PROJECT TITLE DIAMAN Dpts Innovants dAlliages Mtalliques Amorphes
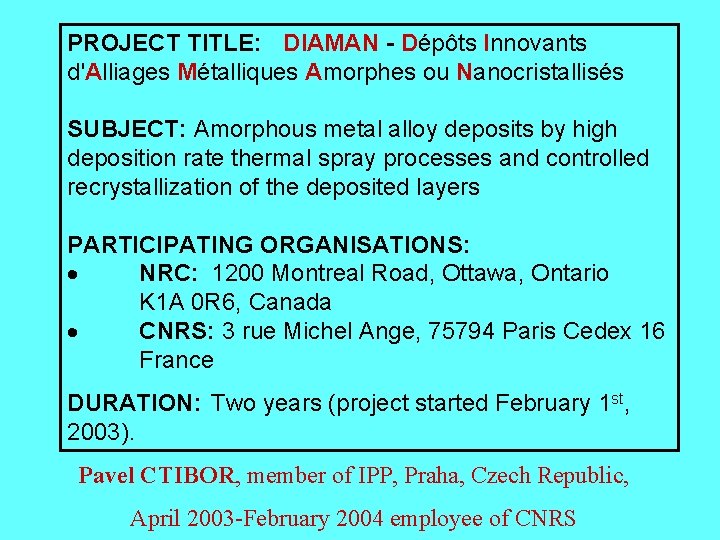
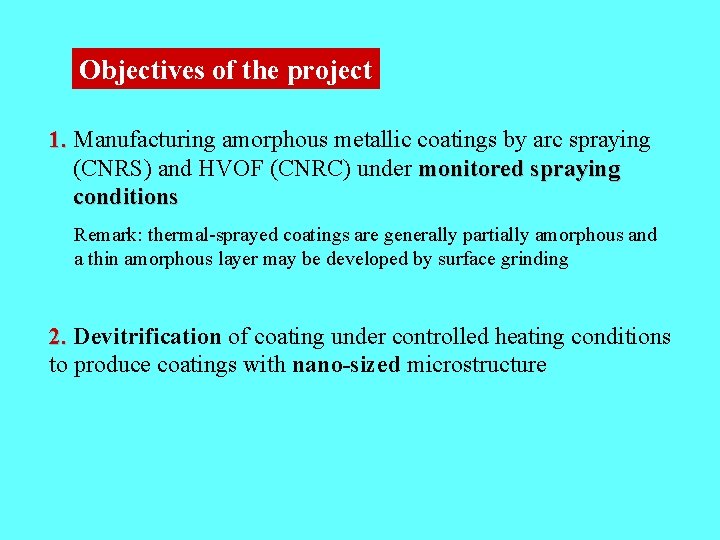
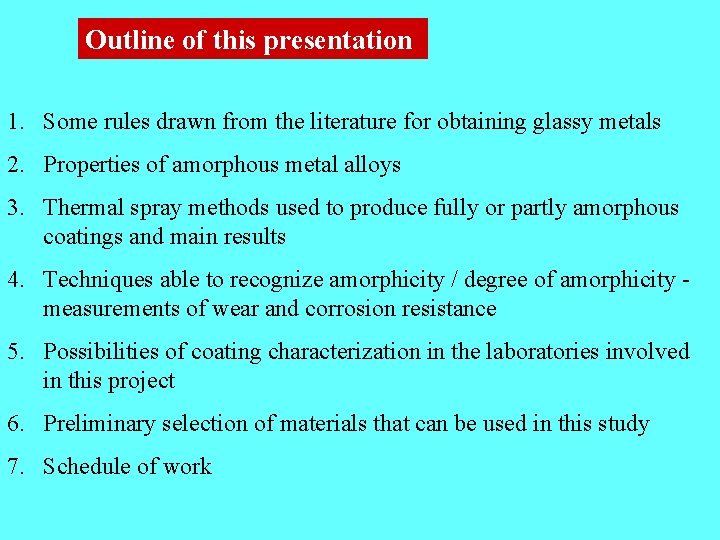
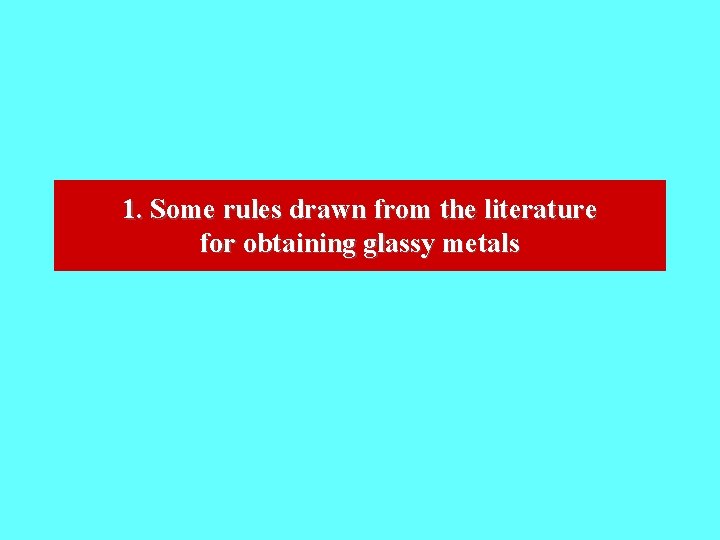
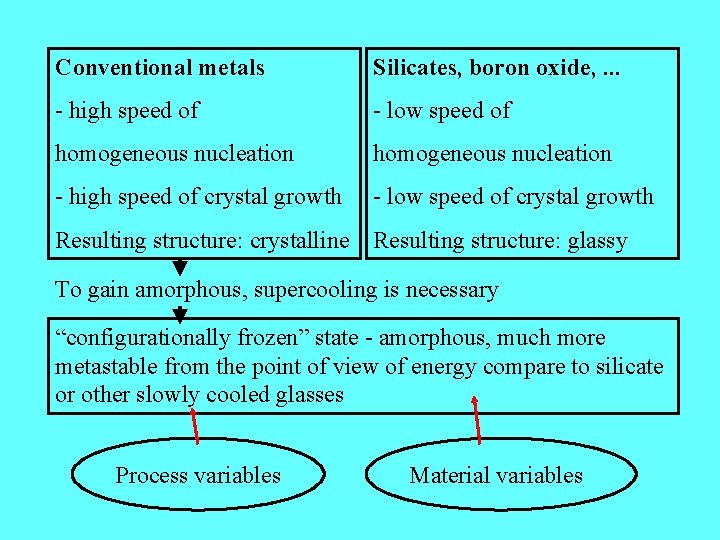

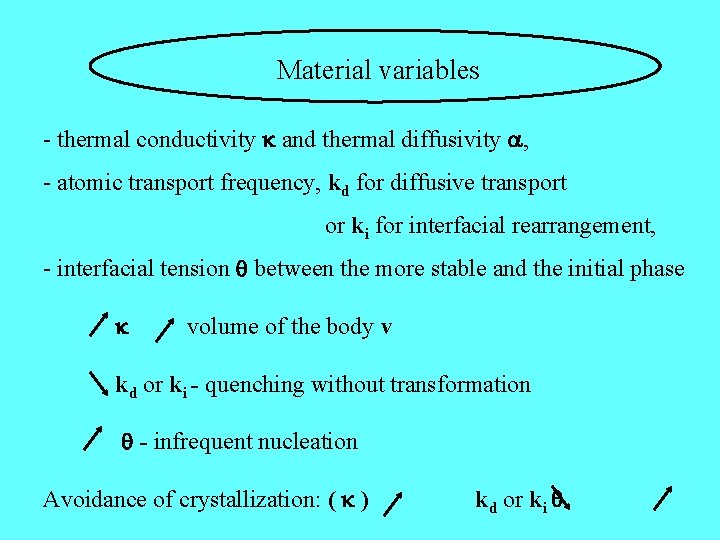
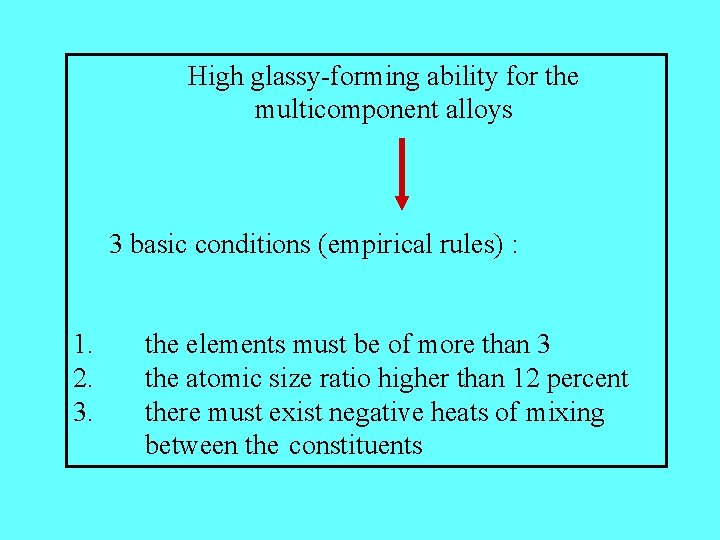
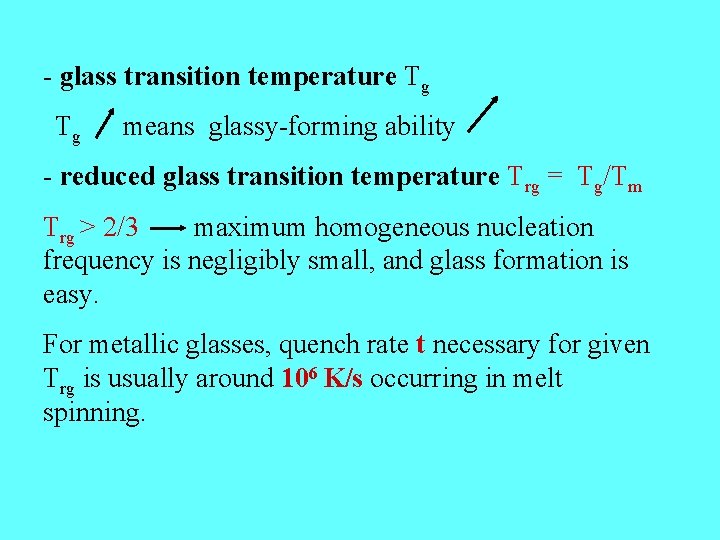
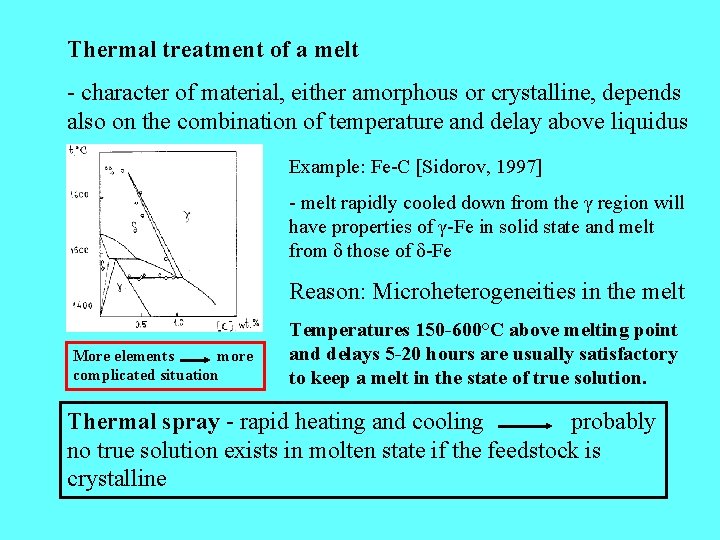
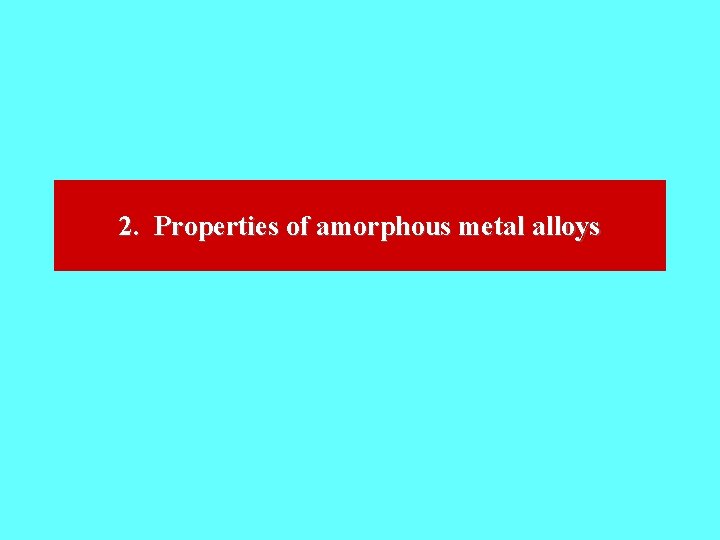
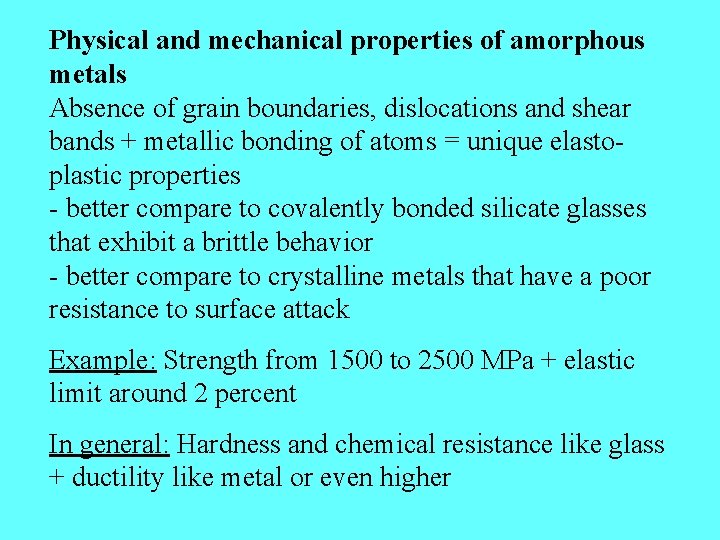
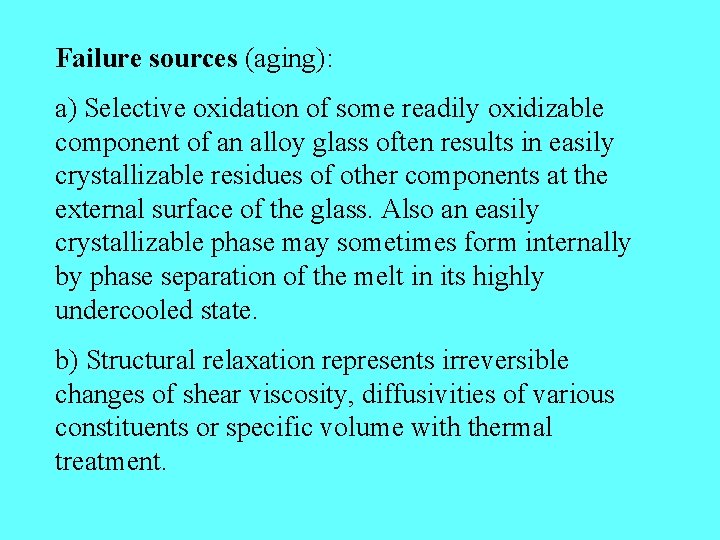
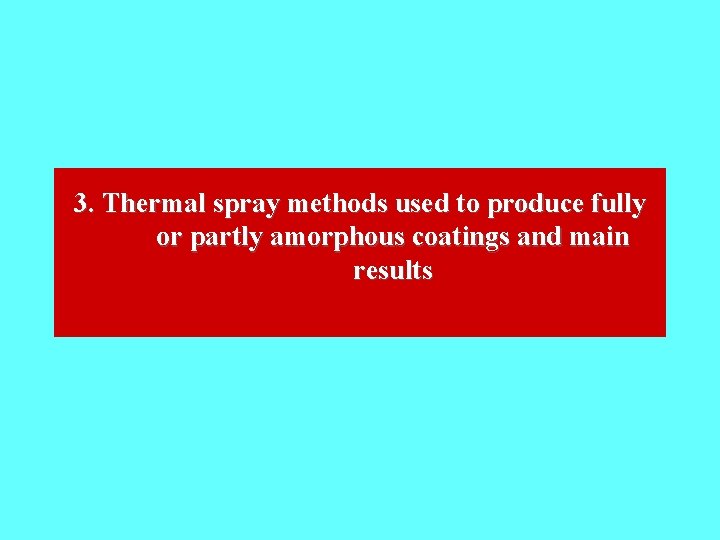
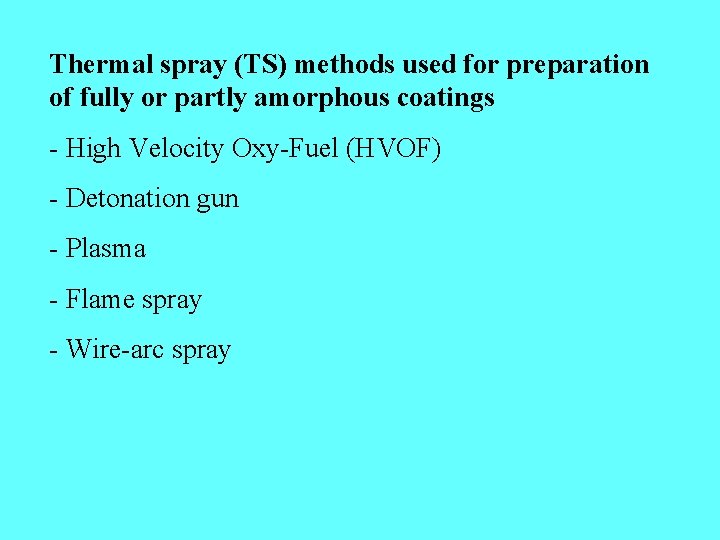
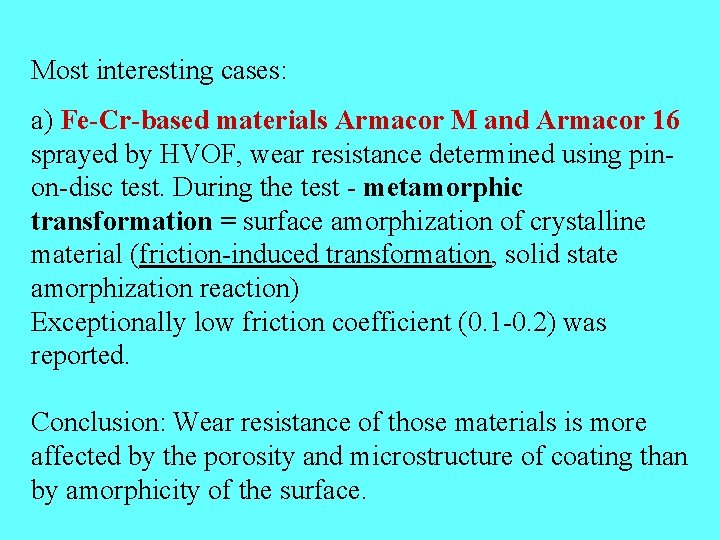
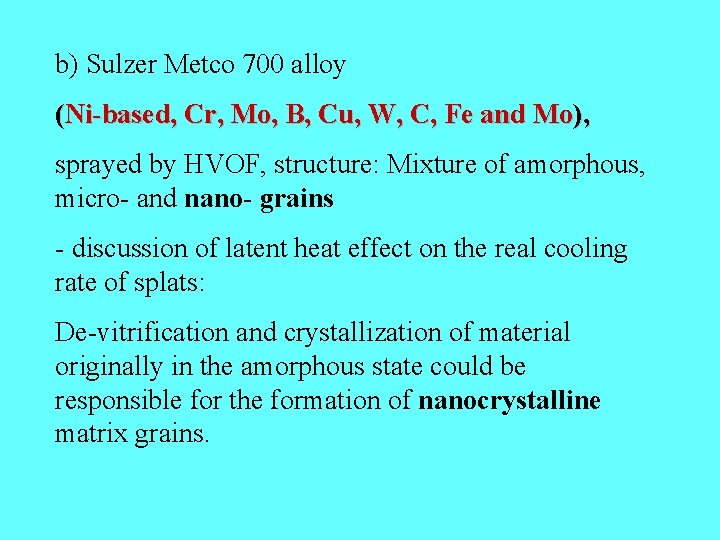
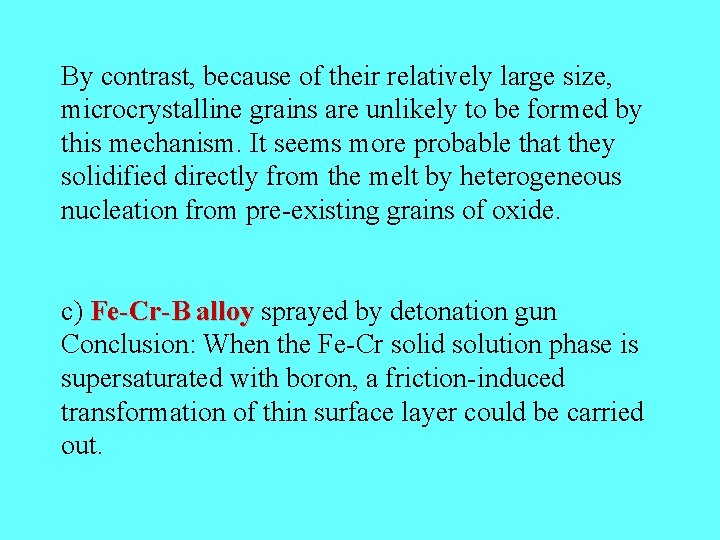
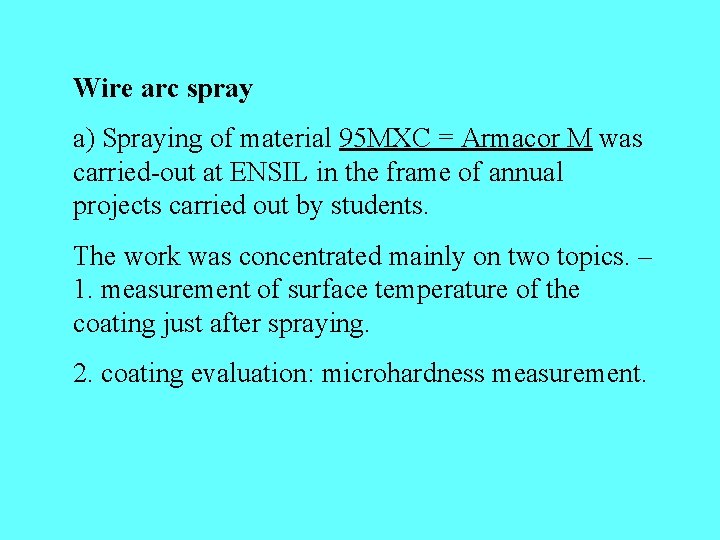
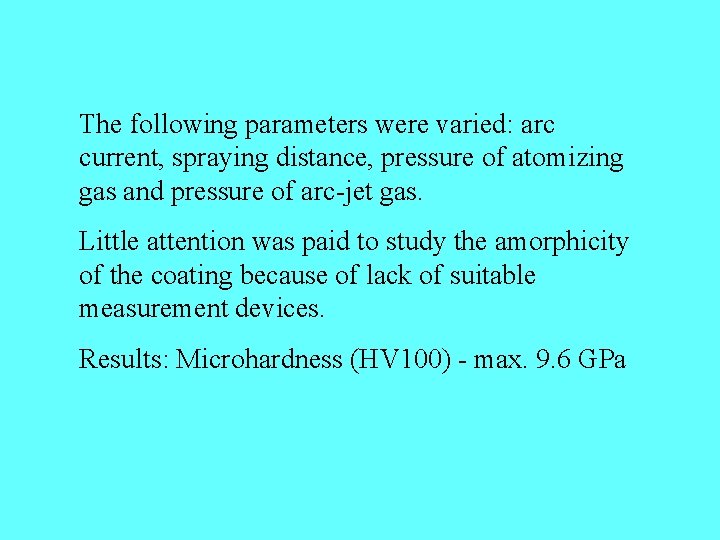
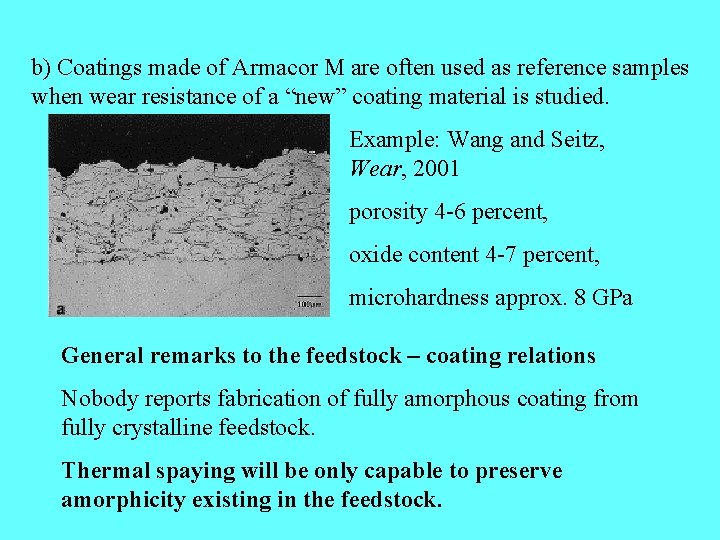
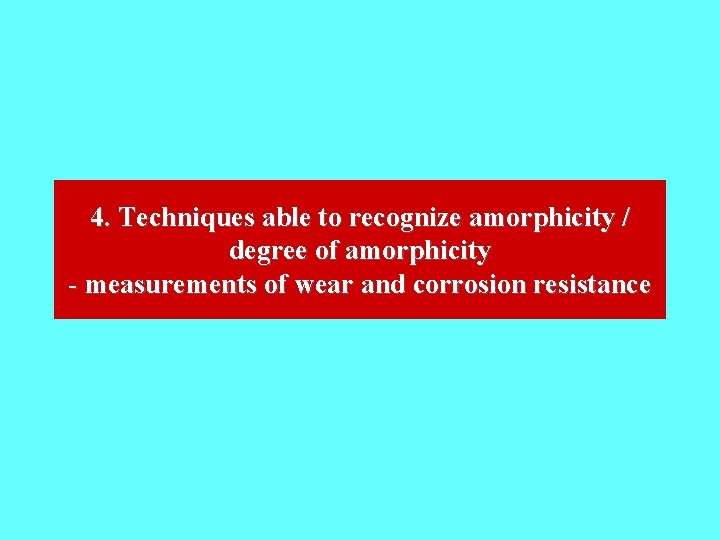
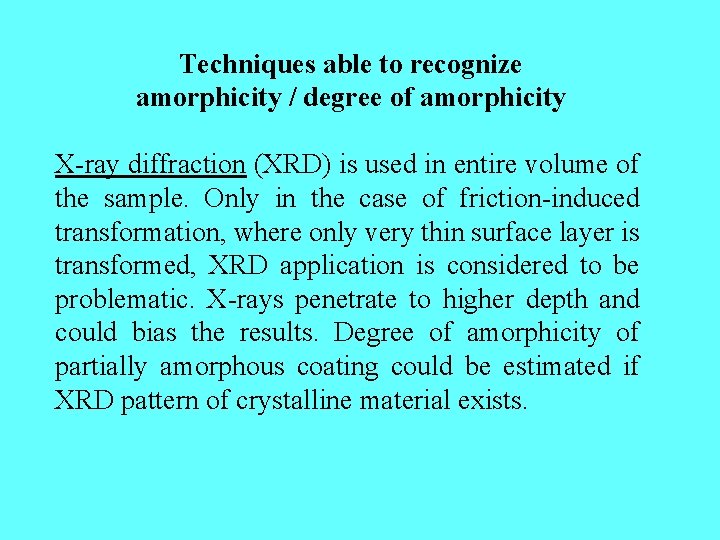
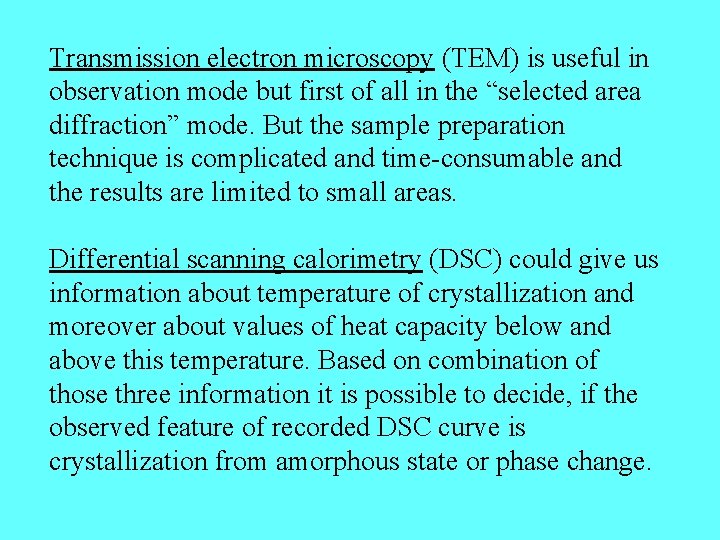
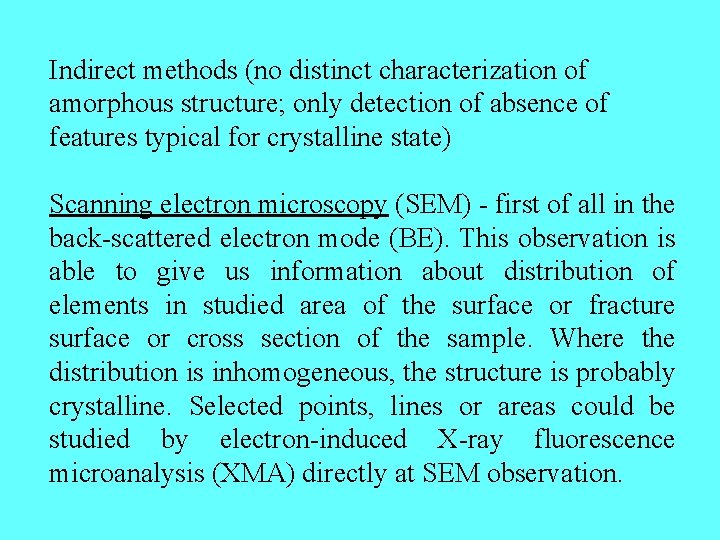
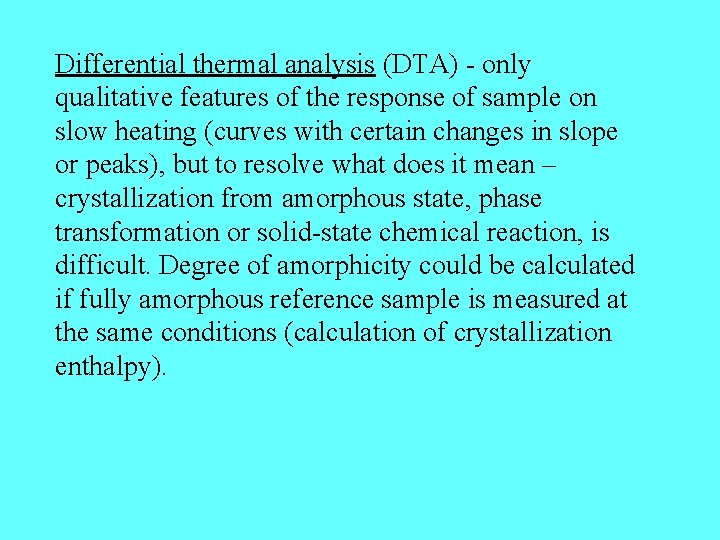
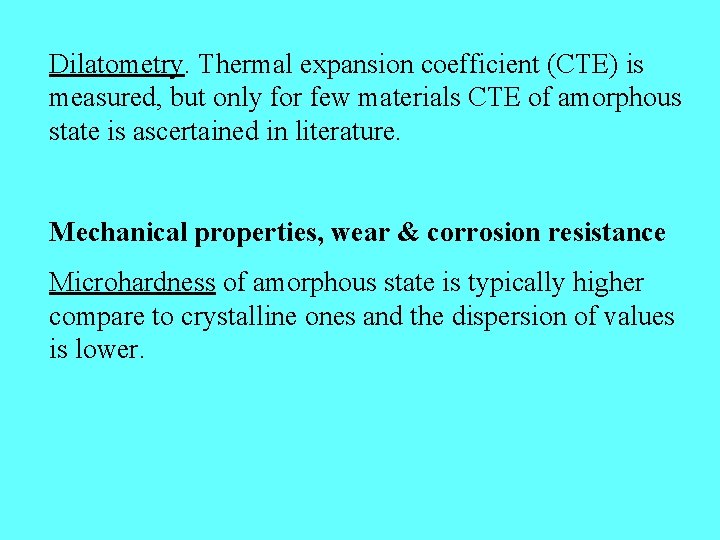
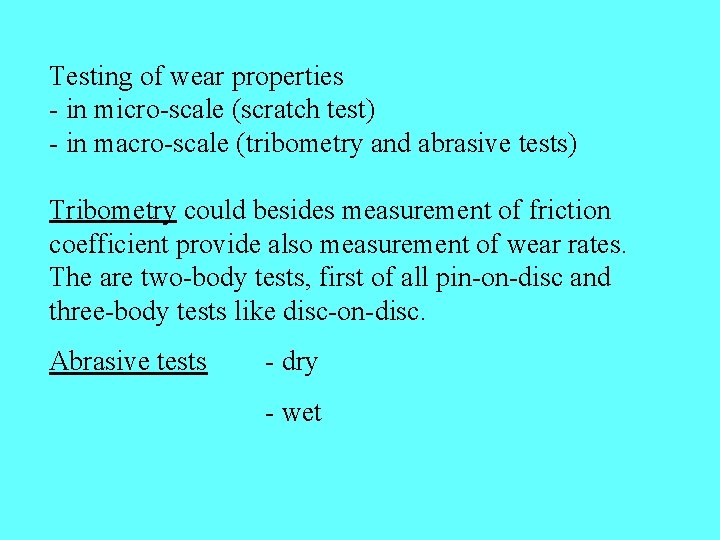
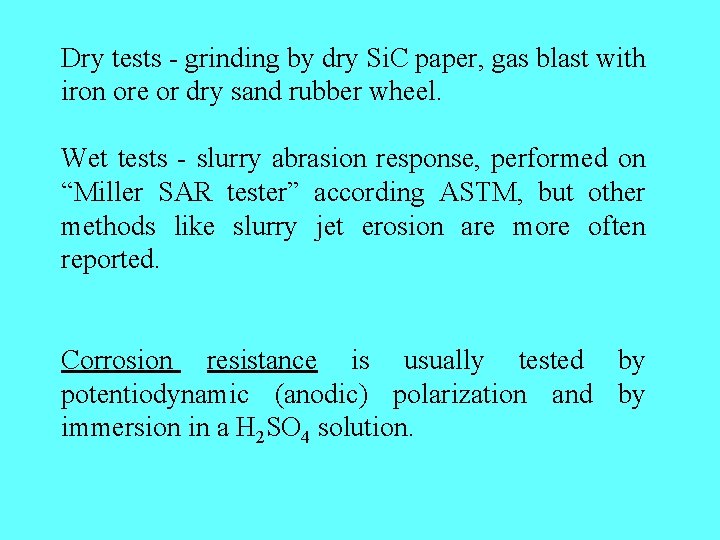
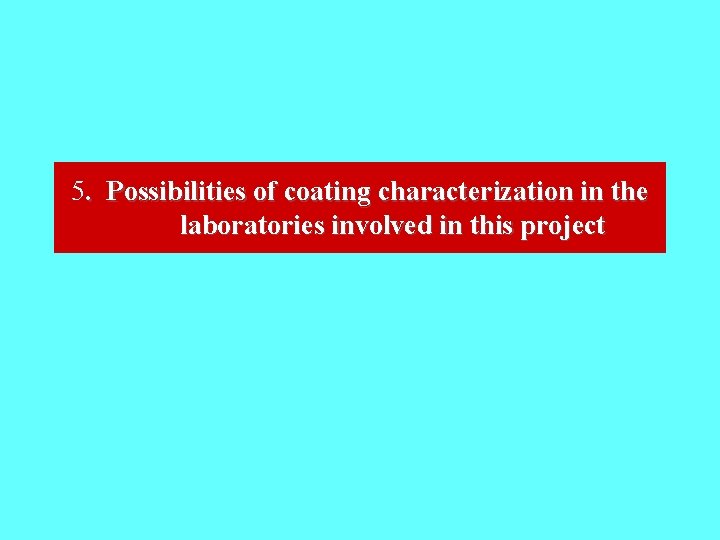
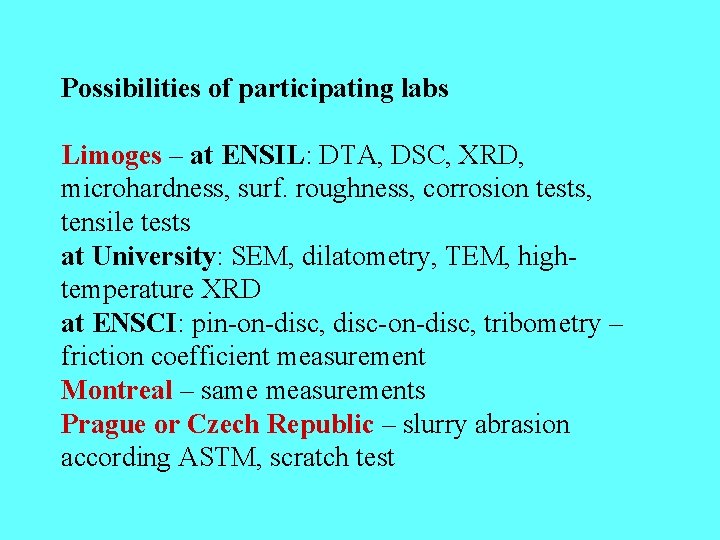

![Materials preliminarily selected a) “Armacor M”, supplier Liquidmetal Technologies, USA Chemical composition [wt. %] Materials preliminarily selected a) “Armacor M”, supplier Liquidmetal Technologies, USA Chemical composition [wt. %]](https://slidetodoc.com/presentation_image_h/0b6d2a08f2ecb8fcb75795df2b7d7109/image-33.jpg)
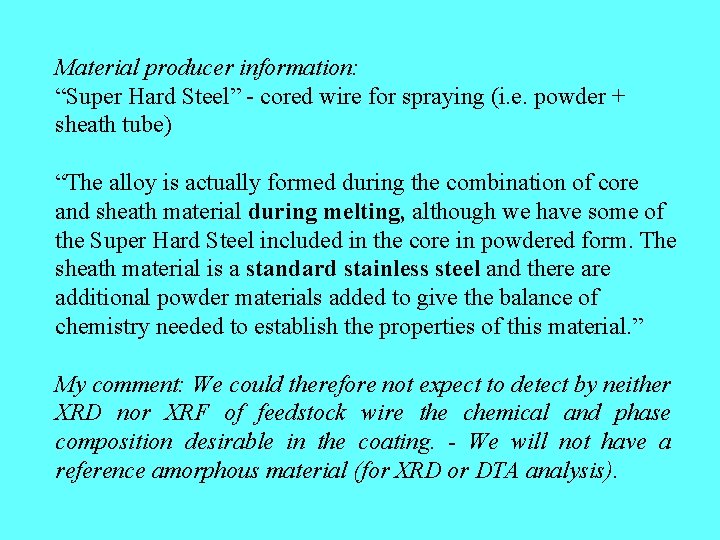
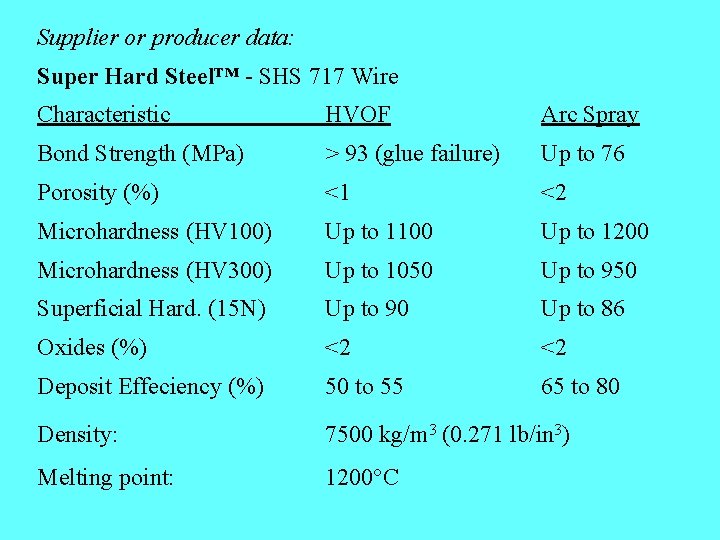
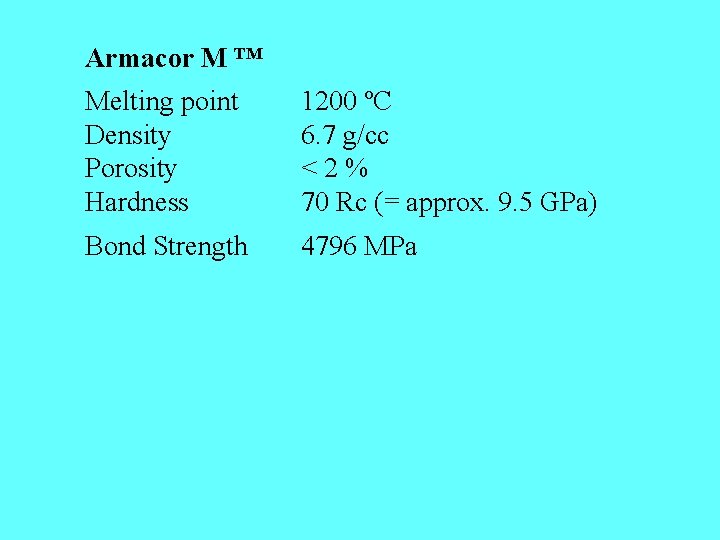
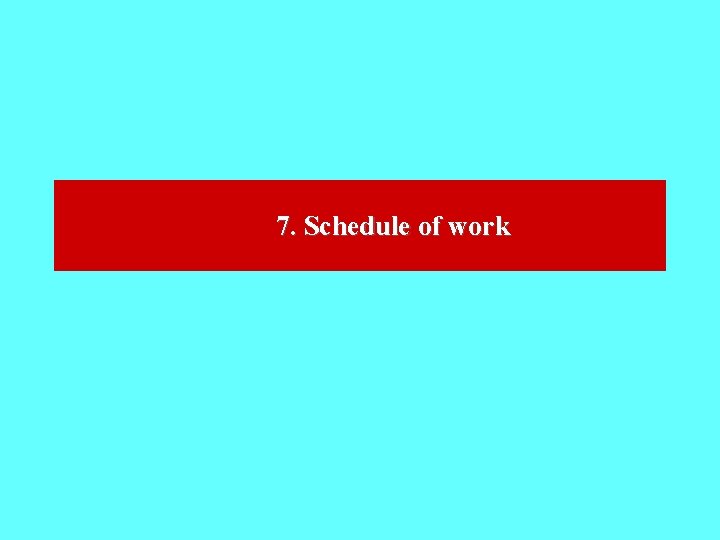
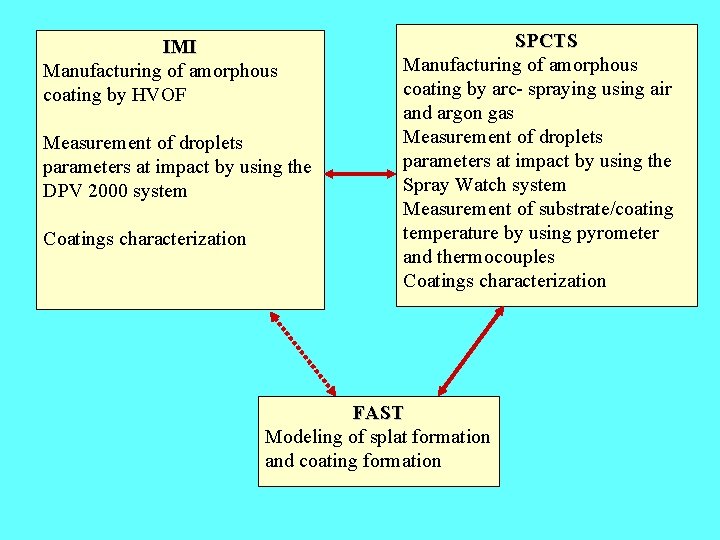
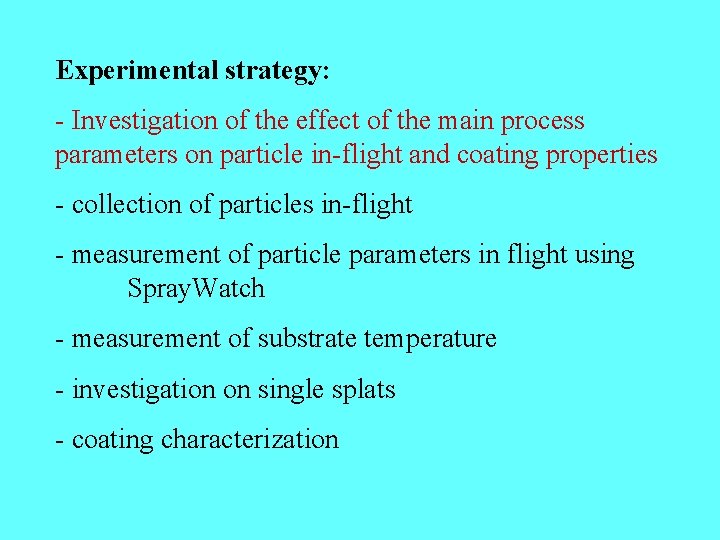
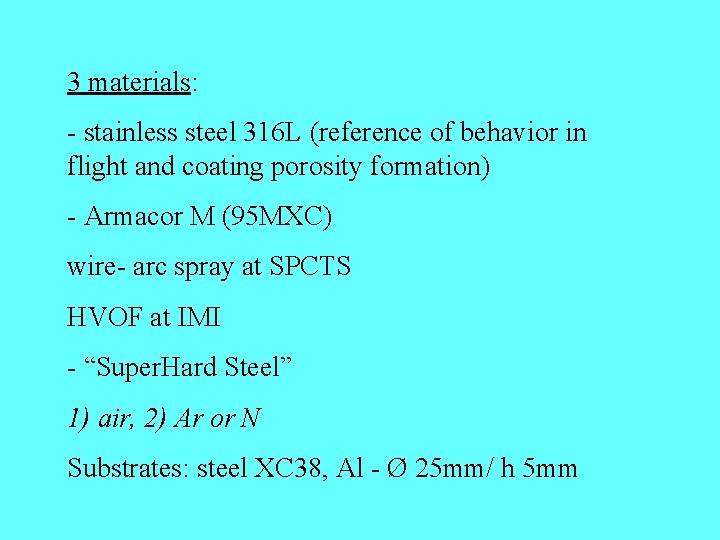
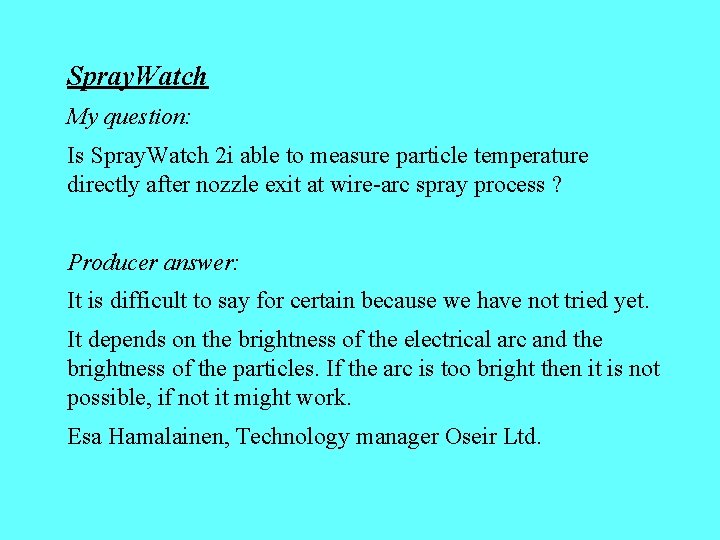
- Slides: 41
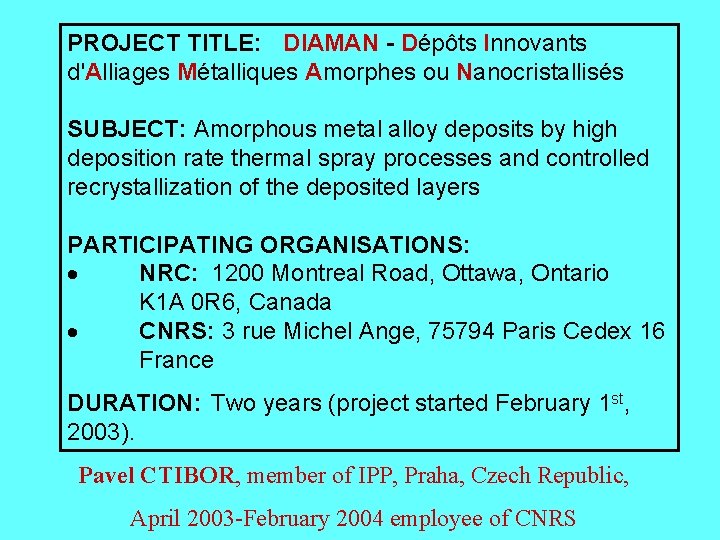
PROJECT TITLE: DIAMAN - Dépôts Innovants d'Alliages Métalliques Amorphes ou Nanocristallisés SUBJECT: Amorphous metal alloy deposits by high deposition rate thermal spray processes and controlled recrystallization of the deposited layers PARTICIPATING ORGANISATIONS: · NRC: 1200 Montreal Road, Ottawa, Ontario K 1 A 0 R 6, Canada · CNRS: 3 rue Michel Ange, 75794 Paris Cedex 16 France DURATION: Two years (project started February 1 st, 2003). Pavel CTIBOR, member of IPP, Praha, Czech Republic, April 2003 -February 2004 employee of CNRS
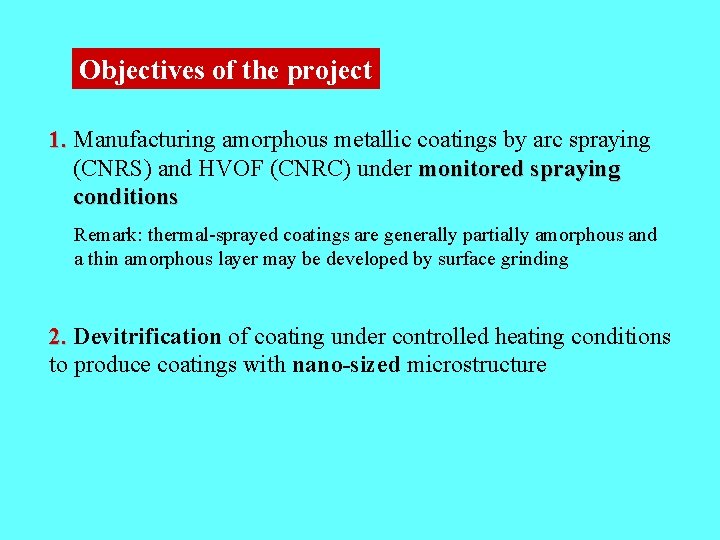
Objectives of the project 1. Manufacturing amorphous metallic coatings by arc spraying (CNRS) and HVOF (CNRC) under monitored spraying conditions Remark: thermal-sprayed coatings are generally partially amorphous and a thin amorphous layer may be developed by surface grinding 2. Devitrification of coating under controlled heating conditions to produce coatings with nano-sized microstructure
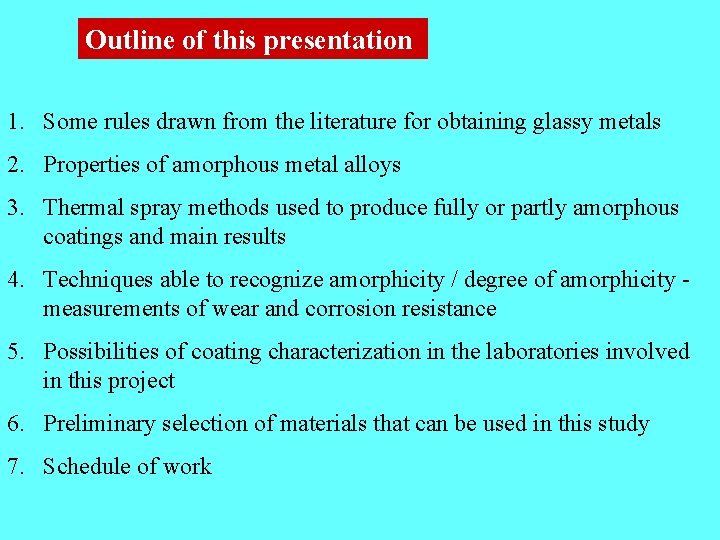
Outline of this presentation 1. Some rules drawn from the literature for obtaining glassy metals 2. Properties of amorphous metal alloys 3. Thermal spray methods used to produce fully or partly amorphous coatings and main results 4. Techniques able to recognize amorphicity / degree of amorphicity measurements of wear and corrosion resistance 5. Possibilities of coating characterization in the laboratories involved in this project 6. Preliminary selection of materials that can be used in this study 7. Schedule of work
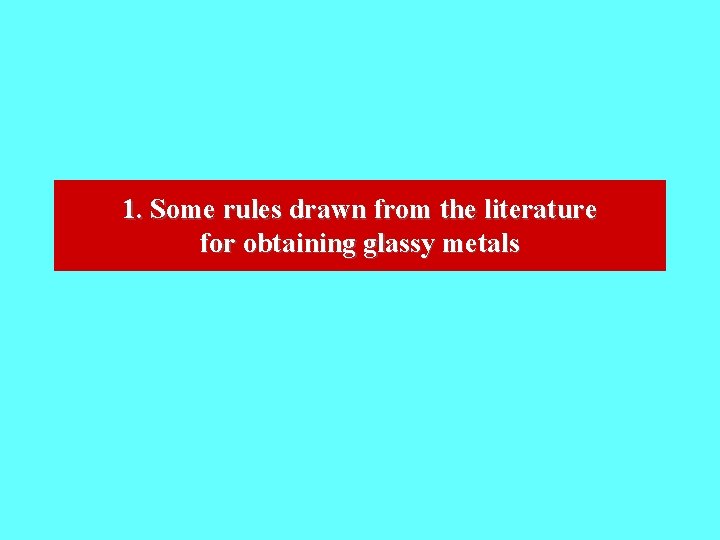
1. Some rules drawn from the literature for obtaining glassy metals
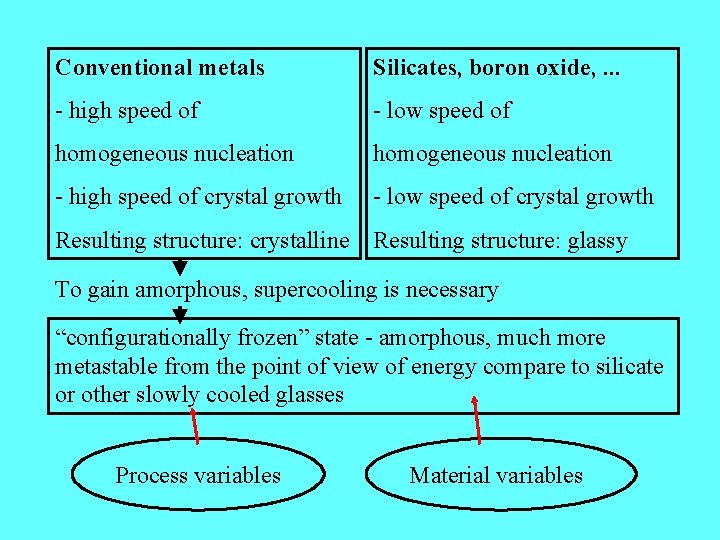
Conventional metals Silicates, boron oxide, . . . - high speed of - low speed of homogeneous nucleation - high speed of crystal growth - low speed of crystal growth Resulting structure: crystalline Resulting structure: glassy To gain amorphous, supercooling is necessary “configurationally frozen” state - amorphous, much more metastable from the point of view of energy compare to silicate or other slowly cooled glasses Process variables Material variables

Process variables - quench rate t, - volume of the body v, - number density of the heterogeneous nucleation sites n Avoidance of crystallization: t v n Thermal spraying - main factors influencing above mentioned parameters t - particle temperature, heat content, area and quality of contact with the underlying surface, substrate temperature and nature v - splat and bead thickness allowed by heat transfer to substrate n - oxidation = loss of chemical purity of the product
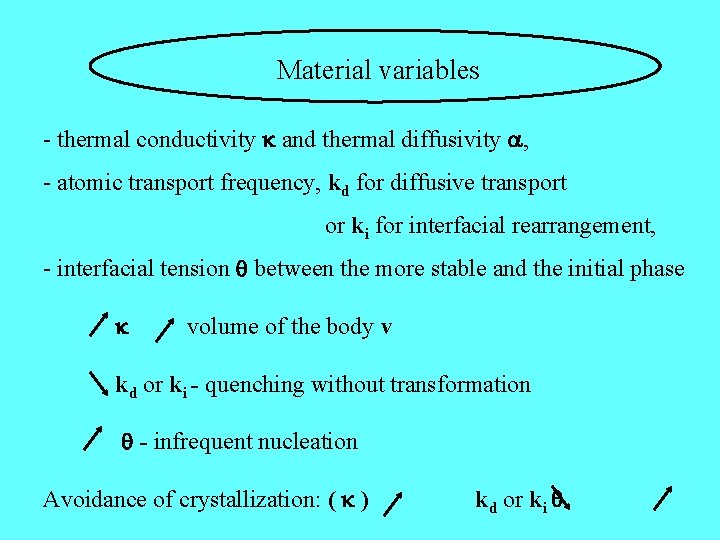
Material variables - thermal conductivity and thermal diffusivity , - atomic transport frequency, kd for diffusive transport or ki for interfacial rearrangement, - interfacial tension between the more stable and the initial phase volume of the body v kd or ki - quenching without transformation - infrequent nucleation Avoidance of crystallization: ( ) kd or ki
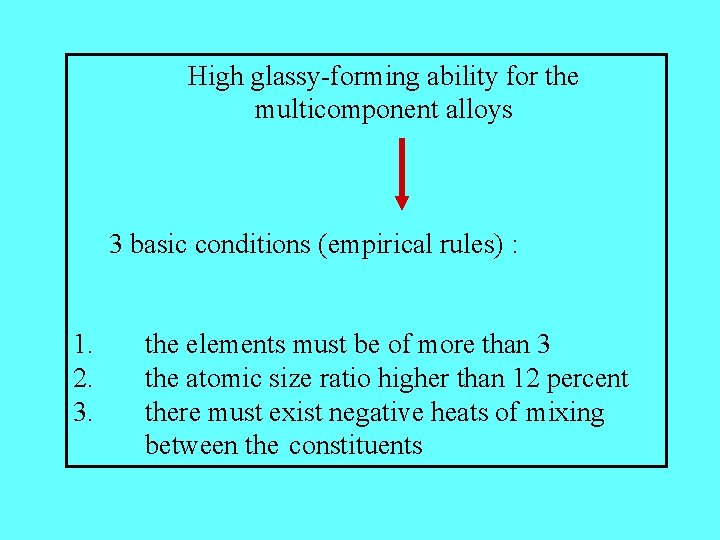
High glassy-forming ability for the multicomponent alloys 3 basic conditions (empirical rules) : 1. 2. 3. the elements must be of more than 3 the atomic size ratio higher than 12 percent there must exist negative heats of mixing between the constituents
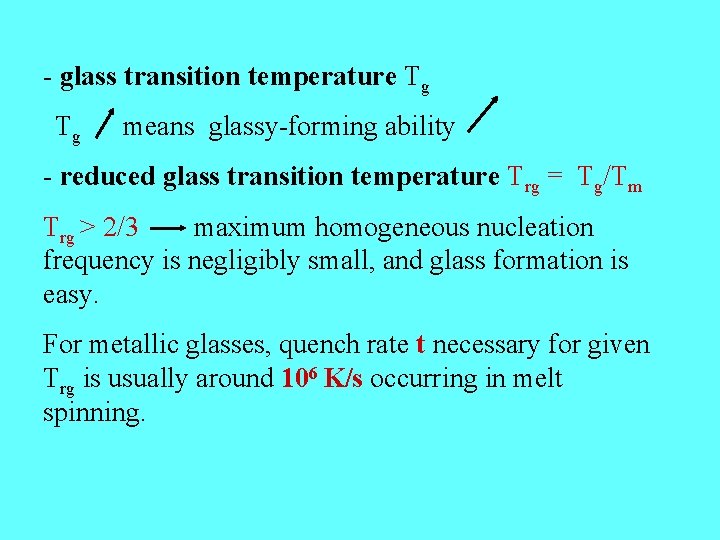
- glass transition temperature Tg Tg means glassy-forming ability - reduced glass transition temperature Trg = Tg/Tm Trg > 2/3 maximum homogeneous nucleation frequency is negligibly small, and glass formation is easy. For metallic glasses, quench rate t necessary for given Trg is usually around 106 K/s occurring in melt spinning.
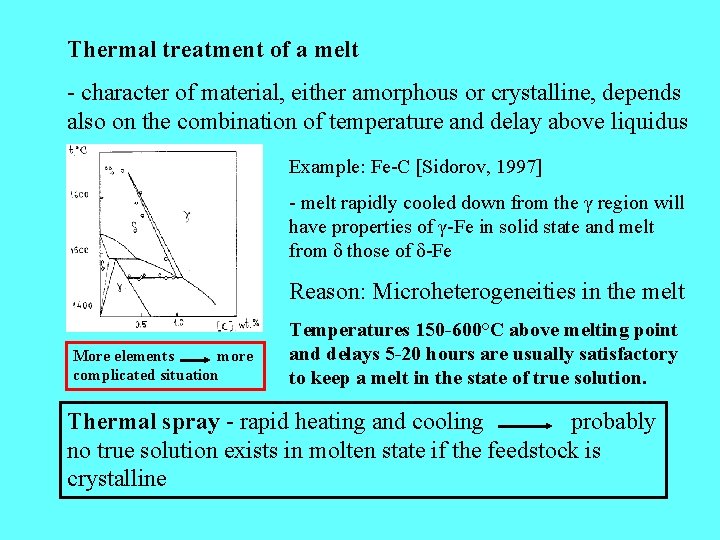
Thermal treatment of a melt - character of material, either amorphous or crystalline, depends also on the combination of temperature and delay above liquidus Example: Fe-C [Sidorov, 1997] - melt rapidly cooled down from the γ region will have properties of γ-Fe in solid state and melt from δ those of δ-Fe Reason: Microheterogeneities in the melt More elements more complicated situation Temperatures 150 -600°C above melting point and delays 5 -20 hours are usually satisfactory to keep a melt in the state of true solution. Thermal spray - rapid heating and cooling probably no true solution exists in molten state if the feedstock is crystalline
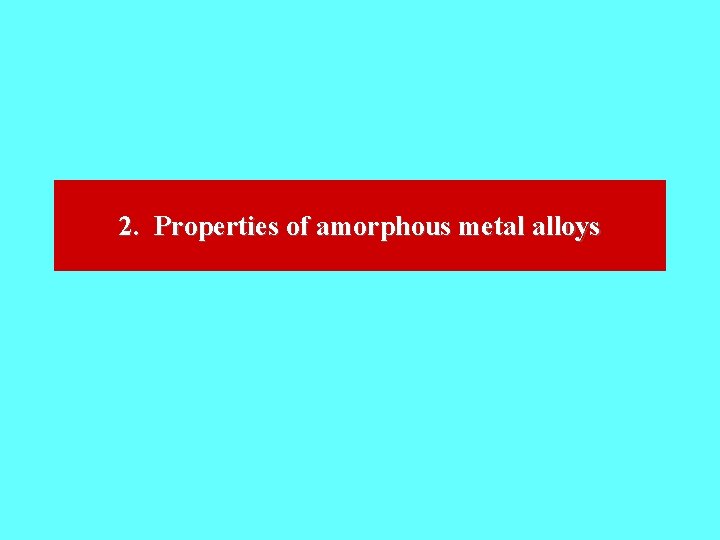
2. Properties of amorphous metal alloys
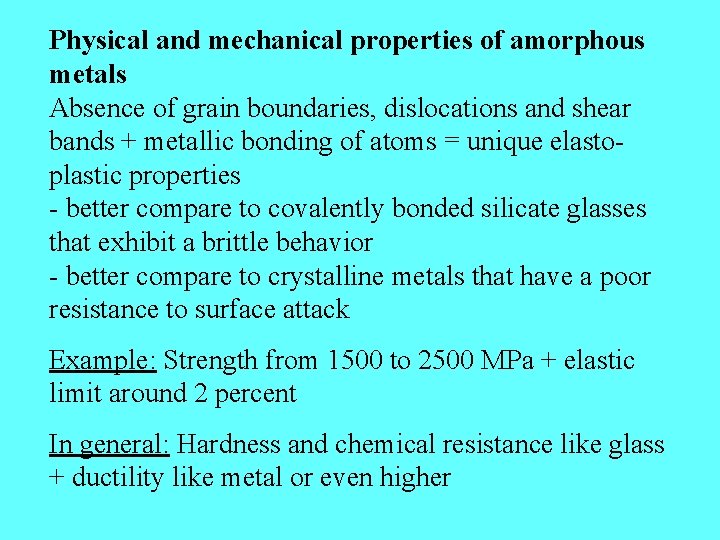
Physical and mechanical properties of amorphous metals Absence of grain boundaries, dislocations and shear bands + metallic bonding of atoms = unique elastoplastic properties - better compare to covalently bonded silicate glasses that exhibit a brittle behavior - better compare to crystalline metals that have a poor resistance to surface attack Example: Strength from 1500 to 2500 MPa + elastic limit around 2 percent In general: Hardness and chemical resistance like glass + ductility like metal or even higher
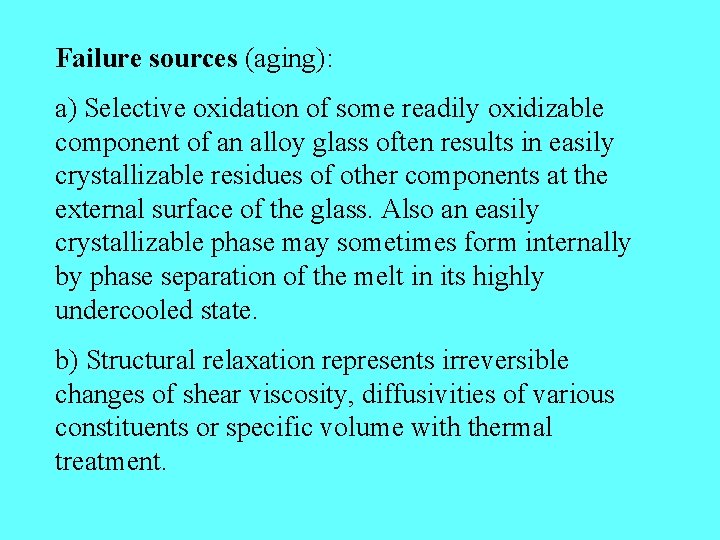
Failure sources (aging): a) Selective oxidation of some readily oxidizable component of an alloy glass often results in easily crystallizable residues of other components at the external surface of the glass. Also an easily crystallizable phase may sometimes form internally by phase separation of the melt in its highly undercooled state. b) Structural relaxation represents irreversible changes of shear viscosity, diffusivities of various constituents or specific volume with thermal treatment.
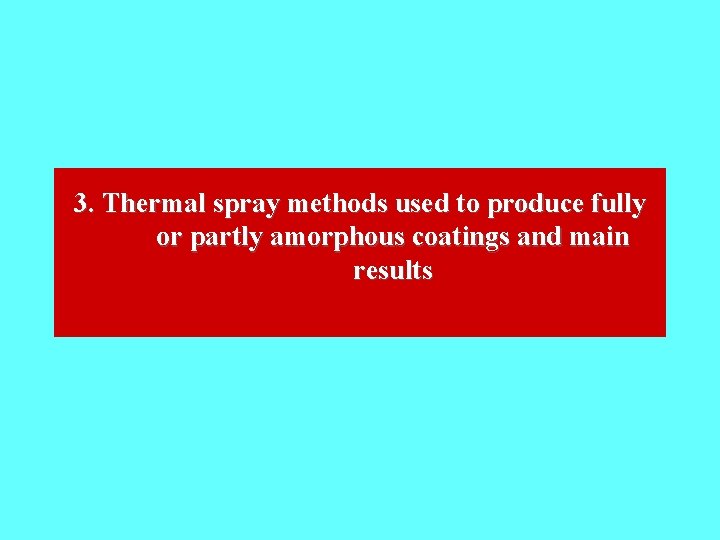
3. Thermal spray methods used to produce fully or partly amorphous coatings and main results
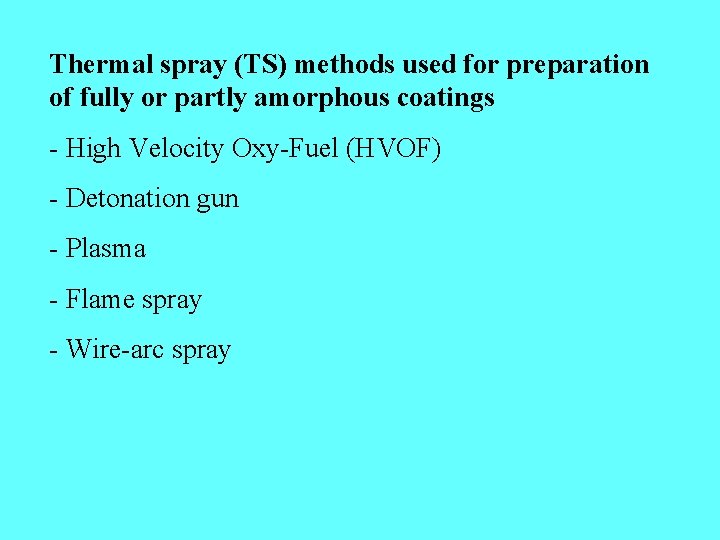
Thermal spray (TS) methods used for preparation of fully or partly amorphous coatings - High Velocity Oxy-Fuel (HVOF) - Detonation gun - Plasma - Flame spray - Wire-arc spray
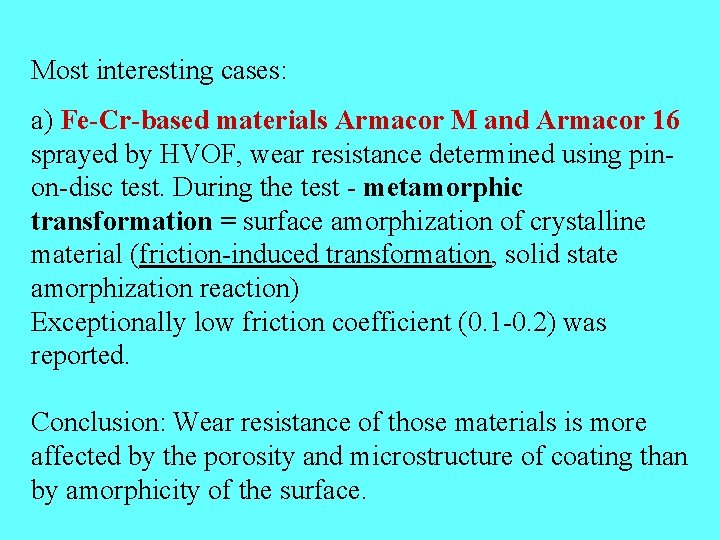
Most interesting cases: a) Fe-Cr-based materials Armacor M and Armacor 16 sprayed by HVOF, wear resistance determined using pinon-disc test. During the test - metamorphic transformation = surface amorphization of crystalline material (friction-induced transformation, solid state amorphization reaction) Exceptionally low friction coefficient (0. 1 -0. 2) was reported. Conclusion: Wear resistance of those materials is more affected by the porosity and microstructure of coating than by amorphicity of the surface.
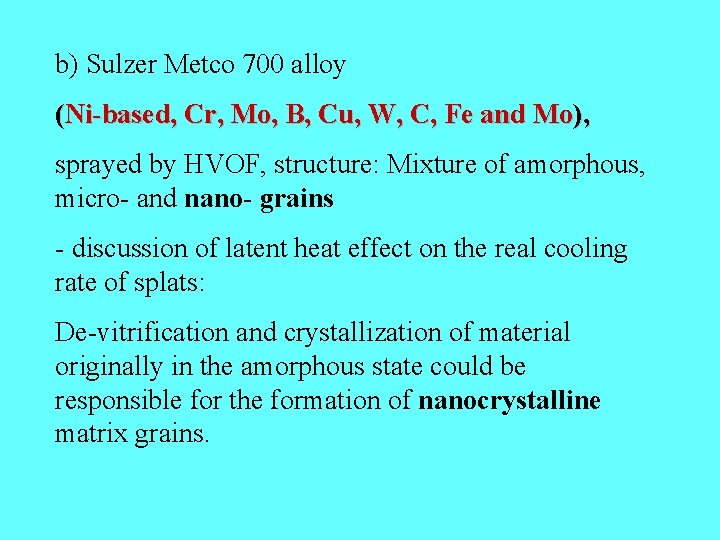
b) Sulzer Metco 700 alloy (Ni-based, Cr, Mo, B, Cu, W, C, Fe and Mo), sprayed by HVOF, structure: Mixture of amorphous, micro- and nano- grains - discussion of latent heat effect on the real cooling rate of splats: De-vitrification and crystallization of material originally in the amorphous state could be responsible for the formation of nanocrystalline matrix grains.
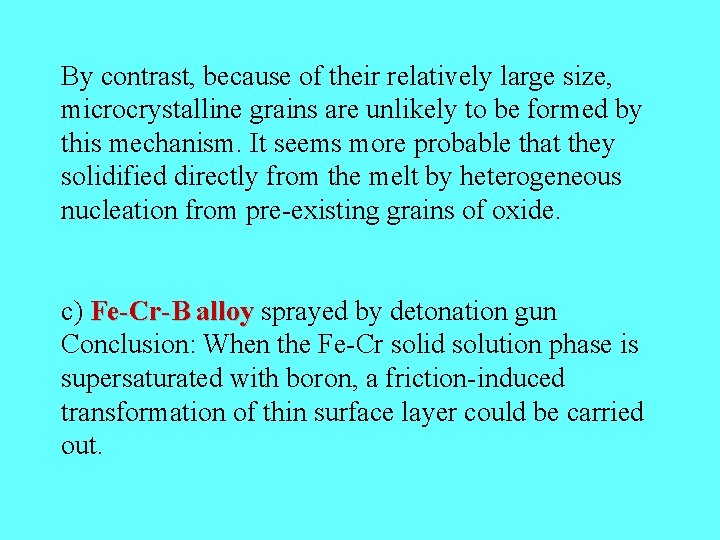
By contrast, because of their relatively large size, microcrystalline grains are unlikely to be formed by this mechanism. It seems more probable that they solidified directly from the melt by heterogeneous nucleation from pre-existing grains of oxide. c) Fe-Cr-B alloy sprayed by detonation gun Conclusion: When the Fe-Cr solid solution phase is supersaturated with boron, a friction-induced transformation of thin surface layer could be carried out.
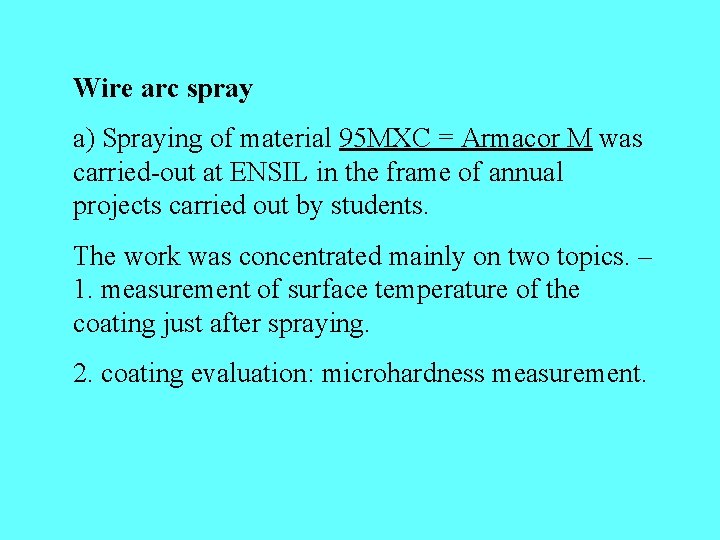
Wire arc spray a) Spraying of material 95 MXC = Armacor M was carried-out at ENSIL in the frame of annual projects carried out by students. The work was concentrated mainly on two topics. – 1. measurement of surface temperature of the coating just after spraying. 2. coating evaluation: microhardness measurement.
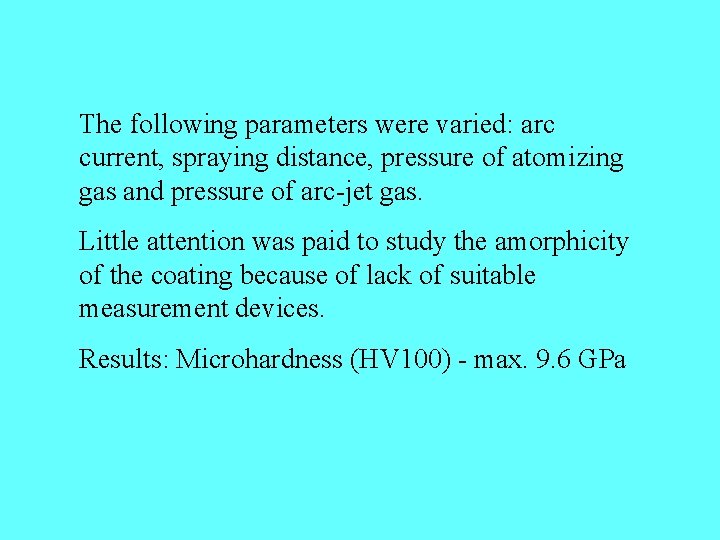
The following parameters were varied: arc current, spraying distance, pressure of atomizing gas and pressure of arc-jet gas. Little attention was paid to study the amorphicity of the coating because of lack of suitable measurement devices. Results: Microhardness (HV 100) - max. 9. 6 GPa
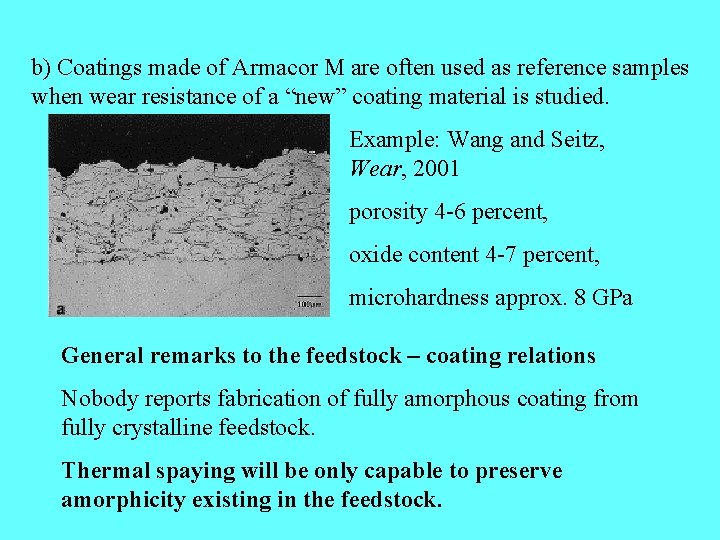
b) Coatings made of Armacor M are often used as reference samples when wear resistance of a “new” coating material is studied. Example: Wang and Seitz, Wear, 2001 porosity 4 -6 percent, oxide content 4 -7 percent, microhardness approx. 8 GPa General remarks to the feedstock – coating relations Nobody reports fabrication of fully amorphous coating from fully crystalline feedstock. Thermal spaying will be only capable to preserve amorphicity existing in the feedstock.
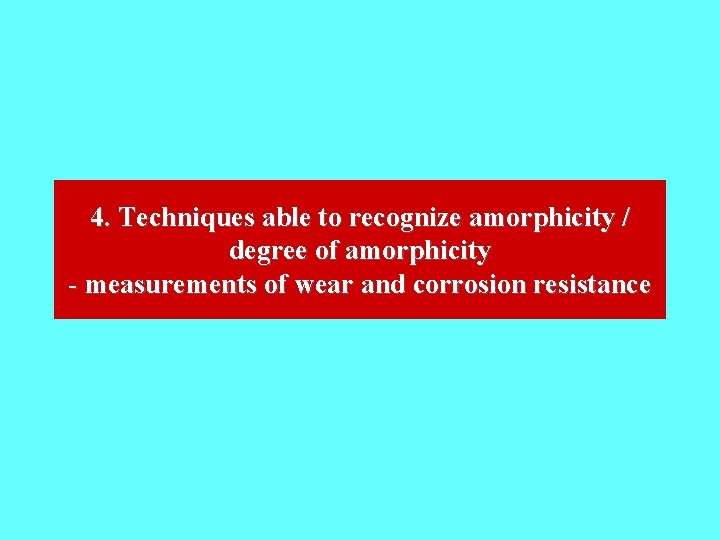
4. Techniques able to recognize amorphicity / degree of amorphicity - measurements of wear and corrosion resistance
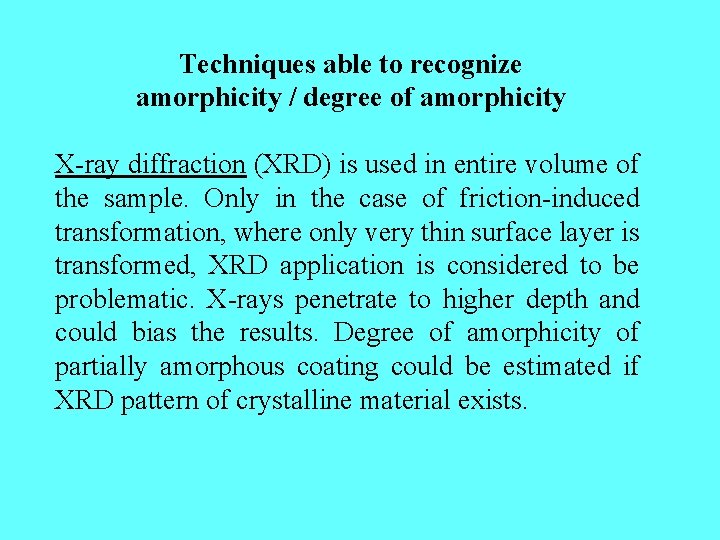
Techniques able to recognize amorphicity / degree of amorphicity X-ray diffraction (XRD) is used in entire volume of the sample. Only in the case of friction-induced transformation, where only very thin surface layer is transformed, XRD application is considered to be problematic. X-rays penetrate to higher depth and could bias the results. Degree of amorphicity of partially amorphous coating could be estimated if XRD pattern of crystalline material exists.
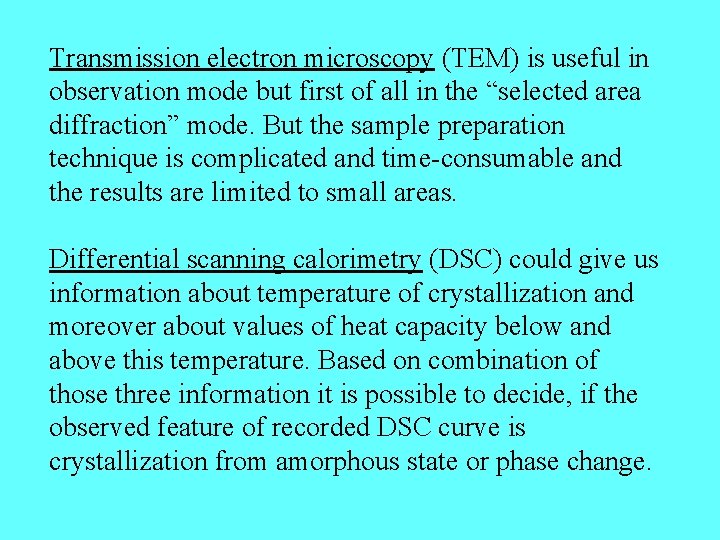
Transmission electron microscopy (TEM) is useful in observation mode but first of all in the “selected area diffraction” mode. But the sample preparation technique is complicated and time-consumable and the results are limited to small areas. Differential scanning calorimetry (DSC) could give us information about temperature of crystallization and moreover about values of heat capacity below and above this temperature. Based on combination of those three information it is possible to decide, if the observed feature of recorded DSC curve is crystallization from amorphous state or phase change.
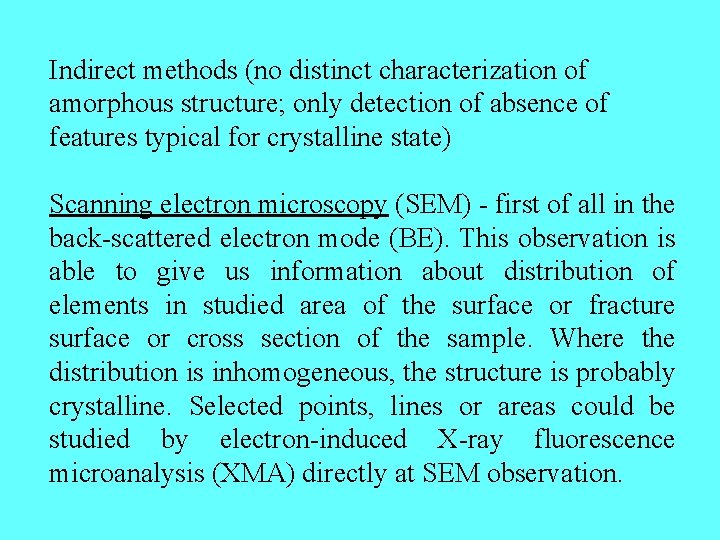
Indirect methods (no distinct characterization of amorphous structure; only detection of absence of features typical for crystalline state) Scanning electron microscopy (SEM) - first of all in the back-scattered electron mode (BE). This observation is able to give us information about distribution of elements in studied area of the surface or fracture surface or cross section of the sample. Where the distribution is inhomogeneous, the structure is probably crystalline. Selected points, lines or areas could be studied by electron-induced X-ray fluorescence microanalysis (XMA) directly at SEM observation.
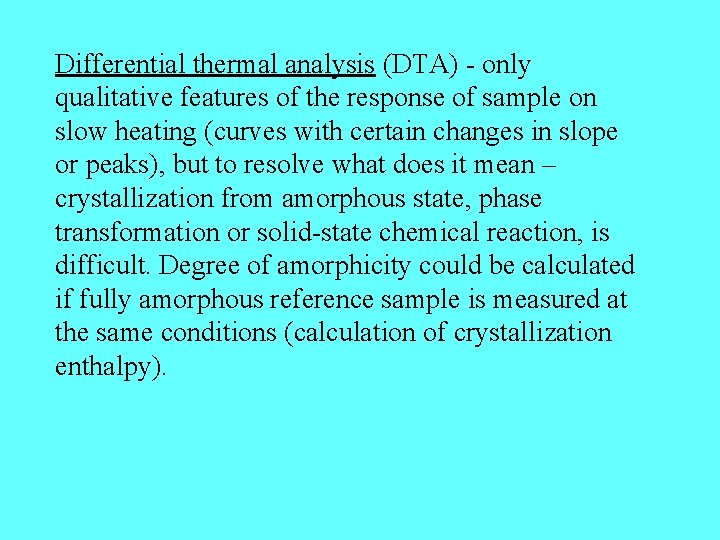
Differential thermal analysis (DTA) - only qualitative features of the response of sample on slow heating (curves with certain changes in slope or peaks), but to resolve what does it mean – crystallization from amorphous state, phase transformation or solid-state chemical reaction, is difficult. Degree of amorphicity could be calculated if fully amorphous reference sample is measured at the same conditions (calculation of crystallization enthalpy).
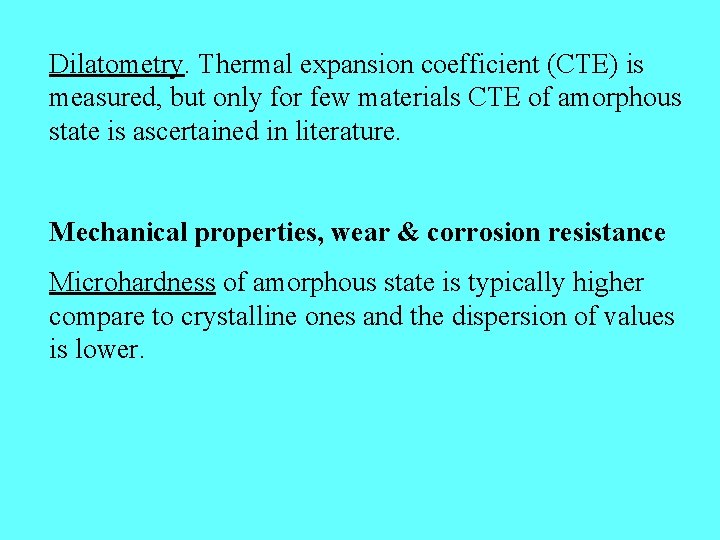
Dilatometry. Thermal expansion coefficient (CTE) is measured, but only for few materials CTE of amorphous state is ascertained in literature. Mechanical properties, wear & corrosion resistance Microhardness of amorphous state is typically higher compare to crystalline ones and the dispersion of values is lower.
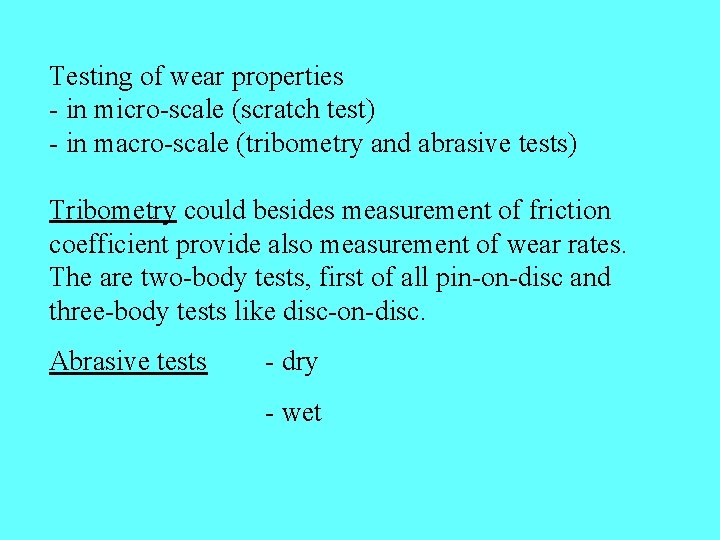
Testing of wear properties - in micro-scale (scratch test) - in macro-scale (tribometry and abrasive tests) Tribometry could besides measurement of friction coefficient provide also measurement of wear rates. The are two-body tests, first of all pin-on-disc and three-body tests like disc-on-disc. Abrasive tests - dry - wet
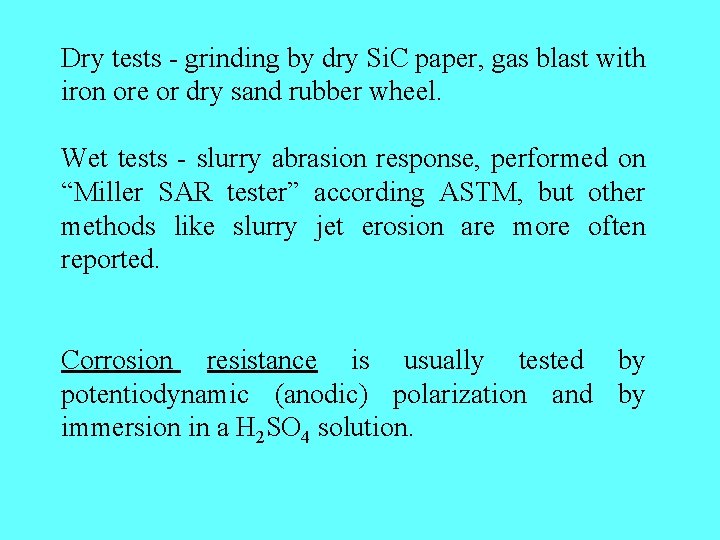
Dry tests - grinding by dry Si. C paper, gas blast with iron ore or dry sand rubber wheel. Wet tests - slurry abrasion response, performed on “Miller SAR tester” according ASTM, but other methods like slurry jet erosion are more often reported. Corrosion resistance is usually tested by potentiodynamic (anodic) polarization and by immersion in a H 2 SO 4 solution.
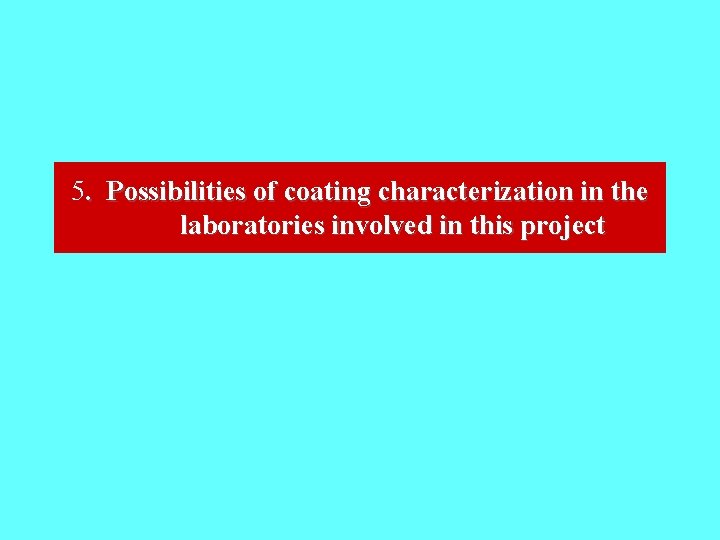
5. Possibilities of coating characterization in the laboratories involved in this project
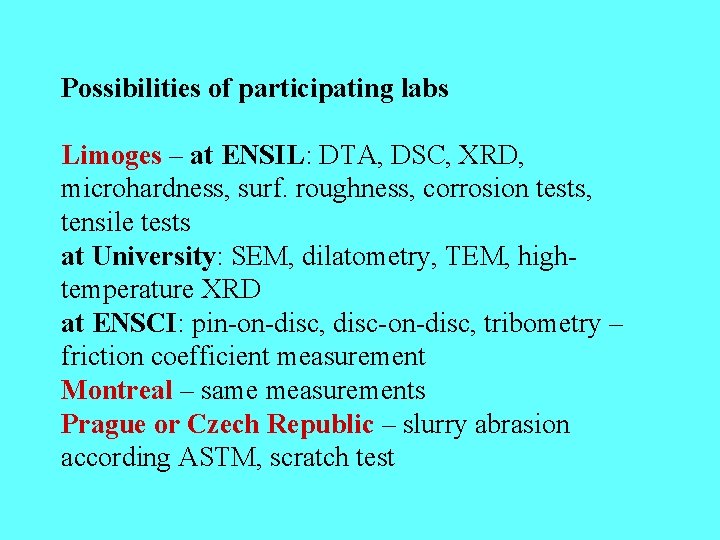
Possibilities of participating labs Limoges – at ENSIL: DTA, DSC, XRD, microhardness, surf. roughness, corrosion tests, tensile tests at University: SEM, dilatometry, TEM, hightemperature XRD at ENSCI: pin-on-disc, disc-on-disc, tribometry – friction coefficient measurement Montreal – same measurements Prague or Czech Republic – slurry abrasion according ASTM, scratch test

6. Preliminary selection of materials that can be used in this study
![Materials preliminarily selected a Armacor M supplier Liquidmetal Technologies USA Chemical composition wt Materials preliminarily selected a) “Armacor M”, supplier Liquidmetal Technologies, USA Chemical composition [wt. %]](https://slidetodoc.com/presentation_image_h/0b6d2a08f2ecb8fcb75795df2b7d7109/image-33.jpg)
Materials preliminarily selected a) “Armacor M”, supplier Liquidmetal Technologies, USA Chemical composition [wt. %] Fe - Cr 28 - B 3. 7 - Mn 2 - Si 1. 7 b) “Super Hard Steel”, supplier Nano. Steel Comp. , USA Chemical composition [wt. %] Fe - Cr<20 - B<5 - Mn<5 - Si<2 - W<10 - Mo<5 - C<2 Delivery: minimum quantity 2 x 25 lb spools, price 20 USD/lb Atomic radii [angstroms]: Fe 1. 26, Cr 1. 3, B 0. 98, Mn 1. 35, Si 1. 32, W 1. 41, Mo 1. 39, C 0. 91 ad a) only B diff. > 12 % , ad b) C, B; Mo, W diff. > 12 %
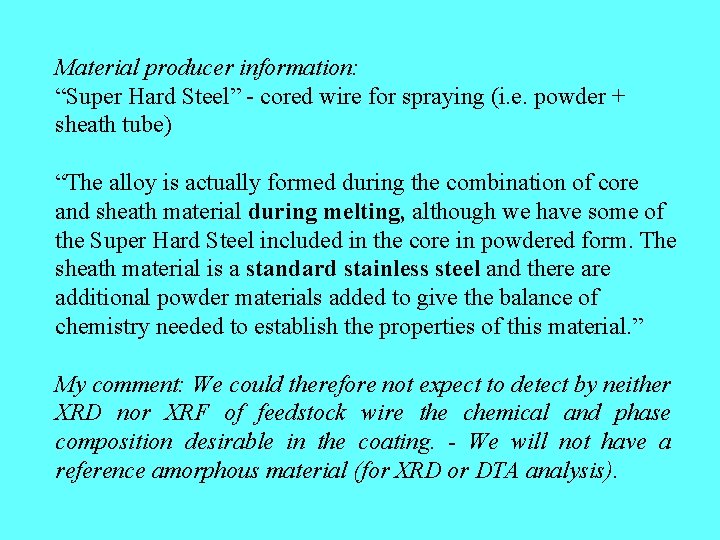
Material producer information: “Super Hard Steel” - cored wire for spraying (i. e. powder + sheath tube) “The alloy is actually formed during the combination of core and sheath material during melting, although we have some of the Super Hard Steel included in the core in powdered form. The sheath material is a standard stainless steel and there additional powder materials added to give the balance of chemistry needed to establish the properties of this material. ” My comment: We could therefore not expect to detect by neither XRD nor XRF of feedstock wire the chemical and phase composition desirable in the coating. - We will not have a reference amorphous material (for XRD or DTA analysis).
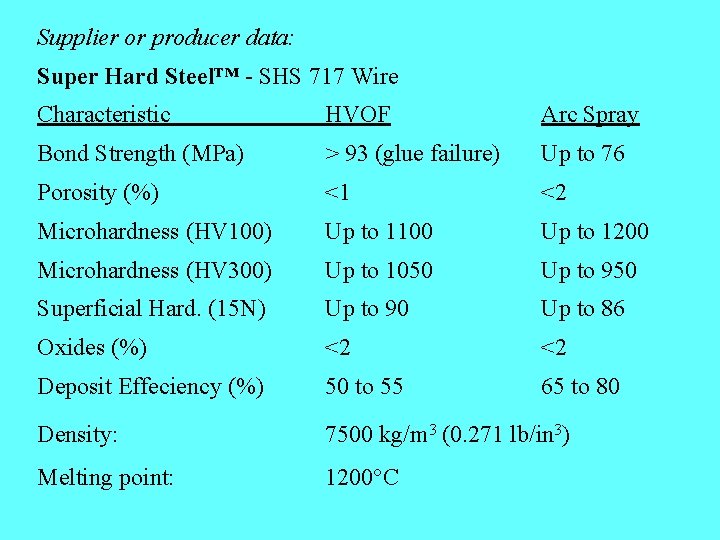
Supplier or producer data: Super Hard Steel™ - SHS 717 Wire Characteristic HVOF Arc Spray Bond Strength (MPa) > 93 (glue failure) Up to 76 Porosity (%) <1 <2 Microhardness (HV 100) Up to 1100 Up to 1200 Microhardness (HV 300) Up to 1050 Up to 950 Superficial Hard. (15 N) Up to 90 Up to 86 Oxides (%) <2 <2 Deposit Effeciency (%) 50 to 55 65 to 80 Density: 7500 kg/m 3 (0. 271 lb/in 3) Melting point: 1200°C
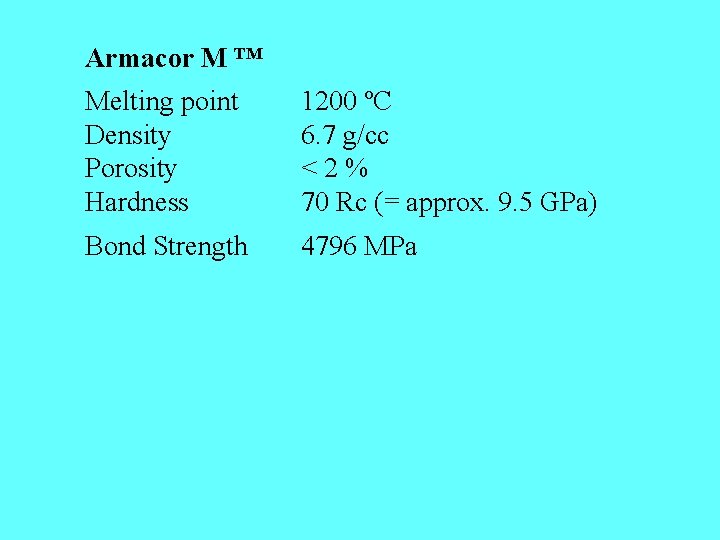
Armacor M ™ Melting point Density Porosity Hardness 1200 ºC 6. 7 g/cc <2% 70 Rc (= approx. 9. 5 GPa) Bond Strength 4796 MPa
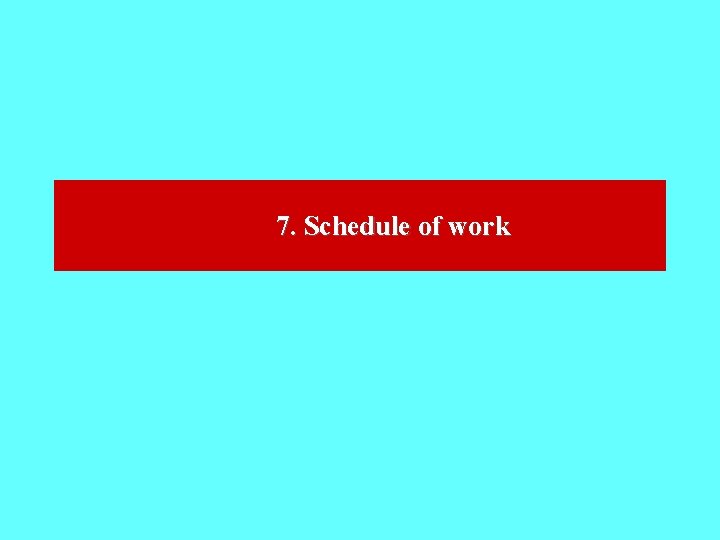
7. Schedule of work
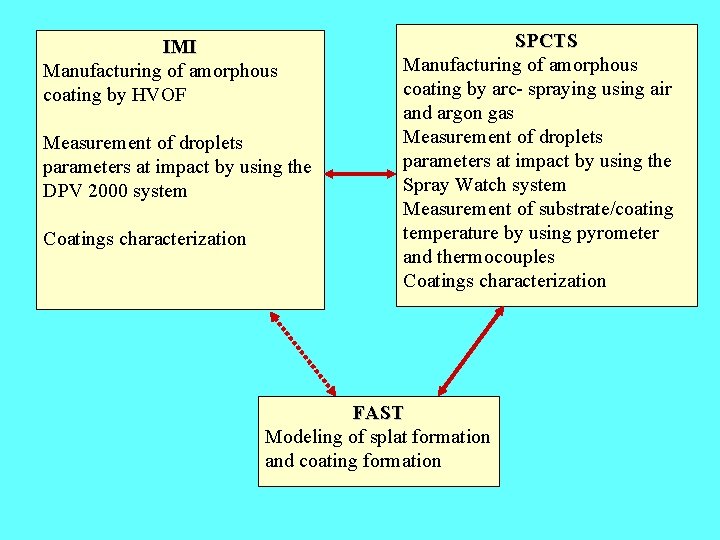
IMI Manufacturing of amorphous coating by HVOF Measurement of droplets parameters at impact by using the DPV 2000 system Coatings characterization SPCTS Manufacturing of amorphous coating by arc- spraying using air and argon gas Measurement of droplets parameters at impact by using the Spray Watch system Measurement of substrate/coating temperature by using pyrometer and thermocouples Coatings characterization FAST Modeling of splat formation and coating formation
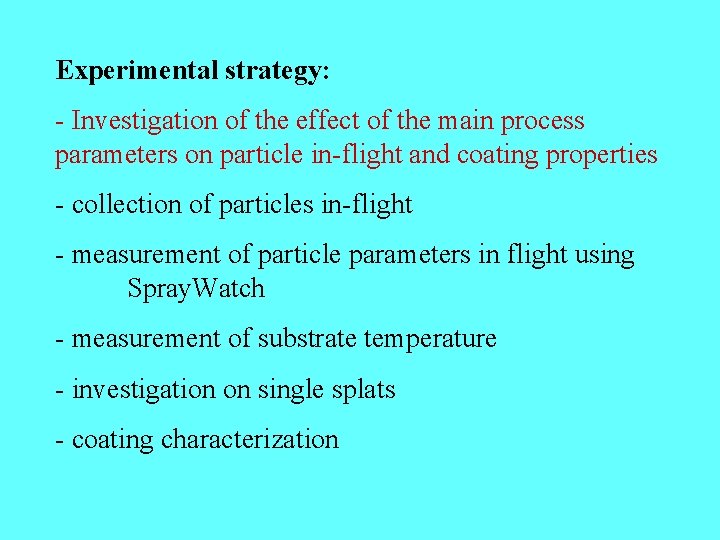
Experimental strategy: - Investigation of the effect of the main process parameters on particle in-flight and coating properties - collection of particles in-flight - measurement of particle parameters in flight using Spray. Watch - measurement of substrate temperature - investigation on single splats - coating characterization
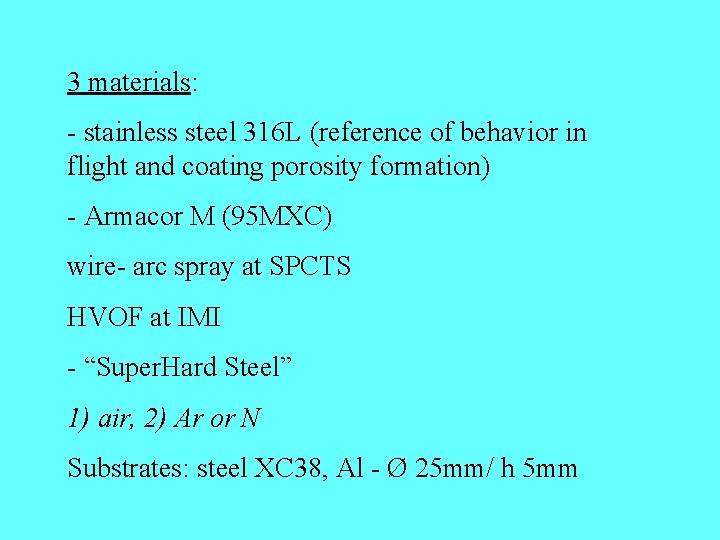
3 materials: - stainless steel 316 L (reference of behavior in flight and coating porosity formation) - Armacor M (95 MXC) wire- arc spray at SPCTS HVOF at IMI - “Super. Hard Steel” 1) air, 2) Ar or N Substrates: steel XC 38, Al - Ø 25 mm/ h 5 mm
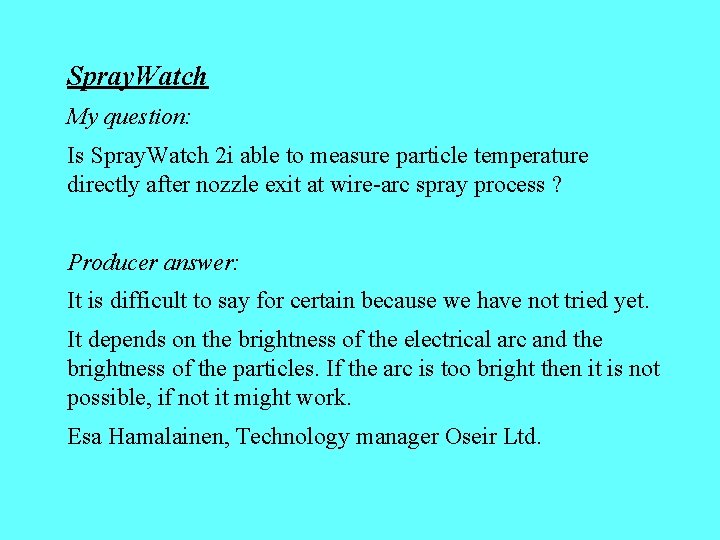
Spray. Watch My question: Is Spray. Watch 2 i able to measure particle temperature directly after nozzle exit at wire-arc spray process ? Producer answer: It is difficult to say for certain because we have not tried yet. It depends on the brightness of the electrical arc and the brightness of the particles. If the arc is too bright then it is not possible, if not it might work. Esa Hamalainen, Technology manager Oseir Ltd.
Attica dpts
Title fly of a report
Title title
Project title page
Example of project title
Research project name
Poc project adalah
Project title design
Project title name
Project title for health and nutrition
Catchy titles for presentations
Date title
Project plan title
Project title names
Acronym project title
Acronym project title
Design project title
Title of project proposal
Term project ideas
Title for project report
Title of project report
Project title names
Project title names
Dps project title
Research project title
Edictive
Catchy title for presentation
The role of project management in achieving project success
How to write a project background
Modern process transitions in spm
How to reduce project duration
Introduction to project management kathy schwalbe
What is strategic assessment in software project management
Traditional project management vs modern project management
When conducting post project audits
Process indicators enable software project manager to
Ms project agile template
Methodology of project proposal
Types of terminations
Geography nea title examples
Title for compare and contrast essay
Title page of essay