SELECTIVE LASER SINTERING SURAJ R S 7 ME
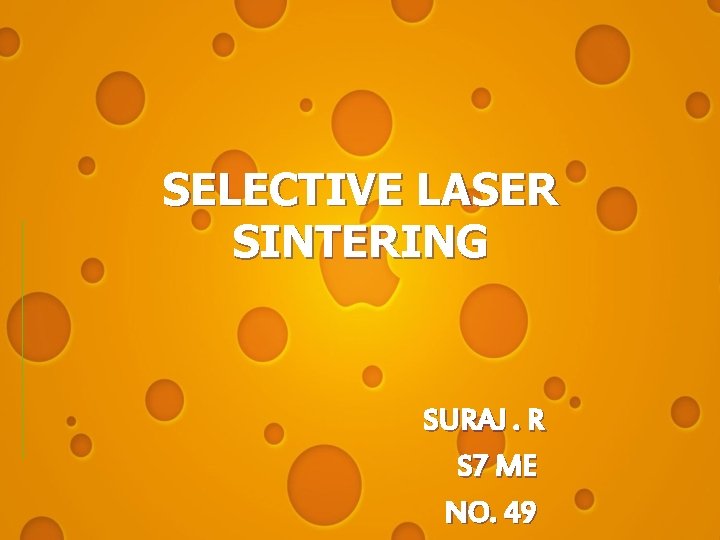
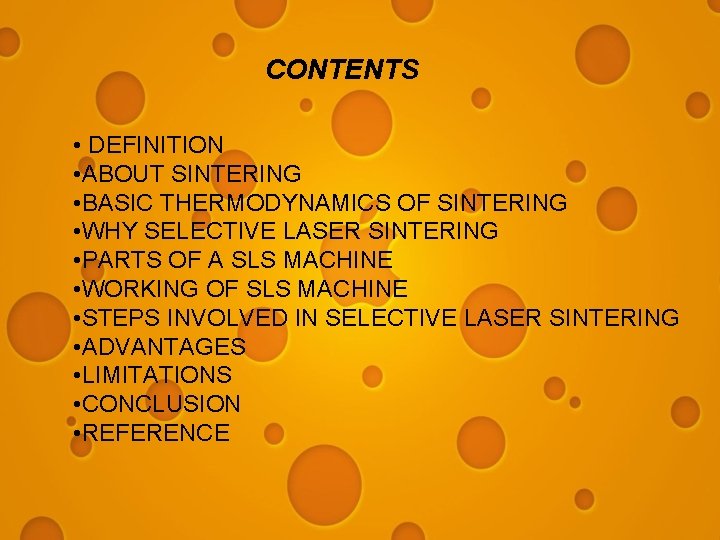
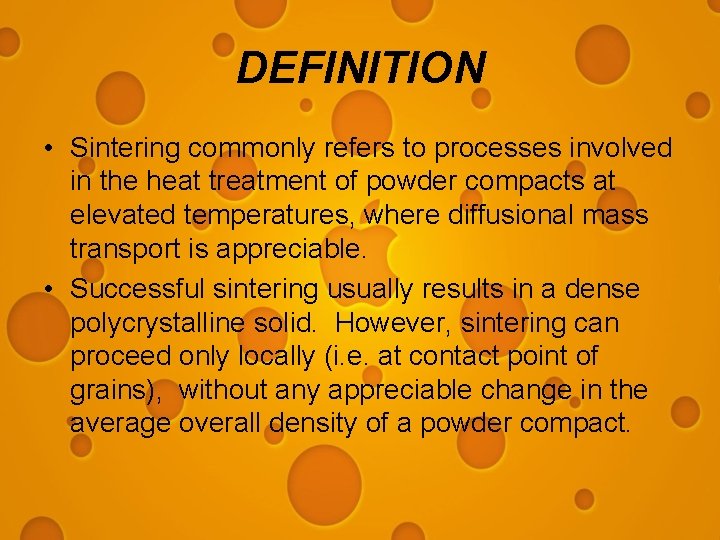
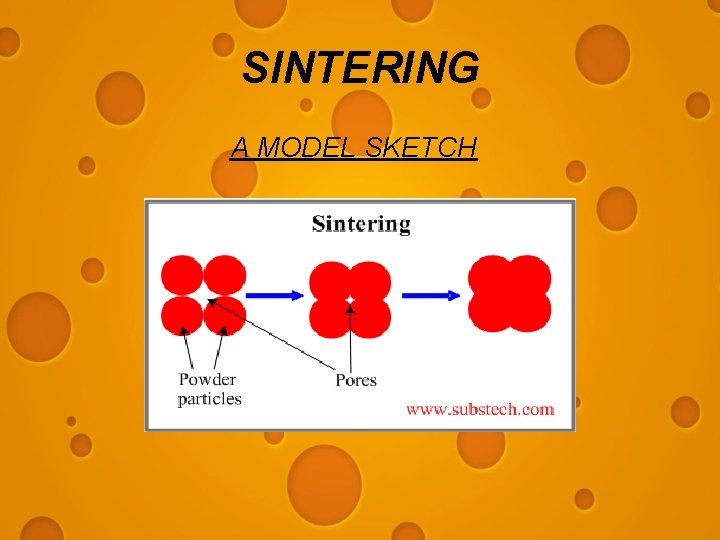
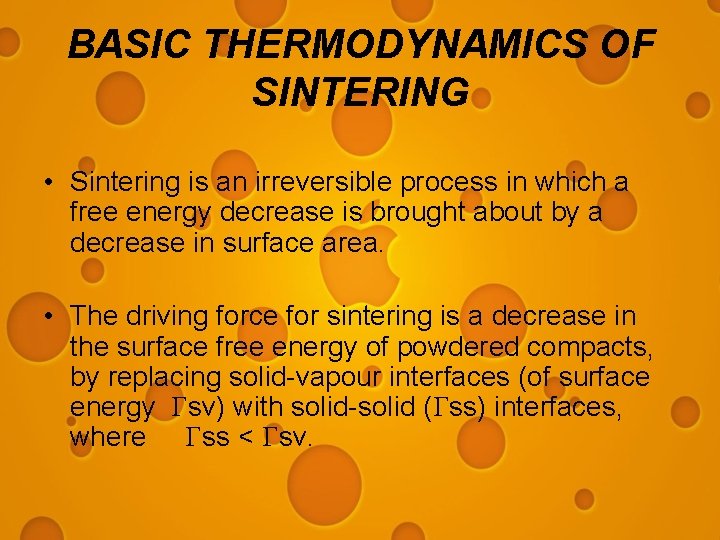
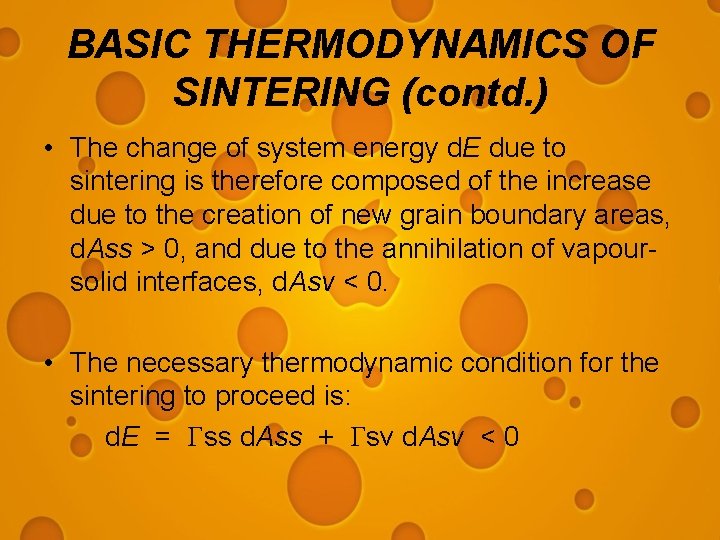
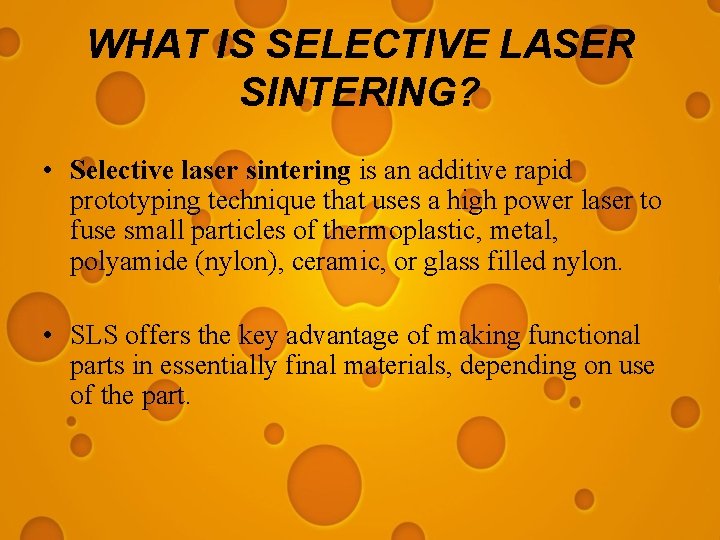
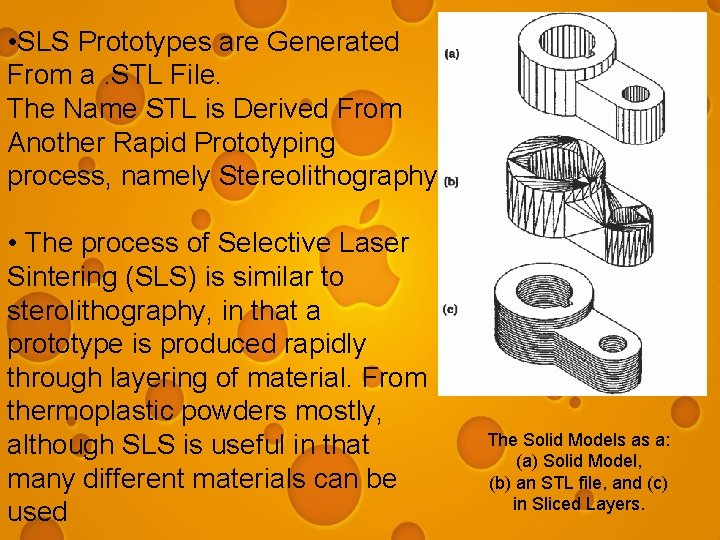
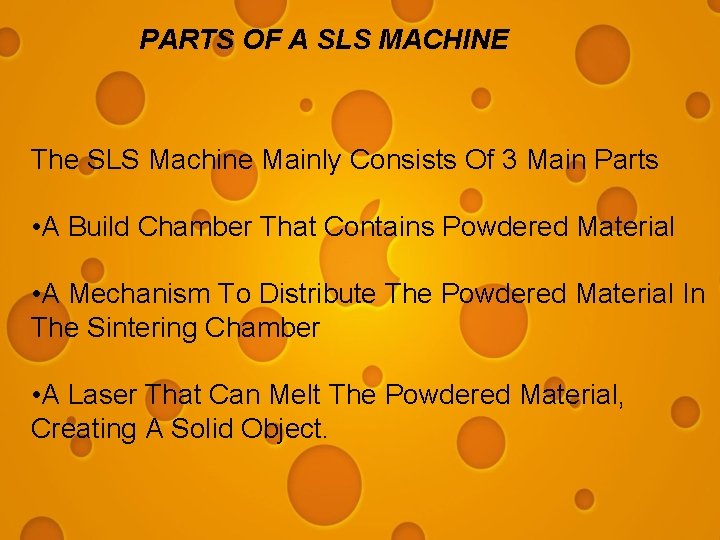
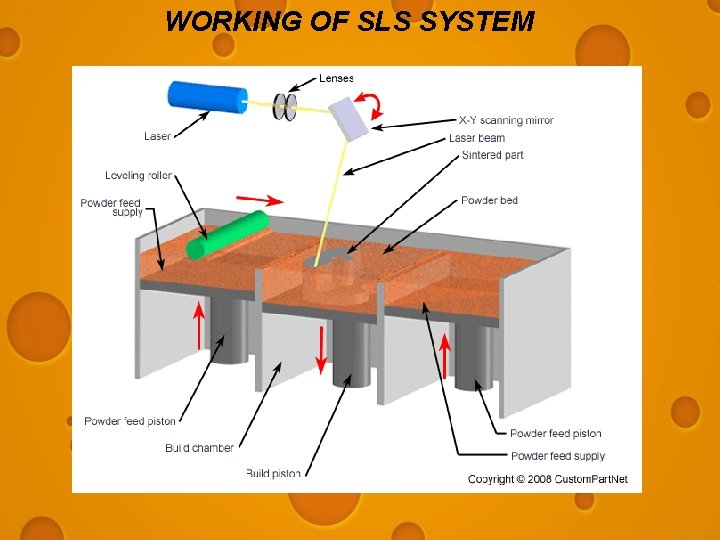
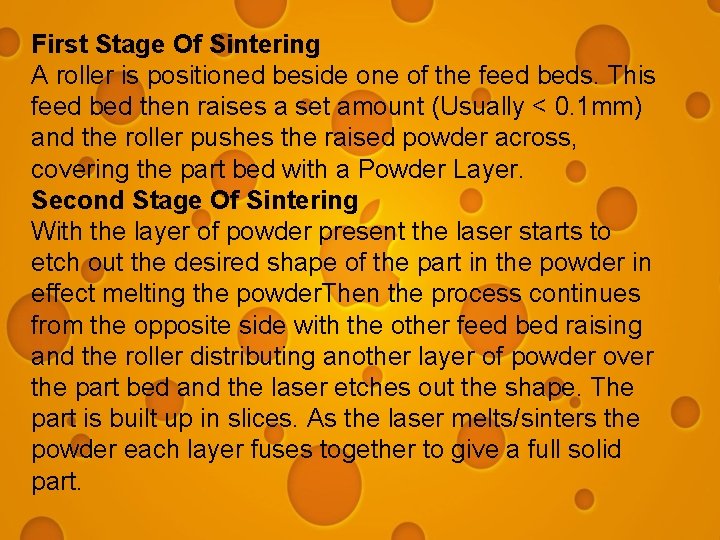
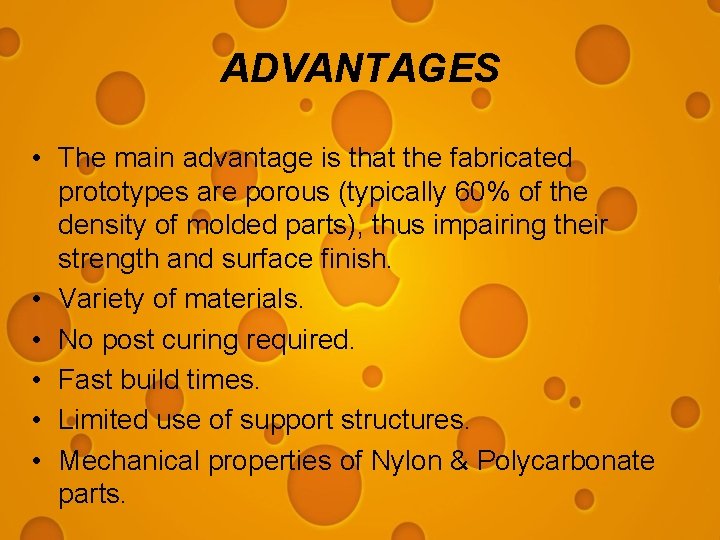
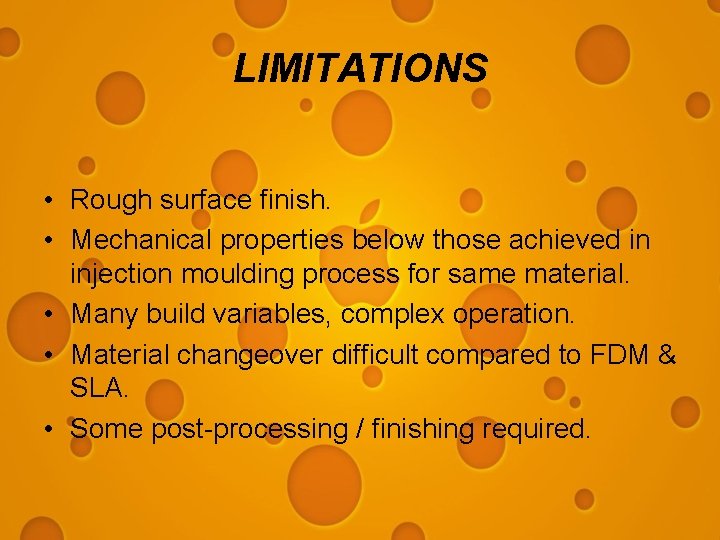
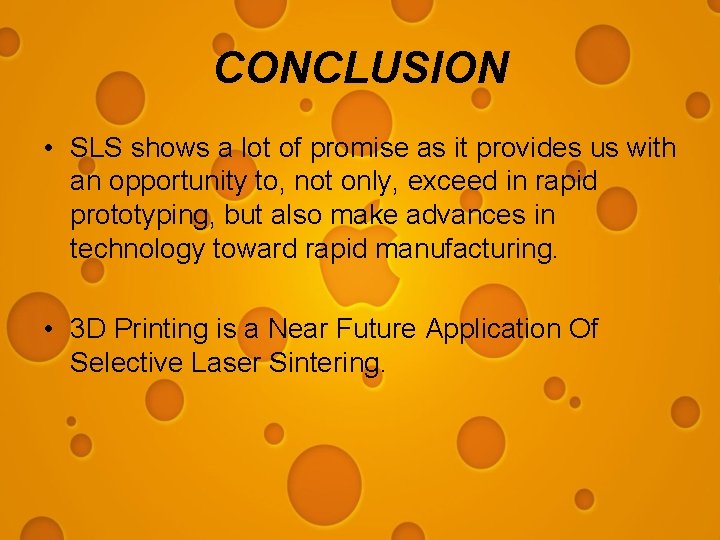
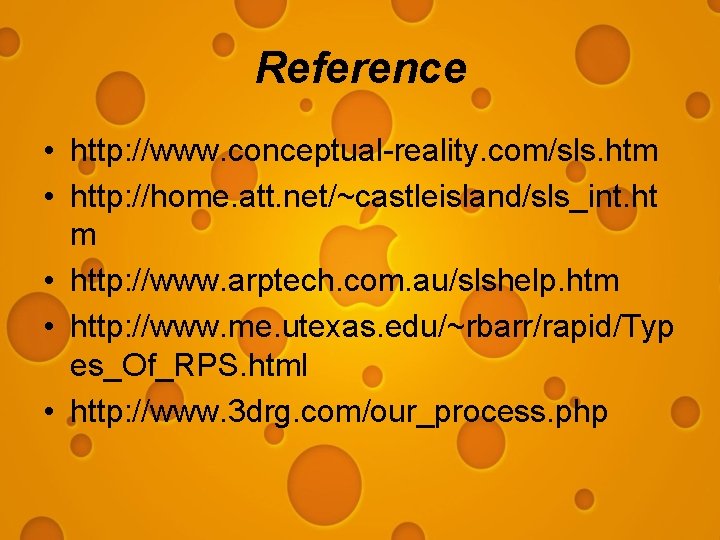
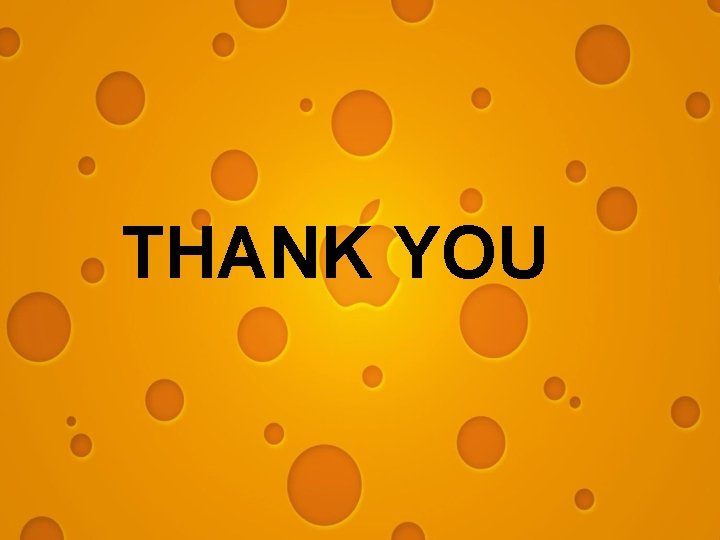
- Slides: 16
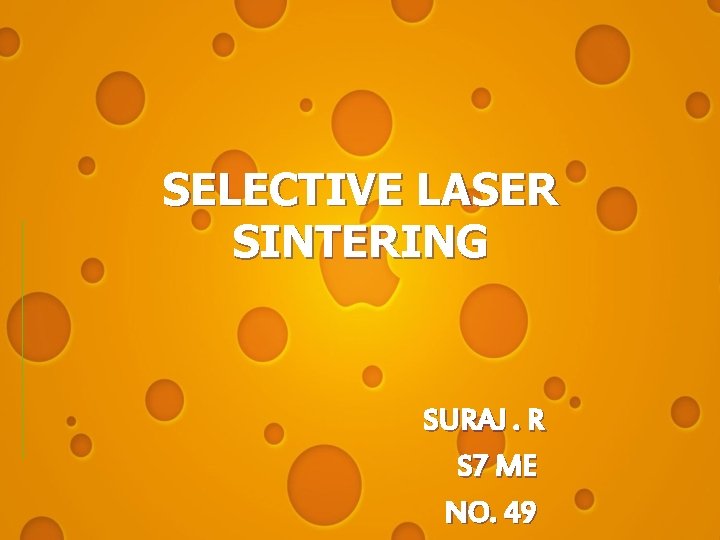
SELECTIVE LASER SINTERING SURAJ. R S 7 ME NO. 49
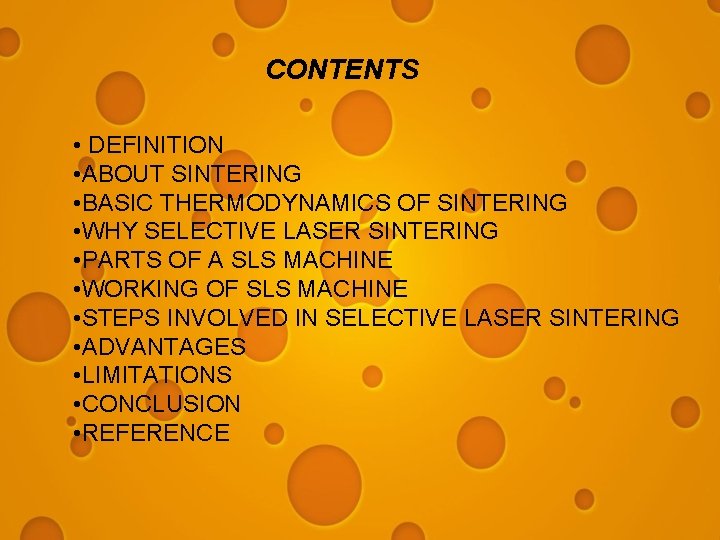
CONTENTS • DEFINITION • ABOUT SINTERING • BASIC THERMODYNAMICS OF SINTERING • WHY SELECTIVE LASER SINTERING • PARTS OF A SLS MACHINE • WORKING OF SLS MACHINE • STEPS INVOLVED IN SELECTIVE LASER SINTERING • ADVANTAGES • LIMITATIONS • CONCLUSION • REFERENCE
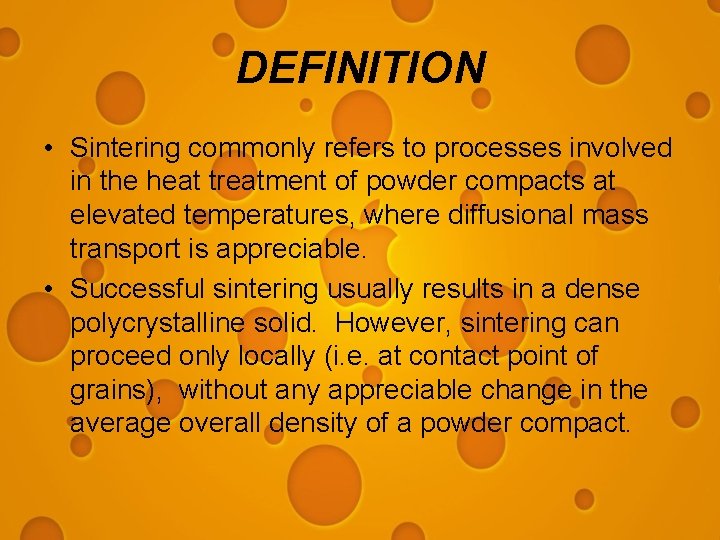
DEFINITION • Sintering commonly refers to processes involved in the heat treatment of powder compacts at elevated temperatures, where diffusional mass transport is appreciable. • Successful sintering usually results in a dense polycrystalline solid. However, sintering can proceed only locally (i. e. at contact point of grains), without any appreciable change in the average overall density of a powder compact.
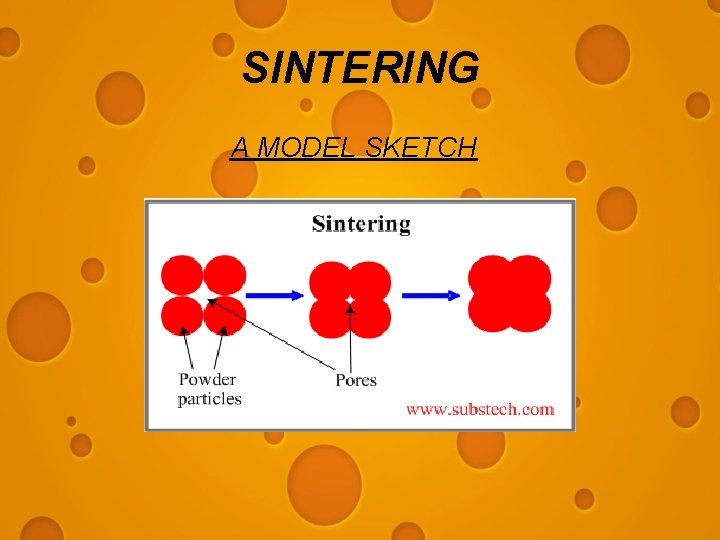
SINTERING A MODEL SKETCH
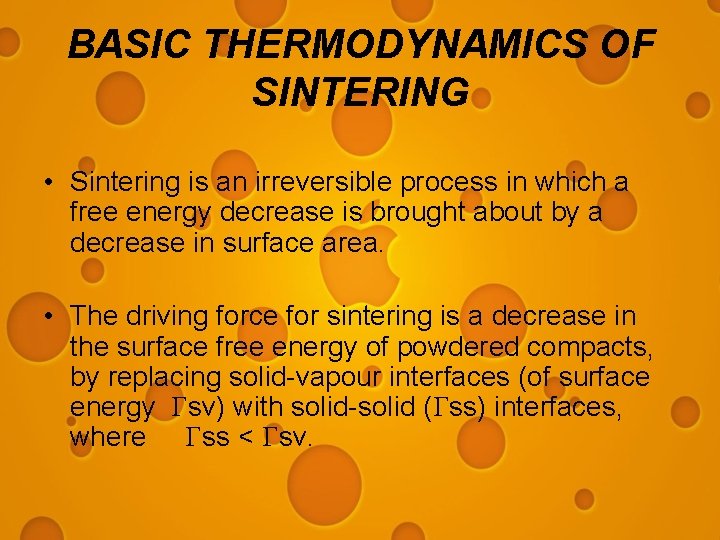
BASIC THERMODYNAMICS OF SINTERING • Sintering is an irreversible process in which a free energy decrease is brought about by a decrease in surface area. • The driving force for sintering is a decrease in the surface free energy of powdered compacts, by replacing solid-vapour interfaces (of surface energy sv) with solid-solid ( ss) interfaces, where ss < sv.
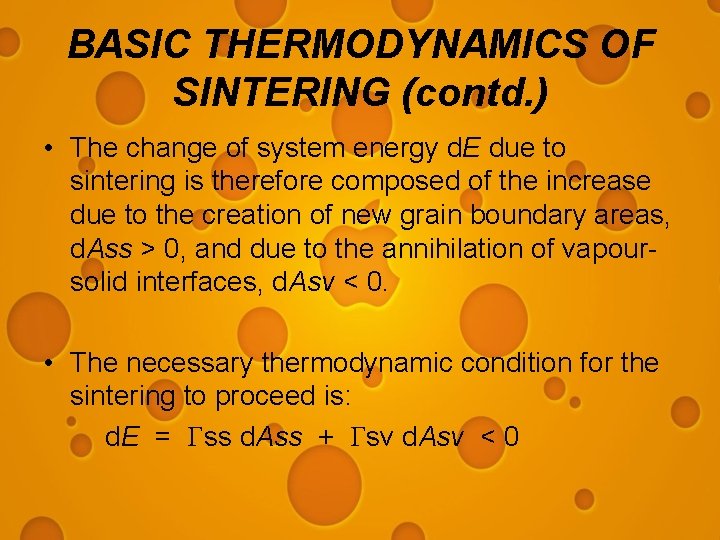
BASIC THERMODYNAMICS OF SINTERING (contd. ) • The change of system energy d. E due to sintering is therefore composed of the increase due to the creation of new grain boundary areas, d. Ass > 0, and due to the annihilation of vapoursolid interfaces, d. Asv < 0. • The necessary thermodynamic condition for the sintering to proceed is: d. E = ss d. Ass + sv d. Asv < 0
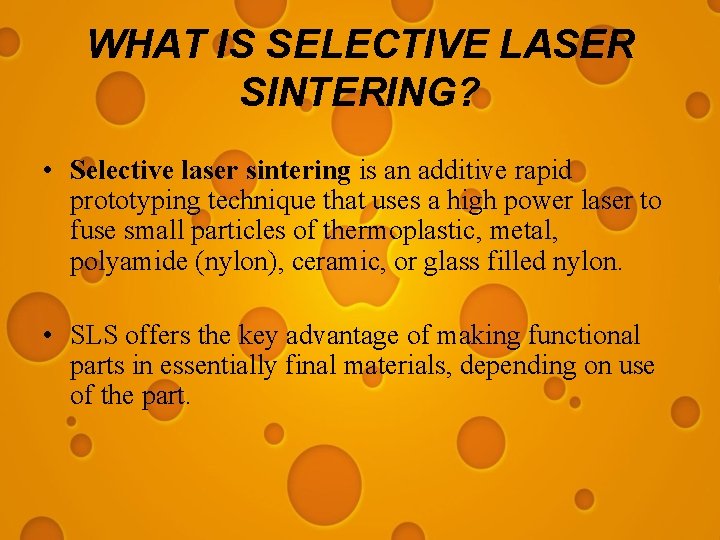
WHAT IS SELECTIVE LASER SINTERING? • Selective laser sintering is an additive rapid prototyping technique that uses a high power laser to fuse small particles of thermoplastic, metal, polyamide (nylon), ceramic, or glass filled nylon. • SLS offers the key advantage of making functional parts in essentially final materials, depending on use of the part.
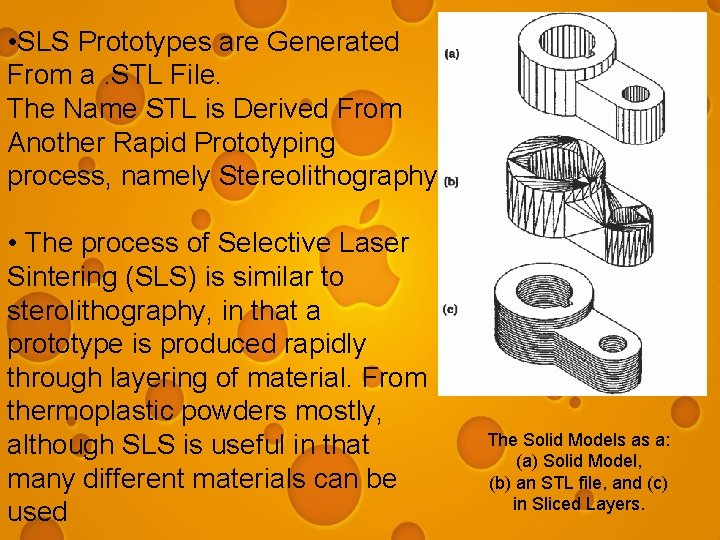
• SLS Prototypes are Generated From a. STL File. The Name STL is Derived From Another Rapid Prototyping process, namely Stereolithography • The process of Selective Laser Sintering (SLS) is similar to sterolithography, in that a prototype is produced rapidly through layering of material. From thermoplastic powders mostly, although SLS is useful in that many different materials can be used The Solid Models as a: (a) Solid Model, (b) an STL file, and (c) in Sliced Layers.
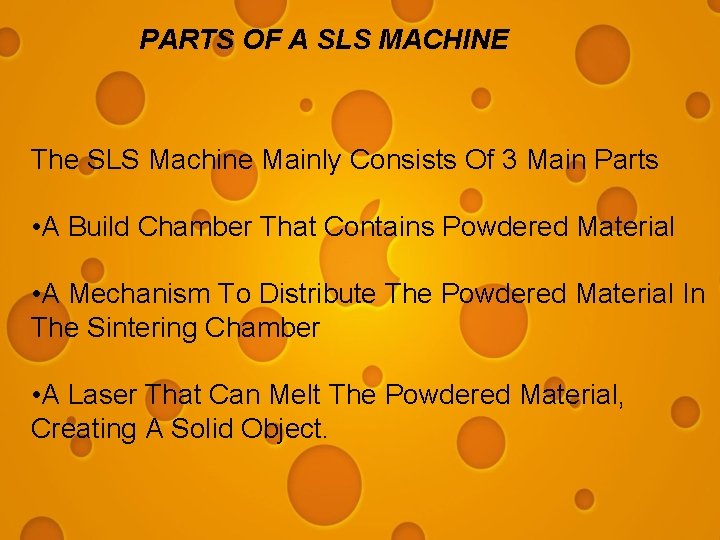
PARTS OF A SLS MACHINE The SLS Machine Mainly Consists Of 3 Main Parts • A Build Chamber That Contains Powdered Material • A Mechanism To Distribute The Powdered Material In The Sintering Chamber • A Laser That Can Melt The Powdered Material, Creating A Solid Object.
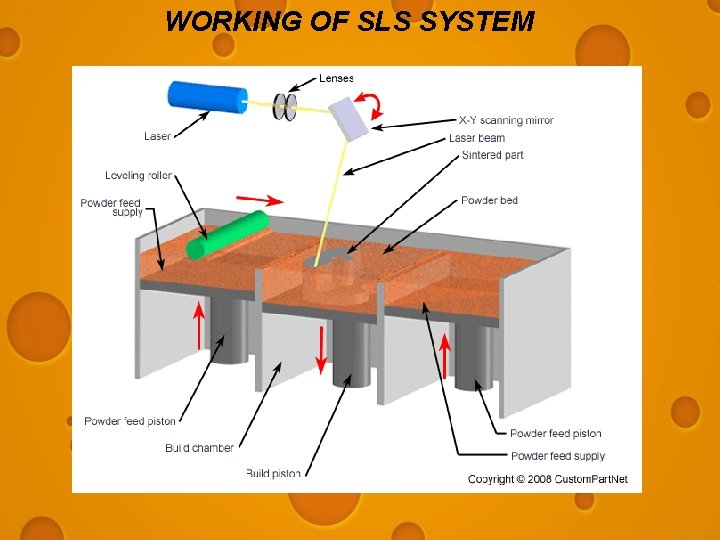
WORKING OF SLS SYSTEM
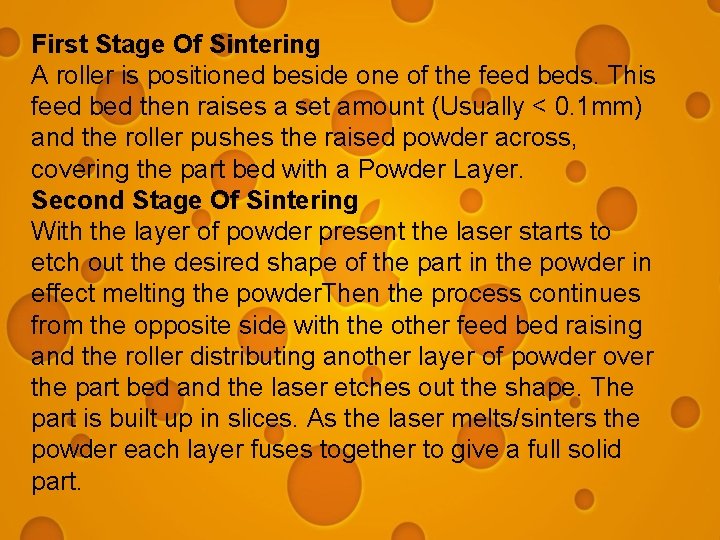
First Stage Of Sintering A roller is positioned beside one of the feed beds. This feed bed then raises a set amount (Usually < 0. 1 mm) and the roller pushes the raised powder across, covering the part bed with a Powder Layer. Second Stage Of Sintering With the layer of powder present the laser starts to etch out the desired shape of the part in the powder in effect melting the powder. Then the process continues from the opposite side with the other feed bed raising and the roller distributing another layer of powder over the part bed and the laser etches out the shape. The part is built up in slices. As the laser melts/sinters the powder each layer fuses together to give a full solid part.
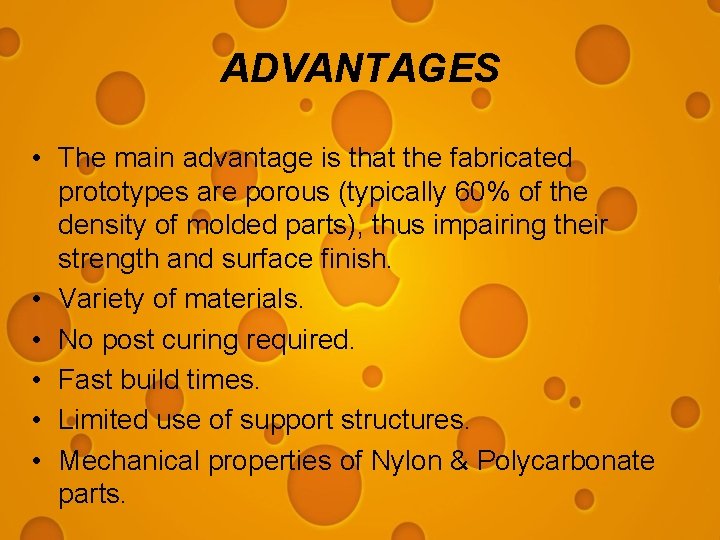
ADVANTAGES • The main advantage is that the fabricated prototypes are porous (typically 60% of the density of molded parts), thus impairing their strength and surface finish. • Variety of materials. • No post curing required. • Fast build times. • Limited use of support structures. • Mechanical properties of Nylon & Polycarbonate parts.
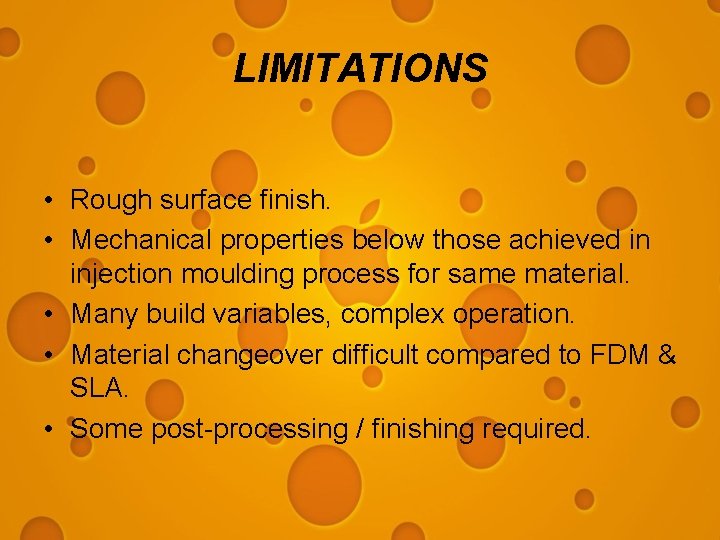
LIMITATIONS • Rough surface finish. • Mechanical properties below those achieved in injection moulding process for same material. • Many build variables, complex operation. • Material changeover difficult compared to FDM & SLA. • Some post-processing / finishing required.
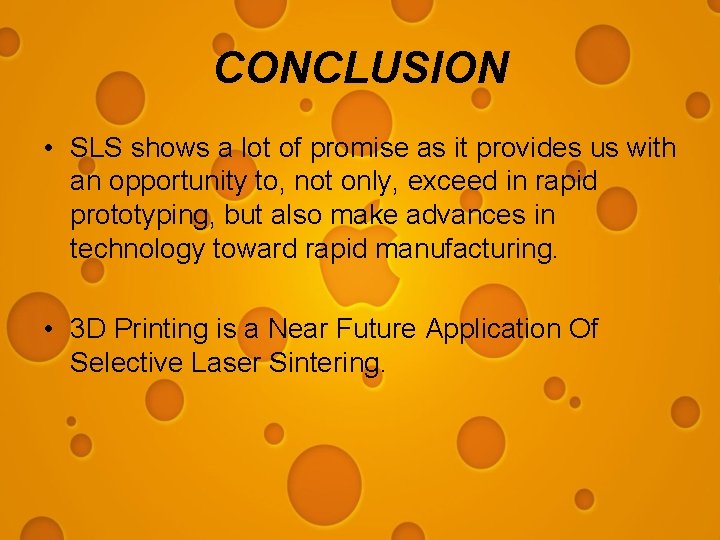
CONCLUSION • SLS shows a lot of promise as it provides us with an opportunity to, not only, exceed in rapid prototyping, but also make advances in technology toward rapid manufacturing. • 3 D Printing is a Near Future Application Of Selective Laser Sintering.
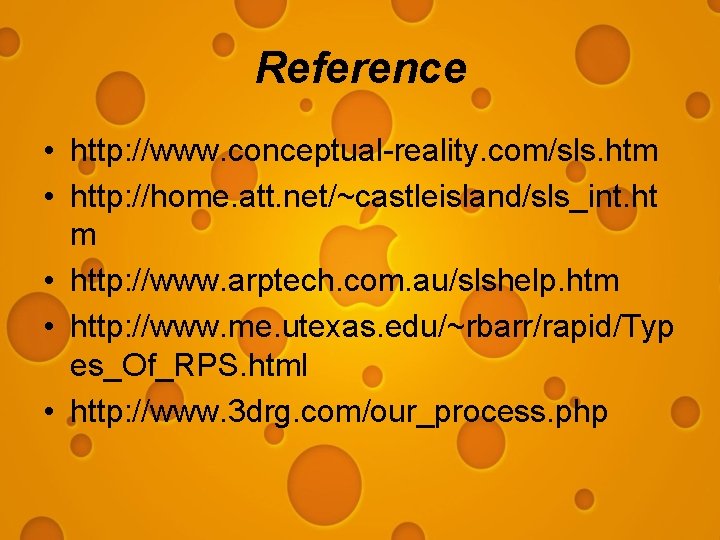
Reference • http: //www. conceptual-reality. com/sls. htm • http: //home. att. net/~castleisland/sls_int. ht m • http: //www. arptech. com. au/slshelp. htm • http: //www. me. utexas. edu/~rbarr/rapid/Typ es_Of_RPS. html • http: //www. 3 drg. com/our_process. php
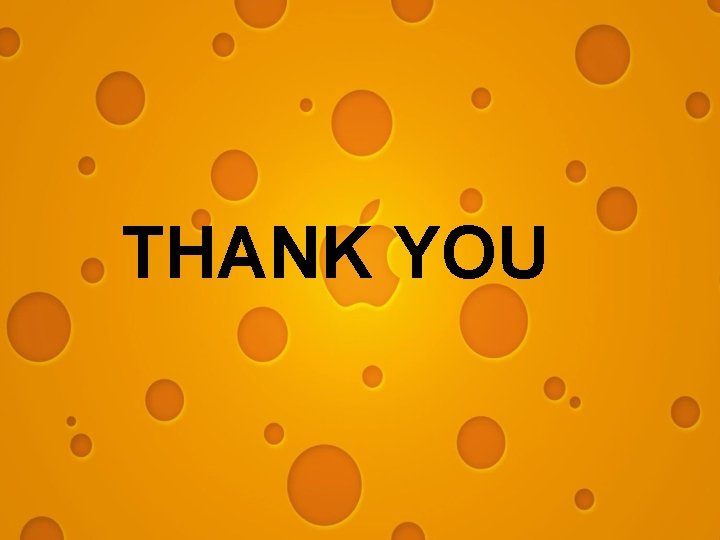
THANK YOU
History of selective laser sintering
Classification of adrenoblockers
Suraj gathani
Dr suraj gathani
Where was this
Suraj vadgama
Dr suraj gathani
Dr suraj gathani
Gear manufacturing process doc
Spark plasma sintering ppt
Types of sintering
Field assisted sintering technique
Selective prime implicants
Differential vs selective media
Cell membrane, selective, screen door
Differential media
Selective service