REINFORCED CONCRETE CLADDING MATERIALS AND STRUCTURAL STEELWORK Prepared
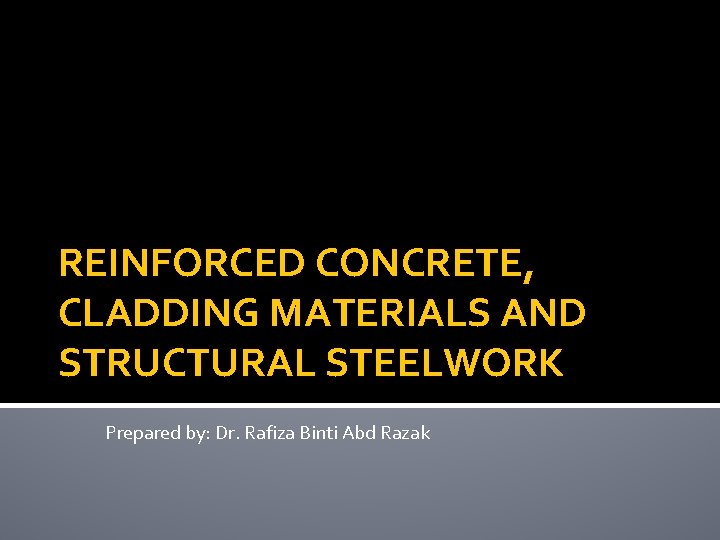
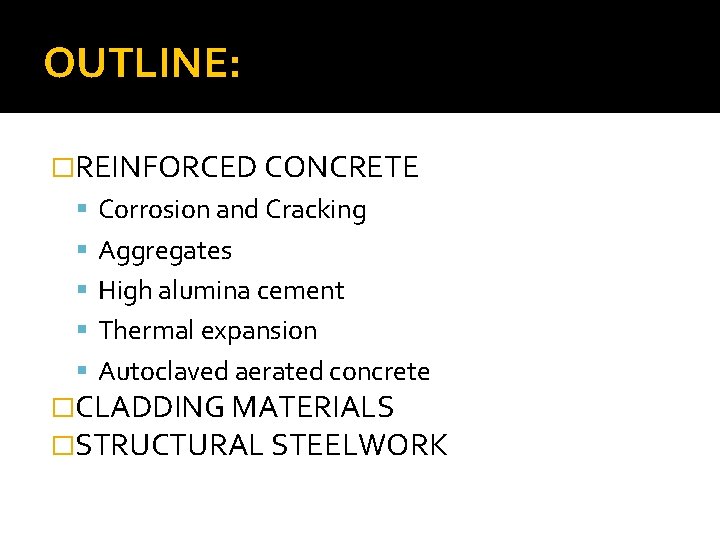
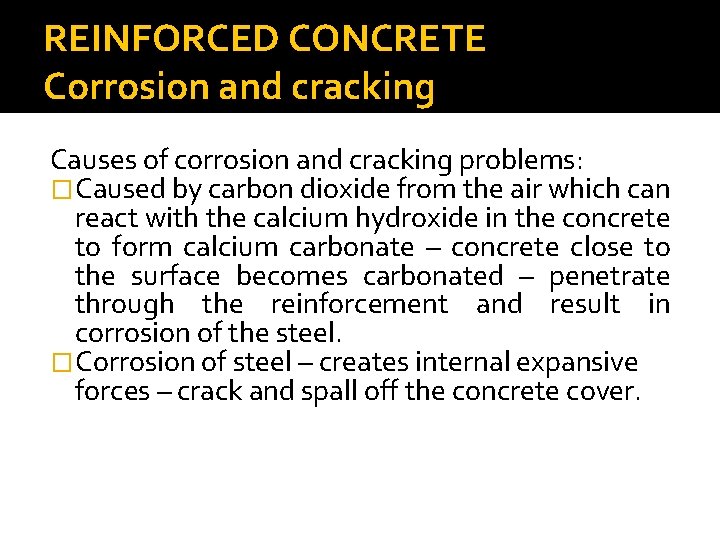
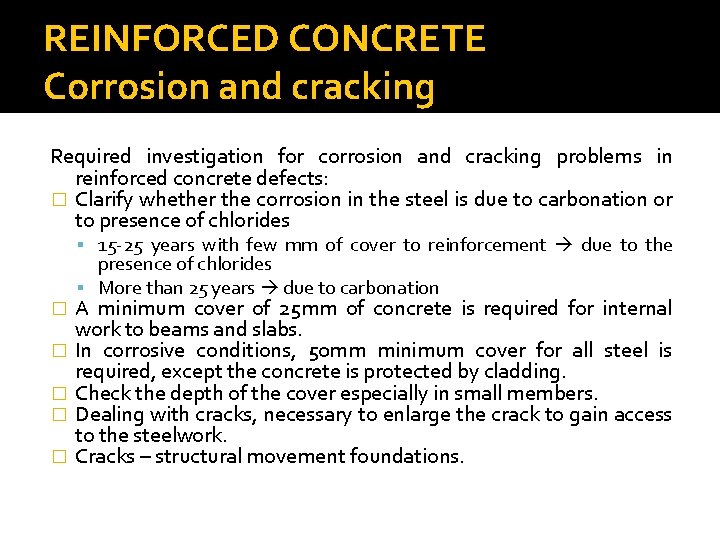
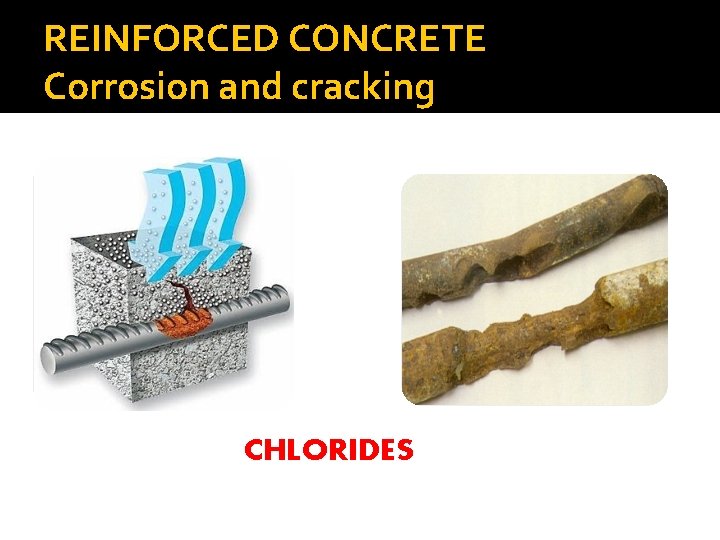
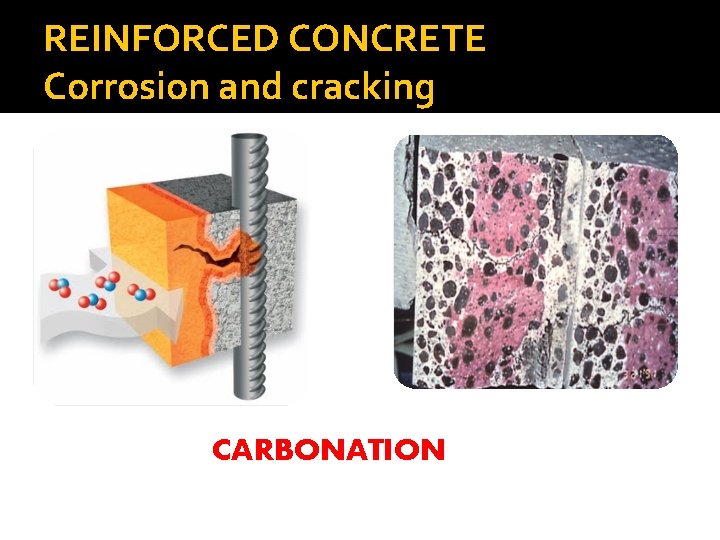
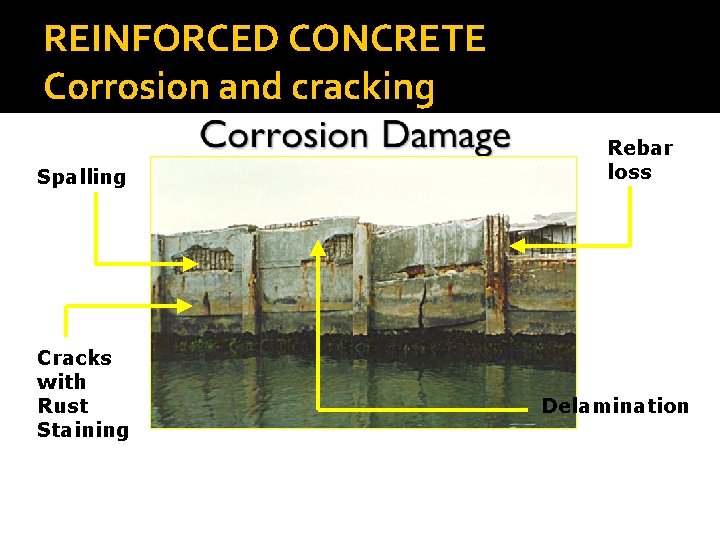
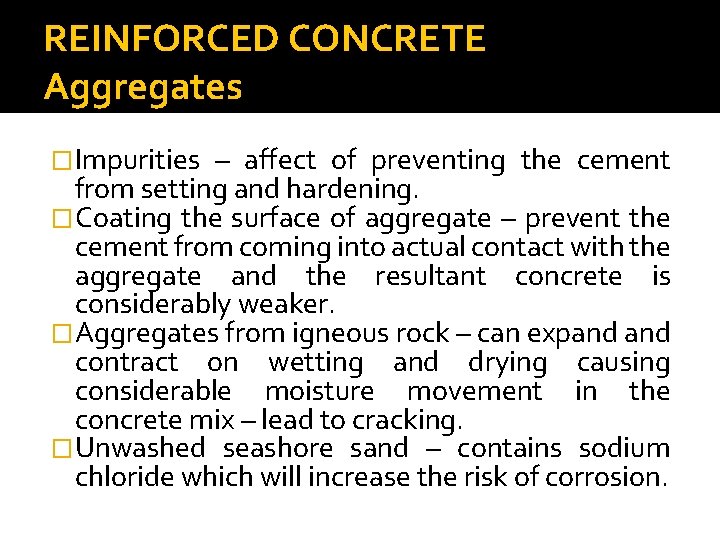
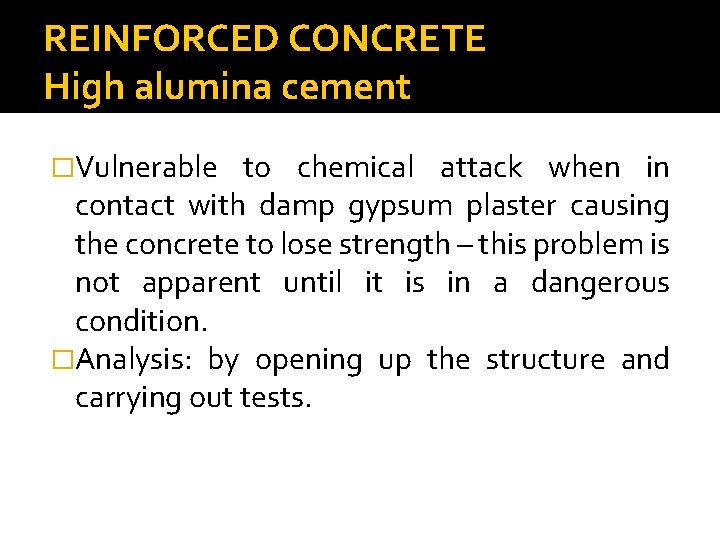
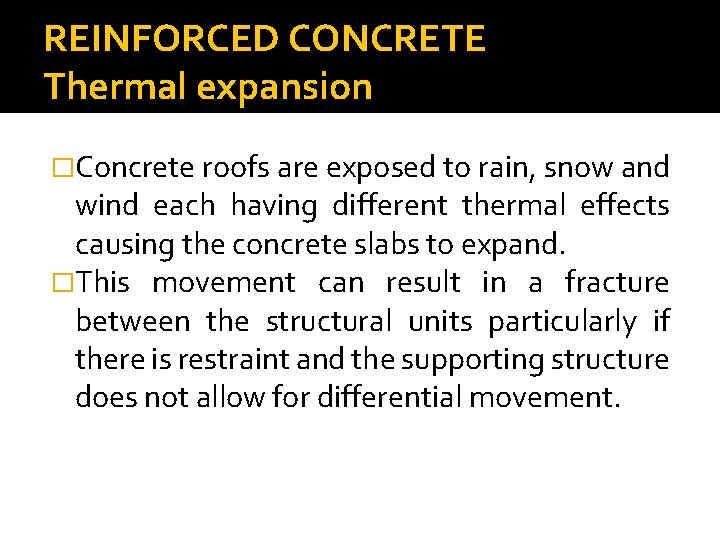
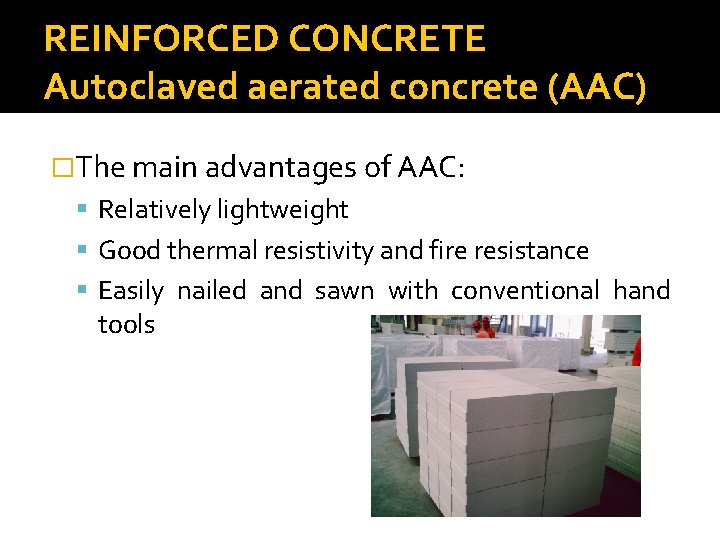
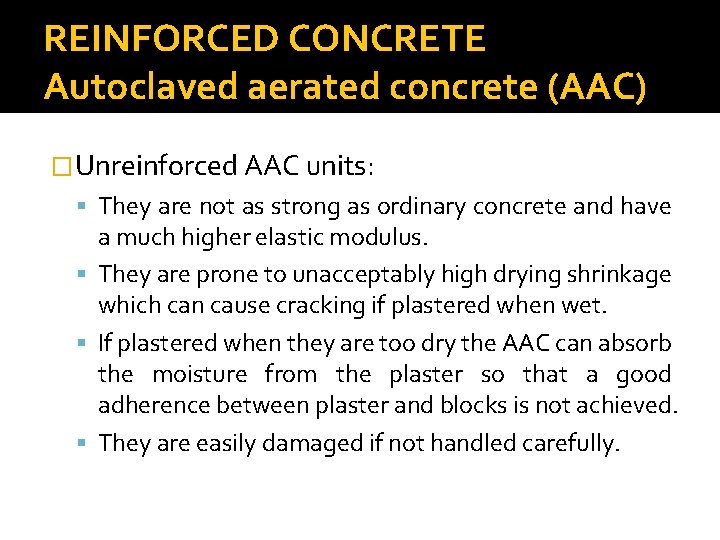
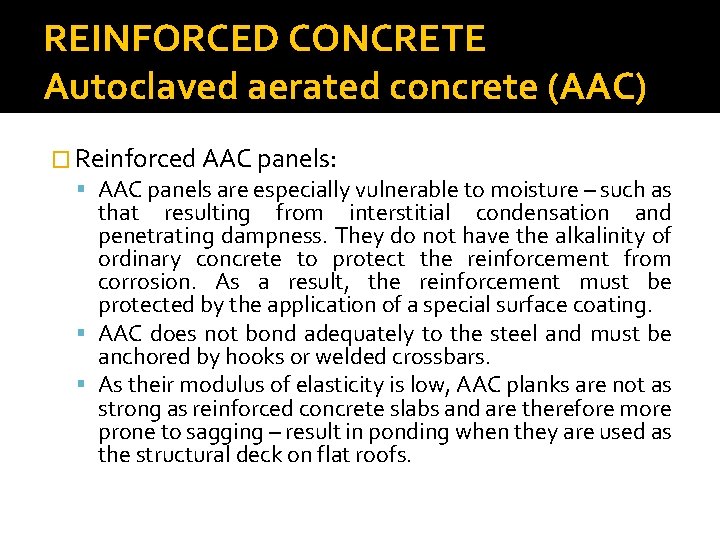
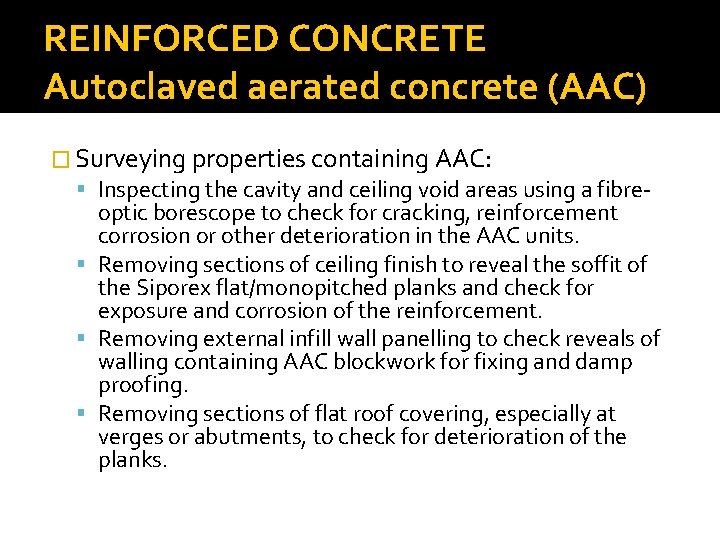
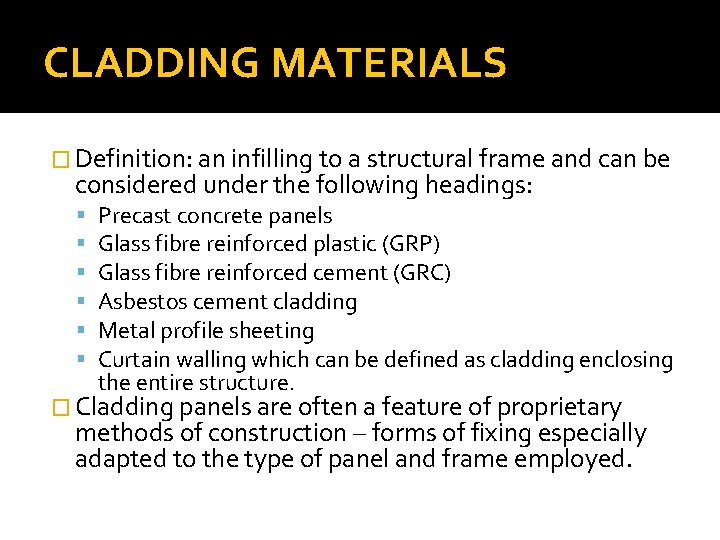
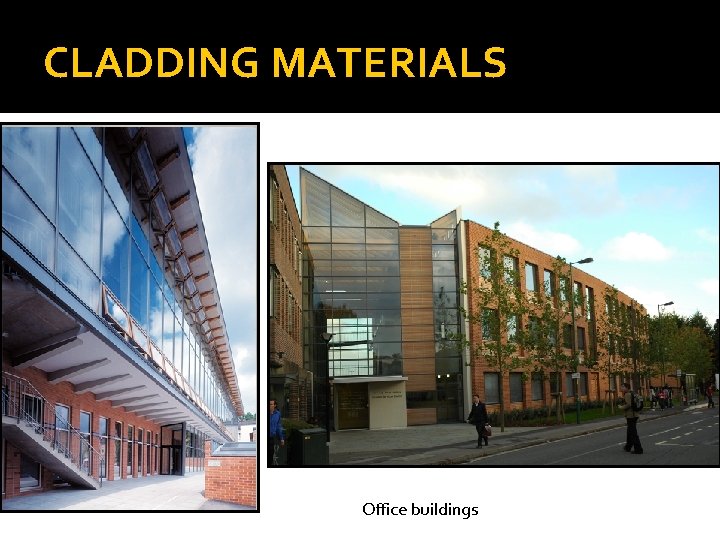
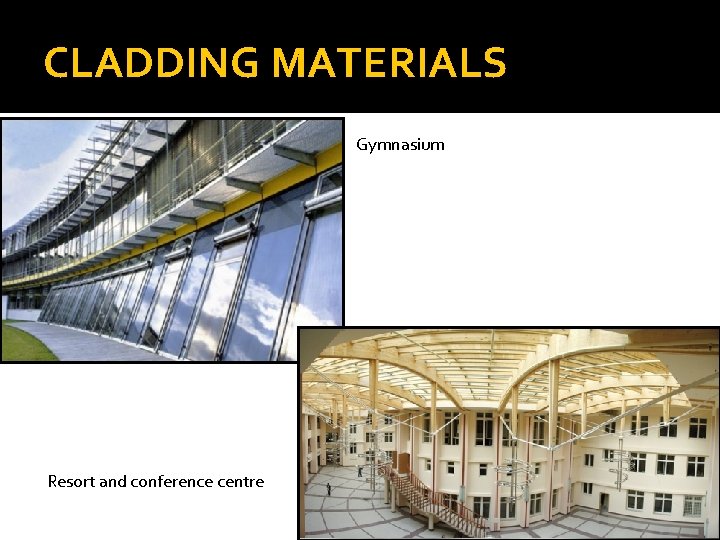
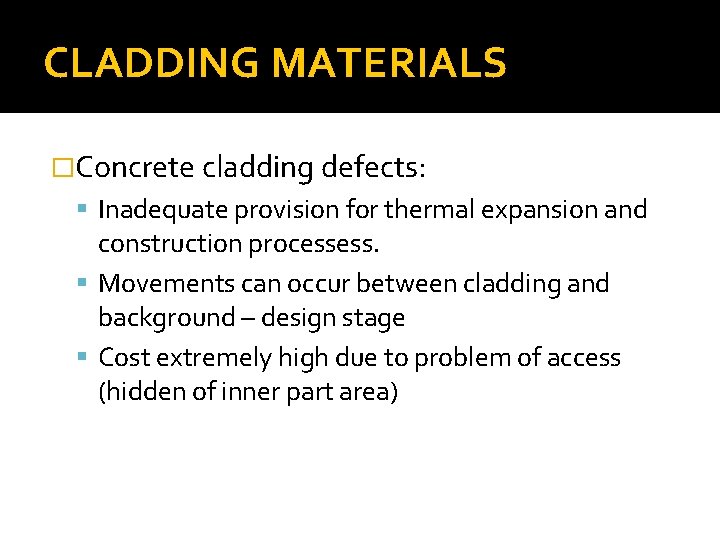
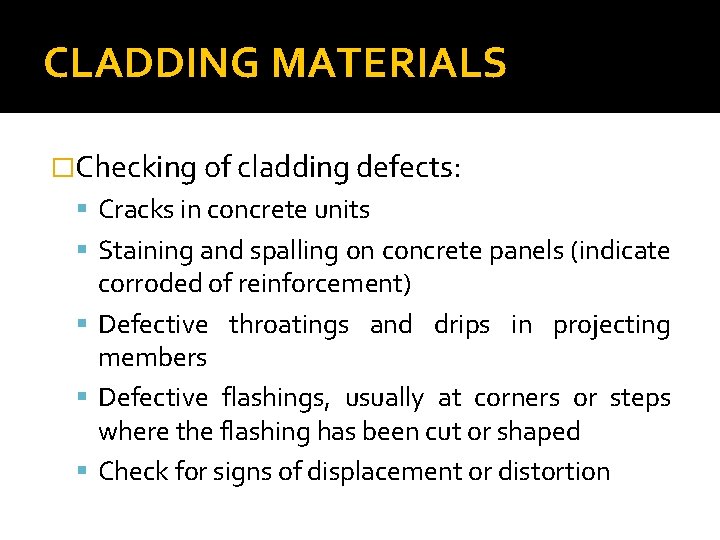
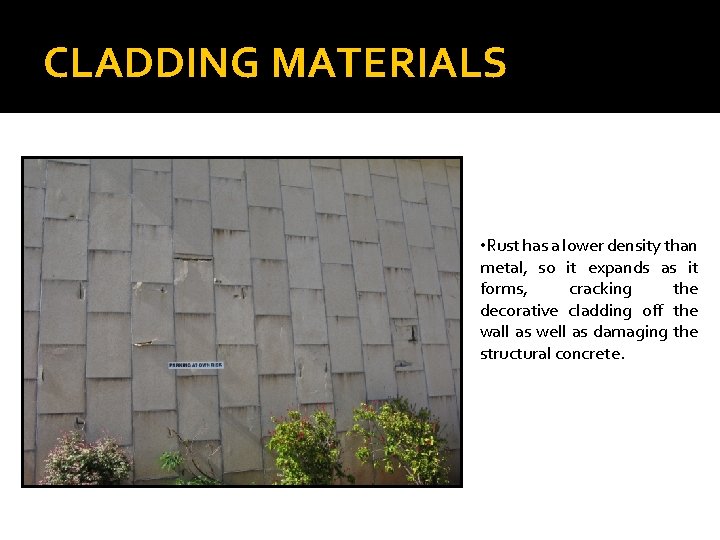
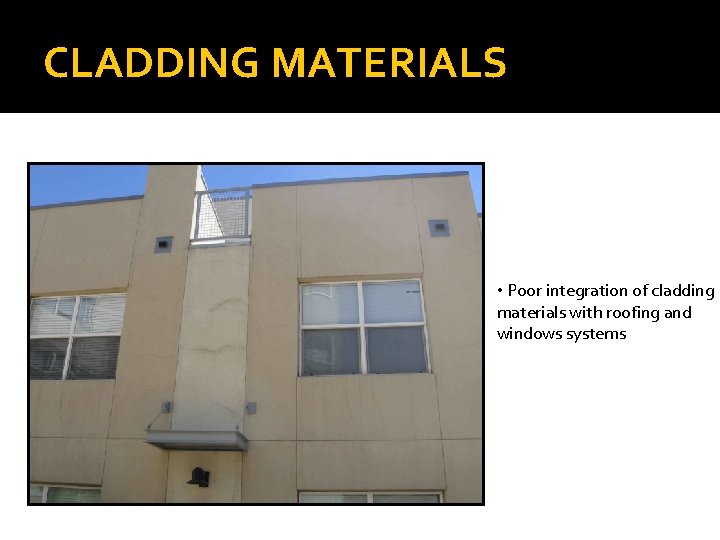
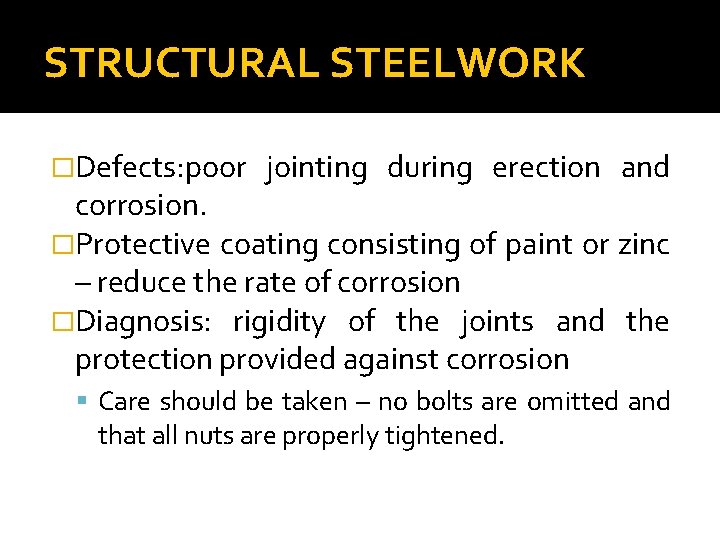
- Slides: 22
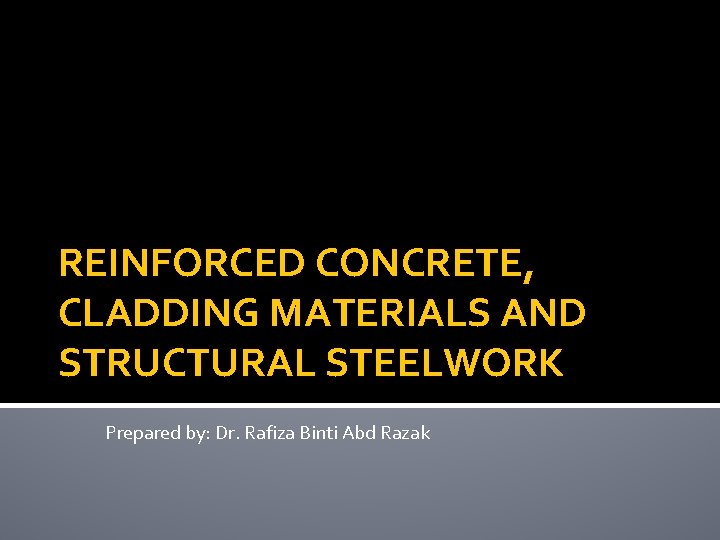
REINFORCED CONCRETE, CLADDING MATERIALS AND STRUCTURAL STEELWORK Prepared by: Dr. Rafiza Binti Abd Razak
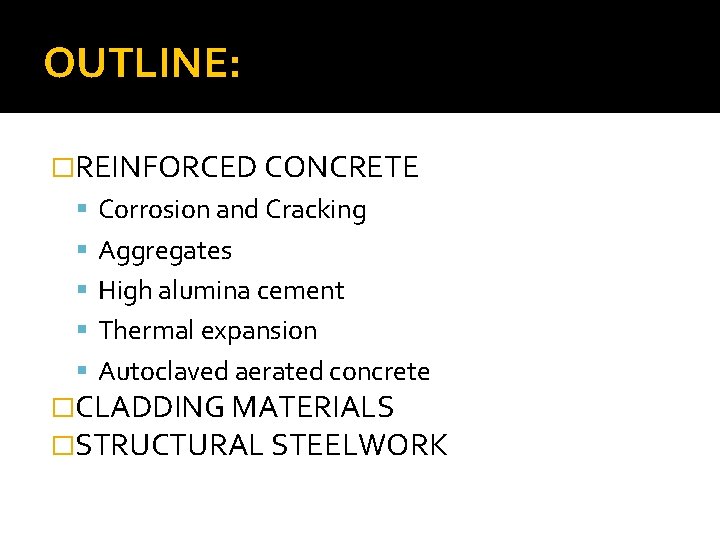
OUTLINE: �REINFORCED CONCRETE Corrosion and Cracking Aggregates High alumina cement Thermal expansion Autoclaved aerated concrete �CLADDING MATERIALS �STRUCTURAL STEELWORK
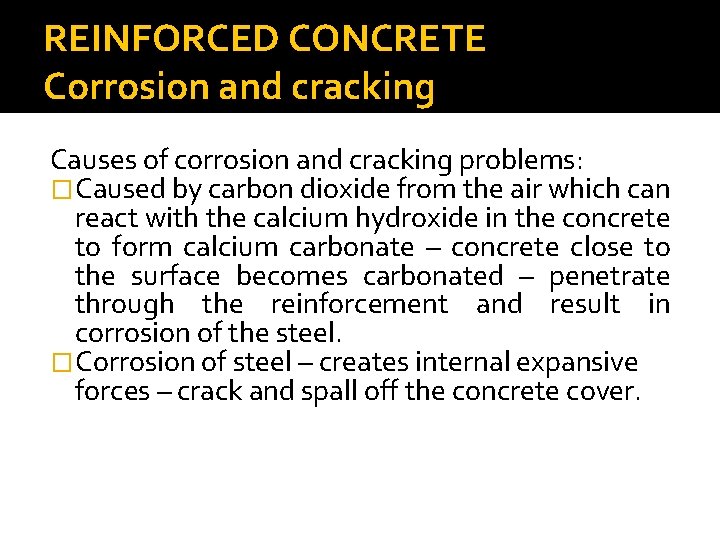
REINFORCED CONCRETE Corrosion and cracking Causes of corrosion and cracking problems: �Caused by carbon dioxide from the air which can react with the calcium hydroxide in the concrete to form calcium carbonate – concrete close to the surface becomes carbonated – penetrate through the reinforcement and result in corrosion of the steel. �Corrosion of steel – creates internal expansive forces – crack and spall off the concrete cover.
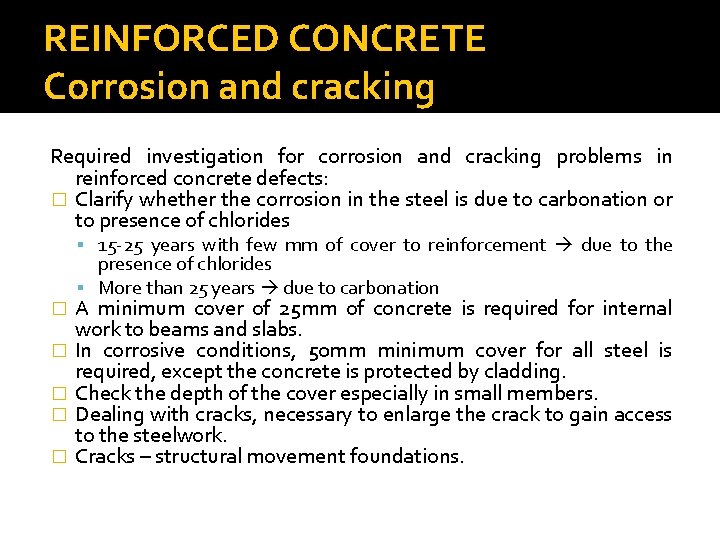
REINFORCED CONCRETE Corrosion and cracking Required investigation for corrosion and cracking problems in reinforced concrete defects: � Clarify whether the corrosion in the steel is due to carbonation or to presence of chlorides 15 -25 years with few mm of cover to reinforcement due to the � � � presence of chlorides More than 25 years due to carbonation A minimum cover of 25 mm of concrete is required for internal work to beams and slabs. In corrosive conditions, 50 mm minimum cover for all steel is required, except the concrete is protected by cladding. Check the depth of the cover especially in small members. Dealing with cracks, necessary to enlarge the crack to gain access to the steelwork. Cracks – structural movement foundations.
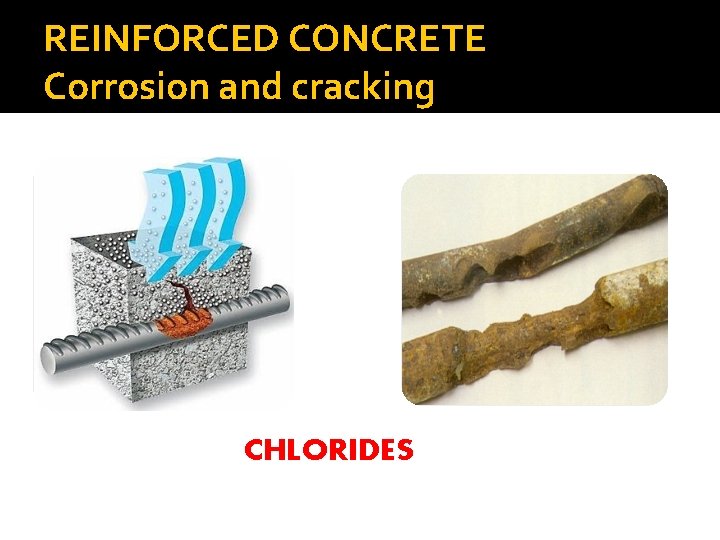
REINFORCED CONCRETE Corrosion and cracking CHLORIDES
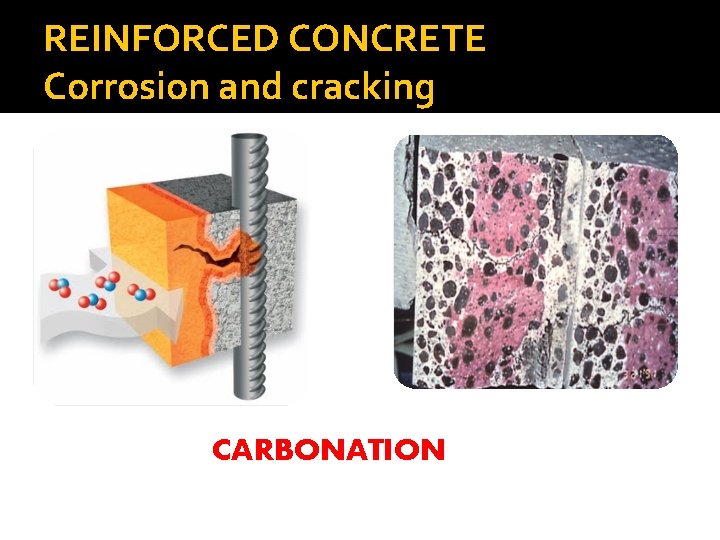
REINFORCED CONCRETE Corrosion and cracking CARBONATION
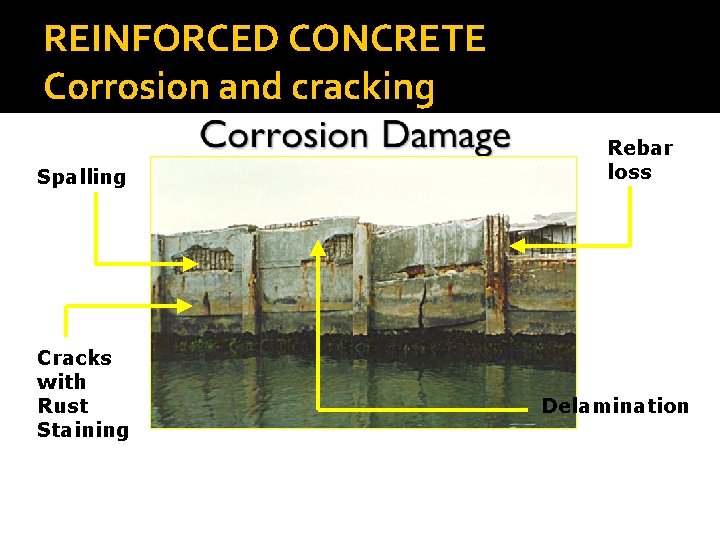
REINFORCED CONCRETE Corrosion and cracking Spalling Cracks with Rust Staining Rebar loss Delamination
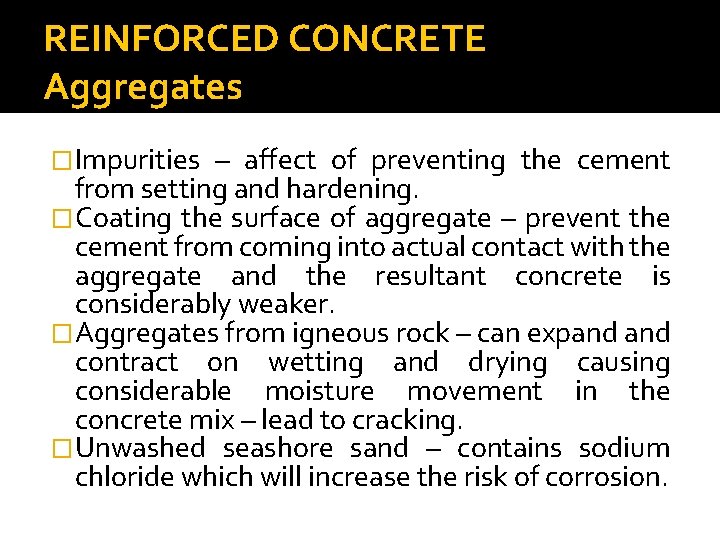
REINFORCED CONCRETE Aggregates �Impurities – affect of preventing the cement from setting and hardening. �Coating the surface of aggregate – prevent the cement from coming into actual contact with the aggregate and the resultant concrete is considerably weaker. �Aggregates from igneous rock – can expand contract on wetting and drying causing considerable moisture movement in the concrete mix – lead to cracking. �Unwashed seashore sand – contains sodium chloride which will increase the risk of corrosion.
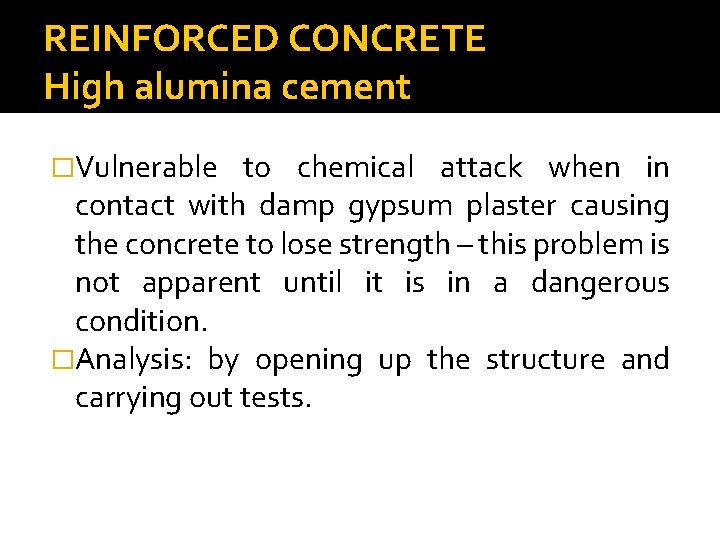
REINFORCED CONCRETE High alumina cement �Vulnerable to chemical attack when in contact with damp gypsum plaster causing the concrete to lose strength – this problem is not apparent until it is in a dangerous condition. �Analysis: by opening up the structure and carrying out tests.
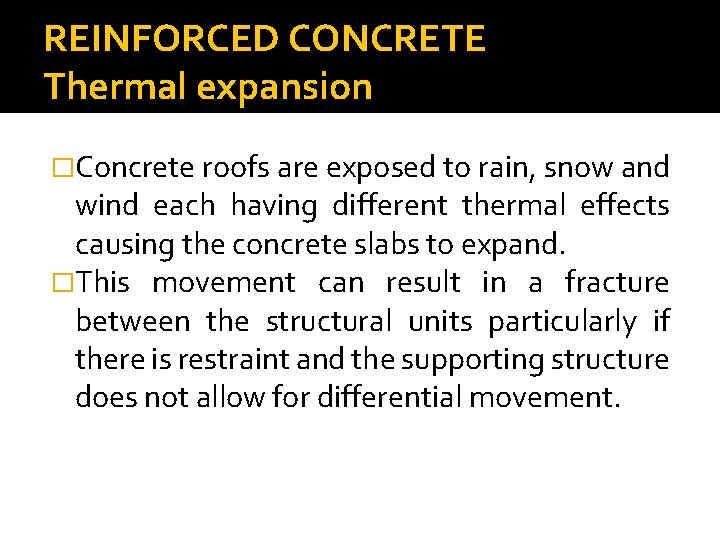
REINFORCED CONCRETE Thermal expansion �Concrete roofs are exposed to rain, snow and wind each having different thermal effects causing the concrete slabs to expand. �This movement can result in a fracture between the structural units particularly if there is restraint and the supporting structure does not allow for differential movement.
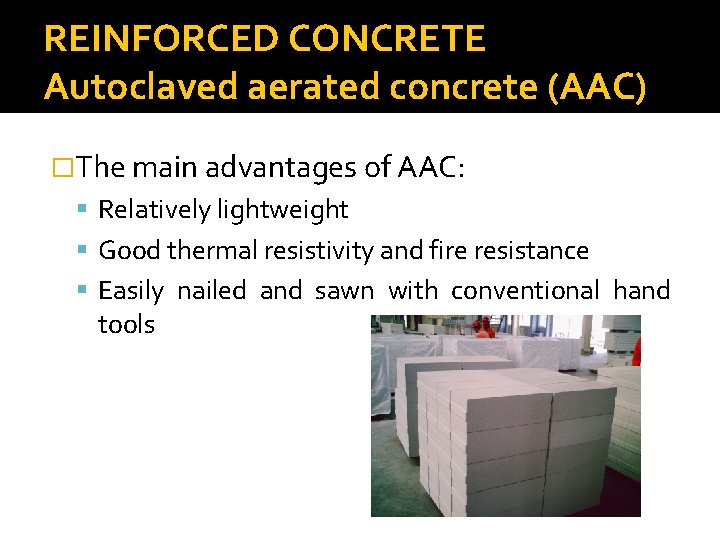
REINFORCED CONCRETE Autoclaved aerated concrete (AAC) �The main advantages of AAC: Relatively lightweight Good thermal resistivity and fire resistance Easily nailed and sawn with conventional hand tools
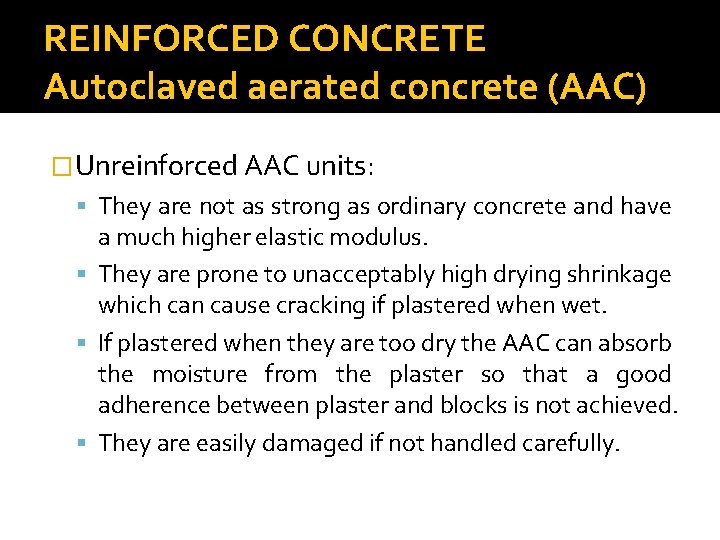
REINFORCED CONCRETE Autoclaved aerated concrete (AAC) �Unreinforced AAC units: They are not as strong as ordinary concrete and have a much higher elastic modulus. They are prone to unacceptably high drying shrinkage which can cause cracking if plastered when wet. If plastered when they are too dry the AAC can absorb the moisture from the plaster so that a good adherence between plaster and blocks is not achieved. They are easily damaged if not handled carefully.
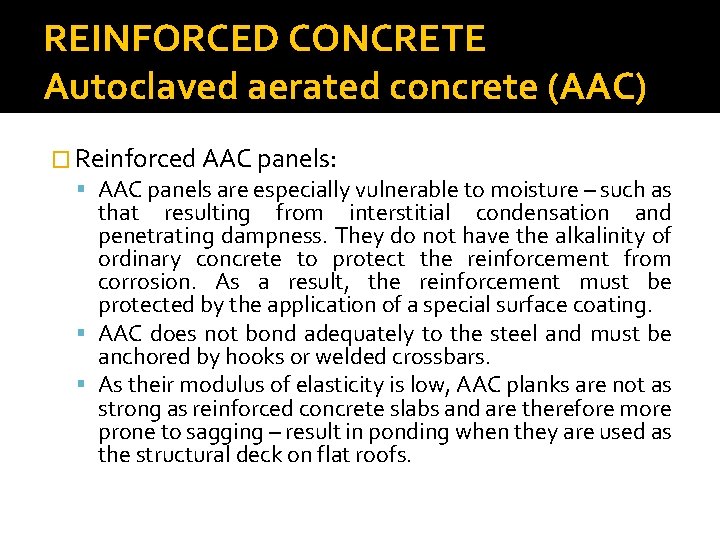
REINFORCED CONCRETE Autoclaved aerated concrete (AAC) � Reinforced AAC panels: AAC panels are especially vulnerable to moisture – such as that resulting from interstitial condensation and penetrating dampness. They do not have the alkalinity of ordinary concrete to protect the reinforcement from corrosion. As a result, the reinforcement must be protected by the application of a special surface coating. AAC does not bond adequately to the steel and must be anchored by hooks or welded crossbars. As their modulus of elasticity is low, AAC planks are not as strong as reinforced concrete slabs and are therefore more prone to sagging – result in ponding when they are used as the structural deck on flat roofs.
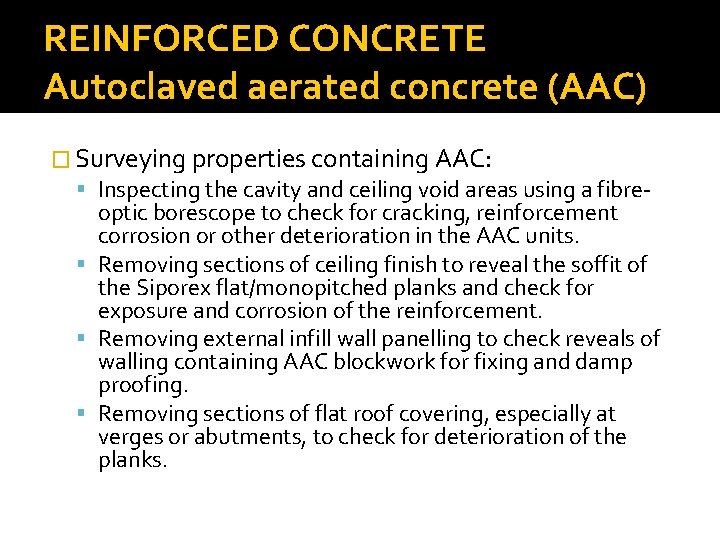
REINFORCED CONCRETE Autoclaved aerated concrete (AAC) � Surveying properties containing AAC: Inspecting the cavity and ceiling void areas using a fibre- optic borescope to check for cracking, reinforcement corrosion or other deterioration in the AAC units. Removing sections of ceiling finish to reveal the soffit of the Siporex flat/monopitched planks and check for exposure and corrosion of the reinforcement. Removing external infill wall panelling to check reveals of walling containing AAC blockwork for fixing and damp proofing. Removing sections of flat roof covering, especially at verges or abutments, to check for deterioration of the planks.
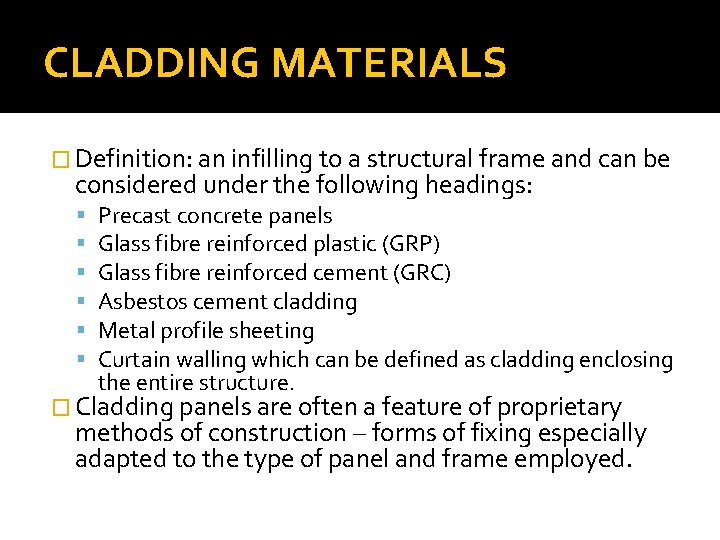
CLADDING MATERIALS � Definition: an infilling to a structural frame and can be considered under the following headings: Precast concrete panels Glass fibre reinforced plastic (GRP) Glass fibre reinforced cement (GRC) Asbestos cement cladding Metal profile sheeting Curtain walling which can be defined as cladding enclosing the entire structure. � Cladding panels are often a feature of proprietary methods of construction – forms of fixing especially adapted to the type of panel and frame employed.
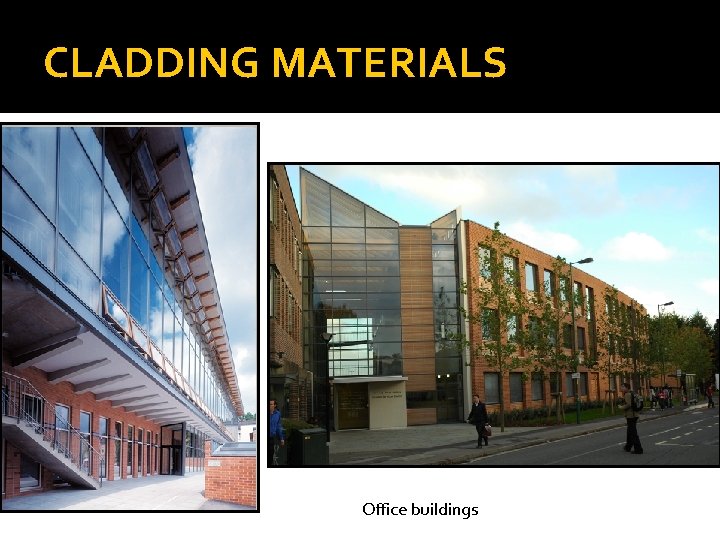
CLADDING MATERIALS Office buildings
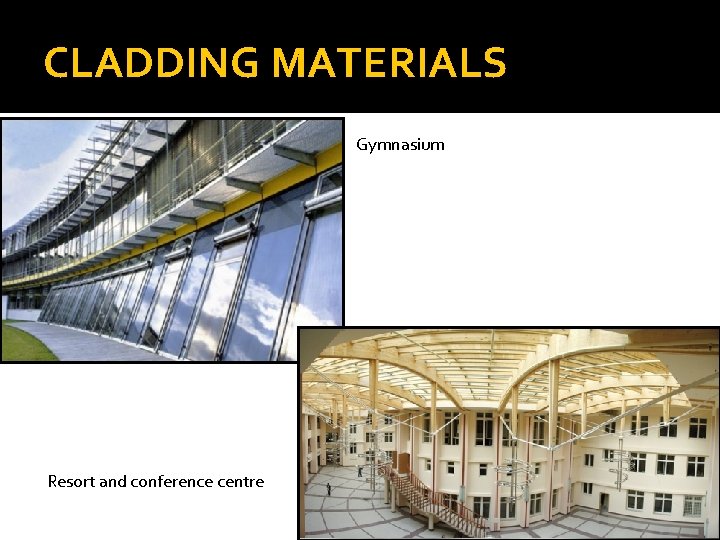
CLADDING MATERIALS Gymnasium Resort and conference centre
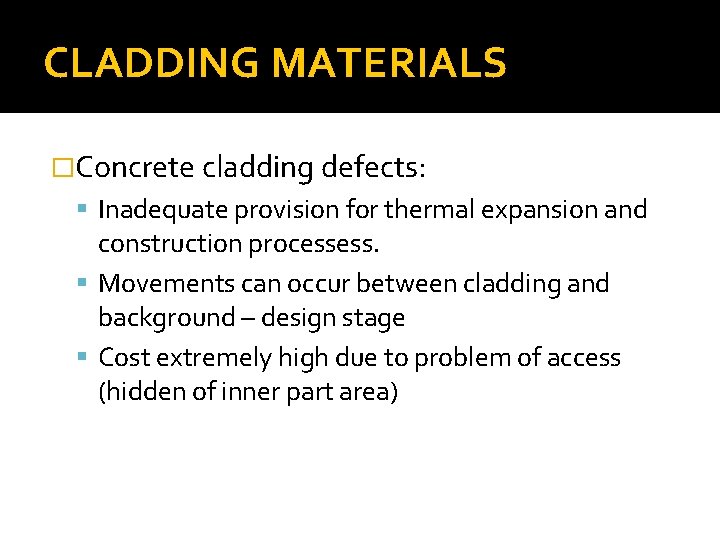
CLADDING MATERIALS �Concrete cladding defects: Inadequate provision for thermal expansion and construction processess. Movements can occur between cladding and background – design stage Cost extremely high due to problem of access (hidden of inner part area)
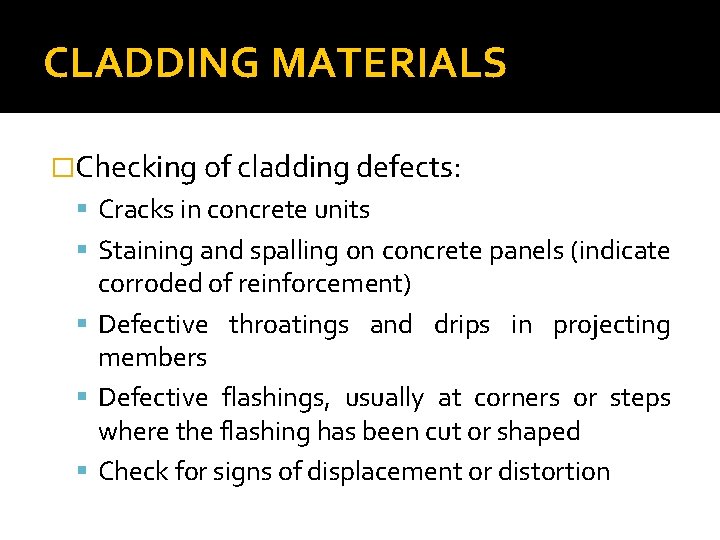
CLADDING MATERIALS �Checking of cladding defects: Cracks in concrete units Staining and spalling on concrete panels (indicate corroded of reinforcement) Defective throatings and drips in projecting members Defective flashings, usually at corners or steps where the flashing has been cut or shaped Check for signs of displacement or distortion
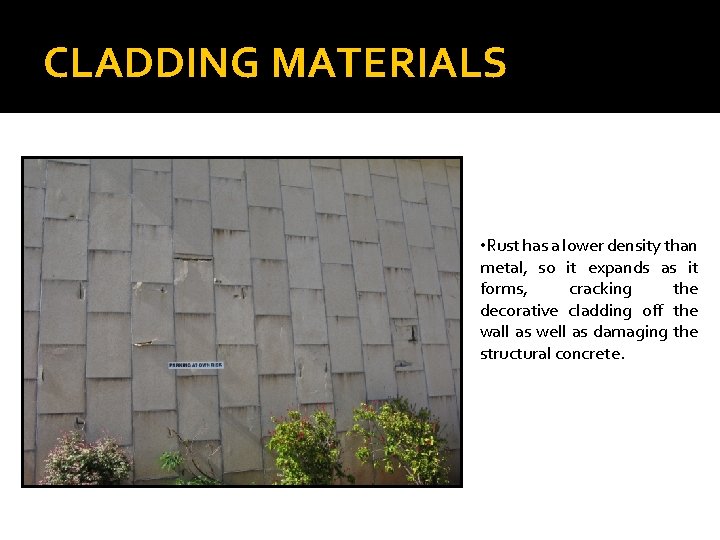
CLADDING MATERIALS • Rust has a lower density than metal, so it expands as it forms, cracking the decorative cladding off the wall as well as damaging the structural concrete.
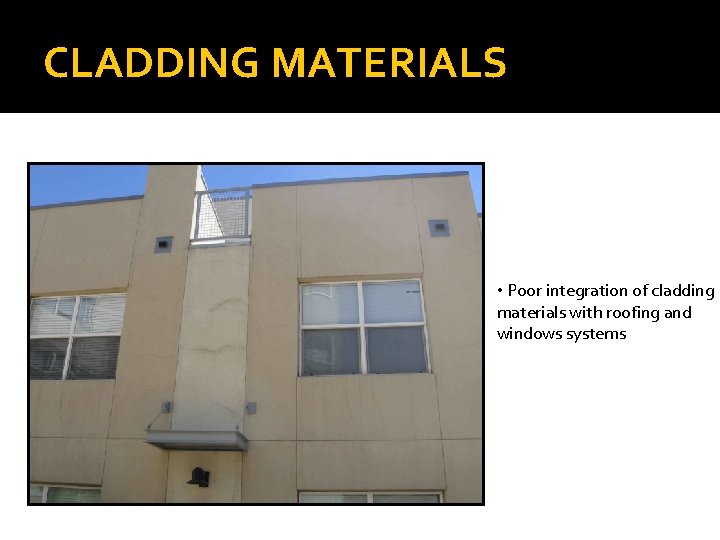
CLADDING MATERIALS • Poor integration of cladding materials with roofing and windows systems
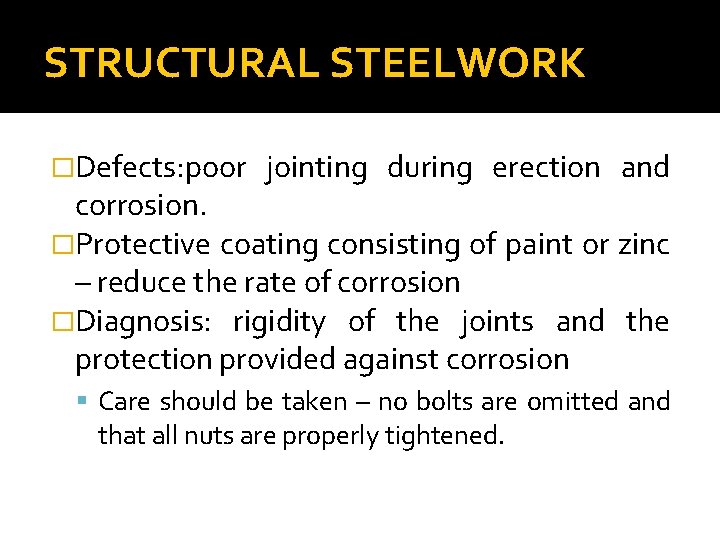
STRUCTURAL STEELWORK �Defects: poor jointing during erection and corrosion. �Protective coating consisting of paint or zinc – reduce the rate of corrosion �Diagnosis: rigidity of the joints and the protection provided against corrosion Care should be taken – no bolts are omitted and that all nuts are properly tightened.
Admixture definition in civil engineering
Who invented rcc
Plastic centroid of column
Cladding deflection limits
Iprs limited
Cladding layer
Column cover and spandrel system
Insulated cladding on cmu
Brittle cladding
Dmc explosion welding
Doubly reinforced t beam
Scip panel construction
Concrete semi concrete abstract
Concrete semi concrete abstract
Social learning theory example
Design of singly reinforced beam
Wallboard that has been reinforced with lexan®:
Bragi god of poetry
Protruding reinforced steel must be guarded
Composite structure
Reaction injection molding advantages and disadvantages
Protruding reinforced steel must be guarded
Vci anticorrosive kraft paper with woven