Shaping Characteristics and Solidification Microstructure under Electromagnetic Confinement
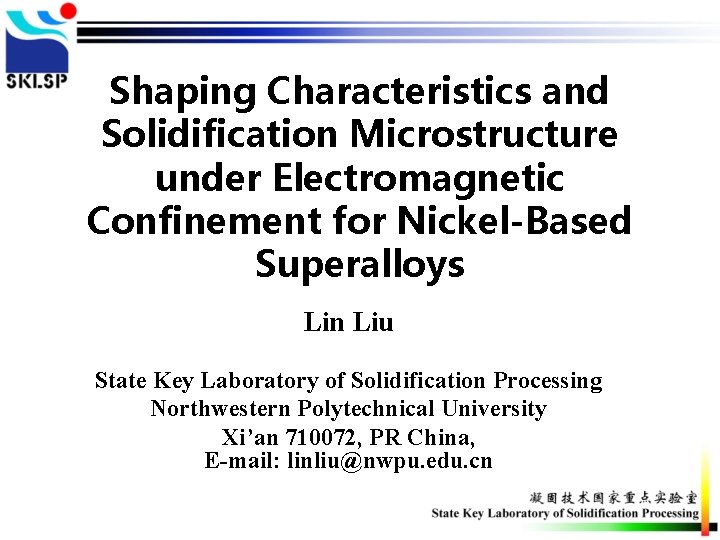
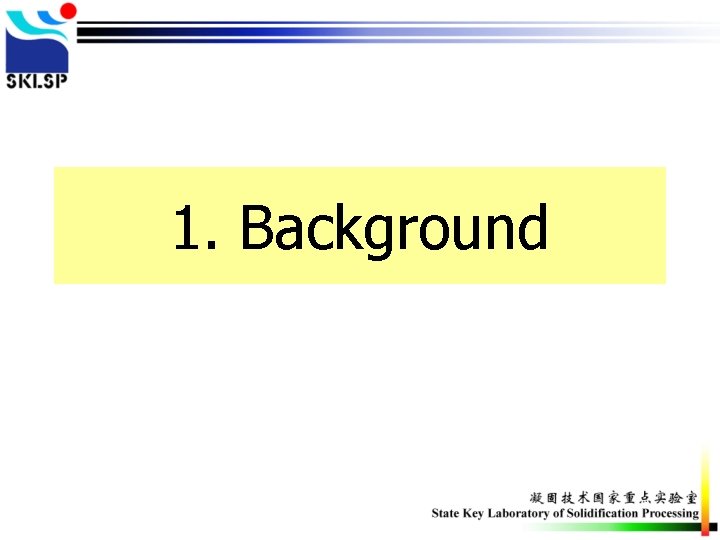
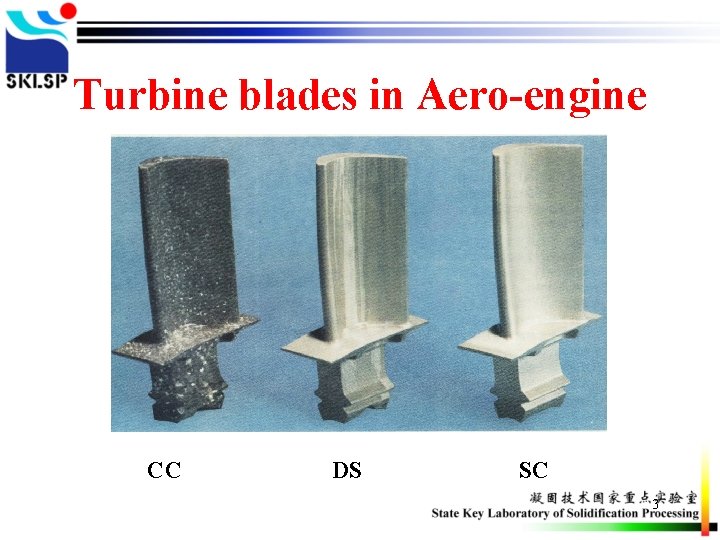
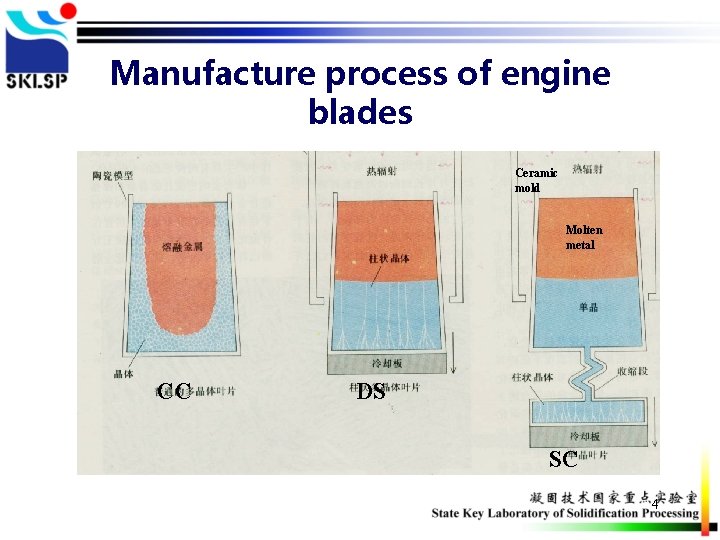
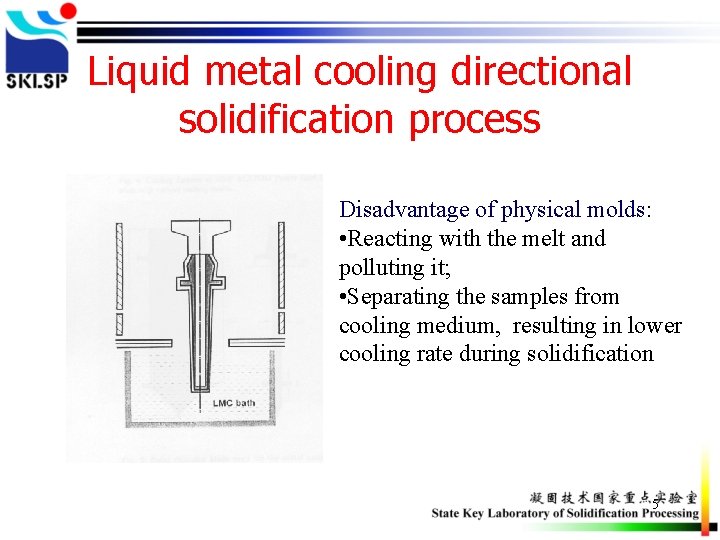
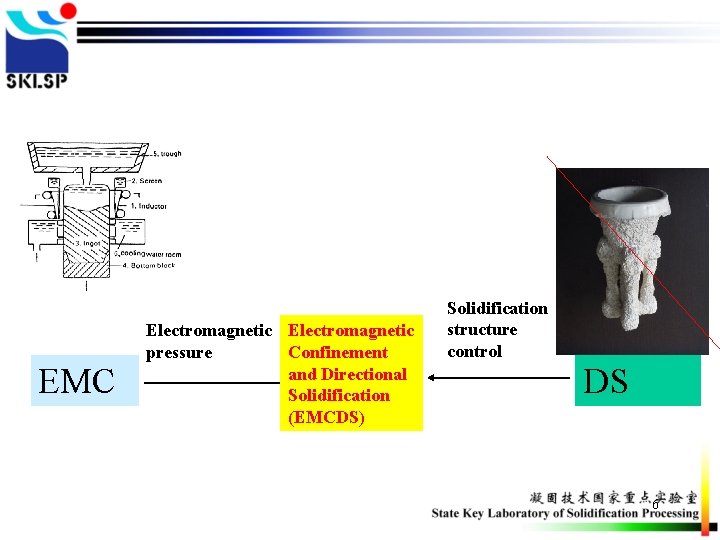
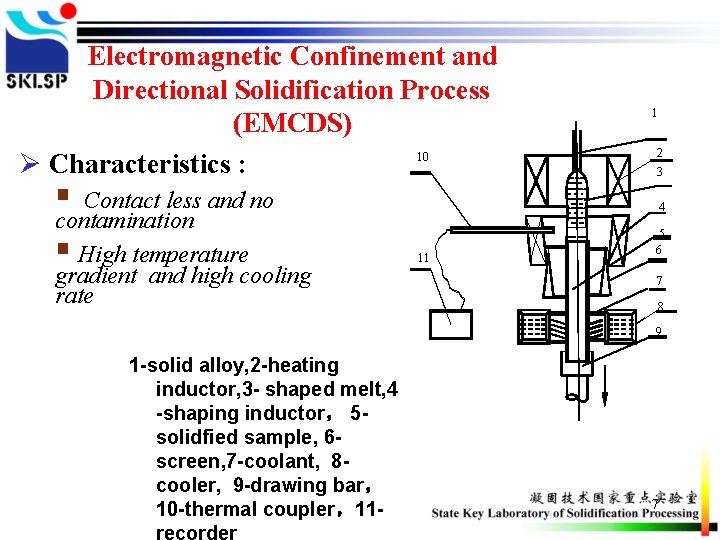
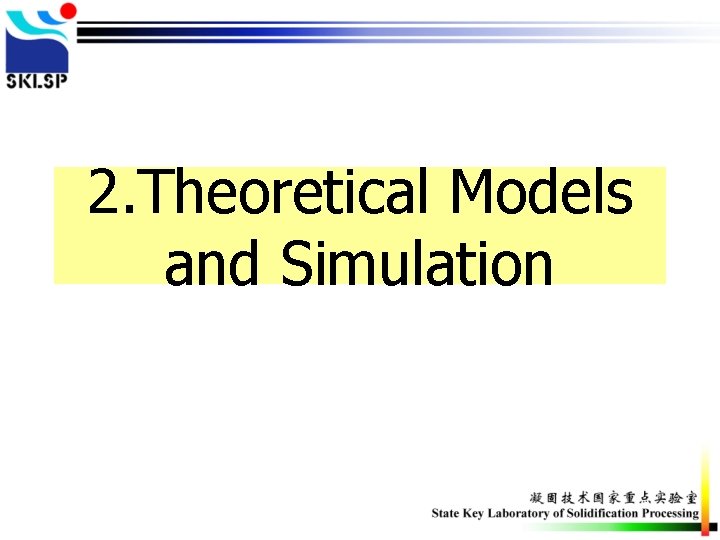
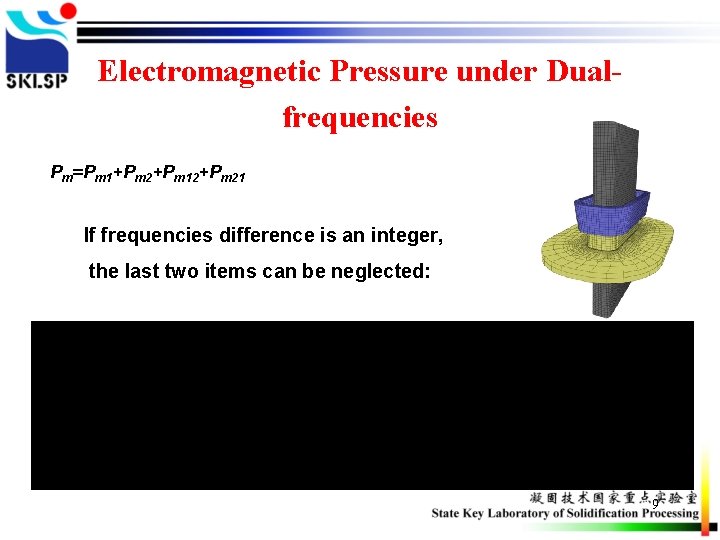
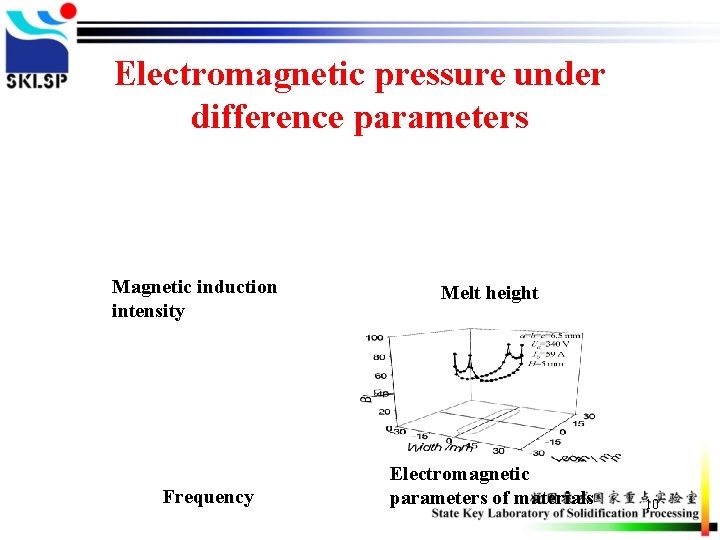
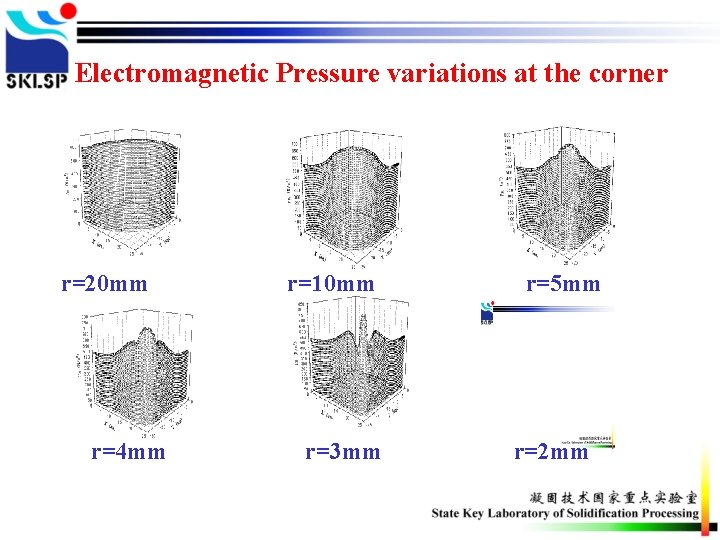
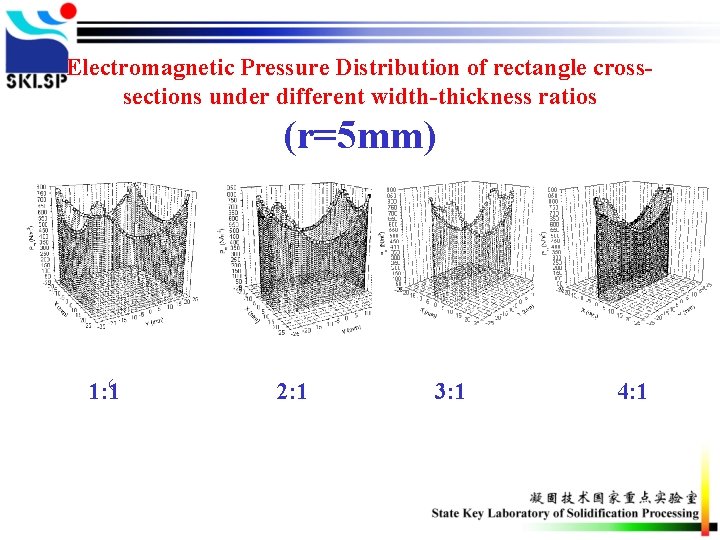
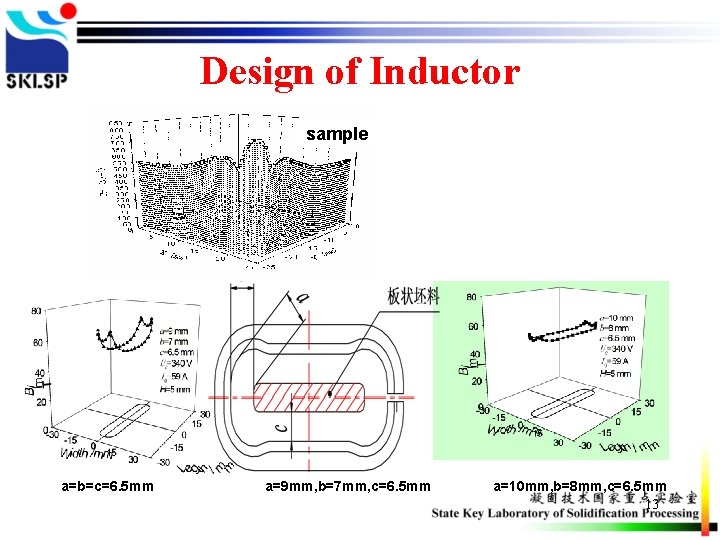
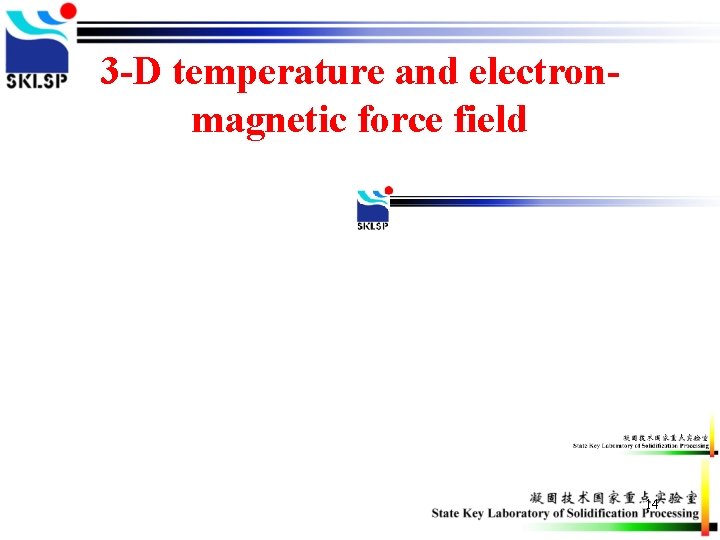
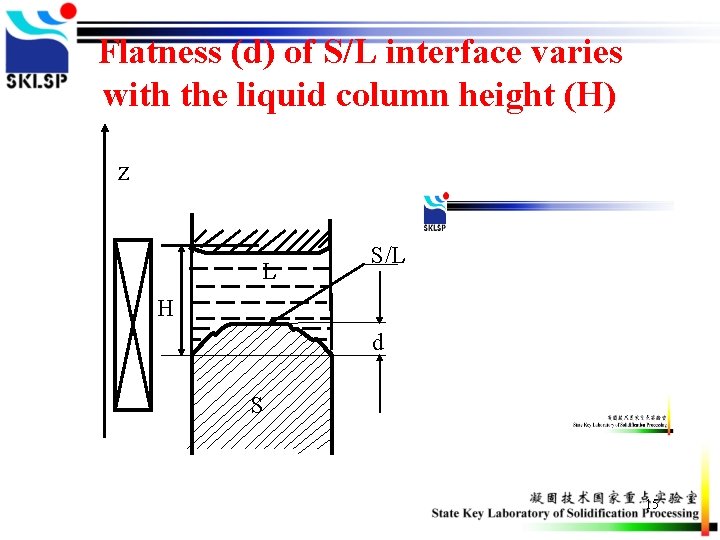
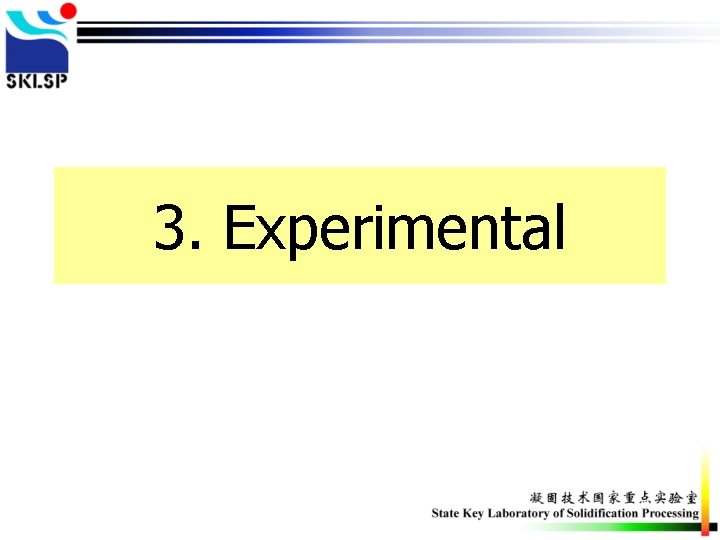
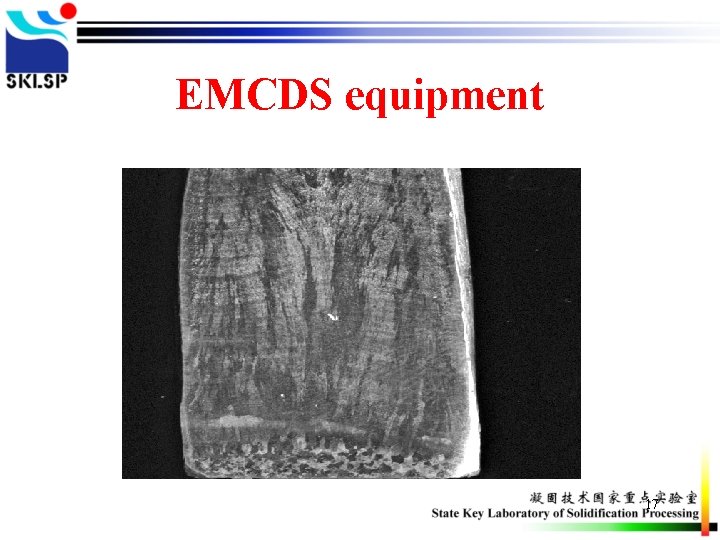
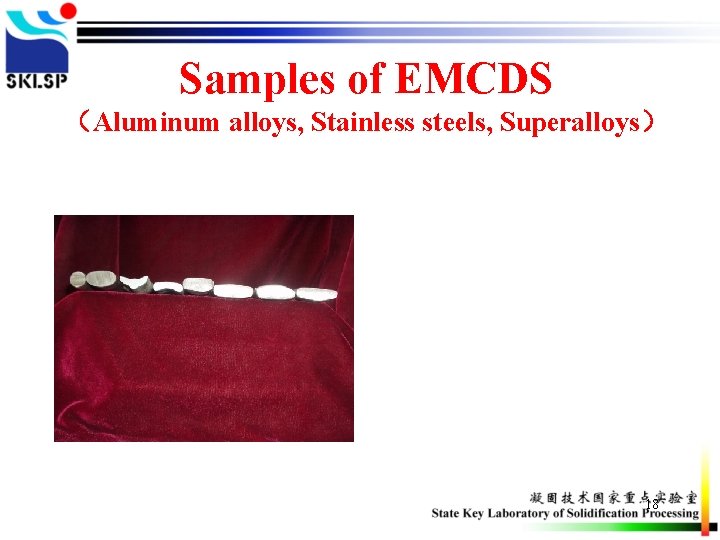
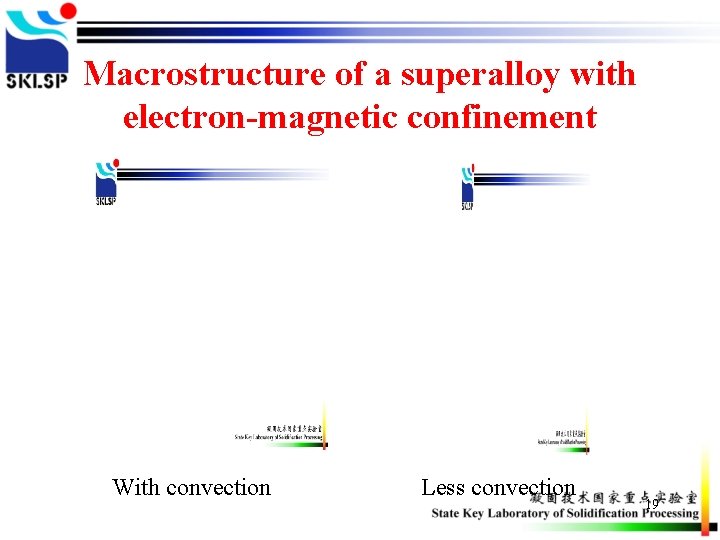
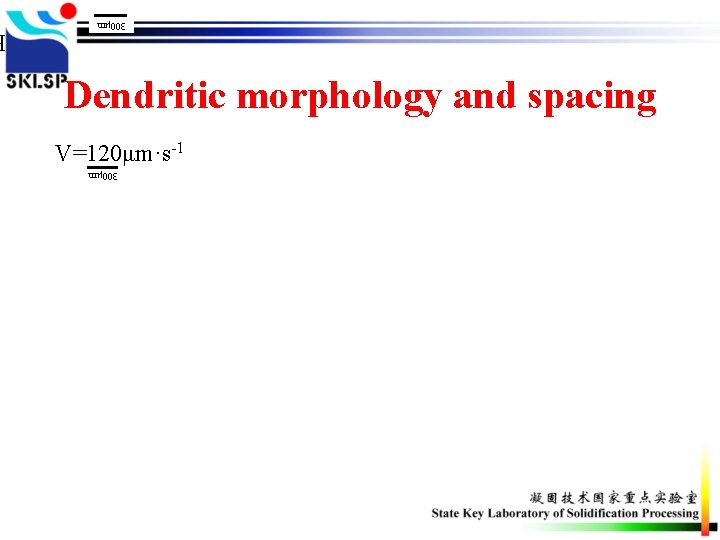
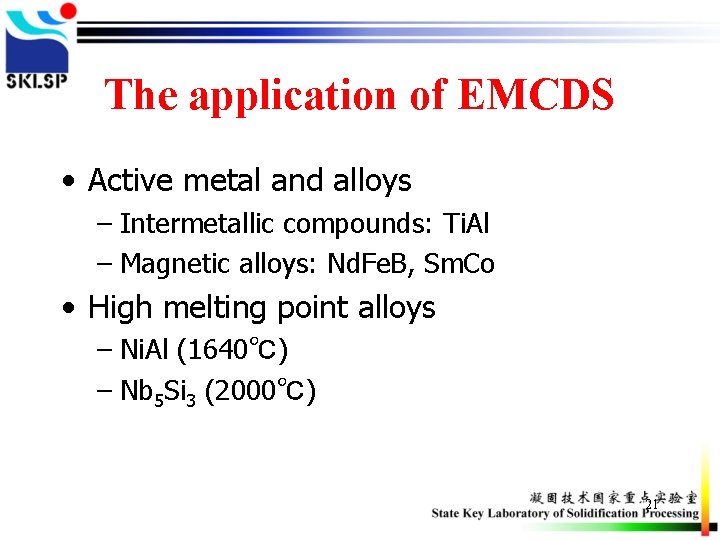
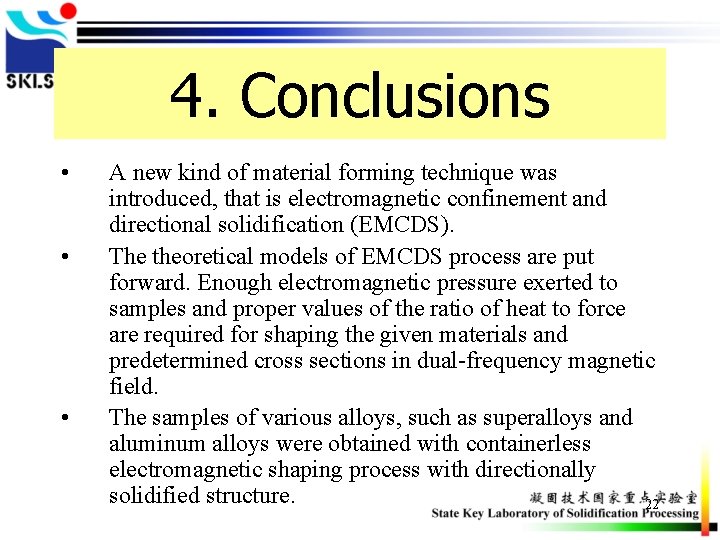

- Slides: 23
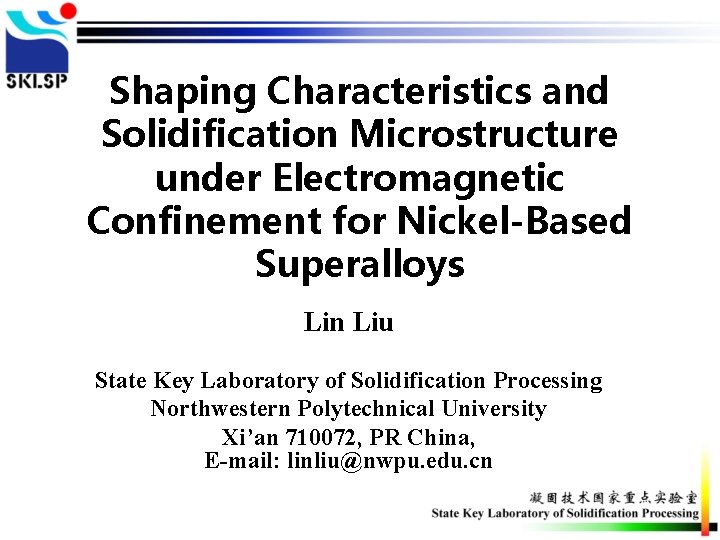
Shaping Characteristics and Solidification Microstructure under Electromagnetic Confinement for Nickel-Based Superalloys Lin Liu State Key Laboratory of Solidification Processing Northwestern Polytechnical University Xi’an 710072, PR China, E-mail: linliu@nwpu. edu. cn
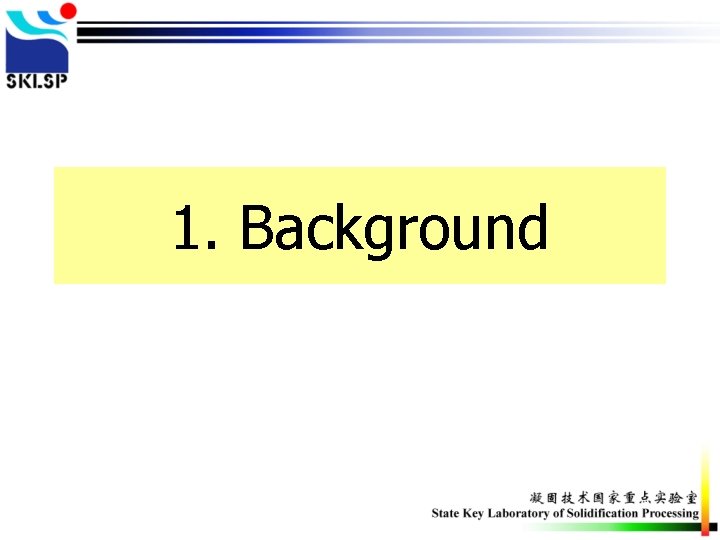
1. Background
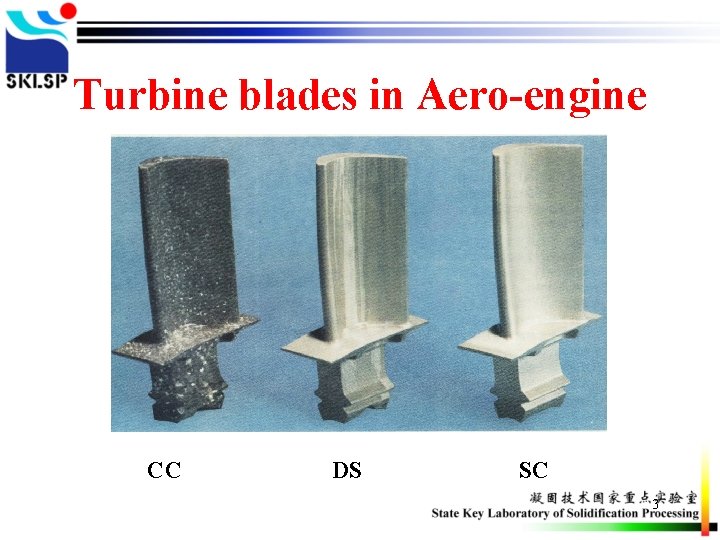
Turbine blades in Aero-engine CC DS SC 3
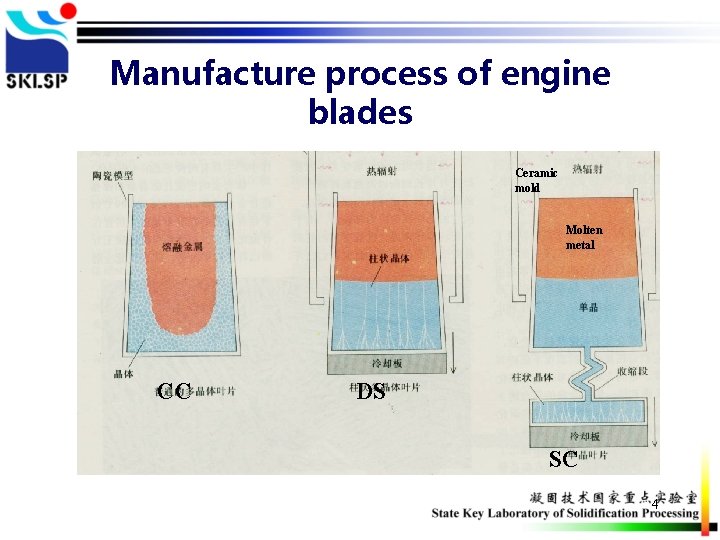
Manufacture process of engine blades Ceramic mold Molten metal CC DS SC 4
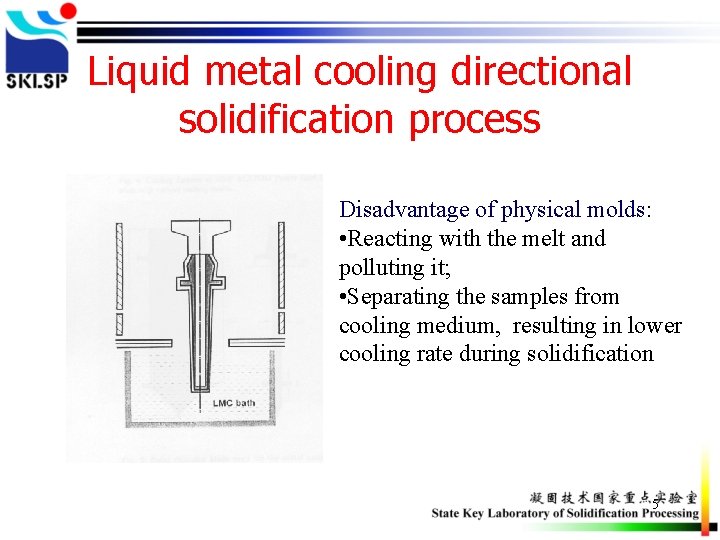
Liquid metal cooling directional solidification process Disadvantage of physical molds: • Reacting with the melt and polluting it; • Separating the samples from cooling medium, resulting in lower cooling rate during solidification 5
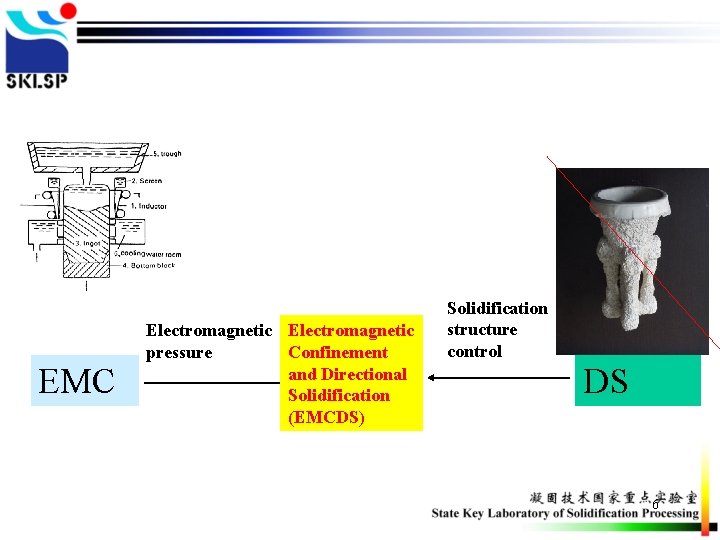
EMC Electromagnetic pressure Confinement and Directional Solidification (EMCDS) Solidification structure control DS 6
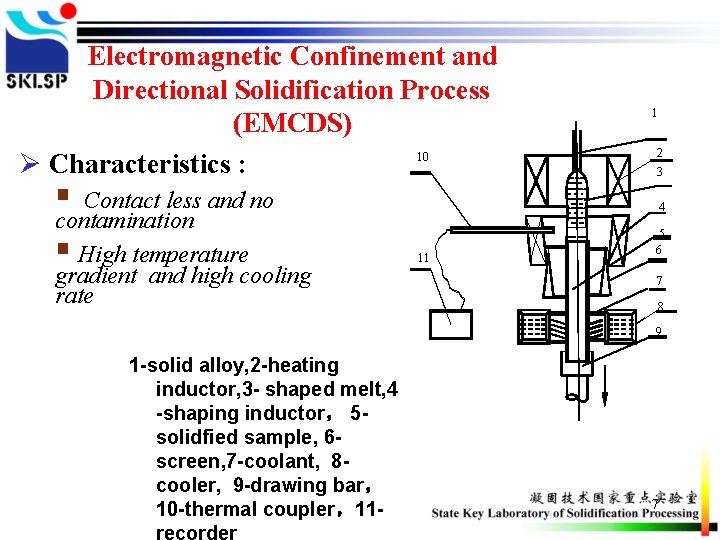
Electromagnetic Confinement and Directional Solidification Process (EMCDS) 9 10 Ø Characteristics : § Contact less and no contamination § High temperature gradient and high cooling rate 10 11 1 2 23 3 4 4 5 56 67 78 89 1 -solid alloy, 2 -heating inductor, 3 - shaped melt, 4 -shaping inductor, 5 solidfied sample, 6 screen, 7 -coolant, 8 cooler, 9 -drawing bar, 10 -thermal coupler,11 - 7
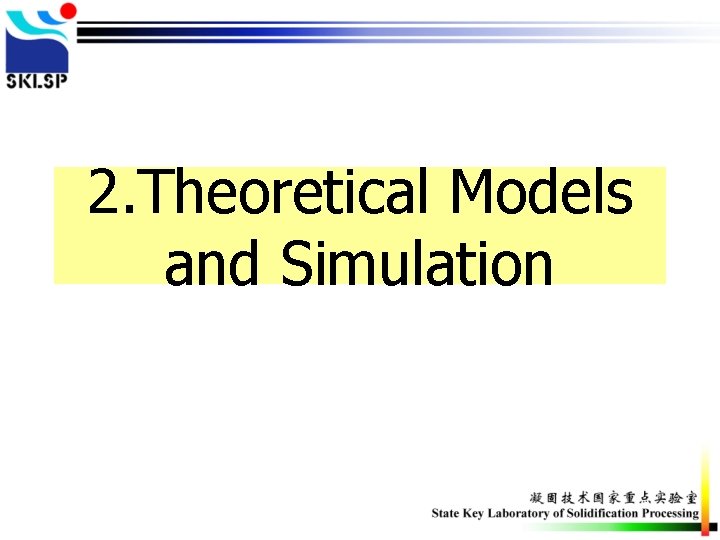
2. Theoretical Models and Simulation
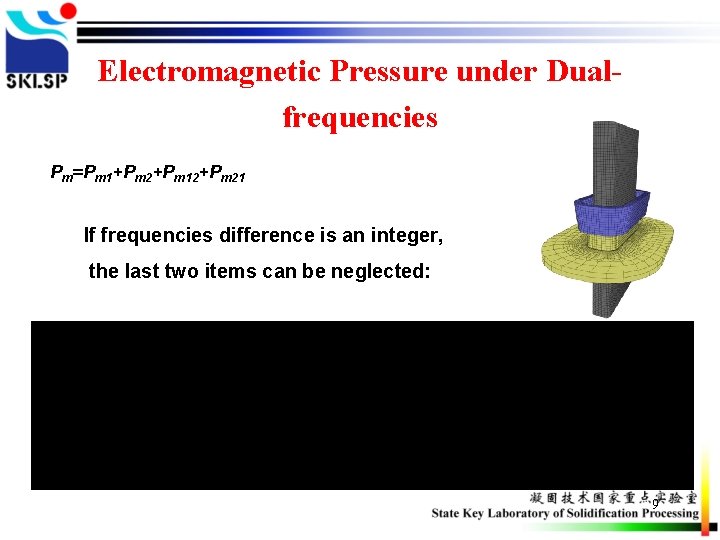
Electromagnetic Pressure under Dualfrequencies Pm=Pm 1+Pm 2+Pm 12+Pm 21 If frequencies difference is an integer, the last two items can be neglected: 9
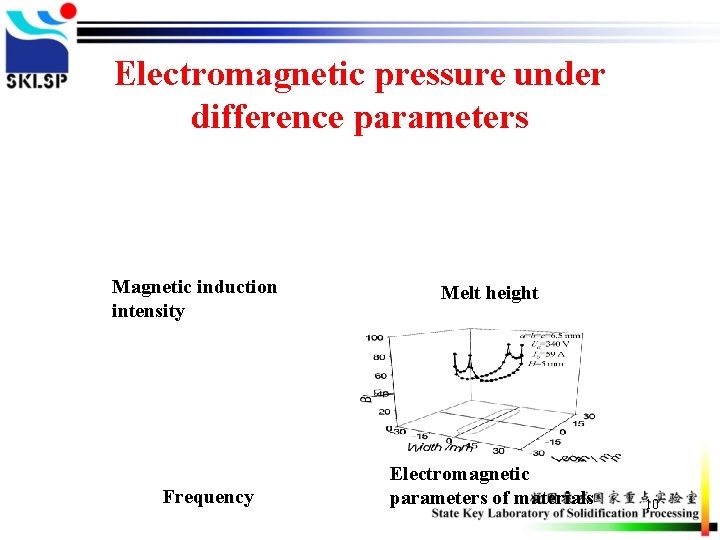
Electromagnetic pressure under difference parameters Magnetic induction intensity Frequency Melt height Electromagnetic parameters of materials 10
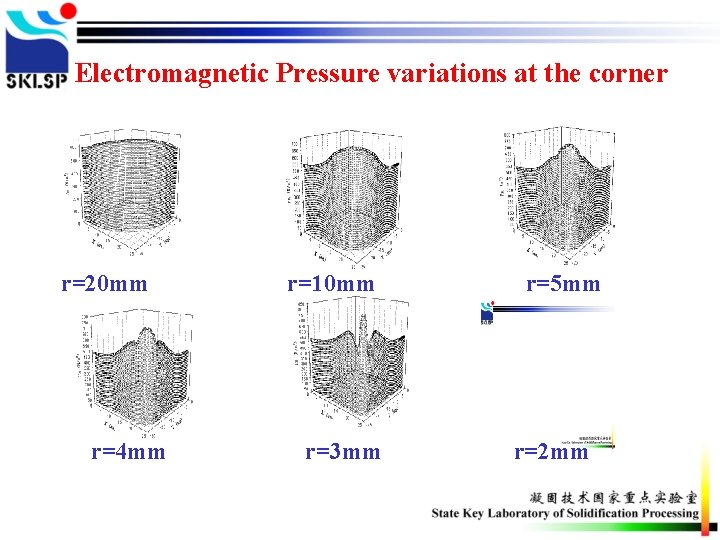
Electromagnetic Pressure variations at the corner r=20 mm r=4 mm r=10 mm r=3 mm r=5 mm r=2 mm
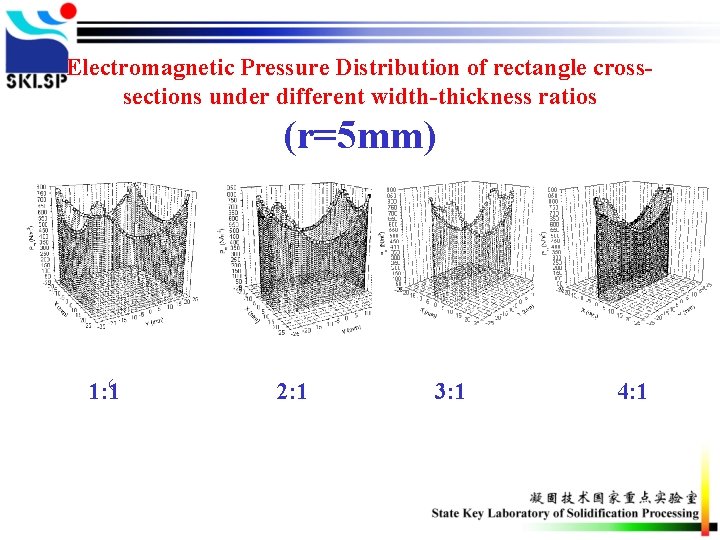
Electromagnetic Pressure Distribution of rectangle crosssections under different width-thickness ratios (r=5 mm) ( 1: 1 2: 1 3: 1 4: 1
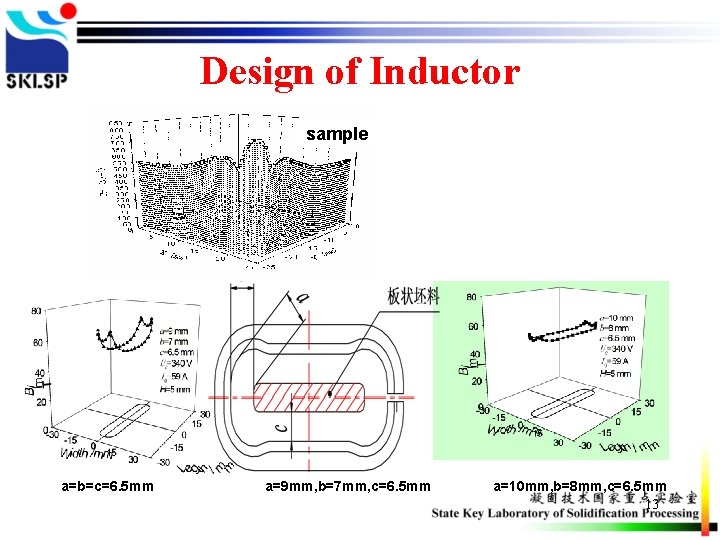
Design of Inductor sample a=b=c=6. 5 mm a=9 mm, b=7 mm, c=6. 5 mm a=10 mm, b=8 mm, c=6. 5 mm 13
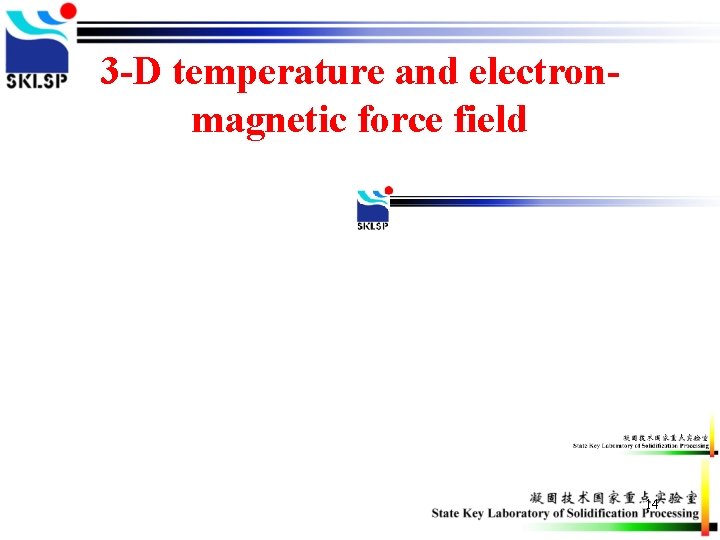
3 -D temperature and electronmagnetic force field 14
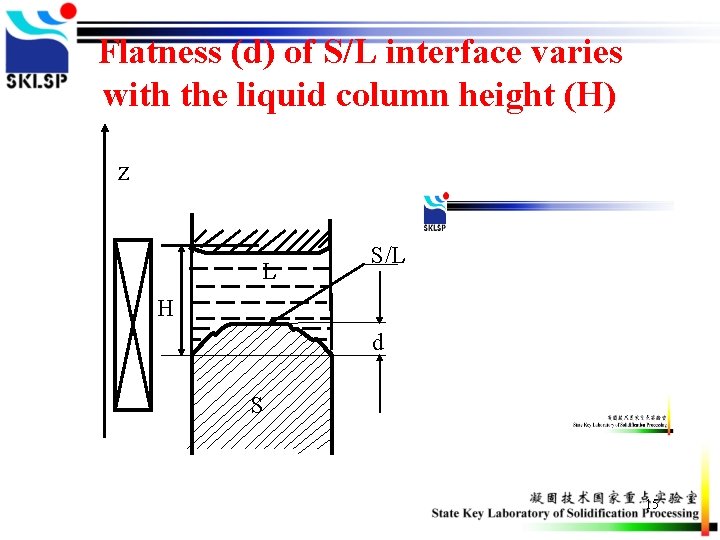
Flatness (d) of S/L interface varies with the liquid column height (H) z L S/L H d S 15
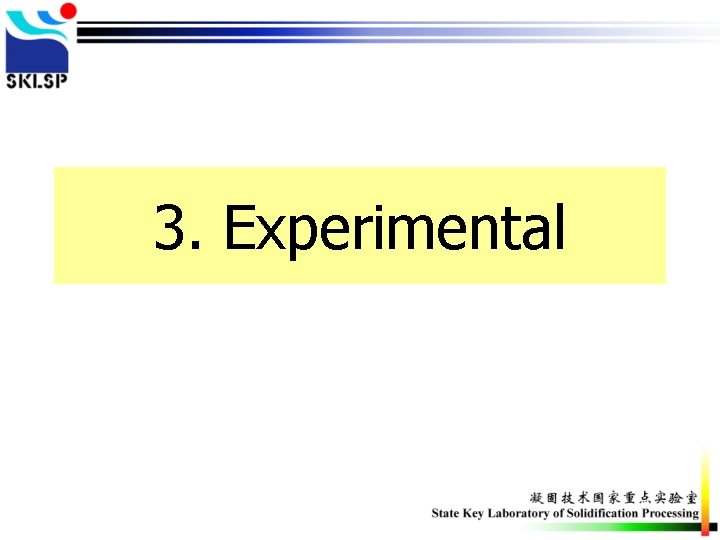
3. Experimental
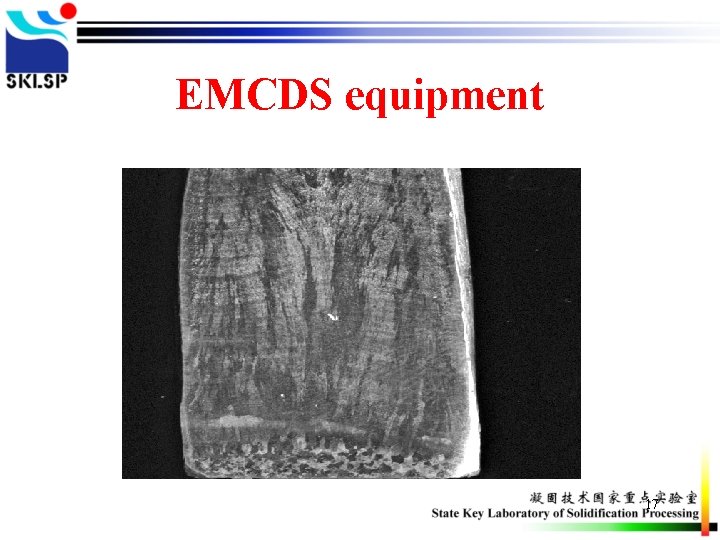
EMCDS equipment 17
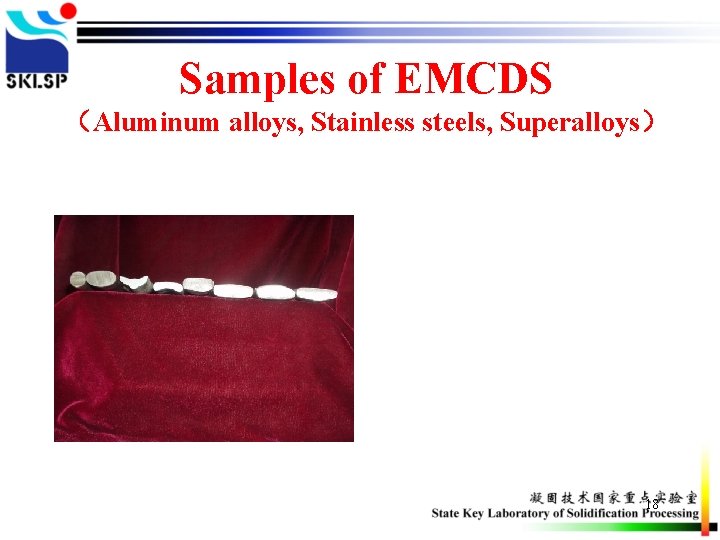
Samples of EMCDS (Aluminum alloys, Stainless steels, Superalloys) 18
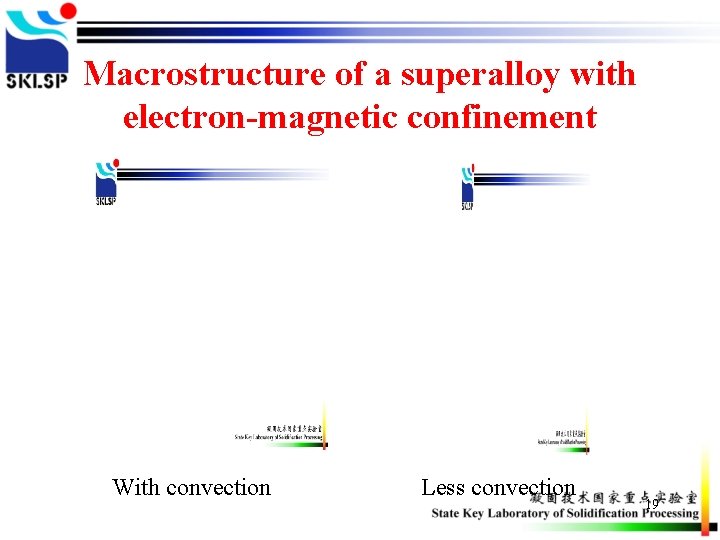
Macrostructure of a superalloy with electron-magnetic confinement With convection Less convection 19
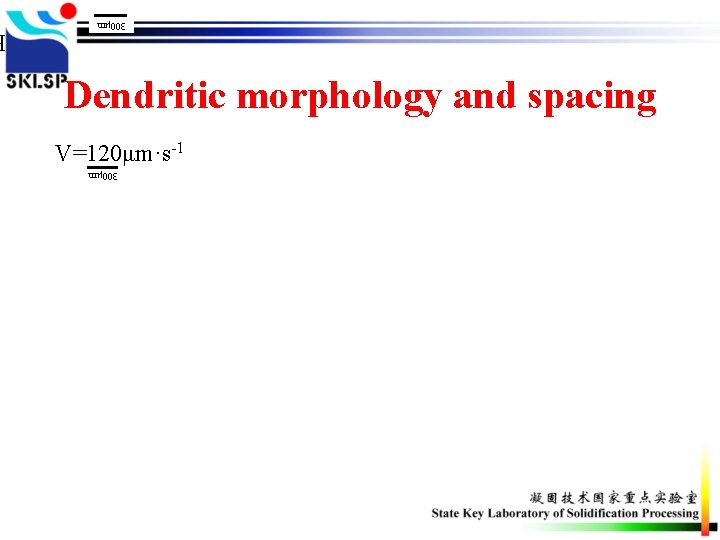
300μm Dendritic morphology and spacing V=120μm·s-1 300μm
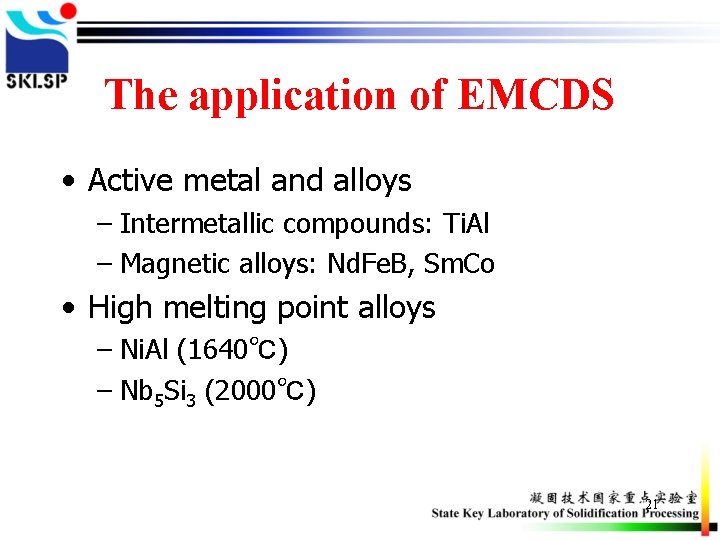
The application of EMCDS • Active metal and alloys – Intermetallic compounds: Ti. Al – Magnetic alloys: Nd. Fe. B, Sm. Co • High melting point alloys – Ni. Al (1640℃) – Nb 5 Si 3 (2000℃) 21
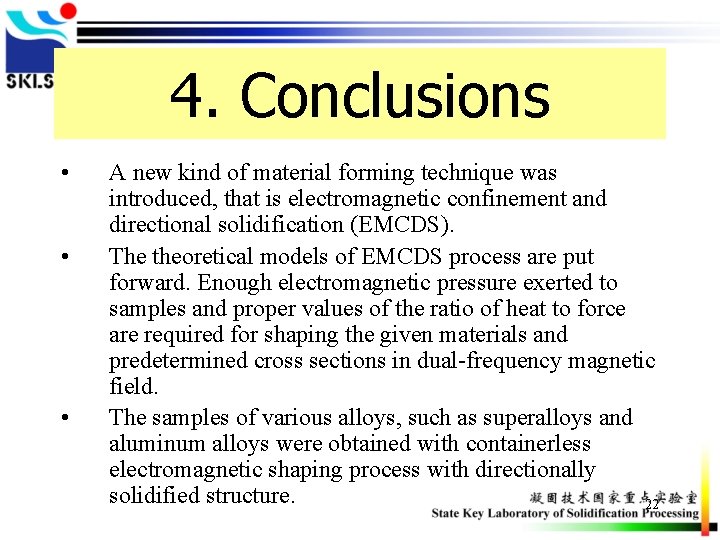
4. Conclusions • • • A new kind of material forming technique was introduced, that is electromagnetic confinement and directional solidification (EMCDS). The theoretical models of EMCDS process are put forward. Enough electromagnetic pressure exerted to samples and proper values of the ratio of heat to force are required for shaping the given materials and predetermined cross sections in dual-frequency magnetic field. The samples of various alloys, such as superalloys and aluminum alloys were obtained with containerless electromagnetic shaping process with directionally solidified structure. 22

Thanks for your attention
Solidification
Solidification
Solidification
Microstructure of a dictionary
Hypereutectoid microstructure
Development of microstructure in isomorphous alloys
Market microstructure trading strategies
Microstructure of ferrous metals
High frequency market microstructure
Empirical market microstructure
Thomas silverstein
Projet enseignement scientifique
Inertial confinement fusion lasers
Confinement qcd
Inertial confinement
Inertial confinement
Confinement principle in computer system security
Solitary confinement effects
Electromagnetic waves characteristics
Demand sensing and shaping
Writing brainstorming planning drafting and editing
Ooqqq
Diaphragms pronunciation
Opportunity recognition shaping and reshaping