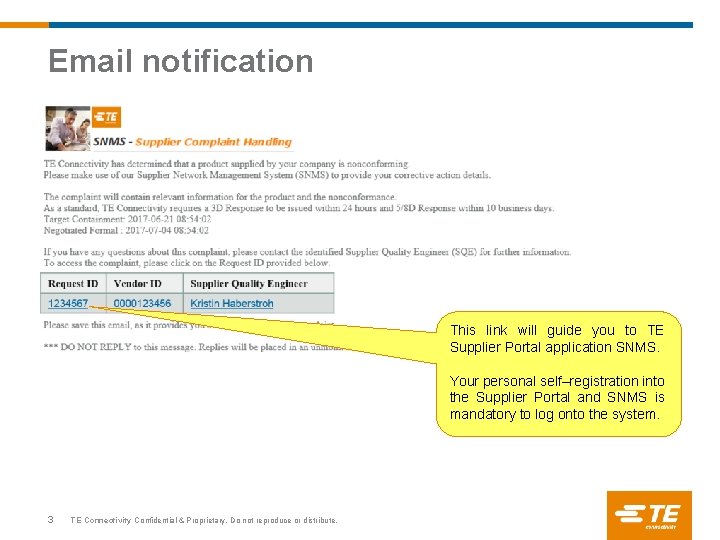
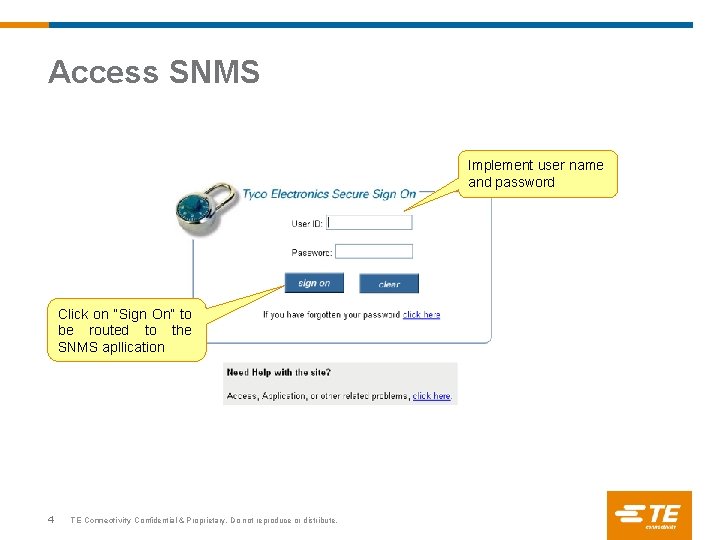
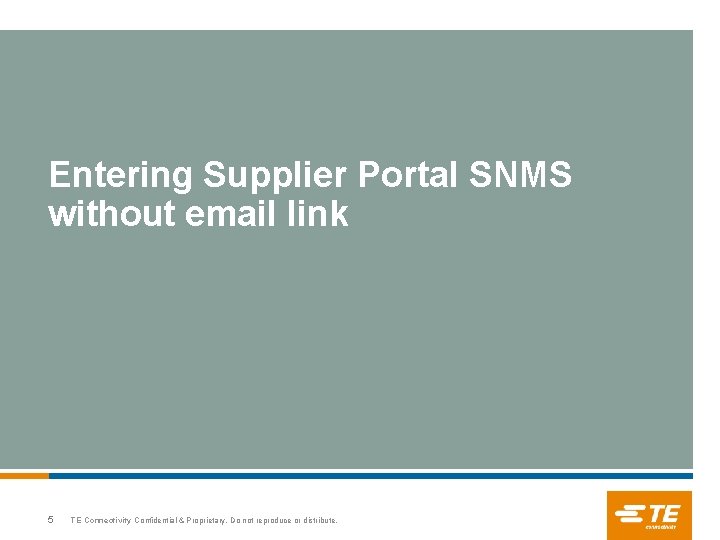
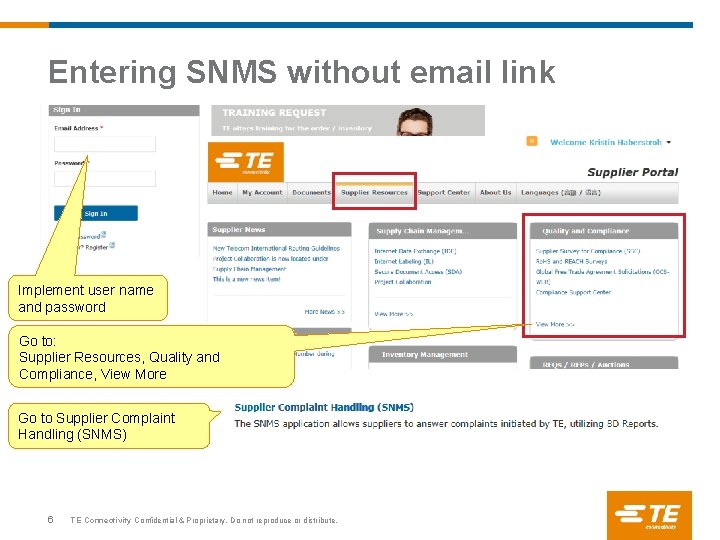
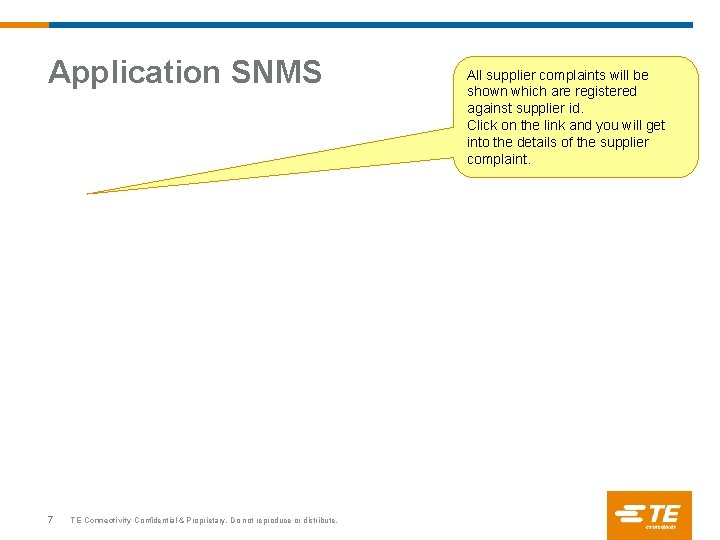
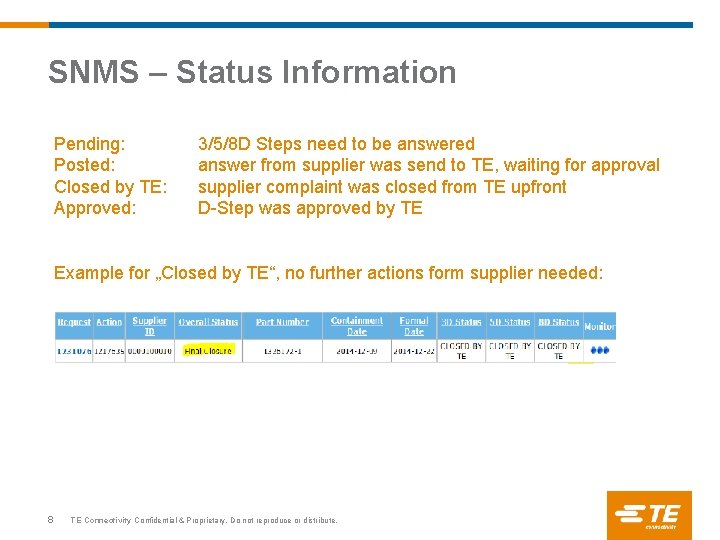
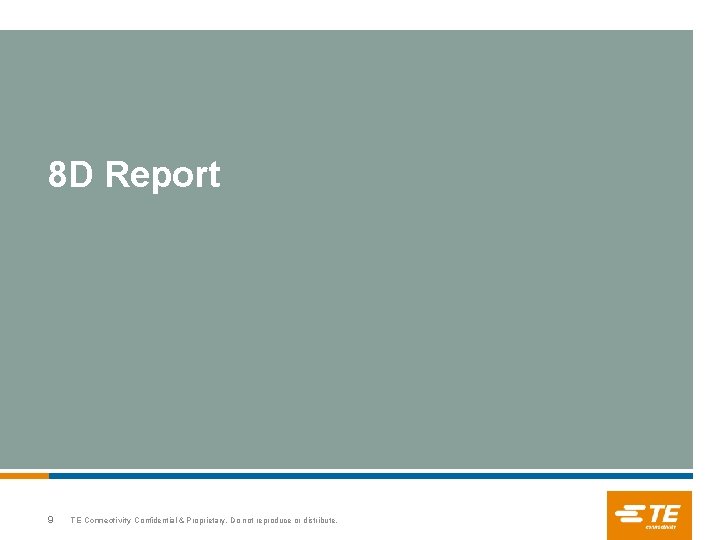
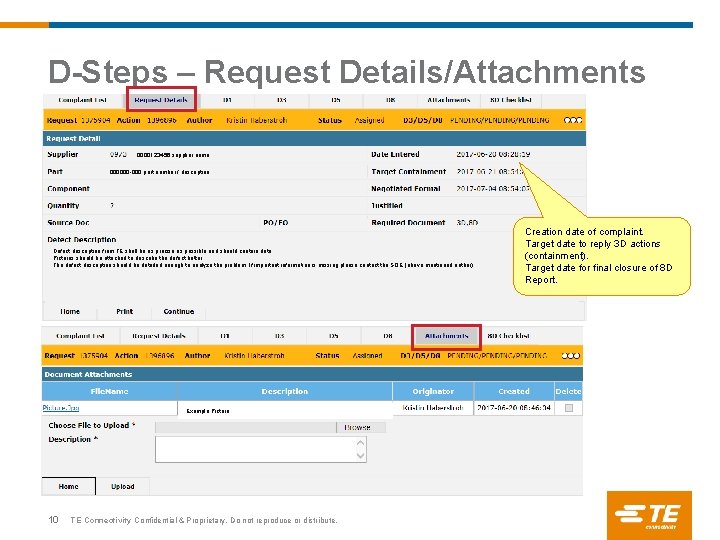
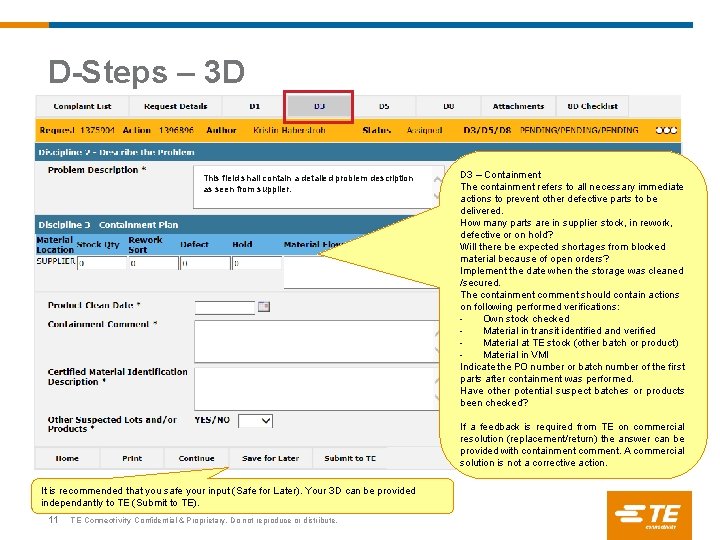
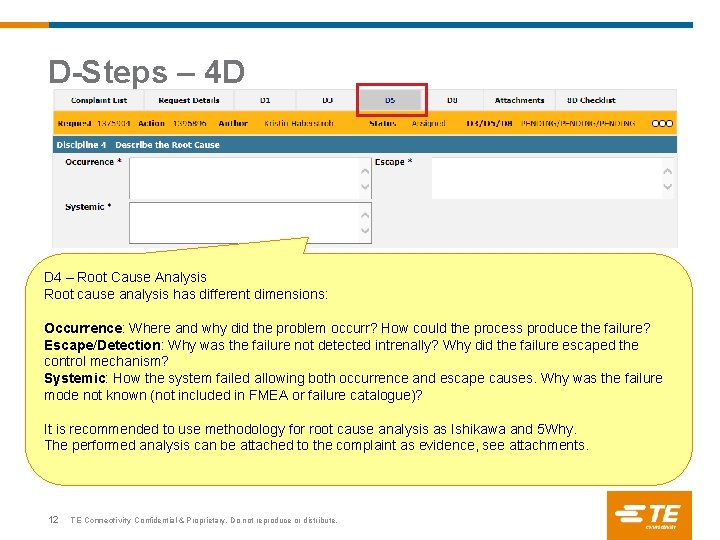
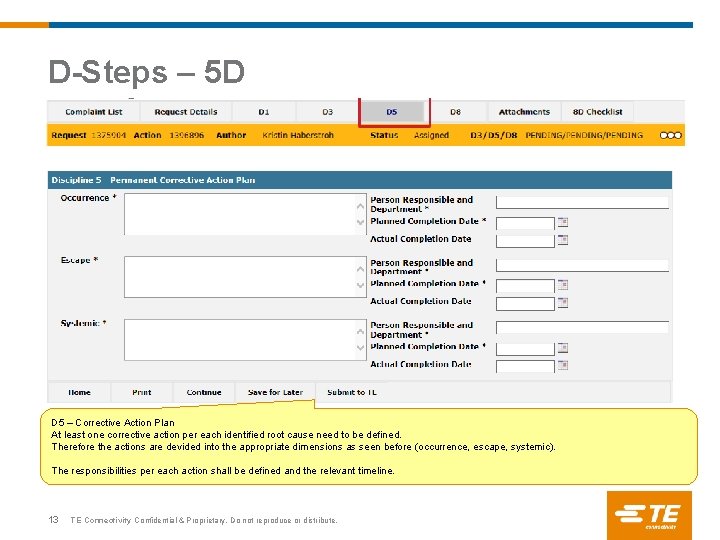
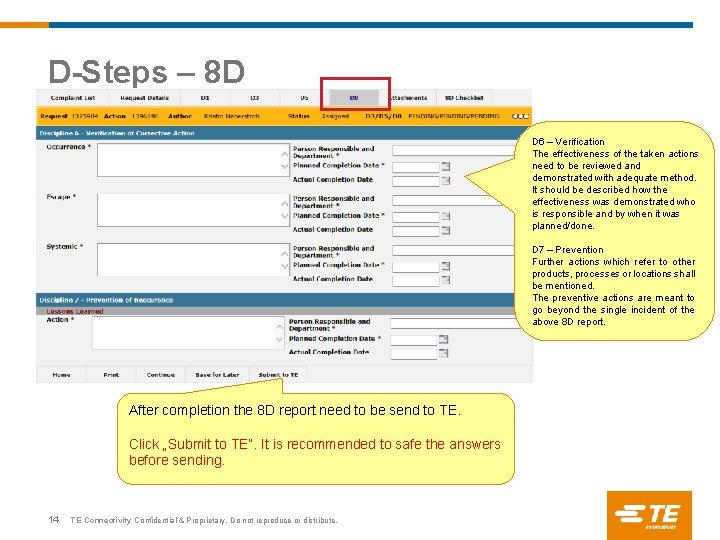
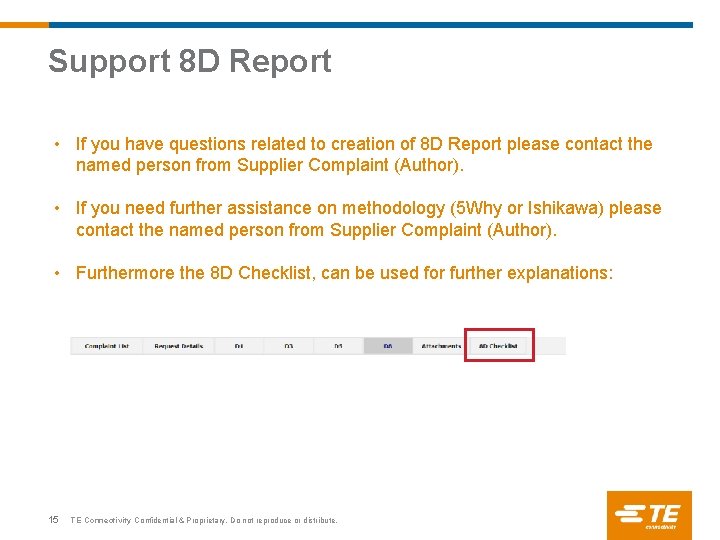
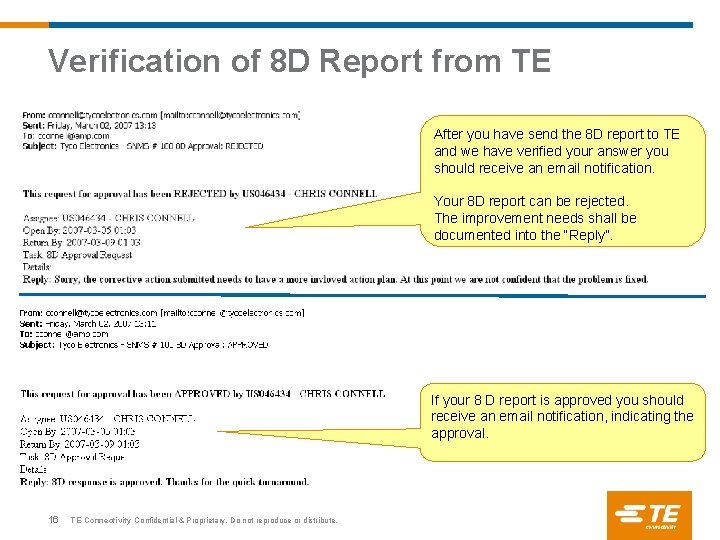
- Slides: 16
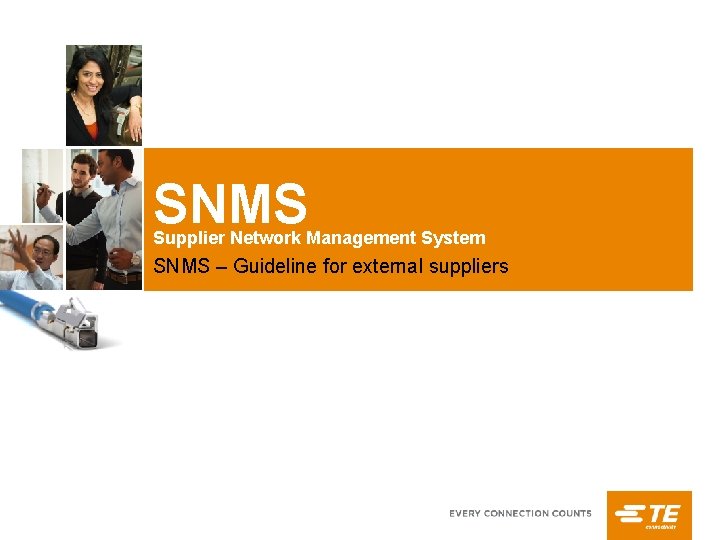
SNMS Supplier Network Management System SNMS – Guideline for external suppliers
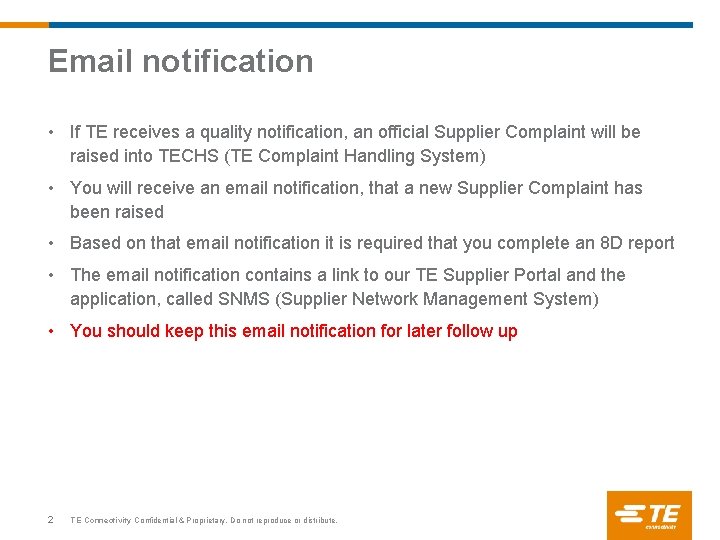
Email notification Supplier Network Management System • If TE receives a quality notification, an official Supplier Complaint will be raised into TECHS (TE Complaint Handling System) • You will receive an email notification, that a new Supplier Complaint has been raised • Based on that email notification it is required that you complete an 8 D report • The email notification contains a link to our TE Supplier Portal and the application, called SNMS (Supplier Network Management System) • You should keep this email notification for later follow up 2 TE Connectivity Confidential & Proprietary. Do not reproduce or distribute.
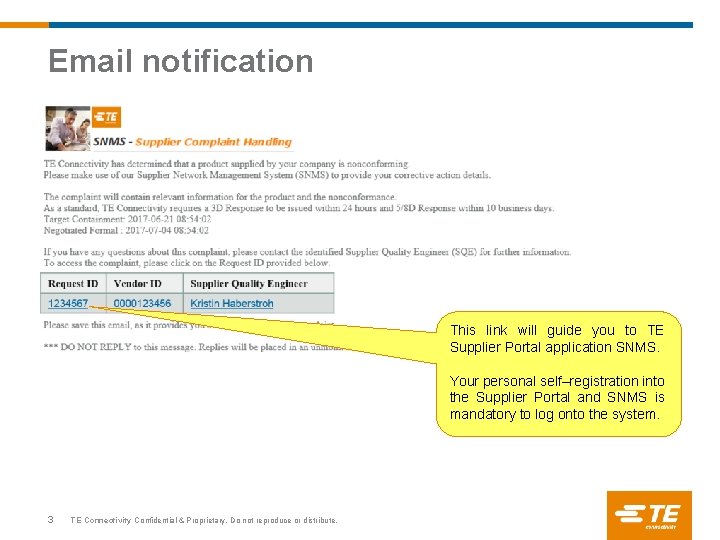
Email notification Supplier Network Management System This link will guide you to TE Supplier Portal application SNMS. Your personal self–registration into the Supplier Portal and SNMS is mandatory to log onto the system. 3 TE Connectivity Confidential & Proprietary. Do not reproduce or distribute.
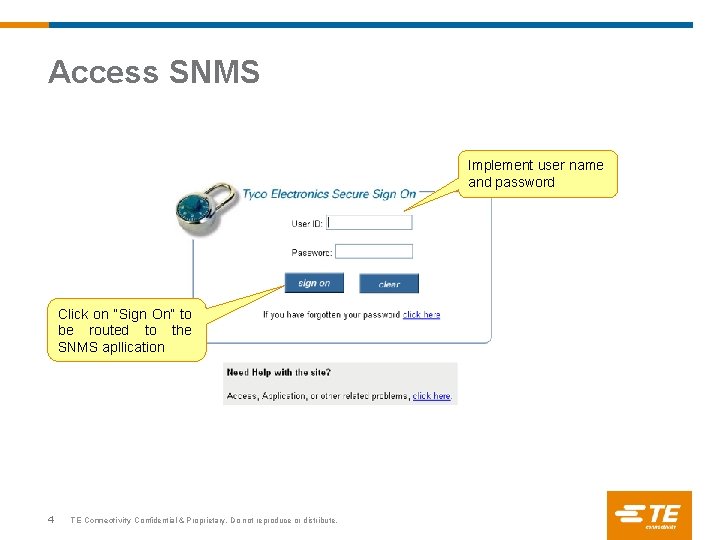
Access SNMS Implement user name and password Click on “Sign On” to be routed to the SNMS apllication 4 TE Connectivity Confidential & Proprietary. Do not reproduce or distribute.
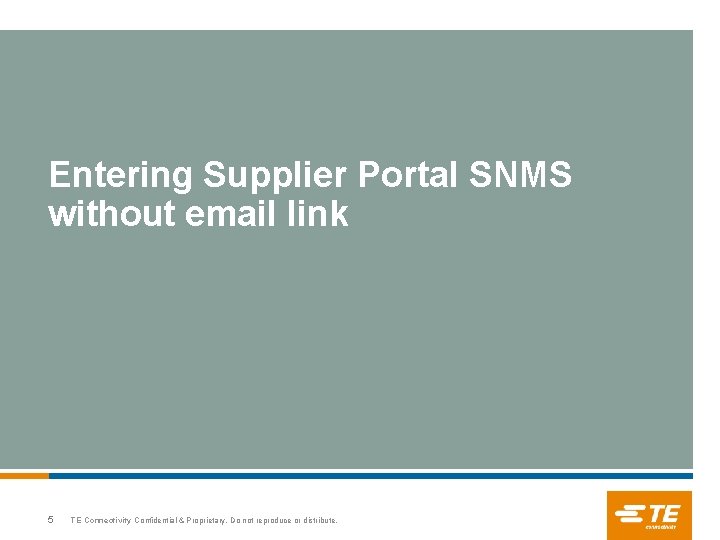
Entering Supplier Portal SNMS without email link 5 TE Connectivity Confidential & Proprietary. Do not reproduce or distribute.
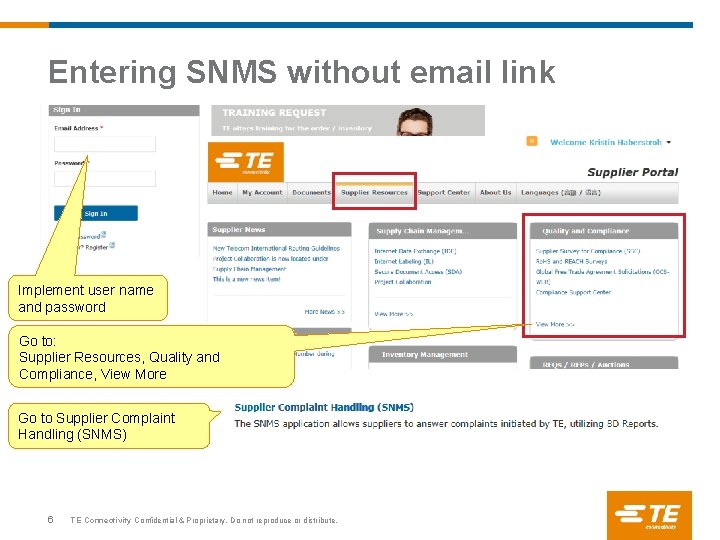
Entering SNMS without email link Implement user name and password Go to: Supplier Resources, Quality and Compliance, View More Go to Supplier Complaint Handling (SNMS) 6 TE Connectivity Confidential & Proprietary. Do not reproduce or distribute.
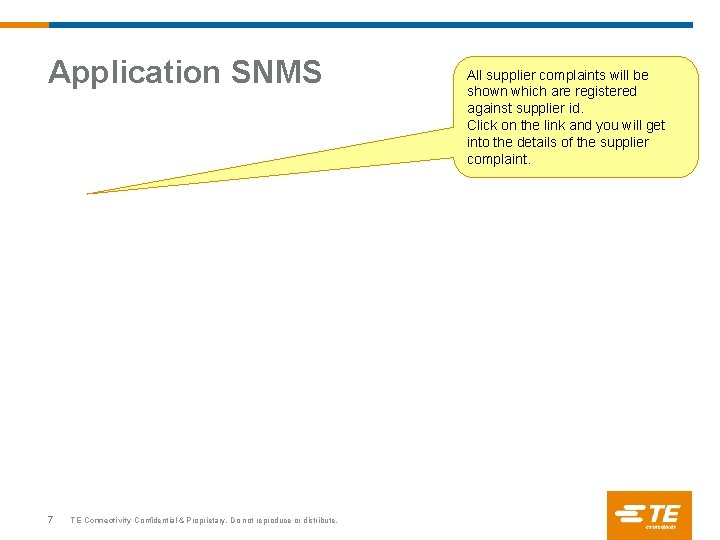
Application SNMS 7 TE Connectivity Confidential & Proprietary. Do not reproduce or distribute. All supplier complaints will be shown which are registered against supplier id. Click on the link and you will get into the details of the supplier complaint.
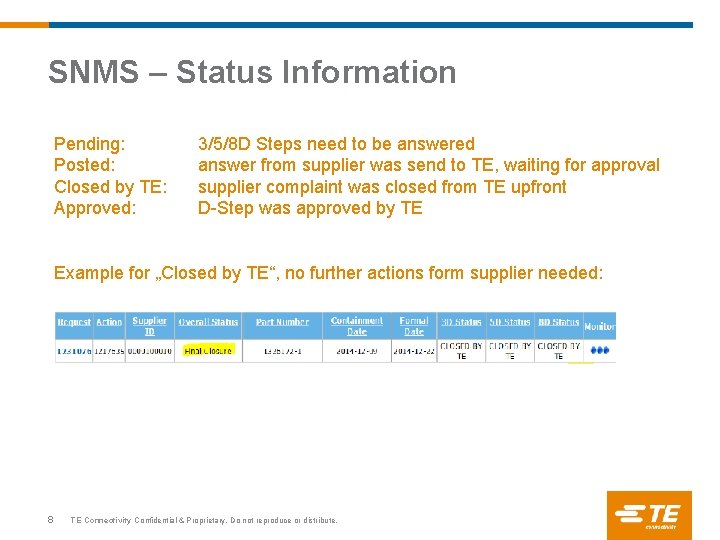
SNMS – Status Information Pending: Posted: Closed by TE: Approved: 3/5/8 D Steps need to be answered answer from supplier was send to TE, waiting for approval supplier complaint was closed from TE upfront D-Step was approved by TE Example for „Closed by TE“, no further actions form supplier needed: 8 TE Connectivity Confidential & Proprietary. Do not reproduce or distribute.
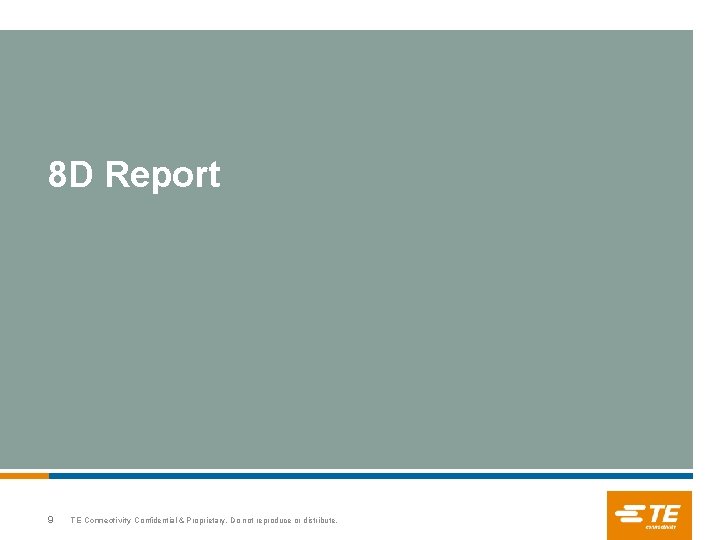
8 D Report 9 TE Connectivity Confidential & Proprietary. Do not reproduce or distribute.
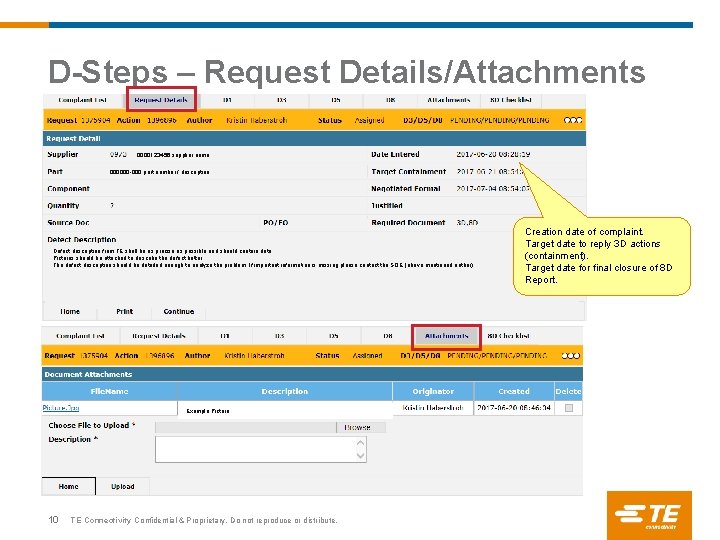
D-Steps – Request Details/Attachments 0000123456 supplier name 000000 -000 part number / description Defect description from TE shall be as precise as possible and should contain data. Pictures should be attached to describe the defect better. The defect description should be detailed enough to analyze the problem. If important information is missing please contact the SQE (above mentioned author). Example Picture 10 TE Connectivity Confidential & Proprietary. Do not reproduce or distribute. Creation date of complaint. Target date to reply 3 D actions (containment). Target date for final closure of 8 D Report.
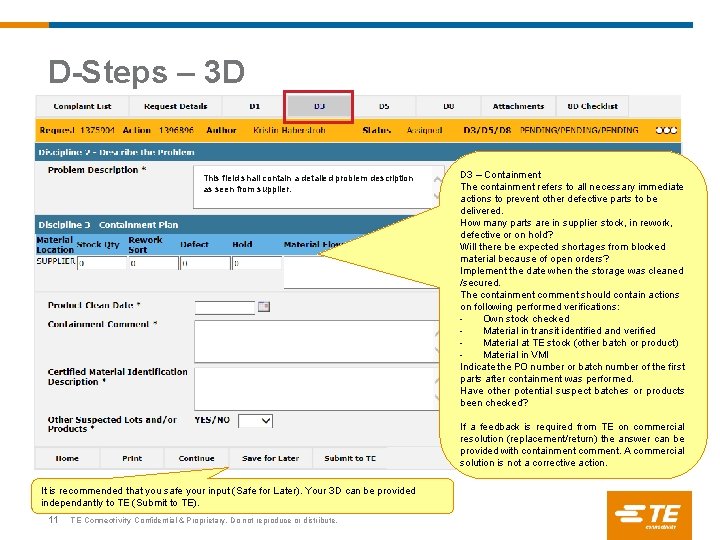
D-Steps – 3 D This field shall contain a detailed problem description as seen from supplier. D 3 – Containment The containment refers to all necessary immediate actions to prevent other defective parts to be delivered. How many parts are in supplier stock, in rework, defective or on hold? Will there be expected shortages from blocked material because of open orders? Implement the date when the storage was cleaned /secured. The containment comment should contain actions on following performed verifications: Own stock checked Material in transit identified and verified Material at TE stock (other batch or product) Material in VMI Indicate the PO number or batch number of the first parts after containment was performed. Have other potential suspect batches or products been checked? If a feedback is required from TE on commercial resolution (replacement/return) the answer can be provided with containment comment. A commercial solution is not a corrective action. It is recommended that you safe your input (Safe for Later). Your 3 D can be provided independantly to TE (Submit to TE). 11 TE Connectivity Confidential & Proprietary. Do not reproduce or distribute.
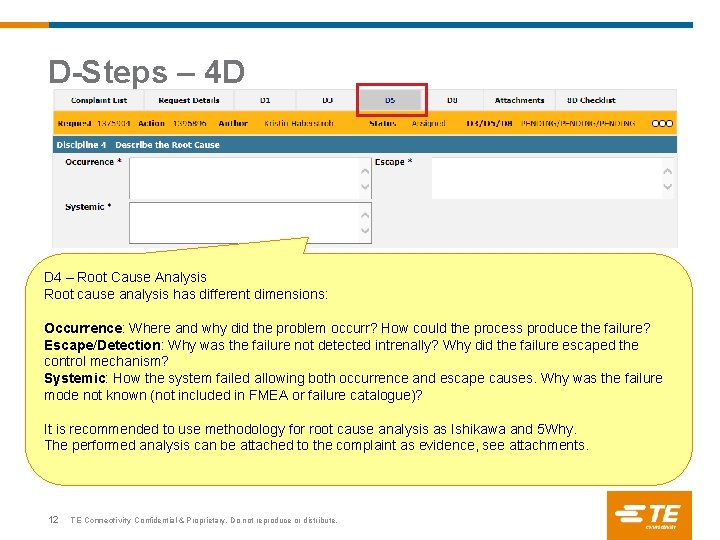
D-Steps – 4 D D 4 – Root Cause Analysis Root cause analysis has different dimensions: Occurrence: Where and why did the problem occurr? How could the process produce the failure? Escape/Detection: Why was the failure not detected intrenally? Why did the failure escaped the control mechanism? Systemic: How the system failed allowing both occurrence and escape causes. Why was the failure mode not known (not included in FMEA or failure catalogue)? It is recommended to use methodology for root cause analysis as Ishikawa and 5 Why. The performed analysis can be attached to the complaint as evidence, see attachments. 12 TE Connectivity Confidential & Proprietary. Do not reproduce or distribute.
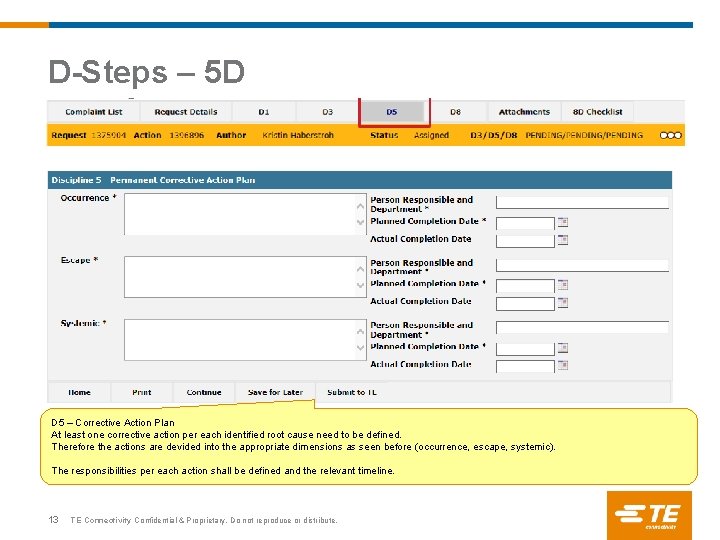
D-Steps – 5 D D 5 – Corrective Action Plan At least one corrective action per each identified root cause need to be defined. Therefore the actions are devided into the appropriate dimensions as seen before (occurrence, escape, systemic). The responsibilities per each action shall be defined and the relevant timeline. 13 TE Connectivity Confidential & Proprietary. Do not reproduce or distribute.
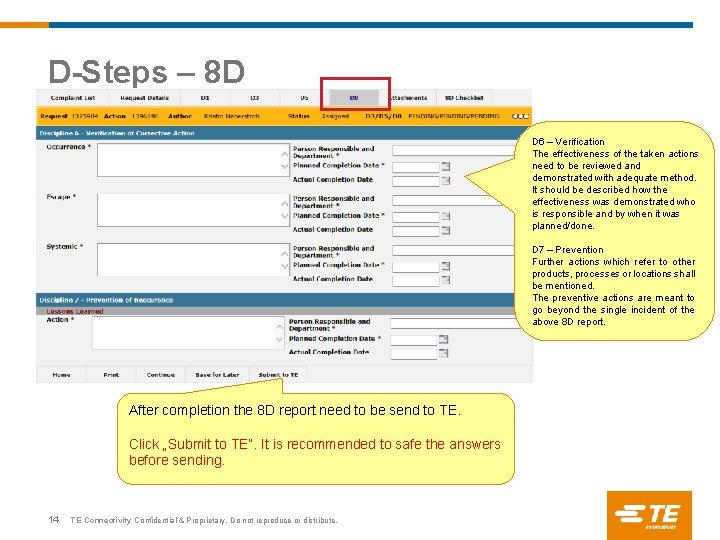
D-Steps – 8 D D 6 – Verification The effectiveness of the taken actions need to be reviewed and demonstrated with adequate method. It should be described how the effectiveness was demonstrated who is responsible and by when it was planned/done. D 7 – Prevention Further actions which refer to other products, processes or locations shall be mentioned. The preventive actions are meant to go beyond the single incident of the above 8 D report. After completion the 8 D report need to be send to TE. Click „Submit to TE“. It is recommended to safe the answers before sending. 14 TE Connectivity Confidential & Proprietary. Do not reproduce or distribute.
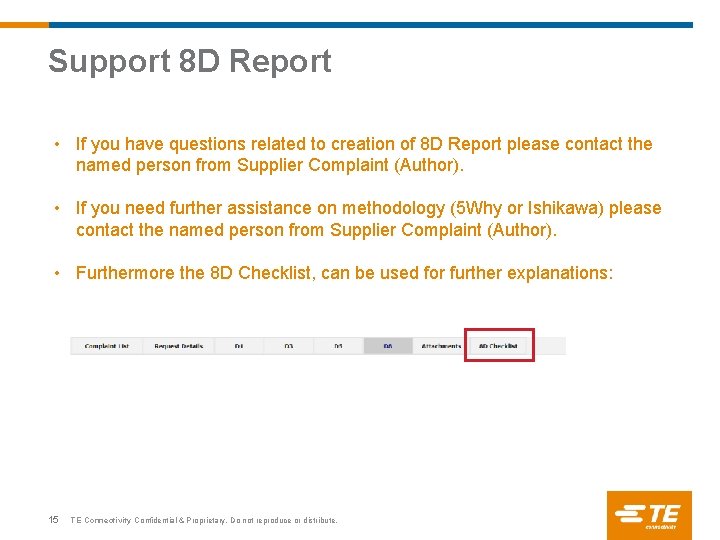
Support 8 D Report • If you have questions related to creation of 8 D Report please contact the named person from Supplier Complaint (Author). • If you need further assistance on methodology (5 Why or Ishikawa) please contact the named person from Supplier Complaint (Author). • Furthermore the 8 D Checklist, can be used for further explanations: 15 TE Connectivity Confidential & Proprietary. Do not reproduce or distribute.
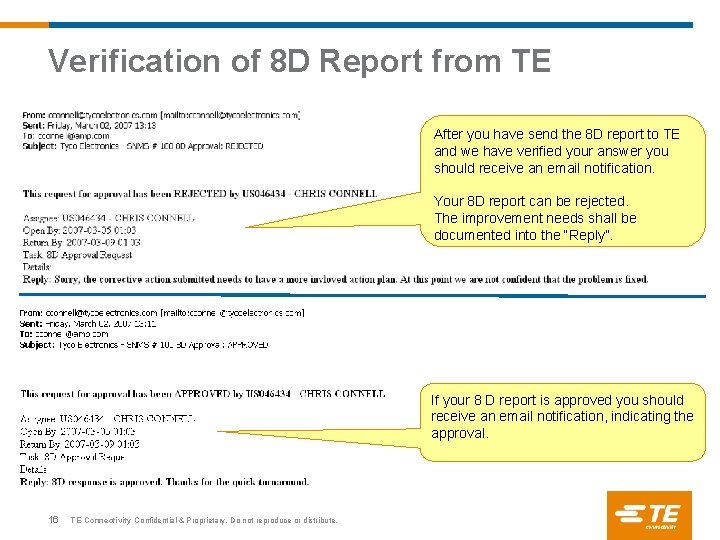
Verification of 8 D Report from TE After you have send the 8 D report to TE and we have verified your answer you should receive an email notification. Your 8 D report can be rejected. The improvement needs shall be documented into the “Reply”. If your 8 D report is approved you should receive an email notification, indicating the approval. 16 TE Connectivity Confidential & Proprietary. Do not reproduce or distribute.
Supplier network management
Waikato stormwater management guideline
Interview guideline template
Anemia in pregnancy guideline
Autoanamnesa
Patient safety incident report form
Msqh standard
Anamnesa psikologi adalah
East practice management guidelines
Enteral feeding guideline
Traveling guide haircut
What is a guideline for hoisting a hoseline?
Turnbull guidelines uk
5 guideline for cumbersome calculations
5% guideline for cumbersome calculations
Who guideline on country pharmaceutical pricing policies
Outside counsel guidelines