NATC International ALARA Symposium Orlando FL January 14
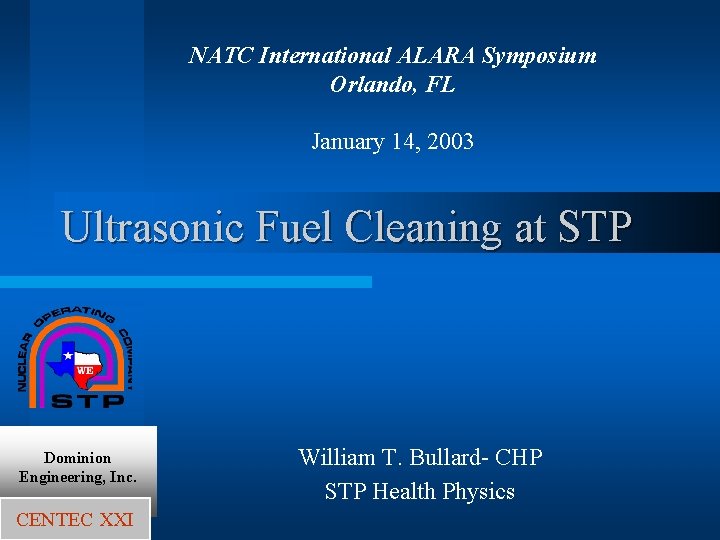
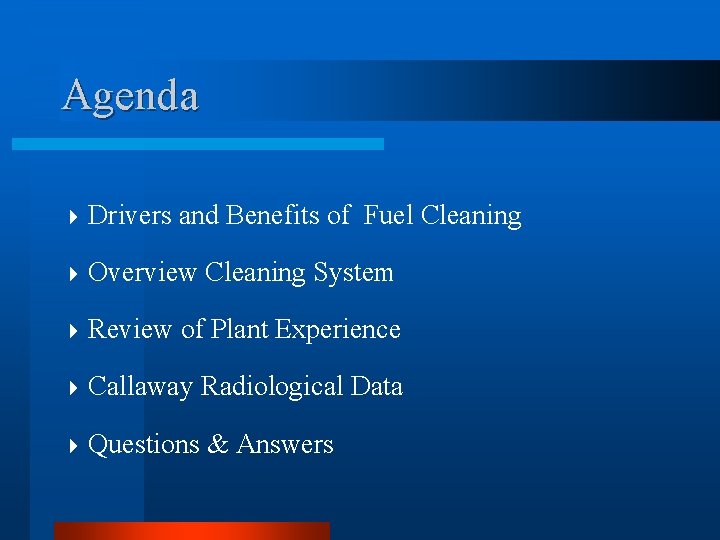
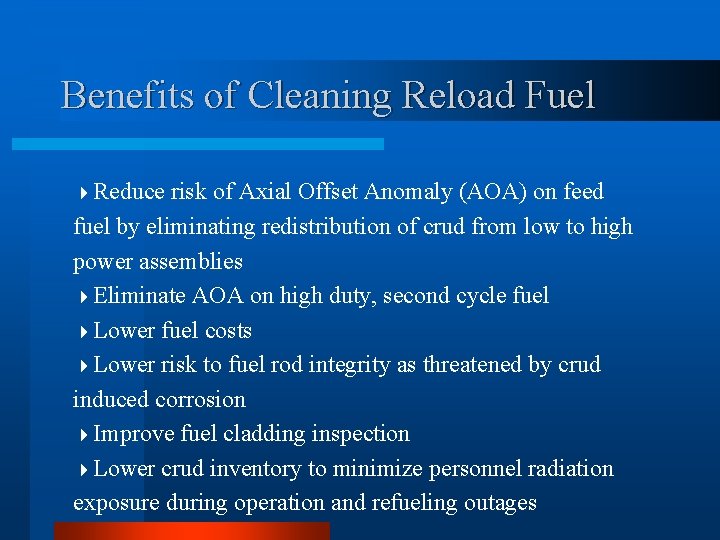
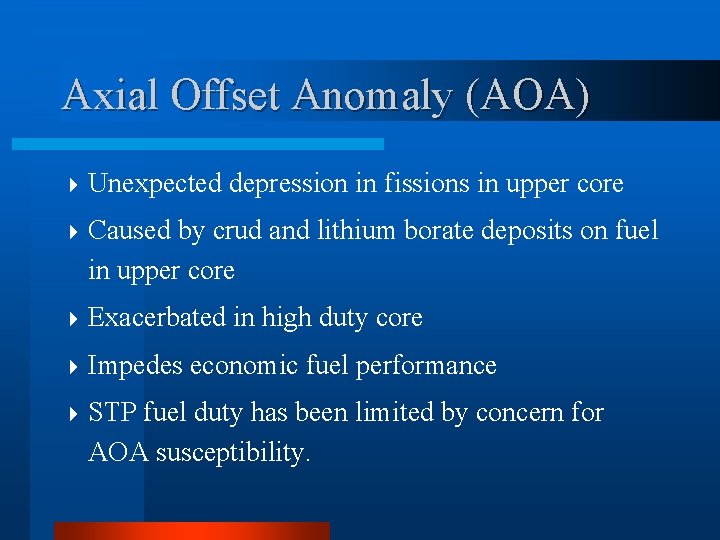
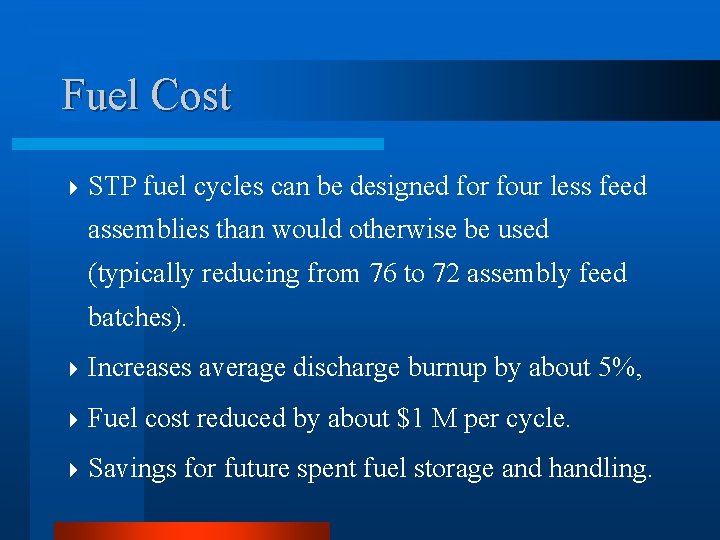
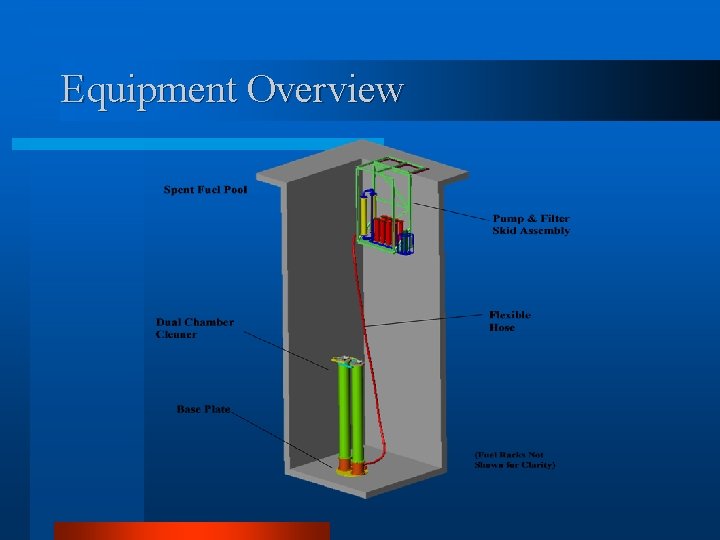
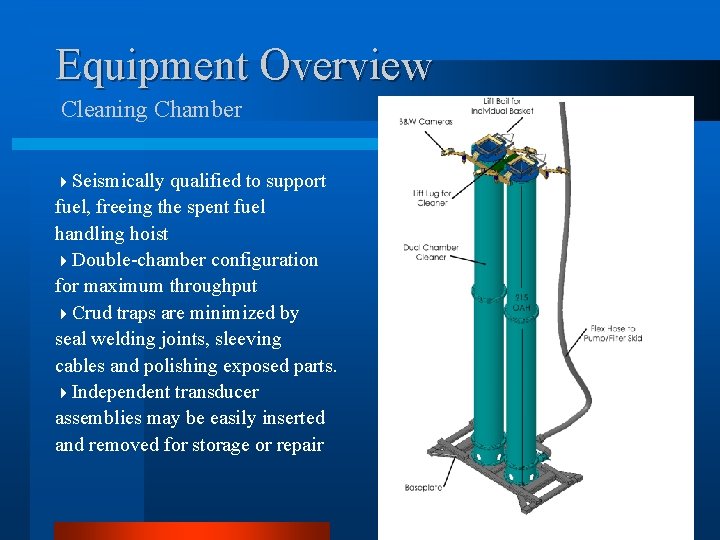
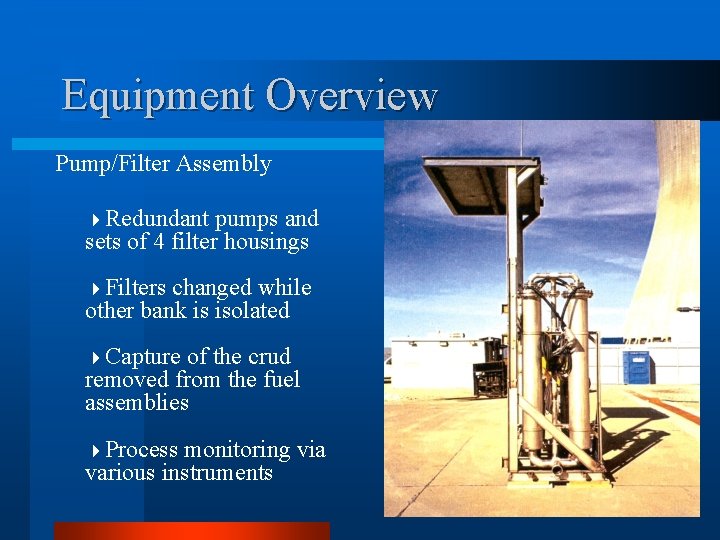
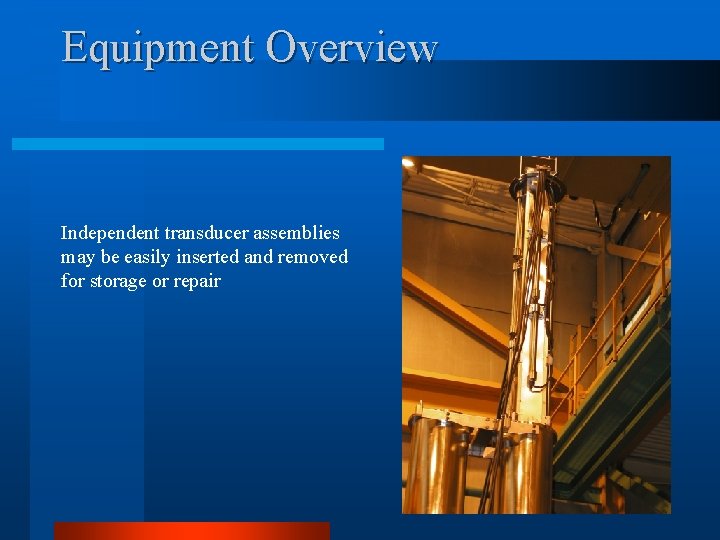
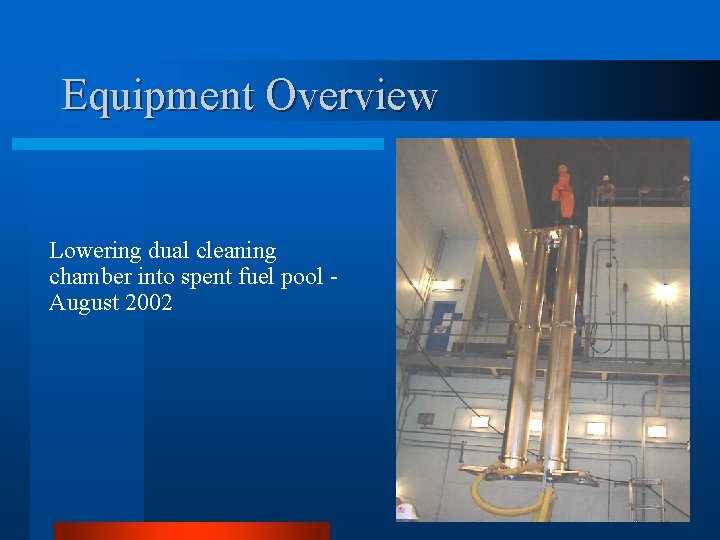
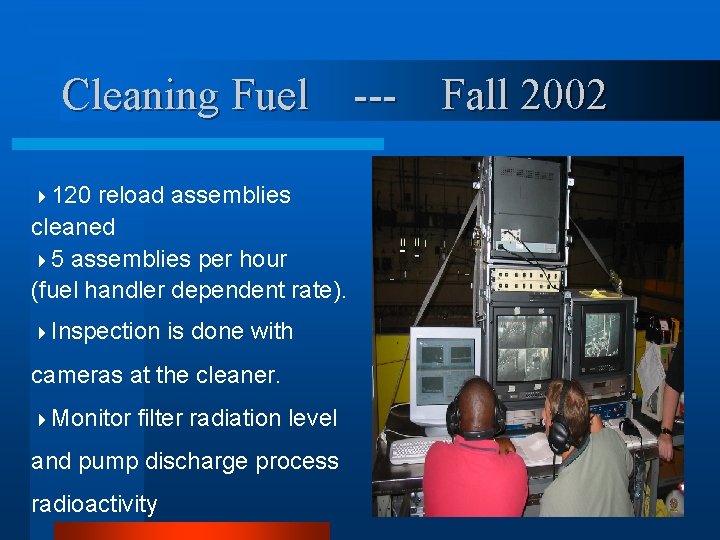
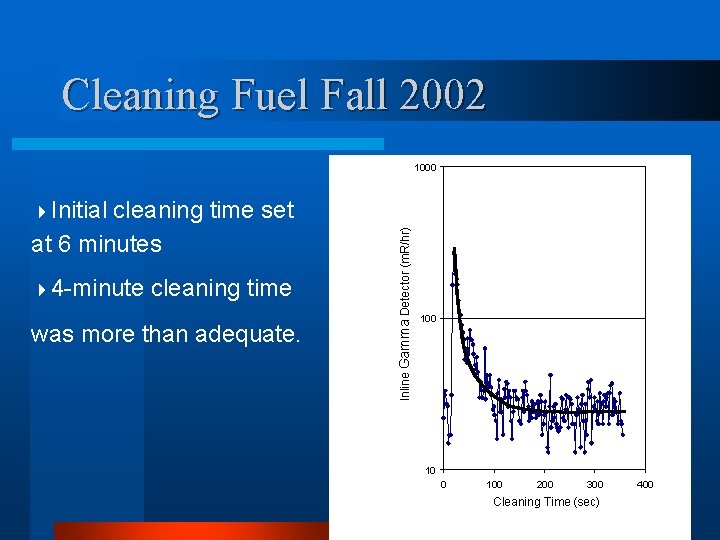
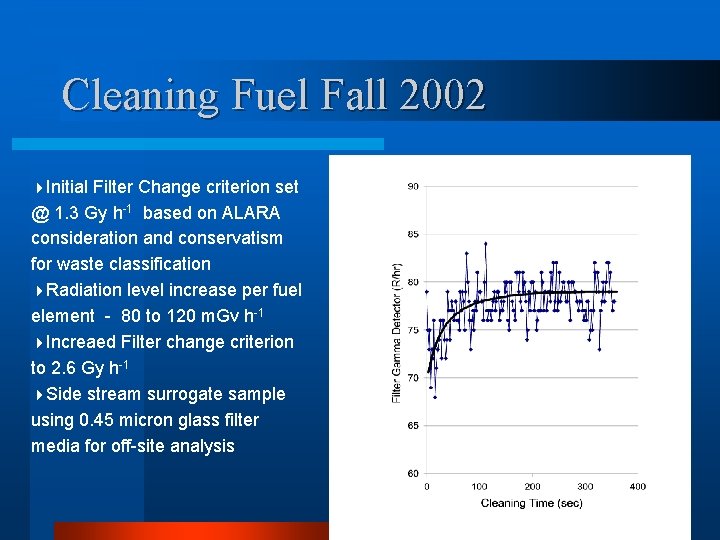
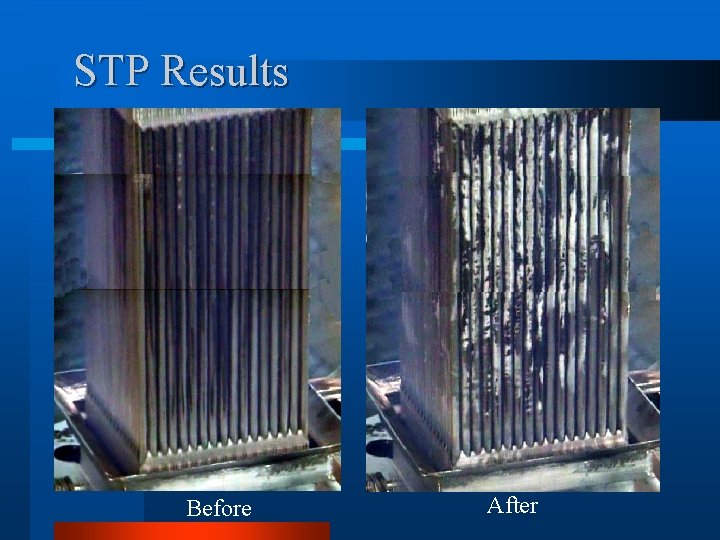
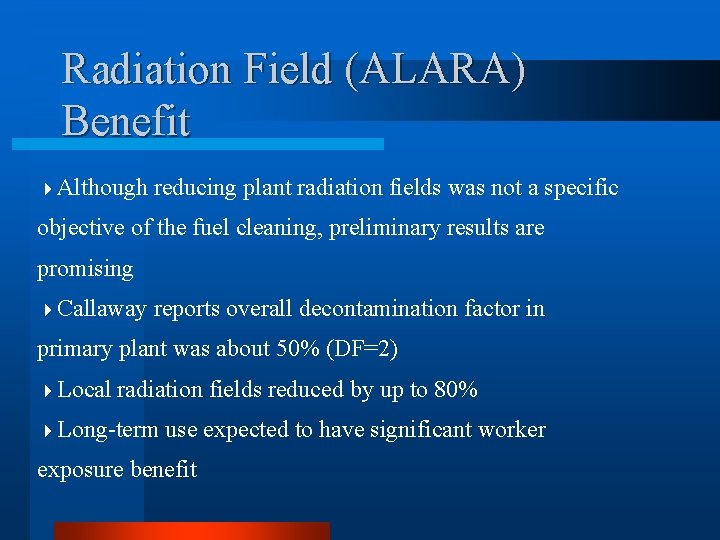
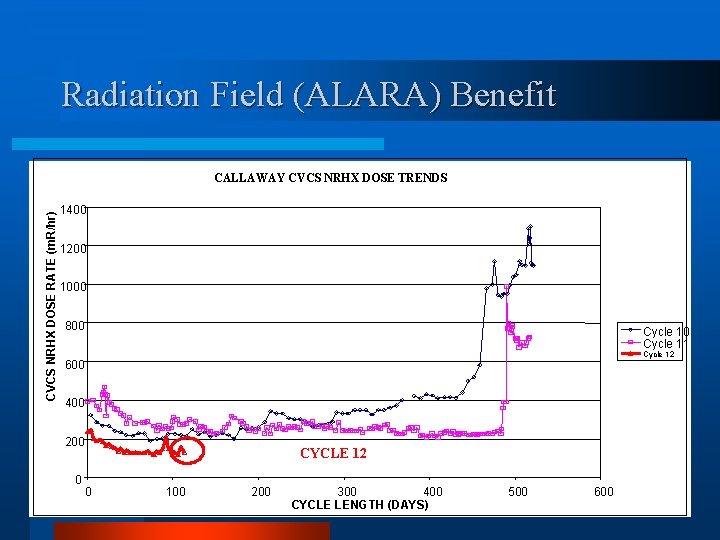
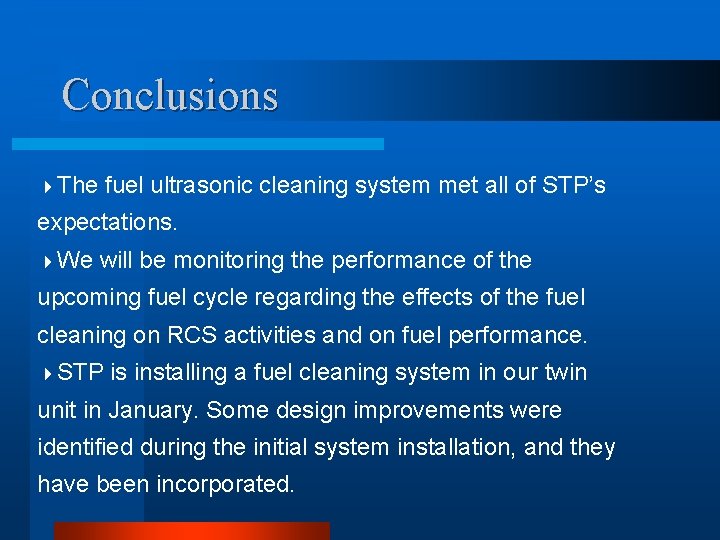
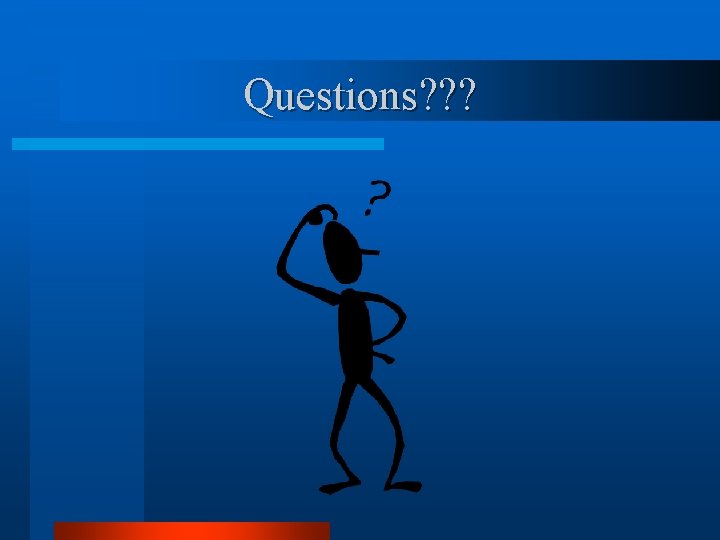
- Slides: 18
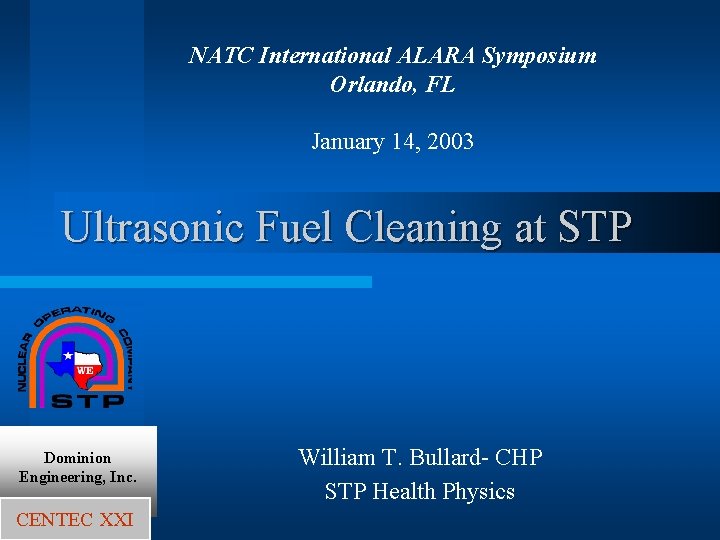
NATC International ALARA Symposium Orlando, FL January 14, 2003 Ultrasonic Fuel Cleaning at STP Dominion Engineering, Inc. CENTEC XXI William T. Bullard- CHP STP Health Physics
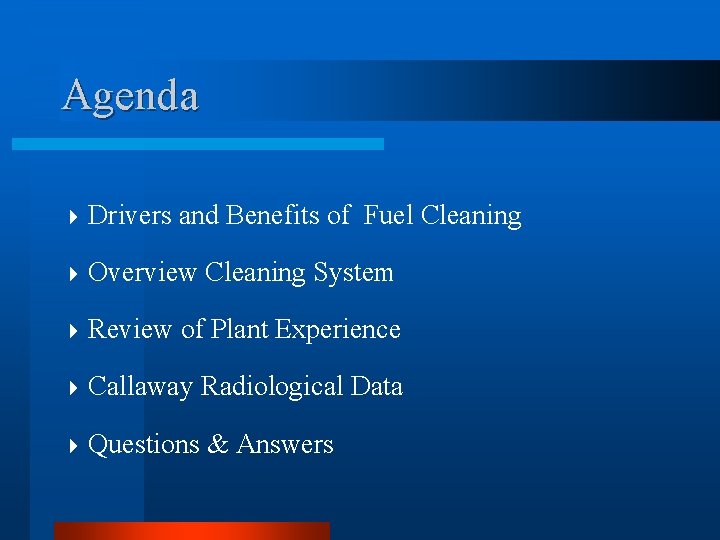
Agenda 4 Drivers and Benefits of Fuel Cleaning 4 Overview 4 Review Cleaning System of Plant Experience 4 Callaway Radiological Data 4 Questions & Answers
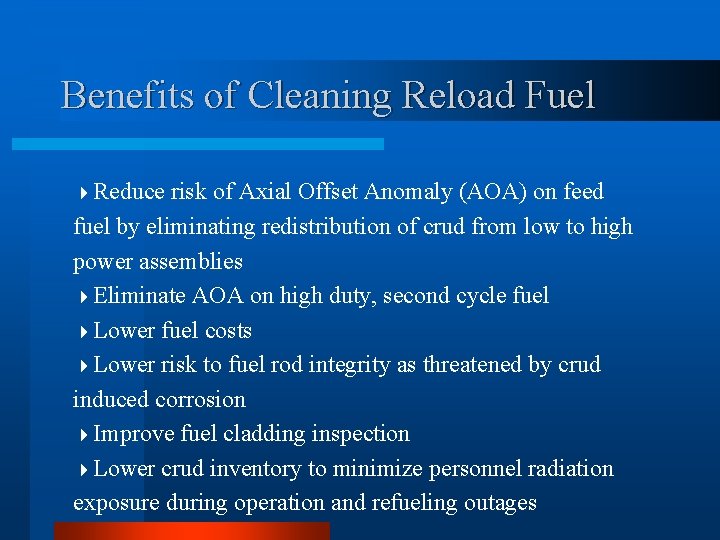
Benefits of Cleaning Reload Fuel 4 Reduce risk of Axial Offset Anomaly (AOA) on feed fuel by eliminating redistribution of crud from low to high power assemblies 4 Eliminate AOA on high duty, second cycle fuel 4 Lower fuel costs 4 Lower risk to fuel rod integrity as threatened by crud induced corrosion 4 Improve fuel cladding inspection 4 Lower crud inventory to minimize personnel radiation exposure during operation and refueling outages
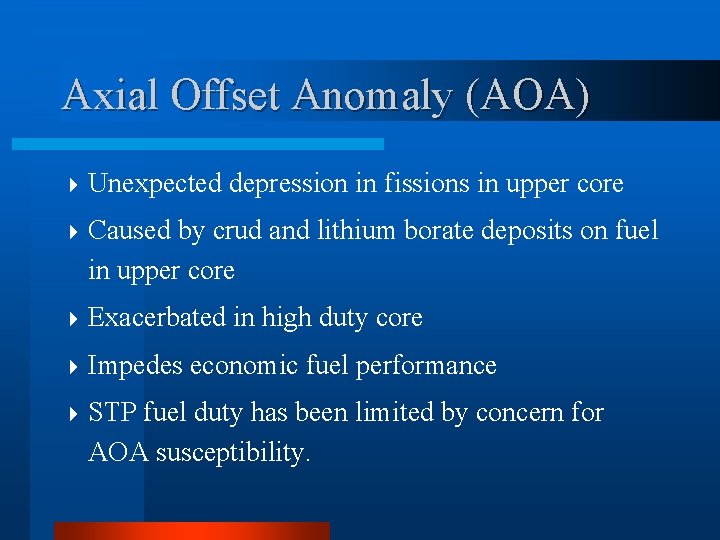
Axial Offset Anomaly (AOA) 4 Unexpected depression in fissions in upper core 4 Caused by crud and lithium borate deposits on fuel in upper core 4 Exacerbated 4 Impedes 4 STP in high duty core economic fuel performance fuel duty has been limited by concern for AOA susceptibility.
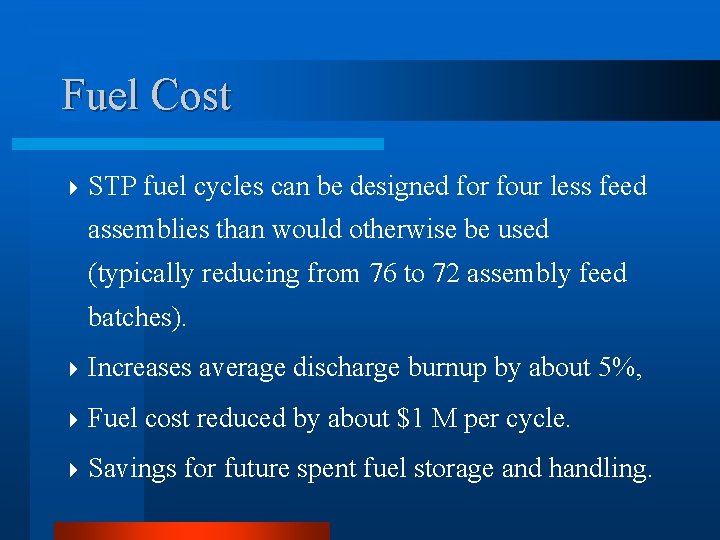
Fuel Cost 4 STP fuel cycles can be designed for four less feed assemblies than would otherwise be used (typically reducing from 76 to 72 assembly feed batches). 4 Increases 4 Fuel average discharge burnup by about 5%, cost reduced by about $1 M per cycle. 4 Savings for future spent fuel storage and handling.
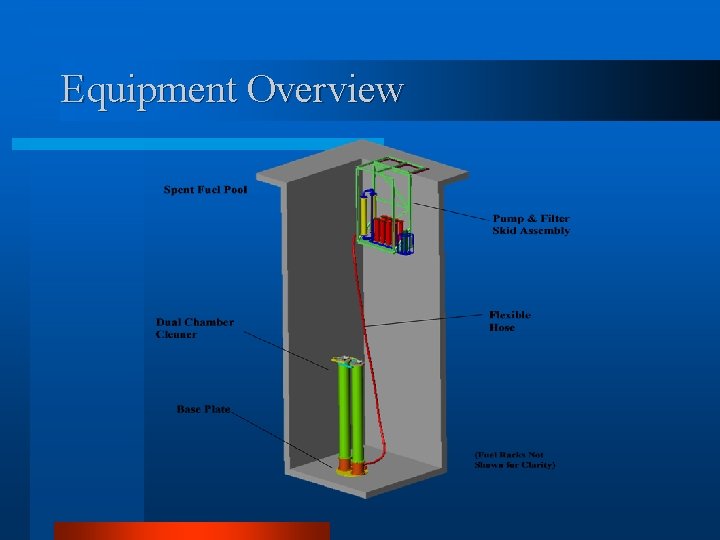
Equipment Overview
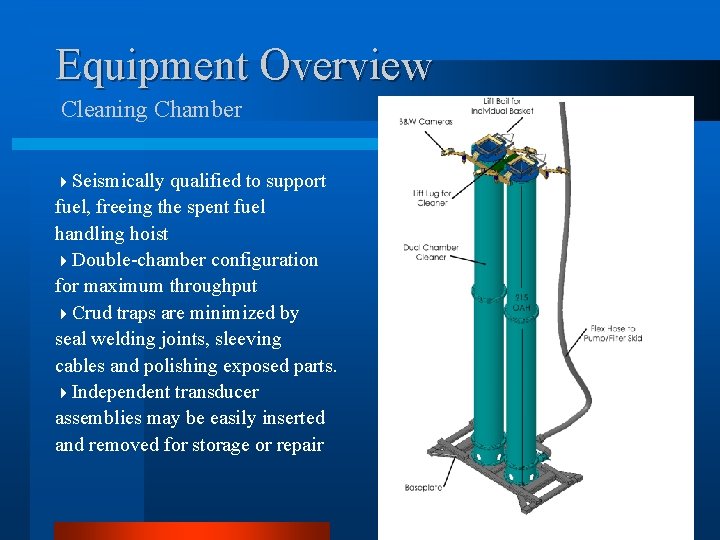
Equipment Overview Cleaning Chamber 4 Seismically qualified to support fuel, freeing the spent fuel handling hoist 4 Double-chamber configuration for maximum throughput 4 Crud traps are minimized by seal welding joints, sleeving cables and polishing exposed parts. 4 Independent transducer assemblies may be easily inserted and removed for storage or repair
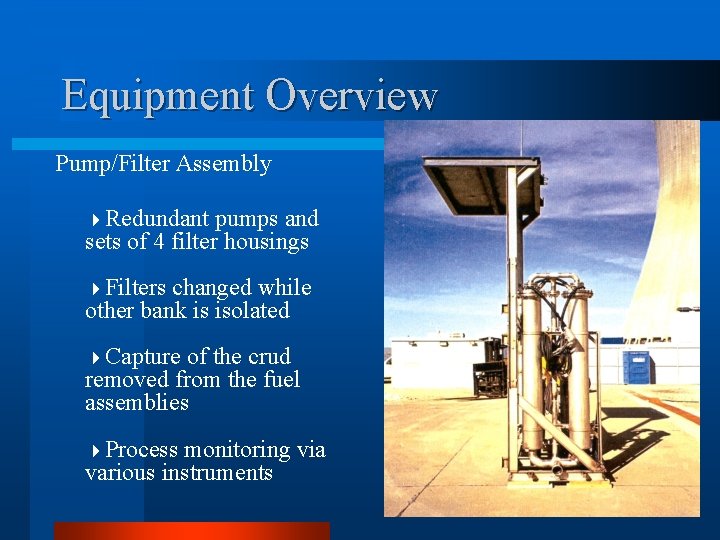
Equipment Overview Pump/Filter Assembly 4 Redundant pumps and sets of 4 filter housings 4 Filters changed while other bank is isolated 4 Capture of the crud removed from the fuel assemblies 4 Process monitoring via various instruments
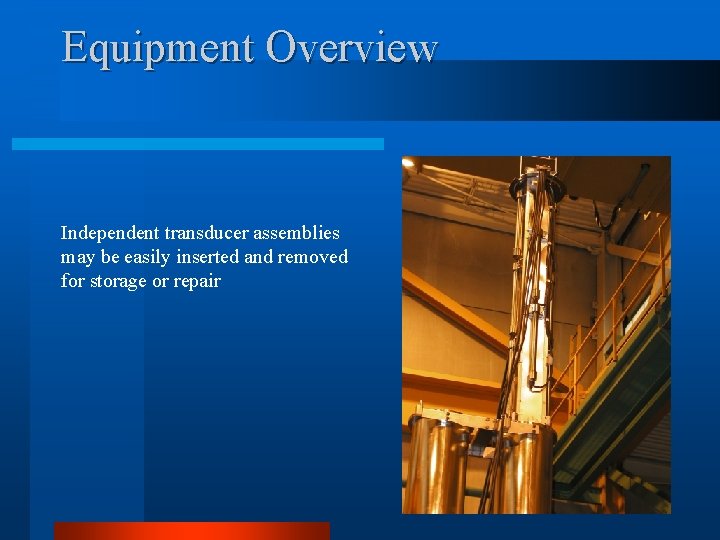
Equipment Overview Independent transducer assemblies may be easily inserted and removed for storage or repair
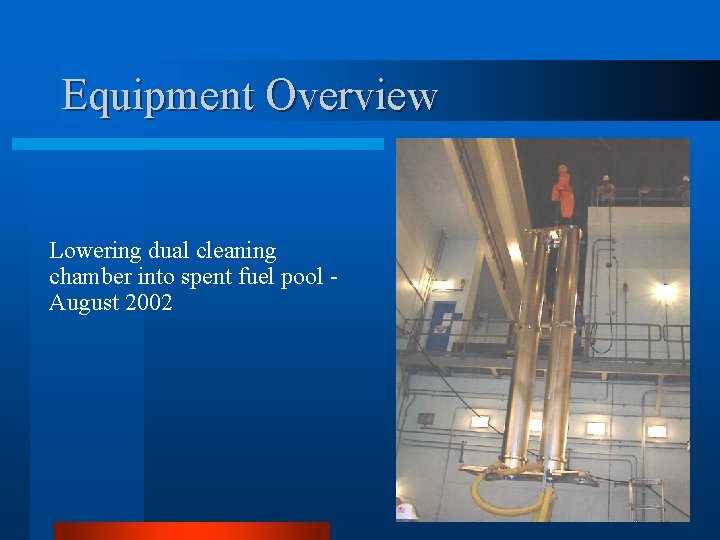
Equipment Overview Lowering dual cleaning chamber into spent fuel pool August 2002
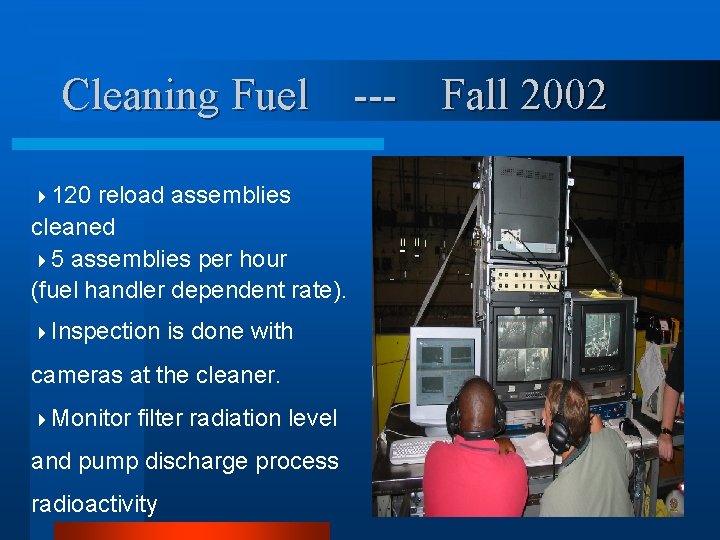
Cleaning Fuel --- Fall 2002 4120 reload assemblies cleaned 45 assemblies per hour (fuel handler dependent rate). 4 Inspection is done with cameras at the cleaner. 4 Monitor filter radiation level and pump discharge process radioactivity
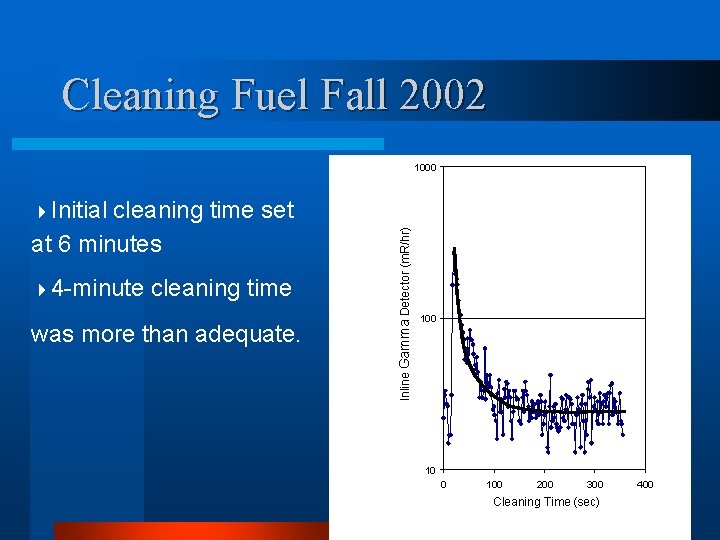
Cleaning Fuel Fall 2002 1000 cleaning time set at 6 minutes 44 -minute cleaning time was more than adequate. Inline Gamma Detector (m. R/hr) 4 Initial 100 100 200 300 Cleaning Time (sec) 400
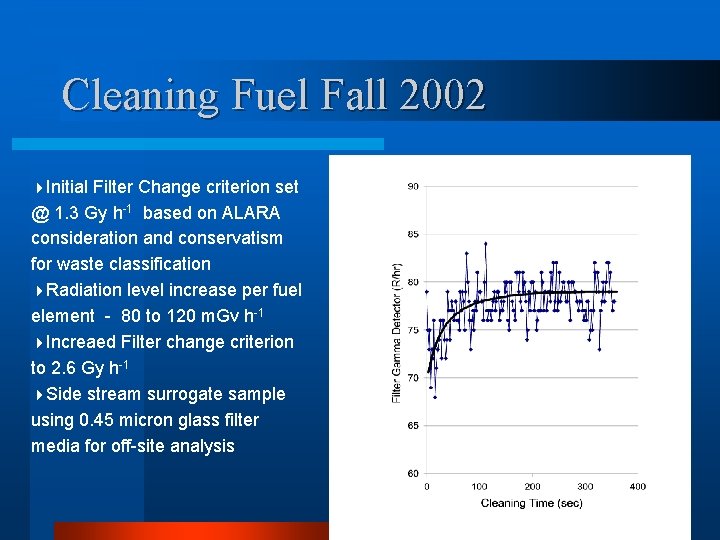
Cleaning Fuel Fall 2002 4 Initial Filter Change criterion set @ 1. 3 Gy h-1 based on ALARA consideration and conservatism for waste classification 4 Radiation level increase per fuel element - 80 to 120 m. Gv h-1 4 Increaed Filter change criterion to 2. 6 Gy h-1 4 Side stream surrogate sample using 0. 45 micron glass filter media for off-site analysis
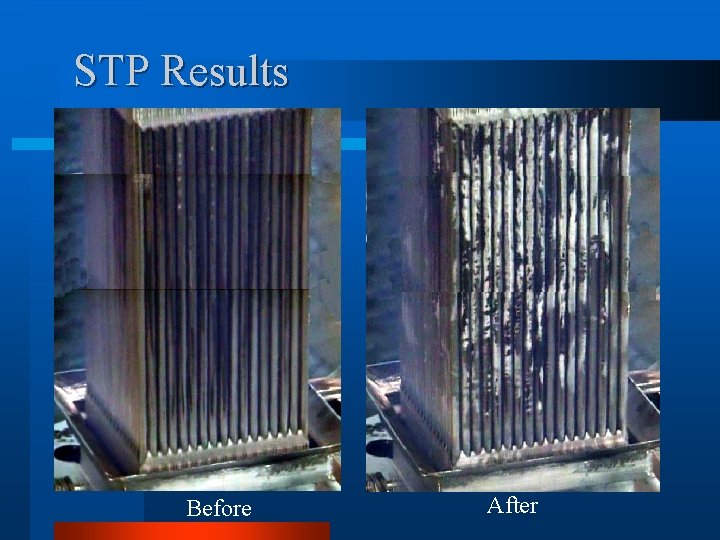
STP Results Before After
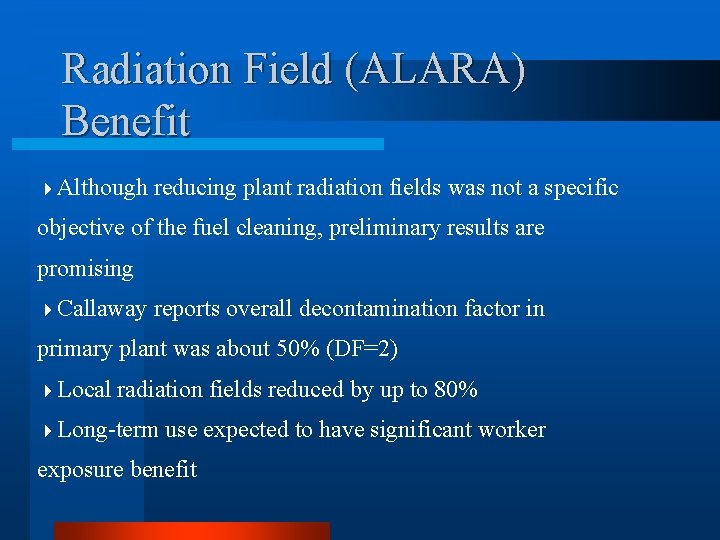
Radiation Field (ALARA) Benefit 4 Although reducing plant radiation fields was not a specific objective of the fuel cleaning, preliminary results are promising 4 Callaway reports overall decontamination factor in primary plant was about 50% (DF=2) 4 Local radiation fields reduced by up to 80% 4 Long-term use expected to have significant worker exposure benefit
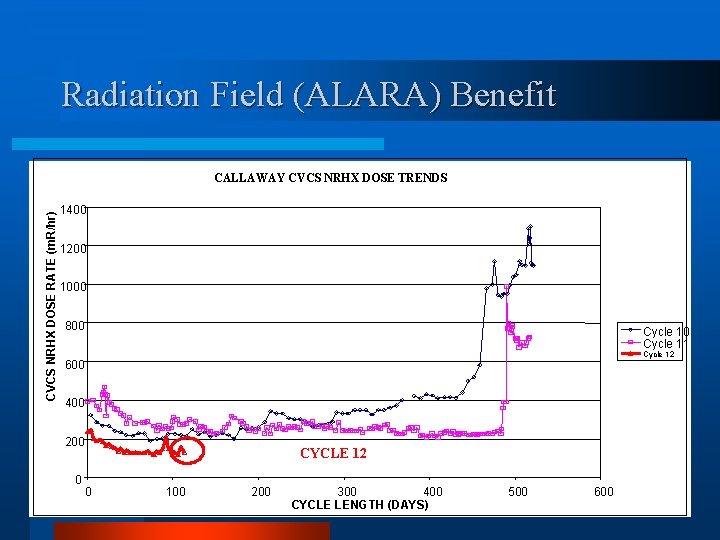
Radiation Field (ALARA) Benefit CVCS NRHX DOSE RATE (m. R/hr) CALLAWAY CVCS NRHX DOSE TRENDS 1400 1200 1000 800 Cycle 11 Cycle 12 600 400 200 0 CYCLE 12 0 100 200 300 400 CYCLE LENGTH (DAYS) 500 600
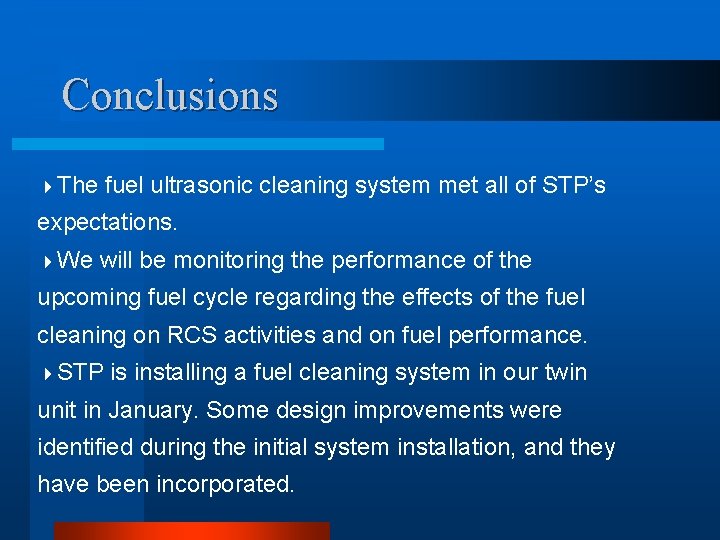
Conclusions 4 The fuel ultrasonic cleaning system met all of STP’s expectations. 4 We will be monitoring the performance of the upcoming fuel cycle regarding the effects of the fuel cleaning on RCS activities and on fuel performance. 4 STP is installing a fuel cleaning system in our twin unit in January. Some design improvements were identified during the initial system installation, and they have been incorporated.
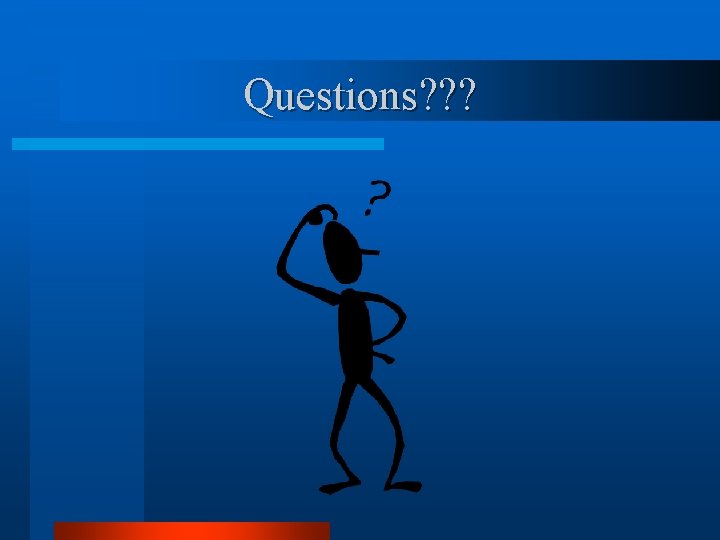
Questions? ? ?
Alara princip
Alara dirik
Alara facility management
Alara ataacar
Alara şevket demirel ortaokulu
Canvas mcboe
International symposium on molecular spectroscopy
International police executive symposium
Ips perforating
International perforating symposium
International perforating symposium
International perforating symposium
International perforating symposium
Ips perforating
"leads international" "international marketing"
"databank"
Vsv symposium
Telpas headphones
Eurographics symposium on rendering